Сварка плавящимся электродом
Сварка плавящимся электродом на сегодняшний день является самым широко используемым способом сварки. При данном способе сварки дуга горит между основным металлом и металлическим стержнем, который подается автоматически в свариваемую зону по мере плавления. Этот вид сварки можно производить одним или несколькими электродами. Двухэлектродной сваркой называют сварку, в которой два электрода подсоединены к одному полюсу источника питания дуги, а многоэлектродной сваркой — если подсоединен пучок электродов. Так же каждый из электродов может получать независимое питание — такую сварку называют двухдуговой (многодуговой) сваркой. Вместе с металлическим стержнем из сварочной головки подается защитный газ, который применяется для защиты от атмосферы. В качестве таких защитных газов могут использоваться углекислый газ, аргон, гелий или их смеси. При применении углекислого газа приходится использовать раскислители (кремний, марганец), так как при высоких температурах выделяется кислород, окисляющий металл и снижающий поверхностное натяжение, что приводит к разбрызгиванию металла. Для того что бы купить сварочное оборудование оптом, обратитесь в отдел продаж представительства компании Nikkey. Вас проконсультируют и посоветуют наиболее подходящие сварочные аппараты оптом, для проведения сварочных работы плавящимся электродом.
Для сварки в защитных газах плавящимся электродом в качестве металлического стержня используют сварочную проволоку близкую по химическому составу к основному металлу. Выбор защитного газа определяется его инертностью к свариваемому металлу, или его активностью, способствующей рафинации металла сварочной ванны. Как правило, для сварки цветных металлов и сплавов на их основе применяют инертные одноатомные газы (аргон, гелий и их смеси). Для сварки меди и кобальта — применяют азот. Для сварки сталей различных классов — применяют углекислый газ, и сварочную проволоку с повышенным их содержанием кремния, марганца. Применение смеси инертных и активных газов, позволяет повысить устойчивость дуги, уменьшить разбрызгивание, улучшить формирование шва, воздействовать на его геометрические параметры. Сварка плавящимся электродом позволяет сваривать металл тонкий и средней толщины.
Сварку в защитных газах плавящимся электродом производят на постоянном токе обратной полярности, т.к. на переменном токе дуга может прерываться, из-за сильного охлаждения столба дуги защитным газом. Сила сварочного тока определяется скоростью подачи сварочной проволоки.
Среди недостатков данного способа сварки можно выделить большой расход электродного металла на угар и разбрызгивание (35-37%), ограничение по сварочному току, мощное излучение дуги, сварка возможна только на постоянном токе.
Среди преимуществ данного способа сварки можно отметить: высокую производительность (по сравнению с дуговой сваркой), не требуется время на замену электродов, нет потерь на огарки, зона сварки надежно защищена, отсутствует шлаковая корка, не происходит окисления, сварка возможна в различных пространственных положениях.
Механизм дуговая сварка плавящимся электродом
Автор zamolotkom. ru На чтение 23 мин. Просмотров 197 Опубликовано
Сварка плавящимся электродом: технология процесса, необходимое оборудование, типы переноса электродного метала
Дуговая сварка плавящимся электродом — это метод, при котором между свариваемым изделием и концом электрода возникает электрическая дуга, под действием которой основной металл и электрод начинают плавиться, образуя сварочную ванну, а обмазочный материал электрода при этом создает газовую защитную среду, необходимую для качественного шва.
Плюсы и минусы метода
Плюсами этого способа сваривания всегда считались:
- простота эксплуатации и низкая цена оборудования для сварного процесса;
- возможность сваривания большого количества разновидностей металлов при широком спектре выбора электродного материала;
- возможность выполнять сварные работы в труднодоступных местах;
- уместно сваривание в любых пространственных положениях.
Из недостатков стоит выделить:
Оборудование для ручной дуговой сварки
Оборудование, необходимое для ручного дугового сваривания, состоит:
- из источника питания, который может быть как переносным, так и стационарным в зависимости от вида выполняемых сварщиком работ;
- из кабеля с электродержателем, в котором фиксируется покрытый специальной обмазкой электрод;
- из кабеля обратного заземления для соединения свариваемого изделия с источником питания.
Также не стоит забывать о дополнительных средствах, таких, как: защитная маска, перчатки сварщика, разнообразные приспособления для удаления шлака и другие вещи, необходимые для удобства специалиста.
Перенос электродного металла делится на три типа:
- крупнокапельный перенос. Случается, если процесс происходит с высоким напряжением на электрической дуге и невысокими параметрами тока при сваривании.
Размер капель плавящегося электрода при этом имеет диаметр больше сечения самого электрода. Процесс сварки в таком случае возможен только в вертикальном пространственном положении, так как сварочная ванна при таком переносе имеет большие размеры и её становится сложно контролировать.
- мелкокапельный перенос. При данном виде переноса металла капли расплавленного электродного материала равны или меньше по диаметру, чем сам электрод. Процесс сварки проходит с высоким напряжением на дуге и высокими параметрами тока. При мелкокапельном переносе увеличивается скорость выполнения работ, шов имеет более аккуратный вид. Такой тип переноса наиболее подходит для сваривания толстостенных металлов.
- струйный перенос. Струйный перенос металла обычно происходит при высокой силе тока и использовании электрода с прямой полярностью. При данном переносе очень мелкие капли металла идут одна за другой непрерывной цепочкой, обеспечивая ровную и гладкую на ощупь поверхность шва.
Этот же тип переноса характерен для полуавтоматической сварки в среде защитного газа.
Сварочный процесс
От источника сварочного тока к электроду поступает электроэнергия. Во время контакта электрода со свариваемым металлом образуется электрическая дуга, которая расплавляет изделие и электрод, вследствие чего возникает сварочная ванна. Электродный материал, поступая в эту ванну, сплавляет кромки металла, который нужно сварить, а обмазка обеспечивает защиту в области формирования шва и образует защитный слой по окончании процесса сваривания.
Сварка плавящимся электродом в защитных газах
Этот тип сварки подразумевает собой сварку с помощью автоматических или полуавтоматических сварочных аппаратов, в процессе сварочная проволока подается в зону формирования шва. В роли защитного газа чаще всего выступают аргон либо углекислый газ, которые подаются в зону действия электрической дуги для обеспечения хорошего соединения металлов и отсутствия дефектов сварочного шва. Высокие сварочные токи и малый диаметр сварочной проволоки делают необходимой большую скорость подачи проволоки в сварочную ванну, скорость сваривания при этом составляет 15-80 м/ч.
Этот способ отличается высокой производительностью и большой скоростью процесса, что способствует его распространению в сфере промышленного производства металлоконструкций, машиностроении.
Из-за отсутствия шлаковых включений и возможности аккуратного выполнения сварки при очень малых толщинах материала данный метод получил широкое распространение на разнообразных СТО и других предприятиях по обслуживанию и ремонту автомобилей.
Опишите ручную дуговую сварку плавящимся электродом
Ручная дуговая сварка выполняется плавящимся или неплавящимся (угольным, графитовым, вольфрамовым, гафниевым) электродом. При сварке плавящимся электродом (рис. 5.1) дуга горит между ним и изделием. Формирование металла шва осуществляется за счет материала электрода и расплавления основного металла в зоне действия дуги. При сварке неплавящимся электродом для формирования металла шва в зону дуги извне подается присадочный материал.
Наибольшее применение нашла сварка плавящимся электродом, так как ее можно применять во всех пространственных положениях, сваривая черные, цветные металлы и различные сплавы. При этом используются электроды диаметром 1÷ 12 мм. Однако основной объем работ выполняется электродами диаметром 3 ÷ 6 мм.
Электроды классифицируются по материалу, из которого они изготовлены, по назначению, по виду покрытия, по свойствам металла шва, по допустимым пространственным положениям сварки или наплавки, по роду и полярности тока.
По назначению электроды подразделяются на следующие группы: для сварки углеродистых и низколегированных конструкционных сталей – У; для сварки теплоустойчивых легированных сталей – Т; для сварки высоколегированных сталей с особыми свойствами – В; для наплавки слоев с особыми свойствами – Н.
48. Свариваемость. Основные технологические приемы для трудно и ограниченно свариваемых сталей.
Ограниченно свариваемые стали имеют содержание углерода от 0,36 до 0,45% и склонны к образованию трещин. Сварка требует обязательного подогрева. Плохо свариваемые стали содержат углерод в количестве более 0,45%. При их сварке требуются специальные технологические процессы.
Легирование стали одним или несколькими легирующими элементами придает ей определенные физико-механические свойства. Как правило, повышение уровня легирования и прочности стали приводит к ухудшению ее свариваемости и первостепенная роль в этом принадлежит углероду.
Низколегированные стали хорошо свариваются всеми способами плавления. Получение же при сварке равнопрочного сварного соединения, особенно у термоупрочненных сталей, вызывает определенные трудности. В зонах, удаленных от высокотемпературной области, возникает холодная пластическая деформация. При наложении последующих швов эти зоны становятся участками деформационного старения. Это в конечном итоге приводит к снижению пластических и повышению прочностных свойств металла и соответственно к появлению холодных трещин.
При сварке высоколегированных хромистых 08X13, 08Х17Т и некоторых других сталей существуют отличительные особенности: высокий порог хладноломкости стали, находящийся обычно в области положительных температур; склонность к значительному охрупчиванию в околошовной зоне;
низкая пластичность и вязкость металла шва, выполненного сварочными материалами аналогичного со сталью химического состава; невозможность устранить охрупчивание термообработкой.
Сварку таких сталей необходимо выполнять с минимальным тепловложением, так как с увеличением погонной энергии возрастает склонность зон сварного соединения к росту зерен, появлению микротрещин и падению пластичности. При этом снижается сопро-тивляемость сварного соединения локальным повреждениям и межкристаллической коррозии. В процессе сварки возникает опасность коробления и появляется повышенный уровень остаточных напряжений. После сварки в ряде случаев требуется термообработка.
Сварка плавящимся электродом.
Выполняется при расплавлении электродной проволоки, подаваемой в плавильное пространство, его защита от воздуха осуществляется подачей защитного газа — инертного, активного или их смесей под давлением, большим атмосферного, вследствие чего воздух оттесняется и образуется соответствующая газовая среда (рис. 7.4). При этом способе сварки дуга горит между электродом 5, который подается в зону сварки с помощью специального механизма со скоростью Упэ, и изделием 4.
Рис. 7.4. Схема сварки плавящимся электродом в среде защитных газов
Капли расплавленного электродного металла 3 смешиваются с расплавленным основным металлом, образуя общую сварочную ванну 2, которая после кристаллизации превращается в сварной шов 1. Перемещение горелки вдоль сварного шва выполняется вручную сварщиком со скоростью сварки VCB. Защита плавильного пространства осуществляется инертным или активным газом б, который подается через сопло 7 под давлением, большим атмосферного. Образованная газовая среда определяет характер взаимодействия между газами и расплавленным металлом. Как и при сварке неплавящимся электродом, надо обеспечивать ламинарное течение газа из сопла, для чего используют такие же средства. Основными параметрами режима являются следующие:
- • род тока, полярность — сварка ведется на постоянном токе обратной полярности, что обеспечивает наиболее стабильное горение дуги;
- • диаметр электродной проволоки — зависит от толщины свариваемого металла и пространственного положения; находится в пределах 0,5—2,0 мм для полуавтоматической сварки и 2—4 мм для автоматической;
- • сила сварочного тока /св = 50—500 А — зависит от диаметра электродной проволоки, пространственного положения и скорости ее подачи;
- • напряжение на дуге Ua = 18—35 В — зависит от пространственного положения, силы сварочного тока, диаметра и состава электродной проволоки и рода защитного газа;
- • скорость сварки VCB при полуавтоматической сварке не задается по тем же соображениям, что и при ручной, при автоматической находится в пределах 10-60 м/ч;
- • вылет электрода /э = 10—30 мм — зависит от диаметра электродной проволоки и ее электрофизических свойств.
При малом вылете возможны оплавление мундштука, увеличение забрызгивания внутренней поверхности сопла, что приводит к нарушению ламинарного течения защитного газа. При большом вылете ухудшается защита плавильного пространства, проволока вследствие перегрева теряет свою жесткость, ухудшается направление ее в место сварки. Однако вследствие подогрева проволоки на участке увеличенного вылета возрастают скорость ее плавления и производительность процесса. Это явление можно реализовать, используя специальные керамические направляющие мундштуки;
- • расход защитного газа QT = 5—30 л/мин — зависит от силы сварочного тока, защитного газа (расход аргона и диоксида углерода в 3—4 раза меньше, чем гелия), состава свариваемого металла, скорости сварки и т.д.
Выбор защитного газа определяется в первую очередь свойствами свариваемого металла. Одни высоколегированные стали и сплавы, титан и его сплавы требуют лишь инертной защитной атмосферы, а другие высоколегированные стали и сплавы, алюминий и его сплавы могут быть сварены как в инертной атмосфере, так и с примесями к ней активных газов, например 2—5 % кислорода. При этом достигается струйный перенос металла, уменьшается разбрызгивание и не появляется пористость от водорода. Сварку углеродистых и низколегированных сталей можно выполнять в активных газах (С02 по ГОСТ 8050—85, С02 + 20—30 % 02), в смеси активных и инертных газов. Так, смесь Аг + 25 % 02 способствует струйному переносу электродного металла и позволяет предотвратить разбрызгивание. Состав защитных газов влияет и на другие технологические характеристики процесса. При сварке в аргоне короткая и длинная дуга обеспечивает благоприятные условия сварки металлов малых и средних толщин в нижнем положении. При сварке в гелии и азоте и в их смесях с аргоном благодаря повышенной тепловой мощности обеспечиваются большая глубина провара и благоприятная его форма, что способствует повышению скорости сварки.
При выборе рассмотренных взаимосвязанных характеристик следует руководствоваться данными, приведенными в табл. 7.1.
Рекомендованные соотношения между диаметром электрода и силой тока, напряжением на дуте и вылетом электрода
Техника полуавтоматической сварки в среде защитных газов плавящимся электродом достаточно проста и имеет много общего с техникой ручной дуговой сварки. Роль сварщика сводится к поддержанию постоянного вылета электрода и расстояния сопла до изделия, равномерного перемещения горелки вдоль свариваемых кромок и иногда к выполнению необходимых манипуляций и колебаний электродом. Форма колебаний зависит от диаметра проволоки; при сварке тонкой проволокой (до 1,6 мм), как и при ручном процессе при больших диаметрах, зависит от типа соединения. Корневые швы сваривают при возвратно-поступательном перемещении электрода, средние слои стыковых швов при перемещении электрода по вытянутой спирали, а верхние слои — с поперечными колебаниями «змейкой». Сварку ведут с наклоном электрода углом вперед и углом назад до 10—30°. В первом случае глубина провара меньше, чем во втором, вследствие подтекания жидкого металла под основание дуги.
Возвратно-поступательные движения горелки уменьшают пористость, особенно при применении активных газов вследствие улучшения защиты, перемешивания и замедления охлаждения жидкой ванны, что способствует извлечению из нее газов.
Подготовка кромок под сварку и размеры сварных швов регламентирует ГОСТ 14771—76, согласно которому можно качественно сваривать металл толщиной начиная с 0,8 мм.
Сварку стыковых швов тонкостенных изделий во всех случаях лучше вести в вертикальном положении сверху вниз или «на весу», а дугу направлять на ванну жидкого металла и выполнять такой шов за один проход. Если детали собраны с зазором, процесс ведут с периодическими остановками, уменьшением мощности или поперечными колебаниями. Кольцевые стыковые швы сваривают, как и прямолинейные. Металл толщиной до 4 мм сваривают в по- лупотолочном или вертикальном положении сверху вниз проволокой малого диаметра или импульсной дугой. Более толстые изделия сваривают в нижнем положении со смещением электрода с зенита в сторону, противоположную вращению детали; размер смещения зависит от диаметра детали, силы тока и скорости сварки. Соединение металла внахлест толщиной до 1,5 мм сваривают, направляя дугу на верхнюю кромку, при большей толщине сваривают «на весу» с наклоном электрода поперек шва, а дугу направляют в угол среза кромки верхнего листа.
Угловые соединения сваривают «лодочкой» наклонным электродом под углом 50—60° к полке. Если толщина металла менее 5 мм, дугу направляют в угол. При большей толщине электрод смещают в сторону полки на 0,8—1,5 мм, а сварку ведут углом вперед.
Сварку электрозаклепками и точками применяют для стыковых, угловых и соединений внахлест металла толщиной до 2 мм во всех пространственных положениях с пробивкой или без пробивки отверстий в верхних листах, а стык деталей обеспечивают прижатием сопла, которое имеет отверстия для выхода газа.
При сварке вертикальных швов на тонком металле используют свободное формирование шва: процесс ведут сверху вниз, углом назад, направляя дугу на переднюю часть ванны, что обеспечивает проплавление кромок и исключает прожоги. Сварка сверху вниз не требует высокой точности сборки деталей и выполняется в 2—2,5 раза быстрее, чем снизу вверх. Сварку металла толщиной более 6 мм выполняют снизу вверх, что обеспечивает надежный провар и отсутствие несплавления по краям шва, короткими частыми замыканиями, пересаживая электродный металл капля за каплей в сварочную ванну. При значительной длине прямолинейные вертикальные швы на стали толщиной от 8 до 40 мм рекомендуется сваривать с принудительным формированием шва с помощью медных водоохлаждаемых ползунов, используя порошковую проволоку или подавая небольшое количество флюса в плавильное пространство. Сварка выполняется специальным автоматом. Использование импульсно-дугового процесса значительно упрощает сварку таких швов.
Сварку горизонтальных швов ведут с наклоном электрода, снизу вверх и углом назад без поперечных колебаний, направляя дугу на сварочную ванну. При толщине металла более 4 мм производят разделку верхней кромки листа, а металл толщиной более 6 мм сваривают с наклоном электрода сверху вниз. При этом корневой шов сваривают тонкой проволокой с частыми короткими замыканиями, импульсной дугой или неплавящимся электродом. Основную разделку заплавляют плавящимся электродом на больших токах, а облицовочный шов — тем же способом, что и корневой.
Потолочные швы — сложные в исполнении, их сваривают углом назад на минимальных силах тока и напряжении, а диаметр электрода выбирают в пределах 0,5—1,4 мм. Дугу и поток защитного газа направляют на ванну жидкого металла для уменьшения ее стекания при увеличенном расходе газа, поперечных колебаниях электрода, частых коротких замыканиях.
Полуавтоматическая сварка в среде защитных газов полностью вытеснила полуавтоматическую сварку под флюсом и стала доминирующей среди механизированных способов сварки при изготовлении металлоконструкций ответственного и особо ответственного назначения благодаря таким преимуществам, как высокая производительность, легкость транспортирования защитной среды к плавильному пространству, отсутствие шлаковой корки и шлаковых включений, уменьшение ширины зоны термического влияния и сварочных деформаций, сварка во всех пространственных положениях, возможность наблюдения за дугой и управления ею.
Углеродистые, низколегированные и некоторые среднелегированные стали можно сваривать в сильно- или слабоокислительной среде, используя электродную проволоку с повышенным содержанием элементов-раскислителей. Дело в том, что углекислый газ только защищает от азота плавильное пространство, а сам образует в нем кислую среду за счет диссоциации:
Жидкий металл в головной части сварочной ванны может реагировать как с самим диоксидом углерода, так и с продуктами его реакции:
в результате чего сварочная ванна насыщается кислородом. При охлаждении расплавленного металла углерод, который присутствует в стали, может окисляться, образуя оксид углерода:
Выделяясь из сварочной ванны в виде пузырей, СО может вызвать пористость; если сварочная проволока легирована кремнием и марганцем, оксиды железа будут раскисляться главным образом в результате взаимодействия с ними, а не с углеродом, обеспечив качественный металл шва и отсутствие пор:
Эти реакции протекают в хвостовой части сварочной ванны, поэтому оксиды кремния и марганца в виде очень тонкой шлаковой корки покрывают поверхность сварного шва. Существенным недостатком использования углекислого газа для сварки является повышенное разбрызгивание: забрызгиваются внутренняя поверхность сопла горелки и околошовная зона, а отделение брызг от основного металла требует применения тяжелого непрестижного ручного труда.
Для предотвращения этого явления используют специальные источники питания, применяют газовые смеси, которые способствуют мелкокапельному переносу электродного металла (С02 + 02) или струйному (Ат + СОД, ведут сварку специальными порошковыми или активированными проволоками или наносят на около- шовную поверхность специальные лакокрасочные покрытия, которые, однако, эффективно действуют только при однопроходной сварке, после чего их нужно обновлять.
С учетом специфики защиты плавильного пространства углекислым газом сварку различных соединений из углеродистых и низколегированных сталей ведут с использованием специальных электродных проволок Св-08Г2С, Св-08ГСМТ, Св-08ХГСМФ и т.д.
При сварке высоколегированных сталей, которые имеют в своем составе элементы, высокоактивные к кислороду (алюминий, титан, ниобий и т.д.), нужно использовать только инертные газы, в других случаях возможно применение смеси аргона с кислородом в комбинации с соответствующими проволоками: Св-01Х19Н9, Св-08Х19Н10Г2Б, Св-08Н50, Св-ХН75М6ТЮит.п.
Медь и ее сплавы сваривают в аргоне, гелии и азоте. С целью экономии аргона и повышения производительности труда рекомендуется газовая смесь 70—80 % Аг + 30—20 % N2. Однако лучшее формирование шва достигается при сварке в аргоне и гелии. В качестве присадки используется проволока из кремнисто-марганцевой бронзы БрКМцЗ—1. Перед началом процесса требуется подогрев кромок до 200—500 °С.
Для механизированной сварки высокопрочной коррозионно-стойкой бронзы марки БрАНМцЖ-8,5—4—4—1,5 разработана специальная композитная проволока, которая обеспечивает получение сварного шва того же состава на параметрах режима: d3 = 2,8 мм, /св — 350-380 А, 1/Д = 24—26 В, QM = 16—17 л/мин.
Титан и его сплавы толщиной более 4 мм сваривают только в среде инертных газов высокой степени чистоты. Размеры сварных швов и их формирование зависят от рода газа. В гелии швы имеют более плавный переход усиления к основному металлу, в аргоне проплавление шва глубже и шов уже. Рекомендуется вести сварку присадочной проволокой марки ВТ 1—00.
Для сварки на монтаже рекомендуется использовать импульсно-дуговой процесс с использованием гелия.
Сварка должна выполняться в палатке, чтобы исключить сдувание защитной струи из плавильного пространства. В цеху надо пользоваться камерой с контролируемой атмосферой.
Алюминий и его ставы толщиной более 4 мм сваривают в среде аргона или в смеси 30 % Аг + 70 % Не. В качестве присадочной проволоки используются сплавы типа АМц и АМг, а также сплавы состава, близкого к основному металлу.
По сравнению со сваркой вольфрамовым электродом сварные швы имеют пониженную на 15 % прочность вследствие большего перегрева электродного металла при переходе через дуговой промежуток. Преимуществами являются надежное перемешивание сварочной ванны и ее очистка от оксидных включений, а также высокая производительность, которую можно значительно увеличить, применяя импульсно-дуговой процесс. Введение модификаторов (циркония, титана, бора) в проволоку повышает стойкость сварных швов к кристаллизационным трещинам.
При сварке высоколегированных термически упрочняемых сплавов прочность может снижаться почти наполовину, поэтому после сварки изделия надо подвергать термической обработке — закалке с последующим старением. Повышение устойчивости куста- лости соединения достигается снятием усиления сварного шва.
Сварку магниевых сплавов плавящимся электродом в аргоне целесообразно выполнять для толщин металла начиная с 6 мм. Лучшие результаты можно получить на параметрах режима сварки, соответствующих струйному переносу металла. При этом скорость плавления магниевой проволоки вдвое больше, чем алюминиевой при той же силе сварочного тока.
Надежная защита обеспечивается при расстоянии от сопла до поверхности изделия и от токоведущего мундштука до среза сопла соответственно 10—15 и 5—10 мм. Листы толщиной до 5 мм сваривают встык без разделки кромок, 10—20 мм — с V-образной разделкой с углом 50—60° и притуплением 2—6 мм, более 20 мм — с Х-образной разделкой с углом 60—80° и притуплением 2—3 мм. Ось электрода составляет угол 90° к изделию при сварке стыковых соединений без разделки или с небольшой разделкой. При большей глубине разделки сварку ведут углом вперед с углом 7—15° к вертикали.
Сварка плавящимся электродом в среде защитных газов производится с помощью полуавтоматов и автоматов, причем наиболее распространены первые.
Для полуавтоматической сварки предназначена установка, основные составные части которой даны на рис. 7.5. Сварочная проволока 7подается из катушки с помощью подающего механизма 5 по специальному шлангу 4к горелке 3. Источник 9 питает как сварочную дугу, которая горит между проволокой горелки 3 и изделием, так и блок управления 6, где размещены элементы пускорегулирующей аппаратуры, источник питания подающего механизма, рукоятка регулирования скорости подачи проволоки, электрогазовый клапан и т. д. Защитный газ подается из баллона через редуктор 10 по шлангу 8 к блоку управления 6 на электрогазовый клапан. Эта магистраль до начала сварки заполнена газом. От электрогазового клапана к подающему шлангу идет магистраль подачи газа 4 к горелке 3, которая перед сваркой заполнена воздухом. С блока управления к подающему шлангу идут провода управления 1 на кнопку, расположенную на горелке. На источнике питания находятся рукоятка регулирования напряжения на дуге, а также амперметр и вольтметр для контроля электрических параметров сварки. Сварочные кабели 2 соединяют изделие с подающими роликами механизма 5. При сварке в среде С02 на газовой магистрали после вентиля баллона устанавливаются подогреватель и осушитель газа.
Рис. 7.5. Монтажная схема установки для полуавтоматической сварки плавящимся электродом в среде защитного газа:
1 — провода управления; 2 — сварочные провода; 3 — горелка; 4 — шланг; 5 — механизм подачи; 6 — блок управления; 7 — кассета; 8 — шланг для газа; 9— источник питания; 10— аппаратура для регулирования и измерения параметров защитного газа
В работе полуавтомата очень важно обеспечить надежность подачи электродной проволоки специальным механизмом по шлангу к горелке. Подавляющее большинство подающих механизмов проталкивает проволоку к горелке по шлангу, и требуемое усилие достигается прижатием проволоки двумя роликами. Эта схема упрощает подающий механизм, уменьшает его габаритные размеры и массу. Однако подача проволоки, особенно тонкой и нежесткой, требует значительных усилий прижима, что ведет к ее деформации, затрудняет прохождение направляющего канала в шланге, приводит к его преждевременному износу, а иногда делает невозможной надежную постоянную работу. Поэтому сейчас применяют четырехроликовые подающие механизмы, значительно улучшающие надежность подачи электродной проволоки. Подающий механизм 5 соединяется с горелкой 3 шлангом 4, по которому транспортируется сварочная проволока, подаются сварочный ток, ток цепи управления, защитный газ и в случае необходимости вода, охлаждающая сопло горелки (при сварке на токах выше 350 А).
Устройство рабочей части горелки для сварки плавящимся электродом показано на рис 7.6. Горелка содержит изогнутый мундштук 7с переходной втулкой 2 и наконечником 5, рукоятку 1 с гашеткой 9, пусковую кнопку, защитный щиток 8 и сопло 4 для создания вокруг зоны сварки защитной атмосферы 6. Сопло электрически изолировано от наконечника и может легко заменяться. Переходная втулка имеет ряд отверстий 3, расположенных перпендикулярно направлению подачи проволоки и предназначенных для подвода защитного газа в зону сопла. Это обеспечивает получение ламинарного газового потока.
При сварке в углекислом газе образующиеся брызги прилипают к соплу и наконечнику, ухудшая газовую защиту зоны сварки и образуя токоведущую перемычку между соплом и наконечником горелки. Для снижения прилипания брызг применяют охлаждаемые сопла, составные с изоляционной прокладкой, металлокерамические и др., а также теплостойкие покрытия или хромирование сопла и защитные смазки, например силиконовые (раствор кремнийорганических соединений). При наличии смазки на поверхности сопла и наконечника брызги металла не привариваются, а только прилипают и потом легко удаляются.
Некоторые зарубежные производители изготовляют горелки, в которых наконечник тела между рукояткой и соплом выполнен из эластичного гибкого материала, что позволяет выгибать сопло под любым углом для достижения любого места сварки.
Для сварки в защитных газах плавящимся электродом используют выпрямители с пологопадающими или жесткими внешними характеристиками.
Р и с. 7.6. Устройство рабочей части горелки для сварки плавящимся электродом в среде защитных газов
В табл. 7.2 приведены итоговые сведения относительно возможности сварки конструкционных материалов с учетом их особенностей, специфики способов и использования оборудования.
Возможности использования сварки металлов и сплавов в среде защитных
Ручная дуговая сварка плавящимся электродом
Ручная сварка производится плавящимся металлическим электродом по способу Славянова (рис. 10.3).
Ручная электродуговая сварка универсальна и широко распространена, так как может выполняться в любом пространственном положении. Она часто применяется при монтаже в труднодоступных местах, где механизированные способы сварки не могут быть применены. Меньшая глубина проплавления основного металла и меньшая производительность ручной сварки из-за пониженной силы применяемого тока, а также меньшая стабильность ручного процесса (по сравнению с автоматической сваркой под флюсом) являются недостатками ручной сварки.
Электродуговая сварка металла представляет собой один из способов сваривания металлов, суть которого заключается в нагреве и расплавлении металла электрической дугой. Это один из самых распространенных методов сварки. Впервые этот способ был открыт ученым Славяновым Н.Г. в 1888 году. Для этого он использовал металлический плавящийся электрод. Сварка происходила под слоем флюса. Электродуговая сварка металла осуществляется постоянным током. При этом плюс находится на свариваемой детали, а минус на электроде. Процесс электросварки выполняется как плавящимся электродом, так и неплавящимся. Такой способ сварки широко применяется в ремонтных работах, монтажных, машиностроении, в строительстве и др. областях.
Электродуговая сварка плавящимся электродом
Электродуговая сварка плавящимся электродом заключается в расплавлении поверхности металла и электрода. При этом электрод служит материалом для получения сварного шва. Чтобы предотвратить окисление шва, применяют такие газы как: гелий, аргон, углекислый, а также их смеси. В процессе работы они подаются из сварочной головки. Легко ионизируемые элементы, входящие в состав электрода, делают электрическую дугу более устойчивой. Такими элементами могут быть: натрий, калий, кальций. Преимущество сварки постоянным током в том, что шов получается более чистым. Это происходит благодаря тому, что при расплавлении электрода количество брызг минимальное. Электродуговая сварка металла плавящимся электродом включает в себя:
- Подготовка свариваемой поверхности металла. Зачищается от грязи и масляных пятен;
- Для образования сварочной дуги, к электроду и заготовке подводится электрический ток;
- Происходит образование дуги. Она достигает 7000 0 С и начинает расплавлять металл;
- Образуется сварочная ванна из расплавленного электрода и поверхности металла. Шлак всплывает и образует защитную пленку. Затем сварочный шов застывает и образуется сварное соединение.
При сварке плавящимся электродом в защитном газе, сварочная проволока похожа по своему химическому составу к свариваемому металлу. Для сварки цветных металлов и их сплавов используют инертные газы: гелий, аргон, а также их смеси.
Параметры тока влияют на глубину проплава. Увеличение тока глубже проплавляет металл, а уменьшение наоборот. Величина тока не влияет на ширину шва, а род тока оказывает влияние. Шов более узкий когда применяют постоянный ток.
Сварочная дуга также влияет на качество шва. Чем меньше сварочная дуга, тем сварной шов более чистый. При этом металл проплавляется спокойно, а количество металлических капель значительно меньше. Это позволяет достичь более глубокое проплавление. Электродуговая сварка металла плавящимся электродом имеет свои преимущества:
- возможность сваривания в любом месте и любом положении;
- можно варить самые разные виды стали;
- сварка достаточно простая, легко транспортировать.
Недостатки такого способа сварки:
- вредность газов во время работы;
- низкий КПД и, в сравнении с другими видами сварки, невысокая производительность;
- качество сварного шва зависит от квалификации сварщика.
Ручная дуговая сварка плавящимся электродом.
Несмотря на большое распространение автоматов для дуговой сварки, ручная дуговая сварка сохранилась и в машиностроении, и в строительстве. Она применяется в монтажных условиях, при сварке швов сложной конфигурации или в труднодоступных местах.
Применение ручной дуговой сварки плавящимся электродом стало возможным только после создания покрытий электродов, предохраняющих зону сварки от воздействия окружающей воздушной атмосферы или уменьшающих это воздействие.
Это позволило значительно повысить качество сварных соединений и сварка стала широко применяться для производства ответственных изделий (паровых котлов, мостов, железнодорожного транспорта и т. д. ).
В самом деле, если сваривать шов обычной стальной проволокой без покрытия, то капли электродного металла, проходя через дуговой разряд, подвергнутся воздействию кислорода и азота воздуха. В результате этого произойдет выгорание углерода, марганца и других активных элементов — металл шва будет насыщаться азотом из атмосферы дугового разряда. Это вызовет резкое ухудшение механических свойств сварного соединения, так как металл шва будет резко отличаться от основного металла по составу и свойствам.
При таких условиях сварки особенно сильно понизятся пластические свойства наплавленного металла, что увеличит его склонность к образованию горячих трещин.
Для того чтобы повысить качество сварных соединений, облегчить труд сварщика и увеличить производительность сварки, разработаны специальные электродные покрытия, содержащие различные вещества, необходимые для улучшения технологии сварки.
Электроды с покрытием, обеспечивающие определенное качество сварных соединений, получили название качественных электродов.
Для вытеснения воздушной атмосферы из зоны сварки в покрытие вводят вещества (мел, мрамор или органические вещества — крахмал, декстрин), при разложении которых в дуговом разряде образуется большое количество газов.
Очень надежную защиту сварочной ванны от окружающей среды обеспечивает слой жидкого шлака. С этой целью в состав электродного покрытия вводят шлакообразующие вещества — полевой шпат, плавиковый шпат, кварцевый песок и другие компоненты. Шлак, взаимодействуя с жидким металлом, извлекает из сварочной ванны окислы, соединения с серой и фосфором, значительно улучшая свойства металла шва.
В состав покрытия вводят также раскислители — сплавы, содержащие высокоактивные элементы (ферросилиций, ферромарганец, ферротитан). Для сохранения определенного состава металла шва и улучшения его свойств можно вводить легирующие элементы в виде порошков ферросплавов (феррохром, ферромолибден и т. д.), которые при плавлении покрытия переходят в металл сварочной ванны.
Для повышения устойчивости дугового разряда в состав покрытия вводят вещества, легко переходящие в ионное состояние, — ионизаторы (соли натрия, калия, кальция).
Введение таких веществ облегчает работу сварщика, так как возрастает устойчивость дугового разряда, обрывы дугового разряда возникают реже, качество сварного шва улучшается.
Все эти перечисленные компоненты покрытий тщательно перемешивают в тонкоизмельченном состоянии и добавляют жидкое стекло (силикат натрия). Оно затвердевает при повышении температуры и связывает все порошковые материалы в общую систему покрытия.
Покрытие наносят на зачищенную до металлического блеска электродную проволоку, предварительно выпрямленную и разрезанную на мерные куски (400— 500 мм), наносят окунанием в жидкий замес (единичное производство) или напрессовкой вязкого замеса в специальных прессах (массовое производство). После сушки и прокаливания электроды испытывают, составляют паспорт, упаковывают в герметичную тару.
При ручной сварке электрод зачищенным концом вставляют в электрододержатель, подключенный к одному полюсу источника питания, другой полюс источника присоединяют к изделию.
Сварка плавящимся электродом в инертном газе
Для тонколистового металла целесообразна сварка в импульсном режиме. Для толстолистового металла (б>10 мм) хорошие результаты дает трехфазная сварка неплавящимся электродом. Сварку плавящимся электродом в инертных газах выполняют при толщинах более 4 мм на постоянном токе обратной полярности /, = (120- I60) Ia, где dg — диаметр сварочной проволоки. Недостатком сварки плавящимся электродом является повышенная пористость. [c.135]Сварка плавящимся электродом в инертных газах не находит широкого применения вследствие повыщенной склонности к образованию пор в металле швов, особенно при выполнении сварных соединений углеродистых и низколегированных сталей. Общие причины образования пор в металле швов при сварке в инертных газах и их смесях следующие повышенное содержание примесей в инертных газах недостаточная защита расплавленного металла повышенное содержание активных газов в основном металле и проволоке [c.

Струйный перенос металла характерен для сварки плавящимся электродом в инертных газах при большой плотности тока. В этом случае образуются мелкие капли, которые следуют одна за другой в виде непрерывной цепочки (струи). [c.20]
Сварка плавящимся электродом в инертных газах [c.208]
Основным оборудованием для дуговой сварки и наплавки являются источники сварочного тока для ручной сварки штучными электродами, полуавтоматы, автоматы, станки и установки для сварки плавящимся электродом без внешней защиты дуги, под флюсом и в защитных газах, оборудование для импульсно-дуговой сварки плавящимся электродом в инертных газах, установки для ру шой и автоматической сварки вольфрамовым электродом, специальное оборудование для сварки конкретных изделий. Универсальное оборудование имеет различные степень сложности и эксплуатационные возможности от простых полуавтоматов и источников со ступенчатым регулированием режимов до сложных с микропроцессорным управлением.
[c.53]
Сварку плавящимся электродом в инертных газах выполняют на автоматах и полуавтоматах с постоянной скоростью подачи электродной проволоки. [c.222]
Сварку плавящимся электродом в инертных газах применяют для изготовления ответственных изделий из нержавеющей стали, алюминия, магния и других металлов и сплавов, активно взаимодействующих с кислородом и азотом воздуха. Используя тонкую электродную проволоку, этим способом можно сваривать изделия толщиной до 4—5 мм без скоса кромок, а для изделий большей толщины рекомендуется применять У-образную подготовку кромок с углом разделки 30—50°. [c.222]
Го ловче и ко В. С. Влияние режимов сварки плавящимся электродом в инертных газах на размеры швов. Автоматическая сварка , 1967, № 8. [c.381]
При сварке плавящимся электродом в инертных газах применяется главным образом постоянный ток обратной полярности. При сварке плавящимся электродом размеры и форма шва определяются
[c. 319]
Сварку плавящимся электродом в инертных газах выполняют на автоматах и полуавтоматах с постоянной скоростью подачи электродной проволоки. При этом используют тонкую электродную проволоку диаметром 0,5—2 мм, имеющую химический состав, близкий к составу металла изделия. Для питания дуги обычно применяют источники постоянного тока с жесткой или возрастающей внешней характеристикой и обратную полярность, так как это повышает стабильность горения дуги и уменьшает разбрызгивание металла. Обусловлено это тем, что вольт-амперная характеристика дуги с высокой плотностью тока в электроде располагается в области III (см. рис. 28.2) и имеет возрастающий характер. [c.278]
Сварку плавящимся электродом в инертных газах выполняют на автоматах и полуавтоматах с постоянной скоростью подачи проволоки. Применяют источники питания постоянного тока с жесткой или возрастающей внешней характеристикой (преобразователи типа ПСГ-500, выпрямители ВС-300, ВДГ-301 и др. ) и обратную полярность. При такой характеристике источника возрастает эффект саморегулирования дуги, что способствует устойчивости процесса.
[c.400]
ДЛЯ СВАРКИ ПЛАВЯЩИМСЯ ЭЛЕКТРОДОМ В ИНЕРТНОМ ГАЗЕ [c.41]
РАБОЧИЕ ПАРАМЕТРЫ МЕХАНИЗИРОВАННОЙ СВАРКИ ПЛАВЯЩИМСЯ ЭЛЕКТРОДОМ В ИНЕРТНОМ ГАЗЕ Сварка в нижнем положении [c.42]
РАБОЧИЕ ПАРАМЕТРЫ ПОЛУАВТОМАТИЧЕСКОЙ СВАРКИ ПЛАВЯЩИМСЯ ЭЛЕКТРОДОМ В ИНЕРТНОМ ГАЗЕ [c.43]
Подварочный шов Не требуется, допустима односторонняя сварка, поперечное сечение должно быть полностью проварено Требуется сварка на твердой подкладке, при статической нагрузке также нужна заварка корня по технологии сварки в углекислом газе, сварки плавящимся электродом в инертном газе и газовой сварки, равнозначная подварочному шву [c.167]
При сварке плавящимся электродом в инертных газах для получения мелкокапельного переноса и предотвращения пор применяют добавки окислительных газов в смесях (в процентах) 80 Аг -ь 20 СО2 80 Аг + 20 О2 75 Аг + 22 СО2 + ЗО2.
[c.44]
Для полуавтоматической и автоматической сварки плавящимся электродом в инертных газах применяют проволоку того же состава, что и свариваемый металл. Для легированных сталей диаметр проволоки 0,8 — 5 мм, для алюминиевых сплавов — 0,8 — 4 мм. [c.152]
Примечания 1. ИН — сварка неплавящимся электродом в инертных газах ИНп — сварка неплавящимся электродом с присадочной проволокой УП — сварка плавящимся электродом в углекислом газе ИП — сварка плавящимся электродом в инертных газах ЛС — лазерная сварка РДС — ручная дуговая сварка. [c.124]
Струйный процесс переноса металла характерен для сварки плавящимся электродом в инертных газах. При струйном переносе (рис. 3.1, б) образуются мелкие капли, которые следуют одна за другой в виде непрерывной цепочки (струи). Струйный перенос электродного металла возникает при сварке с большой плотностью тока проволокой малого диаметра. Например, при сварке полуавтоматом (механизированной) в аргоне проволокой диаметром 1,6 мм струйный перенос металла осуществляется при критическом токе 300 А. При сварке на токах ниже критического наблюдается уже капельный перенос металла. Обычно струйный перенос электродного металла приводит к меньшему выгоранию легирующих элементов в сварочной проволоке и к повышению чистоты металла капель и сварного шва. Скорость расплавления сварочной проволоки увеличивается. Поэтому струйный перенос имеет преимущества перед капельным.
[c.40]
При сварке плавящимся электродом в инертных газах используют обычные полуавтоматы для сварки в защитных [c.328]
В 1948 г. в СССР и других странах был применен высокопроизводительный способ сварки плавящимся электродом в инертных газах. Использование тонкой электродной проволоки (диаметром 1—2,5 мм) и больших плотностей тока (75—200 А/мм и более) дало возможность повысить производительность и эффективность этого процесса. [c.5]
Для питания дуги при механизированной и автоматической сварке плавящимся электродом используют сварочные выпрямители и сварочные преобразователи, имеющие жесткую вольт-амперную характеристику. Сварка неплавящимся электродом в инертных газах находит исключительно широкое применение при изготовлении сварных конструкций из цветных и легких металлов. Технологические особенности дуговой сварки в защитных газах этих металлов рассмотрены в гл. 9.
[c.178]
Сварка вольфрамовым электродом в инертных газах или их смесях выполняется при постоянном токе прямой полярности (за исключением сталей с большим содержанием алюминия, когда применяют переменный ток). Данный способ сварки используют при толщине металла до 5…7 мм для получения корневых швов на стыках повышенной толщины (остальные валики могут выполняться под флюсом, покрытыми электродами или плавящимся электродом в защитных газах). [c.250]
ГОСТ 27580-88 «Дуговая сварка алюминия и алюминиевых сплавов в инертных газах. Соединения сварные под острыми и тупыми углами» распространяется на сварку деталей толщиной от 0,8 до 60 мм (включительно) ручной, полуавтоматической и автоматической дуговой сваркой неплавящимся электродом в инертных газах с присадочным металлом, полуавтоматической и автоматической дуговой сваркой плавящимся электродом, а также автоматической сваркой неплавящимися электродами трехфазной дугой с присадочным металлом.
[c.20]
По данным зарубежной литературы никель (99%-ный) и его сплавы (N1—Си, N1—Сг—Ре, N1—Мо, N1—Мо—Сг, Сг—Мо—Ре) сваривают газовой сваркой, аргонодуговой сваркой вольфрамовым электродом, в инертном газе плавящимся электродом и дуговой сваркой электродами с качественными покрытиями. [c.572]
Пологая внешняя характеристика Дуговая сварка плавящимся электродом в инертном и активном защитном газе. [c.128]
Дуговая сварка плавящимся электродом в инертном защитном газе [c.129]
Представляют интерес три способа сварки алюминия плавящимся электродом в инертных газах, разработанные американской фирмой Кайзер. [c.243]
Сварка методом MIG — дуговая сварка плавящимся электродом в среде инертного газа. [c.225]
Дуговая сварка плавящимся электродом в среде инертных газов. 18-453 273 [c.273]
При сварке плавящимся электродом в инертных газах используют обычные полуавтоматы для сварки в защитных газах и сварочную проволоку диаметром 1—2 м г сила сварочного тока 150— 200 А для проволоки диаметром 1 мм и 300—450 А для проволоки диаметром 2 мм напряжение дуги 22-26 В скорость сварки зависит от сечения шва. При сварке латуней, бронз и медно-никелевых сплавов наиболее широко используют вольфрамовый электрод, так как при сварке плавяш,имся электродом происходит более интенсивное испарение цинка, олова и др.
[c.347]
Г — основная плита, аог = 842 МПа 2 — сварка плавящимся электродом в инертном газе. Он 1 = 945 МПа 3 — термообработка после сварки (904 °С, ) г, о.тлаж-дение в гелии). [c.418]
При сварке плавящимся электродом в инертных газах используют постоянный ток обратной полярности (табл. 8.30). Несмотря на высокую чистоту защитных газов, медь при сварке подвергается окислению, и может возникать пористость, что обусловливает необходимость применения легированных присадочных и электродных проволок БрХ0,7, БрХНТ, БрКМцЗ-1 или медных с добавками. [c.266]
Техническая характеристика генераторов для импульсно-дуговоп сварки плавящимся электродом в инертных газах дана в табл. VI.43. Принципиальные схемы генераторов импульсов на конденсаторах п управляемых вентилях показаны на рис. VI.8, а схемы их включения для работы с генераторами или выпрямителями — на рис. Ч.9. В табл. VI. 14 приведена техническая характеристика осцилляторов.
[c.182]
При сварке плавящимся электродом в инертных газах в качестве защитного газа обычно используют чистый аргон. При сварке толстостенных конструкций из алюминиевых и титановых сплавов и коррозионно-стойких сталей для улучшения проплавления и формирования иногда используют смеси 50 % Аг и 50 % Не, 40 % Аг и 60 % Не. Сварка в чистом гелии ггрименяется редко [c.65]
При сварке плавящимся электродом в инертных газах могут быть получены процессы с крупиокапельным пере носом электродного металла, струйный и имиульсно дуговой. Струйный процесс, характеризующи.йся мелко [c.65]
Сварку плавящимся электродом в инертных газах применяют для стыковых, тавровых и нахлесточных соединений из металла толщиной >4 мм в нижнем положении. Сварку следует проводить при обратной полярности на режимах, гарантирующих струйный перенос металла. При сварке в аргоне меньше разбрызги-ванние металла, больше глубина проплавления, меньше ширина шва и площадь проплавления, чем при сварке в гелии. Однако форма зоны проплавления при свалке в гелии более благоприятна, чем в аргоне. Лучшее формирование шва и стабильность процесса достигаются при использовании смеси из 80 % Не и 20 % Аг. При механизированной сварке применяют проволоку диаметром до 2 мм. В процессе автоматизированной сварки стыковых и угловых соединений используют проволоку диаметром
[c.139]
Сварку сталей всех классов юльфрамовым электродом лучше выполнять постоянным током прямой полярности (минус на электроде) хуже прбЦессИротекает при использовании перёМёнйбГО тока Сварка плавящимся электродом в инертном газе и в смесях аргона с кислородом или углекислым газом выполняется постоянным током обратной полярности (плюс на электроде). [c.390]
ГОСТ 14771-76 «Дуговая сварка в защитном газе. Соединения сварные» устанавливает основные типы, конструктивные элементы и размеры сварных соединений из стали, а также сплавов на железоникелевой и никелевой основах, выполняемых дуговой сваркой плавящимся электродом в углекислом газе и его смесях с кислородом, в инертных газах и их смесях с углекислым газом и кислородом, а также неплавя-щимся электродом в инертных газах с присадочным и без присадочного металла.
[c.19]
Однако даже при получении швов, подобных по составу основному металлу, необходимо учитывать, что часть наиболее важных свойств сварных соединений может быть получена, когда металл шва по составу несколько отличается от свариваемой стали, например имеет меньшую концентрацию углерода, содержит некоторое количество титана и т.д. В связи с тем, что такое регулирование состава металла шва легче обеспечивается при дуговой сварке, этот способ сварки наиболее распространен при изготовлении и ремонте изделий из высокохромистых сталей. Большинство сварочных работ с этими сталями выполняют ручной дуговой сваркой стальными покрытыми электродами. Наряду с этим используют дуговую сварку плавящимся электродом в углекислом газе, в инертных газах (аргоне, аргоногелиевых смесях) и сварку под спещ1альными флюсами. [c.328]
Сварка плавящимся электродом в среде защитного газа. GMAW процесс
GMAW процесс — это процесс соединения металлов плавлением электрической дугой, горящей между непрерывно подаваемым плавящимся электродом и изделием. Зона горения дуги защищается с помощью газа (рис. 7). Защитный газ и подвижный плавящийся электрод — два обязательных участника этого процесса.
Большинство металлов имеют высокую тенденцию к присоединению кислорода (образуют оксиды) и в меньшей степени к присоединению азота (образуют нитриды). Кислород также реагирует с углеродом, содержащимся в металле, с образованием окиси углерода. Оксиды, нитриды и окись углерода при растворении в металле шва образуют дефекты сварного шва. Воздействие атмосферы на расплавленный металл очень велико, так как в ней содержится около 80% азота и примерно 20% кислорода. Основная функция защитного газа — исключить контакт расплавленного металла с окружающей атмосферой.
Рис. 7. Сварка плавящимся электродом в защитном газе
Кроме защиты сварочной ванны, защитный газ влияет на:
- характеристику дуги;
- способ переноса электродного металла;
- глубину проплавления и профиль сварного шва;
- производительность сварки;
- склонность к прожогу;
- степень зачистки сварного шва.
При сварке плавящимся электродом шов образуется за счет проплавления основного металла и расплавления дополнительного металла — электродной проволоки. Поэтому форма и размеры шва помимо прочего (скорости сварки, пространственного положения электрода и изделия и т. п.) зависят также от характера расплавления и переноса электродного металла в сварочную ванну. Характер переноса электродного металла определяется в основном материалом электрода, составом защитного газа, плотностью сварочного тока и рядом других факторов.
Характер переноса расплавленного металла имеет большое значение для качественного формирования сварного шва при сварке плавящимся электродом в защитном газе. Управляя этим процессом различными способами (используя специальные сварочные процессы), можно всегда получить качественное сварное соединение. При MIG/MAG способе сварки можно выделить несколько основных форм расплавления электрода и переноса электродного металла в сварочную ванну:
- циклический режим сварки короткой дугой без разбрызгивания;
- режим сварки оптимизированной короткой дугой;
- крупнокапельный процесс сварки;
- режим импульсной сварки;
- режим струйного (Spray) переноса металла;
- режим непрерывного вращающегося переноса металла (ротационный перенос).
Режим струйного (Spray) и крупнокапельного, а также непрерывного вращающегося переноса металла связан со сравнительно высокой энергией дуги и обычно ограничивается сваркой в нижнем и горизонтальном положении металла толщиной более 3 мм. Циклический режим сварки короткой дугой без разбрызгивания и импульсная сварка имеют низкие энергетические показатели, но обычно позволяют сваривать металл толщиной до 3 мм во всех пространственных положениях.
Циклический режим сварки короткой дугой без разбрызгивания (процесс сварки с периодическими короткими замыканиями). Данный процесс сварки характерен для сварки электродными проволоками диаметром 0,5-1,6 мм при короткой дуге с напряжением 15-22 В и токе 100-200 А.\
Рис. 8. Осциллограмма циклического режима сварки короткой дугой
После очередного короткого замыкания (8 и 9 на рис. 8) силой поверхностного натяжения расплавленный металл на торце электрода стягивается в каплю, приближая ее к правильной сфере (1 — 3), создавая тем самым благоприятные условия для плавного объединения со сварочной ванной. В результате длина и напряжение дуги становятся максимальными.
Во всех стадиях процесса скорость подачи электродной проволоки постоянна, а скорость ее плавления изменяется и в периоды 3 и 4 меньше скорости подачи. Поэтому торец электрода с каплей приближается к сварочной ванне (длина дуги и ее напряжение уменьшаются) до короткого замыкания (4). Во время короткого замыкания капля расплавленного электродного металла переходит в сварочную ванну. Далее процесс повторяется.
При коротком замыкании резко возрастает сварочный ток — до 150-200 А и как результат этого увеличивается сжимающее действие электромагнитных сил (6-7) -, совместное действие которых разрывает перемычку жидкого металла между электродом и изделием (8). Капля мгновенно отрывается, обычно разрушаясь и разлетаясь в стороны, что приводит к разбрызгиванию. Кроме того, ток такой величины, пытаясь пройти через узкую перемычку, образовавшуюся между каплей и ванной, приводит к выплеску металла.
Для уменьшения разбрызгивания электродного металла необходимо сжимающее усилие, возникающее в проводнике при коротком замыкании, сделать более плавным. Это достигается введением в источник сварочного тока регулируемой индуктивности. Максимальная величина сжимающего усилия определяется уровнем тока короткого замыкания, который зависит от конструкции блока питания. Величина индуктивности определяет скорость нарастания сжимающего усилия. При малой индуктивности капля будет быстро и сильно сжата — электрод начинает брызгать. При большой индуктивности увеличивается время отделения капли, и она плавно переходит в сварочную ванну. Сварной шов получается более гладким и чистым. В табл. 12 приведено влияние индуктивности на характер сварки.
Таблица 12. Влияние индуктивности на характер сварки.
Частота периодических замыканий дугового промежутка при циклическом режиме сварки короткой дугой может изменяться в пределах 90-450 замыканий в секунду. Для каждого диаметра электродной проволоки в зависимости от материала, защитного газа и т. д. существует диапазон сварочных токов, в котором возможен процесс сварки с короткими замыканиями. Данный режим удобен для сварки тонколистового металла и пригоден для полуавтоматической сварки во всех пространственных положениях. При оптимальных параметрах процесса потери электродного металла на разбрызгивание не превышают 7%.
Режим сварки оптимизированной короткой дугой. Процесс сочетает в себе циклический режим сварки короткой дугой и очень высокую скорость подачи сварочной проволоки, что позволяет использовать короткую и мощную дугу (напряжение на дуге до 26 В при токе до 300 А). Данный режим позволяет получать сварные соединения с минимальным тепловложением и низкой степенью окисления наплавленного металла.
Крупнокапельный процесс сварки. Увеличение плотности сварочного тока и длины (напряжения) дуги (напряжение на дуге от 22 до 28 В и ток от 200 до 290 А) ведет к изменению характера расплавления и переноса электродного металла, переходу от сварки короткой дугой с короткими замыканиями к процессу с редкими короткими замыканиями или без них. В сварочную ванну электродный металл переносится нерегулярно, отдельными крупными каплями различного размера, хорошо заметными невооруженным глазом. При этом ухудшаются технологические свойства дуги, затрудняется сварка в потолочном положении, а потери электродного металла на угар и разбрызгивание возрастают до 15%.
Крупнокапельный процесс сварки характеризуется некачественным формированием сварного шва.
С положительного электрода, независимо от типа защитного газа, крупнокапельный перенос металла происходит при низких плотностях тока. Крупнокапельный перенос характеризуется размером капли, капля имеет диаметр больше, чем сам электрод.
При использовании инертных защитных газов достигается осеориентированный перенос электродного металла без разбрызгивания. Длина дуги при этом должна быть достаточной, чтобы гарантировать отделение капли прежде, чем она коснется расплавленного металла.
Использование углекислого газа в качестве защитного газа при крупнокапельном переносе всегда дает неосеориентированный перенос капель металла. Это является следствием электромагнитного отталкивающего воздействия на низ расплавленных капель. При углекислотной защите конец электродной проволоки плавится теплом дуги, переданным через расплавленную каплю. Капли в форме бесформенных шариков, произвольно направляемые через дугу, дают сильное разбрызгивание. Сварной шов получается грубый, с волнистой поверхностью.
Дуга, обычно неустойчивая, сопровождается характерным треском. Для уменьшения разбрызгивания необходимо, чтобы конец электрода находился ниже поверхности металла, но в пределах полости, создаваемой дугой. Поскольку большая часть энергии дуги направлена вниз и ниже поверхности сварочной ванны, сварной шов имеет очень глубокое проплавление.
Режим импульсной сварки. Для улучшения технологических свойств дуги применяют периодическое изменение ее мгновенной мощности — импульсно-дуговая сварка. Теплота, выделяемая основной дугой, недостаточна для плавления электродной проволоки со скоростью, равной скорости ее подачи. Вследствие этого длина дугового промежутка уменьшается.
Под действием импульса тока происходит ускоренное расплавление электрода, обеспечивающее формирование капли на его конце. Резкое увеличение электродинамических сил сужает шейку капли и сбрасывает ее в направлении сварочной ванны в любом пространственном положении, т. е., режим импульсной сварки — режим, при котором капли расплавленного металла принудительно отделяются электрическими импульсами. За счет ЭТОГО на токах соответствующих крупнокапельному переносу, можно формировать качественные сварные швы, подобно циклическому режиму сварки короткой дугой без разбрызгивания. Режим импульсной сварки известен также под названием .
Импульсный режим использует одиночные импульсы или группу импульсов с одинаковыми или различными параметрами. В последнем случае первый или первые импульсы ускоряют расплавление электрода, а последующие сбрасывают каплю электродного металла в сварочную ванну. За счет этого металл переносится порциями мелких капель и без разбрызгивания. Кроме того, за счет применения импульсной технологии возникает электромеханическая вибрация сварочной ванны, в результате чего газовые пузырьки выходят из нее, и сварные швы получаются высокой плотности.
Устойчивость режима импульсной сварки зависит от соотношения основных параметров (величины и длительности импульсов и пауз). Соответствующим подбором тока основной дуги и импульса можно повысить скорость расплавления электродной проволоки, изменить форму и размеры шва, а также уменьшить нижний предел сварочного тока, обеспечивающий устойчивое горение дуги.
Преимуществом этого метода является низкое тепловложение, что важно при сварке тонких материалов и при позиционной сварке. Импульсный режим обеспечивает высококачественную сварку низкоуглеродистых и низколегированных сталей. При сварке алюминия можно использовать электродную проволоку больших диаметров, при этом обеспечивается меньшая пористость. Основной недостаток этого процесса — сложный блок питания.
Импульсный режим обеспечивает более высокий коэффициент тепловложения в наплавленный металл, чем циклический режим сварки короткой дугой без разбрызгивания, и осуществляется при напряжении на дуге от 28 до 35 В и токах от 300 до 350 А.
Режим струйного (спрей) переноса металла. При достаточно высоких плотностях постоянного по величине (без импульсов или с импульсами) сварочного тока обратной полярности и при горении дуги в инертных газах (содержание аргона не менее 80%) может наблюдаться очень мелкокапельный перенос электродного металла. Название <струйный> он получил потому, что при его наблюдении невооруженным глазом создается впечатление, что расплавленный металл стекает в сварочную ванну с торца электрода непрерывной струей.
Поток капель направлен строго по оси от электрода к сварочной ванне. Дуга очень стабильная и ровная. Разбрызгивание очень небольшое. Валик сварного шва имеет гладкую поверхность. Энергия дуги передается в металл в форме конуса, поэтому наплавляемый металл имеет поверхностное слияние. Глубина проплавления больше, чем при циклическом режиме сварки короткой дугой, но меньше, чем при крупнокапельном переносе.
Изменение характера переноса электродного металла с капельного на струйный происходит при увеличении сварочного тока до <критического> для данного диаметра электрода.
Значение критического тока уменьшается при активировании электрода (нанесении на его поверхность тем или иным способом некоторых легко ионизирующих веществ), увеличении вылета электрода. Изменение состава защитного газа также влияет на значение критического тока. Например, добавка в аргон до 5% кислорода снижает значение критического тока. При сварке в углекислом газе без применения специальных мер получить струйный перенос электродного металла невозможно. Невозможно его получить и при использовании тока прямой полярности.
При переходе к струйному переносу поток газов и металла от электрода в сторону сварочной ванны резко интенсифицируется благодаря сжимающему действию электромагнитных сил. В результате под дугой уменьшается прослойка жидкого металла, в сварочной ванне появляется местное углубление. Повышается теплопередача к основному металлу, и шов приобретает специфическую форму с повышенной глубиной проплавления по его оси. При струйном переносе дуга очень стабильна — колебаний сварочного тока и напряжений не наблюдается.
Режим струйного переноса металла характеризуется узким столбом дуги и заостренным концом плавящейся электродной проволоки. Расплавленный металл проволоки передается через дугу в виде мелких капель, от сотен до нескольких сотен в секунду. Диаметр капель равняется или меньше, чем диаметр электрода. Поток капель осенаправленый. Скорость плавления проволоки от 42 до 340 мм/с.
Струйный перенос металла происходит при дуге высокой стабильности (напряжение на дуге от 28 до 40 В при токе от 290 до 450 А) и позволяет формировать качественные сварные швы на высоких значениях тока. Данный режим необходим для сварки металлов толщиной более 5 мм.
Режим непрерывного вращающегося переноса металла (ротационный перенос). Ротационный перенос металла возникает при образовании длинного столба жидкости на конце оплавляющегося электрода. Вследствие очень большого тока (напряжение на дуге от 40 до 50 В при токе от 450 до 650 А) и большого вылета электрода температура образовывающейся капли настолько высока, что электрод плавится уже без действия дуги. Расстояние до токоведущего мундштука в этом случае составляет 25-35 мм. По причине продольного магнитного поля столб жидкости вращается вокруг своей оси и конически расширяется. Капли металла переходят в радиальном направлении в основной материал и создают относительно плоское и широкое проплавление.
В зависимости от свариваемого металла и его толщины в качестве защитных газов используют инертные, активные газы или их смеси. В силу физических особенностей стабильность дуги и ее технологические свойства выше при использовании постоянного тока обратной полярности. При использовании постоянного тока прямой полярности количество расплавляемого электродного металла увеличивается на 25-30%, но резко снижается стабильность дуги и повышаются потери металла на разбрызгивание. Применение переменного тока невозможно из-за нестабильного горения дуги.
Инертные газы аргон и гелий и их смеси обязательно используются для сварки цветных металлов, а также широко применяются при сварке нержавеющих и низколегированных сталей. Основное различие между аргоном и гелием — плотность, теплопроводность и характеристика дуги. Плотность аргона приблизительно в 1,4 раза больше плотности воздуха, а гелий в 0,14 раза легче воздуха. Для защиты сварочной ванны более эффективен тяжелый газ. Следовательно, гелиевая защита сварочной ванны для получения того же эффекта требует приблизительно в 2-3 раза большего расхода газа.
Гелий обладает большей теплопроводностью, чем аргон, и энергия в гелиевой дуге распределена более равномерно. Плазма аргоновой дуги характеризуется очень высокой энергией сердцевины и значительно меньшей периферии. Это различие оказывает большое влияние на профиль сварного шва. Гелиевая дуга дает глубокий, широкий, параболический сварной шов. Аргоновая дуга чаще всего характеризуется сосковидной формой сварного шва.
При любой скорости подачи электродной проволоки напряжение на аргоновой дуге будет значительно меньше, чем на гелиевой дуге. В результате будут меньшее изменение напряжения по длине дуги, что, в свою очередь, приводит к большей стабилизации дуги. Аргоновая дуга (включая смеси как с низким, так и с 80%-ным содержанием аргона) производит струйную передачу электродного металла на уровнях выше раздела энергетики переноса.
Гелиевая дуга производит крупнокапельный перенос металла в нормальном рабочем диапазоне. Следовательно, гелиевая дуга имеет большую степень разбрызгивания электродного металла и меньшую глубину проплавления. Легко ионизируемый аргон облегчает зажигание дуги и при сварке на обратной полярности (плюс на электроде) дает очень чистую поверхность сварного шва.
В большинстве случаев чистый аргон используется при сварке цветных металлов. Использование чистого гелия ограничено из-за ограниченной устойчивости дуги. Тем не менее, желаемый профиль сварного шва (глубокий, широкий, параболической формы), получаемый с гелиевой дугой, можно получить, применяя смесь аргона с гелием, кроме того, характер переноса электродного металла приобретает характер, как при аргоновой дуге.
Смесь гелия с аргоном, при 60-90% содержании гелия, используется для получения максимального тепловложения в основной металл и улучшения сплавления. Для некоторых металлов, например нержавеющей и низколегированной стали, замена углекислого газа на гелий позволяет получить увеличение тепловложения, и, поскольку гелий инертный газ, не происходит изменения свойств свариваемого металла.
Чистый аргон и в известной мере гелиевая защита дают отличные результаты при сварке цветных металлов. Тем не менее, эти газы в чистом виде дают не вполне удовлетворительную характеристику при сварке черных металлов. Гелиевая дуга стремится к переходу в неуправляемый режим, сопровождаемый сильным разбрызгиванием. Аргоновая дуга имеет тенденцию к прожогу. Добавление к аргону 1-5% кислорода или 3-10% углекислого газа (вплоть до 25%) дает заметное улучшение характеристики.
Объем добавляемого кислорода или углекислого газа к инертному газу зависит от состояния поверхности (наличие окалины) основного металла, требуемого профиля сварного шва, положения в пространстве и химического состава свариваемого металла. Обычно добавление 3% кислорода или 9% углекислого газа вполне достаточно для проведения качественной сварки.
Добавление углекислого газа к аргону позволяет получить грушевидный профиль сварного шва. Применение различных газов и газовых смесей для сварки различных металлов и на различных режимах приведено в табл. 13-14.
Таблица 13. Выбор защитных газов и газовых смесей для циклического режима сварки короткой дугой без разбрызгивания.
Таблица 14. Выбор защитных газов и газовых смесей для струйного (спрей) переноса металла.
Дуговая сварка плавящимся электродом в защитных газах
Сваркой плавящимся электродом в защитном газе называется процесс, при котором на место стыка, где находится дуга, газ будет подаваться через сопло, защищая материал сварочной ванны от влияния активных веществ, которые находятся в атмосфере.
Чтобы применять такой вид сварки, мастера пытаются подобрать максимально близкую по составу сварочную проволоку к свариваемым сплавам. А подходящий под данный случай газ определяется его способностью быть инертным по отношению к соединяемым конструкциям.
Особенности выбора материала
Для каждого вида металла применяется разный инертный газ. Если требуется сваривать детали из цветного сплава, здесь лучше использовать один из одноатомных газов, таких как гелий или аргон. Чтобы сваривать кобальт или медь, берут азот. Со стальными конструкциями лучше всего справится углекислый газ. Но в этом случае стоит подбирать проволоку, которая будет отличаться преобладанием легирующих компонентов, а также компонентов-раскислителей. Иногда успешно применяются смеси активных и инертных веществ. Это повышает устойчивость дуги и улучшает качество сварного шва.
Важно!
Стыковка в среде защитных газов ведётся с помощью постоянного напряжения обратной полярности. Если применить переменный ток, чрезмерное охлаждение стержня дуги газом приведёт к её прерыванию.
Технология сварки в защитном газе предполагает достаточно высокие потери металла электродов из-за угара и разбрызгивания. Это будет зависеть от выбранных режимов соединения:
- смешанный;
- крупнокапельный;
- мелкокапельный.
Первый режим означает, что брызги образуются в максимальном их количестве. Это происходит из-за замыканий пространства дуги электродным расплавленным металлом и появлением в межэлектродном пространстве капель, которые имеют разную скорость движения и величину.
При крупнокапельном способе, соответственно, будет гораздо меньше брызг, благодаря иногда появляющимся коротким замыканиям дугового промежутка. Высокий показатель содержания тепла в крупных каплях позволит сделать надежные швы.
Самый малый процент разбрызгивания будет характерен для мелкокапельного режима. Капля, которая образуется на электроде, не будет растягиваться или увеличиваться до момента прикосновения с соединяемым металлом, это никогда не приводит к чрезмерным брызгам, коротким замыканиям или взрывам.
Дуговая сварка в срезе защитного газа
Дуговая сварка плавящимся электродом (ТИГ) отличается высокой производительностью. Она не предполагает обязательного использования флюсов и электродного покрытия, при этом успешно выполняя соединение металлических конструкций. Чаще всего её используют для соединения деталей из цветного сплава или стали.
Какими могут быть преимущества такой сварки?
- Шов не взаимодействует с азотом и кислородом.
- Сварка может быть как автоматическая, так и механизированная.
- Не применяются покрытия и флюсы.
- Область структурных повреждений сокращена за счет высокой производительности и степени концентрации тепла источника.
- Отсутствие сложностей в визуальном контроле за процессом сварки.
Иногда для сварочной дуги может применяться двойная защита. Степень надёжности TIG сварки зависит от теплофизических свойств и количества расходованного газа, а также от выбранного режима соединения.
Аргоновая сварка означает, что дуга будет гореть между используемой проволокой и самой деталью. При этом сама дуга может быть косвенной или прямого действия. Подвидом косвенной может выступить дуга, которая во время соединения находится между вольфрамом и сварочной проволокой, беспрерывно подающейся в зону стыковки.
Защитные способности потока инертного газа зависит от его чистоты и режима соединения. Показатель надежности всегда определяется диаметром пространства катодного распыления при получении дуги с переменным током между соединяемой поверхностью и вольфрамовым электродом. В момент, когда катодом выступает сам свариваемый материал, образуется выравнивание частиц металла с верхушки сварочной ванны и близлежащих зон по отношению к холодному металлу.
Заключение
Придерживаясь всех правил, дуговая сварка с использованием плавящегося электрода не станет проблемой даже для неопытного сварщика. Также стоит научиться правильно выбирать автомат для сварки, учитывая его способности и прямое предназначение. Если работы не предполагают сверхсложных соединений, стоит задуматься о приобретении простого агрегата для домашнего использования.
Импульсно-дуговая сварка как основа современных технологий сварки плавящимся электродом / Pulsed arc welding as a basis of modern technologies of consumable electrode welding
ISSN 1993-8322. ВІСНИК Донбаської державної машинобудівної академії. № 2 (38), 2016. 221
УДК 621.791.754
Сидорец В. Н., Жерносеков А. М., Рымар С. В.
ИМПУЛЬСНО-ДУГОВАЯ СВАРКА КАК ОСНОВА СОВРЕМЕННЫХ
ТЕХНОЛОГИЙ СВАРКИ ПЛАВЯЩИМСЯ ЭЛЕКТРОДОМ
Сварочные процессы являются неотъемлемой частью большинства производственных
процессов, например, в машиностроении, строительстве, химической, аэрокосмической, авто-
мобильной, судостроительной промышленности, трубопроводном транспорте. Среди дуговых
процессов сварка плавящимся электродом в защитных газах занимает ведущее место в про-
мышленности Западной Европы, США, Японии, КНР. Этот способ обладает высокой произво-
дительностью, обеспечивает качество сварных соединений, а также предоставляет возмож-
ность автоматизации процесса. Особое место среди дуговых процессов занимает импульсно-
дуговая сварка (ИДС) плавящимся электродом. Она применяется для сварки многих материа-
лов, например, углеродистых конструкционных сталей, алюминиевых сплавов, сплавов на ос-
нове меди [1, 2]. Необходимо также отметить использование ИДС в новых комбинированных,
двухдуговых технологиях, а также в гибридных лазерно-дуговых процессах [3–7].
Целью работы являлось исследование технологической и энергетической эффектив-
ности процесса ИДС. Для этого были решены следующие основные задачи: проанализирова-
ны тенденции совершенствования технологий ИДС и оборудования для реализации этого
способа; исследованы закономерности процесса плавления электрода при сварке плавящим-
ся электродом в среде защитных газов; выявлены пути увеличения скорости его расплавле-
ния за счет применения импульсных воздействий; исследованы особенности применения
импульсной дуги с плавящимся электродом и импульсного лазерного излучения в гибридных
лазерно-дуговых сварочных технологиях.
Импульсно-дуговая сварка плавящимся электродом в защитных газах эффективно
применяется при сварке разнообразных металлов и сплавов, а также во многих комбиниро-
ванных технологиях (рис. 1). Так, например, способ сварки «Speed Pulse» позволяет за один
импульс сбрасывать несколько капель электродного металла. Фирма Fronius предложила
процесс сварки CMT-Advanced-Pulse. При этом отделение капли происходит как в момент
короткого замыкания, так и в момент действия импульсов обратной полярности. Таким обра-
зом, совмещаются два типа переноса металла электрода – перенос с короткими замыканиями
(CMT) и импульсно-дуговой процесс (Pulse). Фирма Fronius также предложила двухдуговой
гибридный процесс CMT Twin, который соединяет преимущества процесса СМТ и импульс-
ного процесса. Развивается направление, связанное с ИДС, при котором базовый ток дуги
изменяет полярность (MАG AC), таким образом, уменьшается тепловложение и устраняется
магнитное «дутье». ИДС получила развитие в технологических процессах Time Twin, Pulse
MIG/MAG-Laser и Time Twin-Pulse MIG/MAG-Laser, где соответственно применяется две
импульсные дуги, импульсная дуга и лазер, три импульсные дуги и лазер.
Дуговые способы сварки плавящимся электродом занимают ведущее место в про-
мышленности передовых стран мира. Они являются основной научной базой для разработки
новых перспективных сварочных технологий. Поскольку виды переноса металла электрода,
во многом, определяют технологию сварки плавящимся электродом, важным остается воз-
действие на процесс посредством источника питания дуги как наиболее быстродействующе-
го и эффективного аппаратного средства, позволяющего изменять параметры и форму сва-
рочного тока.
Таким образом, разработка современного электросварочного оборудования, которое
реализует различные виды переноса металла электрода, должна происходить с применением
импульсно-дугового процесса сварки.
В чем разница между плавящимся и неплавящимся электродами при сварке?
Автор: Майлз Будимир
Старший редактор, WTWH Media
Электроды используются в процессах полностью дуговой сварки. В каждом из этих процессов электрод используется для создания электрической дуги между электродом и свариваемыми металлами, генерируя тепло для плавления основных металлов.
Электроды, используемые при дуговой сварке, обычно можно разделить на расходные и неплавящиеся.Расходуемые электроды становятся частью самого сварного соединения. Электрод служит присадочным металлом и плавится вместе с свариваемыми металлами.
Например, при обычной электродуговой сварке расходуемый электрод представляет собой сварочный пруток с присадочным металлом и содержит флюс, который способствует созданию барьера для защиты сварного шва от любого загрязнения. Напротив, неплавящиеся электроды не расходуются во время сварки, а отдельный сварочный стержень служит в качестве присадочного металла, который плавит и соединяет металлы вместе.
Например, неплавящиеся электроды используются при сварке TIG. Здесь электрод сделан из вольфрама, который имеет высокую температуру плавления около 6000 ° F, поэтому он не расходуется во время сварки.
Расходные электроды требуют дополнительных требований по сравнению с неплавящимся электродом. Поскольку они расходуются в процессе сварки и служат материалом для сварного шва, выбор материала электродов имеет решающее значение. Это связано с тем, что материал электрода должен быть совместим с металлами, которые свариваются вместе; то есть они должны быть химически совместимыми.
Некоторые из наиболее распространенных материалов для расходуемых электродов включают различные типы стали, например, низколегированные или никелевые стали. Кроме того, их можно различать по типу и количеству покрытия или флюса на электродах, от полного отсутствия флюсового покрытия до типов с сильным покрытием.
С другой стороны, поскольку неплавящиеся электроды не расходуются во время сварки, но остаются неповрежденными, вопрос о типе материала электродов не возникает. Обычные электродные материалы включают углерод или графит в дополнение к чистому вольфраму или вольфрамовым сплавам.
Что такое сварочные электроды (и что вы должны знать)?
Независимо от того, являетесь ли вы профессиональным сварщиком или энтузиастом, вы должны знать, что такое сварочные электроды, и их относительные плюсы и минусы.
Так что же такое сварочные электроды? Сварочные электроды — это отрезки проволоки, которые соединяются со сварочным аппаратом для создания электрической дуги. Ток проходит по этой проволоке, образуя дугу, которая выделяет много тепла для плавления и плавления металла для сварки.
Основные типы:
- Расходные материалы
- Нерасходуемые
Эта статья поможет вам различать разные типы сварочных электродов и даст вам хорошее представление об их сильных и слабых сторонах, чтобы вы могли выбрать лучший выбор для вашей сварки Приложения. Читай дальше, чтобы узнать больше.
Электроды сварочные разные
Стержни, используемые для сварки MIG и стержневой сваркой, являются примерами плавящихся электродов.У них есть присадочный материал, который плавится, образуя сварные швы.
С другой стороны, при сваркеTIG используются неплавящиеся электроды. Эти электроды состоят в основном из вольфрама, который не плавится (в отличие от расходуемых электродов) из-за своей высокой температуры плавления. Он просто подает электрическую дугу для сварки. Наполнитель подается с помощью проволоки, подаваемой вручную.
Таким образом, основное различие между ними состоит в том, что расходуемые электроды плавятся, а неплавящиеся электроды — нет.
У этих двух категорий также есть несколько типов электродов.
Расходные электроды
Расходуемые электроды — это ключ к сварке электродуговой сваркой, MIG и порошковой сваркой. Расходуемые электроды, используемые для сварки штангой, называются штучными электродами. К ним относятся электроды с толстым покрытием, экранированная дуга и электроды с легким покрытием.
Электроды с легким покрытием
Как следует из названия, электроды с легким покрытием имеют тонкое покрытие на своей поверхности, которое наносится такими методами, как распыление или кисть.
Эти электроды и их покрытия изготавливаются из нескольких различных материалов. Присадочный материал во многом похож на свариваемый основной металл.
Световое покрытие служит еще одной жизненно важной цели. Это покрытие уменьшает количество примесей, таких как сера и оксид, для обеспечения лучшего качества сварного шва. Он также обеспечивает более равномерное плавление присадочного материала, что позволяет создавать гладкий и надежный сварной шов.
Поскольку покрытие тонкое, получаемый шлак не слишком толстый.Экранированные дуговые электроды имеют некоторое сходство с электродами с легким покрытием. Главное отличие — у них более толстое покрытие. Эти сверхпрочные электроды подходят для более сложных сварочных работ, например, для сварки чугуна.
Электроды неизолированные
Использование неизолированных электродов может быть затруднено, поскольку дуга несколько нестабильна и ее трудно контролировать. Легкое покрытие увеличивает стабильность электрической дуги, облегчая вам управление ею.Применение неизолированных электродов ограничено. Например, они используются для сварки марганцевой стали.
Электроды дуговые экранированные
Экранированные дуговые электроды имеют три различных типа покрытия, которые служат разным целям. Один из видов покрытия содержит целлюлозу и использует слой защитного газа для защиты области сварного шва. Второй тип покрытия содержит минералы, образующие шлак. Третий вид покрытия представляет собой сочетание минералов и целлюлозы.
Экранированные дуговые электроды создают слой защитного газа, который образует эффективный барьер для защиты зоны горячего шва от загрязнения и коррозии окружающим воздухом. Это приводит к более прочным и надежным сварным швам. Нагретая зона сварного шва должна быть защищена от атмосферных газов, таких как азот и кислород, которые реагируют с высокотемпературным металлом с образованием хрупких, пористых и слабых сварных швов.
Экранированные дуговые электроды сводят к минимуму содержание серы, оксидов и других примесей в основном металле, что обеспечивает регулярные, гладкие и чистые сварные швы. Эти покрытые электроды также создают более стабильную электрическую дугу по сравнению с неизолированными электродами, что делает сварку более управляемой и снижает разбрызгивание.
Экранированные дуговые электроды также выделяют шлак из-за минерального покрытия. Этот шлак, кажется, трудно удалить, но он служит полезной цели. Он охлаждается гораздо медленнее, чем экранированные дуговые электроды. Этот процесс вытягивает загрязнения и отправляет их на поверхность. Следовательно, вы получите высококачественные, чистые, прочные и прочные сварные швы.
Нерасходуемые электроды
Неплавящиеся электроды проще понять не только потому, что они не плавятся, но и потому, что их всего два типа.
Электроды угольные
Первый вид — это угольный электрод, который используется как для резки, так и для сварки. Этот электрод сделан из угольного графита. Он может быть покрыт слоем меди или оставлен без покрытия.
Американское общество сварки не выпустило никаких спецификаций для этого типа электродов. Однако для угольных электродов существуют военные спецификации.
Электроды вольфрамовые и их разные
Второй вид неплавящегося электрода — это вольфрамовый электрод, который используется для сварки TIG.Эти электроды состоят из чистого вольфрама (с зеленой маркировкой), вольфрамсодержащего циркония от 0,3 до 0,5% (с коричневой маркировкой), вольфрама с 2-процентным содержанием тория (с красной маркировкой) и 1-процентного вольфрамсодержащего тория (с желтым маркировка).
Неплавящиеся электроды из чистого вольфрама имеют ограниченное применение и подходят для легких сварочных работ. На это есть две причины. Во-первых, чистый вольфрам не обладает прочностью и прочностью вольфрамовых сплавов.Во-вторых, чистый вольфрам может иметь проблемы с большим током.
Вольфрамовые электроды с содержанием циркония от 0,3 до 0,5 процента обеспечивают отличные результаты при переменном токе. Они лучше чистого вольфрама, но не так хороши, как вольфрамовые электроды с содержанием тория.
Вольфрамовые электроды с содержанием тория 1-2% являются одними из наиболее широко используемых неплавящихся электродов, поскольку они служат дольше и имеют более высокое сопротивление, чем другие виды вольфрамовых электродов.Их можно использовать для более высоких токов по сравнению с электродами из чистого вольфрама. Эти электроды также обеспечивают лучший контроль дуги и их легче запускать.
При использовании вольфрамовых электродов лучше использовать максимально допустимый ток, если они имеют гладкую цилиндрическую форму, иначе становится трудно контролировать дугу и поддерживать ее.
Для лучшего контроля дуги и стабильности кончики этих электродов следует заточить до точки, то есть сделать концы конусов.Если вы это сделаете, вам придется выбрать пуск от касания вместо сварочных аппаратов постоянного тока. Помните, что вольфрамовые электроды с торием и цирконием будут более долговечными, чем электроды из чистого вольфрама, если вы выберете конические электроды с использованием сенсорного запуска.
Как читать код на стержневых электродах
Теперь, когда вы хорошо разбираетесь в основах, пора глубже изучить классификацию сварочных стержней.
В этой классификации стержневых электродов учитываются различные факторы, такие как процентное содержание железного порошка, наиболее подходящее положение сварки, предел прочности, материал покрытия и диаметр.
Не используйте плавящиеся электроды, толщина которых превышает толщину свариваемого металла. Наиболее часто используемый диаметр электрода составляет 3/32 дюйма. Однако для некоторых приложений требуются электроды с диаметром, который может быть в пять раз больше или всего 1/16 дюйма.
Предел прочности на разрыв — это максимальное усилие, которое может выдерживать сварной шов. Чтобы сделать прочный и надежный сварной шов, вам необходимо использовать электрод с более прочным присадочным материалом, чем основной металл. Если присадочный материал слабее основного металла, сварное соединение станет слабым местом, которое может легко сломаться.
Процентное содержание порошка железа в электроде также имеет значение, поскольку при расплавлении под действием тепла сварки он превращается в сталь. Более высокий процент порошка железа означает, что каждый электрод может предоставить вам больше присадочного материала для сварки большего количества деталей. Однако следует учитывать, что процентное содержание железа вряд ли превысит 60 процентов.
Поняв эти свойства, вы можете теперь рассмотреть классификационный код для этих электродов.
Например, вы можете встретить E6010.Буква «E» указывает на то, что это электрод. Первые две цифры, следующие за «E», указывают предел прочности на разрыв. «60» здесь означает, что предел прочности на разрыв составляет 60 000 фунтов на квадратный дюйм.
Таким образом, вам нужно добавить четыре нуля к этим двум цифрам, чтобы определить предел прочности электрода на разрыв. Число 70, таким образом, означает предел прочности на разрыв 70 000 фунтов на квадратный дюйм.
Если имеется пять цифр, то первые три цифры после «E» относятся к пределу прочности на разрыв.
Вторая последняя цифра указывает положение, в котором можно использовать электрод. «1» означает, что вы можете использовать электрод в любом положении — над головой, горизонтально, вертикально и горизонтально. «2» означает, что электрод подходит только для горизонтального и плоского положения.
Последняя цифра в сочетании с предпоследней цифрой говорит о покрытии. Эта информация поможет вам выбрать сварочный ток. Производитель электродов предоставит таблицу, в которой перечислены текущие настройки для различных покрытий в соответствии с двумя последними цифрами.
Связанные вопросы
Из чего сделаны сварочные электроды? Сварочный электрод состоит из двух компонентов: настоящего металла и флюсового покрытия. Сплав может отличаться от низкоуглеродистой стали, чугуна, нержавеющей стали, высокопрочной стали, бронзы, алюминия, алюминия или алюминия.
Что означают цифры на сварочном стержне 7018? В рамках этой процедуры классификации самые первые 2 или 3 числа указывают на вязкость при растяжении склеенного продукта, которая может быть измерена в kpi или килограммах на квадратный дюйм.В E7018 70 символизирует 70 000 фунтов на квадратный дюйм или 70 kpi. 1: 3-й рисунок указывает положение сварки.
Для чего используется сварочный стержень 6012? Используйте сварочные стержни 6012 для соединения открытого соединения между двумя соединениями. Профессиональные сварщики используют электроды 6012 в плоском положении из-за собственных быстрых сильноточных угловых швов.
Подобные сообщения:
A | B |
---|---|
Что такое электрическая дуга? | Электрическая дуга — это разряд электрического тока через промежуток в цепи. Он поддерживается ионизированным столбом газа (плазмы), через который протекает ток.Для зажигания дуги в AW электрод приводят в контакт с изделием, а затем быстро отделяют от него на небольшое расстояние. |
Дуговая сварка | Рядом с концом электрода образуется лужа расплавленного металла, и по мере того, как электрод перемещается по стыку, расплавленная сварочная ванна затвердевает в своем следе |
Ручная дуговая сварка и время дуги | Проблемы с ручной сваркой : Качество сварного шва. Производительность. Время дуги = (время зажигания дуги) деленное на (отработанные часы) — Также называется «время зажигания дуги».![]() |
Два основных типа электродов AW | Расходные материалы — расходуются в процессе сварки. Источник присадочного металла при дуговой сварке. Не расходуемый — не расходуется в процессе сварки. Присадочный металл необходимо добавлять отдельно. |
Расходуемые электроды | Формы расходуемых электродов — Сварочные стержни (также известные как стержни) имеют диаметр от 9 до 18 дюймов и 3/8 дюйма или меньше, и их необходимо часто менять.Сварочную проволоку можно непрерывно подавать из катушек с проволокой большой длины, что позволяет избежать частых прерываний. Как в стержневой, так и в проволочной форме электрод расходуется дугой и добавляется в сварное соединение в качестве присадочного металла. |
Неплавящиеся электроды | Изготовлены из вольфрама, стойкого к плавлению.![]() |
Дуговое экранирование | При высоких температурах в AW, металлы химически реактивны по отношению к кислороду, азоту и водороду в воздухе. Эти реакции могут серьезно ухудшить механические свойства соединения.Для защиты работы дуга должна быть защищена от окружающего воздуха в процессах AW. Экранирование дуги достигается с помощью: Защитных газов, например аргона, гелия, CO2. Флюс. |
Flux | Вещество, которое предотвращает образование оксидов и других загрязнений при сварке или растворяет их и облегчает удаление. Обеспечивает защитную атмосферу для сварки. Стабилизирует дугу. Уменьшает разбрызгивание. |
Различные способы нанесения флюса | Заливка гранулированного флюса во время сварки.![]() |
Источник питания при дуговой сварке | Постоянный ток (DC) по сравнению с переменным током (AC) — машины переменного тока менее дороги в приобретении и эксплуатации, но обычно ограничиваются черными металлами. Оборудование постоянного тока может использоваться для всех металлов и обычно отличается лучшим контролем дуги. |
Процессы AW с плавящимся электродом | Дуговая сварка защищенного металла.Газовая дуговая сварка металлов. Дуговая сварка порошковой проволокой. Электрогазовая сварка. Дуговая сварка под флюсом. |
Дуговая сварка экранированного металла (SMAW) | Используется расходный электрод, состоящий из стержня из присадочного металла, покрытого химическими веществами, которые обеспечивают флюс и защиту.![]() |
Сварочная палочка в SMAW | Состав присадочного металла обычно близок к основному.Покрытие: порошкообразная целлюлоза, смешанная с оксидами, карбонатами и другими ингредиентами, удерживаемая силикатным связующим. Сварочная палочка зажимается в электрододержателе, подключенном к источнику питания. Недостатки сварки штангой: Палки нужно периодически менять. Высокий ток может преждевременно расплавить покрытие. |
Применение SMAW | Используется для обработки сталей, нержавеющей стали, чугуна и некоторых цветных сплавов. Не используется или редко используется для алюминия и его сплавов, медных сплавов и титана. |
Газовая дуговая сварка металла (GMAW) | В качестве электрода используется расходуемая неизолированная металлическая проволока, а в качестве защиты достигается заливка дуги газом.![]() |
Преимущества GMAW перед SMAW | Лучшее время дуги благодаря сплошному проволочному электроду. Палки необходимо периодически менять в SMAW. Лучше использовать электродный присадочный металл, чем SMAW. Конец ручки нельзя использовать в SMAW. Более высокая производительность наплавки. Устраняет проблему удаления шлака. Легко поддается автоматизации. |
Дуговая сварка порошковой проволокой (FCAW) | Адаптация дуговой сварки в экранированном металле для преодоления ограничений, связанных с стержневыми электродами.![]() |
Электрогазовая сварка (EGW) | Использует непрерывный расходуемый электрод, порошковую проволоку или неизолированную проволоку с подачей защитных газов извне, а также формовочные башмаки для удерживания расплавленного металла. Когда используется порошковая электродная проволока и не поступают внешние газы, то это особый случай самозащиты FCAW.Когда используется неизолированная проволока электрода с защитными газами от внешнего источника, то особый случай GMAW. |
Дуговая сварка под флюсом (SAW) | Использует непрерывный расходуемый неизолированный проволочный электрод с дуговой защитой, обеспечиваемой покрытием из гранулированного флюса.![]() |
Области применения и продукты для резки на пилы | Изготовление стальных конструкций конструкционных профилей (например,г., двутавры). Швы для труб большого диаметра, резервуаров и сосудов под давлением. Сварные детали для тяжелой техники. Большинство сталей (кроме стали Hi C). Не подходит для цветных металлов. |
Сварочные материалы — Designing Buildings Wiki
Сварка — это процесс соединения металлов и термопластов посредством коалесценции. Это экономичный и эффективный процесс для создания прочных соединений между двумя или более частями. Присадочные металлы плавятся во время сварки, создавая прочное соединение.Флюс обычно используется для создания газовой защиты вокруг сварочной ванны, чтобы предотвратить окисление горячих металлов. Флюс обычно действует как раскислитель, предотвращая образование пористости в сварочной ванне. Флюс и присадочный металл вместе известны как сварочные материалы .
Штанговый электрод, порошковая проволока, сплошная проволока, проволока SAW и флюсы — вот некоторые из сварочных материалов , используемых в процессе сварки. Однако флюс не является частью окончательного сварного шва и поэтому «теряется» в процессе сварки.
Рост сварочной отрасли во многом зависит от мирового потребления стали.
Сварка находит применение в ряде отраслей, таких как; строительство, автомобили и транспорт, судостроение, электроэнергетика, нефть и газ. Прогнозируется, что глобальный рынок сварочных материалов будет быстро расти благодаря позитивным прогнозам в таких отраслях, как автомобильная и транспортная, морская и строительная отрасли. Однако медленное внедрение передовых технологий, особенно в развивающихся странах, создает угрозу этому росту.
Основными тенденциями, положительно влияющими на рост рынка, являются новые разрабатываемые технологии, в частности, технологии, предназначенные для сварки толстых металлических деталей. Кроме того, рынок сварочных материалов движется в сторону автоматизации различных этапов сварочного процесса, и ожидается, что разработка роботов и программного обеспечения для автоматизации положительно повлияет на рост.
Сварочные материалы сегментированы в зависимости от техники сварки, сварочных материалов типа , отрасли конечного использования и региона.
Расходные материалы для сварки подразделяются на:
Сварочные материалы типов включают:
- Электроды стержневые.
- Жесткие провода.
- Порошковые проволоки.
- Проволока SAW.
- Флюсы.
- Прочие (включая газы и др.).
В 2014 году сегмент стержневых электродов доминировал на мировом рынке сварочных материалов , за ним следовал сегмент сплошной проволоки. Однако прогнозируется, что сегмент сплошной проволоки и стержневых электродов потеряет долю из-за растущей популярности сегмента проволоки на ПАВ и порошковой проволоки.
Неплавящиеся электроды и другие присадочные металлы: Maine Welding Company
Нерасходуемые электродыПри сварке обычно используются другие присадочные металлы и специальные изделия. К ним относятся неплавящиеся электроды (вольфрам и углерод) и другие материалы, в том числе подкладочные ленты, подкладочные устройства, флюсовые добавки, припои и припои. Другой тип материала, который используется при сварке, — это расходуемые кольца, используемые для сварки корневого прохода трубы.Также существуют манжеты, используемые для приварки шпилек, и направляющие трубы при электрошлаковой сварке плавящихся направляющих. Другие присадочные материалы — это припои и припои.
Типы неплавящихся электродов. Есть два типа неплавких электродов. Угольный электрод представляет собой электрод из неприсадочного металла, используемый при дуговой сварке или резке, состоящий из стержня из углеродного графита, который может быть покрыт или не покрыт медью или другими покрытиями. Вторым неплавящимся электродом является вольфрамовый электрод, определяемый как электрод без присадочного металла, используемый при дуговой сварке или резке, в основном изготовленный из вольфрама.
Угольные электроды. Американское сварочное общество не предоставляет спецификации для углеродных электродов, но есть военная спецификация, нет. MIL-E-17777C, озаглавленный «Электроды для резки и сварки углерод-графит без покрытия и с медным покрытием». В данной спецификации представлена система классификации, основанная на трех классах: без покрытия, без покрытия и с медным покрытием. Он предоставляет информацию о диаметре, длине и требованиях к допускам по размеру, обеспечению качества, отбору образцов и различным испытаниям.Применения включают сварку угольной дугой, сварку двойной угольной дугой, резку углем, а также резку и строжку угольной дугой.
Вольфрамовые электроды.
Неплавящиеся электроды для газов: чистый вольфрам, вольфрамосодержащая дуговая сварка (TIG) состоит из четырех частей тория на 1,0 процента, вольфрама с содержанием тория 2,0 процента и вольфрама с содержанием циркония от 0,3 до 0,5 процента.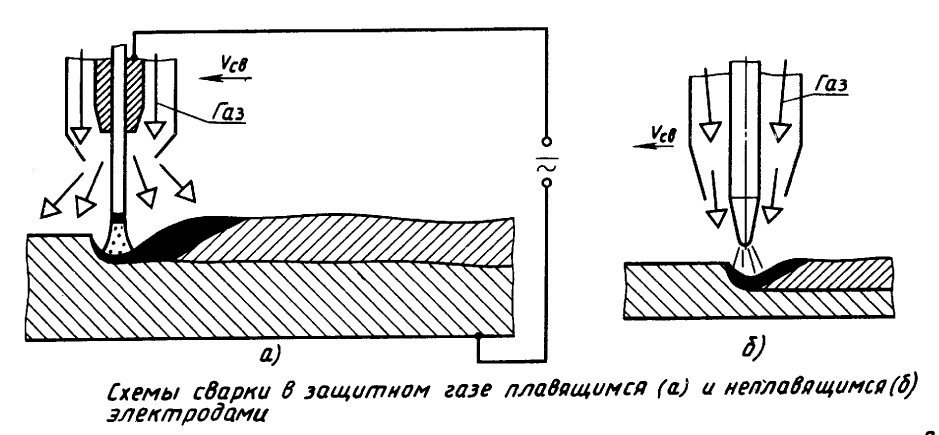
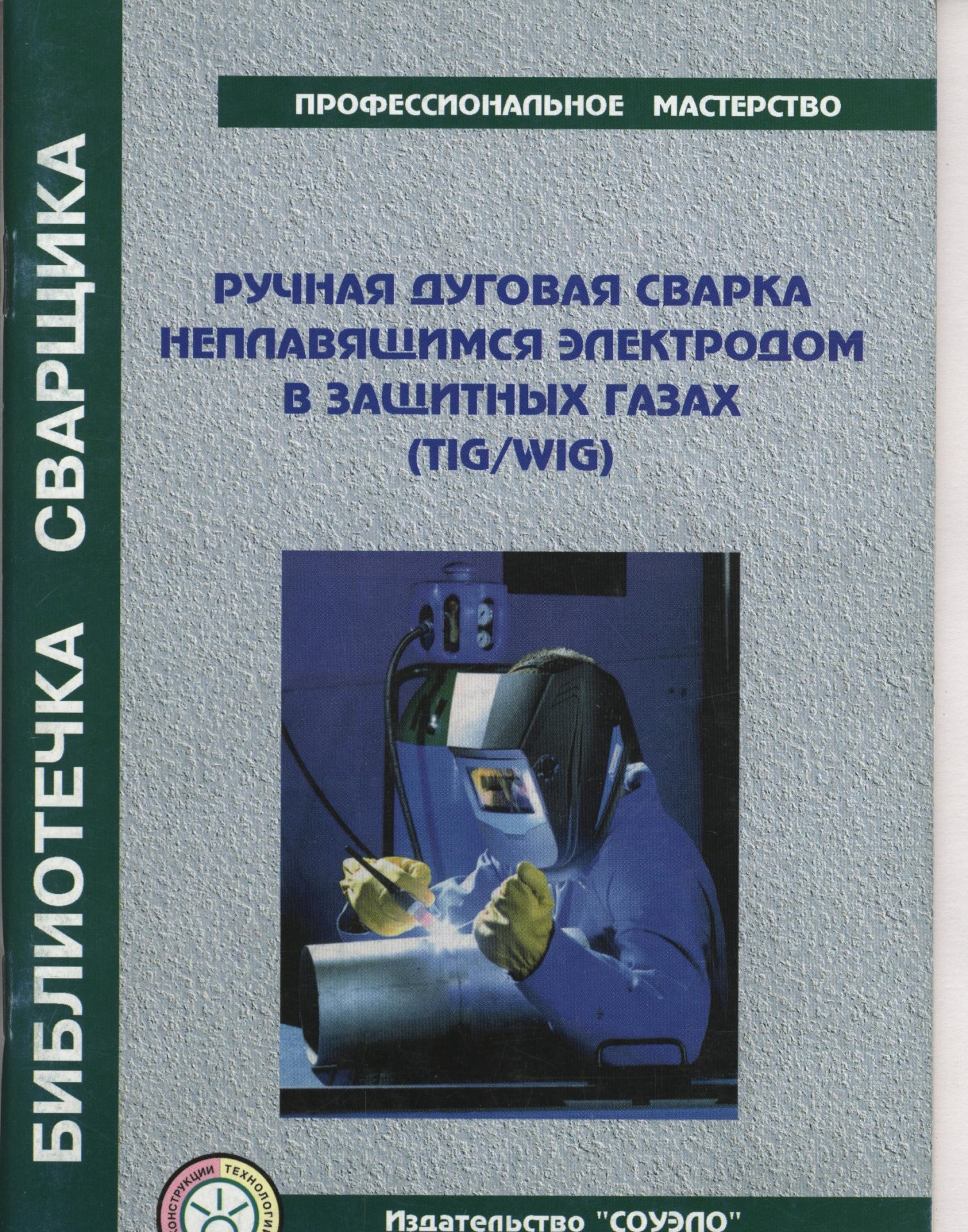

Материалы основы. Для сварки все чаще используются подкладочные материалы.Существуют специальные ленты, некоторые из которых содержат небольшое количество флюса, которым можно закрепить корни суставов. Также существуют различные композитные материалы основы для односторонней сварки. Расходные кольца используются для выполнения стыковых швов труб и насосно-компрессорных труб. Это металлические кольца, которые привариваются прихваточным швом к основанию сварного шва и вплавляются в соединение газовой вольфрамовой дугой. Существует три основных типа колец, называемых расходуемыми инертными кольцами, которые доступны для различных анализов металла на основе стандартных спецификаций.
SMAW против сварки TIG: в чем разница?
Дуговая сварка в среде защитного металла (SMAW) и дуговая сварка вольфрамовым электродом (TIG) — два наиболее распространенных и широко используемых сегодня процесса сварки. Оба они полагаются на использование тепла для плавления и соединения нескольких металлических или термопластичных объектов. Когда металлические предметы остывают, они затвердевают и сплавляются. Но SMAW — это не то же самое, что сварка TIG. Чтобы узнать больше о различиях между сваркой SWAW и TIG, продолжайте читать.
Что такое SMAW?
Также известный как ручная дуговая сварка металлическим электродом, SMAW — это процесс сварки, который характеризуется созданием сварочной дуги между плавящимся электродом, обычно изготовленным из стали, покрытой флюсом, и основным металлом или материалом. Во время SMAW сварочная горелка удерживает этот электрод, в то время как тепло по существу испаряет часть его внешнего покрытия. По мере того, как электродный стержень плавится, он создает газы, которые прилипают к металлу, тем самым устраняя пузырьки или карманы кислорода.
Что такое TIG?
СваркаTIG похожа на SMAW в том смысле, что оба процесса создают дугу между электродом и основным металлом или материалом. Однако при сварке TIG используется неплавящийся электрод. Электрод, используемый при сварке TIG, как следует из названия, сделан из вольфрама.Обладая температурой плавления около 6192 градусов по Фаренгейту, вольфрам способен выдерживать высокую температуру сварочной дуги, а это означает, что электрод можно использовать многократно.
Различия между сваркой SMAW и TIG
Основное различие между сваркой SMAW и TIG заключается в том, что в первой используется расходуемый электрод, а во второй — неплавящийся, многоразовый электрод. Помимо этого нюанса, отличается и материал, из которого изготовлен электрод. При SMAW расходуемый электрод обычно изготавливается из того же материала или материала, аналогичного материалу основного металла или материала. Для сравнения, неплавящийся электрод, используемый при сварке TIG, изготовлен из вольфрама.
Также стоит отметить, что SMAW — это более простой процесс сварки по сравнению с TIG. Он требует меньше инструментов и меньше обучения, чем его аналог для TIG, что делает его популярным среди малых и средних предприятий.
А как насчет GMAW?
В то время как SMAW и TIG являются двумя наиболее распространенными сварочными процессами, третий процесс сварки — это дуговая сварка металлическим электродом в газе (GMAW).Ключевое различие между GMAW и двумя аналогами заключается в том, что в нем используется катанный электрод. Электрод, используемый в GMAW, представляет собой рулон металлической проволоки, который пропускается через устройство, похожее на пистолет. Это же устройство также выделяет газы для вытеснения кислорода, тем самым уменьшая образование шлака и упрощая общий процесс сварки.
4 Важные расходные материалы для дуговой сварки
Эта статья проливает свет на четыре важных расходных материала для дуговой сварки. Расходные материалы: — 1.Электроды с покрытием 2. Сварочные стержни и проволока 3. Сварочные флюсы 4. Защитные газы.
Расходные материалы № 1. Электроды с покрытием:Практически все виды сварки общего назначения выполняются дуговой сваркой в среде защитного металла с использованием покрытых электродов. Электроды с покрытием состоят из сердечника из проволоки с покрытием из материала покрытия. Сердечник, используемый для электродов, изготавливается в соответствии с определенными национальными или международными стандартами, которые определяют калибр проволоки, состав материала, правила приемки и т. Д.
Электроды для ручной и автоматической дуговой сварки низко- и среднеуглеродистых сталей, а также низколегированных сталей в основном изготавливаются из стали с содержанием углерода 012%.
Диаметр сердечника электродов обычно варьируется от 3,15 до 12,50 мм, а промежуточные стандартные диаметры составляют 4,00, 5,00, 6,30, 8,00 и 10,00 мм. Длина этих покрытых электродов варьируется от 350 до 450 мм, причем неизолированная часть (без покрытия) находится в диапазоне от 20 до 30 мм, откуда они удерживаются в электрододержателе.
Химический состав сердечника проволоки для низко- и среднеуглеродистых сталей приведен в таблице 5.1A, а сердечниковой проволоки из низкоуглеродистой стали — в таблице 5.1B .:
Расходные материалы № 2. Сварочные стержни и проволока:
Сварочные проволоки и прутки без оболочки используются короткими отрезками длиной около 1 метра или в бухтах. В то время как короткие длины используются для таких процессов, как GTAW и плазменная дуговая сварка, где они не являются частью сварочного контура, длинные проволоки используются для таких процессов, как GMAW и SAW, где часть проволоки проводит ток, когда сварочная проволока является частью сварочной проволоки. В электрической цепи он называется сварочным электродом, иначе его называют сварочным стержнем.
Большинство проволок, используемых для сварки конструкционной стали, обычно содержат от 0 до 10% углерода и от 0-35 до 0-60% марганца. У других повышенное содержание марганца. Некоторые другие типы содержат повышенное количество углерода, марганца и кремния.
Избыток кремния в сварочной проволоке приводит к сильному разбрызгиванию, образованию газов в сварочной ванне и появлению неметаллических материалов в металле шва. Таким образом, максимально допустимое содержание кремния составляет до 0-95%.
Содержание вредных примесей, таких как сера и фосфор, не должно превышать 0-04% каждая.В некоторых проволоках, особенно тех, которые используются для сварки легированных сталей, максимально допустимое количество серы и фосфора составляет 0–3% каждая.
Диапазон диаметров проволоки от 0-5 до 2-5 мм с 0-5, 0-6, 0-8,0-9,1-0, 1-2, 1-6,2-0,2 Обычно в наличии проволока диаметром 4 и 2-5 мм. Сварочные аппараты используют непрерывную проволоку в бухтах. В зависимости от диаметра проволоки катушка может весить от 5 до 500 кг и иметь диаметр от 150 до 1000 мм.
Сварочные проволоки обычно покрыты медью, чтобы предотвратить ржавление и улучшить прием тока от контактной трубки, это также помогает при протяжке проволоки через матрицы.Чтобы избежать вредных воздействий и отслаивания медного покрытия, его обычно делают очень тонким, а максимальное количество меди указывается на уровне 0-4% от веса проволоки.
Помимо низкоуглеродистых сталей, сварочную проволоку также производят из нержавеющих сталей, алюминия и его сплавов, никелевых сплавов, магниевых сплавов, титановых сплавов и медных сплавов.
Сварочная проволока бывает сплошной и трубчатой, последняя содержит флюс.
Спецификации сплошных проводов и стержней :
Для определения сварочных электродов или стержней используется несколько систем.Спецификация AWS — одна из хорошо известных систем кодификации. Он состоит из буквы или букв префикса, за которыми следуют две цифры и буква S, а затем суффикс, который может быть цифрой, буквой или тем и другим.
Идентификацию AWS для электродов из углеродистой стали без покрытия и стержней для дуговой сварки в среде защитного газа можно объяснить с помощью кода, скажем, ER — 70S-1
ER — Префикс указывает на электрод или сварочный стержень
70 — указывает минимальную прочность на растяжение после сварки 70000 фунтов на квадратный дюйм (5000 Н / мм 2 )
S — указывает на твердый электрод или стержень
1 …….. 6. Число суффикса указывает на химический анализ или другой фактор пригодности, например, 1 означает 0-07% углерода и 0-30% кремния.
Все эти проволоки и стержни обычно предназначены для использования с глубокой полярностью, и большинство из них предназначены для использования с CO 2 в качестве защитного газа.
Система AWS, принятая для идентификации сплошной неизолированной проволоки из углеродистой стали для дуговой сварки под флюсом, выглядит следующим образом:
Он имеет префиксную букву E для обозначения электрода. За ним следует буква L, M или H, чтобы указать уровень марганца; L означает низкое, M — среднее, а H — высокое содержание марганца.За ним следуют одна или две цифры, обозначающие среднее количество углерода в сотых долях процента, например, 8 означает 0,08% углерода. Буква в суффиксе K используется для обозначения содержания кремния выше 0,05%.
Примеры :
EL8 — Низкое содержание марганца (0-30-0-55%), среднее содержание углерода 0-08%, 0-05% кремния
EL8K — (0-30-0-55)% Mn, 0-08% C, (0-10-0-20)% Si
EM12 — (0-85 — 1-25%) Mn, (0-09 — 0-15)% C, 0-05% Si
EH 14 — (1-75-2-25)% Mn, (0-10-0-18)% C, 0-05% Si
Некоторые из этих проволок очень похожи по составу на проволоку, используемую для газовой дуговой сварки.
Трубчатые электроды или порошковая проволока:
Порошковая проволока состоит из металлической оболочки, в которой заключен сердечник из флюса. Флюс, содержащийся в электроде, выполняет по существу те же функции, что и покрытие на покрытом электроде, то есть действует как раскислитель, шлакообразователь, стабилизатор дуги и может обеспечивать легирующие элементы, а также защитный газ.
Есть две основные причины для внедрения порошковой проволоки, а именно: в отличие от сплошной проволоки, для ее производства не обязательно требуются стальные заготовки определенного состава, поскольку ее можно изготавливать из полос желаемого материала; также его легче использовать, особенно для сварки труб, уложенных в фиксированном положении.
Порошковая проволокав нынешнем виде была представлена в США в 1956 году. Сначала полоса, содержащая флюс, была доведена до необходимого диаметра путем складывания, но последующие разработки привели к созданию бесшовной металлической трубки вокруг сердечника, содержащего флюс. Доступны порошковые проволоки различной конфигурации, некоторые из которых показаны на рис. 5.1.
Первоначально порошковые проволоки производились диаметром 3,2 мм, но теперь они доступны и диаметром до 11 мм.
Типичные порошковые проволоки используются с CO 2 в качестве защитного газа с флюсом, содержащим составляющие, образующие шлак, и легирующие элементы. Во многих случаях провода также содержат железный порошок, вставленные провода или металлические полосы, которые частично проводят ток.
Диаметр проволоки обычно колеблется от 1-2 до 4 мм, при этом флюс обычно составляет 5-25% от веса всей проволоки, что дает эффективность наплавки от 85 до 95%.
Типы порошковой проволоки:
Большинство порошковых проволок, доступных для сварки углеродистых сталей, относятся к рутиловому типу, в котором TiO 2 (диоксид титана) является основным шлакообразующим компонентом.Эти проволоки позволяют производить сварку без разбрызгивания и сварные швы с гладкой поверхностью и легко удаляемым шлаком.
Однако более популярны порошковые проволоки основного типа. Шлакообразующие составляющие этих проволок — фторид кальция, известняк, карбонаты и оксиды щелочноземельных металлов. При использовании малых токов эти провода дают больше брызг, однако при более высоком токе перенос металла происходит плавно и с небольшим разбрызгиванием. В случае углеродистой стали основная проволока дает сварные швы с большей ударной вязкостью, чем рутиловые электроды.Еще одна отличительная особенность металла шва, полученного с использованием основной порошковой проволоки, — это его нечувствительность к отжигу для снятия напряжений. После отжига при температуре около 600 ° C страшного падения ударной вязкости не происходит.
В то время как содержание водорода в металле шва в электродах с основным покрытием, даже если они полностью высушены перед использованием, составляет 3 мл / 100 г металла шва, оно может составлять всего 1-2 мл / 100 г металла шва для флюса. -провода.
Существует два основных типа порошковой электродной проволоки:, проволоки одно- и многопроходные. Первое дает более высокое содержание марганца и кремния в металле шва, чем второе. Кроме того, порошковые проволоки могут быть с газовой защитой или с самозащитой (без внешней газовой защиты), то есть она защищена газом, образующимся при разложении и испарении сердечника из флюса. В последнем случае расплавленный шлак экранирует каплю на протяжении всего переноса металла.
CO 2 -экранированные и самозащитные порошковые проволоки все чаще используются, в основном, для сварки стали толщиной более 12 мм, для чего их основным преимуществом является возможность непрерывной и очень быстрой наплавки металла с использованием полуавтоматических сварочных систем. .Одновременно наблюдается рост использования GMAW с газовой смесью, богатой аргоном, для сварки сталей, в основном толщиной менее 12 мм. Основным преимуществом этого является сочетание высокой скорости сварки с хорошей отделкой и минимальным количеством брызг и шлака.
Система кодирования для идентификации порошковой проволоки следует той же схеме, что и для сплошной проволоки GMAW, но специфична для трубчатых электродов.
Возьмем для примера E60T — 7
Здесь,
E — указывает на электрод.
60 — Указывает 60 000 фунтов на квадратный дюйм (420 Н / мм) как минимальную прочность на растяжение после сварки.
T — обозначает трубчатый, сварной электрод или электрод с флюсовой сердцевиной.
7 — Цифра от 1 до 8 в качестве суффикса указывает химический состав наплавленного металла шва, защитный газ и коэффициент пригодности.
Среди наиболее популярных спецификаций — тип рутила (E70T — 1 и E70T — 2), самозащитный тип (E70T — 4) и базовый тип (E70T — 5).
Помимо основной порошковой проволоки из углеродистой стали, были также разработаны порошковые проволоки для низколегированных сталей, которые позволяют изготавливать наплавленный металл, подходящий для большинства видов стали и для различных технических требований.Порошковые проволоки, легированные никелем, молибденом и хромом, могут использоваться для сварки высокопрочных мелкозернистых конструкционных сталей, которые ранее желательно было сваривать электродами с основным покрытием и основными флюсами.
Технология порошковой проволоки заставила пользователей перейти с процесса сплошной проволоки CO 2 на процесс порошковой проволоки для получения различных преимуществ. Этот процесс намного быстрее, проще и экономичнее, чем сварка под флюсом, с более высокой производительностью в определенных областях применения, например, в судостроении. Трубчатая или порошковая проволока также используется для наплавки и сварки под флюсом.
Порошковая проволока, в которой флюс заменен металлическими порошками, используется с богатым аргоном защитным газом для наплавки металла шва с очень высокой скоростью на стальных пластинах толщиной от 5 до 60 мм. Они обладают хорошими механическими свойствами, практически не содержат брызг и мало шлаков. Дымчатость также мала, и удаление шлака между прогонами не требуется.
Порошковая проволока MIG-сварка сочетает в себе лучшие свойства защиты от инертного газа и порошковой порошковой проволоки. Сплошная проволока заменяется порошковой проволокой, в которой сердечник состоит из металлических порошков и раскислителей вместо обычных шлакообразующих флюсов.Когда эта проволока наплавляется в среде защитного газа, состоящего из аргона с небольшим процентным содержанием CO , сварные швы 2 практически идентичны сварным швам MIG, но с более высокими скоростями наплавки, связанными с порошковой проволокой.
Порошковая проволока обычно изготавливается диаметром 1,6 мм и предназначена для сварки во всех положениях с более высоким процентным извлечением при использовании газа, богатого аргоном, и практически не дает шлака. Процент извлечения, который определяется как отношение веса наплавленного металла к весу используемых расходных материалов, умноженное на 100, варьируется от одного процесса к другому, как показано в таблице 5.3.
Расходные материалы № 3. Сварочные флюсы:Флюс является важным аспектом процесса дуговой сварки под флюсом и служит следующим целям:
1. Та часть флюса, которая плавится, плавает как жидкий покров над расплавленным металлом, защищает его от вредного воздействия окружающей атмосферы, тем самым уменьшая поглощение кислорода и азота.
Представление об эффективности флюса для защиты сварочной ванны от атмосферного загрязнения может быть получено из содержания азота в металле сварного шва. При сварке неизолированными электродами содержание азота в металле шва достигает 0-18%. Электроды с толстым покрытием снижают этот показатель до 0–026%, в то время как при сварке под сварку SAW максимальное количество азота в наплавленном шве составляет 0,005%.
2. Он действует как хороший изолятор и концентрирует тепло в относительно небольшой зоне сварки, таким образом улучшая плавление расплавленного металла сварочного электрода и основного материала.
3. Действует как очищающее средство для металла шва, поглощает загрязнения и добавляет легирующие элементы, такие как марганец и кремний.
4. Благодаря флюсу металл шва не только чистый, но и более плотный и, следовательно, имеет отличные физические свойства.
5. Покрытие из флюса повышает эффективность процесса за счет уменьшения потерь от разбрызгивания и горения, которые неизбежны при использовании обычной открытой дуги.
Состав и химическая классификация флюсов на ПАВ:
Составляющие флюсов — это в основном сырье геологического происхождения, которое состоит из кремнезема, силикатов, известняка, глины, оксидов, фторидов и других минералов. Многие составляющие флюса не сильно улучшают его свойства, но присутствуют в основном в виде остатков; однако в некоторой степени они могут влиять на его физическое и химическое поведение.
Обычно флюс на ПАВ состоит из кварца (SiO 2 ), хаусманила (Mn 3 O 4 ), корунда (Al 2 O 3 ), периклаза (MgO), кальцита (CaCO 3 ), флюорит (CaF 2 ), известняк (CaO), диоксид циркония (ZrO 2 ), криолит (Na 3 AlF 6 ), доломит (CaMg (CO 3 ) 2 ), ферро -кремний (FeSi 2 ), магнезит (MgCO 3 ), роденит (MnSi0 3 ), рутил (TiO 2 ), велластонит (CaSiO 3 ), циркон (ZrSiO 3 ), циркон (ZrSiO 4 ) а также оксиды бария, натрия, калия и железа i.е. BaO, Na 2 O, K 2 O и FeO. Он может состоять из всех этих элементов или некоторых из них в желаемых пропорциях. Каждый элемент придает сварочному флюсу разные характеристики, поэтому изменение их пропорций позволяет подобрать флюс, соответствующий требованиям.
В зависимости от количества различных компонентов флюс может быть кислотным, основным или нейтральным.
Эти характеристики определяются с помощью ИНДЕКСА ОСНОВАНИЯ (B.I.) флюса, который определяется как отношение основных оксидов к кислотным оксидам, то есть:
Флюс считается кислым, если B.I. <1, нейтральный для B.I. между 1-0 и 1-5, базовый для B.I. от 1,5 до 2,5 и очень простой для B.I. более 2,5.
Некоторые из флюсов, классифицированных на основании вышеизложенных соображений, приведены в таблице 5.4:
Роли ингредиентов флюса:
1. Кремнезем (SiO 2 ):
Это кислый оксид, который образует главный градиент всех потоков ПАВ. Он обеспечивает необходимую вязкость и токопроводящую способность флюсу в расплавленном состоянии.Чем выше содержание SiO 2 , тем выше вязкость и токонесущая способность флюса. Он улучшает отделение шлака и, как следствие, хороший внешний вид сварного шва без подрезов даже при 1000 А. Однако SiO 2 приводит к потере раскислителей и вызывает диффузию кремния в металл сварного шва, что приводит к ухудшению механических свойств, особенно ударной вязкости.
SiO 2 во флюсе варьируется от 25 до 55% по весу. Но флюсы, содержащие SiO 2 более 40%, показывают быстрое окисление легирующих элементов и повышенное количество неметаллических включений в металле сварного шва, что приводит к снижению ударной вязкости металла шва.
SiO 2 уменьшает отношение ширины к проплавлению сварного шва. Это также снижает стабильность дуги.
2. Оксид марганца (MnO):
Приводит к легированию марганца в металл шва, что улучшает его отрицательные свойства.
MnO способствует более высокой скорости сварки и более глубокому провару. Это снижает чувствительность к пористости ржавчины, но также снижает токонесущую способность и вязкость. Однако MnO улучшает стабильность дуги.
3. Рутил (TiO 2 ):
Это химически нейтральный оксид. Это дает металлургическое преимущество за счет образования игольчатого феррита из-за измельчения зерна. Улучшает стабильность дуги и ударные свойства.
4. Оксид алюминия (Al 2 O 3 ):
Он также улучшает ударные свойства металла шва за счет измельчения зерна и образования игольчатого феррита. Однако он снижает стабильность дуги и вязкость, а также обеспечивает среднюю проплавление.
5. Диоксид циркония (ZrO 2 ):
Удаляет вредные элементы, такие как кислород, азот, сера и фосфор. Однако он действует в основном как измельчающий зерно элемент и способствует образованию игольчатого феррита.
6. Бор, ванадий и ниобий:
Эти элементы отвечают за измельчение зерна в металле шва, но в избытке приводят к дисперсионному твердению.
7. Известняк (CaO):
Это один из основных компонентов флюса с точки зрения стабильности и текучести дуги.CaO — очень стабильный оксид, имеющий основную природу. Это снижает вязкость и делает флюс очень чувствительным к влаге. Этот гигроскопический характер приводит к пористости сварного шва.
CaO удаляет серу и фосфор и увеличивает ударную вязкость металла шва. Однако он дает очень неглубокое проникновение и увеличивает склонность к подрезанию.
8. Фторид кальция (CaF 2 ):
Повышает текучесть расплавленного металла и приводит к распылению.Он помогает удалять растворенный водород из расплавленной металлической стали, образуя фтористый водород, к которому сталь не имеет сродства.
9. Карбонат кальция (CaCO 3 ):
Снижает вязкость и делает флюс более основным. Это предотвращает впитывание влаги.
10. Раскислители (Al, Mn, Ti, Si):
Эти элементы во флюсе помогают удалять кислород из металла шва из-за их более высокого сродства к кислороду, чем у других элементов.Кроме того, Al, Ti и Mn также улучшают механические свойства металла шва за счет измельчения зерна.
11. Оксид натрия (Na 2 O) и оксид калия (K 2 O):
Это элементы с низким потенциалом ионизации, которые являются наиболее нестабильными составляющими потока. Они испаряются и диффундируют в полость дуги, создавая пары с низким потенциалом ионизации в непосредственной близости от дуги и, таким образом, повышая стабильность дуги.
Основные цели различных компонентов флюсовой дуги — достижение стабильности дуги, желаемой текучести расплавленного флюса и легкого отделения затвердевшего шлака после сварки.
Что касается стабильности дуги, то CaF 2 ухудшает ее, хотя его добавление важно для контроля пористости. Следовательно, необходимо найти баланс между этими противоречащими друг другу требованиями. Элементы, улучшающие стабильность дуги, включают калий, натрий и кальций. Благодаря своему влиянию на стабильность дуги состав флюса напрямую влияет на форму сварного шва.
Чрезмерное количество CaF 2 или SiO 2 во флюсе ухудшит стабильность дуги и, как следствие, правильную форму сварного шва. В результате сварной шов будет узким с чрезмерным проваром, поскольку дуга становится короткой и менее маневренной. С другой стороны, присутствие некоторых градиентов, таких как CaO, Na 2 O, K 2 O, делает дугу длинной и гибкой, а полученный шов широким и с нормальным проваром.
Избыточные количества CaF 2 и SiO 2 нежелательны еще и потому, что они вызывают образование ядовитых фторидов, монооксида углерода (CO) и пентаоксида азота, поэтому необходимо постоянно контролировать их содержание в атмосфере сварочного цеха.
Текучесть флюса в расплавленном состоянии также является фактором, влияющим на форму сварного шва. Флюс, текучесть которого в расплавленном состоянии широко меняется в зависимости от температуры, называется коротким потоком, а поток, текучесть которого остается более или менее постоянной, называется длинным потоком, как показано на рис. 5.2. Длинные флюсы вызывают грубую рябь на сварном шве, а короткие — мелкую.
Если флюс имеет низкую текучесть при температуре затвердевания металла шва, поверхность сварного шва будет шероховатой, с множеством выступов и впадин.Шлак легко прилипает к такой поверхности и его очень трудно удалить.
Избыточные количества SiO 2 , MnO и FeO также затрудняют отделение шлака, что снижает скорость сварки, особенно при многопроходной сварке.
Кроме того, флюсы не должны образовывать слишком много пыли, так как это может вызвать силикоз (заболевание легких, вызванное попаданием пыли, содержащей диоксид кремния). В качестве меры предосторожности все операции с флюсом должны быть механизированы.
Физическая классификация флюсов на ПАВ:
Флюсы для дуговой сварки под флюсом гранулируются до контролируемого размера и могут быть одного из двух основных типов, а именно.:
(i) Плавленые флюсы.
(ii) Агломерированные флюсы.
(i) Плавленые флюсы:
Чаще всего используются плавленые флюсы. Они производятся из таких минералов, как песок (SiO 2 ), марганцевая руда (MnSiO 3 ), доломит (CaMg (CO 3 ) 2 ), мел (CaCO 3 ) и т. Д. Название подразумевает, что плавленый флюс получают путем плавления градиентной верхней части печи и гранулирования по мере необходимости. Он не содержит влаги и не гигроскопичен.
Причина слияния ингредиентов заключается в том, что измельчение и механическое смешивание градиентов не позволяет получить однородную массу. Зерна различных минералов различаются по плотности и отличаются друг от друга при обращении. Это разделение неизбежно изменяет состав смеси, и флюс перестает выполнять свою функцию.
Низкоуглеродистые стали чаще всего сваривают плавлеными флюсами.
Некоторые из хорошо известных плавленых флюсов доступны с двумя размерами зерен.Более крупный размер предназначен для автоматов для дуговой сварки, а более мелкий — для полуавтоматических переносных станков для сварки на филе. В первом случае размер зерна составляет от 3-0 до 0-355 мм, а во втором — от 1-6 до 0-25 мм. По внешнему виду зерна представляют собой прозрачные частицы от желтого до красновато-коричневого цвета. Номинальный состав одного из этих флюсов
Другой доступный плавленый флюс также очень мало отличается от указанного выше. Оба приготовлены из песка, содержащего не менее 97% кремнезема, марганцевой руды, содержащей не менее 50% марганца и не более 0-2% фосфора; плавиковый шпат с содержанием CaF 75% 2 и не более 0.2% сера; каустический магнезит с содержанием оксида магния не менее 87%; и углеродосодержащие материалы для раскисления флюса при плавлении, например древесный уголь, антрацит, кокс, опилки и т. д.
(ii) Агломерированные флюсы:
, который также включает керамические флюсы, получают путем смешивания градиентов и связывания зерен жидким стеклом (силикатом натрия). Эти флюсы содержат ферросплавы (ферромарганец, ферро-кремний и ферротитан) и обеспечивают высокое содержание кремния, марганца и других легирующих элементов в металле сварного шва.
Один такой флюс, из которого могут быть получены все другие классификации путем введения легирующих добавок, имеет следующий весовой состав:
С этим составом можно получить высоколегированный металл шва с низкоуглеродистой электродной проволокой.
Недостатком керамических дюкс является то, что они легко впитывают влагу, а их зерна обладают меньшей механической прочностью, из-за чего флюс нельзя использовать повторно.
Керамические флюсы следует хранить в герметично закрытых емкостях и предъявлять претензии перед использованием.Во избежание образования пыли никогда не храните и не перевозите их в мягких мешках.
Факторами, определяющими эффективность флюса в достижении желаемых функций, являются глубина и ширина слоя флюса, а также размер и форма зерен флюса. Обычно слой флюса должен быть не менее 40 мм в глубину и на 30-40 мм шире стыка. Недостаточная глубина или ширина слоя флюса подвергнет зону воздействию воздуха, в результате чего расплавленный металл будет поглощать азот и пластичность металла сварного шва будет снижена. То же касается и крупнозернистых флюсов. По этой же причине стекловидные флюсы лучше пемзовых.
При дуговой сварке металла в защитных слоях электродами с толстым покрытием металл шва легируют ферросплавами, входящими в состав покрытия. Благодаря этому высоколегированный металл сварного шва можно получить даже с помощью обычной низкоуглеродистой электродной проволоки. Однако наиболее часто используемые плавленые флюсы не содержат ферросплавов, а единственными легирующими элементами являются кремний и марганец.
Количество Si и Mn, захваченных металлом шва, зависит от условий сварки, анализа флюса, а также от используемого электрода и основного металла.Обычные цифры составляют от 0-1 до 0-3% кремния и от 0-1 до 0-4% марганца.
Примерная пропорция различных основных компонентов флюсов, производимых крупным производителем в Великобритании, и их влияние на состав металла сварного шва для данной присадочной проволоки приведены в таблице 5.5.
Спецификация флюсов для ПАВ:
Согласно системе кодирования AWS Флюсы для SAW указываются в соответствии с механическими свойствами металла шва для конкретной электродной проволоки.
Поток идентифицируется специальной системой спецификаций, в которой используется префиксная буква F для обозначения потока. Следующая цифра указывает минимальную прочность на разрыв в 10 000 фунтов на квадратный дюйм (70 Н / мм 2 ) металла шва. Следующая цифра или буквенный код указывает на самую низкую температуру, при которой ударная вязкость металла шва будет равна или превышает 27 Дж (20 фут-фунтов).
Этот код выглядит следующим образом:
За этой цифрой кода следует тире, а затем буква E для обозначения электрода.За ним следует буква, обозначающая уровень марганца: L для низкого (0-30 — 0-60%), M для среднего (0-85 -1-40%) и H для высокого (1-75). — 2-25%) марганца. За ним следует число, которое представляет собой среднее количество углерода в точках или сотых долях процента.
Например, F74-EM12 будет указывать поток на ПАВ со следующими характеристиками:
F — флюс
7 — металл сварного шва с минимальным пределом прочности на растяжение 700 Н / мм (700 Н / мм 2 )
4 — шов с ударной вязкостью 27 Дж при -40 ° С
Э — с присадочной проволокой в качестве электрода
М — шов металлический марганец средней степени i. е. От 0-85 до 1-40%
12 — содержание углерода в металле шва 0-12%.
Флюсы для электрошлаковой сварки (ЭШС) похожи на флюсы под ПАВ, но чаще бывают плавлеными. «Флюс должен оставаться полностью в расплавленном состоянии, чтобы проводить электричество, чтобы обеспечить работу процесса ЭШС. Расплавленный флюс обеспечивает необходимое сопротивление току, чтобы поддерживать желаемую температуру.
Флюс также содержит элементы для очистки и раскисления металла шва, а также защищает его от вредного воздействия атмосферного азота и кислорода.Флюс в расплавленном состоянии должен иметь более низкую плотность, чем сталь, чтобы удерживать его на плаву над расплавленным металлом.
Расходные материалы № 4. Защитные газы: Основными защитными газами, используемыми для дуговой сварки вольфрамовым электродом, газовой дуговой сварки металлическим электродом и плазменной сварки, являются аргон, гелий и диоксид углерода. Помимо этих азота, кислород, водород и их смеси с первыми тремя газами также используются для достижения желаемой конфигурации валика и свойств металла сварного шва.
Эти защитные газы можно разделить на две группы, а именно:
а. Инертные газы, такие как (i) аргон и (ii) гелий,
г. Газы, которые растворяются в металле и вступают в реакцию с ним, например, CO 2 , O 2 , H 2 и N 2 .
Аргон:
Это негорючий, невзрывоопасный газ, получаемый из воздуха глубоким охлаждением и фракционированием, в котором он присутствует в количестве 9.3 x 10 Это примерно на 23% тяжелее воздуха.
Обычно аргон продается трех марок, скажем, A, B и C, содержащих 0–01, 0–04, 0–1% примесей соответственно. Товарный аргон содержит 16-7% примесей. Для высококлассных сварочных работ требуется чистота аргона порядка 99-995%.
Аргон нетоксичен, но может вызвать удушье в замкнутых пространствах, замещая воздух.
Аргон хранится и отгружается в стандартных стальных баллонах в газовой среде. Цилиндры для чистого аргона окрашены в черный цвет внизу и в белый цвет вверху, на котором по трафарету нанесены слова «Чистый аргон». В баллоне газ находится под давлением 150 атмосфер (примерно 15 Н / мм 2 ) — когда он полностью заполнен.
Стандартный 40-литровый баллон вмещает 6 кубических метров (6000 литров) аргона. Из баллона аргон подается в точку сварочной операции через регулятор давления, прикрепленный к клапану в горловине баллона. Регулятор давления снижает давление газа до величины, необходимой для сварки (которая обычно ниже 0-5 атмосфер), а также поддерживает постоянное рабочее давление независимо от давления в баллоне.Регуляторы давления для баллонов с аргоном окрашены в черный цвет.
Расход аргона измеряется ротационным расходомером, который прикреплен к регулятору.
Конкретные области применения различных марок аргона для сварки перечислены ниже:
Класс A:
Аргон марки А (чистота 99-99% и более) используется для сварки активных и редких металлов, а также для сварки деталей из других материалов на завершающей стадии производства.
Класс B:
Аргон марки B (чистота 99-96%) используется для сварки сплавов на основе алюминия и магния.
Класс C:
Марка C (чистота 99-9%) аргон используется для сварки нержавеющих и других высоколегированных сталей.
Гелий:
Гелий — инертный газ. Он присутствует в атмосфере лишь в пределах 0-52 x 10 -3 %. Кроме того, гелий присутствует в природном газе до 10%.Он также возникает в результате распада определенных радиоактивных элементов и содержится в некоторых урановых минералах.
Из-за своей высокой стоимости гелий является сравнительно менее используемым инертным газом.
Это легкий газ, который весит всего 1/7 веса воздуха. Это усложняет защиту сварочной ванны и приводит к увеличению расхода газа.
Гелий продается двух марок. Сорт I имеет чистоту 99-6-99-7% и сорт II 98-5-99-5%. Он хранится и отгружается в газообразном состоянии в стандартных баллонах под давлением 15 МПа (150 ат. ). Коммерческий гелий I хранится в цилиндрах, окрашенных в коричневый цвет и не имеющих надписи. Коммерческий гелий II хранится в цилиндрах, выкрашенных в коричневый цвет и имеющих надпись «Гелий», нанесенную белой краской по трафарету.
Гелий имеет самый высокий потенциал ионизации из всех защитных газов, поэтому сварочная дуга может работать при гораздо более высоком потенциале, чем аргон. Таким образом, дуга с гелиевой защитой выделяет большее количество тепла. Из-за своего легкого веса гелий имеет тенденцию улетать из зоны дуги и, следовательно, создает неэффективный экран, если не поддерживаются более высокие скорости потока.
Однако его легкий вес удобен для сварки над головой. Поскольку для гелия требуется более высокая скорость потока, достигаются более высокие скорости сварки. С гелием можно сваривать примерно на 35-40% быстрее, чем при использовании аргона в качестве защитного газа. Он часто используется в процессах газовой дуговой сварки вольфрамом, газовой дуговой сварки металлическим электродом и автоматической сварки MIG.
Двуокись углерода:
Бесцветный газ со слабым запахом. При растворении в воде дает кислый вкус.Это примерно на 1,5 лайма тяжелее воздуха.
Промышленно CO 2 получают путем прокаливания кокса или антрацита в специально разработанных топках котлов и улавливания его из природных источников. Его также получают как побочный продукт производства аммиака и ферментации спирта
Под давлением CO 2 становится жидкостью, которая при достаточном охлаждении затвердевает до снежно-подобного вещества (называемого сухим льдом), испаряющегося при -57 ° C.
Сухой лед и газообразный CO 2 , используемые в промышленных масштабах, получают из жидкого CO 2 , который представляет собой бесцветную жидкость.При испарении при 0 ° C и нормальном давлении (760 мм рт. Ст.) Из одного кг CO 2 образуется 509 литров газообразного CO 2 .
Жидкий CO 2 поставляется в стальных баллонах, в которых он занимает от 60 до 80% общей площади. Стандартный 40-литровый баллон вмещает 25 кг жидкости, из которых получается около 15 куб. газа при испарении. Давление газа в баллоне зависит от температуры, которая понижается по мере того, как из баллона поступает больше газа.
CO 2 , используемый для сварочных целей, может быть двух марок.Класс I должен содержать не менее 99-5% (по объему) чистого CO 2 и не более 0-178 г / м 3 влаги. Соответствующие показатели для Grade II составляют 99-0% и 0-515 г / м 3 .
Характеристики проникновения CO 2 аналогичны характеристикам проникновения гелия из-за сходства масс газов. CO 2 , который используется для сварки, не должен содержать никакой влаги, поскольку влага выделяет водород, который вызывает пористость в металле сварного шва.Поскольку CO 2 имеет большее электрическое сопротивление, уставка тока должна быть на 20-30% выше, чем у аргона и гелия.
CO 2 считается инертным при нормальной температуре и давлении. Однако при повышенных температурах он диссоциирует на 20–30% на CO и O. CO токсичен и имеет безопасную концентрацию всего 175 ppm (частей на миллион) по сравнению с 5000 ppm для CO 2 . Это требует эффективной выхлопной системы для защиты от вредного воздействия CO.
Отрицательной характеристикой образования кислорода является то, что он может снизить номинальную прочность металла. Еще одним важным недостатком использования CO 2 является его чрезвычайная устойчивость к току. Из-за этого сопротивления длина дуги чувствительна. Когда длина дуги слишком велика, она гаснет легче, чем при использовании инертного газа, такого как аргон или гелий.
Дефектные сварные швы чаще всего образуются при использовании CO 2 из верхней или нижней части цилиндра.Это связано с тем, что газ в верхней части несет большую часть примесей (азот, кислород и влагу), а вода, которые могут там быть. 150-200 г / цилиндр собирается под жидким CO 2 внизу. После полного израсходования жидкого CO 2 выходящий из баллона газ будет содержать чрезмерную влажность.
Чтобы избежать дефектов из-за примесей в CO 2 , было бы неплохо, чтобы только что доставленный CO 2 оставался на 15.20 минут, и выпустить верхнюю часть содержимого в атмосферу. Также рекомендуется перевернуть баллон вверх дном и дать ему постоять в этом положении около 15 минут. По истечении этого времени осторожно откройте вентиль, вся вода из баллона вытечет.
Когда CO 2 выпускается с расходом более 1000 л / час (при непрерывной сварке), оператору рекомендуется использовать как минимум два цилиндра, соединенных параллельно.
Если речь идет о больших количествах CO 2 , его можно перевозить в цистернах и выливать в испарители.CO 2 также может поставляться в виде сухого льда и испаряться на территории пользователя. Основными преимуществами использования твердого CO 2 для сварки являются высокая чистота газа и лучшая транспортабельность. Брикеты из твердого CO 2 , поставляемые поставщиком, переводятся на газ в специальных емкостях, нагреваемых электричеством или горячей водой.
Другие газы:
Обычно Ar, He и CO 2 используются по отдельности или в смесях в качестве защитных газов для сварки.Однако довольно часто к этим газам добавляют другие газы, такие как O 2 , H 2 и N 2 , для достижения определенных желаемых форм и характеристик наплавленных покрытий.
Кислород — это активный газ без цвета, запаха и вкуса, который соединяется со многими элементами с образованием оксидов. В стали он может соединяться с углеродом с образованием CO, который может захватываться затвердевающим металлом сварного шва и приводить к образованию пор или пустот. Этот недостаток обычно устраняется добавлением раскислителей, таких как Mn и Si.
Водород — самый легкий газ, присутствующий в атмосфере в количестве 0–01%. Однако водород также может присутствовать в атмосфере дуги из-за влаги или углеводородов, присутствующих на основном металле или присадочной проволоке. Он растворяется в расплавленной стали, но его растворимость в стали при комнатной температуре очень низкая. Таким образом, выходящий водород попадает на границы зерен и может вызвать трещины. Это также вызывает растрескивание под бортом в ЗТВ.
Азот находится в большом количестве в атмосфере.Это бесцветный, без запаха, нетоксичный и почти инертный газ. Он растворим в расплавленной стали, но его растворимость в стали при комнатной температуре очень низкая. Таким образом, это также может вызвать поры и пустоты. В очень небольших количествах нитриты, если они образуются, могут повысить прочность и твердость стали, но снизят ее пластичность, что может привести к растрескиванию. Азот иногда используется для сварки меди, потому что он обеспечивает высокую степень нагрева дуги. Из-за своей низкой стоимости по сравнению с аргоном, он часто используется для продувки труб и систем труб из нержавеющей стали.
Смеси газов:
Смеси газов, обычно используемые в процессах дуговой сварки, включают Ar-He, Ar-CO 2 , Ar-O 2 , Ar-H 2 , Ar-CO 2 — O 2 и т.п. .
Соотношение аргона в смесях Ar-He может варьироваться от 25 до 95% Ar. Однако для сварки алюминия часто используется комбинация Ar-75% He или Ar-80% He. Аргон в качестве защитного газа помогает удалять оксиды, а также демонстрирует определенную степень контроля пористости наплавленного металла.Гелий помогает получить хорошую конфигурацию гранул. Большинство черных и цветных металлов можно сваривать гелием, аргоном или их смесями. Гелий особенно полезен для сварки более тяжелых профилей из алюминия, магния и меди, а также для сварки над головой.
Смесь CO 2 -75% Ar или CO, -SO 2 % Ar довольно популярна для сварки конструкционных и низколегированных сталей. Аргон улучшает характеристики переноса металла, а CO 2 помогает улучшить форму валика и улучшить экономичность процесса.Однако эти смеси используются для обработки более тонких секций стали, когда важен внешний вид борта. Они также используются для сварки в нерабочем положении очень тонких листов.
Кислород иногда добавляют к аргону с целью улучшения формы валика при сварке низкоуглеродистых сталей. Небольшое количество кислорода, добавленного к аргону, вызывает значительные изменения. Например, он расширяет палец с глубоким проникновением в центре бусины; он также улучшает контур валика и устраняет подрезы на краю сварного шва.
Кислород обычно добавляют в количестве 1%, 2% или 5%. Максимальное количество кислорода, используемого для смесей Ar-O 2 , составляет 5%. Добавление более высоких количеств может привести к пористости металла шва. Основная цель добавления кислорода к аргону — образование термоэмиссионного оксида железа на поверхности стального электрода, который улучшает его излучательную способность и делает катодное пятно более широким и стабильным, если электрод сделан отрицательным.
Водород иногда добавляют к аргону, но его количество ограничивается максимум 5%.Обычно используются смеси Ar-2% II или Ar-4% H 2 . Добавление водорода вызывает увеличение напряжения дуги, что приводит к более высокому нагреву дуги. Смесь Ar-H 2 не следует использовать для низкоуглеродистых или низколегированных сталей, так как это может привести к водородному растрескиванию, часто называемому водородным охрупчиванием. Он в основном используется для сварки никеля или никелевых сплавов. Этой смесью сваривают и тяжелые секции нержавеющих сталей.
Смесь CO 2 — O 2 или Ar-CO 2 — O 2 также иногда используется для сварки мягких сталей.Это улучшает режим переноса металла и форму валика. Добавление кислорода приводит к более горячему горению дуги и, таким образом, предотвращает отсутствие плавления.
Использование небольших количеств хлора в качестве защитного газа для алюминия улучшает стабильность дуги. Кроме того, оксид азота в виде очень небольшой добавки (<0–03%) в защитный газ для сварки алюминия помогает снизить содержание озона в зоне сварного шва.
В целом состав защитного газа для дуговой сварки в защитном газе различных металлов и их сплавов может быть основан на рекомендациях, приведенных в таблице 5.