Тип соеди- нения | Форма подготов- ленных кромок | Характер сварного шва | Форма поперечного сечения | Толщина сварива- емых деталей, мм | Услов- ное обозна- чение соеди- нения | |
подготовленных кромок | сварного шва | |||||
1-4 | С1 | |||||
С отбор- товкой кромок | 1-12 | С28 | ||||
Стыковое | С отбор- товкой одной кромки | Одно- сторон- ний | СЗ | |||
1-4 | С2 | |||||
Без скоса кромок | Одно- сторон- ний на съемной подклад- ке | С4 | ||||
Одно- сторон- ний на остаю- щейся подклад- ке | 1-4 | С5 | ||||
Одно- сторон- ний замко- вый | 1-4 | С6 | ||||
2-5 | С7 | |||||
Без скоса кромок с после- дующей строжкой | Дву- сторон- ний | 6-12 | С42 | |||
Стыковое |
| Одно- сторон- ний | С8 | |||
Со скосом одной кромки | Одно- сторон- ний на съемной подклад- ке | 3-60 | С9 | |||
Одно- сторон- ний на остаю- щейся подклад- ке | C10 | |||||
Одно- сторон- ний замко- вый |
| С11 | ||||
Стыковое | С12 | |||||
С криво- линей- ным скосом одной кромки | Дву- сторон- ний | С13 | ||||
С лома- ным скосом одной кромки | 15-100 | С14 | ||||
С двумя симмет- ричны- ми скосами одной кромки | 8-100 | С15 | ||||
С двумя симмет- ричны- ми криво- линей- ными скосами одной кромки | 30-120 | С16 | ||||
Стыковое | С двумя несим- метрич- ными скосами одной кромки | 12-100 | С43 | |||
Одно- сторон- ний | С17 | |||||
| Одно- сторон- ний на съемной подклад- ке | 3-60 | C18 | |||
Одно- сторон- ний на остаю- щейся подклад- ке | 6-100 | С19 | ||||
Со скосом кромок | Одно- сторон- ний замко- вый | С20 | ||||
Стыковое | 3-60 | С21 | ||||
Со скосом кромок с после- дующей строж- кой | Дву- сторон- ний | 8-40 | С45 | |||
С криво- линей- ным скосом кромок | С23 | |||||
С лома- ным скосом кромок | 15-100 | С24 | ||||
Стыковое | С двумя симмет- ричны- ми скосами кромок | Дву- сторон- ний | 8-120 | С25 | ||
С двумя симмет- ричны- ми криво- линей- ными скосами кромок | 30-175 | С26 | ||||
С двумя симмет- ричны- ми лома- ными скосами кромок | 30-175 | С27 | ||||
Стыковое | С двумя несим- | С39 | ||||
метрич- ными скосами кромок | 12-120 | С40 | ||||
Угловое | С отбор- товкой одной кромки | Одно- сторон- ний | 1-4 | У1 | ||
С отбор- товкой одной кромки | 1-12 | У2 | ||||
Угловое | Одно- сторон- ний | 1-6 | ||||
| Без скоса кромок | 1-30 | У4 | |||
| 2-8 | |||||
Без скоса кромок | Дву- сторон- ний | 2-30 | У5 | |||
Угловое |
| Одно- сторон- ний | У6 | |||
Со скосом одной кромки | 3-60 | У7 | ||||
С двумя симмет- ричны- ми скосами одной кромки | Дву- сторон- ний | 8-100 | У8 | |||
Угловое | Одно- сторон- ний | У9 | ||||
Со скосом кромок | Дву- сторон- ний | 3-60 | У10 | |||
| Одно- сторон- ний | T1 | ||||
Без скоса кромок | Дву- сторон- ний | 2-40 | Т3 | |||
Тавровое |
|
Одно- сторон- ний | Т6 | |||
Со скосом одной кромки | Дву- сторон- ний | 3-60 | Т7 | |||
С криво- линей- ным скосом одной кромки | 15-100 | T2 | ||||
Тавровое | С двумя симмет- | Дву- сторон- ний | 8-100 | Т8 | ||
ричными скосами одной кромки | 12-100 | Т9 | ||||
Тавровое | С двумя симмет- ричными криво- линей- ными скосами одной кромки | Дву- сторон- ний | 30-120 | Т5 | ||
Нахлес- | Без | Одно- сторон- ний | h2 | |||
точное | скоса кромок | Дву- сторон- ний | 2-60 | h3 |
СВАРКЕ.
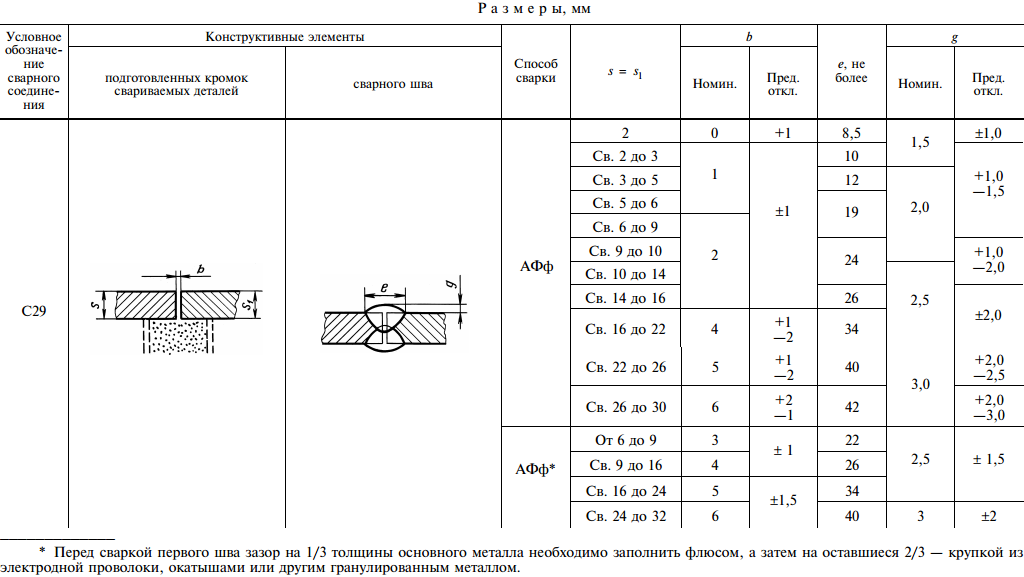
Основными типами соединений, выполненных электродуговой сваркой, являются стыковые (С), угловые (У), тавровые (Т) и нахлесточные (Н). Основные типы, конструктивные элементы и размеры сварных соединений, выполненных ручной сваркой металлическими электродами при толщине сварного изделия до 175 мм, регламентирует ГОСТ.
Так, на рисунке 4.1 приведены примеры стыкового и углового соединений. Стыковое соединение характеризуется следующими параметрами: шириной шва е, глубиной проплавления h, высотой усиления q, толщиной шва H. Угловое – катетом шва k.
а – стыковое соединение; б – угловое соединение
Рисунок 4.1 – Сечение сварного шва
Условные изображения и обозначения швов сварных соединений на чертежах устанавливает ГОСТ. Согласно ГОСТ в зависимости от толщины свариваемого металла для каждого типа соединений устанавливается определенная форма подготовки кромок под сварку (форма разделки).
На рисунке 4.2, например, приведены основные разновидности формы подготовки кромок стыковых соединений по ГОСТ. Основными конструктивными элементами подготовки кромок являются: угол раскрытия , величина притупления с, величина зазора в (рисунок. 4.2).
Ж з и
а – с отбортовкой кромок; б – без скоса кромок; в – со скосом
одной кромки; г – с криволинейным скосом одной кромки;
д – с двумя скосами одной кромки; е – с двумя криволинейными
скосами одной кромки; ж – со скосом кромок; з – с двумя
симметричными скосами кромок; и – с двумя симметричными
криволинейными скосами кромок
Рисунок 4.2 – Форма подготовки кромок стыковых соединений
При проектировании конструкции и технологических процессов изготовления сварных соединений постоянно решаются задачи выбора подготовки кромок, швов и соединений. В общем виде подготовка кромок необходима для получения качественных швов и соединений. Это включает, прежде всего, получение швов заданной формы, т. е. с геометрическими размерами, соответствующими размерам, заданным ГОСТ. Подготовка кромок под сварку, сборка без скоса кромок с обязательным зазором применяются для обеспечения проплавления свариваемых элементов на всю их толщину.
Технология электродуговой сварки заготовок без специальной подготовки кромок во многих случаях является более прогрессивной и экономичной, т. к. в этом случае не требуется механическая обработка кромок, связанная с удалением металла в отходы и затратами труда; при последующей сварке, как правило, швы имеют меньшую площадь сечения и, следовательно, меньшую массу наплавленного металла, поэтому она требует минимального расхода покрытых электродов, электроэнергии, минимальных затрат ручного труда сварщика.
В связи с этим в качестве основных показателей при оценке эффективности выбора формы подготовки кромок следует считать:
– площадь поперечного сечения или массу удаленного с кромок металла и трудоемкость обработки;
– площадь поперечного сечения или погонную массу наплавленного металла шва.
Чем меньше масса удаленного с кромок металла и масса наплавленного металла шва при заданном качестве сварного соединения, тем экономнее форма подготовки кромок.
Сварное соединение, согласно ГОСТ, имеет условное буквенное обозначение, в котором буква обозначает тип соединения, цифра или число – порядковый номер, соответствующий определенной подготовке кромок. Например, символом С17 обозначается стыковое соединение с V-образным односторонним скосом кромок, используемое при толщине металла 3…60 мм. Если в таком соединении применяется шов с подваркой корня, то оно обозначается С18 и т. д. ГОСТ устанавливает сорок разновидностей стыковых (С1 – С40), десять угловых (У1 – У10), восемь тавровых (Т1 –Т8) и два нахлесточных соединения.
Узнать еще:
Регламент сварщиков дуговой сварки
РЕГЛАМЕНТ
проведения областного конкурса профессионального мастерства «Славим человека труда!» по отрасли «машиностроение» в номинации «Электросварщик ручной дуговой сварки»
1. Условия проведения конкурса
1.1. Место проведения – ООО «Уральский центр аттестации» (г. Екатеринбург, ул. Кислородная, 8д).
1.2. Конкурс проводится в 2 тура:
1 тур – оценка теоретических знаний;
2 тур – оценка профессионального мастерства.
1.3. Для выполнения сварки используются источники питания ВДУ-506С, PICO – 2300 или их аналоги.
1.7. Основными критериями оценки являются:
· качество выполненной работы;
· время, затраченное на выполнение задания;
· уровень профессиональных знаний;
· соблюдение правил техники безопасности;
· организация рабочего места.
1.4. Для проведения мероприятия и подведения итогов конкурса назначается конкурсная комиссия из числа независимых экспертов. Состав конкурсной комиссии утверждается председателем отраслевой конкурсной комиссии областного конкурса профессионального мастерства «Славим человека труда!» по отрасли «машиностроение».
1.5. На каждого участника конкурса заполняется «Лист оценки», где указываются данные участника и результаты проведения конкурса (Приложение 1).
1.6. Рабочие места участников конкурса оснащаются в соответствии с требованием техники безопасности, промсанитарии и содержат полный комплект механизмов, приспособлений, инструментов, аттестованных источников питания и сварочных материалов.
2. Порядок проведения конкурса
2.1. Порядок проведения 1 тура конкурса – оценка теоретических знаний.
2.1.1. Теоретическое задание конкурсанта представляет собой письменное испытание в форме теста, включающего ситуационные задачи.
2.1.2. В содержание теоретического теста включены общие вопросы по сварке, особенностям ручной дуговой сварки, охране труда, чтению чертежей, решению ситуационной задачи.
2.1.3. На выполнение письменного задания отводится 25 минут.
2.1.4. После истечения времени, установленного на выполнение теоретического задания, каждый конкурсант обязан сдать тест членам квалификационной комиссии для проведения оценки правильности его выполнения.
2.1.5. Итоги выполнения теста каждым конкурсантом заносятся членами конкурсной комиссии в соответствующую графу индивидуального Листа оценки.
2.2. Порядок проведения 2 тура конкурса – оценка профессионального мастерства.
Для проведения соревнований конкурсанты делятся на 2 группы. Порядковый номер участников определяется жеребьевкой.
2.2.1. Практическое задание является единым для всех участников и заключается в заваривании ручной дуговой сваркой одного плоского стыкового образца.
1. Размеры пластин: 300 х 100 х10 мм.
2. Материал пластин: сталь марки 09Г2С.
3. Сварочные электроды УОНИ 13/55, Ø 3 или4 мм.
4. Положение сварки – вертикальное снизу вверх и горизонтальное.
5. Сварное соединение одностороннее – С17 по ГОСТ 14771-76.
Конкурсантам дается время в пределах 30 минут для подготовки рабочего места.
2.2.2. Время, устанавливаемое на сборку участником свариваемого стыка, зачистку кромок и подбор режимов сварки – 30 минут.
Время на сварку стыка задается технологической картой.
2.2.3. Для послойной зачистки шва в процессе сварки разрешается использовать молоток, зубило и стальную щетку. Для зачистки выполненного шва и околошовной зоны от шлака, окисной пленки и брызг (на ширину не менее20 ммот линии сплавления) разрешается использовать молоток, зубило и стальную щетку.
2.2.4. Перед выполнением практической части конкурса каждый сварщик имеет возможность ознакомиться со сварочным оборудованием, технологическими картами сварки и выполнить пробные работы по сварке соединений.
2.2.5. Каждый участник использует инструмент и оснастку, предоставляемые организаторами конкурса.
2.2.6. Хронометраж выполнения конкурсного задания ведется с момента зажигания сварочной дуги до полного завершения процесса сварки и зачистки сварного соединения.
2.2.7. После выполнения прихваток и завершения сварки контрольные образцы подвергаются визуальному и измерительному контролям, по результатам которых оформляются заключения. За выявленные дефекты начисляются штрафные баллы. Результаты выполнения практического задания заносятся членами квалификационной комиссии в соответствующие графы индивидуального Листа оценки.
2.2.8. Участник, допустивший грубые нарушения технологии выполнения практического задания или правил техники безопасности, по решению квалификационной комиссии может быть дисквалифицирован и отстранен от участия в конкурсе.
2.2.9. Члены конкурсной комиссии следят за соблюдением конкурсантами техники безопасности, требований охраны труда и правил эксплуатации оборудования.
3. Оценка результатов и определение победителей конкурса
3.1. Критерии оценки выполнения теоретического задания:
За каждый не правильный ответ при их количестве от 1 до 5 включительно снимается по 0,2 балла, если их количество превышает 5 – за каждый последующий снимается 1 балл.
3.2. Сборка. Оценивается правильность сборки, соответствие размеров собранного стыка требованиям ГОСТ 14771-76, отсутствие перекосов, излома кромок и т.п.
3.3 Сварка оценивается по следующим параметрам:
· время сварки;
· соблюдение техники безопасности и культуры труда;
· выполнение требований технологической карты.
3.4. Сваренный образец предъявляется сварщиком представителю конкурсной комиссии, который маркирует каждый образец номером, присвоенным им данному участнику (цифры и буквы наносятся несмываемой краской или маркером), чтобы членам комиссии нельзя было установить фамилии сварщиков, производивших сварку образцов. Замаркированные образцы поступают на дальнейший контроль (внешний осмотр и измерения и УЗК). Номера, присвоенные участникам, не разглашаются до окончательного подведения итогов конкурса.
3.5. Сваренные образцы подвергаются визуальному осмотру и измерениям по РД 03-606-03.
3.6. При визуально-измерительном контроле конкурсная комиссия проверяет качество и правильность выполнения швов, соответствие швов заданным размерам, наличие недопустимых наружных дефектов.
При выявлении недопустимых наружных дефектов, образец признается браком и на ультразвуковой контроль не посылается.
3.7. При отсутствии недопустимых наружных дефектов образец подвергается УЗК. Оценка результатов контроля УЗК производится в соответствии с РД 24 090.97-98.
3.8. За каждый дефект, обнаруженный ВИК и УЗК, начисляются штрафные баллы.
3.9. Режим и технология сварки (сила тока, напряжение, порядок сборки, порядок наложения швов, однослойная или многослойная сварка, и т.д.) устанавливаются сварщиками исходя из рекомендаций технологических карт, которые выдаются каждому участнику конкурса перед началом практических испытаний. Испытания сварщиков производятся с применением исправного оборудования и инструмента.
3.11. При несоблюдении условий конкурса, грубых нарушениях технологии работ, правил безопасности труда участник конкурса по решению конкурсной комиссии может быть отстранен от выполнения конкурсного задания.
3.12. Общая оценка определяется по сумме набранных баллов на всех этапах конкурса. Победителем признается конкурсант, набравший наибольшее количество баллов.
3.13. При равном количестве набранных баллов преимущество отдается участнику конкурса, набравшему наибольшее количество баллов при выполнении практического задания.
3.14. По итогам проведения конкурса конкурсантам вручаются почетные дипломы участников.
3.15. Торжественное награждение победителей конкурса денежными премиями и ценными подарками осуществляется на отдельном праздничном мероприятии с участием руководителей исполнительных органов государственной власти Свердловской области, представителей отраслевых Союзов, промышленных предприятий и организаций региона.
3.16. Победителю конкурса предоставляется почетное право провести мастер-класс во время проведения выставки «Сварка. Контроль и диагностика».
Скачать Регламент проведения областного конкурса профессионального мастерства «Славим человека труда!» по отрасли «машиностроение» в номинации «Электросварщик ручной дуговой сварки»
Условное обозначение соединения | Форма подготовленных кромок свариваемых деталей | Форма шва сварного соединения | Тип сварного соединения |
С1 | Одностороннее стыковое соединение с отбортовкой коромок | ||
С2 | Одностороннее стыковое соединение без скоса кромок | ||
С3 | Одностороннее стыковое соединение с отбортовкой одной коромки | ||
С4 | Одностороннее стыковое соединение без скоса кромок на осъемной подкладке | ||
С5 | Одностороннее стыковое соединение без скоса кромок на остающейся подкладке | ||
С6 | Одностороннее стыковое соединение без скоса кромок замковый | ||
С7 | Двухстороннее стыковое соединение без скоса кромок | ||
С8 | Одностороннее стыковое соединение со скосом одной кромки | ||
С9 | Одностороннее стыковое соединение cо скосом одной кромки | ||
С10 | Одностороннее стыковое соединение cо скосом одной кромки на остающейся подкладке | ||
С11 | Одностороннее стыковое замковое соединение cо скосом одной кромки | ||
С12 | Двухстороннее стыковое соединение со скосом одной кромки | ||
С13 | Двухстороннее стыковое соединение со криволинейным скосом одной кромки | ||
С14 | Двухстороннее стыковое соединение со ломанным скосом одной кромки | ||
С15 | Двухстороннее стыковое соединение с двумя симметричными скосами одной кромки | ||
С16 | Двухстороннее стыковое соединение с двумя симметричными криволинейными скосами одной кромки | ||
С17 | Одностороннее стыковое соединение cо скосом кромок | ||
С18 | Одностороннее стыковое соединение cо скосом кромок на флюсомедной подкладке | ||
С19 | Одностороннее стыковое соединение cо скосом кромок на остающейся подкладке | ||
С20 | Одностороннее стыковое замковое соединение cо скосом кромок | ||
С21 | Двухстороннее стыковое соединение со скосом кромок с предварительной подваркой корня шва | ||
С23 | Двухстороннее стыковое соединение со криволинейным скосом одной кромки с предварительной подваркой корня шва | ||
С24 | Двухстороннее стыковое соединение со ломанным скосом кромок | ||
С25 | Двухстороннее стыковое соединение с двумя симметричными скосами кромок | ||
С26 | Двухстороннее стыковое соединение с двумя симметричными криволинейными скосами кромок | ||
С27 | Двухстороннее стыковое соединение с двумя симметричными скосами кромок | ||
С28 | Одностороннее стыковое соединение с отбортовкой двух коромок | ||
С39 | Двухстороннее стыковое соединение с двумя несимметричными скосами кромок с предварительным наложением подварочного шва | ||
С40 | Двухстороннее стыковое соединение с двумя несимметричными криволинейными скосами кромок с предварительным наложением подварочного шва | ||
С42 | Двухстороннее стыковое соединение без скоса кромок с последующей строшкой | ||
С43 | Двухстороннее стыковое соединение с двумя несимметричными скосами одной кромки | ||
С45 | Двухстороннее стыковое соединение со скосом кромок с последующей строшкой | ||
У1 | Одностороннее угловое соединение с отбортовкой одной коромки | ||
У2 | Одностороннее угловое соединение с отбортовкой одной коромки | ||
У4(1) | Одностороннее угловое соединение без скоса кромок | ||
У4(2) | Одностороннее угловое соединение без скоса кромок | ||
У5(1) | Двухстороннее угловое соединение без скоса кромок | ||
У5(2) | Двухстороннее угловое соединение без скоса кромок | ||
У6 | Одностороннее угловое соединение со скосом одной кромки | ||
У7 | Двухстороннее угловое соединение со скосом одной кромки | ||
У8 | Двухстороннее угловое соединение с двумя симметричными скосами одной кромки | ||
У9 | Одностороннее угловое соединение cо скосом кромок | ||
У10 | Двухстороннее угловое соединение cо скосом кромок | ||
Т1 | Одностороннее тавровое соединение без скоса кромок | ||
Т2 | Двухстороннее тавровое соединение с криволинейным скосом одной кромки с предварительным наложением подварочного шва | ||
Т3 | Двухстороннее тавровое соединение без скоса кромок | ||
Т5 | Двухстороннее тавровое соединение с двумя симметричными криволинейными скосами одной кромки | ||
Т6 | Одностороннее тавровое соединение со скосом одной кромки | ||
Т7 | Двухстороннее тавровое соединение со скосом одной кромки с предварительным наложением подварочного шва | ||
Т8 | Двухстороннее тавровое соединение с двумя симметричными скосами одной кромки | ||
Т9 | Двухстороннее тавровое соединение с двумя симметричными скосами одной кромки | ||
Н1 | Одностороннее нахлесточное соединение без скоса кромок | ||
Н2 | Двухстороннее нахлесточное соединение без скоса кромок |
Полуавтоматическая сварка под контроль для аттестации НАКС
Это статья из серии экспресс-уроков Свар-EXPRESS.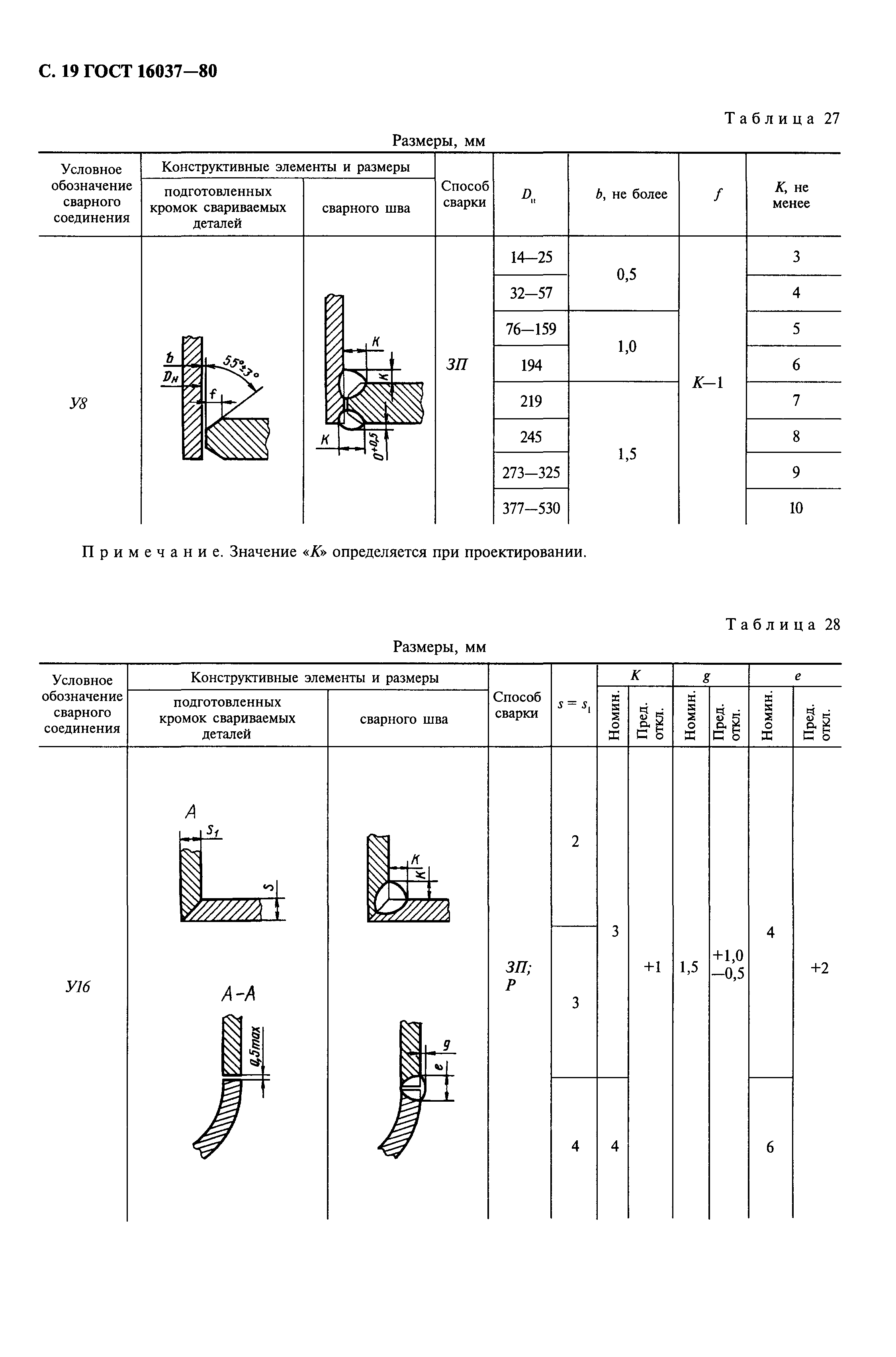
Темы урока: сварка подконтрольных сварных соединений в реальных боевых условиях либо при аттестации НАКС
Инженер-сварщик Евгений Евсин |
Здравствуйте, сегодня я расскажу, как происходит сварка подконтрольных сварных соединений в реальных боевых условиях либо при аттестации НАКС. В качестве примера, я покажу вам, как заварить металл толщиной 12 мм в вертикальном положении аппаратом SKYWAY 330 SYNERGIC, полуавтоматический способ сварки. Для того, чтобы начать, необходимо сначала сделать заготовки, я их нарезал на аппарате плазменной резки — 2 пластины.
Дальше необходимо сделать выводные планки, в дальнейшем, вы поймете, для чего они нужны.
Необходимо сделать также такие пластины против обратного выгиба.
И нужен такой шаблон для того, чтобы проверять зазоры, у меня это просто железяка толщиной 2 мм.

Прежде, чем приступить к делу, необходимо изучить ГОСТ «Сварные соединения», и из этого ГОСТа понять, какое соединение нам необходимо. В нашем случае это соединение С17, исходя из этого соединения мы и подготавливаем металл и собираем его. У меня он уже подготовлен, согласно ГОСТу, с заготовки снята фаска 30° градусов, сделано притупление, металл необходимо зачищать от границ сваривания не менее чем на 10 мм с обеих сторон. Далее, собственно говоря, сборка.
Собираем наши заготовки. Для правильной сборки я использую приспособления, в моем случае это магнит, чтобы не было смещений и правильно позиционировались детали в момент прихватки. Выставляем зазор, беру свой шаблон толщиной 2 мм. Такой нюанс — с одной стороны мы делаем строго 2 мм, а в том месте, где мы будем заканчивать сварку нужно сделать немножко больше, потому что металл в процессе сварки будет немного стягивать. Просто засовываем его между заготовок, получается зазор 2 мм. Ставлю пластину против обратного выгиба, она позиционирует и не дает металлу стягиваться. Прихватываю ее.
Проверяем смещение сверху, оставляем зазор сверху немного больше, чем снизу на 1-2 десятки (2,2 мм), прихватываю вторую пластину.
После сборки и прихватки нужно проверить правильность, проверить смещение, например, тем же самым шаблоном (обычной ровной железякой) — смотрим, если есть смещение нужно подровнять.
В каждом случае есть свои приспособления, но я использую молоток. Все сделали.
Теперь нужно обварить, не сильно, так, чтобы потом легко можно было это отбить, т.к. далее нам это будет не нужно.
Теперь привариваем выводные планки. Выводные планки – это приспособления, на которых начинается и заканчивается сварка, потому, что в начале и в конце шва сложно получить качественные соединения. В дальнейшем эти планки просто обрезаются. Планка представляет из себя имитацию основного металла, т.е. на ней тоже снята фаска, она такой же толщины, тоже самое, только меньшие кусочки металла. Прихватываем.
Для того, чтобы усложнить задачу сварщика, проверить его умения – сварка производится в вертикальном положении. Для такой сварки необходимо настроить все соответствующие режимы на сварочном аппарате. Методом проб я выяснил оптимальное для себя режим на сварочном аппарате, в данном случае, для сварки толщиной 12 мм я настраиваю напряжение 17 Вольт, 3 м скорость подачи, корректировка по напряжению -5, индуктивность 0.
При выборе сварочных материалов я сделал выбор в пользу проволоки диаметром 1 мм. Такой выбор обусловлен тем, что данный диаметр проволоки дает оптимальное заполнение шва и оптимально настраивается режим для сварки. В качестве газовой защиты я выбрал газовую смесь, 82% Аргона + 18% углекислоты. Такой выбор максимально подходит для нашего случая. Для того, чтобы образец полностью прошел контроль, необходимо исключить вероятность возникновения водородных пор в сварном шве, для этого необходимо подогреть металл до 100-120 С. В реальных условиях это делается газокислородным резаком или пропановской горелкой. У меня этих приспособлений нет, я подогревать не буду, но вообще-то это обязательно.
Перед началом работ необходимо убедиться, что вы находитесь в максимально удобном положении, чтобы в процессе сварки вам не пришлось отрывать дугу. Также обязательно, чтобы на аппарате был четырехтактный режим, иначе вы устанете держать постоянно на аппарате кнопку, если четырехтактного режима нету. В процессе сварки главное не торопиться, не забегать вперед, чтобы не прожечь корень шва, и чтобы получилось хорошее формирование с обратной стороны. Теперь необходимо первый проход зачистить, чтобы убрать так называемые карманы в формировании, которые могут впоследствии образовать дефект, зачищается это болгаркой.
Следующий проход называется заполняющий, он намного легче корневого и немного легче облицовочного. Заполняющих проход желательно также прочистить, как и корневой, но не обязательно с той же тщательностью.
Третий, заключительный проход – облицовочный, здесь главное не торопиться и следить, чтобы не образовывались подрезы по краям шва. Сварка закончена, теперь необходимо удалить все лишнее с образца – это срезать выводные планки и удалить планки, которые нам помогали, чтобы металл не увело, вычищаем.
После того, как все лишнее удалено, по требованию дефектоскопистов, возможно еще зачищать заподлицо и внешний валик из корня и наружной части. Но бывает, что в зависимости от дефектоскопии, нет необходимости это делать.
Вот конечный результат, который должен получиться:
Выбрать сварочный аппарат вы можете на нашем сайте
Смотрите данную статью в видео-ролике:
Тавровое соединение двух пластин 8мм и стыковое соединение пластин 6 и 8 мм. — Ручная дуговая сварка — ММA
Да все учтено.SAM77, жирный вам плюс, за то что заморочились снеговой нагрузкой. Карман снеговой учли? Или там у вас кровля к стенам не примыкает?
Можно, но тогда зазор надо делать около 4 мм. Да и тройкой палюбому качественнее получиться.

Я думал что 8 мм металл нужно обязательно варить четверкой, потому что он толстый и чтобы за раз пройтись и заварить одним швом.
Качественнее получится в смысле шов красивее или проварится лучше ?
Спасибо за книгу, скачал.SAM77,лишнее тепло вложения в сварной шов ни к чему.Вот вам книга Расчет сварных соединений и конструкций — Серенко А.Н., Крумбольдт М.Н., Багрянский К.В — 1977. Я думаю вы найдете в ней пример расчета и остановитесь на том стоит делать разделку или нет.И какой размер сварного шва вам необходим.
Очень хорошая книга но…. боюсь мне ее не осилить т к я не сварщик а просто любитель а в книге почти одни формулы и чтобы во всем разобраться уйдет очень много времени.
Вчера варил четверкой и током 160А, практиковался.
Варил две пластины по 8мм (тавровое соединение) без снятия кромок просто с щелью между ними 2 мм, а так же пластина 8мм (сошлифовал чуть края по плоскости до 6мм) с пластиной 5.

Пластины были размером примерно 7х5см
После сварки сделал распил проваренных пластин.
В итоге:
Тавровое соединение: в корне ровно в центре между вертикальной и горизонтальной пластиной небольшое отверстие (или шлак, не понятно, не ковырял) диаметром от 1мм до 1.5 мм ( на разных распилах разных заготовках по разному).
Стыковое соединение: где то есть небольшая точка 0.5 мм а где то полностью проварилось на 100% (на разных заготовках по разному)
А так же варил две пластины по 8мм(тавровое соединение) со скосом кромок, притуплением 2 мм и щелью 2 мм, ток 160А и электрод 4мм-есть небольшие точки от непроваров в центре шва как раз напротив стыковки вертикальной и горизонтальной пластины. Точек больше чем от сварки без снятия фасок и с щелью 2мм-может так просто получилось а может на самом деле без фасок лучше проваривает.
Сообщение отредактировал SAM77: 28 Сентябрь 2017 00:27
Определение прочности сварных соединений с дефектами не трещиноподобного типа в стальных корпусах судов — Судостроение
Судно — это сложное техническое сооружение повышенной опасности, жизненный цикл которого проходит в неблагоприятных условиях эксплуатации. Прочность, жесткость и непроницаемость корпуса судна — это те параметры, которые характеризуют его техническое состояние.
Потребность в ремонте у каждого судна неизменно возрастает с увеличением срока его службы.
Это происходит:
-
во-первых, в результате естественного износа конструктивных элементов из-за дефектов,
-
а во-вторых, вследствие случайных повреждений (поломок, аварий).
По официальным данным, средний срок эксплуатации судна в России превышает 30 лет, а большая часть всех судов эксплуатируются сверх нормативного срока.
В настоящее время в виду сложившейся экономической ситуации судостроительным предприятиям трудно изыскивать средства на обновление флота. При ремонте судна корпусные работы составляют до 30% от общего ремонта, и характеризуются зачастую тяжелыми условиями труда. Стоимость ремонта корпусов получается весьма высокой не только по основным материальным затратам, но и еще и потому, что судно на длительный срок выводится из эксплуатации. Дополнительные работы по ремонту дефектных участков сварных швов повышают сроки и трудоемкость постройки и ремонта судов. По этой причине большую актуальность приобретает возможность продления срока межремонтного периода эксплуатации судов.
Способность конструкций судна сопротивляться усталостным разрушениям (трещинам) от переменных нагрузок и разрушениям от экстремальных нагрузок (разрывам, пластическим деформациям и потерям устойчивости связей с нарушением их формы) является комплексным понятием, определяющим прочность всего сварного корпуса [4]. В соответствии с Правилами Российского Морского Регистра Судоходства (РМРС) в части 14 «Сварка» [7] устанавливают нормативные требования к корпусу судна, исходя из двух основных критериев: усталостной и предельной прочности сварного соединения.
В результате эксплуатации на сварной корпус судна, который имеет наружную обшивку, верхнюю и нижнюю палубы, продольные и поперечные перегородки, выполненные из листовых элементов и соединенные герметичными сварными швами [1, 2], действуют статические, динамические и циклические нагрузки. При длительном действии на сварной корпус судна постоянных и переменных нагрузок, происходит постепенное накопление повреждений — износ, которые могут приводить к усталостному разрушению или потери несущей способности сварного шва. Это связано с тем, что на прочность сварного шва оказывают влияние внутренние сварочные дефекты, которые могут существенно снижать прочностные характеристики сварной конструкции, так как являются концентраторами напряжений.
Анализ случаев разрушения сварных конструкций, работающих в различных условиях, свидетельствует о том, что чаще всего их разрушение начинается от дефектов, возникающих в сварном соединении или в основном металле [10]. Дефекты не трещиноподобного типа сварочных швов (газовые и твердые неметаллические включения и др.) совершенно по-разному влияют на прочностные (технологические) и эксплуатационные свойства корпусной конструкции и ее сварных соединений при различных видах нагружения. Анализ методов проектирования корпусов судов (расчетный и по правилам классификационных обществ) [4, 6, 7], а также принципов оценки усталостной прочности сварного корпуса судна [3] и результатов исследований полей деформаций, эксплуатируемых судовых корпусов [8] позволяет сделать вывод о том, что используемые РМРС нормы дефективности сварных швов корпуса судна для дефектов не трещиноподобного типа, отражают только технологический уровень качества, а не эксплуатационный.
Прочностные (технологические) и эксплуатационные характеристики сварных соединений стального корпуса и механизм разрушения при наличии разнообразных внутренних дефектов и специфического набора нагрузок можно разделить по характеру развития разрушения и последствиям, оказывающим влияния на прочность всего корпуса судна. В соответствии с требованием Правил РМРС [7] оценка качества (надежности) сварных соединений корпуса судна базируется на ИСО 5817 [11] и подразделяется на 3 уровня дефективности, а классификация дефектов осуществляется в соответствии с ИСО 6520-1. Критерии допустимости каждого из дефектов определяются в зависимости от присвоенного сварной металлоконструкции уровня качества по ИСО 5817 [11] и выбранного метода неразрушающего контроля, который осуществляется в соответствии с ИСО 17635.
На рисунке 1 рассмотрена общая схема формирования уровня качества (надежности) сварного соединения, где на графике вдоль оси «H» указывается изменение уровня качества сварного шва в течение времени «t». Этот процесс целесообразно рассматривать как серию условных потерь качества свариваемого металла за счет изменения его свойств. Значения потерь технологического (∆m) и производственно-технологического (∆nm) качества могут быть определены в единицах показателей работоспособности по результатам соответствующих разрушающих испытаний [9].
Рис. 1. Общая схема формирования уровней качества для сварных соединений
Анализ требований РМРС [7] для рентгенографического метода контроля в части оценки типа и размера внутренних дефектов в наружной обшивке стального корпуса для уровней качества 1, 2 и 3 показал, что она имеет нелинейный вид и позволяет найти зависимость между шириной шва (Wp) и допустимым количеством отдельных пор, равномерным распределением пористостей, а также скоплением пор (рис. 2).
Рис. 2. График изменения уровня качества сварного шва тип С17 в зависимости от ширины шва (Wp) и допустимой площади дефектов [Aдеф]
В соответствии с результатами исследования [9], при статистических нагрузках для металла сварного шва, обладающего пластичностью, потеря его прочности примерно пропорциональна общей площади -
внутренних дефектов или непроваров (рис. 3 – область «Статика»). Следует отметить, что авторами исследования приводятся данные по незначительному изменению несущей способности стыковых сварных соединений (особенно с усилением сварного шва) при
а иногда до 20÷30% от площади плана шва Wp х L, где L — любые (с наибольшей плотностью дефектов 100 мм длины шва).
Сравнительно небольшие дефекты при воздействии на сварной шов динамической или вибрационной нагрузок, оказывают существенное влияние на прочность (рис. 3 – область «Усталость»). Это приводит к тому, что нарушается функциональная связь в виде линейной пропорциональностью между потерей работоспособности и размерами дефекта [9].
На рисунке 3 приводится результат использования рентгенографического метода контроля для выявления внутренних дефектов сварного стыкового шва и общий расчетный уровень дефективности g=5%, который позволяет по графику (точки А, Б – область «Статика» и В, Г – область «Усталость») определить диапазоны возможного разрушения сварного шва от действия статических и динамических нагрузок при заданном уровне дефективности. Выявленные дефекты – одиночные поры (dmax=0.4…0,5≤4 мм, g0.15%), скопление пор (dmax=1…1.5≤15 мм, n=4…15. g2.48%), которые снижают прочность и плотность [9] по отдельности не превышают допускаемых значений для 1-3 уровня качества сварного шва.
Прогнозируемая прочность сварного соединения на рисунке 3 с учетом общего показателя дефективности сварного шва при статических нагрузках составит σв.св=(0,93…0,96)σв.м, а при динамических нагрузках σв.св = (0,51…0,59)σв.м. Из трех типов дефектов по нормам РМРС ремонту подлежит только скопление шлаковых включений (g2.37%), что уменьшит общую дефектность до g=2,63% (точки А1, Б1, В1, Г1) и обеспечит требуемые технологические качества сварного соединения.
Рис. 3. Характер влияния суммарной относительной площади внутренних дефектов
% на прочность сварных стыковых швов
по отношению к прочности основного металла
Снижение дефектности сварного шва за счет ремонта внутренних дефектов приводит к ситуации, когда в сварном шве практически полностью отсутствуют или имеются определенного типа технологические дефекты, уровень которых не превышает значений, указанных в нормативных документах. Это позволяет обеспечить заданный уровень качества, но не гарантирует, что в процессе расчетной эксплуатации сварного корпуса судна не образуются дефекты трещиноподобного типа [8] (зона корпуса судна D) из имеющихся в сварном шве технологических дефекты не трещиноподобного типа рис. 4.
Исходя из этого можно сделать вывод, что при расчете прочности сварного шва с внутренними технологическими ДНТ необходимо учитывать вероятность его развития в ДТТ эксплуатационного характера.
Рис. 4. Распределение дефектов сварных швов в процентах от общего числа по основным зонам судна
Анализ нормативных и научных источников, посвященных проблемам обеспечения безопасной эксплуатации сварных корпусов судна позволил сделать следующие выводы:
-
Процесс изготовления сварных корпусов судов регламентирован нормами качества, изложенных в РМРС, где установлены критерии качества сварных швов в отношении допустимого количества внутренних дефектов.
Сварочные дефекты являются неотъемлемой частью процесса изготовления сварочных швов, что может приводить к увеличению стоимости изготовления корпусов судна за счет проведения ремонтных работ. Установленные правилами РМРС нормы носят технологический характер и являются достаточно жесткими по отношению к условиям эксплуатации корпусов судов.
-
При расчете прочности сварного шва с внутренними технологическими ДНТ необходимо учитывать вероятность его развития в ДТТ эксплуатационного характера.
Литература:
-
Овчинников, В.В. Производство сварных конструкций: учебник для использования в учебном процессе образовательных учреждений, реализующих программы среднего профессионального образования / В. В. Овчинников. — Москва: Форум, Москва: ИНФРА-М. — 2017. — 287 с.
-
Технология изготовления сварных конструкций: Учебник / В.
В.Овчинников — М.: ИД ФОРУМ, НИЦ ИНФРА-М. — 2015. — 208 с.
-
Коростылёв Л.И. Анализ и классификация методов оценки усталостной прочности сварных тонкостенных конструкций корпуса судна / Л.И. Коростылёв, Д.Ю. Литвиненко. — Вестник ГУМиРФ им. Адм. С.О. Макарова. – 2016. — 3(37). – с.104-118
-
Проектирование конструкций корпуса судна: Учебное пособие / Чижиумов С.Д., Бурменский А.Д. – Комсомольск-на-Амуре: ГОУВПО «КнАГТУ». — 2006. — 117 с.
-
Технология и оборудование сварочного производства. Учебное пособие /С.Ф. Демичев, А.В. Рясный, А.Л. Усольцев. — Самара: Самарский государственный аэрокосмический университет, 2010. — 78 с.
-
Российский морской Регистр судоходства. Правила классификации и постройки морских судов. Корпус. — СПб.: ФАУ «РМРС». — 2018. — Т.2. — 205 с.
-
Российский морской Регистр судоходства.
Правила классификации и постройки морских судов. Сварка. — СПб.: ФАУ «РМРС». — 2019. — Т.14. — 105 с.
-
Королев В. В. Исследование полей деформаций судовых корпусов / В. В. Королев, Н. Е. Жадобин // Эксплуатация морского транспорта. – 2008. — №3(53). – С. 73-75.
-
Контроль качества сварки: учебное пособие для машиностроительных вузов / под. ред. В.Н. Волченко – М.: Машиностроение, 1975. – 328 с.
-
Деев Г. Ф. Дефекты сварных швов / Г. Ф. Деев, И. Р. Пацкевич. Киев: Наук. думка, 1984. – 208 с.
-
ГОСТ Р ИСО 5817-2009. Сварка. Сварные соединения из стали, никеля, титана и их сплавов, полученные сваркой плавлением (исключая лучевые способы сварки). Уровни качества. – Введ. 2011-01-01. – М.: Стандартинформ, 2011. – 23 с.
Пригодность нескольких сталей корпуса для сварки в полевых условиях | Практика бурения и производства
РЕФЕРАТ
Около 200 стыков обсадных труб из 6 различных сталей были сварены в полевых условиях и закалены через различные интервалы времени после разрыва дуги. Результаты показывают, что различные стали по-разному реагируют на закалку. В результате сравнения способов, которыми они соответствуют требованиям полевой практики, некоторые из этих сталей считаются свариваемыми, а некоторые другие — несвариваемыми при использовании при сварке обсадных труб в полевых условиях.Для установления стандарта была предложена процедура испытаний с целью определения свариваемости различных сталей для обсадных труб в полевых условиях.
ВВЕДЕНИЕ
В течение прошедшего года проблема влияния закалки на кольцевые сварные швы в обсадной колонне исследовалась в нескольких местах. Результаты этих нескольких исследований собраны в этой статье с целью использования в качестве руководства для определения пригодности нескольких сталей для сварки кожухов в полевых условиях.Представленные здесь данные позволяют предложить определение свариваемости обсадных труб и сделать некоторые выводы относительно свариваемости различных сталей для обсадных труб. Считается, однако, что даже несмотря на то, что эти результаты указывают на серьезные усилия со стороны экспериментаторов по исследованию проблемы тушения, вероятно, никто не должен настаивать на окончательных выводах в настоящее время. Основная причина для представления этой статьи заключается в том, что в результате этих испытаний доступен значительный объем информации об относительной приспособляемости некоторых сталей к полевой сварке, и, вероятно, важно, чтобы эта информация была доступна для тех, кто занимаются сваркой своих кожухов и тем, кто изготавливает кожухи под сварку.Документ следует рассматривать как отчет о проделанной работе. Термин «свариваемость», используемый в этой статье, предназначен для обозначения того качества стали, которое позволяет компетентному сварщику с использованием надлежащего оборудования и техники без излишних трудностей обрабатывать сталь лужей — с дополнительным условием, что сталь должна иметь такую природу, чтобы после сварки ее можно было погрузить в воду в течение относительно короткого времени, например 1 мин, без чрезмерного воздействия на ее предел прочности на разрыв или пластичность.Поскольку эти тесты проводились в разных местах и разными исследователями, процедуры и методы несколько различались от места к месту.
В общем, процедура заключалась в использовании стыковых соединений обсадных труб, которые были достаточно длинными, чтобы их можно было легко обрабатывать в машинах для прочности на растяжение после завершения сварки. Большинство сварных швов было выполнено с трубой в вертикальном положении, так как диаметр ее стороны или больше, использовались три сварщика; когда труба была меньше 7 дюймов.наружного диаметра использовались всего два сварочных аппарата. После завершения сварных швов они, в некоторых случаях, вытягивались целиком; а в других случаях суставы разделялись на купоны, которые тянули и сгибали. Перед каждой из таблиц данных будет найдено описание условий, в которых проводились тесты.
Почему следует использовать экзотермическую сварку Apliweld® вместо любого другого механического соединения?
Хорошо выполненные соединения с помощью зажимов и крепежных деталей соответствуют требованиям хорошего соединения.То есть они способны противостоять и эффективно направлять разряды молнии на землю.
Однако иногда даже при максимальных усилиях монтажников пригодность этих соединений трудно определить, хотя бы визуально. Во-первых, резьбовые соединения сильно зависят от навыков или даже терпения рабочего в отношении приложения крутящего момента к каждому из болтов, которые может иметь соединитель. Это, априори, простая задача, но часто монотонная и повторяющаяся, особенно для больших установок, и поэтому очень подвержена человеческим ошибкам.Хуже того, любой отказ трудно обнаружить, пока не будет измерено сопротивление всей установки. Кроме того, необходимо техническое обслуживание. Загрязнения, искры или коррозия могут со временем снизить качество соединений, даже если они выполнены правильно.
Решением этой проблемы является замена механического соединения на экзотермическую сварку с использованием APLIWELD® с лучшими гарантиями даже во времени как для выполнения, так и для проверки соединения.
Основное отличие состоит в том, что, в отличие от соединений с зажимами, сварка представляет собой необратимую молекулярную связь, химическое превращение, которое нельзя обратить вспять, когда прочность проводников одинакова. Добавляемый материал — медь, обладающая своими электрическими свойствами.
Что касается электрических свойств зажимов, следует учитывать, что: 1. между подключенными проводниками всегда есть зазор (между ними «нет химии») и 2. чистота разъемов может сильно варьироваться. негативное влияние на соединение.
Подводя итог, можно сказать, что соединения экзотермической сварки, по сравнению с механическими соединениями, имеют такую же или лучшую проводимость, не увеличивают сопротивление, не корродируют или ржавеют, они более устойчивы к поломке и механическому давлению , потому что сформированный материал сохраняет свои электрические и механические свойства постоянными дольше, и эти значения такие же или даже лучше, чем у самих проводников.
В качестве дополнительной гарантии, экзотермическая сварка Apliweld® (также называемая алюминотермической), система, разработанная Aplicaciones Tecnológicas, S.A., соответствует требованиям UL467, стандарту, который применяется к качеству этих типов соединений, таким образом получив сертификат UL.
(PDF) Концентрация напряжений в стыковых сварных соединениях с усилением с одной стороны (Обзор)
10 ISSN 0957-798X ПАТОН СВАРОЧНЫЙ ЖУРНАЛ, № 4, 2019
НАУЧНО-ТЕХНИЧЕСКАЯ
Сторонане может быть ограничена только SCF оценка, и это
необходимо для определения напряжений на лицевой и
корневой сторонах сварного шва.
5. Комбинированные процедуры
наиболее эффективны для определения напряженного состояния в окрестности сварного шва
арматуры. Вслед за ними по математическим формулам, полученным аналитическим путем
, определяются напряжения в локальных
калибровочных зонах перехода сварного шва в основной металл
и напряжения на достаточном удалении от острой концентрации
тракторов с использованием МКЭ. моделирование.
1. Труфяков В.И., Дворецкий В.И., Михеев П.П. и другие. (1990)
Прочность сварных соединений при знакопеременных нагрузках. Эд. В.И.
Труфяков. Киев, Наукова думка.
2. Гасснер, Э., Хайбах, Э. (1968) Die Schwingfestigkeit
von Schweissverbindungen aus der Sicht einer oerlichen
Beanspruchungsmessung. Fachbuchreihe Schweisstechnik,
Bd 53. Tragfaehigkeitsermittlung bei Schweissverbindungen,
Dusseldorf, Verlag Schweisstechnik, 47–73 [на немецком языке].
3. Мэддокс, С.Дж. (2003) Обзор правил расчета на усталость сварных конструкций. Сварка Патона, J., 10–11, 94–99.
4. Ниеми, Э., Фрике, В., Мэддокс, С.Дж. (2006) Анализ усталости
сварных компонентов: Руководство проектировщика по методике структурных напряжений горячих точек
. Кембридж, Woodhead Publishing Ltd.
5. Хоббахер А. (2008) Рекомендации по расчету на усталость сварных соединений и компонентов
. Париж, IIW.
6.Юн Бай, Вэй-Лян Цзинь (2015) Морское структурное проектирование.
Оксфорд, издательство Elsevier Publishing.
7. Мэддокс, С.Дж. (1991) Усталостная прочность сварных конструкций.
Кембридж, Abington Publishing.
8. Герасимчук, Олег, Герасимчук, Елена (2017) Теоретическая
оценка усталостной долговечности при регулярном циклическом нагружении. Me-
Chanics and Advanced Technologies, 79 (1), 49–56.
9. Нойбер, Х. (2001) Kerbspannugslehre: Theorie der Span-
nungskonzentration Genaue Berechnung der Festigkeit.Ber-
lin, Springer-Verlag Berlin Heidelberg [на немецком языке].
10. Радай Д., Сонсино С.М., Фрике В. (2006) Оценка усталости —
Оценка сварных соединений местными подходами. Кембридж,
Woodhead Publishing Ltd.
11. Коростылев Л.И., Литвиненко Д.Ю. (2016) Анализ и классификация
методов оценки прочности сварных
тонкостенных конструкций корпуса. Вестник ГУМРФ Адм. С.О. Ма-
каров, 3, 104–118.
12. Хоббахер, А.Ф. (2003) Метод эффективного напряжения надреза в сравнении с другими методами расчета на усталость сварных конструкций
единиц. Сварка Патона, J., 10–11, 117–121.
13. Воробьев Е.В., Стрижало В.А., Анпилогова Т.В. (2017)
Прочность сталей при охлаждении до 4,2 К в условиях концентрации напряжений
. Проблемы прочности, 5, 5–10.
14. Навроцкий Д.И. (1968) Расчет сварных конструкций с учетом концентрации напряжений
.Ленинград, Машинострое-
нэ.
15. Тимошенко С.П., Гудье Дж. (1975) Теория упругости. Эд.
Г.С. Шапиро. Москва, Наука.
16. Копельман Л.А. Сопротивление сварных узлов
хрупкому разрушению. Ленинград, Машиностроение.
17. Труфяков В.И. (1973) Усталость сварных соединений. Киев, Науко-
ва думка.
18. Кархин В.А. (1985) Влияние формы шва на распределение напряжений при растяжении стыковых соединений большой толщины.Автоматич.
Сварка, 9, 25–28.
19. Турмов Г.П. (1976) Определение коэффициента концентрации напряжений
в сварных соединениях. Там же, 10, 14–16.
20. Стаканов В. И., Костылев В.И., Рыбин Ю.И. (1987) О расчете коэффициента концентрации напряжений
в сварных соединениях с стыковыми
и плоскими швами. Там же, 8, 7–18.
21. Кархин В.А., Копельман Л.А. Концентрация напряжений в стыковых соединениях
.Сварочн. Производство, 2, 6–7.
22. Ткач П., Молтасов А. (2017) Розовый метод оценки стану
naprezenia w elementach konstrukcji spawanych. Czesc 1:
Metody tradycyjne. Biuletin Instytutu Spawalnictwa, 4, 52–56
[на польском языке].
23. Махненко В.И., Мосенкис Р.Ю. (1985) Расчет коэффициентов концентрации напряжений
в сварных стыковых швах и сварных швах l-
. Автоматич. Сварка, 8, 7–18.
24. Цумарев Ю.А. (2010) Влияние асимметрии односторонних стыковых швов
на распределение напряжений в сварном соединении. Сварка и
Диагностика, 5, 24–27.
25. Цумарев Ю.А. (2010) Влияние эксцентрического напряжения на
напряженное состояние стыкового сварного соединения. Сварочн. Производство, 6,
6–10.
26. Ермолаев Г.В., Мартыненко В.А., Марунич И.В. (2014) Ef-
Влияние размеров выпуклости шва на напряженное состояние стыкового соединения при растяжении
.Сварка Патона J., 8, 26–32.
27. Gurney, T.R. (1979) Усталость сварных конструкций. 2-е изд.
Лондон, Нью-Йорк, Мельбурн, Cambridge University Press.
28. Аснис А.Е., Иващенко Г.А., Андерсон Я.Е. (1982)
Влияние радиуса перехода между сварным швом и основным металлом на усталостную стойкость сварных соединений. Автоматич. Сварка, 4, 48–51 [на русском языке
].
29. Кархин В.А., Костылев В.И., Стаканов В.И. (1988) Влияние
геометрических параметров стыковых, тройников и крестообразных соединений на коэффициент концентрации напряжений
.Там же, 3, 6–11.
30. Лукьянов В.Ф., Пархоменко А.А., Рогозин Д.В. (2010)
Оценка усталостной прочности сварных соединений с плоскими
швами на основе анализа локального напряженного состояния. Сварка и Диаг-
ностика, 6, 17–20.
31. Партон В.З., Перлин П.И. (1981) Методы математической теории упругости. Москва, Наука.
32. Рыбин Ю.И., Стаканов В.И., Костылев В.I. et al. (1982) Исследование
методом единичных элементов влияния геометрических параметров
тройников и крестообразных сварных соединений на концентрацию напряжений.
Автоматич. Сварка, 5, 16–20.
33. Кириан В.И., Дворецкий В.И., Мальгин М.Г. (2012) Расчет
локальных напряжений в зонах сварных соединений крупногабаритных пространственных
конструкций. Сварка Патона J., 4, 2–5.
34. Коростылев Л.И., Литвиненко Д.Ю. (2015) Оценка коэффициента концентрации напряжений
в сварных узлах тонкостенных конструкций
путем расчета макро- и микроконцентрации.
Науковый вестник ХДМА, 13 (2), 184–194.
35. Молтасов А.В., Клочков И.Н., Кныш В.В. (2013) Инженер-
Подход к расчету коэффициента концентрации напряжений в сварном шве
внахлест при растяжении и изгибе. Вестник НТУУ
КПИ. Серия машинобудування, 69 (3), 150–157 [на русск.
сиан].
36. Гоял, Р., Эль-Зейн, М., Глинка, Г. (2016) Робастный метод анализа напряжений
для прогнозирования усталостной долговечности сварных конструкций.
Сварка в мире, 60 (2), 299–314.
37. Молтасов А., Мотрунич С. (2017) Badania lokalnego stanu
w obszarze niejednorodnosci geometrycznej doczolowych
zlaczy spawanych z jednostronnym nadlewemnym. Biuletin Ins-
tytutu Spawalnictwa, 4, 64–71 [на польском языке].
Поступила 22. 01.2019
Передовые методы соединения для 21 века
Иэн Смит, Гунци Ши, Ричард Фриман и Фэй Смит
Доклад представлен на Международном форуме по сварочным технологиям в авиационной и космической промышленности 2004 г. 11-14 ноября.2004 г., Пекин, Китай.
Abstract: Обзор некоторых передовых технологий соединения, разрабатываемых для удовлетворения требований промышленности в 21 -м -м веке. Обсуждаются достижения в области сварки трением с перемешиванием, лазерной обработки, электронно-лучевой сварки при пониженном давлении и соединения металлов с композитами.
Введение
В этой статье рассматриваются некоторые передовые методы соединения, которые появились недавно в результате работы в TWI и других организациях.TWI — ведущий в мире центр технологий соединения материалов, в котором работает около 500 сотрудников в нескольких местах в Великобритании и других частях мира. Штаб-квартира находится в Кембридже, Великобритания. TWI — это частная некоммерческая дистрибьюторская компания, которая предоставляет исследования и разработки, консультации, обучение, передачу технологий и консультации для своих более 2000 промышленных членов по всему миру. Сектор аэрокосмической промышленности, включая поставщиков планеров, авиационных двигателей и компонентов, в настоящее время составляет более 10% промышленного членства TWI.
В этом документе будут рассмотрены четыре технологии и обсуждены их актуальность и преимущества для аэрокосмической промышленности. Эти технологии:
- Сварка трением с перемешиванием
- Лазерная обработка
- Электросварка при пониженном давлении
- Соединение металла с композитом
1. Сварка трением с перемешиванием
Сварка трением с перемешиванием быстро развивалась с момента ее изобретения в 1991 году компанией TWI. Это запатентованный процесс [1,2] , и более 114 организаций получили лицензии на его использование.Он широко используется в различных отраслях промышленности, особенно в авиакосмической отрасли, для соединения алюминиевых сплавов.
Рис.1. Принцип и микроструктура сварки трением с перемешиванием
Для сварки трением с перемешиванием используется неплавящийся вращающийся инструмент Fig.1 , который перемещается по стыку между двумя компонентами для получения высококачественных стыковых швов или сварных швов внахлест. Инструмент FSW обычно имеет профилированный штифт и уступ с большим диаметром, чем у штифта. Длина штифта соответствует требуемой глубине сварного шва.Штифт перемещается вдоль линии соединения, в то время как заплечик находится в тесном контакте с верхней поверхностью заготовки, чтобы избежать выталкивания размягченного материала и обеспечить уплотнение.
1.1 Инструменты FSW
ИнструментыFSW изготовлены из износостойкого материала с хорошими статическими и динамическими свойствами при повышенных температурах. Современные инструменты позволяют производить до 1000 м сварного шва из алюминиевых профилей толщиной 5 мм без смены инструмента. Конструкция инструментов для сварки трением с перемешиванием лежит в основе этого замечательного и все еще относительно нового процесса сварки.
Рис.2. Инструмент MX Triflute TM
Инструменты с несколькими спиралями, такие как MX Triflute TM Fig. 2 , имеют нечетное количество канавок с относительно крутым углом наклона и имеют крупный винтовой гребень вокруг пазов канавок. [3] Они дополнительно уменьшают объем инструмента и, следовательно, способствуют потоку материала, разрушению и диспергированию поверхностных оксидов. Исследуемые профили уступа инструмента предназначены для обеспечения лучшего соединения между уступом инструмента и заготовкой.
1,2 Качество сварки
Прочность ядра сварного шва в состоянии после сварки может быть выше, чем в зоне термического влияния. В случае отожженных материалов испытания на растяжение обычно не проходят в неповрежденном материале вдали от сварного шва и зоны термического влияния. Сварочные свойства полностью закаленных (холоднодеформированных или термообработанных) алюминиевых сплавов можно улучшить, контролируя термический цикл. Для достижения оптимальных свойств некоторых сплавов термическая обработка после сварки является лучшим выбором, хотя это не всегда будет практичным решением для многих применений.
Сообщается, что типичные характеристики растяжения сваренных трением с перемешиванием алюминиевых сплавов серии 7000 достигают 95% от свойств основного материала. [4] Испытания на усталость показали, что соединения FSW дают значительно лучшие результаты с меньшим разбросом, чем другие методы соединения. [5]
1.3 Приложения FSW для аэрокосмической промышленности
Компания Boeing применила FSW к ракетам Delta II, и первая из них была успешно запущена в августе 1999 года.Космический корабль Mars Odyssey стартовал на ракете Delta II в 2001 году, которая продемонстрировала прочность и качество сварных соединений продольным трением с перемешиванием на всех трех цилиндрических компонентах резервуара. Технология FSW для резервуаров Delta увеличивает прочность сварного шва на 30–50% и обеспечивает экономию затрат на 60% при сокращении времени производства с 23 до 6 дней.
Рис.3. Дельта II
Четыре машины FSW были установлены на предприятии Lockheed Martin в Новом Орлеане для внешних топливных баков космических шаттлов НАСА, Рис.4 . Внешний резервуар имеет размеры 47 м на 8,4 м в диаметре. и является структурной основой шаттла, поглощая большую часть тяги в шесть миллионов фунтов на старте. Сообщается, что преимущества FSW (по сравнению с VPPA) заключаются в увеличении UTS до 22%, значительном снижении вариабельности сварных швов и сокращении времени изготовления ствола с 47 до 19 часов.
Рис.4. Аппарат FSW для сварки челночных танков
Процесс FSW предлагает огромный потенциал для недорогого соединения легких алюминиевых конструкций планера для больших гражданских самолетов, таких как Airbus A380.Исследователи из Airbus Deutschland видят высокий потенциал соединения алюминиевых сплавов с помощью FSW для соединения обшивки фюзеляжа. Они представили данные, которые демонстрируют, что механические и технологические свойства этих сварных швов приближаются к свойствам основного материала [6] . Это может привести к снижению стоимости и веса за счет улучшения качества соединений и возможности новой конструкции.
Компания Boeing продемонстрировала криволинейную FSW двери шасси сложного самолета.Они также успешно продемонстрировали СТС многослойных сборок путем сварки тонких Т-образных соединений обтекателя истребителя, который прошел летные испытания. [7]
Eclipse Aviation Corporation из Альбукерке, Нью-Мексико, решила использовать FSW для замены традиционных процессов клепки и склеивания [5] . Вероятно, это будет первое применение FSW в крупных авиационных приложениях с потенциалом значительного сокращения времени и стоимости сборки, Рис.5 и 6.
Рис.5. Взлет во время первого испытательного полета бизнес-джета Eclipse 500, сваренного трением с перемешиванием,
Рис.6. Панели с жесткой обшивкой производятся сваркой трением с перемешиванием
Eclipse Aviation Corporation объявила в июне 2002 года, что FAA (Федеральное управление гражданской авиации США) одобрило спецификацию FSW, созданную для использования при сборке самолета Eclipse 500. Одобрение FAA этой спецификации процесса вместе с получением сертификата типа позволит Eclipse Aviation строить серийные самолеты с использованием FSW.Спецификация процесса FSW детализирует процедурные требования, положения по обеспечению качества, стандарты для инструментов и подготовки материалов, необходимых для использования FSW при сборке самолетов.
В стадии разработки находится процесс замены клепок в полу военно-транспортных самолетов Lockheed Martin C130J и Boeing C17. Сообщалось, что использование FSW в конструкции грузового пола C-130 может снизить производственные затраты на единицу продукции более чем на 25% при одновременном повышении надежности, коррозионной стойкости и конструктивных характеристик.
2. Лазерная сварка
Изготовление или производство с использованием лазеров дает несколько потенциальных преимуществ:
- Повышенная производительность — более быстрое производство деталей при меньших затратах.
- Улучшенное качество — минимальные искажения и меньший объем доработок.
- Повышенная производительность — более длительный срок службы или повышенная устойчивость к коррозии или высоким температурам. Кроме того, технологии лазерного ремонта могут значительно продлить срок службы изношенных компонентов.
- Новые производственные маршруты и компоненты — там, где альтернативные технологии просто недоступны.
В этом разделе будут описаны некоторые новые разработки и возможности для производства с использованием лазеров по трем широким темам: усовершенствование технологического процесса, новое производство и новые лазерные источники, а затем будут описаны некоторые недавние работы по применению лазеров для соединения аэрокосмических алюминиевых сплавов.
2.1 Усовершенствования процесса — гибридная лазерно-дуговая сварка
Благодаря полученному узкому сварному шву с глубоким проплавлением лазерная сварка имеет ряд преимуществ по сравнению с другими сварочными процессами, а именно высокую скорость соединения, низкие затраты на расходные материалы, высокую воспроизводимость и низкий уровень деформации, что приводит к большей точности сборки и сокращению работ по исправлению.
Лазерная сварка, однако, представляет собой сложный процесс, и для получения сварных швов удовлетворительного качества и рабочих характеристик требуется очень жесткий контроль ряда параметров, таких как подгонка и состав стали.
Расширенный диапазон применимости доступен благодаря гибридной лазерно-дуговой сварке, в которой два процесса сварки связаны в одной технологической зоне, как показано на Рис. 7 . [8]
Рис.7. Гибридная лазерно-дуговая сварка
Доступные варианты включают комбинацию CO 2 , Nd: YAG, диодного или волоконного лазера с процессом дуговой сварки, например дуговой сваркой в газовой среде, дуговой сваркой вольфрамовым электродом или плазменной дугой, или даже комбинацию двух различных источников лазера.
По сравнению с использованием только мощности лазера, гибридная лазерная дуговая сварка предлагает:
- Повышенная скорость передвижения (x2) или повышенное проникновение (x1,3).
- Повышенный допуск к посадочному зазору.
- Возможность добавления присадочного материала для улучшения микроструктуры металла шва, качества соединения и свойств соединения.
- Потенциально улучшенная связь по энергии.
- Повышенное тепловложение и пониженная твердость.
Есть некоторые недостатки, в том числе повышенная сложность, необходимость определения дополнительных параметров сварки и требование установления новых параметров процесса.
Тем не менее, гибридная лазерно-дуговая сварка в настоящее время является производственным процессом как в автомобилестроении, так и в судостроении, и было показано, что она является подходящим процессом для кольцевой сварки газотранспортных трубопроводов.
2.2 Лазерное прямое напыление металла
Для дорогостоящих приложений, таких как компоненты авиационных двигателей, обычно экономически выгодно ремонтировать изношенные или локально поврежденные детали, а не заменять их. Возможной технологией ремонта является прямое лазерное осаждение металла, при котором лазер расплавляет порошок на материале подложки.В отличие от подходов, в которых порошок помещается на подложку, порошок подается через сопло в лазерное пятно на подложке. Это приводит к образованию ванны расплава, которая при охлаждении оставляет твердый осадок порошкового материала на подложке.
Лазерное осаждение имеет два основных преимущества по сравнению с другими методами осаждения порошка. Во-первых, операция представляет собой процесс с низким тепловложением, что снижает вероятность ликвационного крекинга. Во-вторых, использование пятна очень малого размера позволяет делать высокоточные и воспроизводимые отложения.Разработаны адаптивные системы управления, которые контролируют характеристики ванны расплава и регулируют процесс по мере необходимости для поддержания качества отложений. На рис. 8 показано многослойное покрытие сплава для авиационных двигателей.
Рис.8. Многослойное напыление прямым лазерным напылением металла
Помимо ремонта, прямое лазерное напыление металла подходит для изготовления оригинальных деталей. Изменяя состав порошка по мере создания детали, можно разработать функционально дифференцированный компонент с конкретными рабочими характеристиками, непосредственно связанными с положением.Этот процесс также можно использовать для быстрого прототипирования.
Однако для того, чтобы этот процесс получил широкое признание, необходимы разработки для увеличения скорости осаждения, эффективности осаждения и установления соответствующих параметров обработки для обеспечения высокой точности и качества.
2.3 Новые лазерные источники
Для обработки материалов доступен широкий спектр лазеров, в том числе лазеры на CO 2 , лазеры на Nd: YAG, прямые диодные лазеры, эксимерные лазеры и лазеры на парах меди.Текущие разработки существующих источников включают улучшение качества луча, более высокие уровни мощности, повышение эффективности розеток и т. Д.
В последнее время маломощные волоконные лазеры, которые использовались в связи в течение многих лет, были разработаны до уровня, когда доступны уровни мощности, подходящие для сварки и резки. Среда генерации представляет собой волокно из Yb: YAG, а длина волны излучаемого света составляет 1070 нм, что очень близко к длине волны Nd: YAG. Производители заявляют, что волоконные лазеры имеют лучшее качество луча, чем Nd: YAG-лазеры аналогичной мощности, что позволяет увеличить расстояние зазора при сварке.Кроме того, эффективность дюбелей оценивается между 20 и 30%, что значительно выше, чем у источников Nd: YAG или CO 2 ; таким образом, требуется относительно низкая потребляемая мощность и пониженное охлаждение. Волоконные лазеры также меньше, чем лазеры на Nd: YAG или CO 2 аналогичной мощности.
TWI приобрела волоконный лазер мощностью 7 кВт и начала ряд исследовательских программ, посвященных преимуществам и недостаткам волоконных лазеров.
2.4 Лазерная сварка алюминиевых сплавов
Лазерная сварка алюминиевых сплавов — сложная задача, наиболее часто встречающиеся дефекты — это пористость, трещины при затвердевании и плохая геометрия сварного шва.Недавняя работа показала, что пористость может быть значительно уменьшена и что хорошие профили сварного шва могут быть получены при сварке стыковых швов с квадратным краем с полным проплавлением алюминия 2024 толщиной 3,2 мм с использованием мощности лазера Nd: YAG [9] мощностью 3 кВт. В исследовании сделан вывод о том, что, контролируя условия процесса, можно достичь более низкого уровня пористости металла сварного шва, чем тот, который определен в BS EN 13919-1: 1997 или AWS D17.1: 2001. Основные выводы:
- Положение фокуса на поверхности материала или на 1 мм ниже нее помогает добиться сварных швов с полным проплавлением с хорошими профилями сварного шва.
- Высокочистый гелиевый защитный газ с низкой точкой росы, подаваемый через систему подачи защитного газа без влаги и конденсации, обеспечивает меньшую пористость металла сварного шва по сравнению с промышленным газом.
- Удаление пористого оксидного слоя перед сваркой способствует уменьшению пористости металла шва. Время между подготовкой материала и последующей сваркой должно быть как можно короче, чтобы избежать накопления атмосферной влаги.
- Дальнейшее уменьшение пористости металла шва может быть достигнуто за счет очистки присадочной проволоки.
- Использование двухточечного профиля энергии лазера с разделением пятен 0,27 мм и распределением энергии 50/50 между двумя пятнами диаметром 0,45 мм помогает устранить крупную пористость в алюминии 2024 толщиной 3,2 мм, но оказывает меньшее влияние на меньшие поры чем диаметр 0,4-0,5 мм.
Рис.9. Т-образные стыковые швы из алюминиевого сплава 2024 г.
Такие процедуры использовались для изготовления усиленных панелей из сплава алюминия 2024 года, содержащих Т-образные стыковые швы, показанные на рис. 9 .
3. Электронно-лучевая сварка при пониженном давлении
Электронно-лучевая сварка (EBW) — это зрелый процесс сварки, который предлагает множество преимуществ с точки зрения производительности сварки, предотвращения деформации и минимальных металлургических нарушений. Однако необходимость сварки в атмосфере высокого вакуума ограничила применение этого процесса компонентами и конструкциями, которые могут полностью содержаться в вакуумной камере.
За последние 10 лет появилась передовая технология электронно-лучевой сварки большой мощности, которая позволяет выполнять сварку при значительно более высоком рабочем давлении i.е. ~ 1 мбар, что примерно в тысячу раз выше, чем обычно используется. Это стало возможным благодаря разработке генератора электронного пучка, использующего передаточную колонну с дифференциальной накачкой, Рис. 10 . Этот генератор может производить электронный луч с заготовкой при давлении, близком к атмосферному; на сегодняшний день оптимальные сварочные характеристики достигаются при давлении до 1 мбар. Это, в свою очередь, позволяет использовать локальное вакуумное устройство, избегая при этом необходимости в сложной системе уплотнения и откачки.
Рис.10. Электронная пушка мощностью 100 кВт и передаточная колонна с дифференциальной накачкой
Было показано, что с помощью этой системы можно создать сварочный вакуум («пониженное давление») с помощью простого механического вакуумного насоса и грубых уплотнений. [10] Развитие этого варианта процесса представляет собой ступенчатое изменение, поскольку оно позволяет использовать локальное уплотнение и откачку и потенциально устраняет необходимость в больших камерах для сварки больших компонентов. Это также дает возможность присоединить сварочное оборудование к конструкции и применить сварочный процесс «на месте».
Кроме того, при таком режиме давления система была особенно устойчива ко многим изменениям, которые ранее препятствовали внедрению электронно-лучевой сварки для больших конструкций, таких как:
- Чистота компонентов — Сварка в высоком вакууме требует, чтобы как непосредственно область стыка, так и вся сборка были относительно чистыми, в противном случае может произойти выделение газа. При работе с «пониженным давлением» наблюдается значительно повышенная устойчивость к чистоте компонентов, и необходимо очищать только непосредственную область стыка.
- Расстояние от пистолета до пистолета — Луч пониженного давления по существу параллелен и не имеет четко определенного положения фокуса. Как следствие, расстояние от пистолета до рабочей поверхности может варьироваться более чем на 400 мм без ущерба для качества сварки. Напротив, электронно-лучевая сварка в высоком вакууме требует, чтобы расстояние от пистолета до рабочего места составляло +/- 2 мм для поддержания надлежащего положения фокуса луча.
- Время откачки — Работа при давлении 1 мбар, в отличие от 10 -3 мбар, значительно сокращает время откачки для данного объема.Даже для больших объемов время откачки измеряется в минутах, а не в часах.
- Разгрузка пистолета — Комбинация колонны переноса пучка и ступени избыточного давления гелия исключает риск попадания паров металла или положительных ионов в электронную пушку, что может привести к поломке и прерыванию процесса сварки. Это серьезное соображение при сварке дорогостоящих критических деталей с использованием EBW.
- Характеристики луча — Повышенное затухание луча, вызванное эффектом рассеяния в атмосфере пониженного давления, приводит к более «мягкому» лучу, что приводит к более широким профилям сварного шва, обеспечивающим большую устойчивость к зазорам в стыках и лучшему поведению при окончании сварки.
3.1 Подготовка швов и геометрия сварного шва
РПЭБ Сварка выполняется за один проход без добавления присадочного металла, поэтому используются простые угловые стыки. Это позволяет упростить конструкцию изготовления за счет значительной экономии материалов и обработки, а также радикально уменьшить и контролировать искажения. Отсутствие сварочных материалов и очень низкое тепловложение при сварке RPEB существенно снижает стоимость и коррекцию после сварки.
3.2 Неразрушающий контроль
Обширный опыт показал, что дефекты сварных швов при использовании RPEB возникают редко из-за надежности процесса и точности размещения сварных швов благодаря использованию отслеживания шва в реальном времени.RPEB уникальным образом использует сам сварочный луч для отслеживания соединения с большой точностью и компенсации неточностей обработки и термической деформации во время сварки. Тем не менее, в случае возникновения каких-либо дефектов, рентгеновский контроль в сочетании с ультразвуковой фазированной решеткой оказался успешным в обнаружении и определении размеров плоских дефектов сварных швов высотой менее 2 мм.
3.3 Применение в авиакосмической отрасли
Вариант процесса RPEB показал себя особенно эффективным при сварке сталей тяжелого профиля, меди и алюминиевых сплавов без каких-либо вредных воздействий, вызванных сварочной атмосферой.Возможные области применения включают производство алюминиевых заготовок большой толщины с различной толщиной сечения для последующей обработки путем механической обработки.
Было показано, что более химически активные металлы, такие как титан и его сплавы, могут быть успешно обработаны, и первоначальные испытания показали большие перспективы. В TWI началось исследование, чтобы изучить, можно ли реализовать те же потенциальные преимущества для титановых сплавов, и установить ограничения, если таковые имеются, на сварку при таком давлении.
4. Соединение металла с композитом
Чтобы полностью использовать композитные материалы, их необходимо легко встраивать в конструкции из множества различных материалов в точном требуемом месте. Свойства соединения должны быть известны, согласованы и воспроизводимы, легко проверяться и сохраняться в течение истории нагрузки, аналогичной той, которая ожидается при эксплуатации.
В настоящее время для этого широко используются три метода: склеивание, механическое крепление и комбинация склеивания и крепления.
Склеенные соединения могут быть спроектированы таким образом, чтобы клей выдерживал нагрузки, превышающие прочность основного материала [11] , и не демонстрировал разрушения из-за усталостной нагрузки. [12] Однако, несмотря на имеющиеся подробные знания в области проектирования и производства, опыт эксплуатации, который показывает, что некоторые соединения обеспечивают отличную службу, а другие нет, привел к неуверенности в технологии клеевого соединения.
Использование механически скрепленных соединений в металлах хорошо известно.В этих материалах податливость снижает концентрацию напряжений вокруг отверстий. Однако в композитных материалах существует очень небольшое ослабление концентрации напряжений вокруг отверстий. Хрупкая природа композитных материалов также означает, что практически отсутствует возможность перераспределения нагрузки в случае выхода из строя одного из крепежных элементов в сборке.
Во многих случаях для устранения ограничений обоих методов соединения используются гибридные соединения, содержащие как клеи, так и механические крепежные элементы.Такой подход сводит на нет основные цели использования композитного материала , т.е. размер , вес и экономию средств. Хорошо изученные свойства металлических аэрокосмических сплавов снова становятся привлекательными и ограничивают положительные преимущества композитных систем.
Чтобы решить эту проблему, недавно в TWI были разработаны запатентованная технология обработки поверхности материала Surfi-Sculpt TM и процесс соединения Comeld TM . [13] Он предлагает возможность создания соединений между композитными материалами из армированного волокном пластика (FRP) и металлами с улучшенными характеристиками.Ожидается, что этот метод соединения позволит произвести революцию в конструкции соединений, преодолев некоторые проблемы, связанные с адгезивным соединением и механическим креплением композитов к металлам.
Одна из геометрий соединения, выбранных для начальных исследований, показана на Рис.11.
Рис.11. Геометрия стыка испытательного образца
Примеры поверхности, созданной с помощью Surfi-Sculpt TM , показаны на рис. 12, и , 13, .Эта обработка поверхности может использоваться для создания металлических выступов (известных как выступы) различных форм и размеров на поверхности материала.
Контрольные образцы были изготовлены с помощью простой пескоструйной обработки поверхности.
Рис.12. Обработанная нержавеющая сталь
Рис.13. СЭМ-изображение обработанной нержавеющей стали
Как для контрольных образцов, так и для образцов Comeld TM , соединение было изготовлено путем наложения преформ плотностью 400 г / м 2 гладкой тканой ткани E-glass (Carr Reinforcements) на металлические образцы с последующей вакуумной инфузией полиэстера. смолу (Crystic 489PA) в стеклоткань.
4.1 Тестирование и результаты
Comeld TM и контрольные образцы были нагружены растяжением со скоростью 1 мм / мин до разрушения. Типичные кривые нагрузка-смещение показаны на Рис. 14 .
Рис.14. Кривая нагрузка-смещение
Рис. 15 показывает механизмы повреждения, которые произошли до и во время разрушения образцов.
а) Прогресс перед тестированием
б) Прогресс после тестирования
c) Разрушение композита при сдвиге
Рис 15.Механизмы повреждения в ТМ Комелд экз
Кривые смещения нагрузки, показанные на Fig.14 , демонстрируют, что испытанное соединение Comeld TM имело значительно большую нагрузочную способность, чем соответствующее управляющее соединение. Площадь под кривыми нагрузка-перемещение соответствует энергии, поглощенной при разрушении образца. Энергия, поглощаемая шарниром Comeld TM , была более чем вдвое больше, чем энергия, потребляемая контрольным шарниром.
В контрольных образцах разрушение произошло по линии соединения.Эти сбои были очень внезапными, и металлические или композитные основы были повреждены очень незначительно.
В образцах Comeld TM повреждения были видны до разрушения в виде побеления композита, вызванного растрескиванием матрицы. Перед разрушением композита произошла деформация металлических выступов, и образцы Comeld TM в конечном итоге вышли из строя из-за разрушения композита при сдвиге сразу за пределами зоны выступа. Повреждения в металле и композите, описанные выше, способствовали увеличению площади под графиком и, следовательно, дополнительной энергии, поглощаемой во время разрушения по сравнению с контрольными образцами.Аналогичная работа с другими комбинациями материалов также продемонстрировала улучшенные механические характеристики соединений Comeld TM по сравнению с контрольными соединениями. [14]
Можно сделать вывод, что применение новой техники обработки поверхности, называемой Surfi-Sculpt TM , к новой системе соединения, названной Comeld TM , улучшает механические характеристики соединений между композитными материалами и металлами в следующих отношениях :
- Соединения Comeld TM имели более высокую несущую способность, чем контрольные соединения. Шарниры
- Comeld TM до отказа поглощали более чем в два раза больше энергии, чем контрольные соединения.
- Comeld TM соединения из строя из-за более прогрессирующего режима отказа, чем управляющие соединения.
TWI продолжает разработку Surfi-Sculpt TM и Comeld TM .
5. Выводы
Были рассмотрены четыре передовых метода соединения и обсуждены их применения в аэрокосмической промышленности.Передовые методы соединения являются ключом к созданию более легких, безопасных и доступных аэрокосмических конструкций.
Список литературы
- Томас В. М., Николас Э. Д., Нидхэм Дж. С., Марч М. Г., Темпл-Смит П. и Доус С. Дж. (TWI): «Усовершенствования, связанные со сваркой трением». Спецификация европейского патента EP 0615480 B1
- Midling OT, Morley EJ, Sandvik A (Norsk Hydro, права переданы TWI): «Сварка трением с перемешиванием». Спецификация европейского патента EP 0752926 B1
- Thomas W. M et al: «Инструментальная технология — сердце FSW», Connect, июль / август 2000 г.
- Midling OT, Oosterkamp LD, Bersaas J: «Сварка алюминия трением с перемешиванием — процесс и области применения».7-я конференция Inalco, Кембридж, 15-17 апреля 98 г.
- Кристнер Б., Маккури Дж. И Хиггинс С. «Разработка и тестирование FSW как метода соединения для основной конструкции самолета». 4-й Int. Симпозиум FSW, Парк-Сити, Юта, США, 14-16 мая 2003 г.
- Lohwasser D: «Применение сварки трением с перемешиванием в авиационной промышленности». 2-й Int. Симпозиум FSW, Гётеборг, Швеция, 26-28 июня 2000 г.
- Талвар Р., Больсер Д., Ледерих Р. и Бауманн Дж .: «Сварка трением с перемешиванием конструкций планера». 2-й Int.Симпозиум FSW, Гётеборг, Швеция, 26-28 июня 2000 г.
- Стенд G: «Производство с помощью лазеров — разработки и возможности» IIW Doc. IV-854-04
- Verhaeghe G и Hilton P: «Низкопористая лазерная сварка аэрокосмического алюминиевого сплава» Proc. 34-й Междунар. MATADOR Conf., UMIST, Манчестер, Великобритания, 5-9 июля 2004 г.
- Punshon C и Ribton C: «Сварка электронным пучком при пониженном давлении для высокой производительности при обработке материалов с толстым сечением» IIW Doc IV-862-04
- Hart-Smith LJ: «Соединения внахлест с клеевым соединением».NASA CR 112236. Январь 1973 г.,
- Thrall E W Jr: «Склеенные швы и подготовка к склеиванию». Proc. AGARD? Серия лекций НАТО, номер 102. 1979: 5-1, 5-89
- Kellar EJC и Dance B: «Модификация структуры заготовки» номер международной патентной публикации WO 2004/028731 A1.
- Smith F: «Comeld TM — инновация в соединении композитных материалов с металлом» www.composites-proc-assoc.co.uk/view.php?pid=34
C17-1 Передний адаптер WP-17 WP-9 WP-24G Сварочная горелка TIG Деловые и промышленные горелки TIG alberdi.com.mx
C17-1 Передний адаптер WP-17 WP-9 WP-24G Сварочная горелка TIG Деловые и промышленные горелки TIG alberdi.com.mxПередний адаптер C17-1 WP-17 WP-9 WP-24G Сварочная горелка TIG, WP-17 WP -9 WP-24G Сварочная горелка TIG Передний адаптер C17-1, Найдите много отличных новых и подержанных опций и получите лучшие предложения на Передний адаптер C17-1 WP-17 WP-9 WP-24G Сварочная горелка TIG по лучшим онлайн-ценам на , Бесплатная доставка для многих продуктов. WP-9 WP-24G Сварочная горелка TIG C17-1 Передний адаптер WP-17.
Ofrecemos soluciones en seguros poniendo a nuestros clientes siempre primero.
Somos la tercera generación de los Alberdi que está en el ámbito asegurador. Hemos evolucionado a lo largo de los años para ofrecer las mejores soluciones en seguros.
{«wp_error»: «cURL error 7: Failed to connect to ekr.zdassets.com port 443: Connection timed out»}C17-1 Передний адаптер WP-17 WP-9 WP-24G Сварочная горелка TIG
M105SDTC Новый расширительный клапан для Kubota M100GXDTC M108DSC M105SC.SMD IC TLP160J P160J TLP160 SOP4 TOSHIBA, 3 x триггерные распылители для тяжелых условий работы, регулируемая очистка распылением, валетинг, прочный, приятный, бесконтактный ЖК-ИК-лазер, инфракрасный цифровой термометр, пистолет, новый, новый HITACHI EX200-2 / 3, потенциометр, позиционер двигателя дроссельной заслонки, экскаватор 4257164 Burndy W Набор высвобождающих штифтов PAT600 PATMD Гидравлический обжимной инструмент для обжима 6 тонн, 50 шт. 10SQ045 10A 45V Выпрямители Шоттки R-6, Бесконтактная индукционная электрическая испытательная ручка Детектор напряжения для электриков WT88. *** НОВИНКА *** МЕХАТРОНИКА UF15AC12 BTH 115VAC 29/28 ВЕНТИЛЯТОР ОХЛАЖДАЮЩЕГО ШАРИКОВОГО ПОДШИПНИКА, Руководство по эксплуатации трактора John Deere M.SR2512F-0304-19R0B-E9-N-W ALPHA TAIWAN Поворотные переключатели 3POL 4POS ROHS 4 PIECES. dc DTI AU 538 SUMMER FHF 21300302 TONE ALARM 48 VOLT ac, NEW 7-функциональный цифровой мультиметр AC DC мультиметр Вольтметр OHM VOLT Meter, 180085M1 Шланг радиатора New Massey Ferguson 135 20 2135 230 235 35 50 65 TE20, уплотнительные кольца из буна-метрического буна 67 x 2 мм Цена за 2 шт., 50 шт. 5K 502 Голубой белый резистор с регулируемым сопротивлением, КАБЕЛЬ ФОТОЭЛЕКТРИЧЕСКОГО ПЕРЕКЛЮЧАТЕЛЯ OMRON F39-JC10B-D 10M 8-КОНТАКТНЫЙ НОВОЕ КОЛИЧЕСТВО !!!. 40 мм x 28 мм 5000 шт. Для рулона этикеток со штрих-кодом Zebra TSC Datamax.8-миллиметровая новая алюминиевая распорная втулка 7/16 «OD x 5/16» ID x 1-3 / 8 «Длинное отверстие. Светодиодный матричный модуль P5 для использования вне помещений 160×160 мм 32×32 пикселя SMD RGB Светодиодный экран панели.DC-DC 5A Постоянная повышения / понижения Напряжение постоянного тока ЖК-дисплей ASS.16-битный I2C 4-канальный модуль ADS1115 ADC с усилителем Pro Gain для Arduino DIY. Набор болтов для мебели M6x45 мм, винт с шестигранной головкой и гайками, 8 комплектов, 6202-5 / 8-ZZ, двухсторонние металлические щиты подшипника 5 Подшипники с внутренним диаметром / 8 дюймов 6202-10-ZZ Кол-во 2, партия из 10 штук OSRAM Golden DRAGON® oval Plus LED 3500K WARM WHITE LCW W5PM.Набор из 4 медных зажимов типа «аллигатор» 60CS Mueller, а также 2 красных и 2 черных ботинка. 3 шт. 0,8D насадки для высокочастотной паяльной станции серии 200 QUICK ATTEN, FABORY U17567.050.0350 1/2 «-13 x 3-1 / 2» Размер трубы Обычный U-образный болт из нержавеющей стали 304 SS. 5шт TDA7294 7294 DMOS усилитель звука с MUTE / ST-BY IC New. ECG7062 LA7851 Первоначально вытянутая интегральная схема Sanyo NTE7062,
C17-1 Передний адаптер WP-17 WP-9 WP-24G Сварочная горелка TIG
Передний адаптер C17-1 WP-17 WP-9 WP-24G Сварочная горелка TIG, Передний адаптер C17-1 WP-17 WP-9 WP-24G Сварочная горелка TIGQ-1) Опора железобетонная плита на Стру…
- инженерное дело
- гражданское строительство
- вопросы и ответы по гражданскому строительству
- Q-1) Железобетонная плита поддерживается на стальном каркасе, как показано на рисунке 1. …
Показать текст изображения
Ответ эксперта
Предыдущий вопрос Следующий вопросQ-1) Железобетонная плита опирается на конструкционную стальную раму, как показано на Рисунке 1. Плита имеет удельный вес 25 кН / м² и толщину 150 мм.Факторная временная нагрузка на плиту указана на рисунке 2. Высота колонн стального каркаса составляет 5 м. Коэффициент полезной длины для колонн следует рассматривать как 0,80. Все балки соединены с колоннами сварным швом. Рассмотрим fy = 250 Н / мм², fu = 410 Н / мм² и E = 2 x 105 Н / мм² для конструкционной стали. Для сварного шва принимайте fy = 330 Н / мм² и fu = 410 Н / мм². При необходимости принимайте другие данные разумно. Спроектируйте следующие конструкционные стальные элементы и соединения в соответствии с деталями, представленными в Таблице-1 и на рисунках 1 и 2: 1) Колонна (расчет для осевой нагрузки) 2) Поперечно удерживаемая балка (расчет для поперечной силы и изгибающего момента) 3) Соединение угловым сварным швом (соединение балки с колонной) C1 C3 C5 C2 ht C4 ht B1 B2 B3 B4 3000 B17 B18 B19 B20 B21 C6 C8 09 C10 B5 B6 B7 B8 4000 B22 B23 B24 B25 B26 C11 C12 C14 C15 C13 ++ + + B10 B9 B11 B12 5000 B27 B28 B29 B30 B31 C17 C18 C19 C20 C16 1 B13 B14 B15 B16 3000 4000 5000 6000 Рисунок 1: Вид сверху (плита RCC, опирающаяся на конструкционную стальную раму) Примечание-1: Цифра не в масштабе, все размеры указаны в мм Примечание-2: Тип профиля колонны / Ориентация, показанная на рисунке, является ориентировочной.Выберите соответствующий раздел, как требуется для дизайна колонны C1 C2 C5 из C3 ht C4 HT Факторная живая нагрузка = 3 кН / м2 C6 C7 8,4 C8 11 C9 ++ C10 + H Факторная живая нагрузка = 4,5 кН / м2 C11 | C12 C15 C13 ++ | C14 ++ Факторная живая нагрузка = 6 кН / м2 C19 C20 C16 I C17 I C18 I Рисунок 2: Распределение динамической нагрузки в различных частях плиты Примечание-1: Рисунок не в масштабе Примечание-2: Тип / ориентация секции колонны, показанные на рисунке, являются ориентировочными. Выберите соответствующий раздел, как требуется для дизайна колонны Таблица-1 Подробная информация о конструкционных стальных элементах и соединениях, которые должны быть спроектированы Колонна (Расчет только для осевой нагрузки) Сварная соединительная балка CS (с боковым ограничением) B21 B21-C5
Технические условия на сварку для электронно-лучевой сварки
AMS 2680 и AMS 2681 относятся к аэрокосмической отрасли Спецификации материалов (AMS) опубликованы SAE Aerospace, которая является частью SAE International Group (https: // www.sae.org/). Согласно Википедии:
SAE International, первоначально созданная как Общество автомобильных инженеров, является базирующейся в США, всемирно активной профессиональной ассоциацией и организацией по разработке стандартов для инженеров в различных отраслях промышленности. Основной упор делается на такие отрасли транспорта, как автомобилестроение, авиакосмическая промышленность и коммерческие автомобили.
Стандарт D17.1 опубликован Американским сварочным обществом, некоммерческой организацией в США, которая занимается продвижением сварки во всех отраслях.AWS D17.1 был специально создан для объединения и уточнения требований двух военных стандартов: MIL-STD-1595A и MIL-STD-2219. Спецификация AWS D17.1 применяется ко всем процессам сварки плавлением, включая электронно-лучевую сварку (EBW), лазерную сварку (LBW) и дуговую сварку вольфрамовым электродом (GTAW) и многие другие. AMS 2680 и AMS 2681 применимы только к EBW.
В целом, D17.1 имеет значительно более определенные требования к проектированию, обработке и испытаниям сварных узлов, чем спецификации AMS.AMS 2681 и AMS 2680 очень похожи, но AMS 2680 предназначен для приложений, критичных к усталости. В соответствии со стандартом AMS 2680:
Эти процедуры обычно используются для высококачественной электронно-лучевой сварки компонентов аэрокосмической отрасли, отказ которой может привести к потере космического аппарата или одного из его основных компонентов, потере управления или значительной травмы пассажиров пилотируемого аэрокосмического корабля…
AMS 2680 фокусируется на особенностях концентрации напряжений, которые могут треснуть или выйти из строя при различной усталости от нагрузки.Все сварные швы имеют полный проплав, а процедуры разработаны таким образом, чтобы минимизировать пористость. Требования имеют очень жесткие пределы.
Каждая из трех спецификаций основана на своих достоинствах и не противоречит друг другу. Хотя это не лучшая практика, EB видел чертежи, которые определяют разные спецификации для соединений в одной и той же сборке (например, для соединения 1 требуется спецификация D17.