Плазмотрон — Энциклопедия по машиностроению XXL
Автомат с плазмотроном для воздушно-плазменной резки. [c.136]Плазмотроны, создающие струи плотной низкотемпературной плазмы, широко применяют в различных областях техники. В частности, с их помощью режут н сваривают металлы, накосят покрытия. [c.290]
Плазменное напыление — это разновидность электродугового напыления сжатой дугой. Способ получения плазменной дуги заключается в сжатии столба сварочной дуги путем ее обдувания потоками холодного газа. Устройство для получения плазменной дуги называется плазмотроном. [c.291]
Что такое низкотемпературная и высокотемпературная плазма, а также плазмотрон [c.307]
Рис. 7.28. Конструкция вихревого плазмотрона |
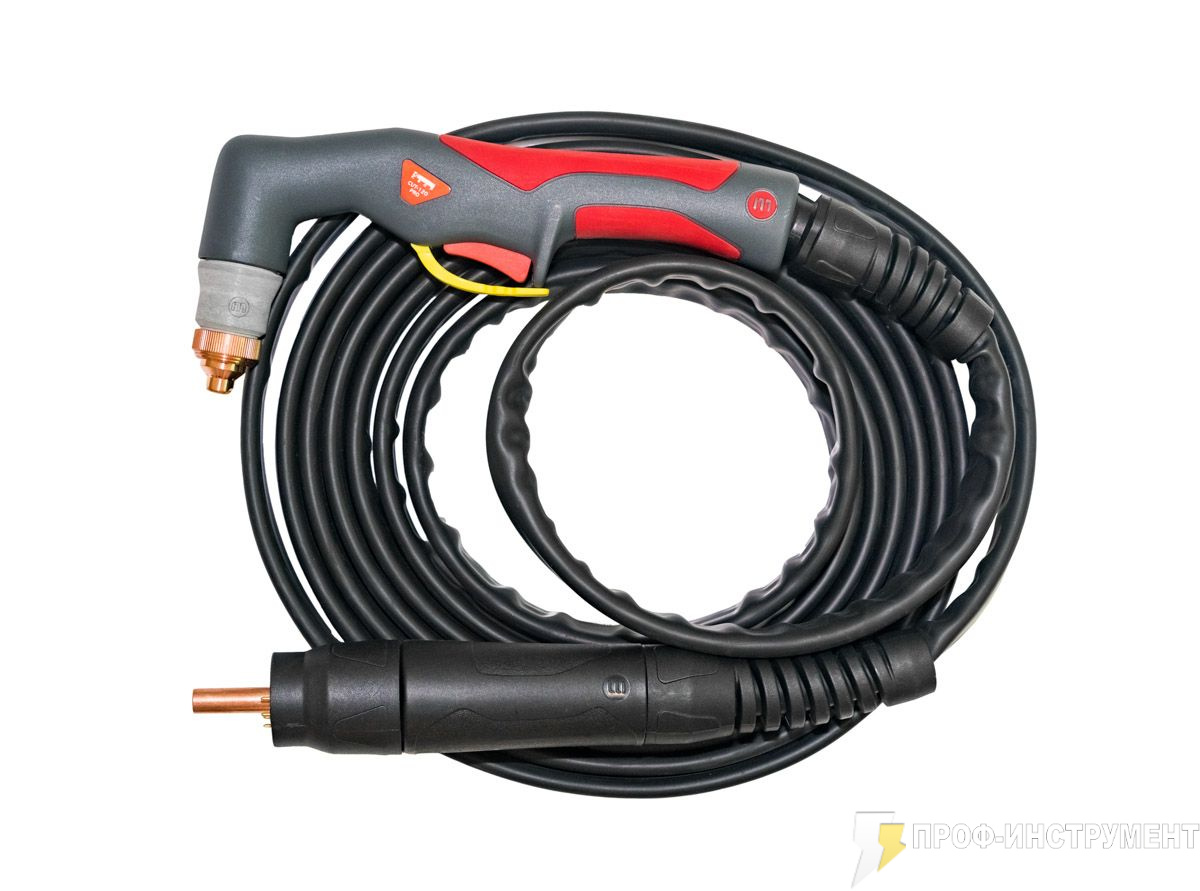
Плазменная струя образуется в канале горелки и стабилизируется стенками канала и холодным газом, отделяющим столб дуги от этих стенок. Сравнительно малый диаметр и достаточная длина канала обеспечивают требуемую для стабилизации плазменного столба скорость газового потока. В наличии стабилизирующего канала и заключается основное отличие плазмотрона от обычной горелки для сварки в защитных газах. [c.103]
Покрытия наносили на образцы из стали 45 на установке плазменного напыления Киев-7 при следующих рабочих режимах напряжение дуги и 220 V, ток плазмотрона I == 210 А, дистанция напыления — 180 мм. [c.62]
При установке оборудования и эксплуатации необходимо учитывать, что для охлаждения плазмотрона и узлов источника питания ИПН 160/600 расходуется 6 — 8 л воды в 1 мин. [c.439]
Рекомендуемые режимы напыления плазмотроном ПП-25 на установке УПУ-ЗД [c.

В спектральном анализе помимо этих основных применяются и другие источники света. К их числу относятся разрядные трубки с полым катодом, плазменные горелки (плазмотроны), представляющие собой генераторы потока плазмы, образующегося при нагревании инертного газа электрической дугой, оптические кван- [c.7]
Плазмотроны. Для исследования обтекания моделей при очень высоких температурах используются электродуговые установки и плазмотроны. Схема одного из плазмотронов, в котором получали струи плазмы с температурой до 12 ООО К, показана на рис. XVI.5. Между цилиндрическим анодом J и катодом 4 образуется электрическая дуга, в область которой через тангенциально расположенные сопла 2 подается вода под давлением. [c.472]
Зажигание плазменного факела 4 производится от внешнего источника, например от дугового разряда, обеспечивающего начальную ионизацию газа. Температура плазмы зависит главным образом от рабочего газа и для аргона составляет 9500—11500 К-Проводимость ионизированного газа много ниже, чем металлов, поэтому плазмотроны работают при частотах 1—40 МГц. В последнее время в связи с увеличением мощности и размеров плазменных факелов происходит переход на более низкие частоты, 440 кГц и ниже. При использовании ферромагнитного сердечника кольцевой разряд возможен даже при средней частоте (10 кГц).
[c.222]
Установки снабжаются блоками плазмотронов для осуществления различных процессов. Мощность подобных установок может достигать 1 МВт и более. [c.222]
Плазменной струей, полученной в столбе дугового разряда независимой дуги, разрезают нез)лектропроводные материалы (напри мер, керамику), тонкие стальные листы, алюминиевые и медные сплавы, жаропрочные сплавы и т. д. При плазменной резке используют аргон, его смесь с водородом, воздух и другие газы. Скорость резки плазменной дугой при прочих равных условиях выше скорости резки плазменной струей. Плазменную резку выполняют специальным резаком, называемым плазмотроном. [c.210]
Плазму получают в плазмотронах (рис.
В комплект оборудования для плазменного напылепия входят плазмотрон источник питания дуги, пускорегулирующая электросиловая аппаратура, система охлаждения, система подачи присадочного материала, манипулятор перемещения плазмотрона при наплавке. [c.292]
В плазмотронных сварочных аппаратах газ ионизируют с помощью высокочастотного электромагнитного поля струю плазмы формируют с помощью электромагнитных катушек. Температура струи до 40000°С. [c.165]
В последние годы закрутку потока стали широко использовать для интенсификации процесса горения.
Вихревые плазматроны или плазмотроны с вихревой стабилизацией плазменного жгута известны давно, и их характеристики можно найти в изданных зарубежных и отечественных монофа-фиях. Однако устройства, генерирующие поток плазмы заданных параметров, целенаправленно использующие характерные особенности эффекта Ранка, впервые были описаны в 1992 г.
В плазмогенераторах с вихревой стабилизацией среднеинте-фальная температура факела возрастает с увеличением интенсивности закрутки потока 5= Vj y — На рис. 7.28 показана схема плазмотрона, использующего в качестве плазмообразующего га- [c.

Периферийный квазипотенци-альный вихрь, выполняя функцию тепловой защиты стенок камеры сгорания и других элементов конструкции, обеспечивает стабилизацию дугового разряда, офани-чивая рост дуги при увеличении рабочего тока [78, 149, 192]. Вихревая характеристика вихревого плазмотрона имеет восходящий участок, наличие которого улучшает технологические качества устройства, обеспечивая возможность гарантированной устойчивой работы дуги на восходящем участке при отсутствии в электрической цепи питания балластного сопротивления. Эго нетрудно показать, воспользовавшись анализом уравнения Кирм-офа, записанного для цепи электропитания плазмотрона [78]. Горение дуги будет устойчивым, если действительные части корней уравнения Кирхгофа отрицательны
Возможность эффективной тепловой зашиты корпусных элементов от больших тепловых потоков успешно используется и при создании экспериментальных СВЧ плазмотронов [64]. Схемы СВЧ плазмотронов с предполагаемыми картинами течений при прямоточно-вихревой и возвратно-вихревой стабилизации плазмы показаны на рис. 7.30, а на рис. 7.31 показана зависимость мощности плазменного СВЧ излучения поглощаемого разрядом, и тепловой мощности fV , вьшеляюшейся в контуре охлаждения плазмотрона. Результаты опытов приведены в виде зависимости доли тепловых потерь WJW от удельного вклада энергии в разряд У = WJG, где G — расход плазмообразуюшего газа — азота. Результаты численного моделирования показаны на рис. 7.32,а — для традиционной прямоточно вихревой стабилизации и на рис. 7.32,6 — для случая с возвратно-вихревой стабилизацией. В первом случае рабочее тело — плазмообразующий газ — азот в виде закрученного потока подается в разрядную камеру, а во втором случае он подается в дополнительную вихревую камеру со скоростями 100 м/с ((7= 1 г/с) и 225 м/с ((7= 1,5 г/с), соответственно. По мнению автора работы [64] возвратный вихрь сжимает зону нагрева, предохраняя стенки камеры плазмотрона от перегрева. Основная часть газа проходит через разрядную зону, а размер зоны рециркуляции незначителен. В традиционной схеме (см.
Рис. 7.25. Зависимость тепловых потерь в плазмотроне от удельного энерговкла-ла и способа формирования вихря |

В качестве плазмообразующего материала обычно применяют газы (аргон, азот, гелий, водород, воздух и их смеси и др.), а также воду (в плазмотронах с водяной стабилизацией), что обеспечивает температуру плазмы до 50 000 К (дуга Гердиена). [c.103]
Режимы напыления плазмотроном ПП-25 на установке УПУ-ЗД приведены в табл. 115. Режимы могут быть скорректированы в зависимости от типа горелки, массы, размеров, марки материала детали, состава напыляемого материала и плазмообразуюшего газа. [c.440]
Скорость перемещения плазмотрона при напылении гиюских поверхностей составляет 0,033 — 0,066 м/с.
[c.441]
Внутренние превращения характерны для поведения рабочих тел многих энергетических и технологических установок двигателей внутреннего сгорания, плазмотронов, металлургических печей. Для определения параметров равновесного состояния здесь уже недостаточно полученных ранее термодинамических соотношений, устанавливающих связь между температурой, давлением, плотностью, энтропией, внутренней энергией и т. п. Но как будет показано далее, термодинамические методы полностью распространимы и на химически реагирующие системы. [c.158]
Конструкции и характеристики плазмотронов — Справочник химика 21
из «Плазма в химической технологии»
В плазмохимических процессах в равной степени могут быть применены как плазменные генераторы постоянного тока, так и переменного, хотя в настоящее время более детально исследованы плазмотроны постоянного тока.
Так как и А /ц мало зависят от величины силы тока, то потери электродах пропорциональны току дуги. Концентрирование тепловой энергии в приэлектродных пятнах снижает ресурс непрерывной работы плазмотрона. Поэтому увеличение мощности за счет увеличения силы тока нежелательно. Необходимо стремиться поднять напряжение на дуге как можно выше за счет выбора наиболее рациональной конструкции плазмотрона. В этой связи большой интерес представляют плазмотроны переменного тока, в которых напряжение на дуге достигает 6 кв. [c.23]
Плазмотроны постоянного тока. Плазмотроны с горячими тугоплавкими электродами (вольфрамовыми, циркониевыми), как правило, проектируются на мощность в несколько десятков и реже — сотен киловатт. Основным недостатком этой группы плазмотронов является быстрый износ электродов из-за значительных тепловых концентраций на торцовой части электрода. Кроме того, наблюдается недостаточная стойкость материала электродов к восстановительной и окислительной средам.

Конструкция осевого плазмотрона с тугоплавким электродом показана на рис. 4. Плазмотрон предназначен для различных химических процессов. [c.24]
Электропитание такого типа плазмотрона возможно постоянным и переменным током. [c.25]
К недостаткам плазмотронов р горячими расходуемыми электродами следует отнести сложность уплотнения электродов, так как при этом нужно сохранить их подвижность в осевом направлении, и также трудность электрической изоляции. [c.25]
Ниже кратко описаны конструкции некоторых плазмотронов.

При некотором значении тока и расхода газа, минимальная длина дуги определяется суммарной длиной диафрагм, а место шунтирования дуги находится сразу же после диафрагмы. При увеличении тока или уменьшении расхода газа опорные точки дуги должны перемещаться в диафрагму. Однако, это происходит не сразу, так как диаметр диафрагмы значительно меньше диаметра электрода. Для пробоя пристеночного слоя в диафрагме сила тока должна достичь определенной величины. Благодаря обжатию дугового столба в диафрагме и фиксированной длине дуги вольтамперная характеристика плазмотрона получается возрастающей. При дальнейшем увеличении тока или при уменьшении расхода газа начинается пробой пристеночного слоя в диафрагмах. При этом установка превра-. щается в обычный линейный плазмотрон с падающей вольтамперной характеристикой. [c.27]
Спинком и Гайлом [134] также исследовано перемещение электрической дуги с током до 10 ООО а под влиянием внешнего мах нитного поля.
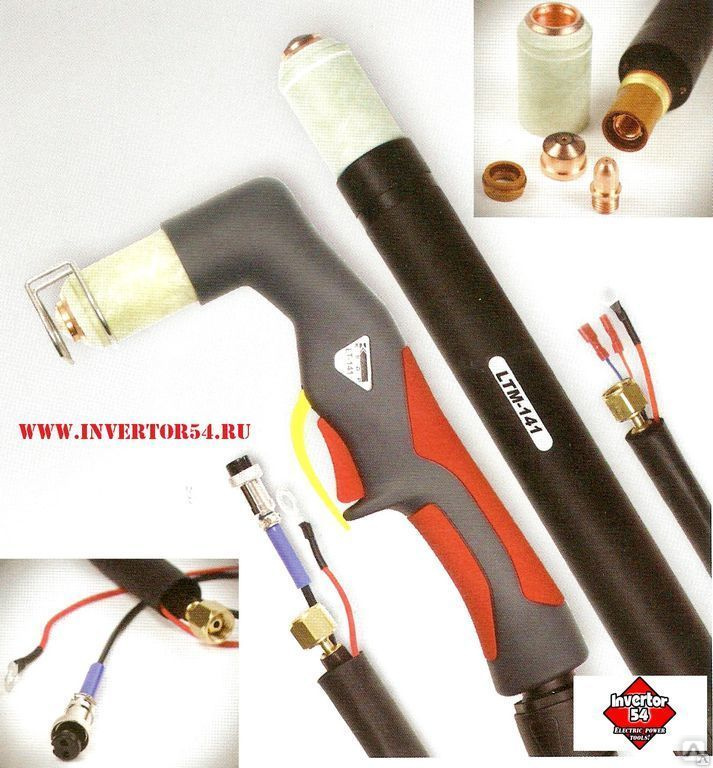
Для уменьшения магнитного сопротивления и созда ния необходимой топологии магнитного поля, корпус 3 и башмаки 2 электромагнита изготовлены из ферромагнитных материалов. Электромагнит соединяется с плазмотроном через изолятор 1. [c.29]
К недостаткам этого плазмотрона следует отнести сложность изготовления пористых электродов и заплавление пор при нарушения оптимальных режимов работы плазмотрона. [c.30]
Пористые электроды могут работать в аргоновой, метановой, водородной и других средах. [c.30]
Плазмотроны с тороидальными электродами работают как на переменном, так и на постоянном токах.

Обычно в плазмотроне с тороидальными электродами дуга горит в зазоре между ними. Вращение дуги осуществляется с помощью магнитного поля, радиальная составляющая которого получается за счет встречного включения соленоидов. Подача газа в межэлектродный зазор может осуществляться различными способами. [c.31]
Существует несколько конструкций плазмотронов с тороидальными электродами. В качестве примера можно привести генератор мощностью 3000 кет типа Марк-30, предназначенный для превращения метана в этилен, ацетилен и синильную кислоту. Общий вид генератора представлен на рис. 10. К основным узлам его следует отнести корпус диаметром 300 и длиной 450 мм, электроды и соленоиды электромагнитов. Дуга вращается со скоростью 1000 об1сек.

Плазмотроны переменного тока. Необходимость создания плазмотронов, работающих на переменном токе, вызвана высокой стоимостью силового оборудования для плазмотронов постоянного тока. Плазмотроны переменного тока условно можно разделить по применяемому току на однофазные, трехфазные и многофазные. Наиболее широко распространены трехфазные плазмотроны, которые, в свою очередь, отличаются электрическими схемами соединения электродов и типом последних. Электроды в таких плазмотронах могут быть соединены звездой, треугольником и звездой с нулевой точкой в плазме. По типу электродов трехфазные плазмотроны можно разделить на генераторы со стержневыми, цилиндрическими, тороидальными и расходуемыми электродами. [c.31]
Рабочее напряжение плазмотронов этого типа достигает нескольких тысяч вольт при рабочем токе в несколько тысяч ампер.

Из анализа литературных данных можно сделать вывод, что ряд конструкций плазмотронов прошел проверку в промышленных установках и может быть рекомендован к дальнейшему использованию. К таким конструкциям следует отнести плазмотроны с расходуемыми графитовыми электродами (применение возможно при осуществлении ряда синтезов с использованием в качестве одного из исходных компонентов углерода) [136], с тороидальными (кольцевыми) электродами [127], с коаксиальным расположением электродов [51, 52], осевые плазмотроны с фиксированной длиной дуги и др. Указанные типы плазмотронов обеспечивают достаточно большой ресурс работы при значительных мощностях генератора. [c.33]
Вернуться к основной статье
10 типичных ошибок при плазменной резке
1. Использование расходных деталей до отказа
При использовании сильно изношенных расходных деталей могут разрушаться другие комплектующие плазмотрона, что может привести к затратным поломкам резака и длительному простою оборудования. Самый лучший способ узнать состояние деталей резака — оценить качество кромки реза металла. Когда качество резки начнет снижаться — это свидетельствует об износе. Ведите учет среднего срока службы деталей (может выражаться в количестве зажиганий или в фактическом времени «на дуге»), имея эти данные оператор будет знать, когда проверять и заменять расходные части, не доводя до возникновения неустранимых отказов.
2. Преждевременная замена расходных деталей
Диаметрально противоположная ситуация возникает, когда выбраковываются расходные детали, не исчерпавшие свой ресурс. Решение о целесообразности замены деталей следует принимать, исходя из их фактического износа, а не количества часов работы. При проведении внешнего осмотра деталей необходимо обратить внимание на следующие моменты: наличие или отсутствие выемок на внутренней или внешней поверхности сопла, правильность формы отверстия сопла. Деталь подлежит замене только при наличии явных признаков износа. Если таковые отсутствуют, скорее всего, деталь пригодна для дальнейшего использования. Степень износа электрода определяют путем визуальной оценки глубины изъязвления гафниевой вставки в самом центре электрода. Если глубина изъязвления превышает нормативные значения, электрод необходимо заменить. Завихрители газа подлежат замене только в тех случаях, когда при тщательном осмотре в отверстиях выявляются грязь или смазка, трещины, дуговые прожоги или чрезмерный износ. То же самое относится и к защитным колпачкам, которые должны заменяться только при наличии признаков физического повреждения. Часто защитные колпачки можно очистить от брызг металла и использовать повторно.
3. Использование неправильных параметров резки и расходных деталей
Выбор расходных деталей зависит от разрезаемого материала и его толщины, силы тока, плазмообразующего газа и других параметров резки. В руководстве оператора указано, какие расходные детали подходят для различных типов резки. Использование неподходящих расходных деталей может привести к сокращению срока службы деталей и снижению качества резки. Особенно важно эксплуатировать детали при номинальной силе тока. Наилучшего качества резки и наиболее продолжительного срока службы деталей можно достичь, если установить силе тока значение, которое составляет 95 % от номинальной характеристики для сопла. Если сила тока слишком низкая, рез будет неоднородным. Слишком высокая сила тока сокращает срок службы сопла.
4. Неправильная сборка резака
Резак должен быть собран так, чтобы его детали были выровнены и плотно прилегали друг к другу. Это позволит обеспечить хороший электрический контакт и правильный поток газа и охлаждающей жидкости через резак. Выполняя замену деталей, храните расходные детали в чистом пакете, чтобы не допустить загрязнения резака грязью или металлической пылью. При сборке резака очень важно соблюдать чистоту. Этим часто пренебрегают. При нанесении смазки на уплотнительное кольцо оно должно лишь слегка блестеть. Если нанести много смазки, завихритель газа может забиться, а резак может загрязниться металлической пылью. Это может привести к неконтролируемому зажиганию дуги в плазменной камере и в конечном итоге к выходу резака из строя. Запрещается наносить смазку на резаки, поскольку это может привести к разрушительному воздействию дуги и возгораниям внутри резака.
5. Несоблюдение расписания планового техобслуживания
При должном уходе резаки могут работать на протяжении месяцев или даже лет. Должна соблюдаться чистота резьбы резака, а опорные поверхности необходимо проверять на загрязнение и механические повреждения. Необходимо очистить резак от любой грязи, металлической пыли или излишней смазки уплотнительного кольца. Для очистки резака воспользуйтесь ватной палочкой со средством для очистки электрических контактов или перекисью водорода.
6. Игнорирование проверки потока газа или охлаждающей жидкости
Поток и давление газа и охлаждающей жидкости следует проверять каждый день. Если скорость потока недостаточна, расходные детали не будут охлаждаться должным образом, вследствие чего уменьшится срок их службы. Неправильный поток охлаждающей воды из-за закупоренных фильтров, низкого уровня охлаждающей жидкости — это самая распространенная причина выхода из строя деталей и резака. Постоянное давление газа важно для поддержки режущей дуги. Избыточное давление газа — самая распространенная причина затрудненного зажигания дуги. Под этим подразумевается ситуация, при которой резаку не удается зажечь дугу, когда все остальные условия для нормальной работы соответствуют требуемым. Слишком высокое давление газа также приведет к быстрому разрушению электродов. Точно так же, необходимо поддерживать чистоту плазмообразующего газа, чтобы не допустить сокращения срока службы расходных деталей и резака. В системах со сжатым воздухом газы особенно подвержены загрязнению маслом и частицами, а также попаданию влаги.
7. Прожиг на слишком низкой высоте
Расстояние между заготовкой и наконечником резака (отклонение) имеет решающе важное значение как для качества резки, так и для срока службы расходных деталей. Даже небольшие изменения высоты резака могут повлиять на угловатость поверхности резки. Особенно важна высота резака при выполнении прожига. Одна из распространённых ошибок — выполнять прожиг слишком низко. Это приводит к тому, что расплавленный металл забрызгивает передний край сопла и защитного колпачка, вызывая повреждения деталей и последующее ухудшение качества резки. «Подавление» дуги может происходить, даже если резак выполняет прожиг в контакте с металлом или скользит по поверхности при резке. «Подавленная» дуги приводит к разрушению электрода, сопла, завихрителя газа, в некоторых случаях и самого резака. Прожиг на высоте, которая превышает рекомендуемую в 1,5–2 раза, защищает резак и детали от повреждений.
8. Слишком быстрая или слишком медленная резка
Слишком быстрая или слишком медленная резка может привести к ухудшению качества реза. Если скорость резки слишком низкая, на кромках вырезанных деталей образуется «окалина низкой скорости резки», которая представляет собой большие пузырчатые отложения окалины вдоль нижней кромки. Низкие скорости могут также привести к расширению реза и вызвать чрезмерное верхнее разбрызгивание. Если скорость резки слишком большая, то дуга будет запаздывать с перемещением по резу, это приведет к образованию скошенных кромок, узкого реза и небольших затвердевших полосок окалины вдоль нижней кромки реза. Окалину, образовавшуюся при высокой скорости резки, тяжело удалить. При правильной скорости резки образование окалины будет минимальным, что позволит получить чистую кромку, которая требует меньше доработки перед передачей детали на следующий этап производственного процесса.
9. «Растяжение» дуги
Растяжение дуги может происходить в начале и конце реза, если дуга должна «растянуться» (отклониться от прямой перпендикулярной траектории), чтобы войти в контакт с металлом. Растяжение дуги может привести к прожигу боковой стенки сопла. При пуске на краю заготовки плазменную дугу нужно зажигать, когда отверстие сопла находится строго по центру над краем заготовки. Об этом важно помнить при комбинированной обработке металла плазменной резкой и вырубным прессом, когда дуга отклоняется от прямой перпендикулярной траектории, чтобы войти в контакт с металлом. Растяжение дуги может привести к прожигу боковой стенки сопла. При пуске на краю заготовки плазменную дугу нужно зажигать, когда отверстие сопла находится строго по центру над краем заготовки. Об этом важно помнить при комбинированной обработке металла плазменной резкой и вырубным прессом, когда дуга зажигается из пробитого отверстия. В таких случаях дуга должна зажигаться на краю, а не в середине пробитого отверстия. Растяжение дуги также может происходить в конце реза, если резак запрограммирован на выход за пределы листа с включенной дугой или «выход» резака следует за разрезом предыдущего листа металла. Выбор времени сигнала гашения дуги и программирование «выхода» могут минимизировать этот эффект.
10. Удар резака
При механизированной резке удары резака о торец изделия или столкновение его с заготовкой могут привести к неустранимой поломке плазмотрона. Столкновения резака с заготовкой можно предотвратить, запрограммировав траекторию движения системы фигурной резки вокруг вырезанных деталей. Датчики высоты резака также могут обеспечить защиту от ударов резака путем корректировки высоты на отклонения ширины материала. Тщательное программирование выхода и работы системы регулировки высоты резака могут минимизировать этот эффект. И наконец, устройства крепления блока отключения резака могут предотвратить повреждение резака при столкновении.
Плазменная система ПЛАЗАРИУМ TPS:
Плазмотроны в составе плазменной системы TPS:
Примечания: 1 — Существует научная версия плазменной системы с единичным плазмотроном мощностью 15 и 25 кВт (доступно для заказа только университетам и научным организациям), а так же версия плазменной системы с единичным плазмотроном мощностью 35, 50, 65 или 90 кВт. , 2 — Источники питания и другие энергетические системы обеспечивают автоматическую адаптацию к любому входному напряжению в диапазоне 380–450 В для трех фаз. 3 — Возможно изготовление плазмотронов мощностью до 2500 кВт включительно по индивидуальному ТЗ заказчика. 4 — Срок службы расходных элементов зависит от технологии изготовления и типа электрода, типа стабилизации дуги, типа плазмообразующей среды и параметров источника питания. 5 — Плазмотроны разрабатываются под конкретный плазмообразующий газ (ПАР / ВОЗДУХ / АЗОТ / АРГОН / КИСЛОРОД / ВОДОРОД / МЕТАН / СИНТЕЗ-ГАЗ и т.д.) согласно параметрам ТЗ заказчика. 6 — Все параметры плазмотронов и плазменной системы изготавливаются в соответствии с ТЗ заказчика. 7 — Конструктивное исполнение плазмотрона и всей плазменной системы определяется Исполнителем с согласованием габаритных и присоединительных размеров с Заказчиком. |
Плазматрон
Плазмотрон — это устройство,
предназначенное для
- Получение сверхвысоких температур (до 150 000 °C, в среднем получают 10 000-30 000 °C), не достижимых при сжигании химических топлив.
- Компактность и надежность.
- Легкое регулирование мощности, легкий пуск и остановка рабочего режима плазмотрона.
Первые плазмотроны, предназначенные
для исследования газодинамических
параметров, параметров тепло- и массообмена,
механизмов разрушения металлических
и композиционных материалов конструкций
были разработаны в 60-х годах прошлого
столетия в СССР и США и получили
достаточно широкое распространение
в ракетно-космической
Принцип действия плазмотрона
достаточно простой: поскольку электрическая
дуга имеет очень высокую
Для электропитания дуги может
использоваться как постоянный, так
и переменный ток. В настоящее
время подавляющее большинство
плазмотронов работает на постоянном
токе. Эта ситуация обусловлена тем
фактором, что дуга постоянного тока
в принципе горит более устойчиво
по сравнению с дугой переменного
тока. Действительно, протекающий
через дугу переменный ток два
раза за период проходит через нуль.
Иными словами, можно считать, что
дуга периодически погасает и зажигается
вновь. Поэтому для устойчивого
горения дуги переменного тока необходимо
обеспечить условия для ее повторного
зажигания после перехода тока через
нуль.Самым распространенным способом
обеспечения устойчивого В то же время идея питания
дуги в плазмотроне переменным током выглядит
весьма привлекательной по следующим
причинам:
•Источниками постоянного
тока являются, как правило, выпрямительные
устройства, снабженные специальными
электронными регуляторами, которые
обеспечивают устойчивое горение дуги.
Для плазмотронов мегаваттного и
мультимегаваттного уровней такие
устройства превращаются в очень
сложные и главное, дорогие сооружения,
стоимость которых намного
• Известно, что в
плазмотронах постоянного тока ресурс
катода обычно в несколько раз
ниже ресурса анода. В плазмотронах
переменного тока катод и анод
меняются местами с частотой сети
(50Гц), поэтому при прочих равных
условиях ресурс электродов плазмотрона
переменного тока примерно в два
раза выше ресурса электродов плазмотрона
постоянного тока.
ФГУП «Исследовательский
центр им. М.В. Келдыша» разрабатывает
и изготавливает плазмотроны
типа «Звезда». Такие плазмотроны
выполнены по модульному принципу и
по сути состоят из трех отдельных
однодуговых плазмотронов, объединенных
общей смесительной камерой с
выходным соплом, что наглядно демонстрирует
фотография такого плазмотрона мощностью
1МВт. Каждый плазмотрон питается от одной
фазы трехфазной сети. Одинаковые условия
горения каждой дуги обеспечивают равномерную
загрузку трехфазной сети. Основной отличительной
особенностью плазмотронов типа «звезда»
является то, что все три дуги
замыкаются между собой в центре
смесительной камеры по схеме «звезда»,
образуя плазменную нуле-вую точку.
Таким образом, в этом плазмотроне
горят три дуги, однако он содержит
только три электрода вместо шести.
Все узлы плазмотрона охлаждаются
водой. Дальнейшим развитием плазмотронов
этого типа является схема «шестилучевая
звезда». Такой плазмотрон состоит
из шести отдельных однофазных плазмотронов,
объединенных общей смесительной камерой,
внутри которой все шесть дуг
замыкаются между собой. Преимущество
такой схемы заключается в
том, что при одинаковой мощности
величина тока в каждой дуге шестилучевого
плазмотрона вдвое меньше по сравнению
с трехлучевой схемой.
Основные преимущества плазмотронов типа «Звезда» следующие: • Однородные распределения температур и давлений в выходном сечении сопла.
• Симметричная загрузка трехфазной сети.
• Модульная конструкция позволяет увеличивать мощность плазмотрона за счет роста числа модулей. В процессе создания и отработки плазмотронов «Звезда» был решен ряд проблем, обеспечивающих их устойчивую работу в широком диапазоне выходных параметров.
1) Была изучена задача
о вращении приэлектродного В те полупериоды,
когда ножка дуги и газовый
вихрь вращаются в разные
| Основные области применения плазмотронов следующие:
|
В электродуговом плазмотроне
газ, нагреваемый в разряде Увеличение площади осаждения
и снижение себестоимости процесса синтеза
лежит на пути повышения мощности установок.
В Пекинском научно-технический университете
для роста алмазных пластин используется
плазмотрон мощностью 100 кВт. Плазмотрон
мощностью 500 кВт создан в Питтсбурге специалистами
научно-технологического центра корпорации
«Вестингхаус электрик», США . В обоих
реакторах предусмотрено, что рабочий
газ не выбрасывается из камеры, а направляется
повторно в неё для максимально полного
использования реагентов. В 90-х годах фирма
«Нортон» (США) на основе дуговых плазмотронов
освоила промышленное производство алмазных
дисков диаметром до 175 мм.
В плазмогенераторе в стандартной
конфигурации с межэлектродными вставками
при мощности, вкладываемой в разряд 3-8
кВт, давлении 50-100 Торр и расходе газа
30 л/мин получены скорости осаждения до
25 мкм/час на площади до 10 см2. Интересный
метод увеличения площади осаждения при
относительно небольшой мощности, основанный
на идее внешнего расширения плазменной
струи после выхода из сопла плазмотрона
посредством организации дополнительного
разряда ниже по направлению применен
в работе.
Разряд поддерживался
между дополнительным кольцевым
электродом (анодом), сквозь который
проходила плазменная струя и
собственно струёй (катодом). Ниже кольца
узкий высокотемпературный
Разработанные плазмотроны условно делятся на два класса — малой мощности (до 100кВт) и большой мощности (100кВт — 50МВт).
Плазмотроны малой мощности
Это однодуговые плазмотроны с двумя соосными цилиндрическими электродами и вихревой стабилизацией дуги. Источником электропитания дуги является специальное устройство, преобразующее трехфазное напряжение 380В частотой 50Гц в однофазное напряжение 500В частотой несколько кГц.
Плазмотроны охлаждаются
водой.
Рабочим телом плазмотрона может быть практически любой газ (воздух, азот, аргон и т.д.), рабочее давление в камере плазмотрона не более 0,2МПа. При работе на воздухе средняя температура выходящего из плазмотрона газа составляет примерно 6000К, тепловой КПД превышает 80%, ресурс работы сменных медных электродов не менее 500 час.
Плазмотроны большой мощности
Это трехфазные плазмотроны типа «Звезда.» Источником электропитания является промышленная трехфазная сеть напряжением 6 или 10кВ. Выпрямители, трансформаторы или другие преобразователи не используются.
Конструктивно плазмотрон типа
«Звезда» выполнен в виде трех
отдельных однофазных плазмотронов
с вихревой стабилизацией дуги, объединенных
общей смесительной камерой с
выходным соплом. Отличительной особенностью
плазмотронов этого типа является то,
что все три дуги замыкаются между
собой в центре смесительной камеры,
образуя «висячую» нулевую точку.
Таким образом, количество электродов
уменьшается с шести до трех, что
существенно повышает надежность плазмотрона
. Другими преимуществами плазмотронов
этого типа являются симметричная нагрузка
трехфазной сети и равномерные поля
температур и давлений в выходном
сечении сопла.
При мощности плазмотрона более 20МВт используется конструктивная схема с шестью дугами, замыкающимися между собой в смесительной камере в висячей нулевой точке. Увеличение числа дуг позволяет уменьшить величину тока в каждой дуге и тем самым повысить ресурс электродов и надежность плазмотрона.
Плазмотроны охлаждаются водой.
Рабочее тело — воздух и другие
газы.
Максимальное давление в камере — 10 МПа.
Максимальная температура газа при работе
на воздухе — 6000К.
Ресурс медных электродов плазмотрона мощностью 1 МВт при работе на воздухе превышает 500 час.
Типы применяемых плазмотронов.
С прямой дугой.
- С косвенной дугой.
- С электролитическим электродом (электродами).
- С вращающейся дугой.
- С вращающимися электродами.
Высокочастотные:
- Индукционные (нагрев движущихся металлических паров).
- Электростатические.
Комбинированные:
Работают при совместном действии токов высоких частот (ТВЧ) и при горении дугового разряда, в том числе с сжатием разряда магнитным полем.
- Для производства плазменной и микроплазменной сварки в настоящее время применяются следующие установки: УПС-501, УПС-804 и УПС-301 для плазменной сварки и установка А-1342 для микроплазменной сварки
Области применения плазмотронов
- сварка и резка металлов и тугоплавких материалов
- нанесение ионно-плазменных защитных покрытий на различные материалы
- нанесение керамических термобарьерных, электроизоляционных покрытий на металлы
- подогрев металла в ковшах при мартеновском производстве
- получение нанодисперсных порошков металлов и их соединений для металлургии
- двигатели космических аппаратов
- термическое обезвреживание высокотоксичных органических отходов
- Синтез химических соединений (например синтез оксидов азота и др.
,
- Накачка мощных газовых лазеров.
- Плазменная проходка крепких горных пород.
- Безмазутная растопка пылеугольных котлов электростанций.
- Расплавление и рафинирование (очистка) металлов при плазменно-дуговом переплаве.
Моделирование процесса перемещения опорного пятна дуги по стенке канала плазмотрона
Открытые информационные и компьютерные интегрированные технологии № 57, 2012
113
Bjuu
t
ur
r
rrr
×+∇−−∇=
∇⋅+
∂
∂
τρρ
, (6)
( )
Dt
Dp
Tj
e
k
BuEjTkTu
t
T
CB
rp +∇⋅+−×+⋅+∇⋅∇=
∇⋅+
∂
∂r
r
r
r
r
r5
4
περ
, (7)
0
, (8)
jA
0
2
µ
−=∇
. (9)
Особенности моделирования турбулентности
Традиционно в численных расчетах применяют модели турбулентности, ко-
торые базируются на осредненных уравнениях Рейнольдса. Наибольшее распро-
странение получили SA и SST модели турбулентности. Их применение оправдан-
но с точки зрения экономии вычислительных ресурсов, они не чувствительны к ка-
честву сетки, и позволяют получать достоверный результат для безотрывных те-
чений в большинстве случаев. В данном случае система уравнений Навье-Стокса
замыкается моделью турбулентности Спаларта-Аллмареса (SA) которая содержит
одно уравнение переноса:
( )
[ ]
( ) ( )
[ ]
{ }
2
12
~~~~
1
UfvvcvvvDP
vD
tb
vv
∆+∇⋅∇+∇+⋅∇+−=
. (10)
Чаще всего при моделировании течений для плазменного оборудования
необходимо учитывать завихренный характер подачи плазмообразующего газа.
Однако большинство авторов, применяя RANS модели турбулентности, игнори-
руют тот факт, что они не пригодны для описания закрученных течений. Хорошо
известно [10], что кривизна линий тока и вращение потока оказывают существен-
ной влияние на характеристики турбулентности и могут приводить как к ее суще-
ственной интенсификации, так и к подавлению. Эти эффекты, в принципе, авто-
матически описываются в рамках моделей переноса Рейнольдсовых напряжений.
В рамках же линейных моделей для их учета необходимо введение специальных
поправок. Наиболее удачной из таких поправок является, по-видимому, поправка
Спаларта-Шура [11], учитывающая единую природу эффектов кривизны линий то-
ка и вращения и применимая, вообще говоря, к любым линейным моделям. Одна-
ко конкретная калибровка поправки, названной “Rotation-Curvature correction” (RC),
была выполнена для SA модели. Соответствующая (при наличии поправки) вер-
сия последней получила название SARC модели.
В рамках SARC модели генерационный член
v
оригинальной SA модели
(10) модифицируется путем домножения на эмпирическую функцию
( )( )
123
1
1
~
1
1*2
rrr
r
r
CrCarctgC
Cr
f−−
=
, (11)
которая зависит от двух параметров
и
, являющихся мерой кривизны линий
тока и вращения.
Убедительным свидетельством возможностей SARC модели являются ре-
зультаты ее применения для расчета развитого турбулентного течения во вра-
щающемся плоском канале, для которого оригинальная версия модели непригод-
на (дает те же результаты, что и при отсутствии вращения). В качестве примера
на рис. 4 сравниваются профили скорости для такого течения, рассчитанные с ис-
Плазменные горелки– обзор
9.4.4 Проект TyGRe
TyGRe (материалы с высокой добавленной стоимостью из отходов Ty re G asification Re sidues) был совместным проектом девяти европейских партнеров: ENEA (итальянская Национальное агентство новых технологий, энергетики и устойчивого экономического развития), ETRA (Европейская ассоциация по переработке шин), IMEC (Венгерская академия наук), LIQTECH (датский конечный пользователь SiC), TUBITAK (Совет по научным и технологическим исследованиям Турции), RWTH (Университет Аахена), FEBE ECOLOGIC (дочернее предприятие ENEA), ELASTRADE (производитель гранулята) и SICAV (производитель активированного угля). Исследования и разработки были сосредоточены на переработке старых шин с помощью термических процессов, в основном связанных с производством субмикронного карбида кремния. На рис. 9.4.5 показана технологическая схема проекта TyGRe.
Рисунок 9.4.5. Технологическая схема проекта TyGRe.
В процессе TyGRe гранулированные изношенные шины подвергались пиролизу в пилотной вращающейся печи при температуре около 800°C для получения полукокса и неочищенного газа. Массовая скорость гранулированной шины составляла около 20 кг в час, а производство полукокса — около 8 кг в час.Полученный полукокс смешивали с техническим кварцевым песком чистотой 99,5 % и подавали в шаровую мельницу, где измельчали до микрометрового размера. Измельченную смесь просеивали на виброфильтре. Частицы диаметром более 50 мкм отбраковывались. Более мелко просеянную смесь подавали в ВЧ-плазмотрон с частотой 2 МГц, где происходил синтез SiC. Для генерации плазмы использовался газообразный аргон. Отходящий газ из реактора с плазменной горелкой, состоящий из аргона и СО, инжектировали с паром и подавали в реактор конверсии водяного газа, где СО с помощью пара превращался в H 2 и CO 2 . Сдвинутый газ проходил через мембранный модуль, в котором извлекались Ar и H 2 , которые рециркулировали в реактор с плазменной горелкой. Неочищенный газ из пиролизера проходил через блок очистки, где удалялись твердые частицы, смола и вода. Синтез-газ смешивался с мембранным отходящим газом и направлялся на установку очистки газа, состоящую из установок паровой конверсии метана и установки конверсии водяного газа, с целью получения газа, богатого водородом. В противном случае он мог бы питать двигатель внутреннего сгорания для производства электроэнергии (40 кВт и ).Технологическая инфраструктура была установлена и запущена в исследовательском центре ENEA-Trisaia (Италия), как показано на рис. 9.4.6.
Рисунок 9.4.6. Строительство завода TyGRe в ВДНХ-Трисая: (A) пиролизер с вращающейся печью; (B) очистка сырого газа; (C) измельчение смеси, просеивание и система подачи в плазмотронный реактор; (Г) двигатель внутреннего сгорания; (E) модернизация газа; (F) мембранный модуль; (G) особенности плазменной горелки; и (H) реактор с плазменной горелкой.
Сердцем технологической инфраструктуры является плазмотронный реактор для синтеза субмикронного SiC.Остальные модули инфраструктуры основаны на хорошо зарекомендовавших себя технологиях; поэтому основные усилия были направлены на оптимизацию и тонкую настройку реактора с плазменной горелкой для успешного синтеза SiC.
Основные отличия, которые можно отнести к процессу TyGRe по сравнению с обычным процессом Ачесона, включают тот факт, что производство SiC с помощью TyGRe является непрерывным и происходит за десятые доли секунды, в отличие от процесса Ачесона, где производство является периодическим и происходит через несколько дней, а размер частиц, производимых TyGRe, является субмикронным, тогда как крупные частицы производятся Acheson.Измельчение крупных частиц требует больших затрат энергии и времени; кроме того, SiC загрязняется материалом, используемым для измельчения. Наконец, SiC из процесса TyGRe имеет более высокую добавленную стоимость (размер и чистоту), что компенсирует более высокое энергопотребление реактора с плазменной горелкой по сравнению с печью Ачесона.
Плазмотрон . Система подачи порошка смеси прекурсоров состоит из бункера и шнека, оснащенного вибрационной системой, которая предотвращает когезионное и липкое поведение смеси.Газ-носитель (Ar) очищает систему подачи. Смесь аксиально попадает в плазмотрон, в середину плазменного факела, вертикальным зондом. Плазмотрон обеспечивался плазменной микросистемой. Это индукционная горелка RF (2 МГц), установленная в верхней части реактора. ВЧ-плазма обеспечивает наибольший объем и наименьшую скорость плазмообразующих газов (и, как следствие, самое продолжительное время пребывания для инжектированных исходных материалов) при заданном уровне мощности по сравнению с любым другим типом плазмы (например,г., дуга, микроволновка). В качестве плазмообразующего газа использовались аргон/гелий. Гелий увеличивает энергию плазмы [48]. Реактор со стенками из нержавеющей стали косвенно охлаждается водой, протекающей в оболочке, чтобы избежать повреждений из-за высокой температуры плазмы. Охлаждаемая стенка реактора препятствует росту зерен SiC с образованием субмикронных зерен. За реактором установлены сборная емкость, электрофильтр и вытяжной вентилятор. С целью повышения производительности процесса под плазменной горелкой была установлена изостатическая графитовая трубка, ограничивающая пламя плазмы.Изостатический графит выдерживает высокие температуры плазмы, сильный тепловой удар при запуске и тепловое расширение [49].
Метод и результаты . После зажигания факела и установки таких рабочих параметров, как расход плазмообразующего газа, расход газа-носителя смеси и мощность факела, смесь подавалась в реактор плазмотрона. Изображение зажженного плазмотрона во время испытания показано на рис. 9.4.6G. После проведения испытания реактор разбирали и собирали порошок продукта.Он состоял из непрореагировавшего углерода, кремнезема и SiC. Углерод окисляли до СО 2 воздухом в муфеле при 700°С по уравнению. 9.4.5:
(9. 4.5)C+SiO2+SiC+O2=CO2(г)↑+SiO2+SiC
SiO 2 выщелачивали избытком раствора фтороводорода, как в уравнении. 9.4.6:
(9.4.6)SiO2+SiC+6HF=h3SiF6(g)↑+SiC+2h3O
После сушки SiC взвешивали и рассчитывали выход. Точная настройка параметров процесса и изостатическая графитовая трубка обеспечили интересный выход процесса.В частности, выходы выше 70% были получены при массовой скорости смеси 0,6 кг в час, имеющей отношение C/Si, равное 1,3; мощность горелки 65 кВт, расход плазмообразующего газа 150 л (Н) в минуту (90 л (Н) в минуту Ar, 60 л (Н) в минуту He) и 70 л (Н) в минуту газа-носителя Ar . Здесь l(N) относится к литрам при 293,15 К и 1 атм. Рентгенофазовый анализ очищенного порошка SiC также может быть связан с четкими сигналами как α-фазы, так и β-фазы. Анализ динамического светорассеяния (DLS) показал получение субмикронного порошка с гауссовым распределением со средним размером в диапазоне 300–400 нм.СЭМ-изображение подтверждает размер частиц, измеренный с помощью динамического анализа светорассеяния. Что касается морфологии, то на изображении СЭМ порошок выглядит как образованный мелкими сфероидальными частицами и более крупными несфероидальными частицами. В результате глубокого рентгенодифракционного анализа были обнаружены некоторые примеси в порошках SiC. Наиболее распространены кварц, корунд, графит, металлический кремний и силикаты. Их количество колебалось в пределах 1–3 мас.% при выходе выше 70% [39].
Проект TyGRe получил приз Оскара Маси, присуждаемый Итальянской ассоциацией промышленных исследований (AIRI), как лучший проект для экономики замкнутого цикла в категории государственных исследовательских организаций и университетов.Презентация проекта была показана на конференции DG ENVIRONMENT «Что делает успешный экотехнологический европейский проект?», состоявшейся в Брюсселе 20 марта 2017 г. Три научных доклада о производстве карбида кремния с помощью процесса TyGRe, характеристике карбида кремния TyGRe и применении были опубликованы [39,50,51]. Поданы заявки на два итальянских патента, касающихся метода очистки прекурсоров и производства SiC [49–52].
Руководство по расходным материалам для плазменной резки
Расходные материалы для плазменной резки — это набор компонентов вашего плазменного резака, которые со временем изнашиваются и требуют замены.
Оптимальная производительность резки:
Расходные материалы имеют жизненный цикл
Все расходные материалы находятся в самом резаке, где сосредоточена большая часть энергии. Отслеживание износа является ключевой частью поддержания эффективной машины, которая хорошо режет и служит долго.
Расходные материалы для плазменного резака включают: завихритель, электрод, сопло, стопорный колпачок и защитный колпачок.
ВИХРЕВОЕ КОЛЬЦО
Это небольшой компонент внутри горелки, который закручивает газ, окружающий плазменную дугу.Этот внешний слой газа помогает сфокусировать и направить дугу для большей точности резки, а завихрение помогает сохранить ее прохладной. Поскольку именно этот защитный слой газа, окружающий дугу, соприкасается с соплом, более низкие температуры предотвращают возгорание сопла и замедляют разрушение.
ЭЛЕКТРОД
Электрод представляет собой узкий кусок меди, содержащий гафний (который является отличным проводником электричества). Его работа состоит в том, чтобы получать электрический ток от катодного блока внутри горелки, к которой он подключен, и фокусировать заряд через его наконечник, что вызывает дуговой разряд на заготовке.
СОПЛО
Сопло фокусирует плазменную дугу и окружающий ее газ для получения чистого и точного реза. Сопло с большим отверстием используется для строжки, в то время как сопло с меньшим отверстием лучше направляет газ и поэтому используется для тонкой, точной работы.
СТОПОРНАЯ КОЛПАЧКА
Крепежная крышка удерживает вместе все расходуемые части резака. Поскольку температура на этом конце машины чрезвычайно высока, изнашиваются не только детали, создающие и фокусирующие дугу; компонент, удерживающий их вместе, также со временем разрушается.
ЗАЩИТНЫЙ КОЛПАЧОК
Защитный экран предназначен для защиты резака и других его компонентов от искр и расплавленного металла, образующихся в процессе плазменной резки. Он принимает на себя основной удар, чтобы максимально снизить износ других компонентов.
КАК ДОЛГО ДЕЙСТВУЮТ РАСХОДНЫЕ МАТЕРИАЛЫ ДЛЯ ПЛАЗМЕННОЙ РЕЗКИ?
Теперь, когда мы рассмотрели роль каждой из этих расходных частей, мы перейдем к обсуждению срока службы этих элементов. Сопло и электрод изнашиваются быстрее, чем другие компоненты, так как они непосредственно участвуют в создании и фокусировке режущей дуги.Вы заметите износ сопла, в первую очередь, по качеству получаемого реза. По мере износа сопла отверстие в наконечнике становится больше, что делает плазменную дугу толще и обеспечивает более широкий разрез (прорезь) в заготовке. С помощью простого визуального осмотра вы сможете увидеть, когда отверстие в форсунке станет слишком большим и потребует замены.
ЗАМЕНА ЭЛЕКТРОДОВ И СОПЕЛ
Когда электрод создает дугу, гафниевая вставка плавится, и со временем фрагменты выбрасываются через горелку в процессе резки, что приводит к образованию ямки на конце электрода. Это совершенно нормально, но когда ямка вырастает глубже 1-1,6 мм, электрод нужно будет заменить, так как гафния останется немного, а сам электрод скоро начнет прогорать. Это чрезвычайно затруднит резку и может значительно повредить остальные компоненты горелки.
Трудно точно сказать, когда вам нужно будет заменить сопло и электрод, так как это зависит от многих факторов, включая скорость резки, толщину заготовки и силу тока, которую вы используете.Тем не менее рекомендуется заменять сопло и электрод одновременно (в зависимости от того, какой из них изнашивается раньше), так как это вернет вам оптимальную производительность резки, а не использование нового электрода с изношенным и непостоянным соплом. Например.
Другие компоненты не нужно будет заменять так часто, и они в основном подвержены падению, образованию шлака в процессе резки, термической динамике и циклам нагрева и охлаждения. Проверьте вихревое кольцо и стопорную крышку на наличие трещин и замените их, как только они появятся. Хорошей практикой является замена завихрителя при каждой пятой замене электрода, если это возможно. Защитную крышку необходимо очистить от шлака, чтобы обеспечить постоянный поток воздуха, и ее следует заменить, если отложения слишком велики, чтобы их можно было удалить.
Своевременная замена расходных материалов необходима для технического обслуживания машины и точности резки. И вы можете быть уверены, что здесь, в Westermans International, наше партнерство с Hypertherm означает, что мы можем поставлять вам оригинальные расходные материалы для плазменной резки высочайшего качества.
3 СОВЕТА ПО ПРОДЛЕНИЮ СЛУЖБЫ РАСХОДНЫХ МАТЕРИАЛОВ ДЛЯ ПЛАЗМЕННОЙ РЕЗКИ
- Параметры резки: Резка слишком быстро, слишком медленно или на неправильном расстоянии от заготовки приведет к более быстрому износу деталей.
- Правильная установка: Тщательная и правильная установка компонентов необходима для их правильной работы. Это включает в себя проверку того, что допуски расходных материалов соответствуют силе тока, которую вы будете использовать, а также правильную сборку.
- Мониторинг: Отслеживание износа ваших компонентов позволит вам предотвратить преждевременный износ одного изношенного компонента для других.Вам придется менять сопло и электрод чаще, чем другие детали, и если вы оставите их слишком долго, это создаст дополнительную нагрузку на всю систему, а также снизит качество резки.
Нужна дополнительная консультация по плазменной резке ?
Прочтите наш блог о четырех лучших газах для плазменной резки
Чтобы получить дополнительные советы и рекомендации, посетите собственный веб-сайт Hypertherm, где вы найдете множество полезных советов по максимально эффективному использованию вашего плазменного резака.
Плазменный резак— Советы и методы плазменного резака
Точная резка стали и других металлов, как правило, представляет собой длительный и утомительный процесс распиловки, шлифовки или их сочетания.Если у вас нет слесарного цеха с полным спектром услуг, где есть гидравлические ножницы и пробойники, старый ручной метод является наиболее часто используемым способом резки металла. В то время как отрезные пилы, сабельные пилы и отрезные круги имеют свое место, плазменный резак — это самый быстрый метод для быстрой и точной резки всего, от тонкого листового металла до 2-дюймовых пластин и труб. Понимание того, как работают плазменные резаки и что их делает не работает имеет решающее значение для правильной работы
Что такое плазма?
Плазменно-дуговая резка похожа на электрическую сварку, за исключением того, что она не соединяет, а разделяет.В 1960-х инженеры обнаружили, что они могут увеличивать подачу газа на электронных сварочных аппаратах, чтобы увеличить скорость сварочных операций, но они достигли точки, когда горелка прекращала сварку и начинала резку. Это открытие привело к созданию плазменных резаков. В этих режущих устройствах используется электрическая дуга с разрядом сжатого воздуха на конце резака. Дуга перегревает сжатый воздух, который затем образует плазму.
Существует 4 формы материи: твердое тело, жидкость, газ и плазма. Когда газ нагревается до экстремальных температур, энергия начинает разрушать молекулы газа, расщепляя атомы, что генерирует огромное количество энергии и невероятную режущую способность. Плазма вокруг нас; неоновые и флуоресцентные лампы использовали холодную плазму, в то время как солнце, по сути, представляет собой гигантский шар плазмы. Поскольку плазма проводит электричество, она режет очень быстро и с минимальными усилиями.
Для генерации плазмы нужна стартовая дуга. Это то, что создает первоначальный выброс плазмы на кончике. Существует 2 распространенных типа пусковых дуг: высокочастотный контакт и пилотная дуга. Хотя оба, безусловно, функциональны, у обоих есть определенные проблемы. ВЧ-дуга идеально подходит для большинства типов плазменных операций, но высокие частоты, генерируемые машиной, могут нанести ущерб ближайшим компьютерам и другой чувствительной электронике, что делает их действительно плохим выбором для плазменных плоттеров с ЧПУ. Хотя это может показаться проблемой только для промышленного применения, существуют доступные плазменные столы с ЧПУ для любителей. Если вы купите его позже, вам нужно будет защитить компьютер от ВЧ-шума. Устройства HF также требуют, чтобы наконечник соприкасался с разрезаемой подложкой для срабатывания дуги, что может привести к выгоранию наконечников и может быть затруднительно для использования на столах с ЧПУ.
В устройствах «пилотной дуги» используется внутренняя дуга более низкого напряжения, которая генерирует плазму внутри наконечника горелки.Это устраняет необходимость прикасаться наконечником к подложке, а значит, расходные материалы служат дольше. Поскольку дуга генерируется внутри, эти устройства не создают высокочастотного шума, что делает их безопасными для использования с ЧПУ.
Недостаток вспомогательной дуги заключается в том, что при повторном срабатывании блока, не находясь в непосредственной близости от подложки, можно повредить внутренние компоненты блока. Тем не менее, конструкция вспомогательной дуги становится лидером среди конструкций плазменных горелок.
Враги плазмы
Плазма может быть самым подлым методом резки, но иногда у самого большого чувака на блоке стеклянная челюсть.Криптонит плазменной резки – это вода. Очевидно, вы дважды подумаете, прежде чем использовать что-либо электронное рядом с водой, но мы говорим о воде/влаге в сжатом воздухе. Большинство любителей используют стандартный воздушный компрессор для производства воздуха, необходимого для операции плазменной резки. Сжатый воздух обычно содержит много влаги, поэтому вам необходимо убедиться, что в воздушной линии есть хотя бы один фильтр-ловушка для воды. Быстрый и простой способ осушить воздух — использовать одноразовые воздушные фильтры с быстроразъемным соединением прямо в месте подключения к плазменной установке.Вы поймете, что в линии есть вода, если операции резки будут неустойчивыми, с большим количеством хлопков и брызг. Плазма НЕНАВИДИТ воду, так что держите ее подальше.
Давление воздуха также является важной проблемой при работе с плазмой. Слишком много воздуха может выдуть плазму; не хватает воздуха, и вы ничего не сможете разрезать — горелка просто расплавит металл до состояния кашицы.Следуйте инструкциям на вашем плазменном резаке, чтобы обеспечить необходимое давление воздуха для качественной работы.
Хорошее заземление чрезвычайно важно для плазменной резки. Во-первых, дуга не будет поддерживать себя, если нет твердого основания. Во-вторых, особенно при работе с большими объектами, на которых вы можете сидеть, плохая земля может означать, что вы станете путем к земле. Мы слышали несколько довольно неприятных историй о том, что происходит, когда пользователя отключают. Не поддавайтесь разряду — практикуйте безопасную плазму.
Безопасность является приоритетом, когда вы имеете дело с экстремальной жарой, светом и электричеством. Используйте плотные сварочные перчатки вместе со сварочным халатом или рукавами для защиты кожи. Перчатки TIG недостаточно толстые, чтобы защитить от экстремальных температур.Плазменные горелки создают тепло в диапазоне 45 000 ° F; Если вы подойдете слишком близко, перчатки MIG сморщатся. Плазма излучает много тепла. Даже высококачественные сварочные перчатки сморщиваются, когда тепло плазменной дуги оказывается слишком близко. Перчатка на картинке действительно сжалась до пальца, и это было довольно больно. Практикуйте безопасную плазму!
Свет, исходящий от плазменной горелки, не такой яркий, как при сварке MIG или TIG, но его все же достаточно, чтобы ослепить вас. Подходят очки для газовой горелки с затемнением № 10, но некоторые предпочитают № 9 или № 11.Дело в том, что вы используете надлежащую защиту для ваших глаз. Автоматический сварочный шлем с регулируемыми настройками еще лучше; таким образом, вы можете четко видеть настройку и не будет никаких проблем с видимостью.
Еще одним важным моментом безопасности является защита органов слуха. Плазменная резка, как правило, является довольно громким процессом с выбросом сжатого воздуха. Если вы просто режете небольшой участок, это не имеет большого значения, но если вы делаете много резки, хорошей идеей будет комплект наушников или затычек.
Методы работы
Существует несколько способов использования плазменного резака. Самый распространенный — перетаскивание. Это звучит так же, как это; факел волочится по металлу. Однако это связано с оговоркой, поскольку вы не можете просто коснуться наконечником металла и уйти. Вам нужен барьер, чтобы наконечник не сплавился с металлом и не выдул наконечник. В зависимости от типа резака, который у вас есть, вам может потребоваться просто держать его на высоте 1/4 дюйма над металлом. Это означает, что для точной резки требуется движение немного медленнее.Подвижные чашки позволяют удерживать резак на металле, пока вы следуете по линии реза, повышая точность и удобство резки. При работе с резаком без форсунки наилучшие результаты часто достигаются при начале резки под углом 45°. Это удалит расплавленный материал от вас и от разреза. Тонкий металл прожигается быстро, и прямой подход работает, но чтобы улучшить видимость реза, держите горелку под углом, чтобы вы могли лучше видеть дугу. Ваша техника будет развиваться с практикой, но основные операции с горелкой просты; держите резак под небольшим углом назад и слегка поверните его в сторону, как показано на рисунке.Всегда убедитесь, что вы сдуваете искры ОТ себя и чувствительных материалов, таких как стекло. Для прокалывания работает прямой подход, но искры будут выбрасываться на 360°, так что будьте осторожны.
Горячий шлак в твоем носке — это не весело!
Резка толстого металла немного отличается от резки листового металла. Толстый металл означает более медленную резку, более широкий разрез или «пропил», большее количество оставшегося шлака (остатки расплавленного металла на краю разреза) и более длительное время прожига. Если вы прокалываете металл, угол 45° жизненно важен.Прямой подход приведет к большому количеству шлака на наконечнике и, что более важно, к огненному дождю вокруг горелки. Расплавленный металл должен куда-то деваться — убедитесь, что он находится подальше от вас. Когда вы начинаете с края металла, прямой подход отлично работает.
После завершения разреза с обеих сторон разреза остается некоторое количество шлака. В большинстве случаев его можно отколоть молотком и зубилом. Более толстые металлы производят больше шлака, и часто его труднее удалить, и для его очистки требуется шлифовальная машина.Строжка — это еще один метод, обычно используемый на более толстых металлах для удаления скоб, заклепок и сварных швов, а также для создания канавок в листовом металле. Это не обязательно является большой необходимостью для использования в автомобиле, но, безусловно, имеет место быть. Строжка выполняется путем удержания резака под небольшим углом к металлу, запуска дуги и вырезания канавки. Этот метод требует много практики, чтобы добиться успеха. Плазменные резаки могут резать практически любой металл, но это также означает, что вы должны быть осторожны с тем, как вы размещаете деталь на столе.Прорезать свой верстак нехорошо. Ребристая металлическая поверхность отлично подходит для плазменного стола.
Вырезать прямые линии или сложные формы может быть немного сложно, но вот отличный совет для быстрых и точных разрезов: используйте 2″x4″ в качестве направляющей для прямой линии. Древесина станет хрустящей, но не загорится, если вы будете осторожны. При необходимости вы можете использовать 3/4-дюймовую МДФ (древесноволокнистую плиту средней плотности) в качестве направляющей для сложных форм.
Использование деревянной направляющей очень хорошо подходит для производственных проектов.
Плазменная резка также является быстрым и простым способом надрезания труб и угловых металлов. Когда вы соединяете трубы, стандартная отрезная пила не может сделать зубчатый срез, необходимый для подгонки заподлицо, а для вырубки соединений требуются дорогие кольцевые пилы и точные настройки, которые не всегда легко выполнить с первого раза. Использование плазменного резака для вырезания гребешка означает более быструю и легкую работу.
Настройка машины
Большинство плазменных резаков не являются автоматическими; есть несколько настроек, которые можно настроить для изменения производительности машины.Мы уже обсуждали давление воздуха, которое обычно составляет около 60 фунтов на квадратный дюйм. Основной регулировкой является напряжение. Вы можете использовать плазменный резак на максимальной мощности, но это приведет к неравномерному резу с большим количеством шлака на более тонких металлах. Используйте соответствующее напряжение для металла, который вы режете. Стали требуется больше тепла, чем алюминию, и более толстые металлы требуют больше тепла. Ржавый металл, такой как листовой металл, имеет тенденцию лопаться и брызгать, поэтому добавление небольшого напряжения может помочь избавиться от ржавчины. Большинство плазменных машин настроены так, что самое низкое напряжение подходит для самых тонких металлов, а самое высокое — для самых толстых.Если у вас нет эталона отношения напряжения к толщине, используйте диапазон машины в качестве ориентира. Так как более толстые металлы требуют большего напряжения, иметь розетку на 220 вольт довольно неплохо.
компании Eastwood имеет возможность работы с двумя напряжениями питания, что позволяет использовать цепи 115 В или 220 В для удобства работы практически в любой ситуации.
Подобрать аксессуары для плазменного резака довольно просто. Чашки для перетаскивания хороши для работы с большими плоскими разрезами, такими как боковые панели и панели пола. Всегда покупайте дополнительные расходные материалы для своего резака, поскольку нет ничего более неприятного, чем просверлить отверстие в наконечнике, а его нет в коробке. Рекомендуется регулярно проверять насадку, сопло и электрод на предмет износа. По мере износа деталей дуга становится неустойчивой и может вызвать больше проблем. Изношенный электрод может привести к тому, что дуга сорвется со стороны наконечника… мы видели, как это происходит. Плазменные резаки имеют расходные детали, которые разрушаются в процессе. Пренебрежение электродом оставит вас с сожженным наконечником.Как только наконечник начинает плавиться, ему не требуется много времени, чтобы взорваться, что снижает точность горелки, если она вообще образует дугу.
Как только вы начнете использовать плазменный резак, вы сразу же удивитесь, почему не купили его раньше. Вы можете даже обнаружить, что ищете вещи, которые можно разрезать; это просто очень весело. Как и в любом другом случае, небольшая практика с плазменным резаком поможет вам получить максимальную отдачу от вашего инструмента. Изучите методы работы с металлоломом, и вскоре вы станете экспертом в области плазменной резки.Плазменные резаки
ВЕРХ | ТЕХЦЕНТР
Плазменный резак | Память Альфа
Множественные реальности(охватывает информацию из нескольких альтернативных линий времени)
Плазменный резак
Плазменный резак был режущим инструментом Звездного Флота, который использовал поток плазмы для разрезания твердых предметов.
Вулканский снеговик
Несмотря на то, что это инструмент, лейтенант Малкольм Рид использовал плазменный резак в 2151 году, чтобы выжечь глаза и рот снеговику на Комете Арчера, а затем воткнул его, чтобы он служил ему носом.(ЭНТ: «Ломая лед»)
Позже в том же году коммандер Такер использовал плазменный резак, чтобы зажечь импровизированную свечу, которую он сделал в Shuttlepod 1 . (ЭНТ: «Шаттл-1»)
После того, как шип из ромуланской мины прижал лейтенанта Рида к корпусу Enterprise NX-01 в 2152 году, капитан Джонатан Арчер нес с собой плазменный факел на корпус и собирался использовать его, чтобы прорезать шип, когда Рид остановил его, обнаружив цепи детонации внутри шипов.После того, как часть корпуса, на которой они находились, была преднамеренно отделена от остальной части корабля, Арчер успешно использовал плазменный резак, чтобы разрезать шип, выпустив Рида, но одновременно активировав мину, хотя им удалось сдержать детонацию. (ЛОР: «Минное поле»)
Во время симуляции 2153 года Дегра использовал плазменный резак, чтобы загерметизировать утечку охлаждающей жидкости на борту смоделированного малосианского грузового шаттла. (ЭНТ: «Стратагема»)
Когда в январе 2154 года «Энтерпрайз» обнаружил штурмовой шаттл зинди-инсектоидов, коммандер Такер сказал, что у него «полудумы взять с собой плазменный факел».(ЭНТ: «Инкубаторий»)
Малкольм Рид использует плазменную горелку
Рид также использовал плазменную горелку, чтобы добраться до заклинившего порта доступа на внешнем корпусе Enterprise в феврале 2154 года. (ENT: «Забытые»)
В 2154 году сварщик использовал плазменный резак, который внес некоторые структурные изменения в капсулу шаттла, Блок 1, для путешествия на Вулкан. (ЭНТ: «Пробуждение»)
В альтернативной временной шкале 2165 года Трип приказал Риду использовать плазменный резак, чтобы «разрезать корабль Йердрина Лека на мелкие кусочки», чтобы выбить из него правду. (ЛОР: «Сумерки»)
В 2369 году командиру Райкеру пришлось лечить травму лица, полученную во время репетиции спектакля «Образ мыслей ». Он был отложен после того, как другой член экипажа вошел в лазарет после того, как ему в лицо взорвался плазменный факел. (ТНГ: «Образ ума»)
В 2375 году USS Voyager получил сигнал бедствия от потерянного USS Equinox . Во время поисково-спасательной миссии на борту Equinox энсину Гарри Киму пришлось использовать плазменный резак, чтобы удалить обломки прижатого к земле Ноя Лессинга.(ВОЙ: «Равноденствие»)
Внешняя ссылка
Лучший плазменный резак: 6 лучших за 2022 г.
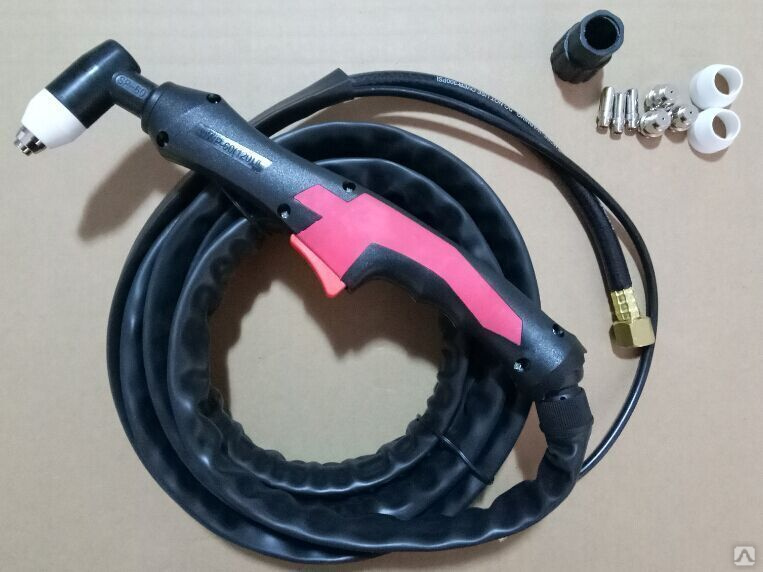
Лучшие плазменные резаки обеспечивают точную резку, сводят к минимуму деформацию и подходят для резки нержавеющей стали, легированной стали, мягкой стали, меди, углеродистой стали, алюминия и других металлов.
С другой стороны, плохой плазменный резак с трудом прорезает мягкое масло.
Итак, чтобы помочь вам отделить хорошее от мусора, мы рассмотрели 6 лучших плазменных резаков 2022 года .
Покупайте с уверенностью, что покупаете один из лучших плазменных резаков на рынке.
Давайте углубимся в обзоры.