Вид контроля |
Метод контроля |
Характеристики метода |
Область применения |
Обозначение стандарта на метод контроля |
|||
Выявляемые дефекты |
Чувствительность |
Особенности метода |
|||||
Технический осмотр |
Внешний осмотр и измерение |
Поверхностные дефекты |
Выявляются несплошности, отклонения размера и формы сварного соединения от заданных величин более 0,1 мм, a также поверхностное окисление сварного соединения |
Метод позволяет обнаруживать дефекты минимального выявляемого размера при осмотре и измерении сварного соединения с использованием оптических приборов с увеличением до 10 ´ и измерительных приборов |
Не ограничивается |
— |
|
Капиллярный |
Цветной Люминесцентный Люмннесцентно-цветной |
Дефекты (несплошности), выходящие на поверхность |
Условные уровни чувствительности по ГОСТ 184412-80 |
Чувствительность и достоверность метода зависят от качества подготовки поверхности соединения к контролю |
Не ограничивается |
ГОСТ 18442-80 |
|
Радиационный |
Радиографический Радиоскопический Радиометрический |
Внутренние и поверхностные дефекты (несплошности), а также дефекты формы соединения |
От 0,5 до 5,0% контролируемой толщины металла От 3 до 8% контролируемой толщины металла От 0,3 до 10% контролируемой толщины металла |
Выявляемость дефектов по ГОСТ 7312-76. Чувствительность зависит от характеристик контролируемого сварного соединения и средств контроля |
По ГОСТ 20426-82 |
ГОСТ 7512-75 |
|
Акустический |
Ультразвуковой |
Внутренние и поверхностные дефекты (несплошности) |
Толщина сварного соединения, мм |
Предельная чувствительность, мм2 |
Размер, количество и характер дефектов определяются в условных показателях по ГОСТ 14782-76 |
По ГОСТ 14782-76 |
ГОСТ 14782-76 |
От1,5 до 10 включ Св. l0 до 50 » » 60 » 150 » » 150 » 400 » » 400 » 2000 » |
0,5 — 5,5
2,0 — 7,0 3,5 — 15,0 10,0 — 80,0 35,0 — 200,0 |
||||||
Магнитный |
Магнитоферрозондовый |
Поверхностные и подповерхностные несплошности |
Условные уровни чувствительности по ГОСТ 21104-80 |
Метод обеспечивает выявление: внутренних несплошностей расположенных на глубине до 10 мм от поверхности соединения; разнонаправленных дефектов. Чувствительность и достоверность метода зависит от качества подготовки соединения к контролю |
По ГОСТ 21104-80 |
ГОСТ 21104-80 |
|
Магнито-порошковый |
Поверхностные и подповерхностные несплошности |
Условные уровни чувствительности по ГОСТ 21105-75 |
Метод обеспечивает выявление внутренних несплошностей, расположенных от поверхности соединения на глубине до 2 мм включительно. Чувствительность и достоверность метода зависят от качества подготовки соединения к контролю |
По ГОСТ 21105-75 |
ГОСТ 21105-75 |
||
Магнито-графический |
Поверхностные, подповерхностные и внутренние несплошности |
От 2 до 7% от толщины контролируемого металла |
Достоверность контроля снижается при наличии неровностей на контролируемой поверхности соединения размером более 1 мм. Чувствительность снижается с увеличением глубины залегания несплошности |
Сварные стыковые соединения, выполненные дуговой газовой сваркой, конструкции из ферромагнитных материалов. Контролируемая толщина не более 25 мм |
— |
||
Течеискание |
Радиационный |
Сквозные дефекты |
|
Радиоактивная опасность |
Обнаружение мест течей в сварных соединениях, работающих под давлением, замкнутых конструкций ядерной энергетики, а также замкнутых конструкций, когда невозможно применение других методов течеискания. Контролируемая толщина не ограничивается |
— |
|
Масс-спектрометрический |
Сквозные дефекты |
По способу: накопления при атмосферном давлении — до 1 × 10-6 мм3 МПа/с вакуумирования — от 1 × 10 -7 до 1 × 10-4 мм3 МПа/с щупа — до l × 10-5 мм3 МПа/с |
Условия эксплуатации течеискателей: температура окружающей среды 10-35 ° С, наибольшая относительная влажность воздуха 80%о |
Способ накопления давления — определение суммарной степени утечек замкнутых конструкции. Способ вакуумирования — определение суммарной степени утечек замкнутых и открытых конструкции. Способ щупа — определение локальных течей в сварных соединениях крупногабаритных конструкций. Контролируемая толщина не ограничивается |
— |
||
Манометрический |
Сквозные дефекты |
По способу: падения давления — от 1 × 10-3 до 7 × 10-3 мм3 МПа/с дифференциального манометра — до l × 10-8 мм3 МПа/с |
Чувствительность метода снижается при контроле конструкций больших объемов. Длительность времени испытания, температура контрольного газа и окружающей среды, а также величина атмосферного давления влияют на погрешность испытаний |
Сварные соединения замкнутых конструкции, работающих под давлением: способ падения давления — для определения величины суммарных утечек; способ дифференциального манометра — для определения локальных утечек. Контролируемая толщина не ограничивается |
— |
||
Галоидный |
Сквозные дефекты |
По фреону12: щуп атмосферный — до 5 × 10-4 мм3 .МПа/с щуп вакуумный — до 1 × 10-6 мм3 МПа/с |
Достоверность и чувствительность контроля снижается, если контролируемая поверхность имеет неровности (наплывы, углубления), препятствующие приближении щупа к контролируемой поверхности |
Обнаружение места и величины локальных течей в сварных соединениях замкнутых конструкций, работающих под давлением. Контролируемая толщина не ограничивается |
— |
||
Газоаналитический |
Сквозные дефекты |
По фреону 12 (90%) в смеси с воздухом от 2 × 10-4 до 4 × 10-4 мм3 -МПа/с |
Достоверность контроля снижается при наличии в окружающей атмосфере различных паров и газов, включая растворители для подготовки поверхности контролируемого соединения, табачный дым и газы, образующиеся при сварке |
Обнаружение места локальных течей в сварных соединениях замкнутых конструкций, работающих под давлением. Контролируемая толщина не ограничивается |
— |
||
Химический |
Сквозные дефекты |
По аммиаку — до 6,65 × 10-4 мм3 МПа/с По аммонию — от 1 × 10-1 до 1 мм3 МПа/с |
Требуется соблюдение правил противопожарной безопасности и правил работы с вредными химическими веществами |
Обнаружение места локальных течей в сварных соединениях открытых и закрытых конструкций, работающих под давлением или предназначенных для хранения жидкостей. Контролируемая толщина не ограничивается |
— |
||
Акустический |
Сквозные дефекты |
Не менее 1 × 10-2 мм3 МПа/с |
Контроль производят при отсутствии шумовых помех. Возможен дистанционный контроль |
Обнаружение мест течей в сварных соединениях подземных водо- и газопроводах высокого давления. Контролируемая толщина не ограничивается |
— |
||
Капиллярный |
Сквозные дефекты |
Люминесцентный — от 1 × 10-2 до 5 × 10-2 мм3 МПа/с Люминесцентно-цветной — от l × 10-2 до 5 × 10-2 мм3 МПа/с Люминесцентно-гидравлический — от 1 × 10-4 до 5 × 10-4 мм3 МПа/с Смачиванием керосином — до 7 × 10-3 мм3 МПа/с |
Требуется тщательная очистка контролируемой поверхности. Чувствительность метода снижается при контроле больших толщин и при контроле сварных соединений, расположенных во всех пространственных положениях, отличных от нижнего. При контроле смачиванием керосином — высокая пожароопасность |
Обнаружение мест течей в сварных соединениях открытых и закрытых конструкции: люминесцентный и люминесцентно-цветной — сварные соединения конструкций, рабочим веществом которых является газ или жидкость; люминесцентно-гидравлический и смачиванием керосином — сварные соединения конструкций, рабочим веществом которых является жидкость. Контролируемая толщина не ограничивается |
— |
||
Наливом воды под напором |
Сквозные дефекты |
От 3 × 10-4 до 2 × .10-2 мм3 МПа/с |
При контроле сварных соединении большой емкости должна быть обеспечена жесткость конструкции |
Обнаружение мест локальных течей в сварных соединениях закрытых конструкции, работающих под давлением. Контролируемая толщина не ограничивается |
ГОСТ 3285-77 |
||
Наливом воды без напора |
Сквозные дефекты |
Не более 1 × 10-3 мм3 МПа/с |
При контроле сварных соединений большой емкости должна быть обеспечена жесткость конструкции |
Обнаружение мест локальных течей в сварных соединениях открытых конструкций. Контролируемая толщина не ограничивается |
ГОСТ 3265-77 |
||
Поливанием струей воды под напором |
Сквозные дефекты |
Не более 1 × 10-1 мм3 МПа/с |
Чувствительность метода повышается при люминесцентно-индикаторном покрытии осматриваемой поверхности. Контроль производят до монтажа оборудования |
Обнаружение мест локальных течей в сварных соединениях открытых конструкций. Контролируемая толщина не ограничивается |
ГОСТ 3285-77 |
||
Поливанием рассеянной струей воды |
Сквозные дефекты |
Не более 1 × 10-1 мм3 МПа/с |
Чувствительность метода повышается при люминесцентно-индикаторном покрытии осматриваемой поверхности. Контроль производят до монтажа оборудования |
Обнаружение мест локальных течей в сварных соединениях открытых конструкций. Контролируемая толщина не ограничивается |
ГОСТ 3285-77 |
||
Пузырьковый |
Сквозные дефекты |
Пневматический: надувом воздуха — от 7 × 10-4 до 1 × 10-3 мм3 МПа/с обдувом струей сжатого воздуха — до 1 × 10-2 мм3 МПа/с Пневмогидравлический: аквариумный — до 1 × 10-3 мм3 МПа/с бароаквариумный — от 5 × 10-4 до 1 × 10-5 мм3 МПа/с Вакуумный (с применением вакуум-камер) — до 1 × 10-2 мм3 МПа/с |
Контроль производится сжатым воздухом. Состав пенообразующих обмазок зависит от температуры воздуха при проведении испытаний пневматическим и вакуумным способами контроля |
Обнаружение мест локальных течей. Пневматический способ: надувом воздуха — сварные соединения замкнутых конструкций, рабочим веществом которых является газ или жидкость; обдувом струей сжатого воздуха — сварные соединения открытых крупногабаритных конструкций. Пневмогидравлический аквариумный и бароаквариумный способы: сварные соединения малогабаритных замкнутых конструкций, работающих под давлением. Вакуумный способ — при одностороннем подходе к контролируемым соединениям. Контролируемая толщина не ограничивается |
ГОСТ 3285-77 |
||
Вскрытие |
Внутренние дефекты |
Выявляются макроскопические дефекты |
Вскрытие производится вырубкой, сверлением, газовой или воздушно-дуговой строжкой, шлифованием, а также вырезкой участка сварного соединения с последующим изготовлением из него послойных шлифов. После контроля требуется запарка некрытого участка сварного соединения |
Сварные соединения, которые не подвергаются термообработке или недоступны для радиационного и акустического контроля. Контролируемая толщина не ограничивается |
— |
||
Технологическая проба |
Внутренние и поверхностные дефекты |
Выявляются макроскопические и микроскопические дефекты |
Контрольная проба выполняется по тому же технологическому процессу и тем же сварщиком (сварщиками), что и контролируемые сварные соединения. |
Не ограничивается |
— |
Технический осмотр | Внешний осмотр и измерение | Поверхностные дефекты | Выявляются несплошности, отклонения размера и формы сварного соединения от заданных величин более 0,1 мм, a также поверхностное окисление сварного соединения | Метод позволяет обнаруживать дефекты минимального выявляемого размера при осмотре и измерении сварного соединения с использованием оптических приборов с увеличением до 10 и измерительных приборов | Не ограничивается | – | |
Капиллярный | Цветной Люминесцентный Люмннесцентно-цветной | Дефекты (несплошности), выходящие на поверхность | Условные уровни чувствительности по ГОСТ 184412-80 | Чувствительность и достоверность метода зависят от качества подготовки поверхности соединения к контролю | Не ограничивается | ГОСТ 18442-80 | |
Радиационный | Радиографический Радиоскопический Радиометрический | Внутренние и поверхностные дефекты (несплошности), а также дефекты формы соединения | От 0,5 до 5,0% контролируемой толщины металла От 3 до 8% контролируемой толщины металла От 0,3 до 10% контролируемой толщины металла | Выявляемость дефектов по ГОСТ 7312-76. Чувствительность зависит от характеристик контролируемого сварного соединения и средств контроля | По ГОСТ 20426-82 | ГОСТ 7512-75 | |
Акустический | Ультразвуковой | Внутренние и поверхностные дефекты (несплошности) | Толщина сварного соединения, мм | Предельная чувствительность, мм2 | Размер, количество и характер дефектов определяются в условных показателях по ГОСТ 14782-76 | По ГОСТ 14782-76 | ГОСТ 14782-76 |
От1,5 до 10 включ Св. l0 до 50 » » 60 » 150 » » 150 » 400 » » 400 » 2000 » | 0,5 – 5,5 2,0 – 7,0 3,5 – 15,0 10,0 – 80,0 35,0 – 200,0 | ||||||
Магнитный | Магнитоферрозондовый | Поверхностные и подповерхностные несплошности | Условные уровни чувствительности по ГОСТ 21104-80 | Метод обеспечивает выявление: внутренних несплошностей расположенных на глубине до 10 мм от поверхности соединения; разнонаправленных дефектов. Чувствительность и достоверность метода зависит от качества подготовки соединения к контролю | По ГОСТ 21104-80 | ГОСТ 21104-80 | |
Магнито-порошковый | Поверхностные и подповерхностные несплошности | Условные уровни чувствительности по ГОСТ 21105-75 | Метод обеспечивает выявление внутренних несплошностей, расположенных от поверхности соединения на глубине до 2 мм включительно. Чувствительность и достоверность метода зависят от качества подготовки соединения к контролю | По ГОСТ 21105-75 | ГОСТ 21105-75 | ||
Магнито-графический | Поверхностные, подповерхностные и внутренние несплошности | От 2 до 7% от толщины контролируемого металла | Достоверность контроля снижается при наличии неровностей на контролируемой поверхности соединения размером более 1 мм. Чувствительность снижается с увеличением глубины залегания несплошности | Сварные стыковые соединения, выполненные дуговой газовой сваркой, конструкции из ферромагнитных материалов. Контролируемая толщина не более 25 мм | – | ||
Течеискание | Радиационный | Сквозные дефекты | По криптону 85(85Kr) – от 110-9 до 110-14 мм3 МПа/с | Радиоактивная опасность | Обнаружение мест течей в сварных соединениях, работающих под давлением, замкнутых конструкций ядерной энергетики, а также замкнутых конструкций, когда невозможно применение других методов течеискания. Контролируемая толщина не ограничивается | – | |
Масс-спектрометрический | Сквозные дефекты | По способу: накопления при атмосферном давлении – до 110-6 мм3 МПа/с вакуумирования – от 110-7 до 110-4 мм3 МПа/с щупа – до l10-5 мм3 МПа/с | Условия эксплуатации течеискателей: температура окружающей среды 10-35С, наибольшая относительная влажность воздуха 80%о | Способ накопления давления – определение суммарной степени утечек замкнутых конструкции. Способ вакуумирования – определение суммарной степени утечек замкнутых и открытых конструкции. Способ щупа – определение локальных течей в сварных соединениях крупногабаритных конструкций. Контролируемая толщина не ограничивается | – | ||
Манометрический | Сквозные дефекты | По способу: падения давления – от 110-3 до 710-3 мм3 МПа/с дифференциального манометра – до l10-8 мм3 МПа/с | Чувствительность метода снижается при контроле конструкций больших объемов. Длительность времени испытания, температура контрольного газа и окружающей среды, а также величина атмосферного давления влияют на погрешность испытаний | Сварные соединения замкнутых конструкции, работающих под давлением: способ падения давления – для определения величины суммарных утечек; способ дифференциального манометра – для определения локальных утечек. Контролируемая толщина не ограничивается | – | ||
Галоидный | Сквозные дефекты | По фреону12: щуп атмосферный – до 510-4 мм3 .МПа/с щуп вакуумный – до 110-6 мм3 МПа/с | Достоверность и чувствительность контроля снижается, если контролируемая поверхность имеет неровности (наплывы, углубления), препятствующие приближении щупа к контролируемой поверхности | Обнаружение места и величины локальных течей в сварных соединениях замкнутых конструкций, работающих под давлением. Контролируемая толщина не ограничивается | – | ||
Газоаналитический | Сквозные дефекты | По фреону 12 (90%) в смеси с воздухом от 210-4 до 410-4 мм3 -МПа/с | Достоверность контроля снижается при наличии в окружающей атмосфере различных паров и газов, включая растворители для подготовки поверхности контролируемого соединения, табачный дым и газы, образующиеся при сварке | Обнаружение места локальных течей в сварных соединениях замкнутых конструкций, работающих под давлением. Контролируемая толщина не ограничивается | – | ||
Химический | Сквозные дефекты | По аммиаку – до 6,6510-4 мм3 МПа/с По аммонию – от 110-1 до 1 мм3 МПа/с | Требуется соблюдение правил противопожарной безопасности и правил работы с вредными химическими веществами | Обнаружение места локальных течей в сварных соединениях открытых и закрытых конструкций, работающих под давлением или предназначенных для хранения жидкостей. Контролируемая толщина не ограничивается | – | ||
Акустический | Сквозные дефекты | Не менее 110-2 мм3 МПа/с | Контроль производят при отсутствии шумовых помех. Возможен дистанционный контроль | Обнаружение мест течей в сварных соединениях подземных водо- и газопроводах высокого давления. Контролируемая толщина не ограничивается | – | ||
Капиллярный | Сквозные дефекты | Люминесцентный – от 110-2 до 510-2 мм3 МПа/с Люминесцентно-цветной – от l10-2 до 510-2 мм3 МПа/с Люминесцентно-гидравлический – от 110-4 до 510-4 мм3 МПа/с Смачиванием керосином – до 710-3 мм3 МПа/с | Требуется тщательная очистка контролируемой поверхности. Чувствительность метода снижается при контроле больших толщин и при контроле сварных соединений, расположенных во всех пространственных положениях, отличных от нижнего. При контроле смачиванием керосином – высокая пожароопасность | Обнаружение мест течей в сварных соединениях открытых и закрытых конструкции: люминесцентный и люминесцентно-цветной – сварные соединения конструкций, рабочим веществом которых является газ или жидкость; люминесцентно-гидравлический и смачиванием керосином – сварные соединения конструкций, рабочим веществом которых является жидкость. Контролируемая толщина не ограничивается | – | ||
Наливом воды под напором | Сквозные дефекты | От 310-4 до 2.10-2 мм3 МПа/с | При контроле сварных соединении большой емкости должна быть обеспечена жесткость конструкции | Обнаружение мест локальных течей в сварных соединениях закрытых конструкции, работающих под давлением. Контролируемая толщина не ограничивается | ГОСТ 3285-77 | ||
Наливом воды без напора | Сквозные дефекты | Не более 110-3 мм3 МПа/с | При контроле сварных соединений большой емкости должна быть обеспечена жесткость конструкции | Обнаружение мест локальных течей в сварных соединениях открытых конструкций. Контролируемая толщина не ограничивается | ГОСТ 3265-77 | ||
Поливанием струей воды под напором | Сквозные дефекты | Не более 110-1 мм3 МПа/с | Чувствительность метода повышается при люминесцентно-индикаторном покрытии осматриваемой поверхности. Контроль производят до монтажа оборудования | Обнаружение мест локальных течей в сварных соединениях открытых конструкций. Контролируемая толщина не ограничивается | ГОСТ 3285-77 | ||
Поливанием рассеянной струей воды | Сквозные дефекты | Не более 110-1 мм3 МПа/с | Чувствительность метода повышается при люминесцентно-индикаторном покрытии осматриваемой поверхности. Контроль производят до монтажа оборудования | Обнаружение мест локальных течей в сварных соединениях открытых конструкций. Контролируемая толщина не ограничивается | ГОСТ 3285-77 | ||
Пузырьковый | Сквозные дефекты | Пневматический: надувом воздуха – от 710-4 до 110-3 мм3 МПа/с обдувом струей сжатого воздуха – до 110-2 мм3 МПа/с Пневмогидравлический: аквариумный – до 110-3 мм3 МПа/с бароаквариумный – от 510-4 до 110-5 мм3 МПа/с Вакуумный (с применением вакуум-камер) – до 110-2 мм3 МПа/с | Контроль производится сжатым воздухом. Состав пенообразующих обмазок зависит от температуры воздуха при проведении испытаний пневматическим и вакуумным способами контроля | Обнаружение мест локальных течей. Пневматический способ: надувом воздуха – сварные соединения замкнутых конструкций, рабочим веществом которых является газ или жидкость; обдувом струей сжатого воздуха – сварные соединения открытых крупногабаритных конструкций. Пневмогидравлический аквариумный и бароаквариумный способы: сварные соединения малогабаритных замкнутых конструкций, работающих под давлением. Вакуумный способ – при одностороннем подходе к контролируемым соединениям. Контролируемая толщина не ограничивается | ГОСТ 3285-77 | ||
Вскрытие | Внутренние дефекты | Выявляются макроскопические дефекты | Вскрытие производится вырубкой, сверлением, газовой или воздушно-дуговой строжкой, шлифованием, а также вырезкой участка сварного соединения с последующим изготовлением из него послойных шлифов. После контроля требуется запарка некрытого участка сварного соединения | Сварные соединения, которые не подвергаются термообработке или недоступны для радиационного и акустического контроля. Контролируемая толщина не ограничивается | – | ||
Технологическая проба | Внутренние и поверхностные дефекты | Выявляются макроскопические и микроскопические дефекты | Контрольная проба выполняется по тому же технологическому процессу и тем же сварщиком (сварщиками), что и контролируемые сварные соединения. | Не ограничивается | – |
ГОСТ 3242-79 Соединения сварные. Методы контроля качества
Текст ГОСТ 3242-79 Соединения сварные. Методы контроля качества
ГОСТ 3242-79
МЕЖГОСУДАРСТВЕННЫЙ СТАНДАРТ
СОЕДИНЕНИЯ СВАРНЫЕ
МЕТОДЫ КОНТРОЛЯ КАЧЕСТВА
Издание официальное
ИПК ИЗДАТЕЛЬСТВО СТАНДАРТОВ
УДК 621.791.052:658.562:006.354 Группа В09
МЕЖГОСУДАРСТВЕННЫЙ СТАНДАРТ
СОВДИНЕНИЯ СВАРНЫЕ Методы контроля качества
Welded joints. Quality control methods
ГОСТ 3242-69
ГОСТ
3242-79
Взамен
Постановлением Государственного комитета СССР по стандартам от 2 августа 1979 г. № 2930 срок действия установлен
с 01.01.81
Ограничение срока действия снято постановлением Госстандарта от 21.10.92 № 1434
1. Настоящий стандарт устанавливает методы контроля качества и область их применения при обнаружении дефектов сварных соединений металлов и сплавов, выполненных способами сварки, приведенными в ГОСТ 19521—74.
Стандарт соответствует рекомендациям СЭВ по стандартизации PC 5246—73, PC 4099-73, PC 789—67 и международному стандарту ИСО 2437—72.
2. Применение метода или комплекта методов контроля для обнаружения дефектов сварных соединений при техническом контроле конструкций на всех стадиях их изготовления, ремонте и модернизации зависит от требований, предъявляемых к сварным соединениям в технической документации на конструкцию.
Методы контроля должны соответствовать приведенным в таблице и указываться в технической (конструкторско-технологической) документации на конструкцию.
3. Допустимость применения неустановленных в настоящем стандарте методов должна быть предусмотрена в технической документации на конструкцию. Технология контроля сварных швов любым методом должна быть установлена в нормативно-технической документации на контроль.
Издание официальное
★
Перепечатка воспрещена
Переиздание. Май 2002 г.
© Издательство стандартов, 1979 © ИПК Издательство стандартов, 2002
Вид контроля | Метод контроля | Характеристика метода | Область применения | Обозначение стандарта на метод контроля | |||
Выявляемые дефекты | Чувствительность | Особенности метода | |||||
Технический осмотр | Внешний осмотр и измерение | Поверхностные дефекты | Выявляются несплошности, отклонения размера и формы сварного соединения от заданных величин более 0,1 мм, а также поверхностное окисление сварного соединения | Метод позволяет обнаруживать дефекты минимального выявляемого размера при осмотре и измерении сварного соединения с использованием оптических приборов с увеличением до 10х и измерительных приборов | Не ограничивается | ||
Капил лярный | Цветной Люминес центный Люминес центно-цвет ной | Дефекты (несплошнос-ти), выходящие на поверхность | Условные уровни чрстви-тельности по ГОСТ 18442-80 | Чувствительность и достоверность метода зависят от качества подготовки поверхности соединения к контролю | Не ограничивается | ГОСТ 18442-80 | |
Радиа ционный | Радиогра фический Радиоскопи- ческий Радиометри ческий | Внутренние и поверхностные дефекты (несп-лошности), а также дефекты формы соединения | От 0,5 до 5,0 % контролируемой толщины металла От 3 до 8 % контролируемой толщины металла От 0,3 до 10 % контролируемой толщины металла | Выявляемое^ дефектов по ГОСТ 7512-82. Чувствительность зависит от характеристик контролируемого сварного соединения и средств контроля | По ГОСТ 20426-82 | ГОСТ 7512-82 | |
Акусти ческий | Ультразву ковой | Внутренние и поверхностные дефекты (неси-лошности) | Толщина сварного соединения, мм | Предельная чувствительность, мм2 | Размер, количество и характер дефектов определяются в условных показателях по ГОСТ 14782-86 | По ГОСТ 14782-86 | ГОСТ 14782-88 |
От 1,5 до 10 ключ. Св. 10 до 50» » 50» 150» » 150.400» » 400.2000» | 0,5-2,5 2.0- 7,0 3,5-15,0 10.0- 80,0 35,0-200,0 | ||||||
Магнит ный | Магнито- феррозондо- вый | Поверхностные и подповерхностные несплош-ности | Условные уровни чрстви-тельностипо ГОСТ 21104-75 | Метод обеспечивает выявление: внутренних несплош-ностей, расположенных на глубине до 10 мм от поверхности соединения; | По ГОСТ 21104-75 | ГОСТ 21104-75 |
2 ГОСТ 3242-79
Вид контроля
Метод контроля
Характеристика метода
Выявляемые
дефекты
Чувствительность
Особенности метода
Область применения
Обозначение стандарта на метод контроля
Магнит-
Магнито-
феррозондо-
Поверх-
Условные уровни чувствительности по ГОСТ 21104-80
подповерхностные не
разнонаправленных
дефектов,
Чувствительность и достоверность метода зависит от качества под-
ГОСТ 21104-75
ГОСТ 21104-75
контролю
Магнито
порошковый
Поверх-
Условные уровни чувствительности по ГОСТ 21105-87
подповерхностные не-
Метод обеспечивает : внутренних несплошностей, расположенных от поверхности соединения на глубине до 2 мм включитель-но, Чувствительность и достоверность метода зависят от качества подготовки соединения к конт-ролю_
ГОСТ 21105-87
ГОСТ 21105-87
Магнито
графический
Поверхностные, подповерхностные и внутренние не-
От 2 до 7 % от толщины контролируемого металла
Достоверность контроля снижается при наличии неровностей на контролируемой поверхности соединения размером более 1мм, Чувствительность снижается с реличением глубины за-
Сварные сты-
дуговои газовой сваркой, конструкции из ферро
риалов, Контролируемая толщина не более 25 мм
Течеис-
Радиа-
Сквозные
дефекты
По криптону 85 (85Кг) — от ■Ю-9 до МО—‘4 мм3 МПа/с
Радиоактивная опас-
Обнаружение мест течей в свар-
работающих под
нутых конструкций ядерной энер-
замкнутых конструкций, когда невозможно применение других ме-
w
ГОСТ 3242-79 С.
Вид контроля | Метод контроля | Характеристика метода | Область применения | Обозначение | ||
Выявляемые дефекты | Чувствительность | Особенности метода | стандарта на метод контроля | |||
Течеис- кание | Контролируемая толщина не ограничивается | |||||
Масс- спектромет- рический | Сквозные дефекты | По способу: накопления при атмосферном давлении-до Ы(Н мм3 МПа/с вакрирования от М0“7 до МО-4 мм3 МПа/с щупа-до МО-5 мм3 МПа/с | Условия эксплуатации течеискателей: температура окружающей среды 10-35 °С, наибольшая относительная влажность воздуха 80 % | Способ накопления давления — определение суммарной степени утечек замири конструкций, Способ вакуумирования-определение суммарной степени утечек замкнутых и открытых конструкций, Способ щупа -определение локальных течей в сварных соединениях крупногабаритных конструкций, Контролируемая толщина не ограничивается | ||
Маномет рический | Сквозные дефекты | По способу: падения давления — от МО-3 до 7-10~3 мм3 МПа/с дифференциального манометра-до Ы(Н мм 3 МПа/с | Чувствительность метода снижается при контроле конструкций больших объемов, Длительность времени испытания, температура контрольного газа и окружающей среды, а также величина атмосферного давления влияют на погрешность испытаний | Сварные соединения замкнутых конструкций, работающих под давлением: способ падения давления-да определения величины суммарных утечек; способ дифференциального манометра-да определения локальных утечек, Контролируемая толщина не ограничивается |
4 ГОСТ 3242-79
Вид контроля | Метод контроля | Характеристика метода | Область применения | Обозначение стандарта на метод контроля | ||
Выявляемые дефекты | Чувствительность | Особенности метода | ||||
Течеис- кание | Галоид ный | Сквозные дефекты | По фреону 12: щуп атмосферный-до 5-10-4 мм3 МПа/с щуп вакуумный-до М0“6 мм3 МПа/с | Достоверность и чувствительность контроля снижается, если контролируемая поверхность имеет неровности (наплывы, углубления), препятствующие приближению щупа к контролируемой поверхности | Обнаружение места и величины локальных течей в сварных соединениях замкнутых конструкций, работающих под давлением, Контролируемая толщина не ограничивается | |
Газоана литический | Сквозные дефекты | По фреону 12 (90 %) в смеси с воздухом от 2’10“4 до 4-10“4 мм3 МПа/с | Достоверность контроля снижается при наличии в окружающей атмосфере различных паров и газов, включая растворители да подготовки поверхности контролируемого соединения, табачный дым и газы, образующиеся при сварке | Обнаружение места локальных течей в сварных соединениях замкнутых конструкций, работающих под давлением, Контролируемая толщина не ограничивается | ||
Химичес кий | Сквозные дефекты | По аммиаку—до 6,65 х х 10-4 мм3 МПа/с По аммонию-от МО-1 до 1 мм3 МПа/с | Требуется соблюдение правил противопожарной безопасности и правил работы с вредными химическими веществами | Обнаружение места локальных течей в сварных соединениях открытых и закрытых конструкций, работающих под давлением или предназначенных да хранения жидкостей, Контролируемая толщина не ограничивается |
О
ГОСТ 3242-79
Продолжение Р а
Вид контроля | Метод контроля | Характеристика метода | Область применения | Обозначение | ||
Выявляемые дефекты | Чувствительность | Особенности метода | СшпДсфш ш MCI УД контроля | |||
Течеис- кание | Акусти ческий | Сквозные дефекты | Не менее МО-2 мм3 МПа/с | Контроль производят при отсутствии шумовых помех, Возможен дистанционный контроль | Обнаружение мест течей в сварных соединениях подземных водо-и газопроводах высокого давления, Контролируемая толщина не ограничивается | |
Капилляр ный | Сквозные дефекты | Люминесцентный-от НО-2 до 5-10-2 мм3 МПа/с Люминесцентно-цветной -от МО-2 до МО “2 мм3 МПа/с Люминесцентно-гидравлический-МО-4 до М0“4мм3 МПа/с Смачивание керосином-до 7’10“3 мм3 МПа/с | Требуется тщательная очистка контролируемой поверхности, Чувствительность метода снижается при контроле больших толщин и при контроле сварных соединений, расположенных во всех пространственных положениях, отличных от нижнего, При контроле смачиванием керосином-высокая пожароопасность | Обнаружение мест течей в сварных соединениях открытых и закрытых конструкций: люминесцентный и люминесцентно-цветной -сварные соединения конструкций, рабочим веществом которых является газ или жидкость; люминесцентно-гидравлический и смачиванием керосином — сварные соединения конструкций, рабочим веществом которых является жидкость, Контролируемая толщина не ограничивается |
6Z.
Вид контроля | Метод контроля | Характеристика метода | Область применения | Обозначение стандарта на метод контроля | ||
Выявляемые дефекты | Чувствительность | Особенности метода | ||||
Течеис- кание | Наливом воды под напором | Сквозные дефекты | От 3-10-4 до НО»2 мм3 МПа/с | При контроле сварных соединений большой емкости должна быть обеспечена жесткость конструкции | Обнаружение мест локальных течей в сварных соединениях закрытых конструкций, работающих под давлением. Контролируемая толщина не ограничивается | Нормативнотехническая документация, утвержденная в установленном порядке |
Наливом воды без напора | Сквозные дефекты | Не более МО»3 мм3 МПа/с | При контроле сварных соединений большой емкости должна быть обеспечена жесткость конструкции | Обнаружение мест локальных течей в сварных соединениях открытых конструкций. Контролируемая толщина не ограничивается | Нормативнотехническая документация, утвержденная в установленном порядке | |
Поливанием струей воды под напором | Сквозные дефекты | Не более МО»1 мм3 МПа/с | Чувствительность метода повышается при лю-минесцентно-индика-торном покрытии осматриваемой поверхности. Контроль производят до монтажа оборудования | Обнаружение мест локальных течей в сварных соединениях открытых конструкций. Контролируемая толщина не ограничивается | Нормативнотехническая документация, утвержденная в установленном порядке | |
Поливанием рассеянной струей воды | Сквозные дефекты | Не более МО»1 мм3 МПа/с | Чувствительность метода повышается при люминесцентно-индикаторном покрытии осматриваемой поверхности. Контроль производят до монтажа оборудования | Обнаружение мест локальных течей в сварных соединениях открытых конструкций. Контролируемая толщина не ограничивается | Нормативнотехническая документация, утвержденная в установленном порядке |
ГОСТ 3242-79 С.
Вид контроля
Течеис-
кание
Характеристика метода
Метод
контроля
Область применения
Обозначение стандарта на метод контроля
Выявляемые
дефекты
Чувствительность
Особенности метода
Сквозные
дефекты
Пневматический: надувом воздуха—от 7-10-4 до МО-3 мм3 МПа/с обдувом струей сжатого воздуха-до МО-2 мм3 МПа/с Пневмогидравлический: аквариумный-до М0“3 мм3 МПа/с бароаквариумный — от МО-4 до МО-5 мм3 МПа/с Вакуумный (с применением вакуум-камер)—до М0“2 мм3 МПа/с
Контроль производится сжатым воздухом, Состав пенообразующих обмазок зависит от температуры воздуха при проведении испытаний пневматическим и вакуумным способами контроля
Обнаружение
Пневматический способ: надувом воздуха-сварные соединения замкнутых конструкций, рабочим веществом которых яв-
Нормативно-техническая документация, утвержденная в установленном порядке
обдувом струей сжатого воздуха — сварные соединения открытых крупногабаритных конструкций,
Пневмогидравлический аквариумный и бароаквариумный способы: сварные соединения малогабаритных замкнутых конструкций, работающих под давлением,
Вакуумный способ— при одностороннем подходе к контролируемым соединениям, Контролируемая толщина не ограничивается
8 ГОСТ 3242-79
Вид контроля | Метод контроля | Характеристика метода | Область применения | Обозначение | ||
Выявляемые дефекты | Чувствительность | Особенности метода | стандарта на метод контроля | |||
Течеис- кание | Вскрытие | Внутренние дефекты | Выявляются макроскопические дефекты | Вскрытие производится вырубкой, сверлением, газовой или воздушно-дуговой строжкой, шлифованием, а также вырезкой участка сварного соединения с последующим изготовлением : ных шлифов, После контроля требуется заварка вскрытого участка сварного соединения | Сварные соединения, которые не подвергаются термообработке или недоступны для радиационного и акустического контроля, Контролируемая толщина не ограничивается | |
Технологическая проба | Внутренние и поверхностные дефекты | Выявляются макроскопические и микроскопические дефекты | Контрольная проба выполняется по тому же технологическому процессу и тем же сварщиком (сварщиками), что и контролируемые сварные соединения | Не ограничивается |
Редактор Т.П. Шашина Технический редактор Л.А. Гусева Корректор В. И. Баренцева Компьютерная верстка И.А. Налейкиной
Изд. лиц. № 02354 от 14.07.2000. Сдано в набор 01.07.2002. Подписано в печать 18.07.2002. Уел. печ. л. 1,40. Уч.-изд.л. 0,80.
Тираж 124 экз. С 6617. Зак. 604.
ИПК Издательство стандартов, 107076 Москва, Колодезный пер., 14. e-mail: Набрано в Издательстве на ПЭВМ
Филиал ИПК Издательство стандартов — тип. «Московский печатник», 103062 Москва, Лялин пер., 6.
Плр № 080102
Швы сварных соединений. Методы контроля качества
КП
fin
ГОСУДАРСТВЕННЫЕ СТАНДАРТЫ СССР
Издание официальное
ЧАСТЬ II
ИЗДАТЕЛЬСТВО СТАНДАРТОВ М о с к • а 1973 г
СОДЕРЖАНИЕ
ГОСТ 15878-70 Соединения сварные, выполняемые контактной электросваркой. Основные типы и конструктивные элементы 3
ГОСТ 14806-69 Швы сварных соединений. Дуговая сварка алюминия и алюминиевых сплавов. Основные типы и конструктивные
элементы………….13
ГОСТ 16037-70 Швы сварных соединений стальных трубопроводов. Основные типы и конструктивные элементы …. 86
ГОСТ 16038-70 Швы сварных соединений трубопроводов из меди и медно-никелевого сплава. Основные типы и конструктивные элементы………….136
ГОСТ 14776-69 Швы сварных соединений электрозаклепочные Основные
типы и конструктивные элементы……178
ГОСТ 9466-60 Электроды металлические для дуговой сварки сталей и
наплавки. Размеры и общие технические требования 185
ГОСТ 10051-62 Электроды металлические для дуговой наплавки поверхностных слоев с особыми свойствами. Типы 198
ГОСТ 9467-60 Электроды металлические для дуговой сварки конструкционных и теплоустойчивых сталей. Типы …. 205
ГОСТ 10052-62 Электроды металлические для дуговой сварки высоколегированных сталей с особыми свойствами. Типы 209
ГОСТ 2246—70 Проволока стальная сварочная……227
ГОСТ 10543—63 Проволока стальная наплавочная……247
ГОСТ 16130-72 Проволока и прутки из меди и сплавов на медной основе сварочные . 256
ГОСТ 7871-63 Проволока сварочная из алюминия и алюминиевых
сплавов………….268
ГОСТ 11545-65 Сормайт. Сплав наплавочный прутковый и порошкообразный ………….274
ГОСТ 11546—65 Сталинит М порошкообразный. Технические требования 281
ГОСТ 2671-70 Прутки чугунные для сварки и наплавки . . 285
ГОСТ 7122-54 Швы сварные. Методы отбора проб для химического и
спектрального анализов………291
ГОСТ 3242—69 Швы сварных соединений. Методы контроля качества 296
ГОСТ 6996—66 Сварные соединения. Методы определения механических
свойств ………….303
ГОСТ 7312-69 Швы сварных соединений. Методы контроля просвечиванием проникающими излучениями …. 354
ГОСТ 14782-69 Швы сварных соединений. Методы ультразвуковой дефектоскопии …………367
Перечень стандартов, включенных в сборник, по порядку номеров . . 381
СВАРКА МЕТАЛЛОВ
Часть II
зд. 60X90’/,«
.ООО Изд. * 3055/02
Редактор С. Г. Вилъкина Обложка художника Г. Ф. Семиреченко Технический редактор //. С. Матвеева Корректор Г. М. Фролова
Сдано в набор 24. 04. 1973 г. Подп. • псч. 27. 10. 1973 г. Форм» Бум. тнпогр. 2 24,0 п. л. + 2 вкл. 2.0 п. л. 23,47 уч.-изд. л. Тираж
I пер.. 3 Зак. 1774
Цена 1 р. 17 к.
Издательство стандартов. Москва. Д-22, НовопресненскШ Калужская типография стандартов, ул. Московская. 256.
ОТ ИЗДАТЕЛЬСТВА
Сборник «Сварка металлов» содержит стандарты, утвержденные до 1 декабря 1972 г.
В стандарты внесены изменения, принятые до указанного срока. Около номера стандарта, в который внесено изменение стоит знак*.
В связи с пересмотром в сборник не включены ГОСТ 11534-65, ГОСТ 11969-66 и ГОСТ 11531-65.
Текущая информация о вновь утвержденных и пересмотренных стандартах, а также о принятых к ним изменениях публикуется в выпускаемом ежемесячно «Информационном указателе стандартов».
(с) Издательство стандартов, 1973
ГОСУДАРСТВЕННЫЙ СТАНДАРТ СОЮЗА ССР
ШВЫ СВАРНЫХ СОЕДИНЕНИЙ Методы контроля качества
Welded joints. Quality control methods
Постановлением Комитета стандартов, мер и измерительных приборов при Совете Министров СССР от 23/V 1969 г. № 598 срок введения установлен
с 1/УИ 1970 г.
Несоблюдение стандарта преследуется по закону
1. Настоящий стандарт распространяется на швы сварных соединений из всех свариваемых металлов и сплавов, выполненные различными способами сварки, и устанавливает методы контроля качества сварных швов с целью выявления наружных, внутренних и сквозных дефектов.
Применение методов предусматривается в стандартах и технических условиях, устанавливающих технические требования на продукцию.
2. Методы контроля качества швов сварных соединений в зависимости от характеристики дефекта и области применения должны соответствовать.
для выявления наружных дефектов — табл. 1;
для выявления внутренних дефектов — табл. 2;
для выявления сквозных дефектов — табл. 3.
Издание официальное | Перепечатка воспрещена |
Из именование М*10*0* контроле | Вид дефекте | Размеры ■ мм | РКПОДОАСИНГ дефекта |
1. Контроль внешним осмотром и измерениями | Наплывы, прожоги, незаверенные кратеры, полрезы. наружные трещины шва н’околошов-ной зоны, выплески, непровары корня шва и несоответствие конструктивных элементов сварного шва | Выявляемые невооруженным глазом или с применением оптических приборов с увеличением не более 10* | Любое |
2. Контроль красками и ЛЮ-минафо-рами | Наружные т ре шины, подрезы, поры, непровары, нсвыявлясмые внешним осмотром | 0,002-0,500 | |
3. Магнитно-порошковый метод | Не менее 0,100 | Перпендикулярно к потоку намагничивания |
| И-lHt 1DOJ |
И i именование методов KOMTpO.1t | Вид дефект* | Р*М«ры 1Сф«К1» > мм | ’кноложеиме дефск!* |
1. Метод технологической про бы | Непровары, перегрев металла шва и иесплап-ление кромок | Не ограни-чикаются | Любое |
2. Металлографический метод | Дефекты структуры шва сварного соединения и зоны термического влияния, внутренние и наружные трешн-ны. непровары, шлаковые и газовые включения. иесллапление кромок | ||
3. Контроль просвечиванием проникающими излучениями | Непровары, газовые поры, шлаковые и мс-таллические включения, грешины в шве сварного соединения и околошов-ной зоне, нciплавление кромок* | Не менее 0.300 | Любое, кроме трещин, расположенных под углом не более 5® по направлению нейтрального луча |
Тип соармого «оезииеки* | C*IOCОй сварен | Сыриысмы* матервмдм | Толщши свариваемы» материалов в мм |
Все ТИПЫ | Все способы спар- КИ | Все свариваемые металлы и сплавы | Не ограничивается |
Не более 100 |
| ГОСТ 3242—** |
| ГОСТ 1242—М | ||||||||||||||||||||||||
* Выявление трещин и нссплавленис кромок методом не гарантируется. ••Метод определяет величину и место расположения дефекта; вид’дефекта не устанавливает. |
Таблица 3 | ||||||||||||||||||
|
Н>!1мс*пв1кие
мстоло»
пипрмя
P.JKTJ.U
дефект*
* ММ
Расположение
дефект*
3. Контроль воз-душ ним давлением
4. Контроль аммн-ако Ы
5. Контроль гидравлическим давлением
Спиши, прожоги, трещины, сплошные непровары
6. Контроль наливом воды
7. Контроль ПОЛИ -HOST водой
8. Метод испытания течеиска-телямк
| ГОСТ 3242-69 |
3. Контроль качества швов сварных соединений смачиванием керосином, гидравлическим давлением и поливом водой (пп. 1; 5 и 7 табл. 3) производят соответственно по ГОСТ 3285-65, ГОСТ 1999—60 и ГОСТ 3845-65.
4. Контроль остальными методами до разработки соответствующих стандартов следует проводить по техническим условиям, утвержденным в установленном порядке.
5. Указанные методы должны применяться при контроле качества швов готовых изделий и на образцах, изготовленных из изделий или из контрольных сварных соединений-
П римечание. Допускается применение других методов контроля, не предусмотренных настоящим стандартом, но обеспечивающих качественное проведение контроля сварных швов, по техническим условиям, утвержденным в установленном порядке.
6. При проведении контрольных испытаний должны соблюдаться действующие правила по технике безопасности и производственной санитарии.
ГОСТ Р 50608-93 Оборудование холодильное. Аппараты стальные. Соединения сварные. Технические требования и методы контроля, ГОСТ Р от 12 ноября 1993 года №50608-93
ГОСТ Р 50608-93
Г87
ОКП 36 4400
Дата введения 1994-07-01
1 РАЗРАБОТАН И ВНЕСЕН Техническим комитетом по стандартизации ТК 271 «Установки холодильные холодопроизводительностью свыше 2,5 тыс. станд. ккал/ч (3,0 кВт)»
2 УТВЕРЖДЕН И ВВЕДЕН В ДЕЙСТВИЕ Постановлением Госстандарта России от 12.11.93 N 240
3 ВВЕДЕН ВПЕРВЫЕ
1 ОБЛАСТЬ ПРИМЕНЕНИЯ
Настоящий стандарт распространяется на стальные теплообменные, емкостные и вспомогательные аппараты, предназначенные для работы в составе аммиачных, углеводородных и хладоновых холодильных машин и установок (далее — аппараты), и устанавливает требования к конструкции сварных швов аппаратов и методы контроля их качества в развитие ГОСТ 5264, ГОСТ 8713, ГОСТ 14771 и ГОСТ 16037.
Стандарт не распространяется на фильтры, смесители, сепараторы, смотровые и другие подобные устройства, встраиваемые в трубопроводы, а также на аппараты и сосуды из труб внутренним диаметром не более 150 мм.
Обязательные требования к качеству сварных швов аппаратов, обеспечивающие их безопасность для жизни, здоровья и имущества населения, изложены в разделе 6 и пунктах 5.1-5.5, 5.8, 5.11-5.17.
Термины и определения — по ГОСТ 2601.
2 НОРМАТИВНЫЕ ССЫЛКИ
В настоящем стандарте использованы ссылки на следующие стандарты:
ГОСТ 2601-84 Сварка металлов. Термины и определения основных понятий
ГОСТ 5264-80 Ручная дуговая сварка. Соединения сварные. Основные типы, конструктивные элементы и размеры
ГОСТ 6996-66 Сварные соединения. Методы определения механических свойств
ГОСТ 8713-79 Сварка под флюсом. Соединения сварные. Основные типы, конструктивные элементы и размеры
ГОСТ 14771-76 Дуговая сварка в защитном газе. Соединения сварные. Основные типы, конструктивные элементы и размеры
ГОСТ 16037-80 Соединения сварные стальных трубопроводов. Основные типы, конструктивные элементы и размеры
ГОСТ 23055-78 Контроль неразрушающий. Сварка металлов плавлением. Классификация сварных соединений по результатам радиографического контроля
3 ОБОЗНАЧЕНИЯ
Приняты следующие обозначения конструктивных элементов свариваемых деталей и сварных швов:
— толщина обечайки;
— толщина патрубка;
— толщина шва;
— глубина разделки под сварку;
— высота шва;
— ширина шва;
— расстояние от поверхности фланца или трубной решетки до сварного шва.
4 КЛАССИФИКАЦИЯ
4.1 Сварные швы аппаратов должны быть отнесены к одной из четырех категорий (рисунок 1).
Рисунок 1
Категория А. Продольные сварные швы обечаек корпуса, распределительной камеры, переходников, патрубков, сварные швы штампованных или плоских днищ, изготовленных из нескольких частей.
Категория В. Кольцевые сварные швы обечаек корпуса, патрубков, кольцевые сварные швы, соединяющие штампованные эллиптические днища с обечайками корпуса, распределительной камеры, отстойников.
Категория С. Сварные швы, присоединяющие фланцы, трубные доски, плоские днища к обечайкам, а также фланцы к эллиптическим и сферическим днищам.
Категория D. Сварные швы, соединяющие патрубки и штуцера с обечайками и днищами.
5 ТЕХНИЧЕСКИЕ ТРЕБОВАНИЯ
5.1 Сварные швы категории А должны быть стыковыми двусторонними или односторонними, выполненными по технологии, обеспечивающей проплавление на всю глубину по ГОСТ 5264, ГОСТ 8713 и ГОСТ 14771.
5.2 Сварные швы категории В должны быть стыковыми двусторонними или односторонними с применением подкладки (остающейся или удаляемой после сварки) по ГОСТ 5264, ГОСТ 8713, ГОСТ 14771 и ГОСТ 16037.
5.3 Сварные швы категории С должны быть:
5.3.1 Для аммиачных и углеводородных аппаратов — стыковыми двусторонними (рисунки 2 и 3) или односторонними, выполненными по технологии, обеспечивающей проплавление на всю глубину, или односторонними с применением подкладки (остающейся или удаляемой после сварки) (рисунки 4 и 5).
Рисунок 2
Рисунок 3
Рисунок 4
Рисунок 5
5.3.2 Для хладоновых аппаратов — угловыми или тавровыми швами (рисунки 6, 7, 8, 9 и 10).
Рисунок 6
Рисунок 7
Рисунок 8
Рисунок 9
Рисунок 10
5.4 Сварные швы категории D должны быть угловыми или тавровыми швами (рисунки 11, 12, 13, 14, 15, 16 и 17).
Рисунок 11
Рисунок 12
Рисунок 13
Рисунок 14
Рисунок 15
Рисунок 16
Рисунок 17
5.5 Стыковые, угловые и тавровые швы полостей, содержащих холодильный агент, должны быть швами с полным проплавлением.
5.6 Допускается применять швы с неполным проплавлением (конструктивным зазором) по типу У5 или У7 ГОСТ 16037, соединяющие фланцы с патрубками хладоновых аппаратов, эксплуатируемых при температуре не ниже минус 28 °С, а также соединяющие фланцы с днищами крышек, не находящихся под давлением холодильного агента.
5.7. Допускается применять швы с неполным проплавлением для соединений гильза — обечайка (рисунок 18), бобышка — обечайка (рисунок 19) для аппаратов, эксплуатируемых при температуре не ниже минус 28 °С.
Рисунок 18
Рисунок 19
5.8 Остающиеся подкладные кольца должны быть изготовлены из стали той же марки, из которой изготовлены свариваемые детали.
5.9 В качестве удаляемых подкладных колец следует применять медные, керамические или флюсовые кольца.
5.10 Приведенные на рисунках 1-19 примеры конструкции сварных швов являются рекомендуемыми.
5.11 Продольные швы смежных обечаек должны быть смещены относительно друг друга на расстояние, равное пятикратной толщине наиболее толстого элемента, но не менее чем на 100 мм между осями швов.
5.12 На всех свариваемых деталях должна быть сохранена маркировка предприятия — поставщика металла. В состав маркировки должны входить:
— марка материала;
— номер плавки.
5.13 В сборочном чертеже сварного узла или на специальном эскизе должны быть указаны схема маркировки деталей, места простановки клейм сварщиков и клейм представителей ОТК, осуществляющих входной контроль материалов и контроль качества сварки на промежуточных операциях.
5.14 Если конструкторской или технологической документацией предусмотрена послесварочная термическая обработка, то окончательный контроль качества сварных швов проводят после нее.
5.15 Кромки подготовленных под сварку деталей и прилегающие к ним поверхности должны быть зачищены с двух сторон до полного удаления окалины, ржавчины, грата и брызг после термической резки, краски, масел и других загрязнений.
5.16 При сварке необходимо защищать внутреннюю поверхность защитным газом (углекислым газом или аргоном).
5.17 Качество и контроль сварных соединений должны обеспечивать прочность и герметичность аппаратов в соответствии с требованиями, установленными в конструкторской документации.
6 МЕТОДЫ КОНТРОЛЯ КАЧЕСТВА СВАРНЫХ ШВОВ
6.1 Технология сварки, а также сварщики и операторы установок для автоматической сварки должны быть аттестованы в соответствии с требованиями отраслевых нормативных документов.
6.2 Методы контроля качества сварных швов различных категорий указаны в таблице 6.1.
Таблица 6.1 — Методы контроля качества сварных швов
Категория сварного шва | Внешний осмотр | Радиографический контроль или ультразвуковая дефектоскопия | Цветная |
А | + | + | |
В | + | + | |
С | + | + | |
D | + | + |
6.3 Объем контроля сварных швов радиографическим или ультразвуковым методами должен быть не менее указанного в Правилах устройства и безопасной эксплуатации холодильных систем, утвержденных Госпроматомнадзором СССР 01.11.91 г.
6.4 При объеме контроля радиографическим или ультразвуковым методами менее 100% общей длины сварных швов обязательному контролю подлежат места пересечений сварных швов категорий А и В для фреоновых аппаратов и сварных швов категорий А, В, С для углеводородных и аммиачных аппаратов, а также участки сварных швов, перекрываемые укрепляющими кольцами.
6.5 По требованию заказчика сварные швы категорий А, В и С аммиачных и углеводородных аппаратов и сварные швы категорий А и В хладоновых аппаратов должны быть проверены радиографическим методом при выполнении следующих условий:
6.5.1 Объем контроля сварных швов аммиачных и углеводородных аппаратов должен составлять 100% независимо от рабочей температуры хладагента в аппарате.
6.5.2 Допускается ультразвуковая дефектоскопия взамен радиографического контроля для замыкающего сварного шва аппарата, если конструкция аппарата не позволяет применить радиографический метод.
6.6 Проверка ударной вязкости
6.6.1 Для аппаратов, изготовленных из углеродистой и низколегированной стали, предназначенных для эксплуатации при температуре ниже минус 28 °С, должны быть подвергнуты испытаниям на ударный изгиб образцы типов IX, Х или XI по ГОСТ 6996 (Шарпи). Испытания следует проводить при минимальной рабочей температуре аппарата.
6.6.2 Минимальное значение ударной вязкости составляет 20 Дж/см (2 кгс·м/см).
6.6.3 Образцы должны быть вырезаны из контрольного стыкового сварного соединения.
6.6.4 При сварке контрольных соединений пластины следует прихватить к свариваемым элементам так, чтобы шов контрольных пластин являлся продолжением шва свариваемого изделия.
6.6.5 Если прихватка пластин невозможна (кольцевые швы и т.д.), то сварку пластин следует проводить отдельно, но с обязательным соблюдением всех условий сварки контролируемых стыковых соединений.
6.6.6 Из каждого контрольного сварного соединения должны быть вырезаны по три образца для испытания наплавленного металла и по три образца для испытания металла околошовной зоны. При этом канавка должна быть расположена перпендикулярно к поверхности пластины.
6.6.7 При получении неудовлетворительных результатов хотя бы одного из видов испытания испытание этого вида должно быть повторено на удвоенном количестве образцов, вырезанных из того же контрольного соединения.
6.6.8 Если при повторном испытании хотя бы на одном из образцов получен неудовлетворительный результат, качество контролируемого сварного соединения сосуда следует считать неудовлетворительным.
6.7 В сварных соединениях не допускаются следующие наружные дефекты:
— несоответствие их форм и размеров требованиям стандартов и чертежей;
— трещины;
— свищи и пористость наружной поверхности шва;
— подрезы;
— наплывы, прожоги и незаплавленные кратеры;
— смещение кромок свариваемых элементов выше максимально допустимого, указанного в таблице 6.2.
Таблица 6.2
В миллиметрах
Толщина свариваемых листов | Максимально допустимое смещение кромок | |
Категория сварного шва | ||
А | В, С | |
До 12 | ||
Св. 12 до 20 | 3,2 |
6.8 В сварных соединениях не допускаются следующие внутренние дефекты:
— трещины, непровары и несплавления;
— поры и включения, количество которых выходит за пределы норм, установленных ГОСТ 23055 для 4-го класса дефектности сварного шва.
Текст документа сверен по:
официальное издание
М.: Издательство стандартов, 1994
Перенос холодного металла: шовная сварка
Сварка швов
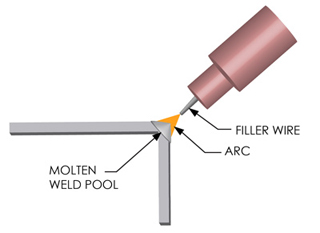
Protocase обеспечивает сварку швов как стандартный процесс. Шовная сварка полезна для непрерывного соединения двух или более кусков листового металла, чтобы они казались бесшовными. Для сварки швом детали надежно зажимаются и свариваются, а затем излишки металла удаляются шлифованием. Полученные непрерывно соединенные швы полезны для защиты от атмосферных воздействий, уменьшения утечки электромагнитных помех и для достижения бесшовного внешнего вида при желании.
Перенос холодного металла: революционная технология сварки
Protocase принял сварку CMT в качестве стандарта для шовной сварки. CMT — это недавно разработанная технология, которая намного превосходит традиционную сварку TIG и MIG для соединения тонкого листового металла. До CMT сварка тонкостенного листового металла всегда была больше видом искусства, чем искусственным производственным процессом. MIG и TIG создают чрезмерное количество тепла, которое может вызвать обратное плавление и коробление, часто разрушая детали и вызывая высокий уровень внутреннего брака.Это увеличило не только наши внутренние затраты, но и вероятность того, что вы опоздаете на работу. Напротив, CMT генерирует только одну десятую теплоты сварки MIG, а деформация и обратное плавление практически исключаются. Это устанавливает новые стандарты в сварке тонкостенных листов, особенно там, где существуют строгие требования к внешнему виду сварных швов. CMT дает вам:
- Качественная сварка всего металла, который у нас есть для изготовления. (Раньше мы не могли сваривать некоторые тонкие материалы.Подробную информацию о металлах, которые мы храним, см. На наших страницах, посвященных холоднокатаной стали, гальванической обработке, нержавеющей стали, алюминию и меди. (медь обычно паяется)
- Снижение затрат за счет сокращения времени сварки и уменьшения количества брака.
- Большой выбор материалов для вашей конструкции корпуса. Все, что мы можем изготовить, теперь можно сваривать.
Как работает CMT Welding
Процесс CMT физически напоминает сварку MIG с подачей проволоки в том, что сварочная проволока и защитный газ пропускаются через сварочную горелку, а электрическая дуга между сварочной проволокой и сварочной поверхностью приводит к тому, что конец сварочной проволоки становится жидким и применяется к сварочной поверхности.Но CMT использует автоматическое включение и выключение нагревательной дуги, чтобы систематически нагревать и охлаждать сварочную проволоку, одновременно вводя проволоку в контакт со сварочной ванной и выходя из нее, много раз в секунду. Поскольку при сварке CMT используется пульсирующее действие, а не непрерывный поток энергии, при сварке CMT выделяется только одна десятая тепла, чем при сварке MIG. Уменьшение тепла — величайшее преимущество CMT, поэтому его называют «холодным» переносом металла.
Во время горения дуги присадочный металл перемещается в сторону сварочной ванны. | Когда присадочный металл погружается в сварочную ванну, дуга гаснет. Сварочный ток снижен. | Движение провода назад способствует отделению капель во время короткого замыкания. Ток короткого замыкания остается небольшим. | Движение проволоки меняется на противоположное, и процесс начинается заново. |
![]() | ![]() | ![]() | ![]() |
Геометрия коробления и сварного шва при сварке швов CMT
Угловые швы (см. Диаграмму A) геометрически стабильны.Напряжениям от изменения температуры и затвердевания противодействуют опоры, предлагаемые обоими краями соединения. Большинство углов геометрии можно полностью сварить швом без коробления с помощью сварки CMT. Это верно для всего металла, который у нас есть.
Т-образные соединения (см. Диаграмму B). Швы, соединяющие край детали с плоской поверхностью, склонны к короблению, так как отсутствует геометрическая опора для противодействия напряжениям от температуры и затвердевания основного металла.Таким образом, даже при сварке CMT, если сделать длинный шовный шов поперек детали, возможно, что плоская поверхность больше не будет плоской после сварки. Особенно это касается нержавеющей стали и алюминия. Одно из решений, которое может работать в определенных ситуациях, — это соединение путем сварки нескольких коротких сегментов, а не создание непрерывного шва. Это может оставить достаточно немодифицированного основного металла, чтобы придать детали достаточную целостность для сохранения плоскостности. Если вам требуется геометрия Т-образного шва, наш технический персонал может помочь вам с проектированием.
Другие геометрии сварных швов необходимо решать в каждом конкретном случае. Свяжитесь с нашим техническим персоналом.
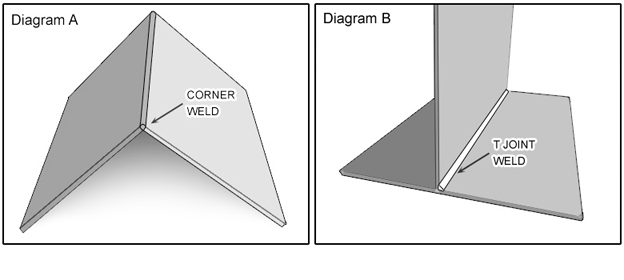
Что такое двоение монитора и как его исправить
Есть несколько способов исправить двоение монитора, большинство из них включает настройку определенных параметров монитора.
Наиболее частым решением является включение функции ускорения.
Этот параметр имеет разные названия в зависимости от производителя монитора и известен как:
- Overdrive для мониторов Acer
- AMA для мониторов BenQ
- Trace Free для мониторов ASUS
- Время отклика для мониторов LG и Samsung
Для у других производителей это обычно отображается как Overdrive или Response Time в настройках монитора.
Теперь, чтобы точно исправить эту проблему, вы должны попробовать тест движения TestUFO, а затем соответствующим образом настроить перегрузку.
Изменяйте уровни перегрузки, пока двоение изображения не будет минимизировано в максимально возможной степени без заметных артефактов короны. Рекомендуемая настройка обычно средняя или на один уровень ниже, когда начинают появляться обратные двоения или артефакт короны.
Некоторые другие настройки, такие как «Perfect Clear», «Автоконтраст», «Сглаживание движения» или «Подавление шума», также могут вызывать ореолы, особенно в темных сценах.
Эти настройки улучшают изображение. Они добавляются к необработанному видеосигналу, увеличивая время отклика, и могут добавлять заметные артефакты изображения.
Обычно они присутствуют на телевизорах, но если вы испытываете артефакты, такие как двоение изображения на мониторе, проверьте эти настройки на панели управления монитора и, если вы обнаружите их, выключите их.
Кроме того, в концентраторе панели управления Nvidia есть параметр «Подавление шума». Рекомендуется отключить эту настройку, чтобы избежать появления ореолов или других артефактов изображения.
Когда артефакт ореола монитора вызван неисправными кабелями или другими устройствами (если изменение настроек ускорения не помогло), вы должны удалить все устройства, которые находятся рядом с вашим монитором (например, принтеры или модемы, динамики безопасны), а затем проверить монитор для ореолов. Если проблема связана с заменой кабеля монитора, это должно решить проблему.
Если ореолы все еще видны, даже если вы изменили настройки ускорения, удалили другие устройства рядом с монитором и поменяли кабель, проблема может быть в неисправном мониторе или неисправных видеопортах.В этом случае единственный вариант — отнести монитор в сервисный центр или заменить его (если он находится на гарантии).
Обратите внимание, что, как мы уже упоминали, более дешевые панели VA и IPS могут показывать артефакты ореола, потому что их время отклика пикселей просто слишком мало. В этом случае вы никак не сможете удалить ореолы.
Еще одно возможное решение — обновить драйверы графической карты, что иногда помогает решить проблемы с двоением монитора.
.