Способы сварки рельсов (Электроконтактная, электродуговая, газопрессовая и алюмотермитная сварка), страница 4
Геометрия стрелочных переводов такова, что применение в пути сварочных машин для электроконтактной сварки затруднено, поэтому для сварки стыков в зоне перевода применяется термитная сварка, выполняемая с использованием специальной оснастки.
Стыки в пределах стрелочных переводов проектов 2726, 2728. 2750 и 2799 подлежат алюминотермитной сварке в соответствии с ТУ «Алюминотермитная сварка рельсов в пределах стрелочных переводов» 1997 г.
Для погашения продольных температурных сил, возникающих в рельсовых плетях, стрелочные переводы отделяются от бесстыкового пути двумя парами уравнительных рельсов с каждой стороны перевода. Это типовое решение, написанное в ТУ-2000, не может быть использовано на участках, примыкающих к сварным стрелочным переводам на скоростных линиях.
На базе Экспериментального кольца ВНИИЖТа проводились опытные работы с
использованием алюминотермитной сварки рельсовых элементов типов Р65 и Р50,
полигонные и эксплуатационные испытания стрелочных переводов со сварными
стыками.
Установленный гарантийный срок службы сварных стыков стрелочных переводов, выполненных алюминотермитным способом, для рельсов типа Р65 составляет 100 млн. т брутто пропущенного по ним груза, но не более трех лет со дня проведения сварочных работ.
Сварка стыков (кроме изолирующих) стрелочных переводов, уложенных на деревянных или железобетонных брусьях, в главных, приемо-отправочных, станционных и горочных путях применяется на железных дорогах Российской Федерации с 1996 г. В Департаменте пути и сооружений разработаны и утверждены Технические условия на алюминотермитную сварку рельсов в пределах стрелочных переводов.
В настоящее время на Экспериментальном кольце продолжают совершенствовать
технологии алюминотермитной сварки рельсовых элементов стрелочных переводов
вместе с фирмами «Электро-Термит» и «Рельтех».
Преимущества сварных стыков, выполненных по данной технологии, такие как: высокие прочностные характеристики, однородность структуры стали, повышенная прямолинейность подтверждены актами ВНИИЖТ и актами проверок качества сварки стыков стрелочных переводов на линии С.Петербург-Москва.
В основе алюминотермитной сварки лежит химическая реакция, происходящая с
большим выделением тепла между основными частями термитной порции (окись
железа и высокочистый алюминий тонкого помола) после ее точечного поджига с
кислородом. К основным составным частям добавляются частицы стали для демпфирования
реакции, а также в зависимости от свариваемого материала различные легирующие
добавки (С, Mn, Cr, V, Мо). В результате образуется сталь определенного качества для
сварки и шлак.
Алюминотермитная сварка осуществляется путем нагрева и расплавления свариваемых металлов теплом термитов порошкообразных горящих смесей металлов с окислами металлов, главным образом, алюминиевого термита (смесь 22 % алюминия и 78 % железной окалины).
Алюминотермитная сварка рельсов состоит из следующих операций:
— рихтовка зазора между свариваемыми торцами рельсов;
— формовка места сварки при помощи огнеупорных материалов;
— прогрев рельсов;
— заливка термитной стали в форму;
— выдержка стали в форме;
— удаление сварочной формы;— обработка сварного шва;
— прогрев шва;
— шлифовка рельсов в зоне сварки.
Алюминотермитная сварка рельсов может применяться для сваривания
объемнозакаленных рельсов с рельсами, имеющими поверхностную закалку, или
поверхностно закаленных рельсов между собой, а также с термически
неупрочненными. При этом применяется термит повышенной прочности марки 1200 (с
временным сопротивлением литого металла 1200 кН/мм). При сварке термически
неупрочненных рельсов применяется термит обычной прочности марки 900.
Алюминотермитная сварка производится при положительной температуре воздуха не ниже +5°С. При отрицательной температуре требуется дополнительный прогрев концов рельсов на длине 1м от стыка.
Рис. 7.6. Термическая обработка стыка.
В таблице 7.3 приведены наименьшие приемочные значения показателей прочности и пластичности рельсов, сваренных термитом, при статическом поперечном изгибе. При испытании образцов рельсов, сваренных по технологиям фирм «Электро-Термит» и «Рельтех», минимальные значения разрушающей нагрузки и стрелы прогиба соответствуют или превышают наименьшие приемочные значения показателей прочности и пластичности.
Таблица 7.3.
Наименьшие значения прочности и пластичности рельсов, при статическом поперечном изгибе.
Зона растяжения образцов на пролете 1 м. | Разрушающая нагрузка, кН, для рельсов типа | Стрела прогиба, мм, для рельсов типа | ||
Р65 | Р50 | Р65 | Р50 | |
Подошва (нагружение на головку) | 1500 | 1000 | 20 | 20 |
Головка (нагружение на подошву) | 1250 | 850 | 15 | 15 |
2.12. Требования охраны труда при алюминотермитной сварке рельсов [ПРАВИЛА ПО ОХРАНЕ ТРУДА ДЛЯ РЕЛЬСОСВАРОЧНЫХ ПОЕЗДОВ] — последняя редакция
2.12. Требования охраны труда при алюминотермитной
сварке рельсов
2.12.1. Работы по алюминотермитной сварке рельсов на станциях в пределах стрелочных переводов должны производиться при температуре окружающего воздуха, указанной в технологической документации, объединенной бригадой, в состав которой входит бригада монтеров пути из 3 — 5 человек (в зависимости от объемов работ), руководимая дорожным мастером, и группа специалистов-сварщиков термитной сварки в составе 3 человек.
Ответственным за охрану труда при производстве сварочных работ является руководитель группы специалистов-сварщиков термитной сварки.
2.12.2. Сварочные работы должны производиться на закрытом для движения поездов участке железнодорожного пути.
2.12.3. При выполнении работ по алюминотермитной сварке рельсов необходимо выполнять требования подпункта 2.3.2 настоящих Правил, а также технических условий по алюминотермитной сварке рельсов в пределах стрелочных переводов.
2.12.4. При сваривании рельсов на железнодорожных путях перегонов и станций в зимнее время снег должен быть удален с площади в 1 м2 вокруг места сварки.
2.12.5. Перед началом проведения работ необходимо проверить целостность тары (упаковки) термитной смеси.
Термитная смесь, литейная форма (литниковый запор), молотый магнезит и термитные спички должны быть сухими. Форма не должна иметь трещин, изломов, сколов.
2.12.6. Применять термит из поврежденных пакетов, пересыпать или досыпать термит из одного пакета в другой запрещается.
2.12.7. Складирование термита, форм, газового и технологического оборудования должно производиться на расстоянии не ближе 5 м от места проведения работ.
2.12.8. Установку тигля, заправленного порцией термита, над полостью формы должны выполнять двое работников плавно, без ударов.
2.12.9. При просушке тигля, подогреве концов рельсов специальной горелкой должны соблюдаться следующие требования безопасности:
— при зажигании горючей смеси в аппаратуре следует первым открыть вентиль кислорода, а затем — вентиль горючего газа и поджечь горючую смесь;
— перекрытие газов производить в обратном порядке;
— при возникновении обратного удара пламени, перегреве горелки необходимо немедленно закрыть вентили на горелке, баллонах, защитном устройстве, а затем охладить горелку;
— после каждого обратного удара необходимо проверить предохранительное устройство, рукава, продуть их инертным газом и, при необходимости, заменить.
— при перерывах в работе пламя горелки должно быть потушено, а вентили на ней плотно закрыты; при длительных перерывах в работе должны быть также закрыты вентили на баллонах.
2.12.10. Запрещается:
— эксплуатировать газовый баллон, имеющий просроченный срок поверки манометра;
— работать при наличии хотя бы незначительных утечек газа, загрязненных выходных каналах мундштуков;
— оставлять без присмотра зажженную горелку;
— проверять плотность соединений с помощью открытого огня.
2.12.11. При присоединении или отсоединении шланга от баллона вентили на шланге и горелке должны быть закрыты.
2.12.12. Плотность мест соединения рукава с баллоном и горелкой следует проверять с помощью мыльной воды.
2.12.13. Газовые баллоны следует закреплять в вертикальном положении и не допускать их падения и ударов.
2.12.14. По окончании работы вентиль на горелке следует закрывать только после прекращения ее горения. После отсоединения от рукава на баллон должен быть надет колпак.
2.12.15. Во время и после предварительного нагрева рельсового стыка, при прохождении сплава в рельсовый стык, остывании стыка нахождение работников в высокотемпературной зоне не допускается. Обрубка грата гратоснимателем, обработка стыков шлифовальной машиной должны выполняться путевой бригадой в термостойкой спецодежде, защитных очках под наблюдением сварщика.
Во время и после подогрева рельсового стыка запрещается касаться полуформ и восстанавливать их обмазку.
2.12.16. Сварочные порции термита, тигли и формы необходимо беречь от влаги. Соприкосновение с водой сварочных порций термита и горячих продуктов реакции не допускается.
Не допускается совместное хранение запальных стержней и порций термита, а также их нахождение в спецодежде сварщика.
2.12.17. Использование термита с повышенной влажностью, добавка термита в тигель во время горения, искусственное охлаждение тигля во время прохождения реакции и после нее мокрой тряпкой, сырой глиной запрещается.
2.12.18. Зажигание горелки должно производится только после установки горелки на специальную стойку.
2.12.19. При работе необходимо следить, чтобы рукава горелки не попали в горячий металл или пламя горелки.
2.12.20. Для зажигания термита следует пользоваться только специальными термитными спичками. Зажигать термит от электродуги сварки или контактного провода, а также горелкой запрещается. Термитную спичку следует зажигать от горелки в перчатках и следить, чтобы рука не попала в пламя горелки. Не допускается зажженную спичку направлять на работников и горючие материалы.
При отсутствии начала реакции повторное зажигание термита следует производить не ранее чем через 30 с. Термитные спички должны храниться у руководителя группы сварщиков термитной сварки в количестве, соответствующем заданию на сварку стыков рельсов, плюс две-три запасные.
2.12.21. При зажигании термитной смеси необходимо пользоваться защитными очками.
2.12.22. От момента зажигания смеси до окончания выпуска металла в форму не допускается выполнять какие-либо работы около свариваемого и противоположного ему стыка.
2.12.23. Во избежание разбрызгивания термитной массы в процессе горения тигель перед зажиганием должен покрываться колпаком из жаропрочного материала. Во время горения термита и выпуске жидкого металла из тигля в форму по сечению рельса руководитель группы сварщиков (сварщик термитной сварки) должен находиться на расстоянии не ближе 2 м от места сварки, а остальные работники — не ближе 3 м от тигля со стороны, противоположной отверстию сопла формы.
Металл из тигля должен выпускать только сварщик термитной сварки, применяя для этой цели специальный «ударник». Замена «ударника» лопаткой, палкой и другими предметами не допускается.
2.12.24. В случае прожога тигля или прорыва формы жидким металлом задерживать льющийся металл глиной или заливать его водой не допускается.
2.12.25. Снимать специальный кювет (ковш) со шлаком следует избегая опрокидывания. Выбрасывать шлак из ковша в воду, на снег или мокрую землю запрещается.
2.12.26. Горячее оборудование, инструмент, отработанный шлак и верхнюю часть формы следует складывать на расстоянии не менее трех метров от места сварки.
2.12.27. Для тушения горячих продуктов реакции (термитной смеси) необходимо применять порошковые огнетушители (ОП-50М, ОП-100, ОП-10). Для тушения небольших по площади очагов пожара (до 0,1 м2) допускается применять только сухой песок или глинозем. Производить тушение горячих продуктов реакции водой, углекислотным огнетушителем, мокрым песком или глиной и другими водосодержащими средствами запрещается.
Способы сварки рельсов (Электроконтактная, электродуговая, газопрессовая и алюмотермитная сварка), страница 2
Берегите глаза | 10.09.2015
Многим известен такой вид сварки, как электродуговая и газовая. Они широко применяются как на производстве, так и в строительстве. Но термитная сварка мало кому известна. Поэтому речь пойдет о ней. Благодаря использованию термитной сварки, получаются, ничем не хуже по качеству соединения, как при электро или газосварке, притом не требуется источник электропитания или газовые баллоны.
Сферы применения
Термитную сварку на сегодняшний день используют для сваривания чугуна, электрических и телефонных коммуникаций, труб, частей двигателя и так далее. Особо часто термит используют для сваривания железнодорожных рельсов. Соединения получаются достаточно надёжные. Место ремонта может быть на любом участке дороги, даже в несколько сот километров от населенного пункта.
Требования и ГОСТ
Правила проведения сварки ванным способом изложены в ГОСТ 14098-91, посвященном соединению арматуры и закладных изделий в ж/б конструкциях.
Примеры:
- Запрещено выполнять работы в условиях нестабильного электроснабжения, при отклонении напряжения от номинального более 5%, на неисправном оборудовании (п. 1.15).
- Соединение сдвоенных арматурных стержней данным методом могут проводить только сварщики с соответствующим удостоверением.
Механизированную сварку прутков производят под флюсами следующих марок (п. 3.4.1):
- встык — АНЦ-I, АН-8, ФН-7, АН-22;
- Т-образно, в т.
ч. с колоннами — ФК-3, АНЦ-1.
Термитная сварка
Появление термитной сварки было обусловлено необходимостью стыкового соединения металлов без использования громоздкого оборудования и наличия электросети. Поэтому в 1859 г. Бекетов Н. Н. обнаружил способ, в основе которого лежит алюминотермия ― процесс получения металла восстановлением их окислов алюминия. Он определил, что смесь порошка алюминия и оксида железа, горя при 3000° C, превращаются в сталь и шлак.
В 1898 г. исследователь из Германии Гольдшмидт, впервые применил термитную сварку на практике, соединив два железных бруска. Сделал он это, образовав форму вокруг места стыка и засыпав его термитным порошком. Сгорев, термитный порошок превратился в расплавленное железо, соединив таким образом два металлических бруска. При этом шлак всплывал на поверхность и мог свободно отделиться.
С того времени состав термита практически не изменился. Чаще всего термит имеет в своём составе опилки алюминия ― 23%, и окись железа― 77%. Фракция порошка составляет ― 0,5 мм. В момент поджига порошка, возникает химическая реакция, благодаря которой выделяется много тепла. Плавясь, окись железа переходит в чистое железо, а расплавленный алюминий окисляется.
Электроконтактный способ
Электроконтактный подход к соединению стыков рельсов основывается на их сильном нагреве и последующем расплаве посредством электрической дуги, которая формируется значительным по величине током низкого напряжения.
Для реализации метода используют специальные машинные комплексы, работающие в автоматическом режиме (МСГР-500, МС-5002 или К-190, например).
Подлежащие обработке рельсы перед началом сварки укладываются либо непосредственно на путях, либо же с небольшим смещением внутри ветки или снаружи колеи (на удалении порядка 260 сантиметров от её оси).
При этом сам сварочный механизм перемещается по восстанавливаемой нитке, то есть представляет собой самоходную рельсосварочную станцию.
youtube.com/embed/P0othxDiPzc?feature=oembed» frameborder=»0″ allow=»accelerometer; autoplay; clipboard-write; encrypted-media; gyroscope; picture-in-picture» allowfullscreen=»»/>В процессе её работы используются сменные контактные головки различного типа, обеспечивающие необходимые режимы сварки (непрерывное оплавление или прерывистый разогрев контактов).
Термитная сварка рельсов
Процесс сваривания рельсов термитом заключается в следующем:
- обрезка рельс с двух сторон, чтобы промежуток между ними был 23 ― 25 мм. Притом они должны быть выставлены горизонтально и вертикально;
- в зазор между рельсами вставляется пластина из углеродистой стали, для образования зазора;
- стык рельсов зажимается прессом;
- на место соединения монтируется огнеупорная форма, а стыки формы с рельсами, засыпаются песком, или замазываются специальной пастой;
- поверх форм прикрепляется тигель (конус в виде лейки из огнеупорного материала) в котором первоначально сжигается термит.
Расплавленный жидкий металл полученный в тигле, в последствии выливают в форму на стыке рельс;
- термит в тигле поджигается термитным карандашом, после чего происходит горение основной смеси 20 ― 30 секунд;
- снизу в воронке тигля установлена заглушка, которая расправляется и освобождает проход жидкому металлу в форму. Сталь и шлак заполняя форму, образуют соединительный шов, притом шлак частично вытесняется наружу в специальные чаши, прикрепленные сбоку тигля;
- горячая сталь заливаемая в форму, проплавляет торцы рельс. После, убирается тигель, и форма сжимается прессом;
- форму снимают, и пока металл ещё горячий, удаляют его избыток;
- получившийся шов, тщательно шлифуют до образования однородной плоскости с рельсой.
Как выполнять ванную сварку
Соединяемые заготовки очищают от грязи и ржавчины. В противном случае шов будет иметь много дефектов.
Необходимое оборудование
Используют следующее:
- Сварочный аппарат переменного или постоянного тока.
- Кондуктор, струбцины или иные приспособления для неподвижной фиксации заготовок.
- Ванночки из стали, меди, керамики или графита. Первая разновидность является одноразовой. Существуют формы 2 типов — для вертикальных и горизонтальных соединений.
- Плавящиеся электроды. Наилучшее качество обеспечивают расходники с покрытием основного типа (фтористо-кальциевым), например УОНИ-13/45. В такой обмазке нет органических веществ, поэтому расплав не насыщается водородом. Начинающим будет сложно работать с этими расходниками. Им лучше воспользоваться рутиловыми МР-3, АНО или аналогичными.
- Баллон с инертным газом. Защищает металл шва от окисления в случае применения тугоплавкого электрода (сварка полуавтоматом и автоматом).
При ванной сварке используют сварочный аппарат постоянного или переменного тока.
В качестве аппарата можно применять самый простой сварочный трансформатор. Более удобен в работе инвертор. Он обладает следующими преимуществами:
- Малыми размерами и весом.
Масса устройства составляет всего 3 кг. Уменьшение габаритов трансформатора обусловлено применением специальной схемы, увеличивающей частоту переменного тока до 40-60 кГц.
- Высоким значением напряжения холостого хода. Это облегчает розжиг дуги, что особенно необходимо при использовании электродов с основной обмазкой. Из-за присутствия фтора она затрудняет горение.
- Наличием дополнительных функций, облегчающих розжиг и поддержание дуги («горячий старт», «форсаж разряда», «антизалипание»).
- Высоким КПД.
Используют ванночки:
- Одноразовые стальные марок С14-Мн, С16-Мо, С15-Рс.
- Керамические.
- Из графита марок ЭЭГ, ЭГО, ГМЗ, ППГ, ЭГ1.
- Из меди М1 или М2.
Применение многоразовых накладок дает двойной эффект:
- снижается расход стали на каждый стык;
- обеспечивается большая толщина защитного слоя бетона, в то время как при наличии стальной формы она сильно сокращается.
Выбор режима
Основными параметрами режима сварки являются:
- диаметр расходника;
- сила тока.
Первую величину подбирают по размеру заготовок. Данные для ванного способа отражены в таблице:
Диаметр свариваемых стержней, мм | Диаметр электрода, мм | Сварочный ток, А при положительной/отрицательной температуре воздуха |
20 | 5 | (225-235)/(250-260) |
22 | (235-250)/(260-280) | |
25 | (250-270)/(280-300) |
Параметры для ванно-шовной сварки — рекомендуемые и допустимые:
Диаметр свариваемых стержней, мм | Диаметр электрода, мм | Сварочный ток, А при положительной/отрицательной температуре воздуха |
36-40 | 6(5) | 300(275)/330(300) |
50-55 | 6(5) | 330(300)/360(330) |
60 | 7(6) | 420(400)/450(430) |
70 | 8(6) | 500(450)/540(470) |
80 | 8(6) | 500(450)/550(480) |
Примечание: в скобках указаны допустимые значения.
Термитные карандаши
В продаже можно найти термитные карандаши. Это кусок проволоки состоящей из углеродистой стали, диаметром до 5 мм. На неё наносят термитную смесь перемешанную с клеем. С одной стороны карандаша имеется место для запала. Что-то вроде бертолетового шнура, но нанесенного в виде дорожки на сам карандаш. Карандаш вставляют в держатель ― как для электросварки, ― и поджигают верхнюю часть. Когда огонь доходит до основного состава на другом конце карандаша, происходит запал термита. Сварку необходимо производить с защитным щитком и рукавицами. Этот же карандаш применяется для поджига основной смеси в тигле. Его поджигают и бросают в тигель с термитной смесью.
Кроме карандашей, существуют ещё термитные шашки и патроны. По принципу работы они схожи с термитным карандашом.
Достоинства термитной сварки
- крепкое и надежное сварочное соединение с высокой стойкостью к разрушению;
- технология сварки отличается простотой и доступностью, что предполагает ее использование как в промышленности, так и в быту;
- самый оптимальный вариант сварки при аварийных ситуациях.
Недостатки
- высокое поглощение влаги;
- смесь из-за способности воспламенятся, считается пожароопасной, что требует бережного отношения и хранения;
- попадание влаги на термитную шашку приводит к образованию взрыва;
- неспособность контролировать процесс горения термита.
Экономия, получаемая от применения сварных рельсов.
Имеются сведения, что, несмотря на более значительные первоначальные затраты, в результате применения длинных сварных рельсов получается значительная экономия за счет меньших затрат на текущее содержание пути. Вследствие отсутствия стыков сварные рельсы имеют больший срок службы, объем работ по смене шпал меньше, сплошную выправку пути по уровню можно производить через большие промежутки времени и случаи необходимости местной выправки пути по уровню сведены до минимума. Другим преимуществом сварных рельсов является значительное снижение количества сменяемых прокладок, стыковых соединителей, стыковых накладок и болтов, а также подлежащих наплавке концов рельсов; при применении сварных рельсов улучшается работа системы сигнализации, улучшаются условия движения поездов и уменьшается количество ударов, воспринимаемых подвижным составом. Специальный комитет AREA проводил исследования, касающиеся экономичности применения длинных сварных рельсов по сравнению с рельсами с обычными стыками и представил доклад по этому вопросу. С помощью данных о расходах и калькуляций, которые Комитет смог получить от дорог, имеющих опытные участки протяжением не менее двух миль, Комитет смог сделать заключение, что применение длинных сварных рельсов повышает первоначальные затраты на 14% в случае применения рельсов весом от 65,0 кг/пог. м до 67,5 кг/пог. я включительно, на 7% — при рельсах весом 55,5 и 57 кг/пог. м и на 13% — при рельсах весом 44,5 кг/пог. м. Однако Комитет сделал следующее заключение: при рельсах весом от 55,5 до 57,0 кг/пог. м дополнительные первоначальные расходы будут компенсированы за счет экономии на текущем содержании пути через 5 лет, а при более тяжелых типах рельсов эта компенсация произойдет через 7 лет. Было также отмечено, что экономия, получаемая от применения длинных сварных рельсов, будет особенно ощутительна на тех участках пути, где не наблюдается особенно интенсивного износа рельсов, вызванного кривыми или уклонами пути.
Оборудование для термитной сварки рельс
- вольфрамовый или керамический тигель с плавящейся заглушкой, и приспособленный для слива жидкого металла в форму;
- отливочные формы для придания расплавленному металлу формы рельсов;
- пресс для сжатия форм после заливки металла;
- дополнительное оборудование: подставка для тигля, термометр, горелка;
- дополнительные материалы и инструменты: болгарка, шлифовальные круги, кувалда, зубило, металлическая щётка, термостойкая одежда, рукавицы, защитные очки для глаз и другое.
Все это обеспечит качественную работу и защитит персонал от разрушительного воздействия тепла и грязи получаемых при сгорании термосмеси. https://www.youtube.com/watch?v=kuydZx-ckTs
Технология сварочной ванны
Соединение арматурных стержней и других элементов сплошного сечения осуществляют следующим образом:
- Их устанавливают в кондукторе с некоторым зазором.
- Ограничивают пространство между заготовками с 3 сторон специальными накладками или U-образной скобой.
- Плавящимся электродом нагревают торцы до разжижения. Их необходимо постоянно поддерживать в таком состоянии, перемещая инструмент от одного изделия к другому. Постепенно зазор между ними заполнится расплавленным металлом.
Различают ванную и ванно-шовную технологии. Во втором случае накладку приваривают к заготовкам фланговыми швами. В результате она усиливает стык, воспринимая часть нагрузки.
С использованием одного электрода
Для заполнения сварочной ванны 1 расходника не хватает. Так, для соединения арматуры диаметром 28 мм требуется 3 электрода толщиной 4 (мм).
Поскольку работу прерывать нежелательно, расходники приходится быстро менять (допустимая пауза составляет 3-5 секунд).
Начинающие сварщики могут с такой задачей не справиться.
Одноэлектродная сварка.
Многоэлектродная сварка
Проще формировать шов одновременно несколькими расходниками — т.н. гребенкой электродов. До начала работ их прихватками крепят к стальной пластине так, чтобы часть ее оставалась свободной. Этот хвостовик помещают в электрододержатель.
После выполнения сварного шва огарки отбивают и используют пластину повторно.
Техника исполнения не отличается от 1-электродного способа.
Трехэлектродная ванная сварка.
Качественная сварка рельсовых стыков
- 10 ноября
- 28 рейтинг
Сварка рельсовых стыков весьма востребована на сегодняшний день. Как известно, когда подвижной состав проходит сборные стыки, они начинают с высокой скоростью расстраиваться. При этом исчезает плавный ход, из-за чего разрушается верхнее покрытие железнодорожного пути. А данный вариант поможет исправить ситуацию.
Схема стыковой сварки.
Основные характеристики
Требуется прокладывать рельсовые пути, которые имеют сваренные стыки, на любых видах путей, в результате получается бесстыковой рельс.
Рельсовая нить разрывается именно в местах, где образован стык. Такой разрыв, даже при установке стыковых накладок, оказывает большое влияние на жесткость конструкции, начинают увеличиваться просадки.
В результате при прохождении подвижного состава рельсового стыка колесо ударяется о головку торца принимающего рельса. Из-за многочисленных ударов в стыковые соединения начинает быстро изнашиваться ходовая часть вагонов, а также уложенных рельсов. За счет сильных ударов колесной пары по набегающему рельсу появляется сколы рельсовых головок и их сминание. Обычно такие дефекты обнаруживаются в 60 см от места стыка. Рельсы начинают ломаться в болтовых отверстиях, изгибаются накладки, деформируются стыковые болты. Все перечисленные недостатки не касаются бесстыкового пути, причем он обладает несколькими положительными качествами:
Схема конструкции контактной сварки.
- почти на 30% снижаются затраты на обслуживание рельсового пути;
- значительно экономится электроэнергия, снижается расход топлива примерно на 10%;
- увеличивается срок эксплуатации верхних путей,
- подвижной состав может работать намного дольше;
- пассажиры испытывают больший комфорт при движении поезда;
- становится надежнее работа автоблокировки и электроцепей.
За счет таких положительных качеств бесстыковой вариант был принят на вооружение всеми главными железнодорожными линиями в мире.
Иногда выбор определенного вида сварки стыков зависит от стоимости работ и производительности. Такой выбор влечет за собой появление в особо ответственных конструкциях сварочных соединений, качество которых находится на очень низком уровне.
Вернуться к оглавлению
Чтобы получить отличное сварное соединение, требуется иметь материал с хорошей свариваемостью. В основном свариваемость характеризует свойства металла, существующую реакцию на сварочный процесс, а также способность получать такое сварочное соединение, которое будет отвечать всем заданным технологическим требованиям.
Когда детали выполнены из материала, свободно поддающегося сварочному процессу, с получением высококачественного шва особых условий не требуется. Но для деталей из плохо свариваемого материала требуются дополнительные технологические условия. Иногда применяется специальный вид сварки, который намного дороже и сложнее. Причем выполнение работ требует строгого соблюдения технологического процесса.
Сварка рельсов востребована на сегодняшний день так как рельсовая нить разрывается и быстро изнашиваться ходовая часть вагонов.
В состав стали для рельсов входит очень много углерода, почти 82%. Этот материал относится к группе материалов, имеющих плохую свариваемость. При сварке возможно появление трещин, что совершенно недопустимо на рельсах. В них концентрируется напряжение, которое может привести к разрушению стыкового соединения и крушению состава.
Сегодня известно два вида сварки рельсовых стыков:
- контактная;
- алюмотермитная.
Большое распространение получила контактная сварка, однако у нее есть несколько серьезных недостатков, ограничений, когда проводятся ремонтные работы железнодорожных путей:
- для сварки требуются специальные рельсосварочные машины, стоящие очень дорого;
- длительности доставки оборудования и его последующая эвакуация;
- для проведения работ необходимо задействовать многочисленные бригады;
- за неимением большого количества времени, приходится постоянно выполнять работу без соблюдения технологического процесса, в результате чего стык получается очень низкого качества;
- невозможно выполнить сварку стыка прямо в том месте, где переводятся стрелки.
Контактная сварка стыков проигрывает алюминотермитной сварке рельсов. Для нее необходимо иметь:
- сложное и очень дорогое оборудование;
- многочисленную бригаду;
- перерывы при движении поездов.
Алюминотермитная сварка рельсов делается очень быстро. На операцию уходит примерно полминуты. Если считать подготовительные работы и завершающую обработку сварочного шва, требуется около 45 минут.
Надо сказать, что такая сварка позволяет одновременно сваривать несколько стыков, в результате сокращается время, затраченное на работу.
Рельсовые стыки с различной формой стыкуемых торцев.
Для сварки стыка необходимо три человека. Их обучение проходит в самые короткие сроки. Масса применяемого оборудования достигает 350 кг. Для проведения сварочных работ, когда используется алюмотермитная сварка и проводятся другие специальные операции, применяются автономные источники подачи топлива.
Чтобы проводить алюминотермитную сварку рельсов, инженерами было создано переносное миниатюрное оборудование, которое может функционировать в автономном режиме прямо в полу.
Технологи смогли подобрать определенный состав термитного раствора и его зернистость. Это помогло добиться термитной реакции, при которой не возникает взрывов, не наблюдается затухания и поддерживается самая оптимальная скорость и нужная температура всех материалов, участвующих в реакции.
Алюминотермитная сварка состоит из нескольких основных технологических шагов:
- начального высокотемпературного подогрева;
- окончательной сварки рельсов.
Вернуться к оглавлению
В качестве подогрева применяется специальная многопламенная горелка.
Операция длится примерно 7 минут. Контроль над подогревом и его окончанием выполняется визуально. Здесь очень важно, чтобы подогрев выполнял высококвалифицированный сварщик.
Схема электроконтактной сварки.
Такой предварительный подогрев является важной составляющей технологического процесса при алюминотермитной сварки рельсов. В результате не происходит несплавлений, сводится к минимуму возникновение закалочных структур. Когда выполняется сварочная операция, заметно снижаются параметры остаточных напряжений сварочного шва и околошовной зоны, не возникает появление трещин.
После того как рельс прошел этап подогрева, выполняются сварочные работы, происходит возгорание термитной смеси. Начинается процесс реакции воспламенения термита. Он в автоматическом режиме выпускается в межстыковой рельсовый зазор.
После долгих экспериментов было доказано, что главными технологическими параметрами, которые влияют на качество будущего сварочного шва, можно считать;
- время предварительного подогрева;
- мощность используемого газового пламени.
Чтобы получить бесстыковой рельсовый путь с применением алюминотермитного способа, разрешается использовать рельсы, бывшие в употреблении, а также их новую модификацию. Для такой сварочной операции применяют:
- упрочненные рельсы;
- неупрочненные рельсы;
- рельсы мартеновского производства;
- рельсы бессемеровского изготовления.
Можно сваривать таким образом рельсы самых разных железнодорожных путей: станционные, подъездные и даже стрелочные переводы.
Но помните: рельсы, которые будут свариваться, должны быть однотипными и обладать одинаковой группой годности.
expertsvarki.ru
Электродуговая сварка стыков рельсов. Качественная сварка рельсовых стыков Сваривают ли рельсы
Владельцы патента RU 2270739:
Изобретение относится к дуговым способам сварки и используется преимущественно для ручной электродуговой сварки железнодорожных рельсов. Способ сварки рельсовых стыков включает установку рельсов с зазором между свариваемыми кромками, введение внутрь зазора плавящегося электрода и сварку с применением форм, установленных у места сварки, при силе тока, обеспечивающей образование жидкой ванны во всем объеме зазора. Предварительно осуществляют механическую обработку кромок рельсов или кромки одного из рельсов, включающую выполнение поперечного разреза по вертикальной плоскости от головки до начала подошвы рельса, выполнение горизонтального разреза по торцевой поверхности рельса перпендикулярно по отношению к ранее произведенному разрезу и снятие на торцевой поверхности подошвы фаски с притуплением у основания подошвы рельса. При образовании жидкой ванны в корне шва дополнительно осуществляют расплавление кромок основного металла рельсов. Это позволит получить сварной шов с механическими свойствами, равнозначными свойствам основного металла, что увеличит срок службы рельсов. 2 ил.
Изобретение относится к дуговым методам сварки, преимущественно используется для ручной электродуговой сварки железнодорожных рельсов.
Известен способ сварки рельсовых стыков, в котором сварку рельсов ведут ручным электродуговым способом (SU 78136, В 23 К 9/02, 1942).
В известном способе рельсы устанавливают с зазором между свариваемыми кромками от 9-14 мм в зависимости от выбранного диаметра электрода, поэтому сварной шов получается, в основном, за счет расплавления электродного материала. Свариваемые кромки настолько сильно разогреваются, что образуется общая ванна расплавленного металла, которая поддерживается в жидком состоянии в течение всего периода сварки. В качестве форм могут служить графитовые пластины, внутренняя поверхность которых изготавливается по форме рельса. Размеры и формы усиления сварного шва зависят от размера и формы соответствующего углубления, которое делается в форме.
Концы рельсов обрезают рельсообрезным станком по плоскости, перпендикулярной к оси рельса. Скос кромок перед сваркой не производят.
Большой зазор между торцами рельсов порядка 9-14 мм не позволяет сварить кромки подошвы рельсов, поэтому для формирования обратной стороны корня шва применяют формирующую подкладку. Сварной шов получается, в основном, за счет расплавления электродного материала, расплавленная масса которого заполняет зазор между торцами подошвы рельсов и формирующей подкладкой.
Наиболее существенным недостатком этого способа является наличие большого зазора между торцами рельсов. Расплавленный электродный металл является естественной перемычкой между свариваемыми рельсами, по которой дуга перемещается от кромки одного рельса к кромке другого. Сварное соединение, полученное таким способом, имеет крупнозернистое строение из-за перегрева электродного металла и, как следствие, более низкие механические свойства, чем у основного металла. В зоне сплавления кромки рельса с расплавленной массой электродного металла возникает большая вероятность возникновения дефектов типа непровара, шлаковые включения, поры.
Технической задачей настоящего изобретения является повышение механических свойств сварного шва путем уменьшения зазора между торцами рельсов до размера, позволяющего сварить металл подошвы рельсов и получить сварной шов с механическими свойствами, которые равнозначны свойствам основного металла.
Способ согласно изобретению, заключается в том, что предварительно осуществляют механическую обработку кромок рельсов или кромки одного из рельсов, при этом производят поперечный разрез по вертикальной плоскости от головки до начала подошвы рельса, а затем горизонтальный разрез по торцевой поверхности рельса перпендикулярно по отношению к ранее произведенному разрезу, и на торце подошвы снимают фаску с притуплением у основания подошвы рельса, устанавливают рельсы с зазором, вводят внутрь зазора электрод и осуществляют сварку с применением форм у места сварки при силе тока, обеспечивающей образование жидкой ванны во всем объеме зазора, причем жидкую ванну в корне шва получают за счет расплавления кромок основного металла.
Отличия предложенного способа сварки рельсовых стыков состоят в том, что предварительно осуществляют механическую обработку кромок рельсов или кромки одного из рельсов, при этом производят поперечный разрез по вертикальной плоскости от головки до начала подошвы рельса, а затем горизонтальный разрез по торцевой поверхности рельса перпендикулярно по отношению к ранее произведенному разрезу, и на торце подошвы снимают фаску с притуплением у основания подошвы рельса, а жидкую ванну в корне шва получают за счет расплавления кромок основного металла.
Сущность предлагаемого способа поясняется чертежами.
На фиг.1 представлен чертеж при механической обработке кромки одного из рельсов, на фиг.2 — кромок рельсов.
На фиг.1 обозначены: 1 — рельс (без обработки кромки), 2 — рельс с подготовленной кромкой, 3 — притупление, 4 — зазор между кромками, α — угол между кромками.
На фиг.2 обозначены: 2 — рельс с подготовленной кромкой, 3 — притупление, 4 — зазор между кромками, α — угол между кромками.
Угол α между кромками лежит в пределах 30-60°.
Сваривают железнодорожные рельсы типа Р65. В механических мастерских дистанции отмеряют кусок рельса длиной 3 м или более в соответствии с ТУ 32 ЦП-670-88 и подготавливают кромки рельса с двух концов для установки на место дефектного рельса. При этом производят поперечный разрез по вертикальной плоскости от головки до начала подошвы рельса. Затем осуществляют горизонтальный разрез по торцевой поверхности рельса перпендикулярно по отношению к ранее произведенному разрезу и на торце подошвы снимают фаску под углом 45° с притуплением 2 мм у основания подошвы рельса. На рельсе, из которого удаляется дефектный участок, делают разметку. Отрезают дефектный кусок рельса, равный по размеру подготовленному, и устанавливают на это место кусок рельса с подготовленными под сварку кромками. Зазор между рельсами составлял 2 мм (см. фиг 1). Концы рельсов перед сваркой зачищают до металлического блеска.
Под подошву свариваемых рельсов устанавливают формирующую обратную сторону шва медную подкладку и закрепляют ее струбциной. Корень шва сваривают электродом марки УОНИ — 13/65, диаметром 3 мм, ток 140-160 А, с последующим заполнением зазора между торцами подошвы рельсов электродом марки УОНИ — 13/65, диаметром 5мм, ток 250-280 А.
Устанавливают на шейку и головку рельсов боковые медные формы и закрепляют их струбциной. Сваривают шейку и головку рельса электродами марки УОНИ — 13/65, диаметром 5 мм, ток 250-280 А.
Предложенный способ позволяет получить сварной шов с механическими свойствами, которые равнозначны свойствам основного металла, при этом полученные механические свойства сварного шва увеличивают срок службы рельсов до срока службы установленных в путь рельсов без сварки.
Способ сварки рельсовых стыков, включающий установку рельсов с зазором между свариваемыми кромками, введение внутрь зазора плавящегося электрода и сварку с применением форм, установленных у места сварки, при силе тока, обеспечивающей образование жидкой ванны во всем объеме зазора, отличающийся тем, что предварительно осуществляют механическую обработку кромок рельсов или кромки одного из рельсов, включающую выполнение поперечного разреза по вертикальной плоскости от головки до начала подошвы рельса, выполнение горизонтального разреза по торцевой поверхности рельса перпендикулярно ранее произведенному разрезу и снятие на торцевой поверхности подошвы фаски с притуплением у основания подошвы рельса, а образование жидкой ванны в корне шва осуществляют расплавлением кромок основного металла рельсов.
Похожие патенты:
Изобретение относится к устройствам для непрерывного изготовления полых труб из плоских металлических лент, и в особенности, к устройствам, позволяющим получать сварные швы без дефектов при остановке и последующем пуске устройства.
Сварка рельсовых стыков весьма востребована на сегодняшний день. Как известно, когда подвижной состав проходит сборные стыки, они начинают с высокой скоростью расстраиваться. При этом исчезает плавный ход, из-за чего разрушается верхнее покрытие железнодорожного пути. А данный вариант поможет исправить ситуацию.
Основные характеристики
Требуется прокладывать рельсовые пути, которые имеют сваренные стыки, на любых видах путей, в результате получается бесстыковой рельс.
Рельсовая нить разрывается именно в местах, где образован стык. Такой разрыв, даже при установке стыковых накладок, оказывает большое влияние на жесткость конструкции, начинают увеличиваться просадки.
В результате при прохождении подвижного состава рельсового стыка колесо ударяется о головку торца принимающего рельса. Из-за многочисленных ударов в стыковые соединения начинает быстро изнашиваться ходовая часть вагонов, а также уложенных рельсов. За счет сильных ударов колесной пары по набегающему рельсу появляется сколы рельсовых головок и их сминание. Обычно такие дефекты обнаруживаются в 60 см от места стыка. Рельсы начинают ломаться в болтовых отверстиях, изгибаются накладки, деформируются стыковые болты. Все перечисленные недостатки не касаются бесстыкового пути, причем он обладает несколькими положительными качествами:
- почти на 30% снижаются затраты на обслуживание рельсового пути;
- значительно экономится электроэнергия, снижается расход топлива примерно на 10%;
- увеличивается срок эксплуатации верхних путей,
- подвижной состав может работать намного дольше;
- пассажиры испытывают больший комфорт при движении поезда;
- становится надежнее работа автоблокировки и электроцепей.
За счет таких положительных качеств бесстыковой вариант был принят на вооружение всеми главными железнодорожными линиями в мире.
Иногда выбор определенного вида зависит от стоимости работ и производительности. Такой выбор влечет за собой появление в особо ответственных конструкциях сварочных соединений, качество которых находится на очень низком уровне.
Читайте также:
Вернуться к оглавлению
Чтобы получить отличное сварное соединение, требуется иметь материал с хорошей свариваемостью. В основном свариваемость характеризует свойства металла, существующую реакцию на сварочный процесс, а также способность получать такое сварочное соединение, которое будет отвечать всем заданным технологическим требованиям.
Когда детали выполнены из материала, свободно поддающегося сварочному процессу, с получением высококачественного шва особых условий не требуется. Но для деталей из плохо свариваемого материала требуются дополнительные технологические условия. Иногда применяется специальный вид сварки, который намного дороже и сложнее. Причем выполнение работ требует строгого соблюдения технологического процесса.
Сварка рельсов востребована на сегодняшний день так как рельсовая нить разрывается и быстро изнашиваться ходовая часть вагонов.
В состав стали для рельсов входит очень много углерода, почти 82%.
Этот материал относится к группе материалов, имеющих плохую свариваемость. При сварке возможно появление трещин, что совершенно недопустимо на рельсах. В них концентрируется напряжение, которое может привести к разрушению стыкового соединения и крушению состава.
Сегодня известно два вида сварки рельсовых стыков:
- контактная;
- алюмотермитная.
Большое распространение получила , однако у нее есть несколько серьезных недостатков, ограничений, когда проводятся ремонтные работы железнодорожных путей:
- для сварки требуются специальные рельсосварочные машины, стоящие очень дорого;
- длительности доставки оборудования и его последующая эвакуация;
- для проведения работ необходимо задействовать многочисленные бригады;
- за неимением большого количества времени, приходится постоянно выполнять работу без соблюдения технологического процесса, в результате чего стык получается очень низкого качества;
- невозможно выполнить сварку стыка прямо в том месте, где переводятся стрелки.
Контактная сварка стыков проигрывает алюминотермитной сварке рельсов. Для нее необходимо иметь:
- сложное и очень дорогое оборудование;
- многочисленную бригаду;
- перерывы при движении поездов.
Алюминотермитная сварка рельсов делается очень быстро. На операцию уходит примерно полминуты. Если считать подготовительные работы и завершающую обработку сварочного шва, требуется около 45 минут.
Надо сказать, что такая сварка позволяет одновременно сваривать несколько стыков, в результате сокращается время, затраченное на работу.
Для сварки стыка необходимо три человека. Их обучение проходит в самые короткие сроки. Масса применяемого оборудования достигает 350 кг. Для проведения сварочных работ, когда используется алюмотермитная сварка и проводятся другие специальные операции, применяются автономные источники подачи топлива.
Чтобы проводить алюминотермитную сварку рельсов, инженерами было создано переносное миниатюрное оборудование, которое может функционировать в автономном режиме прямо в полу.
Технологи смогли подобрать определенный состав термитного раствора и его зернистость. Это помогло добиться термитной реакции, при которой не возникает взрывов, не наблюдается затухания и поддерживается самая оптимальная скорость и нужная температура всех материалов, участвующих в реакции.
Алюминотермитная сварка состоит из нескольких основных технологических шагов:
- начального высокотемпературного подогрева;
- окончательной сварки рельсов.
Монтаж железнодорожных магистралей проводится двумя методами: сборным и сварным. Второй предпочтительнее, потому что сборные стыки снижают скорость движения подвижного состава. Сварка рельсов производится несколькими методами. При выборе способа монтажа бесстыковых линий учитывают свариваемость материала и стоимость работ. Наиболее распространенные: контактная и алюмотермитная сварка, есть и другие виды. О каждом стоит сказать отдельно. Стыки варят с использованием специального оборудования.
Железнодорожный профиль производят из высокоуглеродистых сталей, характеризующихся плохой свариваемостью. При термической обработке на металле образуются трещины, возникают внутренние напряжения. При сварке рельсовых плетей такое недопустимо, дефекты полотна могут стать причиной аварии.
Для работы необходимо:
- профессиональное оборудование;
- качественные расходные материалы;
- контрольные приборы, проверяющие целостность шва.
Для образования прочного соединения толстостенные балки необходимо проваривать на всю глубину. После сварки стыка необходимо выровнять поверхность, чтобы шов не разрушался.
Виды рельсов
Для выбора способа сварки учитывают химический состав сплава. Для каждого вида профилей ГОСТом определены марки стали.
Наименование | Назначение | Марки стали, используемые для изготовления |
Железнодорожные стандартные | Выпускают для магистральных путей | РП50, РП65, РП75. |
Железнодорожные промышленные | Используются на коротких участках.![]() | РП50, РП65, РП75. |
Железнодорожные узкоколейные | Монтируются в шахтах, на подъездных узкоколейках. | Р8, Р11, Р18, Р24. |
Рудничные для шахтных проводников | Применяются для бесстыковых ширококолейных участков, стрелок | Р33, Р38, Р43 |
Рамные | Необходимы для монтажа пересечений линий. | РР65. |
Крановые | Предназначены для движения мостовых и строительных кранов. | КР70, КР80, КР100, КР120 и КР140. |
Остряковые | Необходимы для стрелочных переводов, круговых опорных устройств. | ОР43, ОР50, ОР65 и ОР75. |
Трамвайные с желобами | Используют только для трамвайных путей, они рассчитаны на небольшую нагрузку. | Т58 и Т62 |
Контррельсовые | Монтируют в тупиковых отстойниках. | РП50, РП65, РП75. |
Усиковые | Выпускаются для крестовин с непрерывной поверхностью качения.![]() | УР65 |
Способы сварки рельсовых стыков
При выборе технологии учитывают свариваемость сталей, их текучесть, пластичность. Немаловажный фактор – трудозатраты, стоимость оборудования. С учетом всех составляющих решают, как сваривать рельсы.
Для заделки стыков используют следующие технологии:
- электродуговую;
- электроконтактную;
- алюмотермитную;
- газопрессовую.
На предприятиях чаще используют термитную сварку рельсов, реже контактную. У каждой технологии есть преимущества.
Электродуговой
Сварка рельсов с использованием электродов используется для стыков и плетей. Ванным способом удается получить прочное соединение. Концы укладывают на небольшом возвышении над полотном с зазором 14–16 мм в специальную ванночку, удерживающую расплав. В стык вертикально помещается электрод диаметром 5 или 6 мм. При подаче высокочастотного переменного или постоянного тока прямой полярности мощностью 300–350 ампер в зависмости от толщины профиля, расплав постепенно заполняет весь стык. Диффузионный слой создается по всему сечению. Для сварки рельсов используют электроды с основным видом покрытия:
- отечественные УОНИ 13/45 и УОНИ 13/55,
- японские LB 52U.
Их предварительно прокаливают: в течение 2 часов выдерживают при температуре 180 – 230°С.
Достоинства электродуговой сварки:
- не нужно использовать флюс, обмазка создает слой шлака над ванной, он препятствует окислению;
- не требуется предварительной разделки торцов;
- для образования плотного соединения не нужно дополнительно прикладывать усилий;
- доступность, в качестве генератора тока используют трансформаторы, выпрямители и профессиональные инверторы.
После охлаждения ванны стык зачищают, снимают окалину, выравнивают поверхность головки рельса.
Термитный
Метод основан на способности алюминия восстанавливать окись железа с большим выделением тепла. освоили больше века назад. При поджоге термита в рабочей зоне создается температура от 1200 до 2000°С в зависимости от химического состава сплава. Восстановленное железо затекает в форму, по профилю совпадающую с рельсом.
В термит помимо оксида железа и алюминия входят легирующие добавки, небольшие кусочки металла (они затормаживают химический процесс). Шлак, образующийся при расплаве, всплывает, его удаляют после охлаждения металла.
Самое главное преимущество метода – высокая скорость термитной сварки рельсов. Он применяется для закаленных и холоднокатаных балок. Его используют при монтаже магистральных железнодорожных линий и плетей.
Газопрессовый
Сварку рельсовых стыков этим методом проводят на пластичных сталях. Температура в зоне стыка концов повышается за счет энергии сдвига. Она выделяется при высоком давлении. Образуется качественное соединение за счет однородности диффузного слоя. Для плотной стыковки рельсов торец прорезают рельсорезом. Металл консервируют 4-хлористым углеродом или дихлорэтаном, под составом металл не окисляется. Стык нагревают до температуры вязкости, под 10–15-тонным давлением гидропресса слои сдвигаются, торцы плавятся, образуется диффузный слой.
Главные достоинства газопрессового метода:
- однородность химического состава;
- отсутствие окалины, процесс протекает внутри профиля;
- возможность соединяться профиль любой конфигурации и толщины.
Электроконтактный
Автоматная технология основана на нагреве стыка за счет пронизывающей электродуги, возникающей под воздействием высоких токов небольшого напряжения. Электроконтактная сварка проводится самоходными комплексами МСГР-500, МС-5002, К-190 непосредственно в месте укладки или с небольшим смещением ветки. Для разного вида рельсового профиля используют сменные контактные головки. Работу проводят методом непрерывного оплавления или импульсным прогревом рельсов.
Контроль качества рельсовых стыков
От прочности соединений зависит безопасность движения, поэтому вне зависимости от способа сварки проводится проверка стыков рельсов любым из методов неразрушающего контроля. Особенно внимательно проверяются швы, сделанные ручным сварочным оборудованием. Помимо структуры проверяется ровность головки рельса, на которую опирается колесо во время движения.
При работах с крановыми установками и выполнении монтажа железнодорожного полотна возникает необходимость соединения и сварки рельсов. В данном случае используется специальная технология, которая обеспечивает особую прочность соединения и устойчивость к повышенным нагрузкам. Необходимо сказать, что такие работы относятся к отдельной категории сварочных работ, об особенности которых мы и расскажем в этой статье.
Сварка может выполняться следующими технологиями :
- Термитная.
- Электродуговая.
- Газопрессовая сварка.
Каждая из этих технологий имеет свои определенные недостатки и преимущества. Поговорим поподробнее о таких способах сварки.
Электродуговая сварка стыков рельсов
На сегодняшний день данная технология получила наибольшее распространение, что объясняется простотой оборудования, легкостью самой работой и качеством выполненного соединения. При выполнении сварочных работ рельсы укладываются в нужном положении, после чего имеющееся между стыками послойно пространство заполняется сварочным материалом. Расплавление сварочного материала обеспечивается за счет высоких температур дугового разряда. При необходимости сварки торцов рельсов используется переменный ток от трансформатора. Также возможно использование мобильных сварочных аппаратов, работающих от постоянного тока.
При использовании электродуговой технологии возможно выполнение сварка рельсовых стыков ванным методом, при котором рельсы, обрезанные перпендикулярно своей оси, монтируются внутри ванны. В ванне проводится их качественное сваривание друг с другом. При данном методе сварки рельсы закрепляются с зазором не более 16 миллиметров. Возвышение профиля может колебаться в диапазоне 3-5 миллиметров.
При использовании ванного метода между торцов располагают электрод, по которому подается электрический ток мощностью порядка 350 Ампер. Электрод быстро заполняет зазор между соединяемыми рельсами, равномерно распределяя расплавленный материал по всему сечению. Данный метод исключает растекание металла, при этом обеспечивается максимально качественное закрытие зазора между соединенными металлическими элементами. После завершения сварки необходимо будет зашлифовать соединительный шов по периметру.
Алюминотермитная сварка рельсов
Метод термитной сварки основывается на свойстве окиси алюминия и железа вступать друг с другом в реакцию при высоких температурах. Такую термитную сварку также называют алюминотермитной технологией. Для выполнения такой сварки используется устойчивая к высоким температурам форма, которая по своему внешнему виду идентична геометрии рельсов. Такая форма должна выдерживать температуру больше 2000 градусов, при которой возникает контакт алюминия и железа.
Открыта данная технология сварки еще в конце 19 века. Однако по причине ее технологической сложности распространение она получила лишь относительно недавно. Основные трудности при выполнении такой термитной сварки заключаются в том, что реакция окиси алюминия и железа возникает лишь при температурах в несколько тысяч градусов. Соответственно требовалось нагреть до таких экстремальных температур, как сами рельсы, так и использовать соответствующую форму, способную не расплавляться и сохранять свою геометрию.
Для соединения металлов необходимо поджечь термитную смесь, которая быстро выгорает с образованием высокой температуры. Такая термитная порция содержит не только окиси алюминия и железа, но и разнообразные легирующие добавки. Такие добавки необходимы для получения максимально прочного соединения с нужными параметрами устойчивости к механическим воздействиям. Во время такой температурной реакции происходит послойное разделение легкого шлака и жидкой стали. Шлак при этом оказывается сверху и в последующем с легкостью удаляется из соединения.
Термитный способ сварки рельсов позволяет соединять объемно-закаленные и поверхностно-закаленные материалы. Необходимо сказать, что при помощи подобной технологии обеспечивается прочное и долговечное соединение, поэтому термитный способ сварки нашел применение при изготовлении безстыковых высокоскоростных железнодорожных магистралей.
Газопрессовая технология
Эта оригинальная технология соединения рельсов подразумевает использование температуры ниже точки плавления, однако за счет воздействия высокого давления обеспечивается качественное соединение рельсов. Из преимуществ данной технологии сварки можно отметить следующее:
- Отличные показатели качества выполненного соединения.
- Однородная структура стыка железнодорожного покрытия.
- Высокая производительность.
- Минимальный расход наплавляемых материалов.
Такая газопрессовая сварка широко применяется при соединении тяжелых железнодорожных рельсов. При выполнении используется специальное оборудование, которое позволяет обеспечить максимально высокое давление соединяемых рельсов. Металлические изделия плотно прижимаются друг к другу, после чего при помощи специальной струбцины концы нагреваются, а за счет высокого давления рельсы соединяются друг с другом. В процессе такой работы необходимо обеспечить промывку свариваемых элементов треххлористым углеродом. Это позволяет обеспечить соединение металлических элементов на молекулярном уровне.
Показатели рабочей температуры при газопрессовой технологии составляют порядка 1200 градусов. Для такой работы используются многопламенные горелки и мощные гидравлические прессы. Для качественного разогрева места соединения используют многопламенные горелки, осуществляющие в области сварного стыка многочисленные колебания, что и позволяет качественно разогреть металл. Гидравлический пресс, используемый для соединения рельсов, обеспечивает давление в 13 тонн и более. Усадка рельсов при их соединении данной технологией составляет около 20 миллиметров.
Заключение
Существующие в настоящее время технологии позволяют получить долговечное, надежное и устойчивое к механическим нагрузкам соединение. Выбор той или иной технологии выполняется в зависимости от доступного оборудования и конкретных разновидностей соединяемых рельсов. Необходимо сказать, что качественный выбор такого используемого оборудования и следование всей технологии работ позволит вам гарантировать качественно выполненную сварку рельсов.
Значение дополнительной ковки — TU Delft Research Portal
TY — JOUR
T1 — Остаточные напряжения в рельсах, сваренных термитной сваркой
T2 — значение дополнительной ковки
AU — Josefson, B. Lennart
AU — Bisschop, R.
AU — Messaadi, M.
AU — Hantusch, J.
PY — 2020
Y1 — 2020
N2 — Процесс алюминотермической сварки (ATW) является наиболее часто используемым процессом сварки рельсов (рельсов) в поле.Большое количество сварочного металла, добавляемого в процессе ATW, может привести к образованию широкой неровной поверхности на головке рельса, что в редких случаях может привести к неравномерному износу и пластической деформации из-за высоких динамических сил между колесами и рельсами при прохождении колес. . В данной статье исследуется введение дополнительной ковки в процесс ATW, предназначенной для уменьшения ширины зоны, подверженной воздействию тепла, при этом не создавая более вредного поля остаточных напряжений. Моделирование с использованием новой термомеханической модели FE процесса ATW показывает, что добавление давления ковки приводит к несколько меньшей ширине зоны, подверженной воздействию тепла.Это также обнаруживается при металлургическом исследовании, показывающем, что эта зона (металл шва и зона термического влияния) полностью перлитная. При дополнительной ковке в поле остаточных напряжений обнаруживаются лишь незначительные различия. В обоих случаях большие остаточные напряжения растяжения обнаруживаются в стенке рельса в месте сварного шва. Дополнительная поковка может увеличить риск образования горячих трещин из-за увеличения пластической деформации в зоне сварки.
AB — Процесс алюмотермической сварки (ATW) — это наиболее часто используемый процесс сварки рельсов (рельсов) в полевых условиях.Большое количество сварочного металла, добавляемого в процессе ATW, может привести к образованию широкой неровной поверхности на головке рельса, что в редких случаях может привести к неравномерному износу и пластической деформации из-за высоких динамических сил между колесами и рельсами при прохождении колес. . В данной статье исследуется введение дополнительной ковки в процесс ATW, предназначенной для уменьшения ширины зоны, подверженной воздействию тепла, при этом не создавая более вредного поля остаточных напряжений. Моделирование с использованием новой термомеханической модели FE процесса ATW показывает, что добавление давления ковки приводит к несколько меньшей ширине зоны, подверженной воздействию тепла.Это также обнаруживается при металлургическом исследовании, показывающем, что эта зона (металл шва и зона термического влияния) полностью перлитная. При дополнительной ковке в поле остаточных напряжений обнаруживаются лишь незначительные различия. В обоих случаях большие остаточные напряжения растяжения обнаруживаются в стенке рельса в месте сварного шва. Дополнительная поковка может увеличить риск образования горячих трещин из-за увеличения пластической деформации в зоне сварки.
кВт — алюминотермическая сварка
кВт — FEM
кВт — твердость
кВт — перлит
кВт — остаточное напряжение
UR — http: // www. scopus.com/inward/record.url?scp=85084816072&partnerID=8YFLogxK
U2 — 10.1007 / s40194-020-00912-4
DO — 10.1007 / s40194-020-00912-4
M3 — Артикул
SCOPUS: 85084816072VL — 64
SP — 1195
EP — 1212
JO — Сварка в мире
JF — Сварка в мире
SN — 0043-2288
IS — 7
ER
Презентация PowerPoint
% PDF-1.7 % 1 0 объект > / Метаданные 4 0 R / ViewerPreferences 5 0 R >> эндобдж 6 0 объект / Создатель / rgid (PB: 331950109_AS: 739098079801345 @ 1553226122250) >> эндобдж 2 0 obj > эндобдж 3 0 obj > эндобдж 4 0 объект > ручей Microsoft® PowerPoint® для Office 365

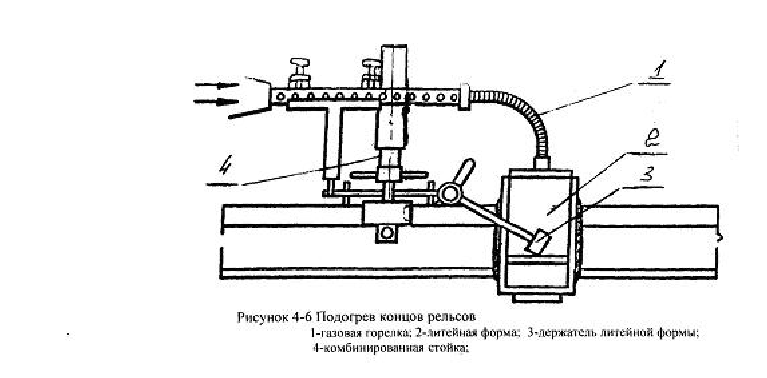


Высокоточная бесшовная железная дорога Hlau алюминотермическая Vuam Pab Neeg Muag Khoom thiab Cov 9000 Cov Lshojam 9000 Cov Lshojam Высокоточная бесшовная алюминотермическая рельсовая направляющая Hlau Кев Паб Вуам
Khoom Taw Qhia
Алюминотермическая сварка рельсов SINCHOLD yog lub vuam txujci raws li cov cua kub hauv cov tshuaj tiv thaiv thaivij cov, los txhim. Алюминоотермическая сварка рельсов SINCHOLD vuam txoj cai yog los ntawm kev teeb tsa kev thermit tom qab ib qho teeb meem hauv lub pob zeb ua rau kub kub aluminium kub molten hlau rau hauv vuam sand pwm thiab nyab qiab hauv cov литье хаув рельс вуам, плавка хов чав юав цум сварной рельс кауг луб нцей муаг. Том каб муаб ков хум пов цег ком тау тхой хлуа тхуас мус рау хаув кев тххим хо.
Khoom Feature thiab Daim Ntawv Thov
Siv cov tshuab txuas rau Бесшовные hauv Suav teb nrog rau txoj kev loj hlob ntawm txoj kev loj hlob ntawm txoj kev tsheb.Qhov kev siv tshiab no siv ceev ceev ntawm kev siv cov кран ntawm ntau lub chaw, шахты cov, коксохимическая промышленность, khoom lag luam, порты thiab wharves. Kev siv cuab yeej hluav taws xob los ntawm kev tsim kev lag luam, kev ua kom zoo dua los yog kev tsim kho rau txhua qhov chaw tsis muaj kev vam taug kev, ntawm txoj keeev tsaub ciavo nqaj hlau, kev tswj txij nkawm thiab nqi, ua kom lub neej muaj kev pab cuam thiab ua kom zoo dua thiab tuav lub peev xwm ntawm cov cuab yeej.
Cov lus qhia ntau lawm
kev kho tsheb ciav hlau
kev ntxuav tsheb rail
nru0003 da71 nru
rhaub xub thawj ntawm lub nplhaib
сварка taub hau с предварительным нагревом
lub rooj sib txoos ua keb sib2
9000 zab2 9000 txoos ua ke sib2 90000003000300030003 teebфлюс горение ras txog
литье hlau
сварка тома qab
0
0 mob tom mob tom qab цоо молдинг
моб т om qab sib tsoo
измеритель расхода кислорода thiab
пропан roj thooj voos kheej kheej thiab txo редуктор
tuom Tsim Nyog
Tuom Tsim Nyog taw
9000 x2 cov khoom muaj peev xwm ua tau raws li ntau hom kev txawv teb chaws thiab tuaj txawv teb chaws txoj kev xav tau ntawm txoj hlua hlau алюминотермический, thiab muab cov neeg siv keiv kev lõv losi, технология сварки los neeg ua haujlwm kev cob qhia dawb xwb.
Lub tuam txhab lees paub ntau txoj kev siv сварка kev sib pab ua ke pab pawg muaj zog, kev siv hlau hlau алюминотермическая сварочная техника siv. Lub tuam txhab txaus siab ua haujlwm nrog tus neeg siv kev sib raug zoo, kev sib pab sib pab thiab nrhiav kev loj hlob. Yog hais tias koj yuav mus lag luam whit высокоточная бесшовная алюминотермическая сварка рельса hlau cov kev pab cuam nyob rau hauv Suav teb, txais tos saib cov nqe lus thiab cov lus nrog peb. Peb yog ib lub tuam txhab ua lag luam hauv Tuam Tshoj thiab cov neeg muag khoom, txais tos yuav lub npe nrov cov khoom hauv cov Tshuag ntawm pheej yig tus nqi ntawm peb.
поездов метро
поездов метро Для правильного отображения страницы необходимо включить Javascript
Выберите маршрут отправления - Good Service — поезда ходят по расписанию до пяти минут.

- Незначительные задержки — время в пути может быть увеличено из-за задержки поездов на 5–15 минут, однако не забывайте придерживаться запланированного маршрута.
- Major Delays — ожидается значительно большее время в пути из-за задержки поездов более чем на 15 минут. Рассмотрите альтернативный транспорт, пока мы устраняем задержку.
- Приостановлено — участок этой линии приостановлен из-за незапланированного сбоя. По возможности будут использоваться запасные автобусы, но следует рассмотреть альтернативный вид транспорта.
- Travel Alert — для этой линии существуют особые инструкции или информация.
- Отмена — для этой линии существуют специальные инструкции или информация об отмененном поезде.
- Предупреждение о проведении работ — запланированные работы по улучшению, проводимые в течение следующих 24 часов, которые изменят запланированные услуги.

Выберите линию и станцию на номер
, чтобы узнать время отправления
Хорошее обслуживание
Планируемые работы
В город
Из города
дюйм 1 м
13:48
13:48
Поезд Белгрейв, экспресс
Выберите линию и станцию, чтобы получать уведомления о поездках и запланированных работах
Белгрейв поезд, экспресс
Платформа
1
Обработка Металлов.
2017 г. 3 (76)
цоо молдинг


, чтобы узнать время отправления
ОБРАБОТКА МЕТАЛЛОВ № 3 (76) 2017 34 ТЕХНОЛОГИЯ Конфликт интересов Автор заявляет об отсутствии конфликта интересов. © 2017 Авторы. Издано Новосибирским государственным техническим университетом. Это статья в открытом доступе по лицензии CC BY (http://creativecommons.org/licenses/by/4.0/). 5. Мохассель А., Кокаби Х., Давами П. Механические и металлургические свойства широкозонных алюминотермических сварных швов рельсов. Иранский журнал материалов и инженерии, 2011, т.8, вып. 4. С. 27–33. 6. Насонов Д.С., Гудков А.В., Борц А.И., Николин А.И. Пути повышения качества алюминотермических сварных соединений рельсов. Развитие железнодорожного транспорта в условиях реформирования: сборник статей ученых и аспирантов. ученики «]. Москва, 2006. С. 189–194. (На русском). 7. Ильиных А.С., Тихомирова Л.Б., ГалайМ.С., Сидоров Е.С. Влияние нормализации на структуру и механические свойства алюминотермитных сварных соединений рельсов.Обработка металлов (технология, оборудование, инструменты) // Металлообработка и материаловедение. 1 (70), стр. 60–66. DOI: 10.17212 / 1994-6309-2016-1-60-66. 8. Каргин В.А., Тихомирова Л.Б., Галай М.С. Упрочнение стыковых соединений рельсовметодомповерхностного пластического деформирования. Обработка металлов (технология, оборудование, инструменты) // Металлообработка и материаловедение. 3 (48), стр. 17–18. 9. Каргин В.А., Тихомирова Л.Б., Абрамов А.Д., Галай М.С. Влияние виброударной обработки на физико-механические свойства поверхностного слоя сварных соединений рельсов. Сварочное производство. 3. С. 38–40. (На русском). 10. Каргин В.А., Тихомирова Л.Б., Галай М.С., Кузнецова Е.С. Повышение эксплуатационных свойств сварных соединений, полученных алюмотермической сваркой.Welding International, 2015, т. 29, вып. 2. С. 155–157. DOI: 10.1080 / 09507116.2014.897809. 11. ТУ 0921-127-01124323–2005. Сварка рельсов алюминотермитным методом промежуточного литья. Технические условия [ТУ 0921-127-01124323–2005. Технологии алюминотермической сварки рельсов промежуточного литья. М .: ВНИИЖТ, 2005.
27 с. 12. Пасько С.В., Тихомирова Л.Б., Болотова О.В. Алюмотермитная сварка рельсов методом промежуточного литья по технологии фирмы «СНАГА».]. Новосибирск: СГУПС, 2010. 99 с. ISBN 5-93461-418-5. 13. Тушинский Л.И. Теория и технология упрочнения металлических сплавов. Новосибирск: Наука, 1990. 306 с. 14. Капуткина Л.М., Берштейн М.Л., Заимовский В.А. Термомеханическая обработка стали. М .: Металлургия, 1983. 480 с. 15. Зубарев Ю.М. Теория и практика повышения эффективности шлифования материалов.М .: Лань, 2010. 304 с. ISBN 978-5-8114-0973-0. 16. Шур Э.А. Повреждения рельсов. М .: Интекст, 2012. 192 с. ISBN 978-5-89277-108-5.
Сделано с FlippingBook
RkJQdWJsaXNoZXIy MTk0ODM1JOIN — P2 Rails
Kurzbeschreibung
Das Themengebiet dieses Projektes handelt vom Verbindungsschweißen von Schienenstählen im Gleis.
Das zurzeit am häufigsten eingesetzte aluminothermische Schweißen (Thermit Schweißen) ist ein Gieß-Prozess und hat deshalb prozessbedingte Nachteile beim Schweißen von Schienen. Diese sind die unzureichende Festigkeit und Zähigkeit des Schweißguts aufgrund des Gußgefüges (Poren und Schlackeneinschlüsse). Des Weiteren werden durch die eingebrachte Wärmemenge die mechanischen Eigenschaften in der breiten Wärmeeinflusszone herabgesetzt. Es ist nur bedingt möglich die geforderten unterschiedlichen Eigenschaften der Schweißung über den Profilquerschnitt zu erreichen. Diese Eigenschaften sind hohe Zähigkeit des Schienenfußes und –stegs, sowie hohe Härte des Schienenkopfes um eine ausreichende Verschleißfestigkeit zu gewährleisten.Zudem hängt die Qualität einer aluminothermischen Schweißung von den Fertigkeiten des ausführenden Schweißers ab da es sich nur um einen semi-automatischen Prozess handelt. Deshalb besteht eine große Nachfrage für die Entwicklung eines neuen, automatisierten und baustellentauglichen Schienenschweißprozesses, basierend auf dem Schutzgasschweißprozess (MAG). Oben genannte Faktoren müssen dabei natürlich berücksichtigt werden. Weiters ist es auch unerlässlich das Umwandlungsverhalten des Werkstoffes genau zu kennen.
Für die Qualifizierung eines neuen Schienenstahls ist das aluminothermische Schweißen ein Pflicht- und Ausscheidekriterium. Für den Eisenbahn Verkehr ist eine manuelle Schweißung der Schienen nicht zulässig, da der Einfluss des Menschen (Qualifikation, Geschicklichkeit, Tagesverfassung) nicht толерантный вирд. Für andere Anwendungen (Straßenbahn, U-Bahn, Kranschienen) ist der manuelle Lichtbogenschweißprozess (E-Hand, MAG). Bis heute ist die Entwicklung eines neuen Schweißprozesses aufgrund folgender Faktoren gescheitert: Geometrie der Schienen, Wetter, Sperrzeit der Strecke, Herstellung der Schweißlücke, Positionieren der Schienenzenenärts Schweßlücke, Positionieren der Schienenzenenägerztelle de Nrachwungen.Die Automatisierung des Prozesses ist daher ein kritischer Faktor. Am Ende des Projektes wird eine Schweißanweisung (WPS) erwartet, welche die Grundlage für die Qualifizierung des Schweißverfahrens legt. Die erfolgreiche Schweißverfahrensprüfung legt wiederum die Grundlage zur Durchführung der Schienen-Verbindungs-Schweißungen mit dem neuen Prozess.