Опрессовка системы отопления водой и воздухом
Домашняя система водяного отопления – это комплексный и сложный механизм, который в осенне-зимний период работает практически непрерывно. Важно поддерживать его в идеальном состоянии, чтобы гарантировать бесперебойное функционирование всех модулей и свести к минимуму потенциальные сбои/неполадки.
Одним из эффективных методов выявления конструкционных проблем отопительной системы, обнаружения изношенных участков и других проблем, является опрессовка.
Опрессовка – основные особенности
Под термином «опрессовка» в общем случае подразумевается процедура гидравлических либо пневматических испытаний трубопроводной системы, функционирующей под давлением, на герметичность и прочность. По итогам проверки могут быть выявлены разнообразные проблем с модулями отопительного комплекса. Тщательному мониторингу поддаются:
- Тепловые обменники и радиаторы;
- Основные линии и насосы;
- Регулирующая и запорная арматура;
- Прочие компоненты.
Совокупность операций опрессовки включает в себя обязательную промывку трубопроводов, проверку/замену изношенных элементов, восстановление целостности изоляционных слоёв. В частных домовладениях с автономной системой отопления проверке поддаётся не только основное оборудование, но также контур горячего водоснабжения, канализация.
Базовые испытания включают в себя:
- Проверку трубопровода с его промывкой и прочисткой;
- Замену деталей при необходимости;
- Восстановление или полную замену тепловой изоляции.
Осмотру поддаются:
- Корпусные конструкции, стенки тепловых обменников, трубы, радиаторы, арматура, прочие компоненты;
- Краны, манометры, клапаны и задвижки всех уровней;
- Закрепления и соединения деталей, компонентов, основных и вспомогательных линий.
Способы опрессовки
В современной практике используются два основных способа опрессовки – это гидравлические и пневматические испытания. Они схожи по алгоритму, однако имеют свои особенности.
Базовой методикой проверки считается опрессовка водой. При использовании такого способа шлангом соединяется водопровод и кран коллектора/котла. Систему заполняют жидкостью, после чего доводят давление внутри контура до полутора атмосфер.
Воздушная опрессовка предопределяет использования пневматического компрессора, нагнетающего в систему воздушную массу с совокупным формированием давления выше рабочего (средний диапазон – 1,5-2 Атм). Пневматическое испытание является альтернативным методом проверки и выполняется при следующих условиях:
- Проектная документация системы отопления допускает замену гидравлических испытаний на воздушные;
- Отсутствует удобный способ подключения к водопроводу;
- Процедуры выполняются в зимний период времени, когда есть вероятность замерзания жидкости в трубах и повреждения оборудования/линий при её расширении.
Если целостность системы при гидравлическом испытании отслеживается очень легко (отсутствие/наличие течи), то в случае проведения пневматического теста основным механизмом мониторинга становится показатели давления манометра.
При пиковой загрузке системы воздушной массой на приборе не должно быть скачков и просадок. Если выявлен потенциальный проблемный участок, то его нужно покрыть мыльным раствором для выявления свищей.
При необходимости можно легко отказаться от приобретения дорогостоящего оборудования для самостоятельного проведения пневматической проверки домашней отопительной системы, заменив его на автомобильный насос достаточной мощности, оснащенный манометром.
Причины и виды проведения опрессовки
Гидравлические или пневматические испытания подразделяются на три категории в зависимости от причин их проведения.
Первичная опрессовка
Организуется перед первым запуском новой отопительной системы в эксплуатацию. Реализуется на этапе полного подключения всех модулей и деталей (в том числе батарей, теплового генератора, расширительного бака), но до финальной «подгонки» обшивочных каркасов, заливки стяжек и иных процедур скрытия компонентов системы.
Вторичная или повторная опрессовка
Выполняется в рамках профилактических мероприятий для контроля работоспособности отопительной системы и предотвращения потенциальных проблем. Профильные специалисты рекомендуют проводить её ежегодно после завершения осенне-зимнего сезона в контексте планового обслуживания всего инфраструктурного хозяйства дома, квартиры.
Внеочередная опрессовка
Проведение внеочередных гидравлических или пневматических испытаний в подавляющем большинстве случаев организуется при аварийной или поставарийной ситуации. Иные типичные причины – проведение ремонтных работ в локализации расположения отопительной системы либо длительный её простой.
Последовательность опрессовки системы отопления
Базовый перечень необходимых процедур включает в себя следующие этапы:
- Изоляция теплового источника нагрева. Для автономных систем полностью отключается тепловой генератор. При наличии централизированного отопления следует перекрыть запорные краны, блокирующие поступление теплоносителя в трубы и радиатор.
- Слив теплоносителя. Производится в обязательном порядке.
- Заполнение водой. Контур отопительной системы заполняется водой с температурой не более 40 градусов Цельсия, после чего поэтапно и порционно сбрасывается попавший внутрь воздух.
- Присоединение и использование компрессора. К системе подключает компрессор, давление в контуре доводится до рабочего штатного уровня в одну атмосферу. Внешнее пространство визуально осматривается на предмет видимых утечек.
- Испытание. С помощью компрессора давление в системе постепенно повышается нужного уровня и удерживается на нем в течение пятнадцати минут. Параллельно проводится тщательный осмотр всех компонентов отопительной системы (арматуры, радиаторов, стенок труб, кранов, клапанов, проч.) на предмет утечек.
- Окончание опрессовки. При отсутствии утечек, свищей и иных проблем давление в системе постепенно снижают и её возвращают к исходному состоянию. Если недочеты обнаружены, то они помечаются визуально и производится их письменная регистрация в соответствующем акте гидравлического или пневматического испытания.
О давлении в трубах
Современные отечественные требования строительных норм и правил в рамках гидравлических/пневматических испытаний предопределяют рекомендованные значения повышения давления в 1,5/2 раза по отношению к рабочим параметрам, но не более 0.65 МПа. При этом дополнительно правила техэксплуатации тепловых сетей утверждают, что верхняя граница рабочего давления не должна превышать 0.2 МПа.
Типичные значения давления в отопительной системе для зданий с разной этажностью:
- Двухэтажные и трехэтажные частные дома – около двух атмосфер;
- Пятиэтажные здания – от трех до шести атмосфер;
- Девятиэтажки – от семи до десяти атмосфер.
При значительном превышении вышеозначенных показателей в подавляющем большинстве случае осуществляется автоматический сброс давления, благодаря специальному защитному клапану.
Насколько просто произвести опрессовку отопительной системы самостоятельно?
В большинстве случаев процедура гидравлического или пневматического испытания может выполняться одним человеком без специальных знаний при условии автономной отопительной системы.
В качестве базового оборудования для опрессовки подойдут простые погружные насосы, манометр, а резервуаром может выступать бочонок необходимой ёмкости либо соответствующая цистерна.
Повторите процедуры по алгоритму, описанному выше. Если неисправности и проблемы обнаружены – устраните их самостоятельно или с помощью профильного специалиста, после чего выполните повторное контрольное испытание.
Герметичность системы воздуховодов
На что влияет герметичность системы воздуховодов и как проверить фактические утечки и подсосы в системе.
На одном из мероприятий в рамках строительной выставки в Санкт-Петербурге прозвучала такая фраза: «Как плохо не спроектируй систему отопления, она всё равно будет работать. Как хорошо не спроектируй систему вентиляции, работать она не будет». Учитывая российские реалии, спорить с этим изречением сложно.
В чём же причина? Почему отлично спроектированная система вентиляции не может выйти на проектные показатели? Проектировщик в полном соответствии со всеми нормативными документами и рекомендациями производителей подбирает элемент за элементом, проверяет себя, а в результате система не обеспечивает нормируемые параметры качества воздуха и потребляет больше энергии, чем предусмотрено проектом. Одна из основных причин – это утечки и подсосы в системе воздуховодов. К сожалению, этому вопросу в российской практике не уделяется достаточного внимания. В результате, мы ставим на объект дорогую и качественную приточно-вытяжную установку, 20–40 % мощности которой используется на вентиляцию венткамеры и запотолочного пространства. Как же такое возможно?
Проектные решения
В актуализированной редакции свода правил «Отопление, вентиляция и кондиционирование воздуха» (СП 60.13330.2012) вопросу герметичности системы воздуховодов посвящён пункт 7.11.8. Согласно вышеуказанному документу, все транзитные воздуховоды и воздуховоды с нормируемым пределом огнестойкости должны соответствовать классу герметичности «В». Остальные воздуховоды должны соответствовать классу «А». В отдельных случаях допускается применение более плотных воздуховодов классов «С» и «D». Более того, вне зависимости от принятого класса герметичности: «Для предотвращения излишних потерь энергии и поддержания необходимого расхода воздуха допустимая утечка в системе не должна превышать 6 %».
Что же происходит на практике? Неужели проектировщик разбивает систему на участки с соответствующим классом плотности и, учитывая давление в системе, делает расчёт утечек/подсосов на каждом участке? Конечно же нет. Наверное, для большей части систем такой расчёт и не нужен. Большинство специалистов ограничивается фразой про максимальную утечку в 6 % и подбирает вентилятор с этим запасом.
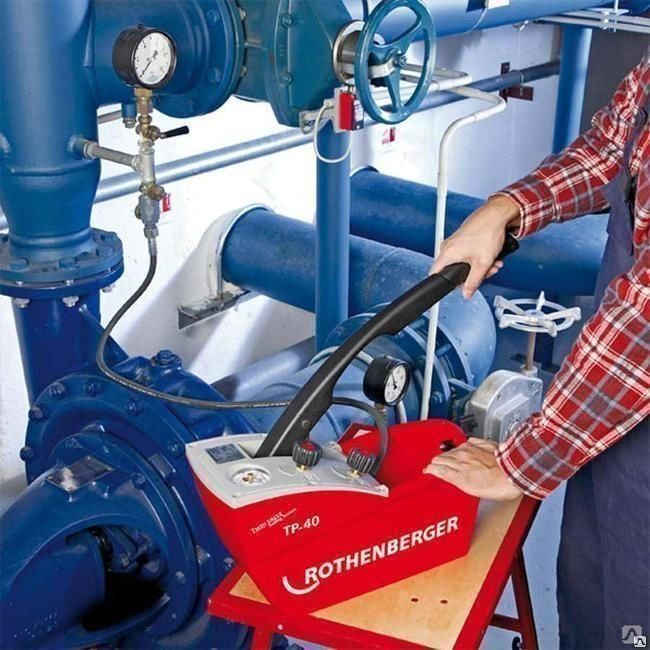
Монтаж
К сожалению, текущая нормативно-правовая ситуация порождает казус – проектировщик учитывает класс герметичности при подборе оборудования и расчёте систем, а при монтаже герметичность не контролируется. Почему так происходит? Обратимся к СТО НОСТРОЙ 2.24.2–2011 «Испытание и наладка систем вентиляции и кондиционирования воздуха». Данный документ не рассматривает работы по проверке герметичности систем вентиляции как обязательные по умолчанию, а только при определённых условиях.
В пункт 5.1.1.3. «Работы по индивидуальной наладке систем вентиляции и кондиционирования воздуха» наряду с другими требованиями включено и «определение герметичности воздуховодов при условии, если это требование предусмотрено рабочей документацией или техническими условиями монтажа». Это само по себе странно, ведь в пункте 7. 11.8 (СП 60.13330.2012) касательно герметичности есть фраза о том, что «Разные части системы могут иметь разные классы герметичности; каждая часть должна испытываться отдельно под давлением, предусмотренным в проекте для этой части». То есть система должна испытываться… или нет?
В пункте 5.1.1.4 СТО НОСТРОЙ отсылает нас к таблице из устаревшего СниП 41.01.2003 в части расчёта утечек, однако уже в пункте 5.1.1.5 заявляет о том, что «Если фактические расходы воздуха не отличаются от проектных более чем на ± 8 %, то система вентиляции и кондиционирования воздуха считается пригодной к эксплуатации». Как это соотносится с 6 % максимальных утечек и подсосов по СП 60.13330.2012? Важны не эти отклонения в процентах, важно то, что на практике, за крайне редким исключением, герметичность воздуховодов после монтажа никто не тестирует.
Проверка системы сводится к определению расходов на оконечных устройствах (решётках, диффузорах). Если расходы в пределах нормы, то герметичность системы обеспечена. При этом методы проверки расхода воздуха на высокую точность не претендуют. О применении регулирующих клапанов или камер статического давления с трубками для подключения дифманометра речь не идёт. Например, одним из способов замера расхода является «шаманство» с анемометрами в сечении воздуховода/плоскости выхода воздуха. Очевидно, что опытный пусконаладчик всегда найдёт нужные ему точки и всегда выйдет на расход с допустимыми отклонениями. Однако допустим, что у заказчика появилось желание предусмотреть в рабочей документации или техусловиях монтажа тест на герметичность систем, хотя бы на участках с давлением выше 400 Па. Как выполнить этот тест?
Р НОСТРОЙ 2.15.3–2011 содержит методику испытаний, которая не менялась с 80-х годов прошлого столетия. Бесспорно, что сама схема (принцип) изменяться и не должна. Но уровень описания теста, порядок проведения работ, используемые приборы и методология оценки результатов в редакции 1989 года мало соответствуют желаниям и требованиям современного заказчика. Поэтому шанс, что поразмыслив, он и вовсе откажется от такого теста, довольно высок.
Выводы
По собственному опыту (автору довелось участвовать в нескольких тестах герметичности в России, – Прим. ред.) могу сказать, что от 15 % до 30 % воздуха утекает из системы только на начальном участке – в венткамере, где давление в сети максимально и, как правило, используются прямоугольные воздуховоды, обеспечить герметичность крайне сложно. Это приводит к таким последствиям как:
• невыполнение нормируемых показателей качества воздуха в помещении;
• значительное увеличение энергопотребления системы;
• шум, свист и прочие неприятные сюрпризы.
Если нормативные документы не требуют проверки герметичности, предусмотренной проектом, а испытания и наладка осуществляются той же организацией, что и монтаж, то ожидать существенного улучшения качества работы вентиляционных систем не приходится.
Впрочем, во всём можно найти плюсы. Для проектировщиков, например, при претензиях по качеству работы системы вентиляции в 90 % случаев можно отписаться тем, что «герметичность воздуховодов» не соответствует проектной. И если дело дойдёт до теста, то он, наверняка, это подтвердит. ●
ОБ АВТОРЕ
Владимир Устинов – специалист в области вентиляции и кондиционирования воздуха
©http://zvt.abok.ru/articles/236/Klassi_plotnosti_vozduhovodov
Проверка двигателя на герметичность: что нужно знать
Причиной нарушений в работе двигателя или его поломки нередко является подсос воздуха или нарушение герметичности. Время от времени полезно делать профилактическую проверку на герметичность двигателя и других систем ДВС. Также данную процедуру проводят при поиске неисправностей или причин, которые вызывали поломку силового агрегата.
Содержание статьи
В каких системах автомобиля требуется герметичность
Полная герметичность для нормальной и безопасной работы автомобиля требуется в следующих системах:
- Тормозной системе. Главный и самый опасный признак – проваливание педали тормоза.
То есть, водитель жмет на нее, но желаемого результата нет, а педаль просто легко уходит вниз.
Также о нарушении герметичности может свидетельствовать увеличение тормозного пути, появление потеков тормозной жидкости, уменьшение уровня жидкости в бачке. Вряд ли стоит напоминать, чем опасно отсутствие или плохая работа тормозов. Кроме того, при таких неисправностях эксплуатация автомобиля запрещена!
- Топливной системе. Если происходит попадание воздуха, то мотор будет работать с перебоями, уменьшается его мощность, так как ухудшается качество топливно-воздушной смеси. Кроме того, возрастает расход топлива и повышается опасность возникновения пожара;
- Системе охлаждения. В этом случае мотор не будет должным образом охлаждаться, что может привести к его перегреву с последующим заклиниванием или повреждением блока цилиндров;
- Блока и головки цилиндров. Как и в предыдущем случае, за счет утечки масла будет происходить перегрев и повысится износ силовой установки.
Не считая повышенного расхода смазки. А нарушение герметичности в ГБЦ негативно скажется на работе газораспределительного механизма, может возникать прорыв газов из камеры сгорания и т.д.
Проверки на герметичность обычно проводятся после ремонтных работ, а также в случае возникновения неполадок в работе автомобиля (при первичной диагностике). При этом важно знать, как проверить двигатель на герметичность, а также каким образом выполняется аналогичная проверка тех или иных систем силового агрегата.
Проверка герметичности систем и двигателя
Первичная проверка системы охлаждения двигателя на герметичность может проводиться при помощи визуального осмотра. Во-первых, нужно обратить внимание на уровень охлаждающей жидкости в расширительном бачке.
Эта процедура должна входить в ежедневный осмотр автомобиля каждым водителем перед выездом из гаража или со стоянки. Во-вторых, следует внимательно осматривать двигатель снаружи для выявления потеков жидкости и масла через микроскопические трещины. Ну и соединения всех трубопроводов системы также нужно осматривать регулярно.
Более тщательный способ заключается в следующем. В систему охлаждения наливают максимально возможный объем воды. После этого поршень первого цилиндра нужно установить в верхнюю мертвую точку на такте сжатия. Далее, через отверстие вывернутой форсунки подается сжатый воздух (давление 0.5 МПа) и наблюдают за изменением уровня воды в расширительном бачке радиатора.
- Проверка топливной системы на герметичность. Проверка герметичности топливной системы начинается с осмотра всех топливопроводов, мест их соединений, внешнего осмотра топливного бака, карбюратора (если он есть), топливного насоса – одни словом, всех узлов системы. После этого можно приступить к более тщательной проверке. Ее необходимо выполнять после каждого ремонта системы, замены фильтров.
Один из самых эффективных способов проверки заключается в использовании специального топливного манометра. Из-за стоимости прибора он редко используется в гараже, чаще в автосервисах. Чаще всего прибор подсоединяется (при помощи переходников) своим выходом к топливной рампе, а на входе соединяется с топливным шлангом. Далее включается зажигание. При этом на манометре устанавливается определенное давление, которое не должно опускаться.
Следующий этап – замерить давление при работающем двигателе. Оно должно быть постоянным и сохраниться после выключения мотора. Величина рабочего давления для разных двигателей может быть разной. Если давление падает, то нужно искать места утечек. Их поиск, как и проверка герметичности двигателя, может проводиться дымогенератором.
Проверка герметичности блока и головки блока цилиндров
Перед проверкой блок необходимо очистить от грязи, а еще лучше вымыть. Первый и самый простой этап заключается в визуальном осмотре, как и с другими системами, о чем было написано выше. Более тщательно блок и головка блока проверяются по раздельности. То есть, головку требуется снять.
Проверка плотности прилегания клапанов знакома каждому, кто ремонтировал мотор своими руками. Заключается она в том, что ГБЦ переворачивается и устанавливается на ровную поверхность. Далее в камеры сгорания наливается керосин (можно и бензин). Его уровень не должен уменьшаться в течение 2-24 часов. Также можно провести опрессовку блока и ГБЦ.
Герметичность самой головки проверяется так. Головка переворачивается и устанавливается на ровную поверхность. В рубашку охлаждения заливается керосин. Если с герметичностью все в порядке, то никаких протечек быть не должно.
Блок цилиндров на наличие трещин в корпусе проверяется примерно так же. Заглушаются отверстия рубашки охлаждения и она заполняется водой под давление 3 кг на квадратный см. Вода не должна уходить в течение хотя бы нескольких минут. Однако не все трещины могут быть выявлены этим способом. Целостность стенок масляных каналов лучше проверить сжатым воздухом.
Проверка герметичности блока и головки сжатым воздухом может производиться и без разборки мотора. Для этого прибор, именуемый пневмотестром, подсоединяется поочередно к каждому цилиндру через отверстие для свечи. При этом поршень цилиндра необходимо выставить в верхнюю мертвую точку. Утечка воздуха через клапаны или в картер двигателя будет определяться не только по показаниям манометра, но также по звуку.
Еще в рамках данной статьи добавим, что проверять нужно также герметичность тормозной системы. Первый и самый доступный способ проверки – визуальный осмотр. При малейших неполадках в тормозах (о них упоминалось выше), водитель обязан проверить бачок с тормозной жидкостью, осмотреть колеса со стороны днища машины – нет ли на них потеков тормозной жидкости.
Также герметичность всех мест соединения трубопроводов этой системы можно проверить при помощи мыльного раствора. Устранить неисправности можно самостоятельно либо обратившись в автосервис.
Что в итоге
Как видно, проверка герметичности двигателя или других систем автомобиля может проводиться как своими силами, так и при помощи специального оборудования в автосервисах. Эту процедуру необходимо проводить после каждого ремонта, связанного с разбором агрегата, а также в целях профилактики.
Данный подход позволит избавиться от случайных утечек технических жидкостей, завоздушивания, а также возможны серьезных последствий для ДВС в отдельных случаях (образование воздушных пробок системы охлаждения, утечки ОЖ в цилиндры, попадание моторного масла в антифриз или тосол и т.д.).
Читайте также
Гидравлические испытания резервуара на водонепроницаемость, герметичность и прочность
Какими средами проводится
Испытания резервуара — комплекс мероприятий, осуществляемый после завершения монтажных работ. Он включает внешний осмотр и проверку на герметичность и плотность. При визуальном осмотре уделяется внимание качеству сварных швов, поскольку непровары, трещины, прожоги и прочие дефекты могут в дальнейшем стать причиной аварий.
Для проверки плотности сварных швов часто используется классический метод с мелом и керосином. Швы покрываются снаружи меловым раствором и, как только он просохнет, изнутри их опрыскивают керосином. Если есть какие-то изъяны, через 2-3 часа на тонкой меловой корке появляются жирные пятна. В резервуарах, изготовленных рулонным способом, на стройплощадке проверяются только монтажные швы, поскольку остальные проходят тесты в заводских условиях после соединения полотнищ.
Качество сварных швов днища определяется с помощью мыльного раствора и специальной вакуум-камеры. Кистью, смоченной в растворе, промазываются соединения, затем на них накладывается камера и рамка, которая выдерживается около минуты при включенном компрессоре. Если есть дефектные участки, раствор начинает пузыриться.
В обязательном порядке требуется проведение гидравлических испытаний резервуара для нефтепродуктов и воды на водонепроницаемость и надежность. В этом случае емкость медленно заполняется пресной водой до уровня, предусмотренного проектом, с соблюдением временных интервалов. В процессе специалисты наблюдают за осадкой металлоконструкции и соединениями, что позволяет своевременно выявить неполадки.
Если емкость предназначается для жидкостей, превышающих плотность воды, и последнюю не представляется возможным подвезти на стройплощадку, разрешается осуществлять испытания с заливом продукта. Но такую операцию обязательно требуется согласовывать со специалистами Ростехнадзора.
Также проводятся пневматические испытания резервуаров на герметичность и прочность посредством создания внутреннего избыточного давления воздухом. В особых ситуациях можно применять иные газы, если обычный воздух не подходит по тем или иным причинам. Показатель давления газа должен быть равен давлению воды, используемой при гидравлических испытаниях.
Программа испытаний
Для проведения испытаний резервуаров обязательно разрабатывается программа, включающая:
- Перечень мероприятий по визуальному осмотру.
- Требования по измерению геометрических значений фундамента и иных составляющих конструкции на всех этапах проверки.
- Последовательность испытаний с уровнями нагружения и временными интервалами.
- Значения избыточного давления.
- Обработку результатов испытаний, расчеты (если в них возникает необходимость).
- Выдачу заключения о пригодности резервуаров к эксплуатации в режимах нагружения.
Надо сказать, что существует внушительный перечень требований, предъявляемых к организации и проведению испытаний резервуаров, которые необходимо строго соблюдать. Любая ошибка, халатность может привести к разрушению емкостей или трагедии. Например, когда выполняются пневматические испытания, важно учитывать опасность энергии, имеющейся в системе. При внезапной разгерметизации соединений или разрушении испытуемой емкости люди и оборудование могут пострадать от ударной волны, разлетающихся осколков и резкого повышения давления окружающей среды в зоне проведения работ. Такие аварии угрожают не только здоровью, но и жизни сотрудников.
Чтобы испытания резервуаров прошли без эксцессов, следует:
- Проводить тесты на прочность и надежность только после завершения монтажных, сварочных работ и их приемки квалифицированными специалистами.
Они должны удостовериться, что швы и другие элементы резервуарных конструкций смогут выдержать давление, создаваемое рабочими средами разного типа.
- Зимой при проведении гидравлических испытаний пожарных, запасных резервуаров и емкостей, используемых для сточных вод, учитывать температуру, поскольку при низких значениях обнаруживать протечки и другие дефекты не получится. Если столбик термометра опускается ниже -5 °С, испытания потребуют применения оборудования, которое не позволит жидкости замерзать в патрубках, задвижках и на поверхности металлической оболочки.
- Внимательно следить за состоянием конструкции и соединительных швов при заполнении водой. Если днище протекает, вода немедленно сливается, а дефекты устраняются.
- Предусмотреть схему аварийного слива воды, которая используется при наличии трещин в корпусе резервуаров. Это важно, так как давление, создаваемое жидкостью, может усугубить изъяны и привести к значительному разрушению конструкции.
- Определять на период испытательных работ границы зоны повышенной опасности с использованием предупреждающих знаков и ограждений (если позволяет стройплощадка).
- После приемки испытаний проводить работы по антикоррозионной защите конструкций, теплоизоляции, монтажу технического оборудования, указанного в сопроводительной документации. При этом все сварочные работы на корпусе емкостей попадают под запрет.
- Выводить временный трубопровод для залива/слива воды за границы обвалования. Схема слива жидкости должна разрабатываться для каждого отдельного случая индивидуально, чтобы не возникало проблем со сливно-наливными операциями.
- Использовать мыльный раствор при проверке плотности швов кровли. Как только в свободном от воды пространстве емкостей будет достигнуто рабочее давление, соединения промазываются раствором и тщательно осматриваются специалистами. Места, где появляются пузыри, отмечаются мелом, чтобы рабочие могли оперативно устранить дефекты.
Как видно из представленного списка, среди всех требований ключевым является то, которое определяет безопасность людей, осуществляющих испытания резервуаров. Все они должны обладать необходимыми знаниями, опытом и хорошо знать технику безопасности. Именно такие специалисты работают в компании «RZMash», регулярно выполняя гидравлические испытания емкостей в вакууме в соответствии с нормами СНиП и ГОСТами.
Доверяя нам решение поставленных задач, клиенты значительно экономят время, получая гарантированный результат. При проведении испытаний мы используем профессиональное оборудование и инструменты, позволяющие обнаруживать скрытые дефекты.
Что касается стоимости испытаний резервуаров, то для каждого проекта она рассчитывается индивидуально. Мы берем во внимание особенности емкостей, подлежащих проверке, условия окружающей среды и другие факторы, которые могут облегчать или усложнять работы. Стоимость работ озвучивается после изучения технической документации и требований заказчика.
Если остались вопросы, вы всегда можете задать их нашим менеджерам, позвонив по телефону, указанному на сайте, или заполнив специальную форму. Консультационная помощь оказывается бесплатно до подписания договора и на всех этапах сотрудничества. При необходимости вы можете приехать в наш офис, если предпочитаете решать дела личным присутствием. Мы гарантируем встречу в оговоренное время и оптимальные условия для комфортного обсуждения.
Проверка на герметичность резервуаров и емкостей может быть произведена научно-производственной лабораторией «ПРОконтроль»
Резервуары, рассчитанные на хранение жидкостей и газов под естественным и низким давлением должны пройти проверку на герметичность. Эта проверка выполняется после окончания проверки качества сварных швов. В зависимости от проектного содержимого, объема, формы и других особенностей выбирается способ проверки. Сосуды, предназначенные для работы под высоким давлением – десятки и сотни атмосфер проходят такие испытания в особом порядке.
Как проверяется резервуар на водонепроницаемость
Проверка на герметичность резервуаров проводится путем забора проб (жидкостных или газовых), осуществляемых в наиболее низкой части пространства между емкостями и оболочками двустенных резервуаров.
Вторым ответом на вопрос — как проверить емкость на герметичность? – является наблюдение за уровнем жидкости и регулярным измерением ее уровня с помощью высокоточных электронных уровнемеров.
Есть еще один способ того, как проверяется резервуар на водонепроницаемость – это проведение периодических пневматических испытаний, опорожненных от жидкостей или газов емкостей, путем нагнетения в них избыточного давления, посредством закачки инертных газов.
Контрольные измерения проводят с использованием радиографических приборов. Чувствительность снимков должна соответствовать определенному ГОСТу.
После проведенных исследований проводится прочистка, продувка каждого сливного отверстия и обвязки с повторной сменой прокладок.
Контроль крупных резервуаров осуществляется так же, как и небольших емкостей – давлением или пртоникновением пенетрантов
Контроль герметичности емкостей и резервуаров должен выполняться тщательно, в противном случае обнаруженная в начале эксплуатации течь требует значительно больших затрат рабочего времени и других ресурсов на устранение.
Виды и особенности контроля емкостей на герметичность
Основной и самый надежный принцип проверки сосудов и резервуаров на герметичность состоит в заполнении их жидкостью или газом и создании в них повышенного давления, иногда – вакуума. Величина такого избыточного давления и рабочее вещество заполнения нормируются.
Самый простой и веками проверенный способ проверки металлов и некоторых других материалов на трещины и неплотности – капиллярный, причем в его традиционном исполнении. Это способ не требует заполнения резервуара чем-либо и создания положительного или отрицательного избыточного давления.
С наружной стороны все сварные швы и прочие важные места и узлы покрывают меловой суспензией, а после ее высыхания с внутренней стороны на все обследуемые места наносят керосин. Спустя какое-то время керосин обязательно просочится через самые малые трещины, если таковые имеются, и оставит хорошо видимые следы на мелу.
Настолько же прост и показателен пневматический метод контроля герметичности. Создав избыточное давление в резервуаре, наружная поверхность всех мест, требующих контроля, покрывается обычным мыльным раствором, который начинает пузыриться там, где воздух выходит наружу.
У этого способа есть более наглядная разновидность, когда швы и прочие требующие проверки места покрывают бумажной или тканой лентой, смоченной фенолфталеином, а в резервуар закачивают смесь воздуха с одним процентом аммиака. Если аммиак проникает сквозь неплотности, он реагирует с фенолфталеином и оставляет хорошо видимые издалека красные характерные следы.
Такой метод хорош очень высокой надежностью и простотой применения на крупных резервуарах, когда следы реакции хорошо заметны.
Применяются и гидравлические методы, при которых емкость заполняется водой или маслом и оставляется на некоторое время, либо же в ней создается избыточное давление. Протечки обнаруживают визуально, для чего жидкость может быть подкрашена. Этот естественный процесс интенсифицируют, простукивая зону швов молотком с округлым бойком.
Проверкам герметичности подвергают емкости стандартного типа. Иногда возникает необходимость проверки такого сосуда, в котором невозможно создать избыточное давление или же требуется проверить на герметичность сварные швы на каком-либо отдельном узле, не образующем замкнутого пространства. В этом случае применяют способ создания местного избыточного давления.
Для этого на обследуемый участок направляют сильную струю сжатого воздуха. В месте соприкосновения такой струи с поверхностью обследуемого объекта возникает зона повышенного давления и она вызывает эффект просачивания воздуха сквозь неплотности, если таковые имеются. Проникновение воздуха фиксируют с обратной стороны обычным способом, применяя мыльный раствор. Этот прием особенно эффективен в угловых швах, где зона повышенного давления образуется более уверенно.
После ликвидации протечек проверку повторяют.
Корпуса металлических судов. Методы испытаний на непроницаемость и герметичность (с Изменением N 1) – РТС-тендер
ГОСТ 3285-77*
Группа Д49
Дата введения 1978-07-01
Постановлением Государственного комитета стандартов Совета Министров СССР от 26 июля 1977 г. N 1834 срок введения установлен с 01.07.78
Проверен в 1982 г. Постановлением Госстандарта от 30.03.83 N 1510 срок действия продлен до 01.07.86
ВЗАМЕН ГОСТ 3285-65
* ПЕРЕИЗДАНИЕ (ноябрь 1983 г.) с Изменением N 1, утвержденным в марте 1983 г. (ИУС 7-83).
Настоящий стандарт распространяется на корпуса металлических судов морских и внутреннего плавания и устанавливает методы испытаний их на непроницаемость и герметичность.
1.1 Испытанию на непроницаемость подвергают все конструкции корпуса (в дальнейшем конструкции), оборудование, дельные вещи, которые в эксплуатации или в предусмотренных расчетом аварийных случаях могут соприкасаться с водой или другой жидкостью и не должны пропускать их.
Под непроницаемостью следует понимать способность конструкций не пропускать воду или другие жидкости.
1.2. Испытанию на герметичность подвергают конструкции, которые по своему назначению и условиям эксплуатации должны защищать ограничиваемые ими пространства от проникновения газообразных веществ и аэрозолей.
Под герметичностью следует понимать способность конструкций не пропускать газообразные вещества и аэрозоли.
1.3. Номенклатуру герметичных конструкций определяют при проектировании судна по согласованию с контролирующей организацией.
1.4. Испытания конструкций на непроницаемость и герметичность проводят согласно схеме испытаний, чертежу или таблице (в дальнейшем схеме испытаний), разработанных проектной организацией в соответствии с технической документацией.
В схеме испытаний должны быть указаны расположение и назначение всех испытываемых конструкций, методы и нормы их испытаний.
1.5. Методы и нормы испытаний конструкций назначает проектная организация по согласованию с контролирующей организацией.
Примечание. Оборудование, дельные вещи, арматура, примыкающие к испытываемым конструкциям или проходящие через них, а также шахты и выгородки испытывают теми же методами и по тем же нормам, что и конструкции.
1.6. В зависимости от применяемости методов и норм испытаний на непроницаемость конструкции делят на:
группу а — отсеки и цистерны, в которых во время эксплуатации временно или постоянно находится жидкость, а также форпик, ахтерпик, отсеки подруливающего устройства, лага и эхолота, пустотелые рули, направляющие насадки, отсеки плавучести, воздушные ящики, крыльевые устройства;
группу б — все прочие конструкции, которые по условиям эксплуатации должны быть непроницаемыми.
1.7. Герметичность корпуса судна подразделяют на:
общую — герметичность наружного контура судна, включая надстройки и рубки;
отсековую — герметичность отсека или группы помещений, ограниченных общим герметичным контуром;
индивидуальную — герметичность отдельного помещения.
Примечание. Под отсеком следует понимать контур, ограниченный главными переборками и палубами.
1.8. Корпус ремонтируемого или модернизируемого судна испытывают на непроницаемость и герметичность теми же методами и по тем же нормам, что и корпус вновь строящегося судна.
Объем испытаний определяют перечнем работ по ремонту и модернизации и согласовывают с контролирующей организацией.
1.9. Если непроницаемые или герметичные конструкции, оборудование, дельные вещи ремонтируемого или модернизируемого судна имеют прочность или уплотнение, недостаточные для восприятия испытательных нагрузок, установленных настоящим стандартом, то проектная организация, ведущая ремонт или модернизацию судна, определяет и согласовывает с контролирующей организацией уменьшение величины испытательных давлений, установку соответствующих подкреплений или замену конструкций.
1.10. Все части корпуса, в том числе и расположенные внутри него, которые обеспечивают нахождение судна на плаву после спуска его со стапеля, а также конструкции, недоступные для осмотра и устранения выявленных дефектов, испытывают до спуска судна на воду на стапеле или в доке.
Конструкции, доступные для осмотра по всему контуру при нахождении судна на плаву, испытывают на плаву или на стапеле, в доке.
1.11. При испытании конструкций, находящихся на плаву, должны быть обеспечены достаточная прочность корпуса, остойчивость судна и контроль за его осадкой, которая не должна превышать осадку судна при полном водоизмещении.
1.12. Качество сварных соединений должно быть проверено в соответствии с требованиями технической документации до начала проведения испытаний на непроницаемость и герметичность.
1.13. Поверхности испытываемых конструкций и соединений должны быть очищены от загрязнений. Контролируемая поверхность конструкций должна быть сухой.
1.14. Конструкции и соединения, подлежащие испытанию на непроницаемость, не должны быть окрашены, заасфальтированы и покрыты специальными покрытиями до окончания испытаний их на непроницаемость, кроме требований, изложенных в п. 1.15.
1.15. Конструкции, включая внутрисекционные соединения, разрешают грунтовать и окрашивать в соответствии со схемами, предусмотренными «табелем назначения красок», до подачи их на стапель или в док и до проверки их на непроницаемость при соблюдении условий:
толщина основных листов, составляющих контур непроницаемости конструкции, должна быть не менее 12 мм, а толщина стенок набора, ограничивающих испытываемый контур и привариваемых к основным листам — не менее 8 мм;
все внутрисекционные соединения конструкций, входящие в непроницаемый контур, должны быть подвергнуты тщательному осмотру по всей длине соединения. Результаты осмотра должны быть зафиксированы в журнале;
стыковые и тавровые сварные соединения, относящиеся к конструкциям группы а, расположенные ниже ватерлинии, перед грунтовкой и окраской проверяют на непроницаемость смачиванием керосином. Двусторонние швы тавровых сварных соединений без сплошного провара проверяют смачиванием керосином после выполнения первого прохода шва с одной стороны;
на всех секциях должны быть закончены сборочно-сварочные работы, работы по правке и установке насыщения (фундаменты, наварыши, наклепыши и т. п.).
1.16. Конструкции, испытанные и принятые на предварительной сборке, должны быть загрунтованы и окрашены за исключением участков шириной 30-40 мм, примыкающих к монтажным кромкам.
Примечание. Если грунт не влияет на процесс сварки и резки, разрешается грунтовать участки, примыкающие к монтажным кромкам.
1.17. Монтажные соединения, выполненные на стапеле или в доке, грунтуют после проведения испытаний их на непроницаемость.
1.18. Конструкции, которые не были испытаны на непроницаемость на предварительной сборке и которые будут длительное время находиться на открытом воздухе и подвергаться влиянию атмосферных осадков, разрешают грунтовать одним слоем.
При этом внутрисекционные сварные соединения и участки, примыкающие к ним на ширине 10 см с каждой стороны шва, не грунтуют.
1.19. На ремонтируемых и модернизируемых судах до проведения испытаний на непроницаемость грунтуют конструкции, на которых во время ремонта или модернизации не будут выполнять сборочно-сварочные работы.
1.20. При доковании судов разрешается грунтовать и окрашивать конструкции, кроме мест, подлежащих при испытаниях внешнему осмотру, до проведения испытаний на непроницаемость.
1.21. При проведении дополнительных сборочно-сварочных, монтажных или ремонтных работ на конструкциях, оборудовании и дельных вещах, испытывают на непроницаемость и герметичность, в случаях, когда общую проверку на непроницаемость и герметичность не проводят, проводят местную проверку конструкций на непроницаемость и герметичность.
По требованию контролирующей организации проводят повторную общую проверку конструкций на непроницаемость и герметичность.
Примечания:
1. Под общей проверкой следует понимать испытание всего объема конструкций.
2. Под местной проверкой следует понимать испытание сварных швов и других соединений, а также части поверхности конструкций, непроницаемость которых могла быть нарушена при проведении дополнительных работ.
1.22. Нормы и правила испытаний конструкций на непроницаемость и герметичность приведены в обязательных приложениях 1 и 2.
1.23. Испытания корпусов металлических судов по назначению и технологической последовательности подразделяют на предварительные, основные и контрольные.
1.24. Предварительные испытания
1.24.1. Предварительные испытания на непроницаемость внутрисекционных соединений конструкций следует проводить при изготовлении секций и блоков корпуса для переноса возможно большего объема работ по испытаниям со стапеля или дока на участки предварительной сборки и сварки и для уменьшения объема работ по исправлению дефектов, выявленных при испытании конструкций на стапелях и в доках.
1.24.2. Объем и методы предварительных испытаний конструкций на непроницаемость устанавливает предприятие-изготовитель в соответствии с технологией постройки судна и технической целесообразностью.
1.24.3. Предварительные испытания на непроницаемость тех конструкций, на которых в дальнейшем на стапеле или в доке не будут выполнять сборочно-сварочные работы, за исключением сборки и сварки монтажных кромок, засчитывают как основные, если методы и нормы этих испытаний соответствуют методам и нормам основных испытаний и при условии согласования с контролирующей организацией.
1.24.4. Предварительные испытания на герметичность проводят после окончания в конструкциях сборочно-сварочных работ.
Необходимость проведения предварительных испытаний на герметичность устанавливает предприятие-изготовитель.
Примечания:
1. Под окончанием сборочно-сварочных работ следует понимать выполнение в испытываемых конструкциях работ, связанных с установкой, сборкой и клепкой всех предусмотренных технической документацией изделий, таких как: фундаменты, наварыши, наклепыши, арматура, съемные стаканы, детали крепления электрокабеля, приборов, механизмов, систем, устройств, оборудования, изоляции.
2. На конструкциях, образующих контур испытываемого отсека, должны быть выполнены сборочно-сварочные работы со стороны смежных отсеков.
1.25. Основные испытания
1.25.1. Основные испытания на непроницаемость и герметичность проводят для проверки конструкций, которые согласно схеме испытаний должны быть непроницаемыми и герметичными.
Основные испытания на непроницаемость проводят после окончания в конструкциях сборочно-сварочных работ и работ по правке.
Основные испытания на герметичность проводят после окончания монтажных, установочных и достроечных работ с обеих сторон конструкций, образующих испытываемый отсек.
1.25.2. Основные испытания на непроницаемость проводят на стапелях, в доках, на плаву и на участках предварительной сборки и сварки.
1.26. Контрольные испытания
1.26.1. Контрольные испытания на непроницаемость проводят для конструкций группы а.
1.26.2. Контрольные испытания на непроницаемость проводят после полного окончания с обеих сторон испытываемых конструкций монтажных работ по всем специальностям.
Примечание. Под полным окончанием монтажных работ по всем специальностям следует понимать выполнение в конструкциях всех работ по монтажу систем, механизмов, устройств, приводов, установке электрокорабля и оборудования, предусмотренных технической документацией.
1.26.3. Контрольные испытания на непроницаемость по согласованию с контролирующей организацией могут быть совмещены с другими испытаниями, такими как: опробование вспомогательных механизмов, электросетей, радиосвязи, проводимыми в несмежных отсеках судна.
1.26.4. Если при контрольных испытаниях на непроницаемость будут обнаружены дефекты, то после обнаружения и устранения их проводят основные испытания повторно. Результаты повторных испытаний считают окончательными.
1. 26.5. Контрольным испытаниям на герметичность подвергают конструкции, в которых после проведения основных испытаний на герметичность проводили работы, связанные с возможным нарушением герметичности.
По требованию контролирующей организации выборочно испытывают и другие конструкции, количество которых должно составлять 5% от общего количества герметичных конструкций, но не менее двух.
Если при проведении испытаний будут обнаружены негерметичные конструкции, проводят повторные испытания на удвоенном количестве конструкций. При неудовлетворительных результатах повторных контрольных испытаний проводят повторные основные испытания всех конструкций, к которым предъявляются требования герметичности. Результаты повторных основных испытаний считают окончательными.
2.1. При испытании корпусов металлических судов применяют следующие методы: налив воды под напором, налив воды без напора, надув воздуха, поливание струей воды под напором, поливание рассеянной струей воды, обдув струей сжатого воздуха, смачивание керосином, применение вакуум-камер — при испытании на непроницаемость;
надув воздуха — при испытании на герметичность.
2.2. Испытания наливом воды под напором
2.2.1. До проведения испытаний наливом воды под напором должны быть проведены мероприятия, исключающие возможные смещения и деформации корпуса во время проведения испытаний.
2.2.2. Гидростатическое давление (напор) на конструкциях, ограничивающих отсек сверху (палуба, платформа, второе дно), создают механическими или ручными насосами, установкой напорной трубы, резинового шланга или штатной измерительной трубы диаметром не менее 25 мм.
2.2.3. Величину гидростатического давления устанавливают в соответствии с проектной документацией на судно и требованиями настоящего стандарта.
2.2.4. Высоту напора отсчитывают от основной линии до уровня воды в напорной трубе или шланге.
Для судов с конструктивным дефферентом высоту напора отсчитывают от килевой линии.
Для цистерн, расположенных на второй и выше палубах, высоту напора отсчитывают от нижней точки цистерны.
Предельные точки отсчета должны быть указаны в схеме испытаний.
2.2.5. Давление, создаваемое в конструкции, измеряют двумя манометрами класса точности 1,5-2,5 с пределом измерения на больше испытательного давления. Манометры устанавливают на испытываемой конструкции и напорном трубопроводе вблизи насоса. На проводящей трубе должен быть установлен запорный кран для регулирования подачи воды.
2.2.6. При заполнении водой не допускается образование воздушных подушек в верхних частях испытываемых конструкций, поэтому в наборе верхнего перекрытия должны быть предусмотрены отводные отверстия или трубки. Для выпуска воздуха просверливают отверстия диаметром 8-10 мм, которые после окончания испытаний заваривают и проверяют на непроницаемость смачиванием керосином или обдувом струей сжатого воздуха.
2.2.7. Для проведения испытаний должна быть использована техническая пресная вода без загрязнений.
По согласованию с контролирующей организацией разрешается использовать морскую воду для испытаний конструкций, кроме цистерн для пресной воды, при соблюдении следующих требований:
поверхности конструкций, соприкасающиеся во время испытаний с морской водой, непосредственно после окончания испытаний и слива воды должны быть промыты пресной водой;
вода из труднодоступных мест, застойных зон, зазоров и др. участков должна быть удалена;
после окончания испытаний поверхности сварных конструкций перед грунтовкой и окраской должны быть очищены;
время нахождения воды в конструкциях должно быть минимальным и не превышать двух суток с начала заполнения.
(Измененная редакция, Изм. N 1).
2.2.8. Продолжительность нахождения конструкции под напором воды определяют временем, необходимым для осмотра всей поверхности конструкции, но не менее 1 ч.
2.2.9. После окончания испытаний вода из отсеков должна быть удалена. При отсутствии откачивающих средств или штатных отверстий воду сливают через заранее высверленные отверстия. В отсеке высверливают одно-два отверстия диаметром до 25 мм.
Для отсеков объемом более 500 м высверливают до четырех отверстий диаметром 25 мм.
Оверстия должны быть расположены в нижней точке отсека на расстоянии не менее 100 мм от стенок близлежащих конструкций.
После слива воды отверстия заваривают и испытывают на непроницаемость смачиванием керосином или обдувом струей сжатого воздуха.
2.2.10. Место расположения вварных штуцеров для подключения контрольных приборов, сливных и воздушных отверстий определяют по схеме, разработанной проектной организацией и согласованной с предприятием-изготовителем.
2.2.11. При температурах наружного воздуха и испытуемых конструкций от 0 °С и ниже температура налитой в отсек воды должна быть достаточной для поддержания температуры наружных поверхностей испытуемых конструкций выше 0 °С и исключения их отпотевания в течение всего времени испытаний.
(Измененная редакция, Изм. N 1).
2.2.12. Конструкции считают непроницаемыми, если на контролируемой поверхности не будут наблюдаться течи в виде струй, потеков и капель.
2.3. Испытания наливом воды без напора
2.3.1. При проведении испытаний на непроницаемость наливом воды без напора уровень воды определяют по нормам, установленным в табл. 1 обязательного приложения 1.
2.3.2. Испытания проводят с учетом требований пп.2.2.7; 2.2.9-2.2.12.
2.4. Испытания надувом воздуха
2.4.1. Перед назначением испытаний на непроницаемость надувом воздуха проектная организация должна произвести расчет прочности конструкций, приборов и аппаратуры, установленных в испытываемых отсеках.
2.4.2. Если при испытании на непроницаемость расчетная прочность окажется недостаточной для восприятия избыточного давления, равного 3·10 Па (0,3 кгс/см), то величина давления может быть уменьшена по согласованию с контролирующей организацией до 2·10 Па (0,2 кгс/см). Если прочность конструкции окажется недостаточной для восприятия уменьшенного давления, то допускается испытывать ее другими методами.
2.4.3. Если при испытании на герметичность расчетная прочность окажется недостаточной для восприятия избыточного давления, равного 2·10 Па (0,02 кгс/см), то величина давления может быть уменьшена по согласованию с контролирующей организацией до 1·10 Па (0,01 кгс/см).
2.4.4. Давление воздуха измеряют манометрами класса точности 1,5-2,5 с пределом измерения на больше испытательного давления. На подводящей трубе устанавливают запорный кран для регулирования подачи воздуха.
Примечание. При объеме конструкций более 250 м следует использовать манометры с ценой деления 2·10 Па (0,02 кгс/см).
2.4.5. На каждой испытываемой конструкции должны быть установлены два манометра и предохранительный клапан.
Штуцеры для установки манометров, предохранительных клапанов и подключения воздушных шлангов устанавливают на крышках горловин, на временных заглушках или в других местах, удобных для обслуживания.
Штатные штуцеры для проведения испытаний на герметичность устанавливают в соответствии с требованиями технической документации, разработанной проектной организацией.
После окончания испытаний штуцеры должны быть закрыты штатными заглушками, испытаны на непроницаемость обдувом струей сжатого воздуха и опломбированы.
2.4.6. Сжатый воздух поступает из заводской магистрали, баллонов или от приточной вентиляции.
2.4.7. Избыточное давление воздуха окончательно устанавливают через 10-15 мин после подачи его в конструкцию.
2.4.8. При проведении испытаний на непроницаемость сварные швы и другие соединения смачивают пенообразующим раствором, приготовленным в соответствии с требованиями технической документации.
2.4.9. Пенообразующий раствор при отрицательной температуре окружающего воздуха должен быть приготовлен на незамерзающем и незагустевающем растворителе, который не должен ухудшать качество пены и вызывать коррозию металла.
2.4.10. При проведении испытаний на непроницаемость сварных соединений внахлестку сжатый воздух давлением 5·10 Па (0,5 кгс/см) подают в зазор между соприкасающимися деталями.
2.4.11. Если падение давления за время испытаний превысит допустимое, сварные швы и другие соединения испытываемых конструкций повторно смачивают пенообразующим раствором.
2.4.12. Испытания на непроницаемость проводят при температуре окружающего воздуха не ниже минус 10 °С, ниже этой температуры испытания проводят по согласованию с контролирующей организацией. Воздух, применяемый при испытаниях, должен быть сухим.
Испытания на герметичность не ограничивают температурой окружающего воздуха.
2.4.13. Сварные швы и конструкции, испытываемые при отрицательной температуре окружающего воздуха, должны быть просушены нагревом до полного удаления замерзшей воды.
2.4.14. Конструкцию считают непроницаемой и герметичной, если при смачивании пенообразующим раствором сварных швов и других соединений не образуются воздушные пузырьки и падение давления за время выдержки конструкции под избыточным давлением не превысит норм, указанных в табл.2 и 3 обязательного приложения 1.
2.5. Испытания поливанием струей воды под напором
2.5.1. Испытания на непроницаемость поливанием струей воды под напором проводят брандспойтом, диаметр выходного отверстия которого должен быть не менее 16 мм.
2.5.2. Напор воды в шланге должен обеспечивать высоту струи воды, выбрасываемой вверх из ствола, не менее 10 м.
2.5.3. Струя воды должна быть направлена перпендикулярно к поверхности шва с расстоянием от ствола до испытываемого участка не более 3 м.
2.5.4. Поливание сварных конструкций проводят с любой стороны, клепаных — по возможности с нечеканенной стороны заклепочных соединений.
При вертикальном расположении сварных и клепаных соединений их поливают струей воды и снизу вверх.
2.5.5. Испытания поливанием струей воды под напором проводят при положительной температуре окружающего воздуха.
Испытания при отрицательной температуре окружающего воздуха проводят по согласованию с контролирующей организацией с использованием воды, подогретой до температуры плюс 40-70 °С.
При этом испытываемые участки конструкций должны быть подогреты до положительной температуры.
2.5.6. Конструкции считают непроницаемыми, если на контролируемой поверхности не будет течей в виде струй, потеков и капель.
2.6. Испытания поливанием рассеянной струей воды
2.6.1. Испытания на непроницаемость проводят поливанием конструкции рассеянной струей воды, направленной перпендикулярно к контролируемой поверхности.
2.6.2. Испытания проводят с учетом требований, установленных в пп.2.5.4-2.5.6.
2.7. Испытания обдувом струей сжатого воздуха
2.7.1. Испытания на непроницаемость обдувом струей сжатого воздуха проводят для местных проверок: мест приварки деталей, участков исправления дефектов сварки, дверей, люков, комингсов и других конструкций, расположенных внутри корпуса и надстроек, а также внутренних конструкций, имеющих клепаные соединения.
2.7.2. Струя воздуха, подаваемая из шланга, должна быть направлена перпендикулярно к контролируемому соединению. Конец шланга должен быть снабжен ниппелем диаметром 10-20 мм и подведен к контролируемому соединению на расстоянии не более 100 мм.
При испытании клепаных соединений струю воздуха направляют с нечеканенной стороны.
2.7.3. Контролируемое соединение одновременно с обдувом струей сжатого воздуха смачивают с противоположной стороны пенообразующим раствором, качество которого должно удовлетворять требованиям, установленным в пп.2.4.8 и 2.4.9.
2.7.4. Испытания обдувом струей сжатого воздуха проводят при температуре окружающего воздуха не ниже минус 10 °С. Испытываемые участки должны быть нагреты до положительной температуры и просушены до полного удаления замерзшей воды. Сжатый воздух должен быть сухим.
2.7.5. Конструкции считают непроницаемыми, если на контролируемых соединениях не образуются воздушные пузырьки.
2.8. Испытания смачиванием керосином
2.8.1. Испытания на непроницаемость смачиванием керосином проводят для контроля сварных соединений, за исключением соединений внахлестку с полным проваром и нахлесточных и тавровых соединений с двусторонними швами без сплошного провара.
Двусторонние швы тавровых сварных соединений без сплошного провара проверяют смачиванием керосином после окончательного выполнения первого прохода шва с одной стороны.
2.8.2. При испытании смачиванием керосином контролируемую сторону сварного шва покрывают меловым раствором. Швы смачивают керосином после высыхания мелового раствора.
Меловой раствор должен быть приготовлен на незамерзающем растворителе, не влияющем на белизну раствора. Если меловой раствор приготовлен на воде, то после нанесения его на сварной шов, он должен быть просушен газовой горелкой.
2.8.3. Поверхность сварного шва во время испытаний должна быть смочена керосином. По мере стекания или высыхания керосина следует периодически смачивать им сварные швы.
2.8.4. При проведении испытаний при отрицательной температуре окружающего воздуха контролируемый сварной шов перед смачиванием керосином должен быть прогрет до положительной температуры и просушен.
2.8.5. Сварные швы считают непроницаемыми, если на контролируемой поверхности с нанесенным меловым раствором за время выдержки, указанное в обязательном приложении 1, не появятся пятна керосина.
2.9. Испытания с применением вакуум-камер
2.9.1. Испытания на непроницаемость с применением вакуум-камер, способных поддерживать устойчивый перепад давлений воздуха в пределах 9·10-9,5·10 Па (0,9-0,95 кгс/см), проводят для местной проверки сварных или других соединений.
Испытания проводят поочередно на отдельных участках.
Примечание. Под перепадом давления следует понимать разность между атмосферным давлением и давлением в вакуум-камере.
2.9.2. При испытании с применением вакуум-камер участки соединений, подлежащие проверке, со стороны установки камеры смачивают пенообразующим раствором, удовлетворяющим требованиям, установленным в пп.2.4.8 и 2.4.9.
2. 9.3. Испытания при отрицательной температуре окружающего воздуха проводят с учетом требований, установленных в п.2.4.13.
2.9.4. Соединения считают непроницаемыми, если при испытании контролируемого участка в пенообразующем растворе не образуются воздушные пузырьки.
3.1. Результаты испытаний на непроницаемость и герметичность, проведенных при постройке, ремонте и модернизации судов, регистрируют в журнале, составленном по форме, приведенной в рекомендуемом приложении 3.
К журналу должна быть приложена схема испытаний на непроницаемость и герметичность.
3.2. Если какая-либо конструкция, подлежащая испытанию на непроницаемость и герметичность, не была испытана, то в журнале должны быть указаны: основание для отмены испытаний, фамилия и должность лица, разрешившего отступить от утвержденной схемы испытаний и согласующая подпись представителя контролирующей организации.
3.3. Перед спуском судна на воду должен быть составлен акт о заделке сливных и воздушных отверстий с указанием расположения этих отверстий.
4.1. К конструкциям, осматриваемым во время испытаний, должен быть обеспечен свободный доступ.
Для конструкций, имеющих высоту более 2 м, должны быть установлены подмости или леса.
4.2. Если в конструкциях, подлежащих испытанию, или соседних с ними конструкциях ранее находилось горючее, то перед испытанием оно должно быть удалено.
Конструкция должна быть пропарена и провентилирована.
4.3. Двери, горловины, крышки и другие подобные устройства должны быть закрыты на все задрайки и болты. Перед задраиванием необходимо убедиться в отсутствии людей в испытываемой конструкции.
Запрещается проводить испытания при неполном количестве крепежных деталей на дверях, люках, крышках, иллюминаторах и при наличии каких-либо неисправностей.
4.4. Конструкции водой или воздухом заполняют плавно, при этом необходимо следить за показаниями манометров. По достижении требуемого давления следует прекратить заполнение конструкций и отключить шланги.
4.5. Во время нахождения конструкций под давлением категорически запрещается проводить работы по устранению дефектов и обстукивать конструкции.
4.6. Перед устранением дефектов должны быть приняты меры, исключающие воспламенение материалов с обеих сторон испытываемой конструкции и ожоги людей.
4.7. Вблизи от места выполнения огневых работ (электросварки, газорезки и т.п.) не должны проводить работы с применением легковоспламеняющихся веществ.
4.8. Во время устранения дефектов в конструкциях должны быть установлены вытяжные вентиляторы для удаления из конструкций вредных газов.
4.9. При осмотре соединений необходимо пользоваться переносными светильниками напряжением не выше 12 В. Светильники должны иметь защитную сетку и исправный провод.
4.10. Измерительная и предохранительная аппаратура должна быть исправной, опломбированной, с непросроченным очередным испытанием Госповерки и должна быть установлена в доступных и хорошо освещенных местах.
4.11. Перед началом проведения испытаний на непроницаемость и герметичность необходимо убедиться в отсутствии людей в испытываемой конструкции. Все посторонние лица должны быть удалены из района испытаний.
4.12. После окончания испытаний необходимо принять меры для безопасности проведения дальнейших работ на испытанной конструкции, а именно: снять давление, удалить испытательные шланги, восстановить ограждение люков и вырезов горловин, крышки люков отдраить и закрепить и т.п.
4.13. При организации и проведении испытаний корпусов металлических судов на непроницаемость и герметичность необходимо руководствоваться требованиями «Общих правил техники безопасности и производственной санитарии для предприятий машиностроения», утвержденных ЦК профсоюза рабочих машиностроения в 1958 г., и «Правил техники безопасности и производственной санитарии для судостроительных и судоремонтных работ», утвержденных ЦК профсоюза рабочих судостроительной промышленности в 1970 г.
ПРИЛОЖЕНИЕ 1
Обязательное
Таблица 1
Наименование конструкции | Нормы основных испытаний на непроницаемость наливом воды под напором, наливом воды без напора, поливанием струей воды под напором, поливанием рассеянной струей воды для | Примечание | |||
морских судов | судов внутреннего плавания классов | ||||
«М-СП» и «М» | «О» | «Р» и «Л» | |||
I. | |||||
Отсеки двойного борта, предназ- наченные для хранения жидких нефтепродуктов | Налив воды под напором до верха воздушной трубы, но не менее чем на 2,5 м от палубы, ограничивающей отсек сверху | Налив воды под напором до верха воздушной трубы, но не ниже палубы переборок | Налив воды под напором до верха воздушной трубы, но не ниже палубы переборок | Налив воды под напором до верха воздушной трубы, но не ниже палубы переборок | Испытания наливом воды под напором могут быть заменены испытаниями надувом воздуха |
Отсеки двойного борта, предназ- наченные для хранения воды | То же | Налив воды под напором до верха воздушной трубы, но не ниже грузовой ватерлинии | Налив воды под напором до верха воздушной трубы, но не ниже грузовой ватерлинии | Налив воды под напором до верха воздушной трубы, но не ниже грузовой ватерлинии | То же |
Цистерны и отсеки, предназ- наченные для хранения воды, расположенные вне двойного дна | Налив воды под напором до верха воздушной трубы, но не менее чем на 2,5 м от настила, ограничивающего верх цистерны | То же | То же | То же | У морских судов с высотой борта менее 5 м высоту напора над палубой (платформой) принимают равной 0,5 высоты борта, но не менее 1,5 м. Для цистерн, воздушные трубы которых сведены в сборный коллектор, величину напора воды принимают до верха сборного коллектора, но не менее 2,5 м от верха цистерны. Испытания наливом воды под напором могут быть заменены испытаниями надувом воздуха |
Цистерны для хранения жидких нефтепродуктов судового запаса, циркуляционные и расходные; цистерны для хранения растительного масла, китового жира и т.п. грузов, расположенные вне двойного дна | Налив воды под напором до верха воздушной трубы, но не менее чем на 2,5 м от настила, ограничивающего верх цистерны | Налив воды под напором до верха воздушной трубы, но не ниже палубы переборок | Налив воды под напором до верха воздушной трубы, но не ниже палубы переборок | Налив воды под напором до верха воздушной трубы, но не ниже палубы переборок | У морских судов с высотой борта менее 5 м высоту напора над палубой (платформой) принимают равной 0,5 высоты борта, но не менее 1,5 м. Испытания наливом воды под напором могут быть заменены испытаниями надувом воздуха |
Отсеки двойного дна, предназ- наченные для хранения воды или нефтепродуктов | Налив воды под напором до палубы переборок или до верха воздушной трубы (по большему напору) | Налив воды под напором до высоты 0,6 м над настилом двойного дна или до верха воздушной трубы (по большему напору) | Налив воды под напором до высоты 0,35 м над настилом двойного дна или до верха воздушной трубы (по большему напору) | Налив воды под напором до высоты 0,35 м над настилом двойного дна или до верха воздушной трубы (по большему напору) | Отсчет уровня воды от настила двойного дна проводят в наиболее высокой точке отсека. Испытания наливом воды под напором могут быть заменены испытаниями надувом воздуха. |
Отсеки наливного судна и трюмы сухогрузных судов, предназ- наченные для перевозки жидких грузов | Налив воды под напором до верха расширительной шахты, но не менее чем на 2,5 м от палубы, ограничивающей отсек сверху | Налив воды под напором до верха расширитель- ной шахты | Налив воды под напором до верха расширитель- ной шахты | Налив воды под напором до верха расширитель- ной шахты | У морских судов с борта, но не менее 5 м высоту напора над палубой (платформой) принимают равной 0,5 высоты борта, но не менее 1,5 м. Испытания наливом воды под напором могут быть заменены испытаниями надувом воздуха. Если конструкции отсеков судов внутреннего плавания не выдерживают заданного напора воды, то такие отсеки испытывают в два этапа: I — на стапеле наливом воды до уровня, превышающего на 0,5 м осадку судна после спуска, а выше этого уровня — поливанием струей воды под напором; II — на плаву наливом воды под напором |
Форпик и ахтерпик, используемые в качестве водяных отсеков | Налив воды под напором до верха воздушной трубы, но не менее чем на 0,9 м над палубой | Налив воды под напором до верха воздушной трубы, но не менее чем на 0,6 м над палубой переборок | Налив воды под напором до верха воздушной трубы | Налив воды под напором до верха воздушной трубы | Ахтерпик на судах испытывают с установленными дейдвудной трубой и гельмпортом. Отсчет уровня воды от настила палубы проводят в наиболее высокой точке отсека. Если воздушные трубы форпика или ахтерпика имеют высоту 915 мм от палубы переборок, то минимальный напор воды при испытании этих отсеков должен быть равен 915 мм от палубы переборок |
Кингстонные ящики, ящики забортной воды, ледовые ящики | Налив воды под напором до уровня 1,25 высоты борта судна | Налив воды под напором до уровня 1,25 высоты борта судна | Налив воды под напором до уровня 1,25 высоты борта судна | Налив воды под напором до уровня 1,25 высоты борта судна | При наличии систем продувания, обогрева и т.п., испытательное давление принимают равным давлению испытания этих систем. При испытании забортных ящиков на судах внутреннего плавания при отсутствии систем продувания напор воды должен быть на 0,35 м выше крышки ящика. Испытания наливом воды под напором могут быть заменены испытаниями надувом воздуха |
Коффердамы, имеющие устройства для приема воды | Налив воды под напором до верха воздушной трубы, но не менее чем на 2,5 м от настила, ограничивающего верх коффердама | Налив воды под напором до верха воз- душной трубы, но не менее чем на 2,5 м от настила, огра- ничивающего верх коффердама | Налив воды под напором до верха воздушной трубы, но не ниже грузовой ватерлинии | Налив воды под напором до верха воздушной трубы, но не ниже грузовой ватерлинии | Испытания наливом воды под напором могут быть заменены испытаниями надувом воздуха |
Съемные водяные, топливные и масляные цистерны | Налив воды под напором до верха воздушной или переливной трубы. | Налив воды под напором до верха воздушной или переливной трубы. Для топливных и масляных цистерн напор не менее чем на 1 м от верхней точки цистерны | Налив воды под напором до верха воздушной или переливной трубы. Для топливных и масляных цистерн напор не менее чем на 1 м от верхней точки цистерны | Налив воды под напором до верха воздушной или переливной трубы. Для топливных и масляных цистерн напор не менее 0,35 м от верхней точки цистерны | Съемные цистерны должны быть испытаны дважды: до и после установки цистер- ны на судне с присоединенными трубопроводами. Испытания наливом воды могут быть заменены испытаниями надувом воздуха |
Плавательные бассейны | Налив воды без напора до верхней кромки бассейна | Налив воды без напора до верхней кромки бассейна | — | — | — |
Фекальные цистерны | Налив воды под напором, равным 1,5 давления столба воды от дна цистерны до нижнего прибора | Налив воды под напором, равным 1,5 давления столба воды от дна цистерны до нижнего прибора | Налив воды под напором, равным 1,5 дав- ления столба воды от дна цистерны до нижнего прибора | Налив воды под напором, равным 1,5 давления столба воды от дна цистерны до нижнего прибора | Испытания наливом воды под напором могут быть заменены испытаниями надувом воздуха |
II. | |||||
Форпик и ахтерпик, не предназ- наченные для заполнения водой | Налив воды под напором не менее чем на 0,3 м над палубой переборок; выше этого уровня — поливание струей воды под напором | Налив воды под напором не менее чем на 0,3 м над палубой переборок; выше этого уровня — поливание струей воды под напором | Налив воды под напором до уровня грузовой ватерлинии; выше этого уровня — поливание струей воды под напором или смачивание керосином | Налив воды под напором до уровня грузовой ватерлинии; выше этого уровня — поливание струей воды под напором или смачивание керосином | Ахтерпик на судах испытывают с установленными дейдвудной трубой и гельмпортом. Отсчет уровня воды от настила палубы проводят в наиболее высокой точке отсека. |
Отсеки двойного борта, не предназ- наченные для хранения жидкостей: | |||||
для судов с двойным дном | Поливание струей воды под напором выше уровня двойного дна | Поливание струей воды под напором выше уровня двойного дна | Поливание струей воды под напором выше уровня двойного дна | Поливание струей воды под напором выше уровня двойного дна | Испытания поливанием струей воды под напором могут быть заменены испыта- ниями сварных швов смачиванием керосином |
для судов без двойного дна | Налив воды без напора на высоту 1 м от наружной обшивки у киля; выше этого уровня — поливание струей воды под напором | Налив воды без напора на высоту 0,6 м от наружной обшивки у киля; выше этого уровня — поливание струей воды под напором | Налив воды без напора на высоту 0,6 м от наружной обшивки у киля; выше этого уровня — поливание струей воды под напором | Налив воды без напора на высоту 0,35 м от наружной обшивки у киля; выше этого уровня — поливание струей воды под напором | Испытания поливанием струей воды под напором могут быть заменены испыта- ниями сварных швов смачиванием керосином |
Грузовые трюмы сухогрузных судов, машинно- котельные, моторные отделения и вертикальные коффердамы: | Испытания поливанием струей воды под напором могут быть заменены испытаниями сварных швов смачиванием керосином | ||||
для судов с двойным дном | Поливание струей воды под напором выше уровня двойного дна | Поливание струей воды под напором выше уровня двойного дна | Поливание струей воды под напором выше уровня двойного дна | Поливание струей воды под напором выше уровня двойного дна | Отсчет уровня воды от наружной обшивки проводят в наиболее высокой точке киля (в пределах данного отсека) |
для судов без двойного дна | Налив воды без напора на высоту 1 м от наружной обшивки днища у киля; выше этого уровня — поливание струей воды над напором | Налив воды без напора на высоту 0,6 м oт наружной обшивки у киля; выше этого уровня — поливание струей воды под напором | Налив воды без напора на высоту 0,35 м от наружной обшивки у киля; выше этого уровня — поливание струей воды под напором | Налив воды без напора на высоту 0,35 м от наружной обшивки у киля; выше этого уровня — поливание струей воды под напором | — |
Отсеки в междупалубном пространстве | Поливание струей воды под напором | Поливание струей воды под напором | Поливание струей воды под напором | Поливание струей воды под напором | Испытания поливанием струей воды под напором могут быть замене- ны испытаниями сварных швов смачиванием керосином |
Междудонные отсеки, включая, туннельный киль и коффердамы, расположенные в междудонном пространстве | Налив воды под напором до палубы переборок | Налив воды под напором до высоты 0,6 м над настилом двойного дна | Налив воды под напором до высоты 0,35 м над настилом двойного дна | Налив воды под напором до высоты 0,35 м над настилом двойного дна | Отсчет уровня воды от настила двойного дна или палубы проводят в наиболее высокой точке отсека. Испытания наливом воды под напором могут быть заменены испытаниями надувом воздуха |
Горизонтальные коффердамы, не имеющие устройства для приема воды и расположенные ниже ватерлинии | Налив воды без напора на высоту комингса люка над коффердамом | Налив воды без напора на высоту комингса люка над коффердамом | Налив воды без напора на высоту 0,35 м от наружной обшивки у киля; выше этого уровня — поливание струей воды под напором | Налив воды без напора на высоту 0,35 м от наружной обшивки у киля; выше этого уровня — поливание струей воды под напором | Испытания наливом воды без напора могут быть заменены испытаниями надувом воздуха. Для морских судов и судов внутреннего плавания классов «М-СП» и «М» в случае отсутствия комингса люка или водолазных труб, высоту напора принимают равной 0,6 м над высшей точкой палубы (платформы) в районе коффердама |
Коффердамы, не имеющие устройства для приема воды и расположенные выше ватерлинии | Поливание струей воды под напором | Поливание струей воды под напором | Поливание струей воды под напором | Поливание струей воды под напором | |
Рули пустотелые (обтекаемые) и направляющие пустотелые насадки, крыльевые устройства | Налив воды под напором | Налив воды под напором | Налив воды под напором | Налив воды под напором над верхней кромкой руля (насадки), равным 1 м | Испытания наливом воды под напором могут быть заменены испытаниями надувом воздуха. Давление водяного столба определяют по формуле , где — осадка судна в полном грузу, м; — скорость судна, узлы |
Шахты лага, эхолота, отсеки подруливающего устройства, воздушные ящики, отсеки плавучести | Налив воды под напором до уровня палубы переборок | Налив воды под напором до уровня палубы переборок | Налив воды под напором до грузовой ватерлинии | Налив воды под напором до грузовой ватерлинии | Испытания наливом воды под напором могут быть заменены испытаниями надувом воздуха |
Коридор гребного вала, включая выгородки и шахты запасного выхода, непроницаемые шахты, включая шахты МКО* кожухи котельных дымоходов и дымовых труб | Поливание струей воды под напором | Поливание струей воды под напором | Поливание струей воды под напором | Поливание струей воды под напором | Испытания поливанием струей воды под напором могут быть заменены испытаниями сварных швов смачиванием керосином. Если конструкции проходят через отсеки, испытываемые наливом воды под напором или надувом воздуха, то соответствующие участки коридора и шахт проверяют на непроницаемость при испытании этих отсеков |
________________ * МКО — машинно-котельные отделения. | |||||
Цепные ящики, расположенные: | |||||
в корму от таранной переборки | Налив воды без напора на высоту 0,6 м от днища ящика; выше этого уровня — поливание струей воды под напором | Налив воды без напора на высоту 0,4 м от днища ящика; выше этого уровня — поливание струей воды под напором | То же | То же | Испытания поливанием струей воды под напором могут быть заменены испытаниями сварных швов смачиванием керосином |
в нос от таранной переборки | Поливание струей воды под напором | Поливание струей воды под напором | Поливание струей воды под напором | Поливание струей воды под напором | Конструкции (или части их) цепного ящика при расположении ящика в нос от таранной переборки, которые испытывали наливом воды под напором при испытании форпика, поливанием струей воды под напором не испытывают |
Отсек в подзоре кормы | Налив воды без напора на высоту, соответствующую грузовой ватерлинии; выше этого уровня — поливание струей воды под напором | Налив воды без напора на высоту, соответствую- щую грузовой ватерлинии; выше этого уровня — поливание струей воды под напором | Налив воды без напора на высоту, соответствую- щую грузовой ватерлинии; выше этого уровня — поливание струей воды под напором | Налив воды без напора на высоту соответствую- щую грузовой ватерлинии; выше этого уровня — поливание струей воды под напором | Испытания поливанием струей воды под напором могут быть заменены испытаниями сварных швов смачиванием керосином. Отсек, предназначенный для приема балласта, испытывают как ахтерпик, используемый в качестве водяного отсека по нормам, установленным для испытания ахтерпика |
Якорные клюзы и цепные трубы | Поливание струей воды под напором | Поливание струей воды под напором | Поливание струей воды под напором | Поливание струей воды под напором | Испытания поливанием струей воды под напором могут быть заменены испытаниями сварных швов смачиванием керосином |
Палубные надстройки и рубки, включая открытые части машинно- котельных шахт и кожухов дымовых труб | То же | То же | То же | То же | Сварные швы конструкций, расположенных внутри надстроек и рубок, могут быть испытаны смачиванием керосином |
Открытые части палуб | « | « | « | « | Открытые части палуб в районе грузовых танков наливных судов испытывают совместно с соответствующими отсеками. Испытания поливанием струей воды под напором могут быть заменены испытаниями сварных швов смачиванием керосином. Клепаные соединения палуб (пазы и стыки) могут быть испытаны обдувом струей сжатого воздуха. Деревянные палубы испытывают поливанием струей воды под напором. Палубы при испытаниях следует поливать сверху |
Комингсы люков и вентиля- ционных труб, расположенные на открытых частях верхней палубы, палубы надстроек и рубок | Поливание струей воды под напором | Поливание струей воды под напором | Поливание струей воды под напором | Поливание струей воды под напором | Комингсы высотой до 100 мм могут быть испытаны смачиванием керосином |
Палубы и выгородки в помещениях, где может скапливаться вода (душевые, умывальные, ванные, прачечные, камбузы, гальюны и т. | Налив воды без напора на высоту комингсов дверей; выше этого уровня — поливание струей воды под напором | Налив воды без напора на высоту комингсов дверей; выше этого уровня — поливание рассеянной струей воды | Налив воды без напора на высоту комингсов дверей, выше этого уровня — поливание рассеянной струей воды | Налив воды без напора на высоту комингсов дверей; выше этого уровня — поливание рассеянной струей воды | Испытания наливом воды без напора проводят после установки и монтажа всех трубопроводов, но до цементирования, укладки метлахских плиток или другого покрытия на палубу. Испытания поливанием струей воды под напором могут быть заменены испытаниями сварных швов смачиванием керосином. Время выдержки при испытании наливом воды без напора — 30 мин. Если при испытании вся палуба в пределах испытываемого отсека не может быть залита водой, то неиспытанные участки палуб проверяют поливанием струей воды под напором или смачиванием керосином. В зимний период по согласованию с контролирующей организацией разрешается проводить испытания всей площади палуб смачиванием керосином |
Устройства для закрывания отверстий в непроницаемых частях корпуса: | |||||
двери в непроницаемых переборках | Поливание струей воды под напором | Поливание струей воды под напором | Поливание струей воды под напором | Поливание рассеянной струей воды | Устройства для закрывания отверстий в непроницаемых конструкциях, расположенных внутри корпуса, надстроек и рубок, могут быть испытаны обдувом струей сжатого воздуха |
двери по наружным стенкам надстроек и рубок | То же | То же | То же | То же | |
лац-порты | « | « | « | « | Устройства для закрывания отверстий (крышки горловин, люков, клинкеты и т. |
крышки световых и сходных люков, иллюминаторы в верхних палубах и бортах основного корпуса, в палубах и наружных переборках надстроек | « | « | « | « | |
крышки горловин в непроницаемых палубах, платформах и переборках | Поливание струей воды под напором | Поливание струей воды под напором | Поливание струей воды под напором | Поливание рассеянной струей воды | Каждая водоне- проницаемая дверь, устанавливаемая под палубой переборок, должна быть испытана напором воды с высотой до палубы переборок, но не менее 5 м. |
наружные бортовые части мусоро- удалителей | То же | То же | То же | То же | Испытания допускается проводить до и после установки двери на место |
металлические закрытия грузовых люков сухогрузных судов | « | « | « | « | Испытания водо- непроницаемых дверей, установ- ленных на судне, поливанием струей воды под напором допускаются в случае, если дверь до установки на судно испытывали наливом воды под напором. Для судов внутреннего плавания класса «О», у которых суммарная величина установленного надводного борта и комингса не менее 1200 мм, испыта- ния поливанием струей воды под напором могут быть заменены испытаниями поливанием рассеянной струей воды |
металлические закрытия грузовых люков сухогрузных судов, перевозящих в трюмах жидкие грузы, включая нефтепродукты | На головном судне испытания на непроницаемость типовых узлов уплотнения проводят на моде- ли в натуральную величину наливом воды под напором. Высота напора должна соответствовать нормам, установленным для данной конструкции. Контроль глубины вдавливания уплотнительной прокладки осуществляют по всему периметру уплотнения всех люков на каждом судне. Глубину вдавливания устанавливает проектная организация. Испытания непроницаемости каждого трюма с люковым закрытием проводят по технической документации, согласованной с контролирующей организацией |
Примечание. Основные испытания на непроницаемость конструкций группы, а на серийных судах внутреннего плавания классов «О», «Р» и «Л» по согласованию с контролирующей организацией допускается проводить смачиванием керосином.
Таблица 2
Нормы испытаний на непроницаемость надувом воздуха
Наименование испытания | Избыточное давление воздуха, Па (кгс/см) | Время выдержки, ч, не менее | Допускаемое падение давления, % |
Основные | 3·10 (0,3) 2·10 (0,2) | 1 | 5 |
Контрольные | 2·10 (0,2) |
Примечания:
1. При проведении основных испытаний избыточное давление, равное 2·10 Па (0,2 кгс/см) применяют в случаях, указанных в п.2.4.2.
2. Для конструкций, в которых хранят нефть, дизельное топливо и легкие нефтепродукты, падение давления не допускается при времени выдержки 1 ч.
3. Контрольные испытания конструкций группы а, прошедших основные испытания на непроницаемость наливом воды под напором, проводят надувом воздуха по указанным нормам.
Таблица 3
Нормы испытаний на герметичность надувом воздуха
Наименование испытания | Избыточное давление воздуха, Па (кгс/см) | Время выдержки, мин, не менее | Допускаемое падение давления, % |
Помещения и отсеки в корпусе и надстройках, граничащие с наружным контуром | 2·10 (0,02) 1·10 (0,01) | 15 | 50 |
Прочие помещения и отсеки | 2·10 (0,02) 1·10 (0,01) | 5 | 50 |
Примечания:
1. Конструкции, не вошедшие в табл.3, испытывают по технической документации.
2. Избыточное давление, равное 1·10 Па (0,01 кгс/см), применяют в случаях, указанных в п.2.4.3.
Нормы испытаний на непроницаемость обдувом струей сжатого воздуха
Давление в шланге должно быть 4·10-5·10 Па (4-5 кгс/см).
Нормы испытаний на непроницаемость смачиванием керосином
Время выдержки при испытании смачиванием керосином определяют в зависимости от толщины свариваемого листа или катета шва и положения шва в пространстве.
Нижнее положение:
толщина листа или катет шва до 6 мм — 40 мин;
» » » » » 6-24 мм — 60 мин;
» » » » » св. 24 мм — 90 мин.
Вертикальное и горизонтальное положение:
толщина листа или катет шва до 6 мм — 60 мин;
» » » » » 6-24 мм — 90 мин;
» » » » » св. 24 мм — 120 мин.
Примечание. Время выдержки удваивают при проведении:
испытаний при отрицательных температурах;
испытаний сварных соединений с двусторонними швами со сплошным проваром.
Нормы испытаний на непроницаемость с применением вакуум-камер
Величина разрежения (вакуума) в вакуум-камере должна быть не менее 6·10 Па (0,6 кгс/см).
ПРИЛОЖЕНИЕ 2
Обязательное
1. Испытания на непроницаемость
1.1. Конструкции группы а испытывают на непроницаемость наливом воды над напором или надувом воздуха.
1.2. Конструкции группы б головных и серийных судов испытывают на непроницаемость одним из следующих методов: наливом воды без напора, обдувом струей сжатого воздуха, поливанием струей воды под напором, поливанием рассеянной струей воды, смачиванием керосином и с применением вакуум-камер.
1.3. Отсеки группы б, состоящие из нескольких отдельных помещений, допускается испытывать по согласованию с контролирующей организацией отдельно по помещениям, составляющим отсек, при соблюдении требований, установленных в пп.1.14-1.19.
1.4. Конструкции группы б, к которым предъявляются требования брызгонепроницаемости, допускается испытывать поливанием рассеянной струей воды по согласованию с контролирующей организацией.
1.5. При проведении испытаний на непроницаемость, одновременно с проверкой сварных соединений, должна быть осмотрена вся поверхность испытываемой конструкции. При обнаружении мест с нарушением непроницаемости конструкции последняя должна быть испытана.
1.6. Двери, люки, горловины, иллюминаторы, вентиляционные заслонки и другие дельные вещи должны быть испытаны на предприятии-изготовителе в соответствии с требованиями технической документации. После установки на место в корпусе судна они должны быть испытаны на непроницаемость и герметичность одновременно с испытанием конструкции, к которой они относятся.
1.7. Вентиляционные каналы, входящие в контролируемые отсеки, испытывают в соответствии с технической документацией.
1.8. При доковании судна в период текущего ремонта или очередного осмотра допускается испытывать междудонные отсеки в два этапа:
когда судно находится в доке, его испытывают наливом воды под напором с последующим устранением дефектов и окраской;
когда судно находится на плаву, осматривают настил, второе дно и другие конструкции междудонных отсеков.
1.9. Съемные листы или части секций, предусмотренные для погрузки механизмов, при испытании конструкций могут быть не заклепаны, а установлены с прокладками на временных болтах.
Испытания на непроницаемость съемных листов и частей секций проводят после их окончательной установки.
В этом случае соединения всех съемных частей на палубах, платформах, переборках и других конструкциях испытывают самостоятельно: сварные соединения — смачиванием керосином или с применением вакуум-камер; клепаные и болтовые — поливанием струей воды под напором, обдувом струей сжатого воздуха или с применением вакуум-камер.
1.10. Главные водонепроницаемые переборки испытывают наливом воды под напором. Эти испытания следует совмещать с испытаниями днищевых отсеков, не имеющих второго дна или непроницаемых платформ.
2. Испытания на герметичность
2.1. При испытании на герметичность каждая конструкция должна быть испытана отдельно.
2.2. Конструкции, к которым, помимо требований непроницаемости, предъявляются требования герметичности и которые в период постройки, ремонта и модернизации подвергались контрольным испытаниям на непроницаемость надувом воздуха, на герметичность не испытывают.
2.3. В период проведения испытаний на герметичность отсеки и помещения задраивают по наружному контуру штатными задраивающими устройствами за исключением систем вентиляции, используемых для создания избыточного давления.
На конструкциях, находящихся внутри испытываемого отсека и помещения, задраивающие устройства должны быть открыты.
2.4. Машинно-котельные отделения, помещения для размещения турбо- и дизельгенераторов электростанций, а также помещения, отсеки и блоки, имеющие вентиляцию, за исключением блоков санитарной обработки, жилых и служебных помещений, испытывают на герметичность при постоянно поддерживаемом вентиляцией избыточном давлении воздуха в соответствии с требованиями технической документации. Продолжительность проведения испытаний не менее 30 мин.
Помещения считают герметичными, если манометры показывают постоянное избыточное давление при работе вентиляции.
2.5. Наружный контур судна испытывают на герметичность надувом воздуха или проходом судна через стойкую завесу нейтрального дыма в течение 10 мин со скоростью, устанавливаемой технической документацией.
2.6. Отсеки и помещения, испытанные ранее на герметичность по группам отсековой и индивидуальной герметичности, повторно не испытывают.
3. Испытания на непроницаемость корпусов несамоходных нефтеналивных судов, поднадзорных Речному Регистру РСФСР
3.1. После проведения ремонтных работ должны быть испытаны на непроницаемость сварные и клепаные швы корпусов несамоходных нефтеналивных судов.
Сварные швы испытывают смачиванием керосином, клепаные швы — поливанием струей воды под напором по нормам, установленным в обязательном приложении 1.
Объем испытаний устанавливают в соответствии с технической документацией, согласованной с контролирующей организацией.
3.2. Балластные отсеки испытывают на непроницаемость наливом воды без напора на высоту, равную половине высоты борта. Выше указанной высоты испытания проводят поливанием струей воды под напором.
3.3. Коффердамы, предназначенные для заполнения водой, испытывают на непроницаемость наливом воды под напором до верха воздушной трубы, но не менее 0,8 м до палубы.
3. 4. Подводную часть обшивки корпуса в районе расположения грузовых отсеков испытывают на непроницаемость «перетопкой».
Примечание. Под «перетопкой» следует понимать положение судна, приспущенного со слипа или дока на воду на 5 см меньше осадки порожнем.
ПРИЛОЖЕНИЕ 3
Рекомендуемое
| Подпись |
| |||||||
Номер испыты- | Наиме- | Метод испы- | Темпе- | Дата испыта- | Резуль- | произ- | мастера ОТК | предста- | Приме- |
Анализаторы герметичности упаковки | wittgas.
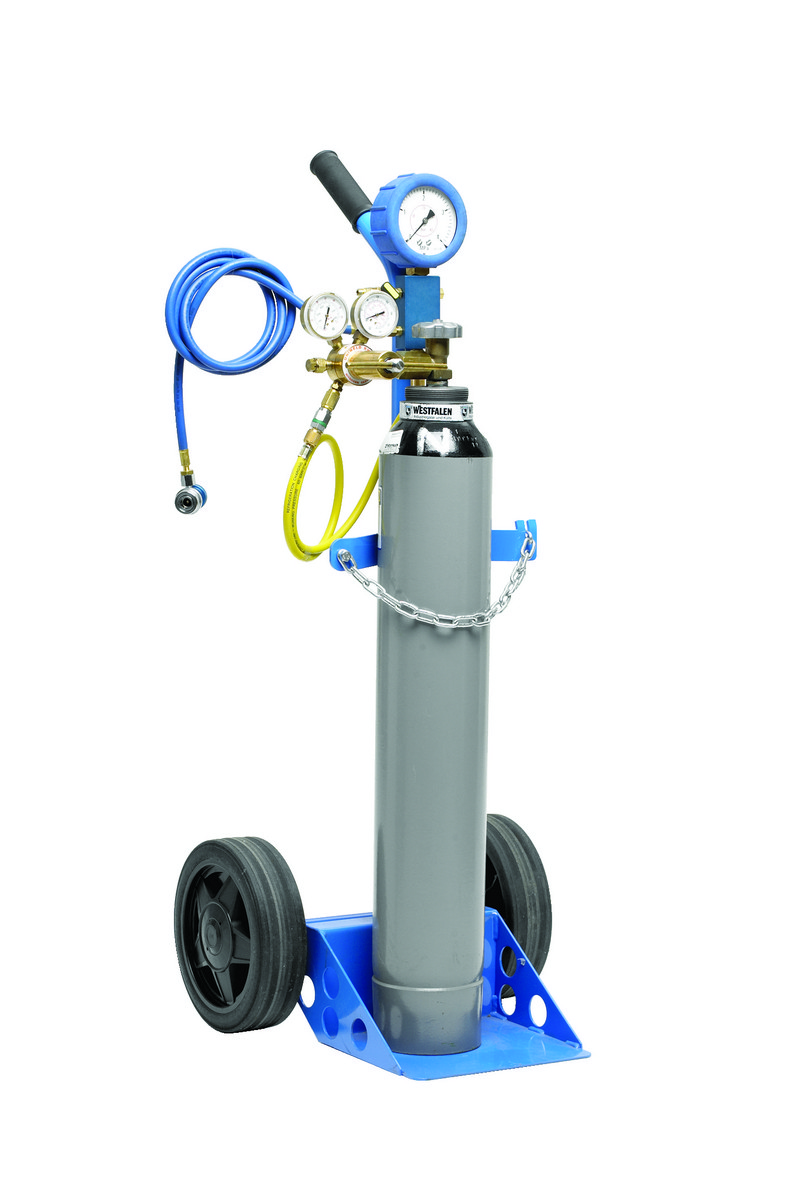
Упаковка должна быть герметичной. Тем не менее, даже с большой осторожностью в процессе упаковки нельзя избежать абсолютно безопасно поврежденных упакованных продуктов. Ошибки в процессе уплотнения или в материале быстро приводят к утечкам, иногда микроскопическим, небольшим. В течение многих лет тестирование герметичности или герметичности швов упаковки является неотъемлемой частью обеспечения качества, как для упаковки пищевых продуктов, так и для других чувствительных продуктов, например, в фармацевтической или химической промышленности.
В модельной серии LEAK-MASTER® компания WITT предлагает различные решения для проверки герметичности упаковки.
Это сертифицированные системы качества для всех типов упаковки — с защитной атмосферой (MAP) или вакуумом. Для оптимизации контроля качества у вас есть выбор между устройствами для проверки герметичности при случайном отборе проб или испытания в линию — на основе CO2 или в качестве испытания на пузырьки воды (рабочее испытание):
испытание на герметичность упаковки в водяной бане на утечку (испытание на герметичность)Система LEAK-MASTER® EASY позволяет обнаруживать даже самые мелкие утечки без использования остаточного газа. Упаковка помещается в заполненную водой камеру для проверки герметичности, а воздух, расположенный выше уровня воды, удаляется через сопло Вентури, приводимое в действие сжатым воздухом. Это приводит к раздуванию упаковки, отжатой под водой. При утечках воздух или заправочный газ выходит в виде пузырьков воздуха и бисер заметно поднимается вверх. Этот тест на наличие пузырьков также может быть использован для определения места утечки упаковки. Это особенно важно для выявления возможных ошибок в процессе упаковки, например, наличие дефекта материала или дефекта уплотнительного шва.
Ваша упаковка герметична? С LEAK-MASTER® PRO вы можете проверить герметичность упаковки методом случайного отбора проб. Принцип действия этой системы для проверки герметичности упаковки также прост и эффективен. В LEAK-MASTER® PRO в качестве остаточного газа используется CO2. Использование CO2 является особенно недорогим методом по сравнению с гелиевым водородом. Продукты, упакованные под инертным газом, в большинстве случаев содержат CO2 в качестве компонента защитной атмосферы — другие продукты сами производят CO2. В измерительной камере создается регулируемый вакуум. Разница давлений между образцом испытания и камерой позволяет защитному газу, содержащему CO2, выходить из самой маленькой утечки в упаковке. Это увеличивает концентрацию CO2 в камере. Чувствительный датчик CO2 реагирует на этот подъем и обнаруживает даже мельчайшие утечки (например, на уплотнительном шве).
LEAK-MASTER® MAPMAX позволяет проводить неразрушающее обнаружение даже самых маленьких утечек с CO2 в качестве следящего газа — в качестве 100%-ного испытания сразу после процесса упаковки. MAPMAX позиционирует упаковку или наружную тару в измерительной камере. Создается регулируемый вакуум, который вызывает разницу давления между образцом испытания и камерой. Наименьшая утечка в упаковке обеспечивает выход защитного газа, который обнаруживается чувствительным датчиком CO2 в течение нескольких секунд. После каждого цикла измерения камера удаляется воздух и испытуемый образец переносится в систему, расположенную ниже по течению. С помощью MAPMAX Вы можете проверить герметичность отдельных упаковок, целых преимуществ или даже внешних упаковок и коробок. Со скоростью 15 циклов в минуту, LEAK-MASTER® MAPMAX обеспечивает полную проверку герметичности всего вашего производства.
Для испытания герметичности упаковки в линию в минимальном пространстве в качестве опции доступна также более короткая версия: LEAK-MASTER® MAPMAX Compact.
100% — Испытание упаковки на утечку является непревзойденным аргументом.
Проверьте герметичность упаковки. С системами WITT для проверки герметичности упаковки, контроля качества и документирования завершено. Таким образом, обеспечивается и проверяется качество продукта, поступающего к потребителю. Ненужные возвраты, неизбежная потеря имиджа, правовые последствия и, в худшем случае, потеря клиента могут быть легко и надежно предотвращены с помощью упаковки для тестирования на герметичность.
Кстати, не только герметичность упаковки пищевых продуктов, но и ПЭТ-бутылок и банок для напитков проверяется с помощью модельного ряда LEAK-MASTER. Системы контроля герметичности также используются во многих других отраслях промышленности: например, в автомобильной промышленности различные компоненты, такие как задние фары, указатели поворота и фары, должны быть водонепроницаемыми и поэтому проверяться на герметичность. Воздушные подушки или пластиковые поплавки также могут быть проверены на герметичность. В косметической и фармацевтической промышленности фармацевтическая упаковка LEAK-MASTER используется для выборочной проверки ампул, флаконов, лабораторных наборов для тестирования и блистерных пакетов на герметичность, поскольку безупречное качество упаковки является решающим конкурентным преимуществом и здесь.
Подробная информация на сайте https://www.leak-master.netwww.leak-master.net
Испытание на герметичность | Что такое испытание на герметичность?
Испытания на герметичность играют важную роль в проверке соответствия новых зданий (как жилых, так и коммерческих).
Что такое испытание на герметичность?
Испытание на герметичность— это общепризнанный метод, используемый для измерения общего количества воздуха, потерянного из-за утечек в ткани здания. Это часто называют неконтролируемой вентиляцией (сквозняками).
Тест важен для определения энергоэффективности нового здания и может выявить низкое качество строительства в новых разработках.С введением более жестких правил при проектировании зданий часто учитывается воздухонепроницаемость на ранних этапах процесса строительства, чтобы обеспечить ее соответствие.
Если рейтинг воздухопроницаемости объекта превышает 10 м³/ч/м² при 50 Па (7 м³/ч/м² при 50 Па в Шотландии), то объект не пройдет испытание из-за значительной неконтролируемой утечки воздуха. Эта утечка может привести к:
- нежелательные потери тепла
- дискомфорт для жильцов (холодные дома)
- повышенные счета за отопление (для борьбы с холодом)
- повышенные выбросы CO² (в результате необходимости дополнительного нагрева)
Когда требуется испытание на герметичность?
Ближе к концу процесса строительства проводится испытание на герметичность в соответствии со строительными нормами и стандартами. Результаты теста используются в расчетах SAP и SBEM и могут повлиять на общий энергетический рейтинг новых зданий.
Крупные жилые комплексы не требуют проведения испытаний на каждом отдельном объекте; вместо этого проводится тестирование различных типов жилья в застройке.
Все коммерческие объекты площадью более 500 м² потребуют проверки давлением воздуха , чтобы соответствовать Строительным нормам/стандартам.
Соответствие строительным нормам/стандартам
Испытания воздуха обычно требуются после постройки здания (жилого или коммерческого).Результаты испытания на герметичность вводятся в Стандартную процедуру оценки (SAP) и расчеты по упрощенной модели энергопотребления здания (SBEM), необходимые для утверждения Управлением по надзору за строительством/верификатором (Шотландия). Это соответствует требованиям Части L строительных норм (и других региональных вариантов).
Как проходит испытание на герметичность?
Испытатели воздуха устанавливают оборудование для проверки дверцы воздуходувки (большие вентиляторы) на внешнее отверстие (обычно дверной проем) и будут использовать его для повышения давления в здании и проверки перепадов избыточного давления. Затем внешнее давление воздуха поступает через трещины и отверстия. Тестеры воздуха уровня 2 могут использовать дверные системы с несколькими вентиляторами вместо систем с одним вентилятором для проверки герметичности больших коммерческих зданий.
Уровни тестера
Существуют различные уровни испытаний на герметичность, установленные в зависимости от размера и сложности здания. Обзор каждого представлен ниже:
Уровень 1: Испытание давлением воздуха для одиночных жилых домов и других небольших нежилых помещений с общим объемом оболочки до 4000 м³, как правило, тестируется с одним дверным вентилятором.
Уровень 2: Испытание давлением воздуха для простых и сложных зданий с общим объемом оболочки более 4000 м³ . Сюда не входят большие и сложные высотные здания (LCHR), а также поэтапно переданные/зональные здания.
Уровень 3: Проверка давления воздуха для зданий LCHR, зданий с поэтапной и зональной передачей.
Обучение проверке герметичности
Если вы хотите пройти обучение по проверке герметичности или другим аспектам оценки энергопотребления, не ищите дальше.Elmhurst Energy Systems Limited, дочерняя компания iATS Limited, предлагает широкий спектр обучения, в том числе обучение уровня 1 и уровня 2, с использованием наших собственных ресурсов или через тщательно отобранных партнеров.
УЗНАТЬ БОЛЬШЕ >
Когда лучше всего провести испытание на герметичность?
Герметичность является основной частью любой конструкции энергоэффективного жилья. Но когда самое подходящее время для проведения испытания на герметичность? Мы делимся этим и многим другим в нашем последнем блоге.
Герметичность — важный этап сборки; это может коренным образом изменить энергоэффективность жилища.
Также известное как испытание на утечку воздуха или испытание под давлением воздуха, это метод, с помощью которого ваше здание измеряется и проверяется на утечку воздуха из-за неконтролируемых утечек в строительной ткани. Это вносит огромный вклад в энергоэффективность здания.
Когда самое подходящее время для проверки на герметичность? Подождите, пока ваше здание не будет в достаточной степени готово к работе, прежде чем пройти тест на герметичность.Тем не менее, есть возможность заранее провести пробный тест, чтобы точно определить любые потенциальные проблемы.
Оставлять такую важную часть сборки на последний момент может быть страшно; в конце концов, если вы потерпите неудачу, вы столкнетесь с серьезным нарушением всего процесса. К счастью, есть вещи, которые вы можете сделать, чтобы защитить себя и убедиться, что вы прошли тест на герметичность с первого раза.
Когда я должен пройти тест на воздух? Ваше жилище должно быть в основном завершено до того, как вы проведете проверку воздуха — это включает в себя готовые стены, установленные окна, плинтус, освещение и выключатели, установленные двери … вы поняли. Вам также понадобится ваш балл SAP, так как он установит цель для воздушного теста.
Несмотря на то, что вам нужно подождать, чтобы провести испытание воздухом, вы можете воспользоваться поддержкой консультанта по энергетике с самого начала, чтобы убедиться, что ваши конструкции были созданы с учетом воздухонепроницаемости. Правильный консультант по энергетике и устойчивому развитию будет рядом, чтобы помочь вам до сборки, во время и затем после, если вы столкнетесь с какими-либо осложнениями во время воздушных испытаний.
Если вы нацелены на чрезвычайно энергоэффективное здание или пассивный дом, мы рекомендуем вам провести по крайней мере два воздушных испытания: одно, когда оболочка здания будет завершена, а другое в конце проекта.Таким образом, вы можете убедиться, что здание работает в соответствии с планом, а если нет, то исправить это до начала отделочных работ.
Нужна ли проверка на герметичность? Любое жилое помещение – и свыше определенного размера (500 м2) должно пройти испытание на герметичность. Если у вас небольшая застройка (одного или двух объектов), то одно из этих зданий должно пройти испытание воздухом. Если свойства имеют различную конструкцию, вам нужно будет протестировать их отдельно.
Как правило, вам не потребуется испытание воздуха для пристроек, существующих жилых помещений или проектов переоборудования, если только вы не пытаетесь улучшить тепловые характеристики, и в этом случае испытание воздуха может быть хорошим средством сравнительного анализа и диагностики. Консультант по энергетике сможет проконсультировать вас по этому вопросу.
Сколько времени занимает испытание на герметичность? Это зависит от размера вашего жилища, количества отверстий, которые необходимо заклеить, и наличия строительных планов.Как правило, тест должен длиться менее двух часов, и вы должны получить результат теста — в случае успеха — либо в тот же, либо на следующий день. Для испытаний Passivhaus мы должны провести испытание как на герметичность, так и на разгерметизацию, что может занять немного больше времени.
Опять же, есть факторы, влияющие на этот ответ, в том числе:
- Сколько жилых помещений требует проверки
- В скольких местах расположено это жилье
Здесь, в Buildpass, наша услуга по проверке воздухонепроницаемости начинается с 85 фунтов стерлингов за квартиру с одной спальней при минимальной плате за посещение объекта в размере 250 фунтов стерлингов.Стоит отметить, что многие исследования показали, что жилье с исключительным показателем воздухонепроницаемости может быть продано по гораздо более высокой цене из-за снижения потребления энергии и затрат в течение срока службы жилья.
Что такое хороший показатель герметичности? В общих чертах, действующие строительные нормы и правила предусматривают, что утечка воздуха в новых домах должна составлять около 10 м3/чм2 или меньше. Это скорость утечки воздуха в час на квадратный метр площади оболочки. Тем не менее, условное здание, которое используется для эталонного строительного законодательства, использует целевое значение 5 м2 / час2. Поэтому мы рекомендуем вам ориентироваться как минимум на 5 или ниже, чтобы убедиться, что здание соответствует требованиям как по выбросам углерода в жилище, так и по энергоэффективности тканей. Если вы устанавливаете механическую вентиляцию с рекуперацией тепла, то значение ниже 5 даст большую эффективность системы.
При этом на цель воздухонепроницаемости может влиять ряд факторов. Для углубленного анализа вашей цели в зависимости от типа здания и вентиляции вы можете загрузить наше БЕСПЛАТНОЕ руководство – 12 шагов к герметичности.
Что, если я не пройду тест на воздух?Прежде всего – не паникуйте! Хотя это не идеально, есть простые шаги, которые вы можете предпринять, чтобы исправить это.
Если вы провалите воздушный тест, вам нужно будет точно определить проблемы, которые привели вас туда. Эти проблемы часто проявляются довольно быстро, но ваш консультант по энергетике может помочь вам найти любую из более скрытых проблем.
Вам нужно решить эти проблемы, а затем пройти еще один тест.Вы будете повторять процесс, пока не пройдете.
В нашем блоге мы описали некоторые основные области, на которые следует обратить внимание, когда речь идет об утечке воздуха – 5 ключевых областей герметичности.
Испытание на герметичность | Что, когда и как | Строительный пропуск
Многие владельцы собственности проверяют свои жилища на герметичность, чтобы уменьшить воздействие на окружающую среду, сэкономить деньги на счетах за электроэнергию и уменьшить потери энергии. Поскольку испытания на герметичность теперь являются частью Строительных норм и правил, все новые постройки (как бытовые, так и нежилые) должны соответствовать стандартам воздухонепроницаемости; Вот почему для нас так важно понимать многослойность испытаний воздуха.
Испытания на герметичность – это практика измерения количества воздуха, выходящего через щели или строительные ткани жилых помещений. Установлено оборудование для испытаний воздуходувных дверей, чтобы создать давление в здании и проверить перепады давления, что помогает определить области, требующие ремонта.
Итак, главный вопрос заключается в том, как получить хороший результат теста на герметичность вашей собственности? Увеличение ваших шансов на получение хорошего результата испытания на герметичность начинается с планирования и подготовки, а также с хорошего общего понимания требований владельца недвижимости.Чтобы помочь вам освоиться, мы вернемся к основам в этом блоге, чтобы действительно дать вам всестороннее представление о тестировании воздуха.
Что такое испытание на герметичность? В апреле 2002 года правительство Великобритании ввело испытания на герметичность наряду с законом о строительных нормах для обеспечения соблюдения стандартов герметичности жилых помещений. Закон был создан для того, чтобы снизить эксплуатационные расходы, проверить стандарты материалов, предотвратить неудобные сквозняки и избежать проблем с конденсатом.
Испытание на герметичность определяет количество утечки воздуха в кубических метрах на квадратный метр площади внутренней поверхности здания м3. Или, проще говоря, испытание на герметичность измеряет количество воздуха, выходящего через щели или строительные материалы. В идеале наличие воздухонепроницаемого здания означает, что меньше энергии будет потрачено впустую из-за утечки нагретого воздуха.
Испытание на герметичность требуется для всех новостроек, как жилых, так и нежилых, в дополнение к требованиям, изложенным в Части L разделов 1A и 1B строительных норм.После испытаний (и улучшения качества воздухонепроницаемости здания) это снизит воздействие здания на окружающую среду, а также сэкономит деньги владельца на счетах за электроэнергию. Где записываемся?!
Как проходит испытание на герметичность? Для проведения теста на герметичность требуется доступ в пустое жилище. Специалисты по тестированию воздуха устанавливают оборудование для тестирования дверцы вентилятора — по сути, большие вентиляторы — к внешнему отверстию, например дверному проему. Затем они будут использовать это для повышения давления в здании и проверки разницы давлений.Затем внешнее давление воздуха поступает через трещины и отверстия.
Вентилятор обычно сбрасывает давление в доме до давления не менее -60 Па. Анемометр покажет внутреннее давление, внешнее давление и силу, с которой вентилятор должен работать, чтобы создать разницу давлений. Это поможет рассчитать утечку воздуха.
Нужна ли проверка на герметичность?С таким количеством строительных норм, которые нужно учитывать, может возникнуть путаница, чтобы узнать, какие из них применимы к вам.С 2006 года все новые разработки в Великобритании должны проходить воздушные испытания в рамках утвержденного документа Part L.
. Жилая недвижимость площадью более 500 м2 должна пройти испытание на герметичность в соответствии со строительными нормами и стандартами для достижения целевых уровней выбросов. Кроме того, при небольших застройках одного или двух объектов одно из зданий должно проходить испытания. Для более крупных застроек требуется, чтобы была протестирована большая часть зданий, в зависимости от размера и конструкции жилых помещений.Есть некоторые исключения из этого, но если вы все еще не уверены, нужно ли тестировать ваше здание, мы будем рады поговорить с вами.
Опять же, есть много факторов, влияющих на цену, например, сколько жилищ требуют проверки и в скольких локациях эти жилища расположены.
Здесь, в Buildpass, стоимость наших услуг по тестированию на герметичность начинается от 110 фунтов стерлингов. Стоит отметить, что многие исследования показали, что жилье с исключительным показателем воздухонепроницаемости может быть продано по гораздо более высокой цене из-за снижения потребления энергии и затрат в течение срока службы жилья.
H Сколько времени занимает испытание на герметичность?
Продолжительность испытания на герметичность будет зависеть от многих факторов, таких как размер здания и уровень утечки воздуха. В среднем тест должен длиться менее двух часов, и в случае успеха вы должны получить результат теста в тот же или на следующий день. Для испытаний Passivhaus мы должны провести испытание как на герметичность, так и на разгерметизацию, что может занять немного больше времени.
Перед испытанием пассивная вентиляция в здании временно перекрыта.Внешняя оболочка и все ее отверстия также закрыты. Внутри все двери временно фиксируются открытыми. Тестеры воздуха устанавливают оборудование для испытаний дверцы вентилятора на внешнее отверстие, которое будет создавать давление в здании и проверять перепад давления. Затем внешнее давление воздуха поступает через трещины и отверстия, помогая нам определить области, требующие ремонта в здании.
Когда лучше всего проводить тест на герметичность? Перед проведением проверки воздуха необходимо, чтобы ваше жилище было полностью укомплектовано. Может показаться, что это много, но это включает в себя стены, окна, плинтус, освещение, выключатели и двери. Вам также понадобится ваш балл SAP, так как он установит цель для воздушного теста.
Несмотря на то, что вам нужно подождать, чтобы провести испытание воздуха, вы можете воспользоваться поддержкой консультанта по энергетике с самого начала, чтобы убедиться, что ваши проекты были созданы с учетом герметичности, чтобы сэкономить ваше время и энергию в долгосрочной перспективе. бегать!
Если вы нацелены на чрезвычайно эффективное здание, мы рекомендуем вам провести по крайней мере два воздушных теста.Один, когда оболочка здания завершена, и один в конце проекта, чтобы убедиться, что здание работает в соответствии с планом, и, если нет, исправить до начала отделочных работ.
Для получения дополнительной информации посетите наш предыдущий блог.
Что такое хороший результат теста на герметичность? Согласно действующим строительным нормам, утечка воздуха в новых домах должна составлять около 10 м3/чм3 или меньше. Это утечка воздуха в час на квадратный метр площади конверта/ткани.Однако для здания, которое используется в качестве контрольного строительного норматива, используется целевое значение 5 м2/ч2. Имея это в виду, мы рекомендуем вам ориентироваться как минимум на 5 или ниже, чтобы убедиться, что здание соответствует целям как по выбросам углерода, так и по энергоэффективности ткани.
В целом, на целевое значение воздухонепроницаемости может влиять ряд факторов. Для углубленного анализа вашей цели в зависимости от типа здания и вентиляции вы можете загрузить наше БЕСПЛАТНОЕ руководство — 12 шагов к герметичности или прочитать наш блог с нашими 10 лучшими советами по улучшению вашего результата теста на воздухопроницаемость.
Чем может помочь Buildpass Если мы убедили вас проверить вашу недвижимость на герметичность, мы можем помочь! Наша команда может помочь с планированием и дизайном вашей собственности в дополнение к проведению воздушных испытаний. Свяжитесь с нашей командой сегодня, чтобы записаться на консультацию и записаться на воздушное испытание на ближайшее время.
Испытание на герметичность — сертифицированное NSAI испытание на герметичность
Испытание на герметичность – 250 евро – Мы не только проведем быстрое и точное испытание на герметичность, но и будем рады предоставить бесплатные консультации по деталям воздухонепроницаемой конструкции.
Звоните: Бернард 086 1061990
Герметичность
Исследования показывают, что до половины всех потерь тепла в зданиях может быть связано с утечкой воздуха и неконтролируемой вентиляцией. Уровни изоляции значительно возросли за последние несколько десятилетий, но нагретый воздух все еще выходит наружу, и его можно определить как основной источник потерь энергии. Климат в Ирландии не страдает от экстремально низких температур, но подвержен экстремальному давлению ветра. В то время как изоляция является центральным элементом строительства с низким энергопотреблением, воздухонепроницаемость также должна иметь центральное значение для энергоэффективной стратегии по сокращению ненужных потерь тепла. Герметизация недорогими герметиками часто может уменьшить утечку воздуха, что приводит к экономии 20% от общего счета за отопление дома. Sheehan Energy Services предоставляет услуги по тестированию дверей как для новых, так и для существующих зданий.
Домашнее испытание на герметичность
Мы можем избавиться от стресса благодаря соблюдению Части L. Наши опытные оценщики воздухонепроницаемости помогут вам пройти через весь процесс, каждый раз гарантируя положительный результат.
НАЦИОНАЛЬНАЯ СЛУЖБА – мы проведем оценку вашей недвижимости в удобное для вас время.
НАДЕЖНОСТЬ — мы сертифицированы NSAI для выполнения каждого теста в соответствии с I.S. Стандарт EN ISO 9972:2015.
СТОИМОСТЬ – Испытание на герметичность за 249 евро для всех домов площадью менее 200 кв. м. -Хороший результат испытания на герметичность улучшит ваш рейтинг BER и снизит счет за отопление дома.
Что такое испытание на герметичность
Испытание на герметичность (также обычно называемое испытанием на утечку воздуха или испытанием на воздухопроницаемость) — это испытание для определения уровня неконтролируемого потока воздуха через зазоры или трещины в ткани здания. Слишком большая утечка воздуха приводит к ненужным потерям тепла и может вызвать дискомфорт у жильцов из-за холодных сквозняков.
Нужен ли мне тест на герметичность
Если вы построили новое жилище, то в Части L Правил указано, что теперь вы должны проверить это здание на герметичность. Испытание на герметичность используется для расчета рейтинга воздухопроницаемости жилого помещения. Именно этот рейтинг должен соответствовать последним строительным нормам по экономии топлива и энергии.
Сколько времени занимает тест
Мы стремимся завершить каждый тест в течение четырех рабочих дней с момента начала взаимодействия. Один из наших опытных оценщиков энергии должен будет посетить объект для проведения теста. Время, в которое мы посещаем сайт, будет удобным для вас, а продолжительность каждого посещения сайта не должна превышать четырех часов, в зависимости от размера и сложности оценки.
Сколько стоит испытание на герметичность
Мы стремимся к тому, чтобы каждое предложение было наиболее конкурентоспособным на рынке, предлагая вам реальную стоимость качественных услуг. Тест на герметичность для дома площадью менее 200 м² обойдется в 249 евро
Что произойдет, если мое здание не пройдет испытание на герметичность
Наши квалифицированные оценщики будут рады оказать вам бесплатную консультационную услугу по всем необходимым ремонтным работам.
Как улучшить воздухонепроницаемость здания
Способы улучшения воздухонепроницаемости здания включают в себя; герметизация любых щелей вокруг окон и дверей; заделка любых отверстий в наружных стенах; нанесение сквозной прокладки между люком чердака и рамой; герметизация любых зазоров, где инженерные трубы и кабели проходят через ткань здания; обеспечение хорошей герметизации вокруг дымоходов котла в местах их прохождения через наружную стену/потолок; герметизация краев помещений и заделка щелей в полу вокруг инженерных труб
Чем Sheehan Energy Services может помочь мне
Помимо предоставления быстрого и точного теста на герметичность по лучшей на рынке цене 249 евро, наши опытные специалисты по оценке герметичности будут рады помочь вам бесплатным советом по деталям воздухонепроницаемой конструкции.
www.berrating.ie
www.berkerry.ie
www.bercork.ie
www.berdublin.ie
www.berlimerick.ie
www.berassessors.ie
Испытание на герметичность достигает совершеннолетия
Вентиляционные дверцы и тестеры воздуховодов стали важными инструментами для высокопроизводительных строителей. Давний ветеран отрасли рассказывает, как мы сюда попали и что будет дальше
Это первая из того, что будет ежемесячной колонкой с моими наблюдениями об искусстве и науке высокоэффективного строительства и домашних испытаний.В этой первой колонке я хочу представиться и помочь вам понять, почему вас должны интересовать эти темы.
Меня зовут Бен Уокер, и с мая 2017 года я являюсь со-генеральным директором Retrotec, крупнейшего в мире производителя оборудования для проверки воздуходувных дверей и воздуховодов. Наша продукция помогает проектировщикам и строителям снизить потребление энергии в зданиях, что способствует созданию более чистой и здоровой окружающей среды. Этот вклад — то, что вдохновляет меня каждый день.
Вентиляционные дверцы и тестеры воздуховодов существуют с 1980-х годов, но поначалу они использовались только небольшой нишей энергоэффективных строителей. Можно с уверенностью сказать, что большинство строителей в те ранние годы практически не знали об этом оборудовании.
Ситуация начала меняться, когда нормы энергопотребления и программы высокоэффективного строительства, такие как Energy Star и LEED, добавили требования к воздухонепроницаемости. Эти требования привлекли внимание среднестатистического строителя к воздушной герметизации и привели к тому, что все большее число из них проводят испытания не только на соответствие, но и для обеспечения качества.
За время работы в отрасли я видел, как строительная наука развивалась и совершенствовалась до такой степени, что построить прочный, эффективный и здоровый дом с минимальным воздействием на окружающую среду стало нетрудно. Я также видел, как испытательное оборудование эволюционировало и стало более универсальным, точным и простым в использовании, чем когда-либо.
Я начал работать в Retrotec в 1995 году. Мне было 22 года, и я жил в Беллингеме, штат Вашингтон, и откликнулся на объявление о поиске сетевого инженера.У меня зазвонил телефон. Это был Колин Джендж, основавший Retrotec в 1980 году.
Несмотря на то, что у меня не было никакого формального образования, я уже десять лет программирую компьютеры. «У меня дома есть три компьютера, объединенных в сеть, и я использую их целыми днями, каждый день», — сказал я ему. Этого было достаточно, чтобы убедить его, что я подхожу для этой работы.
Хотя в настоящее время Retrotec насчитывает более двух десятков сотрудников и поставляет тестеры воздуходувок и воздуховодов в более чем 50 стран, тогда в штате компании было 11 человек, которые производили и отгружали всего 8-10 «инфильтрометров» в месяц.Эти первые дверцы воздуходувки состояли из пары аналоговых датчиков Dwyer Magnehelic, ручки ручного управления скоростью, компьютера HP 95LX или Sharp для расчета результатов и принтера для печати отчета. Все было жестко подключено к вентилятору, установленному в дверном проеме.
Это должно было измениться. Основная причина, по которой Колин нанял меня, заключалась в том, что он хотел разработать цифровой манометр для замены магнитогеликоидных манометров Dwyer, которые мы использовали, которые вскоре устареют.
Я и не подозревал, какой это будет вызов.В течение следующего года я провел бесконечные ночи, работая над первоначальными прототипами того, что стало DM1, одним из первых цифровых микроманометров для HVAC и индустрии чистых агентов. Retrotec продолжал продавать его, прежде чем в конце концов выпустил DM2 в начале 2000-х.
Однако примерно в то же время я решил сменить профессию. Это оказался временный, но случайный редактор.
Это была эра больших интернет-компаний, когда новые интернет-компании росли как сорняки. Мой друг работал в компании электронной коммерции и попросил меня принять участие в управлении их веб-сайтом. Идея работать с некоторыми из моих лучших друзей была настолько привлекательной, что я ушел из Retrotec примерно на Рождество 2001 года. Новая работа не продлилась долго: рынок рухнул, наше финансирование закончилось, и вскоре я ушел в поисках работы. Тем не менее, я встретил свою жену там, поэтому я с любовью вспоминаю этот опыт.
Следующие шесть лет я работал в консалтинговой компании в качестве контрактного разработчика программного обеспечения над проектами для ряда клиентов. Хотя быть брошенным в эти различные среды было болезненно, это был один из самых важных периодов моего роста и обучения.Знакомство с различными бизнес-моделями научило меня многому о том, что работает, а что нет, — знания, которые с тех пор очень хорошо послужили мне.
Летом 2007 года у меня снова зазвонил телефон. Оно было от Колина. Он услышал, что я был в перерыве между работами, и попросил вернуться в Retrotec.
Моим первым проектом была разработка более точного цифрового манометра. Результатом стал первый в отрасли манометр с сенсорным экраном и встроенным Wi-Fi для управления со смартфона. Оператор может установить давление, и он будет автоматически управлять вентилятором, чтобы поддерживать желаемое давление в корпусе.
Мы также разработали приложение для автоматизированного тестирования rCloud , которое определяет место проведения тестирования с помощью геолокации, автоматически выполняет тесты воздуходувки или воздуховода в соответствии с общепринятыми стандартами и создает безопасные цифровые отчеты о соответствии требованиям.
В 2017 году Колин ушел на пенсию, и Retrotec была приобретена уважаемой немецкой технологической компанией Wohler. Их участие поможет нам выйти на новые рынки и разработать еще более передовые технологии испытаний на герметичность.
В разработке находятся: 1.Технологические усовершенствования, помогающие оценщикам быстрее входить, выполнять работу и выходить из нее без ущерба для точности
2. Больше интеграции смартфонов и планшетов
3. Возможность беспроводного управления несколькими устройствами
Например, мы работаем над беспроводным приложением, которое будет запускать несколько вентиляторов одновременно. Это очень важно, особенно в большом здании, где оценщику необходимо, чтобы вентиляционные двери работали одновременно в нескольких проемах. Раньше вам приходилось прокладывать кабели через здание, соединяющие все дверцы вентилятора.Мы значительно сократили количество кабелей, но в течение следующих нескольких лет полностью устраним их.
Как упоминалось выше, мы также видим растущий рынок в сфере обеспечения и улучшения качества. Хотя большая часть наших продаж приходится на места, где соблюдаются энергетические нормы, тестирование стало передовой практикой, которую должны использовать все строители, а испытательное оборудование — важным инструментом диагностики и контроля качества.
Данные, предоставленные тестером дверцы воздуходувки и воздуховода, могут помочь строителям и подрядчикам по ОВКВ улучшить качество, в том числе:
— Уменьшение размера и времени работы системы отопления или охлаждения
. не допускать попадания влажного воздуха в полости стен, где он может привести к гниению и плесени.
Двери воздуходувки и тестеры воздуховодов подтверждают, что рабочие выполнили герметизацию воздуха, необходимую для получения вышеуказанных преимуществ. А сложность современного оборудования позволяет опытным оценщикам легче, чем когда-либо, точно определить источник утечки в воздуховоде или оболочке и показать строителю, как добиться лучших результатов в следующем проекте.
Я подробно расскажу об этих и других проблемах и приложениях в следующих статьях.
Что такое тест дверцы вентилятора? » BEPG проверяет воздухонепроницаемость здания
Завершается испытание двери вентилятора в историческом бревенчатом доме для обнаружения утечек воздуха (и насекомых).
Испытание двери вентилятора измеряет и выявляет утечку воздуха в здании с помощью специальной двери. Дверь выглядит как коробчатый вентилятор, но внутри нее находятся устройства для измерения расхода воздуха и давления. Запуск вентилятора с различными настройками имитирует различные условия и помогает определить скорость и места утечки воздуха.
Зачем проверять дверцу вентилятора?
Этот диагностический инструмент помогает провести энергоаудит, чтобы
- проверить требования строительных норм и правил, а
- помочь выявить и решить проблемы с окнами, дверями и другими внешними системами.
Проверка требований строительных норм и правил
Испытание дверей с воздуходувкой, используемое в качестве инструмента обеспечения качества, может определить, соответствуют ли все механические, инженерные и водопроводные (MEP) системы здания проектным требованиям и строительным нормам.
Например, типичной протестированной механической системой является система HVAC.
Выявление проблем с герметичностью здания
Воздух может просачиваться в здание или выходить из него во многих различных местах. Проблемы с герметичностью здания стоят денег и могут привести к дополнительным проблемам. Например, представьте, что вы пытаетесь нагреть или охладить свой дом с открытыми окнами. Система HVAC будет работать чаще, чтобы поддерживать температуру, установленную на вашем термостате. Результатом всего этого дополнительного потребления энергии являются высокие счета за электроэнергию и чрезмерный износ вашей системы отопления, вентиляции и кондиционирования воздуха!
Остановка утечки воздуха путем выявления и устранения проблем с утечкой позволяет экономить энергию. Кроме того, он предотвращает попадание внутрь здания влаги, загрязняющих веществ и насекомых. Согласно www.Energy.gov, вот несколько причин для обеспечения надлежащей герметичности здания:
- Снижение потребления энергии из-за утечки воздуха
- Предотвращение проблем с конденсацией влаги
- Предотвращение неприятных сквозняков, вызванных утечкой холодного воздуха с улицы
- Определение степени для обеспечения приемлемого качества воздуха в помещении может потребоваться механическая вентиляция.
Как работает проверка дверцы вентилятора?
Испытание двери воздуходувкой создает давление в здании для имитации различных условий и обнаружения утечек воздуха.Вот как:
Во-первых, наружная дверь здания оснащена дверцей с поддувом. Во время испытаний мощный вентилятор на дверце поддува нагнетает воздух в здание или выбрасывает его из здания. Скорость вентилятора увеличивает или уменьшает внутреннее давление в здании и позволяет воздуху проходить через проходы, такие как трещины или отверстия, обнаруживая утечки воздуха в здании. Вентилятор измеряет, сколько воздуха входит или выходит из здания.
Использование результатов измерений давления и количества воздуха, поступающего через вентилятор в здание, позволяет произвести расчеты для определения количества воздуха, выходящего из здания, или скорости утечки воздуха.Затем скорость утечки воздуха сравнивается с историческими данными (например, счетами за электроэнергию), чтобы определить ее влияние на потребление энергии.
Как определить, где в здании происходит утечка воздуха?
BEPG использует дополнительные инструменты для определения места утечки воздуха. Стандартные методы включают инфракрасную термографию (камера способна видеть разницу температур поверхности и отображать ее в виде изображения), дымовые карандаши/ручки или театральный туман. Каждый из этих методов требует знаний в области строительства зданий и науки для надлежащего анализа и определения источников утечек.
Здание какого размера можно проверить с помощью BEPG на утечку воздуха?
BEPG имеет три (3) вентилятора, которые могут производить примерно от 3500 до 4000 кубических футов в минуту. Международный кодекс энергосбережения (IECC) определяет допустимый воздухообмен в час (ACH) при определенном давлении. В зависимости от тестового давления, необходимого для достижения требуемой воздухонепроницаемости по строительным нормам, BEPG может тестировать здания площадью примерно до 200 000 футов3. У нас также есть доступ к дополнительному оборудованию и технике для более значительных зданий, если это необходимо.
Свяжитесь с нами для получения подробной информации об испытаниях на герметичность целых зданий с использованием вентиляционных дверей.
Герметичность: 5 причин, по которым вам следует знать больше
Достижение разумного уровня воздухонепроницаемости в новых зданиях является обязательным требованием части L строительных норм и правил и ключевым аспектом стандарта пассивных домов; и, кроме того, чрезмерная инфильтрация воздуха может иметь серьезные последствия для энергопотребления здания и может быть причиной разрушения ткани из-за сырости.
Утечка воздуха обусловлена перепадом давления в оболочке здания и может быть определена как сопротивление утечке воздуха внутрь или наружу через непреднамеренные точки утечки через зазоры в ткани или компоненты оболочки здания, такие как двери и окна.
- Вы можете не заметить этого сразу, но достижение значения воздухонепроницаемости 10 м3/(ч.м2) при 50 Па примерно эквивалентно наличию отверстия размером с кусок 20 пенсов на каждом м2 площади оболочки.
Это огромно, если учесть площадь всей оболочки здания. Таким образом, вы должны стремиться к гораздо более низкой цифре, чтобы достичь энергоэффективности.
- Любой теплый влажный воздух изнутри здания, проходящий через внешнюю оболочку, может вызвать промежуточную (промежуток между конструкциями или объектами) конденсацию при попадании на холодную поверхность, что может привести к гниению ткани. Увеличение воздухонепроницаемости вашей сборки снизит вероятность возникновения гниения этой ткани.
- Здание никогда не может быть слишком герметичным, но оно может быть недостаточно вентилируемым, поэтому всегда помните: «Строить герметично — правильно проветривать».Распространенной ошибкой является сосредоточение внимания исключительно на уменьшении непреднамеренной утечки воздуха, но важно, чтобы в здании циркулировал адекватный и контролируемый воздух, чтобы предотвратить накопление влаги и переносимых по воздуху загрязнителей, присутствующих в результате проживания / занятия помещения.
- При детализации воздушного барьера важно убедиться, что он находится на теплой стороне изоляции. Это делается для того, чтобы избежать образования конденсата в ткани, вызванного взаимодействием теплого влажного воздуха и холодной поверхности.
- Наконец, всегда рекомендуется проводить аудит утечки воздуха при выполнении теста на герметичность, даже если ваше здание прошло проверку.Таким образом, вы увидите, где здание протекает, и вы сможете улучшить эти детали для вашего следующего строительного проекта.
