Ультразвуковой контроль в литейной промышленности
Применение
Данная инструкция содержит краткое описание примеров использования ультразвукового неразрушающего контроля в литейной промышленности, включая толщинометрию, дефектоскопию и измерение степени шаровидности в литейном чугуне. ПредпосылкаИскусство литья, придание металлу нужной формы, зародилось много тысяч лет назад, но только в последние десятилетия стали доступны современные ультразвуковые приборы НК для контроля качества конечной продукции. Раньше, для проверки качества литья, нужно было постучать по изделию молотком и оценить тональность звучания. Современные ультразвуковые измерительные приборы со встроенным микропроцессором позволяют видеть внутреннюю структуру литых изделий из сплавов черных и цветных металлов. |
Ультразвуковые толщиномеры могут использоваться для измерения стенок пустотелых отливок.
УЗК широко используется для измерения пустотелых отливок сложной формы, например, блоков автомобильных двигателей. Перекос или смещение стержня в процессе литья может привести к тому, что изделие с одной стороны будет слишком тонким, а с другой – слишком толстым. Ультразвуковой толщиномер может измерять толщину изделия при одностороннем доступе, без необходимости разрезания объекта контроля.
В процессе литья, в металле могут возникнуть пустоты, пористость, включения и трещины. Эти неоднородности вызывают определенные сигналы и показания, и выявляются опытным оператором с помощью ультразвукового дефектоскопа и соответствующих преобразователей.
Размер и распределение графитовых включений (степень шаровидности) имеет большое влияние на механическую прочность литейного чугуна. Измерение степени шаровидности особенно актуально для автомобилестроения и других областей, где чрезвычайно важно обеспечить безопасную эксплуатацию компонентов из чугунного литья. При измерении степени шаровидности графита, ультразвуковой неразрушающий контроль представляет альтернативу микроскопическим исследованиям поперечного среза и методу определения предела прочности при растяжении, поскольку скорость распространения продольных волн зависит от крупности графитовых выделений и их количества.
Ультразвуковое измерение толщины
Толщину стенок можно измерить с помощью толщиномеров Olympus 38DL PLUS® или 45MG с ПО для одноэлементных ПЭП. Если толщина металла превышает 12,7 мм, следует использовать ПО повышенного проникновения. Выбор преобразователя зависит от диапазона измеряемых толщин и акустических характеристик литейного металла.
Процедура контроля
Процедуры настройки и калибровки прибора можно найти в прилагаемом руководстве по эксплуатации. Кроме того, на точность измерения литых изделий могут влиять выбор контактной жидкости, состояние поверхности, форма изделия, калибровка прибора и шум при рассеянии лучей.
Контактная жидкость
Грубые поверхности изделий, отливаемых в песчаные формы, ухудшают качество акустического контакта ПЭП, поэтому рекомендуется использовать контактные жидкости высокой вязкости, такие как гель (контактная жидкость D) или глицерин (контактная жидкость B).
Состояние поверхности объекта контроля
При измерении грубой поверхности минимальная толщина, измеряемая ПЭП, возрастает из-за реверберации ультразвука в более толстом слое контактной жидкости. Эти реверберации должны быть погашены. Аналогичным образом, максимальная толщина измерения уменьшается по причине слабого акустического контакта между преобразователем и поверхностью материала. В большинстве случаев, измерения толщины выполняются на необработанных поверхностях, непосредственно после отливки, но в сложных случаях, подготовка поверхности значительно улучшает показатели.
Геометрия изделия
Внутренние и наружные поверхности литого изделия должны быть параллельны или концентричны для выполнения ультразвукового измерения толщины. Если стенки изделия сильно смещены относительно друг друга, ультразвуковые волны отражаются в противоположную от ПЭП сторону, и ни один эхо-сигнал не отображается на экране.
Калибровка прибора
Ультразвуковое измерение толщины будет точным только в том случае, если скорость распространения звука в материале соответствует калибровке прибора. Скорость распространения ультразвука может колебаться как в черных так и в цветных металлах, в зависимости от твердости и гранулярной структуры материала, а также степени шаровидности графита. В крупных отливках, разные зоны остывают с разной скоростью, скорость звука может меняться внутри одного компонента по причине неравномерной гранулярной структуры. Для достижения оптимальной точности измерений, калибровка скорости звука должна всегда производиться на стандартном образце с известной толщиной и схожими с объектом контроля свойствами.
Шум при рассеянии звука
Крупнозернистая структура некоторых литых металлов производит шум по причине рассеяния звука, перед донным эхо-сигналом. Вследствие помех, вызванных внутренними отражениями, толщиномер может показывать ложные показания, особенно при использовании настроек прибора по умолчанию. Данная ситуация должна немедленно диагностироваться путем анализа А-сканов. Внутренние шумы можно устранить путем выбора низкочастотного преобразователя или настройки усиления прибора и/или игнорирования (см. А-сканы 38DL PLUS на Рис. 1 и Рис. 2).
Рис. ![]() | Рис. 2 — Правильное показание после настройки усиления и кривой TDG (донный эхо-сигнал четко виден на экране). |
Ультразвуковая дефектоскопия
Для контроля литых изделий можно использовать любой дефектоскоп Olympus серии EPOCH® (EPOCH 650, EPOCH 6LT или EPOCH 1000). Для контроля качества литья обычно используются раздельно-совмещенные преобразователи, например, серии DHC, работающие на частоте от 1 до 5 МГц, с целью сокращения отражений от контактной жидкости на грубой поверхности отливок, а также для оптимизации отражений от несплошностей неправильной формы. В некоторых случаях, для выявления трещин можно использовать наклонные преобразователи. В более сложных автоматизированных системах контроля используются иммерсионные преобразователи в аналогичном частотном диапазоне.
Процедура контроля
Гранулированная структура литых изделий из сплавов черных и цветных металлов усложняет ультразвуковой контроль по причине многочисленных отражений от границ зерен (гранул), а также избыточного шума, обусловленного рассеянием (от кристаллической структуры материала).
На Рис. 3 и Рис. 4 представлен обычный тест на пористость, на примере чугунной отливки толщиной 40 мм, с использованием дефектоскопа EPOCH 650 и раздельно-совмещенного преобразователя DHC709-RM (5 МГц, диам. 12,7 мм] . На Рис. 3 изображен донный эхо-сигнал от отливки, в правой части экрана, с незначительными поверхностными помехами и шумом вдоль базовой линии. На Рис. 4 изображен сигнал от дефекта (пустоты), который быстро определяется на фоне шума.
Рис 3 — Бездефектная зона отливки | Рис. 4 — Индикатор пористости |
При контроле качества отливок, дефектоскопы чаще всего используются для выявления пустот, пористости, включений; некоторые пользователи также имеют потребность в выявлении трещин. Процедуры контроля трещин должны быть разработаны с учетом геометрической формы литых изделий, местоположения, размера и ориентации предполагаемых трещин, с использованием соответствующих опорных образцов, имеющих известные, или искусственно нанесенные дефекты. Прямые преобразователи используются в случае, если поверхность трещины параллельна контактной поверхности.
Измерение степени шаровидности
Для измерения степени шаровидности мы рекомендуем использовать толщиномеры 38DL PLUS и 45MG с ПО для одноэлементных ПЭП, которые могут напрямую считывать скорость звука в материале на основе введенных значений толщины. Опции повышенного проникновения толщиномеров 38DL PLUS и 45MG рекомендуется использовать в случае, если толщина металла превышает 12,5 мм. Также можно использовать любой дефектоскоп Olympus серии EPOCH; потребуется калибровка скорости звука в материале. Вся эта информация подробно излагается в прикладном примечании «Измерение степени шаровидности в литейном чугуне».
Контроль отливок — Справочник химика 21
Отливки. В этих изделиях возможно образование усадочных пор, горячих трещин и включений. Если толщина отливки позволяет использовать радиографический метод контроля, то этот метод является предпочтительным [24] после обычного визуального осмотра поверхности и контроля магнитно-порошко-вым или капиллярным методами. Отливки, которые имеют большие толщины, превышающие возможности радиографического метода, можно контролировать ультразвуковым методом, но могут возникнуть трудности, если структура отливки крупнозернистая. Поэтому желательно до контроля подвергать отливки термообработке, чтобы разрушить крупнозернистую структуру. Могут также потребоваться искатели на пониженную частоту (до 0,5 МГц), чтобы компенсировать чрезмерное ослабление ультразвука, но в принципе должна использоваться как можно более высокая частота. Ультразвуковой метод может также являться средством проверки толщины стенки и обнаружения отклонения от размеров из-за перекоса литейной формы во время разливки.
Литьевые машины для переработки полиамидов оснащают регулируемым электрообогревом. Нагревательный цилиндр должен иметь две (лучше три) зоны обогрева, каждая — со своей системой контроля температур. Сопло и форма также должны иметь свои собственные системы контроля температуры. В литьевой форме должны быть предусмотрены каналы для охлаждения отливки с целью сокращения цикла литья. При переработке полиамидов отдельных типов и марок необходимо поддержание очень точного температурного режима в различных частях литьевой машины. Это обязательно оговаривается поставщиками полимеров с указанием допустимого интервала изменения температур и оптимальных режимов переработки. [c.173]
Основные преимущества высокого отношения l/d эффективная пластикация при более низких температурах расплава, увеличение скорости пластикации на 25 , уменьшение цикла формования, весьма незначительное коробление изделий, уменьшение напряжений, создание лучшей гомогенности расплава, лучшее перемешивание цветов, возможность осуществлять более точный контроль отливки, получение однородных тонкостенных изделий. [c.44]
Общими дефектами для слитка и отливки являются неметаллические включения. Они возникают от недостаточной очистки зеркала расплавленного металла от шлака и флюса перед разливкой, плохого отвода их в процессе разливки. К включениям относят также окислы железа и различных металлов, добавляемых в процессе плавки, частицы огнеупорного и формовочного материала, электродов и т. п. Специфическим типом включений являются окисные плены в виде тонких и хрупких прослоек окисленного металла. Они образуются на зеркале и в струе расплавленного металла. Перечисленные дефекты при превышении определенных размеров недопустимы как в отливках, так и в слитке. При обработке давлением они лишь деформируются (расплющиваются, раскатываются), но не устраняются. Неметаллические включения обнаруживают радиационными и ультразвуковыми методами контроля, а плены — ультразвуковыми. В случае выхода на поверхность их обнаруживают методами поверхностной дефектоскопии. [c.25]
Отливки из легированных и высоколегированных сталей подвергаются контролю макро- и микроструктуры по требованию. [c.69]
Отливки для фланцев должны подвергаться контролю ультразвуком или другим равноценным методом по инструкции завода-поставщика. [c.69]
Отливки, подвергающиеся индивидуальному контролю [c.10]
При контроле металлургических процессов пробу расплавленного металла отливают в специальную форму — кокиль. После затвердевания проба обычно подвергается ковке, а затем поступает на анализ. Иногда наблюдается неравномерное распределение отдельных элементов в монолитном образце верх нли низ образца оказывается обогащенным определяемым элементом. Если эту неравномерность нельзя устранить выбором формы кокиля и условий охлаждения при отливке, то в твердом образце срезают слой такой толщины, чтобы обнажить для анализа часть образца со средним содержанием определяемых элементов. [c.245]
III Отливки особо ответственного назначения Отливки для деталей, рассчитываемых на прочность и работающих ири динамических и знакопеременных [1а-грузках а) Наружный осмотр б) контроль размеров в) определение химического состава г) определение механических свойств предела текучести, относительного удлинении и ударной вязкости [c. 86]
Отливки из легированных и коррозионностойких сталей подвергаются контролю макро- и микроструктуры при наличии требований в технических условиях или проектах. [c.125]
Ниже 150°С процесс активированной анионной полимеризации протекает медленно с образованием полимера низкого качества. При более высоких температурах реакция идет быстро с выделением тепла, при этом необходим контроль температуры процесса для получения качественных отливок, не имеющих внутренних напряжений. Некоторые инициаторы характеризуются очень продолжительным индукционным периодом, после окончания которого они вступают в реакцию применение инициаторов, отличающихся коротким индукционным периодом, может вызвать трудности при заполнении формы из-за неполного смешения с мономером и, как следствие этого, из-за неравномерного протекания полимеризации возникает разброс показателей свойств в отливке. [c.200]
Как уже говорилось, в отливке и слитке существуют усадочные раковины, вблизи их поверхности возникает усадочная рыхлота. Распространяясь в глубину слитка, рыхлота образует хвост . Поверхность раковины и рыхлого металла сильно окислена и при дальнейшей обработке давлением этот дефект не заваривается, поэтому часть слитка, содержащую раковину и рыхлоту, удаляют. Количество отрезаемого металла определяют чаще всего на основании имеющегося опыта изготовления подобных слитков. При этом для устранения раковины с запасом обрезают также часть здорового металла. Применение радиационного или ультразвукового контроля позволяет более точно определить местоположение усадочной раковины и избежать удаления излишков металла. Полноту удаления рыхлоты проверяют путем контроля места отрезки -методами поверхностей дефектоскопии (визуальными, магнитопорошковыми, капиллярными, вихретоковыми). [c.24]
Полые отливки, предназначенные для использования в системах, работающих под давлением, например корпуса насосов, задвижек, тройников, контролируют на герметичность. Для этого имеющиеся отверстия заглушают (обычно после их механической обработки) и выполняют контроль методами течеискания. [c.26]
Отливки энергетического оборудования. Методики ультразвукового контроля. ОСТ 108.958.03.83. М. Мин-энергомаш 1983. 80 с. [c.851]
Достаточно эффективное устранение дефектов отливок может быть обеспечено соответствующей технологией. Сюда оТ носятся наряду с металлургическими и литейно-технологическими мероприятиями в первую очередь направленная кристаллизация, на которую можно повлиять выбором количества и-расположения литников, питателей и выпоров, применением холодильников и т. д. И наоборот, зная эти технологические особенности, можно заранее предсказать участки отливки, наиболее опасные по дефектам. Поэтому оператор, основываясь на соответствующих указаниях литейщика, может проводить ультразвуковой контроль в критических местах отливки с ориентацией на дефекты и поэтому наиболее экономично. [c.508]
Литье подразделяют на слитки, предназначенные для дальнейшей обработки давлением, и отливки. Ультразвуковой контроль обнаруживает раковины, поры, инородные включения, заливины, неслитины, плены (см. кн. 1 данной серии). Отливки из сталей перлитного класса, прошедшие термообработку типа нормализации, а также из сплавов алюминия, титана имеют мелкозернистую структуру с достаточно малым рассеянием ультразвука. Отливки из сталей аустенитного класса имеют крупнозернистую структуру, измельчить которую термообработкой нельзя. Такой материал не удается контролировать ультразвуком. [c.202]
Объект контроля — контролируемые поверхности сварного соединения, наплавки основного металла, отливки. [c.571]
При отливках серийного производства, если вообще проводится ультразвуковой контроль, обычно ограничиваются точечным контролем особо критических мест после того как технология литья будет оптимизирована с помощью разрушающих и неразрушающих методов контроля [1356]. Затем детали сортируются только по показаниям ультразвукового контроля. В литературе [1029] показан пример ручного контроля серийных отливок из серого чугуна. [c.514]
Определение истинности индикаций в правильно обработанных деталях сложной структуры. Сложные детали, предназначенные для контроля, могут содержать застывшие капли металла, грубые сварные швы, щели, пазы, поверхности, необработанные после отливки и ковки, неточности сборки или подгонки, фрезерованные пазы и другие неоднородности поверхности. [c.702]
Если отвлечься от ограничивающей приставки ультра , то звук уже давно применяется для испытания материалов грубые внутренние дефекты в поковках и отливках можно легко выявить по измененному звучанию при ударе молотком. Любая домашняя хозяйка знает, что трещину в чашке или тарелке, если она есть, можно выявить по звуку. Известно, что уже сами изобретатели керамики пользовались этим способом контроля. Звуковой контроль поэтому можно считать одним из старейших способов неразрушающего контроля изделий для выявления невидимых дефектов. [c.16]
Такая систематика подхода при оценке дефектов в отливках дала удовлетворительные результаты. Затраты времени несколько сокращаются, если использовать специальные эхо-импульс-ные дефектоскопы, у которых изменение частоты контроля возможно без замены искателя. Для этого излучатель должен возбуждаться с определенными частотами, а искатель и усилитель должны быть достаточно широкополосными (техника С8, контролируемый сигнал). Разумеется, при работе по АРД-диаграмме сравнительный (опорный) эхо-импульс должен измеряться отдельно для каждой частоты. [c.394]
На практике в большинстве случаев можно пренебречь затуханием звука в нелегированных и низколегированных стальных отливках, если контроль проводится на частотах 1 и 2 МГц [386]. Для серого чугуна на рис. 27.8 показана зависимость коэффициента затухания звука в зависимости от частоты (при пластинчатом графите, шаровидном графите и ферритоперлитной структуре). Ввиду различных размеров графитовых включений при разных скоростях охлаждения получается представленная зависимость от толщины стенки. В общем можно -сказать, что для чугуна с пластинчатым графитом при высоких значениях временного сопротивления разрыву контроль вполне возможен благодаря более тонким графитовым включениям. Однако его возможности ограничиваются вследствие рассеяния и затухания на крупных и многочисленных графитовых пластинах. Для таких деталей, например станин станков, стоек и т. п., ультразвуковой контроль обычно и не требуется. [c.515]
Промышленный сектор — это определенная отрасль промышленности или вид техники, где используются специалисты по НК. Промышленный сектор может относиться к объекту контроля ОК) (сварное соединение, отливка и. т.п.) или отрасли промышленности (авиация, нефтехимия). [c.30]
Ультразвуковому контролю следует подвергать стальные отливки после высокотемпературной термической обработки, измельчающей структуру. Частота ультразвуковых колебаний 1. .. 2 МГц. Чувствительность дефектоскопа обычно настраивают по плоскодонным отражателям площадью 7. .. 80 мм . Удовлетворительно контролируются отливки центробежного литья (например, трубы). [c.253]
Поковки и отливки находят применение в аппаратах для изготовления фланцев, трубных решеток, крышек, узлов и деталей внутренних устройств, деталей машин, насосов, дробилок и другого технологического оборудования. Поковки и отливки, как правило, подлежат контролю на отсутствие в них внутренних дефектов. [c.89]
Отбор и подготовка пробы, способ ее введения в источник света. При контроле плавки пробу заливают в специальные изложницы или в коки ли и отливают в них чушки трапецеидальной формы массой до нескольких сотен граммов или стержни диаметром 6—10 мм, длиной в несколько сантиметров. Условия отливки и конструкцию кокиля и изложниц выбирают такими, чтобы определяемые элементы распределялись в пробе равномерно, а ее состав отражал средний состав анализируемого жидкого металла. Физические свойства пробы должны совпадать с физическими свойствами эталонов, поэтому при отборе пробы и ее подготовке к анализу принимают меры к устранению возможного несоответствия между ними. Для этого иногда приходится термически и механически обрабатывать пробу например, закаливать, отковывать и т. п. [c.234]
В химической промышленности для изготовления сосудов, работающих в щелочной среде под давлением не выше 10 кгс/см с температурой стенки от —15 до +300 °С, могут применяться отливки из щелочеустойчивых чугунов СЧЩ-1 и СЧЩ-2 по ОСТ 43-108 Главхиммаша. Из таких отливок изготовляют корпуса, крышки и другие детали аппаратуры, предназначенные для работы с водными растворами МаОН и КОН. Отливки подвергаются поплавочному контролю химического состава и механических свойств. [c.99]
Для ультразвукового контроля особой значение имеют отражательные свойства упоминавшихся/выше типичных дефектов отливок. Если не считать треирш, то все дефекты литья имеют более или менее объемный характер. Поэтому их обнаружение в основном не зависит от направления прозвучивания. Это следует из рис. 27.2, где представлены результаты измерений в районе раковины при контроле отливки из чугуна с шаровидным графитом толщиной 110 мм. Здесь показаны соответствующие максимальные амплитуды эхо-импульсов от дефектов над уровнем помех при прозвучивании из различных направлений прямыми и наклонными искателями. Можно ви-видеть, что амплитуда эхо-импульсов практически не зависит от места ввода ультразвука, от направления прозвучивания типа волны и применяемой частоты. [c.508]
I ОТЛ 1ШКИ обычного наз-начення Отливки для деталей, не рассчитываемых на прочность, конфигурация и размеры которых определяются конструктивными и технологическими соображениями а) Наружный осмотр б) контроль размеров в) определение химического состава по фосфору и сере [c.86]
Таким образом, не учитывая всех факторов, влияющих в каждом конкретном случае на структуру высокопрочного чугуна, можно по результатам ультразвукового контроля сделать неправильные выводы, так как в чугуне со сфероидальной формой графита может оказаться низкая скорость УЗК, такая же, как и в сером чугуне. Поэтому необходимо выполнять предварительные исследования для выявления факторов, влияющих на скорость уль- тразвука в данных отливках и при значительном снижении скорости УЗК, как это бывает, например, в результате термообработки, вводить поправочный коэффициент (табл. 11). [c.90]
Ультразвуковой контроль чугунных валов осложняется значительной неоднородностью структуры, характерной для крупногабаритных отливок из чугуна. Как показывает металлографический анализ, размеры графитных включений в таких отливках могут изменяться от 30—50 до 250—300 мкм, а в некоторых зонах обнаруживаются скопления графита в виде сплошных полей. В связи с этим появляется необхойимость использовать разные частоты ультразвука при контроле отдельных участков одного и того же вала. [c.181]
Некоторые сорта металлов, например кипящую сталь, варят таким образом, чтобы расгворенные в металле газы выделялись не полностью. Это уменьшает размеры усадочной раковины, но приводит к образованию газовой пористости, рассеянной по всему объему литого металла. Поры объединяются иногда в более крупные газовые пузыри. Если поры и газовые пузыри в слитке имеют не-окисленную поверхность, то он заваривается в процессе обработки давлением, В высококачественной отливке поры и пузыри недопустимы, для их обнаружения применяют радиационные методы контроля. [c.24]
В случае, если обнаруженные при УЗ-контроле несплошности превышают нормы, приведенные в табл. 3.5, или при контроле прямым преобразователем донный сигнал ослабляется до уровня фиксации, отливка или ее отдельный участок должны быть подвергнуты радиографи-чемкому контролю и качество их оценивают по результатам этого контроля. [c.392]
Стальные отливки для атомных энергетических установок. Правила контроля. ПНАЭ Г-7-025-90. Госпроматом-надзор, М. 1991. 54 с. [c.853]
Электрические методы НК в настоящее время успешно применяются при решении задач дефектоскопии, толщинометрии, структуроскопии, термометрии объектов, анализа состава вещества. Контролю подвергаются как электропроводящие, так и диэлектрические материалы в твердом, жидком и газообразном агрегатном состоянии. В качестве областей наиболее эффективного использования электрических методов можно выделить обнаружение расслоений в прокатном листовом металле, дефектов в отливках, некачественных спаев, дефектных швов, расслоений в биметаллических пластинах, трещин в металлических изделиях, растрескиваний эмалевых покрытий, трещин в электрических изоляторах, сортировка или идентификация металлических изделий, измерение толщин пленок, проверка химического состава и определение степени термообработки металлических деталей, контроль и диагностика трибосопряжений, контроль влажности материалов, кон- [c. 396]
По соображениям экономии энергии все чаще отказываются от полного охлаждения слитка его отливки, сразу же направляя его на ковку. Поэтому в большинстве случаев отпадает ипромежуточный контроль между отдельными операциями ковкиз и отжига, который при охлаждении слитка можно было бы выполнить по нескольким траекториям на поверхности ввиду обычно очень грубой (крупнозернистой) структуры с применением искателей на частоте 0,5 или 1 МГц [845]. Контрол горячих поковок [1039, 1328] на практике пока еще не нашел применения [1319]. Он затрудняется, в частности, следующими [c.410]
При К-образном шве без дефектов серия эхо-импульсов должна исчезнуть по всей ширине. Дефекты соединения и не-провареиные насквозь участки в середине шва (критические дефекты) располагаются благоприятно для их обнаружения. На практике можно вести контроль уже начиная с толщин листа 10 мм, а с применением совмещенных искателей и при меньшей толщине. Для обнаружения дефектных мест в валике сварного шва, например трещин и шлаковых включений, более эффективным молтолщинах стенки менее 30 мм применяют небольшие наклонные искатели на частоте 4—5 МГц с углами 45—60°. С соответствующим ограничением такой способ контроля возможен и при швах, не проваренных насквозь. При контроле со стороны вертикальной стенки, когда полка недоступна или намного толще стенки или если стенка насажена на сложную поковку или отливку, применение таких искателей является единственно воз-монспособом контроля. Лишь при низких стенках, высота которых не превышает десятикратной толщины листового материала, можно вести контроль также и прямыми искателями со стороны свободной плоской кромки, но при этом охватывается только средняя часть проваренного насквозь шва. [c.552]
Затухание звука в чу гуне с шаровидным графитом в диапазоне частот, используемых для контроля, не зависит от количества и размеров глобулей графита и определяется только характером основной структуры. При ферритных и перлитных структурах, обычно наблюдаемых в отливках, оно мало, а в специальном литье с аустенитной основной структурой оно очень высоко [481, 1196]. [c.603]
Поскольку звуковой луч охватывает сразу несколько соседних зерен, контроль становится невозможным, если требуется обнаруживать мелкие раковины и поры размером примерно в горошину. Поэтому контролировать отливки в песчаные формы, в кокиль и даже непрерывнолитые заготовки невозможно. Только если при центробежном литье удается получить величину зерна примерно на два порядка меньше (считая по среднему диаметру), то литая структура сиова становится хорошо прозрачной для звука и поддается контролю почти так же хорошо, как деформированный материал того же химического состава. Это подтвердили измерения Штегера, Шютце и Майстера [1453] на ряде медных сплавов, [c.609]
Для стальных отливок, необходимые данные для которых» отсутс твуют в государ ственных ил й отраслевых стандартах, те хнйчес ких условиях или «в табл. Г приложения 1, значения предела текучести и временного сопротивления принимают равными 85% значения, приведенного в табл. 1 для одноименной марки катаной или кованой стали, ёслй отливкй подвергаются ШО%-ному ультразвуковому или радиографическому контролю 75% указанных выше значений — для остальных отливок. —— [c.23]
Чугун контролируется хуже, чем стальные отливки. Наибольшую чувствительность удается получить при контроле отбеленного чугуна и чугуна с шаровидным графитом. Значительно хуже контролируется серый чугун, особенно при наличии крупных фафитных включений. [c.253]
Тщательный контроль за содержанием серы в сплавах вызывается вредным влиянием, которое она оказывает на их свойства. Содержание серы в сплаве может повыситься в процессе плавки за счет перехода ее в сплав из флюсов, топлива и печных газов. Сера находится в сплавах в виде сульфидов Мп5, Ре5, СаЗ, А1а5з, Сг8 и др., а также входит в состав органического соединения — сернистого метила (СНз)25. Сернистое железо, растворенное в жидкой стали, при затвердевании сосредоточивается по границам зерен феррита, а это приводит к нарушению связи между зернами железа, что в свою очередь является причиной хрупкости металла в нагретом состоянии. Это свойство называется красноломкостью. Увеличение содержания серы делает металл малоподвижным, плохо заполняющим форму для отливки. Внутри отливок образуются пузырьки и раковины. Сера повышает способность к коррозии, понижает кислотоупорность. [c.287]
Отливки с условным проходом 100 мм и более, предназначенные для работы при t > 630 °С и р >100 кг / м следует подвергать дополнительному контролю просве чиванием рентгеновскими или 7 лучами или дру1 ими равноценными методами. Места, подлежащие просвечиванию, устанавливаются техническими условиями. [c.93]
Ультразвуковые дефектоскопы Sonatest
СЕМЕРЕНКО Алексей Владимирович, Руководитель отдела средств НК и ТД, специалист III уровня по УЗК, ООО «Панатест», Москва.
БОГОМОЛОВ Иван Александрович, Научно-исследовательский университет «Московский энергетический институт», Москва.
Как известно, чугун – это сплав железа с углеродом. Различают белый чугун, в котором углерод входит в химическое соединение с железом (цементит), и чугун, в котором углерод содержится в виде графита различной формы. Последний чаще всего применяется в промышленности, но иногда используется также белый чугун, обладающий повышенной твердостью.
Форма графита, содержащегося в чугуне, оказывает непосредственное влияние на механические свойства отливок. Серый чугун (СЧ) содержит включения графита пластинчатой формы, и он является наименее прочным. Высокопрочный чугун (ВЧ) – наиболее прочный из чугунов, характеризуется шаровидной формой включений графита. Чугун с вермикулярной формой графита (ЧВГ) занимает промежуточное положение по прочности между СЧ и В.
Одной из основных проблем при производстве чугунного литья является идентификация отливок с нестандартной формой графита.
Методы УЗК, широко применяемые в последние годы в сталелитейной и сталеобрабатывающей промышленностях, не подходят для контроля чугунных отливок. Появление чугуна с включениями шаровидного и вермикулярного графита не только расширило масштабы производства и применения чугуна, но и вызвало необходимость совершенствования методов НК. Измерение характеристик и сравнительная оценка однородности формы графита, является одной из перспективных областей применения ультразвука.
Обычно высокопрочный чугун получается путем модифицирования магниевым модификатором высокоуглеродистого чугуна с добавлением графитизаторов перед заливкой в форму или в момент заливки. Если модификатор оказывается неоднородным, или же процесс заливки не был проведен должным образом, образуется литье с отклонениями в содержании шаровидного графита (и, соответственно, с нарушением механических свойств и твердости). Это может выражаться в наличии включений пластинчатого графита в отливке из чугуна с шаровидным графитом, что недопустимо. Из-за этих нарушений значительно изменяются механические свойства металла, что требует контроля чугуна с шаровидным графитом на однородность. При этом важную роль играет как распределение включений графита в отливке (они должны распределяться равномерно), так и форма этих включений (шаровидная, вермикулярная или пластинчатая, рис. 1).
|
Для определения формы графита, содержащегося в чугуне, могут быть использованы стандартные лабораторные разрушающие методы контроля (визуально посредством микроскопа) и косвенные (механические) – проверка на прочность. Однако самые быстрые результаты, к тому же без разрушения объекта контроля, дает ультразвуковой метод.
Форма графита в чугуне оценивается по скорости и затуханию продольных ультразвуковых волн. Установлено, что в чугуне с выпавшим графитом скорость ультразвука увеличивается при:
- Уменьшении содержания графита;
- Уменьшении размеров графитовых включений;
- Изменении их формы от пластинчатой к шаровидной;
- Относительном увеличении количества шаровидных графитовых включений;
- Увеличении содержания перлита, цементита в металлической матрице.
Экспериментально выбираются акустические характеристики, сильнее коррелирующие с исследуемыми параметрами чугуна. С учетом этого информацию о графите (содержание, форма, размер) обычно получают по скорости ультразвука, а информацию о металлической основе (матрице) – по его затуханию.
Так как скорость ультразвука в высокопрочном чугуне с шаровидным графитом и сером чугуне различается, по результатам ее измерения может быть сделан вывод о степени содержания шаровидного графита в контролируемой отливке. Точные значения скорости ультразвука зависят от композиции сплава, его зернистости и других технологических переменных. Значения скорости ультразвука должны всегда проверяться на стандартных образцах из материала объекта контроля. При этом рекомендуется, чтобы для каждого конкретного случая измерения пользователь составлял карту скорости ультразвука в зависимости от процентного содержания шаровидного графита.
Частным случаем применения УЗК является определение наличия включений пластинчатого графита в чугуне с шаровидным графитом. Так как скорость ультразвука в сером чугуне ниже, чем в чугуне с шаровидным графитом, время прохождения ультразвука через отливку, содержащую включения серого чугуна, будет больше, чем через отливку, выполненную полностью из чугуна с шаровидным графитом. Для получения данных о других факторах, влияющих на свойства реальных отливок, всегда рекомендуем пользователю проводить настройку приборов на стандартных образцах из чугуна с известной композицией.
Известно, что скорость ультразвука нелинейно зависит от процентного содержания шаровидного графита, и на нее влияет как процентное содержание графита, так и форма его включений. В любом случае, ожидается, что в двух отливках, идентичных по процентному содержанию графита, скорость ультразвука будет значительно различаться, если одна отливка содержит графит пластинчатой формы (серый чугун), а другая – шаровидный (высокопрочный чугун).
В качестве объекта контроля предоставлен набор образцов из чугуна различного вида. Геометрические размеры образов Ш×В×Г — 58×31×28 мм.
|
Для проведения контроля структуры чугуна был выбран прецизионный ультразвуковой толщиномер Microgage III CDLW, производства Sonatest Ltd, Великобритания.
При проведении контроля в первую очередь проводится калибровка ультразвукового преобразователя для установки задержки сигнала ПЭП.
Далее толщиномер Microgage III устанавливается в режим измерения скорости. После этого устанавливаем преобразователь на объект контроля, предварительно задав толщину образца (Рис.3).
|
В процессе контроля можно изменять следующие параметры: начальное и конечное усиление, развертку, ВРЧ, задержку и затенение, что позволяет увеличить соотношение сигнал/шум.
Важной особенностью толщиномера является возможность ввода значения толщины в процессе измерения.
|
|
Таблица 1. Значения скорости ультразвука в материале.
Структура образцов* |
||||
Номер |
Форма графита |
Перлит, |
Феррит, |
Измеренное значение |
1А1 |
Гф 13 |
20 |
80 |
5330 |
1А1Ф |
Гф 13 |
0 |
100 |
5465 |
1А4Ф |
Гф 4 |
0 |
100 |
4135 |
1А6Ф |
Гф 2 |
0 |
100 |
3913 |
1А6П |
Гф 2 |
78 |
22 |
4046 |
1А6 |
Гф 2 |
6 |
94 |
3984 |
Таблица 2. Химический состав образцов.
Содержание химических элементов (% по массе) |
|||||||||
Номер плавки |
С |
Si |
Mn |
Cr |
Ni |
Al |
P |
S |
Mg |
1А |
2,97 |
3,07 |
0,46 |
0,14 |
0,99 |
1,11 |
0,05 |
0,004 |
0,062 |
Для получения шаровидной формы графита в чугуне использовали Ni-Mg лигатуру. Для получения различной формы графита при температуре 1623°К через каждые 10 минут отбирали пробы чугуна.
* Образцы и сведения о них представлены Воронковой Л.В. (АО «НПО «ЦНИИТМАШ»).
Вывод
Результаты испытаний показали стабильную зависимость значений скорости УЗ от структуры чугуна, что позволяет провести разбраковку отливок на соответствие типу чугуна ультразвуковым методом неразрушающего контроля.
Толщиномер Microgage III зарекомендовал себя как прибор, способный быстро и точно измерить скорость ультразвука в материале. Вес прибора составляет всего 230 г, что не создает проблем для работы с ним в течение всей рабочей смены.
Методы дефектоскопии отливок — Энциклопедия по машиностроению XXL
МЕТОДЫ ДЕФЕКТОСКОПИИ ОТЛИВОК [c.180]Внутренние дефекты отливок выявляются радиографическими или ультразвуковыми методами дефектоскопии. [c.180]
Дефектоскопию отливок можно производить радиационным, УЗ и магнитным методами метод и объем контроля определяется ТУ. Чаще всего, контролируют радиационным или УЗ методом, реже магнитным, или сочетанием указанных методов. При необходимости более точной оценки параметров дефектов в зависимости от состояния поверхности и норм браковки выполняют сплошной УЗ контроль отливок и дополнительное просвечивание дефектных участков или же просвечивание и дополнительно— магнитопорошковый контроль, или УЗ контроль и дополнительно— магнитопорошковый. Контролировать можно как перед механической обработкой, так и после черновой механической обработки.
[c.53]
Магнитный или капиллярный метод контроля отливок можно использовать для поиска поверхностных дефектов или уточнения параметров таких дефектов после УЗ дефектоскопии. [c.54]
Обнаружение течи. Течь — это канал или пористый участок отливки или ее элементов, нарушающий их герметичность. Как правило, малые характерные размеры течей исключают возможность их визуального наблюдения или обнаружения всеми другими методами дефектоскопии, кроме методов проникающих веществ. При течеискании, особенно у крупных отливок, предварительно выявляют факт негерметичности, затем выделяют негерметичный участок (локализация течей), а затем уже выявляют места течей.
[c.499]
Еще большее применение получила ультразвуковая дефектоскопия, надежно вскрывающая дефекты во внутренних слоях крупных поковок и отливок. Этим исключительно чувствительным методом дефектоскопии обнаруживают мельчайшие поры, раковины и неметаллические включения в различных деталях, усталостные трещины в осях и валах и трещины в сварных швах. [c.14]
Внутреннее строение отливок и выявление внутренних пороков (раковин, трещин, неметаллических включений и т. п.) производится при помощи физических методов дефектоскопии, к которым относится магнитная дефектоскопия, рентгеновский анализ, ультразвуковой метод и контроль при помощи радиоактивных веществ. [c.142]
Контроль сплошности осуществляется внешним осмотром отливок (деталей), измерением дефектов измерительными инструментами, любыми из применяемых для этой цели методами дефектоскопии.
[c.221]
Метод цветной дефектоскопии рекомендуется для контроля обработанных резанием поверхностей отливок, полученных точными методами литья, а также зачищенных поверхностей отливок, [c.494]
Основными видами брака литья являются газовые, усадочные, шлаковые и песчаные раковины, рыхлость и пористость недостаточное заполнение литейной формы металлом горячие и холодные трещины и коробление несоответствие микроструктуры, химического состава, механических свойств металла отливок требованиям ГОСТов и технических условий. Перечисленные дефекты отливок выявляются различными методами контроля. Контроль размеров отливок позволяет своевременно предупредить массовый брак из-за износа или коробления модели и стержневых ящиков. Механические свойства и микроструктура контролируются испытаниями и исследованием отдельно изготовленных или отлитых совместно с заготовкой образцов. Внутренние дефекты отливок выявляются методами радиографической или ультразвуковой дефектоскопии. Отливки, которые по условию работы должны выдерживать повыщенное давление жидкости или газа, подвергают гидравлическим или пневматическим испытаниям при давлениях, несколько превышающих рабочее давление.
[c.297]
Внутренние дефекты отливок выявляются методами радиографической и ультразвуковой дефектоскопии. Сущность радиографических методов (рентгеноскопии, гамма-дефектоскопии) заключается в облучении отливок рентгеновскими или гамма-лучами. Благодаря ма- [c.205]
Сущность радиографических методов (рентгеноскопии и гамма-дефектоскопии) состоит в облучении отливок рентгеновскими или гамма-лучами. Обладая малой [c.276]
Области применения методов. Из рассмотренных акустических методов контроля наибольшее практическое применение находит эхо-метод. Около 90 % объектов, контролируемых акустическими методами, проверяют эхо-методом. Применяя различные типы волн, с его помощью решают задачи дефектоскопии поковок, отливок, сварных соединений, многих неметаллических ма-
[c. 213]
Образцы ультразвуковых дефектоскопов с теневым методом приема сигнала. На рис. 3-26,а изображена принципиальная схема дефектоскопа с непрерывным излучением для исследования прокатного металла, отливок и других изделий с приемом по теневому методу. На рис. 3-26,6 изображен его внешний вид. [c.107]
Применение дефектоскопов с теневым методом приема с непрерывным излучением. Описанные ультразвуковые дефектоскопы с теневым методом приема могут применяться для обнаружения дефектов в различных изделиях из самых разнообразных материалов. При их -помощи выявляются расслоения в котельных листах различной толщины без обработки поверхности, контролируется качество чугунных отливок и отливок из мелкозернистой стали выявляются раковины и трещины в прокатанных листах и отливках цветных металлов, таких, как алюминий, дюраль и пр. контролируется качество склейки пластических масс, качество керамических материалов, высокочастотных изоляторов и других фарфоровых изделий, качество резиновых изделий, как, например, автопокрышек всех видов проверяется качество гуммирования аппаратов в химической промышленности (отсутствие расслоений между резиной и металлом) и качество железобетонных изделий в железобетонных конструкциях выявляются пустоты, трещины, в некоторых случаях устанавливается и плотность между арматурой и бетоном.
[c.166]
При пом ощи ультразвуковых дефектоскопов, в том числе и дефектоскопов с приемом по теневому методу, удается при некоторых условиях контролировать качество отливок из серого чугуна, что имеет большое значение в практике машино строения, так как из чугуна изготовляется большое количество деталей машин. Однако при этом встречаются некоторые затруднения из-за значительного рассеивания и поглощения ультразвуковой энергии крупными зернами графита в чугуне. [c.168]
Помимо этого, следует иметь в виду, что из-за крайней неоднородности структуры в отдельных сечениях крупногабаритных отливок из серого чугуна при контроле их ультразвуковым методом могут быть резкие колебания величины эхо-сигналов, видимых на экране индикатора дефектоскопа. [c.179]
Ультразвуковые методы. Ультразвуковой контроль (ультразвуковая дефектоскопия) чугунных отливок основан на регистрации параметров упругих ультразвуковых волн, возникающих или возбуждаемых в отливках. Чаще всего используют упругие волны с частотой 0,5-5 МГц. С помощью этих методов определяют наличие и глубину залегания поверхностных и внутренних дефектов литья. Минимальный размер пространственного дефекта, обнаруживаемого ультразвуковым методом, составляет 3-4 мм. Максимальная толщина стенки отливок, на которой можно проводить ультразвуковую дефектоскопию, определяется разной степенью затухания продольных ультразвуковых волн в зависимости от структуры металла отливки (формы графита, типа металлической основы, размера структурных составляющих).
[c.720]
Металлургическими заводами — поставщиками литья, отливки сдаются термически обработанными, с механическими свойствами в соответствии с табл. 19. Прибыли, литники, ли тейные ребра должны быть обрублены. В отливках не допускаются трещины, видимые невооруженным глазом, раковины, пористость, рыхлость и посторонние включения. Выявление дефектов производится методами травления, керосиновой пробы, ультразвуковым дефектоскопом, проникающим излучением. Допустимые дефекты устанавливаются эталонами и техническими условиями. Поверхности отливок должны быть очищены от формовочной земли и окалины. Исправление литейных дефектов на заводе-поставщике допускается путем заварки (пос-
[c.244]
Существуют различные методы радиационной дефектоскопии в зависимости от типа источника ионизирующего излучения. Для контроля качества отливок применяют рентгенодефектоскопию, гамма-дефектоскопию и бетатронную дефектоскопию. [c.211]
Методы, о с н о в а н н ы е на п р и м е н е н и и радиоактивных изотопов, находят все большее применение в машиностроении, так как дают возможность точно и эффективно обнаруживать дефекты не только без разрушения контролируемых объектов, но даже и без контакта с ними. Эти методы используются для дефектоскопии (гамма-дефектоскопия) отливок, деталей и сварных швов, для бесконтактного промера толш,ины листов и лент в процессе обработки, для контроля толщины покрытий, для контроля движения уровня жидкости в закрытых или недоступных сосудах, для контроля движения газов в доменных пёчах и т. д. Приборы — дефектоскопы, толщиномеры, уровнемеры — успешно применяются в различных отраслях народного хозяйства.
[c.313]
Большинству отливок из суперсплавов принадлежит решающая роль в конструкции двигателя. Поэтому средства неразрушающего обнаружения дефектов этих отливок очень важны, затраты на них, включая потери по отбраковке и переработке лома, могут достигать 20 % стоимости отливки. Помимо визуального контроля и проверки размеров наиболее популярны сегодня такие методы инспекции, как фотоавторадиографи-ческая и люминесцентная дефектоскопия. Последние усовершенствования в прямой радиометрической дефектоскопии придали ей чувствительность, фактически не уступающую чувствительности пленочных методов. Инспекция стала экономически выгодной благодаря усовершенствованию средств визуализации (различные выдеокамеры, экраны и другие средства) и использованию компьютерных методов. [c.191]
Все большую поддержку со стороны правительства и промышленности находит автоматизация литья по выплавляемым моделям. Эта деятельность уже привела к улучшению качества и экономических параметров продукпии в части производства изложниц и отливок направленной кристаллизации. Близки к реальности полностью автоматизированные вакуумные печи для литья изделий с равноосной структурой, а некоторые функции поддаются программированию на уже действующем оборудовании. Главным тормозом в настоящее время является осуществление точных замеров температуры. Ранее мы уже упоминали, что началом автоматизации литейного производства будет прогресс в автоматизации неразрушающей дефектоскопии. Большой интерес привлекает развитие компьютерного моделирования процессов кристаллизации. Число переменных, оказывающих свое влияние на свойства продукции весьма значительно принимая во внимание это обстоятельство и учитывая существующие допуски, было бы слишком рано предсказывать степень успеха, который ожидает такое моделирование, тем более что большинство изделий из суперсплавов отличается весьма сложной формой, а сведения об их физических свойствах пока что отсутствуют.
Тем не менее. Конструкторам было бы очень полезно иметь возможность для компьютерного проектирования и анализа пробных отливок при сохранении функций по окончательной отладке процесса за существующими технологическими методами.
[c.195]
В большинстве случаев этот метод применяют для определения качества отливок несложной формы. Однако использование для ввода ультразвуковых колебаний специальных искательных головок с контактными поверхностями, выполненными по форме контролируемого участка детали, позволяет применять этот метод и для контроля отливок сложной конфигурации с грубой, шероховатой поверхностью. Особенно эффективен этот метод в условиях эксплуатации литтлх деталей, так как позволяет обнаруживать дефекты (усталостные трещины и др.) на ранних стадиях их образования без разбора узла машины или прибора. Наиболее часто для контроля качества отливок применяют теневой, резонансный и импульсный (эхо-метод) методы ультразвуковой дефектоскопии.
[c. 496]
Отливки, которые по условиям работы должны выдерживать повышенное давление газа или, жидкости, подвергают гидро- и пневмоиспытаниям при рабочих давлениях или несколько превышающих их. Для определения внутренних дефектов отливок используют методы радиографической и ультразвуковой дефектоскопии. [c.276]
В качестве неразрушающих методов контроля используются рентгенопросве-чивание, магнитопорошковая дефектоскопия и травление поверхности отливок. Объемы контроля и размеры браковочных дефектов указаны в приложениях к ОСТ 108.961.03-79. [c.106]
Следует иметь в виду, что при однощуповой схеме (рис. IX.26) у поверхности отливки наблюдаются мертвые зоны , где дефекты не выявляются в связи со слиянием импульса от дефекта с зондирующим или донным импульсом. При двухщуповой схеме такие зоны существенно уменьшаются. При теневых методах контроля мертвых зон нет однако они не дают координат глубины залегания дефектов. При всем этом следует еще учитывать, что ультразвуковым методом можно производить замеры толщин стенок отливок, имеющих односторонний доступ. Для контроля отлнвок можно рекомендовать дефектоскопы УДМ-ЗМ, ДУК-5В, ДУК-6В, ДУК-8 и толщиномеры ТУК-3, ТУК-4В, выпускаемые кишиневским заводом еЭлектроточприбор .
[c.693]
Основными методами неразрушающего контроля являются ультразвуковая дефектоскопия и просвечивание. Объем их применения обусловливается техническими уатовиямн турбинных заводов. Для сварных соединений отливок и узлов из аустенитных сталей основное применение нашло просвечивание в связи с трудностями расшифровки в этих случаях сигналов ультразвукового дефектоскопа. [c.299]
Для изготовления многих изделий в машиностроении часто применяют аустенитную сталь, имеющую круинозернистую (дендритную) структуру. Попытки контролировать качество отливок из такой стали при помощи ультразвуковых дефектоскопов с теневым методом приема не привели к положительным результатам ультразвуковые колебания даже на частотах менее 300 кгц сильно поглощаются и раосеиваются крупными зернами аусте-нита. Для контроля качества таких отливок приходится применять низкие частоты. Но при этом становится возможным выявлять только очень крупные дефекты. По этой причине до сих пор при помощи теневых методов не удается производить контроль качества паровой арматуры высокого давления на электростанциях, изготовляемой из аустенитной стали, хотя необходимость его контооля чрезвычайно большая
[c.170]
При ультразвуковой дефектоскопии чугунных отливок в больщинстве случаев используют эхо-метод (регистрация отраженного от дефекта сигнала) для определения дефектов типа газовых раковин, трещин и др)тих несплошностей метмла, а также зеркальнотеневой метод (регистрация степени ослабления дефектом звуковой энергии отраженного сигнала) для определения дефектов типа мелких пор, шлаковых и других включений. [c.720]
Контроль структуры (формы графита, толпщны отбеленного слоя, типа металлической основы) ультразвуковым методом наиболее эффективен для больших партий однотипных отливок в серийном производстве. Для осуществления такого контроля используют стандартные перечисленные дефектоскопы или толщиномеры УТ-93П, УТ-55БЭ (г. Кишинев), ОМ2 (Германия), 26МО (США). По мере накопления опыта и уточнения зависимостей в будущем ультразвуковой контроль структуры чугуна составит достойную конкуренцию традиционному металлографическому методу.
[c.723]
InSpect inspection system for electronics, castings and other parts
Система InSpect прекрасно подходит для задач лабораторий, ВУЗов, стоматологий, проведения криминалистической экспертизы, также может применяться в промышленности для контроля электроники, отливок и других изделий. Система поставляется в различных конфигурациях в зависимости от задачи Заказчика. Для того, чтобы обеспечить быстрое и легкое размещение деталей, InSpect имеет несколько направляющих на разной высоте. Специальная полка сделана из радиографически прозрачного материала. Подробнее.
В зависимости от требуемого коэффициента увеличения полка может быть установлена на разной высоте. Это позволяет оператору быстро изменять геометрическое увеличение. Более высокое увеличение приводит не только к уменьшению поля зрения, но и к повышению четкости изображения. Специальные ложементы для деталей могут быть сконструированы по требованию Заказчика. Специальная конструкция шкафа позволяет контролировать различные детали в одной системе.
InSpect оснащен сенсорной панелью высокого разрешения для быстрой и интуитивно понятной работы. Все основные функции системы, такие как напряжение, ток и время экспозиции, могут быть установлены в течение нескольких секунд. Часто используемые параметры могут быть легко сохранены. В зависимости от задачи, InSpect может быть укомплектована как минифокусной, так и микрофокусной трубкой. Правильная комплектация подбирается на основании исследования деталей Заказчика.
Дополнительные возможности. Если система будет встроена в производственную линию Заказчика, VisiConsult предлагает модификацию для автоматической загрузки. Конвейерная лента проходит через InSpect, и система выполняет автоматическое распознавание дефектов изделия (модуль ADR). Такие сиcтемы всегда адаптируются под требования конечного пользователя.
Ультразвуковой метод неразрушающего контроля в Екатеринбурге
Ультразвуковой контроль качества сварных соединений трубопровода (УЗК) и других строительных и промышленных конструкций на объектах в городе Екатеринбург проводят после выполнения визуального контроля и устранения, выявленных после такой проверки дефектов. Поверхность готовят – протирают ветошью и смазывают специальной контактной смазкой. Для этого используют минеральные масла. Поиск дефектов осуществляют перемещением щупа в околошовной зоне. Для этого выполняют продольно-поперечные перемещения и поворотные вокруг своей оси с шагом, который не должен превышать половины размера пьезоэлемента. При появлении на экране дефектоскопа эхо-сигналов от дефектов выполняют измерение необходимых характеристик:
- координат нахождения;
- амплитуды;
- условной высоты и протяженности;
- коэффициента формы;
- количество дефектов на стандартном участке сварного шва.
Полученные результаты вносят в карту контроля и сравнивают с действующей нормативно-технической документацией.
Методика ультразвукового контроля толщины металла, радиографического ультразвукового контроль прочности бетона и сварных соединений разрабатывается для каждого конкретного случаях и должна выполняться предприятиями-изготовителями.
Сварные швы, выполненные из сталей углеродистых и низколегированных толщиной до 15 мм, просвечиваются преобразователями с большим углом наклона призмы или наклонного типа. Швы толщиной от 16 до 30 мм контролируют приборами, имеющими один преобразователь за один проход прямым и однократно отраженным лучом. При этом рекомендуется отдельно проверять прямые участки и корневые.
В некоторых случаях, прежде чем осуществлять контроль ультразвуком, необходимо шов обработать шлифовальным инструментом (листовые конструкции, соединенные односторонним швом).
Металл, толщиной от 30 до 200 мм, который выполнен односторонней сваркой с подваркой корня или двухсторонней сваркой, контролируют наклонными преобразователями на определенной частоте (1,8; 2,5 МГц).
Металл толщиной свыше 200 мм контролируют, понижая частоту до1, 25 МГц и ниже.
Самыми опасными дефектами считаются трещины и непровары. Они возникают в вертикальной плоскости. И тут необходимо применить метод контроля тандем (эхо-зеркальный).
При контроле сварных точек тоже используют ультразвуковой метод. Их контролируют зеркально-теневым методом. Лучше всего этот вид контроля осуществлять в процессе сварки.
Наша лаборатория предлагает услуги проведения УЗК контроля в городе Екатеринбург и по всей территории РФ с выдачей заключения ультразвукового контроля по установленной форме. Компания ООО «НДТ-контроль» имеет свидетельство о регистрации согласно требованиям ПБ 03-372-00 в территориальном Управлении Ростехнадзора РФ и специалистов , которые имеют необходимые допуски, аттестованы в соответствии с Правилами, действующими в области неразрушающего контроля и опыт работы. Цена на проведение ультразвукового контроля формируется в зависимости от фронта работ, которые необходимо выполнить. Она обязательно согласуется с Заказчиком. Оборудование и приборы от лучших производителей и имеют отметку о поверке. Качество выполненных работ гарантируем.
8. Контроль качества и исправление дефектов отливок. Литье по выплавляемым моделям
Похожие главы из других работ:
Вакуумно-пленочный процесс
2.2 Контроль затвердевания отливок
Анализ дефектов ранее изготовленных отливок трака показал, что при затвердевании в теле отливки трака во внутренних секциях имела место усадка и пористость…
Дефекты при выполнении сварки
3. Исправление дефектов
Каждый производственный процесс предполагает определённые отклонения от требований технических норм. Если такие отклонения выходят за пределы установленных допусков для конкретного изделия — это брак, дефект, который должен быть устранён…
Исследование факторов, влияющих на качество холоднокатаного листа для автомобильной промышленности в условиях ЛПЦ-5
7.

Таблица 5 Контрольный листок регистрационных данных…
Литейные свойства сплавов. Прокатный стан. Физические основы сварки
1. Основные литейные свойства сплавов и пути получения отливок без дефектов
Получение качественных отливок без раковин, трещин и других дефектов зависит от литейных свойств сплавов, которые проявляются при заполнении формы, кристаллизации и охлаждении отливок в форме…
Проект реконструкции участка литейного цеха литья под давлением ФГУП «НПЦ АП» – филиал «Сосенский приборостроительный завод» с годовой программой 160 тонн отливок в год
3.2.5 Исправление дефектов отливки
При изготовлении отливок в них возникают различные дефекты, характер и размеры которых зависят от применяемого сплава, способа литья и особенностей приянтого технологического процесса…
Проект цеха точного литья производительностью 500 тонн в год
1.

Исправлять дефекты целесообразно если затраты на исправление забракованной отливки меньше стоимость её изготовления вновь. Наружные раковины могут быть заварены. Заварку следует производить методом электросварки…
Проектирование работ по техническому обслуживанию и ремонту подъемно–транспортного оборудования предприятия
8.6. Контроль качества и устранение дефектов
Контроль качества сварных конструкций должен осуществляться систематически в течение всего производственного цикла, на всех этапах ремонта и изготовления. Предъявляемые к проверке сварные конструкций не должны быть окрашены и зашпаклеваны…
Работа компрессорного завода ОАО «Казанькомпрессормаш
5.11 Контроль годности отливок и их хранение
Различают следующие виды контроля: визуальный, разметка, взвешивание, цветная дефектоскопия, налив керосином, пневмо- и гидроиспытания. Для контроля чугуна производят экспресс-анализ по химическому составу. ..
Разработка технологического процесса ремонта цилиндрической крышки дизеля ПД-1М
Контроль состояния выпускного клапана и методы устранения дефектов
Дефект — трещины Технологический процесс контроля деталей магнитным дефектоскопом состоит из следующих операций: измерения сопротивления изоляции токоведущих частей дефектоскопа и проверки надежности заземления его металлических…
Совершенствование технологии сварки корпуса механизма компенсации морской буровой установки
8. Контроль качества материалов и качества изгтовления изделия
Контроль качества основных, расходных материалов и контроль производственного процесса являются важными составляющей для получения в конечном итоге качественной продукции. Приём материалов, контроль и маркировка…
Технологический процесс изготовления отливки «Кронштейн» на ОАО «МК ОРМЕТО ЮУМЗ»
8. Методы контроля качества отливок
Контроль отливок начинают с внешнего осмотра в два приёма: предварительно до очистки и отжига, а затем после окончательной очистки Геометрические размеры отливок контролируют с помощью шаблонов. ..
Технологический процесс производства катаных помольных шаров
7. Контроль качества. Анализ дефектов термической обработки
…
Технология изготовления детали «Корпус»
4.6 Заливка форм, выбивка, очистка и контроль качества отливок
Заливку форм производят сразу после прокалки — в горячие формы, что способствует улучшению структуры отливок. Затем формы охлаждают до температуры выбивки 300..400 оС. Продолжительность выдержки отливки в форме определим по формуле: , (4…
Технология изготовления отливки «Кокиль» способом литья в песчаную форму в условиях массового производства
12.6 Дефекты отливок и технический контроль качества
Дефекты отливок подразделяют на 5 больших групп по ГОСТ 19200-80 [4]: дефекты поверхности, несоответствие по геометрии, несплошности в теле отливки, включения и несоответствие по структуре…
Технология изготовления отливки «корпус цапфы»
14.
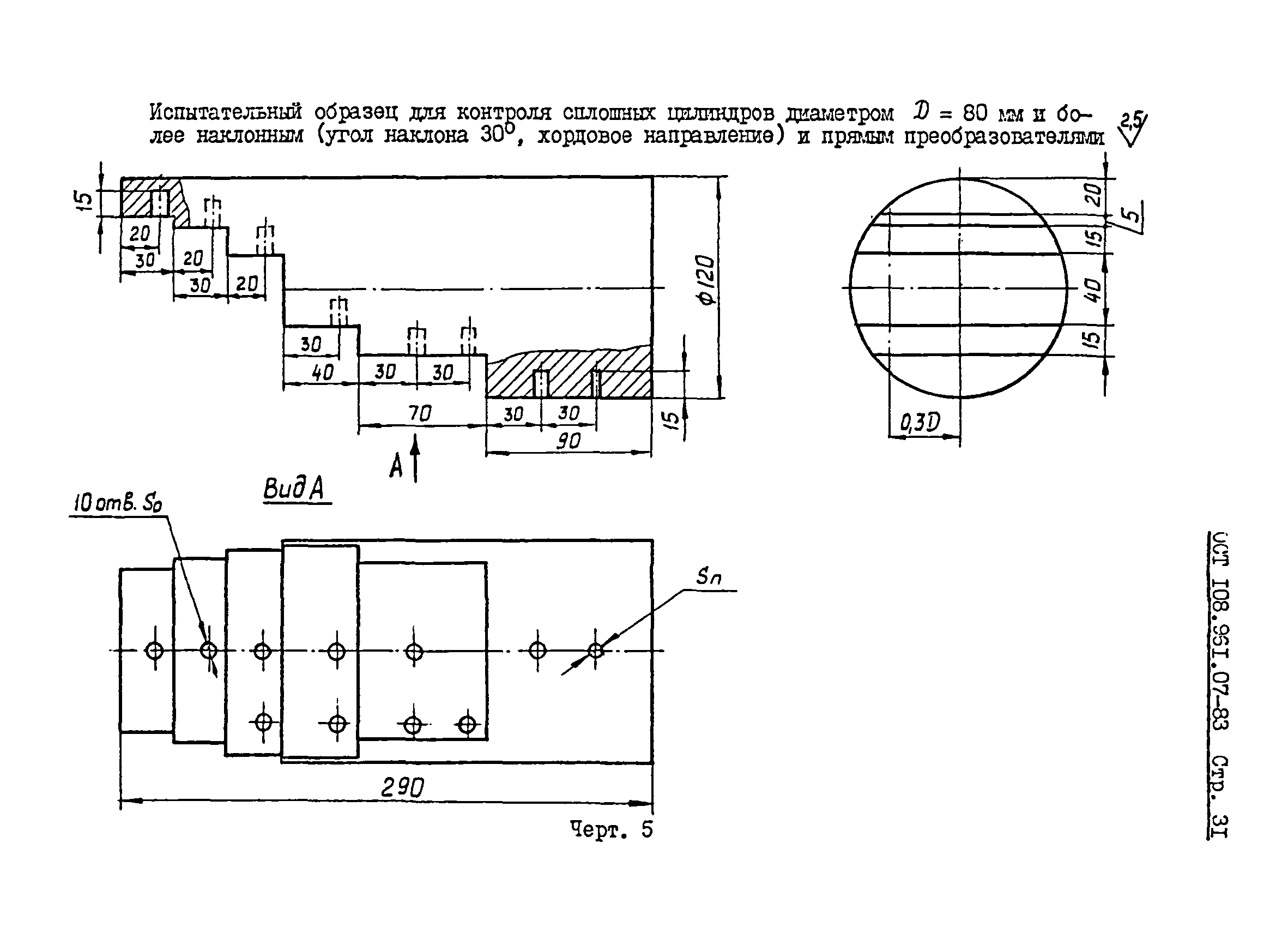
В повышение качества отливок ведущая роль принадлежит контролю, с помощью которого устраняется опасность попадания дефектных отливок на операции механической обработки и сборки…
Ультразвуковой контроль в литейном производстве
Применение
Настоящие указания по применению содержат общий обзор применения ультразвукового неразрушающего контроля в литейной промышленности, включая толщинометрию, дефектоскопию и контроль на шаровидность. Задний план Искусство литья металла в определенные формы практикуется на протяжении тысячелетий, но только в последние десятилетия стали доступны современные ультразвуковые инструменты неразрушающего контроля, помогающие гарантировать целостность продукта.В прошлом литейщик оценивал качество отливки, постукивая по ней молотком, чтобы оценить звук кольца. |
Ультразвуковые толщиномеры могут использоваться для измерения размеров стенок полых отливок. Ультразвуковые дефектоскопы также можно использовать для выявления несплошностей, таких как скрытая пористость, включения, пустоты и трещины.Ультразвуковой контроль на основе скорости с использованием толщиномеров или дефектоскопов также можно использовать для количественного определения сфероидальности графита в чугуне.
Ультразвуковой толщиномер обычно используется для измерения полых отливок сложной формы, таких как блоки автомобильных двигателей. Смещение сердечника в процессе литья может привести к тому, что деталь окажется слишком тонкой с одной стороны и слишком толстой с другой. Ультразвуковой толщиномер может измерять толщину стенки с одной стороны, при этом нет необходимости резать деталь для доступа.
Пустоты, пористость, включения и трещины в металле могут возникать в процессе литья. Эти условия создают ультразвуковые признаки, которые может идентифицировать обученный оператор с помощью ультразвукового дефектоскопа с соответствующими преобразователями.
Размер и распределение включений графита (шаровидность) оказывают большое влияние на механическую прочность чугуна. Проверка на наличие узлов особенно важна в автомобильной промышленности и других областях, где безопасная эксплуатация компонентов из чугуна имеет первостепенное значение.Ультразвуковые методы предлагают неразрушающую альтернативу микроскопическому исследованию поперечного сечения и испытаниям на прочность на растяжение для определения степени узловатости, поскольку узловатость можно коррелировать со скоростью звука.
Ультразвуковой толщиномер
Измерения толщины стенок можно проводить с помощью толщиномеров Olympus 38DL PLUS ® или 45MG с программным обеспечением для отдельных элементов. Если толщина металла превышает приблизительно 12,7 мм (0,5 дюйма), следует использовать программное обеспечение с высокой проникающей способностью.Выбор преобразователя зависит от диапазона измеряемых толщин и акустических свойств конкретного литого металла. Чаще всего используются датчики M106, M1036 (оба 2,25 МГц), M109 и M110 (оба 5 МГц). Для отливок толщиной более 50 мм (2 дюймов) часто рекомендуется низкочастотный преобразователь большого диаметра, такой как 500 кГц M101.
Процедура
Подробные инструкции по установке и калибровке прибора можно найти в руководстве по эксплуатации каждого прибора.Кроме того, выбор контактной жидкости, состояние поверхности, геометрия отливки, калибровка датчика и шум рассеяния могут повлиять на точность измерения отливок.
Контактное вещество
Шероховатая поверхность, обычно встречающаяся на отливках в песчаные формы, ухудшает сцепление преобразователя, поэтому всегда следует использовать контактное вещество с высокой вязкостью, такое как гель (Связующее вещество D) или глицерин (Связующее вещество B).
Состояние поверхности
Когда поверхность соединения очень шероховатая, минимальная толщина, которую можно измерить с помощью данного преобразователя, увеличивается из-за реверберации звука в слое контактной жидкости.Эти реверберации должны быть заглушены. Точно так же максимальная измеряемая толщина уменьшается из-за неэффективной звуковой связи между преобразователем и отливкой. В большинстве случаев измерения толщины могут быть выполнены на отлитых поверхностях, но в сложных случаях подготовка поверхности повышает производительность.
Геометрия
Внутренние и внешние поверхности отливки должны быть приблизительно параллельны или концентричны, чтобы можно было проводить ультразвуковой контроль. Когда стены сильно смещены относительно друг друга, звуковые волны отражаются от преобразователя, и на экране не отображается эхо.
Калибровка прибора
Любое ультразвуковое измерение толщины будет точным только в той степени, в которой скорость звука в материале соответствует калибровке прибора. Скорость звука может различаться как в черном, так и в цветном чугуне из-за изменений твердости и структуры зерна, а также изменений в зернистости графита. В больших отливках, где разные участки охлаждаются с разной скоростью, скорость может изменяться в пределах одной детали из-за неравномерной структуры зерен. Для достижения оптимальной точности измерения калибровку скорости всегда следует выполнять на эталонном эталоне известной толщины, который имеет металлургическое сходство с испытуемыми деталями.
Шум рассеяния
Крупнозернистая структура некоторых литых металлов создает внутренний шум рассеяния, предшествующий отражению от задней стенки. Шум рассеяния может привести к зависанию программного обеспечения толщиномера при ложных показаниях, особенно при использовании настроек толщиномера по умолчанию, а не пользовательских настроек. Это состояние можно легко диагностировать, наблюдая за формой волны. Шум внутреннего рассеяния обычно можно устранить, переключившись на датчик с более низкой частотой или просто отрегулировав усиление и/или гашение прибора (см. осциллограммы 38DL PLUS на Рисунке 1 и Рисунке 2).
Рис. 1. Шум рассеяния, приводящий к ложным показаниям (эхосигнал задней стены справа от дисплея). | Рис. 2. Правильное показание после регулировки усиления и наклона TDG (отчетливо отображается эхосигнал задней стенки). |
Ультразвуковая дефектоскопия
Любой из дефектоскопов Olympus EPOCH ® (EPOCH 650, EPOCH 6LT и EPOCH 1000) можно использовать для контроля отливок.Преобразователи с двойным элементом, такие как серия DHC, с частотами от 1 МГц до 5 МГц, обычно используются при контроле отливок, как для уменьшения отражений от контактной жидкости, захваченной шероховатыми поверхностями отливок, так и для оптимизации отражений от несплошностей неправильной формы. В некоторых случаях для обнаружения трещин могут использоваться преобразователи с наклонным лучом. Специализированные испытательные системы, выполняющие автоматизированное сканирование, будут использовать иммерсионные преобразователи в том же частотном диапазоне.
Процедура
Зернистая природа отливок как из черных, так и из цветных металлов представляет собой проблему для ультразвуковой дефектоскопии из-за отражений, создаваемых границами зерен, при этом уровень шума рассеяния зерен увеличивается по мере увеличения размера зерен.Кроме того, как и при толщинометрии, шероховатая поверхность, обычно присутствующая на отливках в песчаные формы, ухудшает звуковую связь и снижает амплитуду эха. Эти факторы определяют минимальный обнаруживаемый размер дефекта в любом тесте. По этой причине важно уделить особое внимание выбору преобразователя и настройке прибора. Рекомендуемая процедура заключается в оптимизации выбора и настройки преобразователя. Это делается с помощью эталонных образцов, представляющих собой образцы контролируемых деталей, которые содержат известные дефекты, выявленные с помощью разрушающего контроля, радиографии или других неультразвуковых методов. Показания этих известных дефектов затем можно сохранить и сравнить с показаниями испытательных образцов. Полосовая фильтрация, используемая в дефектоскопах EPOCH 650, EPOCH 6LT и EPOCH 1000, очень полезна для снижения шума рассеяния зерен.
На рис. 3 и 4 показан типичный тест на пористость чугунной отливки диаметром 40 мм (1,6 дюйма) с использованием дефектоскопа EPOCH 650 с двойным элементом DHC709-RM (5 МГц, диаметр 12,7 мм [0,5 дюйма]). преобразователь. На Рисунке 3 показан эхо-сигнал задней стенки от отливки с правой стороны экрана, а также типичный низкоуровневый поверхностный шум и зернистый шум вдоль базовой линии.На рис. 4 показан признак пустотного дефекта, который легко различим на фоне фонового шума.
Рисунок 3 – Хорошая зона литья | Рисунок 4 – Индикация пористости |
В то время как наиболее распространенное применение дефектоскопии в отливках связано с пустотами, пористостью и включениями, некоторым пользователям также необходимо проверять наличие трещин или изломов. Испытания на трещины всегда должны разрабатываться с учетом конкретной геометрии отливки, а также местоположения, размера и ориентации предполагаемых трещин.Кроме того, при испытаниях на трещины должны использоваться соответствующие эталонные стандарты, содержащие известные или искусственно созданные дефекты. Преобразователи с прямым лучом используются, когда поверхность трещины параллельна поверхности соединения преобразователя. Угловые балки используются, когда трещина перпендикулярна или наклонена по отношению к поверхности соединения. Обратите внимание, что из-за более низкой скорости звука в чугуне и отливках из цветных металлов фактические углы преломления клиньев, предназначенных для использования на стали, будут ниже. Эти углы должны быть пересчитаны с помощью закона Снеллиуса всякий раз, когда обычные стальные клинья используются на других материалах.
Тестирование на узелковость
Рекомендуемыми приборами для проверки на шаровидность являются толщиномеры 38DL PLUS и 45MG с программным обеспечением для одного элемента, которые могут обеспечить прямое считывание скорости звука на основе введенной толщины детали. Опции программного обеспечения с высокой проникающей способностью для приборов 38DL PLUS и 45MG рекомендуются, если толщина металла превышает примерно 12,5 мм (0,5 дюйма). Также можно использовать любой дефектоскоп Olympus серии EPOCH и получать информацию о скорости путем выполнения процедуры калибровки скорости.Этот важный вопрос подробно обсуждается в Указаниях по применению «Измерение шаровидности в чугуне».
Инспекция: Обеспечение качества отливок | Услуги кастинга
Обнаружение дефектов литья с помощью разрушающего и неразрушающего контроля
Этот неразрушающий контроль качества (NDT) использует ультразвук для проверки внутреннего качества. Каждый шаг в процессе литья металла, от изготовления модели до термообработки, выполняется тщательно, чтобы избежать проблем с прочностью, чистотой поверхности, механическими свойствами и окончательными размерами готовой отливки.Тем не менее, даже отливки, сделанные с усердием, должны проходить проверку на предмет контроля качества. Небольшие проблемы могут возникнуть неожиданно, и многие отливки имеют механические требования, которые могут быть нарушены скрытым дефектом. Инспекция отливок позволяет литейщикам и клиентам быть уверенными в том, что они получают качественное литье.
Методы контроля отливок позволяют выявить любые скрытые дефекты в процессе производства. Некоторые распространенные дефекты литья включают дефекты поверхности, дефекты включения и дефекты охлаждения.
Разрушающие испытания
В каждом производственном цикле литейный цех отбирает несколько образцов и отправляет их на разрушающие испытания. Отливку разрезают и тщательно проверяют свойства металла. Тестер будет искать включения, пористость и усадку. Хотя разрушающее тестирование одной отливки ничего не гарантирует в отношении других отливок в процессе, оно дает представление об общем качестве процесса. Радиографические и ультразвуковые технологии уменьшили важность разрушающего контроля, но они по-прежнему используются для проверки качества и оценки партии.
Неразрушающий контроль (НК)
Неразрушающий контроль проводится литейщиками, клиентами и специалистами по неразрушающему контролю для проверки внутренней и внешней прочности отливки без повреждения самой отливки.
Визуальный осмотр
Этот метод использует человеческий глаз для выявления поверхностных дефектов, трещин, выделения газа, включений шлака или песка, несоответствий, холодных затворов и дефектов литья.
Координатно-измерительная машина (КИМ).Проверка размеров
Этот тип проверки отливок проводится для обеспечения того, чтобы деталь соответствовала размерным требованиям/допускам.Это можно сделать вручную или с помощью координатно-измерительной машины (КИМ), которая использует датчики для получения очень точных измерений.
Контроль проникающей жидкости (LPI)
LPI, или дефектоскопия с помощью проникающих жидкостей, представляет собой неразрушающий контроль (НК) для обнаружения трещин в металлических отливках.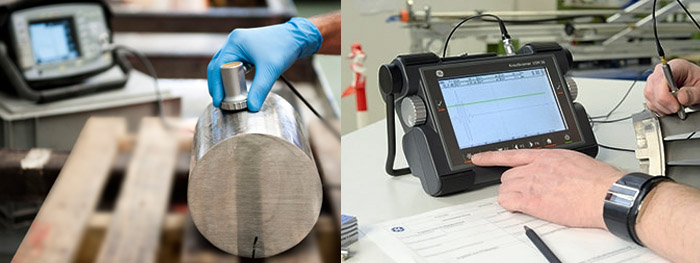
Обнаруживает крошечные трещины, поры и другие дефекты поверхности во всех типах металлических отливок, которые трудно увидеть невооруженным взглядом. Тестер сначала очищает отливку, чтобы удалить любые частицы песка или пыли, которые могут предотвратить попадание жидкого красителя в трещины в металле.
После очистки и высыхания тестер омывает отливку проникающим раствором. В разных типах LPI используются разные растворы, но, как правило, это ярко окрашенное масло с высокой капиллярностью и низкой вязкостью, что означает, что оно будет свободно проникать в трещины в отливке. Этот краситель оставляют на «время выдержки», чтобы он мог проникнуть в любые невидимые щели.
По прошествии времени, достаточного для того, чтобы жидкость сделала свое дело, излишки удаляются с поверхности. Обычно это делается путем осторожного протирания влажной тканью, стараясь не заливать отливку, которая может удалить краску из трещин.
Затем тестер наносит специальный проявитель, и дефекты литья становятся отчетливо видны.
Магнитопорошковая дефектоскопия (MPI)
MPI похож на LPI в том, что он используется для поиска небольших трещин и отверстий на поверхности или неглубокой поверхности отливки. Однако этот процесс можно использовать только для отливок из ферромагнитных металлов, способных создавать магнитное поле, таких металлов, как железо, кобальт, никель и некоторые их сплавы. Отливку намагничивают, обычно с помощью электромагнитов, чтобы начать испытание.
Магнитное поле в металле сильнее, чем в воздухе. Там, где есть дефекты, такие как трещины или отверстия на поверхности или близкой глубине отливки, индуцируемое магнитное поле будет нарушено.
Очень глубокие трещины часто не создают достаточного магнитного искажения на поверхности, чтобы их можно было найти таким образом.
Для обнаружения разрывов отливку опрыскивают пылью или жидкостью, содержащей мелкие частицы оксида железа или другого вещества, реагирующего в магнитном поле.Эти распыленные частицы будут скапливаться вблизи краев искажений, очерчивая места, где магнитный поток низок. Поэтому с помощью магнитов и магнитного порошка можно показать разрывы там, где воздуха больше, чем металла, в любых трещинах или над любыми отверстиями. Метод MPI используется для контроля отливок, а также в полевых условиях для проверки усталости металла уже находящихся в эксплуатации труб и конструкций. Он может обнаруживать растрескивание под напряжением, невидимое невооруженным глазом.
Ультразвуковой контроль (УЗК)
Этот тест выявляет дефекты с использованием высокочастотной акустической энергии, передаваемой в отливку, в технологии, подобной ультразвуку, используемому медицинским персоналом. Звуковые волны проходят через отливку до тех пор, пока не достигнут противоположной поверхности, границы раздела или дефекта. Любой барьер отражает звуковые волны, которые отражаются и записываются для просмотра аналитиком. Характер отклонения энергии может указывать на местонахождение и размер внутреннего дефекта. Этот неразрушающий контроль также можно использовать для проверки толщины стенки и количества конкреций в ковком чугуне.С помощью УЗК можно обнаружить очень маленькие дефекты на очень больших глубинах, что обеспечивает большую точность и уверенность. Опытный техник может даже оценить природу сплава, взглянув на акустическую сигнатуру неизвестного металла.
Ультразвуковой контроль требует знаний и опыта для точной интерпретации результатов. Деталь должна быть очищена от отслоившейся окалины и краски и не должна быть слишком неровной, маленькой или тонкой. В большинстве случаев поверхность, подлежащая ультразвуковому исследованию, должна быть влажной, и часто используется вода: если поверхность будет ржаветь, то вместо нее можно использовать раствор антифриза с ингибиторами ржавчины.
Радиографический контроль (рентген)
Рентгеновские снимки создают изображения, подобные больничным, на которых видны сломанные кости. Призрачные изображения, полученные с помощью рентгеновского литья, показывают темные пятна, где есть полости усадки, небольшие разрывы и щели теплового растрескивания или точечные точки пористости. Эти изображения помогают опытному слесарю определить, ухудшаются ли механические свойства отливки из-за усадки, включений или отверстий, и можно ли их исправить перед отправкой отливок.
В процессе радиографического контроля отливки отливка подвергается облучению рентгеновской трубкой. Отливка поглощает часть излучения, а оставшуюся часть излучения экспонирует рентгенографическая пленка. Более плотные части отливки будут противостоять проникновению излучения, поэтому пленка в этих областях подвергается меньшему воздействию, что придает пленке более светлый вид. Менее плотные части отливки допускают большее проникновение излучения, что приводит к большему облучению пленки.Таким образом, каждое пространство в отливке отбрасывает «тень» на окончательном рентгеновском снимке, вызванную тем, что излучение легче проходит через него, и на рентгеновском снимке любая трещина, пустота или включение отображаются как темная область на пленке.
После того, как литейный завод завершил проверку отливок, проверенная и принятая отливка иногда используется как есть. Обычные неровности поверхности или неоднородности могут не иметь значения для использования в остальном качественного продукта. Иногда отделка может решить наблюдаемые проблемы. Отливка может вернуться к термической обработке или к дальнейшей обработке, которая может включать покраску, антикоррозионные масла, другие виды обработки поверхности, такие как горячее цинкование и механическую обработку.Окончательная подготовка может также включать электроосаждение металлов или порошковое покрытие для косметических или эксплуатационных требований.
Неразрушающий контроль | ИНВЕСТИЦИОННОЕ ЛИТЬЕ
О тестировании литья по выплавляемым моделям
Чтобы обеспечить надежную работу литья по выплавляемым моделям, контроль качества является жизненно важным шагом после производства литья по выплавляемым моделям. Разработано большое количество методов контроля отливок на наличие дефектов, которые могут возникнуть в процессе их изготовления.Такие проверки могут проводиться во время технологических проверок или проверок готовой продукции. Технологические проверки проводятся до того, как все отливки будут завершены, чтобы мы могли принять корректирующие меры для устранения дефекта в оставшихся единицах. Проверка готовой продукции проводится после того, как все отливки по выплавляемым моделям были полностью закончены, что может гарантировать, что наши клиенты получат продукцию высочайшего качества.
Для дефектных отливок мы выборочно предпримем меры по исправлению положения, такие как ремонт сваркой, или полностью откажемся от отливок по выплавляемым моделям для повторного плавления для повторного использования материала в зависимости от степени дефектов.Обычно мы делим методы контроля литья по выплавляемым моделям на разрушающие и неразрушающие испытания в зависимости от степени повреждения, нанесенного отливке во время проверки. Разрушающие методы обычно связаны с распиливанием или отламыванием частей отливок в местах, где легко образуются пустоты или внутренние дефекты. Отливки также могут быть повреждены во время испытаний на прочность.
Неразрушающий контроль
Тем не менее, неразрушающий контроль (НК) является высоко ценимым методом проверки отливок по выплавляемым моделям без повреждения изделий.Все тесты не повлияют на дальнейшее использование продукции. Неразрушающий контроль полезен и полезен для устранения проблем с качеством наших отливок по выплавляемым моделям. Литье CFS сотрудничает с компаниями, занимающимися неразрушающим контролем, в рамках нашего процесса обеспечения качества, что позволяет нам поставлять литые детали высочайшего качества.
Наши возможности неразрушающего контроля включают:- Рентгеновское исследование – разновидность метода испытаний для обнаружения внутренних дефектов отливок по выплавляемым моделям
- Магнитопорошковая дефектоскопия (MPI) — в отличие от рентгенографии используется для проверки внешних дефектов отливок.
- Испытание на твердость — в основном используется для проверки твердости продуктов, особенно для литья по выплавляемым моделям с требованиями к твердости.
- Контроль проникающей жидкости (DPI) — также называемый контролем проникающей жидкости (LPI) или капиллярным контролем (PT), является широко применяемым и недорогим методом контроля, используемым для обнаружения поверхностных дефектов продуктов.
Являясь ведущим поставщиком литья по выплавляемым моделям в Китае, мы можем провести широкий спектр испытаний, чтобы убедиться, что ваши изделия имеют точные размеры и не имеют внутренних и внешних дефектов.Все наши продукты проходят строгие неразрушающие испытания, чтобы работать безопасно и надежно. Наши партнеры – это высококвалифицированные и сертифицированные специалисты. Они обнаруживают любые разрывы, которые могут вызвать проблемы. Для отливок с дефектами при необходимости произведем ремонт сварных швов. Наши услуги по ремонту сварных швов могут помочь снизить процент брака, поддерживать требуемый уровень производительности и, в конечном счете, сэкономить деньги.
Свяжитесь с нами сегодня для получения дополнительной информации о наших услугах по неразрушающему контролю, а также о других дополнительных услугах, вы будете впечатлены нашей специальностью. Просто свяжитесь с нами прямо сейчас!
Ультразвуковой контроль | Ультразвуковой контроль
РЕШЕНИЕ Applus+
Ультразвуковой контроль использует высокочастотную звуковую энергию для проведения исследований и измерений. Ультразвуковой контроль позволяет проверять размеры, толщину, характеристики материала, дефектоскопию и многое другое.
В последнее время в ультразвуковом неразрушающем контроле было достигнуто множество достижений: от применения к обычной толщине до использования более продвинутых методов, охватывающих различные режимы.
В Applus мы сосредоточены на разработке новых приложений и технологий неразрушающего ультразвукового контроля, связанных с ультразвуковым контролем в целом, оставаясь при этом впереди существующих практик и методов контроля неразрушающего контроля.
Компания Appplus+ разработала ряд передовых технологий для следующих ключевых областей применения:
- RTD Vessel Scan: ультразвуковой контроль сварных швов в сосудах под давлением
- RTD RotoScan: ультразвуковой контроль стыковых швов новых труб
- Beetle: для осмотра стенок резервуаров для хранения
- Mapscan: для полуавтоматического картирования коррозии вокруг сложных геометрий
- RTD LNG Scan: для неразрушающего контроля сварных швов крупнозернистых материалов
- Lorus: для проверки коррозии и дефектов в труднодоступных местах, таких как зоны контакта с опорами и осмотр днища резервуара.
- RTD IWEX: инновационная, новая, полнообъемная, прецизионная технология ультразвукового контроля
- EMAT: для скрининга коррозии и измерения толщины через покрытия или при высокой температуре
- PIT: Инструмент для осмотра трубопроводов , , не подлежащий скребку, регулируемый для любых задач
Другие решения для ультразвукового контроля включают, среди прочего, времяпролетную дифракцию (TOFD), ультразвуковые волноводы и ультразвуковые фазированные решетки. Они быстро становятся отраслевым стандартом в современной среде ультразвукового контроля неразрушающего контроля.
В настоящее время у вас недостаточно прав для чтения этого закона
В настоящее время у вас недостаточно прав для чтения этого закона Логотип Public.Resource.OrgЛоготип представляет собой черно-белый рисунок улыбающегося тюленя с усами. Вокруг печати красная круглая полоса с белым шрифтом, на которой в верхней половине написано «The Creat Seal of the Seal of Approval», а в нижней половине «Public.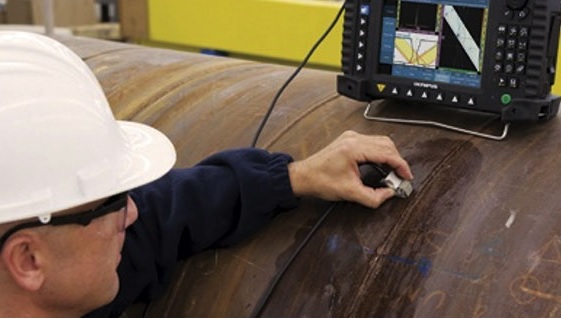
Public.Resource.Org
Хилдсбург, Калифорния, 95448
США
Этот документ в настоящее время недоступен для вас!
Уважаемый земляк:
В настоящее время вам временно отказано в доступе к этому документу.
Public Resource судится за ваше право читать и высказываться в соответствии с законом. Для получения дополнительной информации см. досье этого незавершенного судебного дела:
Американское общество испытаний и материалов (ASTM), Национальная ассоциация противопожарной защиты (NFPA), и Американское общество инженеров по отоплению, охлаждению и кондиционированию воздуха (ASHRAE) v.Public.Resource.Org (общедоступный ресурс), DCD 1:13-cv-01215, Объединенный окружной суд округа Колумбия [1]
Ваш доступ к этому документу, который является законом Соединенных Штатов Америки, был временно отключен, пока мы боремся за
ваше право читать и говорить о законах, по которым мы хотим управлять собой как демократическим обществом.
Чтобы подать заявку на получение лицензии на чтение этого закона, ознакомьтесь со Сводом федеральных правил или применимыми законами и правилами штата. для имени и адреса поставщика.Для получения дополнительной информации о указах правительства и ваших правах как гражданина в соответствии с законом , пожалуйста, прочтите мое свидетельство перед Конгрессом Соединенных Штатов. Более подробную информацию о нашей деятельности вы можете найти на сайте Public Resource. в нашем реестре деятельности 2015 года. [2][3]
Благодарим вас за интерес к чтению закона. Информированные граждане являются фундаментальным требованием для того, чтобы наша демократия работала. Я ценю ваши усилия и приношу извинения за неудобства.
С уважением,
Карл Маламуд
Public.Resource.Org
7 ноября 2015 г.
Примечания
[1] http://www.archive.org/download/gov.uscourts.dcd.161410/gov.uscourts.dcd.161410.docket.html
[2] https://public. resource.org/edicts/
[3] https://public.resource.org/pro.docket.2015.html
Обычные дефекты литья из ковкого чугуна включают некоторые макродефекты, такие как воздушные отверстия, включения песка, шлак включение, усадка или усадочная полость, и некоторые микродефекты, такие как неквалифицированная уровень нодулярности и слишком большой размер зерна и т. д. Методы контроля для пластичных отливки из чугуна включают визуальный осмотр, магнитный порошок тест и ультразвуковой контроль. 1. Визуальный осмотр Визуальный осмотр является самым тяжелым работы, они требуют много шлифовальных работ в сопровождении. Как правило, визуальный осмотр требует соответствия следующим требованиям: а) Без трещин, без сварки, без
включения песка или шлака. При визуальном осмотре трудно различать отверстия для воздуха и отверстия для песка. Отверстия для воздуха обычно имеют гладкие внутренние поверхности и имеют правильную форму, но песчаные отверстия имеют неправильной формы и с остатками грязи или песка внутри.Для отверстия для воздуха, так как они неглубокие, инспектор может измерить их размеры, и проверьте, допустимы ли они, но на остатки песка, большинство из них вызовет более глубокие повреждения отливок, поэтому они должны быть отшлифованы или отремонтированы перед приемкой. Кроме того, инспектор должен проверить пескоструйную обработку. 2. Магнитные частицы (Порошок) Инспекция Магнитопорошковый контроль является своего рода из Неразрушающие испытания . Флуоресцентное магнитопорошковое тестирование подходит для отливок из ковкого чугуна. По нашему опыту, как магнитные чернила для дефектоскопии на водной основе, так и сухие магнитные частица подходит для проверки на ковкий чугун. Поскольку Гладкость поверхности имеет большое влияние на результаты проверки, поэтому вы можете попробовать отшлифовать поверхности, чтобы улучшить осмотр чувствительность.Обычно области литейной головки легко имеют дефекты. 2. Ультразвуковой контроль Ультразвуковой контроль также является проверкой
способ получения отливок из ковкого чугуна. Дом | Другие статьи |
| BS, EN, BS EN и BS ISO | | | | BS EN ISO 10675- 1:2016 Неразрушающий контроль сварных швов.![]() Опубликовано |
Применение | BS ISO 18211:2016 9016 9016 тестирование. Долгосрочная инспекция надземных трубопроводов и установок
трубопроводов с использованием волноводных испытаний с осевым распространением | ISO 18211:2016 Неразрушающий
тестирование. Долгосрочная инспекция надземных трубопроводов и установок
Трубопроводы с использованием тестирования гидна волны с осевым распространением | 8 | ISO / FDIS 19285 Неразрушающее тестирование сварных сварных швов — Техника поэтапных массива (PAUS) — Уровни приема | BS 9690-1:2011 Неразрушающий контроль.Направленное волновое тестирование – общие рекомендации и принципы
Неразрушающий контроль.![]() |
BS EN ISO 16810 :2014 Неразрушающий контроль. Ультразвуковой контроль. Общие принципы | ISO 16810:2012 . Неразрушающий контроль. Ультразвуковой контроль. Ультразвуковое тестирование — Техника передачи | 2 ISO 16823: 2012 Неразрушающее тестирование — Ультразвуковое тестирование — Методика передачи | ||
ISO / TS 16829 Неразрушающее тестирование — автоматическое ультразвуковое тестирование — выбор и применение системы | ||||
ISO 1694 6:2017 Неразрушающий контроль. | ||||
Оборудование и инструменты | BS EN ISO 2400:2012 Ультразвуковой контроль. Спецификация для калибровки. Блок № 1 | ISO 2400:2012 Неразрушающий контроль. Ультразвуковой контроль. Блок № 2 | ISO 7963:2006 Неразрушающий контроль. Ультразвуковой контроль. оборудование для осмотра – Часть 1: Инструменты | |
BS EN 1 2668-2:2010 Неразрушающий контроль. Характеристика и проверка оборудования для ультразвукового контроля. Часть 2. Датчики досмотровое оборудование — Часть 3: Комбинированное оборудование | | |||
CEN / TR 15134: 2005 Неразрушающий контроль — Автоматизированное ультразвуковое исследование — Выбор и применение систем | | |||
| ISO 12710:2002 Неразрушающий контроль.![]() | BS EN 15317:2013 Неразрушающий контроль. Ультразвуковой контроль. Характеристика и проверка ультразвукового оборудования для измерения толщины | ISO 16831:2012 Неразрушающий контроль. | | | ISO 18175: 2004 Неразрушающее тестирование — Оценка производительности Ультразвуковых импульс-эхо-систем тестирования без использования электронных измерительных инструментов |
BS EN ISO 18563-1:2015 Неразрушающий контроль. Характеристика и проверка ультразвукового оборудования с фазированной решеткой.![]() | ISO 18563-3:2015 Неразрушающие тестирование тестирование – Характеристика и проверка ультразвуковых поэтапных оборудование решетки. Часть 3. Комбинированные системы | |||
BS ISO 19675:2017 Неразрушающий контроль. Ультразвуковой контроль. Контроль – Ультразвуковой контроль – Спецификация калибровочного блока для фазированной решетки (PAUT) | ||||
Методы | BS EN ISO 15626:2018 Неразрушающий контроль сварных швов – Метод дифракции во времени ) – Уровни приемки | ISO 15626:2011 Неразрушающий контроль сварных швов. Ультразвуковой контроль – настройка чувствительности и диапазона | ISO 16811:2012 Неразрушающий контроль – ультразвуковой контроль – настройка чувствительности и диапазона 9 0014 | |
BS EN ISO 16826:2014 Неразрушающий контроль.![]() | ISO 16826:2012 Неразрушающий контроль. поверхность | |||
BS EN ISO 16827:2014 Неразрушающий контроль. Ультразвуковой контроль. | ||||
BS EN 14127: 2011 Неразрушающее тестирование — Измерение ультразвуковой толщины | | ISO 16809: 2012 Неразрушительное тестирование — Измерение ультразвуковой толщины | ||
Специальные методы | ISO 4386-1:2012 Подшипники скольжения – Металлические многослойные подшипники скольжения. Часть 1. Неразрушающий ультразвуковой контроль толщины соединения больше или равной 0.5 мм | ISO 4386-1:2012 Подшипники скольжения –
Металлические многослойные подшипники скольжения. Часть 1: Неразрушающий ультразвуковой контроль
испытание толщины соединения более или равной 0,5 мм | ||
BS EN ISO 16828:2014 Неразрушающий – Ультразвуковой контроль – Времяпролетный дифракционный метод как метод обнаружения и определения размера несплошностей | ISO 16828:2012 Неразрушающий контроль –
Ультразвуковой контроль — метод времяпролетной дифракции как метод
для обнаружения и определения размеров несплошностей | |||
BS EN ISO 17405:2014 Неразрушающий контроль.![]() | ||||
BS ISO 10830:2011 Космические системы. Неразрушающий контроль. Автоматический ультразвуковой метод контроля графитовых слитков для твердотопливных ракетных двигателей | . ISO 10830:2011 Космические системы. Неразрушающий контроль. Метод автоматического ультразвукового контроля графитового слитка для твердотопливных двигателей | |||
BS EN ISO 10863:2020 Неразрушающий контроль сварных швов. метод дифракции на лету (TOFD) | ISO 10863:2011 Неразрушающий Контроль сварных швов – Ультразвуковой контроль – Использование метода дифракции на время пролета (TOFD) | |||
BS EN ISO 15626:2013 Неразрушающий контроль сварных швов – Метод дифракции на время пролета (TOFD) – Уровни приемки | ISO 15626:2011 Неразрушающий контроль сварных швов – Метод дифракции на время пролета (TOFD) – Уровни приемки | |||
Неразрушающий контроль сварных швов BS EN ISO 13588:2012 — Ультразвуковые тестирования — использование автоматизированных технологий фазированной массива | | | 2 ISO 13588: 2012 Неразрушающее тестирование сварных швов — Ультразвуковое тестирование — использование технологии автоматизированного фазированного массива | 2 Aerospace | BS EN 4050 -1:2012 Аэрокосмическая серия.![]() | 9 0348
BS EN 4050-2: 2012 Aerospace Series — Тестовый метод для металлических материалов — Ультразвуковая проверка баров, плитов, ковки акций и поковок — Часть 2: Производительность теста | ||||
| ||||
BS EN 4050-4:2012 Авиакосмическая серия. Метод испытаний металлических материалов. Ультразвуковой контроль прутков, плит, поковок и поковок. : Критерии приемлемости | ||||
Железнодорожный транспорт | BS EN 16729-1:2016 Железнодорожное применение – Инфраструктура – Неразрушающий контроль рельсов в пути – Требования к принципам ультразвукового контроля и оценки | |||
Часть 1.![]() | ISO 4992-1:2006 Отливки стальные. Ультразвуковой контроль. Часть 1. Отливки стальные общего назначения | |||
Ультразвуковой контроль. Часть 2. Стальные отливки для высоконагруженных компонентов | ISO 4992-2:2006 Стальное литье. Ультразвуковой контроль. Часть 2. Стальные отливки для высоконагруженных компонентов | |||
2011 * Литье. Ультразвуковой контроль. Часть 3. Отливки из чугуна с шаровидным графитом | ||||
Поковки (f) 9029 3 | BS EN 10228-3: 2016 * Неразрушающее тестирование стальных поковков — часть 3: Ультразвуковое тестирование поковки ферритской или мартенситной стали | |||
| BS EN ISO 17640: 2018 Неразрушительное тестирование | ISO 17640:2010 Неразрушающий контроль сварных швов.![]() | ||
BS EN ISO 21732 Неразрушающий контроль сварных швов. Ультразвуковой контроль. Контроль сварных швов аустенитных сталей и сплавов на основе никеля | ISO 22825:2012 Неразрушающий контроль сварных швов. Ультразвуковой контроль. Контроль сварных швов аустенитных сталей и сплавов на основе никеля. | |||
. | ISO/FDIS 23279 Неразрушающий контроль сварных швов. Ультразвуковой контроль. Характеристика несплошностей в сварных швах. | ISO 11666: 2010 Неразрушающее тестирование сварных швов — Ультразвуковые тестирования — Уровни приема | 2 Трубы и трубы (T) | | BS EN ISO 10893-8: 2011 + A1 2020 Разрушающий контроль стальных труб. Часть 8. Автоматизированный ультразвуковой контроль бесшовных и сварных стальных труб для обнаружения расслоенных дефектов 90 014 | ISO 10893-8:2011 Неразрушающий контроль стальных труб.![]() |
BS EN ISO 10891-9:201 + A1 2020 Неразрушающий контроль стальных труб. Часть 9. Автоматизированный ультразвуковой контроль для обнаружения расслоенных дефектов в полосах/листах, используемых для производства сварных стальных труб | ISO 10893-9:2011 Неразрушающий контроль испытания стальных труб. Часть 9. Автоматизированный ультразвуковой контроль для обнаружения расслоенных дефектов в полосах/листах, используемых для производства сварных стальных труб | |||
разрушающие испытания стальных труб.Автоматизированный полный периферийный ультразвуковой контроль бесшовных и сварных (кроме дуговой сварки под флюсом) стальных труб для обнаружения продольных и/или поперечных дефектов | ISO 10893-10:2011 Неразрушающий контроль стальных труб. Автоматизированный полный периферийный ультразвуковой контроль бесшовных и сварных (кроме дуговой сварки под флюсом) стальных труб для выявления продольных и/или поперечных дефектов | |||
BS EN ISO 10893-11:2011 + A1:2020 Неразрушающий испытания стальных труб.![]() | ||||
BS EN ISO 10893-12:2011 + A1:2020 Неразрушающий контроль стальных труб. Автоматизированный ультразвуковой контроль толщины по всей периферии бесшовных и сварных (кроме дуговой сварки под флюсом) стальных труб сварные (кроме дуговой сварки под флюсом) стальные трубы | ||||
BS ISO 10332:2010* Неразрушающий контроль стальных труб — Автоматизированный ультразвуковой контроль бесшовных и сварных (кроме сваренных под флюсом) стальных труб для проверки гидравлических герметичность | ISO 10332:2010 Неразрушающий контроль стальных труб. Автоматизированный ультразвуковой контроль бесшовных и сварных (кроме сваренных под флюсом) стальных труб для проверки гидравлической герметичности | |||
Кованые изделия (WP) | 28BS EN 10160: 1999 Ультразвуковое тестирование стальной плоский продукт толщины одинаковый или более 6 мм (метод отражения) | |||
BS EN 10306: 2002 Железо и сталь — Ультразвуковой контроль двутавровых балок с параллельными полками и балок из IPE | ||||
BS EN 10307:2001 Неразрушающий контроль – Ультразвуковой контроль плоских изделий из аустенитных и аустенитно-ферритных нержавеющих сталей толщиной равной 6 или более мм (метод отражения) | ||||
BS EN 10308:2002 Неразрушающий контроль – Ultrason IC тестирования стальных прутков | ||||
Терминология | BS EN 1330-4: 2010 Неразрушающий контроль — Терминология — Часть 4: Термины, используемые в УЗК | | ||
BS EN BS EN ISO 5577: 2017 Неразрушительное тестирование — Ультразвуковое тестирование — Словарь | ISO 5577: 2017 ISO 5577: 2017 Неразрушительное тестирование — Ультразвуковое тестирование — Словарь | |||
BS EN 16018: 2011 Неразрушительный тестирование – Терминология – Термины, используемые в ультразвуковом контроле с фазированными решетками |
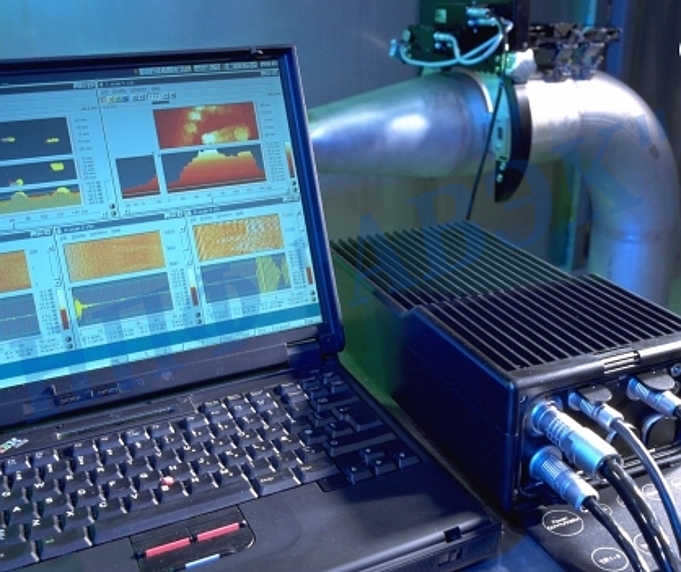