Сварка высоколегированных сталей
Высоколегированная сталь – это сталь, которая содержит в своем составе более 10% легирующих добавок. Это может быть одна или несколько из них. Как правило, высоколегированные стали устойчивы к коррозии, жаропрочные и жаростойкие. Благодаря этому они широко распространились и применяются в промышленности. Высоколегированные стали разделяются на три основные группы: устойчивые к коррозии, жаропрочные и жаростойкие.
Коррозионно устойчивыми высоколегированными сталями называются стали, которые устойчивы к электрической, химической и межкристаллитной коррозии. Жаростойкие называются еще окалина стойкими. Эти стали устойчивы к химическому разрушению при работе в не нагруженном или же слабо нагруженном состоянии при высокой температуре, свыше 500 градусов в газовой среде.
Жаропрочные
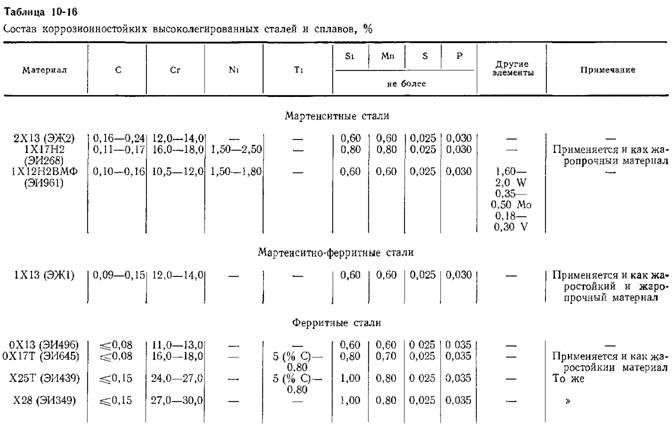
В связи с широким применением сталей данного вида, стоит отметить, что к сварочным соединениям так же должен быть разный подход. Такой подход определяет положение сварочного электрода при сварке, тип сваривания, сварочный ток, способ проведения сварочных работ и т.д. Каждая технология сваривания направлена на сохранение наибольшего количества свойств металла, управляя структурой металла сварочного шва.
Для сваривания высоколегированных сталей может применяться газовая сварка. Данный тип сварки обеспечивает огромную зону разогрева, а также значительный перегрев раскаленного металла и его замедленное охлаждение. В этом случае происходит значительный угар легирующих элементов. Также высоколегированная сталь менее благоприятна для сваривания кислотостойких сталей. В таких сталях может развиваться межкристаллитная коррозия, которая разрушает металлические изделия.
Газовое сваривание может использоваться для проведения сварочных работ с жаропрочными и жаростойкими сталями толщиной 1 – 2 миллиметра. Сваривание производится с мощностью пламени 70 – 75 л/ч на 1 миллиметр толщины металла. Сварочный процесс ведется с большой скоростью, а мундштук следует держать под углом 45 градусов к поверхности.
Нередко
Сварка высоколегированных сталей — Энциклопедия по машиностроению XXL
П некоторых случаях при сварке высоколегированных сталей основной металл в зоне термического влияния после резки также удаляют механическим путем. Перед сборкой кромки и прилегающие участки основного металла (на 40 мм от кромки) должны быть очищены от масла, ржавчины и других загрязнений металлическими щетками, дробеструйной обработкой или химическим травлением. Детали собирают на прихватках (коротких швах)длиной 20—30 мм и более или в специальных сборочных приспособлениях. [c.16]Сварка высоколегированных сталей [c.125]
Технологические особенности сварки высоколегированных сталей связаны с их физическими свойствами и системой легирования. Пониженная теплопроводность и большое электрическое сопротивление (примерно в 5 раз больше, чем у углеродистых сталей) способствуют большей скорости плавления металла, большей глубине проплавления и коэффициенту наплавки, поэтому для сварки высоколегированных сталей требуются меньшие токи и погонные энергии по сравнению с углеродистыми, укороченные электроды при ручной сварке, меньше вылет электрода и больше скорость подачи проволоки при механизированной сварке.
[c.127]
Виды сварки высоколегированных сталей. Для сварки высоколегированных сталей используют ручную дуговую сварку покрытыми электродами, механизированную и ручную в защитных газах, сварку под флюсом, электрошлаковую, лучевые виды сварки, контактную и ряд других.
Сварку под флюсом используют для соединения металла толщиной 3—50 мм. По сравнению со сваркой углеродистых сталей при сварке высоколегированных сталей в 1,5—2 раза уменьшается вылет электрода, применяют электроды диаметром 2—3 мм, сварка многопроходная, на постоянном токе обратной полярности с использованием безокислительных низкокремнистых фтористых и высокоосновных флюсов (АНФ-14, АНФ-16, К-8, АН-26). Серьезным преимуществом сварки под флюсом по сравнению с ручной, наряду с повышением производительности сварки и качества сварных соединений, является уменьшение затрат на разделку кромок. [c.128]
Какие трудности возникают при сварке высоколегированных сталей
[c. 131]
При сварке высоколегированных сталей вылет электрода уменьшают в 1,5 раза из-за пониженной теплопроводности. [c.44]
Электроды для сварки высоколегированных сталей (ГОСТ 10052—62) аустенитного аустенито-ферритного, ферритного, мартен-сито-ферритного, мартенситного классов и специальных сплавов выпускают следующих типов [c.43]
По назначению У — для сварки углеродистых и низколегированных сталей с временным сопротивлением разрыву до 60 кгс/мм Л — для сварки легированных сталей с Ов>60 кгс/мм Т — для сварки теплоустойчивых сталей В — для сварки высоколегированных сталей Н — для наплавки поверхностных слоев с особыми свойствами. [c.64]
СВАРКА ВЫСОКОЛЕГИРОВАННЫХ СТАЛЕЙ [c.428]
Электроды покрытые металлические для ручной дуговой сварки высоколегированных сталей с особыми свойствами. [c.339]
Основные типы покрытых металлических электродов для ручной дуговой сварки высоколегированных сталей с особыми свойствами установлены ГОСТ 10052—75.
В СССР разработаны и изучаются различные пути предупреждения образования горячих трещин при сварке аустенитных сталей применяются электроды и проволока, обеспечивающие образование в швах не только аустенитной, но ферритной фазы модификаторы для улучшения первичной структуры при сварке высоколегированных сталей используются легирующие элементы, устраняющие явления полигонизации и приводящие к дроблению столбчатых кристаллов, возникновению новых зерен, на границах которых образуются микродефекты, переходящие в трещины. В большинстве случаев горячие трещины возникают в наплавленном металле швов, но иногда и в околошовных зонах. [c.130]
Устройство горелок для получения плазменной дуги (рис. 5.12, б) принципиально не отличается от устройства горелок первого типа. Только дуга горит между электродом и заготовкой 7. Для облегчения зажигания дуги вначале возбуждается маломощная вспомогательная дуга между электродом и соплом. Для этого к соплу подключен токопровод от положительного полюса источника тока. Как только возникшая плазменная струя коснется заготовки, зажигается основная дуга, а вспомогательная выключается. Плазменная дуга, обладающая большей тепловой мощностью по сравнению с плазменной струей, имеет более широкое применение при обработке материалов. Ее используют для сварки высоколегированной стали, сплавов титана, никеля, молибдена, вольфрама и других материалов. Плазменную дугу применяют для резки материалов, особенно тех, резка которых другими способами затруднена, например меди, алюминия и др. С помощью плазменной дуги наплавляют тугоплавкие материалы на поверхности заготовок.
Какие технологические мероприятия и с какой целью их применяют при сварке высоколегированных сталей [c.281]
Каковы особенности сварки высоколегированных сталей
[c. 82]
Это ориентировочное значение силы тока, его корректируют в зависимости от свариваемого материала или особенностей соединения. Например, при сварке высоколегированных сталей для уменьшения перегрева металла силу тока уменьшают на 20…30 %. Минимальный ток должен обеспечивать нагрев и плавление торца электрода, максимальный ток не должен перегревать электрод по всей длине и вызывать осыпание покрытия. [c.120]
Для сварки низколегированных низкоуглеродистых сталей используют улучшающие легирующие флюсы. Для сварки высоколегированных сталей — более нейтральные флюсы, состоящие из бескислородных соединений типа фтористого кальция. Однако формирование швов под такими флюсами несколько хуже, чем под флюсами с активными компонентами. Плавленные флюсы бывают стекловидными и пемзовидными, отличаются формой частиц и степенью раскисления. Стекловидный флюс лучше защищает зону сварки, однако формирование шва лучше под пемзовидным флюсом.
[c. 142]
Каховский Н. И. Сварка высоколегированных сталей. Киев Техника, 1975. [c.389]
В — для сварки высоколегированных сталей с особыми свойствами [c.68]
Электроды для сварки высоколегированных сталей разделены на 49 типов (табл. 2.4). Их обозначения аналогичны обозначениям электродов для сварки теплоустойчивых сталей. [c.69]
Химический состав и особые механические свойства металла шва и наплавленного металла, образуемых покрытыми электродами для ручной дуговой сварки высоколегированных сталей
Согласно ГОСТ 9466—75 электроды для сварки и наплавки сталей в зависимости от назначения разделены на классы для сварки углеродистых и низколегированных конструкционных сталей с Он конструкционных сталей с Ов > 60 кгс/мм — Л для сварки теплоустойчивых сталех — Т для сварки высоколегированных сталей с особыми свойствами — В для наплавки поверхностных слоев с особыми свойствами — Н. Этот ГОСТ регламентирует размеры электродов, толщину и типы покрытий, условные обозначения, общие технические требования, правила приемки и методы испытания.
[c.103]
J Электроды для сварки высоколегированных сталей с особыми свойствами должны удовлетворять требованиям ГОСТ 10052—75. Большое разнообразие служебного назначения этих сталей определяет и большой типаж электродов для их сварки. Стандартом предусмотрено 49 типов электродов для сварки хромистых и хромоникелевых сталей, коррозионно-стоЙ1шх, жаропрочных и жаростойких высоколегированных сталей мартепситно-ферритного, ферритного, аустенитно-ферритного и аустенитпого классов. [c.110]
Это обозначение имеет следующие данные электроды типа Э-10Х25Ы13Г2Б по ГОСТ 10052-75, марки ЦЛ-9, диаметром 5 мм для сварки высоколегированных сталей с особыми свой- [c.110]
Таблица / -5.![]() |
В середине 50-х годов Б. И. Медовар и С. М. Гуревич (ИЭС) разработали для сварки высоколегированных сталей и сплавов принципиально новые флюсы — бескислородные или галоидные, которые внесли коренные изменения в металлургию сварки аустенитных сталей [157]. Эти флюсы дали возможность применять титансодержаш ие электродные проволоки и значительно повысить стойкость сварных швов против образования горячих трещин. Создание галоидных флюсов позволило успешно решить задачу автоматизации сварки сплавов алюминия и титана, ряда новых марок жаропрочных и нержавеющих сталей и сплавов. Больше того, создание указанных флюсов сделало автоматическую сварку под флюсом вполне конкурентоспособной в отношении сварки новых материалов и сплавов — с аргонодуговой сваркой. Например, применение автоматической сварки полуоткрытой дугой по слою флюса алюминия и его сплавов оказалось более эффективным, чем аргоно-дуговая сварка.
[c.124]
Так как в состав покрытий электродов, применяемых для сварки высоколегированных сталей, кремнезем (SiOa) не вводится, то основным источником восстановления кремния является сухой остаток жидкого стекла. При этом количество восстановленного кремния пропорционально сухому остатку жидкого стекла 111. [c.191]
В условном обозначении электродов для сварки высоколегированных сталей с особыми свойствами группа индексов, указывающих характеристики наплавленного металла и металла шва, должна содерл[c.339]
Согласно инструкции Института электросварки АН УССР при испытании флюса, предназначенного для сварки высоколегированных сталей (АН-26), производится испытание на склонность к образованию горячих трещин путем пятислойной наплавки и сварки тавровых образцов. Наплавку каждого последующего слоя производят сразу же после удаления шлака с поверхности предыдущего слоя, не ожидая его остывания все пять слоев наплавляются в одном направлении. Рекомендуемый режим наплавки постоянный ток, обратная полярность, сила тока 550—600 а, напряжение 36—40 в, скорость сварки 20—45 м час, проволока марки СвОХ18Н9 с содержанием не менее 0,5% Si и не более 9% Ni, пластина из стали марки 1Х18Н9Т.
[c.288]
Электроды металлические для дуговой сварки конструкционных и теплоустойчивых сталей Электроды металлические для дуговой сварки высоколегированных сталей с особовыми свойствами Технические условия на изготовление, хранение и транспортирование покрытых сварочных электродов для энер-1 омашиностроения [c.517]
По назначению выделяют три группы флюсов для сварки углеродистых и легированных сталей, для сварки высоколегированных сталей, для сварки цветных металлов и сплавов. Внутри этих групп флюсы могут различаться по размеру зерна в зависимости от диаметра электродной проволоки чем больше диаметр проволоки, тем крупнее частицы флюса. По химическому составу различают кислые и основные флюсы в зависимости от соотношения соответствующих окислов в составе. По способу изготовления флюсы разделяют на плавленные и неплавленныс. Неплавленные флюсы изготавливают без плавления компонентов шихты. К ним относят флюсы керамические и изготовленные путем измельчения природных минералов. Керамические флюсы изготавливают из тех же компонентов, что и электродные покрытия, их замешивают на жидком стекле, а затем спекают и дробят. Недостаток таких флюсов — низкая прочность их зерен (много отходов, мелких фракций) и возможная неоднородность состава из-за разделения веществ с разным удельным весом при их перемешивании.
[c.142]
СВАРИВАЕМОСТЬ И ОСОБЕННОСТИ ТЕХНОЛОГИИ СВАРКИ ВЫСОКОЛЕГИРОВАННЫХ СТАЛЕЙ
При сварке высоколегированных аустенитных сталей могут образовываться технологические трещины в металле шва, около — шовной зоне вблизи сплавления и в ЗТВ на некотором расстоянии 272
от шва. Причины появления таких трещин могут быть разными. При сварке аустенитных сталей одна из причин — отсутствие при охлаждении после сварки фазовой перекристаллизации и сохранение первичных аустенитных зерен во всем интервале температур, начиная от кристаллизации до полного охлаждения. При многослойных швах при сварке плавлением в каждом последующем слое кристаллизация аустенитных зерен начинается с зерен предыдущего слоя, и это приводит к образованию непрерывных протяженных границ кристаллитов от первого слоя к последнему с образованием траискристаллитного строения. Такие непрерывные границы зерен, проходящие через весь шов, в связи с особенностями состояния металла в граничных участках являются «трассой» особой предрасположенности к прохождению трещин. 1|Однако одной этой причины для появления кристаллизационных И или холодных трещин может быть и недостаточно, хотя такое И строение металла шва обусловливает его повышенную склонность ™ к образованию трещин.
Другим фактором, определяющим повышенную склонность к образованию, прежде всего, кристаллизационных трещин, может быть повышенная ликвационная загрязненность приграничных областей. В хромоникелевых сталях при высоком содержании основных легирующих элементов при высоких температурах, когда диффузионная подвижность атомов велика, создаются условия для оттеснения примесей (серы и фосфора) в кристаллизующиеся последними приграничные области зерен. Здесь же могут собираться в повышенном количестве атомы других элементов, легирующих сталь в небольших количествах (ниобия, молибдена, титана).
По данным Б. И. Медовара, повышенная склонность к ликвации примесей по границам зерен в высоколегированных сталях приводит к тому, что в этих зонах образуются более легкоплавкие прослойки с меньшей прочностью при температурах кристаллизации, когда ранее закристаллизовавшиеся части приобрели достаточную прочность. Под влиянием усадочных напряжений в них возникают надрывы, переходящие в межкристаллитную трещину. В аустенитном металле сварных швов с транскристаллит — ным строением такая трещина может поразить весь ііюв, проходя по непрерывной межзеренной границе. В связи с рассмотренным для предотвращения появления кристаллизационных трещин в металле аустенитных швов можно использовать особо чистые по сере и фосфору свариваемые стали и присадочные материалы. Хорошо зарекомендовали себя аустенитные стали, рафинированные электрошлаковым переплавом или каким-либо другим методом. Поскольку в процессе сварки нельзя обеспечить снижение содержания фосфора, ибо это достигается окислением, а в стали имеются более легко окисляющиеся элементы, содержание фосфора в свариваемой стзли и присадочных материалах ограничивают 0,01 % и избегают использования флюсов и электродных покрытий, способных загрязнять металл шва вредными примесями.
10 Лившиц Л. G. в ю. 273
Другой мерой предотвращения образования горячих трещин может быть нарушение транскристаллитного строения металла шва. Для этого композицию металла шва (соотношение содержания элементов ферритизаторов и аустенитизаторов) выбирают такой, чтобы шов получился не чисто аустенитным, а аустенитноферритным с небольшим количеством феррита (3—5 %). Этот первичный 5-феррит нарушает сплошность аустенитных зерен, становится прослойкой между аустенитными кристаллитами и нарушает транскристаллизацию. Непрерывная транскристаллитная граница аустенитных зерен прерывается ферритными включениями. Это важно не столько для локализации кристаллизационной трещины, сколько для предотвращения ее образования в связи с тем, что нарушается сплошность межзеренного каркаса легкоплавкой прослойки при кристаллизации.
Выделения феррита в аустенитном шве не должны образовывать сплошной сетки, ибо ферритный каркас может оказать вредное влияние на требуемые свойства металла. Феррит, как более хрупкая фаза, находясь в виде каркаса, может повлиять на хладо — стойкость стали. Он может снизить и пластичность при длительной работе в условиях высоких температур, феррит в большей мере, чем аустенит, склонен к выделению 0-фазы, снижающей пластичность и ударную вязкость. Поэтому присутствие более 8 % феррита в аустенитных швах нежелательно. В то же время разорванные ферритные выделения в аустенитном металле (обычно до 5 % феррита) могут даже оказать положительное влияние на свойства, разрывая непрерывность границ аустенитных зерен.
Помимо горячих кристаллизационных трещин в сварных швах аустенитных сталей могут возникать горячие высокотемпературные полигонизационные трещины, образующиеся в довольно узком интервале температур, находящемся несколько ниже температуры кристаллизации. Б. А. Мовчаи показал, что в литом аустенитном металле при достаточно медленном охлаждении после кристаллизации дефекты кристаллического строения начинают мигрировать, сосредоточиваясь с образованием полигональных границ субзерен. Эти полигональные границы в отдельных местах могут совпадать со старыми границами аустенитных кристаллитов, с участками сосредоточения примесей, здесь могут зарождаться трещины под влиянием напряжений, вызываемых усадкой металла. Для подавления образования таких трещин можно увеличивать скорость охлаждения с тем, чтобы не дать развиться поли — гонизашш. Уменьшение опасности появления полигонизашонных трещин может быть достигнуто специальным легированием, уменьшающим подвижность полигонизационных границ.
I Горячие трещины могут возникать как в металле шва, так /и в околошовных зонах в высокотемпературных участках, подвергаемых оплавлению с прониканием жидкой фазы по границам Ізерен. При этом оплавленные пограничные обогащенные примесями участки могут иметь двоякое значение для образования тре — 274
щин (по дан ним Б. И. Медовара]. С одной сторони, при кристаллизации так же, как и к шве, по рассмотренным выше причинам они могут стать очагами образования трещин, с другой—расплав может играть роль поверхностно-активного вещества и способствовать образованию трещин на примыкающих неоплавленных границах. Г Б сварных соединениях высоколегированных хромоникелевых (сталей при определенных условиях могут образовываться и холодные трещины. Б. И. Медовар указывает на возможность образования таких трещин в двух температурных зонах — в интервале 500—700 °С и после полного охлаждения. Трещины, образующиеся. при 500—700 °С, связаны с фазовыми изменениями, приводящими к повышению жаропрочности, повышению хрупкости и понижению пластичности металла. Причины возникновения холодных трещин были рассмотрены выше.
Процессы, протекающие при сварке различных по назначению и исходному фазовому и структурному состояниям свариваемых сталей, имеют много общего. Эта общность процессов связана со следующим. У всех сталей при сварочном нагреве участки ЗТВ, примыкающие к сварному шву при сварке плавлением, или участки свариваемых поверхностей при сварке давлением являются в основном аустенитными. В тех случаях, когда при нагреве дополнительно образуется феррит, количество его не велико, тем более что небольшое количество феррита оказывает положительное влияние иа уменьшение возможности образования кристаллизационных трещин.
Получение аустенитного состояния в зоне сварки рассматриваемых сталей после завершения сварочного нагрева обеспечивает и после охлаждения создание аустенитной основы в определенных участках ЗТВ, примыкающих к участку сплавления или соединения. В указанных участках даже высокопрочных маргенситно — стареющих и аустенитно-мартенситных сталей после сварки сохраняется аустенитная основа. Это обстоятельство обеспечивает достаточно хорошую свариваемость практически всех высоколегированных хромоникелевых сталей.
Положительное значение для свариваемости рассматриваемых сталей имеет и то обстоятельстве, что рост аустенитного зерна в ЗТВ этих сталей происходит в меньшей степени, чем в ЗТВ углеродистых и низколегированных сталей, и уровень сварочных остаточных напряжений ниже, чем у низколегированных и даже углеродистых сталей. Объясняется это более низким пределом текучести аустенитных сталей. В то же время относительная деформация отдельных участков металла ЗТВ сварного соединения аустенитных сталей по той же причине больше и, по данным В. Н. Земзнна, может достигать при растяжении 5—10 %. Повышенная возможность деформации в сварном соединении связана не только с более низким пределом текучести аустенитных сталей, но и с более высоким уровнем временных напряжений, обусловливаемых их пониженной теплопроводностью.
Сварочный нагрев металла в различных зонах теплового влияния может приводить к протеканию процессов, неблагоприятно влияющих на качество, свойства и работоспособность сварных соединений. В приграничных участках зерен областей ЗТВ, нагреваемых до более высоких температур, может происходить оплавление границ вследствие повышенной загрязненности их примесями. При этом должно происходить дальнейшее повышение концентрации примесей в приграничных участках за счет перемещения их атомов из глубины зерна в зону повышенной растворимости. Таким образом, в этих высоконагретых участках ЗТВ в условиях продолжительного сварочного нагрева состояние границ зерен может сильно ухудшиться, вследствие чего увеличится возможность межкристаллитных разрушений как в процессе сварки, так и при эксплуатации. участка сварного соединения, несмотря на то что сталь содержит стабилизирующие элементы — титан, ниобий. Одновременно в связи с потерей хрома происходят разупрочнение приграничных зон зерна и повышение хрупкости границ с выделившимися по ним карбидами. Одновременно перешедшие в раствор титан, ниобий и другие элементы упрочняют в этих растворах зерно, понижают его деформационную способность. В целом в результате протекания рассмотренных процессов в высоконагревавшемся участке ЗТВ резко возрастает склонность к межзеренному разрушению при длительных нагревах под нагрузкой (локальные разрушения).
Предотвратить повышение склонности металла ЗТВ к МКК и локальным разрушениям можно за счет общего снижения содержания углерода в коррозионно-стойких сталях и вредных примесей в жаропрочных сталях. Стали последнего типа не рекомендуется легировать такими элементами, как титан и ниобий. Восстановить стойкость сварных соединений сталей к МКК можно или общей термообработкой изделия, соответствующей обработке свариваемой стали, или термообработкой с длительным нагревом при 850—900 СС в течение 3—5 ч, приводящим к диффузионному 276
повышению концентрации хрома в обедненных приграничных участках за счет перемещения его из глубины зерна. 900 °С за счет растворения карбидов с границ зерен. Термообработка одновременно снижает уровень остаточных сварочных иа — пряжений.
ТТ участках ЗТВ, нагревающихся до более низких, чем указано выше, температур, могут протекать процессы аустенитизации — получения гомогенного аустенита в сталях типа 18-8, не содержащих активных карбидообразователей. В этих же участках ЗТВ сталей, содержащих титан, ниобий, ванадий, должны сохраняться карбиды указанных элементов в связи с их высокой стойкостью и кратковременностью нагрева, однакс их коагуляция может привести к разупрочнению жаростойких сталей на базе карбидного упрочнения.
В участках ЗТВ, нагреваемых в интервале 750—950 °С, могут проходить с различной степенью интенсивности процессы образования карбидов хрома и выделение их по границам зерен в тех сталях, в которых имеется углерод, не связанный в стойкие карбиды с титаном, ниобием и другими элементами, характеризующимися высокой степенью химического сродства к углероду. Процесс карбидообразования может повысить хрупкость металла в этом участке.
‘ В участках, нагретых ниже 750 °С, может выделяться феррит, а при длительном нагреве и a-фаза. В этой же зоне может развиваться 475’ГРадусная хрупкость. В участках, нагревавшихся /ниже 300 бС, возможно образование мартенсита, которое может закончиться, а может и не завершиться — в зависимости от температуры конца мартенситного превращения. Таким образом, строение ЗТВ высоколегированных хромоникелевых сталей может быть очень сложным.
У разных по составу и назначению высоколегированных хромоникелевых сталей указанные процессы в ЗТВ могут развиваться по-разному, но их развитие, как правило, может оказывать отрицательное влияние на свойства и работоспособность сварных соединений, если эти процессы будут активными. Поэтому, хотя рассматриваемые стали свариваются всеми видами сварки, предпочитать следует такие, при которых тепловое воздействие на свариваемый металл будет наименьшим — в среде защитного инертного газа тонкой проволокой, элект ронно-лучевую и различные способы сварки давлением (шовная, точечная, диффузионная и др. ).
Кинетика распада аустенита в хромоникелевых аустенитномартенситных и мартенситно-ферритных сталях изучена дилатометрическим методом применительно к околошовному участку ЗТВ
В)
сварных соединений при нагреве образцов сталей 10Х12НД, 06Х12Н2Д и 06Х14Н5ДМ до t, mx == 1350 — f — 1400 °С с последующим охлаждением со скоростью от 5 до 100 °С/с (рис. 10 9) [59]. В зависимости от соотношения содержания углерода и легирующих элементов в составе высокохромистой стали при 1350—1400 °С структура металла является либо двухфазной аустенитно-ферритной с незначительным содержанием б-феррита (стали 10Х12НД и 05Х14Н6ДМ), либо однофазной аустенитной (сталь 06Х12Н2Д). С увеличением содержания никеля в составе стали температура начала распада аустенита снижается.
Как видно, в околошовном участке ЗТВ сварных соединений высокохромистых сталей формируется либо полностью мартенситная структура (сталь 06Х12Н2Д), либо смешанная мартенситно — ферритная (сталь 10Х12НД), либо аустенитно-ферритно-мартенситная (сталь 06Х14Н5ДМ). Образовавшийся низкоуглеродистый мартенсит имеет реечную субструктуру, в процессе охлаждения претерпевает самоотпуск, что обеспечивает повышенные показатели прочности и вязкости металла. Наличие в структуре остаточного аустенита способствует дополнительному повышению вязкости и пластичности металла, обеспечивает повышенное сопротивление сварных соединений образованию холодных трещин.
Полагают 159], что для обеспечения повышенной стойкости сварных соединений к образованию холодных трещин необходимо, чтобы в металле шва образовалась однородная структура низкоуглеродистого реечного мартенсита при минимальном содержании 6-феррита и остаточною аустенита. Причем температурный интервал мартенситного превращения металла шва (М„ — Мк) должен быть выше, чем у металла околошовного участка ЗТВ. Если это различие равно или более 100 °С, то мартенситное превращение начинается в наплавленном металле, сопровождаясь увеличением объема, возникновением сжимающих напряжений в шве и растягивающих напряжений в ЗТВ, которые будут активизировать начало мартенситного превращения в ЗТВ, сдвигая его в область повышенных температур. В связи с тем, что процесс у —*■ OL — 278
превращения заканчивается в ЗТВ, в ней не возникают дополнительные растягивающие напряжения, обусловленные превращением в шве и, как следствие, создаются благоприятные условия для релаксации напряжений в закаленной структуре металла.
Для реализации указанных требований ограничивают содержание углерода и азота в сварочной проволоке (С <* 0,015 %), дополнительно легируют 1,2—2,5 % Ni для предотвращения образования б-феррита в количестве более 10 %, обеспечивая соотношение (Сг +1,5 Si)/[Ni + 0,5 Мп + 30 (С + N)] = 3,5-=- 6,0. При ручной дуговой сварке этим условиям удовлетворяют электроды ЦЛ-51, а при автоматической дуговой под флюсом — проволока Св-01 Х12Н2 [591.
Двухфазные аустенитно-ферритные стали обладают высокой технологической прочностью. При содержании феррита свыше 20 % металл шва характеризуется повышенной сопротивляемостью образованию горячих трещин. Поскольку температура начала мартенситного превращения ниже 20 °С, в структуре металла шва и ЗТВ нет опасности образования закалочных структур. Кроме того, уровень остаточных напряжений оказывается ниже, чем у аустенитных хромоникелевых сталей, так как коэффициент теплопроводности аустенитно-ферритных сталей выше, а коэффициент термического расширения ниже, чем у аустенитных сталей. Поэтому сварные соединения аустенитно-ферритных сталей имеют высокую сопротивляемость образованию холодных трещин.
I К числу основных проблем, возникающих при сварке аустенитно-ферритных сталей, относятся пониженные пластичность, |ударная вязкость и склонность к коррозии сварных соединений. Снижению пластичности и ударной вязкости способствуют такие /факторы, как низкое содержание вторичного аустенита в конечной структуре, образование скоплений карбидов типа Me23Cs, Ікарбидов или карботштридов титана в сталях, легированных Ті.
«Для повышения ударной вязкости сварных соединений общепринятая технология сварки ориентируется на пониженную погонную энергию (0,5—2,5 МДж/м) с целью предотвращения роста ферритных зерен. В работе [231 показана эффективность технологии сварки, основанной на обеспечении условий, благоприятных для б -► у’-превращения в ЗТВ вследствие снижения скорости охлаждения в интервале 950—900 °С до 1 °С/с посредством местного сопутствующего подогрева. Эта технология реализована при однопроходной сварке стали 08Х22Н6Т толщиной 16 мм. Местный подогрев осуществляли плазменной дугой до 900—950 °С на поверхности металла. Применение такой обработки позволило увеличить угол загиба при испытании сварных соединений с 45 до 160 СС.
Технология электрошлаковой сварки двухфазных сталей, разработанная Л. А. Ефименко и М. А. Харитоновой, базируется на принципе интенсификации б —► у’-превращения посредством
Рис. 10 10. Микроструктура тарных соединений стали і 10ПЗЛ, выполненных ручной дуговой (а —б) и контактной сваркой оплавлением (в) (По данным О. И. Стеклова, П. А. Беляшина и Э. П. Мотуса): о — шов, Х500; б — ЗТВ, Х500; я — шов, ХІ20 |
замедления охлаждения металла околошейного участка ЗТВ при температурах выше 900 ~С, подавления процесса выделения карбонитридов титана и повышения их дисперсности, увеличением интенсивности охлаждения металла ниже температуры 900 °С.
На рнс. 10.8 показаны микроструктуры сварного соединения стали 08X21Н6М2Т толщиной 30 мм. Электрошлаковая сварка (ЭШС) выполнена при сопутствующем подогреве с помощью газовых горелок и принудительном сопутствующем охлаждении с помощью водовоздушных форсунок. Параметры термического цикла ЭШС в околошовном участке с tn]ax — 1350 °С соответствовали следующим значениям: т’ = 30 с; %» = 80 с. Длительность пребывания металла при температурах выше 900 °С составляет 60 о за счет обеспечения подогрева, а скорость охлаждения па заключительной стадии цикла повышена до 13 °С/с о помощью принудительного охлаждения водовоздушной смесью при расходе воды 0,06 м3/ч. Сварку осуществляли сварочной проволокой ЗСв-06Х20Н11МЗТБ с применением флюса АН-26С. В состоянии после сварки сварные соединения имеют следующие механические свойства: 0„ — 686 МПа, угол загиба 130°, KCU металла около — шовного участка ЗТВ при—40°С 1,8 МДж/м2. В случае применения общепринятой технологии ЭШС для обеспечения повышенного уровня механических свойств сварных соединений выполняют последующую высокотемпературную термическую обработку — нормализацию при 1100 °С.
При ручной дуговой сварке двухфазных сталей можно использовать аустенитный вариант (электроды марок ЦЛ-11 и ЭА-400/10у) или аустенитно-ферритный вариант (ОЗЛ-40 и ОЗЛ-41). В первом варианте содержание ферритной фазы в шве не превышает 10 %, а во втором — феррит является основной фазой в двухфазной аустенитно-ферритной структуре. Преимуществом второго варианта являются равнопрочность швов основному металлу и повы — 280
шейная коррозионная стойкость сварных соединений. В работе [32] описаны исследования коррозионной стойкости сварных соединений двухфазных сталей. Установлено, что сварные соединения стали 08Х22Н6Т после термообработки (нагрев до 1150 °С, выдержка в течение 20 мин) в случае использования электродов ОЗЛ-40 и ЦЛ-11 являются коррозионно-стойкими в 55 %-ной фосфорной кислоте при температуре 90 °С, в 1 %-ной серной и 25 %-ной муравьиной кислотах при температуре 80 °С. Скорость коррозии не превышает 0,01 мм/год. МКК в металле шва не отмечается. При сварке с применением электродов ОЗЛ-40 и ЦЛ-11 МКК отмечена в ЗТВ и у линии сплавления при испытаниях в 55 %-ной фосфорной кислоте. Металл шва обладает высоким сопротивлением МКК в этой среде. В 65 %-ной азотной кислоте при кипении скорость коррозии достигает 3 мм/год за счет коррозионных процессов в ЗТВ, независимо от марки электрода. В этой среде скорость коррозии металла шва, полученного электродом ОЗЛ-40, составляет 0,4 мм/год, основного металла 0,14 мм/год, а ЗТВ — 1,24 мм/год. Соответствующие показатели при сварке электродами ЦЛ-11 составляют 0,45; 0,2; 0,76 мм/год.
В процессе испытания в 92 %-ной серной кислоте при температуре кипения было установлено, что скорость коррозии сварных соединений, выполненных электродами ЭА-400’Т0у и ОЗЛ-41, не превышает 0,14 мм/год, а МКК отсутствует. В 80 %-ной фосфорной кислоте скорость коррозии сварных соединений, полученных электродами указанных марок, не превышает 0,01 мм/год, а МКК металла шва не обнаруживается. У линии сплавления и в ЗТВ проявляется слабая МКК — На основе полученных данных в работе [32] был сделан вывод о целесообразности применения электродов марок ОЗЛ-40 и ОЗЛ-41 при сварке оборудования из аустенитно-ферритных сталей, эксплуатируемого в щелочных, нейтральных и окислительных средах.
В ряде работ было показано, что в аустенитно-ферритных сталях, находящихся в щелочных средах, преимущественному коррозионному разрушению подвергается ферритная структура. Отмеченное подтверждается результатами работы 19], в которой показано влияние погонной энергии на коррозионную стойкость сварных соединений стали типа 10X21Н5Т, выполненных дуговой сваркой иод флюсом. В качестве сварочных материалов использовали проволоку 5Св-04Х19Н10Б (аустенитный вариант) и 5Св-10Х21Н5Т (аустенитно-ферритный вариант). С увеличением погонной энергии от 320 до 3700 кДж/м скорость коррозии сварных соединений при аустенитном варианте в 40 %-ном водном растворе едкого натра возрастает в 6 раз. Это объясняется, с одной стороны, увеличением содержания ферритной фазы в металле околошовного участка ЗТВ, склонной к растворению в коррозионно-активной среде, а с другой — возрастанием тока коррозии в макросистеме аустенитный шов — аустенитно-ферритный основной металл из-за наличия разности потенциалов между ними.
Аустенитно-ферритный вариант сварки предпочтителен аустенитному, так как из-за равенства потенциалов в макросистеме шов — основной металл токи коррозии отсутствуют. Скорость коррозии относительно невелика, сварное соединение отличается повышенной однородностью структуры и механических свойств.
При сварке хромоникелькремнистых сталей в металле шва в процессе кристаллизации по границам дендритов выделяется легкоплавкая кремнистая фаза, снижающая сопротивляемость сварных соединений образованию горячих трещин и их пластичность. Например, сварные соединения, полученные по общепринятой технологии с применением ручной аргонодуговой сварки, имеют следующие показатели механических свойств при 20 °С: 0В — 620 МПа; KCU = 0,24 МДж/м2, угол загиба 15°.
При нагреве в интервале 950—600 °С в структуре стали по границам аустенитных зерен выделяется избыточная фаза, состоящая из сложных карбидов хрома, легированных Si и Ni, и снижающая стойкость сварных соединений к МКК. Ограниченное содержание углерода в составе стали (до 0,015 %) не предотвращает МКК сварных соединений высококремнистых аустенитных сталей [10]. Поэтому общепринятая технология, как правило, предусматривает применение последующей высокотемпературной обработки с нагревом до температур 1050 °С и ускоренным охлаждением. Другой подход к разработке технологии сварки, обеспечивающей повышенную коррозионную стойкость сварных соединений, основан на подавлении процессов роста зерна аустенита и выделения сложных карбидов хрома в ЗТВ посредством ограничения длительности пребывания металла в интервале температур, превышающих 400 °С, и ускоренного охлаждения в интервале 960—600 °С. Для достижения этих целей эффективно применение высококонцентрироваиных источников нагрева, в частности плазменной дуги. Технология сварки, разработанная в МИНГ им. И. М. Губкина, реализована при сварке стали 02Х8Н22С6 [53]. Пластины металла толщиной 6 мм сваривали плазменной проникающей дугой в импульсном режиме, а пластины толщиной 11 мм в непрерывном режиме с сопутствующим принудительным охлаждением водовоздушной смесью с целью обеспечения скорости охлаждения в данном интервале температур на >-120 °С/с.
Аустенитная структура металла шва, полученного при плазменно-дуговой сварке в импульсном режиме, отличается повышенной дисперсностью. Междендритные прослойки силицидной фазы значительно более дисперсны, чем в шве, полученном аргонодуговой сваркой, и разориентированы. Металл околошовного участка ЗТВ имеет аустенитную структуру, выделения вторичной фазы по границам аустенитных зерен отсутствуют, что является следствием уменьшения длительности пребывания в интервале 950—600 °С.
Сварка высокомарганцовистых сталей связана с затруднениями в связи с повышенной склонностью к образованию горячих тре — 282
щин металла шва, пониженной сопротивляемостью металла около — шовного участка ЗТВ хрупкому разрушению из-за интенсивного роста зерна аустенита при температуре выше 1200 °С, образования карбидов типа (Fe, Мп)3С по границам зерен аустенита при замедленном охлаждении.
Применяемые для сварки высокомарганцовистых сталей сварочные материалы можно условно разделить на три группы [7 ]: высокомарганцевые, хромоникелевые и сложнолегированные аустенитные. >1,2 МДж/м2, критическая скорость деформации металла шва t>Rp, определяющая сопротивляемость образованию горячих трещин, составила 3,5—3,7 мм/мин. При сварке порошковыми проволоками 35Х10Г18Н2 и 90ГІЗН4 на тех же режимах показатели механических свойств следующие; ов — соответственно 580 и 510 МПа; 6S соответственно 14,5 и 18 %, KCV —соответственно
1,4 и 1,6 МДж/м2, пкр—соответственно 0,4 и 0,4 мм/мин. На основе этих данных в работе [7] сделан вывод об эффективности применения низкоуглеродистых хромомарганцевых и хромоникелевых электродных материалов для сварки стали 110Г13Л как обеспечивающих повышенную технологическую прочность сварных соединений в процессе кристаллизации.
Для ручной дуговой сварки сталей типа 110Г13Л применяют электроды марки ОЗЛ-19 с рутиловоосновным покрытием и стержнем из низкоуглеродистой высоколегированной хромоиикелевой проволоки 07Х25Н13. По данным работы [2], в ряде случаев электроды ОЗЛ-19 не обеспечивают требуемого уровня прочности и ударной вязкости, установленных для сталей (см. табл. 10.9), кроме сталей типа 110Г13МЛС, а химические составы металла шва и основного металла резко различаются. При этом, естественно, теряется способность металла шва к упрочнению при наклепе, а сопротивляемость износу резко снижается. Другим неблагоприятным фактором является наличие ферритной фазы в металле шва, которая способна превращаться в о-фа з у под действием высокого уровня структурных напряжений из-за разницы физических свойств а — и у-фаз, легированных Мп или Сг и Ni. Отмеченное характерно и для сварных соединений, полученных с применением электродов марки ЦНИИ-48Г, поэтому разрабатываются другие виды сварки. К ним относится термитная сварка, предлагаемая в работе [2] для соединения деталей из сталей типа 1І0Г13Л, отличающаяся энергетической автономностью и способствующая существенному уменьшению длительности пребывания наплавленного металла при критических температурах и сокращению протяженности зон неполного расплав
ления и термического влияния по сравнению о ручной дуговой сваркой. При этом обеспечивается однородность основного и наплавленного металлов по химическому составу и механическим свойствам.
Например, износостойкость крестовин рельсов из стали типа 110Г13Л, полученных термитной сваркой с использованием смеси 0,78 (ЗГе304 + 8А1) и 0,22 (Мп203 + 2А1), составляет не менее 80 % соответствующих характеристик основного металла [2J. Разрушающая нагрузка сварных соединений из стали 110Г13Л при испытаниях на трехточечный изгиб (на базе 1 м) оказалась на 20—30 % выше, чем для соединений, полученных ручной дуговой сваркой электродами ЦНИИ-48Т.
В МИНГ им. И. М. Губкина О. И. Стекловым, П. А. Бе- ляшиным, Э. П. Мотусом была разработана технология сварки высокомарганцовистых сталей, основанная на применении плазменно-дуговой и контактной сварки оплавлением. Сварные соединения стали 110Г13Л толщиной 12 мм с содержанием 1,41 % С, 10,5 % Мп, 2,3 % Сг, 0,74 % Мп, 0,21 % Si, 0,01 % S и 0,01 % Р после закалки с 1100 °С имеют ав — 807 МПа, KCU — = 1,75 МДж/м2.
При ручной дуговой сварке электродами типа ЭА395/9 (сварочная проволока Св-10Х16Н25АМ6, / = 120 A; U = 50 В; псв = = 7 м/ч) в металле шва образуются горячие трещины (см. рис. 10.10, а) по границам кристаллитов, где отмечается выделение карбидов (рис. 10.10, б). В околошовной зоне по границам зерен аустенитной структуры образуются прослойки цементита, легированного марганцем. Для этих сварных соединений ов — 560 МПа, 6 = 8%, ij) = 7,5 %, KCU металла шва и ЗТВ составляет соответственно 1,07 и 0,46 МДж/м2, угол загиба 60°.
При плазменно-дуговой сварке сварочной проволокой Св-07Х25Н12Г2Т (/ = 300 A, U — 25 В, псв = 10 м/ч) выделения карбидов по границам кристаллитов в металле шва более дисперсны, чем при ручной дуговой сварке. Горячие трещины отсутствуют. Механические свойства сварных соединений по отдельным показателям соответствуют следующим значениям: ов = 683 МПа, 6 = 24,7 %, |) = 21,5, угол загиба 150°; KCU металла шва и ЗТВ соответственно 1,69 и 1,13 МДж/м2.
При контактной сварке оплавлением на машине К-617 (время оплавления 135 с, величина осадки 10 мм) сварное соединение имеет относительно однородную мелкодисперсную аустенитную структуру, ов = 812 МПа, 6 = 28 %, >|) = 18,7 %, угол загиба 110е; KCV шва 1,68, околошовной зоны 1,71 МДж/м2.
Технология сварки высоколегированных сталей (часть1)
С развитием атомной энергетики, а также реактивной и ракетной техники появилась необходимость в использовании нержавеющих, жаропрочных и других высоколегированных сталей и сплавов таких толщин, которые целесообразно сваривать электрошлаковым способом. Прежде всего начали применяться аустенитные стали и сплавы.
Среди них наибольшее распространение получили нержавеющая сталь типа 18—8 (1Х18Н9Т, 0Х18Н9 и др.), жаропрочная сталь ЭИ481 (Х12Н8Г8), а также жаропрочные сплавы ЭИ435 (Х20Н80Т), ЭИ437А (Х20Н77Т2ЮР), ЭИ703 (Х20Н35ВЗТ), ЭИ787 (08Х15Н35ВЗТ3ЮР), ЭП126 (Х20Н25В5М3БР) и др.
Указанные стали и сплавы обладают такими физико-химическими свойствами, которые придают технологии электрошлаковой сварки специфические особенности.
Рис. 148. Кольца из аустенитной стали ЭИ435, свариваемые электрошлаковым способом.
К числу их относятся: малая теплопроводность и большой коэффициент расширения при нагреве, высокая склонность к кристаллизационным трещинам в металле шва и основном металле вблизи линии сплавления, наличие в составе свариваемого металла легирующих примесей, обладающих высоким сродством к кислороду (алюминий, титан, цирконий, бор и др. ).
Низкая теплопроводность аустенитных сталей и сплавов на никелевой основе способствует сильному разогреву их в зоне сварки. Поэтому электрошлаковую сварку этих сталей и сплавов необходимо выполнять с применением более широких формирующих приспособлений, чем сварку углеродистых и обычных легированных сталей.
Чтобы избежать кристаллизационных трещин в металле шва, сварку следует выполнять на режимах, которые обеспечивают наибольший коэффициент формы ванны жидкого металла. По этой причине режимы электрошлаковой сварки аустенитных сталей и сплавов на никелевой основе отличаются от режимов электрошлаковой сварки углеродистых и обычных легированных сталей большей шириной зазора между свариваемыми кромками и меньшими значениями тока.
Чтобы избежать потери таких легкоокисляющихся элементов, как алюминий, титан, цирконий и др., которые вводятся в аустенитные стали и сплавы для придания им особых свойств, при электрошлаковой сварке этих сталей и сплавов необходимо применять бескислородные флюсы АНФ-1, АНФ-7 и др.
Из аустенитных сталей и сплавов с применением электрошлаковой сварки в большинстве случаев изготовляют фланцы, различные кольца (рис. 148) и другие детали, в которых свариваемое сечение представляет прямоугольник небольшой высоты.
Такие детали имеют короткие швы, поэтому свариваются пластинчатыми электродами, изготовленными из стали такого же состава, что и свариваемая деталь. В табл. 106 приведены данные, характеризующие электрошлаковую сварку некоторых из указанных деталей.
Таблица 106. Данные, характеризующие электрошлаковую сварку пластинчатым электродом деталей из аустенитных сталей и сплавов.
Сталь и сплав | Свариваемое сечение, мм | Сечение электрода, мм | Флюс | Скорость подачи электрода, м/ч | Сварочный ток, А | Напряжение сварки, В | Ширина зазора в свариваемом соединении, мм |
1Х18Н9Т | 50X50 | 6×50 | АНФ-1 | 3,6 | 900 | 24—26 | 25 |
1Х18Н9Т | 100Х 100 | 10х100 | АНФ-1 | 2,4 | 1200 | 24—26 | 30 |
ЭИ481 | 100X100 | 10×100 | АНФ-1 | 2,9 | 1800 | 23—24 | 30—35 |
ЭИ435 | 125×125 | 10×125 | АНФ-1 | 2,4 | 1800 | 23—24 | 30 |
ЭИ437Б | 100×100 | 10×100 | АНФ-7 | 2,9 | 1800 | 33—25 | 30—33 |
ЭИ703 | 120×120 | 12×120 | АНФ-7 | 2,5 | 1800 | 28—31 | 40 |
ЭИ787 | 80х160 | 10X80 | АНФ-7 | 5,4 | 1800 | 27—28 | 35 |
ЭИ126 | 90×90 | 12×90 | АНФ-7 | 3,0 | 1700 | 28—30 | 36 |
Лазерные технологии
Технологии лазерной сварки
Внедрение технологий лазерной сварки позволяет повысить качество сварных соединений, уменьшить тепловложение и уровень остаточных напряжений и деформаций сварной конструкции, снизить трудозатраты на последующую обработку конструкции, повысить производительность сварочного процесса.
Локальность нагрева и высокие скорости обработки, характерные для лазерной сварки позволяют получать сварные швы с минимальной зоной термического влияния. Высокие скорости нагрева и охлаждения материала при лазерной сварке обеспечивают возможность получения равнопрочных сварных соединений не только однородных, но и разнородных материалов. Наличие глубокого проплавления снижает количество проходов при сварке толстостенных конструкций и позволяет проводить сварку без разделки кромок. При этом необходимо учитывать повышение требований к качеству сборки конструкций под сварку. Возможность транспортировки лазерного излучения с помощью зеркал и оптических волокон позволяет осуществлять сварку в труднодоступных местах.
Институтом лазерных и сварочных технологий разработаны и применяются технологии лазерной сварки нержавеющих сталей, лазерной сварки алюминиевых, титановых сплавов и разнородных соединений, лазерной сварки пластмасс.
Лазерная сварка нержавеющих сталей
Технология сварки нержавеющих сталей отличается от сварки углеродистых рядом особенностей. Практически все нержавеющие стали являются высоколегированными сплавами и обладают другими физико-химическими свойствами. У нержавеющих сталей удельное электрическое сопротивление практически в 6 раз больше, температура плавления на 100 градусов меньше, чем у низколегированного и углеродистого проката. Теплопроводность практически в два раза меньше, что приводит к концентрации теплоты и увеличению области проплавления в зоне сварки. Также у нержавеющих сталей термический коэффициент линейного расширения выше практически на 20%, что способствует существенной деформации во время сварки. Указанные факторы могут способствовать появлению существенных остаточных напряжений, которые могут привести к значительному короблению металлоконструкции и образованию трещин, а неправильный термический режим также может снизить коррозионные свойства сварного соединения.
Классические виды сварки преимущественно осуществляются с существенным перегревом. Перспективные методы лучевой обработки позволяют избежать подобных последствий. Лазерные и лазерно-дуговые методы сварки также позволяют существенно снизить затраты присадочных материалов. Локальный нагрев позволяет получить зону термического влияния толщиной не более 2-3 мм, и избежать коробления конструкции. Высокая скорость сварки позволяет уменьшить остаточные напряжения и, в итоге, избежать образование трещин при сварке и исключить негативное влияние перегрева на коррозионные свойства металла.
Институтом лазерных и сварочных разработана специальная система газовой защиты для сварки высоколегированных сталей толщиной от 0,4 – 15мм. Экспериментальные исследования показали получение качественного сварного соединения, при значениях скоростей сварки в диапазоне от 1 до 5 м/мин., обеспечивающих стабильное формирование сварного шва при отсутствии дефектов. Для определения технологических параметров сварки на базе института была разработана математическая модель процесса сварки в различных пространственных положениях, которая была экспериментально верифицирована. Разработанная модель процесса формирования шва при лазерной сварке является эффективным средством анализа нестационарных процессов и может обоснованно применяться для отбора стабильных технологических режимов для сварки нержавеющих сталей.
Лазерная сварка алюминиевых, титановых сплавов и разнородных соединений
В авиакосмической промышленности, судостроении, транспортном машиностроении и других отраслях промышленности при изготовлении целого ряда ответственных изделий часто бывает необходимо применять сварку разнородных материалов: подобные соединения возникают при изготовлении несущих алюминиевых элементов фюзеляжа, крыльев самолетов, судовой и топливной арматуры из алюминия со стальным корпусом, топливных баков, соединения медно-никелевого сплава с углеродистой сталью при изготовлении холодильных установок, испарителей, сосудов давления и т.п.
Задача сварки разнородных материалов технологически достаточна сложна. Это связано с металлургическими особенностями формирования швов таких соединений при сварке плавлением. Многие сочетания разнородных металлов: медь/алюминий, алюминий/сталь, алюминий/титан, титан/сталь, железо/ниобий и др. имеют ограниченную взаимную растворимость.
В авиастроении требуется применять сварку алюминиевых сплавов со сталями и сплавами на основе титана и меди. Сварка алюминиевых сплавов с другими материалами сопровождается рядом трудностей: большая разница в теплопроводности ведет к интенсивному теплоотводу в сторону алюминия, что препятствует образованию качественного сварного соединения. Металлургические особенности формирования соединения разнородных материалов, одним из которых является алюминиевый сплав, приводят к образованию в зоне сплавления хрупких интерметаллидов, что негативно влияет на свойства сварного соединения. В связи с указанными трудностями только некоторые виды сварки подходят для соединения таких разнородных материалов.
Лазерная сварка является одним из наиболее перспективных методов. В сравнении с другими методами сварки разнородных материалов, данный метод не требует применения дополнительных материалов, специальной обработки кромок, а также обладает высокой скоростью сварки (до 4 м/мин). Данный метод позволяет получить ультратонкую диффузионную зону и избежать появления дефектов. Главной особенностью лазерной сварки и математической модели, разработанной для данного метода сварки, является возможность прогнозирования скоростей диффузионного обмена, которые зависят от регулируемых температурно-временных условий взаимодействия металлов при сварке. Путем варьирования скорости сварки, величины смещения фокуса лазерного пучка в сторону одного из свариваемых металлов, мощности излучения, можно получить требуемую структуру сварного соединения.
Экспериментальные исследования, проведенные в ИЛИСТ с использованием соответствующего технологического и исследовательского оборудования показали, что при варьировании вышеперечисленных параметров можно получить ультратонкую диффузионную зону без непрерывных интерметаллидных прослоек. При этом, в сварном шве отсутствуют такие дефекты, как трещины и поры, а механические свойства сварного соединения соответствуют свойствам используемого алюминиевого сплава.
Лазерная сварка пластмасс
Лазерная сварка является актуальной технологией для соединения термопластов в промышленности. Несмотря на то, что большинство пластиков прозрачны для лазерного излучения диодного лазера, сварка возможна за счет комбинации прозрачных и непрозрачных пластиков, при этом зона высоких температур ограничена областью контакта. При этом поверхность прозрачного пластика не подвержена деструкции. При сварке прозрачных пластиков необходимо использовать поглощающие добавки. Дополнительный контроль температуры активной зоны обеспечивает высокое качество технологического процесса.
Технология сварки легированных сталей | Строительный справочник | материалы — конструкции
Сварка низколегированных и среднелегированных конструкционных сталей
Свариваемость таких сталей зависит от содержания углерода и легирующих компонентов и ухудшается с ростом содержания углерда и легирующих компонентов. Стали кремнемарганцевой группы 15ГС, 18Г2С и 25Г2С сваривают электродами типа Э60А марки УОНИ-13/65. Перед сваркой кромки тщательно зачищают от грязи, ржавчины и окалины.
Сварку выполняют предельно короткой дугой. Изделие перед сваркой подогревают до температуры 200 С, электроды перед сваркой прокаливают при 400°С в течение одного часа.
Кремнемарганцемедистые стали 10Г2СД, 10ХГСНД, 15ХСНД и 12ХГ сваривают электродами типа Э50А марки УОНИ-13/55. Изделие перед сваркой не подогревают.
Сварка низколегированных и среднелегированных конструкционных сталей
Особенности сварки высоколегированных сталей
К высоколегированным относят стали, суммарный состав легирующих элементов в которых составляет не менее 10%, при содержании одного из них не менее 8%. При этом содержание железа должно составлять не менее 45%. В основном это стали, обладающие повышенной коррозионной стойкостью или жаростойкостью. Легирование сталей выполняют углеродом, марганцем, кремнием, молибденом, алюминием, ванадием, вольфрамом, титаном и ниобием, бором, медью, серой и фосфором. Введение легирующих элементов меняет физические и химические особенности стали.
Так, углерод способствует повышению прочности стали и снижению ее пластичности. Окисление углерода в процессе сварки способствует появлению пор. Кремний является раскислителем и содержание его в стали более 1% приводит к снижению свариваемости. Хром также снижает свариваемость, способствуя созданию тугоплавких окислов. Никель повышает прочность и пластичность сварочного шва, не снижая свариваемость стали. Молибден увеличивает прочность и ударную вязкость стали, ухудшая свариваемость. Ванадий в процессе сварочных работ сильно окисляется, поэтому его содержание в стали предусматривает введение раскислителей. Вольфрам тоже сильно окисляется при повышенных температурах, ухудшает свариваемость стали.
Титан и ниобий предотвращают межкристаллитную коррозию. Бор повышает прочность, но затрудняет свариваемость. Медь повышает прочность, ударную вязкость и коррозийную стойкость стали, но снижает ее свариваемость. Повышенное содержание в стали серы приводит к образованию горячих трещин, а фосфор способствует образованию холодных трещин.
Содержание тех или иных легирующих элементов определяют по маркировке стали. Первые две цифры в маркировке означают содержание углерода в сотых долях процента; легирующие элементы обозначают буквенными символами, а стоящие за ними цифры указывают на примерное содержание этих элементов, при этом единицу и меньше не ставят. Символ «А», установленный в конце маркировки, указывает, что сталь высококачественная, с пониженным содержанием серы и фосфора. Наиболее широкое применение получили коррозионно-стойкие хромоникелевые стали (12Х18Н10Т, 10Х23Н18 и некоторые другие).
Из вышесказанного видно, что, как правило, легирование стали приводит к снижению ее свариваемости, а первостепенную роль при этом играет углерод. Поэтому доля влияния каждого легирующего элемента может быть отнесена к доле влияния углерода. Повышенное содержание углерода и легирующих элементов способствует увеличению склонности стали к резкой закалке в пределах термического цикла, происходящего во время сварки. В результате этого околошовная зона оказывается резко закаленной и теряет свою пластичность.
Поэтому при сварочных процессах высоколегированных сталей, происходящих в зоне плавления металла и околошовной области, возникают горячие трещины и межкристаллитная коррозия, проявляющаяся в процессе эксплуатации. Основной причиной появления трещин является образование крупнозернистой структуры в процессе кристаллизации и значительные остаточные напряжения, полученные при затвердевании металла. Легирование влияет на вязкость металла и коэффициент поверхностного натяжения, поэтому у большинства высоколегированных сталей сварочный шов формируется хуже, чем у низколегированных и даже углеродистых сталей.
Межкристаллитная коррозия характерна для всех видов высоколегированных сталей, имеющих высокое содержание хрома. Под действием нагрева образовавшиеся карбиды хрома выпадают по границам зерен, снижая их антикоррозийные свойства.
Препятствует образованию карбидов хрома легирование стали титаном, ниобием, танталом, цирконием и ванадием. Положительное влияние на качество сварочного шва оказывает дополнительное легирование сварочной проволоки хромом, кремнием, алюминием, ванадием, молибденом и бором.
Для сварки высоколегированных сталей используют как ручную дуговую, так механизированную сварку под флюсом и в среде защитных газов. Сварка выполняется при минимальном тепловложении с использованием термообработки и применением дополнительного охлаждения. Введение легирующих элементов меняет и технологические особенности стали. Так, система легирования снижает теплопроводность стали и повышает ее электрическое сопротивление. Это оказывает влияние на скорость и глубину плавления металла, что требует меньшего вложения энергии, и увеличения скорости подачи сварочной проволоки.
Ручную дуговую сварку высоколегированных сталей выполняют при пониженных тока обратной полярности. Сварку ведут короткой дугой ниточными валиками без поперечных колебаний.
Проволока, применяемая для изготовления электродов, должна соответствовать марке стали с учетом ее свариваемости. Защитное покрытие электродов должно иметь состав, снижающий отрицательное действие повышенной температуры. К примеру, для сварки кислотостойкой стали 12X18HI0T электроды типа Э-04Х20Н9 (марки ЦЛ-11) препятствуют образования горячих трещин и межкристаллитной коррозии. Предварительный и сопутствующий подогрев снижает опасность возникновения трещин. Для защиты сварочной ванны используют инертный газ или аргон и его смеси с гелием, кислородом и углекислым газом.
Сварку в среде углекислого газа можно выполнять только в случаях, когда отсутствует опасность возникновения межкристаллитной коррозии. Сварка плавящимся электродом выполняется при значениях тока, обеспечивающих струйный перенос электродного металла.
При сварке возникает опасность коробления и остаточных сварочных напряжений. Поэтому после сварки часто возникает необходимость в термообработке.
Высоколегированные хромоникелевые стали и их сварка
Рекомендуем приобрести:
Установки для автоматической сварки продольных швов обечаек — в наличии на складе!
Высокая производительность, удобство, простота в управлении и надежность в эксплуатации.
Сварочные экраны и защитные шторки — в наличии на складе!
Защита от излучения при сварке и резке. Большой выбор.
Доставка по всей России!
Сплавы на основе железа с высоким содержанием хрома и никеля относятся к особой группе сталей с комплексом свойств, принципиально отличающихся от свойств обычных углеродистых низко- и среднелегированных сталей. Никель, существенно стабилизирующий γ-фазу, расширяет температурную и концентрационную область ее существования, снижает критическую скорость охлаждения при закалке. При легировании стали одновременно большим количеством никеля (более 8%) и хрома (более 18%) критическая скорость охлаждения снижается настолько, что сталь даже при очень медленном охлаждении сохраняет переохлажденный аустенит. При этом снижение температуры начала мартенситного превращения ниже комнатной приводит к сохранению аустенитного состояния таких сталей до комнатной и при определенных условиях — ниже комнатной температур.
Однако в реальных высоколегированных хромоникелевых сталях, содержащих углерод и другие элементы, фазовое состояние как при нагреве, так и после охлаждения может быть более сложным. При этом во всех случаях основой обеспечения свойств является наличие полностью или преимущественно аустенитного состояния сплава в условиях эксплуатации.
Первоначально высоколегированные хромоникелевые стали появились как нержавеющие, кислотостойкие, когда было установлено, что легирование стали свыше 6% Ni резко облагораживает электрохимический потенциал, а одновременное присутствие свыше 12% Сr способствует проявлению защитных свойств окисной пленки, образующейся на поверхности металла, хром оказывает также определенное положительное влияние и на сдвиг в положительную сторону электрохимического потенциала стали. Так возникла широко известная классическая коррозионно-стойкая сталь 18-8, содержащая 18% Cr и 8% Ni.
В дальнейшем на основе изучения связи строения и фазового состояния подобных сталей со свойствами появились другие высоколегированные хромоникелевые стали с более высокой коррозионной стойкостью в особо химически активных средах. Подобные высоколегированные стали с аустенитной основой имеют высокие жаропрочность и хладостойкость. Отдельное место занимают высоколегированные хромоникелевые высокопрочные стали. Хромоникелевые стали широко применяют в сварных конструкциях и изделиях в разных отраслях промышленности. Свойства таких сталей, их коррозионная стойкость, жаропрочность, хладостойкость, свариваемость, технологичность при деформации и резании зависит от химического состава сталей, их фазового и структурного состояния.
Источник: Л.С. Лившиц. «Металловедение для сварщиков». Москва. Машиностроение, 1979.
См. также:
Сварка сталей HSLA — TWI
Существует два метода, с помощью которых достигаются как высокая прочность на разрыв, так и ударная вязкость — микролегированием с добавлением небольших количеств прочных карбидных и нитридных форм и очень тщательным контролем температуры прокатки — контролируемая прокатка или термомеханическая обработка (TMCP). стали).
Наивысшая эффективность достигается за счет комбинации двух методов. Целью обоих методов является получение зерна как можно меньшего размера, мелкого зерна, обеспечивающего наилучшую ударную вязкость, а каждое уменьшение диаметра зерна вдвое дает увеличение прочности на разрыв на 50%.
Повышение свариваемости является дополнительной целью, и это достигается за счет снижения закаливаемости стали, при этом содержание углерода в некоторых сталях составляет менее 0,05% C, и снижения нежелательных элементов, таких как сера и фосфор, до как можно более низкого уровня.
Для компенсации потерь углерода и повышения прочности на разрыв вносятся небольшие добавки легирующих элементов, таких как ниобий (<0,10%), титан (<0,030%) и ванадий (<0,15%), возможно, также с небольшими количествами молибдена. , хром, медь и азот.Эти элементы представляют собой сильные карбидо- и нитридообразователи, образующие тонкую дисперсию стабильных выделений, которые препятствуют росту зерна во время горячей прокатки и способствуют зарождению зародышей мелкозернистого феррита во время охлаждения.
Эти элементы также обеспечивают некоторое увеличение прочности за счет дисперсионного твердения. Контролируемая прокатка методом горячей прокатки TMCP также может использоваться для обеспечения дополнительного измельчения зерна и, следовательно, повышения прочности на разрыв и ударной вязкости. ТМСР проводят при температуре примерно или чуть ниже температуры рекристаллизации стали i.е. ниже примерно 900 ° C, в результате чего образуются удлиненные кристаллы аустенита. Ускоренное охлаждение от температуры прокатки затем вызывает образование очень мелкозернистого феррита на границах аустенитных зерен.
Несмотря на улучшенную свариваемость этих сталей, существуют некоторые производственные проблемы. Во-первых, водород вызывает холодное растрескивание.
Низкое содержание углерода — и, следовательно, низкий углеродный эквивалент, иногда менее 0,30CE v — означает, что эти стали имеют низкую чувствительность к водородному холодному растрескиванию (см. Рабочие знания 45, но обратите внимание, что стандартная формула эквивалента углерода IIW недействительна. для всех этих сталей, и на них нельзя всегда полагаться при расчете температур предварительного нагрева).
Таким образом, стали HSLA можно сваривать с меньшим предварительным нагревом, чем было бы допустимо для обычных углеродисто-марганцевых сталей, несмотря на их более высокую прочность. Таким образом, наибольший риск образования холодных трещин в этих типах сталей связан с металлом сварного шва, а не в ЗТВ. На это есть несколько причин; a) Высокая прочность основного металла означает более высокие остаточные напряжения во время сварки. b) Чтобы соответствовать пределу прочности и ударной вязкости основной стали, присадочные металлы должны быть более высоколегированными и, следовательно, будут иметь более высокий CE v , возможно, до 0.6CE v (IIW) при согласовании прочности на разрыв стали с пределом текучести 700 МПа с электродом E11018-G. c) Металл сварного шва превращается из аустенита в феррит при более низкой температуре, чем основная сталь (как правило, в обычной углеродисто-марганцевой стали все наоборот), что означает, что любой водород в HAZ переходит в все еще аустенитный металл сварного шва, который имеет высокую растворимость в водороде. Поэтому рекомендуется предварительный нагрев в зависимости от состава металла сварного шва и использовать методы с низким содержанием водорода.
Исключением из этого правила являются трубопроводные стали HSLA, специально предназначенные для сварки целлюлозными электродами. Консультации относительно температуры предварительного нагрева для конкретных сталей следует запрашивать у производителя стали.
Во-вторых, даже несмотря на то, что стали обычно имеют очень низкий уровень серы, стали, содержащие менее 0,05% C, могут страдать от трещин при затвердевании в корневом проходе стыковых соединений, особенно если корневой валик наплавляется при высокой скорости сварки. Причина этого в том, что из-за высокого разбавления присадочного металла металл шва образуется с низким содержанием углерода.Это низкое содержание углерода, в свою очередь, приводит к чрезмерному росту зерен аустенита во время сварки, и эти большие зерна увеличивают риск растрескивания центральной линии затвердевания в корневом валике. Эта проблема, по-видимому, наиболее распространена при сварке стыковых соединений труб с использованием целлюлозных электродов, вероятно, из-за возможности использования быстрой техники сварки вертикально вниз.
В-третьих, могут возникнуть проблемы с твердостью и прочностью в ЗТВ. Производитель стали уделяет большое внимание контролю температуры прокатки и скорости охлаждения для обеспечения желаемых свойств.Затем деталь сваривается, образуя зону термического влияния, которая подверглась неконтролируемому циклу термообработки. Микроструктура в ЗТВ будет варьироваться в зависимости от состава стали и подводимого тепла в процессе сварки. Большое количество тепла будет способствовать росту зерна, что отрицательно скажется как на прочности, так и на ударной вязкости. Как показывает практический опыт, тепловложение должно быть ограничено максимумом примерно 2,5 кДж / мм, а температура между проходами должна поддерживаться на уровне не более 250 ° C, хотя некоторые стали, содержащие титан и бор, могут выдерживать тепловложение до 4.5 кДж / мм без чрезмерной потери прочности. Для окончательного утверждения о контроле теплоподвода следует обратиться за советом к производителю стали.
Эти стали ни в коем случае нельзя подвергать нормализации или отпуску, хотя термообработка после сварки (PWHT) часто является требованием, когда толщина компонента превышает примерно 35-40 мм. При применении PWHT необходимо соблюдать осторожность, чтобы температура выдержки не превышала 600 ° C; часто указывается диапазон температур от 550 ° C до 600 ° C. Причина этого в том, что многие стали TMCP подвергаются ускоренному охлаждению до температуры около 620 ° C; термообработка при этой температуре или близкой к ней приведет к существенному снижению прочности на разрыв из-за чрезмерного отпуска.То же ограничение применяется к любой горячей обработке — лист не должен подвергаться горячей прокатке, а температура местного нагрева для коррекции деформации не должна превышать 600 ° C.
Дополнительные рекомендации по сварке этих сталей можно найти в специальной литературе и в спецификации EN 1011 Часть 2 Сварка — Рекомендации по сварке металлических материалов: Дуговая сварка ферритных сталей .
Эту статью написал Джин Мазерс .
(PDF) Влияние сварки на механические и микроструктурные характеристики соединений высокопрочных низколегированных сталей
2
1234567890 ‘’ «»
KOD 2018 IOP Publishing
IOP Conf. Серия: Материаловедение и инженерия 393 (2018) 012020 doi: 10.1088 / 1757-899X / 393/1/012020
является результатом специфической микроструктуры, полученной с помощью микролегирования и строго контролируемых производственных процессов
. Эти стали следует рассматривать иначе, чем обычные стали, которые они заменили в сварных конструкциях общего назначения.С другой стороны, характеристики и свойства
этих сталей в эксплуатации являются результатом их микроструктуры и дополнительных факторов. Количество
и сложность факторов, влияющих на эксплуатацию, подразумевают, что механические характеристики, свойства
и ответ на нагрузку могут быть определены только путем экспериментальных испытаний в реальных эксплуатационных условиях
. Концентрация напряжений изменила распределение напряжений, положение максимальных напряжений и, к
, положение критического поперечного сечения с точки зрения целостности и безопасности.Численное моделирование
конструкций из высокопрочных низколегированных сталей является одним из наиболее эффективных инструментов
для определения наилучшей проектной концепции конкретных сварных конструкций. Но проверка концепции конструкции
сварной конструкции из высокопрочных сталей может быть проведена только путем экспериментальных испытаний
. В настоящее время сварка представляет собой один из многих способов соединения металлов. Технология
и процедуры сварки постоянно развиваются путем применения, а
— внедрения новых достижений в фундаментальных научных дисциплинах.На этом этапе появляется
идентификация наиболее подходящего для конкретного случая в связи с факторами, упомянутыми выше.
Выбор адекватных сварочных процедур с подходящими параметрами, в том числе термическая обработка
сварных соединений, при необходимости чередование структурных преобразований может быть сведено к минимуму или даже
может быть превращено в полезное. Идентификация процесса сварки и его параметров стала предметом исследования
, особенно с точки зрения специфической свариваемости высокопрочных низколегированных сталей.
Ссылка [1] систематически подчеркивает влияние сварочных процессов и условий на микроструктуру
, механические свойства и коррозионную стойкость дуплексных нержавеющих сталей и их различных комбинаций
на основе взаимосвязи структуры и свойств.
Вукич и др. в ссылке [2] указано, что существующие, очень скудные и часто нечеткие и недостаточные
рекомендаций по выбору оптимальной технологии сварки являются одной из причин большого
количества дефектов сварных соединений.Сделан вывод о том, что указанные проблемы
могут быть успешно решены путем правильного выбора процедуры, присадочного металла и технологии сварки, подтвержденных экспериментами
, проведенными в лабораторных условиях или в реальных условиях эксплуатации. Таким образом, частично благодаря результатам, представленным в этой статье
, технологи получат возможность заранее, за очень короткий период времени, предсказать механические и металлургические свойства
соединений этого класса высокопрочных сталей.Это будет
без проведения большого количества практических тестов и без использования личного опыта дизайнера
.
Фидрих с сотрудниками в работе [3] охарактеризовали проблемы свариваемости высокопрочной стали в условиях подводной влажной сварки
. Вода как сварочная среда усиливает действие
неблагоприятных факторов, влияющих на склонность сварных стыков стали к холодному растрескиванию. Экспериментально оценена подверженность холодному растрескиванию
стали С355Ж2Г3 и стали С500М во влажных условиях.Был сделан вывод о том, что рассматриваемые стали характеризуются высокой склонностью к образованию трещин в
сварных швах.
Представленный краткий обзор литературы указывает на научный интерес и актуальность исследований, представленных в статье
. Несмотря на высокий интерес к сварке высокопрочных низколегированных сталей
до сих пор не выделены в деталях с четкими предписаниями стандартами и нормами.
2. Экспериментальные испытания
Модели, которые проходят экспериментальные испытания, изготовлены из высокопрочной низколегированной стали марки
, соответствующей марке S690QL согласно стандарту EN 10025-6, сталь № 1.8928
классификация 3.1 / 3.2 — EN 10204 / TCM. Использованная сталь производится SSAB Oxelösund AB, 613 80
Oxelösund, Швеция под коммерческим названием Weldox 700. Химический состав стали Weldox 700
представлен в таблице 1. Механические свойства использованной высокопрочной низколегированной стали Weldox 700
представлены в Таблице 2.
Сварка плавлением высокопрочной низколегированной стали: Мини- Отзыв
Мини-обзор Открытый доступ
Сварка плавлением высокопрочной низколегированной стали. Отзыв
Ле Зай, Синь Тонг *
Колледж материаловедения и инженерии, Чунцинский университет, Чунцин, Китай
* Автор, ответственный за переписку: Синь Тонг, Колледж материаловедения и инженерии, Чунцинский университет, Чунцин, 400045, Китай. Эл. Почта: @Поступила: 09.05.2020 г .; Принята в печать: 20 мая 2020 г .; Опубликовано: 26 марта 2019 г.
Высокопрочная низколегированная (HSLA) сталь демонстрирует превосходный предел прочности на растяжение.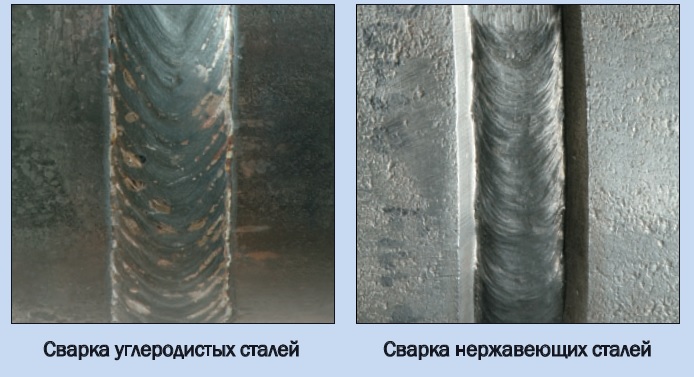
Ключевые слова: Сталь высокопрочная низколегированная; Сварка плавлением; Сварочный дефект; Микроструктура; Механические свойства
Стали HSLA классифицируются как низкоуглеродистые стали, и их высокая прочность достигается за счет добавления небольшого процента легирующие элементы, вызывающие дисперсионное твердение и зернистость упрочнение путем термомеханической обработки [1]. Стали HSLA широко используются для транспортировки трубопроводов природный газ и нефть, сосуды под давлением, морские платформы, атомные электростанции и мосты [2-5], в которых процесс сварки является одним наиболее ответственных производственных процессов для производства вышеуказанные сопутствующие товары.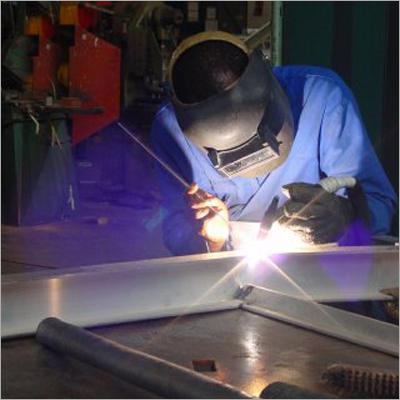
Состояние исследований сварки плавлением сталей HSLA
Дуговая сварка Дуговая сварка использует дугу в качестве источника тепла для преобразования электрического тока.
энергии в тепловую энергию и плавить деталь, тем самым достигая
цель соединения металлов. Алипоромирабад и др. [6] присоединились
Трубопроводная сталь X70 сваркой вольфрамовым электродом в среде инертного газа (TIG) с низким
тепловложения, и обнаружил высокий уровень остаточного напряжения
в металле шва (WM) и зоне термического влияния (HAZ), которые
был связан с микроструктурой бейнита и видманштеттеном
феррит.Ли и др. [7] исследовали микроструктуру и
механические свойства LW, TIG и Metal Active Gas (MAG)
сварили стык DP780, и выяснили, что размеры сварного шва
и HAZ увеличились с увеличением погонной энергии при сварке (MAG
> TIG> LW). Соединения, сваренные LW и TIG, имеют более высокую
прочности, чем у сваренных MAG, потому что микроструктура
зоны плавления LW и TIG состоит из мартенсита. Тем не мение,
скорость охлаждения при сварке MAG относительно низкая, поэтому
микроструктура в основном состоит из феррита, как показано на (рис. 1) Guo et al.[8] исследовали потерю прочности высокопрочной стали S960.
производства GMAW, прочность сварного шва составляла 100
МПа ниже, чем у основного металла (BM). Авторы также
установлено, что зона разрушения находится в ЗТВ из-за
смягчающий эффект. Lan et al. [9] провели многократную дугу под флюсом
сварка стали HSLA несколькими микролегированными электродами. В
результаты показали, что сварной шов имел хорошую вязкость, а
основным режимом разрушения было вязкое разрушение, которое в основном произошло из-за
к образованию игольчатого феррита.Однако стойкость
ЗТВ значительно уменьшилась с увеличением погонной энергии, что
объясняется изменением микроструктуры реечного бейнита /
от мартенсита до крупнозернистого бейнита.
Его можно найти в
Вышеупомянутый обзор литературы показал, что размягченная ЗТВ обычно была одной
самых слабых мест стыка из-за большого тепловложения
дуговой сварки. Между тем, холодные трещины всегда были
произведены в ЗТВ, что также серьезно ухудшило характеристики
сварного шва.
Плазменная сварка
Linet al.[10] подготовили сварное соединение D6AC методом плазменно-дуговой сварки, и
затем закалили соединение при 300 ° C, 450 ° C и 600 ° C в течение 1000 мин.
Результаты показали, что V-образный предел прочности на разрыв (V-образный надрез
прочность на разрыв: NTS) стыка без муравьиной дополнительной обработки
значительно увеличился. Однако хрупкость соединения привела к
значительное снижение NTS из-за зернограничного скольжения
после отпуска, особенно при более высоком отпуске
температуры (например, 450 oc и 600 oc). Ахиали и др. [11] изучал
микроструктура и многоцикловая усталость DP590
соединение изготовлено GMAW и PAW.Результаты показывают, что PAW
образец имел более высокую усталостную долговечность, относительно пологий уклон S-N и
более высокие пределы выносливости по сравнению с образцом GMAW (как показано на рисунке 2). Более длительный срок службы и более высокие пределы выносливости
Образцы соединений внахлест PAW можно отнести к уменьшенным
эффект надреза на носке сварного шва по сравнению с одинарной сваркой GMAW
образцы соединений внахлест.
Рис. 1: Изображения , полученные с помощью оптической микроскопии, демонстрирующие микроструктуру (a и b) лазерной сварки, (c и d) TIG и (e и f) материалов, сваренных MAG: (a, c, e) в целом и (б, г, е) области металла сварного шва [7].
Рис. 2: S-N-графики образцов, сваренных GMAW и PAW [11].
Лазерная сваркаВо избежание размягчения ЗТВ, сварочных трещин и некоторые другие сварочные дефекты возникли из-за большого погонного тепла. при обычной сварке плавлением LW с более концентрированной плотность энергии и меньшее тепловложение также применяются для сварка стали HSLA [12-14]. [12] исследовали разницу в микроструктура и механические свойства сварной стали Д406А с помощью LW и TIG, и обнаружил, что деформация соединения LW после сварки было около 21% деформации TIG сустав (рисунок 3).
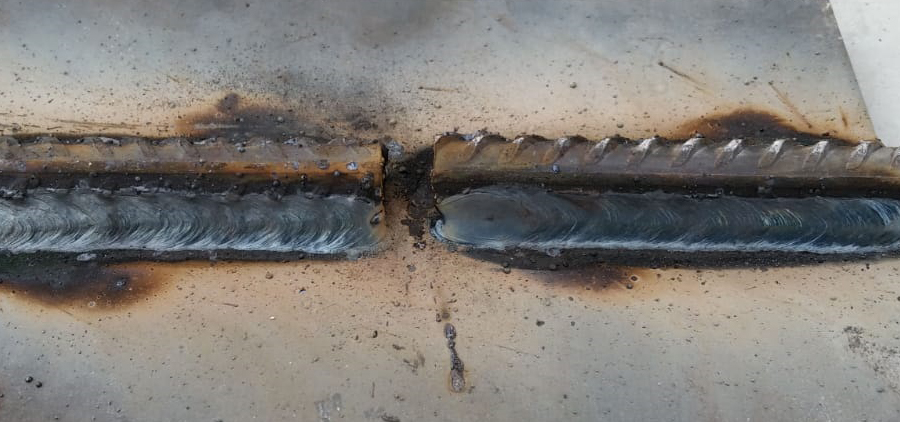
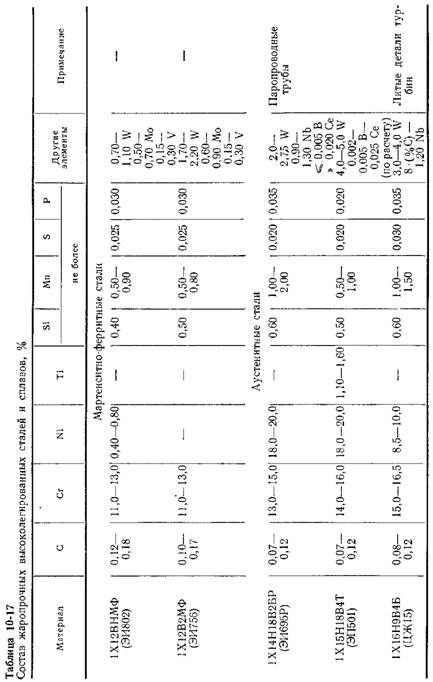
Электронно-лучевая сварка
Во время EBW ускоренный и сфокусированный электронный пучок
применяется для бомбардировки заготовки, а кинетическая энергия
электрон преобразуется в тепловую энергию для плавления детали
и осознаем присоединение. Вакуумная электронно-лучевая сварка (VEBW) — это
в настоящее время наиболее широко используемая технология EBW. [15] сравнили
и изучили различия микроструктуры и производительности
между состоянием после сварки и состоянием отпуска 300M
сверхвысокопрочная сталь производства EBW.Результаты показали
микроструктура зоны сварного шва состояла из нижних
бейнит, остаточный аустенит и доэвтектоидный феррит, а
микроструктура зоны отпущенного шва содержала отпущенный
мартенсит. Прочность соединения на разрыв после отпуска
обработка доходила до 1900 МПа. Жангет др. [16] изучили
влияние послесварочной термообработки на микроструктуру и
Рисунок 3: Контуры искажения для (a) сварного шва TIG и (b) сварного шва LW, полученные с трехмерного бинокулярного стереоизображения XJTUDIC. система сканирования [12].
механических свойств сверхвысокопрочной стали 300M, соединенной методом ЭЛС, и сравнение этого соединения с обычным закаленным и закаленный образец БМ. Результаты показали, что процессы термообработки не могут устранить столбчатые дендриты в сварном шве. шов, а прочность и ударная вязкость образца W-N2QT лучше, чем у закаленного состояния BMat. Хотя EBW также имеет преимущество высокой плотности энергии, большая часть EBW должна работать в вакуумной камере. Поскольку степень вакуума сильно зависит от размера камеры, EBW предъявляет более высокие требования к размеру заготовки (Рисунок 4)
Рисунок 4: Микрофотографии DSEM WM при различных условиях PWHT: (a) W-QT (870 o c / 1 h / OQ + 300 o c / 2 h / AC / два раза), ( б) W-N1QT
(970oc / 0.25 ч / AC + 870 o c / 1 час / OQ + 300 o c / 2 ч / AC / два раза), (c) W-N2QT (970 o c / 1 час / AC + 870 o c / 1 ч / OQ + 300 o c / 2 ч / AC / два раза), и (d) WN2TQT (
970 o c / 1 ч / AC + 700 o c / 2 ч / AC + 870 o c / 1 ч / OQ + 300 o c / 2 ч / AC / два раза) [16] .
Резюме и перспективы
Несмотря на то, что стали HSLA были успешно соединены различными
процессы сварки плавлением, дефекты сварки, такие как сварка
растрескивание, пористость при сварке и размягчение ЗТВ также легко
генерироваться во время обработки.В настоящее время исследователи
в первую очередь направлен на улучшение свойств растяжения
сварное соединение плавлением из стали HSLA, в то время как
внимание к их коррозионным и усталостным свойствам. В то же
времени, построив модель взаимосвязи между
эволюция микроструктуры и распределение напряжений во время
процедура сварки может дать рекомендации по производительности
прогнозирование полученных соединений стали HSLA.
Это исследование не получало какого-либо специального гранта от финансирования. агентства в государственном, коммерческом или некоммерческом секторе.
- Cao X, Wanjara P, Huang J, Munro C, Nolting A. Гибридный волоконный лазер — дуговая сварка толстого сечения высокопрочной низколегированной стали.
Материалы и дизайн. 2011; 32 (6): 3399-3413. DOI: 10.1016 / j.matdes.2011.02.002.
- Вильялобос Дж., Посо А., Кампильо Б., Майен Дж., Серна С. Микролегированные стали на протяжении истории до 2018 г .: Обзор химического состава, обработки и обслуживания водорода. Металлы. 2018; 8 (5): 351. DOI: 10.3390 / met8050351.
- Шао Ю., Лю Ц., Янь З., Ли Х, Лю Ю.Механизм образования и методы контроля игольчатого феррита в стали HSLA: обзор. Журнал материаловедения и технологий. 2018; 34 (5): 737-744. DOI: 10.1016 / j.jmst.2017.11.020.
- Ким Ю.М., Ким СК, Ким Нью-Джерси. Простой метод подбора оптимальной микроструктуры высокопрочных низколегированных сталей с помощью определяющего уравнения. Материаловедение и инженерия. 2019; 743: 138-147. DOI: 10.1016 / j.msea.2018.11.058.
- Нин Дж., Чжан Л.Дж., Сунь М.Дж., Инь XQ, Ню Дж., Чжан Дж.Исследование характеристик и размерных эффектов зоны разупрочнения сварного лазером соединения 20MnTiB. Журнал технологий обработки материалов.
2017; 243: 405-419. DOI: 10.1016 / j.jmatprotec.2017.01.006.
- Алипурамирабад Х., Гомащи Р., Парадовска А., Рид М. Взаимосвязь остаточного напряжения, микроструктуры и механических свойств в многопроходных сварных швах из стали HSLA. Журнал технологий обработки материалов. 2016; 231: 456-467. DOI: 10.1016 / j.jmatprotec.2016.01.020.
- Ли Дж. Х., Пак Ш., Квон Х. С., Ким Г. С., Ли К. С..Сварка стали DP780 лазером, вольфрамом в инертном газе и металлоактивным газом: сравнение твердости, прочности на растяжение и сопротивления усталости. Материалы и дизайн. 2014; 64: 559-565. DOI: 10.1016 / j.matdes.2014.07.065.
- Го В., Ли Л., Донг С., Кроутер Д., Томпсон А. Сравнение микроструктуры и механических свойств сверхузкой лазерной сварки и высокопрочной стали S960, сваренной с помощью газо-металлической дуговой сварки. Оптика и лазеры в технике. 2017; 91: 1-15. DOI: 10.1016 / j.optlaseng.2016.11.011.
- Lan L, Kong X, Qiu C, Zhao D.Влияние микроструктурных аспектов на ударную вязкость многопроходных сварных соединений стали HSLA под флюсом.
Материалы и дизайн. 2016; 90: 488-498. DOI: 10.1016 / j.matdes.2015.10.158.
- Lin CM, Lu CH. Влияние температуры отпуска на эволюцию микроструктуры и механические свойства высокопрочных низколегированных плазменно-дуговых швов D6AC. Материаловедение и инженерия. 2016; 676: 28-37. DOI: 10.1016 / j.msea.2016.08.090.
- Ахиале Г.К., Йонг Дж., Чой В.Д., Ли КБ, Юнг Дж. Г., Нам SW.Микроструктура и сопротивление усталости высокопрочной двухфазной стали, сваренной методами газовой дуговой сварки и плазменной сварки. Металлы и материалы Интернэшнл. 2013; 19: 933-939. DOI: 10.1007 / s12540-013-5005-3.
- Ning J, Zhang LJ, Yang J, Yin XQ, Wang XW, Wu J. Характеристики многопроходной узкозазорной лазерной сварки сверхвысокопрочной стали D406A. Журнал технологий обработки материалов. 2019; 270: 168-181. DOI: 10.1016 / j.jmatprotec.2019.02.026.
- Joshi JR, Potta M, Adepu K, Katta RK, Gankidi MR.Сравнительная оценка микроструктурных и механических характеристик сварных швов разнородных сверхвысокопрочных сталей, сваренных пучком волоконного лазера и вольфрамовым инертным газом.
Оборонные технологии. 2016; 12: 464-472. DOI: 10.1016 / j.dt.2016.08.003.
- Li J, Nayak SS, Biro E, Panda SK, Goodwin F, Zhou Y. Влияние положения и геометрии линии сварки на формуемость высокопрочных низколегированных и двухфазных стальных заготовок, сваренных лазером. Материалы и дизайн. 2013; 52: 757-766. DOI: 10.1016 / j.matdes.2013.06.021.
- He X, Yang X, Zhang G, Li J, Hu H. Закалочная микроструктура и свойства сварных электронно-лучевых соединений сверхвысокопрочной стали 300M. Материалы и дизайн. 2012; 40: 386-391. DOI: 10.1016 / j.matdes.2012.04.010.
- Zhang G, Yang X, He X, Li J, Hu H. Улучшение механических свойств и механизма разрушения сварных электронно-лучевых сварных соединений сверхвысокопрочной стали 300M. Материалы и дизайн. 2013; 45: 56-66. DOI: 10.1016 / j.matdes.2012.09.004.
Исследование по совершенствованию технологии сварки и механизма упрочнения Zr на металле шва стали Q960
Реферат
Высокопрочная сталь Q960 широко используется в сосудах высокого давления, мостах, морских платформах и других важных стальных конструкционных элементах из-за своей высокой прочности и хорошая пластическая вязкость, но легирующие элементы, добавленные в этот вид стали, обладают высокой закаливаемой способностью, особенно после сварки, поэтому прочность и ударная вязкость не могут соответствовать требованиям, что ограничивает их применение в более широком диапазоне. В этой статье, с точки зрения металлургической обработки сварного шва, целью является повышение прочности и ударной вязкости сварочного металла из высокопрочной стали Q960. Для анализа влияния Zr на процесс сварки стали Q960 и упрочняющий и упрочняющий эффект металла шва, в этой статье Fe-Mn-Mo-Cr-Ni используется в качестве основной системы сплава, BaF 2 -CaF 2 -Al-Mg в качестве основной системы шлака и используется метод плавления плавящегося самозащитного электрода для сварки, а также анализирует процесс сварки, микроструктуру, свойства растяжения и ударную вязкость сварного соединения.Результаты экспериментов показывают, что, когда металл шва содержит 0,0061% Zr, минимальная скорость разбрызгивания составляет всего 7%, максимальная скорость удаления шлака составляет 95%, максимальная твердость составляет 357HV, максимальное удлинение составляет 34%, а ударная вязкость составляет самый высокий. В это время содержание игольчатого феррита в микроструктуре сварного шва является самым высоким, имеется определенное количество равноосного мелкозернистого феррита и наименьшее содержание доэвтектоидного феррита, что эффективно улучшает прочность и ударную вязкость металла шва.
.
Ключевые слова: высокопрочная сталь Q960, самозащитная порошковая проволока, легирующий агент, игольчатый феррит, механизм упрочнения и закалки
1. Введение
Высокопрочная низколегированная сталь (HSLA) широко используется в сосудах под давлением , мосты, морские платформы и другие крупномасштабные конструкции из-за своей высокой прочности и хорошей пластичности, ударной вязкости [1,2,3,4,5]. С постоянным появлением новых материалов и процессов, а также постоянным совершенствованием производственных технологий и технологий формования, «энергосбережение, защита окружающей среды и сокращение количества материалов» стали целью развития машиностроительной отрасли, особенно спрос на легкий вес становится все больше. и более срочные [6,7,8,9,10,11].В продукции строительной техники необходимо сваривать от 50% до 70% стали. Качество сварочной конструкции напрямую определяет качество продукции, а также безопасность и надежность компонентов [11,12,13,14]. Однако в процесс выплавки низколегированной высокопрочной стали добавляется большое количество легирующих элементов, что приводит к большей прокаливаемости. После сварки легко возникают проблемы свариваемости, такие как трещины, охрупчивание и разупрочнение зоны термического влияния, и особенно низкотемпературная ударная вязкость не соответствует требованиям, что ограничивает широкое использование низколегированной высокопрочной стали в сварке. более широкий спектр приложений [13,14,15,16].
Результаты показывают, что более высокая температура плавления оксида, более очевидное препятствие для роста аустенитного зерна, может способствовать зарождению игольчатого феррита и улучшить ударную вязкость металла шва [17]. Zr — сильный углерод, азот и оксидообразующий элемент. Энергия образования оксида Zr ниже, чем у Ti, а температура плавления Zr выше, чем у Ti. Как элемент микролегирования, Zr много изучался на предмет влияния микроструктуры и свойств стали [18], но исследований влияния Zr на микроструктуру и свойства металла сварного шва относительно мало.
Самозащитная порошковая проволока — это новый тип сварочного материала, который можно сваривать без дополнительных мер защиты. Он обладает такими характеристиками, как сильное сопротивление ветру, простое сварочное оборудование и подходит для полевого строительства, поэтому может сваривать высококачественные сварные швы. В этой статье, принимая Fe-Mn-Mo-Cr-Ni в качестве основной системы сплава и BaF 2 -CaF 2 -Al-Mg в качестве основной системы шлака, мы определяем правило и механизм влияния элемента Zr в сварочной проволоке. порошка на микроструктуру и механические свойства металла шва, исследован механизм упрочнения и упрочнения металла шва из высокопрочной стали.
2. Материалы и методы
Стальной лист для испытания — это Q960, низкоуглеродистая закаленная и отпущенная сталь, производимая Wuyang Iron and Steel Co., Ltd. (Wugang, Китай), толщиной 10 мм. Его основной химический состав показан на, а его механические свойства показаны на. Стальная полоса, используемая для испытания, представляет собой холоднокатаную коммерческую сталь Steel Plate Cold Commercial (SPCC) марки H08A, которую производит Shanghai Baosteel (Шанхай, Китай) и изготавливается методом холодной прокатки. Ширина стальной полосы 10 мм, толщина 0.3 мм. Его химический состав показан на.
Таблица 1
Химический состав высокопрочной стали Q960 (мас.%).
Компонент | C | Si | Mn | Cr | Ni | Mo | Nb | Ti | B | S | P | 0,5 | 1,6 | 0,8 | 1,0 | 0.![]() | 0,05 | 0,03 | 0,005 | 0,002 | 0,011 |
---|
Таблица 2
Механические свойства высокопрочной стали Q960.
Свойство | Предел прочности на разрыв Rm / МПа | Удлинение, A /% | Энергия удара Akv (−20 ° C) / Дж |
---|---|---|---|
Значение | ≥960 | > 960 | ≥30 |
Таблица 3
Химический состав стальной полосы (мас. %).
Компонент | C | Si | Mn | P | S | Fe |
---|---|---|---|---|---|---|
Содержание | 0,03 | 0,01 | 0,19 |
Металлический порошок для изготовления порошковой проволоки содержит порошок электролитического марганца, порошок никеля, порошок молибдена, металлический хром, порошок алюминия, порошок циркония и порошок железа, а размер частиц составляет 80–100 меш. Mn, Si, Ni, Mo, Cr, Ti, B, Al часто используются в качестве самозащитной порошковой проволоки для сварки высокопрочной стали. Mn может реагировать с S, продуктом MNS, помогает предотвратить горячие трещины, вызванные включениями FES. Cr, Si, B могут образовывать прочный карбид с C, что увеличивает прокаливаемость и прочность сварного шва. Ni и Mo могут сдвигать кривую перехода непрерывного охлаждения металла шва вправо и способствовать образованию игольчатого феррита. Ti, B может способствовать зарождению и росту игольчатого феррита и улучшать ударную вязкость металла сварного шва.Добавление Al может значительно снизить содержание O и N и чувствительность к пористости [3,4,5]. В этом эксперименте содержание другого порошка не изменяется, регулируется только содержание порошка Zr. Формула порошка приведена в.
Таблица 4
Состав порошка порошковой проволоки (мас.%).
Компонент | Zr | Mn | Si | Ni | Mo | Cr | Ti | B | Al | Fe |
---|---|---|---|---|---|---|---|---|---|---|
1,20 | 0,20 | 0,60 | 0,40 | 0,60 | 0,25 | 0,005 | 0,20 | Бал. | ||
0,004 | 1,20 | 0,20 | 0,60 | 0,40 | 0,60 | 0,25 | 0,005 | 0,20 | Бал.![]() | |
0,008 | 1,20 | 0,20 | 0,60 | 0,40 | 0,60 | 0.25 | 0,005 | 0,20 | Бал. | |
0,012 | 1,20 | 0,20 | 0,60 | 0,40 | 0,60 | 0,25 | 0,005 | 0,20 | Бал.![]() | |
0,016 | 1,20 | 0,20 | 0,60 | 0,40 | 0,60 | 0,25 | 0,005 | 0,20 | Бал. |
По данным химического анализа, содержание Zr в металле шва составляет 0%, 0.0028%, 0,0061%, 0,0087% и 0,0135% соответственно, а состав других элементов сплава металла шва показан на. Система шлаков порошковой проволоки — BaF 2 -CaF 2 -Al-Mg. Вышеупомянутый металлический порошок и минеральный порошок предоставлены Sichuan Kehui Industry Co., Ltd. (Чэнду, Китай). Состав металлического порошка показан на.
Таблица 5
Массовая доля исследуемого порошка (мас.%).
Компонент | Электролитический марганец | Никелевый порошок | Молибденовый порошок | Металлический Хром | Циркониевый порошок | Алюминиевый порошок | Железный порошок | 99,9 | 99,5 | 99 | 99,99 | 99,5 |
---|
Производство сердечника порошковой проволоки должно проходить через четыре процесса: смешивание порошка, спекание порошка, просеивание порошка и смешивание порошка. Обработанная стальная полоса и порошковый сердечник отправляются в машину для формования проволоки, а порошковая проволока, необходимая для эксперимента, получается путем волочения и уменьшения диаметра до 1,6 мм. Степень наполнения порошком 35%.Сварка осуществляется плавящимся самозащитным электродом. В качестве сварочного оборудования выбран сварочный аппарат YD-500 (Panasonic, Таншань, Китай). Положение сварки — плоская сварка. Количество слоев сварного шва составляет пять слоев и семь проходов сварки. Параметры процесса сварки и принципиальная схема сварного соединения показаны соответственно на и.
Схема сварного шва.
Таблица 6
Параметры процесса сварки.
Layer | Скорость подачи проволоки м / мин | Сварочное напряжение U / V | Сварочный ток I / A | Скорость СВАРКИ мм / мин | Удлинитель проволоки L / mm | Interpass Температура / ° C | |
---|---|---|---|---|---|---|---|
1 проход | 2 | 28 ~ 30 | 200 ~ 250 | 230 | 18 ~ 20 | 150 ± 10 | |
2–5 проходов | 2–5 проходов | 30 ~ 32 | 250 ~ 300 | 230 | 18 ~ 20 | 150 ± 10 | |
6–7 проходов | 2 | 28 ~ 30 | 200 ~ 250 | 230 | 18 ~ 20 | 150 ± 10 |
В процессе сварки самозащитной порошковой проволокой следует учитывать скорость разбрызгивания и удаление шлака. Плохая скорость разбрызгивания вызовет загрязнение заготовки, низкий коэффициент перехода элементов из сплава повлияет на качество сварки, сварочная дуга будет нестабильной, а эффективность наплавки снизится. Низкая скорость удаления шлака увеличит рабочую силу сварщика, снизит эффективность сварочного производства и сделает металл шва склонным к включению шлака и другим дефектам. Интенсивность разбрызгивания измерялась анализом качества. Самодельное устройство для сбора сварочных брызг показано на рис.Правильно нанесенное количество средства для предотвращения разбрызгивания на внутреннюю стенку устройства перед сваркой будет способствовать улавливанию сварочных брызг после сварки. На платформе внутри устройства размещается стальная пластина размером 300 мм × 200 мм × 10 мм, с обеих сторон канавки стальной пластины наносится средство против разбрызгивания, и взвешивается стальная пластина массой м 0 . В настоящее время. Поверхность стального листа сваривается с параметрами, указанными в, и время сварки составляет 1 минуту.
После сварки частицы брызг на внутренней стенке и поверхности стального листа должны быть немедленно собраны и взвешены м 1 . При этом фиксируется масса сварного стального листа м 2 . В соответствии с уравнением (1) получается интенсивность разбрызгивания при сварке:
Скорость разбрызгивания = m1m2 − m0 + m1
(1)
Принципиальная схема оборудования для испытания сварочного разбрызгивания.
Таблица 7
Химический состав металла шва (мас.%).
Компонент | Zr | Mn | Si | Mo | Cr | Ni | Ti | B | Al | O | N | 1,09 | 0,37 | 0,85 | 0,89 | 1,19 | 0,29 | 0,002 | 0,18 | 0,016 | 0,028 |
---|---|---|---|---|---|---|---|---|---|---|---|
0,0028 1 | 140,35 | 0,80 | 0,90 | 1,18 | 0,33 | 0,006 | 0,16 | 0,016 | 0,019 | ||
0,0061 | 0,28 | 0,004 | 0,18 | 0,015 | 0,020 | ||||||
0,0087 | 1,21 | 0,38 | 0,88 | 0,90 | 1.![]() | 0,30 | 0,003 | 0,19 | 0,010 | 0,017 | |
0,0135 | 1,20 | 0,36 | 0,82 | 0,88 | 0,014 |
Метод ударного молотка используется для измерения удаления шлака сварочного шва. Удаление шлака проводилось для сварных образцов с помощью испытания падающим шариком, принцип испытания показан на рис.Вес стального шара — 3000 г, время испытания — 1 мин после сварки. Положение удара стального шара — это задняя часть стального листа, соответствующая сварному шву, а высота падения стального шара составляет 500 мм.
Принципиальная схема машины для испытания на падение шара.
Длину без удаления шлака, серьезного налипания шлака и небольшого налипания шлака на поверхность сварного шва следует подсчитать и рассчитать в соответствии с уравнением (2):
D = l− (l0 + 0,5l1 + 0,2l2) l
(2)
где D — скорость удаления шлака сварного шва; l — длина шва, мм; l 0 — длина бесшлакового съема, мм; l 1 — длина серьезного налипания шлака, мм; l 2 — длина легкого налипания шлака, мм.
Сварные образцы обрабатывают с помощью электроэрозионной обработки проволокой (WEDM) для получения металлографических образцов, образцов передачи, образцов для испытаний на растяжение и образцов для испытаний на удар.
Металлографические образцы для наблюдений ОМ и СЭМ были приготовлены путем шлифовки с использованием абразивной бумаги SiC от № 240 до № 2000, механической полировки с использованием алмазного абразива 2,5 мм, а затем химического травления 4% раствором нитала и травления. время 10 с ~ 15 с.Используемая модель оптического микроскопа — GX – 51 (Olympus, Токио, Япония). Металлографические образцы, разрушение при растяжении и ударное разрушение анализировали с помощью сканирующего электронного микроскопа S-3400N (Hitachi, Токио, Япония), а фазовый состав включений анализировали с помощью энергодисперсионной спектрометрии (EDS).
ТЭМ-диски толщиной не менее 500 мкм были вырезаны из калибровочных сечений разрушенных образцов перпендикулярно оси нагружения. Диски диаметром 3 мм вырубались после механического шлифования до толщины около 50 мкм.Тонкие фольги для ПЭМ-наблюдений были приготовлены двухструйной электрополировкой в растворе 10 об.% Хлорной кислоты и 90 об.% Этанола при 20 В и -19 ° C. Микроструктуру и микроанализ проводили с помощью автоэмиссионного просвечивающего электронного микроскопа TECNAI G2 F20.
Химический состав Zr, Mn, Si, Mo, Cr, Ni, Ti, B, Al в металле сварного шва был проанализирован с помощью фотоэлектрического спектрометра прямого считывания ARL4460 (Thermo Fisher, Waltham, MA, USA). Содержание O и N в металле шва измеряли кислородно-азотным анализатором ON 900 (Eltra, Гамбург, Германия).
Твердость металла шва измерялась на микротвердомере THVS-5 (Beijing Times peak Technology Co., Ltd, Пекин, Китай). Нагрузка составляла 500 г, время выдержки — 15 с. Расстояние между местом измерения и верхней поверхностью сварного шва составляет 2 мм. На каждом образце было измерено пять баллов, и было получено среднее значение. Интервал между точками: 500 мкм, как показано на Рисунке 9.
Образцы излома при растяжении и образцы излома при ударе очищаются только раствором ацетона без какой-либо другой обработки.Испытания на растяжение проводились в соответствии со стандартом «порошковая проволока для низколегированных сталей» (GB / T 17493–2008). В качестве испытательной машины использовалась электронная универсальная испытательная машина GNT 200 (CNS, Шанхай, Китай). Были измерены прочность на разрыв и удлинение при разрыве, три параллельных образца для каждого состояния и получены средние значения прочности на разрыв и удлинения.
Зона сварного шва и HAZ подверглись механической обработке в образцах для испытания на удар. Согласно GB / T 17493-2008 испытание на ударную вязкость должно проводиться при 25 ° C, 0 ° C; и −60 ° C.Испытание на удар проводилось на ударной машине JB-30B (Kocheng testing machine Co., Ltd, Chengde, Китай). Размер образцов для испытаний составляет 10 мм × 10 мм × 55 мм, V-образные надрезы были подготовлены на протяжном станке для ударных образцов, модель CSL-A (Liangong testing equipment Co., Ltd, Цзинань, Китай). Положение надреза — это центр испытуемого образца, то есть центр сварного шва, а его глубина составляет 2 мм. Мгновенная скорость маятника составляет 5 м / с, были получены 5 параллельных выборок для каждого условия и средние значения энергии удара. Испытание на удар проводится в соответствии со стандартом GB / T 2650-2008 «Метод испытания сварного соединения на удар». Ориентация механической обработки образцов для испытаний на растяжение и образцов для испытаний на ударную вязкость перпендикулярна сварному шву, как показано на. Размеры образцов для испытаний на растяжение и удар показаны на рисунках 10 и 12.
Принципиальная схема ориентации механической обработки образцов для испытаний на растяжение и удар.
3. Результаты и обсуждение
3.1. Влияние содержания Zr на скорость разбрызгивания и удаление шлака
По данным химического анализа, содержание Zr в металле шва составляет 0%, 0.0028%, 0,0061%, 0,0087% и 0,0135% соответственно, а состав других элементов сплава металла шва показан на. показывает влияние содержания Zr в металле шва на скорость разбрызгивания и удаление шлака. Видно, что с увеличением содержания элемента Zr интенсивность сварочного разбрызгивания постепенно уменьшается. Когда металл шва содержит 0,0061% Zr, минимальная скорость разбрызгивания металла шва составляет всего 7%; с увеличением содержания Zr в металле шва интенсивность сварочного разбрызгивания снова начинает увеличиваться. Соотношение между скоростью удаления шлака и содержанием Zr в металле шва прямо противоположно скорости разбрызгивания.Когда содержание Zr в металле шва достигает 0,0061%, максимальная степень удаления шлака составляет 95%.
Влияние содержания Zr на скорость разбрызгивания при сварке и скорость удаления шлака.
Zr — сильный восстановитель в металле шва высокопрочной стали. Когда Zr в порошковой проволоке меньше (0,0028% Zr), во время процесса сварки легко происходит разбрызгивание мелких частиц из-за высокого содержания O и низкого поверхностного натяжения капель. С увеличением содержания Zr в порошковой проволоке Zr будет реагировать с O с образованием ZrO 2 , что снизит содержание O в капле, а ZrO 2 имеет ионную связь.Энергия связи больше, что увеличивает поверхностное натяжение капли. Следовательно, с увеличением содержания Zr (0,0061% Zr) поверхностное натяжение капли будет все больше и больше, а скорость разбрызгивания при сварке будет меньше. Однако, когда содержание Zr слишком велико (0,0135% Zr), капля станет крупной из-за чрезмерного поверхностного натяжения капли, образуя большое разбрызгивание частиц, что увеличит скорость разбрызгивания. Следовательно, в этом испытании с точки зрения уменьшения скорости разбрызгивания содержание Zr в металле сварного шва установлено равным 0.0061%.
Скорость удаления шлака сварным швом зависит от физических свойств самого шлака. В этом эксперименте ZrO 2 , продукт окисления Zr, имеет различную кристаллическую структуру при разных температурах [17,18,19]. Оксид ZrO 2 при температуре ~ 1170 ° C имеет моноклинную структуру; при 1170 ° C ~ 2370 ° C оксид ZrO 2 имеет тетрагональную структуру; при 2370 ° C ~ 2706 ° C оксид ZrO 2 имеет кубическую структуру, а доля трех различных структур в металле шва равна 5.68: 6.10: 6.27. Среди них тетрагональная структура оксида ZrO 2 является метастабильной и легко трансформируется в моноклинную структуру под действием внешней силы. В процессе трансформации при объемном расширении 8% шлак легко отделяется от поверхности металла шва и имеет хорошие характеристики удаления шлака. Однако, когда содержание Zr в металле сварного шва увеличивается, кубическая структура оксида ZrO 2 будет увеличиваться, а FeO на поверхности металла шва также имеет кубическую структуру, сила связи между ними велика, что приводит к плохому удалению шлака. производительность, снижая скорость удаления шлака.
3.2. Влияние содержания Zr на микроструктуру металла шва
показывает влияние содержания элементов Zr на микроструктуру металла шва. Можно видеть, что, когда металл сварного шва не содержит элемента Zr, структура состоит в основном из доэвтектоидного феррита и гранулированного бейнита с небольшим количеством игольчатого феррита и перлита, как показано на а. В матрице металла сварного шва много включений, размер частиц включений большой и неравномерный, а размер зерна матрицы металла сварного шва также относительно велик. Когда металл шва содержит 0,0028% элемента Zr, содержание эвтектоидного феррита и гранулированного бейнита в структуре металла шва уменьшается, и начинает выделяться равноосный мелкозернистый феррит и игольчатый феррит. Размер частиц включений большой, но распределение равномерное, как показано на b. Когда металл шва содержит 0,0061% Zr, содержание игольчатого феррита в металле сварного шва увеличивается, содержание равноосного мелкозернистого феррита начинает уменьшаться, появляется небольшое количество перлита, размер частиц металла шва небольшой. , и размер частиц включения невелик, что показывает распределение дисперсии, как показано на c.Когда металл шва содержит 0,0087% Zr, структура игольчатого феррита начинает уменьшаться, равноосный мелкозернистый феррит продолжает уменьшаться, количество эвтектоидного феррита увеличивается, а распределение включений неравномерно, как показано на d. Когда металл шва содержит 0,0135% Zr, игольчатый феррит значительно уменьшается, в структуре присутствует большое количество гранулированного бейнита, небольшое количество перлита и доэвтектоидного феррита, размер частиц включений большой, а распределение неравномерное.
, как показано на e.Результаты показывают, что с увеличением содержания Zr в металле шва содержание игольчатого феррита и равноосного мелкодисперсного феррита в микроструктуре сначала увеличивается, а затем уменьшается. Когда содержится 0,0061% Zr, содержание игольчатого феррита в металле сварного шва является самым высоким, имеется определенное количество равноосного мелкодисперсного феррита, а содержание доэвтектоидного феррита является самым низким.
Влияние содержания Zr на морфологию металла шва ( a ) 0% Zr ( b ) 0.0028% Zr ( c ) 0,0061% Zr ( d ) 0,0087% Zr ( e ) 0,0135% Zr.
Игольчатый феррит является продуктом среднетемпературного превращения и часто включается в бейнитное превращение. Обычно считается, что игольчатый феррит состоит из множества мелких непараллельных пучков ферритовых реек. Пучки планок расположены в шахматном порядке и излучают со средним размером зерна 4 мкм ~ 5 мкм, соотношением длины и ширины 4: 1 ~ 8: 1 и углом около 20 ° между игольчатыми ферритовыми планками, так что это большой угол. граница зерна [20,21].
Когда в металле сварного шва есть трещины, рост трещины вблизи крупноугловой границы зерна блокируется, и расширяющаяся трещина блокируется и останавливается при непрерывном увеличении приложенной нагрузки. В это время большое количество дислокаций с высокой плотностью в игольчатом феррите будет собираться на границе зерна, что приведет к существованию внутреннего напряжения на границе зерна, которое приведет к тому, что дислокация внутри зерна вызовет поперечное скольжение, но направление движения дислокации Существует определенный угол с первоначальным направлением трещины, то есть образуется новая трещина.При дальнейшем увеличении напряжения исходная трещина и новая трещина соединяются друг с другом и медленно изменяют направление роста трещины. Следовательно, крупногабаритная граница зерна блокирует рост трещины, что затрудняет ее расширение.
Под ПЭМ высокого разрешения видно множество субструктур из игольчатого феррита, которые являются M-A-компонентами и дислокациями высокой плотности. Образование компонента M-A происходит из-за образования в аустените частиц, которые способствуют зарождению игольчатого феррита во время трансформации металла шва, что препятствует росту границы раздела аустенит-феррит.Вокруг границы зерен выделяется слишком много углерода. В процессе последующего охлаждения аустенит не успевает превратиться в феррит, но происходит мартенситное превращение с образованием мартенсита. Эти мартенситы и остатки, богатые углеродом, образуются. Оставшийся аустенит образует компонент M-A, как показано на.
Схематические рисунки, показывающие распределение M-A в игольчатом феррите.
Под сканирующим электронным микроскопом компонент M-A представляет собой однородную ярко-белую ткань с небольшой выпуклостью, как показано на a.Под просвечивающим электронным микроскопом можно отчетливо увидеть детали, как показано на b.
Морфология M-A в игольчатом феррите ( a ) SEM-фотография ( b ) TEM-фотография.
Элементы сплава могут повысить стабильность аустенита и сделать распределение игольчатой ферритовой планки более очевидным, а компонент M-A распределен между игольчатыми ферритовыми планками в форме полосы. Правильное увеличение скорости охлаждения может уменьшить количество компонента M-A в игольчатом феррите и сделать его мелким и дисперсным.Когда скорость охлаждения увеличивается, компонент M-A увеличивается, и его размер увеличивается, он имеет стержневую форму и массив; когда скорость охлаждения замедляется, островок аустенита разлагается на феррит и цементит, например верхний бейнит. Компонент M-A в игольчатом феррите не только улучшает прочность металла сварного шва, но также хорошо влияет на ударную вязкость. Это связано с тем, что компонент M-A представляет собой твердую хрупкую фазу, благодаря которой игольчатый феррит имеет более высокую твердость, что способствует повышению прочности металла сварного шва.
показывает морфологию продольного сечения ударного разрушения металла шва. Можно видеть, что когда трещина распространяется до игольчатого феррита в металле сварного шва, путь распространения трещины становится зигзагообразным, трещина распространяется вдоль границы игольчатого феррита, и путь является изогнутым, как показано на рисунке a; Когда трещина распространяется до верхнего бейнита, путь расширения трещины становится прямым, и трещина проникает внутрь верхнего бейнита, сопротивление распространению невелико, как показано на b. Когда металл сварного шва растрескивается, трещина распространяется около компонента M-A, дислокация, образованная трещиной, будет заблокирована компонентом M-A и изогнута, и дислокация будет собираться вокруг компонента M-A с образованием кластеров дислокаций. Кластер дислокаций закреплен компонентом M-A, который препятствует росту трещины и меняет ее направление. Когда приложенное напряжение увеличивается, трещины соединятся вместе и пересекут компонент M-A, вернутся в исходное направление распространения и продолжат расширяться вперед.Следовательно, наличие компонента M-A в игольчатом феррите сделает дислокацию, образованную трещиной, фиксированной, повлияет на движение трещины и изменит направление трещины, чтобы улучшить ударную вязкость игольчатого феррита.
Распространение трещины ударного разрушения металла шва. ( a ) через AF ( b ) через BF.
3.3. Влияние Zr на твердость металла шва №
показывает влияние содержания Zr на твердость металла шва. Можно заметить, что когда содержание Zr равно 0, твердость сварного шва самая низкая.
Влияние содержания Zr на твердость металла шва по Виккерсу.
С увеличением содержания Zr твердость постепенно увеличивалась. Когда содержание Zr составляло 0,0061%, твердость достигала максимального значения 357HV. С увеличением содержания Zr твердость начала снижаться. По результатам анализа, при содержании Zr равном 0 микроструктура крупная, игольчатый феррит меньше и распределен неравномерно, а твердость невысока.С увеличением содержания Zr форма и распределение зерен игольчатого феррита при рафинировании становятся более разумными, а значение твердости явно возрастает. При дальнейшем увеличении содержания Zr в структуре появляется большое количество гранулированного бейнита, небольшое количество перлита и доэвтектоидного феррита, поэтому твердость снижается.
3.4. Влияние Zr на свойства при растяжении металла шва
показывает влияние содержания Zr в металле шва на свойства при растяжении. Можно видеть, что, когда содержание Zr в металле сварного шва равно 0, предел прочности на разрыв и удлинение металла шва были низкими; с увеличением содержания Zr в металле шва прочность на разрыв и удлинение металла шва сначала увеличиваются, а затем уменьшаются. Когда в металле сварного шва содержится 0,0061% Zr, удлинение металла шва достигает максимального значения 34%, относительное удлинение после разрушения начинает снижаться с увеличением содержания Zr, пластическая вязкость металла сварного шва ухудшается, но Прочность металла шва продолжает увеличиваться.Когда содержание Zr в металле сварного шва достигает 0,0087%, предел прочности металла шва на растяжение достигает максимального значения 1110 МПа, а затем продолжает увеличиваться содержание Zr, и предел прочности металла шва на растяжение начинает снижаться.
Влияние содержания циркония на предел прочности и удлинения сварных соединений.
— это СЭМ-изображение разрушения при растяжении сварных швов с 0% Zr, 0,0061% Zr и 0,0135% Zr, а анализ состава ямчатых включений, указанных стрелками на рисунке, показан на рис. Из разрушения металла шва при растяжении видно, что, когда металл шва не содержит элемента Zr, разрушение при растяжении характеризуется поперечным распределением большой лунки и маленькой лунки с небольшой глубиной лунки, а включений очень мало. ; когда в металле сварного шва содержится 0,0061% Zr, радиальная зона излома характеризуется небольшой ямкой с большой глубиной; когда металл сварного шва содержит 0,0135% Zr, трещина при растяжении характеризуется большой впадиной, которая разделена вокруг большой впадины. Небольшие впадины распределены, а глубина каждой впадины небольшая.Глубина лунки излома тесно связана со способностью металла шва к пластической деформации. При этом количество включений увеличивается, а распределение равномерное. Когда пластичность металла шва велика, глубина впадины велика; в противном случае ямочка неглубокая. Размер ямки трещины зависит от размера и количества частиц второй фазы. Когда размер частиц второй фазы большой, размер ямок велик; когда количество частиц второй фазы невелико, размер ямок велик.
Размер включения обычно составляет 0,5–1 мкм.
Морфология разрушения металла шва при растяжении ( a ) 0% Zr ( b ) 0,0061% Zr ( c ) 0,0135% Zr.
Таблица 8
Состав включений трещины при растяжении.
Компонент | Mn | Ti | Mg | Al | O | N | Zr | Fe |
---|---|---|---|---|---|---|---|---|
0% Zr | .![]() | 12,4 | 18 | 13,2 | 9,5 | 0 | 40,7 | |
0,0061% Zr | 1,1 | 0,6 | 80328 1,84,7 | 4,7 | ||||
0,0135% Zr | 0 | 1,1 | 0,65 | 7,1 | 3,2 | 5,2 | 3,3 | 79,7 |
r В зависимости от металла и Структура металла сварного шва в основном состоит из доэвтектоидного феррита и гранулированного бейнита, с грубой структурой и плохой прочностью металла шва и пластической вязкостью. С увеличением содержания Zr в металле сварного шва количество доэвтектоидного феррита и гранулированного бейнита в металле сварного шва уменьшается, количество игольчатого феррита увеличивается, микроструктура прекрасна и появляются дислокации высокой плотности, поэтому металл шва имеет высокую прочность и лучшая пластическая вязкость. Когда содержание Zr в металле сварного шва продолжает увеличиваться, дуга будет нестабильной во время сварки, и контакт между каплей и наружным воздухом будет увеличиваться. Свариваемость будет плохой, а структура в основном состоит из бейнита.Следовательно, прочность и пластическая вязкость металла сварного шва низкие.
Были измерены составы включений в 0% Zr, 0,0061% Zr и 0,0135% Zr, в каждой группе было измерено пять включений, в каждой группе указан один состав включений в. Из этого видно, что с изменением содержания Zr в металле шва, состав микровключений в трещине также различается, а изменение состава и количества включений влияет на размер включений, тем самым влияя на производительность сваривать металл. Когда металл шва содержит 0% Zr, основными компонентами включений в трещинах при растяжении являются Fe, Al, Mg, O и N, тогда как Al и Ti являются сильными раскисляющими и фиксирующими азот элементами, что указывает на то, что включения представляют собой оксиды и нитриды металлов. Результаты показывают, что AlN присутствует во включениях, а AlN представляет собой гексагональное включение, которое оказывает режущее действие на металл сварного шва. С увеличением содержания Zr в металле шва увеличивается и содержание Zr во включениях, и основной компонент включений меняется на Fe.По сравнению с включениями без Zr содержание n значительно снижается. Когда содержание Zr в металле шва достигает 0,0135%, основными компонентами включений являются Fe и Zr, а содержание Al и N снова увеличивается. Обнаружено, что содержание Zr во включениях намного выше, чем в матрице металла сварного шва, что указывает на то, что Zr более вероятно присутствует во включениях, чем в твердом растворе, образованном металлом шва.
3.5. Влияние элементов Zr на ударную вязкость металла шва
показывает влияние содержания Zr в металле шва на энергию удара металла шва.Видно, что с увеличением содержания Zr энергия удара металла шва сначала увеличивается, а затем уменьшается при комнатной температуре и низкой температуре, и максимальное значение появляется при 0,0061% Zr. При содержании Zr 0% средняя энергия низкотемпературного удара металла шва при –60 ° C составляет 48 Дж; при содержании Zr 0,0061% средняя низкотемпературная энергия удара металла шва при –60 ° C составляет 126 Дж; при содержании Zr 0,0135% средняя низкотемпературная энергия удара металла шва при –60 ° C составляет 10 Дж, что даже ниже, чем энергия удара металла шва без элемента Zr.Это связано с тем, что при очень высоком содержании Zr может образоваться игольчатая ферритная структура, но содержание C в непревращенном аустените увеличивается из-за разряда C из феррита в аустенит. В процессе охлаждения часть аустенита превращается в мартенсит, становясь хрупкой фазой компонента M-A, который легко становится источником трещин, что приводит к снижению ударной вязкости металла сварного шва.
Влияние содержания Zr на энергию удара металла шва.
показывает морфологию ударного разрушения металла шва при температуре –60 ° C, когда содержание Zr в металле шва составляет 0%, 0,0061% и 0,0135% соответственно. Когда содержание Zr в металле сварного шва составляет 0%, радиальная область ударного разрушения металла сварного шва представляет собой излом скола, показывающий веерообразный узор; когда содержание Zr в металле сварного шва составляет 0,0061%, ударное разрушение металла сварного шва содержит большое количество ямок, демонстрирующих пластичный излом; когда содержание Zr в металле сварного шва составляет 0,0135%, ударное разрушение имеет характер хрупкого разрушения с плохой ударной нагрузкой.
Морфология ударного разрушения металла шва при −60 ° C ( a ) 0% Zr ( b ) 0,0061% Zr ( c ) 0,0135% Zr.
Согласно и, когда содержание Zr в металле шва составляет 0%, микроструктура металла шва представляет собой доэвтектоидный феррит и гранулированный бейнит, микроструктура является относительно крупной, что неблагоприятно для ударной вязкости металла шва. С увеличением содержания Zr в металле шва количество доэвтектоидного феррита и гранулированного бейнита в структуре уменьшается, количество игольчатого феррита увеличивается, и структура становится меньше.Поскольку игольчатый феррит имеет дислокации и субструктуру высокой плотности, он обладает сильным сопротивлением росту трещин, что обеспечивает хорошую ударную вязкость металла шва. Когда содержание Zr в металле сварного шва достигает высокого уровня, металл шва состоит из гранулированного бейнита с крупными зернами, что отрицательно сказывается на ударной вязкости металла шва.
3.6. Механизм упрочнения и закалки металла шва из высокопрочной стали
Для повышения прочности и ударной вязкости металла шва из высокопрочной стали, с одной стороны, необходимо добавить легирующие элементы в металл шва, изменить состав С другой стороны, необходимо учитывать, что при движении дислокаций матричная ткань должна сохранять достаточную пластичность.
Эксперимент на пропускание проводился на лучшем образце (0,0061% Zr). показывает микроструктуру игольчатого феррита, полученную методом просвечивающей электронной микроскопии в этом испытании. В это время микроструктура металла шва составляет 1,2% Mn, 0,31% Mo, 0,35% Si, 0,67% Ni, 0,53% Cr, 0,21% Al, 0,35% Ti, 0,005% B и 0,0061% Zr. Из вышеизложенного можно видеть, что игольчатый феррит представляет собой серию чередующихся непараллельных игольчатых структур, сплетенных вместе, с крупноугловой границей зерен и дислокациями высокой плотности, а угол между соседними границами зерен больше 15 °.Следовательно, когда микротрещины в металле сварного шва распространяются между переплетенным игольчатым ферритом, путь является зигзагообразным, что требует большего расхода энергии, что приводит к повышению прочности и ударной вязкости.
Морфология игольчатого феррита в металле сварного шва с содержанием Zr 0,0061%, полученного методом просвечивающей электронной микроскопии.
Согласно теории, выведенной Бхадешиа, соотношение между числом дислокаций и температурой перехода при сдвиговом превращении выглядит следующим образом [22]:
lnρ = 21,3772 + 15843,4663 / T − 4099430 / T2
(3)
где T — температура перехода, единица: К; ρ — плотность дислокаций, единица — м 2 .
Поскольку температура перехода бокового феррита составляет от 1023 К до 923 К, плотность дислокаций составляет 2 × 10 14 ~ 4 × 10 14 из уравнения (3) [23]; температура перехода игольчатого феррита составляет от 873 К до 723 К, а плотность дислокаций находится между 6 × 10 14 ~ 2 × 10 15 . Плотность игольчатого феррита намного выше, чем у бокового феррита, поэтому прочность игольчатого феррита намного выше, чем у бокового феррита.
При испытании на растяжение не было обнаружено явного предела текучести в процессе растяжения. Это связано с тем, что, хотя игольчатый феррит имеет дислокации высокой плотности, поскольку содержание C в самом сварочном материале очень низкое, C недостаточно для блокировки движения дислокаций, поэтому имеется объемно-центрированная кубическая структура с высокой энергией дефекта упаковки. , непросто создать протяженные дислокации и привести к поперечному скольжению, поэтому дислокации обладают большой подвижностью.
представляет собой анализ энергетического спектра ламеллярной матрицы игольчатого феррита.Видно, что содержание Mn, Ni и других элементов в матрице игольчатого феррита высокое, что указывает на то, что эти элементы действительно могут проникать в матрицу, чтобы играть роль упрочняющего твердого раствора.
Анализ энергетического спектра игольчатого феррита в наплавленном металле с содержанием Zr 0,0061%.
Согласно методу анализа энергии коттеля, формула критического напряжения, необходимого для роста трещины, имеет следующий вид [24]:
где σ c — номинальное напряжение разрушения трещины, МПа; G — модуль упругости, МПа; γ с — поверхностная энергия на единицу площади трещины, МДж / м 2 ; k y — коэффициент закрепления дислокаций; d — диаметр зерна, мм.Видно, что с уменьшением размера зерна критическое напряжение, необходимое для роста трещины, становится больше, и пластическая вязкость материала лучше.
Из уравнения (4) видно, что для повышения пластической вязкости материала можно увеличить значение G , k y γ s или значение d можно уменьшить. Поскольку значения G и k y связаны с физическими величинами материала, при определении материала критическое напряжение, необходимое для роста трещины, может быть увеличено только за счет уменьшения значения d , т.е. .е., измельчение зерен.
Температура хрупкого перехода между T c и ln d −1/2 показана в уравнении (5) [25]:
где K и β — константы, а d — размер зерна.
Добавляя микроэлемент Zr, Zr может сфероидизировать и измельчать включения в металле сварного шва, он также может увеличивать количество включений, которые подходят для индукции зародышеобразования игольчатого феррита, и увеличивать количество игольчатого феррита.С увеличением содержания Zr в металле шва микроструктура металла шва постепенно улучшалась, преэвтектоидный феррит на границе зерен подавлялся, и в зернах появлялось большое количество мелкодисперсного и однородного игольчатого феррита. Из формулы (5) видно, что существует линейная зависимость между температурой перехода T c из пластического хрупкого состояния и размером зерна ln d -1/2 . Другими словами, измельчение слоя игольчатого феррита может снизить температуру пластического хрупкого перехода и улучшить низкотемпературную ударную вязкость металла сварного шва.
Исследование чувствительности высокопрочных хладостойких судостроительных сталей к термическому циклу дуговой сварки | Международный журнал машиностроения и материаловедения
Расчетное время охлаждения и начальная температура мартенсита
Значения t 8/5 , M s , A c1 , A c3 и максимальная твердость были рассчитаны в соответствии с методы, описанные ниже.
Время охлаждения
Время охлаждения при сварке обычно описывается как t 8/5 , что представляет собой время охлаждения от 800 до 500 ° C, поскольку эти температуры обычно соответствуют температурам рекристаллизации сталей.Время охлаждения можно измерить с помощью термопар или рассчитать теоретически по следующей формуле (EN 1011-2):
$$ {t} _ {\ raisebox {1ex} {$ 8 $} \! \ Left / \! \ Raisebox { -1ex} {$ 5 $} \ right.} = \ Left (6700-5 {T} _p \ right) \ times Q \ times \ left (\ frac {1} {500- {T} _p} — \ frac { 1} {800- {T} _p} \ right) \ times F $$
, где t 8/5 — время охлаждения (с), Tp — температура предварительного нагрева (° C), Q — тепловложение (кДж / мм), а F — правильный коэффициент формы, который зависит от формы сварного шва, который равен 1 для стыкового шва.
Начальная температура мартенсита
Это снижение ударной вязкости является результатом мартенситно-аустенитной фазы, которая часто образуется во время повторного нагрева и последующего охлаждения ЗТВ. Когда крупнозернистая микроструктура повторно нагревается до двухфазной области фазовой диаграммы, островки аустенита образуются на границах зерен и вблизи предыдущих границ аустенита. Образовавшийся аустенит имеет высокое содержание сплава, что снижает как начальную (Ms), так и конечную (Mf) температуру мартенсита, а также способность образовывать перлит и феррит при высоких скоростях охлаждения.Из-за низких температур Ms и Mf островки аустенита образуют смесь хрупкого мартенсита и остаточного аустенита. Уменьшение влияния элементов сплава на температуру Ms можно увидеть из уравнения (Hansen 2012):
$$ {M} _s = 539-423 \ left (\ mathrm {wt} \% \ mathrm {C} \ вправо) -30,4 \ влево (\ mathrm {wt} \% \ mathrm {Mn} \ right) +17,7 \ left (\ mathrm {wt} \% \ mathrm {Ni} \ right) +12,1 \ left (\ mathrm { wt} \% \ mathrm {C} \ mathrm {r} \ right) +7.8 \ left (\ mathrm {wt} \% \ mathrm {Mo} \ right) $$
Температуры превращения, обозначенные как Ac1 и Ac3, можно найти экспериментально по кривой дилатометра.{\ raisebox {1ex} {$ 1 $} \! \ left / \! \ raisebox {-1ex} {$ 2 $} \ right.} — 15.2 \ left (\ mathrm {wt} \% \ mathrm {Ni} \ right ) +44,7 \ left (\ mathrm {wt} \% \ mathrm {Si} \ right) +104 \ left (\ mathrm {wt} \% \ mathrm {V} \ right) +31,5 \ left (\ mathrm {wt } \% \ mathrm {Mo} \ right) +13,1 \ left (\ mathrm {wt} \% \ mathrm {W} \ right) $$
Одним из наиболее часто используемых критериев для оценки качества сварного шва является измерение твердости. Твердость измеряется экспериментально, и следующая формула также может оценить максимальную твердость HAZ для сталей HSLA:
$$ HV = 90 + 1050 \ left (\ mathrm {wt} \% \ mathrm {C} \ right) + 47 \ left (\ mathrm {wt} \% \ mathrm {Si} \ right) +75 \ left (\ mathrm {wt} \% \ mathrm {Mn} \ right) +30 \ left (\ mathrm {wt} \ % \ mathrm {Ni} \ right) +31 \ left (\ mathrm {wt} \% \ mathrm {C} \ mathrm {r} \ right) $$
Это уравнение утверждает, что содержание углерода определяет значения твердости HAZ.Из практических наблюдений было отмечено, что если твердость ЗТВ превышает твердость основного металла более чем на 20–30%, вероятность образования холодных трещин значительно возрастает, ударная вязкость снижается, а неоднородность сварного шва становится высокой.
Для исследуемых сталей расчет прогнозных значений приведен в таблице 5.
Таблица 5 Расчетные значения для исследуемых сталейОсобенности структуры и свойств сварных соединений SAW низколегированной судостроительной марки TMCP Сталь 09Г2ФБ
Проведена оценка свариваемости образцов стыкового шва с кромками К-образного стыка листовой стали 09Г2ФБ толщиной 50 мм производства ТМКП.
Анализ микроструктуры после сварки с низкой погонной энергией 1,5 кДж / мм показал образование нижнего бейнита в CGHAZ с размером зерна 44–88 мкм (рис. 2c), что соответствует размеру зерна 4–6. согласно ISO 643: 2003. После сварки с высокой погонной энергией (5 кДж / мм) на границе линии плавления наблюдается значительный рост зерна (до 150 мкм, что соответствует размеру зерна 2–3 согласно ISO 643: 2003) вблизи линии плавления и наблюдается образование феррита неправильной формы на границах аустенитных зерен (рис.2б). Это приводит к увеличению длины ЗТВ с 2–2,5 до 6–7 мм (таблица 3) с увеличением погонной энергии.
Рис. 2Микроструктура 09Г2ФБ в различных областях ЗТВ. a Линия для плавления с подводимой теплотой сварки 1,5 кДж / мм. b Линия плавления с подводимой теплотой сварки 5 кДж / мм. c CGHAZ область с подводимой теплотой сварки 1,5 кДж / мм. d Область CGHAZ с подводимой теплотой сварки 5 кДж / мм
Микроструктура HAZ на расстоянии 2 мм от линии плавления представляет собой нижний бейнит, а микроструктура HAZ на расстоянии 5 мм от линии плавления представляет собой смесь феррита и нижнего бейнита.Эта микроструктура вызывает повышение твердости и снижение значений энергии удара.
В результате снижения скорости охлаждения формируется неблагоприятная структура крупнозернистого верхнего бейнита с выделениями свободного феррита по его границам при увеличении тепловложения от 1,5 до 5 кДж / мм (рис. 2г). , который имеет низкие ударные вязкости при -40 ° C. Расчетное время охлаждения t 8/5 составило 8 с для подводимого тепла 1,5 кДж / мм и 26 с для подводимого тепла 5 кДж / мм. Микротвердость и ударная вязкость представлены в таблицах 6, 7 и 8.
Таблица 6 Твердость (среднее значение) в различных областях ЗТВ сварного соединения стали 09Г2ФБ Таблица 7 Механические свойства сварных соединений стали 09Г2ФБ Таблица 8 Значения ударных испытаний сварных соединений стали 09Г2ФБ при -40 ° C (Дж / см 2 )Значения испытаний на ударную вязкость выше при сварке с меньшим тепловложением, как видно из таблицы 8. Значение испытания на удар на линии плавления для подводимого тепла 5 кДж / мм довольно низкое — 33 Дж / см 2 .
Методика TMCP позволяет сохранить желаемую микроструктуру ЗТВ при нагреве стали до точки A c3 из-за повышенного содержания легирующих элементов.Однако этот подход не ограничивает значительный рост зерна при более высоких температурах. Следовательно, тепловложение при сварке этой марки стали TMCP должно быть ограничено 2,5–3,5 кДж / мм, чтобы гарантировать приемлемую ударную вязкость на линии плавления и избежать чрезмерного роста зерна в ЗТВ (Счастливцев и др., 2013).
Увеличение тепловложения приводит к росту зерен аустенита и снижению скорости охлаждения по сравнению со сваркой с низким тепловложением. В результате преобразования в γ → α низкоуглеродистая низколегированная сталь начинается с выделения свободного феррита.Следовательно, повышенное содержание углерода приводит к образованию непревращенного аустенита, а граница образуется за счет сплавления неблагоприятной структуры крупного бейнита с выделениями свободного феррита на его границах, как это видно на рис. 2, имеющем низкие значения энергии удара.
Особенности структуры и свойств сварных соединений легированной судостроительной стали QT (сваркой MMA и SAW)
Сталь QTСтыковые сварные швы MMA и SAW выполнены из хромоникель-молибденовой стали 10XN2MD, стали с бейнитно-мартенситной структурой 08XN3MD , и стали мартенситной марки 12ХН3МФ.
Дуговая сварка
Сравнительные исследования микроструктуры ЗТВ и свойств сваренных ММА сталей марок 10XN2MD, 08XN3MD и 12XN3MF показали, что с увеличением содержания углерода и легирующих элементов ширина ЗТВ увеличивается с 1,8 до 5,4 мм, так как приведено в таблице 3.
Размер зерна на первом участке ЗТВ (рис. 1) имеет крупнозернистую мартенситную структуру, зерна которой в стали 12ХН3МФ в 1,5–2 раза больше, чем в стали 10ХН2МД, где размер зерна не превышает 110 мкм, а структура преимущественно бейнитная, что определяет снижение микротвердости на участке 1 ЗТВ в стали 10ХН2МД и способствует повышению ударной вязкости.Образование в основном бейнитной структуры в результате снижения содержания углерода в высокопрочной хромоникель-молибденовой стали способствует снижению твердости в ЗТВ на 25% и повышению ударной вязкости (таблица 9).
Таблица 9 Твердость ЗТВ сварных швов MMA и SAWРаздел 2 ЗТВ 12XN3MF состоит в основном из мартенситной структуры, которая улучшается по мере удаления от границы плавления и превращается в бейнитно-мартенситную структуру сечения. 3.Сталь 10ХН2МД не имеет четкой границы между участками 2 и 3, которые представляют собой дисперсную бейнитно-ферритную структуру.
Анализ ЗТВ сварки под флюсом марки 10ХН2МД показал, что микротвердость не превышает 235 Hv, а значения микротвердости постепенно снижаются от линии плавления к основному металлу в пределах от 235 до 187 Hv (таблица 9).
Исследование стали марок 10ХН2МД и 08ХН3МД, сваренных методом сварки SAW, показало, что участок 1 ЗТВ представляет собой крупнозернистую структуру бейнита с участками феррита по границам, а участки 2 и 3 преимущественно представляют собой бейнитно-ферритную смесь, в которой размер зерна уменьшается с расстояние от линии плавления.Участок 4 ЗТВ имеет более крупнозернистую структуру бейнитного феррита, соответствующую структуре основного металла, с карбидами по границам зерен. При переходе к структуре основного металла карбиды, входящие в границы, исчезают.
Сталь 08ХН3МД с высоким содержанием хрома и никеля, но с меньшим содержанием углерода (0,08 против 0,10%) была сварена методом SAW. Микротвердость ЗТВ самая низкая: 171–183 Hv, т.е. на 28% ниже, чем у стали 10ХН2МД.Сталь 10ХН2МД имеет более низкие значения Рсм (0,23%) из-за меньшего содержания легирующих элементов. Максимальная твердость наблюдается на участках ЗТВ 1 (крупнозернистая) и 2 (мелкозернистая), прилегающих к металлу шва, имеющих игольчатую структуру. Ударная вязкость сварного соединения при температуре испытания — 40 ° С имеет значения 183–171 (сталь 08ХН3МД) и 235–187 Дж / см 2 (сталь 10ХН2МД).
Таким образом, уменьшение содержания углерода, количества легирующих элементов и образование бейнитной структуры в стали никель-никель-молибденового состава приводит к повышению уровня ударной вязкости и снижению твердости ЗТВ как в Сварка MMA и SAW.Было замечено, что более низкое содержание углерода в стали сильнее влияет на ударную вязкость сварного соединения, чем увеличение процентного содержания легирующих элементов.
За счет увеличения содержания углерода и легирующих элементов в стали 12ХН3МДФ ширина ЗТВ увеличивается и имеет максимальную твердость области ЗТВ с игольчатой структурой. Образование в основном бейнитной структуры за счет снижения содержания углерода в хромоникель-молибденовой стали 10ХН2МД позволяет снизить твердость ЗТВ сварных соединений на 25%, а также повысить пластичность почти до уровня основного металла.
Для сварных высокопрочных стальных конструкций часто требуется отпуск после сварки для снятия остаточных напряжений. Однако после отпуска сварных соединений, выполненных из высокопрочных сварных хромоникель-молибденовых сталей, наблюдается растрескивание, локализованное в ЗТВ или непосредственно по линии шва.
При испытании моделируемой зоны сварного шва металла (ЗТВ) на образцах с острым надрезом при температуре испытания + 20, + 40 и — 60 ° C было установлено, что максимальный уровень ударной вязкости при всех температурах соответствует скорость охлаждения 6 ° C / с.После отпуска образцов твердость увеличивается, а ударная вязкость значительно снижается во всем диапазоне скоростей охлаждения (рис. 3). Это может быть связано с закреплением дислокаций во время сегрегации при отпуске, что обычно приводит к повышенной твердости и хрупкости.
Рис. 3Изменение твердости ( a ) и вязкости ( b ) в зоне ЗТВ в зависимости от температуры испытательных образцов стали 10XN3MD при различных скоростях охлаждения после сварки до и после отпуска при 600 (2) и 640 ° C (3), а также после моделирования нагрева (1)
Для исследования возможных остаточных напряжений при сварке были выполнены исследования структуры и характера разрушения (рис.4в, е). При исследовании использовались следующие параметры: основной металл и крупнозернистая область ЗТВ после нагрева до 600 ° C и медленная скорость деформации растяжения с 5,5 × 10 — 6 с — 1 .
Рис.4Структура ( a , b , d , e ) и излом ( c , f ) основного металла 10XN3MD после отпуска 600 ° C ( a ) и моделировали на крупнозернистой области ЗТВ Gleeble-3800 и стали 10XN3MDF после нагрева до 600 ° C и отпуска 1350 ° C ( г ) и после деформации на скорости 5.5 × 10 — 6 с — 1 при температуре 600 ° C ( b , c , e , f ), основной металл ( b , c ), и крупнозернистая область ( d , f )
Отпуск без деформации незначительно изменяет структуру основного металла и крупнозернистую область. После комбинированного воздействия температуры и медленной деформации структура стали 10ХН3МД полностью теряет свою первоначальную мартенситно-бейнитную структуру, которая превращается в ферритно-карбидную смесь ферритных зерен, вытянутых в направлении нагрузки (рис.4б). Большинство зерен феррита имеют размер 12–15 мкм, но есть мелкие зерна размером 3–5 мкм. При этом в структуре наблюдаются отдельные крупные зерна размером около 100 мкм. Они возникают в результате развития рекристаллизации in situ (рис. 4). Время до отказа составляет 23 070 с, а относительное удлинение — 14% (см. Таблицу 10).
Таблица 10 Результаты испытаний после деформации растяжением при температуре 600 ° C стали 10XN3MDСтруктура крупнозернистой области после комбинированного воздействия температуры и медленной деформации — отпущенный крупнозернистый мартенсит с трещинами по длине. границы и тройные стыки зерна (рис.4д). Время наработки на отказ сокращено до 4970 с, а относительное удлинение — до 1%.
Приложенная деформация вызывает разрушение механизма зернограничного скольжения, что приводит к концентрации напряжений в тройных стыках и образованию клиновидных трещин. Очевидно, что скопление межузельных атомов (предположительно углерода) на крупнозернистых границах при выбранной температуре отпуска затрудняет скольжение, способствуя возникновению трещин и появлению хрупких изломов.Более продолжительный отпуск может способствовать образованию карбидов на границах зерен, кавитации, а также привести к разрушению. В связи с этим, если требуется отпуск сварных соединений, его режимы следует оптимизировать с учетом эффектов возможного снижения деформации металла.
Урок 1 — Основы дуговой сварки
Урок 1 — Основы дуговой сварки © АВТОРСКИЕ ПРАВА 1999 УРОК ГРУППЫ ЭСАБ, ИНК. I, ЧАСТЬ А элементы добавляются для повышения прочности и ударной вязкости, для уменьшения или увеличения реакция на термическую обработку и на замедлить ржавление и коррозию.Низколегированная сталь обычно обычно определяется как имеющий от 1,5% до 5% общее содержание сплава. Обычные легирующие элементы — марганец, кремний, хром, никель, молибден и ванадий. Низколегированные стали могут содержат целых четыре или пять эти сплавы в разном количестве. 1.2.2.1 Низколегированные стали обладают более высоким пределом прочности. и предел текучести по сравнению с конструкцией из низкоуглеродистой стали или углеродистой стали стали. Поскольку они имеют высокое отношение прочности к весу, они уменьшают мертвую вес в железной дороге легковые автомобили, рамы грузовиков, тяжелая техника и т. д.1.2.2.2 Обычные углеродистые стали, демонстрирующие хрупкость при низких температурах, ненадежны в критические приложения. Поэтому низколегированные стали с добавками никеля часто используются для низких температурные ситуации. 1.2.2.3 Стали теряют большую часть своей прочности при высоких температурах. Чтобы восполнить эту потерю прочность при повышенных температурах, небольшое количество хрома или молибдена добавлен. 1.2.3 Высокий Легированная сталь — Эта группа дорогих и специализированных сталей содержит уровни сплава более 10%, что придает им исключительные свойства.1.2.3.1 Аустенитная марганцовистая сталь содержит высокий уровень углерода и марганца, который дает это два исключительных качества: способность затвердевать при холодной работе и большая стойкость. Термин аустенитная относится к кристаллической структуре этих сталей. 1.2.3.2 Нержавеющая сталь Стали — это высоколегированные стали, устойчивые к коррозии. Этот характеристика в основном из-за высокое содержание хрома, то есть 10% или больше. Никель также используется в значительных количествах в некоторых нержавеющих сталях.1.2.3.3 Инструментальные стали используются для резки и формовочные операции. Это высококачественная сталь используется при изготовлении инструментов, штампов, штампов, штампов для экструзии, поковок и т. д. В зависимости от их свойств и их иногда называют водоотверждающими, ударопрочная, масляная закалка, закалка на воздухе и инструментальная сталь для горячей обработки. 1.2.3.4 Потому что высокого уровня легирующих элементов, особый уход и методы требуется при сварке высоколегированных сталей.Исследование технологии сварки низколегированной высокопрочной стали
[1] Хуан Цисю.Welding Technology of WELDOX960 Low Alloy High Strength Steel [D]. Chongqing University, (2008).
[2] Wang Zhiling, Wei Fuxiang, Yu Hexi.Влияние согласования прочности на микроструктуру и свойства сварных соединений стали WELDOX960 [J]. Горячий рабочий процесс, 2014 (5): 175-177.
[3] SI Zihua.Технология сварки MAG высокопрочной стали WELDOX960 [J]. Технологии аэрокосмического производства, 2012 (2).
[4] ЯН Чжэнкай.Исследование процесса сварки низколегированной высокопрочной стали [J]. Машиностроение и автоматизация, 2007 (1): 171-172.
[5] Ван Цзибо, Го Линлин, Чжан Янь и др.Исследование процесса сварки сложной коробки из низколегированной высокопрочной стали Q690D [J]. Металлообработка (горячая обработка), 2016 (24): 57-60.
[6] Исследование процесса двусторонней двухдуговой поперечной сварки толстого листа низколегированной высокопрочной стали [D].Харбинский технологический институт, (2011).
[7] Хуан Цисю. Исследование процесса сварки низколегированной высокопрочной стали WELDOX960 [D].Чунцинский университет, (2008).
[8] Чжан Минь, Ван Сяодун, Чжао Сяохуэй. Экспериментальное исследование процесса сварки закаленной и отпущенной высокопрочной стали Weldox 960E [J].Рефераты по машиностроению (сварочная книга), 2013 (2): 29-30.
.