Как плавят металл от А до Я
Как плавят металл и какое место занимает Украина на международной арене
Металлургия является одной из старейших отраслей промышленности в мире. Первые свидетельства о производстве металла были найдены во время раскопок в разных странах Европы и Ближнего Востока. Древние народы сначала использовали только самородки металлов: серебра, меди, олова, и метеоритное железо. Из них производили орудия труда и оружие. Однако началом настоящей металлургии считают время, когда люди научились добывать металлы из горной породы. Тогда из медных и оловянных руд, стопивши два металла, получили первый сплав – бронзу. Железо начали добывать из руды намного позже. Металлургия стала развиваться особенно быстрыми темпами с началом промышленных переворотов XVIII века – вырос объем производства металлов и совершенствовались способы их добычи.
Металлургия состоит из трех взаимосвязанных производств: горнодобывающей промышленности, черной металлургии и цветной металлургии.
В структуре внешнего товарооборота Украины, черная металлургия занимает 1-е место, что составляет около 45% стоимости всего экспорта страны. По объему экспорта стали, Украина занимает 6-е место в мире. Основным способом выплавки чугуна и стали в Украине длительное время был доменно-мартеновский. А с 1956 года, используется прогрессивный кислородно-конвертерный способ выплавки металла. Доля металла, производимого кислородно-конвертерным способом, постоянно растет и в последние годы составляет 70% от всей выплавляемой в мире стали (около 750 млн. т в год).
Предприятия, производящие чугун, сталь и прокат, сосредоточены в трех частях страны: Приднепровье, Приазовье и на Донбассе. Крупнейшие металлургические комбинаты в Украине:
- «Криворожсталь»,
- «Азовсталь» (Мариуполь),
- «Запорожсталь»,
- Днепровский (Днепродзержинск),
- Алчевский,
- Макеевский.
В Приазовье действуют мощные металлургические предприятия Мариуполя, которые дают около 20% продукции черной металлургии страны. Одно из них — «Азовсталь» — самый большой металлургический комбинат Украины. «Азовсталь» является частной собственностью крупнейшей горно-металлургической холдинговой компании «Метинвест», вы можете ознакомиться с продукцией компании здесь www.metinvest-smc.com. Кроме Украины, ее металлургические предприятия работают в странах ЕС и Америке. Металлургические предприятия «Метинвеста» в Украине производят и экспортируют плоский, сортовой и фасонный прокат, трубы для тепловых сетей, и трубы общего назначения. В последние годы для европейских заказчиков освоено производство атмосферостойкого проката, который не подвергается коррозии. Кроме того, выпускается оцинкованный рулонный прокат.
Кислородно-конвертерный процесс – это способ выплавки стали из жидкого чугуна в конвертере с основной футеровкой и продувкой кислородом через водоохлаждаемую фурму. Кислородный конвертер это сосуд грушевидной формы, изготовлен из листа стали и выложенный изнутри огнеупорным кирпичом. Его верхняя часть имеет открытую горловину для введения кислородной фурмы и загрузки шихтовых материалов.
Сущность процесса плавки металла заключается в следующем: исходные материалы (жидкий чугун, стальной лом, известь для наведения шлака) вводятся через горловину конвертера. Стальной лом должен содержать 25-30% от массы чугуна. Чугун в свою очередь, содержит 0,7-1% марганца; 3,7-4,4% углерода; 0,03-0,08% серы; 0,4-0,8% кремния и 0,3% фосфора. Температура чугуна обычно составляет 1400°С. После ввода исходных материалов, внутрь конвертера опускается кислородная фурма и начинает подаваться кислород под давлением 0,9-1,4 МПа.
Источник: metinvest-smc.com
Информация размещена на правах рекламы
Металлургия — как надо плавить металлы, чтобы они выдерживали любые условия
Развитие топливно-энергетической отрасли было бы совершенно невозможно без параллельного развития металлургии. В свою очередь, металлурги мобилизовывали для решения поставленных задач специалистов самых разных отраслей знания. Наша машинная цивилизация стоит на достижениях металлургов: они создали технику, которая не только использует топливные ресурсы, но и позволяет их добыть, транспортировать и переработать.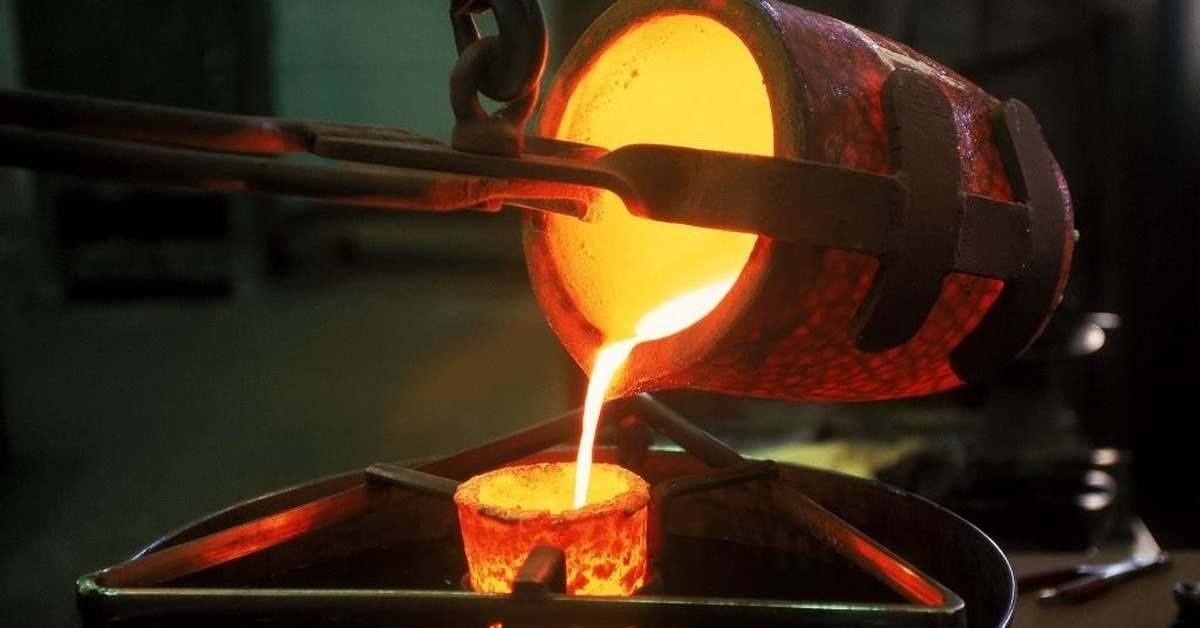
История металлургии, и в первую очередь металлургии железа, уходит в седую древность, когда древних энергетиков перестал удовлетворять каменный топор. Его сменил бронзовый, а потом и железный. Поначалу производство железа было примитивным — его выплавляли даже из болотной руды в примитивных плавильных горнах. Это железо было низкого качества.
И у оружейников, и у производителей инструмента тех времен была одна и та же проблема — изделия из твердого железа были крайне хрупкими и постоянно ломались, а те что, из мягкого, стремительно тупились. Над решением этой задачи колдовали веками лучшие кузнецы и алхимики своего времени. Больше всего расстраивал металлургов побочный продукт плавки — чугун. Этот сплав железа и углерода отличается твердостью, но и исключительной хрупкостью, то есть непригодный для производства чего-либо методом ковки — он просто рассыпался на куски. Его столетиями выбрасывали в отвалы. Но в ХIV веке кто-то вновь загрузил чугун в печь и переплавил его вместе с новой рудой. Это позволило наладить производство стали.
В начале XVIII века стали расти требования к качеству стали. Процесс придания стали различных качеств называется легированием, и он был известен достаточно давно, но был весьма сложным и хлопотным делом. То, что годилось для меча правителя, не годилось для заступов лопат, передаточных колес, шестерен и других изделий. В 1740 году Бенджамин Хантсмен в поисках рецепта стали для изготовления пружин и маятников разработал так называемую тигельную технологию изготовления стали, которая позволяла делать сталь разных свойств.
В первой половине XIX века Якоб Берцелиус и Иоганн Карстен смогли сформулировать представления о влиянии фосфора и серы, а также кислорода на свойства стали. Исследования показали также изменения свойств стали при добавке в ее состав других металлов. Чтобы объективно оценивать свойства различных сплавов, пришлось развивать раздел механики о прочностных свойствах, известный как «сопротивление материалов». Многие ученые отметились на этом поприще, в частности, значительный вклад внес в изучение сплавов известный физик Майкл Фарадей.
Во второй половине XIX века появились не только новые способы получения стали, но и новые потребности. В частности, была нужна сталь, которая использовалась бы для изготовления тех же самых труб, которые стали все шире использоваться в поиске и добыче нефти. Пионером в деле создания такого инструмента стал Робер Мюше, который создал в 1864 году легированную вольфрамом сталь, твердость которой не падала при нагревании, а даже росла. Появились сплавы устойчивые к истиранию, как, например, победит — сплав вольфрама и кобальта, созданный в СССР в 1929 году. Победит уже скоро 100 лет как используется для буровых коронок благодаря своей твердости и стойкости. Режущие элементы из победита используются также в пилах по камню и другом инструменте с особо тяжелыми условиями работы.
Таким образом, к началу ХХ века сформировался целый комплекс научных дисциплин, связанных с созданием новых сплавов с заданными свойствами, обусловленными конкретными нуждами промышленности.
Например, свои требования выдвигает буровая индустрия. Собственно бурильные трубы, обсадные, турбобуры и прочий инструмент должны быть изготовлены из соответствующих сплавов. Особые требования предъявляются и к трубам для магистральных нефте- и газопроводов.
Металлургия — как надо плавить металлы, чтобы они выдерживали любые испытания
Так, если до 50-х годов ХХ века трубы производились из обычной, легированной хромом или марганцем, стали, то уже в следующем десятилетии металлурги предложили трубопрокатчикам другую, более качественную, сталь. Причина была проста — обычная сталь склонна к хрупкому разрушению, которое становится тем более вероятным, чем ниже температура.
Именно поэтому сначала появилась новая кремнемарганцевая сталь, трубы из которой могли выдержать гораздо большее давление. А снижение содержания углерода повысило вязкость этой стали. Совершенствовалась также прокатка металла. Однако новые проекты поставили новые требования — трубы должны были быть еще более устойчивыми к низким температурам, металл должен был быть еще более вязким и прочным.
Сейчас российские производители, в частности Челябинский трубопрокатный завод, выпускают трубы из стали нового поколения. Эти новые сорта стали позволяют поднять рабочее давление и прокладывать трубопроводы в условиях Крайнего Севера и в холодных морях.
Ученые тем временем колдуют над новыми сплавами, которые будут востребованы уже очень скоро, — они потребуются для трубопроводов повышенного давления, поскольку повышение давления — это прямой путь и к повышению экономической эффективности трубопроводов. Буровики требуют новых инструментов — жаро- и хладостойких одновременно, прочных, но легких. Отдельная страница — это разработки металлов для установок нефте- и газохимических предприятий.
Плюс турбины тепловых электростанций, котельные и многое другое — все нуждается в своих металлах и их сплавах, которые надо рассчитать, создать, исследовать и только потом отправлять машиностроителям, которые создадут из них нужную продукцию. Так что то, что может показаться «простой железякой», на самом деле является продуктом серьезных научных исследований, конца-краю которым не видно.
Вконтакте
Одноклассники
Google+
обзор ТОП7 самоделок + еще одна / Хабр
Микроволновые печи…
Они достаточно давно вошли в нашу жизнь и занимают в ней прочное место, благодаря своим уникальным качествам, которые дают возможность любому пользователю быстро и беспроблемно согревать любые продукты, а также производить их готовку.
Однако, многие даже не догадываются, что их обычный бытовой аппарат — способен на гораздо большие «подвиги», чем принято считать. Вот об этом мы и поговорим ниже.
Автор статьи также является многолетним владельцем микроволновой печи, впрочем, как и достаточно большое число людей в России (рискнем сделать такое смелое предположение).
Как и у любой техники, у микроволновой печи существует свой срок эксплуатации, по истечении которого, она выходит из строя или подаёт симптомы к скорому наступлению данного события.
На написание такой статьи автора подтолкнуло то, что его микроволновая печь стала подавать явственные признаки, что конец её близок. В нашем случае, это заключается не в выходе из строя электронной части, а скорее в физическом износе самой камеры нагрева: износилось лакокрасочное покрытие, ввиду чего, есть риск получить пищу, с кусочками краски в её составе (Ммм вкуснотишша! Всё, как мы любим! Sarcasm mode: off).
Справедливо рассудив, что этот ингредиент никоим образом не может улучшить вкус приготовляемых продуктов, а встроенная на уровне прошивки жаба не даёт автору выкинуть микроволновку, — он решил «пуститься во все тяжкие». А именно: посмотреть, а что ещё можно сотворить на базе микроволновки, если её полностью разобрать или же использовать как-то в других целях. Для этого было решено «прошерстить» просторы YouTube, который дал пищу для размышлений относительно того, какую судьбу для микроволновки стоит выбрать…
Следствием данных поисков стал личный хит-парад поделок, среди которых наблюдаются весьма любопытные применения микроволновой печи. Предлагаем вам тоже знакомиться с данными «поделиями».
Сразу оговоримся, что данная подборка не претендует на исключительную полноту и корректность ранжирования. Возможно даже, кто-то может посчитать мнение автора некорректным. Будем рады, если Вы выскажите своё мнение в комментариях к статье.
Автор также предупреждает, что для выполнения всего нижеописанного строго обязательно выполнение техники безопасности. Осуществляя какие-либо эксперименты, описанные в статье, вы делаете это на свой страх и риск,
автор не несёт ответственности за последствия.
▍ Итак, начнем!
Проводя любой поиск на тему самоделок, на основе микроволновки, любой исследователь обязательно натолкнется на такого известного блогера, как
«Креосан». Это имя является нарицательным и широко известно на просторах Рунета. Поэтому он не нуждается в специальном представлении. Мнения относительно его опытов, как правило, достаточно полярны. Однако сейчас мы сосредоточимся не на особенностях рассмотрения субъективных оценок его опытов.
В своё время он провел достаточно любопытный опыт, который поднял широкую волну на просторах интернета. Опыт заключался в том, что магнетрон микроволновки был использован в качестве излучающего устройства, которое позволяло (по утверждениям его автора) создать некую дальнобойную микроволновую пушку. Ввиду запрета на встраивание видео, вы можете его посмотреть по ссылке, на youtube.
Видео вызвало нешуточный вал споров. Вал дошел даже до зарубежного сегмента интернета и ряд блогеров, в частности, известный блогер Allen Pan взялся проверить утверждения, изложенные в ролике выше.
Судя по анализу этого блогера, показанное в рассматриваемом ролике — «не совсем соответствует» реальности :-).
Но автор статьи решил пойти дальше, так как не планировал поджаривать соседей микроволновой пушкой.
Следующее видео, которое заставляет задуматься, это рассказ о том, как на основе трансформатора микроволновки сделать свой сварочный аппарат.
Кстати, если интересно, можно ознакомиться с устройством типичного трансформатора микроволновки:
Хммм уже интересней… Если кратко обобщить изложенную информацию, то переделка трансформатора под сварочный аппарат, как правило, заключается в том, что видоизменяется вторичная обмотка, в целях понижения напряжения и увеличения силы тока.
Однако, ввиду того, что у автора уже есть хороший сварочный аппарат инверторного типа, — такие самоделки его не заинтересовали. Это связано с тем, что современные инверторные сварочные аппараты дают своему пользователю достаточно широкие возможности по регулировке как силы тока, так и обеспечивают его интеллектуальными алгоритмами зажигания дуги. Не говоря уже о том, что физические размеры таких аппаратов весьма скромны и цена их более чем приемлема.
А вот следующая поделка, является достаточно полезной и заинтересует многих: создание аппарата точечной сварки. Для любого домашнего мастера, такой аппарат является весьма полезным, так как позволяет быстро соединять различные детали. Аппарат точечной сварки может быть весьма полезным в разработке собственных блоков питания (пауэрбанков), для чего потребуется быстрая приварка контактных пластин к различным аккумуляторным батареям, в частности, литий-ионным. Батареи такого типа весьма не рекомендуется перегревать, ввиду чего, в заводских сборках широко используется точечная сварка для прикрепления контактов:
Как можно было легко понять из предыдущих опытов, трансформатор микроволновки является достаточно мощным и легко переделывается в целях разнообразных самоделок. Благодаря этому, он является частой основой для создания разнообразных систем питания, таких широко известных и эффектных конструкций, работающих на основе токов высокого напряжения, — как катушка Тесла и лестница Иакова:
Говоря о первой самоделке, — катушке Тесла, можно сказать, что она является весьма частой в изготовлении различными «энтузиастами высокого напряжения». Такая катушка позволяет производить разнообразные интересные опыты, в числе которых широко известный опыт по созданию «поющего» разряда:
Этот опыт широко вышел за пределы разнообразных лабораторий и комнатушек самодельщиков, с применением данного эффекта проводятся даже разнообразные шоу (весьма эффектные, надо сказать):
Если кто заинтересовался этой темой, то по следующему адресу можно найти достаточно
подробное описание по созданию катушек Тесла, с длиной получаемых разрядов
до полутора метров!
И потихоньку, мы начинаем приближаться к самым интересным, на взгляд автора, самоделкам на базе микроволновки, — первой из которых является способ плавления стекла.
Способ выглядит так — предварительно измельченное стекло помещается в специальный теплоизолированный корпус печки для плавления, в котором и происходит его последующее спекание:
Работа печей для фьюзинга базируется на 2 различающихся способах:
1) на дно специальной камеры для плавления укладывается кружок из карбида кремния или несколько подобных кружков. Они и являются тепловыделяющим(и) элементом(элементами), которые преобразуют энергию микроволн — в тепло;
2) камера плавления представляет собой герметичную теплоизолированную камеру, которая изнутри выложена слоем карбида кремния. Данное покрытие также играет роль тепловыделяющего элемента, который и нагревает собственно камеру — изнутри.
Это занятие является достаточно увлекательным и занимаются им широкие слои, преимущественно женского, населения и их можно понять!
Если посмотреть на результаты удачных примеров «фьюзинга», то бишь спекания стекла, — то они поражают своей эстетической красотой и осознанием того факта, что подобные изделия могут быть получены в домашних условиях!
Для получения настоящего культурного удовольствия и изучения того, что в мире делается по этому направлению, рекомендуется поиск по сайту www. pinterest.com, по ключевым словам: «microwave melting glass», «microwave fusing glass», «microwave fusing».
Если вы всерьез заинтересовались этим занятием, то на известном сайте имеются наборы начинающего.
При анализе информации, доступной в интернете по теме фьюзинга, была выявлена явная проблема, с которой сталкивается большинство энтузиастов этого дела: отсутствие четко контролируемого процесса нагрева и охлаждения. Такая проблема приводит к тому, что в получившемся изделии остаются остаточные напряжения, которые могут в любой момент привести к неожиданному его разрушению. Легко представить себе последствия, если предположить, что данное изделие является некой декоративной подвеской на шее, или серьгами в ушах!
Поэтому, здесь наблюдается явная возможность для знатоков программирования и физической «железной» части, такой, как плата Arduino или более продвинутой версии — esp32. С использованием данного подхода, можно, после проведения ряда тестовых итераций, разработать соответствующую программу оптимального нагрева и охлаждения, которая позволит получать достойные стеклянные изделия с минимальным содержанием остаточных напряжений или совсем без оных.
И наконец, мы подошли к самому интересному моменту нашего хит-парада: плавление металла в обычной микроволновке! (на этом месте автор начинает ходить из угла в угол, с безумным взглядом, что то бормочет и машет руками. Успокоившись – продолжает дальше…)
В это сложно поверить, однако существует способ, который позволяет легко плавить металлы, имеющие температуру плавления до 1200 градусов в обычной микроволновке, мощностью не менее 700 Вт!
Способ заключается в том, что для плавления используется тигель из графита, с покрытием из карбида кремния, который и является радиопоглощающим материалом, эффективно переводящим энергию микроволнового излучения — в тепло. Это позволяет плавить металлы (если на примере бронзы), — то в районе 80 грамм, за одну закладку.
Способ плавления металлов с использованием микроволновки является особенно интересным в связи с тем, что эта технология практически полностью укладывается в один из принципов ТРИЗ (теории решения изобретательских задач), который, утрированно, звучит примерно так: «идеальная машина — это та, которой не существует, однако её функции – выполняются».
Под этим подразумевается, что для плавления можно использовать специализированные устройства, однако лучше использовать обычное бытовое устройство, которое изначально не предназначено для данных целей и по сути, можно сказать, что мы «плавим металл в отсутствующей плавильной печи».
Рассмотренный в микроволновом способе плавки тигель у автора выдерживал 50 плавок без каких-либо признаков разрушения.
Там же, продаются доступные по цене комплекты для плавления. Да, конечно, можно приобрести на известном сайте Aliexpress «муфельную плавильную печь», однако она тоже не лишена существенных недостатков.
Если например, рассмотренная выше технология по плавлению в микроволновке занимает по времени в среднем (от закладки — до расплава) около 8-9 минут, то способ плавления металлов с использованием муфельной плавильной печи только для разогрева печи требует не менее 30-40 минут, с соответствующими энергозатратами. И это мы ещё не учитываем тот момент, что печь должна быть доставлена с Aliexpress, и она укомплектована тиглем, с достаточно малым сроком наработки на отказ.
Если же брать индукционную плавильную печь, то она требует подключения воды — для охлаждения и так же не является слишком дешевой, а также требует времени на доставку.
Плавление же с использованием микроволновки является особенно интересным, если учесть возможность литья металла по выплавляемой модели, например, как в этой статье.
Или же в этих видео:
Единственной проблемой при таком подходе, на взгляд автора, является то, что при литье по выплавляемой модели, — требуется предварительно выплавить данную модель из подготовленных для литья форм. Даже если мы используем для предварительной 3D печати легкоплавкий пластик PLA, его удаление из готовой формы может стать определенной проблемой. А именно, потребуется достаточно высокая температура, чтобы выплавить его или даже выжечь из такой формы.
Проанализировав опыт других людей, автор пришел к выводу, что наиболее приемлемым подходом в данном случае является использование высокотемпературной горелки, в качестве которой можно воспользоваться, например, паяльной лампой.
Конечно, этот процесс вряд ли можно воспроизвести «в ванной комнате, пока жена спит» и потребуется, как минимум, выйти во двор.
Однако сама вероятность создания металлических изделий с использованием 3D принтера и имеющейся в наличии микроволновки, — является весьма примечательной и достойной внимательного рассмотрения!
Творчески сочетая 2 рассмотренных выше способа, а именно, — плавление металла и стекла, можно получать весьма интересные вещи, как например, заливка расплавленным стеклом — металлических форм. В итоге получаются практически ювелирные изделия. Способ базируется на заполнении пустот в металлической форме — специальной «горячей эмалью», которая представляет собой смесь стеклянного порошка различных цветов со связующим:
Освоив данную связку двух технологий, вы сможете делать весьма любопытные вещи, как в видео ниже. Автор для прогрева использует горелку, но у вас есть способ лучше — микроволновка! Это видео вы можете использовать для ориентира, что вообще возможно делать:
Примечание.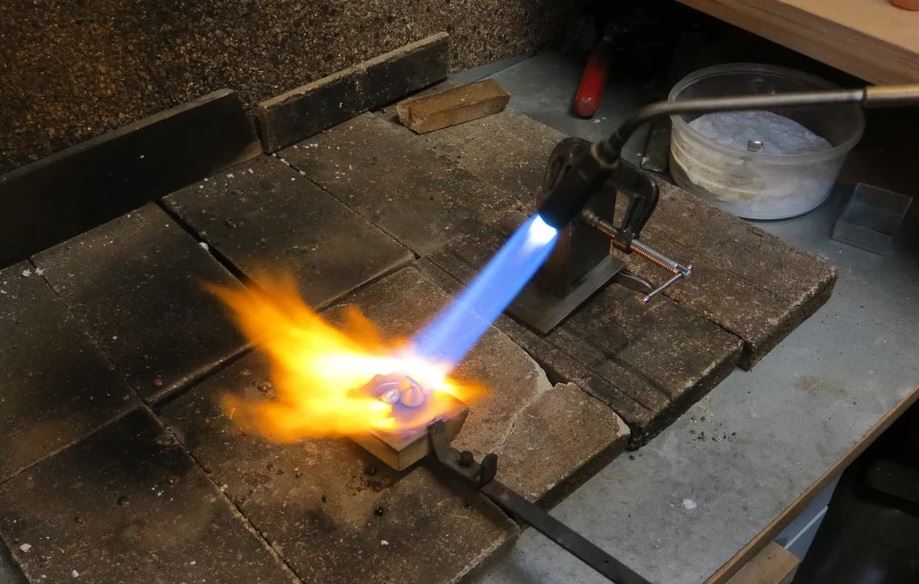
Таким образом, зная температуру плавления металла, который вы используете и снимая показания температуры с помощью термопары (например), возможно плавить только стекло и не доводить до плавления металл. И стекло заполнит все нужные места в металле, а сам металл — не повредится!
▍ Бонус
Завершая рассказ, нельзя не упомянуть еще одну достаточно забавную поделку, которая была в своё время изготовлена упомянутым ранее блогером Allen-ом Pan-ом. Для её создания он использовал трансформатор от микроволновки, который был переделан в электромагнит.
Кроме того, в её составе были использованы следующие компоненты: плата Arduino Pro Mini, аккумулятор на 12 вольт, твердотельное реле, емкостной датчик, подключенный к рукоятке и сканер отпечатка пальца. Всё это было помещено в компактный корпус в форме молота («Мьёльнир»-а), принадлежащего Богу грома «Тору» (согласно Вселенной «Марвел»).
Работает устройство следующим образом: как только кто-либо берется за рукоятку, срабатывает емкостный датчик и включается электромагнит, благодаря чему молот намертво приклеивается к любой металлической поверхности, на которую он был предварительно установлен.
Любой, кто попытается оторвать молот от поверхности — потерпит неудачу, так как касание рукоятки включает электромагнит!
Оторвать же молот от поверхности и отключить его магнит, — может только хозяин, так как система откалибрована на распознавание отпечатка именно его пальца, которым он должен предварительно коснуться сканера. Получилось смешно:
Если кто-то задумает повторить такую самоделку, следующее видео может ему в этом помочь: здесь достаточно подробно показывается процесс изготовления электромагнита — из трансформатора микроволновки:
Также, в настоящее время возможно упростить конструкцию молота, если взять вместо платы Arduino Pro Mini — плату esp32: она содержит сенсорные пины, к которым можно подключить металлические площадки на рукоятке молота (предусмотрительно размещенные ранее). И вести обработку события «отпустить молот» исключительно логическим путём («если площадка 1 удерживается и по площадке 2 в этот момент — два раза постучали пальцем, то отпустить молот» и т.д.). В таком случае, самоделка будет еще привлекательней, так как пропадет существенный демаскирующий признак — сканер отпечатка пальца.
Как можно видеть из этого длинного рассказа, микроволновка, — это не только средство для приготовления и разогрева пищи, но и неисчерпаемый кладезь компонентов, которые позволят вам создать свои экспериментальные и даже вполне полезные вещи.
Для некоторых из этих неординарных применений, даже не требуется каких-либо её переделок!
Что же касается самого автора рассказа, то в списке его предпочтений, так сказать, «личного хит-парада», — первое место прочно занимает методика плавки металла в микроволновке.
К описанной технологии плавки хотелось бы добавить еще одно примечание, что в микроволновке плавится партия металла не более 80 грамм за один раз. Соответственно — для заливки такого объема металла не нужна слишком большая форма, и форма может быть легко обожжена на обычной бытовой газовой плите кухонного назначения (если у вас в наличии имеется таковая, а не электрическая плита).
При таком подходе, — процесс плавки металла становится поистине домашним и, можно даже сказать, уютным (в этом месте на заднем плане должен звучать зловещий хохот безумного учёного).
В любом случае, надеемся, что этот рассказ был для вас полезным и интересным, дав каждому читателю пищу для размышлений!
Плазма плавит металл | Плавка и транспортировка металла
Как известно, нагревание веществ ведет к увеличению энергии теплового движения молекул. При нагреве до 2000° С начинает проявляться нарушение молекулярного состояния. Распадаются на атомы многоатомные молекулы. Вблизи 3000° С наблюдается диссоциация уже « двухатомных молекул, происходит и их распад. Когда температура достигает 4000°С, почти все вещества находятся не в молекулярном, а в атомарном состоянии. Свыше 5000° С начинается процесс распада атомов на ионы; нарушаются внутриатомные связи. При 6000—7000° С происходит деформация электронных оболочек атомов, отрыв электронов от атомных ядер. К 8000° С вещества находятся уже не только в атомарном, но и, частично, в ионизированном, плазменном, состоянии. Плазма — это ионизированная газовая система.
Плазменная струя газа обладает необычными свойствами. Газы — диэлектрики в плазменном состоянии становятся проводниками электрического тока. В обычном состоянии газы нейтральны, а в ионизированном они обладают уже электрическим зарядом. В плазме наблюдается очень высокая концентрация энергии (до 100 кВт/см2).
Если плазменную струю сжать, нагреть электрической дугой и направить на поверхность металла, то металл будет плавиться. На этом принципе созданы плазменные горелки. Чем меньше сечение плазменной струи, чем больше плотность тока, сопротивление и мощность установки, тем выше температура, развиваемая плазменной горелкой — плазмотроном. Плазмотроны уже серийно выпускаются как в СССР, так и в США, Японии и ФРГ. Используются они для резки металлов, сварки, наплавки и напыления, а в ряде случаях и для плавки тугоплавких металлов.
В плазменных печах плавят от нескольких килограммов до нескольких тонн металла. На них устанавливают от одного до пяти плазмотронов. В качестве газов используют аргон или азот. На каждый килограмм полученного расплава расходуется 0,8 кВт, т. е. примерно столько же, сколько и на дуговой электропечи. Азотная плазма развивает температуру более 6000° С. Это позволяет получить очень высокий коэффициент полезного действия: 60—70% больше, чем у любых других печей.
В плазменных печах возможно получение металла весьма высокого качества. Металл не соприкасается с воздухом и не образует окислов и нитридов. В печи нет графитовых электродов и поэтому не происходит науглероживания расплава. Медная водоохлаждаемая ванна исключает попадание в металл неметаллических включений. Все это обеспечивает высокую пластичность и достаточную прочность металлов, выплавляемых в плазменных печах.
На рис. 28 приведены схемы плазменно-дуговых печей. Печь с огнеупорной футеровкой (рис. 28, а) аналогична обычной электродуговой печи с той разницей, что вместо обычных графитовых электродов через свод печи в ванну вводятся плазменные горелки — плазмотроны. На рис. 28, б показана плазменно-дуговая печь с водоохлаждаемым кристаллизатором, в котором расплавляемый металл затвердевает на поддоне, равномерно опускающимся вниз.
Рис. 28. Схема устройства плазменной дуговой печи:
а — с огнеупорной футеровкой; б — с водоохлаждаемым катализатором
конвертерщики плавят металл, основываясь на интуиции и на законах химии
Производственный процесс на Медногорском медно-серном комбинате осуществляется круглосуточно. В таком же режиме — 24/7 работает сменный персонал медеплавильного цеха. Всего в МПЦ под руководством мастеров трудятся пять технологических смен. В состав каждой смены входят конвертерщики, плавильщики, разливщики, загрузчики, шлаковщики, крановщики и сигналисты-стропальщики. Братья по горячим делам
Особым, металлургическим, братством в среде представителей горячих профессий выделяются конвертерщики, чье рабочее место — в «святая святых» комбината: у конвертеров и плавильного агрегата «Победа». Их главная задача — получение основной товарной продукции — черновой меди. Для того чтобы на остывшем штыке контролер ОТК проставил номер плавки, конвертерщики, облачившись в металлургические «доспехи» — суконку, валенки и вачеги, опустив «забрало» — щиток лицевой маски, ведут переработку штейнов.
В смене № 4 мастера Дениса Кутуманова — восемь конвертерщиков. Рядом с опытными Сериком Шудобаевым, Андреем Могиным, Виктором Петровым, Сергеем Маляновым, братьями Салаватом и Радмиром Кульсаитовыми постигают премудрости профессии новички Иван Сергеев и Анатолий Бортник.
Формула профессии
Основываясь на показаниях контрольно-измерительных приборов и результатах лабораторных анализов, выданных управлением контроля продукции, конвертерщики регулируют режимы работы основного и вспомогательного оборудования, подачу воздуха и кислорода, обслуживают механизмы, а также определяют готовность продуктов плавки.
— Работа на конвертере — очень ответственная, она требует не только отточенных профессиональных навыков. Конвертерщики должны обладать знаниями в таких областях, как металлургия цветных металлов, теплотехника, аналитическая и физическая химия, обогащение руд, — говорит бригадир смены № 4, конвертерщик 6-го разряда Серик Шудобаев. Его стаж в профессии — 30 лет.
Мы — сплоченная команда!
Каждый из конвертерщиков четвертой смены пришел в металлургию по своей причине. Дело отцов продолжили Виктор и Салават. Оставили службу по контракту ради семьи Иван и Салават. Радмир устроился на ММСК вслед за братом и понял, что именно здесь он полезен. Нравится профессия и трудолюбивый, дружный коллектив Сергею и Андрею. Высоким и стабильным заработком привлекателен труд металлурга для Анатолия.
А мастер смены Денис Кутуманов говорит, что эта профессия выбрала его сама. Действительно, как иначе объяснить, если в семье он — первый металлург. Если высшее образование начал приобретать, собираясь специализироваться в сфере машиностроения, завершил по профилю металлургии. Если, пройдя через проходную цеха 18-летним студентом индустриального техникума, работает здесь уже 21 год, из них 10 — сменным мастером.
— Это мой второй дом. Коллеги стали близкими людьми. Все, что я сегодня имею (семья, жилье, стабильность, то, чего достиг в жизни), — все это благодаря профессии, — подытоживает Денис Александрович.
Именно так, по имени-отчеству, называют своих мастеров рабочие в сменах. По-другому здесь нельзя. Работа с огнем и металлом не терпит панибратства и небрежности, она требует высокой исполнительской дисциплины, а коллективная ответственность за результат — умения работать в команде.
Нина ПАВЛОВА
Плавильщица завода УГМК рассказала, почему металл «варят» как борщ и разливают половником » Вечерние ведомости
Екатерина Николаева, плавильщица Челябинского цинкового завода (УГМК) в преддверии Международного женского дня в рамках спецпроекта о женщинах-металлургах рассказала о том, как плавит и разливает редкоземельный металл индий.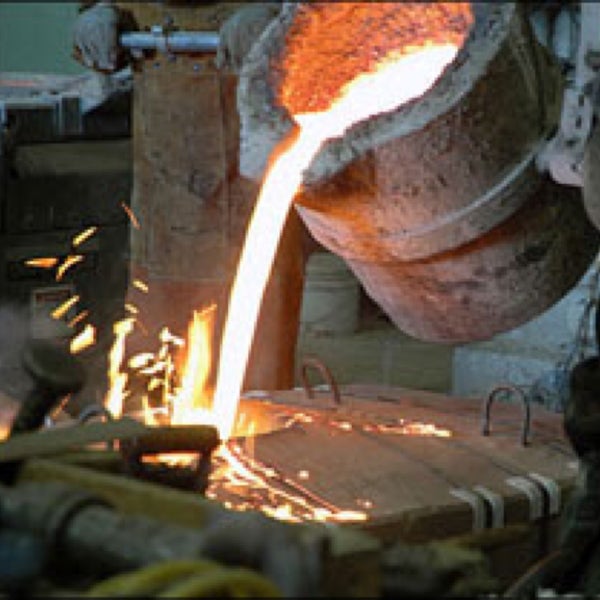
«Все, кто впервые видят, как мы работаем, сразу говорят, – что у вас за советские технологии? Плавите металл в кастрюле, как борщ, разливаете половником, – рассказывает Николаева, – Если индий соприкоснется с другим металлом, он будет заражен. И его по технологии можно плавить только в эмалированной титановой кастрюле и разливать поварёшкой из нержавейки. Это ГОСТ, это актуальная технология.
Я за раз разливаю по изложницам по пять половников, это приблизительно пять килограммов, плюс сама кастрюля весит. Ну, где-то шесть килограмм выходит в весе. За четыре недели мы должны сделать около восьми плавок. Каждая плавка от 123 килограммов. Когда к нам приходили мужчины и пробовали эту кастрюльку держать, лить металл из нее, удивлялись, как мы держим ее на весу».
Плавильщица также рассказала, что работа с индием – щепетильная и аккуратная и с мужской грубой силой она не сочетается.
«Индий нельзя просто взять и налить, нужно лить аккуратнее. То есть, если я перегрею металл, у меня он будет плавиться буграми. Если недогрею, будет плавиться волнами, если буду лить слишком быстро, он будет весь в пузырьках. Слишком медленно – он будет застывать неровно. Нужно держать в одном режиме струю, которую я лью в изложницы. Потому что если будет литься быстро, оно испортится, медленно – будет застывать волнами, и не станет товарного вида уже, брусок будет забракован», – рассказала рабочая.
Добавим, что индий – яркий, блестящий металл, имеющий температуру плавления 156.6 °C. Индий находит своё применение в производстве жидко-кристаллических дисплеев телевизоров, планшетов и смартфонов в виде тонких плёнок оксида индия-олова. Важнейшая область применения индия в современной технике — производство плат с использованием полупроводников. Главное преимущество индиевых сплавов — возможность полностью заполнять и герметизировать мельчайшие поры и пустоты изделий при низкой температуре плавления. Это позволяет качественно соединять тонкие изделия, боящиеся повышенной температуры, например, медные.
© Вечерние ведомости
Как плавят металл — ZAVODFOTO.RU
Новолипецкий комбинат производит 17% всей российской стали. Его строительство началось в 1931 году, а 7 ноября 1934 года доменная печь дала первую партию чугуна. В годы войны производство эвакуировали в Челябинск, после её окончания завод вернулся обратно и в советские годы активно рос: число доменных печей увеличилось до шести, а в 1986-м заработал крупнейший на тот момент в Европе цех прокатки динамной стали. В ходе приватизации завод перешёл в частную собственность — сейчас группой НЛМК, в которую также входит несколько угольных месторождений в России и заводы за рубежом, владеют структуры Владимира Лисина.
Площадь предприятия — 28 кв. км. В 2011 году на комбинате открылась новая доменная печь «Россиянка». Всего на предприятии их семь. Доменная печь состоит из пяти элементов: колошника для загрузки сырья, высокой шахты для нагрева материалов и восстановления железа, цилиндрического распара для плавки металла, заплечиков, где образуется восстановительный газ, и горна. Домна работает непрерывно — остановка производства даже на короткое время потребует длительного восстановления.
Шихтовые материалы, заполняющие всю печь, непрерывно опускаются вниз под действием силы тяжести, а снизу вверх поднимается горячий газ, который нагревает шихту и участвует в восстановительных процессах металла. В горне при температуре 1 800–2 000 °С сгорает кокс. Он соединяется с кислородом в воздухе и образует углекислый газ. Под влиянием высокой температуры газ превращается в оксид углерода, который отнимает у железорудных материалов кислород, восстанавливая железо. Так, стекая вниз через слой раскалённого кокса, железо насыщается углеродом и превращается в чугун.
Чугун скапливается в нижней части печи — горне. На его поверхности собирается шлак — более легкий слой пустой породы. Потом расплавленный металл выпускают через лётки. Чугун разливают в ковши и везут в конвертерный цех, шлак попадает в чаши, которые идут в цех переработки. Потом он может использоваться в строительстве.
Для выплавки стали на комбинате используют конвертеры — ёмкости грушевидной формы, обложенные изнутри огнеупорным кирпичом.
При производстве стали из чугуна путём окисления удаляются примеси. Через вертикальную водоохлаждаемую фурму вдувается технически чистый кислород, который окисляет примеси (углерод, кремний, марганец, фосфор и серу), переводя их в шлак или газовую фазу. После этого металл поступает в цех горячей прокатки.
Она начинается с предварительного разогрева металлических слитков (слябов) до температуры 1 150–1 250 °С в печах прокатного стана. Затем слябы выдаются на рольганг, который перевозит их к черновой группе из пяти клетей.
Гидросбивы струёй воды под давлением 12,0–16,0 МПа очищают поверхность металла.
Из черновой группы клетей прокат везут к чистовой группе клетей — здесь заготовка приобретает свою конечную толщину.
Затем полоса поступает на одну из трёх моталок, где металл сматывают в рулон (температура смотки — около 650 градусов). На выходе получается горячекатаный прокат.
Этот металл используется в строительстве, производстве оборудования, энергетическом и сельскохозяйственном машиностроении, производстве труб, автомобилей и бытовой техники.
Источник
Плавка — обзор | ScienceDirect Topics
Bloomery Iron
При выплавке железа использовались методы, установленные для производства цветных металлов, которые применялись в некоторых частях Ближнего Востока почти 2000 лет. Простые чашеобразные очаги — неглубокие и обычно выложенные глиной или камнем ямы — были окружены низкими круглыми глиняными стенками. Эти стены иногда были высотой всего по колено (римляне выплавляли большую часть своего металла в печах высотой не более 1 м и внутренним диаметром менее полуметра), но в некоторых частях Старого Света (включая Центральную Африку) они со временем достигли высоты более 2 м (Van Noten & Raymaekers, 1988).Печи были заполнены древесным углем и измельченной (и часто обожженной) железной рудой, а относительно высокие температуры достигались путем продувки воздухом через фурмы, узкие глиняные трубки, вставленные близко к поверхности (см. Приложение B для определений некоторых основных технических терминов, связанных с производство чугуна и стали).
Фурмы были соединены с кожаными мехами, чтобы нагнетать воздух в очаг и повышать температуру плавки. Маленькие мехи приводились в движение вручную, более крупные — весом человека (с помощью педали или качающейся штанги), а самые мощные мехи в конечном итоге приводились в движение водяными колесами. Температура внутри этих угольных печей обычно не превышала 1100–1200°С (а часто была и ниже 900°С), достаточно высокой для восстановления оксида железа и далеко не достаточной для расплавления металла и получения жидкого железа (чистого Fe сжижается при 1535°C): конечным продуктом этой плавки была корка, губчатая масса, состоящая из железа и богатого железом шлака, состоящего из неметаллических примесей (Bayley, Dungworth, & Paynter, 2001). Отсюда и общее название этих печей — блумеры, а продукта — блумеры.
Современные эксперименты продемонстрировали относительно узкий диапазон условий, необходимых для успешной плавки (Tylecote, Austin, & Wraith, 1971). Когда условия внутри печи недостаточно восстановительны, металл не производится, только богатый железом шлак, но когда они слишком восстановительны, шлак становится слишком вязким и его трудно отделить от металла. Промежуточные условия дают хорошее цветение; большая часть шлака образуется из железной руды, около 30 % — из кремнистой футеровки печи и менее 5 % — из золы (Paynter, 2006). Блюмы, изготовленные в самых маленьких ранних печах, весили менее 1 кг, более типичный средневековый диапазон составлял 5–15 кг, а масса блюма увеличивалась до 30–50 кг (или даже до более 100 кг) только с введением более высоких печей и мехи с приводом от водяного колеса.
Блумерийское железо обычно содержало от 0,3% С до 0,6% С, и в Европе это был единственный железосодержащий материал, доступный в значительных количествах в древности и до позднего средневековья. Железо, произведенное в блюмериях, было консолидировано и сформировано последующей кузнечной обработкой: для получения массы кованого железа, содержащей всего 0, требовалось повторное нагревание и ковка блюма.04–0,08% C, пластичный, ковкий и поддающийся сварке. Кованое железо использовалось для изготовления все большего количества оружия, утилитарных и декоративных предметов, от наконечников стрел до болтов и топоров (Ashkenazi, Golan, & Tal, 2013; Barrena, Gómez de Salazar, & Soria, 2008), а также для современных металлургических экспертиз. найти небольшое количество шлака, попавшего в эти продукты.
Блюмерии поставляли все железо в Европу во время первого заметного роста спроса на металл на континенте, который начался в одиннадцатом веке — с введением железной кольчуги, первоначально в виде небольших металлических бляшек, позже в виде кованых вручную и клепаных узлов — и расширился. в течение двенадцатого и тринадцатого веков.Возросло производство ручного оружия (от ножей до булав) и шлемов, а также сельскохозяйственных и транспортных орудий и орудий, из железа изготовлялись плуги, вилы, серпы, мотыги, оси телег, обручи (для бочек, повозки и ветряные мельницы) и подковы. Первое задокументированное использование мощных кузнечных молотов, приводимых в движение водяными колесами, датируется 1135 годом в знаменитом цистерцианском монастыре Клерво. Больше железа также использовалось в строительстве в качестве болтов, решеток, стержней и застежек, а в тринадцатом веке металлические ленты использовались в Нотр-Дам-де-Пари. Столетие спустя папский дворец в Авиньоне израсходовал 12 т металла (Caron, 2013).
Плавка в блюмери практиковалась практически во всех культурах Старого Света, и тысячи таких простых временных очагов (иногда с нетронутыми частями стен) были раскопаны в регионах как Сахелианской, так и южнее Сахары Африки (Haaland & Shinnie, 1985). к кочевым обществам в степях Центральной Азии (Sasada & Chunag, 2014) и от побережья Шри-Ланки (Juleff, 1996; 2009Juleff, 1996Juleff, 2009) до Скандинавии (Olsson, 2007; Svensson et al., 2009) и Корее, где эта практика, возможно, была перенесена из региона, который сейчас является тихоокеанским побережьем России, а не из Китая, где преобладал чугун (Park & Rehren, 2011).
Большая часть свидетельств самой ранней выплавки чугуна в Евразии известна давно, многочисленные остатки более простых и низких конструкций (часто называемых корсиканскими горнами) и более прочных и высоких печей (называемых каталонскими горнами) были найдены от Атлантики до Урал. Напротив, новые раскопки древних цветников и новые углеродные датировки изменили наши взгляды на развитие металлургии железа в Африке (Holl, 2009; Zangato & Holl, 2010).Эти находки указывают на раннюю плавильную деятельность в регионах от долины Среднего Сенегала на западе до долины Нила на востоке и от бассейна Эгаззер в Нигере до района Великих озер в Восточной Африке, причем многие даты относятся к более чем 2500 лет назад. в настоящее время и с предполагаемой температурой печи 1100–1450°C.
Стойкость этой технологии выплавки подтверждается тем фактом, что испанские цветочные заводы в Сан-Хуан-Капистрано (построенные в 1790-х годах) были старейшими металлургическими заводами в Калифорнии, а действующие цветочные заводы сохранились в некоторых частях Англии до восемнадцатого века; в некоторых частях Испании и на юге Франции они все еще присутствовали к середине девятнадцатого века.Плавка в блюмерии была лишь первым шагом к получению полезного металла: железистую губку, смешанную со шлаком, нужно было многократно обрабатывать (ковать) попеременным нагревом и ковкой (требуется до 30–50 циклов) для удаления вкраплений. примесей и для производства кованого железа, из которого можно выковать оружие, подковы, наконечники колтера, гвозди и другие мелкие железные предметы. На протяжении столетий весь этот горячий и тяжелый труд повсеместно выполнялся вручную, и только внедрение более крупных водяных колес позволило строить механизированные горны с использованием более тяжелых молотов.Тем не менее, это традиционное сочетание цветочных заводов и кузниц имело свои очевидные производственные ограничения.
Будучи мелкомасштабной периодической операцией (каждая плавка прекращалась для удаления относительно небольших масс твердой шихты), выплавка чугуна в традиционных малоэтажных блочных заводах никогда не могла экономически удовлетворить крупномасштабный спрос на металл, а рабочая сила — интенсивная (а также высокоэнергоемкая) ковка удорожала (дополнительно увеличивалась из-за значительных потерь железа в процессе ковки).Неудивительно, что с ростом спроса некоторые европейские шарманки, например, средневековые немецкие и австрийские Stucköfen , стали выше ( Technisches Museum в Вене имеет прекрасную модель). Эти печи по-прежнему производили небольшие массы металла ( Застрявший ), удаление которых требовало разрыва передней стенки конструкции, но поскольку процесс плавки длился немного дольше, а сильфоны с приводом от водяного колеса обеспечивали более мощное дутье и температуру в нижних частях печи. печи были выше, в результате налет часто представлял собой смесь губчатого железа и стали.
Выплавка металлов — обзор
Загрязнение воздуха в древних городах
Основными источниками загрязнения воздуха были запах из открытых канализационных коллекторов; разложение мусора, мертвых животных и экскрементов; древесный дым; выплавка и изготовление металлов; и производство различных товаров. Доступная информация из различных источников дает косвенные, но положительные предположения о том, что уровни загрязнения воздуха в древних городах были значительными. Один из первых зарегистрированных эпизодов загрязнения воздуха произошел в деревне Хит к западу от древнего Вавилона, где египетский царь Тукульти описал неприятный запах, исходящий от добычи битума, в результате которого в 2900 г. до н.э. выделялись высокие концентрации едких газов.
Загрязнение воздуха в Риме, особенно в классический период, было вызвано сжиганием большого количества топлива из биомассы (включая древесину, другие растительные материалы или навоз животных) для отопления и приготовления пищи огромным населением (по оценкам, более 1 млн. до 2,5 миллионов при Константине) и для обогрева общественных бань. Некоторым отраслям промышленности Рима требовалось огромное количество топлива из биомассы для изготовления кирпичей и черепицы, которые использовались для строительства Рима и восстановления его после знаменитого пожара Нерона, а также для строительства огромных и великолепных зданий, которыми был известен город (таких как Термы Каракаллы).Другие источники загрязнения воздуха включали сжигание животных и растительных масел в терракотовых лампах, сжигание свечей и благовоний, а также кустарное производство. Луций Анней Сенека Младший в 61 г. н. э. изумлялся: «Как только я выбрался из тяжелого воздуха Рима, из вони дымоходов и чумы, паров и копоти воздуха, я почувствовал перемену в моем расположение». Хотя некоторые люди могли страдать от неприятного воздействия летучих органических соединений из разлагающегося мусора, загрязненный воздух в помещении был причиной значительной доли болезней и болезней, связанных с экологическими причинами в древние времена.
Китайский кан — это древняя технология, разработанная примерно 2500 лет назад во времена династии Чжоу (722–481 г. до н.э.). Это интегрированная домашняя система для приготовления пищи, сна и отопления дома, которая до сих пор широко используется. Недавнее крупномасштабное исследование обнаружило канги почти в 85% сельских домов на севере Китая, где в основном холодно и сухо, а отопительный сезон длинный, но использование этого приспособления распространено по всей стране. Подобные системы отопления были также разработаны и приняты другими культурами, такими как ондоль (пол с подогревом) в Корее и гипокауст в Древнем Риме.Хотя дизайн немного различается от региона к региону, так называемый заземленный кан был наиболее широко использован в Китае. У заземленных кангов есть два основных недостатка: эффективность горения (примерно 14–18 % для тела и 8–10 % для печи) низкая, что приводит к значительным потерям топлива, и большое количество загрязняющих веществ выбрасывается в атмосферу. воздух в помещении, особенно когда печь и корпус кан находятся в одном помещении. Кроме того, заземленные канги с плохой конструкцией вентиляции часто приводят к обратному потоку дыма и засорению дымохода.В сельских районах Китая воздействие загрязнения воздуха внутри помещений из-за сжигания биомассы в канах связано с рядом заболеваний, таких как острые респираторные инфекции, хроническая обструктивная болезнь легких, рак легких и астма; Уровень смертности, связанный с загрязнением воздуха внутри помещений, также оценивается как значительный (примерно 425 000 смертей в Китае в 2000 г.), и это происходит с древних времен. Кан — это передовая технология по сравнению с простыми и импровизированными печами и дровяными устройствами, используемыми людьми в других частях мира, где можно было бы ожидать более высоких показателей заболеваемости и смертности от загрязнения воздуха внутри помещений.
Дарио Камуффо предпринял некоторые попытки оценить степень загрязнения воздуха в Риме отложениями на мраморной колонне Траяна, построенной в 105 году нашей эры архитектором Аполлодором Дамаскином. Износ колонны был типичен для других древних памятников с изъязвлением, растворением, следами так называемой scialbatura (серо-розовый поверхностный слой оксалата кальция, покрывающий мрамор) и черными корками. Камуффо предположил, что патины (особенно scialbatura) образовались в результате осаждения оксалатов кальция из щавелевой кислоты, выделяемой микроорганизмами, такими как лишайники или синие водоросли, которые колонизировали памятники.Он показал, что scialbatura обычно отсутствовала, когда население Рима превышало 150 000–200 000 человек, порог, который он связывал с токсичными для лишайников уровнями загрязняющих веществ в древней городской атмосфере. С падением Рима и улучшением качества воздуха расцвела биологическая деятельность, что было связано с образованием патины на следующие 13 столетий. Высокий уровень загрязнения атмосферного воздуха, приведенный Камуффо, не подтверждается результатами других исследователей.
Железная руда | HowStuffWorks
Еще до того, как многие древние цивилизации начали переход от бронзового века к железному, некоторые производители инструментов уже создавали железные орудия из космического источника: метеоритов.Названное египтянами «черной медью», метеоритное железо — это не то вещество, которое можно найти в огромных, объединенных местах. Скорее, мастера находили его кусочки, разбросанные на огромных расстояниях. Таким образом, этот небесный металл в основном использовался в Хотя кузнецы иногда использовали метеоритное железо для изготовления мечей, это ценное оружие обычно предназначалось для людей великой силы, таких как халифы седьмого века, чьи клинки, как говорили, были выкованы из того же материала, что и Святой Черный камень. Мекки [источник: Рикард].
Большая часть земного железа, однако, содержится в железной руде . Сырая руда, добываемая прямо из-под земли, представляет собой смесь собственно руды и рыхлой земли, называемой пустой породой . Собственно руду обычно можно отделить, измельчив необработанную руду и просто вымыв более легкую почву. Однако разбить собственно руду сложнее, так как она представляет собой химическое соединение карбонатов, гидратов, оксидов, силикатов, сульфидов и различных примесей.
Чтобы добраться до кусочков железа в руде, вам нужно выплавить ее.Плавка включает в себя нагрев руды до тех пор, пока металл не станет губчатым и химические соединения в руде не начнут разрушаться. Самое главное, он выделяет кислород из железной руды, которая составляет большую часть обычных железных руд.
Самым примитивным оборудованием для выплавки железа является плавильня . Там кузнец сжигает уголь с железной рудой и хорошим запасом кислорода (обеспечивается мехами или воздуходувкой). Древесный уголь — это, по сути, чистый углерод. Углерод соединяется с кислородом с образованием двуокиси углерода и угарного газа (выделяя при этом много тепла). Углерод и монооксид углерода соединяются с кислородом в железной руде и уносят его, оставляя металлическое железо.
В камине огонь не нагревается настолько, чтобы полностью расплавить железо. Вместо этого железо нагревается и превращается в губчатую массу, содержащую железо и силикаты из руды. Нагревание и измельчение этой массы (называемой блюмом) вытесняет примеси и смешивает стеклообразные силикаты с металлическим железом, создавая кованое железо . Кованое железо прочное и легкое в обработке, что делает его идеальным для создания инструментов.
Производители инструментов и оружия научились плавить медь задолго до того, как железо стало доминирующим металлом. Археологические данные свидетельствуют о том, что кузнецы на Ближнем Востоке плавили железо еще в 2500 году до нашей эры, хотя прошло более тысячи лет, прежде чем железо стало доминирующим металлом в регионе.
Чтобы создать железо более высокого качества, кузнецам потребуются лучшие печи. Технология постепенно развивалась на протяжении веков. К середине 1300-х годов более высокие печи и мехи с ручным управлением позволили европейским печам гореть достаточно жарко, чтобы не только размягчать железо, но и плавить его.
Знаете ли вы, что добытая руда разлагается во время плавки?
Выберите страну / регион * Выберите страну / regionUnited StatesCanadaAfghanistanAlbaniaAlgeriaAmerican SamoaAndorraAngolaAnguillaAntarcticaAntigua и BarbudaArgentinaArmeniaArubaAustraliaAustriaAzerbaijanBahamasBahrainBangladeshBarbadosBelarusBelgiumBelizeBeninBermudaBhutanBoliviaBosnia и HerzegovinaBotswanaBouvet IslandBrazilBritish Индийского океана TerritoryBrunei DarussalamBulgariaBurkina FasoBurundiCambodiaCameroonCape VerdeCayman IslandsCentral африканского RepublicChadChileChinaChristmas IslandCocos (Килинг) IslandsColombiaComorosCongoCongo, Демократической Республика ofCook IslandsCosta RicaCote D’IvoireCroatiaCubaCyprusCzech RepublicDenmarkDjiboutiDominicaDominican RepublicEast TimorEcuadorEgyptEl SalvadorEquatorial GuineaEritreaEstoniaEthiopiaFalkland остров (Мальвинские острова)Фарерские островаФиджиФинляндияПремьер Югославская Республика МакедонияФранцияФранцузская ГвианаФранцузская ПолинезияФранцузские Южные ТерриторииГабонГамбияГрузияГерманияГанаГибралтарГрецияГренландияГренадаГваделупаГуамГватемалаГуин eaGuinea-BissauGuyanaHaitiHeard и McDonald IslandsHoly Престол (Ватикан) HondurasHong KongHungaryIcelandIndiaIndonesiaIran (Исламская Республика) IraqIrelandIsraelItalyJamaicaJapanJordanKazakstanKenyaKiribatiKorea, Корейские Народно-Демократической RepKorea, Республика ofKuwaitKyrgyzstanLao Народный Демократической RepLatviaLebanonLesothoLiberiaLibyan Arab JamahiriyaLiechtensteinLithuaniaLuxembourgMacauMadagascarMalawiMalaysiaMaldivesMaliMaltaMarshall IslandsMartiniqueMauritaniaMauritiusMayotteMexicoMicronesia, Федеративные StatesMoldova, Республика ofMonacoMongoliaMontserratMoroccoMozambiqueMyanmarNamibiaNauruNepalNetherlandsNetherlands AntillesNew CaledoniaNew ZealandNicaraguaNigerNigeriaNiueNorfolk IslandNorthern Mariana IslandsNorwayOmanPakistanPalauPanamaPapua Нового GuineaParaguayPeruPhilippinesPitcairnPolandPortugalPuerto RicoQatarReunionRomaniaRussian FederationRwandaSaint HelenaSaint Киттс и НевисСент-ЛюсияСент-Пьер и МикелонСамоаСан-МариноСао-Томе и ПринсипиСаудовская АравияСенегалСейшельские острова ierra LeoneSingaporeSlovakiaSloveniaSolomon IslandsSomaliaSouth AfricaSpainSri LankaSth Georgia & Sth Sandwich Институт социальных Винсент и GrenadinesSudanSurinameSvalbard и Ян MayenSwazilandSwedenSwitzerlandSyrian Arab RepublicTaiwan, провинция ChinaTajikistanTanzania, Объединенная Республика ofThailandTogoTokelauTongaTrinidad и TobagoTunisiaTurkeyTurkmenistanTurks и Кайкос IslandsTuvaluUgandaUkraineUnited Арабские EmiratesUnited KingdomUruguayUS Малые отдаленные IslandsUzbekistanVanuatuVenezuelaVietnamVirgin острова (Британские) Виргинские острова (U. S.)Острова Уоллис и ФутунаЗападная СахараЙеменЮгославияЗамбияЗимбабве
Больше для плавки | ||||||||
Мы кратко рассмотрим четыре темы
здесь:
| ||||||||
Пределы до Размер плавильни | ||||||||
Из вышеупомянутого
положений (извините, но я вынужден читать много юридической
настоящее время) то, что вы узнали в предыдущих модулях, ограничения на размер
плавильного завода станет ясно, как только мы посмотрим, что нужно для запуска большого:
| ||||||||
| ||||||||
| ||||||||
Прежде всего, если цветение слишком
большой, из плавильни его не вытащишь.Снос плавильного завода после одного
использовать можно, если он относительно небольшой и его легко перестроить. Вы не
Однако каждый раз, когда вы производите цветение, вы хотите снести большую плавильню. Во-вторых, вы должны обработать цветок, пока он еще горячий. ![]() | ||||||||
Люди разрезали цветы пополам топором прямо
после того, как один был извлечен из печи. Это требует использования двух
кузнецы для последующего стука. Вы могли бы придумать несколько других трюков, но
ничего не помогает, пока вы работаете с человеческой силой: блумери очень ограничен в
размер. Ваш единственный выход в какой-то степени — использовать большие молоты, приводимые в движение силой воды, как эта мать.Добавьте «мощность сильфоны», и вы можете производить 50 кг цветов. ![]() | ||||||||
Как жарко Должно получиться? | ||||||||
Природа вашего топлива определяет
максимум
температура, которую можно получить в наилучших возможных условиях.За
хороший уголь это был T max » 2000 o C (3600 o F) .
Подача кислорода (не то же самое, что
«воздух»!) и теплоизоляция определяет максимальную
температура, которую вы можете достичь в вашей конкретной настройке.![]() | ||||||||
Предельное значение для паяльной трубки составляет около 1 200 o C
(2 192 o F), и эту температуру можно рассматривать как предел для раннего
металлургия.Он достаточно высок для плавления .
металлов, таких как свинец, олово, медь, бронза, золото и серебро, и почти достаточно
для (беспорядочной) плавки меди, олова и
свинец, но маргинален для выплавки чугуна и способен полностью расплавить только отливку железо . С помощью мехов и хорошо спроектированной плавильной печи вы можете легко получить 1 500 o C. (2 732 или Ф). Естественная тяга или ветряные печи также могут быть в состоянии получить это далеко. Решают ли такие высокие температуры все проблемы с плавкой/плавлением? | ||||||||
| ||||||||
Две проблемы, касающиеся очень высокого
температуры общие для всего пиротехнического оборудования:
| ||||||||
Медь
в выплавке почти всегда участвует железо. Некоторая железная руда является любой частью
пустой породы или был добавлен намеренно, потому что это хороший «флюс»
и обычно используется, когда шлак производится преднамеренно, т.е. всякий раз, когда медь
выплавлено в количествах, см. ниже. Почти неизбежно, что некоторое количество железа
получают при плавке меди. Железо есть
растворим в жидкой меди в незначительной степени при температурах, близких к температуре плавления
точки меди, но ее растворимость быстро увеличивается с увеличением
температура.![]() Если у вас слишком высокая температура, вы получите богатую железом медь, а это не так. хорошо! Медно-железные сплавы не обладают желаемыми свойствами и должны быть избегали. | ||||||||
За первые два тысячелетия
серьезная плавка железа , большинство операторов нацелены
для «кованого железа» или железа с относительно низким содержанием углерода. Что
необходимо было избежать случайного производства чугуна. Только
Китайцы умоляли быть
разные. Если у вас слишком высокая температура, возможно, из-за того, что соотношение древесного угля и руды было слишком большой, или из-за того, что вы сильно напрягли мехи, вы произвели то ли чугун, то ли налет со слишком большой концентрацией углерода, то ли и то и другое одновременно. Раньше это не нравилось «западным» металлургам 1500 или около того. Они также не могли иметь дело с высокоуглеродистой сталью, как «Индийцы» ни с чугуном как китайцы. ![]() | ||||||||
Можно было бы добавить еще многое, но я уверен, что вы поняли идея! | ||||||||
Роль шлака | ||||||||
Пришла тема «шлак»
много в предыдущих модулях, и два следующих пункта должны быть
уже довольно ясно:
| ||||||||
Давайте посмотрим на первый пункт. Почему производство шлака «почти» неизбежно, спросите вы? То основная реакция плавления Me y O + CO Þ y Me + CO 2 нужен только руда и окись углерода (СО) и не образует шлака. Если я позабочусь о том, чтобы я только кормил очищать руду и уголь в плавильне, почему должен производиться шлак? | ||||||||
Вы, безусловно, правы.Если вы сделаете именно это, шлак производиться не будет. Вы также будете , а не производят шлак — материал, который был скорее
жидкость однократно — если у вас температура в среднем слишком низкая (ниже примерно
1.![]() На самом деле, очень ранняя выплавка меди, по-видимому, была довольно «безшлаковый». У меня есть эта часть информации и многое из того, что описано здесь и в соответствующих модулях из Андреас Книга Гауптмана: «Археометаллургия меди», настоящая сокровищница (но не все так легко читается) и Книга Редера, уже упомянул. Бесшлаковая плавка вызывает определенную проблему, потому что археологи обучены ищите шлак, если ищут плавку. Легко не заметить признаки плавка, если шлака нет или его очень мало. И это практически невозможно выяснить, использовался ли 5000-летний тигель для «бесшлаковая» плавка s или только для расплавить немного меди. | ||||||||
Теперь ко второму
точка.![]() Есть несколько моментов, которые в принципе достаточно универсальны, если разные в деталях. Я дам их вам один за другим. Сначала давайте посмотрим на микроструктура некоторых шлаков: | ||||||||
| ||||||||
«Медный шлак» справа выше из
ранняя выплавка меди в районе Фаян / Иордания.![]() Нет, не буду объяснять. Поверь мне: ты нет хочу узнать подробности о шлаке. Достаточно хорошо знать, что есть люди, которые знают (почти) все, что нужно знать о шлаке. Давайте сосредоточимся о том, что шлак делает для нас. | ||||||||
1. Жидкий шлак транспортирует металл туда, куда вам нужно. Процесс восстановления обычно происходит при средние температуры. То руда превращается в пористый металл, покрывающий рудное тело, и этот композит до сих пор покрыт коркой. Производимый металл занимает меньший объем чем руда, и это вызовет напряжение и, возможно, растрескивание, обнажая больше руды в восстановительный газ. ![]() Теперь вы хотите, чтобы ваши металлические частицы двигались через окисляя горячую зону вашего плавильного завода , не становясь окисленный и, в случае железа, сильно науглероженный. Если они это сделают что, поскольку твердые тела движутся вниз с медленной скоростью бремени, шансы невелики что они проходят через окислительную зону, не окисляясь полностью снова. Если металл должен перейти в жидкое состояние уже в зоне восстановления, он просачиваться вниз, и это намного быстрее.Затем части жидкого металла могут его на дно и собирают там в жидком состоянии. Это может случиться для меди и почти наверняка произойдет для свинца и олова. Тем не менее, вы потеряет часть произведенного металла. Он окислится и попадет в шлак. Если вы расплавите железо, оно не станет жидким. Но мелкие частицы железа производится в верхней части плавильного завода, все еще необходимо перемещаться ниже фурмы, где они собираются и спекаются вместе в своего рода самодвижущемся порошковая металлургия процесс. ![]() Как металлическая частица, вы не можете избежать некоторого окисления в горячем и неподвижном состоянии. богатая кислородом зона вокруг фурмы. Если вы будете двигаться быстро, вы можете избежать но полное окисление. Быстрое движение потребует, чтобы время пребывания вашего процесса должно быть коротким. Но как это сделать? Время пребывания хорошо работающего процесса в значительной степени исправлено, и вы не можете изменить его по своему желанию.Более того, если вы слишком быстро двигаетесь по горячие зоны, ваш металл может не расплавиться или стать достаточно перегрет, чтобы оставаться в расплавленном состоянии. Как ни посмотри, у тебя проблема | ||||||||
Вот решение проблемы: Приложить
ваш металл в чем-то жидком, что защищает его и перемещает его вниз быстрее, чем бремя
движется.![]() Возьмите ведро, проделайте в дне множество мелких отверстий, наполните его обычным угля для барбекю и налейте немного воды сверху.Что будет просачиваться в дно довольно грязная вода, так как она унесла все мелкие кусочки древесного угля с ним, когда он просочился вниз. Если вы посмотрите внимательно, вы также заметите, что мелкие частицы пыли внутри капли воды сплавляются вместе, цепляясь за друг с другом. То же самое с металлическими частицами внутри жидкого шлака. Внутри жидкости при падении они имеют тенденцию к комку, потому что это уменьшает их поверхность и, следовательно, поверхность энергия. Не имеет большого значения, твердые или жидкие частицы металла; Это работает в любом случае.Ключевое слово — «поверхность». напряжение», но я не буду вдаваться в подробности здесь. | ||||||||
Пришло время сделать два замечания о
плавки, которые редко упоминаются в литературе.![]()
| ||||||||
2. Шлак избавляется от пустой породы . Это немного тривиально, но подумайте: как бы работала ваша плавильная печь, если бы пустая порода не сжижается, а остается твердым? Вы бы собирали все больше и больше «камни» и каменная пыль внутри плавильни. ![]() | ||||||||
3. Шлак избавляет от некоторых нежелательных примесей . Если повезет, некоторые примеси, которые вы не хотите иметь в своем металле, предпочтут раствориться в шлаке. Это поддерживает концентрацию в металле ниже, чем то, что вы бы получили без шлака. | ||||||||
Это работает для некоторых, но не для всех примесей.![]() Может быть, скорректировав состав шлака, можно избавиться еще от нескольких примеси? Получить к нему! | ||||||||
4. Шлак защищает бассейн расплавленного металла на самом дне вашей печи. Шлак может сделать это, потому что он никогда не смешивается с расплавленным металлом (как, например, вода и спирт), но всегда разделяются (как вода и масло).Ключевое слово вот «поверхность напряжение» или энергия еще раз. Шлак всегда сверху, потому что его плотность меньше, чем у металлов. который можно плавить с углеродом. | ||||||||
Этого должно быть достаточно, чтобы убедить вас
этот шлак не только почти неизбежен, но и полезен.![]() Шлак – это всегда достаточно сложная смесь нескольких компонентов (см. выше!).Поскольку большинство «камней» и таким образом, большая часть пустой породы содержит силикаты, вы всегда найдете там силикаты. Поскольку «грязный кремнезем» — это просто другое слово для обозначения стекло, шлак обычно демонстрирует стекловидное поведение. Он не тает, когда нагревается, он просто становится менее вязкий. Сделайте его достаточно горячим, и его текучесть (почти) похожа что воды. Температура, необходимая для достижения хорошей текучести, зависит от ингредиенты. | ||||||||
Важный первый пункт об оптимизации шлака
заключается в том, что у вас достаточно (как правило, больше, чем металла), и что это будет
достаточно жидкий, скажем, при 1 100 90 234 o 90 235 C (2 012 90 234 o 90 235 F).![]() Поиск правильного типа и количества флюса является одним из секретов превосходного качества. плавка. Вот один из таких секретов выявлено для выплавки чугуна: Флюс «Брауншпат» (коричневый шпат) и «Eisenkalk» (железистый мел) в точном количестве — и оба флюса по существу сидерит или карбонат железа (FeCO 3 ).Сидерит обычно является лучшим флюсом, чем другие железные руды. но все железные руды «работают» и использовались всеми кому не лень на всем протяжении тысячелетия. Не только для выплавки железа, но и для выплавки меди! Это причина, по которой древние шлаки от выплавки меди или от выплавки железа часто очень похожи по составу. ![]() | ||||||||
Тот факт, что железные руды являются очень хорошими флюсами
означает, что выплавка чугуна может быть « самофлюсующаяся «.Красиво, но расточительно, потому что
много вашего железа тогда окажется в шлаке. На самом деле, вы можете произвести
ничего, кроме шлака в вашем плавильном цеху, если вы точно не знаете, кто вы
делает. Довольно интересно, не правда ли? Парни, у которых, к счастью, есть немного сидерита в их железные руды (как протоавстрийцы, которые подлизывались к римлянам), автоматически получают лучшую плавку по сравнению с теми ребятами, которым приходится обходиться без это (как протошлезвиг-голштинцы в моем районе, которые боролись с римляне). | ||||||||
Анализ
состава древнего шлака и, используя полученные знания, вернуться к
техника плавки, довольно сложная и разочаровывающая, но полезная
предприятие.![]() Однако здесь я оставлю эту тему сейчас, пока она не стала слишком очевидной. что я ничего об этом не знаю. | ||||||||
| ||||||||
«Грязная и неэффективная» Древняя плавка: Горнило и Паяльная трубка | ||||||||
Первая крупная плавка
произведена медь. Это определенно был , а не .
на плавильном заводе, таком большом и сложном, как
тот, который я использовал
объяснить основы плавки.Многие люди предполагают, что это не было сделано
в плавильне, но случайно попал в костер, делая
глиняной посуды или во время обжига
горение извести. Фактически,
Я не читал о последнем, так что я претендую на кредит. Обжиг извести, после
все, это техника гораздо более древняя, чем выплавка или гончарное дело, и уже довольно
развивались до того, как появилась плавка.![]() Может ли это быть правдой? Не могли бы вы понюхать что-то простое вроде олова, свинца или меди случайно в костре или в печи? Ответ: это почти невозможно — но не совсем.Давайте посмотрим, почему. | ||||||||
1. Вам нужно иметь руду в огне. Банка
руды довольно редки. Поэтому очень маловероятно, но не невозможно, что
некоторые случайно попадают в костер. То же самое для свинцовой и медной руды,
даже в этом случае они не так уж редки. 2. Вам нужен угарный газ для восстановления руды. Или ты? как мы будем см. ниже, вы можете восстановить руду без угарного газа, но это не тут очень помогают.Угарный газ образуется, если некоторое количество углерода достаточно горячее (около 1 000 или С; 1 832 или Ф) и лишенный кислорода/воздуха. Это очень маловероятно — но не невозможно — происходит в типичном дровяном костре. ![]() 3. Если, несмотря ни на что, вам удастся произвести кусок металла, он немедленно плавится в случае свинца и олова, поглощаясь пеплом и куски угля. Медь не плавится (такого огня не бывает в походном костре), а образует небольшие хлипкие кусочки, склонные к немедленному окислению.Другими словами: если вы не посмотрите очень внимательно на остатки вашего костра, вы бы этого не заметили вы произвели немного металла. 4. Как насчет керамики? Вы украшаете некоторые горшки некоторыми красочные медные руды и затем уволить их. Вы бы не понюхали эти руды? Хорошо, может быть. В правильном печь, бег при высоких температурах выше, скажем, 1 000 90 234 o 90 235 °С; (1 832 o F) и с специально созданной восстановительной атмосферой (иначе она всегда была бы окисляющей), может случиться выплавка меди — но эта продвинутая керамика появилась намного позже того, как была изобретена плавка! В виде до тех пор, пока горшки обжигали, помещая их в своего рода прославленный лагерь огонь — см. ![]() | ||||||||
Ф.Оверман, в «А
Трактат о металлургии (Нью-Йорк и Лондон, 1852 ) с. 656., написал
вслед за темой: «Если западный глубинник
хочет выстрела или пуль, он разожжет огонь в дупле дерева или старом пне
дерева, поместите немного галенита на обугленное дерево и расплавьте его. После
остывая, он находит металл на дне дупла». Если это действительно так, мы все равно должны принять к сведению, что это не было случайное плавление в костре но преднамеренная плавка в очень примитивной печи. | ||||||||
Люди во время плавки
возникла медь, были одержимы «зелеными камнями»,
используется для изготовления украшений. Иногда они сталкиваются с самородной медью (выглядящей зеленой).
так как окислился снаружи), и иногда они признавали, что это
что-то другое работало это в
бисер и шило.![]() Каким-то образом, и я не претендую на то, чтобы знать, как именно, они, должно быть, плавили медь. случайно при работе с зеленью так или иначе.Большинство из время никто не заметил. Иногда кто-то замечал, но не мог воспроизвести «экспериментировать» и потерял интерес. Но в конце концов кто-то где-то начали намеренно производить медь, и эта техника прижилась. Как убедительно свидетельствуют современные данные, очень ранняя «медная «промышленность» носила надомный характер. Вы работали дома с «привозной» медной рудой. Признаков плавки меди никогда не было обнаружены при самых ранних разработках медной руды; кажется, это было сделано в поселения в другом месте. Первая преднамеренная плавка меди была произведена в самой простой плавильне. можно представить: «стандартная» керамическая миска диаметром около (20–30) см. и (16 — 30) см в высоту. Мы называем такую чашу тиглем , но нет никакой принципиальной разницы с тиглем. чаша, используемая, например, для варки пива. ![]() Вот как это выглядело схематически, настоящие чаши здесь. | ||||||||
| ||||||||
Для плавки вы складываете свой уголь — руда
смесь больше на одной стороне и окуните свою паяльную трубку в слой древесного угля.![]() Да, это грязно и неэффективно, но есть преимущества: вы можете легко манипулируйте содержимым вашей «плавильни»: таскайте угли, добавляйте топливо и руда здесь или там, удар в том или ином месте и так далее. ![]() | ||||||||
Обычно вы не получите лужу жидкости таким образом медь покрыта жидким шлаком. Ваша средняя температура слишком низкая, а пространственная и временная однородность процесса недостаточно хорошая. То, что вы получаете, представляет собой грязную смесь меди . гранулы , погруженные в расплавленную массу частично сжиженного шлака, древесного угля куски и остатки руды. | ||||||||
Ранняя медь
«промышленность», оказывается, состояла в основном из обработки тигля
содержимое, ударив по нему каменными молотками, чтобы оторвать драгоценные маленькие кусочки
там меди. Следующим шагом будет плавление (и, таким образом, также автоматически
рафинирование) меди.![]() Как я уже заявил раньше, если вы не умеете плавить, у вас будут большие проблемы, чтобы просто расплавить самородную медь.Но если вы владеете плавильной технологией, плавка теперь легко по нескольким причинам:
| ||||||||
Все, что вам нужно сделать, это подуть прямо на
слой древесных углей сверху Прямо под поверхностью (фактическое расстояние
смотря как сильно дуть) температура будет на пиковых значениях и жарко
достаточно, чтобы расплавить там медь.![]() Ваш « слиток » после охлаждения станет круглым плосковыпуклый диск — и это то, что археологи склонны находить в ранней меди плавильных обществ. | ||||||||
Процесс, однако, беспорядочный и неэффективный. Он не подходит для «массового производства» меди. Тем более пока работает — не ну а именно так — с оксидными или карбонатными рудами найдено на поверхности вблизи Госсан или немного ниже месторождения медной руды, типичные сульфиды находятся немного глубже будет иметь тенденцию создавать проблемы.Ядовитые серосодержащие пары, выходящие из ваш тигель будет первой, но не единственной проблемой. | ||||||||
Плавка в тигле с подогревом снаружи | ||||||||
Плавка в тигле может производиться в
способ, совершенно отличный от того, что указано выше.![]() Это не важный метод, и даже неясно, использовался ли он когда-либо в древность. Однако, по некоторым данным, вариант знаменитого индийского тигельная (или воотц) сталь может быть сделано таким образом. | ||||||||
Один из способов сделать это — припудрить ингредиенты. Вы не продуваете воздух через них, поэтому вам не нужно обеспечивать много свободного места, чтобы уменьшить сопротивление воздуха.Так как углерод там будет очень жарко, а так как вокруг много CO 2 вы делаете, чтобы сделать тигель очень горячим, есть вероятность, что вы будете производить углерод монооксид внутри вашего тигля и уменьшить руду. Но вам даже не нужно сделай это! Сюрприз: | ||||||||
| ||||||||
Вы можете восстанавливать руду напрямую с помощью твердого углерода ! Одна возможная реакция (из многих) это: | ||||||||
| ||||||||
Это так называемое карботермическая реакция не очень
эффективная реакция, поскольку она может происходить только там, где твердый углерод соприкасается
твердая руда, и этот контакт даже разрушается реакцией! Имея небольшой
частицы, тщательно перемешанные, помогут добиться максимально возможной площади контакта
возможный.![]() | ||||||||
| ||||||||
Окислительная атмосфера — это то, что у вас есть в обычных
костров или дровяных печей, потому что вы всегда даете больше кислорода, чем потребляете
топливом, если не принять специальных мер.![]() Есть улов, из курс. Все должно быть правильно, потому что у вас мало контроля о том, что происходит в вашем тигле, как только вы зажжете огонь. Ваш тигель должен быть изготовлен из огнеупорных материалов и очень хорошего качества, чтобы быть в состоянии выдержать жару и не стать частью шлака и так далее. То тигли, используемые для плавки труб с прямым дутьем, напротив, практически не нагреваются. снаружи, и в большинстве случаев, если внутри не бывает очень высоких температур либо.Также может существовать опасность того, что реакция «запустится». прочь», и газ выбрасывается так быстро, что камера взрывается. | ||||||||
Редер подозревает, что плавка
в нагретой форме тигля внешняя сторона могла широко использоваться для всех
виды металлов. К сожалению, легко узнаваемых артефактов не осталось
позади.![]() | ||||||||
Плавка | Encyclopedia.com
Добытая руда перерабатывается для обогащения нужных минералов. В случае металлических руд эти минеральные концентраты обычно нуждаются в дальнейшей переработке для отделения металла от других элементов в рудных минералах.Плавка — это процесс отделения металла от примесей путем нагревания концентрата до высокой температуры, чтобы металл расплавился. При плавке концентрата образуется металл или высококачественная металлическая смесь вместе с твердыми отходами, называемыми шлаком.
Основными источниками загрязнения, вызванного плавкой, являются загрязненные выбросы в атмосферу и технологические отходы, такие как сточные воды и шлак.
Одним из видов загрязнения, связанного с выбросами в атмосферу, являются кислотные дожди. Плавка сульфидных руд приводит к выбросу газообразного диоксида серы, который вступает в химическую реакцию в атмосфере с образованием тумана серной кислоты.Когда эти кислотные дожди падают на землю, они повышают кислотность почв, ручьев и озер, нанося вред здоровью растительности, рыб и популяций диких животных.
На старых плавильных заводах выбросы в атмосферу содержали повышенные уровни различных металлов. Медь и селен, например, которые могут выделяться из медеплавильных заводов, важны для организмов в качестве микроэлементов, но они токсичны, если их слишком много. Эти металлы могут загрязнять почву вблизи плавильных заводов, уничтожая большую часть растительности.Кроме того, твердые частицы, выбрасываемые плавильными заводами, могут включать оксиды таких токсичных металлов, как мышьяк (кумулятивный яд), кадмий (болезнь сердца) и ртуть (повреждение нервов).
По сравнению с загрязнением, вызванным выбросами в атмосферу, технологические отходы и шлак вызывают меньшую озабоченность. На современных плавильных заводах большая часть образующихся сточных вод возвращается в технологический процесс. Если экономическая ценность металлического концентрата в шлаке достаточно высока, шлак может быть возвращен в процесс, тем самым уменьшая количество, требующее постоянного удаления.
Новые технологии играют важную роль в снижении или даже предотвращении загрязнения металлургических заводов. Старые металлургические комбинаты выбрасывали большую часть образующегося диоксида серы, и теперь почти весь он улавливается перед выбросом с использованием новых технологий, таких как электростатические осадители, которые улавливают частицы пыли и возвращают их в процесс. Замена или отказ от сырья, например переработка свинцовых аккумуляторов и алюминиевых банок, снижает потребность в переработке руды, что снижает загрязнение окружающей среды.
Некоторые основные федеральные законы и постановления, применимые к металлургии, аналогичны тем, которые применялись к горнодобывающей промышленности с тех пор, как Закон о чистом воздухе (CAA) 1970 года стал законом. CAA установило единые национальные стандарты, которые контролируют определенные опасные загрязнители воздуха.
Садбери, Онтарио, Канада, является одним из крупнейших в мире плавильных комплексов, имеющим международную репутацию сильно загрязненного района, где ведется разработка полезных ископаемых уже более ста лет. Воздействие на окружающую среду заключалось в полностью или частичном оголении растительности на более чем 46 000 га и 7 000 поврежденных кислотой озер.Плавка нанесла большую часть экологического ущерба из-за кислотных дождей и повышенного содержания меди и никеля в непосредственной близости от плавильных заводов. Усилия правительства и промышленности с 1970-х годов устранили большую часть выбросов диоксида серы в этом районе, и был достигнут значительный прогресс в достижении устойчивых экосистем.
см. также Кислотный дождь; Загрязнение воздуха; Вести; Добыча полезных ископаемых; Суперфонд.
Библиография
Ганн, Джон М. (1995). Восстановление и оздоровление промышленного района. Нью-Йорк: Springer-Verlag.
Вайс, Норман Л., изд. (1985). Справочник по переработке полезных ископаемых для малого и среднего бизнеса. Кингспорт, Теннесси: Kingsport Press.
Интернет-ресурсы
Агентство по охране окружающей среды США. (1995). «Отраслевой блокнот Управления по обеспечению соблюдения нормативных требований Агентства по охране окружающей среды: Профиль отрасли цветных металлов». Документ Агентства по охране окружающей среды США № EPA/310-R-95-010. Доступно на http://es.epa.gov.
Геологическая служба США. (2001). «Расположение рудников и заводов по переработке полезных ископаемых — дополнительная информация к карте USGS I-2654.Доступно на http://pubs.usgs.gov.
Геологическая служба США. (2001). «USGS отслеживает кислотные дожди». Информационный бюллетень FS-183-95. Доступно на http://pubs.usgs.gov.
Майкл Дж. МакКинли
Загрязнение от А до Я МакКинли, Майкл Дж.
Что такое плавка? — Золото и серебро Манхэттена
Если вы не проводите выходные за просмотром средневековых боевиков, вы, вероятно, никогда не слышали о термин «плавка». Нет, это не опечатка, это процесс, в результате которого кузнецы производили металлы, необходимые для создания мечей и ножей.Читайте дальше, чтобы узнать, что такое плавка, как она работает и почему она играет важную роль в истории.
Плавка Определено
Плавка – это процесс извлечения металла из руды. Услышав это, вы можете представить себе, как просто отделяете кусок металла от огромного куска камня, но это еще не все. Руда — это не просто смесь горной породы и металла. Металл, содержащийся в руде, часто окисляется, поэтому вам потребуется химическое превращение, чтобы удалить кислород. Таким образом, руда, содержащая металл, должна быть сброшена в доменную печь вместе с топливом и флюсом (химическим чистящим средством).
Когда руда нагревается в печи, расплавленный металл стекает вниз в виде «налета», представляющего собой каплю горячего металла, которую вы вытаскиваете щипцами. Помимо извлечения нужного металла, вы также получите шлак — примеси, отделяемые от руды.
Проблемы плавки
Плавка может быть невероятно сложным процессом. Во-первых, нет никакой гарантии, что вы получите нужный металл при плавке. Вы можете пройти весь процесс сбора руды и плавки только для того, чтобы получить кусок шлака.Во-вторых, ковка только что извлеченного металла в любую форму может быть утомительной. Возможно, вам придется растирать кусок металла в течение нескольких часов, разогревать его и еще раз растирать, чтобы придать ему пригодную для использования форму.
История плавки
Плавка использовалась на протяжении всей истории для создания важных инструментов и оружия. Этот процесс можно проследить вплоть до 5000 г. до н.э., когда на Ближнем Востоке был выплавлен первый металл, медь. Открытие таких металлов, как медь и бронза, оказало значительное влияние на историю человечества.Эти металлы были достаточно прочными, чтобы создавать оружие, такое как боевые топоры, копья и наконечники стрел, в дополнение к шлемам, щитам, наголенникам и другим бронежилетам.