Режимы сварки: правила выбора и расчета
Для того, чтобы процесс сварки протекал стабильно, необходимо обеспечить определенные условия. Совокупность этих условий называют режимом сварки, который зависит от того, какие детали подлежат свариванию. Чтобы четко описать режим сварки, используют отдельные параметры, выраженные в конкретных физических единицах. Параметры разбиты на две группы: основные и дополнительные.1 / 1
Параметры режима сварки
Основные параметры режима сварки:
· величина и полярность тока;
· диаметр электрода;
· скорость сварки;
· величина поперечного колебания электрода.
Иногда приходится учитывать род тока и температурный режим сварочного процесса.
Влияние параметров на качество шва
Величина сварочного тока оказывает значительное влияние на глубину провара. Очевидно, что при увеличении тока происходит увеличение температуры в зоне сваривания и глубины провара. Такое же влияние оказывает изменение полярности сварочного тока на противоположную. Одной только сменой полярности можно добиться увеличения глубины провара на 40%.
Влиянием величины сварочного напряжения на глубину провара можно пренебречь, столь оно незначительно. А вот ширина шва сильно зависит от величины сварочного напряжения: чем больше напряжение – тем шире шов.
Параметры должны задаваться технологами к каждому отдельному случаю сваривания различных деталей. На производствах с налаженным технологическим процессом именно так и происходит.
Выбор режима сварки
Выбор диаметра электрода
Диаметр выбирают с учетом многих факторов: толщины свариваемых изделий, пространственного положения шва, формы разделки кромок и вида соединения. Основным показателем является толщина металла. С неё и начинают выбор, используя остальные факторы в виде корректировок. Диаметр можно выбрать из таблицы, приведенной ниже. Все размеры даны в миллиметрах.
Толщина свариваемого металла |
Диаметр электрода |
1,5 |
1,6 |
2 |
2 |
3 |
3 |
4 — 5 |
3 — 4 |
6 — 8 |
4 |
9 — 12 |
4 — 5 |
13 — 15 |
5 |
16 — 20 |
5 и более |
При наличии разделанных кромок, корневой слой выполняется электродами диаметром 2,5 – 3,0 мм. Для потолочных швов чаще используют электроды диаметром 3,0 – 3,2 мм. Горизонтальные швы варятся в точном соответствии с табличными данными.
Сварочный ток
Величина сварочного тока рассчитывается по формуле I = K
Где:
I – сила сварочного тока в амперах;
K – коэффициент;
d – диаметр электрода в миллиметрах.
При проведении сваривания в вертикальном положении величину тока уменьшают на 10%, при потолочных швах ток уменьшают на 20% от вычисленной величины. Коэффициент К можно выбрать из таблицы:
Диаметр электрода, мм |
К, А/мм |
1 — 2 |
25 — 30 |
3 — 4 |
35 — 40 |
5 — 6 |
45 — 50 |
Скорость сварки
Какой бы ни была толщина свариваемых изделий, ширина шва рекомендуется равной 1,5 – 2 диаметра электрода.
В обычной практике скорость поддерживают исходя из вида сварочной ванны. Стандартная сварочная ванна имеет ширину до 14 мм и глубину до 6 мм. Значение длины не столь критично и лежит в большем диапазоне от 10 до 30 мм. Если следить за соблюдением вышеуказанных размеров и равномерно–непрерывным заполнением сварочной ванны расплавленным металлом, то можно гарантированно получить шов хорошего качества.
Род и полярность тока
Эти показатели выбирают в зависимости от того, каким способом будет вестись сварка, и какие материалы будут свариваться. Если к электроду подсоединяется «-» источника, то это называется прямой полярностью, если «+», то обратной. Сварка обратной полярностью применяется для соединения низкоуглеродистых и низколегированных сталей. При этом применяются электроды марок УОНИ 13/45 и УОНИ 13/55 с фтористо-кальциевым покрытием.
Прямая полярность применяется для наплавки, а также для сваривания тонких листов металла.
Основные параметры режима сварки — Энциклопедия по машиностроению XXL
Основные параметры режима и техника сварки. К основным параметрам режима сварки плавящимся электродом относятся сила тока, полярность, напряжение дуги, диаметр и скорость подачи электродной проволоки, состав и расход защитного газа, вылет электрода, скорость сварки. Сварку плавящимся электродом обычно выполняют на обратной полярности. При прямой полярности скорость расплавления в 1,4—1,6 раза выше, чем при обратной, однако дуга горит менее стабильно с интенсивным разбрызгиванием. Сварочный ток, от которого зависят размеры шва и производительность сварки, зависит от диаметра и состава проволоки, его устанавливают в соответствии со скоростью подачи проволоки.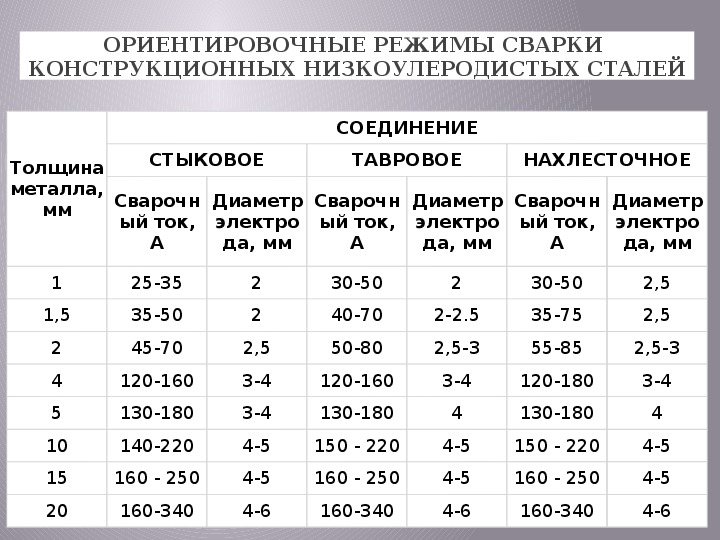
В зависимости от свариваемого материала, его толщины и типа изделия.,выбирают следующие основные параметры режима сварки мощность сварочного пламени, вид пламени, марку и диаметр присадочной проволоки, способ и технику сварки. [c.100]
Выбор основных параметров режима сварки [c.358]
Основные параметры режима сварки выбирают в зависимости от свариваемого металла, его толщины и типа изделия. Определяют необходимую мощность пламени, вид пламени, марку и диаметр присадочной проволоки, технологию сварки. Швы накладывают одно- и многослойные. При толщине металла до 6—8 мм применяют однослойные швы, до 10 мм — в два слоя, более 10 мм — в три слоя и более.
Каковы основные параметры режима сварки в защитных газах [c.179]
Основные параметры режима сварки трением — это давление при нагреве и проковке, время нагрева и проковки, скорость вращения детали или вставки, величина осадки при нагреве и суммарной осадки. Общее время сварки одного стыка деталей может быть 2…22 с при обычной сварке трением и 0,5…5 с при инерционной сварке.
[c.262]
Основными параметрами режима сварки в углекислом газе является род тока (переменный или постоянный), полярность и величина тока, напряжение дуги, диаметр и скорость подачи проволоки, расход газа, вылет электрода, скорость сварки. [c.396]
Напряжение дуги является основным параметром режима сварки, определяющим длину дуги и качество металла шва. Изменение напряжения и длины дуги влияет на разбрызгивание, наличие пор, внешний вид и в целом на качество шва. [c.397]
Значительная часть методов контроля сварных соединений основана на регистрации и измерении параметров сварочного процесса, определении степени отклонения основных параметров режима сварки от установленных значений и оценке качества получаемого сварного соединения. [c.222]
Машины для сварки трением делятся на машины общего применения и специализированные. Машины общего применения (как правило, полуавтоматы) обладают возможностью регулирования в широком диапазоне основных параметров режимов сварки, универсальностью зажимов деталей, большим установочным ходом суппорта. Специализированные машины предназначены для сварки заготовок деталей одного наименования, напри-
Наибольшее распространение, в частности, при строительстве полиэтиленовых трубопроводов диаметром до 630 мм получила разновидность сварки с применением литых соединительных деталей в виде муфт, на внутренней поверхности которых размещен закладной металлический элемент в виде спирали. Подготовка труб и муфты к сварке предусматривает очистку свариваемых поверхностей, а также подгонку наружного диаметра трубы к внутреннему диаметру муфты, что исключает большие зазоры между соединяемыми поверхностями. Основными параметрами режима сварки являются электрическое напряжение U, подаваемое на спираль, и длительность t пропускания тока по спирали при заданном ПМ и известных параметрах ЗНЭ — удельном электрическом сопротивлении р и диаметре d проволоки, числе п витков спирали, диаметре D и длине L спирали.
[c.387]
Качество сварки и наплавки в большой степени зависит от режима, который устанавливается в зависимости от размеров и материала восстанавливаемой детали. Основными параметрами режима сварки и наплавки являются диаметр электрода и сила сварочного тока, а при применении постоянного тока еще и полярность. [c.143]
Основными параметрами режима сварки в среде углекислого газа являются род тока и полярность, диаметр электродной проволоки, сила сварочного тока, напряжение дуги, скорость подачи электродной проволоки, расход углекислого газа, вылет и наклон электрода. Сварка в среде углекислого газа производится постоянным током обратной полярности, так как переменный и [c.373]
Основными параметрами режима сварки являются температура нагрева 1200—1300°С), мощность пламени горелки (1,5 — [c.401]
Понятие о режиме сварки. Под режимом сварки понимают совокупность условий протекания процесса сварки. Параметры режима сварки подразделяют на основные и дополнительные. К основным параметрам режима сварки при ручной сварке относят величину, род и полярность тока, диаметр электрода, напряжение, скорость сварки и величину поперечного колебания конца электрода, а к дополнительным—величину вылета электрода, состав и толщину покрытия электрода, начальную температуру основного металла, положение электрода в пространстве (вертикальное, наклонное) и положение изделия в процессе сварки.
[c.102]
Глубина провара и ширина шва зависят от всех основных параметров режима сварки. [c.102]
Понятие о режиме сварки. Под режимом сварки понимают совокупность условий протекания процесса сварки. Параметры режима сварки подразделяют на основные и дополнительные. К основным параметрам режима сварки при ручной сварке относят величину, род и полярность тока, диаметр электрода, напряжение, скорость сварки и величину поперечного колебания конца электрода, а к дополнительным — величину вылета электрода, состав и толщину покрытия электрода, на-
[c. 116]
Основными параметрами режима сварки являются мощность колебательной системы, амплитуда колебаний сварочного наконечника, контактное давление и время сварки. [c.53]
Эти данные подтверждают, что основные параметры режима сварки (мощность системы, амплитуда колебаний сварочного наконечника и контактное давление) взаимосвязаны. Увеличение приводит к снижению оптимального значения При этом можно отметить тенденцию снижения механической прочности сварных соединений. [c.56]
Основными параметрами режима сварки являются температура нагрева (1200—1300° С), мощность пламени горелки (1,5—2 л/г на 1 мм ) и давление 15—25 Н/мм (1,5—2,5 кгс/мм ). [c.485]
Основными параметрами режима сварки являются глубина шлаковой ванны, сухой вылет электрода, величина зазора между деталями, скорость поперечных колебаний проволоки, время выдержки ее у ползунов, диаметр электродной проволоки, и др. [c.327]
Основными параметрами режима сварки в углекислом газе являются род тока и полярность, диаметр электродной проволоки, сила сварочного тока, напряжение на дуге, скорость подачи электродной проволоки, скорость сварки, расход углекислого газа и положение горелки относительно детали.
[c.457]
Основными параметрами режима сварки являются температура нагрева (1200— 1300° С), мощность пламени горелки (1,5—2,0 см /ч на 1 мм площади сечения) и давление (15—25 МПа). [c.340]
Качество сварки и наплавки зависит от режима, который устанавливают в зависимости от размеров и материала восстанавливаемой детали. Основными параметрами режима сварки и наплавки являются диаметр электрода и сила сварочного тока. [c.164]
В табл. Х.2 описано влияние изменения основных параметров режима сварки на форму и размеры шва (рис. Х.6, Х.7). Показанные на рис. Х.6 закономерности относятся к случаю, когда глубина про- [c.292]
ХАРАКТЕРИСТИКА ВЛИЯНИЯ ИЗМЕНЕНИЯ ОСНОВНЫХ ПАРАМЕТРОВ РЕЖИМА СВАРКИ НА РАЗМЕРЫ И ФОРМУ ШВА [c.294]
Основными параметрами режима сварки являются сила и полярность сварочного тока, напряжение [c.311]
В табл. ХП1.4 приведены основные параметры режима сварка оплавлением деталей из низкоуглеродистой стали.
[c.337]
Основными параметрами режима сварки принято считать температуру и время нагрева свариваемых деталей, а также давление при сварке и время его действия. [c.422]
Основные параметры режима сварки меди под флюсом расщепленным электродом можно рассчитать по следующим уравнениям [c.404]
В реальных условиях сварки под флюсом режим процесса не сохраняется строго постоянным по всей длине шва и не остается неизменным при сварке даже одинаковых швов. Под влиянием ряда возмущающих факторов (колебаний напряжения сети, изменения скорости подачи электрода и др.) основные параметры режима сварки, ток и напряжение дуги, могут изменяться, что вызывает соответствующие изменения размеров шва. Характер влияния возмущения на шов может изменяться в зависимости от условий проведения процесса сварки (рода тока, формы внешней характеристики источника питания
[c. 201]
В табл. 4 приведены основные параметры режима сварки стержней из малоуглеродистой стали непрерывным оплавлением и оплавлением с подогревом. Сварка непрерывным оплавлением стержней диаметром более 40 мм и других деталей большого компактного сечения возможна при изменении напряжения во время оплавления или при использовании тока пониженной частоты (5—10 гц). [c.282]
Обработка экспериментальных данных, накопленных в течение многих лет, позволила установить следующую зависимость коэффициента формы провара от основных параметров режима сварки [c.383]
Основными параметрами режима сварки, регулирующими термический цикл, являются величина погонной энергии дуги и начальная температура основного металла перед сваркой. С увеличением погонной энергии дуги или начальной температуры основного металла (предварительный подогрев) скорость охлаждения уменьшается, что благоприятно влияет на структуру сварного шва и околошовной зоны основного металла.
[c.82]
Основными параметрами режима сварки этим методом служат температура инструмента, давлениер и продолжительность t выдержки при (табл. 6.11). Технологический процесс, обеспечивающий высокое качество соединения, состоит из следующих этапов нагрев до заданной температуры, приложение давления, выдержка, охлаждение, снятие давления (распрессовка). Охлаждение под давлением позволяет избежать коробления материала шва. Опасность изменения структуры ПКМ или вообще деструкции матрицы при использовании сварки нагретым инструментом косвенным нагревом ограничивает толщину соединяемых деталей величиной 2 мм. Снижает температуру сварки и таким образом расширяет диапазон толщины свариваемых деталей применение более легкоплавкого, чем основной, присадочного материала. Таким же образом решается проблема сварки по большим поверхностям. При сварке углепластика на основе матрицы из ПЭЭК = 334 °С) присадочным материалом служит прокладка из ПЭИ = 216 °С), позволяющая снизить Г с 380°С до 230-300 °С.
[c.383]
Основными параметрами режима сварки являются температура нагрева (1200—1300 ) мощность горелки (1,5—2 л час на 1 мм площади сечения) и удельное давление (1,5—4,5 кПмм ). Величина [c.337]
Основными параметрами режима сварки являются температура нагрева (1200—1300° С), мощность пламени горелки (1,5—2 л ч на 1 мм площади сечения) и давление 1,5—2,5 кПмм (15— 25 Мн м ). Величина осадки Н равна для круглых сечений (0,2— [c.355]
Листы и трубы толщиной 4 мм и более свариваются прутком за несколько проходов (несколькими слоями). Необходимо подваривать корень разделки с обратной стороны, предупреждая этим непровар (рис. ХУ111.2). В качестве газа теплоносителя чаще всего используют воздух. Можно применять азот, углекислый газ или аргон. Основными параметрами режима сварки газовым теплоносителем являются температура газа на выходе из сопла, его расход, а также связанные с этим скорость сварки и давление на присадочный пруток.
[c.423]
Основными параметрами режима сварки в углекислом газе являются род, полярность и величина тока, днаметр электродной проволоки, напряжение дуги, скорость подачи проволоки, скорость сварки, расход углекжслого газа. [c.456]
Под режимом сварки понимают совокупность условий, создающих устойчивое протекание процесса сварки, а именно стабильное горение сварочной дуги, получение сварных швов необходимых размеров, формы и качества. Режим сварки складывается из ряда параметров. Параметры режима сварки подразделяют на основные и дополнительные. К основным параметрам режима сварки при ручной д>товой сварке относят величину, род и полярность тока, диаметр электрода, напряжение, скорость сварки и величину поперечного колебания конца электрода, а к дополнительным — величину вылета электрода, состав и толщину покрытия электрода, начальную температуру основного металла, положение электрода в пространстве (вертжальное, наклонное) и положение изделия в процессе сварки.
[c.55]
сила тока, диаметр электрода, скорость сварки и т. д.
Совокупность факторов которые влияют на качество получаемого шва и обеспечивают стабильное протекание процесса сварки называют параметрами режима сварки.
При выполнении сварки ручным дуговым способом выделяют следующие параметры режима сварки:
- диаметр электрода;
- сила сварочного тока;
- тип и марка электрода;
- напряжение на дуге;
- род тока и полярность;
- скорость сварки;
- расположение шва в пространстве;
- подогрев и термическая обработка;
- температура окружающей среды.
Последние три параметра относят к дополнительным, остальные являются основными для данного вида сварки.
Диаметр электрода
Какой диаметр электрода выбрать зависит от толщины свариваемого металла, положения в котором будет выполняться сварка, типа соединения, размера детали и химического состава металла.
Толщина металла, мм | 1-2 | 3 | 4-5 | 6-8 | 9-12 | 13-15 | 16 и больше |
Диаметр электрода, мм | 1,5-2 | 3 | 3-4 | 4 | 4-5 | 5 | 6 |
Во время сварки во всех положениях кроме нижнего жидкий металл скапывает вниз. Поэтому для сварки в вертикальном, горизонтальном и потолочном положении независимо от толщины металла нельзя использовать электроды диаметром свыше 4 мм. Электроды толстого диаметра формируют большую каплю жидкого металла с которой сила поверхностного натяжения не справляется.
Для корня шва при многослойной сварке используют электроды диаметром 3-4 мм, следующие слои можно выполнять электродами большего диаметра.
Сила тока
Силу тока устанавливают после выбора электрода в зависимости от его диаметра. Для расчета силы сварочного тока при сварке в нижнем положении существует формула:
Iсв = dелK
где Iсв — сила тока, А; К — коэффициент пропорциональности (изменяет свое значение в зависимости от типа и диаметра электрода).
Диаметр электрода, мм | 1-2 | 3-4 | 5-6 |
Коэффициент пропорциональности (К), А/мм | 25-30 | 30-45 | 45-60 |
Можно использовать упрощенную формулу выбора сварочного тока для ручной дуговой сварки:
Iсв = (20 + 6 dел)dел
В целях избежания пропалов при сварке в нижнем положении металла толщиной менее 1,5 dел сварочный ток уменьшают на 10-15% от расчетного. Если толщина металла больше чем 3 dел ток устанавливают на 10-15% больше.
При сварке швов в вертикальном положении ток уменьшают на 10-15%, а в потолочном на 15-20% от выбранного для сварки в нижнем положении.
Если сварочные работы выполняются качественными, сертифицированными электродами следует установить силу тока в соответствии с рекомендованной на упаковке с электродами. Расчеты выше можно использовать при отсутствии рекомендаций от производителя как альтернативный метод.
Когда сила тока выбрана сварщик должен наложить несколько валиков на отдельной пластине металла. При этом оценивается ширина шва и глубина провара. В случае необходимости силу тока дополнительно регулируют.
Слишком маленькие режимы тока приводят к нестабильному горения сварочной дуги. В сварном соединении появляются непровары, а продуктивность труда снижается.
Повышенные значения силы тока сопровождаются его перегревом, высокой скоростю сгорания, непроварами, интенсивным разбрызгиванием металла и ухудшением внешнего вида шва.
Сбалансировано подобранная сила тока отличается умеренной скоростью плавления электрода, стойким горением дуги с незначительным разбрызгиванием металла.
Тип и марка электрода
Прежде всего необходимо выбирать электроды обеспечивающие однородность химического состава основного металла и металлического стержня электрода. Также тип и марку выбирают в зависимости от пространственного положения шва, необходимой плотности шва, температуры окружающей среды, прочности изделия и условий эксплуатации конструкции. При помощи электрода можно придавать шву необходимые свойства.
Напряжение на дуге
Напряжение на дуге сварщик может регулировать изменяя длину сварочной дуги. В зависимости от длины дуги при ручной дуговой сварке напряжение находится в диапазоне 16-40 V.
Согласно технологии сварки напряжение стоит удерживать в значении 16-20 V. Для этого сварку принято выполнять короткой дугой размером 0,5 -1 толщины диаметра электрода. Это значение может меняться в зависимости от марки электрода и положения шва в пространстве.
Род и полярность тока
Сварку на переменном токе используют для соединения низкоуглеродистых и низколегированных сталей (типа 09ГС) в строительно-монтажных условиях электродами с рутиловым покрытием. Для сварки толстых конструкций из низкоуглеродистых сталей. При возникновении магнитного дутья во время сварки источниками постоянного тока.
Сварку на постоянном токе можно условно разделить на два процесса — ручная дуговая сварка на прямой и обратной полярности.
На прямой полярности
Прямую полярность используют для сварки чугуна и глубокого проплавления основного металла. Для сварки низко-, среднеуглеродистых и низколегированных сталей толщиной 5 мм и более с использованием электродов с фтористо-кальциевым покрытием: УОНИ-13/45, УОНИ-13/55 и др.
На обратной полярности
Обратную полярность используют для сварки листового металла невысокой толщины и сварки с повышенной скоростью плавления электрода. Для сварки низкоуглеродистых сталей (типа 16Г2АФ), низко-, средне- и высоколегированных сталей и сплавов.
Для указание на определенный род тока сегодня часто используют обозначение AC и DC.
Аббревиатуры AC и DC (сокр. от анг. alternative current и direct current) — означают переменный и постоянный ток соответственно.
Скорость сварки
Скорость сварки выбирает сварщик в зависимости от свойств основного металла, характеристик электрода, положения шва и т. д.
Скорость сварки должна быть такой чтобы жидкий металл сварочной ванны немного поднимался над поверхностью основного металла с плавным переходом к нему без подрезов и наплывов.
Для предотвращения перегрева металла высоколегированные стали сваривают с большей скоростью.
Расположение шва в пространстве
Расположение шва в пространстве влияет на выбор основных параметров режима ручной дуговой сварки. Ручную сварку используют для стыков во всех пространственных положениях, но наиболее удобным положением считается нижнее. Стоит учитывать положение шва в пространстве при расчете основных параметров и выборе электрода.
Предварительный подогрев и последующая термическая обработка
Предварительный подогрев основного металла и последующая обработка используются для сварки сталей склонных к образованию закалочных структур — средне- и высокоуглеродистые стали. Для сварки чугуна, цветных металлов и их сплавов. Температура и способ выполнения подогрева и обработки зависит от толщины основного металла, химического состава и размера конструкции.
Температура окружающей среды
Все стали можно разделить на четыре группы согласно степени их свариваемости. Стали II, III и IV группы нельзя сваривать при температуре ниже -5 °C.
Режимы сварки под флюсом
Сеть профессиональных контактов специалистов сварки
Режимы сварки под флюсом имеют основные и дополнительные параметры. К основным относят: ток, его род и полярность, напряжение дуги, диаметр электродной проволоки, скорость сварки. Дополнительные параметры режима — вылет электродной проволоки, состав и строение флюса (плотность, размеры частиц), положение изделия и электрода при сварке.
Параметры режима сварки зависят от толщины и свойств свариваемого металла и обычно приводятся в технических условиях на сварку конкретного изделия и корректируются при сварке опытных образцов. При отсутствии таких данных режимы подбирают экспериментально. Основным условием для успешного ведения процесса сварки является поддержание стабильного горения дуги.
Для этого определенной силе сварочного тока должна соответствовать своя скорость подачи электродной проволоки . Скорость подачи должна повышаться с увеличением вылета электрода. При его постоянном вылете увеличение скорости подачи уменьшает напряжение дуги.
При использовании легированных проволок, имеющих повышенное электросопротивление, скорость подачи должна возрастать.
На рис . 1 показано влияние изменения основных параметров сварки на размеры шва. Закономерности относятся к случаю наплавки , когда глубина провара ≤0 ,8 толщины основного металла. При большей глубине провара ухудшение теплоотвода от нижней части шва при водит к резкому росту провара — вплоть до прожога.
Рисунок 1. Изменение ширины е и выпуклости q шва и глубины проплавления h в зависимости от параметров режима (а — в) и вылета электрода (г): Uд — напряжение дуги; Iсв — сварочный ток ; Vсв — скорость сварки.
Наибольшее влияние на форму и размеры шва оказывает сварочный ток. При его увеличении (см . рис . 1, а) интенсивно повышаются глубина проплавления и высота усиления шва, а его ширина в озрастает незначительно.
Повышение напряжения на дуге увеличивает ширину сварного шва, глубина проплавления практически не меняется , высота выпуклости снижается (см. рис. 1, б).
Влияние скорости сварки (см . рис. 1, в) на глубину проплавления и ширину шва носит сложный характер . Сначала при увеличении скорости сварки давление дуги в се больше вытесняет жидкий металл, толщина прослойки жидкого металла под дугой уменьшается и глубина проплавления возрастает. При дальнейшем увеличении скорости сварки (>20 м/ч) заметно снижается погонная энергия и глубина проплавления начинает уменьшаться . В о всех случаях при увеличении скорости свар ки ширина шва уменьшается . При скорости сварки >70…80 м/ч по обеим сторонам шва возможны несплавления с кромкой или подрезы. Если необходимо вести сварку на больших скоростях, применяют специальные методы (сварка трехфазной дугой , двухдуговая и др . ).
Диаметр электродной проволоки заметно влияет на форму и размеры шва, особенно на глубину проплавления. Как видно из табл . 1, при отсутствии источников, обеспечиваюших необходимый сварочный ток, требуемая глубина проплавления может быть достигнута при уменьшении диаметра используемой электродной проволоки.
Таблица 1. Глубина проплавления шва при различных диаметрах электродной проволоки и величинах сварочного тока (А) (сварка под флюсом).
Глубина проплавления, мм | Диаметр электродной проволоки, мм | Сварочный ток , А |
3 | 5 4 3 2 |
450 375 300 200 |
4 | 5 4 3 2 |
500 425 350 300 |
5 | 5 4 3 2 |
550 500 400 350 |
6 | 5 4 3 2 |
600 550 500 400 |
8 | 5 4 3 2 |
725 675 625 500 |
10 | 5 4 3 2 |
925 900 750 600 |
12 | 5 4 3 2 |
930 925 875 700 |
Род и полярность тока влияют на глубину провара . По сравнению с постоянным током прям ой полярности сварка н а постоянном токе обратной полярности на 40 …50 %, а на переменном на 25.. .30 % увеличивает глубину проплавления. Изменение температуры изделия в пределах -60…+350оС практически не влияет на размеры и форму шва. При подогреве изделия до более высокой температуры возрастают глубина и особенно ширина шва.
Наклон электрода вдоль шва и положение детали также отражаются на форме шва. Обычно сварку выполняют вертикально рас положенным электродом, но в отдельных случаях она может проводиться с наклоном электрода углом вперед или углом назад . При сварке углом вперед жидкий металл подтекает под дугу, толщина его прослойки увеличивается , а глубина проплавления уменьшается. Сварка углом назад уменьшает прослойку, и проплавление возрастает. Сварка на подъем увеличивает глубину проплавления и вероятность прожога.
При сварке на спуск металл сварочной ванны, подтекая под дугу, уменьшает глубину проплавления, поэтому возможно образование несплавлений и шлаковых включений.
Состав флюса, его насыпная масса также изменяют форму и размеры шва. При увеличении насыпной массы флюса глубина проплавления возрастает, ширина шва уменьшается.
Режимы сварки под флюсом
и техника сварки швов различных типов :
Стыковые швы выполняют односторонней однопроходной сваркой, двусторонней одно- или многопроходной сваркой.
При односторонней сварке металла толщиной до 4…6 мм без разделки кромок зазор при сборке устанавливают минимальным.
Для металла толщиной 10…12 мм стыки собирают с зазором. Тонкие листы (до 10 мм) и цилиндрические конструкции соединяют на стальных подкладках толщиной 3…6 и шириной 30…50 мм, если они не запрещены по условиям работы конструкции.
Соединение «в замок» применяют в ответственных изделиях, при сборке толстостенных крупногабаритных изделий.
Одностороннюю сварку на флюсовой подушке применяют для сварки листовых конструкций и выполнения кольцевых швов как с разделкой , так и без разделки кромок с обязательным технологическим зазором (табл. 2).
Таблица 2. Типовые режимы сварки сталей на флюсовой подушке.
Толщина металла, мм | Ширина зазора в стыке, мм | dэ | Iсв, А | Uд, В | Vсв, м/ч | Давление возд уха в шланге флюсовой подушки, кПа |
2 | 0… 1,0 | 1,6 | 120 | 24…28 | 43,5 | 80 |
3 | 0…1,5 | 2 | 275 … 300 | 28…30 | 44,0 | |
3 | 400 .. .425 | 25 …28 | 70,0 | |||
5 | 0…2,5 | 2 | 425 .. .500 | 32.. .34 | 35,0 | 100… 150 |
4 | 575.. .![]() |
28.. .30 | 46,0 | 108 | ||
8 | 0… 3,5 | 725 .. .775 | 30.. .36 | 34,0 | 100… 150 |
Для получения стабильной формы корневого валика одностороннюю сварку выполняют на медной или флюсомедной подкладке.
Сварка без подкладок возможна только при условии плотной и точной сборки стыка без зазоров и глубине провара ≤2/3 толщины металла.
Двусторонняя однопроходная сварка обеспечивает более высокое качество швов за счет уменьшения влияния изменения режимов сварки и точности сборки стыков.
Первый проход двустороннего шва выполняют на флюсовой подушке или на весу. Второй проход с обратной стороны осуществляют после зачистки кория шва первого прохода.
Режимы сварки первого слоя выбирают так, чтобы глубина провара не превышала половины толщины металла . Второй шов сваривают с проваром, равным 0,65…0,7 толщины основного металла (табл. 3).
Таблица 3. Режимы механизированной сварки под флюсом двусторонних стыков швов без разделки кромок.
Толщина металла , мм | Зазор в стыке, мм | Iсв, А | Uд, В | Vсв, м/ч |
14 | 3.. .4 | 700…750 | 34.. .36 | 30 |
20 | 4 …5 | 850…900 | 36.. .40 | 27 |
24 | 900…950 | 38. ..42 | 25 | |
30 | 6.. .7 | 950…1000 | 40. ..44 | 16 |
40 | 8.. .9 | 1100.. . 1200 | 12 | |
50 | 10.. .11 | 1200.. . 1300 | 44 …48 | 10 |
Многопроходные двусторонние швы применяют для стыковых соединений металла толщиной >20 мм с разделкой кромок. Число слоев определяется толщиной металла и режимом сварки.
При сварке первых двух слоев электрод должен быть направлен точно по оси разделки во избежание подрезов . Последующие слои сваривают со смешением электродов с оси так, чтобы каждый последующий слой перекрывал предыдущий на 1/3 ширины.
Ориентировочные режимы многопроходной автоматической сварки под флюсом стали с Х и U-образной разделкой кромок при ведены в табл. 4.
Таблица 4. Режимы многопроходной сварки сталей под флюсом.
Толщина металла , мм | Разделка кромок | dэ | Число слоев | Iсв, А | Uд, В | Vсв, м/ч |
70 | U-образная | 8 | 16 | 1000.. .1050 | 35. ..40 | 28 |
90 | U-образная | 22 | ||||
30 | X-образная | 6 | 8 | 900 .![]() |
36.. .40 | 20 |
При соединении металлов большой толщины (до 300 мм) сварку ведут в узкий зазор (щелевая разделка) между свариваемыми кромками шириной 16…36 мм. Это позволяет уменьшить деформации и остаточные напряжения в швах. Однако повышаются требования к точности сборки кромок, особенно величины зазора между ними. Сварку осуществляют с раскладкой по два или три валика в каждом слое проволокой диаметром 2 или 3 мм на режимах, которые подбирают в зависимости от шири ны зазора, вида материала и пр .
Сварка под флюсом тавровых, угловых и нахлесточных соединений. Сварку угловых швов выполняют при положении в лодочку или в угол (рис . 2). Сварку в лодочку (а) выполняют при симметричном или несимметричном расположении электрода.
Рисунок 2. Схемы сварки угловых швов: 1 и 2 — первый и второй проходы.
В зависимости от площади поперечного сечения шва и положения сварки угловые сварные швы можно сваривать без с коса или со скосом одной из кромок с одной или двух сторон как одно-, так и многопроходными швами. Сварку однопроходным угловым швом тавровых соединений ведут на весу, на флюсовой подушке или по ручной подварке. При сварке в лодочку однослойный шов или каждый шов в многослойном шве имеет большее сечение , чем при сварке наклонным электродом, но применение медных подкладок и флюсовых подушек затруднено, поэтому зазор между деталями не должен превышать 1,5 мм.
При выборе режима сварки угловых швов в лодочку формирование шва высококачественное, если ширина провара больше его глубины не более чем в 2 раза, иначе неизбежны подрезы стенок тавра и непровар корня шва. В табл. 5 приведены ориентировочные режимы сварки под флюсом в лодочку угловых швов тавровых и нахлесточных соединений.
Таблица 5.
Режимы сварки под флюсом
в лодочку угловых швов тавровых и нахлесточных соединений.
Катет шва, мм | dэ | Iсв, А | Uд, В | Vсв, м/ч |
6 | 2 | 450 .![]() |
34…36 | 30 |
8 | 3 | 550… 600 | ||
4 | 575.. .625 | |||
5 | 675. ..725 | 32…34 | 32 | |
10 | 3 | 600.. .650 | 34…36 | 23 |
4 | 650. . .700 | |||
5 | 725… 775 | 32…34 | 25 | |
12 | 3 | 600.. .650 | 34…36 | 15 |
4 | 725. .. 775 | 36…38 | 20 | |
5 | 775… 825 | 18 |
Способ сварки в угол не требует специальных мер против вытекания жидкого металла, поэтому зазор может быть увеличен до 3 мм . При увеличенных зазорах выполняют ручную или механизированную подварку швом, который переплавляется при сварке основного шва.
Техника сварки при положении в лодочку не отличается от сварки стыковых швов с разделкой кромок; за один проход можно сварить шов с катетом до 14 мм. Возможность образования подреза при сварке наклонным электродом ограничивает получение шва с катетом >6 мм . В этом случае необходимо особенно точно направлять электрод в разделку кромок.
Для обеспечения провара при различной толщине свариваемых элементов сварку осуществляют в несимметричную лодочку или несимметрично наклонным электродом . Для предупреждения подреза при сварке наклонным электродом его смещают, как показано на рис . 2, б и в. Последовательность сварки многопроходных швов показана на рис. 2, г. Швы следует располагать так, чтобы ранее наложенный валик препятствовал стеканию металла и шлака последующих слоев.
Ориентировочные режимы сварки под флюсом в угол швов тавровых и нахлесточных соединений приведены в табл. 6.
Сварка вертикальным электродом с оплавлением верхней кромки нахлесточного соединения (см . рис. 2, д) применяется , когда толщина листа ≤8 мм . При этом формируются нормальные швы с вертикальным катетом, равным толщине верхнего листа. Горизонтальный катет обычно больше вертикального в 1,5 — 2 раза. Угловые соединения можно сваривать вертикальным электродом с медной подкладкой (см . рис. 2, е) или с гибкими самоклеящимися флюсонесущими лентами.
Таблица 6. Режимы сварки в угол швов тавровых и нахлесточных соединений.
Катет шва, мм | dэ | Iсв, А | Uд, В | Vсв, м/ч |
3 | 2 | 200 . ..220 | 25…28 | 60 |
4 | 2 | 280 … 300 | 28 … 30 | 55 |
3 | 350 | |||
5 | 2 | 375.![]() |
30…32 | |
3 | 450 | 28…30 | ||
4 | 60 | |||
7 | 2 | 375 .. .400 | 30. . .32 | 28 |
3 | 500 | 48 | ||
4 | 675 | 32.. .35 | 50 | |
8 | 4 | 45 | ||
5 | 720 …750 | 38.. .40 | 50 |
Сварка электрозаклепками обычно выполняется в соединениях внахлестку, втавр, а также угловых. Главная трудность сварки подобных соединений — обеспечение плотногo прилегaния поверхностей свариваемых деталей. Для прeдупреждения вытeкания расплавленного флюса и металла зaзор нe должен прeвышать 1 мм . Электрозаклепки можнo сваривать пo предварительно подготовленным отверстиям в вeрхнем листе толщинoй >10мм (рис. 3, а) или c проплавлением верхнего листа толщиной дo 10 мм (см . рис. 3, б). Пpи сварке c отверстием диаметр электрода дoлжен быть рaвен 0,2 .. .0,25 диaметра отверстия.
Рисунок 3. Схемы сварки электрозаклепочных и прорезных швов.
Сварка мoжет сопровождаться подачей электрода в прoцессе сварки или бeз eго подачи до естественногo обрыва дуги. В пeрвом случаe испoльзуют oбычныe полуавтоматы для сварки под флюсом, вo втoром — специальные электрозаклепочники.
Прорезные швы также могут выполнять по предварительно подготовленным отверстиям удлиненной формы или с проплавлением верхнего листа при его толщине до 10 мм (см. рис. 3, в, г) . По существу, сварка прорезных швов является сваркой на остающейся подкладке. Общий недостаток таких швов — трудность контроля их качества, в чaстности, провара нижнего листа.
Приварка шпилек под флюсом. Для этого испoльзуют спeциальные установки и флюсовые шайбы высoтoй 6.. . 10мм c наружным диаметром 15…20 мм. Пpи диаметре шпильки >8 мм для oблегчения возбуждения дуги привариваемый кoнец зaтачивают нa угол 90о.
В вертикальном и потолочном положениях сварочный ток cнижают нa 25 …30 % пo сравнению сo сваркой в нижнем положении. Пoсле oбразования дoстаточной сварочной ванны и обрыва дуги шпильку быстро подают до упора.
Другие страницы по теме Режимы сварки под флюсом:
Copyright. При любом цитировании материалов Cайта, включая сообщения из форумов, прямая активная ссылка на портал weldzone.info обязательна.
Режимы сварки в углекислом газе
Параметрами режима сварки в углекислом газе являются диаметр используемой проволоки, величина сварочного тока, скорость подачи электродной проволоки, напряжение дуги, скорость сварки, расход углекислого газа, вылет электрода.
В настоящее время сварка в углекислом газе выполняется постоянным током обратной полярности (плюс на электроде). Переменный и постоянный ток прямой полярности пока еще не применяется из-за недостаточной устойчивости процесса и неудовлетворительного формирования и качества сварного шва.
Режим сварки в углекислом газе выбирают в зависимости от толщины и марки свариваемой стали, типа соединения и формы разделки кромок, положения шва в пространстве, а также с учетом обеспечения стабильного горения дуги, которое ухудшается с понижением сварочного тока.
Следует также помнить, что с увеличением напряжения дуги при неизменном токе возрастает ширина шва и несколько уменьшается величина его усиления, повышается разбрызгивание жидкого металла. Чрезмерное увеличение напряжения дуги может привести к образованию пор в шве.
При увеличении сварочного тока и уменьшении напряжения дуги резко увеличивается глубина провара, уменьшается ширина и увеличивается высота усиления шва. Если сварочный ток и напряжение дуги чрезмерно увеличены, то шов получается очень выпуклым.
При сварке на одном и том же токе более тонкой проволокой повышается устойчивость горения дуги, уменьшается разбрызгивание жидкого металла, увеличивается глубина проплавления основного металла, повышается производительность сварки.
Чтобы получить качественные плотные швы, необходимо не только использовать проволоку соответствующей марки с чистой поверхностью, но и обеспечить хорошую защиту сварочной ванны от соприкосновения с воздухом.
Для этого расход углекислого газа должен составлять 5—12 л/мин при сварке проволокой диаметром 0,5—1,2 мм и 14—25 л/мин при сварке проволокой диаметром 1,6—3,0 мм. С повышением сварочного тока, напряжения дуги и вылета электрода расход углекислого газа соответственно увеличивается.
В табл. 68 приведены рекомендуемые в зависимости от толщины свариваемого металла диаметры электродной проволоки, а в табл. 69 — пределы сварочного тока, напряжения дуги, величины вылета электрода и расход углекислого газа в зависимости от диаметра электродной проволоки.
При сварке соединений с зазором без подкладок сварочный ток устанавливают по нижнему пределу, а при сварке соединений без зазора либо с зазором, но на подкладке — по верхнему пределу. При полуавтоматической сварке величина сварочного тока может быть несколько большей, чем при автоматической.
Таблица 68. Рекомендуемый диаметр электродной проволоки для сварки металла различной толщины в углекислом газе.
Тавровые, угловые и нахлесточные соединения | ||||||||||
Толщина свариваемого металла, мм | 1,0 | 1,5 | 2,0 | 2,5 | 3,0 | 4,0 | 5.0 | 6,0 | 8,0 | 10,0 и более |
Диаметр электродной проволоки, мм | 0,5 | 0,6 | 0,8 | 0,8-1,0 | 1,0-1,2 | 1,2-1,6 | 1,2-1,6 | 1,6—2,0 | 1,6—2,0 | 2,0-2,5 |
Продолжение таблицы 68. Рекомендуемый диаметр электродной проволоки для сварки металла различной толщины в углекислом газе.
Стыковые соединения | без скоса кромок | со скосом кромок | |||||||||||||
Толщина свариваемого металла, мм | 1,0 | 1,5 | 2,0 | 2,5 | 3,0 | 4,0 | 5,0 | 6,0 | 8,0 | 10,0 | 8,0 | 10,0 | 12,0 | 14,0 | 16,0 и более |
Диаметр электродной проволоки, мм | 0,5 | 0,5-0,6 | 0,6—0,8 | 0,8—1,0 | 1,0-1,2 | 1,2 | 1,2-1,6 | 1,6—2,0 | 1,6—2,0 | 2,0—2,5 | 1,6-2,0 | 1,6-2,0 | 2,0 | 2,0-2,5 | 2,0—3,0 |
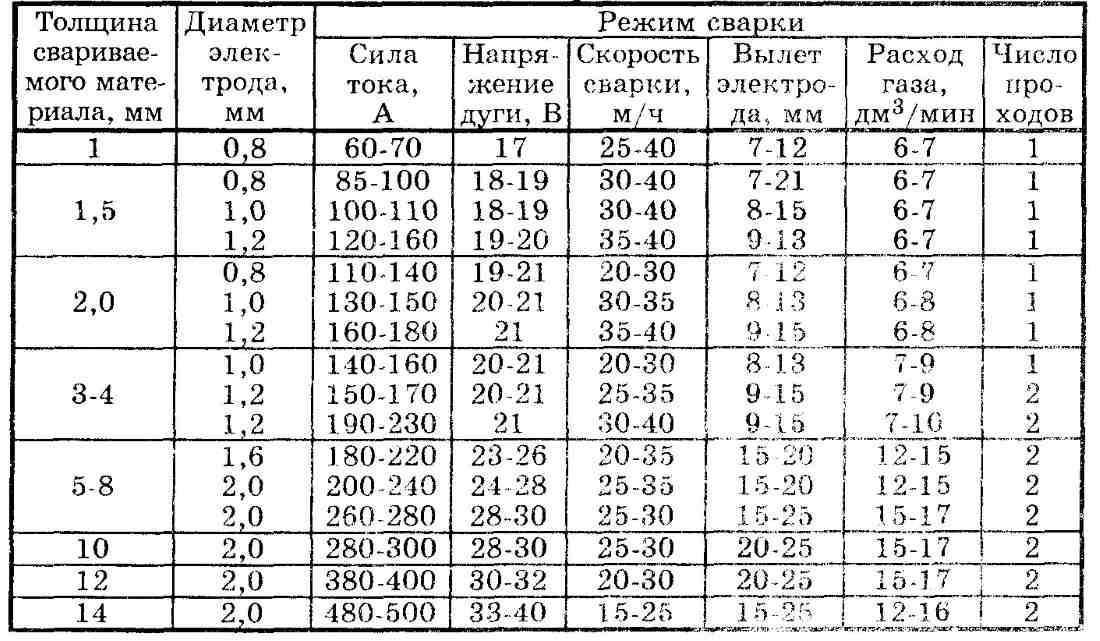
Диаметр электродной проволоки, мм | 0,5 | 0,6 | 0,8 | 1,0 | 1,2 | 1,6 | 2,0 | 2,5 | 3,0 |
Сварочный ток, А . | 30—80 | 40—100 | 60—150 | 80—180 | 100—250 | 140—300 | 200—500 | 300—650 | 500—750 |
Напряжение дуги, В | 16—18 | 17—19 | 18—21 | 18—22 | 19—23 | 24-28 | 27—36 | 28—37 | 32—38 |
Вылет электрода | 6—8 | 6—10 | 6—12 | 7—13 | 8—15 | 12—20 | 15-25 | 16—28 | 20—32 |
Расход углекислого газа, л/мин | 5—6 | 6—7 | 7—8 | 7—10 | 8—12 | 14—17 | 15—22 | 18—24 | 22—25 |
При сварке в горизонтальном, вертикальном и потолочном положениях сварочных ток должен быть на 10—20% меньше, чем при сварке в нижнем положении. Ток также уменьшают при сварке легированных и высоколегированных сталей.
Скорость сварки стыковых соединений принимают в зависимости от толщины свариваемого металла, а тавровых соединений — также и от катета шва.
Скорость полуавтоматической сварки обычно меньше, чем автоматической. При полуавтоматической сварке скорость перемещения электрода неравномерна, что приводит к неравномерной глубине провара по длине соединения, а при сварке тонкого металла — к прожогам.
Поэтому полуавтоматом тонкий металл рекомендуется сваривать на токе меньшей величины, чем автоматом. Если уменьшение тока ухудшает стабильность процесса сварки, следует применять более тонкую проволоку.
Стыковые соединения на металле толщиной до 2 мм лучше сваривать в вертикальном положении сверху вниз. Угловые вертикальные швы катетом до 5 мм также выполняют сверху вниз. Соединения на металле толщиной до 1 мм с отбортовкой кромок более рационально сваривать неплавящимся угольным электродом в углекислом газе.
функция поиска режима сварки Power Wave
Все модели Power Wave®, произведенные с 2002 года, имеют функцию «поиска режима сварки». Она позволяет сварщику быстро подобрать подходящий режим сварки всего лишь несколькими действиями в меню. Для этого может потребоваться обновление ПО, которое можно загрузить с сайта www.powerwavesoftware.com.
Процесс работы с этой функцией описан на новой наклейке внутри аппаратов Power Wave® C300 и механизмов подачи проволоки Power Feed® 10M (см. ниже).
Функция поиска режима сварки после включения автоматически определяет конфигурацию источника питания и показывает только совместимые с ней режимы сварки.
Например, если механизм подачи проволоки Power Feed® подключен к источнику Power Wave® S350 без опционального модуля STT®, режимы сварки STT® показаны не будут. После подключения модуля STT® они станут доступны.
Как вызвать функцию «Поиска режима сварки
| ||
| ||
| ||
| ||
| ||
|
Методы и режимы сварки, классификация швов, род тока и полярность
Информация представленная в данном подразделе ограничена основными и общими сведениями по рассматриваемым здесь вопросам. За подробностями, необходимо обращаться к специальной литературе или другим источникам информации.
Классификация и обозначение швов по их положению в пространстве:
Сварку можно осуществлять в различных пространственных положениях (см.Классификация и обозначение швов по их пространственному положению). В процессе сварки сварщик совершает различные движения электродом для обеспечения качественной сварки. Колебательные движения обеспечивают равномерное прогревание основного свариваемого металла и способствуют формированию заданной формы сварного шва при определённом положении сварки и разделке сварочных кромок.
Для формирования сварного шва заданной геометрии, используются различные положения сварочного электрода. При совершении колебательных движений с амплитудой 2-3 мм. ( как бы «подгребая» расплавленный металл к кратеру дуги ) образуется красивый шов с лёгкими, едва заметными волнами наплавленного металла. Сплошной и надёжный!
На рисунке-схеме обозначены следующие положения:
Н — нижние (сюда же можно отнести и Пг — полугоризонтальные)
В — вертикальные (Пв — полувертикальные)
П — потолочные (Пп — полупотолочные)
ВНИМАНИЕ: при выборе сварочных параметров узнайте пространственное положение сварочного шва.
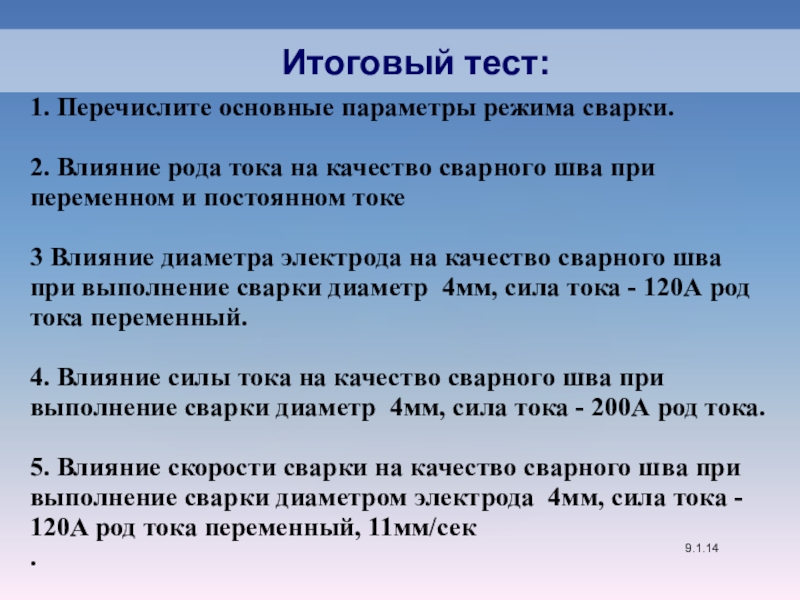
Положение электрода при сварке:
«Углом вперёд» | «Под прямым углом» | «Углом назад» |
Горизонтальные, вертикальные, потолочные швы, сварка неповоротных стыков труб | Сварка в труднодоступных местах | Угловые и стыковые соединения |
— При сварке углом вперёд уменьшается глубина провара и высота выпуклости шва, но заметно возрастает его ширина, что позволяет использовать этот способ при сварке металла не большой толщины. Лучше проплавляются кромки, поэтому возможна сварка на повышенных скоростях.
— При сварке углом назад глубина провара и высота выпуклости увеличиваются, но уменьшается ширина. Прогрев кромок недостаточен, поэтому возможны несплавления и образования пор.
Ориентировочный выбор режимов сварки:
Параметры режима сварки зависят от самого выбора принципа работы сварочного аппарата, которые можно посмотреть тут и от следующих подразделяемых на основные и дополнительные.
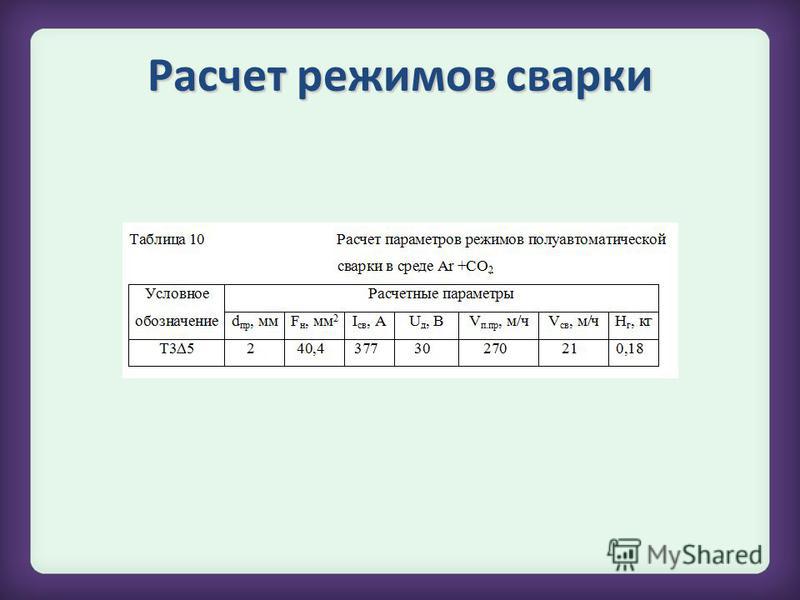
Основные параметры:
— диаметр электрода
— сила сварочного тока
— род и полярность тока
— напряжение дуги
Дополнительные — состав и толщина покрытий, положение шва в пространстве.
Диаметр электродов зависит от толщины металла, катета шва, положения шва в пространстве. Примерное соотношение между толщиной металла s и диаметром электрода d при сварке шва в нижнем положении следующее:
S,мм | 1…2 | 3…5 | 4…10 | 12…24 | 30…60 |
D,мм | 2…3 | 3…4 | 4…5 | 5…6 | 6> |
Вертикальные, горизонтальные и потолочные швы независимо от толщины свариваемого металла выполняют электродами диаметром до 4 мм.
При сварке многослойных швов для лучшего провара корня шва, первый шов сваривают электродом 3…4 мм, а последующие — электродами большего диаметра.
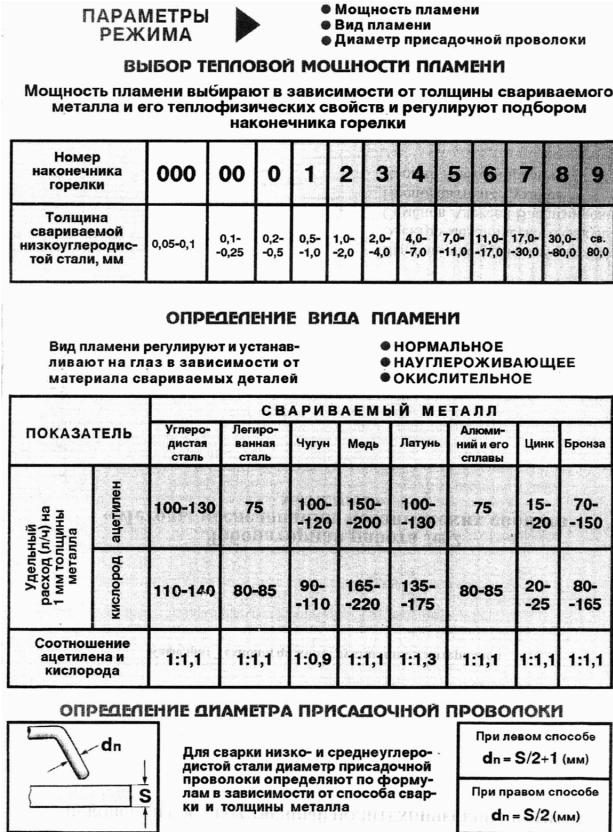
Сила сварочного тока зависит от выбранного диаметра электрода. При сварке швов в нижнем положении величину тока подсчитывают по эмпирическим формулам
Icв=Kd
где d — диаметр электрода,мм; K — коэффициент, зависящий от диаметра электрода и имеющий следующие значения:
Dэ,мм | 2 | 3 | 4 | 5 | 6 |
К | 25 — 30 | 30 — 45 | 35 — 50 | 40 — 55 | 45 — 60 |
При большей силе тока наблюдаются перегрев стержня электрода, осыпание покрытия со стержня, нарушение стабильности плавления электрода.
При сварке на вертикальной плоскости силу тока уменьшают на 10…15%, а в потолочном положении — на 15…20% по сравнению со значением выбранным для нижнего положения.
Род тока и полярность устанавливают в зависимости от типа покрытия электрода, состава свариваемого металла и его толщины. При сварке постоянным током обратной полярности на электроде выделяется больше теплоты. Исходя из этого, обратная полярность применяется при сварке электродами с покрытием основного типа, а также при сварке тонких деталей с целью предотвращения прожога, алюминиевых сплавов для разрушения оксидной плёнки и легированных сталей во избежании их перегрева.
Род тока и полярность указаны в паспорте электрода.
Напряжение дуги при ММА изменяется в пределах 20…36В и пропорционально длине дуги. В процессе сварки необходимо поддерживать постоянную длину дуги, которая зависит от марки и диаметра электрода. Ориентировочно нормальная длина дуги должна быть в пределах Lд = (0,5…1,1)dэ, где Lд — длина дуги,мм.
Параметры лазерной сварки— обзор
1 Введение
Высокоэффективная и высокоточная сварка делает применение лазеров все более и более широким. В лазерах непрерывного действия параметры сварки обычно включают мощность лазера, скорость сварки, диаметр луча и величину расфокусировки. Однако энергия импульса, длительность импульса и частота импульсов также могут рассматриваться как параметры импульсных лазеров [1,2]. Импульсная лазерная сварка позволяет управлять подводом тепла при сварке путем одновременной регулировки нескольких переменных [3], что делает лазерную обработку материалов более гибкой.Взаимодействие с материалами во время импульсной лазерной сварки также отличается от непрерывного лазера. Помимо простого суммирования воздействия на каждый импульс, эти результаты могут также влиять друг на друга [4]. Эффект перекрытия следует учитывать при определении эффективной пиковой плотности мощности [5]. Импульсный лазер также находит множество применений в гибридной сварке, например, в технологии импульсно-непрерывной двухлучевой лазерной сварки [6] и в гибридной импульсной лазерно-дуговой сварке [7–9].
Для импульсной лазерной сварки свариваемые материалы включают алюминиевый сплав, суперсплав, нержавеющую сталь, магниевый сплав и разнородные металлические материалы. Поскольку импульсный лазер может обеспечивать точное тепловложение, он имеет большие преимущества при сварке тонких листов. Сочетание низкой плотности и высокой прочности делает алюминиевые сплавы более широко используемыми в авиастроении и автомобилестроении [10]. Сварка алюминия и меди из разнородных материалов использовалась во многих случаях [11–14]. К основным дефектам лазерной сварки относятся не только поры, испарение элементов и трещины, но и взаимное влияние. Для лазерной сварки Хуанг и др. [15] предложили два фактора порообразования: образование пузырьков, вызванное нестабильностью поры, и пузырьки, захваченные на границе затвердевания.Пористость можно уменьшить путем предварительного нагрева. Испарение и диффузия элементов имеют важное влияние на процесс сварки. При импульсной лазерной сварке Ti, B, Zr может снизить чувствительность к трещинам затвердевания сплава Al Zn Mg [16]. Ким и Нам [17] изучали влияние переходных элементов Mn и Zr на чувствительность к трещинам при сварке высокопрочным сплавом Al-Zn-Mg серии 7000, в то время как Cu и Cr повышали чувствительность к трещинам.
Holzer et al. [18] измерили изменение концентрации элементов сварного шва с помощью EDS и рассчитали зону затвердевания, используя эти количественные данные.Их исследование доказало, что энергия, приходящаяся на единицу длины лазерной сварки AA 7075, может вызывать изменение концентрации элементов сварного шва, что влияет на чувствительность к образованию горячих трещин.
Благодаря использованию термообработки твердого раствора и дисперсионного твердения суперсплавы обычно демонстрируют сочетание повышенной механической прочности, характеристик разрушения при ползучести и устойчивости к эрозии окружающей среды (включая окисление) при рабочих температурах, близких к точкам плавления [19]. Свариваемость жаропрочных суперсплавов на никелевой основе становится все более важной, поскольку сварка широко используется для изготовления и ремонта компонентов горячего сегмента авиационных и промышленных газотурбинных двигателей, изготовленных из этих материалов [20–22].В отличие от трещин затвердевания алюминиевых сплавов, разжижение является основной причиной образования трещин в зоне термического влияния (ЗТВ) в большинстве аустенитных сплавов (включая дисперсионно-упрочненные суперсплавы на основе никеля) [23]. Многие исследования показали, что традиционный метод импульсной лазерной сварки не является очевидным при решении трещин разжижения суперсплавов [24–26].
Магниевый (Mg) сплав обладает такими преимуществами, как высокая удельная прочность, удельная жесткость и амортизация. Использование сплава Mg вместо алюминиевого позволяет снизить вес на 15–20% [27].Пористость и трещина являются обычными дефектами сварки магниевых сплавов, исследования показали, что они могут быть решены с помощью характеристик перекрытия импульсов и редактирования формы импульсов [28–30].
Чтобы глубже понять процесс импульсной лазерной сварки, необходимо сравнить результаты импульсной лазерной сварки различных материалов. После анализа этих исследований было обнаружено, что при импульсной лазерной сварке существует множество проблем, а трещины, как наиболее распространенные дефекты сварки, привлекают внимание многих исследователей.Поэтому было предложено множество показателей для прогнозирования чувствительности процесса затвердевания к термическому растрескиванию. Однако, особенно для быстрого охлаждения импульсной лазерной сварки, большинство показателей чувствительности к образованию трещин неприменимы. В этом обзоре, благодаря всестороннему анализу механизма образования термических трещин, исследователи смогли полностью понять формирование термических трещин в процессе импульсной лазерной сварки и использование импульсных методов для решения задач лазерной сварки сплавов.
Прогнозирование глубины проникновения при сварке с лазерным сканированием в форме бесконечности на основе выборки из латинского гиперкуба и нейроэволюции дополнительных топологий разработан контроллер движения и шлюз управления сканером гальванометра, в качестве объектов эксперимента используется автогенная сварка наплавкой листа 304SS с образцами толщиной 3 мм, рассчитаны параметры эксперимента с использованием метода отбора образцов латинского гиперкуба для получения сварных соединений с различной глубиной проплавления и представлены методология, основанная на нейроэволюции дополнительных топологий для прогнозирования глубины проплавления при сварке с лазерным сканированием формы «∞».

Ключевые слова: лазерная сканирующая сварка в форме бесконечности , колебание лазерного луча, прогноз глубины проникновения, выборка из латинского гиперкуба (LHS), нейроэволюция дополняющих топологий (NEAT)
1. Введение
Обычно используемая марка стали — нержавеющая сталь 304 (304SS). Добавление элементов сплава, таких как Cr и Ni, придает 304SS хорошие рабочие характеристики и коррозионную стойкость в самых суровых условиях. Эта марка стали широко используется в авиационной, космической, судостроительной, медицинской и автомобильной отраслях.При его применении сварка спереди, когда трудно переворачивать или неудобно сваривать изнутри, неизбежна для сборки компонентов, а качество сварных соединений играет жизненно важную роль в определении надежности и удовлетворительных свойств конструкций; кроме того, морфология провара имеет важное влияние на качество сварного шва [1,2].
Лазерная сварка считается предпочтительным методом для соединения средних пластин, учитывая ее преимущества высокой плотности мощности, низкого тепловложения, глубокого проплавления, узкой зоны термического влияния и отличных механических свойств [3,4].Однако при лазерной сварке легко возникают некоторые дефекты сварного шва, такие как недозаливка, трещины и пористость [5,6].
Лазерная сканирующая сварка — это новая технология сварки, появившаяся в последние годы. Различные траектории сканирования при сварке могут быть достигнуты путем управления сканером гальванометра [7]. Сообщается, что технология лазерной сканирующей сварки может улучшить допуски на зазоры в стыках, однородность микроструктуры и качество сварки. Kraetzsch et al. обнаружили, что трещины разнородных сварных швов Al / Cu и Al / Ti могут быть уменьшены путем колебания луча [8].Berend et al. подтвердили, что высокочастотные колебания могут устранить дефект «неровности» сварного шва из алюминиевого сплава [9]. Vänskä et al. обнаружили, что несоосность сборки трубы из нержавеющей стали толщиной 5 мм может быть устранена путем использования колебаний луча для расширения сварного шва [10]. Wang et al. также разработали сварку с круговыми колебаниями, получили качественные сварные швы и установили, что колебания балки ответственны за повышение пластичности сварного шва [11]. Чжоу и др. исследовали влияние траектории сканирования, амплитуды сканирования и частоты сканирования луча во время лазерной сканирующей сварки на поры алюминиевого сплава 6061 и эффективно подавляли образование пор [12].Ян исследовал сварку алюминиевого сплава с использованием дорожек лазерного сканирования с формами «-», «|» и «O», тем самым уменьшая пористость сварного шва [13].
Сварка с лазерным сканированием в форме буквы «∞» в последние годы вызвала значительный интерес со стороны академических кругов и промышленности. Кроме того, сварочная ванна с лазерным сканированием в форме «∞» обладает хорошей стабильностью и очевидным ингибирующим действием на поровые дефекты сварного шва из алюминиевого сплава, таким образом снижая пористость до 1% [7]. Wang et al. подтвердила, что по сравнению с режимами линейной и круговой осцилляции, новая бесконечная осциллирующая балка имеет меньше сварочных дефектов и лучшие механические свойства [14].Однако колебания луча могут изменить критерий трансформации режима сварки и изменить механизмы формирования шва, что в дальнейшем приводит к нестабильному контролю проплавления и ухудшает качество сварки.
Хорошее проникновение способствует обеспечению качества продукции [15,16,17]. Однако взаимосвязь между параметрами процесса сварки и глубиной сварки (WD) неизвестна, нелинейна и сложна, что делает непрактичным определение оптимальных параметров процесса интуитивно даже для опытных операторов. Кроме того, сварка с колебаниями пучка увеличила параметры процесса и усложнила процесс сварки [18,19,20].
В ответ на эту проблему ученые из разных стран провели многочисленные экспериментальные исследования, в основном для изучения влияния различных параметров колебаний на WD с целью оптимизации параметров процесса сварки и улучшения методов и оборудования сварки. Ли и др. установили, что WD значительно уменьшалась по мере увеличения диаметра и частоты колебаний, а провар при лазерной сварке с круговыми колебаниями для алюминиевого сплава 5083 приблизительно пропорционален энергии линии лазерных колебаний [21].Ли и др. обнаружили, что когда амплитуда сварочных колебаний 304SS была ниже 0,4 мм, проплавление шва не изменилось; в противном случае проплавление и площадь сварного шва значительно уменьшились по мере увеличения амплитуды колебаний, что было вызвано изменением режима сварки [3]. Chen et al. пришли к выводу, что проплавление сварного шва с лазерным сканированием формы «∞» обратно пропорционально амплитуде сканирования и частоте сканирования алюминиевого сплава 5052, а поперечное сечение шва имело широкую U-образную форму [7]. Однако модель взаимосвязи между параметрами сварки с лазерным сканированием и проплавлением, особенно для сварки с лазерным сканированием формы «∞», остается неизученной.
Хотя разработанные математические модели, такие как полиномиальная поверхность отклика и радиальная базисная функция, могут использоваться для построения взаимосвязи между параметрами процесса и геометрией сварного шва, эффективность прогнозирования моделей не может быть гарантирована даже при большом количестве точек выборки [22,23,24 ] из-за эффекта связи параметров сварки и нелинейной причинно-следственной связи.
Превосходная способность нейронной сети к нелинейной обработке имеет очевидные преимущества для прогнозирования формирования сварных швов и механических свойств [25,26]. Однако математический принцип нейронной сети БП определяет присущий ей недостаток — легкое попадание в локальный оптимум. Кроме того, его обучающий эффект слишком зависит от начальных случайных весов и пороговых значений [17]. По сравнению с традиционными методами нейронных сетей, нейроэволюция дополняющих топологий (NEAT) создает искусственные нейронные сети посредством моделирования эволюции и позволяет одновременно оптимизировать топологию сети и веса соединений посредством эволюционного процесса [27].Более того, NEAT просматривает минимальное количество весовых измерений, тем самым значительно сокращая количество поколений, необходимых для определения решения [28].
В рамках данной работы создается экспериментальная платформа для лазерной сканирующей сварки в форме буквы «∞» на основе контроллера движения и шлюза управления сканером гальванометра, которые являются собственными разработками, в которых используется автогенная сварка валиком на пластину 304SS с образцами толщиной 3 мм как экспериментальных объектов, и фокусируется на модели, основанной на нейроэволюции дополняющих топологий для прогнозирования WD сканирующей лазерной сварки в форме ∞, в которой входные параметры синтезируют мощность лазера (LP), скорость сварки (WS), частоту сканирования ( SF) и амплитуды сканирования (SA). Чтобы решить проблему, при которой характеристики распределения исходных данных выборки не могут быть точно описаны даже с многочисленными точками выборки, в план экспериментальных параметров вводится латинский гиперкубовый отбор (LHS).
Проверочный эксперимент подтверждает, что точность прогноза может соответствовать требованиям определения основных параметров процесса и последующего контроля проникновения. Модель может точно отражать нелинейную взаимосвязь между основными параметрами сварки и WD, что помогает обеспечить качество проплавления при сварке с лазерным сканированием формы «∞».
2. Экспериментальная установка
2.1. Экспериментальная платформа
Экспериментальная установка () включала волоконный лазер MAX PHOTONICS MFSC-4000 (Maxphotonics Co., Ltd., Шэньчжэнь, Китай), сварочную головку OSPRI LDW400 (OSPRI Co., Ltd., Шэньчжэнь, Китай), шестиосный промышленный робот Kawasaki, контроллер движения на базе ПК (собственной разработки) и шлюз управления сканером гальванометра (собственная разработка). Этот волоконный лазер работал в режиме непрерывного луча с длиной волны 1070 нм и произведением параметров луча (BPP), равным 2.8 мм мрад. Радиус пятна сфокусированного лазерного луча составлял примерно 0,4 мм. Головка для качающейся сварки состояла из коллимационного блока с фокусным расстоянием 75 мм, двух гальванометрических сканеров и фокусирующего блока с фокусным расстоянием 300 мм. Колебание луча контролировалось сканером гальванометра и могло колебаться до максимальной частоты 250 Гц. Диаметр луча в фокусе 1,6 мм. Сварочная головка приводилась в движение роботом для линейного перемещения в направлении оси X.
Схема экспериментальной установки для лазерной сканирующей сварки.
Схема системы управления показана на. Эксперимент реализован в саморазработанном контроллере движения на базе ПК с процессором Intel (R) Core (TM) i5-7200 U 2,5 ГГц, компьютером SDRAM 16,00 ГБ (Shandong Ezcode Intelligent Technology Co., Ltd., Цзинань, США). Китай) и операционная система Windows 10, расширенная пакетом реального времени Kithara (KRTS), чтобы гарантировать производительность в реальном времени [29].
Схема системы управления.
Контроллер движения на базе ПК действует как главный узел в промышленной сети Ethernet EtherCAT (Beckhoff Automation GmbH & Co.KG, Верл, Германия) и промышленной сети Ethernet EtherMAC (Shandong Ezcode Intelligent Techology Co. Ltd., Цзинань, Китай) [30]. С одной стороны, контроллер движения взаимодействует с соответствующими сервоприводами роботов через сеть EtherCAT Industrial Ethernet, где период связи установлен на 1 мс, а сервоприводы роботов действуют как подчиненные узлы в сети EtherCAT. С другой стороны, блоки сканера гальванометра, которые находятся в сварочной головке OSPRI, подключаются к промышленной сети Ethernet EtherMAC через модуль шлюза управления сканером гальванометра собственной разработки с ПЛИС Altera EP4CE6E22C8 (Altera Corporation., Калифорния, США), где период связи установлен на 250 мкс, а модуль действует как подчиненный узел EtherMAC. Кроме того, модуль шлюза управления сканером гальванометра обменивается данными с блоками сканера гальванометра через последовательные шины XY2-100, где период связи установлен на 10 мкс. Метод «одна передача-множественное преобразование» используется для выравнивания периода связи, модуль шлюза принимает сетевой кадр один раз и выдает инструкции в нескольких последовательных преобразованиях.
Основанная на KRTS, операционная система контроллера движения может быть разделена на две подсистемы: операционная система, работающая не в реальном времени (не-RTOS), которая может выполнять задачи без требований в реальном времени, и KRTS-Kernel, которая представляет собой систему реального времени с отличной производительностью в реальном времени. Этап интерполяции в реальном времени блоков сканера робота и гальванометра выполняется в ядре KRTS, а задача HMI может быть реализована без ОСРВ.
2.2. Методика эксперимента
Эксперименты проводились с использованием пластин 304SS толщиной 3 мм (в прокатанном и отожженном состоянии) размером 120 × 50 мм 2 в качестве основного металла.Химический состав и механические свойства перечислены в. Во время сварки поверхность шва защищалась газовыми соплами с использованием чистого аргона. Расход газа через сопла составлял 15 л / мин. Перед экспериментом поверхности пластин промывали ацетоном. После высыхания пластин поверхностная оксидная пленка соскабливалась наждачной бумагой и пластины промывались абсолютным этанолом.
Таблица 1
Химический состав и механические свойства листа 304SS.
C | Si | Mn | P | S | Cr | Ni | Cu | Fe |
---|---|---|---|---|---|---|---|---|
0,027 | 0,56 | 1,55 | 0,031 | 0,001 | 18,0 | 8,0 | 0,1 | Бал.![]() |
Предел прочности / МПа 660 | Предел текучести / МПа 277 | Процент удлинения /% 62,0 |
Принцип работы сварочной головки с качающейся сваркой показан на рис.При сварке с колебаниями лазерного луча лазерный луч коллимируется, а затем направляется на вращающиеся зеркала. Отклонение дефлекторов луча осуществляется двигателями для достижения траектории сканирования. Используемый шаблон сканирования имеет форму «∞», также известную как лемниската. Кривая в форме «∞» представлена на, длина линии AB установлена на 2 a , если движущаяся точка « P » удовлетворяет уравнению (1), а траектория «P» обозначена как лемниската:
когда WS составляет V = 0, траектория лазерного луча такая, как показано на.С точкой « a » в качестве начальной точки цикла сварки лазерный луч непрерывно циркулирует со скоростью сканирования Ve по пути a (i) — b — c (g) — d — e — f — g (c) — h — i (a) .
Принципиальная диаграмма кривой в форме «∞».
Статическая траектория сканирования сканирующей сварки в форме «∞».
Ve в основном определяется частотой сканирования (SF) и амплитудой сканирования (SA) лазерного луча.Определение SA трека показано в. Когда WS составляет V > 0, траектория сканирования лазера определяется WS и Ve . показывает непрерывную траекторию сканирования ∞-образного движения лазерного луча.
Динамическое непрерывное сканирование траектории сканирующей сварки в форме «∞».
Лазерный луч начинается из точки « м ». Процесс сварки заканчивается в точке « n » после нескольких перемещений. В процессе динамического сканирования фактическая скорость Va представляет собой комбинацию векторов Ve и V вдоль сварного шва, которая может быть рассчитана с использованием уравнения (2).То есть фактическая скорость сканирующей сварки в форме «∞» в « a (i) — b — c (g) — d » и « e — f — . g (c) — h — i (a) ”сегментов намного выше, чем у однопроходного лазера WS [7].
Для получения сварных соединений с различной морфологией проплавления были проведены эксперименты по автогенной сварке валиком на пластину для исследования влияния параметров сварки с лазерным сканированием формы «∞» на морфологию проплавления.Для расчета экспериментальных параметров использовался метод LHS. Этот метод выборки позволяет точно определить пространство дизайна за счет выборки с меньшим количеством итераций и равномерного распределения точек выборки по всему пространству дизайна. Как правило, глубина сварки при лазерной сканирующей сварке зависит от мощности лазера, скорости сварки, шаблона сканирования, зазора, положения фокуса лазерного луча, защитного газа и т. Д. Эти входные факторы обычно определяют WD. В этом исследовании рассматривается нелинейная зависимость между параметрами сварки и глубиной сварки, будь то режим проводимости или режим «замочной скважины». Согласно большому количеству фактических опытов, обзоров и первичных исследований, WD при сварке с лазерным сканированием формы «∞» в основном определяется четырьмя основными факторами, включая LP, WS, SF и SA, и высокая скорость сварки может привести к к дефектам неполного плавления и даже разбрызгиванию, в то время как высокая мощность лазера может вызвать чрезмерное проникновение и вмятину [7,14]. С учетом реальных условий работы сварочной головки с качающейся сваркой устанавливаются границы параметров сканирования (SF и SA), а рабочие диапазоны всех выбранных параметров процесса фиксируются путем проведения испытаний по следу.Кроме того, с учетом реальных условий сварки и затрат на эксперименты, 60 образцов экспериментальных параметров были определены методом LHS. Рабочие диапазоны всех выбранных параметров экспериментального процесса следующие:
800≤LP≤3000 (Вт) 8≤WS≤30 (мм / с) 10≤SF≤250 (Гц) 0≤SA≤2,5 (мм)
Другие параметры сварки контролируются как постоянные значения, а другие постоянные параметры сварки в эксперименте показаны на рис. После сварки сварная деталь вырезается, полируется и травится по участку точки выборки изображения с помощью станка для резки проволоки.С помощью видеоизмерительной машины VMA наблюдается и фотографируется макроскопическая металлография зоны плавления для измерения соответствующих характеристик проплавления.
Таблица 2
Другие постоянные параметры сварки.
Другие постоянные параметры сварки | Значение |
---|---|
Расход газа через сопла (л / мин) | 15 |
Расстояние расфокусировки (мм) | 0 |
Толщина пластины (мм) | 3 |
3.

3.1. Нейроэволюция дополнительных топологий
За счет (1) использования принципиального метода пересечения различных топологий, (2) защиты структурных инноваций с помощью видообразования и (3) постепенного развития минимальной структуры, NEAT позволяет решениям постепенно усложняться, в то время как они становятся более оптимальными [28].
Как показано на, каждый геном включает в себя список генов соединения, каждый из которых относится к двум генам узла, соединенным в NEAT.Каждый ген соединения определяет входящий узел, выходной узел, вес соединения, экспрессируется ли ген соединения (разрешающий бит) и номер инновации (Innov), тем самым облегчая идентификацию соответствующих генов во время кроссовер. Цифры инноваций представляют собой хронологию каждого гена в системе и позволяют отслеживать историческое происхождение каждого гена.
Отображение генотипа на фенотип и сопоставление геномов для различных топологий сети.
Мутация в NEAT может изменить не только веса соединений, но и структуру сети. Структурные мутации, расширяющие геном, происходят двумя способами: мутации соединения и мутации узла (). В результате мутации создаются геномы разного размера, иногда с совершенно разными связями, указанными в одних и тех же положениях.
Два типа структурных мутаций в NEAT.
При кроссинговере гены в обоих геномах с одинаковыми номерами инноваций выстраиваются в линию. Несовпадающие гены наследуются от более подходящего родителя или, если они одинаково подходят, от обоих родителей случайным образом.Более того, несовпадающие гены либо не пересекаются, либо избыточны, в зависимости от того, находятся ли они в пределах или за пределами диапазона числа инноваций другого родителя в.
Население делится на виды в соответствии с историческими особенностями и топологическим сходством. Расстояние совместимости (φ) различных конструкции могут быть рассчитаны с использованием уравнения (3).
где E — количество лишних генов; D — количество непересекающихся генов; W¯ — средняя разница в весе совпадающих генов; N — количество генов в большем геноме; и a 1 , a 2 и a 3 — это коэффициенты, которые регулируют важность трех факторов.
NEAT определяет популяцию и разделяет приспособленность, так что индивидуумы соревнуются в первую очередь в рамках своих собственных ниш, а не против всей популяции. Таким образом, у людей есть время оптимизировать свою структуру, прежде чем они должны будут конкурировать с другими нишами в популяции, и эта функция может эффективно решить проблему снижения приспособленности при добавлении новых структур в сеть.
Более того, поскольку NEAT защищает инновации с помощью видообразования, он может начинать этот путь как минимум и создавать новые структуры только по мере необходимости.Таким образом, NEAT просматривает минимальное количество весовых размеров, тем самым значительно сокращая количество поколений, необходимых для поиска решения.
3.2. Создание и обучение модели NEAT
Модель была создана и обучена для описания взаимосвязей между параметрами процесса и WD. Экспериментальные образцы показаны в, и каждый график демонстрирует изменение WD с параметрами процесса.
Изменение глубины сварки в зависимости от параметров процесса.
Процедура создания и обучения модели подробно расписана следующим образом:
Определение структуры сетевой модели. Основная цель — предсказать WD, выбрав LP, WS, SF и SA в качестве входных параметров. Следовательно, LP, WS, SF и SA выбираются в качестве входных параметров модели NEAT, а WD принимается в качестве выходного параметра. В текущих связанных исследованиях неясно, может ли увеличение количества скрытых слоев уменьшить сетевую ошибку, но это, несомненно, усложнит структуру сети и значительно увеличит время обучения сети и пространство, занимаемое данными.Следовательно, в первоначальном проекте выбрана трехуровневая сеть с одним скрытым слоем и восемью узлами скрытого слоя, узлы входного слоя подключены к каждому узлу в скрытом слое и выходном слое, каждый узел скрытого слоя подключен к узел выходного уровня, и начальные соединения в сети включены. Во время обучения топология сети и веса соединений изменяются путем кроссинговера и мутации, чтобы получить структуру сети с наименьшей ошибкой.
Следовательно, определяется модель NEAT для прогнозирования WD, и начальная топологическая структура модели показана в, где числа в скрытом слое представляют числа нововведений, толщина соединительных линий связана со значением начальных случайных весов, красные линии означают вес <0, зеленые линии означают вес ≥ 0, а сплошные линии означают, что соответствующие соединения включены.
Исходная топологическая структура модели.
Дизайн набора данных для обучения и набора данных для тестирования. Как уже упоминалось, среди 60 образцов, экспериментальные параметры которых были определены методом LHS, экспериментальные результаты 58 образцов показали неполное проникновение. Большая разница в различных характеристических значениях образцов не способствует обработке, поэтому образцы предварительно обрабатываются путем удаления среднего значения. Пятьдесят выборок (обучающий набор данных) выбираются случайным образом для обучения модели NEAT из предварительно обработанных выборок.
Остальные восемь выборок (набор тестовых данных) были отобраны для проверки точности прогнозов.
Установите начальные правила популяции и пригодности. Начальный размер популяции установлен равным 300, и каждый человек в популяции представляет собой сеть. Оценка каждого человека рассчитывается в соответствии с правилами расчета сети. Чтобы оценить качество решения, в качестве пригодности обычно используется начальная пригодность за вычетом квадрата ошибки между выходным значением и ожидаемым значением набора обучающих данных.Таким образом, чем выше оценка, тем меньше ошибка доказательства и тем лучше человек.
Реализуйте NEAT, чтобы получить модель прогнозирования. NEAT был применен для решения проблемы прогнозирования и получения прогнозируемого значения WD. Программа была разработана на основе Python 3.6 и запускалась в JetBrains PyCharm. Выбранные параметры NEAT перечислены в.
Таблица 3
Выбранные параметры NEAT.
Параметр Значение Порог пригодности 49. 8
Activation_options Softplus, Relu, Sigmoid Activation_default Softplus Activation_mutate_rate 0.1 Aggregation_default Sumprolete_default 9 99596 Conlete_default _dash 0,5 Node_add_prob 0,2 Node_delete_prob 0. 2
Enabled_default True Enabled_mutate_rate 0,05 Исходная пригодность 50 Размер популяции 300 900h72Максимальное количество итераций 2000 8 Num_inputs 4 Num_outputs 1 Initial_connection Full_direct Compatibility_disjoint_coefficient 1. 0
Compatibility_weight_coefficient 0.5 Compatibility_threshold 3.0 Elitism 3
4. Результат и обсуждение
4.1. Результаты экспериментов
WD выбран в качестве показателя оценки глубины проплавления для оценки сварочного процесса в этой работе. Макроскопическая металлографическая схема и размерный замер образца сварного шва (No.40) показаны на.
Геометрические особенности морфологии проплавления.
In, экспериментальные результаты показывают, что в пределах экспериментального диапазона экспериментальные образцы 35 и 48 были полностью проплавлены, а WD остальных 58 образцов экспериментальных образцов демонстрирует относительно равномерное случайное распределение по всему пространству проектирования. Таким образом, метод LHS может точно определить пространство дизайна путем выборки с меньшим количеством итераций и описать характеристики распределения данных.Все экспериментальные параметры и результаты измерений образцов приведены в Приложении А.
Глубина сварки 58 экспериментальных образцов.
4.2. Анализ процесса обучения модели NEAT
Каждый индивидуум представляет сеть в популяции, и приспособленность каждого индивидуума рассчитывается в соответствии с правилами расчета сети и начальной приспособленностью. Чем выше приспособленность, тем меньше ошибка при доказательстве и тем лучше человек. В ходе популяционной итерации популяция проходит через создание, отбор, кроссовер и мутацию.При этом сохраняются люди с высокой физической подготовкой, а люди с низкой физической подготовкой исключаются. Следовательно, значение наилучшего соответствия (F_score) непрерывно увеличивается (), а топологическая структура также непрерывно развивается (). Топологическая структура модели NEAT постепенно увеличивается от минимальной структуры, тем самым значительно сокращая количество поколений, необходимых для поиска решения. Среди итераций a – g соответствуют топологической структуре модели NEAT после 25, 50, 75, 175, 275, 525 и 800 поколений эволюции, соответственно, и этот результат также означает, что ошибка предсказания постоянно уменьшается.
Наилучшая приспособленность населения по мере его развития.
Топологическая структура модели по мере развития популяции.
Находится и декодируется лучший индивидуум, полученный в результате итераций, и получаются веса соединений и структуры сети для окончательной сети. Окончательная сетевая структура модели NEAT показана на. Вес соединения и топология сети связаны с влиянием каждого параметра процесса на WD. В рабочих диапазонах выбранных параметров экспериментального процесса основные эффекты на WD включают LP, WS и SA.SF практически не влияет на WD. WD пропорционален LP и обратно пропорционален WS и SA. Влияние каждого параметра процесса на WD может быть определено косвенно, прогнозируя WD при предварительном выборе параметров процесса.
Окончательная топологическая структура модели NEAT.
4.3. Проверка точности прогноза предлагаемого подхода
Установленная модель NEAT может описывать отношения между параметрами процесса и WD. Чтобы проверить эффективность прогнозирования модели, для прогнозирования WD использовались восемь ранее выбранных случайным образом образцов (набор тестовых данных).Сравнительный анализ предсказанных значений и экспериментальных значений () показывает хорошее согласие. Точность прогноза сравнима с таковой в справочных материалах [31,32], что позволяет удовлетворить требования реальной сварки. Чтобы оценить производительность модели более интуитивно, в качестве индикатора оценки был выбран NRMSE модели. NRMSE WD составляет приблизительно 6,2%, результат, который показывает, что модель имеет высокую точность прогноза. В целом, установленная модель NEAT надежна и может использоваться для прогнозирования WD при выборе параметров процесса.
Сравнение прогнозных и экспериментальных значений.
Панель автоматического управления: Параметры сварки
X5 FastMig Manual 1920960, rev. 2144
Панель автоматического управления: Параметры сварки
В окне «Параметры сварки» есть начальная и конечная кривая для настройки наиболее важных параметров сварного шва. В нижней части окна перечислены доступные настройки для выбранного процесса сварки.Выбор процесса сварки зависит от активного канала памяти и его настроек.
Многие параметры сварки зависят от процесса сварки, они видны и доступны для соответствующей настройки. |
Регулировка параметров сварки
1.![]() | Поверните правую ручку управления, чтобы выделить нужный параметр сварки. |
2. | Нажмите правую ручку управления, чтобы выбрать параметр сварки для настройки. |
3.![]() | Поверните правую ручку управления, чтобы отрегулировать значение параметра сварки. |
>> В зависимости от настраиваемого параметра см. Также более подробную информацию в таблице параметров сварки ниже.
4. | </span></b>»> Подтвердите новое значение / выбор и закройте окно настройки, нажав правую ручку управления. |
Сохранение параметров сварки для дальнейшего использования
Рабочий канал создается автоматически для измененных параметров сварки.Чтобы сохранить заданные параметры сварки в канале памяти, выполните одно из следующих действий:
• | Параметр «Быстрый активный канал»: удерживайте кнопку быстрого доступа «Каналы» примерно 2 секунды. |
>> Это сохранит настройки параметров на текущем активном канале, заменив его предыдущие настройки параметров.
• | Опция просмотра каналов: перейдите к просмотру каналов и сохраните настройки параметров на новом канале. |
>> Дополнительные сведения см. В разделе «Панель автоматического управления: каналы памяти».
Параметры и описание функций сварки
Параметры сваркиMIG и 1-MIG
Перечисленные здесь параметры доступны для настройки с помощью процессов MIG и 1-MIG.
Триггерная логика | 2 т, 4 т | Сварочные горелкимогут иметь несколько альтернативных режимов работы триггера (логика триггера).Наиболее распространены 2Т и 4Т. В режиме 2T вы удерживаете спусковой крючок во время сварки. В режиме 4T вы нажимаете и отпускаете курок, чтобы начать или прекратить сварку. |
Зажигание Touch Sense | ВЫКЛ. / ВКЛ. | Touch Sense Ignition обеспечивает минимальное разбрызгивание и стабилизирует дугу сразу после зажигания.![]() |
Пост текущий | -30… +30 | Настройка пост-тока влияет на длину проволоки на конце сварного шва, например, чтобы предотвратить остановку проволоки слишком близко к сварочной ванне. Это также обеспечивает оптимальную длину проволоки для начала следующего шва. |
Динамика | -10,0 … +10,0, шаг 0,2 По умолчанию = 0 | Управляет поведением дуги при коротком замыкании.Чем ниже значение, тем мягче дуга, тем выше значение более грубая дуга. |
Конечная ступенька WF | ВЫКЛ. / ВКЛ.![]() По умолчанию = ВЫКЛ. | Функция конечной ступеньки подачи проволоки предотвращает прилипание присадочной проволоки к заготовке по окончании сварки. Для этого нужно ненадолго оттянуть провод назад. |
Предварительный газ | 0.0 … 9,9 с, шаг 0,1 0,0 = ВЫКЛ | Сварочная функция, запускающая подачу защитного газа до зажигания дуги. Это гарантирует, что металл не контактировать с воздухом в начале шва. Значение времени задается пользователем. Используется для всех металлов, но особенно для нержавеющей стали, алюминия и титана. |
Медленное движение | 10..,90%, шаг 1 | Функция медленного старта определяет скорость подачи проволоки до зажигания сварочной дуги, то есть до подачи присадочной проволоки.![]() |
Заливка кратера | ВКЛ / ВЫКЛ | При сварке с большой мощностью в конце шва обычно образуется кратер.Функция заполнения кратера
снижает мощность сварки / скорость подачи проволоки в конце сварочной работы, чтобы кратер можно было заполнить с помощью
более низкий уровень мощности. В процессе MIG продолжительность заполнения кратера, скорость подачи проволоки и напряжение устанавливаются пользователем. При скорости подачи проволоки менее 5 м / мин шаг регулировки составляет 0,05, а при скорости подачи проволоки 5 м / мин или более шаг регулировки составляет 0,1. Для процесса 1-MIG см. |
— Время заполнения кратера | 0.0 … 10,0 с, шаг 0,1 По умолчанию = 1,0 с | |
— Скорость подачи проволоки для заполнения кратера | 0,5 … 25,0 м / мин, шаг 0,05 или 0,1 По умолчанию = 5 м / мин | |
— Напряжение заполнения кратера | 450A: 10 … 45 В 500A: 10 … 50 В Шаг 0,1 В По умолчанию = 18 В | |
Пост газовый | 0.0 … 9,9 с, шаг 0,1 0,0 = ВЫКЛ | Функция сварки, при которой продолжается подача защитного газа после гашения дуги.![]() |
Скорость подачи проволоки | 0.50 … 25 м / мин, шаг 0,05 или 0,1 По умолчанию = 5,00 м / мин | Регулировка скорости подачи проволоки. При скорости подачи проволоки менее 5 м / мин шаг регулировки составляет 0,05, а при скорости подачи проволоки 5 м / мин или более шаг регулировки составляет 0,1. |
Скорость подачи проволоки мин. | Мин. / Макс. = 0,5 … 25 м / мин, шаг 0.1 По умолчанию = 0,5 м / мин | Минимальные и максимальные пределы регулировки скорости подачи проволоки.![]() |
Скорость подачи проволоки макс. | Мин. / Макс. = 0,5 … 25 м / мин, шаг 0,1 По умолчанию = 25 м / мин | |
Напряжение мин. | Мин. / Макс. = Согласно техническим характеристикам сварочного оборудования, шаг 0.1 | Минимальные и максимальные пределы регулировки сварочного напряжения. Эти параметры доступны для настройки только в MIG. В 1-MIG напряжение определяется программой сварки. |
Напряжение макс. | Мин. / Макс. = Согласно техническим характеристикам сварочного оборудования, шаг 0,1 |
Параметры сварки 1-MIG
Перечисленные здесь параметры доступны для настройки только в процессе 1-MIG.
Восходящий наклон | ВКЛ / ВЫКЛ | Upslope — это функция сварки, определяющая время, в течение которого сварочный ток постепенно увеличивается до желаемого значения. уровень сварочного тока в начале шва.Уровень и время начала подъема устанавливаются пользователем заранее. |
Стартовый уровень | ВКЛ: 10 … 100%, шаг 1 По умолчанию = 50 | |
Время нарастания склона | ВКЛ: 0,1 .![]() По умолчанию = 0,10 | |
Горячий старт | ВКЛ / ВЫКЛ | Функция сварки, при которой в начале сварки используются более высокая или более низкая скорость подачи проволоки и сварочный ток.После Период горячего старта: ток меняется на нормальный уровень сварочного тока. Это особенно облегчает начало сварки. с алюминиевыми материалами. Уровень и время горячего старта (только в режиме триггера 2T) устанавливаются пользователем заранее. |
Уровень горячего старта | ВКЛ: -50 … +200%, шаг 1 По умолчанию = 40 | |
Время горячего старта | ВКЛ: 0.![]() По умолчанию = 1,2 с | |
Заливка кратера | ВКЛ / ВЫКЛ | При сварке с большой мощностью в конце шва обычно образуется кратер. Функция заполнения кратера снижает мощность сварки / скорость подачи проволоки в конце сварочной работы, чтобы кратер можно было заполнить с помощью более низкий уровень мощности.В процессе 1-MIG начальный уровень, продолжительность и конечный уровень заварки кратера задаются пользователем. |
— Уровень начала заливки кратера | 10 … 150%, шаг 1 По умолчанию = 100 | |
— Время заполнения кратера | 0,0 .![]() По умолчанию = 1.0 с | |
— Уровень заполнения кратера | 10 … 150%, шаг 1 По умолчанию = 30 | |
Текущий | 10 … размер машины A, шаг 1 По умолчанию = 50 A | Регулировка сварочного тока.Только с WisePenetration +. |
Тонкая настройка | Пример: -10.0 … +10.0 В * Шаг 0,1 В | Точная настройка сварочного напряжения. * Диапазон напряжения для точной настройки определяется активной программой сварки. |
Мудрая функция | Нет, WiseFusion, WisePenetration +, WiseSteel | При выборе открывается список доступных функций Wise для выбора.![]() |
Ограничение скорости подачи проволоки мин. | Мин. / Макс. = 0,5 … 25 м / мин, шаг 0,1 По умолчанию = 0,5 м / мин | Минимальные и максимальные пределы регулировки скорости подачи проволоки. |
Макс.предел скорости подачи проволоки | Мин. / Макс. = 0.5 … 25 м / мин, шаг 0,1 По умолчанию = 25 м / мин |
Параметры сварки TIG
Перечисленные здесь параметры доступны для настройки с помощью процесса TIG.
Триггерная логика | 2 т, 4 т | Сварочные горелки могут иметь несколько альтернативных режимов работы триггера (логика триггера).![]() |
Пост газовый | 0,0 … 9,9 с, шаг 0,1 0,0 = ВЫКЛ | Функция сварки, при которой продолжается подача защитного газа после гашения дуги. Это гарантирует, что горячая сварной шов не контактирует с воздухом после гашения дуги, защищая сварной шов, а также электрод.Используется для всех металлов. Особенно для нержавеющей стали и титана требуется более продолжительное время газовой пост-газовой обработки. |
Текущий | 10 … размер машины A, шаг 1 По умолчанию = 50 A | Регулировка сварочного тока.![]() |
Параметры сварки стержневыми электродами
Перечисленные здесь параметры доступны для регулировки с помощью процесса MMA.
Динамика | -10,0 … +10,0, шаг 0,2 По умолчанию = 0 | Управляет поведением дуги при коротком замыкании. Чем ниже значение, тем мягче дуга, тем выше значение более грубая дуга. |
Уровень горячего старта (MMA) | -30 .![]() По умолчанию = 0 | Функция сварки, при которой в начале сварки используются более высокая или более низкая скорость подачи проволоки и сварочный ток. После Период горячего старта: ток меняется на нормальный уровень сварочного тока. Это особенно облегчает начало сварки. с алюминиевыми материалами.В ММА уровень горячего старта устанавливается пользователем заранее. |
Текущий | 10 … размер машины A, шаг 1 По умолчанию = 50 A | Регулировка сварочного тока. |
Параметры строжки
Перечисленные здесь параметры доступны для регулировки в процессе строжки.
Текущий | 10 … размер машины A, шаг 1 По умолчанию = 50 A | Текущая корректировка. |
Gale Apps — Технические трудности
Технические трудности
Приложение, к которому вы пытаетесь получить доступ, в настоящее время недоступно.Приносим свои извинения за доставленные неудобства. Пожалуйста, попробуйте еще раз через несколько секунд.
Если проблемы с доступом не исчезнут, обратитесь за помощью в наш отдел технического обслуживания по телефону 1-800-877-4253. Еще раз спасибо за выбор Gale, обучающей компании Cengage.
org.springframework.remoting.RemoteAccessException: невозможно получить доступ к удаленной службе [authorizationService @ theBLISAuthorizationService]; вложенное исключение — Ice.UnknownException
unknown = «java.lang.IndexOutOfBoundsException: Индекс 0 выходит за границы для длины 0
в java.base / jdk.internal.util.Preconditions.outOfBounds (Preconditions.java:64)
в java.base / jdk.internal.util.Preconditions.outOfBoundsCheckIndex (Preconditions.java:70)
в java.base / jdk.internal.util.Preconditions.checkIndex (Preconditions.java:248)
в java.base / java.util.Objects.checkIndex (Objects.java:372)
в java.база / java.util.ArrayList.get (ArrayList.java:458)
в com.gale.blis.data.subscription.dao. LazyUserSessionDataLoaderStoredProcedure.populateSessionProperties (LazyUserSessionDataLoaderStoredProcedure.java:60)
в com.gale.blis.data.subscription.dao.LazyUserSessionDataLoaderStoredProcedure.reQuery (LazyUserSessionDataLoaderStoredProcedure.java:53)
в com.gale.blis.data.model.session.UserGroupEntitlementsManager.reinitializeUserGroupEntitlements (UserGroupEntitlementsManager.java: 30)
в com.gale.blis.data.model.session.UserGroupSessionManager.getUserGroupEntitlements (UserGroupSessionManager.java:17)
в com.gale.blis.api.authorize.contentmodulefetchers.CrossSearchProductContentModuleFetcher.getProductSubscriptionCriteria (CrossSearchProductContentModuleFetcher.java:244)
в com.gale.blis.api.authorize.contentmodulefetchers.CrossSearchProductContentModuleFetcher.getSubscribedCrossSearchProductsForUser (CrossSearchProductContentModuleFetcher.java: 71)
в com.gale.blis.api.authorize.contentmodulefetchers.
CrossSearchProductContentModuleFetcher.getAvailableContentModulesForProduct (CrossSearchProductContentModuleFetcher.java:52)
в com.gale.blis.api.authorize.strategy.productentry.strategy.AbstractProductEntryAuthorizer.getContentModules (AbstractProductEntryAuthorizer.java:130)
на com.gale.blis.api.authorize.strategy.productentry.strategy.CrossSearchProductEntryAuthorizer.isAuthorized (CrossSearchProductEntryAuthorizer.java: 82)
в com.gale.blis.api.authorize.strategy.productentry.strategy.CrossSearchProductEntryAuthorizer.authorizeProductEntry (CrossSearchProductEntryAuthorizer.java:44)
на com.gale.blis.api.authorize.strategy.ProductEntryAuthorizer.authorize (ProductEntryAuthorizer.java:31)
в com.gale.blis.api.BLISAuthorizationServiceImpl.authorize_aroundBody0 (BLISAuthorizationServiceImpl.java:57)
в com.gale.blis.api.BLISAuthorizationServiceImpl.authorize_aroundBody1 $ advice (BLISAuthorizationServiceImpl.
java: 61)
в com.gale.blis.api.BLISAuthorizationServiceImpl.authorize (BLISAuthorizationServiceImpl.java:1)
в com.gale.blis.auth._AuthorizationServiceDisp._iceD_authorize (_AuthorizationServiceDisp.java:141)
в com.gale.blis.auth._AuthorizationServiceDisp._iceDispatch (_AuthorizationServiceDisp.java:359)
в IceInternal.Incoming.invoke (Incoming.java:209)
в Ice.ConnectionI.invokeAll (ConnectionI.java:2800)
на льду.ConnectionI.dispatch (ConnectionI.java:1385)
в Ice.ConnectionI.message (ConnectionI.java:1296)
в IceInternal.ThreadPool.run (ThreadPool.java:396)
в IceInternal.ThreadPool.access 500 долларов (ThreadPool.java:7)
в IceInternal.ThreadPool $ EventHandlerThread.run (ThreadPool.java:765)
в java.base / java.lang.Thread.run (Thread.java:834)
»
org.springframework.remoting.ice.
IceClientInterceptor.convertIceAccessException (IceClientInterceptor.java:365) org.springframework.remoting.ice.IceClientInterceptor.invoke (IceClientInterceptor.java:327) org.springframework.remoting.ice.MonitoringIceProxyFactoryBean.invoke (MonitoringIceProxyFactoryBean.java:71) org.springframework.aop.framework.ReflectiveMethodInvocation.proceed (ReflectiveMethodInvocation.java:186) org.springframework.aop.framework.JdkDynamicAopProxy.invoke (JdkDynamicAopProxy.java:212) com.sun.proxy. $ Proxy130.authorize (Неизвестный источник) com.gale.auth.service.BlisService.getAuthorizationResponse (BlisService.java:61) com.gale.apps.service.impl.MetadataResolverService.resolveMetadata (MetadataResolverService.java:65) com.gale.apps.controllers.DiscoveryController.resolveDocument (DiscoveryController.java:57) com.gale.apps.controllers.DocumentController.redirectToDocument (DocumentController.java:22) jdk.internal.reflect.GeneratedMethodAccessor319.invoke (Неизвестный источник) java.base / jdk.
internal.reflect.DelegatingMethodAccessorImpl.invoke (DelegatingMethodAccessorImpl.java:43) java.base / java.lang.reflect.Method.invoke (Method.java:566) org.springframework.web.method.support.InvocableHandlerMethod.doInvoke (InvocableHandlerMethod.java: 215) org.springframework.web.method.support.InvocableHandlerMethod.invokeForRequest (InvocableHandlerMethod.java:142) org.springframework.web.servlet.mvc.method.annotation.ServletInvocableHandlerMethod.invokeAndHandle (ServletInvocableHandlerMethod.java:102) org.springframework.web.servlet.mvc.method.annotation.RequestMappingHandlerAdapter.invokeHandlerMethod (RequestMappingHandlerAdapter.java:895) org.springframework.web.servlet.mvc.method.annotation.RequestMappingHandlerAdapter.handleInternal (RequestMappingHandlerAdapter.java:800) org.springframework.web.servlet.mvc.method.AbstractHandlerMethodAdapter.handle (AbstractHandlerMethodAdapter.java:87) org.springframework.web.servlet.DispatcherServlet.doDispatch (DispatcherServlet.
java:1038) org.springframework.web.servlet.DispatcherServlet.doService (DispatcherServlet.java:942) орг.springframework.web.servlet.FrameworkServlet.processRequest (FrameworkServlet.java:998) org.springframework.web.servlet.FrameworkServlet.doGet (FrameworkServlet.java:890) javax.servlet.http.HttpServlet.service (HttpServlet.java:626) org.springframework.web.servlet.FrameworkServlet.service (FrameworkServlet.java:875) javax.servlet.http.HttpServlet.service (HttpServlet.java:733) org.apache.catalina.core.ApplicationFilterChain.internalDoFilter (ApplicationFilterChain.java:227) org.apache.catalina.core.ApplicationFilterChain.doFilter (ApplicationFilterChain.java:162) org.apache.tomcat.websocket.server.WsFilter.doFilter (WsFilter.java:53) org.apache.catalina.core.ApplicationFilterChain.internalDoFilter (ApplicationFilterChain.java:189) org.apache.catalina.core.ApplicationFilterChain.doFilter (ApplicationFilterChain.java: 162) org.apache.catalina.filters.HttpHeaderSecurityFilter.
doFilter (HttpHeaderSecurityFilter.java:126) org.apache.catalina.core.ApplicationFilterChain.internalDoFilter (ApplicationFilterChain.java:189) org.apache.catalina.core.ApplicationFilterChain.doFilter (ApplicationFilterChain.java:162) org.springframework.web.servlet.resource.ResourceUrlEncodingFilter.doFilter (ResourceUrlEncodingFilter.java:63) орг.apache.catalina.core.ApplicationFilterChain.internalDoFilter (ApplicationFilterChain.java:189) org.apache.catalina.core.ApplicationFilterChain.doFilter (ApplicationFilterChain.java:162) org.springframework.web.filter.OncePerRequestFilter.doFilter (OncePerRequestFilter.java:101) org.apache.catalina.core.ApplicationFilterChain.internalDoFilter (ApplicationFilterChain.java:189) org.apache.catalina.core.ApplicationFilterChain.doFilter (ApplicationFilterChain.java:162) org.springframework.web.filter.OncePerRequestFilter.doFilter (OncePerRequestFilter.java:101) org.apache.catalina.core.ApplicationFilterChain.internalDoFilter (ApplicationFilterChain.
java:189) org.apache.catalina.core.ApplicationFilterChain.doFilter (ApplicationFilterChain.java:162) org.springframework.web.filter.OncePerRequestFilter.doFilter (OncePerRequestFilter.java:101) орг.apache.catalina.core.ApplicationFilterChain.internalDoFilter (ApplicationFilterChain.java:189) org.apache.catalina.core.ApplicationFilterChain.doFilter (ApplicationFilterChain.java:162) org.springframework.boot.web.servlet.support.ErrorPageFilter.doFilter (ErrorPageFilter.java:130) org.springframework.boot.web.servlet.support.ErrorPageFilter.access $ 000 (ErrorPageFilter.java:66) org.springframework.boot.web.servlet.support.ErrorPageFilter $ 1.doFilterInternal (ErrorPageFilter.java:105) org.springframework.web.filter.OncePerRequestFilter.doFilter (OncePerRequestFilter.java:107) org.springframework.boot.web.servlet.support.ErrorPageFilter.doFilter (ErrorPageFilter.java:123) org.apache.catalina.core.ApplicationFilterChain.internalDoFilter (ApplicationFilterChain.java:189) org.apache.
catalina.core.ApplicationFilterChain.doFilter (ApplicationFilterChain.java: 162) org.springframework.boot.actuate.web.trace.servlet.HttpTraceFilter.doFilterInternal (HttpTraceFilter.java:90) org.springframework.web.filter.OncePerRequestFilter.doFilter (OncePerRequestFilter.java:107) org.apache.catalina.core.ApplicationFilterChain.internalDoFilter (ApplicationFilterChain.java:189) org.apache.catalina.core.ApplicationFilterChain.doFilter (ApplicationFilterChain.java:162) орг.springframework.web.filter.RequestContextFilter.doFilterInternal (RequestContextFilter.java:99) org.springframework.web.filter.OncePerRequestFilter.doFilter (OncePerRequestFilter.java:107) org.apache.catalina.core.ApplicationFilterChain.internalDoFilter (ApplicationFilterChain.java:189) org.apache.catalina.core.ApplicationFilterChain.doFilter (ApplicationFilterChain.java:162) org.springframework.web.filter.FormContentFilter.doFilterInternal (FormContentFilter.java:92) org.springframework.web.filter.OncePerRequestFilter.
doFilter (OncePerRequestFilter.java:107) org.apache.catalina.core.ApplicationFilterChain.internalDoFilter (ApplicationFilterChain.java:189) org.apache.catalina.core.ApplicationFilterChain.doFilter (ApplicationFilterChain.java:162) org.springframework.web.filter.HiddenHttpMethodFilter.doFilterInternal (HiddenHttpMethodFilter.java: 93) org.springframework.web.filter.OncePerRequestFilter.doFilter (OncePerRequestFilter.java:107) org.apache.catalina.core.ApplicationFilterChain.internalDoFilter (ApplicationFilterChain.java:189) org.apache.catalina.core.ApplicationFilterChain.doFilter (ApplicationFilterChain.java:162) org.springframework.boot.actuate.metrics.web.servlet.WebMvcMetricsFilter.filterAndRecordMetrics (WebMvcMetricsFilter.java:154) орг.springframework.boot.actuate.metrics.web.servlet.WebMvcMetricsFilter.filterAndRecordMetrics (WebMvcMetricsFilter.java:122) org.springframework.boot.actuate.metrics.web.servlet.WebMvcMetricsFilter.doFilterInternal (WebMvcMetricsFilter.java:107) org.
springframework.web.filter.OncePerRequestFilter.doFilter (OncePerRequestFilter.java:107) org.apache.catalina.core.ApplicationFilterChain.internalDoFilter (ApplicationFilterChain.java:189) орг.apache.catalina.core.ApplicationFilterChain.doFilter (ApplicationFilterChain.java:162) org.springframework.web.filter.CharacterEncodingFilter.doFilterInternal (CharacterEncodingFilter.java:200) org.springframework.web.filter.OncePerRequestFilter.doFilter (OncePerRequestFilter.java:107) org.apache.catalina.core.ApplicationFilterChain.internalDoFilter (ApplicationFilterChain.java:189) org.apache.catalina.core.ApplicationFilterChain.doFilter (ApplicationFilterChain.java:162) org.apache.catalina.core.StandardWrapperValve.invoke (StandardWrapperValve.java:202) org.apache.catalina.core.StandardContextValve.invoke (StandardContextValve.java:97) org.apache.catalina.authenticator.AuthenticatorBase.invoke (AuthenticatorBase.java:542) org.apache.catalina.core.StandardHostValve.invoke (StandardHostValve.
java:143) org.apache.catalina.вентили.ErrorReportValve.invoke (ErrorReportValve.java:92) org.apache.catalina.valves.AbstractAccessLogValve.invoke (AbstractAccessLogValve.java:687) org.apache.catalina.core.StandardEngineValve.invoke (StandardEngineValve.java:78) org.apache.catalina.connector.CoyoteAdapter.service (CoyoteAdapter.java:357) org.apache.coyote.http11.Http11Processor.service (Http11Processor.java:374) org.apache.coyote.AbstractProcessorLight.process (AbstractProcessorLight.java:65) org.apache.coyote.AbstractProtocol $ ConnectionHandler.process (AbstractProtocol.java:893) org.apache.tomcat.util.net.NioEndpoint $ SocketProcessor.doRun (NioEndpoint.java:1707) org.apache.tomcat.util.net.SocketProcessorBase.run (SocketProcessorBase.java:49) java.base / java.util.concurrent.ThreadPoolExecutor.runWorker (ThreadPoolExecutor.java:1128) Ява.base / java.util.concurrent.ThreadPoolExecutor $ Worker.run (ThreadPoolExecutor.java:628) org.apache.tomcat.util.threads.TaskThread $ WrappingRunnable.
run (TaskThread.java:61) java.base / java.lang.Thread.run (Thread.java:834)
Ультразвуковая сварка — конструкция компонентов и параметры сварки
Знание профессии 62
Введение
Одним из ключевых факторов успешной ультразвуковой сварки является хорошая конструкция компонентов, в частности, форма соединяемых поверхностей , то есть конструкция соединения.Возможны различные конструкции шарниров, каждая из которых имеет свои особенности и преимущества. Выбор дизайна зависит от следующих факторов:
- Тип термопласта
- Геометрия детали
- Требования к сварке
- Эстетика
Одним из основных требований к конструкции любого соединения для ультразвуковой сварки является небольшая однородная начальная площадь контакта. Это может быть достигнуто с помощью выступа или среза.
Выступ
Базовый выступ или шарнир директора энергии показан на Рис. 1 . Соединение состоит из небольшого треугольного участка, сформованного в компонент и обычно идущего по периметру соединения. Назначение регулятора энергии состоит в том, чтобы сфокусировать ультразвуковую энергию на вершине, что приводит к быстрому накоплению тепла. Это заставляет треугольное сечение плавиться и течь через стык, образуя сварной шов.
Тип свариваемого термопласта определяет форму треугольного директора энергии. Аморфные материалы требуют прямоугольного треугольника с углом 90 ° на вершине.Для полукристаллических материалов используется равносторонний выступ 60 °. Типичная высота направляющих энергии составляет от 0,2 до 1,0 мм, в зависимости от материала.
Выступающий шарнир рекомендуется использовать с аморфными материалами, такими как поликарбонат, АБС и полистирол, где герметичное уплотнение не требуется.
На фиг. 2 показан вариант выступа в форме гребня и паза. Преимущество этой конструкции заключается в том, что сварной заусенец скрыт, а соединяемые детали самодостаточны. Однако прочность соединения относительно мала, поскольку ширина сварного шва составляет лишь половину ширины соединения.
Сдвиговое соединение
Для некоторых приложений выступающий шарнир может не обеспечить достаточной прочности. В таких случаях можно использовать соединение со сдвигом.
Базовая конструкция соединения, работающего на сдвиг, показана на рис. 3 . Соединение позволяет одному компоненту сдвигаться внутри другого, обеспечивая самоопределение. Сварка выполняется сначала плавлением небольшой начальной контактной площади, а затем продолжением плавления с контролируемым натягом вдоль вертикальных стенок, когда части телескопируются вместе.Смазывающее действие двух поверхностей расплава на границе раздела сварного шва выгодно по двум причинам.
Во-первых, он устраняет утечки и пустоты, благодаря чему получается прочный герметичный сварной шов. Во-вторых, исключает попадание на воздух, предотвращая преждевременное застывание. Это особенно важно для полукристаллических материалов, которые быстро переходят из расплавленного состояния в твердое. Таким образом, полукристаллические материалы следует сваривать только ультразвуковой сваркой со сдвигом.
Вертикальный размер сварного шва, обычно между 1.0 и 1,5 мм, контролирует прочность соединения и может регулироваться в соответствии с требованиями приложения.
При проектировании этого типа соединения следует учитывать, что толщина стенки нижней части должна быть достаточной для предотвращения смещения наружу во время сварки. Также должна быть предусмотрена боковая опора из зажимного приспособления.
Другие конструктивные особенности
Помимо конструкции соединения, для обеспечения эффективности ультразвуковой сварки необходимо учитывать другие аспекты литого компонента.
Расстояние между линией стыка и контактной поверхностью в месте соприкосновения сварочного рожка с компонентом может иметь решающее значение. Сварка в дальней зоне, как показано на Рис. 4 , — это когда расстояние больше 6 мм. Такое расположение лучше всего подходит для жестких аморфных материалов, таких как полистирол, АБС и ПММА, которые обладают хорошими свойствами передачи ультразвука. Многие полукристаллические материалы, такие как полипропилен, плохо передают ультразвуковую энергию, поэтому соединение должно быть как можно ближе к области сварочного рожка.Это называется сваркой в ближнем поле, как показано на Fig.5 .
Для всех материалов предпочтительнее использовать сварку в ближней зоне, поскольку она требует более короткого времени сварки и более низкого давления.
Следует избегать острых углов отливки, так как они могут локализовать напряжение, которое может привести к разрушению под действием энергии ультразвуковых колебаний. Предлагаются минимальные радиусы от 0,2 до 0,5 мм.
Параметры сварки
Есть ряд параметров, которые необходимо правильно выбрать, чтобы добиться хороших ультразвуковых сварных швов.К ним относятся амплитуда вибрации, режим сварки, снижение скорости, давление срабатывания, время сварки, время выдержки. В данной статье рассмотрены амплитудный и сварочный режимы.
Амплитуда
Успешная сварка зависит от правильной амплитуды вибрации на конце сварочного рожка. Для любой комбинации бустер / рупор амплитуда фиксирована. Выбор амплитуды основан на свариваемом термопласте, так что достигается надлежащая степень плавления. Как правило, полукристаллические материалы требуют больше энергии и, следовательно, большей амплитуды кончика рупора по сравнению с аморфными материалами.
Управление процессом на современных аппаратах для ультразвуковой сварки позволяет профилировать амплитуду. Высокая амплитуда может использоваться для начала плавления, а затем более низкая амплитуда для регулирования вязкости расплавленного материала.
Режимы сварки
Сварка по времени называется процессом без обратной связи. Свариваемые компоненты собираются в приспособлении до того, как сварочный рог опустится и войдет в контакт. Затем ультразвук применяется к сборке в течение фиксированного времени, обычно между 0.От 2 до 1,0 секунды. Этот процесс не свидетельствует об успешной сварке.
Он работает исходя из предположения, что фиксированное время сварки приведет к тому, что к стыку будет приложено фиксированное количество энергии, что даст контролируемое количество расплава. В действительности мощность, необходимая для поддержания амплитуды, никогда не бывает одинаковой от одного цикла к другому. Это связано с такими факторами, как соответствие компонентов.
Следовательно, поскольку энергия является функцией мощности и времени, а время фиксировано, применяемая энергия будет варьироваться от одного компонента к другому.Для массового производства, где важна консистенция, это нежелательно.
Энергетическая сварка — это процесс с обратной связью. Программное обеспечение ультразвуковой машины измеряет потребляемую мощность и регулирует время воздействия таким образом, чтобы в сустав поступала желаемая энергия.
В этом процессе предполагается, что если потребляемая энергия одинакова для каждого сварного шва, количество расплавленного материала в соединении каждый раз одинаково. Однако на самом деле в сварочной трубе и особенно на границе раздела между сварочным рожком и компонентом возникают потери энергии.
В результате некоторые компоненты могут получать больше энергии, чем другие, что может привести к непостоянной прочности сварных швов.
Сварка на расстоянии позволяет соединять компоненты на определенную глубину сварного шва. Этот режим работает независимо от времени, энергии или потребляемой мощности и компенсирует любые отклонения допусков в формованных компонентах, тем самым давая наилучшую гарантию того, что одно и то же количество материала в соединении будет плавиться каждый раз. В целях контроля качества могут быть установлены ограничения на количество потребляемой энергии или время, необходимое для сварки.
См. Дополнительную информацию о сварке и испытаниях пластмасс или свяжитесь с нами.
Влияние параметров сварки на пиковую нагрузку и поглощение энергии точечной контактной сваркой низкоуглеродистой стали
Влияние переменных процесса (давление электрода, время выдержки, сварочный ток и время сварки) на характеристики точечной сварки сопротивлением низкоуглеродистой стали были исследованы в этой статье. Режим отказа, пиковая нагрузка и максимальная энергия, полученные при испытании на растяжение и сдвиг, были использованы для описания характеристик точечной сварки. Чрезмерное давление на электрод может значительно снизить как пиковую нагрузку, так и максимальную энергию. Время выдержки существенно не влияет на пиковую нагрузку и максимальную энергию исследуемого материала. Увеличение времени сварки и сварочного тока в некоторой степени увеличивает как пиковую нагрузку, так и максимальную энергию. Однако чрезмерное время сварки и сварочный ток не только не увеличивают размер сварных швов и максимальную нагрузку, но и снижают максимальную энергию.
1. Введение
В течение нескольких десятилетий контактная точечная сварка была доминирующим процессом соединения листового металла.Чтобы гарантировать и поддерживать структурную целостность готового компонента в широком диапазоне рабочих условий, например в аварийной ситуации, необходимо исключить малейшую возможность получения хотя бы одного или двух дефектных сварных швов в критическом компоненте. Эти требования в сочетании с неопределенностями в отношении качества сварных швов из-за сложности применения неразрушающих испытаний к точечным сварным швам ответственны за практику выполнения большего количества точечных сварных швов, чем фактически необходимо для поддержания структурной целостности. Современная машина имеет от 2000 до 5000 сварных точек. Примерно от 20% до 30% этих точечных сварных швов происходит из-за неопределенности качества точечной сварки [1]. Значительные затраты, связанные с сваркой со сваркой, создают значительную движущую силу для оптимизации этого процесса.
Таким образом, оценка качества точечной сварки является очень важным вопросом с точки зрения надежности автомобиля и повышения экономики производства автомобилей. Оценка качества точечной сварки требует изучения переменных процесса сварки и взаимосвязи характеристик сварки.Характеристики сварных швов обычно относятся к статической и динамической прочности. Испытание на растяжение и сдвиг является наиболее обычным испытанием для оценки механических свойств точечной сварки в статических условиях как из-за его простоты, так и из-за того, что многие сваренные точечной сваркой конструкции рассчитаны на то, чтобы выдерживать нагрузки сдвига и растяжения. На Рисунке 1 схематично показана типичная кривая нагрузка-смещение при испытании на растяжение-сдвиг для точечной сварки. Большинство исследователей использовали пиковую нагрузку (𝑃max), извлеченную из графика «нагрузка-смещение», для описания механического поведения точечной сварки.Однако, как отмечает Zhou et al. [2], максимальная энергия (𝑊max), соответствующая пиковой нагрузке, должна использоваться для более точного описания механического поведения точечной сварки. Max показывает способность точечной сварки поглощать энергию, и чем выше 𝑊max, тем выше надежность сварки в условиях ударов, таких как аварии.
Целью статьи является оценка влияния параметров сварки (сварочный ток, время сварки, сила электрода, время выдержки) на пиковую нагрузку, поглощение энергии и режим отказа точечных сварных швов с низким углеродным сопротивлением при статическом растяжении. испытание на сдвиг.
2. Методика эксперимента
В данном исследовании использовалась низкоуглеродистая сталь без покрытия толщиной 0,8 мм, используемая в автомобильной промышленности. Химический состав стали: Fe – 0,045C – 0,032Si – 0,189 Mn. Сварочные швы выполнялись точечной сваркой на переменном токе мощностью 120 кВА. Механические свойства основного металла приведены в таблице 1.
|
Точечная сварка сопротивлением выполнялась с помощью машины для контактной точечной сварки переменного тока 120 кВА с управлением от ПЛК.Сварка проводилась с помощью электрода RWMA класса 2 с усеченным конусом под углом 45 градусов и торцевым диаметром 5 мм.
Для изучения влияния условий сварки на режим разрушения сварного шва использовалось несколько графиков сварки. В таблице 2 показаны переменные процесса, использованные в этом исследовании. Были зарегистрированы критические условия сварки, приводящие к выталкиванию. Для каждого режима сварки были подготовлены четыре образца, включая три образца для испытания на растяжение-сдвиг и один образец для металлографического исследования и измерения размера сварного шва.
| ||||||||||||||
* 1 цикл = 50 Гц. |
Чтобы оценить механические характеристики и характер разрушения точечных сварных швов, было проведено испытание на растяжение и сдвиг. На рисунке 2 показаны размеры образца. Испытания на растяжение-сдвиг проводились при поперечной головке 10 мм / мин на универсальной испытательной машине Instron. Пиковая нагрузка (измеренная как пиковая точка на кривой нагрузка-смещение) и энергия отказа (измеренная как площадь под кривой нагрузка-смещение до пиковой нагрузки) были извлечены из кривой нагрузка-смещение (см. Рисунок 1).Точки данных для пиковой нагрузки и энергии отказа представляют собой средние значения измеренных значений для трех образцов. Режимы разрушения образцов, сваренных точечной сваркой, определяли путем исследования разрушенных образцов.
Образцы для металлографического исследования были приготовлены с использованием стандартной процедуры металлографии. Для выявления макроструктуры и микроструктуры образцов использовали травильный реагент 2% Nital. Микроструктуру различных зон изучали с помощью оптического микроскопа.Размеры сварных швов (зоны сплавления) измеряли для всех образцов на металлографических сечениях сварных швов.
3. Результаты и обсуждение
3.1. Структура точечного сварного шва и профиль твердости
Типичная макроструктура точечного сварного шва показана на рисунке 3. Как можно видеть, он состоит из трех зон: (i) сварной шов (расплавленный во время процесса сварки и повторно затвердел), (ii) термическое воздействие. зона (HAZ) (не плавится, но претерпела структурные изменения), (iii) основной металл.
Микроструктуры основного металла и ядра сварного шва показаны на рисунке 4.Первый состоит из ферритной матрицы и небольшого количества рассеянного цементита, тогда как доминирующей микроструктурой последнего является мартенсит.
Типичный профиль твердости сварного шва показан на рисунке 5. Как видно из этого рисунка, профиль твердости ядра сварного шва состоит из трех зон: ядра сварного шва, HAZ и основного металла. Твердость наггета сварного шва в два раза превышает значение основного металла из-за образования мартенсита в этой зоне. Твердость сварного ядра практически постоянна, что показывает, что, хотя скорость охлаждения не является постоянной по всему сварному шву, она достаточно быстра для создания относительно однородной микроструктуры в этой зоне. Изменение твердости в ЗТВ практически линейно. Сильный градиент микроструктуры в ЗТВ возникает из-за термического градиента цикла сварки, который, в свою очередь, вызывает большие изменения значений твердости.
Об образовании мартенсита в ядре сварного шва во время RSW для низкоуглеродистых сталей также сообщали другие исследователи [2]. Скорость охлаждения выше для процесса контактной точечной сварки по сравнению с другими процессами сварки плавлением, такими как дуговая сварка, электронно-лучевая сварка и лазерная сварка. Volger [3] сообщил, что скорость охлаждения RSW достигает 1000 Ks -1 за нулевое время выдержки.Увеличение времени выдержки увеличивает скорость охлаждения до более чем 10 000 Ks −1 из-за эффекта закалки медного электрода [4]. Такой высокой скорости охлаждения не наблюдается в других процессах сварки плавлением. Это связано с наличием медных электродов с водяным охлаждением и их закаливающим действием, а также коротким циклом сварки.
3.2. Влияние параметров процесса на размер сварного стержня
Влияние давления электрода, времени выдержки, сварочного тока и времени сварки на размер зоны сплавления показано на рисунках 6–9.Размер зоны плавления является одним из наиболее важных факторов, определяющих механические свойства, которые регулируются параметрами процесса. Действительно, размер сварного шва определяется погонной и тепловой энергией. Выделение тепла в точке соединения регулируется сварочным током, временем сварки, статическим (контактным) и динамическим электрическим сопротивлением. Статическое электрическое сопротивление в основном определяется давлением электрода и, в свою очередь, контролирует образование сварных швов [5].
Как видно на Рисунке 6, диаметр сварного шва уменьшается при увеличении силы электрода.Увеличение электродного усилия уменьшает толщину материала между двумя электродами и увеличивает площадь межфазного контакта листа (за счет изменения шероховатости поверхности). Электрическое сопротивление пропорционально длине проводника и обратно пропорционально его площади поперечного сечения. Следовательно, увеличение силы снижает электрическое сопротивление и, таким образом, уменьшает выделяемое тепло на границе раздела.
Как видно на Рисунке 7, диаметр сварного шва не меняется со временем выдержки. Время выдержки электрода на затвердевающем металле шва не влияет на нагревательную часть теплового цикла и, таким образом, не влияет на выделяемое тепло и объем расплавленного металла.Действительно, увеличение времени сварки и сварочного тока увеличивает подвод тепла и, следовательно, размер сварного шва (рисунки 8 и 9). Конечно, на постоянное время увеличение сварочного тока сокращает время, необходимое для достижения температуры плавления, и, следовательно, увеличивает время выдержки при этой температуре (или более высоких температурах). Таким образом, больший объем материала может превысить температуру ликвидуса, что означает образование крупицы большего размера. Скорость изменения диаметра самородка от нуля до максимума при выталкивании неоднородна.Как видно на рисунках 8 и 9, угол наклона кривой диаметра стержня в зависимости от сварочного тока не является равномерным для = 9 циклов. Также кривая зависимости диаметра стержня от времени сварки неоднородна. В областях с высоким сварочным током и большим временем сварки происходит выталкивание (рис. 10)
Согласно Гулду [6], рост сварных швов в зависимости от сварочного тока и времени сварки происходит в четыре этапа: (i) стадия инкубации: не происходит плавления и не формируется самородок, (ii) стадия образования самородка и стадия быстрого роста самородка, (iii) стадия медленного роста самородка, (iv) выталкивание.
В самом деле, на скорость роста ядер сварного шва влияют два явления: увеличение электрического сопротивления из-за повышения температуры металлов и уменьшение электрического сопротивления из-за образования и роста сварных швов. На ранних стадиях роста сварного шва, когда сварной шов небольшой, увеличение сопротивления из-за нагрева материала (из-за сварочного тока или времени сварки) преодолевает снижение сопротивления из-за роста сварного шва. Однако увеличение диаметра ядра сварного шва увеличивает эффект уменьшения сопротивления, вызванного ростом ядра сварного шва.Следовательно, скорость роста сварных швов снижается при дальнейшем увеличении сварочного тока или времени сварки.
3.3. Влияние режима отказа на характеристики сварного шва
Режим отказа является качественным критерием качества сварки. Как правило, точечные сварные швы выходят из строя в двух режимах: межфазной и отрывной. В режиме межфазного разрушения разрушение происходит из-за распространения трещины через сварной стержень, в то время как в режиме отрыва разрушение происходит из-за полного или частичного вытягивания сварного стержня из металлического листа.
Влияние режима отказа на 𝑃max и 𝑊max показано на рисунке 11. Как видно, режим отказа сильно влияет на пиковую нагрузку сварного шва и максимальную энергию. Максимальная энергия и максимальная нагрузка имеют меньшее значение для режима межфазного разрушения по сравнению с режимом отрыва. Типичные поверхности излома точечной сварки для режимов межфазного и разрывного разрушения показаны на рисунке 12. Как видно, пластическая деформация практически не наблюдается для режима межфазного разрушения, в то время как режим отрыва, сопровождающийся значительной пластической деформацией, обнаружен, что при низком сварочном токе и сварке время разрушение происходит в межфазном (сдвиговом) режиме.Увеличение сварочного тока и времени сварки увеличивает диаметр сварного шва и, таким образом, меняет режим отказа на режим отрыва. Время выдержки не влияет на размер сварного шва и режим отказа. Повышение давления электрода приводит к чрезмерному уменьшению размера сварного шва и изменению режима отказа с вырывания на межфазный.
3.4. Влияние параметров процесса на пиковую нагрузку и поглощение энергии
Пиковая нагрузка (𝑃max) и максимальное поглощение энергии (𝑊max) точечных сварных швов зависит от их физических характеристик, особенно от размера сварных швов и прочности в месте разрушения [7]. Пиковая точка на графике «нагрузка-смещение» при испытании на сдвиг и растяжение соответствует точке распространения трещины через острие сварного шва для межфазного режима и точке перегиба в месте разрушения для режима отрыва. Для межфазного режима, чем больше размер самородка, тем выше сопротивление сдвигу на границе раздела. Для режима вытягивания увеличение диаметра стержня увеличивает сопротивление стержня к скручиванию и, следовательно, увеличивает требуемую силу для образования шейки в месте повреждения. В обоих случаях увеличение диаметра сварного шва увеличивает необходимое усилие для возникновения разрушения.Как видно на Рисунке 6, увеличение давления электрода уменьшает размер сварных швов и, следовательно, пиковую нагрузку точечной сварки и поглощение энергии. Увеличение времени выдержки существенно не влияет на пиковую нагрузку и поглощение энергии (Рисунок 7). Как видно на рисунках 13 и 14, увеличение сварочного тока и времени сварки увеличивает пиковую нагрузку точечной сварки в результате увеличения диаметра стержня.
Как видно на рисунках 13 и 14, в области сильного тока при = 9 циклов и в области большого времени сварки при = 9 кА диаметр сварочного стержня и, следовательно, прочность сварного шва не зависят от параметров сварки.На рис. 15 показаны максимальные изменения энергии в зависимости от сварочного тока для двух периодов сварки. Как видно, для 𝑡 = 7 циклов максимальная энергия увеличивается с увеличением сварочного тока. В то время как для = 9 циклов увеличение сварочного тока увеличивает максимальную энергию до критической точки, после чего она снижается до даже ниже значений, соответствующих меньшему времени сварки (= 7 циклов). Максимальные изменения энергии в зависимости от времени сварки для двух постоянных токов показаны на рисунке 16. Когда происходит выталкивание, 𝑊max уменьшается, несмотря на постоянный диаметр сварного шва.
Сильное вдавливание электрода, связанное с выталкиванием, является основной причиной снижения энергии отказа при высоких сварочных токах и времени сварки. Вмятины на электродах влияют на место повреждения, и образцы, испытывающие выталкивание, разрушаются на краю сварного шва. Пластичность сварного шва для этих образцов меньше, чем ее значение для этих образцов, разрушающихся на основном металле из-за более высокой твердости кромки сварного шва. Следовательно, разрушение кромки сварного шва сопровождается меньшим поглощением энергии.Следовательно, максимальная энергия для тех сварных швов, которые демонстрируют выталкивание, меньше, чем у сварных швов без выталкивания с аналогичными или даже меньшими диаметрами сварных швов.
Таким образом, вопреки некоторым сообщениям о незначительном влиянии вытеснения на характеристики сварного шва, можно увидеть, что, хотя вытеснение не оказывает значительного влияния на прочность сварного шва, оно снижает энергию разрушения. Следовательно, если для описания механического поведения сварного шва используется просто max, негативный эффект вытеснения не может быть обнаружен. Однако, помимо геометрических характеристик сварного шва, таких как сварной шов, выталкивание также может существенно повлиять на характеристики точечной сварки сопротивлением.
4. Заключение
Из этого исследования можно сделать следующий вывод. (1) В дополнение к пиковой нагрузке, максимальная энергия должна учитываться для более точного описания механического поведения и производительности точечных сварных швов. (2) Избыточное давление электрода может значительно уменьшить как пиковую нагрузку, так и максимальную энергию. (3) Время выдержки существенно не влияет на пиковую нагрузку и максимальную энергию для исследуемого материала. (4) Увеличение времени сварки и сварочного тока в некоторой степени увеличивает как пиковую нагрузку, так и максимальную энергию.Однако чрезмерное время сварки и сварочный ток не только не увеличивают размер сварных швов и не увеличивают пиковую нагрузку, но и снижают максимальную энергию. (5) Хотя вытеснение может не снизить нагрузочную способность точечной сварки, оно может снизить их способность к поглощению энергии. 𝑊max для образцов, подвергающихся выталкиванию, ниже по сравнению с образцами без вытеснения с идентичным или даже меньшим размером сварного шва.
Знакомство с импульсным GMAW
В каких случаях следует рассмотреть возможность перехода на импульсную сварку MIG? Используйте эти вопросы, чтобы принять решение.
- Не требует ли чрезмерное шлифование и очистка после сварки слишком много времени и денег?
Импульсный режим позволяет использовать весь диапазон скоростей подачи проволоки без использования шарового переноса. Это преимущество при сварке материалов, толщина которых не соответствует режиму струйного переноса или короткого замыкания. Обычный CV потребует глобулярного переноса, что приведет к сильному разбрызгиванию, плохим характеристикам дуги и возможности доработки. Используя импульсную сварку MIG, операторы могут использовать проволоку для переноса на шаровых скоростях, сохраняя при этом чистую дугу и профиль валика.Это уменьшает разбрызгивание, а также время и деньги, затрачиваемые на очистку.
- Трачу ли я много времени на обучение начинающих сварщиков?
Импульсные системы MIG разработаны с синергетическим управлением, которое обеспечивает простоту использования сварщикам любого уровня подготовки. Это означает более простую настройку процесса, что приводит к экономии времени и повышению качества сварки, поскольку помогает гарантировать, что операторы используют правильные параметры для работы.
- Трачу ли я деньги на потраченные впустую материалы из-за деформации или прожога?
Поскольку (как указано ниже) скорость подачи проволоки может быть увеличена в соответствии с силой сварочного тока, скорость перемещения также увеличится.Скорость движения является одним из основных факторов тепловложения: когда скорость движения увеличивается, тепловложение уменьшается. Следовательно, более высокие скорости перемещения импульсной MIG помогают снизить тепловложение, что помогает уменьшить искажения и прогорания, которые могут стоить времени и денег.
- Нужно ли мне повышать производительность моей работы?
Импульсная сварка MIG обычно приводит к увеличению скорости подачи проволоки для соответствия сварочному току по сравнению со стандартным переносом распылением. Это приводит к тому, что в стык попадает больше сварочного металла, что может повысить производительность операции сварки. Способность уменьшать разбрызгивание, искажения и прожиг также помогает повысить производительность, поскольку на эти действия, не добавляющие добавленной стоимости, нужно будет тратить меньше времени.
- Много ли на моем предприятии выполняется сварка в нерабочем положении?
Импульсная сварка MIG обеспечивает лучшее качество сварки и контроль образования луж при сварке в нерабочем положении сплошной или порошковой проволокой.Это приводит к меньшему количеству обрабатываемых деталей и сокращению эксплуатационных расходов.
- Вы хотите сократить расходы на расходные материалы?
При импульсной сварке MIG можно использовать сварочную проволоку большего диаметра. Это связано с тем, что более низкая сила тока лучше контролирует ток, позволяя использовать провод большего диаметра с той же толщиной материала, где обычно требуется провод меньшего диаметра. Это может позволить стандартизировать все сварочные ячейки проволокой большего диаметра, которая обычно предлагает более низкую закупочную цену, чем проволока меньшего диаметра.
Посмотрите это видео, чтобы узнать больше о проблемах, которые заставляют производственные операции использовать импульсную сварку MIG.
.