Величина сварочных напряжений и деформаций
С увеличением толщины свариваемых деталей и их жесткости температура подогрева обычно повышается на 100—200 против используемой при сварке конструкций относительно небольшой жесткости. Этим достигается уменьшение неравномерности распределения температур, а следовательно, и снижение величины сварочных напряжений и деформаций, обусловленных ею. В условиях сварки деталей повышенной жесткости, когда возникающие сварочные напряжения могут носить характер реактивных напряжений п. 2, глава П1), снижение величины последних за счет повышения температуры подогрева будет уменьшать опасность образования трещин. [c.87]Разновидности и величина сварочных напряжений и деформаций 293 [c.293]
РАЗНОВИДНОСТИ И ВЕЛИЧИНА СВАРОЧНЫХ НАПРЯЖЕНИЙ И ДЕФОРМАЦИЙ [c.293]
Методы снижения напряжений и деформаций в процессе сварки.
Сварка вызывает в изделиях появление напряжений, существующих без приложения внешних сил. Напряжения возникают по ряду причин, прежде всего из-за неравномерного распределения температуры при сварке, что затрудняет расширение и сжатие металла при его нагреве и остывании, так как нагретый участок со всех сторон окружен холодным металлом, размеры которого не изменяются. Вследствие структурных превращений участков металла околошовной зоны, нагретых в процессе сварки выше критических точек, в свариваемых конструкциях возникают структурные напряжения. В отличие от напряжений, действующих на конструкцию во время ее эксплуатации и вызываемых внешними силами, эти напрял ения называют внутренними (собственными) и остаточными сварочными напряжениями. Если значения сварочных напряжений достигнут предела текучести металла, они вызовут изменение размеров и формы, т.
Сварочные напряжения и деформации в процессе нагрева изменяются по величине и по знаку. Изменение активных и реактивных напряжений
Технологичность конструкции заключается в том, что при разработке конструкции с целью уменьшения сварочных напряжений и деформаций изделие комплектуют из отдельных сварных узлов и под-узлов. В отдельных сварных узлах и конструкциях в целом должны предусматриваться сварные швы с наименьшим объемом наплавленного металла, при этом не следует допускать концентрации и пересечения сварных швов в местах, подвергающихся растяжению, ударным и вибрационным нагрузкам. Кроме того, не следует допускать применение различных вставок, накладок и косынок, создающих замкнутые контуры, резких переходов сечений швов. Предусматривать преимущественно стыковые соединения как наиболее технологичные. Применять разделку кромок и величину зазоров по минимальным допускам, регламентируемым ГОСТом. Прерывистые Швы большого сечения нужно заменять на сплошные меньшего сечения. При конструировании необходимо широко использовать гнутые и штампованные профили, сварно-кованые и сварно-литые элементы соединений.
[c.167]
В теории сварочных напряжений и деформаций достаточно подробно рассмотрены особенности работы элементов, имеющих начальные сварочные напряжения.
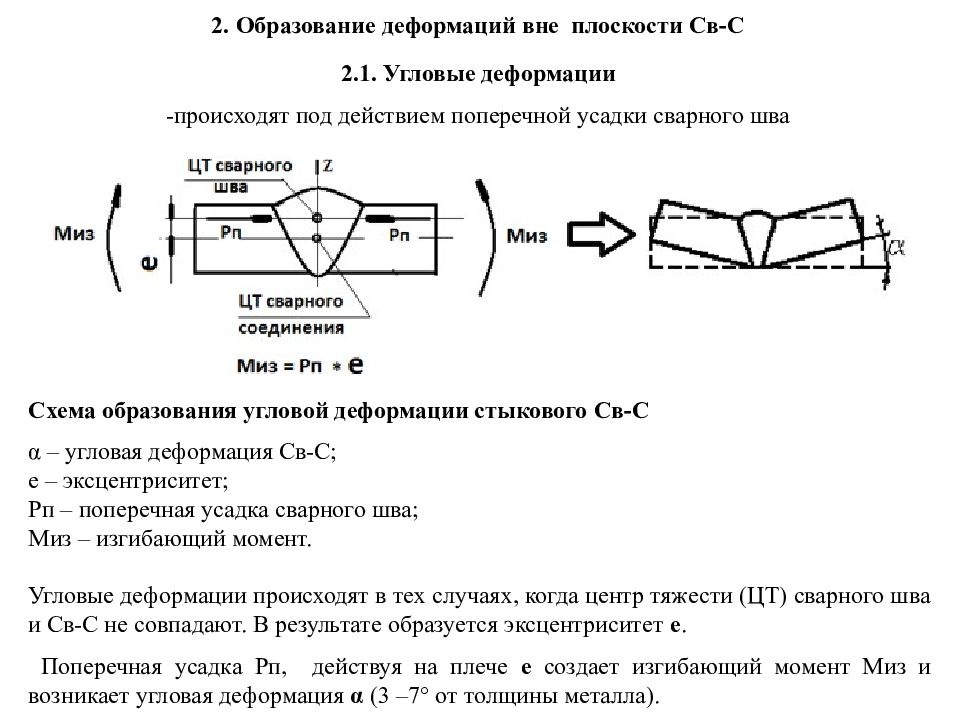
Величину обратной деформации определяют расчетным или опытным путем Способ обеспечивает уменьшение сварочных деформаций По сравнению со сваркой в свободном состоянии при условии, если зона нагрева до температуры свыше 6(Ю° С не превышает 0,15 от общей ширины свариваемого элемента. В случае превышения размеров указанной зоны нагрева деформации могут увеличиться Проковка способствует снижению сварочных напряжений и деформаций. При проковке необходимо соблюдать следующие условия
Величина и распределение напряжений и деформаций зависят от жесткости свариваемых конструкций, при этом большое значение имеет толщина металла. При сварке металла толщиной до 3 мм проявляются преимущественно большие деформации, а напряжения очень малы. Сварка металла толщиной 4—20 мм сопровождается значительными деформациями, одновременно с увеличением толщины металла начинают проявляться остаточные напряжения. При сварке металла толщиной свыше 20 мм деформации ничтожны, но остаточные напряжения могут достигать значительных величин. Остаточные сварочные напряжения проявляются в ближайших к шву слоях металла и резко затухают на расстоянии 50—70 мм от шва. Различают остаточные сварочные напряжения и деформации —> продольные, поперечные и угловые.
[c.86]
Величина и характер сварочных напряжений и деформаций определяются рядом факторов. Рассмотрим влияние некоторых из них. [c.163]
Величина и характер сварочных напряжений и деформаций определяются рядом технологических и конструктивных факторов. Рассмотрим влияние некоторых из них. [c.77]
Выбор режима сварки. Величина и характер сварочных напряжений и остаточных деформаций находятся в прямой зависимости от погонной энергии сварки, которая определяется выбранным режимом.
[c.35]
Высокая концентрация теплоты способствует сужению зоны, подвергающейся пластическим деформациям, и уменьшению деформаций конструкций. С этой точки зрения наиболее благоприятной является замена ручной сварки покрытыми электродами автоматической или полуавтоматической сваркой под флюсом или в защитных газах. Для обеспечения минимальной деформации сварной конструкции следует накладывать сварные швы наименьшего сечения и не допускать их увеличения в процессе изготовления конструкции. Величина и характер сварочных напряжений и остаточных дефор-
На величину и характер сварочных напряжений и остаточных деформаций влияет погонная энергия сварки и режим сварки. Увеличение сечения шва, как правило, способствует росту деформаций. Величина остаточных деформаций и напряжений зависит и от порядка наложения швов по длине и сечению. Например, при сварке листовых конструкций вначале выполняют поперечные швы отдельных поясов, а затем соединяют (сваривают) пояса между собой.
Величина остаточных свароч- ддд. ных напряжений или деформаций будет тем больше, чем больше сечение шва, свариваемого за один проход, т. е. больше сварочный ток и меньше скорость сварки (чем больше погонная энергия сварки). Кроме того, величина напряжений будет тем больше, чем больше разность температур между нагреваемыми и холодными участками металла при сварке. При сварке на морозе эта разность значительно больше, чем при сварке на тех же режимах летом, поэтому в первом случае величина возникающих напряжений и скорость их роста будет большей, чем во втором случае. [c.39]
Растягивающие остаточные напряжения появлялись также при плазменно-механическом фрезеровании кромок листовых заготовок при 5 мм, тогда как при фрезеровании без нагрева в тех же условиях имели место напряжения сжатия. Различие объясняется, по-видимому, возникновением термических деформаций от плазменного нагрева, обусловливающих достаточно обширную область распространения термических растягивающих напряжений (см.
Внутренние напряжения и деформации, возникающие при сварке, зависят от вида сварки. При газовой сварке возникают значительно большие деформации, чем при дуговой. По направлению действия различают продольные, расположенные параллельно оси шва, и поперечные, расположенные перпендикулярно оси шва, линейные сварочные напряжения (рис. 52). Распределение продольных напряжений в стыковом шве таково, что на его концах из-за возможности свободной усадки они незначительны, а в средней части имеют достаточно большую величину, достигая предел а теку чести. При сварке встык продольные сокращения [c.
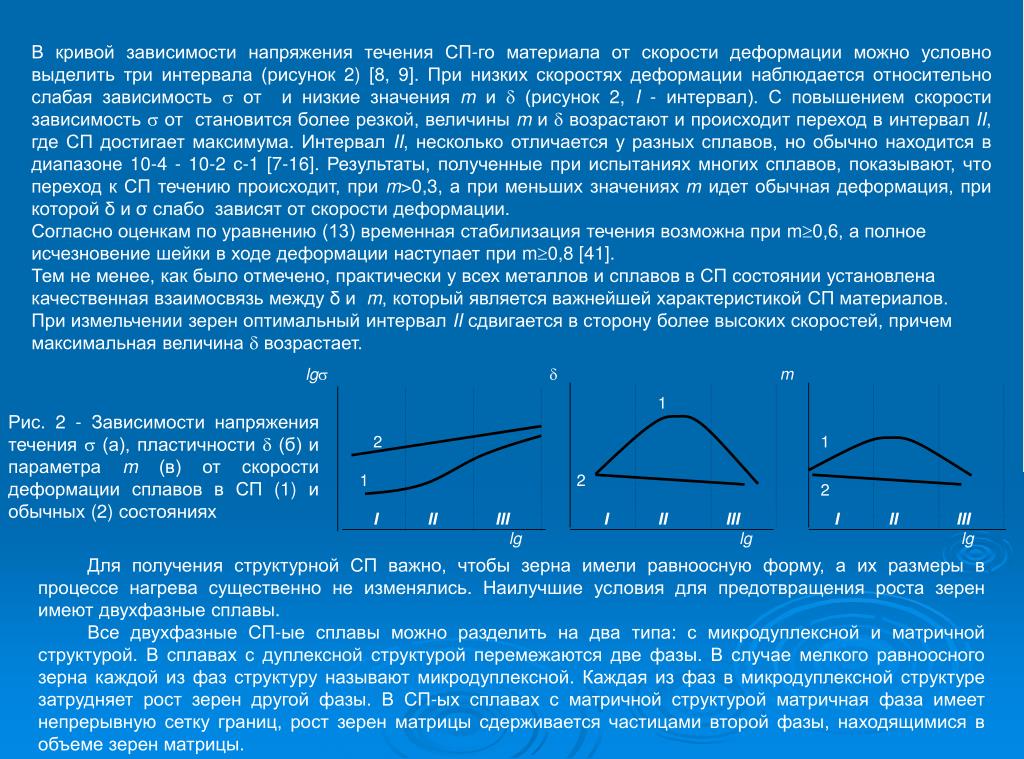
Режим сварки. Величина и характер сварочных напряжений и остаточных деформаций находятся в прямой зависимости от погонной энергии сварки, которая определяется выбранным режимом сварки. С уменьшением погонной энергии деформации снижаются. [c.77]
Мероприятия, применяемые преимущественно для снятия сварочных напряжений, влияют на деформации и, наоборот, мероприятия, применяемые преимущественно для уменьшения деформаций, влияют на величину напряжений. Рассмотрим основные способы уменьшения сварочных деформаций и напряжений. [c.35]
Для ряда сварных изделий необходимо также учитывать коробление в процессе механической обработки или эксплуатации конструкции. Снятие припусков при механической обработке изменяет напряженное состояние изделия и приводит к нарушению взаимной уравновешенности напряжений. Для перехода в новое равновесное напряженное состояние, необходимое по условию существования сварочных напряжений без приложения внешних сил, в конструкции должны пройти определенные деформации, вызывающие ее коробление.
Внешние наблюдаемые деформации сварных заготовок (например, укорочение пластины после сварки, соответствующее перемещению ее фани 1 в положение 4) не совпадают с внутренними упругопластическими деформациями, а их величины противоположны чем больше внешние деформации, тем меньше внутренние деформации. Величина и знак собственных сварочных напряжений определяются внутренними деформациями. [c.275]
Деформации, напряжения и перемещения относятся к сопутствующим сварочным процессам, оказывающим отрицательное воздействие на конструкцию в процессе ее изготовления и в последующем, снижая ее эксплуатационные характеристики, ухудшая качество. Так, напряжения в сварной конструкции уменьшают величину усталостной прочности, особенно если в сварном соединении имеется концентратор напряжений. В реальных конструкциях роль надреза, т. е. концентратора напряжений, может выполнять непровар, трещина и т. п. Форма шва также определяет характер распределения напряжений наличие усиления сверху и снизу шва вызывает в месте перехода от шва к основному металлу концентрацию напряжений.
[c.498]
Деформации и напряжения при сварке стыковых соединений. По продолжительности сварочные напряжения бывают технологические и остаточные. Первые возникают во время сварки (в процессе изменения температуры), вторые — после окончания сварки и полного охлаждения изделия. По направлению действия различают продольные, расположенные параллельно оси шва, и поперечные, расположенные поперек оси шва, линейные сварочные напряжения (рис. 31). Распределение продольных напряжений при сварке в стыковом шве таково, что на его концах из-за возможности свободной усадки они незначительны, а в средней части имеют достаточно большую величину, достигают предела текучести (рис. 32). При сварке встык продольное сокращение шва вызывает не только продольные, но и поперечные
[c.91]
Сварочные напряжения вызывают остаточные деформации в сварной конструкции, величина которых может быть значительно больше допуска на готовую деталь. Действие сварочных напряжений важно учитывать при конструировании и изготовлении технологической оснастки, так как от этого зависит точность обработки и сборки. Сварочные напряжения могут быть значительно уменьшены при правильном конструировании детали (узла), рациональным выбором режима сварки, а также последующей термической правкой детали. [c.129]
В то же время, известно, что сварочные напряжения снижают прочность конструкций из хрупких материалов, неспособных давать пластические деформации. Следовательно, в конструкциях из малоуглеродистых и низколегированных конструкционных сталей, внутренне уравновешенные сварочные напряжения могут снизить прочность сварного соединения лишь в том случае, если материал сварного соединения будет приведен в хрупкое состояние, т. е. практически полностью потеряет способность пластически деформироваться. Такое состояние материала может иметь место при температурах ниже критической температуры хрупкости, которая зависит от формы образца. В этом случае сварочные напряжения, суммируясь с напряжениями от внешней нагрузки, приведут к снижению величины разрушающей нагрузки. Однако, если этим исключительно тяжелым условиям работы предшествовала работа конструкции в более легких условиях (например, при положительной температуре), то снижения разрушающей нагрузки не произойдет вследствие смягчения остроты концентратора напряжений за счет пластических деформаций, происшедших при предшествующих нагружениях. Этим и объясняется то обстоятельство, что в реальных конструкциях при статических нагрузках практически не наблюдается снижения прочности от действия остаточных напряжений.
[c.97]
Выбор источника тепла. На величину сварочных деформаций и напряжений оказывает влияние степень концентрации тепла источника.
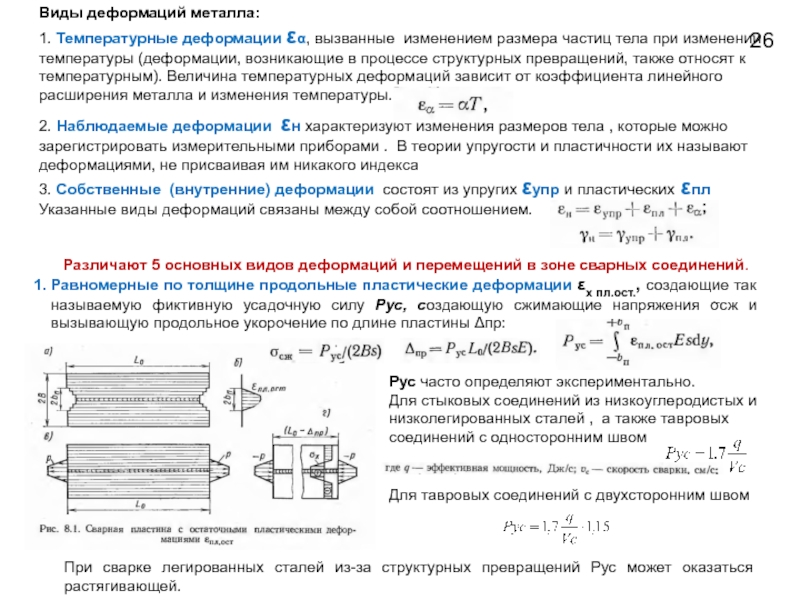
При охлаждении полоса / будет стремиться укоротиться на величину полученной деформации сжатия Д/пл. но этому препятствуют полосы // и III. После полного охлаждения лист в целом получит усадку Д ост. меньшую, чем Д/пл- Вместе с этим в полосе I возникнут остаточные напряжения растяжения, в полосах И и /// — остаточные напряжения сжатия. Поле остаточных сварочных напряжений в листе в целом будет находиться в равновесии. [c.354]
Изменение размеров и формы сварной конструкции в некоторых случаях снижает ее работоспособность и портит ее внешний вид. Если остаточные деформации достигают заметной величины они могут привести к неисправимому браку. При разработке, технологии сборки и сварки конструкции следует учитывать необходимость снижения остаточных деформаций до величины, при которой они не отражаются на работоспособности и внешнем виде конструкции и не затрудняют сборку отдельных элементов. Если величина остаточных деформаций выходит за допускаемые пределы, следует проводить правку конструкции. Правка конструкции является весьма трудоемкой операцией, требует высокой квалификации рабочих, и ее так же, как и снятие сварочных напряжений, следует проводить только в случае действительной необходимости.
[c.163]
Режим сварки. Величина и характер сварочных напряжений и остаточных деформаций находятся в прямой зависимости от погонной энергии сварки,-которая определяется режимом сварки и зависит от сечения шва или слоя. Увеличение сечения шва или слоя приводит к заметному росту величины остаточной деформации. Для обеспечения минимальной деформации сварной конструкции следует назначать наименьшие (допустимые из условий прочности конструкции) сечения швов и не допускать их увеличения в процессе изготовления конструкции. В отношении уменьшения сечения шва наиболее рациональной является двусторонняя рюмкообразная разделка рис. 4-18). На зависимости между величиной остаточной деформации и режимом сварки (погонной энергией) основан расчетный метод определения остаточных деформаций.
[c.164]
В сварочной лаборатории МВТУ им. Баумана разработан метод определения объемных остаточных напряжений в стыковых сварных соединениях большой толщины. Метод позволяет определять напряжения как в глубине сварного соединения (объемные напряжения), так и на его поверхности (двухосные напряжения). Сущность его состоит в следующем в сварном соединении большой толщины сверлят специальные ступенчатые отверстия, ориентированные по главным осям поля напряжений или под некоторым углом к ним. В эти отверстия помещают специальные цилиндрические вставки с наклеенными на их поверхность тензодатчиками сопротивления. Перед установкой в образец вставки тарируют на машине для испытаний на растяжение. Коме того, перед проведением измерения напряжений вставке сообщают определенный предварительный натяг, который дает возможность регистрировать его деформации обоих знаков. После установки вставки и снятия прибором показания соответствующего напряжения предварительного натяга из образца вырезают столбик с отверстием и вставкой. Затем снимают повторное показание прибора. Практика измерений показала, что оптимальными размерами вырезаемого столбика является размер АОХА мм. Увеличение этого размера ведет к увеличению степени осреднения искомого компонента напряжения, а его уменьшение — к усилению влияния отверстия на результат измерения деформации. По разности произведенных замеров определяют величину упругой деформации, вызванной снятием остаточных напряжений, и подсчитывают величину этих напряжений.
[c.215]
Нагрев изделия в процессе отпуска до 650—750° в зависимости от марки стали приводит к снятию сварочных напряжений за счет прохождения процесса релаксации. Однако в процессе охлаждения после отпуска в разнородных соединениях, в отличие от однородных, вновь возникают остаточные напряжения, но уже вызванные не неравномерностью нагрева при сварке, а разностью коэффициентов линейного расширения контактируемых материалов. Так, при охлаждении аустенитная составляющая стремится получить большее укорочение, чем перлитная, за счет того, что коэффициенты линейного расширения аустенита на 20—40% больше, чем перлита. Наличие в сварном соединении жесткой связи между ними препятствует свободной деформации отдельных составляющих и вызывает появление в сварных соединениях L новых остаточных напряжений. Вслед- в,кГ1мм г ствие этого в аустенитных ободе и шве возникают напряжения растялнапряжения сжатия, причем в зоне сплавления наблюдается скачок величины напряжений с переменой их знака.
[c.49]
Сварочные напряжения относятся к группе так называемых внутренних напряжений, существующих в изделии без приложения внешних сил. Внутренние напряжения возникают практически при всех технологических про-щёссах изготовления конструкций (литье, ковке, прокатке, сварке, механической и термической обработке), достигая в ряде случаев значительной величины (предела текучести) и вызывая заметные деформации изделий. Основными причинами их развития могут являться неравномерный разогрев изделия Б процессе изготовления, неравномерное распределение усилий, а также структурные изменения, приводящие к появлению в отдельных участках пластических или термопластических деформаций. Отличительной особенностью внутренних напряжений является их взаимная уравновешенность в пределах изделия.
[c.59]
Другим технологическим приемом снижения реактивных напряжений является проколачивание сварных швов. При проколачивании зона шва подвергается принудительному расширению, что несколько снижает жесткость изделия, а следовательно, и величину реактивных напряжений. Использование проколачивания является в ряде случаев полезным и с точки зрения уменьшения сварочных деформаций. Эта операция является желательной в сварных соединениях перлитных сталей. [c.64]
Рассмотренный кратко термодеформационный цикл сварки, обусловливая появление уравновешенных упругих деформаций в зоне сварного соединения, приводит к возникновению остаточных сварочных напряжений в сварном соединении. В зонах, где должны происходить деформации сжатия, возникают растягивающие остаточные напряжения, а уравновешивающие их сжимающие напряжения соответственно появляются в зонах с деформацией растяжения. На величину и распределение остаточных напряжений кроме неравномерных деформаций изменения объема металла при охлаждении оказывают влияние и объемные изменения, протекающие ниже температуры распада аустенита. Эти изменения у различных сталей протекают по-разиому и зависят от содержания в стали углерода и легирующих элементов. На рис. 4 представлена схема распределения остаточных напряжений в сварном соединении. Уровень напряжений и размеры растянутых и сжатых зон зависят от условий сварки и состава свариваемой стали. По данным табл. 2 можно судить о роли состава стали в возникновении остаточных напряжений в сварном соединении. Экспериментально определенные величина и распределение остаточных напряжений в сварных соединениях труб с толщиной стеики 30—36 м.м из стали 15ХМ, выполненных ручной дуговой сваркой с получением металла шва близкого состава, приведены на рис. 5.
[c.408]
Влияние остаточных сварочных напряжений возрастает по мере перехода от пластических форм разрушения, т.


В процессе сварки конструкции в ней возникают напряжения в результате неравномерных объемных изменений, вызванных неодинаковым нагревом основного и наплавленного металлов, усадкой расплавленного металла после сварки, структурными изменениями металла из-за быстрого охлаждения, жестким закреплением деталей или изделия в ходе их изготовления. Появление указанных натряжений в сварном соединении может обусловливаться также и изменением растворимости газов, окружающих сварной шов при охлаждении. Эти напряжения в отличие от напряжений, действующих на конструкцию во время ее эксплуатации и вызываемых внешними силами, называют внутренними или остаточными сварочными напряжениями. Внутренние напряжения могут вызвать не только деформацию сварного изделия, но и его разрушение. Величина оста- [c.119]
Стойкость сварных соедипений протпв образования трещпн характеризует способность составляющих его материалов образовывать соединение без трещин и является комплексной характеристикой, зависящей как от технологических свойств металлов, так и от интенсивности и величины сварочных деформаций или напряжений. Ее определяют путем сварки образцов технологических проб отраслевого назначения, включающих основной и сварочный материалы, тип и жесткость сварного соедпнения, термические и климатические условия сварки, применительно к определенному виду сварных конструкций. Степень (или группа) стойкости оценивается указанным выше комплексо.м условий сварки образца пробы, при которых еще не образуется трещин.
[c.190]
Деформации и напряжения при сварке
Деформации и напряжения при сварке
Категория:
Сварка металлов
Деформации и напряжения при сварке
Классификация деформаций и напряжений. Помимо напряжений и деформаций, возникающих в деталях под действием приложенных нагрузок, в них могут быть так называемые собственные напряжения и деформации, которые существуют в телах даже при отсутствии каких-либо внешних сил.
В зависимости от продолжительности существования собственные напряжения и деформации при сварке разделяют на временные, т. е. существующие период выполнения свари или сопутствующих технологических операций, и на остаточные, т. е. устойчиво сохраняющиеся в теченидц длительного времени сварки.
Различают собственные напряжения I рода, которые уравновешиваются в макрообъемах тела, II рода—в пределах зерен, III рода в пределах кристаллической решетки.
В зависимости от характера напряженного состояния собстве ные напряжения могут быть одноосными — линейными, двухо ными — плоскостными и трехосными — объемными.
Различают деформации в плоскости, проявляющи еся в изменении формы и размеров детали или конструкции в пло кости, например, в виде продольных и поперечных деформаци деформации вне плоскости, например в виде угловых деформаци грибовидности, серповидности и т. д.
Деформации, которые изменяют размеры всего изделия, иска; жают его геометрические оси, называются общими. Деформации относящиеся к отдельным элементам изделия в виде выпучин, хло-
32 пуНов, волнистости и других местных искажений, называются устными.
Следует различать деформации непосредственно в зоне сварных соединений и деформации элементов конструкции в целом. Последние являются следствием деформаций и напряжений в сварном соединении.
Образование сварочных деформаций и напряжений. Основными причинами образования собственных напряжений и деформаций в сварных соединениях и конструкциях являются неравномерный нагрев и охлаждение металла при сварке, структурные и фазовые превращения, механическое (упругое и пластическое) деформирование при сборке, монтаже и правке сварных узлов и конструкций.
Представление о причинах возникновения тепловых сварочных деформаций и напряжений дает последовательное ознакомление с элементарным процессом нагрева и охлаждения стержня при разных условиях его заделки (закрепления).
Если точно на расстоянии поставить жесткую преграду, препятствующую удлинению стержня, и вновь нагревать его, то при расширении стержень будет давить на левую и правую преграды, со стороны которых возникают противодействующие силы реакции на давление стержня R, которые по отношению к стержню являются внешними сжимающими силами. В стержне возникнут напряжения о- сжатия, которые будут расти по мере роста температуры Т в соответствии с выражением а—аЕТ, где произведение аТ Равно относительному удлинению, а Е — модуль упругости. Если нагревать стержень до температур, вызывающих только упругое Деформирование, то при его охлаждении до исходной температуры Е нем не возникнет никаких напряжений и остаточных деформаций, его длина останется неизменной.
Рис. 1. Схема деформации стержня с различными условиями закрепления при нагреве
При нагреве стального стержня выше 100 °С в нем возможно появление пластических деформаций.
Рассмотрим, наконец, случай, когда стержень закреплен жестко с обоих концов, закрепление препятствует как его удлинению, так и укорочению.
После нагрева до температур, не вызывающих пластического деформирования , и последующего охлаждения в стержне не останется никаких напряжений, так как при нагреве
стержень деформировался (сжимался) только упруго. На стадии нагрева в нем воз-i никали сжимающие напряжения.
Нагрев до температур, превышающих температуру достижения от (>100 °С), приводит к пластическому обжатию стержня и возникновению напряжений сжатия аг. При остывании стержень будет стремиться укоротиться на величину обжатия А/Пл. Однако жесткое закрепление будет препятствовать сокращению. Реакция закрепления вызовет появление в стержне растягивающих напряжений. Эти остаточные напряжения растяжения не появились бы, если бы стержень при нагреве не претерпел пластического обжатия.
Нагрев стержня из низкоуглеродистой стали при жестком его закреплении до температур >200° С приводит к появлению в нем после остывания растягивающих напряжений, равных пределу текучести и даже к пластическим деформациям растяжения.
Процессами, происходящими при нагреве и охлаждении защемленного стержня, объясняется образование временных и остаточ ных напряжений.и деформаций, действующих в сварном шве и при легающей зоне, где металл подвергается упругопластическому де формированию при нагреве и охлаждении в процессе сварки. Зон нагрева при сварке ведет себя как защемленный нагреваемый стержень, а холодные участки металла как защемление.
Обязательным условием возникновения остаточных деформация и напряжений является наличие пластической деформации при нагреве. Чем выше нагрев и больше его неравномерность, тем более вероятно появление при нагреве пластических деформаций, а cледовательно, и остаточных напряжений и деформаций.
Величина остаточных напряжений для углеродистых сталей достигает предела текучести, для сталей высоколегированных может превышать условный предел текучести, для титана, алюминия, меди, и тугоплавких металлов, как правило, меньше предела текучести.
При сварке закаливающихся сталей наряду с тепловыми деформациями и напряжениями возникают структурные напряжения связи с образованием закалочной, мартенситной структуры, так как образование мартенсита сопровождается увеличением объема по сравнению с объемом феррита и перлита.
—
Основные понятия. Изменение формы и размеров твердого тела под влиянием внешней или внутренней силы называется деформацией. Если форма и размеры восстанавливаются после прекращения действия силы, то такая деформация будет упругой. Если тело не принимает первоначальной формы, оно получило остаточную, или пластическую, деформацию. Размеры деформации определяются величиной приложенного усилия. Чем больше усилие, тем больше вызываемая им деформация. О величине усилия судят по напряжению, вызываемому данным усилием в теле. Напряжением называется внутренняя сила, приходящаяся на единицу площади поперечного сечения тела. Таким образом, между напряжением и вызываемой им деформацией существует прямая зависимость.
Напряжения и деформации, возникающие от неравномерного нагревания и охлаждения материала, называются тепловыми или термическими. Величина расширения металла зависит от температуры его нагрева и коэффициента линейного расширения — величины в миллиметрах, на которую удлиняется металлический стержень длиной 1 м при нагревании его на 1 °С. Чем больше коэффициент термического линейного расширения и выше температура нагрева, тем большую деформацию будет испытывать металл при нагревании и охлаждении.
Если закрепить концы стержня так, что он не сможет свободно удлиняться или укорачиваться, то термические деформации стержня вызовут в нем термические напряжения, соответствующие этим деформациям. Чем большую нагрузку будет испытывать закрепленный стержень, тем больше будет его деформация и тем выше будут возникающие в нем напряжения.
На величину деформаций при сварке влияет теплопроводность металла. Чем выше теплопроводность свариваемого металла, тем равномернее распределяется по его сечению тепловой поток и деформация будет меньше. Так, например, при сварке нержавеющих сталей, обладающих меньшей теплопроводностью и большим коэффициентом термического линейного расширения, чем малоуглеродистая сталь, деформации получаются больше, чем при сварке малоуглеродистой стали. Наоборот, алюминий, обладающий более высоким коэффициентом термического линейного расширения, но значительно лучше проводящий теплоту, чем низкоуглеродистая сталь, дает при сварке меньшие деформации по сравнению с малоуглеродистой сталью.
Термические напряжения могут возникать в металле и без действия внешних усилий. Такие напряжения называются собственными. Из собственных термических напряжений наибольшее значение имеют те, которые возникают во время охлаждения изделия. Если они действуют только вдоль шва, это не сказывается на прочности сварного соединения. Более опасны напряжения, действующие перпендикулярно оси шва (поперечные), так как они могут вызвать появление трещин в шве и околошовной зоне.
Причины возникновения деформаций. Внутренние напряжения возникают только в том случае, если свободному расширению и сокращению детали что-либо препятствует. Таким препятствием являются соседние участки металла, оставшиеся более холодными вследствие неравномерного нагрева и потому менее расширившиеся. Наличие сосредоточенного источника теплоты (электрическая дуга), перемещающегося вдоль шва с определенной скоростью и вызывающего неравномерное нагревание металла при сварке, является основной причиной возникновения внутренних напряжений и деформаций в сварных изделиях.
Усадка наплавленного металла возникает в следующих случаях. При переходе наплавленного металла из жидкого состояния в твердое объем его уменьшается, происходит усадка. Явление усадки объясняется тем, что при затвердевании металла он становится более плотным, вследствие чего объем его сокращается. В результате усадки возникают растягивающие напряжения в соседних частях детали, которые вызывают соответствующие им напряжения и деформации. Различные металлы имеют разную усадку. Она обычно измеряется в процентах от первоначального линейного размера. Так, усадка алюминия 1,7…1,8; бронзы — 1,45…1.6; латуни — 2,06; меди — 2,1; малоуглеродистой стали — 2.
Напряжения, вызванные усадкой, возрастают до тех пор, пока металл не начнет вытягиваться”. Если он недостаточно пластичен, деталь может дать трещину в наиболее слабом месте. Этим местом часто бывает околошовная зона термического влияния. Вследствие усадки или сокращения объема металла образуются трещины в процессе сварки, называемые горячими трещинами. При сварке происходит продольная и поперечная усадка.
Продольная усадка вызывает сокращение длины листов при сварке продольных швов. Если центр тяжести поперечного сечения шва не совпадает с центром тяжести сечения свариваемого элемента, то от продольной усадки неизбежно возникает коробление этих элементов в продольном направлении. Поперечная усадка дает коробление листов. Усадка всегда больше там, где больше объем наплавленного металла. Поэтому при поперечной усадке листы будут коробиться вверх, в сторону усиления шва. Если деталь закрепить, не давая ей деформироваться от усадки, то это вызовет напряжения в закрепленных участках изделия.
Величина деформаций и связанных с ней напряжений зависит от величины зоны нагрева при сварке. Чем больший объем металла разогревается при сварке, тем сильнее будут деформации и коробление. Поэтому различные способы сварки дают различную величину деформаций.
Рис. 1. Деформации от поперечной усадки наплавленного металла: а — соединение до сварки, б — после сварки
Рис. 2. Продольная усадка и вызываемые ею деформации:
а — при симметричном б, в, г — при несимметричном расположении швов относительно центра тяжести сечения элемента;
Размеры и положения швов влияют на величину деформации при сварке. Наибольшие деформации возникают в длинных швах, расположенных несимметрично относительно сечения свариваемого профиля. Чем сложнее форма детали, чем больше в ней различных швов, тем больше она может деформироваться.
Искусственное охлаждение детали в процессе сварки уменьшает величину деформации.
Способы снижения напряжений и деформаций. Для снижения сварочных напряжений и деформаций при разработке черте;;;ей металлических конструкций учитывают следующее. Сварные соединения конструируют таким образом, чтобы объем наплавленного металла был минимальным. С этой целью прерывистые швы заменяют сплошными меньшего сечения. Стыковые швы проектируют с минимальным углом раскрытия шва и минимальным зазором. Избегают резких переходов сечений, а также применяют преимущественно стыковые соединения. Не допускают концентрации и пересечений сварных швов.
Порядок сборки под сварку, способ сварки, режимы сварки и последовательность наложения шва по его длине и сечению оказывают влияние на величину деформаций и напряжений при сварке.
Чтобы уменьшить остаточные деформации и напряжения конструкций и изделий при сборке, по возможности не допускают скрепления деталей прихватками, которые создают жесткие закрепления. Для обеспечения подвижного состояния закрепленных деталей используют клиновые, центровочные и другие сборочные приспособления.
На образование остаточных деформаций и напряжений значительное влияние оказывает способ сварки. На величину и характер сварочных напряжений и остаточных деформаций влияют энергия и режим сварки. Увеличение сечения шва, как правило, способствует росту деформаций. Величина остаточных деформаций и напряжений зависит и от порядка наложения швов по длине и сечению. Например, при сварке листовых конструкций вначале выполняют поперечные швы отдельных поясов, а затем сваривают пояса между собой.
Для того чтобы предотвратить деформации в процессе сварки, применяют следующие способы.
Уравновешивание деформаций заключается в том, что устанавливают определенную последовательность наложения швов, при которой деформации от предыдущих швов снижаются при выполнении последующих швов. Этот способ широко применяют при сварке конструкций симметричного сечения.
Обратные деформации выполняют так. Перед сваркой конструкций или элемента для уменьшения остаточной деформации искусственно создают деформацию, обратную по отношению к той, которая может возникнуть при сварке. На рис. 3 показаны примеры использования обратной деформации.
Жесткое закрепление деталей перед сваркой обеспечивает уменьшение сварочных деформаций.
Проковка швов и околошовной зоны легкими ударами молотка способствует снижению напряжений и деформаций. При выполнении проковки необходимо соблюдать следующие условия. При многослойной сварке проковку выполняют послойно, а первый и последний швы не проковывают; шов проковывают участками длиной 150…200 мм сразу после сварки или подогрева его до 150…200 °С; при сварке металла толщиной более 16 мм проковывают и металл околошовной зоны.
Рис. 3. Использование обратных деформаций при сварке: а — клиновидный зазор, равный 10 … 20 мм на 1 м шва, б, в —предварительный выгиб (/, II — положения до и после сварки)
Общий отжиг сварных конструкций делают тогда, когда они изготовлены из сталей, имеющих склонность к образованию закаленных зон вблизи сварного шва (особенно при большой толщине свариваемого металла), а также в том случае, когда конструкции работают в сооружении при знакопеременных нагрузках.
Механическую правку конструкций производят приложением ударной или статической нагрузки при холодном или нагретом состоянии металла.
Термическую правку конструкций выполняют наплавкой валиков с обратной стороны шва или местным нагревом.
Для получения сварных конструкций заданных проектных размеров необходимо давать припуски на усадку сварных швов. На один поперечный стыковой шов проката листов толщиной 8… 16 мм припуск должен составлять около 1 мм.
Реклама:
Читать далее:
Способы уменьшения сварочных деформаций м напряжений
Статьи по теме:
Рекомендуем приобрести: Установки для автоматической сварки продольных швов обечаек — в наличии на складе! Сварочные экраны и защитные шторки — в наличии на складе! Возникновение собственных сварочных деформаций и напряжений обусловлено неравномерным распределением температуры при сварке, фазовыми превращениями, протекающими с изменением удельного объема, и жесткостью свариваемых элементов, препятствующей развитию деформаций. В отличие от тепловых процессов, процессы изменения полей внутренних деформаций и напряжений первого рода при сварке изучены в меньшей степени, и расчеты их, как правило, весьма сложны. В настоящее время инженерные расчеты, разработанные в СССР В. П. Вологдиным, Н. О. Окербломом, Г. А. Николаевым, Н. Н. Рыкалиным, используются главным образом для определения конечных деформаций формоизменения и остаточных напряжений. Наиболее достоверные данные о кинетике изменения внутренних деформаций и напряжений в процессе сварки получены путем экспериментальных исследований на сталях с применением разработанного Н. Измерение Н. Н. Прохоровым продольных деформаций в околошовной зоне с помощью механических тензометров на базе 20 мм в условиях наплавки валика на кромку пластины показало, что в сплавах, не претерпевающих фазовых превращений (сталь ОХ18Н9Т), при нагреве происходит развитие упругопластических внутренних сжимающих деформаций и напряжений. В табл. 4 приведены данные о деформациях и напряжениях в околошовной зоне, полученные при следующих условиях: размеры пластины 300x100x8 мм, наплавка на кромку длиной 200 мм электродами из малоуглеродистой стали; погонная энергия дуги q/v=3,3—4,2 ккал/см; скорость охлаждения при 550° около 6—8 град/сек; напряжения были измерены на модели в виде тонкостенных трубчатых образцов, нагреваемых током и воспринимающих сжимающие напряжения, которые создавались активными силами и имитировали реакцию соседних с околошовной, зоной участков металлов; для сталей Ст.3, 40Х и 25ХН4 остаточные напряжения были дополнительно проверены методом разрезания на пластинах с наплавленными на кромку валиками. К моменту полного выравнивания температурного поля внутренняя деформация растяжения достигает 1,65%, а остаточное растягивающее напряжение, уравновешивающее упругую составляющую деформации, около 24 кг/мм2. В легированных сталях (например, 25ХН4), претерпевающих бейнитное и особенно мартенситное превращения, влияние этих фазовых превращений на кинетику развития деформаций и напряжений оказывается более существенным (см. Величина растягивающих деформаций перед началом превращения аустенита определяется коэффициентом линейного расширения стали и температурой начала превращения. Чем ниже эта температура, тем больше величина растягивающих деформаций к началу превращения. В зависимости от состава стали деформация растяжения может достигать 0,7— 1,8%. Например, в сталях Ст.3 и Ст.20 к началу превращений аустенита в феррит и перлит (680—670°) деформация равна 0,78—0,72%; в сталях 30ХГСА и 40Х к началу бейнитного превращения (440—430°) она составляет 1,2—1,4%; в сталях 25НХ4, 35СГ и 50ХВС к началу мартенситного превращения (300—300°) деформация равна 1,3—1,75%: При анализе этих данных следует иметь в виду, что наплавку производили электродами из малоуглеродистой стали, вследствие чего превращение аустенита в наплавленном металле во всех случаях протекало при относительно высоких температурах ( ∼ 600°) с образованием феррито-перлитной структуры. Поэтому при наплавке на легированные стали, в околошовной зоне которых аустенит сохранялся до более низких температур, чем в шве, деформация растяжения аустенита в зоне возрастала также и вследствие дополнительного влияния увеличения удельного объема шва при превращении и разницы в коэффициентах теплового расширения шва и зоны при последующем охлаждении. Таким образом, перед началом превращения аустенит подвергается небольшой по величине внутренней деформации растяжения, продольная составляющая которой равна 0,7—1,8%. Эта деформация тем больше,чем ниже температура начала превращения аустенита в околошовной зоне и чем выше эта температура превращения в шве. Хотя по своей величине упругопластическая деформация аустенита невелика, она может оказывать существенное влияние на кинетику мартенситного превращения и на сопротивляемость металла околошовной зоны образованию холодных трещин. При этом существенное значение приобретает разница в температурах превращения аустенита в шве и околошовной зоне, однако не столько в связи с изменением величины деформации, сколько из-за возникновения различий в условиях и степени развития релаксационных процессов в аустените. В процессе последующего превращения аустенита в околошовной зоне развиваются небольшие сжимающие деформации и напряжения. Величина их в легированных сталях больше, чем в малоуглеродистых (см. рис. 12, б и в). Одновременно с понижением температуры начала превращения аустенита в мартенситную область (особенно ниже 350°) восстановление растягивающих продольных напряжений к моменту полного выравнивания температуры становится маловероятным. Например, в сталях 25ХН4, 35СГ и 50ХВС возникают даже заметные сжимающие напряжения. Существенное увеличение влияния превращения аустенита на величину и знак остаточных внутренних деформаций и особенно напряжений при переходе от малоуглеродистых к легированным сталям в сравнении со сталью ОХ18Н9Т обусловлено тремя основными причинами: 1) протеканием ферритного и перлитного превращений (малоуглеродистая сталь) при высоких температурах, когда металл слабо сопротивляется пластической деформации, а бейнитного и мартенситного превращений (легированная сталь) — при относительно низких температурах, при которых металл обладает более высокой сопротивляемостью пластической деформации и значительными упругими свойствами; 2) большей величиной разности между удельными объемами мартенсита и аустенита, чем феррита (или феррито-карбидных смесей (Справедливо для сталей с содержанием углерода примерно до 0,5%, так как удельный объем у карбидов, как правило, больше, чем у мартенсита)) и аустенита; 3) возрастанием этой разности с понижением температуры, так как коэффициент линейного расширения у мартенсита меньше, чем у аустенита. В. Н. Земзин [88] и П. А. Мельников [89] также показали, что в околошовной зоне закаливающихся легированных сталей развиваются продольные деформации и напряжения сжатия. Кроме того, они обнаружили, что по обе стороны от околошовной зоны при переходе к шву или основному металлу продольные напряжения изменяются скачкообразно. При этом в основном металле они всегда растягивающие, а в шве их знак зависит от типа электродов, т. е. состава наплавленного металла. Чем ниже температура превращения аустенита в металле шва, тем вероятнее развитие в нем сжимающих напряжений. Для анализа кинетики развития деформаций при сварке и их влиянияна технологическую прочность, а также структуру и свойства околошовной зоны весьма важно располагать сведениями об изменении скорости деформации в процессе нагрева и охлаждения. В работе [86] показано, что и для малоуглеродистых и для закаливающихся легированных сталей развитие внутренних деформаций в околошовной зоне с относительно высокими скоростями (0,02—0,03 мм/сек) происходит только в период нагрева и в начальной стадии охлаждения при высоких температурах. Скорости изменения поперечных деформаций в процессе охлаждения практически такие же, как и продольных. Разница заключается лишь в величине и знаке внутренних деформаций после полного охлаждения соединения [86]. На величину деформаций и напряжений существенное влияние оказывает ряд факторов: «жесткость» или размеры (до определенного предела) и конструкция соединяемых элементов; реактивные силы, возникающие обычно вследствие ограничения деформаций свариваемых элементов; активные силы от собственного веса изделия или от полезной нагрузки; последовательность наложения швов; режим сварки и число слоев; температура подогрева; различия в составе, теплофизических свойствах, в характере и температурных интервалах фазовых превращений металла шва и основного металла и т. Существенное влияние закреплений и близкого расположения швов на величину остаточных продольных и поперечных напряжений часто используется при разработке конструкции жестких проб, предназначенных для оценки склонности сталей и сплавов титана к образованию холодных трещин. Н. О. Окерблом [81, 82] показал, что в общем случае для стыковых соединений при данной ширине свариваемых листов с увеличением погонной энергии величина напряжений в околошовной зоне сначала возрастает, а затем по достижении некоторого максимума снижается. Наибольшие напряжения возникают при определенном соотношении между объемом расплавленного металла и шириной листов. В частности он предположил, что при сварке малоуглеродистой стали аустенитными электродами снижение продольных (от 35 до 30 кГ/мм2) и повышение поперечных напряжений (от 5 до 10 кГ/мм2) по сравнению со сваркой ферритными электродами обусловлены не столько различиями в характере фазовых превращений и свойствах металла шва, сколько неодинаковыми тепловыми режимами сварки за счет разных коэффициентов наплавки. Рациональными методами снижения остаточных напряжений при сварке являются общий подогрев, ограничение температуры охлаждения шва при многослойной сварке, повышение погонной энергии дуги при укладке второго слоя или отжигающего валика [86, 81]. Однако наиболее часто используется отпуск или отжиг изделий после сварки. О кинетике изменения и величине внутренних деформаций и напряжений в околошовной зоне при сварке титана данных очень мало. Однако, располагая сведениями о коэффициенте линейного расширения титана (8,5 * 10-6 0/1°С при 0—100° в сравнении с 11,7 * 10-6 1/°С для железа), о модуле упругости (11250 в сравнении с 21000 кГ/мм2 для железа) и характере изменений удельного объема при протекании фазовых превращений, можно в первом приближении оценить знак и порядок величин остаточных деформаций и напряжения. Таким образом, следует полагать, что в отличие от закаливающихся сталей при сварке титана и его сплавов в околошовной зоне растягивающие деформации и напряжения развиваются не только поперек шва, но и вдоль него, т. М.Х. Шоршоров. Металловедение. Сварка стали и сплавов титана |
Предотвращение и снижение сварочных напряжений и деформаций
Величина и характер сварочных напряжений и деформаций определяются рядом факторов. Рассмотрим влияние некоторых из них.
Вид и способ сварки. Значительное влияние на величину сварочных деформаций оказывает степень концентрации теплоты. Высокая концентрация теплоты способствует сужению зоны, подвергающейся пластическим деформациям, и уменьшению деформаций конструкций. Это подтверждается опытом применения автоматической сварки под флюсом.
При практически одной и той же погонной энергии сварка под флюсом благодаря большей скорости перемещения дуги (изотермы вытянуты и сдвинуты в область, уже пройденную дугой) вызывает меньшие остаточные деформации, чем ручная дуговая сварка. Снизить величины остаточных деформаций можно также, заменив ручную дуговую сварку покрытыми электродами автоматической или полуавтоматической сваркой в углекислом газе, аргоне, порошковой проволокой или активированной проволокой без дополнительной защиты. Применение полуавтоматической сварки в угл ‘кислом газе позволило ~простить технологию изготовления ряда тонколистовых конструкций (кузова тепловозов, электровозов и пр.) и сократить расходы на последующую правку.
Влияние конфигурации шва. От конфигурации шва в известной мере зависят величина и характер остаточных деформаций. При прочих равных условиях Х-образная подготовка кромок благодаря симметричному расположению шва относительно нейтральной оси вызывает меньшую угловую деформацию, чем У- образная. С целью уменьшения деформаций в некоторых случаях целесообразно применять двустороннюю сварку. При сварке под флюсом меньшие деформации происходят в соединениях без скоса кромок. В случае электрошлакового процесса, где сама техника выполнения сварки предопределяет симметричное расположение шва относительно нейтральной оси, угловые деформации весьма невелики. Эффективной мерой уменьшения деформаций является уменьшение сечения шва за счет применения сварочных материалов, обеспечивающих более высокую прочность металла шва. Как показали исследования, при сварке соединения с угловыми швами сечение может быть уменьшено до 40 %.
Режим сварки. Величина и характер сварочных напряжений и остаточных деформаций находятся в прямой зависимости от погонной энергии сварки, которая определяется режимом сварки и зависит от сечения шва или слоя. Увеличение сечения шва или слоя приводит к заметному росту величины остаточной деформации. Для обеспечения минимальной деформации сварной конструкции следует назначать наименьшие (допустимые из условий прочности конструкции) сечения швов и не допускать их увеличения в процессе изготовления конструкции. В отношении уменьшения сечения шва наиболее рациональной является двусторонняя рюмкообразная разделка (рис. 1). На зависимости между величиной остаточной деформации и режимом сварки (погонной энергией) основан расчетный метод определения остаточных деформаций.
Рис. 1. Зависимость между толщиной металла, формой и сечением разделки
Порядок сварки и закрепление свариваемых деталей. На величину возникающих при сварке остаточных деформаций и напряжений существенно влияет порядок наложения шва по его длине и сечению. Наибольшие остаточные деформации образуются при сварке на проход, т.е. при наложении шва от начала до конца без длительных перерывов. При ручной сварке для уменьшения величины деформации швы накладывают от середины к концам. Этот метод эффективен при выполнении шва двумя сварщиками.
При правильном выборе длины ступени обратноступенчатая сварка резко уменьшает величину напряжений и деформаций. При этом способе шов следует разбивать на участки таким образом, чтобы к началу сварки последующего участка температура металла составляла 200-300ºС. При однослойной сварке это условие обеспечивается, если длина ступени равна участку, образованному за счет расплавления одного электрода (при сечении шва, равном 1,2 сечения стержня электрода). Уменьшение деформаций и напряжений при обратноступенчатой сварке связано с тем, что ее выполняют по увеличенному зазору. При охлаждении одновременно с уменьшением ширины шва уменьшается и предварительно расширенный зазор, что способствует уменьшению реактивных напряжений и деформаций.
Для уменьшения величины остаточных напряжений и деформаций при сварке многопроходных швов применяют каскадный метод сварки. Существенное влияние на величину напряжений и остаточных деформаций оказывает направление сварки отдельных швов. Эффективной мерой снижения остаточных деформаций является закрепление свариваемых деталей в специальных приспособлениях-кондукторах.
Предварительный изгиб свариваемых деталей. В производственных условиях для борьбы с деформациями часто применяют предварительный обратный изгиб свариваемых деталей. Этот метод используют для борьбы с угловыми деформациями при сварке стыковых и нахлесточных соединений. При сварке листов небольшой ширины с V-образной разделкой кромок их располагают с предварительным выгибом в сторону, обратную ожидаемой деформации (рис. 2). Листы большой ширины можно укладывать с предварительным изгибом свариваемых кромок (рис. 3). Монтажные стыки с закрепленными листами рекомендуется сваривать с предварительно отогнутыми кромками, что достигается при помощи домкратов или специальных приспособлений (рис. 4). Для предотвращения деформаций из плоскости тавровых или двутавровых сечений производят упругую или пластическую деформацию пояса (рис. 5). С целью устранения продольных деформаций в плоскости при сварке тавровых балок применяют приспособления, которые изгибают балку в сторону, обратную ожидаемой деформации (рис. 6).
Рис. 2. Укладка свариваемых деталей для предотвращения угловой деформации при стыковом соединении
Рис. 3. Обратный изгиб свариваемых деталей для предотвращения угловой деформации при стыковом соединении
Рис. 4. Обратный изгиб свариваемых кромок в местах монтажных стыков
Рис. 5. Обратный изгиб пояса для
предотвращения грибовидной деформации
Предварительный обратный изгиб можно создать с помощью наклепа кромок и стенки балок либо нагревом до температуры 700 — 750º С (рис. 7). Эффективной мерой предотвращения выпучивания стенки в двутавровой балке, вызываемой сваркой поясных швов, является сборка с предварительным натяжением стенки. Для натяжения стенки используют сборочные стенды с домкратным устройством. Повысить жесткость тонких листов в сварных конструкциях с целью уменьшения деформаций можно путем гофрирования. При помощи прессов на тонких листах предварительно выдавливают узоры жесткости или гофры. Мерой уменьшения сварочных напряжений может быть предварительное растяжение или сжатие элемента с помощью продольно сжимающей силы.
Рис. 6. Обратный изгиб балки
Рис. 7. Место нагрева (или наклепа) кромки вертикальной стенки тавровой балки для создания обратного изгиба 1 — область нагрева или на клена
Рис. 8. Характер распределения температуры при сварке стыкового соединения:а — с искусственным охлажден нем, б — без охлаждения
Резкое охлаждение свариваемых деталей. При резком охлаждении сварного соединения нагреваемый при сварке участок, в котором возникают пластические деформации, сужается, что приводит к уменьшению остаточных деформаций и напряжений. На рис. 8 схематически показаны характер распределения температуры и размеры участков пластических деформаций при искусственном охлаждении и без него. При охлаждении участок пластической деформации значительно короче, чем при сварке в обычных условиях.
Однако искусственное охлаждение применимо только при сварке низкоуглеродистых сталей. Для уменьшения остаточных деформаций и напряжений при сварке сталей с повышенным содержанием углерода и легированных закаливающихся сталей метод искусственного охлаждения неприменим, так как он может привести к образованию малопластичных закалочных структур. Некоторое влияние на величину сварочных деформаций оказывает также и начальная температура изделия. При сварке в условиях естественных низких температур деформации снижаются весьма мало.
Влияние подогрева свариваемых деталей. При предварительном или сопутствующем подогреве уменьшается перепад температур между участками сварного соединения, благодаря чему несколько снижаются напряжения. Установлено, что при подогреве до температуры 200º С остаточные напряжения по сравнению со сваркой без подогрева снижаются на 30%. При более высокой температуре подогрева достигаются еще более благоприятные результаты.
Значительный эффект дает и сопутствующий подогрев. При сварке можно проводить как общий, так и местный сопутствующий подогрев. Общий подогрев назначают при сварке деталей небольших размеров или непластичных материалов, например чугуна. При местном подогреве нагревают участок шириной не менее 40 — 50 мм по обе стороны от шва. Нагрев только свариваемых кромок не дает заметного эффекта. При сварке с предварительным или сопутствующим подогревом в большинстве случаев не требуется последующей термообработки (отпуска) конструкции. Подогрев можно осуществлять индукционным способом, газовым пламенем и электрическими нагревателями.
Температура предварительного подогрева зависит от химического состава и толщины металла, а также жесткости конструкции. С увеличением содержания углерода и легирующих примесей, толщины металла и жесткости конструкции необходим подогрев до более высоких температур.
При изготовлении особо ответственных конструкций из низко- углеродистых сталей при толщине металла выше 40 мм иногда применяют предварительный подогрев до температуры 100- 120º С. При сварке среднеуглеродистых и низколегированных конструкционных сталей целесообразно применять предварительный подогрев до температуры 150—200ºС при толщине металла более 30 мм.
%PDF-1.4 % 406 0 объект > эндообъект внешняя ссылка 406 81 0000000016 00000 н 0000002826 00000 н 0000003055 00000 н 0000003099 00000 н 0000003135 00000 н 0000003751 00000 н 0000003979 00000 н 0000004127 00000 н 0000004313 00000 н 0000004461 00000 н 0000004645 00000 н 0000004795 00000 н 0000004977 00000 н 0000005126 00000 н 0000005311 00000 н 0000005459 00000 н 0000005642 00000 н 0000005792 00000 н 0000005946 00000 н 0000006094 00000 н 0000006245 00000 н 0000006391 00000 н 0000007569 00000 н 0000007606 00000 н 0000007709 00000 н 0000007795 00000 н 0000008009 00000 н 0000009294 00000 н 0000010478 00000 н 0000010697 00000 н 0000012037 00000 н 0000013226 00000 н 0000014657 00000 н 0000016250 00000 н 0000017439 00000 н 0000017586 00000 н 0000018297 00000 н 0000018482 00000 н 0000018947 00000 н 0000020503 00000 н 0000021044 00000 н 0000021173 00000 н 0000022813 00000 н 0000024002 00000 н 0000025248 00000 н 0000026554 00000 н 0000029247 00000 н 0000037149 00000 н 0000042098 00000 н 0000042166 00000 н 0000042481 00000 н 0000042673 00000 н 0000043075 00000 н 0000043139 00000 н 0000043642 00000 н 0000043839 00000 н 0000044366 00000 н 0000044475 00000 н 0000047505 00000 н 0000047544 00000 н 0000048092 00000 н 0000048226 00000 н 0000070504 00000 н 0000070543 00000 н 0000074175 00000 н 0000074247 00000 н 0000074447 00000 н 0000074557 00000 н 0000074669 00000 н 0000074795 00000 н 0000074925 00000 н 0000075051 00000 н 0000075216 00000 н 0000075356 00000 н 0000075479 00000 н 0000075644 00000 н 0000075770 00000 н 0000075897 00000 н 0000076025 00000 н 0000076160 00000 н 0000001916 00000 н трейлер ]/предыдущая 11007857>> startxref 0 %%EOF 486 0 объект >поток hb«`g`e`c`bg@
Факторы, влияющие на вызванные сваркой остаточные напряжения и деформации в сталях для сосудов под давлением, и методы их смягчения: обзор
Сосуды под давлением относятся к критически важному производственному оборудованию в промышленных операциях. Тот факт, что сосуд работает под давлением и может содержать токсичное, опасное или опасное содержимое, требует принятия мер для обеспечения безопасности людей, работающих с ним, и окружающей среды, в которой он работает. Остаточные напряжения, возникающие при сварке конструкций сосудов высокого давления, отрицательно сказываются на усталостной долговечности таких конструкций, снижая вязкость разрушения. Образование остаточных напряжений при сварке происходит, когда неравномерный нагрев металлических поверхностей создает значительные температурные градиенты, которые, в свою очередь, вызывают пластическую деформацию различных участков материала свариваемой детали, тем самым подвергая ее послеохлаждению внутренним напряжениям, которые могут ее ослабить.Был проведен ряд исследований по параметрическому анализу сварки с помощью планирования экспериментов (DoE), математического программирования, эволюционных алгоритмов и методов конечных элементов с целью количественной оценки влияния факторов сварки на результирующее остаточное напряжение.
Цель этого обзора состоит в том, чтобы организовать такую литературу в соответствии с конкретными областями анализа, чтобы улучшить доступ к ней и выяснить ее актуальность для справочной работы и дальнейших исследований.В документе определены три категории влияющих факторов: условия перед сваркой, параметры в процессе и условия после сварки. Показано, что условия предварительной сварки, такие как выбор процесса сварки, должны выбираться в соответствии с характером свариваемых материалов, эксплуатацией конструкции и компромиссом между сроком службы и себестоимостью производства. Тепловложение (которое зависит от напряжения дуги, сварочного тока и скорости перемещения) является наиболее важным технологическим параметром, связанным с аппаратом, в формировании остаточного напряжения во время сварки.Также отмечается, что при применении смягчающих факторов следует соблюдать осторожность, чтобы не усугубить ситуацию остаточного напряжения из-за неоптимальной параметрической настройки.
%PDF-1. 7
%
509 0 объект
>
эндообъект
внешняя ссылка
509 151
0000000016 00000 н
0000004154 00000 н
0000004382 00000 н
0000004424 00000 н
0000004460 00000 н
0000004926 00000 н
0000005030 00000 н
0000005145 00000 н
0000005253 00000 н
0000005361 00000 н
0000005473 00000 н
0000005588 00000 н
0000005702 00000 н
0000005817 00000 н
0000005932 00000 н
0000006046 00000 н
0000006160 00000 н
0000006265 00000 н
0000006368 00000 н
0000006476 00000 н
0000006584 00000 н
0000006692 00000 н
0000006796 00000 н
0000006904 00000 н
0000007012 00000 н
0000007092 00000 н
0000007172 00000 н
0000007253 00000 н
0000007333 00000 н
0000007413 00000 н
0000007493 00000 н
0000007573 00000 н
0000007654 00000 н
0000007734 00000 н
0000007814 00000 н
0000007894 00000 н
0000007973 00000 н
0000008052 00000 н
0000008132 00000 н
0000008211 00000 н
0000008291 00000 н
0000008370 00000 н
0000008449 00000 н
0000008529 00000 н
0000008609 00000 н
0000008688 00000 н
0000008767 00000 н
0000008847 00000 н
0000008925 00000 н
0000009005 00000 н
0000009084 00000 н
0000009163 00000 н
0000009242 00000 н
0000009321 00000 н
0000009400 00000 н
0000009478 00000 н
0000009558 00000 н
0000009638 00000 н
0000009718 00000 н
0000009799 00000 н
0000009879 00000 н
0000009960 00000 н
0000010040 00000 н
0000010120 00000 н
0000010234 00000 н
0000010292 00000 н
0000010413 00000 н
0000010459 00000 н
0000010493 00000 н
0000010981 00000 н
0000011692 00000 н
0000011888 00000 н
0000012046 00000 н
0000012447 00000 н
0000012893 00000 н
0000013107 00000 н
0000013329 00000 н
0000013407 00000 н
0000014721 00000 н
0000014909 00000 н
0000015070 00000 н
0000015367 00000 н
0000015558 00000 н
0000015614 00000 н
0000015760 00000 н
0000016088 00000 н
0000016480 00000 н
0000017802 00000 н
0000018454 00000 н
0000018657 00000 н
0000018952 00000 н
0000019021 00000 н
0000019199 00000 н
0000020448 00000 н
0000021737 00000 н
0000023011 00000 н
0000024305 00000 н
0000024557 00000 н
0000024909 00000 н
0000025818 00000 н
0000027027 00000 н
0000033170 00000 н
0000033452 00000 н
0000034814 00000 н
0000035194 00000 н
0000040921 00000 н
0000044633 00000 н
0000046360 00000 н
0000051762 00000 н
0000101023 00000 н
0000134375 00000 н
0000134919 00000 н
0000135049 00000 н
0000150365 00000 н
0000150404 00000 н
0000150456 00000 н
0000150505 00000 н
0000150557 00000 н
0000150640 00000 н
0000150700 00000 н
0000150814 00000 н
0000150894 00000 н
0000150964 00000 н
0000151043 00000 н
0000151122 00000 н
0000151201 00000 н
0000151259 00000 н
0000151619 00000 н
0000151728 00000 н
0000151829 00000 н
0000151957 00000 н
0000152077 00000 н
0000152255 00000 н
0000152452 00000 н
0000152667 00000 н
0000152846 00000 н
0000152983 00000 н
0000153102 00000 н
0000153305 00000 н
0000153422 00000 н
0000153559 00000 н
0000153723 00000 н
0000153903 00000 н
0000154105 00000 н
0000154331 00000 н
0000154515 00000 н
0000154719 00000 н
0000154941 00000 н
0000155147 00000 н
0000155385 00000 н
0000003316 00000 н
трейлер
]>>
startxref
0
%%EOF
659 0 объект
>поток
x ڤS[Ha~Ayt �`tcS»* ©[Vy2
«н
!nz_{=}
Прогнозирование остаточных сварочных напряжений и перераспределения/релаксации из-за циклического нагружения на JSTOR
Абстрактный Трехмерный градиент остаточных напряжений неизбежен практически для любого процесса сварки из-за термического цикла. Ожидалось, что при последующем циклическом нагружении эти остаточные напряжения изменят усталостную долговечность с тенденциями, аналогичными тем, которые наблюдались для одноосных экспериментов со средними напряжениями. Однако пластическая деформация во время циклических событий может привести к перераспределению и релаксации остаточных напряжений. Были проведены эксперименты для определения характеристик одноосной усталости поперечного двустороннего стыкового сварного шва из низкоуглеродистой стали. Для определения как начальных остаточных напряжений, так и остаточных напряжений после определенного количества циклов использовалась автоматизированная система сверления отверстий с помощью лазерной спекл-интерферометрии.Моделирование методом конечных элементов использовалось для моделирования эволюции остаточного напряжения во время термического цикла сварки и последующего циклического нагружения при комнатной температуре. Была разработана определяемая пользователем подпрограмма для включения в модель соответствующей циклической пластичности и зависящих от времени механизмов ползучести.
Была продемонстрирована превосходная корреляция между экспериментально измеренными начальными измерениями остаточного напряжения и уточненным аналитическим моделированием. Во время циклического нагружения экспериментально наблюдались остаточные напряжения, и аналитически прогнозировалось, что они будут перераспределяться и релаксировать нелинейно в зависимости от приложенной номинальной нагрузки и коэффициента нагрузки.Параметр повреждения критической плоскости Финдли был использован для оценки взаимодействия многомерного поля остаточных напряжений с одноосной номинальной нагрузкой после того, как было показано, что простые одноосные теории неадекватны. Принимая во внимание стабилизированные остаточные напряжения, зависящие от амплитуды и отношения нагрузки, исходные данные сварного шва могут быть пересчитаны с точки зрения параметра Финдли, что сводит на нет экспериментальные данные постоянной амплитуды. Разработанные концепции позволили оценить гипотетическую последовательность «высокий-низкий», моделирующую первоначальную приспособляемость, что привело к значительному увеличению усталостной долговечности для «нормальных» условий эксплуатации, когда в анализ долговечности были включены перераспределение и релаксация остаточных напряжений.
Представленные концепции представлены в формате, который легко распространяется на более сложные геометрические формы и нагрузки.
SAE International — это глобальная ассоциация, объединяющая более 128 000 инженеров и соответствующих технических экспертов в аэрокосмической, автомобильной и коммерческой отраслях промышленности. Основными компетенциями SAE International являются обучение на протяжении всей жизни и добровольная разработка согласованных стандартов. Благотворительным подразделением SAE International является Фонд SAE, который поддерживает множество программ, в том числе A World In Motion® и серию Collegiate Design Series.
Численный анализ термической деформации и остаточных напряжений в автомобильном глушителе при сварке МИГ | Журнал вычислительного дизайна и инженерии
Аннотация
В автомобильной промышленности для изготовления автомобильных глушителей широко используется металлический инертный газ (MIG) сварочной технологии. Однако глушитель деформируется термической деформацией в процессе сварки. В этой статье прогнозирование деформации и остаточного напряжения, вызванных сваркой MIG, моделируется программным обеспечением SYSWELD.Формы поперечного сечения ванны расплава, предсказанные численным анализом, сравниваются с экспериментальными результатами. В результате напряжения, в то время как сжимающие напряжения возникают в областях, удаленных от сварного шва, высокие растягивающие напряжения возникают в областях, близких к сварному шву. Значения деформации рассчитаны как 2,5 мм. Расположение фактической сварочной деформации было аналогично экспериментальным результатам. На основе результатов SYSWELD предложит методы оптимизации процедуры сварки для повышения производительности глушителя.
Прогноз деформации и остаточных напряжений, вызванных сваркой MIG, моделируется программным обеспечением SYSWELD.
Формы поперечного сечения ванны расплава, предсказанные численным анализом, сравниваются с экспериментальными результатами.
Расположение фактической сварочной деформации аналогично экспериментальным результатам.
На основании результатов SYSWELD предложит методы повышения производительности глушителей.
Графический реферат
Графический реферат
1. Введение
Выбросы автомобильных газов наносят значительный ущерб окружающей среде. В последнее время широкое внимание привлекли исследования по изготовлению автомобильных глушителей для уменьшения повреждений. Роль глушителя заключается в снижении температуры и давления выхлопных газов и уменьшении шума. Различные компоненты глушителя собираются сваркой.В частности, сварка металлов в среде инертного газа (МИГ) широко используется при сборке и является одним из наиболее распространенных процессов дуговой сварки. Сварка MIG может применяться для широкого диапазона толщин листа благодаря простоте операции и относительно высокой производительности. Однако глушитель может деформироваться из-за термической деформации во время сварки, что может вызвать проблемы с размерами при изготовлении.
Технология сварки используется в качестве основного метода изготовления многочисленных изделий, таких как корабли, автомобили, поезда и мосты.Например, процесс сборки в автомобильной промышленности по существу включает в себя соединение различных компонентов. При изготовлении глушителей сварочная деформация в основном вызвана высокой температурой в процессе сварки. Следовательно, в реальном процессе сварки сварочные деформации могут привести к проблемам с размерами. Сварочная деформация отрицательно влияет на точность изготовления и внешний вид. Кроме того, это не только ухудшает характеристики сварных конструкций, но и увеличивает стоимость сборных конструкций.Кроме того, задержки графиков сборки могут вызвать проблемы. Хотя полностью устранить деформацию чрезвычайно сложно, прогнозирование сварочной деформации позволяет избежать таких проблем в процессе сборки. Кроме того, сварочная деформация должна быть решена до фактического процесса сварки, чтобы улучшить качество сварных конструкций (Deng & Murakawa, 2007; Deng & Murakawa, 2008; Yu, Li, & Zhang, 2013; Yupiter et al., 2015; Чжу, Донг, Линь, Лу и Ли, 2014 г.).
Сварочная деформация изучалась с помощью экспериментальных измерений и эмпирических формул за последние несколько десятилетий.Однако эти опыты и формулы не могут точно предсказать величину сварочной деформации (Ю и др., 2013). Для получения точных результатов наряду с экспериментами и численным моделированием используется термоупруго-пластический метод конечных элементов (МКЭ). Когда сварка MIG анализируется с помощью программного обеспечения SYSWELD на основе FEM, очень важно смоделировать процесс сварки с использованием подходящей модели источника тепла для получения точных результатов деформации. Кроме того, результаты моделирования следует сравнивать с экспериментальными методами для проверки.
В этом исследовании прогнозы термической деформации и остаточного напряжения автомобильного глушителя были смоделированы с использованием программного обеспечения SYSWELD. Трехмерная модель конечных элементов (КЭ) для тепловых деформаций была разработана для создания типа твердой оболочки с низкими вычислительными затратами. Мелкая сетка используется в областях вблизи зоны термического влияния (ЗТВ), а более крупная сетка используется в областях, удаленных от зоны сварки. Параметры моделирования сварки включают скорость перемещения источника тепла, энерговклад на единицу длины, форму сварочной ванны, глубину провара, последовательность сварки, направление сварки и условия зажима.Для прогнозирования теплового и механического поведения автомобильного глушителя в процессе сварки был применен термоупругий-пластический МКЭ. Метод установки источника тепла (HSF) SYSWELD использовался для управления источником тепла при сварке MIG. Трехмерная модель детали была оптимизирована путем определения источника тепла итерационным методом. Результаты HSF сравнивались с поперечным сечением фактической свариваемой детали. Наиболее подходящей моделью источника тепла для процедур сварки MIG является использование двойного эллипсоидального источника тепла.
Деформацию автомобильного глушителя, предсказанную численным анализом, сравнили с экспериментальными результатами, и они оказались практически идентичными. Было подтверждено, что зазор возникает в том же месте, что и фактическая сварочная деформация. Возникло остаточное напряжение в виде более высокой концентрации напряжений в зоне сварки и окружающей ЗТВ. Концентрация напряжений в ЗТВ произошла за счет затвердевания расплавленной ванны и усадки основного металла. Следовательно, растягивающее напряжение возникало в зоне сварки и вокруг расплавленной зоны, где вдали от зоны сварки возникает сжимающее напряжение.Это остаточное напряжение является основным фактором, вызывающим сварочную деформацию. Основываясь на результатах, SYSWELD предлагает метод оптимизации процедуры сварки для повышения производительности глушителя (Friedman, 1975; Kwon, Lee, & Chae, 2006; Gu & Goldak, 1991; Näsström, Wikander, Karlson, & Lindgren, 1991). ; Norrish, Tieu, & Darmadi, 2012; Osawa, Hashimoto, Sawamura, Nakai, & Suzuki, 2007; SYSWELD, 2015; Ueda & Yamakawa, 1971).
2. Численный метод анализа
2.1. Взаимодействие термометаллургических явлений
В последнее время широко изучается численный анализ процесса сварки. Результаты моделирования получены для объяснения сложных физических явлений, таких как взаимодействие тепловых, механических и металлургических явлений процесса сварки. Однако моделирование сложного сварочного процесса — непростая задача. В процессе сварки и термической обработки взаимодействие физических явлений обобщено на рис. 1. Сварочные явления SYSWELD связаны с затвердеванием зоны плавления (FZ), тепловым потоком сварки и электро-тепло-механическим моделированием (SYSWELD, 2015). ).В процессе сварки происходят различные физические явления, которые влияют друг на друга. SYSWELD может определять остаточное напряжение и деформации, возникающие в результате сварки или термической обработки, а также диффузионное осаждение и диффузию водорода. Чтобы справиться с таким сложным моделированием, было использовано программное обеспечение SYSWELD, основанное на методе термоупругого пластического конечного элемента (Deng & Murakawa, 2007; Deng & Murakawa, 2008; Ueda & Yamakawa, 1971; Yu et al. , 2013; Юпитер и др., 2015; Чжу и др., 2014).
Рис. 1
Взаимосвязанные физические явления в SYSWELD.
Рис. 1
Взаимосвязанные физические явления в SYSWELD.
2.2. Геометрическое моделирование автомобильного глушителя
Это исследование было разработано для прогнозирования деформации и остаточного напряжения автомобильного глушителя с использованием коммерческого программного обеспечения SYSWELD. На рис. 2 показана процедура моделирования сварки с помощью SYSWELD (Osawa et al., 2007).Как показано на схематической диаграмме, перед термическим анализом были предприняты следующие шаги. Была смоделирована геометрия образца и построена сетка. Затем источник тепла был приспособлен к реальному способу сварки. Начальные и граничные условия применялись соответственно в виде тепловых потерь и температуры окружающей среды. Автомобильный глушитель представляет собой конструкцию, различные компоненты которой соединены пластиной. Он изготавливается сваркой по всей окружности компонентов.Деформацию глушителя исследовали с помощью МКЭ. Чтобы точно подтвердить деформацию автомобильного глушителя, сварочная деформация была спрогнозирована с использованием 3D-модели конечных элементов. Геометрия структуры сварного шва, показанная на рис. 3, была смоделирована с использованием двух типов элементов, таких как трехмерные объемные элементы и двумерные мембранные элементы. Они используются для базовой конструкции кузова и для поверхности свариваемой детали соответственно. На рис. 3 показана сетка основного металла и наплавленного валика. Видно, что для сетки использовались дифференциальные размеры элементов.Плотность сетки была выше вблизи осевой линии, чтобы представить возникновение движения источника тепла.
Мелкая сетка была расположена в расплавленной зоне для создания высокой температуры. Таким образом, размер сетки мелкий вблизи осевой линии сварного шва и постепенно становится более крупным по мере удаления от зоны сварки, чтобы сократить время вычислений (Gu & Goldak, 1991; Näsström et al., 1991; Osawa et al., 2007). ).
Рис. 2
Схематическая диаграмма, иллюстрирующая структуру моделирования сварки в SYSWELD.
Рис. 2
Схематическая диаграмма, иллюстрирующая структуру моделирования сварки в SYSWELD.
Рис. 3
Геометрия и КЭ модель автомобильного глушителя.
Рис. 3
Геометрия и КЭ модель автомобильного глушителя.
2.3. Свойства материала
SYSWELD позволяет использовать предопределенные данные для свойств материалов или разрабатывать данные о термометаллургических и механических характеристиках (Sulaiman et al., 2011). В данной работе в качестве материала был выбран SUS 436. Химический состав основного металла содержит 0,12 % C, 1,00 % Si, 1,00 % Mn, 0,03 % S и 0,04 % P, что можно считать эквивалентным используемому стальному материалу в экспериментах (табл. 1). Свойства материала, такие как коэффициент Пуассона, коэффициент конвекционной теплопередачи, постоянная Стефана-Больцмана и коэффициент излучения, перечислены в таблице 2. В расчетах термоупругой-пластической сварки материал, а также физические свойства сильно нелинейны и зависят от температуры. .На рис. 4 показаны физико-механические свойства основного металла (International Stainless Steel Forum (ISSF), 2007).
Рис. 4
Физико-механические свойства ферритной нержавеющей стали 436.
Рис. 4
Физико-механические свойства ферритной нержавеющей стали 436.
Таблица 1Химический состав SUS 436 (в мас.%).
С . | Си . | Мн . | П . | С . | Кр
.![]() | Мо . |
---|---|---|---|---|---|---|
0,12 Макс. | 1,00 Макс. | 1,00 Макс. | 0,040 Макс. | 0,030 Макс. | 16.00–8.00 | 0,75–1,50 |