Технология изготовления СВЧ элементов конструкций РЭС
БЕЛОРУССКИЙ ГОСУДАРСТВЕННЫЙ УНИВЕРСИТЕТ ИНФОРМАТИКИ И РАДИОЭЛЕКТРОНИКИ
Кафедра ЭТТ
РЕФЕРАТ
На тему:
«Технология изготовления СВЧ элементов конструкций РЭС»
МИНСК, 2008
Для передачи энергии СВЧ колебаний миллиметрового, сантиметрового и дециметрового диапазонов используются волноводные системы или волноводные тракты, которые сокращенно называются волноводами. Обычно волноводное звено состоит из отрезка трубы с соединенными фланцами на концах.
Рис.1. Волновод.
Все звенья должны иметь хорошо проводящие внутренние поверхности. По форме поперечного сечения волноводные звенья из труб разделяются на прямоугольные, эллиптические и круглые. По конструкции стенок звенья подразделяются на жесткие и гибкие. Жесткие звенья делятся на прямые и изогнутые.
Для генерирования СВЧ колебаний в качестве контуров применяются полые резонаторы различной формы.
Рис.2. Виды полых резонаторов: цилиндрический, прямоугольный, тороидальный.
Для излучения и приема СВЧ энергии в пространство используются различные металлические и металлизированные поверхности. Идеальным отражателем является гладкая металлическая поверхность. Однако в ряде случаев для изменения веса и снижения ветровых нагрузок применяются решетчатые и сетчатые конструкции.
Основная технологическая задача при изготовлении элементов СВЧ –трактов передачи энергии – это: 1. высокая чистота внутренней поверхности волноводов и резонаторов и наружной отражательной поверхности антенных излучателей; 2. их высокая электропроводность; 3. защита поверхности проводящего слоя от коррозии.
Широко распространен способ изготовления волноводных звеньев из стандартных труб прямоугольного или круглого сечения. В качестве материала применяют латунь (марки ЛС–50, Л–62, Л–96), алюминий (марки А–00, А–Л) и медь (марки М–1, М–3).
При одинаковых способах обработки чистота поверхности латунных деталей получается выше, чем у других материалов.
Алюминиевые волноводы отличаются малой массой и более простой технологией изготовления, чем латунные и медные.
Процесс изготовления волноводных звеньев складывается из следующих этапов:
– нарезка заготовок;
– изгибание и скручивание (по мере надобности) заготовок;
– изготовление фланцев;
– пайка фланцев к трубам;
– обработка проводящих поверхностей;
– сборка волноводных звеньев в волноводы.
Нарезка заготовок. Куски труб нарезают дисковой фрезой с припуском на обработку на горизонтальном фрезерном станке, после чего торцы их зачищают от заусенцев.
При необходимости выполнения отводов (ответвлений) в стенках трубы фрезеруют отверстия, а в торцах соединяемых труб – уступы.
Изгибание заготовок должно осуществляться способами, при которых не изменяется форма и внутренние размеры сечения заготовок и не ухудшается чистота обработки внутренних поверхностей.
Наиболее производительным способом получения изогнутых звеньев без заполнения заготовки является способ чеканки (насечки). Изгибание труб прямоугольного сечения производится на гибочном станке в результате возвратно-поступательного движения верхнего пуансона одновременно с движением двух боковых пуансонов, находящихся в обжимной головке.
Рис.3. Процесс изгиба.
При этом заготовка через равные промежутки времени перемещается в продольном направлении (шаг подачи), подвергаясь одновременно с трех сторон ударам чеканов, вызывающих пластические деформации в металле стенок трубы. В результате труба изгибается в сторону нижней стенки.
Изготовление фланцев. Фланцы, укрепляемые на концах труб, по форме торцовой поверхности могут быть прямоугольными или круглыми, причем те и другие изготавливают плоскими и с уступами. Плоские фланцы выполняют на металлорежущих станках с сверлением круглых крепежных отверстий, фрезерованием и калибровкой прямоугольных отверстий.
Рис.4. Фланец.
Латунные и алюминиевые фланцы с уступами (объемные) обычно изготавливают путем штамповки с последующей пробивкой и калибровкой окон.
Пайка фланцев к трубам. Соединение труб с фланцами производят посредством пайки. Латунные и медные звенья паяют серебренными припоями. Алюминиевые трубы и фланцы наиболее надежно соединяются посредством газовой сварки с последующей зачисткой сварного шва.
Обработка проводящих поверхностей. Перед полированием внутренняя поверхность волноводного звена очищается механическим путем при помощи щеток из тонкой медной проволоки. Полирование осуществляется на пневматической установке.
Рис.5. Обработка проводящей поверхности.
Сжатый воздух поступает поочередно в правый и левый фланец, в результате чего полирующий вкладыш из плотного фетра совершает с большой быстротой прямолинейные возвратно-поступательные движения, полируя внутреннюю поверхность трубы абразивным порошком или полировальными пастами. Изогнутые звенья полируют вкладышами из мягкого фетра. После полирования звенья счищают от абразивных частиц и обезжиривают.д.ля увеличения электропроводности и повышения антикоррозионных свойств внутреннюю поверхность латунных волноводов покрывают слоем электролитического серебра. Для защиты серебра от коррозии осуществляют покрытие поверхности пленкой лака. В местах разъемных контактных соединений для повышения стойкости серебряного покрытия наносят пленки палладия и родия толщиной 0,1 мкм.
Волноводные звенья из алюминия не нуждаются в серебрении. Для защиты от коррозии после полирования внутреннюю поверхность алюминиевых труб подвергают пассивированию. Наружную поверхность волноводных звеньев покрывают антикоррозионными лакокрасочными покрытиями, выбор которых определяется эксплуатационными условиями.
Изготовление литых волноводных звеньев
По сравнению с методом изготовления волноводов из труб метод литья является наиболее прогрессивным – требует меньшей затраты времени и средств, использует недорогие и недефицитные материалы; обеспечивает более высокую стабильность характеристик волноводов за счет их монолитности и идентичности размеров.
Волноводные элементы изготавливаются литьем по выплавляемым моделям и имеют внутренние каналы прямоугольного, эллиптического или круглого сечения и сложной конфигурации. Для изготовления волноводов чаще всего используют сплавы АЛ9 и ЛС59–1Л. Они имеют хорошие литейные и механические свойства, коррозионную стойкость, легко обрабатываются резанием.
Изготовление наращенных волноводных звеньев
При изготовлении единичных образцов сложных по конструкции волноводных звеньев применяется способ электролитического осаждения металла на предварительно изготовленные модели. По технологическому признаку эти модели разделяют на возвратимые и невозвратимые. Технологический процесс изготовления деталей по возвратным моделям состоит в следующем: на поверхность модели, выполненной из изоляционного материала, сначала наносят тонкий электропроводящий слой (серебро или медь), после чего загружают в ванну с цианистым электролитом, в котором осаждается слой серебра толщиной 20–40 мкм. Затем медь переносят в ванну из комплексной медно-цианистой соли, где на нее наносят слой меди 2–3 мм и более. Особенностью возвратимых моделей является возможность изготовления по одной модели большого количества изделий.
Сущность применения невозвратимой модели заключается в том, что после осаждения на ее поверхности металла медь разрушается и осаждает все внутренние полости изделия.
Изготовление гибких волноводных звеньев
Наибольшее распространение получили волноводы в виде металлического шланга. Их изготовляют из посеребренной листовой бронзы Бр КМЦ3–1 толщиной 0,15–0,3 мм, а также латуни Л80, Л622М толщиной 0,1–0,15 мм. Заготовки нарезают гильотинными ножницами в виде полос такой ширины, чтобы после свертывания их на прямоугольной оправке один край заходил на другой 5–10 мм. Свертывание осуществляется намоткой по спирали с загибанием краев лент для соединения витков между собой.
Рис.6. Гибкие звенья.
Выбором режима наматывания ленты достигается надежный электрический контакт между витками и увеличивается срок службы волновода.
Бесшовный гофрированный волновод получают прокаткой тонкостенной медной трубы в специальном приспособлении. После прокатки труба принимает вид «гармошки», которая обеспечивает его гибкость.
Методы изготовления полых резонаторов
Наиболее распространенными методами изготовления полых резонаторов являются: точное литье, литье под давлением и электролитическое осаждение метала.
Внутренняя поверхность полых резонаторов должна достигать высокой степени чистоты, поверхностный слой металла должен быть однородным, без разрушений. Это достигается механическими видами обработки: чистовым точением, обработкой алмазным резцом, полированием, суперфинишированием.
Чистовое точение осуществляется токарной обработкой с применением резцов из сверхтвердых сплавов.
Принципиальной особенностью чистового точения являются большие скорости резания (30–50 м/с) при малой глубине резания (0,05–0,1) мм и малой подачи (00,1–0,2 мм/об).
Обработка алмазным резцом. Она следует после чистового точения. Для этого режущие грани алмазного резца придается полукруглый профиль с радиусом кривизны 100–120 мкм.
Обточка внутренней поверхности резонатора производится на токарном станке при подаче резца в осевом направлении порядка 0,8–1 мкм на один оборот, скорости резания 17–20 м/с и интенсивном охлаждении струей азота. При таком режиме обработки средняя высота микронеровности составляет не более 0,001 мкм (10).
Полирование. Применяется для уменьшения микрогеометрии шероховатости. Полирование образует гладкую поверхность, но не дает возможности довести обрабатываемую поверхность до заданного размера.
При высокой чистоте отполированная поверхность после обрезания тонкой оксидной пленки приобретает повышенную антикоррозионную стойкость.
Суперфиниширование. Является заключительной стадией механической обработки поверхности и проводится с целью удаления поверхностного разрушенного слоя металла, оставшегося от предшествующей операции.
После полного удаления гребешков микронеровностей между бруском и поверхностью резонатора образуется неразъемная пленка смазки, снятие металла с обрабатываемой поверхности больше не происходит и процесс обработки прекращается.
Неметаллические покрытия
Неметаллические покрытия получают в процессе химической и электрохимической обработки.
На поверхности деталей образуются тонкие плотные пленки окислов и других химических соединений, защищающих изделия от влияния внешней среды или обладающих другими желаемыми свойствами, например изоляционными.
К неметаллическим покрытиям относятся: анодирование, оксидирование, пассивирование, фосфотирование.
Анодирование применяется как покрытие на алюминии и его сплавах. В результате анодирования на поверхности изделия образуется прочная оксидная пленка.
Электрохимическое анодирование производят в 20% растворе серной кислоты, детали присоединяют к аноду, катодом служит свинцовая пластина. Для получения золотисто-желтого цвета детали дополнительно обрабатывают в 10% растворе хромпика (К2Cr2O7), молочного цвета – в хромовом агнедриде.
Оксидирование – получение окисных пленок путем обработки в растворах щелочей и кислот. Оксидируются стальные детали, медные и латунные.
Пассивирование – получение тонких защитных пленок на стали и цветных сплавах с использованием окислов хрома.
Фосфотирование – применяется как антикоррозионное и изоляционное покрытие алюминиевых и стальных деталей. При фосфотировании изделие покрывается нерастворимой пленкой солей фосфорной кислоты.
Фосфорная пленка пориста, поэтому фосфотированные детали покрывают лаком или промасливают.
1. Технология производства ЭВМ / А.П. Достанко, М.И. Пикуль, А.А. Хмыль: Учеб. – Мн. Выш. Школа, 2004 – 347с.
2. Технология деталей радиоэлектронной аппаратуры. Учеб. пособие для ВУЗов / С.Е. Ушакова, В.С. Сергеев, А.В. Ключников, В.П. Привалов; Под ред. С.Е. Ушаковой. – М.: Радио и связь, 2002. – 256с.
3. Тявловский М.Д., Хмыль А.А., Станишевский В.К. Технология деталей и пе-риферийных устройств ЭВА: Учеб. пособие для ВУЗов. Мн.: Выш. школа, 2001. – 256с.
4. Технология конструкционных материалов: Учебник для машиностроительных специальностей ВУЗов / А.М. Дольский, И.А. Арутюнова, Т.М. Барсукова и др.; Под ред.А.М. Дольского. – М.: Машиностроение, 2005. – 448с.
5. Зайцев И.В. Технология электроаппаратостроения: Учеб. пособие для ВУЗов. – М.: Высш. Школа, 2002. – 215с.
6. Основы технологии важнейших отраслей промышленности: В 2 ч. Ч.1: Учеб. пособие для вузов / И.В. Ченцов, И.А.
Изготовление фланцев по чертежу | tokarnaja-obrabotka.ru
Изготовление фланцев по чертежу от ООО “Токарная обработка” на ЧПУ okuma B400, 1К62, 16К20, токарных автоматах. Есть закалка, шлифовка, гальваника. Пошлите запрос с чертежами на электронную почту:
[email protected]
Изготовление фланцев по чертежу
Наша компания предлагает изготовление фланцев по чертежу. Это достаточно сложная задача, которую только можно поставить перед производством. Сложность связана с тем, что на чертежах фланцев отсутствует документация и то, какая технологическая оснастка требуется.
Для расчета стоимости изготовления фланцев на станках ЧПУ, пошлите запрос с чертежами на электронную почту:
[email protected] Ответим на любые вопросы: 8 3439 38 00 81, 8 3439 38 98 01, доставка по всей России.
Предназначением для фланцев служит цель, которая состоит в соединении труб и арматуры. Фланцы делятся на два типа. Во-первых, речь идет о нержавейке, и из черного металла. Также можно использовать сталь различных марок. Они также хорошо подходят, что и детали, требуемые при производстве отводов и переходов. Важно отметить, что фланцам присуща конструктивная особенность монтажа, поэтому они делятся на несколько типов. Рассмотрим их.
Во-первых, стальной фланец, который является плоским и называется приварным. В этом случае его надевают на трубу и приваривают к ней по кругу, используя два сварных шва. Во-вторых, стальной фланец, которые приваривается встык. Отличается он от плоского фланца тем, что для его прикрепления требуется только один шов. То есть соединяется воротник встык. Так можно во много раз сократить время и стоимость монтажа. В-третьих, стальной фланец, который является свободным и приваривается на кольце.
Для того чтобы разработать новую оснастку и технологическую карту, требуется много дополнительного времени. Именно по этой причине, цена на фланцы может быть выше, чем на другие детали, изготавливаемые по чертежу. Выходит, что при производстве изделия стандартного образца можно получить изделие много дороже, чем оно есть на самом деле. И все из-за того, что требуется дополнять чертежи.
Также многое связано с тем, что фланцы производят серийно, для чего нужно много времени. Отметим, что подготовить и разработать техническую документацию, которая нужна для небольшой серии деталей, а также вообще одной, требуются совсем немного, но чтобы изготовить большую серию фланцев, тем самым подготовить больше документации, требует больше времени и затрат. Также получается, что если заказ на один фланец имеет высокую стоимость, то при большой серии стоимость распределяется на каждый экземпляр, выходит, что они стоят по отдельности дешевле.
Что же касается единичного экземпляра фланца, то его изготавливать совсем невыгодно. Поэтому лучше подождать некоторое время, чтобы потребовались токарные работы ЧПУ большей серии. Получается, что несколько фланцев обходятся дешевле. Значит, для компаний, которые продают фланцы, мы готовы изготовить на целый ряд больше деталей, что во многом их удешевит, а значит, сделает доступными простому человеку.
Когда выполняется чертеж фланца, то речь идет о создании документа, который позволит изготовить технологическую карту для данной детали. Производство и изготовление фланца по чертежу в полной мере во многом связано с дополнительными усилиями, требуется больше времени. Поэтому при чертеже важно соблюсти все нюансы. Это позволит даже менять по необходимости параметры, которые требуются, чтобы изготовить деталь.
Например, изделие на чертеже может не соответствовать ГОСТу, поэтому фланец важно производить только по правильным параметрам. В частности, учитывается геометрия, материал, который нужен для изготовления, давление при работе, область применения. Когда речь идет о фланцах, а также о соединениях этих деталей, то нужны дополнительные усилия, чтобы произвести эти детали. А как показывает практика, мало кто из существующих компаний готов к созданию подобного рода деталей. У нас же для этого есть все необходимое оборудование и квалификация, которые позволят достигать большой серийности, а также качества при единичном изобретении.
Те, кто производят фланцы, должны знать, что на чертеже не всегда установлено все в должном порядке, поэтому многое нужно доделывать. Требуется создать дополнительную базу, которая бы включала в себя серьезно подготовленных работников, которые бы умело пользовались необходимой документацией. Получается, что для изготовления фланцев по чертежам важно уметь правильно читать чертежи именно этой детали.
Процессы достаточно сложны при изготовлении фланцев и их соединений. Выходит, что для этого дела важно быть сосредоточенным, полностью понимать все возможные трудности, а также осознавать, насколько сложен процесс изготовления фланцев, тогда не будет невозможного. А что касается специалистов, то потребуется много умений и стараний, чтобы увеличить квалификацию, которая бы позволила создавать фланцы по чертежам.
Изготовление и производство фланцев из нержавейки по чертежу, любые размеры, любой сплав
Такое изделие, как фланец часто на слуху, а что это такое? Фланец – диск, изготовленный из нержавеющей стали, по телу которого равномерно распределены отверстия. Это изделие используется в различных отраслях: водопровод, газопровод, бытовые и промышленные соединения труб, валов или вращающихся элементов. Отверстия на фланце предусматривают герметичное соединение деталей друг с другом, емкостями, аппаратами и т.д.
Нержавеющие фланцы изготавливаются из нержавеющих сталей. Наиболее популярна 12Х18Н10Т, но используются и другие хромоникелевые сплавы. Такой материал обеспечивает изделиям высокую износостойкость, в том числе в агрессивных средах, прочность и устойчивость в коррозии.
Ассортимент фланцев из нержавейки обусловлен вариантами их применения. Обычный сортамент, производимый по технической нормативной документации, составляет три вида:
- Плоские,
- Резьбовые,
- Воротниковые.
Возможно изготовление фланцев и под заказ, по индивидуальным чертежам и размерам.
Методы производства
Есть несколько технологий производства нержавеющих фланцев, выбор нужной зависит в основном, от материала из которого они изготавливаются. Наиболее популярен метод центробежного электрошлакового литья. Он предусматривает переплавку металла и литье с помощью центробежной машины. Такая технология позволяет получить наилучшие показатели ударной вязкости у готового изделия.
Также часто применяется для получения фланцевой заготовки – горячая штамповка. Она позволяет получить наиболее прочный и долговечный метиз, в частности, применяющийся для трубопроводов высокого давления или других экстремальных условиях. Возможно изготовление нержавеющих фланцев путем вырубки заготовки из нержавеющего листа или полосы.
Наиболее популярный раньше, а сейчас все реже используемый – метод точения фланца из поковки. Кованые изделия имеют хорошие прочностные характеристики, но высок процент брака из-за внутренних дефектов поковок.
После обработки заготовки, на сверлильном станке изготавливаются крепежные отверстия. В зависимости от назначения изделия, проводится его соответствующая термообработка. Все нержавеющие фланцы проходят многоступенчатый контроль качества на соответствие нормативной документации по физическим свойствам и техническим параметрам изготовления.
Преимущества нержавеющих изделий
Нержавеющие фланцы наиболее востребованы, по сравнению с другими материалами. Во-первых, нержавеющая сталь известна своей долговечностью и устойчивостью к коррозии. Во-вторых, этот материал позволяет использовать фланцы в самых разных областях применения. Их преимущества очевидны:
- Стойкость к агрессивным средам, делает возможным применение таких деталей в газо- и нефтепроводах, трубопроводах высокого давления.
- Возможность использования в различных атмосферных условиях дает возможность использовать их на улице, в условиях повышенной влажности или низких температурах.
- Безопасность для здоровья человека. Нержавеющая сталь относится к экологичным материалам и может применяться в пищевой промышленности.
- Долговечность и прочность – нержавеющие фланцы успешно применяются в тяжелом машиностроении, кораблестроении, атомной и химической промышленностях.
Фланцы из нержавеющей стали – простое, но важное изделие. Без него невозможна работа механизмов и систем. Качественно выполненный фланец обеспечивает прочное и герметичное крепление на длительный срок.
Компания МеталлНефтеПроект является производителем фланцев 12х18н10т и других сплавов. Сроки, стоимость и оформить заказ вы можете по электронной почте [email protected] или по телефону +7 (343) 243-53-50
Металлоконструкции, резка металла, токарно-фрезерные работы
На многих промышленных предприятиях, которые используют для работы нестандартное или импортное оборудование, возникает необходимость устанавливать нестандартные фланцы, фланцы по стандартам отличным от гост или же особые варианты, изготавливаемые по чертежам заказчика. На нашем предприятии не проблема изготовить фланцы любой сложности с учетом требований и пожеланий клиентов. Мы готовы выполнить полный комплекс работ по изготовлению нестандартных фланцев, начиная от разработки и проектирования подобных деталей, заканчивая изготовлением деталей, которыми не оснащены трубопроводы и оборудование.
Особенности изготовления нестандартных фланцев
Не на всех машиностроительных предприятиях можно изготовить фланцы по нестандартным проектам. Это объясняется очень просто – на многих предприятиях оборудование рассчитано на массовое производство, и изготовление деталей небольшими партиями невыгодно с экономической точки зрения. Как показывает практика нашего предприятия, изготовление специальных фланцев производится или штучно, или минимальными партиями. Одним из неоспоримых достоинств сотрудничества с нашим предприятием является то, что для наших специалистов изготовление фланцев, которые не регламентированы соответствующими справочниками, нормами или стандартами, не является проблемой. Отдельного внимания заслуживает тот факт, что на нашем предприятии уже не один год изготавливаются фланцы различного уровня сложности, при этом стоимость изготовления заметно снижается, так как мы имеем специально разработанные приспособления для изготовления и определенные наработки.
Технологии изготовления нестандартных фланцев
Специалисты нашего предприятия уже не один год занимаются изготовлением фланцев, которые применяются на трубопроводах, построенных по гостам, а также с разнообразным оборудованием по стандартам asme, ansi, en. в своей работе мы применяем несколько основных методов:
• ковки. Фланцы, которые изготовлены таким методом прочные с механической точки зрения, в них отсутствуют дефекты. Но изготовление фланцев таким способом относительно дорогостоящий, так ка для каждого конкретного случая необходимо изготовление ковочной формы;
• штамповки. Прочность аналогична кованным, но такой метод оптимален для производства большими сериями. изготовление производится по заранее составленным чертежам;
• из поковок и листового проката. фланцы, изготовленные таким методом, мало затратны, поэтому соотношение цены и качества в них оптимально.
Если возникает необходимость изготовления фланцев нестандартного размера, то не стоит доверять этот процесс «кулибиным», которые делают фланцы при помощи подручных средств, а к нашим специалистам. Мы готовы изготовить не только нестандартные фланцы, но и фланцево-муфтовые переходы, рассчитанные на использование в различных средах и под высоким давлением согласно нормативно-технической документации заказчика или по его особым требованиям.
9. Изготовление фланцев. Разработка технологии изготовления цилиндрического аппарата
Похожие главы из других работ:
Абсорбер тарельчатого типа
8. Расчет трубных решеток и фланцев кожуха
Толщина трубной решетки, исходя из закрепления труб развальцовкой с обваркой, определяется из условия: tp = 32 мм dн = 25 мм Sp = 0,125 · dн + 5 Sp = 8.1 мм где: dн — наружный диаметр трубы, равный 25 мм; tp — шаг между трубами, равный 32 мм; В соответствии с ГОСТ 28759…
Абсорбционная тарельчатая колонна для газовой смеси «метанол+воздух»
2.6 Выбор фланцев для обечайки, люка и штуцеров аппарата
Принимаем плоские приварные фланцы, [4] т.4.9 с.29, т.4.19 с.49 Р МПа Dу мм Dф мм D мм D1 мм Dн мм h мм h2 мм d мм dб, мм n шт 0,3 1000 1130 1090 1052 1016 30 3 23 М20 36 0,3 300 435 395 365 325 22 3 22 М20 12 0. ..
Абсорбционная тарельчатая колонна для газовой смеси Nh4 + воздух
2.5 Выбор фланцев для обечайки, люка и штуцеров аппарата
Принимаем плоские приварные фланцы, [4] т.4.9 с.29, т.4.19 с.49 Рисунок 2.2 Таблица 2.1 Р МПа Dв мм D1 мм D2 мм D3 мм Ds мм В мм d мм dб мм n шт 0,6 800 920 880 842 816 35 23 М20 32 Рисунок 2.3 Таблица 2…
Вертикальный аппарат с механическим перемешивающим устройством типа ВКЭ-2110
2.5.1 Расчетная температура фланцев и болтов
Tф = tp = 100C Tб = 0.95tp = 0.95100C = 95C…
Однокорпусная выпарная установка для концентрирования водного раствора NaOH
4.6 Выбор фланцев
Соединение царг между собой и с днищами осуществляется с помощью плоских приварных фланцев с по ГОСТ 28759.2-90 (Р<1,6МПа) Рис. 4.6.1 Фланец «аппаратный» ГОСТ 28759.2-90 (исполнение 1) Табл. 4.6.1 Конструктивные размеры фланца «аппаратного» ГОСТ 28759. 2-90 Dобеч…
Определение конструктивных параметров аппаратов выпарных установок
5.4 Выбор фланцев
Фланцевые соединения являются прочноплотными разъемными соединениями. С их помощью к аппарату присоединяются все возможные днища, крышки и трубы. Фланцы различают по способу соединения с трубой и конструкции…
Проект ректификационной установки с тарельчатой колонной непрерывного действия
4. Расчет проходного диаметра штуцеров колонны и выбор фланцев
…
Проект ректификационной установки с тарельчатой колонной непрерывного действия
4.6 Изготовление штуцеров и выбор фланцев
Для упрощения конструктивных деталей колонны, будем изготовлять штуцера из отрезков труб соответствующих диаметров. Внешний вылет штуцеров составляет 1.5 от диаметра штуцера, внутренний — 0.3…
Проектирование приводной станции к передвижному вибратору для снятия фруктов путем встряхивания
5.

b = 1,5 d = 1…
Проектирование производства по получению карбинола (метанола)
4.2.4. Расчет штуцеров реактора и подбор фланцев к ним
Необходимо рассчитать штуцера и подобрать фланцы к ним для исходной смеси, для продуктов реакции, для холодного байпаса, для выгрузки катализатора. Приведем пример расчета штуцера для подачи исходной смеси…
Разработка технологического процесса сборки и сварки крышки бака из сплава 1420
6.2 Директивный технологический процесс в варки штуцеров и фланцев в крышку бака
Табл. № 8 № Наименование операций Оборудование и приспособления Режимы и вспомогательные материалы Эскизы операции 1 Химическая обработка свариваемых деталей Ванна 1.Травление 5% водном растворе NaOH-2мин 60?С 2…
Расчёт сушилки с псевдоожиженным слоем
4.8 Подбор фланцев
l1 dб…
Система планово-предупредительного ремонта оборудования
4.

Аппарат имеет два люка и два фланцевых соединения. Д люка = 675 мм Д фланцев =150 мм Исполнительная толщина обечайки люка определяется по формуле: S= + С (мм) где: Д = dдиаметр люка = 675 мм Р = 0.95 мПа = 0.95 С =0.3мм С2 = 0.22мм 0.95 — 675 S= 2* 138-0.95- 0.95 + С 3 = 2.45 + 0.22 + 0…
Система планово-предупредительного ремонта оборудования
4.Подбор фланцев и крышек люков
Аппарат имеет два люка и два фланцевых соединения. Д люка = 675 мм Д фланцев =150 мм Исполнительная толщина обечайки люка определяется по формуле: S= + С (мм) где: Д = dдиаметр люка = 675 мм Р = 0.95 мПа = 0.95 С =0.3мм С2 = 0.22мм 0.95 — 675 S= 2* 138-0.95- 0.95 + С 3 = 2.45 + 0.22 + 0…
Теплообменная аппаратура
4.5.1 Выбор фланцев
Фланцы для теплообменника выбраны исходя из максимального давления в аппарате и габаритных размеров самого аппарата. Для соединения обечайки с крышкой и днищем фланцы взяты плоские приварные, как и для штуцеров. ..
Изготовление детали фланец — Flancev.ru
Внешне фланец выглядит как плоское кольцо с расположенными по кругу отверстиями. Его задача герметично соединить трубопроводы и арматуру, надежно прикрепить трубы с емкостями, сосудами, аппаратами, механизмами. Используются фланцы не поодиночке, а попарно и зачастую крепятся друг к другу.
Изготовление детали фланец
Различаются по размеру, форме, методу крепления и уплотнительной плоскости. Существуют воротниковые фланцы и плоские. Воротниковые, используются в тех случаях, когда соединение должно быть максимально надежно: например, на трубах с большим давлением, где воротник или шея фланца помогала бы стенкам выдерживать давление содержимого. Воротниковый фланец существует с различными способами присоединения и в зависимости от этого имеет:
Пришлите ваши чертежи или эскизы на [email protected]
Либо звоните 8-800-250-88-72. Доставка по России и СНГ!!!
- шипы,
- пазы,
- впадины,
- выступы.
Фланцы это составные части валов, труб, фитинга, корпусных деталей. К изделиям их либо привинчивают с помощью болтов и шпилек либо приваривают. В зависимости от среды использования и диаметра фланца подбирают прокладки для уплотнения. Закажите у нас прямо сейчас изготовление фланцев по невероятно низкой цене.
Где востребованы фланцы?
Производство фланцев востребовано машиностроением, строительными компаниями, коммунальными предприятиями, нефте- и газодобывающими компаниями и пр. Существует стандартные формы и размеры фланцев и нестандартные.
Компания «Flancev.ru» предоставляет свои услуги заказчикам, которые ищут производителя фланцев по адекватным ценам.
Наше предприятие уже не первый год занимается качественным изготовлением фланцев и его комплектующих. Наше ценообразование носит демократичный характер, а в своем сотрудничестве с клиентами мы стремимся принимать компромиссные решения. У нас можно легко заказать крупную партию фланцев стандартных типов, однако, мы без проблем создадим изделия и по проекту заказчика.
Индивидуальный подход
Обычно индивидуальные и нестандартные заказы обходятся клиентам несколько дороже. Цена увеличивается, поскольку существует необходимость в разработке отдельного пакета технологических документов на нестандартные изделия.
Пришлите ваши чертежи или эскизы на [email protected]
Либо звоните 8-800-250-88-72. Доставка по России и СНГ!!!
Также в некоторых случаях при сложном изготовлении детали фланец потребуется время, чтобы перенастроить оборудование на нестандартное производство. Тем не менее, качество наших изделий и скорость дополнительных услуг гораздо выше, чем предприятиях-конкурентах.
Квалифицированный штат сотрудников
Технологические карты составляются маститыми и опытными инженерами с помощью программ автоматического проектирования. Также мы не являемся пассивным производителем, который только пользуется современными разработками и стандартными программами – мы используем свои наработки и технологи для ускорения процесс и повышения его качества при изготовлении фланцевых соединений.
Все это вкупе, со сверхточными металлообрабатывающими станками по штампованию, литью и ковке позволяет нам создавать любые фланцы на предельно высоком уровне за самое короткое время. Для того чтобы цена заказа стала меньше мы рекомендуем делать заявки на массовое и серийное производство. Таким образом, себестоимость отдельного изделия может значительно сократится. Кроме того, регулярным заказчикам мы обещаем скидки и бонусы. В любом случае, при составлении заказа менеджеры «Flancev.ru» проконсультируют вас, обсудят всевозможные варианты производства и вместе с вами поищут наиболее экономически целесообразные варианты изготовления детали фланец.
Стандартные решения
Стандартные фланцы мы изготавливаем на основании ГОСТ, нестандартные изделия могут ГОСТу не всегда соответствовать, и мы их выполняем, руководствуясь требованиями заказчика.
В любом случае перед выполнением заказа нам важно знать следующую информацию относительно будущей продукции:
- тип фланца,
- его геометрическая форма,
- возможные отклонения (допуски),
- степень шероховатости,
- материал изготовления (либо характеристики, которыми он должен обладать),
- проверки, которые должен пройти фланец.
После того как вся вышеперечисленная техническая документация будет известна, инженеры «Flancev.ru» займутся выбором оптимальной технологии изготовления фланцев стальных.
Беремся за самые сложные заказы
Стоит сказать, что не все предприятия готовы изготовить фланцы любых размеров и форм. Обычно те компании, что нацелены на массовое производство не могут делать нестандартную продукцию в малых количествах (это либо очень дорого, либо технологически нецелесообразно).
Пришлите ваши чертежи или эскизы на [email protected]
Либо звоните 8-800-250-88-72. Доставка по России и СНГ!!!
Другие компании настроенные на мелкие партии изделий, не могут реализовать крупные заказы на фланцы. Наше предприятие не только изготовит изделия самого широкого ассортимента в различных масштабах, но и готово доставить произведенные фланцы по всей России.
Обширные площади наших цехов позволяют изготовлять с помощью всех осиновых технологий производства. Среди них стоит выделить:
- изготовление фланцев на токарных и сверлильных станках методом металлообработки;
- производство фланцев из листового металла с помощью рубочных и гибочных станков;
- литье фланцев;
- ковка и штампование фланцев и его составляющих.
Технология изготовления детали фланец выбирается в зависимости от требований к изделию, которые описаны в конструкторской документации. Вкратце остановимся на всех этих методах.
Ковка фланцев
Данная технология позволяет минимизировать дефекты поверхности. Полученные таким образом изделия лишены трещины, раковин и обладают предельно возможной прочность. Ковка осуществляется с помощью пуансона и матрицы, которые для каждого размера изготавливаются отдельно.
Обычно данное условие и приводит к удорожанию изделий, изготовленных этим методов. Идеальный заказ для ковки – крупный. Тогда можно говорить об экономической целесообразности. Также этот способ предполагает значительное количество расходуемого сырья.
Штамповка фланцев
Штампованные изделия прочны и надежны в эксплуатации. Данный метод предполагает высокую производительность, а потому экономически выгодно с помощью него делать крупные заказы. Кроме этого, сам по себе штамп – инструмент дорогостоящий, что не позволяет производство мелких партий на данном оборудовании.
Фланцы из листового проката
Данным методом можно изготовить фланцы на заказ лишь плоские. Этот метод наиболее прост и несложен. Для изготовления требуется гибочное и режущее оборудование. Тем не менее, технология не отличается высокой производительностью, но позволяет создавать небольшие партии за самую выгодную цену.
Литье фланцев
Осуществляется специальным методом электрошлакового литья. Производство мелких партий продукции на данном оборудовании изготовить, возможно, но цена каждого фланца будет существенной.
Пришлите ваши чертежи или эскизы на [email protected]
Либо звоните 8-800-250-88-72.

Полученные литые фланцы имеют повышенной ударной вязкостью и обладают отменной прочностью, поскольку изготавливаются из шихты и металла. Многочисленные независимые исследования продемонстрировали, что данный метод, несмотря, на уверения отдельных специалистов, не приводит к каким-либо мелким и скрытым дефектам. Если и говорить о недостатках метода, то можно упомянуть только о приличной стоимости создания литейной емкости с помощью, которой производятся отливки.
Компания «Flancev.ru» специализируется на изготовлении детали фланец с помощью широкого круга технологий. Заказывая у нас, вы имеете возможность производить изделия различными методами по наиболее выгодным ценам. Компания производит доставку фланцев по России.
Технология изготовления фланца
Определение параметров заготовки.
●Класс
точности-1 для авиационного производства
в условии серийного производства для
трудно обрабатываемого дорогостоящего
материала сталь 20Х3МВФ-Ш.
●Группа материала-М2, так как содержание легирующих элементов в стали 20Х3МВФ-Ш более 2%.
●Степень
сложности заготовки-С2, так как 4 наружнии
и 2 внутренние поверхности.
Предварительная масса заготовки Мзаг
Где:
Мдет масса детали=0,15
К- коэффициент использования заготовки=0,5
Проверка:
УТз – УТд = ΣZmax – Σzmin
93,178-90=(2+0,81+0,518)-(
0,178=0,178
Таб2 Расчёт припусков и операционных размеров на обработку табличным методом для отверстия Φ800,019
Тех маршрут поверхности детали | Квалитет точности и шероховатость | Расчётный припуск | Расчётный размер | Допуск | Предельные размеры | Предельные припуски | ||
Дmax | Дmin | Zmax | Zmin | |||||
Φ80 | — | — | — | — | — | — | — | — |
Заготовка | Класс точности1√ 0,4 -0,8 | — | 76,819 | +0,4 -0,8 | 76,619 | 75,619 | — | — |
Точение черновое | Н12 | 2 | 78,819 | 0,3 | 79,819 | 78,519 | 2,9 | 2 |
Точение чистовое | Н10 | 0,8 | 79,619 | 0,12 | 79,619 | 79,499 | 0,98 | 0,8 |
шлифование | Н6 | 0,4 | 80,019 | 0,019 | 80,019 | 80 | 0,501 | 0,4 |
Проверка:
ТДз – ТДд =Σ Zmax – Σzmin
1,2=(2,9+0,98+0,501)-(2+0,
1,2-0,019=4,381-3,2
1,181=1,181
По результатам таблиц 1 и 2 определяется исполнительный размер на переходы обработки и заносятся в таблицу 3 и 4
Таб3. Тех маршрут обработки вала Φ90-0,022
Переходы обработки | Исполнительные размеры | Шероховатость |
Заготовка | 93,5 | |
Точении черновое | 91,5-0,350 | |
Точение чистовое | 90,5-0,140 | |
Шлифование | 90-0,022 |
Расчёт исполнительных размеров заготовки
dн = dmax-es
dн = 94.378 – 0.8 = 93.578 принимаем размер заготовки Φ93,5
Таб4. Тех маршрут обработки отверстия Φ800,019
Переходы обработки | Исполнительные размеры | Шероховатость |
Заготовка | 76,5 | |
Точении черновое | 78,50,3 | |
Точение чистовое | 79,50,12 | |
Шлифование | 800,019 |
Расчёт исполнительных размеров заготовки
Дн = Дmax-ЕS
Дн = 76. 819– 0.4 = 76.419
принимаем размер заготовки Φ76,5
Размеры
заготовки из таблиц 3 и 4 проставляем
на чертёж заготовки В1КП151.001.001.001. Остальные
размеры рассчитываем по укрупнённым
нормативам.
Таб5. Расчёт размера заготовки по укрупненным нормативам.
Размер детали | Шероховатость Ra | Припуск | Основание | Расчетный размер | Принятый размер с допуском | примечание |
Φ84 | 1,5 | Курсовое проектирование по предмету «технология машиностроения» И. С. Добрыднев (стр. 149 таб. 1.2) | Φ87 | Φ87 | ||
Φ72 | 1,5 | Φ69 | Φ69 | |||
18 | 1,4 | 20 | 23 | |||
2,5 | 1,4 | 4 | 5,5 | |||
9,5 | 1,4 | 9,5 | 9,5 | |||
2,5 | 1,7 | 3,5 | 6 | |||
Φ96 | — | Φ96 | Φ96 | |||
R12 | — | R12 | R12 | |||
R7 | — | R7 | R7 |
Размеры
заготовки проставляем на чертёж заготовки
(В1КП151001. 001.001).
Расчёт массы заготовки.
где:
V=объём заготовки (мм3)
g=7,8 плотность материала заготовки сталь
V=V1+ V2+ V3+ V4
где:
Д- наружный диаметр элементарной фигуры
d- внутренний диаметр элементарной фигуры
Н-высота элементарной фигуры
К- коэффициент
отклонения наружного диаметра от правильной
формы (К=0,5 ;К=1)
N | Д | d | Н | К |
V1 | 87 | 76 | 6,5 | 1 |
V2 | 96 | 76 | 4 | 0,5 |
V3 | 93 | 76 | 6 | 1 |
V4 | 93 | 69 | 3,5 | 1 |
Расчёт объёмов элементарных фигур
Расчёт полной массы заготовки
V=1407,505+7426,1+7393,5675+
Рассчитываем массу заготовки
Коэффициент использования
материала.
2.5 Разработка РТК для станка с ЧПУ.
Операция №1110 выполняется на станке с ЧПУ модели 16К20Ф3. Операция содержит 2 перехода:
а) 1 переход: подрезание торца до размера 19-0,2 протачивание диаметра до размера Ф84,5-0,05 подрезание до размера 4-0,3 (смотри чертёж РТК В1КП 150001.002.004) переход выполняется в 2 прохода черновой и чистовой.
б) 2 переход: проточить диаметр до размера Ф72+0,3 проточить фаску до размера 1,1+0,2 × 450 , (смотри чертёж РТК В1КП 150001.002.004) переход выполняется в 2 прохода черновой и чистовой.
Инструменты для переходов:
— для 1 перехода резец проходной упорный,
— для 2 перехода резец расточной.
Параметры резцов смотри пункт 2.6
Определяются точки обрабатываемого контура и указывается на эскизе точек обрабатываемого контура.
Расчёт координат точек обрабатываемого контура:
Точка | Х | Z |
A | 36 | -2.![]() |
B | 38.5 | -2.85 |
C | 38.5 | 14.25 |
D | 39.6 | 15.35 |
E | 42.25 | 15.35 |
F | 42.25 | 4 |
G | 58.3 | 4 |
Первый переход
Расчёт координат точки Т
ХТ
где:
Дз – максимальный диаметр заготовки=117
Зб — зона безопасности 50 . . . 100 принимаем 50
Дрц – диаметр резцедержателя =295
lr – вылет резца
lr= 1,5Н
Н — высота державки резца =25
lr= 1,5*25=37,5
ZТ
где:
lз – длинна заготовки =20
Зб — зона безопасности 50 . . . 100 принимаем 50
Zu – 5 . . . 10 принимаем 10
1 точка
Х1=ХТ-Хu=293,5-185=108,5
Z1= ZТ- Zu=75-5=70
2 точка
Х2= 0,5Двз-Ru-у1
где:
Двз – внутренний диаметр заготовки=79
Ru – радиус инструмента =2,5
у1, у2 недобег и перебег резца 2,2 . . . 5 принимаем
2,5
Х2= 0,5*79-2,5-2,5=34,5
Z2= ZТ=70
3 точка
Х3= Х2 =34,5
Z3= ZD+ Ru =15.35+2.5=17.85
4 точка
Х4= ХЕ + Ru =42,25+2,5=44,75
Производство фланцев Производственный процесс — производитель трубопроводной арматуры, фланцев и трубопроводов
Ковка — это производственный процесс, включающий формование металла с использованием локализованных сжимающих сил. Удары наносятся молотком (часто силовым молотком) или плашкой. Ковку часто классифицируют по температуре, при которой она выполняется: холодная ковка (вид холодной обработки), теплая ковка или горячая ковка (вид горячей обработки).
Процесс производства фланца в основном делится на ковку, литье, резку и прокатку.
Понимание требований клиентов и обеспечение поставок в соответствии с этими требованиями осуществляется с помощью службы обеспечения качества в Sunny Steel. Мы являемся одним из лучших производителей фланцев в Китае, в наш ассортимент входят все типы фланцев, такие как фланец MS (низкоуглеродистая сталь), фланец с выступом, фланец приварной шейки, фланец сильфона и фланцы в соответствии с индивидуальными требованиями.
Сырье
Начиная с этого процесса, система контролирует качество всех поступающих материалов в соответствии с сертификатом испытаний сырья.Фланцы из низкоуглеродистой стали (MS) имеют высшее качество, которое обеспечивает высокую долговечность, прочность и удельное сопротивление в различных не поддерживающих условиях. Кроме того, проверка химических и физических свойств этих материалов каждого размера в лаборатории, утвержденной правительством.
Защита от ржавчины для стальных фланцев
Обычная обработка для защиты от ржавчины для стальных фланцев включает покрытие желтой (золотой) краской, покрытие черной краской или обработку черным фосфатированием, покрытие лаковой краской, лакокрасочное антикоррозийное масляное покрытие, электрооцинкование (холодное), горячее цинкование и т. д.
Завод по упаковке стальных фланцев
Стальные фланцы должны быть упакованы морским методом упаковки, а затем доставлены клиентам, обычно способ упаковки включает деревянный ящик, деревянный поддон, железо-стальной каркас, железный и стальной поддон и т. Д. деревянные ящики или деревянные поддоны должны подвергаться фумигации, мы обычно используем фанерные поддоны или фанерные ящики или коробки для упаковки стальных фланцев без фумигации. Независимо от способа упаковки фанеры или чугуна и стали они должны быть мореходными, прочными, водонепроницаемыми и удобными для погрузки и разгрузки.
Наклейка транспортной марки снаружи упаковки.
Последний процесс отправки — самый утомительный из всех, и для этого используются краны большой грузоподъемности. С помощью нашей обширной цепочки поставок мы можем обеспечить своевременные поставки по просьбе наших уважаемых клиентов. Для нас действительно большая честь быть в состоянии служить и оправдать их ожидания и занимать беспрецедентное положение производителей фланцев в Китае.
Процесс производства фланца
Процесс производства фланца в основном делится на ковку, литье, резку и прокатку.Литые и ковочные фланцы имеют преимущества, заключающиеся в том, что их заготовки имеют точную форму, размер, низкие затраты и требуют только простого процесса. Но поковки фланцы имеют производственные дефекты, такие как раковины, трещины и т. Д., И не очень гладкую внутреннюю организацию обтекаемой формы. Очевидные преимущества ковки фланцев заключаются в том, что они могут быть кованы различной формы и имеют низкую стоимость.
Кованые фланцы обычно имеют более низкое содержание углерода, чем литые, и их нелегко ржаветь.Они имеют гладкую обтекаемую форму, однородную внутреннюю организацию и лучшие механические характеристики, чем у литых фланцев. На литых фланцах отсутствуют дефекты в виде раковин и трещин. Кованые фланцы способны выдерживать более высокие усилия сдвига и волочения, чем литые фланцы. Однако, если использовать неправильный процесс ковки, это также вызовет появление крупных неровных зерен и явление растрескивания при затвердевании, что приведет к более высокой стоимости, чем литые фланцы.

Мы можем различать литые фланцы и кованые фланцы в зависимости от производственного процесса.Если взять в качестве примера центробежный фланец, это своего рода литой фланец. Центробежные фланцы изготавливаются методом прецизионного литья, который делает организацию фланцев меньше, чем те, которые обычно производятся литьем в песчаные формы, и улучшает качество фланцев, уменьшая появление рыхлой ткани, пор, песчаных отверстий и т. Д.
Процесс резки относится к изготовлению фланцев путем непосредственного вырезания круглой пластины с внутренним диаметром, внешним диаметром и толщиной, которая может быть дополнительно обработана позже из средней пластины, а затем обработки отверстия для болта и ватерлинии.Максимальный диаметр таких фланцев ограничен шириной средней пластины.
Процесс резки относится к изготовлению фланцев путем вырезания полос на средней пластине и последующего скатывания их в круглую форму. Этот процесс в основном используется для производства больших фланцев.
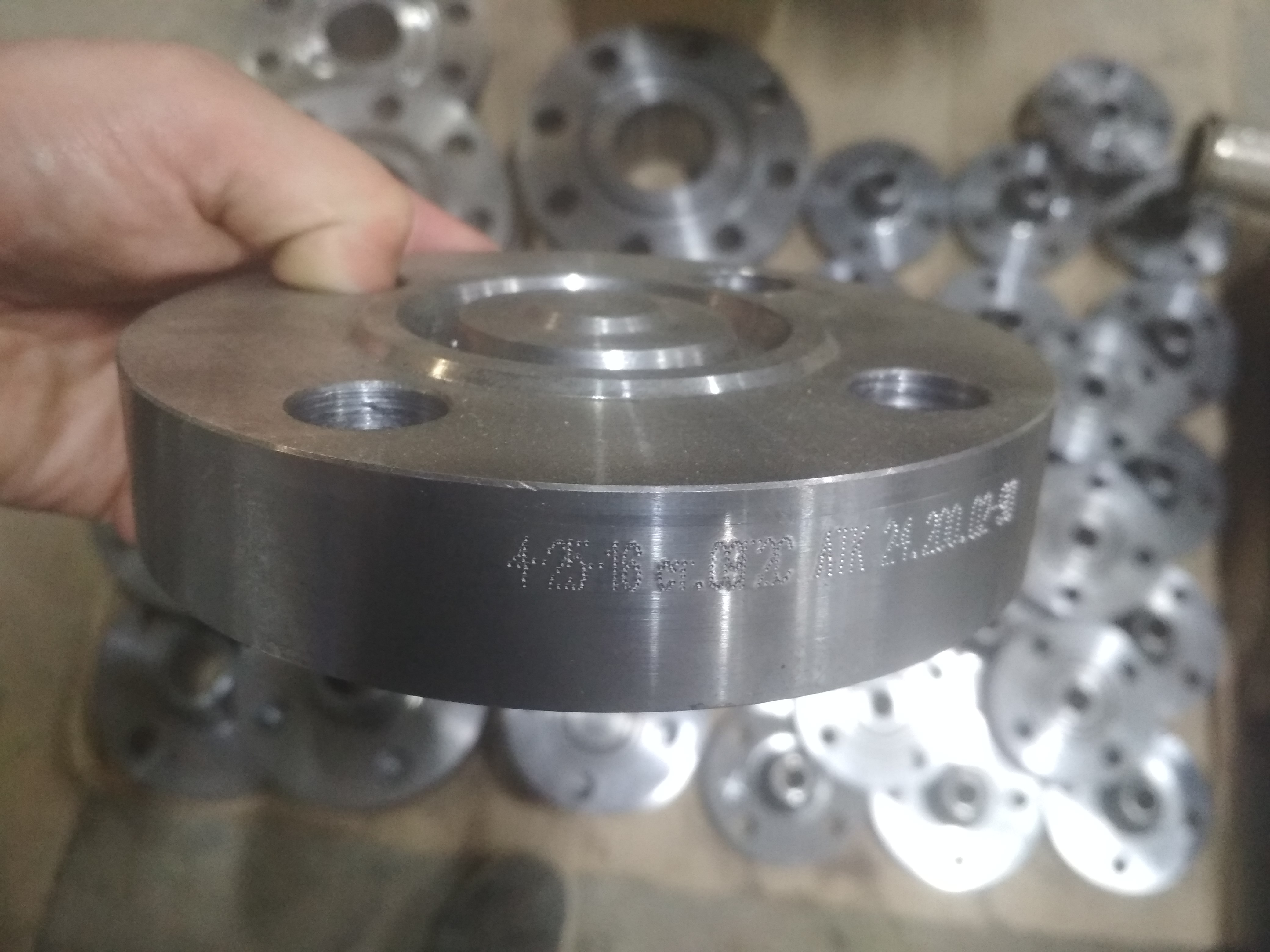
Процесс производства фланцев — Yaang
Производство фланцев
Сырье:
Начиная с этого процесса, система контролирует качество всех поступающих материалов в соответствии с сертификатом испытаний сырья на материал.Проверка каждого размера на химические и физические свойства этих материалов в лаборатории, утвержденной правительством.
Система обработки:
На стадии обработки сырья он проверяется визуально на наличие любых дефектов поверхности, таких как трещины, швы, нахлесты, точечная коррозия, а также размерные. Перед выбором сырья проводится химико-физический тест.
После приемки сырья выдается контрольный номер, который наносится / маркируется на всем сырье, предназначенном для использования.
При изготовлении фланцев. Во время резки контрольный номер переносится на каждую вырезанную деталь, и то же самое передается после каждой операции ковки или формовки в случае невидимости того же самого. После каждой ковки или формовки материал визуально проверяется на наличие трещин на поверхности.
Термическая обработка проводится после окончательной штамповки или формовки в соответствии с требованиями норм. После окончательной штамповки или термообработки партии присваивается номер партии, и этот номер партии проштампован на каждом фланце.и на графике температуры, который автоматически создается самописцем температуры, соединенным с нагревательной печью. Время окончательной штамповки / формовки и дата также указаны на графике.
Обработка:
После окончательной штамповки / формовки и термообработки все фланцы. отправляются на механическую обработку, т. е. на подготовку, согласование O / D и I / D в соответствии с кодами размеров. Эксперт Q.C. в этом участвует инженер, который постоянно следит за каждой операцией обработки.Пошаговая обработка выполняется в соответствии с требованиями кодексов. Датчики GO и NO-GO используются для проверки O / D и I / D фитингов, фланцев и т. Д.
Тестирование:
Испытание на растяжение проводится на образце, взятом из исходного сырья или из партии фланцев. в соответствии с требованиями покупателя на универсальной испытательной машине, которая откалибрована и одобрена уполномоченными инспекционными органами.
Испытания на твердость проводятся не менее чем на 10% каждой партии, и результаты регистрируются в отдельном регистре.
Проведен 100% рентгеновский контроль всех фланцев.
Чистовая:
Все стальные фланцы протравливаются и пассивируются травлением, удаляется вся окалина, которая образуется во время операций ковки / формовки. После травления выполняется операция шлифования, чтобы удалить след штампа и внутренние / внешние заусенцы, образовавшиеся во время операций формовки и механической обработки. Окончательная проверка размеров выполняется и фиксируется.
Артикул:
После окончательной проверки размеров на каждом фитинге проставляется штамп / маркировка с указанием размера, спецификации, спецификации фитингов, марки нагрева и номера партии.
Завод по упаковке стальных фланцев:
Все стальные фланцы должны быть упакованы морским методом упаковки, а затем доставлены клиентам, обычно способ упаковки включает деревянный ящик, деревянный поддон, железный и стальной каркас, железный и стальной поддон и т. Д. Из-за использования обычных деревянных ящиков или деревянных поддонов. обработка фумигацией, мы обычно используем фанерный поддон или фанерный ящик или ящик для упаковки стальных фланцев без обработки фумигацией. Независимо от способа упаковки фанеры или чугуна и стали они должны быть мореходными, прочными, водонепроницаемыми и удобными для погрузки и разгрузки.
Отгрузочная маркировка наклеена снаружи упаковки.
Отправка:
Последний процесс отправки — самый утомительный из всех, и для этого используются краны большой грузоподъемности. С помощью нашей обширной цепочки поставок мы можем обеспечить своевременные поставки по просьбе наших уважаемых клиентов. Нам действительно повезло, что мы можем служить и оправдать их ожидания и занимать беспрецедентное положение среди производителей фланцев в Китае.
Изучение трех методов изготовления фланцев
Нет никаких сомнений в том, что шкивы являются одним из важнейших механических компонентов многих машин и устройств, от которых мы используем каждый день.Однако не менее важны шкив с фланцами .
При нормальной работе шкива ремень, вращающийся вокруг шкива, естественным образом стремится двигаться к одной стороне шкива. Эта тенденция, называемая угловым смещением, может со временем привести к износу краев ремня или полному отказу системы. Назначение фланцев — удерживать ремень на месте, предотвращая его износ. Таким образом, прочные и эффективные фланцы имеют решающее значение для бесперебойной работы системы шкивов и нулевого простоя ваших механических процессов.
Чтобы удовлетворить эти требования, необходимы мощные и производительные процессы производства фланцев, и существует несколько различных производственных методов, которые высококачественные производители используют для создания продуктов для вашего приложения и предприятия.
Ниже мы рассмотрим производственный процесс, а также некоторые методы изготовления фланцев, которые использует компания Illinois Pulley and Gear для создания нестандартных качественных фланцев шкивов. Прочтите, чтобы начать.
Производственный процесс
Тип 1: Штамповка на станках с ЧПУ
Штамповка металла — это общий процесс преобразования плоского листового металла в определенные формы.Когда дело доходит до изготовления фланцев, при штамповке используются различные методы обработки металлов давлением, включая вырубку, штамповку, гибку и прошивку. Обычно процесс выполняется на холодном листовом металле с помощью штамповочного штампа, изготовленного на заказ, что позволяет получать безупречный конечный продукт.
Штамповка может быть полезна в широком спектре отраслей и сфер применения. Этот метод дает производителям возможность создавать фланцы очень быстро и в больших объемах, а также помогает избежать сварки или точечной сварки, которые могут создать слабые места в конструкции. Когда ваше приложение требует точности и более толстых материалов, штамповка — идеальный вариант.
Тип 2: Лазерная резка
Мощный углекислый газ и волоконный лазер для резки обеспечивает наиболее точные разрезы при любом процессе производства фланцев. Эффективность и точность лазерной резки, контролируемой компьютеризированной системой, делает ее идеальной техникой для высокотехнологичных приложений или других отраслей с жесткими требованиями.
Лазерная резка также является экономичным решением и потребляет значительно меньше энергии, чем другие методы.Однако лазерная резка может превосходить альтернативные методы и в некоторых других областях.
С точки зрения скорости: точный симметричный дизайн может быть создан за считанные секунды в зависимости от ваших требований и материалов.
С точки зрения гибкости: лазерные станки не требуют изготовления штампа по индивидуальному заказу, как те, которые необходимы для процессов штамповки. Мы просто перенастраиваем компьютер, управляющий лазером, в точном соответствии с вашими проектными требованиями. Это позволяет нам быстро корректировать производимые нами продукты, что особенно полезно, если вам требуется более одного типа и размера фланца.Лазерная резка также может использоваться для обработки широкого спектра материалов, включая пластик и многие типы металлов.
Как упоминалось ранее, качество резки и эффективность производства лазерной резки остаются непревзойденными на момент написания этой статьи. Когда вы объединяете все эти преимущества, лазерная резка помогает нашим специалистам из компании Illinois Pulley and Gear конструировать и создавать именно тот продукт, который вам нужен.
Продолжение процесса — Приложение
После того, как ваш фланец создан, его необходимо прикрепить к синхронизирующему шкиву.Есть несколько способов достижения этой цели, три из которых мы используем в наших собственных процессах и описаны ниже.
Стейкинг рулона
Изготовление полного обжима по всему краю фланца, роликовая разбивка является предпочтительным методом крепления Illinois Pulley and Gear. При большинстве обычных методов разбивки на шкив удерживается лишь небольшой процент фланца, соединяющий его в нескольких точках. Полная «герметичная» установка валков гарантирует долговечное соединение и, следовательно, высокое качество детали в целом.
Термоусадочная
Еще один исключительный метод крепления тяжелых фланцев большого диаметра к зубчатым шкивам — это термоусадка. Во время термоусадки фланец нагревается до температуры более 450 градусов по Фаренгейту, прежде чем помещаться на ступеньку фланца шкива. Когда металл остынет, фланец идеально сжимается на ступеньке фланца шкива, создавая прочное уплотнение между ними.
Фланцы с болтовым креплением
Возможно, наиболее эффективным способом соединения фланцев с зубчатыми шкивами является использование фланцев с болтовым креплением. Эти тяжелые и прочные фланцы удерживаются сбоку от зубчатого шкива винтами с плоской головкой. Помимо создания значительной прочности, этот метод отбортовки позволяет обслуживающему персоналу снимать фланец для ремонта ремня и т. Д. Это полезное преимущество недоступно при использовании любого другого метода отбортовки.
Отбортовка со шкивом и шестерней Illinois
В компании Illinois Pulley and Gear мы обладаем опытом в использовании широкого спектра методов отбортовки, чтобы гарантировать, что у вас есть лучший нестандартный фланец для всех ваших потребностей.Мы также гарантируем надежный и надежный процесс отбортовки.
Чтобы узнать больше о наших компонентах или процессе отбортовки, позвоните по телефону 847.407.9595 или заполнив нашу онлайн-форму. Мы с нетерпением ждем возможности поговорить с вами, выслушать ваши потребности и решить проблемы с помощью дружелюбного обслуживания клиентов и быстрой обработки.
Что такое процесс ковки фланца
Кованые фланцы используются в качестве соединительной детали для создания сети трубопроводов для цилиндров, клапанов, насосов и других устройств. Кованые фланцы включают в себя две разные части оборудования. Чтобы сделать сущность сильнее, они должны быть прикреплены к раме. Промышленные фланцы имеют несколько применений, включая соединительные листы, насосы, трубы и конструкции, которым явно требуется промежуточная точка соединения. Фланцы из нержавеющей стали бывают разных форм. Каждая форма удовлетворяет свои потребности. К основанию НКТ крепятся большие фланцы приварной горловины. То, как этот фланец приварен, гарантирует, что диаметр будет таким же, как длина трубы, к которой он был прикреплен.Такие фланцы также обычно используются в приложениях с высоким давлением.
Преимущества кованых фланцев
Фланцы обычно привариваются к трубам или устанавливаются на конце вала с резьбой, а затем соединяются для обеспечения контакта с помощью болтов. Он обычно используется при ковке основных компонентов и поковок в ограниченных количествах. Оборудование для свободной ковки оснащено пневмомолотом, паровоздушным молотом и гидравлическим прессом, что позволяет производить мелкие и широкие поковки. Высокая производительность, быстрая работа, простая обработка и автоматизация. Размер штамповки большой, припуск на обработку небольшой, а тканевая ковка более подходящая и еще больше увеличивает срок службы деталей.
Процесс ковки фланца
Метод ковки обычно состоит из следующих процедур, а именно выбора стандартной стальной заготовки, нагрева, формовки и охлаждения. Метод ковки включает операции свободной ковки, штамповки и штамповки шин.Введите массу компонентов поковки, количество партии различных процессов поковки на выходе. Он обычно используется при ковке основных компонентов и поковок в ограниченных количествах. Высокая эффективность, быстрый процесс, простота обработки и автоматизации. Масштаб штамповки высок, припуск на механическую обработку снижен, а ковка ткани лучше всего адаптирована, увеличивая срок службы деталей.
Простой метод свободной ковки: ковка медленно выковывает структуру ковки за счет определенного механизма деформации.Простой метод ковки и ковки — это жирный, широкий, перфорированный, гибочный и режущий. Неприятным препятствием является этап операции, на котором уменьшается высота исходного материала и увеличивается поперечное сечение. Этот процесс используется для штамповки зубчатых заготовок и других поковок в форме диска. Заголовок подразделяется на общий заголовок и минимальную сварку.
Поковка в штампе, как известно, является штампованной штамповкой, и ее помещают в штамповочное устройство, соединенное с штамповочным оборудованием.Основной метод штамповки штампа: упаковка, нагрев, предварительная штамповка, вытяжка, резка, обрезка, струйная очистка и т. Д. Метод подъема предназначен для разрушения, толкания, скручивания, штамповки и формовки.
Широко используемое кузнечно-прессовое оборудование включает штамповку с молотком, пресс для горячей штамповки, систему плоской штамповки и пресс трения. Поковки фланца обычно более высокого качества, как правило, путем штамповки, кристаллическая структура хорошая, прочность и цена, конечно, дороже.
Pipingmart — это портал B2B, специализирующийся на промышленных, металлических и трубных продуктах. Кроме того, делитесь последней информацией и новостями, связанными с продуктами, материалами и различными типами сортов, чтобы помочь ведению бизнеса в этой отрасли.
Различия между коваными фланцами и литыми фланцами
Фланцы кованые или литые?
Фланцы могут быть коваными или литыми. Оба метода производства имеют свои преимущества и недостатки в зависимости от области применения, которую вы планируете использовать для фланца.Здесь, в Texas Flange, мы в основном имеем дело с коваными фланцами из-за устаревшего характера и более низкого стандарта качества литых фланцев. Ниже мы рассмотрим преимущества и недостатки как фланцев из кованой стали, так и фланцев из чугуна.
ЧУГУННЫЕ ФЛАНЦЫ
Литье — это процесс, при котором металл нагревают до расплавления, а затем выливают в форму или сосуд для придания желаемой формы. Их часто используют в слишком больших, сложных или иным образом не подходящих для поковок ящиках. Некоторые из преимуществ изготовленных таким образом фланцев включают более низкую стоимость производства, возможность изготавливать более сложные детали с меньшими затратами, а также отсутствие истинного верхнего предела размера, когда речь идет о вашей детали.
Однако у чугунных фланцев есть некоторые недостатки. Наиболее важным из них является то, насколько они подвержены внутренним дефектам. По этой причине литые фланцы не подходят для приложений высокого давления или приложений, в которых высока вероятность коррозии.Несмотря на прогресс в технологии литья и компьютерную оптимизацию процесса и конструкции литья, по-прежнему трудно соответствовать стандартам, необходимым для применения в нефтехимической промышленности.
ФЛАНЦЫ ИЗ КОВАНЫЙ СТАЛИ
Ковка — это приложение механической и тепловой энергии к стальным заготовкам или слиткам для изменения формы материала, оставаясь твердым. Поковки обладают неизменным составом и структурой. Из-за характера производства кованых фланцев производственные затраты выше, чем у литых фланцев. Хотя они не могут иметь сложную форму, из которой могут изготавливаться литые фланцы, их внутренняя структура более компактна и поэтому редко имеет дефекты, которые часто затрагивают литые фланцы. Ковка устраняет дефекты, обнаруженные в отливке, такие как усадка, пористость, пустоты или проблемы холодной заливки.
Как правило, кованые фланцы прочнее и надежнее, чем литые, поскольку поток зерна в стали изменяется в соответствии с формой детали. Поковка с плотной структурой зерна делает детали механически более прочными и более устойчивыми к общему износу, чем литые фланцы.Благодаря более высокому качеству, надежности, прочности и долговечности мы в основном имеем дело с коваными фланцами, а не литыми.
Здесь, в Texas Flange, мы предлагаем кованые фланцы от 1/2 ″ номинального диаметра трубы до 203 ″ OD из более чем дюжины различных марок материалов. Мы ценим качество и стремимся к тому, чтобы вы получали нужную деталь для своего приложения по цене и срокам, которые подходят для вашего бизнеса. Наши продавцы работают с вами, чтобы обеспечить это. Если вам нужен фланец, позвоните нам по телефону 281-484-8325 или отправьте электронное письмо на [адрес электронной почты защищен], чтобы начать свой запрос.Пока вы здесь, не стесняйтесь просматривать наши бесплатные информационные сообщения в блоге, бесплатные трехмерные чертежи и чертежи САПР или фланцевые диаграммы.
Производственный процесс ковки корпуса клапана с боковым фланцем — китайский поставщик трубопроводных решений
В настоящее время фланцевые клапаны высокого и среднего давления широко используются в нефтехимической отрасли. Корпус клапана — это основная часть клапана. Согласно спецификации Американской нефтяной ассоциации (API) для устьевого и рождественского оборудования, корпус масляного клапана часто требуется для работы в условиях высокого давления, агрессивных газов и высокой герметичности, а также в тяжелых условиях эксплуатации.Уже давно существуют процессы сварки, литья и ковки корпуса клапана с фланцем. Процесс сварки, как правило, представляет собой сварку фланцевой части поковки основного корпуса клапана. Его недостатком является то, что в сварном шве легко образуются поры и горячие трещины, а процесс сварки сложен, а эффективность производства невысока. Недостатком процесса литья является то, что внутри отливки имеется множество дефектов, таких как газовые раковины, включения, пористость и трещины. С учетом номинального рабочего давления гидроблока, используемого в нефтехимической промышленности, составляет 13.8МПа-138МПа. Ввиду недостатков недостаточной герметичности, неудовлетворительной опоры давления и низкого качества готовой продукции в процессах сварки и литья, процесс ковки все чаще используется для производства поковок нефтяных корпусов клапанов.
В настоящее время корпус клапана с фланцем обычно выковывают отдельно, а затем корпус клапана и фланец соединяют сваркой. Однако сварные детали легко получить дефекты, которые повлияют на общее качество клапана. Некоторые производители также применяют процесс мембранной ковки, состоящий из ступенчатой ковки и местного формования. Недостатком этого процесса является то, что рабочий процесс разнообразен, а разделение материалов точное в процессе изготовления заготовки, в противном случае поковку легко сломать. корпус чрезвычайно нестабилен, и технология многонаправленной штамповки может решить вышеуказанные проблемы. За счет одной поковки можно формировать поковки сложной конструкции, втулки или полости.
Таким образом, в данной статье описан процесс изготовления по технологии многонаправленной штамповки корпуса клапана с боковым фланцем.Ковка корпуса клапана сложной формы с внутренним отверстием может быть выкована за один обжиг, и на этом обтекаемость ковки завершена. Затем проводится необходимая послепоковочная обработка, чтобы обеспечить общую производительность корпуса клапана, что дает новую идею для применения этого или аналогичного процесса производства корпуса клапана.
Технологический маршрут
В данной статье исследуется процесс изготовления корпуса клапана Q345B с боковым фланцем. Детали корпуса клапана в основном используются в нефтехимической промышленности.Традиционный процесс обрабатывается непосредственно баром. Требования к механическим характеристикам приведены в таблице 1.
Таблица 1 Требования к механическим свойствам поковок
Параметр | Предел прочности на разрыв / МПа | Предел текучести / МПа | Относительное удлинение /% | Энергия удара / Дж |
Численная величина | ≥520 | ≥335 | ≥20 | ≥27 |
Его можно найти на рисунке.1 видно, что внутренняя часть корпуса клапана состоит из двух вертикальных и горизонтальных отверстий. Площадь проекции вертикальной плоскости корпуса клапана больше площади горизонтальной плоскости. Объем бокового фланца гидроблока большой, его сложно подделать. Строение гидроблока сложное и неправильное. Поэтому в процессе ковки предлагается использовать технологию многонаправленной штамповки, а после штамповки проводится термообработка, чтобы обеспечить соответствие механических свойств корпуса клапана требованиям.
Конструктивная форма поковки корпуса клапана, показанная на рис. 2, в зависимости от формы деталей, требований к производительности и мощности гидравлического пресса, спроектирована и изготовлена на многонаправленном штамповочном гидравлическом прессе 40Mn и вспомогательном оборудовании. Основной технологический маршрут определяется следующим образом: 1) компьютерное численное моделирование → 2) подготовка к возврату материалов → 3) нагрев возвращаемых материалов → 4) подготовка штампа → 5) многонаправленная штамповка штамповки → 6) неразрушающий контроль поковок → 7 ) термообработка поковок → 8) дробеструйная обработка поковок, среди которых 1) и 2) являются ключевыми звеньями управления.
Рис.1 часть схема
Рис.2 структурная схема поковки гидроблока с боковым фланцем
Компьютерное моделирование ковки
В соответствии с требованиями параметров процесса штамповки корпуса клапана, трехмерное моделирование заготовки, верхнего штампа, нижнего штампа и пуансона показано на рисунке 3 с использованием программного обеспечения SolidWorks. Формат 3D-модели преобразуется и импортируется в программу DEFORM-3D для моделирования и анализа процесса штамповки.
Рис.3 Трехмерный чертеж поковки и штампа
1-вертикальный пуансон 2-верхний штамп 3-ковочный 4-горизонтальный пуансон 5 нижний штамп
В процессе моделирования методом конечных элементов стержень выбирается как заготовка, а начальный Температура ковки составляет 1150 ℃, а температура штампа — 200 ℃. Заготовка выполнена в виде пластикового корпуса, а матрица — в виде жесткого тела. В процессе формовки используется модель жесткого вязкопластического течения. Модель трения сдвига выбирается между заготовкой и модулем, а коэффициент трения равен 0.15.
В процессе ковки с использованием технологии многонаправленной штамповки пуансон может оказывать давление на заготовку в штампе со всех направлений, а последовательность перемещений, расстояние перемещения и перемещение пуансона можно произвольно комбинировать. Эта комбинация оказывает большое влияние на эффект ковки, нагрузку и срок службы штампа. Согласно анализу конструкции и формы поковки корпуса клапана, фланец легко заполняется и является неполным, поэтому его сложно формировать. Следовательно, процесс многонаправленной штамповки выглядит следующим образом: закрытие верхней и нижней матрицы → горизонтальное перемещение пуансона → вертикальное перемещение пуансона → сброс.
В процессе многонаправленной штамповки последовательность движения пуансона влияет на поток материала и поле смещения в штамповке. Диаметр полости горизонтального отверстия корпусной части клапана невелик. Усилие, действующее на пуансон, велико при формировании полости горизонтального отверстия расчетным моделированием, что выходит за рамки возможностей оборудования. Кроме того, горизонтальный пуансон имеет большую деформацию, которую трудно вытягивать и легко ломать. Следовательно, регулируя смещение вертикального пуансона, заготовка может быть упорядоченно заполнена полостью под действием небольшой силы деформации, и можно избежать внутреннего разрыва и поверхностного складывания поковки.
Подводя итог, заготовка помещается горизонтально в В нижней полости формы верхняя и нижняя матрицы закрываются, а затем левый и правый горизонтальные пуансоны совместно выдавливаются и перемещаются, чтобы задать смещение, как показано на рис.4Б. Во время всего процесса металл сначала течет к боковому фланцу, и в середине заготовки в вертикальном направлении образуется барабан, как показано на фиг. 4A и 4B. После того, как горизонтальный пуансон достигнет обозначенной точки, внешняя кромка фланца и нижняя нижняя поверхность поковки не будут полностью заполнены золотом. В это время заготовка выдавливается вертикальным движением пуансона, чтобы металл заполнил полость формы. , как показано на фиг. 4D. Результаты моделирования показывают, что поковка имеет хороший формовочный эффект без дефектов.Требуемое усилие зажима составляет 20 Мн, усилие прижатия вертикального пуансона — 3,2 м, а усилие прижатия горизонтального пуансона — 5,6 м. Путем сравнения выбранная мощность кузнечно-прессового оборудования может соответствовать проектным требованиям.
Заготовка и штамп
Технические требования к прокатному пруту диаметром 145 мм соответствуют требованиям GB / T 1591 и GB / T 702. Пильный станок используется для вырубки. При расчете веса резки следует учитывать скорость окисления и потери при распиловке, а вес вырубки следует точно контролировать в 76.2-76,5 кг.
Рис. 4 Поточный процесс металла
По заводским условиям заготовку можно нагревать в камерной печи или среднечастотной печи. Температура нагрева составляет 1200 ℃, а начальная температура ковки выше 1150 ℃. Удаление накипи необходимо проводить после нагрева.
Температура предварительного нагрева формы должна быть выше 200 ℃, а смазка для формы должна быть графитовой эмульсией на водной основе.
Многонаправленная штамповка
Процесс многонаправленной штамповки поковки с боковым фланцем явно отличается от процесса поковки обычных тройников.Таким образом, верхний и нижний штампы, вертикальный и горизонтальный пуансоны регулируются давлением. В процессе формования давление в горизонтальном и вертикальном цилиндрах регулируется в зависимости от ситуации для получения наилучших параметров процесса. В то время как боковой фланец формируется горизонтальным пуансоном, синхронизация симметричного пуансона в горизонтальном направлении должна быть обеспечена во время процесса формования. Конкретный процесс формования выглядит следующим образом: ① закрытие верхней и нижней матрицы → ② левый и правый горизонтальный пуансон перемещается к указанное положение хода → ③ вертикальный пуансон перемещается в указанное положение хода → ④ сбрасывается вертикальный пуансон → ⑤ сбрасывается горизонтальный пуансон → сбрасывается верхняя матрица → ⑦ извлечение поковки из формы → и (8) входит в следующий цикл
Основные параметры управления многонаправленной штамповки показаны в таблице 2.
Таблица 2 основные параметры управления формованием
Формовочный процесс | Режим управления | Давление / МПа | Начальная точка | Точка прекращения | Смещение / мм |
Нисходящий канал в верхнем режиме | Смещение управления | 一 | 0 | 390 | 390 |
Нисходящий канал в верхнем режиме | Контрольное давление | 50 | 390 | 一 | 一 |
Горизонтальное движение пуансона | Смещение управления | 一 | 0 | 290 | 290 |
Горизонтальное движение пуансона | Контрольное давление | 50 | 290 | 一 | 一 |
Вертикальное движение пуансона | Смещение управления | 一 | 0 | 435 | 435 |
Вертикальное движение пуансона | Контрольное давление | 15 | 435 | 一 | 一 |
Сброс и извлечение из формы |
Последующая обработка поковок
После охлаждения был проведен 100% ультразвуковой контроль внешней поверхности поковок в соответствии с GB / T 6402, дефектов обнаружено не было. После нормализации при 910 ℃ и времени выдержки 5ho поверхность поковок должна быть подвергнута дробеструйной очистке для удаления оксидной пленки. Основные параметры дробеструйной обработки приведены в таблице 3.
Таблица 3 основные параметры дробеструйной обработки
Параметр | Диаметр стальной дроби / мм | Скорость выброса / м, мин | Время дробеструйной обработки / мин |
Численная величина | 1.2 | 80 | 8 |
Производственная проверка
Согласно технологической схеме, опытное производство данной продукции осуществлялось на многонаправленном ковочно-штамповочном гидравлическом прессе 40Мн. Согласно фактической структуре и форме поковки, результаты штамповки поковки в основном соответствовали результатам моделирования. Квалифицированные изделия были выкованы за один обжиг, фланец был полностью заполнен. После проверки механические свойства изделий оказались лучше проектных. См. Таблицу 4, и внешний вид поковок был хорошим, как показано на Рисунке 5.
Таблица 4 механические свойства поковок
Параметр | Предел прочности на разрыв / МПа | Предел текучести / МПа | Относительное удлинение /% | Энергия удара / Дж |
Численная величина | 575 | 395 | 24 | 138 |
Инжир.5 пробное производство
На основе опытного производства было осуществлено мелкосерийное производство, и процент первого прохода достиг 91%. В то же время в процессе проектирования в полной мере учитывались напряжения пуансона при деформации металла, использование небольшого усилия прижатия, отсутствие вертикального скопления металла пуансона, отсутствие явной царапины канавки в полости формы, увеличили срок службы плесень.
Вывод
- (1) Процесс формовки поковки корпуса клапана с боковым фланцем смоделирован компьютерным численным моделированием.Анализируются законы течения металла, распределения напряжений и деформации, что обеспечивает техническую поддержку практического производства.
- (2) По этой схеме могут быть изготовлены квалифицированные поковки корпуса клапана с боковым фланцем, что хорошо согласуется с результатами численного моделирования.
- (3) Технология изготовления корпуса клапана, основанная на процессе многонаправленной штамповки, может быть откована в одном огне. Поковка имеет отличные механические свойства и внешний вид, а также позволяет экономить энергию и материалы.
- (4) Посредством разумной последовательности движений, смещения и усилия прижатия матрицы и пуансона может быть сформирована поковка корпуса клапана с фланцем.
Автор: Song Changzhe
Источник: Network Arrangement — Поставщик клапанов в Китае : www. epowermetals.com
(Yaang Pipe Industry — ведущий производитель и поставщик изделий из никелевых сплавов и нержавеющей стали, включая фланцы из супердуплексной нержавеющей стали, фланцы из нержавеющей стали, фитинги из нержавеющей стали, трубы из нержавеющей стали. Продукция Yaang широко используется в судостроении, атомной энергетике, судостроении. машиностроение, нефтяная, химическая, горнодобывающая промышленность, очистка сточных вод, резервуары для природного газа и высокого давления и другие отрасли.)
Если вы хотите получить дополнительную информацию о статье или поделиться с нами своим мнением, свяжитесь с нами по адресу [email protected].
.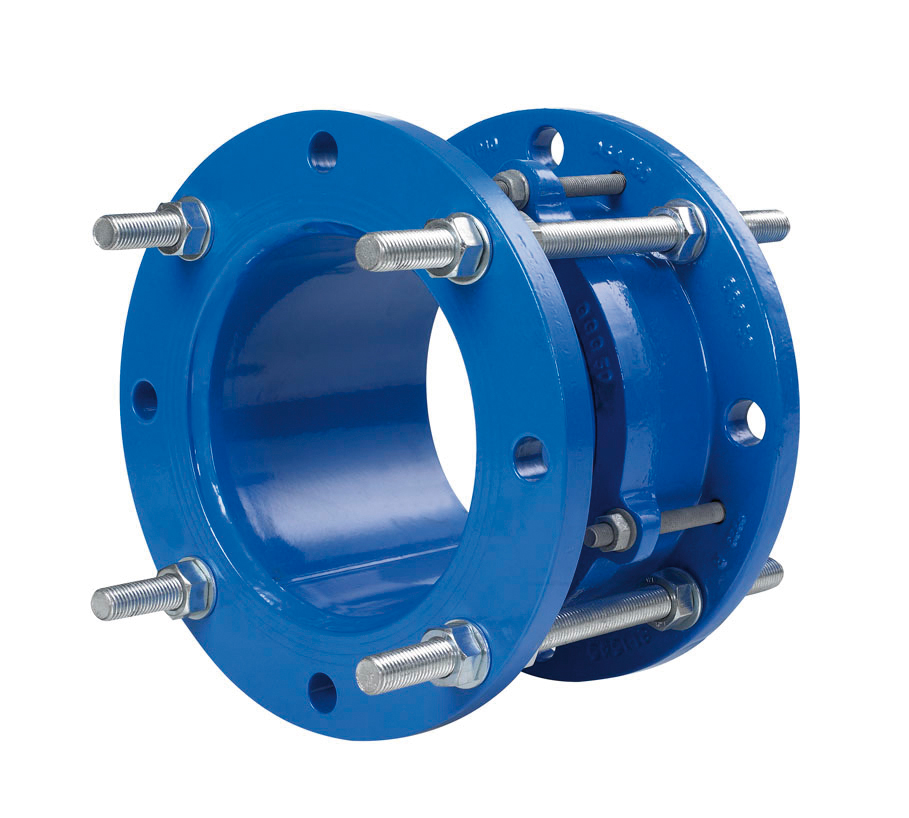