Контроль сварных швов на непроницаемость
Контроль швов на непроницаемость применяется в сварных изделиях, предназначенных для хранения жидкостей, газов или работающих в условиях вакуума.
Испытание на плотность производится после предварительного контроля сварных швов наружным осмотром. Эти испытания выполняются с помощью керосина, а также воздуха или воды под давлением.
Способы испытания зависят от назначения конструкции и технических условий на изготовление. Испытания на плотность обычно производятся не менее двух раз: предварительное для выявления пороков и повторное после их исправления.
Испытание керосином.
Для испытания открытых сосудов и различных стационарных резервуаров часто используется керосин. Швы сосудов для лучшего выявления пороков покрываются мелом, разведенным на клее. Швы с обратной стороны обильно смазывают керосином и выдерживают от 10 мин. до 3 час, в зависимости от толщины материала и назначения конструкции.
Испытание воздухом.
Испытание сжатым воздухом применяется только для закрытых сосудов. Для испытания в сосуд с предварительно заглушенными отверстиями подается сжатый воздух под давлением 1,0—2,0 атм. Снаружи все швы смачиваются мыльной водой, и сжатый воздух, выходя через неплотности, образует мыльные пузыри, по которым определяют пороки в швах и исправляют их.
Необходимо отметить, что испытание воздухом при неправильной подготовке изделий или подаче воздуха без чувствительного манометра и предохранительного клапана представляет значительную опасность. Крышки и заглушки перед испытанием должны быть надежно закреплены.
Применять сжатый воздух давлением свыше 2 атм не рекомендуется вследствие опасности разрушения конструкций.
Гидравлическое испытание.
При гидравлическом испытании проверяется прочность и плотность различных сосудов, котлов и трубопроводов, работающих под давлением. При этом испытании сосуд с плотно закрытыми отверстиями наполняется водой. Воздух из него выходит через верхнее отверстие, которое после заполнения также заглушается. Затем давление доводится до необходимой величины, и сосуд подвергается тщательному осмотру. Швы, имеющие пороки, дают течь и потение, а слабые места даже разрушаются. После выдержки и осмотра давление в сосуде доводится до рабочего, и металл сосуда на расстоянии 15—20 мм от швов подвергается обстукиванию легкими ударами молотка (весом 0,4—1,5 кг) с круглым бойком для предупреждения образования вмятин. Величина давления при испытании устанавливается соответствующими инструкциями по контролю и правилами освидетельствования. Обычно испытательное давление на 25—100% больше рабочего. Рабочее место, где производится испытание, должно быть оборудовано в соответствии с правилами по технике безопасности.
Испытание аммиаком.
При этом способе внутрь испытуемого изделия подается аммиак в количестве 1% от объема воздуха, находящегося в изделии при нормальном давлении. После этого в сосуд нагнетается воздух до давления, принятого для испытания. Швы, подлежащие испытанию, покрываются бумажной лентой, пропитанной 5%-ным водным раствором азотнокислой ртути. Бумажная лента может быть заменена обычным медицинским бинтом, пропитанным тем же раствором. Бинт более выгоден, так как после промывки в воде вновь пригоден к употреблению.
Фиг.110.Схема испытания плотности швов аммиаком.
При наличии в шве пор, трещин или других дефектов, влияющих на плотность швов, аммиак проходит через них и действует химически на пропитанную азотнокислой ртутью бумагу. В местах неплотностей на бумаге остаются черные пятна. Выдержка под давлением составляет 1—5 мин, после чего бумагу (или бинт) снимают. Она служит документом при определении качества шва.
Схема испытания плотности аммиаком показана на фиг. 110.
Испытание аммиаком более производительно, дешевле и точнее, чем способ испытания воздухом.
Большим преимуществом проверки на плотность швов аммиаком является возможность применить этот способ в зимних условиях при низких температурах.
Обнаружение неплотностей в сварном шве галоидным течеискателем типа ГТИ-2. Для выявления полной непроницаемости сварных соединений в сосудах, работающих в условиях глубокого вакуума или в сосудах (системах), в которых находятся под давлением различные газы (или воздух), с успехом может быть применен весьма чувствительный галоидный течеискатель типа ГТИ-2. С его помощью выявляются такие микроскопические неплотности, через которые в течение года вытекает 0,5 г фреона (Ф-12) под давлением 5—6 атм.
Течеискатель ГТИ-2 — переносный прибор, состоящий из выносного щупа, оформленного для удобства пользования в виде пистолета, и измерительного блока (электроаппаратуры с регулирующими и измерительными устройствами). Питание производится от сети переменного тока промышленной частоты напряжением 220 в. Вес выносного щупа 2 кг, измерительного блока 11,5 кг.
При отыскании неплотностей в сосуде или другом каком-либо объекте его предварительно испытывают сжатым воздухом для выявления сравнительно больших течей и устранения их. Затем внутренний объем сосуда заполняется газом, содержащим галоиды — фреон, четыреххлористый углерод, хлороформ, йодоформ под давлением, несколько превышающим атмосферное. Эти газы могут применяться как в чистом виде, так и в смеси с воздухом.
По шву, который проверяют, медленно проводят наконечник щупа. Появление звукового сигнала (увеличение частоты звука) и отклонение стрелки выходного прибора указывают на наличие неплотности в шве.
Проверка непроницаемости сварных швов и соединений
Рекомендуем приобрести:
Установки для автоматической сварки продольных швов обечаек — в наличии на складе!
Высокая производительность, удобство, простота в управлении и надежность в эксплуатации.
Сварочные экраны и защитные шторки — в наличии на складе!
Защита от излучения при сварке и резке. Большой выбор.
Доставка по всей России!
Сварные швы и соединения ответственных изделий и сооружений должны быть непроницаемыми для различных жидкостей и газов Неплотности в швах снижают их прочность при вибрационных нагрузках, уменьшают коррозионную стойкость, вызывают утечку хранимых и транспортируемых продуктов и создают недопустимые условия эксплуатации сварных конструкций.
Контроль непроницаемости сварных соединений проводят в соответствии с ГОСТ 3242-79, включая следующие виды испытаний: керосином, обдувом, аммиаком, воздушным давлением, гидравлическим давлением, наливом и поливом.
Кроме этого, непроницаемость сварных соединений определяют вакуумным методом и газоэлектрическими течеискателями.
Перед проведением испытаний должны быть устранены все дефекты, выявленные внешним осмотром.
Испытание керосином основано на способности многих жидкостей подниматься по капиллярным трубкам, какими в сварных швах являются сквозные поры и трещины. Керосин обладает высокой смачивающей способностью и сравнительно малой вязкостью, что обеспечивает большой эффект этого способа контроля. Например, в отличие от воды (полярная жидкость) керосин под действием поверхностных сил проникает в мельчайшие (10 -3 — 2,10-4 мм) неплотности в металле.
Испытание сварных соединений керосином проводят следующим образом. После внешнего осмотра простукивают молотком или подвергают вибрации основной металл на расстоянии 30—40 мм от шва и тщательно очищают сварное соединение от шлака, ржавчины, масла и других загрязнений. Такое простукивание или вибрация способствует лучшему удалению шлака и развитию несквозных дефектов в сквозные.
Затем с помощью пульверизатора сварные швы покрывают меловым раствором (350—450 г молотого мела или каолина на 1 л воды) с той стороны, которая более доступна для осмотра.
После высыхания мелового раствора другую сторону шва обильно смачивают керосином и выдерживают в течение определенного времени.
Исходя из экспериментальных данных Института электросварки им. Е. О. Патона, Всесоюзного научно-исследовательского института строительства трубопроводов и ряда монтажных организаций время выдержки под керосином обычно устанавливают не менее 12 ч при окружающей температуре выше 0° и не менее 24 ч — при температуре ниже 0°.
Ввиду того что при повышении температуры вязкость керосина уменьшается и скорость проникания его через неплотности шва увеличивается, для сокращения времени контроля рекомендуется швы перед испытанием нагревать до температуры 60—70° С. В этом случае время выдержки под керосином сокращается до 1,5—2 ч. Керосин наносят в процессе испытания 3—5 раз.
Соединения внахлестку, у которых один шов сплошной, а второй прерывистый, опрыскивают струей керосина под давлением co стороны прерывистого шва. Соединения внахлестку, сваренные сплошным швом с обеих сторон, испытывают керосином путем нагнетания его под давлением в межнахлесточное пространство через специально просверленное отверстие.
О наличии пор, свищей, сквозных трещин и непроваров свидетельствуют жирные желтые точки или полоски керосина на меловом слое, которые с течением времени расплываются в пятна. Поэтому необходимо тщательно следить за появлением первых точек или полосок и своевременно отмечать границы дефектных участков.
Обнаруженные дефекты устраняют, после чего сварной шов подвергают повторному контролю.
Для лучшего наблюдения за керосиновыми пятнами применяют керосин, окрашенный в красный цвет краской «Судан-III» в количестве 2,5—3 г на литр.
Эффективность контроля непроницаемости сварных швов с помощью керосина можно повысить, применяя дополнительно продувку швов сжатым воздухом под давлением 3—4 кгс/см2, разрежение атмосферного воздуха с меловой стороны шва при помощи специальных камер, вибрацию швов. Все эти меры ускоряют проникание керосина через неплотности.
С помощью керосина выявляют не только сквозные, но и поверхностные дефекты. Для этого поверхность контролируемого сварного соединения после тщательной очистки обезжиривают бензином или ацетоном и обильно смачивают окрашенным керосином. По истечении 15—20 мин керосин вытирают или смывают 5%-ным водным раствором кальцинированной соды с последующим просушиванием. Затем на поверхность сварного соединения при помощи пульверизатора наносят тонкий слой разведенного в воде мела (или каолина).
Когда мел высохнет, изделие около шва обстукивают молотком, а сам шов прогревают горячим воздухом. При этом керосин, задержавшийся ранее на дефектных участках (в случае их наличия), просачивается на меловую краску в виде пятен и полосок, по которым судят об имеющихся дефектах.
При испытании обдувом одну сторону сварного шва промазывают мыльным раствором (вода 1 л, мыло хозяйственное 100 г), а другую — обдувают сжатым воздухом, подаваемым по гибкому шлангу с наконечником под давлением 4—5 кгс/см2. Расстояние между наконечником и швом должно быть не более 50 мм.
Если испытание проводят при температуре ниже 0° С, мыльный раствор готовят с частичной заменой воды спиртом (до 60%) или с применением незамерзающей жидкости, растворяющей мыло.
Сквозные дефекты обнаруживают по появлению пузырей на промазанной мыльным раствором стороне шва.
В основу испытания аммиаком положено свойство некоторых индикаторов, например спирто-водного раствора фенолфталеина или водного раствора азотнокислой ртути, изменять окраску под воздействием щелочей, в данном случае сжиженного аммиака.
Перед началом испытаний тщательно очищают металлической щеткой сварное соединение от шлака, ржавчины, масла и других загрязнений. Если сварку вели электродами с обмазкой основного типа, то швы, кроме того, промывают водой, иначе остатки щелочных шлаков будут реагировать в процессе испытания с индикатором, изменяя его окраску.
После такой подготовки на одну сторону шва укладывают бумажную ленту или светлую ткань, пропитанную 5%-ным раствором азотнокислой ртути (индикатором), а с другой стороны создают давление аммиака.
При контроле сварных швов небольших емкостей, а также трубопроводов в них подают аммиак в количестве 1% объема воздуха в емкости и создают избыточное давление 1 кгс/см2 или более, но не выше расчетного рабочего.
При контроле отдельных участков шва над ними устанавливают герметичную камеру, в которой создают давление аммиака.
В обоих случаях спустя 1—5 мин аммиак, проникая через неплотности сварного шва, окрашивает пропитанную индикатором бумагу или ткань в серебристо-черный цвет. Скорость и интенсивность окраски, а также величина пятен характеризуют размеры дефектов, границы которых отмечают мелом или краской.
При использовании в качестве индикатора спирто-водного раствора фенолфталеина его тонкой струей льют на контролируемый шов. Если в шве имеются неплотности, аммиак проходит через них и окрашивает раствор фенолфталеина в ярко-красный цвет с фиолетовым оттенком.
Для испытания сварных швов днищ резервуаров или газгольдеров аммиак подают в пространство между днищем и основанием по трубкам с отверстиями и создают избыточное давление 8 — 10 мм вод. ст. Поливая швы спирто-водным раствором фенолфталеина, определяют неплотности в сварных швах и устраняют их.
Испытанию давлением газа подвергают емкости и трубопроводы, работающие под давлением, с целью контроля общей непроницаемости сварной конструкции.
Малогабаритные изделия герметизируют газонепроницаемыми заглушками и полностью погружают в ванну с водой. Затем в изделие через редуктор от воздушной сети или из баллона подают газ (воздух, азот, инертные газы) под давлением, величина которого на 10—20% больше величины рабочего. Имеющиеся неплотности определяют по появлению пузырьков газа в воде.
Крупногабаритные сварные изделия испытывают следующим образом. После герметизации в них создают испытательное давление и промазывают сварные швы мыльным раствором (100 г мыла на 1 л воды). Появление мыльных пузырей на промазанной поверхности свидетельствует о проницаемости шва.
Величину давления и время выдержки под ним устанавливают в соответствии с техническими условиями.
При испытании сжатыми газами следует тщательно соблюдать правила техники безопасности. Работы должны проводиться в изолированном помещении с ограждениями (на случай взрыва). Трубопроводы испытывают отдельными изолированными участками с предупредительными знаками об опасности. Гидравлическим давлением проверяют прочность и плотность сварных соединений различных емкостей, котлов паропроводов, водопроводов, газопроводов и других сварных конструкций, работающих под высоким давлением.
Перед испытанием сварное изделие герметизируют водонепроницаемыми заглушками, обтирают или обдувают сжатым воздухом сварные швы до получения сухой поверхности.
После полного заполнения изделия водой с помощью насоса или гидравлического пресса создают избыточное контрольное давление, величину которого принимают в соответствии со стандартами, инструкциями или техническими условиями (обычно в 1,5—2 раза больше рабочего). В процессе испытания давление определяют по проверенным и опломбированным манометрам.
В самой высокой точке испытываемого изделия устанавливают контрольную заглушку на резьбе для наблюдения за заполнением всего объема водой и выпуском воздуха в атмосферу. В противном случае не исключено образование воздушной подушки, находящейся под большим давлением, что может привести к разрыву изделия в процессе испытания.
По истечении 5—6 мин давление уменьшают до рабочего, а околошовную зону слегка обстукивают молотком на расстоянии 15—20 мм от края шва. Боек молотка должен быть круглым, чтобы не повредить основной металл изделия.
Проницаемость сварных швов и места сквозных дефектов устанавливают по снижению испытательного давления и появлению течи или просачиванию воды в виде капель, а также по запотеванию поверхности шва или вблизи него.
Во избежание ошибочных выводов следует иметь в виду, что при температуре воды в сосуде ниже температуры воздуха в помещении возможно полное запотевание всей поверхности металла испытуемого изделия. Кроме того, уменьшение испытательного давления не всегда указывает на наличие дефектов, а может быть вызвано неплотностями в нагнетательной системе, присоединительной арматуре, заглушках.
Недостатками этого способа контроля являются необходимость в источниках водоснабжения и трудности, возникающие при испытаниях в зимнее время на открытом воздухе.
Вертикальные резервуары для хранения нефти и нефтепродуктов, газгольдеры и другие крупные емкости испытывают наливом воды.
До испытания сварные швы тщательно обтирают ветошью или обдувают воздухом до получения сухой поверхности. Затем емкость заполняют водой и наблюдают за сварными швами и падением уровня воды. Продолжительность испытания, необходимого для осмотра всех швов, составляет от 2 до 24 ч в соответствии с техническими условиями. Если в течение этого времени не обнаружено пропусков воды и уровень ее не снизился, емкость считают выдержавшей испытание.
Категорически запрещается обстукивать сварные швы резервуаров, газгольдеров и других крупных емкостей в процессе испытания во избежание их разрушения. Испытание проводится при температуре окружающего воздуха не ниже 0° С и температуре воды не ниже +5° С.
Когда швов немного, их непроницаемость определяют, полива одну сторону шва водой из брандспойта под давлением 1—10 кгс/см2, устанавливаемым техническими условиями. Одновременно осматривают противоположную сухую сторону шва.
Проницаемость сварных швов и места дефектов определяют, следя за появлением течи, просачиванием воды в виде капель, запотеванием поверхности шва или вблизи его.
Вакуумный контроль сварных швов применяют в тех случаях, когда применение других способов почему-либо исключено. В частности, этот метод широко применяется при контроле сварных днищ резервуаров, газгольдеров, цистерн, гидроизоляционных ящиков. Он позволяет обнаружить отдельные поры диаметром до 0,004— 0,005 мм, а производительность при его использовании достигает 40—60 м сварных швов в час.
Вакуум создают при помощи переносной вакуум-камеры, которую устанавливают на наиболее доступной стороне проверяемого участка шва.
В зависимости от формы контролируемого изделия и типа соединения применяются плоские, угловые и кольцевые вакуум-камеры.
Механизированная вакуум-тележка укомплектована набором переносных вакуум-камер, позволяющих контролировать различные типы сварных соединений во всех пространственных положениях.
Контроль швов газоэлектрическими течеискателями. В настоящее время применяют два вида газоэлектрических течеискателей: гелиевые и галоидные.
Чувствительность газоэлектрических течеискателей к выявлению неплотностей в швах очень высока, но ввиду сложности конструкции и значительной стоимости изготовления их применяют только для контроля особо ответственных сварных конструкций.
Принцип работы гелиевого течеискателя основан на высокой способности гелия при определенном вакууме проходить сквозь неплотности сварных швов.
В зависимости от конфигурации и объема испытуемой сварной конструкции контроль неплотностей швов гелиевыми течеискателями производят следующими методами.
а) Контроль избыточным давлением состоит в том, что испытуемую емкость помещают в газонепроницаемую металлическую камеру, соединенную с насосами течеискателя. Внутри камеры создают вакуум, а в емкость подают под давлением гелий. При наличии сквозных дефектов в сварных швах гелий проникает в камеру и попадает в течеискатель, где фиксируется одновременно миллиамперметром и звуковым сигналом.
По окончании испытаний гелий перекачивают в другую емкость, подготовленную для контроля, или в резервуар для хранения.
б) При контроле с помощью гелиевой камеры вакуум создают в испытуемой емкости, а гелий подают в газонепроницаемую камеру. Если в сварных швах имеются неплотности, то гелий просачивается в испытуемый сосуд и попадает в течеискатель.
в) Метод установки специальной герметичной камеры-муфты применяют в основном для испытания стыков трубопроводов.
Камеру соединяют с насосом течеискателя, создают в ней вакуум и подают в трубопровод гелий. При наличии неплотностей в сварных швах гелий попадает в течеискатель и вызывает сигнал.
Эти три метода являются наиболее чувствительными к выявлению неплотностей в сварных швах, но не определяют место их расположения. С этой целью применяют обдувание струей гелия наружной поверхности испытуемой емкости, в которой создают вакуум. Места неплотностей фиксируют по сигналу течеискателя, соединенного с емкостью.
Для более точного определения расположения дефектных участков используют специальный щуп-улавливатель, соединенный с течеискателем. Щуп перемещают вдоль швов по наружной поверхности емкости, в которой находится гелий под давлением выше атмосферного. Малейшая неплотность в шве тотчас же фиксируется течеискателем.
Гелиевые течеискатели применяются для обнаружения неплотностей в сварных швах трубопроводов, находящихся под землей. Для этого над трубопроводами пробуривают несколько скважин, в которые опускают специальный щуп-улавливатель, а в каждую трубу подают гелий. Примерное место течи определяют в зависимости от того, какая из скважин показывает максимальную концентрацию гелия.
Контроль качества сварных швов
Контроль качества сварных швов
Для своевременного выявления дефектов необходим тщательный и систематический контроль сварных соединений трубопроводов на всех стадиях производства сварки. В зависимости от требований проекта или технических условий контроль сварных соединений технологических трубопроводов осуществляется путем наружного осмотра всех стыков, механических испытаний и физических методов контроля (металлографического исследования, просвечивания рентгеновскими или гамма-лучами, ультразвука, магнитографического способа), а также проверки плотности сварных стыков гидравлическим или пневматическим испытанием. В отдельных случаях в зависимости от материала труб и назначения трубопровода сварные швы проверяют на коррозионную стойкость.
Наружному осмотру подвергают каждый сваренный стык трубопровода. Путем осмотра выявляют внешние дефекты шва: наплывы, подрезы, кратеры, прожоги, трещины, свищи, наружные поры.
Механические испытания сварных соединений производят, чтобы определить их прочность и пластичность. Обязательными, видами механических испытаний являются испытания на растяжение, загиб или сплющивание и на ударную вязкость. Для проведения механических испытаний каждый сварщик одновременно со сваркой трубопровода осуществляет сварку контрольных (пробных) стыков, из которых вырезают образцы. Механические испытания контрольных стыков выполняют только при сварке трубопроводов, подведомственных органам Госгортехнадзора, на газопроводах, подведомственных органам газовой инспекции, а также на внутризаводских трубопроводах, транспортирующих огне- и взрывоопасные или токсичные газообразные и жидкие продукты. Механические испытания производят в соответствии с ГОСТ 6996—54.
Металлографическое исследование осуществляют, чтобы определить структуру металла шва и околошовной зоны, выявить в сварном шве газовые или шлаковые включения, волосяные трещины, непровары. При металлографическом исследовании проверяют излом сварного шва и определяют его макро- и микроструктуру. Эти исследования обязательны только для паропроводов первой и второй категорий, подведомственных Госгортехнадзору, и трубопроводов специального назначения. Исследованию подвергаются образцы, вырезанные из контрольного стыка.
Просвечивание рентгено- и гамма-лучами — наиболее распространенный способ контроля сварных швов без разрушения. Просвечивание позволяет обнаружить внутренние дефекты сварки — трещины, непровар, шлаковые включения и поры. Для просвечивания сварных швов применяют стационарные (РУП-200, РУП-400-5) и переносные (РУП-120-5-1 иИРА-1д) рентгеновские установки. Стационарные установки из-за больших габаритных размеров используют на заводах и в лабораториях; переносные — в монтажных условиях.
Гамма-лучи возникают в результате процессов, происходящих при распаде ядер элементов или изотопов, обладающих искусственной или естественной радиоактивностью. Эти лучи способны проникать через слой металла значительной толщины и действовать на рентгенопленку, приложенную к шву с обратной стороны. В тех местах, где имеются дефекты, поглощение лучей металлом будет меньше, и они окажут более сильное воздействие на эмульсию пленки. В данном месте на пленке появится темное пятно, по форме соответствующее дефекту шва. Для просвечивания пользуются гамма-лучами радиоактивных элементов цезия-137,. туллия-170, кобальта-60, иридия-192, европия-152. Для просвечивания радиоактивные вещества, излучающие гамма-лучи, помещают в специальные ампулы, заключенные в свинцовые кожухи (контейнеры). Рентгеновское и гамма-просвечивание проводят в соответствии с ГОСТ 7512—55. Недостатком способа контроля гамма-лучами является его вредность, требующая особых мер к охране людей от их воздействия.
Магнитографический способ контроля сварных швов основан на принципе изменения магнитного рассеивания, возникающего во время намагничивания контролируемого изделия в местах расположения дефектов. Особенностью этого способа является «запись» обнаруживаемых дефектов на специальную магнитофонную пленку (ленту).
Данный способ контроля применяют для труб толщиной до 20 мм, он позволяет четко выявить такие дефекты сварных швов, как продольные трещины, непровар, шлаковые включения и поры.
Ультразвуковой способ контроля сварных швов основан на различном отражении направленного пучка высокочастотных звуковых колебаний от металла (сварного шва) и имеющихся в нем дефектов.
Ультразвуковой контроль применяют для труб с внутренним диаметром 80 мм и более и стенками толщиной свыше 10 мм. Наибольшее применение для контроля нашли ультразвуковые дефектоскопы УЗД-7Н, НИИМ-5 и УЗД-39.
Недостатком данного способа контроля является то, что он позволяет определить лишь место дефекта, а не его характер.
Контролю физическими методами подвергают наихудшие стыки из отобранных по внешнему осмотру, в количестве:
Для трубопроводов I и II категорий. ……………………. 3%
Для трубопроводов III категории ……………………….. 2%
Для трубопроводов IV категории…………………………. 1%
Количество стыков определяется от общего числа сваренных каждым сварщиком стыков, но оно должно быть не менее одного. Контролю необходимо подвергать весь периметр стыка.
При физических методах контроля сварные швы полагается браковать, если в них обнаружены следующие дефекты: трещины любых размеров; непровар глубиной более 15% от толщины стенки трубы, если она не превышает 20 мм, а при толщине стенки свыше 20 мм — более 3 мм; шлаковые включения и поры глубиной более 10% от толщины стенки трубы, если она не превышает 20 мм и 3 мм — при толщине стенки свыше 20 мм; скопления включений и пор в виде сплошной сетки дефектов в шве независимо от их глубины. Шлаковые включения глубиной до 10% от толщины стенки и длиной не более 30 мм, а также скопления пор длиной не более 15 мм не являются признаками брака.
Исправление дефектов сварных стыков трубопроводов допускается, если при условном диаметре трубопровода до 100 мм длина трещин меньше 20 мм и при условном диаметре свыше 100 мм — меньше 50 мм, а также если протяженность участков с недопустимыми дефектами меньше ¼окружности стыка. В процессе исправления необходимо вырубить дефектные места и вновь их заварить. В остальных случаях дефектный стык должен быть удален из трубопровода и на его место вварена катушка. Все подвергавшиеся исправлению участки стыков должны быть проверены физическими методами контроля.
1. Какие применяют способы контроля сварных швов?
2. В чем сущность просвечивания гамма-лучами? Какие радиоактивные элементы используются при этом?
3. Как производится исправление дефектов сварного шва?
Все материалы раздела «Сварка труб» :
● Способы сварки трубопроводов и виды сварных соединений
● Подготовка труб под сварку
● Технология газовой сварки и резки
● Кислородно-флюсовая и дуговая резка
● Технология ручной электродуговой сварки, электроды
● Источники питания сварочной дуги
● Автоматическая и полуавтоматическая сварка под флюсом
● Автоматическая и полуавтоматическая сварка в защитных газах
● Сварка трубопроводов из легированной стали
● Сварка трубопроводов высокого давления, термообработка сварных соединений
● Сварка трубопроводов из алюминия и его сплавов, из меди и ее сплавов
● Пайка трубопроводов, дефекты сварных швов
● Контроль качества сварных швов
● Виды сварки и применяемое оборудование
● Сварка и склеивание винипластовых труб
● Сварка полиэтиленовых трубопроводов
● Правила техники безопасности при резке и сварке трубопроводов
Физические методы контроля сварных швов
ФИЗИЧЕСКИЕ МЕТОДЫ КОНТРОЛЯ СВАРНЫХ ШВОВ [c.
Сварные швы бракуются, если физическим методом контроля будут обнаружены трещины, непровары швов глубиной более 10% толщины стенок труб, шлаковые включения и поры глубиной более 10% толщины стенок труб, а также скопления включений и пор в виде сплошной сетки в швах независимо от их глубины. [c.363]
В настоящее время методы контроля сварных соединений делятся на следующие группы методы контроля подготовки изделий под сварку н наружных дефектов (сюда относится люминесцентный метод контроля) методы контроля с частичным или полным разрушением сварных швов физические методы контроля без разрушения (гамма- и рентгеновский контроль, магнитные и ультразвуковой методы контроля) методы контроля герметичности сварных швов (контроль керосином вакуумный, гидравлический, пневматический методы контроля метод химических реакций и метод течеискателей) методы контроля сварных соединений, образованных с помощью прессовых способов сварки (проверка параметров режима сварки, которые характеризуют степень нагрева и величину осадки).
[c.327]
СНиПом оговариваются допускаемые дефекты сварных швов, обнаруживаемые как нри наружном осмотре, так и физическими методами контроля, а также способы устранения дефектов. [c.358]
Контроль качества сварных соединений, выполненных дуговой сваркой. Контроль сварных швов производится путем внешнего осмотра сваренного стыка и путем проверки сплошности стыков физическими методами контроля без разрушения (рентгеном, гамма-лучами, магнитографическим и ультразвуковым контролем). Физическим методам контроля подвергаются 2″/о стыков, а на участках подводных переходов— 100%. [c.324]
Проверке физическими методами контроля сплошности сварных швов трубопроводов водоснабжения и канализации рабочим давле- [c.352]
Ж. Увеличение объема выборочного контроля сварных швов физическими методами с доведением его объема в особо ответственных случаях до 100%.
[c.299]
В местах ремонта швов разрешается увеличение усиления на 1 мм. Трубы с отремонтированными сварными швами подвергают повторному гидравлическому испытанию или места ремонта подвергают физическим методам контроля без разрушения металла. [c.69]
Все исправленные места сварных швов подлежат обязательному повторному контролю и гидравлическому испытанию. В тех случаях, когда сварные швы должны подвергаться контролю физическими методами без разрушения, такой контроль является обязательным для всех исправленных мест сварных швов. [c.246]
Цикл изготовления узлов трубопроводов заканчивается контролем качества и выполнением отделочных операций — грунтовки, маркировки, комплектации и складирования готовых узлов с отгрузкой готовой продукции потребителям. В процессе контроля качества проверяется геометрическая форма узла, производится внешний осмотр сварных швов и в некоторых случаях проверка швов физическими методами. Кроме трех основных операций по изготовлению узлов трубопро водов вы полня-
[c.128]
При осуществлении контроля качества сварных швов физическими методами (просвечиванием, ультразвуком и др.) расчетные сопротивления стыковых соединений при сжатии, растяжении, изгибе равны расчетным сопротивлениям основного металла. [c.31]
В ответственных трубопроводах и конструкциях контролю физическими методами (например, гаммаграфированию) подвергаются 100% сварных швов или стыков. Как правило, при ограниченном объеме контроля обязательна проверка сомнительных и опасных мест (например, пересечений швов, швов в труднодоступных местах и т. д.). При обнаружении недопустимых дефектов контролю подвергается удвоенное количество швов (или образцов). В случае обнаружения трещин контролю физическими методами должны быть подвергнуты все 100% сварных швов данного изделия. По результатам повторного контроля конструкция бракуется полностью или частично. Исправленные места подлежат повторному контролю теми же методами. Исправление дефектов на одном и том же участке шва должно производиться не более двух раз дефектные участки, как правило, удаляют механическим способом без нагрева.
[c.167]
Физические методы контроля сварных швов. Рентгенокон-т р о л ь. Просвечивание швов рентгеновскими лучами позволяет обнаружить в них внутренние дефекты сварки — непровар, поры, шлаковые включения, трещины. Рентгеновские лучи способны проникать через металл и действовать на фотографическую пленку, покрытую светочувствительной эмульсией и прикладываемую к шву с обратной стороны. В тех местах шва, где имеется дефект (пора, трещина и пр,), поглощение лучей металлом будет меньше и он1 окажут более сильное действие на эмульсию пленки, поэтому на [c.482]
От электросварщика ручной дуговой сварки требуется знание сварочного оборудования, физических особенностей процесса сварки, методов контроля сварных швов и соединений, а также умеше практически вьшолнять сварочные работы. На рис. 1 приведена схема ручной дуговой сварки металлическим электродом с покрытием.
[c.4]
Выбор физического метода контроля без разрушен определяется характером получения необходимой информации, особенностями конгролируемого объекта и возможностью его применения в конкретных условиях. Применение любого метода НК для диагностирования сварных аппаратов осложняется отмеченными ранее спещ1фическими конструктивными и функциональными особенностями этих аппаратов. Прежде всего, следует обратить внимание на такую особенность аппаратов, например, колонной аппаратл -ры и сферических газгольдеров, как значительные поверхности диагностирования и большая при этом протяженность сварных швов. С другой стороны, для них характерны большие поверхности контакта металла с рабочей средой, которая часто может проявлять коррозионную и эрозионную активность. [c.183]
Для систематической проверки качества сварки физическим методом контроля организации, производящей сварочно-монтажные работы по тепловым сетям, нужно иметь передвижную лабораторию. В комплект лаборатории входит дефектоскоп типа МД-10, дисковый магнит ДМ-61, магнитная лента, намагничивающее устройство с преобразователем ПО-380А на напряжение 127/220 в и аккумулятор ВСТМ-128. Все перечисленное оборудование устанавливается на автомобиле УАЗ-450А. Передвижная лаборатория для дефектоскопии сварных швов магнитографическим методом изготовляется Киевским экспериментальным механическим заводом Главгаза.
[c.363]
К акту сдачи-приемки прилагаются паспорт магистрали, паспорта арматуры и акты ревизии и испытаний, сертификаты на трубы, электроды, акты лабораторных исследований прочности сварных швов на растяжение и загиб, заключения по проверке сварных стыков физическим методом контроля, копии паспортов сварщиков, журнал сварочных работ, а также все акты на скрытые работы промежуточной приемки разбивки трассы, устройства оснований и засыпки траншей и котлованов, сварки труб и закладных частей сборных конструкций, антикоррозионной изоляции труб, укладки трубопроводов, монтажа строительных конструкций, заделки и омоноличивания стыков сборных элементов, тепловой изоляции трубопроводов, дренажных устройств и гидроизоляции, устройства электрозащиты, гидравлического или пневматического испытания, промывки трубопроводов и продувки паропроводов.
[c.365]
Контроль сварных швов рулонных заготовок. Сварные швы контролируются постоянно проверяется правильность применения установленных режимов оварки, швы осматривают, испытывают на плотность, проверяют физическими методами. Соблюдение установленных режимов должно обеспе-чивать заданные гео-.метрическне размеры сварного шва и глубину проплавления. [c.83]
Контроль качества сварных соединений корпуса цементной печи. Перед сваркой проверяют качество обработки кромок, зазо ро,в, притуплений, углов раскрытия и чистоты поверхности. Сварные соединения корпуса цементной неч И контролируют как в процессе сварки, так после ее окончания. В процессе сварочных работ кантролируют последовательность наложения слоев (И режимы сварки, а также отсутствие в наплавленном металле трещин, пор и друпих дефектов. После сварки производят внешний осмотр сварных швов. и исправляют обнаруженные дефекты 5% длины швов подвергают физическим методам контроля. Результаты контроля оформляют актом.
[c.212]
Собранные блоки трубопроводов Dy до 400 мм включительно должны подвергаться на заводе гидравлическому испытанию давлением на 50% выше рабочего, сварные стыки трубопроводов )у>400 мм до сборки в блоки подвергаются испытанию на керосин. Гидравлические испытания блоков или проверка швов на плотность керо сином могут быть заменены физическими методами контроля (рентгеноскопия, ультразвуковая дефектоскопия или гамма-трафирование) с охватом 100% стыков по всему иериметру. Все концы блока должны быть закрыты специальными заглушками. [c.414]
При выявлении недопустимых дефектов в сварных швах, под вергаемых физическим методам контроля, должен производиться по вторный контроль качества швов. В случае выявления недопусти мых дефектов при повторном контроле должны быть проконтроли рованы все стыки, выполненные данным сварщиком. [c.353]
Для предотвращения оквозняков в трубе и быстрого охлаждения металла шва торцы свариваемых звеньев или секции следует закрывать инвентарными заглушками или иными приспособлениями. Запрещается опускать в снег стыки газопровода после сварки. Проверка качества сварных швов городских газовых сетей производится путем систематического пооперационного контроля, осуществляемого в процессе сборки и сварки газопроводов, внешнего осмотра электродов, проверки сплошности стыков, выполняемой физическими методами контроля без разрушения, путем просвечивания сварных стыков гамма-лучами или магнитографического контроля
[c.58]
Вводимый в дополнение к 0,55 по СНиП коэффвдиент надежности (запаса) по материалу свидетельствует о фактическом использовании предельного состояния наступления разрушения для угловых швов, так же как и коэффициент 0,85 для неконтролируемых физическими методами стыковьк швов в табл.З СНиП, который вводит понижение расчетного сопротивления металла сварных стыковых соединений, назначаемого по пределу текучести металла. Так как физические методы контроля обнаруживают лишь несплошности и не дают сведений о механических свойствах металла по 0 2, то коэффи-
[c. 291]
При серийном контроле прямыми искателями, например при контроле стальных листов или прутков, к оператору предъявляют минимальные требования. Часто достаточно обучения в течение нескольких часов, если оператор хорошо понимает задачу и имеет достаточно умелые руки, чтобы перемещать искатель, не вызывая его износа. Для работ с поперечными поверхностными волнами и волнами в пластинах, например для контроля сложных изделий типа осей, труб или даже сварных швов, нужно больше опыта и необходимо некоторое обучение, по крайней мере изучение руководства по проведению контроля, учебные курсы или учебная практика под руководством опытного оператора. В этом случае требуется также и некоторое техническое образование, нужны элементарные математические знания и хорошее пространственное воображение. Для перехода к самостоятельной работе по контролю сварных швов и дорогостоящих изделий индивидуального произвоства обязательно необходимо основательное знание материала, по крайней мере в объеме экзаменов для квалифицированного рабочего в данной области производства нужны также и особые черты характера, например прилежность и добросовестность, причем в гораздо большей степени, чем при других способах контроля. Для самостоятельного применения многих разнообразных и недавно разработанных методов испытания требуется по крайней мере физическое и математическое образование в объеме среднетехнического учебного заведения и кроме того длительный личный опыт работы в синей спецодежде с грязными промасленными пальцами.
[c.399]
Все (применяемые для изготовления узлов трубопроводов детали, основные сварочные материалы и изделия должны удовлетворять требованиям нормативных документов и иметь сертификаты и паспорта заводов-изготовителей. Материалы и изделия, не имеющие сертификатов или паспортов, могут применяться для изготовления узлов только после их проверки и испытания в соответствии со стандартами и техническими условиями. Проверке и испытанию подвергаются также сварные соединения, выполненные при изготовлении узлов трубопроводов. В частности, кроме пооперационного контроля и внешнего осмотра сварных швов осуществляют проверку сплошности сварных стыков физическими методами (рентгеновским или у-просвечкванием, магни-тографированием, ультразвуковым контролем или комбинированными способами), а также механические испытания образцов из пробных стыков.
[c.126]
Контроль искажений — предотвращение с помощью технологий изготовления
Методы сборки
В целом, сварщик мало влияет на выбор процедуры сварки, но методы сборки часто могут иметь решающее значение для сведения к минимуму деформации. Основные методы сборки:
- прихватка
- встык в сборе
- усиление
Щелкните здесь , чтобы посмотреть наши последние технические подкасты на YouTube .
Прихватка
Прихваточные швы идеально подходят для установки и поддержания зазора в стыке, но также могут использоваться для предотвращения поперечной усадки. Чтобы быть эффективным, следует подумать о количестве прихваточных швов, их длине и расстоянии между ними. При слишком малом количестве существует риск постепенного смыкания соединения по мере сварки. При длинном шве с использованием MMA или MIG края шва могут даже перекрываться. Следует отметить, что при использовании процесса сварки под флюсом соединение может открыться, если оно не будет надлежащим образом прихвачено.
Последовательность прихватки важна для поддержания равномерного корневого зазора по всей длине соединения. Три альтернативные последовательности прихватки показаны на рис. 1:
.а) прихваточный шов насквозь до конца стыка (рис. 1а). Необходимо зажать пластины или использовать клинья для сохранения зазора стыка во время прихватки
b) прихватите один конец, а затем используйте технику обратного шага для прихватки остальной части соединения (рис. 1b)
c) прихватите центральную часть и завершите прихватку, отступив назад (рис. 1c).
a) прихваточный шов насквозь до конца соединения
b) прихваточный шов с одного конца, затем используйте технику обратного шага для прихватки остальной части соединения
c) прихваточный шов по центру, затем завершите прихватку методом обратного шага
Направленная прихватка является полезной техникой для контроля зазора в стыке, например, для закрытия зазора в стыке, который стал (или стал) слишком большим.
При прихватке важно, чтобы прихватки, которые должны вплавляться в основной шов, выполнялись в соответствии с утвержденной процедурой с использованием сварщиков с соответствующей квалификацией.Процедура может потребовать предварительного нагрева и одобренных расходных материалов, указанных для основного сварного шва. Удаление прихваток также требует тщательного контроля, чтобы избежать появления дефектов на поверхности компонента.
Спина к спине в сборе
Путем сварки прихватками или зажима двух одинаковых компонентов вплотную друг к другу сварка обоих компонентов может быть уравновешена вокруг нейтральной оси комбинированного узла (рис. 2а). Перед разделением компонентов рекомендуется снять напряжение со сборки.Если снятие напряжения не выполнено, может потребоваться вставить клинья между компонентами (рис. 2b), чтобы после удаления клиньев детали возвращались к правильной форме или выравниванию.
а) сборки, скрепленные перед сваркой
б) использование клиньев для компонентов, деформирующихся при разделении после сварки
Усиление жесткости
Продольная усадка в стыковых сварных швах часто приводит к искривлению, особенно при изготовлении тонколистовых конструкций. Продольные ребра жесткости в виде лысков или уголков, приваренные вдоль каждой стороны шва (рис. 3), эффективны для предотвращения продольного прогиба. Важно расположение ребер жесткости: они должны располагаться на достаточном расстоянии от стыка, чтобы не мешать сварке, если только они не расположены с обратной стороны стыка, сваренного с одной стороны.
Процедура сварки
Подходящая процедура сварки обычно определяется требованиями к производительности и качеству, а не необходимостью контролировать деформацию.Тем не менее, процесс, техника и последовательность сварки влияют на уровень деформации.
Процесс сварки
Общие правила выбора сварочного процесса для предотвращения угловой деформации:
- как можно быстрее нанесите наплавленный металл
- использовать наименьшее количество проходов для заполнения шва
К сожалению, выбор подходящего процесса сварки на основе этих правил может увеличить продольную усадку, приводящую к искривлению и короблению.
При ручной сварке MIG, процесс с высокой скоростью наплавки, предпочтительнее, чем MMA. Металл сварного шва следует наплавлять с использованием электрода с наибольшим диаметром (MMA) или с использованием самого высокого уровня тока (MIG), не вызывая непроваров. Поскольку нагрев происходит намного медленнее и более рассеянно, газовая сварка обычно дает больше угловых искажений, чем дуговые процессы.
Механизированные методы, сочетающие высокую скорость наплавки и высокую скорость сварки, обладают наибольшим потенциалом для предотвращения деформации.Поскольку искажение более постоянное, простые методы, такие как предварительная настройка, более эффективны для контроля углового искажения.
Техника сварки
Общие правила предотвращения искажений:
- сохранить сварной шов (галтель) до минимального указанного размера
- использовать сбалансированную сварку вокруг нейтральной оси
- свести время между запусками к минимуму
При отсутствии ограничения угловая деформация как в угловых, так и в стыковых соединениях будет зависеть от геометрии соединения, размера сварного шва и количества проходов для данного поперечного сечения. Угловая деформация (измеряемая в градусах) в зависимости от количества проходов для углового сварного шва длиной 10 мм показана на рис. 4.
Если возможно, сбалансированная сварка вокруг нейтральной оси должна выполняться, например, на двухсторонних угловых соединениях, двумя сварщиками одновременно. В стыковых соединениях порядок выполнения может иметь решающее значение, поскольку сбалансированная сварка может использоваться для исправления угловой деформации по мере ее развития.
а) Сварка в обратном направлении
б) Сварка скипов
Последовательность сварки
Последовательность или направление сварки важны и должны быть направлены к свободному концу соединения.Для длинных швов весь шов не выполняется в одном направлении. Короткие прогоны, например, с использованием техники обратной ступенчатой или скиповой сварки, очень эффективны для контроля деформации (рис. 5).
- Сварка с обратным уступом включает наплавку коротких смежных участков сварного шва в направлении, противоположном общему направлению (рис.
5а).
- Скиповая сварка представляет собой укладку коротких отрезков шва в заданной, равномерно расположенной последовательности вдоль шва (рис. 5б). Длины сварных швов и промежутки между ними обычно равны естественной длине одного электрода.Направление наплавки для каждого электрода одинаково, но направление сварки не обязательно должно быть противоположным направлению общего прогрессирования.
Передовая практика
Для контроля искажений используются следующие методы изготовления:
- использование прихваточных швов для установки и поддержания зазора в стыке
- идентичные компоненты, сваренные спиной к спине, так что сварку можно сбалансировать вокруг нейтральной оси
- крепление продольных ребер жесткости для предотвращения продольного изгиба в стыковых сварных швах тонколистовых конструкций
- , где есть выбор процедуры, процесса и техники сварки, должен быть направлен на наплавку металла шва как можно быстрее; MIG предпочтительнее MMA или газовой сварки и механизированной, а не ручной сварки
- на длинных участках весь шов не должен выполняться в одном направлении; следует использовать методы обратной ступенчатой или скиповой сварки.
Билл Лукас подготовил эту статью в сотрудничестве с Гертом Верхаге, Риком Леггаттом и Джином Мазерсом.
Для получения дополнительной информации свяжитесь с нами.
Шовная сварка — Как сварить сопротивлением
Чтобы ответить на этот вопрос, предположим, что мы делаем сварной шов, непроницаемый для жидкости. Это касается любой толщины материала. Многие из перечисленных ниже условий являются общими для точечной сварки. При шовной сварке швы перекрываются, когда сварочные колеса катятся вперед.В шовном шве технологический ток создается для обеспечения шунтирования тока через уже выполненные замыкающие швы.
УДАЛЕНИЕ ИНТЕРФЕЙСА УДАЛЕНИЕ ПОВЕРХНОСТИ
Выход из интерфейса или поверхности может привести к прожогу.
Читать далее …
Существует два типа приводов для шовных сварочных кругов. Один приводится в движение центральной ступицей, прямой привод. Другой приводится в движение рифлеными колесами, едущими по периметру шва сварочными колесами, непрямой привод. Плюсы и минусы есть у обеих систем.
В другой статье этого блога обсуждаются различия:
КАК ПРИВОДЯТСЯ КОЛЕСА ДЛЯ ШОВНОЙ СВАРКИ?
Здесь речь пойдет о шовных сварочных кругах с прямым приводом. Вопрос стоит ли гнать
• Оба колеса
• Одно колесо
• или, возможно, нет
Читать далее …
Вал для шовной сварки, как правило, представляет собой стержень из медного сплава большого диаметра, прецизионно обработанный для передачи силы тока и вращения во время операции шовной сварки. Вал тяжело работает в тяжелых режимах, токах и силах. Вал работает в корпусе, который заполнен токопроводящей смазкой и имеет токопроводящие башмаки, которые перемещаются по валу для подачи тока. Со временем эти проводники и вал требуют износа и обслуживания.
Износ вала встречается чаще, чем поломка, но возможен.
АППАРАТ ДЛЯ ШОВНОЙ СВАРКИ С НАКАТЧИКАМИ
Читать далее …
Некоторая информация по шовной сварке сплавов железа с высоким содержанием никеля и хрома опубликована Американским обществом сварщиков в их стандартах сварки. Там выставлены примеры текущих значений, которые могут работать.
Стандарт AWS C1.1:2019 «Рекомендуемые методы контактной сварки»
Читать далее …
Информация о шовной сварке нержавеющей стали опубликована Американским обществом сварщиков в их стандартах сварки.
«Стандарт AWS C1.1:2019 «Рекомендуемые методы контактной сварки»
Читать далее …
Методы профилирования сварных швов на основе активного распознавания зрения для интеллектуальной роботизированной сварки
Pires JN, Loureiro A, Bölmsjo G (2006) Сварочные роботы: технология, системные проблемы и применение. Springer Science & Business Media
Wilson WJ, Hulls CCW, Bell GS (1996) Относительное управление концевым рабочим органом с использованием декартова визуального слежения на основе положения. IEEE Trans Robot Autom 12(5):684–696
Статья Google Scholar
Xu D, Tan M, Zhao X, Tu Z (2004) Отслеживание шва и визуальный контроль при роботизированной дуговой сварке на основе структурированного светового стереовидения. Int J Autom Comput 1(1):63–75
Статья Google Scholar
Xu D, Wang L, Tan M (2004) Метод обработки изображений и визуального контроля для робота для дуговой сварки. В: Робототехника и биомиметика, 2004. ROBIO 2004. Международная конференция IEEE (стр. 727–732). IEEE
Xu D, Jiang Z, Wang L, Tan M (2004) Извлечение признаков структурированного светового изображения сварочного шва с нарушением дуги и брызг. В: Конференция по управлению, автоматизации, робототехнике и зрению, 2004 г. ICARCV, 2004 г., 8-е (том 3, стр. 1559–1563). IEEE
Ланцетта М., Санточи М., Тантусси Г. (2001) Онлайн-контроль роботизированной дуговой сварки металлическим газом.CIRP Ann Manuf Technol 50(1):13–16
Статья Google Scholar
Clarke T, Wang X (2000) Управление рабочим органом робота с помощью фотограмметрии. Int Arch Photogramm Remote Sens 33(B5/1; PART 5), 137–142
Chen XZ, Huang YM, Chen SB (2012) Модельный анализ и экспериментальная техника вычисления точности информации о пространственном положении пласта на основе Стереовидение для сварочного робота. Ind Robot: Int J 39(4):349–356
Статья Google Scholar
Cook GE, Andersen K, Fernandez KR, Shepard ME, Wells Jr AM (1987) Датчик электрической дуги для управления позиционированием робота. IFS (Publications) Ltd., Robotic Welding, 181–216
Park YW, Rhee S (2008) Моделирование процессов и оптимизация параметров с использованием нейронных сетей и генетических алгоритмов для автоматизации лазерной сварки алюминия. Int J Adv Manuf Technol 37(9–10):1014–1021
Статья Google Scholar
Чаки С., Шанмугараджан Б., Госал С., Падманабхам Г. (2015) Применение интегрированных методов мягких вычислений для оптимизации гибридного процесса сварки CO 2 -лазер-MIG.Appl Soft Comput 30:365–374
Статья Google Scholar
Неле Л., Сарно Э., Кешари А. (2013) Моделирование множественных характеристик дугового сварного соединения. Int J Adv Manuf Technol 69(5–8):1331–1341
Статья Google Scholar
Fridenfalk M (2003) Разработка интеллектуальных робототехнических систем на основе сенсорного управления. Лундский университет
Fang Z, Xu D, Tan M (2013) Начальное позиционирование точки сварки на основе визуализации с использованием геометрического соотношения между двумя швами. Int J Adv Manuf Technol 66(9–12):1535–1543
Статья Google Scholar
Kiddee P, Fang Z, Tan M (2014) Визуальное распознавание начальной и конечной точек соединения внахлест для сварочных роботов. В: Информация и автоматизация (ICIA), 2014 г. И.Е. Международная конференция (стр. 513-518). IEEE
Конг М., Ши Ф.Х., Чен С.Б., Лин Т. (2007) Распознавание начального положения сварного шва на основе обнаружения угла для сварочного робота в глобальной среде. В: Роботизированная сварка. Springer, Берлин, стр. 249–255
Google Scholar
Zhu ZY, Lin T, Piao YJ, Chen SB (2005) Распознавание начального положения сварного шва на основе технологии сопоставления шаблона изображения для сварочного робота. Int J Adv Manuf Technol 26(7–8):784–788
Статья Google Scholar
Чжоу Л., Линь Т., Чен С.Б. (2006) Автономное получение координат шва для робота для дуговой сварки на основе визуального слежения. J Intel Robot Syst 47(3):239–255
Статья Google Scholar
Dinham M, Fang G (2013) Автономная идентификация и локализация сварного шва с использованием стереозрения «глаз в руке» для роботизированной дуговой сварки. Robot Comput Integr Manuf 29(5):288–301
Статья Google Scholar
Микаллеф К., Фанг Г., Динхэм М. (2011) Автоматическое обнаружение шва и планирование пути при роботизированной сварке. В кн.: Роботизированная сварка, интеллект и автоматизация. Springer, Берлин, стр. 23–32
Глава Google Scholar
Li L, Fu L, Zhou X, Li X (2007) Обработка изображений системы отслеживания швов с использованием лазерного зрения. В кн.: Роботизированная сварка, интеллект и автоматизация. Springer, Берлин, стр. 319–324
Глава Google Scholar
Chen XZ, Chen SB (2010) Автономное обнаружение и управление начальным положением сварки для робота для дуговой сварки. Ind Robot: Int J 37(1):70–78
Статья Google Scholar
Wei SC, Wang J, Lin T, Chen SB (2012) Применение морфологии изображения для обнаружения и выделения начального положения сварки. J Shanghai Jiaotong Univ (Sci) 17:323–326
Статья Google Scholar
Chen XZ, Chen SB, Lin T (2007) Распознавание макроскопических швов в сложной среде роботизированной сварки. В кн.: Роботизированная сварка, интеллект и автоматизация. Springer, Берлин, стр. 171–178
Глава Google Scholar
Dinham M, Fang G (2014) Обнаружение угловых сварных соединений с использованием адаптивного алгоритма увеличения линии для роботизированной дуговой сварки. Robot Comput Integr Manuf 30(3):229–243
Статья Google Scholar
Chen X, Chen S, Lin T, Lei Y (2006) Практический метод определения начального положения сварного шва с использованием визуальных технологий. Int J Adv Manuf Technol 30(7-8):663–668
Статья Google Scholar
Неле Л., Сарно Э., Кешари А. (2013) Система сбора изображений для отслеживания швов в реальном времени. Int J Adv Manuf Technol 69(9–12):2099–2110
Статья Google Scholar
Chen SB, Chen XZ, Qiu T, Li JQ (2005) Получение информации о размерах сварного шва для робота для дуговой сварки на основе компьютерных вычислений. J Intel Robot Syst 43(1):77–97
Статья Google Scholar
Shen HY, Wu J, Lin T, Chen SB (2008) Роботизированная система дуговой сварки с отслеживанием шва и контролем сварочной ванны на основе пассивного зрения. Int J Adv Manuf Technol 39(7–8):669–678
Статья Google Scholar
Xu Y, Fang G, Chen S, Zou JJ, Ye Z (2014) Обработка изображений в реальном времени для визуального отслеживания сварных швов в роботизированной GMAW. Int J Adv Manuf Technol 73(9–12):1413–1425
Статья Google Scholar
Gao X, Zhong X, You D, Katayama S (2013)Фильтрация Калмана, компенсированная радиальной базовой функцией нейронной сети для отслеживания шва лазерной сварки. IEEE Trans Control Syst Technol 21(5):1916–1923
Статья Google Scholar
Баскоро А.С., Масуда Р., Кабутомори М., Суга Ю. (2009) Применение генетического алгоритма для обнаружения краев расплавленной ванны при сварке стационарных труб. Int J Adv Manuf Technol 45(11–12):1104–1112
Статья Google Scholar

Баскоро А.С., Масуда Р., Кабутомори М., Суга Ю. (2008) Сравнение оптимизации роя частиц и генетического алгоритма для обнаружения краев расплавленной ванны при сварке стационарных труб. В: SCIS & ISIS (Vol.2008, № 0, с. 1743–1748). Японское общество нечеткой теории и интеллектуальной информатики
Баскоро А.С., Кабутомори М., Суга Ю. (2009) Контроль проплавления неподвижной трубы при сварке TIG с использованием системы нечеткого вывода. J Solid Mech Mater Eng 3(1):38–48
Статья Google Scholar
Баскоро А.С., Кабутомори М., Суга Ю. (2008) Система автоматической сварки алюминиевых труб путем отслеживания изображения обратной стороны расплавленной ванны с помощью датчика технического зрения.J Solid Mech Mater Eng 2(5):582–592
Артикул Google Scholar
Ge J, Zhu Z, He D, Chen L (2005) Алгоритм визуального обнаружения шва в процессе PAW для труб большого диаметра из нержавеющей стали. Int J Adv Manuf Technol 26(9–10):1006–1011
Статья Google Scholar
Gao J, Wu C, Liu X, Xia D (2007) Отслеживание сварного шва на основе зрения при дуговой сварке металлическим газом.Front Mater Sci Chin 1(3):268–273
Статья Google Scholar
Gao XD, Na SJ (2005) Обнаружение положения сварного шва и отслеживание шва на основе фильтрации Калмана изображений сварочной ванны. J Manuf Syst 24(1):1–12
Статья Google Scholar
Shen H, Lin T, Chen S, Li L (2010) Технология отслеживания шва в режиме реального времени сварочного робота с визуальным датчиком. J Intel Robot Syst 59(3–4):283–298
Статья МАТЕМАТИКА Google Scholar
Ошима К., Морита М., Фуджи К., Ямамото М., Кубота Т. (1992) Датчики и цифровое управление сварочной ванной при импульсной сварке МИГ. Trans Jpn Weld Soc 23(1):17–23
Google Scholar
Bae KY, Lee TH, Ahn KC (2002) Система оптических датчиков для отслеживания шва и контроля сварочной ванны при дуговой сварке металлическим электродом стальных труб. J Mater Process Technol 120(1):458–465
Статья Google Scholar
Gao X, Ding D, Bai T, Katayama S (2011) Алгоритм центроида изображения сварочной ванны для визуальной модели отслеживания шва в процессе дуговой сварки. IET Image Process 5(5):410–419
Статья Google Scholar
Gu WP, Xiong ZY, Wan W (2013) Автономная система обнаружения и отслеживания шва для многопроходной сварки на основе датчика технического зрения. Int J Adv Manuf Technol 69(1–4):451–460
Статья Google Scholar
Iakovou D, Aarts R, Meijer J (2005) Интеграция датчиков для роботизированных процессов лазерной сварки
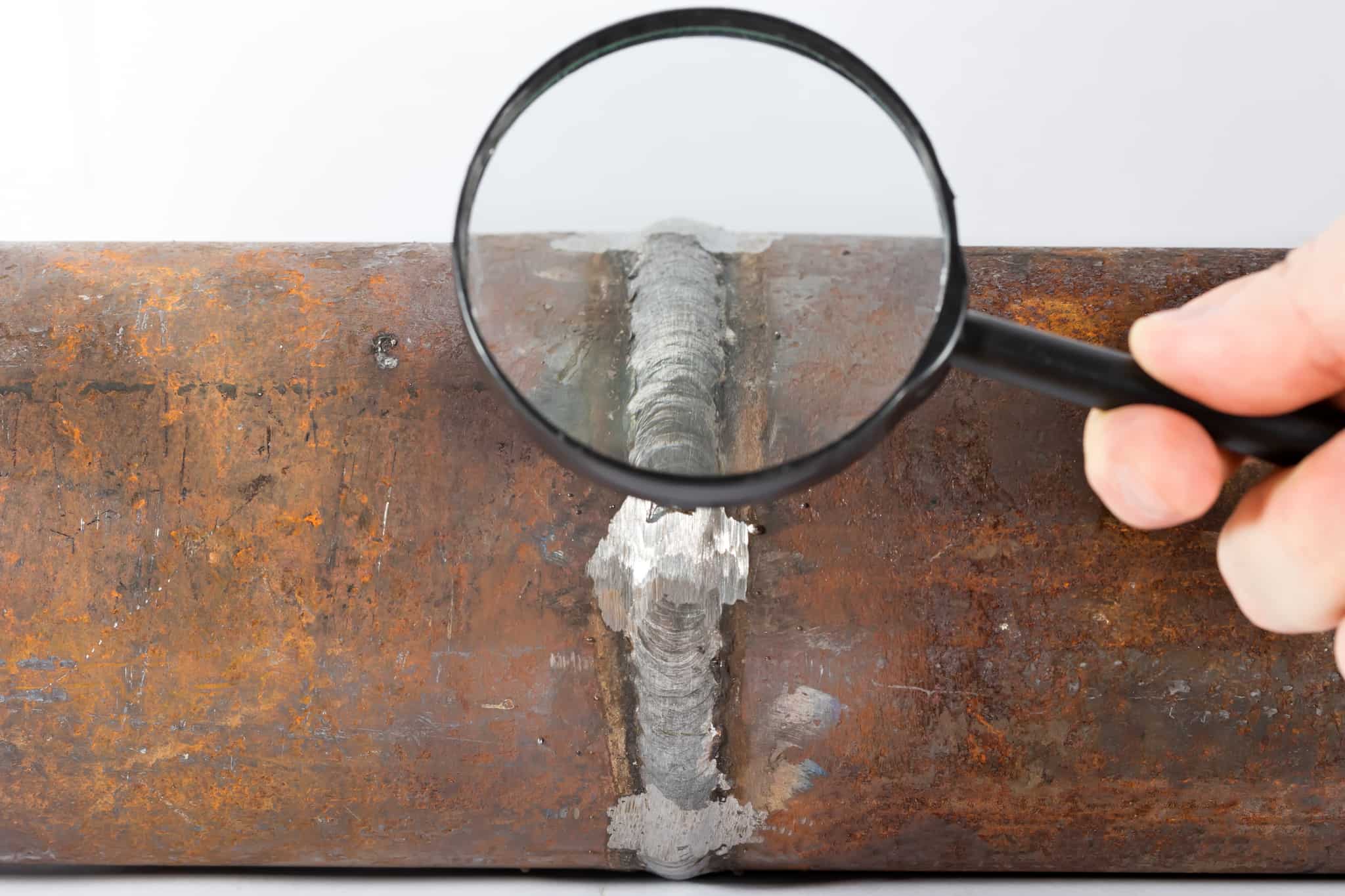
Forest J, Salvi J, Cabruja E, Pous C. (2004) Пиковый детектор лазерной полосы для 3D-сканеров. Подход с КИХ-фильтром. В: Распознавание образов, 2004 г. ICPR 2004 г. Материалы 17-й Международной конференции (том 3, стр. 646–649). IEEE
Xu P, Xu G, Tang X, Yao S (2008) Система визуального отслеживания шва для роботизированной дуговой сварки. Int J Adv Manuf Technol 37(1–2):70–75
Статья Google Scholar
Zhang L, Ye Q, Yang W, Jiao J (2014) Обнаружение и отслеживание линии сварки с помощью пространственно-временных каскадных скрытых марковских моделей и кросс-структурированного света. IEEE Trans Instrum Meas 63(4):742–753
Статья Google Scholar
Xiao Z (2011) Исследование трехлинейного лазерного датчика технического зрения для отслеживания шва при сварке. В кн.: Роботизированная сварка, интеллект и автоматизация. Springer, Берлин, стр. 139–144
Глава Google Scholar
Вильян А.Ф., Асеведо Р.Г., Альварес Э.А., Лопес А.С., Гарсия Д.Ф., Фернандес Р.У., … и Санчес Дж.М.Г. (2011) Недорогая система отслеживания сварных швов на основе искусственного зрения. IEEE Trans Ind Appl 47(3):1159–1167
Caggiano A, Nele L, Sarno E, Teti R (2014)Цифровая 3D-реконфигурация автоматизированной сварочной системы для железнодорожного производства. Procedia CIRP 25:39–45
Статья Google Scholar
Hang K, Pritschow G (1999) Уменьшение искажений, вызванных сварочной дугой, в системе лазерных датчиков для автоматического отслеживания шва.В кн.: Промышленная электроника, 1999. ИСИЭ’99. Материалы Международного симпозиума IEEE (том 2, стр. 919–924). IEEE
Huang W, Kovacevic R (2012) Разработка лазерной системы машинного зрения в режиме реального времени для контроля и управления сварочными процессами. Int J Adv Manuf Technol 63(1–4):235–248
Статья Google Scholar
Li Y, Li YF, Wang QL, Xu D, Tan M (2010) Измерение и обнаружение дефектов сварного шва на основе визуального контроля в режиме онлайн.IEEE Trans Instrum Meas 59(7):1841–1849
Статья Google Scholar
Kim JK, Hong JI, Kim JW, Choi DJ, Rhee SY (2012) Геометрические измерения формы сварки с использованием двойной лазерной системы технического зрения. В: Управление, автоматизация и системы (ICCAS), 12-я Международная конференция, 2012 г. (стр. 195–198). IEEE
Сунг К., Ли Х., Чой Ю.С., Ри С. (2009 г.) Разработка многолинейного лазерного датчика технического зрения для отслеживания соединений при сварке.Weld J
Iakovou D (2009) Разработка и интеграция датчиков для роботизированной лазерной сварки. Университет Твенте (докторская диссертация)
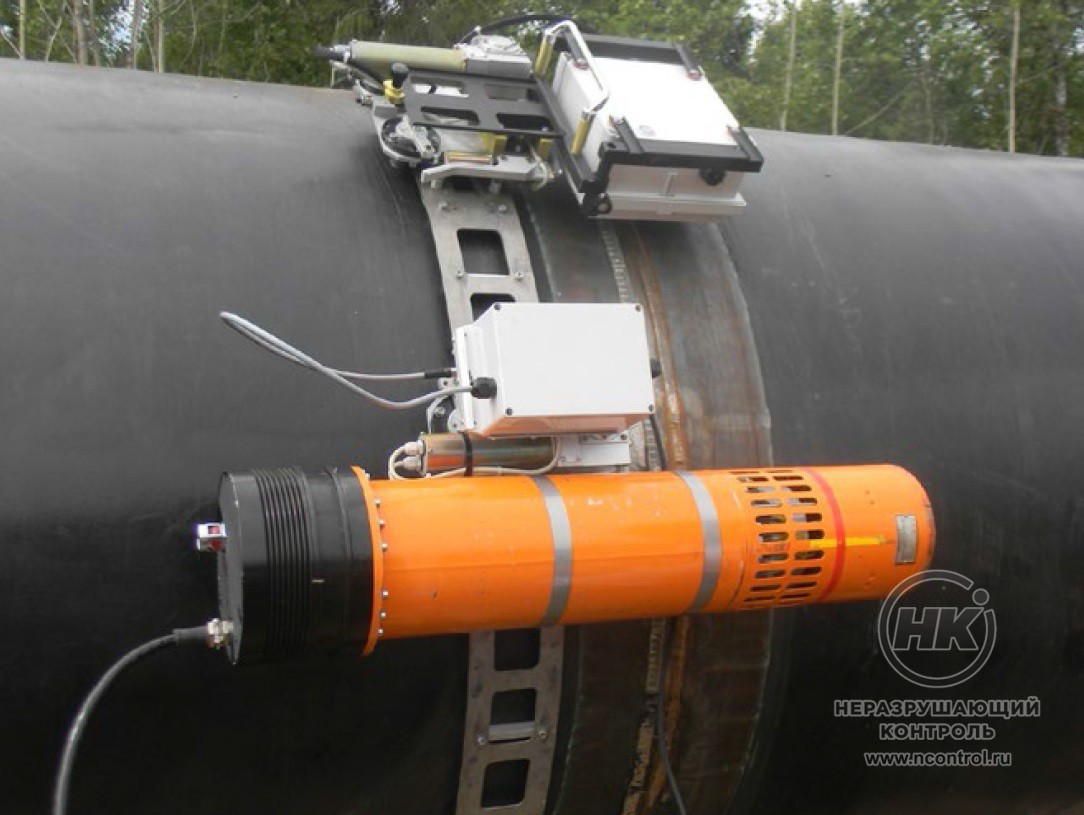
Ши Ю.Х., Ван Г.Р., Ли Г.Дж. (2007) Адаптивная роботизированная сварочная система, использующая лазерное зрение для подводной техники. В: Управление и автоматизация, 2007. ICCA 2007. Международная конференция IEEE (стр. 1213–1218). IEEE
Lee JP, Wu QQ, Park MH, Park CK, Kim IS (2014) Исследование оптимальных алгоритмов для отслеживания соединения при сварке GMA.Int J Eng Sci Innov Technol 3:370–380
Google Scholar
Zhang L, Wu C, Zou Y (2009) Сенсорная система визуального отслеживания шва в режиме онлайн во время лазерной сварки. В: Информационные технологии и компьютерные науки, 2009. ITCS 2009. Международная конференция (том 2, стр. 361–364). IEEE
Вильян А.Ф., Асеведо Р.Г., Альварес Э.А., Лопес А.С., Гарсия Д.Ф., Фернандес Р.У., … и Санчес Дж.М.Г. (2011) Недорогая система отслеживания сварных швов на основе искусственного зрения.IEEE Trans Ind Appl 47(3), 1159–1167

Huang W, Kovacevic R (2011) Лазерная система технического зрения для контроля качества сварки. Датчики 11(1):506–521
Артикул Google Scholar
Fang Z, Xu D (2009) Система визуального отслеживания швов на основе изображений для угловых соединений. В кн.: Робототехника и биомиметика (РОБИО), 2009 г. И.Е. Международная конференция (стр. 1230–1235). IEEE
Fang Z, Xu D, Tan M (2010) Система визуального отслеживания шва для стыковой сварки тонкого листа.Int J Adv Manuf Technol 49(5–8):519–526
Статья Google Scholar
Piccardi M (2004) Методы вычитания фона: обзор. В кн.: Системы, человек и кибернетика, 2004 г. И.Е. международная конференция (том 4, стр. 3099–3104). IEEE
Otsu N (1975) Метод порогового выбора из гистограмм уровней серого. Автоматика 11(285–296):23–27
Google Scholar
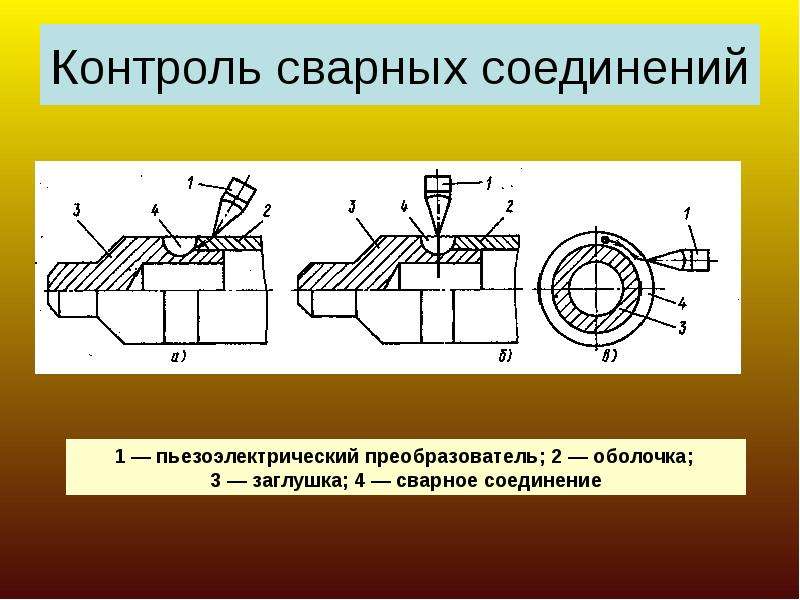
Тофт П.А., Соренсен Дж.А. (1996) Теория преобразования Радона и реализация (докторская диссертация, Датский технический университет Датского технического университета, кафедра информатики и математического моделирования, Институт информатики и математического моделирования)
Ballard DH (1981) Обобщение преобразования Хафа для обнаружения произвольных форм. Распознавание образов 13(2):111–122
Артикул МАТЕМАТИКА Google Scholar
Li Y, Wang QL, Li YF, Xu D, Tan M (2008) Визуальное измерение и проверка сварного шва в реальном времени с использованием структурированного света. В: Материалы конференции по приборостроению и измерительным технологиям, 2008 г. IMTC 2008. IEEE (стр. 2038–2043). IEEE
Найду Д.К., Фишер Р.Б. (1991) Сравнительный анализ алгоритмов определения положения пика полосы с субпиксельной точностью. В: BMVC91, 1991-е изд. Springer, Лондон, стр. 217–225
Глава Google Scholar

Usamentiaga R, Molleda J, García DF (2012) Быстрое и надежное извлечение лазерных полос для трехмерной реконструкции в промышленных условиях. Mach Vis Appl 23(1):179–196
Статья Google Scholar
Haug K, Pritschow G (1998) Надежный лазерный датчик для автоматизированного отслеживания сварных швов в судостроении. В: Общество промышленной электроники, 1998. IECON’98. Материалы 24-й ежегодной конференции IEEE (т.2, стр. 1236–1241). IEEE
Гонг И, Дай С, Ли С (2010). Совместное распознавание на основе структурированного света с использованием комбинированной визуальной обработки снизу вверх и сверху вниз. В: Анализ изображений и обработка сигналов (IASP), Международная конференция 2010 г. (стр. 507–512). IEEE
Blais F, Rioux M (1986) Численный пиковый детектор в реальном времени. Signal Process 11(2):145–155
Артикул Google Scholar
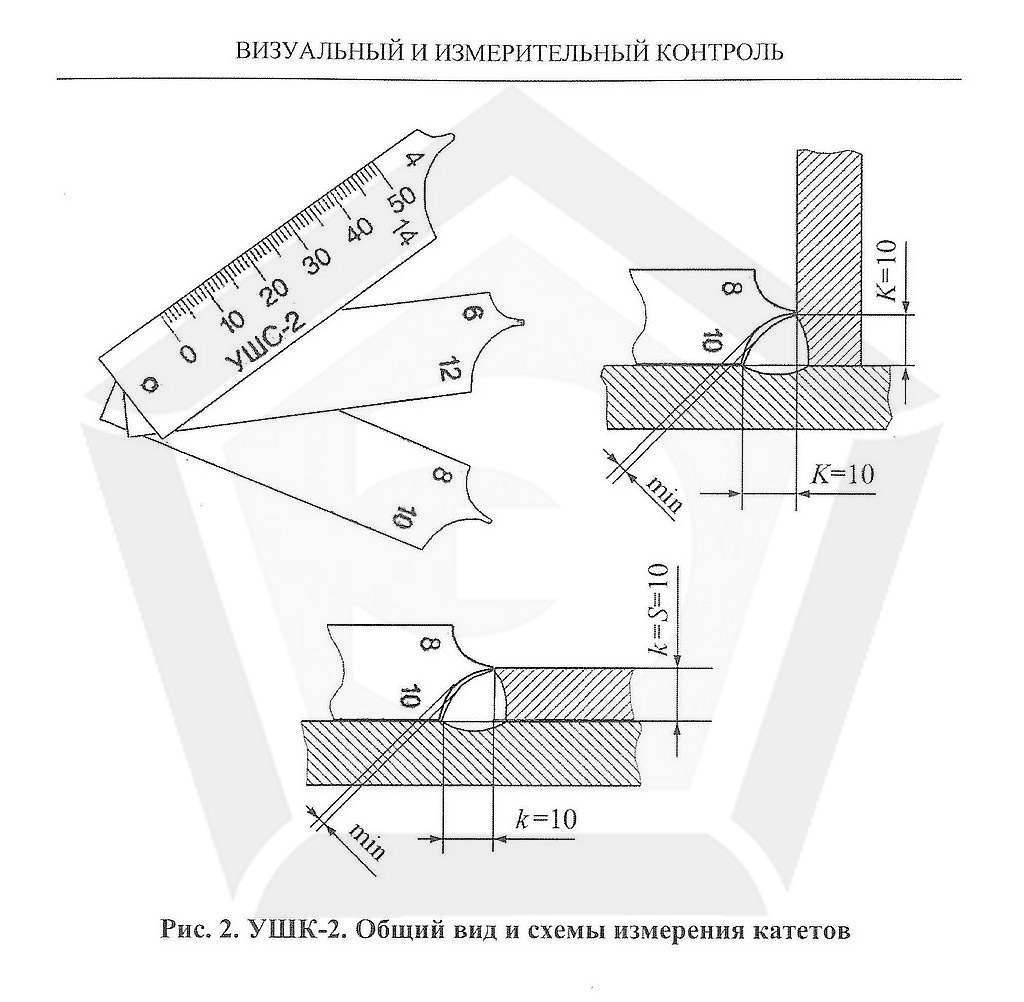
Trucco E, Fisher RB, Fitzgibbon AW, Naidu DK (1998) Калибровка, согласованность данных и получение модели с помощью лазерных стрейперов. Int J Comput Integr Manuf 11(4):293–310
Статья Google Scholar
Forest Collado J (2004) Новые методы получения формы на основе триангуляции с использованием лазерных сканеров. Universitat de Girona
Khoury JM (1999) Патент США № 5,931,898. Ведомство США по патентам и товарным знакам, Вашингтон, округ Колумбия
Google Scholar
Kim JW, Bae HS (2005) Исследование системы видеодатчиков для отслеживания двутавровых стыковых сварных соединений. J Mech Sci Technol 19(10):1856–1863
Статья Google Scholar
Fang Z, Xu D, Tan M (2011) Самонастраивающийся нечеткий контроллер на основе технического зрения для отслеживания угловых сварных швов. IEEE/ASME Trans Mechatron 16(3):540–550
Статья Google Scholar
Эдди С.Р. (1996) Скрытые марковские модели.Curr Opin Struct Biol 6(3):361–365
Статья Google Scholar
Zhang L, Jiao J, Ye Q, Han Z, Yang W (2012) Надежное обнаружение линии сварки с помощью кросс-структурированного света и скрытой марковской модели. В: Мехатроника и автоматизация (ICMA), Международная конференция 2012 г. (стр. 1411–1416). IEEE
Zhang L, Ke W, Han Z, Jiao J (2013) Световой датчик с перекрестной структурой для обнаружения линии сварки на роботе, передвигающемся по стене.В: Мехатроника и автоматизация (ICMA), 2013 И.Е. Международная конференция (стр. 1179–1184). IEEE
Canny J (1986) Вычислительный подход к обнаружению границ. IEEE Trans Pattern Anal Mach Intel 6: 679–698
Статья Google Scholar
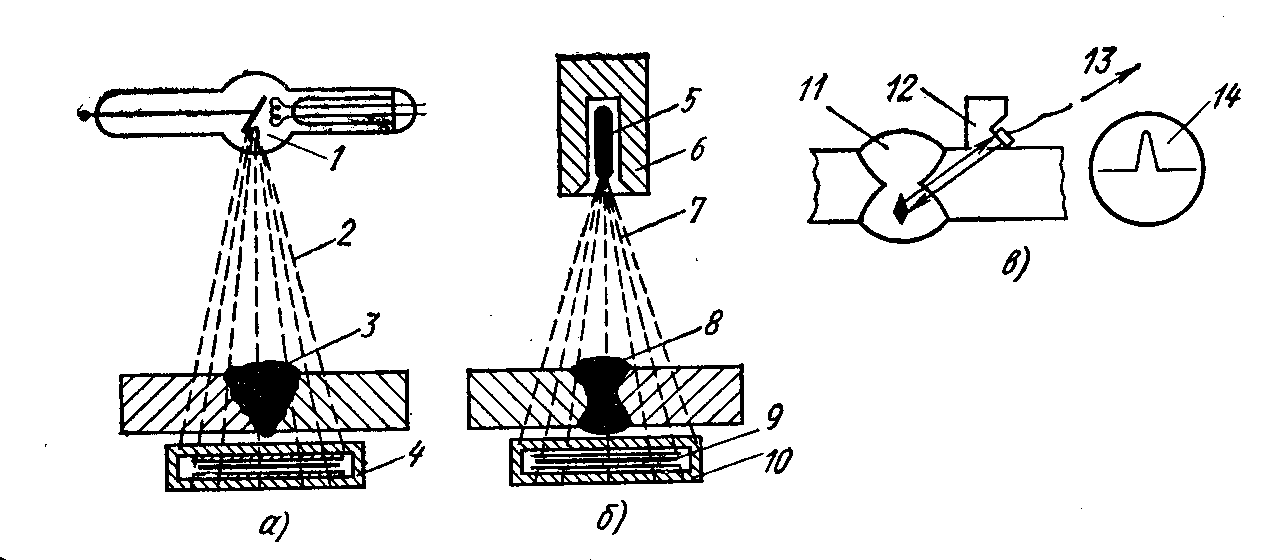
Марр Д., Хилдрет Э. (1980) Теория обнаружения границ. Proc R Soc Lond B Biol Sci 207(1167):187–217
Статья Google Scholar
Kim JS, Son YT, Cho HS, Koh KI (1996) Надежная система визуального отслеживания шва для роботизированной дуговой сварки. Мехатроника 6(2):141–163
Статья Google Scholar
Kim JS, Son YT, Cho HS, Koh KI (1995) Надежный метод визуального отслеживания шва при роботизированной дуговой сварке. В: Интеллектуальное управление, 1995 г. Материалы 1995 г. I.E. Международный симпозиум по (стр. 363–368). IEEE
Xiao Y, Zou JJ, Yan H (2001) Адаптивный метод разделения и слияния для сжатия данных контура бинарного изображения.Pattern Recognin Letter 22(3):299–307
Статья МАТЕМАТИКА Google Scholar
Aubert G, Kornprobst P (2006) Математические проблемы обработки изображений: дифференциальные уравнения в частных производных и вариационное исчисление (Том 147). Springer Science & Business Media
Sicard P, Levine MD (1989) Распознавание и отслеживание соединений для роботизированной дуговой сварки. IEEE Trans Syst Man Cybern 19(4):714–728
Статья Google Scholar
Nan H, Beattie RJ, Davey PG (1988) Основанная на правилах система интерпретации изображений сварных швов. Int J Adv Manuf Technol 3(3):111–121
Статья Google Scholar
Павлидис Т., Горовиц С.Л. (1974) Сегментация плоских кривых. IEEE Trans Comput 8: 860–870
MathSciNet Статья МАТЕМАТИКА Google Scholar
Berkan RC, Trubatch S (1997) Принципы проектирования нечетких систем.Wiley-IEEE Press
Wu J, Smith JS, Lucas J (1996) Система размещения сварных швов для многопроходной сварки. IEE Proc: Sci Meas Technol 143(2):85–90
Google Scholar
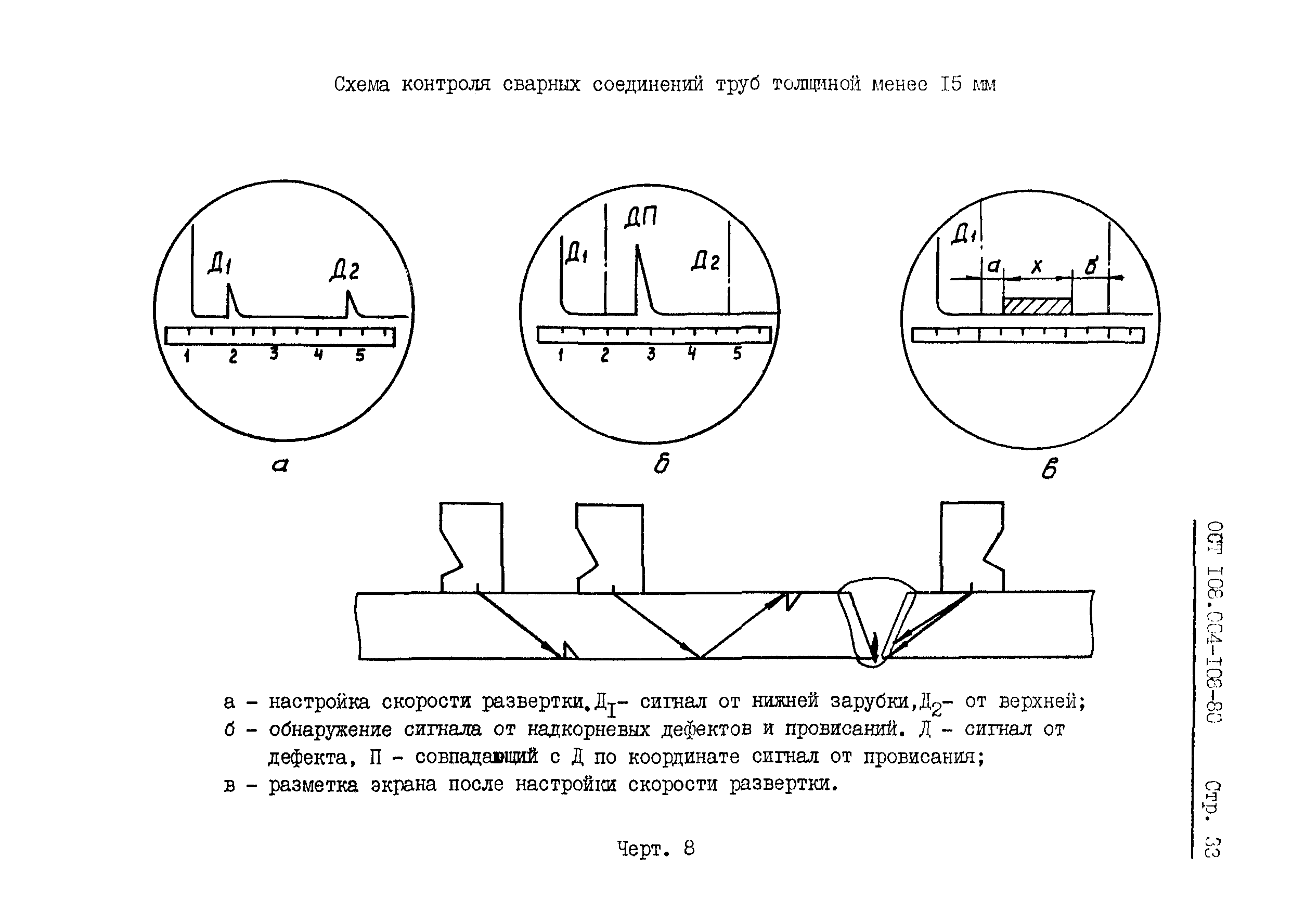
Harris C, Stephens M (1988) Комбинированный детектор углов и краев. В: Конференция по видению Alvey (Том 15, стр. 50)
Фишлер М.А., Боллес Р.К. (1981) Консенсус случайных выборок: парадигма подбора модели с приложениями для анализа изображений и автоматизированной картографии.Сообщество ACM 24(6):381–395
MathSciNet Статья Google Scholar
York D (1968) Аппроксимация прямой линии методом наименьших квадратов с коррелированными ошибками. Earth Planet Sci Lett 5:320–324
Статья Google Scholar
(PDF) Трекинговое управление сварочными роботами-манипуляторами на основе адаптивной безвибрационной технологии скользящего режима управления
Интеллектуальные технологии, большое внимание уделяется трекинговому управлению роботизированными манипуляторами
.
Управление слежением необходимо для того, чтобы каждое соединение отслеживало желаемую траекторию как можно ближе. Многие алгоритмы управления
, такие как компьютерный метод крутящего момента (Craig, 1989), оптимальное управление
(Ruderman, 2014), адаптивное управление (Slo-
tine and Li, 1987), управление переменной структурой (VSC)
(Cao and Ren, 2012), нейронные сети (NN) (Yan
и Wang, 2012) и нечеткая система (Cruz and Mor-
ris, 2006) были предложены для решения этой проблемы управления роботом
.Однако роботы-манипуляторы сильно нелинейны, сильно зависят от времени и сильно связаны. Более того, в модели системы
всегда существует неопределенность, такая как внешнее возмущение, неопределенность параметров, ошибки датчиков и т. д., которые вызывают нестабильную работу роботизированной системы (Guo and
Woo, 2003).
В этой статье выведен новый алгоритм адаптивного управления
режимом скольжения (ASMC) для решения проблемы управления швом
сварочного робота-
манипулятора в процессе крупномасштабной компоновки конструкции.
позиционная сварка.Хорошо известно, что классическое скользящее
управление режимами (SMC) вызывает вибрацию, что является критическим недостатком для стабильности системы,
делая проектирование контроллера чрезвычайно
хлопотным. Надежность контроллеров подтверждена
теорией устойчивости по Ляпунову, а аналитические результаты показывают, что предложенный алгоритм обеспечивает более высокую точность слежения
без вибраций, чем классический SMC.
Макет бумаги выглядит следующим образом. В разделе 2
представлена динамическая модель сварочного робота-манипулятора
, и обсуждаются некоторые важные свойства.
В разделе 3 разработан и проанализирован новый адаптивный контроллер скользящего режима
для управления слежением за сварочными роботами-манипуляторами
. Примеры моделирования
даны для демонстрации производительности контроллера
, предлагаемого в разделе 4.Наконец, мы предлагаем краткие
выводы и предложения для дальнейших исследований.
2 ДИНАМИЧЕСКАЯ МОДЕЛЬ
СВАРОЧНОГО РОБОТА
МАНИПУЛЯТОРЫ
В целом динамическая модель 3-звенного сварочного робота
представлена следующим образом
M(q)¨q+ )˙q+g(q) + d(t) = u, (1)
где M(q) = MT(q)∈R3×3 — симметричная положительно определенная
матрица инерции; q∈R3 обозначает вектор положения соединения
; C(q,˙q)∈R3×3 – кориолисовский и
центробежный моменты; g(q)∈R3 — вектор гравитационных моментов; d(t)∈R3 обозначает ограниченное возмущение; и u∈R3 представляет входной вектор крутящего момента.
Несколько основных свойств модели робота
(1) можно получить следующим образом.
Свойство 1. Матрица ˙
M(q)−2C(q,˙q) является кососимметричной
метрической матрицей, т. е.
xT˙
M(q)−2C(q,˙ q)x=0,∀x∈R3.
Свойство 2. Для произвольных x,y∈R3 получаем, что
M(q)x+C(q,˙q)y+G(q) = Y(q,˙q,x,y)θ ,
, где Y(q,˙q,x,y) обозначает матрицу регрессии, θявляется
вектором постоянных неизвестных параметров.
Недвижимость 3.Неизвестное возмущение d(t) предполагается неизвестным, но ограниченным, т. е. kd(t)k<η.
3 КОНСТРУКЦИЯ КОНТРОЛЛЕРА
3.1 Контроллер адаптивного режима скольжения
Целью разработанного контроллера является перемещение положения сустава
qв желаемое положение траектории qd.
Сначала определим ошибку слежения следующим образом:
˜q=q−qd.(2)
Пусть поверхность скольжения =diag[β1,β2,β3], где βii — положительная
константа.
Цель контроллера может быть достигнута путем
выбора управляющего входа u таким образом, чтобы поверхность скольжения удовлетворяла достаточному условию (Slotine and Li,
1989; Slotine and Li, 1991). Пусть эталонное состояние
˙qr=˙q−s=˙qd−β˜q,(4)
и ¨qr=¨q−˙s=¨qd−β˙
˜q.(5)
Тогда закон управления ui оформляется как
где ˆ
M(q),ˆ
C(q,˙q) и ˆg(q) — оценки M(q),C(q,˙q) и g(q) соответственно; Kr=
diag[Kr11,Kr22,Kr33] — диагональная положительно определенная
матрица; sgn(s)α определяется как
sgn(x)α=|x1|αsign(x1),|x2|αsign(x2),|x3|αsign(x3)T,(7)
и x∈ R3, 0 <α<1.
ICINCO-2014-11-я Международная конференция по информатике в управлении, автоматике и робототехнике
Контроллеры шовной сварки на базе микроконтроллера: CSM
ХАРАКТЕРИСТИКИ
|
[развернуть название=»ТЕХНИЧЕСКИЕ ХАРАКТЕРИСТИКИ»]
Источник питания | : | 230 В / 415 В переменного тока, 50 Гц / 60 Гц |
Выход | : | Сигнал управления затвором и катодом для управления парой тиристоров любой емкости. |
Компенсация | : | Компенсация колебаний напряжения питания. (Выходное напряжение остается в пределах ± 3 % по сравнению с ± 15 % колебания сетевого напряжения).![]() |
Триггер | : | Внешний нормально открытый контакт педали или концевого выключателя. |
[/развернуть]
[expand title=»ВОЗМОЖНА РЕГУЛИРОВКА РАЗЛИЧНЫХ ПАРАМЕТРОВ ПО ТАБЛИЦЕ»]
Время сжатия | 0-99 полупериодов |
Наклон для сварки (W1) | 0-9 полуциклов |
Время сварки | 0-99 полупериодов |
Энергия сварки | 0–99 % Программируется |
Прохладное время | 0-99 полуциклов |
Время удержания | 0-99 полупериодов |
[/развернуть]
[раскрыть заголовок=»ПРИЛОЖЕНИЯ»]
- Машины контактной шовной сварки любой мощности/любого производителя.
[/развернуть]
Что такое радиочастотная сварка?
Наши пакеты для упаковки медицинских инструментов, изготовленные из термопластичной полиуретановой пленки (ТПУ) FlexShield
Радиочастотная сварка или (высокочастотная сварка) — это процесс соединения материалов с помощью электромагнитной энергии. Два электрода создают колеблющееся электрическое поле, которое начинает смещать и перемещать полярные молекулы внутри материалов, чтобы ориентироваться в соответствии с электромагнитным полем.Движение этих молекул высвобождает энергию в виде тепла. Когда прикладывается достаточно энергии, молекулы начинают плавиться и связываться друг с другом. Внешнее тепло не применяется. Сварка завершается приложением давления к склеиваемой области, что обеспечивает успешную герметизацию.
Многие факторы влияют на прочность и качество сварки при ВЧ-сварке. Расположение инструментов, толщина сварного шва, толщина материала и управление станком являются одними из наиболее важных факторов в создании хорошего уплотнения.Привлекательность радиочастотной сварки заключается в полноте сварного шва. С помощью этого метода можно создавать очень прочные герметичные швы. Многие сварные швы подвергаются испытаниям на растяжение, испытаниям на герметичность и оптическим испытаниям, чтобы определить, были ли достигнуты правильные условия.
Некоторые материалы более сложны для радиочастотной сварки, чем другие, и могут даже потребовать специального процесса. Независимо от уровня сложности, UFP Technologies уверена в своей способности профессионально выполнять ВЧ-сварку следующих материалов:
- ПЭТ
- ПЭТГ
- ПВХ
- Термопластичные полиуретаны (ТПУ)
- Полиуретаны с открытыми порами
- ПЭНП/ЭВА
Существует несколько альтернатив ВЧ-сварке, включая шитье, склеивание или использование горячего воздуха.Зачем использовать радиочастотную сварку?
Радиочастотная сварка и шитье
СваркаRF обеспечивает постоянное воздухонепроницаемое уплотнение, в отличие от шитья. Когда сшитые швы натянуты, нить воспринимает давление и может порваться. Сварные швы RF равномерно распределяют напряжения по всему материалу, обеспечивая гораздо более прочный шов, предотвращая попадание внутрь воздуха, влаги или мусора.
Радиочастотная сварка и склеивание/адгезивы
Склеивание может обеспечить воздухонепроницаемое решение, но склеивание занимает намного больше времени, чем радиочастотная сварка, и часто используются опасные растворители, которые вредны для окружающей среды. Клеевые швы также могут выйти из строя после того, как клей изнашивается.
ВЧ-сварка по сравнению с горячим воздухом
Горячий воздух — это метод нагревания материала снаружи, чтобы расплавить его и создать связь. Этот метод эффективен только до определенной толщины. Слишком толстые материалы не будут склеиваться посередине, так как сердцевина будет изо всех сил пытаться расплавиться, а внешние слои будут перегреваться или сгорать. ВЧ-сварка нагревается изнутри наружу и является лучшим методом формирования герметичных швов.
Наш сваренный RF упаковочный пакет из ТПУ FlexShield для медицинских инструментов
Наш упаковочный пакет, изготовленный из термопластичной полиуретановой пленки (ТПУ) FlexShield® , является одной из наших новейших инноваций для индустрии медицинского оборудования. Пакет FlexShield® TPU изготавливается с помощью радиочастотной сварки и обеспечивает стойкость к проколам и истиранию, что позволяет безопасно транспортировать медицинские инструменты без повреждения внешней упаковки. Использование пакетов FlexShield в ваших упаковочных системах обеспечит целостность стерильного барьера между вашими инструментами и внешними загрязнениями.
Для функциональности продукта крайне важно, чтобы радиочастотная сварка на пакете FlexShield сохраняла целостность на протяжении всей цепочки поставок. ВЧ-сварка также используется в ряде приложений для ухода за ранами, которые помогают пациентам в процессе заживления. Для безопасного хранения дефибуляторов компания UFP Technologies производит трехкамерную многоразовую систему хранения пакетов, герметизированную с помощью радиочастотной сварки. Мы также используем эти возможности для производства промышленных чистящих средств.
В феврале 2018 года UFP Technologies приобрела Dielectrics, Inc., лидер в области проектирования, разработки и производства медицинских устройств с использованием термопластичных материалов, сваренных методом радиочастотной сварки. Наши объединенные возможности и опыт позволяют нам улучшать результаты лечения пациентов, сводя к минимуму вероятность заражения, повышая комфорт пациентов и способствуя более быстрому заживлению. Чтобы узнать больше о компании Dielectrics, посетите их веб-сайт по адресу www.dielectrics.com .
— MITUSA, Inc.
Машина для продольной сварки, внешние, внутренние, линейные, комбинированные, системы сварки плоских швов.
MITUSA Inc разрабатывает большие нестандартные сварочные машины с дополнительными инструментами для обработки деталей. Стандартные системы сварки швов большой длины. Зашивочные машины с электроприводом, наружные, внутренние, комбинированные, продольные зашивочные машины. От малых до больших продольных сварочных аппаратов длиной от 1 фута до 40 футов. Диапазон диаметров деталей от 1 дюйма до 20 футов.
Наши машины для сварки продольных швов используют прочные линейные направляющие с опорными блоками для плавного процесса сварки швов. Это позволяет оборудованию для продольной сварки прилагать давление для зажима концов стыкового сварного шва вместе.Сварка частичных швов выполняется на токопроводящих вставках с водяным охлаждением, таких как медь или алюминий, с переменным требуемым усилием, применяемым вдоль зажимного соединения. Это исключает возможность деформации детали во время сварки швов. Наша конструкция обеспечивает надежное сцепление гусеницы и свободный ход каретки боковой балки. Перевозка путешествия автомобиль везет.
Применение линейных сварочных аппаратов для сварки швов труб. Шовная сварочная машина для линейной сварки шовных соединений цилиндрических деталей.Включая сварку швов труб, труб или цилиндров. Некоторые формованные соединения краев коробки могут быть сварены швом. Квадратные или прямоугольные детали могут быть сварены продольным швом вдоль чистого стыкового соединения в зависимости от толщины металла.
Наши сварочные органы управления работают вместе с тележкой закаточной машины, когда она перемещается по линейным рельсам боковых балок. Использование двух контроллеров двигателей 24 В постоянного тока, один для каретки, а другой для механизма подачи проволоки Capstan. Эти устройства управления сваркой обеспечивают точную обратную связь с энкодером для точного плавного управления скоростью перемещения каретки на прецизионной машине для сварки боковых балок с линейными рельсами.
MITUSA обеспечивают прочность и точность в процессе сварки продольных швов. Возможность установки всего необходимого сварочного оборудования на тележке боковой балки линейного рельса. В результате провода меньше запутываются, что снижает потребность в обслуживании более длинных кабелей управления. Обеспечение удобного доступа оператора к блоку управления сваркой и источнику питания. Полный эргономичный доступ к контроллерам сварки на всем нашем оборудовании для линейных сварочных швов.
Траектория линейного перемещения обработана до 0.005-in допуск на прямолинейность, чтобы сварной шов был как можно более прямым в зависимости от подготовки стыка. Прецизионные сварочные аппараты предназначены для продольной сварки всех типов стыковых металлов со 100%-ным проваром.
Основание сварочной машины MITUSA очень широкое, чтобы вместить инструмент для загрузки деталей с гидравлическим ножничным подъемником. Детали загружаются и выгружаются без каких-либо препятствий на пути. Не требуются краны или цепи, чтобы плавно направить деталь в положение для шовной сварки зажимного соединения.
Мы разрабатываем нашу машину для продольной сварки с учетом безопасности оператора и эргономичной закаточной машины, в отличие от других типов машин для линейной сварки.
Когда-то замена мешка с воздушной камерой отнимала много времени, теперь на наших закаточных машинах требуется всего несколько часов, а не дней, в отличие от других моделей. MITUSA является первоначальным разработчиком эргономичного инструмента для баллонов, открывающегося к концам станины закаточной машины. Это позволяет запатентованному инструменту обслуживания замены мочевого пузыря.В закаточных машинах MITUSA используются ребристые линейные боковые балки с двумя направляющими для облегчения обслуживания направляющих. Машины для сварки швов MITUSA созданы для простой продуктивной работы и самых простых в обслуживании закаточных машин, доступных на сегодняшний день!
MITUSA Сварочная закаточная машина стандартных размеров
- Удобные, легко читаемые органы управления воздушным модулем на передней панели с кнопками и индикаторами.
- MLSW-24 2 фута (0,6096) Система шовной сварки 24 дюйма
- MLSW-36 3 фута (0,9144) Система шовной сварки 36 дюймов
- MLSW-48 4 фута (1.2192) Система для шовной сварки 48 дюймов
- MLSW-60 5 футов (1,524) Система шовной сварки 60 дюймов
- MLSW-72 6 футов (1,8288) Система шовной сварки 72 дюйма
- MLSW-84 7 футов (2.1336) Система шовной сварки 84 дюйма
- MLSW-96 8 футов (2,4384) Система шовной сварки 96 дюймов
- MLSW-120 10 футов (3,048) Система шовной сварки 120 дюймов
- MLSW-144 12 футов (3,6576) Система шовной сварки 144 дюйма
- MLSW-168 14 футов (4.2672) Система шовной сварки 168 дюймов
- MLSW-192 16 футов (4.8768) Система шовной сварки 192″
- MLSW-216 18 футов (5,4864) Система шовной сварки 216 дюймов
- MLSW-240 20 футов (6,096) Система шовной сварки 240 дюймов
- MLSW-264 22 фута (6.7056) Система шовной сварки 264 дюйма
- MLSW-288 24 фута (7.3152) Система шовной сварки 288 дюймов
- MLSW-312 Система шовной сварки 26 футов (7,9248) 312 дюймов
- MLSW-336 28 футов (8,5344) Система шовной сварки 336 дюймов
- MLSW-360 Система шовной сварки 30 футов (9,144 дюйма) 360 дюймов
- MLSW-384 32 фута (9.
7536) Система шовной сварки 384 дюйма
- MLSW-480 Система шовной сварки 40 футов (12,192 дюйма) 480 дюймов
- Доступны более длинные заказные системы шовной сварки MITUSA
Индивидуальные сварочные закаточные системы MITUSA.
В конструкции закаточной машиныMITUSA используются высококачественные зажимные приспособления для охлаждения столешницы для дуговой сварки швов. Стандартные или изготовленные по индивидуальному заказу медные кончики пальцев и инструменты для вставок поглощают и рассеивают тепло благодаря нашей запатентованной вставке закаточной станины с резервным стержнем с водяным охлаждением.Инструменты закаточной машины могут быть изготовлены из меди, нержавеющей стали или алюминия в зависимости от требований заказчика.
Модернизация вашей компании, занимающейся сваркой швов, с помощью специально разработанной системы MITUSA для сварки швов, отвечающей вашим требованиям к изготовлению сварных швов. Сроки изготовления нестандартных закаточных машин могут варьироваться, а стандартные сварочные машины есть в наличии.
Наша компания, базирующаяся в США, имеет полный инженерный и производственный отделы, которые изготовят ваш сварочный аппарат от стали до полных систем сварки швов.Мы производим машины для шовной сварки по индивидуальному заказу для сварки швов продольной дугой. Мы производим всю нашу продукцию на нашем предприятии в Хантингтон-Парке, Калифорния, США.
Шовные машины построены со встроенным оборудованием для шовной сварки MIG, TIG, плазменной или субдуговой сварки. Монтаж любых типов систем электроснабжения дуговой сварки по вашему выбору. MITUSA установит камеры дуговой сварки Xiris или полную систему сварки GTAW (TIG) горячей или холодной проволокой
Сварочный аппарат используется для шовной сварки, чтобы соединить края металлических сосудов, резервуаров, фонарных столбов, дымоходных труб, баллонов с пропаном, воздуховодов из листового металла, труб, конусов, плоских листов из листовой стали, сварных швов кромок коробок. и многое другое!
Зашивщики используют несколько процессов дуговой сварки, таких как MIG, TIG или Sub Arc, для сварки деталей из нержавеющей стали, алюминия, меди, алюминиевой бронзы, высоколегированных сплавов Inconel и углеродистой стали, черного чугуна и многого другого! Консультация требуется в зависимости от ваших требований к сварке швов.
Модернизация контроллера последовательности сварки для замены устаревшего контроллера системы шовной сварки без дорогостоящих обновлений? Наши средства управления сваркой MITUSA Universal PLC позволяют производителям восстановить полный контроль над сварочным аппаратом и процессом сварки швов одним касанием.
Мы проектируем и изготавливаем вашу систему продольной сварки с учетом требований оператора, чтобы обеспечить простоту эргономичного функционирования и техническое обслуживание системы шовной сварки. Обеспечьте безотказную работу сварочных машин благодаря нашему превосходному обслуживанию клиентов и поддержке, которые имеют первостепенное значение для MITUSA и их клиентов.