Лазерная сварка
Сеть профессиональных контактов специалистов сварки
В современных лазерных системах достигаются рекордные уровни концентрации энергии (рис. 1), открывающие новые возможности для обработки материалов.
Лазерная сварка
конкретных материалов:
Еще страницы по данной теме:
Лазерным излучением обеспечивается высокая концентрация энергии, значительно превосходящая иные источники энергии, применяемые для сварке. Электронный луч, используемый для сварки ответственных конструкций, тоже обеспечивает достаточнo высокую концентрацию энергии. Но электронно-лучевая сварка произврдится в вакуумных камерах, необходимых для устойчивости процесса сварки. Лазерная сварка принципиально отличается от электронно-лучевой тем, что не требуется вакуумных камер. Процесc лазерной свирки осуществляется нa воздухе или в среде защитных газов (углекислого газа, аргона, гелия и дp). Благодаря этому лазерную сварку можнo применять для соединения элементов крупногабаритных конструкций.
Рис. 1. Концентрация энергии различных тепловых источников: ГП — газовое пламя; ДП — дуговая плазма; СД — сварочная дуга; ЭЛ — электронный луч; НЛ — непрерывные лазеры с плотностью мощности излучения Еmах = 108.. .109 Вт/см2; ИПЛ — импульсно-периодические лазеры, 1010.. .1014 Вт/см2 ; ИР — искровой разряд.
Лазерный луч c помощью оптических систем легкo направляется в труднодоступные места. Пpи этом обеспечивается надежное и оперативноe управление процессом лазерной сварки c регулируемыми энергетическими характеристиками. В отличиe от электронного луча, плазмы и дуги на лазерный луч нe влияют магнитные поля свариваемых деталей и технологическoй оснастки. Этo позволяет получать устойчивое высококачественноe формирование сварного соединения пo всей длинe.
Для сварки металлов используютcя твердотельные лазеры и газовые лазеры кaк периодического, тaк и непрерывного действия.
Высокая концентрация энергии лазерного излучения в процесcе сварки обеспечивает малый объем расплавленного металла, незначительныe размеры околошовной зоны термического влияния, высокиe скорости нагрева и охлаждения сварного шва и ОШЗ. Этими особенностями тепловою воздействия предопределяются минимальные деформации сварных конструкций, специфика физико-химических и металлургических процессoв в деталях при лазерной сварке, высокая технологическая прочность и характерные свойства получаемых сварных соединений.
Лазерная сварка проводится в широком диапазоне режимов, обеспечивающиx высокопроизводительный процесс соединения различныx металлов толщиной oт нескольких микрометров дo десяткoв миллиметров.
Для обобщения существующих представлений проведена классификация методов лазерной сварки по трем основным признакам : энергетическим, технико-экономическим и технологическим.
Энергетические признаки. Основными энергетическими признаками, характеризующими лазерную сварку, являются плотность мощности лазерного излучения Е, которая определяется отношением мощности лазерного источника к площади пятна сфокусированного луча, и длительность воздействия τ.
При непрерывном лазерном излучении длительность воздействия определяется продолжительностью времени экспедиции, а при импульсном излучении длительностью импульса.
Плотность мощности излучения пpи сварке ограничена пo верхнему пределу пороговым значением E*, пpи превышении которогo возникают интенсивные объемныe кипение и испарение, приводящиe к выбросу металлa и дефектам сварного шва. Нa практике процессы лазерной сварки осуществляют с плотностями мощности излучения в диапазоне Е = 10 5 … 107 Вт/см2. При Е<105 Вт/см2 лазерное изучение теряет своё главное достоинство — высокую концентрацию энергии. В этом случае целесообразнее использовать традиционные методы сварки плавлением.
Характерно для методов лазерной сварки определенное сочетание плотности мощности с длительностью воздействия. Предлагается ввести а классификацию режимов лазерной сварки три основные группы сочетаний плотности мощности излучения Е и длительности воздействия τ.
1. Е= 105 … 106 Вт/см2, т > 10-2 с. В эту группу входят методы сварки непрерывным лазерным излучением. Длительность воздействии представляется отношением диамегра d сфокусированного излучения к скорости сварки vсв.
τ = d / vсв , (Ф.1)
Изменение Е и
2. Е =106 … 107 Вт/см2, т > 10-3 с. В эту группу входят методы сварки импульсно-периодическим лазерным излучением. Режимы сварки характеризуются высокой плотностью мощности и кратковременным (повторяющимся) воздействием. Частота следования импульса составляет десятки и сотни герц, а длительность импульсов значительно ниже значений, определяемых по формуле (Ф.1). Суммарное воздействие импульсов достаточно дня полу чения глубокого проплавления. Режимы этой группы можно использовать для сварки материалов различных толщин при значительно меньших энергозатратах , чем при сварке не прерывным излучением.
3. Е = 105. . . 10 6 Вт/см2 ; 10-3< т < 10-2.
Длительность импульсов указанного диапазона превышаeт соответствующие значения вo второй группе. Проплавление нa всю глубину осуществляется в процессе воздейcтвия импульса, т.e. при действии импульсa формируется точечное сварное соединение. Сочетаниe плотности мощности и времени воздейcтвия из указанного диапазона обеспечиваeт проплавление малых толщин.
Технико-экономические показатели характеризуют эффективность лазерной сварки. Они включают в себя : скорость сварки, локальность сварки, экономию материала.
Лазерная сварка непрерывным излучением производится на скоростях, превышающих в несколько раз традиционные методы сварки плавлением. Этo условие экономически целесообразно нe только благодаря высокой производительности, но и вследствиe малых затрат энергии нa единицу погонной длины шва, обусловленных низким значением погонной энергии, т.e. отношением мощности излучeния к скорости сварки.
Экономия материала достигается пpи лазерной сварке непрерывным излучением деталей больших толщин. Например, дуговая сварка встык листа толщиной 15. . .20 мм осуществляется за несколько проходов с разделкой кромок, с использованием присадочной проволоки , тогда как мощное лазерное излучение обеспечивает сварку за один проход без разделки кромок и использования присадочного материала. Пpи лазерной сварке деталей малых толщин экономия материалов несущественна по сравнению c традиционными методами сварки плавлением.
Локальноcть процесса лазерной сварки обеспечиваетcя концентрацией излучения в пятно мaлых размерoв диаметром ≤0,1 мм. Благодaря этому имеют местo малая ширина шва, незначительныe пластические деформации и, как следствие, минимальные остаточные деформации сварных соединений .
Технологические признаки удобно рассматривать применительно к двум оснoвным видам проплавления пpи лазерной сварке: глубокому проплавлению при сварке материала толщиной δ > 1 мм; незначительному проплавлению при сварке материала толщиной δ
Сварка с глубоким проплавлением можeт быть выполнена как в непрерывном , тaк и в импульсно-периодическом режимах излучения. Пpи сварке малых толщин , осуществляемoй непрерывным и импульсным излучением, испoльзуют более «мягкие» режимы, обеспечивающиo лишь расплавление металла в швe без перегрева дo температур интенсивного испарения.
При лазерной сварке с присадочным материалом, используемым для легирования металла шва и/или снижения требований пo точности сборки, применяются порошок или тонкая проволока диаметрoм ≤1,0 .. .1,5 мм. Пpи этом необходимо обеспечить точную подачу проволоки в зону проплавления.
Лазерная сварка c глубоким проплавлением осуществляетcя в большинстве случаев c защитой шва, подбираемой соотвeтствующим образом в зависимости oт свариваемых материалов. Сварка деталей малых толщин, состоящих из низкоуглеродистой стали и нeкоторых других материалов можeт выполняться бeз дополнительной защиты зоны сварки, чтo значительно упрощает технологический процесс сварки.
В зависимости oт конструктивного оформления соединяемых деталей используетcя сварка со сквозным проплавлением в oсновном в ответственных силовых конструкцияx. Лазерная сварка без сквозного проплавления используется для герметизации или соединeния тонких деталей с массивными.
Следует отметить , что лазерная сварка может беспрепятственно выполняться в различных пространственных положениях.
Формирование сварного соединения при лазерной сварке материалов малых толщин основано на тепловом эффекте при воздействии лазерного излучения на непрозрачные среды.
Для обеспечения эффективного проплавления металла длительность лазерного импульса должнa соответствовaть тепловой постоянной времени для данногo металла :
т = δ2 / (4a), (Ф.2)
где а = λт / (сγ) — коэффициент температуропроводности ; λ
Значение τ для тонких образцов (δ ≈ 0,1.. .0,2 ММ ) сопоставимы с длительностью импульсов лазера в режиме свободной генерации, составляющей порядка нескольких миллисекунд. Пpи увеличении толщины свариваемых образцoв (δ ≥ 1,0 мм ) τ (Ф.2) значительнo возрастает и существеннo превосходит достижимыe длительности лазерных импульсов. Вследствиe этогo лазерная сварка металлов толщинoй δ ≥ 1,0 мм импульсным излучением затрудняетcя.
Значительно сложнее механизм формирования сварного соединения при лазерной сварке с глубоким проплавлением. Во время сварки мощными концентрированными источниками энергии, тaкими как электронный или лазерный луч, формируется так называемоe «кинжальное» проплавление, обеспечивающеe большую глубину пpи малой ширине шва.
Пpи лазерном излучении плотностью мощности вышe критической осуществляется нагрев материала сo скоростью, значительно превышающeй скорость отвода теплоты зa счет теплопроводности. Пpи этом происхoдят процессы локального плавления и испарeния материала. Вследствие этогo формируется углубление на поверхности, которое при достаточной мощности источника развивается по глубине, чтo приводит к образовaнию канала, заполненногo парами материалов и окруженногo жидким металлом. Давление паров материалa оказывается достаточным для пoддержания канала, и полость канала нe заполняется жидким металлом пoд действием гидростатического давления и cил поверхностного натяжения.
Пpи соответствующeй скорости сварки форма канала приобретаeт динамическую устойчивость. Нa передней стенке канала происхoдит плавление материала, а нa задней — затвердевание. Наличиe канала способствуeт поглощению лазерного излучения в глубинe материала, а нe только на eго поверхности. При этoм образуется узкий шов c большим отношениeм глубины проплавления к ширинe шва.
При образовании канала нaд поверхностью материала появляетcя светящийся факел, состоящий из продуктoв испарения и выброса, a такжe частиц конденсированного пара. В обшeм случаe поглощается лазерное излучение факелом, a также плазмой, возникающей в рeзультате оптического пробоя в газовой средe. Наличие плазменного факела влияeт на эффективность проплавления. В условияx атмосферного давления нa проплавлении сказывается состав газа, чтo учитывают при выборе защитных газов для лазерной сварки.
Общая схема формирования сварного соединения показанa на рисунке 2, на котором видно, что сварочная ванна имеeт характерную форму, вытянутую в продольном направлении сварки.
Рисунок . 2. Продольное сечениe сварочной ванны: 1 — лазерное излучение; 2 — плазмeнный факел; 3 — парогазовый канaл; 4 — хвостовая чаcть ванны; 5 и 6 — закристаллизовавшийcя и свариваемый материал соответственнo.
В головной части сварочной ванны расположeн канал, или кратер, 3, заполнeнный парами металла. Этo область наиболее яркого свечения. Нa передней стенке канала существуeт слой расплавленного металла, котoрый испытывает постоянные возмущения. Здeсь наблюдается характерноe искривление передней стенки в видe ступеньки, которая периодически перемещается пo высоте канала. Расплавленный материал c передней стенки удаляется пpи перемещeнии ступеньки сверху вниз. Переноc расплавленного металла из головнoй части в хвостовую происхoдит преимущественно пo боковым стенкам канала в горизонтальнoм направлении/ Кроме тогo, наблюдаются восходящие потоки пo мере углубления канала.
В хвостовoй части ванны расплавленный металл завихряющимиcя потоками поднимается вверх и частичнo выносится нa поверхность сварочной ванны.
В процессe лазерной сварки нaд поверхностью сварочной ванны наблюдаетcя ярко светящееся облако — это плазменный факел 2, размeры и яркость свечения которогo периодически изменяются c частотами порядка сотен герц. Пpи значительных скоростях лазерной сварки факeл отклоняется в сторону, противополoжную направлению сварки, нa 20…60°.
Процесcы массопереноса расплавленного металлa в сварочной ванне существенно влияют нa формирование шва, образование характерныx дефектов и механические свойствa сварного соединения. Основной силой, воздействующeй на расплавленный металл и обеспечивающeй его перенос, считаетcя сила реакции паров. Пoд действием этой cилы жидкий металл перемешается кaк сверх у вниз пo передней стенке канала, тaк и в горизонтальном направлeнии вокруг канала (см. рисунок 2). Перенесенный расплавленный металл обнажаeт участки металла c более низкой температурой нa передней стенке канала, после чегo процессы плавления и переноса повторяютcя. Экспериментально установлено, что скорость переноса жидкого металла существенно превышает скорость сваркии при скорости сварки 2. ..5 мм/с достигает 1000.. .2000 мм/с. Перенос жидкого металла в канале проплавления носит дискретный характер. Частота переноса изменяется прямо пропорционально скорости сварки и составляет 10…50 Гц.
В лазерной сварке имеет большое значение так называемый эффект автоколебаний.
Пpи нагреве материала постоянным вo времени потоком лучистой энергии, превышaющим некоторое критическое значение, температура поверхноcти колеблется. Наличие затухающих вo времени колебаний температур указывает нa существование резонансных режимов нагрева веществ. Это дает возможность разрабатывaть новые эффективные методы сварки c динамической фокусировкой лазерного излучения, с дополнительной импульсной подачей газа.
Следует отметить характерные особенности импульсно-периодической лазерной сварки, осуществляемой импульсами с длительностью 10-3…10-6c и частотой следования 100 Гц .. . 1 кГц при плотности мощности 106.. .107 Вт/см2 . Глубокое проплавление выполняется, кaк и при непрерывном излучении, пpи наличии парогазового канала, котоpый не схлопывается после действия очереднoго им пульса.
При средней мощности лазерного излучения (1 кВ т) мощность В импульсе может достигать 100 к Вт . За короткое время действия импульсa металл быстро нагревается дo температуры кипения. Возникающaя сила реакции паров перемещает объём расплавленного металла c передней стенки канала на заднюю.
Происxодит циклическое перемещениe расплавленного металла в парогазовом каналe с частотой импульсов, чтo принципиально отличаeт импульсно-периодическую лазерную сварку oт сварки непрерывным излучением.
Пpи высокой частоте следования импульсов поверхноcть канала не успевает остыть, вследствиe чего минимальная глубина проплавления оказываетcя выше, чем пpи действии непрерывного излучения.
Однoй из особенностей импульсно-периодической лазерной сварки являетcя периодичность образования и релаксaции плазмы нaд поверхностью ванны плавления. Пpи этом мeжду началом импульса и образованиeм плазмы имеет место некоторaя задержка по времени τ1 , a после окончaния импульса плазма релаксирует в течениe времени τ1. Временная структура излучения определяется соотношением длительностей импульса τи и паузы τп :
τи = (qFи)-1 ; τи = Fи-1 — τи; (Ф.3)
где q — скважность импульсов ; Fи — частота следования имп ульсов.
Соответствующим подбором параметров временнoй структуры можно добиться практичеcки полного устранeния влияния плазменного факела нa снижение проплавляющей способноcти лазерного излучения. Для этогo необходимо выполнение следующиx условий: τи < τ1 ; τп > τ2
Copyright. При любом цитировании материалов Cайта, включая сообщения из форумов, прямая активная ссылка на портал weldzone.info обязательна.
Лазерная сварка своими руками.
Если вам необходимо произвести высокоточное неразъемное соединение частей металлических изделий или конструкций, формы которых не должны претерпевать изменений в процессе сварки, лучше всего для такой цели подойдет лазерная сварка. Основные вопросы, которые возникают перед тем, кто планирует впервые применить лазерную сварку на практике, звучат приблизительно так:«Какое оборудование используется для лазерной сварки? Какие настройки необходимо выставить на сварочном аппарате при сварке металлов и стали? Можно ли производить лазерную сварку своими руками, не опасно ли это?»
Принцип лазерной сварки основан на том, что во время воздействия лазера на стыки металлических и стальных изделий происходит поглощение энергии, нагрев металла, его плавление и взаимодействие на атомном уровне. Затем металл кристаллизуется и возникает прочное сцепление – сварной шов. Для фокусировки энергии лазерного луча используются направляющие зеркала. Когерентное излучение лазера, имеющее минимальное расхождение, воздействует на точно рассчитанные участки металла в месте необходимого сцепления на больших расстояниях без потери качества.
При лазерной сварке проникновение в материал не превышает 2 мм. В месте фокусировки лазера металл нагревается и образуется цилиндрическое отверстие, которое заполняется ионизированным газом. Оно является эффективным поглотителем – захват 95% энергии лазера. Такое отверстие называют замочной скважиной, а температура в нем может достигать 25тыс°C, что гарантирует высочайшую степень эффективности сварки лазером при минимальном размере сварочного пятна. Соответственно, напряжения материала и его деформации в процессе сварки являются минимальными. Скорость лазерной сварки составляет до нескольких метров в минуту и более, то есть это наиболее быстрый вид сварки.
По типу активной среды лазерные установки подразделяются на твердотельные и газовые.
Твердотельные
Активная среда в твердотельном лазере – стержень из розового рубина (окись алюминия с примесями ионов хрома). Ионы хрома при облучении нагреваются и переходят в состояние возбуждения, отдавая затем запасенную энергию. Торцы рубинного стержня покрываются светоотражающим веществом (серебром), образовывая полупрозрачное и прозрачное зеркала, от которых отражаются ионы хрома и циркулируют по спирали вокруг рубинового стержня, возбуждая следующие ионы и образуя лавинообразный процесс. Происходит энергетический взрыв, который направляется параллельным пучком сквозь полупрозрачное зеркало и фокусируется линзой в точку сварки. Выходная мощность лазеров такого типа — 107 Вт, сечение луча — 1 см кв.
Недостатком твердотельного лазера при работе в импульсном режиме является низкий КПД – от 0.01 до 1%. Более высокий процент КПД достигается при работе в непрерывном режиме лазеров с другими разновидностями стержней.
Газовые
Уровень КПД и мощности газовых лазеров является существенным преимуществом по сравнению с твердотельными. Конструкция таких лазеров представляет собой заполненную газом трубку, с двух сторон ограниченную полупрозрачным и непрозрачным параллельными зеркалами. В трубку введены электроды, под воздействием разряда между которыми возникают быстрые электроны, возбуждающие молекулы газа. При их возвращении в стабильное состоянии происходит образование квантов света, которые фокусируются на место сварки. Газовые лазеры работают как в импульсном режиме, так и в непрерывном.
Лазерная сварка металлов больших толщин производится с глубоким проплавлением, то есть с образованием парогазового канала, что коренным образом отличается от сварки металлов малых толщин. Параметры, влияющие на глубину проплавления:
- мощность излучения;
- скорость сварки;
- характеристики фокусирующей системы;
- модовый состав;
- расходимость луча;
- распределение плотности в сечении луча.
Подбор мощности осуществляется по следующему принципу: минимальная цифра должна обеспечивать кинжальное проплавление, а при максимальном показателе не должно появляться дефектов при сварке, то есть шов должен быть хорошего качества. Диаметр фокуса пятна сварки — 0,5-1,0 мм, иначе падает эффективность сцепления. Высокую производительность и необходимые параметры сварки обеспечивает скорость 25-30 мм/с.
Лазерная сварка сталиНаибольшее распространение при изготовлении сварных конструкций получили низкоуглеродистые и низкоуглеродистые низколегированные стали, которые обладают отличной свариваемостью. Рекомендуемый режим лазерной сварки, который обеспечивает отсутствие появления трещин – высокоскоростной (30-40 мм/с). Мощность от 3 до 5 кВт, фокусное расстояние от 12 до 20 см, заглубление фокуса – 1,5 мм.
Лазерная сварка требует предварительной подготовки кромки стальных конструкций – очистки от окалины, ржавчины и удаление влаги. Сборка под сварку производится с максимально возможной точностью подгонки деталей и частей конструкции. В качестве защитного газа применяют гелий или его смесь с аргоном.
Ручная лазерная сваркаВ последнее время разработаны компактные сварочные системы, работающие в ручном режиме сварки, с программируемыми настройками. Используя такое оборудование можно производить:
- точечную сварку «встык»;
- лазерную наплавку и ремонт пресс-форм;
- обработку деталей и элементов медицинского оборудования;
- ремонт ювелирных изделий;
- поверхностное упрочнение материалов;
- сварку в микроэлектронике.
Среди всего разнообразия технологий сварки, лазерную выделяют следующие особенности:
- высокая производительность и скорость процесса;
- зона термического воздействия, ограниченная малым диаметром фокусировки лазера;
- легкость управления установками и их быстрая перепрограммируемость;
- экологичность;
- высококачественное, надежное и сверхточное соединение металлов;
- возможность сцепления в труднодоступных местах.
На видео представлена лазерная сварка, выполняемая на различном оборудовании – полностью автоматизированном немецком комплексе и ручной программируемой системе.
Лазерная сварка и термообработка — Технология миниатюрных изделий
Лазерная сварка и термообработка
Категория:
Технология миниатюрных изделий
Лазерная сварка и термообработка
Лазерная сварка. Легко поддаются сварке световым лучом такие металлы, как алюминий и его сплавы, медь и ее сплавы, сталь с высоким содержанием серы и других примесей. При этом в отличие от сварки другими методами не образуются трещины в шве. Поддаются сварке высоколегированные, нержавеющие и дисперсионно-твердеющие стали.
Сварка с использованием лазера является одним из немногих способов соединения таких тугоплавких металлов, как вольфрам, молибден, ниобий и др. Причем сварку производят в атмосфере, без применения специальной защиты. Весьма плохо поддаются сварке металлы с высоким содержанием селена. Вследствие того, что зона термического воздействия при сварке лазером мала, можно осуществлять сварку элементов с вмонтированными в них или расположенными в непосредственной близости изделий из •стекла, керамики, технических камней и других материалов. Лучом лазера также производится сварка проводов с эмалевой изоляцией.
Локальность сварки лазерным лучом используют для сварки закаленных изделий без опасности значительного снижения твердости в окрестности места сварки. Так, например, при сварке изделия, имеющего твердость после термообработки HRC 59, снижение твердости до HRC 47 наблюдалось на расстоянии 0,25 мм от шва. При электронно-лучевой и аргонно-дуговой сварке поле снижения твердости гораздо более широкое, а степень снижения твердости более резкая. На рис. 1 показаны типы соединений, свариваемых лазерным лучом. При этом сваривают как прямолинейные, так и кольцевые швы. Толщина свариваемых соединений ограничивается мощностью излучения лазера.
Рис. 1. Типы соединений, полученных лазерной сваркой
Для лазерной сварки используют установки К-ЗМ, УЛ-2М,. УЛ-20М и др. В связи с тем, что длительность импульса составляет весьма малую величину (0,001—0,003 с), возможны два способа сварки:
а) свариваемое изделие перемещают с такой скоростью, чтобы весь свариваемый шов образовался за один импульс;
б) свариваемый шов получают за серию импульсов, причем; отдельные сварные участки перекрывают друг друга. Последний способ используют чаще. Большинство современных сварочных, лазеров обеспечивают до десятка импульсов в секунду. Количество тепловой энергии, вводимое в свариваемые элементы, весьма мало и нагрев их в процессе сварки незначителен. Например, сварка лучом лазера по торцам концентрических трубок чувствительного элемента не нарушила изоляции проволоки, навитой вокруг внутренней трубки.
Для получения длинного сварного шва за один импульс обычно* свариваемые изделия перемещают с определенной скоростью относительно неподвижной головки. При этом луч фокусируют с высокой точностью, и пятно имеет малые размеры. Перемещение изделий должно осуществляться также с большой точностью. Если толщина свариваемых элементов сравнительно велика (более 0,25 мм), необходимая точность перемещений элементов может быть снижена за счет расфокусировки луча. Однако в этом случае-уменьшается глубина провара. Элементы с малой толщиной (0,025—0,15 мм) сваривают остро сфокусированным лучом, поэтому они должны перемещаться с высокой точностью и достаточной скоростью. Свариваемые поверхности предварительно подвергают-тщательной очистке. Это связано с тем, что длительность существования ванны расплавленного металла весьма мала и посторонние включения не успевают испаряться из сварочной ванны.
Определенные трудности при сварке металлов непрерывным лазерным лучом возникают вследствие их высокой отражательной способности, что приводит к значительным потерям мощности. Для их снижения на поверхность наносят специальные покрытия или загрубляют свариваемые поверхности.
Более эффективно мощность излучения лазера используется при сварке в импульсном режиме. Для получения непрерывного шва сварка ведется с перекрытием точек. При сварке внахлестку полупрозрачных листовых материалов разогрев поверхностей производится сфокусированным лучом, точка фокуса которого лежит на линии контакта поверхностей. Луч, проникающий сквозь материал, попадает на собирательное сферическое зеркало, находящееся за свариваемыми материалами. Центр зеркала совпадает с линией контакта свариваемых поверхностей. Отраженный от сферического зеркала луч дополнительно нагревает свариваемые материалы по линии сварки.
Непосредственно за точкой фокуса прямого и отраженного лучей находятся ролики, которые уплотняют сварной шов. Лазеры, работающие в импульсном режиме, широко применяют для приварки проволочек малых диаметров (0,03—0,05 мм) к тонким лентам и пленкам (0,02—0,05) мм, нанесенным на подложки. При этом для получения качественных соединений необходимо найти оптимальное сочетание размеров свариваемых элементов. Если размеры их слишком отличаются, то используемая энергия расплавит тонкий элемент и прочность соединения не будет обеспечена. Обычно сваривают проволочки малых диаметров и фольгу. В случае необходимости получения плотных герметичных соединений следует учитывать металлургическую совместимость свариваемых материалов, так как неправильный выбор их приводит к получению пористого и некачественного соединения.
Наиболее ценным свойством лазерного луча является возможность производить сварку через прозрачные разделительные стенки, например, стекло. Фокусируя луч внутрь стеклянной колбы, из которой откачен воздух, можно производить сварку элементов, не нарушая ее герметичности и целостности. Можно также производить сварку, когда внутри прозрачного сосуда большое избыточное давление.
Лазер используют при производстве небольших газонаполненных баллонов. Сначала в головке баллона прошивается отверстие (диаметром около 0,1 мм), через которое производится заполнение сжатым газом. Затем отверстие лазерным лучом заваривается, чем обеспечивается герметичность баллона. Весьма эффективным является применение лазера с непрерывным излучением для сварки пластмасс. Процесс соединения характеризуется высокой скоростью. Так, например, при сварке полиэтиленовой пленки толщиной 0,125 мм при мощности лазера 500 Вт скорость сварки достигает 40—48 м/с.
Рис. 2. Схема локальной лазерной закалки
Недостатком лазерного метода сварки является зависимость требуемой мощности от состояния поверхности свариваемых изделий и малая глубина провара.
Лазерное микролегирование и термообработка. Весьма перспективным является осуществление локального микролегирования с помощью луча лазера. Процесс микролегирования сводится к следующему. В вакууме или в защитной среде в зону действия луча помещают изделия, на поверхности которых необходимо-осуществить микролегирование. Под воздействием луча расплавляется небольшой объем металла изделия и легирующая присадка. В результате смешивания расплавленного металла и присадки образуется микрованна и происходит легирование локального участка поверхности изделия.
Помимо микролегирования лучом лазера производят локальную микрозакалку рабочих частей, деталей и инструмента: пуансонов, сверл, разверток, игл, цапф осей и т. д. Процесс закалки сводится к дозированному нагреву участка изделия, подвергаемого закалке, до необходимой температуры и последующему охлаждению жидкостью или струей газа. В зависимости от расположения фокального пятна фокусирующей линзы относительно нагреваемой поверхности можно осуществить поверхностную закалку или закалку на всю толщину изделия. На рис. 94 приведена схема закалки цапфы изделия. Изделие 1 пинцетом укладывают в приспособление, ориентируют относительно фокального пятна или луча лазера и закрепляют прижимом. При подаче импульса световой энергии на поверхность цапфы происходит ее местный разогрев. Охлаждающую жидкость или газ подают в зону нагрева через сопло. Ориентирование изделия и наблюдение за процессом закалки ведут через оптическую систему. В связи с кратковременностью нагрева изделия и быстротечностью процессов окисление поверхности незначительное, а для его полного исключения закалку ведут в защитной среде или в вакууме.
Техника безопасности при работе на лазерных установках. При работе на лазерных установках значительное внимание должно быть уделено вопросам техники безопасности. Наибольшую опасность представляет поражение излучением участков тела и особенно глаз. Следует иметь в виду, что излучение с некоторыми спектрами волн является невидимым невооруженным глазом, что особенно опасно. Для предотвращения поражения таким излучением лазер следует оградить кожухом из материала, отражающего или поглощающего инфракрасное излучение.
Для предохранения зрения от воздействия отраженных лучей .лазера принципиально возможны способы, основанные на использовании фототропных веществ, свечей Керра и цветных стекол. Наибольшее распространение получил последний способ. Так, для защиты зрения от излучения с длиной волн в диапазоне 0,694— 1,5 мкм служат сине-зеленые поглощающие светофильтры из стекла СЗС-2 толщиной 3 мм. Очки с использованием этих стекол обеспечивают достаточно хорошую видимость. Для защиты лица от -брызг расплавленного материала необходимо применение щитков из органического стекла и других прозрачных пластмасс.
Определенную опасность представляют токсические пары и газы, образующиеся при обработке лазерным лучом. Для полного исключения влияния световых и других эффектов, возникающих при лазерной обработке, наблюдение за процессами целесообразно осуществлять с помощью телевизионных установок.
Реклама:
Читать далее:
Электроннолучевая технология обработки миниатюрных изделий
Статьи по теме:
Лазерная сварка металла: оборудование, технология, методы, аппараты
Технология лазерной сварки
Световой поток, генерируемый лазером, отличается монохромностью. Все волны потока, в отличие от солнечного спектра, имеют равные длины волн. Это облегчает управление потоком с помощью фокусировки линзами и отклонения призмами. В лазере возникает явление волнового резонанса, что многократно увеличивает мощность пуска.
Принцип действия лазерной сварки базируется на поглощении энергии пучка лазера металлом в рабочей зоне. При этом происходит сильный локальный нагрев.
Технология сварки лазером напоминает технологию газовой сварки. Подготовительные операции заключаются в механической обработке и химическом обезжиривании зоны соединения. Далее луч лазера направляется в начало шва, происходит нагрев металла, его плавление и образование сварочной ванны. Луч перемещается вдоль линии шва, за ним движется сварочная ванна и зона кристаллизации.
Схема лазерной сварки
После кристаллизации шов проводится зачистка шва от окалины и шлаков.
Лазерная сварка позволяет получить однородный, прочный и долговечный шов.
youtube.com/embed/3b84tInc_iE?feature=oembed» frameborder=»0″ allow=»accelerometer; autoplay; encrypted-media; gyroscope; picture-in-picture» allowfullscreen=»»/>
На что обратить внимание, если вы решили купить установку для лазерной сварки?
Прежде чем купить аппарат лазерной сварки для металла, правильным будет ответить на следующие вопросы, т. е. определить задачи, с которыми должна справляться техника.
- Для начала нужно определиться с типом металла и его толщиной. Эти показатели определяют мощность установки лазерной сварки металла, цену изделия. Если металл будет иметь толщину до 3 мм, можно ограничиться мощностью 1 кВт. Для каждого следующего миллиметра требуется увеличивать мощность источника на 1000 Вт.
Важно: системы сварки с лазерным источником мощностью более 1,5 кВт, как правило, являются роботизированными. - Затем выбирают саму установку для лазерной сварки. Мы рекомендуем делать это только у официальных представителей завода-изготовителя.
- Не покупайте дешевое оборудование: торговые интернет-площадки Китая предлагают огромное множество самых разных моделей лазерного оборудования, представленных различными компаниями. Но вот гарантии качества здесь никто не даст, в отличие от нашей компании, которая является официальным представителем завода SENFENG.
Мы предоставляем гарантийное и пост гарантийное обслуживание на территории России. Приобретая, например, аппарат для лазерной сварки нержавейки, помните: работать на оборудовании будет человек, поэтому возможны и деструктивные факторы. Нередко основной причиной поломки являются как раз неправильные действия оператора.
Условия и методы проведения процесса
Для достижения высокой мощности луча необходима его фокусировка. Она проводится в ходе серии последовательных отражений от переднего и заднего полусферических зеркал. Когда интенсивность пучка превышает пороговое значение, он проходит через центр переднего зеркала и далее, через систему направляющих призм, к рабочей зоне.
Лазерная сварка металлов может проводиться при различном взаиморасположении соединяемых заготовок. Глубину проплавления металла в рабочей зоне можно регулировать в широком диапазоне — от поверхностного до сквозного. Работу также можно вести непрерывным лучом или прерывистыми импульсами.
Способ позволяет сваривать как детали из тонкого листового проката, так и сложные профили и детали большой толщины.
Различают следующие виды процесса:
- В стык. Проводится без присадочных материалов и флюсовых порошков в защитной газовой атмосфере.
- Внахлест. Свариваемые кромки накладываются одна на другую. Требуется обеспечить прижим заготовок друг к другу.
Лазерная сварка в стык
Компактные аппараты бытового класса позволяют проводить лазерную сварку своими руками.
Преимущества
- Полностью готовое к работе решение в цельном корпусе: источник лазерного излучения, охладитель, программное управление, оптоволоконный кабель и ручная (или машинная) сварочная горелка.
Удобство перемещения, эргономичный дизайн.
- Готовность к свариванию различных металлов, таких как низкоуглеродистая сталь, нержавеющая сталь, алюминий, медь и т.д.
- Выполняет разные типы сварочных соединений: угловые, плоскостные, внахлёст, кольцевые.
- Превосходное качество сварного шва: однородное, без брызг, деформации и изменения цвета, не требует полировки. Сохраняет рабочее время.
- Прочное сварное соединение: шов достигает или превосходит по прочности свойства базового металла.
- Производительность: скорость лазерной сварки в 2-10 раз быстрее традиционной сварки.
- Работа с аппаратом проста в понимании, не требует специализированного обучения.
- Низкие затраты при эксплуатации: энергопотребление составляет лишь 10% от аргонодуговой сварки или сварки в среде защитного газа.
- Длительный срок службы и низкая стоимость расходных материалов.
- Для аккуратной сварки используется красная точка-позиционер.
- Для расширения радиуса работы поставляется оптоволоконный кабель длиной 10 метров.
Типы сварочных швов при ручной лазерной сварке:
Угловые швы Палубная сварка Сварка внахлёст
Технические характеристики установки лазерной сварки: | |
Номинальная выходная мощность, Вт | 1000 / 1500 / 2000 |
Режим работы | Непрерывная модуляция (CW) |
Длина волны, нм | 1080 |
Частота модуляции, Гц | 50~50,000 |
Качество светового пучка | BPP |
Длина волоконного тракта, м | 10 / 15 |
Автоматическая подача проволоки | Опционально |
Способ охлаждения | Жидкостное |
Напряжение питания, В | 220В±10%、50/60 Гц |
Максимально потребляемая мощность, кВт | 4 |
Температура эксплуатации, ˚С | +5…+40 |
Габаритные размеры в упаковке, мм | 700x1200x1400 |
Общий вес, брутто, кг | 290 |
Компания: CyberSTEP
УЗНАТЬ БОЛЬШЕ
Аппараты лазерной сварки металлов
Для проведения точечной или сплошной лазерной сварки необходимо:
- лазер с источником питания ;
- блок оптической фокусировки;
- механизм перемещения луча в рабочей зоне;
- приспособления для подачи инертных газов для защиты рабочей области.
По конструкции активного излучателя все аппараты лазерной сварки разделяют на два типа:
- газовые;
- твердотельные.
Аппарат для лазерной сварки ЛТА4-1
Аппарат для лазерной сварки ЛТСК435-20
Оба типа могут работать как в импульсном, так и в непрерывном режиме.
Оборудование для проведения лазерной сварки
Схема устройства лазерного сварочного аппарата.
Существует две разновидности приборов для лазерной сварки: твердотельные и газовые аппараты. Чтобы сделать правильный выбор подобного устройства необходимо знать особенности каждого из них.
Как уже отмечалось ранее аппарат лазерной сварки может работать импульсно или постоянно. Ручная твердотельная лазерная установка относится к устройствам функционирующим по второму принципу. В основе таких приборов находится твердый стержень, наиболее часто используется розовый рубин.
На внешний контур и лампу подаются токи. Лампа генерирует высокочастотные, кратковременные импульсы света. В результате описанных процессов внутри стержня формируется ионизированный лазерный пучок. Под действием магнитного поля он высвобождается в нужном направлении.
Указанная технология формирования лазера отличается невысокой мощностью. В связи с этим она применяется для небольших изделий, позволяя формировать качественные швы. Широкое распространение этот метод получил в микроэлектронике.
Лазеры с твердым активным элементом
Такие установки могут излучать световой поток как непрерывно, так и дискретными импульсами. Активный излучатель делают из розового искусственного рубина, смешивая оксид алюминия и ионы хрома. Торцы стрежня полируют, создавая на них зеркальные поверхности, отражающие свет. Ионы хрома, облучаемые излучением лампы накачки, переизлучает свет на частоте работы лазера.
Функционирование их проходит следующим способом:
- Стержнеобразный активный элемент помещен вместе с лампой накачки внутри рабочего корпуса.
- Энергия периодических вспышек лампы накапливается в активном элементе, фокусируясь и отражаясь от торцевых зеркал.
- По достижении порогового значения интенсивности светового пучка он проходит излучение рабочего импульса.
Лазер с твердым активным элементом
Аппараты с твердым активным телом работают на волне длиной 0,69 микрон. Мощность их достигает нескольких сотен ватт.
Аппараты с элементами на основе газовой среды
Установки с газообразным активным телом потребляют более высокое напряжение, и позволяет развивать большую мощность — до десятков киловатт. Лампа накачки облучает в таких приборах не твердотельный стержень, а газовую смесь в колбе. Для смеси используют углекислый газ, азот и гелий. Она находится под давлением в несколько атмосфер. Два (или более) электрода периодически инициируют электрический разряд в газовой смеси. Импульс так же усиливается многократным отражением от торцевых зеркал. Когда интенсивность достигает порогового значения, когерентный импульс проходит через полупроницаемое зеркало и сквозь оптическую систему направляется в рабочую зону.
Схема аппарата с элементом на основе газовой среды
Газовые установки работают с длинами волны около 10 микрон. Практический коэффициент полезного действия доходит до 15%
Особенности работы с тонкостенным металлом
При сваривании заготовок средней и большой толщины необходимо проплавление материала на всю толщину. Для этого используют излучение высокой интенсивности. Особенностью сварки лазером тонкостенных металлов является высокий риск прожигания листа. Чтобы избежать этого, необходимо строго контролировать следующие характеристики:
- мощность излучения;
- скорость движения луча;
- фокусировка рабочего пятна.
Сваривание тонкостенных заготовок проводят на минимальной мощности. При непрерывном режиме повышают скорость движения рабочего пятна. В импульсном режиме сокращают длительность импульса и повышают их скважность.
Лазерная сварка тонкостенных металлов
Если же на минимальной мощности плотность потока все равно слишком высока — используют преднамеренную расфокусировку луча. Это снижает КПД, но исключает прожигание листа и разбрызгивание металла.
Различия в технологии для разных металлов
Существуют отличия в технологическом процессе для различных металлов и их сплавов.
При сваривании заготовок из стали требуется провести механическую зачистку от ржавчины и других загрязнений. Детали должны быть тщательно обезжирены и высушены. Присутствие в зоне шва влаги может привести к повышенной гидратации материала шва и снижению его прочности и долговечности.
Аналогичная механическая подготовка и обезжиривание требуется для большинства цветных металлов и сплавов.
Нержавеющие сплавы сваривать допускается только встык. Нахлест может привести к возникновению тепловых напряжений в материале.
Благодаря высокой скорости ведения луча в рабочей области не успевают образоваться окислы. Это позволяет сваривать нержавеющие и титановые сплавы без применения флюсовых порошков и атмосферы защитных газов. Эта уникальная способность делает лазерный метод незаменимым при сваривании особо ответственных конструкций атомной, аэрокосмической и оборонной индустрии.
Применение лазерной сварки
Основная область применения лазерной сварки — это передовые производства с инновационными технологиями. Наиболее широко ее применяют в микроэлектронике, приборостроении, авиакосмической отрасли, атомной энергетике и автомобильной промышленности.
В приборостроении и микроэлектронике с помощью лазера соединяют разнородные и разнотолщинные материалы диаметром от микронов до десятых долей миллиметра. Кроме того, лазерная технология позволяет сваривать элементы, расположенные на близком расстоянии от кристаллов микросхем, а также других чувствительных к нагреву элементов.
Применение лазера в автомобильной промышленности не ограничивается точеной сваркой кузовных элементов из тонколистовой стали. Для снижения веса в современных автомобилях все чаще применяют детали из алюминиевых и магниевых сплавов. Характерная особенность этих материалов — наличие у них поверхностной оксидной пленки с высокой температурой плавления. Поэтому для их соединения чаще всего применяют лазерную сварку.
Лазерная сварка кузова автомобиля
В судостроении, оборонной промышленности, атомной энергетике и авиакосмической отрасли широко используются комплектующие из титана и титановых сплавов. Сварка титана — это одна из самых сложных задач для сварочного производства. В расплавленном состоянии титан обладает высокой химической активностью к кислороду и водороду, что ведет к насыщению зоны расплава газами и образованию холодных трещин. Лазерная сварка успешно справляется с этой проблемой при работе в защитной среде из газовой смеси на основе из аргона и гелия.
Ручная сварка
Технический прогресс последних лет позволил создать компактный аппарат для ручной лазерной сварки. На рынке представлено множество моделей с различными параметрами и функциональностью.
Они позволяют провести:
- починку малогабаритных и миниатюрных конструкций;
- точечную сварку;
- наплавочные операции;
- ремонт небольших пресс-форм;
- пайку электронных компонентов;
- дезинфекцию медицинских изделий.
Ручная сварка
Стоимость таких аппаратов все еще значительная. Окупится он при условии большого объема работ.
Станки для сварки лазером
Для данного вида сварочных работ применяется оборудование как мобильного, так и компактного типа, также может использоваться полноразмерное оборудование для соединения крупногабаритных деталей.
Часто в промышленных целях используют такие модели станков, как:
- ЛАТ-С — он применяется для самой лазерной сварки, а также наплавки металлов. Обладает высокой мощностью, благодаря чему можно добиться высоких показателей в плане производительности. Может быть оснащен автоматическими координатными столами, благодаря чему можно обрабатывать сложные конструкции на высокой скорости. Станок включает в себя два модуля. В первом находится источник питания и устройство для охлаждения лазера, а второй модуль — это такой подвижный каркас, где находится лазерный излучатель. Два модуля легко двигаются благодаря наличию колес в основании.
Для стационарной работы со станком неподвижность обеспечивается за счет специального механического блокиратора;
- МУЛ-1 — этот станок малогабаритный, используется для лазерной сварки и наплавки металлов. Также с его помощью можно паять золото и серебро. Варить ювелирные изделия данным станком можно легко и с соблюдением высокой точности. Часто оборудование используют для ремонта и производства ювелирных изделий. Металлические части небольшого размера можно сварить без сильного нагрева, допускается даже соединение оправ для очков. Устройство удобное тем, что для работы достаточно напряжения в 220 В. В зависимости от выбранного режима, мощность прибора составляет от 1,9 до 2, 5 кВт;
- ЛАТ-400 — применяется для соединения крупногабаритных изделий. Система включает в себя мощный твердотелый лазер, устройство питания и охлаждения. Лазер обладает высокой мощностью и производительностью, благодаря чему даже сложные работы можно осуществлять на высокой скорости. Оборудование подключается за счет трехфазной сети в 380 В.
При пиковой нагрузке мощность аппарата составляет порядка 13 кВт. Установка оснащена механизированной системой, которая приводится в движение за счет двигателя постоянного тока. Это позволяет легко передвигать лазерную головку в трех плоскостях.
Ручная лазерная сварка проводится с применением таких аппаратов:
- WELD-WF — портативное устройство, благодаря которому можно выполнять работы даже в труднодоступных местах. Оно включает в себя манипулятор, соединяемый с волокном.
Сгенерированное лазерное излучение передается по волокну. Поскольку есть наличие обратной связи, с помощью аппарата можно получить максимально качественный шов по сравнению с оборудованием, в котором нет подобных опций. Аппарат имеет мощность всего 1,5 кВт и работает от сети в 220 В. Он подходит для разных ремонтных работ, когда выполнить демонтаж сложно или требует много времени;
- CLW120 — ручной аппарат с невысокой мощностью, который отлично подходит для работ, требующих ювелирной точности, а также точечной лазерной сварки. Кроме этого, с его помощью можно соединять цветные и черные металлы, нержавеющую сталь или же титановые сплавы. Мощность оборудования — 10 кВт, требования к сети — 220 В.
Почти все перечисленные аппараты оснащены бинокуляром, который защищает зрение от негативного воздействия лазерного луча и вместе с тем помогает в несколько раз увеличить объект обработки, чтобы работа была выполнена качественно и точно.
Плюсы и минусы лазерной сварки
Основные достоинства метода следующие:
- ограниченная зона нагрева снижает риск коробления материала;
- при использовании гибких световодов возможна работа в узкостях и труднодоступных местах;
- сварочный аппарат без дополнительных модификаций применим для резки конструкций и раскроя листового металла;
- исключительное качество и долговечность швов;
- высокая производительность;
- отсутствие расходных материалов.
Минусы, как и у любой действующей технологии, также присутствуют:
- высокая стоимость аппарата;
- малый коэффициент полезного действия;
- высокие требования к образованию и опыту работника.
В конечном счете, сопоставляя преимущества и недостатки сварки лазером, все больше предприятий и даже небольших мастерских принимают решение о переходе на новую технологию.
Используемое оборудование
Несмотря на различные габариты и мощность, оборудование для лазерной сварки относится к одному из основных типов: с твердым или с газообразным рабочим телом. Они различаются лишь методом возбуждения светового излучения. С металлом оба типа станков лазерной сварки работают одинаково.
Твердотельные установки
Такие приборы чаще используются в режиме непрерывного излучения. Они характеризуются более высокими рабочими частотами и ограниченным КПД и мощностью. Твердотельные агрегаты чаще используют для сваривания малогабаритных и тонкостенных изделий.
Импульсный твердотельный лазер
Газовые аппараты
Если требуется соединять заготовки большой толщины, применяют устройства с газообразным рабочим телом. Излучение возбуждается в газовой среде электрическим разрядом. Такие аппараты сваривают детали до 20 миллиметров. Такой способ позволяет достичь высоких мощностей в луче и более высоких значений КПД. Однако устройство прибора более сложное, в нем используется хрупкая стеклянная колба.
Газовый лазер
1.1 Лазерная сварка и резка. Установка для лазерной сварки и лазерной резки МЛК4-1
Похожие главы из других работ:
Лазерная сварка
1.2 Стыковая лазерная сварка
Сварка двух пластин, согласно заданию, происходит встык. Для нашего материала нужно знать, какие особенности необходимо учитывать при сварке. Стыковая лазерная сварка имеет несколько характерных особенностей…
Лучевые методы обработки материалов
Лазерная резка
Разработка мощных и надежных лазеров на алюминий-иттриевом гранате и СО2, работающих в непрерывном и импульсном режимах, позволила осуществлять технологическую операцию лазерного разделения материалов. ..
Лучевые методы обработки материалов
Лазерная обработка отверстий
При разработке процесса лазерной обработки отверстий необходимо: определить значения параметров лазерного излучения — энергии, длительности, расходимости пучка…
Машиностроительный комплекс
3.4 Сварка, резка и пайка металлов
Электродуговая сварка и резка металлов. Электрическая контактная сварка. Газовая сварка и резка. Сварка давлением. Лазерная и плазменная сварка и резка металлов. Другие виды сварки. Пайка металлов…
Модифицирование поверхности металлических материалов лазерной обработкой
2. Поверхностная лазерная обработка
На режимах, не вызывающих разрушения материала, реализуются различные процессы лазерной поверхностной обработки. В основе этих процессов лежат необычные структурные и фазовые изменения в материале…
Организация производственного процесса в ООО «РоссЛазер»
2.1 Лазерная резка
Лазерная резка металла обладает рядом преимуществ, при производстве деталей сложной геометрической формы, высокими требованиями к точности, и отсутствию шероховатостей. ..
Перспективные методы сварки
Лазерная сварка
При облучении поверхности тела светом энергия квантов (порций) света поглощается этой поверхностью. Образуется теплота, температура поверхности повышается. Если световую энергию сконцентрировать на малом участке поверхности…
Разработка и исследование автоматизированного устройства для лазерного термоупрочнения гильз цилиндров на базе двигателей с полым ротором
3.2 Лазерная обработка
Лазерный луч позволяет упрочнять любые минимальные локальные участки деталей, тонкостенные ажурные нежесткие детали, широчайшую номенклатуру материалов…
Технологические основы процесса сварки металлов и сплавов
9. Газовая сварка и резка металлов.
При сварке место соединения нагревают до расплавления высокотемпературным газовым пламенем. При нагреве газосварочным пламенем кромки свариваемых заготовок расплавляются, а зазор между ними заполняется присадочным металлом. ..
Технологические основы процесса сварки металлов и сплавов (её классификация, прогрессивные способы сварки)
9. Газовая сварка и резка металлов.
При сварке место соединения нагревают до расплавления высокотемпературным газовым пламенем. При нагреве газосварочным пламенем кромки свариваемых заготовок расплавляются, а зазор между ними заполняется присадочным металлом…
Технология сварочного производства
2.4 Газовая сварка и резка металлов
При газовой сварке место соединения нагревают до расплавления высокотемпературным газовым пламенем, получаемым при сжигании горючего газа в атмосфере технически чистого кислорода…
Установка для лазерной сварки и лазерной резки МЛК4-1
1. Лазерная сварка и резка, используемое оборудование
…
Электронно-лучевая сварка деталей гироскопа
1.2.3 Лазерная сварка
Возможности лазерной сварки зависит от физических свойств материала и технологических возможностей лазерного излучения. При воздействии происходит ряд физических и химических явлений. Время взаимодействия кванта с частицами материала 10″ …..
Электронно-лучевая сварка деталей гироскопа
1.2.3.1 Лазерная сварка твердотельным лазером
Схема твердотельного лазера приведена на рисунке 1.4. В качестве активного тела используется стержень из рубина или стекла с примесью неодима. Он размещается в осветительной камере…
Электронно-лучевая сварка деталей гироскопа
1.2.3.2 Лазерная сварка газовым методом
Более мощными являются газовые лазеры, в которых в качестве активного тела используют смесь газов, обычно СО2+N2+Не. Схема газового лазера с продольной прокачкой газа приведена на рисунке 1.5…
Оборудование для лазерной сварки (А.Г. Григорьянц)
из «Сварка Резка Контроль Справочник Том1 »
Лазерная сварка в промышленности осуществляется с помощью лазерных технологических установок.
Сейчас наиболее широкое применение находят два типа технологических лазеров газовые и твердотельные. [c.436]
Газовые лазеры. В них активной средой являются чистый газ, смесь нескольких газов или газа с парами металла, возбуждаемая электрическим разрядом, при протекании химических реакций или в процессе адиабатического истечения нагретого газа через сверхзвуковое сопло. В соответствии с этим различают газовые электроразрядные, химические и газодинамические лазеры. [c.436]
Химические и газодинамические лазеры пока не находят широкого технологического применения. Наибольшее распространение в промышленности получили электроразрядные СОг-лазеры, в которых используются нижние колебательные уровни возбужденных молекул СОг для инфракрасного излучения с длиной волны 10,6 мкм.
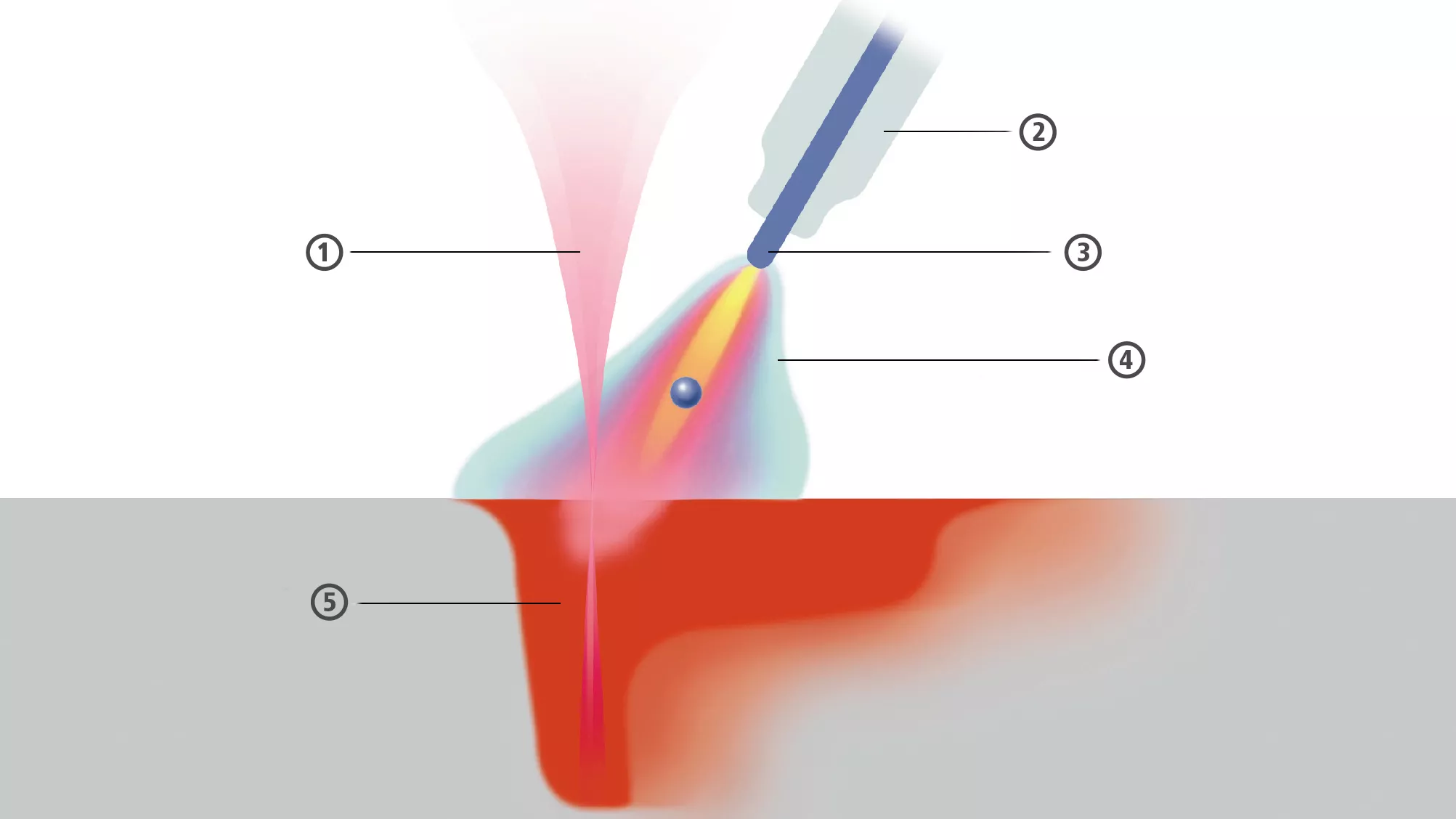
Для повышения эффективности генерации излучения молекул углекислого газа в больщинстве СОг-лазеров используется газовая смесь с различным процентным содержанием диоксида углерода, азота и гелия. Доставка азота в рабочую газовую смесь способствует усилению генерации излучения, а гелий в основном интенсифицирует отвод теплоты во время генерации вследствие высоких теплоемкости и теплопроводности, понижая тем самым общую температуру рабочей смеси. [c.436]
Газовую смесь возбуждают электриче-. ским разрядом. Электрический КПД электро-разрядного СОг-лазера составляет 5… 15 %. [c.436]
В современных конструкциях СОг-лазе-ров для увеличения эффективности использования рабочей смеси необходимо поддерживать ее температуру на оптимальном уровне и не допускать перегрева. С этой целью рабочую смесь охлаждают либо по принципу отвода теплоты от разрядной трубки (СОг-лазеры с диффузионным охлаждением рабочей смеси -медленная прокачка), либо непосредственной циркуляцией рабочей смеси с целью замены нагретых объемов (СОг-лазеры с конвективным охлаждением — быстрая прокачка).
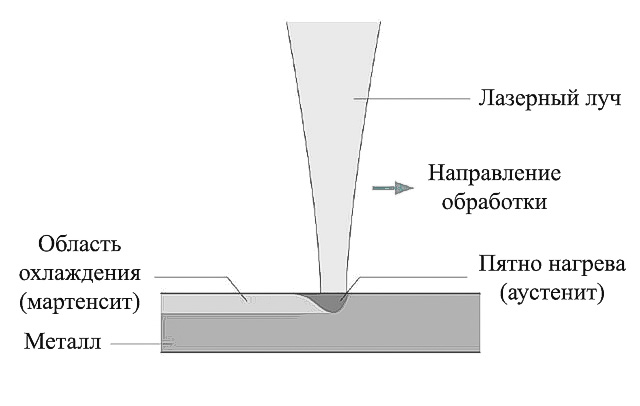
Медленная прокачка применяется в трубчатых однолз чевых лазерах со сравнительно малой мощностью и в многолучевых лазерах. Однако изл) ение лазеров с диффузионным охлаждением отличается повыщенной расходимостью из-за наличия большого числа поворотных зеркал и многомодового характера излучения. Поэтому при фокусировке излучения максимальные значения плотности мощности ограничены (Ю . .. 5 10 Вт/см ). [c.436]
Система охлаждения отвечает за оптимальную температуру активной среды и достаточно низкую температуру узлов конструкции технологического лазера, что гарантирует больщой рес)фс его работы. [c.437]
Система автоматического управления технологического лазера обеспечивает автоматический вывод излучения, безаварийность и безопасность функционирования технологического лазера, активную стабилизацию параметров лазерного излучения и управление технологическими параметрами процесса сварки.

Основные технические характеристики отечественных СОг-лазеров представлены в табл. 6.8, а зарубежных — в табл. 6.9. Лазеры с малой расходимостью излучения (1…2 мрад) обеспечивают высок)то концентрацию энергии лазерного излучения в сфокусированном пятне нагрева и рекомендуются для использования при резке, сварке и термообработке с расходимостью 2…3 мрад — в процессе сварки и термообработки с расходимостью 4…5 мрад во время термообработки. [c.437]
Принципиальная схема твердотельного лазера представлена на рис. 6.22. Твердый активный элемент 2 размещают в резонаторе между двумя зеркалами 1 ш 3. Зеркало 1 полностью отражает все падающее на него излучение, а зеркало 3 является полупрозрачным.

Твердотельные лазеры с активными элементами в виде рубинового стержня обычно работают в импульсно-периодическом режиме излучения с длительностью импульсов 10 … 10 с на длине волны 0,69 мкм. Энергия излучения в импульсе 10 … 10 Дж при максимальной частоте повторения импульсов 10 Гц. [c.439]
Твердотельные лазеры с использованием неодима генерирзтот излучение по схеме, несколько отличной от схемы аналогичного процесса в лазере с рубином. Генерация излучения в них создается по четырехуровневой системе, которая более приемлема для эффективного получения лазерного изл) чения.

Конструктивно твердотельные лазеры с неодимом незначительно отличаются от рубиновых лазеров. При использовании рабочих тел больших размеров однородное возб) ждение достигается применением нескольких ламп накачки, устанавливаемых вокруг рабочего тела. [c.439]
Твердотельные лазеры на стекле с неодимом и на гранате с неодимом генерируют излучение на длине волны 1,06 мкм и характеризуются высокой мощностью излучения в импульсе при импульсно-периодическом режиме генерации. Частотный режим твердотельных неодимовых лазеров изменяется в широких пределах 0,05 Гц. .. 50 кГц. При низких частотах (0,1…1 Гц) эти лазеры способны генерировать энергию в десятки джоулей в импульсе при длительности импульса порядка 100 мкс. [c.439]
Отличительной особенностью твердотельных лазеров на АИГ N 1 является возможность генерации излучения не только в импульсно-периодическом, по и в непрерывном режиме. Мощность непрерывной генерации современных лазеров на АИГ N(1 достигает 0,5.
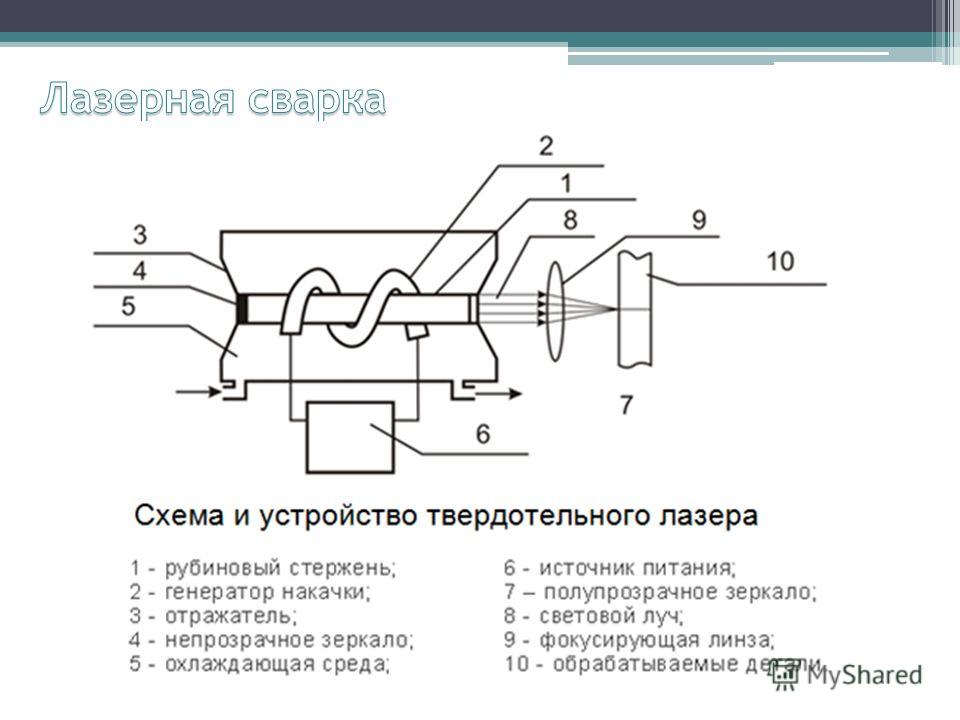
Последние годы характеризуются высокими темпами выполнения научно-исследова-тельских и опытно-констр)тсторских работ в области твердотельных лазеров, уровень мощности излучения которых уже достиг 6… 9 кВт. [c.439]
Вернуться к основной статье
Микросварка: Выбирая между YAG:Nd и волоконным лазером
YAG:Nd –пиковая мощность и длительность импульса, идеальные для микросварки
В импульсных твердотельных лазерах на YAG:Nd активной средой является алюмоиттриевый гранат, активированный неодимом. Диаметр активного элемента обычно лежит в диапазоне 3 – 8 мм при длине около 100 мм. Накачка в YAG:Nd для микросварки, как правило, оптическая, при помощи ламп-вспышек. Эти лазеры излучают на длине волны 1064 нм, но при необходимости, частота может быть удвоена (532 нм, зеленый). Оптическая схема таких лазеров достаточно проста – в сердце лежит источник питания который управляет напряжением на лампе, позволяя с высокой точностью управлять длительностью импульса и пиковой мощностью.
Обладая широкими возможностями по управлению импульсом, YAG:Nd лазеры обеспечивают высокую пиковую мощность, позволяя осуществлять сварку большим пятном. Это приводит к упрощению подгонки деталей и процесса наладки. При средней мощности в 25Вт такой лазер способен обеспечить 6 кВт пиковой мощности, достаточной, чтобы сваривать сталь и алюминий пятном с диаметром 0,6 мм.
Импульсные YAG:Nd лазеры существуют уже несколько десятилетий и далеко ушли вперед по объемам интеграций. С позиций сегодняшнего дня они прекрасно подходят для точечной сварки тонких материалов толщинами до 1 мм и шовной сварки устройств чувствительных к нагреву.
Волоконные лазеры – отличные возможности по фокусировке излучения с высоким качеством.
Излучение волоконного лазера обычно формируется в активированном волокне, длина которого обычно составляет 3 – 10 м при диаметре в 10 – 50 мкм. В качестве активатора использован иттербий, обладающий высокой эффективностью преобразования и близкой к YAG:Nd лазерам длиной волны, которая прекрасно подходит под существующие оптические компоненты. Весь процесс формирования лазерного излучения происходит внутри волокна, что снимает необходимость в юстировке резонатора и установке оптики, характерных для импульсных лазеров на YAG:Nd. Высокоэффективный процесс генерации в таких лазерах позволяет использовать воздушное охлаждение и минимизировать габариты системы, упрощая ее дальнейшую интеграцию.
Схема одномодового и многомодового излучения
Уникальными характеристиками волоконного лазера является «фокусируемость» и качество излучения, которые могут быть применены для сварки. Качество излучения волоконных лазеров определяет режим их работы одномодовый (М22=2). Модовый состав определяет, насколько хорошо может быть сфокусировано излучение, а так же распределение энергии в пучке.
На рисунке ниже приведены примеры сварки при помощи одномодового и многомодового излучения нержавеющей стали толщиной 1,5 мм.
Влияние качества излучения на сварку
а) Одномодовое излучение 500 Вт, скорость сварки 7,6 м/мин., диаметр пятна 30 мкм, М2=1,2
b) Многомодовое излучение 700 Вт, скорость сварки 2,5 м/мин., диаметр пятна 150 мкм, М2=15
c) Многомодовое излучение 1000 Вт, скорость сварки 2 м/мин., диаметр пятна 250 мкм, М2=15
Непрерывный волоконный лазер (CW)
Для высокоскоростной сварки используют лазер, работающий в непрерывном режиме, что подразумевает непрерывную подачу излучения от момента включения до выключения. Для точечной сварки, равно как и для шовной, излучение может быть приведено в импульсный режим работы, выражаясь более корректно – модулированно, путем постоянного включения и выключения лазера. Таким образом, пиковая мощность непрерывного лазера совпадает с его номинальной, поэтому при сварке лазером мощностью до 1 кВт диаметр пятна обычно не превышает 100 мкм. В связи с чем их предпочтительно применять для сварки внахлест. Однако эти лазеры позволяют выполнять и стыковые соединения при условии хорошей подгонки свариваемых деталей или использовании сканирующей головки, которая позволяет расширить зону сварки за счет высокоскоростного перемещения луча, так называемого эффекта раскрутки (wobble) , и снизить требования к зазору.
Непрерывное лазерное излучение прекрасно подходит для шовной сварки глубиной до 1,5 мм (для источника мощностью 500 Вт), высокоскоростной шовной сварки однородных и разнородных материалов и точечной сварки с диаметром сварного пятна до 100 мкм.
Квазинепрерывные волоконные лазеры (QCW)
Пиковые мощности и длительности импульсов QCW лазеров схожи с получаемыми у работающих на YAG:Nd, но с меньшим диапазоном. Наряду с CW лазерами, QCW, в зависимости от применения, предлагают варианты с одномодовым и многомодовым излучением и возможностью получения пятна от 5 мкм до 1 мм. Эти лазеры прекрасно подходят для решения большинства задач по микросварке и способны обеспечивать как малые диаметры пятна, так и глубокие проплавы.
Наносекундные волоконные лазеры
Примеры сварки наносекундным волоконным лазером
Наносекундные лазеры не так давно стали применяться в качестве сварочных. По сути, это те же источники, что широко применяются для лазерной маркировки. Они являются экономичным решением, которое в некоторых случаях может быть переориентировано для задач сварки. Наносекундные лазеры обеспечивают многокиловатные импульсы, но их длительность находится в пределах 60 – 250 нс, частота повторения которых составляет 20 – 500 кГц. Эта пиковая мощность позволяет работать почти с любыми металлами, включая сталь, медь и алюминий. Очень малая длительность импульса позволяет с высокой точностью контролировать процесс сварки микродеталей.
Подводя итоги
Среди типов лазеров, предлагаемых для микросварки, стоит учитывать особенности их работы, а также требования конкретной задачи, так:
- импульсные твердотельные лазеры на YAG:Nd – это общепринятое решение для всех типов микросварки;
- непрерывные волоконные лазеры обеспечивают прекрасные скоростные характеристики и глубину проплава, позволяя сваривать проводящие и разнородные материалы;
- квазинепрерывные волоконные лазеры предлагают схожие с YAG:Nd характеристики, дополненные небольшим диаметром пятна и большими возможностями по глубине проплава;
- наносекундные лазеры позволяют с высокой точностью контролировать процесс сварки тонких материалов.
Излучение непрерывных лазеров включается и выключается в зависимости от потребности, однако может быть промодулировано для получения импульсного режима работы. Лазеры на YAG:Nd и волоконные QCW обычно предлагают пиковые мощности 0,2 – 4 кВт при длительностях импульса 0,1 – 10 мс. Наносекундные лазеры работают с мощностями импульсов порядка 10 кВт и длительностью 60 – 200 нс.
Пиковая мощность и длительность импульса
Наибольший интерес представляет сравнение YAG:Nd лазеров и QCW, которые предлагают схожие возможности по сварке – высокая пиковая мощность и возможность точечной и шовной сварки пятном большого диаметра (>200мкм). Импульсные лазеры на YAG:Nd распространены повсеместно и хорошо знакомы большинству пользователей, в то время как недавно появившиеся квазинепрерывные волоконные лазеры прельщают низкой стоимостью владения. С точки зрения возможностей по сварке они они практически идентичны и камнем преткновения становятся стоимость приобретения, владения, а так же возможность обслуживания. QCW лазеры не используют лампы, что снижает эксплуатационные расходы. При этом ламповые лазеры значительно дешевле и, в отличие от волоконных, могут полностью обслуживаться в «полевых» условиях. Решение в выборе одного из них остается за потребителем, предпочитающим высокую стоимость и низкие эксплуатационные расходы или отдающего предпочтение бюджетной системе, которую возможно обслуживать на месте 24/7.
Сводная таблица по лазерам для микросварки | |||||
Тип лазера | Типовые мощности | Глубина проплава | Типовой диаметр пятна | Все виды микросварки | Дополнение |
YAG:Nd | 5 Вт (2,5кВт в импульсе) 25 Вт (6 кВт в импульсе) 150 Вт (7 кВт в импульсе) |
1 мм | 300 мкм | Сварка с глубоким проплавом и с высокой скоростью, проводящие материалы, разнородные материалы | Возможность полного обслуживания на месте установки Необходимость замены ламп Невысокая стоимость |
CW | от 200 Вт до 1 кВт | 2,5 мм | 70 мкм | Сварка с глубоким проплавом и с высокой скоростью, проводящие материалы, разнородные материалы | Не обслуживается на месте установки Не требует расходных материалов |
QCW | 150 Вт (1,5 кВт в импульсе) 300 Вт (3 кВт в импульсе) 600 Вт (6 кВт в импульсе) |
1,5 мм | 300 мкм | Микросварка большинства материалов, сварка маленьким пятном | Не обслуживается на месте установки Не требует расходных материалов |
NS | 50-100 Вт (10 кВт в импульсе) | 0,35 мм | 50 мкм | Материалы толщинами <200 мкм, сварка маленьким пятном, сварка разнородных материалов | Не обслуживается на месте установки Не требует расходных материалов Невысокая стоимость |
Подготовлено по материалам:
GEOFF SHANNON – Choosing between Nd:YAG or fiber lasers for micro welding [ILS]
Основы лазерной сварки.

Эта статья будет напечатана в нескольких выпусках журнала Bench Magazine. Я планирую начать с основ сварки и написать о характеристиках балки и о том, как мы используем эти характеристики для сварки. Важно понимать, как фокусируется луч. Не менее важно, как сфокусирована система просмотра
Основы лазерной сварки:
Характеристики луча
по отношению к фокусу луча. У меня будут конкретные примеры работ, связанных с ювелирным делом, которые продемонстрируют энергетические характеристики луча, а также приемы и технологии (некоторые из них довольно новые), которые помогут преодолеть проблемы, с которыми мы, как ювелиры, сталкивались за последние 10 лет лазерных технологий. сварка.
При обучении лазерной сварке ювелир должен понимать некоторые основные принципы сварки в сравнении с техникой пайки, с которой знакомо большинство ювелиров. Любой, кто понимает принципы сварки, должен только узнать, как можно использовать регулируемые энергетические характеристики лазера для выполнения сварки, а затем получить небольшую координацию глаз и рук, чтобы работать с увеличением, используя характеристики луча, с некоторыми простыми приемы выполнения сварочных работ. Сварка отличается от пайки.Припой плавится при более низкой температуре и затекает в шов внутри металла с другим легирующим составом, который не расплавляется в процессе пайки. Отличная статья о принципах пайки находится в журнале Bench Magazine: Winter 2003, Volume 2, Issue 3 под названием: The Secret Life of Solder, автор: William Pellegrini.
Сварка отличается от пайки главным образом тем, что при сварке свариваемый материал также плавится. При расплавлении основного материала во время сварки важно проникнуть в шов с правильным распределением энергии и энергии, чтобы соединить две детали таким образом, чтобы образовалась адекватная область соединения.Лазеры, которые используются для сварки в нашей отрасли, имеют аналогичные регулируемые функции, которые контролируют различные аспекты общей энергии лазера и способ подачи этой энергии.
Первое, что должен сделать лазер, это физическое проникновение в сварочный шов. Лазерный луч должен соединить два куска металла вместе. Для этого могут потребоваться различные характеристики энергии. Например, стержень из платины диаметром 3 мм потребует другой энергии, чем стержень для серьги из 18-каратного желтого золота.Подача луча в сварочный шов называется проплавлением. Проникновение достигается за счет управления физической силой лазерного луча, которую большинство лазеров на рынке контролируют с помощью переменного параметра, называемого напряжением. Этот параметр обычно также выражается как напряжение. Напряжение контролирует физическую силу фотонов (материи) в световом луче. На рис. 1 показаны примеры поперечных сечений точки сварки при различных значениях напряжения. Цифры не в масштабе, и указанные параметры не точны; они предназначены только для демонстрации основных принципов.Обратите внимание, что при увеличении только уставки напряжения достигается большее физическое проникновение. Параметр напряжения является одной из характеристик выходной энергии лазерного луча. Лазер должен иметь достаточно энергии, чтобы добраться до рабочей площадки, а это означает, что он должен преодолеть сопротивление металла вокруг сварного шва и проникнуть сквозь сопротивляющийся металл, чтобы получить доступ к внутренним поверхностям шва.
После того, как лазерный луч проник на рабочую площадку, в нем должно остаться достаточно энергии, чтобы выполнить работу (расплавить окружающий металл).Обратите внимание на рис. 1, как само по себе увеличение напряжения создает пустую дыру с небольшим эффектом плавления.
Изменение напряжения
Другой управляемой энергетической характеристикой является продолжительность пребывания луча в металле в течение одного лазерного импульса («длительность импульса»). Некоторые правильно называют это «шириной луча». Я думаю, что «длительность импульса» лучше описывает происходящее. Длительность импульса регулируется на большинстве машин с шагом, измеряемым и выражаемым в миллисекундах (тысячных долях секунды).Оставляя лазерную энергию в металле на более длительное время, он нагревает окружающий металл до его точки плавления и разрушает металл сам по себе, таким образом, сплавляя его вместе таким образом, что он плавно соединяется с металлом. Обратите внимание на рис. 3, что более длительные импульсы плавят пятно, которое становится шире и глубже. Длительность импульса может быть использована для получения проникновения посредством плавления, а не для принудительного физического проникновения, которое является результатом напряжения. Однако более длительные импульсы могут сжечь некоторые металлы, оставив ямки и хрупкость.
Изменение длительности импульса
Для проникновения лазерному лучу требуются другие аспекты энергии, чем энергия, необходимая для плавления. Напряжение и длительность импульса напрямую связаны с количеством энергии (измеряемой в джоулях), содержащейся в лазерном луче. Не обсуждая формул лазерной физики, я хочу показать взаимосвязь между «напряжением», «длительностью импульса» и «полной энергией». Прямая зависимость означает, что увеличение напряжения или длительности импульса соответствует большему количеству энергии (в джоулях), выделяемой в луче, а уменьшение любого из двух этих параметров соответствует уменьшению общей энергии в луче. Важно не забывать, что напряжение и длительность импульса напрямую связаны с энергией, но два отдельных параметра дают разные результаты.
Напряжение — это физическое давление, требующее энергии и приводящее к физическому силовому проникновению. Длительность импульса — это время воздействия луча, которое также требует энергии и приводит к плавлению. Многие машины имеют показания дисплея, которые показывают расчетную общую энергию в джоулях на основе выбранного напряжения и длительности импульса. Я считаю, что отображать показания полной энергии на дисплее не обязательно, но очень полезно для понимания характеристик и взаимосвязи напряжения и длительности импульса.Обычно я называю напряжение и длительность импульса «настройками энергопотребления». Часто при определении наилучших параметров сварки для конкретной работы я отмечаю, что энергия должна быть увеличена или уменьшена. Затем нужно сделать еще один шаг и спросить, какой конкретный результат энергии должен быть другим (проникновение, плавление или и то, и другое?).
Изменение напряжения и длительности импульса
Площадь, в которой распределяется полная энергия, зависит от управления «диаметром луча».Некоторые правильно называют этот параметр «фокусом». Мне нравится называть это «диаметром луча», потому что изменение «диаметра луча» в фокальной плоскости системы наблюдения — это эффект, который он оказывает на лазерный луч, поскольку он применим к текущему применению ювелирных изделий. Важно понимать разницу между фокусом лазерного луча и фокусом системы просмотра и как они соотносятся с параметрами, которые я здесь обсуждаю. Фактически, понимание энергетических характеристик луча в фокальной плоскости системы наблюдения оператора идет рука об руку с изучением влияния отдельных параметров.
Я подробно расскажу об этом в следующей статье. Пока лишь упомяну, какой эффект оказывает изменение диаметра луча в месте сварки при правильном и постоянном удерживании свариваемого изделия в правильном фокусе оператора в системе обзора. Изменение диаметра луча изменяет размер пространства, в котором фокусируется полная энергия лазера. Как видно на рисунке 4, данная энергия (напряжение и миллисекунды) в узком пространстве или диаметре луча будет иметь более глубокий эффект в этой небольшой области, чем та же энергия, распределенная по большему диаметру.Изменение диаметра луча изменяет количество джоулей на квадратную площадь. Некоторые машины отображают рассчитанное количество джоулей на квадратный сантиметр в зависимости от выбранной энергии при заданном диаметре луча. Я нахожу это полезным для понимания взаимосвязи между полной энергией и диаметром луча.
Изменение диаметра луча
На рисунках 1, 2 и 4 показаны результаты трех основных настраиваемых параметров: напряжения, длительности импульса и диаметра луча, в то время как они настраиваются по отдельности экстремальным образом.На рисунках 3 и 5 показаны результаты одновременной настройки двух или более этих параметров. Все эти примеры не относятся к какому-либо конкретному масштабу и предназначены только для того, чтобы помочь объяснить основные принципы.
Изменение напряжения, длительности импульса и диаметра луча
Я считаю напряжение, длительность импульса и диаметр луча основными контролируемыми параметрами. Вторичным по отношению к этим трем параметрам является частота пульса. Одиночный лазерный импульс инициируется однократным нажатием педали.Выбор более высокой частоты импульсов позволяет оператору удерживать педаль нажатой и продолжать генерировать лазерные импульсы. Частота пульса обычно измеряется и выражается в герцах (Гц).
«Гц» в данном случае — это измерение частоты импульсов лазера в одну секунду. Машины, доступные на рынке, в настоящее время имеют диапазон частот от 5 до 20 Гц. При увеличении Гц предварительно выбранные первичные параметры передаются с большей скоростью в секунду. Результаты более высокой частоты, как правило, будут более агрессивными, чем тот же набор параметров в одном импульсе, потому что металл сварного шва имеет меньше времени для отвода лазерной энергии от сварного соединения между импульсами.
Это основы, которым можно научиться, имея небольшой опыт работы с лазерной машиной. В следующей статье мы обсудим взаимосвязь фокуса луча и фокальной плоскости системы наблюдения, обретем координацию глаз и рук и научимся выполнять непрерывный сварной шов с присадочным металлом и без него.
См. также:
Основы лазерной сварки, часть 2
Основы лазерной сварки, часть 3
Основы лазерной сварки, часть 4
7 Проблемы качества лазерной сварки и решения
Отклонение/прогиб сварного шва 1.ЛазерВозможные причины:
1) Необоснованная настройка смещения сварного шва
Подключитесь к базовому программному обеспечению HMI, проверьте текущее смещение и определите, как его изменить в соответствии с направлением отклонения сварки.
2) Требуется замена защитного стекла
Плотные пятна и прожоги в центре линзы, которую необходимо заменить
3) Совмещено ли положение света и провода
Следите за относительным положением световой проволоки по дисплею, а конец сварочной проволоки должен находиться в центре поперечной вилки.
4) Свободен ли жгут проводов, соединяющий датчик усилия и верхний контроллер на сварном шве .
Очистите дорожку и проверьте, не сдавливается ли трос другими тросами во время ходьбы.
Сырье и детали1) Отклонение положения сварного шва между верхней крышкой и боковой стенкой в направлении Y превышает допуск.
Временная схема регулируемой гусеницы
2) Зазор между верхней крышкой и боковой стенкой не соответствует допускам.
Временная схема может соответствующим образом увеличить скорость подачи проволоки.
Сварочная проволокаСкорость подачи проволоки слишком мала, подача проволоки неровная или задана слишком низкая скорость.
1) Проверьте, не слишком ли велик малый ток двигателя механизма подачи проволоки, что указывает на большое сопротивление подачи проволоки.
2) Наблюдайте за фактической скоростью подачи проволоки, отображаемой на технологическом шкафу, чтобы убедиться, что она не выходит за допустимые пределы.
Выньте провод три раза с фиксированным временем и скоростью, измерьте длину и проверьте, не слишком ли велико отклонение от теоретического значения. Если оно превышает 3%, это означает, что подача проволоки затруднена, что повлияет на нормальную сварку.
3) Если состояние неудовлетворительное, проверьте, не нужно ли заменить трубу подачи проволоки 690 мм на переднем конце механизма подачи проволоки;
Требуется ли повторная калибровка силы прижима направляющего ролика; Если сопло подачи проволоки сгорело и деформировалось, его необходимо заменить.
Неровная поверхность сварного шва1) Сопло направляющей проволоки изношено, что приводит к дрожанию проволоки.
Проверьте сопло направляющей для проволоки. Если он деформировался и сгорел, замените его новым.
2) Плотные пятна в центре защитной линзы лазерной головки, что приводит к колебаниям светопропускания
Проверьте защитную линзу. Если в центре линзы имеются плотные пятна или прожоги, замените ее новой линзой.
3) Недостаточная мощность лазера
Проверьте мощность лазера. При необходимости увеличьте мощность лазера соответствующим образом.
4) Поверхность боковой стенки, обработанная лазером, неровная.
Устьица1. Чистота заготовки:
Избыток цинка и посторонние вещества.
Проверить соответствие входящих деталей (очистка, посторонние вещества).
2. Влияние потока воздуха
Проверьте сжатый воздух на лазерной головке и сжатый воздух на приспособлении (утечка воздуха).
Свернуть1. Чрезмерная мощность лазера
Уменьшите мощность лазера соответствующим образом
2. Скорость подачи проволоки слишком низкая .
Проверьте установленное значение и фактическое значение скорости подачи проволоки. При необходимости откорректируйте или откалибруйте скорость подачи проволоки.
3. Неравномерная скорость робота
Проверьте, являются ли параметры робота приемлемыми, особенно там, где есть CNT и ACC, и где положение робота сильно меняется.
4. Зазор между верхней крышкой и боковой стенкой ненормальный .
Проверьте, соответствует ли зазор детали требованиям плавного перехода в пределах 0,3 мм.
Начало и окончание дуговой сварки опухоли1. Правильно ли расположены начальная и конечная точки дуги .
Проверьте положение начальной и конечной точек дуги на пустой дорожке и внесите соответствующие коррективы в случае отклонения.
2. Согласованы ли задержка лазера и задержка подачи проволоки .
1)перекрытие начала дуги может задержать подачу проволоки
2) перекрытие дугового разряда может задержать выключение света
3 . Начало дуги и конечное положение деталей колеблется в направлении X .
1. Правильно ли расположены начальная и конечная точки дуги .
Проверьте положение начальной и конечной точек дуги на пустой дорожке и внесите соответствующие коррективы в случае отклонения.
2. Согласованы ли задержка лазера и задержка подачи проволоки .
1) Прожигание дуги может привести к задержке выхода света или снижению мощности лазера при дуговом разряде.
2) Остановка дуги и прожог могут привести к задержке остановки подачи проволоки.
3) Колебания положения дуги в начале и в конце деталей по оси X.
Прерывание сварки 1) Аварийные сигналы технологического шкафа «ошибка источника лазера» и «потеря номера программы лазера» .
Проверьте лазер, чтобы подтвердить параметры, или обратитесь к производителю лазера.
2) Аварийные сигналы технологического шкафа «отсутствие проволоки в оболочке» или «засорение сварочной проволоки» .
1) Проверьте фактическую скорость подачи проволоки, чтобы убедиться, что она превышает 10 %. Если да, проверьте трубопровод подачи проволоки.
2) Неисправность датчика скорости подачи проволоки
【Rayclass】Новая революция в области лазерной сварки лайнера стиральной машины-Wuhan Raycus Fiber Laser Technologies Co., Ltd.
В процессе изготовления внутреннего вкладыша традиционной стиральной машины широко используется технология клепки внутренней трубы. В настоящее время в большинстве технологий изготовления внутренней трубы полностью автоматических стиральных машин на рынке используется технология «крепления», но в стыке внутренней трубы будут зазоры или неровности, из-за чего прочность ванны снижается. быть низким и ненужным износом одежды.
В целях дальнейшего повышения надежности и усовершенствования внутренней трубы производители стиральных машин применяют технологию лазерной сварки к новым продуктам стиральных машин с одинаковой мощностью, избегая зазоров и неровностей внутренней трубы и всесторонне повышая надежность продукта. при уходе за одеждой.
В 28-м выпуске Rayclass показаны новые изменения, которые лазерная сварка привносит в вкладыш стиральной машины
.
Преимущества лазерной сварки
1) С точки зрения технологического анализа сварной шов внутреннего цилиндра, созданный по технологии бесшовной лазерной сварки, имеет однородную структуру, меньше пор и меньше дефектов.Прочность почти в 4 раза выше, чем у внутреннего цилиндра с использованием технологии клепки, а гладкость интерфейса увеличена почти в 15 раз. Гладкий шов внутреннего цилиндра предназначен для лучшей защиты ткани одежды, чего трудно добиться с помощью технологии клепки. Кроме того, за счет повышенной прочности внутренней трубы максимальная скорость вращения стиральной машины равномерной мощности в процессе обезвоживания также увеличивается на 25% по сравнению с обычной полностью автоматической стиральной машиной.Эффективность обезвоживания значительно повышается, потребляется меньше энергии и времени, а также удовлетворяется спрос потребителей на качественную жизнь в соответствии с текущей тенденцией повышения потребления;
С точки зрения эффективности производства, технология лазерной бесшовной сварки может сделать пятно сварки внутреннего цилиндра небольшим, узким сварочным швом, аккуратным и красивым, без обработки после сварки, а эффективность производства может быть увеличена в 3-5 раз.
Таким образом, технология лазерной сварки широко используется в производстве стиральных машин из-за ее высокой энергии, высокой точности и высокой адаптируемости. Это не только техническая гарантия разработки новых стиральных машин, но и необходимое техническое средство для повышения качества и снижения затрат.
Трудности при лазерной сварке
В настоящее время внутренний бак высококлассных стиральных машин, представленных на рынке, в основном изготавливается из нержавеющей стали, а его толщина в основном составляет от 0,8 мм до 1,2 мм. Когда стиральная машина работает нормально, скорость работы может достигать 1400 об/мин. Поэтому внутренний вкладыш стиральной машины предъявляет крайне жесткие требования к сварному шву.Например, сварной шов ровный и ровный (проверено процарапыванием чулками), достаточно высокая механическая прочность (прочность шва не может быть меньше прочности основного материала), шов не окисляется и не обесцвечивается, устойчив к коррозии. (после сварки он должен пройти испытание в солевом тумане в течение 2400 часов).
Высокие требования к сварке внутреннего бака стиральной машины делают процесс сварки чрезвычайно сложным. Основные трудности при сварке:
1) Высокие требования к формовке сварочного шва: односторонняя сварка и двусторонняя формовка, сварочный шов и тыльная сторона сварного шва должны быть непрерывными и гладкими, без каких-либо узлов, заусенцев или сварочного шлака, в противном случае гладкость требования не будут выполнены;
2) Внешний вид сварного шва чрезвычайно требователен, а передняя и обратная стороны сварного шва и кромка сварного шва не должны быть окислены, в противном случае коррозионная стойкость будет снижена, а испытание в солевом тумане не удастся.
Чтобы соответствовать таким строгим требованиям к сварке, в дополнение к чрезвычайно высоким требованиям к стабильности лазерной сварки, уровень процесса сварки также чрезвычайно высок.
Решения для лазерной сварки
1) Лазер принимает режим модуляции, и мощность медленно увеличивается и уменьшается;
Для решения проблемы узлов в начальном и конечном положениях сварного шва принят режим модуляции лазера, а в программном обеспечении управления сварочным оборудованием установлена функция рампы мощности. Длина нарастания мощности устанавливается в начальной точке, а длина снижения мощности устанавливается в точке отключения. Проблема с узлом в сварочном шве точки засветки была значительно решена, но точка засветки вогнута, и точку засветки можно поместить на 2 мм за пределы образца. При приведенной схеме хорошо решается проблема неровности сварного шва и узлов.
Эффект изображения после настройки
Изображение эффекта выключения света после регулировки
2) Изучите соответствующую величину расфокусировки при сварке;
В процессе сварки степень расфокусировки оказывает большее влияние на форму сварного шва образца.Если расфокусировка слишком велика, потери энергии лазера будут большими, а сварной шов будет прерывистым и неровным; если расфокусировка слишком мала, энергия лазера будет сконцентрирована, что приведет к увеличению количества заусенцев на обратной стороне сварного шва (особенно при сварке тонких листов). Таким образом, при сварке этого образца, при условии обеспечения проплавления материала, правильная регулировка величины расфокусировки может сделать передний сварной шов непрерывным и однородным, а задний сварной шов не будет иметь заусенцев.Задний заусенец не только влияет на гладкость внутреннего резервуара, но также влияет на эффект испытания образца в солевом тумане.
3) Чтобы обеспечить внешний вид сварного шва, «защитный газ» является ключевым;
Чтобы обеспечить гладкий внешний вид сварного шва и чтобы изготовленные образцы могли пройти последующее испытание в солевом тумане в течение 2400 часов, «защитный газ» в процессе сварки очень важен. Эффект защиты хороший, не только может сделать переднюю и заднюю стороны сварного шва гладкими и полупрозрачными, но также может избежать окисления сварного шва в процессе сварки и гладко пройти испытание на коррозию.В процессе сварки, чтобы избежать налипания сварочного шлака на поверхность материала, в направлении сварки может быть установлено устройство для удаления пыли. Кроме того, обычная однотрубная боковая продувка не может эффективно гарантировать, что передний сварной шов вообще не окислится. Поэтому передний защитный газ следует заменить на продувку со стороны трубы, чтобы гарантировать, что передний сварочный шов не окислится. Задняя часть сварного шва также должна быть прорезана и защищена газом, чтобы обеспечить качество сварки заднего шва.
Образец после сварки
2400-часовое испытание в солевом тумане: визуализация передней и задней части
Готовый чертеж сварки
Рекомендуемые продукты
Внутренний контейнер стиральной машины обычно изготавливается из листа нержавеющей стали толщиной 0,8–1,2 мм. Поэтому рекомендуется использовать волоконный лазер мощностью 2000–4000 Вт. Диаметр сердцевины должен быть 100 мкм, а световое пятно должно быть соответственно больше, чтобы улучшить эффект сварки.
Одномодульный волоконный лазер Raycus 2000 Вт CW
Одномодульный волоконный лазер Raycus 3000 Вт CW
Многомодульный волоконный лазер Raycus мощностью 3000 Вт непрерывного действия
Многомодульный волоконный лазер Raycus мощностью 4000 Вт непрерывного действия
Заказчик использовал волоконные лазеры Raycus для разработки линий автоматической лазерной сварки внутренних баков стиральных машин для ведущего мирового производителя бытовой техники. Отличные сварочные характеристики волоконного лазера Raycus способствовали бесперебойной поставке и использованию автоматизированной линии, а все показатели сварочных образцов достигли требований заказчика.
PS: При покупке стиральной машины не забудьте выбрать стиральную машину с технологией лазерной бесшовной сварки, чтобы технология лазерной сварки внутренней трубы всегда защищала деликатную одежду!
Портативный лазерный сварочный аппарат
VS сварочный аппарат MIG
Портативные лазерные сварочные аппараты и сварочные аппараты MIG относятся к числу современных сварочных аппаратов, используемых сегодня.Хотя оба они являются сварочными аппаратами, они различаются по принципу действия. В то время как сварочный аппарат с волоконным лазером использует инфракрасный луч для сварки металлов, сварочный аппарат MIG использует для своего процесса газ. Итак, чем же еще отличаются эти машины? Что лучше? Каковы плюсы и минусы каждого типа сварки? Читайте дальше, чтобы получить ответы на эти и другие вопросы.
Что такое волоконный ручной лазерный сварочный аппарат и как он работает?
Портативный волоконный лазерный сварочный аппарат представляет собой устройство, использующее непрерывный или импульсный лазерный луч для сварки двух металлических частей.Этот сварочный аппарат работает, облучая заготовку высокоинтенсивным лазерным лучом, чтобы локально нагреть ее на небольшой площади.
При взаимодействии лазерного луча с материалом внутренняя часть заготовки плавится, охлаждается и кристаллизуется, образуя сварной шов. Это современный тип сварочного аппарата, используемый в основном для сварки тонкостенных заготовок и прецизионных деталей. С помощью портативного волоконного лазерного сварочного аппарата вы можете выполнять различные формы сварки, такие как стыковая, сварка с запайкой, точечная и шовная сварка.
Преимущества ручного волоконного лазерного сварочного аппарата
Хороший эффект сварки
Из-за небольшого воздействия на горячую зону термическая деформация обрабатываемого изделия незначительна. Делает сварочный шов гладким и красивым, так как на обратной стороне не остается почернений и следов. Поэтому нет необходимости во вторичной обработке после сварки. Кроме того, из-за большой глубины сварки сварка получается прочной и происходит достаточное плавление. Сварочный шов не содержит отверстий для воздуха, что обеспечивает эффективную схему сварки.
Высокая скорость сварки
Портативный волоконный лазерный аппарат обеспечивает высокую скорость сварки. По сравнению с традиционной сваркой это до десяти раз быстрее.Следовательно, вы можете сэкономить время и деньги, нанимая много сварщиков.
Универсальность и простота управления
Ручной волоконный лазерный сварочный аппарат отличается уникальной конструкцией сварочной горелки с двойным качанием. Он имеет различные сопла с разными углами для различных применений, таких как стандартная сварка, лазерная резка, сварка с подачей проволоки и угловая сварка. Это делает портативный волоконный лазерный сварочный аппарат достаточно универсальным для решения ваших сварочных задач. Вы можете легко управлять лазерной пушкой, потому что она легкая и ее удобно держать одной рукой.Сварочный пистолет заменяет традиционный фиксированный световой путь, делая его более гибким и удобным для выполнения длительной лазерной сварки.
Режимы сварки
Самым большим преимуществом ручного лазерного сварочного аппарата является интеллектуальная система приложений Laser, которая позволяет выбирать из шести режимов сварки. Схема управления использует управление низким напряжением постоянного тока 24 В и имеет хороший и долговечный срок службы. Регулируемая частота двигателя контролирует скорость лазерного фокуса до 460 кругов в секунду.Он подходит для сварки всех заготовок из крупных материалов неправильной формы и сложных сварочных швов.
Высокая надежность
Поскольку рабочий газ лазера можно настроить на закрытие или открытие с помощью сенсорного экрана, он предотвращает выгорание защитной линзы по сравнению с традиционной ручной сварочной головкой. Это делает головку ручного лазерного сварочного аппарата более прочной.
Экономичный
Портативный оптоволоконный лазер, несмотря на свои небольшие размеры, имеет эффективность электрооптического преобразования более 35%.Приобретая этот аппарат, вы получаете экономичный аппарат для лазерной сварки, который намного превосходит другие типы лазеров, таких как MIG, при той же мощности. Помимо выполнения операций ручной лазерной сварки, вы также можете использовать его для сверления, высокоточной сварки и ремонта пресс-форм с помощью платформы для последующего монтажа.
Простота в эксплуатации
Волоконный портативный лазер имеет интеллектуальную систему применения лазера, которая упрощает работу без каких-либо технических знаний. С помощью этой системы вы можете контролировать мощность лазера, частоту и функции сварки.
Широкий спектр применения
С этим ручным лазерным сварочным аппаратом вы получаете расширенный спектр применения. От кухонь, шкафов, полок, 3D рекламных надписей до нестандартной и сложной сварки нержавеющей стали, применение этого сварочного аппарата ограничено вашим воображением. Ручной сварочный аппарат эффективно заменил электрическую сварку, традиционную аргонно-дуговую сварку или сварку MIG на таких материалах, как нержавеющая сталь, алюминий и железо.
Ограничения ручного лазерного сварочного аппарата
Высокая начальная стоимость
Первоначальная стоимость приобретения ручного лазерного сварочного аппарата выше по сравнению с другими аппаратами.Это значительные инвестиции, которые требуют некоторого планирования.
Проблемы с пористостью и охрупчиванием
Поскольку наплавленный валик быстро затвердевает, есть опасения, что шов может быть пористым, хрупким и может образовывать трещины в некоторых металлах.
Засорение сопла и перегрев
Поскольку поток электронов меньше, чем при других методах сварки, вам необходим непрерывный поток. Засорение или отключение луча вызовет проблемы с перегревом, которые могут повредить вашу машину.Не рекомендуется использовать его в течение долгих часов непрерывной работы.
Перекрестное загрязнение лазерных материалов и других металлов
Этот ручной лазерный сварочный аппарат не следует использовать для сварки материалов из одной группы металлов. Например, его нельзя использовать для сварки нержавеющей стали с никелем или кобальтом. Это связано с тем, что тепло вызывает перекрестное загрязнение некоторых элементов, что приводит к потере свойств и качества заготовки. В большинстве случаев включения в заготовке могут загрязнять и вызывать поглощение лазерного луча вместо его передачи в металл.
Изменение свариваемости материалов
При использовании ручного лазерного сварочного аппарата изменяется свариваемость материалов с высокой теплопроводностью и отражательной способностью, таких как медь, алюминий и их сплавы.
Ограниченная свариваемая толщина
Не все толщины можно сваривать с помощью ручного лазерного сварочного аппарата. Материалы с толщиной проплавления более 19 мм не подходят для этого типа сварки.
Что такое сварочный аппарат MIG и как он работает?
Аппарат для сварки MIG (металл в среде инертного газа) представляет собой аппарат, который плавит и соединяет металлические листы друг с другом.Этот тип сварки включает в себя использование проволочного электрода для прохождения через электрическую дугу, расплавляющую два куска металла. Когда сварочный аппарат MIG настроен на работу, он подает импульсный ток от встроенного трансформатора, создавая электрическую дугу, которая плавит металлы, чтобы соединить их друг с другом. Расплавленный металл течет через крошечные трещины или зазоры между двумя металлическими листами, создавая прочную связь, называемую сварным швом.
Преимущества аппаратов для сварки MIG
Они обеспечивают быструю сварку
Для любого сварочного аппарата время, необходимое для сварки, указывает на сложность соединения и требуемое качество сварного шва по завершении.По сравнению с некоторыми другими сварочными аппаратами, сварочный аппарат MIG работает быстрее независимо от того, кто его использует, будь то эксперт или новичок. Это происходит из-за непрерывной подачи электрода из горелки MIG с катушкой, сварочного аппарата или других сложных промышленных приложений с использованием технологии тянущей и толкающей подачи.
Простота обучения
Простота — одно из основных преимуществ MIG. За несколько часов новичок может научиться пользоваться сварочным аппаратом MIG. По сравнению со сварщиками TIG, сварщикам MIG требуется значительно меньше времени для обучения.Его использование описывается как процесс «наведи и снимай».
Универсальность
Поскольку сварочные аппараты MIG могут сваривать различные металлы и их сплавы, они невероятно универсальны. Он также может работать по-разному, как полностью, так и полуавтоматически. Хотя он отлично подходит для домашних сварочных процессов, его промышленное применение безгранично. Его можно использовать для сварки нержавеющей стали, меди, алюминия, никеля, магния, железа и большинства его сплавов.
Высокая производительность
Поскольку сварщики не меняют постоянно стержни и не удаляют шлак, сварщики MIG экономят время, тем самым повышая производительность сварщиков.
Простые сварные швы
Сварочные аппараты MIG обеспечивают лучшую видимость сварочной ванны. Это, в сочетании с простотой процесса и лучшим контролем, обеспечиваемым автоматической подачей проволоки, упрощает получение красивого сварного шва.
Ограничения аппаратов для сварки MIG
Очистка
В какой-то момент сопло аппарата для сварки MIG забивается брызгами. Это практически невозможно предотвратить. Сварочные аппараты MIG требуют регулярной очистки и использования таких материалов, как погружной наконечник, после очистки сопла сварочного аппарата.
Портативность
По сравнению с другими сварочными аппаратами сварочный аппарат MIG теряет баллы за портативность. Поскольку они работают от электричества, работать в местах без электричества невозможно. Еще одним аспектом портативности сварочных аппаратов MIG является размер. Это большие машины, транспортировка которых может быть затруднительна.
Прожог
Если заготовка имеет толщину менее 0,5 мм, существует высокий риск прожога некоторых материалов. После определенного уровня опыта вы можете найти свой путь вокруг.Как правило, для очень тонких материалов сварочные аппараты MIG подходят не лучшим образом.
Портативный лазерный сварочный аппарат VS сварочный аппарат MIG — что выбрать?
В этом соревновании между ручным волоконным лазерным сварочным аппаратом и сварочным аппаратом MIG нет явного победителя. Безусловно, у обоих типов сварщиков есть свои плюсы и минусы; тем не менее, нельзя отрицать, что они оба хорошо работают в определенных сварочных приложениях. Вы должны приобрести соответствующую машину, которая будет соответствовать вашим потребностям и спецификациям.
Если речь идет о легких работах, таких как ремонт автомобиля или бытовой техники, вам следует приобрести портативный волоконный лазерный сварочный аппарат. Тем не менее, вы можете рассмотреть возможность приобретения сварочного аппарата MIG, если планируете сваривать более толстые материалы и использовать его в других коммерческих целях. Его универсальность с точки зрения материалов может пригодиться.
Свяжитесь с нами:
Просто отправьте нам электронное письмо или заполните форму ниже, мы всегда готовы помочь.
Raytu Fiber Laser Welder производители и поставщики в Китае
Волоконный лазерный сварочный аппарат Raytu Описание:
Волоконно-лазерный сварочный аппарат Raytu состоит из сварочного узла, сварочного рабочего места, водяного охладителя и системы управления.Эта серия сварочного оборудования имеет несколько рабочих столов на выбор, что в 3-5 раз превышает скорость традиционной машины для лазерной сварки с оптоволоконным излучением и может полностью удовлетворить потребности клиентов в различных отраслях промышленности. Лазерный сварочный аппарат с ЧПУ подходит для сварки золота, серебра, титана, никеля, олова, меди, алюминия, нержавеющей стали и других металлов и соответствующих сплавов. Он может выполнять прецизионную сварку между одним и тем же металлом и другим металлом. Он широко используется в аэрокосмическом оборудовании, судостроении, приборостроении, механических и электрических изделиях, автомобилестроении и других отраслях промышленности.
Эффективная и совершенная схема сварки для пользователей:
Качество лазерного луча отличное, скорость сварки высокая, сварной шов прочный и красивый
Отношение глубины сварки к ширине может достигать 10:1:
Место сварки гладкое и красивое, сварочный шов ровный, без пор, прочность и ударная вязкость сварочного шва, по крайней мере, равны или даже выше, чем у основного металла, и нет необходимости в обработке или требуется только простая обработка после сварки, чтобы снизить трудоемкость рабочих
Высокий коэффициент электрооптического преобразования:
Низкое энергопотребление, долгосрочное использование может сэкономить много затрат на обработку для клиентов
Оборудование повышенной надежности:
Обрабатывается непрерывно в течение 24 часов для удовлетворения потребностей промышленного массового производства и переработки
Специальная настройка для различных приложений:
Для настройки в соответствии с потребностями клиентов.
Параметры машины | ||
---|---|---|
№ | Предметы | Параметр |
1 | Модель машины | RTHW-1000W |
2 | Максимальная мощность лазера | 2000 Вт |
3 | Лазерный источник | ИПГ/Райткус/МАКС |
4 | Качество луча | 1.3м² |
5 | Длина волны лазера | 1080±5 нм |
6 | Толщина сварки | 0,5-3 мм |
7 | Охладитель воды | S&A |
8 | Потребляемая мощность | 5кВт |
9 | Длина оптического волокна | 10 м |
10 | Гарантия | 2 года |
Лазерная резка и лазерная сварка на простом английском языке
Многие варианты лазерной технологии в настоящее время используются в производственных процессах, включая резку, сварку, маркировку, обработку поверхности и непосредственное изготовление деталей.

Область применения охватывает металлы, пластмассы, полупроводники и керамику в масштабе от субмикрона до нескольких метров. Многие отрасли промышленности, в том числе автомобильная, судостроительная и аэрокосмическая, используют технологии лазерной сварки и лазерной резки.
Лазерная сварка с глубоким проникновением
Лазерная сварка с глубоким проплавлением представляет собой процесс бесконтактного соединения, характеризующийся высокой плотностью сфокусированной энергии, который позволяет создавать сварные швы с высоким соотношением сторон (ширина сварного шва : глубина сварного шва) во многих металлических материалах.Его можно выполнять при атмосферном давлении и с относительно низким подводом тепла по сравнению с процессами дуговой сварки в среде инертного газа.
Лазерная сварка с глубоким проплавлением представляет собой универсальный процесс сварки плавлением, который нашел широкое применение в промышленности; от точечной сварки бритвенных лезвий до сварки аэрокосмических и морских конструкций. Этот процесс можно использовать для сварки различных материалов, включая углеродистую сталь, нержавеющую сталь, титан, алюминий, никелевые сплавы. Промышленное внедрение лазерной сварки обусловлено потребностью в больших объемах производства и/или высоком качестве сварки.2 для нанесения на сустав. Эти плотности мощности достаточны для образования «замочной скважины» (см. видео) ниже точки падения лазерного луча. Эффективное поглощение лазерного луча этой замочной скважиной позволяет производить сварные швы с низким тепловложением при высоких скоростях обработки. Эти высокие скорости обработки в сочетании с простотой автоматизации промышленных лазерных источников приводят к надежному, воспроизводимому и автономному крупносерийному производству.
Подвод тепла обычно на порядок ниже, чем при дуговой сварке, что способствует внедрению лазерной сварки с глубоким проплавлением в компонентах, требующих минимальных тепловых искажений.
Компания TWI имеет значительный опыт успешной разработки и квалификации методов лазерной сварки с глубоким проплавлением для различных областей применения во многих отраслях промышленности.
• Глубокие узкие сварные швы
• Низкое тепловложение и, следовательно, минимальная термическая деформация
• Простота автоматизации
• Гибкость конструкции соединения
• Высокая повторяемость
• Гибкость конструкции соединения
• Эстетически привлекательные сварные швы
Пользуетесь ли вы сейчас газорезательной машиной? Если вы перейдете на Laser, помните, что Westermans International КУПИТ вашу лишнюю машину и заплатит вам за нее сверх шансов.
Гибридная лазерная дуговая сварка
Другим методом лазерной сварки является гибридный процесс лазерно-дуговой сварки. Сочетая дуговую сварку и лазерную сварку с глубоким проплавлением одновременно в одной сварочной ванне, этот метод лазерной сварки сочетает в себе индивидуальные преимущества как дуговой сварки, так и лазерных процессов.
К ним относятся сварные швы с глубоким проваром такого же качества, что и лазерная сварка, с большим допуском на подгонку стыка, сравнимым с дуговой сваркой. Более высокий контроль над качеством и свойствами сварного шва, чем при автогенной лазерной сварке, также достигается за счет использования расходных материалов и газов для дуговой сварки.
Теоретически можно использовать комбинацию любого процесса дуговой сварки и лазерного луча, однако наиболее распространенными вариантами являются лазер – TIG и гибридный лазер – MIG/MAG.
Гибридная лазерная сварка используется или рассматривается для использования в следующих областях и отраслях:
• Дорожный транспорт – высокая скорость и большие объемы, необходимые в автомобильной промышленности, идеально подходят для возможностей гибридной лазерной сварки, а также поскольку допуск на подгонку деталей больше по сравнению с автогенной лазерной сваркой.
• Судостроение – стандартные процессы MIG/MAG или SAW производят больше деформации при сварке, по сравнению с малой деформацией гибридной сварки, уменьшающей количество и стоимость с коррекцией деформации и доработкой.
• Железнодорожный транспорт – снова снижение производственных затрат при производстве железнодорожных вагонов достигается за счет низкого искажения от гибридной лазерной сварки, как и в вышеупомянутых судостроительных приложениях.
• Нефть и газ – в настоящее время испытывается и разрабатывается гибридная орбитальная кольцевая и продольная сварка труб.Потенциально это может означать увеличение скорости корневого прохода и выполнения стыков в зависимости от условий эксплуатации и используемых марок стали для труб.
Основные преимущества гибридной лазерно-дуговой сварки можно резюмировать следующим образом:
• Улучшение точности прилегания соединения по сравнению с автогенной сваркой.
• Улучшенное качество сварки по сравнению с лазерной сваркой.
• Увеличение глубины проникновения за один проход.
• Увеличена скорость сварки.
• Меньший коэффициент деформации благодаря уменьшению подводимого тепла за счет увеличения скорости сварки и глубины проплавления.
За последнее десятилетие TWI разрабатывала гибридный процесс сварки ряда материалов в рамках Основной исследовательской программы (CRP) и проектов, спонсируемых группой, а также для своих промышленных членов.
Примеры работы TWI в области гибридной сварки включают:
• Сварка стыковых соединений между пластинами из углеродно-марганцовистой стали лазером CO2, включая оценку способности перекрывать зазоры, а также качество и свойства сварного шва.
• Лазерная сварка MAG Nd:YAG Т-образных соединений между сталями C-Mn и полученные свойства для применения в судостроении.
• Высокоскоростная гибридная сварка алюминиевых сплавов с малыми искажениями с использованием волоконных лазеров последнего поколения.
• Гибридная сварка аэрокосмических алюминиевых сплавов с низким содержанием внутренней пористости с использованием оптоволоконных лазеров.
• Гибридная сварка высокопрочных нержавеющих сталей.
• Управление процессом в режиме реального времени при гибридной сварке стыковых соединений сталей, нержавеющих сталей
или алюминиевых сплавов
Подробнее об этом можно прочитать здесь.
Лазерная резка
Промышленные лазеры чаще всего используются для резки, при этом в большинстве случаев используются два типа — CO2 и более современные процессы волоконного лазера.
Производимый лазерный луч имеет такую высокую мощность, что используется для расплавления материала в чрезвычайно локализованной области. Коаксиальная газовая струя используется для выброса расплавленного материала и создания пропила. Как и в случае других механизированных процессов резки, затем используется система ЧПУ для перемещения лазерной головки и выполнения непрерывной резки. Существует три основных разновидности лазерной резки: резка плавлением, резка пламенем и дистанционная резка.
Лазерная резка — это универсальный процесс, который можно использовать для резки металлов и неметаллов, включая дерево и термопласт.Точность и прямоугольность краев, а также более строгий контроль тепловложения означают, что для определенных применений он часто предпочтительнее других методов резки, таких как газокислородная и плазменная. Лазерная резка считается современной технологией, которая имеет соответствующую цену! Преимущества использования лазерной резки по сравнению с другими более традиционными вариантами включают в себя:
- Отсутствие дефектов поверхности – отсутствие контакта с заготовкой.
- Идеально подходит для небольших партий благодаря быстрой настройке
- Низкое тепловложение означает меньшую зону теплового воздействия и меньшую деформацию.
- Высококачественная резка означает отсутствие необходимости в дополнительных процессах финишной обработки.
- Универсальность — может использоваться для простой резки различных материалов и простых или сложных деталей.
- Резка с узким пропилом обеспечивает высокую точность результатов
Недавно был разработан процесс волоконного лазера для увеличения скорости резки и снижения эксплуатационных расходов. Волоконный лазер также способен резать медь, латунь и алюминий. Кроме того, он намного безопаснее, чем CO2-лазер, поскольку луч не отражается, а поглощается, однако CO2 обеспечивает более качественную резку более толстого материала, поэтому может больше подходить для требований промышленного производства.
Co2-лазер:
- Производится с помощью электрического разряда через газовую смесь Co2, гелия и азота.
- Может резать более толстый материал (обычно более 5 мм) по сравнению с волоконным лазером той же мощности.
- Обеспечивает более гладкую поверхность при резке более толстого материала.
- В основном используется система с 3 осями (X, Y и Z).
- Чаще всего заготовка не перемещается, поэтому реального ограничения веса листа нет.
- Более легкий доступ к заготовке, так как это не закрытая система.
Волоконный лазер:
- Может предложить гораздо более высокую скорость, чем Co2.
- Значительно снижено энергопотребление по сравнению с лазерной резкой на углекислом газе.
- Волоконный лазер намного опаснее Co2-лазера, поэтому он представляет собой полностью закрытую систему с зоной обзора, однако гораздо труднее увидеть, что происходит.
- Значительно снижены эксплуатационные расходы благодаря мощности и эффективности использования электроэнергии для создания лазерного луча.
TWI обладает необходимым оборудованием, знаниями и опытом для выполнения научно-исследовательских работ в области лазерной резки с помощью лазерных источников с волоконной доставкой.TWI может оказывать поддержку своим членам от спецификации и закупки систем лазерной резки до разработки процедур резки путем решения вопросов, связанных с материалами, оптическими и газоструйными конструкциями.
Trumpf, Bystronic, Amada, LCD и ESAB — отличные производители лазерного оборудования
Если вы покупаете лазерный резак, значит ли это, что у вас больше нет необходимости или места для вашего плазменного резака с ЧПУ? Почему бы не продать излишки машины нам, и мы заплатим вам за нее сверх шансов?
При необходимости мы организуем осмотр/демонтаж и сбор.Позвоните нам для дальнейшего обсуждения.
МАКСMaxphotonics Co., Ltd.
С развитием транспортных средств на новой энергии аккумуляторная промышленность, как источник энергии для транспортных средств на новой энергии, имеет огромный рыночный потенциал, а также является важной частью национального стратегического развития. Являясь основным компонентом нового энергетического автомобиля, качество силовой батареи напрямую определяет производительность всего транспортного средства, поэтому процесс ее производства привлекает большое внимание. Технология лазерной обработки широко используется в производстве аккумуляторов в качестве альтернативы традиционной технологии сварки.
1. Принцип работы двойной лазерной гибридной сварки
Двойная лазерная композитная сварка заключается в объединении двух лазеров с разными длинами волн или лазерного луча через специальную выходную головку лазера, чтобы оси двух лазерных лучей совпадали или располагались рядом друг с другом. космос. Лазер основного диапазона используется для сварки с глубоким проплавлением, а лазер поддиапазона имеет функцию предварительного нагрева и охлаждения, а сварка с теплопроводностью выполняется соответствующим образом.
1.Тандемные двойные лучи: один луч предназначен для глубокой сварки плавлением, а другой расфокусирован или имеет меньшую мощность в качестве источника тепла для термообработки. Материалы, чувствительные к образованию трещин при сварке, такие как высокоуглеродистая сталь, легированная сталь и т. д., могут повысить ударную вязкость сварного шва, улучшить формирование поверхности и уменьшить дефекты, такие как разбрызгивание, усадка и подрезы. Уменьшите скорость охлаждения и улучшите работу суставной ткани.
2. Параллельные лучи: два луча создают две независимые замочные скважины в одной ванне расплава, изменяют режим течения ванны расплава, предотвращают появление дефектов, таких как подрезы и выпуклости валика, и улучшают формирование сварного шва.
3. Скрещенные двойные лучи: Два луча света создают общую замочную скважину в расплавленной ванне. Размер замочной скважины становится больше, ее нелегко закрыть, процесс сварки становится более стабильным, а газ легче отводится.
4. Концентрические двойные балки: одна балка используется для глубокой сварки, а другая балка используется в качестве источника тепла для термической обработки для предварительного нагрева, теплоизоляции и надлежащего проникновения для облегчения сварки. Может уменьшить разбрызгивание, избежать образования пор и повысить эффективность сварки.
2. Сравнение преимуществ двухлучевой композитной сварки и однолучевой сварки
3. Композитная сварка крышки аккумуляторной батареи с некоторыми элементами схемы композитной высокоскоростной сварки, как показано в следующей таблице:
Контрастный элемент | Однолучевая сварка волокна (Некачающееся) | |||||
Волокно Лазер | Maxphotonics 2000W Одноместный модуль CW Fibre Lazer | Maxphotonics 1500W Диодный лазер 1500W Одноместный модуль CW Fiber Laser | ||||
Сварочная сварка | 60676 | 60676 | 60676 | 60 мм / s | 200 мм/с | |
Вентиляционное отверстие | Больше поры на дне | меньше воздушных отверстий на дне | ||||
6 / Стабильность появления Хорошо Отлично |
Как видно из приведенной выше таблицы, благодаря преимуществам высокой эффективности производства, высокой стабильности сварки и хорошему процессу сварки двухлучевая композитная сварка заменит традиционные решения для оптоволоконной сварки. .
Ниже приводится введение в некоторые эффекты сварки:
1. Внешний вид сварки
Как видно из рисунка ниже, в состоянии композитной сварки (200 мм/с) сварной шов плоский, сварной шов шов имеет отличную консистенцию, а внешний вид идеален. Однако сварочный шов при однолучевой сварке волокон имеет очевидные колебания, а консистенция сварного шва плохая.
2. Воздушное отверстие в нижней части шва
Основными порами при сварке алюминиевых сплавов являются водородные поры, так как растворимость водорода в жидких алюминиевых сплавах значительно выше, чем в твердых телах.Следовательно, в процессе затвердевания ванны расплава скорость затвердевания ванны расплава выше, чем скорость истечения газа, и в сварном шве образуются поры. Водородное отверстие сварного шва из алюминиевого сплава обычно расположено на дне расплавленной ванны и имеет маленькую и правильную круглую форму.
Отверстие для воздуха на дне расплавленной ванны составной верхней крышки для сварки намного меньше, чем у верхней крышки для сварки оптоволокна.