Испытание механических свойств сварных швов и соединений
Для оценки механических свойств сварных швов определяют пределы прочности и текучести, относительное удлинение и сужение металла швов при растяжении образцов Гагарина (вырезанных из металла шва) при комнатной (рис. 52, а) и повышенной температуре (рис. 52, б).
Определяют также предел прочности сварного соединения испытанием на разрыв плоских образцов (рис. 52, д), вырезанных поперек шва. Кроме того, определяют пластичность сварного соединения испытанием на загиб плоских образцов, вырезанных поперек шва (рис. 52, ж).
Ударную вязкость металла шва и различных зон термического влияния определяют испытанием на удар образцов с круглым надрезом Менаже по центру шва (рис. 52, з), по линии сплавления и в зоне термического влияния в основном металле на различном расстоянии (от 1 до 15 мм) от шва.
При необходимости (в зависимости от условий эксплуатации) испытания на растяжение и на ударную вязкость проводят не только при комнатной температуре (17—20°С), но и при повышенных и отрицательных температурах.
В этом случае для определения ударной вязкости служат те же образцы Менаже, а для испытания на разрыв — стандартные цилиндрические образцы с головками, имеющими метрическую нарезку.
Образцы Менаже перед испытанием охлаждают в керосине или бензине вместе с сухой углекислотой либо в сжиженных газах — кислороде, азоте, водороде или гелии.
Для определения порога хладноломкости металла полученные данные испытаний на ударную вязкость наносят на график зависимости ударной вязкости от температуры (рис. 53). Температура, при которой наблюдается значительное падение ударной вязкости одного или нескольких испытуемых образцов, является порогом хладноломкости данного металла.
Рис. 52. Образцы для испытаний:а — металла шва на разрыв при комнатной температуре, б —металла шва на разрыв при повышенных температурах, в — металла шва на длительную прочность, г — сварного соединения на длительную прочность, д — сварного соединения на разрыв, е — металла шва на разрыв, ж — сварного соединения на загиб, з — металла шва на ударную вязкость при различной толщине свариваемого металла.
Определяя ударную вязкость сварных швов, выполненных на стали толщиной 10 мм и более, испытывают образцы сечением 10X10 мм с надрезом сверху шва по его центру (по зоне слабины), а при толщине менее 10 мм — образцы с надрезом по центру шва с боковой его стороны.
Механические испытания сварных швов и соединений
Механические испытания сварных швов и соединений. Порядок и методы механических испытаний сварных швов и соединений регламентирован ГОСТ 6996-54 Методы определения механических свойств металла шва и сварного соединения . [c.66]Механические испытания сварных швов и соединений [c.583]
ПО величине и направлению большое количество раз. Порядок механических испытаний сварных швов и соединений регламентирован ГОСТ 6996—54. [c.584]
Характер механических испытаний образцов зависит от того, какую нагрузку несет сварное соединение при эксплуатации.

Испытание механических свойств сварных швов и соединений. Для оценки механических свойств сварных швов определяют пределы прочности и текучести, относительное удлинение и сужение металла швов при растяжении образцов Гагарина (вырезанных из металла шва) при комнатной (рис. 52, а) и повышенной температуре (рис. 52, б). Определяют также предел прочности сварного соединения испытанием на разрыв плоских образцов (рис. 52, д), вырезанных поперек шва. Кроме того, определяют пластичность сварного соединения испытанием на загиб плоских образцов, вырезанных поперек шва (рис. 52, ж).
[c. 94]
Характеристиками механических свойств сварных швов и соединений при их работе под статической нагрузкой являются предел прочности, о,,, предел текучести а , относительное удлинение при разрыве б, коэффициент поперечного сужения г ), угол загиба а. Испытания проводятся согласно ГОСТу 6996—66 на круглых выточенных образцах длиной 18, 36 и 60 мм. диаметром 3,6 и 10. мм. В отдельных случаях заменяют нахождение а условного предела текучести напряжением, вызывающим заданную относительную остаточную деформацию е.
Характеристиками механических свойств сварных швов и соединений при их работе под статической нагрузкой являются предел прочности а д предел текучести о . относительное удлинение при разрыве д, коэффициент поперечного сужения ф, угол загиба а, модуль упругости Е. Испытания проводятся согласно ГОСТу 6996-54. [c.48]
Механические испытания сварных швов и изделий. Кроме механических свойств металла шва во многих случаях надо определить и механические свойства сварного соединения в целом. При этом сравнивают свойства металла шва и зоны термического влияния
[c.468]
Механические испытания сварных швов. Основные виды испытаний механических свойств металла шва и сварного соединения приведены в табл. 164. [c.478]
Механические испытания производятся с целью определения прочности сварных соединений, в процессе работы подвергающихся действию статических или динамических нагрузок. Если требуется испытать целую конструкцию, то ее нагружают усилиями, характер которых соответствует эксплуатационным. Механическую прочность сварных швов и сварных соединений чаще всего определяют на образцах, вырезанных из планок, заваренных при тех же условиях, что и испытуемое изделие. [c.135]
Важное значение приобретают методы контроля сварных швов и соединений без их разрушения и без изготовления образцов для механических испытаний. К таким методам относятся люминесцентный и цветной методы контроля, магнитная, ультразвуковая, рентгеновская и гамма-дефектоскопия сварных швов и соединений.
В отличие от схемы сварки по фиксированному времени , при которой выбор продолжительности сварочного импульса совершенно не связан с образованием сварного соединения, схема сварки по фиксированной осадке частично связана с кинетикой образования сварного соединения. В этом случае вероятность появления бракованного соединения определяется только нестабильностью исходной толщины свариваемой пластмассы. Сравнительные механические испытания сварных швов, полученных при сварке по описанным выше двум схемам ограничения продолжительности импульса, подтверждают большую эффективность второго способа. Однако последний способ ограничения требует получения изделия с малым допуском по разнотолщинности. Технологические операции по переработке пластмасс (литье, вакуумная формовка и др.) не всегда обеспечивают это условие. [c.85]
До настоящего времени еще не разработаны единые условия механических испытаний сварных соединений пластмасс.
Испытания на усталость. Различные структуры и механические свойства сварных швов, зоны термического влияния иод воздействием переменных нагрузок могут привести к образованию микротрещин, а затем и к разрушению сварного соединения. Такое разрушение носит название усталостного, а состояние металла при этом называется усталостью. Для имитации процессов, происходящих в реальной конструкции, подверженной усталостному разрушению, образец сварного соединения подвергают действию переменных нагрузок — растяжению, сжатию, изгибу, кручению или комбинации этих нагрузок. Испытания проводят в той среде и при той температуре, которые соответствуют производственным условиям.
Для контроля качества сварного соединения в готовом изделии существуют следующие методы наружный осмотр и проверка размеров швов механические испытания швов гидравлические испытания сварных сосудов и трубопроводов на прочность и непроницаемость радиационный акустический магнитный электромагнитный и др. [c.292]
Прочность соединений определяют по результатам механических испытаний образцов на срез (разрыв) и реже на отрыв (точечные соединения) и ударную вязкость (соединения стыковой сварки). Образцы испытывают на специальных разрывных машинах в лаборатории механических испытаний. Образцы для испытаний точек на срез (5—10 образцов) выполняют одноточечными шириной 15—40 мм и длиной 75—150 мм (каждая пластина) соответственно для металла толщиной 0,5— 4 мм. Образцы для испытаний сварных швов на срез шириной 15—30 мм вырезают из карт с длиной шва 250—300 мм.
[c.114]
Контроль качества соединений и готовых изделий включает осмотр и обмеры сварных швов и изделий металлографические исследования физико-химические исследования металла шва соединения механические испытания комплексное применение неразрушающих методов контроля.
Объем дефектоскопии при изготовлении резервуара включал контроль качества в объеме 100% длины сварных швов оболочки резервуара методом ультразвуковой дефектоскопии и 15% длины сварных швов в местах пересечении меридиональных и горизонтальных (поясных) швов радиографическим методом. Механические испытания и металлографические исследования сварных соединений выполнялись а объеме требований ОСТ 26-291.
[c.14]
Все сварные соединения были изготовлены в соответствии со стандартом [6], и их качество было удовлетворительным, что подтверждено стандартными механическими испытаниями образцов на растяжение и радиографическим контролем швов. [c.177]
Химическую стойкость сварных соединений проверяют при определении прочности и пластичности сварных образцов, прошедших обработку в условиях химических или газовых сред. Сравнительные механические испытания образцов, сохранившихся после сварки в обычных условиях, и образцов, выдержанных в коррозионных средах различное время, показывают как изменилась прочность и пластичность сварных швов в результате химического воздействия. [c.217]
Сравнение механических свойств большой группы сталей и сварных швов близкого легирования к основному металлу подтверждает отмеченные закономерности о влиянии условий выполнения сварки и жесткости соединения на свойства швов. Большая прочность сварных швов сохраняется обычно до температур интенсивного разупрочнения, что в условиях обычных скоростей деформирования при механических испытаниях составляет около 600—650° С для перлитных сталей и 700—750° С для аустенитных. Выше этих температур обычно упрочнение швов за счет развитой субструктуры оказывается уже не эффективным.
[c.45]
На рис. 51 показано сопротивление удару соединения на поверхности раздела между алюминием и сталью. При ударных испытаниях по Изоду плакированный образец разрушался, предпочтительно, по алюминию 1100, а не в зоне поверхности раздела. Сопротивление усталости переходных соединений, приведенное в табл. 9, значительно больше сопротивления усталости эквивалентных механических соединений и лучше, чем у алюминиевых сварных швов, полученных с сопряженными алюминиевыми конструкциями. На рис. 52 представлены конструкционные детали кораблей, изготовленные с использованием данного переходного соединения. [c.101]
Методы дефектоскопии применяются при контроле сварных стыковых соединений на месте производства монтажных работ. По сравнению с механическими испытаниями и металлографическими исследованиями эти методы имеют то существенное преимущество, что качество сварных швов оценивается без разрушения соединений.
[c.302]
Последующие механические испытания и технологические пробы выявляют прочность сварных соединений, Чтобы получить точные данные о прочности швов, иногда применяют пробные образцы (если непосредственное изучение прочности швов требует их разрушения). [c.334]
Качество сварных изделий может проверяться разрушающими, а также неразрушающими методами контроля сварных соединений, швов и сварного изделия в целом. Разрушающими методами проверяют контрольные сварные образцы, вырезанные из сварного изделия или заваренные одновременно со сваркой его. Образцы, в зависимости от вида и назначения сварного изделия подвергают механическим, металлографическим и коррозионным испытаниям. [c.178]
Испытание швов и сварных соединений на механическую прочность. [c.218]
Следует особо подчеркнуть, что при статических испытаниях сварных соединений по ГОСТ6996-66 выявляются их относительные механические характеристики. Действительная прочность сварных соединений в изделиях будет зависеть от соотношения геометрических характеристик сварных швов и размеров поперечного сечения соединений в конструкции /4/. Для их определения по результатам РОСТОВСКИХ испытаний нами разработана специальная методика /4/.
[c.213]
Для контроля качества сварных соединений одновременно со сваркой стыкоь коллектора завариваются в тех же производственных условиях пробные стыки на планках, из которых потом выре- аются образцы для проведения механических испытаний. В комплекс испытаний сварных швов входят испытания на разрыв, на аагиб и на ударную вязкость, а также металлографическое исследование или просвечивание швов гамма-лучами. [c.198]
Сосуды, предназначенные для хранения и переработки веществ, обладающих токсичными или вэрыво- и пожароопасными свойствами, должны изготовляться по технологии, обеспечивающей высокую герметичность и прочность сварных швов. Контроль качества сварных соединений производится ультразвуковой дефектоскопией и просвечиванием рентгеновскими или гамма-лучами в пределах объема, указанного в табл. 11.23. Кроме того, сварные швы должны подвергаться механическим и металлографическим исследованиям с целью проверки их прочности и пластических характеристик. Механические испытания сварных соединений должны выполняться в соответствии с требованиями ГОСТ 6996-81.
[c.421]
Лавинообразное разрушение корпуса теплообменника, находившегося под действием внутреннего давления, произошло в ноябре 1987 г., при остановке технологической линии. В момент, предшествующий разрушению, потока среды в межтруб-ном пространстве аппарата не было, однако в корпусе сохранялось рабочее давление (вероятнее всего жидкой фракции). Теплообменник представлял собой горизонтальный цилиндрический аппарат с двумя неподвижными трубными решетками, сферическими днищами и компенсатором на трубной части. Он рассчитан на эксплуатацию с некоррозионной средой под давлением в корпусе 3 МПа, в трубной части 3,8 МПа при температуре -18 °С. Корпус, днища и трубные решетки аппарата изготовлены из стали 09Г2С. Размеры теплообменника длина (между трубными решетками) 5000 мм диаметр 1200 мм толщина стенки корпуса 20 мм. В соответствии с технологической схемой обвязки Т-231 теплообменник эксплуатировался при температуре-36 °С. На основании анализа результатов исследований установлено следующее. Зарождение и докритический рост трещины, вызвавшей разрушение корпуса теплообменника, произошли на оси кольцевого шва обечайки в зоне приварки штуцера входа этановой фракции. Трещина развивалась вдоль оси кольцевого шва, и при достижении критической длины (200 мм) произошел переход в лавинообразное разрушение с разветвлением трещины по трем направлениям вдоль шва и в обе стороны поперек оси шва по основному металлу. Химический состав и механические свойства основного металла 09Г2С корпуса теплообменника в основном соответствовали требованиям НД. Температура перехода материала днища (Т50) в хрупкое состояние по данным серийных испытаний составила -20 °С. Для материала обечайки она составляет от О до -20 °С.
При температуре -40 °С вязкая составляющая в изломе отсутствовала. Механические свойства металла швов и сварных соединений отвечали требованиям, предъявляемым НД к качеству сварных соединений сосудов и аппаратов.
[c.51]
Качество сварного соединения термопластов определяется его механическими и физико-химическими свойствами. Эти основные свойства различных по конструкции сварных соединений для наиболее широко применяемых в строительстве термопластов (винипласт, поливинилхлорид, полиэтилен, пластикат и др.) и методы их определения установлены ГОСТ 16971—71. Стандарт дредусматривает проведение механических испытаний сварных соединений на растяжение, напряженный и ударный изгиб и герметичность. Он также предусматривает испытание сварных швов термопласта на растяжение после воздействия на них агрессивных сред. Образцы сварных соединений для всех видов испытаний при толщине основного материала более 1 мм вырезают фрезерованием, а для пленочных материалов — специальным приспособлением (ГОСТ 14236—69).

Обжатие (нагартовка) сварных швов и околошовной зоны при продольной прокатке роликами увеличивает прочность соединений. Так, обжатие сварных швов нагартованного сплава АМгб повышенной чистоты приводит к росту временного сопротивления разрыву на 30— 50 МПа, условного предела текучести на 100—120 МПа. При испытании на разрыв образцов сварных соединений до прокатки разрушение происходит, как правило, в зоне сплавления, а после прокатки — преимущественно в зоне отжига. Прочность соединений во втором случае выше. В табл, 29 приведены типичные значения механических свойств стыковых соединений, выполненных аргонодуговой сваркой на металле толщиной 10 мм. [c.72]
Особые требования предъявляются к контролю ка-1ества сварки. Согласно Правил Госгортехнадзора я действующим инструкциям сварные соединения трубо-11роводов, сосудов и трубных элементов котлов подвергаются следующим видам контроля внещнему осмотру механическим испытаниям металлографическим исследованиям дефектоскопии — ультразвуковому контролю, просвечиванию швов гамма- или рентгеновскими лучами, магнитографическому контролю
[c. 295]
Все (применяемые для изготовления узлов трубопроводов детали, основные сварочные материалы и изделия должны удовлетворять требованиям нормативных документов и иметь сертификаты и паспорта заводов-изготовителей. Материалы и изделия, не имеющие сертификатов или паспортов, могут применяться для изготовления узлов только после их проверки и испытания в соответствии со стандартами и техническими условиями. Проверке и испытанию подвергаются также сварные соединения, выполненные при изготовлении узлов трубопроводов. В частности, кроме пооперационного контроля и внешнего осмотра сварных швов осуществляют проверку сплошности сварных стыков физическими методами (рентгеновским или у-просвечкванием, магни-тографированием, ультразвуковым контролем или комбинированными способами), а также механические испытания образцов из пробных стыков. [c.126]
До последнего времени основными методами контроля сварных соединений металлических конструкций были радиография и магнитография, а соединений железобетонных конструкций — механические испытания и внешний осмотр. Широко распространенный в некоторых отраслях промышленности радиографический контроль достаточно эффективен, но неприемлем для контроля сварных соединений арматуры железобетонных конструкций и малоэффективен при контроле сварных швов металлических конструкций большой толщины.
[c.3]
Контроль качества сварных соединений, проводимый при изготовлении, реконструкции и ремонте крандв отделом технического контроля должен осуществляться внешним осмотром и измерением, просвечиванием (рентгеио- или гам-ма-графирование) стыковых швов и механическими испытаниями. [c.15]
Опасность разрушения сварных пзделий прп понижении температуры возрастает. Началом разрушенпя являются технологические дефекты швов — ненровары и трещины, а также резкие переходы от усиления шпа к основному материалу п другие концентраторы напряженпп. При этом образцы для стандартных механических испытаний основного металла п сварных соединений могут иметь высокую прочность, удовлетворительную пластичность и вязкое разрушение.
[c.53]
Механические испытания
Механическим испытаниям подлежат: пробные (допускные) сварные стыки, выполненные при квалификационных испытаниях сварщиков и проверке технологии сварки стыков стальных и полиэтиленовых газопроводов; сварные стыки стальных газопроводов; не подлежащие контролю физическими методами, и стыки подземных газопроводов, сваренных газовой сваркой. Стыки отбирают в период производства сварочных работ в количестве 0,5% общего числа стыковых соединений, сваренных каждым сварщиком, но не менее двух стыков диаметром 50 мм и не менее одного стыка диаметром свыше 50 мм, сваренных им в течение календарного месяца.
Стыки стальных газопроводов испытывают на статическое растяжение и на изгиб или сплющивание по ГОСТ 6996. Допускные стыки полиэтиленовых газопроводов испытывают на растяжение.
Механические свойства стыков стальных труб с условным диаметром свыше 50 мм определяют испытаниями на растяжение и изгиб образцов (вырезанных равномерно по периметру каждого отобранного стыка) со снятым усилением в соответствии с ГОСТ 6996.
Результаты механических испытаний стыка считаются неудовлетворительными, если:
- среднее арифметическое предела прочности трех образцов при испытании на растяжение менее нормативного предела прочности основного металла трубы;
- среднее арифметическое угла изгиба трех образцов при испытании на изгиб менее 120° — для дуговой сварки и менее 100° — для газовой сварки;
- результат испытаний хотя бы одного из трех образцов по одному из видов испытаний на 10% ниже нормативного значения прочности или угла изгиба.
Механические свойства сварных стыков стальных труб условным диаметром до 50 мм включительно должны определяться испытаниями целых стыков на растяжение и сплющивание. Для труб этих диаметров половину отобранных для контроля стыков (с неснятым усилением) следует испытывать на растяжение и половину (со снятым усилением) — на сплющивание.
Результаты механических испытаний сварного стыка считаются неудовлетворительными, если:
- предел прочности при испытании стыка на растяжение менее нормативного предела прочности основного металла трубы;
- просвет между сжимающими поверхностями пресса при появлении первой трещины на сварном шве при испытании стыка на сплющивание превышает значение 55, где 5— номинальная толщина стенки трубы.
При неудовлетворительных испытаниях хотя бы одного стыка проводят повторные испытания удвоенного количества стыков.
Проверка должна производиться по виду испытаний, давшему неудовлетворительные результаты.
В случае получения при повторной проверке неудовлетворительных результатов испытаний хотя бы на одном стыке все стыки, сваренные данным сварщиком в течение календарного месяца на данном объекте газовой сваркой, должны быть удалены, а стыки, сваренные дуговой сваркой, проверены радиографическим методом контроля.
Коррозионные испытания сварных соединений
Рекомендуем приобрести:
Установки для автоматической сварки продольных швов обечаек — в наличии на складе!
Высокая производительность, удобство, простота в управлении и надежность в эксплуатации.
Сварочные экраны и защитные шторки — в наличии на складе!
Защита от излучения при сварке и резке. Большой выбор.
Доставка по всей России!
Сварные соединения из углеродистых, легированных и высоколегированных сталей, работающие в условиях химически активной среды, подвержены коррозии (разъеданию).
По своему действию на металл коррозию разделяют на химическую и электрохимическую.
Химическая коррозия представляет собой процесс непосредственного химического взаимодействия между металлом и средой, как, например, окисление железа на воздухе при высоких темпера турах с образованием окалины.
Электрохимическая коррозия — это разрушение металла с участием электрического тока, который возникает при работе металла в воде, растворах кислот, солей и щелочей.
Различают два вида коррозии: общая и межкристаллитная.
При общей коррозии вся поверхность металла или часть его химически взаимодействует с агрессивной средой. С течением времени поверхность разъедается и толщина металла соответственно уменьшается.
При межкристаллитной коррозии происходит разрушение металла по границам зерен. Внешне металл не меняется, но связь между зернами значительно ослабевает, и при испытании на изгиб в растянутой зоне образца образуются трещины по границам зерен.
Испытывая сварные соединения на коррозионную стойкость, сварные образцы (для ускорения процесса испытания) подвергают действию более сильных коррозионных сред, чем те, в которых конструкцию будут эксплуатировать.
Оценку стойкости сварных соединений против общей коррозии проводят несколькими методами.
Весовой метод заключается во взвешивании сварных образцов размером 80 X 120 мм и толщиной 6—10 мм со швом посредине до и после испытания и определении потерь в весе (в г/м2) за определенное время. Усиление шва снимают. Перед испытанием образцы взвешивают с точностью до 0,01 г и замеряют их общую поверхность по всем шести граням. Затем образцы кипятят несколькими циклами по 24—48 ч в азотной или серной кислоте соответствующей концентрации в зависимости от условий работы сварного соединения.
После кипячения с образцов мягкими скребками из дерева, алюминия или меди полностью удаляют продукты коррозии и образцы снова взвешивают. Вычитая вес образца после испытания из первоначального веса и отнеся разность к общей площади поверхности образца (в м2) и одному часу испытания, получают показатель коррозии по потере веса в г/м2*ч и пересчитывают его на потерю веса в г/м2*год.
Скорость проникания коррозии П в мм/год определяют по формуле
П = (К/δ)*10-3
где К — потеря веса, г/м2*год;
δ — плотность металла, г/см3.
Полученные расчетные данные сравнивают с данными ГОСТа.
По ГОСТ 13819—68 оценку коррозионной стойкости черных и цветных металлов, а также их сплавов при условии их равномерной коррозии проводят по десятибалльной шкале коррозионной стойкости (табл. 15).
Таблица 15. Десятибалльная шкала коррозионной стойкости
Коррозионную стойкость металлов при скорости коррозии 0,5 мм/год и выше оценивают по группам стойкости, а при скорости ниже 0,5 мм/год — по баллам.
Этой шкалой нельзя пользоваться при наличии в металле межкристаллитной коррозии и коррозионного растрескивания.
Профилографический метод состоит в определении степени коррозирования (глубины разъедания) различных участков сварного соединения (основного металла, зоны термического влияния и металла шва). Образцы испытают в среде, аналогичной по действию той, в которой будет работать сварное соединение, но более быстродействующей с определенным коэффициентом ускорения. Глубину разъедания измеряют с помощью специальных профилографов и профилометров (рис. 116), после чего на бумаге вычерчивают профиль сварного соединения после коррозии.
При электрохимическом (потенциометрическом) методе определяют разность потенциалов в той или иной коррозионной среде между сварным швом, зоной термического влияния и основным металлом. Это дает довольно правильные представления о направлении процесса коррозии.
Объемный метод применяют для коррозионных испытаний только основного металла. Он заключается в определении количества газов, образующихся в результате коррозии.
При методе определения коррозионной стойкости по изменению механических свойств для испытания подбирают сильно действующую среду, как, например, раствор серной или соляной кислоты. Образцы выдерживают в коррозионной среде определенное время, а затем подвергают механическим испытаниям, по результатам которых судят о стойкости сварных швов против коррозии.
Качественную оценку коррозионных поражений проводят внешним осмотром, а также исследованием с помощью лупы или микроскопа сварных соединений после коррозионных испытаний. Эта оценка служит дополнением к методам количественной оценки коррозионных поражений.
Межкристаллитной коррозии подвержены главным образом аустенитные и аустенитно-ферритные нержавеющие стали с большим содержанием хрома.
Рис. 116. Определение коррозионной стойкости шва профилометром
а — общий вид профилометра; б — образцы для испытаний: 1 — после сварки; 2 — перед испытанием; 3 — после испытания; в — профиль сварного соединения: I — до испытания; II — после испытания; г — глубина проникания коррозии
При сварке этих сталей отдельные участки основного металла, расположенные по обе стороны от шва, подвергаются действию температур, которые могут вызвать распад твердого раствора и выпадение карбидов железа и хрома на границах зерен. Снижение содержания хрома приводит к потере коррозионной стойкости металла и развитию межкристаллитной коррозии (рис. 117), которая может поразить также участки шва, подверженные повторному воздействию сварочного нагрева.
Рис. 117. Межкристаллитная коррозия в результате выпадения карбидов а — при сварке пересекающихся швов; б — при возобновлении сварки шва после смены электрода; в — при двустороннем сварном шве
Испытания на межкристаллитную коррозию аустенитных, аустенитно-ферритных и аустенито-мартенситных коррозиестойких сталей проводят по ГОСТ 6032—58*.
Образцы (рис. 118) вырезают механическим способом. Контрольную поверхность толщиной до 10 мм состругивают на глубину до 1 мм. Образцы толщиной более 10 мм вырезают поперек шва с таким расчетом, чтобы толщина его была 5 мм, а ширина равнялась толщине основного металла. Чистота поверхности образцов перед испытанием должна быть не ниже Δ7.
Рис. 118. Образцы для испытания на межкристаллитную коррозию
а — при толщине металла до 10 мм; б — при толщине металла более 10 мм; S — толщина металла: I — место вырезки образца; II — контрольная поверхность; III — отход
Склонность металла к межкристаллитной коррозии определяют по методам A, AM, В:
А — в водном растворе медного купороса и серной кислоты;
AM — в водном растворе медного купороса и серной кислоты в присутствии медной стружки;
В — в водном растворе медного купороса и серной кислоты с добавкой цинковой пыли.
Все испытания проводят в колбе или специальном бачке из хромоникелевой стали с обратным холодильником. В реакционный сосуд загружают образцы и заполняют его соответствующим раствором на 20 мм выше образцов. Затем образцы кипятят в растворе: для метода А — 24 ч, AM — 15 или 24 ч; В — 144 ч.
После кипячения образцы промывают, просушивают и загибают на угол 90°. При этом радиус закругления губок или оправки должен быть равен: при толщине образцов до 1 мм — 3 мм, от 1 до 3 мм — не более трехкратной толщины образца и свыше 3 мм — 10 мм.
Поверхность в зоне изгиба образца тщательно осматривают с помощью лупы при увеличении в 8—10 раз. Если на поверхности будут обнаружены поперечные трещины, то это значит, что металл склонен к межкристаллитной коррозии и непригоден для эксплуатации.
Кроме методов A, AM и В существуют еще методы Б и Д.
При методе Б производят анодное травление участков поверхности деталей или зоны термического влияния. Металл сварного шва этим методом не контролируют. Метод Б основан на анодной поляризации и состоит в воздействии коррозионной среды и электрического тока на поверхность испытуемой детали.
Сосуд для коррозионной среды (рис. 119) состоит из свинцовой воронки с резиновой манжетой, плотно прилегающей к поверхности контролируемой детали. Для испытаний собирают установку по схеме, приведенной на рис. 120.
Рис. 119. Сосуд для испытания анодным травлением
а — горизонтальных поверхностей; б — вертикальных поверхностей; I — свинцовая воронка; 2 — резиновая манжетка; 3 — поверхность контролируемой детали
Рис. 120. Электрическая схема для испытания методом анодного травления
1 — источник постоянного тока; 2 — амперметр с ценой деления не более 0.1 а; 3 — реостат или магазин сопротивления; 4 — выключатель; 5 — свинцовый сосуд; 6 — резиновая манжета; 7 — контролируемый образец
Испытания проводят по обеим сторонам сварного шва в шахматном порядке, а в случае перекрытых швов — во всех местах перекрещивания (рис. 121). Поверхность контролируемых участков шлифуют наждачной бумагой и промывают чистым авиационным бензином и спиртом. На отшлифованную поверхность плотно устанавливают сосуд и наливают в него 3—5 мл электролита (60% серной кислоты и 0,5% уротропина), включают электрический ток и в течение 5 мин подвергают металл коррозированию. Полярность устанавливают таким образом, чтобы испытуемое изделие служило анодом, а свинцовый сосуд — катодом. С помощью реостата устанавливают ток плотностью 0,65 а/см2 при напряжении 5—9 в.
Рис. 121. Схема проведения контроля перекрывающихся сварных швов методом анодного травления
1 — сварной шов; 2 — место анодного травления
По прошествии 5 мин ток выключают, детали промывают водой и протирают спиртом. Образовавшиеся пятна на поверхности образца рассматривают под микроскопом при увеличении не менее чем в 30 раз. При контроле готовых сварных конструкций, когда применение микроскопа невозможно, допускается применение бинокулярной лупы или оптических трубок с 20-кратным увеличением. Если пятно анодного травления имеет однородный светлый или темный цвет, то это значит, что металл не склонен к межкристаллитной коррозии. Браковочным признаком является образование в нем непрерывной сетки.
По методу Д образцы испытывают в кипящей 65% ной азотной кислоте. Перед испытанием образцы взвешивают на аналитических весах с точностью до 0,1 мг. Затем их помещают в стеклянную колбу с обратным холодильником, заливают кислотой из расчета не менее 9 мл кислоты на 1 см2 поверхности образца и кипятят в течение 48 ч.
Всего проводят три цикла кипячения (каждый раз в новом растворе), промывая, просушивая, обезжиривая и взвешивая образцы после каждого цикла. Коррозионную стойкость определяют по скорости коррозии образцов, выраженной в мм/год за каждые 48 ч. Если скорость коррозии превысит 2 мм/год или будет иметь место ножевая коррозия, металл бракуют.
Л.П. Шебеко, А.П. Яковлев. «Контроль качества сварных соединений»
Испытание сварного соединения на статическое растяжение
Испытанием сварного соединения на статическое растяжение определяют прочность наиболее слабого участка стыкового или нахлесточного соединения, а также прочность металла шва в стыковом соединении.
Контроль сварных соединений проводят в соответствии с требованиями Правил устройства и безопасной эксплуатации сосудов, работающих под давлением . Качество сварных соединений, выполненных при изготовлении баллонов, контролируют внешним осмотром 100% сварных соединений, механическими испытаниями образцов, просвечиванием проникающими излучениями, гидравлическими и пневматическими испытаниями. Обязательными видами механических испытаний сварных соединений являются испытания на статическое растяжение и загиб, при этом временное сопротивление на разрыв должно быть не менее 38 кгс/мм , а угол загиба— не менее 100°. [c.42]
Испытание сварного соединения на статическое растяжение [c.271]
Статические испытания на двухосное растяжение стыковых сварных соединений [c.136]
Механические испытания сварных соединений, а также измерение твердости металла различных участков сварного соединения и наплавленного металла проводят при нормальной температуре, равной (20 10) °С [(293 10) К]. Испытания различных участков сварного соединения на статическое растяжение, ударный изгиб и стойкость металла против механического старения проводят при нормальной температуре или при повышенных или пониженных температурах, если это предусмотрено стандартами или другой технической документацией. [c.261]
Испытание металла различных участков сварного соединения и наплавленного металла на статическое (кратковременное) растяжение [c.262]
Определение механических свойств сварного соединения на статическое растяжение, изгиб или сплющивание (для труб с толщиной стенки до 5= 12 мм — на ударный изгиб), а также испытания на статическое растяжение для металла щва, металла различных участков околощовной зоны и наплавленного металла при всех видах сварки, место вырезки, форма и размеры образцов, их количество, условия проведения испытаний, оценка результатов испытаний должны соответствовать требованиям ГОСТ 6996 — 66. [c.223]
А. Определение прочности наиболее слабого участка сварного соединения. При испытании сварного соединения на статическое растяжение определяют временное сопротивление наиболее слабого участка. Для испытания применяют, как правило, образцы, толщина или диаметр которых равны толщине или диаметру основного металла. Если сварное соединение выполнено из листов разной толщины, то толщина более толстого листа. механической обработкой доводится до толщины тонкого листа. [c.271]
При испытании сварного соединения на статическое растяжение определяют временное сопротивление наиболее слабого участка. [c.166]
Испытания сварного соединения на статический изгиб и растяжение, а также ударный разрыв и замеры твердости проводят при нормальной температуре, равной 20 10°С. Температура образца принимается равной температуре помещения, в котором проводят испытания. Испытания металла различных участков сварного соединения и наплавленного металла на статическое (кратковременное) растяжение, ударный изгиб (на надрезанных образцах), а также испытания на стойкость против механического старения проводят при нормальной температуре или по требованию, оговоренному в соответствующих стандартах или другой технической документации, при повышенных или пониженных температурах. При испытании при пониженной или повышенной температуре температуру образца принимают равной температуре среды, в которой проводят нагрев или охлаждение. При этом допускается определение температуры на образцах-свидетелях. [c.58]
При испытании сварного соединения на статическое растяжение определяют временное сопротивление наиболее слабого участка. Подсчет временного сопротивления ведется по ГОСТ 1497. При испытании определяют место разрушения образца (по металлу шва, по металлу околошовной зоны, по основному металлу). [c.85]
Испытания при постоянной общей деформации. При этих испытаниях статические растягивающие напряжения в образцах создаются путем заданной начальной деформации изгибом или растяжением. Испытания при одноосном изгибе с постоянной общей деформацией проводят при напряжениях (во внешних волокнах), меньших предела текучести, обычно а = 0,7-ь0,9 Ох, и больших предела текучести (петлевые и подковообразные образцы). Образцы второго типа более чувствительны к растрескиванию в связи с наличием в них, наряду с упругой (напряжения), пластической деформации. Однако напряженное состояние в таких образцах весьма сложно и неопределенно, поэтому испытания с их использованием следует рассматривать как относительно грубый, сравнительный экспресс-метод. Для сварных соединений эти способы применять нецелесообразно, так как при деформации образцов (в связи с неоднородностью прочностных и деформационных свойств в различных зонах сварного соединения) неизбежно неоднородное нагружение сварного соединения и еще большая по сравнению с основным металлом неопределенность напряженного состояния Для испытаний сварных соединений широко используют образцы в виде скоб [43] (рис. 16). Изменяя стрелу прогиба, можно создавать различные начальные напряжения. [c.59]
Испытание на статическое растяжение в соответствии с Правилами по котлонадзору допускается не производить для контроля поперечных сварных соединений сосудов, камер, трубопроводов (в том числе в пределах котла) и труб поверхностей нагрева, если они подвергнуты 100%-ному контролю ультразвуком или просвечиванием. [c.243]
РАЗМЕРЫ ОБРАЗЦОВ, ПРИМЕНЯЕМЫХ ПРИ ИСПЫТАНИИ НА СТАТИЧЕСКОЕ РАСТЯЖЕНИЕ РАЗЛИЧНЫХ УЧАСТКОВ СВАРНОГО СОЕДИНЕНИЯ (ПО ГОСТ 6996 — 66), мм [c.262]
Сварные соединения, помимо выявления внутренних дефектов, подвергаются, в соответствии с Правилами, механическим испытаниям на статическое растяжение, статический изгиб или сплющивание, на ударную вязкость в зависимости от толщины стенки сосуда или его элементов и рабочей температуры. [c.128]
Если нет других указаний в стандартах или другой технической документации, то испытания на статическое растяжение и статический изгиб проводят не менее чем на двух образцах испытания на ударный изгиб, на стойкость против механического старения и ударный разрыв — не менее чем на трех обр цах измерение твердости — не менее чем на четырех точках для каждого свиного соединения. Если размеры сварного соединения исключают возможность размещения четырех точек, то допускается уменьшать их количество в соответствии с реальными возможностями. [c.57]
Механические испытания сварных стыков производят на растяжение, статический загиб, отдир и сдвиг (для раструбных соединений). Испытание на растяжение выполняют на трубных образцах при Д до 50 мм и на линейных образцах при Д более 50 мм и толщине стенки более 10 мм. Испытание на статический загиб проводят на линейных образцах при Дн более 50 мм и толщине стенки до 10 мм, а на отдир —при Д более 50 мм независимо от толщины стенки. Испытание на сдвиг вьшолняют на трубчатых образцах, вырезанных из середины раструба с высотой, равной половине его глубины. [c.131]
Примечания 1. Показатели механических свойств сварных соединений должны определяться как среднеарифметическое значение результатов испытаний отдельных образцов. Результаты испьттаний на стаггическое растяжение и статический изгиб считаются неудовлетворительными, если хотя бы один из образцов показал значение ниже установленных требований более чем на 10 %. Результаты [c. 111]
Обобщенный анализ механических характеристик. 06обш1ен-ные результаты механических испытаний основного металла и сварных соединений приведены в табл. 2. По механическим свойствам (растяжение, ударный изгиб при комнатной и пониженной температуре, статический изгиб для сварных соединений) металл труб и сварные соединения соответствуют сертификату завода-изготовителя и действующей НТД для труб МГ класса прочности К50. Химический состав и механические свойства металла разрушенной трубы в непосредственной близости от места повреждения и на удалении от места повреждения одинаковы и соответствуют стали марки 19Г. [c.384]
Исследования проводили в условиях постоянной растягивающей нагрузки и при циклическом нагружении образцов. Статические испытания при постоянном напряжении производили на специально сконструированной многопозиционной установке, позволяющей создавать в образцах различные по величине растягивающие напряжения. Испытания на циклическую выносливость проводили в условиях напряжения растяжения переменной величины на разрывной машине ГРМ-1 с гидропульсатором. Условия испытания нагрузка знакопостоянная, асимметричная (коэффициент асимметрии 0,5) при частоте нагружения 200 циклов в минуту на базе испытания ЫО циклов. Одновременно произво-дпли испытания натурных образцов сварных стыковых соединений и основного металла, вырезанных из труб действующего рассолонровода с размерами, аналогичными экспериментальным. [c.236]
Сварка в машиностроении.Том 3 (Николаев Г.А. — Сварка в машиностроении) — DJVU, страница 9
4, а и б и регламентированы ГОСТ 6996 — 66, Поперечная ось образцов должна совпадать с осью шва. Временное сопротивление Р где й — поправочный коэффициент; Р— максимальное усилие, кгс; г — площадь поперечного сечения образца в наименьшем сечении до испытания, ммз, 47 46 СВОЙСТВА Механические свойства сварных соединений Для углеродистых и низколегированных конструкционных сталей коэффициент к принимают равным 0,9. Для других металлов коэффициент я устанавливается соответствующей технической документацией, Утолщение шва должно Рис. 4, Образец для определения прочности металла шва в стыковом соединении при испытаниях сварного соеди- нения на статическое растяжение быть снято механическим способом до основного металла.
Строгать утолщение следует поперек шва. Испытание сварного соединения на статический изгиб. Испытания проводят для стыковых сварных соединений. При испытании определяют способность данного соединения принимать заданный по размеру и форме изгиб. Эта способность характеризуется углом изгиба я при образовании первой трещины в растянутой зоне образца (рис.
5). Если трещина не образуется, то испытания в соответствии с требованиями, оговоренными в технической документации, продолжаются до получения нормируемого угла изгиба, паралрис 5 Схема испытания ле. Ьности стоРОН нли сплющиваниЯ Обо . ца. сварного соединения на ста- Появление надрывов длиной до 5 мм по кромкам тический изгиб » и а овеРхности 06Разца не Развивающих дальше в процессе испытания, браковочным признаком не является. Форма и размеры образцов для испытания на изгиб представлены соответственно на рис. 6, а и б и регламентируются ГОСТ 6996 — 66. Утолщение и1ва удаляется механическим путем до основного металла, Строгать утолщение для Рис. б. Образцы для испытания сварного соединения на статический изгиб образца, представленного на рис.
б, а, следует вдоль, а для образца, представленного на рис, б, б, поперек шва. Испытание сварного соединения на ударный разрыв. Испытание на сопротивление ударному разрыву производят для сварных стыковых соединений листов толщиной до 2 мм, Форма и размеры образца должны соответствовать рис, 7, у годы определения механических свойств Кето ь Испытание проводят на маятниковых копрах с приспособлением для закрепл нпя 11лоских образцов.
Удельная ударная работа Ат и, юи У вЂ” объем расчетной части образца, равный произведению толщины основгде ного металла иа расчетную длину и ширину образца, смз. Условия проведения испытаний. Выбор видов испытаний и применения метода предусм у-мотрен в стандартах и технических условиях на продукцию, устанавливаю;цих механические требования на нее. Образцы, имеющие отступления от чертежных размеров по шероховатости ; .ботки, а также механические повреждения в рабочей части, к испытаниям обре от нс допу допускаются и заменяются таким же числом новых образцов, изготовленных из той же пробы или контрольного соединения.
дд Все перечисленные виды испытаний, кроме испытания сварного соединения на статический изгиб и измерения твердости, если нет указаний в соответствующих стандартах или Ягд другой технической документации, чэ Б0 4е проводят не менее чем на трех образцах. Испытание сварного соединения иа статический изгиб проводят не менее чем на двух образцах. Твердость измеряют не менее чем в пяти точках длЯ каждого Участка сваРного Рис, 7, Образец для испытания свар- соединения. Испытание сварных сое- ного соединения на ударный разрыв динений, выполненных точечной и шовной контактной сваркой, если нет других указаний в стандартах, проводят не менее чем на 10 образцах.
Результаты по всем видам испытаний определяют как среднее арифметическое результатов, полученных при испытании всех образцов. Методика определения размеров образцов, требования, предъявляемые к оборудованию для испытаний, условия проведения испытаний, подсчет и оценка результатов должны соответствовать ГОСТ 6996 — 66, а также: а) при испытании на статическое растяжение при нормальной температуре— ГОСТ 149? — 73, при пониженных температурах — ГОСТ 11150 — 75, при повышенных температурах — ГОСТ 9651 — 73; 6) при измерении твердости — ГОСТ 2999 — 75, ГОСТ 9013 — 59 и ГОСТ 90! 2 — 59.
Другие требования к условиям проведения испытаний, определению размеров образцов, оборудованию для испытаний и подсчету результатов должны оговариваться стандартом или другой технической документацией. В протоколе испытания указывают тип образца, место его отбора, место разрушения (для сварных соединений), температуру испытания, результаты испытания для всех образцов и наличие дефектов в изломе образцов. Для определения прочности и пластичности сварных соединений и металла шва проводят испытания при температурах, предусмотренных техническими условиями эксплуатации в соответствии с ГОСТами. Для определения механических свойств в отдельных локальных зонах шва и зоны термического влияния производят испытание микрообразцов с измерением микротвердости соответствующих участков, Применяют также специальные (нестандартные) методы испытаний, 49 48 Свойства Предел прочности (временное сопротивление) сварных соединений ниэкоуглеродистых сталей прн различной температуре, кгс/ммз Определяемые характеристики прочности и пластичности могут относиться к металлу шва, зоне термического влияния, к сварному соединению в нслом и, для сравнения, к основному металлу.
Прочность и пластичность сварных соединений углеродистых н легированных сталей. В зависимости от механических свойств при растяжении стали, применяемые для стальных строительных конструкций, часто подразделяют на условные классы прочности, именуемые как «классы стали», согласно табл. 1 (12, 2Ц. Современные способы сварки низкоуглеродистых и низколегиронапных сталей обеспечивают равнопрочность сварного соединения основному металлу при пластичности, практически не уступающей исходным показателям (табл. 2).
УОНИ-13/55 Зпсб 12 Исходное После старения Исходное 49,8 61,5 49,3 57,0 50,0 60,0 460 078 МР-3 УОНИ-13/55 УОНИ-13~55 Зпсб 3 Зпсо 12 20 !. Классы стали для строительных конструицнй 52,0 ~ о2,5 в Класс стали 5,, у Металл или сварное соедине- ние кгс/см’ не ниже 4. Свойства сварных швов соединений конструкционных сталей кгс/мм’ б. Ф 25 3800 Свариваемая сталь, сварочные материалы и’ кгс м/смз Тв ‘С 21 кгс/мм’ 45,о СтЗ в состоянии поставки, образцы диаметром 6 мм 29,3 21 4600 Б СтЗкп Сз-08А СтЗ, полуавтоматическая сварка 12Х1ЗН! ОТ ЭП!С 12Х!8Н10Т, в защитных газах, 6=14 мм 14,0 0,47 6.5 14,1 3,55 5200 32,4 47,0 30,1 16 6000 7000 12Х18Н10Т, ручная сварка Электроды ЦЛ2, 5 = 8 мм 10 8500 50 Сталь 15ХСНД в состоянии поставки (без термической обработки) 6.
Механические свойства при 20 ‘С 65,0 46,0 Металл шва после автоматической сварки в среде СОз пластин нз стали 15ХСНД толщиной !4 мм ыполи мм Ти элекзр згиба, усы Свойства сварных соединений сталей зависят от температуры эксплуатации. На прочность и пластичность сварных соединений влияет тсрмическзя либо механическая обработка после сварки. В табл. 3 — б приведены цифровые данные, характеризующие свойстаа сварных соединений ннзкоуглеродистых и низколегированных сталей при различных температурах испытания с применением и без применения термической сбработки.
Одним из показателей хрупкости и пластичности является ударная вязкость сталей, которая существенным образом зависит от температуры (рис. 8). 38 С 23 С— 44 29 46 зз 52 40 60 45 С вЂ”. 70 60 С— 75 » При отсутствии выраженной площадки текучести эа предел текучести принимают напряжение, соответствующее остаточному относительному удлинению 0,2% (и,,) Примечание. Цифры в индексе класса обозначают; числитель — минимальное временное сопротивление из разрыв (кгс/мм’).
знаменатель — минимальный предел теиучести) (к г с/м м’). Механические свойства сварных соединений 2. Свойства металла швов в стыковых сварных соединениях Сварное соединение иэ стали Стз под керамическим флюсом, сварка в три слоя, толщина 13 мм, образцы диаметром 6 мм вырезаны поперек шза ЭЗЗ Э42 Э46 Э00 Э42А Э*16А Э50 А Э55 Э60 Э70 Эвв Э!00 Э!25 Э 150 20 — 183 20 20 -180 +2Π— 70 — 196 20 — 40 — 75 — 183 41,8 55,1 57,5 102 5 60,4 89,4 !20,2 68,7 89 90,8 109 ! 7. 8 36.7 — 45 17,6 — 18,0 38,2 48,! ЗЗ’ 37 3! 2!) 18 52 Механические свойства сварных соединений Свойства Механические сво ст й ва зоны термического влияния зависят также от темпеат ы наи ольшего н р б агрева.
Предел текучести и поперечное сужение ра Р )р сматчески пе зависят от температурь ратуры максимального нагрева металла ЗТВ в рас ел п очтемператур. В то же время с уменьшением ее предел прориваемом диапазоне н е инение сначала незна. ности металла несколько снижается, а относительное удл н м снижается. Небольшое повышение относительного удличительно растет, а потом снижается.
Механические испытания — Испытания на растяжение, часть 2
Для утверждения процедуры стыковой сварки большинство спецификаций, таких как ISO 15614 и ASME IX, требуют проведения испытаний на растяжение. Обычно это испытания на растяжение поперечного соединения (CJ) квадратного или прямоугольного сечения, которые, как следует из названия, ориентированы поперек сварного шва, так что испытываются оба основных металла, обе зоны термического влияния (ЗТВ) и сам металл сварного шва ( Рис. 1 ). Излишки металла шва в верхней части шва можно оставить на месте или обработать.
Несмотря на возможность измерения предела текучести, удлинения и уменьшения площади образцов CJ, тот факт, что существуют по крайней мере три различных участка с разными механическими свойствами, делает такие измерения неточными и ненадежными, хотя иногда они проводятся исключительно для информационные цели.
Упомянутые выше спецификации требуют регистрации только UTS и положения трещины. Обычно требуется, чтобы прочность поперечного соединения превышала минимальную указанную UTS основного металла.В большинстве случаев металл сварного шва прочнее основного металла, т. е. превосходит его, так что разрушение основного металла или ЗТВ происходит при напряжении выше указанного минимума.
В тех случаях, когда сварной шов и/или ЗТВ слабее, чем основной металл – хорошим примером являются сварные дисперсионно-упрочненные или холоднодеформированные алюминиевые сплавы – это рассматривается в большинстве спецификаций.
Конструктор также должен принять это во внимание в проектных расчетах и предусмотреть какой-либо метод компенсации этой потери прочности.
Испытание на растяжение стыковых сварных швов плоских пластин не вызывает проблем с формой образцов, но образцы, изготовленные из стыкового соединения труб, не являются плоскими, и эта кривизна может повлиять на результаты. В контексте испытаний на одобрение технологии сварки это не имеет значения, поскольку испытание используется только для определения UTS и положения разрыва. Для получения более точных результатов образец может быть сужен и может быть обработан плоско, как показано на Рис. 2 .
Может потребоваться обработка нескольких образцов по всей толщине сварного шва, особенно на очень толстых соединениях, где мощность разрывной машины недостаточна для вытягивания образца полной толщины, Рис.3 .
Для испытания трубы малого диаметра в отверстие трубы вставляется твердый стержень, чтобы предотвратить разрушение трубы, когда образец зажимается в разрывной машине.
Большинство испытаний сварных швов проводится с CJ-образцами, но продольно ориентированные образцы полезны, особенно когда металл сварного шва или ЗТВ очень прочный, но пластичность низкая.
В образце CJ основной металл может деформироваться и, в конце концов, разрушиться без существенной деформации металла шва или ЗТВ, в то время как в образце для продольного испытания нагрузка распределяется более равномерно.
Хрупкий сварной шов или ЗТВ не будут удлиняться вместе с основным металлом, но будут трескаться, при этом трещины раскрываются, но не обязательно распространяются на основной металл по мере проведения испытаний.
Описанное выше испытание требуется в соответствии со спецификациями утверждения процедуры сварки. Они не дают гарантии того, что сварные швы в конструкции будут соответствовать своему назначению, например, для эксплуатации на высоте или при криогенных температурах, и многие стандарты применения, такие как сосуды под давлением без огня PD 5500 и сосуды под давлением ASME VIII, требуют дополнительных испытаний.
Поскольку прочность металла падает с повышением температуры, эти спецификации требуют проведения испытаний на растяжение при повышенной температуре при максимальной расчетной температуре.
Эти испытания должны проводиться только на металле сварного шва и с использованием продольно ориентированного образца с круглым поперечным сечением, по которому можно получить точное измерение предела текучести.
Многие прикладные стандарты, такие как PD 5500, требуют испытаний в дополнение к тем, которые требуются, например, в соответствии с ISO 15614-1.Это необходимо помнить, когда документация по утверждению процедуры представляется на утверждение проверяющему органу или заказчику.
Достоверность данных о растяжении
Предполагается, что взятые пробы представляют основную массу материала, но это не всегда так.
Прочность отливки на растяжение, например, часто определяется по образцу, полученному механической обработкой из стояка, и он будет иметь размер зерна, отличный от крупности отливки.
Стальной прокат имеет различные свойства в продольном, поперечном и поперечном направлениях и по толщине.Таким образом, спецификации материалов, такие как BS EN 10028, Плоские стальные изделия для работы под давлением, требуют, чтобы испытание на растяжение проводилось поперек направления прокатки, чтобы сталь испытывалась поперек «зерен» — более низкая прочность, более низкая пластичность. направление.
Размер продукта также может влиять на свойства, так как во время термообработки толщина среза будет влиять на скорость охлаждения с более низкими скоростями охлаждения и, следовательно, более мягкими структурами в центре более толстых срезов.Это рассматривается в стандартах на материалы путем указания так называемого «ограничивающего линейного сечения», максимального диаметра стержня, при котором в центре могут быть достигнуты требуемые механические свойства.
В дополнение к изменениям свойств из-за формы образцов и температуры испытаний, на результаты также влияет скорость нагружения.
На рис. 4 показано, как прочность на растяжение увеличивается, а пластичность снижается по мере увеличения скорости испытания.Следовательно, необходимо контролировать скорость траверсы растягивающей машины, и в стандарте BS EN 10002 указан диапазон скорости напряжения от 6 МПа в секунду до 60 МПа в секунду. Спецификации ASTM имеют схожие, но не идентичные требования.
Излишне говорить, что калибровка испытательного оборудования, чтобы гарантировать работу в пределах допустимых параметров, является обязательной.
Соответствующие спецификацииBS EN 10002 Методы испытаний металлических материалов на растяжение.BS EN 876 Разрушающие испытания сварных швов металлических материалов — испытание на продольное растяжение. BS EN 895 Разрушающие испытания сварных швов металлических материалов — испытание на поперечное растяжение. BS EN ISO 7500-1 Машины для испытаний на растяжение/сжатие. поверка и калибровка силоизмерительной системы. ![]() ASTM A370 Механические испытания стальных изделий. ASTM E8 Испытание металлических материалов на растяжение. ASTM B557 Испытание на растяжение кованых и литых изделий из алюминия и магниевого сплава. |
Эта статья была подготовлена Джином Мазерсом.
Эта статья о профессиях была первоначально опубликована в журнале Connect за май/июнь 2004 г. Она была обновлена, поэтому веб-страница больше не отражает точно печатную версию.
(PDF) ИСПЫТАНИЯ НА ПРОЧНОСТЬ СВАРНЫХ СОЕДИНЕНИЙ НОВЫХ И Б/У МАТЕРИАЛОВ НА РАСТЯЖЕНИЕ
87
16-я Международная научно-экспертная конференция
«Тенденции развития машиностроения и сопутствующих технологий»
TMT 2012, 10-11 ОАЭ, Дубай Сентябрь 2012
ИСПЫТАНИЯ НА ПРОЧНОСТЬ СВАРНЫХ СОЕДИНЕНИЙ НОВЫХ И
ИСПОЛЬЗУЕМЫХ МАТЕРИАЛОВ
Бахрудин Хрница, Фадил Исламович, Дженана Гачо
Университет в Бихаче – Факультет технического строительства Бихач
5 dr.

Босния и Герцеговина
Zijah Burzić
Военно-технический институт
ul. R. Resanovića 1, 11000 Белград
Сербия
РЕФЕРАТ
Процесс ремонта сварной стальной конструкции (резервуара) требует ряда сложных испытаний, имеющих
, чтобы определить, соответствуют ли сварные соединения всем требуемым стандартам. В работе рассмотрены испытания стыкового сварного соединения
, выполненного из 40-летнего эксплуатируемого материала, а также неиспользованного материала идентичного состава
.Процедура испытаний включала ряд предварительных процедур, предшествующих самому испытанию прочности на растяжение
. Помимо выбора подходящей технологии сварки, необходимо было произвести извлечение
старых стальных листов из резервуара и приварить их к новому материалу. Первоначально мы
подготовили старый материал к сварке, провели сварочный процесс, исследовали сварной шов микроскопическими и макроскопическими
, вырезали образцы и проверили их на прочность при растяжении. Помимо результатов испытаний
, в этом документе также рассматривается технология сварки, используемая в процессе сварки нового материала
с тем, который эксплуатировался более 40 лет.
Ключевые слова: Предел прочности, Резервуар, Сварное соединение, Сварка
1. ПОДГОТОВКА И СОЕДИНЕНИЕ ПЛАСТИН
Ремонт существующих металлоконструкций является очень ответственной работой, и одной из таких операций является
сварка процесс нового материала к эксплуатируемому материалу, расположенному на конструкции.В работе
представлены результаты испытаний на растяжение при ремонте резервуара большого объема. В процессе подготовки
мероприятия проводились по нескольким направлениям, такие как закупка новых стальных листов, которые
должны соответствовать характеристикам эксплуатируемой стали на конструкции резервуара, резка листов
существующего резервуара и закупка электродов для сварочного процесса. А именно, вся конструкция бака
изготовлена из стали S235, что обусловило закупку новых пластин, которые должны быть из той же стали марки
. Заготовка эксплуатируемого материала производилась из одного из вертикальных цилиндрических резервуаров
на терминале в Бихаче. Пластины были нарезаны на заданную длину в соответствии с планом
эксперимента. После того, как основной материал был доставлен, первым шагом было соединение пластин из старой и новой стали
и. Процесс требовал строгих критериев и условий процесса соединения, так как эти
были сварными соединениями высокого уровня безопасности.На рис. 1 показано положение и способ обработки пластины
и процесс сварки, а также форма сварного шва. После завершения процесса сварки,
, в результате серии контрольных мероприятий был выдан сертификат на сварные соединения, что позволяет проводить дальнейшие
экспериментальные действия. Резка пробирок проводилась таким образом, чтобы оптимально использовать поверхность, чтобы
бракованных пластин было как можно меньше, чтобы минимизировать затраты на эксперимент.После испытания
Сварное соединение – обзор
1 Введение
Процесс сварки широко применяется для соединения конструкционных компонентов в широком диапазоне промышленных применений, особенно в области машиностроения и гражданского строительства. Как правило, структурные компоненты рассчитаны на предполагаемую усталостную долговечность. В случае конструкций, включающих сварные соединения, наиболее очевидным местом усталостного разрушения является подошва или корень сварного шва. Крайне важно, чтобы сварные соединения были спроектированы таким образом, чтобы эти соединения не вышли из строя до истечения их предполагаемой усталостной долговечности.В то же время сварные соединения с завышенной конструкцией приведут к громоздким конструкциям, что приведет к увеличению стоимости и снижению эффективности. Следовательно, очень важно точно определить усталостную долговечность сварных соединений на раннем этапе проектирования. Непрерывное расширенное использование методов виртуального проектирования и проверки стало хорошо принятой стратегией во всех отраслях, чтобы уменьшить зависимость от дорогостоящих и трудоемких физических сборок в соответствии с философией проектирования «с первого раза правильно». Однако виртуальное проектирование и проверка сварных соединений сопряжены со многими проблемами из-за ряда связанных с этим сложностей.
Большинство вопросов, связанных с виртуальным проектированием и прогнозированием усталостной долговечности сварных соединений, можно в целом разделить на три категории:
- (a)
Геометрический коэффициент концентрации напряжений: в конструкциях сварные швы в основном необходимы для облегчения переноса нагрузки от одной детали к другой. Однако эта передача нагрузки должна проходить через сложную геометрическую форму сварного шва. Дуговые сварные швы, как правило, имеют угловой или канавочный тип, которые могут применяться для соединения деталей для получения пяти типов соединений, а именно стыковых, Т-образных, нахлесточных, угловых и кромочных, что приводит к сложной геометрической форме в макромасштабе.На геометрическую форму сварного шва также влияет процесс сварки, т.е. сварной шов в форме самородка может быть получен с помощью процессов контактной, лазерной сварки или сварки трением. Дополнительная сложность возникает из-за геометрического перехода между сварным швом и основным материалом с точки зрения малого радиуса и угла перехода, также известных как микрогеометрические особенности.
Как макро-, так и микрогеометрические особенности сварного соединения создают концентрацию напряжений, то есть сопротивление передаче нагрузки, что в конечном итоге влияет на усталостную долговечность соединения.В то время как геометрия сварного шва на макроуровне определяется конструкцией на чертежах и контролируется с помощью различных стандартов качества сварки, например. AWS D14.3 или ISO 5817 не содержит положений о микрогеометрических особенностях сварного шва. Авторы твердо убеждены в необходимости включения этих микрофункций в процедуры проектирования и контроля качества. В любом случае они должны быть тщательно учтены при расчетной усталостной долговечности сварных конструкций.
- (b)
Изменения материалов, связанные со сваркой и ЗТВ: Свойства материала играют ключевую роль в влиянии на прочность и усталостные характеристики конструкции.Добавление микролегирующих элементов для измельчения зерна или дальнейшей обработки материала, такой как прокатка или термообработка, являются довольно распространенными методами улучшения конкретных физических свойств, твердости, прочности и усталостных свойств конструкционных материалов.
Процесс сварки обычно включает плавление основного материала и может включать присадочную проволоку с определенным химическим составом (обычно обогащенным марганцем и кремнием), что приводит к изменению химического состава затвердевшего сварного шва по сравнению с основным материалом.Кроме того, рядом с зоной сварки некоторая часть основного материала подвергается воздействию термического нагрева (известная как зона термического влияния или ЗТВ) и, как правило, подвергается размягчению или упрочнению из-за микроструктурных изменений, влияющих на прочность и усталостные характеристики всего сварного шва. соединение.
- (c)
Остаточное напряжение и деформация: Процесс сварки включает в себя локальное плавление, нагрев и охлаждение материала в конструкции, обычно ограниченной с помощью приспособлений и зажимов, что приводит к дифференциальным деформациям и смещениям.Сложные термические циклы от подводимого тепла при сварке также приводят к состоянию остаточного напряжения в сварном соединении и вокруг него, что может отрицательно сказаться на усталостной долговечности сварного соединения.
Деформация, вызванная процессом, может вызвать перекос в сварном узле, вызывая дополнительные напряжения, которые могли не учитываться при проектировании. С другой стороны, остаточное сжимающее напряжение может способствовать увеличению усталостной долговечности сварных соединений. Некоторые из методов повышения усталостной долговечности сварного шва основаны на этом фундаментальном принципе введения сжимающих остаточных напряжений на кромке сварного шва либо с использованием сварочной проволоки с низкотемпературным преобразованием (LTT), либо с помощью методов высокочастотной механической ударной обработки (HFMI).
Усталость приводит к необратимому повреждению компонента, подвергающегося многократному нагружению, что приводит к трещинам и выходу из строя. Условно общую усталостную долговечность делят в основном на две части – усталостные циклы до зарождения трещины и последующие циклы, необходимые для распространения этой начальной трещины до окончательного разрушения. Это удобное, но произвольное разделение общего срока службы на фазы зарождения и распространения связано с дилеммой начального размера трещины, что, возможно, является самым большим недостатком теории из-за отсутствия последовательности.Не существует универсального согласованного определения начального размера трещины, в то время как общепризнано, что начальный размер трещины оказывает значительное влияние на срок службы распространения трещины. Начальный размер трещины в идеале должен быть размером, который может быть измерен последовательным образом и зависит от разрешающей способности методов неразрушающего контроля, используемых для этой цели. Однако с инженерной точки зрения обычно считается, что начальная трещина представляет собой полуэллиптическую поверхностную трещину глубиной около 0,5 мм и длиной 2 мм для типичных промышленных применений.
Усталостное повреждение сварных конструкций является одним из наиболее частых видов разрушения инженерных конструкций, приводящим к разрушению ответственных силовых сварных соединений, подвергающихся циклическим или переменным нагрузкам. Для появления явлений усталости материалу должна быть придана некоторая пластичность приложенными циклическими нагрузками. Несмотря на то, что глобальные рабочие нагрузки, прикладываемые к сварной конструкции, могут находиться в пределах предела упругости материала, локальное напряжение на кромке или в корне сварного шва из-за геометрической концентрации напряжений может быть достаточно высоким, чтобы вызвать локальную пластичность.Это основная причина того, что усталостные трещины возникают либо в подошве, либо в корне сварных швов в сварных конструкциях. Величина и профиль распределения напряжений в потенциальной плоскости трещины контролируют относительные пропорции зарождения и распространения трещины.
Из-за важности предмета явление усталости изучалось в течение нескольких десятилетий в самых разных промышленных приложениях с использованием металлических и неметаллических материалов, например. в исх. [1–4]. Несмотря на то, что был достигнут значительный прогресс в понимании процесса усталости и механики, связанной с этим явлением, не существует универсального подхода к оценке усталости сварных соединений. Существует огромное количество доступной литературы, охватывающей как теоретические, так и инженерные аспекты проектирования и анализа сварных соединений.
На рис. 3.1 показана краткая, но очень информативная блок-схема, описывающая информационный путь для анализа напряжения и усталости. Важными входными данными, необходимыми для любого анализа усталостной долговечности, являются геометрия, история нагрузки и свойства материала. Анализ напряжения-деформации необходимо выполнять для получения соответствующей информации о напряжении или деформации в соответствии с требованиями метода, используемого для анализа усталости.
Рис. 3.1. Блок-схема анализа напряжения и усталости.
При любом анализе усталостной прочности и долговечности выполняется аналогичная последовательность шагов, как показано на рис. 3.1. Во-первых, необходимо осуществить выбор материала и определение его свойств. Во-вторых, геометрия анализируемого компонента или конструкции должна быть адекватно определена и описана. Нагрузка или история напряжений — это третий сегмент входных данных, необходимых для любого анализа механической усталости. Содержание каждого сегмента входных данных варьируется в зависимости от выбранного для анализа метода усталости.Следовательно, анализ напряжения и характер используемого напряжения варьируются в зависимости от выбранного метода анализа усталости. Последним шагом любого анализа усталости является оценка усталостного повреждения и прогнозирование усталостной долговечности. Другими словами, содержимое каждого входного сегмента и используемый параметр напряжения варьируются в зависимости от выбранного метода анализа усталости.
Также стоит отметить, что входные данные зависят от нескольких факторов, таких как процесс изготовления материала (свойства материала), метод изготовления объекта (геометрия компонента и остаточные напряжения) и история нагружения.История нагрузки или напряжения является единственной, которая почти одинакова для различных методов анализа усталости.
Существует огромное количество литературы [5–34] по рекомендациям по расчету усталостных элементов сварных компонентов и конструкций, включая подробное руководство по проектированию, выпущенное Международным институтом сварки (IIW). Несмотря на это, практическая проблема заключается в том, что имеющиеся теоретические знания бесполезны, когда речь идет о систематической реализации метода расчета усталостной прочности сварных соединений в реальных условиях.Другая проблема заключается в том, что разные процедуры расчета на усталость требуют в качестве входных данных разных параметров напряжения/деформации, что обычно приводит к путанице и ошибкам, если они применяются неправильно.
Анализы усталостной прочности и долговечности сварных соединений требуют использования нескольких дисциплин, таких как механика материалов, экспериментальный анализ напряжений, материаловедение, процесс производства сварных швов и теория вероятностей. Таким образом, существует несколько доступных методов анализа усталости сварных швов в зависимости от страны происхождения или интересующей инженерной области. Тем не менее, можно выделить три наиболее популярных методологии анализа усталости сварных соединений, которые в настоящее время используются в различных отраслях промышленности, таких как авиация, автомобилестроение или сектор землеройных машин, использующих сварные конструкции. Три основные философии анализа усталостной долговечности, которые используются в настоящее время, можно классифицировать следующим образом: обозначается как метод ε-N и
Метод механики разрушения обозначается как метод da/dN-ΔK.
Как показано на рис. 3.1, анализ напряжения-деформации является первым важным шагом к оценке усталостной долговечности. Точная оценка усталостной долговечности требует информации о соответствующих данных напряжения-деформации.
Локальное пиковое напряжение в кромке (или корне) сварного шва, σ пиковое — основной параметр напряжения (рис. 3.2), который влияет на усталостную долговечность сварного соединения в критическом месте. Для проведения анализа усталостной прочности при деформации (метод Ɛ — N) требуется величина пикового напряжения или история пикового напряжения.Для проведения анализа распространения трещин с использованием подхода механики разрушения требуется нелинейное распределение напряжения по толщине (рис. 3.2) в критическом сечении. Это нелинейное распределение напряжения по толщине и метод весовой функции можно использовать для определения коэффициентов интенсивности напряжения и для анализа последующего роста усталостной трещины. Поэтому определение концентрации и распределения напряжений в критических точках сварной конструкции играет важную роль для анализа усталости.Подход, основанный на анализе долговечности при деформации, и подход, основанный на механике разрушения, помогают определить соответственно срок возникновения усталостной трещины и срок ее распространения.
Рис. 3.2. Величины напряжения, необходимые для анализа усталости в сварном соединении.
Перед детальным рассмотрением методов анализа усталости в разделах 2 и 3 будут рассмотрены вычислительная механика сварного шва и параметры напряжения, необходимые для анализа усталости сварного шва соответственно. В разделах 4–6 подробно описаны три основных метода анализа усталости с точки зрения наиболее важного параметра, т.е.е. циклическое напряжение, используемое для оценки усталостного повреждения и усталостной долговечности. Разделы 7 и 8 посвящены обсуждению упрощенных методик, разработанных для получения требуемых величин напряжений для анализа усталости сварных соединений с использованием оболочечной конечно-элементной модели (метод GY2) и твердотельной модели (модель GR3).
Микроструктура и механические свойства сварных соединений современных жаропрочных сталей 11%Cr
4.1. Микроструктура стали Т155 в исходном состоянии
Типичные микроструктуры стали Т155 в исходном состоянии представлены в и .В исходном состоянии сталь Т115 имела структуру мартенсита отпуска с многочисленными частицами, наблюдаемыми на границах первичных аустенитных зерен (ПАГ), блоках мартенситных реек, границах мартенситных реек и внутри реек/зерен ( и ). Пакеты реечного мартенсита формировались внутри границ ПАГ. Ориентация и размер пакетов и прорезей в блоках были переменными. Электронно-микроскопические исследования показали, что микроструктура мартенсита отпуска имеет субзеренную структуру с низкой плотностью дислокаций внутри субзерен и многочисленными выделениями М 23 С 6 и МХ ( и ).В стали в исходном состоянии наблюдаются выделения двух типов: карбиды М 23 С 6 и выделения МХ (NbX, VX) также наблюдались, например, в [1, 23, 24]. Частицы M 23 C 6 представляют собой осадки, богатые хромом [1,24,25]. Богатые хромом M 23 C 6 карбиды являются преобладающим типом выделений в этой группе сталей. По данным [22], они составляют более 90 % всех выделений в высокохромистых сталях.Частицы этих выделений наблюдаются на границах ПАГ и мартенситного пакета и реек, а также единичные выделения внутри реек. Карбиды M 23 C 6 в сталях с содержанием 9–12 % Cr играют важную роль, стабилизируя реечную структуру мартенсита отпуска [1, 26, 27, 28].
Микроструктура стали Т115 в исходном состоянии по данным сканирующей электронной микроскопии (СЭМ).
Микроструктура Thor 115 в исходном состоянии по данным просвечивающей электронной микроскопии (ПЭМ).
Осадки в стали Thor 115 в исходном состоянии: ( a ) M 23 C 6 ; ( б ) МС.
В свою очередь, частицы MX (выделения, богатые ниобием и/или ванадием) могут наблюдаться внутри мартенситных реек, и часть их выделяется на дислокациях. В матрице эти осадки распределены неоднородно. В отличие от карбидов М 23 С 6 выделения MX в сталях с 9% Cr характеризуются низкой скоростью укрупнения.Высокая термическая стабильность этих выделений и когерентные (полукогерентные) границы раздела с матрицей обусловливают то, что, несмотря на их малую объемную долю (примерно 0,020–0,025), эти выделения вызывают сильное дисперсионное твердение стали и являются эффективным барьером для свободной дислокации. движение за счет эффекта пиннинга [1,4].
4.2. Микроструктура зоны термического влияния сварных соединений Т155
Макроскопические виды сварных соединений Т115 показаны на рис. Воздействие тепла в процессе сварки изменяет микроструктуру в областях, прилегающих к линии сплавления, — эта область называется зоной термического влияния (ЗТВ).В зависимости от температуры опыта можно выделить следующие зоны: крупнозернистая зона термического влияния (КЗТВ), мелкозернистая зона термического влияния (ФГЗТ) и межкритическая зона термического влияния (ИЧАЗ). Структура конкретной ЗТВ определяется пиком температуры.
Макроскопическое изображение пробных стыков: ( a ) стык № 1; ( б ) стык № 2; где: WM-сварка; ЗТВ – зона термического влияния; БМ – основной материал.
В ЦГАЗ вблизи линии сплавления температура значительно выше температуры перехода A C3 [29,30].Высокая пиковая температура сварочного цикла в зоне способствует растворению выделений в матрице, в основном частиц М 23 С 6 [29,31,32]. Это растворение приводит к исчезновению эффекта закрепления границ и приводит к образованию крупного аустенитного зерна (). Измеренный размер ПАГ в этой области составил 33 ± 8 мкм, что соответствует 7 по стандартной шкале ASTM. В этой области наблюдается структура мартенсита отпуска с многочисленными выделениями различной морфологии.Выделения располагаются так же, как и в основном материале, т. е. на границах ПАГ, мартенситных реек и внутри реек ( и ). В ЗТВ, как и в основном материале, выделения M 23 C 6 в основном наблюдаются на границах/реек/блоках, а выделения MX наблюдаются внутри реек/субзерен [31,32]. Размер первичного аустенитного зерна в мартенситных сталях является важным фактором, влияющим на свойства стали, такие как: предел прочности при растяжении, ударная вязкость, сопротивление ползучести, а также подверженность механизму повреждения, т.е.г., растрескивание IV типа [31,33,34,35].
Микроструктура стыка № 1 в районе линии сплавления – крупнозернистой околошовной зоны (КГТВ).
Как и в стыке № 1, в районе линии сплавления в стыке № 2 также наблюдалась крупнозернистая мартенситная микроструктура с многочисленными выделениями. Однако, в отличие от стыка № 1, наличие участка На границах зерен в этой области наблюдался δ-феррит (). Рассчитанная объемная доля δ-феррита в этой области стыка №.2 составил 1,54%.
δ-феррит в районе линии сплавления – ЦГАЗ, стык № 2; WM – металл шва.
Склонность к возможному выделению δ-феррита вблизи зоны сплавления можно определить, например, с помощью следующих уравнений [36]:
Creq=%Cr+6%Si+4%Mo+1,5%W+11% V+5%Nb+12%Al+8%Ti−40%C−2%Mn−4%Ni −2%Co−30%N−%Cu
Ферритовый фактор Кальтенхаузера FF = %Cr+6%Si+ 4%Mo+8%Ti+2%Al+4%Nb-2%Mn-4%Ni-40%C-40%N
Для структуры без δ-феррита значение Cr равно и параметры FF должно быть ниже 10 и 8 соответственно.Для исследуемой стали значение параметров Cr eq и FF составило 11,88 и 9,18 соответственно. Это указывает на тенденцию к образованию δ-феррита, который будет расти при увеличении содержания ферритообразующих элементов (в основном Cr, а также Mo) в области линии сплавления.
По данным [31,33], наличие δ-феррита в этой зоне сварного соединения также может быть обусловлено составом основного металла и присадочного материала, широким интервалом затвердевания, высокой тепловкладом, а также скоростью охлаждения .В свою очередь, согласно [37], большое тепловложение при многопроходной сварке приводило к замедлению скорости охлаждения и влияло на образование δ-феррита в области вблизи линии сплавления.
Видно, что внутренняя часть области δ-феррита свободна от выделений, а границы украшены выделениями карбида (). Наличие в стали участка δ-феррита ускоряло скорость восстановления мартенситной структуры и скорость роста фазы Лавеса и, следовательно, снижало ползучесть и усталостную прочность стали [33].
В свою очередь, на ФГАЗ/ИЧАЗ пиковая температура ниже, чем на ЦГАЗ — несколько выше А с3 для ФГАЗ и между А с1 и А с3 для ИЧАЗ [20,30]. Пиковая температура в этих областях приводит к частичному растворению осадков в матрице [20,32,33]. Нерастворившиеся частицы тормозят рост аустенитных зерен, закрепляя границы аустенитных зерен и способствуя формированию мелкозернистой структуры ( и ). В обоих случаях температура тепловложения и скорость охлаждения аналогичны параметрам отжига стали.Расчетный размер зерна в FGHAZ составил 16 ± 6 мкм, что соответствует размеру зерна 9 по стандартной шкале ASTM. Влияние температуры термоцикла в этой области может не только способствовать растворению некоторых выделений в матрице, но и приводить к коагуляции нерастворившихся карбидов М 23 С 6 [32,33]. Частичное растворение частиц в этой части ЗТВ приводит к укрупнению нерастворившихся осадков. Следовательно, в этой области наблюдаются как крупные, так и мелкие выделения, распределенные так же, как и в основном материале.В этой области наблюдается значительная деградация микроструктуры, видна практически полная потеря реечной структуры мартенсита отпуска в пользу ферритной микроструктуры с многочисленными частицами ().
Микроструктура мелкозернистой околошовной зоны (ФГАЗ)/межкритической околошовной зоны (ИКЗТ) в стыке стали Т115 — стык № 1.
Микроструктура ФГАЗ/ИЧАЗ в стыке стали Т115 — стык № 2.
Аналогичные результаты испытаний представлены в [31,38].Согласно [33], помимо частиц M 23 C 6 и MX в этой области также наблюдаются выделения фазы Лавеса. Образование фазы Лавеса на границах зерен снижает ползучести стали, что приводит к снижению прочности твердого раствора. Фаза Лавеса также снижает ударную вязкость [39]. В этой области также наблюдается ускоренное восстановление реечной структуры отпущенного мартенсита по сравнению с другими участками соединения [27,34]. Относительно высокая скорость деградации микроструктуры на этих участках связана не только с влиянием термического цикла, но и с обработкой соединений после сварки.Вышеуказанные изменения в микроструктуре этой области выражаются в более быстром разупрочнении по сравнению с другими участками соединения, что приводит к склонности этой области к ускоренному повреждению ползучести, что называется растрескиванием IV типа [35]. В суставе № 2 микроструктура в этой области сустава была аналогичной ().
Кроме того, на линии сплавления в анализируемом соединении наблюдалось возникновение характерных несмешанных участков между швом и основным материалом, т. е. так называемых пальцев Нернста (НП).Их наличие в стыке обусловлено наличием неподвижного слоя жидкости в ванне, примыкающей к линии сплавления, во время сварки [9]. Также образование НФ происходит в основном из-за разницы температур плавления основного материала и присадочного металла [38,40]. Поэтому в стыке № 1 эти участки не наблюдались. Подробный механизм образования НФ и его влияние на свойства полученных стыков представлены в [41,42].
Пальцы Нернста в сварном шве стыка №2.
4.3. Механические свойства испытательных соединений
Результаты механических исследований анализируемых сварных соединений представлены в , и и . Механические свойства испытательных соединений соответствовали требованиям [43].
Профиль распределения твердости по поперечному сечению соединения, сваренного с: ( a ) CrMo91, ( b ) EPRI P87.
Прочность на растяжение испытательных соединений, сваренных при определенной температуре.
Энергия удара сварных соединений для обоих присадочных металлов.
Таблица 5
Результаты измерения микротвердости опытных сварных соединений и δ-феррита.
Расположение измерения | Составление № | ||
---|---|---|---|
1 (WCRMO91) | |||
WM | Face | 234 -244 | 124-143 |
237-247 | |||
CHHAZ | 273-285 | ||
FGHAZ / ICHAZ | 191-207 | 185-206 | |
BM | 212-216 | ||
145-168 * |
Основное расследование, проведенное на сварных суставах №1 и № 2 – измерение твердости по поперечному сечению соединения. К основным факторам, влияющим на твердость соединений в исследуемой стали, относятся: микроструктура, площадь фракций M 23 C 6 и выделений MX, плотность дислокаций, наличие атомов C и N в твердом растворе и размер предшествующего аустенитного зерна. Измерения показали, что полученные результаты твердости по поперечному сечению испытуемых соединений не превышали значения 290HV. В рассматриваемом случае высокая твердость вблизи линии сплавления на ЦГАЗ стыка № 1.1, возможно, из-за осаждения частиц M 23 C 6 и MX. Нагрев этого участка при сварке приводит к растворению карбидов M 23 C 6 и выпадению в матрице части обогащенного ванадием MX [31,32]. PWHT приводит к осаждению дисперсионных частиц, что приводит к значительному дисперсионному твердению. В свою очередь, более низкая твердость ФГАЗ/ИЧАЗ по сравнению с ЦГАЗ является результатом коагуляции карбидов М 23 С 6 и более выраженного разупрочнения матрицы при ПТО [20].
Различия в микротвердости в окрестности линии сплавления между стыком № 1 и стыком № 2, вероятно, обусловлены наличием в микроструктуре стыка № 2 участка мягкого δ-феррита ( , ). Влияние δ-феррита на снижение твердости зоны сплавления также представлено Pandey [31,34]. Плохие механические свойства δ-феррита подтверждают плохое сопротивление деформации и влияют на склонность к разрушению при ползучести [33]. Следовательно, следует избегать образования δ-феррита в ЗТВ стали.Наблюдаемые различия в твердости материала сварного шва в испытательных соединениях являются результатом использования присадочных материалов с различным химическим составом. Это приводит к различной микроструктуре в зоне сварного шва — мартенситной (стык № 1) или аустенитной (стык № 2) микроструктуре.
При этом измерения () показали, что наименьшее значение микротвердости по сечению соединения наблюдается у ФГАЗ/ИЧАЗ. Низкая микротвердость этой мягкой зоны обусловлена опережающей деградацией микроструктуры этой зоны ( и ) и связана с размягчением мартенсита (процесс восстановления) и ростом и укрупнением выделений [34,35]. Низкая твердость/микротвердость в этой области свидетельствует о высокой степени деградации микроструктуры. Высокая степень деградации структуры в этой области и ее более низкие свойства приводят к увеличению ее восприимчивости к растрескиванию типа IV [32,35].
Испытание сварных соединений на статическое растяжение проводили как при комнатной, так и при повышенной температуре. Значения прочности на растяжение анализируемых соединений превышали требуемый минимум для основного материала (). Независимо от температуры значения TS для испытуемых соединений были одинаковыми и сравнимыми со значениями, полученными для основного материала.Тем не менее TS при 600 и 650 °С был чуть меньше половины TS при комнатной температуре. Из-за возможности более быстрой диффузии повышенная температура облегчает движение дислокации и позволяет избежать осаждения путем подъема [44]. Это приводит к уменьшению взаимодействия между выделениями и матрицей, поэтому механизм упрочнения выделений постепенно ослабевает, а прочность на растяжение впоследствии снижается. Согласно Сяо и соавт. [45], это явление может быть связано с укрупнением субзерен и уменьшением плотности дислокаций.Сопоставимые значения TS анализируемых соединений независимо от температуры свидетельствуют о незначительном влиянии δ-феррита на этот параметр прочности. Разрыв анализируемых образцов произошел в основном материале.
В жаростойких ферритных/мартенситных сталях высокая энергия удара используется в качестве основного критерия для обеспечения стойкости материала к охрупчиванию и повышению температуры вязко-хрупкого превращения. Из-за наличия в ЗТВ различных участков энергия удара сварного соединения будет различной.Минимальная энергия удара стальных сварных соединений была рекомендована около 52 Дж/см 2 согласно [43]. Результаты испытаний на ударную вязкость испытательных соединений, которые являются мерой способности материала передавать динамические нагрузки, обобщены в . Вообще говоря, энергия удара металлических материалов зависит в основном от размера зерна (измельчение структуры), а также от морфологии выделений и наличия хрупких фаз на границах зерен. Независимо от используемого присадочного металла ударная вязкость сварных соединений была выше требуемой для основного материала.Меньшая энергия удара ЗТВ в соединении № 2, вероятно, связана с наличием участка δ-феррита с карбидами на границах зерен вблизи линии сплавления (). Частицы, осажденные на межфазной границе δ-феррит/мартенсит, приводят к ухудшению сцепления между PAG и δ-ферритом [33,35]. Однако влияние накладки δ-феррита на ударную вязкость и пластичность неоднозначно. Одни исследователи пришли к выводу о его негативном влиянии [33,46], а другие – о положительном [10]. Согласно Муну [46], энергия удара отпущенного мартенсита выше, чем у мартенсита и δ-феррита.Более высокая энергия удара ЗТВ в соединении № 1 обусловлена однородной микроструктурой, лишенной δ-феррита (). Как и в случае с пределом прочности, различия в энергии удара сварного шва были вызваны используемым для сварки присадочным металлом ( и ). В случае соединения № 2 это был аустенитный наполнитель, характеризующийся высокой ударной вязкостью и пластичностью при относительно невысоких прочностных свойствах ( и ).
Испытание сварных швов | Американская сварка трением
Разрушающий контроль
Разрушающие испытания сварных швов включают физическое разрушение компонентов, сваренных трением.Для оценки характеристик сварного шва можно использовать различные методы испытаний. Мы проводим эти испытания на всех сварных швах прототипа в соответствии с требованиями заказчика.
Выборочный контроль производственных сварных швов проводится до:
- Квалификация характеристик сварки
- Устранение неполадок с помощью анализа отказов
- Исследовать процессы проверки для улучшения или проверки существующих методов тестирования
Проверка качества сварного шва в разрезе
- С помощью испытания на макротравление (и в зависимости от основного материала(ов), соединяемых в сварном шве) на поверхность поперечного сечения наносится слабокислотная смесь.
- Полученное травление обеспечивает превосходное изучение внутренней структуры сварного шва, что также полезно при обнаружении проблем со сваркой.
Крупный план зоны сварки трением
Испытание на изгиб в действии
Выявление проблем с целостностью
- Глубина проникновения
- Отсутствие слияния
- Недостаточное корневое проникновение
- Внутренняя пористость
- Трещины или включения
Могут применяться дополнительные испытания для подтверждения пластичности, прочности сварных соединений, прочности на растяжение или любого наличия шлаковых включений или нарушений качества сварного шва по всей длине сварного шва.
В зависимости от характеристик, требующих контроля, мы используем различные методы разрушающего контроля сварных швов трением:
- Испытания на изгиб : свободный изгиб, управляемый изгиб, продольный изгиб, поперечный изгиб
- Испытание травлением
- Испытания на твердость : твердость по Бринеллю, твердость по Роквеллу
- Испытание на удар
- Испытание на разрыв
- Испытание на растяжение
- Испытание на крутящий момент
Проверка резьбового стержня
Труба с поперечным сечением
Неразрушающий контроль качества сварки
Ультразвуковой контроль регулярно используется для обеспечения целостности сварных швов. Этот тест проводится в соответствии с требованиями заказчика.
Неразрушающий контроль также включает проверку сварных компонентов, подвергая их требуемым условиям эксплуатации для определения пригодности. Эти тесты предназначены для выявления дефектов, которые могут ухудшить качество обслуживания. Они не разрушат и не изменят структуру или внешний вид детали, сваренной трением.
Видеосварка трением
Неразрушающий контроль
Испытание сварки трением на прочность
Параметры сварки разработаны для обеспечения надежности.Прочность, равная или превышающая прочность исходного материала на каждой детали.Шток поршня из закаленной нитридом стали сломан за пределами зоны сварки трением. Вмятина рядом с изломом является результатом усилия пресса.
Тонкостенная трубка, приклеенная к прочному основанию. Это показывает тест разреза и изгиба. Зона сварки трением не затрагивается.
Этот полый вал приварен к цельному поршню. Срез проверяли усилием на изгиб.Основной материал отклонился до того, как какое-либо воздействие достигло зоны сварки трением.
Этот тест показывает отрезок тонкостенной трубы, разрезанный на полоски, которые согнуты вниз в виде «лепестков».
Это испытание на изгиб вала, приваренного трением к кованому кольцу, демонстрирует невероятную прочность процесса сварки трением.
В этом испытании на изгиб эта толстостенная труба, прикрепленная к твердому основанию, разрушилась раньше, чем сварной шов трением.
Штифт из закаленной нитридом стали был приварен трением к стальной монтажной пластине.Это испытание на изгиб показывает, что металлическое покрытие разрывается без разделения сварного шва трением.
Кованая скоба была приварена трением к закаленному хромированному штоку гидравлического поршня. Испытание на изгиб показывает, что стержень сломался на испытательном прессе без разрушения зоны сварки.
Эта ось прицепа класса 8 изготовлена из толстостенной трубы, приваренной трением к кованому шпинделю. Этот отрезанный участок был испытан на гибочном прессе. Вы можете видеть, что труба поддалась силе до того, как в зоне сварки трением произошло какое-либо повреждение.
Этот резьбовой стержень приварен трением к литому кулачку. Испытание на изгиб показывает, что зона сварного шва трением прочнее основного материала.
OEM-производители требуют специальных испытаний на прочность, чтобы убедиться, что характеристики деталей соответствуют конструкции. Этот шток клапана был испытан на прочность при растяжении, и он сломался за пределами сварного соединения трением, где вал встречается с диском. Испытание на растяжение показывает, что соединение, сваренное трением, прочнее, чем основной материал.
ПРИМЕЧАНИЕ. Этот готовый образец также показывает, что зону сварки трением можно обрабатывать так же, как сплошной основной материал.
Как и в других тестах на изгиб «лепестком» на этой странице, этот образец показывает, что соединение сваркой трением между тонкостенной трубой и сплошной крышкой выполнено успешно.
Здесь термообработанная закаленная сталь 8620 соединяется с нержавеющей сталью. Полую трубку из нержавеющей стали разрезали для «лепесткового теста». Параметр сварки трением доказал свою эффективность в этом тестовом примере.
Еще одно испытание на изгиб, еще одна победа сварки трением.
Этот стальной стержень диаметром 1/8 дюйма наполовину состоит из закаленной нитридом стали, соединенной с другой половиной из необработанной мягкой стали. Вы можете видеть, что сварной шов трением прочнее, чем обе стороны основного материала.
Влияние конфигурации сварного соединения на напряженные компоненты, остаточные напряжения и механические свойства
Ссылки
1 D.Moratal: Анализ методом конечных элементов, Sciyo, Chapters Published, Spain (2010), DOI: http://dx.doi. org/10.5772/58224Поиск в Google Scholar
2 W.Фрикке: Влияние остаточных напряжений на усталостное поведение сварных стальных конструкций, Матем.-вис. ты Werkstofftech. 36 (2005), № 11, стр. 642–649 DOI: http://dx.doi.org/10.1002/mawe.200500933Search in Google Scholar
Исследование влияния зажатия на остаточные напряжения и деформации в пластинах, сваренных встык, Scientia Iranica Transactions B: Mechanical Engineering17 (2010), стр. 387–394. Поиск в Google Scholar
4 C.Heinze, C.Schwenk, M.Ретмайер: Численный расчет остаточного напряжения и развитие многопроходной дуговой сварки металлическим газом, Journal of Constructional Steel Research72 (2012), стр. 12–19. DOI: http://dx.doi.org/10.1016/j.jcsr. 2011.08.011Search in Google Scholar
5 А.М.Корсунский, Г.М.Регино, Д.Ноуэлл: Вариационный анализ собственных деформаций остаточных напряжений в сварной пластине, International Journal of Solids and Structures44 (2007), стр. 4574–4591 DOI: http:/ /dx.doi.org/10.1016/j.ijsolstr.2006.11.037Поиск в Google Scholar
6 H.Н.Хан, Дж.К.Ли, С.Дж.Ким: Наблюдение за постоянной деформацией во время рекристаллизации и роста стали под действием внешнего напряжения, Materials Letters59 (2005), стр. 158–161 DOI: http://dx.doi.org/10.1016 /j.matlet.2004.07.030Search in Google Scholar
7 SLSmith, WAWood: Рентгеновская структура и упругая деформация меди, Proceedings of the Royal Society of London A: Mathematical and Physical Sciences176 (1940), стр. 398 –411 DOI: http://dx.doi.org/10.1098/rspa.1940.0096Поиск в Google Scholar
8 Y.Озкаталбаш, А. Озер: Стальная балка с внутренним предварительным напряжением, номер патента. TR200400366, Турция (2004 г.) Поиск в Google Scholar
9 Ю. Озкаталбас, А. Озер: Исследование изготовления и механических свойств стальной двутавровой балки с внутренним предварительным напряжением, Материалы и конструкция 28 (2007 г.), № 6, стр. 1988–1993 DOI: http://dx.doi.org/10.1016/j.matdes.2006.04.007Search in Google Scholar
10 A.Özer, Y.Ozçatalbaş: Измерение остаточных/постоянных напряжений с использованием метода сверления отверстий и калибровки розетки тензорезисторы, Журнал инженерно-архитектурного факультета Университета Гази26 (2011), №3, стр. 657–666Поиск в Google Scholar
11 Б.Чевик; А. Озер; Ю. Озчаталбаш: Анализ напряжений, возникающих в угловых швах, с использованием метода фотоупругости, Proc. 6 th International Advanced Technologies Symposium, Elazıg, Turkey (2011), pp. 409–414Search in Google Scholar
12 Vishay Tech-Note TN-701-1, Калибровка покрытия PhotoStress ® ; Малверн, США (2009 г.), стр. 1–6Поиск в Google Scholar
13 Н. Озден: Термическая обработка сварки, Nurettin Uycan Printing Industry, Стамбул, Турция (1985)Поиск в Google Scholar
14 E.П. Попов: Введение в механику твердых тел, Prentice-Hall of India Private Limited, Нью-Дели, Индия (1976) ISBN 0-13-571356-0 Поиск в Google Scholar
15 С. П. Тимошенко, М. Дж. Гере: Механика материалов, D Компания Van Nostrand, Нью-Йорк, США (1972 г.) ISBN 0442226373 Поиск в Google Scholar
16 ASTM E 837-01: Стандартный метод испытаний для определения остаточного напряжения методом тензодатчика при сверлении отверстий, ASTM International, США (2002 г. ) DOI: http://dx.doi.org/10.1520/E0837Поиск в Google Scholar
%PDF-1.4 % 1 0 объект >поток 2016-10-11T09:05:37-04:00Microsoft® Word 20102022-01-13T19:37:29-08:002022-01-13T19:37:29-08:00iText 4.2.0 by 1T3XTapplication/pdf
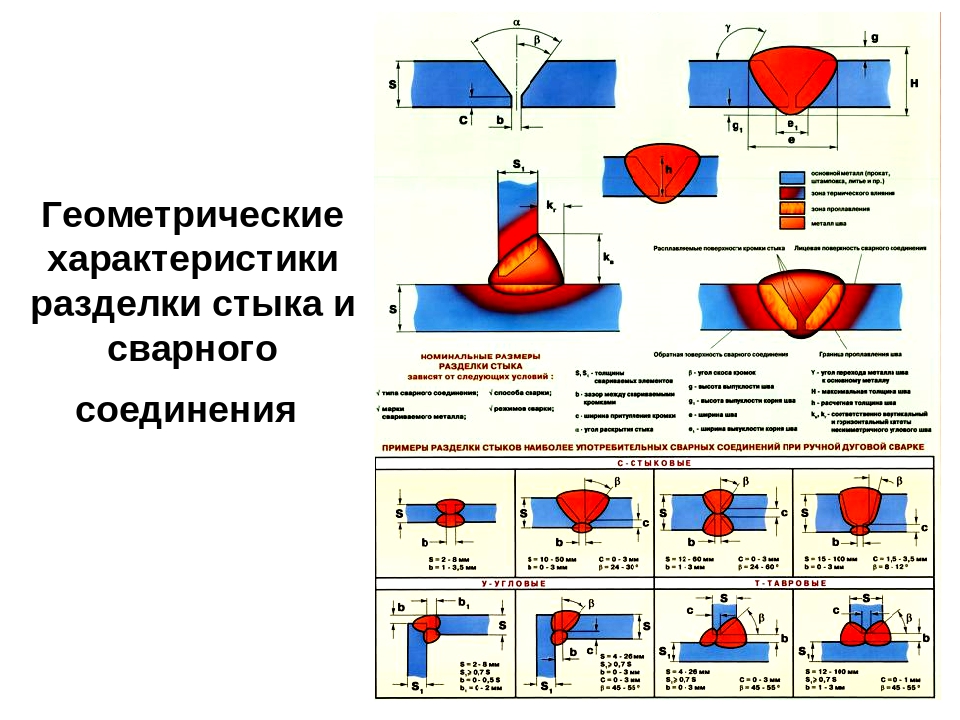