каким лучше аппаратом, как электродом с инвертором или полуавтоматом, как правильно на сломанной раме грузовика – Определенных деталей и элементов на Svarka.guru
Износ элементов механизмов происходит неравномерно. При этом из-за небольшого по сравнению с размерами детали повреждения, теряется ее работоспособность. Соответственно ухудшается или прекращается функционирование узла или даже всего механизма.
Из методов реставрации металла восстановление деталей сваркой и наплавкой стоит на первом месте по распространенности. Главных причин две:
- Восстановление исходных свойств элемента.
- Относительная дешевизна.
В статье мы остановимся на практическом применении методик восстановления, применительно к кузовным сварочным работам легковых и грузовых автомобилей.
В чем заключается ремонт?
Процессы сварки и наплавки принципиально отличаются мало. В первом случае расплав используется для соединения частей. Во втором выступает рабочим слоем, который наносят на поверхность детали, с целью восстановления ее первоначальных размеров.
Бывают ситуации, когда эти функции совпадают. Пример — восстановления днища кузова автомобиля, поврежденного коррозией. При этом, сильно разрушенные места заменяются листами металла, трещины и отверстия восстанавливаются наплавкой.
В других случаях, выработка на оси, либо обойме детали кузова полностью реставрируется методом наплавки. Одновременно сваркой может быть устранена (к примеру) трещина на этом же элементе.
Еще один пример: сварка рамы грузового автомобиля. Здесь свариваются элементы несущего каркаса, где возникли трещины, а наплавляются места выработок в проушинах и пазах крепления узлов, тяг, осей и пр.
Что касается износа железа, выбрать ремонт наплавкой не всегда целесообразно. Если автомобильный завод выпускает необходимые узлы, ремонт может свестись к вырезанию изношенной детали с последующей приваркой новой.
Как правило сварка кузова автомобиля применяется чаще чем наплавка на его деталях. Причина — характер износа, вызванный схожестью причин повреждений при эксплуатации.


Не важно какая это марка: ВАЗ 2109, грузовик «Хюндаи портер», «Лексус» или старенькая «Нива» — основное количество повреждений кузова приходится на коррозию и деформацию листового металла при авариях.
Применяемое оборудование
При всем разнообразии методики работ и инструментального обеспечения, классификация сварки при ремонтах автомобилей сводится всего к двум типам:
- Электрическая, преимущественно дуговая с использованием защитных газов либо флюсов.
- Газовая, с применением ацетилена или пропана.
Электрическая подразделяется на ручную, полуавтоматическую в среде инертных газов, под флюсом и пр.
Существуют и другие способы, например сварка лазерная, трением, диффузионная. Однако для ремонтов автомобилей они практически не используются.
В некоторых случаях используется такая разновидность сварки, как пайка. Применяют ее для ремонта повреждений патрубков из цветных металлов, блоков радиаторов, деталей оборудования рефрижераторов, выполненных из тонкой меди.
Какой сваркой лучше варить кузов автомобиля зависит от характера повреждений, а также особенностей места или детали, которую необходимо восстановить.
На сегодня выполнение основного объема работ осуществляют с помощью электричества. Газосварка, некогда бывшая чуть ли не единственным способом ремонта, на сегодня используется для соединения деталей из тонкого металла.
Кроме того, кислородно-ацетиленовая сварка по-прежнему популярна там, где к кузову крепятся различные тяги, создающие динамические нагрузки.
Из электрических приборов для небольших, ремонтов применяется сварка автомобиля инвертором, обычным ручным сварочным аппаратом. Для тонких работ, требующих высокого качества, а также наплавки используют полуавтоматы с углекислым или инертным газом.
С распространением алюминиевых и титановых сплавов арсенал механиков по ремонту пополнился аппаратами дуговой сварки неплавким электродом в среде инертных газов. С подачей плавящегося присадочного прутка рукой либо автоматически.
Требования к подготовке детали
Металл тщательно зачищают от ржавчины с помощью угловой шлифовальной машины (УШМ), более известной как «болгарка». Либо ручной щеткой. При необходимости снимают фаску или выравнивают.
В ответственных случаях, при наплавке, пайке поверхность обезжиривают.
Хороший эффект дает обработка пескоструйными либо гидроабразивными аппаратами.
Трещины разделывают заточными дисками УШМ на всю глубину, чтобы получить на их месте V-образные канавки. Толстый металл обрабатывают с двух сторон. На их концах для устранения напряжений, предотвращения дальнейшего развития сверлят сквозные отверстия диаметром 4-6 мм.
Перед тем как наплавлять отверстия, их края зенкуют с одной либо двух сторон, при наличии резьбы ее высверливают.
Учитывая, что сварка авто электродом либо газовым пламенем, создает высокую температуру следует позаботится о сохранности примыкающих элементов отделки, эл. оборудования, пластиковых деталей.
Для этого снимают ремонтируемый элемент либо детали, могущие быть поврежденными. Если это по каким-либо причинам невозможно, применяют меры к их защите (закрывают, обкладывают мокрой ветошью).
Используемые электроды
Подбор электродов либо сварочной проволоки осуществляется исходя из трех параметров:
- Вида металла.
- Необходимой толщины детали либо слоя наплавки.
- Уровня ответственности восстанавливаемой детали.
Выполняя кузовной ремонт полуавтоматом с углекислотой используют порошковую сварочную проволоку, омедненную либо простую.
Наплавку слоя с высокими характеристиками по твердости выполняют электродами типа Т-620, с толстой обмазкой включающей графит, карбид бора и пр.
Необходимый диаметр электрода подбирают исходя из толщины свариваемого металла, по специальным таблицам.
Алюминиевые детали соединяют газовой (кислородно-ацетиленовой) либо дуговой сваркой. В последнем случае применяются электроды типа ОЗА-2. При технологии с неплавящимся вольфрамовым электродом, используют в качестве присадки пруток соответствующего алюминиевого сплава.
При наплавке изношенных деталей двигателя для получение легированных покрытий применяют проволоку типа Нп-65, с высоким содержанием углерода. Работы ведут под флюсом, в среде инертных газов.
Способы сварного ремонта кузовов легковых и грузовых автомобилей
Для сварки кузова как легковых авто, так и грузовозов используют самые различные технологии. Принципиально все они сводятся к электрической дуге либо раскаленной струе газа, но при этом нередко имеют существенные технологические отличия.
Ручной дуговой
Для работы применяют аппараты как переменного, так и постоянного тока. К первым относятся сварочные трансформаторы различны типов. Вторые представлены сварочными машинами и генераторами.
Трансформатор дает неустойчивую дугу, требует значительной силы тока на диаметре электрода (эта характеристика называется плотностью тока). При этом растет температура дуги, что чревато прожогом и перекаливанием.
Эта опасность для старых сварочных трансформаторов была актуальной, да и сейчас на вопрос: можно ли варить машину электросваркой, не всегда дают положительный ответ. Как минимум, если речь идет о самодельных устройствах либо обычных сварочных трансформаторах.
Ситуация изменилась с появлением инверторных аппаратов, но для соединения элементов из тонкого металла этот тип соединения применяют ограничено.
Как правило таким способом делают ремонт массивных деталей, наподобие станин или узлов из толстого металла, например — глушителей.


А. Тархомов сварщик со стажем 20 лет: «Современным инвертором кузов заварить можно в большинстве поломок. Разумеется, аппаратом профессионального уровня. Все от сварщика зависит. Не спецу заниматься подобными вещами не стоит категорически».
Автоматическая наплавка под флюсом
Используется достаточно широко для ремонта промышленного оборудования, особенно уникального. Для автомобильных ремонтов распространение невелико обычно, для восстановления путем наплавки деталей вращения (к примеру — распредвала)
.Смысл метода заключается в том, что сварочная дуга горит не открыто, а под слоем специального порошка — флюса. Он защищает металл от окисления и соединения с азотом воздуха. Шов или слой наплавки по качеству не уступает исходному металлу, а при использовании специальных электродов может превосходить его по твердости и износостойкости.
Вибродуговой метод
Как и наплавка под флюсом применяется исключительно в заводских условиях, поскольку требует громоздких установок, обеспечивающих точное позиционирование детали.
Смысл заключается в колебательных движениях плавящегося электрода с частотой 100-120Гц, при напряжении 12-18 Вольт. При этом наплавка выполняется крохотными частичками металла с одновременным охлаждением.
В газовых защитных средах
Метод дающий наиболее качественный результат в условиях станций технического обслуживания и ремонтных мастерских
Сварка либо наплавка ведется в среде инертного газа с помощью неплавящегося электрода (TIG), либо плавким электродом в окружении инертного, либо активного газа (MIG/MAG сварка соответственно).
Позволяет получать соединение, не уступающее выполненному в заводских условиях. Но главное с помощью этого метода автомобилистам впервые стал доступен текущий ремонт деталей, изготовленных из титановых и алюминиевых сплавов, высокопрочных легированных сталей.
Полуавтоматические способы
Один из наиболее популярных на сегодня методов, используемых небольшими мастерскими и частными мастерами.
Процесс ведется на воздухе либо под углекислым газом. В качестве плавящегося электрода используется сварочная проволока нужного состава. Подается она, сматываясь с катушки, по мере необходимости.
При этом даже устройства бытового уровня способны автоматически подстраивать скорость подачи проволоки в зависимости от силы дуги.
Альтернативная технология восстановления под давлением
Для восстановления деталей под давлением наплавка либо сварка не требуется. Деталь лишь предварительно нагревают до пластичности.
Смысл метода в изменении геометрических размеров деталей при их деформации. Различают три основных способа:
- осадка;
- обжатие;
- обсадка.
В первом случае при сжатии цилиндрических деталей типа втулок, с уменьшением высоты уменьшается внутренний диаметр. Обжатием деталь уменьшаю боковыми деформациями, а при обсадке наоборот — увеличивают (см. рисунок фото 8)
В некоторых случаях такие операции дополняют либо предваряют наплавкой.
Особенности сварки рамы грузовых автомобилей
Сварка деталей грузовика и легковой машины принципиально одинакова. Несущественные различия вызваны разной толщиной металла кузова.
Другое дело, когда речь идет о том, как правильно сварить сломанную раму на грузовике воспринимающую нагрузку перевозимого груза, порой весящего не меньше, чем сама машина.
При значительных повреждениях, вызванных авариями либо неправильно эксплуатацией целесообразно вырезать деформированный участок, заменив его целым.
При этом следует использовать исключительно методы, не перекаливающие металл.


Выполняя сварочные работы на каркасах старайтесь спланировать работу так, чтобы швы не располагались поперек сечения. Особенно в местах, где предполагается повышенная нагрузка.
При наплавке трещин их предварительно обрабатывают как рассказывалось в разделе о подготовке. Затем шов зачищают, а участок дополнительно усиливают металлической накладкой.
Ремонт деталей сваркой
Ремонт деталей сваркой — выбор оборудования
Сварка — часто используемый метод для ремонта. В общем объеме ремонтных работ она занимает 70%. Значит, в этом непростом деле без нее не обойтись никак. Так же как и без инвертора, выбор которого зависит от габаритов и марки материала ремонтируемого.
Если говорить о марке, то выбирать оборудование нужно следующим образом:
• для сталей используют ручную сварку ММА на токе DС.
• для алюминиевых сплавов — инверторы TIG на токе AC.
Вся премудрость технологии сводится к сварке и наплавке.
Подготовка деталей к сварке и наплавке
ремонт распредвала
Уделите этому моменту достойное внимание.
Дефекты типа «скол» необходимо тщательно зачистить металлической щеткой, не желательно оставлять острые кромки, они – концентраторы напряжения. Поэтому кромки нужно скруглить, либо «притупить».
Сварка трещины
Трещины требуют полного удаления путем их разделки (то же с порами, раковинами), иначе оставшаяся внутри и заплавленная снаружи трещина при знакопеременных нагрузках, снова разрастется с выходом на наружный диаметр или поверхность.
При восстановлении деталей наплавкой
«Прохудившиеся» диаметры, требующие наплавки, просто тщательно защищаются металлической щеткой.
Не забывайте, что перед заваркой дефектов алюминиевых сплавов изделия и присадочный материал необходимо протравить в 4-5%-ном растворе едкого натра и 20-25%-ом растворе азотной кислоты, либо зачистить до металлического блеска и немедленно варить.
Какие изъяны устраняют?
Заваривают трещины на платформах и рамах, так же делают заплаты и разнообразные накладки и т.д. и т.п.
Производят восстановление резьб путем наплавки с последующей обработкой и нарезанием резьбы плашкой или метчиком. Соответственно, ремонтируют наружные и внутренние резьбы.
Выбор технологии восстановления деталей
Детали машин ремонтируют автоматической и полуавтоматической сваркой в углекислоте.
Автоматическая представляет собой полностью автономный процесс, нужно только лишь зафиксировать деталь и нажать кнопку, то же касается сварочных роботов.
При проведении ремонтно-восстановительных работ в автосервисе наиболее простой способ – полуавтоматической сварки, когда проволока подается с заданной скоростью, а горелка перемещается вручную вдоль шва. КПД полуавтомата существенно проще по сравнению с ручным инвертором и лучше качество шва. Газ, используемый для защиты: углекислота – активный , существенно окисляет расплавленную углеродистую сталь, а связывает и выводит кислород на поверхность марганец, в большом количестве присутствующий в проволоке 08Г2С. Сварка полуавтоматом в углекислоте идеальна для ремонта пальцев, фланцев карданных валов и т.д.
Популярна в деле ремонта и восстановления так же сварка под флюсом благодаря тому, что она обеспечивает высокую производительность и прочность, обеспечивая надежную защиту ванной. Она и названа так потому, что во время процесса дуга, зажженная между металлом и электродом скрыта под слоем флюса. Таким образом ремонтируют, например, распредвалы.
При небольшом износе на деталях с малым диаметром практикуют восстановление электроимпульсной наплавкой.
Лекция №10. Ремонт деталей сваркой и наплавкой
Сваркой называется процесс образования неразъемного соединения деталей или их отдельных частей вследствие межатомарного взаимодействия или действия сил молекулярного сцепления. Сваркой соединяют металлы и неметаллические материалы, например, стекло, пластмассы и др. При сварке металлов, за исключением холодной сварки, производят местный нагрев соединяемых частей до перехода их в пластическое (сварка давлением) или в расплавленное состояние (сварка плавлением). Стремятся, чтобы металл шва обладал одинаковыми свойствами с основным металлом. Это определяет подбор присадочного материала и режима сварки.
Оборудование, используемое при ремонте деталей сваркой, такое же, как и при сварке новых деталей. Сваркой соединяют отдельные части деталей, заваривают трещины, раковины и устраняют другие дефекты.
Наплавка — процесс нанесения расплавленного металла необходимого состава на поверхность детали, нагретую до температуры плавления, При наплавке нанесенный слой металла прочно соединяется с основным металлом вследствие образования металлической связи.
Наплавку применяют для восстановления размеров детали и придания заданных свойств ее поверхности путем правильного выбора химического состава и структуры наплавленного металла.
Наплавка является разновидностью сварки. Однако наплавочные процессы отличаются от сварочных. При наплавке сварочный процесс используется для наращивания на основной металл слоя металла или сплава со свойствами, иногда отличающимися от свойств основного металла.
В связи с этим к процессу наплавки предъявляются следующие основные требования;
1) для обеспечения заданных физико-механических свойств в наплавленном слое процесс наплавки не должен изменять исходного химического состава и структуры наносимого металла, т.е. при наплавке доля основного металла в наплавленном слое должна быть минимальной;
2) для сохранения прочности ремонтируемой детали процесс наплавки не должен изменять ее исходного химического состава, структуры и напряженного состояния;
3
Виды наплавки


Ручная
Механизированная
















Рисунок 10.1 – Виды ремонта деталей наплавкой
Лекция №10. Ремонт деталей сваркой и наплавкой
Сваркой называется процесс образования неразъемного соединения деталей или их отдельных частей вследствие межатомарного взаимодействия или действия сил молекулярного сцепления. Сваркой соединяют металлы и неметаллические материалы, например, стекло, пластмассы и др. При сварке металлов, за исключением холодной сварки, производят местный нагрев соединяемых частей до перехода их в пластическое (сварка давлением) или в расплавленное состояние (сварка плавлением). Стремятся, чтобы металл шва обладал одинаковыми свойствами с основным металлом. Это определяет подбор присадочного материала и режима сварки.
Оборудование, используемое при ремонте деталей сваркой, такое же, как и при сварке новых деталей. Сваркой соединяют отдельные части деталей, заваривают трещины, раковины и устраняют другие дефекты.
Наплавка — процесс нанесения расплавленного металла необходимого состава на поверхность детали, нагретую до температуры плавления, При наплавке нанесенный слой металла прочно соединяется с основным металлом вследствие образования металлической связи.
Наплавку применяют для восстановления размеров детали и придания заданных свойств ее поверхности путем правильного выбора химического состава и структуры наплавленного металла.
Наплавка является разновидностью сварки. Однако наплавочные процессы отличаются от сварочных. При наплавке сварочный процесс используется для наращивания на основной металл слоя металла или сплава со свойствами, иногда отличающимися от свойств основного металла.
В связи с этим к процессу наплавки предъявляются следующие основные требования;
1) для обеспечения заданных физико-механических свойств в наплавленном слое процесс наплавки не должен изменять исходного химического состава и структуры наносимого металла, т.е. при наплавке доля основного металла в наплавленном слое должна быть минимальной;
2) для сохранения прочности ремонтируемой детали процесс наплавки не должен изменять ее исходного химического состава, структуры и напряженного состояния;
3) наплавленный слой должен обладать достаточно высокой прочностью сцепления с основным металлом.
Рисунок 10.1 – Виды ремонта деталей наплавкой
Для ручной газовой и электродуговой наплавки обычно используют металлические электроды, что объясняется сравнительной простотой процесса наплавки и возможностью широкого регулирования химического состава и свойств наплавленного слоя. Регулирование химического состава и свойств наплавленного слоя осуществляют через покрытие или через электродный стержень, или комбинированным методом. Для предотвращения появления деформаций и трещин при наплавке применяют предварительный нагрев детали в пределах 200—400°С, предварительный изгиб детали в направлении, обратном деформации, погружение детали в воду без смачивания наплавляемой поверхности, наложение наплавляемых валиков в определенной последовательности, высокий температурный отпуск детали после наплавки.
Ручная газовая сварка и наплавка. При ручной газовой сварке и наплавке расплавление основного и присадочного материала осуществляется теплом, выделяющимся в процессе сгорания горючих газов (ацетилена, пропанбутановых смесей и других) в среде кислорода (рис. 5.10). Наиболее распространенным горючим газом, применяемым на ремонтных предприятиях, является ацетилен.
В зависимости от соотношения подаваемых в горелку ацетилена и кислорода можно получить нормальное, науглероживающее и окислительное пламя. Нормальное или, как его часто называют, нейтральное пламя образуется при соотношении кислорода и ацетилена в смеси, равном 1,0—1,2. Нормальное пламя является восстановительным в отношении к свободной закиси железа и в зоне I плавления ограничивает окисление поверхности. При соотношении кислорода и ацетилена, составляющем 0,8—0,9, возникает науглероживающее, а при соотношении, равном 1,2—1,5, окислительное пламя. Выбор сварочного пламени влияет на качество сварного шва или наплавки, а также на производительность процесса.
Сварку деталей из алюминиевых сплавов, а также из стали с содержанием углерода до 0,5% ведут нормальным пламенем. Науглероживающее пламя обычно используют для сварки деталей из серого чугуна и стали с содержанием углерода более 0,5%.
Для сварки деталей из цветных металлов, заварки трещин и раковин небольшой длины в чугунных деталях при толщине стенок 10—15 мм, а также для сварки деталей из малоуглеродистой стали толщиной до 7 мм применяют бензинокислородное пламя и горелку ГКУ-01-55.
Рисунок 10.2 – Ручная газовая наплавка
К недостаткам газовой наплавки следует отнести неравномерность толщины наплавленного слоя.
Электродуговая сварка и наплавка. Ручная электродуговая сварка и наплавка. При электродуговой сварке и наплавке источником тепла для расплавления металлов является электрическая сварочная дуга, возникающая между электродом и свариваемым металлом. Качество сварного шва и наплавленного слоя определяется диаметром электрода, типом и маркой электрода, величиной сварочного тока, напряжением на дуге, родом и полярностью тока, скоростью сварки и положением шва в пространстве.
При ручной электродуговой сварке и наплавке чаще всего используются металлические электроды, представляющие собой металлический стержень, на поверхность которого нанесен слой покрытия, предназначенного для стабилизации горения дуги, защиты расплавленного металла от кислорода и азота воздуха, легирования наплавленного металла. В состав электродных покрытий входят следующие группы компонентов: стабилизирующие, шлакообразующие, газообразующие, раскисляющие, легирующие и связующие. Электроды изготовляют диаметром 1,6—12 мм и длиной 225—450 мм. В зависимости от назначения стальные электроды подразделяются на типы. Тип и марку электродов выбирают в зависимости от химического состава металла ремонтируемой детали и требований, предъявляемых к сварному шву или наплавленному слою.
Диаметр электрода выбирают в зависимости от толщины наплавляемого слоя. При толщине наплавки менее 2 мм рекомендуется применять электроды диаметром 3 мм, а при большей толщине наплавки — электроды диаметром 4—5 мм.
При ремонте закаленных деталей ненаплавляемую часть детали погружают в воду во избежание отпуска. Наплавку легированных сталей производят при большой плотности тока с предварительным подогревом поверхности.
Ручную электродуговую наплавку целесообразно применять при небольшом объеме работ, а также при наплавке труднодоступных мест.
К преимуществам ручной
электродуговой наплавки относятся
удобство и простота процесса.
Недостатки ее — низкая производительность ,
низкая стабильность дуги и невысокое
качество наплавки.
Автоматическая электродуговая наплавка под слоем флюса. При указанном виде наплавки электрическая дуга горит под слоем флюса, подаваемого систематически в зону наплавки. В зоне горения дуги оплавляются поверхность детали, электрод и прилегающий слой флюса. Электродная проволока по мере оплавления автоматически подается в зону дуги одновременно с флюсом. При плавлении флюса выделяется газ и образуется газовая оболочка, защищающая расплавленный металл от взаимодействия с окружающим воздухом выгорания легирующих элементов. Кроме того, флюсовое покрытие способствует сохранению тепла дуги и препятствует разбрызгиванию жидкого металла.
На рис.10.3 представлена схема наплавки под слоем флюса тел вращения. Между поверхностью детали 5 и электродной проволокой 3 возбуждена электрическая дуга. Расплавленная капля металла электрода 3, смещаясь в направлении вращения детали, смешивается е расплавленным основным металлом детали, образуя сварочную ванночку. При остывании образуется наплавленный валик, который покрыт шлаковой коркой 7 и частично неиспользованным флюсом 1.
Наплавка в среде защитных газов. При этом виде наплавки защитный газ, подаваемый в зону наплавки под избыточным давлением, изолирует сварочную дугу и плавильное пространство от кислорода и азота воздуха.
Рисунок 10.3 – наплавка под
слоем флюса
Наплавка в среде защитных газов. При этом виде наплавки защитный газ, подаваемый в зону наплавки под избыточным давлением, изолирует сварочную дугу и плавильное пространство от кислорода и азота воздуха.
Наплавку углеродистых, легированных сталей и чугуна производят в среде углекислого газа; для высоколегированных сталей применяют аргон. При высокой температуре сварочной дуги происходит диссоциация углекислого газа. Образовавшийся атомарный кислород окисляет металл, что приводит к выгоранию железа и других примесей стали. Чтобы прекратить окисление, а также пополнить выгоревшие примеси при наплавке в углекислом газе применяют электродную проволоку, легированную марганцем и кремнием, которые связывают кислород и раскисляют ранее образовавшуюся закись железа. Образующиеся окислы марганца и кремния переходят в шлак.
Наплавку в среде защитных газов применяют, когда невозможна или затруднительна подача флюса и удаление шлаковой корки, например при наплавке мелких деталей, внутренних поверхностей и деталей сложной формы.
Преимуществами наплавки в среде защитных газов являются высокая производительность и простота ведения и управления процессом.
Недостатки ее — сложность работы на открытом воздухе из-за срыва струи углекислого газа под действием ветра и окислительная способность углекислого газа.
Вибродуговая наплавка. Автоматическая вибродуговая наплавка основана на использовании тепла кратковременной электрической дуги, возникающей в момент разрыва цепи между вибрирующим электродом и наплавляемой поверхностью. Отличительной особенностью этого вида наплавки является возможность получения наплавленного слоя малой толщины 0,3—2,5 мм, охлаждение поверхности наплавки в результате прерывистого характера процесса, что позволяет значительно уменьшить нагрев детали, снизить в ней остаточные напряжения и предотвратить ее деформирование.
Автоматическую вибродуговую наплавку применяют для наращивания изношенных наружных и внутренних цилиндрических поверхностей, в частности, шеек валов, штоков буровых насосов, замков бурильных труб и других деталей.
К преимуществам вибродуговой наплавки относятся: возможность получения тонких и прочных покрытий, малая глубина зоны термического влияния, небольшой нагрев детали и незначительное выгорание легирующих электродной проволоки.
Производительность при вибродуговой наплавке выше, чем ручной электродуговой, но ниже, чем при наплавке под флюсом.
Наплавка металлов трением. Сущность процесса наплавки металлов трением, предложенного и разработанного Я.М. Кершенбаумом и Б.А. Авербухом, заключается в плавлении наносимого металла за счет теплоты трения и соединении его с деталью при повышенных температуре и давлении. Наносимый металл или сплав в гранулированном состоянии (в виде стружки) плавится в закрытом пространстве за счет трения о наплавляемую деталь или специальный инструмент. Трение обеспечивается вращением наплавляемой детали или инструмента относительно массы наносимого металла или сплава.
Литература: 2 осн. [43-47], 3 осн. [122-143], 5 осн. [81-148].
Контрольные вопросы:
1. Какие особенности процессов сварки и наплавки?
2. Какие виды сварки и наплавки Вы знаете и объясните их различия в зависимости от технологических процессов?
Восстановление деталей сваркой и наплавкой: каким лучше аппаратом, как электродом с инвертором или полуавтоматом, как правильно на сломанной раме грузовика
Износ элементов механизмов происходит неравномерно. При этом из-за небольшого по сравнению с размерами детали повреждения, теряется ее работоспособность. Соответственно ухудшается или прекращается функционирование узла или даже всего механизма.
Из методов реставрации металла восстановление деталей сваркой и наплавкой стоит на первом месте по распространенности. Главных причин две:
- Восстановление исходных свойств элемента.
- Относительная дешевизна.
В статье мы остановимся на практическом применении методик восстановления, применительно к кузовным сварочным работам легковых и грузовых автомобилей.
В чем заключается ремонт?
Процессы сварки и наплавки принципиально отличаются мало. В первом случае расплав используется для соединения частей. Во втором выступает рабочим слоем, который наносят на поверхность детали, с целью восстановления ее первоначальных размеров.
Бывают ситуации, когда эти функции совпадают. Пример — восстановления днища кузова автомобиля, поврежденного коррозией. При этом, сильно разрушенные места заменяются листами металла, трещины и отверстия восстанавливаются наплавкой.
В других случаях, выработка на оси, либо обойме детали кузова полностью реставрируется методом наплавки. Одновременно сваркой может быть устранена (к примеру) трещина на этом же элементе.
Еще один пример: сварка рамы грузового автомобиля. Здесь свариваются элементы несущего каркаса, где возникли трещины, а наплавляются места выработок в проушинах и пазах крепления узлов, тяг, осей и пр.
Что касается износа железа, выбрать ремонт наплавкой не всегда целесообразно. Если автомобильный завод выпускает необходимые узлы, ремонт может свестись к вырезанию изношенной детали с последующей приваркой новой.
Как правило сварка кузова автомобиля применяется чаще чем наплавка на его деталях. Причина — характер износа, вызванный схожестью причин повреждений при эксплуатации.
Не важно какая это марка: ВАЗ 2109, грузовик «Хюндаи портер», «Лексус» или старенькая «Нива» — основное количество повреждений кузова приходится на коррозию и деформацию листового металла при авариях.
Применяемое оборудование
При всем разнообразии методики работ и инструментального обеспечения, классификация сварки при ремонтах автомобилей сводится всего к двум типам:
- Электрическая, преимущественно дуговая с использованием защитных газов либо флюсов.
- Газовая, с применением ацетилена или пропана.
Электрическая подразделяется на ручную, полуавтоматическую в среде инертных газов, под флюсом и пр.
Существуют и другие способы, например сварка лазерная, трением, диффузионная. Однако для ремонтов автомобилей они практически не используются.
В некоторых случаях используется такая разновидность сварки, как пайка. Применяют ее для ремонта повреждений патрубков из цветных металлов, блоков радиаторов, деталей оборудования рефрижераторов, выполненных из тонкой меди.
Какой сваркой лучше варить кузов автомобиля зависит от характера повреждений, а также особенностей места или детали, которую необходимо восстановить.
На сегодня выполнение основного объема работ осуществляют с помощью электричества. Газосварка, некогда бывшая чуть ли не единственным способом ремонта, на сегодня используется для соединения деталей из тонкого металла.
Кроме того, кислородно-ацетиленовая сварка по-прежнему популярна там, где к кузову крепятся различные тяги, создающие динамические нагрузки.
Из электрических приборов для небольших, ремонтов применяется сварка автомобиля инвертором, обычным ручным сварочным аппаратом. Для тонких работ, требующих высокого качества, а также наплавки используют полуавтоматы с углекислым или инертным газом.
С распространением алюминиевых и титановых сплавов арсенал механиков по ремонту пополнился аппаратами дуговой сварки неплавким электродом в среде инертных газов. С подачей плавящегося присадочного прутка рукой либо автоматически.
Требования к подготовке детали
Качество восстановления во многом зависит от того, насколько правильно мы будем готовить деталь. Это касается сварки, а особенно наплавки.
Металл тщательно зачищают от ржавчины с помощью угловой шлифовальной машины (УШМ), более известной как «болгарка». Либо ручной щеткой. При необходимости снимают фаску или выравнивают.
В ответственных случаях, при наплавке, пайке поверхность обезжиривают.
Хороший эффект дает обработка пескоструйными либо гидроабразивными аппаратами.
Трещины разделывают заточными дисками УШМ на всю глубину, чтобы получить на их месте V-образные канавки. Толстый металл обрабатывают с двух сторон. На их концах для устранения напряжений, предотвращения дальнейшего развития сверлят сквозные отверстия диаметром 4-6 мм.
Перед тем как наплавлять отверстия, их края зенкуют с одной либо двух сторон, при наличии резьбы ее высверливают.
Учитывая, что сварка авто электродом либо газовым пламенем, создает высокую температуру следует позаботится о сохранности примыкающих элементов отделки, эл. оборудования, пластиковых деталей.
Для этого снимают ремонтируемый элемент либо детали, могущие быть поврежденными. Если это по каким-либо причинам невозможно, применяют меры к их защите (закрывают, обкладывают мокрой ветошью).
Используемые электроды
Подбор электродов либо сварочной проволоки осуществляется исходя из трех параметров:
- Вида металла.
- Необходимой толщины детали либо слоя наплавки.
- Уровня ответственности восстанавливаемой детали.
Выполняя кузовной ремонт полуавтоматом с углекислотой используют порошковую сварочную проволоку, омедненную либо простую.
Наплавку слоя с высокими характеристиками по твердости выполняют электродами типа Т-620, с толстой обмазкой включающей графит, карбид бора и пр.
Необходимый диаметр электрода подбирают исходя из толщины свариваемого металла, по специальным таблицам.
Алюминиевые детали соединяют газовой (кислородно-ацетиленовой) либо дуговой сваркой. В последнем случае применяются электроды типа ОЗА-2. При технологии с неплавящимся вольфрамовым электродом, используют в качестве присадки пруток соответствующего алюминиевого сплава.
При наплавке изношенных деталей двигателя для получение легированных покрытий применяют проволоку типа Нп-65, с высоким содержанием углерода. Работы ведут под флюсом, в среде инертных газов.
Способы сварного ремонта кузовов легковых и грузовых автомобилей
Для сварки кузова как легковых авто, так и грузовозов используют самые различные технологии. Принципиально все они сводятся к электрической дуге либо раскаленной струе газа, но при этом нередко имеют существенные технологические отличия.
Ручной дуговой
Для работы применяют аппараты как переменного, так и постоянного тока. К первым относятся сварочные трансформаторы различны типов. Вторые представлены сварочными машинами и генераторами.
Трансформатор дает неустойчивую дугу, требует значительной силы тока на диаметре электрода (эта характеристика называется плотностью тока). При этом растет температура дуги, что чревато прожогом и перекаливанием.
Эта опасность для старых сварочных трансформаторов была актуальной, да и сейчас на вопрос: можно ли варить машину электросваркой, не всегда дают положительный ответ. Как минимум, если речь идет о самодельных устройствах либо обычных сварочных трансформаторах.
Ситуация изменилась с появлением инверторных аппаратов, но для соединения элементов из тонкого металла этот тип соединения применяют ограничено.
Как правило таким способом делают ремонт массивных деталей, наподобие станин или узлов из толстого металла, например — глушителей.
А. Тархомов сварщик со стажем 20 лет: «Современным инвертором кузов заварить можно в большинстве поломок. Разумеется, аппаратом профессионального уровня. Все от сварщика зависит. Не спецу заниматься подобными вещами не стоит категорически».
Автоматическая наплавка под флюсом
Используется достаточно широко для ремонта промышленного оборудования, особенно уникального. Для автомобильных ремонтов распространение невелико обычно, для восстановления путем наплавки деталей вращения (к примеру — распредвала).
Смысл метода заключается в том, что сварочная дуга горит не открыто, а под слоем специального порошка — флюса. Он защищает металл от окисления и соединения с азотом воздуха. Шов или слой наплавки по качеству не уступает исходному металлу, а при использовании специальных электродов может превосходить его по твердости и износостойкости.
Вибродуговой метод
Как и наплавка под флюсом применяется исключительно в заводских условиях, поскольку требует громоздких установок, обеспечивающих точное позиционирование детали.
Смысл заключается в колебательных движениях плавящегося электрода с частотой 100-120Гц, при напряжении 12-18 Вольт. При этом наплавка выполняется крохотными частичками металла с одновременным охлаждением.
В газовых защитных средах
Метод дающий наиболее качественный результат в условиях станций технического обслуживания и ремонтных мастерских.
Сварка либо наплавка ведется в среде инертного газа с помощью неплавящегося электрода (TIG), либо плавким электродом в окружении инертного, либо активного газа (MIG/MAG сварка соответственно).
Позволяет получать соединение, не уступающее выполненному в заводских условиях. Но главное с помощью этого метода автомобилистам впервые стал доступен текущий ремонт деталей, изготовленных из титановых и алюминиевых сплавов, высокопрочных легированных сталей.
Полуавтоматические способы
Один из наиболее популярных на сегодня методов, используемых небольшими мастерскими и частными мастерами.
Процесс ведется на воздухе либо под углекислым газом. В качестве плавящегося электрода используется сварочная проволока нужного состава. Подается она, сматываясь с катушки, по мере необходимости.
При этом даже устройства бытового уровня способны автоматически подстраивать скорость подачи проволоки в зависимости от силы дуги.
Альтернативная технология восстановления под давлением
Для восстановления деталей под давлением наплавка либо сварка не требуется. Деталь лишь предварительно нагревают до пластичности.
Смысл метода в изменении геометрических размеров деталей при их деформации. Различают три основных способа:
- осадка,
- обжатие,
- обсадка.
В первом случае при сжатии цилиндрических деталей типа втулок, с уменьшением высоты уменьшается внутренний диаметр. Обжатием деталь уменьшаю боковыми деформациями, а при обсадке наоборот — увеличивают (см. рисунок фото
В некоторых случаях такие операции дополняют либо предваряют наплавкой.
Особенности сварки рамы грузовых автомобилей
Сварка деталей грузовика и легковой машины принципиально одинакова. Несущественные различия вызваны разной толщиной металла кузова.
Другое дело, когда речь идет о том, как правильно сварить сломанную раму на грузовике воспринимающую нагрузку перевозимого груза, порой весящего не меньше, чем сама машина.
При значительных повреждениях, вызванных авариями либо неправильно эксплуатацией целесообразно вырезать деформированный участок, заменив его целым.
При этом следует использовать исключительно методы, не перекаливающие металл.
Выполняя сварочные работы на каркасах старайтесь спланировать работу так, чтобы швы не располагались поперек сечения. Особенно в местах, где предполагается повышенная нагрузка.
При наплавке трещин их предварительно обрабатывают как рассказывалось в разделе о подготовке. Затем шов зачищают, а участок дополнительно усиливают металлической накладкой.

Восстановление деталей сваркой — Техническое Обслуживание и Ремонт Автомобилей
Сварка в ремонтном производстве находит очень широкое применение. Многие дефекты и повреждения устраняются сваркой, в том числе различные трещины, отколы, пробоины, срыв или износ резьбы и т. п. Сваркой называется процесс соединения металлических частей в одно неразъемное целое при помощи нагрева металла в местах соединения. При ремонте автомобильных деталей нагрев металла осуществляют газовым пламенем или электрической дугой. Так как детали изготавливаются из различных металлов (сталь, серый и ковкий чугун, цветные металлы и сплавы), то применяют соответствующий способ сварки.
Заваривают трещины на платформах и рамах, так же делают заплаты и разнообразные накладки и т.д.
Производят восстановление резьб путем наплавки с последующей обработкой и нарезанием резьбы плашкой или метчиком. Соответственно, ремонтируют наружные и внутренние резьбы.
Выбор технологии восстановления деталей:
Детали машин ремонтируют автоматической и полуавтоматической сваркой в углекислоте.
Автоматическая представляет собой полностью автономный процесс, нужно только лишь зафиксировать деталь и нажать кнопку, то же касается сварочных роботов.
При проведении ремонтно-восстановительных работ в автосервисе наиболее простой способ – полуавтоматической сварки, когда проволока подается с заданной скоростью, а горелка перемещается вручную вдоль шва. КПД полуавтомата существенно проще по сравнению с ручным инвертором и лучше качество шва. Газ, используемый для защиты: углекислота – активный , существенно окисляет расплавленную углеродистую сталь, а связывает и выводит кислород на поверхность марганец, в большом количестве присутствующий в проволоке 08Г2С. Сварка полуавтоматом в углекислоте идеальна для ремонта пальцев, фланцев карданных валов и т.д.
Популярна в деле ремонта и восстановления так же сварка под флюсом благодаря тому, что она обеспечивает высокую производительность и прочность, обеспечивая надежную защиту ванной. Она и названа так потому, что во время процесса дуга, зажженная между металлом и электродом скрыта под слоем флюса. Таким образом ремонтируют, например, распредвалы.
При небольшом износе на деталях с малым диаметром практикуют восстановление электроимпульсной наплавкой.
Сварка стальных деталей. Автомобильные детали изготавливают из углеродистых и легированных сталей. Малоуглеродистые и среднеуглеродистые стали хорошо свариваются газовой сваркой. Труднее сваривать газовым пламенем стали с содержанием углерода более 0,4%, термически обработанные и легированные стали. Это связано с тем, что с повышением содержания углерода температура плавления углеродистой стали понижается и пламенем газовой горелки легко ее пережечь.
При сварке легированных сталей образуются тугоплавкие окислы, которые остаются в сварных швах и придают им хрупкость. Поэтому для деталей, изготовленных из высокоуглеродистых, термически обработанных и легированных сталей, рекомендуется применять сварки электрической дугой, так как температура сварочной зоны у нее ниже, чем у газовой сварки.
Сварка чугунных деталей имеет определенные трудности, так как серый чугун из твердого состояния сразу переходит в жидкое. При местном нагреве возникают большие внутренние напряжения, которые могут привести к появлению трещин в основном металле. Быстрое охлаждение деталей, особенно тонкостенных, ведет к отбеливанию чугуна в зоне сварки. Это придает чугуну высокую твердость и хрупкость, и деталь становится непригодной для механической обработки.
Сварку чугуна можно выполнять двумя способами: холодным, т. е. без предварительного нагрева детали, и горячим, при котором деталь предварительно подогревают в печи.
При горячей сварке деталь медленно нагревают до температуры 600—650°С в специальных печах или горнах. Чем больше содержание углерода в чугуне, тем медленнее должна быть скорость нагрева. Предварительный нагрев осуществляют при сварке и заварке трещин в ответственных деталях и деталях сложной конфигурации. После подогрева деталь помещают в термоизоляционный кожух со специальными задвижками или закрывают листовым асбестом, оставляя открытым только место сварки.
В процессе сварки допускается охлаждение детали до температуры 350—400°С. Если за это время сварка не закончена, то необходимо деталь вновь нагреть и продолжать сварку. После сварки деталь следует медленно охлаждать. Рекомендуется предусмотреть отпуск для деталей сложной конфигурации и разной толщины стенок. Для этого их нагревают до температуры 600—650°С и медленно охлаждают.
Сварку можно вести электрической дугой или газовым пламенем. При газовой сварке применяют нейтральное пламя или пламя с небольшим избытком ацетилена. В качестве присадочного материала используют чугунные прутки диаметром 6—8 мм или малоуглеродистую сварочную проволоку. При сварке чугунными прутками применяют флюсы следующего состава; бура; смесь, состоящая из 50% буры, 47% двууглеродистого натрия и 3% окиси кремния; смесь, состоящая из 56% буры, 22% углекислого натрия и 22% углекислого калия. Флюс вносят в сварочную ванну путем погружения в него нагретого конца присадочного прутка.
Сварка деталей, изготовленных из сплавов цветных металлов. Латунные детали сваривают газовой сваркой. Применяют окислительное пламя с небольшим избытком кислорода. В качестве присадочного материала используют латунные прутки, содержащие кремний и алюминий, снижающие выгорание цинка из сварочной ванны.
Бронзовые детали также сваривают газовой сваркой. Сварочное пламя должно быть нейтральным. В качестве присадочного материала применяют бронзовые прутки с содержанием фосфора до 0,4%. Последний хорошо раскисляет металл шва и затрудняет выгорание олова и других примесей. После сварки деталь нагревают до 450—500°С, а затем быстро охлаждают.
Детали из алюминия и его сплавов лучше сваривать ацетилено — кислородным пламенем. При плавлении на поверхности сварочной ванны образуется тугоплавкая пленка окиси алюминия, которая препятствует процессу сварки. Температура плавления пленки окиси алюминия составляет 2050°С, ч.то значительно превышает температуру плавления сплава или алюминия, равную 660°С. Для растворения окислов и удаления их из сварочного шва применяют специальные флюсы. Наиболее распространенными являются два вида флюсов, имеющие в составе (%): первый— хлористого натрия—17, хлористого калия— 83; второй — хлористого калия — 45, хлористого натрия — 30, хлористого лития — 15, фтористого калия — 7, сернокислого натрия — 3.
В качестве присадочного материала используют прутки или кусочки такого же материала, из которого изготовлена деталь. Перед сваркой рекомендуется подготовленную деталь медленно нагреть до 250—300°С. Сварку следует вести быстро нормальным пламенем и держать мундштук сварочной горелки под углом наклона не более 30° к поверхности свариваемой детали. Для удаления остатков флюса и предотвращения коррозии шва осуществляют промывку его слабым раствором азотной кислоты с добавлением в раствор 2% хромпика. Для улучшения механических свойств сварного шва ответственные детали отжигают с нагревом до 300—350°С и последующим медленным охлаждением.
Контрольные вопросы
1. Какие существуют виды дефектов и износов?
2. В чем сущность способа восстановления посадки применением деталей ремонтных размеров и дополнительных деталей?
3. Расскажите о способах восстановления деталей до номинальных размеров.
Восстановление деталей электродуговой сваркой и наплавкой
Категория:
Техническое обслуживание дорожных машин
Публикация:
Восстановление деталей электродуговой сваркой и наплавкой
Читать далее:
Восстановление деталей электродуговой сваркой и наплавкой
При восстановлении деталей ручную электродуговую сварку применяют для заварки трещин, приварки обломанных частей и заплат на пробоины, заплавки изношенных отверстий, наращивания изношенных кулачков и зубьев, а также для устранения повреждений в деталях из алюминиевых сплавов, чугуна и стали.
При ручной электродуговой сварке больше, чем при любом другом процессе, применяемом при восстановлении деталей, качество и производительность процесса зависят от квалификации сварщика, его умения правильно выбрать марку и диаметр электрода, режим сварки, приемы манипулирования концом электрода.
Газовую сварку используют при ремонте кабин и облицовки, а также для заплавки изношенных отверстий, наращивания обломанных ушков. Она основана на использовании теплоты, выделяющейся при сгорании ацетилена или других горючих газов в смеси с кислородом.
Рекламные предложения на основе ваших интересов:
При восстановлении деталей чаще всего в качестве горючего газа применяют ацетилен. Температура ацетилено-кислородного пламени в самой его горячей точке 3000—3150° С. При газовой сварке скорость нагрева и расплавления металла значительно меньше, чем при дуговой, а зона термического влияния значительно больше, поэтому не рекомендуется применять газовую сварку для устранения повреждений в деталях, изготовленных из чугуна.
Дуговая сварка в среде углекислого газа — один из наиболее эффективных процессов для устранения повреждений в тонколистовых стальных деталях. Она все больше вытесняет газовую и ручную электродуговую сварку при ремонте кабин, кузовов и ответственных металлоконструкций. Этот вид сварки отличается высокой производительностью, хорошим формированием сварного шва, легкостью ведения процесса во всех пространственных положениях, концентрацией теплоты в зоне сварки.
Автоматическая наплавка под слоем флюса (рис. 86) обеспечивает наиболее высокое качество наплавленного металла, так как сварочная дуга и ванна жидкого металла полностью защищены от вредного влияния кислорода воздуха, а медленное охлаждение способствует наиболее полному удалению из наплавленного металла газов и шлаковых включений. При автоматической наплавке заданный режим почти не изменяется.
При наплавке под слоем флюса электрическая сварочная дуга горит в закрытой полости из расплавленного минерального вещества (флюса). Флюс предотвращает разбрызгивание жидкого металла, обеспечивает формирование нормального сварного шва, защищает расплавленный металл от действия кислорода и азота воздуха, влияющих отрицательно на свойства наплавленного металла. Электродная проволока из кассеты к месту наплавки подается автоматической головкой.
Рис. 86. Схема механизированной наплавки под слоем флюса:
1 — источник тока для питания дуги, 2 — оболочка из жидкого флюса, 3 — устройство для подвода флюса, 4 — мундштук, 5 — электродная проволока, 6 — электрическая дуга, 7 — шлаковая корка, 8 — наплавленный слой, 9 — наплавляемая деталь, 10 — скользящий контакт
Применение флюса дало возможность использовать голую (без покрытия) электродную проволоку. Ток к проволоке подведен по скользящему контакту 10 на небольшом расстоянии от дуги, что уменьшило длину электрода, по которому протекает сварочный ток. Плотность тока при этом увеличилась в несколько раз, возросла и производительность наплавки. Питание дуги чаще всего осуществляется током от сварочных генераторов или выпрямителей.
Наплавкой под слоем флюса можно восстанавливать изношенные плоские, цилиндрические, резьбовые и другие поверхности деталей. Цилиндрические поверхности деталей, наплавляемые под слоем флюса, должны иметь наружный диаметр свыше 50 мм, так как на меньших сечениях расплавленный флюс и шлак из-за большого разогрева не успевают затвердевать и стекают с деталей. Механизированной наплавкой под слоем флюса восстанавливают катки, колеса, башмаки, валы, ролики, барабаны и др.
Разновидностями электродуговой наплавки под слоем флюса являются более производительная наплавка ленточным электродом, а также сварка и наплавка порошковой проволокой.
Автоматическая наплавка ленточным электродом производится специальным электродом, изготовленным из металлической ленты холодного проката толщиной 0,4—1,0, шириной 20— 100 мм. Благодаря тому, что при этом способе наплавки сварочная дуга непрерывно перемещается по торцу ширины ленты, проплавление основного металла неглубокое и его доля в наплавленном слое составляет 8—10%. Таким образом, влияние наплавки на структуру и механические свойства основного металла незначительно. Химический состав ленты и марку флюса выбирают в зависимости от назначения наплавки.
Способ обеспечивает высокую производительность работ: за один проход можно наплавить слой толщиной 2—7 мм и шириной, соответствующей ширине ленты.
Недостатки способа: потребности в ленте различной ширины для наплавки разнотипных деталей; невозможность применения наплавки для валов малых диаметров, шлицевых соединений, внутренних отверстий.Полуавтоматическая сварка и наплавка порошковой проволокой — это сравнительно новый процесс в ремонтном производстве. Сущность способа заключается в том, что в качестве электродного материала применяют специальную проволоку, в состав которой наряду с легирующими элементами введены защитные газо- и шлакообразующие вещества, благодаря чему достигается высокая твердость и износостойкость наплавленного металла. Для наплавки порошковой проволокой используют те же автоматы и полуавтоматы, что и для сварки и наплавки сплошными электродными проволоками под слоем флюса. Наплавку порошковой проволокой рекомендуется применять прежде всего для восстановления деталей с большим износом.
При устранении дефектов в корпусных чугунных деталях (трещин, обломов, пробоин) применяют самозащитную проволоку ПАНЧ-11 без подогрева и дополнительной защиты. По сравнению со специальными никелевыми электродами проволока ПАНЧ-11 обладает высокой стойкостью сварных соединений против околошовных трещин. Заваривают трещины самозащитной проволокой ПАНЧ-11 открытой дугой на постоянном токе прямой полярности участками длиной 20—50 мм с проковкой и охлаждением каждого участка до температуры 50° С. Для сварки рекомендуются полуавтоматы ПДПГ-500, ПДГ-300, А-547У, А-825М в комплекте с выпрямителями ВС-300.
При полуавтоматической сварке чугуна самозащитной проволокой ПАНЧ-11 процесс протекает стабильно, без разбрызгивания металла, сварочный шов формируется без подрезов, наплывов и других наружных дефектов. Металл шва имеет высокую обрабатываемость, плотность и прочность. Этот метод находит все большее применение на ремонтных предприятиях, его можно рекомендовать для холодной заварки трещин длиной до 200 мм, обломов, а также обварки заплат у тонкостенных чугунных деталей.
Вибродуговая наплавка — разновидность автоматической электродуговой наплавки. Она ведется колеблющимся электродом, что дает возможность наплавлять металл при низком напряжении источника тока. Благодаря этому образуется минимально возможная сварочная ванна, мелкокапельный переход металла с электрода на деталь. При вибродуговой наплавке получается достаточно хорошее сплавление основного металла с электродным, небольшой нагрев детали и малая по глубине зона термического влияния. Наиболее широкое применение получила вибродуговая наплавка в среде охлаждающей жидкости.
Принципиальная схема установки для вибродуговой наплавки в среде жидкости показана на рис. 87. К установленной в станок изношенной детали с помощью роликов по направляющему мундштуку подается проволока, которая сматывается с барабана. Одновременно с подачей проволоки от вибратора электроду сообщается колебательное движение частотой 50—100 Гц. Установка вибратора позволяет уменьшить мощность дуги, не уменьшая стабильности процесса. От источника постоянного тока через ролики и мундштук к электроду подводится плюс, а к детали через шпиндель станка — минус.
Рис. 87. Схема установки для вибродуговой наплавки в струе жидкости:
1—индуктивность, 2—генератор, 3—трубопровод, 4 — подающие ролики, 5 — барабан для электродной проволоки, 6 — вибратор, 7 — пружины, 8 — шестеренный насос, 9 — бак-отстойник, 10 — деталь с наплавленным слоем, 11 — зона наплавки, 12 — мундштук
В зону наплавки по трубопроводу непрерывной струей подается жидкость. С детали жидкость стекает в поддон станка, откуда попадает в бак-отстойник и далее насосом по трубопроводам снова подается к детали.
Вибродуговым способом могут наплавляться цилиндрические поверхности диаметром от 15 мм и выше, поверхности изношенных отверстий, подвижных и неподвижных соединений; поверхности под обоймы шариковых и роликовых подшипников; шейки валов, работающих в подшипниках скольжения, не испытывающие ударной нагрузки; шейки в местах прессовых посадок. Вибродуговая наплавка нежелательна для профильных поверхностей в виде резьб, мелких шлиц и т. д. Вибродуговую наплавку можно производить также под слоем флюса и в среде защитного газа.
Способ вибродуговой наплавки и сварки различных материалов в потоке воздуха применяют при восстановлении чугунных деталей. Деталь наплавляют с помощью автоматической вибродуговой головки, а для получения плотных и легко обрабатываемых слоев в зону сварки подают атмосферный воздух. С увеличением подачи воздуха наружная пористость наплавляемого металла уменьшается. Наименьшая пористость получается при расходе воздуха свыше 1600—2000 л/ч.
Рис. 89. Полуавтомат А-547У в комплекте с выпрямителем ВС-300:
1 — баллон с углекислым газом, 2 — подогреватель, 3 — редуктор-расходомер, 4 — держатель со шлангом, 5 — подающий механизм, 6 — сварочный выпрямитель, 7 — пульт управления
Наплавленный металл обладает невысокой твердостью, что позволяет производить токарную обработку слоя обычным инструментом. Для наплавки используют установку, состоящую из токарного станка, источника тока (три выпрямителя ВСГ-ЗА) и автоматической вибродуговой головки.
При наплавке в среде углекислого газа сварочная дуга и расплавленный металл защищаются от вредного влияния воздуха струей углекислого газа, специально подаваемого в зону сварки. Электродная проволока из кассеты непрерывно подается в зону сварки с заданной скоростью. Ток к проволоке подводится с помощью мундштука и наконечника, расположенного внутри газовой горелки, которая подает защитный газ в зону сварки.
Рис. 88. Схема процесса наплавки в среде углекислого газа:
1 — горелка, 2 — электродная проволока, 3 — мундштук, 4 — наконечник, 5 — сопло горелки,6 — основной металл, 7 — сварочная дуга, 8 — сварочная ванна, 9 — шов
Электродная проволока плавится под действием теплотыдуги; электродный металл переходит в сварочную ванну и смешивается с расплавленным основным металлом. В результате сплавления электродного и основного металлов образуется наплавленный валик, прочно соединенный с основным металлом.
При наплавке углекислый газ из баллона (рис. 89) проходит через подогреватель газа, осушитель, редуктор и расходомер (ротаметр). При выходе из баллона углекислый газ расширяется и температура его резко падает. Чтобы исключить резкое охлаждение газа и замерзание содержащейся в углекислом газе влаги, его сразу после выхода из баллона пропускают через подогреватель. Затем углекислый газ попадает в осушитель, представляющий собой цилиндр, заполненный веществом, которое поглощает влагу из углекислого газа (сили- кагель, обезвоженный медный купорос или хлористый кальций).
Наплавка в среде углекислого газа имеет ряд преимуществ перед другими методами наплавки: более высокая производительность труда по сравнению с наплавкой под слоем флюса, высокая экономичность процесса, хорошее качество наплавленного металла; возможность наплавки внутренних поверхностей изделий сложной формы и малых диаметров; улучшение условий труда рабочих. Кроме того, отпадает необходимость в применении различных приспособлений для удержания флюса и расплавленного шлака, как при наплавке под слоем флюса, что позволяет повысить автоматизацию процесса. Недостатки способа наплавки в среде углекислого газа: большие потери металла на разбрызгивание, потребность в применении специальных типов проволоки и особых источников питания.
Сущность процесса электроконтактной приварки стальной ленты заключается в приварке к поверхности деталей стальной ленты мощными импульсами электрического тока. В сварочной точке под действием импульса тока расплавляются металлы присадочного материала и детали. Присадочный материал (стальная лента) расплавляется не по всей толщине, а лишь в тонком поверхностном слое, в зоне контакта с деталью. Слой приваривают ко всей изношенной поверхности регулируемыми импульсами тока при вращательном движении детали со скоростью, пропорциональной частоте импульсов, и поступательном перемещении сварочной головки. Схема процесса приварки ленты приведена на рис. 90.
Для приварки ленты применяют установку 011-1-02, которая позволяет восстанавливать наружные и внутренние цилиндрические поверхности деталей. Технологический процесс целесообразно применять при восстановлении шеек валов под подшипники качения, посадочных отверстий стаканов подшипников и других деталей при износе до 0,4 мм.
Изношенную поверхность предварительно шлифуют, удаляя слой металла толщиной 0,15—0,2 мм. После этого деталь подают на установку. Накладывают на подготовленную поверхность мерный отрезок стальной ленты толщиной 0,4—0,8 мм (в зависимости от величины износа), который прижимают сварочными роликами установки. Материал ленты — средне- и высокоуглеродистые стали марок 45, 50, 65Г и др.
Импульсами тока прихватывают ленту в нескольких местах. Перемещая ролики в крайнее положение, переключают установку на рабочий режим и приваривают ленту.
Рис. 90. Схема процесса электроконтактной приварки стальной ленты:
1 — центры, 2 — восстанавливаемая деталь, 3 — ролики, 4 — лента, 5 — трансформатор, 6 — прерыватель тока
Процесс ведут при подаче жидкости (воды), которая охлаждает ролики сварочной головки и одновременно эффективно отводит теплоту от зоны приварки. При этом твердость восстанавливаемой поверхности увеличивается до HRC.55 и более. Этим достигается совмещение технологий нанесения покрытия и термической обработки. Последующую механическую обработку после приварки ленты производят на круглошлифовальных станках.
Использование электроконтактной приварки стальной ленты взамен вибродуговой наплавки позволяет повысить производительность восстановления деталей в 2,5 раза, снизить расход присадочных материалов в 4—5 раз, трудоемкость работ в 2,5 раза и повысить ресурс детали до уровня новой.
Электроконтактную приварку стальной проволоки применяют преимущественно для восстановления резьбы. Проволоку подают во впадину изношенной резьбы и прижимают контактным роликом. После включения тока ее приваривают. Диаметр проволоки подбирают с таким расчетом, чтобы после ее приварки и осадки металл заполнил впадину между витками восстанавливаемой резьбы и при этом оставался припуск на механическую обработку. Наилучшие результаты получаются в том случае, если диаметр присадочной проволоки равен шагу резьбы или больше его на 5—10%.
Рекламные предложения:
Читать далее: Газопламенное и плазменное напыление и наплавка
Категория: — Техническое обслуживание дорожных машин
Главная → Справочник → Статьи → Форум
Восстановление деталей сваркой и наплавкой
Восстановление деталей сваркой и наплавкой
Категория:
Ремонт промышленного оборудования
Восстановление деталей сваркой и наплавкой
Сварка и наплавка широко применяются при ремонтных работах. Сваркой исправляют детали с изломами, трещинами и отколами.
Наплавка является разновидностью сварки и заключается в том, что этим способом не соединяют металлические детали или части в одно целое, а наращивают, наплавляя на основной металл присадочный материал. Наплавкой восстанавливают изношенные поверхности деталей, посадочные размеры которых затем получают механической обработкой на станках.
В ремонтном деле применяют главным образом два вида сварки: дуговую и газовую.
Дуговая сварка может осуществляться металлическим и угольным электродами. Широко применяют сварку на переменном токе (по сравнению с постоянным током) вследствие меньшего расхода электроэнергии, небольшой стоимости оборудования и простоты ухода за оборудованием. При этом применяют электроды со стабилизирующими обмазками.
Газовая сварка также широко используется в ремонтном производстве. Сущность газовой сварки стальных и чугунных деталей заключается в плавлении металла при горении ацетилена в избыточной среде кислорода, при этом развивается температура 3300 °С и выше.
Решая вопросы восстановления деталей сваркой и наплавкой, необходимо учитывать недостатки данного метода. При этом происходит нагрев, вызывающий деформация и возникновение внутренних напряжений. Для ликвидации последних приходится осуществлять термическую обработку, которая также может быть причиной деформации деталей.
Сварка и наплавка стальных деталей. Свариваемость стали зависит от ее химического состава, главным образом от содержания углерода. Большое влияние оказывают и легирующие элементы — хром, марганец, никель и др. С увеличением количества углерода и легирующих элементов в стали ее свариваемость ухудшается.
Хорошо сваривающиеся стали можно сваривать или наплавлять в оГычных производственных условиях без предварительного нагрева и баз последующей термической обработки. Это же относится и к удовлетворительно сваривающимся сталям. Однако детали из этих сталей большой толщины и большого диаметра нужно перед сваркой назреть, чтобы предотвратить образование трещин. Стали с ограничен эй и тем более с плохой свариваемостью могут давать трещины (в зоне теплового влияния в наплавленном металле), поэтому рекомендуется детали из них перед сваркой отжигать при температуре 600—650 °С, а по окончании сварки подвергать закалке и отпуску.
В ремонтной практике применяют главным образом дуговую сварку металлическими электродами.
Наплавкой восстанавливают многие детали, в том числе и вращающиеся в подшипниках скольжения цапфы валов и осей. Прежде чем приступить к наплавке, поверхность детали очищают до металлического блеска. Наплавку ведут слоями параллельно оси цапфы, причем слои наплавляют поочередно на диаметрально противоположных участках цапф, чтобы предупредить деформацию детали. Ширина наплавленного слоя не должна превышать двойной толщины электрода. Наплавив слой, зачищают его стальной щеткой. Следующий слой должен покрывать предыдущий на одну треть ширины.
Сварка и наплавка деталей из чугуна. При восстановлении чугунных деталей (а также деталей из углеродистых сталей толщиной менее мм) применяют главным образом газовую сварку. Сварочный шов получают, используя присадочный материал в виде прутков или проволоки. Чугунные отливки (детали) сваривают обычно при помощи чугунного же присадочного материала. Сварка чугуна ведется кислородно-ацетиленовым пламенем с небольшим избытком ацетилена (пламя получается восстановительное). Чтобы предохранить расплавленный металл шва от окисления, применяют флюсы.
Детали из серого чугуна можно сварить с предварительным общим нагревом, с местным подогревом или без подогрева. Сварку деталей с предварительным подогревом до 500—700 °С условно называют горячей сваркой, при подогреве до 250—450 °С— полугорячей, а без подогрева — холодной сваркой. Лучшие результаты дает горячая сварка. Детали нагревают в печах или горнах.
В ремонтной практике широко распространен способ восстановления корпусных деталей из чугуна методом сварка-пайка латунной проволокой и прутками, отлитыми из медно-цинковых оловянных сплавов. Этот способ не требует нагрева свариваемых кромок до расплавления, а лишь до температуры плавления припоя.
Ковкий чугун плохо поддается сварке. Наиболее простым способом восстановления деталей из ковкого чугуна является сварка с применением латунных электродов или электродов из монель-металла.
Для высококачественной сварки необходима соответствующая подготовка поверхности для сварки и режим охлаждения соединения деталей. Сварное соединение охлаждают медленно. Крупные детали охлаждают вместе с печью, в которой они были нагреты, мелкие помещают в сухой горячий песок или золу. При быстром охлаждении образуется твердый и хрупкий отбеленный чугун. Неравномерное охлаждение приводит к возникновению внутренних напряжений и появлению трещин.
Наплавка цветных металлов
Изношенные детали, изготовленные из меди, бронзы, латуни, алюминия и его сплавов, восстанавливают газовой наплавкой. В качестве присадочных материалов применяют стержни, близкие по составу к основному металлу.
При восстановлении размеров деталей из бронзы в качестве присадочного материала могут служить латуни Л62, Л К-62-03, ЛСЖ-1-03, которые дают плотный наплавленный металл, хорошо сопротивляющийся изнашиванию. Детали больших размеров и массой более кг предварительно подогревают горелкой или в специальных печах до 400—460 °С. После наплавки рекомендуется быстрое охлаждение на воздухе, а для бронз с высоким содержанием меди — в воде.
Детали из меди наплавляют медной проволокой. Большие детали наплавляют двумя горелками, одной из которых осуществляют подогрев, а другой ведут наплавку. Наплавленный слой можно дополнительно уплотнить проковкой в горячем состоянии.
Алюминиевые детали восстанавливают газовой наплавкой с применением флюса АФ-4А. В качестве присадки выбирают металл, близкий по составу к основному металлу.
Детали из черных металлов можно наплавлять медью, латунью, бронзой при помощи ацетилено-кислородной горелки с применением газообразных флюсов БМ-1 или БМ-2. При этом получается плотный слой цветного металла, хорошо сплавленного с основным.
Поверхность детали, подлежащую наплавке, тщательно очищают и обезжиривают, затем нагревают газовой горелкой до температуры, близкой к температуре плавления присадочного металла. При больших размерах наплавляемой поверхности наплавку нужно выполнять с предварительным нагревом.
В ряде случаев целесообразно выполнять наплавку двумя горелками, одну из которых располагают впереди (по ходу процесса наплавки) и подогревают ею металл, а второй с флюсом БМ-1 ведут наплавку. Флюс БМ-1 обеспечивает полную защиту от окисления расплавленного слоя цветного металла, что не достигается в присутствии порошковых флюсов. Поверхность металла после остывания получается ровной, блестящей и неокисленной.
Для наплавки рекомендуются латуни различных марок (например, Л62), не содержащие кремния, свинца, олова, бронзы, в частности БрКМЦЗ-0,5, дающие плотный слой при наплавке на чугун и сталь. Прочность соединения с чугуном и сталью соответствует прочности литой латуни.
Наплавка поверхностей твердыми сплавами
Для восстановления деталей и Повышения их износостойкости применяют наплавку легированными сплавами, обладающими высоким сопротивлением износу (повышение срока службы в 2—6 раз и более). При ремонте деталей часто применяют сормайт, литой твердый сплав, порошковый твердый сплав, а также электроды со специальной обмазкой, компоненты которой в процессе плавления, соединяясь с основным металлом и металлом электрода, образуют однородный износостойкий слой.
Сормайт № применяют в виде прутка диаметром от до мм. Этими сплавами ремонтируют кулачковые муфты, фиксаторы, различные упоры и др. После охлаждения наплавленную деталь обрабатывают шлифованием.
Реклама:
Читать далее:
Восстановление и упрочнение изношенных деталей электролитическими и химико-термическими способами
Статьи по теме:
Процедуры ремонтной сварки и наплавки
Для ремонтной сварки существует три важнейших комплекса операций:- Подготовка к сварке
- Ремонтная сварка
- Операция после сварки
Подготовка к сварке
Прежде чем приступить к работе, необходимо учитывать большое количество факторов и принимать решения. сварка.Безопасность. Место или зона ремонтной сварки должны быть обследованы и все соображения безопасности выполнены. Это может включать в себя размещение необходимой площади согласно определенным правилам, удаление всех горючих материалов с территории, слив топлива из баков строительной техники, самолетов, лодок, грузовиков и т. д. Другое меры предосторожности включают устранение токсичных материалов, таких как толстые слои свинцовой краски, пластиковые покрытия металлов и др.
Очистка. Непосредственно рабочая зона должна быть чистой от всех загрязнений. и это включает удаление грязи, жира, масла, ржавчины, краски, пластиковых покрытий и т. д., с поверхности свариваемых деталей. Метод очистки зависит от удаляемый материал и расположение заготовки. Для большинства строительных и производственного оборудования рекомендуется чистка паром. Когда это невозможно, растворитель можно использовать чистку. Также применяется пескоструйная очистка абразивными материалами.Для мелких деталей можно использовать травление или очистку погружением в растворитель и, наконец, очистку электроинструмента с щетки, шлифовальные круги, шлифовальный круг и т.д. Время, потраченное на уборку участок ремонта сварного шва окупится в долгосрочной перспективе.
Разборка. Кроме простейших ремонтных работ, возможна разборка. обязательный. Это может быть связано с элементами, упомянутыми выше, но также применимо к смазке. линии, КИПиА, электропроводку и т. д. Иногда бывает необходимо разобрать основные компоненты, такие как машины из рам машин и т. д.
Защита смежных машин и обработанных поверхностей. При ремонте сварка выполняется на оборудовании, многие части, которые не снимаются, должны быть защищены от брызги сварочного шва, искры газовой резки и другие посторонние предметы, образующиеся при ремонте обработать. Ограждения или перегородки из листового металла используются для защиты смежного оборудования. Для обработанные поверхности можно использовать асбестовую ткань. Целесообразно обеспечить защиту материал с помощью проволоки, зажимов или других временных связей.Обработанные поверхности в пределах пяти ноги во время сварочных работ должны быть защищены.
Стяжки и зажимы. При сложных ремонтных работах возможна установка распорок или зажимов. быть обязательным. Это происходит из-за большого веса деталей или из-за того, что нагрузки могут воздействовать на ремонтируемую деталь. Если необходимо разрезать основные элементы конструкции груз должен переноситься временными скобами. Подтяжки можно временно приварить к ремонтируемое сооружение.
Планировка ремонтных работ. При большинстве ремонтных работ необходимо удалять металла, чтобы можно было сделать сварной шов с полным проплавлением. Должен быть сделан макет, показывающий металл, который необходимо удалить путем резки или строжки для подготовки детали к сварке. В необходимо удалить минимальное количество металла, чтобы получить сварной шов с полным проплавлением. Расположение следует выбирать так, чтобы сварка могла быть сбалансирована, если это возможно, и чтобы большая часть сварку можно производить из более удобного сварочного положения.
Предварительный нагрев. Предварительный нагрев и газовая резка или строжка являются частями подготовка к сварке, но может считаться частью сварочной операции. когда Газовая резка или строжка обязательны, предварительный нагрев должен быть таким же, как при сварке. Это может быть не столь важным, поскольку напряжения намного меньше; однако термический Удар по металлу может произойти как при строжке, так и при сварке.
Резка и строжка. Горелка газовая на кислородном топливе чаще всего используется для этого приложения. Доступны специальные насадки для строжки, и они должны быть выбирается исходя из конкретной геометрии подготовки шва. Возможно, по внимательно следить за поверхностью реза, чтобы найти и проследить трещины во время строжки пламенем операция. Края трещин будут видны, так как они станут немного горячее. Воздух Процесс резки и строжки угольной дугой также широко используется для подготовки к ремонту.Соответствующие источники энергии и угли должны быть выбраны в соответствии с объемом металла. удалено. Следует выбрать технику, чтобы избежать нагара на подготовленном металле. поверхность. Для некоторых металлов горелка или угольная дуга могут не подходить, и в этих случаях можно использовать механическое измельчение и измельчение.
Шлифовка и очистка. Полученные поверхности могут быть не такими гладкими по желанию и может включать обожженные участки, оксид и т. д.Отшлифовать поверхности до яркого металл перед началом сварки. Для критических работ или при подозрении на дополнительные трещины рекомендуется проверить поверхность с помощью магнитопорошкового контроля, чтобы убедитесь, что все трещины и дефекты устранены.
Приведенные выше девять шагов представляют собой список шагов по подготовке к сварке. Некоторые из они могут быть устранены, но все они должны быть рассмотрены для надлежащей подготовки стык под сварку.
Ремонт Сварка
Успешная ремонтная сварка также предполагает соблюдение логической последовательности, чтобы убедиться, что что все факторы учтены и адекватно представлены.Порядок сварки. Процедура сварки должна быть доступна для использование сварщиков. Он должен включать в себя используемый процесс, конкретные присадочные металлы, требуемый предварительный нагрев и любая другая конкретная информация, касающаяся сварного соединения техника.
Сварочное оборудование. Должно быть в наличии достаточное сварочное оборудование чтобы не было задержек. Также может потребоваться резервное оборудование. Это не включает только сварочное оборудование, но включает в себя достаточное количество электрододержателей, шлифовальных машин, механизмы подачи проволоки, если требуется, кабели и т. д.
Материалы. Также должно быть достаточно материалов для всего работа. Сюда входят присадочные материалы, хранящиеся должным образом для использования при ремонте. Это также включает в себя такие материалы, как вставки, армирующие детали и т. д. Материалы также включить топливо для поддержания предварительного нагрева и температуры промежуточного прохода, защитные газы, если они используются, и топливо для сварочных аппаратов с приводом от двигателя.
Маркеры совмещения. Перед выполнением сварных швов маркеры соосности иногда используется.Это может быть не что иное, как следы керна, нанесенные на стыке в разных местах.
Последовательности сварки. Последовательность сварки должна быть подробно описана в процедура сварки и может включать блочную сварку, последовательную сварку с обратным шагом, блуждающая последовательность сварки и отслаивания.
Наконец, должно быть достаточное количество сварщиков. назначены для работы, чтобы ее можно было выполнить быстро.
Безопасность. Наконец, во время сварки нельзя упускать из виду безопасность операция. Например, при использовании топливных газов для предварительный нагрев и т. д.
Качество сварки. Качество сварного шва необходимо постоянно проверять. Окончательный сварной шов должен быть ровным, без зазубрин и арматуры, если она используется, должен плавно переходить в существующую структуру. При необходимости следует произвести шлифовку для поддержания плавных, плавных контуров.
Операция после сварки
После того, как сварка будет завершена, ему нужно дать медленно остыть. Так не должно быть подвергаться воздействию ветра или сквозняков, а также нельзя подвергать отремонтированный части, пока температура не вернется к нормальной температуре окружающей среды.Осмотр. Готовый сварной шов следует проверить на гладкость и качественный. Это может включать неразрушающий контроль, такой как магнитопорошковый, ультразвуковой, или рентген.Ремонтный шов должен быть качественным, поскольку заменяет оригинальный металл. высокого качества.
Операция по очистке. Это включает удаление сильных спинок и плавное шлифование точек, где они крепились. Это также предполагает удаление других креплений и защитных кожухов и т. д. Кроме того, все сварные штыри, сварочные брызги, сварочный шлак и другие остатки должны быть удалены из зоны ремонта, чтобы она стала чище чем было изначально.Шлифовальная пыль доставляет особые хлопоты и прилагает все усилия необходимо удалить его полностью, так как он абразивный и может начать работать шарниры, подшипники и т. д. и создают проблемы в будущем.
Перекраска. После очистки сварного шва и прилегающей зоны ремонта его следует перекрасить, а другие участки следует повторно смазать в рамках подготовки к повторная эксплуатация техники.
Повторная сборка. После чистки, покраски и т. Д., части оборудования что были отобраны, возвращаются. Это включает в себя повторную сборку оборудования.
Восстановление и наложение
Восстановление и наплавка наплавленным металлом или наплавленным металлом считаются наплавкой. операции. Наплавка — это нанесение присадочного металла на основной металл для получения желаемого размеры или свойства. Накладкой считается наплавленный металл или наплавленный металл, который имеет специфические свойства, иногда отличающиеся от свойств исходной поверхности.Восстановление используется для восстановления исходных размеров и свойств деталей, такие как восстановление изношенных валов, ремонт деталей, которые были обработаны меньшего размера, Наплавка используется для возврата детали к исходным размерам, но со сварным швом. металл, обладающий особыми свойствами по уменьшению износа, эрозии, коррозии и т. д.
Восстановление и наложение, или всеобъемлющий термин, покрытие, могут быть выполнены многими из сварочные процессы и процессы термического напыления.Выбор процесс основан на тех же факторах, которые используются при выборе процесса сварки для изготовление или ремонт.
В некоторых ситуациях следует выбирать процессы термического напыления. В процессы термического напыления не вносят столько тепла в работу, сколько сварка процессы. Если это важное требование, следует использовать метод термического напыления. используемый. Возможно термическое напыление некоторых материалов, на которые нельзя наносить сварочные процессы.Это особенно относится к керамическим напыленным покрытиям или другие неметаллические материалы.
Выбор процесса сварки
Выбор процесса сварки, а также процедуры и техники сварки: Важен также выбор наплавленного сплава. Практически все процессы дуговой сварки и некоторые другие могут использоваться для нанесения наплавленного наплавленного металла.Процесс дуговой сварки металлическим экраном , вероятно, является наиболее часто используемым из любой из сварочных процессов для наплавки.Его можно использовать в поле и в shop и может применяться к мелким и крупным деталям в любом положении.
Сварка под флюсом также используется во многих областях, но имеет ограничения. сварке в горизонтальном положении. Чаще всего он используется для работы завода, а не используется в поле. Часто используется для повторяющихся приложений, когда одна и та же часть всплывает на регулярной основе.
Порошковая сварка с защитным газом и без него — популярный полуавтомат. сварочный процесс.Его можно использовать в поле или в магазине и не ограничивается плоское положение.
Процесс газовой сварки вольфрамовым электродом используется во многих небольших сферах, обычно для работы в магазине, когда деталь можно принести в магазин и манипулировать и переехал для удобства сварки. Газовая вольфрамовая дуга может использоваться вручную или в автоматическом режиме. режим с автоматами подачи проволоки, осцилляторами и т. д. Он дороже других процессов и по этой причине ограничивается более техническим типом работ.
Плазменная сварка также используется во многом так же, как газовая вольфрамовая дуга. Это имеет более высокую температуру и по этой причине может использоваться в определенных случаях, когда Газовая вольфрамовая дуговая сварка не применяется. Он снова ограничивается меньшими виды работ.
Электрошлаковая сварка также используется в некоторых особых случаях. Он широко используется для восстановления молотков дробилок. Их можно перестроить с помощью специальное крепление и выполняется довольно быстро с помощью электрошлакового процесса.
Кислородно-ацетиленовая сварка также используется для определенных применений. Широко используется для нанесения специализированных кобальтовых сплавов на относительно тонкие кромки.
Как правило, процесс выбирается на основе обычных факторов выбора процесса и изменен некоторыми из приведенных выше комментариев. После того, как процесс выбран, следующий требованием является подбор наплавленного металла для обеспечения необходимого свойства.
.Поверхностные дефекты, ухудшающие качество сварки | Качество и проблемы сварки | Основы автоматизированной сварки
В принципе, сварочные процессы должны соединять материалы в соответствии с чертежами на основе соответствующей конструкции сварки. Кроме того, важно обеспечить качество сварки, в том числе внешний вид и прочность сварного шва. На этой странице представлены типичные дефекты поверхности, ухудшающие качество сварки.
Обязательно к прочтению всем, кто занимается сваркой! Это руководство включает в себя базовые знания о сварке, такие как типы и механизмы сварки, а также подробные знания, касающиеся автоматизации сварки и устранения неисправностей.Скачать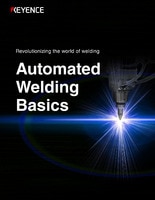
Ямки (открытые дефекты) — это поверхностные дефекты, образующиеся при затвердевании газовых полостей внутри металла сварного шва после выхода газа с поверхности валика. Газовые полости, оставшиеся внутри валика, являются внутренним дефектом, известным как газовые раковины. Причины этих дефектов включают использование неподходящего защитного газа; недостаточный раскислитель; масло, ржавчина, галька или другие вещества, приставшие к поверхности канавки в основном материале; и влага, содержащаяся в материале.
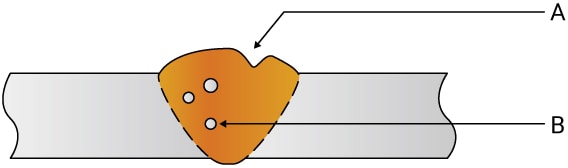
Поднутрение — это канавка на носке сварного шва, образованная основным материалом на выходе из сварного шва. Типичные причины — слишком высокий сварочный ток или скорость сварки. Слишком большая ширина плетения также может быть причиной подрезов.
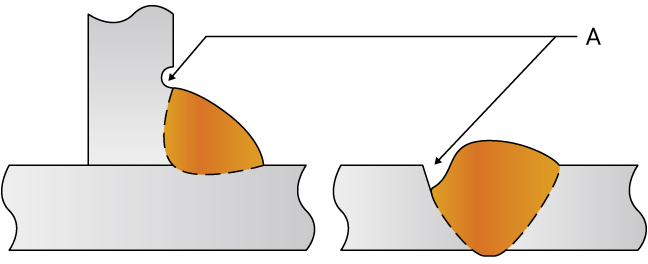
Перекрытие происходит, когда расплавленный металл течет по поверхности основного материала, а затем охлаждается без сплавления с основным материалом. Типичной причиной перекрытия является подача слишком большого количества сварочного металла из-за низкой скорости сварки. Перекрытие угловых сварных швов вызывается опусканием излишка расплавленного металла под действием силы тяжести.Необходимая контрмера — пересмотреть условия сварки (например, установить более высокую скорость сварки или более низкий сварочный ток).
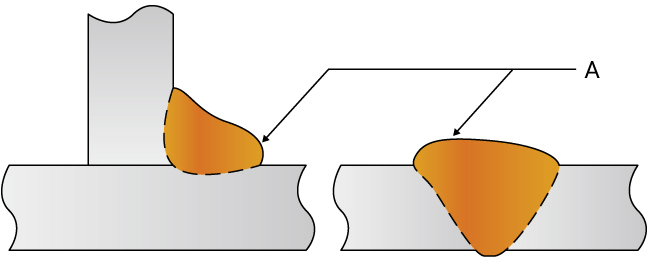
Армирование — металл сварного шва, нарастающий над поверхностью сверх требуемого размера в канавке или угловом шве. Типичной причиной является высокая скорость сварки (скорость движения источника тепла), из-за которой наплавление металла шва в канавке оказывается недостаточным.
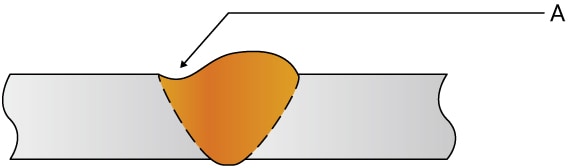
- Недостаточное армирование
Поверхностное растрескивание приводит к образованию трещин на поверхности горячих сварных швов сразу после сварки.Он широко делится на крекинг при затвердевании и крекинг при разжижении. Растрескивание при затвердевании происходит при затвердевании сварного шва. Растрескивание в результате разжижения возникает при многослойной сварке, когда предыдущий сварочный слой плавится при последующей сварке. Другая классификация относится к сформированному положению и форме трещины, например, к продольному растрескиванию, растрескиванию пальцев ног, поперечному растрескиванию, растрескиванию кратера и так далее.
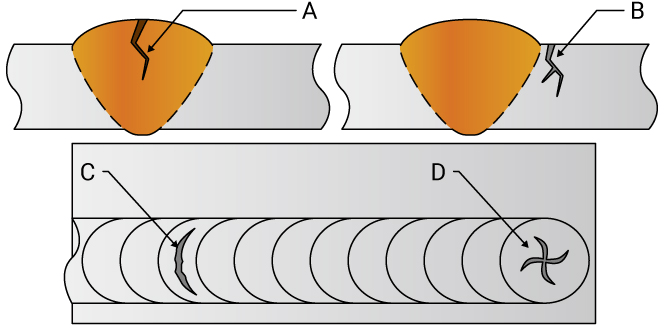
- Продольное растрескивание
- Растрескивание пальцев ног
- Поперечное растрескивание
- Кратер трещины
Это дефект, вызванный мгновенным зажиганием дуги на основном материале.Другими словами, зажигание дуги — это место неудачного зажигания дуги, которое не оплавилось при последующей сварке и осталось на основном материале. Удар дуги может стать причиной растрескивания основного материала.
Подобный дефект может возникнуть, когда крупные частицы брызг прилипают и остаются на поверхности.
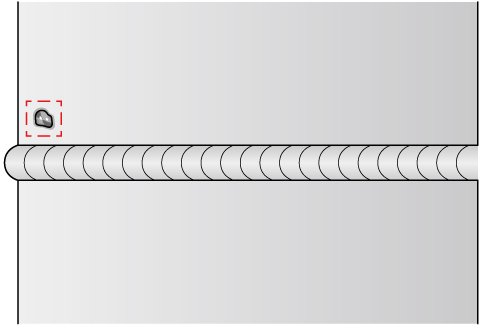
Этот дефект возникает, когда валик изгибается и отклоняется от линии сварки. Возможные причины включают в себя волну или изгиб автоматически подаваемой сварочной проволоки, которая не исправляется должным образом, или направления линии сварки и изгиба проволоки под прямым углом друг к другу.Этот дефект также может возникать, когда настройки скорости подачи проволоки и сварочного тока не совпадают.

Это состояние, когда части канавки не свариваются и остаются открытыми, потому что процесс не может образовать бортик, продолжающийся от начальной точки до конечной точки канавки. Когда этот дефект обнаруживается при роботизированной сварке около начальной или конечной точки, это может быть проблемой в управлении роботом. Если подача дуги, газа или проволоки нестабильна, канавка также может оставаться открытой в середине валика.
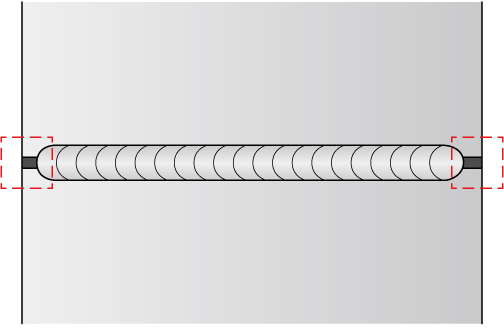
Дом
.Основные меры безопасности и меры предосторожности
Безопасность судов в море зависит от знаний, навыков и самостоятельности экипажа при выполнении работ по техническому обслуживанию и ремонту во время рейса и между постановкой в сухой док. Для их владельцев суда также зависят от здорового и компетентного экипажа, чтобы свести к минимуму производственные травмы, непредвиденные расходы и время нахождения судна вне дома.
Техническое обслуживание во время полета является неотъемлемой частью работы члена экипажа, а такие задачи, как сварка на борту, являются обычным делом.Даже в этом случае важно, чтобы бригада, выполняющая сварочные работы на борту, выполняла это в соответствии со строгими принципами безопасности. Последствия несоблюдения правил техники безопасности или обслуживания оборудования могут быть очень серьезными. Для экипажа существует риск получения травм и долгосрочной опасности для здоровья.
Для судна риски для безопасности и целостности оборудования столь же серьезны, и в конечном итоге, если судно будет повреждено или перенаправлено из-за проблем со здоровьем или оборудованием, последствия могут быть также финансовыми.Крайне важно, чтобы со сварочным оборудованием и газами обращались безопасно и надежно — безопасность при эксплуатации всегда должна быть приоритетом. Вот правила техники безопасности и меры предосторожности, которые экипаж должен соблюдать до и во время электродуговой сварки на борту.
переменного тока
Переменный ток (AC) всегда будет доступен на борту судна от электросети, но экипаж должен принять во внимание оборудование, которое им предлагается использовать, и принять соответствующие решения.
Доступны два типа сварочных аппаратов; трансформатор, который принимает переменный ток и подает переменный ток, но с более низким напряжением, и выпрямительные / инверторные машины, которые преобразуют переменный ток в постоянный ток (DC) на выходе при более низком напряжении.
Мы советуем экипажу избегать использования переменного тока при сварке на борту судна. Это связано с тем, что в случае случайного поражения электрическим током через тело человека передается переменный ток, что может вызвать судороги, которые могут привести к остановке сердца. Напротив, постоянный ток будет течь по поверхности сварщика, если он случайно окажется частью электрической цепи.
Напряжение и частота
Основная цель всех сварочных аппаратов — снизить высокое напряжение до подходящего безопасного рабочего напряжения.Рабочее напряжение сварочного аппарата называется напряжением холостого хода (OCV) или иногда называется напряжением без нагрузки. Определение OCV — это напряжение между выводами сварочного аппарата, который включен, но не используется.
В Кодексе правил безопасной работы для моряков торговых судов Управления морского судоходства и береговой охраны Соединенного Королевства указано, что максимальное напряжение должно быть следующим:
Для выпрямителей и инверторов постоянного тока: макс. 70 В постоянного тока
Для трансформаторов переменного тока макс. 25 В переменного тока
Поэтому первое, что должен проверить любой член экипажа перед началом работы, это соответствие сварочного аппарата на борту этим значениям.На большинстве сварочных аппаратов это указано на табличке оборудования.
WSS также рекомендует избегать использования сварочных аппаратов, которые используют высокие частоты (HF) для запуска процесса вольфрамового инертного газа (TIG). ВЧ могут создавать помехи для оборудования радиосвязи, а также могут мешать управлению пуском / остановом оборудования с электронным управлением, такого как насосы. Доступны низковольтные системы запуска TIG, использующие процесс «подъемной дуги», и поэтому нет необходимости использовать ВЧ для запуска процесса сварки.
Соответствие
В пределах Европейского Союза и на судах, плавающих под флагами стран-членов ЕС, экипаж также должен проверить, соответствует ли машина знаку соответствия европейскому (CE). Это форма «паспорта», которая позволяет товарам беспрепятственно въезжать в Европу и по всей Европе, а также гарантирует соответствие машины директивам и стандартам ЕС по электричеству.
Стандарты, которым должно соответствовать сварочное оборудование в странах-членах ЕС, следующие:
EN 60974-10 Европейские нормы электромагнитной совместимости.
EN 60974-1 / 5 Европейские нормы для аппаратов для дуговой сварки: источники тока для сварки.
Операторы также должны искать знак «S», указывающий на то, что оборудование подходит для использования в зонах с повышенной опасностью поражения электрическим током. Это особенно важно при работе в потенциально влажных, влажных и тесных местах, таких как двойное дно или балластные цистерны.
Обратный кабель
Еще одна область, требующая определенности, — это использование таких терминов, как «земля» и «земля».Обратный кабель сварочного аппарата часто называют землей или землей, но это не так.
Термины «земля» и «заземление» используются в электротехнике США для обозначения электрического оборудования, которое надежно соединено с землей по соображениям безопасности. В Великобритании эквивалентными терминами являются «земля» и «заземление».
Обратный кабель аппарата дуговой сварки пропускает столько же тока, сколько и сам сварочный кабель. Сварочный и обратный кабели являются частью электрической цепи.В результате для безопасной сварки бригадир должен использовать возвратный зажим и кабель, которые должны быть размещены как можно ближе к месту сварки.
Размещение возвратного зажима к ближайшей арматуре с лампой накаливания приведет к тому, что корпус корабля окажется в этой зоне, что создаст риск поражения электрическим током. Фактически сварщик будет стоять на обратном пути, возможно, в некачественной обуви, в грязных перчатках, во влажных условиях, возможно в соленой воде (отличный проводник электричества).
Если он лежит на животе или на спине в вспотевшем комбинезоне, он подвергает большие части тела живой палубе.Если сварочный кабель плохо изолирован, то использование корпуса в качестве обратного кабеля также может вызвать короткое замыкание, создавая искры и опасность взрыва. Этот вид операции в сочетании с использованием трансформатора, подающего переменный ток с высоким OCV, может быть фатальным для сварщика.
Также следует помнить, что подключение обратного кабеля непосредственно к корпусу судна может также вызвать прохождение тока через шарикоподшипники и поршни, что приведет к повреждению. При сварке оборудования двигателя бригадир всегда должен протягивать обратный кабель и зажим к месту сварки и закреплять его как можно ближе к зоне сварки.
Безопасная сварка
Во избежание поражения электрическим током и риска поражения электрическим током, а также для обеспечения безопасной работы судовой персонал должен принимать следующие меры предосторожности:
- Используйте только источники питания постоянного тока с OCV ниже 70 вольт;
- Поместите возвратный зажим и кабель как можно ближе к месту сварки;
- Помните, что через обратный кабель проходит столько же тока, сколько через сварочный кабель;
- Использование корпуса в качестве возвратного кондуктора противоречит правилам государства флага;
- Носите сухую изолированную защитную одежду и перчатки в хорошем состоянии, меняя их по мере необходимости, чтобы они оставались сухими;
- Изолируйте себя от обрабатываемой детали и обратного кабеля, надев обувь на резиновой подошве или встаньте на сухой изолированный коврик.Не прикасайтесь к возвратной плате другими частями тела;
- Используйте полностью изолированные держатели электродов;
- Не используйте изношенные, поврежденные кабели, кабели недостаточного размера или плохо сращенные;
- Не обматывайте тело проводом с током;
- Не прикасайтесь к электроду под напряжением голыми руками;
- Выключайте все оборудование, когда оно не используется;
- Используйте только исправное оборудование. Отремонтируйте или замените поврежденные детали перед дальнейшим использованием;
- Следует избегать влажных условий труда.Даже потоотделение может снизить сопротивляемость организма поражению электрическим током.
Эти моменты могут показаться очевидными, но, по нашему опыту, часто бывают случаи, когда бригада работает небезопасно. Результаты могут быть серьезными — и наиболее серьезными для задействованной команды.
Пример использования 1
Судовой слесарь настраивал свое сварочное оборудование, и, когда он устанавливал хлыст на питатель, одна рука коснулась металлического сопла хлыста, а другая рука касалась проволоки из питателя.Это замкнуло электрическую цепь, которая позволила электричеству 80 вольт пройти через его грудь. Сотрудник получил ожоги рук и был доставлен в больницу для лечения.
Пример использования 2
Судовой слесарь прибыл на борт корабля в начале смены и обнаружил на палубе воду после ночного ливня. Он знал об опасности поражения электрическим током, поэтому стоял на комингсе вокруг дверного проема, прежде чем потянуться за сварочным аппаратом. К сожалению, его ботинки и рабочие перчатки были уже мокрыми.Когда сотрудник прикоснулся к сварочному аппарату, он замкнул цепь, и через него прошел ток, получив травмы, которые потребовали лечения в больнице.
Пример использования 3
Член экипажа вернулся на палубу корабля после ливня. Он торопился перевезти сварочный аппарат и закончить работу до обеда. Слесарь знал, что нельзя стоять в воде при работе с электрооборудованием, но он не заметил, что тонкая фанера, на которой он стоял, погрузилась в воду в тот момент, когда он наступил на нее.Его одежда и ботинки были уже мокрыми от бури. Когда он коснулся оборудования, цепь замкнулась, и по его телу прошел ток. Его тоже пришлось доставить в больницу на лечение.
Посетите наш каталог сварочной продукции
.Sz-hcs04 Машина для ремонта наплавки и сварки Машина для ремонта депозита
Применения оборудования:
1. Литейное производство
Продукты для литья автозапчастей: автомобильный карданный вал, поршень, цилиндр, выхлопная труба, тормозной диск и другое литье ремонт дефектов, таких как трахома, устьица и так далее.
Машиностроение и станкостроение: для изменения допуска или износа заготовки, например, направляющих для ремонтных станков, станины, вала больших машин, деталей зубьев, холодной прокатки, горячего валка, гидравлического стержня инженерного оборудования, сварки различных запасных частей части.
Авиационная и судостроительная промышленность: кожух компрессора, кожух воздушного компрессора, прецизионные детали из нержавеющей стали, прецизионные валы и т. Д.
2. Производство меди, алюминия, магния, цинка и других цветных металлов
Различные отрасли производства деталей из цветных металлов, такие как энергетический трансформатор из алюминиевого сплава SF6, цилиндр из алюминиевого сплава для автомобильной промышленности, головка цилиндра, колеса, вентилятор крыльчатка из алюминиевого сплава, алюминиевый радиатор.
Сантехнические клапаны из медного сплава, трубопроводная арматура, рабочие колеса, турбины, изделия из меди и т. Д.
3. Формовочная промышленность
Литейная форма: износ формы, неровности, шрамы и другие сварочные работы
Форма для литья под давлением: износ формы, неровности, шрамы и другие сварочные работы для устранения продукта вспышки
Форма для литья под давлением: эрозия формы для литья под давлением цинк-алюминия, выпадение, повреждение и т. д., а также полость и устье рта для укрепления формы для продления срока службы.
Применимые сварочные материалы:
Благодаря уникальному режиму управления SZ-HCS04 выходная энергия высокая, а управление точное, поэтому сварочный материал очень подходит.В дополнение к профессиональным сварочным материалам для электроэрозионных станков, другим сварочным аппаратам, используемым в большинстве случаев для сварки прямых стержней диаметром 0,2-1,0 мм, можно также использовать обычный сварочный электрод для durg.
Преимущество:
1. Передовые технологии
2. Эффективная энергия
3. Высокая сварочная прочность
4.Медь, алюминий, магний, цинк Отличный сварочный эффект
5. Матрица без отжига и деформации
6. Высокая точность ремонта
7. Станок универсальный
8. Защита окружающей среды: Отсутствие загрязнения при работе
9 Удобство использования: любой может использовать, нет необходимости работать с картой, трудно сваривать место также может быть наплавка
10. Экономия: немедленный ремонт на месте, повышение эффективности производства и экономия средств
.