Ультразвуковой метод контроля — неразрушающий метод (УЗК)
УЗК (ультразвуковой метод контроля) – современная диагностическая методика, отличающаяся высокой точностью по сравнению с рентгенодефектоскопией, радио-дефектоскопией и т. д. Она позволяет выявлять широкий спектр дефектов, а также получать достоверные данные о месторасположении, характеристиках и размерах дефектов.Листовая сталь – это прокат, используемый в промышленном и гражданском строительстве, при возведении железнодорожных и автодорожных мостов. Каркасы зданий и сооружений такого масштаба должны отличаться повышенной надёжностью и прочностью. Поэтому этап контроля качества является обязательным и должен выполняться в соответствии с установленными нормативами.
Принцип УЗК
Ультразвуковая диагностика основывается на том, что колебания с высокой частотой (примерно 20 тысяч Гц) способны проникать в металл и отражаться от дефектов. Узконаправленная волна, создаваемая дефектоскопом, проходит сквозь проверяемое изделие. При наличии дефекта она распространяется с отклонениями, которые можно зафиксировать на экране прибора. Показания, полученные в ходе УЗК, позволяют узнать информацию о характере выявленного дефекта. Например: по времени прохождения ультразвукового сигнала – измеряется расстояние до неровности; по амплитуде колебания отражённой волны – примерные размеры дефекта.Разновидности УЗК
Сегодня в промышленной сфере используют четыре основных методики выполнения ультразвукового метода неразрушающего контроля. Их отличия заключаются в способах, применяемых для получения и оценки информации о дефектах:2. Теневая методика. По разные стороны от контролируемой зоны устанавливают два преобразователя. Один из них формирует УЗ-волну, а второй регистрирует отражённый сигнал. При использовании теневого метода о наличии дефекта можно говорить в случае исчезновения УЗ-колебаний. В потоке возникает «глухая зона». Она говорит о том, что в этом месте сигнал не смог пройти из-за дефекта.
3. Зеркальный эхо-метод. В этом случае оба преобразователя устанавливаются на одной стороне. Первый прибор формирует УЗ-колебания, которые отражаются от неровности, а второй регистрирует их. Данный метод особенно эффективен, если необходимо найти дефекты, расположенные под прямым углом относительно поверхности исследуемого изделия (трещины и пр.).
4. Зеркально-теневая методика. По сути – это теневой метод. Однако приборы размещаются на одной стороне. В ходе дефектоскопии оператор регистрирует не прямой, а отражённый от второй поверхности контролируемой зоны поток УЗ-волн. О наличии дефекта говорят «глухие зоны» в отражённых колебаниях.
Неразрушающаяся на первый взгляд конструкция может быть повреждена дефектами, которые возникают во внутренних структурах металла. Поэтому данные методики способны обеспечить безопасную эксплуатацию сооружений, возведённых их продуктов проката.
Выявляемые дефекты
Ультразвуковой неразрушающий контроль используется для выявления:- воздушных пор и пустот;
- трещин;
- недопустимых утолщений;
- флокенов;
- зон крупнозернистости;
- отложений шлака;
- неоднородных химических вкраплений;
- ликвационных скоплений и так далее.
Преимущества ультразвукового метода контроля
- Доступная стоимость. УЗК обходится значительно дешевле, чем ряд других методов дефектоскопии;
- Безопасность. Ультразвуковое излучение не оказывает негативного влияния на оператора, проводящего исследование;
- Мобильность. Портативные аппараты для дефектоскопии позволяют проводить проверку на выезде. Это существенно расширяет сферы использования УЗК;
- Высокая точность. Высокая скорость и точность УЗК даёт возможность получать объективные данные о состоянии и о качестве листового металла без значительных погрешностей. Проверенные листы могут использоваться для создания прочных и неразрушающихся в течение долгого времени конструкций;
- Неразрушающее воздействие. Изделия сохраняются в своём первозданном виде, что позволяет избежать дополнительных финансовых затрат.
Основные минусы УЗК
Одним из недостатков УЗК является необходимость тщательной подготовки поверхности перед проведением контроля. Требуется создать шероховатости пятого класса. Они необходимы для хорошего контакта с жидкой массой, которая наносится для того, чтобы УЗ-волны беспрепятственно проникали внутрь. Помимо этого, УЗК не позволяет получить точную информацию о размерах дефекта. Однако по сравнению с другими способами дефектоскопии УЗК является наиболее точной, эффективной и надёжной методикой.Порядок выполнения УЗК
Порядок проведения дефектоскопии будет зависеть от класса металла, который нужно проверить, а также от требований, предъявляемых к нему. Образно можно разделить весь процесс на несколько этапов, это:2. Выбор характеристик и методов контроля. В зависимости от класса заготовки выбирается метод выполнения УЗК.
3. Подготовка поверхности. С поверхности удаляют остатки шлака, лакокрасочных покрытий, крупные неровности и следы коррозии. Зона выполнения УЗК покрывается специальным составом, включающим воду, минеральные масла или особые густые клейстеры. Это даёт ультразвуковым сигналам возможность проникать внутрь металлического листа без препятствий.
4. Подготовка оборудования. В зависимости от выбранного метода выполнения УЗК мастер размещает, подключает и настраивает приборы.
5. Проведение дефектоскопии. Оператор медленно сканирует металлический лист. При возникновении сигналов от дефектов подбирается контрольный уровень чувствительности. Все данные фиксируются оператором.
6. Подготовка результатов. Информация о найденных дефектах заносится в специальный журнал. Также на основании полученных данных определяется качество стального листа в зависимости от требований, которые к нему предъявляются.
Некоторые предприниматели, занимающиеся производством и реализацией листовой стали, игнорируют этап обязательного неразрушающего контроля. Это может обернуться массой негативных последствий. Листовой металл, не прошедший дефектоскопию, часто становится причиной аварий. Для создания прочных, ответственных и неразрушающихся конструкций он не годится. Поэтому лучше выполнить УЗК в профессиональной лаборатории. Если вас интересуют подобные услуги, обратитесь в ТД «Ареал». Наши специалисты обладают высокой квалификацией, а также оформляют все документы согласно установленным стандартам.
Вид контроля | По характеру взаимодействия физических полей с контролируемым объектом | По первичному информативному параметру | По способу получения первичной информации |
---|---|---|---|
Магнитный | Магнитный | Коэрцитивной силы, Намагниченности, Остаточной индукции, Магнитной проницаемости, Напряженности Эффекта Баркгаузена | Индукционный, Феррозондовый, Магнитографический, Пондеромоторный, Магниторезисторный |
Электрический | Электрический, Трибоэлектрический, Термоэлектрический, | Электропотенциальный, Электроемкостный | Электростатический порошковый, Электропараметрический, Электроискровой, Рекомбинационного излучения, Экзоэлектронной эмиссии, Шумовой, Контактной разности потенциалов |
Вихретоковый | Прошедшего излучения, Отраженного излучения | Амплитудный, Фазовый, Частотный, Спектральный, Многочастотный | Трансформаторный, Параметрический |
Радиоволновой | Прошедшего излучения, Отраженного излучения, Рассеянного излучения, Резонансный | Амплитудный, Фазовый, Частотный, Временной, Поляризационный, Геометрический | Детекторный (диодный), Болометрический, Термисторный, Интерференционный, Голографический, Жидких кристаллов, Термобумаг, Термолюминофоров, Фотоуправляемых полупроводниковых пластин, Калориметрический |
Тепловой | Тепловой контактный, Конвективный, Собственного излучения, | Термометрический, Теплометрический | Пирометрический, Жидких кристаллов, Термокрасок, Термобумаг, Термолюминофоров, Термозависимых параметров, Оптический, Интерференционный, Калориметрический |
Оптический | Прошедшего излучения, Отраженного излучения, Рассеянного излучения, Индуцированного излучения | Амплитудный, Фазовый, Частотный, Временной, Поляризационный, Геометрический, Спектральный | Интерференционный, Нефелометрический, Голографический, Рефрактометрический, Рефлексометрический, Визуально-оптический, |
Радиационный | Прошедшего излучения, Рассеянного излучения, Активационного анализа, Характеристического излучения, Автоэмиссионный | Плотности потока энергии, Спектральный | Сцинтилляционный, Ионизационный, Вторичных электронов, Радиографический, Радиоскопический |
Акустический | Прошедшего излучения, Отраженного излучения (эхо-метод), Резонансный, Импедансный, Свободных колебаний, Акустико-эмиссионный | Амплитудный, Фазовый, Временной, Частотный, Спектральный | Пьезоэлектрический, Электромагнитно-акустический, Микрофонный, Порошковый |
Проникающими веществами | Молекулярный | Жидкостной, Газовый | Яркостный (ахроматический), Цветной (хроматический), Люминесцентный, Люминесцентно-цветной, Фильтрующихся частиц, Масс-спектрометрический, Пузырьковый, Манометрический, Галогенный |
Виброакустический | Механические колебания — движение точки или механической системы, при котором происходят колебания характеризующих его скалярных величин | Статистические параметры колебательного процесса (механических колебаний) | Пьезоэлектрический. Электромагнитно-акустический |
Ультразвуковые дефектоскопы — Ультразвуковой контроль — НЕРАЗРУШАЮЩИЙ КОНТРОЛЬ — Оборудование и комплектующего для неразрушающий контроля, физико-механических испытаний, пробоподготовки, спектрального анализа 8 (495) 134-69-69
Ультразвуковые дефектоскопы предназначены для обнаружения дефектов в изделиях из различных металлических и неметаллических материалов методами ультразвуковой дефектоскопии. В зависимости от задач они бывают следующих видов: импульсные, импедансные, резонансные.
У нас вы можете купить дефектоскопы USM 36, USM-Go+, Mentor UT, Phasor XS (CV/DM), USN 60, USLT2000, Spotchecker, USM Vision +, ультразвуковые дефектоскопы серии А12, УД и УИУ Сканер.
Линейка Krautkramer представлена несколькими передовыми ультразвуковыми дефектоскопами: USM Go +; USM 36, USN 60.
Преимуществами всех приборов и комплектующих производства GE Sensing & Inspection Technologies являются:
-
Высочайшее качество всех компонентов, составляющих приборы этого производителя;
-
Контроль на всех этапах производства каждого аппарата;
-
Мощный интеллектуальный резерв компании.
Оборудование Krautkramer широко применяется для контроля качества в нефтяной и газовой промышленности, энергетической, аэрокосмической, транспортной, строительной, металлообрабатывающей, химической, металлургической и других отраслях.
Основные технические преимущества линейки ультразвуковых дефектоскопов Krautkramer:
-
Высокая частота повторения импульсов 15…2000 Гц (6000 для USN 60)
-
Генератор прямоугольных импульсов ( 300 В для USM и 450 B для USN). Данное преимущество позволяет прозвучивать большие толщины и материалы с высоким затуханием (поковки из черных и цветных металлов, литье), чем не могу похвастаться конкуренты, такие как А1212, А1214
-
Большой диапазон частот 0,2 … 20 МГц и большое количество узкополосных фильтров (1,0, 2,0, 2,25, 4, 5, 7,5, 10, 15 МГц)
-
Диапазон прозвучивания до 14000 мм.
-
Класс надежности дефектоскопов Krautkramer не ниже IP66, этим они превосходят такие дефектоскопы как А1212, А1214, Epoch, OmniScan.
USM Go+ — аналог УСД46
Если вы хотитекупить ультразвуковой дефектоскопи выбираете между двумя моделями — USM Go+ из линейки Krautkramer и дефектоскопом УСД 46, то следующий абзац поможет вам узнать наиболее важные различия данных моделей.
-
Дефектоскоп компании GE USM Go+ имеет генератор прямоугольных импульсов, с амплитудой 300В, что на 100 больше, чем у УСД 46. Это преимущество дает возможность контролировать поковки и литье, что дефектоскоп УСД 46 не способен сделать.
-
Диапазон ЧПИ намного шире, от 15 до 2000 Гц, когда как у УСД 46— от 40 до 400 Гц. Широкий диапазон ЧПИ дает возможность контролировать с высокой вероятностью выявления дефекта как тонких, так и толстых изделий.
-
Полоса пропускания USM Go+ шире, чем у дефектоскопа УСД 46.
USM Go+ имеет нижнюю границу 0,2 МГц, когда как УСД 46 только 0,5. Это дает возможность подключения специализированных низкочастотных датчиков, которые могут контролировать крупнозернистые стали и поковки, материалы с высоким затуханием ультразвука.
Ультразвуковые дефектоскопы USM 36 и УСД-50: сравнительные характеристики
Если вы хотите купить ультразвуковой дефектоскоп и выбираете между моделями USM 36 и УСД 50, то вам поможет эта статья, в ней сравниваются самые важные характеристики данных дефектоскопов.
-
Ультразвуковой дефектоскоп USM 36 обладает большей мощностью по сравнению с дефектоскопом УСД 50. Амплитуда прямоугольного импульса в 300В в комбинации с максимальным усилением до 110 Дб значительно превосходят аналогичные характеристики у дефектоскопа УСД 50 (200В, усиление 110 Дб). Тем самым возможности контроля увеличиваются за счет увеличения диапазона прозвучивания.
-
Диапазон ЧПИ (15-2000 Гц) дефектоскопа USM 36 превосходит аналогичную характеристику дефектоскопа УСД 50 (40/800). Тем самым можно производить контроль с большой скоростью на малых толщинах c высокой вероятностью выявления дефектов.
Ультразвуковой дефектоскоп Phasor XS 16/16 на фазированных решетках
Простой, удобный и практичный в эксплуатации ультразвуковой дефектоскоп Phasor XS 16/16 отличается высокой производительностью и минимальными расходами, что считается оптимально пригодным для производственной оценки.
Прочный и надежный корпус портативного дефектоскопа Phasor XS 16/16, небольшой вес (менее 4,0 кг) позволяют эксплуатировать прибор на самых сложных участках работы. Показатели влаго- и пылезащиты соответствуют классу IP54. Простое управление настройками дефектоскопа подходит для специалистов, имеющих аттестацию II уровня по ультразвуковому методу контроля и не требует дополнительного обучения. Все необходимые данные легко собираются, анализируются и архивируются.
Основным преимуществом является возможность контролировать поковки из черных и цветных металлов методом фазированных решеток.
Phasor XS — отличная замена ультразвуковому дефектоскопу УСД-60
Дефектоскоп УСД-60 может реализовывать только стандартную дефектоскопию, когда как Phasor XS сочетает в себе возможность использования метода Фазированных решеток с удобством стандартного УЗ канала.
Ультразвуковой дефектоскоп Phasor превосходит УСД-60 по многим параметрам:
-
ЧПИ: 15-2000 Гц (стандартный УЗ канал), 15-7680 Гц (канал на ФР), когда как у УСД 60 он 20…2000 Гц.
-
Генератор импульсов Phasor XS 16/16 гораздо мощнее чем у ультразвукового дефектоскопа УСД 60. Phasor выдает 300В (с шагом 10В) прямоугольного импульса с возможностью усиления до 110 Дб, когда УСД 60 может либо 50 либо 200В без промежуточных значений амплитуды сигнала с усилением до 100 Дб. Данное преимущество позволяет контролировать большие толщины, материалы с высоким затуханием и высоколегированные стали.
Контроль сварных швов: ультразвуковые дефектоскопы
При ультразвуковом контроле сварных соединений применяют методы отраженного излучения и прошедшего излучения по ГОСТ 18353, а также их сочетания, реализуемые способами (вариантами методов), схемами прозвучивания, регламентированными настоящим стандартом.
Основным стандартом является ГОСТ Р 55724 — 2013 Контроль неразрушающий. Сварные соединения. Методы ультразвуковые.
Технология проведения ультразвукового контроля
Технология акустического контроля сварки зависит от типа сварного соединения и от требований, предъявляемых к качеству изделия. Технология проведения акустического контроля можно условно разделить на несколько основных этапов:
1. Контроль сварного соединения внешним осмотром;
2. Выбор метода контроля и типа преобразователя;
3. Определение границ перемещения преобразователя;
4. Подготовка поверхности сварного соединения для контроля;
5. Размещение, включение, проверку работоспособности приборов и оборудования для контроля, их настройкам;
6. Прозвучивание металла сварного шва и зоны термического влияния;
7. Оформление данных, полученных при контроле;
8. Определение качества сварки, исходя из результатов;
9. Оценка качества сварки, исходя из результатов контроля.
Выбор ультразвукового дефектоскопа для контроля сварных соединений
Рассмотрим основные факторы, влияющие на выбор дефектоскопа для контроля сварных швов.
Выбор дефектоскопа для сварных соединений зависит от многих параметров:
Для металлов с крупнозернистой структурой следует выбирать дефектоскопы с высокой амплитудой прямоугольного импульса для обеспечения прохождения УЗ волны через границы зерен. Сигнал с малой амплитудой может сильно исказиться и затухнуть.
Для основного металла сварного соединения более 60мм применяются те же требования, что указаны выше. Данными особенностми генератора обладают дефектоскопы GE линейки Krautkramer: USM Go+, USM 36, USN 60, Phasor XS.
Чем лучше зачищена поверхность объекта контроля, тем меньше она будет влиять на сигнал. Неровная поверхность рассеивает волну, искажая достоверность результатов контроля.
Некачественно удаленное усиления шва препятствует перемещению преобразователя над корнем шва.
Соответственно, в зависимости от поверхности, применяются преобразователи с различными типами протекторов (твердые, мягкие, истираемые). От выбора преобразователя будет зависеть качество получаемых результатов.
У каждого сварного соединения есть своя специфика и сложности контроля. До некоторых дефектов бывает добраться очень сложно, что заставляет усложнить схему контроля. Дефектоскоп для контроля сварных соединений должен обладать возможностью использовать все типы преобразователей и схемы их подключения. Многоканальная система позволяет расширить возможности, вплоть до подключения большого количества преобразователей. USIP 40 является многоканальной системой, как раз решающей большинство из перечисленных выше задач.
Дефекты могут иметь различную форму и размеры, быть протяженными и точечными, одиночными и скоплениями. Стандартный УЗ метод зачастую не может охватить несколько дефектов сразу и не создается полной картины дефектного участка. Методом фазированных решеток можно провести секторное сканирования участка сварного соединения и наблюдать скопления пор, трещин и прочих несплошностей.
Phasor XS как раз способен использовать все возможности фазированных решеток для поиска дефектов. После выявления можно переключить на стандартный УЗ канал и провести контроль уже в месте, где точно расположен дефект и далее по ГОСТу его задокументировать.
Важно: Ультразвуковой дефектоскоп для сварных швов должен соответствовать ГОСТ 23667-85
Спецпредложение от НПФ «АВЭК»
Официальный дистрибьютор GE Sensing & Inspection Technologies, НПФ «АВЭК» предлагает Вам особые условия по приобретению дефектоскопов линейки Krautkramer, а именно:
-
Дилерские цены за счёт прямых поставок от завода-изготовителя в Европе;
-
Весь комплект сертификатов и сопутствующей документации;
-
Гарантийную и послегарантийную техническую и метрологическую поддержку силами собственной сервисной службы и специалистов, прошедших обучение в Германии;
-
Доставку в любой регион России и СНГ.
-
Оперативную отгрузку со склада (приборы в наличии!)

Производитель: GE Inspection Technologies
Компактный ультразвуковой дефектоскоп USM 36.
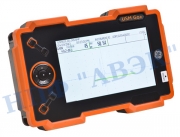
Производитель: GE Inspection Technologies
Компактный ультразвуковой дефектоскоп универсального применения.
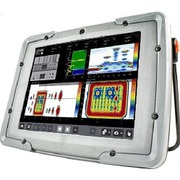
Производитель: GE Inspection Technologies
Дефектоскоп на фазированных решетках Mentor UT сочетает в себе высокую производительность ультразвукового контроля в сочетании с существующими достижениями в программном обеспечении.
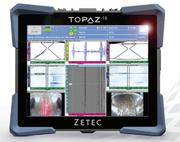
Производитель: ZETEC
TOPAZ 16 — ультразвуковой дефектоскоп с полностью интегрированными 16 активными каналами фазированных решеток.
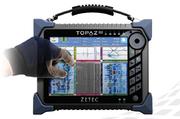
Производитель: ZETEC
TOPAZ 32 — ультразвуковой дефектоскоп с полностью интегрированными 32 активными каналами фазированных решеток.

Производитель: ZETEC
TOPAZ 64 — ультразвуковой дефектоскоп с полностью интегрированными 64 активными каналами фазированных решеток, беспечивающий более быструю и точную проверку.
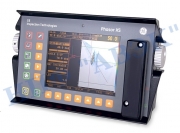
Производитель: GE Inspection Technologies
Ультразвуковой дефектоскоп на фазированных решетках Phasor XS 16/64.
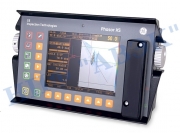
Производитель: GE Inspection Technologies
Дефектоскопы на фазированных решетках Phasor XS 16/16. ООО НПФ «АВЭК» является официальным дистрибьютором GE Sensing & Ispection Technologies.
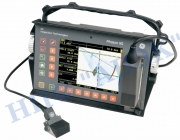
Производитель: GE Inspection Technologies
Ультразвуковой дефектоскоп на фазированных решетках Phasor XS CV/DM.
Неразрушающий контроль: методы, ГОСТ, приборы
В ходе эксплуатации или изготовления различного оборудования, его узлов и деталей, постоянно требуется оценить его состояние. Делать это необходимо без остановки, вывода из эксплуатации, разборки или взятия образцов материалов, поскольку такие действия обходятся очень дорого.


Для этого разработаны и широко применяются методы неразрушающего контроля, или non-destructive test. Обследование конструкции, механизма, детали проводят не прерывая его использования, не вызывая простоев. Периодическое обследование позволяет своевременно обнаружить предпосылки к возникновению неисправности механизма или усталости конструкции и предпринять действия по устранению причин возможных неисправностей или разрушений. Это существенно повышает безопасность эксплуатации и снижает стоимость и продолжительность внеплановых ремонтов.
С помощью неразрушающего контроля в конструкциях, узлах и деталях находят дефекты на ранней стадии их возникновения:
- пористость;
- растрескивание;
- механические или термические напряжения;
- сдвиговые деформации;
- посторонние включения;
- и многие другие.
Классификация методов неразрушающего контроля по ГОСТ 18353- 79
Основные методы неразрушающего контроля основаны на применении различных физических явлений и измерении характеризующих эти явления физических величин. Наиболее широко применяются следующие виды неразрушающего контроля:
- ультразвуковой;
- радиоволновый;
- электрический;
- акустический;
- вихревых токов;
- магнитный;
- тепловой;
- радиационный;
- проникающими веществами;
- оптический.
Общие виды неразрушающего контроля могут включать в себя несколько конкретных методов, различающихся по таким признакам, как:
- способ взаимодействия с контролируемым объектом;
- физические величины, измеряемые в ходе наблюдения;
- способ получения и интерпретации данных.
Правильный выбор способа позволяет предприятию сэкономить средства и обеспечить высокую надежность контролируемого оборудования и конструкций.
Радиоволновой метод неразрушающего контроля
Заключается в облучении исследуемого объекта радиочастотным излучением и измерении параметров прошедшей, отраженной или рассеянной электромагнитной волны.


Радиоволновой метод
Он применим к диэлектрическим, полупроводниковым материалам, а также к тонкостенным металлическим оболочкам и конструкциям, в которых хорошо распространяются радиоволны. Используется для проверки однородности, габаритов и формы изделий из пластика, резины, композитных материалов. Измеряют при этом амплитудные, фазовые или поляризационные характеристики волны. Неразрушающий контроль радиоволновым методом позволяет обнаружить в массе материала неоднородности, посторонние включения, некачественные клеевые и сварные соединения и другие дефекты.
Электрический метод неразрушающего контроля
Группа методов неразрушающего контроля металлов и диэлектриков основана на измерении и интерпретации характеристик электростатического поля, приложенного к контролируемому объекту. Чаще всего измеряют электрический потенциал и емкость.
Для работы с токопроводящими материалами применяют эквипотенциальный способ, к диэлектрическим материалам чаще применяют емкостной. Термоэлектрический способ применим для достаточно точного определения химического состава материала без взятия образцов и применения дорогих масс-спектрографических установок.


Неразрушающий контроль электрический
С использованием электрических методик находят различные скрытые дефекты:
- пустоты и пористость в отливках;
- микротрещины в металлопрокате;
- непровар и другие пороки сварки;
- некачественные лакокрасочные покрытия и клеевые швы.
Акустический, или ультразвуковой контроль
Способ основан на возбуждении в конструкции колебаний определенной частоты, амплитуды, скважности импульсов и анализе отклика конструкции на эти колебания. Интерпретация результатов с помощью специализированных компьютерных программ позволяет воссоздать двумерные сечения исследуемого объекта, не разрушая его. Различают две основных группы методик акустической дефектоскопии:
- Активные — установка осуществляет излучение колебаний и последующий прием отклика от конструкции.
- Пассивные — осуществляется только измерение колебаний и импульсов.


Ультразвуковой неразрушающий контроль
Звуковые колебания с частотой выше 20 килогерц называют ультразвуком. Ультразвук является одним из самых популярных способов акустической дефектоскопии в промышленности и позволяет проверять качество и пространственную конфигурацию практически любых материалов. Популярность ультразвука определяется его преимуществами перед другими методами:
- низкая цена оборудования;
- компактность установок;
- безопасность для персонала;
- высокая чувствительность и пространственное разрешение.
Ультразвуковой способ мало применим к конструкциям, имеющим крупнозернистую структуру или сильно шероховатую поверхность.
Безопасность ультразвука для человека позволяет широко использовать его в медицинской диагностике, включая обследование ребенка в утробе матери и раннее определение его пола.
Вихретоковый метод неразрушающего контроля
Способ основан на наведении в исследуемом объекте вихревых (приповерхностных) токов малой интенсивности и частотой до нескольких мегагерц помещения его в электромагнитное поле, создаваемое вихретоковым преобразователями измерения. Применяется для металлов и других электропроводящих материалов. На основании неоднородностей приповерхностного вихревого поля можно судить о наличии неоднородностей и других дефектов в наружном слое металла (до глубины в несколько миллиметров). Измерения с высокой точностью определяют также дефекты лакокрасочных и защитных покрытий, нанесенных на металлическую деталь. В роли вихретокового преобразователя служить мощная катушка индуктивности, генерирующая высокочастотное электромагнитное поле. Вихревые токи, наводимые этим полем в приповерхностном слое металла, измеряют этой же катушкой (совмещенная схема) или отдельной (разнесенная схема). По пространственной картине распределения интенсивности измеренных токов определяют места неоднородностей, вносящих искажение в поле.


Вихретоковый метод неразрушающего контроля
На применении вихревых токов основано большое количество различных конструкций дефектоскопов, специализирующихся на определении толщины и однородности листов металлопроката и покрытий на конструкциях, непрерывного измерения диаметра проволоки и пруткового проката во время их производства. Применяются вихретоковые устройства, наряду с ультразвуковыми, и для определения состояния лопаток турбин и других ответственных высоконагруженных узлов.
Магнитный метод неразрушающего контроля
Эта группа методик имеет в своей физической основе измерение взаимодействия исследуемого объекта с магнитным полем. Применяются для дефектоскопии ферромагнитных материалов и сплавов. Три основных вида магнитных исследований – это:
- магнитопорошковый;
- феррозондовый;
- магнитографический.


Магнитный метод
Чтобы обнаружить неоднородность в структуре магнитного материала, его намагничивают, а поверхность смазывают специальной суспензией или гелем, содержащим калиброванные металлические частицы. Эти частицы концентрируются вдоль силовых линий магнитного поля, простым и наглядным способом визуализируя его. В местах неоднородностей и дефектов магнитное поле искажено, и линии его будут искривлены. Магнитографические опыты проводились учеными еще в XVIII веке, но для целей дефектоскопии были приспособлены только в XX.
Тепловой метод
Тепловые методики основаны на измерении интенсивности тепловых полей, излучаемых контролируемым устройством или конструкцией. Распределение температур на поверхности и градиент их изменения отражает распределение тепла внутри объекта. В местах дефектов и неоднородностей равномерная тепловая картина будет искажена.


Использование тепловизора для неразрушающего контроля
Исследователи путем расчетов и экспериментов определили типовые изменения в тепловом портрете изделия, характерные для тех или иных дефектов, и в настоящее время распознавание таких особенностей доверяют компьютерам и нейронным сетям. Измерения тепловой картины на поверхности производят как с помощью контактных термометров, так и путем дистанционной пирометрии. С помощью теплового портрета обнаруживают дефекты сварки и пайки, нарушения герметичности сосудов, места концентрации внутренних напряжений и неисправные электронные компоненты. Самое широкое применение тепловой способ находит в электронике и приборостроении.
Радиационный метод неразрушающего контроля
Этот способ чрезвычайно эффективный, он позволяет получать информацию о самых крупных установках и конструкциях (практически без ограничения размера) путем просвечивания их проникающим ионизирующим излучением.


Радиационный метод неразрушающего контроля
Применяется в следующих диапазонах:
- гамма-лучи;
- рентгеновское излучение;
- нейтронное излучение.
Физической основой способа является возрастание плотности потока заряженных частиц в местах скрытых дефектов. На основании сравнения интенсивности прошедшего и отраженного потока делают вывод о глубине расположения неоднородности. Применяется при определении качества сварных швов на крупных изделиях, таких, как корпуса атомных или химических реакторов, турбин, магистральных трубопроводов и их запорной арматуры.
Метод неразрушающего контроля проникающими веществами
Суть способа заключается в том, что во внутренние полости контролируемого устройства или конструкции запускают специально подготовленную жидкость, реже — химически активное или радиоактивное вещество. По его скоплению или следам и определяют место дефекта.
Различают две разновидности:
- капиллярный, для нахождения поверхностных капиллярных трещин, по которым и просачивается вещество – индикатор;
- течеискание — для обнаружения утечек в трубопроводах и емкостях.


Метод неразрушающего контроля проникающими веществами
Поверхность тщательно очищают, далее наносят на нее вещество-индикатор, или пенетрант. После определенной выдержки наносят вещество — проявитель и наблюдают картину дефектов визуально. В случае применения радиоактивных маркеров обнаружение дефектов производят соответствующей рентгенографической аппаратурой. Методика обладает следующими достоинствами:
- высокая чувствительность;
- простота применения;
- наглядность представления.
Он хорошо сочетается с другими методиками и служит им для взаимной проверки.
Оптический метод неразрушающего контроля
Оптический способ дефектоскопии основан на анализе оптических эффектов, связанных с отражением, преломлением и рассеянием световых лучей поверхностью или объемом объекта.


Оптический метод
Внешние оптические методики позволяют определять чистоту и шероховатость поверхностей, особо важную в точном машиностроении. При измерении размеров мелких деталей применяется физическое явление дифракции, шероховатость поверхностей определяется на основе интерференционных измерений.
Внутренние дефекты возможно выявить лишь для прозрачных материалов, и здесь оптическим методикам нет равных по дешевизне и эффективности.
Выгодно отличаются они своей простотой и малой трудоемкостью и при нахождении пороков поверхностей, таких, как трещины, заусенцы и забоины.
Особенности выбора метода неразрушающего контроля
В ряде отраслей промышленности, таких, как :
- атомная;
- химическая;
- аэрокосмическая;
- оборонная;
выбор способов дефектоскопии строго регламентирован государственными стандартами и нормами сертифицирующих организаций, таких, ка МАГАТЭ или Госатомнадзора.
Вне этих отраслей руководитель подразделения качества предприятия выбирает методики дефектоскопии, руководствуясь следующими параметрами:
- физико-химические свойства применяемого материала;
- размеры и прежде всего — толщина конструкции;
- тип контролируемого объекта, соединения или конструкции;
- требования технологического процесса;
- стоимостные параметры того или иного способа дефектоскопии.
Универсального способа определить все дефекты и сразу не существует. При планировании стратегии качества изделия необходимо определить дефекты, наиболее значимые по степени привносимого ими риска неисправности. Далее находится та комбинация средств измерения и методик неразрушающего контроля, которая:
- позволит выявить все критически значимые дефекты с заданной вероятностью;
- минимизирует финансовые издержки трудозатраты;
- окажет минимальное влияние на основной производственный процесс.
Средства неразрушающего контроля применяются сегодня практически на всех производствах — от авиазавода и судоверфи до авторемонтной мастерской и кондитерской фабрики. Контролируют прочность сварных швов и герметичность сосудов высокого давления, качество лакокрасочного покрытия и однородность массы для приготовления зефира в шоколаде. Экономя предприятиям средства на проведение выборочных испытаний на разрушение, применение неразрушающей дефектоскопии сказывается и на цене выпускаемых на рынок продуктов при одновременной гарантии их высокого качества.