Мощность лазера для резки металла
Мощность лазера для резки металла определяет его максимальные возможности. Одно из главных правил при покупке такого устройства — станок для резки металла лазером нужно покупать с запасом. Ведь наличие запаса силы гарантирует большую производительность и возможность дальнейшего развития организации.
- Что это за показатель — мощность лазера для резки?
- Для резки металла
Что это за показатель — мощность лазера для резки?
Мощность лазера для резки металла — золотая середина модельного ряда LaserFor BSR, которая находится в районе от 500 Вт до 3 кВт. Это оборудование — надежный инструмент, которому можно доверить большое количество работы и при этом не бояться подводных камней.
Лазерные установки включают в себя три главных параметра:
- рабочую среду;
- источник энергии;
- оптический резонатор.
По виду рабочей среды устройства для нарезания бывают следующих видов:
- Твердотельные .
Их основной узел заключается в осветительной камере. В ней расположен источник энергии, а также рабочее тело.
Справка. К твердотельному типу относятся также и волоконные устройства. В них излучение становится выше, а в качестве источника энергии выступает полупроводниковый лазер.
- Газовые. В них рабочим телом выступает углекислый газ, который прокачивается насосом сквозь газоразрядную трубку и заряжается электрическими разрядами. Чтобы усилить излучение, ставят прозрачное зеркало.
- Газодинамические. Они являются самыми мощными. Рабочее тело в них — углекислый газ, который нагрет до 3000 градусов. Он заряжается маломощным лучом. Газ с большой скоростью прокачивается через узкий канал, резко расширяется и охлаждается. В итоге его атомы переходят из заряженного в простое состояние, и газ становится источником излучения.
Для резки металла
Мощность нарезания материала лазером зависит от его теплопроводности: чем она выше, тем эффективнее будет процедура, в среднем это 0,15–12,5 м/с. Мощностная характеристика определяется плотностью потока и достигает 10 в 8 степени Ватт на один квадратный сантиметр. Также она определяется в зависимости от толщины заготовки и в среднем достигает 0,5–1,5 кВт.
В зависимости от типа используемых материалов
Справка. Чтобы нарезать металл с помощью специального оборудования, потребуется сила, которая в среднем составляет 450–500 Вт. Эффективным данный способ считается при толщине заготовок не выше 6 мм. При 20–40 мм подобное оборудование используется редко. Для материала большой толщины резка не осуществляется.
Резка лучом возможна, если материалом выступает:
- Сталь. Максимальная толщина листа не должна быть выше 20 мм, иначе необходимо использовать другой метод.
- Нержавеющая сталь. В этом случае ограничение составляет 16 мм. При таких показателях удастся избежать появления облоя и его можно легко удалить.
- Латунь. Для резки этого материала подойдут 12 мм листы, так как его сопротивление достаточно большое.
- Алюминиевый сплав. Можно резать металлические листы толщиной не выше 10 мм.
Каждому из этих видов материала соответствует свой вид оборудования.
Справка. Нарезание материала лучом не используется на вольфраме, титане, молибдене. Они обладают высокой прочностью, которая приведет к выходу устройства из строя.
В зависимости от толщины
Для качественной нарезки материала нужно учитывать несколько факторов. К примеру, для малоуглеродистых сталей параметры будут такими:
- При толщине в 1 мм мощность должна быть 100 Вт, а скорость резки заготовки 1,6 м в минуту.
- Для изделий плотностью в 1,2 мм — 400 Вт, а скорость резки — 4,6 м в минуту.
- Изделия в 2,2 мм и выше нуждаются в оборудовании силой 850 Вт и резке около 1,8 м в минуту.
Если обработке подвержена нержавеющая сталь, то параметры следующие:
- Для заготовки в 1 мм хватит мощности в 100 Вт.
- Если заготовка имеет толщину 1,3 мм, то сила вырастает до 400 Вт.
- Изделия толщиной в 2,5 мм обрабатывают лазером такой же силы, как и в предыдущем пункте, но в этот раз скорость падает до 1,3 м в минуту.
При резке титана параметры следующие:
- Материал толщиной 0,6 мм обрабатывают устройством, имеющим силу 250 Вт.
- Заготовки толщиной 1 мм обрабатывают с силой в 600 Вт.
В зависимости от производительности
Чем мощнее источник лазерного станка, тем толще может быть лист материала. У лампового устройства мощностью 500 Вт есть два достоинства, которых нет у оборудования меньшей силы. Им можно разрезать латунь и алюминий, что нельзя осуществить оборудованием меньшей мощности из-за большой отражательной способности этого материала.
Если потребности в производстве и производственные задачи высокие, то вы свободно достигнете их, используя силу 250 или 500 Вт. Если предполагается нарезка металла, то понадобится 500 Вт мощности, а если нужен просто станок для резки деталей, то хватит и 100 Вт.
Станки для лазерной резки металла — современное решение, которое нацелено на будущее. Их главные отличия состоят в качестве и сбалансированности всех элементов вместе с современными разработками в области ПО.
- 01 ноября 2020
- 5097
Получите консультацию специалиста
Как выбрать лазерный станок для резки листового металла с ЧПУ?
- Главная
- / Станки
- / Лазерные org/ListItem»> / Для резки металла
- / Часто задаваемые вопросы и ответы о станке лазерной резки металла с ЧПУ
От мощности лазерного источника зависят такие параметры резки как:
- Качество резки
Толщина разрезаемого материала
1кВт/12мм | 2кВт/12мм | 3кВт/12мм | 4кВт/12мм |
На фотографии 1кВт/12мм видно, что на выходе из материала мощности лазерного источника недостаточно и рез происходит по полупараболе. На двухкиловатном источнике
отклонение от вертикали уменьшается, а на трех и четырехкиловатном практически отсутствует.
Таблица подбора мощности лазерного источника в зависимости от толщины материала и марки стали
Черная сталь (Q235A)Нержавейка (201)АлюминийЛатунь
Толщина, мм | 1000 Вт | 1500 Вт | 2000 Вт | 3000 Вт | 4000 Вт | 6000 Вт | ||||
---|---|---|---|---|---|---|---|---|---|---|
1 мм | 8.0-10 | 15-26 | 24-30 | 30-40 | 33-43 | 35-44 | ||||
2 мм | 4.0-6.5 | 4.![]() |
4.7-6.5 | 4.8-7.5 | 15-25 | 20-28.0 | ||||
3 мм | 2.4-3.0 | 2.6-4.0 | 3.0-4.8 | 3.3-5.0 | 7.0-12 | 13-17 | ||||
4 мм | 2.0-2.4 | 2.5-3.0 | 2.8-3.5 | 3.0-4.2 | 3.0-4.0 | 3.0-4.5 | ||||
5 мм | 1.5-2.0 | 2.0-2.5 | 2.2-3.0 | 2.6-3.5 | 2.7-3.6 | 3.0-4.2 | ||||
6 мм | 1.4-1.6 | 1.6-2.2 | 1.8-2.6 | ![]() |
2.5-3.4 | 2.5-3.5 | ||||
8 мм | 0.8-1.2 | 1.0-1.4 | 1.2-1.8 | 1.8-2.6 | 2.0-3.0 | 2.2-3.2 | ||||
10 мм | 0.6-1.0 | 0.8-1.1 | 1.1-1.3 | 1.2-2.0 | 1.5-2.4 | 1.8-2.5 | ||||
12 мм | 0.5-0.8 | 0.7-1.0 | 0.9-1.2 | 1.0-1.6 | 1.2-1.8 | 1.2-2.0 | ||||
14 мм | 0.5-0.7 | 0.7-0.8 | 0.9-1.4 | 0.9-1.2 | 1.![]() |
|||||
16 мм | 0.6-0.7 | 0.7-1.0 | 0.8-1.0 | 0.8-1.3 | ||||||
18 мм | 0.4-0.6 | 0.6-0.8 | 0.6-0.9 | 0.6-0.9 | ||||||
20 мм | 0.5-0.8 | 0.5-0.8 | 0.5-0.8 | |||||||
22 мм | 0.4-0.8 | 0.4-0.8 | ||||||||
25 мм | 0.![]() |
Толщина, мм | 1000 Вт | 1500 Вт | 2000 Вт | 3000 Вт | 4000 Вт | 6000 Вт | ||||
---|---|---|---|---|---|---|---|---|---|---|
1 мм | 18-25 | 20-27 | 24-30 | 30-35 | 32-45 | 42-52 | ||||
2 мм | 5-7.5 | 8.0-12 | 9.0-15 | 13-21 | 16-28 | 20-33 | ||||
3 мм | 1.8-2.5 | 3.0-5.0 | 4.0-6.5 | 6.0-10 | 7.![]() |
15-22 | ||||
4 мм | 1.2-1.3 | 1.2-2.4 | 3.0-4.5 | 4.0-6.0 | 5.0-8.0 | 10-15 | ||||
5 мм | 0.6-0.7 | 0.7-1.3 | 1.8-2.5 | 3.0-5.0 | 3.5-5.0 | 8.0-12 | ||||
6 мм | 0.7-1.0 | 1.2-2.0 | 2.0-4.0 | 2.5-4.5 | 4.8-8.0 | |||||
8 мм | 0.7-1.0 | 1.5-2.0 | 1.2-2.0 | 3.0-4.0 | ||||||
10 мм | 0.![]() |
0.8-1.2 | 1.6-2.5 | |||||||
12 мм | 0.4-0.6 | 0.5-0.8 | 0.8-1.5 | |||||||
14 мм | 0.4-0.6 | 0.6-0.8 | ||||||||
20 мм | 0.3-0.5 | |||||||||
25 мм | 0.2-0.4 | |||||||||
30 мм | ||||||||||
40 мм |
Толщина, мм | 1000 Вт | 1500 Вт | 2000 Вт | 3000 Вт | 4000 Вт | 6000 Вт | ||||
---|---|---|---|---|---|---|---|---|---|---|
1 мм | 6.![]() |
10-20 | 15-25 | 25-38 | 35-45 | 42-55 | ||||
2 мм | 2.8-3.6 | 5.0-7.0 | 7-10 | 10-18 | 13-24 | 20-40 | ||||
3 мм | 0.7-1.5 | 2.0-4.0 | 4.0-6.0 | 6.5-8.0 | 7.0-13 | 15-25 | ||||
4 мм | 1.0-1.5 | 2.0-3.0 | 3.5-5.0 | 4.0-5.5 | 9.5-12 | |||||
5 мм | 0.7-1.0 | 1.2-1.8 | 2.![]() |
3.0-4.5 | 5.0-8.0 | |||||
6 мм | 0.7-1.0 | 1.5-2.5 | 2.0-3.5 | 3.8-5.0 | ||||||
8 мм | 0.6-0.8 | 0.7-1.0 | 0.9-1.6 | 2.0-2.5 | ||||||
10 мм | 0.4-0.7 | 0.6-1.2 | 1.0-1.5 | |||||||
12 мм | 0.3-0.45 | 0.4-0.6 | 0.8-1.0 | |||||||
16 мм | 0.![]() |
0.5-0.8 | ||||||||
20 мм | 0.5-0.7 | |||||||||
25 мм | 0.3-0.5 | |||||||||
30 мм |
Толщина, мм | 1000 Вт | 1500 Вт | 2000 Вт | 3000 Вт | 4000 Вт | 6000 Вт | ||||
---|---|---|---|---|---|---|---|---|---|---|
1 мм | 6.![]() |
8.0-13 | 10-16 | 20-35 | 25-35 | 35-45 | ||||
2 мм | 2.8-3.6 | 3.0-4.5 | 4.5-7.5 | 6.0-10 | 8.0-12 | 20-30 | ||||
3 мм | 0.5-1.0 | 1.5-2.5 | 2.5-4.0 | 4.0-6.0 | 5.0-8.0 | 12-18 | ||||
4 мм | 1.0-1.6 | 1.5-2.0 | 3.0-5.0 | 3.2-5.5 | 5.0-8.0 | |||||
5 мм | 0.5-0.7 | 0.9-1.2 | 1.![]() |
2.0-3.0 | 4.5-6.0 | |||||
6 мм | 0.4-0.7 | 1.0-1.8 | 1.4-2.0 | 3.0-4.5 | ||||||
8 мм | 0.5-0.7 | 0.7-1.2 | 1.6-2.2 | |||||||
10 мм | 0.2-0.5 | 0.8-1.2 | ||||||||
12 мм | 0.2-0.4 | |||||||||
14 мм |
Скорость резки
Не все обращает внимание на такой важный параметр, как скорость резки металла.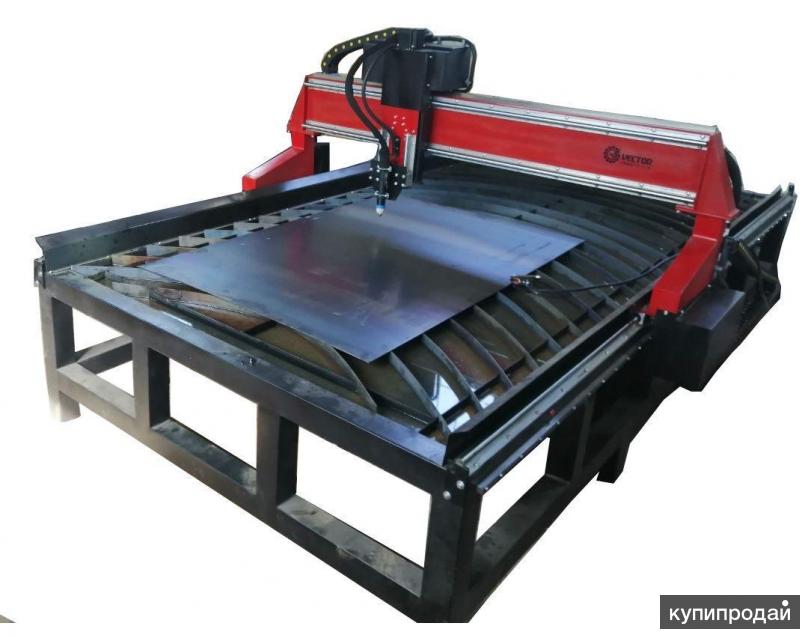
Она зависит от многих параметров. От механической части станка и приводов, от используемого газа и его давления, а самое главное от мощности источника излучения.
На видеоролике ниже Вы можете увидеть эту зависимость.
2. Конструкция станины.
3. Комплектующие.
3. Скорость холостых перемещений
4. Программное обеспечение
Комментарии и вопросы:
Комментариев пока нет, но ваш может быть первым.Разметить комментарий или вопрос
Связанные товары
Код товара: 59784
Лазерный труборез для круглых и профильных труб FLT-12035ETP
Мощность лазера, Вт1000
Лазерный источникRaycus
Макс.
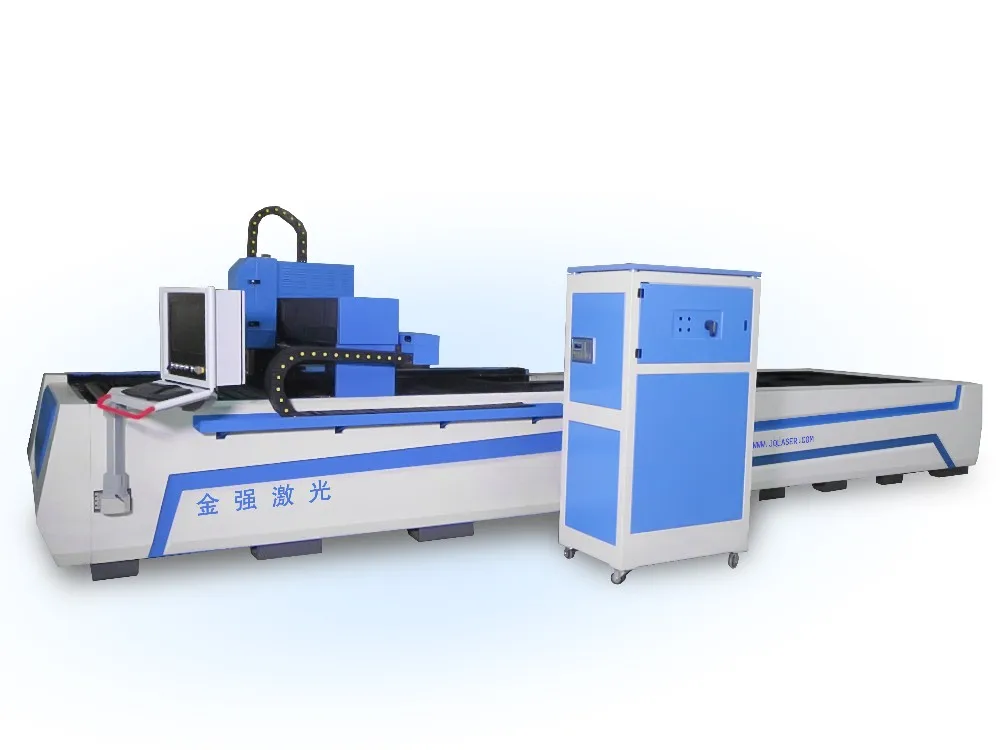
Макс. длина трубы12000 мм
Максимальный вес трубы, кг560 кг
Напряжение380В
Масса19000 кг
Код товара: 58456
Станок лазерной резки металла со сменным столом и кабинетной защитой G-Weike LF3015GA 3000вт IPG
Мощность лазера, Вт3000
Лазерный источникIPG
Длина стола3000 мм
Ширина стола1500 мм
Мощность 25.00 кВт
Напряжение380В
Код товара: 50492
Настольный лазерный маркировщик по металлу Raptor ABN-20R (Raycus 20Вт)
Мощность лазера, Вт20
Длина стола175 мм
Ширина стола175 мм
Мощность 0.70 кВт
Напряжение220В
Масса27 кг
Код товара: 57892
Станок лазерной резки металла со сменным столом и кабинетной защитой G-Weike LF3015GA 3000вт Raycus
Мощность лазера, Вт3000
Лазерный источникRaycus
Размер стола3000х1500
Длина стола3000 мм
Ширина стола1500 мм
Мощность 25.
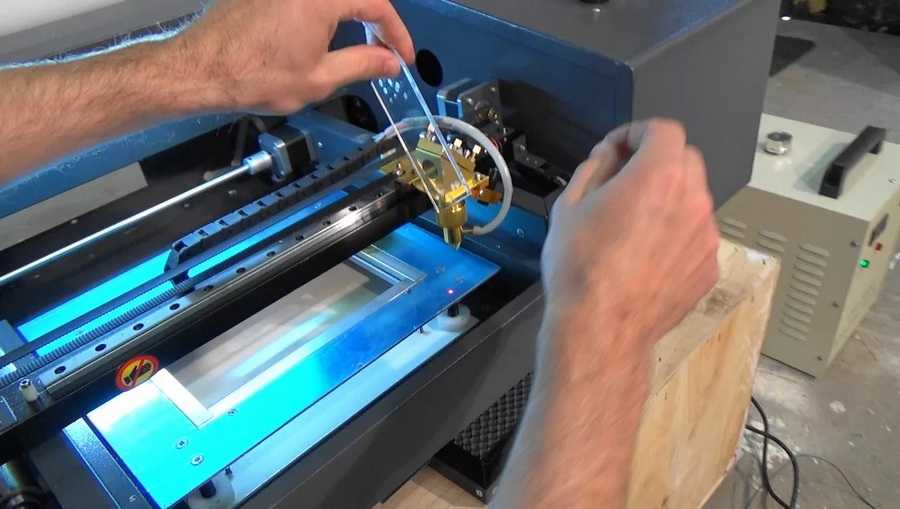
Напряжение380В
Код товара: 57860
Под заказ. 60 дней.
Высокоточный лазерный станок для резки металла с автофокусом G-WEIKE LF1390 Raycus 1000 Вт
Мощность лазера, Вт1000
Лазерный источникRaycus
Размер стола1300х900
Длина стола1300 мм
Ширина стола900 мм
Мощность 16.00 кВт
Напряжение380В
Масса1500 кг
Код товара: 59279
Лазерная очистка металла Raptor HS-LC1000 (CW 1000w)
Мощность лазера, Вт1000
Мощность 4.00 кВт
Напряжение220В
Масса280 кг
Код товара: 48560
Лазерный станок для резки и гравировки TS 1390 (100W, W4 RECI)
Мощность лазера, Вт100
Размер стола1300×900
Длина стола1300 мм
Ширина стола900 мм
Напряжение220В
Масса280 кг
Код товара: 57925
Лазерный труборез для круглых и профильных труб LF60M-1000W (Raycus 1 кВт)
Мощность лазера, Вт1000
Лазерный источникRaycus
Макс.

Макс. длина трубы6000 мм
Максимальный вес трубы, кг200 кг
Мощность 24.00 кВт
Напряжение380В
Масса5400 кг
Код товара: 48541
Лазерный станок для резки и гравировки TS 1625 (130W, W6 RECI)
Мощность лазера, Вт130
Размер стола1600х2500
Длина стола2500 мм
Ширина стола1600 мм
Напряжение220В
Масса1300 кг
Код товара: 57927
Лазерный станок для резки металла LF3015CN-2000 с автофокусом (IPG 2кВт)
Мощность лазера, Вт2000
Лазерный источникIPG
Размер стола3000х1500
Длина стола3000 мм
Ширина стола1500 мм
Мощность 25.00 кВт
Напряжение380В
Масса4500 кг
Код товара: 57919
Под заказ. 60 дней.
Лазерный станок для резки металла с труборезом LF3015LNR с автофокусом (IPG 1,5 кВт)
Мощность лазера, Вт1500
Лазерный источникIPG
Размер стола3000х1500
Длина стола3000 мм
Ширина стола1500 мм
Мощность 22.
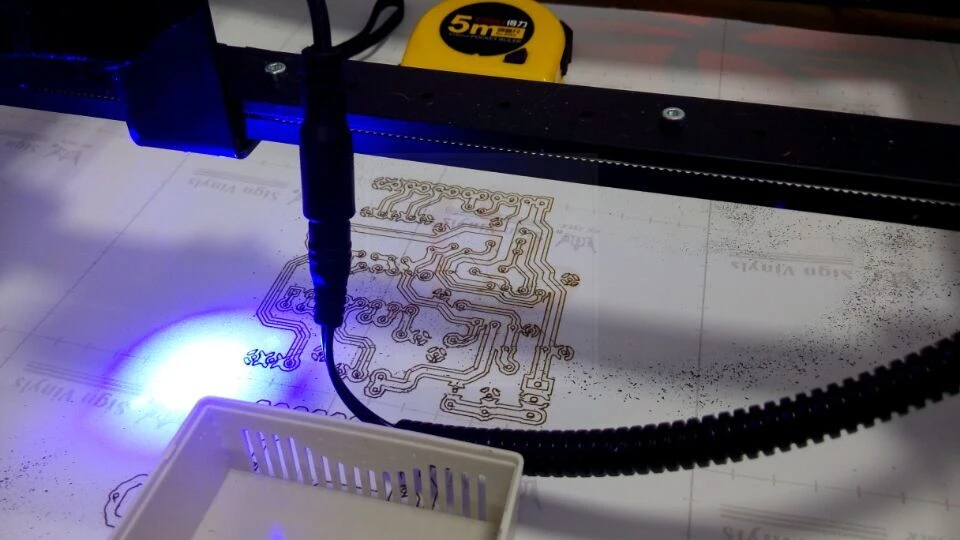
Напряжение380В
Масса6500 кг
Код товара: 48587
Лазерный станок для резки и гравировки TS 1060 (130W, W6 RECI)
Мощность лазера, Вт130
Размер стола1000×600
Длина стола1000 мм
Ширина стола600 мм
Напряжение220В
Масса210 кг
Вверх
Как выбрать мощность излучателя лазерного станка по металлу
Современные лазерные станки для резки и обработки металлов комплектуются твердотельными иттербиевыми лазерными излучателями оптоволоконного типа различных брендов.
ИзлучателиКакие факторы учитываются при выборе излучателя для станка
Компания Wattsan комплектует свои лазерные металлорезы продукцией, наиболее востребованной рынком, выпуск которой налажен производителями: IPG, MAX Photonics, Raycus.
Диапазон мощности упомянутых излучателей достаточно широк, 0.35-25.0 кВт. Заявленные изготовителем сроки службы изделий превышают 5 лет. Изделия отличаются существенной эффективностью и надёжностью, а КПД (соотношение энергии потребляемой и её результирующего значения) может достигать 30, а у отдельных моделей, 50%.
У станков линейки Wattsan просматривается прямая зависимость толщины рамы и мощности установленных на них излучателей:
- Оборудование с рамой, толщина которой не превышает (8.0-10.0) мм, чаще всего, получает излучатели, мощность которых не превышает 2кВт;
- Оборудование с более мощными (10.0-12.0) мм рамами комплектуется излучателями, мощность которых задаётся диапазоном (1.5-6.0) кВт;
- Самые прочные рамы, толщина которых составляет (12.0-16.0) мм получают излучатели с N≥4кВт.
Станки Wattsan спроектированы с учётом работы на максимально доступных скоростях с излучателями до 6 кВт (включительно). Даже когда в качестве заготовки выступает тонколистовой металл.
Взаимосвязь таких параметров оборудования, как корпус и максимальные разрешённые скорости, затронута в специальной статье и подробно рассмотрена в данном видео.
Практика показывает, что подавляющее большинство материалов заготовок, имеющих различную толщину, может качественно обрабатываться волоконным лазером подобной мощности. Поэтому более «крутой» станок приобретать экономически нецелесообразно.
Самый большой процент приобретённых станков имеет излучатели мощностью один-два киловатта.
Определяемся с выбором требуемой мощности
Для взвешенного принятия решения следует выполнить небольшой сравнительный анализ возможностей излучателей различной мощности. Пусть это будут устройства: 0.5Вт, 1.5Вт, 3.0Вт, 6.0Вт.
- Лазер мощностью 0.5 кВт способен резать металлический лист толщиной 1 мм, выполняя данную работу на скорости порядка 12 м/мин. Но предельная толщина заготовки, для подобного устройства, составляет 3 мм. При этом скорость реза упадёт до 0.7 м/мин.
- Более мощный излучатель в полтора киловатта с миллиметровым листом справится значительно быстрее. Обработка возможна на скоростях ≤26 м/мин.
Заготовку толщиной в 3 мм он качественно режет, перемещаясь со скоростью 4 м/мин. Максимально доступной толщиной для этого устройства является 6 мм. Скорость реза упадёт, в данном случае, до 1 м/мин.
- Трёх киловатт достаточно, чтобы резать миллиметровую заготовку на скоростях до 34 м/мин. С листом в 3 мм подобный станок работает, перемещаясь со скоростью 8.5 м/мин. Толщина 6 мм поддаётся сложнее. Скорость падает до 3 м/мин. Максимально возможная для обработки толщина возрастает до 12 мм. а скорость реза падает до 0.5 м/мин.
- Шестикиловаттный излучатель является безусловным лидером «скоростных режимов». Лист в 1 мм режется на скоростях, которые могут достигать 41 м/мин. 3мм обрабатывается с перемещением на (15-16) м/мин. Толщина 6 мм обрабатывается медленнее, всего 5 м/мин. А предельная толщина заготовки в 16 мм, 0.6 м/мин.
Следует иметь в виду, что скорость обработки напрямую зависит не только от толщины заготовки, но и от материала, из которого она изготовлена. А также газа, применяемого в процессе работы.
Примеры:
- излучатель мощностью в 500Вт, выполняет рез листа нержавеющей стали толщиной 1 мм, перемещаясь с V≤12 м/мин;
- этот же лазер прорежет лист углеродистой стали аналогичной толщины (с кислородом) при V≤8 м/мин;
- если предстоит обработка миллиметрового листа меди, алюминия (азот) на этом же станке, скорость упадёт до 5 м/мин.
Именно этим объясняется практически незаметная разница в работе 3.0 кВт и 1.5 кВт волоконного лазера при изготовлении средних и мелких деталей из тонколистовой заготовки. Оборудование не успевает выйти на максимально доступный скоростной режим.
Положение кардинально меняется, когда рез выполняется на длинной большой заготовке. В этом случае ощутимая разница видна даже при работе с тонколистовыми металлами.
А, при увеличении толщины обрабатываемого материала, различие становится колоссальным. Эту толщину предварительно следует пробить.
Зная соотношение между мощностью и скоростью реза и тем, какие предельные толщины может брать излучатель, можно определиться с тем какой выбор будет для вас оптимальным. Потому что иногда взять более мощный излучатель выгоднее так как он будет работать быстрее.
Несмотря на то, что для решения большинства задач достаточно 6 кВт, компания Lasercut готова изготовить станок с излучателем до 25 кВт.
Но здесь стоит отметить, что для подобного оборудования нужна специальная усиленная станина. Представьте, какие толщины такой станок будет брать. Соответственно нужно, чтобы он выдерживал этот материал.
Если вы из тех редких людей, которым нужно такое специфическое оборудование, обращайтесь по любому из контактов, указанных на сайте.
Защита волоконного лазера от отражённых лучей
Важно понимать, что отдельные металлы представляют определённую опасность для лазера, которым их обрабатывают. Это обусловлено свойственным им значительным коэффициентам отражения.
Достоинства продукции IPG заключается в том, что в ней конструктивно предусмотрена защита волоконных излучателей от возникающих отражённых лучей.
Лазеры данного бренда предлагаются в двух вариантах исполнения защиты:
- LK – имеют пассивную систему, датчики которой ловят переотражения и информируют оператора о выявленной опасности;
- LS – активная система.
Позволяет нивелировать выявленные опасные отражения. Прерывать работу для этого не придётся.
Станки в исполнении второго типа являются лучшим решением для обработки заготовок из таких материалов, как алюминий, латунь, зеркальная нержавейка, медь.
Ещё одним бесспорным преимуществом продукции IPG является лучший Гауссов пучок, что обеспечивает более стабильный рез. Однако на толщину прорезаемых заготовок и скорость резки это не влияет.
Перспективы рынка
Аналитики компании выявили интересную закономерность. Большая часть наших клиентов осуществляет замену имеющихся лазерных излучателей на более мощные.
Сегодняшний рынок, усиливающаяся конкуренция требуют повышенных скоростей и большей мощности.
Поэтому решение приобрести сегодня лазеры, мощность которых меньше 1 кВт, дальновидным назвать нельзя.
Гарантии на оборудование
Практика подтверждает бесспорное мировое лидерство бренда IPG в сегменте изготовления лазерных излучателей любых типов. Этому производителю принадлежит внушительное количество запатентованных технологий.
IPG — единственный производитель, лазеры которого эксплуатируются свыше десяти лет. Бренд фактически подтвердил заявленную долговечность собственной продукции.
Ещё одним существенным плюсом выбора именно данной продукции, является наличие в России (Фрязино, Московская область) собственной сервисной службы, выполняющей комплексный ремонт излучателей этого бренда. Для сравнения, для восстановления излучателя «Райкус», его потребуется отправить в Китай.
Lasercut даёт годовую гарантию на реализуемые станки. Любая проблема, возникающая у их пользователей, будет оперативно решена нашими специалистами.
Компания ведёт любую сделку до её логического конца.
Наши контакты с потенциальным заказчиком начинаются с предварительных бесплатных консультаций по любым вопросам, касающимся нашего оборудования и лазерных станков по металлу в целом.
Мы помогаем с выбором, доставляет приобретённые станки и запасные части к ним, выполняем установку и пусконаладочные работы. При необходимости, обучим персонал заказчика. в течение трёх рабочих дней ваши будущие операторы получат информацию о конструкции станка, основных моментах его эксплуатации, обслуживания.
Наши сотрудники научат их подбирать требуемые настройки с учётом толщины и марки материала. Продемонстрируют порядок и особенности работы на режимах, упрощающих процесс, обеспечивающих экономию материалов и времени.
Длительный успешный опыт сотрудничества с различными производствами существенно обогатил и разнообразил профессиональное мастерство наших сотрудников.
Что позволяет им надлежащим образом организовать обучение, передать собственный опыт и уникальные наработки, позволяющие оптимизировать производство с использованием лазерного оборудования.
Купить станок, предназначенный для лазерной резки металла, клиент может в различных организациях. Но таким багажом знаний, практического опыта, который накоплен нашими мастерами сервисной службы, менеджерами, обладают далеко не все продавцы.
Лазер какой мощности нужен для моих целей?| Trotec Laser FAQ
- Trotec Laser
- Обучение и поддержка
- Часто задаваемые вопросы
- Лазерный станок какой мощности нужен для моих целей?
Самым важным критерием при выборе мощности лазерного станка является вопрос, для чего вы будете использовать его чаще всего. Если лазерное оборудование используется главным образом для гравировки, то лазерный станок с мощностью от 25 до 80 ватт обеспечит хорошие результаты. Для лазерной резки или работ с очень высокой скоростью рекомендуем лазерный станок мощностью более 80 ватт.
В этой статье мы постараемся как можно лучше объяснить тему «Оптимальная мощность лазерного станка». В целом, для определения оптимальной для вас мощности лазерного оборудования рекомендуем воспользоваться индивидуальной консультацией.
Свяжитесь с нами
На что влияет мощность лазерного станка в практическом плане?
Максимальная мощность вашего лазерного станка влияет как на качество ваших изделий, так и на время работы. Разницу между двумя уровнями мощности лучше всего показать на примерах. Итак, мы выгравировали алюминиевую табличку данных и вырезали логотип Trotec из акрила.
Пример 1: Резка акрила — сравнение лазерных станков на 80 и 120 ватт
При 120 ваттах резка занимает 29 секунд, при 80 ваттах за это время выполнено только 65% работы. При мощности более 120 ватт можно сэкономить еще больше времени при том же качестве.
Мощность лазерного станка | 80 Вт | 120 Вт |
Выполнено | готово на 100% | готово на 100% |
Время на 1 изделие | 55 сек | 29 сек |
Пример 2: Гравировка по анодированному алюминию — сравнение лазерных станков на 30 и 80 ватт
Лазерный станок на 80 ватт работает более, чем вдвое быстрее. То же самое применимо к другим материалам, например, к гравировке резиновых штемпелей.
Мощность лазерного станка | 30 Вт | 80 Вт |
Выполнено | готово на 48% | готово на 65% |
Время на 1 изделие | 55 сек | 29 сек |
Рекомендуемая мощность лазерного станка для различных материалов
В зависимости от типа материала для достижения оптимального результата требуется разная мощность лазера. Например, для гравировки по бумаге обычно требуется меньшая мощность, чем для гравировки по дереву. При работе с акрилом для равномерной, не слишком глубокой гравировки достаточно небольшой мощности. А при обработке специальных материалов для гравировки (таких как пластиковый ламинат TroLase) более высокая мощность позволяет ускорить работу.
Мощность лазера можно легко регулировать с помощью программного обеспечения. Однако максимальная мощность зависит от лазерного оборудования. Из чего следует: лазер высокой мощности дает большую гибкость и позволяет вам работать с разными материалами.
В таблице показаны минимальные значения мощности, необходимые для разных материалов.
Значения приблизительные. Более высокая мощность лазера, как правило, означает более высокую скорость работы и большую производительность.
Материал | Рекомендуемая мощность лазера (ватт) | |
---|---|---|
Гравировка | Гравировка и резка | |
ДВП (6 мм) | 40 | 60 |
Ламинат/пластик для гравировки (1,6 мм) | 40 | 40 |
Бумага | 25 | 40 |
Акрил (3 мм) | 30 | 40 |
Штемпель (2,3 мм) | 30 | 30 |
Анодированный алюминий | 30 | — |
Оптимальная мощность лазерного станка для резки
Чем толще материал, подлежащий резке, тем важнее иметь мощный лазерный станок, чтобы обеспечить хорошее качество. Для акрила используется следующее практическое правило: 10 ватт на миллиметр.
Сравнение времени резки листов акрила разной толщины при мощности 200 ватт и 400 ватт показано на графике.
Кроме акрила, лазерный станок может работать с другими пластиками, например, поликарбонатом или сополимером стирола и акрилонитрила. Чтобы обеспечить чистую резку этих пластиков, требуется высокая мощность, равная 200 или 400 ватт даже для сравнительно небольшой толщины в 2-3 см.
Какая мощность требуется для оптоволоконного лазерного станка?
Даже для оптоволоконного лазера при выборе мощности важно знать, для каких целей он вам нужен. Высокая мощность лазера необходима при гравировке по металлу. Для наведенной окраски и нанесения отметок необходим лазерный станок мощностью 20 или 30 ватт.
Какой из лазерных станков мне больше всего подходит?
Мы будем рады помочь вам сделать оптимальный выбор для ваших целей.
Воспользуйтесь нашим многолетним опытом, запросите консультацию, бесплатную тестовую обработку ваших материалов или демонстрацию лазерного станка.
Обращайтесь к нам
Так как индивидуальные запросы требуют индивидуальных рекомендаций!
Мы проконсультируем вас бесплатно.
Запросите 30-минутную встречу сейчас.
Связаться с нами
Параметры лазерной резки металла на волоконном лазерном станке | Основы подбора лазерного излучателя
18сен 2019
Статья содержит в себе рекомендации, параметры и настройки лазерной резки металла при помощи лазерного станка с волоконным (иттербиевым) излучателем, отличие волоконного станка от плазмы, а также рекомендации по подбору мощности излучателей относительно материала, экономические выгоды.
Для качественной и предельно точной лазерной резки металла мы рекомендуем в качестве излучателя использовать иттербиевый (волоконный) лазерный излучатель (ссылка на каталог с излучателями), более точного излучателя в современном мире не существует.
Основные отличительные черты волоконного излучателя от плазмыВолоконный излучатель | Плюсы/минусы | Плазма | Плюсы/минусы | |
1 | Ширина лазерного луча по линии резки, не более от 0,03 -1 мм.![]() | плюс | Ширина плазменного луча по линии, 1-3 мм. и более, в зависимости от толщины материала | минус |
2 | Конусность вырезанных деталей — отсутствует | плюс | Конусность вырезанных деталей, от 15-30° | минус |
3 | Резка небольших отверстий (менее 12 мм.) в материалах толщиной более 6-10 мм. | плюс | Резка небольших отверстий (менее 12 мм.) в материалах толщиной более 6-10 мм. — не возможна | минус |
4 | Детали с внешними и внутренними углами при любой толщине материала — идеальна | плюс | Детали с прямыми углами сделать не возможно.![]() | минус |
5 | При правильном подборе мощности, скорости, и давления газа, облой исключен, допонительной обработки детали не требуют | плюс | При резке образуется большое количество облоя, что требует дополнительной обработки детали шлифовальными кругами | минус |
6 | Цена на комплект станок+излучатель выше, чем на станок+плазма | минус | Стоимость станка плазма+станок значительно ниже, чем иттербиевый (волоконный) станок | плюс |
7 | Экологичность при обработке в разы выше, так как при резке волоконным излучателем меньшее сжигание металла при резки, что значительно снижает выбросы в атмосферу.![]() | плюс | Большие выхлопы угарного газа при резке+высокое потребление электроэнергии | минус |
Выше в таблице мы произвели сравнение двух видов резки металла, при помощи лазерного волоконного (иттербиевого) станка и станка плазменной резки. Выбор очевиден, если требования к товару высокие, по точности размеров отверстий и прямых углов, по однородности торца детали, без зубцов и облоя, по конусности торца, то стоит остановить свой выбор на волоконном (иттербиевом) станке.
Если нужны детали без требований точности, с допустимыми погрешностями в размерах +3-+5 мм., под сварку, то следует остановить свой выбор на плазменном станке.
Итак, чтобы подобрать волоконный (иттербиевый) излучатель, нужно определиться с толщинами металлов для лазерной резки. К примеру, если 80% материалов составляет сталь толщиной от 8-10 мм. , а 20% нержавеющая сталь и цветные металлы, то мы рекомендуем рассматривать к приобретению станок с мощностью не менее 1500 Ватт.
Излучатель с мощностью от 1,5 кВт, сможет резать сталь с адекватными параметрами скорости, что экономически будет выгодно. Сталь толщиной 8-10 мм., сможет порезать станок с мощностью 1000 Ватт, но скорость резки будет достаточно низкой (см. таблицу ниже), что влечет за собой большой расход газа и большое количество времени на обработку детали, что становится экономически не выгодно, на рынке лазерной резки.
Рассмотрим другие обстоятельства выбора излучателя, к примеру 80% материалов из стали до 6 мм., 10% времени материалы из металла 8-10 мм., при таких обстоятельствах, в целях экономии, выгодно приобрести лазерный станок с максимальной мощностью 1000 Ватт, потому что скорость обработки металла на станке с мощностью 1 кВт., достаточно высокая на толщинах до 6 мм., а 10% рабочего времени, как факультатив, можно резать и 8, и 10 мм., для более подробного анализа, можно воспользоваться таблицей данных скоростных характеристик ниже.
Таблица скорости реза металла
Мощность источника | 500Вт | 750Вт | 1000Вт | 1500Вт | 2000Вт | 3000Вт | 4000Вт | 6000Вт | 8000Вт | 10000Вт | ||
Материал / Газ | Толщина, мм | Размер сопла, мм. | Скорость, м/мин | |||||||||
Углеродистая (Кислород) | 1 | 1.2 | 8 | 9 | 10 | 22 | 26 | 34 | 38 | 42 | 46 | 50 |
2 | 1.5 | 4 | 5 | 6,2 | 6,8 | 7,2 | 7,5 | 7,8 | 8,2 | 36 | 9 | |
3 | 2.0 | 2,6 | 2,8 | 3 | 3,6 | 4 | 4,4 | 5 | 5,5 | 6 | 6.![]() | |
4 | 2.0 | 1,6 | 1,8 | 2,2 | 2,8 | 3,2 | 3,8 | 4,4 | 5 | 5.5 | 6.1 | |
5 | 2.0 | 1 | 1,4 | 1,8 | 2,4 | 2,8 | 3,2 | 3,4 | 3,6 | 3.8 | 4.2 | |
6 | 2.5 | 1 | 1,6 | 2 | 2,4 | 2,8 | 3,2 | 3,4 | 3.6 | 4.![]() | ||
8 | 2.5 | 0,8 | 1,2 | 1,4 | 1,6 | 2,2 | 2,6 | 3 | 3.3 | 3.5 | ||
10 | 2.5 | 0,7 | 1 | 1,2 | 1,6 | 2 | 2,4 | 2.8 | 3.2 | |||
12 | 3 | 0,6 | 0,8 | 1 | 1,4 | 1,8 | 2 | 2.2 | 2.4 | |||
14 | 3 | 0,6 | 0,9 | 1 | 1,2 | 1,3 | 1.![]() | 1.6 | ||||
16 | 4 | 0,5 | 0,8 | 0,8 | 1 | 1,1 | 1.3 | 1.4 | ||||
18 | 4 | 0,7 | 0,7 | 0,9 | 1 | 1.2 | 1.3 | |||||
20 | 4 | 0,6 | 0,8 | 0,9 | 1.1 | 1.35 | ||||||
22 | 4 | 0,5 | 0,7 | 0,8 | 1 | 1.![]() | ||||||
24 | 4 | 0,4 | 0,6 | 0.8 | 0.9 | |||||||
26 | 5 | 0.5 | 0.65 |
Мощность источника | 500Вт | 750Вт | 1000Вт | 1500Вт | 2000Вт | 3000Вт | 4000Вт | 6000Вт | 8000Вт | 10000Вт толщина до 40 мм. | ||
Нержавеющая (Азот) | 1 | 1.5 | 12,4 | 18,5 | 23,8 | 26,4 | 30 | 34 | 38 | 41,4 | 57 | 65 |
2 | 1.5 | 4,7 | 5,1 | 10,8 | 11,9 | 12,7 | 15,4 | 24,4 | 28,6 | 38 | 58 | |
3 | 1.5 | 0,7 | 1,2 | 2,3 | 4,1 | 6,1 | 8,6 | 12,8 | 15,8 | 22 | 30 | |
4 | 1.![]() | 0,8 | 1,3 | 2,2 | 4,2 | 5,5 | 7,4 | 9,4 | 16 | 22 | ||
5 | 1.5 | 0,7 | 1,2 | 2 | 4,3 | 5,1 | 6 | 11 | 17 | |||
6 | 1.5 | 1 | 1,8 | 3,1 | 3,8 | 4,7 | 5 | 15 | ||||
8 | 1.5 | 0,9 | 2 | 2,4 | 3,3 | 3.![]() | 8.5 | |||||
10 | 1.5 | 0,8 | 1,1 | 1,3 | 1.9 | 5.9 | ||||||
12 | 1.5 | 0,5 | 0,7 | 1,1 | 1.5 | 3.4 | ||||||
14 | 1.5 | 0,6 | 0,8 | 1.1 | 2.3 | |||||||
16 | 1.5 | 0,6 | 0. | 1.6 | ||||||||
Мощность источника | 500Вт | 750Вт | 1000Вт | 1500Вт | 2000Вт | 3000Вт | 4000Вт | 6000Вт | 8000Вт | 10000Вт | ||
Алюминий (Азот) | 1 | 1.5 | 5,2 | 6,4 | 8,4 | 16 | 22 | 34 | 38 | 42 | 57 | нет данных |
2 | 1.![]() | 2,2 | 3,4 | 6,6 | 8,4 | 15 | 21 | 25,5 | 38 | нет данных | ||
3 | 1.5 | 1,4 | 3,8 | 5,5 | 7,6 | 11,5 | 14,6 | 22 | нет данных | |||
4 | 1.5 | 1,4 | 2,6 | 4 | 5,2 | 5,8 | 16 | нет данных | ||||
5 | 1.5 | 1,7 | 3,3 | 4,4 | 4,9 | 11 | нет данных | |||||
6 | 1.![]() | 0,9 | 2,1 | 3,4 | 4,1 | 7 | нет данных | |||||
8 | 1.5 | 0,9 | 1,3 | 2 | 3.6 | нет данных | ||||||
10 | 1.5 | 0,6 | 1,1 | 1,7 | 2.5 | нет данных | ||||||
12 | 1.5 | 0,5 | 0,8 | 1.![]() | нет данных | |||||||
14 | 1.5 | 0,4 | 0,6 | 1.1 | нет данных | |||||||
16 | 1.5 | 0,5 | 0.9 | нет данных | ||||||||
Мощность источника | 500Вт | 750Вт | 1000Вт | 1500Вт | 2000Вт | 3000Вт | 4000Вт | 6000Вт | 8000Вт | 10000Вт | ||
Медь (Азот) | 1 | 1. | 5,2 | 6 | 8 | 12 | 14 | 22 | 26 | 32 | 57 | нет данных |
2 | 1.5 | 1,8 | 3,2 | 4 | 6 | 8 | 10 | 12 | 38 | нет данных | ||
3 | 1.5 | 1 | 2,2 | 3,4 | 5,2 | 6 | 6,4 | 22 | нет данных | |||
4 | 1. | 1,4 | 1,8 | 4 | 4,8 | 5,4 | 16 | нет данных | ||||
5 | 1.5 | 1,2 | 1,8 | 2,6 | 3,2 | 11 | нет данных | |||||
6 | 1.5 | 0,6 | 1,4 | 1,8 | 2,2 | 7 | нет данных | |||||
8 | 1. | 0,6 | 0,9 | 1,2 | 3.6 | нет данных | ||||||
10 | 1.5 | 0,4 | 0,6 | 2.5 | нет данных | |||||||
12 | 1.5 | 0,4 | 1. | нет данных |
Рекомендуемые товары
Для волоконного лазерного станка Чиллер CWFL-500 Мощность компрессора, кВт — 0.8 Охлаждающая способность, кВт — 2.33
От 168 200
Заказать консультациюМы готовы проконсультировать и подобрать подходящий лазерный станок, который будет отвечать вашим бизнес задачам. Это поможет сэкономить на покупке и на обслуживании станка.
Ваш телефон
Основы лазерной резки — знания, которые вам пригодятся
Лазеры впервые были использованы для резки в 1970-х годах.
В современном промышленном производстве лазерная резка более широко применяется в обработке листового металла, пластмасс, стекла, керамики, полупроводников и таких материалов, как текстиль, дерево и бумага.
В ближайшие несколько лет применение лазерной резки в прецизионной обработке и микрообработке также получит значительный рост.
Во-первых, давайте посмотрим, как работает лазерная резка.
Когда сфокусированный лазерный луч попадает на заготовку, область облучения быстро нагревается, расплавляя или испаряя материал.
Как только лазерный луч проникает в заготовку, начинается процесс резки: лазерный луч движется по контуру и расплавляет материал.
Обычно для удаления расплава из разреза используется струйный поток, оставляя узкий зазор между режущей частью и рамой.
Узкие швы получаются почти такой же ширины, как и сфокусированный лазерный луч.
Примечание: данная статья является переводом
Газовая резка
Газовая резка — это стандартная техника, используемая для резки низкоуглеродистой стали. В качестве режущего газа используется кислород.
Перед вдуванием в разрез давление кислорода повышается до 6 бар. Там нагретый металл вступает в реакцию с кислородом: он начинает гореть и окисляться.
В результате химической реакции высвобождается большое количество энергии (в пять раз больше энергии лазера).
Рис.1 Лазерный луч плавит заготовку, а режущий газ сдувает расплавленный материал и шлак в зоне разреза
Резка плавлением
Резка плавлением — это еще один стандартный процесс, используемый при резке металла, который также может применяться для резки других легкоплавких материалов, например, керамики.
В качестве газа для резки используется азот или аргон, а воздух под давлением 2-20 бар продувается через разрез.
Аргон и азот являются инертными газами, что означает, что они не вступают в реакцию с расплавленным металлом в надрезе, а просто выдувают его на дно.
Между тем, инертный газ может защитить режущую кромку от окисления воздухом.
Резка сжатым воздухом
Сжатый воздух также можно использовать для резки тонких листов.
Давления воздуха, увеличенного до 5-6 бар, достаточно, чтобы сдуть расплавленный металл в разрезе.
Поскольку почти 80% воздуха — это азот, резка сжатым воздухом — это, по сути, резка плавлением.
Плазменная резка
Если параметры выбраны правильно, то в разрезе плазменной резки с применением плазменного наплавления появляются плазменные облака.
Плазменное облако состоит из ионизированного пара металла и ионизированного газа для резки.
Плазменное облако поглощает энергию CO2-лазера и переводит ее в заготовку, позволяя соединить больше энергии с заготовкой, что позволяет быстрее плавить металл и ускоряет процесс резки.
Поэтому процесс резки также называют высокоскоростной плазменной резкой.
Плазменное облако фактически прозрачно для твердого лазера, поэтому плазменная резка может использоваться только при лазерной резке CO2.
Газифицирующая резка
Газифицирующая резка испаряет материал и минимизирует тепловое воздействие на окружающий материал.
Использование непрерывной обработки CO2-лазером для испарения материалов с низким тепловыделением и высоким поглощением позволяет достичь вышеуказанных эффектов, например, тонкой пластиковой пленки и неплавящихся материалов, таких как дерево, бумага и пенопласт.
Ультракороткоимпульсный лазер позволяет применить эту технику к другим материалам.
Свободные электроны в металле поглощают лазер и резко нагреваются.
Лазерный импульс не вступает в реакцию с расплавленными частицами и плазмой, и материал сублимируется напрямую, не успевая передать энергию окружающему материалу в виде тепла.
В материале для пикосекундной импульсной абляции нет явного теплового эффекта, нет плавления и образования заусенцев.
Рис.3 Газификационная резка: лазер заставляет материал испаряться и гореть. Давление пара вытягивает шлак из разреза
На процесс лазерной резки влияют многие параметры, некоторые из которых зависят от технических характеристик лазерного генератора и станка для лазерной резки, а другие варьируются.
Степень поляризации
Степень поляризации показывает, какой процент лазера преобразуется.
Типичная степень поляризации составляет около 90%. Этого достаточно для высококачественной резки.
Диаметр фокусировки
Диаметр фокуса влияет на ширину разреза и может изменяться путем изменения фокусного расстояния фокусирующей линзы. Меньший диаметр фокуса означает более узкие разрезы.
Фокусное положение
Рис. 4 Положение фокуса: внутри, на поверхности и на восходящей стороне заготовки.
Мощность лазера
Мощность лазера должна соответствовать ьипу обработки, а также типу и толщине материала.
Мощность должна быть достаточно высокой, чтобы плотность мощности на заготовке превышала порог обработки.
Рис.5 Более высокая мощность лазера позволяет резать более толстый материал
Рабочий режим
Непрерывный режим в основном используется для резки стандартного контура металла и пластика толщиной от миллиметра до сантиметра.
Для выплавки отверстий или получения точных контуров используются низкочастотные импульсные лазеры.
Скорость резки
Мощность лазера и скорость резки должны соответствовать друг другу. Слишком высокая или слишком низкая скорость резки может привести к увеличению шероховатости и образованию грата.
Рис. 6 Скорость резания уменьшается с увеличением толщины пластины
Диаметр сопла
Диаметр сопла определяет форму потока газа и воздушного потока из сопла.
Чем толще материал, тем больше диаметр газовой струи и, соответственно, больше диаметр отверстия сопла.
Чистота и давление газа
Кислород и азот часто используются в качестве газов для резки.
Чистота и давление газа влияют на эффект резки.
При резке кислородным пламенем чистота газа составляет 99,95 %.
Чем толще стальной лист, тем ниже давление газа.
При резке азотом чистота газа должна достигать 99,995 % (в идеале 99,999 %), что требует более высокого давления при плавлении и резке толстых стальных листов.
Технические параметры
На ранней стадии лазерной резки пользователь должен определить настройки параметров обработки путем пробной операции.
Теперь необходимые параметры обработки хранятся в управляющем устройстве системы резки.
Для каждого типа и толщины материала имеются соответствующие данные.
Технические параметры позволяют людям, не знакомым с технологией, беспрепятственно управлять оборудованием для лазерной резки.
Оценка качества резки
Существует множество критериев для определения качества кромок лазерной резки.
Например, стандарт формы грата, провисания и зернистости можно оценить невооруженным глазом.
Прямолинейность, шероховатость и ширина надреза должны быть измерены специальными приборами.
Осаждение материала, коррозия, область термического воздействия и деформация являются важными факторами для измерения качества лазерной резки.
Рис.7
Перспективы в будущем
Непрерывный успех лазерной резки находится за пределами досягаемости большинства других методов. Эта тенденция продолжается и сегодня. В будущем применение лазерной резки будет становиться все более и более перспективным.
Какой толщины металл можно резать лазером?
Лазерная резка — невероятно полезная разработка, возникшая за последние полвека. Лазерная резка, излучающая чрезвычайно высокую температуру невероятно узким потоком, позволяет производителям и сварщикам вырезать из металла нестандартные детали и детали с предельной точностью. Как и многие другие технологии, она способствует повышению надежности и надежности многих деталей современных машин.
Конечно, как и все технологии, лазерная резка является постоянно развивающейся областью, а это означает, что она никогда не бывает идеальной. Всегда есть препятствия, которые нужно преодолеть, и ограничения, которые нужно преодолеть. Когда дело доходит до лазерной резки толстой стали, эти ограничения проявляются в первую очередь в таких факторах, как материалы, которые можно резать, мощность лазеров и, как следствие, максимальная толщина металла, с которой могут работать лазеры.
Какие металлы можно резать лазером?
Лазеры могут резать многие материалы и обычно используются для обработки нескольких избранных типов металлов, в частности, углеродистой стали, мягкой стали, нержавеющей стали, стальных сплавов и алюминия.
Углеродистая сталь: Сталь представляет собой смесь железа и углерода. Углеродистая сталь – это сталь с особенно высоким содержанием углерода.
Мягкая сталь: Мягкая сталь имеет более низкую концентрацию углерода по сравнению с углеродистой сталью.
Нержавеющая сталь: Нержавеющая сталь содержит небольшое количество хрома для придания устойчивости к коррозии.
Другие стальные сплавы: Легированная сталь связана с одним или несколькими другими элементами для ее усиления.
Алюминий: Алюминиевые материалы удобны тем, что они легче стальных.
Помимо этих металлов, лазеры могут использоваться для резки многих неметаллических материалов, от дерева до пластика и керамики. Однако чаще всего его используют для резки металла, в частности перечисленных выше.
Какую максимальную толщину может резать лазер?
Кажется достаточно простым запросить единый максимальный предел толщины для всех лазерных резаков, но все гораздо сложнее. Многие переменные влияют на то, как лазер прорезает кусок металла, поэтому максимальная толщина лазерной резки зависит, среди прочего, от конкретного лазера и используемого материала.
Чтобы назвать конкретное число, мы можем соединить лазер высокой мощности — 6000 Вт — с таким металлом, как нержавеющая сталь. В этом случае максимальная толщина лазерной резки обычно составляет около 2,75 дюйма.
Но эта толщина зависит от этих конкретных переменных. Тот же лазер в сочетании с углеродистой сталью, вероятно, мог обрабатывать только до 1 5/8 дюйма, в то время как лазер мощностью 4000 Вт мог проникать только в 1 дюйм нержавеющей стали.
Максимальная толщина значительно возрастет для неметаллических материалов, таких как дерево и пластик, поскольку они гораздо менее плотные и прочные, чем сталь или алюминий.
Мощность лазерной резки в зависимости от материала
При рассмотрении максимальной толщины лазерной резки необходимо проанализировать два фактора, в частности, — мощность лазера и материал. Лазер одной мощности не сможет прорезать такой же толстый материал, как лазер другой мощности. Точно так же один и тот же лазер не сможет прорезать углеродистую сталь той же толщины, что и алюминий.
Наиболее часто встречаются лазеры мощностью 3500, 4000 и 6000 ватт. Лазеры мощностью 6000 Вт отлично подходят для резки особо толстых или прочных металлов, хотя во многих случаях более низкой мощности более чем достаточно для выполнения работы.
Прочность материала
Прочность данного металла может варьироваться в зависимости от таких факторов, как соотношение различных элементов в сплаве, но по-прежнему существует тенденция к тому, чтобы одни типы металлов были прочнее или слабее других. Вот краткий обзор того, как ранее упомянутые материалы сочетаются друг с другом, от самых сложных до самых простых для резки.
Углеродистая сталь: Большое количество углерода придает металлу дополнительный слой прочности.
Мягкая сталь: Поскольку содержание углерода ниже, чем в углеродистой стали, мягкая сталь легче режется. Однако готовые изделия из мягкой стали, несмотря на то, что их легче резать, прочнее и эластичнее, чем изделия с большим содержанием углерода.
Нержавеющая сталь: Присутствие хрома борется с ржавчиной и часто делает материал менее пластичным и трудным для резки. Однако он не имеет такого же эффекта, как углерод.
Алюминий: Алюминий, как правило, очень пластичный материал, как известно любому, кто имеет дело с алюминиевой фольгой. Это редко оказывается серьезной проблемой для лазеров.
Неметаллические материалы: Неудивительно, что в конце списка находятся такие материалы, как дерево, пластик и керамика, которые обладают гораздо меньшей прочностью, чем металл.
Другие стальные сплавы также могут появляться в разных местах списка, в зависимости от конкретного сплава и соотношения включенных элементов. Опять же, ни один из этих рейтингов не является окончательным, поскольку они могут варьироваться от случая к случаю в зависимости от структуры конкретного металла. Например, один тип нержавеющей стали может быть намного мягче другого. Но приведенный выше список может помочь дать представление о том, как часто обстоят дела.
Скорость резки
Также стоит учитывать скорость. Лазеры с более высокой режущей способностью могут прорезать большую толщину, но они также могут прорезать меньшую толщину за меньшее время. Точно так же лазер может прорезать более слабые материалы быстрее, чем более прочные. Иногда это может повысить ценность использования лазера высокой мощности, даже если вы не имеете дело с особенно толстым или прочным металлом.
Однако на скорость также влияет использование газа в процессе. Металл нельзя просто небрежно прорезать, так как это оставит заусенцы и другие несоответствия на кромках реза. По мере выполнения разрезов газ должен подаваться под высоким давлением, чтобы сгладить эти проблемы. Например, в нержавеющей стали используется азот, а в углеродистой стали — кислород. Тип газа и время, необходимое для его правильного применения, могут повлиять на скорость процесса, что является еще одним способом, которым процесс зависит от разрезаемого материала.
Принимая решение о том, какая мощность лазерного резака вам нужна, вы должны сопоставить эти факторы друг с другом, а также с тем, для чего вам нужен лазер. Возможно, вам не понадобится самый мощный лазер для определенной работы.
Свяжитесь с APX York Sheet Metal для прецизионной лазерной резки
Если вы ищете место, где ваши металлические детали могут быть вырезаны с точностью лазера, обратите внимание на APX York Sheet Metal. Наше производство листового металла отличается высоким качеством и надежностью, и мы выполняем всю нашу работу собственными силами — без привлечения других предприятий. Наш процесс начинается с лазерной резки, а затем проходит гибку, вставку, сварку, шлифовку и покраску, прежде чем производить необходимую вам готовую продукцию.
Вы можете рассчитывать на то, что мы используем первоклассное оборудование для выполнения работы, поэтому вы получаете детали самого высокого качества. Чтобы начать, просто свяжитесь с нами сегодня!
Лазерная резка металла: Руководство эксперта [2022]
Лазерная резка — это эффективный способ высокоточной и сложной резки металла.
Несмотря на высокую плотность и прочность металлов, соответствующий лазер может прорезать их, практически мгновенно испаряя.
Однако способность лазера выполнять чистые разрезы с минимальным временем цикла напрямую зависит от толщины и типа металла.
В то время как некоторые металлы можно резать с чистой кромкой, другие могут создавать проблемы, из-за которых их трудно резать лазером.
В этой статье представлено полное руководство по лазерной резке металла и обсуждаются проблемы, которых следует опасаться во время процесса.
Что в этой статье?
- Лазерная резка металла
- Как резать металл лазером
- Лазерная гравировка металла
- Преимущества лазерной резки металла
- Проблемы лазерной резки металла
- Лучшие лазерные резаки для металлов
- Лазерные онлайн-сервисы для резки металла
- Заключение
- Направляющие для лазерной резки различных материалов
- Часто задаваемые вопросы (FAQ)
Лазерный резак с номинальной мощностью в несколько киловатт (1-12 кВт) рекомендуется для промышленной резки листового металла. Однако лазер мощностью 500 Вт можно использовать для резки тонких металлических заготовок в малосерийных проектах. Лазерная резка — это быстрый и эффективный способ получения чистых резов в тонких металлических листах.
Лазерная резка металла
Лазерная резка мягкой стали (Источник: Kernlasers)Лазерная резка использует высокоэнергетический лазерный луч для сжигания, плавления и испарения металла для получения желаемого разреза.
Лазер проходит через фокусирующую линзу, которая сводит его в узкий пучок, тем самым увеличивая плотность энергии лазера.
Этот концентрированный лазер нагревает поверхность металла и поднимает температуру до достаточной для выполнения резки.
Металлы обычно более плотные, чем неметаллы, и для испарения материала с поверхности требуется более мощный лазер, что увеличивает стоимость оборудования для лазерной резки.
Однако способность лазера нагревать металл и производить разрез зависит от типа используемого лазера.
Длина волны волоконного лазера (1060 нм) легко поглощается металлами, поэтому он считается лучшим вариантом для лазерной резки листового металла.
В то время как лазеры CO 2 имеют длину волны 10 600 нм, которая плохо поглощается металлами, и значительная часть энергии теряется на отражение.
В результате металлом поглощается только часть лазерной энергии, которой недостаточно для повышения температуры, достаточной для испарения металла.
Тем не менее, мощные CO 2 лазеры с высокой частотой способны выполнять лазерную резку металла, поскольку лазерные лучи достигают поверхности металла с чрезвычайно высокой скоростью, чтобы компенсировать потерю энергии при отражении.
При сравнении волоконных лазеров с лазерами CO 2 волоконные лазеры лучше подходят для обработки металлов из-за их высокой скорости поглощения и лучшей способности резать, маркировать и гравировать металлические поверхности.
Кроме того, диодные лазеры с длиной волны 450-950 нм также подходят для резки металла, но низкая выходная мощность диодных лазеров ограничивает их использование в металлургической промышленности.
Хотя недавние разработки представили мощные промышленные диодные лазеры, которые могут выполнять чистые разрезы в металлах, технология является относительно новой и не всегда доступна.
При сравнении волоконных лазеров с диодными лазерами волоконные лазеры легко доступны в вариантах с большей мощностью, что делает их лучшим выбором для операций резки металла.
Таким образом, волоконные лазеры, за которыми следуют мощные CO-лазеры 2 , являются предпочтительным выбором лазеров для приложений, связанных с резкой металлов.
Лазерная резка металла
Лазерная резка миниатюрного металлического велосипеда (Источник: Kernlasers)Лазерная резка металла обычно дает высококачественные результаты с чистыми краями, которые не требуют вторичной обработки.
Однако отражающая природа и высокая плотность металлов делают их одним из самых сложных материалов для резки лазером.
Чтобы решить эти проблемы, вы должны использовать соответствующий лазер с оптимальными настройками для разрезаемого металла.
Кроме того, отражающая природа металлов может представлять опасность для лазера, поскольку рассеянное лазерное излучение может попасть в глаза оператора и вызвать серьезное повреждение.
Поэтому настоятельно рекомендуется носить подходящие защитные очки для работы с лазером, следовать протоколу безопасности при работе с лазером и обеспечивать надлежащий контроль процесса для выполнения безопасной и успешной резки металла.
Подготовка дизайна для лазерной резки металла
Подготовка дизайна в LightBurnПроект состоит из цифрового файла, представляющего необходимый разрез в графической форме.
При подготовке дизайна всегда рекомендуется, чтобы толщина каждого элемента дизайна была больше толщины заготовки.
Обеспечивает структурную целостность конструкции и предотвращает ее рассыпание.
Кроме того, рекомендуется установить порядок вырезов таким образом, чтобы элементы дизайна, расположенные близко друг к другу, не вырезались последовательно.
Уменьшает зону термического влияния на определенном участке и предотвращает перегрев металла.
Существует различное бесплатное и платное программное обеспечение для лазерной резки, которое можно использовать для подготовки дизайна (CAD), преобразования дизайна в G-код (CAM) и взаимодействия с лазерным резаком для установки параметров лазера.
Установка параметров для лазерной резки металла
Оптимальные параметры для лазерной резки варьируются от одного металла к другому.
Поэтому важно установить оптимальные параметры в соответствии с используемым металлом и поддерживать хороший контроль процесса для получения чистых резов с высоким качеством поверхности.
Parameter | Recommendation |
---|---|
Type of Laser | Fiber laser or high powered CO 2 laser |
Laser Power | Above 500W |
Cutting Speed | Slow cutting скорость |
Вспомогательный газ | Кислород для более высокой скорости резки, Азот для более чистого реза |
Выхлопная система | Рекомендуется |
Лазерный фокус | Наименьший размер пятна для высокой концентрации энергии |
Рекомендуемые параметры для лазерной резки металлов
Тип металла
Лазерная резка — это универсальный метод резки различных металлов.
Однако некоторые металлы, такие как алюминий, латунь, медь, серебро и золото, обладают большей отражательной способностью, чем другие, что затрудняет их лазерную резку.
Эти металлы требуют более высокой мощности лазера, чем другие металлы, и специального оборудования для определения количества отраженного лазера, попадающего в лазерную головку, поскольку это может повредить лазерное оборудование.
Мощность лазера для резки металла
Мощность — один из важнейших параметров лазера, определяющий способность лазера резать различные материалы.
Чем выше мощность, тем выше способность лазера выполнять чистые разрезы в различных металлах.
Как правило, для эффективной лазерной резки металлов рекомендуется мощность лазера в несколько киловатт.
Промышленные лазерные станки для резки металла, подходящие для крупных предприятий, могут иметь мощность лазера от 3 до 12 кВт.
Однако волоконный лазер с номинальной мощностью более 500 Вт может помочь вам начать лазерную резку тонких металлических листов за несколько проходов.
Импульсный CO-лазер 2 с номинальной мощностью более 500 Вт может генерировать высокоэнергетические лазерные импульсы мощностью, эквивалентной нескольким киловаттам.
Таким образом, высокочастотный импульсный CO-лазер 2 может использоваться для лазерной резки определенных металлов с гораздо меньшей скоростью, чем волоконный лазер того же калибра.
Однако при лазерной резке металлов с высокой отражающей способностью предпочтительным выбором лазера является волоконный лазер из-за его высокой совместимости с металлами по поглощению энергии.
Высокая отражательная способность золота и серебра затрудняет их резку даже с помощью импульсного лазера CO 2 или стандартного волоконного лазера.
Поэтому импульсный волоконный лазер используется для резки/гравировки золота и серебра для изготовления ювелирных изделий.
Подпишитесь на Mellowpine Lasers, чтобы получать еженедельные видеоролики о лазерной резке и гравировкеСкорость лазерной резки металла
Скорость лазерной резки зависит от двух основных факторов: мощности лазера и толщины материала.
Мощный лазер может резать относительно более толстые металлы, но он также может выполнять резку тонких металлических листов с более высокой скоростью.
Чем выше мощность лазера, тем быстрее он сможет прорезать тонкую заготовку.
Кроме того, для резки толстого металла требуется больше энергии лазера. В результате скорость резки лазера уменьшается по мере увеличения толщины металла.
Замедление процесса резки увеличивает время выдержки лазера, что, в свою очередь, увеличивает количество энергии, поглощаемой металлом, и выделяет больше тепла для его испарения.
Как правило, волоконные лазеры могут прорезать тонкие металлы с большей скоростью, чем CO-лазер 2 , но по мере увеличения толщины металла способность CO-лазеров 2 прорезать металл увеличивается.
Поэтому лазеры CO 2 рекомендуются для резки толстых металлов (более 0,3 дюйма для нержавеющей стали и более 0,5 дюйма для мягкой стали).
Чистота поверхности резки, выполненной лазером CO 2 и волоконным лазером (Источник: автоматизация Espirit) Конфигурации мощности и скорости для различных толщин некоторых из наиболее часто используемых лазером металлов приведены в таблице ниже.
Материал (толщина в дюймах) | 6 кВт волоконно -волоконно0236 | 450 | 200 |
---|---|---|---|
Aluminum (0.20) | 150 | 80 | |
Mild Steel (0.20) | 165 | 150 | |
Stainless Steel (0.20) | 236 | 106 | |
Mild Steel (0.40) | 80 | 75 | |
Stainless Steel (0.40) | 51 | 60 |
Cutting speed of a 6kW fiber and CO 2 лазер для различных металлов
Помимо демонстрации скорости резки различных металлов, в таблице также показано снижение скорости резки алюминия по сравнению с другими металлами с меньшей отражающей способностью.
Вспомогательный газ
Вспомогательный газ играет жизненно важную роль в лазерной резке металлов.
Направляет поток сжатого газа в зону резки и защищает фокусирующую линзу от осколков горячего расплавленного металла, сохраняя при этом температуру под контролем.
Вспомогательный газ также выдувает расплавленный металл из пропила и повышает скорость и качество резки.
Новые технологии форсунок, такие как сенсорная форсунка, улучшают подачу вспомогательного газа и повышают производительность.
Сокращает потери вспомогательного газа и обеспечивает более чистый рез с более высокой скоростью резки.
Сенсорное сопло (Источник: Air Liquide)Как правило, для лазерной резки металла используются три типа вспомогательных газов: кислород, азот и воздух.
Воздух – самый дешевый вспомогательный газ, способный защитить фокусирующую линзу от повреждений, но не оказывающий существенного влияния на качество лазерной резки металла.
Кислород повышает скорость резки, так как способствует сгоранию и ускоряет испарение металла.
Однако окислительные свойства кислорода могут привести к образованию оксидного слоя, что снижает качество реза и может потребовать финишной обработки заготовки шлифованием, шлифовкой и т. д.
Это свойство делает его непригодным для лазерной резки высокореактивных металлов, такие как алюминий и медь, которые легко реагируют с кислородом.
В отличие от кислорода азот не облегчает процесс горения, но повышает качество реза, выдувая расплавленный металл из пропила, не окисляя металл.
Сравнение качества кромки (Источник: Kernlasers)Азотная добавка обеспечивает наилучшее качество резки и может использоваться для всех металлов, но более низкая стоимость кислорода делает его популярным выбором для лазерной резки металлов, таких как мягкая сталь, которые менее подвержен окислению.
Выхлопная система
Лазерная резка включает сжигание и плавление материала, в результате чего образуется дым.
В то время как некоторые металлы выделяют минимальное количество дыма при лазерной резке, другие выделяют сильный дым.
Тем не менее, этот дым может быть вреден для оператора, так как вызывает тошноту и раздражение легких.
Этот дым также может влиять на качество резки, рассеивая лазер и снижая его способность испарять металл.
Поэтому настоятельно рекомендуется использовать хорошую вытяжную систему для надлежащего удаления вредных паров от оператора и заготовки.
Лазерный фокус
Влияние расфокусированного лазера на размер пятнаЛазерный фокус играет важную роль в получении качественного реза, так как напрямую влияет на ширину пропила и зону термического влияния.
Как правило, фокусировка лазера на поверхности металла дает наилучшие результаты, но при резке толстого металла рекомендуется расфокусировать лазер и установить новый фокус на 1/3 толщины заготовки.
Луч волоконных лазеров может быть собран в более тонкое пятно, чем CO 2 лазеров, что приводит к более высокой плотности энергии лазера и более тонким резкам.
Однако более мелкая резка уменьшает ширину пропила, что затрудняет выдувание расплавленного металла вспомогательным газом из узкого пропила.
Следовательно, для резки металла волоконным лазером требуется более высокое давление вспомогательного газа, чем CO 2 лазер.
Это увеличивает количество газа, используемого в процессе, и приводит к более высоким эксплуатационным затратам на волоконный лазер, чем на CO 2 лазер.
Помимо фокусировки лазера, регулировка системы подачи луча также играет решающую роль в получении чистого реза.
Смещение лазера может привести к увеличению размера пятна. Это увеличивает околошовную зону и ухудшает качество реза за счет перегрева металла.
Эффект несоосности лазера (Источник: автоматизация Espirit) Исправление несоосности в лазерах CO 2 является более сложной задачей, поскольку система доставки луча состоит как минимум из трех зеркал, которые необходимо точно выровнять.
Выполнение тестовых прогонов для лазерной резки металла
Оптимальные параметры лазера для лазерной резки металлов варьируются от одной установки к другой.
Поэтому всегда рекомендуется выполнять пробные прогоны на заготовке из того же металла, прежде чем приступать к фактической резке заготовки.
Тестовые прогоны помогают понять поведение материала при обработке лазером и найти наилучшее сочетание мощности, скорости и фокусировки лазера для получения желаемого разреза.
Некоторые металлические детали могут стоить очень дорого. Улучшение результатов путем выполнения тестовых прогонов сводит к минимуму вероятность ошибки и помогает получить идеальные результаты на реальной заготовке.
Выполнение резки
После выбора соответствующего лазера и выполнения пробных запусков можно приступать к резке.
Настоятельно рекомендуется следить за процессом лазерной резки и следить за любым нежелательным поведением процесса, чтобы предотвратить несчастные случаи.
Хотя металлическая заготовка с меньшей вероятностью загорится, отраженные лазеры могут вызвать пожар, отражаясь от поверхности и вступая в контакт с горючим материалом.
Поэтому рекомендуется хранить дополнительные газовые баллоны вдали от лазерного резака, желательно в огнеупорном контейнере.
После завершения процесса резки осмотрите заготовку на наличие острых краев и выполните чистовую обработку, например, шлифование, чтобы улучшить чистоту поверхности реза.
Лазерная гравировка металла
Лазерная гравировка алюминия (Источник: Kernlasers)Помимо выполнения сквозных разрезов, лазерный резак также может использоваться для гравировки металлических поверхностей.
Основное различие между лазерным резаком и лазерным гравером заключается в максимальной глубине реза, которую он может сделать в материале.
Как правило, хороший лазерный гравер по металлу может удалить материал с поверхности металлической заготовки на максимальную глубину около 0,01 дюйма (~0,25 мм).
Хотя принцип лазерной гравировки аналогичен процессу резки, существуют некоторые различия между параметрами
Тип лазера
Лазерная гравировка обычно требует меньшей мощности лазера по сравнению с лазерной резкой, и волоконный лазер лучше всего подходит для лазерной гравировки металлов
Кроме того, волоконный лазер MOPA может выполнять цветную гравировку на таких металлах, как алюминий, нержавеющая сталь и титан.
Образцы цветной лазерной гравировки (Источник: Trotec)Хотя мощный углекислотный лазер 2 может выполнять сквозную резку, его не рекомендуется использовать для маркировки или гравировки металла.
Энергия диодного лазера легко поглощается металлами, что делает их подходящими для лазерной гравировки металлов.
Однако низкая мощность диодных лазеров больше подходит для лазерной гравировки анодированного алюминия и других специальных металлов, таких как латунь, поддающаяся лазерному гравированию.
Лазер CO 2 можно использовать для лазерного травления металлов путем нанесения чернил для лазерной маркировки на поверхность гравируемого металла.
Подача воздуха
Подача воздуха используется для выдувания расплавленного металла из пропила, что повышает скорость и качество резки.
Использование газообразного кислорода увеличивает скорость резки, но может привести к плохому качеству поверхности из-за чрезмерного тепловыделения.
С другой стороны, считается, что азот обеспечивает более холодный рез при одновременном повышении скорости резки за счет выдувания расплавленного металла из пропила.
Поэтому для лазерной гравировки металла рекомендуется использовать азотную добавку, поскольку она обеспечивает чистый срез с высоким качеством поверхности.
Однако это может привести к разбрызгиванию расплавленного металла по поверхности гравировки.
Это напыление ухудшает качество гравировки и требует финишной обработки шлифованием или чисткой щеткой для очистки выгравированной поверхности.
Лазерный фокус
При лазерной гравировке металла рекомендуется соблюдать небольшой размер пятна, так как это позволяет выполнять сложные гравировки с хорошим качеством поверхности.
Однако при гравировке криволинейных поверхностей рекомендуется определить самый низкий и самый высокий края заготовки и отрегулировать фокус лазера так, чтобы фокус находился посередине расстояния между двумя краями.
Кроме того, если вам необходимо часто гравировать криволинейные поверхности, рекомендуется использовать вращающуюся насадку.
Ротационная гравировка нержавеющей стали (Источник: Kernlasers)Преимущества лазерной резки металла
Лазерная резка предлагает различные преимущества по сравнению с традиционными методами резки металла, что повышает ее популярность в сфере обработки листового металла.
Бесконтактный процесс
Лазерная резка — это бесконтактный процесс, при котором высокоэнергетический лазер прожигает, плавит и испаряет металлическую поверхность для получения желаемого разреза.
Это устраняет риск нежелательного механического напряжения в заготовке.
Кроме того, при традиционных методах резания к металлу прикладывается большая сила резания, что требует надежного зажима заготовки.
Этот зажим может вызвать нежелательное напряжение и деформировать заготовку, особенно такие пластичные металлы, как алюминий и латунь.
Бесконтактный характер лазерной резки исключает необходимость жесткого закрепления заготовки на рабочем столе, тем самым снижая риск ее деформации.
Качество
Лазерная резка низкоуглеродистой стали (Источник: kernlasers)Лазерная резка хорошо известна своими высококачественными резами с малой шириной пропила.
В отличие от традиционных процессов резки, которые склонны к образованию заусенцев по краю реза, лазерная резка дает чистую поверхность с минимальными поверхностными дефектами.
Кроме того, высокая точность и точность лазерных резаков делают их идеальными для выполнения сложных разрезов металлов.
Скорость и воспроизводимость
Лазерная резка использует высокосфокусированный лазерный луч, способный почти мгновенно испарить металл.
В результате получается высококачественная резка с минимальным временем цикла, что делает лазерную резку идеальной для крупных производств, где время является ценным активом.
Кроме того, лазерные резаки представляют собой станки с ЧПУ, обеспечивающие высокий индекс повторяемости около ±0,0005 дюйма.
Это означает, что он может точно воспроизвести разрез и производить одинаковые изделия каждый раз.
Сочетание высокой скорости и высокой повторяемости делает лазерную резку одной из самых популярных и успешных технологий обработки листового металла.
Проблемы лазерной резки металла
Несмотря на то, что это один из лучших методов резки металла, вам следует опасаться некоторых проблем, связанных с лазерной резкой металла.
Высокая начальная стоимость
Хотя лазерная резка предлагает различные преимущества по сравнению с традиционными процессами резки, высокая начальная стоимость оборудования ограничивает его использование малыми предприятиями.
Для лазерной резки металла обычно требуется волоконный лазерный резак, который сравнительно дороже, чем CO-лазер 2 .
Кроме того, использование вспомогательного газа (кислорода или азота) для лазерной резки металла еще больше увеличивает стоимость оборудования.
Отражающая природа металлов
Отражающая природа металлов приводит к потере лазерной энергии в виде отраженных лазерных лучей.
В результате для резки металлических заготовок требуется более мощный лазер.
Следует отметить, что использование малярной ленты для покрытия отражающей поверхности металла не предотвращает отражение лазера.
Это связано с тем, что основным источником отражения является блестящая расплавленная ванна, образующаяся в процессе лазерной резки.
Помимо снижения эффективности лазерного резака, эти отраженные лучи могут быть опасны.
Эти лучи могут причинить серьезные травмы, если попадут в глаза оператору.
Кроме того, это также увеличивает риск возгорания, поскольку эти лучи могут отражаться от металлической заготовки и ударять по легковоспламеняющимся материалам, таким как дополнительный бензобак.
Толщина заготовки
Сравнение отделки поверхности резов, выполненных лазером и плазмой в толстой металлической заготовке (Источник: автоматизация Espirit) Лазерная резка металла дает высококачественные результаты с коротким временем цикла.
Однако по мере увеличения толщины металла способность лазера выполнять чистые разрезы снижается.
Например, лазер мощностью 6 кВт может резать нержавеющую сталь максимальной толщиной около 2,75 дюйма, тогда как максимальная толщина углеродистой стали, которую может резать лазер мощностью 6 кВт, составляет около 1,65 дюйма.
Хотя использование вспомогательного газа под высоким давлением может улучшить способность лазера резать толстые металлы, качество резки толстых металлов с помощью плазменной резки намного превосходит лазерную резку.
Таким образом, при сравнении плазменной резки с лазерной резкой лазерная резка лучше всего подходит для тонких металлических листов, но плазменная резка обеспечивает более чистый рез толстых заготовок.
Лучшие лазерные резаки для металлов
Kern FiberCell
Kern FiberCell FiberCell от Kern — это мощный лазерный резак с иттербиевым волоконным лазером мощностью 0,5–3 кВт, способный резать и гравировать металлы различной толщины.
Это промышленный лазерный резак с рабочей зоной 52 x 50 дюймов и площадью около 74 x 85 x 75 дюймов.
Мощный лазерный модуль в сочетании с высоким индексом воспроизводимости около 0,0016 дюйма в минуту делает FiberCell идеальным решением для крупных производств.
Это многофункциональный лазерный резак со встроенной вытяжной системой и охладителем, который обеспечивает долгую работу без перегрева.
Кроме того, стандартный комплект Kern FiberCell также включает в себя монитор с компьютерной системой и регулируемый кронштейн монитора на передней части лазерного резака.
Это обеспечивает легкий доступ к управлению процессом лазерной резки и повышает производительность.
Защитный кожух класса 2 и другие функции безопасности, такие как кнопка аварийной остановки и функция блокировки, делают его безопасным для использования даже в загруженных цехах.
Купить Kern FiberCell
Kern LaserCell
Kern LaserCell LaserCell — еще один мощный лазерный резак от Kern, в котором установлен лазер CO 2 с вариантами мощности от 100 Вт до 650 Вт.
Он имеет размеры около 74 x 87 x 53 дюймов и обеспечивает рабочую зону 52 x 50 дюймов с дополнительной функцией, включающей раздвижные двери спереди и сзади для легкой загрузки и выгрузки тяжелых заготовок.
Технология Super Pulsed, разработанная Kern, позволяет LaserCell выполнять чистые пропилы в плотных металлах с высокой отражающей способностью
Вакуумная рабочая платформа облегчает укладку заготовки на рабочий стол, а также действует как вытяжка дыма
Kern Лазеры включают в себя монитор и компьютерную систему во всех своих стандартных моделях.
Кроме того, встроенный охладитель предохраняет машину от перегрева, а ее многочисленные функции безопасности, такие как защитный кожух, кнопка аварийного останова и т. д., делают ее работу безопасной.
Купить Kern LaserCell
Плоский волоконный лазер FSL MC
Плоский волоконный лазер FSL MC Серия MC представляет собой крупногабаритный промышленный волоконный лазер, занимающий площадь около 173 x 90 x 55 дюймов. площадью 4 x 8 футов (48 x 96 дюймов).
Внутри находится волоконный лазер мощностью от 200 Вт до 2 кВт, который может резать и гравировать различные металлы.
Небольшая ширина пропила около 0,001 дюйма делает его идеальным для выполнения сложных резов с высокой точностью. высокая повторяемость (±0,02 мм)
Все эти характеристики в сочетании с мощным лазерным модулем и встроенной системой охлаждения делают серию MC отличным металлорежущим станком для крупных производств
Материал | Макс. толщина резки | Макс. cutting speed |
---|---|---|
Carbon Steel | 0.23″ (6 mm) | 31 ipm |
Stainless Steel | 0.12″ (3mm) | 59 ipm |
Galvanized plate | 0.![]() | 39 IPM |
Алюминий | 0,12 «(3 мм) | 31 IPM |
Mopper | 0.08″ | |
Mopper | 0.08 « | |
0.08″ | ||
.0236 |
Возможности лазерной резки Full Spectrum серии MC для резки металла
Купить FSL MC-Flat Bed
Лазерные онлайн-услуги для резки металла
Для лазерной резки металла требуются мощные лазеры и подходящий вспомогательный газ, которые могут быть довольно дорогими .
Если вы являетесь энтузиастом «сделай сам» или представляете малый бизнес, которому время от времени требуется лазерная резка металлических деталей, вы можете положиться на аутсорсинг.
Существуют различные онлайн-поставщики лазерных услуг, которые учитывают ваши требования и доставляют готовое металлическое изделие к вашему порогу.
Вот список некоторых популярных поставщиков лазерных услуг, которые предлагают услуги по резке металла в США.
- Factory
- OSH Cut
- SendCutSend
- eMachine Shop
- Ponoko
Заключительные мысли
Лазерная резка — это эффективный способ резки тонких листов сложной формы с минимальным временем цикла.
Волоконный лазер дает наилучшие результаты при резке тонких листов металла, а CO 2 рекомендуется для резки сравнительно более толстых заготовок.
Кроме того, волоконный лазер можно использовать для гравировки различных металлов, а использование волоконного лазера MOPA позволяет выполнять цветную лазерную гравировку.
Однако лазерная резка не рекомендуется для толстых заготовок, поскольку с увеличением толщины металла скорость резки снижается.
Это приводит к избыточному выделению тепла вокруг зоны реза, что ухудшает качество реза и повреждает заготовку.
Направляющие для лазерной резки различных материалов
Ознакомьтесь с этими руководствами по лазерной резке и гравировке некоторых популярных материалов.
Направляющие для лазерной резки других материалов
Часто задаваемые вопросы (FAQ)
Может ли диодный лазер резать тонкие листы металла?
Да, диодный лазер может резать очень тонкие металлические листы за несколько проходов. Однако выполнение слишком большого количества проходов увеличивает ширину пропила, снижая точность резки и ухудшая качество из-за перегрева материала.
Выделяет ли лазерная резка металла вредные пары?
Да, лазерная резка металла выделяет вредные пары, которые могут вызывать раздражение глаз и дыхательных путей. Некоторые металлы, такие как нержавеющая сталь, содержат хром в качестве легирующего элемента. При горении и испарении хрома могут образовываться канцерогенные пары, которые могут повредить глаза и горло.
Поэтому настоятельно рекомендуется использовать хорошую вытяжную систему при лазерной резке металлов.
Сколько стоит лазерный резак по металлу?
Лазерный резак для металла стоит от 8000 до 300 000 долларов. Недорогие лазерные резаки больше подходят для энтузиастов-любителей, которые работают с очень тонкими металлическими заготовками и малосерийными проектами. Однако для коммерческого применения лазерный резак хорошего качества будет стоить более 20 000 долларов.
Является ли волоконный лазерный маркер лазерным резаком по металлу? – OMTech Laser
Объяснение станков для лазерной резки металла
Металлы являются одним из самых прочных материалов для использования в лазерной промышленности. Чаще всего новички в индустрии лазерной маркировки часто предполагают, что маркер с волоконным лазером может выполнять как резку, так и маркировку. Но это не совсем так. Типичный металлический лазерный резак имеет характеристики, отличные от характеристик волоконного лазерного маркера. Одним из основных различий между этими двумя разными машинами является интенсивность/фокус лазерного источника. Обычно волоконный лазерный маркер имеет длину волны лазера от 800 до 2200 нм. Но металлический лазерный резак имеет длину волны между 9000-11000 нм, что означает, что он намного мощнее. Это показывает проникающую способность обеих машин при использовании.
Может ли волоконный лазер резать металл?
Да, вы можете резать металлы с помощью волоконного лазера, однако это должен быть чрезвычайно мощный источник волокна мощностью около 2000 Вт. Вы не можете лазером резать любой металл стандартным волоконным лазером мощностью от 20 Вт до 50 Вт. Это означает, что лазерная резка металла возможна только для крупного бизнеса. Волоконный лазер может легче проникать в металлы, чем CO2-лазер, потому что фокусная точка намного меньше, а это означает, что лазерный луч более плотный и концентрированный. Даже в этом случае стандартные оптоволоконные источники мощностью до 50 Вт не обладают достаточной мощностью для лазерной резки металла.
Какая мощность волоконного лазера может резать металл?
Для лазерной резки металлов с помощью источника волоконного лазера это должен быть промышленный волоконный лазер мощностью не менее 2000 Вт или 2 кВт. Такие мощные станки для лазерной резки металла чрезвычайно дороги, в диапазоне от 60 000 до 100 000 долларов и выше, что делает их недоступными для большинства малых предприятий.
Поэтому, чтобы обеспечить правильность и эффективность, для лазерной маркировки следует использовать только стандартный волоконный лазерный маркер. Это связано с тем, что для резки или даже гравировки металла волоконным лазерным маркером мощностью 50 Вт вам пришлось бы потратить столько времени из-за многочисленных проходов металла через станок. Именно по этой причине маркеры с волоконным лазером предназначены только для маркировки металла и не используются в качестве лазерной резки металла. И как малый бизнес, вы должны рассмотреть возможность добавления волоконного лазерного маркера к вашему оборудованию из-за его универсальности, скорости и доступности. Вы можете выполнить множество проектов, таких как нестандартные стаканы, украшения, медали и многое другое. Таким образом, лазерный гравер CO2 пригодится в качестве лазерной резки металла.
Если вы хотите создавать металлические вывески с лазерной резкой, имейте в виду, что вы не можете самостоятельно резать металл с помощью волоконного лазерного маркера. Вам нужно будет купить металлические листы, предварительно нарезанные по размеру, прежде чем добавлять настройки для каждого клиента.
Краткий обзор волоконных лазерных маркеров
CO2-лазерные граверы были первыми, кто был представлен в лазерной промышленности, но потребность в волоконных лазерных маркерах возникла из-за особой потребности в маркировке металлов, а не только в резке. Так было до 1990-х годов, прежде чем этот тип машины попал в центр внимания. Волоконный лазер производится из лазерного источника, который представляет собой смесь кварцевого стекла и редкоземельных металлов. По этой причине волоконные лазеры называются твердотельными лазерами и могут работать до 100 000 часов, прежде чем потребуется плановое техническое обслуживание. Вот краткое изложение шагов, необходимых для создания луча волоконного лазера:
- Преобразование электричества в свет или фотоны.
- Созданные фотоны закачиваются в оптоволоконный кабель и направляются для формирования единого светового луча.
- Одиночный луч света, проходящий по оптоволоконному кабелю, входит в резонатор лазера и усиливается в лазерный луч.
- Определенная длина волны лазерного луча формируется на основе легирующего элемента резонатора лазера.
- Лазерный луч сформирован и готов к использованию для маркировки.
Топ-5 металлов, наиболее популярных для лазерной маркировки
Если вы собираетесь маркировать металл, наличие подходящей машины, такой как от OMTech, принесет вам много пользы. Вам было бы интересно узнать, что существуют бесконечные возможности дизайна, который вы можете нанести на любой металл по вашему выбору. Но из всех металлов, которые вы могли бы отметить, некоторые выделяются как самые популярные и по праву. С учетом сказанного, давайте углубимся в:
Алюминий
Алюминий является одним из наиболее часто используемых металлов в лазерной промышленности благодаря его легкости и прочности. Он поставляется в различных формах, таких как голый, анодированный и литой. Вы обнаружите, что анодированный алюминий быстрее белеет при маркировке меньшей интенсивностью луча. Если это голый или литой алюминий, лучше использовать более темную маркировку, а более высокая интенсивность луча подойдет. В любом случае крайне важно всегда сохранять маркировку как можно более глубокой с правильным контрастом для эстетической привлекательности.
Нержавеющая сталь
После алюминия чаще всего используется нержавеющая сталь, особенно в областях с высокими гигиеническими требованиями. Различные проекты, которые можно сделать из нержавеющей стали, включают кухонную утварь, столовые приборы, аксессуары и многое другое. Этот металл поддерживает все формы маркировки, такие как гравировка, травление и даже отжиг. По этой причине он очень универсален и адаптируется к любым параметрам маркировки, которым он подвергается, не повреждаясь. При гравировке или травлении он выдерживает высокую температуру, сопровождающую процесс. Тем не менее, большой контраст достигается, когда маркировка сделана.
Серебро и золото
Когда речь заходит о украшениях, на ум обязательно приходят эти два драгоценных металла. Они достаточно мягкие и хрупкие, поэтому при лазерной маркировке с ними нужно обращаться осторожно. Известно, что во время маркировки верхняя поверхность серебра быстро окисляется, в то время как поверхность золота более стабильна, что облегчает маркировку. При небольшой мощности лазера можно отжигать золото с хорошим контрастом. Из-за мягкости этих металлов гравировка и травление могут быть неприятными для них, поэтому их лучше отжигать. Когда вы маркируете поверхность отжигом, с поверхности материала снимается минимальный материал.
Титан
Это легкий сплав, который специально используется в аэрокосмической, автомобильной и медицинской промышленности. Сочетание долговечности, прочности и легкости делает его совершенно выдающимся. Для медицинской промышленности маркировка должна быть выполнена таким образом, чтобы не оставалось места для загрязнения.
Гравировка и травление подходят для медицинских целей, а отжиг идеально подходит для аэрокосмических целей. Это связано с тем, что в аэрокосмической промышленности титановые детали подвергаются испытаниям на усталость, чтобы гарантировать отсутствие повреждений детали во время эксплуатации. По этой причине структурные повреждения из-за воздействия чрезмерного тепла во время маркировки должны быть ограничены. Это показывает, что титан необходимо тщательно маркировать и обращать внимание на его конкретную область применения.
Вольфрам и карбид
Одним из общих свойств этого металла является то, что его твердость уступает алмазу с твердостью по шкале Мооса 9. Вольфрам естественно светлее по цвету, чем карбид, поэтому для маркировки вашего изделия следует использовать волоконный лазер более высокой интенсивности. дизайн. По возможности маркировка должна быть отожженной для надлежащего контраста. Область применения этих металлов включает режущие инструменты, абразивы, прокалывающие инструменты и некоторые виды ювелирных изделий.
Возьми домой
Волоконные лазерные маркеры предназначены только для лазерной маркировки, и это отличает их от станков для лазерной резки металла. На практике часто используются некоторые металлы из-за их желаемых свойств и простоты обращения. Поэтому лучше всего покупать лазерный станок для маркировки или резки у известной компании, такой как OMTech, чтобы вы могли легко обрабатывать любой материал, который попадется вам на пути. Независимо от того, изучите ли вы их машины в Интернете или посетите их лично, вы найдете разнообразную линейку волоконных лазерных маркеров и станков для лазерной резки CO2. Вы также можете рассчитывать на множество аксессуаров, которые сопровождают каждый лазерный станок, обеспечивая дополнительные преимущества и непревзойденную функциональность.
Назад к Является ли волоконный лазерный маркер лазерным резаком по металлу?
Повышение мощности
Промышленные тенденции показывают, что производители металлов все чаще выбирают более мощные лазеры для резки. Два года назад наиболее распространенными уровнями мощности были от 1500 до 2000 Вт. Тем не менее, статистический обзор, проведенный группой продуктов AMT Laser System, указывает на устойчивый рост в течение последних 12 месяцев установок мощных лазерных систем мощностью от 3000 до 4000 Вт и снижение продаж лазеров мощностью менее 2000 Вт. . Совсем недавно на рынке Северной Америки проявился интерес к лазерам мощностью от 4000 до 6000 Вт.
Сегодня некоторые опытные изготовители переходят к приобретению более высоких уровней мощности для своих вторых систем, чтобы расширить часть своего бизнеса, связанную с лазерной резкой, на более толстые диапазоны материалов. Некоторые новые пользователи лазеров покупают более мощные системы, чтобы выделиться среди конкурентов. У этих пользователей может не быть приложения, требующего большой мощности, но они готовы развивать рыночные возможности, существующие для этой работы.
В этой статье представлены некоторые технические аспекты, связанные с мощной лазерной резкой толстых профилей, а также рассмотрены области применения и сегменты рынка для этой технологии.
Резка нержавеющей стали
Мощные лазеры могут обрабатывать толстую нержавеющую сталь с кромкой без оксидов. Лазер мощностью 6000 Вт может обрабатывать таким образом нержавеющую сталь толщиной до 11/4 дюйма. В этом приложении азот под высоким давлением обычно используется в качестве вспомогательного газа. При резке под высоким давлением или инертным газом основной функцией вспомогательного газа является защита режущей кромки от накопления оксида и быстрое и чистое выдувание расплавленного материала через пропил до того, как он прилипнет к кромке и образует заусенец.
Инертный газообразный азот мало помогает процессу горения материала. Это отличается от резки реактивным газом, для которой вспомогательный газ — обычно кислород — обеспечивает достаточное количество энергии, используемой для сжигания материала. При резке инертным газом лазер обеспечивает почти всю энергию, необходимую для сжигания материала.
Вспомогательный газ азот подается в сопло соосно сфокусированному лазерному лучу. Газ проходит через отверстие сопла и с высокой скоростью опускается в пропил. Фокус луча — самая мощная часть — устанавливается глубоко в материал. Это позволяет верхней части разреза стать шире, увеличивая поток лазерного газа в разрез.
Наконечник высокого давления используется для резки с помощью азота. Это устройство предназначено для максимизации скорости и силы, с которой вспомогательный газ выходит из сопла. Давление вспомогательного газа обычно находится в диапазоне от 300 до 400 фунтов на квадратный дюйм (PSI) при резке толстой нержавеющей стали. Более тонкую нержавеющую сталь можно резать при давлении в нижнем диапазоне от 100 до 200 фунтов на квадратный дюйм.
Отсутствие оксидного слоя или почернения на кромке лазерной резки означает, что детали из нержавеющей стали можно сваривать без интенсивной шлифовки. Оксидный слой должен быть удален с деталей, которые вырезаются с использованием кислородного вспомогательного газа, чтобы обеспечить целостность сварного шва.
Вторичное шлифование может занять много времени, особенно на более толстой нержавеющей стали, с которой необходимо удалить значительное количество загрязненной оксидом кромки. Поскольку большая часть этой шлифовки выполняется вручную, детали могут быть трудно подогнаны и закреплены для сварки. В результате этого несоответствия эти детали часто бывает трудно сварить вручную и почти невозможно сварить роботизированным способом.
Детали, вырезанные с использованием азота, имеют блестящую блестящую кромку и могут сразу же перейти к сварке, как только они будут сняты со станка. Готовые детали имеют квадратные края без конусности и без заусенцев. Не требуется доработка деталей; они просто удаляются из станка для лазерной резки и передаются в следующую ячейку для операций с добавленной стоимостью.
Рисунок 1 |
Поток газа под высоким давлением также способствует охлаждению детали. Это, в сочетании с очень маленьким, но концентрированным размером пятна лазера, приводит к уменьшению зоны термического влияния (ЗТВ) (см. Рисунок 1 ).
Мощность и производительность. С помощью лазера мощностью от 4000 до 6000 Вт можно обрабатывать нержавеющую сталь толщиной 3/4 и 1,0 дюйма с конкурентоспособной скоростью подачи. Хотя скорость подачи часто не такая высокая, как у плазмы, вторичные операции, связанные с плазмой, сокращаются или исключаются.
В тех случаях, когда малая ЗТВ лазера может представлять проблему, некоторые производители считают экономически выгодным сначала вырезать заготовку на лазере, а затем обрезать деталь с помощью фрезы. Лазер используется для черновой обработки детали с более высокой скоростью подачи, чем может достичь фрезерная или электроэрозионная обработка (EDM), освобождая эти машины для дополнительной работы.
Лазер мощностью 6000 Вт также быстро режет более тонкие материалы с хорошим качеством кромки. Например, нержавеющая сталь толщиной 0,160 дюйма может быть обработана в три раза быстрее с помощью лазера мощностью 6000 Вт по сравнению с лазером мощностью 2000 Вт. Один и тот же материал можно разрезать лазером мощностью 6000 Вт более чем в два раза быстрее, чем лазером мощностью 3000 Вт.
Эксплуатационные расходы. Эксплуатационные расходы на обработку толстой нержавеющей стали должны быть тщательно изучены. Почасовые затраты на обработку нержавеющей стали толщиной от 1/2 до 1-1/4 дюйма с помощью лазера мощностью 6000 Вт могут достигать 120 долларов в час. При обработке нержавеющей стали азотом используются большие объемы вспомогательного газа азота, поэтому более 90 процентов почасовых эксплуатационных расходов связаны с использованием вспомогательного газа. Менее 10 процентов эксплуатационных расходов поглощаются фактическими затратами на эксплуатацию и техническое обслуживание лазера.
Первоначально затраты могут показаться высокими, но для обоснования использования лазера требуется комплексный подход к оценке стоимости этого типа работ. В то время как стоимость обработки толстых деталей из нержавеющей стали с помощью лазера, как правило, выше, чем лазерная обработка углеродистой стали, толстые детали из нержавеющей стали, вырезанные лазером, обычно представляют собой детали, которые можно разрезать только с помощью более дорогостоящих процессов, таких как механическая обработка и проволочная электроэрозионная обработка. Устранение большинства второстепенных и не добавляющих ценности операций, таких как шлифовка и снятие заусенцев, обычно компенсирует эти затраты.
Дальнейшая экономия времени достигается за счет сокращения времени фиксации и улучшения подгонки после лазерной обработки. Во многих случаях скорость подачи, достигаемая с помощью лазера, также позволяет производить деталь быстрее, поэтому общее время цикла сокращается.
Например, деталь из нержавеющей стали толщиной 3/4 дюйма, которая раньше обрабатывалась на фрезерном станке за 100 минут, теперь может быть обработана на режущей системе мощностью 6000 Вт за 18 минут. Кроме того, деталь, изготовленная на лазере, не требует дополнительных операций. Поскольку деталь тратит меньше времени на станок, она производится с меньшими затратами, и станок высвобождается для выполнения дополнительных работ.
Резка углеродистой стали
Еще одним применением мощных лазеров является резка углеродистой стали. Лазер мощностью 4000 Вт может обрабатывать углеродистую сталь толщиной до 1,0 дюйма, а лазер мощностью 6000 Вт может обрабатывать углеродистую сталь толщиной 1-5/8 дюйма.
Кислород всегда используется для обработки листа в этом диапазоне толщины материала. При обработке толстой углеродистой стали основной функцией кислорода является помощь в сжигании листа. Это также помогает выталкивать расплавленный материал. Как правило, давление и объем вспомогательного газа очень низкие. Например, для обработки листа толщиной 1-5/8 дюйма обычно используется кислород от 6 до 8 фунтов на квадратный дюйм.
Как и при резке инертным газом, вспомогательный газ (кислород) проходит через отверстие сопла и попадает в пропил. В то время как для выброса расплавленного материала из пропила требуется сплошной поток вспомогательного газа, слишком высокое давление вспомогательного газа может вызвать неконтролируемое горение. Как только процесс горения начался, для поддержания процесса горения требуется очень мало вспомогательного газа.
Тем не менее, расплавленный материал все равно должен очищаться твердым потоком вспомогательного газа. Если используется стандартное сопло, ударные волны в столбе вспомогательного газа приведут к тому, что обрезанная кромка будет выглядеть очень бороздчатой и выемчатой. Сопла с кольцевым потоком могут предотвратить эту проблему, и они обсуждаются более подробно далее в этой статье.
Мощность и производительность. Более высокая мощность лазера полезна в первую очередь для увеличения производительности при обработке углеродистой стали. Как правило, увеличение скорости подачи является номинальным при увеличении мощности. Существует пороговое значение мощности/скорости подачи, при котором данная толщина материала может быть разрезана с использованием кислорода. Вливание большего количества энергии в материал не обязательно увеличивает скорость обработки материала, поскольку наступает момент, когда процесс должен ждать, пока экзотермическая реакция кислорода закрепится. Материал можно обрабатывать только настолько быстро, насколько кислород позволяет ему гореть, поэтому кривая производительности выравнивается при более высоких мощностях при обработке более тонких материалов.
Некоторые производители оригинального оборудования (OEM) в настоящее время экспериментируют с азотной резкой более тонкой углеродистой стали. Поскольку азот является инертным газом, можно использовать дополнительную мощность для увеличения скорости подачи, не дожидаясь, пока произойдет экзотермическая реакция кислорода. В результате получается кромка без оксидного слоя или заусенцев.
Однако этот процесс несколько ограничен толщиной материала, который можно разрезать. Для лазера мощностью 4000 Вт углеродистая сталь толщиной 3/8 дюйма обычно является максимальной практической толщиной; с помощью лазера мощностью 6000 Вт толщина материала может быть увеличена до 1/2 дюйма. В более толстых материалах образуется небольшой, но очень твердый и трудно удаляемый заусенец. Обработка углеродистой стали азотом, как правило, решает некоторые проблемы, связанные с прилипанием краски к кромкам реза, поскольку оксидный слой не является проблемой.
Эксплуатационные расходы. Типичные эксплуатационные расходы на обработку углеродистой стали кислородом составляют от 9 до 14 долларов в час. Стоимость лазерной резки листа из углеродистой стали ниже, чем у нержавеющей, и не так сильно различается для разных толщин материала. В первую очередь это связано с тем, что при обработке углеродистой стали используются более низкое давление и объем вспомогательного газа. Типичный диапазон давления вспомогательного кислорода для углеродистой стали составляет от 5 до 25 фунтов на квадратный дюйм. Давление азота часто может варьироваться от 100 до 400 фунтов на квадратный дюйм.
Из-за разности давлений и того, что кислород дешевле азота, вспомогательный газ составляет значительно меньший процент от общей стоимости резки углеродистой стали, в отличие от резки нержавеющей стали. Фактически менее 10 процентов стоимости обработки углеродистой стали приходится на вспомогательный газ.
Качество листа
Наиболее важным фактором при лазерной резке толстолистового проката является качество листа. Качество пластины может сильно различаться, и получение стабильных результатов с помощью лазера зависит исключительно от получения пластины хорошего качества. Включения или высокое содержание кремнезема вызовут разрушение или извержение при резке. Прилипание накипи, содержание углерода и соотношение остаточных элементов также являются факторами получения стабильных высококачественных результатов. На скорость подачи может сильно повлиять химический состав пластины.
Пользователи часто ошибочно предполагают, что им придется платить высокую цену за лист, который хорошо режется лазером. На самом деле качественная плита доступна по ценам, сравнимым со стандартной плитой. В последнее время многие поставщики пластин проводят эксперименты и разрабатывают сорта пластин, специально предназначенные для лазерной резки. Рис. 2 Отчасти это связано с ранним внедрением мощных лазеров для обработки толстых листов в этих областях. В США ведущие производители пластин сотрудничают с поставщиками мощных лазеров и крупными производственными компаниями, которые вырезают лазером толстые пластины, чтобы лучше понять, что делает материал хорошего качества для лазерной резки.
Для лазерной обработки очень толстого листа важно сначала связаться с производителем стали. Чтобы получить требуемое качество и толщину, производители могут получить наилучшие результаты, работая напрямую с листопрокатными заводами.
Нетрудно получить листы, пригодные для лазерной обработки. Эти сорта не намного дороже, чем стандартные сорта, и дешевле, чем платить за протравку стандартных сортов толстого листа, а затем бороться с непостоянными результатами (см. 9).0013 Рисунок 2 ).
Конструкция режущего сопла
Конструкция режущего сопла вызывает беспокойство при обработке нержавеющей стали, но более серьезная проблема при обработке толстой углеродистой стали. В толстолистовом материале выталкивание является ключом к достижению качественного реза, поскольку при резке углеродистой стали толщиной 1-5/8 дюйма необходимо выбрасывать огромное количество расплавленного материала.
Важно, чтобы в пропил попало как можно больше кислорода, чтобы помочь сжечь материал и обеспечить его чистый выход из пропила. Для оптимизации этого процесса можно использовать кольцевое сопло.
Как и стандартное режущее сопло, кольцевое сопло имеет одно отверстие, через которое центрируется лазер и через которое проходит столб вспомогательного газа. В отличие от стандартного сопла, кольцевое сопло имеет несколько других отверстий, окружающих основное отверстие. Эти дополнительные отверстия используются для подачи большего количества вспомогательного газа в разрез. Поскольку основное отверстие окружает большее количество струй вспомогательного газа, большие объемы газа перемещаются в разрез при более низких давлениях и не вызывают турбулентности или ударных волн, характерных для одной более мощной струи вспомогательного газа.
Если используется стандартное сопло с одним отверстием, требуется слишком большое давление, чтобы направить газ в разрез. Повышенная сила струи вспомогательного газа создает турбулентность или ударные волны в пропиле на фронте резки. Волны приводят к тому, что разрез бесконтрольно горит и выдавливает материал, а не разрезает его чисто и гладко.
Конструкция системы резки высокой мощности
Одним из наиболее важных аспектов доставки луча для мощной лазерной системы является продувка луча. Продувку луча можно определить как слабый поток чистого, сухого воздуха или азота, который вводится в замкнутый путь лазерного луча. Этот поток газа поддерживает положительное давление внутри замкнутого пути луча, чтобы не допустить попадания загрязняющих веществ (частиц или паров) на путь лазерного луча.
Хорошая продувка луча необходима для обеспечения стабильной работы любой лазерной системы, независимо от уровня мощности; на уровнях мощности выше 3000 Вт это абсолютно необходимо, поскольку проблемы, создаваемые некачественной продувкой пучка, часто усугубляются при этих уровнях мощности.
В любой лазерной системе CO 2 используется несколько внешних оптических устройств для транспортировки несфокусированного необработанного луча от лазерного источника к заготовке. Путь, который проходит между каждой внешней оптикой, заключен в жесткий канал или складной сильфон. Это покрытие обеспечивает защиту от случайного воздействия на луч и предохраняет луч от воздействия загрязнения.
Внешний тракт луча подвержен загрязнениям, таким как грязь, шлифовальная пыль и другие крупные частицы, которые могут исказить форму необработанного луча при попадании на путь луча. Менее очевидные загрязняющие вещества, такие как пары краски и химикатов, масляный туман, водяной пар и другие источники углеводородов, также могут вызвать искажение необработанного луча, что приведет к катастрофическим последствиям. Это искажение известно как тепловое размытие или аномальное расширение лазерного луча. Возможность фокусировки необработанного луча изменяется по мере того, как фокусная точка смещается в материал и выходит из него, создавая противоречивые и неприемлемые результаты резки.
Чтобы предотвратить это и сохранить постоянную точку фокусировки, необходимо использовать надлежащую продувку луча. Большинство производителей лазерных систем обычно очищают внешний тракт луча чистым сухим потоком газа или воздуха. Это поддерживает положительное давление протекающего газа в тракте подачи луча и предотвращает попадание загрязнения в цех.
Пользователи лазеров часто ошибочно полагают, что система может работать с отключенной продувкой пучком и при этом поддерживать максимальную производительность. В качестве альтернативы для экономии денег вместо азота в качестве газа для продувки пучка можно использовать воздух. Однако воздух должен быть чистым, сухим и обезжиренным. Недостаточно использовать стандартный воздух из заводского компрессора для продувки тракта луча. Масляный туман, водяной пар и углеводороды можно найти в самом чистом воздухе цеха, даже если используется компрессор с осушителем воздуха.
Лучшее решение — приобрести осушитель вторичного воздуха и разместить его рядом с лазерной установкой. Осушитель воздуха должен фильтровать воздух до 1 микрона и регулировать точку росы до 40 градусов по Фаренгейту или ниже. Использование специального осушителя воздуха и постоянно включенная продувка помогут избежать бесчисленных часов поиска и устранения неисправностей низкого качества резки.
Линзы с низким поглощением и выходные ответвители
В последнее время производители оптики продвигают покрытия с низким поглощением на оптике, используемой в сочетании с мощными лазерными источниками. Эти покрытия наносятся специально на выходной ответвитель и фокусную линзу и предназначены для продления срока службы оптики для приложений с высокой мощностью.
В приложениях с более высокой мощностью как выходной ответвитель, так и фокусирующая линза подвергаются воздействию огромного количества концентрированной энергии и тепла. Покрытия с низким поглощением работают, чтобы свести к минимуму количество оптических искажений из-за этого эффекта и, таким образом, уменьшить преждевременное тепловое линзирование выходного ответвителя и смещение фокусной точки объектива.
Несмотря на то, что оптика с низким поглощением является относительно новой для отрасли, она предлагает некоторые теоретические преимущества по сравнению со стандартной оптикой. Преимущества их использования зависят от области применения. Оптика с низким поглощением стоит на 30-50 процентов дороже, чем оптика без покрытия, но если смещение фокуса или преждевременное линзирование вызывают проблемы, стоит рассмотреть оптику с низким поглощением.
Устройства с постоянным лучом
Еще одной недавней разработкой является использование устройств с постоянным лучом для мощных систем. Эти устройства поддерживают постоянную или почти постоянную длину траектории луча, чтобы обеспечить одинаковое качество резки во всех квадрантах стола станка.
Мощные системы обычно имеют большие столы, и большинство из них представляют собой летающие оптические машины. Оптический путь этих систем может варьироваться в среднем от 7 метров в ближнем поле (где режущая головка расположена ближе всего к источнику лазерного излучения) до 12 метров в дальнем поле (где режущая головка находится дальше всего от лазера). источник). Это большое расстояние может привести к небольшому изменению диаметра луча в ближней и дальней областях, что, в свою очередь, изменяет режущие возможности лазера в этих областях.
Поскольку мощные лазеры предназначены для того, чтобы пользователи могли максимизировать производительность резки за счет резки толстого материала, в большинстве этих систем используется устройство с постоянным ходом луча того или иного типа. Эти устройства подразделяются на несколько категорий, в том числе:
1. Шарнирный рычаг. Этот тип устройства по существу представляет собой шарнирный сегментированный трубчатый рычаг. Один конец рычага подключен к выходу лазера; другой конец прикреплен к режущей головке. В каждом суставе руки есть зеркало, чтобы направить луч с выхода лазера на режущую головку. Диаметр трубки подобран таким образом, чтобы несфокусированный пучок проходил без каких-либо помех. Шарнирная рука также должна быть оснащена продувкой воздухом или азотом.
Использование манипулятора гарантирует, что траектория луча сохраняется на постоянном расстоянии, независимо от того, где находится режущая головка. Это гарантирует, что лазер будет постоянно резать материал максимальной толщины, независимо от квадранта стола, в котором происходит резка.
2. Оптический слайд — еще одним типом устройства с постоянным ходом луча является оптический слайд, часто называемый тромбонным стилем. Устройство работает аналогично шарнирному рычагу, но использует отражающую оптику, установленную на слайде. Ползун управляется серводвигателем и системой привода, которые синхронизированы для перемещения по осям X и Y для поддержания заданного расстояния оптического пути.
Как шарнирный рычаг, так и оптическое скользящее устройство одинаково эффективны для получения постоянного качества резки как в ближней, так и в дальней зоне. Их следует считать необходимыми, если пользователь лазера планирует использовать лазер с максимальной производительностью резки и получать стабильные результаты резки.
Максимально эффективное использование мощных лазеров
Мощные лазерные источники предоставляют производителям металла расширенные возможности обработки для резки толстых сечений, а также возможность быстрее обрабатывать тонкие материалы. Они позволяют этим пользователям расширяться до приложений, ранее зарезервированных для фрезерного и проволочного электроэрозионного оборудования с числовым программным управлением (ЧПУ), в то же время обеспечивая узкий пропил, отсутствие фаски, небольшую ЗТВ, а также сокращение вторичных операций и брака.
Конечно, производители предъявляют разные требования к резке, и не всем будет полезно использовать мощный лазер. Лучший способ определить, подходит ли мощный лазер для конкретного применения, — это проконсультироваться с поставщиком лазерного источника.
Лазерная резка металлов и плазменная резка металлов |
Станки для лазерной и плазменной резки помогут вам сэкономить время и деньги. Оба имеют схожие качества, но есть уникальные особенности, которые отличают их друг от друга. Прежде чем выбрать, какая машина лучше всего соответствует вашим потребностям, вы должны понять все тонкости каждой из них. Мы надеемся помочь вам найти подходящую форму.
Наши отношения с клиентами так же надежны, как и металлы, с которыми мы работаем, и основаны на качественном обслуживании для получения деталей высочайшего качества. Glenn Metalcraft является продолжением каждого клиента. Мы хотим расти в правильном направлении, поэтому мы внимательно относимся к типу работы, которую мы принимаем, и стремимся достичь хорошего соответствия, прежде всего.
Если вы когда-либо использовали увеличительное стекло, чтобы направить солнечный свет в концентрированный луч, вы создали лазер! Направление прямого солнечного света через линзу создает сфокусированный столб света. Этот столб также известен как лазерный луч.
Когда вы думаете о лазерах, вы можете вспомнить научно-фантастические фильмы или лазерные световые шоу. Лазеры, которые вы себе представляете, аналогичны тем, которые используют станки для лазерной резки. Концентрированный луч направляется через станок на материал, который вы хотите разрезать. Этот луч управляется сложной сетью частей, и все они управляются компьютером.
Компьютер управляет машиной и направляет лазерный луч с фантастической точностью. Лазерная резка металлов — это процесс, хорошо известный своими чистыми резами и жесткими допусками.
Станки плазменной резки создают поток электричества, протекающий через газ, и пропускают его через небольшое отверстие с помощью сжатого воздуха. Этот поток перескакивает с электрода в сопле на разрезаемый токопроводящий материал. Вот почему плазменная резка ограничивается только проводящими материалами.
Машины для плазменной резки предлагают мощные возможности резки, но обеспечивают меньшую точность, чем машины для лазерной резки. В отличие от станков для лазерной резки, многие станки для плазменной резки являются ручными. Они представляют собой доступный и эффективный способ легко разрезать металлические листы.
Различия в точности: лазерная и плазменная резка металлов
Как вы понимаете, лазерная резка является более точным вариантом. Лазер может разрезать металлический лист с предельной точностью, потому что ширина разреза очень мала. Большинство лазеров имеют толщину всего одну тысячную дюйма. Эта тонкая ширина разреза обеспечивает идеальный разрез.
Станки плазменной резки мощные, но не соответствуют тому же уровню точности, что и лазеры. Толщина струи, которую машины плазменной резки выпускают для разрезания материалов, составляет одну сотую дюйма. Это почти в десять раз менее точно, чем лазерная резка.
Сравнение качества резки: металлы, вырезанные лазером, и металлы, вырезанные плазмой
Плазменная резка требует больше времени на «очистку».Плазменная резка часто оставляет на деталях зазубренные края и дефекты. Это означает, что вы можете вернуться к куску после резки, чтобы очистить края разреза.
При столкновении машин для лазерной и плазменной резки становятся очевидными различия в качестве и скорости резки.
Ограничения по материалам для станков лазерной резки:
Станки для лазерной резки создают четкие края, но они привередливы в еде.
В отличие от плазмы, станки для лазерной резки могут работать только с материалами толщиной менее ½ дюйма. Любой больше, и вам может понадобиться очень большой, чрезвычайно специализированный лазер. Лазерная резка металлов ограничивается чистыми металлическими материалами без ржавчины и без зеркального отражения.
Лазерные станки для резки различных металлических материалов.Они варьируются от обычного картона до толстого акрилового картона. Учитывая, насколько хорошо он может резать металлы, идеальной толщиной является стальной или алюминиевый лист толщиной ¼ дюйма. Основное правило заключается в том, что эти поверхности должны быть безупречными и неокрашенными, чтобы лазерный резак работал правильно.
Ограничения по материалам для машин плазменной резки:
Для работы машин плазменной резки требуется проводящий материал. Фаворитами этих машин являются сталь и алюминий. Одним из преимуществ плазменной резки является то, что они не требуют чистых разрезов материала и будут работать надлежащим образом, удаляя ржавчину и пятна на поверхности.
Более толстые материалы, требующие простой резки, идеально подходят для плазменной резки. Плазменная резка возможна при толщине до 6 дюймов. Максимальная толщина, возможная для каждого плазменного резака, зависит от мощности и настройки машины. Плазменные резаки могут быть ручными или настольными системами.
Здесь можно задать вопросы о лазерной и плазменной резке металлов.
Наши отношения с клиентами так же надежны, как и металлы, с которыми мы работаем, и основаны на качественном обслуживании для получения деталей высочайшего качества. Glenn Metalcraft является продолжением каждого клиента. Мы хотим расти в правильном направлении, поэтому мы внимательно относимся к типу работы, которую мы принимаем, и стремимся достичь хорошего соответствия, прежде всего.
Введение в прядение металлов
Гленн Металкрафт 25 ноября 2020 г.
Прядение металла, иногда называемое вращением, существует уже много столетий и восходит к гробнице египетского фараона. Увлекательно, но что
Подробнее »
Введение в роботизированную сварку
Glenn Metalcraft 1 декабря 2020 г.
Производство играет огромную роль в нашей повседневной жизни. От стульев, на которых мы сидим, до автомобилей, на которых мы ездим, роботизированная сварка коснулась многих из этих предметов.
Подробнее »
Резка волоконным лазером по сравнению с традиционной резкой листового металла
Просмотреть всю лазерную продукцию IPG Photonics — ПОСЕТИТЬ КОРПОРАТИВНЫЙ ВЕБ-САЙТ✕
Вернуться к блогу
Лазерная резка низкоуглеродистой и нержавеющей стали имеет долгую историю и является одним из основных применений CO 2 лазеров. Однако лазеры CO 2 традиционно не являются хорошим решением для резки материалов с высокой отражающей способностью.
Волоконные лазеры имеют длину волны излучения около 1,07 мкм по сравнению с 10,6 мкм у традиционных альтернатив CO 2 . Лазерный свет с длиной волны 1,07 мкм не только меньше отражается и, следовательно, легче поглощается, но и более короткая длина волны может быть сфокусирована в пятно, которое составляет около 1/10 диаметра луча CO 2 . Это обеспечивает значительно более высокую удельную мощность, облегчая проникновение в металл. При таких высоких уровнях плотности мощности такие металлы, как медь и латунь, быстро претерпевают фазовый переход в расплавленное состояние, поэтому лазерный луч быстро преодолевает барьер отражения таких металлов, инициируя эффективный процесс резки. Резка таких металлов с использованием CO 9 оказалась сложной задачей.0169 2 лазеры или лазеры ближнего ИК-диапазона с низкой пиковой мощностью.
Медь, латунь, бронза, серебро, золото и алюминий хорошо отражают инфракрасный свет в твердом состоянии. Алюминий, однако, не считается отражающим металлом для практических целей резки волоконным лазером .
Почему лазерная резка латуни и меди так сложна?
- Низкое поглощение инфракрасного лазерного излучения затрудняет резку этих металлов.
- Медь и латунь (медно-цинковый сплав) являются хорошими отражателями (и, следовательно, плохими поглотителями) инфракрасного (ИК) лазерного излучения, особенно в твердом состоянии.
- Чистая медь отражает > 95 % ближнего ИК-излучения (длина волны ~ 1 мкм) в твердом состоянии.
- Отражательная способность меди и других отражающих металлов уменьшается, когда металл нагревается, и резко падает, когда материал плавится (например, до <70% для меди в расплавленном состоянии), как показано на рисунке ниже. Эти металлы поглощают значительно больше лазерной энергии в расплавленном состоянии.
Распространенные проблемы при лазерной резке отражающих металлов.
При выборе оптимизированного лазера, оптики и процесса резки лазерный луч быстро плавит поверхность отражающих материалов, чтобы затем взаимодействовать с более абсорбирующим расплавленным металлом и инициировать эффективный и стабильный процесс резки. Неправильный выбор лазерной/оптической установки или использование неоптимальных параметров процесса может привести к чрезмерному задержке лазера в твердом металле и, следовательно, к чрезмерному количеству обратно отраженного света. Слишком сильное отражение, в свою очередь, приводит к неэффективности процесса резки и потенциальному повреждению оптики.
Критической стадией резки отражающего металла является начало процесса, особенно стадия прожига, когда лазер взаимодействует с твердым металлом. После того, как разрез установлен, лазерный луч в основном взаимодействует с расплавленным материалом.
Следующие параметры процесса относятся к прошивке и резке меди и латуни с помощью волоконных лазеров:
Скорость резки
Отклонение от максимальной скорости подачи, которую может поддерживать процесс, примерно на 10–15 %, чтобы избежать любого риска того, что рез погаснет, тем самым применяя высокие уровни энергии луча к материалу в его наиболее отражающем состоянии. . Если вы сомневаетесь, начните с более медленной скорости, чем, как вы знаете, может поддерживать процесс. Подождите достаточное время, чтобы просверлить отверстие, прежде чем перемещать луч, чтобы начать резку.
Положение фокуса
Как для прокалывания, так и для резки установите положение фокуса как можно ближе к верхней поверхности, насколько позволяет качество резки. Это сводит к минимуму количество поверхностного материала, взаимодействующего с лучом в начале процесса, тем самым максимизируя плотность мощности луча, что приводит к более быстрому плавлению.
Толщина меди | 0,04 дюйма 1 мм | 0,06 дюйма 1,5 мм | 0,08 дюйма 2 мм | 0,12 дюйма 3 мм | 0,16 дюйма 4 мм | 0,25 дюйма 6 мм |
Минимальная необходимая пиковая мощность | 1000 Вт | 1000 Вт | 1500 Вт | 2000 Вт | 3000 Вт | 4000 Вт |
Настройка мощности
Использование максимальной пиковой мощности, доступной для прокалывания и резки, сокращает время, в течение которого материал находится в наиболее отражающем состоянии.