Баллон кислородный 1 литр — Сварпост. Переносные газосварочные посты ПГСП
3 100 р.
Технические характеристики и параметры
Тип баллона | БДГ 0,75.150.192 |
Рабочее давление (Р) | 14,7 МПА (150 кгс/кв.см) |
Пробное давление (П) | 22,1 МПа (225 кгс/кв.см) |
Размеры баллона : | |
— высота | 245 мм |
— диаметр | 89 мм |
-толщина стенки | 3,5 мм |
Вместимость | 1 литр |
2,5 кг | |
Резьба на горловине баллона | W 19,2 |
Уплотнение на горловине | лента ФУМ |
Температурный режим эксплуатации |
от — 40 до плюс + 50 град.![]() |
Резьба на вентиле баллона | G 3/4 |
Максимальное количество заправок | 10000 |
Расчетный срок службы с даты изготовления | 20 лет |
На верхней сферической части баллона нанесена маркировка, содержащая следующую информацию:
- товарный знак изготовителя
- порядковый номер баллона
- дата изготовления и год следующего освидетельствования
- параметры и характеристики, влияющие на безопасность (рабочее и пробное давление)
- знак ОТК
Баллон кислородный 1 литр изготовлен в полном соответствии с ТР ТС 032/2013, ГОСТ 949-73 и ТУ 1411100-54553586-2013.
Взрывобезопасность кислородных баллонов.
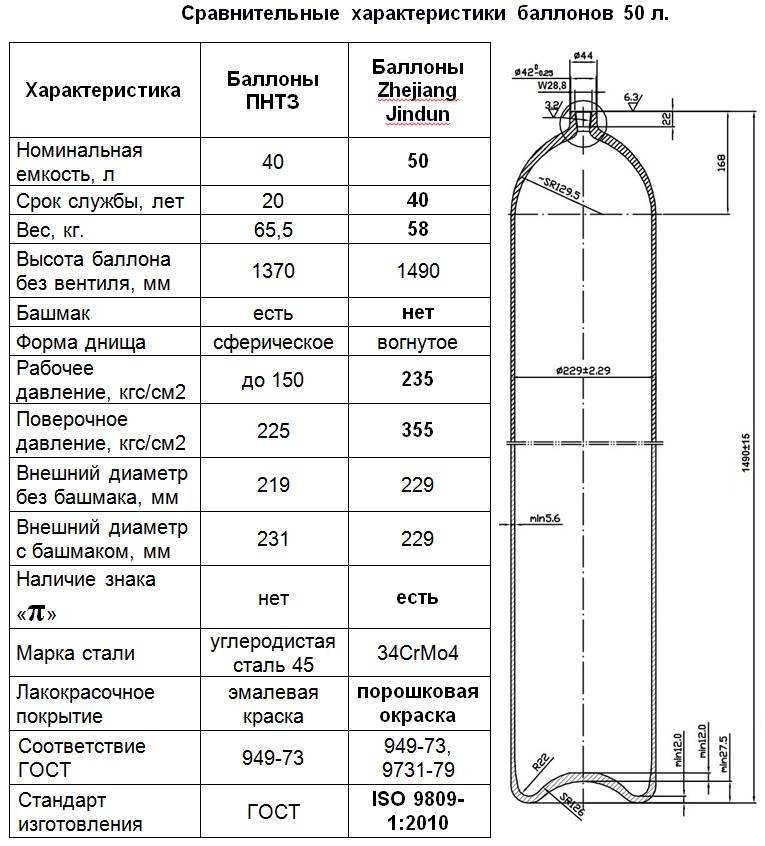
Взрывобезопасность кислородных баллонов. Журнал «ТЕХНИЧЕСКИЕ ГАЗЫ» 6/2009
Автор: Чижиченко Вадим Петрович
Продолжающиеся взрывы кислородных баллонов на территории Украины свидетельствуют о том, что данной проблеме уделяется не должное внимание. К сожалению, все взрывы кислородных баллонов сопровождались человеческими жертвами и нанесли значительный материальный ущерб.
Следует обратить внимание, что подавляющее число аварий произошло у потребителей в момент подключения кислородного редуктора и открытия кислородного вентиля на баллоне.
Кислородные баллоны в соответствии с ГОСТ 949-73 изготавливаются из углеродистой стали, толщина стенок корпуса не менее s=6,8 мм, горловина и днище имеют толщину не менее 15 мм, диаметр D=219 мм, высота баллона L=1370 мм. Рабочее давление указанных баллонов 15,0 МПа. Завод – изготовитель гарантирует запас прочности равный 2,7, что соответствует давлению разрушения баллона при давлении не менее 42,0 МПа.
Уменьшение толщины стенки корпуса баллона может происходить в результате длительной эксплуатации баллона и коррозии внутренних стенок. Коррозия возникает при заправке баллона влажным кислородом, остатке воды после гидроиспытания. Поэтому своевременное (через каждые 5 лет) проведение технического освидетельствование кислородных баллонов является обязательным условием при эксплуатации кислородных баллонов. Кроме этого, специальными постановлениями Кабинета Министров Украины (№687 от 26.05.2004 г.) и Госпромнадзора Украины (№16 от 20.12.2006 г.) контроль за проведением техосвидетельствования проводит только эксперт технический по надзору, который прошел курс специального обучения Организации, которые проводят техосвидетельствование баллонов и не имеющие у себя такого эксперта, в дальнейшем получать Разрешение на проведение указанных работ не будут.
Типичные разрушения баллонов при техосвидетельствовании показаны на фото (коррозия стенки баллона).
Если своевременное техническое освидетельствование и случившиеся при этом разрушение баллона не приводит к последствиям, то взрыв кислородного баллона при заправке или во время эксплуатации всегда приводит к тяжелым последствиям.
За последний год на территории Украины произошли несколько взрывов кислородных баллонов, каждый из которых привел к человеческим жертвам и материальному ущербу. Следует подчеркнуть, что взрыв кислородного баллона сравним со взрывом авиабомбы. Расследование аварий специально созданными комиссиями с привлечением специалистов завода-изготовителя баллонов, различных институтов, экспертов, проведение анализа осколков во всех случаях привели к выводам, что взрывы произошли в результате возгорания внутри баллона кислорода и горючего газа (пропан, метан, ацетилен). При мгновенном возгорании взрывоопасной смеси образуется сверхвысокое давление 100 МПа – 200 МПа , которое и приводит к взрыву баллона.
При взрыве газоопасной смеси внутри баллона он разрушается на мелкие осколки, днище и горловина отрываются от корпуса.
Подключенный редуктор обычно разрушается со стороны камеры высокого давления, сильфонная трубка манометра высокого давления разрывается. Части разорвавшегося баллона находят за сотни метров от места взрыва, что доказывает большую опасную зону.
Причины, по которым в кислородные баллоны попали горючие газы, могут быть следующие:
а) использование кислородных баллонов потребителем не по назначению, с последующей сдачей его на кислородонаполнительную станцию;
б) попадание горючего газа во время эксплуатации через резак (если мундштук закупорен) в кислородный баллон при условии, что давление в нём или отсутствует или ниже, чем в газовом.
Таким образом, основным условием исключения аварийной ситуации является недопущение попадания в кислородный баллон горючего газа. «Типовая инструкция по охране труда при наполнении кислородных баллонов и обращении с ними у потребителей» и дополнение к Инструкции «Инструкция по проверке остаточного газа в кислородных баллонах сигнализатором СГГ-4М-3 (или аналогичным) с приспособлением» являются обязательными для выполнения.
Перед заправкой кислородных баллонов проверить наличие в нем остаточного давления и в истекающей струе проверить наличие горючего газа с помощью чувствительного газоанализатора. При визуальном и звуковом сигнале «зараженный» баллон к наполнению не допускается.
У потребителей кислородных баллонов ввести за правило обязательную установку на резаке (горелке) огнепреградительных клапанов (кислород, горючий газ) для предотвращения обратного удара и невозможности перетекания одного газа в другой.
Освидетельствование баллонов – технические нюансы
Работа с техническими газами требует неукоснительного соблюдения правил эксплуатации газоиспользующего оборудования и газовых резервуаров, которые должны периодически подвергаться аттестации. Важно понимать, что плановое освидетельствование баллонов – это не прихоть контролирующих органов, а необходимая мера для своевременного выявления дефектов конструкции и предотвращения опасных ситуаций на производстве.
Существует немало частных компаний-поставщиков техгазов, которые, пренебрегая процедурой аттестации, предоставляют клиентам просроченные баллоны. Получая в свое распоряжение более дешевый продукт, покупатель зачастую не подозревает о возможных последствиях. Чем грозит эксплуатация несертифицированных резервуаров, читайте в статье: серые производители технических газов.
Вместе с тем, ответственные организации заботятся о безопасности своих клиентов, выполняя требования ФНП, которые касаются обустройства испытательных пунктов для освидетельствования баллонов. Чтобы получить разрешения от контролирующих органов на проведение испытаний, компания должна иметь:
- подходящее по площади помещение;
- технические средства;
- аттестованных специалистов;
- клеймо с шифром организации;
- производственную инструкцию.
Когда выполняется аттестация газовых емкостей
Периодичность технической аттестации для работающих под избыточным давлением сосудов составляет 5 лет. То есть с даты изготовления каждые 5 лет баллон должен обязательно подвергаться испытаниям, во время которых определяют целостность корпуса и вентиля, массу конструкции, внутреннюю емкость и способность выдерживать повышенное давление.
Однако в некоторых ситуациях освидетельствование выполняют раньше установленного срока, когда:
- сломан вентиль;
- в месте соединения баллон-вентиль обнаружена утечка;
- на горловине неисправно или отсутствует кольцо;
- поврежден башмак;
- окраска наружной поверхности является некачественной.
Решение о ремонте или выбраковке таких сосудов принимают только по результатам визуального осмотра и технических исследований.
Освидетельствование баллонов: последовательность операций
Проверку состояния осуществляют в следующей последовательности:
1) Подготовка.
На этапе подготовки из емкости удаляют остаток газа, демонтируют вентиль, после чего осуществляют продувку воздухом и тщательную очистку поверхности с применением воды и, при необходимости, растворителя. Демонтированный вентиль подвергают отдельной проверке, а в случае неисправности направляют в ремонт или бракуют с последующей заменой.
Подготовка баллона перед проверкой
2) Визуальный осмотр.
Целью визуального осмотра является выявление любых дефектов конструкции: трещин, вмятин, плен, раковин, глубоких рисок (более 10% толщины стенки), износа резьбы и т.п. Для внутреннего осмотра допускается применение осветительного прибора с напряжением питания до 12 В. В случае обнаружения ослабления кольца на горловине или неправильной насадки башмака, испытание приостанавливается до устранения данных неисправностей.
Осмотр на наличие дефектов
3) Проверка массы и вместительности.
Чтобы определить, насколько коррозия и другие физико-химические преобразования металла уменьшили толщину стенок, осуществляют измерение массы и внутреннего объема изделия, а также сравнение полученных показателей с первоначальными данными из паспорта. Взвешивание выполняют на весах с точностью 200 г. Для определения вместимости сначала взвешивают пустой сосуд, а затем наполненный водой, после чего по разности показателей находят массу воды с дальнейшим расчетом ее объема.
Проверка массы и вместимости взвешиванием
4) Гидравлическое испытание.
Для определения прочности емкости ее наполняют водой под высоким давлением. Величину проверочного давления устанавливает завод-производитель, оно должно быть как минимум в 1,5 раза выше рабочего показателя. Длительность проверки составляет не меньше 1 минуты. Гидроиспытание считается успешным, если во время его выполнения манометр показывал стабильную величину, а на корпусе не были обнаружены трещины, течи, слезы и видимые деформации.
Гидравлическое испытание
Выдержка под проверочным давлением при гидроиспытании
5) Монтаж вентиля.
Перед соединением вентиля и резервуара оба компонента подвергают обезжириванию, после чего просушивают и продувают воздухом. Установка осуществляется с применением уплотнителя, а сила затяжки для резьбы W27,8 составляет 300-400 н. м.
Установка вентиля
6) Нанесение клейма.
Если по результатам тестирования резервуар допускается к дальнейшей эксплуатации, организация, проводившая аттестацию, выбивает на корпусе индивидуальное клеймо, а также дату проведенной и следующей проверки.
Нанесение клейма
7) Покраска корпуса.
В случае неудовлетворительного качества внешнего покрытия цилиндрический корпус покрывается масляной или эмалевой краской или нитроэмалью. При этом не допускается производить окраску емкости под давлением.
Покраска и сушка
Какие сосуды подлежат выбраковке
При наличии одного из приведенных ниже условий баллон не подлежит освидетельствованию и подвергается выбраковке:
- наличие видимых дефектов корпуса;
- уменьшение фактической массы на 7,5% или увеличение объема на 1%;
- выявление недостаточной прочности во время гидравлического испытания.
- отсутствие хотя бы одного из следующих паспортных клейм: знак завода-изготовителя, заводской номер, фактическая масса и вместимость, дата изготовления и следующего испытания, рабочее и пробное давление, метка ОТК, вид термообработки.
На резервуарах, которые не прошли освидетельствование, деформируется резьба горловины посредством нанесения насечек или сверлится отверстие в корпусе. Это делается для того, чтобы дальнейшая эксплуатация бракованного сосуда была невозможной.
Поскольку некоторые недобросовестные компании восстанавливают выбракованные сосуды и потом предоставляют их клиенту в качестве новых изделий, важно покупать и делать заправку только у проверенных поставщиков, где вся продукция соответствует строгим государственным нормам. Подробнее о типах заправляемых газов и емкостей Вы можете узнать здесь.
пустых промышленных кислородных баллонов типа D (46,7 л),
О компании
Год основания1999
Юридический статус фирмы Физическое лицо — собственник
Характер деятельностиОптовый торговец
Количество сотрудниковДо 10 человек
Годовой оборот2008-09 рупий. 2–5 крор прибл.
2009-10 рупий. 2–5 крор прибл.
2010-11 рупий. 2–5 крор прибл.
IndiaMART Участник с апреля 2007 г.
GST27ACLPM6801A1ZV
Мы, AA, трейдеры , основанные в 1999 годах, являемся одним из ведущих оптовиков, розничных продавцов, экспортеров, и трейдеров , а также обширного ассортимента газовых баллонов и промышленных сжиженных газов .Наш предлагаемый ассортимент состоит из баллонов с кислородом высшего качества , баллонов с гелием, газообразного азота ULTRA High Pure и многого другого. Составленный в соответствии с руководящими принципами качества ведущих производителей, мы гарантируем, что предлагаемые жидкие газы имеют надлежащий состав различных ингредиентов. В дополнение к этому, эти продукты известны своим длительным сроком хранения, высокой чистотой, нетоксичностью и точным составом.Чтобы помочь клиентам с самыми эффективными газовыми баллонами и промышленными сжиженными газами, нас поддерживает эффективная команда квалифицированных профессионалов.

Видео компании
Маленький кислородный баллон
AirLocus поставляет маленькие кислородные баллоны.Маленький кислородный баллон объемом от 2 л до 20 л. Их можно использовать для промышленных или медицинских приложений, таких как сталелитейный завод, больница, дом, скорая помощь. Наши небольшие кислородные баллоны изготавливаются строго в соответствии с международными стандартами из высокопрочного алюминия 6061 или бесшовного стального материала. Небольшие кислородные баллоны из алюминия обычно используются в медицинских целях. Небольшие кислородные баллоны, изготовленные из стали, обычно используются для промышленного применения, а также для медицинского применения.
1. Малые кислородные баллоны (стальной тип)
Спецификация малого кислородного баллона 5 л-150 бар | |||
Тип | ИСО140-5-150 | Наружный диаметр | 140 мм |
Объем воды | 5.0л | Высота без клапана | 455 мм |
Рабочее давление | 150 бар | Мин. толщина стенки | 3,6 мм |
Испытательное давление | 250 бар | Вес без клапана | 8.2кг |
Производственный стандарт | ИСО9809-3 | Материал | 37Мн |
Спецификация малого кислородного баллона 10 л-150 бар | |||
Тип | ИСО140-10-150 | Наружный диаметр | 140 мм |
Объем воды | 10. | Высота без клапана | 815 мм |
Рабочее давление | 150 бар | Мин. толщина стенки | 3,6 мм |
Испытательное давление | 250 бар | Вес без клапана | 13.6 кг |
Производственный стандарт | ИСО9809-3 | Материал | 37Мн |
Спецификация малого кислородного баллона 15 л-150 бар | |||
Тип | ИСО159-15-150 | Наружный диаметр | 159 мм |
Объем воды | 15.0л | Высота без клапана | 956 мм |
Рабочее давление | 150 бар | Мин. | 4,2 мм |
Испытательное давление | 250 бар | Вес без клапана | 19.9 кг |
Производственный стандарт | ИСО9809-3 | Материал | 37Мн |
2. Малые кислородные баллоны (алюминиевого типа)
Спецификация малого кислородного баллона размера D | |||
Тип | LWh211-3.0-15 | Наружный диаметр | 111 мм |
Объем воды | 3,0 л | Высота без клапана | 490 мм |
Рабочее давление | 150 бар | Мин. толщина стенки | 5. |
Испытательное давление | 225 бар | Вес без клапана | 3,1 кг |
Производственный стандарт | ИСО7866 | Материал | 6061А |
Спецификация малого кислородного баллона размера E | |||
Тип | LWh211-4.6-15 | Наружный диаметр | 111 мм |
Объем воды | 4,6 л | Высота без клапана | 685 мм |
Рабочее давление | 150 бар | Мин. толщина стенки | 5.6мм |
Испытательное давление | 225 бар | Вес без клапана | 4,2 кг |
Производственный стандарт | ИСО7866 | Материал | 6061А |
Спецификация малого кислородного баллона 60CF | |||
Тип | LWh284-10. | Наружный диаметр | 184 мм |
Объем воды | 10,0 л | Высота без клапана | 591 мм |
Рабочее давление | 150 бар | Мин. толщина стенки | 9.3мм |
Испытательное давление | 225 бар | Вес без клапана | 11,4 кг |
Производственный стандарт | ИСО7866 | Материал | 6061А |
Спецификация малого кислородного баллона 90CF | |||
Тип | LWh284-15.0-15 | Наружный диаметр | 184 мм |
Объем воды | 15,0 л | Высота без клапана | 831 мм |
Рабочее давление | 150 бар | Мин. | 9.3мм |
Испытательное давление | 225 бар | Вес без клапана | 15,2 кг |
Производственный стандарт | ИСО7866 | Материал | 6061А |
Примечание:
1.Небольшой кислородный баллон из стали может быть изготовлен в соответствии со стандартами ISO9809, EN ISO9809 и DOT-3AA.
2. Небольшой кислородный баллон из алюминия может быть изготовлен в соответствии со стандартами ISO7866, EN ISO7866 и DOT-3AL.
3. Малый кислородный баллон может быть изготовлен с рабочим давлением 139 бар, 150 бар, 159 бар, 200 бар, 230 бар, 300 бар.
4. Малый кислородный баллон может быть изготовлен по индивидуальному заказу по цвету, клапану, крышке.
5. Перечислены не все малые кислородные баллоны.
49 CFR § 178.

§ 178.37 Спецификация Бесшовные стальные цилиндры 3AA и 3AAX.
(a) Тип, размер и рабочее давление. В дополнение к требованиям § 178.35 баллоны должны соответствовать следующим требованиям:
(1) Баллон DOT-3AA представляет собой цельнотянутый стальной цилиндр с вместимостью по воде (номинальной) не более 1000 фунтов и рабочим давлением не менее 150 фунтов на квадратный дюйм.
(2) Цилиндр DOT-3AAX представляет собой бесшовный стальной цилиндр с вместимостью по воде не менее 1000 фунтов и рабочим давлением не менее 500 фунтов на кв. дюйм, соответствующий следующим требованиям:
(i) Предполагается, что цилиндр должен поддерживаться горизонтально только двумя концами и равномерно нагружен по всей его длине, состоящей из веса на единицу длины прямой цилиндрической части, заполненной водой и сжатой до установленного испытательного давления; сумма двухкратного максимального растягивающего напряжения в нижних волокнах из-за изгиба плюс напряжение в тех же волокнах (продольное напряжение) из-за гидростатического испытательного давления не может превышать 80 процентов минимального предела текучести стали при таком максимальном напряжении . Толщина стенки должна быть увеличена, если это необходимо для удовлетворения требований.
(ii) Для расчета максимального растягивающего напряжения из-за изгиба необходимо использовать следующую формулу:
S = Мк/И
(iii) Для расчета максимального продольного растягивающего напряжения из-за гидростатического испытательного давления необходимо использовать следующую формулу:
С = А 1P/A 2
(b) Утвержденная сталь. Должна использоваться мартеновская, кислородно-кислородная или электротехническая сталь одинакового качества. Плавка стали, изготовленная по техническим условиям таблицы 1 настоящего пункта (b), контрольный химический анализ которой незначительно выходит за пределы указанного диапазона, считается приемлемой, если она удовлетворительна во всех других отношениях, при условии соблюдения допусков, указанных в таблице 2 настоящего пункта параграф (b) не превышаются.При использовании углеродисто-бористой стали испытание на прокаливаемость необходимо проводить на первом и последнем слитке каждой плавки стали. Результаты этого испытания должны быть зарегистрированы в Протоколе химического анализа материала для баллонов, требуемом § 178.35. Этот тест на твердость должен быть сделан
5/16 дюйма от закаленного конца закалочного стержня Джомини, а твердость должна быть не менее Rc 33 и не более Rc 53. Разрешены следующие химические анализы:
Таблица 1 – Разрешенные материалы
Обозначение | 4130X (в процентах) (см. Примечание 1) | NE-8630 (в процентах) (см. Примечание 1) | 9115 (в процентах) (см. Примечание 1) | 9125 (в процентах) (см. Примечание 1) | Углерод-бор (проценты) | Марганец промежуточный (проценты) |
---|---|---|---|---|---|---|
Углерод | 0.25/0,35 | 0,28/0,33 | 0,10/0,20 | 0,20/0,30 | 0,27-0,37 | 0,40 макс.![]() |
Марганец | 0,40/0,90 | 0,70/0,90 | 0,50/0,75 | 0,50/0,75 | 0,80-1,40 | 1,35/1,65. |
Фосфор | 0,04 макс. | 0,04 макс. | 0,04 макс. | 0,04 макс. | 0,035 макс. | 0,04 макс. |
Сера | 0.05 макс | 0,04 макс. | 0,04 макс. | 0,04 макс. | 0,045 макс. | 0,05 макс. |
Кремний | 0,15/0,35 | 0,20/0,35 | 0,60/0,90 | 0,60/0,90 | 0,3 макс. | 0,10/0,30. |
Хром | 0,80/1,10 | 0,40/0,60 | 0,50/0,65 | 0,50/0,65. | ||
Молибден | 0.15/0,25 | 0,15/0,25 | ||||
Цирконий | 0,05/0,15 | 0,05/0,15 | ||||
Никель | 0,40/0,70 | |||||
Бор | 0,0005/0,003.![]() |
Таблица 2. Проверка допусков анализа
Элемент | Указанный предел или максимум (проценты) | Допуск (в процентах) выше максимального предела или ниже минимального предела | |
---|---|---|---|
Ниже минимального предела | Превышение максимального предела | ||
Углерод | К 0.15 вкл. | 0,02 | 0,03 |
Более 0,15 до 0,40 вкл. | .03 | .04 | |
Марганец | До 0,60, включая | .03 | .03 |
Более 0,60 до 1,15 вкл. | 0,04 | 0,04 | |
Свыше 1,15 до 2,50, включая | 0,05 | 0,05 | |
Фосфор | Все диапазоны | .![]() | |
Сера | Все диапазоны | .01 | |
Кремний | До 0,30, включая | .02 | .03 |
Более 0,30 до 1,00, включая | .05 | .05 | |
Никель | До 1,00, включая | .03 | .03 |
Хром | До 0,90, включая | .03 | .03 |
0.от 90 до 2,90, включая | .05 | .05 | |
Молибден | До 0,20, включая | .01 | .01 |
Более 0,20 до 0,40 | .02 | .02 | |
Цирконий | Все диапазоны | .01 | .05 |
(c) Идентификация материала. Материал должен быть идентифицирован любым подходящим методом, за исключением того, что плиты и заготовки для горячетянутых цилиндров должны быть маркированы номером плавки.
(г) Производство. Баллоны должны изготавливаться с использованием оборудования и процессов, обеспечивающих соответствие каждого произведенного баллона требованиям настоящего подраздела. Не допускается наличие трещин или других дефектов, которые могут заметно ослабить готовый баллон. Требуется достаточно гладкая и однородная поверхность. Если изначально такие дефекты отсутствуют, поверхность может быть подвергнута механической обработке или другой обработке для устранения этих дефектов. Толщина днищ цилиндров, сваренных или сформированных методом прядения, ни при каких условиях не должна быть менее двухкратной минимальной толщины стенки цилиндрической обечайки; такая толщина днища должна быть измерена в пределах области, ограниченной линией, представляющей точки контакта между цилиндром и полом, когда цилиндр находится в вертикальном положении.
(e) Сварка или пайка. Сварка или пайка в любых целях запрещены, за исключением следующих случаев:
(1) Сварка или пайка разрешены для крепления шейных и опорных колец, которые не являются частями, работающими под давлением, и только к верхней и нижней части баллонов, работающих под рабочим давлением 500 фунтов на кв. дюйм или менее. Цилиндры, шейки и опорные кольца должны быть изготовлены из свариваемой стали, содержание углерода в которой не может превышать 0,25%, за исключением стали 4130X, которую можно использовать при соблюдении надлежащей процедуры сварки.
(2) В соответствии с пунктом (d) настоящего раздела.
(f) Толщина стенки. Толщина каждого цилиндра должна соответствовать следующему:
(1) Для баллонов с рабочим давлением менее 900 фунтов на квадратный дюйм напряжение стенки не может превышать 24 000 фунтов на квадратный дюйм. Минимальная толщина стенки 0,100 дюйма требуется для любого цилиндра с внешним диаметром более 5 дюймов.
(2) Для баллонов с рабочим давлением 900 фунтов на кв. дюйм или более минимальная стенка должна быть такой, чтобы напряжение стенки при минимальном установленном испытательном давлении не превышало 67 процентов минимального предела прочности стали на растяжение, определенного в результате необходимых физических испытаний. в параграфах (k) и (l) этого раздела и не должно превышать 70 000 фунтов на квадратный дюйм.
(3) Расчет должен производиться по формуле:
S = [P(1.3D 2 + 0,4д 2)]/(Д 2-й 2)
(ж) Термическая обработка. Готовые баллоны перед испытаниями должны быть подвергнуты однородной и надлежащей термообработке. Термическая обработка баллонов разрешенных анализов должна быть следующей:
(1) Все цилиндры должны охлаждаться маслом или другой подходящей средой, за исключением случаев, предусмотренных в параграфе (g)(5) настоящего раздела.
(2) Температура стали при закалке должна соответствовать рекомендованной для анализа стали, но не должна превышать 1750 °F.
(3) Все стали должны быть отпущены при температуре, наиболее подходящей для этой стали.
(4) Минимальная температура отпуска не может быть ниже 1000 °F, за исключением случаев, указанных в параграфе (g)(6) данного раздела.
(5) Сталь 4130X может быть нормализована при температуре 1650 °F вместо закалки, а цилиндры, нормализованные таким образом, не нуждаются в отпуске.
(6) Промежуточные марганцевые стали могут подвергаться отпуску при температуре не ниже 1150 °F, и после термической обработки каждый цилиндр должен быть подвергнут магнитному испытанию для выявления наличия закалочных трещин.Баллоны с трещинами подлежат отбраковке и уничтожению.
(7) За исключением случаев, предусмотренных в параграфе (g)(6) настоящего раздела, все баллоны, закаленные водой или жидкостью, обеспечивающей скорость охлаждения, превышающую 80 процентов скорости охлаждения воды, должны быть проверены. магнитопорошковым, проникающим или ультразвуковым методом для выявления наличия закалочных трещин. Любой баллон, спроектированный в соответствии с требованиями спецификации 3AA и имеющий закалочную трещину, должен быть забракован и не может быть переаттестован.Цилиндры, разработанные в соответствии с требованиями спецификации 3AAX и имеющие трещины, должны быть удалены механическими средствами до прочного металла. Цилиндры с такой спецификацией 3AAX будут приемлемыми, если отремонтированный участок впоследствии будет проверен на предмет отсутствия дефектов и будет установлено, что требования к проектной толщине соблюдены.
(h) Отверстия в цилиндрах и соединения (клапаны, плавкие вставки и т. д.) для этих отверстий. Резьба обязательна на отверстиях.
(1) Резьба должна быть чистой, ровной, без заусенцев и калибра.
(2) Коническая резьба, если она используется, должна иметь длину не менее длины, указанной для трубной конической резьбы американского стандарта.
(3) Разрешена прямая резьба, имеющая не менее 6 зацепляемых витков. Прямая резьба должна иметь плотную посадку и расчетную прочность на сдвиг, по крайней мере, в 10 раз превышающую испытательное давление баллона. Требуются прокладки, достаточные для предотвращения утечки.
(i) Испытания под давлением. Каждый баллон должен успешно выдержать следующие испытания под давлением:
(1) Испытание должно проводиться методом водяной рубашки или прямым расширением, как предписано в CGA C-1 (IBR; см. § 171.7 настоящего подраздела). Испытательное оборудование должно быть откалибровано в соответствии с требованиями CGA C-1. Все испытательное оборудование и устройства для индикации давления должны иметь точность в пределах параметров, определенных в CGA C-1.
(2) Каждый баллон должен быть испытан как минимум 5/3-кратное рабочее давление.
(3) Минимальное испытательное давление должно поддерживаться в течение не менее 30 секунд и достаточно дольше, чтобы обеспечить полное расширение. Любое внутреннее давление, прикладываемое после термической обработки и до официального испытания, не должно превышать 90 % испытательного давления.Если из-за отказа испытательного оборудования или ошибки оператора испытательное давление невозможно поддерживать, испытание можно повторить в соответствии с CGA C-1, раздел 5.7.2.
(4) Постоянное объемное расширение не должно превышать 10 процентов от общего объемного расширения при испытательном давлении.
(j) Испытание на сплющивание. Испытание на сплющивание должно быть выполнено на одном цилиндре, выбранном наугад из каждой партии в 200 или менее штук, путем помещения цилиндра между лезвиями клиновидных ножей, имеющих угол прилегания 60°, закругленных до
Радиус 1/2 дюйма. Продольная ось цилиндра должна быть под углом 90 градусов к кромкам ножей во время испытания. Для партий из 30 и менее разрешается проводить испытания на сплющивание кольца длиной не менее 8 дюймов, вырезанного из каждого цилиндра и подвергнутого той же термической обработке, что и готовый цилиндр. Цилиндры могут быть подвергнуты испытанию на изгиб вместо испытания на сплющивание. Два образца для испытаний на изгиб должны быть взяты в соответствии с ISO 9809-1 или ASTM E 290 (IBR, см. § 171.7 настоящего подраздела) и должны быть подвергнуты указанному в нем испытанию на изгиб.
(k) Физический тест. Необходимо провести физическое испытание для определения предела текучести, предела прочности при растяжении, относительного удлинения и уменьшения площади материала следующим образом:
(1) Испытание требуется на 2 образцах, вырезанных из 1 цилиндра, взятых случайным образом из каждой партии в 200 или менее штук. Для партий из 30 и менее разрешается проводить физические испытания на кольце длиной не менее 8 дюймов, вырезанном из каждого цилиндра и подвергнутом той же термической обработке, что и готовый цилиндр.
(2) Образцы должны соответствовать следующим требованиям:
(i) Расчетная длина 8 дюймов при ширине не более 1 1/2 дюйма, калибровочная длина 2 дюйма при ширине не более 1 1/2 дюйма или расчетная длина, по крайней мере, в 24 раза превышающая толщину, а ширина не более чем в 6 раз превышающая толщину, если толщина стенки цилиндра не превышает 3/16 дюйма.
(ii) Образец, за исключением концов захвата, нельзя сплющивать. Концы захвата могут быть сплющены в пределах 1 дюйма от каждого конца уменьшенной секции.
(iii) Если размер цилиндра не позволяет закреплять прямые образцы, образцы можно брать в любом месте и в любом направлении и их можно выпрямлять или сплющивать в холодном виде, только давлением, а не ударами. Когда образцы отобраны и подготовлены таким образом, отчет инспектора должен содержать подробную информацию о таких образцах в связи с записью физических испытаний.
(iv) Нагрев образца для любых целей не разрешается.
(3) Предел текучести при растяжении должен соответствовать напряжению, соответствующему остаточной деформации в 0,2 процента от расчетной длины. Применяются следующие условия:
(i) Предел текучести должен быть определен либо методом «смещения», либо методом «удлинения под нагрузкой», как предписано в ASTM E 8 (IBR, см. § 171.7 данного подраздела).
(ii) При использовании метода «растяжение под нагрузкой» общая деформация (или «растяжение под нагрузкой»), соответствующая напряжению, при котором 0.2-процентная остаточная деформация может быть определена с достаточной точностью путем расчета упругого удлинения расчетной длины при соответствующей нагрузке и добавления к нему 0,2% расчетной длины. Расчеты упругого растяжения должны основываться на модуле упругости 30 000 000. В случае разногласий должна быть построена вся диаграмма напряжения-деформации, а предел текучести определен по смещению в 0,2 процента.
(iii) Для целей измерения деформации первоначальная деформация должна быть установлена, когда образец находится под нагрузкой 12 000 фунтов на квадратный дюйм, при этом показания индикатора деформации должны быть установлены на рассчитанную соответствующую деформацию.
(iv) Скорость траверсы испытательной машины не может превышать 1/8 дюйма в минуту при определении предела текучести.
(l) Приемлемые результаты физических испытаний, испытаний на сплющивание и изгиб. Приемлемым результатом физических испытаний и испытаний на сплющивание является удлинение не менее 20 процентов для 2 дюймов расчетной длины или не менее 10 процентов в других случаях. Требуется сплющивание без образования трещин до 6-кратной толщины стенки цилиндра. Приемлемым результатом альтернативного испытания на изгиб является отсутствие трещин, когда цилиндр изгибают внутрь вокруг оправки до тех пор, пока расстояние между внутренними краями не станет больше диаметра оправки.
(м) Испытание на герметичность. Все вращающиеся цилиндры и цилиндры с заглушками должны быть проверены на утечку с помощью газа или давления воздуха после того, как дно будет очищено и полностью очищено от влаги. К одной стороне готового днища на площади не менее
1/16 общей площади днища, но не менее
3/4 дюйма в диаметре, включая крышку, в течение не менее одной минуты, в течение которых другая сторона дна, находящаяся под давлением, должна быть покрыта водой и тщательно осмотрена на наличие признаков утечки. За исключением случаев, предусмотренных в пункте (n) настоящего раздела, баллон должен быть забракован, если есть какая-либо утечка.
(1) Прядильный цилиндр – это цилиндр, в котором торцевая заглушка готового цилиндра приварена в процессе прядения.
(2) Цилиндр с заглушкой – это цилиндр, в котором необратимое закрытие нижней части готового цилиндра осуществляется заглушкой.
(3) В качестве меры предосторожности, если изготовитель решит провести это испытание перед гидростатическим испытанием, изготовитель должен спроектировать испытательное оборудование таким образом, чтобы давление прикладывалось к наименьшей практически возможной площади вокруг точки закрытия и таким образом, чтобы использовать минимально возможный объем воздуха или газа.
(n) Бракованные баллоны. Обработка повторным нагревом разрешена для забракованных баллонов. После этого баллоны должны пройти все предписанные испытания, чтобы быть приемлемыми. Ремонт сваркой или вращением не разрешается. Цилиндрические цилиндры, забракованные в соответствии с положением пункта (m) настоящего раздела, могут быть исключены из категории цилиндрических цилиндров путем сверления для удаления дефектного материала, нарезания резьбы и закупоривания.
IRJET-Запрошенная вами страница не найдена на нашем сайте Февраль 2022 Публикация в процессе…
Просмотр статей
IRJET Получил «Научный журнал Импакт-фактор: 7.529 » на 2020 год.
Подтвердить здесь
IRJET Получен сертификат регистрации ISO 9001:2008 для своей системы управления качеством. февраль 2022 г.)
Отправить сейчас
IRJET Vol-9 Выпуск 2, февраль 2022 г. Публикация в процессе…
Просмотр статей
IRJET Получено «Научный журнал Импакт-фактор: 7. 529 » на 2020 год.
Подтвердить здесь
IRJET Получен сертификат регистрации ISO 9001:2008 для своей системы управления качеством. февраль 2022 г.)
Отправить сейчас
IRJET Vol-9 Выпуск 2, февраль 2022 г. Публикация в процессе…
Просмотр статей
IRJET Получено «Научный журнал Импакт-фактор: 7.529 » на 2020 год.
Подтвердить здесь
IRJET Получен сертификат регистрации ISO 9001:2008 для своей системы управления качеством. февраль 2022 г.)
Отправить сейчас
IRJET Vol-9 Выпуск 2, февраль 2022 г. Публикация в процессе…
Просмотр статей
IRJET Получено «Научный журнал Импакт-фактор: 7.529 » на 2020 год.
Подтвердить здесь
IRJET Получен сертификат регистрации ISO 9001:2008 для своей системы управления качеством. февраль 2022 г.)
Отправить сейчас
IRJET Vol-9 Выпуск 2, февраль 2022 г. Публикация в процессе. ..
Просмотр статей
IRJET Получено «Научный журнал Импакт-фактор: 7.529 » на 2020 год.
Подтвердить здесь
IRJET Получен сертификат регистрации ISO 9001:2008 для своей системы управления качеством. февраль 2022 г.)
Отправить сейчас
IRJET Vol-9 Выпуск 2, февраль 2022 г. Публикация в процессе…
Просмотр статей
IRJET Получено «Научный журнал Импакт-фактор: 7.529 » на 2020 год.
Подтвердить здесь
IRJET Получен сертификат регистрации ISO 9001:2008 для своей системы управления качеством. февраль 2022 г.)
Отправить сейчас
IRJET Vol-9 Выпуск 2, февраль 2022 г. Публикация в процессе…
Просмотр статей
IRJET Получено «Научный журнал Импакт-фактор: 7.529 » на 2020 год.
Подтвердить здесь
IRJET Получен сертификат регистрации ISO 9001:2008 для своей системы управления качеством. февраль 2022 г. )
Отправить сейчас
IRJET Vol-9 Выпуск 2, февраль 2022 г. Публикация в процессе…
Просмотр статей
IRJET Получено «Научный журнал Импакт-фактор: 7.529 » на 2020 год.
Verify Here
IRJET получила сертификат регистрации ISO 9001:2008 для своей системы менеджмента качества.
%PDF-1.3
%
1 0 объект
/CreationDate (D:20130114150428-05’00’)/Creator/Keywords/Producer/Subject/Title >>
эндообъект
2 0 объект
>>>
эндообъект
3 0 объект
>
эндообъект
4 0 объект
>
эндообъект
5 0 объект
>/ProcSet [/PDF /Text /ImageB /ImageC /ImageI ]/XObject >>>/Type /Page >>
эндообъект
6 0 объект
>/ProcSet [/PDF /Text /ImageB /ImageC /ImageI ]/XObject >>>/Type /Page >>
эндообъект
7 0 объект
>/ProcSet [/PDF /Text /ImageB /ImageC /ImageI ]/XObject >>>/Type /Page >>
эндообъект
8 0 объект
>/ProcSet [/PDF /Text /ImageB /ImageC /ImageI ]/XObject >>>/Type /Page >>
эндообъект
9 0 объект
>/ProcSet [/PDF /Text /ImageB /ImageC /ImageI ]/XObject >>>/Type /Page >>
эндообъект
10 0 объект
>/ProcSet [/PDF /Text /ImageB /ImageC /ImageI ]/XObject >>>/Type /Page >>
эндообъект
11 0 объект
>/ProcSet [/PDF /Text /ImageB /ImageC /ImageI ]/XObject >>>/Type /Page >>
эндообъект
12 0 объект
>/ProcSet [/PDF /Text /ImageB /ImageC /ImageI ]/XObject >>>/Type /Page >>
эндообъект
13 0 объект
>/ProcSet [/PDF /Text /ImageB /ImageC /ImageI ]/XObject >>>/Type /Page >>
эндообъект
14 0 объект
>/ProcSet [/PDF /Text /ImageB /ImageC /ImageI ]/XObject >>>/Type /Page >>
эндообъект
15 0 объект
>/ProcSet [/PDF /Text /ImageB /ImageC /ImageI ]/XObject >>>/Type /Page >>
эндообъект
16 0 объект
>/ProcSet [/PDF /Text /ImageB /ImageC /ImageI ]/XObject >>>/Type /Page >>
эндообъект
17 0 объект
>/ProcSet [/PDF /Text /ImageB /ImageC /ImageI ]/XObject >>>/Type /Page >>
эндообъект
18 0 объект
>/ProcSet [/PDF /Text /ImageB /ImageC /ImageI ]/XObject >>>/Type /Page >>
эндообъект
19 0 объект
>/ProcSet [/PDF /Text /ImageB /ImageC /ImageI ]/XObject >>>/Type /Page >>
эндообъект
20 0 объект
>/ProcSet [/PDF /Text /ImageB /ImageC /ImageI ]/XObject >>>/Type /Page >>
эндообъект
21 0 объект
>/ProcSet [/PDF /Text /ImageB /ImageC /ImageI ]/XObject >>>/Type /Page >>
эндообъект
22 0 объект
>/ProcSet [/PDF /Text /ImageB /ImageC /ImageI ]/XObject >>>/Type /Page >>
эндообъект
23 0 объект
>/ProcSet [/PDF /Text /ImageB /ImageC /ImageI ]/XObject >>>/Type /Page >>
эндообъект
24 0 объект
>/ProcSet [/PDF /Text /ImageB /ImageC /ImageI ]/XObject >>>/Type /Page >>
эндообъект
25 0 объект
>/ProcSet [/PDF /Text /ImageB /ImageC /ImageI ]/XObject >>>/Type /Page >>
эндообъект
26 0 объект
>/ProcSet [/PDF /Text /ImageB /ImageC /ImageI ]/XObject >>>/Type /Page >>
эндообъект
27 0 объект
>/ProcSet [/PDF /Text /ImageB /ImageC /ImageI ]/XObject >>>/Type /Page >>
эндообъект
28 0 объект
>/ProcSet [/PDF /Text /ImageB /ImageC /ImageI ]/XObject >>>/Type /Page >>
эндообъект
29 0 объект
>/ProcSet [/PDF /Text /ImageB /ImageC /ImageI ]/XObject >>>/Type /Page >>
эндообъект
30 0 объект
>/ProcSet [/PDF /Text /ImageB /ImageC /ImageI ]/XObject >>>/Type /Page >>
эндообъект
31 0 объект
>/ProcSet [/PDF /Text /ImageB /ImageC /ImageI ]/XObject >>>/Type /Page >>
эндообъект
32 0 объект
>/ProcSet [/PDF /Text /ImageB /ImageC /ImageI ]/XObject >>>/Type /Page >>
эндообъект
33 0 объект
>/ProcSet [/PDF /Text /ImageB /ImageC /ImageI ]/XObject >>>/Type /Page >>
эндообъект
34 0 объект
>/ProcSet [/PDF /Text /ImageB /ImageC /ImageI ]/XObject >>>/Type /Page >>
эндообъект
35 0 объект
>/ProcSet [/PDF /Text /ImageB /ImageC /ImageI ]/XObject >>>/Type /Page >>
эндообъект
36 0 объект
>/ProcSet [/PDF /Text /ImageB /ImageC /ImageI ]/XObject >>>/Type /Page >>
эндообъект
37 0 объект
>/ProcSet [/PDF /Text /ImageB /ImageC /ImageI ]/XObject >>>/Type /Page >>
эндообъект
38 0 объект
>/ProcSet [/PDF /Text /ImageB /ImageC /ImageI ]/XObject >>>/Type /Page >>
эндообъект
39 0 объект
>/ProcSet [/PDF /Text /ImageB /ImageC /ImageI ]/XObject >>>/Type /Page >>
эндообъект
40 0 объект
>/ProcSet [/PDF /Text /ImageB /ImageC /ImageI ]/XObject >>>/Type /Page >>
эндообъект
41 0 объект
> поток
xSMo0W(ин. v(v'(йMZ˿/)JX$E=RO/;0k2U
Поддержка | Алюминиевые газовые баллоны высокого давления
Все алюминиевые баллоны DOT/TC должны подвергаться визуальному осмотру во время их повторного 5-летнего испытания. Резьба и осмотр горловины можно проводить только при снятом с цилиндра клапане и удалении всех посторонних материалов (т. е. грязи, коррозии и т. д.) с уплотнительного кольца и резьбы. источник и стоматологическое зеркало 2X, и может поддерживаться использованием вихретокового устройства для контроля резьбы.
Вихретоковый контроль баллонов из алюминиевого сплава 6061 не предусмотрен Департаментом транспорта (DOT). Catalina Cylinders изготавливает цилиндры только из алюминиевого сплава 6061. Только баллоны из алюминиевого сплава 6351 должны проходить проверку Департаментом транспорта каждые 5 лет во время переквалификации.
Catalina Cylinders рекомендует, чтобы элементы, определенные ниже, были включены в проверку резьбы и шейки цилиндров Catalina Cylinders, подлежащих ежегодному визуальному осмотру. Критерии отклонения для каждого элемента перечислены под этим элементом.
Минимальное количество потоков
Минимальное количество полных резьб, необходимых для цилиндров Catalina Cylinders:
Рабочее давление | Минимальное количество потоков |
1800–2216 фунтов на кв. дюйм | 6,0 |
3000 фунтов на кв. дюйм | 8,0 |
3300 фунтов на кв. дюйм | 9,0 |
Минимальное количество полных нитей считается от верхней нити вниз.Минимальное количество полных витков не может быть прервано какими-либо разрывами (например, впадинами, складками, коррозией, трещинами или повреждениями).
Критерии отклонения:
Цилиндры с количеством полной резьбы меньше минимального, необходимого для указанных выше рабочих давлений, неприемлемы.
Политика замены:
Политика разрешения на возврат цилиндров Catalina распространяется на цилиндры, изготовленные с меньшим числом полных резьб, чем требуется.
Долина
Впадина – это отсутствие состояния металла в нижней части резьбы. Впадина создается во время операции формирования кроны. Впадина имеет вид перевернутой буквы «U» в нижней части резьбы. Контур долины сильно округлен.
Критерии отклонения:
Долина неприемлема, если:
- прерывает требуемое минимальное количество завершенных потоков и
- создает дисбаланс потоков в 6 или более потоков
Впадина может быть обнаружена, но не исключена исключительно с помощью вихретокового контроля резьбы.Впадина не будет отображаться в виде пика на устройстве Visual Plus.
Политика замены:
Неприемлемая долина — это производственный дефект, подпадающий под действие Политики авторизации возврата баллонов Catalina.
Дисбаланс резьбы
Дисбаланс резьбы — это количество неполных нитей в цилиндре. Дисбаланс нитей — это разница между количеством полных нитей и количеством полных нитей (полных нитей и неполных нитей) в цилиндре.
Критерии отклонения:
Дисбаланс потоков недопустим, если:
- Прерывает требуемое минимальное количество нитей в цилиндре или
- Он измеряет 6 нитей или более
Дисбаланс резьбы может быть обнаружен, но не исключен исключительно с помощью вихретокового контроля резьбы.
Политика замены:
Недопустимый дисбаланс резьбы — это производственный дефект, подпадающий под действие Политики авторизации возврата цилиндров Catalina.
Складки
Складка – это отсутствие состояния металла в нижней части резьбы или в буртике цилиндра. Складка создается во время операции формирования венца и фактически представляет собой сгибание металла во время операции формирования. Складка — это статическое состояние, она не распространяется и не увеличивается в размерах.Складка имеет вид перевернутой буквы «V» в нижней части нитей. Обычно сгиб имеет линейную индикацию, идущую вниз по самой глубокой части сгиба. Контур складки резкий в самой глубокой точке. Складка внешне похожа на трещину и часто ошибочно принимается за нее, динамическое состояние, которое может возникнуть в цилиндрах из сплава 6351.
Критерии отклонения:
Сгиб недопустим, если:
- прерывает требуемое минимальное количество завершенных потоков или
- прерывает два полных потока или
- вызывает потерю содержимого цилиндра
Устройство вихретокового контроля резьбы может обнаруживать складки на резьбе цилиндра.
Политика замены:
Недопустимая складка — это производственный дефект, на который распространяется политика разрешения на возврат баллонов Catalina.
Коррозия
Коррозия может возникнуть в резьбе цилиндра, если в цилиндр попадает влага, возможно, из-за наполнения цилиндра влажным воздухом. Коррозия обычно начинается с 9-й или 10-й резьбы, в том месте, где нижняя часть резьбовой части клапана заканчивается резьбой цилиндра. Клапан акваланга, не полностью хромированный, может ускорить процесс коррозии в резьбовой части баллона.Коррозия может возникать на верхней поверхности цилиндра и в уплотнительном кольце цилиндра.
Критерии отклонения:
Коррозия недопустима, если:
- прерывает требуемое минимальное количество завершенных потоков или
- прерывает два полных потока или
- вызывает потерю содержимого цилиндра
Вихретоковый контроль резьбы позволяет обнаружить коррозию резьбы цилиндра.
Политика замены:
Коррозия не связана с производством и не подпадает под действие Политики авторизации возврата баллонов Catalina.
Трещины резьбы
Трещина представляет собой линейный разрыв, который обычно проходит линейно сверху вниз в резьбе. Трещина обычно начинается в нижней части резьбы и распространяется вверх. Трещина может, но редко начинается в верхней части резьбы. Трещина — это динамическое состояние, которое распространяется или увеличивается в размерах с течением времени, как правило, когда цилиндр находится под давлением. Трещина в цилиндре из сплава 6351 внешне похожа на складку, статическое состояние.
Критерии отклонения:
Трещина недопустима.
Трещины могут быть идентифицированы и отклонены с помощью устройства вихретокового контроля резьбы. Рекомендуется, чтобы баллоны, в которых трещина была обнаружена с помощью вихретокового датчика резьбы и не может быть обнаружена визуально, были возвращены в компанию Catalina Cylinders по разрешению на возврат (RA) для оценки до их изъятия.
Политика замены:
Трещина, признанная производственным дефектом, подпадает под действие Политики разрешения на возврат баллонов Catalina.
Вихретоковый прибор «Шип» Индикация
Вихретоковый контроль баллонов из алюминиевого сплава 6061 не предусмотрен Департаментом транспорта (DOT). Catalina Cylinders изготавливает цилиндры только из алюминиевого сплава 6061. Только баллоны из алюминиевого сплава 6351 должны проходить проверку Департаментом транспорта каждые 5 лет во время переаттестации.
Вихретоковый прибор «Шип» измеряет длину двух витков. Эти показания измеряются после того, как устройство было откалибровано, работало в режиме 1X, а линия трассировки была сброшена и центрирована ниже пороговой линии.
Критерии отклонения:
Любая линейная индикация, которая прерывает два полных потока и идентифицируется вихретоковым устройством как индикация всплеска, является причиной отклонения (не осуждается). Цилиндр с условиями отбраковки вихретокового устройства должен визуально проверяться перед отбраковкой баллона.
Политика замены:
Коррозионные язвы, приемлемая ендова и 1 изгиб нити не подпадают под действие Политики разрешения на возврат цилиндров Catalina.
Цилиндр с неприемлемыми производственными условиями (т. е. складки, трещины или отсутствие полной резьбы), удлиняющий две резьбы, как определено вихретоковым устройством, подпадает под действие Политики разрешения на возврат цилиндров Catalina.
Метки остановки инструмента
Метки остановки инструмента отображаются в виде линейных индикаторов на 1–3 витках нижней резьбы цилиндра. Как правило, когда резьба завершена, в нижней части резьбы в цилиндре видны шесть меток остановки инструмента, расположенных на равном расстоянии друг от друга.Инструмент, который нарезает резьбу в цилиндре, создает метки остановки инструмента. Метка остановки инструмента представляет собой небольшое нарастание металла в месте, где останавливается инструмент для нарезания резьбы, отсюда и название «метка остановки инструмента». Метки остановки инструмента не являются отклонением.
Вихретоковые устройства контроля резьбы обычно не обнаруживают метки остановки инструмента.
Критерии отклонения:
Нет.
Политика замены:
Остановочные метки на инструменте не являются неприемлемым производственным условием, подпадающим под действие Политики авторизации возврата цилиндров Catalina.
Урон
Повреждение верхней поверхности, уплотнительного кольца или резьбы цилиндра может быть нанесено во время изготовления цилиндра и после того, как цилиндр был в эксплуатации.
Критерии отклонения:
Повреждение верхней поверхности, уплотнительного кольца или резьбы цилиндра недопустимо, если:
- вызывает потерю содержимого баллона, или
- прерывает требуемое минимальное количество полных витков в цилиндре
Вихретоковый контроль резьбы может обнаруживать или не обнаруживать повреждение резьбы цилиндра.
Политика замены:
Политика разрешения на возврат баллонов Catalina распространяется на неприемлемые повреждения, возникшие в процессе изготовления баллона.
Если в какой-либо момент целостность цилиндра со штампом «CATALINA» и/или «M4002» на заводной головке вызывает сомнения, мы просим вас немедленно связаться с Catalina Cylinders и попросить поговорить с представителем Catalina Cylinders Return Authorization (RA). Наш офис RA работает с понедельника по пятницу с 8:00 до 17:00. Прежде чем звонить, подготовьте маркировку головки цилиндра (штамп) и объясните, что вас беспокоит по поводу цилиндра. Наличие этой информации во время звонка поможет ускорить решение ваших проблем. Информация, которую вы предоставите представителю RA, определит, следует ли создать отчет RA и вернуть баллон в Catalina Cylinders.
Композитный баллон – обзор
1.6 Композитные транспортные сосуды
Композитные транспортные баллоны, используемые для доставки газообразного водорода, были представлены на рынке без льготных правил.Поэтому для перевозки композитных баллонов под давлением требовались разрешения регулирующих органов в виде специальных разрешений или исключений из правил. Были разработаны отраслевые стандарты, которые послужили основой для разрешений регулирующих органов. DOT разрешает хранение водорода в виде исключения в композитных сосудах. Руководящие принципы, используемые для исключения композитных сосудов под давлением, включают FRP-1 31 , FRP-2 32 , FRP-3 33 и CFFC 34 .
FRP-1 (баллоны с полной оболочкой) и FRP-2 (баллоны с кольцевой оболочкой) были разработаны Ассоциацией сжатых газов (CGA) в сотрудничестве с DOT в начале 1970-х годов и с тех пор практически не изменились. Эти стандарты были разработаны для переносных баллонов меньшего размера. Коэффициенты безопасности были установлены на уровне 3,0 для разрыва и 3,33 для напряжения на основе использования армирования стекловолокном для полностью обернутых баллонов. Баллоны с кольцевой обмоткой используют коэффициент запаса прочности 2,5 на разрыв. Оба стандарта допускали использование только бесшовных алюминиевых вкладышей. FRP-1 и FRP-2 также используют тесты производительности для квалификации конструкции цилиндра, а не по конструкции в соответствии с правилами и анализом. Номер
CFFC был разработан Министерством транспорта США в 1997 году для использования в дыхательных баллонах, армированных углеродным волокном, с алюминиевым покрытием, и основывался на запросах об освобождении от трех или четырех производителей.Коэффициент безопасности по давлению разрыва был установлен на уровне 3,4 на основании общности конструкций в приложениях, что было необходимо для удовлетворения требований к неразрушаемости (огнестрельное оружие), падению и циклической усталости гильзы на основе общих размеров, материалов и условий. использования.
FRP-3 был разработан в 1990-х годах на основе ANSI NGV2 35 . Он был разработан CGA как документ C-19 для композитных баллонов с гильзами без распределения нагрузки. FRP-3 был в большей степени основан на характеристиках, чем стандарты цилиндров FRP-1 и FRP-2, и предназначался для включения большего разнообразия материалов, различных подходов к проектированию и больших размеров.Он имеет те же коэффициенты безопасности, что и NGV2: 2,25 для цилиндров, армированных углеродным волокном, 3,0 для цилиндров, армированных арамидным волокном, и 3,5 для цилиндров, армированных стекловолокном.
ISO 11119 36 разработан на основе FRP-1, FRP-2, NGV2 и европейских стандартов. Он в большей степени основан на характеристиках, чем FRP-1 и FRP-2, но он больше основан на цилиндрах меньшего размера, как указано в FRP-1 и FRP-2, а не на больших транспортных цилиндрах.
Недавно при поддержке Министерства энергетики США (DOE) были разработаны большие суда для хранения и транспортировки сжатого природного газа и водорода.