РЕЖИМЫ СВАРКИ ПОД ФЛЮСОМ | Инструмент, проверенный временем
Режим автоматической сварки под флюсом включает ряд параметров. Основные из них — сила сварочного тока, напряжение дуги, скорость сварки, диаметр электрода, род и полярность тока. Дополнительные параметры — вылет электрода, наклон электрода и др.
Параметры режима сварки выбирают исходя из толщины свариваемого металла и требуемой формы сварного шва, которая определяется глубиной проплавления и шириной шва. Режим сварки определяют по экспериментальным (справочным) таблицам или приближенным расчетом с последующей проверкой на технологических пробах. Обычно режим сварки выбирают в следующем порядке: в зависимости от толщины свариваемого металла выбирают диаметр электродной проволоки, затем в зависимости от диаметра устанавливают силу сварочного тока, далее скорость подачи электрода и скорость сварки. Примерные режимы автоматической сварки под флюсом приведены в таблице 13.2.
Таблица 13. Режимы сварки под флюсом
|
Ниже рассматривается влияние перечисленных параметров режимов на формирование шва и приводятся рекомендации к их выбору.
Сила сварочного тока. От силы тока зависит тепловая мощность дуги. При увеличении силы тока количество выделяющейся теплоты возрастает и увеличивается давление дуги на ванну. Это приводит к увеличению глубины проплавления основного металла и доли участия его в формировании швов.
а б |
10м/ч 40 м/ч 100 м/ч Рис. 13.4. Влияние параметров режима на форму шва: а — варочный ток; б — напряжения дуги; в — скорость сварки |
Диаметр электродной проволоки. При увеличении диаметра электродной проволоки и неизменном сварочном токе плотность тока на электроде уменьшается, одновременно усиливается блуждание дуги между концом электрода и поверхностью сварочной ванны, что приводит к возрастанию ширины шва и уменьшению глубины провара. И, наоборот, при уменьшении диаметра электродной проволоки плотность тока в ней увеличивается, уменьшается блуждание дуги, происходит концентрация теплоты на малой площади сварочной ванны и глубина провара возрастает, ширина шва при этом уменьшается. Это позволяет при сварке тонкой электродной проволокой сравнительно на небольших токах получать глубокий провар.
Напряжение дуги. Из всех параметров режимов автоматических способов дуговой сварки напряжение дуги (рис. 13.4, б) оказывает наибольшее влияние на ширину шва. С повышением напряжения дуги увеличиваются ее длина и подвижность, в результате чего возрастает доля теплоты, идущей на плавление поверхности основного металла и флюса. Это приводит к значительному увеличению ширины шва, причем глубина проплавления уменьшается, что особенно важно при сварке тонкого металла. Несколько уменьшается и высота выпуклости шва.
С повышением напряжения дуги увеличение ширины шва зависит и от рода тока. При одних и тех же напряжениях дуги ширина шва при сварке на постоянном токе, а в особенности при обратной полярности, значительно больше ширины шва, выполненного на переменном токе.
Род токаи полярность. Характер зависимости формы и размеров шва от основных параметров режимов сварки при переменном токе примерно такой же, как и при постоянном. Однако полярность постоянного тока оказывает различное влияние на глубину проплавления, что объясняется разным количеством теплоты, выделяемой на катоде и аноде. При дуговой сварке под флюсом постоянным током применяется, как правило, обратная полярность.
Скорость сварки. Влияние скорости сварки (рис. 13.4, в) на глубину проплавления и ширину шва носит сложный характер.
Сначала при увеличении скорости сварки столб дуги все больше вытесняет жидкий металл, толщина прослойки жидкого металла под дугой уменьшается и глубина проплавления возрастает. При дальнейшем увеличении скорости сварки (более 40-50 м/ч) заметно уменьшается погонная энергия и глубина проплавления начинает уменьшаться. Во всех случаях при увеличении скорости сварки ширина постоянно уменьшается. При скорости сварки более 70-80 м/ч основной металл не успевает достаточно прогреваться, в результате чего по обеим сторонам шва возможны несплавления кромок или подрезы. При необходимости ведения
Скорость подачи электродной проволоки. Этот параметр режима сварки тесно связан с силой сварочного тока и напряжением дуги. Для устойчивого процесса сварки скорость подачи электродной проволоки должна быть равна скорости ее плавления. При недостаточной скорости подачи проволоки возможны периодические обрывы дуги, при слишком большой скорости происходят частые короткие замыкания электрода на сварочную ванну. Все это ведет к появлению непроваров и неудовлетворительному формированию шва.
Вылет электрода. С увеличением вылета электрода возрастает интенсивность его предварительного подогрева проходящим сварочным током. Электрод плавится быстрее, а основной металл остается сравнительно холодным. Кроме того, увеличивается длина дуги, что приводит к уменьшению глубины проплавления и некоторому увеличению ширины шва. Обычно вылет составляет 40-60 мм.
б |
Рис. 13.5. Влияние наклона при сварке на форму шва: а — электрода; б — детали При сварке углом вперед жидкий металл подтекает под дугу, толщина его прослойки увеличивается, а глубина проплавления уменьшается. |
Наклон электрода вдоль шва. Обычно сварку выполняют вертикально расположенным электродом, но в отдельных случаях она может производиться с наклоном электрода углом вперед или углом назад (рис. 13.5, а).
наплавленным и образованием пористости шва. Учитывая это, данный метод применяют ограниченно, в основном при сварке металла большой толщины на больших скоростях, например при двухдуговой сварке или выполнении кольцевых швов небольшого диаметра.
Наклон изделия. Обычно автоматическая и механизированная сварка под флюсом производится в нижнем положении (рис. 13.5, а). Возможна сварка на подъем или на спуск (рис. 13.5, б). При сварке на подъем жидкий металл под действием собственного веса вытекает из-под дуги, толщина его прослойки уменьшается, что приводит к увеличению глубины проплавления и уменьшению ширины шва. При угле наклона 6-8° по обе стороны шва могут образоваться подрезы, ухудшающие форму шва.
При сварке на спуск расплавленный металл подтекает под дугу, что приводит к увеличению толщины его прослойки. Глубина проплавления при этом уменьшается. Этот метод, позволяющий несколько увеличить скорость сварки при хорошем формировании шва и небольшой глубине проплавления, применяется при сварке тонкого металла. При угле наклона более 15-20° происходит сильное растекание электродного металла, который только натекает на поверхность свариваемого изделия, но не сплавляется с ним, поэтому не применяется.
Марка флюса и его грануляция. Различные флюсы обладают разными стабилизирующими свойствами, с повышением которых увеличиваются длина дуги и ее напряжение, в результате чего возрастает ширина шва и уменьшается глубина проплавления. Чем крупнее флюс, тем меньше его объемная масса. Флюсы с малой объемной массой (крупнозернистые стекловидные и пемзовидные) оказывают меньшее давление на газовую полость зоны сварки, что способствует получению более широкого шва с меньшей глубиной проплавления. Применение мелкозернистого флюса с большей объемной массой приводит к увеличению глубины проплавления и уменьшению ширины шва.
Режимы под флюсом — Энциклопедия по машиностроению XXL
Опытные данные показывают, что в условиях автоматической и полуавтоматической сварки под флюсом, а так ке в среде углекислого газа, в диапазоне режимов, обеспечивающих удовлетворительное формирование, коэффициент полноты валика [Хв изменяется в узких пределах и практически имеет устойчивое значение рв =- 0,73. [c.
Таблица 53. Режимы сварка под флюсом |
Ширина зоны термического влияния зависит от толщины металла, вида и режимов сварки. При ручной дуговой сварке она составляет обычно 5—6 мм, при сварке под флюсом средних толщин около 10 мм, при газовой сварке до 25 мм. [c.30]
Участки I и II ВАХ соответствуют режимам сварки, применяемым при ручной сварке плавящимся покрытым электродом, а также неплавящимся электродом в среде защитных газов. Механизированная сварка под флюсом соответствует II области и частично захватывает III область при использовании тонких электродных проволок и повышенной плотности тока, сварка плавящимся электродом в защитных газах соответствует III области ВАХ. Для питания дуги с падающей или жесткой ВАХ применяют источники питания с падающей или пологопадающей внешней характеристикой.
Параметры режима сварки под флюсом. Основными составляющими режима сварки под флюсом являются величина тока, его род и полярность, напряжение дуги, скорость сварки, диаметр электрода, скорость подачи электродной проволоки. Дополнительные параметры режима — вылет электрода, наклон электрода и изделия, марка флюса, подготовка кромок и вид сварного соединения. [c.75]
Примерные режимы автоматической и полуавтоматической сварки под флюсом на переменном токе низкоуглеродистой стали толщиной 10 мм приведены в табл. 3. [c.76]
Назовите параметры режима сварки под флюсом. [c.79]
Процесс электрошлаковой сварки возник в свое время как дальнейшее развитие процесса дуговой сварки под флюсом, когда было установлено, что при определенных режимах электрод закорачивается на слой расплавленного шлака и выделение
[c. 129]
В остальном, с учетом указанных особенностей, расчет режимов при сварке под флюсом аналогичен расчету режимов сварки в среде защитных газов (пункты 1 — 14). [c.55]
Сварка автоматическая под флюсом—Режимы 5—541 [c.118]
Сварка автоматическая под флюсом — Режимы 5 — 541 [c.282]
Головки для автоматической сварки под флюсом конструкции ЦНИИТМАШ построены по принципу независимой скорости подачи электродной проволоки. Рациональная конструкция сварочной головки с независимой скоростью подачи электродной проволоки должна допускать плавное регулирование скорости электрода без перерыва процесса сварки. Это облегчает подбор сварочных режимов и позволяет в случае значительного падения напряжения сети путём замедления скорости подачи электрода поднять напряжение на дуге и улучшить форму шва. [c.243]
Трансформаторы СТЭ-23, -24, -32, -34, СТАН-0, -I предназначены для ручной сварки.
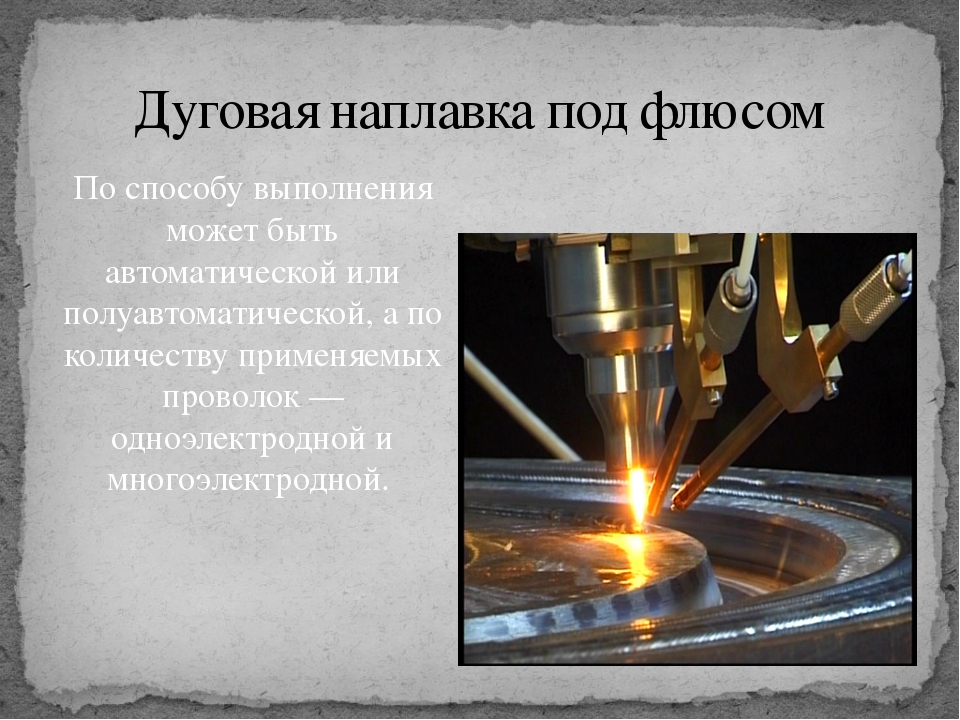
Неравномерность усиления шва по высоте при ручной сварке может возникнуть при неправильных приемах заварки прихваток, возвратных движениях ири заварке кратеров, при плохом формировании шва из-за неправильно выбранного режима сварки и низкого качества электродов. При автоматической сварке под флюсом неравномерные по высоте швы получаются при заниженной величине тока относительно требуемого для принятой скорости сварки. [c.464]
Основные технологические данные о подготовке кольцевых стыковых кромок под сварку и режимы автоматической сварки под флюсом с предварительной ручной подваркой приведены в табл. 29—32. [c.116]
Режимы автоматической сварки под флюсом основных кольцевых наружных швов, выполняемых после ручной подварки
[c. 116]
В табл. 32 приведены режимы автоматической сварки под флюсом основных кольцевых наружных швов, выполняемых после ручной подварки. [c.117]
Для питания дуги на участке II с жесткой характеристикой применяют источники с падающей или пологопадающей характеристикой (ручная дуговая сварка, автоматическая под флюсом, сварка в защитных газах неплавящимся электродом). Режим горения дуги определяется точкой пересечения характеристик дуги б и источника тока I (рис. 5.4, б). Точка В соответствует режиму неустойчивого горения дуги, точка С — режиму устойчивого горения дуги (/св и f/д), точка А — режиму холостого хода в работе источника тока в период, когда дуга не горит и сварочная цепь разомкнута. Режим холостого хода характеризуется повышенным напряжением (60. .. 80 В). Точка D соответствует режиму короткого замыкания при зажигании дуги и ее замыкании каплями жидкого электродного металла. Короткое замыкание характеризуется малым напряжением, стремящимся к нулю, и повышенным, но ограниченным током.
[c.225]
Химический состав сварочной ванны в первую очередь определяется составом электродной проволоки и основного металла в зависимости от доли его участия в шве. Доля участия основного металла определяется способом и режимом сварки и может изменяться от 0,15 до 0,6 для ручной сварки покрытыми электродами и автоматической под флюсом соответственно. Конечный состав шва устанавливается [c.227]
Повышенное качество сварных швов обусловлено получением более высоких механических свойств наплавленного металла благодаря надежной защите сварочной ванны флюсом, интенсивному раскислению и легированию вследствие увеличения объема жидкого шлака, сравнительно медленного охлаждения шва под флюсом и твердой шлаковой коркой, улучшением формы и поверхности сварного шва и постоянством его размеров по всей длине вследствие регулирования режима сварки, механизированных подачи и перемещения электродной проволоки. [c.232]
Режим сварки. Определение режима сварки производится по экспериментально-расчетной методике с использованием эмпирических соотношений, полученных обработкой опытных данных. Параметрами режима автоматической сварки под флюсом являются сварочный ток, напряжение дуги, скорость сварки и скорость подачи сварочной проволоки. Основной параметр — сварочный ток — в случае сварки по стыку с зазором без разделки кромок определяется исходя из условия полного провара свариваемого сечения на величину Я. При односторонней сварке Я принимается равным толщине листа 6 (см), при двусторонней сварке больше Л 5 на 10. .. 15 % с учетом перекрытия первого и второго слоев.
[c.233]
Дуговую сварку под флюсом выполняют неподвижными подвесными автоматическими сварочными головками и передвижными сварочными автоматами (сварочными тракторами), перемещающимися непосредственно по изделию. Назначение сварочных автоматов — подача электродной проволоки в дугу и поддержание постоянного режима сварки в течение всего процесса. Автоматическую сварку под флюсом применяют в серийном и массовом производствах для выполнения длинных прямолинейных и кольцевых швов в нижнем положении на металле толщиной 2. .. 100 мм. Под флюсом сваривают стали различных классов. Автоматическую сварку широко применяют при изготовлении котлов, резервуаров для хранения жидкостей и газов, корпусов судов, мостовых балок и других изделий. Она является одним из основных звеньев автоматических линий для изготовления сварных автомобильных колес и станов для производства сварных прямошовных и спиральных труб (рис. 5.9).
[c.234]
Методика определения параметров режима сварки аналогична рассмотренной ранее для автоматической сварки под флюсом. Исходным условием остается получение полного провара свариваемого сечения на величину Я (см. с. 233), см [c.238]
Основные параметры режима дуговой сварки под флюсом — это сила сварочного тока, его род и полярность, напряжение дуги, скорость сварки, диаметр и скорость подачи электродной проволоки. Дополнительные параметры — вылет электрода (расстояние от его торца до мундштука), наклон электрода или изделия, марка флюса, подготовка кромок и вид сварного соединения. С увеличением силы сварочного тока возрастает давление дуги, вследствие чего жидкий металл сварочной ванны более интенсивно вытесняется из-под электрода и дуга погружается в глубь основного металла. Глубина проплавления основного металла при этом увеличивается, дуга укорачивается и становится менее подвижной. Вследствие этого ширина шва при увеличении силы тока остается неизменной, несмотря на увеличение объема сварочной ванны. Швы становятся глубокими, но не широкими (рис. 76). Величина усиления такого шва велика, так как растет количество электродного металла, расплавленного в единицу времени. Такие швы менее стойки к образованию трещин и плохо работают при вибрационных нагрузках. Следует отметить, что с ростом силы тока при неизменных остальных условиях уменьшается количество расплавляемого флюса.
[c.143]
При сварке плавящимся электродом в защитных газах зависимости формы и размеров шва от основных пара. метров режима такие же, как и при сварке под флюсом (см. рис. 28). Для сварки используют электродные проволоки малого диаметра (до. 3 мм). Поэтому швы имеют узкую форму провара и в них может наблюдаться повышенная зональная ликвация (см. рис. 2У). Применяя ионерочиые колебания электрода (с м. рис. 30, а), изменяют форму шва и условия кристаллизации металла сварочной вапны и уменьшают вероятность зональной ликвации. Плюется опыт примопе-ния для сварки в углекислом га ю электродных проволок диаметром 3—5 мм. Сила сварочного тока в этом случае достигает 2000 А, что значительно повыша( т производительность сварки. Однако при подобных форсированных режимах наблюдается ухудшенное формирование стыковых швов и образование в иих подрезов. Формирование и качество угловых швов вполне удовлетворительны.
[c.58]
Значительно более жесткие требования по точности выполнения устанавливаемых режимов предъявляются к манипуляторам и механизмам перемещения сварочного источника теплоты в автоматизированных установках. Допустимы следуюн(ие колебания скорости перемещения при сварке под флюсом 5% при аргонодуговой сварке тонколистовых металлов 2% в установках для электронно-лучевой и лазерной сварки менее ztl%. Точность установки свариваемых изделий и отклонение положения стыка при сварке не должно нревын1ать 20—25% поперечного размера площади пятна ввода теплоты в изделие, т. е. при сварке под флюсом это составляет J —2 мм при микроплазмен-ной — не более 0,25 мм нри электронно-лучевой и лазерной (в зависимости от диаметра луча) от tO,l мм до 10 мкм.
[c.123]
Рассмотрим вопросы построения критериев подобия по методу анализа размерностей и основы теории многофакторного эксперимента. Формулы для выбора режимов сварки и приближенного расчета геометрических размеров сварных швов и их механических свойств приведены только для механизированной сварки под флюсом и только для низкоуглеродистых и пизколегированпых сталей. Для этих сталей и метода сварки указанные форму гы про1нли многократную опытную проверку и дают надежные результаты с точностью до 10 — 12%.
[c.174]
Основные параметры режима механизированной сварки (автоматической и полуавтоматической) под флюсом и в защитных газах, оказывающие существенное влияние на размеры и форму швов, — сила сварочного тока, плотность тока в электроде, напряжение дуги, скорость сварки, химический состав (марка) и граггуляция флюса, род тока и ого полярность. [c.185]
Повышение коррозионной стойкости швов в морской воде достигается использованием электродной проволоки марки Св-08ХГ2С. Структура и свойства металла шва и околошовной зоны на низкоуглеродистых и низколегированных сталях зависят от марки использованной электродной проволоки, состава и свойств ОСЕОВПОГО металла и режима сварки (термического цикла сварки, доли участия основного металла в формировании шва и фо])мы шва). Влияние этих условий сварки и технологические рекомендации примерно такие же, как и при ручной дуговой сварке и сварке под флюсом. [c.226]
В связи с этим в шов с расплавленным основным металлом поступают легирующие элементы, содержащиеся в свариваемой стали, в том числе и углерод, концентрация которого в сталях этой группы достаточно высока. Влияние содержания углерода, серы и марганца в шве на склонность к образованию горячих трещин схематически представлепо на рис. 124. Линия I служит границей раздела составов с низким содержанием углерода ( ] m. при которых образуются или не образуются горячие трещины. При повышенном содержании углерода [С] , ш такой границей будет линия 5, в этом случае даже при низком содержании серы и большой концентрации марганца в шве могут возникнуть горячие трещины. При механизированной сварке под флюсом необходимы подготовка кромок, техника и режимы сварки, при которых доля основного металла в шве будет минимальной.
[c.252]
При использовании для сварки низкоуглеродистых проволок в полной мере можно реализовать преимущество сварки под флюсом получать швы с глубоким проплавлением, используя при однопроходной сварке стыковых соединений без разделки кромок повышенный сварочный ток и скорость сварки.
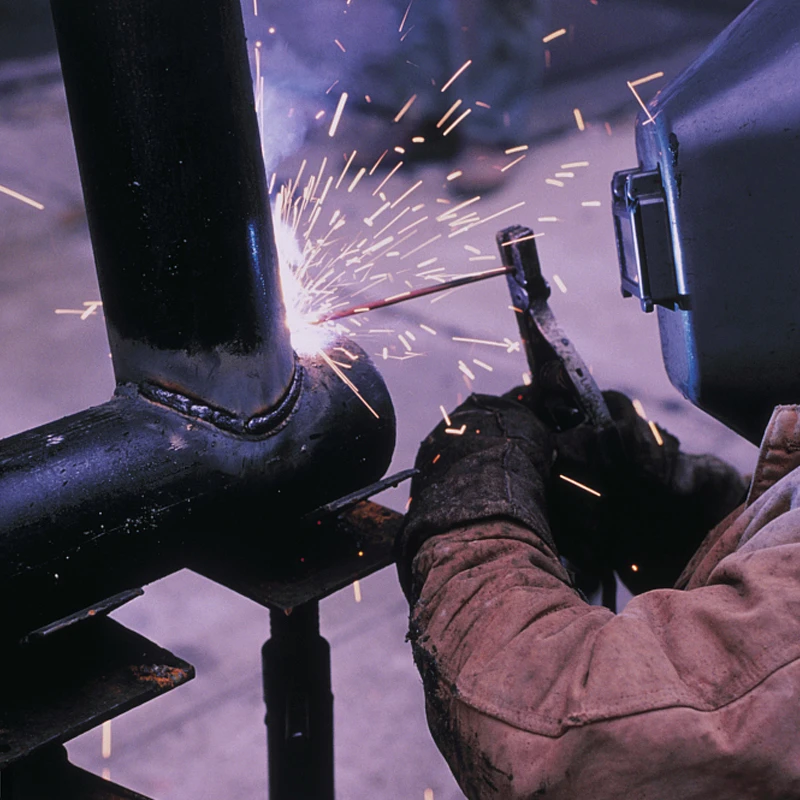
Аналогично может влиять и примепепие при поплавке, выполняемой под флюсом НЛП в защитных газах, электродной лепты, спрессованной из порошков, но сравнению с прокатной. ]Зольшее электрическое сопротивление спрессованной ленты и се меньшая теплопрозо/нюсть приводят к более быстрому ее расплавлению (большему а,1 при том же, как при прокатанной ленте, режиме [c.397]
При массовом производстве однотипных изделий (трубы, резервуары, балки) для повышения производительнвети повышают скорость сварки. Для обеспечения хорошего формирования шва при больших скоростях для сварки стыковых соединений под флюсом применяют многодуговую автоматическую сварку. При многодуговой сварке шов выполняют несколькими раздельными дугами, допускающими независимое регулирование и режимы, обычно электродные проволоки плавятся в одну общую ванну. [c.74]
Влиянне параметров режима сварки на развитие металлургических процессов при сварке под флюсом. Главными параметрами режима сварки являются напряжение на дуговом промежутке (7д, связанное с длиной дуги, сила тока /д и скорость сварки U Вместе они определяют энерговложение при сварке или значение погонной энергии. [c.374]
На основе проведенных исследований и результатов опытно-промышленного опробования подготовлены нормативные технологические инструкции по ручной электроду го-вой сварке, по полуавтоматической сварке в среде углекис.то го газа и по автоматической сварке под флюсом регламентирующие применение разработанных технологий сварки, [5 этих руководящих документах регламентированы конструктивные формы и размеры элементов подготовки кромок, последовательность и требования к сборке, допустимые параметры твердых прослоек во взаимосвязи с геометрическими размерами и степенью их механической неоднородности, порядок выполнения сварки, выбор сварочных материалов и ре комендуемые режимы сварки, параметры сопутствую щег ) охлаждения с учетом толщины металла свариваемых элементов и рабочих условий эксплуатации. [c.106]
При изготовлении полотнищ для последующего монтажа стенок резервуара листы разных поясов в специальных контейнерах подают на верхний ярус стенда и укладывают за один ход самоходной кран-балки, несущей необходимое число траверс с вакуумными или магнитными захватами. Укладка листов производится на медные водоохлаждаемые подкладки о точностью до 1 мм, что обеспечивается специальными упорами и улавливателями. Кромки листов поджимаются к медной подкладке пневморычажными прижимами. Обычно сварка полотнищ ведется под флюсом, при этом для повышения производительности используют двухд> говые автоматы, которые позволяют сваривать полотнища из листов переменной толщины. Сварку ведут в направлении от более толстых листов к тонким, изменяя режим отключением одной из д>т при сохранении непрерывности движения аппарата по всей длине стыка. Одновременно ведут автоматическую сварку швов в перпендикулярном направлении, состыковывая пару разнотолщинных листов и корректируя по мере перехода на очередной шов режимы сварки. После сварки полотнища с одной стороны, оно при помощи барабана передастся на нижний ярус, где осуществляется сварка в той же последовательности, но без прижимных устройств [c.14]
Свойства многослойных сварных соединений, моделирующих кольцевые швы, исследовали на плоских образцах (пакетах) толщиной 100 мм, собранных из пластин толщиной 4 мм. Торцы пакетов обрабатывали под наплавку механическим способом. Наплавку торцов пакетов осуществляли в один слой высотой 8 мм металлической крошкой типа 08А проволокой Св-08Г2С диаметром 3 мм под флюсом АН-60 с поперечными колебаниями электрода по режиму сила тока 750— 800 А напряжение дуги 38—40 В скорость наплавки 4,4 м/ч, скорость колебаний электродов 116 м/ч, амплитуда колебаний 100 мм. Автоматическую сварку наплавленных пакетов выполняли с предваритель- [c.116]
Кольцевые швы выполнены проволокой Св-10ХГСН2МТ диаметром 3 мм под флюсом АН-17М на режиме /св = 400—450 А, ид = = 36—38 В, Уев = 18 м/ч, ток постоянный, полярность — обратная. Предварительный подогрев сварных соединений 150—200 С. [c.124]
Шлаковые включения наблюдаются при сварке электродами, покрытыми обмазкой, и при автоматической сварке под флюсом. При сварке непокрытыми или тонкопокрытыми электродами, а также при газовой сварке они встречаются редко. Шлаковые включения образуются вследствие применения несоответствуюш,их марок электродов или обмазок, а также при неправильном режиме сварки и низкой квалификации или небрежности сварщика. [c.359]
Для обеспечения пластических свойств металла шва и околошов-ной зоны на уровне свойств основного металла следует выбирать режимы, обеспечивающие получение швов повышенного сечения, применять двухдуговую сварку или производить предварительный подогрев металла до температуры 150…200 °С. Среднеуглеродистые и среднелегированные стали рекомендуется сваривать под флюсом при толщине свариваемого металла не менее 4 мм. Сварку можно вести как на переменном, так и на постоянном токе. Диаметр электродной проволоки выбирают 2…5 мм. При сварке с одной стороны не допускается использование медных и медно-флюсовых подкладок из-за возможности попадания в шов меди и образования вследствие этого горячих трещин. Для увеличения сопротивляемости сварных швов горячим трещинам, а также повышения пластичности и ударной вязкости металла шва используют основные флюсы, такие как АН-26, АН-20, 48-ОФ-10, уменьшающие содержание серы и окисных включений в металле шва. Во избежание пористости и наводоражи-вания швов флюсы перед сваркой необходимо прокаливать при температуре 300…350 °С в течение 2…3 ч, чтобы их влажность не превышала 0,1 %. Конструкционные среднеуглеродистые и среднелегированные стали под флюсом сваривают, как правило, без подогрева. Только в случае сварки жестких узлов и узлов из сталей ЗОХГСА и ЗОХГСНА при большой толщине изделий применяют подогрев до температуры 250…300 °С. После сварки во всех случаях необходим общий отпуск при температуре 600 °С или местный послесварочный отпуск при температуре 300 ° С для предупреждения образования холодных трещин. [c.150]
Автоматическая сварка под флюсом.
Сварку под флюсом выполняют на постоянном токе обратной полярнос-ти. Сила сварочного тока не превышает 800А, напряжение дуги до 40 В, ско-рость сварки изменяют в диапазоне 13…30 м/ч. Одностороннюю однопроход-ную сварку применяют длясоединений толщиной до 8 мм и выполняют на ос-тающейся стальной подкладке или флюсовой подушке.
Максимальная толщина соединений без разделки кромок, свариваемых двусторонними швами, не должна превышать 20 мм. Для стыковых соединений без скоса кромок (односторонних и двусторонних) используют проволоку марки Св-08ХН2М. Применять более легированные проволоки для таких сое-динений нецелесообразно, поскольку в этом случае швы имеют излишне высо-кую прочность.
Наиболее часто стыковые соединения подготавливают со скосом кромок. Сварку корневых швов стыковых соединений высокопрочных сталей с V- или Х-образной разделкой кромок обычно выполняют проволоками марок Св-08ГА или Св-10Г2. Заполнение разделок кромок осуществляется проволоками марок Св-08ХН2ГМЮ или Св-08ХН2ГСМЮ последовательным наложением слоев.
Основные параметры режима автоматической сварки под флюсом: сваро-чный ток, напряжение дуги и скорость перемещения дуги.
С увеличением сварочного тока дуга больше погружается в основной ме-талл, возрастает погонная энергия и количество расплавленного в единицу вре-мени электродного металла. В результате глубина провара и доля участия ос-новного металла в металле шва увеличиваются. Увеличение диаметра свароч-ной проволоки при неизменном сварочном токе приводит к уменьшению глу-бины провара и выпуклости шва при одновременном увеличении его ширины. В зависимости от толщины свариваемых кромок применяют проволоку диа-метром 2…5 мм.
Увеличение напряжения дуги приводит к повышению ее подвижности, в результате чего увеличивается ширина шва, а глубина остается практически не-изменной. При сварке под флюсами АН-17М и АН-43 напряжение дуги не дол-жно превышать 40 В. Скорость перемещения дуги при сварке стыковых соеди-нений высокопрочных сталей изменяют от 13 до 30 м/ч. Повышение скорости сварки в этом диапазоне обусловливает увеличение глубины проплавления. Автоматической сваркой под флюсом выполняют стыковые, угловые и нахлес-точные швы, расположенные в нижнем положении.
Стыковые соединения можно выполнять односторонними и двусторонни-ми швами с разделкой и без разделки кромок. Швы с разделкой кромок могут быть однопроходными и многопроходными.
Односторонней однопроходной сваркой соединяют высокопрочную сталь толщиной до 8 мм. Для более толстого металла использовать односторон-нюю сварку нецелесообразно, поскольку это приводит к перегреву металла око-лошовной зоны.
Односторонние стыковые соединения сваривают с использованием тех-нологических приемов, которые позволяют обеспечивать высокое качество сварных швов: на остающейся стальной подкладке, на медной или флюсомед-ной подкладке, на флюсовой подушке. Подкладные планки изготовляют из низкоуглеродистой стали СтЗсп толщиной 3…6 мм и шириной 40…50 мм. Зазор между подкладкой и кромками не должен превышать 0,5… 1 мм для пре-дотвращения затекания металла в корневом участке шва. В противном случае в корне шва могут образоваться дефекты (прожоги, шлаковые включения, трещи-ны). После окончания кварки подкладную планку, как правило, удаляют, а поверхность шва зачищают шлифовальной машинкой заподлицо с основным ме-таллом.
При использовании медных или флюсомедных подкладок, флюсовых по-душек необходимо обеспечивать плотное под-жатие подкладки к корню свар—ного соединения. Рекомендуемые режимы односторонней сварки под флюсом стыковых соединений толщиной до 8 мм без скоса кромок на флюсовой по-душке приведены в табл. 23. Металл большей толщины без скоса кромок сва-ривают двусторонними швами.
Таблица 23. Режимы автоматической сварки под флюсом стыковых соединений без скоса кромок на флюсовой подушке
Двусторонняя автоматическая сварка является основным методом полу-чения высококачественных швов, так как этот тип соединений наиболее тех-нологичен, надежен, позволяет получать сварные соединения с минимальными деформациями и высоким качеством. Двусторонняя автоматическая сварка бо-лее надежна по сравнению с односторонней, так как в этом случае на качество швов в меньшей степени влияет колебание режима сварки, смещение электрода от оси шва, точность подготовки кромок и сборки. Первый проход двусторон-него шва обычно выполняют на флюсовой подушке или «на весу».
Максимальная толщина металла, свариваемого двусторонними швами при бескосной разделке кромок, не должна превышать 20 мм. В противном слу-чае сварку необходимо вести на форсированных режимах, что приводит к сни-жению пластичности и хладостойкости металла околошовной зоны. Техника сварки первого прохода такая же, как и односторонних швов. Глубина проплав-ления должна быть равна (0,6…0,7) металла. После кантования изделия второй проход шва выполняют с таким расчетом, чтобы перекрытие слоев состав-ляло 3…4 мм. Наиболее рационально такие швы сваривать с обязательным за-зором в стыке. Режимы двусторонней автоматической сварки под флюсом сты-ков без скоса кромок обычно выбирают с таким расчетом, чтобы оба слоя шва сваривались без переналадки сварочной аппаратуры (табл. 23).
Для стыковых соединений без скоса кромок (односторонних и двусторон-них) используют сварочную проволоку Св-08ХН2М. Применять более легиро-ванные проволоки для таких соединений нецелесообразно, поскольку в этом случае механические свойства швов имеют излишне высокую прочность.
Наиболее часто при сварке высокопрочных сталей стыковые соединения подготовляют со скосом кромок. Корневые швы стыковых соединений высоко-прочных сталей с V- или X-образной разделкой кромок обычно выполняют то-ком прямой полярности проволоками Св-08ГА или Св-10Г2 (табл. 24).
Заполнение V-образной разделки кромок осуществляется током обратной полярности проволоками Св-08ХН2ГМЮ или Св-08ХН2Г2СМЮ последова-тельным наложением слоев. При выполнении слоев многопроходного шва пер-вые два-три слоя выполняют по оси разделки, а все последующие — со смеще-ниями последовательно то к одной, то к другой стороне разделки.
Порядок многопроходной сварки швов при Х-образной симметричной разделке кромок следующий: выполняют сварку с одной стороны, заполняя разделку на одну треть или наполовину по глубине; кантуют соединение, зачи-щают корень шва и выполняют сварку с этой стороны, заполняя разделку на одну треть или наполовину сечения по глубине; снова кантуют и окончательно сваривают шов с первой стороны, а затем — со второй стороны соединения.
При сварке толстолистовых соединений высокопрочных сталей более предпочтительна разделка с двумя несимметричными скосами двух кромок.
При автоматической сварке под флюсом угловых швов тавровых и нахле-сточных соединений при положении в угол формирование швов затруднено, в результате чего появляются условия для образования подрезов вертикальной стенки и наплывов металла шва на горизонтальную полку. Основным условием получения качественных швов является правильный выбор режима сварки и точное расположение конца электрода относительно кромок свариваемого из-делия. Электрод располагают таким образом, чтобы угол, образуемый электро-дом и вертикальной стенкой, составлял 35…40°.
Сварку тавровых, угловых и нахлесточных соединений выполняют в двух основных положениях — в «лодочку» и в угол (табл. 25, 26).
Узнать еще:
Сварка под флюсом
На первый взгляд может показаться, что одно из основных преимуществ сварки под флюсом — возможность получения большой глубины проплавления свариваемого металла — противоречит условиям сварки тонколистовой стали. Однако при определенных условиях сварка под флюсом допускает регулирование глубины проплавления металла, начиная от долей миллиметра, и поэтому хорошо известные ее достоинства могут быть использованы для сварки тонколистовой стали.
Успешное внедрение в производство сварки под флюсом изделий из тонколистовой стали стало возможным, главным образом, благодаря применению тонкой сварочной проволоки. Известны примеры сварки тонколистовой стали и обычной электродной проволокой диаметром, например, 4 мм. Однако в этом случае удавалось сваривать сталь толщиной не менее 3—4 мм при условии весьма тщательной сборки изделия.
Для сварки тонколистовой стали большое значение имеет применение приспособлений, облегчающих точную сборку изделия и обеспечивающих надежное поджатие к свариваемому стыку медной или флюсомедной подкладки, флюсовой подушки и т. п. Опыт показывает, что производительность автоматической сварки изделий из тонколистовой стали со сравнительно короткими швами зависит не столько от машинной скорости сварки, сколько от затрат времени на подготовительные и вспомогательные операции. Поэтому важной задачей является разработка эффективно действующих сборочных и сборочно-сварочных приспособлений.
Чем меньше величина тепловой энергии, передающейся от дуги основному металлу в процессе сварки, тем меньше глубина его проплавления и, следовательно, тем более тонкий металл можно сваривать без прожогов. Тепловая энергия, передаваемая основному металлу, может быть уменьшена за счет уменьшения мощности дуги или увеличения скорости ее перемещения по свариваемому соединению.
Для сварки тонколистовой стали в основном применяют уменьшение мощности дуги, а не увеличение скорости сварки. Это в значительной мере объясняется тем, что применение больших скоростей сварки (более 150—200 м/час) связано с жесткими требованиями к точности поддержания режима сварки, необходимостью тщательной очистки свариваемых кромок, с очень точной сборкой стыков, в ряде случаев со специальным наклоном изделия и электрода и т. п. При указанных скоростях сварки металл шва может быть поражен порами, поперечными трещинами и другими дефектами. Если при этом учесть, что производительность сварки тонколистовой стали, как указывалось выше, главным образом, зависит от затрат времени на установочные и подготовительные операции, то станет ясным, почему увеличение скорости не стало основным способом уменьшения погонной тепловой энергии.
Устойчивость процесса сварки
При сварке тонколистовой стали равномерность глубины проплавления имеет особенно важное значение. Если сваривая сталь толщиной более 4—5 мм, можно допустить колебание глубины проплавления в пределах ± 1 мм, не опасаясь возникновения прожогов, то в случае сварки тонких листов стали такое же колебание совершенно недопустимо.
Равномерность глубины проплавления зависит от устойчивости режима сварки, главным образом, от колебаний сварочного тока. Колебания скорости сварки, а также напряжения дуги сказываются в меньшей степени. Исходя из этого, для сварки тонколистовой стали следует рекомендовать сварочные автоматы с постоянной скоростью подачи электродной проволоки, так как они обеспечивают практически почти постоянные значения тока при колебании напряжения в сети или случайных изменениях длины дуги в процессе сварки. При этом сохраняются почти постоянной глубина проплавления, а также количество наплавляемого металла. Сварочные головки с регулируемой скоростью подачи электродной проволоки в тех же условиях не обеспечивают постоянство тока и поэтому применять их не рекомендуется.
Понижение мощности дуги, требующееся для сварки тонколистовой стали, может быть осуществлено только до определенного предела, зависящего от диаметра электродной проволоки. Дальнейшее снижение мощности резко ухудшает устойчивость процесса сварки и приводит к неудовлетворительному формированию шва. В случае сварки переменным током этот предел достигается при значительно большей мощности дуги, чем в случае сварки постоянным током обратной полярности. Поэтому сварку тонколистовой стали рекомендуется осуществлять постоянным током обратной полярности (положительный полюс присоединен к электроду). В табл. 1 приведены полученные опытным путем значения минимально-допустимых сварочных токов для электродной проволоки различных диаметров при сварке под флюсом АН-348 постоянным током обратной полярности.
Таблица 1
Как следует из табл. 1, для обеспечения устойчивого горения дуги при понижении ее мощности необходимо увеличивать плотность тока в электроде, что практически достигается путем уменьшения диаметра электродной проволоки. Эту таблицу можно использовать для выбора диаметра электродной проволоки при сварке на заданном режиме.
При рассмотрении условий устойчивого горения электрической дуги пользуются ее статическими вольтамперными характеристиками. Вольтамперной характеристикой называется зависимость между током и напряжением дуги при постоянной ее длине. На фиг. 1 приведены такие характеристики для дуг различной длины. Каждая вольт- амперная характеристика дуги состоит из нескольких участков: падающего (с ростом тока напряжение падает), почти горизонтального (жесткий участок) и растущего (с ростом тока напряжение увеличивается). В зависимости от условии сварки, дуге соответствует тот или иной участок характеристики. Так, например, при сварке неплавящимся угольным или вольфрамовым электродом, при ручной сварке качественными электродами, при автоматической сварке под флюсом со сравнительно небольшой плотностью тока и в некоторых других случаях характеристика сварочной дуги является падающей с переходом к жесткой. При сварке под флюсом или в защитной газовой среде с повышенной плотностью тока в плавящейся электродной проволоке характеристика дуги становится растущей.
Если дуга имеет падающую вольтамперную характеристику, то устойчивое ее горение возможно только при том условии, что внешняя характеристика сварочного генератора также будет падающей, т. е. напряжение холостого хода генератора значительно превышает напряжение дуги при сварке.
С ростом плотности тока в плавящемся электроде изменяются свойства сварочной дуги. Эти изменения настолько существенны, что позволяют предъявить совершенно другие требования к характеристикам источников питания постоянного тока.
Еще в 1950 г. в Институте электросварки им. Е. О. Па- тона было доказано, что при повышении плотности тока в плавящемся электроде может быть получен устойчивый процесс сварки при использовании в качестве источника питания генератора постоянного тока с жесткой внешней характеристикой (напряжение холостого хода генератора практически равно напряжению дуги при сварке). В отечественной и зарубежной практике в последние годы такие генераторы нашли широкое применение.
Генераторы с жесткими внешними характеристиками значительно более экономичны, чем обычные сварочные генераторы с крутопадающими характеристиками и высоким напряжением холостого хода, так как пропорционально снижению напряжения холостого хода генератора снижаются затраты на активные материалы, уменьшается вес генератора и его стоимость.
Чем больше скорость подачи электродной проволоки п меньше сварочный ток, тем труднее возбудить дугу путем непосредственной подачи электродной проволоки к изделию. Опыт показывает, что при использовании обычных сварочных генераторов с крутопадающей внешней характеристикой в ряде случаев этот способ возбуждения дуги практически оказывается неосуществимым. Совершенно иное наблюдается в случае применения генераторов с жесткими внешними характеристиками. Резкое нарастание тока при закорачивании электрода на изделие обеспечивает безотказное возбуждение дуги. Короткое замыкание не наносит ущерба генератору, так как тонкая электродная проволока выполняет роль плавкой вставки в цепи, ограничивая время протекания и величину тока короткого замыкания.
В тех случаях, когда генераторы с жесткими внешними характеристиками по какой-либо причине не могут быть применены для сварки тонкого металла, следует применять генераторы с весьма пологопадающими характеристиками, т. е. с большой величиной тока короткого замыкания.
Чем резче изменяется ток в цепи при случайных изменениях длины дуги, тем интенсивнее протекают процессы саморегулирования и тем быстрее восстанавливается заданный режим сварки. Генераторы с крутопадающими внешними характеристиками дают значительно меньшие изменения тока при случайных колебаниях длины дуги, чем генераторы с пологопадающими, жесткими или растущими характеристиками, благодаря чему обеспечивают большую устойчивость процесса сварки тонкой электродной проволокой.
Весьма характерно влияние внешних характеристик генераторов на процесс сварки и формирование шва при изменении величины зазора в соединении. Опыт показывает, что в случае питания дуги от генераторов с жесткой или пологопадающей внешней характеристикой можно допустить большие по величине зазоры в стыке, не нарушая нормального формирования шва. Такое же явление наблюдается при увеличении плотности тока в электроде.
Таблица 2
В табл. 2 приведены режимы сварки стыковых соединений стали толщиной 3 мм, собранных с постепенно возрастающим зазором от 0 до 5 мм при длине образцов 500 мм. Образцы сваривались электродной проволокой диаметром 3 мм при питании от генератора с крутопадающей внешней характеристикой и генератора с пологопадающей характеристикой. Один из образцов был сварен электродной проволокой диаметром 1,6 мм при питании от генератора с крутопадающей характеристикой. Как следует из табл. 2 и фиг. 2, где изображены образцы сварных соединений, в случае внешней характеристики генератора, приближающейся к жесткой (пологопадающей), а также в случае большей плотности тока в электроде (меньший диаметр электрода), максимальный зазор, при котором еще происходит правильное формирование шва, значительно больше.
Не следует считать, что приведенные в таблице максимальные зазоры могут быть рекомендованы как допустимые при сборке стыков. В данном случае имеет место плавное возрастание зазора, что не равноценно резким изменениям зазоров, которые могут наблюдаться в практике.
Влияние формы внешней характеристики, а также плотности тока на формирование швов при сварке с зазорами в стыке связано, по-видимому, с изменением интенсивности процессов саморегулирования.
При автоматической сварке стыкового соединения одно из активных пятен дуги расположено на расплавленном металле ванны, заполняющей разделку. В отдельные моменты времени скорость перемещения ванны расплавленного металла может отличаться от скорости движения электрода вдоль стыка. Одной из причин этого бывает изменение величины зазора между свариваемыми кромками или изменение зазора между подкладкой и свариваемыми листами.
При увеличении зазора в стыковом соединении или возникновении большего зазора между подкладкой и свариваемыми листами скорость перемещения ванны расплавленного металла уменьшается. Так как скорость движения электрода при этом остается прежней, имеет место рост дугового промежутка. Резкое увеличение дугового промежутка вызывает обрыв дуги и нарушение процесса сварки. При плавном удлинении дуги процесс может не нарушиться, активное пятно успеет занять новое положение, обеспечивая восстановление прежней длины дуги.
Если питание дуги осуществляется от генератора с крутопадающей внешней характеристикой, то при удлинении дуги, как показали исследования, наблюдается рост ее мощности, что ведет к дополнительному оплавлению кромок в месте повышенного зазора, где начала удлиняться дута. При этом электродного металла окажется недостаточно для заполнения зазора между оплавленными кромками, в результате чего образуется не заполненный металлом участок — прожог.
Увеличение интенсивности саморегулирования дуги, имеющее место в случае применения генераторов с жесткими внешними характеристиками или при повышенной плотности тока в электроде, в известных пределах может предотвратить возникновение прожогов. Благодаря интенсивному саморегулированию значительное удлинение или обрывы дуги не будут наблюдаться при отставании ванны жидкого металла в месте увеличившегося зазора. При этом длина дуги будет поддерживаться постоянной и опасный участок с увеличенным зазором может быть пройден без нарушения процесса сварки (без обрывов дуги, прожогов и пр.). Этот участок от остальной части шва будет отличаться только меньшим усилением шва или даже полным отсутствием усиления.
Как известно из практики автоматической сварки под флюсом, с увеличением плотности тока в электроде глубина проплавления заметно возрастает. Например, при сварке на токе 500 а увеличение плотности тока приблизительно в 3 раза, за счет уменьшения диаметра электродной проволоки от 5 до 3 мм, вызывает увеличение глубины проплавления на 25%. Так как переход к сварке тонкой электродной проволокой связан с еще большим увеличением плотности тока в электроде, то возникает опасение, не может ли интенсивный рост глубины проплавления в этом случае стать препятствием на пути применения тонкой электродной проволоки и повышенной плотности тока для сварки тонколистовой стали. Проведенные опыты показали, что это опасение несостоятельно.
На фиг. 3 приведен график зависимости глубины проплавления от диаметра электродной проволоки. Как видно из графика, рост глубины проплавления с увеличением плотности тока (уменьшением диаметра электрода) наблюдается только при сварке на токах, превосходящих 300—350 а. Что же касается интересующего пас диапазона токов, применяемых для сварки тонкой стали (до 300—350 а), то в нем увеличение плотности тока не вызывает изменения глубины проплавления. Это объясняется некоторыми особенностями, отличающими маломощные электрические дуги от дуг большей мощности.
Также по теме:
Сварка стальных листов. Методы сварки тонких листов стали.
Сварочные станки. Оборудование для сварки тонколистовой стали.
Инструкция по автоматической дуговой под флюсом и электрошлаковой сварке с порошковым присадочным металлом (ППМ)
МИНИСТЕРСТВО МОНТАЖНЫХ И
СПЕЦИАЛЬНЫХ
СТРОИТЕЛЬНЫХ РАБОТ СССР
УТВЕРЖДАЮ:
Заместитель министра монтажных
и специальных строительных
работ СССР
К.К. Липодат
10 февраля 1977 г.
ИНСТРУКЦИЯ
ПО АВТОМАТИЧЕСКОЙ ДУГОВОЙ
ПОД ФЛЮСОМ И ЭЛЕКТРОШЛАКОВОЙ
СВАРКЕ С ПОРОШКОВЫМ
ПРИСАДОЧНЫМ МЕТАЛЛОМ (ППМ)
ВСН 375-77
ММСС СССР
ЦЕНТРАЛЬНОЕ
БЮРО
НАУЧНО-ТЕХНИЧЕСКОЙ ИНФОРМАЦИИ
Москва — 1978
СОДЕРЖАНИЕ
Инструкция разработана Всесоюзным научно-исследовательским институтом по монтажным и специальным строительным работам (ВНИИмонтажспецстрой) Минмонтажспецстроя СССР с участием Института электросварки (ИЭС) им. Е. О. Патона АН СССР и Московского высшего технического училища (МВТУ) им. Н. Э. Баумана Министерства высшего и среднего специального образования СССР.
Инструкция подготовлена кандидатами техн. наук И. И. Ивочкиным, А. И. Алексеевым, Б. Д. Малышевым, Ю. А. Черновым, А. Ф. Соседовым, Н. П. Рощупкиным; инженерами К. А. Илюковичем, Л. М. Матвеевой (ВНИИМонтажспецстрой) при участии докт. техн. наук О. И. Стеклова, канд. техн. наук Б. Ф. Якушина (МВТУ им. Н. Э. Баумана), доктора техн. наук Б. Ф. Лебедева, В. А. Богдановского (ИЭС им. Е. О. Патона).
Инструкция предназначена для специалистов сварочного производства, работающих по изготовлению и монтажу металлических конструкций.
Минмонтажспецстрой СССР |
Ведомственные строительные нормы |
ВСН 375-77 |
Инструкция по автоматической дуговой под флюсом и электрошлаковой сварке с порошковым присадочным металлом (ППМ) |
ММСС СССР |
|
Впервые |
1.1. Инструкция распространяется на следующие способы сварки металлических конструкций:
автоматическую дуговую сварку под флюсом с применением порошкового присадочного металла (ППМ) в нижнем положении стыковых и угловых соединений из низкоуглеродистых сталей марок ВСт3кп, ВСт3пс, ВСт3сп и низколегированных сталей марок 09Г2С, 14Г2, 10Г2С1, 10ХСНД, 15ХСНД, 16Г2АФ и 14Х2ГМР толщиной до 60 мм;
электрошлаковую сварку с применением ППМ низкоуглеродистых сталей марок ВСт3кп, ВСт3пс, ВСт3сп и низколегированных сталей марок 10Г2С1, 09Г2С, 10ХСНД, 15ХСНД, 16Г2АФ толщиной 30-60 мм.
При обоих способах сварки с ППМ следует руководствоваться общими требованиями СНиП III-18-75 «Металлические конструкции. Правила производства и приемки работ» и положениями СНиП III-A.11-70 «Техника безопасности в строительстве», а также указаниями «Инструкции по изготовлению стальных конструкций из углеродистой и низколегированной сталей» МСН 97-65/ГМСС СССР и «Инструкции по электрошлаковой сварке кожухов доменных печей».
1.2. Введение в зону сварки ППМ повышает тепловую эффективность процесса и качество сварного соединения. Благодаря таким свойствам ППМ, как автономность, развитая поверхность и малая масса частиц, введение его в зону сварки позволяет значительно уменьшить потери тепла и повысить коэффициент полезного действия источника сварочного тепла.
Внесены |
Утверждены |
Срок введения |
1.3. В качестве ППМ используется крупка, приготовленная на простейшем станке (приложение 1) из сварочной проволоки диаметром 0,8-2,0 мм. При этом длина частицы крупки должна быть равна диаметру проволоки.
1.4. Сварочная проволока, применяемая для изготовления крупки, должна быть очищена от технологических и противокоррозионных смазок, масел, грязи и ржавчины.
1.5. ППМ должен иметь неокисленную поверхность и храниться в металлических закрытых сосудах в сухом помещении.
1.6. Изготовлять ППМ можно на любом стандартном и нестандартном оборудовании, обеспечивающем требуемые размеры металлической крупки.
1.7. Сварочный флюс АН-348А, АН-60, АН-22, АН-8 по ГОСТ 9082-69 перед сваркой необходимо прокалить при температуре 200-250 °С в течение 1,0-1,5 ч, если влажность флюса превышает 0,1 %, в соответствии с техническими условиями на эти материалы.
2.1. Автоматическая дуговая сварка под флюсом с ППМ производится на стандартном сварочном оборудовании: сварочных тракторах ТС-17МУ, ДТС-38, ТС-35, АДС-1000, сварочных самоходных автоматах подвесного типа АБСК, А-639К и др.
В качестве источников питания рекомендуются выпрямители ВКСМ-1000, ВДМ-1601, ВДМ-3001, ВСЖ-1600 и преобразователи типа ПСМ.
2.2. ППМ в зону сварки вводят двумя способами:
путем предварительной засыпки ППМ в зазор или разделку перед сваркой (рис. 1, а) простейшими устройствами;
путем подачи ППМ с ферромагнитными свойствами на вылет электрода в процессе сварки (рис. 1, б).
Дозировку и подачу ППМ на вылет электрода осуществляют дозатором конструкции ВНИИмонтажспецстроя, который устанавливают на любой сварочный трактор (рис. 2).
2.3. Поставляемый для сварки металл и сварочные материалы должны иметь сертификаты заводов-изготовителей.
2.4. Для обеспечения требуемых свойств металла шва необходимо применять ППМ и сварочную проволоку определенного химического состава (табл. 1), флюс марки АН-348А по ГОСТ 9087-69.
Рис. 1. Принципиальные схемы
сварки:
а — с предварительной засыпкой ППМ в зазор или
разделку; б — с подачей ППМ на вылет электрода в процессе сварки
Рис. 2. Сварочный трактор АДС-1000 с установленным на нем дозатором-приставкой для подачи ППМ на вылет электрода
Таблица 1
Сварочная проволока, используемая для приготовления ППМ в зависимости от свариваемого металла и марки электродной проволоки
Основной металл |
Электродная проволока |
ППМ в виде крупки из проволоки |
|
марка |
диаметр, мм |
||
Низкоуглеродистые стали |
Св-08А Св-08ГА |
4-5 4-5 |
Св-08А или Св-08Г2С Св-08А |
Низколегированные стали: |
|
|
|
09Г2С |
Св-08ГА |
4-5 |
Св-08ГА или Св-08Г2С |
Св-10Г2 |
4-5 |
Св-10Г2 или Св-08Г2С |
|
10Г2С1 |
Св-08ГА |
4-5 |
Св-10Г2 или Св-08Г2С |
Св-10Г2 |
4-5 |
Св-10Г2 или Св-08Г2С |
|
14Г2 |
Св-08ГА |
4-5 |
Св-08Г2С или Св-10Г2 |
Св-10Г2 |
4-5 |
Св-10Г2 или Св-08Г2С |
|
16Г2АФ |
Св-08НМА или Св-08ХМ |
4-5 |
Св-08Г2С |
10ХСНД 15ХСНД |
Св-08ХМ |
4-5 |
Св-08Г2С или Св-08ГА |
Примечание. При сварке стали марки 14Х2ГМР необходимо применять электродную проволоку марки Св-08ХН2ГМЮ с ППМ из проволоки Св-08Г2С, флюс АН-17М.
Можно применять также флюсы АН-60 и АН-22 или смесь флюсов АН-348А и АН-60.
2.5. Типы сварных соединений, конструктивные элементы подготовки свариваемых кромок (углы разделки, притупления и т.п.) должны соответствовать данным табл. 2 и 3.
2.6. При оборке деталей конструкции под сварку и подготовке поверхности необходимо руководствоваться указаниями СНиП III-18-75 «Металлические конструкции. Правила изготовления, монтажа и приемки» и «Инструкции по изготовлению стальных конструкций из углеродистой и низколегированной сталей» МСН 97-65/ГМСС СССР.
При подготовке под сварку стыковых соединений качество реза должно удовлетворять требованиям ГОСТ 14792-69. При этом допускается неперпендикулярность кромок реза к поверхности листов на величину h, которая не должна превышать значений, определяемых по формуле:
,
где lmin — минимальная ширина шва по ГОСТ;
b - зазор по табл. 2.
Таблица 2
Швы стыковых соединений без скоса кромок, двухсторонние на стальной подкладке или флюсовой подушке
Тип шва по ГОСТ 8713-70 |
Подготовка кромок |
Выполненный шов |
|||
С2 |
|||||
Параметры, мм: |
|
|
|
|
|
S = S1 |
10 |
20 |
30 |
40 |
50 |
b |
4 |
6 |
7 |
8 |
9 |
l = l1 |
20 ± 4,0 |
22 ± 4,0 |
35 ± 5,0 |
34 ± 5,0 |
35 ± 5,0 |
q = q1 |
|
2,5 ± 2,0 |
|
|
|
Таблица 3
Швы тавровых соединений без скоса кромок, двухсторонние и односторонние
Тип шва по ГОСТ 8713-70 |
Подготовка кромок |
Выполненный шов |
||
T1 и Т5 |
||||
Параметры, мм: |
|
|
|
|
S1 ³ S |
3-5 |
6-10 |
12-16 |
18-40 |
b |
0+1,0 |
0+1,5 |
0+1,5 |
0+1,5 |
При сборке стыкового соединения листы с неперпендикулярно обработанными кромками необходимо размещать так, чтобы зазор в корне шва соответствовал значениям b согласно табл. 2 (рис. 3).
Рис. 3. Сборка стыков с неперпендикулярно обработанными кромками
2.7. При сборке конструкций прихватки нужно выполнять ручной электродуговой сваркой электродами типа Э-42А с фтористо-кальциевым покрытием (марки УОНИ-13/45, УП-2/45 и др.), типа Э-46Т с рутилово-карбонатным покрытием (марки МР-3, ОЗС-4, АНО-3 и др.) или полуавтоматической сваркой в среде СО2, а также в смеси газов. Перед сваркой прихватки и свариваемые кромки должны быть тщательно очищены от шлака.
2.8. В тех местах, где зазоры в стыках деталей, собранных под сварку, превышают величины, указанные в табл. 2-3, в виде исключения разрешается производить подварку стыков либо наплавку кромок ручной дуговой или полуавтоматической сваркой в среде СО2.
2.9. Способ сварки с предварительной засыпкой ППМ (см. рис. 1, а) предназначен для двухсторонней сварки стыковых соединений без разделки кромок, а также для выполнения соединений с разделкой кромок и тавровых «в лодочку». Для предотвращения просыпания ППМ сварку первого прохода стыков следует производить на металлическом листе. Для этих целей разрешается применять флюсовую подушку или подушку из ППМ.
При сварке листов толщиной до 36 мм зазор в стыке следует заполнять ППМ заподлицо с поверхностью листов; для толщин 36-60 мм зазор заполняют на 2/3 толщины свариваемого металла.
Толщина слоя ППМ при сварке тавровых соединений «в лодочку» должна быть на 2 мм больше величины катета шва.
2.10. Режим автоматической сварки под флюсом с предварительной засыпкой ППМ стыков без разделки и «в лодочку» следует назначать в соответствии с табл. 4-5.
При сварке стыковых соединений других толщин, не указанных в табл. 4, скорость сварки следует корректировать в соответствии с разделом «Расчет технологических параметров сварки» (приложение 2).
На режимах, указанных в табл. 5, сваривают соединения «в лодочку» из низкоуглеродистых сталей. Режимы сварки низколегированных сталей «в лодочку» следует выбирать по методике, изложенной в приложении 3.
Сварку за один проход угловых соединений «в лодочку» с катетом шва более 14 мм осуществляют на более мощных источниках питания.
При использовании источников сварочного тока ВДМ-1601, ВДМ-3001 и ВСЖ-1600 сварку швов тавровых соединений «в лодочку» до катетов 18-20 мм можно производить за один проход.
На режимах, указанных в табл. 4, сваривают стыковые соединения из низкоуглеродистых и низколегированных сталей без предварительного подогрева, кроме сталей 16Г2АФ и 14Х2ГМР толщиной свыше 40 мм, режимы сварки этих сталей следует выбирать по методике приложения 3.
2.11. Сварку стыковых соединений толщиной до 60 мм следует производить с двух сторон, по одному проходу с каждой стороны. Сварку второго прохода осуществляют в соответствии с табл. 4 на режиме первого, при этом засыпки ППМ не требуется. Сварку следует производить постоянным током обратной полярности.
2.12. Дозировка ППМ при сварке «в лодочку» осуществляется с помощью шаблона (рис. 4). Для выполнения сварки «в лодочку» необходимо заменить направляющее колесо трактора другим, более широким, имеющим выточку по окружности такой глубины, чтобы колесо не касалось слоя ППМ, предварительно засыпанного в разделку.
Таблица 4
Режимы однодуговой автоматической двухсторонней сварки стыковых соединений без скоса кромок под флюсом с предварительной засыпкой ППМ
Толщина металла, мм |
Оптимальный зазор, мм |
Диаметр электродной проволоки, мм |
Скорость подачи проволоки, м/ч |
Сила сварочного тока, А |
Напряжение, В |
Скорость сварки, м/ч |
Расход ППМ, г/см |
20 |
6 |
5 |
103 |
1000-1100 |
40-44 |
35 |
5,0 |
30 |
7 |
5 |
103 |
1000-1100 |
42-45 |
19,5 |
8,0 |
40 |
8 |
5 |
128 |
1200-1300 |
43-48 |
16 |
12,0 |
50 |
9 |
5 |
140 |
1300-1400 |
44-48 |
12 |
16,0 |
60 |
11 |
5 |
163 |
1350-1450 |
45-50 |
12 |
18,0 |
20 |
6 |
4 |
154 |
900-950 |
42-45 |
35 |
5,0 |
30 |
7 |
4 |
163 |
950-1000 |
42-46 |
19 |
8,0 |
40 |
8 |
4 |
163 |
950-1000 |
43-48 |
14 |
12,0 |
50 |
9 |
4 |
210 |
1100-1200 |
44-49 |
14 |
16,0 |
60 |
11 |
4 |
240 |
1300-1400 |
46-50 |
12 |
18,0 |
Таблица 5
Режимы однодуговой автоматической сварки под флюсом угловых соединений «в лодочку» из низкоуглеродистых сталей с предварительной засыпкой ППМ
Катет шва, мм |
Сторона шаблона для ППМ, мм |
Диаметр проволоки, мм |
Сварочный ток, А |
Напряжение, В |
Скорость подачи проволоки, м/ч |
Скорость сварки, м/ч |
Расход ППМ, г/см |
Количество проходов |
8 |
10 |
5 |
750-800 |
36-38 |
68,5 |
54,5 |
2 |
1 |
10 |
12 |
5 |
800-850 |
38-40 |
74,5 |
47,0 |
3 |
1 |
12 |
14 |
5 |
850-900 |
40-42 |
81,0 |
37,5 |
4 |
1 |
14 |
16 |
5 |
900-950 |
40-42 |
87,5 |
32,0 |
5 |
1 |
Технология сварки под флюсом | svarnoy.info
Конструктивные элементы основных типов швов сварных соединений из углеродистых или низколегированных сталей, свариваемых автоматической и полуавтоматической сваркой под флюсом, установлены ГОСТ 8713-79. В зависимости от толщины свариваемого металла и способа сварки ГОСТ устанавливает формы разделки кромок для каждого вида соединения. Требования к подготовке кромок и сборке изделия под сварку более высокие, чем при ручной сварке. Эти требования вытекают из условий автоматической сварки. Настроенный под определенный режим автомат точно выполняет установленный процесс сварки и не может учесть и выправить отклонения в разделке кромок и сборке изделия. Разделку кромок производят машинной кислородной или плазменно-дуговой резкой, а также на металлорежущих станках.
Свариваемые кромки перед сборкой должны быть тщательно очищены от ржавчины, грязи, масла, влаги и шлаков. Это особенно важно при больших скоростях сварки, когда различные загрязнения, попадая в зону дуги, приводят к образованию пор, раковин и неметаллических включений. Очистку кромок производят пескоструйной обработкой или протравливанием и пассивированием. Очистке подвергается поверхность кромок шириной 50…60 мм по обе стороны от шва. Перед сваркой детали закрепляют на стендах или иных устройствах с помощью различных приспособленний или прихватывают ручной сваркой электродами с качественным покрытием. Прихватки длиной 50…70 мм располагают на расстоянии не более 400 мм друг от друга, а крайние прихватки — на расстоянии не менее 200 мм от края шва. Прихватки должны быть тщательно очищены от шлака, брызг металла.
При сварке продольных швов для ввода электрода в шов и вывода его из шва за пределы изделия по окончании сварки к кромкам приваривают вводные и выводные планки. Форма разделки планок должна соответствовать разделке кромок основного шва.
Режим автоматической сварки: сварочный ток, напряжение дуги, диаметр, угол наклона и скорость подачи электродной проволоки, скорость сварки и основные размеры разделки кромок — выбирают в зависимости от толщины свариваемых кромок, формы разделки и свариваемого металла.
Стыковые швы выполняют с разделкой и без разделки кромок. При этом шов может быть одно- и двусторонним, одно- и многослойным.
Односторонняя стыковая сварка применяется в малоответственных сварных соединениях или в случаях, когда конструкция изделия не позволяет производить двустороннюю сварку шва. Значительный объем расплавленного металла, большая глубина проплавления и некоторый перегрев ванны могут привести к вытеканию металла в зазоры и нарушению процесса формирования шва.
Рис 1.
Флюсовая подушка
Чтобы избежать этого, следует закрыть обратную сторону шва стальной или медной подкладкой, флюсовой подушкой или проварить шов с обратной стороны.
В практике применяют четыре основных приема выполнения односторонней сварки стыковых швов, обеспечивающих получение качественного сварного шва.
Сварка на флюсовой подушке (рис. 1) заключается в том, что под свариваемые кромки изделия 1 подводят флюсовую подушку 2 — слой флюса толщиной 30…70 мм. Флюсовая подушка прижимается к свариваемым кромкам под действием собственной массы изделия или с помощью резинового шланга 3, наполненного воздухом. Давление воздуха в зависимости от толщины свариваемых изделий составляет 0,05…0,06 МПа для тонких и 0,2…0,25 МПа для толстых кромок. Флюсовая подушка не допускает подтекания расплавленного металла и способствует хорошему формированию металла шва.
Сварка на медной подкладке применяется для большего теплоотвода в целях предупреждения пережога металла кромок. Вместе с тем подкладка, установленная с нижней стороны шва, предупреждает протекание жидкого металла сварочной ванны. Подкладка прижимается к шву с помощью механических или пневматических приспособлений. После сварки подкладка легко отделяется от стальных листов. При зазоре между свариваемыми кромками более 1…2 мм медную подкладку делают с желобком, куда насыпают флюс. В этом случае на обратной стороне шва образуется сварной валик. Ширина медной подкладки составляет 40…60 мм, а толщину подкладки (5…30 мм) выбирают в зависимости от толщины свариваемых кромок.
Институтом электросварки им. Е. О. Патона разработан метод сварки, при котором по обратной стороне шва перемещается медный башмак, охлаждаемый водой (рис. 2). При этом свариваемые листы собирают с зазором 2…3 мм и через каждые 1,2…1,5 м скрепляют сборочными планками путем прихватки короткими сварными швами. Сварочный трактор 2 имеет нож 5, устанавливаемый в зазор стыка и прижимающий пружиной 1 тягу 4 с роликами 6 и медным башмаком 3 к нижней стороне свариваемых кромок. Нож направляет трактор вдоль свариваемого шва. Башмак, перемещаясь вместе с трактором, все время находится под сварочной дугой, предупреждая протекание жидкого металла и формируя нижнюю сторону шва. По мере приближения трактора к сборочным планкам их удаляют ударами молотка.
Рис. 2 .
Метод сварки, при котором по обратной стороне шва перемещается медный башмак, охлаждаемый водой.
Сварка на стальной подкладке производится в тех случаях, когда конструкция изделия допускает приварку подкладки с обратной стороны шва. Стальную подкладку плотно подгоняют к плоскости свариваемых кромок и прикрепляют короткими швами ручной дуговой сваркой. Затем автоматической сваркой выполняют основной шов, проваривая одновременно основной металл и металл подкладки. Размеры подкладки зависят от толщины свариваемых кромок. Обычно подкладку изготовляют из стальной полосы шириной 20…60 мм и толщиной 4…6 мм.
Сварка после предварительного наложения подварочного шва вручную применяется для упрощения процесса сборки изделия. Однако такой способ автоматической сварки значительно увеличивает затраты труда и материалов и поэтому, его следует применять реже.
Режимы автоматической сварки стыковых швов тонколистовых изделий представлены в табл. 1.
Таблица. 1.
Толщина кромок, | Способ сварки | Зазор, мм | Сварочный ток, А | Напряжение, | Диаметр электрода мм. | Скорость сварки, |
1,5 | На медной подкладке | 0,3 | 150-170 | 26 | 1,6 | 50-60 |
1,5 | На весу | 0,2 | 100-115 | 26 | 1,2 | 50 |
2,0 | На флюсовой подушке | 0,8 | 120-130 | 24-28 | 1,6 | 40-50 |
2,0 | На стальной подкладке | 0,7 | 270-300 | 23-27 | 3,0 | 75-80 |
2,0 | На весу | 0,3 | 120-130 | 26-28 | 1,6 | 50-60 |
3,0 | На флюсовой подушке | 1,5 | 270-300 | 28-30 | 2,0 | 35-60 |
3,0 | На стальной подкладке | 0,7 | 270-300 | 23-27 | 3,0 | 50-60 |
3,0 | На весу | 0,8 | 160-200 | 28-30 | 1,0 | 70-80 |
4,0 | На флюсовой подушке | 1,5 | 375-400 | 28-30 | 2,0 | 40-50 |
5,0 | На флюсовой подушке | 2,5 | 550-625 | 28-30 | 4,0 | 35-45 |
Двусторонняя стыковая сварка дает более высококачественный шов, обеспечивая хороший провар шва даже при некотором смещении свариваемых кромок. При изготовлении строительно-монтажных конструкций двусторонний способ сварки является основным. Стыковое соединение сваривают автоматом сначала с одной стороны так, чтобы глубина проплавления составляла 60…70% толщины металла шва. Зазор между кромками должен быть минимальным, не более 1 мм. При этом сварку выполняют на весу без подкладок и уплотнений с обратной стороны стыка.
При невозможности выдержать зазор между кромками менее 1 мм принимают меры по предупреждению подтекания жидкого металла, так же как это делают при односторонней сварке, т. е. производят сварку на флюсовой подушке, медной подкладке, на стальной подкладке или применяют прихватку ручной дуговой сваркой.
Примерные режимы двусторонней автоматической сварки стыковых соединений без разделки кромок на флюсовой подушке электродной проволокой диаметром 5…6 мм даны в табл. 2.
Таблица № 2.
Толщина кромок, мм | Наименование шва | Зазор, мм | Сварочный ток, А | Напряжение дуги, В | Скорость подачи электродной проволоки, м/ч | Скорость сварки. м/ч |
6 | Основной | 0…1,5 | 600 | 34…30 | 47,0 | 55,0 |
Подварочный | 500 | 50,0 | 43,5 | |||
8 | Основной | 0.. .1,5 | 650 | 34…36 | 46,0 | 62,2 |
Подварочный | 550 | 50,0 | 40,3 | |||
10 | Основной | 0…2,0 | 720 | 36…38 | 43,0 | 69,7 |
Подварочный | 650 | 38…40 | 60,8 | |||
14 | Основной | 0…2,5 | 850 | 36…38 | 34,0 | 87,7 |
Подварочный | 750 | 73,5 | ||||
20 | Основной | 3 | 950 | 38…40 | 24,0 | 111,0 |
Подварочный | 900 | 102,0 | ||||
24 | Основной | 4 | 1050 | 38…40 | 18,0 | 72,8 |
Подварочный | 19,0 | |||||
30 | Основной | 4,5 | 1150 | 40…42 | 15.0 | 82,4 |
Подварочный | 16.0 | |||||
40 | Основной | 6,5 | 1200 | 40…42 | 8,5 | 87,0 |
Подварочный | 9,5 | |||||
50 | Основной | 9,0 | 1300 | 42…44 | 6,0 | 98,8 |
Подварочный | 7,0 |
Тавровые и нахлесточные соединения сваривают вертикальным электродом при положении шва «в лодочку» (рис. 3, а) или наклонным, если один из листов занимает горизонтальное положение (рис. 3, б).
Рис. 3.
Тавровые и нахлесточные соединения сваривают вертикальным электродом при положении шва «в лодочку» (а)
Наклонным, если один из листов занимает горизонтальное положение (б)
При этом в зависимости от толщины свариваемых кромок и назначения соединения сварка может быть выполнена без разделки кромок, с одно- или с двусторонней разделкой кромок (рис. 4, а, б, в).
Рис. 4.
Разделка кромок с одно- или с двусторонняя.
При зазоре между кромками менее 1 мм сварку «в лодочку» выполняют на весу. При больших зазорах сварку производят на флюсовой подушке или на подкладках. Допускается заделка зазора асбестовым уплотнением или подварка шва с обратной стороны. Сварка «в лодочку» обеспечивает равномерное проплавление свариваемых кромок и получение качественного шва большого сечения за один проход; в большинстве случаев для выполнения сварного соединения изделие устанавливают на кантователь.
Сварку тавровых и нахлесточных соединений при горизонтальной или вертикальной полке производят наклонным электродом с углом наклона к горизонтальной полке 20…30°. Недостатком такого способа сварки является невозможность получить шов с катетом более 16 мм, что иногда приводит к необходимости многослойной сварки. Примерные режимы автоматической сварки швов тавровых и нахлесточных соединений, выполняемых «в лодочку» электродной проволокой диаметром 5 мм, даны в табл. 3.
При полуавтоматической сварке сварщик перемещает дугу вдоль свариваемого шва либо на себя, либо справа налево. Держатель опирается на кромки свариваемого изделия и тем самым поддерживается постоянство вылета электродной проволоки в пределах 15…25 мм. Благодаря повышенной плотности тока и более сосредоточенному вводу теплоты глубина провара при шланговой сварке возрастает на 30 … 40%. Устойчивость горения дуги также значительно повышается, что позволяет сваривать листы малых толщин (0,8…1,0 мм) и угловые швы катетом до 2 мм при сварочных токах 80 … 100 А.
Стыковые швы с зазором более 1,0… 1,5 мм сваривают на флюсовой подушке или на подкладках. При этом держателю придают поперечные колебательные Движения. Тавровые и нахлесточные соединения рекомендуется выполнять электродной проволокой диаметром 1,6…2,0 мм на постоянном токе обратной полярности. Зазор между свариваемыми кромками не должен превышать 0,8…1,0 мм. Примерные режимы шланговой сварки электродной проволокой диаметром 2 мм под флюсом АН-348-А стыковых швов даны в табл. 4, а угловых швов тавровых соединений — в табл. 5.
Качественный шов за один проход шланговой сваркой можно получить при катете шва не более 8 мм. При катетах более 8 мм производят многослойную сварку шва.
Таблица № 3.
Катет шва, мм | Сварочный ток, А | Напряжение дуги, В | Скорость сварки. м/ч | Скорость подачи электродной проволоки, м/ч |
5 6 7 8 9 10 12 14 16 | 600…650 650…700 700…730 700…750 750…780 750…800 850…900 900…950 950… 1000 | 34…36 34…36 34…36 34…36 34…36 34…36 34…36 36…38 38…40 | 58,0 47,0 38,5 32,0 27,5 24,0 19,0 16,0 13,0 | 60,7 67,3 71,1 73,5 78,0 81,3 95,3 103,0 111,0 |
Таблица № 4.
Толщина кромок, мм | Сварочный ток, А | Напряжение дуги, В | Скорость подачи электродной проволоки, м/ч | Скорость сварки, м/ч |
4 6 8 10 12 | 220…240 300…350 450…475 475…525 525…575 | 30…32 32…34 34…36 36…38 38…40 | 101,0 156,0 308,0 346,0 378,0 | 20…24 20…24 22…26 24…30 24…30 |
Таблица № 5
Катет шва, мм | Сварочный ток, А | Напряжение дуги, В | Скорость подачи электродной проволоки, м/ч | Скорость сварки, м/ч |
4 6 8 | 250…300 300…350 350…400 | 30…32 32…34 34…36 | 126 156 260 | 35…40 24…30 20…24 |
Сварка под флюсом — Технологический центр
Kjellberg Finsterwalde − сварочная техника с 1922-го года
Kjellberg Finsterwalde Schweisstechnik und Verschleissschutzsysteme GmbH продолжает традиции разработки и производства сварочной техники Kjellberg , всходящие к 1922-му году. Лишь на нескольких квадратных метрах от современной территории в г. Финстервальде швед Оскар Къеллберг, совместно с шестью другими инвесторами, основал предприятие Kjellberg Elektro-Maschinen GmbH.
Целью этого предприятия было изготовление подходящих сварочных генераторов для сварочных электродов с покрытием — изобретения Kjellberg. Всего за несколько лет фирма Kjellberg стала крупнейшим в мире производителем сварочной техники. Ее основным продуктом уже в конце 1930-х годов стала автоматизированная сварка под флюсом. Этот многолетний опыт продолжает питать новые разработки вплоть до сегодняшнего дня. На двух предприятиях в Германии Kjellberg Finsterwalde ведет исследования для конструирования сварочной техники высочайшего качества. Предприятие Kjellberg Finsterwalde Schweisstechnik und Verschleissschutzsysteme GmbH (KSV) основано в 2008-м году. Оно возникло в результате разделения фирмы Kjellberg Finsterwalde Elektroden und Maschinen GmbH − богатого традициями предприятия, основанного в 1922-м году в городе Финстервальде.
На двух предприятиях − в южнобранденбургском городе Финстервальде и в городе Виттене земли Северный Рейн-Вестфалия − заняты 17 сотрудников.
KSV входит в состав группы Kjellberg. Центральной задачей предприятия является разработка и производство высококачественной сварочной техники для соединения и наплавки. Современная техника для сварки под флюсом, плазменно-порошковой наплавки и сварки в среде защитного газа поступает в широкую международную сеть продавцов и клиентов. Обладая большим ноу-хау, Kjellberg Finsterwalde изготовляет и поставляет индивидуальные решения автоматизации для самых высоких требований.
Техника для сварки под флюсом
При сварке под флюсом электрическая дуга и ванна расплава не видны, так как они находятся под флюсом в виде зернистого порошка. Сварка под флюсом является высокопроизводительным методом, экономично применяемым начиная с толщины листа 6 мм. Этим методом можно сваривать нелегированные, низколегированные и высоколегированные стали. Сварка под флюсом применяется, прежде всего, в судостроении, мостостроении, при возведении стальных конструкций и при производстве резервуаров.
Гибкая модульная концепция автоматов Kjellberg для сварки под флюсом образует основу для индивидуальных системных решений с большой технологический широтой применения. Kjellberg предлагает автоматы как для однопроволочной сварки и сварки параллельными проволоками, с одношарнирной или двухшарнирной рукой.
Автоматы KA представляют собой мобильные аппараты, легко транспортируемые на новое рабочее место и приспосабливаемые к различным обрабатываемым деталям. Модульная структура серии KA облегчает расширение автомата дополнительными устройствами, например, для отслеживания шва и подачи флюса. Благодаря этому можно оптимально выбирать подходящие компоненты для каждого сварочного процесса.
Автоматизированные системы для сварки под флюсом (СКАЧАТЬ PDF)
Некоторые особенности сварки и влияние параметров режима на формирование шва
Сварку под слоем флюса производят электродной проволокой, которую подают в зону горения дуги специальным механизмом, называемым сварочной головкой автомата.
Металл сварочной проволоки расплавляется дугой и переносится каплями в сварочную ванну. В сварочной ванне металл сварочной проволоки смешивается с расплавленным основным металлом.
Токоподвод к проволоке осуществляется через мундштук, изготовляемый из меди или ее сплавов.
Малый вылет электрода, отсутствие покрытия, большая скорость подачи электродной проволоки позволяют значительно увеличить силу сварочного тока по сравнению с ручной сваркой электродами тех же диаметров. Это приводит к ускорению процесса плавления сварочной проволоки, увеличению глубины проплавления основного металла и, как следствие, значительному повышению производительности. Достаточно толстый слой флюса (до 60 мм), засыпаемый в зону сварки, расплавляется на 30%. Это делает дугу закрытой (невидимой) и обеспечивает надежную защиту расплавленного металла от окружающего воздуха, стабилизирует сварочный процесс. Существенным достоинством сварки под флюсом являются незначительные потери на угар металла и его разбрызгивание. Вследствие увеличения эффективной тепловой мощности дуги может быть расширен диапазон толщин деталей, свариваемых без скоса кромок.
Например, при обычных режимах сварки под флюсом деталей встык без скоса кромок, можно сваривать металл толщиной 15-20 мм. В этом случае увеличивается проплавление основного металла, и его доля в металле шва составляет 0,5-0,7. При этом значительно снижается расход электродной проволоки.
При сварке угловых швов увеличенная глубина провара обеспечивает большее сечение, чем это достигается при ручной сварке с одинаковым катетом шва.
Как отмечалось ранее, флюсы влияют на устойчивость горения дуги, формирование и химический состав металла шва. Флюсы в значительной мере определяют стойкость металла шва против образования пор и кристаллизационных трещин.
Требуемые механические свойства, структура металла шва и сварного соединения в целом обеспечиваются применением сочетания флюса и электродной проволоки.
Размеры и форма шва при сварке под флюсом характеризуются глубиной провара, шириной шва, высотой выпуклости и т.д. Закономерности изменения формы шва обусловлены главным образом режимом сварки и практически мало зависят от типа сварного соединения.
Зазор между деталями, разделка кромок и вид сварного соединения не оказывают значительного влияния на форму шва. Очертание провара и общая высота шва остаются практически постоянными. Чем больше зазор или разделка кромок, тем меньше доля основного металла в металле шва .
В зависимости от зазора или разделки кромок шов может быть выпуклым, нормальным или вогнутым. Наиболее существенное влияние на форму и качество шва влияет непосредственно зазор между деталями. При сварке вручную сварщик может сам выправить дефект сборки (заплавить увеличенный зазор) и обеспечить требуемую форму шва. При автоматической сварке это осуществить невозможно. Плохая сборка не обеспечит заданные зазоры и получение качественного шва.
Sub-Arc Manipulator или SWR
Дуговая сварка под флюсом (SAW) — это обычный процесс дуговой сварки, который обычно выполняется в автоматическом или механизированном режиме. Этот процесс, также известный как Sub-Arc, использует слой порошкообразного флюса поверх свариваемой области, чтобы предотвратить загрязнение из атмосферы, и обычно используется на трубах и сосудах высокого давления с более толстыми стенками (более ½ дюйма в толщину). Системы дуговой сварки обычно устанавливаются на манипуляторы X-Y и используются только для заливки и заглушки.
Робот для сварки катушек (SWR) использует модифицированные формы волны короткого замыкания, такие как RMD, LSC и STT, для корневого прохода и процесс сварки GMAW-P для проходов заполнения и закрытия. Сварка GMAW — это процесс, в котором для покрытия свариваемой области используется инертный газ, а не флюс. В этом процессе сварки используется защитный газ, такой как смеси CO2 / аргона, для защиты процесса от загрязнений в воздухе и предотвращения попадания атмосферного азота / кислорода в расплавленные металлы.
SWR или Манипуляторы Sub-Arc
Хотя процесс дуговой сварки намного эффективнее, чем процесс GMAW из-за более высоких скоростей наплавки, при принятии решения о покупке подходящего механизированного манипулятора необходимо учитывать все производственные факторы.
Время сварки корня и горячего прохода, а также время погрузочно-разгрузочных работ
Обычно при сварке труб или резервуаров с помощью систем дуговой сварки корневой проход выполняется вручную на другой сварочной станции, а затем трубу или катушку необходимо переместить на станцию дуговой сварки для заполнения и заглушки. Также перед проходом SAW требуется горячий проход над корнем. Для сравнения, SWR использует GMAW от корня до кончика в одной сварочной станции, что приводит к гораздо более эффективному процессу на трубах или резервуарах с показателем менее 0.75 дюймов по сравнению с манипуляторами Sub-Arc. В результате более быстрое время наплавки в процессе Sub-Arc будет смыто дополнительным корневым швом и сваркой горячего прохода, а также дополнительным временем обработки материала для толщины менее 0,75 дюйма.
Система транспортировки флюса
ПроцессSAW требует наличия системы обработки флюса, но SWR не требует такой системы, а также удаления шлака после сварки, и он может стабильно создавать высококачественные сварные швы, исключая возможность дефектов улавливания шлака.Сложность и стоимость систем обработки / восстановления флюса следует учитывать в общей стоимости владения.
Комплекс проектов
МанипуляторыSub-Arc также требуют более длительного времени настройки, что имеет экономический смысл только для крупных проектов, которые могут оправдать установку манипуляторов Sub-Arc. Напротив, SWR может сваривать трубы менее 0,75 дюйма и использоваться для небольших или нечастых проектов сварки труб или сосудов с толщиной более 0,75 дюйма.Наличие аппарата для сварки труб, который можно использовать в обоих сценариях, является огромным преимуществом для руководителей производства, которым приходится иметь дело с большим количеством проектов в своей деятельности. Удобный в использовании человеко-машинный интерфейс SWR и простота позиционирования от стыка к стыку обеспечивают самое быстрое время настройки в отрасли при охвате самого большого разнообразия катушек (катушки длиной до 30 футов, диаметры от 2 до 60 дюймов, съемные фланцы и т. Д.).
Подводя итог, покупка манипуляторов Sub-Arc оправдана только при постоянном потоке проектов, требующих сварки толстых труб или сосудов (больше 0.75 дюймов) может быть гарантировано.
Хотите узнать больше о максимальном увеличении производительности сварки трубных катушек или сосудов высокого давления? Свяжитесь с нами, чтобы узнать больше о бесплатных консультационных услугах и подробном расчете окупаемости инвестиций с учетом ваших текущих производственных потребностей!
Что такое дуговая сварка под флюсом, ее применение и принципы работы
Сварка под флюсом (SAW)
Сегодня я расскажу о том, что такое сварка под флюсом, и о принципах ее применения.Ранее была опубликована статья о дуговой сварке порошковой проволокой (FCAW). Проверить!
Принципы работы дуговой сварки порошковой проволокой, ее достоинства и недостатки
Что такое сварка под флюсом (SAW)
Сварка под флюсом — это еще один тип процесса дуговой сварки, в котором используется плавящийся трубчатый электрод с непрерывной подачей. Может эксплуатироваться в автоматическом или механизированном режиме. Он также может работать на полуавтоматических (ручных) пушках для резки SAW с подачей флюса под давлением или под действием силы тяжести.Этот процесс не подходит для плоского или горизонтального положения присадочной сварки, поскольку горизонтальное положение было выполнено с помощью специального приспособления для поддержки флюса.
В этом процессе сварки зона дуги и сварочная ванна защищены от атмосферного загрязнения за счет слоя гранулированного флюса, состоящего из извести, кремния, оксида марганца, фторида кальция и некоторых других соединений. Расплавленный флюс становится проводящим и создает ток между электродами и основным металлом.Толстый слой флюса полностью покрывает металл, предотвращая образование искр и брызг, а также поддерживая интенсивное ультрафиолетовое излучение и пары, которые являются частью процесса сварки.
SAW была первым патентом в 1935 году и покрывала электрическую дугу под слоем гранулированного флюса. Первоначально он был разработан Джонсом, Кеннеди и Ротермундом. Этот процесс имеет некоторые отличительные особенности, которые отличают его от других процессов дуговой сварки, в том числе:
- Сварочная головка: подает флюс и присадочный металл к сварному шву.
- Бункер для флюса: он помогает хранить флюс и контролирует скорость осаждения флюса на сварное соединение.
- Флюс: гранулированный флюс защищает сварной шов от атмосферного загрязнения. Он также очищает металл шва и снижает его химическое загрязнение. Хотя некоторые другие способы дуговой сварки, такие как MIG, SMAW предлагают это.
- Электрод: присадочный материал представляет собой стандартную проволоку, а также другие специальные формы. Толщина этой проволоки обычно составляет от 1,6 мм до 6 мм.
Принцип работы
Как и другие процессы дуговой сварки, SAW передает ток на электрод от сварочного аппарата переменного или постоянного тока.Он отдельно наносил флюс в зону сварного шва до того, как произойдет соединение. Этот флюс не проводит электричество в холодном состоянии, но становится хорошим проводником при расплавлении с помощью тепла дуги. Это также позволяет току течь между электродом и заготовкой. Поток, видимый в атмосфере, остается зернистым (неизменным), что позволяет использовать его повторно. Более низкий расплавленный флюс становится шлаком, что делает его отходами и должен быть удален после сварки,
Электрод непрерывно подается в соединение с заданной скоростью.В полуавтоматических сварочных установках сварка выполняется вручную вдоль стыка. В автоматическом режиме отдельный привод перемещает либо сварочную головку над стационарной сварочной головкой, либо работа вращается под неподвижной сварочной головкой.
Приложения
Следующие области применения процесса SAW:
ПроцессSAW подходит для сварки углеродистых сталей (конструкционных и судостроительных). Он также используется для обработки низколегированных сталей, нержавеющих сталей, сплавов на никелевой основе и для наплавки.
Также проверьте:
В этой статье мы расскажем, что такое дуговая сварка под флюсом, принципы ее работы и области применения. Я надеюсь, тебе это нравится. Если да, прокомментируйте и поделитесь. Спасибо, что прочитали!
AWS Сварщики | Изготовление индивидуальной сварки
Дуговая сварка под флюсом (SAW) — это распространенный процесс сварки, который идеально подходит для продольных и кольцевых стыковых и стыковых сварных швов из-за высокой текучести сварочной ванны. Для SAW требуются расходуемые твердые или трубчатые электроды с непрерывной подачей.Расплавленная проволока и зона дуги защищены от атмосферного загрязнения путем погружения под слой плавкого флюса, состоящего из извести, кремнезема, оксида марганца, фторида кальция и других соединений. Этот процесс сварки обычно выполняется в автоматическом или механизированном режиме с использованием одной проволоки и переменного или постоянного тока.
Метод SAW используется специалистами по сварке Weldall Manufacturing. Сварочные изделия Weldall по индивидуальному заказу подходят для использования в автоматизации и производстве, в строительной отрасли, погрузочно-разгрузочных работах, в горнодобывающей промышленности, в муниципальных и государственных контрактах, атомной промышленности, электроэнергетике, железнодорожной промышленности и ветроэнергетическом оборудовании.
Некоторые типы сварки имеют высокую пористость, что приводит к целостности конструкции. Другие типы не имеют достаточного проплавления свариваемых металлических поверхностей. Скорость плавления из-за высокого тока также может быть проблемой. И все же другие процессы сварки создают на поверхности ямки, которые не только не радуют глаз, но и могут поставить под сомнение целостность изготовленной детали.
ВWeldall Manufacturing работают высококвалифицированные сварщики, которые являются сварщиками AWS, которые применяют индивидуальные сварочные работы для средних и крупных сварных швов.Сварка SAW — это высокопроизводительный инструмент для их производителей. Сварщики Weldall Manufacturing понимают и контролируют этот тип сварочного процесса благодаря опыту и образованию, обеспечивая высокое качество сварки, высокую скорость наплавки и глубокое проплавление. При дуговой сварке под флюсом образуется легкий дым и создается атмосфера для высокоскоростной сварки.
Weldall Manufacturing — средний и крупный производитель сварных деталей с высококвалифицированными и преданными своему делу рабочими. Сварщики AWS, а также вторичные операции по механической обработке необходимы для выполнения сложных проектов по изготовлению тяжелого оборудования на заказ.Благодаря гибкости и изобретательности своей команды они превзойдут ваш прототип для производственных нужд — независимо от размера.
Автоматический аппарат для дуговой сварки под флюсом по цене 275000 рупий за единицу | Сектор 9 | Bahadurgarh
Автоматический аппарат для дуговой сварки под флюсом по цене 275000 рупий за единицу | Сектор 9 | Бахадургарх | ID: 21597199162Спецификация продукта
КПД | 87% | ||||
Размеры | 1010x580x930 мм | ||||
Номер модели | MZ-630IGBT | Мощность | |||
Номинальная входная мощность | 33 кВА | ||||
Номинальный входной ток | 50 A | ||||
Номинальный выходной ток | 630 A | ||||
Номинальное выходное напряжение 44 | |||||
Номинальное напряжение холостого хода | 80 В | ||||
Номинальный рабочий цикл | 100% (40 ° C) | ||||
Коэффициент мощности | 0.92 | ||||
Диапазон регулировки выходного тока | 60-630 A | ||||
Регулировка глубины сварки от мелкой до глубокой | DC, A, B, C, D (A — стандартный) | ||||
Режим охлаждения | Воздушное охлаждение | ||||
Класс изоляции | F | ||||
Пылевлагозащита | IP21S | ||||
Вес нетто | 68 кг | ||||
Диапазон регулировки скорости подачи проволоки | 135-600 см / мин | ||||
Диапазон регулировки скорости сварки | 0-170 см / мин | ||||
Диапазон регулировки сварочной головки по вертикали | 93 мм | ||||
Диапазон регулировки по горизонтали сварочной головки | + -30 мм | ||||
Диапазон регулировки по вертикали для костыля | 140 мм | ||||
Колесная колея | 300 мм | ||||
Колесная база | Емкость потока | 10 л |
Описание продукта
Основные характеристики:- Технология контроля проплавления сварного шва
- Конструкция технологии плавного переключения с хорошими сварочными характеристиками
- 30% веса, 50% объема, 80% входной мощности традиционного аппарата
- Конструкция с высоким рабочим циклом, подходящая для тяжелой промышленности
- Выбор режима CC / CV
- Цифровой дисплей сварочного тока и напряжения
- Источник питания может использоваться для сварки под флюсом, ленточной сварки, а также MMA, строжки и электродно-шлаковой сварки
Применение продукта:
- Подходит для нержавеющей стали, углеродистой стали и ее сплавов
Заинтересовал этот товар? Получите последнюю цену у продавца
Связаться с продавцом
Изображение продукта
О компании
Год основания 1996
Юридический статус компании с ограниченной ответственностью (Ltd./Pvt.Ltd.)
Характер бизнеса Производитель
Количество сотрудников от 11 до 25 человек
Годовой оборот2012-13 рупий. 1-2 крор Прибл.
2011-12 руп. 1-2 крор Прибл.
2010-11 рупий. 1-2 крор Прибл.
IndiaMART Участник с декабря 2003 г.
GST06AAACE2900Q1ZO
Код импорта и экспорта (IEC) 05970 *****
Elektroweld Automations India Pvt Ltd — ведущая организация, занимающаяся производством и экспортом сварочного оборудования в Индии.За короткий промежуток времени организация заняла нишу в своей сфере деятельности и стала признанным производителем и поставщиком сварочного оборудования.Заслуга этой уважаемой позиции заключается в стремлении компании обеспечивать лучшее качество по доступным ценам. Благодаря своим настойчивым усилиям и инновациям компания стала законодателем мод в области сварочного оборудования в Индии.
Видео компании
Вернуться к началу 1 Есть потребность?
Получите лучшую цену
Есть потребность?
Получите лучшую цену
Аппарат для дуговой сварки под флюсом, процедура и оборудование
Дуговая сварка под флюсом — Сварка — одна из многих технологий, которые с каждым годом развиваются.Потому что бизнес многообещающий, а наука — сложная. С развитием технологий автоматизации попытки скрестить сварку и автоматизацию (таким образом, превратившись в автоматическую сварку), уже являются прогрессивными.
Однако знаете ли вы, что автоматическая сварка существует уже несколько десятилетий? На практике сварка выполняется не только вручную сварщиком, но и на самом деле существует машина, которая способна сваривать безупречно без сварщика. Вы знаете, о чем я говорю, если вы когда-нибудь слышали название «Сварка под флюсом» (сокращенно — ПИЛА).Не волнуйтесь, если у вас нет, просто прочтите эту статью, и вы узнаете чудо дуговой сварки под флюсом.
Применение дуговой сварки под флюсом при сварке трубОпределение дуговой сварки под флюсом
Это первая автоматическая сварочная машина, на которую был выдан первый патент в 1930-х годах. Там, где процесс сварки обычно виден, при дуговой сварке под флюсом дуга буквально погружена в ванну с расплавленным флюсом, поэтому дугу невозможно увидеть.
Присадочная проволока и флюс непрерывно подаются на дугу, поскольку сварочный аппарат постепенно продвигается вперед по пути сварки. Флюс имеет форму зерна и выглядит как обычный песок. Он состоит из смеси различных ингредиентов, а именно извести, кремнезема, оксида марганца, фторида кальция и других соединений.
Сварочная дуга погружается в слой гранулированного флюса.Благодаря тому, что сварка под флюсом является полностью автоматической или механизированной, она очень производительна благодаря высокой производительности наплавки.В диапазоне от 9 до 10 раз по сравнению с такими показателями наплавки. Однако дуговая сварка под флюсом также имеет несколько недостатков. Сама по себе механизированная сварка ограничивает применение SAW с точки зрения положения при сварке.
Если сварка невозможна в каком-либо другом положении, кроме плоского, в некоторой степени также может применяться для углового шва. Более того, сварка SAW может быть очень горячей, она имеет большее тепловложение по сравнению со сваркой штучной сваркой из-за ее относительно больших сварочных параметров.Тепло от дуги не может уйти, как при сварке штучной сваркой, потому что дуга погружена во флюс, который действует как изолятор.
Таким образом, тепло распространяется по основному металлу, что приводит к большему разбавлению и зоне термического влияния (HAZ). Тем не менее, SAW популярна и нашла свое применение во многих отраслях промышленности и на производстве.
Оборудование для дуговой сварки под флюсом
Аппарат для дуговой сварки под флюсом — это собственный аппарат, состоящий из нескольких важных частей.Аппарат Basic SAW выглядит как диаграмма на рисунке 3. Как и в каждом сварочном аппарате, особенно в аппарате для дуговой сварки, есть трансформатор, который генерирует требуемый сварочный ток и напряжение от вашей обычной электрической розетки. В большинстве случаев этот трансформатор и его панель управления в основном цифровые и выглядят довольно продвинутыми.
Панель управления также может быть оснащена множеством других функций, включая, помимо прочего, управление переменными (сварочный ток, сварочное напряжение и скорость движения), устранение неисправностей и память для сохранения наиболее часто используемых параметров сварки.Катушка с электродной проволокой предназначена для непрерывной подачи присадочного металла через двигатель подачи проволоки.
Подобно механизму подачи проволоки в GMAW и FCAW, разница в том, что при SAW диаметр присадочной проволоки больше, чем в GMAW или FCAW. Бункер для флюса предназначен для удерживания гранулированного флюса и его непрерывной подачи в сварочную ванну. Неиспользованный флюс, который находится в верхней части сварочной ванны (та, которая не плавится), будет собираться вручную или с помощью какого-либо устройства для вакуумирования, аналогичного трубке для извлечения незаплавленного флюса на рисунке 3.Иногда применяется подкладка сварного шва, чтобы избежать прожога из-за непрерывной сварочной активности.
Базовый механизм SAWДругой вариант SAW — добавление дополнительного механизма подачи проволоки. Одновременно можно использовать до четырех устройств подачи проволоки для дальнейшего повышения производительности сварки. Следовательно, за один проход можно правильно соединить толстые куски металла, а не за несколько проходов.
Работающий станок для резки SAW с несколькими механизмами подачи проволокиSAW также работают в стационарном режиме, когда заготовка перемещается вместо станка.Стационарная модель применяется в стыке труб, в то время как традиционная подвижная машина в основном применяется в стыке пластин. Режим движения регулируется перилами, которые необходимо настроить на прямолинейность перед началом сварки.
Установка направляющей так же важна, как и установка параметров сварки, потому что после запуска не рекомендуется прерывать процесс до его завершения. Кроме того, небольшой наклон повлияет на геометрию сварки и создаст такую проблему, как отсутствие плавления.
Сварка под флюсом — это высокопроизводительный сварочный процесс. Из-за этого этот процесс применяется в максимально возможной степени, несмотря на его ограничения с точки зрения положения при сварке.
Помимо сложности обращения с гранулированным флюсом, так как его необходимо восстанавливать, и некоторых других проблем при очистке шлака, сварка под флюсом является довольно чистым процессом, при этом не образуются брызги или искры, поскольку слой флюса полностью покрывает сварочную ванну. , не допуская выхода брызг или искр.
Другая причина, по которой сварка под флюсом является предпочтительной, заключается в том, что для нее не требуется квалифицированный сварщик. Обучение сварщика занимает гораздо меньше времени по сравнению с обучением сварщика навыкам.
См .: Аппарат для стержневой сварки
Сварка под флюсом в основном используется для сварки толстых материалов с длинными стыками. Например, в конструкции корпуса корабля продольный стык сосуда высокого давления и цистерны. Также возможно соединение толстых и больших диаметров трубы с помощью SAW.Однако из-за того, что процесс очень горячий, его применение ограничено только материалом, который на самом деле не реагирует на тепло.
В основном это углеродистая сталь и некоторые разновидности сплава на основе никеля. Тепло также может деформировать материал, поэтому необходимо принять меры для предотвращения деформации, такие как прерывистая сварка или установка стопора в критической точке. Но в любом случае дуговая сварка под флюсом исключает любую человеческую ошибку и увеличивает вероятность получения качественного сварного шва быстрее, чем любой сварочный процесс.
Проблема безопасности, связанная с этим процессом, уникальна по сравнению с любым другим процессом сварки. SAW полностью автоматизирован и механизирован, при этом сварщикам нужно только направить сварочный путь и нажать кнопку, чтобы начать сварку. После этого сварщик может безопасно наблюдать за процессом сварки с безопасного расстояния.
В процессе сварки не образуется столько дыма по сравнению с любым другим процессом сварки, и это большая мера безопасности. Слой флюса также полностью закрывает ультрафиолетовый свет дуги от выхода, тогда как в другом процессе сварки УФ-свет часто вызывает проблемы у сварщика, вызывая такие осложнения, как глазная дуга (фотокератит) и ожог кожи.
производителей аппаратов для дуговой сварки под флюсом в Мумбаи, Индия
Аппарат для дуговой сварки под флюсом
Дуговая сварка под флюсом (SAW) — это распространенный процесс дуговой сварки. Для этого требуется расходный твердый или трубчатый (порошковый) электрод с непрерывной подачей. Расплавленный сварной шов и зона дуги защищены от атмосферного загрязнения за счет того, что они «погружены» под слой гранулированного плавкого флюса, состоящего из извести, кремнезема, оксида марганца, фторида кальция и других соединений.В расплавленном состоянии флюс становится проводящим и обеспечивает прохождение тока между электродом и изделием. Толстый слой флюса полностью покрывает расплавленный металл, предотвращая разбрызгивание и искры, а также подавляя интенсивное ультрафиолетовое излучение и пары, которые являются частью процесса SMAW.
SAW обычно работает в автоматическом или механизированном режиме, однако доступны полуавтоматические (ручные) SAW-пушки с подачей флюса под давлением или под действием силы тяжести. Процесс обычно ограничивается плоскими или горизонтальными положениями угловой сварки.При этом процессе возможна производительность наплавки до 45 кг / час. Для этого требуется источник питания постоянного напряжения.
Источник питания на ПАВ на диоде
Диодный источник питания на ПАВ имеет регулируемое выходное напряжение ступенчато без обратной связи по напряжению или току. Тележка с электроприводом для напряжения или тока. Тележка с электроприводом используется для транспортировки сварочной головки с механизмом подачи проволоки, катушкой с проволокой и бункером для флюса. Доступны дисплеи для сварочного напряжения, тока, скорости подачи проволоки и скорости тележки.Эти источники питания рассчитаны на непрерывный режим работы и сваривают вместе в течение нескольких часов без остановки.
Тиристоризованные источники питания на ПАВ
Тиристорный источник питания имеет обратную связь по напряжению. Это также имеет функцию, которая ограничивает ток до расчетного уровня в качестве защиты. Этот тип источника питания позволяет плавно регулировать выходное напряжение и поддерживает постоянное заданное напряжение.
Источник питания на инвертированной ПАВ
Инвертированный источник питания на ПАВ имеет характеристики постоянного напряжения / постоянного тока.Они позволяют бесступенчато выбирать выходное напряжение. Этот тип источника питания обеспечивает превосходное качество сварки.
Что такое дуговая сварка под флюсом?
Принцип и процедура сварки
При дуговой сварке под флюсом неизолированный металл или электрод с медным покрытием действует как наполнитель и плавится вместе с процессом сварки, а гранулированный флюс защищает от атмосферного загрязнения. Тепло создается за счет образования дуги между электродом и металлической заготовкой, которая остается скрытой под флюсом.Флюс становится проводящим, когда образуется расплавленная ванна, а путь тока застревает между электродом и металлической заготовкой. Этот флюс также служит защитой от брызг.
Процесс сварки под флюсом может быть полуавтоматическим или автоматическим. Сварочное оборудование в основном будет иметь источник постоянного тока, приводные ролики для непрерывной подачи электрода, сварочную горелку с бункером для флюса и соплом.
В процессе полуавтоматической сварки нажимается спусковой крючок горелки, и флюс начинает оседать на свариваемом соединении детали.Здесь тип используемого пистолета может быть с подачей потока под действием силы тяжести или нагнетанием флюса под давлением. Флюс не проводит ток и в холодном состоянии не уступает изолятору, поэтому дуга зажигается либо путем постукивания электрода по металлической заготовке, либо перед подачей сварочного тока между металлической заготовкой и электродом остается стальная вата. В качестве альтернативы для этого процесса сварки также используется ток высокой частоты. Во всех трех упомянутых выше методах для покрытия дуги и расплавленного металла используется флюс.
Включены источники питания, и сварочный ток может протекать между электродом и металлической заготовкой.Флюс становится очень проводящим и поддерживается расплавленным флюсом. Опорная пластина, сделанная из стали или меди, используется для поддержки проникновения и расплавленного металла, который находится в большом количестве. Из-за контакта флюса с атмосферой верхняя часть флюса, которая видна, продолжает оставаться в твердой гранулированной форме, что позволяет повторно использовать ее и экономить на затратах. Сварочная головка в таких полуавтоматах перемещается вручную вместе с металлическими соединениями заготовок, тогда как в автоматическом сварочном оборудовании либо сварочная головка перемещается по металлической заготовке, закрепленной отдельными приводами, либо заготовка вращается и перемещается под сварочной головкой.Принцип саморегулирующейся дуги применяется здесь для поддержания постоянной длины дуги, при этом, если длина дуги уменьшается по каким-либо причинам, одновременно уменьшаются и напряжение дуги, и ток дуги. Следовательно, скорость выгорания увеличивается, что приводит к удлинению дуги, и происходит обратное, если длина дуги увеличивается по сравнению с нормальной.
SAW подходит только для плоской или горизонтальной угловой сварки.
Преимущества дуговой сварки под флюсом
Высокая скорость наплавки
Высокая глубина проплавления шва
Сварные соединения прочные и хорошего качества
Высокая скорость производства благодаря возможности автоматизации
Требуемые навыки сварщика могут не быть высоким
Из-за низкой защиты дуги от флюса, дыма и света дуги
Ограничения SAW
Ограничения на сварку только низкоуглеродистой стали, нержавеющей стали и никелевых сплавов
Положения сварки ограничены
Годно только непрерывная и длинномерная сварка
Возможности нерегулярной подачи проволоки
Обработка флюса требует много времени и дополнительных работ
Удаление шлака после сварки
.