чем зачистить сварочный шов? Как зачищать сварочный шов болгаркой? ГОСТ. Чем зачистить шов в труднодоступном месте?
В процессе сварки различных изделий и конструкций образуются сварочные швы. Они могут полностью испортить внешний вид предмета, поэтому от них лучше избавиться. Сделать зачистку можно различными способами. Сегодня мы поговорим о том, как просто убрать такие швы и чем это можно сделать.
Особенности
Зачистка сварочных швов после сварки является необходимой процедурой. В процессе таких работ происходит сильное нагревание металлических элементов до температуры плавления, что приводит к напряжению внутри и изменению формы. Помимо этого, на швах будут образовываться мелкие частицы и шлак. В настоящее время существует большое количество всевозможных методов и способов, позволяющих удалять сварочные швы с металлических изделий.
Зачем нужна?
Сильное внутреннее напряжение в металлической конструкции, которое образуется в процессе сварочных работ, может привести не только к деформации детали, но и к ее дальнейшему быстрому разрушению. Кроме того, в местах, где был неравномерный нагрев, может измениться структура кристаллической решетки. Это приводит к ухудшению различных химических и физико-механических свойств материала. Специальная термическая обработка дает возможность восстановить внутреннее строение металлических деталей, а также улучшить их свойства.
Процедура позволяет сделать металл достаточно прочным и устойчивым к образованию коррозии.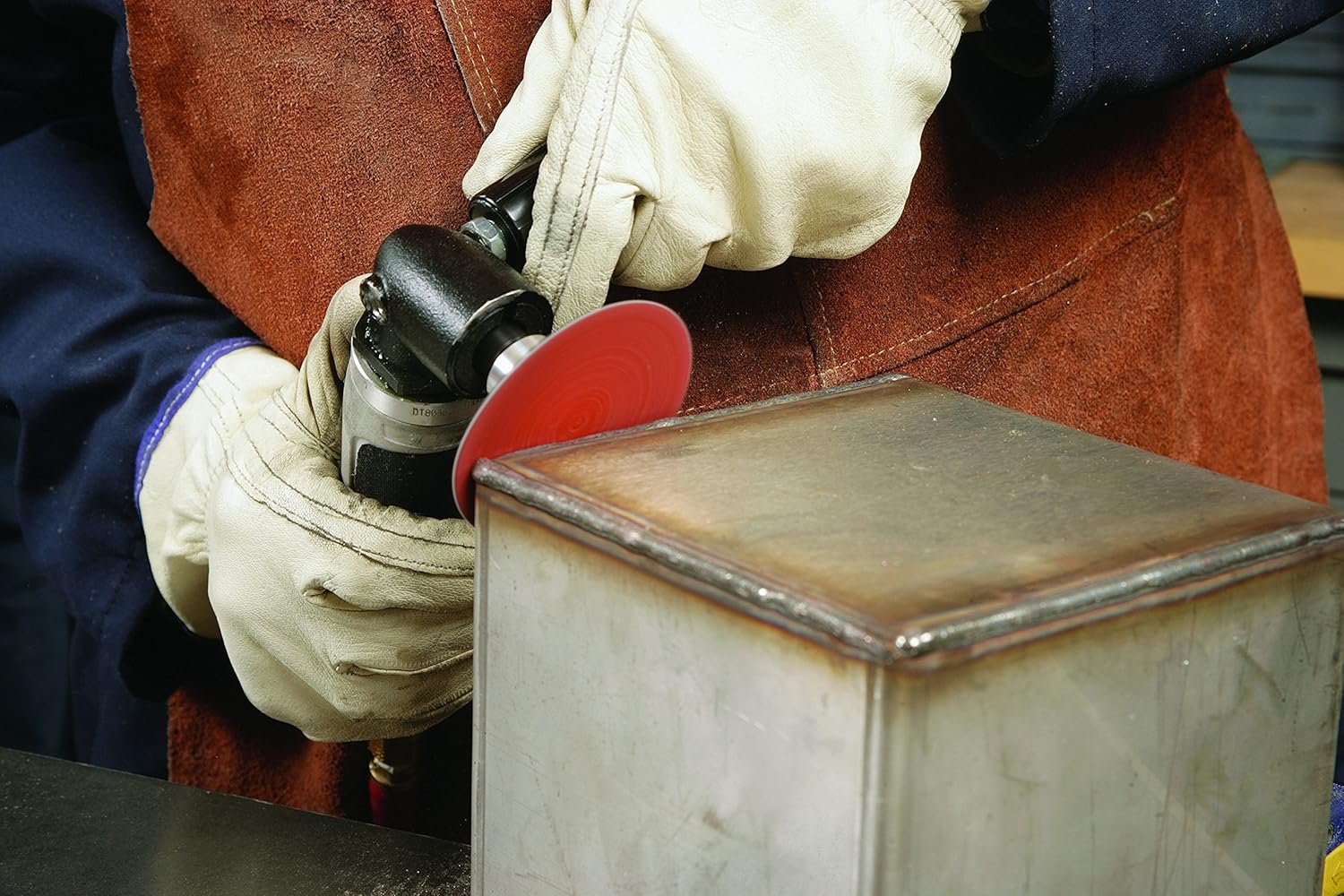
Способы
Избавиться от сварочных швов на металле можно различными способами:
- термическая обработка;
- механическая обработка;
- химическая обработка.
Термическая обработка
Она используется в том случае, если необходимо зачищать остаточные напряжения во внутренней части. Данный тип обработки обязателен после сварки тонкостенных металлических конструкций. Чтобы произвести такую процедуру, следует слегка нагреть деталь, а затем охладить ее по заданному температурному графику.
Данный способ осуществляется в три этапа. На первом этапе нужно нагреть область вокруг сварочного шва, затем надо оставить элемент нагретым в течение небольшого времени, в конце все остужается. Такой способ позволяет восстановить свойства материала (пластичность и прочность), снять внутреннее напряжение и обеспечить долговечность сварки.
Термическая обработка позволяет бесшумно снять весь шлак со швов.
Для контроля за температурным режимом можно использовать различные агрегаты: пирометр и тепловизор (электронные аппараты, они измеряют нужные показатели дистанционно), термокраска и термокарандаш (изменяют свою расцветку при смене температуры).
Механическая обработка
Этот способ позволяет убирать шлак, металлические «брызги» и окалины со сварочных швов посредством шлифовки. Для механического типа понадобится или проволочная прочная щетка, или специальный абразивный диск. На промышленных предприятиях такие элементы закрепляются в шлифовальных машинках (нередко в бытовых условиях такой аппарат называют болгаркой). Перед обработкой стоит подобрать подходящий круг.
Оптимальным вариантом для сварочных швов на нержавеющей стали будет цирконат алюминия, так как он не оказывает на такие изделия коррозийных воздействий. Также часто используются особые
Самым простым и дешевым вариантом станут насадки на бумажной основе. Чаще всего их делают с напылением из оксида алюминия. Но уровень цены будет полностью соответствовать и уровню качества шлифовки швов. Помните, что подобные насадки следует подбирать с учетом типа работы. Если вам нужно зачистить швы в труднодоступных местах в угловых сложных металлических конструкций, то тогда размер абразивного элемента насадки лучше взять небольшого размера.
Для запиловки самого верхнего наиболее грубого слоя с окалинами и шлаком допустимо использовать насадку самого большого размера. В данном случае она не сможет повредить сам материал.
Финишная обработка всегда осуществляется самым маленьким шлифовальным инструментом, поэтому при проведении таких процедур будут использоваться сразу несколько видов насадок разных по размеру.
Химическая обработка
Самый лучший результат можно достичь, совместив механическую и химическую обработку швов.
Кроме того, эта процедура дает возможность удалять места, где скапливается окисленный хром или никель. Если их своевременно не удалить, они могут быть поражены коррозией. Если сварочные швы небольшие, то тогда можно просто нанести на их поверхность химический состав. Иногда деталь полностью окунают в вещество. После травления следует выполнить пассивацию, которая позволит придать металлу дополнительную прочность. Пассивация представляет собой обработку детали специальным раствором, который позволяет формировать на поверхности изделия защитную пленку, не дающую образовываться коррозийному слою.
После проведения химической обработки обязательно нужно смыть все остатки растворов водой. При этом сточную воду нужно утилизировать максимально осторожно. Ведь жидкость будет содержать в себе большое количество вредных тяжелых металлов и кислот. Их можно немного нейтрализовать с помощью щелочей.
После все это тщательно фильтруют и только потом выливают в безопасное место.
Контроль качества
При проведении сварочных работ и затирки образовавшихся швов на металле следует руководствоваться правилами и нормами,
Также там можно найти и таблицы с максимальными значениями выпуклости швов в миллиметрах (в зависимости от их размеров), перечень методов, позволяющих производить контроль за качеством сварных соединений.
О том, как идеально зачистить сварочные швы на профильной трубе, вы можете узнать из видео ниже.
чем зачистить сварочный шов? Как зачищать сварочный шов болгаркой? ГОСТ. Чем зачистить шов в труднодоступном месте?
В процессе сварки различных изделий и конструкций образуются сварочные швы. Они могут полностью испортить внешний вид предмета, поэтому от них лучше избавиться. Сделать зачистку можно различными способами. Сегодня мы поговорим о том, как просто убрать такие швы и чем это можно сделать.
Особенности
Зачистка сварочных швов после сварки является необходимой процедурой. В процессе таких работ происходит сильное нагревание металлических элементов до температуры плавления, что приводит к напряжению внутри и изменению формы. Помимо этого, на швах будут образовываться мелкие частицы и шлак. В настоящее время существует большое количество всевозможных методов и способов, позволяющих удалять сварочные швы с металлических изделий.
Зачем нужна?
Сильное внутреннее напряжение в металлической конструкции, которое образуется в процессе сварочных работ, может привести не только к деформации детали, но и к ее дальнейшему быстрому разрушению. Кроме того, в местах, где был неравномерный нагрев, может измениться структура кристаллической решетки. Это приводит к ухудшению различных химических и физико-механических свойств материала. Специальная термическая обработка дает возможность восстановить внутреннее строение металлических деталей, а также улучшить их свойства. Процедура позволяет сделать металл достаточно прочным и устойчивым к образованию коррозии.
Способы
Избавиться от сварочных швов на металле можно различными способами:
- термическая обработка;
- механическая обработка;
- химическая обработка.
Термическая обработка
Она используется в том случае, если необходимо зачищать остаточные напряжения во внутренней части. Данный тип обработки обязателен после сварки тонкостенных металлических конструкций. Чтобы произвести такую процедуру, следует слегка нагреть деталь, а затем охладить ее по заданному температурному графику.
Данный способ осуществляется в три этапа. На первом этапе нужно нагреть область вокруг сварочного шва, затем надо оставить элемент нагретым в течение небольшого времени, в конце все остужается. Такой способ позволяет восстановить свойства материала (пластичность и прочность), снять внутреннее напряжение и обеспечить долговечность сварки. Но при этом она имеет и ряд недостатков: необратимость (если вы не смогли провести обработку в соответствии с графиком температуры, то исправить брак будет почти невозможно), для такой процедуры требуется дорогостоящее профессиональное оборудование.
Термическая обработка позволяет бесшумно снять весь шлак со швов.
Для контроля за температурным режимом можно использовать различные агрегаты: пирометр и тепловизор (электронные аппараты, они измеряют нужные показатели дистанционно), термокраска и термокарандаш (изменяют свою расцветку при смене температуры).
Механическая обработка
Этот способ позволяет убирать шлак, металлические «брызги» и окалины со сварочных швов посредством шлифовки. Для механического типа понадобится или проволочная прочная щетка, или специальный абразивный диск. На промышленных предприятиях такие элементы закрепляются в шлифовальных машинках (нередко в бытовых условиях такой аппарат называют болгаркой). Перед обработкой стоит подобрать подходящий круг.
Оптимальным вариантом для сварочных швов на нержавеющей стали будет цирконат алюминия, так как он не оказывает на такие изделия коррозийных воздействий. Также часто используются особые лепестковые абразивные насадки. Последние должны иметь лепестки, созданные на тканевой основе. Они считаются наиболее надежными по сравнению с остальными разновидностями. Элементы с лепестками на тканевой основе и с нанесением из цирконата алюминия обладают относительно высокой стоимостью, но и очистка посредством их отличается особым уровнем качества.
Самым простым и дешевым вариантом станут насадки на бумажной основе. Чаще всего их делают с напылением из оксида алюминия. Но уровень цены будет полностью соответствовать и уровню качества шлифовки швов. Помните, что подобные насадки следует подбирать с учетом типа работы. Если вам нужно зачистить швы в труднодоступных местах в угловых сложных металлических конструкций, то тогда размер абразивного элемента насадки лучше взять небольшого размера.
Для запиловки самого верхнего наиболее грубого слоя с окалинами и шлаком допустимо использовать насадку самого большого размера. В данном случае она не сможет повредить сам материал.
Финишная обработка всегда осуществляется самым маленьким шлифовальным инструментом, поэтому при проведении таких процедур будут использоваться сразу несколько видов насадок разных по размеру.
Химическая обработка
Самый лучший результат можно достичь, совместив механическую и химическую обработку швов. Последняя может производиться посредством травления или пассивации. Такой тип удобен для зачистки углом. Травление чаще всего выступает в качестве подготовительного этапа перед механической обработкой. Оно должно выполняться с использованием специальных химических веществ. Они позволят создать надежное покрытие, стойкое к образованию коррозии.
Кроме того, эта процедура дает возможность удалять места, где скапливается окисленный хром или никель. Если их своевременно не удалить, они могут быть поражены коррозией. Если сварочные швы небольшие, то тогда можно просто нанести на их поверхность химический состав. Иногда деталь полностью окунают в вещество. После травления следует выполнить пассивацию, которая позволит придать металлу дополнительную прочность. Пассивация представляет собой обработку детали специальным раствором, который позволяет формировать на поверхности изделия защитную пленку, не дающую образовываться коррозийному слою.
После проведения химической обработки обязательно нужно смыть все остатки растворов водой. При этом сточную воду нужно утилизировать максимально осторожно. Ведь жидкость будет содержать в себе большое количество вредных тяжелых металлов и кислот. Их можно немного нейтрализовать с помощью щелочей.
После все это тщательно фильтруют и только потом выливают в безопасное место.
Контроль качества
При проведении сварочных работ и затирки образовавшихся швов на металле следует руководствоваться правилами и нормами, закрепленными в ГОСТ 31385-2008 (требования к сварке и контролю качества сварных соединений). В данном ГОСТ можно найти общие требования к проведению таких работ, отдельные требования к различным свойствам изделий (прочность, ударная вязкость, технологические испытания на изгиб таких соединений).
Также там можно найти и таблицы с максимальными значениями выпуклости швов в миллиметрах (в зависимости от их размеров), перечень методов, позволяющих производить контроль за качеством сварных соединений.
О том, как идеально зачистить сварочные швы на профильной трубе, вы можете узнать из видео ниже.
чем зачистить сварочный шов? Как зачищать сварочный шов болгаркой? ГОСТ. Чем зачистить шов в труднодоступном месте?
В процессе сварки различных изделий и конструкций образуются сварочные швы. Они могут полностью испортить внешний вид предмета, поэтому от них лучше избавиться. Сделать зачистку можно различными способами. Сегодня мы поговорим о том, как просто убрать такие швы и чем это можно сделать.
Особенности
Зачистка сварочных швов после сварки является необходимой процедурой. В процессе таких работ происходит сильное нагревание металлических элементов до температуры плавления, что приводит к напряжению внутри и изменению формы. Помимо этого, на швах будут образовываться мелкие частицы и шлак. В настоящее время существует большое количество всевозможных методов и способов, позволяющих удалять сварочные швы с металлических изделий. Сделать это можно и при помощи специальных инструментов (наждачник, фреза), и вручную при помощи проволочных щеток.
Зачем нужна?
Сильное внутреннее напряжение в металлической конструкции, которое образуется в процессе сварочных работ, может привести не только к деформации детали, но и к ее дальнейшему быстрому разрушению. Кроме того, в местах, где был неравномерный нагрев, может измениться структура кристаллической решетки. Это приводит к ухудшению различных химических и физико-механических свойств материала. Специальная термическая обработка дает возможность восстановить внутреннее строение металлических деталей, а также улучшить их свойства. Процедура позволяет сделать металл достаточно прочным и устойчивым к образованию коррозии.
Способы
Избавиться от сварочных швов на металле можно различными способами:
- термическая обработка;
- механическая обработка;
- химическая обработка.
Термическая обработка
Она используется в том случае, если необходимо зачищать остаточные напряжения во внутренней части. Данный тип обработки обязателен после сварки тонкостенных металлических конструкций. Чтобы произвести такую процедуру, следует слегка нагреть деталь, а затем охладить ее по заданному температурному графику.
Данный способ осуществляется в три этапа. На первом этапе нужно нагреть область вокруг сварочного шва, затем надо оставить элемент нагретым в течение небольшого времени, в конце все остужается. Такой способ позволяет восстановить свойства материала (пластичность и прочность), снять внутреннее напряжение и обеспечить долговечность сварки. Но при этом она имеет и ряд недостатков: необратимость (если вы не смогли провести обработку в соответствии с графиком температуры, то исправить брак будет почти невозможно), для такой процедуры требуется дорогостоящее профессиональное оборудование.
Термическая обработка позволяет бесшумно снять весь шлак со швов.
Для контроля за температурным режимом можно использовать различные агрегаты: пирометр и тепловизор (электронные аппараты, они измеряют нужные показатели дистанционно), термокраска и термокарандаш (изменяют свою расцветку при смене температуры).
Механическая обработка
Этот способ позволяет убирать шлак, металлические «брызги» и окалины со сварочных швов посредством шлифовки. Для механического типа понадобится или проволочная прочная щетка, или специальный абразивный диск. На промышленных предприятиях такие элементы закрепляются в шлифовальных машинках (нередко в бытовых условиях такой аппарат называют болгаркой). Перед обработкой стоит подобрать подходящий круг.
Оптимальным вариантом для сварочных швов на нержавеющей стали будет цирконат алюминия, так как он не оказывает на такие изделия коррозийных воздействий. Также часто используются особые лепестковые абразивные насадки. Последние должны иметь лепестки, созданные на тканевой основе. Они считаются наиболее надежными по сравнению с остальными разновидностями. Элементы с лепестками на тканевой основе и с нанесением из цирконата алюминия обладают относительно высокой стоимостью, но и очистка посредством их отличается особым уровнем качества.
Самым простым и дешевым вариантом станут насадки на бумажной основе. Чаще всего их делают с напылением из оксида алюминия. Но уровень цены будет полностью соответствовать и уровню качества шлифовки швов. Помните, что подобные насадки следует подбирать с учетом типа работы. Если вам нужно зачистить швы в труднодоступных местах в угловых сложных металлических конструкций, то тогда размер абразивного элемента насадки лучше взять небольшого размера.
Для запиловки самого верхнего наиболее грубого слоя с окалинами и шлаком допустимо использовать насадку самого большого размера. В данном случае она не сможет повредить сам материал.
Финишная обработка всегда осуществляется самым маленьким шлифовальным инструментом, поэтому при проведении таких процедур будут использоваться сразу несколько видов насадок разных по размеру.
Химическая обработка
Самый лучший результат можно достичь, совместив механическую и химическую обработку швов. Последняя может производиться посредством травления или пассивации. Такой тип удобен для зачистки углом. Травление чаще всего выступает в качестве подготовительного этапа перед механической обработкой. Оно должно выполняться с использованием специальных химических веществ. Они позволят создать надежное покрытие, стойкое к образованию коррозии.
Кроме того, эта процедура дает возможность удалять места, где скапливается окисленный хром или никель. Если их своевременно не удалить, они могут быть поражены коррозией. Если сварочные швы небольшие, то тогда можно просто нанести на их поверхность химический состав. Иногда деталь полностью окунают в вещество. После травления следует выполнить пассивацию, которая позволит придать металлу дополнительную прочность. Пассивация представляет собой обработку детали специальным раствором, который позволяет формировать на поверхности изделия защитную пленку, не дающую образовываться коррозийному слою.
После проведения химической обработки обязательно нужно смыть все остатки растворов водой. При этом сточную воду нужно утилизировать максимально осторожно. Ведь жидкость будет содержать в себе большое количество вредных тяжелых металлов и кислот. Их можно немного нейтрализовать с помощью щелочей.
После все это тщательно фильтруют и только потом выливают в безопасное место.
Контроль качества
При проведении сварочных работ и затирки образовавшихся швов на металле следует руководствоваться правилами и нормами, закрепленными в ГОСТ 31385-2008 (требования к сварке и контролю качества сварных соединений). В данном ГОСТ можно найти общие требования к проведению таких работ, отдельные требования к различным свойствам изделий (прочность, ударная вязкость, технологические испытания на изгиб таких соединений).
Также там можно найти и таблицы с максимальными значениями выпуклости швов в миллиметрах (в зависимости от их размеров), перечень методов, позволяющих производить контроль за качеством сварных соединений.
О том, как идеально зачистить сварочные швы на профильной трубе, вы можете узнать из видео ниже.
чем зачистить сварочный шов? Как зачищать сварочный шов болгаркой? ГОСТ. Чем зачистить шов в труднодоступном месте?
В процессе сварки различных изделий и конструкций образуются сварочные швы. Они могут полностью испортить внешний вид предмета, поэтому от них лучше избавиться. Сделать зачистку можно различными способами. Сегодня мы поговорим о том, как просто убрать такие швы и чем это можно сделать.
Особенности
Зачистка сварочных швов после сварки является необходимой процедурой. В процессе таких работ происходит сильное нагревание металлических элементов до температуры плавления, что приводит к напряжению внутри и изменению формы. Помимо этого, на швах будут образовываться мелкие частицы и шлак. В настоящее время существует большое количество всевозможных методов и способов, позволяющих удалять сварочные швы с металлических изделий. Сделать это можно и при помощи специальных инструментов (наждачник, фреза), и вручную при помощи проволочных щеток.
Зачем нужна?
Сильное внутреннее напряжение в металлической конструкции, которое образуется в процессе сварочных работ, может привести не только к деформации детали, но и к ее дальнейшему быстрому разрушению. Кроме того, в местах, где был неравномерный нагрев, может измениться структура кристаллической решетки. Это приводит к ухудшению различных химических и физико-механических свойств материала. Специальная термическая обработка дает возможность восстановить внутреннее строение металлических деталей, а также улучшить их свойства. Процедура позволяет сделать металл достаточно прочным и устойчивым к образованию коррозии.
Способы
Избавиться от сварочных швов на металле можно различными способами:
- термическая обработка;
- механическая обработка;
- химическая обработка.
Термическая обработка
Она используется в том случае, если необходимо зачищать остаточные напряжения во внутренней части. Данный тип обработки обязателен после сварки тонкостенных металлических конструкций. Чтобы произвести такую процедуру, следует слегка нагреть деталь, а затем охладить ее по заданному температурному графику.
Данный способ осуществляется в три этапа. На первом этапе нужно нагреть область вокруг сварочного шва, затем надо оставить элемент нагретым в течение небольшого времени, в конце все остужается. Такой способ позволяет восстановить свойства материала (пластичность и прочность), снять внутреннее напряжение и обеспечить долговечность сварки. Но при этом она имеет и ряд недостатков: необратимость (если вы не смогли провести обработку в соответствии с графиком температуры, то исправить брак будет почти невозможно), для такой процедуры требуется дорогостоящее профессиональное оборудование.
Термическая обработка позволяет бесшумно снять весь шлак со швов.
Для контроля за температурным режимом можно использовать различные агрегаты: пирометр и тепловизор (электронные аппараты, они измеряют нужные показатели дистанционно), термокраска и термокарандаш (изменяют свою расцветку при смене температуры).
Механическая обработка
Этот способ позволяет убирать шлак, металлические «брызги» и окалины со сварочных швов посредством шлифовки. Для механического типа понадобится или проволочная прочная щетка, или специальный абразивный диск. На промышленных предприятиях такие элементы закрепляются в шлифовальных машинках (нередко в бытовых условиях такой аппарат называют болгаркой). Перед обработкой стоит подобрать подходящий круг.
Оптимальным вариантом для сварочных швов на нержавеющей стали будет цирконат алюминия, так как он не оказывает на такие изделия коррозийных воздействий. Также часто используются особые лепестковые абразивные насадки. Последние должны иметь лепестки, созданные на тканевой основе. Они считаются наиболее надежными по сравнению с остальными разновидностями. Элементы с лепестками на тканевой основе и с нанесением из цирконата алюминия обладают относительно высокой стоимостью, но и очистка посредством их отличается особым уровнем качества.
Самым простым и дешевым вариантом станут насадки на бумажной основе. Чаще всего их делают с напылением из оксида алюминия. Но уровень цены будет полностью соответствовать и уровню качества шлифовки швов. Помните, что подобные насадки следует подбирать с учетом типа работы. Если вам нужно зачистить швы в труднодоступных местах в угловых сложных металлических конструкций, то тогда размер абразивного элемента насадки лучше взять небольшого размера.
Для запиловки самого верхнего наиболее грубого слоя с окалинами и шлаком допустимо использовать насадку самого большого размера. В данном случае она не сможет повредить сам материал.
Финишная обработка всегда осуществляется самым маленьким шлифовальным инструментом, поэтому при проведении таких процедур будут использоваться сразу несколько видов насадок разных по размеру.
Химическая обработка
Самый лучший результат можно достичь, совместив механическую и химическую обработку швов. Последняя может производиться посредством травления или пассивации. Такой тип удобен для зачистки углом. Травление чаще всего выступает в качестве подготовительного этапа перед механической обработкой. Оно должно выполняться с использованием специальных химических веществ. Они позволят создать надежное покрытие, стойкое к образованию коррозии.
Кроме того, эта процедура дает возможность удалять места, где скапливается окисленный хром или никель. Если их своевременно не удалить, они могут быть поражены коррозией. Если сварочные швы небольшие, то тогда можно просто нанести на их поверхность химический состав. Иногда деталь полностью окунают в вещество. После травления следует выполнить пассивацию, которая позволит придать металлу дополнительную прочность. Пассивация представляет собой обработку детали специальным раствором, который позволяет формировать на поверхности изделия защитную пленку, не дающую образовываться коррозийному слою.
После проведения химической обработки обязательно нужно смыть все остатки растворов водой. При этом сточную воду нужно утилизировать максимально осторожно. Ведь жидкость будет содержать в себе большое количество вредных тяжелых металлов и кислот. Их можно немного нейтрализовать с помощью щелочей.
После все это тщательно фильтруют и только потом выливают в безопасное место.
Контроль качества
При проведении сварочных работ и затирки образовавшихся швов на металле следует руководствоваться правилами и нормами, закрепленными в ГОСТ 31385-2008 (требования к сварке и контролю качества сварных соединений). В данном ГОСТ можно найти общие требования к проведению таких работ, отдельные требования к различным свойствам изделий (прочность, ударная вязкость, технологические испытания на изгиб таких соединений).
Также там можно найти и таблицы с максимальными значениями выпуклости швов в миллиметрах (в зависимости от их размеров), перечень методов, позволяющих производить контроль за качеством сварных соединений.
О том, как идеально зачистить сварочные швы на профильной трубе, вы можете узнать из видео ниже.
Очистка и пассивация сварного шва
Прежде чем ответить на этот вопрос, важно сначала понять состав и физические свойства нержавеющей стали.
Итак, приступим.
Нержавеющая сталь по своей природе пассивна?
По своей сути нержавеющая сталь — это стальной сплав, состоящий в основном из железа с добавлением хрома (минимум 10-12%).
При воздействии нормальных атмосферных условий (воздуха) хром вступает в реакцию с кислородом и создает защитный слой на поверхности сплава.
Пассивный слой очень тонкий, но достаточно прочный, чтобы предотвратить проникновение дополнительного кислорода и влаги внутрь. По этой причине нержавеющая сталь обладает непревзойденными антикоррозийными свойствами.
Итак, является ли нержавеющая сталь пассивной по своей природе? Ответ-да.
Может ли нержавеющая сталь ржаветь?
Поверхность из нержавеющей стали становится активной при повреждении или разрушении слоя оксида хрома.
Если поверхность нержавеющей стали не сильно повреждена, пассивный слой, вероятно, восстановится естественным образом, когда произойдет новая реакция между частицами хрома и кислорода.
Однако различные производственные процессы, такие как резка, шлифовка и сварка, могут необратимо разрушить защитный слой на стальной поверхности.
Это создает идеальные условия для образования ржавчины и других загрязнений.
Нарушение пассивного слоя после сварки.
Давление и тепло как неотъемлемые части процесса сварки непосредственно ответственны за образование ржавчины на поверхностях из нержавеющей стали.
Поскольку структура стали изменяется в результате плавления, частицы свободного железа начинают накапливаться на поверхности, где они вступают в реакцию с кислородом и вызывают коррозию.
Как объяснялось ранее, нержавеющая сталь не была бы нержавеющей без защитного слоя хрома.
Концентрация частиц хрома уменьшается даже в зонах термического влияния, а не только на поверхности, подверженной плавлению.
Когда это происходит, необходимо искусственно восстановить пассивное состояние нержавеющей стали.
Однако эффективная пассивация невозможна без тщательной очистки и обработки поверхности после сварки.
Защитный слой оксида хрома не может полностью восстановиться, если все загрязнения не будут удалены с пораженных участков.
Почему шлифование не гарантирует пассивацию сварного шва?
Сварка часто приводит к появлению значительного количества дефектов на поверхности нержавеющей стали. Некоторые из ярких примеров — ржавчина, окалина и цвета побежалости.
Традиционные методы, такие как механическое шлифование или чистка проволочной щеткой, могут быть весьма эффективными при решении этих проблем. Однако эффект от этого процесса носит преимущественно эстетический характер.
Механическое удаление загрязняющих частиц не восстанавливает пассивный слой на поверхности нержавеющей стали и нет гарантий, что слой оксида хрома будет сформирован, чтобы предотвратить повторное появление ржавчины.
Неправильное использование механических шлифовальных станков также может полностью разрушить поверхность и остановить образование нового пассивного слоя.
Кроме того, очистка сварных швов абразивом может привести к более нежелательным последствиям, таким как изменение внешнего вида, появление царапин.
Итак, как правильно очистить и защитить поверхность из нержавеющей стали?
Электрохимический процесс – это очистка и пассивация за один проход.
Сочетания электричества и специальных электролитов достаточно для успешной очистки и пассивации поверхности нержавеющей стали за один прием.
Электрохимический процесс не только удалит дефекты на поверхности после сварки, но и восстановит оксидный слой, который возвращает нержавеющую сталь в ее нормальное пассивное состояние.
В отличие от шлифовки, этот метод очистки успешно удаляет все загрязнения и осветляет сварной шов. Это очень важно для успешного восстановления пассивного слоя.
Аппараты для очистки сварных швов Surfox, Inox System Revolution, Clinox предназначены для очистки сварного шва, инициирования и индуцирования образования пленки оксида хрома на поверхности нержавеющей стали. Таким образом, вы можете быть уверены, что ржавчина и другие загрязняющие факторы не появятся снова на сварных швах после их успешного устранения.
Очистка и пассивация зоны термического влияния
Зона термического влияния (ЗТВ) — это участок на поверхности металла, микроструктура которого изменилась под воздействием тепла во время сварки.
Это нерасплавленная часть металлической поверхности, находящаяся между неповрежденным основным металлом и металлом сварного шва (см. Изображение ниже).
Размер зоны термического влияния зависит от нескольких факторов.
• количество тепла
• типа сварки
• тип используемого материала
Изменение микроструктуры делает сталь более слабой и менее устойчивой к коррозии и растрескиванию под напряжением.
Правильная обработка после сварки (очистка и пассивация) — единственный способ восстановить структурную стабильность стали и предотвратить дальнейшее разрушение.
Но в какой степени? Какую часть поверхности вам действительно нужно обработать? Всю деталь или только зону термического влияния (зону сварки)?
Ответ на самом деле очень прост..
Лучше всего активно очищать и пассивировать только ту часть поверхности, на которую действительно повлиял процесс сварки. Во всех случаях эта область включает сам сварной шов и зону термического влияния (область, где обычно появляются цвета побежалости и другие дефекты после сварки).
Пассивация непораженных участков не повредит, хотя эти области и не требуют целенаправленного и активного лечения, если они не были повреждены механически.
Нейтрализация электролита – важный этап электрохимического метода очистки.
Электрохимическая очистка производится с помощью пищевой кислоты на основе фосфора.
Несмотря на свою мягкость, кислоты часто оставляют белый осадок на поверхности стали после очистки и пассивации.
Удаление этих белых кислотных следов выполняется по двум основным причинам — снижение уровня pH и сохранение привлекательного внешнего вида поверхности.
Поскольку остатки иногда становятся видимыми только через пару дней, важно нейтрализовать поверхность сразу или вскоре после очистки и пассивации.
В большинстве случаев невозможно решить эту проблему с помощью воды, если не использовать мойку высокого давления. Вот почему необходимо использовать специальные нейтрализующие жидкости. Мы рекомендуем использовать нейтрализатор FORSTEX-N.
Компания «СУРФОКС» поставляет Оборудование для очистки сварных швов, пассиваторы во все города России, в том числе в г. Москва, Санкт-Петербург, Челябинск, Пермь, Тюмень, Ульяновск, Казань, Калуга, Новосибирск, Екатеринбург, Нижний Новгород, Калининград, Самара, Омск, Уфа, Саратов, Красноярск, Владивосток, Ростов-на-Дону, Воронеж, Волгоград, Махачкала и другие, а также в Белоруссию, Казахстан, Армению и Киргизию.
У нас вы можете купить Установки для очистки сварных швов, пассиваторы следующих производителей: SURFOX, CLINOX (Nitty-Gritty), INOX SYSTEM (Ricerca Chimica) и другие.
Купить Оборудование для очистки сварных швов, пассиваторы у нас легко:
• Выберите интересующее оборудование в разделе Установки для очистки сварного шва
• Узнайте характеристики, посмотрите фото и видео, нажав на название модели
• Позвоните по номеру +7 495 661 62 42 или отправьте запрос на [email protected] или [email protected]
Компания Сурфокс является специалистом в области электролитической и химической очистки нержавеющей стали, постоянно обновляет свои знания, а также сотрудничает только с проверенными, сертифицированными европейскими производителями оборудования и химии для обработки металла.
Почему выбирают установки SURFOX (Walter), CLINOX (Nitty-Gritty), INOX SYSTEM (Ricerca Chimica) ?
• Травление и пассивация
Вся линия оборудования одновременно выполняет травление и пассивацию.
Применение инвертора, по сравнению с оборудованием, которое работает на основе трансформатора, позволяет в случае короткого замыкания, отсекать ток в тысячную долю секунды, избегая повреждений.
• Полировка
Процедура полировки сварных швов происходит в одну стадию, без необходимости использования пасты или абразивной бумаги, что позволяет добиться максимальных результатов без дополнительной траты времени.
• Питтинговая коррозия
Возникновение точечных сквозных разрушений нержавеющих сталей. Микротрещины препятствуют процессу полной и правильно выполненной пассивации обрабатываемой поверхности. На всех пассиваторах SURFOX, CLINOX (Nitty-Gritty) и INOX SYSTEM установлено специальное оборудование, которое управляется микропроцессором, который улавливает и сокращает возможность короткого замыкания, избегая любой возможности возникновения питтинговой коррозии.
Как купить Оборудование для очистки сварных швов, пассиваторы ?
Компания «СУРФОКС» поставляет Оборудование для очистки сварных швов, пассиваторы во все города России, в том числе в г. Москва, Санкт-Петербург, Челябинск, Пермь, Тюмень, Ульяновск, Казань, Калуга, Новосибирск, Екатеринбург, Нижний Новгород, Калининград, Самара, Омск, Уфа, Саратов, Красноярск, Владивосток, Ростов-на-Дону, Воронеж, Волгоград, Махачкала и другие, а также в Белоруссию, Казахстан, Армению и Киргизию.
Очистка сварных швов и металла от прокатной окалины
После выполнения сварного шва, его необходимо зачистить. Очистка сварного шва улучшает внешний вид металлоконструкций, позволяет избежать проблем, связанных с коррозией металла в зоне сварного шва.
Коррозия – это процесс физико-химического разрушения металла под воздействием внешней среды.
Сварные швы и соединения часто работают в агрессивных средах — атмосферная влажность, морская вода, растворы щелочей и кислот – они способны вызвать разрушающую коррозию.
По характеру процесса различают химическую и электрохимическую коррозию.
Химическая коррозия – разрушение металла под воздействием окружающей среды без присутствия электрического тока. Окисление железа и его сплавов происходит на воздухе, в дистиллированной воде.
Электрохимическая — разрушение металла в электролитах (растворах солей, кислот, щелочей – проводниках эл. тока) и сопровождается появлением электрического тока.
Во время ремонта корпусов речных/морских судов, установлено, что наружная поверхность судов, подводной части корпуса имеет участки корродированного металла. Проанализировав причины коррозии, выяснилось, что окалина, не удаленная с поверхности металла корпуса — это катод (обладает более высоким потенциалом). Участки корпуса судов, где нет окалины — это анод и поэтому металл подвергается не просто химической, но и электрохимической коррозии (т.е. разрушению). Для защиты металлических изделий и сварных швов от воздействия коррозии, сварные швы обрабатывают/очищают и окрашивают специальными грунтовыми красками или покрытиями.
Обработка сварного шва условно делится на три группы. Первая — это очистка сварного шва от шлаков, окалины, цветов побежалости. Вторая, это грубая зачистка, т.е. удаление усиления сварного шва. В-третьих, это доводка поверхности и ее подготовка к окончательной обработке – покраске или нанесению защитных поверхностей.
Очистка сварного шва возможна путем шлифовки сварного шва щеткой из нержавеющей стали, шлифмашинкой, но этот способ не эффективен, да и не возможен в тех случаях, когда доступ к сварному шву ограничен.
В труднодоступных местах оптимальным вариантом будет обработка сварного шва гидро песко стуйным методом с применением оборудования высокого давления (АВД ЛМ/Лименс/Limens). Очистка сварного шва происходит водой с песком, которые подаются под высоким давлением.
Зачистка мест сварки и швов
При подводной сварке для зачистки места сварки и швов, а также для удаления наплывов, брызг металла, шлака и других дефектов сварщик-водолаз должен иметь проволочную щетку, ручной молоток-секач, зубило и щуп для проверки зазоров и правильности подгонки привариваемых листов и заплат.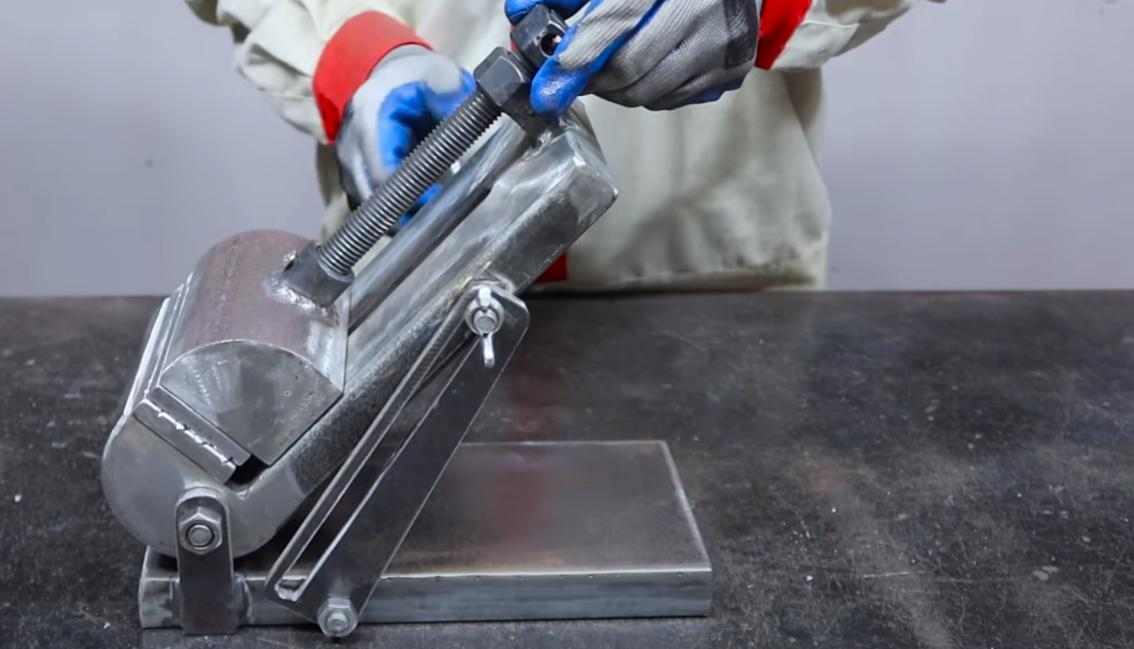
Электросварщик должен иметь при себе следующий инструмент для зачистки места сварки и сварных швов. [c.291]
Проковка и зачистка сварочных швов применяется для их уплотнения с целью создания лучшей герметичности, а также для придания панелям нужного профиля. Проковку производят пневматическим пистолетом с помощью комплекта поддержек. Зачистка мест сварки производится шлифовальными кругами, установленными в пневматических или электрических шлифовальных машинках. [c.336]
Проковка и зачистка сварочных швов. Для упрочнения места сварки и придания ему необходимого профиля панели, а также для создания лучшей герметичности кузова или кабины все сварные швы следует проковывать. Проковку выполняют пневматическим рихтовочным молотком при помощи комплекта поддержек. Места сварки зачищают пневматическими шлифовальными или полировальными машинами.
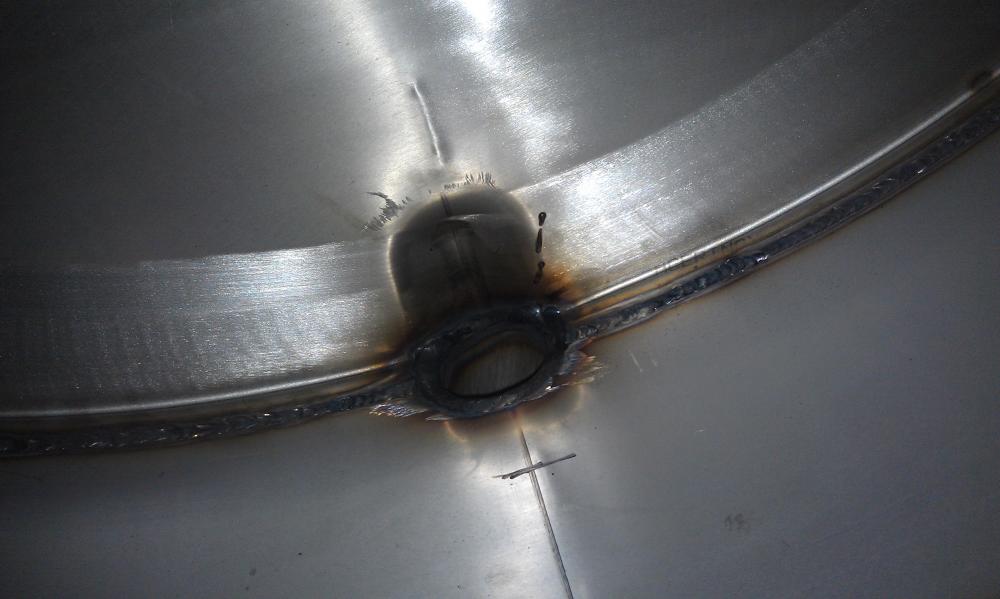
Панели могут быть сварены встык («стыковая сварка) при помощи дуговой или газовой сварки. В этих случаях плавится не только материал детали, но и подводимая к месту сварки проволока. Швы сварки на наружной поверхности кузова подл ежат зачистке и оплавлению. В концах ответственных сварочных швов обычно устанавливаются две-три заклёпки, которые гарантируют сварку от разрыва, если она выполнена недостаточно надежно. [c.160]
Вспомогательное время при ручной дуговой сварке складывается из времени, затрачиваемого на установку детали на рабочее место, поворот детали в процессе сварки, снятие ее с рабочего места, включение и выключение рубильника сварочной машины, смену электродов, зачистку швов от шлака, клеймение швов, регулирование режима сварки, переходы от одного участка шва к другому при сварке прерывистых швов и др. [c.518]
Проковка и зачистка сварочных, швов необходима для упрочнения места сварки, улучшения герметичности и придания кузову нужного профиля. Для проковки используют пневматический рихтовочный молоток и комплект поддержек. Места
[c.182]
Шлаковые включения (рис. 124, в) в сварном шве возникают из-за плохой зачистки свариваемого металла и присадочной проволоки, а также неправильного выбора режимов сварки. Шлаковые включения ослабляют сечение шва, вызывают снижение прочности и являются зонами концентрации напряжений. Места швов со шлаковыми включениями вырубают и заваривают вновь. [c.270]
Сборка обвязок производилась на сварке в специальных стапелях, обеспечивших точность размеров и предотвративших деформации после сварки. Стапели представляли собой сваренную из стальных швеллеров раму, на которой были установлены зажимы-фиксаторы. Для удобства сварки и зачистки швов фиксаторы были несколько удалены от углов обвязок, а стапели были сделаны поворотными относительно продольной оси, так что все швы можно было накладывать в горизонтальном или слегка наклонном положении. Сварка производилась вручную при помощи серийных аппаратов для аргоно-дуговой сварки присадка — проволока АК. В тех местах, где швы могли затруднить дальнейшую работу или отразиться на внешнем виде, они зачищались.
[c.278]
Чугунные эмалированные трубы выпускают только по особым требованиям, так как производство их весьма сложно в связи с необходимостью тщательной очистки внутренней поверхности. Большей частью из чугуна изготовляют отводы, тройники, переходы и арматуру, имеющие небольшие размеры в этом случае все части поверхности можно равномерно по крыть эмалью. На фасонных деталях, изготовленных из отрезков труб на сварке, имеется много мест, трудно поддающихся эмалированию, поэтому детали изготовляют цельными или сварными больших размеров с тем, чтобы удобно было производить зачистку и подварку швов. [c.183]
За основное время сварки принимается время горения дуги, которое определяется с учетом технологии сварки, производительности оборудования и заданных режимов сварки.
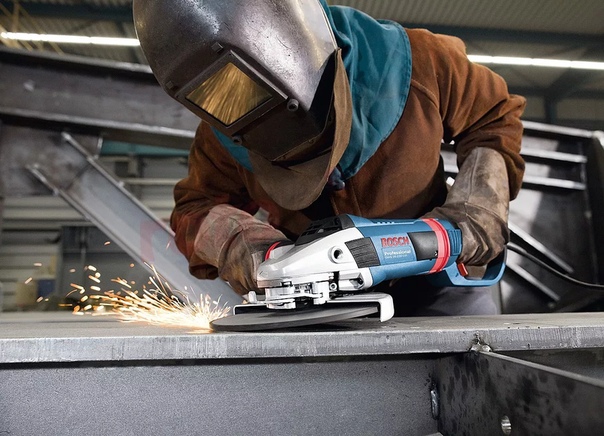
В процессе сварки внутренних и наружных швов аппаратов возникает необходимость в зачистных операциях для удаления дефектных мест, снятия усиления сварного шва и зачистки шва перед нанесением подварочного шва, так называемая зачистка корня шва. [c.155]
Изделия должны своевременно подаваться на рабочее место и немедленно убираться после сварки. Сварщик не должен быть загружен вспомогательными работами по транспортировке изделий. Зачистка сварных швов от шлака и деталей от брызг металла должна выполняться вспомогательными рабочими с тем, чтобы квалифицированный рабочий-сварщик не был загружен этой работой.
[c.630]
Техника сварки деталей из тонких стальных листов, приварки панелей и заварки трещин имеет своп особенности. При сварке новых вставных панелей или заплат в стык расширение металла в местах нагрева ограничено вследствие этого расширяющийся металл поднимается вверх или опускается вниз, образуя выступ или впадину. Чем больше поверхность и интенсивность нагрева, тем больше коробление. Если кромки новой панели заходят на старую панель кузова, получается неисправимый брак. В этом случае сварка получается непрочной, а шов невозможно сделать заподлицо с поверхностью панелей. Зазор, образовавшийся с противоположной стороны нахлестки и заполненный при сварке присадочной проволокой, осложняет зачистку и отделку панели. Во избежание коробления металла и получения некачественных швов прибегают к приварке внакладку и к прихватке панели в нескольких точках. Место соединения выравнивают молотком и гладилкой так, чтобы кромки панелей плотно прилегали друг к другу. По обеим сторонам шва на металл панели кладут смоченный в холодной воде листовой асбест, оставляя зазор в 30 мм для проведения сварки.
[c.138]
Щетки ручные угловые предназначены для очистки металлических поверхностей от ржавчины, окалины и старой краски, могут применяться для зачистки сварных швов и мест под сварку. [c.161]
Допустимость дефектов и необходимость их исправления зависит от -степени ответственности данного соединения в конструкции сварного узла (изделия) и указывается в ТУ и действующих технологических инструкциях по сварке. В зависимости от вида, расположения и размера дефектов их исправляют повторной точечной или шовной сваркой обработкой резанием дефектного места и последующей газовой ли дуговой электросваркой в среде защитных газов сверлением отверстий и постановкой заклепок зачисткой поверхности сварных швов термической обработкой сварного узла. Дефекты сварных узлов (изменение формы и размеров) исправляют путем местного нагрева, постановки холостых точек , прокаткой между стальными роликами, а также правкой ударом и обжатием.
[c.109]
Сварка в заводских условиях выполнялась автоматами. После выверки и зачистки балки отправлялись на железнодорожных платформах иа место монтажа, где осуществляли монтаж главных балок (рис. 135), наложение вертикальных швов (рис. 136) производили автоматами под флюсом с принудительным формированием. [c.62]
Для получения хорошего качества швов при сварке на шовных машинах необходимо, чтобы ширина роликов соответствовала требуемой. Это постигается наличием на рабочем месте запасных комплектов роликов или специальным приспособлением для калибрования и зачистки роликов (фиг. 180). Зачистка контактной поверхности ролика производится резцом 2, а калибрование специальным калибрующим роликом 3. Такое приспособление устанавливается в зависимости от конструкции и размеров свариваемой детали или у одного, или у обоих роликов шовной машины.
[c.345]
Слабым местом в сварном соединении является корень шва. Поэтому при выполнении особо ответственных швов проводится подварка корня шва, что значительно улучшает качество сварного соединения. После окончания сварки шов должен медленно охлаждаться. Быстрое искусственное охлаждение шва, особенно при сварке листов толщиной более 10 мм, может привести к его растрескиванию. После охлаждения и зачистки сварные швы проверяют на плотность. [c.50]
Проковкаи зачистка сварных швов необходима для упрочнения места сварки, улучшения герметичности и придания кузову нужного профиля. Для проковки используют пневматический рихтовочный молоток и комплект поддержек. Места сварки зачищают шлифовальными кругами, установленными в пневматических или электрических шлифовальных машинках. [c.221]
Вспомогательное В1ремя при ручной дуговой сварке включает следующие операции установку детали на рабочее место, поворот детали в процессе сварки, снятие ее с рабочего места, включение и выключение рубильника сварочной машины, смену электродов, зачистку швов
[c. 460]
Самой высокой эффективностью обладают совмещенные технологические процессы, когда на одном операционном поле одновременно или последовательно (без снятия детали) выполняется несколько разнородных технологических операций. Примером такого решения является технологический процесс, осуществляемый на автоматизированной установке с системой числового программного управления (ЧПУ) для механообработки, сборки и сварки крупногабаритных узлов и агрегатов с одного установа на одном рабочем месте. При этом производится также автоматизированная зачистка кромок под сварку, правку сварных швов и их рентгенокои- [c.70]
Штамповка деталей должна производиться на хорошо отлаженных и доведенных штампах. После штамповки детали должны обязательно проходить операции снятия грата и заусениц, Детали перед отливкой должны быть хорошо отформованы, а после отливки дефекты поверхности должны быть устранены на месте. Сварные детали должны иметь ровные швы, без раковин, свищей и шлаковых включений. При изготовлении сварных деталей и узлов, которые должны иметь хороший декоративный вид, рекомендуется производить автоматическую сварку под слоем флюса, обеспечивающую хорошее качество и ровную поверхность сварных швов. При изготовлении деталей методом литья рекомендуется широко применять точные методы отливки деталей — в кокиль, в корковые формы, под давлением и т. д. Перед окраской все дефекты поверхности деталей должны быть тщательно исправлены. Раковины и прожоги литых деталей должны быть заварены и зачищены. В отдельных случаях применяются специальные замазки или пасты. Наплывы и литники удаляются механическим способом. Сварные швы зачищаются, удаляются грат и брызги металла. Заусенцы и грат после штамповки снимаются запиловкой, зачисткой или на гратоснимающих машинах.
[c.86]
Подготовка кромок деталей из листовой нержавеющей стали аустенит-ного класса под сварку может производиться механическим способом, сжатой дугой или методом газофлюсовой резки с обязательной последующей механической обработкой или зачисткой огнерезных кромок наждачным кругом на глубину не менее 0,8 мм. Подготовка кромок труб под сварку должна производиться только механическим способом. Все детали перед сборкой должны быть зачищены и обезжирены в местах наложения швов на ширину не менее 20 мм.
[c.77]
Как очистить алюминий после сварки
Несколько любителей сварки своими руками вместе с профессионалами, работающими со сваркой алюминия, знают, как он окрашивается в процессе сварки. Тонировка снижает эстетический вид алюминия в готовом проекте и придает ему дилетантский вид. Это причина, по которой большинство сварщиков всегда ищут, как лучше всего очистить алюминий после сварки.
В этой статье мы объясним, как очищать алюминий после сварки, различные виды очистки и основное оборудование, необходимое для обеспечения эффективной очистки.
Что нужно и чего нельзя делать при очистке алюминиевых сварных швов Очистка алюминиевых сварных швов — это процесс, требующий особой осторожности и внимания. Неправильная очистка сварного шва может привести к бракованному алюминиевому изделию. При зачистке сварных швов алюминия необходимо соблюдать несколько правил. Каждый шаг в процессе очистки должен быть сделан тщательно. Вот список того, что можно и чего нельзя делать при очистке алюминиевых сварных швов.
- Методы резки, которые оставляют отшлифованную или смазанную поверхность, не должны использоваться ни при каких обстоятельствах.Например, распиленная лентой поверхность может стать причиной появления пятен. Для резки алюминия следует использовать высокоскоростную циркулярную пилу. Точно так же следует держать подальше шлифовальные машины, чтобы получить чистый алюминиевый сварной шов. При необходимости можно использовать грубые шлифовальные машины с круговой шлифовальной машиной. Смысл резки должен быть острым и быстрым, без размазывания или смазывания. Перед сваркой алюминия пятна на поверхности необходимо очистить, чтобы избежать непровара.
- Следует избегать использования газокислородной резки, резки угольной дугой, калибровочных процессов или кислородно-топливного пламени для предварительного нагрева.
Они вызывают повреждение участков, подверженных тепловому воздействию, и способствуют росту и гидратации оксидной пленки, присутствующей на поверхности. Плазменная резка и строжка в большей степени способствуют получению более чистых алюминиевых сварных швов. Это связано с тем, что эти процессы обычно не позволяют водороду и влаге смешиваться с оксидным слоем.
- Запрещается использовать смазочные материалы при сварке алюминия. Смазочные материалы на нефтяной основе состоят из углеводородов, которые растворяются в процессе сварки и, таким образом, позволяют добавлять водород в соединение.Это вызывает пористость и растрескивание — два процесса, которые снижают качество готового алюминиевого изделия ниже нормы.
- Масло и смазка поставляются прикрепленными к алюминию на заводе. Перед сборкой соединение должно быть очищено. Это можно сделать с помощью обезжиривающих растворителей. После этого можно использовать марлю или бумажное полотенце, чтобы очистить и высушить точку сварки.
Марля и бумажные полотенца обеспечивают эффективную очистку, потому что они пористые и, следовательно, впитывают больше масла и влаги.Противоположная сторона соединения также должна быть протерта начисто, чтобы предотвратить проникновение загрязнений через алюминий в сварочную ванну.
- Никогда не используйте ветошь для очистки сварного соединения. Масло и грязь могут переноситься с этих тряпок на поверхность сварки.
- Проволочную щетку можно использовать для очистки соединения только после завершения очистки растворителем, в противном случае углеводороды и другие загрязняющие вещества осядут на поверхности сварного соединения.
- Никогда не продувайте соединение сжатым воздухом.В сжатом воздухе часто присутствуют влага и масляные загрязнения.
Типы очистки алюминиевых сварных швов
Существует три различных типа очистки алюминия после сварки. Ниже приводится обзор методов очистки:
1. Механическая очистка сварных швов
Это распространенный и недорогой метод очистки алюминия. Он включает в себя шлифовальные станки и абразивы для обеспечения надлежащей очистки верхнего слоя алюминиевой поверхности, где образуются частицы ржавчины и других шлаков.
Однако известно, что этот процесс занимает много времени, и редко удается достичь 100% результата очистки с правильным эстетическим значением. Это идеальный метод для использования в местах, которые легко доступны.
2. Химическая очистка сварных швов
Это самый популярный метод очистки алюминия после сварки. Он включает использование химической травильной пасты, которую обычно наносят на пораженные участки с помощью распылителя или кисти и оставляют на поверхности на некоторое время для взаимодействия с металлическим алюминием.Через несколько часов его удаляют и нейтрализуют поверхность с помощью нейтрализующего средства.
Химическая очистка сварных швов считается очень эффективным процессом очистки после производственного процесса, хотя некоторые сварщики избегают его использования по ряду причин.
Известно, что химическая травильная паста содержит различные токсичные кислоты, такие как серная, азотная и плавиковая кислоты. Известно, что эти химические вещества весьма опасны для человеческого организма и способны вызывать долгосрочные и серьезные повреждения внутренних органов и кожи человека при вдыхании или употреблении внутрь.
Рекомендуется, чтобы с травильной пастой для химикатов работал только сертифицированный оператор. Оператор должен будет убедиться, что его тело полностью покрыто, чтобы его тело было полностью закрыто, поэтому кислота не может попасть в его тело. По этой причине травильная паста обычно используется в коммерческих целях или только на автоматизированных площадках.
3. Электрохимическая очистка сварных швов
Электрохимическая, также известная как электрополировка, является наиболее эффективной, когда речь идет о очистке алюминия после сварки.Это безопаснее и быстрее, поэтому большинство сварщиков предпочитают использовать его по сравнению с другими методами. Нет никаких серьезных рисков для здоровья, связанных с использованием этого метода.
Помимо очистки алюминия после сварки, этот метод также эффективен для удаления ржавчины, перекрестного загрязнения и других видов загрязнений с алюминиевых поверхностей.
Основное оборудование для очистки алюминия после сварки
1. Чистые и свежие тряпки из микрофибры
Рекомендуется приобрести новые тряпки, которые помогут протирать влажные алюминиевые поверхности после удаления смазки.Убедитесь, что ветошь чистая и сухая, прежде чем начинать протирать алюминиевые поверхности после завершения процесса раскисления.
2. Спрей для удаления окислов и уксус
Распылители для удаления окислов обычно выпускаются в виде веществ в бутылках или аэрозольных спреев. Белый уксус также является важным средством для удаления оксидов, особенно при использовании на алюминиевых поверхностях.
3. Проволочная щетка
Настоятельно рекомендуется использовать проволочную щетку с мягкой щетиной, чтобы удалить следы окисления с поверхности алюминия.
4. Горячая вода
Для обеспечения оптимального эффекта обязательно погрузите алюминий в горячую воду перед началом процесса очистки.
5. Коричневая крафт-бумага
Коричневая крафт-бумага очень важна, когда речь идет о хранении алюминия после очистки. Если вы не планируете в ближайшее время выполнять еще одну сварку и не хотите снова чистить, убедитесь, что вы обернули алюминий коричневой крафт-бумагой, чтобы предотвратить повторное окисление и загрязнение.
6.Упаковочная лента
Упаковочная лента не является частью чистящего оборудования, но очень важна, когда речь идет об очистке алюминия. Когда вы закончите оборачивать алюминий коричневой крафт-бумагой, вам понадобится упаковочная лента, чтобы удерживать его на месте.
Убедитесь, что упаковочная лента не соприкасается напрямую с алюминием во избежание любого загрязнения.
Процедура очистки
Грязь и любые другие загрязнения всегда влияют на качество сварки алюминия. Всякий раз, когда вы закончите сварку алюминия, рекомендуется выполнить два шага, описанных ниже.
Обезжирить алюминий, чтобы избавиться от влаги или остаточных загрязнений
Загрязнения, такие как жир и масло, всегда влияют на качество сварки. Хотя можно использовать тряпку, чтобы вытереть масло или жир, это ненадежный и эффективный метод, так как вы рискуете распространить жир или масло на другие части алюминия.
Чтобы убедиться, что вы удалили все загрязнения, рекомендуется использовать жидкие обезжиривающие средства, такие как органические растворители и щелочные растворы.Некоторые прекрасные примеры включают ацетон, толуол, растворитель лака и метилэтилкетон.
Удалите все оксидные слои
После того, как вы удалили жир, теперь вы можете избавиться от присутствующих оксидов алюминия. Это процесс, который включает ручное удаление материала с поверхности алюминия. Вы всегда можете использовать химический раствор или проволочную щетку.
Всякий раз, когда вы используете проволочную щетку, выбирайте щетку с мягкой щетиной, а не с жесткой щетиной. Убедитесь, что вы выбрали сильный щелочной химический раствор в качестве агента для удаления оксидов.
Заключение
Очистка алюминия после сварки очень важна, так как помогает обеспечить прочность сварного шва. Обезжиривание и раскисление — отличные варианты очистки, на которые вы всегда можете положиться. Однако, прежде чем приступать к процессу очистки, рекомендуется убедиться, что у вас есть все оборудование, которое вы собираетесь использовать, на месте.
Надеемся, теперь вы знаете, как очистить алюминий после сварки.В случае возникновения каких-либо вопросов или разъяснений, не стесняйтесь обращаться к нам.
СВЯЗАННЫЕ ПОСТЫПрощай, обесцвечивание сварных швов!
Цвета отжига: что за ними стоит и как от них избавиться?
Сварка относится к наиболее распространенным методам соединения в металлоконструкциях. Истоки соединения деталей из железа и стали лежат в кузнечном процессе сварки огнем и давлением уже несколько сотен лет назад.
Но примерно в середине 19 века утвердила себя техника кислородно-ацетиленовой сварки с помощью кислорода и горючих газов. Сто лет спустя, в 1940-х и 50-х годах, электродуговая сварка и сварка сопротивлением приобретали все большее значение, и, в свою очередь, несколько лет спустя появился процесс сварки TIG как дальнейшее развитие дуговой сварки углеродом. Вскоре после этого был изобретен процесс сварки MIG, наиболее часто используемый сегодня в секторе нержавеющей стали.
Независимо от того, какой метод соединения сваркой выбран, вероятно, наиболее важной причиной использования нержавеющих сталей, несомненно, является их коррозионная стойкость.
Всегда ли нержавеющая сталь не ржавеет?
То, что нержавеющие стали обычно не ржавеют, как, например, мягкая сталь, сильно не ржавеют, не означает, что они не могут подвергаться коррозии! Для этого существуют другие формы коррозии, которым подвержены нержавеющие стали, причем в большей или меньшей степени, в зависимости от сплава. Прежде всего, при производстве сварных швов важно сохранить особые свойства этих материалов. Часто в процессе сварки параллельно сварному шву возникает цветное обесцвечивание (зона термического влияния). На техническом жаргоне отжиг красок называется отжигом и может сильно отрицательно сказаться на коррозионной стойкости высоколегированных материалов.
Что вызывает появление цветов отжига в сварных соединениях и что это означает?
Изменение цвета является термическим оксидированием и происходит из-за одновременного воздействия тепла и кислорода.Следовательно, это всегда означает снижение коррозионной стойкости. Несмотря на профилактические защитные меры, такие как сварка MIG в виде инертного защитного газа (например, аргона), обычно пассивный слой нержавеющей стали может изменяться в процессе сварки из-за окисления поверхности металла. Хром разрушается и образуется слой оксида железа, который больше не защищает поверхность материала от коррозии. В зависимости от степени, обесцвечивание очень сильно способствует, в частности, образованию ямок. Поддерживаемые агрессивными средами, такими как, например, соленая вода, могут возникать точечные повреждения. Затем коррозия продолжается внутри материала и может привести к кавернообразной эрозии.
Краски для отжига, оставить или удалить?
Интенсивность цвета цвета отжига является показателем толщины вышеупомянутого оксидного слоя. Как правило, чем темнее цвет, тем толще оксидный слой и выше потенциал коррозии, а это означает, что в процессе работы цветовой спектр варьируется от светло-желтого/соломенно-желтого до пурпурного/фиолетового и сине-серого/серого.
Когда цвет отжига, то есть оксидный слой, удаляется, пассивный слой может снова образоваться под действием кислорода, и материал может вернуться к прежней коррозионной стойкости. На практике желтые пятна обычно допускаются, но степень, в которой можно оставить цвет грунтовки, в конечном итоге зависит от области применения и оператора. Тем не менее, для предотвращения коррозии в основном рекомендуется удалять изменения цвета.
Как удаляется цвет отжига со сварного соединения внутри трубы?
В то время как большинство методов очистки и/или ремонта относительно просты для выполнения на внешнем сварном шве, очистка сварного шва внутри трубы бывает сложной или невозможной.Особенно, когда косяк лежит в нескольких метрах. Если необходим ремонт, в большинстве случаев остается только вариант вскрытия и повторной сварки с сопутствующим увеличением временных и финансовых затрат.
Как INSPECTOR SYSTEMS ремонтирует сварной шов внутри трубы?
Для этого INSPECTOR SYSTEMS предлагает свою роботизированную технологию шлифовки и полировки, проверенную на протяжении многих лет и признанную престижными международными компаниями и экспертами морской нефтегазовой и атомной промышленности, для обработки сварных швов и внутренних поверхностей. трубы.
Опыты показали, что все степени обесцвечивания можно удалить с помощью полировального круга. При этом съем материала лежал в диапазоне сотых долей миллиметра. Однако для сварных швов с большим смещением может потребоваться модификация верхней части шва с помощью шлифовального круга, прежде чем боковое изменение цвета можно будет впоследствии удалить с помощью полировального диска.
Обработка сварных швов | ABICOR BINZEL
Обработка сварных швов | АБИКОР БИНЗЕЛЬГермания | английский
Устройства и раствор электролита для очистки сварных швов
Это знакомо каждому сварщику: После сварки металлов остается непривлекательный налет – как при сварке МИГ, так и при сварке МАГ и ТИГ.В частности, высокочувствительные металлы, такие как нержавеющая сталь или алюминий, должны иметь красивую поверхность и зачастую идеальный блеск после обработки. Кроме того, оксидный слой, который отсутствует в процессе сварки, должен быть восстановлен, чтобы предотвратить коррозию. Когда дело доходит до последующей обработки сварного шва, правильный выбор чистящего средства и оборудования имеет решающее значение для получения желаемого результата и одновременной защиты окружающей среды.
На рынке представлены различные вспомогательные средства и инструменты.Однако обычные шлифовальные инструменты слишком агрессивны для чувствительных поверхностей. Травильные пасты также опасны при использовании и должны утилизироваться специальным образом. С помощью устройств ABICLEANER и соответствующего раствора электролита ABICLEAN от ABICOR BINZEL очистка сварных швов выполняется быстро, легко и безвредно для окружающей среды — и результат убедителен.
Головной офисAlexander Binzel SchweisstechnikGmbH & Co. KGKiesacker 7-9
35418 BuseckGoogle Maps0049 (0) 64 08 / 59-0 Канал ABICOR BINZEL на YouTubeПосетите канал нашей компании на YouTube и узнайте больше о ABICOR BINZEL.© 2022 АБИКОР БИНЗЕЛЬ Изменить настройки файлов cookie
Нам нужно ваше согласие на загрузку сервиса Youtube!
Мы используем Youtube для встраивания контента, который может собирать данные о вашей активности.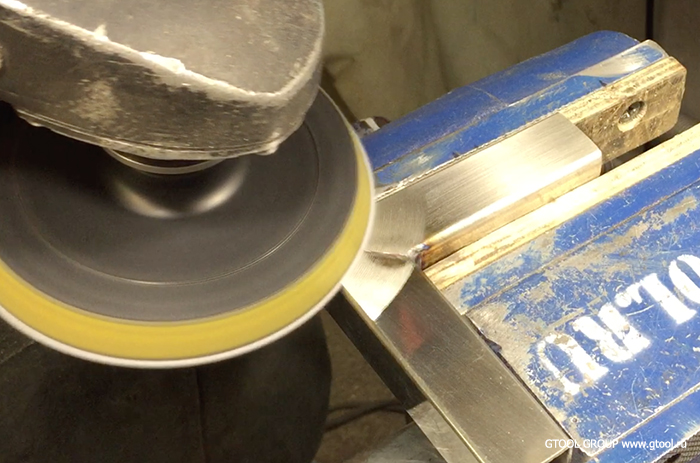
Электролит для очистки сварных швов
Электролит для очистки сварных швов | АБИКОР БИНЗЕЛЬالإمارات العربية المتحدة | английский
Коррозия является постоянным спутником обработки металлов – это также проблема дуговой сварки, поскольку свойства материала должны быть сохранены.Однако процесс сварки сводит на нет эти свойства вдоль сварного шва. Причиной этого является образующийся оксидный слой, который проявляется в так называемом потускнении. Он делает металл в сварных швах чувствительным к коррозии и должен быть соответствующим образом удален. Но и с визуальной точки зрения, особенно при сварке нержавеющей стали или алюминия, необходимо удалить оксидный слой. Это делается аккуратно и быстро с раствором электролита ABICLEAN от ABICOR BINZEL. В конце концов, кто хотел бы иметь царапины на благородной нержавеющей стали или алюминиевых поверхностях?
ABICLEAN представляет собой раствор электролита «все в одном» и используется с устройствами ABICLEANER от ABICOR BINZEL для электрохимической очистки сварных швов.Этот очищающий раствор электролита очень удобен в использовании: в то время как многие устройства электрохимической очистки требуют различных жидкостей для самой очистки, подготовки и отделки сварного шва, все эти свойства объединены в ABICLEAN от ABICOR BINZEL.
Вместе с устройствами ABICLEANER и щеткой из углеродного волокна ABIBRUSH от ABICOR BINZEL вы можете быстро и бережно очищать и одновременно пассивировать чувствительные металлы, такие как нержавеющая сталь или алюминий. С помощью чистящего устройства ABICLEANER 1000 можно полировать даже очень чувствительные металлические поверхности.
Просто окуните специальную щетку ABIBBRASH ABICLEANER в раствор электролита «все в одном» ABICLEAN и приступайте к процессу очистки или полировки.
Краткий обзор всей информации
Как появляется потускнение при сварке
В процессе сварки вдоль сварного шва часто происходит обесцвечивание – термические оксиды, также известные как потускнение. Эти обесцвечивания вызваны одновременным действием тепла и кислорода и имеют большое влияние на коррозионную стойкость, особенно высоколегированных материалов.Например, при сварке MIG инертный газ аргон может помочь сохранить нормальный пассивный слой, но нагрев при сварке нержавеющей стали изменяет его поверхность. В этом процессе хром соединяется с углеродом с образованием карбида хрома и, следовательно, больше не используется для защиты от коррозии. Это означает, что поверхность из нержавеющей стали больше не защищена от коррозии.
В зависимости от условий окружающей среды этот процесс может привести к так называемой точечной коррозии. Например, соленая вода может способствовать образованию точечных ямок, которые продолжаются внутри материала.
Применение ABICLEAN
Чистящий электролит ABICLEAN поставляется в литровых бутылях вместе с меньшим пустым пластиковым контейнером. Перед очисткой сварного шва во второй пластиковый контейнер наливается небольшое количество ABICLEANER. Щетку из углеродного волокна ABIBRUSH погружают в залитый раствор и круговыми движениями зачищают сварной шов. Просто смочите поверхность заготовки кисточкой. После использования остатки чистящего раствора можно просто смыть чистой водой и высушить заготовку тряпкой.Это лучше всего: с ABICLEAN не остается никаких остатков, таких как, например, некрасивые отложения, которые остаются после травления.
Полировка работает по тому же принципу и оставляет после себя блестящие металлические поверхности.
В отличие от обычных травильных паст раствор для электролитической очистки ABICLEAN не содержит фтористоводородной кислоты, поэтому его легко транспортировать, хранить, использовать и утилизировать.
Альтернатива травильным пастам
Травильные пасты являются одним из стандартных чистящих средств для сварных швов, которые широко использовались в прошлом. Однако текущие требования по охране труда и технике безопасности, а также по охране окружающей среды требуют альтернатив. Травильные пасты все еще используются, потому что они оставляют поверхности, которые очень хорошо очищаются. Однако их использование должно осуществляться с соблюдением строгих мер предосторожности, поскольку они не должны попадать на кожу, а их пары нельзя вдыхать. В дополнение ко всему этому, их обработка требует много времени, потому что они требуют длительного времени пребывания. Остатки травильных паст нужно не просто смывать, а правильно утилизировать.
Электрохимическая очистка с помощью ABICLEAN от ABICOR BINZEL делает очистку сварных швов безопасной, быстрой и надежной.
Для электрохимической очистки с помощью устройства ABICLEANER в дополнение к чистящему электролиту ABICLEAN вам также потребуется щетка из углеродного волокна для нанесения раствора на заготовку: ABIBBRUSH от ABICOR BINZEL. Эта щетка из углеродного волокна состоит примерно из 1,5 миллиона нитей, каждая из которых при использовании создает столько же микродуг. Благодаря этому химическому процессу остатки сварки, такие как налет, удаляются быстро и бережно, и в то же время прямо восстанавливается антикоррозионная защита поверхности заготовки.То же самое относится и к полировке с помощью ABICLEANER 1000 (AC/DC).
Щетка для чистки ABIBRUSH — оригинальный продукт ABICOR BINZEL, только с пурпурным волокном в центре — предназначена для легкого доступа даже к узким щелям и труднодоступным углам. Длину щетинок можно регулировать индивидуально в зависимости от применения.
Ручка щетки для чистки имеет эргономичную форму и выглядит как ручка сварочной горелки. Его очень удобно держать в руке, а также он подходит для постоянного использования.Отдельные компоненты чистящей щетки ABIBRUSH устойчивы к воздействию кислот. Резьбовая часть рукоятки и адаптер щетки изготовлены из высококачественной нержавеющей стали 1.4571, а насадка щетки изготовлена из кислотостойкого пластика PTFE, который также может выдерживать высокие температуры.
Видео о очистке сварных швов
Удаление некрасивых потускнений после сварки экологически безопасно
ABICOR BINZEL Middle East FZEСвободная зона Рас-эль-ХаймаGoogle Maps00 971 7 2432355 Канал ABICOR BINZEL на YouTubeПосетите канал нашей компании на YouTube и узнайте больше о ABICOR BINZEL.
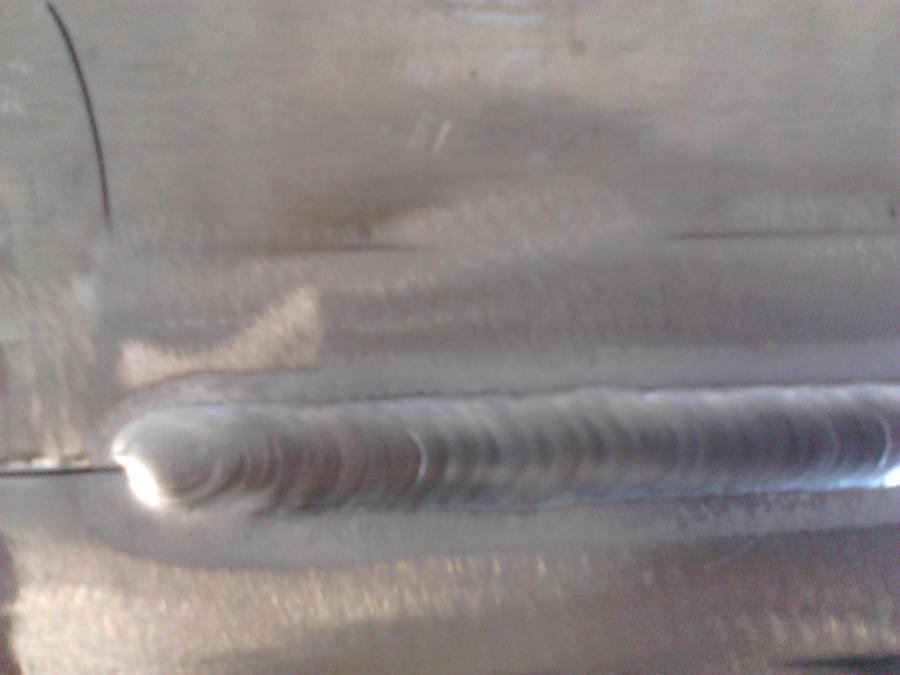
Нам нужно ваше согласие на загрузку сервиса Youtube!
Мы используем Youtube для встраивания контента, который может собирать данные о вашей активности. Пожалуйста, ознакомьтесь с деталями и примите услугу, чтобы увидеть этот контент.Неоднородная коррозия на сварных швах 316L
«Образование, алоха и развлечения… с 1989 года»
Сегодня вторник, 15.02.22, и ваши вопросы или ответы приветствуются.
Звоните прямо сейчас! (сайт без регистрации)
Недавно наша компания поставила готовые изделия из стали 316L на объект, расположенный на острове на северо-западе Тихого океана. Изделия находились на стройплощадке около 2 недель, и теперь около 15 % сварных швов имеют ржавчину на швах. Наша процедура очистки сварного шва заключалась в использовании проволочной щетки из нержавеющей стали с последующей пассивацией лимонной кислотой.
Первое, что вам нужно сделать, это устранить обычных подозреваемых.Возьмите немного азотной кислоты и смочите в ней кисти. Если они быстро чернеют, значит, они не из нержавеющей стали. Затем попробуйте свою сварочную проволоку с тем же тестом. Если у вас нет под рукой азотной кислоты, попробуйте проверить сварные швы и щетки магнитом.
Фотографии, которые вы прислали, были страшными, но если ваша проблема окажется в плохих щетках, то работа будет решена механической очисткой сварных швов и хорошей полевой репассивацией. Качество работы не будет поставлено под угрозу, и кроме задержки, пока вы выполняете уборку, все будут довольны.
Если же окажется, что это сварочная проволока, то у вас будет очень большая проблема. Вы можете зашлифовать проблемные сварные швы, но удаление всех следов углеродистой стали будет гигантской задачей, и, вероятно, будет более рентабельно начать все сначала со свежим материалом. Если вы обнаружите, что это материал сварного шва, и вы решите переделать сварные швы, пожалуйста, свяжитесь со мной напрямую, так как у меня есть некоторые предложения относительно того, как наиболее эффективно удалить все следы углеродистой стали.
Я очень подозрительно отношусь к сварочной проволоке, потому что даже если бы вы использовали щетки из углеродистой стали, а затем пассивировали лимонной кислотой, вы не должны были бы столкнуться с такой проблемой, если бы ваша пассивация не была выполнена должным образом.
Это очень интересно для меня, у нас была аналогичная проблема с конструкциями из 304L для шоковой заморозки. Оказалось, что это произошло из-за использования Очистка щеткой с питанием от 302ss. К нам пришла компания, которая указана на этом веб-сайте, чтобы нанести травильный гель на поврежденные участки. Оно работает! Причина, по которой я не верю, что вы использовали щетку из углеродистой стали, заключается в том, что обработка лимонной кислотой удалит ее, но не удалит загрязнения от механической чистки 302 и 304. Азотно-фтористоводородная и щеточная электрополировка — единственное, что мы нашли, чтобы удалить это.
Я уже видел это раньше. Проволочная щетка была из нержавеющей стали, но это была нержавеющая сталь 410. В основном это железо с небольшим количеством хрома. Провод обрывается в
316L очень-очень мелкими кусочками. Мы пассивировали деталь в нескольких резервуарах для азотной и хромовой пассивации буквально в течение нескольких дней, и она все еще не пропускала солевой туман. Поэтому я сомневаюсь, что лимонная кислота может решить проблему. Абразивное удаление «кожи» или, возможно, электрополировка щеткой, вероятно, единственные вещи, которые будут работать. В следующий раз я бы определенно использовал колеса скотчбрайта.
Фотографии действительно страшные.
Совет, который вы дали до сих пор, очень хорош. Судя по фотографиям, степень ржавчины заставляет меня предположить, что проблема не в проволочной щетке. Начните с магнита, чтобы увидеть, является ли сварной шов сильно магнитным или нет. Если это так, у вас, вероятно, есть некоторые проблемы. Возьмите образец той же нержавеющей стали и выполните пробную сварку, используя ту же сварочную проволоку. Очистите его настоящей проволочной щеткой из нержавеющей стали и погрузите место сварки примерно на 6 часов в 20-процентный раствор азотной кислоты. Если материал сварного шва вытравлен (съеден), значит, сварочная проволока не из нержавеющей стали, и вам придется начинать все сначала со всеми вытекающими последствиями. Если он еще полностью цел, можно вздохнуть с облегчением. В этом случае возьмите пластиковую щетку и нанесите травильный гель на основе азота/HF на ржавый сварной участок и оставьте на 15 минут. Смойте массу пластиковой губкой и снова промойте чистой губкой, смоченной деионизированной водой. Затем промойте участок деионизированной водой. Смачивайте его деионизированной водой в течение 24 часов, чтобы увидеть, не появится ли снова ржавчина.
Кевин:
Я видел эту ситуацию несколько раз. Я согласен с Брэдом Маасом, что проблема в проволочной щетке. Вы поместили так много встроенного железа в поверхность, что потребовался более длительный процесс пассивации. Есть несколько способов исправить ситуацию. В полевых условиях это сложнее, но вы можете исправить это с помощью горячего геля лимонной кислоты или геля азота / HF (если вы можете справиться с опасностью).
После повторной пассивации вы можете легко проверить сварные швы, чтобы убедиться, что свободное железо, ферриты и т. д.
9 сентября 2011 г.
Сэр
Я был в южной части Тихого океана (Гуам) во флоте, работая над атомными подводными лодками в течение многих лет. Да, убедитесь, что электрод правильный (внешний анализ), использование квалифицированного сварщика и процедуры и, самое главное, что основной материал правильно прослеживается до слитка?
Попросите своего сварщика использовать тот же основной материал и присадочный металл, подвергнуть его испытанию в солевом тумане, а затем разделить сварной шов пополам и посмотреть, с какой стороны ЗТВ исходит коррозия. Если 316L, процедура и очистка верны, моя ставка на дешевую / фарфоровую тарелку.
этот текст заменяется на bannerText
Отказ от ответственности: На этих страницах невозможно полностью диагностировать проблему чистовой обработки или опасность операции. Вся представленная информация предназначена для общего ознакомления и не является профессиональным мнением или политикой работодателя автора. Интернет в значительной степени анонимен и непроверен; некоторые имена могут быть вымышленными, а некоторые рекомендации могут быть вредными.
Если вы ищете продукт или услугу, связанную с отделкой металлов, проверьте следующие каталоги:
О нас/Контакты — Политика конфиденциальности — ©1995-2022 finish.com, Пайн-Бич, Нью-Джерси, США
TWS — отличный вариант обучения для всех
Узнайте больше о том, как мы можем подготовить вас к карьерному росту.
Независимо от материала или способа сварки важно работать с чистыми металлами.Металлы с поверхностной ржавчиной, грязью, сажей и другими формами коррозии могут усложнить задачу сварки, а также привести к более слабому сварному шву. Примеси на поверхности основного металла или наполнителя могут увеличить пористость и даже растрескивание. Эти примеси включают грязь, жир, ржавчину, краску, пластик и другие загрязнения. Для большинства материалов и оборудования очистка паром позволяет надежно удалить загрязнения с поверхности. Пескоструйная очистка и очистка растворителем являются распространенными альтернативами. Электроинструменты, такие как щетки, шлифовальные круги и шлифовальные круги, также могут использоваться для определенных целей.Рекомендуется потратить дополнительное время на очистку поверхности основного металла, чтобы создать максимально прочный и долговечный сварной шов. Сварщики должны ознакомиться с требованиями к очистке различных металлов, особенно алюминия.
Подготовка основного металла к сварке алюминия
Aluminium представляет собой специальный чехол для чистки. В дополнение к тому, что на поверхности не должно быть различных примесей, алюминий также должен быть свободен от оксидов, иначе это приведет к значительной пористости. Сварщики должны подготовить как основной металл, так и присадочный материал, чтобы ни одна из поверхностей не содержала оксида.Чтобы предотвратить конденсацию и накопление воды, сварщики должны хранить весь основной металл и присадочные материалы в вертикальном положении и при комнатной температуре, если это возможно. Хранение их накрытыми тканью во время хранения также может помочь уменьшить загрязнение поверхности посторонними веществами. Сама ткань тоже должна быть чистой. Магазинные тряпки на самом деле могут переносить больше грязи и масла, чем изначально было на металле.
Очистка алюминиевых соединений перед сваркой
Материалы, поступающие из другого цеха, часто покрыты смазкой или маслом для защиты металла.Эти поверхности следует обезжирить растворителем, а затем протереть бумажным полотенцем (не тряпкой). Важно очищать все поверхности, а не только рабочую поверхность, потому что сварной шов может проникать через загрязнения с другой стороны материала. Сварщики также должны избегать использования ненужных смазочных материалов, особенно смазок на нефтяной основе, которые разрушаются в процессе сварки и выделяют водород в соединение.
Очистка шва после сварки
После сварки соединения не используйте сжатый воздух для удаления излишков материала из соединения. Он содержит влагу и масляные загрязнители, которые привносят новые загрязнения на поверхность. Вместо этого следует нанести другой растворитель, а затем использовать проволочную щетку из нержавеющей стали для очистки сварного шва. Эта щетка должна быть предназначена только для обработки алюминиевых сплавов или ее следует предварительно тщательно очистить. Если щетка используется для других металлов и не очищается, она может впитать углеводороды и другие загрязняющие вещества в основной металл.
Сварщики могут научиться надлежащим методам подготовки и очистки в рамках программы обучения сварщиков.Для получения дополнительной информации об обучении навыкам сварщика обращайтесь в школу сварщиков Талсы, чтобы записаться на профессиональное обучение в Оклахоме или Флориде.
Заполните форму, чтобы получить информационный пакет без обязательств.
Ресурсов:
http://www.millerwelds.com/resources/articles/cleaning-aluminum-welding-wire-metals/
http://www. keytometals.com/page.aspx?ID=CheckArticle&site=kts&NM=130
Сварка и пассивация
Подготовка швов и резка
Резка или подготовка кромок должны выполняться гильотиной, механической обработкой, шлифованием или плазменной дугой. Кромки, отрезанные плазменной дугой, должны быть гладкими, без желобков или зазубрин, а также должны быть удалены окислы. Все остальные края должны быть зачищены. Любая резка или подготовка, выполненная с помощью процесса угольной дуги или порошковой резки, должна иметь зачистку на 1,5 мм от кромки реза.Строжка угольной дугой не рекомендуется для резки нержавеющих сталей ни при каких обстоятельствах. Все брызги должны быть удалены, а поверхность основного металла зачищена.
Уход за электродами
Электроды, которые были извлечены из упаковки, должны быть перенесены в печь для выдержки или сварочный бокс и выдержаны при температуре 110ºC, чтобы предотвратить поглощение влаги до тех пор, пока они не потребуются для использования. Электроды, которые стали влажными, должны быть повторно высушены при 250ºC в течение 2 часов перед использованием.
Очистка
Очистка может быть необходима перед сваркой и во время сварки (междупроходная сварка), а также обычно необходима после сварки для обеспечения максимальной коррозионной стойкости.
Очистка перед сваркой включает обработку кромки реза и удаление всех загрязнений, таких как масло, краска, жир, следы карандаша, клейкие ленты и т. д. Область с обеих сторон сварного шва должна быть очищена перед сваркой щеткой из нержавеющей стали. и протер тряпкой, смоченной в растворителе.Вся влага должна быть удалена, и если используется пламя, необходимо следить за тем, чтобы вода (продукт горения) не оставалась на поверхности или в зоне подготовки сварного шва. Сжиженный нефтяной газ особенно выделяет большое количество воды при сгорании.
Каждый сварочный проход должен быть тщательно очищен от шлака и брызг, прежде чем переходить к следующему проходу. Используемый метод очистки (обдирка, чистка щеткой, шлифовка) будет зависеть от процесса сварки, формы валика и т. д., но следует соблюдать осторожность, чтобы в процессе сварки не загрязнилась зона сварки.Любое чистящее оборудование должно подходить для нержавеющей стали и храниться для этой цели.
Во время сварки может быть полезной продувка газом с обратной стороны.
После сварки необходимо удалить сварочные брызги, флюс, окалину, вспышки дуги и общее обесцвечивание от нагрева. Это может включать шлифовку и полировку, пескоструйную очистку и чистку проволочной щеткой из нержавеющей стали, а также использование раствора или пасты для удаления накипи. Предпочтительная процедура обычно определяется конечным использованием.
Шлифование и правка должны производиться щетками, не содержащими железа, абразивами и т.п.и не должны быть настолько тяжелыми, чтобы привести к обесцвечиванию и перегреву металла. Колеса на резиновой и полимерной связке удовлетворительны. Колеса следует регулярно чистить, чтобы они не нагружались и не образовывали нежелательных царапин. При дробеметных работах запрещается использовать стальную дробь.
Процедура сварки
Эффективное зажигание дуги имеет важное значение при сварке всех типов нержавеющих сталей, поскольку неизбирательное зажигание дуги имеет тенденцию к царапанию или сжиганию поверхности стали, что создает зоны для преждевременного химического воздействия.Для получения удовлетворительного начала и возобновления сварки на непрерывных швах требуются осторожность и навыки. Поскольку как прожог на легком материале, так и холодный непровар на более тяжелом материале могут легко возникнуть из-за несовершенной техники, предлагаемая процедура заключается в том, чтобы ударить электродом в стыке примерно на 8-10 мм вперед от фактической начальной точки. При установленной дуге и правильном наклоне электрода его можно быстро переместить в начальную точку для полного проплавления предыдущего шва и/или корня шва нового шва.
Эффективная сварка прихватками аустенитных сталей имеет важное значение для контроля деформации. Длина прихваточных швов варьируется от 12 до 40 мм в зависимости от толщины листа или листа. Обычно прихваточные швы располагаются более близко друг к другу, чем при сварке низкоуглеродистой стали аналогичных размеров.
Использование длинной дуги или чрезмерного тока может привести к потерям марганца и хрома, что может ухудшить коррозионную стойкость сварного соединения. Поэтому длина дуги должна быть как можно меньше, чтобы обеспечить удовлетворительные характеристики сварки, т.е.минимальное разбрызгивание, полное сплавление, приемлемая форма валика.
Сварка должна выполняться на самом низком токе, обеспечивающем хорошее плавление при выбранной скорости сварки, чтобы свести к минимуму тепловложение и искажения управления. Более высокие скорости сварки могут быть преимуществом.
Стрингерные бусы рекомендуются вместо плетения, чтобы поддерживать подвод тепла на приемлемом уровне. Там, где необходимо ткачество, как ширина плетения, так и время боковой выдержки должны быть сведены к минимуму. Межпроходные температуры, как правило, не должны превышать 150ºC, за исключением мартенситных сплавов.
Резкий разрыв дуги может привести к шлаковым включениям и усадочным трещинам. Кратеры следует заполнять круговыми движениями в конце сварного шва с последующим постепенным удлинением дуги до момента ее гашения.
Условия и техника сварки должны быть такими, чтобы обеспечить гладкую поверхность сварного шва, требующую минимальной зачистки.
Угловые сварные швы должны иметь полную толщину шва и правильный контур, соответствующий хорошей работе.Следует избегать вогнутых угловых швов.
Корневая часть сварного шва должна быть защищена от окисления, особенно при дуговой сварке в защитных газах. Обычно применяется защита защитным газом. Выдалбливание (шлифовка) корня и сварка с обратной стороны соединения также могут быть использованы, когда это позволяет конструкция.
Рекомендуемые присадочные металлы для сварки разнородных металлов
Родитель | 201 | 303(1) | 309 | 310 | 317 | 317л | 321 | S30815 |
---|---|---|---|---|---|---|---|---|
Металл | 202 | 304 | 309С | 310С | 316 | 316L | 347 | (253МА) |
ASTM | 304л | 316Ti | ||||||
(AISI) | ||||||||
201 | 308 | 308 | 308 | 308 | 308 | 308 | 347 | 308 |
202 | 308л | 308л | 308л | 308л | 308л | 308л | 318 | 347 |
312 | 347 | 347 | 347 | 318 | 308 | |||
318 | ||||||||
304(1) | 308 | 308 | 308 | 308 | 308 | 347 | 22.![]() | |
304л | 308л | 308л | 308л | 308л | 308л | 308 | 308 | |
303 | 347 | 347 | 347 | 347 | 347 | 308л | 347 | |
318 | ||||||||
309 | 309 | 309 | 309 | 309 | 374 | 22.12.НТ | ||
309С | 309л | 309л | 309л | 309л | 308 | 309 | ||
310 | 316L | 308л | 347 | |||||
318 | ||||||||
310 | 310 | 317л | 317л | 347 | 22.![]() | |||
310С | 310л | 316L | 316L | 308 | 310 | |||
318 | 318 | 308л | 309 | |||||
309 | 309 | 310 | ||||||
309л | ||||||||
317 | 317 | 317л | 347 | 22.12.НТ | ||||
316 | 316 | 316L | 318 | 309 | ||||
318 | 316 | 316 | ||||||
318 | ||||||||
317L | 317л | 347 | 22.![]() | |||||
316L | 316L | 318 | 309 | |||||
316Ti | 318 | 308 | ||||||
316L | ||||||||
321 | 347 | 22.12.НТ | ||||||
347 | 318 | 309 | ||||||
308 | 347 | |||||||
S30815 | 22.![]() | |||||||
(253MA) | ||||||||
409 | ||||||||
410 | ||||||||
430 | ||||||||
446 | ||||||||
S31500 | ||||||||
S31803 | ||||||||
S32304 | ||||||||
NiCrFe(2) | ||||||||
Сплавы | ||||||||
Родитель | 409 | 446 | Дуплекс | NiCrFe(2) |
---|---|---|---|---|
Металл | 410 | S31500 | Стали | |
ASTM | 430 | S31803 | ||
(AISI) | S32304 | |||
201 | 309 | 309 | 22.![]() | NiCr-3 |
202 | 310 | 310 | 309 | NiCrFe-6 |
304(1) | 309 | 309 | 22.8,3 л | NiCr-3 |
304л | 310 | 310 | 309л | NiCrFe-6 |
303 | 309 | |||
309 | 309 | 309 | 22.8,3 л | NiCr-3 |
309С | 310 | 310 | 309 | NiCrFe-6 |
309л | ||||
310 | 309 | 310 | 22.![]() | NiCr-3 |
310С | 310 | 309 | 309 | NiCrFe-6 |
309л | ||||
317 | 309 | 309 | 22.8,3 л | NiCr-3 |
316 | 310 | 310 | 309Мо | NiCrFe-6 |
309 | ||||
317L | 309 | 309 | 22.8,3 л | NiCr-3 |
316L | 310 | 310 | 309Мо | NiCrFe-6 |
316Ti | 317л | |||
316L | ||||
321 | 309 | 309 | 22.![]() | NiCr-3 |
347 | 310 | 310 | 309 | NiCrFe-6 |
S30815 | 22.12.НТ | 22.12.НТ | 22,8,3 л | NiCr-3 |
(253MA) | 309 | 309 | 309 | NiCrFe-6 |
310 | 310 | 310 | ||
409 | 410 | 446 | 22.8,3 л | NiCr-3 |
410 | 309 | 310 | 309 | NiCrFe-6 |
430 | 309 | 309л | ||
446 | 446 | 309 | NiCr-3 | |
310 | 309л | NiCrFe-6 | ||
309 | ||||
S31500 | 22.![]() | NiCr-3 | ||
S31803 | 309Мо | NiCrFe-6 | ||
S32304 | ||||
NiCrFe(2) | NiCr-3 | |||
Сплавы | NiCrFe | |||
Сплавы |
Родитель | Углерод(1) | Низкий(1) | 501 |
---|---|---|---|
Металл | Стали | Легированная сталь | 502 |
ASTM | 505 | ||
(AISI) | |||
201 | 309 | 309 | 309 |
202 | |||
304(1) | 309 | 309 | 309 |
304л | |||
303 | |||
309 | 309 | 309 | 309 |
309С | |||
310 | 310 | 310 | 310 |
310С | 309 | 309 | 309 |
317 | 309 | 309 | 309 |
316 | |||
317L | 309 | 309 | 309 |
316L | |||
316Ti | |||
321 | 309 | 309 | 309 |
347 | |||
S30815 | 22.![]() | 22.12.НТ | 22.12.НТ |
(253MA) | 309 | 309 | |
310 | 310 | ||
409 | 309 | 309 | 309 |
410 | |||
430 | |||
446 | 309 | 309 | 309 |
S31500 | |||
S31803 | |||
S32304 | |||
NiCrFe(2) | |||
Сплавы | |||
Примечания :
(1) Эта группа включает автоматные стали. Когда такая сталь является элементом соединения, необходимо принять определенные меры предосторожности. Смазывание стали 312 перед сваркой стыка присадочным металлом, подходящим для другой части соединения, или сварка всего стыка 312 обычно является безопасной процедурой.
(2) Более высокую прочность можно получить при использовании NiCrFe-6 с последующей термообработкой.
Общие примечания:
• Если разбавление высокое, т.е. при дуговой сварке под флюсом часто предпочитают специальные марки с высоким содержанием феррита.
• Если рабочие условия требуют термической обработки, возможно, придется пересмотреть выбор присадочного металла. Из-за бесконечных комбинаций материалов и условий работы нельзя применять какие-либо общие правила.
• Присадочные металлы указаны в порядке предпочтения. Обычно предполагается MMA, TIG, поддуговая сварка. Для сварки MIG с более высоким содержанием кремния, напр. 308LSi, 308Si являются предпочтительными.
• Там, где указано 309, можно использовать 309MoL. Там, где указано 309, обычно можно использовать присадочные металлы 310, 312, NiCr-3, однако при этом выборе следует соблюдать осторожность: например.i) чтобы избежать высоких уровней феррита (расходуемый материал 312), который может привести к охрупчиванию сигма-фазы, ii) чтобы избежать высокого содержания никеля (NiCr-3), который может разрушаться в серосодержащих высокотемпературных средах.
• Там, где специальные расходные материалы недоступны, можно использовать более высоколегированные марки. Однако к их выбору следует отнестись с должным вниманием.
• Для высокотемпературных переходных соединений необходимо учитывать диффузию углерода. В таких случаях рекомендуется 310 или NiCr-3.
• При сварке разнородных, но очень коррозионностойких сталей часто требуется наплавка без феррита. Хотя каждый случай необходимо рассматривать отдельно, часто можно рекомендовать использование NiCr-3, 20,25,5LCu или 27,31,4LCu.
• В дополнение к указанным здесь маркам доступны присадочные металлы со специфическими свойствами, например. низкое содержание феррита, высокое содержание углерода, сверхнизкое содержание промежуточных частиц, высокая чистота и т. д.
• Эта таблица не является исчерпывающей. Другие сплавы также могут быть подходящими.
Пассивация
Пассивация — это обработка поверхности нержавеющих сталей, часто растворами кислот (или пастами), для удаления загрязнений и содействия образованию пассивной пленки на только что созданной поверхности (например, путем шлифовки, механической обработки или механического повреждения).
Обычные способы пассивации включают растворы или пасты азотной кислоты (HNO3), которые очищают стальную поверхность от свободных примесей железа. Необходимо соблюдать осторожность при выборе и использовании пассивирующих обработок, чтобы гарантировать, что выбранная обработка будет нацелена на загрязняющее вещество.Пассивация также способствует быстрому образованию пассивной оксидной пленки на поверхности стали. Пассивирование обычно не приводит к заметному изменению внешнего вида стальной поверхности.
В растворах для травления и пассивации могут использоваться опасные кислоты, которые при неправильном обращении могут нанести вред как оператору, так и окружающей среде. Кислоты для травления нержавеющей стали сильно разъедают углеродистую сталь.
Важно, чтобы все кислоты были тщательно удалены путем промывки компонента после завершения процесса.Остаточная фтористоводородная кислота вызывает точечную коррозию.
Может оказаться целесообразным нейтрализовать кислоту щелочью перед этапом ополаскивания.
Стандарт ASTM A380по очистке, удалению окалины и пассивации деталей, оборудования и систем из нержавеющей стали является ценным источником информации о травлении и пассивации. Другие источники информации можно получить, связавшись с ASSDA.
На коррозионную стойкость нержавеющей стали влияет шероховатость поверхности после полировки, с заметным снижением коррозионной стойкости по мере увеличения шероховатости поверхности выше значения Ra около 0.