Как отличить шлак от металла при сварке и как его выгнать | ММА сварка для начинающих
Как отличить шлак от металла при сварке и как его выгнатьКак отличить шлак от металла при сварке и как его выгнать
Во время сварки новички сталкиваются с большим количеством вопросов, один из которых, как отличить шлак от металла. Шлак отличается от металла не только цветом и плотностью, но и текучестью. Однако когда учишься варить, контролировать полностью процесс сварки, следить за дугой и движением электрода, да ещё и обращать внимание на шлак, не имеющему опыта сварщику очень трудно.
Тем не менее, научившись разжигать дугу и вести электрода, с данным вопросом разобраться все-таки придется, ведь в процессе сварки нужно не просто различать, где металл, а где шлак, но и уметь выгнать его из сварочной ванны. В данной статье сайта про сварку mmasvarka.ru будет рассказано о том, как отличить шлак от металла, и выгнать его во время сварки.
Из-за чего появляется шлак на металле
Наверняка вы не раз замечали, что прямо над сварочным швом и по его краям, сразу после сварки, образуется темная сильнопористая корка, которая легко отлетает от металла при ударе молотком. Это и есть тот самый пресловутый шлак — не что иное, как продукт сгоревшей электродной обмазки и окислившегося металла.
Что такое сварочный шлак?
Ни в коем случае не стоит думать, что шлак это зло. Конечно же, нет, ведь главной его задачей, является перекрыть доступ кислорода к сварочной ванне, и защитить тем самым металл от окисления. Однако, если шлак попадёт непосредственно в сам сварочный шов, то, быть беде. При попадании в сварочную ванну, шлак серьезно ослабляет прочность сварного соединения и может стать причиной его разрушения в дальнейшем.
Как отличить шлак от металла при сварке
Чтобы отличить шлак от раскалённого металла в процессе сварки, достаточно запомнить следующее:
- Шлак имеет более темный цвет, чем нагретый металл;
- Текучесть металла намного выше шлака;
- Шлак и металл имеют разную плотность;
- Шлак остывает намного медленнее, чем металл;
- Шлак легче металла.
О чем это все говорит? На самом деле, все очень просто, и в процессе сварки отличить шлак от металла, совсем несложно.
Шлак при сварке металла вредит сварному швуШлак при сварке металла вредит сварному шву
Достаточно лишь приглядеться к самому процессу, и станет понятно, что шлак зачастую стремится сбежать в сварочную ванну, он темного цвета и легко сдувается, если изменить угол движения электродом. Следует помнить всегда о том, что шлак не должен попасть в сварочную ванну, и это самое главное правило при сварке металлов.
Как выгнать шлак во время сварки
Чтобы полностью выгнать шлак при сварке, достаточно выдерживать большой наклон электрода. Кстати, так легче будет распознать этот самый шлак от металла. При этом важно заметить, что большой наклон электрода способен сдуть не только шлак, но и раскалённый металл, поэтому здесь важно найти «золотую середину».
Разрушение сварочного соединения вследствие попадания шлакаРазрушение сварочного соединения вследствие попадания шлака
Для начинающих сварщиков, которые еще не умеют отличать шлак от металла, держать электрод во время сварки нужно вертикально. Делая небольшие колебательные движения электродом поперёк шва, нужно добиться, тем самым, перекрывания кромки фасок. Также можно попробовать варить углом назад, таким образом, отличить шлак от металла будет намного проще.
Как отличить шлак от металла при сварке?
Ну и последнее, при сварке электродами с основным покрытием, распознать шлак намного проще. Выгнать его получится как самим электродом (изменив его наклон), так и повышением силы тока или же короткой дугой. Не бойтесь экспериментировать, и у вас, наверняка, все получится!
Сварочная ванна…, или Горе от ума — Ручная дуговая сварка — ММA
Доброго времени суток!
Для начала:
Варить самостоятельно начал лет 5 назад, первый аппарат — самопальный брал у товарища, не ахти мощный, электрод 2-3 какие попались подруку. Первый нормальный опыт пришел с вваркой в раму калитки листа 1мм. Причем так как электроды товарища (двойка) кончились быстро, в сарае откопалось запрятанное в далекие годы сокровище — 5кг электродов тройки, варить которыми было «невозможно» ! :cray:))
Пришедший на помощь друг сказал — «ешкин кот! УОНИ!»
Так был добавлен самопальный выпрямитель. Забыл сказать, что ток регулировался трехпозиционной перемычкой обмоток, так что выбор был не ахти и учеба протекала в жестких условиях. 😉
Чтоб бороться с прожигом тонкого листа и залипами была придумана кнопка на держаке которая управляла пусковой релюхой на первичной обмотке (вентилятор охлаждения был включен до нее). Стало учиться уже не через «ешь твою медь» каждые пять минут. ИМХО — полезная весчь не только для новичков!
Было все! И прожиг тонкого металла, и зайцы вплоть до два дня — ничего не вижу, и перекосы от напряжений в конструкциях, и …да много чего, вообщем все как у всех. Потом появился навык. И полдюймовка начала свариваться и прожиги размером с монету 3коп. СССР начали завариваться…
Начало нравиться и появилось желание варить все и везде где можно :)))
Но появилась лень! Лень возить тяжеленную хрень от товарища и обратно, а потому что он переехал на 5 км подалее от меня.
И был куплен САИ-200 (не будем обсуждать аппарат, это делается на другом форуме, желающим дам ссылку).
Переварив все что нужно и не нужно первая волна эйфории прошла. Вроде как все тип-топ.
И от предисловия переходим к сути:
С прошлой осени сам не брал держак в руки, решил полазить по инету, посмотреть на новинки ибо еще один товарищ похвастался приобретением инвертора «который можно носить в кармане». Залез сюда, наткнулся на ветку http://www.chipmaker.ru/index.php?showtopic=608&st=600 прочитал с удовольствием, почерпнул для себя новое.
НО! Чудо со знаком минус!!! — На выходных варил каркас вольера, стал думать во время процесса, искать ванну. Результат — прожоги-непровары, чешуйчатый шов! Трындец! :(((
Как же я раньше варил? на ощупь, чуствовал электродом что и куда вести… на место сварки пристально смотрел только в момент поджега и в момент заклепки…
Сразу скажу — в маске стекло №3 чтоб видеть куда электрод в начале тыкать (это после зайцев сильных страх за глаза, сначала примеряюсь потом кивок-маска и тыкаю уже куда надо чуть видя в сумраке что не промазал). Я так понимаю что я варил на ощупь электродом, практически не глядя на сам шов… ванну я так и не увидел… варить стал хуже…
ИТОГ: Что делать? 🙁
Сижу на пеньке, закусываю горькую пирожком…
хотелось бы услышать мнения WOW и Вжик …
как отличить от металла при сварке? Что это такое и по какой причине его образуется много? Состав отхода и плотность, утилизация
В процессе выполнения сварки рабочая область стыка двух металлических деталей подвергается контакту с элементами окружающей среды: кислородом, смесью защитных газов, а также расплавом шлака. Такое контактное взаимодействие происходит при высоких температурных режимах плавления металла. В некоторых случаях подобное взаимодействие может оказаться положительным для металла, но в большей мере газы, кислород и шлаки изменяют химический состав металла и его физические свойства.
Что это такое и как появляется?
В процессе выполнения сварочных работ в области стыка двух металлических деталей образуется много побочных продуктов, называемых шлаком. Сварочный шлак выглядит как черная корка рыхлой плотности и неоднородной структуры. Причина его появления естественна, так как шлак является побочным продуктом сварки, появляющимся на сварочном шве. Состав отхода включает в себя оплавленные элементы флюса или компонентов обмазки сварочных электродов, а также оксиды металлов. Побочный продукт сварочного процесса, образующийся во время стыковки металлических деталей и в процессе оплавления электрода, заполняет собой плавильную ванну шва.
Побочный продукт появляется при любом виде сварочных работ, и его наиболее важные функции таковы:
- обеспечивает формирование прочного сварного шва и гарантирует последовательность процесса сварки;
- предотвращает окислительное влияние кислорода на области проведения сварных работ;
- создает постоянство химического состава сплава металлов в области шва;
- обеспечивает необходимые технологические условия для соединительного сварного соединения металла;
- предупреждает возникновение дефектов шва в процессе сварки.

Как отличить от металла при сварке?
- нагретый металл светлее, чем шлак, который обладает более насыщенным и темным оттенком;
- шлак обладает низкой текучестью, тогда как расплавленный металл более текучий и подвижный;
- плотность металла гораздо выше, чем плотность сварочного шлака;
- расплавленный металл застывает намного раньше, чем расплавленный шлак;
- металл имеет больший вес, если сравнивать его со шлаком.
Отличия существующие между расплавленными металлом и побочным продуктом сварочных работ основываются на плотности и текучести металлов. Металл и шлак имеют разную скорость нагрева. Когда начинается сварочный процесс, металл нагревается, плавится и при этом приобретает ярко-красный цвет. После того как процесс сварки завершается, шов постепенно остывает и приобретает темный оттенок, при этом шлак поднимается на поверхность шва. Сначала шлак имеет темный цвет, но когда он остывает, то становится светлее, чем металл.
Если зачистить шов, постучав по нему молотком и обработав напильником, можно легко отличить ярко выраженный блеск металла и темные матовые вкрапления шлака.
Зачем и как удалять?
Сразу после окончания процесса сварки оксиды металлов защищают сварочный шов от чрезмерно быстрого остывания.
После выполнения сварочных работ готовый шов требуется зачищать, особенно важно делать это, когда соединяют детали, имеющих большую толщину, и для надежности стыка выполняют несколько сварочных швов, поверх предыдущих. Если не убрать побочные продукты сварки, то выполнить следующий шов будет невозможно, так как шлак будет погашать дугу сварки. В случае когда сварочный шлак обладает повышенной вязкостью, его необходимо удалить, иначе шов будет формироваться непоследовательно и хаотично, образуя корку и дефекты. У такого шва температура при удалении шлака после сварки падает равномерно, и это дает возможность для формирования ровного стыка.
Сварочный шлак имеет пористое строение и образует с металлом слабые связи, его удаляют путем механической обработки поверхности готового шва. Отходы сварки в расплавленном виде являются причиной того, что шов будет непрочен и быстро разрушится.

После того как с поверхности сварочного шва шлак удален, он уже не препятствует дальнейшей обработке стыка и становится ненужным побочным продуктом сварочного процесса, подлежащим утилизации. Отходы, получаемые в процессе сварки, относятся к 4 классу опасности. Из этого следует, что такие отходы подлежат контролю за их утилизацией и на них оформляется специальный паспорт. Утилизация либо вторичная переработка сварочных отходов является довольно простой – электроды и побочные продукты сварки отправляют в переплавку, но прежде их подвергают сортировке исходя из состава их примесей. Благодаря переплавке сварочных отходов можно получать готовую легированную сталь с заданным химическим составом компонентов.
Кроме добавления шлака в сплавы, их в небольшом количестве можно включать и в состав флюсов.
Все о сварочном шлаке смотрите в следующем видео.
Как увидеть шлак при сварке и не спутать с металлом
Как увидеть шлак при сварке и не спутать с металломОсновная проблема начинающих сварщиков заключается в том, что они не понимают, что происходит в процессе сварки, и не умеют отличать шлак от расплавленного металла. Всё это доставляет массу проблем и нежелание заниматься электросваркой в дальнейшем.
А ведь от того, насколько быстро новичок начнёт отличать шлак от металла, зависит скорость обучения и качество сварного шва. Научись отличать шлак от металла — и ты поймёшь, как варить! Именно так говорят опытные сварщики, но не дают толком никакого разъяснения.
Как научиться отличать шлак от металла при сварке
На самом деле существует достаточно много советов и способов отличать шлак при сварке. Чем быстрее вы научитесь это делать, тем лучше для вас в плане опыта и дальнейшей практики.
Итак, первое, что нужно знать начинающему сварщику, так это то, что учиться отличать шлак лучше всего при сварке электродами с основным покрытием. Рутиловые электроды хоть и лучше, но шлак рассмотреть при их использовании гораздо сложнее из-за его большей плотности.
При сварке электродами с основным покрытием, шлак выглядит чуть темнее расплавленного металла. Он имеет большую текучесть, и как бы следует за электродом, образуя собой корку для защиты сварочной ванны от кислорода. Это такая себе плёнка, которая после застывания превращается в шлак.
Поэтому, исходя из всего вышеперечисленного, нужно выделить основные моменты, которые связаны вот с чем:
- Цвет шлака темнее, чем металла;
- Шлак более подвижен, чем металл, он как пенка, хорошо растекается;
- Плотность у шлака и металла разная;
- После того, как дуга погасла можно увидеть, что металл быстро остывает и меняет цвет в отличие от шлака;
- Металл тяжелее шлака.
Наиболее просто учиться отличать шлак от металла, если варить основными электродами, в верхнем положении. В таком случае жидкие капли шлака, которые образуются за сварочной ванной, начнут сразу же стекать вниз.
Практический способ определения шлака
Также можно воспользоваться и другим способом, как отличить шлак от металла при сварке. Для этого понадобится целый электрод, на котором нужно счистить покрытие на некотором расстоянии. Берём плоскогубцы и через каждые 5 см сдираем электродное покрытие, оставляя только один металлический стержень.
Для чего это нужно делать? Всё просто, и при дальнейшем обучении сварки используем именно этот электрод. Теперь при сгорании электрода будет отчётливо видно, где шлак, когда электрод начнёт плавиться с покрытым обмазкой участком, а где металл.
Достаточно немного посмотреть под углом, чтобы увидеть, как шлак прирастает к металлу тонкой корочкой. Таким образом, используя все вышеперечисленные советы можно быстро научиться в процессе сварки определять, где шлак, а где жидкий металл.
Как отличить шлак от металла?
Array ( [TAGS] => [~TAGS] => [ID] => 104585 [~ID] => 104585 [NAME] => Как отличить шлак от металла? [~NAME] => Как отличить шлак от металла? [IBLOCK_ID] => 1 [~IBLOCK_ID] => 1 [IBLOCK_SECTION_ID] => 115 [~IBLOCK_SECTION_ID] => 115 [DETAIL_TEXT] =>Как отличить шлак от металла?
Сварщики-новички сталкиваются с множеством проблем и вопросов, возникающих в процессе. Так, на первых этапах многим сложно отличить шлак от металла, и то, как выгонять этот шлак во время сварки. В этой статье мы расскажем о том, как это сделать, и что нужно для того чтобы сварочный шов получился качественным.
Главным отличием плавящегося металла от шлака, во время сварки, является его текучесть. Металл является более жидким и подвижным, а в процессе самой сварки отчетливо видно, как он закипает в сварочной ванне. В свою очередь, шлак является более тягучим и имеет более темный оттенок.
![]()
Часто возникают ситуации, когда шлак наплывает на сварочную ванну. В такой ситуации сварщику практически ничего не видно, и чтобы избежать это, ему приходится наклонять электрод таким образом, чтобы струя газа (которая испаряется из обмазки) выдувала шлак обратно на сварочный шов. После этого, сварочная ванна вновь открывается и место сварки становится отчетливо видно.
Проводя аналогию, можно привести пример тазика с мыльной водой. Чтобы увидеть воду через пенку, её необходимо сдуть и только тогда вам откроется вид на воду, и всё содержимое в ней.
Таким образом, начинающему сварщику всегда необходимо держать в голове одно правило – шлак ни в коем случае не должен сбегать в сварочную ванну, и тогда качество сварочных швов станет на порядок лучше.
Источник: vse-o-svarke.org
[~DETAIL_TEXT] =>
Сварщики-новички сталкиваются с множеством проблем и вопросов, возникающих в процессе.
Так, на первых этапах многим сложно отличить шлак от металла, и то, как выгонять этот шлак во время сварки. В этой статье мы расскажем о том, как это сделать, и что нужно для того чтобы сварочный шов получился качественным.
Главным отличием плавящегося металла от шлака, во время сварки, является его текучесть. Металл является более жидким и подвижным, а в процессе самой сварки отчетливо видно, как он закипает в сварочной ванне. В свою очередь, шлак является более тягучим и имеет более темный оттенок.
Часто возникают ситуации, когда шлак наплывает на сварочную ванну. В такой ситуации сварщику практически ничего не видно, и чтобы избежать это, ему приходится наклонять электрод таким образом, чтобы струя газа (которая испаряется из обмазки) выдувала шлак обратно на сварочный шов. После этого, сварочная ванна вновь открывается и место сварки становится отчетливо видно.
Проводя аналогию, можно привести пример тазика с мыльной водой.
Чтобы увидеть воду через пенку, её необходимо сдуть и только тогда вам откроется вид на воду, и всё содержимое в ней.
Таким образом, начинающему сварщику всегда необходимо держать в голове одно правило – шлак ни в коем случае не должен сбегать в сварочную ванну, и тогда качество сварочных швов станет на порядок лучше.
Источник: vse-o-svarke.org
[DETAIL_TEXT_TYPE] => html [~DETAIL_TEXT_TYPE] => html [PREVIEW_TEXT] => Сварщики-новички сталкиваются с множеством проблем и вопросов, возникающих в процессе. Так, на первых этапах многим сложно отличить шлак от металла, и то, как выгонять этот шлак во время сварки. В этой статье мы расскажем о том, как это сделать, и что нужно для того чтобы сварочный шов получился качественным. [~PREVIEW_TEXT] => Сварщики-новички сталкиваются с множеством проблем и вопросов, возникающих в процессе. Так, на первых этапах многим сложно отличить шлак от металла, и то, как выгонять этот шлак во время сварки.В этой статье мы расскажем о том, как это сделать, и что нужно для того чтобы сварочный шов получился качественным. [PREVIEW_TEXT_TYPE] => text [~PREVIEW_TEXT_TYPE] => text [DETAIL_PICTURE] => [~DETAIL_PICTURE] => [TIMESTAMP_X] => 16.10.2019 10:46:02 [~TIMESTAMP_X] => 16.10.2019 10:46:02 [ACTIVE_FROM] => 16.10.2019 [~ACTIVE_FROM] => 16.10.2019 [LIST_PAGE_URL] => /news/ [~LIST_PAGE_URL] => /news/ [DETAIL_PAGE_URL] => /news/115/104585/ [~DETAIL_PAGE_URL] => /news/115/104585/ [LANG_DIR] => / [~LANG_DIR] => / [CODE] => kak_otlichit_shlak_ot_metalla [~CODE] => kak_otlichit_shlak_ot_metalla [EXTERNAL_ID] => 104585 [~EXTERNAL_ID] => 104585 [IBLOCK_TYPE_ID] => news [~IBLOCK_TYPE_ID] => news [IBLOCK_CODE] => news [~IBLOCK_CODE] => news [IBLOCK_EXTERNAL_ID] => clothes_news_s1 [~IBLOCK_EXTERNAL_ID] => clothes_news_s1 [LID] => s1 [~LID] => s1 [NAV_RESULT] => [DISPLAY_ACTIVE_FROM] => 16.
10.2019 [IPROPERTY_VALUES] => Array ( [SECTION_META_TITLE] => Как отличить шлак от металла? [SECTION_META_KEYWORDS] => как отличить шлак от металла? [SECTION_META_DESCRIPTION] => Сварщики-новички сталкиваются с множеством проблем и вопросов, возникающих в процессе. Так, на первых этапах многим сложно отличить шлак от металла, и то, как выгонять этот шлак во время сварки. В этой статье мы расскажем о том, как это сделать, и что нужно для того чтобы сварочный шов получился качественным. [SECTION_PAGE_TITLE] => Как отличить шлак от металла? [ELEMENT_META_TITLE] => Как отличить шлак от металла? [ELEMENT_META_KEYWORDS] => как отличить шлак от металла? [ELEMENT_META_DESCRIPTION] => Сварщики-новички сталкиваются с множеством проблем и вопросов, возникающих в процессе. Так, на первых этапах многим сложно отличить шлак от металла, и то, как выгонять этот шлак во время сварки. В этой статье мы расскажем о том, как это сделать, и что нужно для того чтобы сварочный шов получился качественным.
[ELEMENT_PAGE_TITLE] => Как отличить шлак от металла? [SECTION_PICTURE_FILE_ALT] => Как отличить шлак от металла? [SECTION_PICTURE_FILE_TITLE] => Как отличить шлак от металла? [SECTION_DETAIL_PICTURE_FILE_ALT] => Как отличить шлак от металла? [SECTION_DETAIL_PICTURE_FILE_TITLE] => Как отличить шлак от металла? [ELEMENT_PREVIEW_PICTURE_FILE_ALT] => Как отличить шлак от металла? [ELEMENT_PREVIEW_PICTURE_FILE_TITLE] => Как отличить шлак от металла? [ELEMENT_DETAIL_PICTURE_FILE_ALT] => Как отличить шлак от металла? [ELEMENT_DETAIL_PICTURE_FILE_TITLE] => Как отличить шлак от металла? ) [FIELDS] => Array ( [TAGS] => ) [DISPLAY_PROPERTIES] => Array ( ) [IBLOCK] => Array ( [ID] => 1 [~ID] => 1 [TIMESTAMP_X] => 15.02.2016 17:09:48 [~TIMESTAMP_X] => 15.
02.2016 17:09:48 [IBLOCK_TYPE_ID] => news [~IBLOCK_TYPE_ID] => news [LID] => s1 [~LID] => s1 [CODE] => news [~CODE] => news [NAME] => Пресс-центр [~NAME] => Пресс-центр [ACTIVE] => Y [~ACTIVE] => Y [SORT] => 500 [~SORT] => 500 [LIST_PAGE_URL] => /news/ [~LIST_PAGE_URL] => /news/ [DETAIL_PAGE_URL] => #SITE_DIR#/news/#SECTION_ID#/#ELEMENT_ID#/ [~DETAIL_PAGE_URL] => #SITE_DIR#/news/#SECTION_ID#/#ELEMENT_ID#/ [SECTION_PAGE_URL] => #SITE_DIR#/news/#SECTION_ID#/ [~SECTION_PAGE_URL] => #SITE_DIR#/news/#SECTION_ID#/ [PICTURE] => [~PICTURE] => [DESCRIPTION] => [~DESCRIPTION] => [DESCRIPTION_TYPE] => text [~DESCRIPTION_TYPE] => text [RSS_TTL] => 24 [~RSS_TTL] => 24 [RSS_ACTIVE] => Y [~RSS_ACTIVE] => Y [RSS_FILE_ACTIVE] => N [~RSS_FILE_ACTIVE] => N [RSS_FILE_LIMIT] => 0 [~RSS_FILE_LIMIT] => 0 [RSS_FILE_DAYS] => 0 [~RSS_FILE_DAYS] => 0 [RSS_YANDEX_ACTIVE] => N [~RSS_YANDEX_ACTIVE] => N [XML_ID] => clothes_news_s1 [~XML_ID] => clothes_news_s1 [TMP_ID] => bdc319b578d4e21260366365054decb9 [~TMP_ID] => bdc319b578d4e21260366365054decb9 [INDEX_ELEMENT] => Y [~INDEX_ELEMENT] => Y [INDEX_SECTION] => Y [~INDEX_SECTION] => Y [WORKFLOW] => N [~WORKFLOW] => N [BIZPROC] => N [~BIZPROC] => N [SECTION_CHOOSER] => L [~SECTION_CHOOSER] => L [LIST_MODE] => [~LIST_MODE] => [RIGHTS_MODE] => S [~RIGHTS_MODE] => S [SECTION_PROPERTY] => N [~SECTION_PROPERTY] => N [PROPERTY_INDEX] => N [~PROPERTY_INDEX] => N [VERSION] => 1 [~VERSION] => 1 [LAST_CONV_ELEMENT] => 0 [~LAST_CONV_ELEMENT] => 0 [SOCNET_GROUP_ID] => [~SOCNET_GROUP_ID] => [EDIT_FILE_BEFORE] => [~EDIT_FILE_BEFORE] => [EDIT_FILE_AFTER] => [~EDIT_FILE_AFTER] => [SECTIONS_NAME] => Разделы [~SECTIONS_NAME] => Разделы [SECTION_NAME] => Раздел [~SECTION_NAME] => Раздел [ELEMENTS_NAME] => Новости [~ELEMENTS_NAME] => Новости [ELEMENT_NAME] => Новость [~ELEMENT_NAME] => Новость [CANONICAL_PAGE_URL] => [~CANONICAL_PAGE_URL] => [EXTERNAL_ID] => clothes_news_s1 [~EXTERNAL_ID] => clothes_news_s1 [LANG_DIR] => / [~LANG_DIR] => / [SERVER_NAME] => www.
alfa-industry.ru [~SERVER_NAME] => www.alfa-industry.ru ) [SECTION] => Array ( [PATH] => Array ( [0] => Array ( [ID] => 115 [~ID] => 115 [TIMESTAMP_X] => 2015-11-25 18:37:33 [~TIMESTAMP_X] => 2015-11-25 18:37:33 [MODIFIED_BY] => 2 [~MODIFIED_BY] => 2 [DATE_CREATE] => 2015-09-29 20:10:16 [~DATE_CREATE] => 2015-09-29 20:10:16 [CREATED_BY] => 1 [~CREATED_BY] => 1 [IBLOCK_ID] => 1 [~IBLOCK_ID] => 1 [IBLOCK_SECTION_ID] => [~IBLOCK_SECTION_ID] => [ACTIVE] => Y [~ACTIVE] => Y [GLOBAL_ACTIVE] => Y [~GLOBAL_ACTIVE] => Y [SORT] => 500 [~SORT] => 500 [NAME] => Технические статьи [~NAME] => Технические статьи [PICTURE] => [~PICTURE] => [LEFT_MARGIN] => 21 [~LEFT_MARGIN] => 21 [RIGHT_MARGIN] => 22 [~RIGHT_MARGIN] => 22 [DEPTH_LEVEL] => 1 [~DEPTH_LEVEL] => 1 [DESCRIPTION] => [~DESCRIPTION] => [DESCRIPTION_TYPE] => text [~DESCRIPTION_TYPE] => text [SEARCHABLE_CONTENT] => ТЕХНИЧЕСКИЕ СТАТЬИ [~SEARCHABLE_CONTENT] => ТЕХНИЧЕСКИЕ СТАТЬИ [CODE] => [~CODE] => [XML_ID] => 115 [~XML_ID] => 115 [TMP_ID] => [~TMP_ID] => [DETAIL_PICTURE] => [~DETAIL_PICTURE] => [SOCNET_GROUP_ID] => [~SOCNET_GROUP_ID] => [LIST_PAGE_URL] => /news/ [~LIST_PAGE_URL] => /news/ [SECTION_PAGE_URL] => /news/115/ [~SECTION_PAGE_URL] => /news/115/ [IBLOCK_TYPE_ID] => news [~IBLOCK_TYPE_ID] => news [IBLOCK_CODE] => news [~IBLOCK_CODE] => news [IBLOCK_EXTERNAL_ID] => clothes_news_s1 [~IBLOCK_EXTERNAL_ID] => clothes_news_s1 [EXTERNAL_ID] => 115 [~EXTERNAL_ID] => 115 [IPROPERTY_VALUES] => Array ( [SECTION_META_TITLE] => Технические статьи [SECTION_META_KEYWORDS] => технические статьи [SECTION_META_DESCRIPTION] => [SECTION_PAGE_TITLE] => Технические статьи [ELEMENT_META_TITLE] => Технические статьи [ELEMENT_META_KEYWORDS] => технические статьи [ELEMENT_META_DESCRIPTION] => [ELEMENT_PAGE_TITLE] => Технические статьи [SECTION_PICTURE_FILE_ALT] => Технические статьи [SECTION_PICTURE_FILE_TITLE] => Технические статьи [SECTION_DETAIL_PICTURE_FILE_ALT] => Технические статьи [SECTION_DETAIL_PICTURE_FILE_TITLE] => Технические статьи [ELEMENT_PREVIEW_PICTURE_FILE_ALT] => Технические статьи [ELEMENT_PREVIEW_PICTURE_FILE_TITLE] => Технические статьи [ELEMENT_DETAIL_PICTURE_FILE_ALT] => Технические статьи [ELEMENT_DETAIL_PICTURE_FILE_TITLE] => Технические статьи ) ) ) ) [SECTION_URL] => /news/115/ )
16. 10.2019
Сварщики-новички сталкиваются с множеством проблем и вопросов, возникающих в процессе. Так, на первых этапах многим сложно отличить шлак от металла, и то, как выгонять этот шлак во время сварки. В этой статье мы расскажем о том, как это сделать, и что нужно для того чтобы сварочный шов получился качественным.
Главным отличием плавящегося металла от шлака, во время сварки, является его текучесть. Металл является более жидким и подвижным, а в процессе самой сварки отчетливо видно, как он закипает в сварочной ванне. В свою очередь, шлак является более тягучим и имеет более темный оттенок.
Часто возникают ситуации, когда шлак наплывает на сварочную ванну. В такой ситуации сварщику практически ничего не видно, и чтобы избежать это, ему приходится наклонять электрод таким образом, чтобы струя газа (которая испаряется из обмазки) выдувала шлак обратно на сварочный шов. После этого, сварочная ванна вновь открывается и место сварки становится отчетливо видно.
Проводя аналогию, можно привести пример тазика с мыльной водой. Чтобы увидеть воду через пенку, её необходимо сдуть и только тогда вам откроется вид на воду, и всё содержимое в ней.
Таким образом, начинающему сварщику всегда необходимо держать в голове одно правило – шлак ни в коем случае не должен сбегать в сварочную ванну, и тогда качество сварочных швов станет на порядок лучше.
Источник: vse-o-svarke.org
Просмотров: 285
Электроды с толстым или качественным покрытием
Электроды с толстым или качественным покрытием
Категория:
Сварка металлов
Электроды с толстым или качественным покрытием
Эти электроды называют также качественными. Их легко отличить по внешнему виду: слой покрытия имеет значительную толщину, 1—3 мм; вес покрытия 15—60% и более от веса электродного стержня. Покрытия, помимо стабилизации дуги, защищают сварочную ванну от вредного влияния атмосферного воздуха, улучшают химический состав, структуру и механические свойства наплавленного металла, обеспечивают достаточно устойчивое горение дуги.
Основой металлургического процесса при сварке, как и в сталеплавильных печах, является взаимодействие между шлаком и металлом. Шлак при сварке образуется главным образом из расплавленного покрытия электрода, в которое вводят в тонкоразмо-лотом виде различные минеральные вещества, руды, горные породы и т. п. Шлак, образующийся вместе с расплавленным металлом при плавлении электрода, защищает ванну от доступа воздуха; при затвердевании ванны шлак замедляет охлаждение. При замедленном охлаждении разлагаются нестойкие соединения азота с яшлезом, причем освободившийся азот удаляется из металла, и содержание азота в металле снижается до допустимой нормы 0,01 — 0,03%. Содержание вредных примесей, в особенности серы и фосфора, в материалах для изготовления покрытий доводится до возможного минимума. Все материалы должны строго контролироваться по содержанию фосфора и серы.
Существующие разнообразные качественные электродные покрытия могут быть классифицированы по различным признакам, например по характеру шлака. По химическому составу шлаки, получаемые при расплавлении электродных покрытий, могут быть разделены на кислые и основные. Важнейшими кислотными окислами в электродных обмазках являются: двуокись кремния Si02 и двуокись титана ТЮ2. Основными окислами являются Na20, CaO, MgO, MnO, FeO и др. Окислы А1203, Fe203, Сг203 являются промежуточными, нейтральными или амфогерными. Преобладание кислотных или основных окислов делает шлак соответственно кислым или основным.
Кислые шлаки могут уменьшать содержание кислорода в наплавленном металле, что объясняется следующим образом. Кислород содержится в расплавленном железе в форме закиси железа FeO, имеющей ясно выраженный основной характер и реагирующей с кислотными окислами шлака, если они имеются в избытке; образуемые силикаты или титанаты закиси железа 2Fe0-Si02 и 2FeO -Ti02 в ванне металла практически нерастворимы. В результате происходит непрерывный переход закиси железа из металла в шлак, т. е. экстрагирование закиси железа из металла шлаком. Подобный процесс раскисления металла кислым шлаком называется диффузионным раскислением.
Большое распространение имеют покрытия, дающие шлаки сильно основного характера с большим содержанием окиси кальция СаО; эти шлаки обеспечивают получение наплавленного металла особенно высокого качества. Шлаки основного характера не производят диффузионного раскисления металла, и для уменьшения содержания кислорода в ванне в обмазки приходится вводить сильные раскислители (кремний, титан) в форме ферросплавов.
По характеру металлургических реакций, протекающих в сварочной ванне, качественные электроды можно разделить на две группы.
Для быстрого и энергичного проведения подобной реакции в обмазку вводят в большом количестве окислы железа в форме железных руд либо железной окалины или же другие окислы, легко отдающие кислород и способные интенсивно окислять металл ванны, например двуокись марганца Мп02 в виде минерала пиролюзита. Дополнительным источником углерода, сверх содержащегося в основном металле, служит обычно ферромарганец, вводимый в значительном количестве в подобные обмазки. Протекающие в ванне экзотермические реакции освобождают значительное количество тепла и дополнительно разогревают ванну.
Весьма важны физические свойства шлака. Температура плавления шлака, как показывает опыт, должна находиться в пределах 1100—1200 °С. При температуре плавления стали 1400— 1500 °С шлак должен обладать малой вязкостью, большой подвижностью и жидкотекучестью, что важно для правильного формирования сварного шва. Существенное значение имеет характер затвердевания расплавленного шлака. Шлаки не имеют строго определенной температуры плавления. При повышении температуры вязкость шлака постепенно падает, а при понижении возрастает. Переход от жидкого состояния к твердому может быть
растянут на значительный температурный интервал, такие шлаки называются длинными. Если же переход от твердого состояния к жидкому происходит в небольшом температурном интервале, то шлаки называются короткими (рис. 43). Опыт показывает, что при сварке лучшие результаты при прочих равных условиях обычно дают короткие шлаки.
Одной шлаковой защиты недостаточно, как бы ни была она совершенна. Для получения высококачественного наплавленного металла необходимо легирование, т. е. введение в металл таких элементов, как марганец, хром, никель и т. д. Наиболее важное значение имеет легирование марганцем, которое в практике применяется чаще всего. Легирующие элементы вводят в обмазку в виде тонкоизмельчен-ных ферросплавов, ферромарганца, ферросилиция, феррохрома и т. п. Ферросплавы, кроме того, являются сильными раскис-лителями и уменьшают содержание кислорода в ванне, восстанавливая закись железа.
Помимо минеральных веществ для образования шлаков и ферросплавов для восстановления и легирования в обмазки часто вводят органические вещества: целлюлозу, крахмал, декстрин, сахар, пищевую муку, древесную муку и т. п. Органические вещества под воздействием высокой температуры при сварке разлагаются с образованием смеси газов, имеющих восстановительные свойства, устраняющие доступ кислорода к ванне; соединения железа с азотом в присутствии водорода или газов, богатых водородом, как показывает опыт, при сварке вообще не образуются. Введение органических веществ, в особенности целлюлозы, позволяет уменьшить количество обмазки на электроде, что особенно важно для электродов, предназначенных для сварки в вертикальном и потолочном положениях. Для качественной обмазки важен не только ее состав, но и количество, наносимое на электрод, так как ход и конечный результат металлургической реакции зависят от количества шлака, взаимодействующего с металлом.
Рис. 1. Диаграмма затвердевания шлаков
Реклама:
Читать далее:
Классификация покрытых электродов
Статьи по теме:
Основы сварки самозащитными порошковыми проволоками
Основы сварки самозащитными порошковыми проволоками: высокая скорость, отсутствие необходимости в газовых баллонах
Процессом сварки самозащитной проволокой редко овладевают в начале карьеры. Тем не менее, это один из самых эффективных методов дуговой сварки.
Авторы: Том Майерс (Tom Myers) и Фрэнк Драголич Мл. (Frank Dragolich, Jr.)
Сварка порошковой самозащитной проволокой (FCAW-S) – это самый универсальный процесс в отрасли дуговой сварки. Такая проволока самостоятельно выделяет защитный газ, удаляет загрязняющие вещества на стали, образует отвечающее всем нормативным требованиям наплавление и быстрозастывающий шлак.
Метод FCAW-S скорее напоминает ручную руговую сварку штучными электродами (SMAW), чем сварку газозащитными порошковыми проволоками. Сварщики с большим опытом ручной дуговой сварки обычно очень быстро овладевают процессом FCAW-S, в то время как тем, кто знаком только с процессом газозащитной сварки контролируемыми короткими замыканиям (GMAW), на это приходится потратить чуть больше времени.
Как и РДС, FCAW-S не требует использования внешнего источника защитного газа, поэтому этот процесс хорошо подходит для сварки под открытым небом (см. Рисунки 1 и 2). Тем не менее, в отличие от РДС, процесс сварки самозащитной порошковой проволокой имеет намного более высокую производительность наплавки. Она аналогична, а в некоторых случаях даже превышает производительность сварки газозащитной проволокой. В случае штучных электродов марки E6010 и E6013 производительность наплавки составляет 1-1,5 кг металла в час. Для E7018 этот показатель составляет 2-2,5 кг. Что касается процесса FCAW-S, то в его случае сварщик может наплавить до 4 кг металла при вертикальной сварке и более 6 кг при сварке в горизонтальном и нижнем положении, в зависимости от используемой проволоки. Кроме того, производительность можно увеличить до более 10 кг металла в час с помощью процедур с увеличенным вылетом электрода.
Рисунок 1: Самозащитная порошковая проволока часто используется для сварки в неудобных пространственных положениях. |
Рисунок 2: Благодаря отсутствию необходимости в газовых баллонах процесс FCAW-S часто используется для сварки в монтажных условиях или под открытым небом как более эффективная альтернатива РДС. |
Основные сведения о процессе
Для GMAW (MIG) и сварки газозащитной порошковой проволокой (FCAW-G) лучше всего подходит постоянный ток обратной полярности (DC+). Однако для самозащитной проволоки рекомендуемая полярность зависит от состава сердечника (стабилизаторов дуги) конкретной марки проволоки. Большая часть проволок FCAW-S лучше всего себя показывает на постоянном токе прямой полярности (DC-), но некоторые из них больше подходят для работы на токе обратной полярности.
В случае GMAW сцепление для бесперебойной подачи проволоки обеспечивается гладкой V-образной насечкой на приводных роликах механизма подачи. К сожалению, такая насечка может повредить порошковые проволоки. Для того, чтобы обеспечить такое же толкающее усилие без сильного сжатия проволоки, в случае FCAW-S используются приводные ролики с V-образным гофрированием, которое захватывает оболочку проволоки и обеспечивает ее плавную подачу без деформаций.
Обратите внимание: если после сварки порошковой проволокой Вы возвращаетесь к режиму GMAW, не забудьте заменить приводные ролики на ролики с гладкой V-образной насечкой. Ролики с гофрированием могут повредить медное покрытие сплошных проволокок и привести к его расслоению. Сейчас эта проблема не так актуальна, как раньше, но о ней все равно не стоит забывать.
Напряжение
Все самозащитные порошковые проволоки очень чувствительны к колебаниям напряжения и поэтому требуют применения источника питания с режимом сварки на жесткой вольтамперной характеристике (CV). В некоторых случаях сварка газозащитной проволокой имеет более широкий диапазон допустимого напряжения. В случае FCAW-S Вы должны точно придерживаться необходимого напряжения.
При сварке самозащитной проволокой во время работы дуги между расплавленным металлом наплавления и окружающим воздухом нет ничего, кроме шлака и выделенного самой проволокой газа. Повышенное напряжение приводит к увеличению длины дуги, что, в свою очередь, увеличивает ширину конуса дуги. Соответственно, дуга большой длины и ширины более подвержена воздействию атмосферы. Из-за этого длина дуги имеет крайне большое значение, а источники питания на жесткой ВАХ позволяют сохранять ее на постоянном уровне.
Обратите внимание, что, если расплавленный металл вступит контакт с окружающим воздухом (который содержит 79% азота, 20% кислорода и 1% процент других элементов), он начнет поглощать азот и кислород. Если этому никак не помешать, после застывания металла часть этих газов улетучится и оставит после себя отверстия (т. е. пористость). Оставшиеся внутри газы приведут к образованию очень ломкого металла с низкими механическими характеристиками. Поэтому расплавленный металл нужно защищать от контакта с воздухом, пока он не застынет. Это относится ко всем процессам сварки.
Теперь представьте, как от самозащитной проволоки отделяется расплавленная капля. Практически сразу же вокруг нее образуется тонкий слой шлака. Материал проволоки включает определенные элементы, которые вступают в химическую реакцию с азотом и кислородом (т. е. денитрификаторы или восстановители) и затягивают их в шлак, тем самым не давая им попасть в металл наплавления. Также при этом образуются другие побочные продукты реакций в дуге, например, двуокись углерода, которая замещает собой воздух. Эти две особенности защищают расплавленную каплю металла во время ее перемещения к сварочной ванне.
Но чем больше длина дуги, тем большее расстояние должны пройти капли металла и тем сильнее становится воздействие азота, кислорода и других составляющих воздуха. Если оно становится слишком большим, системы защиты проволоки с ним не справятся и газ окажется поглащен металлом наплавления. Эти примеси скажутся на механических свойствах наплавления, в том числе ударной вязкости. Для ее измерения проводится тест по Шарпи с V-образным надрезом. Когда содержание примесей достигает определенного порогового значения, в металле возникает пористость. Слишком низкое напряжение, напротив, приводит к чрезмерному укорачиванию дуги. В таком случае проволока втыкается в пластину, что приводит к образованию неровного сварного шва.
В случае FCAW-S после завершения сварки над кончиком проволоки образуется маленький шарик шлака, который выступает в роли изолятора и мешает зажиганию дуги при возобновлении сварки. Поэтому для упрощения зажигания дуги кончик проволоки нужно аккуратно отломить или отрезать кусачками.
Также проверьте расстояние, на которое выступает проволока от контактного наконечника. Для стандартных процедур сварки эта величина обычно составляет 19-25 мм, иногда до 95 мм в случае высокопроизводительной сварки на спуск. Вылет электрода так же важен, как и длина дуги. Для сохранения стабильности дуги его колебания не должны превышать ±3 мм. Силшком большой вылет электрода приведет к короткой, нестабильной дуге и сильному разбрызгиванию, слишком маленький – избыточной длине дуги и большому риску загрязнения расплавленного металла окружающим воздухом.
Также никогда не ведите сварку с упреждающим наклоном горелки. Это не сварка GMAW короткими замыканиями. При сварке самозащитной проволокой используется шлак, поэтому Вы можете использовать старый принцип: удерживайте шлак, направляя на него поток газа. Если горелку расположить под небольшим углом на отставание, она будет удерживать шлак позади дуги. Если направить горелку вперед, она будет подталкивать расплавленный шлак перед сварочной ванной. Из-за этого возникнет риск того, что он окажется погружен под слоем металла.
Особенности сварки в сложных пространственных положениях
Производительность наплавки и общие сварочно-технологические характеристики зависят от использованной проволоки. Проволоки класса AWS E71T-8–которые подходят для сварки в любых пространственных положений на постоянном токе прямой полярности–имеют схожий металлургический состав, но при этом каждая из них имеет свои особенности.
Самое большое влияние оказывает система шлакообразования проволоки. Она представляет собой вещества, которые вступают в реакцию с другими химическими элементами, застывают быстрее металла наплавления и всплывают к поверхности соединения, чтобы защитить его от атмосферного воздуха (см. Рисунок 3). Некоторые проволоки имеют щелочную систему шлакообразования на основе фторидов, аналогичных использованных в электродах марки E7018. В других используется более кислая система, которая вступает в реакцию и застывает быстрее. Именно она помогает сварщикам достигунть упомянутой производительности 4 кг/час (чтобы узнать о системах шлакообразования подробнее, см. Техническое письмо: Обзор составов шлака ниже).
Техническое письмо: Обзор составов шлака
При сварке самозащитной порошковой используются другие системы шлакообразования. Большей частью они основаны на восстановлении алюминия и магния и деазотировании системы. Эти элементы попадают в сварочную ванну и образуют оксид алюминия и оксид магния, которые имеют высокие температуры плавления. Если к этому добавить элементы шлака с низкими температурами плавления, можно получить эффективную систему шлакообразования. Элементы шлака–оксид алюминия и оксид магния–быстро плавятся и всплывают к поверхности сварочной ванны, защищая наплавление от атмосферного воздуха.
Процесс FCAW-S имеет очень высокую усойчивость к азоту именно благодаря системам шлакообразования. Молекулы алюминия и магния привлекают к себе атомы кислорода и азота, в результате образуются оксиды алюминия и магния. Эти легкие вещества с высокой температурой плавления (т. е. быстрозастывающие) быстро поднимаются на поверхность сварочной ванны. По сути, система шлакообразования превращает азот и кислород–потенциальные загрязняющие вещества–в химические соединения, которые защищают наплавление.
Во многих проволоках FCAW-S используется одна из двух систем шлакообразования – основная или кислотная. В основных системах фторид кальция вместе с соединениями алюминия и магния образует систему, которая немного напоминает шлак, образующийся при сварке штучными электродами, например, класса E7018. В кислотных системах вместо фторида кальция используется оксид железа.
Основные системы имеют хорошие характеристики очистки. Они больше подходят для сварки конструкций ответственного назначения, имеют высокую ударную вязкость при низких температурах и другие прочностные характеристики. Кислотные системы отличаются плавным и быстрым процессом сварки.
Это связано с тем, как кислотные и основные элементы вступают в реакцию с другими элементами в металле наплавления. Это сводится к тому, как быстро происходят химические реакции. Во время сварки молекулы ионизируются, что заставляет атомы покидать одни молекулы и присоединяться к другим. В разных системах шлакообразования для этого требуется разная температура. Во фторидных системах на разделение молекул требуется очень много тепла. Для разделения кислотных, железооксидных молекул, напротив, нужна меньшая температура. Быстрая химическая реакция в таком случае приводит к более быстрому застыванию шлака и, в конечном итоге, большей производительности наплавки.
Рисунок 3: Самозащитная проволока FCAW имеет внешнюю оболочку, которая защищает сердечник из флюсообразующих веществ. Она немного похожа на вывернутый наизнанку штучный электрод.
Техника сварки зависит от рекомендаций производителя, обратитесь к нему за более подробными инструкциями. Техника также зависит от основного металла и поставленной задачи, но при этом у всех проволок есть некоторые общие свойства.
Возьмем, например, две проволоки класса E71T-8 – Innershield® NR-203MP и NR-203 Nickel (1%), в которых используется основная (некислотная) система шлакообразования. Проволоки NR-203 напоминают электроды марки E7018, за исключением более высокой производительности наплавки и, разумеется, отсутствия необходимости в смене электродов. Проволоки можно использовать в любых пространственных положениях, проводить сварку по открытому зазору и создавать соединения с очень высокой ударной вязкостью при низких температурах. Кроме того, они позволяют проводить сварку на спуск.
При сварке V-образных или угловых соединений проволокой NR-203 нужно использовать технику поперечных колебаний. Направьте проволоку на кромку лицевой поверхности шва и сделайте небольшую паузу–это обеспечит большую глубину проплавления и даст шлаку время подняться к поверхности–и затем быстро переместитесь на другую сторону шва и опять сделайте паузу. Будьте внимательны: если слишком задержитесь в центре шва, Вы можете наплавить слишком много металла и создать шов выпуклой формы, который не только ухудшит механические характеристики, но и сделает соединение более уязвимым к таким дефектам, как подрезание.
Всегда старайтесь точно сфокусировать дугу на сварочной ванне. Такое волнообразное движение–паузы у кромок шва и затем быстрое перемещение на другую сторону–позволяет металлу наплавления поступать с обеих сторон. Кроме этого, небольшая пауза у одной кромки шва позволяет застыть шлаку с другой. Если сравнивать с другими самозащитными проволоками, NR-203 образует довольно тонкий слой флюса, который может удерживать лишь ограниченный объем металла. Поэтому производительность наплавки составляет всего 2,5-3 кг/час–больше, чем при ручной сварке, но меньше, чем у остальных самозащитных проволок,
например, NR-232 и NR-233. Эти проволоки имеют кислотную систему шлакообразования, которая очень быстро вступает в реакцию в металле наплавления и образует более тяжелый шлак, что делает возможной сварку с производительностью 3,5-4 кг/час даже в неудобных пространственных положениях.
В отличие от сварки проволокой NR-203, когда Вы следите за сварочной ванной, с NR-232 и NR-233 нужно обратить внимание на образующуюся позади переднего края дуги линии шлака. Вместо традиционного метода воспользуйтесь сваркой узкими валиками с небольшими колебаниями. Если линия шлака получается неровной, Вы сможете быстро сделать исправление. Например, если линия шлака с левой стороны оказалась ниже, Вы должны немного сдвинуть горелку влево, выровнять ее и затем продолжить сварку узкими валиками. При вертикальной сварке на подъем представьте, что Вы создаете «полку» с наплавленным металлом и штабелируете валики друг на друга.
Скорость штабелирования определяет скорость сварки. Если Вы будете это делать слишком быстро и расположите дугу немного выше сварочной ванны, проволока может проникнуть в пластину и даже привести к прожиганию.
Также нельзя забывать о контроле тепловложения. Для этого можно регулировать вылет электрода – такая техника сварки используется не только при сварке FCAW-S, но и любых других процессах на жесткой ВАХ. Если Вы, например, ведете вертикальную сварку на подъем, опираясь на «полку» из расплавленного металла наплавления NR-232, Вы можете почувствовать, что ванна становится слишком горячей, а дуга проникает внутрь пластины. В таком случае Вы можете немного увеличить вылет электрода – это приведет к падению силы тока и немного охладит сварочную ванну. И наоборот, если температура слишком мала и у Вас не получается обеспечить нужную глубину проплавления, вылет электрода можно немного уменьшить – это увеличит силу сварочного тока и глубину проплавления.
Гибкие, мобильные и эффективные
Процесс сварки FCAW-S завоевал большую популярность в США – стране, которая постоянно работает над улучшением инфраструктуры. Он сочетает мобильность, способность противостоять тяжелым погодным условиям,эффективность сварки проволокой и гибкость РДС. Процессом сварки самозащитной проволокой редко овладевают в начале карьеры. Тем не менее, это один из самых эффективных методов сварки.
Том Майерс – это старший технический специалист, а Фрэнк Драголич Мл. – техник компании Lincoln Electric Co., 22801 St. Clair Ave., Cleveland, OH 44117, 216-481-8100.
Технические данные предоставлены компанией Lincoln Electric
Что такое шлак при сварке и как он работает? Руководство на 2022 год
0Последнее обновление
Сварочный шлак можно определить как «каменистые отходы, которые отделяются от металлов во время плавки или рафинирования руды». Хотя мы не имеем дело с рудой при сварке, сварочный шлак также отделяется от основного и присадочного металла во время сварки. Затем он отколотается и позже очищается. Но это не чистая трата. Шлак служит цели, которая способствует структурной целостности сварного шва.
Как это работает?
Шлак является побочным продуктом некоторых процессов дуговой сварки. Он образуется при сварке из флюса. Когда дуга инициализируется и стабилизируется, присадочный металл электрода начинает разжижаться и осаждается в зоне сварного шва. Поскольку расплавленный металл является текучим и не охлаждается, он гораздо более склонен к образованию дефектов в процессе сварки и в период охлаждения сразу после него.
Сварочные процессы, в которых используется шлак, имеют электроды, покрытые флюсом (дуговая сварка защищенным металлом) или флюсом, заделанным внутри трубчатой проволоки (дуговая сварка порошковой проволокой).Этот флюс плавится с присадочным металлом и выделяет газы, которые создают защитную зону для сварного шва, отталкивая другие атмосферные газы, такие как кислород. Но не весь флюс испаряется или превращается в газ. Остальная его часть остается в зоне сварного шва и поднимается к вершине сварного шва, оставляя шлак, который также служит для защиты сварного шва при охлаждении.
По окончании сварки шлак необходимо удалить с помощью молотка для откола (также называемого отбойным молотком) или игольчатого пистолета. Поскольку шлак действует как защита сварного шва и является неметаллическим, он также может вызвать отсутствие плавления, если дополнительный сварной шов будет наплавлен без удаления старого шлака.
Какие бывают виды шлаков при сварке?
При сварке шлаки бывают разных видов. Флюсы производятся из различных карбонатных и силикатных материалов. Некоторые шлаки удалить легче, чем другие. Рутиловые или кислотные флюсы, поскольку они не содержат фторидов, создают шлак, который легче удалить. Основные флюсы создают шлак, содержащий фторид кальция, что затрудняет его удаление. Несмотря на то, что характеристики флюса различаются в зависимости от электрода, лучший способ классифицировать различные типы шлака для наших целей — это отсортировать его по процессу сварки.
Дуговая сварка защищенного металла
Дуговая сварка защищенным металлом (SMAW) или сварка палкой — это процесс, в котором используется электрод, покрытый флюсом. Металл осаждается, когда электрод плавится вместе с флюсом. При этом образуется шлак, который затем необходимо отколоть. Перед добавлением сварного шва важно удалить весь шлак.
Кредит изображения: Мати Нусерм, Shutterstock
Дуговая сварка порошковой проволокой с двойным экраном
Дуговая сварка порошковой проволокой с двойным экраном (FCAW-G) — это полуавтоматический процесс сварки, при котором присадочный металл откладывается из механизма подачи проволоки.Проволока трубчатая и заполнена флюсом, отсюда и название «порошковая». Одного этого флюса недостаточно для защиты сварного шва, но требуется дополнительное покрытие от защитного газа. Вот почему этот процесс также называется Dual Shield.
Характеризуется довольно гладкой дугой, что также приводит к образованию одинаково гладкого шлака. Почти во всех случаях этот шлак исключительно легко удалить, часто целиком. Это отличает Dual Shield от своего аналога Self-Shield.
Самозащитная порошковая сварка
Самозащитная порошковая сварка (FCAW-S или Innershield) использует то же оборудование, что и Dual Shield. Однако используемый в этом процессе флюс самодостаточен и не требует дополнительного газового покрытия. Дуга менее гладкая, поскольку работает больше по принципу шарового переноса (в отличие от дуги со струйным переносом). Это означает, что перенос перемещается по дуге большими каплями расплава. Этот тип сварки используется на открытом воздухе, где газовое покрытие будет унесено ветром. Шлак удалить сложно.
Сварка под флюсом
Для дуговой сварки под флюсом (SAW) используется проволока с металлическим сердечником и механизм подачи проволоки, аналогичный сварке порошковой проволокой.Однако обычно в проволоку нет флюса для образования шлака. Поскольку этот процесс чаще всего используется для автоматизации, путь сварки задается, и в него закладывается зернистый проводящий флюс. Более эффективным является бункер для флюса, который распределяет флюс при сварке. Этот флюс плавится и превращается в шлак. В то же время он помогает стабилизировать дугу под флюсом. Вот почему это называется дуговой сваркой под флюсом, поскольку дуга не видна за пределами флюса. Образующийся шлак обычно легко удалить.
Кредит изображения: Greeneries, Shutterstock
Электрошлаковая сварка
Электрошлаковая сварка (ESW) — это однопроходный процесс, предназначенный для сварки толстых листов, обычно толщиной более 1¼ дюйма. Его описывают скорее как процесс плавления, чем как сварку. Флюс добавляется к стыку заранее. Электрод вставляется поверх флюса. Поскольку флюс не является хорошим проводником электричества, дуги нет. Вместо этого происходит то, что сопротивление между электродом и заготовкой генерирует тепло, которое расплавляет лужу флюса.После того, как он станет расплавленным, добавляется еще флюс для стабилизации дуги и соединения ванны расплавленного шлака с массой присадочного металла.
Где это используется?
Шлак используется везде, где вы видите FCAW, SMAW, SAW и ESW. Эти виды сварки чаще используются в цехах по изготовлению металлоконструкций, а также на стройплощадках, где работают с металлоконструкциями. Защитный характер шлака помогает предотвратить дефекты, вызванные ненастной погодой. Использование сварки MIG или проволоки не будет работать в ненастную погоду или на большом количестве конструкционной стали, поскольку она не проникает так же хорошо, как вышеупомянутые процессы.
Преимущества шлака при сварке
Очевидным преимуществом шлака является то, что он помогает защитить сварной шов от внешних дефектов в процессе сварки. Шлак также может сохранять заданную форму и надлежащие размеры сварных швов, что может иметь решающее значение в зависимости от области применения.
Недостатки шлака при сварке
Хотя цель сварочных процессов, в которых используется флюс и шлак, состоит в том, чтобы они поднимались на поверхность во время сварки, это не всегда так.Вероятно, самым большим недостатком является то, что вы рискуете получить включения шлака и отсутствие плавления. Хотя шлак создается для предотвращения дефектов, таких как пористость и червоточины, он также может вызывать дефекты и сам по себе, если сварщик не очистит свои сварные швы или не использует надлежащую технику.
Изображение предоставлено: Игорь В. Подкопаев, Shutterstock
Часто задаваемые вопросы (FAQ)
Можно ли оставить шлак на сварном шве?
Короткий ответ — нет. Сварные швы следует чистить всегда.Однако, если это последний проход многопроходного сварного шва, если вы не планируете окрашивать сварную конструкцию, оставление шлака сверху не должно быть проблемой. Это часто случается с приспособлениями и другими временными конструкциями, используемыми, чтобы помочь производителям выполнить реальную работу.
Сейчас бывают времена, когда люди не следуют протоколу. Иногда сварщики Dual Shield FCAW сваривают корневой проход многопроходного углового шва и снимают шлак в соответствии с процедурой. Однако в следующих двух последовательных проходах, составляющих второй слой сварного шва, между ними не будет отслаиваться шлак.Это происходит только потому, что шлак уже легко удалить, а лужа может стать достаточно горячей, чтобы предыдущий шлак поднялся на вершину новой лужи. Опять же, это не рекомендуется (особенно для ответственных сварных швов), и это все равно может вызвать включения шлака. Но в такой ситуации это не должно повредить общей целостности сварного шва, поскольку шлак откалывается между слоями сварного шва.
Что вызывает включения шлака?
Шлаковые включения обычно возникают из-за плохой очистки сварного шва между проходами.Это также может быть вызвано плохой техникой сварки. Например, FCAW предназначена для сварки под небольшим углом сопротивления, так что электродная проволока может тянуться за лужей. Если вы измените этот угол на толкание лужи, вы потенциально можете сваривать ранее образовавшуюся лужу и, следовательно, улавливать шлак. Вкрапления шлака обычно возникают из-за ошибки пользователя.
Кредит изображения: Pixabay
Как лучше всего удалить шлак между проходами углового шва?
Самый простой способ удалить шлак — воспользоваться молотком для шлака.Один конец заострен, а другой конец имеет плоский край. Другой способ — использовать воздушный инструмент, например, игольчатый пистолет. Просто нажмите на спусковой крючок и ударьте им по сварному шву. Это полезно при сварке со шлаком, который трудно удалить, например самозащищенным.
Другой метод — использовать угловую шлифовальную машину. Хотя это не лучший метод удаления шлака, он может быть более эффективным, чем иногда использование игольчатого пистолета. Например, если вы выполняете сварку стыков труб с помощью стержня E6010 для прокладки корневого прохода, из-за быстрого замораживания шлака в сочетании с методом сварки с паузой шлака шлак будет отрываться небольшими частями. .Используйте угловую шлифовальную машину для очистки корневого прохода и выравнивания сварного шва для следующих проходов.
Заключение
Шлак грязный. При сварке он проникает повсюду и вызывает много дыма. Тем не менее, это то, как он служит своей цели. Но без надлежащей очистки и подготовки металла это может вызвать проблемы, которые могут повлиять на структурную целостность ваших сварных швов. Утомительная работа по очистке сварного шва избавит вас от строжки угольной дугой или притирки дефектного сварного шва для его устранения.
Изображение предоставлено: К. Каргона, Shutterstock
Дефекты / несовершенства сварных швов — включения шлака
Описаны характерные особенности и основные причины дефектов шлака.
Идентификатор
Шлак обычно представляет собой удлиненные линии, непрерывные или прерывистые по длине сварного шва. Это легко определить на рентгенограмме. Рис. 1. Включения шлака обычно связаны с процессами флюса, т.е. MMA, FCA и дугой под флюсом, но они также могут возникать при сварке MIG.
Нажмите здесь, чтобы увидеть наши последние подкасты по технической инженерии на YouTube .Причины
Поскольку шлак является остатком покрытия флюсом при сварке стержневым электродом, он в основном является продуктом раскисления в результате реакции между флюсом, воздухом и поверхностным оксидом. Шлак захватывается сварным швом, когда два соседних сварных валика осаждаются с недостаточным перекрытием и образуется пустота. При нанесении следующего слоя уловленный шлак не расплавляется.Шлак также может задерживаться в полостях многопроходных сварных швов из-за чрезмерного подреза в подошве сварного шва или неровного профиля поверхности предыдущих прогонов сварного шва, Рис. 2.
Поскольку оба они влияют на легкость удаления шлака, на риск дефектов шлака влияет
- Тип покрытия флюсом
- Сварочная техника
Тип и конфигурация соединения, положение сварки и ограничения доступа — все это влияет на риск образования дефектов шлака.
Тип покрытия флюса
Одна из основных функций флюсового покрытия при сварке — это образование шлака, который будет свободно течь по поверхности сварочной ванны, защищая его от окисления. Поскольку шлак влияет на рабочие характеристики ММА-электрода, его поверхностное натяжение и скорость замерзания могут быть не менее важными свойствами. Для сварки в плоском и горизонтальном / вертикальном положениях предпочтительным является относительно вязкий шлак, поскольку он дает гладкий профиль сварного шва, с меньшей вероятностью захватывается и при затвердевании обычно легче удаляется.При вертикальной сварке шлак должен быть более текучим, чтобы вытекать к поверхности сварочной ванны, но иметь более высокое поверхностное натяжение, чтобы поддерживать сварочную ванну и быстро замерзать.
Состав покрытия из флюса также играет важную роль в риске образования шлаковых включений из-за его влияния на форму сварного шва и легкости удаления шлака. Сварочная ванна с низким содержанием кислорода будет иметь высокое поверхностное натяжение, приводящее к выпуклому сварному шву с плохим смачиванием основного металла.Таким образом, окисляющий флюс, содержащий, например, оксид железа, создает сварочную ванну с низким поверхностным натяжением и более вогнутым профилем валика сварного шва и способствует смачиванию основного металла. Высокосиликатный флюс дает стекловидный шлак, часто самоотверждающийся. Флюсы с содержанием извести образуют налипший шлак, который трудно удалить.
Простота удаления шлака для основных типов флюсов:
- Рутиловые или кислотные флюсы — большие количества оксида титана (рутила) с некоторыми силикатами.Уровень кислорода в сварочной ванне достаточно высок, чтобы получить плоский или слегка выпуклый сварной шов. Текучесть шлака определяется содержанием фторида кальция. Покрытия без фтора, предназначенные для сварки в плоском положении, создают гладкие профили валика и легко удаляются шлаки. Более жидкий фторидный шлак, предназначенный для позиционной сварки, удалить труднее.
- Основные флюсы — высокая доля карбоната кальция (известняк) и фторида кальция (фторошпар) во флюсе снижает содержание кислорода в сварочной ванне и, следовательно, ее поверхностное натяжение.Шлак более жидкий, чем шлак с рутиловым покрытием. Быстрое замерзание также способствует сварке в вертикальном и верхнем положениях, но шлаковое покрытие удалить труднее.
Следовательно, риск включения шлака значительно выше при использовании основных флюсов из-за присущего им выпуклого профиля сварного шва и сложности удаления шлака с подошв сварного шва, особенно при многопроходных сварных швах.
Сварочная техника
Сварочная техника играет важную роль в предотвращении образования шлаковых включений.Манипуляции с электродами должны обеспечивать соответствующую форму и степень перекрытия сварных швов, чтобы избежать образования карманов, в которых может скапливаться шлак. Таким образом, правильный размер электрода для подготовки шва, правильный угол к заготовке для хорошего проплавления и гладкий профиль сварного шва — все это важно для предотвращения уноса шлака.
При многопроходной вертикальной сварке, особенно с использованием основных электродов, следует позаботиться о расплавлении любых оставшихся мелких шлаковых карманов и минимизации подрезов.При использовании переплетения небольшая задержка на крайних краях переплетения будет способствовать сплавлению боковых стенок и созданию более плоского профиля сварного шва.
Слишком высокий ток в сочетании с высокой скоростью сварки также приведет к подрезу боковой стенки, что затруднит удаление шлака.
Очень важно удалить весь шлак перед нанесением следующего цикла. Это может быть сделано между прогонами путем шлифовки, легкого скалывания или чистки проволочной щеткой. Инструменты для очистки должны быть идентифицированы для различных материалов, например, стали или нержавеющей стали, и разделены.
При сварке сложными электродами, в стыках с узкими клиновыми стыками или когда шлак задерживается из-за подрезов, может потребоваться шлифовка поверхности сварного шва между слоями, чтобы обеспечить полное удаление шлака.
Лучшая практика
Для предотвращения шлаковых включений можно использовать следующие методы:
- Используйте методы сварки для получения гладких сварных швов и соответствующей сварки между прогонами, чтобы избежать образования карманов для захвата шлака
- Используйте правильный ток и скорость движения, чтобы избежать подреза боковой стенки, что затруднит удаление шлака
- Удаляйте шлак между прогонами, уделяя особое внимание удалению шлака, застрявшего в щелях
- Используйте шлифование при сварке сложных стыковых соединений, в противном случае для удаления шлака может быть достаточно обработки проволочной щеткой или небольшого скола.
Стандарты приемки
Включения шлака и флюса являются линейными дефектами, но поскольку они не имеют острых краев по сравнению с трещинами, они могут быть разрешены определенными стандартами и правилами. Пределы для стали указаны в BE EN ISO 5817: 2007 для трех уровней качества.
Статья подготовлена Биллом Лукасом с помощью Джин Мэтерс и Колин Эйлинс.
Эта статья о вакансиях изначально была опубликована в Connect, сентябрь / октябрь 1999 г.Он был обновлен, поэтому веб-страница больше не отражает в точности печатную версию.
Что такое шлаковые включения? Причины, профилактика и устранение
Сварщик — профессия, требующая отличных навыков и разнообразия. Это может привести к достойной карьере, если вы вложите в нее всю душу.
Однако его многовариантный характер также делает его склонным к ошибкам. Новые сварщики должны быть морально подготовлены к решению таких проблем.
Один из самых проблемных дефектов при сварке — это включения шлака.
В этой статье объясняется, что это такое, как его идентифицировать, что его вызывает и что можно сделать, чтобы этого не произошло.
Что такое включения шлака?
Пример включения шлакаВключения шлака — распространенный дефект сварки, который возникает, когда шлак, побочный продукт сварки, застревает внутри сварного изделия. Это неблагоприятное условие, которое в дальнейшем создает проблемы с производительностью.
В большинстве случаев это результат плохой техники сварки или неправильного выбора компонентов и параметров.
Этот дефект в основном возникает при сварке под флюсом, например при сварке стержнем и дуговой сварке порошковой проволокой.
Почему только методы на основе флюса ?.
Чтобы прояснить это, давайте начнем с обсуждения флюса и шлака…
Чем шлак отличается от сварочного флюса?
Флюс — это комбинация соединений, которая попадает в расплавленную сварочную ванну с присадочным металлом.
При плавлении он реагирует с кислородом / азотом в окружающей атмосфере с образованием соответствующих оксидов / нитридов. Это предотвращает окисление основных металлов этими газами.
Часть его растворяется в сварочной ванне и вступает в аналогичные реакции с примесями внутри основного металла.
Эти неметаллические продукты этих химических реакций известны под общим названием шлак.
Шлак поднимается в верхнюю часть бассейна из-за своей низкой плотности. Достигнув поверхности сварного изделия, он затвердевает, создавая слой защиты между расплавленным металлом и воздухом, блокируя дальнейшие реакции между ними.
Таким образом, флюс, который в конечном итоге становится шлаком, защищает сварочную ванну от воздуха и очищает ее от внутренних примесей.
Подводя итог, флюс является важным ингредиентом, который сохраняет сварную деталь чистой от неметаллических примесей. Шлак — это отходы, которые необходимо удалить из стыка после окончания сварки.
Вот небольшой видеоролик о том, как происходит включение шлака в процессе переноса холодного металла:
youtube.com/embed/us66qtKRODY?feature=oembed» frameborder=»0″ allow=»accelerometer; autoplay; clipboard-write; encrypted-media; gyroscope; picture-in-picture» allowfullscreen=»»/>
Почему это неблагоприятно?
Сварное соединение хорошего качества определяется по однородному составу.Любые нарушения целостности его внутренней структуры, микро или макро, делают его неисправным.
Включения шлака создают эти неоднородности, приводя к дефектному сварному шву. Зазоры, заполненные шлаком, подвержены концентрациям напряжений и локальным деформациям, которые отрицательно сказываются на прочности сварного изделия. Кроме того, шлак предотвращает естественное взаимодействие между отдельными зернами, что еще больше ухудшает механическую целостность сварного соединения.
Шлаковые включения также могут пропускать жидкости / газы через них.В таких конструкциях, как водонепроницаемые сосуды или герметичные газовые баллоны, это может иметь катастрофические последствия.
Ржавчина — еще одна проблема, если шлак имеет склонность к коррозии. Если на сварной детали образуется ржавчина, вредное воздействие этих микродефектов может возрасти.
Как определить включения шлака?
Полностью избежать включения шлака невозможно. Следовательно, каждый сварщик должен знать, как их идентифицировать.
В большинстве случаев включения видны невооруженным глазом. Такие включения имеют вид прозрачного стекла.Они бывают либо в виде тонких линий, либо в виде точечных отверстий. Они разбросаны беспорядочно, иногда группами, а иногда и в укромных местах. Неразрушающие методы, такие как проверка проникновения красителя, могут точно определить их местоположение.
В других случаях включения шлака находятся глубоко внутри сварного изделия. Их можно обнаружить с помощью рентгеновского или ультразвукового исследования.
Ультразвуковой контроль (UT)Общие методы удаления шлака
После идентификации сварщики используют различные методы для удаления включений шлака.
Если они находятся на поверхности или рядом с ней, достаточно простой металлической щетки или отбойного молотка. Помол подходит для обработки более глубоких включений.
Когда производительность важна, полное устранение дефекта также является профессиональной практикой. В таких случаях сварщики переделывают полость и заполняют все отверстия новым наполнителем.
Основные причины шлаковых включений
Как упоминалось в начале, сварка не является однофакторным процессом. Есть несколько факторов, которые необходимо учитывать.
Следовательно, шлаковые включения вызваны множеством причин. Чтобы не усложнять задачу, мы обсудим ее основные причины одну за другой.
Тип используемого флюса
Флюс становится шлаком. Этого факта достаточно, чтобы подчеркнуть важность состава флюса.
Свойства материала шлака играют огромную роль в создании шлаковых включений. Основными качествами, которые следует учитывать, являются смачиваемость, поверхностное натяжение и скорость замерзания.
Некоторые флюсы в этом отношении отличаются высоким качеством.Например, рутиловые флюсы обладают высоким поверхностным натяжением, что способствует получению более плоского сварного шва. Образовавшийся шлак быстро поднимается наверх и скапливается в легкодоступных местах.
Основные флюсы, особенно содержащие карбонат кальция, известны тем, что вызывают включения шлака. Шлак имеет тенденцию погружаться в ванну из-за своей высокой смачиваемости, а не подниматься на поверхность. Он также создает гораздо более твердый шлак, который труднее сломать и удалить, особенно когда он полностью находится внутри сварного соединения.
Параметры сварки
Профессиональная сварка — это все о настройке правильных параметров. Скорость и сила тока — два самых важных фактора, определяющих степень включения шлака.
Сила тока
Amperage устанавливает плотность энергии, которая связана с тем, как наполнитель / флюс осаждается в бассейне.
Установка слишком низкой силы тока означает, что шлак будет метаться вдоль электрода, а не оставаться в ванне, которую он оставляет. Это усиленное движение приводит к большему перемешиванию шлака в ванне, что означает большее количество включений.
Низкая сила тока также означает более низкую общую температуру. В этом случае лужа быстро затвердевает и захватывает шлак, который еще не поднялся на поверхность.
Скорость сварки
Скорость сварки — еще один фактор, который следует учитывать. Высокая скорость передвижения делает то же самое, что и низкая сила тока. Он концентрирует шлак в более холодных регионах (перед перемещением стержня), а не в более горячей ванне, которая с большей вероятностью преждевременно затвердеет.
Низкая скорость перемещения электрода вызывает другие проблемы.Если электрод остается на месте слишком долго, в окружающей ванне откладывается много наполнителя и шлака. Больший вес и более высокая массовая доля шлака неизбежно приводят к большему количеству включений.
Плохая сварочная техника
Отсутствие опыта сварщика или несоблюдение рекомендованных практик также могут стать причиной образования шлаковых включений.
Выбор размера и угла электрода являются важными факторами. Слишком большой электрод — лишний шлак, что явно является проблемой.
Угол электрода также должен быть в определенном диапазоне.Если он расположен слишком близко к горизонтали, шлак упадет рядом или впереди точки контакта электрода с ванной, затвердевая раньше.
С другой стороны, слишком крутой угол не оставляет места для ручного управления перемещением шлака через стержень. Это вызывает брызги, и решение о том, куда они пойдут, в значительной степени зависит от местных сил.
Также очень важны поддержание постоянного дугового зазора и угла между электродами. Малейшее их нарушение приводит к иному поведению шлака.
Плохие методы
При сварке грязных и неровных поверхностей могут образовываться включения шлака. На неровных поверхностях есть щели и кратеры, в которых может скапливаться шлак. Кроме того, очень легко создать поднутрения на несовершенной поверхности, даже если вы используете правильную технику.
Включения шлака — более серьезная проблема в многопроходных сварных соединениях. Каждый проход требует очистки ранее уложенного сварного шва, поэтому больше шансов на ошибку. Более того, поскольку поверхности сами по себе являются валиками сварного шва, обязательно должны быть некоторые неровности и участки глубины вокруг пальцев шва.
Если вы используете ткацкие движения, неперекрывающиеся рисунки плетения могут создавать полости возле выступов сварных швов, в которых скапливается шлак. Сварщики должны следить за тем, чтобы «длина волны» или «частота» каждого переплетенного прохода была одинаковой, чтобы минимизировать включения шлака.
Плохие многопроходные сварные швы могут вызвать включенияКак предотвратить включения шлака?
Совершенно очевидно, что включения шлака являются серьезной проблемой при сварке по нескольким причинам. Недостаточно выявить проблемы; вы должны действовать, чтобы искоренить их.
Предотвращение включения шлака может быть непростой задачей. Именно поэтому сварка — это высокотехнологичная работа!
Подготовка и постобработка
То, что вы делаете до и после сварки, имеет большое значение. Если вы стремитесь к минимальным дефектам, перед сваркой необходимо очистить поверхность от влаги, масел и пыли.
Также необходимо использовать шлифовальный станок для создания ровной поверхности желаемой формы. Будьте осторожны, чтобы не вызвать подрезов или плохих краев.
После сварки удалите весь возможный шлак перед наложением дополнительных сварных швов. Если вам посчастливилось получить вогнутую / плоскую бусину, то это совсем несложно. Для выпуклых бусинок не стоит игнорировать шлак в пальцах ног.
Оптимальные параметры и методы
Мы уже рассмотрели вопросы, связанные с параметрами и методами сварки. Избегание неправильной практики и поиск правильного баланса между оптимальными рабочими диапазонами — ключ к получению безшлакового шва.
Важно установить достаточно высокую силу тока, чтобы избежать преждевременного затвердевания шлака и его прилипания к электроду.
Скорость должна быть постоянной и в желаемом диапазоне. Это должно позволить шлаку пройти полный цикл: реакция, смачивание, подъем наверх, замерзание. Если вы чувствуете, что это не так, подумайте о том, чтобы немного сбавить скорость.
Сварщику также необходимо найти оптимальное место для угла электрода. В идеальном случае угол оптимизирован для максимального использования силы тяжести (как для горизонтальных, так и для вертикальных сварных швов).
Это означает, что шлак просто скользит в сварочную ванну и всплывает на поверхность автоматически без особых манипуляций. Конечно, для этого необходимо изменить угол наклона электрода!
Заключение
Сварка никогда не бывает легкой задачей. Глубина этого поля, бесспорно, не имеет себе равных в сфере производственных процессов.
Мы надеемся, что эта попытка разрушить шлаковые включения помогла. Однако помните, что знание всего не сделает вас хорошим сварщиком.Важен опыт, дополненный знаниями.
Другие дефекты сварки
Урок 7 — Электроды для дуговой сварки углеродистых и низколегированных сталей с порошковой сердцевиной
Урок 7 — Электроды для дуговой сварки углеродистых и низколегированных сталей УРОК VII © АВТОРСКИЕ ПРАВА 2000 ГРУППА ЭСАБ, ИНК. 7.3.2 Шлак Системы — Компоненты сердечника определяют свариваемость электрода и механические свойства металла шва.Электроды с перевес компонентов флюса кислой природы образуют шлак кислотного типа. Те электроды, которые состоят из большего количества компонентов основного характера, как говорят, производят шлак основного типа. Электроды произведенные с использованием кислотно-шлаковой системы, обладают отличной свариваемостью. Это означает, что дуга гладкая и похожа на брызги с очень небольшим количеством брызг. и эти электроды имеют высокую операторскую привлекательность. Механические свойства хорошие и соответствовать или превосходить спецификации AWS.7.3.2.1 Электроды наличие основной системы шлака позволяет получать сварной металл с отличной пластичностью и ударная вязкость.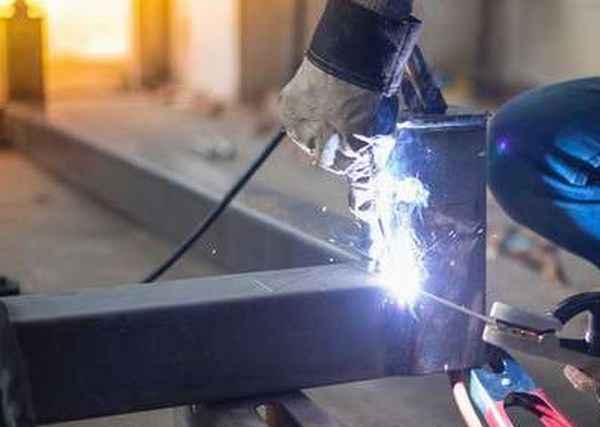

Как отличить металл от шлака при сварке электродом
Друзья, приветствую вас на нашем канале для всех начинающих самоучек в сварке и слесарях.Самые первые шаги в сварке электродами должны заключаться в понимании того, как отличить металл от шлака. Только тогда можно будет продолжить обучение сварке швов в разных положениях.
А вообще рекомендаций для новичков как отличить металл от шлака в интернете довольно много. Также на этом канале есть старые статьи, в которых по-разному можно увидеть эту разницу. Но совсем недавно у меня появилась интересная идея, как это сделать максимально просто и быстро.
Нужно взять кусок металла хорошей толщины. Минимум миллиметр 4. Важно отшлифовать поверхность до металлического блеска. В противном случае грязь и ржавчина будут смешиваться со шлаком, и эта масса будет более подвижной и текучей, чем просто шлак от электрода. Нормальную границу между металлом и шлаком будет сложно увидеть.
Поставьте сварочный аппарат рядом с местом, где сваривается эта железка. Разместите его на таком расстоянии, чтобы одной рукой можно было направлять электрод, а другой держаться за ручку регулировки сварочного тока.
Кстати, это мой инвертор Torus 200. Аппарат российского производства на честные 200 ампер — отличный запас мощности для сварки в гараже, на участке, на даче. Работаю на них уже 4 месяца, по ощущениям как девайс из Советского Союза, простой мощный, без гламурных пластиковых деталей, не более того!
Подключаем сварочные кабели с обратной полярностью. Значит подключаем держатель к плюсу прибора, провод массы к минусу.Сейчас я покажу наглядную теорию этого метода.
Разложенные в направляющей диски шлифовального станка будут копией сварного шва. Поджигаем электрод, направляем и начинаем совершать небольшие колебательные движения.
Прямо под кончиком электрода у нас будет сварочная ванна — красное озеро расплавленного металла. Но чуть дальше образуется шлак. Шлак волнообразно течет по поверхности сварочной ванны. Ну а он полностью закроет уже сварной шов, а видимая волна будет границей шлака и металла.
Нам нужно увидеть, чтобы поймать наш взгляд на эту волну-границу. Тогда будет понимание, где металл, а где шлак. Посмотрите, как можно научиться точно видеть шлаковую волну на границе с металлом сварочной ванны.
Поджигаем электрод, начинаем водить им по поверхности нашей толстой чистой железки. И сразу начинаем плавно изменять значения сварочного тока. Для нас не имеет значения, какими будут эти значения, просто мы меньше скручиваем во время самой сварки. И вот такое случается.
При слабом токе эта волна будет приближаться к кончику электрода. Как только мы добавляем ток, эта граница волны начинает двигаться все дальше и дальше.
Итак, мы пытаемся уловить взглядом движение этой пограничной волны. Все будет предельно понятно и интуитивно понятно даже для тех, кто только начал заниматься сваркой.
Добавьте волну тока, перемещающуюся дальше от кончика электрода, уменьшите приближение волны тока к кончику электрода.Все просто, достаточно нескольких минут, чтобы все это разобраться. И так новички увидят и запомнят, как можно увидеть эту разницу между шлаком и металлом. Далее освоить сварку электродами станет проще и увлекательнее!
ПРОИСХОЖДЕНИЕ Стальной шлак, побочный продукт производства стали, образуется во время отделения жидкой стали от примесей в сталеплавильных печах. Практически вся сталь в настоящее время производится на металлургических комбинатах с использованием версии основного кислородного процесса или на специальных сталеплавильных заводах (мини-заводах) с использованием процесса электродуговой печи. Процесс мартеновской печи больше не используется. В кислородном процессе горячий жидкий доменный металл, лом и флюсы, состоящие из извести (CaO) и доломитовой извести (CaO.MgO или «долим») загружаются в конвертер (печь). В конвертер опускается фурма и впрыскивается кислород под высоким давлением. Кислород соединяется с примесями заряда и удаляет их. Эти примеси состоят из углерода в виде газообразного оксида углерода и кремния, марганца, фосфора и некоторого количества железа в виде жидких оксидов, которые соединяются с известью и долимом с образованием стального шлака. В конце операции рафинирования жидкая сталь выпускается (выливается) в ковш, в то время как стальной шлак остается в емкости, а затем выпускается в отдельную емкость для шлака. Существует множество марок стали, которые можно производить, и свойства стального шлака могут значительно изменяться с каждой маркой. Марки стали можно разделить на высокие, средние и низкие, в зависимости от содержания углерода в стали. Высококачественные стали имеют высокое содержание углерода. Чтобы уменьшить количество углерода в стали, в процессе производства стали требуются более высокие уровни кислорода. Это также требует добавления повышенных уровней извести и долима (флюса) для удаления примесей из стали и повышенного образования шлака. В процессе производства стали образуется несколько различных типов стального шлака. Эти различные типы называются печным или выпускным шлаком, скребковым шлаком, синтетическим или ковшевым шлаком, а также карьерным или очистным шлаком. На рисунке 18-1 представлена диаграмма общего потока и производства различных шлаков на современном металлургическом заводе. Стальной шлак, образующийся на первичной стадии производства стали, называется печным шлаком или выпускным шлаком. Рисунок 18-1. Обзор производства шлака на современном металлургическом комбинате. Шахтный шлак и очистной шлак — это другие виды шлака, обычно встречающиеся при производстве стали. Обычно они состоят из стального шлака, который падает на пол установки на различных этапах работы, или шлака, который удаляется из ковша после выпуска. Поскольку стадия рафинирования в ковше обычно включает сравнительно высокие добавки флюса, свойства этих синтетических шлаков сильно отличаются от свойств печного шлака и, как правило, непригодны для переработки в качестве агрегатов стального шлака. Эти различные шлаки необходимо отделить от печного шлака, чтобы избежать загрязнения производимого шлакового агрегата. Помимо извлечения шлака, жидкий печной шлак и ковшевые шлаки обычно перерабатываются для извлечения черных металлов.Эта операция по извлечению металлов (с использованием магнитного сепаратора на конвейере и / или электромагнита крана) важна для сталелитейщика, поскольку затем металлы можно повторно использовать на сталеплавильном заводе в качестве исходного материала для доменной печи для производства чугуна. Дополнительную информацию об использовании агрегатов стального шлака в США можно получить по адресу: Национальная шлаковая ассоциация улица 808 Норт-Фэрфакс, Арлингтон, Вирджиния 22314 ОПЦИИ ТЕКУЩЕГО УПРАВЛЕНИЯ Переработка По оценкам, между 7. Выбытие Хотя большая часть печного шлака перерабатывается для использования в качестве заполнителя, избыток стального шлака от других операций (грабли, ковш, очистка или карьерный шлак) обычно отправляется на свалки для утилизации. ИСТОЧНИКИ НА РЫНКЕ Стальной шлак обычно получают от переработчиков шлака, которые собирают шлак на сталеплавильных предприятиях. Переработчики шлака могут работать с различными материалами, такими как стальной шлак, ковшевый шлак, карьерный шлак и использованный огнеупорный материал для извлечения металлической стали. Эти материалы должны быть отделены от источника, и должны применяться четко определенные методы обращения, чтобы избежать загрязнения агрегата стального шлака. Переработка стальных шлаков для извлечения металлов важна не только для удаления излишков стали у источника на рынке для повторного использования на сталелитейном заводе, но также важна для облегчения использования неметаллического стального шлака в качестве строительного заполнителя. Этот неметаллический шлак можно дробить и просеивать для использования в качестве заполнителя (агрегаты стального шлака) или спекать и повторно использовать в качестве флюсового материала в чугунных и сталеплавильных печах. Агрегаты стального шлака обычно имеют склонность к расширению.Это связано с наличием свободной извести и оксидов магния, которые не вступили в реакцию с силикатными структурами и могут гидратироваться и расширяться во влажной среде. Этот потенциально расширяющийся характер (изменения объема до 10 процентов или более, связанные с гидратацией оксидов кальция и магния) может вызвать трудности с продуктами, содержащими стальной шлак, и является одной из причин, по которой заполнители стального шлака не подходят для использования в портландцементном бетоне. Стальной шлак, предназначенный для использования в качестве заполнителя, следует складировать на открытом воздухе в течение нескольких месяцев, чтобы подвергать материал воздействию влаги от естественных осадков и / или нанесения воды путем распыления. Целью такого хранения (старения) является обеспечение возможности потенциально разрушительной гидратации и связанного с ней расширения до использования материала в совокупных применениях. Существует широкий диапазон времени, необходимого для адекватного воздействия элементов. Для гидратации экспансивных оксидов может потребоваться до 18 месяцев. ТРЕБОВАНИЯ К ЭКСПЛУАТАЦИИ И ОБРАБОТКЕ НА ДОРОГАХ Асфальтобетонный заполнитель, гранулированное основание и насыпь или насыпь Использование стального шлака в качестве заполнителя считается стандартной практикой во многих юрисдикциях, с применением, которое включает его использование в гранулированной основе, насыпях, инженерных насыпях, обочинах шоссе и асфальтовом покрытии из горячего асфальта. Перед использованием стального шлака в качестве строительного заполнителя необходимо измельчить и просеять стальной шлак, чтобы он соответствовал установленным требованиям по градации для конкретного применения.От переработчика шлака также может потребоваться соответствие критериям содержания влаги (например, ограничение количества влаги в заполнителе стального шлака перед отправкой на завод по производству горячего асфальта) и применение методов обращения с материалами (обработки и складирования), аналогичных применяемым. в индустрии обычных заполнителей, чтобы избежать потенциальной сегрегации. Кроме того, как отмечалось ранее, перед использованием следует рассмотреть вопрос о расширении из-за реакций гидратации. СВОЙСТВА МАТЕРИАЛА Физические свойства Стальные шлаковые агрегаты имеют очень угловатую форму и шероховатую структуру поверхности.У них высокий объемный удельный вес и умеренное водопоглощение (менее 3 процентов). Таблица 18-1. Типичные физические свойства стального шлака.
Химические свойства Химический состав шлака обычно выражается в простых оксидах, рассчитанных на основе элементного анализа, определенного с помощью рентгеновской флуоресценции.В Таблице 18-2 приведен диапазон соединений, присутствующих в сталеплавильном шлаке типичной кислородно-кислородной печи. Практически все стальные шлаки попадают в эти химические диапазоны, но не все стальные шлаки подходят в качестве заполнителей. Таблица 18-2. Типичный химический состав стального шлака. (4)
Скорость охлаждения стального шлака достаточно низкая, поэтому обычно образуются кристаллические соединения. Преобладающими соединениями являются силикат дикальция, силикат трикальция, феррит дикальция, мервинит, алюминат кальция, оксид кальция-магния и железа, а также некоторая свободная известь и свободная магнезия (периклаз).Относительные пропорции этих соединений зависят от технологии выплавки стали и скорости охлаждения стального шлака. Свободные оксиды кальция и магния не полностью расходуются в стальном шлаке, и в технической литературе есть общее согласие, что гидратация негашеной извести и магнезии при контакте с влагой в значительной степени ответственна за расширяющуюся природу большинства стальных шлаков (1). 2) Свободная известь гидратируется быстро и может вызывать большие изменения объема в течение относительно короткого периода времени (недели), в то время как магнезия гидратируется гораздо медленнее и способствует долгосрочному расширению, на формирование которого могут уйти годы. Стальной шлак является слабощелочным, с pH раствора обычно в диапазоне от 8 до 10. Однако pH выщелачивания из стального шлака может превышать 11, уровень, который может вызвать коррозию алюминиевых или оцинкованных стальных труб, находящихся в прямом контакте с шлак. Туфоподобные осадки, возникающие в результате воздействия на агрегаты стального шлака как воды, так и атмосферы, описаны в литературе. Туф представляет собой белый порошкообразный осадок, состоящий в основном из карбоната кальция (CaCO 3 ).Встречается в природе и обычно встречается в водоемах. Осадки туфа, связанные со стальными шлаками, относятся к выщелачиванию, смешанному с атмосферным диоксидом углерода. Свободная известь в стальных шлаках может соединяться с водой с образованием раствора гидроксида кальция (Ca (OH 2 )). Под воздействием атмосферного углекислого газа кальцит (CaCO 3 ) осаждается в виде поверхностного туфа и порошкообразного осадка в поверхностных водах. Механические свойства Обработанный стальной шлак имеет подходящие механические свойства для использования в качестве заполнителя, включая хорошую стойкость к истиранию, хорошие характеристики прочности и высокую несущую способность. В Таблице 18-3 перечислены некоторые типичные механические свойства стального шлака. Таблица 18-3. Типичные механические свойства стального шлака. (3)
Тепловые свойства Из-за своей высокой теплоемкости агрегаты стального шлака сохраняют тепло значительно дольше, чем обычные природные агрегаты. Характеристики теплоудержания стальных шлаковых агрегатов могут быть полезными при ремонтных работах с горячим асфальтом в холодную погоду. ССЫЛКИ
Предыдущая | Содержание | Следующий |
Есть ли разница между пайкой и сваркой?
В то время как многие люди используют термины «сварка» и «изготовление» как синонимы, другие путают «сварку» и «пайку». Однако и не совсем так.
Оба метода представляют собой отдельные методы соединения листового металла в рамках общего процесса изготовления листового металла, но каждая операция немного отличается.Короче говоря, сварка — это технология, при которой металлы соединяются путем плавления основного металла и образования плавления, в то время как пайка соединяет металлы путем плавления и вливания присадочного металла в соединение.
Большая разница
При пайке и сварке производители добавляют в стык присадочный металл. Наполнителем может быть алюминий-кремний, латунь, бронза, медь, медь-серебро, золото-серебро, никелевый сплав или серебро.
Однако основные отличия заключаются в следующем:
- При пайке присадочный металл имеет более низкую температуру плавления, чем прилегающий металл.При сварке присадочный металл имеет более высокую температуру плавления, как при пайке.
- При пайке производители не плавят основной металл.
При сварке производители плавят основной металл и каждую деталь вместе.
- Пайка использует капиллярное действие, а сварка — плавление.
Процесс
В процессе сварки происходит плавление. Плавление — это общий термин для соединения металлов схожего состава и точек плавления. Ванна расплавленного материала, называемая сварочной ванной, образуется из-за высоких температур плавления деталей.
Эта ванна охлаждается, образуя соединение, которое прочнее, чем основной металл, и давление в виде тепла может использоваться для облегчения производства сварных швов.
Сварка также требует формы экрана для защиты присадочного металла от загрязнения или окисления, что является потерей электронов и вызывает образование оксида железа (более известного как ржавчина) на металле.
В процессе пайки присадочный металл втекает в стык между плотно прилегающими деталями за счет капиллярного действия, которое представляет собой способность жидкости течь в узких пространствах без помощи или противодействия внешним силам, таким как сила тяжести.
Затем присадочный металл немного превышает температуру плавления, при этом его защищают флюсом, химическим очищающим и очищающим средством. Затем он течет по основному металлу (также известное как смачивание) и затем охлаждается, чтобы соединить детали вместе.
Методы
Сварка и пайка — это методы обработки листового металла, но существуют отдельные методы для каждой операции. Типы пайки следующие:
- Горелка для пайки
- Печь для пайки
- Серебряная пайка
- Сварка припоем
- Сварка чугуна
- Вакуумная пайка
- Пайка погружением
Виды сварки включают следующие:
- Сварка сопротивлением
- Электрошлаковая сварка
- Порошковая сварка
- Газовая дуговая сварка металлическим электродом
- Газовая дуговая сварка вольфрамом
- Сварка стекла
- Газокислородная сварка
- Пластмассовая сварка
- Дуговая сварка в экранированном металле
- Сварка под флюсом
Преимущества пайки
Сварка листового металла является более распространенным методом, но пайку нельзя сбрасывать со счетов как надежный процесс.
Самым большим преимуществом пайки является то, что производители листового металла могут соединять вместе одинаковые или разные металлы и при этом создавать прочное соединение. При сварке для получения готового продукта необходимо использовать металлы схожей температуры и состава, которые обеспечивают более прочные соединения.
Пайка также обеспечивает более жесткий контроль, обеспечивает более чистое соединение, чем сварка, без необходимости вторичной обработки, и вызывает меньшую тепловую деформацию, чем сварка. При пайке используется одинаковая температура, в отличие от сварки, при которой используются разные температуры.
Пайка также легко адаптируется для массового производства. Техника листового металла позволяет легко автоматизировать, потому что параметры проекта редко меняются.
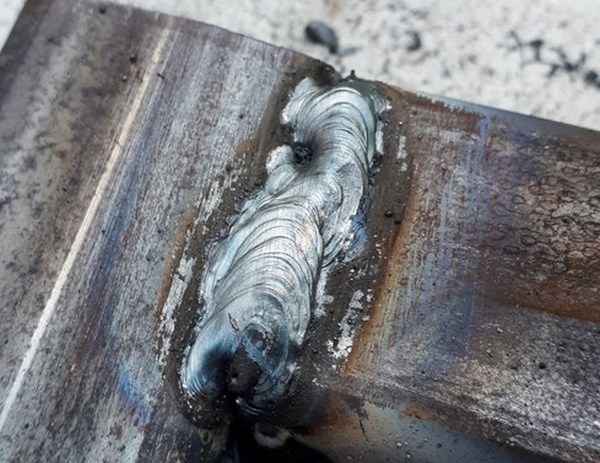