обзор видов обработки и оборудования
Рассказываем о напылении металла: особенности и назначение технологии. Современные способы. Применяемое оборудование и приборы. Особенности ионно-плазменного и плазменного напыления. Лазерное, вакуумное и порошковое напыление.
Напыление металла – это технология изменения структуры поверхности изделия с целью приобретения определенных качеств, повышающих эксплуатационные характеристики. Обработку выполняют путем нанесения однородного металлического слоя на деталь или механизм. В качестве расходного материала используют специальные порошковые составы, которые подвергают термической обработке и придают им значительное ускорение. При ударном соприкосновении с поверхностью частицы осаждаются на плоскости.
Технология появилась в начале XX века в качестве альтернативы традиционным способам поверхностной модификации металлов. По мере изучения и развития методов напыления металлических изделий была образована отдельная отрасль – порошковая металлургия.
В современной промышленности напыление металлов считается одним из самых экономичных способов обработки. По сравнению с объемным легированием технология дает возможность получить необходимые эксплуатационные свойства поверхности при меньших затратах.
Сущность и назначение напыления металлов
Нанесение защитных покрытий на металл необходимо для многих отраслей промышленности. Цель напыления изделий – повышение базового эксплуатационного ресурса заготовки. Защитный слой обеспечивает надежную защиту от следующих вредных факторов:
- воздействия агрессивных сред;
- вибрационных и знакопеременных нагрузок;
- термического воздействия.
Состав многокомпонентного порошка подбирают исходя из требуемых эксплуатационных качеств.
Использование нескольких составляющих повышает риск получения неоднородного покрытия ввиду расслаивания защитного слоя.
Для решения этой проблемы используют специальные материалы канатного типа, где порошок фиксируется пластичной связкой.
В процессе напыления поток частиц направляют на поверхность металла. При взаимодействии с поверхностью распыляемые элементы деформируются, что обеспечивает надежный контакт с изделием. Качество адгезии с заготовкой зависит от характера взаимодействия частиц с подложкой, а также процедуры кристаллизации защитного слоя.
Способы напыления, применяемое оборудование
На заре развития технологии обработка изделий осуществлялась с помощью сопла горелки и обычного компрессора, которые обеспечивали нагрев расходного материала и скоростной перенос на осаждаемую поверхность. По мере развития технологии были разработаны новые методы получения защитного покрытия. Следующим этапом развития стало использование электродугового оборудования. Конструкция такого металлизатора проволочного типа была разработана в 1918 году.
- Газодинамическое.
Обработка осуществляется мельчайшими частицами, размер которых не превышает 150 мкм.
- Вакуумное. Процедура протекает в условиях пониженного давления. Образование защитного слоя происходит в процессе конденсации напыляемого материала на базовой поверхности.
Рассмотрим основные способы обработки, а также особенности используемого оборудования для напыления.
Напыление в магнетронных установках
Технология магнетронной вакуумной металлизации основана на действии диодного газового разряда в скрещенных полях. В процессе работы установки в плазме тлеющего заряда образуются ионы газа, которые воздействуют на распыляемое вещество. Основными элементами магнетронной системы являются:
- анод;
- катод;
- магнитный узел.
Функция последнего элемента заключается в локализации плазмы у основания распыляемого вещества – катода. Любая магнитная система состоит из центральных и периферийных магнитов постоянного действия.

Преимущества магнетронного метода:
- высокая производительность;
- точность химического состава осажденного вещества;
- равномерность покрытия;
- отсутствие термического воздействия на обрабатываемую заготовку;
- возможность использования любых металлов и полупроводниковых материалов.
С помощью установок получают тонкие защитные пленки в среде специального газа. Напыляемым материалом могут выступать металлы, полупроводники или диэлектрики. Скорость образования слоя зависит от силы тока и давления рабочего газа.
Ионно-плазменное напыление
Одна из разновидностей вакуумного напыления металла на поверхность. Метод является следующим этапом развития технологии термического осаждения, которая основана на нагреве исходных материалов до точки кипения с их дальнейшей конденсацией на заготовках.

В состав принципиальной схемы оборудования для ионно-плазменного насаждения входят следующие элементы:
- анод;
- катод-мишень;
- термокатод;
- камера;
- заготовка.
Алгоритм действия установки:
- В камере создается пониженное давление.
- На термокатод, который является вспомогательным источником электронов, подается ток.
- Вследствие нагрева возникает термоэлектронная эмиссия.
- В камеру подают инертный газ. Наибольшей популярностью пользуется аргон.
- Между анодом и термокатодом возникает напряжение, которое инициирует образование плазменного тлеющего заряда.
- На катод подают мощный заряд.
- Положительные ионы воздействуют на распыляемый материал-мишень.
- Распыленные атомы осаждаются на заготовке в виде тонкого покрытия.
Ионно-плазменное осаждение используют в качестве декоративных или защитных покрытий, которые характеризуются высокой плотностью и прочностью, а также отсутствием изменений в стереохимическом составе.
Для изменения цвета изделия в технологический цикл добавляют реактивные газы: кислород, ацетилен, азот или углекислоту.
Плазменное напыление
Один из самых эффективных – метод диффузионной металлизации. Особенности технологического процесса:
- Рабочая температура плазмы может достигать 6000 ºC. Это способствует высокой скорости осаждения состава на поверхности. Длительность процесса – десятые доли секунды.
- Существует возможность изменения структурного состава поверхности заготовки. Вместе с горячей плазмой в верхние слои изделия могут диффундировать отдельные химические элементы.
- Плазменная струя отличается неизменными показателями давления и температуры. Это положительно влияет на качество напыления.
- Благодаря малому времени обработки заготовка не подвергается вредным поверхностным факторам, таким как перегрев или окисление.
» src=»about:blank» frameborder=»0″ allow=»accelerometer; autoplay; encrypted-media; gyroscope; picture-in-picture» allowfullscreen=»» data-rocket-lazyload=»fitvidscompatible» data-lazy-src=»https://www.youtube.com/embed/k5ie1Y-XoHQ?feature=oembed&wmode=opaque»/>
В качестве источника энергии для образования плазмы используют искровой, импульсный или дуговой разряд.
Лазерное напыление
Лазерное напыление металла применяют для достижения следующих целей:
- повышения прочности поверхностного слоя;
- восстановления геометрии изделия;
- снижения коэффициента трения;
- защиты от коррозионных процессов.
В отличие от прочих методов металлизации источником тепла является энергия излучения лазера. Высокая точность фокусировки позволяет добиться концентрации энергии точно в зоне работы. Это снижает термическое воздействие на заготовку, что позволяет избежать изменения геометрии изделия и дает возможность осуществить напыление практически любого материала.
Благодаря высокой скорости охлаждения в поверхностном слое металла образуются структуры с высокой твердостью, что повышает эксплуатационные характеристики детали.
Вакуумное напыление
Вакуумное напыление металла – эффективный и универсальный способ металлизации поверхности. С помощью данного метода можно обрабатывать практически любое изделие. За время технологического цикла с материалом происходит ряд превращений:
- испарение;
- конденсация;
- адсорбция;
- кристаллизация.
Производительность процесса зависит от многих факторов: структуры заготовки, типа наносимого материала, скорости потока заряженных частиц и многих других.
Вакуумные установки отличаются принципом действия. Существует непрерывное, полунепрерывное, а также периодическое оборудование.
Порошковое напыление
Порошковое напыление металлов полимерными материалами является наиболее эффективным способом получения высококачественного покрытия с декоративными или защитными свойствами.
Порошок для распыления представляет собой смесь каучука и цветного пигмента. Его наносят на поверхность с помощью специального электростатического пистолета. При этом порошок приобретает заряд, который способствует эффективному сопряжению с заготовкой.
Для получения качественного покрытия необходимо тщательно подготовить поверхность. Суть процедуры заключается в очистке заготовки от загрязнений и следов коррозии с последующим обезжириванием.
Для использования технологии в промышленных масштабах используют специальные покрасочные линии автоматического или ручного действия.
Напыление металла – одна из самых эффективных технологий модификации поверхности. Обработка позволяет получить покрытие с декоративными или защитными качествами, которые повышают эксплуатационные свойства изделия. А что вы думаете о данной технологии? Какой метод считаете наиболее перспективным? Напишите ваше мнение в блоке комментариев.
Способы напыления металлов
Традиции производства металлических изделий накапливались столетиями. Наука многократно модернизировала общепринятые технологические схемы, но всегда оставались существенными сырьевые и энергетические потери на всех этапах техпроцесса. Идея его кардинального изменения зародилась в начале ХХ века, когда известный русский инженер-металлург Соболевский П.Г. порекомендовал применить напыление металла в производстве машиностроительных изделий. Усовершенствование этой технологии способствовало образованию инновационной специализации – порошковой металлургии, обуславливающей замену традиционной обработки металла автоматизированными операциями прессовки и спекания материалов.
Технология напыления металлов является современным способом нанесения однородного металлического слоя на деталь при использовании раскаленной скоростной струи, имеющей в своем составе порошковые элементы, осаждающиеся на базисном металле при ударном столкновении с ним. Для выбора оптимального метода напыления металла следует принимать во внимание форму и размерные габариты деталей; точность и характер погрешности покрытия, его технико-эксплуатационные особенности; расход на базовое и дополнительное оснащение, порошковые материалы, на черновое и заключительное обрабатывание покрытий и прочее.
Способы и оборудование для напыления металлов
Однако порошковое напыление металла вовсе не ограничивается одним лишь производством деталей из порошков. Не менее важным является такое ее направление, как нанесение на металлическую поверхность слоя мелкодисперсной среды из огнеупорных, коррозионно- и износостойких материалов для улучшения функциональных, реставрационных и декоративных характеристик. При использовании в этих целях многокомпонентных порошковых материалов возрастает риск возникновения неоднородности покрытия, связанной с сегрегацией (расслаиванием) порошков. Такая проблема разрешается применением пластичных шнуровых материалов, имеющих в своем составе порошок, который фиксируется пластичной связкой. При обработке поверхности вещество связки целиком испаряется и на подложку изделия оседает лишь непосредственно порошок.
Сущность вакуумного напыления металлов состоит в том, что требуемый материал в результате сильного нагревания в вакуумном пространстве переходит в пар, который конденсируется в виде плоской пленки на наружной стороне тех или иных изделий.
Процесс термонапыления относительно прост и включает такие операции: расплавка металлического сырья в специальном пистолете (горелке) и напыление металла в жидком состоянии на заблаговременно обработанную поверхность при помощи сжатого воздуха. В ходе газопламенного напыления металла непрерывно перемещающийся напыляемый материал в форме проволоки или стержня продвигается через пистолет и плавится в конусовидном потоке горючего газа (диметилметана или топлива с содержанием ацетилена и кислорода). Кончик расплавленной проволоки встраивается в конусовидный поток и наносится на поверхность подложки. При контакте с поверхностью микрочастицы наносимого вещества моментально остывают и трансформируются, прочно сцепляясь с ней. В связи с этим, газотермическое напыление отличается мельчайшей ленточной или планарно-зернистой структурой.
Данный способ обработки идеально подходит для напыления труднодоступных участков. При его использовании следует контролировать дистанцию между пистолетом и обрабатываемым изделием, поддерживать оптимальную температуру напыления, соблюдать чистоту. Соблюдение точно выбранного промежутка и скорости передвижения пистолета обеспечивает оптимальную дозу материала и толщину наносимого слоя. Поскольку в ходе напыления металла создается пыль, следует регулярно прочищать фронтальную часть аппарата, чтобы гарантировать нанесение свежего слоя на очищенную поверхность. Использование газопламенного способа нанесения позволяет создавать покрытия с достаточной пористостью (до 12 %) и небольшой адгезией к основе, что связано с невысокой скоростью воздушно-газовой струи (менее 50 м/с). Температурный режим горения пламени лимитирует спектр металлов, которые можно наносить таким способом.
При осуществлении плазменного или газоплазменного напыления металла в качестве источника тепла выступает электродуга, возникающая между парой электродов. В зону ее горения нагнетается инертный газ, способный ионизироваться и образовывать плазму (температурой до 15000 °С). В плазменную струю поступает порошок наносимого металла, который плавится и переходит на обрабатываемую подложку. Вопреки высоким температурам в месте горения электродуги, изделие не подвергается перегреву, поскольку при переходе из участка дуги температурные показатели резко снижаются. Оборудование для такого типа нанесения металла сложнее, в сравнении с газопламенным из-за дополнительной потребности в электроаппаратуре.
В наиболее ответственных задачах для получения максимальной адгезии и прочности покрытий плазменную обработку осуществляют в вакуумном оборудовании для напыления металлов при низком давлении. Снижение давления обеспечивает возрастание скорости микрочастиц, что способствует получению более прочных химически стойких покрытий с повышенной твердостью.
Газодинамическое напыление металла заключается в образовании покрытий при взаимном ударении холодных микрочастиц металла, убыстренных ультразвуковой газовой струей, с подложкой детали. При контакте не расплавленных микрочастиц с поверхностью получается их пластическая трансформация и кинематическая энергия переходит в тепловую и адгезионную, способствуя образованию однородного слоя из прочно уложенных частиц металла. Отличительная особенность такого напыления – отсутствие повышенных температур при нанесении металлических покрытий, а значит, и отсутствие оксидации металлических частиц и подложки, явления неоднородной кристаллизации, повышенных внутренних напряжений в готовых изделиях.
Лазерное напыление металла представляет собой технологию восстановления изделий путем обработки их лазерным лучом света, генерируемым при работе оптико-квантового генератора. Из-за узкой сосредоточенности лазерного потока и повышенной энергетической плотности в месте его контакта с поверхностью можно производить наплавку любого металла. Самой востребованной является порошковая форма. Локальное фокусирование излучения дает возможность производить наплавление в труднодоступных зонах. При этом первичная структура практически не деформируется, но достигается повышенная износостойкость деталей.
Разработаны многочисленные установки для напыления металла. Как правило, они производятся в двух исполнениях: стационарном и мобильном, кроме этого могут функционировать как в закрытых цехах, так и на открытой местности для обработки крупногабаритной продукции. Покрытия, образованные перечисленными способами напыления, имеют высокие параметры прочности и пониженную степень остаточных напряжений.
Напыление металла — Центр защитных покрытий — Урал
Напыление металла это множество разных процессов в которых, главным образом, происходит нанесение покрытия частицами металла распыленными или уже в порошке. Cуть данного метода заключается в том, что расплавленный металл под воздействием струи сжатого газа распыляется на мелкие частицы, которые, ударяясь о покрываемую поверхность, расплющиваются и сцепляются с ней и между собой, образуя покрытие слоистого строения толщиной от 0,02 мм. На нашем предприятии, ООО ЦЗПУ, открылась роботизированная линия по напылению металла. В результате чего возросли качество и точность обрабатываемых изделий. Напыление металла проводится в специализированной камере, нанесение покрытий методом HVOF (высокоскоростное напыление) из порошка.
Напыление металла, для нанесения защитных покрытий на металлические поверхности преследует цель: создание функциональных свойств поверхности, упрочнение деталей для предотвращения их разрушения под воздействием окружающей среды и изменение формы изделия и ее восстановление, наращивание поврежденной в процессе эксплуатации поверхности.
Напыление металла
В зависимости от назначения детали, ее материала и условий эксплуатации при восстановлении используют различные методы напыления металла. Все они основаны на нагреве мелких частиц напыляемого материала до высоковязкого или расплавленного состояния и переносе их на поверхность изделия. Соударяясь с поверхностью изделия частицы металла закрепляются на ней и формируют покрытие. Чем больше скорость металлических частиц, тем выше качество покрытия, его плотность и прочность сцепления с основой. Материал для напыления подается в пламя горелки в виде проволоки или порошка, где происходит нагрев и распыление частиц, которые тепловым потоком источника нагрева разгоняются и попадают на поверхность напыляемой детали.
Металлизированные поверхности можно подвергать дальнейшей обработке. Реализуемые свойства покрытий: износостойкость, коррозиестойкость, термостойкость, антифрикционность, жаростойкость. Напыление металла проводится с применением различных материалов покрытий: на основе Cu, Fe, Ni, Co, нитридов, карбидов, бориды, оксидов, многокомпонентных, композиционных.
Напыление металла преимущества
- различные по габаритам (до 8 метров в длину и/или диаметром 1500мм)
- высокая гибкость процесса, что выражается в возможности нанесения покрытий на различные по габаритам изделия
- меньшее влияние процесса нанесения покрытия на свойства материала детали:
с наплавкой, т.к. деталь не нагревается выше 130 грС и не возникает напряжений в изделии, с гальваникой — экологичность, качество покрытия, ремонтопригодность у напыления выше
Напыление металлов — все способы и необходимое оборудование
Напыление металлов позволяет улучшить характеристики деталей, работающих в условиях, связанных сильным изнашиванием и механическими концентрированными нагрузками. Металлизация поверхностей повышает устойчивость и увеличивает срок службы. Кроме решения технических задач, напыление используется во время производства декоративных изделий, бижутерии, в пищевой, фармацевтической и химической промышленностях. Для напыления могут применяться различные металлы, конкретный выбор зависит от технического задания.
Химическое хромирование
Используется для обработки деталей со сложной геометрической формой, процесс основан на восстановлении хрома из растворов солей при помощи гипофосфита натрия. Осадок имеет серый цвет, блеск приобретается после полирования. Химическое хромирование протекает в ваннах с таким составом растворов.
Состав растворов для химического хромирования
- Фтористый хром, г — 17
- Хлористый хром, г — 1,2
- Лимоннокислый натрий, г — 8,5
- Гипофосфит натрия, г — 8,5
- Вода, л — 1
- Температура, °С — 70-87
Хромированная деталь
Скорость процесса хромирования может достигать 2,5 мкм/ч, для изготовления ванн используется устойчивый пластик. Металлизация сопровождается выделением ядовитых химических соединений, растворы негативно влияют на кожу людей. Во время производства работ следует соблюдать правила техники безопасности, для очистки воздушной среды устанавливается принудительная вентиляция. Мощность вентиляции рассчитывается исходя из объема помещения или рабочей зоны с учетом минимальной кратности обмена.
На промышленных предприятиях монтируется вентиляция пластиковая, она позволяет выдерживать рекомендованные технологические параметры при минимальных финансовых потерях. Для промышленного хромирования химическим методом применяются специально разработанные растворы с улучшенными показателями.
Промышленные растворы для химического хромирования
При приготовлении растворов первым растворяется хлористый хром. Затем согласно схеме могут растворяться лимонно-кислый натрий и фтористый хром. Для ускорения химических процессов в состав добавляется щавелевая кислота. Ионы хрома образуют с ней химически активный ион, скорость покрытия возрастает до 7 мкм/ч и более. Процентное содержание ингредиентов корректируется технологами с учетом поставленных конечных задач по обработке деталей.
Для получения расчетного покрытия необходимо выполнять следующие требования:
- Качественная подготовка поверхностей.
Детали очищаются механическим и химическим способами, при необходимости поверхности шлифуются.
- Оборудование должно обеспечивать максимальную автоматизацию процесса для исключения вредного влияния человеческого фактора.
- Постоянный контроль за состоянием раствора, фильтрование, поддержание заданной концентрации, своевременная замена катода.
Нарушение рекомендованной технологии может становиться причиной отслоений покрытий или образования глубоких раковин. Необходимость исправления дефектов приводит к значительному увеличению себестоимости производства.
Линия химического хромирования
Визуальный контроль химических процессов производится за счет определения количества выделяемого водорода, технологи рекомендуют для улучшения процесса одновременно покрывать детали из нескольких металлов. Слишком интенсивное выделение водорода может становиться причиной появления раковин, скорость процесса регулируется в каждом конкретном случае.
Газоплазменное напыление
Газоплазменное напыления позволяет получать чистое покрытие с высокими показателями адгезии. Процесс протекает при температурах до +50 000°С, скорость струи оставляет 500 м/с, температура поверхности обрабатываемой детали составляет не более +200°С.
Газоплазменное напыление металлов
Шероховатость поверхности напыляемых деталей до 60 Rz, зона обдува должна на 2–5 мм превышать номинальный размер напыляемого участка. Для работы используются порошки одной фракции по размерам, необрабатываемые участки детали закрываются специальными экранами. Перед процессом поверхность деталей предварительно прогревается до рабочих технологических температур.
Режимы работы оборудования при газоплазменном напылении
Технология напыления
Схема оборудования для напыления
Оборудование для порошкового напыления состоит из подвода газа (1), катода плазмотрона (2), корпуса катода (3), теплоизолятора (4), корпуса анода (5), порошкового питателя (6), подвода газа-носителя (7), плазменной дуги (8) и источника питания (9).
Газоплазменное напыление допускает финишную обработку покрытий для улучшения характеристик деталей, в таком случае толщина покрытия должна учитывать механическую шлифовку.
Напыление в вакууме
Перенос напыляемых металлов выполняется при разрежении 10-2 Па, напыление может быть катодным, магнетронным или ионно-плазменным. Вакуум увеличивает прочность сцепления поверхностей. Оборудование для технологии может быть многокамерным или многопозиционным однокамерным. Первые линии состоят из нескольких установок, в каждой из которых выполняется определенное напыление металлов, агрегаты между собой соединены технологическими линиями для транспортировки деталей. Многопозиционные имеют несколько отдельных постов для напыления в одном объеме. Вакуумное напыление производится по следующим этапам:
- Создание вакуума заданной глубины. Мощные компрессоры откачивают воздух из камеры, металлизация контролируется автоматическими приборами.
- Распыление покрывающего материала. В зависимости от особенностей процесса напыление металлов может выполняться несколькими способами.
- Транспортировка деталей в зависимости от их состояния.
Установка вакуумного напыления
Технологические определенияВакуумное напыление – сложный технологический процесс, зависящий от нескольких параметров:
- Критическая температурная точка напыления. Выше этого значения весь объем направляемых частиц отражается от поверхности детали, напыление металлов приостанавливается. Параметр зависит от металла детали, состояния ее рабочей поверхности и свойств напыляемых материалов.
- Критическая плотность давления. Минимальная плотность, при которой осадочная пленка адсорбируется и становится неспособной принимать атомы металла, напыление прекращается. Контроль критической плотности в установках выполняется непрерывно, при необходимости параметры условий корректируются. В зависимости от состава пленки могут быть моно- или поликристаллическими и аморфными.
Для повышения производительности вакуумное оборудование комплектуется механизмами автоматизированной транспортировки деталей в камеру и из нее, экранами и манипуляторами, заслонками и прочими механизмами. Напыление осуществляется в полуавтоматическом режиме.
Использование вакуумного оборудования позволяет получать напыление металлов с максимальным коэффициентом адгезии, увеличивается скорость протекания процесса, покрытия отличаются повышенной твердостью и химической устойчивостью. Недостаток – высокая энергоемкость процесса. Кроме того, вакуумное напыление не рекомендуется использовать для деталей со сложным профилем поверхностей.
Технология напыления металлов — В помощь хозяину
Напыление металлов
Напыление металлов позволяет улучшить характеристики деталей, работающих в условиях, связанных сильным изнашиванием и механическими концентрированными нагрузками. Металлизация поверхностей повышает устойчивость и увеличивает срок службы. Кроме решения технических задач, напыление используется во время производства декоративных изделий, бижутерии, в пищевой, фармацевтической и химической промышленностях. Для напыления могут применяться различные металлы, конкретный выбор зависит от технического задания.
Химическое хромирование
Используется для обработки деталей со сложной геометрической формой, процесс основан на восстановлении хрома из растворов солей при помощи гипофосфита натрия. Осадок имеет серый цвет, блеск приобретается после полирования. Химическое хромирование протекает в ваннах с таким составом растворов.
Состав растворов для химического хромирования
- Фтористый хром, г — 17
- Хлористый хром, г — 1,2
- Лимоннокислый натрий, г — 8,5
- Гипофосфит натрия, г — 8,5
- Вода, л — 1
- Температура, °С — 70-87
Скорость процесса хромирования может достигать 2,5 мкм/ч, для изготовления ванн используется устойчивый пластик. Металлизация сопровождается выделением ядовитых химических соединений, растворы негативно влияют на кожу людей. Во время производства работ следует соблюдать правила техники безопасности, для очистки воздушной среды устанавливается принудительная вентиляция. Мощность вентиляции рассчитывается исходя из объема помещения или рабочей зоны с учетом минимальной кратности обмена.
На промышленных предприятиях монтируется вентиляция пластиковая, она позволяет выдерживать рекомендованные технологические параметры при минимальных финансовых потерях. Для промышленного хромирования химическим методом применяются специально разработанные растворы с улучшенными показателями.
Промышленные растворы для химического хромирования
При приготовлении растворов первым растворяется хлористый хром. Затем согласно схеме могут растворяться лимонно-кислый натрий и фтористый хром. Для ускорения химических процессов в состав добавляется щавелевая кислота. Ионы хрома образуют с ней химически активный ион, скорость покрытия возрастает до 7 мкм/ч и более. Процентное содержание ингредиентов корректируется технологами с учетом поставленных конечных задач по обработке деталей.
Для получения расчетного покрытия необходимо выполнять следующие требования:
- Качественная подготовка поверхностей. Детали очищаются механическим и химическим способами, при необходимости поверхности шлифуются.
- Оборудование должно обеспечивать максимальную автоматизацию процесса для исключения вредного влияния человеческого фактора.
- Постоянный контроль за состоянием раствора, фильтрование, поддержание заданной концентрации, своевременная замена катода.
Нарушение рекомендованной технологии может становиться причиной отслоений покрытий или образования глубоких раковин. Необходимость исправления дефектов приводит к значительному увеличению себестоимости производства.
Линия химического хромирования
Визуальный контроль химических процессов производится за счет определения количества выделяемого водорода, технологи рекомендуют для улучшения процесса одновременно покрывать детали из нескольких металлов. Слишком интенсивное выделение водорода может становиться причиной появления раковин, скорость процесса регулируется в каждом конкретном случае.
Газоплазменное напыление
Газоплазменное напыления позволяет получать чистое покрытие с высокими показателями адгезии. Процесс протекает при температурах до +50 000°С, скорость струи оставляет 500 м/с, температура поверхности обрабатываемой детали составляет не более +200°С.
Газоплазменное напыление металлов
Шероховатость поверхности напыляемых деталей до 60 Rz, зона обдува должна на 2–5 мм превышать номинальный размер напыляемого участка. Для работы используются порошки одной фракции по размерам, необрабатываемые участки детали закрываются специальными экранами. Перед процессом поверхность деталей предварительно прогревается до рабочих технологических температур.
Режимы работы оборудования при газоплазменном напылении
Схема оборудования для напыления
Оборудование для порошкового напыления состоит из подвода газа (1), катода плазмотрона (2), корпуса катода (3), теплоизолятора (4), корпуса анода (5), порошкового питателя (6), подвода газа-носителя (7), плазменной дуги (8) и источника питания (9).
Газоплазменное напыление допускает финишную обработку покрытий для улучшения характеристик деталей, в таком случае толщина покрытия должна учитывать механическую шлифовку.
Напыление в вакууме
Перенос напыляемых металлов выполняется при разрежении 10 -2 Па, напыление может быть катодным, магнетронным или ионно-плазменным. Вакуум увеличивает прочность сцепления поверхностей. Оборудование для технологии может быть многокамерным или многопозиционным однокамерным. Первые линии состоят из нескольких установок, в каждой из которых выполняется определенное напыление металлов, агрегаты между собой соединены технологическими линиями для транспортировки деталей. Многопозиционные имеют несколько отдельных постов для напыления в одном объеме. Вакуумное напыление производится по следующим этапам:
- Создание вакуума заданной глубины. Мощные компрессоры откачивают воздух из камеры, металлизация контролируется автоматическими приборами.
- Распыление покрывающего материала. В зависимости от особенностей процесса напыление металлов может выполняться несколькими способами.
- Транспортировка деталей в зависимости от их состояния.
Установка вакуумного напыления
Технологические определения Вакуумное напыление – сложный технологический процесс, зависящий от нескольких параметров:
- Критическая температурная точка напыления. Выше этого значения весь объем направляемых частиц отражается от поверхности детали, напыление металлов приостанавливается. Параметр зависит от металла детали, состояния ее рабочей поверхности и свойств напыляемых материалов.
- Критическая плотность давления. Минимальная плотность, при которой осадочная пленка адсорбируется и становится неспособной принимать атомы металла, напыление прекращается. Контроль критической плотности в установках выполняется непрерывно, при необходимости параметры условий корректируются. В зависимости от состава пленки могут быть моно- или поликристаллическими и аморфными.
Для повышения производительности вакуумное оборудование комплектуется механизмами автоматизированной транспортировки деталей в камеру и из нее, экранами и манипуляторами, заслонками и прочими механизмами. Напыление осуществляется в полуавтоматическом режиме.
Использование вакуумного оборудования позволяет получать напыление металлов с максимальным коэффициентом адгезии, увеличивается скорость протекания процесса, покрытия отличаются повышенной твердостью и химической устойчивостью. Недостаток – высокая энергоемкость процесса. Кроме того, вакуумное напыление не рекомендуется использовать для деталей со сложным профилем поверхностей.
Способы напыления металлов
Традиции производства металлических изделий накапливались столетиями. Наука многократно модернизировала общепринятые технологические схемы, но всегда оставались существенными сырьевые и энергетические потери на всех этапах техпроцесса. Идея его кардинального изменения зародилась в начале ХХ века, когда известный русский инженер-металлург Соболевский П.Г. порекомендовал применить напыление металла в производстве машиностроительных изделий. Усовершенствование этой технологии способствовало образованию инновационной специализации – порошковой металлургии, обуславливающей замену традиционной обработки металла автоматизированными операциями прессовки и спекания материалов.
Технология напыления металлов является современным способом нанесения однородного металлического слоя на деталь при использовании раскаленной скоростной струи, имеющей в своем составе порошковые элементы, осаждающиеся на базисном металле при ударном столкновении с ним. Для выбора оптимального метода напыления металла следует принимать во внимание форму и размерные габариты деталей; точность и характер погрешности покрытия, его технико-эксплуатационные особенности; расход на базовое и дополнительное оснащение, порошковые материалы, на черновое и заключительное обрабатывание покрытий и прочее.
Способы и оборудование для напыления металлов
Однако порошковое напыление металла вовсе не ограничивается одним лишь производством деталей из порошков. Не менее важным является такое ее направление, как нанесение на металлическую поверхность слоя мелкодисперсной среды из огнеупорных, коррозионно- и износостойких материалов для улучшения функциональных, реставрационных и декоративных характеристик. При использовании в этих целях многокомпонентных порошковых материалов возрастает риск возникновения неоднородности покрытия, связанной с сегрегацией (расслаиванием) порошков. Такая проблема разрешается применением пластичных шнуровых материалов, имеющих в своем составе порошок, который фиксируется пластичной связкой. При обработке поверхности вещество связки целиком испаряется и на подложку изделия оседает лишь непосредственно порошок.
Сущность вакуумного напыления металлов состоит в том, что требуемый материал в результате сильного нагревания в вакуумном пространстве переходит в пар, который конденсируется в виде плоской пленки на наружной стороне тех или иных изделий.
Процесс термонапыления относительно прост и включает такие операции: расплавка металлического сырья в специальном пистолете (горелке) и напыление металла в жидком состоянии на заблаговременно обработанную поверхность при помощи сжатого воздуха. В ходе газопламенного напыления металла непрерывно перемещающийся напыляемый материал в форме проволоки или стержня продвигается через пистолет и плавится в конусовидном потоке горючего газа (диметилметана или топлива с содержанием ацетилена и кислорода). Кончик расплавленной проволоки встраивается в конусовидный поток и наносится на поверхность подложки. При контакте с поверхностью микрочастицы наносимого вещества моментально остывают и трансформируются, прочно сцепляясь с ней. В связи с этим, газотермическое напыление отличается мельчайшей ленточной или планарно-зернистой структурой.
Данный способ обработки идеально подходит для напыления труднодоступных участков. При его использовании следует контролировать дистанцию между пистолетом и обрабатываемым изделием, поддерживать оптимальную температуру напыления, соблюдать чистоту. Соблюдение точно выбранного промежутка и скорости передвижения пистолета обеспечивает оптимальную дозу материала и толщину наносимого слоя. Поскольку в ходе напыления металла создается пыль, следует регулярно прочищать фронтальную часть аппарата, чтобы гарантировать нанесение свежего слоя на очищенную поверхность. Использование газопламенного способа нанесения позволяет создавать покрытия с достаточной пористостью (до 12 %) и небольшой адгезией к основе, что связано с невысокой скоростью воздушно-газовой струи (менее 50 м/с). Температурный режим горения пламени лимитирует спектр металлов, которые можно наносить таким способом.
При осуществлении плазменного или газоплазменного напыления металла в качестве источника тепла выступает электродуга, возникающая между парой электродов. В зону ее горения нагнетается инертный газ, способный ионизироваться и образовывать плазму (температурой до 15000 °С). В плазменную струю поступает порошок наносимого металла, который плавится и переходит на обрабатываемую подложку. Вопреки высоким температурам в месте горения электродуги, изделие не подвергается перегреву, поскольку при переходе из участка дуги температурные показатели резко снижаются. Оборудование для такого типа нанесения металла сложнее, в сравнении с газопламенным из-за дополнительной потребности в электроаппаратуре.
В наиболее ответственных задачах для получения максимальной адгезии и прочности покрытий плазменную обработку осуществляют в вакуумном оборудовании для напыления металлов при низком давлении. Снижение давления обеспечивает возрастание скорости микрочастиц, что способствует получению более прочных химически стойких покрытий с повышенной твердостью.
Газодинамическое напыление металла заключается в образовании покрытий при взаимном ударении холодных микрочастиц металла, убыстренных ультразвуковой газовой струей, с подложкой детали. При контакте не расплавленных микрочастиц с поверхностью получается их пластическая трансформация и кинематическая энергия переходит в тепловую и адгезионную, способствуя образованию однородного слоя из прочно уложенных частиц металла. Отличительная особенность такого напыления – отсутствие повышенных температур при нанесении металлических покрытий, а значит, и отсутствие оксидации металлических частиц и подложки, явления неоднородной кристаллизации, повышенных внутренних напряжений в готовых изделиях.
Лазерное напыление металла представляет собой технологию восстановления изделий путем обработки их лазерным лучом света, генерируемым при работе оптико-квантового генератора. Из-за узкой сосредоточенности лазерного потока и повышенной энергетической плотности в месте его контакта с поверхностью можно производить наплавку любого металла. Самой востребованной является порошковая форма. Локальное фокусирование излучения дает возможность производить наплавление в труднодоступных зонах. При этом первичная структура практически не деформируется, но достигается повышенная износостойкость деталей.
Разработаны многочисленные установки для напыления металла. Как правило, они производятся в двух исполнениях: стационарном и мобильном, кроме этого могут функционировать как в закрытых цехах, так и на открытой местности для обработки крупногабаритной продукции. Покрытия, образованные перечисленными способами напыления, имеют высокие параметры прочности и пониженную степень остаточных напряжений.
Плазменное напыление металлов
Напыление плазменное, которое иногда называют диффузионной металлизацией, образуется вследствие термического диссоциации атомов металла под воздействием высокотемпературной плазмы с последующим осаждением и диффундированием внутрь заготовки. Это простой и дешёвый способ формирования покрытий.
Особенности и назначение плазменного напыления
Особенность покрытия — пластинчатая зернистая структура, возникающая в результате термической диффузии мелких частиц.
Стадии плазменного напыления металла:
- Ионизация частиц.
- Распыление.
- Осаждение.
- Затвердевание.
На каждом из этапов необходимо проводить контроль температуры и скорости движения напыляемых частиц.
Осаждение представляет собой совокупность двух, одновременно протекающих процессов – химической связи, которая активируется вследствие высоких температур в зоне обработки, и механических взаимодействий, обусловленных повышенной кинетической энергией частиц напыляемого металла. Дополнительным интенсифицирующим фактором считается наличие промежуточной среды – газа/жидкости — молекулы которой ускоряют и стабилизируют процесс металлизации. При этом образуются дополнительные соединения, улучшающие качество напылённого слоя. Например, азот формирует высокотвёрдые нитриды металлов, гелий предотвращает окисление поверхности, а медь улучшает условия трения.
Процесс используется для формирования оптимальных характеристик поверхностного слоя, а также как метод восстановления изношенных стальных деталей.
Технология процесса напыления
Исходный материал подается в столб плазмы в форме порошка или проволоки. Ионизированные газы высвобождают активные молекулы газов, некоторые из которых (например, водород) дополнительно поднимают температуру внутри плазменного столба, ускоряя процесс превращения молекул исходной заготовки в парообразное состояние. В результате ускоряется оседание движущихся частиц на подложку. Ионизация возможна не только из газа, но и из жидкости, испаряющейся в столбе дуги.
Напыляющие порошки разнообразят состав и свойства покрытий, поскольку в мелкодисперсное состояние может быть переработан широкий спектр металлов.
Плазменное напыление осуществляется в результате:
- Инициализации плазмы высоковольтным разрядом, который образует электрическую дугу постоянного тока, образующуюся между двумя электродами — медным анодом и металлическим катодом (чаще – вольфрамовым).
Электроды должны постоянно охлаждаться;
- Генерирования потока высокотемпературного ионизированного плазменного газа, который обычно состоит из аргона/водорода или аргона/гелия;
- Нагрева газа, с последующим ускорением его движения через сужающееся сопло;
- Переноса мелкодисперсного порошка в плазменной струе на подложку.
Высококачественное покрытие образуется вследствие сочетания высокой температуры (до 15000°C), концентрированной тепловой энергии плазменной струи, инертной среды распыления и скоростей частиц, достигающих 300 м/с.
Последующая обработка покрытия
Процесс распыления в потоке плазмы ограничен материалами, которые имеют более высокую температуру плавления, чем пламя. При более низких температурах и скоростях (до 40 м/с), энергетические характеристики движущихся частиц уменьшаются, что приводит к окислообразованию, пористости и наличием различных включений в готовом покрытии. Снижается прочность сцепления и адгезии между покрытием и подложкой. Такие покрытия подвергают шлифовке или полированию. В обоснованных случаях предусматривается термическая обработка – закалка, отпуск, нормализация.
Оборудование плазменного напыления
Для диффузионной металлизации производят три вида устройств – со сжиганием кислородной смеси, с подачей инертного газа и с термическим разложением жидкости. Толщина покрытия достигает 100…120 мкм.
Установки плазменного напыления, использующие энергию высокоскоростной кислородной плазмы, работают при гиперзвуковых скоростях газа, достигающих 1600…1800 м/с в момент удара струи по подложке. Так производят плазменное напыление износостойкими карбидами металлов, когда не требуется полного расплавления ионизированных частиц.
Оборудование, где поток плазмы формируется в струе инертного газа, используется для производства покрытий, требующих сочетания хорошей износостойкости и ударопрочности. Нагрев приводит к тому, что газ достигает экстремальных температур, диссоциирует и ионизируется.
Установки третьего типа выполняют металлизацию в конечный момент формообразования поверхности или полости электродуговым разрядом, сжатым поперечным потоком рабочей среды. Такие установки наиболее производительны. В качестве примера рассмотрим станок типа «Дуга-8М», состоящий из следующих узлов:
- Инструментальной головки с электрододержателем.
- Герметизированной рабочей камеры.
- Насосной станции.
- Резервуара с диэлектриком.
- Генератора плазмы.
- Узлов контроля и слежения.
Диффузионная металлизация происходит так. Исходное изделие фиксируется в рабочей камере и герметизируется. Электрододержатель с электродом (имеющим сквозное отверстие) устанавливается над заготовкой, после чего через зону обработки производится прокачка среды под высоким давлением. Включается генератор плазмы, и производится перемещение электрода до момента пробоя межэлектродного промежутка. Высокая концентрация тепловой мощности в дуге приводит к размерному испарению материалов электрода и рабочей среды. В результате одновременно происходит съём металла и насыщение поверхности атомами элементов.
Оборудование для плазменного напыления своими руками изготовить крайне сложно, поскольку кроме мощных источников питания, необходимых для создания дугового разряда, необходимы высокоточные узлы подачи рабочей среды к плазменному столбу.
Расходные материалы
Выбор исходных материалов определяется свойствами покрытия и стоимостью его получения.
Металлы. Предпочтение отдают интерметаллидам алюминия, железа, титана, никеля и кобальта, потому что они имеют высокие температуры плавления и сравнительно невысокие плотности, что уменьшает энергоёмкость плазменного напыления.
Самофлюсующиеся порошки. Используются порошки самофлюсующихся сплавов (типа бор-кремний). В процессе обработки расплавы порошков образуют металлургические соединения, устойчивые к коррозии и износу.
Минералокерамика. Для плазменного напыления используют исходные материалы, содержащие алюминий и кремний: они не дают трещин или отслаиваний. Добавка железа, марганца, меди, цинка и магния приводит к улучшению свойств покрытия.
Металлоорганические соединения. Используются преимущественно неполярные жидкости, которые хорошо растворяются в минеральных и синтетических маслах малой вязкости.
Технология напыления металлов: основные способы металлизации изделий
Автор: Анастасия Исакова · Опубликовано 27.11.2017 · Обновлено 22.11.2017
Производство металлических изделий модернизируется по мере развития передовых технологий. Металл в большей степени подвержен воздействию влаги, поэтому для обеспечения высокого срока эксплуатации и придания деталям, рабочим механизмам и поверхностям требуемых свойств, в современной промышленности широко используют напыление металлов. Технология порошковой обработки заключается в нанесении на базовую металлическую основу защитного слоя, обеспечивающего высокие антикоррозийные характеристики напыляемых изделий.
Задачи и варианты напыления
Металлическая поверхность после порошковой обработки приобретает важные защитные свойства. В зависимости от назначения и области применения, металлическим деталям придают огнеупорные, антикоррозийные, износостойкие характеристики.
Основная цель напыления базовой основы из металла – обеспечить продолжительный эксплуатационный ресурс деталей и механизмов в результате воздействия вибрационных процессов, высоких температур, знакопеременных нагрузок, влияния агрессивных сред.
Процессы напыления металлов выполняют несколькими способами:
- Вакуумная обработка – материал при сильном нагревании в вакуумной среде преобразуется в пар, который в процессе конденсации осаживается на обрабатываемой поверхности.
- Плазменное или газоплазменное напыление металла – в основу метода обработки положено использование электродуги, образующейся между парой электродов с нагнетанием инертного газа и ионизацией.
- Газодинамический способ обработки – защитное покрытие образуется при контакте и взаимодействии микрочастиц холодного металла, скорость которых увеличена ультразвуковой струей газа, с подложкой.
- Напыление лазерным лучом – генерация процесса происходит с использованием оптико-квантового оборудования. Локальное лазерное излучение позволяет проводить обработку сложных деталей.
- Магнетронное напыление – выполняется при воздействии катодного распыления в плазменной среде для нанесения на поверхность тонких пленок. В технологии магнетронных способов обработки используются магнетроны.
- Защита металлических поверхностей ионно-плазменным способом – основана на распылении материалов в вакуумной среде с образованием конденсата и осаждением его на обрабатываемой основе. Вакуумный метод не дает металлам нагреваться и деформироваться.
Технологический метод напыления деталей, механизмов, поверхностей из металла подбирают, в зависимости от характеристик, которые нужно придать напыляемой основе. Поскольку метод объемного легирования экономически затратный, в промышленных масштабах широко используют передовые технологии лазерной, плазменной, вакуумной металлизации.
Напыление в магнетронных установках
Металлизация поверхностей по технологии магнетронного напыления основана на расплавлении металла, из которого выполнена мишень магнетрона. Обработка происходит в процессе ударного действия ионами рабочей газовой среды, сформированными в плазме разряда. Особенности использования магнетронных установок:
- Основными элементами рабочей системы являются катод, анод, магнитная среда, которая способствует локализации плазменной струи у поверхности распыляемой мишени.
- Действие магнитной системы активизирует использование магнитов постоянного поля (самарий-кобальт, неодим), установленных на основании из магнитомягких материалов.
- При подаче напряжения от источника электропитания на катод ионной установки происходит распыление мишени, причем силу тока нужно поддерживать на стабильно высоком уровне.
- Магнетронный процесс основан на использовании рабочей среды, которой выступает соединение инертных и реакционных газов высокой чистоты, подающихся в камеру вакуумного оборудования под давлением.
Преимущества магнетронного напыления позволяют применять данную технологию обработки для получения тонких пленок металлов. Например, алюминиевые, медные, золотые, серебряные изделия. Происходит формирование пленок полупроводников – кремний, германий, карбид кремния, арсенид галлия, а также образование покрытий диэлектриков.
Главное достоинство магнетронного метода – высокая скорость распыления мишени, осаждения частиц, точность воспроизведения химического состава, отсутствие перегрева обрабатываемой детали, равномерность нанесенного покрытия.
Использование при напылении магнетронного оборудования дает возможность обрабатывать металлы и полупроводники с высокой скоростью осаждения частиц, создавать на напыляемой поверхности тонкие пленки с плотной кристаллической структурой, высокими адгезивными свойствами. К основному перечню работ по магнетронной металлизации относятся хромирование, никелирование, реактивное напыление оксидов, карбо- и оксинитридов, сверхскоростная наплавка меди.
Технология ионно-плазменной наплавки
Чтобы получать многомикронные покрытия на изделиях из металла, широко используют метод ионно-плазменного напыления. Он основан на использовании вакуумной среды и физико-химических свойств материалов испаряться и распыляться в безвоздушном пространстве.
Технологически сложный процесс позволяет решать важные технические задачи по металлизации изделий благодаря использованию установки ионно-плазменного напыления:
- Увеличение параметров износоустойчивости, исключение спекания при эксплуатации изделий в условиях высоких температур.
- Повышение коррозийной устойчивости металлов при эксплуатации в агрессивных водных, химических средах.
- Придание электромагнитных свойств и характеристик, эксплуатация в границах инфракрасного и оптического диапазона.
- Получение высококачественных гальванических покрытий, придание изделиям декоративно-защитных свойств, обработки деталей и механизмов, используемых в разных отраслях промышленности.
Процесс ионно-плазменного напыления базируется на использовании вакуумной среды. После поджига катода формируются пятна первого и второго уровня, которые перемещаются с высокой скоростью и образуют плазменную струю в ионном слое. Полученная в результате эродирования катодов струя проходит через вакуумную среду и вступает во взаимодействие с конденсируемыми поверхностями, осаживаясь плотнокристаллическим покрытием.
Использование ионно-плазменного напыления позволяет наносить защитные покрытия при температуре поджига катода до 100°C, отличается достаточно простой схемой получения слоев толщиной до 20 мкм.
С помощью ионно-плазменного напыления на металл удается придавать требуемые свойства конструктивно сложным изделиям нестандартной геометрической формы. После обработки металлическую поверхность не требуется покрывать финишным слоем.
Особенности плазменной металлизации
Наряду с ионно-плазменным напылением и магнетронными способами обработки металлов применяют еще один метод – плазменная металлизация. Главная задача технологии – защита изделий от окислительных процессов в агрессивных средах, повышение эксплуатационных качеств, упрочнение обрабатываемой поверхности, усиление сопротивляемости механическим нагрузкам.
Плазменное напыление алюминия и других металлов основано на высокоскоростном разгоне металлического порошка в потоке плазмы с осаждением микрочастиц в виде покрывающего слоя.
Особенности и преимущества технологии плазменного напыления на металл:
- Высокотемпературный метод нанесения защитного слоя на обрабатываемую поверхность (порядка 5000-6000 °C) происходит за доли секунд.
- Используя методы регулирования газового состава, можно получать комбинированное насыщение металлической поверхности атомами порошковых покрытий.
- Благодаря равномерности потока плазменной струи удается получать одинаково пористое, качественное покрытие. Конечная продукция превосходит результаты традиционных способов металлизации.
- Длительность процесса напыления невысока, что помогает достичь стопроцентной экономической эффективности использования плазменного оборудования в разных производственных масштабах.
Основные компоненты рабочей установки – высокочастотный генератор, камера герметизации, резервуар газовой среды, насосная установка для подачи давления, система управления. Использовать технологию плазменного напыления на металл допускается в домашних условиях при наличии необходимого оборудования с вакуумной камерой – воздействие кислорода приводит к окислению горячих металлических поверхностей и мишени.
На видео: восстановление деталей напылением.
Процесс лазерной обработки
Наплавка металлов лазерным методом позволяет восстанавливать детали и механизмы потоками света, генерируемыми от оптико-квантового оборудования. Вакуумное напыление лазером является одним из наиболее перспективных методов получения наноструктурированных пленок. В основу процесса положено распыление мишени световым лучом с последующим осаждением частиц на подложке.
Преимущества технологии: простота реализации металлизации, равномерное испарение химических элементов, получение пленочных покрытий с заданным стехиометрическим составом. Благодаря узкой направленности лазерного потока в месте его сосредоточения удается получить наплавку изделия любыми металлами.
Механизмы формирования жидкокапельных фаз:
- Крупные капли частиц расплавленной мишени образуются путем воздействия гидродинамического механизма. При этом диаметр крупных капель варьируется в диапазоне 1-100 мкм.
- Капли среднего размера формируются вследствие процессов объемного парообразования. Размер капель колеблется в диапазоне 0,01-1 мкм.
- При воздействии на мишень коротких и частых импульсов лазерного луча в эрозийном факеле образуются частицы мишени небольшой величины – 40-60 нм.
Если в лазерной установке при наплавке металлов на мишень одновременно действуют все три механизма рабочего процесса (гидродинамика, парообразование, высокочастотный импульс), приобретение изделием требуемых характеристик зависит от величины влияния конкретного механизма наплавки.
Одно из условий качественной лазерной обработки – воздействие на мишень таким режимом облучения, чтобы на выходе получить лазерные факелы с наименьшим включением жидкокапельных частиц.
Оборудование для холодного напыления
Существует два варианта защиты металлов от негативного воздействия внешних и рабочих факторов – легирование и напыление с вакуумным оборудованием. То есть, в сплав добавляют атомы химических элементов, придающих изделиям требуемые характеристики, или наносят на базовую поверхность защитное покрытие.
Чаще всего в отрасли металлизации используют технологию нанесения гальванических покрытий, применяют методы погружения деталей в расплав, задействуют в процессах обработки вакуумную среду, пользуются магнетронным оборудованием.
Иногда используют детонационно-газовое напыление, которое разгоняет частицы до невероятных скоростей. Широко применяют плазмотроны, электродуговую металлизацию, газопламенную обработку, ионное напыление. Задачи промышленности диктуют свои условия, и перед инженерами возникла необходимость создать недорогое, простое в обращении оборудование, для которого можно использовать свойства нагретого сжатого воздуха.
Появилось понятие порошковой металлизации с добавлением в металлический порошок мелкодисперсионной керамики либо частиц твердого металла. Используется для работы с алюминием, никелем, медью.
Результат экспериментов превзошел ожидания, позволив решить следующие задачи:
- Нагревание сжатого воздуха в камере приводит к повышению давления, что вызывает увеличение скорости вытекания наплава из сопла в установках.
- При наборе металлическими частицами в газовой среде высокой скорости они ударяются о подложку, размягчаются и прикипают к ней. А керамические частицы уплотняют образовавшийся слой.
- Использование порошковой технологии подходит для металлизации пластичных металлов – медь, алюминий, никель, цинк. После напыления изделия можно поддавать механической обработке.
Благодаря успешной работе инженеров удалось создать переносной аппарат, позволяющий выполнять металлизацию покрытий на всех промышленных предприятиях и в домашних условиях. Требования для успешной работы оборудования – наличие компрессорной установки (или воздушной сети) с давлением сжатого воздуха в пять-шесть атмосфер и электропитание.
В таблице ниже приведены данные для хромирования алюминия в домашних условиях. Перед нанесением гальванического покрытия требуется «положить» на деталь промежуточный металлический слой, а потом выполнять напыление алюминия.
Таблица 1. Хромирование алюминия
Использование передового оборудования для металлизации изделий позволяет решить технические вопросы, связанные с повышением антикоррозийных, прочностных, эксплуатационных характеристик, а также приданием машинам, деталям и механизмам требуемых свойств для работы в сложных эксплуатационных условиях.
Лазерная сварка (2 видео)
Напыление металлов. БЛЕСК-АВТО
В процессе напыления поток мелкодисперсных расплавленных или нагретых до кипения частиц направляют на поверхность металла. При взаимодействии с поверхностью распыляемые элементы осаждаются на поверхности заготовки, обеспечивая надёжный неразрушаемый контакт.
В общем виде существует два основных вида напыления: газодинамическое и вакуумное. При вакуумном напылении перенос напыляемых частиц осуществляется при разрежении 10-2 Па, что способствует более плотному прилеганию напыляемого слоя и производится в магнетронных, катодных или ионно-плазменных установках. В этих установках на обрабатываемую поверхность подаётся поток расплавленных мелкодисперсных частиц, поскольку считалось, что для создания устойчивого, малопористого и однородного слоя это условие является обязательным.
Технология газодинамического напыления включает в себя подачу через сверхзвуковое (600-700 м/с) сопло мелкодисперсных частиц металла (0,01-50 мкм) и нагрев сжатого воздуха до 400-600°C. В результате образуется слой металла, который обладает высокой адгезией (40-100 Н/мм2) и низкой пористостью (1-3%).
Напыление металлов — одна из самых современных и перспективных технологий кузовного ремонта.
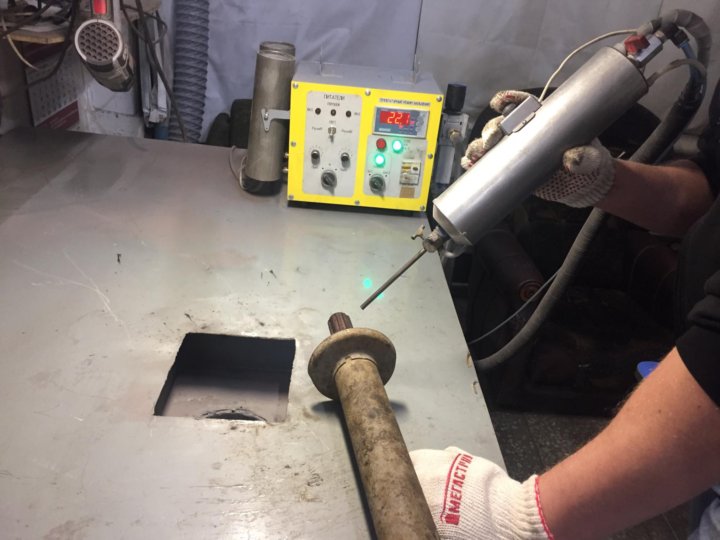
Напылением решается задача восстановления изношенных поверхностей, геометрии кузова, ремонт легкосплавных деталей и механизмов (устранение трещин, сколов).
Кроме того, напыление цинка или цинкование — лучшая защита металла и сварочных соединений от коррозии.
Если даже не нагревать напыляемые частицы до температуры плавления, а направить поток на обрабатываемую поверхность со сверхзвуковой скоростью 600-700 м/с (скорость звука составляет 331 м/с), то показатели полученного покрытия: на отрыв, микротвёрдость, пористость и однородность, ничем не уступали покрытиям, полученным при высокотемпературном напылении.
Дело в том, что при нагревании давление воздуха в камере в соответствии с законом Шарля повышается, а следовательно, повышается и скорость истечения из сопла. Частицы металла, набравшие в струе газа огромную скорость, при ударе о подложку размягчаются и привариваются к ней.
MIG-пайка кузова
Процесс пайки не разрушает цинковый защитный слой и тем более металл. MIG-Пайка происходит при более низкой температуре плавления припоя — приблизительно 900°C. Кроме того, медная пайка обладает отличными антикоррозийными свойствами.
Ремонт алюминия
Использование алюминия в автомобилестроении снижает вес автотранспорта и при этом это очень прочный металл. Кроме того, алюминий поглощает силу удара — деформации кузова при этом расположены в месте, где был нанесен удар.
Защита металлов от коррозии
Коррозия — это разрушение металла или сплава в результате его окисления под воздействием окружающей среды. В наибольшей степени коррозии подвергаются кузовные элементы автомобиля (особенно сварочные соединения). Коррозия не только ослабляет металл, но и может стать причиной разрушения кузова.
Реставрация авто
Плохое состояние кузова совершенно не говорит о том, что ему вынесен окончательный приговор. Реставрацией называется комплекс ремонтно/изготовительных процессов для восстановления первоначальных форм и функциональных характеристик автомобиля.
Ультразвуковая обработка
Ультразвук позволяет снять напряжения с поверхности металла методом образования «микроребер жесткости», которые возникают под действием акустической энергии. При ультразвуковом поверхностном упрочнении повышаются микротвёрдость и износостойкость металла.
Цинкование кузова
Самым распространённым способом защиты металлов от коррозии является цинкование, дающее наиболее длительную — 25-30 лет защиту. На воздухе цинк покрывается тонкой оксидной или карбонатной плёнкой, которая защищает железо от взаимодействия с окружающей средой.
Напыление цинка
Технологическим прорывом в сфере ремонта и восстановления металла стала технология напыления. Покрытие цинком или цинкование — лучшая защита металла и сварочных соединений от коррозии.
Лужение кузова
Лужение — нанесение на поверхность металла слоя олова или сплава на его основе. Оловянное покрытие применяется для защиты металлических изделий от коррозии. Его основные преимущества — хорошая адгезия и защита от коррозии, а также легкая обрабатываемость.
Please enable JavaScript to view the comments powered by Disqus.
Порошковое напыление металла | ОКБ «Поток
Порошковое напыление металла полимерными материалами — это на сегодняшний день самый современный и эффективный метод получения декоративно-защитного покрытия металлических изделий, которые используются в различных отраслях народного хозяйства. На данный момент аналогов порошковой покраске на рынке не существует, так как она обладает многими неоспоримыми экономическими и технологическими достоинствами, и что самое главное, не наносит никакого вреда экологической обстановке. В отличие от традиционных жидких красок порошковые в своем составе растворителей не содержат, поэтому и являются полностью безопасными как для работающих с ними людей, так и для окружающей среды.
Порошок, используемый для напыления металла, представляет собой смесь мельчайших частиц каучука и красящего пигмента. В процессе напыления частицы порошка, имеющие электрический заряд, распыляются на поверхность изделия, являющуюся нейтральной. Происходит это с помощью специального электростатического пистолета-распылителя. После того, как напыление будет закончено, изделие из металла (или иного материала) транспортируется в другое помещение — камеру полимеризации, в которой происходит нагревание и размягчение порошка. Краска расплавляется и растекается по поверхности ровным слоем, в результате чего получается стойкое, долговечное и очень привлекательное покрытие, обладающее, к тому же, защитными свойствами.
Технология порошкового напыления металлов развивается очень быстрыми темпами, повсеместно вытесняя с рынка традиционные жидкие краски. В настоящее время ведутся работы по разработке новых методов порошкового напыления, что способствует еще большему ее распространению.
Порошковое напыление металла позволяет получать очень качественное покрытие, которое представляет собой слой порошка, нанесенного на поверхность изделия, а затем расплавленного в печи с высокой температурой.
Таким образом, порошковое напыление состоит из трех основных этапов:
- Предварительная обработка поверхности и подготовка к напылению. Заключается она в удалении окислов и загрязнений, фосфатировании и обезжиривании, чтобы обеспечить хорошую адгезию и защитить окрашенное изделие от коррозии.
- Непосредственное нанесение слоя порошковой краски на деталь из металла в камере напыления.
- Нагревание и полимеризация порошкового слоя в камере полимеризации, формирование прочной пленки, остывание и отверждение.
Для порошкового напыления изделий из металла используются специальные окрасочные линии, которые могут быть автоматическими, полуавтоматическими и ручными. Для напыления крупногабаритных конструкций предусмотрена специальная транспортная система, которая перемещает их из камеры в камеру. Принцип ее работы состоит в том, что окрашиваемые предметы подаются на тележках или подвесках, которые передвигаются по рельсам. С помощью транспортной системы можно обеспечить непрерывный процесс напыления, что существенно увеличивает производительность окрасочных линий.
В начале процесса порошкового напыления детали из металла загружаются на конвейерную ленту и отправляются в камеру предварительной подготовки. Там они подаются в пятиступенчатый очиститель и проходят обработку очистителем, фосфатированию, антикоррозионной обработке, после чего ополаскиваются чистой водой. После этого изделия высушиваются в специальной печи. Это делается для того, чтобы полностью исключить попадание на поверхность влаги. После сушки изделия охлаждаются. Затем они перемещаются в окрасочную камеру и на них напыляется порошок. В камере полимеризации он расплавляется о получается качественное покрытие.
Нужно сказать, что порошковое напыление металла позволяет получать очень качественные покрытия. Достигается это за счет того, что на всех этапах производственного процесса осуществляется постоянный контроль. Для этого применяются современное оборудование. Например, для качественного контроля параметров полимеризации о формирования покрытий на поверхности деталей используется томограф. Степень заряда порошковой краски также контролируется, равно как и заземление деталей.
Смотрите также:
Что такое напыление металла / термическое напыление?
Металлическое напыление, также известное как Термическое напыление включает нанесение металлического покрытия на различные поверхности с помощью распыления расплавленных частиц.
Существует целый ряд методов напыления металла, включая напыление пламенем, напыление проволочной дугой, плазменное напыление, детонационное напыление, высокоскоростное кислородно-топливное напыление (HVOF), теплое напыление, холодное напыление и высокоскоростное воздушное топливо.
Техника распыления, которая подходит именно вам, будет зависеть от ряда различных факторов, включая используемое вами приложение, а также ваш бюджет, рабочие сроки и предпочтительную отделку.
Мы создали полезное руководство, в котором изложено все, что вам нужно знать о напылении металлов — мы надеемся, что оно окажется для вас полезным!
Как работает напыление металла?
Распыление металла — это процесс, который используется в самых разных отраслях промышленности и предполагает использование высокой степени нагрева для достижения расплавленного состояния.
По достижении расплавленного состояния материал тщательно распыляется на мельчайшие частицы, а затем распыляется на поверхность, с которой вы работаете.Как только частицы попадают на поверхность, они мгновенно выравниваются, выравниваются и затвердевают, образуя прочный, долговечный и водостойкий слой.
Хотя этот метод используется во многих различных секторах, он в основном связан с антикоррозийным и инженерным рынками, где важны точность, качество, противопожарная защита, защита и долговечность. Помня об этом, вы быстро обнаружите, что этот метод используется для нанесения финишных покрытий, создания антикоррозионных слоев и термобарьеров, а также для оптимизации износостойкости.
Преимущества металлического напыления
Вот еще несколько преимуществ, связанных с напылением металла…
- Повышенная прочность
- Измененные электрические свойства
- Повышенная или пониженная защита от коррозии
- Повышенная твердость
- Повышенное или пониженное трение
- Повышенная износостойкость
- Дополнительная защита поврежденных материалов
Но одна из основных причин того, почему этот метод так популярен и широко используется, заключается в том, что скорость осаждения поверхности выше и легче, чем при любых других процессах нанесения покрытия.
Системы и процессы термического напыления IRS
Ниже подробно описаны системы и процессы термического напыления, предлагаемые IRS Surfacing Technologies.
HVOF Металлургическая и керамическая химия
Для высококачественных покрытий с низкой пористостью и отличной прочностью сцепления. Карбиды вольфрама + хрома — полные керамические диапазоны до 1450 Hv. Химические, жаропрочные и износостойкие покрытия с пористостью менее 0,5%. Доступны химически стойкие сплавы G30, C22, C276, Ultimet и титан.
Высокоэнергетическое жидкое топливо — 8-осевая робототехника и встроенный поворотный стол ABB.
Для высококачественных, плотных и толстослойных наплавок из мягких сплавов, антикоррозионных и износостойких материалов. Диапазон карбида вольфрама превышает 1699Hv. Отложения с чрезвычайно низкой пористостью толщиной более 3,0 мм. Inconel 625, Hastelloy C276, Ultimet и большинство коррозионно-стойких сплавов. Мягкие алюминиевые подшипниковые сплавы, полный ассортимент карбида вольфрама, хрома и титана в стандартных или запатентованных матрицах.Доступен чистый титан. Собственный анализ для удовлетворения особых требований. Включает полностью скоординированную 8-осевую робототехнику и поддержку программного обеспечения.
Плазменная дуга (N.T.A.)
Полностью керамическая износостойкая, химически стойкая и термобарьерная серия, включая оксид хрома, чистый оксид алюминия, оксид алюминия, диоксид титана и оксид циркония иттрия. Износостойкость карбида вольфрама и хрома.
Плазменный спрей (NTA)
Покрытия, указанные выше, по внутреннему диаметру и отверстию.
Плазменная дуга (P.T.A.)
Твердые непористые покрытия с молекулярной связью. Все сплавы, карбиды вольфрама, хрома, титана и никеля. Сплавы с высоким содержанием никеля и бронзы и т.д. Стеллит, хастеллой, инконель, монель и т.д.
Плазменный спрей (PTA)
Покрытия, нанесенные на отверстия, стволы, линии подачи, штампы и т. Д.
Плазменный спрей (PTA)
Покрытия для отверстий, стволов, линий подачи, штампов и т. Д.
Плазменный распылитель (PTA)
Покрытия, нанесенные на отверстия, стволы, линии подачи, штампы и т. Д.
Гиперзвуковой спрей с двойным барабаном
Хромовые сплавы, Алюминий Магний, Бронза, Нержавеющие и Углеродистые сплавы, Хастеллой и Карбиды Вольфрама, а также восстановление компонентов, подшипников. журналы и покрытия роликов и т. д. Морское и химическое антикоррозионное покрытие. Хромированные сплавы и псевдометаллические покрытия для блоков Capstan Bull и канатных шкивов.Сплавы Hastelloy C22 и G30.
Techni-Chorde
Полный спектр наплавочных сплавов плюс керамическое оборудование среднего размера. Рокдур варьируется в хордах. Никелевые сплавы плюс многие другие анализы.
Высокоскоростной дуговой распылитель
Высокоскоростные напыления дуговым напылением с использованием высокоплотных покрытий с более высокими связями во всех расходных материалах. Значительно лучшая целостность и меньшая структура частиц, чем стандартные напыления дугового распыления.
Распылитель ArcSpray Bore-Spray
Полностью углеродистая сталь, никель и бронзовые сплавы.
Пламя-спрей
Стандартные устройства для пламенного напыления флюсовых сплавов. Самые распространенные системы в эксплуатации.
Fusion
Полный спектр процессов сварки, включающий системы всех ведущих производителей. Восстановление прессовой оснастки и штампов. Твердые, плотные, практически без пористости, молекулярно-сплавленные отложения, при которых подвод тепла к субстрату не является чрезмерной проблемой.
Rokide / Norton Ceramics.
Мы являемся единственным центром приложений Rokide / Norton, оборудованным и одобренным в Великобритании.Система распыления Rokide запатентована и уникальна тем, что она проецирует на подложку только полностью расплавленные частицы, в отличие от плазмы процессов пламенного распыления. В результате значительно улучшена антикавитационная стойкость, особенно в приложениях с точечным контактным давлением, таких как конусы для волочения проволоки и т. инструмент для волочения проволоки.
Спрей для нейлона и пластика
Антикоррозийные, химически стойкие покрытия с низким коэффициентом трения для шкивов, желобов и компонентов, которые должны противостоять кислотному воздействию при низких температурах неабразивных материалов, где требуется относительно дешевое решение.Также подходит для улучшения декора большинства цветов. Нейлон 1 и пластик EVA.
Новинка! Карбид вольфрама 80 Rc на инструментальной стали
С молекулярной связью. Не сколоть и не отсоединить !!! Может применяться для шнеков для литья под давлением, компонентов поворотных клапанов, гильотинных лезвий и т. Д.
Почему выбирают IRS Surfacing Technologies Ltd
IRS Surfacing специализируется на предоставлении полного спектра собственной технологии создания термоизоляции, которая была разработана с учетом индивидуальных требований, возникающих в различных отраслях промышленности.
Обладая более чем 20-летним опытом работы в отрасли, мы продолжаем предоставлять высококачественные и экономичные решения проблем преждевременного и серьезного износа в аэрокосмической, оффшорной, химической и производственной отраслях.
Прежде всего, IRS действительно придерживается принципа «могу сделать — могу помочь» как с нашей очень ценной армией сторонников, так и с новыми клиентами.
Если у вас есть какие-либо вопросы о наших услугах, не стесняйтесь обращаться к нам или посетите страницу https: //www.adl-usa.com /. Наша дружелюбная и услужливая команда всегда готова ответить на любые ваши вопросы, чтобы вы всегда находили правильное решение для ваших нужд.
Обратите внимание: Процедурная и химическая помощь и техническая поддержка на месте предоставляется без каких-либо обязательств.
Для получения более подробной информации о наших услугах по напылению металла, пожалуйста, свяжитесь с нами.
Дата публикации: 01.01.2019Категория: Металлическое напыление, Системы термического напыления
Металлическое напыление | Металлургия для чайников
Распыление металла — это распыление горячего металла на поверхность для создания покрытия.Методы термического напыления — это процессы нанесения покрытия, при которых расплавленные (или нагретые) материалы напыляются на поверхность. «Сырье» (предшественник покрытия) нагревается электрическими (плазма или дуга) или химическими средствами (пламя горения).
Напыление металла
Термическое напыление может обеспечить толстые покрытия (приблизительный диапазон толщины от 20 микрометров до нескольких мм, в зависимости от процесса и сырья) на большой площади при высокой скорости осаждения по сравнению с другими процессами нанесения покрытий, такими как гальваника, физическое и химическое осаждение из паровой фазы. .Материалы покрытия, доступные для термического напыления, включают металлы, сплавы, керамику, пластмассы и композиты.
Их подают в виде порошка или проволоки, нагревают до расплавленного или полурасплавленного состояния и ускоряют по направлению к подложкам в виде частиц микрометрового размера.
Процесс термического напыления проволоки сгорания
Горение или электрический разряд дуги обычно используются в качестве источника энергии для термического напыления. Получающиеся покрытия образуются за счет скопления множества распыленных частиц.Поверхность может не сильно нагреваться, что приведет к покрытию легковоспламеняющимися веществами.
Распыление металла — порошок и проволока
Качество покрытия обычно оценивается путем измерения его пористости, содержания оксидов, макро- и микротвердости, прочности сцепления и шероховатости поверхности. Как правило, качество покрытия повышается с увеличением скорости частиц.
Различают несколько разновидностей термического напыления:
- Плазменное напыление
- Детонационное распыление
- Сварочная дуга для напыления
- Распыление пламенем
- Высокоскоростное газокислородное напыление покрытия (HVOF)
- Теплое распыление
- Холодное напыление
В классических (разработанных между 1910 и 1920 гг.), Но все еще широко используемых процессах, таких как напыление пламенем и напыление дуги проволокой, скорость частиц обычно низкая (<150 м / с), и сырье должно быть расплавлено для осаждения.Плазменное напыление, разработанное в 1970-х годах, использует высокотемпературную плазменную струю, создаваемую дуговым разрядом с типичными температурами> 15000 K, что позволяет распылять тугоплавкие материалы, такие как оксиды, молибден и т. Д.
Предварительная обработка:
Поверхностная адгезия является чисто механической, поэтому требуется твердый ключ, свободный от жира или других загрязнений. Поэтому очень важны тщательная очистка и предварительная обработка окрашиваемой поверхности. Придание шероховатости поверхности обычно происходит путем дробеструйной обработки сухим корундом.Кроме того, для некоторых применений используются другие среды, такие как закаленный чугун, стальная крошка или SiC.
Предварительная обработка металла Spryaing
Все детали проходят пескоструйную очистку с использованием острого абразивного зерна для достижения шероховатости поверхности приблизительно 100-300 мкм. Помимо типа абразива, другие важные факторы включают размер частиц, форму частиц, угол струи, давление и чистоту абразивной среды. Подходящие материалы подложки — это те материалы, которые могут выдерживать процедуры струйной очистки для придания шероховатости поверхности, обычно имеющие твердость поверхности около 55 Rockwell C или ниже.Для получения более твердой основы требуются специальные методы обработки.
Некоторые из доступных материалов для распыления металла включают:
Покрытия алюминиевые
обеспечивают защиту от агрессивных атмосферных сред. Алюминиево-кремниевые покрытия используются для ремонта и восстановления оснований на основе алюминия и для низкотемпературных уплотнений в компрессорах. Добавление кремния в алюминиевый сплав обеспечивает улучшенную обрабатываемость по сравнению с покрытиями из чистого алюминия.
Бронзовые покрытия
дает плотное износостойкое покрытие, которое особенно хорошо подходит для неправильно обработанных деталей, ремонта, восстановления или для обеспечения опорной поверхности на другой основе.
Покрытия из чистой меди
обеспечивает хорошую проводимость для электрических применений. Покрытия из медных сплавов используются при работе с элементами машин, утилизации, ремонте и восстановлении подложек на основе меди.
Сталь углеродистая и низколегированная
Доступны, подходящие для универсального износа.Различные марки с разным содержанием углерода влияют на твердость и износостойкость покрытия. Также легко доступны сплавы из нержавеющей стали. Все эти продукты подходят для общего восстановления, восстановления и наращивания изношенных и неправильно обработанных компонентов, а более твердые сплавы обеспечивают дополнительную износостойкость.
Покрытия на основе свинца (эквивалент белого металла)
обеспечивает самосмазывающуюся поверхность подшипника и демонстрирует хорошую стойкость к кислотам и другим сильным реагентам.Идеально подходят для регулируемых башмаков подшипников в станках.
Молибденовые покрытия
производит твердые, смазанные поверхности, устойчивые к истиранию, истиранию и истиранию, а также с очень низким коэффициентом трения. Эти характеристики являются результатом образования оксида молибдена на поверхности. Основные области применения этого материала — компоненты автомобильного и другого транспортного оборудования.
Процесс плазменного распыления
Процесс плазменного распыления — это в основном распыление расплавленного или размягченного при нагревании материала на поверхность для получения покрытия.Материал в виде порошка вводится в пламя очень высокой температуры плазмы, где он быстро нагревается и ускоряется до высокой скорости.
Принципиальная схема процесса плазменного распыления
Горячий материал ударяется о поверхность подложки и быстро остывает, образуя покрытие. Этот правильно выполненный процесс плазменного напыления называется «холодным процессом» (относительно материала подложки, на которую наносится покрытие), поскольку температура подложки может поддерживаться низкой во время обработки, избегая повреждений, металлургических изменений и искажения материала подложки.
Распыление пламенной проволоки
При газопламенном напылении проволоки, типичном методе газового напыления, проволока последовательно подается в газовое пламя, такое как оксиацетилен или оксипропан, расплавляется и распыляется с использованием сжатого воздуха для образования покрытий.
Схема распыления пламенной проволокиХарактеристики:
- Использование легкого оборудования, пригодного для строительства на месте
- Незначительное или полное отсутствие термической деформации основных металлов
- Диапазон регулировки толщины (0.1 ~ 10 мкм)
- Большой выбор материалов
- Высокая износостойкость покрытий
Для этого метода напыления можно использовать все виды металлов, из которых можно сделать проволоку, включая цинк, алюминий, углеродистую сталь, нержавеющую сталь и молибден. Диапазон толщины широк — от 0,1 до 10 мкм.
Распыление стержнем пламени
Этот метод, использующий тот же принцип, что и газопламенное напыление, требует использования оксидно-керамического стержня в качестве материала покрытия.Керамический стержень попадает в кислородно-ацетиленовое пламя, нагревается и расплавляется, затем тонко измельчается сжатым воздухом и затвердевает на основном металле, образуя покрытие. Поскольку в этом методе используется керамика, этот метод подходит для напыления для защиты от коррозии или для контроля износа, что улучшает термостойкость вокруг горячих участков.
Распыление пламенной проволоки
Характеристики:
- Распыляет только полностью расплавленные частицы
- Обеспечивает отличное сцепление частиц и образует высококогезионные покрытия.
- В три или четыре раза быстрее, чем при порошковом напылении
- Менее подвержен нагреву, чем плазменное напыление
- Ограниченный выбор материалов покрытия (только оксидная керамика)
Пламя порошкового напыления
В этой форме напыления порошковый материал подается в пистолет-распылитель через порошковый насос и расплавляется и нагревается в высокотемпературном пламени, образуя покрытие.Существует три основных метода подачи порошка: подключение порошкового насоса непосредственно к пистолету-распылителю, использование отдельного порошкового насоса и подача в пистолет-распылитель с использованием неактивного газа (например, азота).
Схема распыления порошка пламенем
Характеристики:
- Широкий выбор материалов, включая металлы, сплавы, пластмассы и керамику
- Длительное время плавления в пламени обеспечивает превосходную адгезионную прочность материалов (эффективность 90% для самофлюсующихся сплавов).
- Очень низкий уровень шума
- Использует сжатые газы для ускорения и охлаждения частиц
- Использование легкого краскопульта позволяет производить опрыскивание вручную
HVOF Пламенное напыление
Этот метод формирует покрытия за счет мощного распыления, создаваемого повышенной скоростью распыления.Используя тот же топливный газ, что и при напылении пламенем, он делится на HVOF (высокоскоростное кислородное топливо), использующее смесь топлива и кислорода, и HVAF (высокоскоростное воздушно-топливо), использующее смесь топлива и воздуха. Он работает по принципу
- Горение происходит внутри трубы
- Горючий газ распыляется с высокой скоростью через сопло
- Порошок подается в распыляемый газ и нагревается, расплавляется и распыляется с высокой скоростью, в конечном итоге образуя покрытие.
Схема газового напыления HVOF
Характеристики:
- Распыление в два или четыре раза быстрее
- Может образовывать деликатные покрытия
- Окисление происходит меньше
- Требуются более мелкие порошки
- Может вызвать засорение пистолета-распылителя
- Генерирует ультразвук
- Работа должна выполняться в изолированном звукоизолированном помещении
Дуговое напыление
В этом типичном электрическом напылении две металлические проволоки генерируют электрический дуговый разряд, расплавляются и подаются в соответствии со скоростью плавления.Затем расплавленные металлы тонко разделяются сжатым воздухом и последовательно формуются на основном металле, образуя покрытие. По сравнению с методами напыления пламенем он показывает отличные характеристики. Поскольку материал покрытия может быть полностью расплавлен при высокой температуре, он обеспечивает отличную адгезию к основному материалу. Однако материалы покрытия ограничиваются только электропроводящими.
Схема дугового напыления
Характеристики:
- Быстрое напыление (в два-четыре раза быстрее, чем напыление пламенем)
- Высокая адгезия и прочность покрытия
- Из различных материалов можно формировать покрытия из сплавов.
- Низкие эксплуатационные расходы
Процесс термического распыления с детонацией
Принципиальная схема процесса детонационного термического напыления
Детонационное ружье в основном состоит из длинного ствола с водяным охлаждением и впускными клапанами для газов и пороха.Кислород и топливо (чаще всего ацетилен) подаются в ствол вместе с порохом. Искра используется для воспламенения газовой смеси, и возникающая в результате детонация нагревает и ускоряет порох до сверхзвуковой скорости вниз по стволу. Пульс азота используется для продувки ствола после каждого взрыва. Этот процесс повторяется много раз в секунду. Высокая кинетическая энергия частиц горячего порошка при ударе о подложку приводит к образованию очень плотного и прочного покрытия.
Возможно вам понравится
Случайные сообщения
- Коррозия
Коррозия — это распад искусственного материала на составляющие его атомы из-за химических реакций с ним… - Фазовые диаграммы Fe-Mn, Fe-Co, Fe-Mo
В чистом железе превращения A4 (1394 ° C) и A3 (912 ° C) происходят при постоянных температурах. Если элемент попадает … - Биомиметика (биомимикрия)
Биомиметика относится к искусственным процессам, веществам, устройствам или системам, которые имитируют природу. Искусство и наука … - Глубокая вытяжка
Технология производства глубокой вытяжки — это вытягивание листового металла, обычно называемого заготовкой, вокруг a… - Сплав с памятью формы
Сплав с памятью формы (SMA, интеллектуальный металл, металл с памятью, сплав с памятью, мышечный провод, интеллектуальный сплав) — это сплав, который «запоминает …
Что такое металлический спрей? | MSSA
Распыление металла — это процесс, который используется более 100 лет во всем мире, когда расплавленный металл или размягченные частицы наносятся на подготовленную поверхность (подложку), чтобы улучшить ее свойства (твердость, защита от коррозии, износ, диэлектрическая проницаемость, восстановление габаритов и т. д.). Без растворителей или химических веществ , только чистого металла . Распыление металла, часто используемое в качестве альтернативы процессу цинкования, имеет низкое тепловложение во время напыления, что устраняет риск деформации компонентов. Не существует ограничений по размеру компонентов, на которые наносится покрытие методом Metal Spray, и эти компоненты можно обрабатывать на месте, что означает отсутствие проблем с транспортировкой или ожиданием. Особые работы требуют дополнительной защиты в критических областях, процесс металлического напыления позволяет оператору изменять толщину покрытия, чтобы удовлетворить эту потребность.
Наше оборудование для металлического напыления состоит из дугового напыления, пламенного напыления, плазменного напыления, высокоскоростного воздушного топлива (HVAF), высокоскоростного кислородного топлива (HVOF), оборудования для лазерной наплавки, оборудования для сварки распылением, а также вспомогательного оборудования. Более подробную информацию о каждом процессе можно получить, щелкнув соответствующие вкладки.
Этот процесс преимущественно используется для защиты от коррозии, модификации / улучшения поверхности и восстановления инженерных размеров и используется во всех мыслимых отраслях, включая аэрокосмическую, автомобильную, морскую, биомедицинскую, сельское хозяйство, космические путешествия, производство электроэнергии, инфраструктуру, горнодобывающую промышленность и многие другие. Приложения.
Распространенное заблуждение относительно антикоррозионных покрытий состоит в том, что они могут быть завершены только цинком, тогда как на самом деле Metal Spray может предложить 4 варианта антикоррозионных покрытий, каждое из которых имеет свою собственную идентичность: цинк 99,99%, цинк-алюминий Сплав 85/15, алюминий 99,5% и алюминий-магний 5% .
Применение технических покрытий включает, помимо прочего: замену твердого хрома, рекультивацию, наплавку, искробезопасные, антипригарные и нескользящие покрытия.
Metal Spray — это идеальная поверхность от до для нанесения любого верхнего покрытия от окраски до порошковой окраски .
Картины, напыленные цинком и металлическим напылением, с верхним слоем краски — Изображение предоставлено Ironic Art, Gatton QLD.
Процесс металл / термическое напыление / металлизация — это процедура нанесения покрытия, используемая для изменения свойств поверхности детали путем добавления слоя (слоев) материала для увеличения многих факторов, включая:Материалы, используемые в этой процедуре нанесения покрытия, могут включать:
Материалы подложки включают:
- Металлы, стекло, углеродное волокно, пластмассы, гипс, полистирол, керамика и дерево.
Катодная защита бетонных мостов
Чем отличается металлический баллончик от покраски?
- Материалы неизменно высокого качества и чистоты, перед нанесением смешивание не требуется.
- Материалы имеют неограниченный срок хранения при правильном хранении .
- Требуется меньше этапов процесса.
- Это упрощает контроль качества и снижает вероятность ошибки.
- Распыляемые компоненты не требуют времени для длительного отверждения или высыхания , что обеспечивает превосходное использование площади пола. Цинк, алюминий и их сплавы
- обеспечивают эффективную коррозионную стойкость и немедленную защиту .
- Напыленные металлы на прочнее , чем краски и , выдерживают более грубое использование .
- Даже , если напыляемый слой поврежден, жертвенное действие предотвращает коррозию .
- Металлы можно распылять в более широком диапазоне климатических условий (температура и влажность) , чем краски.
- материалов , используемых с начала 1900-х годов не изменились и используются до сих пор , тогда как многочисленные системы окраски были заменены много раз.
Чем отличается распыление металла от цинкования?
- Низкое тепловложение во время напыления исключает риск деформации компонентов .
- Низкое тепловложение исключает риск термической металлургической деградации .
- Герметичные пустотелые конструкции можно обрабатывать без риска взрыва .
- Нет ограничений на размер обрабатываемого компонента .
- Компоненты можно обработать на площадке , что означает отсутствие проблем с транспортировкой или ожиданием.
- Нет проблем с удалением сточных вод.
- Требуются уменьшенные запасы цинка.Оборотный капитал не привязан к ванне с расплавленным цинком.
- Топливо не требуется для сохранения расплавленного цинка, когда технологический процесс не работает.
- Распыление металла восстанавливает защиту от коррозии на поврежденных участках сварной оцинкованной стали (для этого существуют международные стандарты).
- Толщина покрытия может варьироваться. обеспечивает дополнительную защиту в критических областях.
- Процесс распыления металла не ограничивается цинком .
- Алюминий, сталь, бронза и т. Д. Также могут применяться в различных областях.
- При цинковании окалины не требуется никаких дополнительных работ.
- Покрытие Metal Spray пористое и, следовательно, поверхность идеальна для приема краски (это если требуется, поскольку в этом нет необходимости).
- Нет необходимости в предварительном травлении и т. Д.
Знаете ли вы? Доктор Макс Ульрих Шоп (на фото выше) первым изобрел напыление металла в начале 1900-х годов, когда он, стреляя гранулами из игрушечной пушки, которую купил для своего маленького сына, обнаружил, что расплавленный свинец и цинк могут прилипать практически к любой поверхности.
Есть еще вопросы? Позвоните нам по телефону (07) 3823 1004 или нажмите здесь, чтобы написать нам по электронной почте.Метод напыления металла
Металлическое напыление — это собирательный термин для различных технологий термического напыления. Термическое напыление основано на взаимодействии кинетической и тепловой энергии.
Распыление металла было разработано в начале 20 века и первоначально включало распыление частиц расплавленного металла. Термическое напыление позволило наносить материалы на правильно подготовленные элементы, не достигая подводимого тепла, необходимого для сварки или плавления.
Высокая кинетическая энергия, генерируемая методом напыления металла, привела к механическому прижатию расплавленных частиц к детали без выделения тепла. Основываясь на этих выводах, все чаще применялось термическое напыление, первоначально в основном при ремонте. Благодаря возможности использования различных устройств при напылении пламенем, покрытия при напылении металла могут быть предоставлены — в зависимости от требований и области применения — из молибдена, стали, нержавеющей стали и металлов NE, таких как медь, бронза, алюминий, цинк ) так далее.а также оксидная керамика.
Для подготовки деталей к напылению металла их обезжиривают, нагревают прибл. 100 ° C, напыленный стальной дробью, карбидом кремния или оксидом алюминия и сразу после этого покрытый для предотвращения коррозии. Если термическое напыление невозможно для покрытий, обработку можно проводить путем сухого точения или сухого шлифования в определенных случаях.
Окончательная обработка покрытий методом напыления металла может производиться вращением, круглым шлифованием и чистовой обработкой.При термическом напылении покрытие часто также наносят без дополнительной обработки. Поверхности, обработанные металлическим напылением, следует затем смазать или загерметизировать в зависимости от использования.
Различные технологии термического напыления получили дальнейшее развитие, и благодаря новым открытиям они стали неотъемлемым элементом защиты от износа и коррозии. Сегодня методы напыления металлов, такие как напыление проволокой в пламени, напыление пучком пламени, напыление порошка с самофлюсом или без него, высокоскоростное напыление пламенем (HVOF), стандартизированы термическим напылением DIN EN 657.
Распыление металла покрывает применение для ремонта и защиты от брака из-за дефектов высоких технологий указанными методами. Возможности термического напыления нигде еще почти не исчерпаны и всегда доступны для решения технических проблем. Термическое напыление сегодня является частью современных технологий.
Распыление металла — Распыление бронзы — Распыление молибдена
Мы предлагаем услугу напыления металла с использованием ряда Sulzer Metco12E. Пистолеты (с подачей проволоки) и пистолеты Sulzer Metco 5P mk11 (с подачей порошка).
Широкий ассортимент покрытий могут применяться в том числе из высокоуглеродистой стали право до нержавеющей стали, меди, бонза, алюминий, материалы на основе молибдена и свинца. Приложения почти бесконечные, но некоторые примеры включают диаметры уплотнений, шпиндели станков, опорные поверхности и печатные ролики.
Быстро Срок сдачи: , потому что напыление металла может быть довольно быстрым. время оборота может быть значительно сокращено по сравнению к гальванике (т.е. наш процесс жесткого хромирования). Это особенно полезно для аварийных служб, например, для ремонта шпинделя на станке. поломки. Напыление металла полезно и при ремонтных работах. который был неправильно обработан или был неожиданно поврежден. Толстые покрытия могут быть созданы и впоследствии отшлифованы до требуется допуск.
Обзор:
В процессе газопламенного напыления используется источник тепла из кислорода и ацетилена.Наносимый материал подается в пламя в форме
проволоки, затем сжатый воздух используется для распыления расплавленного
металл и ускоряет частицу к подложке.
В процессе горения порошка используется аналогичная технология, но
порошок заменяет проволоку в качестве сырья, таким образом, больший выбор
материалов для распыления доступно, так как не все материалы для распыления
могут быть изготовлены в виде проволоки.
Предварительная обработка: Адгезия к поверхности является чисто механической и, как таковая,
Требуется прочный ключ, свободный от жира или других загрязнений.Поэтому тщательная очистка и предварительная обработка поверхности
быть покрытым очень важно. Шероховатость поверхности обычно
происходит пескоструйной очисткой сухим корундом. Кроме того,
используются другие среды, такие как закаленный чугун, стальная крошка или SiC
для некоторых приложений. Все предметы прошли пескоструйную обработку острым
абразивное зерно для достижения шероховатости поверхности примерно
100-300 мкдюймов. Помимо типа зернистости, другие важные
факторы включают размер частиц, форму частиц, угол взрыва,
давление и чистота песчаной среды.
Подходящие материалы подложки — это те, которые выдерживают взрывные работы.
процедуры для придания шероховатости поверхности, обычно имеющие поверхность
твердость около 55 ° C по Роквеллу или ниже. Специальная обработка
Для подготовки подложек с более высокой твердостью требуются техники.
Некоторые из доступных материалов для распыления металла включают:
Алюминий покрытия обеспечивают защиту от коррозионных атмосферных воздействий. среды.Алюминиево-кремниевые покрытия используются для ремонта. и восстановление подложек на основе алюминия и при низких температурах уплотнения в компрессорах. Добавление кремния в алюминиевый сплав обеспечивает улучшенную обработку более покрытия из чистого алюминия.
бронза покрытия образуют плотное износостойкое покрытие, которое особенно хорош для неправильно обработанных деталей, ремонта, восстановления или обеспечить опорную поверхность на другом основании
Покрытия из чистой меди обеспечивает хорошую проводимость для электрических Приложения.Покрытия из медного сплава используются для элементов машины. работы, утилизация, ремонт и восстановление оснований на основе меди.
Углерод и низколегированная сталь , подходящая для универсального износа доступны приложения. Различные сорта с разными содержание углерода влияет на твердость покрытия и износостойкость. Нержавеющая легкодоступны также стальные сплавы. Все эти продукты подходят для общей реставрации, утилизации и наращивания изношенных и неправильно обработанных компонентов, с более твердыми сплавами, обеспечивающими дополнительная износостойкость.
Свинец Покрытия на основе (эквивалент белого металла) обеспечивают самосмазывающиеся несущую поверхность и обладают хорошей устойчивостью к кислотам и другим сильнодействующие реагенты. Идеально подходит, включает регулируемый подшипник обувь в станках.
молибден покрытия создают твердые, смазанные поверхности, которые устойчив к истиранию, истиранию и истиранию и очень хорошо низкий коэффициент трения.Эти характеристики являются результатом образования оксида молибдена на поверхности. Ключевые приложения для этого материала предназначены для автомобильного и другого транспорта компоненты оборудования.
Антикоррозийное напыление металла — Защита от коррозии стальной проволоки
Алюминиевая проволока
Алюминий с термическим напылением (TSA) — чрезвычайно прочное покрытие, обеспечивающее полную защиту от коррозии и значительное увеличение срока службы по сравнению с обычными барьерными покрытиями.Узнать больше »
Цинк / цинковые сплавы
Металлические цинковые покрытия являются анодными по отношению к стали, цинкование и цинкование, нанесенное дуговым напылением, защищают сталь точно так же, цинк обеспечивает защитный слой поверх стали.Подробнее »
Одним из наиболее экономичных способов защиты стали от коррозии является нанесение защитного покрытия. Благодаря принципу протекторного анода эти покрытия обеспечивают более длительный срок службы. Это покрытие должно выдерживать не только определенные условия окружающей среды, но и обладать определенными механическими свойствами.По этим причинам наиболее широко используемые коррозионно-стойкие материалы включают такие металлы, как цинк, алюминий или цинк / алюминий.
Опции для антикоррозионного напыления металла
Состав материала | Идентификационный номер продукта / лист данных | Диаметр | В упаковке | Вес |
---|---|---|---|---|
Алюминий | ||||
Алюминий 99,5% | TH600 | 1/16 дюйма (1,6 мм) (2 мм) 3/32 дюйма (2.3 мм) 1/8 дюйма (3,2 мм) 3/16 дюйма (4,8 мм) | Катушка Большая катушка | 20 фунтов (9,1 кг) 30 фунтов (13,6 кг) 160 фунтов (72,6 кг) |
Алюминий 99,00% | TH601 | 1/16 дюйма (1,6 мм) (2 мм) 3/32 дюйма (2,3 мм) 1/8 дюйма (3,2 мм) 3/16 дюйма (4,8 мм) | Катушка Большая катушка | 20 фунтов (9,1 кг) 30 фунтов (13,6 кг) 160 фунтов (72,6 кг) |
Цинк / алюминий (85/15) | TH650 | 1/16 дюйма (1.6 мм) (2 мм) 3/32 дюйма (2,3 мм) 1/8 дюйма (3,2 мм) 3/16 дюйма (4,8 мм) | Катушка Барабан | 44 фунта (20 кг) 450 фунтов (204 кг) |
цинк | ||||
Цинк 99,8% | TH700 | 1/16 дюйма (1,6 мм) (2 мм) 3/32 дюйма (2,3 мм) 1/8 дюйма (3,2 мм) 3/16 дюйма (4,8 мм) | Катушка Барабан | 55 фунтов (25 кг) 550 фунтов (250 кг) |
Нажмите здесь, чтобы отправить запрос на расценки
, или позвоните нам сегодня по телефону 877-884-3428
Распыление металла: значение и применение | Отрасли промышленности
В этой статье мы обсудим значение и применение металлического напыления в промышленности.
Значение металлического напыления:
Распыление металла или металлизация буквально означает обработку или покрытие металла или металлического соединения. Металлизация как процесс обычно включает подготовку основного материала, напыление на металл и, наконец, шлифовку поверхности.
В основном, для напыления металла используется два типа оборудования. Один из них — металлический пистолет, который состоит из газовой горелки с отверстием в центре наконечника для проволоки, небольшой воздушной турбины и шестерен для подачи проволоки через наконечник в пламя так же быстро, как оно тает, и воздуха. колпачок вокруг наконечника горелки и сопла, который подает струю воздуха для распыления расплавленного металла и нанесения его на подготовленную поверхность.
В другом методе порошкообразный металл подается из контейнера через резиновый шланг к распылителю и выходит через центр пламени, аналогично проволочному пистолету. В этом случае металл уже находится в распыленной форме, и, следовательно, необходимого воздуха достаточно для осаждения расплавленного металла на покрываемой поверхности.
Применение обоих методов важно в своих областях. Порошковый пистолет, не имеющий турбины или шестерен, стоит меньше, легче в обращении и без струи распыляющего воздуха может более эффективно использоваться для нагрева основного металла, когда такое тепло необходимо.С другой стороны, металл в виде проволоки дешевле, чем в виде порошка; металл в форме проволоки более доступен и с ним легче обращаться.
Чаще всего используется металлическая пушка, использующая металл в форме проволоки. Проволока подается в пистолет-распылитель с определенной скоростью, расплавляется кислородно-ацетиленовым пламенем, а затем продувается сжатым воздухом на покрываемую поверхность. Вид в разрезе пистолета-распылителя для металла показан на рис. 8.1.
Поверхность основного металла подготовлена должным образом, поскольку связь между напыленным металлом и основным металлом является чисто механической.Поверхность очищается струйной очисткой острым кварцевым песком или стальной стальной крошкой. Цилиндрические объекты изготавливаются путем обработки небольших канавок на поверхности с последующим накатыванием вершин этих канавок с помощью инструмента, подобного инструменту для накатки.
Оба метода делают поверхность шероховатой и обеспечивают необходимые сцепляющиеся поверхности, так что пластик может легко приклеиваться к поверхности. Расплавленный материал выдувается со значительной силой, что вызывает сцепление с неровностями поверхности.Напыленный металл сам по себе обеспечивает подходящую поверхность для последовательных покрытий и позволяет создавать слой значительной толщины.
При напылении металла на основной металл исходные свойства изменяются. Увеличивается пористость, прочность на сжатие и твердость, но уменьшается прочность на разрыв. Также качество напыленного металла хорошее.
В наши дни этот процесс стал очень популярным из-за его экономичности и скорости, с которой можно наносить металл.Также в деталях не возникает перекосов и внутренних напряжений.
Применение металлического напыления:Некоторые области применения металлического напыления:
(1) Защита от коррозии:
Самым распространенным применением напыления металла является нанесение алюминия и цинка на железо и сталь. Калибровка часто выполняется путем распыления алюминия толщиной 0,1 мм на сталь с последующим нагревом детали с образованием на поверхности соединения железа и алюминия.
(2) Твердая и благородная поверхность:
Одним из основных применений металлизации является нанесение специальной металлической поверхности на большие массы менее дорогостоящего металла, например, большой вал, требующий устойчивости к коррозии, не обязательно должен быть полностью из нержавеющей стали. Его можно было сначала сделать из любого металла, а затем металлизировать благородным металлом.
Аналогичным образом металлизация может применяться для обеспечения устойчивости к истиранию или износу, защиты от коррозии, а также для улучшения электрических или магнитных свойств и т. Д.Большинство обычных твердых материалов для наплавки доступны в виде порошка и могут быть распылены при приготовлении тонких покрытий.
(3) Поверхности пайки:
Медь с напылением часто используется на неметаллических деталях, когда требуется прикрепить детали пайкой. Эта процедура также может быть применена к твердым припоям, таким как магний, когда гальваническая коррозия не рассматривается.
(4) Электропроводность:
Проводящее покрытие из меди и серебра может быть получено на плохом проводнике e.g., распыляя медь на большинство угольных щеток двигателей и генераторов для лучшего электрического соединения.
(5) Теплопроводность:
Иногда желательно иметь поверхность, отводящую тепло от горячих точек на плохих проводниках. В этом случае можно распылять медь, и это имеет еще одно преимущество: она идеально вписывается в непроводящую часть и обеспечивает максимальную эффективность.
(6) Другие приложения:
Другое его применение — создание декоративных пленок, отражающих поверхностей и специальных металлических форм.