Учебные плакаты по капиллярному методу
Плакаты предназначены для обучения и повышения квалификации специалистов неразрушающего контроля. На данной странице фотографии представлены в уменьшенном виде. Все плакаты печатаются на матовой бумаге формата А1 (594×841мм), плотность бумаги 170 г. Каждая серия плакатов, посвящена определенному методу неразрушающего контроля. В настоящее время выпущены следующие серии:
1. Визуальный и измерительный контроль – 6 плакатов:
2. Радиографический контроль – 7 плакатов:
- Транспортные и транспортно-перезарядные контейнеры
- Гамма дефектоскопы
- Строение и характеристики радиографических пленок
- Устройство и принцип действия двухэлектронной трубки с накаленным катодом
- Схемы радиографического контроля
- Факторы, влияющие на формирование радиационного изображения и чувствительность контроля
- Основные дефекты сварных соединений
3.
4. Капиллярная дефектоскопия – 3 плаката:
5. Магнитопорошковая дефектоскопия – 4 плаката:
6. Контроль герметичности – 11 плакатов:
7. Металлография – 4 плаката:
8. Стилоскопирование – 3 плаката:
Слайд-шоу Плакаты по неразрушающему контролю
Подпишитесь на наш канал YouTube
Учебные плакаты по неразрушающему контролю можно купить с доставкой до двери или до терминалов транспортной компании в следующих городах: Москва, Санкт-Петербург, Екатеринбург, Саратов. Амурск, Ангарск, Архангельск, Астрахань, Барнаул, Белгород, Бийск, Брянск, Воронеж, Великий Новгород, Владивосток, Владикавказ, Владимир, Волгоград, Волгодонск, Вологда, Иваново, Ижевск, Йошкар-Ола, Казань, Калининград, Калуга, Кемерово, Киров, Кострома, Краснодар, Красноярск, Курск, Липецк, Магадан, Магнитогорск, Мурманск, Муром, Набережные Челны, Нальчик, Новокузнецк, Нарьян-Мар, Новороссийск, Новосибирск, Нефтекамск, Нефтеюганск, Новочеркасск, Нижнекамск, Норильск, Нижний Новгород, Обнинск, Омск, Орёл, Оренбург, Оха, Пенза, Пермь, Петрозаводск, Петропавловск-Камчатский, Псков, Ржев, Ростов, Рязань, Самара, Саранск, Смоленск, Сочи, Сыктывкар, Таганрог, Тамбов, Тверь, Тобольск, Тольятти, Томск, Тула, Тюмень, Ульяновск, Уфа, Ханты-Мансийск, Чебоксары, Челябинск, Череповец, Элиста, Ярославль и другие города, кроме того, в Республике Крым.
Капиллярный метод неразрушающего контроля (кнк) (капиллярная дефектоскопия)
Капиллярный метод неразрушающего контроля (кнк) (капиллярная дефектоскопия)Этот метод пригоден только для выявления дефектов, проявляющихся на поверхности контролируемого объекта. Он основан на проникновении специальной жидкости — пенетранта — в полости поверхностных и сквозных несплошностей объекта контроля, в извлечении пенетранта из дефектов с помощью проявляющего покрытия и фиксировании пенетранта. Глубина дефектов, обнаруживаемых КНК должна значительно превышать их ширину. Если ширина поверхностного повреждения больше его глубины (риска, царапина), то оно легко заполняется пенетрантом и так же легко удаляется из повреждений. Такие дефекты, как правило, КНК не выявляются.
КНК обычно используют для обнаружения дефектов, не видимых невооруженным глазом. Его абсолютную чувствительность определяют средним раскрытием дефекта типа трещин длиной 3-5 мм. выявляемого с заданной вероятностью.
Индикаторные рисунки, образующиеся при контроле, либо обладают способностью люминесцировать в ультрафиолетовых лучах, либо имеют окраску, вызываемую избирательным поглощением (отражением) части падающих на них световых лучей. Линии индикаторного рисунка имеют ширину от 0.05 до 0.3 мм (на расстоянии наилучшего зрения это соответствует угловой ширине от 15″ до Г30″). яркостный контраст 30-60% и более, а также высокий цветовой контраст. Это значительно выше соответствующих параметров поверхностных дефектов, обнаруживаемых визуально (угловой размер от Г до 10″. яркостный контраст 0-5%. цветовой контраст отсутствует).
При КНК ставятся следующие задачи: обнаружение дефекта, определение направления дефекта относительно конфигурации детали, определение размеров и формы дефекта.
В процессе КНК осуществляется следующая маркировка дефектов;
а — по количеству дефектов: А — одиночные дефекты.
б — по направлению дефектов:
|| -дефекты, параллельные направлению изделия:
_|_ — дефекты, перпендикулярные направлению изделия;
Z -дефекты, расположенные под углом к направлению изделия.
Основными объектами КНК являются неферромагнитные материалы: лопатки турбин из никелевых сплавов, в том числе авиационных турбин: титановый крепеж для летательных и космических аппаратов: литые детали из цветных металлов для электроники и систем автоматического управления: детали приборов и аппаратов нефтяной и химической промышленности.
КНК позволяет диагностировать объекты контроля любых размеров и форм, изготовленных из чёрных и цветных металлов и сплавов, пластмасс, стекла, керамики, а также других твёрдых неферромагнитных материалов. При этом выявляются такие дефекты, как трещины, пористость, рыхлоты.
При КНК применяют следующие материалы:
1. В качестве пенетранта — различные жидкие растворы, чаше всего на основе керосина, в который добавляются красители или люминофоры, светящиеся под действием ультрафиолетового излучения.
Люменисцирующие пенетранты представляют собой смеси органических растворителей, масел, керосина с добавками поверхностно-активных веществ (ПАВ) и люминесцирующих веществ: масел, нефти, норнола, эмульсола и др.
2. Очищающую жидкость, которая предназначена для удаления пенетранта с поверхности контролируемого объекта. В качестве очищающих жидкостей используются вода, вода с добавлением ПАВ. органические растворители, смесь масла с керосином и другие жидкости. Например, масло МК-8-65% объема, толуол — 30%. эмульгатор ОП-7
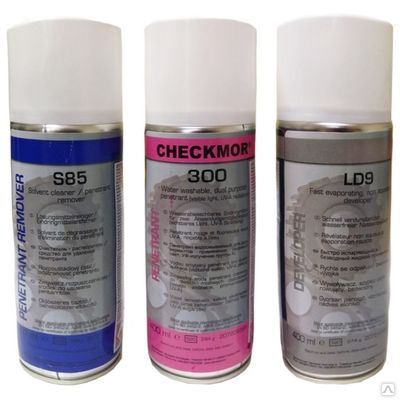
4. В качестве проявляющих веществ — агар-агар, крахмал, порошок окиси магния, суспензия каолина в ацетоне и многие другие материалы, которые адсорбируют пенетрант. проникший в дефекты, и тем самым позволяют фиксировать их на поверхности контролируемого объекта.
Для выполнения КНК применяется следующая аппаратура:
1 — ванны для мойки и насыщения изделия пенетрантом:
2 — шкафы для сушки изделий:
4 — оптические устройства для фиксации дефектов визуально, с помощью фотосъёмок и для облучения пенетранта ультрафиолетовыми лучами в случае применения люминесцирующих веществ.
Проникающую жидкость наносят на предварительно очищенную поверхность деталей, чтобы заполнить полости возможных поверхностных дефектов. Продолжительность контакта жидкости с поверхностью детали зависит от физических свойств жидкости, характера обнаруживаемых дефектов и способа заполнения жидкостью полостей дефектов.
В табл. 4.1 приведены способы заполнения полостей дефектов пенетрантом. Наиболее простым и распространенным в производственных условиях является капиллярный способ. При этом для улучшения проникновения жидкости в полости может подогреваться проникающая жидкость или проверяемая деталь.
При вакуумном способе
При компрессионном способе жидкость быстро заполняет полости дефектов под действием капиллярного и внешнего избыточного давлений. При этом достигается более полное заполнение полостей дефектов, однако многие пенетранты изменяют свои свойства при увеличении давления — увеличивается вязкость, ухудшается смачиваемость твердых тел. в результате эффективность способа невелика.
При ультразвуковом способе ускоряется процесс заполнения полостей дефектов, особенно загрязненных. Высокой эффективности способ достигает при использовании пенетрантов средней и высокой вязкости (нориола, шубнкола. смесей масла с керосином), когда направление колебаний совпадает с плоскостью полости дефекта.
Под воздействием статических сил увеличивается ширина раскрытия полости дефектов, улучшаются условия заполнения этих полостей н выявления дефектов ннзковязкимн жидкостями.
При обычных условиях, например, заполнение поверхностных трещин раскрытием 0.002 мм и глубиной происходит за 20 с: такая же трещина глубиной 3 мм полностью заполняется примерно за 40 с.
Скорость заполнения сквозных дефектов зависит от их размеров и конфигурации, время заполнения измеряется секундами.
Индикаторные пенетранты для красок и люминофоров, приготовленные на основе растворителей (керосин, бензин и т.п.). достаточно быстро испаряются. Длительная выдержка пенетранта на контролируемой поверхности может привести к его высыханию и выпадению в виде осадка из частиц красителя или люминофора. Эти частицы, являясь сорбентом, могут привести к извлечению пенетранта из устья дефекта: в результате выявление дефектов при контроле ухудшается. Для предотвращения высыхания можно периодически наносить дополнительно пенетрант. однако это процесс трудоемкий, особенно при контроле больших площадей, поэтому время нахождения пенетранта на контролируемой поверхности обычно ограничено 3-5 мин. После этого индикаторный пенетрант необходимо удалить с поверхности КО.
Способы удаления проникающей жидкости с поверхности выбирают с учетом необходимости сохранения ее в полостях дефектов, а также типа пенетранта. шероховатости поверхности, условий контроля, объема работ и требуемой производительности труда. При локальном контроле условиях в случае использования невысыхающих жидкостей детали протирают ветошью или бумагой. При большом объеме работ или при контроле шероховатых деталей (с чистотой обработки поверхности ниже пятого класса) этот способ непригоден. В этих случаях применяют промывку органическими растворителей!, водой и пр. Для удаления невысыхающих жидкостей применяют обдувку струей песка, дроби, косточковой крошки, опилок и т.п. Гашением устраняется люминесценция или окраска при использовании специальных проникающих жидкостей. При контроле массовых деталей в цеховых условиях применяют комбинированный способ удаления проникающей жидкости с поверхности деталей.
Если фон обнаружен, для повторной очистки используют очиститель типа O-l или 0-2. При температуре окружающего воздуха ниже 8°С индикаторный пенетрант с поверхности КО снимают бязью, смоченной в спирте. Влагу с поверхности изделия удаляют влажной бязью до полного исчезновения с нее капель воды, после чего поверхность считается подготовленной к следующей операции. Проявитель чаще всего наносят кистью. При этом расход проявителя значительно меньше, чем при нанесении его краскораспылителем, окружающий воздух меньше насыщается вредными для человека парами растворителей и аэрозолей.
В цеховых условиях применяют также способ посыпания и способ наложения липких пленок. Затем происходит медленное перемещение мениска в глубь трещины (рис. 4.2) и незначительное увеличение индикаторного следа. Размер индикаторного следа определяется объемом пенетранта. извлеченного из устья трещины, после образования мениска по всей ее протяженности.
Средняя ширина индикаторного следа определяется в основном раскрытием поверхностной единичной трещины. Следовательно, для надежного выявления поверхностных дефектов при проведении технологических операций контроля необходимо обеспечить сохранение пенетранта в устье дефекта от момента нанесения до момента его извлечения из дефекта, поэтому операции по нанесению и удалению проникающей жидкости и нанесению проявителя должны проводиться непосредственно одна за другой с минимальным интервалом времени, не следует допускать длительной сушки поверхности после удаления пенетранта. длительной промывки КО и т.п.
Освещенность исследуемой поверхности должна быть не ниже 50 лк. Контроль проводят в затененном помещении, а в полевых условиях — при местном затемнении. При цветном контроле естественное или искусственное освещение на контролируемом участке должно быть не менее 3000 лк. С поверхностей деталей, прошедших контроль и признанных годными, удаляют проявитель и следы других дефектоскопических материалов одним из перечисленных способов: протиркой, промывкой, анодной обработкой, выжиганием, органическими растворителями.
В некоторых случаях в условиях производства возникает необходимость многократного контроля. Перед повторным контролем проводят полный цикл подготовки изделий, тщательно промывая КО ацетоном, бензином или другими растворителями для удаления остатков дефектоскопических материалов из поверхностных дефектов. Небольшие изделия перед повторным контролем рекомендуется помещать на несколько часов в растворители индикаторного красителя. В качестве иллюстрации влияния первичного контроля на последующие проверки на рис. 4.3 приведены результаты двух серий (каждая по пять раз) контроля образцов из стали, на которых при первичном осмотре было обнаружено 11 единичных трещин.
Осмотр контролируемой поверхности, как правило, проводят дважды: через 5-6 мин для обнаружения крупных дефектов и через 25-60 мин для обнаружения мелких. При люминесцентном методе контроля используют ультрафиолетовое излучение с длиной волны Сумма площадей индикаторных следов, обнаруженных на образцах, изменяется в зависимости от числа проведенных ранее испытаний.
Между сериями испытаний образцы помешали на 8-10 ч в растворители индикаторного красителя. Из рис. 4.3 видно, что такая обработка образцов почти полностью исключает влияние загрязнений дефектов остатками дефектоскопических материалов, используемых на предыдущих стадиях контроля.
КНК подразделяется на четыре уровня, как указано в табл. 4.2.
Чувствительность КНК определяется геометрическим к. и оптическим ко факторами: KKHK=f(kr. ko). где f- знак функции.
Геометрический фактор определяется как k=l-y/b, где у— ширина устья дефекта, a b — ширина выделившегося пенетранта. как показано на рис. 4.4.
Здесь 1 — контролируемое изделие. 2 — проявитель. 3 — дефект. В6 и Ва — интенсивности света, отражённого от проявителя (фон) и от выделившегося из дефекта пенетранта. Оптический фактор определяется отношением интенсивностей света: ко= В./ Вп .
Приборы для КНК выпускаются серийно. В качестве примеров приведём отечественный прибор ЛДА-3 н прибор США «Тнн-Kq) АФБ». Последний позволяет контролировать в течение часа до 500 лопаток турбин.
Основные положения, которые необходимо знать при КНК. следующие.
1. Подготовку изделий к контролю (удаление жидкостей из поверхностных дефектов) можно проводить путем их нагрева или нанося на их поверхность проявитель. При нагреве изделий выше температуры кипения жидкостей происходит удаление жидкости из дефектов за счет образования пузырьков пара. Температура, при которой происходит выброс жидкости из дефекта, зависит от величины раскрытия дефекта. При широких является практически мгновенно. При нагреве изделий ниже температуры кипения жидкости очистка дефектов происходит за счет испарения жидкостей и пленочного массопереноса ее по стенкам дефекта. Нанесение проявителя на контролируемую поверхность обеспечивает удаление жидкости из устья дефектов приблизительно за 20 мин.
2. Размер индикаторного следа от поверхности единичной трещины определяется в основном объемом индикаторного пенетранта. находящегося в устье трещины, поэтому надежное выявление поверхностных дефектов обеспечивается при условии сохранения пенетранта в устье дефекта от момента его нанесения до момента извлечения его из дефекта.
3. Осмотру с целью обнаружения дефекта не подвергаются детали, состояние проявителя в зонах контроля которых затрудняет видимость индикаторных рисунков. Например, при цветовом варианте КНК осмотру не подвергаются детали, если в слое проявителя имеются пятна не удаленной красной проникающей жидкости, пятна и потеки масляно-керосиновой смеси, непокрытые проявляющей краской участки зоны контроля, частицы пыли, ветоши, следы каких-либо посторонних материалов (из-за применения загрязненных инструментов, приспособлений — краскораспылителей, кистей, захватов и др.).
Общий осмотр проводят невооруженным глазом или с применением луп малого увеличения с большим полем зрения 2.
Размер индикаторного следа от поверхности единичной трещины определяется в основном объемом индикаторного пенетранта. находящегося в устье трещины, поэтому надежное выявление поверхностных дефектов обеспечивается при условии сохранения пенетранта в устье дефекта от момента его нанесения до момента извлечения его из дефекта.
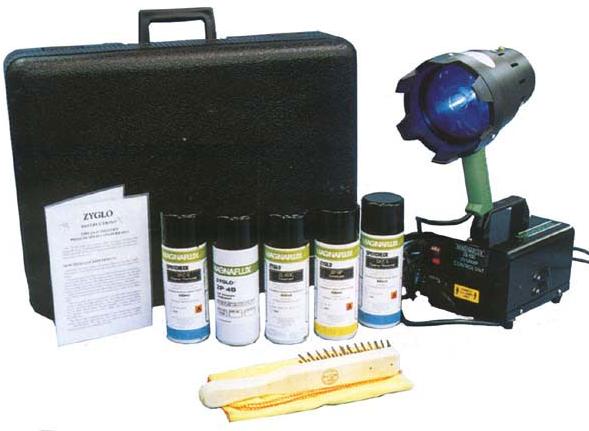
3. Осмотру с целью обнаружения дефекта не подвергаются детали, состояние проявителя в зонах контроля которых затрудняет видимость индикаторных рисунков. Например, при цветовом варианте КНК осмотру не подвергаются детали, если в слое проявителя имеются пятна не удаленной красной проникающей жидкости, пятна и потеки масляно-керосиновой смеси, непокрытые проявляющей краской участки зоны контроля, частицы пыли, ветоши, следы каких-либо посторонних материалов (из-за применения загрязненных инструментов, приспособлений — краскораспылителей, кистей, захватов и др.).
Общий осмотр проводят невооруженным глазом или с применением луп малого увеличения с большим полем зрения. При осмотре отыскивают окрашенный или люминесцирующнй индикаторный рисунок, обращая внимание на основные признаки:
— Трещины любого происхождения, волосовины, закаты, неслитнны. непровары. неспаи, плены выявляются в виде четких, иногда прерывистых окрашенных линий различной конфигурации (рис. 4.5. 4.6)
— Растрескивание материала, межкристаллнтная коррозия участков поверхности крупнозернистых сплавов проявляются в виде группы отдельных коротких линий или сетки (рис.4.7. б)
— Межкристалльная коррозия участков поверхности мелкозернистых сплавов выявляется в виде пятен, размытых полос:
— Поры, язвенная коррозия, выкрашивание материала, эрозионные повреждения поверхности выявляются отдельными точками, звездочками (рис.4.7, а).
Обнаружение рисунка, соответствующего указанным выше основным признакам, служит основанием для анализа допустимости дефекта по его размеру, положению, характеру.
К недостаткам КНК следует отнести высокую трудоемкость контроля при отсутствии механизации; сложность механизации и автоматизации процесса контроля: большую длительность процесса (от 0.5 до 1.5 ч): снижение достоверности результатов при отрицательных температурах, необходимость удаления лакокрасочных покрытий и тщательной предварительной очистки контролируемых деталей: низкую вероятность обнаружения дефектов, перекрытых окисными пленками или сжатых значительными остаточными или рабочими напряжениями в детали: громоздкость стационарного оборудования: вредность некоторых дефектоскопических материалов для персонала и необходимость использования защитных приспособлений и вентиляции: субъективность контроля, зависимость достоверности результатов от умения и состояния контролера: ограниченный срок хранения дефектоскопических материалов, зависимость их свойств от продолжительности хранения и температуры среды.
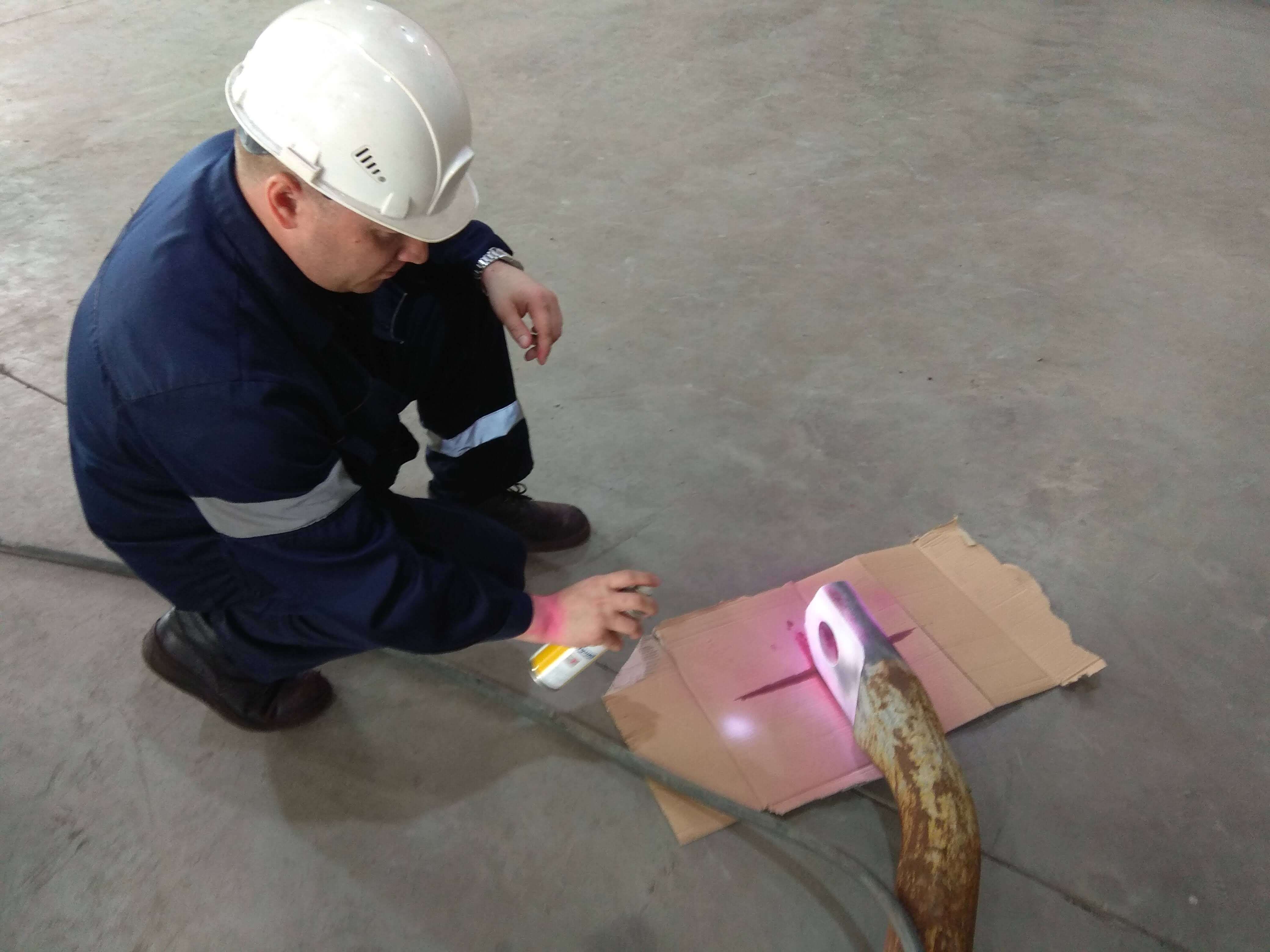
Капиллярный контроль, цветная дефектоскопия, капиллярный метод неразрушающего контроля
Капиллярный контроль. Цветная дефектоскопия. Капиллярный метод неразрушающего контроля.
_____________________________________________________________________________________
Капиллярная дефектоскопия — метод дефектоскопии, основанный на проникновении определенных контрастных веществ в поверхностные дефектные слои контролируемого изделия под действием капиллярного (атмосферного) давления, в результате последующей обработки проявителем повышается свето- и цветоконтрастность дефектного участка относительно неповрежденного, с выявлением количественного и качественного состава повреждений (до тысячных долей миллиметра).
Существует люминесцентный (флуоресцентный) и цветной методы капиллярной дефектоскопии.
В основном по техническим требованиям или условиям необходимо выявлять очень малые дефекты (до сотых долей миллиметра) и идентифицировать их при обычном визуальном осмотре невооруженным глазом просто невозможно. Использование же портативных оптических приборов, например увеличительной лупы или микроскопа, не позволяет выявить поверхностные повреждения из-за недостаточной различимости дефекта на фоне металла и нехватки поля зрения при кратных увеличениях.
В таких случаях применяют капиллярный метод контроля.
При капиллярном контроле индикаторные вещества проникают в полости поверхностных и сквозных дефектов материала объектов контроля, в последствие образующиеся индикаторные линии или точки регистрируются визуальным способом или с помощью преобразователя.
Контроль капиллярным методом осуществляется в соответствии с ГОСТ 18442-80 “Контроль неразрушающий. Капиллярные методы. Общие требования.”
Главным условием для обнаружения дефектов типа нарушения сплошности материала капиллярным методом является наличие полостей, свободных от загрязнений и других технических веществ, имеющих свободный доступ к поверхности объекта и глубину залегания, в несколько раз превышающую ширину их раскрытия на выходе. Для очистки поверхности перед нанесением пенетранта используют очиститель.
Назначение капиллярного контроля (капиллярной дефектоскопии)
Капиллярная дефектоскопия (капиллярный контроль) предназначена для обнаружения и инспектирования, невидимых или слабо видимых для невооруженного глаза поверхностных и сквозных дефектов (трещины, поры, непровары, межкристаллическая коррозия, раковины, свищи и т.д.) в контролируемых изделиях, определение их консолидации, глубины и ориентации на поверхности.
Применение капиллярного метода неразрушающего контроля
Капиллярный метод контроля применяется при контроле объектов любых размеров и форм, изготовленных из чугуна, черных и цветных металлов, пластмасс, легированных сталей, металлических покрытий, стекла и керамики в энергетике, ракетной технике, авиации, металлургии, судостроении, химической промышленности, при строительстве ядерных реакторов, в машиностроении, автомобилестроении, электротехники, литейном производстве, медицине, штамповке, приборостроении, медицине и других отраслях. В некоторых случаях этот метод является единственным для определения технической исправности деталей или установок и допуск их к работе.
Капиллярную дефектоскопию применяют как метод неразрушающего контроля также и для объектов из ферромагнитных материалов, если их магнитные свойства, форма, вид и расположение повреждений не позволяют достигать требуемой по ГОСТ 21105-87 чувствительности магнитопорошковым методом или магнитопорошковый метод контроля не допускается применять по техническим условиям эксплуатации объекта.
Капиллярные системы также широко применяются для контроля герметичности, в совокупности с другими методами, при мониторинге ответственных объектов и объектов в процессе эксплуатации. Основными достоинствами капиллярных методов дефектоскопии являются: несложность операций при проведение контроля, легкость в обращение с приборами, большой спектр контролируемых материалов, в том числе и немагнитные металлы.
Преимущество капиллярной дефектоскопии в том, что с помощью несложного метода контроля можно не только обнаружить и индентифицировать поверхностные и сквозные дефекты, но и получить по их расположению, форме ,протяженности и ориентации по поверхности полную информацию о характере повреждения и даже некоторых причинах его возникновения (концентрация силовых напряжений, несоблюдение технического регламетна при изготовлении и пр. ).
В качестве проявляющих жидкостей применяют органические люминофоры — вещества, обладающие ярким собственным излучением под действием ультрафиолетовых лучей, а также различные красители и пигменты. Поверхностные дефекты выявляют посредством средств, позволяющие извлекать пенетрант из полости дефектов и обнаруживать его на поверхности контролируемого изделия.
Приборы и оборудования применяемые при капиллярном контроле:
• Наборы для капиллярной дефектоскопии Sherwin, Magnaflux, Helling (очистители, проявители, пенетранты)
• Пульверизаторы
• Пневмогидропистолеты
• Источники ультрафиолетового освещения (ультрафиолетовые фонари, осветители).
• Испытательные панели (тест-панель)
• Контрольные образцы для цветной дефектоскопии.
Параметр «чувствительность» в капиллярном методе дефектоскопии
Чувствительность капиллярного контроля – способность выявления несплошностей данного размера с заданной вероятностью при использовании конкретного способа, технологии контроля и пенетрантной системы. Согласно ГОСТ 18442-80 класс чувствительности контроля определяют в зависимости от минимального размера выявленных дефектов с поперечными размером 0,1 — 500 мкм.
Выявление поверхностных дефектов, имеющих размер раскрытия более 500 мкм, капиллярными методами контроля не гарантируется.
Класс чувствительности Ширина раскрытия дефекта, мкм
I Менее 1
II От 1 до 10
III От 10 до 100
IV От 100 до 500
технологический Не нормируется
Физические основы и методика капиллярного метода контроля
Капиллярный метод неразрушающего контроля (ГОСТ 18442-80) основан на проникновении внутрь поверхностного дефекта индикаторного вещества и предназначен для выявления повреждений, имеющих свободный выход на поверхность изделия контроля. Метод цветной дефектоскопии подходит для обнаружения несплошностей с поперечными размером 0,1 — 500 мкм, в том числе сквозных дефектов, на поверхности керамики, черных и цветных металлов, сплавов, стекла и другие синтетических материалов. Нашел широкое применение при контроле целостности спаек и сварного шва.
Цветной или красящий пенетрант наносится с помощью кисти или распылителя на поверхность объекта контроля. Благодаря особым качествам, которое обеспечиваются на производственном уровне, выбор физических свойств вещества: плотности, поверхностного натяжения, вязкости, пенетрант под действием капиллярного давления, проникает в мельчайшие несплошности, имеющие открытый выход на поверхность контролируемого объекта.
Проявитель, наносимый на поверхность объекта контроля через относительно недолгое время после осторожного удаления с поверхности неусвоенного пенетранта, растворяет находящийся внутри дефекта краситель и за счет взаимного проникновения друг в друга “выталкивает” оставшийся в дефекте пенетрант на поверхность объекта контроля.
Имеющиеся дефекты видны достаточно четко и контрастно. Индикаторные следы в виде линий указывают на трещины или царапины, отдельные цветовые точки — на одиночные поры или выходы.
Процесс обнаружения дефектов капиллярным методом разделяется на 5 стадий (проведение капиллярного контроля):
1. Предварительная очистка поверхности (используют очиститель)
2. Нанесение пенетранта
3. Удаление излишков пенетранта
4. Нанесение проявителя
5. Контроль
Капиллярный контроль. Цветная дефектоскопия. Капиллярный метод неразрушающего контроля.
- Хиты продаж
- Новинки
- Акции
Капиллярная дефектоскопия (контроль жидкими пенетрантами)
В статье рассмотрен контроль жидкими пенетрантами — основной метод дефектоскопии поверхности. Приводятся физические основы, принцип действия и особенности метода. Сравниваются отечественные и зарубежные пенетранты; с точки зрения чувствительности метода анализируются класс чувствительности капиллярного контроля, эталоны и контрольные образцы.
0б авторе
Дамаскинский Евгений Алексеевич
Заместитель генерального директора ООО «Зайферт-Рентген» (Санкт-Петербург). Кандидат физико- математических наук. Научные интересы — методы неразрушающего контроля, детекторы ионизирующих излучений.
Особенности капиллярных методов неразрушающего контроля
Среди разнообразных методов неразрушающего контроля (НК) капиллярная дефектоскопия занимает особое положение. Во-первых, этот метод пригоден только для контроля поверхности материала или изделия, и, во-вторых, среди различных методов контроля поверхности капиллярный метод отличается универсальностью. Так, если метод течеискания применим только для определения сквозных деформаций, а магнитопорошковый метод применяется для контроля ферромагнитных материалов и изделий с относительной магнитной проницаемостью не менее 40, то капиллярный метод используется независимо от материала и формы объекта контроля (ОК), геометрии и направления дефектов. Он пригоден для выявления несплошностей с поперечными размерами 0,1 — 500 мкм, в том числе сквозных, на поверхности черных и цветных металлов, сплавов, керамики, стекла и т. п. За рубежом его называют методом контроля проникающими жидкостями (Liquid penetrant testing). По совокупности качеств: возможности выявления микроскопических дефектов на поверхности, недоступных другим методам НК, стоимости контроля единицы площади изделия, простоте, отсутствию сложной аппаратуры, портативности и мобильности — капиллярный метод превосходит все другие методы.
Развитие методов дефектоскопии поверхностей тесно связано с техническим прогрессом. Современное промышленное оборудование изготавливается при минимальном расходе материала, а эксплуатируется при больших, почти предельных нагрузках. В таком режиме именно трещины на поверхности представляют собой наиболее опасные дефекты, т. к. локальные напряжения в надрезе могут привести к скорому разрыву. Для обнаружения поверхностных дефектов и был предложен пенетрантный метод. Произошло это во время Второй мировой войны, когда сотрудник компании Юнкерс Хельмут Клумпф запатентовал красно-белый капиллярный метод обнаружения поверхностных дефектов. Как это часто бывает в истории техники, параллельно и независимо аналогичный метод стал применяться по другую сторону океана, в США.
Сегодня десятки компаний предлагают различные пенет- ранты, которые нашли широкое применение в энергомашиностроении, судостроительной промышленности, авиационной и космической технике, в атомной энергетике, при контроле оборудования, подведомственного Госгортехнадзору и т.д.
Физические основы и принцип действия
Метод основан на капиллярном проникновении внутрь дефекта индикаторной жидкости, хорошо смачивающей материал ОК, с последующей регистрацией индикаторных следов.
Красящий пенетрант наносится на поверхность. Благодаря особым качествам, которые обеспечиваются подбором определенных физических свойств пенетранта: поверхностного натяжения, вязкости, плотности, он под действием капиллярных сил проникает в мельчайшие открытые на поверхности дефекты.
Проявитель растворяет находящийся внутри дефекта краситель, во время испарения несущей жидкости сорбирует его и за счет диффузии «вытягивает» оставшийся в дефекте пенетрант на поверхность.
Имеющиеся дефекты видны достаточно контрастно. Индикаторные следы в виде ветвящихся линий указывают на трещины или царапины, отдельные точки — на поры.
Контроль цветными пенетрантами
Процесс обнаружения дефектов капиллярным методом разделяется на 5 стадий, четыре из которых схематично показанны на рисунке.
Стадия I. Предварительная очистка поверхности Чтобы краситель мог проникнуть в дефекты на поверхности, ее предварительно следует тщательно очистить водой или органическим очистителем. Все загрязняющие вещества (масла, ржавчина, накипь и т. п.), любые покрытия (металлизация, краска и т. п.) должны быть удалены с контролируемого участка. После этого поверхность и полости дефектов должны быть высушены, чтобы внутри дефекта не осталось следов воды или очистителя.
Стадия 2. Применение пенетранта Пенетрант, обычно красного цвета, наносится на поверхность путем распыления, кистью или погружением ОК в ванну, чтобы контролируемый участок хорошо пропитался и полностью покрылся пенетрантом. Рекомендуемое время контакта от 5 до 30 мин. при температуре 5-50o С.
Стадия 3. Удаление избытка пенетранта Избыток пенетранта удаляется протиркой салфеткой, промыванием водой, либо используя тот же самый очиститель, который применялся на первой стадии. При выполнении этой операции важно иметь в виду, что пенетрант следует удалить с поверхности, но не из полости дефекта. Контролируемую поверхность далее высушивают безворсовой материей или струей воздуха. Теплый воздух с температурой до 50o С ускоряет процесс сушки.
В случае наличия на поверхности дефектов с шириной раскрытия более 0,1 мм обычно применяют эмульгатор. При промежуточном промывании водой краситель эмульгирует, т. е. образует желатиноподобную смесь, и, тем самым, препятствует вымыванию красителя из дефекта. Если же использовать очиститель, то есть опасность вымывания пенетранта и неправильной индикации дефекта.
Стадия 4. Применение проявителя
Сразу же после просушки на контролируемую поверхность наносится проявитель обычно белого цвета. Проявитель наносится тонким, равномерным слоем, поскольку толстый слой будет маскировать дефекты и затруднять индикацию. Для этого подходят как разбрызгиватели, так и распылители. Наиболее удобны для выполнения этой операции аэрозольные баллончики, которые дают наиболее тонкий слой на поверхности. Нанесение проявителя кистью недопустимо. После нанесения проявителя следует выждать некоторое время, чтобы достичь максимальной визуализации дефекта. Время изменяется от 5 мин. для больших разрывов до 1 ч для тонких дефектов. Поверхностные дефекты будут проявляться как красные следы на белом фоне. Могут использоваться как смываемые, так и водостойкие проявители. В смываемом проявителе индикаторный рисунок дефекта во время проявки постоянно увеличивается, «кровоточит». В водостойком проявителе следы сразу же после испарения несущей жидкости (примерно через одну-две минуты) жестко фиксируются. В этом случае результат контроля можно документировать каким-нибудь способом, например, используя сканер, записать его в память компьютера.
Стадия 5. Контроль
Инспектирование ОК начинается непосредственно после окончания процесса проявки и заканчивается согласно разным стандартам не более, чем через 30 мин. Относительная оценка глубины дефекта возможна по цветовому пятну. Если пятно проявляется как бледно-красное, дефект залегает неглубоко в материале. Темно-красные линии указывают на более глубокие дефекты. После проведения контроля смываемый проявитель легко удаляется с поверхности. Водостойкий проявитель удаляется очистителем.
Сквозные трещины на тонкостенных контролируемых деталях можно обнаружить, если с одной стороны ОК нанести красящий пенетрант, а с другой — проявитель. Прошедший насквозь краситель будет хорошо виден в слое проявителя.
Флуоресцентный метод контроля
Все описанные выше стадии применения цветных пенетрантов присутствуют и во флуоресцентном методе. Отличие состоит в том, что вместо красящего пенетранта применяется флуоресцирующее вещество, которое под действием ультрафиолетового излучения с длиной волны 315-400 нм излучает в видимой части спектра.
Класс чувствительности капиллярного контроля
Согласно ГОСТ 18442-80 класс чувствительности контроля определяется в зависимости от размера выявляемых дефектов. В качестве параметра размера дефекта принимается поперечный размер дефекта на поверхности ОК — так называемая ширина раскрытия дефекта (табл. 1).
Таблица 1
Класс чувствительности |
Ширина раскрытия дефекта, мкм |
I |
менее 1 |
II |
от 1 до 10 |
III |
от 10 до 100 |
IV |
от 100 до 500 |
технологический |
не нормируется |
За рубежом установлены другие шкалы чувствительности пенетрантов. Например, в немецком промышленном стандарте DIN 54 152, который применяется и в ряде других стран Европы, чувствительность пенетрантов также разделяется на четыре класса, но шкала чувствительности обратная (табл. 2).
Таблица 2
Класс чувствительности |
Ширина раскрытия дефекта, мкм (± 20 %) |
Толщина никелевого покрытия, мкм (± 10 %) |
I — низкий |
4 |
100 |
II — средний |
2 |
60 |
III — высокий |
1 |
60 |
IV — очень высокий |
0,6 |
50 |
Обратим внимание на очень высокую шкалу чувствительности по DIN в сравнении с ГОСТ 18442-80. А именно, все четыре класса чувствительности по DIN «укладываются» в полтора высших класса чувствительности по ГОСТ.
Эталоны и контрольные образцы
Чувствительность отечественных дефектоскопических материалов определяется на контрольных образцах, т. е. на пластинах с заранее нормируемыми свойствами, изготовленными по определенной технологии. Образцы представляют собой стальные или титановые пластины с заданной шероховатостью поверхности, на которую нанесены трещины определенных размеров и формы. Контрольные образцы позволяют, прежде всего, получить представление о возможностях индикации трещин на ОК. Кроме того, контрольные образцы служат для постоянного периодического контроля важнейших свойств пенетрантов: чувствительности и смываемости. В частности, по контрольным образцам можно определить степень ухудшения свойств пенетрантных наборов; выбрать технологические режимы контроля.
Процедура определения чувствительности зарубежных пенетрантов отличается от описанной выше. Согласно DIN 54 152 все пенетранты подвергаются квалификационному тесту на соответствие качеству, который проводится независимыми организациями. Для сравнения чувствительности различных пенетрантов в качестве «эталонной поверхности» используются никелированные пластины с различной толщиной покрытия. Калиброванные трещины наносятся на «стандартную» поверхность, обеспечивая одинаковые условия сравнения.
Квалификационный тест включает также измерение физических величин (вязкость, плотность и т. п.), от которых зависит качество пенетрантов. При положительных результатах производитель получает сертификат качества продукции.
Кроме того, DIN 54 152 предусматривает тестирование пенетрантов, которое выполняется пользователем. Эталоны пользователя позволяют правильно оценить качество применяемых пенетрантов и сравнить результаты применения разных технологических методик.
Жидкие пенетранты
Эффективность капиллярного контроля при прочих одинаковых условиях определяется свойствами дефектоскопических материалов: пенет- ранта, проявителя, очистителя. Последовательное применение этих материалов в определенным образом подобранном сочетании (в наборе), позволяет получать наилучшие результаты. Отечественные наборы хорошо известны. Опыт показал, что их применение позволяет надежно решать весь круг задач капиллярной дефектоскопии. К сожалению, отечественные жидкие пенетранты выпускаются только в разливном виде и не производятся в аэрозольной упаковке.
Аэрозольный баллончик удобен, когда объектом контроля является не все изделие, а лишь отдельные участки его поверхности, в труднодоступных для контроля участках поверхности изделия, в случаях применения на открытом воздухе. Такая упаковка обеспечивает экономичность расходования пенетранта, энерго- и ресурсосберегаемость при проведении НК. Пе- нетрант (проявитель, очиститель), содержащийся в баллончике, имеет гарантированные качество и свойства, т. е. может использоваться без дополнительной проверки. Отсюда и надежность контроля, и экономия рабочего времени. Аэрозольные баллончики делают НК портативным и мобильным. Они компактны (объем 400 или 500 мл), имеют небольшой вес (не более 0,5 кг), легко удерживаются в одной руке и позволяют вести распыление почти из любого положения.
Контроль пенетрантами в аэрозольной упаковке широко распространен в Европе и США. В нашей стране этот способ контроля только начал применяться. Важно заметить, что ГОСТ 18442-80 не накладывает никаких ограничений на тип и состав используемых дефектоскопических материалов.
Десятки европейских фирм могут предложить более сотни типов пенетрантов. Возникает естественный вопрос: какой набор пенетрантов является наилучшим? Не представляется возможным теоретически показать преимущества одного набора пенетрантов перед другим. Путь прямого сравнения некоторых технических показателей, таких, например, как класс чувствительности, также не позволяет выявить лучший набор пенетрантов, т. к. выбор класса чувствительности определяется задачами, для решения которых выпускаются разные по чувствительности пенетрантные наборы. Лучшим является тот набор, который надежно решает Вашу задачу в соответствии с требованиями технической документации на ОК.
В табл. 3 и 4 приведены наборы для цветного и люминесцентного методов контроля жидкими пенетрантами, выпускаемых фирмами, которые до настоящего времени были представлены на российском рынке.
Два слова о пенетрантах, работающих при различных температурных условиях. Диапазон температур, при которых работают пенетранты (т. е. температур ОК) составляет 10-35° С для отечественных наборов и от -10 до +100° С для зарубежных. Отечественный набор № 2 допускает применение при самой низкой температуре (-40° С), наборы для работы при самой высокой температуре предлагают фирмы HELLING (до 175°С) и BYCOSIN (до 200°С).
С большим удовольствием я приношу благодарность сотрудникам тех компаний, которые любезно откликнулись на предложение прислать информацию о своих фирмах и выпускаемой ими продукции.
НАБОРЫ ДЛЯ ЦВЕТНОГО КОНТРАСТНОГО МЕТОДА
Таблица 3
НАБОРЫ ДЛЯ ФЛУОРЕСЦЕНТНОГО МЕТОДА
Таблица 4
Принятые сокращения: 1) Пенетрант: кр — красный; гол — голубой. 2) Очиститель: Н — гидрофильный, V — липофильный.3) Проявитель: сух. — сухой.
Капиллярный контроль, цветная дефектоскопия | ООО «Квалитест»
Проведение капиллярного метода контроля: особенности, назначение, применение
Одним из наиболее распространенных методов диагностики качества деталей и оборудования без нарушения их целостности является капиллярный контроль (цветная дефектоскопия). Данный метод позволяет выявить и охарактеризовать дефекты, расположенные на поверхности изделия, либо сквозные повреждения (коррозия, трещины, свищи, полости, непровары и другие). Для качественной покраски и избежания появления подобных дефектов мы советуем пользоваться специальными аппаратами для электростатического распыление краски.
Наиболее целесообразен капиллярный метод контроля для обнаружения предельно малых повреждений, которые невозможно заметить при осмотре невооруженным глазом и путем применения увеличительных приборов. Как правило, дефект недостаточно контрастирует с общим фоном материала, поэтому даже использование лупы или микроскопа не позволяет его обнаружить.
Для проведения капиллярного метода неразрушающего контроля может быть использовано оборудование разных производителей. Сегодня на рынке одними из наиболее востребованных являются наборы для капиллярной дефектоскопии Magnaflux: линии, установка, ультрафиолетовые лампы.
Как реализуется капиллярный метод контроля?
При проведении капиллярного неразрушающего контроля изделия на его поверхность наносится специальное вещество — пенетрант. Но перед этим исследуемую поверхность следует тщательно очистить от жира, ржавчины, пыли и загрязнений, а затем — просушить. После этого на поверхность обрабатывается пенетрантом для капиллярного контроля (например Magnaflux SKL-SP2), который проникает в существующие дефекты. Излишки пенетранта удаляются с поверхности, таким образом, остается только вещество в полостях дефектов.
Для того чтобы извлечь пенетрант, заполнивший дефект, на поверхность, используется проявитель (например Magnaflux SKD-S2). Результат (наличие дефекта) может быть оценен визуально либо (при использовании люминесцентного пенетранта) путем просвечивания в темном помещении. Для этой цели используется ультрафиолетовый светильник с длиной волны 365 нм, а повреждения проявляются в виде светящихся точек или линий.
Капиллярный неразрушающий контроль: разновидности
В зависимости от способа получения результата, различают следующие виды капиллярного контроля:
- цветная дефектоскопия;
- люминесцентная дефектоскопия;
- люминесцентно-цветная дефектоскопия.
Капиллярный контроль: востребованность и применение
Диагностика с помощью капиллярного метода контроля дает возможность исследовать объекты разных размеров, форм, изготовленные из разных материалов, в том числе металла (например, капиллярный контроль сварных соединений и сварных швов), пластмассы, стекла, чугуна и других. Применяется капиллярный метод в ракетостроении, машиностроении, электротехнике, медицине, атомной энергетике и других отраслях промышленности.
Купить оборудование для цветной дефектоскопии или люминесцентной дефектоскопии вы можете в компании Квалитест в Москве, Санкт-Петербурге и других городах России.
Учебные плакаты по неразрушающему контролю
Учебные плакаты по неразрушающему контролю — капиллярная дефектоскопия
Все плакаты печатаются на матовой бумаге формата А1 (594×841мм) или А0 (1189х851мм), плотность бумаги 150г.
Мы можем изготовить комплект учебных плакатов по капиллярному контролю специально под Ваши требования.
Также предлагаем двустороннюю ламинацию, которая сохранит плакаты от выгорания и влаги.
Капиллярный контроль – комплект 3 плаката:
-
Капиллярный контроль: основные понятия, методы, применяемые материалы согласно ГОСТ 18442-80
- Методы проведения контрастного капиллярного контроля согласно ГОСТ 18442-80
- Методы проведения флуоресцентного капиллярного контроля согласно ГОСТ 18442-80
Процесс оформления для юридических и физических лиц:
Для покупки товара в нашем интернет-магазине выберите понравившийся товар и добавьте его в корзину. Далее перейдите в Корзину и нажмите на «Оформить заказ» или «Быстрый заказ».
- Выберите тип покупателя (Юридическое лицо или Физическое лицо) и регион доставки
- Укажите способ доставки до терминала транспортной компании в вашем городе (самовывоз) или доставка курьером (DHL, СДЭК и т др.) в любом случае доставку можно будет изменить после разговора с менеджером компании или в личном кабинете в разделе заказы
- Укажите Счёт для банковского перевода с вашего расчётного счёта Юр. лица (или личного счёта для Физ. лица)
Оформление заказа в полном режиме выглядит следующим образом. Заполняете полностью форму начиная с обязательных полей: Название компании* (или ФИО),Контактное лицо*,E-Mail*
Телефон*, адрес, способ доставки, оплаты, данные о себе. Советуем в комментарии к заказу написать информацию, которая поможет сотруднику более детально ответить на ваши вопросы.
Нажмите кнопку «Оформить заказ».
Как во время оформления заказа так и после вы можете связаться с нами для уточнения любых вопросов
Оплачивайте покупки удобным способом. В интернет-магазине доступно 3 варианта оплаты:
- Банковский перевод для Юридических лиц при самовывозе или доставке курьером. Специалист свяжется с вами после оформления заказа. Вы переводите денежные средства после формирования счёта в личном кабинете или разговора с нашим сотрудником который отправит вам счёт для оплаты. Дальше стандартно подписываете товаросопроводительные документы (УПД) при получении товара.
- Безналичный расчет при самовывозе или оформлении в интернет-магазине: карты Visa и MasterCard.
Чтобы оплатить покупку, система перенаправит вас на сервер системы ASSIST. Здесь нужно ввести номер карты, срок действия и имя держателя.Доступно для карт привязанных к расчетному счёту Юридических лиц.
- Электронные системы при онлайн-заказе: PayPal, WebMoney и Яндекс.Деньги. Для совершения покупки система перенаправит вас на страницу платежного сервиса. Здесь необходимо заполнить форму по инструкции.
Экономьте время на получении заказа. В интернет-магазине федеральной компании NDT Rus доступно 3 варианта доставки:
- Курьерская доставка работает с 9.
00 до 19.00. Когда товар поступит на склад, курьерская служба свяжется для уточнения деталей. Специалист предложит выбрать удобное время доставки и уточнит адрес. Осмотрите упаковку на целостность и соответствие указанной комплектации.
- Самовывоз из пункта выдачи. Список точек для выбора появится в корзине. Когда заказ поступит на склад, вам придет уведомление. Для получения заказа обратитесь к сотруднику в кассовой зоне и назовите номер.
- Самовывоз из терминала транспортной компании
Наш интернет магазин создан в первую очередь для удобной работы с Юридическими лицами
Мы сохраняем возможность нашим клиентам «старыми» способами оформить заказ: когда вы звоните по телефону и диктуете своему менеджеру заявку или отправляете сформированное ТЗ на e-mail и дополняем возможность оформить заказ через социальные сети, мессенджеры, онлайн консультант на сайте.
Но самое главное мы внедрили удобную систему создания счёта для оплаты Юридическим лицом прямо в личном кабинете. Больше не прийдётся ждать ответа от сотрудника, если вы сами знаете какой прибор или расходные материалы вам сейчас необходимо приобрести.
Оформив заказ один раз вы сохраните данные для последующих заказов.
В любой момент можно позвонить нам для получения консультации.
УСЛУГИ ПО ПРОВЕДЕНИЮ КАПИЛЛЯРНОГО КОНТРОЛЯ
Капиллярная дефектоскопия неразрушающего контроля (НК) предназначена для обнаружения открытых дефектов, выходящих на поверхность: трещин, пор, раковин, непроваров и других несплошностей поверхности изделий без их разрушения и, следовательно, дает возможность проводить 100% контроль продукции.
Классически капилярная дефектоскопия осуществляется контролем проникающими веществами.
Контроль проникающими веществами
Капиллярная дефектоскопия – является одним из основных методов неразрушающего контроля и предназначена для обнаружения поверхностных и сквозных дефектов в объектах контроля, определения их расположения, протяженности (для протяженных дефектов типа непроваров, трещин) и их ориентации на поверхности. Капиллярный метод неразрушающего контроля (ГОСТ 18442-80) основан на капиллярном проникновении внутрь дефекта индикаторных жидкостей, хорошо смачивающих материал объекта – поверхность контроля и последующей регистрации индикаторных следов (благодаря чему так же носит название цветная дефектоскопия).
В соответствии с техническими требованиями в большинстве случаев необходимо выявлять настолько малые дефекты, что заметить их при визуальном осмотре невооруженным глазом практически невозможно. В то же время, применение оптических приборов, например лупы или микроскопа, не позволяет выявить поверхностные дефекты из-за недостаточной контрастности изображения дефекта на фоне металла и малого поля зрения при больших увеличениях.
В таких случаях наиболее применим — капиллярный метод контроля.
Капиллярная дефектоскопия позволяет контролировать объекты любых размеров и форм, изготовленные из различных материалов: черных и цветных металлов, сплавов, пластмасс, стекла, керамики и т.п. Капиллярный контроль широко востребован при дефектоскопии сварных швов.
При контроле красящий пенетрант наносится на контролируемую поверхность и благодаря своим особым качествам под действием капиллярных сил проникает в мельчайшие дефекты, имеющие выход на поверхность объекта контроля. Проявитель, наносимый на поверхность объекта контроля через некоторое время после осторожного удаления с поверхности пенетранта, растворяет находящийся внутри дефекта краситель и за счет диффузии “вытягивает” оставшийся в дефекте пенетрант на поверхность объекта контроля. Имеющиеся дефекты видны достаточно контрастно. Индикаторные следы в виде линий указывают на трещины или царапины, отдельные точки — на поры.
Процесс капиллярного контроля состоит из 5 этапов:
1 – предварительная очистка поверхности.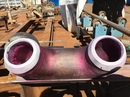
Чтобы краситель мог проникнуть в дефекты на поверхности, ее предварительно следует очистить водой или органическим очистителем. Все загрязняющие вещества (масла, ржавчина, и т.п.) любые покрытия (ЛКП, металлизация) должны быть удалены с контролируемого участка. После этого поверхность высушивается, чтобы внутри дефекта не оставалось воды или очистителя.
2 – нанесение пенетранта.
Пенетрант, обычно красного цвета, наносится на поверхность путем распыления, кистью или погружением объекта контроля в ванну, для хорошей пропитки и полного покрытия пенетрантом. Как правило, при температуре 5…50°С, на время 5…30 мин.
3 — удаление излишков пенетранта.
Избыток пенетранта удаляется протиркой салфеткой, промыванием водой, или тем же очистителем, что и на стадии предварительной очистки. При этом пенетрант должен быть удален только с поверхности контроля, но никак не из полости дефекта. Затем поверхность высушивается салфеткой без ворса или струей воздуха.
4 – нанесение проявителя.
После просушки сразу же на поверхность контроля тонким ровным слоем наносится проявитель (обычно белого цвета).
5 — контроль.
Выявление имеющихся дефектов начинается непосредственно после окончания процесса проявки. При контроле выявляются и регистрируются индикаторные следы. Интенсивность окраски которых говорит о глубине и ширине раскрытия дефекта, чем бледнее окраска, тем дефект мельче. Интенсивную окраску имеют глубокие трещины. После проведения контроля проявитель удаляется водой или очистителем.
Дефектоскопические материалы для цветной дефектоскопии выбирают в зависимости от требований, предъявляемых к контролируемому объекту, его состояния и условий контроля. Их укомплектовывают в целевые наборы, в которые входят полностью или частично взаимообусловленные совместимые дефектоскопические материалы.
Достоинства капиллярного контроля
Капиллярный контроль наряду с другими физическими методами ( визуально-измерительный контроль , рентгенографический контроль , ультразвуковой контроль , магнитно-порошковый контроль) является надежным и высокоэффективным средством для выявления возможных поверхностных дефектов.
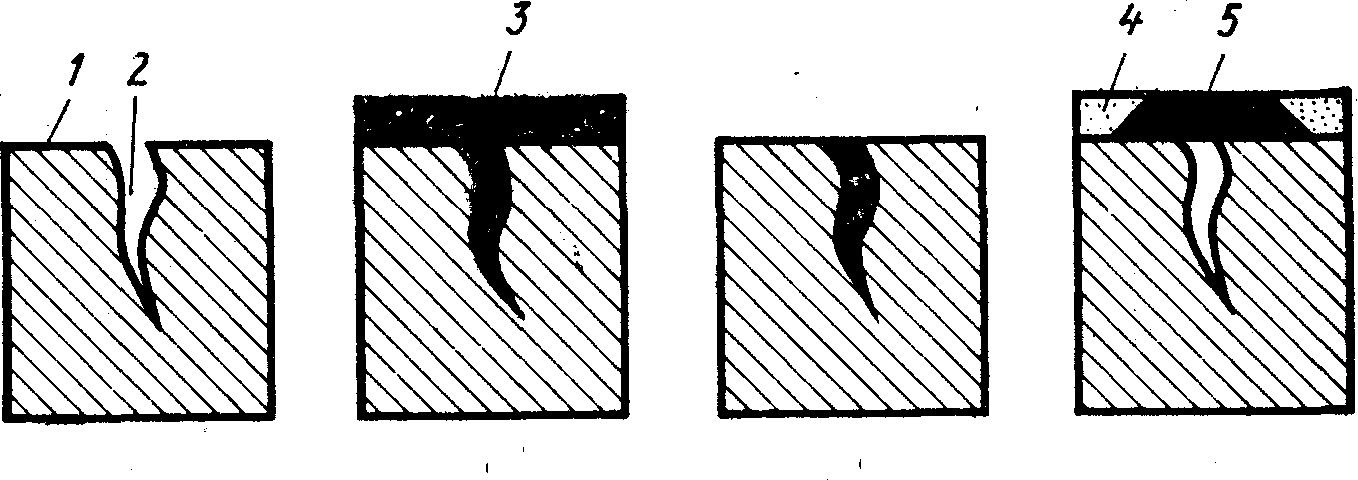
К недостаткам капиллярного контроля следует отнести его высокую трудоемкость при отсутствии механизации, большую длительность процесса контроля (от 0.5 до 1.5 ч), а также сложность механизации и автоматизации процесса контроля; снижение достоверности результатов при отрицательных температурах; субъективность контроля — зависимость достоверности результатов от профессионализма оператора; ограниченный срок хранения дефектоскопических материалов, зависимость их свойств от условий хранения.
Некоторые производители в целях экономии или некомпетентности игнорируют проведение неразрушающего контроля продукции или вспоминают о нём только на последней стадии — уже непосредственно перед сдачей объекта (а это приводит к дополнительной потери времени и непредусмотренным расходам), когда контроль бывает технически неосуществим. Подобное отношение к контролю качества чаще всего приводит к аварийным ситуациям в процессе эксплуатации и способно привести даже техногенным катастрофам.
Обращайтесь к нам вовремя!
Наша лаборатория неразрушающего контроля качественно выполнит капиллярный контроль сварных швов и основного металла трубопроводов, емкостей, сосудов и металлоконструкций различного назначения.
Penetrant Testing — обзор
Новые физические эффекты в гидродинамике пенетрантных испытаний
При пенетрантных испытаниях размерный эффект пенетрантной вязкости проявляется как на стадии заполнения микродефектов, так и в значительно большей степени при поглощении пенетранта проникающим веществом. слой мелкодисперсного проявителя на стадии разработки. Физический смысл предложенной интерпретации эффекта размерной вязкости заключается в следующем. Эффект обнаружен в полярных жидкостях, молекулы которых не только сдвигающие, но и моментные напряжения действуют между компонентами такой микрополярной жидкости. В результате жидкие ассоциаты не только совершают поступательное движение, но и имеют собственные угловые скорости. Таким образом, энергия, затрачиваемая на абсорбцию жидкости на определенную глубину, тратится на преодоление как сдвиговых, так и моментных напряжений между ассоциатами, т.е. при заданном перепаде давления расход жидкости уменьшается, а эффективная вязкость возрастает. В частности, было получено выражение для расчета смещения пенетрантного мениска в тупиковом цилиндрическом капилляре длиной l o и радиусом R от устья на глубину [1, 2] °:
(1 ) t = 6μHℓ02ψH6 cos θ [ν22− (1 − ψ) (ν + ψℓnψ − νψ)] x x (k∼H) 2 (k∼H) 2 + 3δ¯ [2− (k∼H) cth (k ∼H / 2)],
, где ψ = pk / (pk − pa); pk = 26 cos θ / H — капиллярное давление, μ H — табулированная сдвиговая вязкость пенетранта при заданной температуре; σ — коэффициент поверхностного натяжения; θ — угол смачивания; v = 1/10; Па — атмосферное давление; k∼ и δ¯ — параметры микроструктуры пенетранта.
Впервые разработан и использован метод определения микроструктурных параметров пенетрантов k∼ и δ¯. Полученные значения k∼ и δ¯ для некоторых пенетрантов, широко используемых при испытаниях пенетрантов, были впервые использованы для описания размерного эффекта пенетрантной вязкости в капиллярных дефектах различной геометрии и в пористых материалах [3].
Предлагаемая модель развития дефекта [4] основана на трех уравнениях, описывающих поглощение пенетранта, содержащегося в дефекте, пористым слоем сорбционного проявителя.Это уравнение Навье-Стокса для потока жидкости на фронте пропитки в слое проявителя и соотношение баланса массы жидкости, которое замыкает уравнения. Из-за нехватки места мы не будем здесь приводить вывод уравнений кинетики развития дефекта, который был описан в [4, 5], а лишь перечислим основные характеристики процесса, важные для качества и чувствительности теста. . Это проникающая вязкость μ и поверхностное натяжение σ, толщина h, пористость ρ, проницаемость и эффективный радиус R e слоя проявителя, остаточное заполнение полости дефекта пенетрантом перед нанесением проявителя на исследуемую поверхность n.
Последнее количество особенно важно для чувствительности теста. Поэтому полное двустороннее заполнение тупиковых конических капилляров жидкими пенетрантами, сопровождающееся существенным (на 2 или 3 порядка) увеличением скорости растворения газа, запертого в капилляре, в жидкости, представляется особенно интересным для теории. и практика пенетрантного тестирования [6]. Установлено, что некоторые жидкости (вода, ацетон, этиловый и бутиловый спирты и др.) Заполняют конические капилляры длиной 1 o ≲ 2 · 10 −3 м и радиусом R o ∼ 20 мкм, а не только от устья, но также и от тупика капилляра, где образуется и поднимается еще один столб жидкости.
Оба столба жидкости движутся в капилляре навстречу друг другу и в момент слияния (полного заполнения капилляра) их объемы становятся сравнимыми по порядку величины. Некоторые специальные эксперименты показали, что эффект можно объяснить переконденсацией жидкости в канале из-за наличия двух менисков с разной кривизной.
Проведенные эксперименты по определению влияния полного двухстороннего заполнения капилляров жидкостью на пенетрантное тестирование позволили выработать практические рекомендации по повышению чувствительности теста.Например, у сорбционных порошковых проявителей эффект снижает порог чувствительности теста. Между тем, замена суспензии порошкового проявителя с подобранными физико-химическими свойствами существенно увеличивает чувствительность теста. Выбор осуществляется с помощью соотношений, лежащих в основе другого эффекта, который мы наблюдали в капилляре, когда две разные жидкости контактируют. Исследования кинетики миграции жидкостей после их соприкосновения в капилляре выявили особый тип взаимодействия, заключающийся в извлечении одной жидкости из капилляра другой [7].Мы предложили физическую модель процесса, основанную на предположении, что одна жидкость течет относительно другой по стенке капилляра в виде тонкой пленки. Термодинамический анализ [8] показал, что такой процесс действительно возможен, если свойства жидкости L 1 , контактирующей в капилляре с жидкостью L 2 , удовлетворяют соотношению
(2) δL1 cos θ1≥δL2cos θ2,
, где δL1,2 и θ 1,2 — поверхностное натяжение и угол смачивания капиллярного материала жидкостями L 1 и L 2 . Эксперименты показали, что соотношение (2) выполняется для всех жидкостей, для которых наблюдался эффект экстракции, а именно для воды, ацетона, этилового и бутилового спиртов, реальных индикаторов и других жидкостей, используемых при пенетрантных испытаниях.
Эффект негистерезисный. Когда (2) не выполняется, жидкость L 1 блокируется в капилляре жидкостью L 2 , контактирующей с первым.
Исследования капилляров как модельных дефектов подтверждены реальными промышленными пенетрантными испытаниями.В [9] мы показали, в частности, что жидкая фаза проявителя оказала существенное влияние на обнаружение дефектов и была очень важна для процесса тестирования.
Принимая во внимание эффект извлечения одной жидкости из капилляра другой, можно выбрать лучшие составы наборов для пенетрантного тестирования и повысить надежность теста. Мы использовали этот критерий при разработке метода испытаний пористых материалов.
Соотношение (2) должно соблюдаться при составлении новых наборов для отбора жидкостей, последовательно взаимодействующих друг с другом во время пенетрантных испытаний (шайба, индикатор, очиститель, жидкий носитель проявителя) и для замены новых материалов, более эффективных и экологически чистых, в используемые комплекты.
Неразрушающий контроль — Проверка проницаемости красителя
Что такое инспекция на проникновение красителя ..
Dye Penetrant Inspection (DPI), также называемый Liquid Penetrant Inspection (LPI) или Penetrant Testing (PT), является одним из старейших и упрощенных методов неразрушающего контроля, самые ранние версии которого (с использованием керосина и масляной смеси) относятся к 19 веку.
Жидкостный проникающий контроль используется для обнаружения любых связанных с поверхностью неоднородностей, таких как трещины от усталости, закалки и шлифования, а также трещины, пористость, неполное сплавление и дефекты в соединениях.
Принципы
DPI основан на капиллярном действии, при котором жидкость с низким поверхностным натяжением проникает в чистые и сухие неоднородности, разрушающие поверхность. Пенетрант может быть нанесен на тестовый компонент окунанием, распылением или кистью. По истечении достаточного времени проникновения избыток пенетранта удаляется и наносится проявитель. Разработчик помогает извлечь пенетрант из дефекта, где невидимая индикация становится видимой инспектору. Проверка проводится в ультрафиолетовом или белом свете, в зависимости от типа используемого красителя — флуоресцентный или нефлуоресцентный (видимый).
Материалы
Пенетранты классифицируются по уровням чувствительности. Видимые пенетранты обычно красного цвета и представляют самую низкую чувствительность. Флуоресцентные пенетранты содержат два или более красителя, которые флуоресцируют при возбуждении ультрафиолетовым (УФ-A) излучением (также известным как черный свет). Поскольку флуоресцентный пенетрантный контроль проводится в затемненной среде, а возбужденные красители излучают яркий желто-зеленый свет, который сильно контрастирует с темным фоном, этот материал более чувствителен к дефектам.
При выборе уровня чувствительности необходимо учитывать множество факторов, включая среду, в которой будет проводиться испытание, качество поверхности образца и размер искомых дефектов. Также необходимо убедиться, что исследуемые химические вещества совместимы с образцом, чтобы исследование не привело к постоянному окрашиванию или разложению. Этот метод может быть довольно портативным, потому что в его простейшей форме для проверки требуется всего 3 баллончика с аэрозольными баллончиками, несколько безворсовых салфеток и достаточное количество видимого света.Стационарные системы со специальными станциями для нанесения, промывки и проявки более дороги и сложны, но приводят к большей чувствительности и увеличению пропускной способности образцов.
Этапы проверки
- Предварительная очистка ..
Испытуемая поверхность очищается для удаления любой грязи, краски, масла, жира или любых отслаивающихся отложений, которые могут либо удерживать пенетрант от дефекта, либо вызывать несоответствующие или ложные показания. Методы очистки могут включать растворители, этапы щелочной очистки, парообразование или струйную очистку.Конечная цель этого шага — получить чистую поверхность, на которой все дефекты будут открытыми, сухими и свободными от загрязнений.Обратите внимание, что если используется струйная очистка, она может «проработать» небольшие неоднородности детали, и ванна для травления рекомендуется в качестве обработки после струйной очистки.
- Нанесение пенетранта ..
Затем пенетрант наносится на поверхность испытуемого объекта. Пенетранту дают «время выдержки», чтобы проникнуть в любые дефекты (обычно от 5 до 30 минут).Время выдержки в основном зависит от используемого пенетранта, испытываемого материала и размера искомых дефектов. Как и ожидалось, меньшие дефекты требуют большего времени проникновения. Из-за их несовместимости необходимо соблюдать осторожность, чтобы не наносить пенетрант на основе растворителя на поверхность, которая должна быть проверена с помощью водосмываемого пенетранта. - Удаление излишков пенетранта.
Затем излишки пенетранта удаляются с поверхности. Метод удаления зависит от типа используемого пенетранта.Обычно выбираются смываемые водой, удаляемые растворителем, липофильные постэмульгируемые или гидрофильные постэмульгируемые.Эмульгаторы представляют собой наивысший уровень чувствительности и химически взаимодействуют с масляным пенетрантом, что позволяет удалить его с помощью водной струи. При использовании средства для удаления растворителя и безворсовой ткани важно не распылять растворитель непосредственно на тестируемую поверхность, поскольку это может удалить пенетрант с дефектов. Если избыток пенетранта не удалить должным образом, после нанесения проявителя он может оставить фон в проявленной области, который может скрыть признаки или дефекты.Кроме того, это также может привести к ложным показаниям, что серьезно затруднит вашу способность провести надлежащий осмотр.
- Нанесение проявителя.
После удаления излишков пенетранта на образец наносится белый проявитель. Доступны несколько типов проявителя, в том числе … неводный влажный проявитель, сухой порошок, суспендируемый в воде и растворимый в воде. Выбор проявителя определяется совместимостью пенетранта (нельзя использовать водорастворимый или суспендируемый проявитель с водосмываемым пенетрантом) и условиями проверки.При использовании неводного влажного проявителя (NAWD) или сухого порошка образец необходимо высушить перед нанесением, в то время как растворимые и суспендируемые проявители наносятся на часть, еще влажную после предыдущего шага. NAWD коммерчески доступен в аэрозольных баллончиках и может использовать ацетон, изопропиловый спирт или пропеллент, который является их комбинацией. Проявитель должен образовывать полупрозрачное ровное покрытие на поверхности.
Проявитель вытягивает пенетрант из дефектов на поверхность, чтобы сформировать видимую индикацию, широко известную как просачивание.Любые просвечивающие участки могут указывать на расположение, ориентацию и возможные типы дефектов на поверхности. Для интерпретации результатов и определения дефектов по обнаруженным показаниям может потребоваться определенная подготовка и / или опыт. - Осмотр ..
Инспектор будет использовать видимый свет соответствующей интенсивности (обычно 100 фут-свечей или 1100 люкс) для видимого пенетранта красителя.Ультрафиолетовое (УФ-A) излучение адекватной интенсивности (обычно 1000 микроватт на квадратный сантиметр) наряду с низким уровнем окружающего освещения (менее 2 фут-кандел) для флуоресцентных проникающих исследований.Осмотр тестовой поверхности следует проводить через 10-30 минут, в зависимости от типа продукта. Эта временная задержка позволяет осуществить промокание. Инспектор может наблюдать образец для формирования индикации при использовании видимого красителя. Также хорошей практикой является наблюдение за показаниями по мере их формирования, потому что характеристики истечения являются важной частью интерпретации характеристик дефектов.
- Последующая очистка ..
Испытательную поверхность часто очищают после проверки и регистрации дефектов, особенно если запланированы процессы нанесения покрытия после проверки.
Преимущества и недостатки
Основные преимущества и недостатки по сравнению с другими методами неразрушающего контроля:
Преимущества
- Высокая чувствительность (можно обнаружить небольшие неоднородности).
- Некоторые ограничения по материалам (можно проверять металлические и неметаллические, магнитные и немагнитные, а также проводящие и непроводящие материалы).
- Оперативный контроль больших площадей и объемов.
- Подходит для деталей сложной формы.
- Обозначения наносятся непосредственно на поверхность детали и представляют собой визуальное представление дефекта.
- Портативный (материалы доступны в аэрозольных баллончиках)
- Низкая стоимость (относительно недорого материалы и сопутствующее оборудование)
Недостатки
- Обнаруживаются только дефекты поверхностного разрушения.
- Проверять можно только материалы с относительно непористой поверхностью.
- Предварительная очистка имеет решающее значение, поскольку загрязнения могут маскировать дефекты.
- Металлические пятна от механической обработки, шлифования, абразивоструйной или пароструйной обработки должны быть удалены.
- Инспектор должен иметь прямой доступ к проверяемой поверхности.
- Шероховатость и шероховатость поверхности могут повлиять на чувствительность контроля.
- Необходимо выполнять и контролировать несколько технологических операций.
- Требуется дополнительная очистка допустимых деталей или материалов.
- Требуется обращение с химическими веществами и надлежащая утилизация.
Стандарты
Международная организация по стандартизации (ISO)
- ISO 3452-1, Неразрушающий контроль — Пенетрантный контроль — Часть 1.Общие принципы
- ISO 3452-2, Неразрушающий контроль. Пенетрантные испытания. Часть 2. Испытания проникающих материалов.
- ISO 3452-3, Неразрушающий контроль — Пенетрантный контроль — Часть 3. Контрольные образцы
- ISO 3452-4, Неразрушающий контроль — Пенетрантный контроль — Часть 4. Оборудование
- ISO 3452-5, Неразрушающие испытания. Испытания на проницаемость.
Часть 5. Испытания на проницаемость при температурах выше 50 ° C.
- ISO 3452-6, Неразрушающий контроль. Пенетрантный контроль. Часть 6.. Испытание на проницаемость при температурах ниже 10 ° C
- ISO 3059, Неразрушающий контроль — Пенетрантный контроль и испытание магнитными частицами — Условия просмотра
- ISO 12706, Неразрушающий контроль. Пенетрантное тестирование. Словарь .
- ISO 23277, Неразрушающий контроль сварных швов. Проникающий контроль сварных швов. Уровни приемки .
Европейский комитет по стандартизации (CEN)
- EN 1371-1, Литье — Жидкостный контроль — Часть 1.. Песок, гравитационная матрица и отливки под низким давлением
- EN 1371-2, Литье — Жидкостный контроль — Часть 2 .. Литье по выплавляемым моделям
- EN 10228-2, Неразрушающий контроль стальных поковок — Часть 2 .. Испытание на проницаемость
- EN 10246-11, Неразрушающий контроль стальных труб — Часть 11. Испытание на проницаемость бесшовных и сварных стальных труб для обнаружения поверхностных дефектов
Американское общество испытаний материалов (ASTM)
- ASTM E 165, Стандартная практика проверки проницаемости жидкости для общей промышленности
- ASTM E 1417, Стандартная практика испытаний на проникновение жидкости
Американское общество инженеров-механиков (ASME)
- Нормы ASME по котлам и сосудам под давлением, раздел V, ст.
6, Жидкостная проникающая экспертиза
- Нормы ASME по котлам и сосудам под давлением, раздел V, ст. 24 Стандартный метод испытаний на проникновение жидкости SE-165 (идентичный ASTM E-165)
Жидкостный проникающий контроль
Это простой и недорогой метод обнаружения поверхностных дефектов, таких как трещины, перехлесты, пористость и т. Д. Для обнаружения дефект должен достигнуть проверяемой поверхности.Пенетрантное тестирование — это шаг вперед по сравнению с визуальным осмотром и предлагает множество преимуществ, таких как скорость, покрытие большой площади и дешевизна.
Обычно это шестиэтапный процесс:
a) очистка поверхности (обезжиривание и т. Д.)
b) нанесение проникающей жидкости (окунание, распыление, кисть)
c) удаление излишков пенетранта (растворитель, вода)
г) нанесение проявителя
д) осмотр тестовой поверхности (визуальная, телекамера)
е) постинспекционная очистка (антикоррозионные растворы).
Есть три основные группы процессов пенетранта:
a) водорастворимые
b) постэмульгируемые с промывкой водой
c) удаляемые растворителем, разница заключается в методе, используемом для удаления избытка пенетранта.
В каждой из этих трех групп пенетрантный раствор может содержать краситель, делающий указание видимым в белом свете, или флуоресцентный материал, который флуоресцирует в подходящем ультрафиолетовом (УФ-A) свете.
Выбор метода для любого конкретного применения основан на:
a) чистоте поверхности образца
b) совместимости материалов с образцом
c) требуемой чувствительности
d) размере, форме и доступность проверяемой области
e) конечное использование компонента.
Флуоресцентные пенетранты обычно используются, когда требуется максимальная чувствительность к дефектам.
Принцип испытания проникающей жидкостью заключается в том, что проникающая жидкость всасывается в трещину, разрушающую поверхность, за счет капиллярного действия, а затем удаляется излишек поверхностного пенетранта; Затем на поверхность наносится проявитель (обычно сухой порошок), чтобы вывести пенетрант из трещины и создать указание на поверхности. Могут быть обнаружены трещины шириной до 150 нанометров. Показания намного шире, чем фактический дефект, и поэтому их легче увидеть.
Испытание на проникновение жидкости можно применять к любому непористому чистому материалу, металлическому или неметаллическому, но оно не подходит для грязных или очень грубых поверхностей. Очистка поверхности — важная часть методики пенетрантного тестирования. Метод может быть ручным, полуавтоматическим или полностью автоматизированным. Контроль проницаемости, непрерывные производственные линии, в которых образцы очищаются, погружаются, промываются, сушатся и т. Д., Являются обычным явлением.
Недавно было представлено оборудование для полной автоматизации стадии визуального контроля процесса путем роботизированной обработки образца по запрограммированной процедуре с просмотром телекамерой и распознаванием образов для выявления и распознавания дефектов.Могут быть включены процессы улучшения телевизионного изображения.
Иногда используется специальный проникающий процесс с очень высокой чувствительностью с использованием радиоактивных индикаторов, но он требует очень строгих процедур безопасности.
Определение, сущность, классификация, характеристика, способы и особенности применения
После сварки проводится обязательная дефектоскопия для определения качества сварного шва, его структуры поверхности и параметров дефекта. Осмотр должен проводиться неразрушающим образом, чтобы не повредить обрабатываемую деталь или используемую конструкцию.Этим требованиям отвечает метод капиллярного контроля, широко применяемый как в строительстве, так и в отраслях, связанных с применением сварочных работ.
Что такое дефектоскопия капилляров?
Это один из самых популярных методов обнаружения дефектов на поверхности целевой заготовки. Важно подчеркнуть применимость контроля именно для выявления параметров внешних возмущений — этот метод не используется для диагностики внутренней структуры шва.После завершения сварки методом капиллярного контроля мастер может записать такие характеристики дефектов, как положение поверхности, длина, ориентация и т. Д. Трещины и недостаточные проплавления чаще всего являются целевыми дефектами.
Но почему так важно использовать специальную технику, игнорируя стандартный визуальный осмотр, пусть даже с подключением профессиональной оптики? Одним из основных преимуществ этого метода является возможность обнаружения мелких дефектов, которые можно не заметить при традиционном визуальном осмотре.Использование оптического оборудования, например микроскопа или лупы, не позволит вам обнаружить дефекты из-за их низкого контраста на фоне металлической поверхности, не говоря уже о небольшом поле зрения при значительном увеличении. В свою очередь, капиллярная техника позволяет с высокой точностью исправлять дефекты в больших заготовках.
Требования к организации работ и методике их выполнения регламентируют стандарты нормативного документа на метод капиллярного контроля — ГОСТ 18442.В соответствии с официальным определением, эта технология проверки качества сварных швов представлена как способ анализа и регистрации сквозных и поверхностных неоднородностей материала. Кстати, происхождение заготовки в производственной или строительной среде не имеет значения: помимо черных и цветных металлов, технология успешно работает с керамикой, пластиком и стеклом.
Суть метода
Принцип действия метода капиллярного контроля заключается в выявлении структуры дефекта с помощью красящего пенетранта, обрабатывающего поверхность мишени.Высокая проникающая способность активного состава позволяет ему проникать в мельчайшие поры поверхности, обозначая контуры трещин или неплавления ярким цветом. Поэтапную технологию производства капиллярного метода контроля сварных швов можно представить следующим образом:
- Подготовка поверхности. От качества дефектоскопии будет зависеть чистота рабочей зоны. Малейшее препятствие в виде грязи, пыли и жира может помешать процессу маркировки капилляров.Поэтому проводится очистка поверхности, а иногда и шлифовка с последующей доводкой.
- Нанесение красящего состава. Как правило, используется красный пенетрант.
Его распыляют или наносят кистью в достаточном объеме, чтобы масса могла беспрепятственно заполнить все имеющиеся дефекты.
- Очистка от излишков пенетранта. Чтобы в дальнейшем было удобнее контролировать дефектную зону, с поверхности удаляют ненужный красящий раствор. Важно не прикасаться непосредственно к обозначенным контурам трещин.
- Приложение разработчика. Через некоторое время после высыхания пенетранта наносится проявитель — состав белого цвета, что позволит на контрасте выявить структурные нарушения.
- Контроль качества. После завершения процесса разработки оператор фиксирует следы и контуры дефектов.
Функциональную сущность метода капиллярного контроля можно свести к двум технологическим факторам обнаружения дефектов. Во-первых, это описанный процесс точечного визуального проявления структуры трещин и несращения.Во-вторых, это процедура прямой регистрации, измерения и анализа параметров дефекта, но с помощью других функциональных инструментов.
Классификация основных методов капиллярной дефектоскопии
Наиболее значимым признаком разделения разных методов капиллярного контроля является тип индикаторной смеси — один и тот же пенетрант. Выше был рассмотрен наиболее популярный состав красных маркеров, но есть и другие варианты, которые выгодно проявляют себя в различных условиях дефектоскопии.И в этом контексте можно предложить следующую классификацию методов контроля капилляров:
- Люминесцентный. Этот метод предполагает использование раствора или суспензии люминофора в сочетании с органическими растворителями, маслами и керосином. В процессе анализа выявленной дефектной структуры специального ультрафиолетового облучения не требуется — даже в темном помещении люминофор обеспечивает достаточный контраст, позволяя зафиксировать микротрещины толщиной до 0,1 мкм.
- Люминесцентный цветной метод.Дает максимально чувствительный эффект обнаружения внешних дефектов. Модификация люминесцентного индикатора, заключающаяся в использовании длинноволнового ультрафиолетового излучения.
Метод используется в лабораторных условиях для фиксации узоров сверхмалых трещин.
- Метод яркости. Его еще называют ахроматическим и является одним из наиболее доступных и простых методов контроля капилляров, возможностей которого достаточно для проверки качества большинства сварных швов. В работе используется керосин-меловая индикаторная жидкость, обеспечивающая контрастное проявление очертаний возможного дефекта.
- Фильтрованный суспензионный метод. В данном случае это не жидкость, а своеобразный порошковый подход к проявлению дефекта, что приводит к его крайне низкой чувствительности. Тем не менее использование отфильтрованных дисперсных частиц суспензии в качестве маркера — лучший вариант контроля, когда не допускается обработка поверхности заготовки жидкими растворами.
Комбинированные методы капиллярной дефектоскопии
Группа методов, особенностью которых является сочетание с другими методами неразрушающего контроля поверхности.Причем в основе обязательно должен быть способ обозначения дефекта. Итак, различают следующие комбинированные методы капиллярного контроля сварных швов:
- Капиллярный электростатический. Позволяет идентифицировать дефекты неметаллических деталей по индикаторному следу, который образован частицами наэлектризованного порошка на поверхности пенетранта.
- Капиллярный электроиндуктивный. В качестве дополнительного активного фактора используется электрический проводник, который работает непосредственно по контурам пенетранта без других посторонних включений.
- Капиллярная магнитная частица. Этот метод специально разработан для ферромагнитных намагничиваемых изделий с контролем дефектов вдоль индикаторного следа, образованного ферромагнитным порошком над проникающим слоем.
- Капиллярное излучение. Контроль осуществляется на основании анализа спектра ионизирующего излучения в области дефектной зоны, предварительно обработанной жидкостным индикатором.
Отдельного внимания заслуживает капиллярный метод неразрушающего контроля с использованием стабильных нитроксильных радикалов. Они смешаны с основным составом пенетранта и благодаря парамагнетизму нитроксилов позволяют использовать спектроскопию парамагнитного резонанса. Это высокоточный метод обнаружения микротрещин, глубоко проникающих в структуру материала, где обычные средства внешнего анализа неэффективны.
Характеристики метода контроля капилляров
В общей группе методов неразрушающего контроля этот метод соответствует второму уровню чувствительности, при котором могут возникать дефекты с потенциалом открытия до 1 мкм.К несплошностям мишени можно отнести дефекты, поперечное сечение которых варьируется в пределах 0,1-500 мкм. Основные физические и рабочие характеристики неразрушающего контроля капилляров включают вязкость, плотность, растяжение и пенетрацию. Во многом показатели по этим параметрам зависят от конкретного индикаторного состава. Например, пропитка со средней проникающей способностью характеризуется хорошей смачиваемостью и высоким поверхностным натяжением. Составы на основе керосина, бензола, жидких масел и скипидара, в частности, обеспечивают поверхностное натяжение до 10-2 Н / м. Что касается коэффициента яркостного контраста, то он может увеличиваться на 30-50% в зависимости от исходных данных маркера и условий применения метода.
Рабочие требования
В нормативно-технической документации приведен следующий набор общих требований к контролю неразрушающими капиллярными методами:
- Технология предназначена для неразрушающего дефектоскопа с целью выявления сквозных и поверхностных неоднородностей. в заготовках после сварочных работ.
- В процессе дефектоскопии капиллярными методами необходимо определять размеры трещин, зазоров, сколов и других технологических повреждений, включая их положение и ориентацию на поверхности.
- Капиллярные методы предназначены для управления объектами независимо от их формы и размера.
- Технология также может использоваться для управления деталями из ферромагнитных материалов. Но в этом случае конфигурация расположения дефектов и магнитные свойства изделия должны соответствовать эксплуатационным характеристикам нанесенного маркировочного состава.
Согласно требованиям ГОСТ при капиллярном методе неразрушающего контроля обращение с пенетрантами и другими индикаторными пропитками из-за химической активности также должно основываться на правилах пожарной безопасности, утвержденных другим ГОСТом — 12.1.004-91.
Подготовка к работе
Сначала проводится визуальный осмотр заготовки и ее поверхностей. Важно заранее отметить участки, которые будут подлежать контролю. Зонирование позволит провести комплексную диагностику без пропуска труднодоступных поверхностей.Далее на условно обозначенных участках проводится зачистка. На этапе подготовки к выполнению капиллярного контроля сварных соединений ответственных конструкций рекомендуется использовать растворители и обрабатывающие средства. Жидкости для растворения веществ устранят следы масляных и жирных пятен на поверхности, а, например, пескоструйный аппарат удалит с покрытия окалину и ржавчину. Если под рукой нет пневматического инструмента, можно использовать простые абразивные материалы, например, металлическую щетку или наждачную бумагу. После механической шлифовки проводят промывку и сушку поверхности.
При использовании спецтехники также потребуется операция по устранению неисправностей. Типичный метод капиллярного контроля сварных соединений предполагает использование следующих приборов и устройств:
- Комплексное оборудование неразрушающей диагностики, в состав которого входят проявители, очистители, средства защиты от проникновения и другие устройства.
- Пистолеты. Средство для распыления жидкого индикатора.
- Пневмогидропистолеты.Также позволяет производить операции по очистке в процессе работы и проводить нанесение технологических составов, ,
- УФ-прибор. Скорее дополнительная оснастка, но если требуется качественная диагностика, то без нее не обойтись. Обычно используют УФ-лампы, фонарики и другие осветители с контрастным излучением.
- Тестовая панель. Своеобразная тестовая площадка, на которой выполняются рабочие процедуры. Более того, в некоторых случаях дефектоскопия проводится на дороге, когда необходимо обследовать сварной шов стационарной конструкции.
В таких случаях для удобства используются мобильные панели.
- Фотоаппаратура для визуального контроля. На завершающем этапе работы такое оборудование позволяет автоматически регистрировать параметры дефекта на программном уровне.
Капиллярная дефектоскопия
Самый трудоемкий и в то же время ответственный этап дефектоскопии, который можно разделить на отдельные процедуры:
- Заполнение полостей пенетрантом. После зачистки приготовленный раствор наносится в рабочую полость.Техника нанесения может варьироваться от обычной чистки до ультразвукового распыления. Чаще всего для таких целей используют краскопульт. Покрытие формируется ровно, без проседаний и пропусков. Согласно ГОСТу по методу капиллярного контроля для обеспечения высокой проникающей способности температура поверхности должна находиться в пределах +10 … + 50 ° С. Температурный режим самого маркера зависит от его состава, но превышает его. та же +50 ° С нежелательна.
- Регулировка проницаемости.
С помощью тряпки или салфетки необходимо удалить излишки нанесенной жидкости, при необходимости аккуратно заполняя недостающий объем в местах ее расхождения по трещинам. Поверхности несплошностей не должны соприкасаться с другими объектами. После этого рабочие зоны оставляют сохнуть.
- Приложение разработчика. Тонкий проявитель белого цвета также наносится распылителями или ручным инструментом в 2-3 слоя. Эта операция, как уже было сказано, требуется для создания контраста между зоной отображения и основанием заготовки.Если капиллярный контроль сварного соединения был проведен правильно, то ширина сформированного маркерного следа будет в несколько раз больше фактической ширины условной трещины стыка, что позволит легко обнаруживать мелкие дефекты.
Регистрация дефектов
Заключительный этап, в ходе которого фиксируются не только факты наличия тех или иных дефектов поверхности, но и их специфические характеристики. Для непосредственного документирования результатов дефектоскопии можно использовать фото- и видеоаппаратуру. Если условия не подходят для использования специализированных методов визуального осмотра, то используется липкая лента, на которой сохраняется несплошность. Напротив, капиллярный метод неразрушающего контроля в лабораторных условиях предполагает возможность высокоточной обработки с помощью фото- и рентгеновского оборудования. Отснятые материалы передаются через специальный интерфейс на компьютер, где соответствующее программное обеспечение отображает результаты дефектоскопии в виде наглядных графиков и шаблонов мельчайших трещин в структуре детали.
Заключение
Данный метод неразрушающей диагностики сварных соединений может быть использован как самостоятельная дефектоскопическая операция, так и при комплексном обследовании конструкций. Во втором случае в первую очередь будет выполняться метод контроля цвета капилляров с указанием возможных очагов несплошности. Далее используются методы внутренней диагностики, выявляющие пустоты и крупные поры в структуре детали. Насколько эффективен этот метод по сравнению с альтернативными методами анализа поверхности после сварки? На сегодняшний день это далеко не самый технологичный метод дефектоскопии — особенно на фоне электромагнитных и ультразвуковых приборов, которые с высокой точностью и с минимальными организационными затратами позволяют получить не менее достойный результат. Тем не менее именно из-за своей простоты и финансовой доступности капиллярный контроль по-прежнему популярен при обследованиях на удаленных объектах, где невозможно полностью использовать современное оборудование.
Тестирование на проникновение жидкости — предварительное тестирование и проверка
Также известно как: Проверка на проникновение красителя (DPI), Проверка на проникновение жидкости (LPI), Тестирование на проникновение (PT) и флуоресцентное тестирование. Жидкостный пенетрантный контроль — один из старейших методов неразрушающего контроля, который все еще используется сегодня, благодаря его простоте и замечательной чувствительности к обнаружению очень мелких неоднородностей поверхности.Используемый для черных, цветных и даже неметаллических материалов, дефектоскопический контроль красителя является наиболее распространенным и экономически эффективным из всех методов контроля неразрушающего контроля.
ПРЕИМУЩЕСТВА
- Быстрый
- Портативный
- Экономически выгодно
- Высокая чувствительность
- Дефекты визуально обозначены на поверхности
- Для больших и сложных форм
КАК РАБОТАЕТ ЖИДКИЙ ПЕНЕТРАНТ NDT?
Как следует из названия, испытание на проницаемость жидкости включает окрашенную проникающую жидкость, которая наносится на поверхность испытываемого материала. Жидкость втягивается в дефектные участки на поверхности материала за счет капиллярного действия, а затем вытягивается, чтобы обнаружить себя с помощью УФ-излучения или других методов, в зависимости от типа используемого пенетранта и красителя.
Frontline Testing Laboratories предоставляет полный спектр экономичных услуг по неразрушающему контролю проникающих жидкостей. Будь то крупносерийное производство или тестирование отдельных, крупных или сложных объектов, мы предлагаем быстрое выполнение работ и высокую степень надежности
ПРОЦЕСС ИСПЫТАНИЯ НА ПЕРЕДАЧУ
- Шаг 1: Подготовка: Поверхность подготавливается путем удаления любых загрязнений, которые могут помешать процессу.
- Шаг 2: Нанесение пенетранта: Пенетрант наносят распылением, кистью или погружением в ванну. Затем его оставляют на месте на некоторое время, чтобы позволить как можно большему проникновению красителя.
- Этап 3: Удаление: На этом этапе инспектор тщательно удаляет излишки пенетранта, не удаляя пенетрант из дефектов.
Иногда используют воду или эмульгаторы.
- Шаг 4: Нанесение проявителя: На поверхность наносится слой проявителя, который вытягивает пенетрант из дефектов и на поверхность, делая его видимым.
- Шаг 5: Осмотр: При правильном освещении выполняется визуальный осмотр для выявления любых возможных признаков.
- Шаг 6: Очистка: Последний шаг — удалить проявитель с участков поверхности, на которых отсутствуют дефекты.
|
Услуги по неразрушающему контролю — Услуги
Ультразвуковой контроль (UT)
— это метод обнаружения подповерхностных дефектов путем направления
высокочастотный звуковой луч сквозь материал под разными углами. Когда путь звукового луча наталкивается на разрыв в материале
непрерывность, часть звука отражается обратно. Звук
собираются прибором, усиливаются и отображаются в виде вертикальной
след на экране — ответ помогает определить местоположение,
размер и тип дефекта, например, трещины, неплавление, шлак
включения, пористость и др.
Магнитопорошковый контроль (MPI, MT)
MPI — это неразрушающий контроль (NDT) процесс обнаружения поверхностных неоднородностей в ферромагнитных материалах.
Мелкодисперсные магнитные частицы, нанесенные на намагниченные части, привлекают и очерчивают узор любого магнитные поля рассеяния, создаваемые неоднородностями.
Проверка проницаемости или проникновения красителей (PT, иногда именуется Dye Pen)
Дефекты поверхности, невидимые невооруженным глазом, могут быть
обнаружен с помощью пенетрантной проверки красителя. Он широко используется для
обнаружение поверхностных трещин в цветных и непористых
такие материалы, как алюминий и нержавеющая сталь.
Проникающая жидкость может быть либо цветовой контрастной (видимой), либо флуоресцентный. Пенетрант наносится на поверхность детали до быть исследованным. Капиллярное действие вытягивает жидкость на поверхность отверстия, а излишки затем удаляются. «Разработчик» используется для нанести пенетрант на поверхность, и в результате появится при просмотре в естественном или искусственном свете или в ультрафиолетовом (черном) свете. Высокая контрастность позволяет обнаруживать мельчайшие следы пенетрант, указывающий на неоднородность поверхности.
Визуальный осмотр
Быстрый и простой метод проверки и дополняет все другие дисциплины в области неразрушающего контроля. Вышеуказанные методы могут необходимо использовать для подтверждения выводов.
.