Что такое ультразвуковая дефектоскопия и для чего она нужна
Ультразвуковые дефектоскопы на фазированных решетках одни из самых совершенных приборов неразрушающего контроля. Ультразвуковые колебания прибора позволяют без труда находить скрытые микроповреждения в труднодоступных местах магистральных трубопроводов и промышленных резервуарах.
Ультразвуковой контроль
Использование акустических (механических) колебаний ультразвукового частотного диапазона является в настоящее время обычным делом при решении многих научных вопросов и технических задач.
Применение ультразвуковых колебаний в научных целях сопряжено, прежде всего, с исследованиями микро- и мезоструктуры различных материалов и с определениями интегральных материальных констант. Приборы используемые данную технологию неразрушающего контроля — ультразвуковые дефектоскопы.
Для жидкостей это концентрация растворенных веществ, а для твердого агрегатного состояния это модули упругости, различные физико-механические константы, определяющие пьезоактивные свойства твердых тел.
Исследование свойств материалов с помощью ультразвуковых колебаний естественным образом трансформируется в неразрушающий контроль качества изготовления изделий из этих материалов. Контроль качества может осуществляться в двух направлениях.
Первое, и основное по объему практических применений ультразвуковых колебаний, направление контроля качества изготовления изделий ориентировано на выявление различного рода дефектов, которые могут появиться в ходе выполнения различных технологических операций. Это, прежде всего, различного сорта нарушения однородности материала (трещины, раковины, расслоения, инородные включения) и отклонения основных размеров (в основном толщины листового проката) от заданных значений.
Совокупность научных и технических знаний, технических средств и технологических приемов, нацеленных на практическое решение задач неразрушающего контроля и диагностики качества изделий и материалов, образует научно-техническое направление, которое называется ультразвуковой дефектоскопией.
Вторым направлением дефектоскопии можно считать исследование зернистости металлов. Размеры зерен в значительной степени определяют прочностные характеристики металлов и могут послужить отправной точкой для прогнозирования условий появления усталостных трещин.
Определение размеров зерен по коэффициентам затухания ультразвуковых волн на различных частотах позволяет судить о качестве металлов, которые используются для изготовления тех или иных изделий.
Ультразвуковая дефектоскопия в энергомашиностроении
В монографии Е.Ф.Кретова «Ультразвуковая дефектоскопия в энергомашиностроении» приведены современные понятия качества и системы менеджмента качества. Изложены сведения о дефектах листового проката, поковок и сварных соединений. Дана информация о методах НК применяемых в энергомашиностроении. Подробно рассмотрены физические основы ультразвуковой дефектоскопии, средства и технологии ручного УЗК и толщинометрии металлоконструкций. Сведения о функциональной схеме, основных технических параметрах и сервисных возможностях ультразвуковых дефектоскопов даны применительно к современным цифровым приборам.
Четвертое издание дополнено рассмотрением принципа работы ультразвуковых фазированных решеток, особенностей УЗК стального литья, изложены основные принципы дифракционно-временного метода.
Книга рекомендована в качестве учебного пособия для студентов ВУЗов обучающихся по специальности 200102 «Приборы и методы контроля качества и диагностики», а также для обучения специалистов по ультразвуковой дефектоскопии и подготовке к сертификации на I, II и III уровни квалификации. Издание: 4-е. Год издания: 2014. Объем: 312 стр. Формат: 60х 90 1/16, цена – 690р
Содержание
Глава 1. Основы металловедения
1.1. Металлы и сплавы
1.1.1. Металлы
1.1.2. Кристаллическая структура металла
1.1.3. Строение слитка
1.1.4. Диаграмма состояния железо-углерод
1.1.5. Термическая обработка сталей
1.1.6. Термомеханическая обработка стали
1.1.7. Классификация легированной стали
1.1.8. Маркировка углеродистой стали
1. 1.9. Маркировка легированной стали
1.1.10. Хромникелевые не ржавеющие стали
1.1.11. Исследование материалов с применением макро- и микроанализа
1.2. Сварка металлов
1.2.1. Физические основы сварки металлов
1.2.2. Геометрические параметры кромок под сварку
1.2.3. Виды сварных соединений и разделок кромок под сварку
1.2.4. Общие требования к сварке
1.2.5. Структурное строение сварных швов
1.3. Дефекты металлов
1.3.1. Классификация дефектов металла
1.3.2. Типы дефектов металла
1.3.2.1. Литейные дефекты
1.3.2.2. Дефекты прокатного и кованного металла
1.3.2.3. Дефекты сварных соединений
1.3.2.4. Дефекты возникающие при различных видах обработки деталей
1.3.2.5. Дефекты возникающие при эксплуатации изделий
Глава 2. Общие сведения по неразрушающему контролю
2.1. Задачи решаемые с применением НК и требования к нему
2. 2. Виды контроля полуфабрикатов и изделий
2.3. Требования к обеспечению дефектоскопической технологичности изделий
2.4. Общие требования к средствам НК
2.5. Требования к персоналу НК
2.6. Выбор метода НК
Глава 3. Методы неразрушающего контроля
3.1. Методы оптического вида
3.3. Методы магнитного вида контроля
3.4. Методы вихретокового вида НК
3.5. Методы радиационного вида НК
Глава 4. Физические основы ультразвуковой дефектоскопии
4.1. Колебательный процесс
4.2. Гармонические колебания
4.3. Ультразвуковые волны
4.4. Параметры ультразвуковой волны. Акустические свойства среды
4.5. Шкала децибел
4.6. Явления на границе раздела двух сред
4.6.1. Частные случаи
4.6.2. Энергетические соотношения
4.6.3. Отражение от двугранного угла
4.7. Нормальные волны
4.8. Головные волны
4.9. Формирование акустического поля
4. 10. Дифракция ультразвуковых волн
4.11. Затухание ультразвука в твердых средах
4.12. Расчет акустического тракта прямого контактного преобразователя
4.13. Поле излучения-приема наклонного преобразователя
4.15. Пересчет отражателей одного вида в отражатели другого вида
4.16. Отражение от реальных дефектов
4.17. Электроакустический тракт ультразвукового дефектоскопа
4.18. Способы возбуждения ультразвуковых колебаний
Глава 5. Методы акустического контроля металлов
5.1. Классификация акустических методов НК
5.2. Теневой метод (амплитудный)
5.3. Эхо-метод
5.4. Зеркальный эхо-метод
5.5. Дельта-метод
5.6. Дифракционно-временной метод
5.7. Зеркально-теневой метод (ЗТМ)
5.8. Эхо-теневой метод
5.9. Сквозной эхо-метод
5.10. Акустико-эмиссионный метод
Глава 6. Средства ультразвукового контроля
6.1. Состав средств ультразвукового контроля
6.2. Классификация ультразвуковых дефектоскопов
6. 3. Функциональная схема дефектоскопа общего назначения
6.4. Технические параметры ультразвукового дефектоскопа
6.6. Технические параметры ультразвуковых толщиномеров
6.7. Ультразвуковые пьезоэлектрические преобразователи
6.8. Параметры преобразователей
6.9. Ультразвуковые фазированные решетки
6.10. Образцы для ультразвукового контроля
6.10.1. Стандартные образцы
6.10.2. Стандартные образцы предприятия
6.11. Метрологическое обеспечение средств ультразвукового контроля
Глава 7. Основные параметры контроля и измеряемые характеристики несплошностей
7.1. Основные параметры ультразвукового контроля
7.2. Измеряемые характеристики несплошностей
7.3. Классификация несплошностей на протяженные и не протяженные
7.4. Измерение координат отражателей
Глава 8. Технология ультразвукового контроля
8.1. Руководящие документы на ультразвуковой контроль
8. 2. Выбор преобразователя, параметров контроля и режимов настройки
8.2.1. Тип и конструкция преобразователя
8.2.2. Диапазон контроля
8.2.3. Зона автоматической сигнализации дефектов (АСД)
8.2.4. Система временной регулировки чувствительности
8.2.5. Отсечка
8.2.6. Частота следования зондирующих импульсов
8.2.7. Мощность
8.3. Настройка глубиномера
8.4. Настройка чувствительности дефектоскопа и оценка размеров несплошностей по амплитудному признаку
8.4.1. Способ стандартных образцов предприятия
8.4.2. Способ АРД диаграмм
8.4.2.1. Оценка коэффициента затухания волн
8.4.2.2. Настройка чувствительности дефектоскопа
8.4.2.3. Определение эквивалентных размеров несплошностей
8.4.3. Способ DAC кривых
8.5. Схемы прозвучивания
8.5.1. Листовой прокат
8.5.2. Поковки
8.5.3. Сварные швы
8.5.4. Наплавки
8.6. Подготовка к контролю
8.7. Проведение контроля
8.7.1. Общие положения

8.7.3. Особенности ультразвукового контроля сварных отливок
8.7.4. Особенности ультразвукового контроля аустенитных сварных соединений
8.8. Формулирование нормативных требований
8.9. Оформление заключения
8.10. Получение дополнительной информации о форме ориентации и реальных размеров несплошности
8.10.1. Общие сведения
8.10.2. Способы азимутального озвучивания
8.10.3. Способы озвучивания под разными углами ввода
8.10.4. Способы коэффициента формы
8.10.5. Способ коэффициента µ
8.10.6. Характер индикации на экране
8.10.7. Другие способы
8.10.8. Алгоритм определения характера дефекта
8.10.9. Определение реальных размеров дефекта
8.11. Импульсы помех
8.12. Надежность достоверность и воспроизводимость результатов ультразвукового контроля
Приложение к гл. 8 Государственные стандарты на ультразвуковой контроль металлопродукции
Глава 9. Ультразвуковая толщинометрия
9.1. Терминология
9.2. Условия применимости ультразвуковой толщинометрии
9.3. Средства ультразвуковой толщинометрии
9.4. Подготовка к измерению толщины
9.5. Проведение измерений
9.6. Некоторые сведения об ошибках измерений
9.7. Методика определения погрешности измерения толщины
Список литературы
Дефектоскопия металлов и сплавов — Энциклопедия по машиностроению XXL
Дефектоскопия металлов и сплавов. Наряду с исследованием структуры металлов и сплавов в технике широко применяется дефектоскопия, позволяющая выявить внутренние дефекты ме-таллов без нарушения целостности деталей. Существуют магнитная и ультразвуковая дефектоскопия — простые и удобные методы выявления дефектов. [c.30]Ультразвуковая дефектоскопия металлов и сплавов. Способность ультразвуковых волн высоких частот распространяться в металлах на большие расстояния без значительного поглощения можно использовать для просвечивания ультра-
[c. 390]
Ультразвуковая дефектоскопия металлов и сплавов. Способность ультразвуковых волн высоких частот распространяться в металлах на большие расстояния без значительного поглощения можно использовать для просвечивания ультразвуком образцов различного рода изделий в целях выяснения их качества. При отливке и последующей обработке металлов в них могут появиться раковины, трещины и различного рода неоднородности. Оставаясь незамеченными, эти дефекты при последующей работе изделия могут привести к тому, что деталь выйдет из строя. Для ответственных деталей машин и механизмов — коленчатых валов, шатунов, самолетных винтов и пр. — такие изъяны, разумеется, недопустимы. Дефектоскопия рентгеновскими лучами дает возможность просвечивать металлы лишь на небольшие глубины, ультразвуком же можно осуществить просвечивание металлов на глубину более 10 м. [c.495]
Дефектоскопия металлов и сплавов [c.199]
Из зарубежных дефектоскопов наиболее совершенны приборы Ин-та д-ра Ф. Ферстера (ФРГ). В нашей стране их успешно применяют для контроля труб, прутков, проволоки из ферромагнитных (преимущественно) и неферромагнитных металлов и сплавов.
[c.143]
Для контроля линейно-протяженных объектов круглого сечения (прутки, трубы) применяют сканирующие дефектоскопы с вращающимися вокруг объекта накладными ВТП. К ним относится серия приборов типа ВД-40Н, ВД-41Н, ВД-43Н, различающихся диапазонами диаметров изделий. Они предназначены для выявления поверхностных дефектов в изделиях из ферромагнитных и слабомагнитных сталей, а также из цветных металлов и сплавов (табл. 11). [c.144]
Ультразвуковые дефектоскопы (УЗД) предназначены в основном для НК объектов из металлов и сплавов, а также сварных соединений в таких ОК. Возможен контроль объектов из пластиков, резины, стекла, фарфора, керамики, бетона, т. е. материалов с высоким коэффициентом затухания а ультразвука (расстоянием, на котором амплитуда плоской акустической волны убывает в е раз). Максимальная глубина прозвучивания УЗД обратно пропорциональна а. Минимальная глубина прозвучивания, или мертвая зона, определяется минимальной глубиной залегания искусственного дефекта в виде цилиндра диаметром
[c.333]
Неразрушающий контроль качества металлов и сплавов вьшолняют с использованием магнитной, ультразвуковой и рентгеновской дефектоскопии, а также других методов контроля. [c.107]
Ультразвуковую дефектоскопию применяют для контроля качества отливок, поковок и готовых деталей не только из ферромагнитных, но из любых металлов и сплавов и для выявления макро-и микродефектов, залегающих на значительной глубине (до 10 м). При проверке качества деталей с помощью ультразвуковых дефектоскопов различной конструкции применяют ультразвуковые упругие колебания с частотой 10 —10 гц. [c.110]
Рентгеноскопия просвечивание) металлов и сплавов основана на способности рентгеновских лучей проходить через оптически непрозрачные среды и предназначена для выявления внутренних дефектов (пористости, трещин, газовых пузырей, шлаковых включений и др.

В технике используются механические колебания в очень широком интервале частот — от нескольких герц до 200 МГц, или от инфразвука до ультразвука. Широкий интервал применяемых частот обусловлен тем, что характер их распространения и поглощения зависит от частоты. Ею определяются контролируемая зона, минимальная измеряемая толщина, степень поглощения и характер возбужденных волн. В ультразвуковой дефектоскопии используется целая гамма различных видов волн, которые отличаются друг от друга как направлениями распространения колебаний, так и характером колебаний. Механические колебания используются для выявления нарушения сплошности и измерения толщины. Свойство их поглощения при прохождении через контролируемую среду используется для нахождения мелких рассеянных инородных включений и пустот, оценки неоднородности зерна, структуры, определения плотности массы, внутренних напряжений, коэффициента вязкости, межкристаллитной коррозии, зоны поверхностного распространения. Большим достоинством методов и средств неразрушающего ультразвукового контроля является их универсальность — возможность применения как для металлов и сплавов, так и для керамики, полупроводников, пластических масс, бетона, фарфора, стекла, ферритов, твердых сплавов, т. е. таких синтетических материалов, которые находят все большее применение в технике.
[c.548]
Исследование структуры металлов и сплавов имеет важное практическое значение. К важнейшим методам исследования структур металлов и сплавов относятся макроанализ, микроанализ, рентгеновский анализ, спектральный, термический анализы и дефектоскопия (рентгеновская, магнитная и ультразвуковая).
[c.27]
Методом магнитной дефектоскопии можно контролировать лишь детали, изготовленные из ферромагнитных материалов (чугун, сталь). Для контроля деталей из цветных металлов и сплавов, пластмассы, керамики, твердых сплавов и других материа- [c.207]
Работами НИИХИММАШа было установлено [79 ], что для ультразвукового контроля величины зерна в сталях, цветных металлах и сплавах относительным методом следует применять более высокие частоты ультразвука по сравнению с теми, которые используются в современных отечественных ультразвуковых дефектоскопах УЗД-7Н, УЗД-12Т, 86-ИМ и 86-ИМ-2 и др. (верхняя граница частот у этих приборов не превышает 2,5—2,8 Мгц). [c.130]
Применение этой методики исследования позволило получить ряд практически важных сведений о жидкостях, применяемых для люминесцентной дефектоскопии, сравнить их смачивающую способность по отношению к различным металлам и сплавам. [c.267]
Детали машин изготовляют в большинстве случаев из различных сплавов стали, чугуна, бронзы, латуни, дюралюминия и т. д. Состав, структура и свойства металлов и сплавов характеризуют их качество и подвергаются контролю. Химический состав и структуру материала металлических заготовок и деталей проверяют методами макро- и микроанализа, рентгеновскими лучами и т. д. Для выявления поверхностных и внутренних пороков применяют следующие методы дефектоскопии просвечивание, магнитный, люминесцентный, цветной и ультразвуковой.
[c.197]
Данный метод контроля применяют для выявления только открытых поверхностных дефектов, например микротрещин. По сравнению с методом магнитной дефектоскопии, при помощи которого можно обнаруживать дефекты только в магнитных материалах (стали, чугуне), люминесцентный метод применим для контроля деталей, изготовленных из магнитных и немагнитных материалов (из стали аустенитного класса, цветных металлов и сплавов, твердых сплавов), а также из неметаллических материалов (например, пластмасс). При помощи люминесцирующих веществ можно выявлять поверхностные трещины шириной около
[c. 37]
Большой интерес представляет электромагнитный индуктивный дефектоскоп типа ЭМИД-4М, позволяющий осуществлять контроль комплекса свойств заготовок и готовых деталей из ферромагнитных и Неферромагнитных металлов и сплавов. Указанным дефектоскопом можно оценить качество термической и химико-термической обработки по твердости, структуре и прочности выявить наличие трещин определить наличие внутренних напряжений сортировать детали по маркам стали. [c.184]
Методом магнитной дефектоскопии можно контролировать лишь детали, изготовленные из ферромагнитных материалов (чугун, сталь). Для контроля деталей из цветных металлов и сплавов, пластмассы, керамики, твердых сплавов и других материалов применяют капиллярные методы, основанные на проникновении специальных растворов в область дефекта. К числу их относится люминесцентный (флуоресцентный) метод. [c.82]
Радиоактивные изотопы могут широко использоваться в качестве меченых атомов для исследования и разработки различных технологических вопросов (контроль качества деталей, оценка износа движущихся частей, анализ металлов и сплавов, выяснение влияния вредных примесей и др. ). Большие перспективы имеет применение радиоактивного излучения для изучения структуры сплавов, дефектоскопии и других целей.
[c.76]
При выборе изотопа для использования в промышленной дефектоскопии необходимо прежде всего учитывать для контроля каких металлов и сплавов, каких толщин и выявления каких пороков в основном он будет применен. С увеличением удельного веса контролируемого металла и его толщины предпочтительнее изотоп с большей энергией излучения — с более жесткими лучами. Наоборот, при контроле металла малых толщин или металла с малым удельным весом лучше использовать изотоп, обладающий мягким излучением. [c.109]
За последние 20 —- 25 лет ультразвук начинает играть всё ббльшую роль не только в научных исследованиях, но и в решении большого круга технических и практических задач — в подводной сигнализации и связи, ультразвуковой дефектоскопии металлов и сплавов, в медицине и т. д. [c.161]
Радиационная дефектоскопия >0,5 мм Кроме трещин и непроваров, расположенных под углом более 5— 10 к направлению цросвечивания Все металлы и сплавы [c. 77]
РАДИОАКТИВНЫЕ ИЗОТОПЫ — неустойчивые, самопроизвольно распадающиеся изотопы хнмич. элементов. В процессе радиоактивного распада происходит превращение атомов Р. и. в атомы др. химия. элемента (неразветвленпый распад) или яеск. др. химич. элементов (разветвленный распад). Известны след, тины радиоактивного распада а-распад, р-распад, К-захват, деление атомных ядер. В технике, не связанной с атомной энергетикой, используются Р. и. с распадом первых трех типов (в основном с р-распадом). В природе существует ок. 50 естественных Р. п. с помощью ядерных реакций получено ок. 1000 искусственных Р. и. В технике используются только нек-рые из искусственных Р. и. — наиболее дешевые, достаточно долговечные и обладающие легко регистрируемым излучением. Основной количественной хар-кой Р.и. является активность,определяемая числом радиоактивных распадов, происходящих в данной порции Р. и. в единицу времени. Осн. единица активности — кюри. соответствует 3,7-10 распадов в сек. Осн. качественные хар-ки Р. и. — период полураспада (время, в течение к-рого активность убывает вдвое), тин и энергия ( жесткость ) излучения. Р. и. широко используются в науке и технике как радиоактивные индикаторы и как источники излучений. Наиболее важные области применения — радиационная химия, изучение процессов в доменных и мартеновских печах, кристаллизации слитков, износа деталей машин и режущего инструмента, процессов диффузии и самодиффузии в металлах и сплавах. В измерит, технике Р. и. применяются для бесконтактного измерения таких параметров, как плотность, хим. сост. различных материалов, скорость газовых потоков и др. В гамма-дефектоскопии используются
[c.103]
Для проведения исследований целесообразно применять электромагнитные приборы универсального типа, имеющие широкий диапазон рабочих частот. Это обеспечивает контроль различных металлов и сплавов, как ферромагнитных, так и неферромагнит-ных. В частности, для измерения глубины кольцевой трещины использовали [106] универсальный электромагнитный дефектоскоп типа ДУЭТ [132], разработанный в Физико-механическом институте АН УССР и предназначенный для решения подобных задач. Существенное значение для проведения исследований имеет выбор
[c.208]
Рентгеновский метод исследования металлов и сплавов Ёключает 1) рентгеновскую дефектоскопию (просвечивание) 2) рентгеновский структурный анализ 3) рентгеновский спектральный анализ [1] [25] [381 [581- [c.59]
Физические методы контроля качества металлов и сплавов (дефектоскопия) являются методами контроля цзделий без их разрушения. В современной технике существуют различные методы выявления дефектов деталей и изделий. [c.32]
Методом люминесцентной дефектоскопии можно контролировать любые материалы (металлы, керамика, пластмассы), выявляя в сварных швах трещины шириной 0,01 жл1 и глубиной 0,03—0,04 мм. Высокая чувствительность метода позволяет применять его для выявления трещин в околошовной зоне многих сварных соединений и особенно соединений из немагнитных сталей, цветных металлов и сплавов. Люминесцентный метод можно применять также для контроля непроницаемости сварных швов. В основу этого метода контроля положено свойство веществ, поглощающих лучистую энергию, светиться под действием ультрафиолетовых лучей. Контроль основан на капиллярном введении в полость дефекта люминесцирующего раствора, адсорбции его с помощью порошкового адсо1рбента и люминесценции в невидимом ультрафиолетовом свете. Под действием ультрафиолетовых лучей происходит интенсивное видимое свечение раствора, адсорбированного из полости дефекта.
[c.267]
Дефектоскоп тппа ИПП-1М предназначен для выявления в поточном производстве поверхностных дефектов в прутках круглого и шестигранного профилей, выполненных из ферромагнитных и неферромагнптных металлов и сплавов, диаметром 4—47 мм, Глубина порогового дефекта 1—2% от диаметра, но не менее 0,1 мм длина 2 мм. [c.135]
Прибор ИДП-1 предназначен для выявления в прутках диаметром 1—5 мм из неферромагнитных п ферромагнитных металлов и сплавов поверхностных дефектов типа трещин, волосовпн, раковин п т, п. Глубина порогового дефекта 0,05 мм. Дефектоскоп ИДП-1 отличается от прибора ИПП-1М рабочей частотой и узлом блокировки, исключающим влиянпе концевых участков контролируемого изделия. В нем блокировка построена по индукционному принципу и устранены недостатки, присущие фотоблокировке, связанные с ее засорением в нроизвод-ственных условиях окалиной, маслом, пылью и т, п.
[c.135]
Методом магнитной дефектоскопии можно контролировать лишь детали, изготовленные из ферромагнитных материалов (чугун, сталь). Для контроля деталей из цветных металлов и сплавов, пластмассы, керамики, твердых сплавов и других материалов применяют капиллярные методы, основанные на проникновении специальных растворов в полость дефекта. К числу их относят люминесцентный (флуоресцентный) метод контроля. Сущность его заключается в следующем. Очищенные и обезжиренные детали погружают в ванну с флуоресцирующей жидкостью на 10—15 мин. Жидкость проникает в имеющиеся трещины и там задерживается. Затем раствор удаляют с поверхности струей холодной воды, а деталь просушивают подогретым сжатым воздухом. Для лучшего выявления трещин поверхность просушенной детали припудривают тальком, порошком углекислого магния или селикагеля. При освещении ультрафиолетовым излучением трещины обнаруживаются по яркому зелено-желтому свечению. Глубокие трещины светятся в виде широких полос, а микроскопические — тонкими линиями. Скрытые дефекты хорошо выявляются и ультразвуковой дефектоскопией.
[c.137]
Усовершенствование фотографического метода гамма-дефектоскопии и других методов регистрации излучения является важной задачей дефектоскопии. Как уже указывалось, чувствительность, фотометода для данной толщины материала зависит от энергии излучения и остроты фокуса источника излучения. Особое значение острота фокуса приобретает при просвечивании изделий из тонкой стали и легких металлов и сплавов. Таким образом, наличие источника гамма-лучей, имеющего острый фокус, большой период полураспада, изменяемую по желанию энергию излучения, позволило бы повысить качество фотометода гамма-дефектоскопии и в какой-то мере приблизить ее к рентгеновской дефектоскопии.
[c.25]
Дефектоскоп типа ИПП предназначен для выявления в условиях поточного производства поверхностных дефектов в прутках круглого и щестигранного профилей диаметром 4…47 мм, выполненных из ферромагнитных и неферромагнитных металлов и сплавов. Глубина порогового дефекта 1…2 % диаметра, но >0,1 мм длина 2 мм. [c.343]
Diex — Ультразвуковая дефектоскопия
Ультразвукова́я дефектоскопи́я — метод основанный С.Я. Соколовым, позволяющий осуществлять поиск дефектов в материале изделия путём излучения и принятия ультразвуковых колебаний, отраженных от внутренних несплошностей (дефектов), и дальнейшего анализа их амплитуды, времени прихода, формы и других характеристик с помощью специального оборудования — ультразвукового дефектоскопа. Является одним из самых распространенных методов неразрушающего контроля.
Принцип работыЗвуковые волны не изменяют траектории движения в однородном материале.
Отражение акустических волн происходит от раздела сред с различными удельными
акустическими сопротивлениями. Чем больше различаются акустические
сопротивления, тем большая часть звуковых волн отражается от границы раздела
сред. Так как включения в металле часто содержат воздух, имеющий на несколько
порядков большее удельное акустическое сопротивление, чем сам металл, то
отражение будет практически полное.
Разрешающая способность акустического исследования определяется длиной используемой звуковой волны. Это ограничение накладывается тем фактом, что при размере препятствия меньше четверти длины волны, волна от него практически не отражается. Это определяет использование высокочастотных колебаний — ультразвука. С другой стороны, при повышении частоты колебаний быстро растет их затухание, что ограничивает доступную глубину контроля. Для контроля металла наиболее часто используются частоты от 0.5 до 10 МГц.
Возбуждение и прием ультразвукаСуществует несколько методов возбуждения ультразвуковых волн в исследуемом
объекте. Наиболее распространенным является использование пьезоэлектрического
эффекта. В этом случае излучение ультразвука производится с помощью
преобразователя, который преобразует электрические колебания в акустические с
помощью обратного пьезоэлектрического эффекта. Отраженные сигналы попавшие на
пьезопластину из-за прямого пьезоэлектрического эффекта преобразуются в
электрические, которые и регистрируются измерительными цепями.
Также используются электромагнитно-акустический (ЭМА) метод, основанный на приложении сильных переменных магнитных полей к металлу. КПД этого метода гораздо ниже, чем у пьезоэлектрического, но зато может работать через воздушный зазор и не предъявляет особых требований к качеству поверхности.
Классификация методов исследования
Методы отражения
- Эхо-импульсный
метод контроля сварного соединения без дефекта (сверху) и с дефектом (снизу). В
правой части изображения представлен экран дефектоскопа с изображённым на нём
зондирующим импульсом (сверху) и импульсом от дефекта (снизу).
- Эхо-метод или эхо-импульсный метод — наиболее распространенный: преобразователь генерирует колебания (т.е. выступает в роли генератора) и он же принимает отражённые от дефектов эхо-сигналы (приёмник). Данный способ получил широкое распространение за счёт своей простоты, т.к. для проведения контроля требуется только один преобразователь, следовательно при ручном контроле отсутствует необходимость в специальный приспособлениях для его фиксации (как, например, в дифракционно-временном методе) и совмещении акустических осей при использовании двух преобразователей. Кроме того, это один из немногих методов ультразвуковой дефектоскопии, позволяющий достаточно точно определить координаты дефекта, такие как глубину залегания и положение в исследуемом объекте (относительно преобразователя).
- Зеркальный или Эхо-зеркальный метод — используются два преобразователя с
одной стороны детали: сгенерированные колебания отражаются от дефекта в сторону
приемника.
На практике используется для поиска дефектов расположенных перпендикулярно поверхности контроля, например трещин.
- Дифракционно-временной метод — используется два преобразователя с одной стороны детали, расположенные друг напротив друга. Если дефект имеет острые кромки (как, например, трещины) то колебания дифрагируют на концах дефекта и отражаются во все стороны, в том числе и в сторону приёмника. Дефектоскоп регистрирует время прихода обоих импульсов при их достаточной амплитуде. На экране дефектоскопа одновременно отображаются оба сигнала от верхней и от нижней границ дефекта, тем самым можно достаточно точно определить условную высоту дефекта. Способ достаточно универсален, позволяет производить ультразвуковой контроль на швах любой сложности, но требует специального оборудования для фиксации преобразователей, а также дефектоскоп, способный работать в таком режиме. Кроме того, дифрагированные сигналы достаточно слабые.
- Дельта-метод — разновидность зеркального метода — отличаются механизм отражения волны от дефекта и способ принятия.
На практике не используется.
- Ревербационный метод — основан на постепенном затухании сигнала в объекте контроля. При контроле двухслойной конструкции, в случае качественного соединения слоёв, часть энергии из первого слоя будет уходить во второй, поэтому ревербация будет меньше. В обратном случае будут наблюдаться многократные отражения от первого слоя, так называемый лес. Метод используется для контроля сцепления различных видов наплавок, например баббитовой наплавки с чугунным основанием. Основным недостатком данного метода является регистрация дефектоскопом эхо-сигналов от границы соединения двух слоёв. Причиной этих эхо-сигналов является разница скоростей упругих колебаний в материалах соединения и их различное удельное акустическое сопротивление. Например на границе баббит-сталь возникает постоянный эхо-сигнал даже в местах качественного сцепления. В силу конструкционных особенностей некоторых изделий, контроль качества соединения материалов ревербационным методом может быть невозможен именно из-за наличия на экране дефектоскопа эхо-сигналов от границы соединения.
- Акустическая микроскопия благодаря повышенной частоте ввода ультразвукового пучка и применению его фокусировки, позволяет обнаруживать дефекты, размеры которых не превышают десятых долей миллиметра.
- Когерентный метод — помимо двух основных параметров эхо-сигнала, таких как амплитуда и время прихода, используется дополнительно фаза эхо-сигнала. Использование когерентного метода, а точнее нескольких идентичных преобразователей, работающих синфазно, позволяет получить изображение дефекта, близкое к реальному. При использовании специальных преобразователей, таких как преобразователь бегущей волны или его современный аналог — преобразователь с фазированной решёткой, метод позволяет значительно уменьшить время, затрачиваемое на контроль изделия.
Методы прохождения
Методы
прохождения подразумевают под собой наблюдение за изменением параметров
ультразвуковых колебаний, прошедших через объект контроля, так называемых
сквозных колебаний. Изначально для контроля применялось непрерывное излучение,
а изменение его амплитуды сквозных колебаний расценивалось как наличие дефекта
в контролируемом объекте, так называемой звуковой тени. Отсюда появилось
название теневой метод. Со временем непрерывное излучение сменилось импульсным,
а к фиксируемым параметрам помимо амплитуды добавились также фаза, спектр и
время прихода импульса и появились другие методы прохождения. Термин теневой
потерял свой первоначальный смысл и стал означать один из методов прохождения.
В англоязычной литературе метод прохождения называется through transmission
technique или through transmission method, что полностью соответствует его
российскому названию. Термин теневой в англоязычной литературе не
применяется.
- Теневой —
используются два преобразователя, которые находятся по две стороны от
исследуемой детали на одной акустической оси.
В данном случае один из преобразователей генерирует колебания (генератор), а второй принимает их (приёмник). Признаком наличия дефекта будет являться значительное уменьшение амплитуды принятого сигнала, или его пропадание (дефект создает акустическую тень).
- Зеркально-теневой — используется для контроля деталей с двумя параллельными сторонами, развитие теневого метода: анализируются отражения от противоположной грани детали. Признаком дефекта, как и при теневом методе, будет считаться пропадание отраженных колебаний. Основное достоинство этого метода в отличие от теневого заключается в доступе к детали с одной стороны.
- Временной теневой основан на запаздывании импульса во времени, затраченного на огибание дефекта. Используется для контроля бетона или огнеупорного кирпича.
- Метод многократной тени
аналогичен теневому, с тем исключением, что ультразвуковая волна несколько
раз проходит через параллельные поверхности изделия.
- При эхо-сквозном методе используют два преобразователя, расположенные по разные стороны объекта контроля друг напротив друга. В случае отсутствия дефекта, на экране дефектоскопа наблюдают сквозной сигнал и сигнал, двукратно отражённый от стенок объекта контроля. При наличии полупрозрачного дефекта, также наблюдают отражённые сквозные сигналы от дефекта. При отсутствии дефекта на экране дефектоскопа наблюдаются только 1 и 2 импульсы. При наличии полупрозрачного дефекта, дополнительно 3 и 4-й. На рисунке для наглядности отражения ультразвуковых волн, неверно показаны направления их распространения. Ультразвуковые волны распространяются вдоль акустической оси передатчика (верхнего преобразователя).
- Ревербационно-сквозной
метод включает в себя элементы ревербационного метода и метода
многократной тени. На небольшом расстоянии друг от друга, как правило с
одной стороны изделия, устанавливают два преобразователя — передатчик и
приёмник.
Ультразвуковые волны, посылаемые в объект контроля после многократных отражений, в конечном счете попадают на приёмник. Отсутствие дефекта позволяет наблюдать стабильные отраженные сигналы. При наличии дефекта изменяется распространение ультразвуковых волн — изменяется амплитуда и спектр принятых импульсов. Метод применяется для контроля многослойных конструкций и полимерных композитных материалов.
- Велосиметрический метод основан на регистрации изменения скорости упругих волн в зоне дефекта. Применяется для контроля многослойных конструкций и для изделий из полимерных композиционных материалов.
Ультразвуковое исследование не разрушает и не повреждает исследуемый
образец, что является его главным преимуществом. Возможно проводить контроль
изделий из разнообразных материалов, как металлов, так и неметаллов. Кроме того
можно выделить высокую скорость исследования при низкой стоимости и опасности
для человека (по сравнению с рентгеновской дефектоскопией) и высокую
мобильность ультразвукового дефектоскопа.
Особенности ультразвуковой дефектоскопии
Использование пъезоэлектрических преобразователей требует подготовки поверхности для ввода ультразвука в металл, в частности создания шероховатости поверхности не ниже класса 5, в случае со сварными соединениям ещё и направления шероховатости (перпендикулярно шву). Ввиду большого акустического сопротивления воздуха, малейший воздушный зазор может стать неодолимой преградой для ультразвуковых колебаний. Для устранения воздушного зазора, на контролируемый участок изделия предварительно наносят контактные жидкости, такие как вода, масло, клейстер. При контроле вертикальных или сильно наклоненных поверхностей необходимо применять густые контактные жидкости с целью предотвращения их быстрого стекания.
Для контроля изделий с внешним диаметром менее 200мм, необходимо
использовать преобразователи, с радиусом кривизны подошвы R, равным 0,9-1,1R
радиуса контролируемого объекта, так называемые притертые преобразователи,
которые в таком виде непригодны для контроля изделий с плоскими поверхностями.
Например, для контроля цилиндрической поковки, необходимо производить
перемещение преобразователя в двух взаимно перпендикулярных направлениях, что
подразумевает под собой использование двух притёртых преобразователей — по
одному для каждого из направлений.
Как правило, ультразвуковая дефектоскопия не может дать ответ на вопрос о реальных размерах дефекта, лишь о его отражательной способности в направлении приемника. Эти величины коррелируют, но не для всех типов дефектов. Кроме того, некоторые дефекты практически невозможно выявить ультразвуковым методом в силу их характера, формы или расположения в объекте контроля.
Практически невозможно производить достоверный
ультразвуковой контроль металлов с крупнозернистой структурой, таких как чугун
или аустенитный сварной шов (толщиной свыше 60 мм) из-за большого
рассеяния и сильного затухания ультразвука. Кроме того, затруднителен контроль
малых деталей или деталей со сложной формой.
Ультразвуковая дефектоскопия металлов — Справочник химика 21
Наиболее распространенный ультразвуковой метод. Он достаточно хорошо разработан, освоен и оснащен приборами. В основе ультразвукового метода лежит способность ультразвука распространяться в физических телах (н в первую очередь в металлах) с определенной скоростью и при возникновении каких-либо несплошностей больше длины волны ультразвука отражаться от их границы. По отраженному сигналу можно судить о наличии дефектов в металле и их величине (ультразвуковая дефектоскопия) или в отсутствие таковых о толщине металла, т. е. о развитии общей коррозии (ультразвуковая толщинометрия). Разработанные ультразвуковые приборы позволяют анализировать состояние металла толщиной до 100 мм с точностью около 0,1 мм. [c.99]Ультразвуковая дефектоскопия металлов. Под ред. Л. М, Хинчина, ЦБНТИ, [c.
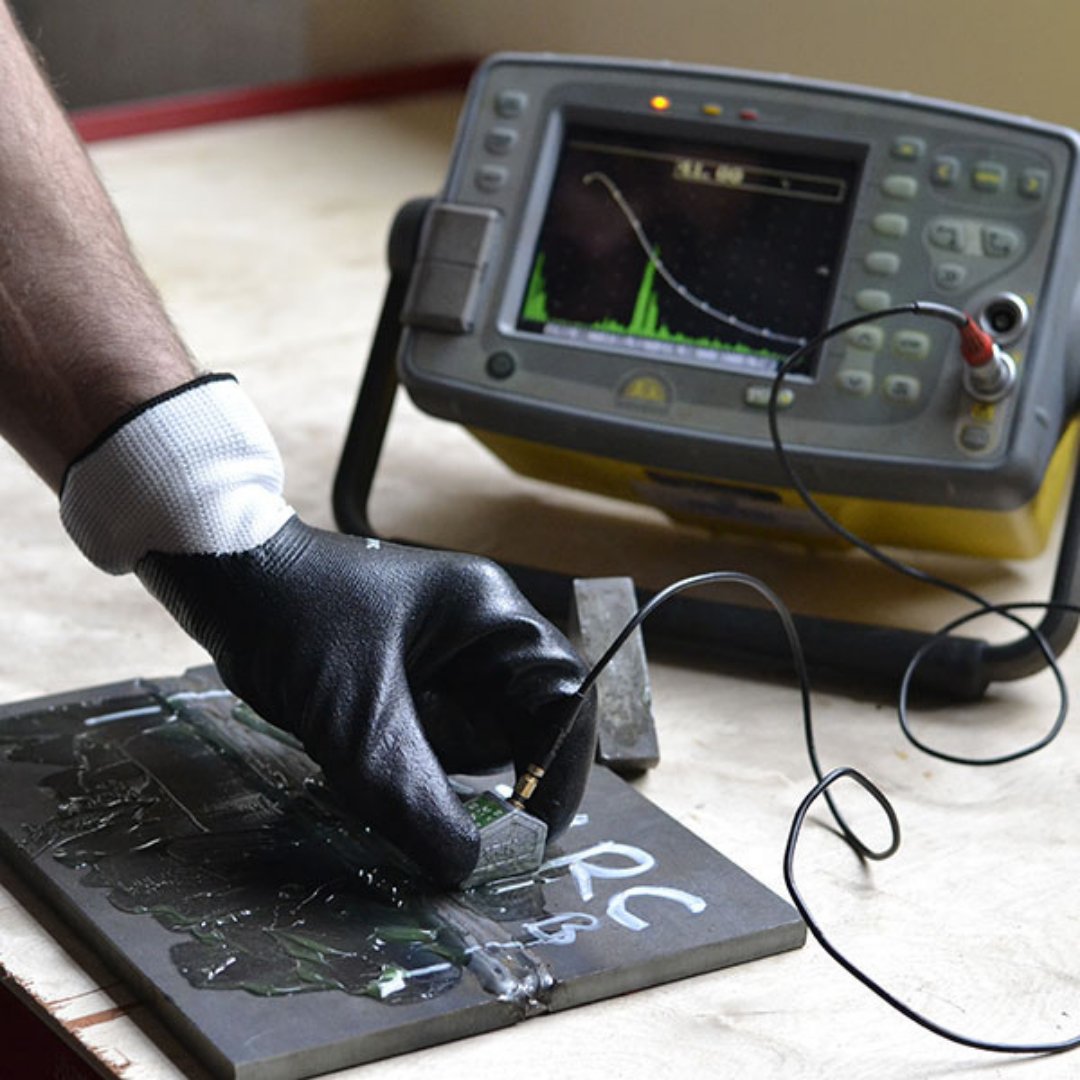
Авторами были выполнены сравнительные исследования величины погрешностей при контроле резонансным толщиномером ТУК-3 (УРТ-6) и импульсным ультразвуковым дефектоскопом-толщиномером УДМ-Ш. На эталонных образцах исследовали влияние на показания приборов таких геометрических факторов, как толщины металла, непараллельности стенок, кривизны поверхности, а также изучали возможность контроля коррозии при различной степени ее развития. Данные ультразвуковых измерений сопоставляли с результатами определения толщины образцов на одних и тех же участках металла микрометром или специальным индикатором-толщиномером и оценивали относительную ошибку измерений. [c.54]
Внутритрубную дефектоскопию проводят, как правило, в сложных нестационарных условиях, осуществляя дискретные по времени многоканальные измерения. Поскольку настроить чувствительность дефектоскопа на каждый встречающийся вид дефектов одновременно практически невозможно, измерения проводят в оптимальных режимах, то есть устанавливают один уровень настройки для всех видов дефектов. Естественной при этом является настройка прибора по наиболее жесткому уровню измеряемых параметров, который принят для поверхностных дефектов. Такую настройку проводят по искусственному дефекту глубиной 1-1,5 мм и регистрацию сигнала от него ведут на уровне полной амплитуды. Этот уровень по чувствительности на 15-25 с1В выще, чем средний уровень чувствительности, принимаемый для выявления несплошностей типа расслоений. Стандартная настройка ультразвукового дефектоскопа (УЗД) на выявление наиболее опасных видов поверхностных дефектов приводит к завышению нормативной чувствительности к несплошностям металла типа расслоений или скоплений включений. В результате данные, получаемые путем проведения обычного неразрушающего контроля и внутритрубной дефектоскопии, существенно отличаются. [c.95]
На фиг. 4 приведена схема прозвучивания изделий импульсным методом, получившим наибольшее применение в ультразвуковой дефектоскопии металлов. [c.35]
Необходимо предусмотреть звуковую и световую сигнализацию,, срабатывающую при уменьщении pH среды ниже восьми. Через каждые 450 ч работы нужно проверять целостность трубопроводов от тройника до аппаратов с тем, чтобы своевременно выявить износ металла, вызванный коррозией. В случае обнаружения коррозии на одном участке необходимо проверить и другие линии, а также аппараты. Проверку нужно проводить методом ультразвуковой дефектоскопии. При проверке необходимо замерять толщину стенок трубопровода перед и после запорной арматуры, диафрагм, колен трубопроводов и др. [c.87]
Для контроля толщины стенок аппаратов, находящихся в рабочем состоянии, осуществляется настройка дефектоскопа по образцу с параллельными поверхностями из этого же металла известной толщины. Ультразвуковые дефектоскопы позволяют определять размеры дефекта и глубину его залегания. Толщина контролируемых деталей может составлять 1—2000 мм, минимальный размер определяемого дефекта — 1 мм». [c.140]
При наличии повреждений наружной поверхности (вмятин, коррозионных разрушений и др. ) необходимо удалить дефектный металл шлифованием. Надежность ликвидации поверхностных дефектов контролируют магнитной или ультразвуковой дефектоскопией. Допускается глубина повреждения в пределах 10— 20 % толщины стенки в зависимости от размеров повреждения. [c.354]
УЛЬТРАЗВУКОВЫЕ ДЕФЕКТОСКОПЫ (общего назначения и специализированные) для контроля качества сварных соединений и основного металла [c.285]
Обнаружение трещин с помощью дефектоскопа, движущегося внутри трубы, связано с определенными трудностями. Дефектоскопы указанного типа были разработаны для обнаружения дефектов и расслоений металла, общей и язвенной коррозии [119,120]. Применительно к КР сложно отличить трещины от других дефектов. Кроме того, не все трещины могут быть зарегистрированы в связи с малой чувствительностью диагностических комплексов указанного типа к продольным трещинам. Специально разработанный ультразвуковой дефектоскоп для поиска продольных трещин прошел проверку в США на магистральном нефтепроводе (КР проявляется только на магистральных газопроводах) [219]. Последнее, по-видимому, связано с трудностью обеспечения акустического контакта между стенкой трубы и приемниками-излучателями. По данным национального совещания по безопасности магистраль- [c.90]
Трещины в образцах могут быть обнаружены также рентгеновской, гамма-лучевой и ультразвуковой дефектоскопией. Применяется также трибоэлектрический способ, при котором либо поверхностный потенциал появляется в результате трения одного металла о другой, либо тонкий металлический порошок электрически заряжается при продувании его через сопло из эбонита. В результате в трещинах образуются скопления порошка. [c.185]
Когда плакирующий слой состоит из цветного или благородного металла, например серебра, то может оказаться, что Н — — к между слоями путем ввода ультразвуковых колебаний со стороны стали. Однако расслоения, соизмеримые с площадью пьезоэлемента искателя, можно обнаружить, так как на участке с расслоением путь, пройденный ультразвуковым импульсом, становится меньше, чем на участке без расслоения. И в этом случае на экране трубки дефектоскопа можно наблюдать как бы смещение донного сигнала в сторону начального (рис. 7, в). Процесс контроля сводится к измерению толщины. Предположим, что указанным способом необходимо проверить биметалл сталь—серебро, толщина которого Я = 16 мм, а Н — к = 2,5 мм. Длительность импульса ультразвукового дефектоскопа УДМ-1М на частоте 2,5 Мгц составляет 1,5 МКС. Теоретическая разрешающая способность в этом случае равна 2,7 мм, т. е. сигнал от расслоения не будет разрешаться . Однако толщина плакирующего слоя составляет около 15% от общей толщины листа, и такое изменение толщины на участке с расслоением можно определить этим дефектоскопом. Точность измерения толщин дефектоскопом УДМ-1М составляет 2—3%. Более высокую точность обеспечивает ультразвуковой резонансный толщиномер. [c.17]
Один из забракованных валов был подвергнут дополнительному исследованию. Для проверки данных ультразвуковой дефектоскопии из щеки вала вырезали образец. При визуальном осмотре поверхности образца дефектов обнаружено не было. Магнитный контроль выявил трещины протяженностью от 1—2 до 15—20 мм, расположенные параллельно боковой поверхности щеки (рис. 133, б). Металлографическое исследование подтвердило, что выявленные ультразвуковым и магнитным методами нарушения сплошности материала являются дефектами типа трещин, расположенных преимущественно по границам зерен металла. Сравнение истинной площади дефектов с установленной на эталонах показало хорошее совпадение результатов. [c.180]
Ультразвуковой метод позволяет достаточно уверенно выявлять внутренние дефекты и в цилиндрической части вала. Так, на одной из торцовых поверхностей заготовки вала ротора турбокомпрессора оказалась поверхностная трещина. Возникло подозрение, что трещина проникает на значительную глубину в толщу металла. Проверку производили с боковой поверхности вала на частоте 2,5 МГц прямыми и наклонными искателями. Было установлено, что трещина имеет протяженность в глубину до 200 мм. Контроль остальной части вала выявил еще одну трещину протяженностью около 340 мм в центре сечения вала. Когда вал разрезали, наличие внутренней трещины подтвердилось (рис. 133, в). Дефекты возникли, по-видимому, вследствие нарушения режима ковки. Результаты ультразвуковой дефектоскопии позволили пересмотреть технологию изготовления вала ротора турбокомпрессора. [c.180]
Посредством ультразвуковой дефектоскопии проверяют толщину стенок аппаратов и трубопроводов, по изменению толщины стенки судят о необходимости замены аппарата или его отдельных элементов. Толщину стенки проверяют в первую очередь на тех участках, где предполагаются интенсивная коррозия или растрескивание металла. К таковым относятся участки трубопроводов, где поток меняет направление, застойные зоны в аппаратах, участки аппаратов с повышенной температурой и т.д. [c.366]
Контроль неразрушающий. Поковки из черных металлов. Методы ультразвуковой дефектоскопии. [c.839]
Общеизвестно применение ультразвуковой дефектоскопии для контроля внутренних пороков, дефектов в металлоизделиях. Большая проникающая способность ультразвуковых колебаний ставит ее на одно из первых мест среди прочих разнообразных физических методов дефектоскопии без разрушения испытуемых изделий. Область применения импульсной ультразвуковой дефектоскопии металлов весьма многообразна детали турбин и двигателей внутреннего сгорания, детали автомобилей, паровозов и самолетов, рельсы, поковки, листовые материалы, трубопроводы, крепежные шпильки, закленочныо соединения котлов и самая разнообразная продукция прокатных, кузнечных и прессовых цехов. Кроме импульсных методов ультразвуковой дефектоскопии, существует несколько различных по своей физической природе методов дефектоскопии с помощью незатухающих колебаний. К ним следует отнести проверку резонансным методом толщин изделий, доступ к которым возможен с одной стороны. С подобного вида измерениями мы встречаемся при проверке зон коррозионного разъедания стенок котлов, трубопроводов и общивки судов. Незатз хающие [c.7]
В процессе изготовления и монтажа металл конструкций нефтегазопроводов и ТЭС проходит дефектоскопический контроль, включая рентгеновскую и ультразвуковую дефектоскопию. Контроль на этих объектах в процессе эксплуатации до недавнего времени носил выборочный характер. [c.80]
В настоящее время существует несколько типов приборов, позволяющих производить испытания качества бетона в толще до 20-> 30 м. Испытания обычно производятся импульсным методом. В качестве пьезопреобразователей используются щуиы с пакетами пз сегнетовой соли, имеющие значительно большую чувствительность, чем обычно применяемые в ультразвуковой дефектоскопии металлов щупы с пластинками кварца или титаната бария. Кроме того, ввиду неровной поверхности изделий из бетона, применяют специальные нхуиы с топким резиновым донышком (см. рис. 65). [c.134]
ГОСТ 24507-80. Контроль неразрушающий. Поковки из черных и цветных металлов. Методы ультразвуковой дефектоскопии. [c.21]
Установка позволяет осуществлять ультразвуковой контроль дефектов основного металла и сварных соединений с помощью ультразвуковых дефектоскопов, а также контроль поверхностных дефектов изделий капиллярным, магнитопорошковым и электромагнитным методами, [c.594]
К внутренним дефектам относят дефекты, расположенные в толще наплавленного металла трещины, непровары, поры, шлаковые включения и др. Причины появления перечисленных де ктов указаны выше. Внутренние дефекты выявляются просвечиванием или ультразвуковой дефектоскопией сварных соединений. [c.226]
В практике ультразвуковой дефектоскопии металлов применяют УЗК частотой от 0,5—0,8 до 10,0 МГц. Для получения ультразвука таких частот применяют пьезоэлектрические, магнитострикционньге, электромагнитно-акустические (ЭМА) и другие преобразователи. Наибольшее распространение получили пьезоэлектрические преобразователи, в которых активным элементом являются пьезоэлементы, изготовленные из монокристалла кварца или пьезокерамических материалов — титаната бария, цирконат титаната свинца (ЦТС) и др. (ГОСТ 13927—74). На поверхности пьезоэлементов наносят тонкие слои серебра, служащие электродами. При подведении к электродам переменного электрического напряжения пьезоэлемент совершает вынужденные механические колебания (растягивается и сжимается) с частотой электрического напряжения (обратный пьезоэффект). При воздействии на пьезоэлемент упругих механических колебаний на его электродах возникает переменное электрическое напряжение с частотой воздействующих механических колебаний (прямой пьезоэффект) (рис. 23). [c.55]
ООО гц — ультразвуковыми. В практике ультразвуковой дефектоскопии металлов применяются ультразвуковые колебания частотой более 500 ООО гц, т. е 0,5 мггц [24]. [c.71]
Толщину стенок трубопроводов определяют обстукиванием молотком, ультразвуковым толщиномером или при помощи засверловок с последующей заваркой (на трубопроводах, выполненных из сталей 0Х18НС0Т, Х18Н10Т и др. ). Для трубопроводов, работающих в средах, вызывающих межкристаллитную коррозию, не допускаются сквозные засверловки. Сварные стыки подвергают рентгено-гаммапросвечиванию и ультразвуковой дефектоскопии (УЗД). Механические свойства металла проверяют в том случае, если обнаружены какие-либо изменения. [c.200]
Сварные швы по результатам металлографических исследований, рентгеноконтроля или ультразвуковой дефектоскопии, цветной дефектоскопии бракуются, если выявлены следующие дефекты трещины всех видов и направлений, расположенные в металле шва, по линии сплавления и в околошовной зоне основного металла, в том числе и микротрещины, выявленные при микроисследовании межкристаллитная коррозия (для сталей типа 12Х18Н10Т), коррозия сварных швов с их износом (по толщине) до отбраковочных величин, коррозионное растрескивание. [c.226]
Метоп, ультразвуковой дефектоскопии основан на принципе отражения ультразвуковых колебаний (УЗК)- В испытуемый объект сводятся пучки УЗК если они встречают на своем пути препятствие в виде дефекта, то часть их отражается и воз-вращаетгя в дефектоскоп, другая же часть достигает раздела объект — воздух и возвращается в прибор с некоторым за-поздани( м. На экране дефектоскопа эти отражения располагаются па расстоянии, соответствующем времени их возвращения. По их изображению на экране можно судить о размерах и месте залегания дефекта. С помощью ультразвукового метода мсжио точно определить координаты дефекта метод обладает высокой чувствительностью к дефектам малых размеров, а также расноложенным на большой глубине. Он позволяет контролировать состояние металла резервуаров и трубо-проводоЕ без их опорожнения, а при проверке угловых сварных шво является единственно возможным. [c.277]
Должен знать. Основы электротехники и материаловедения типы сварных соединений виды дефектов основные типы ультразвуковых волн, применяемые при дефектоскопии сварных соединений и основного металла физическую сущность ультразвуковых методов контроля эхоимпульсного, теневого, зеркально-теневого способы обеспечения акустического контакта устройство ультразвуковых дефектоскопов эталоны и тест-образцы для проверки и настройки ультразвуковых дефектоскопов и искателей. Методики контроля листового проката, стыковых сварных соединений металлоконструкций и трубопроводов из малоуглеродистых и низколегированных сталей различных толщин. Правила оформления учетной технической документации по результатам контроля. Правила техники безопасности при проведении НК на АЭС. [c.63]
Указанный контроль сварных соединений осуществляется следующими методами внешним осмотром и измерением швов механическими испытаниями металлографическим исследованием стилоскопированием ультразвуковой дефектоскопией просвечиванием (рентгено- или гаммаграфированием) замером твердости металла шва испытанием на межкристаллитную коррозию гидравлическим или пневматическим испытанием и другими методами (магнитографией, цветной дефектоскопией и т. д.), если они предусмотрены в чертежах и ТУ. [c.96]
Растрескивание сварного соединения корпуса шарового клапана ЛК8/ШКМ с хвостовиком произошло по истечении года эксплуатации в условиях ОНГКМ. Корпус и хвостовик изготовлены из стали А352СгЬСС-М (% С верхней части кольцевого шва обнаружена трещина длиной 300 мм, а методами ультразвуковой дефектоскопии зафиксировано ее развитие в металле шва на расстояние 1200 мм. Характер разрушения хрупкий, поверхность излома покрыта продуктами коррозии, растрескивание начинается от непровара (рис. 13). В зоне термического влияния под корневым слоем в области очага разрушения обнаружен участок укрупненного бейнитного зерна с твердостью 266-285 НУ. В следующих далее слоях сварного соединения в зоне термического влияния наблюдается мелкозернистая нормализованная структура с твердостью 210-221 НУ. Сероводородное растрескивание сварного соединения инициировал концентратор напряжений — непровар в сочетании с бейнитной структурой металла, обладающей высокой твердостью. [c.42]
Ультразвуковые колебания применяют в технике ( просвечивание металла на большую глубину — ультразвуковая дефектоскопия, получение эмульсий из несмешйвающихся жидкостей и мн. др.), физике, химии, медицине, биологии. [c.517]
На практике большее распространение получили ультразвуковые дефектоскопы, работающие на принципе использования импульсных ультразвуковых колебаний. В указанных приборах пьезоэлектрическим излучателем, возбуждаемым радиоимпульсами специального генератора, посылаются в исследуемый металл не непрерывные (незатухающие) упругие колебания, а чрезвычайно короткие импульсы =0,5-5- Юмкс) с относительно продолжительными промежутками между ними (/ = 1 -ь 5 мс), распространяющиеся узким пучком. [c.41]
При производственном контроле сварных швов ультразвуковые колебания вводятся в металл шва через основной металл с помощью наклонных искателей, применяя для этого эхо-метод. Наклонные искатели для ультразвукового дефектоскопа были разработаны в 1951 г. ЦНИИТМАШем. Это позволило НИИхим-машу в 1951—1952 гг. провести первые исследования, в результате которых была установлена возможность использования ультразвукового метода для контроля качества сварных швов химической и нефтяной аппаратуры [112]. Отработку методики контроля производили на специально подготовленных сварных образцах, выполненных многослойной сваркой с различными естественными и искусственными дефектами. Были отработаны основные приемы сканирования, позволявшие отличать опасные протяженные дефекты типа непроваров и трещин от мелких допустимых, округлых по форме пор и шлаковых включений. Чувствительность контроля выбирали близкой к максимальной, но при которой еще отсутствовали помехи. [c.26]
Коленчатые валы. Для проверки качества металла крупногабаритных валов компрессоров, детандеров, трубокомпрессоров используют ультразвуковую, магнитную и в некоторых случаях цветную дефектоскопию. Несмотря на сложную конфигурацию этих изделий (рис. 133), сочетание магнитной и ультразвуковой дефектоскопии позволяет уверенно выявлять в них как поверхностные дефекты, так и дефекты в толще металла. [c.179]
Исследование влияния структуры и фазового состава на акустические свойства металла швов нержавеющих сталей в связи с проблемой дефектоскопичности.— В кн. Ультразвуковая дефектоскопия сварных конструкций. Л., НИИмостов, 1973. с. 69—71. Авт. Н. В. Химченко, В. А. Бобров, В, В. Волокитин и др. [c.258]
Основными дефектами трубопровода, обнаруживаемыми внутритрубными снарядами — профилемерами Калипер и ультразвуковыми дефектоскопами Ультраскан , являются дефекты формы трубы (вмятины, гофры) и дефекты стенки трубы — дефекты потери металла коррозионного и механического происхождения. [c.15]
При обнаружении зон, в которых 1фа1а> Цкр, рекомендуется вскрыть теплоизоляцию над поврежденной зоной и провести ультразвуковую дефектоскопию и металлографический анализ металла с помощью реплик. При обнаружении зон, поврежденных МКК, необходим обязательный ремонт конструкции. Эксплуатация оборудования с трещинами МКК, особенно при низких и сверхнизких температурах, недопустима, т. к. приводит к снижению надежности и резкой потере запасов пластичности металла (табл. 1.4.51). [c.122]
Дефекты стенок, связанных с потерей металла, определяются ультразвуковыми дефектоскопами Ультраскан , которые перемещают внутри трубопровода также с потоком нефти. Предполагается, что указанными приборами будут обследованы все нефтепроводы России к 2000 г. [c.80]
Ультразвуковая дефектоскопия металлов, сварных соединений и швов, рельсов
Когда необходима ультразвуковая дефектоскопия металлов?
Мы проводим ультразвуковую дефектоскопию рельсов, трубопроводов, сварных соединений (швов) и различных изделий из металлов для обнаружения несовершенств и дефектов в них при помощи теневого и эхо-импульсного метода (отраженных колебаний).
Мы выполняем проверку заготовок неразрушающим методом в собственной лаборатории, которая оснащена всем необходимым оборудованием, среди которого дефектоскопы с А-, В- и С-сканом, для выполнения процедуры на высоком уровне. Для выявления дефектов, которые залегают на небольшой глубине, мы используем коротковолновые звуковые колебания.
Как проводится исследование?
Ультразвуковую дефектоскопию мы проводим под прямым лучом и под углом. Мы выявляем возможные трещины, поры, пустоты и другие неоднородные включения при помощи звуковых волн частотой от 20 КГц до 500 МГц, которые во время проведения дефектоскопии отражаются в разных направлениях. В работе мы используем тестовые образцы и метод сравнения с ними. При обнаружении дефекта дефектоскоп фиксирует соответствующие эхосигналы, и переносной измерительный прибор записывает его.
При ультразвуковой дефектоскопии сварных соединений мы используем эхоимпульсный метод контроля. Способ заключается в отправке от излучателя малых зондирующих импульсов в шов, который исследуется, и регистрации амплитуды и времени получения на приемник эхосигналов, которые отражаются от дефектов.
Метод позволяет выявить трещины, непровары, шлаковые и газовые включения в угловых, стыковых, нахлесточных и тавровых соединениях, которые выполнены газовой, дуговой, контактной и электрошлаковой сваркой. Способ используется как для контроля сварных швов из стали, так и из цветных металлов и сплавов из них.
Ультразвуковая дефектоскопия рельсов и различных заготовок из металла проводится нами согласно требованиям ГОСТ 15467-79, ГОСТ 23667-85, ГОСТ 23829-85, а также других стандартов и нормативных актов. В результате исследования рельс мы выявляем дефекты, которые образовались на стадии их изготовления, при сварке, а также дефекты, которые появились в процессе их укладки и эксплуатации.
Кроме дефектоскопии ультразвуком в лаборатории мы проводим исследования неразрушающими методами контроля с использованием магнитных порошков и проникающими методами (капиллярный способ).
Заказать ультразвуковую дефектоскопию металлов
Для обсуждения сроков, стоимости и других условий исследования позвоните нашим экспертам: +7 812 577-18-87 (Россия), +7 812 577-46-16 (Санкт-Петербург) или напишите на почту.
Ультразвуковой неразрушающий контроль металлоконструкций – дефектоскопия и толщинометрия сварных соединений
Лаборатория неразрушающего контроля СК «Олимп» проводит ультразвуковую толщинометрию и дефектоскопию сварных швов, околошовной зоны, основного металла. Услуга предоставляется в Москве и на всей территории России.
Выезд специалистов НК на объект возможен на следующий день после получения заявки. Испытания и измерения проводят сотрудники, аттестованные на II и III уровень квалификации.
Заключениям о соответствии объекта проверки требованиям технической документации, выданным ЛНК компании СК «Олимп», доверяет Ростехнадзор и другие контролирующие ведомства.
Узнать стоимость услуги — отправить заявку
Лаборатория аттестована на проведение ультразвукового контроля, следующих объектов:
- строительных конструкций;
- трубопроводов;
- оборудования опасных производств;
- объектов котлонадзора;
- систем газоснабжения;
- оборудования нефтегазовой промышленности;
- подъемных сооружений.
Физическая природа ультразвукового контроля
Ультразвуковые волны, используемые в дефектоскопии и толщинометрии, представляют собой упругие колебания, возбуждаемые в материале объекта, при этом частицы объекта не перемещаются вдоль направления движения волн – каждая частица, совершив колебательное движение относительно своей первоначальной ориентации, снова занимает первоначальное положение, а колебательное движение совершает следующая за ней частица. В зависимости от скорости распространения импульса выявляется тот или иной дефект.
В металлах возбуждаются волны пяти типов поверхностные, растяжения, изгиба, продольные и поперечные. Для обнаружения дефектов с помощью специальных излучателей применяют теневой (используется только при наличии двустороннего доступа к объекту контроля), резонансный и эхо-метод.
Ультразвуковой метод контроля наряду с рентгеновским, предназначен для определения местоположения и характера внутренних дефектов. В отличие от РК, где требуется наличие объемного оборудования и получение результатов гарантировано через достаточно длительное время, ультразвуковой метод более мобилен, оперативен, безопасен для здоровья и ниже по стоимости. Весь комплект оборудования может поместиться в небольшую сумку. Для его проведения потребуется ультразвуковой дефектоскоп, смазка (гель для УЗК, солидол, технический вазелин, моторное или техническое масло) датчик (ПЭП) с кабелем. Как правило специалисты прибывают на объект уже с настроенными параметрами в дефектоскопе и наличие настроечных образцов на объекте не так обязательно. Обследуя объект контроля, дефектоскопист видит картину на экране прибора в режиме онлайн, поэтому результаты контроля специалист может сообщить вам сразу.
УЗК проводят при шероховатости поверхности не более Rz 40. Поверхность должна быть зачищена от грязи, выли, ржавчины, окалин, застывших брызг металла, забоин и других неровностей. Подготовка к контролю, настройка дефектоскопа, порядок проведения ультразвукового контроля регламентруется ГОСТ Р 55724-2013. Ультразвуковая дефектоскопия широко применима во всей линейке объектов контроля по ПБ 03-440-02. Ультразвуковой метод можно применять при контроле сварных швов на резервуарах, металлических и полиэтиленовых трубопроводах, металлических конструкциях, а также полуфабрикатах, поковках, отливках и пр.
Наиболее распространенным и востребованным является эхо-импульсный метод, при котором обнаруживают более 90% дефектов. Отличительной особенностью метода является то, что при контроле изделий регистрируются и анализируются практически все сигналы, приходящие из изделия после излучения зондирующих колебаний.
Среди дефектов, плохо поддающихся обнаружению при проведении ультразвукового контроля, можно отнести поры малых размеров. За счет сферической формы заметная часть лучей рассеивается при обнаружении волны препятствия и, собственно, не происходит «эха».
Ультразвуковая дефектоскопия позволяет решить следующие практические задачи:
- Установить качество неразъемных соединений (стыковых, угловых, тавровых сварных швов) – выявить наличие пор, раковин, кратеров, прожогов, непроваров, шлаковых включений, трещин и иных дефектов.
- Проверить сплошность (расслоение) основного металла в околошовной зоне.
Выявленные поверхностные и подповерхностные дефекты классифицируются на допустимые, недопустимые и возможно допустимые.
Ультразвуковую дефектоскопию сочетают с методами рентгено- и гаммографировании для контроля сварных швов, если необходимо:
- Уточнить размеры и характер выявленных ультразвуком дефектов.
- Повысить надежность и объективность контроля путем выборочного просвечивания участков, в которых по данным ультразвуковой дефектоскопии отсутствуют недопустимые дефекты.
Ультразвуковая толщинометрия дает возможность:
- Определить фактическую толщину металла объектов с односторонним доступом, например: ёмкостей, каркасов, магистральных труб, баллонов, днищ морских/речных судов.
- Измерить толщину гальванических, лакокрасочных, керамических и других изоляционных, немагнитных, неэлектропроводящих металлических либо неметаллических покрытий.
По результатам проведения ультразвукового неразрушающего контроля оформляется технический отчет, включающий в себя:
- Заключение о соответствии объекта проверки требованиям технической документации.
- Копию свидетельства об аттестации лаборатории неразрушающего контроля.
- Копию свидетельства об аттестации дефектоскописта.
- Копию свидетельства о поверке прибора (дефектоскопа).
- Технологические карты (по требованию заказчика).
Цена ультразвукового контроля определяется с учетом следующих факторов:
- применяемого метода контроля;
- стоимости расходных материалов;
- параметров участка контроля;
- количества обследуемых неразъемных соединений (сварных швов) – учитывается при проведении дефектоскопии;
- времени, необходимого для проведения УЗК;
- количества специалистов НК, привлекаемых к выполнению работ.
Цель проведения неразрушающего контроля ультразвуковым методом:
- Установить соответствие объекта обследования требованиям нормативно-технической документации.
- Дать качественную и количественную оценку поверхностных/подповерхностных дефектов, определив степень их потенциальной опасности.
- Повысить уровень безопасности эксплуатации оборудования на промышленных объектах, отнесенных к категории особо опасных.
- Обеспечить безопасную эксплуатацию ответственных трубопроводов и предотвратить вероятные аварии.
- Своевременно выявить недопустимые дефекты конструкций на различных стадиях строительства зданий и сооружений.
Проведение неразрушающего контроля исключительно на стадии ввода объекта в эксплуатацию с высокой долей вероятности может привести к дополнительным повышенным расходам на устранение опасных дефектов, а полное игнорирование НК – к авариям и даже катастрофам техногенного характера.
Передвижная лаборатория неразрушающего контроля «СК «ОЛИМП» – это:
- Гарантия точности результатов ультразвуковой дефектоскопии и толщинометрии.
- Полный комплект поверенного оборудования, сертифицированных материалов, калиброванных контрольных образцов необходимых для выполнения всех измерений и испытаний методами неразрушающего контроля с помощью ультразвука в рамках области аттестации лаборатории. Средства измерения внесены в государственный реестр.
- Наработанный годами опыт решения нестандартных задач неразрушающего контроля.
- Компетентный персонал – сотрудники аттестованы на II и III уровень квалификации, стаж специалистов НК более 10 лет.
- Обширная база постоянных клиентов, каждому из которых предоставляется скидка при следующем обращении или заказе других услуг компании.
Том Неллиган 1. Основная теория: Звуковые волны — это просто организованные механические колебания, проходящие через среду, которая может быть твердым телом, жидкостью или газом. Частота: Все звуковые волны колеблются с определенной частотой или числом колебаний или циклов в секунду, которые мы воспринимаем как высоту тона в знакомом диапазоне слышимого звука.Человеческий слух имеет максимальную частоту около 20 000 циклов в секунду (20 кГц), в то время как большинство приложений ультразвуковой дефектоскопии используют частоты от 500 000 до 10 000 000 циклов в секунду (от 500 кГц до 10 МГц). На частотах в мегагерцовом диапазоне звуковая энергия не распространяется эффективно через воздух или другие газы, но она свободно проходит через большинство жидкостей и обычные технические материалы. Скорость: Скорость звуковой волны зависит от среды, через которую она распространяется, на нее влияют ее плотность и упругие свойства. Длина волны: Любой тип волны будет иметь связанную длину волны, которая представляет собой расстояние между любыми двумя соответствующими точками в волновом цикле, когда она распространяется через среду. Длина волны связана с частотой и скоростью простым уравнением λ = c / f Длина волны является ограничивающим фактором, который контролирует количество информации, которая может быть получена от поведения волны.При ультразвуковой дефектоскопии общепринятым нижним пределом обнаружения небольшого дефекта является половина длины волны. Все, что меньше этого, будет невидимым. При ультразвуковом измерении толщины — теоретическая минимальная измеряемая толщина на одной длине волны. Режимы распространения: Звуковые волны в твердых телах могут существовать в различных режимах распространения, которые определяются типом участвующего движения. Переменные, ограничивающие передачу звуковых волн: Расстояние, которое пройдёт волна с заданной частотой и уровнем энергии, зависит от материала, через который она проходит.Как правило, твердые и однородные материалы передают звуковые волны более эффективно, чем мягкие, неоднородные или зернистые. Три фактора определяют расстояние, на которое звуковая волна будет проходить в данной среде: распространение луча, затухание и рассеяние. По мере продвижения луча передняя кромка становится шире, энергия, связанная с волной, распространяется по большей площади, и в конечном итоге энергия рассеивается. Затухание — это потеря энергии, связанная с передачей звука через среду, по сути, степень поглощения энергии при движении фронта волны вперед.Рассеяние — это случайное отражение звуковой энергии от границ зерен и подобной микроструктуры. С понижением частоты расширение луча увеличивается, но эффекты ослабления и рассеяния уменьшаются. Отражение на границе: Когда звуковая энергия, проходящая через материал, встречает границу с другим материалом, часть энергии будет отражаться назад, а часть будет проходить через нее.Количество отраженной энергии или коэффициент отражения зависит от относительного акустического импеданса двух материалов. Акустический импеданс, в свою очередь, — это свойство материала, определяемое как плотность, умноженная на скорость звука в данном материале. Для любых двух материалов коэффициент отражения в процентах от падающего энергетического давления можно рассчитать по формуле
где Угол отражения и преломления: Звуковая энергия на ультразвуковых частотах сильно направлена, а звуковые лучи, используемые для обнаружения дефектов, четко определены. В ситуациях, когда звук отражается от границы, угол отражения равен углу падения. Звуковой луч, падающий на поверхность перпендикулярно, будет отражаться прямо назад.Звуковой луч, падающий на поверхность под углом, будет отражаться вперед под тем же углом.
2. Ультразвуковые преобразователи Поперечное сечение типичного контактного преобразователя Существует пять типов ультразвуковых преобразователей , обычно используемых в приложениях для обнаружения дефектов: – Контактные преобразователи — Как следует из названия, контактные преобразователи используются в непосредственном контакте с испытуемым образцом. Они вводят звуковую энергию перпендикулярно поверхности и обычно используются для обнаружения пустот, пористости и трещин или отслоений, параллельных внешней поверхности детали, а также для измерения толщины. — Преобразователи углового луча — Преобразователи углового луча используются в сочетании с пластиковыми или эпоксидными клиньями (угловыми балками) для введения поперечных или продольных волн в испытательный образец под заданным углом по отношению к поверхности. – Погружные преобразователи — Погружные преобразователи предназначены для передачи звуковой энергии в испытуемый образец через столб воды или водяную баню.Они используются в приложениях для автоматического сканирования, а также в ситуациях, когда требуется четко сфокусированный луч для улучшения разрешения дефектов. Более подробную информацию о преимуществах различных типов преобразователей, а также о диапазоне частот и предлагаемых диаметров можно найти в разделе «Преобразователи » нашего веб-сайта. 3. Ультразвуковые дефектоскопы 4. Процедура В некоторых специализированных случаях тестирование выполняется в режиме сквозной передачи, когда звуковая энергия проходит между двумя преобразователями, расположенными на противоположных сторонах испытательного образца.Если на пути прохождения звука имеется большой дефект, луч будет заблокирован, и звуковой импульс не достигнет приемника. Типовая угловая балка в сборе
Угловой звуковой луч очень чувствителен к трещинам, перпендикулярным дальней поверхности испытательного образца (испытание первой ноги) или, после отражения от дальней стороны, к трещинам перпендикулярно поверхности сцепления (испытание второй ноги).Различные углы наклона луча и положения зонда используются для приспособления к деталям разной геометрии и типам дефектов, и они подробно описаны в соответствующих правилах и процедурах проверки, таких как ASTM E-164 и Кодекс по сварке конструкций AWS. Полный список примечаний по применению дефектоскопа Olympus.![]() |
Что такое ультразвуковой контроль Это работает?
Ультразвуковой контроль (UT) включает в себя ряд методов неразрушающего контроля (NDT), при которых ультразвуковые волны проходят через объект или материал.Эти высокочастотные звуковые волны передаются в материалы для определения характеристик материала или для обнаружения дефектов. В большинстве приложений контроля UT используются короткие импульсные волны с частотами от 0,1 до 15 МГц, хотя могут использоваться частоты до 50 МГц. Одним из распространенных применений этого метода испытаний является ультразвуковое измерение толщины, которое используется для определения толщины объекта, например, при оценке коррозии трубопроводов.
Как это работает?
Ультразвуковой контроль использует пьезоэлектрический преобразователь, подключенный к дефектоскопу, который в своей основной форме представляет собой приемник импульсов и дисплей осциллографа.Преобразователь проходит над исследуемым объектом, который обычно соединяется с тестируемым объектом с помощью геля, масла или воды. Это связующее вещество требуется для эффективной передачи звуковой энергии от преобразователя в деталь, однако это связующее вещество не требуется при проведении испытаний с использованием бесконтактных методов, таких как электромагнитный акустический преобразователь (ЭМАП) или с помощью лазерного возбуждения.
Импульсное эхо и сквозная передача
Ультразвуковой контроль может выполняться двумя основными методами — эхо-импульсным и сквозным.
При импульсном эхо-тестировании тот же преобразователь излучает и принимает энергию звуковой волны. В этом методе используются эхо-сигналы на интерфейсе, например на задней части объекта или дефекте, для отражения волн обратно к датчику. Результаты показаны в виде линейного графика с амплитудой на оси Y, представляющей интенсивность отражения, и расстояние или время на оси x, что показывает глубину сигнала через материал.
При тестировании на сквозное пропускание используется излучатель для отправки ультразвуковых волн с одной поверхности и отдельный приемник для приема звуковой энергии, достигшей противоположной стороны объекта.Дефекты материала уменьшают количество получаемого звука, что позволяет обнаруживать дефекты.
Контактные и иммерсионные испытания
Ультразвуковой контроль также можно разделить на два основных типа: контактный или иммерсионный контроль .
Контактный ультразвуковой контроль обычно используется для проверки доступности или портативности на месте. Контактный ультразвуковой контроль может выполняться там, где доступна только одна сторона испытательного образца, или если детали, подлежащие испытанию, имеют большие размеры, неправильную форму или трудны для транспортировки.
Иммерсионный ультразвуковой контроль — это неразрушающий контроль в лаборатории или на заводе, который лучше всего подходит для изогнутых компонентов, сложной геометрии и для разработки ультразвуковой техники. В этом методе компонент или материал погружают в воду, которая действует как связующее вещество вместо гелей, используемых для контактного ультразвука. Погружной UT обычно использует метод эхо-импульса, и траектории роботизированных зондов могут использоваться для проверки сложных поверхностей, которые было бы трудно покрыть контактными зондами.Погружной UT можно использовать для широкого диапазона толщин стенок и типов материалов, что делает его подходящим методом испытаний для различных приложений и отраслей.
Почему это используется?
Ультразвуковой контроль как метод неразрушающего контроля идеален для обнаружения дефектов и дефектов без повреждения объекта или материала. Периодические ультразвуковые осмотры также могут использоваться для проверки на коррозию или рост известных дефектов и, таким образом, потенциально предотвращать выход из строя части, компонента или всего актива. Он используется в широком спектре отраслей, включая аэрокосмическую, автомобильную, строительную, медицинскую, металлургическую и производственную.
Какие материалы можно испытывать?
Ультразвуковой контроль используется во многих отраслях промышленности из-за его пригодности для многих различных материалов. UT идеально подходит для проверки плотных кристаллических структур, таких как металлы. Керамику, пластмассы, композиты и бетон также можно успешно обследовать, но с меньшим разрешением, поскольку затухание в этих материалах выше.
Ультразвуковая технология успешно используется в медицинском секторе в течение многих десятилетий и становится все более предпочтительным вариантом как для рутинной диагностической визуализации, так и для медицинских исследований из-за отсутствия ионизирующего излучения.
Преимущества
К преимуществам ультразвукового контроля можно отнести:
- Высокая проникающая способность, позволяющая обнаруживать дефекты глубоко внутри детали
- Высокая чувствительность, позволяющая обнаруживать очень мелкие дефекты
- Может использоваться для проверки, когда доступна только одна сторона объекта
- Более высокая точность по сравнению с другими методами неразрушающего контроля для определения глубины внутренних дефектов и толщины деталей с параллельными поверхностями
- Возможность оценить размер, форму, ориентацию и характер дефектов
- Возможность оценить структуру сплава компонентов с различными акустическими свойствами
- Неопасно для находящегося рядом персонала, оборудования или материалов
- Возможны высокоавтоматизированные и портативные операции
- Могут быть получены немедленные результаты, позволяющие принимать немедленные решения
Ограничения
Однако существует несколько ограничений для ультразвукового контроля, а именно:
- Требуются опытные специалисты для проверки и интерпретации данных
- Ложные положительные результаты, также известные как ложные сигналы, могут быть результатом допустимых аномалий, а также самой геометрии компонентов
- Шероховатые предметы, объекты неправильной формы, очень маленькие или тонкие или неоднородные, труднодоступны для проверки
- Отслаивающуюся окалину или краску необходимо удалить перед началом испытания, хотя чистую, должным образом склеенную краску можно оставить на месте
- Муфты, необходимые для испытаний с использованием стандартного UT
- UT может иметь меньшую чувствительность к объемным дефектам, особенно металлическим включениям, чем радиографические испытания
Приложения
Ультразвуковой контроль применяется в различных отраслях промышленности, включая проверку целостности материала или компонента. Это может включать в себя испытание сварных швов для определения наличия разрывов. Это испытание может проводиться как на черных, так и на цветных материалах, а также на более толстых сечениях и тех, которые доступны только с одной стороны. УЗИ также может обнаруживать более мелкие дефекты и плоские дефекты, которые не могут быть легко оценены с помощью радиографических исследований.
Приложения для UT включают в себя те, которые используются в аэрокосмической, автомобильной, строительной, железнодорожной, медицинской и нефтегазовой отраслях.
Услуги и курсы TWI
TWI предоставляет ряд услуг по ультразвуковому тестированию нашим промышленным членам, а также ряд учебных курсов по неразрушающему контролю для тех, кто желает узнать о применяемых методах.
Мы можем предоставить полный спектр услуг и экспертных знаний, включая такие методы, как ультразвуковой контроль с фазированной решеткой (PAUT), лазерный ультразвуковой контроль и ручной ультразвуковой контроль.
Дефектоскопы | Instrumart
Дефектоскопы используют хорошо зарекомендовавшую себя и полностью неразрушающую ультразвуковую технологию для пропускания звуковых волн через металлы, композиты, пластмассы и керамику для обнаружения скрытых дефектов, таких как в виде трещин, пустот и мягкости, которые могут привести к поломке.Звуковые волны действуют очень предсказуемым образом и создают характерные эхо-паттерны, которые могут отображаться и записываться портативными устройствами. инструменты, делающие их весьма полезными в качестве инструмента проверки.
В качестве ультразвукового устройства дефектоскопы используют преобразователь как для создания вибраций, так и для приема отраженного эхо-сигнала. Когда эти колебания проходят через среду, они происходят в предсказуемом
направление и скорости и скорости, специфичные для среды. Когда граница, такая как новая среда или дефект, достигается, вибрации отражаются обратно на преобразователь, снова в
предсказуемым образом. Возвращаемый сигнал преобразуется в шаблон формы волны, который может быть проанализирован на предмет несоответствий.
Ультразвуковая дефектоскопия — сравнительный метод. Используя соответствующие эталоны, а также знания о распространении звуковых волн и общепринятые процедуры испытаний, обученный Оператор может определить конкретные характеристики, в том числе дефекты, по форме волны исследуемого материала.
Дефектоскопы состоят из прибора и преобразователя.Доступны различные типы преобразователей для различных методов измерения и приложений. Обычно бывает два типа методик измерения:
Тестирование прямым лучом: Тестирование прямым лучом включает размещение преобразователя перпендикулярно испытуемому материалу. Он используется для поиска параллельных трещин и отслоений. поверхности образца, а также пустот и пористости. Тестирование прямым пучком может выполняться с помощью четырех типов преобразователей, каждый из которых предназначен для конкретного применения:
- Контактные преобразователи используются в прямом контакте с испытуемым образцом.
- Преобразователи линии задержки включают короткий пластиковый волновод или линию задержки между активным элементом и испытательным образцом, что улучшает разрешение вблизи поверхности а также защищает преобразователь при высоких температурах.
- Двухэлементные преобразователи используют отдельные элементы передатчика и приемника в единой сборке, что улучшает разрешение при обнаружении пористости или при работе с шероховатыми поверхностями или крупнозернистыми материалами.
- Погружные преобразователи передают звуковую энергию в испытуемый образец через столб воды или водяную баню, что также полезно при автоматизированном сканировании. как в ситуациях, когда для улучшения разрешения дефектов необходим остро сфокусированный луч.
Испытание угловым пучком: Испытание угловым пучком решает основную проблему обнаружения дефектов: дефекты, перпендикулярные поверхности испытательного образца, обычно невидимы с прямой
лучи из-за их ориентации относительно звукового луча. Преобразователи углового луча , в которых используются пластиковые клинья для ввода звуковой энергии в испытуемый образец на выбранной
угол, решите эту проблему. Они особенно полезны при контроле сварных швов.
Калибровка
Как и большинство испытательного и измерительного оборудования, дефектоскопы необходимо периодически калибровать для поддержания точности. В случае оборудования неразрушающего контроля калибровка выполняется с использованием прецизионных испытательных блоков, которые моделируют условия и служат эталонами.Различные типы тестовых блоков моделируют разные условия. Блоки тестов могут включать в себя этапы разных толщины для использования с толщиномерами, отверстиями и другими «дефектами» для использования с дефектоскопами или заданной твердости для датчиков твердости.
Что следует учитывать при выборе дефектоскопа:
- Какой параметр (толщина, дефектоскопия и т. Д.) Проверяется?
- Требует ли оборудование специальной подготовки?
- Какие аксессуары (преобразователи, контакт, калибровочные блоки) необходимы?
- Существуют ли профессиональные стандарты, которых необходимо придерживаться?
Если у вас есть какие-либо вопросы относительно дефектоскопов, не стесняйтесь обращаться к одному из наших инженеров, отправив нам электронное письмо по адресу sales @ instrumart. com или по телефону 1-800-884-4967.
Ультразвуковая дефектоскопия
Обычно используются импульсные ультразвуковые лучи, а в простейших приборах на поверхность образца помещается ручной зонд. Дисплей осциллографа с временной разверткой показывает время, за которое ультразвуковой импульс проходит до отражателя (дефекта, задней поверхности или другой свободной поверхности) с точки зрения расстояния по экрану осциллографа — так называемого A -сканирование дисплея. Высота отраженного импульса зависит от размера дефекта, видимого из зонда передатчика.Взаимосвязь между размером дефекта, расстоянием до дефекта и отражательной способностью дефекта сложна, и для интерпретации изображения требуются значительные навыки.Также используются сложные многозондовые системы с механическим перемещением зонда и оцифровкой сигналов с последующим хранением в компьютере; методы компьютерной интерпретации быстро развиваются.
Существует несколько форм механической вибрации, в зависимости от направления движения частиц в волновом движении, поэтому существует несколько форм ультразвуковых волн, наиболее широко используемыми в неразрушающем контроле являются волны сжатия и поперечные (сдвиговые) волны.
Благодаря подходящей конструкции зонда ультразвуковые лучи можно вводить в твердый материал практически под любым углом.
Волны сжатия также распространяются через жидкости, и распространенный метод заключается в погружении образца в большой резервуар и использовании стояночного зонда с механизированным перемещением. С помощью такого оборудования возможны альтернативные методы отображения сигналов и может быть получено двумерное ультразвуковое изображение (дисплеи B-сканирования и C-сканирования).
Как правило, один зонд действует как передатчик и приемник, поэтому контроль можно проводить только с одной стороны образца.Крупнозернистые материалы, такие как сварка аустенитной стали, медные отливки и т. Д., Вызывают сильное затухание и рассеяние, и в настоящее время их трудно контролировать с помощью ультразвука, но большие толщины мелкозернистого материала, такого как кованая сталь, могут быть протестированы без труда.
Поскольку обычным признаком дефекта является импульс на осциллограмме, дефекты должны быть охарактеризованы, а также определены их размеры. Новые методы, такие как времяпролетная дифракция, TOFD, были разработаны, чтобы помочь этому методу.
Измерения затухания и скорости ультразвука используются для изучения различных свойств материалов.
Использование ультразвука для определения размеров дефектов
После обнаружения дефектов часто бывает желательно определить их размер. Для дефектов, меньших ширины ультразвукового луча, можно получить псевдоразмер путем сравнения амплитуды сигнала дефекта с амплитудой эталонного отражателя (плоскодонное или просверленное сбоку отверстие) в том же диапазоне. Когда размер дефекта больше ширины ультразвукового луча, для оценки размера дефекта часто можно использовать обычные методы определения размера движения зонда.Метод максимальной амплитуды использует меру движения датчика между максимальными сигналами от конечностей дефекта до дефекта размера. Методы падения на 6 дБ и 20 дБ используют уменьшение амплитуды сигнала от дефекта, когда датчик проходит через край дефекта в качестве индикатора размеров дефекта. Однако взаимодействие между ультразвуковым лучом и дефектом, в зависимости от природы и ориентации дефекта, ограничивает эффективность этих методов при работе со сложными и неправильно ориентированными дефектами.
Методы, использующие дифрагированный сигнал от краев дефекта для обнаружения и определения размеров дефектов, наиболее эффективны при определении размеров плоских дефектов. В методе времяпролетной дифракции (TOFD) используется время прохождения ультразвука между датчиком (датчиками) и конечностями дефекта для обнаружения и определения размера дефектов. Точность определения размера дефекта лучше ± 2 мм может быть достигнута с помощью оптимизированных методов (см. Также усовершенствованные ультразвуковые методы).
Ранняя история металлоискателей
Часто провозглашенный отцом ультразвуковых исследований, Сергей Юрьевич.Соколов , знаменитый советский ученый из Института имени В.И. Ленинградский электротехнический институт им. Ульянова (Ленина) родился в 1897 году в одноименном городе России.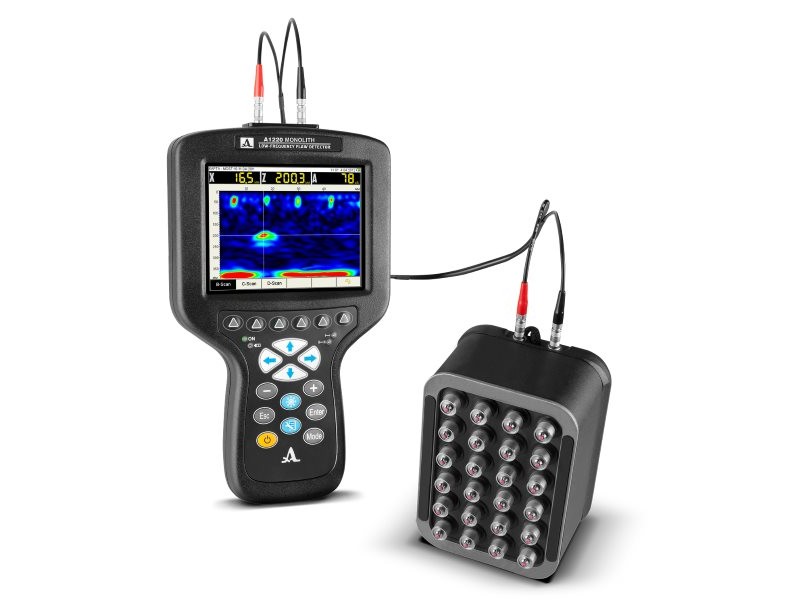
Как и в случае с ранним использованием ультразвука, обширная работа по дефектоскопии металлов проводилась в Германии в начале 1930-х годов.В 1933 году О. Мюльхаузер запатентовал систему передачи ультразвуковой энергии в исследуемую деталь, обнаруживая ее по мере появления с помощью второго преобразователя. В 1935 году Соколов опубликовал подробности экспериментальной конструкции кварцевых генераторов, методы соединения генераторов с испытуемым образцом для достижения максимальной передачи энергии, а также различные методы определения ультразвуковой энергии после прохождения через испытательный образец. Он предложил первую «ультразвуковую камеру», с помощью которой можно было получить реальное изображение дефекта. Он предвидел, что, используя звуковые волны с частотой 3000 мегагерц (МГц), можно получить разрешение, равное разрешению оптического микроскопа. В его методе использовался большой пьезоэлектрический приемный преобразователь, на котором заряды, генерируемые приходящими акустическими сигналами, оставались изолированными. Затем поверхность преобразователя сканируется механическим контактом или лучом, создавая «картину» дефекта. Однако разрешение экспериментальных устройств, которые он изготовил, было недостаточно хорошим для практического использования.
В Германии к 1936 году Раймар Польман разработал метод ультразвуковой визуализации, основанный на передаче с использованием акустических линз и преобразовании полученного акустического изображения в визуально наблюдаемое изображение в том же интересующем объеме. В Германии его устройство для преобразования изображений стало известно как «ячейка Польмана». Широко использовался в конце Второй мировой войны в Германии, когда ультразвуковые испытания материалов стали важными при выборе боеприпасов для зенитной обороны Берлина. Польман экспериментировал в том же направлении с распространением ультразвука через металлы, содержащие дефекты, но применил совершенно другой подход к методу обнаружения выходящего луча. В его детекторе использовалась суспензия хлопьев коллоидного алюминия в ксилоле, запечатанная в прозрачном контейнере. Ультразвуковой луч, выходящий из испытательного образца, воздействовал на алюминиевые чешуйки, заставляя их выравниваться перпендикулярно направлению луча. В случае наличия каких-либо дефектов в тестируемом материале будут отбрасываться теневые области, где чешуйки сохраняют свою первоначальную ориентацию.
В 1939 году исследователи из Британского института черной металлургии решили исследовать возможность обнаружения микротрещин в стали с помощью ультразвуковой волны, проводимой с помощью прибора типа Польмана, но оказалось, что он недостаточно чувствителен. В 1942 году Дональд Спроул успешно применил принцип эхолота для обнаружения дефектов в стали. В его аппарате использовались отдельные передающие и приемные преобразователи. Почти одновременно, но независимо, американский ученый Флойд Файерстоун изобрел «рефлектоскоп» — прибор, работающий по аналогичным принципам, но использующий один преобразователь для передачи и приема].
В методе отражения импульсная звуковая волна передается с одной стороны образца, отражается от дальней стороны и возвращается в приемник, расположенный в начальной точке. При столкновении с дефектом или трещиной в материале сигнал отражается, и время его прохождения изменяется. Фактическая задержка становится мерой местоположения дефекта; карта материала может быть создана, чтобы проиллюстрировать расположение и геометрию дефектов. В способе сквозной передачи передатчик и приемник расположены на противоположных сторонах материала; прерывания прохождения звуковых волн используются для обнаружения и измерения дефектов.Обычно используется водная среда, в которую погружены передатчик, проба и приемник. Аналогичная технология также была исследована в Германии и Японии, но разработка была свернута из-за Второй мировой войны.
Ключевые лица, Флойд Файерстоун , Дональд Спроул и Адольф Трост , не знали друг друга, поскольку работали строго в секрете. Не были опубликованы даже их заявки на патенты. Спроул и Трост использовали метод передачи с отдельными зондами передатчика и приемника. Trost изобрел так называемый « Trost-Tonge ». Два зонда контактировали на противоположных сторонах пластины, удерживались на одной оси с помощью механического устройства — тонж — и соединялись с обеими поверхностями с помощью непрерывно протекающей воды. Sproule поместил 2 зонда на одной стороне заготовки. Поэтому он изобрел двухкристальные зонды. Он использовал эту комбинацию также с переменным расстоянием друг от друга. Firestone был первым, кто реализовал технику отражения.Он модифицировал радиолокационный прибор и разработал передатчик с короткими импульсами и усилитель с короткой мертвой зоной. Sproule в конечном итоге отказался от метода передачи и в 1952 году подал патент, озаглавленный «Улучшения / или относящиеся к устройству для обнаружения дефектов и измерения скорости методами ультразвукового эхо».
Компания Firestone сделала следующие презентации и / или зарегистрировала следующие патенты в период с 1940 по 1951 год:
- 1940 Дефектоскоп и измерительный прибор
- 1943 Метод резонансного контроля; Метод и аппаратура поверхностных и поперечных волн
- 1945 Сверхзвуковой рефлектоскоп, прибор для исследования внутренней части твердых частей с помощью звуковых волн.
- 1946 Уточнения в сверхзвуковом рефлекторе, Поляризованный звук
- 1948 Трюки со сверхзвуковым рефлектометром
- 1951 Способ и средства для создания и использования колебательной волны в пластине
Sproule и Firestone нашли промышленных партнеров для своих инструментов: Kelvin-Hughes и Sperry Inc . Кельвин-Хьюз выпустил свою первую коммерческую машину в 1952 году. Несколько лет спустя, в , Германия, , , 1949, , информация о Firestone-Sperry-Reflectoscope была получена в виде публикаций в технических статьях: Josef Krautkrmer in Cologne и Karl Deutsch в Вуппертале. Оба приступили к разработке — не зная друг друга. Йозеф Крауткрмер и его брат Герберт были физиками, работавшими в области осциллографов.Они могли самостоятельно разработать ультразвуковые инструменты. Карлу Дойчу, инженеру-механику, понадобился партнер по электронике, и он нашел его вместе с Хансом-Вернером Браншайд, который во время войны получил некоторый технический опыт в области радиолокационной техники. Всего за год и молодые, и крошечные компании смогли представить свои ультразвуковые дефектоскопы, положив начало конкурсу, который существует и сегодня.
Ранние испытания труб на аппарате Крауткрмера (1950-е годы)
Позже на международном рынке появилось больше устройств для ультразвуковых испытаний: Siemens и Lehfeldt в Германии, Kretztechnik в Австрии, Ultrasonique во Франции и Kelvin-Hughes в Великобритании.Все они прекратили производство до 1970-х годов. Kelvin-Hughes также остановился в то же время, Sperry позже был переименован в Automation Industries Inc .
Krautkrme r стала мировым лидером на рынке в начале 60-х годов и сохраняет эту позицию до сегодняшнего дня. Помимо Карла Дойча, появились новые имена: Nukem в Германии, Panametrics и Stavely (после Sonic и Harisonic) в США, Sonatest и Sonomatic в Бриатайне, Gilardoni в Италии.
Четыре немецких дефектоскопа в 1950-е годы.
вверху слева: Крауткрамер, справа: Сименс. слева внизу: Lehfeldt, справа: Карл Дойч.
Исследования в области ультразвука и дефектоскопии металла в Японии были значительно сокращены, когда разразилась Вторая мировая война в 1941 году, когда американцы и немцы усердно исследовали ультразвуковое оборудование и разработку радара. Изучение радиолокационных технологий в Японии также оказалось в невыгодном положении. По окончании войны в 1945 году исследования в области электроники большой мощности были запрещены в Японии на некоторое время (до 1948 года, когда возобновились разработки невоенной электроники).
Японские предприятия взяли на себя исследования из США и Англии и вскоре разработали собственные дефектоскопы для неразрушающего контроля. Примерно в 1949 году четыре японские компании начали производить собственные дефектоскопы. Это были: Mitsutbishi Electric Corporation , Japan Radio Company (позже стала Aloka Company ), Shimadsu Manufacturing Company и Toyko Ultrasonic Industrial Company .Только Mitsubishi продолжила расширяться в области неразрушающего контроля, а другие компании перешли в другие области и, в частности, на диагностические медицинские ультразвуковые исследования. Японское общество неразрушающего контроля официально признало 1952 год первым годом проведения неразрушающего контроля в Японии.
Информация предоставлена NDT.net и другими источниками.
Назад к истории ультразвукового исследования в акушерстве и гинекологии .
Отображать | Отображать Любой совместимый Apple® iPad (iOS 10 и выше) | Отображать TFT 8. | Отображать TFT 8.4 « | Отображать TFT 8.4 « | Отображать TFT 8. | Отображать TFT |
объем памяти | объем памяти До 1 ТБ (в зависимости от модели iPad) | объем памяти | объем памяти | объем памяти | объем памяти | объем памяти |
Подключения | Подключения Зашифрованное соединение Wi-Fi с iPad | Подключения | Подключения | Подключения | Подключения | Подключения |
Улучшение сигнала | Улучшение сигнала Цифровые фильтры, режекторные, усредненные | Улучшение сигнала Цифровые фильтры, сглаживание, контур, подавление, усреднение | Улучшение сигнала Цифровые фильтры, сглаживание, контур, подавление, усреднение | Улучшение сигнала Фильтры цифровые, сглаживающие, контурные, подавляющие | Улучшение сигнала Фильтры цифровые, сглаживающие, контурные, подавляющие | Улучшение сигнала Режим эха в эхо (только Zonotip +) |
Архитектура | Архитектура 1 канал | Архитектура 2 канала, истинная частота дискретизации 200 МГц | Архитектура 1 канал, истинная частота дискретизации 200 МГц | Архитектура 16 активных каналов | Архитектура 16 активных каналов, мультиплексированных более 64 | Архитектура 1 канал |
Частота оцифровки | Частота оцифровки 125 МГц | Частота оцифровки 50 МГц, 100 МГц, 200 МГц | Частота оцифровки 50 МГц, 100 МГц, 200 МГц | Частота оцифровки 65 МГц | Частота оцифровки 65 МГц | Частота оцифровки |
Законы очага | Законы очага | Законы очага | Законы очага | Законы очага 128 | Законы очага 128 | Законы очага |
Макс.![]() | Макс.длина сканирования | Макс.длина сканирования 8192 | Макс. 8192 | Макс.длина сканирования 4096 | Макс.длина сканирования 4096 | Макс. |
Поддерживаемые сканирования | Поддерживаемые сканирования A-Scan, сетка | Поддерживаемые сканирования А-скан | Поддерживаемые сканирования A-скан и TOFD | Поддерживаемые сканирования S-сканирование и L-сканирование | Поддерживаемые сканирования S-сканирование и L-сканирование | Поддерживаемые сканирования Толщина и А-скан (только Zonotip +) |
Количество сканирований | Количество сканирований | Количество сканирований До 2 | Количество сканирований 1 TOFD + 1 Обычный UT | Количество сканирований 1 (до 3 извлеченных сканов A) | Количество сканирований 1 (до 3 извлеченных сканов A) | Количество сканирований |
Количество макетов | Количество макетов | Количество макетов 18 | Количество макетов 18 | Количество макетов 35 | Количество макетов 35 | Количество макетов Zonotip: 2, Zonotip +: 3 |
Измерения | Измерения Длина пути, глубина, расстояние до поверхности, DAC, AWS | Измерения Длина пути, глубина, расстояние до поверхности, DAC, AWS, DGS | Измерения Глубина, длина | Измерения Длина пути, глубина, расстояние до поверхности, DAC, AWS, DGS | Измерения Длина пути, глубина, расстояние до поверхности, DAC, AWS, DGS | Измерения Нормальный режим, режим памяти и режим А-сканирования (только Zonotip +) |
Размер файла | Размер файла | Размер файла До 3 ГБ | Размер файла До 3 ГБ | Размер файла До 3 ГБ | Размер файла До 3 ГБ | Размер файла Память до 50 000 измерений |
Генерация отчетов | Генерация отчетов Индикационная таблица, экспорт в HTML | Генерация отчетов Настраиваемый отчет в формате pdf, снимок экрана PNG, опция вывода файла CSV | Генерация отчетов Настраиваемый отчет в формате pdf, снимок экрана PNG, опция вывода файла CSV | Генерация отчетов Настраиваемый отчет в формате pdf, снимок экрана PNG, опция вывода файла CSV | Генерация отчетов Настраиваемый отчет в формате pdf, снимок экрана PNG, опция вывода файла CSV | Генерация отчетов Файл CSV |
Кодировщик | Кодировщик | Кодировщик 1 или 2 оси (квадратурный вход) | Кодировщик 1 или 2 оси (квадратурный вход) | Кодировщик 1 или 2 оси (квадратурный вход) | Кодировщик 1 или 2 оси (квадратурный вход) | Кодировщик Нет |
Языки | Языки английский, немецкий, французский, испанский, китайский, японский, корейский | Языки Английский, немецкий, французский, испанский, русский, китайский, венгерский, итальянский, португальский и японский | Языки Английский, немецкий, французский, испанский, русский, китайский, венгерский, итальянский, португальский и японский | Языки Английский, немецкий, французский, испанский, русский, китайский, венгерский, итальянский, португальский и японский | Языки Английский, немецкий, французский, испанский, русский, китайский, венгерский, итальянский, португальский и японский | Языки Английский, немецкий, французский, испанский, русский, китайский, итальянский и португальский |
Срок службы батареи | Срок службы батареи | Срок службы батареи 7 часов | Срок службы батареи 7 часов | Срок службы батареи 6 часов | Срок службы батареи 6 часов | Срок службы батареи 9 часов |
Аккумулятор | Аккумулятор Съемный блок, 6 батарей AA (NiMH), безопасный для полетов | Аккумулятор | Аккумулятор | Аккумулятор | Аккумулятор | Аккумулятор |
Срок службы батареи | Срок службы батареи 5 часов | Срок службы батареи | Срок службы батареи | Срок службы батареи | Срок службы батареи | Срок службы батареи |
Особые возможности | Особые возможности IP67 | Особые возможности | Особые возможности | Особые возможности | Особые возможности | Особые возможности |
Неразрушающий контроль — Ультразвуковой контроль
Что такое ультразвуковой контроль.

Ультразвуковой неразрушающий контроль, также известный как ультразвуковой неразрушающий контроль или просто УЗ, представляет собой метод определения толщины или внутренней структуры испытуемого образца с помощью высокочастотных звуковых волн. Частоты или высота тона, используемые для ультразвукового контроля, во много раз превышают предел человеческого слуха, чаще всего в диапазоне от 500 кГц до 20 МГц.
Какие материалы можно тестировать ..
В промышленных приложениях ультразвуковой контроль широко используется для металлов, пластмасс, композитов и керамики.Единственными распространенными инженерными материалами, которые не подходят для ультразвукового контроля с помощью обычного оборудования, являются изделия из дерева и бумаги. Ультразвуковая технология также широко используется в биомедицине для диагностической визуализации и медицинских исследований.
Принцип ультразвукового контроля.
LEFT .. Зонд посылает звуковую волну в исследуемый материал. Есть два показания, одно от начального импульса зонда, а второе от эхо-сигнала от задней стенки.
ВПРАВО .. Дефект создает третью индикацию и одновременно снижает амплитуду индикации задней стенки.
Как это работает ..
Высокочастотные звуковые волны очень направленные, и они будут проходить через среду (например, кусок стали или пластика) до тех пор, пока не встретят границу с другой средой (например, воздухом), после чего они отражаются обратно к своему источнику. Анализируя эти отражения, можно измерить толщину испытательного образца или найти признаки трещин или других скрытых внутренних дефектов.
При ультразвуковом контроле ультразвуковой преобразователь, подключенный к диагностическому аппарату, проходит над проверяемым объектом.Преобразователь обычно отделяется от тестируемого объекта связующим веществом (например, маслом) или водой, как при испытании иммерсией.
Есть два метода приема ультразвуковой волны: отражение и затухание.
В режиме отражения (или эхо-импульса) преобразователь выполняет как отправку, так и прием импульсных волн, поскольку «звук» отражается обратно в устройство. Отраженный ультразвук исходит от поверхности раздела, например, от задней стенки объекта или от дефекта внутри объекта.Диагностическая машина отображает эти результаты в виде сигнала с амплитудой, представляющей интенсивность отражения, и расстояние, представляющее время прибытия отражения.
В режиме ослабления (или сквозной передачи) передатчик посылает ультразвук через одну поверхность, а отдельный приемник определяет количество, которое достигло его на другой поверхности после прохождения через среду. Дефекты или другие условия в пространстве между передатчиком и приемником уменьшают количество передаваемого звука, таким образом обнаруживая их присутствие.Использование связующего увеличивает эффективность процесса за счет снижения потерь энергии ультразвуковой волны из-за разделения между поверхностями.
Контроль труб с помощью ультразвукового дефектоскопа
В чем преимущества ультразвукового контроля .

Ультразвуковой контроль полностью неразрушающий. Образец для испытаний не нужно разрезать, разрезать или подвергать воздействию вредных химикатов. Требуется доступ только к одной стороне, в отличие от измерения с помощью механических инструментов для измерения толщины, таких как штангенциркуль и микрометры.В отличие от рентгенографии, ультразвуковые исследования не представляют потенциальной опасности для здоровья. Когда тест настроен должным образом, результаты будут стабильными и надежными.
Каковы потенциальные ограничения ультразвукового контроля.
Для ультразвуковой дефектоскопии требуется обученный оператор, который может настроить испытание с помощью соответствующих эталонов и правильно интерпретировать результаты. Проверка некоторых сложных геометрических объектов может быть сложной задачей. Ультразвуковые толщиномеры должны быть откалиброваны в соответствии с измеряемым материалом, а для приложений, требующих широкого диапазона измерения толщины или измерения акустически различных материалов, может потребоваться несколько настроек. Ультразвуковые толщиномеры дороже механических.
На строительной площадке техник проверяет сварной шов трубопровода на предмет дефектов с помощью ультразвукового прибора с фазированной решеткой. Сканер, состоящий из рамы с магнитными колесами, удерживает датчик в контакте с трубой с помощью пружины. Влажная зона — это ультразвуковая связка, которая позволяет звуку проходить в стенку трубы.
Ультразвуковой контроль сварных швов
Одной из наиболее полезных характеристик ультразвукового контроля является его способность определять точное положение несплошности в сварном шве.Этот метод тестирования требует высокого уровня подготовки и компетентности оператора и зависит от создания и применения подходящих процедур тестирования. Этот метод тестирования может использоваться для черных и цветных металлов, часто подходит для тестирования более толстых участков, доступных только с одной стороны, и часто может обнаруживать более тонкие линии или более простые дефекты, которые не так легко обнаружить с помощью радиографического тестирования.
Стандарты
Международная организация по стандартизации (ISO)
- ISO 7963, Неразрушающий контроль. Ультразвуковой контроль. Технические условия на калибровочный блок No.2
- ISO / DIS 11666, Неразрушающий контроль сварных швов. Ультразвуковой контроль сварных соединений. Уровни приемки .
- ISO / DIS 17640, Неразрушающий контроль сварных швов. Ультразвуковой контроль сварных соединений
- ISO 22825, Неразрушающий контроль сварных швов. Ультразвуковой контроль. Испытание сварных швов аустенитных сталей и сплавов на никелевой основе
Европейский комитет по стандартизации (CEN)
- EN 583, Неразрушающий контроль — Ультразвуковой контроль
- EN 1330-4, Неразрушающий контроль — Терминология — Часть 4.. Термины, используемые при ультразвуковом контроле
- EN 1712, Неразрушающий контроль сварных швов. Ультразвуковой контроль сварных соединений. Уровни приемки .
- EN 1713, Неразрушающий контроль сварных швов — Ультразвуковой контроль — Определение показаний сварных швов
- EN 1714, Неразрушающий контроль сварных швов — Ультразвуковой контроль сварных соединений
- EN 12223, Неразрушающий контроль — Ультразвуковой контроль — Технические условия на калибровочный блок № 1
- EN 12668-1, Неразрушающий контроль — Характеристики и проверка оборудования для ультразвукового исследования — Часть 1.. Инструменты
- EN 12668-2, Неразрушающий контроль. Определение характеристик и проверка оборудования для ультразвукового исследования. Часть 2. Зонды .
- EN 12668-3, Неразрушающий контроль — Характеристики и проверка оборудования для ультразвукового исследования — Часть 3. Комбинированное оборудование
- EN 12680, Основание — Ультразвуковое исследование
- EN 14127, Неразрушающий контроль — Ультразвуковое измерение толщины

Часто задаваемые вопросы по ультразвуковому тестированию
- Что такое ультразвуковой преобразователь.
.
Преобразователь — это любое устройство, преобразующее одну форму энергии в другую. Ультразвуковой преобразователь преобразует электрическую энергию в механические колебания (звуковые волны), а звуковые волны в электрическую энергию. Как правило, это небольшие портативные сборки, которые бывают самых разных частот и стилей, чтобы удовлетворить специфические потребности тестирования. - Что такое ультразвуковой толщиномер ..
Ультразвуковой толщиномер — это прибор, который генерирует звуковые импульсы в контрольном образце и очень точно измеряет временной интервал до получения эхо-сигнала.Запрограммированный на скорость звука в исследуемом материале, датчик использует эту информацию о скорости звука и измеренный временной интервал для вычисления толщины с помощью простого соотношения [расстояние] равно [скорость], умноженное на [время]. - Насколько точен ультразвуковой толщиномер.
При оптимальных условиях коммерческие ультразвуковые датчики могут достигать точности до +/- 0,001 мм, с точностью +/- 0,025 мм или выше, возможной для большинства распространенных технических материалов.Факторы, влияющие на точность, включают однородность скорости звука в исследуемом материале, степень рассеяния или поглощения звука, состояние поверхности, а также точность и осторожность, с которыми прибор был откалиброван для конкретного применения.
- Кто использует ультразвуковые датчики ..
Основное применение ультразвуковых датчиков — измерение остаточной толщины стенок в корродированных трубах и резервуарах. Измерение может быть выполнено быстро и легко, без необходимости доступа внутрь или необходимости опорожнения трубы или резервуара.Другие важные приложения включают измерение толщины формованных пластиковых бутылок и аналогичных контейнеров, лопаток турбин и других прецизионных обработанных или литых деталей, медицинских трубок малого диаметра, резиновых шин и конвейерных лент, корпусов лодок из стекловолокна и даже контактных линз. - Что такое ультразвуковой дефектоскоп.
Звуковые волны, проходящие через материал, будут предсказуемым образом отражаться от дефектов, таких как трещины и пустоты.Ультразвуковой дефектоскоп — это инструмент, который генерирует и обрабатывает ультразвуковые сигналы для создания отображения формы волны, которое может использоваться обученным оператором для выявления скрытых дефектов в испытательном образце.Оператор идентифицирует характерный образец отражения от хорошей детали, а затем ищет изменения в этом образе отражения, которые могут указывать на дефекты.
- Какие дефекты можно найти с помощью одного ..
С помощью ультразвуковых дефектоскопов можно обнаружить и измерить широкий спектр трещин, пустот, отслоений, включений и подобных проблем, влияющих на структурную целостность. Минимальный размер обнаруживаемого дефекта в данном приложении будет зависеть от типа испытываемого материала и типа рассматриваемого дефекта. - Кто использует ультразвуковые дефектоскопы.
Ультразвуковые дефектоскопы широко используются в критических областях, связанных с безопасностью и качеством, включая сварные швы, стальные балки, поковки, трубопроводы и резервуары, авиационные двигатели и рамы, автомобильные рамы, железнодорожные рельсы , силовые турбины и другое тяжелое оборудование, корпуса судов, отливки и многие другие важные приложения. - Какие другие типы инструментов доступны?
Системы ультразвуковой визуализации используются для создания высокодетализированных изображений, похожих на рентгеновские лучи, отображающих внутреннюю структуру детали с помощью звуковых волн.Технология фазированных решеток, первоначально разработанная для медицинской диагностической визуализации, используется в промышленных условиях для создания изображений поперечного сечения. Крупные системы сканирования используются в авиакосмической промышленности и поставщиками металлообработки для выявления скрытых дефектов как в сырье, так и в готовых деталях. Ультразвуковые генераторы / приемники и анализаторы сигналов используются во множестве приложений исследования материалов.
Ссылки .. www.olympus-ims.com и Welding and Cutting United States
.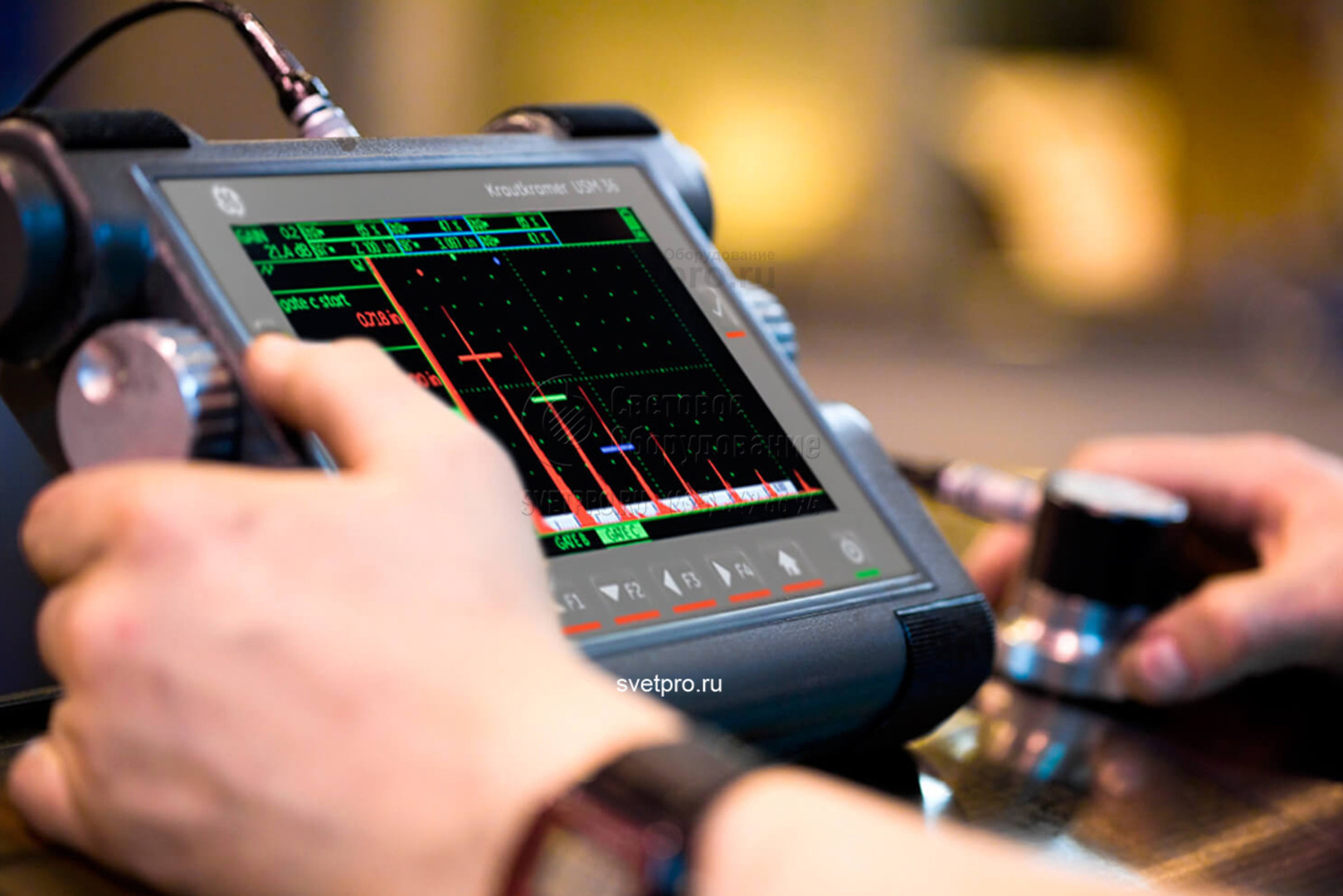