пластиковое ведро, таз, полипропиленовую трубу
Одной из проблем, с которыми сталкиваются дачники, это невозможность быстро добраться до магазина в случае необходимости. К примеру, упала и лопнула лейка, а половина грядок осталась сухой, или ведро, в котором носили воду, дало течь. Именно о том, как решить подобные вопросы быстро и без затрат, расскажет сегодня Маннанов Альберт Олегович из города Усолье Сибирское Иркутской области. Его статья поможет домашним мастерам справиться не только с поломанными вёдрами и тазами, но и с другими протечками.
Это лето 2019 года для меня изначально не задалось. Приехав после холодов на дачный участок, я обнаружил выбитые стёкла в домике. Брать внутри было нечего, почти всё я увожу на зиму в гараж или в квартиру, а железный ящик с инструментом вскрыть им не удалось, как и унести (он намертво приварен). Видимо это воров и разозлило. Восстановив окна, я принялся за привычную работу по саду. Однако, едва пришло время полива, снова проблема – пластиковое ведро (единственное оставшееся) оказалось треснутым. Ехать за новым у меня не было ни средств, ни настроения, а потому было решено попробовать запаять старое. И сейчас я расскажу, что из этого вышло.
Содержание статьи
Обработка площади вокруг трещины в днище ведра
Перед тем, как приступить к пайке пластика требуется тщательно очистить поверхность и обезжирить её, чем я и занялся. Ведро было довольно старым, к тому же, раньше в нём была какая-то шпатлёвка, которую перемешивали миксером, в результате чего на поверхности образовались царапины. Забившаяся в них грязь никак не хотела отмываться, поэтому пришлось поработать ещё и наждачной бумагой. При этом поверхность нужно было очистить и обезжирить с обеих сторон, ведь пайка только наружной или лишь внутренней части ничего не даст. При первом же наполнении водой, ведро лопнет, деформировавшись намного сильнее, нежели было до начала ремонта.
Приступаем к работе: какие инструменты и материалы понадобятся для пайки
Для того, чтобы отремонтировать ведро, помимо наждачной бумаги и растворителя, понадобится паяльник и полоска пластика. Лучше всего, если это будет именно такой материал, из которого изготовлена сломанная ёмкость. В крайнем случае, можно попробовать использовать обычную пластиковую бутылку или полиэтиленовый хомут.
Проблема инородного пластика заключается в том, что он может иметь слабую адгезию с ремонтируемым предметом. Честно говоря, об этом я узнал уже позже. Мне просто повезло. Я использовал полосу, отрезанную от пластиковой бутылки и никаких проблем с «совместимостью» не заметил. Но, узнав о подобной проблеме, стал наливать меньше воды в ведро во избежание новых протечек.
Вот такая пластиковая полоска помогла мне в ремонте ведраПроцесс пайки и его нюансы
Первым делом необходимо пропаять внутреннюю часть ведра, иначе, при ремонте внешней стороны, трещина будет прогибаться внутрь, что не позволит сторонам разлома склеиться. На моих фотопримерах пайки нет процесса работы с внутренней стороной. Причина в том, что на них попросту ничего не видно. При работе обе руки находятся внутри ведра, и ничего сфотографировать невозможно. Поэтому придётся поверить на слово: пайка внутри и снаружи ничем не отличается.
Для начала, паяльнику нужно дать разогреться максимально сильно. Маломощные приборы можно сразу убрать в сторону, толку от них не будет. Раскалённым жалом, с небольшим надавливанием, начинаем как бы «зашивать» разлом, двигая влево-вправо. Слишком усердствовать тоже не стоит, при избыточном давлении жало паяльника просто провалится внутрь, после чего ремонт пластикового ведра будет значительно осложнён.
Начинаем аккуратно прогревать разлом, спаивая части ведраДополнительное усиление шва по трещине в дне ведра
После того, как шов предварительно пропаян, его нужно усилить. Для этого я использовал полоску, отрезанную от пластиковой бутылки. Мне повезло, при прогреве пластик спаялся достаточно плотно.
При производстве этой работы нужно следить за тем, чтобы плавилась не только полоска пластика от бутылки, но и основа. Если упустить этот момент, то заплатка после остывания будет отслаиваться, а значит, ни о каком усилении шва речи уже идти не будет. При прогреве основы также не следует слишком усердствовать, чтобы не прожечь в днище ведра дыру. Запаять её вполне возможно, однако времени такая работа займёт значительно больше. В целом же, на ремонт своего пластикового ведра, я потратил немногим более получаса, включая чистку и обезжиривание поверхности. Думаю, что если придётся в следующий раз ремонтировать подобную утварь, времени понадобится ещё меньше.
Что получилось после производства ремонта ведра
Когда все работы были завершены, я налил воды около половины объёма и оставил ведро на полчаса. Это требовалось для того, чтобы проверить, не протекает ли получившийся шов. Но подобная процедура, по сути, была необязательна. Ведь я не собирался пользоваться им для хранения воды. Ведро у меня на даче служило для полива, а значит, даже при наличии небольшой течи, оставалось вполне функциональным.
В моём случае, разлом в днище ведра был скромным, поэтому ремонт не затянулся. Но бывает, что на больших ёмкостях появляются крупные трещины. Здесь уже придётся паять немного по-другому. В подобных ситуациях потребуется сначала прихватить отломившиеся части, после зашить разлом медной проволокой, а уже третьим шагом наложить слой пластика, который предотвратит протечки.
К слову, такой метод подойдёт даже для ремонта резервуара стиральной машинки-автомат. Подобная пайка, при обращении к специалистам, потребует больших финансовых вложений. Самостоятельный же ремонт довольно прост и займёт немного времени.
Днище ведра запаяно и ёмкость снова готова к эксплуатацииЧто ещё можно починить при помощи паяльника
Мало кто задумывается, но при помощи паяльника можно починить даже пробитые полипропиленовые трубы водопровода. Однако здесь стоит отнестись с особым вниманием к выбору «донора». Неподходящий пластик приведёт к повторной протечке, ведь давление в системе водоснабжения значительное. Стоит разобраться, каким образом производится пайка полипропиленовых труб и все ли из них можно ремонтировать.
Если говорить о соединениях, которые начинают протекать по причине некомпетентности мастера, который их собирал, то их отремонтировать достаточно просто. Другой вопрос – долговечность такой трубы. Нужно понимать, что как бы качественно не была отремонтирована сама труба или спайка соединения, это всего лишь временная мера, дающая отсрочку капитального ремонта. Утверждение «нет ничего более постоянного, чем временное» здесь не работает. Но и этого порой бывает вполне достаточно, а значит, не стоит обходить вниманием подобную проблему, как и пути её решения. Попробуем разобраться, что делать, если в полипропиленовой трубе образовалась течь. Конечно, это очень редкий случай, но такое развитие событий вполне возможно.
Труба, которую мы будем ремонтировать. На заднем плане «донор»Заведомо продуманная порча магистрали водопровода
Для того чтобы показать на примере, как можно отремонтировать водопроводную полипропиленовую трубу, изначально я решил испортить её. Конечно, пробивать действующую водопроводную магистраль я не стал, а вот испортить ненужный отрезок, а после отремонтировать его было очень неплохой мыслью. Поэтому специально, чтобы на примере было проще разобраться, я прожёг паяльником приличную дыру в полипропиленовой трубе. Именно на этом отверстии я и покажу, каким образом можно устранить течь без замены повреждённого участка и привлечения специалистов, услуги которых, скажем прямо, дешёвыми не назовёшь.
Ремонт прожжённой трубы при помощи паяльника
Для того, чтобы запаять такое отверстие, требуется аналогичный полипропилен. При этом обычная пайка приемлема только для ремонта труб в частном доме, где давление воды, нагнетаемое насосом из скважины, не слишком высоко. Если же устранение течи производится в многоквартирном доме, где оборудовано централизованное водоснабжение, лучше предварительно впаять в магистраль сетку или кусочки проволоки, армировав отверстие, и только после этого приступать к пайке.
Для того, чтобы заплавить брешь, нужно отделять от трубы-«донора» полипропилен небольшими кусочками, накладывая их на отверстие. При этом, не стоит забывать и о прогреве ремонтируемой трубы, чтобы адгезия была максимальной. Именно поэтому наплавляемые кусочки должны быть маленькими.
Постепенно отверстие закрывается. Здесь необходимо немного проталкивать расплавленный полипропилен внутрь трубы, не кидаясь при этом в крайность. Если переусердствовать, то можно полностью заполнить пространство внутри ремонтируемой магистрали, вплоть до полной непроходимости воды. Думаю, что не нужно никому объяснять, к чему это приведёт.
Аккуратно, шаг за шагом заплавляем отверстие, немного продавливая расплавленный полипропилен внутрьТруба после ремонта: особенности эксплуатации
После того, как полипропиленовая труба будет отремонтирована, следует обращать внимание на некоторые особенности её эксплуатации. Ни в коем случае нельзя допускать механических воздействий на место пайки. За самим отремонтированным пробоем нужно постоянно следить, не начнёт ли он мокнуть. Это не всегда можно заметить невооружённым взглядом, однако определить место даже самой минимальной протечки поможет обычная туалетная бумага, прислонённая к трубе. На ней моментально станут видны пятна влаги.
Хочу напомнить, что подобная мера является лишь временной. При первом удобном случае необходимо поменять повреждённый участок трубы. Такую работу можно выполнить самостоятельно, если есть возможность взять на «прокат» у знакомых утюжок, которым и производится пайка. Алгоритм производства работ, кстати, я видел на страницах этого журнала. При этом, описано всё было достаточно грамотно, насколько мне показалось. По крайней мере, я выполнял пайку в своей квартире, руководствуясь именно этой инструкцией.
Вот так будет выглядеть отремонтированная труба после пайкиПодводим итог
Часто подобный ремонт на скорую руку остаётся единственной возможностью закончить начатую работу в саду или обеспечить нормальную подачу воды в кран. Но следует помнить, что такая пайка не является панацеей, она может существовать только как временная мера. И насколько бы качественно она ни была выполнена, по прочности отремонтированный участок никогда не сможет сравниться с тем, что было до повреждения. Нельзя забывать и о том, что ремонтное место требует от владельца постоянного повышенного контроля.
Я буду рад, если всё, о чём сегодня было написано, пригодится дачникам и другим любителям делать всё своими руками. Любые вопросы по теме можно задать в обсуждениях ниже. Я постараюсь максимально подробно пролить на них свет.
Интересно было бы узнать, доверяете ли вы подобному ремонту или лучше сразу менять испорченные пластиковые изделия на новые. Прошу оставить свой отзыв. Для меня очень важно мнения со стороны. Если вам понравилась моя статья, то не забудьте её оценить.
Редакция Homius приглашает домашних мастеров и умельцев стать соавторами рубрики «Истории». Полезные рассказы от первого лица будут опубликованы на страницах нашего онлайн-журнала.
ФОТО: Альберт Маннанов
ПредыдущаяИСТОРИИПросто и практично: складной походный стул своими руками
СледующаяИСТОРИИНе выкидывайте аккумулятор от ноутбука: полезные идеи от читателя Homius
Понравилась статья? Сохраните, чтобы не потерять!
ТОЖЕ ИНТЕРЕСНО:
ВОЗМОЖНО ВАМ ТАКЖЕ БУДЕТ ИНТЕРЕСНО:
Ремонт пластиковых деталей
Ремонт пластиковых деталейНа главную В мастерскую
Ремонт пластмассовых деталей
В современном автомобиле множество запчастей изготовленных из
пластмассы. Само собой что по ряду причин иногда они ломаются. Самое досадное
в данной ситуации то что наряду с высокой ценой их довольно проблематично купить,
даже под заказ. Может конечно повезти и нужная запчасть найдется на авторазборке,
но чтобы не зависеть от случая будет не лишним освоить их ремонт в «домашних
условиях».
Прежде чем начать разговор о собственно ремонте, давайте определимся с некоторыми терминами и понятиями принятыми в данной сфере деятельности.
Полимеры (от греч. polys — многочисленный, обширный и meros — доля, часть) — вещества, молекулы которых состоят из большого числа повторяющихся звеньев.
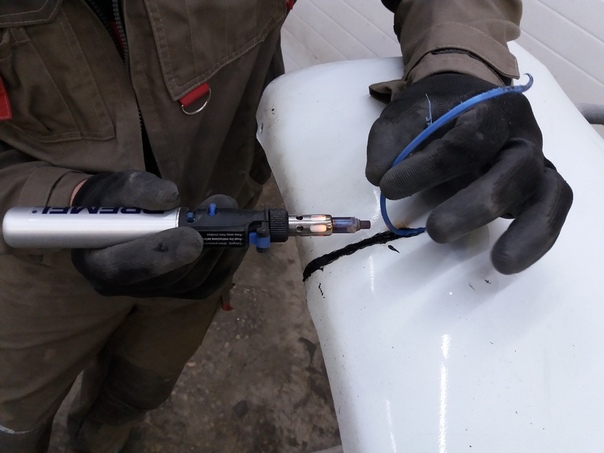
Термопласты (термопластичные пластмассы) — материалы, сохраняющие способность многократно плавиться при нагревании. Поэтому детали, изготовленные из термопласта, поддаются сварке.
Реактопласты (термореактивные пластмассы) — материалы, в которых при формовании изделия происходят необратимые химические реакции, приводящие к потере способности плавиться при нагревании. Они стойки к растворителям или незначительно набухают под их воздействием. Детали из этого вида пластмасс НЕ поддаются сварке.
Адгезия (от лат. adhaesio — прилипание) — способность одного материала удерживаться на другом при различных механических и климатических воздействиях. Например: лакокрасочного покрытия на стали, клея на пластмассе и т.д.
Виды повреждений, которые могут получить пластиковые детали:
Царапины — несквозные дефекты поверхности в виде борозд. Бывают поверхностные — нарушающие только лакокрасочное покрытие (ЛКП), и глубокие, из-за значительной глубины которых при дальнейшей эксплуатации возможно образование трещин.
Вмятины — изменение формы поверхности (деформация) из-за местного растяжения пластмассы.
Трещины
Проломы — сквозное разрушение, при котором происходит отламывание фрагментов и образуется отверстие.
Определение типа полимера
Первым делом необходимо определится к какому типу пластмасс принадлежит материал, из которого изготовлена наша деталь. Полимер обозначают с помощью буквенного кода на внутренней стороне детали (в большинстве случаев).
Как наиболее часто встречающиеся можно выделить следующие типы:
ABS — Акрилонитриловый бутадиен стирол (очень часто из этого материала сделан обвес мотоциклов и мопедов)
PA — Полиамид
PC — Поликарбонат
PE — Полиэтилен
PP/EPDM — Полипропиленовая/ этилен-пропиленовая резина
PС/PВТ — Поликарбонат/терефталат полибутилена
PBT/PC — Терефталат полибутилена/ поликарбонат
PUR — Полиуретан
GF — Усиленный стекловолокном
При отсутствии маркировки тип пластмассы можно определить косвенно. Для этого используют отломившийся кусок или отделяют его в малозаметном месте. Дальше плавим- поджигаем — смотрим и вдыхаем «аромат»:
ABS — Хрупкий, при попытке согнуть изгиб белеет. Переход из твердой фазы в жидкую происходит очень быстро. Очень текучий. При перегреве пузырится. Сильно коптит. Пламя со вспышками, оранжевым пламенем. Запах, как каучук. Не гасит себя. Легко растворяется в ацетоне.
PA — При попытке согнуть изгиб белеет. Плавится тяжело, вязкий. Горит плохо.
Пламя с желтым цветом, синим в основании и вспышки пламени. Тает и пенится. Резкий запах, как муравьиная кислота. Гасит себя. Не растворяется.
PE — Пламя с ясным пламенем, синим в основании, желтой вершиной, капли во время горения и запах, как стеарин. Не гасит себя.
PP — Гибкий и прочный на разрыв.

В принципе, через некоторое время, необходимость в поджигательстве пропадает — с опытом вы научитесь уже по внешнему виду определять большинство типов пластмасс, а также стоит или нет затевать ремонт 🙂
Выбор вида ремонта.
От характера повреждения детали и ее материала зависит способ ремонта. Если царапины неглубокие и нарушают только лакокрасочное покрытие (ЛКП), ремонт сводится к восстановлению внешнего вида. Глубокие царапины зашпаклевывают перед покраской. В тех случаях когда из-за значительной глубины повреждения при дальнейшей эксплуатации возможно образование трещин, дефект подвергают сварке или склеиванию.
Ремонт нагревом
Используется для устранения вмятин на термопласте. После постепенного прогрева
деформированной поверхности(желательно чтобы температура не превышала 200 градусов),
прикладывается механическое усилие до восстановления первоначальной формы изделия.
Не рекомендуется откладывать ремонт, особенно в теплое время, так как пластмассе
будет сложнее придать первоначальную форму.
Склеивание
Это процесс создания неразъемного соединения за счет адгезии клеящего состава (клеевой композиции) к соединяемым деталям.
Ремонт склеиванием не менее распространен, чем сварка, и является единственно возможным способом ремонта изделий из термореактивных пластмасс. Использование современных клеевых композиций позволяет ремонтировать как термопласты, так и реактопласты.
Клеевые композиции (клеи) для ремонта пластмассовых деталей представляют в своем большинстве высокомолекулярные соединения, которые после затвердевания превращаются в полимерный материал.
Правильный выбор клея необходим для высокого качества ремонта. Это обеспечит лучшую адгезию клеевой композиции к данному типу пластика и одинаковые физические свойства материалов бампера и шва после его отвердения. Для проверки желательно производить контрольное склеивание. (более подробно данный вид ремонта рассмотрен в статье Ремонт пластикового бампера)
Сварка
Процесс получения неразъемного соединения фрагментов (осколков) поврежденного участка путем их местного сплавления. Сварка — более прочный способ ремонта, чем склеивание, поэтому она предпочтительнее для изделий из термопластов. Этот вид ремонта мы разберем более подробно.
Сварка пластмасс
Формально ничего сложного в сварке пластмассы нет. Нагрел до нужной температуры, соединил, дал остыть. Однако важный момент — нагрев до нужной температуры. Я бы выделил такие градации нагрева:
1. Нагрев до температуры пластичности — материалу можно придать определенную форму, изгиб в нужном направлении.
2. Нагрев до температуры плавления — можно сваривать поврежденные участки, добавлять недостающие вставки.
3. Нагрев до температуры разрушения — материал после этого остынет и внешне вам даже будет казаться что процесс пайки увенчался успехом, однако шов будет хрупким и будет содержать продукты разложения пластмассы — что естественно скажется на его прочности.
Тип материала |
Температура плавления, градусы |
Температура разрушения пластика, градусы |
Рекомендуемая температура сварки, градусы |
ABS | 350 |
380-400 |
350-370 |
PA | 400 |
450-470 |
400-440 |
PC | 350 |
380-400 |
350-370 |
PE(мягкий/твердый) | 270/300 |
||
PP | 300 |
350-370 |
300-340 |
Обычно проблемы с перегревом случаются при сварке-пайке обычным
паяльником, поскольку невозможно строго выдержать нужную температуру, кроме
того немалую роль играет температура окружающей среды. Так надежно спаять деталь
из ABS паяльником у меня не получалось, но однажды осенью, когда похолодало,
спаял на ура. Мощность паяльника осталась неизменной, а часть тепла шла на «борьбу
с похолоданием». Вот и получилось что эффективная температура как раз в
пределах допуска температуры плавления. Хорошо паяется паяльником полиамид,
результат вполне надежный. Полипропилен пережигается, но результат тоже сносный.
ABS я бы не советовал ремонтировать используя паяльник.
А так вообще незаменимый инструмент. Только нужно чтобы был
достаточно мощный (я использую 100W), и с загнутым жалом, чтобы можно было разравнивать
расплавленный пластик. Не лишним будет и старый добрый выжигатель по дереву,
когда нужно сделать тонкую работу, без него не обойтись, да и температура там
регулируется. По большому счету мелкие и несложные дефекты можно устранить этими
инструментами, для более сложных и запущеных случаев понадобится специальный
инструмент — фен (термовоздуходувка). В магазинах много строительных фенов,
они нам не подойдут. Поскольку обычно у них только две температуры 350/550 и
нерегулируемая подача воздуха. Специальный фен имеет плавную регулировку температуры
и подачи воздуха, ну и цену на порядок больше чем у строительного фена. Профессиональные
термовоздуходувки (Leister, Steinel) не совсем напоминают фен, легкие и удобные
в использовании, единственный недостаток — высокая цена.
Я для себя решил эту проблему купив полупрофессиональный фен Steinel 2310LCD, с плавной регулировкой (шаг 10 градусов) от 50 до 650 градусов, и регулировкой потока воздуха.
Кроме фена понадобятся также насадки для сварки.
Редукционная насадка, насадка для быстрой сварки, шлицевая насадка
Сварка происходит так. Деталь зачищают по обе стороны от будущего сварного шва на ширину 15 мм. Концы трещин засверливают для предотвращения их роста, а кромкам придают V-образный профиль с углом 90° глубиной до 5 мм например специальной фрезой.
Подбирают присадочные прутки из пластика соответствующего состава — идентичного материалу детали. Желательно производить пробную сварку для проверки однородности (совместимости) материалов прутка и детали, а также для подбора температуры нагрева, скорости перемещения фена и усилия вдавливания. В течение 5-10 минут прогревают фен, чтобы температура горячего воздуха стабилизировалась. А вы пока складываете из обломков всю «картинку». Обломки проще всего закрепить в нужном положении при помощи специальных струбцин-прищепок. Чтобы облегчить начальную стадию сварки, нужно заострить конец прутка.
При сварке нужно наклонить пруток под углом 45° (или использовать насадку для быстрой сварки) и придавливать его в сторону шва с усилием. Поток горячего воздуха направлять больше в сторону прутка припоя.
Термопласты не имеют явно выраженной точки плавления, а постепенно переходят из твердого состояния в вязкотекучее. Поэтому для получения сварного шва необходимо упереть пруток в зону плавления и после размягчения пластика вдавить в шов до требуемого сечения.
Для сохранения первоначальных свойств пластика нагрев при сварке должен быть кратковременным и производиться потоком воздуха строго определенной температуры.
Сварку проводят в два этапа. Сначала скрепляют края поврежденного участка с помощью предварительной (скрепляющей) сварки. Она позволяет зафиксировать взаимное положение соединяемых фрагментов и исправить их небольшую деформацию. Для облегчения операции используют струбцины. Скрепляющая сварка выполняется короткими швами (прихватками) по всей длине будущего соединения. После нее производят окончательную сварку. Получаемый шов должен незначительно возвышаться над свариваемой поверхностью и быть гладким.
В зависимости от характера повреждения и доступности места ремонта сварку производят с внутренней или лицевой стороны. При толщине стенки 5 мм и более — с двух сторон.
После того как место сварки остынет производим окончательную доводку и подготовку
под покраску — шлифуем (начинаем с наждачки 100-120, потом 180, доводка 320),
шпаклюем (специальной шпаклевкой для пластмассы). Дальше красим и пользуемся.
Как видите процесс не особо сложный, но позволяющий сэкономить и деньги и время.
Дополнительные материалы:
Сварка горячим воздухом
Сварка пластмассовых автодеталей (Leister)
Справочник по сварке и склеиванию пластмасс.
В статье использовались материалы с сайтов http://www.scs.clan.su и http://vitz.ru, а также материалы руководства по сварке пластмассовых автодеталей аппаратом горячего воздуха Leister Triac «S».
Используются технологии uCoz
насадки для сварочных фенов.
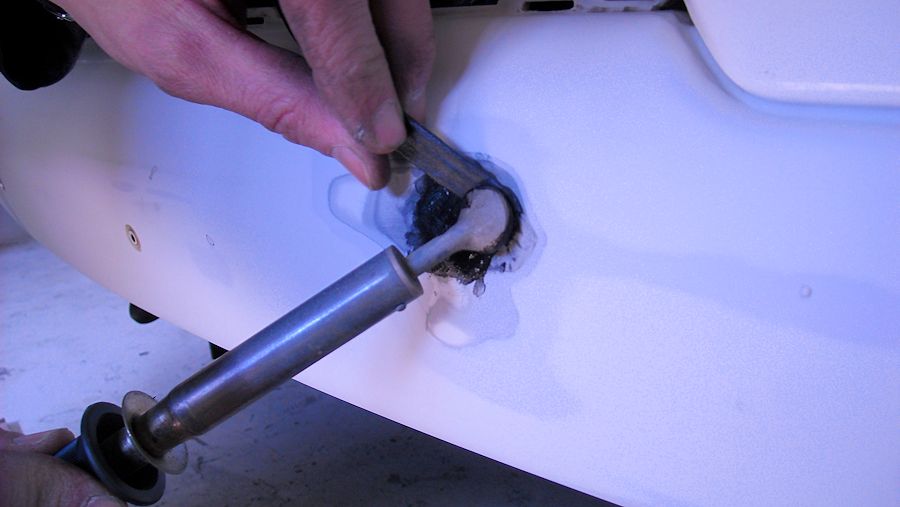
Строительный фен (или термофен) является востребованным инструментом при осуществлении различных ремонтных работ. В круг его возможностей входят сушка, пайка, сваривание, нарезка и изгиб материала. Но потенциалы его применения значительно обширнее. Находчивый человек способен придумать массу возможностей применения данного инструмента, поскольку современный термофен для сварки пластика даёт возможность производить работы различной сложности за короткий промежуток времени. Даже недорогие образцы способны помочь произвести простой ремонт ПВХ труб в жилище, не говоря уже о специализированных строительных (технических, промышленных) устройствах, предназначенных для выполнения крупномасштабных работ.
Особенности
Процедура пайки строительным феном сопряжена с большой затратой энергоресурсов, потому как мощность нагревателя порою достигает 2,5 кВт. Это способствует высокой производительности – 300-400 л/мин. Поток разогретых воздушных масс оказывает воздействие на большую площадь, что порой неудобно при необходимости воздействия на определённую точку. В связи с этим сварку пластика посредством фена осуществляют с использованием насадок для быстрой пайки, которые дают возможность подать присадочный материал прямиком в область соединения.
Виды фенов и насадок
Ручные термофены для пайки полимеров бывают 2-х видов:
- бытовой;
- промышленный.
Конструкция у них одинаковая, различия лишь в возможностях и вспомогательных функциях.
Промышленные устройства имеют большую мощность и высокую температуру разогрева воздуха. Посредством их, к примеру, выполняют сборку крупных трубопроводов. Более того, подобные устройства практикуются в связке со специализированной паяльной установкой.
В домашних условиях вы едва ли станете использовать подобное оснащение, к тому же оно очень дорогое.
Бытовые сварочные фены функционируют от простой розетки и разогревают воздух до 600° C. Таким образом, с их помощью можно сделать следующее:
- отремонтировать ПВХ трубы на дачном участке;
- восстановить лопнувший пластмассовый бампер на собственном автомобиле и т. д.
Бытовые приборы малогабаритные и лёгкие, не отнимают много пространства и довольно экономны в вопросе потребления электрической энергии.
При реализации фена он комплектуется разными насадками. Их другое наименование – сопла либо форсунки. Зачастую для работы комплекта не хватает, но приспособления можно докупить отдельно. Большой выбор увеличивает возможности применения термофена посредством изменения мощи и формы потока воздуха.
Рассмотрим особенно используемые насадки:
- Круглая фокусирующая требуется для неконтактной пайки медных трубок. Присадочный материал (прутки, изготовленные из полиэтилена либо пропилена) для пластика дают возможность запаивать щели во всевозможных конструкциях, наклеивать мебельный шпон.
- Плоская – посредством её убирают старую шпатлёвку либо лакокрасочное покрытие, остатки облицовочных материалов.
- Рефлекторная прогревает пластиковые трубы перед их загибом.
- Шлицевая (щелевая) требуется для пайки изделий из поливинилхлорида.
- Режущая (резная) требуется для вырезки разнообразных фигур из пластмассы.
- Сварное зеркало практикуется при стыковом способе пайки полимеров.
- Сварная насадка предназначена для соединения сварных кабелей.
Насадка подбирается исходя из планируемой работы с термофеном.
Сопло для пайки пластмассы
Выполнить ремонт изделий из пластика значительно проще, нежели из металла. Для этого не требуется большая температура, использование трансформаторов. Достаточно задействовать промышленный термофен и верно подобрать вспомогательные компоненты.
Для пайки предметов из пластика сгодится специализированное плоское V-образное сопло. Оно оснащается сварочным прутком, который является припоем. Структура прутка должна быть такой же, что и соединяемый материал.
Насадка – сварочный наконечник
Он состоит из 2 трубок, соединённых под углом. По одной трубке идёт разогретый воздушный поток в рабочую область, по другой – размягчённый сварочный пруток. Его структура полностью совпадает с материалом свариваемого предмета.
Сопло для фена
Сопло являет собой трубку с разным сечением, становящуюся к выходу уже. Благодаря этому возрастает скорость и давление выходящего разогретого воздушного потока.
Можно практиковать для разогрева труб из поливинилхлорида перед загибом, наклеивания предохранительной и клеящей ленты либо шпона, сваривания деталей.
Насадка для оформления швов промеж полотен
Для пайки линолеума практикуют насадку, оснащённую держателем для ленты из полимерных материалов, посредством которой и осуществляется сварка.
Сферы применения
В настоящее время термофен с насадками практикуется как в домашних условиях, так и на больших предприятиях для решения различных задач. Один инструмент не в силах исполнять большинство функций, однако с комплектом насадок устройство становится многофункциональным и применяется:
- для соединения и обработки швов;
- заделки трещин, деформаций, неровностей;
- спаивания предметов из плёнки на базе полимеров, пластика с иными материалами;
- работ по устройству кровель;
- монтажных, демонтажных, восстановительных работ в автомобильной сфере.
Помимо указанных выше мероприятий, термофен с насадками может выполнить массу иных работ, где практикуются мягкие полимерные материалы и необходимо термическое воздействие.
Как паять своими руками
Надо сказать, что термофеном для пайки пластика не так легко работать, как может выглядеть со стороны, поскольку у полимеров температура плавления различается. У поливинилхлорида она составляет 150-220° C, у полипропилена – 160° C.
Отступление в какую-либо из сторон повлечёт непровар стыкового соединения либо перегрев, что равным образом неудовлетворительно скажется на качестве окончательного результата.
Новичкам желательно попробовать спаять какой-нибудь черновой материал.
Для осуществления пайки термопластичного полимера понадобятся:
- сам термофен;
- ряд сопел к нему;
- сварочный пруток (лента).
От верно подобранного сопла на фен находится в зависимости надёжность выполненного соединения. Для пайки толстых предметов желательно применять насадку диаметром 5-8 миллиметров.
Имейте в виду, что не все термофены комплектуются нужным количеством сопел, поэтому потребуется их докупать.
Припой представляет собой специальные прутки полимера, которые при нагревании плавятся и заполняют собой пространство промеж соединяемых заготовок.
Наряду с этим края деталей также плавятся, что ведёт к спаиванию элементов в одно целое. Стык выходит крепким благодаря молекулярным связям припоя с пластмассовыми заготовками. Под любой тип пластика потребуется искать свой тип прутка.
Следует приготовить определённый вспомогательный инструментарий и материалы для пайки. Понадобится напильник либо наждачка, растворитель, ножик для обрезки лишнего припоя после его затвердевания.
Процесс пайки:
- Первым делом, как говорилось ранее, подбирают прутки пластика под материал спаиваемых деталей, дополнительно настраивается режим температуры пайки.
Для этого требуется точно знать разновидность пластика. Обозначение, как правило, находится с оборотной стороны изделия.
- Выполняют зачистку сопрягаемых областей наждачкой либо напильником, а при необходимости используют растворитель.
- Затем в область пайки вставляют пруток. Вся область разогревается феном, принимая во внимание температуру плавления. Следует выдержать нужное время, чтобы припой и края деталей как следует прогрелись. При этом необходимо одинаково греть оба изделия.
- После того как пластик под воздействием термофена станет плавиться, пруток вдавливают в область соединения. При применении промышленных термофенов практикуется специализированная машинка, посредством которой осуществляется уплотнение расплавленного прутка промеж пластиковых деталей. Под давлением машинки совершается уплотнение. Это укрепляет стык.
- После завершения работ, как только пластик охладится и будет прочным, необходимо срезать весь лишний материал до поверхности сопрягаемых деталей.
Для этой цели, как правило, применяется специализированный серпообразный нож.
Если выполнить это трудно, в таком случае надо немножко разогреть место сопряжения тем же термофеном.
Только не перестарайтесь! Излишний нагрев пластика способен спровоцировать расслаивание.
Наглядный обзор пайки пластика термофеном на примере бака от стиральной машины представлен в следующем видео.
Как запаять бампер
Как запаять бампер? Вот вопрос, который может встать перед владельцем современного авто. Металлические бампера понемногу отошли в прошлое. Теперь для их изготовления используется исключительно пластик. Простота ремонта – одно из его преимуществ. Заметим, что пластик, используемый для бамперов, весьма различен. От хрупкого, разлетающегося при малейшем ударе, до такого, который после получения вмятины, способен полностью распрямиться.
Паять или не паять бампер, такой вопрос не должен возникать. Паять треснувший бампер можно и нужно. Особенно, в том случае, когда не произошло потери элементов. Должен возникнуть вопрос как запаять бампер? Чтобы это сделать, вам понадобится технический фен, мощный паяльник (минимум 80Вт), мягкая проволока или металлическая сетка, а также куски пластика, желательно, аналогичного материалу бампера. Можно обойтись без фена, но с ним намного удобнее.
Если бампер окрашиваемый, поверхность отремонтированной трещины должна получиться немного ниже по отношению к основной плоскости. Она будет выравниваться шпатлевкой.
Перед тем, как запаять бампер, края трещины необходимо совместить. Затем трещину разделываем, т.е., нагретым паяльником проводим вдоль трещины так, чтобы образовалась канавка. В эту канавку с двух сторон паяльником же сдвигаем материал. Или, заполнив желобок пластиковой стружкой, плавим ее, скрепляя кромки. Фен нужен для того, чтобы в процессе пайки бампера равномерно прогревать материал. Кроме того, после заполнения шва при помощи фена и гладилок удобно окончательно выровнять поверхность.
Второй этап пайки пластикового бампера – армирование шва. Особенно это актуально для длинных трещин. Нарезав из проволоки скоб, вплавляем их поперек шва с шагом от 2 до 5 см. Разогревать вплавляемую проволоку можно паяльником, но лучше – фен. Далее пластиковый бампер можно шпатлевать и красить.
Если бампер поврежден сильно и куски отсутствуют, возможно, собрать один пластиковый бампер из двух ломанных. В любом случае, это обойдется дешевле даже покупки на разборе. Технология пайки та же, но в этом случае поможет металлическая сетка. Вплавленная в пластик с внутренней стороны, она станет основой для отсутствующих элементов.
Запаянный таким образом пластиковый бампер может прослужить еще очень долго.
Еще по теме
электрика — резка пластмассы в домашних условиях
резка пластмассы в домашних условияхОбщее назначение.
В этой статье мы разберем, как можно разрезать и запаять пластмассовые изделья. На примере будет разбираться прозрачная пластмассовая коробка для посева растений в малой посудине. Для работы с этим оборудованием надо хорошее проветривание, так как от процедуры выделяется чадный газ, но для малых масштабов это не угроза.
Подготовка материала для изготовления нихромового резака.
Для изготовления резака пластмассы, нам понадобится:
— медный провод монолит, диаметром с карандаш, длиной два по 18 см
— текстолит 5 х 1 см – 2 шт
— нихромовый провод от плитки на 1,5 кВатт — 7 см
— трансформатор, минимальная мощность 100 Ватт
— гибкий двухжильный провод с сечением 2,5 кв мм – 1 мерт
— монолитный провод с сечением 1 кв мм – до 2-х метров
— клемма на 2 линии
— трапяная изолента
Намотка трансформатора.
Для намотки трансформатора, не надо специальные счетчики, берем сам трансформатор и наматываем поверх изолированной вторичке монолитный провод с сечением 1 кв мм. Если трансформатор около 100 Ватт и ниже тогда наматываем 12 витков вплотную. Чтобы они не ссунулись прикрепите их трапяной изолентой и потом посадите на клемник, как видно на рисунке.
Держатель нихромового резака.
Держатель изготавливается с меди монолита с диаметр простого карандаша, можно по уже. Выгибаем, как видно на рисунке. Края расклепываем, для надежного контакта к нихромового провода, и заклепываем нихромовый провод, от плитки на 1,5 кВатт, так чтобы он был почти в натяжку. Нижние части тоже расклепываем, но не так интенсивно, только чтобы прикладывалась шайба и просверливаем. Садим на винтики со шайбами гибкий двухжильный провод, с сечением 2,5 кв мм – 1 мерт и подключаем к трансформатору на клемник.
Работа с нихромовым резаком.
Подаем питание на первичку трансформатора. Примечание: соблюдайте технику безопасности! На выходе нашей намотки должно бить примерно 3 вольта и наше чудо расжаривает спираль. Берем, плавным движением, режем пластмассовые заготовки и также, при нагреве нихрома, склеиваем вращающимся движением. Если у вас рвется спираль – работайте помедленнее или срежьте пару витков, которые вы намотали.
Как отремонтировать пластиковый радиатор дома с помощью набора «Сделай сам» — BackYardMechanic
Если у вас протекает пластиковый радиатор, его можно устранить с помощью наборов для самостоятельной сборки или даже с помощью паяльника.
Часто, когда на пластиковом радиаторе видна утечка, многие думают, что его необходимо заменить, когда он может быть отремонтирован человеком типа «сделай сам».
Устранение течи — простая задача, с которой может справиться любой домашний механик.
Есть три способа ремонта пластикового радиатора.
3 способа ремонта пластикового радиатора
- Используйте паяльник, чтобы вернуть пластик на место.
- Используйте эпоксидную смолу, которая плавится в радиаторе, устраняя утечку.
- Запаяйте место утечки, затем нанесите эпоксидную смолу.
Если у вас есть паяльник, применить свои навыки пайки будет самым дешевым вариантом.
Для тех, у кого нет паяльника, это недорогие вещи.
Промышленный паяльник Weller D650
Использование эпоксидной смолы также дает хорошие результаты.Эпоксидная смола вплавляется в пластик, закрывая утечку.
Многие наборы, такие как этот, доступны на Amazon.
Versachem
Третий вариант – использовать пайку и эпоксидную смолу, что удваивает протечку, продлевая срок службы, если не навсегда.
Как отремонтировать пластиковый радиатор Метод пайки
Слейте жидкость из радиатора, если жидкость вытекает, так как место должно быть сухим.
Очистите место утечки и удалите всю смазку. На цель можно распылить WD-40 или что-то подобное, что хорошо ее очистит.
Затем используется пайка, чтобы пройти вдоль утечки, расплавив пластик и герметизировав его.
Это будет зависеть от того, насколько велика трещина, насколько сильно нужно расплавить пластик.
После расплавления пластика проверить его, чтобы убедиться, что он все еще протекает, — единственный способ узнать, исправлено ли оно.
Часто эпоксидная смола используется в сочетании, чтобы гарантировать, что утечка не вернется.
Как отремонтировать пластиковый радиатор Метод эпоксидной смолы
Использование эпоксидной смолы — это распространенный метод, в котором используются химические вещества, когда они смешиваются, чтобы вызвать реакцию, при которой происходит плавление всего вместе.
Дополнительным преимуществом эпоксидной смолы является добавление большего количества материала к месту утечки, что может стать проблемой, если стенки радиатора слишком тонкие.
Смешивание веществ, входящих в набор, — очень простая работа.Обязательно очистите область перед нанесением.
Резюме
Самостоятельный ремонт радиатора позволяет значительно сэкономить, особенно при поиске замены.
Большинство утечек легко исправить, и их можно устранить в течение часа или около того.
Соединения сложнее ремонтировать, но используется тот же принцип. Часто сустав сложнее, так как он находится в неудобном месте, что иногда требует удаления мешающей части.
Снятие всего радиатора для труднодоступных мест — лучший способ его починить.Идеально иметь хороший доступ к проблемной зоне.
Вы уже чинили пластиковый радиатор? Дайте нам знать об этом в комментарии ниже.
Лучшие паяльники 2022 года
Наш выбор
X-Tronic Model 3020-XTS LED паяльная станция
Надежная X-Tronic быстро нагревается и предлагает безопасную и прочную подставку, эргономичную рукоятку и цифровую температуру дисплей — функции, за которые обычно приходится платить в два раза больше.
Светодиодная паяльная станция X-Tronic Model 3020-XTS удивила своей надежностью. Некоторые его функции обычно встречаются только в моделях, которые стоят в два раза дороже. Его ручку удобно держать и она не горячая на ощупь, а утюг поставляется с тяжелой, прочной подставкой и полезными аксессуарами. Это также один из немногих протестированных нами утюгов с цифровым дисплеем — функция, которая делает отслеживание и изменение температуры особенно простым. Во время сборки нашего комплекта электроники нам иногда приходилось ждать, пока паяльная станция X-Tronic не восстановится до заданной температуры; Вы могли бы потратить примерно на 40 долларов больше на утюг с более быстрым восстановлением температуры, но мы почти не заметили разницы.Утюг поставляется с прочной подставкой для удержания горячего утюга во время использования, катушкой для припоя, а также губкой и латунной губкой для очистки наконечника утюга.
Отмычка для модернизации
Hakko FX-888D
Быстрое время нагрева и восстановление температуры, прочная конструкция и полированный внешний вид делают этот паяльник идеальным выбором для любителей, которые планируют часто паять.
Варианты покупки
*На момент публикации цена составляла 100 долларов США.
Hakko FX-888D стоит обновить, если вы планируете часто паять, так как он нагревается немного быстрее, чем X-Tronic, поэтому вы можете паять с меньшими паузами.Он оснащен цифровым дисплеем и тонким пером, которое удобно держать в руке и которое не нагревается. FX-888D кажется особенно прочным, с тяжелой подставкой и станцией, которые, как кажется, прослужат дольше, чем конкурирующие модели. Кроме того, тот факт, что подставка и станция представляют собой две отдельные части, дает вам больше гибкости при настройке рабочей зоны.
Бюджетный вариант
Если 50 долларов — это больше, чем вы хотите потратить, мы рекомендуем комплект паяльника Vastar Full Set 60 Вт 110 В.Эта регулируемая модель является самым дешевым утюгом, который мы тестировали, но он хорошо работает и поставляется с большим количеством аксессуаров, чем любая другая, включая припой и наконечники разных размеров. Но входящая в комплект подставка не прочная — мы не чувствовали себя в безопасности, ставя на нее горячий утюг, — поэтому вам следует подумать о добавлении нашей любимой подставки Hakko FH-300. Рукоятка Vastar стала самой теплой среди протестированных нами утюгов, и температуры, отмеченные на колесе регулировки Vastar, также оказались совершенно неточными. Vastar показал самую высокую максимальную температуру из всех опробованных нами утюгов, хотя любой из утюгов, которые мы рекомендуем, может достигать температуры, достаточно высокой для обычного хобби.
Также отлично подходит
Hakko FH-300
Hakko FH-300 достаточно тяжелый, чтобы стоять на рабочей поверхности, и занимает мало места.
Варианты покупки
*На момент публикации цена составляла 32 доллара США.
Если у вас уже есть паяльник и вам нужна прочная подставка для него, мы рекомендуем Hakko FH-300, который весит достаточно, чтобы не скользить, когда вы кладете паяльник в держатель. Установка занимает несколько секунд и поставляется с губкой и чистящим средством для наконечников.Это также самая маленькая из всех протестированных нами подставок, что оставляет больше места на вашем рабочем месте для других паяльных наконечников и бобышек.
НАКОНЕЧНИКИ ДЛЯ СВАРКИ ТЕРМОПЛАСТИКОВ | King Plastic Corporation
Из архива IAPD
Сварка – это процесс соединения поверхностей путем их размягчения под действием тепла. При сварке термопластов одним из ключевых компонентов является сам материал. Пока существует сварка пластмасс, многие люди до сих пор не понимают основ, что имеет решающее значение для правильного сварного шва.
Правило номер один при сварке термопластов: вы должны сваривать подобный пластик с подобным пластиком. Чтобы получить прочный, стабильный сварной шов, необходимо убедиться, что ваша подложка и сварочный стержень идентичны; например, полипропилен в полипропилен, полиуретан в полиуретан или полиэтилен в полиэтилен.
Вот несколько советов по сварке различных видов пластика и шаги, необходимые для обеспечения качественного сварного шва.
Полипропилен (ПП) — один из термопластов, который легче всего сваривать, и он используется для самых разных целей.Полипропилен обладает отличной химической стойкостью, низким удельным весом, высокой прочностью на растяжение и является наиболее стабильным полиолефином. Доказанные области применения полипропилена: гальваническое оборудование, резервуары, воздуховоды, травильные станки, вытяжные шкафы, скрубберы и ортопедия.
Для сварки полипропилена сварочный аппарат должен быть настроен примерно на 572°F/300°C; определение вашей температуры будет зависеть от того, какой тип сварочного аппарата вы покупаете, и рекомендаций производителя. При использовании сварочного аппарата для термопластов с нагревательным элементом мощностью 500 ватт 120 вольт регулятор подачи воздуха следует установить примерно на 5 п.с.и. и реостат на 5. Выполняя эти шаги, вы должны быть в районе 572°F/300°C.
Сварочный полиэтилен Другой термопласт, который довольно легко сваривается, — это полиэтилен (ПЭ). Полиэтилен отличается ударопрочностью, исключительной стойкостью к истиранию, высокой прочностью на растяжение, поддается механической обработке и имеет низкое водопоглощение. Доказанными областями применения полиэтилена являются контейнеры и вкладыши, резервуары, лабораторные сосуды, разделочные доски и горки.
Самое важное правило сварки полиэтилена заключается в том, что можно сваривать низкое к высокому, но не высокое к низкому.Это означает, что вы можете приваривать сварочный стержень из полиэтилена низкой плотности (LDPE) к листу из полиэтилена высокой плотности (HDPE), но не наоборот. Причина довольно проста. Чем выше плотность, тем труднее разрушить компоненты для сварки. Если компоненты не могут быть разрушены с одинаковой скоростью, они не могут правильно соединиться. Помимо обеспечения совместимости плотностей, полиэтилен довольно легко сваривается. Для сварки полиэтилена низкой плотности необходимо, чтобы температура была примерно 518°F/270°C, регулятор установлен примерно на 5-1/4 до 5-1/2, а реостат установлен на 5. Как и полипропилен, HDPE можно сваривать при температуре 572°F/300°C.
Перед сваркой термопластов необходимо выполнить несколько простых шагов, чтобы обеспечить надлежащую сварку. Очистите все поверхности, включая сварочный стержень, МЭК или подобным растворителем. Вырежьте на подложке достаточно большую канавку, чтобы принять сварочный стержень, а затем обрежьте конец сварочного стержня под углом 45°. После того, как сварочный аппарат настроится на правильную температуру, вам необходимо подготовить подложку и сварочный стержень.Используя автоматический наконечник скорости, большая часть подготовительной работы выполняется за вас.
Удерживая сварочный аппарат примерно в дюйме над поверхностью, вставьте сварочный стержень в наконечник и перемещайте его вверх-вниз три-четыре раза. Это приведет к нагреву сварочного стержня при нагреве подложки. Признаком того, что подложка готова к сварке, является появление эффекта запотевания, похожего на дуновение на кусок стекла.
Приложив сильное и постоянное давление, надавите на наконечник наконечника.Ботинок будет вдавливать сварочный стержень в подложку. Если вы решите, как только сварочный стержень приклеится к подложке, вы можете отпустить стержень, и он автоматически протянется.
Большинство термопластов поддаются шлифованию, и прочность сварного шва не пострадает при шлифовании. Используя наждачную бумагу с зернистостью 60, отшлифуйте верхнюю часть сварного шва, затем доведите до мокрой наждачной бумаги с зернистостью 360, чтобы получить чистую поверхность. При работе с полипропиленом или полиэтиленом можно восстановить их глянцевую поверхность, слегка нагрев поверхность желтой пропановой горелкой с открытым пламенем.(Имейте в виду, что необходимо соблюдать обычные правила пожарной безопасности.) После выполнения этих шагов у вас должен получиться сварной шов, похожий на фото внизу слева.
Заключение Принимая во внимание приведенные выше советы, процесс сварки термопластов может быть довольно простым в освоении. Несколько часов практических занятий сваркой дадут «чувство» поддержания правильного равномерного давления на стержень прямо в зону сварки. А эксперименты с разными видами пластики помогут освоить процедуру.Чтобы узнать о других процедурах и стандартах, обратитесь к местному дистрибьютору пластмасс.
Дополнительные советы по сварке пластмасс
Сварка термопластов и термореактивных пластмасс
Решение об использовании термореактивных материалов или термопластов не так просто, как кажется, когда речь идет о сварке пластиковых деталей. Являясь ведущими национальными экспертами по сварке пластмасс, Trinetics Group предоставляет экспертные знания многим профессионалам в автомобильной, аэрокосмической, морской и потребительской отраслях в отношении того, какие типы пластмасс являются лучшим выбором для их продукта для использования во время ультразвуковой сварки. производственный процесс.
Во-первых, давайте посмотрим на свойства термопластов.
A Термопласт представляет собой полимер, который становится мягким при нагревании и твердым при охлаждении. Преимущество использования термопластичного материала заключается в том, что его можно охлаждать и нагревать несколько раз без каких-либо изменений в его молекулярной химии или механических свойствах. Термопласты имеют низкую температуру плавления, могут быть переплавлены и переформованы, поэтому материал очень хорошо поддается сварке пластмасс. Термопласты имеют малый вес и обычно имеют плотность от .от 9 до 2 г/куб.см.
Термопластический материалтакже имеет относительно низкую стоимость обработки и прост в производстве в больших объемах с высокой точностью. Термопласты являются твердыми, хорошими электрическими изоляторами и могут противостоять химическим веществам. Преимущества Термопласты чаще всего используются для литья под давлением. Если принято решение о сварке деталей, то необходимо выбирать термопластичные материалы.
Существует множество термопластов, которые имеют характеристики, аналогичные термореактивным пластикам. Некоторые гибкие ПВХ имеют характеристики силикона или резины и могут быть сварены ультразвуком. Trinetics Group может помочь вам найти подходящий термопласт для использования, когда вы рассматриваете возможность ультразвуковой сварки вашего продукта или деталей.
Наиболее распространенными формами термопластичных полимеров являются ABS, акрил, поликарбонат, полиэтилен высокой плотности (HDPE) и ПВХ или поливинилхлориды.
Преимущества термопластов:- Размягчается и становится более жидким при повышении температуры
- Легко перерабатывается, так как может быть переформован и изменен
- Может быть переформован и переработан без ущерба для физических свойств материала для производства в больших объемах, с высокой точностью и низкими затратами на обработку
- Может использоваться в приложениях с низким или высоким напряжением
- Гибкость и удлинение пленки покрытия
- Способность выдерживать коррозионные материалы и среды
- Способность переносить материалы при очень низких температурах или при высоких температурах
- Может герметизировать твердые предметы для электроизоляции и оборудования
- Чрезвычайно прилипает к металлу
- Может использоваться для упаковки
- Устойчивость к сколам
- Превосходная отделка
1:
:
:
:
- Имеет относительно низкую температуру плавления.
- Может размягчаться при повторном нагревании
- Может плавиться при длительном воздействии солнечных лучей
- Плохая стойкость к органическим растворителям, углеводородам и высокополярным растворителям
- Склонен к ползучести при длительном воздействии стрессовых нагрузок и более низкой температуре плавления
- Может разрушаться, а не деформироваться в условиях высокого напряжения
- Может быть дороже термореактивного пластика
Создание деталей изделия с использованием термореактивных смол представляет собой постоянную экзотермическую химическую реакцию. В термореактивных пластмассах используется отвердитель, вызываемый теплом или излучением под высоким давлением, который навсегда изменяет пластик. Это означает, что при отверждении смола выделяет тепло и газы. Как только происходит фазовый переход или реакция отверждения, деталь готова и всегда остается в постоянном твердом состоянии. Термореактивные пластмассы не могут вернуться в расплавленное состояние.
Все термореактивные смолы, такие как двухкомпонентные эпоксидные смолы, каучуки и силиконы, нельзя переплавлять.
По всем этим причинам термореактивные пластмассы нельзя сваривать ультразвуком. Термореактивные материалы, как правило, лучше подходят для литья или экструзии деталей.
Наиболее распространенными формами термореактивных пластмасс являются эпоксидная смола, полиэфирная смола, силикон, сантопрен и другие каучуки. В конечном итоге Trinetics Group не рекомендует использовать термореактивные пластмассы для ультразвуковой сварки деталей.
Преимущества термореактивных пластмасс:- Термическая стабильность – Сохраняют прочность и форму даже при нагревании
- Имеют высокие температуры плавления без потери структурной целостности
- Не подвержены дополнительному тепловому воздействию
- Устойчивы к химическим веществам, коррозии и механической ползучести
- Требуют жестких допусков
- Отлично характеристики удельной прочности
- Структурная целостность – превосходная диэлектрическая прочность
- Хорошо подходит для производства неразъемных компонентов и крупных цельных форм
- Меньшие затраты на оснастку и настройку
- Снижение производственных затрат при замене металлических компонентов
- Доступны литые детали -в допусках
- Выбор цвета и отделки поверхности
- Низкая теплопроводность и прозрачность для микроволнового излучения
- Не подлежит повторной формовке или нагреву после первоначальной формовки
- Низкая прочность на растяжение и пластичность требуют конструкции с толстыми стенками
- Используемые соединения представляют собой реактивные системы и могут влиять на срок годности
- Процессы Баха могут демонстрировать большие вариации и меньшую согласованность от партии к партии .
- Высокое содержание некоторых присадочных материалов может привести к чрезмерному износу инструмента
- Качество продукции зависит от степени сшивания в процессе формования
- Трудно поддается ультразвуковой сварке
Когда Trinetics Group сваривает пластмассовые детали одним из наших многочисленных методов, мы вырабатываем необходимое количество тепла на нашем ведущем в отрасли оборудовании Dukane для расплавления пластмассы на двух половинках пластмассовой детали.Расплавленный пластик течет и создает связь на молекулярном уровне между двумя частями. Часто вы даже не можете увидеть, где раньше был тот или иной пластик. Поток материалов из каждой половины термопластичных деталей настолько сильно взаимодействует друг с другом, что мы можем достичь примерно от 80 до 100% прочности основного материала в сварном шве. Вот почему так важно найти лучший пластиковый полимер для вашей конкретной детали или продукта.
Окончательное решение о том, какой тип пластика использовать для сварки пластиковых деталей, может в конечном итоге сделать производственный процесс менее напряженным и привести к лучшим результатам и результатам.Если у вас есть какие-либо вопросы о различиях между термореактивными и термопластами, свяжитесь с Trinetics Group по телефону 321.622.8485 или по электронной почте [email protected] для получения дополнительной информации.
Об авторе
Джеймс Стерн
Джеймс Стерн — вице-президент и генеральный директор Trinetics Group — контрактного производителя из Мельбурна, Флорида, специализирующегося на услугах по сварке и сборке пластмасс.Trinetics Group является производителем, предоставляющим услуги по разработке, сборке, сварке пластиковых деталей и оборудованию. Наше оборудование для сварки пластмасс включает в себя спиновую сварку, ультразвуковую сварку, инфракрасную сварку и экструзионную сварку горячим газом.
Чем отличается литье пластмасс под давлением?
Пластмассы чрезвычайно универсальны, что делает их востребованными материалами в различных отраслях промышленности. Например, в Соединенных Штатах транспортная/автомобильная и строительная отрасли являются двумя из трех основных рынков, на долю которых ежегодно тратится более 31 миллиарда долларов на пластиковые компоненты и изделия. 1
Популярность и повсеместное использование приводят к некоторым проблемам. Для пластика это надежное соединение пластиковых заготовок друг с другом или с другими материалами. Существует несколько проверенных решений для соединения пластмасс, в том числе многослойное формование пластмасс, но процесс, наиболее подходящий для конкретного проекта и бюджета, не всегда очевиден.
Этот краткий обзор основных методов соединения пластиков содержит основные сведения, которые помогут вам сделать правильный выбор.
4 Методы сварки соединений пластмасс
Механическое крепление с помощью винтов, болтов или заклепок, а также склеивание растворителем или клеем когда-то было единственным выбором при соединении пластмасс. Эти простые методы все еще доступны и в целом эффективны. Однако в качестве вторичных процессов они также могут быть трудоемкими и дорогостоящими.
Эволюция материалов, знаний о пластмассах и технологий расширила возможности соединения пластмасс, включив в них несколько вариантов сварки:
Ультразвуковая сварка сочетает вибрационные импульсы и давление для соединения достаточно жестких пластиков. Когда материалы вибрируют и трутся друг о друга, они нагреваются и в конечном итоге сплавляются друг с другом.Сборка с помощью ультразвуковой сварки выполняется быстро и универсально. Ультразвук можно использовать для вставки металлических компонентов в пластик, соединения металлических и пластиковых деталей вместе, а также для точечной сварки пластика.
Сварка вращением соединяет пластмассы с использованием поверхностного трения для создания кругового сварного шва. Одна из двух соединяемых частей вращается с высокой скоростью, при этом прикладывается усилие, удерживающее две части вместе. Возникающее в результате трение нагревает и плавит пластмассы, а после вращения применяется большее давление, чтобы соединить материалы вместе.Сварочные швы отличаются высокой прочностью, герметичностью и наиболее экономичным способом получения круглых сварных швов.
Вибрационная сварка подходит для создания герметичных соединений в пластмассовых деталях неправильной формы, как правило, больших размеров или из разнородных материалов с разными температурами плавления. Вибрационный нагрев вызывает трение, которое в сочетании с давлением плавит и склеивает пластмассы. Прочность полученного сварного шва сравнима с прочностью используемых материалов, а время цикла составляет в среднем от 5 до 8 секунд для ручных или автоматических операций.
Сварка горячей плитой соединяет две пластмассовые детали, расплавляя их относительно точно нагретой плиты в течение заданного периода времени. Пластина снимается, и две части соединяются вместе. В результате соединение получается прочным, постоянным и часто герметичным.
Усовершенствованное соединение пластмасс: инфракрасное, термическое и литьевое формование
Некоторые передовые методы соединения пластмасс используют тепло для управления температурой расплава, адгезией и другими характеристиками пластмасс:
Инфракрасная сварка — это быстрый бесконтактный метод, при котором на пластмассовые детали воздействует инфракрасное излучение, которое преобразуется в тепло и расплавляет поверхности.Части соединяются с помощью давления, чтобы удерживать их вместе до соединения.
Лазерная сварка использует концентрированное тепло и направленность лазерного луча для соединения пластмасс. Лазерная сварка может использоваться в приложениях, предназначенных для пластмасс различной толщины, и идеально подходит для крупносерийного производства деталей, требующих узких и глубоких сварных швов.
Многослойное формование является предпочтительным методом соединения пластмасс, поскольку он не просто объединяет несколько материалов. Пластмассовое литье улучшает конструкцию и производительность компонентов или устройств, поскольку его можно использовать для гашения звуковых и вибрационных воздействий, изоляции чувствительной электроники и повышения химической/влагостойкости — и все это без дополнительной сборки. Кроме того, в пластик можно отлить множество цветов для более легкого использования (например, клавиатуры, функциональные кнопки и т. д.), прочной дифференциации бренда и индивидуальной эстетики. Многокомпонентное литье обеспечивает эти и другие преимущества в комплексном процессе, который сокращает количество отходов, повышает эффективность и снижает производственные затраты.
Сложность соединения пластмасс варьируется от проекта к проекту и от процесса к процессу. Использование опыта индивидуального литья под давлением полезно и необходимо для достижения успешных результатов и использования преимуществ передовых методов, таких как литье пластмасс под давлением, для вашего приложения. Узнайте больше в нашем техническом документе Основы многокомпонентного формования для OEM-производителей . Нажмите кнопку ниже, чтобы загрузить копию сейчас.
1 Энциклопедия.com, Отраслевые профили: изделия из пластмассы, без даты
Перманентный ремонт пластика, который часто прочнее нового
Настоящая сварка
Сварка пластика — это *настоящая* сварка. Это не эпоксидная смола, сумасшедший клей или пистолет для горячего клея. Я использую горелку горячего воздуха, чтобы нагреть детали до тех пор, пока они не расплавятся (около 450 градусов, в зависимости от типа пластика). Я использую пластиковый наполнитель, сделанный из того же типа пластика, чтобы соединить детали или нарастить недостающие детали. Отремонтированные детали на 90 % прочнее исходной детали, если они обработаны до исходных размеров, или потенциально прочнее, если деталь наращивается или армируется.
Однако не все вещи, которые выглядят как пластик, являются пластиковыми. Стекловолокно, баколит, некоторые виды нейлона, пропитанного стекловолокном, и некоторые смеси не поддаются сварке. Иногда я использую продукт под названием Fiber Flex для пайки некоторых несвариваемых пластиковых или пластиковых деталей. Однако паяная деталь не будет такой прочной, как сварная.
Недоступные детали стоит починить
Это крышка главного выключателя двери водителя, которая снята с производства.
Переключатель окон Toyota продолжает падать в дверь
Это сломанный пластиковый выступ на нижней стороне крышки, который удерживает переключатель на крышке.Без выступа выключатель проваливается в дверную панель.
Сваривать можно только одинаковые виды пластика (а их очень много).
Различные пластмассы нельзя сваривать вместе. Вот несколько типов пластмасс: PE, PP, ABS, PVC, HDPE и нейлон. Хотя это далеко не полный список. Самый простой способ — найти на детали маркировку или символ переработки. Если метки нет, попытайтесь приварить каждый тип стержня к детали, пока один из них не приклеится и не будет отрываться. Эта часть АБС.
Подготовьте место для сварки, сошлифовав старый пластик
Затем я стачиваю оставшуюся часть выступа твердосплавной насадкой с широкой канавкой, оставляя плоскую поверхность. Подготовив поверхность, я добавляю пластиковый наполнитель небольшими витками, охлаждая пластик водой после каждого витка. Это затвердевает уже нанесенный пластик, облегчая наращивание.
Восстановите сломанную часть
Теперь грубая форма выступа построена.
При тщательной шлифовке выступ возвращается к исходному размеру.
Также была трещина под выступом. Трещина зашлифовывается (так же, как при сварке металла), затем заполняется канавка. В этой работе я зашлифовал очень глубоко, чтобы добраться до центра выступа с другой стороны. Это позволит убедиться, что наконечник хорошо прикреплен.
Теперь, когда все трещины и повреждения устранены, а новые отверстия для винтов просверлены и нарезаны резьба, деталь готова к повторной сборке.
Вот и все отремонтированные детали. Поскольку все повреждения были в невидимых местах, он выглядит как новый.
Насколько долговечна сварка пластика? + [Тест на долговечность]
Пластик в нашей обычной жизни часто бывает тонким и хлипким. Он предназначен для того, чтобы его можно было разорвать и легко раздавить в наших руках. Поэтому неудивительно, что многие сомневаются в прочности и преимуществах сварки пластика и задаются вопросом, насколько долговечны этот материал и техника по сравнению с несварным куском полиэтилена высокой плотности (ПЭВП).
Насколько долговечна сварка пластика
Сварка пластмасс существует уже несколько десятилетий и находит применение в медицинской промышленности, при производстве упаковки и в автомобильной промышленности. Его долговечность зависит от многих факторов, но при оптимальных настройках может быть невероятно прочной и долговечной.
Если все сделано правильно (это означает, что место было соответствующим образом подготовлено заранее), проверено, выбран правильный сварочный электрод и множество других факторов дважды и трижды проверено, то сварка пластика может иметь прочность до 98% основного материала. .
Для чего используется сварка пластмасс?
Сварка пластмасс используется во многих отраслях промышленности, в частности, в автомобильной промышленности. Чтобы проиллюстрировать, насколько долговечной может быть сварка пластика при определенных обстоятельствах, просто учтите, что этот метод используется профессионалами на пластиковых бамперах, которые должны иметь высокую прочность, чтобы соответствовать требованиям безопасности.
Что может повлиять на прочность и долговечность сварного шва?
Как уже говорилось, сварка пластика может быть очень прочной и долговечной, если все сделано правильно, но на ее долговечность влияет множество факторов, от материала до опыта сварщика.Плохая или неправильная процедура сварки часто является причиной снижения ожиданий долговечности.
Возможно, был выбран неправильный сварочный пруток, место могло быть неправильно подготовлено, температура могла быть неправильной, или сам материал слишком слаб, чтобы его можно было обрабатывать и гарантировать сварку пластика. Все эти факторы могут снизить долговечность сварки пластика, но будьте уверены, что при правильном выполнении и использовании правильных материалов он достаточно прочен для выполнения тяжелых работ.
Как правильно подготовить помещение
Надлежащая очистка области имеет решающее значение и означает, что исходный материал необходимо будет тщательно промыть и зачистить. Не может быть никакой краски, масла, жира или ультрафиолетового излучения, чтобы сварка пластика была эффективной.
Другой этап подготовки зависит от используемого метода сварки. От маятниковой сварки для коротких сварочных швов до скоростной сварки для длинных швов. Правильная предварительная подготовка сварного шва является ключом к долговечности сварного шва.
Как проверяется долговечность?
Долговечность сначала проверяется с помощью комплекта для испытаний стержней, который является ключевым фактором при выборе правильного стержня для конкретной работы. Испытания также проводятся путем приваривания небольших полос исходного материала к самому себе, так как это наиболее совместимый материал.