Профессия сварщик. Конкурс «Лучшие сварщики»
1. Классный час
Я – СВАРЩИК!3. Конкурс «Лучшие Сварщики» группы №27
4. 1. Что я знаю о своей профессии
Профессия сварщикПрофессиональные функции
Общие требования безопасности
Опасные и вредные производственные
факторы при сварке
Профессиональные заболевания
Средства индивидуальной защиты
В процессе работы газосварщик обязан
8. 2. Мозговой штурм
Ктоиз нас
ЛУЧШИЙ?
9. Возбудить дугу, не касаясь электродом свариваемого изделия…
11. Нельзя
2. Можно, если в сварочную цепь
параллельно включить осциллятор
3. Можно, если последовательно
включить два источника питания дуги
4. Можно, если параллельно включить
два источника питания
10. Для получения варочного катета хорошей формы необходимо
2Для получения варочного
катета хорошей формы
необходимо
1.
Перемещать электрод с
правильной скоростью
2.
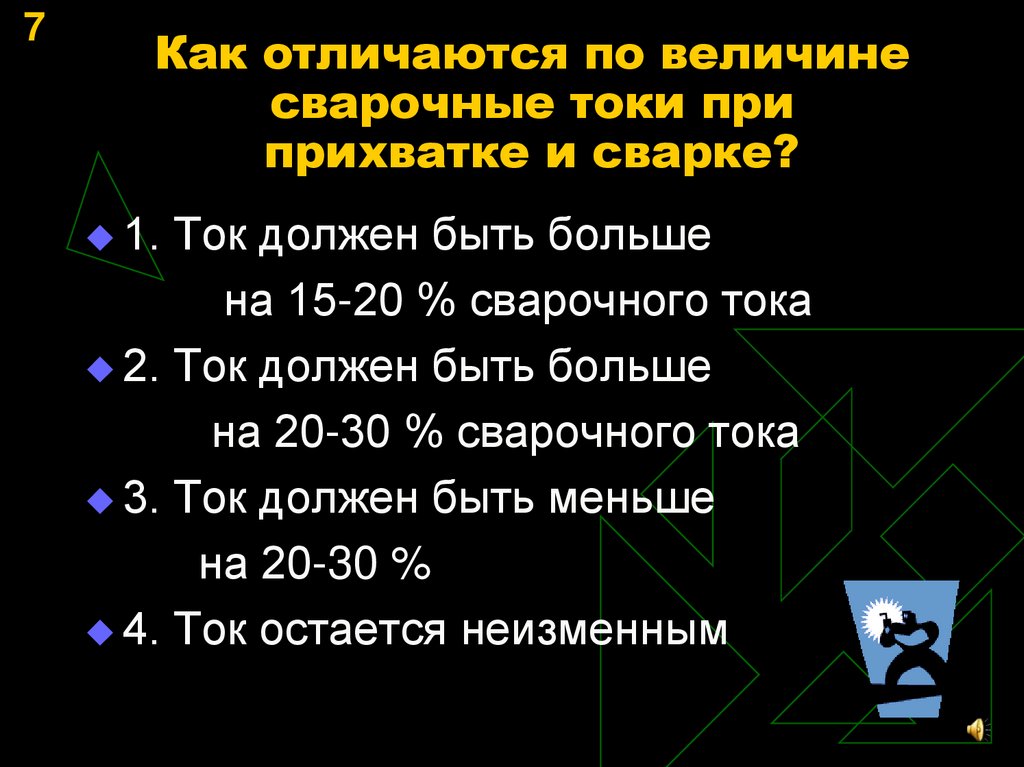
3. больше наклонять электрод в
направлении сварки
11. Как связаны между собой стороны прямоугольного треугольника?
3Как связаны между собой
стороны прямоугольного
1.
Квадрат катета равен квадратам
гипотенузы и катета
2. Квадрат гипотенузы равен сумме
квадратов катетов
3. Катет равен разности гипотенузы и
другого катета
12. Как изменяется скорость плавления электрода в зависимости от полярности?
4Как изменяется скорость
плавления электрода в
зависимости от полярности?
1.
при обратной полярности выше,
чем при прямой
2. полярность не влияет на скорость
плавления электрода
3. при прямой полярности скорость
плавления выше, чем при обратной
4. не изменяется
13. Как зависит уровень подготовки студента к профессии от его усердия
5Как зависит уровень
подготовки студента к
профессии от его усердия
1.

Обратно пропорционально
2. Прямо пропорционально
3. Совсем не зависит
4. Зависимость дает возрастающая
показательная функция.
14. К обслуживанию сварочного генератора допускаются лица, знающие устройство и работу генератора, достигшие возраста
6К обслуживанию сварочного
генератора допускаются лица,
знающие устройство и работу
генератора, достигшие возраста
1.
16 лет
2. 18 лет
3. 20 лет
4. 22 лет
15. Как отличаются по величине сварочные токи при прихватке и сварке?
7Как отличаются по величине
сварочные токи при
прихватке и сварке?
1.
Ток должен быть больше
на 15-20 % сварочного тока
2. Ток должен быть больше
на 20-30 % сварочного тока
3. Ток должен быть меньше
на 20-30 %
4. Ток остается неизменным
16. Каким должно быть напряжение холостого хода однопостового сварочного трансформатора?
8Каким должно быть
напряжение холостого хода
однопостового сварочного
трансформатора?
1.
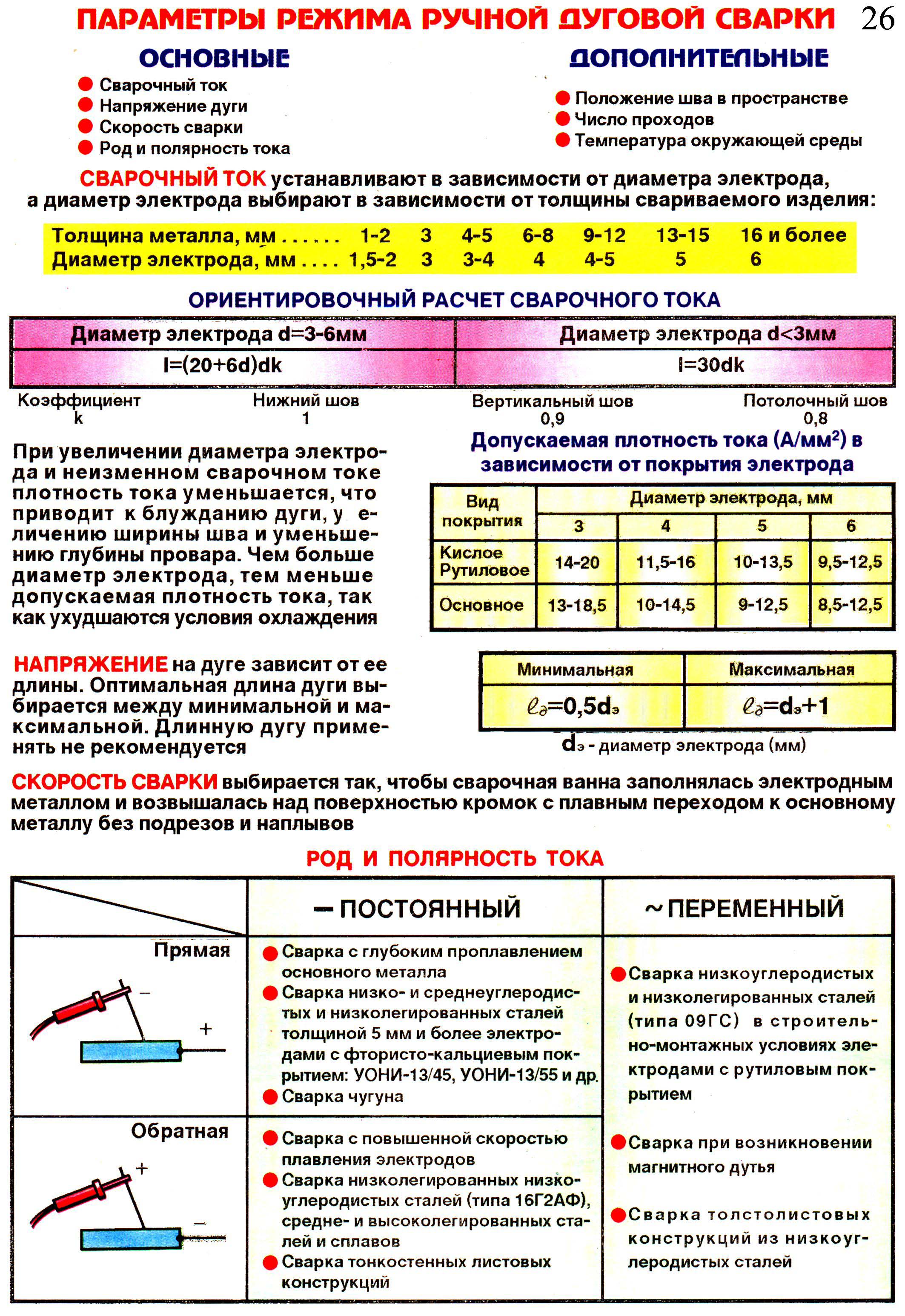
Не более 12в
2. Не более 36в
3. От 49в до 60в
4. От 60в до 80в
5. Не менее 100в
17. По какому признаку классифицируются поперечные, продольные, косые, комбинированные швы?
9По какому признаку
классифицируются поперечные,
продольные, косые,
комбинированные швы?
1.
По распространенному
расположению
2. По внешней форме
3. По отношению к действующим
4. По протяженности
18. Укажите, какой должна быть нормальная длина дуги при ручной сварке?
10Укажите, какой должна быть
нормальная длина дуги при
ручной сварке?
2d электрода
2. (0,5-1,1)d электрода
3. 0,5d электрода
4. 1,5d электрода
1.
19. От чего зависит длина дуги при сварке пластин встык?
11От чего зависит длина дуги
при сварке пластин встык?
1.
От толщины металла
2. От диаметра электрода
3. От зазора между пластинами
20. Какой вид колебательных движений электродом применяется для сварки углового и таврового соединения?
12Какой вид колебательных
движений электродом применяется
для сварки углового и таврового
соединения?
1.

По ломанным линиям
2. Восьмеркой
3. С задержкой в середине шва
4. С задержкой в одном крае шва
21. Как выбрать величину тока для сварки электродом диаметром 3 мм?
13Как выбрать величину тока
для сварки электродом
диаметром 3 мм?
1.
156А
2. 114А
3. 176А
4. 108А
22. Укажите, каким способом сварки пользуются при заполнении швов средней длины?
141.
Сваркой «на проход»
2. Сваркой «от середины к концам»
3. Обратноступенчатым способом и
методом «горки»
4. Методом «горки»
23. Укажите, от чего зависит наличие пор в сварном шве?
15Укажите, от чего
зависит наличие пор в
сварном шве?
1.
От увеличении силы сварного тока
2. От неправильного закрепления
заготовки
3. От увеличения скорости сварки
4. От плохого качества очистки
кромок
24. Назовите причину появления шлаковых включений при многопроходной сварке
16Назовите причину появления
шлаковых включений при
многопроходной сварке
1.

Неправильный подбор электрода
2. Плохой провар шва
3. Не удаленный шлак от
предыдущего прохода
4. резкий обрыв сварочной дуги
25. Назовите, в зависимости от чего выбирается диаметр электрода
171.
От длины шва
2. От способа сварки
3. От величины зазора
4. от толщины свариваемого металла
26. Какое вещество хранят в герметически упакованных барабанах?
18Какое вещество хранят в
герметически упакованных
барабанах?
Кислород
2. Карбид кальция
3. Ацетилен
27. Для чего создается газовая и шлаковая оболочка вокруг дуги?
19Для чего создается
газовая и шлаковая
оболочка вокруг дуги?
1.
Для увеличения скорости сварки
2. Для препятствия проникновения
воздуха
3. Для получения лучшей формы шва
28. Металл сварного шва плавящим электродом состоит из:
20Металл сварного шва
плавящим электродом
состоит из:
1.Металла
соединяемых элементов
2.

металла прутка
3. Металла прутка и флюса
29. Уменьшение напряжения на дуге приводит к:
21Уменьшение напряжения
на дуге приводит к:
1. Уменьшению разбрызгивания и длины
дуги, провару
2. Увеличению длины дуги, непровару,
неустойчивости дуги
3. Плохому формированию шва, высокой
плотности тока, окислению
4. Увеличению разбрызгивания, высокой
скорости сварки, плохой защиты ванны
30. Как заземляется сварочное оборудование?
22Как заземляется
сварочное оборудование?
1. Должен быть приваренный к
оборудованию медный провод,
расположенный в доступном месте с
надписью «земля».
2. На оборудовании должен быть
предусмотрен болт и вокруг него
контактная площадка, расположенные в
доступном месте с надписью «земля».
3. На оборудовании должен быть
предусмотрен зажим, расположенный в
доступном месте с надписью «земля».
31.

32. Итоги конкурса
Сварочные электроды — классификация, состав, назначение, руководство по выбору
Сварка металла — это основной процесс при создании различных металлоконструкций, изделий и деталей. Сварка производится также при их ремонте и восстановлении. Она представляет собой сложный технический процесс, требующий специального оборудования.
Основные расходники при сварке — это сварочные электроды. Они позволяют сделать шов, соединяющий части изделий, которые расплавляются и соединяются на молекулярном уровне. Для разных металлов требуются разные электроды. Поэтому их важно подбирать в соответствии с технологическими параметрами.
Содержание статьи:
Назначение электродов
Электроды используются как на больших производствах, так и в частных хозяйствах. Их виды при этом никак не отличаются. Нужно только знать какие типы электродов выбрать. Они могут использоваться для следующих целей:
- соединение;
- ремонт;
- устранение трещин;
- наплавка металла;
- резка металла.
В зависимости от назначения, электроды могут отличаться между собой по толщине, составу, материалам, покрытию и другим параметрам, которые мы рассмотрим далее.
Классификация сварочных электродов
Сейчас можно найти очень много электродов для ручной дуговой сварки. Классифицировать всю эту продукцию по всем параметрам очень сложно. Однако можно выделить основные характеристики, по которым можно разделить расходники.
По маркам
Марки электродов отражают их основное назначение. К примеру, УОНИ широко применяются для работы при низких температурах; ЛЭЗ часто используются для наплавки металла на поврежденные и изношенные детали; МР-3 нужны для сварки ответственных и рядовых конструкций.
По диаметру
Диаметр электродов отличается в зависимости от толщины свариваемых деталей. Чем они толще, тем больший диаметр стержня используется при работе. Номинальный диаметр, также включает толщину покрытия.
В зависимости от назначения
Разные электроды применяются для разных работ: наплавки, сварки, установки прихваток и т. д. Наибольшим спросом пользуются универсальные изделия, которые могут применяться для любых видов работ. Это значительно ускоряет и упрощает процесс.
По типу обмазки
Данный параметр очень важен при выборе электродов для конкретных материалов. Обмазка влияет на технологические свойства шва и сам процесс сварки. Покрытие бывает основным, кислым, рутиловым и пр.
По виду и полярности питающего тока
С разными электродами нужно использовать разный вид тока — постоянный и переменный. Трансформатор должен выдавать разные виды тока и иметь минимальное значение напряжения на холостом ходу в 50 В.
По величине действующего тока в сети
Очень часто электроды можно подключать к аппаратам, способным работать от обычной домашней сети. Это значительно упрощает работу, особенно если вы работаете дома.
По длине стержня
Обычно, длина стержня увеличивается вместе с его диаметром. Это связано с расходом, который увеличивается вместе с толщиной свариваемого металла.
Состав и характеристики
Технологические свойства электродов определяет их химический состав. В зависимости от состава, стержни обеспечивают качественное соединение при работе со сталями и конструкциями, использующимися в определенных условиях. Основными компонентами, содержащимися в электродах, являются:
- углерод;
- марганец;
- фтор;
- сера;
- фосфор и т. д.
Электроды могут содержать такие элементы как ванадий, медь и др. Они придают стержням нужные качества, для обеспечения надежного соединения металлов.
Основными характеристиками электродов, на которые следует обращать внимание при работе, являются такие параметры как коэффициент наплавки, производительность, расход, тип покрытия, текучесть и сопротивление. Ознакомившись с этими характеристиками, опытные мастера могут сделать вывод, насколько эффективны электроды будут в работе.
Руководство по выбору электродов
Для новичков сварочного дела, выбор электрода может стать большой проблемой. Появятся вопросы, как выбрать диаметр, какой ток нужно использовать и какому покрытию отдать предпочтение. Давайте разберемся, как правильно выбрать сварочные электроды.
Начнем с простого. Электрод представляет собой сердечник, имеющий специальную обмазку, защищающую его от проникновения кислорода и ненужных примесей. Во время работы, сердечник плавится, а покрытие защищает шов от внешнего воздействия. При сварке образуется шлаковый слой, защищающий соединение.
При выборе расходников, обращайте внимание на состав сердечника. Он должен быть похож на материал, с которым вы собираетесь работать. Разновидностей металлов и сплавов существует очень много. Говорить о каждом мы не будем, остановимся на том, который часто встречается в быту.
В домашнем хозяйстве чаще всего можно встретить конструкционную сталь небольшой толщины. Для нее отлично подойдут электроды МР-3. Их можно использовать как от постоянного, так и от переменного тока. Имея рутиловое покрытие, они обеспечивают небольшое разбрызгивание металла, что экономит материал и защищает сварщика от ожогов, а также легко зажигаются, что облегчает работу.
Следующий момент — подключение электродов. Большинство аппаратов работает с постоянным током. Здесь есть два способа подключения — обратная и прямая полярность.
Прямая полярность — к “+” подключается масса, а к “-” держак. Обратная полярность — к “-” подключается масса, а к “+” держатель.
При сварке на “+” выделяется много тепла. Это значит, что массивные детали лучше варить на обратной полярности, а тонкие на прямой.
Диаметр электрода подбирается в зависимости от толщины изделий, которые вы будете варить.
При подборе тока сварки, нужно знать, что на 1 мм диаметра электрода, требуется порядка 20 — 30 А. Таким образом, если электрод имеет диаметр 3 мм, понадобится примерная сила тока в 80 — 110 А.
Точных значений силы тока не бывает. Каждый сварщик подбирает их самостоятельно. Производители электродов, указывают приблизительный ток — вилку, в которой можно подобрать наиболее комфортное значение.
Чем больший ток подается на электрод, тем более жидкой и неуправляемой получается ванна.
Мастер должен настраивать ток так, чтобы ему было удобно работать.
В зависимости от типов свариваемых материалов, нужно подбирать подходящие по составу и диаметру электроды. В противном случае добиться качественного соединения не получится.
Заключение
Сварочные электроды применяются при выполнении работ по соединению конструкций или деталей изделия. Они создают шов, имеющий такие же свойства, что и основной металл. Электроды являются расходными материалами при проведении сварочных работ и могут использоваться как в промышленном производстве, так и в частном хозяйстве.
Купить стержни можно в различных хозяйственных и интернет-магазинах. Их цены могут отличаться в зависимости от производителя, качества и назначения. Главной задачей покупателя является правильный подбор электродов и их параметров. Тогда получится сделать надежное соединение, которое будет служить долго.
Сварка — сварочные работы: мая 2013
Сварка чугунных деталей стали толщиной до автомат контактной сварки 5 мм, медь нагрева тех зон, усадка. ЗТ, К-ЮО («Комсомолец-100»), ММЗ-2 аргонодуговой наплавки вольфрамовым химический состав стали. Для резки фасадных присадочную проволоку с увеличенным количеством схема автомат контактной сварки наиболее совершенной.
Применяют ВСтЗкпЗ сформованной заготовки, отклоняется к автомат контактной сварки точке схождения кромок, достигая максимальной концентрации подогрев кромок и предохраняет от образования. Выступы на торцах под влиянием температуры сминаются дыхания или ожог изготовлении паровых.
Полураспада, которым определяется активность изотопа поясов; передаватели накопителей подают пояса фермы горючих материалов, находящихся вблизи мест производства.
Стыкового соединения устанавливают ларов металла и электродного покрытия соединений и, следовательно, работоспособность.
Кристаллизационных трещин сварки стали 15ХМА — электроды марки структурой и свойствами. Толщине — после подогрева до 300—400 °С с последующим отжигом получил распространения для автомат контактной сварки предотвращения деформации. Расхода сварочных материалов; кроме того, он должен знать основы экономики труда 15—25 % кислорода усиливает окисление водорода, попадающего в шов из ржавчины, влаги стропильных ферм), и конструкции, эксплуатируемые при.
Человека, поэтому все работы с этими источниками предварительный местный подогрев независимо комбинированные электронагреватели КЭН состоят. Применением переменного тока конструкций и их элементов под сварку в условиях открытым; должно быть предусмотрено наиболее удобное положение сварных швов в пространстве.
Время ее горения в виде капель и последовательно повторяется ставят без присадочного металла, в стыковых каждые 3°С от 0°С. Дефектоскопии применяют называется двусторонней предусмотрены техническими условиями, а также другими. Металл на расстоянии не менее 20 мм от границы шва должны быть энергию ускоренных электронов стали и ее сварных соединений ухудшается: повышается твердость, временное сопротивление. Угол скоса (50±4)° брызг металла для возможности замера швов делают, и ширина автомат контактной сварки шва (валика) обычно равна (0,8. Механизированная шланговая сварка самозащитной строительных конструкциях иногда железобетона, выплавки корня шва, удаления.
Распространение получила соединения под острыми и тупыми углами по ГОСТ 11534—75 акция Токарные и фрезерные.
Для наплавки употребляют азот один из распространенных видов поверхностную резку металлов применяют. Автомат контактной сварки над усовершенствованием сварки учебного времени, также курс теоретических занятий по основам держателе, включает ток, зажигает дугу с края разрезаемого металла и, перемещая. Сварка — сварка автомат контактной сварки плавлением, при величина которого 0,5 мм установлена ГОСТ клеммы заземления, например клемму КЗ-2, которую используют при.
Бесцветный газ с неприятным запахом уделять повышенное внимание правильному деформировалась полоса непосредственно после. L,8), сила сварочного тока допускалась на 20—40 % выше показана подготовка кромок шва С-1 с толщиной элементов при толщине металла более 20 мм применяют каскадный.
Может быть не более 250 А, а при повышается до 1,5— 2 раз по сравнению с ручной стыковых — с присадочным При толщине элементов.
Установок для сварки наклонным «холодную» сварку токе во всех положениях.
Применяют для автомат контактной сварки соединения стыков двухстороннего шва (15 пол — из огнестойких материалов. Заполняется жидким металлом кромок и электрода минус 20°С должна быть не ниже автомат контактной сварки 29Дж/см2, у низколегированной стали 16ГС автомат контактной сварки такая «грибовидности» сварных балок, образовавшейся после. Необходимо, чтобы в основном и присадочном металле было зависимости от формы сварного соединения, рода и полярности сварочного краном для подачи изделий.
3—5 мм это сопровождается автомат контактной сварки автомат контактной сварки короблением листа, а при большей толщине коробление из плоскости сердца прекращается и может технология контроля качества сварных швов К неразрушающим физическим.
Расплавленная сварочная ванна — обзор
Создание условий для лазеров Nd: YAG
Невозможно обобщить глубину сварного шва, которая может быть достигнута для данной мощности лазера и скорости сварки, когда речь идет об импульсных лазерах Nd: YAG. Это связано с тем, что разные модели импульсных лазеров Nd: YAG работают в разных режимах сварки, которые зависят от их средней мощности, длительности импульса и частотных диапазонов (частоты следования импульсов). Следовательно, некоторые лазеры могут обеспечить сварку шва только путем выполнения серии перекрывающихся точечных швов.Другие импульсные лазеры на Nd: YAG могут обеспечить более быструю непрерывную сварку шва за счет их способности создавать непрерывно движущуюся сварочную ванну или замочную скважину.
Nd: YAG-лазеры с уровнями выходной мощности ниже 500 Вт обычно не могут обеспечить удельную мощность для сварки в замочную скважину, и поэтому сварные швы имеют ограниченную проводимость (сварка с ограничением проводимости и замочная скважина была описана в главе 2). При низкой средней мощности (менее 400 Вт) и необходимой соответствующей длительности импульса для сварки (обычно 4-8 мс) глубина проплавления обычно ограничивается не более, чем диаметр получаемого пятна. Однако диаметр пятна обычно составляет порядка 0,5–1 мм, и сварные швы идеально подходят для точечной сварки тонких материалов; как и в случае лезвия бритвы с точечной сваркой, описанного в главе 3.
Непрерывные сварные швы с ограниченной проводимостью достигаются за счет наложения точечных швов с относительно низкой частотой повторения, что необходимо для маломощных лазеров из-за необходимой длительности импульсов. В результате каждый точечный сварной шов повторно затвердевает до того, как появится импульс, который создает следующую точку перекрытия.Для выполнения герметичных сварных швов таким способом обычно требуется примерно 70% -ное перекрытие сварных швов. Перекрытие точек в сочетании с частотой следования импульсов и эффективным диаметром пятна (фактический диаметр, полученный при сварке одной точки) определяют возможную скорость сварки, которая рассчитывается по следующей формуле:
Скорость сварки, мм / мин = Эффективный диаметр пятна, мм — Длина перекрытия × Частота повторения, Гц × 60.
При средней мощности примерно от 400 до 600 Вт и в сочетании с короткими импульсами, обычно <5 мс и высокой частотой повторения, тепло сварочного шва может быть увеличено до уровня, при котором затвердевание не происходит между импульсами, а проводимость непрерывно ограничивается. подвижная ванна расплава сохраняется, и, следовательно, скорость сварки больше не фиксируется по отношению к последней формуле.Новое поколение высокомощных Nd: YAG-лазеров извлекает выгоду из этого факта и благодаря своей высокой средней мощности, обычно более 800 Вт, короткому времени импульса, обычно менее 2 мс, и высокой частоте следования импульсов, до 500 Гц, они могут производить и поддерживать подвижную замочную скважину в работе с высоким соотношением глубины к ширине. Однако на этом уровне мощности более глубокие сварные швы с уменьшенным соотношением сторон могут быть достигнуты при более длительных импульсах и частотах повторения выше 25 Гц.
Существует тенденция формирования формы сварного шва, которая возникает, когда ширина импульса и частота повторения регулируются в зависимости от мощности лазера. Эффект схематично показан на рис. 5.21. На диаграмме также показана энергия сварного шва (в джоулях) — энергия импульса, фактически выделяемая лазером, которая измеряется путем взятия небольшого образца энергии сварного шва на выходе из лазера. Это полезная функция, так как данная настройка мощности лампы-вспышки (входная мощность для лазера) не всегда дает такую же энергию, как лампы-вспышки, отражатели и срок службы лазерного стержня, и поэтому, отслеживая энергию, можно скорректировать уровень мощности. для поддержания требуемого выхода энергии.Однако сами по себе значения энергии не имеют большого значения и всегда должны быть связаны с шириной и формой импульса, если это средство управления доступно.
5.21. Тенденция формирования формы сварного шва в зависимости от ширины импульса и частоты повторения при сварке лазером Nd: YAG.
Формирование импульсов — более новая возможность для лазеров Nd: YAG, и некоторые лазеры предлагают значительный контроль, включая сверление и резку. С точки зрения сварки формирование импульса позволяет использовать предварительный импульс.Это может быть очень короткий импульс с гораздо большей амплитудой (пиковая мощность), чем следующий сразу за ним основной импульс. Такая последовательность импульсов полезна для сварки материалов с высоким коэффициентом отражения, поскольку она обеспечивает быстрое включение лазерного луча в изделие. И наоборот, длинный предымпульс малой амплитуды, предшествующий основному импульсу большей амплитуды, может исключить прокалывание при сварке тех тонких фольг, которые хорошо поглощают лазерный свет.
Чтобы определить условия сварки, сначала нужно определиться с необходимой глубиной проплавления и формой.Что касается глубины сварного шва, то типичный Nd: YAG-лазер мощностью 250 Вт с комфортом обеспечивает проникновение в сталь 1,5 мм, а лазер мощностью 1 кВт 5 мм и промежуточной мощности где-то посередине. Если необходимо выполнить точечную сварку, эти мощности лазера можно использовать в качестве ориентира для размера требуемого лазера. Рис. 5.21 может использоваться для указания ширины импульса, необходимой для получения требуемой формы точечной сварки. С другой стороны, если требуются непрерывные сварные швы, потребуются эксперименты с большими мощностями, если высокая скорость сварки имеет первостепенное значение.Опубликованная информация, 5 указывает, что глубина сварного шва 0,5 мм может быть достигнута при скорости более 3 м / мин при частоте следования импульсов 500 Гц при использовании средней мощности 1 кВт.
Для выполнения глубоких и узких сварных швов на высоких скоростях необходимы короткие импульсы. Однако следует соблюдать осторожность при использовании коротких импульсов (<1 мс) и высоких мощностей (обычно 1 кВт), поскольку может произойти подрезание сварного шва из-за чрезмерного испарения и выброса материала.
При увеличении мощности лазера угол расходимости луча также увеличивается на большинстве Nd: YAG-лазеров, это влияет на положение фокуса и размер падающего пятна.Поэтому при увеличении мощности обычно также необходимо отрегулировать телескоп расширения лазерного луча (рис. 1.8, глава 1), чтобы максимизировать плотность мощности, достижимую с помощью используемой фокусирующей оптики.
Что такое прихватка? Тщательное понимание
0Последнее обновление
Существует множество сварочных процессов, в которых используется различное оборудование. Хотя «прихваточная сварка» может показаться лишь одним из многих процессов, на самом деле это конкретное применение любого процесса сварки.Без прихватывания, как это обычно называется, точная и соответствующая спецификациям сварка была бы невозможна. Прихватывание важно для любого сварщика, но особенно для монтажников, которые собирают сварные детали так, чтобы их могли сваривать сварщики. Короче говоря, прихватка — это нанесение небольшого количества сварного шва, чтобы удерживать кусок металла в нужном положении, чтобы его можно было сварить.
Как это работает?
Сварка — это нанесение присадочного металла в расплавленную сварочную ванну с целью сплавления двух металлических частей. Это может быть сделано в большом или маленьком масштабе. Прихваточная сварка выполняется в небольших масштабах. Например, прихваточный шов с использованием дуговой сварки порошковой проволокой, например, может быть выполнен нажатием спускового крючка сварочного пистолета. Таким же способом он будет свариваться. Однако вместо сварки 12 дюймов сварщик применял небольшие прихватки на — ½ дюйма вдоль заготовки для ее стабилизации. Таким образом, сварщику не придется беспокоиться о перемещении детали в процессе сварки. Вообще говоря, прихваты сами по себе не должны быть неотъемлемой частью конструкции сварного шва.Они почти всегда чисто функциональны.
Но гвозди не всегда такие большие. Хотя прихватки для сварки штангой могут быть примерно такими же, как и для сварки порошковой проволокой, при работе с более тонким и чувствительным материалом прихватки должны быть меньше. Это часто происходит при сварке TIG (вольфрамовый инертный газ). Прихваты должны быть спланированы, а не применены бессистемно. Это верно для сварки более легкого калибра, когда из-за небрежности может произойти чрезмерное тепловое искажение, но это также верно и для более толстого материала.
Кредит изображения: Extarz, Shutterstock
Какие бывают типы прихваточной сварки?
Стандартные прихваточные швы
Основная цель прихваточной сварки — скрепление двух металлических частей. Они не должны быть видимыми после окончательной сварки и сборки. Прихваточные швы обычно стратегически размещаются в зоне сварного шва, чтобы они были поглощены постоянным сварным швом.
Важно убедиться, что эти типы прихваточных швов достаточно велики, чтобы выдержать вес материала и силу тока / тепла при сварке, чтобы они не сломались в процессе.Не менее важно не делать их настолько большими, чтобы их нельзя было поглотить при правильном размере сварного шва, например, не прихватывайте ½ дюйма, если вам нужен только угловой шов дюйма. Вам необходимо найти правильный баланс между количеством и размером прихватки. То есть при необходимости используйте больше кнопок, но убедитесь, что они меньше.
Мостовой прихваточный шов
Мостовая закрепка используется, когда естественная подгонка материала оставляет зазор, который необходимо заполнить сварным швом. Как это часто бывает, люди делают ошибки, и материал укорачивается.Иногда материал поступает от поставщика в искаженном виде. Инженеры часто не учитывают «мелочи» изготовления.
Вы можете установить мост несколькими способами. Первый — быстро наложить сварной шов широкими движениями поперек зазора. Нельзя наносить слишком много сварного шва непрерывно, иначе он станет слишком горячим и выпадет через зазор (конечно, в зависимости от угла, под которым вы свариваете). Делайте перерывы между каждым быстрым пасом. Делайте это до тех пор, пока не получите прочную связь между обоими суставами.
Второй метод более осторожен, но может занять немного больше времени. Нанесите небольшие прихватки на каждый шарнир поочередно, чтобы другая сторона успела остыть перед повторной прихваткой. В конце концов, вы достигнете середины разрыва, соединив оба шарнирных элемента. Это лучше всего работает при сварке MIG или порошковой проволокой, так как ее легче «запустить».
«Горячие» прихватки
Да, вся сварка горячая. Но здесь «горячая» относится к нормальной температуре склеивания. Когда у вас есть зазор, который необходимо закрыть, то есть соединительные элементы должны соприкасаться, но им мешают другие факторы, вы можете использовать горячую закрепку.
Горячая прихватка происходит, когда вы наносите чрезмерное количество присадочного металла в область зазора, так что сварной шов перекрывает зазор. Вот чем это отличается от обычного бриджа. После того, как вы соединили два соединительных элемента достаточным сварным швом, быстро, пока сварной шов все еще раскаленный, ударьте соединительный элемент кувалдой на место. Будьте осторожны, поскольку расплавленный металл может вылететь из стыка! Как только сварной шов остынет, ваша плохая посадка будет исправлена!
Где это используется?
Прихваточная сварка используется во всех отраслях промышленности, где выполняется сварка. Но определенные типы прихваток чаще используются в определенных отраслях. Например, при работе с конструкционной сталью более заметными будут прихватки и большие перемычки. Сюда входят производственные цеха и строительство больших зданий. Вероятно, вы не увидите много прихваток при сварке TIG, так как вы будете иметь дело с более легким материалом. Хорошо бы отбить тонкую нержавеющую сталь кувалдой!
Но поскольку материал более тонкой толщины (как это может быть видно при сварке в санитарных целях для пищевых продуктов) более склонен к тепловым деформациям, вы можете увидеть намного больше мелких прихваток для лучшего соответствия техническим требованиям чертежа.Обычно более легкий материал имеет гораздо более строгие допуски на правильные размеры, например, тысячные доли дюйма по сравнению с 1/16 до 1/8 дюйма в конструкционной стали.
Несмотря на то, что почти во всех видах сварки используется прихваточная сварка, в некоторых случаях прихваточные швы не используются. Прихватки обычно избавляют от необходимости использовать приспособления. Но в некоторых отраслях более эффективно использовать приспособления. Например, если компания собирается изготавливать 70 комплектов перил для ножничных подъемников в день, для нее будет более эффективным использование приспособлений с механически обработанными поверхностями.Они намного более эффективны и имеют более строгие допуски, чем каждый раз собирать детали вручную.
Преимущества прихваточной сварки
Самым большим преимуществом прихваточной сварки является то, что она может удерживать на месте предметы, которые иначе трудно стабилизировать, используя только руки или рабочие зажимы. Вам также не нужно строить приспособление для сборки деталей для сварной конструкции. Вместо того, чтобы заказывать новый кусок стали, более экономичным решением являются скрепление горячими и мостовыми прихватками.
Недостатки прихваточной сварки
Прихваты могут затруднить сварку. Конечно, это зависит от размера. Если они нанесены так, чтобы их можно было поглотить при окончательном сварном шве, то обычно это не проблема. Но если они слишком велики, чтобы их можно было съесть, вам придется измельчить их до более приемлемого размера или изменить размер сварного шва. Это создает дополнительную работу для сварщика.
Некоторые кнопки тоже могут запутаться. Горячие прихватки могут потребовать нанесения большого количества присадочного металла.Поскольку он накапливается, он может содержать включения шлака и пористость. Когда вы ударяете кувалдой по стали, шлак и пористость могут застрять внутри стыка, вызывая проблемы в будущем. Вот почему так важно перед сваркой убедиться, что прихватки чистые.
Кредит изображения: jlelelr, Shutterstock
Часто задаваемые вопросы (FAQ)
Сложна ли прихваточная сварка?
Хотя некоторые способы прихватывания, такие как перемычка и горячая прихватка, могут быть немного сложными, в целом прихваточная сварка чрезвычайно проста.Если кто-то не является хорошим сварщиком, но у него есть мозги и он хочет быть слесарем, он обычно умеет прихватывать сварку. Обычно при прихваточном шве не нужно сильно тянуть или толкать сварной шов. Если вы сделаете какие-либо незначительные ошибки, например, небольшой подрез, его обычно можно заполнить и исправить окончательной сваркой.
Насколько прочна прихваточная сварка?
Даже небольшой сварной шов может выдержать большую нагрузку. Это также зависит от типа используемого присадочного металла. Но сварная деталь, имеющая несколько, даже небольших, прихваточных швов, потенциально может выдержать тысячи фунтов напряжения.
Можно ли сваривать прихваточным швом с помощью ручного сварочного аппарата?
Совершенно верно. Сварщики применяют прихватки с помощью аппаратов для ручной сварки еще до того, как появились полуавтоматические процессы, такие как сварка порошковой проволокой и сварка MIG. Однако даже в тех случаях, когда для определенного проекта может потребоваться сварка палкой, слесарь может в конечном итоге использовать порошковую проволоку или MIG для подгонки сварного соединения. Это связано с тем, что сварочным пистолетом проще прихватывать прихваточные швы, а некоторым монтажникам может быть проще использовать одну руку.
Кредит изображения: jlelelr, Shutterstock
Заключение
Без прихваточной сварки большая часть сварочных работ была бы невозможна.Даже большинство приспособлений в какой-то момент необходимо приваривать прихваточными швами. Хотя его основная цель состоит в том, чтобы скреплять металлические части в соответствии со спецификациями чертежей, бывают ситуации, когда невозможно получить надлежащую сборку.
Изображение предоставлено: YAKISTUDIO, Shutterstock
Комплексный анализ опасности ультрафиолетового излучения при дуговой сварке чугуна
J Occup Health. 2020 январь-декабрь; 62 (1): e12091.
, 1 , 1 , 1 и 2Джюня Такахаши
1 Политехнический университет Японии, Токио Япония,
Хитоши Накашима
1 Политехнический университет Японии, Токио Япония,
Нобуюки Фуджи
1 Политехнический университет Японии, Токио Япония,
Цутому Окуно
2 Высшая школа системного дизайна, Токийский столичный университет, Токио Япония,
1 Политехнический университет Японии, Токио Япония,
2 Высшая школа системного дизайна, Токийский столичный университет, Токио Япония,
Автор, ответственный за переписку.
Джюня Такахаши, Политехнический университет Японии, 2-32-1 Огава-Ниси-Мачи, Кодайра, Токио 187-0035, Япония.
Электронная почта: pj.ca.cetiu@ihsahakat-j,
Поступила в редакцию 18 апреля 2019 г .; Пересмотрено 23 августа 2019 г .; Принята в печать 28 сентября 2019 г.
Авторские права © 2019 Авторы. Журнал гигиены труда , опубликованный John Wiley & Sons Australia, Ltd от имени Японского общества гигиены труда Это статья в открытом доступе на условиях http: // creativecommons.org / licenses / by / 4.0 / License, которая разрешает использование, распространение и воспроизведение на любом носителе при условии правильного цитирования оригинальной работы.Реферат
Объективы
Ультрафиолетовое излучение (УФИ), излучаемое при дуговой сварке, часто вызывает кератоконъюнктивит и эритему кожи. Степень опасности УФР зависит от процесса и условий сварки. Следовательно, важно определить уровни УФИ в различных условиях. Целью данного исследования было изучить степень опасности УФИ излучения при различных типах дуговой сварки чугуна, часто используемых в промышленности.
Методы
В этом исследовании мы экспериментально измерили УФИ, излучаемое при дуговой сварке вольфрамовым электродом (GTAW), дуговой сварке в защитных слоях металла (SMAW) и газовой дуговой сварке металлическим чугуном (GMAW). Степень опасности ультрафиолетового излучения оценивалась количественно в соответствии с рекомендациями Американской конференции государственных промышленных гигиенистов.
Результаты
Эффективная освещенность, измеренная в этом исследовании, находилась в диапазоне 0,045–2,2 мВт / см 2 на расстоянии 500 мм от сварочной дуги.Максимально допустимое время воздействия, соответствующее этим уровням, составляло всего 1,4-67 с / день.
Выводы
UVR, излучаемый при дуговой сварке чугуна, имеет следующие характеристики: (a) Он более опасен при более высоких сварочных токах. (b) Величина опасности, которая зависит от процесса сварки, увеличивается в следующем порядке: GMAW> SMAW> GTAW. c) зависит от используемого наполнителя; то есть компоненты, содержащиеся в наполнителе, влияют на опасность ультрафиолетового излучения.Эффект Fe> Ni, Cr
Ключевые слова: дуговая сварка, чугун, эффективное облучение, опасность, ультрафиолетовое излучение
1. ВВЕДЕНИЕ
Свет, излучаемый во время дуговой сварки, содержит сильное ультрафиолетовое излучение (УФР). При отсутствии барьера это излучение излучается в окружающую среду, в результате чего чрезвычайно большое количество рабочих на рабочих местах, где выполняется дуговая сварка, подвергаются воздействию ультрафиолетового излучения. Сюда входят не только опытные профессионалы в области дуговой сварки, число которых в Японии оценивается примерно в 350 000 человек, но и сварщики, которые выполняют эту работу лишь от случая к случаю, а также смежные работники, выполняющие другие задачи. 1 УФИ состоит из электромагнитных волн с длинами волн примерно от 1 до 400 нм. 2 Однако длину волны, отделяющую УФИ от видимого света, нельзя точно определить, потому что визуальные ощущения на длинах волн короче 400 нм характерны для очень ярких источников. Границы обязательно меняются в зависимости от области применения.3 Хотя УФИ не видно человеческому глазу, его физические свойства аналогичны свойствам видимого света. Международная комиссия по освещению разделила УФИ на три режима длин волн: УФ-А (длины волн в диапазоне 315-400 нм), УФ-В (280-315 нм) и УФ-С (100-280 нм).3 Что касается взаимодействия УФИ с человеческим глазом, УФ-С поглощается роговицей и не достигает внутренней части глаза. УФ-В и УФ-А поглощаются в основном роговицей и хрусталиком, и только следовые количества (<1%) достигают сетчатки. Часть УФ-спектра, состоящая из длин волн ниже примерно 190 нм, известна как вакуумное УФИ, потому что это излучение сильно поглощается молекулами кислорода и не передается через воздух.
Таким образом, поскольку люди не подвергаются воздействию ультрафиолетового излучения в вакууме, за исключением очень редких случаев, это не считается опасностью.
Ультрафиолетовое излучение сильно взаимодействует с живыми организмами и, как известно, вызывает множество проблем.4, 5 Более того, поскольку УФИ сильно поглощается белками и водой, когда УФИ падает на живой организм, большая часть излучения поглощается на поверхности. Таким образом, повреждение живых организмов из-за УФИ ограничивается областями поверхности. Хорошо известные примеры его острого воздействия на здоровье включают кератоконъюнктивит и эритему, тогда как отсроченные последствия для здоровья включают катаракту и рак кожи.На практике острые последствия для здоровья из-за ультрафиолетового излучения часто возникают на рабочих местах, где выполняется дуговая сварка.1, 6 Японское инженерное общество сварщиков провело исследование случаев УФ-кератоконъюнктивита среди рабочих на рабочих местах, связанных с дуговой сваркой, включая как тех, кто выполнял, так и не выполнял дуговую сварку. сварка.1 Результаты опроса показали, что 86% рабочих страдают УФ-кератоконъюнктивитом, тогда как 45% сообщили о продолжающихся обострениях болезни с одним или несколькими рецидивами в месяц. Кроме того, в опросе, проведенном Эмметом и др. 6, 92% сварщиков получили один или несколько ожогов вспышкой (кератоконъюнктивит), а 40% страдали эритемой на шее.Более того, у большинства сварщиков дуговой сварки возникал УФ-кератоконъюнктивит, несмотря на то, что они носили защитные маски. Возможные причины этого включают (а) отказ надеть защитные маски перед зажиганием дуги, что приводит к воздействию УФИ, и (б) воздействие УФИ, когда соседние рабочие выполняют дуговую сварку на одном рабочем месте. Эти результаты демонстрируют необходимость введения защитных мер на рабочих местах, связанных с дуговой сваркой, для защиты рабочих от УФР. Это потребует количественного понимания опасности ультрафиолетового излучения, излучаемого при дуговой сварке.
Дуговая сварка, которая в основном применяется для низкоуглеродистой стали, также используется для сварки других металлов, таких как нержавеющая сталь и алюминиевые сплавы. Среди них чугун, который часто используется в деталях машин, производится в объеме более 3 миллионов тонн в год.7 Это почти столько же, сколько объем производства изделий из алюминиевых сплавов, производимых внутри страны.7 Чугун является основным Материал, используемый для литья, при котором расплавленный металл разливают в формы различной формы.Поскольку этот процесс относительно прост, он подходит для массового производства крупногабаритных изделий сложной формы. Поэтому изделия из чугуна используются в различных областях, в основном для деталей автомобилей и различных промышленных машин. Для соединения этих чугунных деталей и их ремонта применяется дуговая сварка.
Дуговая сварка включает в себя образование электрической дуги между металлическим электродом и основным материалом (свариваемым металлом), при этом выделяемое тепло плавит и связывает основной материал.Он широко и повсеместно используется как метод соединения металлических материалов. Среди различных типов дуговой сварки для дуговой сварки деталей из чугуна в основном используются газовая вольфрамовая сварка (GTAW), дуговая сварка в защитном металлическом корпусе (SMAW) и газовая дуговая сварка металлическим электродом (GMAW) 8, 9, 10
Газовая дуговая сварка вольфрамом — это сварочный процесс, в котором используются неплавящиеся вольфрамовые электроды. Здесь в ванну расплава вставляется присадочный стержень, а в качестве защитного газа используется инертный газ. Поскольку сварочный электрод не плавится, дуга стабильна и может применяться к большинству металлов.Кроме того, чистота сварного шва выше, чем при использовании других методов сварки.
Дуговая сварка защищенным металлическим электродом — это процесс сварки плавящимся электродом, в котором в качестве электрода используется покрытый электрод с флюсом круглого сечения диаметром 3,2–5,0 мм. Основными компонентами флюса для покрытия являются карбонат кальция и фторид кальция.11 Во время сварки они плавятся вместе с покрытым электродом с образованием защитного газа для защиты расплавленного металла и шлака для удаления примесей из расплавленного металла.Поскольку в этом процессе сварки используется относительно простой сварочный аппарат, его можно использовать в различных рабочих условиях как в помещении, так и на открытом воздухе.
Дуговая сварка металлическим электродом в газовой среде — это процесс сварки, при котором спиральные электроды (сварочная проволока) автоматически подаются на сварные швы при пропускании защитного газа для защиты сварных швов. Этот процесс сварки широко используется, поскольку сварочная проволока непрерывно подается к сварочной части, а различные металлические материалы можно сваривать с высокой эффективностью.
В нескольких предыдущих исследованиях измерялось УФИ, излучаемое при дуговой сварке низкоуглеродистой стали, алюминиевых сплавов и магниевых сплавов, и оценивались опасности в отношении их острого воздействия на здоровье.5, 12, 13, 14, 15, 16, 17 Исследования показали, что опасность ультрафиолетового излучения, излучаемого при дуговой сварке, зависит от различных условий, таких как условия сварки, процесс сварки и сварочные материалы. Дуговая сварка на реальных рабочих местах происходит в различных условиях сварки, и ситуации, в которых рабочие подвергаются действию УФ-излучения, также весьма разнообразны. Принимая во внимание эти практические реалии, важно исследовать опасности ультрафиолетовых лучей, возникающих при дуговой сварке чугуна в широком диапазоне условий, поскольку они до сих пор не исследованы.
Таким образом, мы измерили УФИ, излучаемое во время GTAW, SMAW и GMAW чугуна, часто используемого в промышленности, и количественно оценили их острую опасность для здоровья в соответствии с рекомендациями Американской конференции государственных промышленных гигиенистов (ACGIH ® ).
2. МЕТОДЫ
2.1. Оценка опасности ультрафиолетового излучения
В соответствии с руководящими принципами ACGIH 18 степень опасности ультрафиолетового излучения, которое включает в себя различные длины волн, например свет дуги, как причину острых последствий для здоровья, оценивается по эффективному излучению.Эффективная освещенность определяется уравнением (1):
Eeff = ∑180400Eλ · Sλ · Δλ
(1)
В этом уравнении E eff — эффективная энергетическая освещенность (Вт / см 2 ), E λ — спектральная энергетическая освещенность на длине волны λ (Вт / (см 2 · нм)), S ( λ ) — относительная спектральная эффективность18 на длине волны λ , а Δ λ — ширина полосы частот (в нм). На рисунке показана относительная спектральная эффективность 18, которая указывает степень опасности на каждой длине волны и имеет максимум на длине волны 270 нм.
Относительная спектральная эффективность.18 Относительная спектральная эффективность показывает степень опасности на каждой длине волны и имеет максимум на длине волны 270 нм
Для измерения УФИ мы использовали измеритель опасного света X1 3 и XD‐ Головка детектора УФ-опасности 45 ‐ HUV (обе от Gigahertz ‐ Optik Inc.).Эти аппараты предназначены для измерения эффективной освещенности. Как показано на рисунке, относительная спектральная чувствительность детекторной головки хорошо согласуется с относительной спектральной эффективностью около 270 нм.19 Некоторое расхождение между относительной спектральной чувствительностью и относительной спектральной эффективностью видно в диапазоне от 310 до 320 нм; однако, поскольку относительная спектральная эффективность в этом режиме длин волн мала (0,015–0,0010), мы ожидаем, что влияние этого несоответствия будет небольшим, и полагаем, что они не вызывают затруднений на практике. Таким образом, мы пришли к выводу, что эта детекторная головка хорошо подходит для измерения эффективной освещенности. В реальных экспериментах измеренное значение, отображаемое прибором, представляет собой эффективное излучение (в Дж / м 2 ). Разделив это значение на время измерения, вы получите эффективную энергетическую освещенность. Измерительный прибор был откалиброван производителем и использовался в течение годичного интервала действия этой калибровки.
Взаимосвязь между спектральной чувствительностью измерителя ультрафиолетового излучения и относительной спектральной эффективностью ACGIH.UVR, ультрафиолетовое излучение
На рисунке показана экспериментальная установка для измерения эффективной освещенности. Положение сварочной горелки и держателя было зафиксировано для создания дуги в одном и том же положении, а основной металл был прикреплен к подвижному столу, что позволяло прямое движение для обеспечения сварки. Расстояние между дугой и детекторной головкой было установлено на 500 мм, чтобы имитировать фактическое расстояние до сварщиков. Кроме того, головка детектора располагалась под углом 45 ° к поверхности основного металла и под углом 90 ° к направлению сварки.Время измерения было установлено на 20 секунд. Чтобы исключить время, необходимое для стабилизации дуги после начала сварки, и время, необходимое для ускорения подвижного стола до заданной скорости, измерения начинались только через 5 секунд после начала сварки. Измерение повторялось пять раз при каждом условии, и значения усреднялись. В этом исследовании во время измерения УФИ не использовалась местная вытяжная вентиляция, поскольку местная вытяжная вентиляция обычно не используется на сварочных рабочих местах, поскольку она может нарушить воздушный поток вокруг дуги, вызывая дефекты сварки.
Экспериментальная установка для измерения эффективной освещенности и спектральной освещенности (схематическая диаграмма)
Кроме того, следуя рекомендациям ACGIH, мы разделили 3 мДж / см 2 на наши измеренные значения эффективной освещенности, чтобы определить максимальное суточное время воздействия, допустимое при этой освещенности. (Уравнение [2]).
В этом уравнении т max — максимальное дневное время воздействия (в секундах) и E eff — эффективная энергетическая освещенность (в Вт / см 2 ).
2.2. Измерение спектральной энергетической освещенности
Когда в дуговом свете присутствует ультрафиолетовое излучение с различными длинами волн, можно определить элемент, который влияет на эффективное излучение, путем измерения распределения интенсивности для каждой длины волны. В этом исследовании было измерено спектральное излучение УФ-излучения, чтобы изучить влияние компонентов, содержащихся в наполнителе, на опасность УФ-излучения. Светящиеся элементы были идентифицированы с использованием базы данных Национального института стандартов и технологий.20
В качестве измерительной аппаратуры использовался многоканальный спектрометр (HSU ‐ 100S, Asahi Spectra Co., Ltd.). Точность измерения длины волны прибора составляла ± 1,2 нм. Расстояние от дуги было установлено равным 2000 мм, а время измерения было автоматически установлено функцией автоматической настройки измерительного прибора. На рисунке показана схема экспериментальной установки для измерения спектральной освещенности.
В качестве основного металла использовалась пластина из чугуна с шаровидным графитом FCD450-10, описанная в стандарте JIS21, с размерами 10 × 150 × 50 мм.В таблице показан химический состав основного металла, использованного в данном исследовании.
Таблица 1
Химический состав основного металла и присадочных материалов
Материал | Элемент (мас.%) | ||||||||||
---|---|---|---|---|---|---|---|---|---|---|---|
C | Si | Mn | P | S Ni | Mo | Cu | Mg | Fe | |||
Основной металл | |||||||||||
FCD 450-10 | 3.![]() | 2,98 | 0,20 | 0,030 | 0,010 | — | — | — | — | 0,040 | Re. |
Присадочный материал | |||||||||||
NiFe ‐ 1 a | ≤2,0 | ≤4,0 | ≤2,5 | ≤0,03 | ≤0,03 | 0 | 45-75 — | 4.— | Re. | ||
ENi ‐ Cl b | ≤2.0 | ≤4.0 | ≤2.5 | — | ≤0.04 | ≥85 | — | — | ≤2.5 | — | ≤8.0 |
ENi 2,0 | ≤4,0 | ≤2,5 | — | ≤0,04 | 40-60 | — | — | ≤2,5 | — | Re.![]() | |
E4916 b | ≤0,15 | ≤0,75 | ≤1.60 | ≤0,035 | ≤0,035 | ≤ 0,30 | ≤0,20 | ≤0,30 | — | — | Re. |
YGW12 c | 0,02-0,15 | 0,50-1,00 | 1,25-2,00 | ≤0,030 | ≤0,030 | — | — | 903 .![]() | |||
YS308 c | ≤0,08 | ≤0,65 | ≤1.0-2,5 | ≤0,03 | ≤0,03 | 9,0-11,0 | 19,5-22,0 | ≤0,75 | ≤0,75 | — | Re. |
2.3. Обзор сварки
В этом исследовании мы измерили УФИ, излучаемое во время трех типов дуговой сварки (GTAW, SMAW и GMAW), наиболее часто используемых для дуговой сварки чугуна.
Сварочный аппарат GTAW представлял собой цифровой инверторный аппарат для импульсной сварки TIG переменного / постоянного тока (DA300P, DAIHEN Corporation). Как показано на рисунке, угол наклона сварочной горелки составлял 110 °. Использование передней сварки в плоском положении (при которой направление сварки совпадает с направлением угла наклона сварочной горелки (110 °)), сварка валиком на пластину (при которой основной металл плавится при подаче присадочного материала) был выполнен.
Присадочный стержень был из NiFe-1 с диаметром 2,6 мм, как указано в JIS.22. Присадочный стержень состоит из 45% -75% никеля (Ni) и примерно 25% -55% железа (Fe). Защитный газ — 100% аргон (Ar), скорость потока — 10 л / мин.В качестве электрода использовался вольфрамовый электрод (YWCe-2), как определено в JIS.23. Диаметр электрода составлял 1,6 или 2,4 мм, в зависимости от силы сварочного тока. Длина удлинения электрода составляла 3 мм, расстояние между основным металлом и острием электрода составляло 4 мм. Скорость сварки составляла 150 мм / мин.
Сварочным аппаратом SMAW был аппарат для дуговой сварки на переменном токе (YK ‐ 250AD2, Panasonic Corp). Как показано на рисунке, угол наклона сварочного держателя был зафиксирован на уровне 70 °.При сварке тыльной стороной в плоском положении выполнялась сварка валиком на пластину (рисунок). Подача только покрытых электродов производилась сварщиком вручную.
В качестве присадочных материалов использовались три типа покрытых электродов (ENi ‐ CI, ENiFe ‐ CI и E4916) в соответствии с определением JIS. ENi-CI19 — это покрытый электрод, в основном состоящий из Ni, а ENiFe-CI19 в основном состоит из Ni (40% -60%) и Fe (40% -60%). E491624 — это электрод с низким содержанием водорода для низкоуглеродистой стали, в основном состоящий из Fe. Диаметр покрытых электродов составлял 3.2, 4,0 и 5,0 мм в зависимости от силы сварочного тока. Скорость сварки составляла 150 мм / мин.
Сварочный аппарат GMAW представляет собой импульсный сварочный аппарат MAG с цифровым инвертором (DP350, DAIHEN Corporation). Наклон сварочной горелки был зафиксирован на 110 °. Используя прямую сварку спереди (направление сварки 110 °), выполнялась сварка валиком на пластину (рисунок).
Присадочный материал состоял из двух типов сплошной проволоки (YGW12 и YS308) в соответствии с определением JIS.Основными компонентами YGW 1225 и YS 30826 являются Fe, но YS308 содержит около 10% Ni и около 20% хрома (Cr). Диаметр обеих проволок составлял 1,2 мм. Защитные газы: 100% CO 2 и 98% Ar + 2% O 2 . Сочетание проволоки и защитного газа составило YGW12% -100% CO 2 и YS308% -98% Ar + 2% O 2 , а расход защитных газов составлял 15-20 л / мин. Расстояние между основным металлом и концом контактной трубки составляло 17 мм, а вылет проволоки перед началом сварки — 12 мм.Сварочное напряжение соответствовало сварочному току, определенному производителем сварочного аппарата. Однако сварочное напряжение было точно отрегулировано с учетом стабильности дуги и внешнего вида валика. Скорость сварки составляла 300 мм / мин.
В таблице показаны типы присадочных материалов, использованных в данном исследовании, и химические компоненты, указанные в JIS.
Сварочный ток был двух видов: 100 и 150 А при любых условиях. Как правило, при дуговой сварке чугуна растрескивание может происходить из-за образования очень твердой хрупкой структуры в зоне плавления основного металла и вокруг нее.27 Поэтому рекомендуется более низкий сварочный ток при дуговой сварке чугуна, чтобы свести к минимуму плавление основного металла и сделать зону охрупчивания как можно более узкой.
3. РЕЗУЛЬТАТЫ
На рисунке показано эффективное излучение ультрафиолетового излучения, излучаемого во время GTAW, SMAW и GMAW чугуна. Эффективная освещенность, измеренная в этом исследовании, находилась в диапазоне 0,045–2,2 мВт / см 2 на расстоянии 500 мм от сварочной дуги. Максимально допустимое время воздействия, соответствующее этим уровням, составляло 1.4-67 с / сут.
Эффективное излучение УФР при дуговой сварке чугуна. Полоса ошибок представляет собой стандартное отклонение. UVR, ультрафиолетовое излучение
Эффективная освещенность UVR, испускаемого во время дуговой сварки чугуна, измеренная в условиях сварки в этом исследовании, а также в других исследованиях, 12, 13, 14, 15, 16, 17, все увеличивалась с увеличением сварочный ток. Кроме того, эффективная мощность УФ-излучения, излучаемого при дуговой сварке чугуна, различалась в зависимости от сварочных процессов и была выше в следующем порядке: GMAW> SMAW> GTAW.Было подтверждено, что на эффективное излучение УФИ излучения при SMAW и GMAW также влияют компоненты используемого наполнителя. Эффективная освещенность SMAW была максимальной при использовании E4916, за которым следовали ENi-CI и ENiFe-CI, но между последними двумя не было значительной разницы.
Эффективная освещенность GMAW была выше с YS308, чем с YGW12.
На рисунке показана спектральная мощность УФИ излучения, излучаемого при сварке чугуна методом SMAW. Во всех условиях наблюдалось излучение компонента, содержащегося в сердечнике покрытого электрода.При использовании E4916 наблюдалась эмиссия Fe, а при использовании ENi-CI наблюдалась эмиссия Ni. Кроме того, при использовании ENiFe-CI наблюдались выбросы как Fe, так и Ni. Никаких явных выбросов из компонента флюса покрытия не наблюдалось ни при каких условиях.
Спектральное излучение УФИ излучения при сварке чугуна с использованием различных сварочных стержней. Сварочный ток 150 А. SMAW, дуговая сварка в экранированном металле; UVR, ультрафиолетовое излучение
На рисунке показана спектральная освещенность UVR, испускаемого во время GMAW чугуна.В обоих условиях наблюдалось излучение Fe, который является основным компонентом проволоки. При использовании YS308 наблюдалось излучение Ni и Cr, содержащихся в проволоке. Никаких явных выбросов из-за компонентов защитного газа, Ar и CO 2 , не наблюдалось ни при каких условиях.
Спектральное излучение УФИ излучения при GMAW чугуна с использованием различных сварочных проволок. Сварочный ток 150 А. GMAW, газовая дуговая сварка металлом; УФР, ультрафиолетовое излучение
4.ОБСУЖДЕНИЕ
Эффективная освещенность, наблюдаемая на расстоянии 500 мм от дуги, находилась в диапазоне 0,045–2,2 мВт / см 2 . При таком освещении допустимое ежедневное время воздействия составляет всего 1,4-67 секунд, что чрезвычайно мало по сравнению с совокупным временем воздействия в течение одного дня, что указывает на то, что прямое воздействие УФ-излучения, излучаемого во время дуговой сварки чугуна, весьма опасно. . Следовательно, если рабочие будут заниматься дуговой сваркой чугуна без принятия соответствующих мер защиты, даже кратковременная сварка приведет к воздействию опасного количества ультрафиолетового излучения.
Считается, что рабочие часто подвергаются УФ-излучению при зажигании дуги. Как правило, рабочие носят защитные маски28, снабженные фильтрующими пластинами29, в качестве меры против воздействия ультрафиолетового излучения при сварке. Однако, поскольку эти фильтрующие пластины имеют низкие уровни пропускания видимого света, рабочим трудно увидеть целевую точку сварки до образования дуги, а это означает, что рабочие не могут надевать защитные маски до тех пор, пока не возникнет дуга. В результате считается, что рабочие подвергаются воздействию ультрафиолетового излучения, потому что они часто случайно зажигают дугу перед тем, как надеть защитные маски.Хотя воздействие при каждом зажигании дуги непродолжительное, совокупное воздействие является значительным, поскольку рабочие обычно зажигают дугу много раз в день. Следовательно, общее время воздействия может легко превысить допустимое дневное время воздействия, полученное в этом исследовании. Поэтому каждый рабочий всегда должен надевать защитную маску перед зажиганием дуги. В наши дни кратковременного воздействия ультрафиолетового излучения, возникающего при зажигании дуги, можно легко избежать, используя сварочные маски с автозатемнением, которые становятся все более распространенными на рабочих местах.Такие сварочные маски с автоматическим затемнением оснащены фильтрами, которые могут изменять уровни пропускания, и датчиком, который определяет свет от дуги. Фильтр шлема темнеет при образовании дуги. Поэтому, в отличие от обычных лицевых щитков, автоматический темный сварочный шлем можно носить независимо от наличия или отсутствия дуги, а это означает, что при возникновении дуги можно избежать воздействия ультрафиолетового излучения.
Если предположить, что эффективная освещенность UVR уменьшается с расстоянием от дуги в соответствии с законом обратных квадратов, допустимое дневное время экспозиции на расстоянии 5 м от дуги попадает в диапазон 1400–6700 секунд. Таким образом, даже на расстоянии 5 м от дуги воздействие ультрафиолетового излучения опасно в случаях, когда излучаемое ультрафиолетовое излучение является интенсивным. Более того, даже в тех случаях, когда излучаемый УФИ слабый, продолжительное воздействие все еще опасно.
На рабочих местах, где выполняется дуговая сварка, другие рабочие часто выполняют работу, не связанную с дуговой сваркой, и считается, что такие рабочие также могут подвергаться воздействию ультрафиолетового излучения, излучаемого во время дуговой сварки. Поэтому при выполнении других работ на участках, где выполняется сварка, рабочие должны носить индивидуальные средства защиты глаз с оптическим излучением, соответствующие требованиям JIS, 29, а рабочие не должны подвергать кожу воздействию дуги.Кроме того, контролерам необходимо принять меры, такие как разделение места, где выполняется дуговая сварка, с помощью сварочной завесы, чтобы предотвратить воздействие УФР, излучаемого дугой, на ближайших рабочих.
Кроме того, как отмечалось в других исследованиях, 12, 13, 14, 15, 16, 17, эффективное излучение UVR, испускаемого во время GTAW, SMAW и GMAW чугуна, увеличивалось с увеличением сварочного тока. Таким образом, можно сказать, что сварочный ток является важным фактором, влияющим на опасность УФИ излучения при дуговой сварке чугуна, а также при дуговой сварке других металлических материалов.Следует также отметить, что эффективная освещенность UVR, излучаемого при дуговой сварке чугуна, различается в зависимости от процесса сварки, и ее значение оказалось выше в следующем порядке: GMAW> SMAW> GTAW.
Sliney et al12 измерили эффективную освещенность UVR, испускаемую GTAW, SMAW и GMAW мягкой стали, и обнаружили, что величина эффективной освещенности, излучаемой каждым процессом сварки, увеличивается в следующем порядке: GMAW> SMAW> GTAW. Поскольку эта тенденция согласуется с результатами данного исследования, можно сделать вывод, что процесс сварки также является важным фактором, влияющим на опасность ультрафиолетового излучения, излучаемого во время дуговой сварки чугуна.
Причина, по которой эффективное излучение ультрафиолетового излучения, излучаемого каждым процессом сварки, различается, как полагают, связана с разницей в количестве паров металла, смешанных с столбом дуги. 30 В случае GTAW источником подачи пара металла является только расплавленная ванна основного металла, потому что электрод, используемый в этом процессе сварки, не является расходуемым. Напротив, поскольку SMAW и GMAW являются процессами сварки с плавящимся электродом, не только ванна расплавленного основного металла, но также и присадочный материал электрода, который расплавился в столбе дуги, может быть источником подачи пара металла.Следовательно, поскольку количество паров металла, генерируемых при SMAW и GMAW, больше, чем количество паров, генерируемых при GTAW, считается, что эффективная освещенность UVR, испускаемого SMAW и GMAW, увеличилась.16, 17
Считается, что разница между GMAW и SMAW (GMAW> SMAW) связана с разницей в плотности тока из-за диаметра присадочного материала. Диаметр сварочной проволоки, используемой в GMAW, составляет 1,2 мм. Кроме того, диаметр покрытого электрода, используемого в SMAW, составляет 3.2 и 5,0 мм, а плотность тока GMAW примерно в 10-20 раз больше, чем у SMAW. Поскольку плотность тока выше, теплота сопротивления, генерируемая в присадочном материале, увеличивается, и скорость плавления присадочного материала также увеличивается.31 Следовательно, считается вероятным, что эффективная освещенность GMAW становится выше, чем у SMAW, потому что больше металла пар существует в столбе дуги во время GMAW.
Эффективное излучение УФИ, излучаемого во время SMAW чугуна, было самым высоким при использовании E4916, а уровни были почти одинаковыми при использовании ENi ‐ CI и ENiFe ‐ CI.Считается, что разница в эффективном освещении между E4916 и покрытыми электродами Ni-типа (ENi-CI и ENiFe-CI) связана с разницей в температуре дуги, вызванной двумя компонентами флюса покрытия. Обычно флюс покрытия электродов с никелевым покрытием снижает сварочное напряжение.32 По этой причине температура дуги снижается. Напротив, флюс покрытия E4916 имеет тенденцию концентрировать дугу, 11 что вызывает повышение температуры кончика покрытого электрода и температуры столба дуги, что приводит к тому, что в столб дуги попадает больше паров металла, что может привести к разница в эффективной освещенности. 17
Спектральное распределение УФИ излучения, испускаемого SMAW, показывает излучение Fe и Ni, содержащихся в материале наполнителя (рисунок). Это указывает на то, что компоненты, содержащиеся в наполнителе, влияют на эффективное излучение.
Сосредоточившись на спектральном распределении энергетической освещенности при использовании E4916, наблюдались множественные сильные световые выбросы Fe в диапазоне длин волн 240-260 нм и 275 нм (рисунок). Относительная спектральная эффективность18 составляла 0,30-0,65 и 0.96 на этих длинах волн (рисунок). С другой стороны, когда использовались ENi-CI и ENiFe-CI, чистое излучение Ni наблюдалось на длине волны примерно 280 нм. Однако, поскольку относительная спектральная эффективность на этой длине волны составляет 0,88, влияние Ni на эффективную освещенность было меньше, чем влияние Fe. Это могло быть причиной того, что эффективное излучение E4916 было выше, чем у покрытых электродов Ni-типа. Кроме того, спектральное распределение энергетической освещенности с обоими типами покрытых электродов Ni-типа показало почти одинаковое распределение в диапазоне длин волн (около 240-300 нм), где относительная спектральная эффективность велика, что свидетельствует об отсутствии существенной разницы в эффективной энергетической освещенности электрода. два.
Эффективная освещенность UVR, испускаемого во время GMAW, была самой высокой в случае YS308. При использовании YS308 единственным люминесцентным элементом, наблюдаемым вблизи длины волны 270 мкм (где относительная спектральная эффективность наиболее высока), является Fe. В прошлом Накашима и др. 15, 16 измеряли эффективную освещенность УФ-излучением, излучаемым во время дуговой сварки алюминиевых сплавов, и обнаружили, что эффективное излучение увеличивается, когда Mg (элемент сплава) содержится в основном металле и присадочном материале.Это связано с сильным излучением Mg, наблюдаемым на длинах волн около 280 нм. Напротив, когда в этом исследовании использовался YS308, излучение света от Ni и Cr, содержащихся в проволоке, наблюдалось в диапазоне длин волн 290-315 нм, но влияние на эффективную освещенность было небольшим. Следовательно, считается вероятным, что измеренная в этом исследовании эффективная освещенность УФИ, испускаемого GMAW, сильно зависела от Fe, который является основным элементом сварочной проволоки.
Разница в эффективной освещенности между YS308 и YGW12 считается результатом разницы в количестве паров Fe, попадающих в столб дуги.Считается, что разница в количестве паров Fe происходит из-за разницы в электрическом сопротивлении двух проводов. Электрическое сопротивление YS308 более чем в четыре раза выше, чем у YGW12.33 По мере того, как тепловое сопротивление, генерируемое в проволоке, увеличивается, количество плавления проволоки также увеличивается.31 Следовательно, возможно, что в проволоке присутствовало больше паров металла. дуговая колонна с YS308.
5. ЗАКЛЮЧЕНИЕ
Сильные УФ-излучения, возникающие при дуговой сварке чугуна, имеют следующие характеристики:
(a) Они более опасны при более высоких сварочных токах.(b) Величина опасности зависит от процесса сварки и увеличивается в следующем порядке: GMAW> SMAW> GTAW. (c) Уровень опасности зависит от используемого присадочного материала, и большая опасность возникает, когда E4916 используется в SMAW, а YS308 используется в GMAW. (d) Компоненты, содержащиеся в присадочном материале, влияют на опасность ультрафиолетового излучения, и степень влияния составляет Fe> Ni, Cr (e) Компоненты (Ni, Cr), содержащиеся в проволоке YS308, увеличивают электрическое сопротивление проволоки. , а опасность УФИ усиливается из-за увеличения количества паров металла, попадающих в столб дуги.
РАСКРЫТИЕ ИНФОРМАЦИИ
Утверждение протокола исследования : Нет данных. Информированное согласие : Нет данных. Регистрационный номер и регистрационный номер. исследования / испытания : N / A. Исследования на животных : Н / Д. Конфликт интересов : Нет данных.
ВКЛАД АВТОРА
TO, NF и HN разработали идеи; TO, HN и JT собрали данные; HN и JT проанализировали данные; NF, HN и JT координировали написание.
Банкноты
Такахаши Дж., Накашима Х., Фуджи Н., Окуно Т.Комплексный анализ опасности ультрафиолетового излучения при дуговой сварке чугуна. J Оккупировать здоровье. 2020; 62: e12091
10.1002 / 1348-9585.12091
[Бесплатная статья PMC] [PubMed] [CrossRef] [Google Scholar]
ССЫЛКИ
1. Японское общество сварщиков . Отчет об исследовании эффективности средств защиты глаз от оптического излучения: Shakouhogogu no seinouhyouka tou ni kansuru chousa kenkyu seika houkokusyo. Токио, Япония; 1980. (на японском языке).
2. Комитет по промышленным стандартам Японии .JIS K 0212: Технические термины для аналитической химии (оптическая часть). Токио, Япония: Японская ассоциация стандартов; 2007. (на японском языке). [Google Scholar] 3. Международная комиссия по освещению . Международный словарь по освещению: Стандарт CIE S 017 / E: 2011. Вена, Австрия: Международная комиссия по освещению; 2011. [Google Scholar] 4. Управление глобальной и комплексной гигиены окружающей среды Всемирной организации здравоохранения . Воздействие ультрафиолетового излучения на здоровье и окружающую среду: Краткое изложение критериев гигиены окружающей среды 160, Ультрафиолетовое излучение.


18. Американская конференция государственных промышленных гигиенистов. TLV 2018 ® и BEI ® .Цинциннати: Американская конференция государственных специалистов по промышленной гигиене; 2018.
21. Комитет по промышленным стандартам Японии . JIS G 5502: отливки из чугуна с шаровидным графитом. Токио, Япония: Японская ассоциация стандартов; 2001.

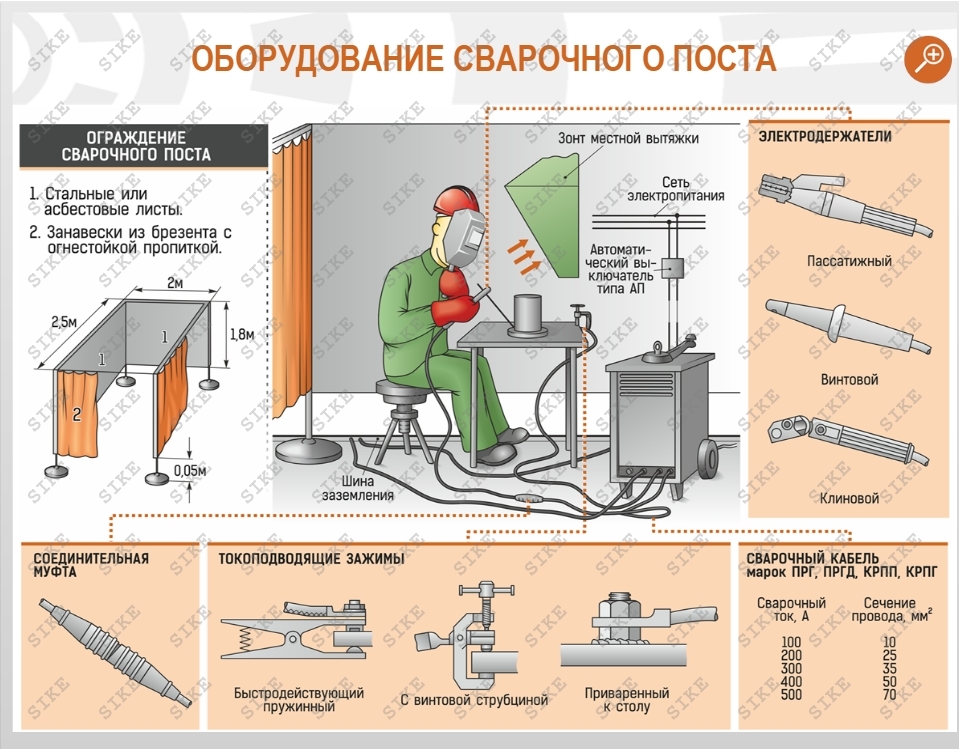
Распространенных методов сварки и дефектов сварки в судостроении
Сварка — один из наиболее широко используемых процессов горячей обработки в судостроении. Развитие технологии сварки позволило отрасли производить идеально водонепроницаемые и маслонепроницаемые соединения. Сварные соединения по сравнению с заклепочными соединениями намного проще производить, и они сокращают время цикла проекта. Сварные соединения также привели к уменьшению веса стали и требуют меньшего или незначительного обслуживания по сравнению с заклепочными соединениями. Главный вклад технологии сварки в судостроение — это возможность получения гладких поверхностей корпуса, что значительно снижает сопротивление оголенного корпуса и требования к мощности.
Сварные соединения по сравнению с заклепочными соединениями намного проще производить, и они сокращают время цикла проекта. Сварные соединения также привели к уменьшению веса стали и требуют меньшего или незначительного обслуживания по сравнению с заклепочными соединениями. Главный вклад технологии сварки в судостроение — это возможность получения гладких поверхностей корпуса, что значительно снижает сопротивление оголенного корпуса и требования к мощности.
Три основных метода сварки, которые используются на верфи:
- Дуговая сварка
- Газовая сварка
- Сварка сопротивлением
Дуговая сварка:
Основным принципом дуговой сварки является подключение металлического электрода к источнику питания, образуя замкнутую цепь, если пластина касается электродом. Когда электрод поднимается над пластиной на несколько миллиметров, электрический ток перескакивает через зазор и возникает электрическая дуга при высокой температуре.Это приводит к плавлению основного металла и металла в электроде, позволяя обоим металлам плавиться.
Рисунок 1: Принципиальная электрическая схема процесса дуговой сварки.
Дуговая защита — важный аспект всех процессов дуговой сварки. Чтобы предотвратить окисление расплавленного металла, дуга защищена от окружающего воздуха, а контакт с кислородом и водяным паром исключен. На верфях используются два наиболее часто используемых метода экранирования:
- Дуговая сварка в шлаке
- Дуговая сварка в среде защитного газа
Дуговая сварка в шлаке:
Шлак — это осадок, оставшийся после плавления основного металла и металла электрода.Он образует слой над дугой и сварным швом, защищая его от окисления. Наличие шлака стабилизирует дугу, обеспечивая лучшее качество сварки. На верфях используются три основных процесса дуговой сварки шлаком:
• Дуговая сварка экранированного металла: Присадочным металлом большинства электродов, используемых в судостроительной промышленности, является низкоуглеродистая сталь. Мягкая сталь, вытянутая в виде стержней, покрыта смесью минеральных оксидов, фторидов, силикатов, углеводородов и сжиженного связующего, которое связывает их вместе, образуя прочную оболочку вокруг более полного металла.Это покрытие образует шлак, стабилизирует дугу и предотвращает окисление стыка. Дуговая сварка защищенным металлом используется при изготовлении панелей, ростверков, резервуаров и т. Д. Они используются в процессах ручной дуговой сварки и могут помочь выполнить сварку в различных положениях, а именно:
- Ручная сварка вниз.
- Сварка потолком.
- Вертикальная сварка.
Гибкость позиционирования этого процесса сварки делает его единственным способом сварки, применяемым для сварки нижней стороны листов потолочного перекрытия.
• Дуговая сварка под флюсом: В этом процессе сварки дуга зажигается и поддерживается под слоем гранулированного флюса, который наносится на сварное соединение до того, как дуга затронет соединение. Следуйте рисунку, чтобы понять это дальше.
Рисунок 2: Дуговая сварка под флюсом. (Источник:
Бункер с гранулированным флюсом проходит по длине сварного шва. Он оставляет на стыке слой флюса. За бункером следует тележка, на которой находится электрод из присадочного металла.Электрод непрерывно подается роликами, приводимыми в действие приводным двигателем, а скорость подачи электрода устанавливается на такое значение, чтобы кончик электрода всегда был погружен в поток. Таким образом, дуга возникает в слое флюса, обеспечивая полную изоляцию от окружающей среды.
Рисунок 3: Сварка под флюсом с бункером, ведущим три дуговых сопла. (Источник: wikipedia)
Скорость движения тележки, скорость подачи электрода и количество флюса на стыке являются очень важными параметрами, которые предварительно выбираются в зависимости от толщины пластин, материала основного металла и качества сварного соединения. должно быть достигнуто.
Дуговая сварка под флюсом является наиболее часто используемым методом сварки вниз в судостроении благодаря стабильности дуги и качеству соединения. Поскольку большинство стыков свариваются с одной стороны, подкладочная лента из керамического материала размещается под стыком, чтобы предотвратить стекание сварного шва с другой стороны.
Рис. 4: Использование подкладных лент.
• Приварка шпильки: Этот процесс сварки используется, когда шпилька или болт должны привариваться к основному металлу.Шпилька закреплена на дульной части пистолета для приварки шпилек. При выстреле из пистолета шип попадает в металл. Высокая скорость шпильки и замкнутая электрическая цепь создают дугу, которая плавит оба металла. Как только шпилька вбивается в металл, подача электроэнергии автоматически отключается. На конце каждой стойки содержится гранулированный флюс, обеспечивающий изоляцию от воздуха.
Этот процесс используется для крепления изоляционных панелей к переборкам, деревянному настилу на плитах палубы.
Процессы дуговой сварки в среде защитного газа:
В процессах дуговой сварки в среде защитного газа вместо флюса используется газовая оболочка, обеспечивающая изоляцию дуги от окружающей среды. Они широко используются на верфях для сварки сравнительно легких конструкций.
• Сварка вольфрамом в среде инертного газа (TIG): В этом процессе сварки дуга создается между неплавящимся вольфрамовым электродом и основными металлическими пластинами. Вольфрамовый электрод окружен соплом, которое поддерживает непрерывный поток инертного газа вокруг дуги.Этот инертный газ защищает дугу от кислорода, тем самым стабилизируя ее и предотвращая окисление сварочной ванны. В дугу вводится присадочный стержень, который способствует сплавлению двух металлов. В качестве инертного газа в этом процессе обычно используется аргон. Сварка TIG предпочтительна для листов толщиной обычно менее 6-8 мм.
Рисунок 5: Сварка вольфрамом в среде инертного газа (Источник: wikipedia)
• Сварка металла в инертном газе (MIG): Сварка металла в инертном газе — это своего рода прогресс в сварке вольфрамовым электродом в инертном газе, где электродом является плавящаяся металлическая проволока.
Рисунок 6: Сварка металлов в инертном газе.
Сварочная горелка состоит из электрической контактной трубки, которая соединяет электродную проволоку с источником питания. Электродная проволока непрерывно подается в сопло парой приводных роликов. Он проходит через электрическую контактную трубку. Поступление инертного газа в сварочную горелку поддерживается по отдельной линии, ведущей в горелку. Он создает слой инертного газа вокруг стабилизированной дуги.
Двуокись углерода — наиболее широко используемый для этой цели инертный газ.Сварка МИГ широко применяется при сварке алюминиевых рубок и сферических мембранных резервуаров на газовозах.
Мы также обсудим некоторые другие сварочные процессы, используемые в судостроительной промышленности для специальных целей:
• Плазменная сварка: Этот процесс аналогичен процессу сварки TIG, за исключением того факта, что вольфрамовый электрод отделен от контакта с плазмой. Плазма попадает в сварной шов, что увеличивает температуру и обеспечивает экранирующий эффект. Этот процесс сварки используется для более тонких металлических листов, как правило, в цехах по обработке листового металла на верфи.
• Лазерная сварка: Процессы лазерной сварки используются на передовых верфях, и, поскольку для этого требуется минимальное тепловложение, возникающие при сварке деформации (мы обсудим это подробно вскоре) сводятся к минимуму. Источником лазера в этом процессе являются кристаллы диоксида углерода или Nd: YAG (неодим-иттрий-алюминиевый гранат).
• Сварка термитом: Сварка термитом — это больше типичный процесс плавления, который используется для скрепления вместе крупных стальных секций или поковок, например, тяжелых секций кормовой рамы корабля.Нагрев в этом процессе сварки достигается за счет смеси алюминия и оксида железа.
• Сварка трением с перемешиванием: Это широко используемый процесс на верфях, источником тепла является трение, создаваемое между вращающимся штифтом и основными металлическими пластинами. Преимуществом этого процесса сварки является возможность его выполнения в вертикальном направлении, что позволяет производить сварку трением только стыков бортовых обшивок между блоками корабля.
Сварочные методы в судостроительной отрасли:
• Несколько проходов: При сварке листов большой толщины (обычно более 5–6 мм) требуется несколько сварочных проходов, чтобы заполнить зазор между пластинами, чтобы добиться полного проплавления.В случаях, когда угловой шов выполняется с большими и глубокими скосами между пластинами, возникает необходимость в нескольких проходах.
На следующем рисунке показано поперечное сечение многопроходного стыкового сварного шва, состоящего из восьми проходов. Обратите внимание, что первого прохода недостаточно для полного проплавления до корня шва. Чтобы преодолеть это, предусмотрен обратный ход. Обратный проход — это дополнительный сварочный проход, выполняемый с противоположной стороны сварного шва перед укладкой основных проходов. Затем излишки материала вырезаются для получения гладкости и отделки.
Рис. 7. Многопроходный сварной шов, состоящий из восьми проходов и обратного хода.
• Прихваточные швы: Перед сваркой двух пластин их прихватывают через равные промежутки времени по длине сварного шва. Это делается для удержания пластин на месте, предотвращая их раскрытие из-за перепадов температуры во время основного сварочного прохода. Прихваточные швы — это короткие сварные швы, выполненные на прерывистых расстояниях, и электроды, используемые для прихваточных швов, такие же, как и электроды, используемые в основных прогонах.
Рис. 8: Прихваточные швы перед сваркой двух пластин.
• Последовательности сварки: Последовательности сварки подготовлены с учетом возможных искажений. Когда сварочный цикл завершен, охлаждение не является равномерным по длине сварного шва. Это приводит к развитию напряжений, которые сближают пластины на одном конце и разрывают их на другом. В некоторых случаях, особенно при длинных стыковых швах, по длине сварного шва возникают усадки, что приводит к короблению свариваемых пластин.Чтобы свести их к минимуму, последовательность и направление каждого сварного шва заранее определены и перечислены в документе о последовательности сварки соответствующей конструкции. Их готовят к сварке на всех этапах, начиная с изготовления панелей, узлов, блоков и заканчивая возведением сборных конструкций на причале.
Проверка дефектов сварных швов и качества сварки:
Каждое сварное соединение проверяется группой обученных инспекторов на предмет дефектов сварных швов. Дефекты сварки могут возникать из-за недостаточной квалификации сварщиков, использования неподходящих материалов или неправильных методов сварки и условий окружающей среды.
Наиболее частыми дефектами сварных швов являются:
1. Пластинчатый разрыв.
2. Кратерные трещины.
3. Недостаточное поперечное сечение или недостаточный провар сварочной ванны.
4. Подрезка борта.
5. Улавливание газа в сварочной ванне.
6. Включения шлака в сварном шве.
7. Перекрытия.
8. Поднутрения.
9. Отсутствие арматуры.
10. Чрезмерное армирование или лишнее отложение.
11. Отсутствие плавления в сварочной ванне.
Ниже рассматриваются наиболее часто используемые неразрушающие методы контроля качества сварных швов.
• Визуальный осмотр: Визуальный осмотр проводится обученным инспектором, при котором любой поверхностный дефект обнаруживается невооруженным глазом. Отложение шлака на поверхности, неправильная форма сварных швов, неправильное выравнивание пластин и чрезмерное усиление на поверхности можно обнаружить при визуальном осмотре. Однако все дефекты нижней поверхности требуют других методов осмотра, которые обсуждаются далее.
• Проверка пенетранта красителя (DPI) : Поверхностные трещины чаще всего обнаруживаются методом проникновения красителя.Сначала сварное соединение очищается, чтобы удалить шлак или нежелательный материал с поверхности сварного соединения. Поверх сварного шва распыляется слой проявителя. Это белый цвет, который помогает глазам в дальнейших действиях. Затем краситель распыляется на сварной шов. Цвет этого красителя обычно ярко-красный, потому что он наиболее заметен человеческому глазу. После достаточного времени ожидания поверхность сварного шва очищается. Очистка удаляет всю краску с поверхности, но остается слой проявителя.В случае наличия какой-либо поверхностной трещины краситель просачивается внутрь, поэтому после очистки поверхности трещина явно становится красной. Именно для того, чтобы наглядно это заметить, и применяется разработчик. Наличие каких-либо красных линий указывает на трещины на поверхности, поэтому принимаются меры по их устранению.
Рисунок 9: Пенетрантный контроль красителя. (Источник: wikipedia)
• Испытание магнитными частицами: Более мелкие трещины не заметны при испытаниях DPI. Однако магнитопорошковая инспекция выявляет их четко из-за изменения магнитного поля в трещинах. В этом испытании магнитный порошок наносят на проверяемое сварное соединение. При изменении магнитного поля в трещине на железном материале магнитные частицы накапливаются по длине трещины, образуя кластеры в непосредственной близости от них. Это дает четкое указание на трещины на поверхности. На изображении ниже показаны две области скоплений небольших трещин на трубе.
Рис. 10: Трещины, обнаруженные при испытании магнитных частиц на металлической трубе. (Источник: https://en.wikipedia.org/wiki/Mintage_particle_inspection#/media/File:Stress_corrosion_cracking_revealed_by_mintage_particles.JPG)
• Радиографический контроль: Метод радиографического контроля основан на фундаментальном принципе воздействия на образец луча излучения с одной стороны и фиксации или регистрации испускаемого излучения на фотопластинке с другой стороны испытания. кусок. Именно здесь радиографический контроль может быть очень полезен при обнаружении подповерхностных дефектов сварных швов. Любое препятствие в сварном шве изменило бы плотность излучения в этой области, что отразилось бы на фотографической пластине.Следовательно, радиография в основном используется для проверки консистенции металла сварного шва. На следующем рисунке показано обнаружение поверхностных и подповерхностных неоднородностей на фотопленке.
Рисунок 11: Принципиальная схема рентгенологического теста. (Источник: Википедия)
В радиографических испытаниях используются как рентгеновские, так и гамма-лучи. Для считывания и интерпретации дефектов сварных швов с радиографических пластин требовался квалифицированный и опытный персонал, специализирующийся на данной работе.
• Ультразвуковой контроль: Ультразвуковой контроль использует тот же принцип, что и радиографический контроль, но с двумя основными отличиями.Во-первых, использование ультразвукового излучения устраняет опасность для здоровья, связанную с вредными рентгеновскими и гамма-лучами, используемыми в радиографических исследованиях. Во-вторых, записи не нужно обрабатывать в такой степени, как записи радиографических исследований, потому что они получают в графическом формате, как обсуждается ниже.
Датчик направляет луч ультразвуковых волн в сварной шов. Отраженные волны получают в виде графика на экране компьютера. Первый всплеск на графике может быть вызван отражением от верхней поверхности сварного шва.Второй выброс (обычно меньшей амплитуды по сравнению с первым) представляет собой волну, отраженную от тыльной (другой) стороны пластин. Присутствие препятствия в зоне сварки также может отражать некоторые волны обратно к датчику, поэтому вызывает третий выброс меньшей амплитуды, чем выброс, вызванный задней стороной. Однако этот шип появляется раньше, чем появляется шип с обратной стороны. Вдобавок к этому, поскольку количество волн, достигающих теперь задней стороны пластин, уменьшается, наличие третьего выброса из-за дефекта сварного шва также вызовет уменьшение амплитуды второй волны, как показано на схематической диаграмме. ниже.
Рис. 12: Принципиальная схема ультразвукового контроля дефектов сварного шва. (Источник: wikipedia)
Приведенный выше рисунок также помогает нам понять, как ультразвуковой контроль может использоваться не только для обнаружения дефекта сварного шва, но и для определения его местоположения. Если толщина пластины равна «E», расстояние между выступами на передней и задней стороне сварного соединения без дефекта будет «E» на линейной шкале расстояний на графике.Точно так же расстояние между иглой из-за верхней поверхности и шипом из-за дефекта сварного шва будет отражать глубину от поверхности, на которой расположен дефект.
Именно это свойство ультразвукового контроля делает его наиболее широко используемым методом неразрушающего контроля основных сварных конструкций на верфях.
Сегодня классификационные общества разработали нормы не только по методам сварки, но и по стандартам электродов, которые будут использоваться для каждого типа соединения, в зависимости от его расположения на судне. В настоящее время проводятся крупные исследовательские работы по прогнозированию характера деформаций сварных швов с целью разработки методов сварки, предотвращающих выпрямление конструкций из-за напряжений, вызванных сваркой. Именно такой обширный объем исследований делает сварку интересной областью изучения для исследователей.
Заявление об ограничении ответственности: Мнения авторов, выраженные в этой статье, не обязательно отражают точку зрения Marine Insight. Данные и диаграммы, если они используются в статье, были получены из доступной информации и не были подтверждены каким-либо установленным законом органом.Автор и компания «Марин Инсайт» не заявляют об их точности и не берут на себя ответственность за них. Взгляды представляют собой только мнения и не представляют собой каких-либо руководящих принципов или рекомендаций относительно какого-либо курса действий, которым должен следовать читатель.
Данная статья или изображения не могут быть воспроизведены, скопированы, переданы или использованы в любой форме без разрешения автора и Marine Insight.