Система | Марка сплава | Химический состав % (по массе) | Свариваемость (сварка плавлением) | Рекомендуемые марки сварочной проволоки | Горячеломкость | |||
без присадки | С присадкой, гр. А. | С присадкой гр. Б | Крестовая проба К, % | Проба МВТУ А, мм/мин | ||||
Алюминиевые сплавы. | ||||||||
А. Термические неупрочняемые | ||||||||
Аl | АД1 | 99,3 Аl | св | св | св | св. А97; св. А85 | 5,0 | 9,0 |
Аl-Мn | АМц | 1,3 Мn | св | св | — | св. | 0,7 | 7,0 |
Аl-Mg | AMгl | 1,1 Mg | св | св | — | св. АМн | 12,0 | 6,0 |
АМг2 | 2,2 Mg; 0,4 Мn | нс | нс | св | св. АМгЗ | 12 | 6,0 | |
АМг3 | 3,6 Mg; 0,6 Si; 0,5 Мn | св | св | — | св. АМгЗ | 8,0 | 8,0 | |
АМг4 | 4,3 Mg; 0,6 Мn; 0,06 Ti | св | св | св | св. АМг4 | 10 | 7,0 | |
АМг5 | 5,3 Mg; 0,6 Мn; 0,06 Ti | св | св | св | св. | 10 | 7,0 | |
АМг6 | 6,3 Mg; 0,6 Мn; 0,06 Ti | св | св | св | св. АМг6 | 8,0 | 8,0 | |
Б. Термически упрочняемые | ||||||||
Аl-Сu | Д20 | 6,5 Сu; 0,6 Мn; 0,15 Ti | св | св | — | Д20 | 15 | 6,0 |
1201 | 6,3 Сu; 0,3 Мn; 0,06 Ti; 0,17 Zr; 0,1 V | св | — | св. 1201 | 5,0 | 10 | ||
1205 | 6,3 Сu; 0,6 Мn; 0,06 Ti; 0,11 Zr; 0,15 Cd | нс | нс | св | св. 1201 | 12 | 6,0 | |
Al-Mg-Si | АД31 | 0,6 Mg; 0,5 Si | нс | нс | св | св. | 15 | 6,0 |
АД33 | 1,1 Mg; 0,25 Сu; 0,6 Si; 0,25 Сг | нс | нс | св | св. АК5 | 12 | 6,0 | |
АД35 | 1,1 Mg; 1,0 Si; 0,7 Мn; 0,25 Сг | нс | нс | св | св. АК5 | 12 | 6,0 | |
АВ | 0,7 Mg; 0,3 Си; 0,85 Si; 0,25 Мn | нс | нс | св | св. АК5 | 10 | 7,0 | |
Al-Zn-Mg | В92ц | 4,4 Mg; 3,2 Zn; 0,8 Мn; 0,13 Zr; 0,14 Cr | св | св | нс | св. В92ц | 12 | 6,0 |
1915 | 1,1 Mg; 3,7 Zn; 0,4 Mn 0,18 Zr | нс | нс | св | св. | 10 | 7,0 | |
Al-Mg-Cu | ВАД1 | 2,5 Mg; 4,1 Cu; 0,6 Mn; 0,06 Ti; 0,15 Zr | св | св | нс | ВАД1 | 10 | 7,0 |
Д1 | 0,6 Mg; 4,3 Cu; 0,6 Mn | нс | нс | нс | D1 | 40 | 2,0 | |
Д16 | 1,5 Mg; 4,3 Cu; 0,6 Mn | нс | нс | нс | D16 | 50 | 1,0 | |
Д19 | 2,0 Mg; 4,0 Cu; 0,75 Mn | нс | нс | нс | Д19 | 45 | 2,0 | |
Al-Mg-Cu-Zn | В95 | 2,3 Mg; 1,7 Cu; 6,0 Zn; 0,4 Mn; 0,18 Cr | нс | нс | нс | В95 | 50 | 1,0 |
В96 | 2,6 Mg; 2,3 Cu; 8,5 Zn | нс | нс | нс | В96 | 60 | 1,0 | |
Al-Mg-Si-Cu | АК6 | 0,6 Mg; 2,2 Cu; 0,9 Si;0,6 Mn | нс | нс | нс | АК6 | 45 | — |
АК8 | 0,6 Mg; 4,3 Cu; 0,9 Si; 0,7 Mn | нс | нс | нс | АК8 | 50 | — | |
Al-Mg-Cu-Fe-Si | АК4 | 1,6 Mg; 2,2 Cu; 1,2 e; 1,3 Ni | нс | нс | нс | АК4 | 60 | — |
АК4-1 | 1,6 Mg; 2,2 Cu; 1,2 e; 1,2 Ni | нс | нс | нс | АК4 | 65 | — | |
Магниевые сплавы | ||||||||
А. | ||||||||
M-Мn | MA1 | 1,9 Мn | св | св | нс | MA1 | 10 | — |
MA8 | 1,9 Мn; 0,25 Се | нс | нс | св | MA2-1 | 20 | — | |
Mg-Zn | MA20 (ВМД8) | 1,25 Zn; 0,2 Се; 0,09 Zr | нс | нс | св | MA20-1 | 10 | — |
Mg-Al-Zn | MA2 | 3,5 Al; 0,5 Zn; 0,3 Мn | нс | нс | св | MA2-1 | 15 | — |
MA2-1 | 4,4 Al; 1,1 Zn; 0,4 Мn | св | св | нс | MA2-1 | 20 | — | |
Mg-Zn-Cd-La | MA15 (ВМД3) | 1,6 Cd; 3,0 Zn; 0,9 La; 0,7 Zr | нс | нс | нс | MA15 | 30 | — |
Mg-Zn-Cd-Nd | MA19 (ВМД6) | 0,6 Cd; 6,2 Zn; 1,7 Nd; 0,7 Zr | нс | нс | нс | MA19 | >30 | — |
Б. | ||||||||
Mg-Zn | MA14 (BM65-1) | 5,5 Zn; 0,6 Zr | нс | нс | нс | MA14 | >40 | — |
Mg-Nd | MA12 | 3,0 Nd; 0,6 Zr | св | св | нс | MA12 | 15 | — |
Mg-Al-Zn | MA5 | 8,5 Al; 0,5 Zn; 0,3 Mn | св | св | нс | MA5 | 20 | — |
Mg-Mn-Nd | МА11 | 3,0 Nd; 2,0 Mn: 0,2 Ni | нс | нс | нс | МА11 | >40 | — |
Свариваемость алюминия и его сплавов
Свариваемость алюминия и его сплавов [c.
Свариваемость алюминия и его сплавов в первую очередь определяется возможностью получения металла шва без трещин и пор при высоких механических свойствах п коррозионной стойкости сварных соединений. Кроме того, свариваемость алюминия и его сплавов характеризуется некоторыми затруднениями получения хорошего сплавления и плотного металла шва без шлаковых включений в связи с образованием в процессе сварки на поверхности металла шва пленки окиси алюминия и наличием ее на поверхности свариваемого металла. Пленка имеет значительно более высокую температуру плавления (2050°), чем алюминий (658°), и больший удельный вес (3,9), чем алюминий (2,7). При сварке алюминия и его сплавов необходимо учитывать высокую теплопроводность их (у алюминия в три раза больше, чем у железа), что вызывает быстрый отвод тепла от места сварки, Высокая теплопро-
СВАРИВАЕМОСТЬ АЛЮМИНИЯ И ЕГО СПЛАВОВ [c.375]
Свариваемость алюминия и его сплавов. Проблемы металлургического характера-.
[c.378]
Особенности свариваемости алюминия и его сплавов. [c.127]
Свариваемость сталей — ОсноБНые характеристики 23 Сварка алюминия и его сплавов 27 [c.555]
При аргонно-дуговой и газовой сварке алюминия и его сплавов сварочная проволока и присадочные прутки следует применять того же или аналогичного состава, что и свариваемый металл. [c.29]
Для автоматической сварки сжатой дугой применяют установку УПС-501, рассчитанную на силу тока до 500 А. Для ручной сварки используют установку УПС-301, позволяющую сваривать на постоянном токе прямой и обратной полярности силой 4…315 А в непрерывном и импульсном режимах коррозионно-стойкие стали толщиной до 5 мм, медь и ее сплавы от 0,5 до 3 мм, алюминий и его сплавы толщиной 1…8 мм. Напряжение холостого хода этой установки 80 В, рабочее напряжение дуги 18…40 В. Плазмотрон установки УПС-301 имеет комплект сменных сопел с различными диаметрами канала и обеспечивает сварку на токах силой 25. ..315 А при прямой и 25…70 А при обратной полярности. Его конструкция обеспечивает возможность возбуждения дуги касанием свариваемого изделия.
[c.231]
Зависимость зазоров, расстояний между прихватками и их размеров от толщины свариваемых встык деталей из алюминия и его сплавов [c.340]
Электрошлаковую сварку алюминия и его сплавов осуществляют для толщин металла 50. .. 250 мм. Сварку ведут на переменном токе пластинчатыми электродами или плавящимися мундштуками. Применяют флюсы АН-301, АН-302 на основе галогенидов щелочных и щелочноземельных металлов. Формирование шва осуществляют медными водоохлаждаемыми или графитовыми кристаллизаторами. Плотность тока в электроде около 2,5 А/мм , скорость сварки 6. .. 8 м/ч. Прочность сварных соединений составляет 80. .. 100 % прочности основного металла. Технико-экономическая эффективность данного способа сварки возрастает с увеличением толщины свариваемых изделий. [c.448]
Сварка стали с алюминием и его сплавами. Процесс затруднен физико-химическими свойствами алюминия. Выполняется в основном аргонодуговая сварка вольфрамовым электродом. Подготовка стальной детали под сварку предусматривает для стыкового соединения двусторонний скос кромок с углом 70°, так как при таком угле скоса прочность соединения достигает максимального значения (см. рис. 13.7, б). Свариваемые кромки тщательно очищают механическим или пескоструйным способом или химическим травлением, затем на них наносят активирующее покрытие. Недопустимо применение дробеструйной очистки, так как при этом на поверхности металла остаются оксидные включения. Наиболее дешевое покрытие — цинковое, наносимое после механической обработки.
[c.499]
Алюминий и его сплавы сваривают автоматической сваркой по флюсу (рис. 93,6). Флюс с помощью дозирующего приспособления 1 непрерывно в процессе сварки насыпается впереди дуги 2 тонким слоем, при этом флюс не закрывает дугу, а слой жидкого флюса 4 надежно защищает сварочную ванну 3 и удаляет пленку окислов.
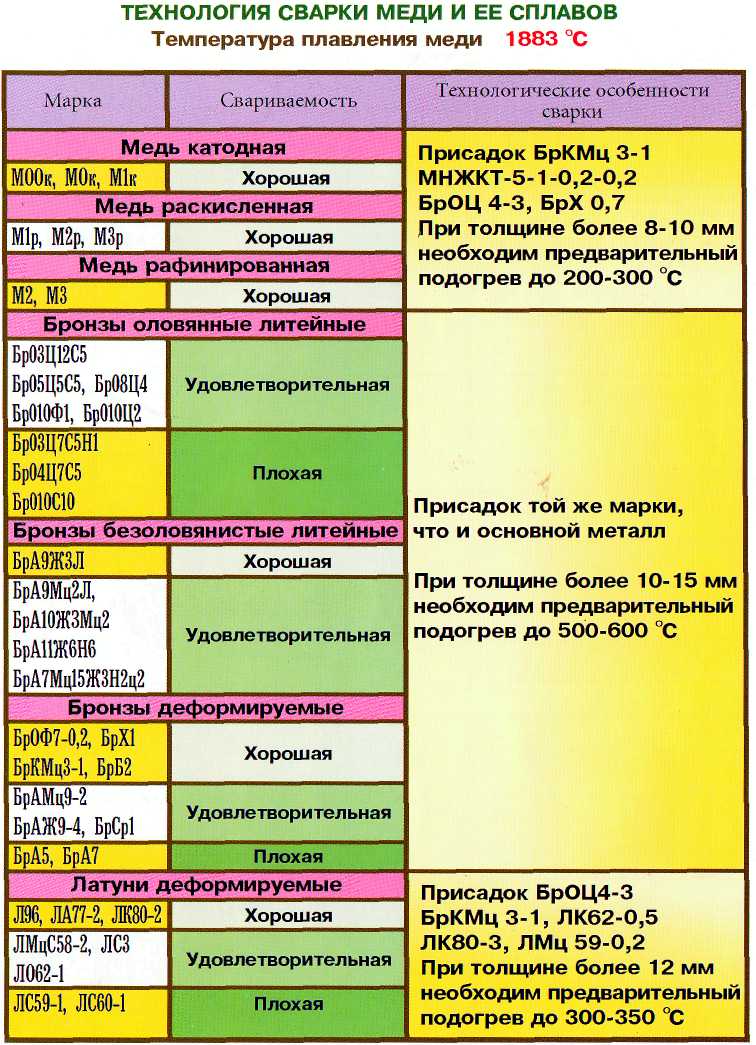
При сварке алюминия и его сплавов в качестве присадки применяют проволоку того же химического состава, что и химический состав свариваемого металла. Хорошие результаты при сварке сплава АМц и некоторых термически обрабатываемых алюминиевых сплавов дает применение присадочной проволоки марки АК, содержащей около 5% 51. Эта проволока обеспечивает повышенную жидкотекучесть металла шва и меньшую усадку его при остывании. [c.495]
При сварке алюминия и его сплавов угольным электродом берут присадочную электродную проволоку марок АО, А1 или прутки из сплава АК, содержащего 5 % кремния. Для растворения оксидной пленки служат специальные флюсы, в состав которых входят хлористые натрий, калий, литий, фтористые натрий и калий, сернокислый калий и криолит. Флюсы разводят на чистой питьевой воде и в виде кашицы наносят (окунанием или кисточкой) на присадочные стержни слоем 0,2—0,3 мм. После этого стержни сушат на воздухе при 20—25 °С в течение 25—30 мин. Флюс можно наносить также на свариваемые кромки.
[c.64]
Выбор мощности пламени при газовой сварке алюминия и его сплавов в зависимости от толщины свариваемого металла [c.517]
Газы — заменители ацетилена При сварке и резке металлов можно применять также другие горючие газы и пары горючих жидкостей. Для эффективного нагрева и расплавления металла при сварке необходимо, чтобы температура пламени примерно в два раза превышала температуру плавления свариваемого металла. Поэтому использовать газы — заменители ацетилена целесообразно только при сварке металлов с более низкой температурой плавления, чем сталь (алюминия и его сплавов, латуни, свинца) при пайке- и т. п. [c.35]
Сварка в инертных газах. Алюминий и его сплавы в инертных газах сваривают неплавящимся вольфрамовым электродом или плавящимся электродом. Сварку вольфрамовым электродом выполняют со сварочной проволокой или без нее. Состав электродной или сварочной проволоки принимается близким к составу свариваемого металла.
[c.407]
Технологические особенности сварки алюминия и его сплавов полуоткрытой дугой (по флюсу). Получение качественных сварных соединений из алюминия и его сплавов требует тщательного удаления перед сваркой жировой смазки со свариваемых кромок и электродной проволоки, а также обезжиривания поверхности металла на ширине 100—150 мм от кромки ацетоном или другими растворителями. Оксидную пленку, находящуюся под жировой смазкой на ширине 25—30. мм, удаляют механической зачисткой НЛП химическим травлением с последующей промывкой в проточной воде, осветлением, повторной промывкой и сушкой сжатым воздухом. Зачищенная поверхность алюминия сохраняет свои свойства в течение 3—4 дней. При более длительном хранении на зачищенной поверхности может образоваться оксидная пленка, адсорбирующая влагу из воздуха. [c.423]
Способность материалов свариваться ультразвуком различна. Хорошо свариваются медь, алюминий и его сплавы, титан и многие другие пластичные металлы хуже — жаропрочные стали к числу материалов, сваривающихся плохо, относятся инструментальные стали. Наибольшая толщина верхней свариваемой детали зависит в основном от подводимой к ней акустической мощности. Например, при мощности 2 кет удается сваривать плакированный дур-алюмин толщиной до 1—1,5 мм, а при мощности 4 кет до 2—2,5 мм.
[c.606]
Газовая сварка. Этот способ сварки алюминия и его сплавов малоэффективен. Основной его недостаток — необходимость применения флюсов и малая концентрация тепла по сравнению с дуговой сваркой. Мощность пламени выбирают в зависимости от толщины свариваемого металла [c.406]
Пламя должно быть строго нормальным. В качестве присадочного металла применяют сварочную проволоку из алюминия и его сплавов. Диаметр присадочной проволоки зависит от толщины свариваемого металла [c.408]
При сварке алюминия и его сплавов избыток кислорода не допускается, так как образуется при этом большое количество трудноудаляемой пленки окиси алюминия. При избытке образуется большое количество пор з сварном шве. Расход ацетилена зависит от толщины свариваемого металла (табл. 13).
[c.92]
Какова роль окисной пленки А12О3 при рассмотрении проблем свариваемости алюминия и его сплавов Каким образом эта пленка удаляется из зоны сварки [c.413]
Свариваемость алюминия и его сплавов. Алюминий и его сплавы имеют большую теплопроводность, теплоемкость и скрытую теплоту плавления. Теплопроводность алюминия в три раза выше теплопроводности низкоуглеродис-той стали при нагреве от 20 до 600°С разница в теплопроводности еще более возрастает. Следовательно, сварка алюминия и его сплавов должна выполняться с относительно мощным и концентрированным источником нагрева. [c.164]
Наиболее широко применяют сварку алюминия и его сплавов в атмосфере защитных газов неплавящимся (толщины 0,5—10 мм) и плавящимся (толщины более 10 мм) электродом. В этом случае получают более высокое качество сварных швов по сравнению с другими видами дуговой сварки. Применяют также автоматическую сварку плавящимся электродом полуоткрытой дугой по слою флюса, при которой для формирования корня шва используют медные или стальные подкладки. Возможна газовая (ацетилено-кислородная) сварка алюминия и его сплавов. Флюс наносят на свариваемые кромки в виде пасты или вводят в сварочную ванну на разогретом конце присадочного прутка. Алюминий и его сплавы также сваривают плазменной и электрошлаковой сваркой они достаточно хорошо свариваются контактной сваркой. Учитывая высокую теплопроводность и электропроводимость алюминия, для его сварки необходимо применять большие силы тока.
[c.237]
Таким образом, наиболее склонен к порообразованию алюминий и его сплавы. В сварочной технологии на возникновение пор влияет время пребывания сварочной ванны в жидком состоянии, что зависит от скорости сварки. При малой скорости сварки алюминия водород успевает покинуть ванну и наплавленный металл будет плотным, при больших скоростях сварки (Исв>50м/ч) водород не успевает выделиться из кристаллизующегося металла и образовать поры, а при скорости сварки 20 м/ч обычно возникают поры. При сварке алюминия и его сплавов типа АМгб требуются особые меры для очистки кромок свариваемых изделий и тщательная подготовка электродной проволоки, а также использование аргона, имеющего минимальную влажность (Г. Д. Никифоров).
[c.346]
Сварка алюминия и его сплавов. При сварке деталей из алюминия и его сплавов возникают трудности, связанные с тугоплавкостью пленки окислов (AI2O3) на поверхности деталей, температура плавления которой 2050 °С. Пленка мешает соединению свариваемых деталей, поскольку температура плавления алюминия 658 °С. Коэффициент линейного расширения алюминия в 2 раза, а теплопроводность в 3 раза больше, чем эти же параметры для стали, что приводит к значительным деформациям свариваемых деталей. [c.120]
Больщое значение при сварке алюминия и его сплавов имеет правильный выбор присадочного металла. Чтобы получить для металла шва свойства, близкие к свойствам основного металла (прочность, пластичность, коррозионная стойкость, теплофизические характеристики и т. д.), целесообразно использовать присадочный металл того же состава, что и основной. Однако из-за повышенной склонности большинства сплавов алюминия к кристаллизационным трещинам более рационально применять присадочный материал, который, отличаясь по составу от свариваемого сплава, обеспечил бы проведение эффективного комплексного легирования с использованием модификаторов.
[c.371]
При аргоно-дуговой сварке неплавящимся электродом (рис. У.14) через специальную горелку 4, в которой установлен вольфрамовый электрод 3, пропускают нейтральный газ — аргон (или гелий). Возбуждение дуги происходит между электродом и свариваемым изделием. Для заполнения разделки кромок в зону вводят присадочный пруток 2, химический состав которого близок к составу основного металла. Применяют электроды диаметром 2—6 мм. Аргон подается в горелку под давленпем 0,3—0,5 ат (0,03—0,05 МПа). Аргоно-дуговая сварка применяется для сварки легированных сталей, алюминия и его сплавов, титана, магниевых сплавов и дает хорошие результаты.
[c.275]
В качестве электродов или присадочного материала при сварке чистого алюминия и его сплавов используют прутки или проволоку, по химическому составу близкие к свариваемому металлу. В покрытия электродов или в флюс вводят хлористые и фтористые соли лития, калия, энергично растворяющиеся и ошлаковывающие оксид алюминия. Сварку ведут постоянным током обратной полярности, [c.79]
Сварка алюминия и его сплавов. Алюминий и его сплавы хорошо свариваются газовой сваркой только нормальным пламенем. Присадочную проволоку применяют такого же состава, как свариваемый металл. Для удаления пленки оксида алюминия используют флюсы АФ-4А, АН-4А, АН-А201, содержащие хлористые и фтористые соли лития, натрия, калия и бария. После сварки остатки флюса удаляют горячей водой. Оксидную пленку можно удалять так же, как при дуговой сварке, специальным скребком. В этом случае сварщик должен иметь большой навык, так как в шов могут попадать остатки оксидной пленки и вызывать не-сплавление металла.
[c.85]
ЭШС алюминия и его сплавов. Электрошлаковую сварку алюминия и его сплавов целесообразно осуществлять прн толщине металла свыше 40 мм. В этом случае экономический эффект составляет более 50 % затрат, имеющих место при многопроходипй механизированной дуговой сварке. С увеличение1М толщины свариваемого металла, как и при сварке других цветных металлов и сплавов, технико-экономическая эффективность процесса сварки возрастает. [c.492]
При газовой сварке алюминия и его сплавов пламя берется нормальное. Избыток кислорода и горючего газа не допускается, так как свободный кислород окисляет алюминий, а избыток горючего газа приводит к сильной пористости шва. Мощность сварочиого пламени выбирается из расчета расхода ацетилена 75 дм ч на 1 мм толщины свариваемого изделия. Расход ацетилена в зависимости от толщины свариваемого металла приведен ниже
[c. 261]
Основной трудностью при сварке алюминия является образование на поверхности алюминия тугоплавкой окис-ной пленки А1гОз с температурой плавления 2060° С, которая затрудняет плавление металла и сплавление свариваемых кромок. Другая трудность заключается в том, что при нагреве алюминий не меняет своего цвета и поэтому трудно уловить момент начала его плавления. От сваршика требуется большой навык и опыт по сварке алюминия и его сплавов. [c.92]
Влияние водорода на сварные соединения из алюминия гораздо сильнее, чем на медь и ее сплавы, так как растворимость водорода ничтожна в твердом алюминии и его сплавах, а изменение ее в процессе кристаллизации очень велико. В отличие от меди, алюминий почти не растворяет свой тугоплавкий окисел А1гОз, который всегда образуется на свариваемых кромках и на присадочном металле. Окисные включения (пленки) способствуют зарождению газовых пузырей и образованию пор. [c.335]
Сварка алюминия и его сплавов
Сварка алюминия и его сплавов
Категория:
Сварка различных металлов
Сварка алюминия и его сплавов
Алюминий обладает низкой прочностью; поэтому его не применяют для конструкций, работающих под динамической нагрузкой. Его употребляют в химическом аппарато-строении, рамных конструкциях, для оконных и дверных переплетов и декоративных изделий в строительстве. Он обладает малой массой (плотность 2,7 г/см3), повышенной коррозионной стойкостью и большой пластичностью по сравнению с низкоуглеродистой сталью.
Повышенную прочность имеют сплавы алюминия с марганцем, магнием, кремнием, цинком и медью.
Алюминий и его сплавы делят на литейные и деформируемые (катаные, прессованные, кованые). Деформируемые сплавы подразделяют на термически не упрочняемые, к которым относятся сплавы алюминия с марганцем и магнием, и термически упрочняемые, к которым относятся сплавы алюминия с медью, цинком, кремнием.
Наиболее высокой прочностью обладают термически упрочняем мые алюминиевые сплавы. Например, механические свойства дюр алюминия Д16 (3,8—4,9% меди, 1,2—1,8% магния, 0,3—0,9% мар ганца, остальное — алюминий) следующие: до термической обра-ботки — 6В = 22 кгс/мм2 и 6б = 2%; после термической обработки ств=42 кгс/мм2 и 65=18%. Наибольшей прочностью из термиче ски упрочняемых алюминиевых сплавов обладает сплав В95 (ав = 60 кгс/мм2, огт = 55 кгс/мм2 и 65 — около 12%), сплав по, строен на основе алюминий — медь — магний — цинк.
Однако термически упрочненные алюминиевые сплавы разуп рочняются при сварке со значительной потерей механических свойств. Применение этих сплавов для сварных конструкций воз» можно лишь при условии обеспечения термической обработки после сварки для повышения прочности сварных соединений.
Из термически неупрочняемых сплавов наибольшей прочностью обладают сплавы системы А1 — Mg — Ti, например сплав АМгб, механические свойства которого следующие: сгв = 32—38 кгс/мм2, стт = 1 б— 18 кгс/мм2, бБ= 15—20% и ак=3—4 кгс-м/см2. Конструкции из алюминиево-магниевого сплава АМгб изготовляются в основном сварными.
Свариваемость алюминия и его сплавов. Алюминий и его сплавы имеют большую теплопроводность, теплоемкость и скрытую теплоту плавления. Теплопроводность алюминия в три раза выше теплопроводности низкоуглеродистой стали; при нагреве от 20 до 600° С разница в теплопроводности еще более возрастает. Следовательно, сварка алюминия и его сплавов должна выполняться с относительно мощным и концентрированным источником нагрева.
Коэффициент линейного расширения алюминия в два раза выше, чем коэффициент расширения железа. Это способствует увеличенным деформациям и короблению при сварке алюминиевых изделий.
Низкая удельная плотность (2,7 г/см3) и температура плавления (660° С) алюминия по сравнению с высокой удельной плотностью окисла алюминия А120э (3,85 г/см3) и его температурой плавления (2060° С) затрудняют процесс сварки. Тугоплавкий и тяжелый окисел AI2O3 может оставаться в металле шва и снижать работоспособность сварного соединения. При сварке алюминия и его сплавов необходимо применять различные способы борьбы с окислом А1203. Во всех случаях поверхность металла изделия должна зачищаться непосредственно перед сваркой и процесс сварки должен протекать с защитой расплавленного металла от действия газов воздуха.
Используют три способа борьбы с окислом алюминия: сварка с растворителем окислов (электродные покрытия, флюсы), сварка без растворителей, но с так называемым катодным распылением, и сварка с механическим удалением окислов из сварочной ванны.
Растворителями окисла А1203 и других окислов являются галоидные соли щелочноземельных металлов (хлористый, фтористый литий и др.), которые растворяют окислы и вместе с ними подни-1аЮтся из сварочной ванны в сварочный шлак. Так как раствор обладает пониженной температурой плавления, меньшей удельной плотностью и меньшей вязкостью, чем каждый компонент в отдельности, то он выводится из металла шва в сварочный шлак.
Сущность катодного распыления состоит в том, что при дуговой сварке в аргоне на постоянном токе при обратной полярности происходит дробление окисной пленки А1203 с последующим распылением частиц окисла на поверхности сварного изделия. Тонкая окисная пленка, покрывающая сварочную ванну, разрушается под ударами тяжелых положительных ионов защитного газа аргона, образующихся при горении дуги. Так как положительный ион обладает большей массой, чем электрон, то образующийся поток ионов способен дробить окнсные пленки алюминия и магния, которые создаются при сварке. При этом надо учитывать большую скорость движения ионов, позволяющую распыленным окислам через защитную газовую среду выходить из сварочной зоны.
Другие газы, обладающие низкой атомной массой (например, 4 у гелия вместо 40 у аргона), не способны дробить и распылять окислы.
Механический способ удаления окисла А1203 из сварочной ванны заключается в том, что сварщик опускает в сварочную ванну стальной пруток диаметром 3—4 мм и вынимает его с прилипшим к поверхности прутка окислом, который легко отделяется от прутка при его встряхивании и легком ударе. Опытные рабочие, выполняющие газовую или дуговую сварку угольным электродом, часто используют этот способ, не прибегая к флюсам.
Алюминиевые сплавы обладают повышенной склонностью к образованию пор. Пористость металла при сварке алюминия и его сплавов вызывается водородом, источником которого служит адсорбированная влага на поверхности основного металла и особенно проволоки, а также воздух, подсасываемый в сварочную ванну. В этом случае алюминий в сварочной ванне взаимодействует с влагой по реакции 2А1+ЗН20->-А120з+6Н.
Для получения беспористых швов при сварке алюминия и его сплавов даже небольшой толщины иногда требуется подогрев, снижающий скорость охлаждения сварочной ванны и способствующий более полному удалению водорода из металла при медленном охлаждении. Так, например, при наплавке на лист алюминия толщиной 8 мм беспористый шов может получить при подогреве металла до 150 °С. При увеличении толщины металла до 16 мм даже подогрев до температуры 300 °С не обеспечивает беспористых швов.
Однако подогрев листов для сварки некоторых сплавов следует применять осторожно. Например, при сварке толстолистовых алю-миниево-магниевых сплавов допускается подогрев до температуры не выше 100—150 °С. Более высокая температура подогрева может усилить пористость шва за счет выделения из твердого раствора магния и образования при этом водорода по реакции Mg + h30-vMg0 + 2H. Кроме того, при сварке подогретого металла
Флюс АФ-4а разводят дистиллированной водой и наносят на свариваемые кромки и присадочный пруток.
При газовой сварке применяют присадочную проволоку той же марки, что и свариваемый металл.
Для получения и сохранения мелкозернистой структуры изделие после сварки в некоторых случаях, например при сварке литых деталей, подвергают отжигу при 300—350 °С с последующим медленным охлаждением.
—-
Алюминий обладает малой плотностью, хорошей тепло- и электропроводностью, высокой коррозионной стойкостью и пластичностью. В технике алюминий применяют в виде алюминия разной степени чистоты и в виде сплавов.
В зависимости от содержания примесей (Fe, Si, Си, Zn, Ti) алюминий бывает особой чистоты А999 (0,001 % примесей), высокой чистоты А995, А99, А97, А95 (0,005—0,5% примесей) и технической чистоты А85, А8 и др. (0,15—1,0% примесей). Технический алюминий, выпускаемый в виде деформируемого полуфабриката (листы, профили, прутки и др.), используют в сварных конструкциях, маркируется АД0 и АД1.
Из-за низкой прочности (сгв=804-110 МПа) алюминий применяют для ненагруженных деталей и элементов конструкций, когда от материала требуется легкость, свариваемость, пластичность, коррозионная стойкость (рамы, двери, трубопроводы, емкости, фольга и др. ). Для нагруженных изделий используют сплавы алюминия. В качестве основных легирующих элементов алюминиевых сплавов применяют Си, Mg, Si, Mn, Zn, реже — Li, Ni, Ti, Be, Zr.
Алюминиевые сплавы классифицируют по технологии изготовления, способности к термической обработке и свойствам. В зависимости от технологии изготовления различают деформируемые (для полуфабрикатов и изделий обработкой давлением), литейные (для отливок) и спеченные сплавы. По способности к термической обработке они разделяются на термические неупрочняемые и термические упрочняемые.
К литейным сплавам относятся сплавы системы А1—Mg, А1— Si, А1—Си. Наиболее распространенными литейными сплавами с повышенным содержанием кремния (от 4 до 13%) являются силумины. Сварку литейных сплавов выполняют при ремонтных работах.
Материалы из спеченной алюминиевой пудры (САП) и спеченных алюминиевых сплавов (САС) состоят из порошков алюминия или его сплавов и окиси алюминия. Получают САП и САС последовательным брикетированием, спеканием и прессованием окисленной с поверхности алюминиевой пудры. алюминием (р=3,85 г/см3). Окисная пленка затрудняет сплавление, способствует непроварам и охрупчивает металл. Поэтому окисную пленку удаляют со свариваемых кромок механическими и химическими способами перед сваркой, во время сварки защищают зону сварки инертным газом, катодным распылением, применяют покрытия и флюсы на основе солей щелочных и щелочноземельных металлов (NaCl, NaF, КС1 и др.).
2. Склонность к образованию горячих трещин в связи с большой литейной усадкой кристаллизующегося металла, грубой столбчатой структурой сварного шва и наличием примесей. Для борьбы с горячими трещинами ограничивают содержание примесей в свариваемом металле, для измельчения структуры добавляют в металл и сварочную .проволоку модификаторы (Zr, Ti, В), регулируют режимы сварки.
3. Термически упрочняемые сплавы весьма чувствительны к термическому циклу сварки в связи с ростом зерна, распадом перенасыщенных твердых растворов, процессами старения, рекристаллизацией.
4. Для ряда сплавов, особенно содержащих в качестве основного легирующего элемента магний, характерна повышенная пористость при сварке, связанная с насыщением расплавленного металла водородом. Для уменьшения пористости рекомендуется тщательная подготовка свариваемых кромок и проволоки перед сваркой для удаления следов влаги с их поверхности; тщательная защита сварочной ванны, увеличение диаметра присадочной проволоки, чтобы уменьшить удельную поверхность присадки; предварительный подогрев, чтобы увеличить время существования сварочной ванны и чтобы пузырьки водорода успели выйти из ванны.
5. Высокие теплопроводность и теплоемкость алюминия требуют применения мощных источников тепла, а в ряде случаев подогрева. Высокий коэффициент линейного расширения и малый модуль упругости способствуют появлению значительных сварочных деформаций, что требует применения надежных зажимных приспособлений и устранения деформаций после сварки в ответственных конструкциях. В алюминии отсутствует пластическое состояние при нагреве и переходе из твердого в жидкое состояние, при этом алюминий не меняет своего цвета, а в области температур более 400—450 °С имеется провал прочности и пластичности, поэтому рекомендуется сварка на подкладках.
Высокий коэффициент вязкости и быстрый теплоотвод затрудняют формирование шва, поэтому требуется соблюдение необходимых разделок кромок. Все перечисленные трудности и особенности свар-; ки алюминия требуют тщательной подготовки под сварку и тщательное соблюдение технологии сварки.
Способы сварки алюминия и его сплавов. Основными способами сварки алюминия и его термонеупрочняемых сплавов являются сварка в инертных газах, по флюсу и под флюсом, ручная покрытыми электродами, контактная. Используют также газовую сварку, электрошлаковую сварку угольным электродом. Для термически упрочняемых сплавов применяют преимущественно механизированные способы сварки в инертных газах, электронно-лучевую, плаз-менно-дуговую.
Для тонколистового металла целесообразна сварка в импульсном режиме. Для толстолистового металла (6>10 мм) хорошие результаты дает трехфазная сварка неплавящимся электродом. Сварку плавящимся электродом в инертных газах выполняют при толщинах более 4 мм на постоянном токе обратной полярности /св = (120-г-160)da, где da — диаметр сварочной проволоки. Недостатком сварки плавящимся электродом является повышенная пористость.
Газовую сварку выполняют нормальным пламенем с использованием защитного флюса в виде порошка или пасты, наносимого на свариваемые кромки и присадочной проволоки типа АФ-4А (КО— 50%, LiCl — 14%, NaCl—28%. NaF—8%), с подогревом металла при сварке больших толщин. Ориентировочную мощность сварочного пламени выбирают из расчета расхода ацетилена 75 дм3/ч на 1 мм толщины свариваемого металла.
При использовании флюсовой защиты применяют следующие способы электрической сварки плавлением: дуговую автоматическую по флюсу и под флюсом и электрошлаковую. При сварке по слою флюса используют флюсы на основе солей щелочных и щелочноземельных металлов (например, АН-А1 системы Na3AlF3—КС1—NaCl), которые обладают высокой электропроводностью, поэтому погруженная дуга закорачивается и горит по слою флюса. Дополнительным параметром режима при сварке по слою флюса является высота насыпного слоя флюса перед дугой. Добавление во флюсы для сварки алюминия компонентов, уменьшающих электропроводность флюса, позволило разработать способ сварки под слоем флюса. В качестве такого компонента во флюс ЖА-64 введен кремнезем SiOa (система Na3AlF3—КС1—NaCl—Si02).
Контактную точечную и шовную сварку применяют для соединения листов и профильного проката преимущественно из деформируемых сплавов. Контактную стыковую сварку выполняют преимущественно методом оплавления. Тацгкак алюминий и его сплавы отличаются высокой тепло- и электропроводностью, то необходимо при электроконтактной сварке, особенно точечной, применение больших токов и мощных машин, для повышения эффективности нагрева целесообразно сваривать при малой длительности импульсов тока.
Пластичные сплавы алюминия хорошо свариваются другими видами сварки термомеханического и механического классов.
Реклама:
Читать далее:
Сварка титановых сплавов
Статьи по теме:
СВОЙСТВА АЛЮМИНИЕВЫХ СПЛАВОВ
АЛЮМИНИЕВЫЕ СПЛАВЫ
Содержание
— классификация сплавов
— физические свойства
— коррозионные свойства
— механические свойства
— круглый и профильный алюминиевый прокат
— плоский алюминиевый прокат
— интересные интернет-ссылки
Классификация алюминиевых сплавов.
Алюминиевые сплавы условно делятся на литейные (для производства отливок) и деформируемые (для производства проката и поковок). Далее будут рассматриваться только деформируемые сплавы и прокат на их основе. Под алюминиевым прокатом подразумевают прокат из алюминиевых сплавов и технического алюминия (А8 – А5, АД0, АД1). Химический состав деформируемых сплавов общего применения приведен в ГОСТ 4784-97 и ГОСТ 1131.
Деформируемые сплавы разделяют по способу упрочнения: упрочняемые давлением (деформацией) и термоупрочняемые.
Другая классификация основана на ключевых свойствах: сплавы низкой, средней или высокой прочности, повышенной пластичности, жаропрочные, ковочные и т.д.
В таблице систематизированы наиболее распространенные деформируемые сплавы с краткой характеристикой основных свойств присущих для каждой системы. Маркировка дана по ГОСТ 4784-97 и международной классификации ИСО 209-1.
Характеристика сплавов | Маркировка | Система легирования | Примечания | |
СПЛАВЫ УПРОЧНЯЕМЫЕ ДАВЛЕНИЕМ (ТЕРМОНЕУПРОЧНЯЕМЫЕ) | ||||
Сплавы низкой прочности и высокой пластичности,свариваемые, коррозионносойкие | АД0 | 1050А | Техн.![]() | Также АД, А5, А6, А7 |
АД1 | 1230 | |||
АМц | 3003 | Al – Mn | Также ММ (3005) | |
Д12 | 3004 | |||
Сплавы средней прочности и высокой пластичности,свариваемые, коррозионносойкие | АМг2 | 5251 | Al – Mg (Магналии) | Также АМг0.![]() АМг4 и т.д. |
АМг3 | 5754 | |||
АМг5 | 5056 | |||
АМг6 | — | |||
ТЕРМОУПРОЧНЯЕМЫЕ СПЛАВЫ | ||||
Сплавы средней прочности и высокой пластичности свариваемые | АД31 | 6063 | Al-Mg-Si (Авиали) | Также АВ (6151) |
АД33 | 6061 | |||
АД35 | 6082 | |||
Сплавы нормальной прочности | Д1 | 2017 | Al-Cu-Mg (Дюрали) | Также В65, Д19, ВАД1 |
Д16 | 2024 | |||
Д18 | 2117 | |||
Свариваемые сплавы нормальной прочности | 1915 | 7005 | Al-Zn-Mg | |
1925 | — | |||
Высокопрочные сплавы | В95 | — | Al-Zn-Mg-Cu | Также В93 |
Жаропрочные сплавы | АК4-1 | — | Al-Cu-Mg-Ni-Fe | Также АК4 |
1201 | 2219 | Al-Cu-Mn | Также Д20 | |
Ковочные сплавы | АК6 | — | Al-Cu-Mg-Si | |
АК8 | 2014 |
Состояния поставки Сплавы, упрочняемые давлением, упрочняются только холодной деформацией (холодная прокатка или волочение). Деформационное упрочнение приводит к увеличению прочности и твердости, но уменьшает пластичность. Восстановление пластичности достигается рекристаллизационным отжигом. Прокат из этой группы сплавов имеет следующие состояния поставки, указываемые в маркировке полуфабриката:
1) не имеет обозначения — после прессования или горячей прокатки без термообработки
2) М — отожженное
3) Н4 — четвертьнагартованное
4) Н2 — полунагартованное
5) Н3 — нагартованное на 3/4
6) Н — нагартованное
Полуфабрикаты из термоупрочняемых сплавов упрочняются путем специальной термообработки. Она заключается в закалке с определенной температуры и последующей выдержкой в течение некоторого времени при другой температуре (старение). Происходящее при этом изменение структуры сплава, увеличивает прочность, твердость без потери пластичности. Существует несколько вариантов термообработки. Наиболее распространены следующие состояния поставки термоупрочняемых сплавов, отражаемые в маркировке проката:
1) не имеет обозначения — после прессования или горячей прокатки без термообработки
2) М — отожженное
3) Т — закаленное и естественно состаренное (на максимальную прочность)
4) Т1 — закаленное и искусственно состаренное (на максимальную прочность)
Для некоторых сплавов производится термомеханическое упрочнение, когда нагартовка осуществляется после закалки. В этом случае в маркировке присутствует ТН или Т1Н. Другим режимам старения соответствуют состояния Т2, Т3, Т5. Обычно им соответствует меньшая прочность, но большая коррозионная стойкость или вязкость разрушения.
Приведенная маркировка состояний соответствует российским ГОСТам.
Физические свойства алюминиевых сплавов.
Плотность алюминиевых сплавов незначительно отличается от плотности чистого алюминия (2.7г/см3). Она изменяется от 2.65 г/см3 для сплава АМг6 до 2.85 г/см3 для сплава В95.
Легирование практически не влияет на величину модуля упругости и модуля сдвига. Например, модуль упругости упрочненного дуралюминия Д16Т практически равен модулю упругости чистого алюминия А5 (Е=7100 кгс/мм2). Однако, за счет того, что предел текучести сплавов в несколько раз превышает предел текучести чистого алюминия, алюминиевые сплавы уже могут использоваться в качестве конструкционного материала с разным уровнем нагрузок (в зависимости от марки сплава и его состояния).
За счет малой плотности удельные значения предела прочности, предела текучести и модуля упругости (соответствующие величины, поделенные на величину плотности) для прочных алюминиевых сплавов сопоставимы с соответствующими значениями удельных величин для стали и титановых сплавов. Это позволяет высокопрочным алюминиевым сплавам конкурировать со сталью и титаном, но только до температур не превышающих 200 С.
Большинство алюминиевых сплавов имеют худшую электро- и теплопроводность, коррозионную стойкость и свариваемость по сравнению с чистым алюминием.
Ниже в таблице приведены значения твердости, тепло- и электропроводности для нескольких сплавов в различных состояниях. Поскольку значения твердости коррелируют с величинами предела текучести и предела прочности, то эта таблица дает представление о порядке и этих величин.
Из таблицы видно, что сплавы с большей степенью легирования имеют заметно меньшую электро- и теплопроводность, эти величины также существенно зависят от состояния сплава (М, Н2, Т или Т1):
марка | твердость, НВ | электропроводность в % по отношению к меди | теплопроводность в кал/оС | ||||||
М | Н2 | Н,Т(Т1) | М | Н2 | Н, Т(Т1) | М | Н2 | Н, Т(Т1) | |
А8 — АД0 | 25 | 35 | 60 | 0.![]() | |||||
АМц | 30 | 40 | 55 | 50 | 40 | 0.45 | 0.38 | ||
АМг2 | 45 | 60 | 35 | 30 | 0.34 | 0.30 | |||
АМг5 | 70 | 30 | 0.28 | ||||||
АД31 | 80 | 55 | 55 | 0.![]() | |||||
Д16 | 45 | 105 | 45 | 30 | 0.42 | 0.28 | |||
В95 | 150 | 30 | 0.28 |
Из таблицы видно, что только сплав АД31 сочетает высокую прочность и высокую электропроводность. Поэтому «мягкие» электротехнические шины производятся из АД0, а «твердые» — из АД31 (ГОСТ 15176-89). Электропроводность этих шин составляет (в мкОм*м):
0,029 – из АД0 (без термообработки, сразу после прессования)
0,031 – из АД31 (без термообработки, сразу после прессования)
0. 035 – из АД31Т (после закалки и естественного старения)
Теплопроводность многих сплавов (АМг5, Д16Т, В95Т1) вдвое ниже, чем у чистого алюминия, но все равно она выше, чем у сталей.
Коррозионные свойства.
Наилучшие коррозионные свойства имеют сплавы АМц, АМг, АД31, а худшие – высоко-прочные сплавы Д16, В95, АК. Кроме того коррозионные свойства термоупрочняемых сплавов существенно зависят от режима закалки и старения. Например сплав Д16 обычно применяется в естественно-состаренном состоянии (Т). Однако свыше 80оС его коррозионные свойства значительно ухудшаются и для использования при больших температурах часто применяют искусственное старение, хотя ему соответствует меньшая прочность и пластичность (чем после естественного старения). Многие прочные термоупрочняемые сплавы подвержены коррозии под напряжением и расслаивающей коррозии.
Свариваемость.
Хорошо свариваются всеми видами сварки сплавы АМц и АМг. При сварке нагартованного проката в зоне сварочного шва происходит отжиг, поэтому прочность шва соответствует прочности основного материала в отожженном состоянии.
Из термоупрочняемых сплавов хорошо свариваются авиали, сплав 1915. Сплав 1915 относится к самозакаливающимся, поэтому сварной шов со временем приобретает прочность основного материала. Большинство других сплавов свариваются только точечной сваркой.
Механические свойства.
Прочность сплавов АМц и АМг возрастает (а пластичность уменьшается) с увеличением степени легирования. Высокая коррозионная стойкость и свариваемость определяет их применение в конструкциях малой нагруженности. Сплавы АМг5 и АМг6 могут использоваться в средненагруженных конструкциях. Эти сплавы упрочняются только холодной деформацией, поэтому свойства изделий из этих сплавов определяются состоянием полуфабриката, из которого они были изготовлены.
Термоупрочняемые сплавы позволяют производить упрочнение деталей после их изготовления если исходный полуфабрикат не подвергался термоупрочняющей обработке.
Наибольшую прочность после упрочняющей термообработки (закалка и старение) имеют сплавы Д16, В95, АК6, АК8, АК4-1 (из доступных в свободной продаже).
Самым распространенным сплавом является Д16. При комнатной температуре он уступает многим сплавам по статической прочности, но имеет наилучшие показатели конструкционной прочности (трещиностойкость). Обычно применяется в естественно состаренном состоянии (Т). Но свыше 80 С начинает ухудшаться его коррозионная стойкость. Для использования сплава при температурах 120-250 С изделия из него подвергают искусственному старению. Оно обеспечивает лучшую коррозионную стойкость и больший предел текучести по сравнению с естественно-состаренным состоянием.
С ростом температуры прочностные свойства сплавов меняются в разной степени, что определяет их разную применимость в зависимости от температурного диапазона.
Из этих сплавов до 120 С наибольшие пределы прочности и текучести имеет В95Т1. Выше этой температуры он уже уступает сплаву Д16Т. Однако, следует учитывать, что В95Т1 имеет значительно худшую конструкционную прочность, т.е. малую трещиностойкость, по сравнению с Д16. Кроме того В95 в состоянии Т1 подвержен коррозии под напряжением. Это ограничивает его применение в изделиях, работающих на растяжение. Улучшение коррозионных свойств и существенное улучшение трещиностойкости достигается в изделиях обработанных по режимам Т2 или Т3.
При температурах 150-250 С большую прочность имеют Д19, АК6, АК8. При больших температурах (250-300 С) целесообразно применение других сплавов — АК4-1, Д20, 1201. Сплавы Д20 и 1201 имеют самый широкий температурный диапазон применения (от криогенных -250 С до +300 С) в условиях высоких нагрузок.
Сплавы АК6 и АК8 пластичны при высоких температурах, что позволяет использовать их для изготовления поковок и штамповок. Сплав АК8 характеризуется большей анизотропией механических свойств, у него меньше трещиностойкость, но он сваривается лучше, чем АК6.
Перечисленные высокопрочные сплавыт плохо свариваются и имеют низкую коррозионную стойкость. К свариваемым термоупрочняемым сплавам с нормальной прочностью относится сплав 1915. Это самозакаливающийся сплав (допускает закалку со скоростью естественного охлаждения), что позволяет обеспечить высокую прочность сварного шва. Сплав 1925, не отличаясь от него по механическим свойствам, сваривается хуже. Сплавы 1915 и 1925 имеют большую прочность, чем АМг6 и не уступают ему по характеристикам сварного шва.
Хорошо свариваются, имеют высокую коррозионную стойкость сплавы средней прочности — авиали (АВ, АД35, АД31,АД33).
АЛЮМИНИЕВЫЙ ПРОКАТ.
Из алюминия и его сплавов производятся все виды проката – фольга, листы, ленты, плиты, прутки, трубы, проволока. Следует иметь в виду, что для многих термоупрочняемых сплавов имеет место «пресс-эффект» — механические свойства прессованных изделий выше, чем у горячекатаных (т.е. круги имеют лучшие показатели прочности, чем листы).
Прутки, профили, трубы
Прутки из термоупрочняемых сплавов поставляются в состоянии «без термообработки» или в упрочненном состоянии (закалка с последующим естественным или искусственным старением). Прутки из термически неупрочняемых сплавов производятся прессованием и поставляются в состоянии «без термообработки».
Общее представление о механических свойствах алюминиевых сплавов дает гистограмма, на которой представлены гарантированные показатели для прессованных прутков при нормальных температурах:
Из всего приведенного многообразия в свободной продаже всегда имеются прутки из Д16, причем круги диаметром до 100 мм включительно обычно поставляются в естественно состаренном состоянии (Д16Т). Фактические значения (по сертификатам качества) для них составляют: предел текучести ?0.2 = (37-45), предел прочности при разрыве ?в = (52-56), относительное удлинение ?=(11-17%). Обрабатываемость прутков из Д16Т очень хорошая, у прутков Д16 (без термообработки) обрабатываемость заметно хуже. Их твердость соответственно 105 НВ и 50 НВ. Как уже отмечалось, деталь, изготовленная из Д16 может быть упрочнена закалкой и естественным старением. Максимальная прочность после закалки достигается на 4-е сутки.
Поскольку дуралюминиевый сплав Д16 не отличается хорошими коррозионными свойствами, желательна дополнительная защита изделий из него анодированием или нанесением лако-красочных покрытий. При эксплуатации при температурах выше 80-100 С проявляется склонность к межкристаллитной коррозии.
Необходимость дополнительной защиты от коррозии относится и к другим высокопрочным сплавам (Д1, В95, АК).
Прутки из АМц и АМг обладают высокой коррозионной стойкостью, допускают возможность дополнительного формообразования горячей ковкой (в интервале 510-380оС).
Разнообразные профили широко представлены из сплава АД31 с различными вариантами термообработки. Применяются для конструкций невысокой и средней прочности, а также для изделий декоративного назначения.
Прутки, трубы и профили из АД31 имеют высокую общую коррозионную стойкость, не склонны к коррозии под напряжением. Сплав хорошо сваривается точечной, роликовой и аргонно-дуговой сваркой. Коррозионная стойкость сварного шва такая же, как у основного материала. Для повышения прочности сварного шва необходима специальная термообработка.
Уголки производятся в основном из АД31, Д16 и АМг2.
Трубы производятся из большинства сплавов, представленных на рисунке. Они поставляются в состояниях без термообработки (прессованные), закаленные и состаренные, а также отожженные и нагартованные. Параметры их механических свойств примерно соответствуют, приведенным на гистограмме. При выборе материала труб кроме прочностных характеристик учитывается его коррозионная стойкость и свариваемость. Наиболее доступны трубы из АД31.
Наличие кругов, труб и уголков — см. на странице сайта «Алюминиевые круги, трубы и уголки»
Плоский алюминиевый прокат.
Листы общего назаначения производятся по ГОСТ 21631-76, ленты — по ГОСТ 13726-97, плиты по ГОСТ 17232-99.
Листы из сплавов с пониженной или низкой коррозионной устойчивостью (АМг6, 1105, Д1, Д16, ВД1, В95) плакируются. Химический состав плакирующего сплава обычно соответствует марке АД1, а толщина слоя составляет 2 – 4% от номинальной толщины листа.
Плакирующий слой обеспечивает электрохимическую защиту основного металла от коррозии. Это означает, что коррозионная защита металла обеспечивается даже при наличии механических повреждений защитного слоя (царапины).
Маркировка листов включает в себя: обозначение марки сплава + состояние поставки + вид плакировки (если она присутствует). Примеры маркировки:
А5 — лист марки А5 без плакировки и термообработки
А5Н2 — лист марки А5 без плакировки, полунагартованный
АМг5М — лист марки Амг5 без плакировки, отожженный
Д16АТ — лист марки Д16 с нормальной плакировкой, закаленный и естественно состаренный.
На гистограмме приведены основные характеристики механических свойств листов в различных состояниях поставки для наиболее используемых марок. Состояние «без термообработки» не показано. В большинстве случаев величины предела текучести и предела прочности такого проката близки к соответствующим значениям для отожженного состояния, а пластичность ниже. Плиты выпускаются в состоянии «без термообработки».
Из рисунка видно, что выпускаемый ассортимент листов дает широкие возможности для выбора материала по прочности, пределу текучести и пластичности с учетом коррозионной стойкости и свариваемости.Для ответственных конструкций из прочных сплавов обязательно учитывается трещиностойкость и характеристики сопротивления усталости.
Листы из технического алюминия (АД0, АД1, А5-А7).
Нагартованные и полунагартованные листы используются для изготовления ненагружен-ных конструкций, резервуаров (в т. ч. для криогенных температур), требующих обеспечения высокой коррозионной стойкости и допускающих применение сварки. Они используются также для изготовления вентиляционных коробов, теплоотражающих экранов (отражательная способность алюминиевых листов достигает 80%), изоляции теплотрасс.
Листы в мягком состоянии используются для уплотнения неразъемных соединений. Высокая пластичность отожженных листов позволяет производить изделия глубокой вытяжкой.
Технический алюминий отличается высокой коррозионной устойчивостью во многих средах (см. страницу «Свойства алюминия»). Однако, за счет разного содержания примесей в перечисленных марках, их антикоррозионные свойства в некоторых средах всё-таки различаются.
Алюминий сваривается всеми методами. Технический алюминий и его сварные соединения обладают высокой коррозионной стойкостью к межкристаллитной, расслаивающей коррозии и не склонны к коррозионному растрескиванию.
Кроме листов, изготавливаемых по ГОСТ21631-76, в свободной продаже имеются листы, произведенные по Евростандарту, с маркировкой 1050А. По химическому составу они соответствуют марке АД0. Фактические параметры (по сертификатам качества) механических свойств составляют (для листов 1050АН24): предел текучести ?0. 2 = (10.5-14), предел прочности при разрыве ?в=(11.5-14.5), относительное удлинение ?=(5-10%), что соответствует полунагартованному состоянию (ближе к нагартованному). Листы с маркировкой 1050АН0 или 1050АН111 соответствуют отожженному состоянию.
Листы (и ленты) из сплава 1105.
Из-за пониженной коррозионной стойкости изготавливается плакированным. Широко применяется для изоляции теплотрасс, для изготовления малонагруженных деталей, не требующих высоких коррозионных свойств.
Листы из сплава АМц.
Листы из сплава АМц хорошо деформируются в холодном и горячем состояниях. Из-за невысокой прочности (низкого предела текучести) используются для изготовления только малонагруженных конструкций. Высокая пластичность отожженных листов позволяет производить из них малонагруженные изделия глубокой вытяжкой.
По коррозионной стойкости АМц практически не уступает техническому алюминию. Хорошо свариваются аргонно-дуговой, газовой и контактной сваркой. Коррозионная стойкость сварного шва такая же, как у основного металла.
Листы из сплавов АМг.
Чем больше содержание магния в сплавах этой группы, тем они прочнее , но менее пластичны.
Механические свойства.
Наиболее распостранены листы из сплавов АМг2 (состояния М, Н2, Н) и АМг3 (состояния М и Н2), в том числе рифленые. Сплавы АМг1, АМг2, АМг3, АМг4 хорошо деформируются и в горячем и в холодном состоянии. Листы обладают удовлетворительной штампуемостью. Нагартовка заметно снижает штампуемость листов. Листы этих марок применяются для конструкций средней нагруженности.
Листы из АМг6 и АМг6 в упрочненном состоянии не поставляются. Применяются для конструкций повышенной нагруженности.
Коррозионная стойкость. Сплавы АМг отличаются высокой коррозионной стойкостью в растворах кислот и щелочей. Сплавы АМг1, АМг2, АМг3, АМг4 имеют высокую коррозионную стойкость к основным видам коррозии как в отожженном так и в нагартованном состонии.
Сплавы АМг5, АМг6 склонны к коррозии под напряжением и межкристаллитной коррозии. Для защиты от коррозии листы и плиты из этих сплавов плакируются, а заклепки из АМг5п ставят только анодированными.
Свариваемость.Все сплавы АМг хорошо свариваются аргоннодуговой сваркой, но характеристики сварного шва зависят от содержания магния. С ростом его содержания уменьшается коэффициент трещинообразования, возрастает пористость сварных соединений.
Сварка нагартованных листов устраняет нагартовку в зоне термичес-кого влияния сварного соединения, механические свойства в этой зоне соответствуют свойствам в отожженном состоянии. Поэтому сварные соединения нагартованных листов АМг имеют меньшую прочность по сравнению с основным материалом.
Сварные соединения АМг1, АМг2, АМг3 обладают высокой стойкостью против коррозии. Для обеспечения коррозионной стойкости сварного шва АМг5 и АМг6 требуется специальная термообработка.
Листы и плиты из Д1, Д16, В95.
Высокопрочные сплавы Д1, Д16, В95 имеют низкую устойчивость к коррозии. Поскольку листы из них используются в конструкционных целях, то для коррозинной защиты они плакируются слоем технического алюминия. Следует помнить, что технологические нагревы плакированных листов из сплавов, содержащих медь (например Д1, Д16), не должны даже кратковременно превышать 500 С.
Наиболее распространены листы из дуралюминия Д16. Фактические значения механических параметров для листов из Д16АТ (по сертификатам качества) составляют: предел текучести ?0.2 = (28-32), предел прочности при разрыве ?в= (42-45), относительное удлинение ?=(26-23%).
Сплавы этой группы свариваются точечной сваркой, но не свариваются плавлением. Поэтому основной способ их соединения — заклепки. Для заклепок используется проволока из Д18Т и В65Т1. Сопротивление срезу для них соответственно 200 и 260 МПа.
Из толстолистового проката доступны плиты из Д16 и В95. Плиты поставляются в состоянии «без термообработки», но возможно термоупрочнение уже готовых деталей после их изготовления. Прокаливаемость Д16 допускает термоупрочнение деталей сечением до 100-120 мм. Для В95 этот показатель составляет 50-70 мм.
Листы и плиты из В95 имеют большую (по сравнению с Д16) прочность при работе на сжатие.
Наличие листов и плит — см. на странице сайта «Алюминиевые листы»
********************
Выше кратко рассмотрены свойства алюминиевых сплавов общего назначения. Для специальных целей применяются или другие сплавы, или более чистые варианты сплавов Д16 и В95. Чтобы представить многообразие специальных сплавов, применяемых в авиа-ракетной технике, стоит зайти на сайт http://www.viam.ru.
Подход к выбору материалов для корабля «Буран» интересно отражен на сайте http://www.buran.ru/htm/inside. htm
Очень интересные материалы об истории создания и применении алюминиевых сплавов в масштабных проектах СССР содержатся в воспоминаниях академика Фридляндера:
- http://vivovoco.rsl.ru/VV/JOURNAL/VRAN/2004/ALLOYS.HTM
- http://www.arcan7.ru/library/articles/230.html
- http://vivovoco.rsl.ru/VV/JOURNAL/VRAN/02_01/FRID.HTM
- http://scilib.narod.ru/Avia/Fridlyander/contents.htm
На главную
Свариваемость металлов и сплавов. Свариваемость алюминия и его сплавов. Лабораторная работа №3
1. Лабораторная работа №3 по дисциплине 43349 «Свариваемость металлов и сплавов»
«Свариваемость алюминия и его сплавов»Выполнил:
Принял: Минаева Н.И.
Материал АМг-2, тип соединения –стыковое
Наличие вставок, покрытий — нет
Дефект соединения- трещины
Материал АМг-2, тип соединения – наплавка
Наличие вставок, покрытий — нет
Дефект соединения- трещина
Материал АМг-2, тип соединения – стыковое
Наличие вставок, покрытий – вставка из Ti
Дефект соединения- нет
Материал АМг-2, тип соединения – по отбортовке кромок
Наличие вставок, покрытий — нет
Дефект соединения- трещина в корне шва от
окисной пленки
Глубина проплавления- 0,24 мм
Материал АМг-2, тип соединения – по отбортовке кромок
Наличие вставок, покрытий — нет
Дефект соединения- кристаллизационные
трещины
Материал АМг-2, тип соединения – по отбортовке кромок
Наличие вставок, покрытий – титановая прослойка
толщиной 50 мкм
Дефект соединения- нет
Глубина проплавления- 0,5 мм
Материал АД-1, тип соединения – по отбортовке кромок
Наличие вставок, покрытий — нет
Дефект соединения- трещина в корне шва
Глубина проплавления- 0,14 мм
Материал АД-1, тип соединения –по отбортовке
кромок(продольное сечение)
Наличие вставок, покрытий — нет
Дефект соединения- поры
Глубина проплавления-
Материал АД-1, тип соединения – по отбортовке
кромок(продольное сечение)
Наличие вставок, покрытий — нет
Дефект соединения- поры
Глубина проплавления-
Материал АД-1, тип соединения – по отбортовке кромок
Наличие вставок, покрытий — нет
Дефект соединения- поры
Глубина проплавления-
Материал АД-1, тип соединения – по отбортовке кромок
Наличие вставок, покрытий — нет
Дефект соединения- поры
Глубина проплавления- 1,4 мм
Выводы:
Алюминиевые сплавы при лазерной
сварке подвержены образованию пор и
трещин.

применяют металлургические и
конструкционные приемы.
Алюминий АМг5 — сплав, свойства, характеристики обзорная статья, доклад, реферат
Применительно к сплаву системы алюминий — магний (АМг5), подходят такие определения, как: средняя прочность и пластичность, средняя теплопроводность и электропроводность, хорошая свариваемость, но относительно невысокая коррозионная стойкость.
Сравнение АМг5 с другими сплавами системы Al-Mg
Прочность и твёрдость у этого материала выше, чем у АМг2 или АМг3, которые, однако, обладают большей пластичностью, по сравнению с ним. С увеличением содержания магния в сплаве, увеличивается и его прочность, благодаря чему сплавы АМг5 и АМг6 могут успешно применяться для изготовления элементов конструкций средней нагруженности. Также, с повышением твёрдости этого материала, улучшается обрабатываемость заготовок из его механическим способом на станках.
Одновременно с увеличением прочности в зависимости от увеличения состава магния, в сплавах системы Al- Mg происходит ухудшение антикоррозионных свойств. В частности АМг5 и АМг6 плохо противостоят межкристаллитной коррозии, под воздействием напряжения. Сварные швы на поверхности этих материалов также подвержены коррозии, поэтому для обеспечения их защиты, поверхность свариваемого металла, требуется обработать термически, прежде, чем проводить её сварку.
Химический состав сплава и физические свойства
Химический состав АМг5 описывается в ГОСТ 4784-97. Это деформируемый сплав на основе Al, хорошо обрабатывается в холодном или горячем состоянии под давлением, и удовлетворительно обрабатывается на станках.
Механические и технологические свойства АМг5
Листы из АМг5, применяемые для изготовления нагруженных элементов конструкций, как правило, плакируются, а заклёпки, изготавливаемые из этого сплава, обязательно проходят процедуру анодирования, так как под нагрузкой на них проявляется межкристаллическая коррозия, если не прибегнуть к дополнительной защите.
То же касается сварных швов. Поверхность металла должна подвергнуться термопоготовке, прежде чем проводить процедуру сварки. При этом желательно пользоваться точечной сваркой.
Несмотря на относительно высокую прочность, среди сплавов системы Al-Mg — сплав АМг5 упрочняется только в холодном состоянии с помощью давления и не может соревноваться по прочности с термоупрочняемыми сплавами. Зато из него выпускают отожжённые заготовки, которые обладают хорошей пластичностью перед обработкой.
АМг5 или АМг2 — что выбрать?
Интересно было бы сравнить механические свойства у прутков из сплавов этой системы. К примеру, прутки из АМг5 выпускаются в обычном и отожжённом состоянии. Согласно информации, представленной на гистограммах ниже, можно заключить, что по пластичности в обычном состоянии АМг5 даже немного превосходит АМг2, а по прочности превосходит его в несколько раз. В отожжённом же состоянии АМг2 проявляет лучшие показатели относительно пластичности, однако эта разница не столь велика. Следовательно, с учётом механических свойств, АМг5 является лучшим выбором, за исключением ситуаций, когда очевидно важна стойкость к коррозии, лучшая свариваемость, лучшая теплопроводность или электропроводность.
Область применения АМг5
Из АМг5 выпускают:
Профили из этого материала обладают средней прочностью и могут применяться в средненагруженных конструкциях. Листы ленты и плиты — хорошо обрабатываются давлением в холодном или горячем состоянии. Пластичные отожжённые листы могут использоваться для изготовления деталей сложной формы. Плакированные плиты, листы и ленты могут применяться при возведении средненагруженных конструкций, рассчитанных для работы в умеренной или влажной среде. Нагартованные заготовки, естественно обладают большей прочностью чем материал в обычном состоянии, но при расчёте прочности обычно ориентируются на состояние самого материала.
Pатруднение свариваемости алюминиевых сплавов при температурах ниже точки затвердевания.
Автор admin На чтение 3 мин. Просмотров 219 Опубликовано
Свариваемость алюминиевых сплавов затруднена также тем, что при температурах ниже точки затвердевания значительно снижается их прочность. В том случае, если возникающие напряжения в результате усадки превысят прочность на растяжение при температуре ниже точки затвердевания, деталь трескается. Эта опасность появляется при сварке упрочняемых алюминиевых сплавов, в которых при затвердевании в результате изменения объема образуются ликвации. Трещины могут быть вызваны и включениями газов.
Прочность алюминия в диапазоне температур 423… 473 К, то есть 150… 200 °С, значительно снижается. С целью повышения прочности алюминий легируют. В то же время известно, что легирующие элементы во многом влияют на свариваемость. Поэтому перед сваркой в первую очередь необходимо определить состав сплава и разработать технологию сварки и термообработки.
Имеющиеся трещины в отливках и листах из алюминия заделывают и ручной дуговой сваркой. Дуговая сварка алюминия возможна лишь с применением электродов, имеющих требуемые покрытия. Точка плавления покрытия примерно равна точке плавления алюминия, а плотность меньше, в результате чего шлаковые включения в сварочной ванне не остаются. Материал покрытий главным образом состоит из солей галогенов, растворимых в воде.
Состав проволоки электродов обычно соответствует основному материалу. Сплавы из Al — Mg — Si и Al — Си рекомендуется сваривать проволокой Al — Si. Для улучшения качества шва часто добавляют ТЛ в количестве 0,2%, который уменьшает образование газовых пузырей. Сварка на постоянном токе проводится при обратной полярности. Выдержка оптимального расстояния для получения стабильной дуги требует большого практического навыка. Кроме того, деталь перед сваркой необходимо подогреть до температуры около 423 К (150 °С). Новые способы дуговой сварки алюминия — полуавтоматическая и автоматическая сварка и наплавка алюминиевых деталей в атмосфере защитного газа аргона плавящимся электродом.
Восстановление деталей металлизацией
В последние годы широкое распространение получили многочисленные методы металлизации (например, электрический, газопламенный, плазменный и т. д.). Для восстановления деталей сельскохозяйственных машин наиболее широко применяются порошковый, газопламенный методы, например технология UTP и Messer — Griesheim.
Сущность метода Messei — Griesheim и UTP заключается в том, что он не требует сложного оборудования,
Рис. 109. Газовая горелка для напыления порошка.
Соединение в зависимости от состава металлического порошка и предварительного нагрева детали может быть адгезионное, диффузионное и когезионное. С помощью различных смесей порошков, подобранных в оподающего сжатый воздух, а Дозатор порошка (рис. 109) установлен прямо на горелке. Принцип действия аппарата следующий. Металлический порошок, находящийся в баке (1) с закрывающейся крышкой, с помощью клапана (5), открываемого рычагом (4), подается в регулируемом количестве в поток газа. Поток ацетилена и кислорода направляется в горелку (3) через инжектор (2), расположенный под баком (1). Проходя через пламя, металлический порошок оплавляется и, ударяясь о поверхность детали, образует сплошной слой металла.
13. ПАРАМЕТРЫ МЕТАЛЛИЧЕСКИХ ПОРОШКОВ ТИПА UTP
Рис. 110.
Рис. 111
Из таблицы видно, что в зависимости от выбора металлических порошков с помощью напыления можно восстанавливать различные детали. Область применения этого метода расширяется за счет того, что с его помощью можно получать тонкие и толстые покрытия, а также паять.
Из вышесказанного следует, что этот способ отлично применим как для повышения срока службы режущих кромок, так и для наплавки изношенных деталей, а также для герметизации и сварки деталей, имеющих трещины и поломки. Для демонстрации этого приведены примеры на рисунках ПО, 111, 112 и 113.
Широкое распространение метода напыления, несмотря на его многочисленные преимущества, лимитируется стоимостью и наличием порошков.
Свариваемость материалов — алюминиевые сплавы
Профессиональные знания 21
Алюминий и его сплавы используются в производстве из-за их малого веса, хорошей коррозионной стойкости и свариваемости. Несмотря на обычно низкую прочность, некоторые из более сложных сплавов могут иметь механические свойства, эквивалентные стали. Определены различные типы алюминиевых сплавов и даны рекомендации по изготовлению компонентов без ухудшения коррозионных и механических свойств материала или внесения дефектов в сварной шов.
Нажмите здесь , чтобы посмотреть наши последние технические подкасты на YouTube .
Типы материалов
Поскольку чистый алюминий относительно мягок, в него добавляют небольшое количество легирующих элементов для придания ему ряда механических свойств. Сплавы сгруппированы по основным легирующим элементам, отдельные товарные сплавы имеют четырехзначное обозначение в соответствии с международными спецификациями для деформируемых сплавов или буквенно-цифровой системой ISO.
Сплавы могут быть далее классифицированы в соответствии со средствами, с помощью которых легирующие элементы приобретают механические свойства, на нетермообрабатываемые или термообрабатываемые сплавы.
Нетермообрабатываемые сплавы
Прочность материала зависит от эффекта деформационного упрочнения и упрочнения на твердый раствор легирующих элементов, таких как магний и марганец; легирующие элементы в основном встречаются в сплавах серий 1ххх, 3ххх и 5ххх. При сварке эти сплавы могут терять эффект деформационного упрочнения, что приводит к разупрочнению ЗТВ, прилегающей к сварному шву.
Термообрабатываемые сплавы
Твердость и прочность материала зависят от состава сплава и термической обработки (термическая обработка на твердый раствор и закалка с последующим естественным или искусственным старением приводит к тонкой дисперсии легирующих компонентов). Основные легирующие элементы определены в сериях 2ххх, 6ххх и 7ххх. Сварка плавлением перераспределяет упрочняющие компоненты в ЗТВ, что локально снижает прочность материала.
Процессы
Большинство деформируемых марок 1ххх, 3ххх, 5ххх, 6ххх и средней прочности 7ххх (напр.грамм. 7020) можно сваривать плавлением с использованием процессов TIG, MIG и кислородной сварки. В частности, сплавы серии 5ххх обладают отличной свариваемостью. Высокопрочные сплавы (например, 7010 и 7050) и большинство сплавов серии 2ххх не рекомендуются для сварки плавлением, поскольку они склонны к ликвации и растрескиванию при затвердевании.
Техника сварки трением с перемешиванием особенно подходит для алюминиевых сплавов. Он способен обеспечивать прочные сварные швы многих сплавов, в том числе термообрабатываемых сплавов, склонных к горячему растрескиванию при сварке плавлением.
Присадочные сплавы
Состав присадочного металла определяется:
- свариваемость основного металла
- минимальные механические свойства металла шва
- коррозионная стойкость
- Требования к анодному покрытию
Номинально соответствующие присадочные металлы часто используются для нетермообрабатываемых сплавов. Однако для материалов с низким содержанием сплава и термообрабатываемых сплавов используются неподходящие наполнители для предотвращения растрескивания при затвердевании.
Выбор состава присадочного металла для различных свариваемых сплавов указан в BS EN 1011 Pt 4:2000 для сварки TIG и MIG; рекомендуемые составы присадочного металла для наиболее часто используемых сплавов приведены в таблице .