Области применения капиллярных методов контроля
Капиллярный метод выявляет только дефекты, имеющие выход на поверхность детали. Если дефект будет неглубоким, то пенетрант не будет задерживаться и будет вымываться из дефекта и такой дефект нельзя обнаружить капиллярным методом. Чтобы работал капиллярный метод, надо чтобы глубина дефекта не менее чем в 10 раз превосходила раскрытие дефекта.
Капиллярным методом можно контролировать детали из любых конструкционных материалов: чёрных и цветных металлов (магнитных и немагнитных), пластмасс, стекла и керамики. Но! Незаменимая область применения капиллярных методов – контроль изделий из немагнитных, неметаллических, композиционных и других перспективных материалов, где капиллярный метод является одним из немногих, а зачастую и единственным.
Капиллярные методы позволяют контролировать объекты любых форм и размеров, начиная от корпуса ракеты и кончая миниатюрной лопаткой турбореактивного двигателя, которые имеют очень сложную форму и выполнены из немагнитных материалов. И только капиллярные методы обеспечивают полный контроль всей поверхности лопатки, гарантируя безопасную работу авиадвигателя и всего летательного аппарата.
В настоящее время уже разработаны методы капиллярного контроля пористых изделий и материалов, например, таких перспективных материалов, как керамические изделия, находящие все большее применение в машиностроении, автомобильной промышленности, медицине.
Важным достоинством капиллярного метода, особенно люминесцентного, является высокая чувствительность — 0,1 мкм. С помощью капиллярного метода выявляются сварочные, термические, шлифовочные, усталостные, деформационные трещины, пористость, трещины на фоне пористости и т.п. Основными объектами контроля являются ответственные детали массового производства, особенно сложной формы, такие как лопатки турбин, крепеж, литье, детали корпусов и элементов систем управления из легких сплавов и аналогичные детали энергетических и транспортных машин из коррозионно-стойких немагнитных никелевых и титановых, а также других термостойких сплавов.
Важно, что капиллярный метод используется не только при контроле качества деталей при их изготовлении в цехах завода и лабораториях. Он применяется широко и в полевых условиях при необходимости технического обследования таких сооружений, как мосты, грузоподъемные краны, трубопроводы и сосуды под давлением и других сложных технических объектов. Ведь весь комплект необходимых материалов для цветного капиллярного контроля размещается в небольшой переносной сумке.
Можно контролировать и внутренние поверхности труб, отверстий, пазов, но на глубину не больше диаметра трубы, отверстия или ширины паза. При использовании роботов и волоконной оптики капиллярный метод доступен для неразрушающего контроля внутренних полостей большой протяженности.
Авторитет капиллярного контроля ощутимо подняла аэрозольная упаковка дефектоскопических материалов. Аэрозольные баллончики сделали капиллярный контроль портативным и мобильным. Такие баллончики удобны, когда объектом контроля является не все изделие, а лишь отдельные участки поверхности, в труднодоступных местах, в случае применения на открытом воздухе. Пенетрант, содержащийся в баллончике, имеет гарантированное качество и может использоваться без дополнительной проверки. Баллончики экономичны, компактны, имеют небольшой вес и легко удерживаются в одной руке.
Постоянно расширяется температурный диапазон капиллярного метода. Образцы отечественных наборов российского производства допускают применение (от –40 °С до +100 °С), фирма Неlling предлагает наборы до +175 °С, а ВYCOSIN до +200 °С.
Универсальность капиллярного метода позволяет его использовать в самых различных областях машиностроения: от общего до атомного и космического, на транспорте (авиационный, железнодорожный, морского и др.), в химической и нефтеперерабатывающей отраслях, при транспортировке нефти и газа и множестве других.
Широка номенклатура деталей авиационной техники, контролируемых капиллярным методом: рабочие лопатки, диски тяговых двигателей и компрессоров, силовые шпангоуты, стрингеры, лонжероны, лопасти воздушных винтов самолётов и вертолётов, стойки и колёса шасси и др.
Для капиллярного контроля элементов ракет и управляемых снарядов из-за опасности контакта жидкого кислорода с индикаторной жидкостью на нефтепродуктах используются специальные пенетранты на водной основе.
Для нефтеперерабатывающих и химических предприятий методы капиллярной дефектоскопии применяются для контроля наличия коррозии деталей под воздействием хлоридов, для контроля дефектов в резервуарах и сварных швах трубопроводов.
Главные недостатки капиллярного неразрушающего контроля:
- большая трудоёмкость и многооперационность;
- сравнительно большая доля ручного труда;
- трудно поддается автоматизации;
- некоторые дефектоскопические материалы токсичны и пожароопасны;
- ультрафиолетовое облучение влияет на здоровье дефектоскописта;
- большая продолжительность всего процесса контроля;
- чувствительность к точности выполнения технологических операций;
- результаты контроля во многом зависят от квалификации дефектоскописта, его самочувствия в момент контроля, а также его добросовестности;
- переработка отходов капиллярного контроля при его массовом применении требует проведения специальных мероприятий по пожарной безопасности и охране окружающей среды.
Процесс развития капиллярных методов контроля в настоящее время связан прежде всего с ликвидацией указанных выше недостатков. Выпуск новых малотоксичных, пожаробезопасных и экологически чистых дефектоскопических материалов, автоматизация контроля и оценка его результатов с помощью современной вычислительной и телевизионной техники, сделают его еще более привлекательным.
Отдельно следует упомянуть, что капиллярный контроль может входить в состав комплекса методов (капиллярный, ультразвуковой, вихретоковый), которые применяются для критичных деталей, например, лопатки турбин отдельных видов газотурбинных двигателей.
определение, суть, классификация, характеристика, методы и особенности применения
После сварочных работ производится обязательная дефектоскопия, позволяющая определить качество шва, его поверхностную структуру и параметры изъянов. Контроль должен осуществляться неразрушающим способом, чтобы не повредить заготовку или эксплуатируемую конструкцию. Таким требованиям соответствует метод капиллярный контроля, который широко используется как в строительстве, так и на производствах, связанных с применением сварочных операций.
Что такое капиллярная дефектоскопия?
Это один из наиболее востребованных способов обнаружения дефектов на поверхности целевой заготовки. Важно подчеркнуть применимость контроля именно для выявления параметров внешних нарушений – для диагностики внутренней структуры шва данная техника не используется. После завершения сварочных работ с помощью капиллярного метода контроля мастер может зафиксировать такие характеристики дефектов, как положение на поверхности, протяженность, ориентацию и т. д. Целевыми изъянами чаще всего выступают трещины и недостаточные провары.
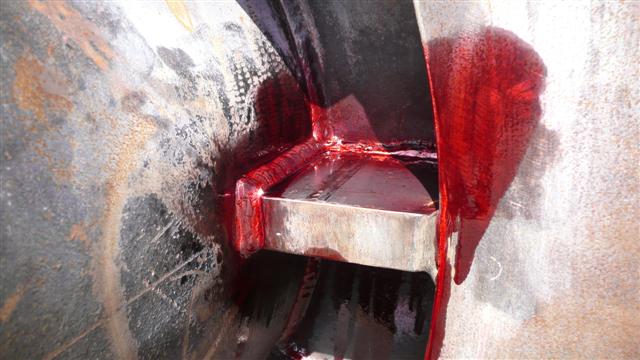
Но почему так важно использовать именно специальную методику, игнорируя стандартный визуальный осмотр, пусть и с подключением профессиональной оптики? Одним из главных преимуществ этого метода является возможность выявления малых дефектов, которые можно упустить при традиционном визуальном контроле. Использование оптической техники наподобие микроскопа или лупы, к примеру, не позволит обнаружить дефекты в силу их слабой контрастности на фоне металлической поверхности, не говоря о малом поле зрении при значительных увеличениях. В свою очередь, капиллярная методика вполне позволяет фиксировать изъяны в заготовках крупных размеров с высокой точностью.
Требования к организации работ и технике их выполнения регулируют стандарты нормативного документа для капиллярного метода контроля – ГОСТ 18442. В соответствии с официальным определением, данная технология проверки качества швов представляется как способ анализа и регистрации сквозных и поверхностных несплошностей материала. К слову, происхождение заготовки в производственной или строительной среде значения не имеет: кроме черных и цветных металлов, технология успешно работает с керамикой, пластмассами и стеклом.
Суть метода
Принцип действия капиллярного способа контроля заключается в проявлении структуры дефекта с помощью красящего пенетранта, которым обрабатывается целевая поверхность. Высокая проникающая способность активного состава позволяет ему проникать в мельчайшие поры поверхности, ярким цветом маркируя контуры трещин или непроваров. Поэтапно технологию производства капиллярного метода контроля сварных швов можно представить так:
- Подготовка поверхности. Качество выполнения дефектоскопии будет зависеть от чистоты рабочей зоны. Малейшие препятствия в виде грязи, пыли и жировых следов могут помешать процессу капиллярной маркировки. Поэтому выполняется зачистка поверхности, а иногда и шлифовка с последующей доработкой.
- Нанесение красящего состава. Как правило, используется красный пенетрант. Его распыляют или наносят кисточкой в достаточном объеме, чтобы масса могла свободно заполнить все имеющиеся дефекты.
- Очистка излишков пенетранта. Чтобы в дальнейшем удобнее было производить контроль дефектной зоны, с поверхности удаляется ненужный красящий раствор. Важно не затронуть маркированные контуры непосредственно трещин.
- Нанесение проявителя. Через некоторое время после высыхания пенетранта производится укладка проявителя – состава белого цвета, который позволит на контрасте выявить нарушения структуры.
- Контроль качества. После завершения проявочного процесса оператор фиксирует следы и контуры дефектов.
Функциональную сущность капиллярного метода контроля можно свести к двум технологическим факторам обнаружения дефектов. Во-первых, это описанный процесс точечного визуального проявления структуры трещин и непроваров. Во-вторых, это процедура непосредственной регистрации, измерения и анализа параметров дефекта, но уже с помощью другого функционального инструментария.
Классификация основных способов капиллярной дефектоскопии
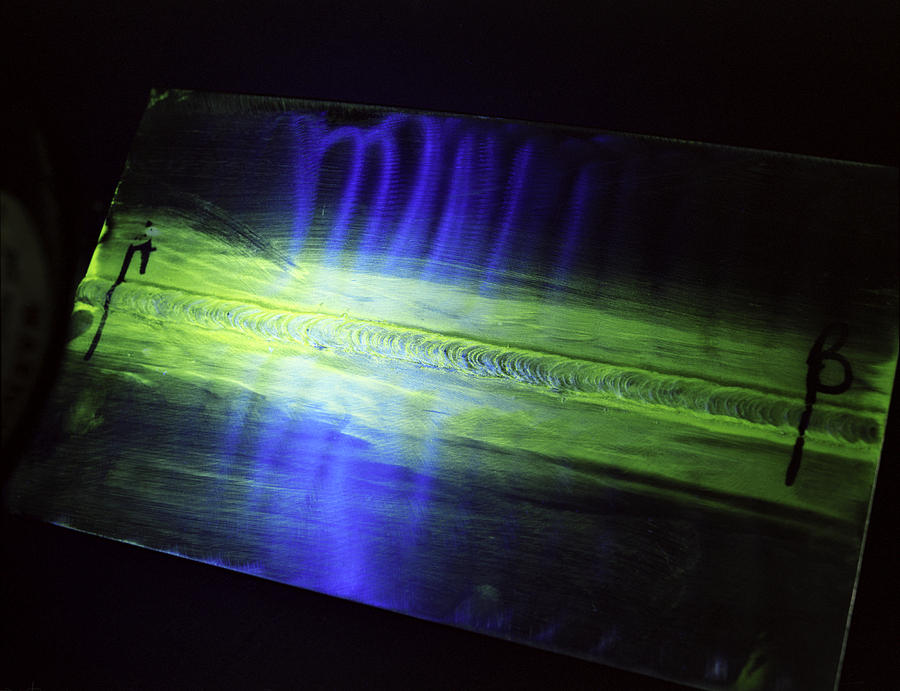
Наиболее существенным признаком разделения разных способов капиллярного контроля является тип индикаторной смеси – того самого пенетранта. Выше был рассмотрен наиболее популярный красный маркерный состав, но существуют и другие вариации, которые выгодно проявляют себя в тех или иных условия дефектоскопии. И в этом контексте можно предложить следующую классификацию капиллярных методов контроля:
- Люминесцентный. Этот способ предполагает использование раствора или суспензии люминофора в сочетании с органическими растворителями, маслами и керосином. В процессе анализа выявленной структуры дефекта не требуется специальное облучение ультрафиолетом – даже в темном помещении люминофор обеспечивает достаточный контраст, позволяя фиксировать микротрещины толщиной до 0,1 мкм.
- Люминесцентно-цветной способ. Дает наиболее чувствительный эффект выявления внешних дефектов. Модификация люминесцирующего индикатора, которая заключается в применении длинноволнового ультрафиолетового излучения. Метод используется в лабораторных условиях для фиксации сверхмалых рисунков трещин.
- Яркостный способ. Также называется ахроматическим и представляет собой один из самых доступных и простых методов капиллярного контроля, возможностей которого достаточно для проверки качества большей части строительных сварочных швов. В работе используется керосино-меловая индикаторная жидкость, обеспечивающая контрастное проявление очертаний возможного дефекта.
- Метод фильтрующейся суспензий. В данном случае применяется не жидкостный, а своего рода порошковый подход к проявлению дефекта, что обуславливает его крайне низкую чувствительность. Тем не менее, использование отфильтрованных дисперсных частиц суспензии в качестве маркера является оптимальным вариантом контроля, когда не допускается обработка поверхности заготовки жидкими растворами.
Комбинированные способы капиллярной дефектоскопии
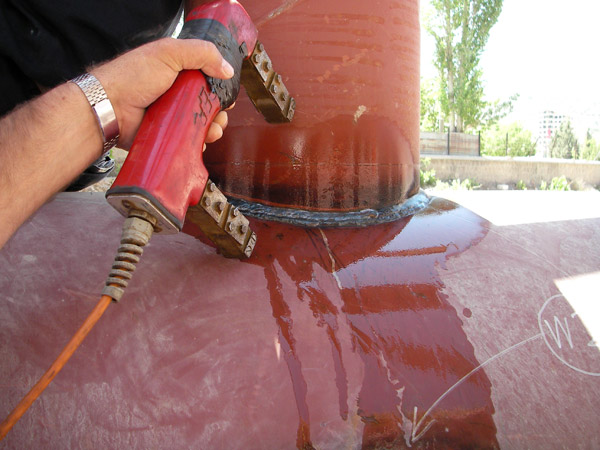
Группа методов, особенностью которой является сочетание с другими техниками неразрушающего поверхностного контроля. Причем основой обязательно должен выступать способ маркировки дефекта. Итак, выделяют следующие комбинированные методы капиллярного контроля сварных швов:
- Капиллярно-электростатический. Позволяет выявлять дефекты неметаллических заготовок по индикаторному следу, который был сформирован частицами наэлектризованного порошка на поверхности пенетранта.
- Капиллярно-электроиндуктивный. В качестве дополнительного активного фактора применяется электрический проводник, работающий непосредственно по контурам пенетранта без других инородных включений.
- Капиллярно-магнитопорошковый. Способ предназначен конкретно для ферромагнитных намагничиваемых изделий с контролем дефектов по индикаторному следу, образованному ферромагнитным порошком над слоем пенетранта.
- Капиллярно-радиационный. Контроль осуществляется на основе анализа спектра ионизирующего излучения в области дефектной зоны, предварительно обработанной жидкостным индикатором.
Отдельного внимания заслуживает капиллярный метод неразрушающего контроля с применением стабильных нитрокроксильных радикалов. Они смешиваются с базовым составом пенетранта и благодаря парамагнетизму нитроксилов дают возможность применения спектроскопии парамагнитного резонанса. Это высокоточный метод обнаружения микротрещин, глубоко проникающих в структуру материала, где обычные средства внешнего анализа неэффективны.
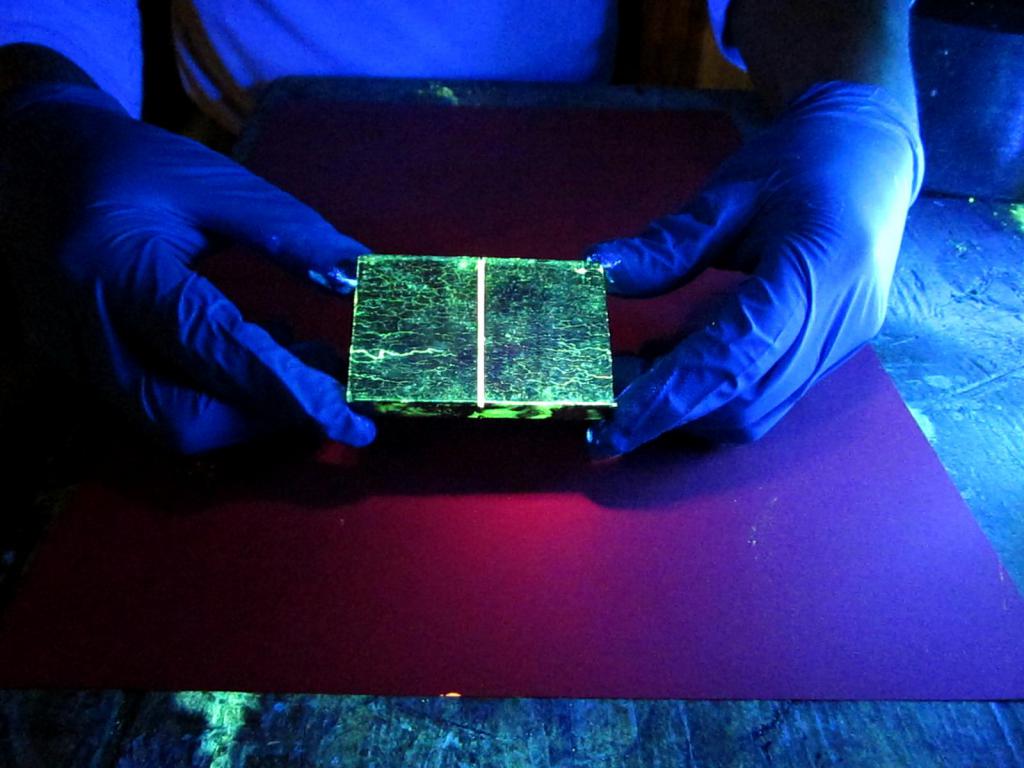
В общей группе техник неразрушающего контроля данный способ соответствует второму уровню чувствительности, при котором возможно проявление дефектов с потенциалом раскрытия до 1 мкм. К целевым несплошностям можно отнести сквозные изъяны, поперечное сечение которых варьируется в диапазоне 0,1-500 мкм. К основным физико-эксплуатационным характеристикам капиллярного неразрушающего контроля относят вязкость, плотность, натяжение и проникновение. Во многом показатели по этим параметрам зависят от конкретного индикаторного состава. Например, средняя пропитка пенетрантом отличается хорошей смачиваемостью и высоким поверхностным натяжением. Составы на основе керосина, бензола, жидких масел и скипидара, в частности, обеспечивают поверхностное натяжение до 10-2 Н/м. Что касается коэффициента яркостного контраста, то он в зависимости от изначальных данных маркера и условий применения метода может увеличиваться на 30-50 %.
Требования к проведению работ
В нормативно-технической документации приводится следующий набор общих требований к контролю неразрушающими капиллярными методами:
- Технология предназначена для проведения неразрушающей дефектоскопии с целью выявления сквозных и поверхностных несплошностей в рабочих заготовках после проведения сварочных мероприятий.
- В процессе дефектоскопии капиллярными методами должны выявляться размеры трещин, разрывов, сколов и других технологических повреждений, в том числе их положение и ориентация на поверхности.
- Капиллярные методы предназначены для контроля объектов независимо от их форм и размеров.
- Допускается применение технологии и для контроля заготовок, выполненных из ферромагнитных материалов. Но в данном случае конфигурация расположения дефектов и магнитные свойства изделия должны соответствовать рабочим характеристикам применяемого маркировочного состава.
Согласно требованиям ГОСТа по капиллярному методу неразрушающего контроля, обращение с пенетрантами и другими индикаторными пропитками ввиду химической активности также должно основываться на правилах пожарной безопасности, утвержденных уже другим ГОСТом – 12.1.004-91.
Подготовка к работам
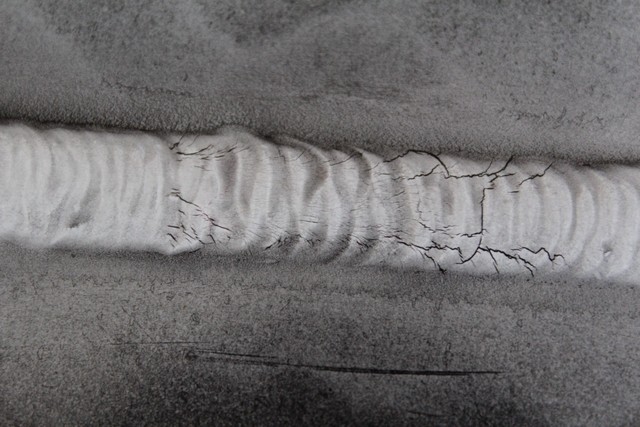
Сначала проводится визуальный осмотр заготовки и ее поверхностей. Важно заранее разметить участки, которые будут подвергаться контролю. Зонирование даст возможность комплексной диагностики без упущения труднодоступных поверхностей. Далее по условно размеченным участкам производится зачистка. На этапе подготовки к выполнению капиллярного контроля сварных соединений в ответственных конструкциях рекомендуется использовать растворители и средства механической обработки. Жидкости для растворения веществ позволят ликвидировать следы масляных и жировых пятен на поверхности, а, к примеру, пескоструйный аппарат устранит с покрытия окалины и ржавчины. Если пневматического инструмента под рукой нет, то можно использовать простые абразивы наподобие металлической щетки или наждачной бумаги. После механической шлифовки выполняется промывка поверхности и сушка.
Потребует применения специального оборудования и сама операция дефектовки. Типовой метод капиллярного контроля сварных соединений предусматривает использование следующих приборов и устройств:
- Комплексная оснастка для проведения неразрушающей диагностики, в состав которой входят проявители, очистители, средства содержания пенетрантов и другие приспособления.
- Пульверизаторы. Инструмент для распыления жидкостного индикатора.
- Пневмогидропистолеты. Также позволяет выполнять зачистные операции по ходу работы и осуществлять нанесение технологических составов,
- Ультрафиолетовый прибор освещения. Скорее опциональная оснастка, но если требуется высокое качество диагностики, то без нее не обойтись. Обычно используют УФ-лампы, фонари и другие осветители с контрастным излучением.
- Испытательная панель. Своего рода тестовая платформа, на которой производятся рабочие процедуры. При этом в некоторых случаях дефектоскопия выполняется на выезде, когда нужно обследовать сварной шов стационарной конструкции. В таких случаях для удобства используют мобильные панели.
- Фотографическая аппаратура для визуального контроля. На финальном этапе работ такое оборудование позволяет автоматически на программном уровне регистрировать параметры дефектов.
Техника проведения капиллярной дефектоскопии
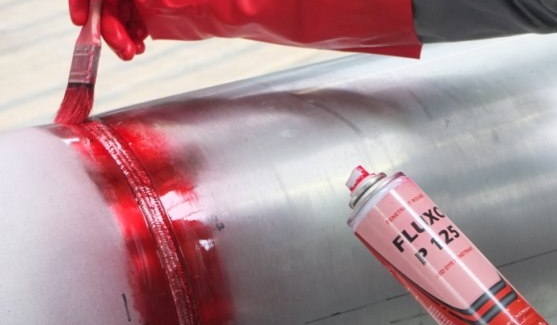
Наиболее трудоемкий и в то же время ответственный этап дефектоскопии, который можно разделить на отдельные процедуры:
- Заполнение полостей пенетрантом. После зачистки подготовленный раствор наносится на рабочую полость. Техники нанесения могут быть разными – от обычного смачивания кисточкой до ультразвукового распыления. Чаще всего для таких целей используется пульверизатор. Покрытие формируется плавно, без образования наплывов и пропусков. Как отмечает ГОСТ по капиллярному методу контроля, для обеспечения высокой проникающей способности температура поверхности должна укладываться в диапазон +10…+50 °C. Температурный режим самого маркера зависит от его состава, но превышения тех же +50 °C нежелательны.
- Корректировка пенетранта. С помощью ветоши или салфетки необходимо удалить излишки нанесенной жидкости, при необходимости аккуратно восполняя недостающий объем в зонах ее расхождения по трещинам. Поверхности несплошностей при этом не должны контактировать с другими объектами. После этого рабочие участки оставляются на просушку.
- Нанесение проявителя. Также с помощью распылителей или кистевого инструмента в 2-3 слоя наносится тонкий проявитель белого цвета. Данная операция, как уже говорилось, требуется для создания контраста между зоной индикации и основой заготовки. Если капиллярный контроль сварного соединения был правильно выполнен, то ширина образованного маркерного следа будет в несколько раз превосходить фактическую ширину условной трещины шва, что позволит без труда обнаружить и мелкие дефекты.
Регистрация дефекта
Завершающая стадия, в ходе которой не просто фиксируются факты наличия тех или иных изъянов поверхности, но также их конкретные характеристики. Для непосредственного документирования результатов дефектоскопии может применяться фото- и видеоаппаратура. Если условия не приспособлены для использования специализированной техники визуального контроля, то применяют клейкую ленту, на которой остается рисунок несплошности. И наоборот, в лабораторных условиях капиллярный метод неразрушающего контроля предполагает возможность высокоточной обработки посредством фотографической и рентгеновской аппаратуры. Снимаемые материалы через специальный интерфейс передаются в компьютер, где соответствующее программное обеспечение отражает результаты дефектоскопии в виде наглядных графиков и схем расположения мельчайших трещин в структуре заготовки.
Заключение
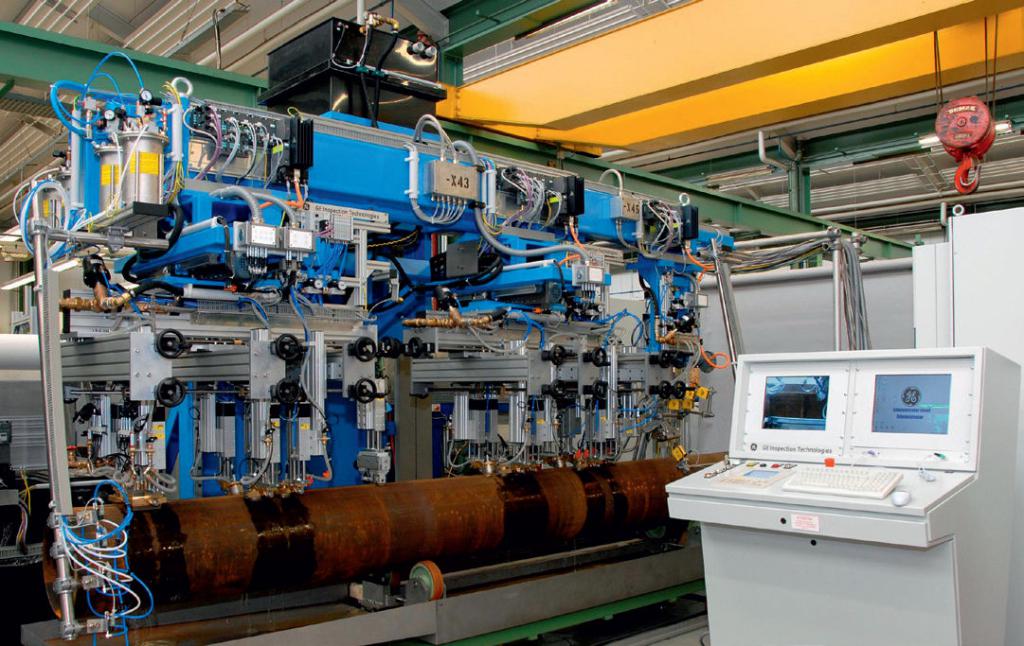
Данный способ неразрушающей диагностики сварных соединений может применяться и в качестве самостоятельной операции дефектоскопии, и в комплексном обследовании конструкций. Во втором случае метод капиллярного цветного контроля будет выполняться в первую очередь, указывая на возможные очаги местоположения несплошностей. Далее задействуются способы внутренней диагностики, выявляющие пустоты и крупные поры в структуре заготовки. Насколько эффективен данный метод по сравнению с альтернативными техниками анализа поверхностей после сварочных работ? На сегодняшний день это далеко не самый технологичный способ дефектоскопии – особенно на фоне электромагнитных и ультразвуковых приборов, которые с высокой точностью и с минимальными организационными затратами позволяют получить не менее достойный результат. Тем не менее, именно в силу своей простоты и финансовой доступности капиллярный контроль все еще сохраняет популярность в обследованиях на удаленных объектах, где нет возможности в полной мере использовать современную аппаратуру.
Классификация капиллярных методов контроля
Основными разновидностями капиллярных методов являются цветной, люминесцентный, люминесцентно-цветной, яркостный и фильтрующихся суспензий.
При цветном методе в качестве индикаторной жидкости используются ярко окрашенные жидкости. Красный цвет обеспечивает наиболее высокий цветовой контраст, он обладает наибольшим возбуждающим действием на человека, обеспечивает наиболее быстрое возникновение зрительного ощущения и быструю реакцию дефектоскописта. Красный цвет даёт индикаторный рисунок дефекта, который легко отличить от рисунков, похожих на трещины, внешних повреждений: рисок, царапин, заусенцев и других внешне похожих на дефекты, но не представляющих опасности повреждения металла. Красные красители видны в очень тонком слое проявителя.
Дефекты выявляются по индикаторным следам на фоне проявителя (обычно белого цвета). Для цветного метода используется естественное освещение, лампы накаливания или комбинированное освещение. Чувствительность цветного метода соответствует II уровню, при котором выявляются дефекты с раскрытием не менее 1 мкм. Цветной метод является наиболее распространенным среди капиллярных методов неразрушающего контроля. Одним из его серьезных преимуществ является то, что он может быть использован при обычном освещении, а комплект необходимых материалов может быть размещён в небольшой переносной сумке.
Люминесцентный метод контроля обладает большей чувствительностью, но требует применения специального облучения ультрафиолетовым светом и затемненного помещения для осмотра изделия. При люминесцентном методе контроля дефект заполняется индикаторной жидкостью, которая представляет собой раствор либо суспензию люминофора в смеси органических растворителей, керосина, масел и ПАВ. При проявлении извлеченный из дефекта люминофор дает на темном фоне контрастный, светящийся под действием ультрафиолетовых лучей след, что позволяет выявлять дефекты раскрытием более 0,1 мкм. В связи с повышенной чувствительностью человеческого глаза в желто-зеленой области применяются люминофоры с максимальной световой отдачей именно в этой области спектра.
Люминесцентно-цветной метод – самый высокочувствительный метод выявления поверхностных дефектов. Это жидкостный метод капиллярного неразрушающего контроля, основанный на регистрации контраста цветного или люминесцирующего индикаторного рисунка на фоне поверхности объекта контроля в видимом или в длинноволновом ультрафиолетовом излучении. Более высокая чувствительность метода достигается в ультрафиолетовом свете и растет с увеличением освещённости контролируемой поверхности. Этот комбинированный метод объединил и расширил возможности двух различных методов дефектоскопии.
Один из наиболее простых методов капиллярного контроля –
Метод фильтрующихся суспензий использует в качестве жидкого проникающего вещества индикаторные суспензии, которые образуют индикаторный рисунок из отфильтрованных частиц дисперсной фазы. Обладает сравнительно низкой чувствительностью. Различают его цветную, люминесцентную и люминесцентно-цветную разновидности.
Кроме перечисленных выше основных методов контроля применяются комбинированные капиллярные методы, которые классифицируются в зависимости от характера используемых для интенсификации контроля физических полей и особенностей их взаимодействия с контролируемым объектом.
используемые методы, порядок проведения и необходимые материалы
Для определения качества сварного шва проводится его контроль. Капиллярный контроль является одним из основных контрольных методов, которые на сегодняшний день активно применяются для проверки швов.
Что такое капиллярный контроль
Данный метод относится к группе неразрушающих и предполагает наличие множества способов его проведения с применением различных расходных материалов.
С помощью такого метода выявляются наружные и внутренние недостатки шва. Описываемый метод позволяет определить практически все дефекты: непровары, поры, трещины и т. д. Капиллярный контроль позволяет определить местонахождение дефекта, его ориентацию к поверхности детали, а также его размеры.
Данный метод применяется для проверки любых металлов (чёрных и цветных), а также для контроля соединения стекла, пластмасс, керамики и т. д. Капиллярный метод получил широкую область применения при определении недостатков сварочных швов.
Суть процесса проверки состоит в том, что на полученное соединение наносятся специальные индикаторы в виде жидкости. Они с лёгкостью проникают в любой материал, если в нём имеются пустоты, проходят даже через самые маленькие трещины и возникают на обратной стороне от места их распыления. Где проявляется цветной индикатор, там и находится дефект.
Используемые методы
Существует две группы способов проведения капиллярного контроля: основные и комбинированные.
Основные
Основные методы предполагают использование исключительно капиллярной проверки с жидкими индикаторами.
Основные методы контроля:
- По видам используемых растворов:
- проникающие растворы;
- фильтрующие суспензии.
- По способу получения результата:
- яркостный;
- люминесцентный;
- люминесцентно-цветной;
- цветной.
Комбинированные
Комбинированные способы подразумевают применение ряда способов проверки неразрушающего характера, одним из которых является капиллярный.
Комбинированные способы:
- магнитный;
- электростатический;
- радиационный способ излучения или поглощения;
- электроиндукционный.
Перечисленные методы различаются в зависимости от их технологии воздействия на поверхность, поддающуюся проверке.
Процесс проведения капиллярного контроля
Перед началом проверки необходимо зачистить и просушить участок, который будет проверяться. Далее наносится индикаторная жидкость, часть которой проникает в поры и трещины, а остатки нужно тщательно удалить. После этого для вытягивания жидкости применяется проявитель. Индикатор проявляется на поверхности соединения в виде цветных пятен, которые и обозначат местонахождение изъяна, его размер и форму.
Материалы для капиллярной дефектоскопии
Необходимый перечень материалов для проведения капиллярного контроля:
- Индикаторная жидкость:
- флуоресцентная жидкость;
- цветная жидкость.
- Промежуточные очистители:
- растворитель или вода;
- водочувствительный эмульгатор;
- растворимый жидкий очиститель.
- Проявители:
- жидкий проявитель на водной основе;
- жидкий проявитель на основе растворителя;
- водный растворитель в виде суспензии.
Подготовка металла к проверке
Перед началом нужно провести зачистку поверхности сварочного шва. Рекомендуется использовать комбинацию механического и химического способов.
Сперва проводят механическую обработку металлической щёткой. Но не стоит сильно усердствовать: при интенсивном воздействии затираются поверхностные недостатки, и индикаторная жидкость не сможет проникнуть вглубь металла. Это приведёт к ошибочным суждениям о качестве шва.
Химическая обработка обычно проводится спиртом или растворителем. Нужно помнить, что химикаты могут вступать в реакцию с индикаторами, поэтому нужно их тщательно смывать водой или специальными реагентами. Важно, чтобы проверяемый участок был хорошо просушен, иначе результаты проверок будут неточными.
Нанесение индикатора
Индикаторная жидкость может наноситься различными способами:
- Стандартный капиллярный способ – при таком методе жидкость сама проникает в сварочный шов без специального вмешательства. Нанесение проводится путём смачивания, нанесения струёй погружения детали в жидкость.
- Ультразвуковой способ – заполнение пустот пор и трещин проводится посредством ультразвукового эффекта.
- Вакуумный – детали помещаются в вакуумную установку, с помощью которой из внутренних полостей откачивается воздух. Давление в этих пустотах ниже, чем атмосферное. Поэтому нанесённая жидкость легко проникает в них.
- Компрессионный – способ, при котором на индикаторную жидкость воздействуют высоким давлением, и она заполняет пустоты, выталкивая воздух.
- Деформационный – индикатор проникает внутрь сварочного шва при помощи воздействия звуковых волн, но при этом увеличивается размер выявленного дефекта.
Промежуточная очистка поверхности
Проводить очистку поверхности шва нужно аккуратно, чтобы не удалить индикатор с поверхностных недостатков. Очищать можно:
- Обычной водой, при помощи губки или тряпки. Температура воды не должна превышать +50оС.
- Эмульгаторами на основе масел. Вначале поверхность металла промывается водой, затем наносится эмульгатор, который также смывается водой.
- Растворителями. Поверхность шва просушивается, а затем протирается тканью, пропитанной растворителем.
- Комбинированный способ – сначала проверяемый участок промывается водой, а затем вытирается губкой, смоченной растворителем.
- После промежуточной очистки необходимо хорошо просушить сварочный шов.
Нанесение проявителя
Сразу после просушки на проверяемый участок равномерным тонким слоем наносится проявитель. Разновидности проявителей:
- Сухой. Его использование возможно только в комплексе с флуоресцентными индикаторами. Наносится равномерным слоем при помощи обычного напыления.
- Жидкий на основе растворителя. Такой проявитель наносится методом равномерного распыления, чтобы образовалась тонкая и однородная плёнка.
- Жидкий на основе водной суспензии или водного раствора. Наносится методом распыления или способом замачивания свариваемых деталей в жидком проявителе. Однако после погружения в жидкость заготовки нужно быстро достать и тщательно просушить.
Стандартно время проявления занимает от 10 до 30 мин. в зависимости от используемого растворителя.
Последовательность операций капиллярного контроля
Капиллярный контроль предназначен для обнаружения невидимых или слабовидимых дефектов типа несплошностей, выходящих на поверхность объекта контроля. Применение капиллярных методов позволяет определить расположение и геометрические размеры поверхностных и сквозных несплошностей в объектах контроля, дающие объективную информацию об опасности этих дефектов для безаварийной работы детали, узла и всего механизма в целом.
Суть капиллярного контроля заключается в проникновении специальной индикаторной жидкости в трещину, последующем извлечении ее из трещины в слой проявителя в месте выхода трещины на поверхность детали и окрашивании этой части проявителя в яркий цвет. Форма цветного пятна, его размеры и яркость позволяют опытному дефектоскописту судить об объеме полости трещины и других ее параметрах (ширина и проч.).
Основные операции капиллярного контроля представлены на рисунке, где схематически изображена деталь 1 с дефектом 2, имеющим выход на поверхность П. Чтобы выявить этот дефект (трещину), на поверхность детали наносится индикаторная жидкость (пенетрант) 3, которая заполняет трещину под действием капиллярных сил.
Индикаторным пенетрантом (пенетрант – от английского «penetrate» – проникать) называют дефектоскопическую жидкость, обладающую способностью проникать в несплошности объекта контроля и образовывать при ее последующем полном или частичном извлечении слоем проявителя визуализируемый индикаторный рисунок дефекта.
В зависимости от свето-колористических свойств индикаторной проникающей жидкости и соответственно способа получения первичной информации от индикаторного рисунка, индикаторные пенетранты разделяются на цветной, люминесцентно-цветной и люминесцентный. Цветной пенетрант обнаруживается в видимом свете, люминесцентный пенетрант различим под действием ультрафиолетового излучения, люминесцентно-цветной пенетрант имеет характерный цвет в видимом излучении и люминесцирует под воздействием ультрафиолетового излучения.
Последовательность операций при капиллярной дефектоскопии: а – дефект в изделии; б – нанесение пенетранта; в – удаление пенетранта с поверхности; г – нанесение проявителя и проявление; 1 – изделие; 2 – дефект; 3 – пенетрант; 4 – проявитель; 5 – след дефекта (окрашенный проявитель).
Заполнение полостей дефектов индикаторными пенетрантами происходит прежде всего благодаря капиллярным явлениям. Эта операция ставит своей целью предельно возможное заполнение полости дефекта индикаторной жидкостью. Для этого полость дефекта должна быть чистой, а смачиваемость ее пенетрантом – наибольшей. Поэтому процессу нанесения индикаторного пенетранта на поверхность с целью его проникновения в трещину предшествует подготовка объекта к контролю.
Цель подготовки объекта к контролю – освободить полость дефекта и контролируемую поверхность от всего, что мешает жидким дефектоскопическим материалам контактировать с поверхностью и обеспечивать ее равномерное смачивание индикаторной жидкостью. Она включает очистку контролируемой поверхности и полостей дефектов от всевозможных загрязнений, остатков рабочей среды предыдущих технологических операций, лакокрасочных покрытий, моющих составов и дефектоскопических материалов, оставшихся от предыдущих операций контроля.
После заполнения пенетрантом полостей трещин и других дефектов часть индикаторной жидкости остается на поверхности контролируемого объекта. Поэтому следующая операция – удаление излишков пенетранта с поверхности изделия. Если пенетрант остается на бездефектной поверхности, он даст ложную информацию о наличии на поверхности трещины или иного дефекта. Но главное – чтобы пенетрант остался в трещине.
Для получения информации о месте расположения дефекта необходимо извлечь индикаторный пенетрант из трещины. Для этого после удаления излишков пенетранта вся контролируемая поверхность покрывается ровным и тонким слоем проявителя (порошкообразного или суспензионного), который вступает во взаимодействие с индикаторным пенетрантом. Этот процесс носит название проявление. Он заключается в извлечении проявителем из капиллярной несплошности такого количества индикаторной жидкости, которое позволило бы пропитать слой проявителя на всю толщину и образовать на месте выхода дефекта окрашенный или люминесцирующий рисунок.
Проявителем называют дефектоскопический материал, предназначенный для извлечения индикаторного пенетранта из капиллярной несплошности с целью образования четкого индикаторного рисунка в месте выхода трещины на поверхность и создания контрастирующего с ним фона. Роль проявителя в капиллярном контроле заключается, с одной стороны, в том, чтобы он извлекал пенетрант из дефектов за счет капиллярных сил, с другой стороны, проявитель (чаще всего – белый) должен создать контрастный фон на поверхности контролируемого объекта, чтобы достоверно выявлять окрашенные или люминесцирующие индикаторные следы дефектов. Чем больший контраст достигается между цветным рисунком (след) и проявителем (фон), тем выше чувствительность и тем большая вероятность обнаружения дефекта. В начале появления окрашенный рисунок на фоне проявителя имеет очертания, близкие к форме дефекта, в дальнейшем отдельные элементы рисунка сливаются.
В основе процесса проявления лежат явления смачивания, сорбции, адсорбции и диффузии. Пенетрант 3 из трещины 2 извлекается капиллярными силами проявителя в слой проявителя 4 и, окрашивая его, указывает место, где расположена трещина. Эту окрашенную пенетрантом часть поверхности детали после завершения процесса появления принято называть следом дефекта.
След дефекта представляет собой индикаторный рисунок (изображение), образованный индикаторной жидкостью в месте расположения несплошности и подобный форме трещины у выхода на поверхность объекта контроля. Обычно ширина следа по величине значительно больше раскрытия (ширины) несплошности на поверхности. При правильной технологии проявления ширина следа в 10 – 20 и более раз может превосходить ширину дефекта. Этот эффект увеличения позволяет опытным специалистам даже невооруженным глазом выявлять очень маленькие трещины.
По месту расположения следа дефекта, его форме и протяженности можно судить не только об опасности дефекта, но и получить ценную информацию о причинах его возникновения (концентрации напряжений, несоблюдение технологии и пр.).
После операции проявления деталь осматривают и следует операция расшифровки результатов контроля. Сначала исключают ложные дефекты, а сведения о выявленных дефектах заносят в журнал, используя условные обозначения обнаруженных дефектов и сокращенную запись технологии контроля. Расшифровка результатов контроля заканчивается оценкой степени их опасности.
Окончательная очистка от дефектоскопических материалов заканчивает процесс контроля. Она заключается в удалении слоя проявителя, лакового слоя или пленки проявителя с объекта контроля. При необходимости объекты контроля после окончательной очистки подвергаются антикоррозионной обработке в соответствии с техническими условиями.
Таким образом, основными операциями капиллярного контроля являются:
- подготовка объекта к контролю;
- нанесение индикаторного пенетранта на изделие и заполнение им полостей дефектов;
- удаление излишков пенетранта;
- проявление;
- расшифровка результатов контроля и выявление дефектов;
- регистрация результатов контроля;
- окончательная очистка объектов контроля.
Представление о длительности полного технологического цикла капиллярного контроля может дать пример контроля такого относительно небольшого объекта, как турбинная лопатка. Он составляет 0,5 – 1,4 часа в зависимости от применяемых дефектоскопических материалов и требований к чувствительности контроля.
Затраты времени в минутах распределяются следующим образом:
- подготовка объекта к контролю 5 – 20 мин;
- нанесение индикаторного пенетранта на изделие и заполнение им полостей дефектов 10 – 30 мин;
- удаление излишков пенетранта 3 – 5 мин;
- проявление 5 – 25 мин;
- осмотр 2 – 5 мин;
- окончательная очистка (если она необходима, 3 – 5 мин).
Обычно выдержку при заполнении дефекта пенетрантом или проявлении одного изделия совмещают с контролем другого изделия, в результате чего среднее время контроля изделия сокращается в 5 – 10 раз.
Искать все виды документовДокументы неопределённого видаISOАвиационные правилаАльбомАпелляционное определениеАТКАТК-РЭАТПЭАТРВИВМРВМУВНВНиРВНКРВНМДВНПВНПБВНТМ/МЧМ СССРВНТПВНТП/МПСВНЭВОМВПНРМВППБВРДВРДСВременное положениеВременное руководствоВременные методические рекомендацииВременные нормативыВременные рекомендацииВременные указанияВременный порядокВрТЕРВрТЕРрВрТЭСНВрТЭСНрВСНВСН АСВСН ВКВСН-АПКВСПВСТПВТУВТУ МММПВТУ НКММПВУП СНЭВУППВУТПВыпускГКИНПГКИНП (ОНТА)ГНГОСТГОСТ CEN/TRГОСТ CISPRГОСТ ENГОСТ EN ISOГОСТ EN/TSГОСТ IECГОСТ IEC/PASГОСТ IEC/TRГОСТ IEC/TSГОСТ ISOГОСТ ISO GuideГОСТ ISO/DISГОСТ ISO/HL7ГОСТ ISO/IECГОСТ ISO/IEC GuideГОСТ ISO/TRГОСТ ISO/TSГОСТ OIML RГОСТ ЕНГОСТ ИСОГОСТ ИСО/МЭКГОСТ ИСО/ТОГОСТ ИСО/ТСГОСТ МЭКГОСТ РГОСТ Р ЕНГОСТ Р ЕН ИСОГОСТ Р ИСОГОСТ Р ИСО/HL7ГОСТ Р ИСО/АСТМГОСТ Р ИСО/МЭКГОСТ Р ИСО/МЭК МФСГОСТ Р ИСО/МЭК ТОГОСТ Р ИСО/ТОГОСТ Р ИСО/ТСГОСТ Р ИСО/ТУГОСТ Р МЭКГОСТ Р МЭК/ТОГОСТ Р МЭК/ТСГОСТ ЭД1ГСНГСНрГСССДГЭСНГЭСНмГЭСНмрГЭСНмтГЭСНпГЭСНПиТЕРГЭСНПиТЕРрГЭСНрГЭСНсДИДиОРДирективное письмоДоговорДополнение к ВСНДополнение к РНиПДСЕКЕНВиРЕНВиР-ПЕНиРЕСДЗемЕТКСЖНМЗаключениеЗаконЗаконопроектЗональный типовой проектИИБТВИДИКИМИНИнструктивное письмоИнструкцияИнструкция НСАМИнформационно-методическое письмоИнформационно-технический сборникИнформационное письмоИнформацияИОТИРИСОИСО/TRИТНИТОсИТПИТСИЭСНИЭСНиЕР Республика КарелияККарта трудового процессаКарта-нарядКаталогКаталог-справочникККТКОКодексКОТКПОКСИКТКТПММ-МВИМВИМВНМВРМГСНМДМДКМДСМеждународные стандартыМетодикаМетодика НСАММетодические рекомендацииМетодические рекомендации к СПМетодические указанияМетодический документМетодическое пособиеМетодическое руководствоМИМИ БГЕИМИ УЯВИМИГКМММНМОДНМонтажные чертежиМос МУМосМРМосСанПинМППБМРМРДСМРОМРРМРТУМСанПиНМСНМСПМТМУМУ ОТ РММУКМЭКННАС ГАНБ ЖТНВННГЭАНДНДПНиТУНКНормыНормы времениНПНПБНПРМНРНРБНСПНТПНТП АПКНТП ЭППНТПДНТПСНТСНЦКРНЦСОДМОДНОЕРЖОЕРЖкрОЕРЖмОЕРЖмрОЕРЖпОЕРЖрОКОМТРМОНОНДОНКОНТПОПВОПКП АЭСОПНРМСОРДОСГиСППиНОСНОСН-АПКОСПОССПЖОССЦЖОСТОСТ 1ОСТ 2ОСТ 34ОСТ 4ОСТ 5ОСТ ВКСОСТ КЗ СНКОСТ НКЗагОСТ НКЛесОСТ НКМОСТ НКММПОСТ НКППОСТ НКПП и НКВТОСТ НКСМОСТ НКТПОСТ5ОСТНОСЭМЖОТРОТТПП ССФЖТПБПБПРВПБЭ НППБЯПВ НППВКМПВСРПГВУПереченьПиН АЭПисьмоПМГПНАЭПНД ФПНД Ф СБПНД Ф ТПНСТПОПоложениеПорядокПособиеПособие в развитие СНиППособие к ВНТППособие к ВСНПособие к МГСНПособие к МРПособие к РДПособие к РТМПособие к СНПособие к СНиППособие к СППособие к СТОПособие по применению СППостановлениеПОТ РПОЭСНрППБППБ-АСППБ-СППБВППБОППРПРПР РСКПР СМНПравилаПрактическое пособие к СППРБ АСПрейскурантПриказПротоколПСРр Калининградской областиПТБПТЭ |
все, что вы хотели знать
Дефектоскопия сварных швов — обязательный этап после любой коммерческой сварки. Для тех, кто не знает, поясним. Дефектоскопия — поиск в сварном шве скрытых от глаз дефектов с применением специальных приборов или жидкостей. Один из недорогих способов дефектоскопии — капиллярный контроль сварных соединений.


Главное преимущество капиллярного контроля — он не разрушает металл и не изменяет его качественные характеристики. К тому же, такой контроль не требует дополнительного обучения сотрудников, поскольку он очень прост в применении и расшифровке. Но, несмотря на это, у капиллярного контроля есть свои особенности, которые нужно учитывать. О них мы и расскажем в этой статье. Также вы узнаете, какова сущность и технология капиллярного контроля.
Содержание статьи
Общая информация
Капиллярный контроль сварных швов — метод контроля качества, суть которого заключается в применении специальных жидкостей. Их еще называют индикаторами или пенетрантами. Такие жидкости обладают особыми свойствами. Они способны проникать в самые мелкие трещинки, оставляя при этом следы яркого цвета. Следы хорошо заметны невооруженным глазом, так что сварщик без труда может определить точное местоположение дефекта. Если дефекты очень маленькие, то можно использовать увеличительные лупы. Подобные методы контроля сварных швов эффективны и просты в использовании.


Используя капиллярный метод контроля можно обнаружить многие дефекты: начиная от трещин и пор, заканчивая прожогами и непроварами. Словом, все основные дефекты можно увидеть, не используя при этом дорогостоящего оборудования. Также можно узнать физические размеры дефекта и его точное местоположение.
Читайте также: Визуально-измертельный контроль качества
Капиллярный контроль применим ко многим материалам, будь то черный или цветной металл, различные искусственные полимеры (например, пластмасса или полипропилен), стекло и даже керамика. Так что область применения действительно большая, капиллярный контроль может найти себе применение во многих отраслях.
Разновидности капиллярного контроля
Существует две разновидности капиллярного контроля: основной и комбинированный. Основной метод заключается в том, что вы используете только технологию капиллярного контроля и ничего более. А при комбинированном методе капиллярный контроль может использоваться до любого другого контроля. Например, радиографического.
Эти методы в свою очередь имеют свои разновидности. В основном методе капиллярного контроля можно использовать либо специальный раствор, либо фильтрующую суспензию. А чтобы обнаружить результаты контроля, можно использовать хроматический, ахроматический, люминесцентный или люминесцентно-хроматический способ. Все этого относится к основному методу.


В комбинированном методе всегда используется капиллярный контроль, а также магнитный, индукционный, радиографический или любой другой метод контроля качества. Во всех этих способах нужно применять специальные жидкости, но для обнаружения результатов контроля используются приборы, характерный для каждого отдельного типа контроля качества. Например, в радиографическом методе таким прибором будет рентгеновский аппарат. В таком случае деталь сначала подвергают капиллярному контролю, а затем делают рентгеновский снимок, чтобы точно обнаружить, где располагаются дефекты.
Технология
Выше мы писали, что метод капиллярного контроля очень простой, и это правда. Сейчас мы вам подробно расскажем, как провести такой контроль. Вы сможете повторить его самостоятельно.
Для начала очистите поверхность шва. Это можно сделать с помощью любого растворителя. На поверхности не должны быть грязи, пятен от краски или от масла. Также просушите деталь, можно сделать это естественным образом на свежем воздухе. Также рекомендуем зачистить металл металлической щеткой или наждачкой. Так вы точно удалите все загрязнения и лишние вкрапления.
Но здесь есть один нюанс. Использовать щетку или наждачку нужно только в том случае, если поверхность металла неровная или пористая. Если металл относительно ровный и гладкий, то лучше ограничиться растворителем. В противном случае вы просто затрете наружные дефекты и не сможете потом обнаружить их при проведении контроля.
Далее нужно нанести пенетрант на поверхность шва. Есть несколько методов нанесения, о них мы поговорим позже. Скажем лишь, что самый простой метод — нанесение прямо из баллончика, с помощью кисти и погружение детали в емкость с пенетрантом. В последнем случае деталь нужно выдержать в жидкости от 5 минут и выше. Затем нужно удалить с поверхности излишки пенетранта. О том, как это сделать, мы тоже подробно рассказываем далее.


После того, как мы нанесли пенетрант, а затем убрали его излишки, нужно деталь просушить. После просушки нанесите на поверхность металла проявитель. Все готово. Согласитесь, ничего сложного. Так что можете приобрести баллончики с пенетрантом и проявителем, чтобы поэкспериментировать у себя в гараже. Поверьте, результата вас приятно удивит. Возможно, вы всегда считала свою сварку идеальной. Но только благодаря контролю получите по-настоящему объективную картину.
Обращаем ваше внимание, что к покупке пенетрантов нужно отнестись серьезно. Сейчас в магазинах появилось много дешевых жидкостей от неизвестных производителей, которые в лучше случае просто не дают должного результата, а в худшем — могут быть взрывоопасными или опасными для здоровья. Не экономьте на жидкостях для капиллярного контроля, они и так стоят не очень дорого по сравнению с другими способами контроля качества. Самый удобный формат жидкости — это, конечно, в баллончиках. Они равномерно распыляются на поверхность металла, что очень удобно. Рекомендуем новичкам именно жидкости в баллончиках.
Также капиллярная дефектоскопия может проводиться с помощью флуоресцентных пенетрантов. Это пенетранты, которые светятся в темноте. Для наблюдения за результатом не нужно использовать специальные очки, достаточно просто осмотреть деталь в затемненном помещении. При этом нужно использовать ультрафиолетовые лампы. В самом помещении не должно быть никаких посторонних предметов, которые могут отсвечивать.
Если используются обычные цветные пенетранты, то можно проводить осмотр детали и при дневном свете. Но мы все же рекомендуем использовать специальные яркие лампы.
Способы нанесения жидкостей
Выше мы упоминали, что пенетранты можно наносить с помощью аэрозольного баллончика или кисти. Это, пожалуй, самый примитивный и простой способ нанесения жидкости на контролируемую поверхность металла. В таких случаях жидкость сама распределяется по вглубь металла. Чтобы добиться лучших результатов можно погрузить деталь в емкость, наполненную пенетрантом. Температура пенетранта может быть от 5 до 50 градусов по Цельсию, так что можно проводить контроль даже на улице.
Но это не единственные методы нанесения жидкостей. Существуют и более продвинутые. Например, компрессионный метод, когда пенетрант подается на шов под определенным давлением. Благодаря давлению жидкость быстрее и эффективнее проникает вглубь металла. А сам контроль дает лучшие результаты по сравнению с простыми методами нанесения.
Также существует абсолютно противоположный способ нанесения жидкостей — вакуумный. Этот способ дорогостоящий, но очень эффективный. Деталь нужно поместить в вакуумную камеру и лишают ее воздуха. В результате в местах, где есть скрытые дефекты, давление сильно падает. Далее наносится жидкость, которая тут же заполняет все дефектные полости. Способ не из простых и дешевых, так что применяется в случаях, когда нужно добиться высокого качества шва и нет возможности использовать другие методы контроля.
Также можно использовать звуковые или ультразвуковые волны, которые будут воздействовать на жидкости, вгоняя их глубоко в металл. Но нужно учитывать, что такой метод деформирует дефекты, так что применяется он крайне редко.
Способы очистки
Как вы помните из технологии, после нанесения пенетранта и его выдержки нужно удалить излишки. Самый простой способ сделать это — смочить теплой водой мягкую тряпку или губку для мытья посуды и протереть ею поверхность шва. Такой способ самый экономный, не очень эффективный.
Вместо воды можно использовать растворитель. Но перед этим поверхность детали нужно как следует просушить. Этот способ очистки куда лучше тряпки с водой, но все равно недостаточно эффективен. Мы рекомендуем комбинировать протирание водой и протирание растворителем. Если вы готовы потратиться, то можете использовать специальные очистители в баллончиках. Они отлично справляются со своей задачей.
После очистки деталь нужно снова высушить. Если время позволяет, то оставьте деталь на свежем воздухе на некоторое время. Но не оставляйте на солнцепеке. Если времени мало и нет никаких приборов, то можно просто хорошо протереть тряпкой без ворса. Если в вашем распоряжении есть фен, то можете удалить влагу таким способом. Он самый эффективный и быстрый.
Способы нанесения проявителя
Итак, мы разобрались, как правильно наносить пенетрант и очищать деталь от ее излишков. Но что насчет проявителя? Ведь от него во многом зависит конечный результат. Здесь метод нанесения не так важен, как в случае с пенетрантом. Важнее выбрать подходящий тип проявителя и нанести его на очищенную и высушенную поверхность.
Проявители бывают разные. Есть сухие, их не очень удобно наносить, они используются только в сочетании с флуоресцентными пенетрантами. Стоят недешево. Используются редко, понятно, по каким причинам. Но результат контроля отличный.
Второй вид — жидкий проявитель. Может быть изготовлен с применением разных основ. Самый популярный — жидкий на основе водной суспензии. Можно наносить разными способами: и распылять, и замачивать в емкости. Если решите использовать емкость, то погружение должно быть кратковременным. За ним должна следовать просушка с применением специального фена.
Также есть жидкий проявитель на основе веществ, сходных по свойствам с растворителями. Недорогие и вполне эффективные, наносятся равномерным слоем с помощью распыления. Больше нечего добавить.
Проявлять нужно около 10-20 минут. Если результат не достигнут, то можно добавить еще минут 10 к основному времени.
Повторный контроль
В процессе капиллярного контроля могут произойти многие ситуации, из-за которых результат контроля будет неудовлетворительным. Например, вы решили погрузить деталь в емкость с пенетрантом, но выдержали меньше времени, чем должны были. И произошло это не по вашей вине. Или же вы случайно допустили ошибку при выполнении технологии капиллярного контроля. В таких случаях новички часто спрашивают: «Можно ли провести повторный контроль?». Наш ответ: да, можно.
Самое главное — хорошо очистить металл от остатков пенетранта и проявителя. Также используете те же жидкости, не нужно брать жидкости другого производителя. Соблюдая эти простые правила, вы сможете провести повторный контроль, который может оказаться куда успешнее предыдущего.
Вместо заключения
Капиллярный метод контроля сварных соединений очень простой, при этом экономически выгодный и вполне эффективный. Поэтому данный метод контроля качества используется повсеместно. Вы наверняка встретите баллончик с пенетрантом как в цеху крупного завода, так и в гараже у домашнего мастера.
Конечно, с помощью такого метода можно обнаружить далеко не все возможные дефекты, скрытые от глаз сварщика. Но если вы в полевых условиях или высокое качество шва не так уж важно, то можно ограничиться и капиллярным контролем. Также капиллярный контроль незаменим в маленьких частных мастерских, где прибыль небольшая и экономическая сторона вопроса играет главную роль. А вы использовали в своей практике капиллярный метод контроля качества швов? Расскажите об этом в комментариях ниже. Не забывайте делиться этой статьей в социальных сетях. Желаем удачи в работе!