история создания и основные способы применения
История создания, метод работы и принцип работы с различными металлами с использованием сварочной дуги был известен еще в XIX веке.Русский физик Василий Петров создал условия для функционирования устойчивого электрического разряда (1802). В дальнейшем его идеи сварки использовал на практике другой наш соотечественник – Николай Бенардос. Ему удалось соединить металлические части эл дугой, которую создавали между собой неплавящийся угольный электрод и свариваемое плавлением изделие (1882).
Дуговая сварка это основа основ соединения металла
Уже первый сварочный агрегат обеспечивал подачу газа для эффективного процесса, где взаимодействовали два электрода или один электрод и обрабатываемая с его помощью деталь.
Развитие дуговой сварки
Следующим этапом исторического развития дуговой сварки стали опыты русского инженера Николая Славянова. Произошла замена неплавящегося угольного электрода на металлический, который плавился и исключал необходимость в отдельном присадочном металле (1888).
Эти открытия русских испытателей и стали той основой, на которой построено современное производство агрегатов для дуговой сварки во всем мире. Все, что происходило в дальнейшем, шло по путям:
- изыскания защитных средств и способов обработки расплавляемого для сварки металла;
- автоматизации различных способов сварочного процесса.
Способов защиты к настоящему времени известно несколько:
- газовая,
- газошлаковая,
- шлаковая.
Автоматизация сварки, в том или ином виде позволяет классифицировать ее на три основные группы:
- полностью автоматическая,
- механизированная,
- ручная.
Используемый эл разряд должен иметь нужную продолжительность. Для этого применяется специальный источник питания дуги (для краткости написания используется аббревиатура ИПД). Поэтому в формате переменного тока используется сварочный трансформатор, а если ток постоянный – генератор или выпрямитель.
youtube.com/embed/s6HXXOPjn0w» allowfullscreen=»» frameborder=»0″/>
Разновидности дуговой сварки
Сварка с использованием покрытых электродов
Весь сварочный процесс при этом идет ручным способом, плавлением обрабатываемой поверхности. Предполагается использование плавящихся и неплавящихся электродов. Из первой группы предпочтение отдается:
- алюминиевым,
- медным,
- стальным
электродам и некоторым другим, в зависимости от конкретных параметров сварки. Из второй группы характерно использование:
- вольфрамовых,
- графитовых,
- угольных
электродов различного диаметра.
Чаще всего в ход идут стальные электроды. При этом осуществляются:
- подача электрода в район места предполагаемого процесса,
- процесс перемещения сварочной дуги по всей длине обрабатываемой поверхности детали, на которой плавлением образуется шов.
Этот способ соединения деталей электрической дугой входит в число самых распространенных. Он выгодно отличается от остальных тем, что предельно прост и универсален, когда сварочный аппарат используется для изготовления конструкций различного профиля. Отлично зарекомендовал себя данный способ в случаях, когда необходимо работать:
- в горизонтальном, вертикальном положении или вести сварочные работы под углом;
- в местах, куда бывает трудно обеспечить нормальный доступ.
К числу недостатков следует отнести:
- малую производительность этого вида дуговой сварки,
- прямую зависимость результатов труда от профессионализма специалиста, выполняющего данную работу.
Дуговая сварка не плавящимся электродом в среде аргона
Сварка при помощи штучных электродов
В современной терминологии этот процесс дуговой сварки называется ММА. Это англоязычное название (от Manual Metal Arc), в наших учебных пособиях и инструкциях иногда применяется аббревиатура РДС. При этом способе эл ток в постоянном или переменном формате подводится на электрод и свариваемую деталь.
Дуга естественным плавлением обрабатывает электрод и поверхность детали. При этом электрод образует отдельными каплями материал для смешивания с расплавляемой поверхностью детали. Глубина проплавления регулируется сварщиком и зависит от того, каковыми являются:
- сила подаваемого эл тока,
- диаметр используемого электрода,
- положение (вертикальное, угловое или горизонтальное) сварки,
- скорость перемещения сварочной дуги по обрабатываемой площади предполагаемого шва,
- вид соединения (одинарный, двойной и так далее),
- форма и размеры обрабатываемой кромки детали
и другие факторы, влияющие на процесс сварки.
Отдельно можно рассмотреть процесс зажигания и поддержания дуги, установку необходимых параметров сварочного тока. Однако в большинстве случаев при сварке используется аппарат в виде инвертора, где эти функции прописываются отдельно, в прилагаемой инструкции, применительно к каждой модели и диаметру используемого электрода.
Дуговая сварка под флюсом
Наиболее часто этот способ используется в промышленных отраслях, когда есть необходимость в сварке изделий, содержащих:
- различные сплавы,
- сталь,
- цветные металлы,
поскольку этот способ:
- высокопроизводителен,
- отличается отменным качеством работ и стабильным соединением свариваемых поверхностей,
- заметно улучшает условия трудового процесса,
- значительно меньше расходует эл энергии и материалов для сварки.
Дуговая сварка под флюсом
В углекислом газе предполагается наличие смесей с инертными/активными газами, для создания максимальной эффективности горения дуги. Недостатком (и весьма существенным) данного способа специалисты считают ограниченность положений для ведения работ. Поскольку отклонение от горизонтального даже на 10 градусов приводит к стеканию флюса и металла, сварочный процесс можно осуществлять только в положении снизу.
Этот способ используется в режиме однодуговой сварки, при котором используется один электрод. При этом происходит горение сварочной дуги между подаваемой проволокой (играющей роль электрода) и деталью (свариваемой поверхностью), которая находится под слоем флюса. Постепенным плавлением флюса, в образуемом при этом газе происходит образование полости (так называемый газовый пузырь), где и обеспечивается горение дуговой сварки.
Этот вид сварки возможен, как в режиме переменного тока, так и при постоянном токе. Иногда используется двухдуговая или многодуговая сварка, при этом аппарат для подачи питания может быть один или несколько.
Способ ручной дуговой сварки TIG
Такой способ возможен при использовании неплавящегося электрода в защитном инертном и углекислом газе, образующих эффективно действующую смесь. Современный метод сварки TIG закладывается в качестве одной из функций практически во всех новинках инверторов.
Любой аппарат XXI века обладает ей, в совокупности с другими вспомогательными функциями. Расшифровывается эта аббревиатура, как Tungsten Inert Gas, а поскольку лучший неплавящийся материал – это вольфрам, то зачастую можно встретить аббревиатуру WIG.
При этом способе происходит ручная или автоматическая подача проволоки, играющей роль электрода. В любом случае, в углекислом газе смешивается один из инертных газов, чаще всего аргон. Поэтому такую сварку называют еще аргонно-дуговой (АДС). Помимо аргона применяются также:
- всевозможные газовые смеси,
- азот,
- гелий,
а иногда используется атомно-водородная сварка, похожая на сварку TIG. С момента открытия преимуществ сварки в углекислом газе и его смесях с инертными газами этот способ стал широко использоваться в промышленных отраслях. При этом дуговая сварка плавлением обрабатываемой поверхности неплавящимся электродом может производиться во всех трех указанных выше режимах, начиная от ручного режима и заканчивая режимом автоматическим. Используемый сварочный аппарат позволяет применять все виды электродов, начиная от самого тонкого и заканчивая самыми толстыми.
Дуговая сварка в режиме MIG/MAG. Это сварка с использованием плавящегося электрода. Она также производится в углекислом газе со всевозможными инертными/активными газами:
- азотом,
- гелием,
- кислородом,
- аргоном
и другими.
При этом, соединяясь в углекислом газе, эти дополнительные компоненты образуют наиболее эффективную смесь для полноценного поддержания дуговой сварки, происходящей плавлением электрода и обрабатываемой детали. Этот современный метод также поддерживает любой аппарат из числа имеющихся на российском рынке сварочных инверторов. Использование различных смесей с углекислым газом необходимо соотносить с конкретными параметрами предполагаемого технического задания.
Какие нужны электроды для электродуговой сварки?
В работе со сваркой наблюдается такая тенденция: комфорт и быстрота выполнения работ напрямую зависит от качества электродов, которые Вы использовали для сварки того или иного изделия. Низкое качество, неподобающие условия хранения или использование просроченных электродов – все это и образует качество изделия.
При дуговой сварке температура составляет более 3000 градусов. Осуществляется она путем сваривания частей будущего изделия при нагреве. Используется дуговая сварка для того, чтобы получить неразъемные конструкции, которые могли бы выдерживать большое давление. Также она часто применяется и в слесарном деле.
Среди достоинств можно привести следующее:
- — Высокая прочность швов;
- — Большая экономия денежных ресурсов;
- — Имеется прекрасная возможность соединения деталей разных сортов стали;
- — Возможность производить ремонт чугунных изделий;
С помощью этого вида сварки Вы можете осуществлять соединение одинаковых по типу металлов. Электрическая дуга возникает вследствие того, что электрический ток проходит между деталями и электродом.
Электродуговая сварка делится на несколько видов:
- Сварка плавящимся электродом;
- Сварка под флюсом;
- Ручная дуговая сварка;
1.) Если сваривание происходит с помощью плавящегося электрода, то электрическая дуга производит расплавку электрода. В этом случае защитные газы используются для того, чтобы защитить процесс сваривания от атмосферных воздействий. В качестве газов-защитников выступают гелий, аргон и СО2.
2.) В случае использования сварки под флюсом, электрод подается под слой флюса. Само горение дуги осуществляется за счет образующегося газового пузыря, расположенного между свариваемым металлом и слоем флюса. Благодаря использованию этого метода сваривания увеличивается глубина проплавления и защита металла от воздействия окружающей среды становится еще большей.
3.) Если же Вы решили использовать метод ручной дуговой сварки, то Вам нужно обязательно использовать электроды с покрытием. Когда происходит плавление, создается специфический слой защиты, который гарантирует надежную защиту от атмосферных воздействий.
Также этот метод сваривания способствует правильному формированию шва, легированию шва, устранение неметаллических включений и стабильности горения дуги, которое очень важно. Этот способ является самым сложным из всех вышеперечисленных.
Также для более качественного и быстрого сваривания Вам нужно придерживаться правил техники безопасности, которые не только обезопасят Вашу жизнь, но еще и ускорят процесс работы. Для этого Вы можете сделать выгодные покупки в одного или нескольких заводов-изготовителей электродов и сварочного оборудования. Ссылки на их сайты Вы можете найти на странице этого сайта «Контакты». Также на этих сайтах Вы можете оформить заказ на любое сварочное оборудование и совершить выгодные покупки у наших партнеров.
Ручная электродуговая сварка и наплавка
Рис. 1. Схема сварки по способу Бенардоса Н. Н.:
1 — электрическая дуга; 2 — присадочный пруток; 3 — угольный электрод; 4 — держатель; 5 — свариваемый металл.
Температура дуги зависит от силы тока, приходящейся на единицу площади поперечного сечения электрода, — плотности тока. Чем она больше, тем выше температура дуги. При ручной дуговой сварке плавящимся электродом плотность тока от 10 до 20 А/мм2 и напряжение 18…20 В.
В ремонтной практике для сварочных работ используют переменный и постоянный ток. Сварочная дуга на переменном токе малой плотности горит неустойчиво. Чтобы повысить стабильность дуги, увеличивают плотность тока. По этой причине при сварке мелких деталей возрастает опасность их прожигания, однако из-за простоты источников питания сварку на переменном токе применяют достаточно широко. При сварке на постоянном токе дуга горит стабильно. Это позволяет использовать малые токи и сваривать тонкие детали, а кроме того, можно изменять полярность тока. Поэтому, несмотря на более сложное и дорогое оборудование источников питания, постоянный ток применяют в практике все шире.
Коэффициент наплавки зависит от присадочного материала, материала электродов и состава их покрытия, рода и полярности тока, а также от потерь при сварке. Для различных условий коэффициент наплавки находят опытным путем. При ручной сварке он колеблется в пределах от 6 до 18 г/ (А • ч) или составляет в среднем 8…12 г/ (А- ч).
Под действием высокой температуры в зоне сварки молекулы кислорода и азота, попадающие из воздуха, частично распадаются на атомы. Кислород образует оксиды железа и способствует выгоранию ценных легирующих элементов (марганца, кремния и др.), тем самым резко ухудшая свойства наплавленного слоя. Азот образует нитриды, которые увеличивают твердость, снижают пластичность и способствуют образованию коробления и трещин. Водород, попадающий в зону сварки из влаги и ржавчины, способствует образованию пор и трещин. Чтобы уменьшить вредное воздействие этих элементов, место сварки зачищают, а зону сварки защищают нейтральными газами и шлаками.
Сварочная проволока и электроды. Качество наплавленного материала и производительность процесса сварки или наплавки во многом определяются материалом электродов и их покрытий. В зависимости от способа сварки применяют сварочную проволоку, плавящиеся и неплавящиеся электродные стержни, пластины и ленты. Наибольшее применение в качестве электродного материала находит выпускаемая промышленностью электродная сварочная проволока. При механизированных способах сварки ее используют без покрытия, а для ручной дуговой сварки проволоку рубят на стержни длиной 350…400 мм и на их поверхность наносят покрытие. Плавящийся стержень с нанесенным на его поверхность покрытием называют сварочным электродом.
Стальная сварочная проволока изготавливается диаметром от 0,3 до 12 мм. В зависимости от химического состава стальную сварочную проволоку разделяют на низкоуглеродистую, легированную и высоколегированную.
Низкоуглеродистые проволоки Св-08, Св-08А, Св-08ГА, Св-ЮГА и другие — всего шесть марок, содержащие не более 0,12% углерода, предназначены для сварки мало- и среднеуглеродистых, а также некоторых низколегированных сталей.
Легированные проволоки Св-08Г2С, Св-08ХН2М, Св-08ХГСМФА и другие включают в себя до шести легирующих элементов с их общим содержанием не более 6%. Эти проволоки применяют для сварки и наплавки углеродистых и легированных сталей. Проволоки марок Св-15ГСТЮЦА и Св-20ГСТЮА можно использовать для изготовления стержней и применять при сварке без дополнительной защиты.
Высоколегированные проволоки Св-12X13, Св-06Х19М9Т и другие — всего 41 марка — содержат в своем составе легирующих элементов более 6%. Эти проволоки применяют для сварки нержавеющих, жаростойких и других специальных сталей.
Сварочные электроды выпускаются промышленностью как плавящиеся, так и неплавящиеся. Угольные неплавящиеся электроды изготавливают в виде стержней длиной до 300 мм и диаметром от 6 до 30 мм. Плавящиеся электроды, занимающие ведущее место в сварке, выпускают покрытыми различными элементами Для защиты зоны сварки. По своему назначению покрытия электродов делят на стабилизирующие, или тонкие, и качественные, или толстые.
Стабилизирующие покрытия содержат вещества, атомы которых легко ионизируются и поддерживают устойчивое горение дуги, а также облегчают ее возбуждение, особенно при сварке на переменном токе. Лучше всего ионизируются пары калия, а также кальция, который входит в состав мрамора и мела в виде углекислого кальция СаСОз. Наиболее простое и распространенное стабилизирующее покрытие—меловое: на 15…20 частей по массе натрового жидкого стекла берут 80…85 частей мела. Покрытие наносят на электрод тонким слоем — 0,1.—0,3 мм, и оно составляет 1…2% от массы электрода. Стабилизирующие покрытия не защищают наплавляемый металл от кислорода и азота воздуха, поэтому сварной шов получается сравнительно хрупким, со многими посторонними включениями.
Качественные защитные покрытия предохраняют наплавленный слой от кислорода и азота окружающего воздуха, а легирующие элементы, входящие в состав покрытия, позволяют получить сварной шов, не уступающий по механическим свойствам основному, металлу, а иногда и превосходящий его. 1,80), Г — с особо толстым покрытием (D:d3 > 1,80).
Защитные качественные покрытия по составу основных входящих в них веществ делят на группы: А — с кислым покрытием; Б — с основным покрытием; Ц — с целлюлозным покрытием; Р — с рутиловым покрытием; П — с покрытием прочих видов.
В соответствии с ГОСТ 9467—75 электроды для ручной дуговой сварки подразделяют на несколько типов, в каждый из которых входит несколько марок, обеспечивающих определенное качество сварочного шва.
Электроды типа Э42, Э42А, Э46, Э46А, Э50 и Э50А (марки АНО-1, АНО-5, УОНИ-13/45, УОНИ-13/55 и др.) предназначены для сварки углеродистых и низколегированных сталей с временным сопротивлением разрыву до 500 МПа. Буква А указывает на то, что электрод дает сварочный шов повышенного качества по пластичности и ударной вязкости.
Электроды типа Э55 и Э60 (марки УОНИ-13/55У и УОНИ-13/65) используют для сварки сталей с временным сопротивлением разрыву до 600 МПа.
Электроды типа Э70, Э85, Э100 и Э150 (марки УОНИ-13/85, НИАТ-3, НИАТ-ЗМ и др. ) используют для сварки сталей высокой прочности с временным сопротивлением разрыву свыше 600 МПа.
Электроды типа Э-09МХ, Э-09Х1МФ, Э-10ХЗМ16Ф и другие предназначены для сварки легированных высококачественных и теплоустойчивых сталей. К этим типам относят электроды марок ЦЛ-55, ЦЛ-20, ЦЛ-36, ЦЛ-26М и др.
Электроды типа Э-10Г2, Э-12Г4, Э-30Г2ХМ и другие (марки ОЗН-ЗООУ, ОЗН-400У и др.) используют преимущественно для наплавки деталей, работающих в тяжелых условиях ударных нагрузок и повышенного износа.
Выбор электродов и рода тока зависит от толщины и химического состава свариваемого материала, от конфигурации детали, расположения накладываемых швов и других факторов. Поэтому марку электрода в каждом конкретном случае должен выбирать квалифицированный специалист по сварке. Общие же положения по выбору электродов, силы и рода тока можно свести к следующему.
Детали толщиной более 5 мм хорошо сваривать на переменном токе. Стальные детали толщиной менее 5 мм, а также чугун и цветные металлы лучше варить на постоянном токе. При сварке на постоянном токе стабильно горение дуги на малых токах и, кроме того, можно маневрировать полярностью тока. Если сваривают тонкие детали, то, чтобы избежать прожога, их подключают к катоду (на минус), а электрод — к аноду (на плюс). При сварке толстых деталей анод подключают к детали, а катод — к электроду.
Толщину стержня электрода выбирают в зависимости от толщины свариваемой детали. Для сварки металла большей толщины берут электрод с более толстым стержнем и, наоборот, тонкие детали сваривают более тонким стержнем электрода. В ремонтной практике используют преимущественно электроды со стержнем диаметром от 2 до 5 мм.
Аргонно-дуговая сварка — разновидность сварки в инертных газах. Сущность ее заключается в том, что зону сварки и электрод защищают от воздуха аргоном, гелием или их смесями. Инертные газы хорошо ионизируются и создают условия для устойчивого горения дуги. Так как из инертных газов наибольшее распространение получил аргон, сварку называют аргонно-дуговой.
Преимущества такой сварки: надежная защита зоны сварки от действия кислорода и азота окружающего воздуха, более высокая производительность сварки из-за большей тепловой мощности дуги и, самое главное, возможность сварки многих трудносваривающих-ся металлов и сплавов, в том числе разнородных. Этим способом сваривают нержавеющие стали, алюминий и его сплавы, магнитные и жаропрочные сплавы, титан, медь, латунь, бронзу и другие металлы. При данной сварке используют неплавящиеся и плавящиеся электроды.
В качестве неплавящихся электродов применяют вольфрамовые стержни диаметром от 0,8 до 6 мм или такие же стержни с добавками оксида циркония, лантана или тория, которые более стойкие, чем чисто вольфрамовые. Присадочный материал в виде проволоки направляют в зону сварки вручную или специальным подающим механизмом. Сварку ведут на постоянном и переменном токе.
Горелки ручной аргонно-дуговой сварки неплавящимся вольфрамовым электродом состоят из головки и корпуса, к которому присоединен кабель с шлангом для аргона и токопроводом воздушного или водяного охлаждения. Вольфрамовый электрод закреплен под колпаком. Сопло служит для формирования потока защитного газа вокруг зоны сварки. При механизированной подаче присадочного материала проволоку в гибком шланге крепят к корпусу горелки.
Рис. 2. Горелка для аргонно-дуговой сварки не-плавящимся электродом:
1 — проволока; 2 — вольфрамовый электрод; 3 — сопло; 4 — головка; 5 — колпак; 6 — корпус.
Для сварки цветных металлов и легированных сталей толщиной до 2,5 мм используют горелки ЭЗР-З-66 с естественным воздушным охлаждением. Для сварки крупных деталей из чугуна и легированных сталей применяют горелки с водяным охлаждением типа ГНР-160, ГНР-315 и др.
Источники питания током. На ремонтных предприятиях в качестве источников питания током при электродуговой сварке широко используют сварочные трансформаторы, преобразователи и выпрямители. Все источники питания снабжены устройством для регулировки тока.
Сварочные трансформаторы используют для питания сварочной дуги переменным током. Применяются трансформаторы СТН-350, СТН-500, ТСК-300, ТСМ-500, ТД-300 и ТД-500. Цифры в марке трансформатора указывают значение номинального тока. Лучшие — трансформаторы последних моделей типа ТД. Они могут работать в двух диапазонах малых токов, но с повышенным напряжением холостого хода.
Сварочные преобразователи используют для питания сварочной дуги постоянным током. Преобразователь чаще всего состоит из генератора постоянного тока и электродвигателя, смонтированных на одной раме. Якорь генератора и ротор электродвигателя обычно размещены на одном валу и снабжены вентилятором для охлаждения во время работы.
На ремонтных предприятиях широко применяют преобразователи марок ПСО-300-2У2, ПСО-300-2Т2, ПСО-315МУ2, ПСО-500, ПСГ;500 и универсальные преобразователи ПСУ-300, ПСУ-500, А.СУМ-400 и др. Последние, кроме устройств для регулировки тока, оборудованы приспособлениями для регулировки напряжения.
Для сварки в полевых условиях промышленность выпускает сварочные агрегаты с двигателем внутреннего сгорания. Сварочный генератор и двигатель смонтированы на одной раме и соединены эластичной муфтой. Наибольшее применение получили передвижные агрегаты АСБ-300-МУ1, АСД-300-7МУ1, АСБ-300-7У1. Их характеристики: номинальный сварочный ток 320 А с пределами регулирования 75…320 А и номинальное напряжение 30 В.
Сварочные выпрямители получают все большее распространение в качестве источников питания сварочной дуги постоянным током. Они состоят из понижающего трехфазного трансформатора и выпрямительного блока с кремниевыми или германиевыми и селеновыми вентилями. Кроме того, они снабжены вентилятором и пускорегулирующей аппаратурой. Все механизмы смонтированы в одном корпусе. Сварочные выпрямители имеют ряд преимуществ перед сварочными преобразователями: меньший удельный расход энергии, меньшую массу и габариты, проще в обслуживании. Для сварки при ремонте машин используют выпрямители марок ВД-306, ВД-502 и универсальные модели ВДУ-305, ВДУ-504 и др.
Особенности технологии ручной электродной сварки и наплавки заключаются в следующем.
Сварка и наплавка стальных деталей. Хорошее качество сварки и наплавки стальных деталей во многом зависит от химического состава металла, от содержания в нем углерода и легирующих примесей.
Малоуглеродистые и низколегированные стали удовлетворительно свариваются обычным способом. Многослойную заварку или наплавку этих сталей ведут так, чтобы при наложении последующего слоя предыдущий не успевал охладиться до температуры ниже 200°С. Сталь, легко поддающуюся закалке, перед сваркой подогревают до температуры 200…250 °С; то же выполняют при сварке на морозе. Углеродистые и низколегированные стали сваривают и наплавляют преимущественно электродами типов Э42 и Э46 с рутиловым покрытием марок АНО-4, АНО-5, ОЗС-4 и др. При сварке деталей из конструкционных сталей наилучшее качество дают электроды типа Э42А с фтористокальциевыми покрытиями УОНИ-13/45, ОЗС-2. Для наплавки быстроизнашивающихся поверхностей, работающих в абразивной среде, когда необходима их повышенная твердость, лучше применять электроды марок Т-590, Т-620, 13 КН, Х-5. Шов получается менее пластичный, но с твердостью порядка HRC 56…62 без термообработки.
Детали с цементованными поверхностями и высокой твердостью (кулачки распределительных валов, тарелки толкателей и. др.) восстанавливают электродами ОЗН-400У и ЦН-4. Эти электроды обеспечивают твердость слоя HRC 45…55 без термической обработки. Перед наплавкой с кулачков распределительных валов снимают наждачным кругом верхний наклепанный слой металла толщиной 1…2 мм. При наплавке распределительный вал частично погружают в воду, чтобы уменьшить коробление и избежать нарушения термической обработки участков, расположенных близко к зоне сварки. Так же наваривают тарелки толкателей клапанов.
Тонкостенные стальные детали кабин, оперения, топливных баков и других толщиной менее 2 мм сваривают с отбортовкой кромок на 90 или 180°. Отбортованные кромки лучше сваривать угольным электродом без присадочного материала. При сварке тонкостенных деталей плавящимся электродом используют источники питания постоянным током, позволяющие получать малый ток при повышенном напряжении.
Стальные детали толщиной от 1 мм до сотых долей миллиметра успешно сваривают аргонно-дуговой сваркой неплавящимся электродом с применением специальных транзисторных источников питания типа АП-4, АП-5 и АП-6. Они позволяют вести сварку на постоянном импульсном токе прямой и обратной полярности. Пределы регулирования тока в этих аппаратах от 0,05 до 300 А.
Баки, бочки, автоцистерны и другие сосуды из-под топлива перед сваркой тщательно очищают от следов нефтепродуктов или заполняют отработавшими газами карбюраторных двигателей, предварительно очистив их пропусканием через воду.
Сварка чугунных деталей. Восстановление чугунных деталей сваркой — трудный процесс, обусловливаемый химическим составом чугуна, его структурой и особыми механическими свойствами. По химическому составу чугун — сплав железа с углеродом (2…3,6%), содержащий некоторое количество кремния, марганца, фосфора, серы и других примесей.
Механические свойства чугуна во многом зависят от того, в каком виде находится углерод. Если большая часть углерода содержится в связанном состоянии в виде цементита (ЕезС), то такой чугун более светлого цвета, очень тверд, хрупок и не поддается механической обработке. Его часто называют белым и почти не применяют для изготовления деталей. Наиболее широкое применение получил серый чугун. В нем большая часть углерода находится в структурно-свободном состоянии в виде пластинчатых включений графита. Серый чугун также хрупок, но достаточно мягок и легко поддается обработке.
При быстром охлаждении серого чугуна, расплавленного или нагретого до температуры выше 750 °С, графит легко переходит в цементит (то есть чугун отбеливается) и, кроме того, закаливается. Относительное удлинение чугуна при разрыве практически равно нулю, поэтому при неравномерном нагреве или остывании почти всегда возникают большие внутренние напряжения и трещины. В расплавленном состоянии чугун текуч и мгновенно переходит из жидкого состояния в твердое, минуя пластическое. Все эти свойства чугуна в большой степени затрудняют его сварку.
Разработано и применяется много способов сварки чугуна, но рекомендовать какой-либо из них для восстановления конкретной детали весьма затруднительно, так как даже у одной корпусной детали со стенками разной толщины может быть различная структура чугуна и потребуются различные способы их сварки. Прибли-’ женно все способы сварки чугунных деталей делят на два вида: горячую и холодную.
Горячая сварка. Деталь перед сваркой подогревают, а после — медленно охлаждают. Лучшая температура, обеспечивающая высокое качество сварки, 600…650°С. Более высокий нагрев вызывает рост графитных зерен, а при нагреве свыше. 750°С происходят уже химические и структурные изменения. Скорость охлаждения от начала затвердевания наплавленного металла до 600°С должна быть не более 4 °С в секунду. При большей скорости охлаждения ухудшается процесс графитизации и происходит отбеливание чугуна.
Мелкие детали подогревают до температуры 150…200 °С. Чтобы избежать появления деформаций и трещин, подогрев и охлаждение ведут медленно и равномерно.
Заварку дефекта ведут чугунными электродами больших диаметров (12…14 мм) на повышенном сварочном токе (1200…1300 А), при большой ванне жидкого металла, чтобы создать необходимые условия для удаления газов и неметаллических включений из расплава. Сварку ведут только в нижнем положении шва и без перерыва до полного заполнения трещин. Перед сваркой концы трещины засверливают и вдоль трещины делают разделку под шов. Чтобы предупредить растекание жидкого чугуна,’ место заварки заформовывают графитными или угольными пластинами.
Сварка чугуна с предварительным подогревом обеспечивает, как правило, хорошее качество наплавленного металла, но очень трудоемка, поэтому ее применяют все реже и реже.
Холодная сварка. Ее выполняют без предварительного подогрева детали различными способами и с применением специальных электродов.
I. Сварка чугуна стальными электродами обычным способом почти всегда вызывает образование зоны отбеленного чугуна и зоны закаленного чугуна вдоль завариваемой трещины, а наплавленный валик представляет собой закаленную высокоуглеродистую сталь. Кроме того, вдоль наплавленного валика очень часто появляется одна новая трещина или несколько. Чтобы избежать, этих дефектов, применяют многослойную наплавку электродами из малоуглеродистой стали, или так называемый способ отжигающих валиков.
Вдоль трещины чугунной детали наносят V-образную глубокую разделку кромок и по обе стороны снимают литейную корку на расстоянии, примерно равном ширине разделки. На первый сварочный валик длиной 40…50 см сразу же накладывают второй, отжигающий валик. При наложении второго валика первый больше прогревается и затем остывает с меньшей скоростью. Значительная часть цементита распадается, выделяется графит, а закаленная часть шва частично отпускается и нормализуется. Верхний (отжигающий) валик уже меньше подвержен закалке, в результате чего резко снижается твердость всего шва и частично снимаются оста-’ точные напряжения.
Для повышения надежности заварки трещин в сильно нагруженных деталях (корпуса коробок передач, корпуса трансмиссий тракторов и др. ) на разделанных кромках трещин часто ставят в шахматном порядке на резьбе упрочняющие стальные шпильки или скобы. Диаметр шпилек d рекомендуют брать в пределах (0,15… 0>2) S, где S — толщина стенки, но не менее диаметра электрода. Расстояние между шпильками берут равным (4…6) of, глубину посадки 2d, расстояние от кромок не менее (l,5…2)cf. Сначала шпильки обваривают кругом, а затем наплавляют весь сплошной шов.
Первые слои в разделке трещины или обварку упрочняющих Шпилек выполняют специальным электродом ЦЧ-4, а все последующие — электродами типа УОНИ-13/55 или другими из стержней малоуглеродистой стали.
Восстановление чугунных деталей способом отжигающих валиков в сочетании с установкой упрочняющих шпилек, скоб И других связей дает удовлетворительные результаты. Однако при этом способе требуется большая подготовительная слесарная работа. Способ трудоемок, малопроизводителен, требует большого расхода электродного материала. Поэтому, когда не нужна высокая прочность сварочного шва, применяют сварку биметаллическими электродами.
II. Сварка чугуна электродами на основе никеля ПАНЧ-11 и ЦЧ-ЗА обеспечивает достаточно высокую прочность, отсутствие трещин и хорошую обрабатываемость наплавленного металла. Электроды ПАНЧ-11 изготавливают из никелевой проволоки ПАНЧ-11. В состав проволоки входят редкоземельные элементы, которые обеспечивают самозащиту в процессе сварки. Электроды типа ЦЧ-ЗА изготавливают из никельсодержащей проволоки Св-08Н50. В металле, наплавленном этим электродом, содержится 48… 50% никеля.
Электроды предназначены для холодной сварки серого и высокопрочного чугуна. Они рекомендуются для устранения дефектов в чугунных головках блоков, в блоках двигателей и в других ответственных деталях.
За рубежом широкое применение получили электроды с содержанием никеля до 90%. Однако эти электроды очень дорогие.
III. Сварку чугуна электродами на основе меди ведут во всех случаях, когда не требуется высокая прочность сварного шва.
Медно-железные электроды ОЗЧ-2 изготавливают из медного стержня с фтористокальциевым покрытием, в которое добавляют 50% железного порошка. Эти электроды используют при заварке трещин в водяных рубашках блоков двигателей, головках блока, резервуарах радиаторов и в других деталях. Слой, наплавленный электродами ОЗЧ-2, представляет собой медь, насыщенную железом с вкраплением закаленной стали, имеющей большую твердость. По границе шва отдельными участками располагаются зоны отбеливания. Несмотря на достаточно высокую твердость, шов можно обрабатывать твердосплавным инструментом.
Медно-никелевые электроды МНЧ-2 представляют собой стержни из монель-металла (28% меди, 2,5% железа, 1,5% марганца, остальное никель) или из сплава МНМц (40% никеля, 1,5% марганца, остальное медь). Никель этих электродов не образует соединений с углеродом, поэтому наплавленный шов имеет малую твердость и почти отсутствует зона отбеленного чугуна. Зона закаленного чугуна характеризуется высокой твердостью, которую можно легко снизить небольшим отпуском. Наплавленный шов обладает меньшей склонностью к образованию пор и трещин, легко поддается обработке, но прочность его низкая, поэтому медно-никелевые электроды часто применяют в сочетании с электродами ОЗЧ-2. Первый слой, чтобы обеспечить плотность, и последний, чтобы улучшить обработку, наносят электродами МНЧ-2, а остальное заплавляют электродами ОЗЧ-2.
Хорошие результаты при холодной сварке чугуна дают электроды АНЧ-1 со стержнем из аустенитной хромоникелевой проволоки Св-04Х19Н9 или Св-06Х19Н9Т, снабженным медной оболочкой и фтористо-кальциевым покрытием типа УОНИ-13/55. Сварку этим электродом ведут постоянным током 100… 120 А обратной полярности. Наплавленный шов плотный, легко поддается обработке, но недостаточно прочен, так как электрод содержит 75…80% меди.
Сварка цветных металлов и сплавов, особенно алюминиевых, достаточно широко применяется при ремонте, так как в современных тракторах и автомобилях многие детали изготовлены из цветных металлов.
Медь, бронза и латунь обычной дугой и плавящимся электродом свариваются плохо. Это объясняется тем, что в расплавленном состоянии медь и сплавы на ее основе обладают большой жидко-текучестью, хорошо растворяют газы, особенно кислород, легко окисляются. У них большой коэффициент линейного расширения и они подвержены значительным структурным изменениям в зоне сварки.
Медь и ее сплавы удовлетворительно свариваются электродами марок «Комсомолец-100», МН-5 и ОЗБ-1, а также угольным электродом на постоянном токе прямой полярности и достаточно хорошо свариваются аргонно-дуговой сваркой вольфрамовым электродом. Присадочным материалом служат круглые или прямоугольные прутки примерно такого же химического состава, что и свариваемый металл. При сварке угольным электродом в качестве флюса используют прокаленную до 500…550 °С буру. Наплавленный шов проковывают при температуре не выше 500°С, чтобы улучшить его механические свойства.
При сварке латуни и других медно-цинковых сплавов применяют прутки с повышенным содержанием цинка. При сварке выделяются ядовитые пары цинка, поэтому необходимы хорошая вентиляция рабочего места сварщика и применение респираторов.
Алюминий и его сплавы легко окисляются на воздухе, и поверхности деталей всегда покрыты плотной пленкой оксида алюминия AI2O3, температура плавления которого 2050°С (в то время как температура плавления чистого алюминия 660°С). Тугоплавкая и механически прочная пленка оксида алюминия создает основные трудности при его сварке. Кроме того, при нагревании алюминий и сплавы не изменяют цвета, а в расплавленном состоянии характеризуются большой жидкотекучестью, что также затрудняет сварку.
В качестве электродов или присадочного материала при сварке чистого алюминия и его сплавов используют прутки или проволоку, по химическому составу близкие к свариваемому металлу. В покрытия электродов или в флюс вводят хлористые и фтористые соли лития, калия, энергично растворяющиеся и ошлаковывающие оксид алюминия. Сварку ведут постоянным током обратной полярности, при которой в результате катодного распыления улучшаются условия разрушения оксидной пленки. При диаметре электрода 4…6 мм используют ток 120…150 А. После сварки во избежание разъедания металла шлак со шва удаляют, промывая горячей или подкисленной водой и тщательно протирая стальными щетками. Перед сваркой поверхность детали обезжиривают бензином или ацетоном и подвергают очистке механическим или ручным способом (стальной щеткой).
Для сварки чистого алюминия используют электроды ОЗА-1. Алюминиево-кремнистые сплавы (типа силумин) сваривают электродами ОЗА-2.
Чтобы избежать коробления, образования трещин и улучшить качество сварки, детали из алюминия и его сплавов перед сваркой подогревают до температуры 200…350°С (крупные детали до более высокой температуры). Температуру подогрева определяют термопарами или специальными карандашами. Концы трещин в деталях засверливают, а кромки разделывают под углом 60…90°. Расплавленный металл удерживают от растекания стальными или глиняными подкладками. Для получения мелкозернистой структуры металла шва деталь после сварки медленно охлаждают, а шов слегка проковывают. Внутренние напряжения снимают нагревом до температуры 300…350°С с последующим медленным охлаждением.
Аргонно-дуговая сварка вольфрамовым электродом дает возможность получать хорошие результаты сварки алюминия и его сплавов без применения флюса. Однако оксидную пленку и загряз-чения с поверхности детали перед сваркой требуется удалять более тщательно, чем при использовании флюса.
Меры борьбы со сварочными напряжениями и деформациями. При сварке и наплавке в деталях возникают собственные (внутренние) напряжения. Во многих случаях эти напряжения бывают настолько велики, что появляются трещины или коробление детали.
Основные причины образования напряжений и деформаций — неравномерный нагрев металла, литейная усадка расплавленного металла и структурные изменения, вызываемые большим нагревом и последующим быстрым охлаждением.
Наиболее эффективное средство снижения собственных напряжений — это подогрев детали перед сваркой и медленное охлаждение после нее. Предварительный подогрев в значительной степени снижает тепловые и усадочные напряжения, а медленное охлаждение предотвращает резкие структурные превращения, особенно в околошовной зоне.
Стали, податливые закалке, с содержанием углерода 0,35% и более подогревают до температуры 150…280 °С. Для получения наплавленного слоя хорошего качества высокоуглеродистые (более 0,55% углерода) и легированные стали после сварки или наплавки подвергают термической обработке, которая не только улучшает качество шва, но и снимает собственные напряжения. В некоторых случаях применяют высокотемпературный отпуск после наплавки, то есть нагрев до температуры 600…650 °С, выдержку при этой температуре из расчета 2…3 мин на 1 мм толщины металла и медленное охлаждение вместе с печью.
Рис. 3. Методы снижения деформаций при сварке и наплавке деталей:
а — последовательность наложения швов на симметричные детали; б — создание обратных деформаций.
Для подогрева деталей используют индукторы, много- и одно-пламенные газовые горелки, специальные печи и др. Применение предварительного нагрева, отпуска и термообработки всегда связано со значительным усложнением процесса и снижением производительности. Поэтому для уменьшения собственных напряжений и деформаций разработаны и успешно применяются менее трудоемкие способы.
При сварке и наплавке симметричных деталей сварочные швы накладывают в определенной последовательности, вызывающей уравновешивающие деформации. Иногда при подготовке деталей к сварке создают деформации, обратные деформациям, ожидаемым после сварки. При многослойной наплавке деталей рекомендуется послойная проковка швов пневматическим зубилом с закругленным лезвием. Чтобы не вызвать трещин и надрывов, первый и последний швы не проковывают. Не рекомендуется проковывать хрупкие и закаленные швы.
Деформации, возникшие в деталях после наплавки, устраняют механической или термической правкой. Для механической правки применяют молоты, различные правильные вальцы и прессы. При термической правке быстро нагревают до температуры 700…800 °С и охлаждают выпуклую сторону деформированной детали. Возникающие при этом уравновешивающие деформации выравнивают деталь.
Сварочные электроды нашли широкое применение в строительстве
Даже в эпоху инновационных технологий ручная электродуговая сварка по-прежнему сохраняет актуальность. Ее активно применяют в строительстве жилых, административных, промышленных зданий, транспортных магистралей, трубопроводов, машиностроении и многих других сферах. Привлекательность данной технологии состоит в том, что она позволяет сваривать металлоконструкции в любых пространственных положениях, независимо от вида стали.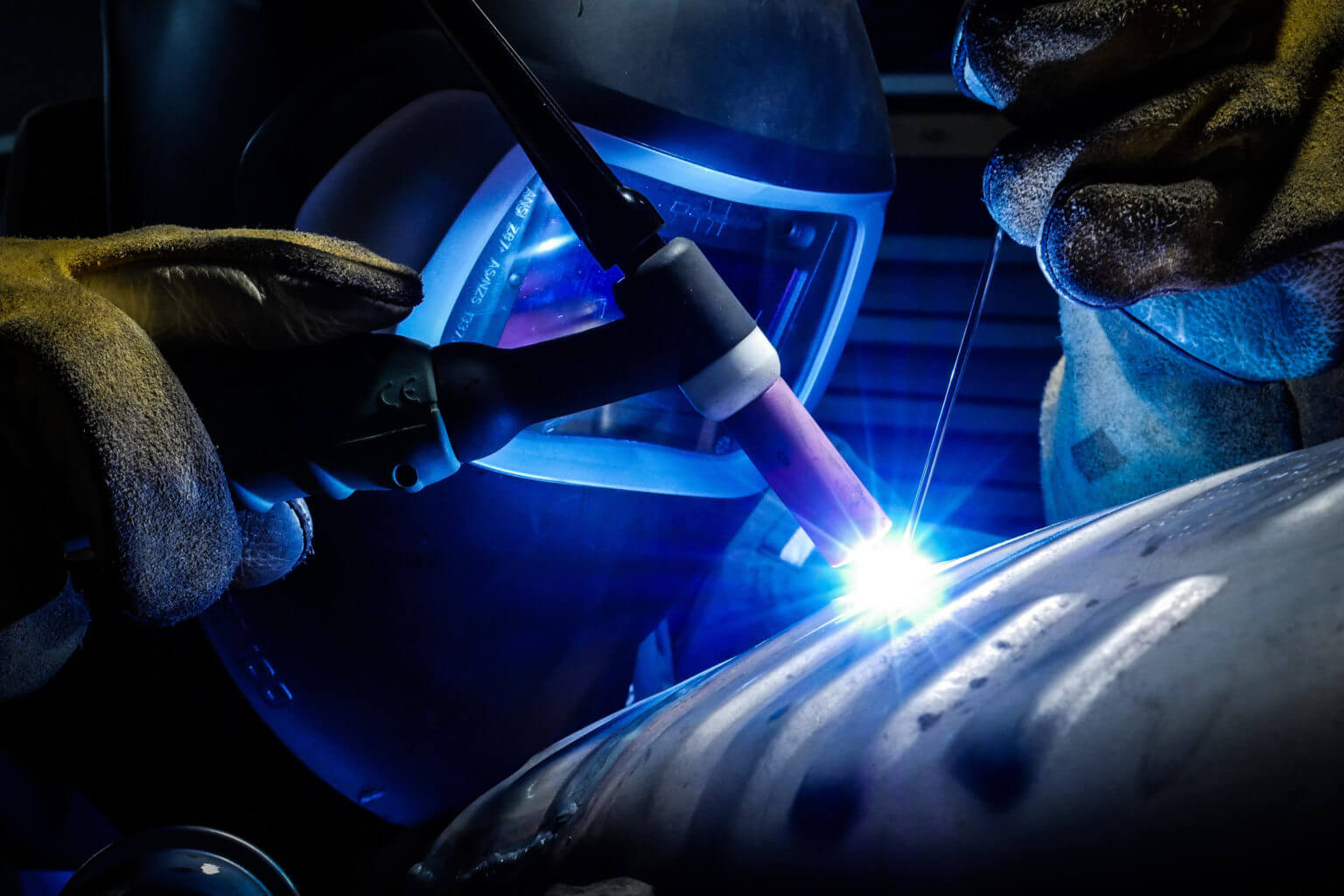
Огромным спросом на рынке СНГ пользуются сварочные электроды торговой марки «СпецЭлектрод». Их эксплуатационные характеристики с самого начала не вызывают сомнений. Этот факт подтверждается, в частности, сертификацией НАКС, Морского и Речного Регистра, Гост Р. Товары описываемого бренда действительно заслуживают внимания. По уровню качества они значительно превосходят китайские и украинские аналоги.
На сегодняшний день продукты ТМ «СпецЭлектрод» представлены потребителю в широком ассортименте. Среди них можно отметить АНО-21, ОЗС-12, МР-3. Этим марки электродов применяют для сварки углеродистых и низколегированных сортов стали. Эти же металлы, но с повышенными требованиями к качеству шва варят электродами УОНИ-13/55. Для нержавеющих сталей используют ЦЛ-11, ОЗЛ- 8, ЦТ-10, ЦТ-15 и др. Первые две марки электродов пригодны также для сварки пищевой нержавеющей стали.
Ввиду растущих требований к качеству расходных материалов, производителям приходится постоянно совершенствовать методологию. Ведь для того, чтоб электроды получили высокую оценку потребителя, они должны отвечать многим критериям. Например, обеспечивать стабильную электрическую дугу. Это позволит стержню не прожигать, а равномерно оплавлять металл, направляя его в сварочную ванну. Далее, защитить ванну, в свою очередь, призван шлак, образующийся при сгорании обмазки поверхности При этом важно, чтобы оплавление электрода и сгорание поверхности происходило синхронно. В противном случае дуга исчезнет. Кстати, после выполнения сварного шва шлак должен свободно осыпаться от легких ударов молотка.
Качественное соединение деталей возможно, если электрод обеспечивает хорошее формирование шва при минимальном разбрызгивании. Важно понимать, что во время эксплуатации металлоконструкция будет подвергаться различным нагрузкам. Степень ее надежности будет непосредственно зависеть от механической прочности шва. Решающим фактором при этом является качество электродов.
Как известно, ручная дуговая сварка – это не только сложный, но и достаточно вредный процесс. Она сопряжена с выделением продуктов горения, неизбежно вдыхаемых сварщиком. Уменьшить степень негативного воздействия на органы дыхания — тоже задача производителя электродов. В процессе оплавления они должны выделять как можно меньше дыма.
Электродуговая ручная сварка выполняется с помощью не только переменного, но и постоянного тока. В первом случае применяют однофазные или трехфазные трансформаторы, а во втором – выпрямители, преобразователи. Полярность при сварке переменным током не имеет значения, так как она все время меняется. При постоянном же токе возможна прямая или обратная полярность.
Электродуговая сварка — обзор
10.1.1.5 Сварочные установки
Типовые установки для дуговой сварки как для одиночных, так и для нескольких сварочных аппаратов описаны в национальных директивах, например, Директива по ОТОСБ № 118 Великобритании «Электробезопасность при дуговой сварке». При подключении сварочного контура следует придерживаться следующих передовых методов:
- •
соединение между источником сварочного тока и заготовкой должно быть как можно более прямым;
- •
использовать изолированные кабели и соединительные устройства соответствующей допустимой токовой нагрузки;
- •
посторонние токопроводящие части не должны использоваться как часть сварочного обратного контура, если только они не являются частью самой заготовки;
- •
зажим обратного тока должен располагаться как можно ближе к сварочной дуге.
При подключении кабелей сварочного тока и обратного тока важно обеспечить эффективный электрический контакт между соединительным устройством и заготовкой, чтобы предотвратить перегрев и искрение. Например, токовые и возвратные зажимы должны быть надежно прикреплены к «блестящему» металлу, т.е. любые ржавчины или грунтовочные покрытия должны быть локально удалены.
Источник питания и заземление Обычной практикой в Великобритании было обеспечение отдельного заземления для заготовки.Причина в том, что в маловероятном случае пробоя изоляции между первичной и вторичной цепями сгорают предохранители. Однако отдельное заземление увеличивает риск паразитных токов, которые могут вызвать повреждение другого оборудования и проводов.
Поскольку современные источники питания спроектированы с гораздо более высоким уровнем изоляции (так называемая двойная или усиленная изоляция), отдельное заземление не рекомендуется.
Потенциальная проблема заключается в том, что обе конструкции источника питания часто можно найти в одном сварочном цехе. Более новый источник питания (с двойной или усиленной изоляцией) можно определить по паспортной табличке источника питания (, рисунок 10.12, ), на которой будет указано, что он был изготовлен в соответствии с действующими стандартами, например EN 60974-1 или IEC 60974-1.
В старых конструкциях источников питания сварочная цепь иногда подключалась к корпусу источника питания внутри. Однако опасность заключается в том, что даже при отключенном обратном сварочном проводе и отдельном заземлении сварка возможна с током, протекающим через землю.Из-за риска повреждения защитного заземления и других разъемов этот тип источника питания считается устаревшим и не должен использоваться.
Требования к источнику питания Источникам питания потребуется одно- или трехфазное питание при 230 В переменного тока. или 400 В переменного тока Во многих частях Европы напряжение 230 В составляет 16 А, но в Великобритании стандартная кольцевая сеть составляет 13 А. Следовательно, относительно низкая выходная мощность системы 230 В дополнительно снижается, если установлена вилка на 13 А и специальный схема может потребоваться.
Трехфазные источники питания могут быть ограничены до 30 А, но для сварочного оборудования более высокой мощности может потребоваться источник питания на 45 или даже 60 А. Действующий ток указан на паспортной табличке. Это значение следует использовать для определения размера кабеля и требований к предохранителям.
Помимо очевидных опасностей, связанных с перегрузкой источника питания, например, перегрев и перегорание предохранителей могут вызвать проблемы с другим оборудованием. Если источник питания имеет высокий импеданс (обычно называемый мягким), как это может иметь место в сельской местности, питаемой по воздушным кабелям, большой ток потребления может привести к падению напряжения источника питания ниже уровней, что может вызвать проблемы с другим оборудованием.
Двигатели и моторные приводы Для оборудования, не питаемого от сети, такого как генераторы, предоставляется информация о характеристиках двигателя, нагрузке и скорости холостого хода, а также потребляемой мощности. Хотя этот тип оборудования может быть идеальным для сварки на открытом воздухе в удаленных местах, он, как правило, создает высокий уровень акустического шума. Уровни шума ограничены директивой ЕС, но могут достигать 97 дБА.
Окружающая среда Все источники питания должны иметь степень защиты IP, которая дает информацию о степени защиты оборудования от воды.Обычно оборудование имеет IP 21 или IP 23. Первая цифра означает, что нельзя прикасаться к токоведущим частям, а вторая цифра описывает защиту от проникновения воды. Источник питания с маркировкой IP 21 защищен от вертикальных капель воды, которые могут возникнуть, например, при протечке крыши. Если оборудование имеет маркировку IP 23, это означает, что оборудование защищено от воды под углом до 60 ° от вертикали и, таким образом, подходит для использования на открытом воздухе. Дополнительные буквы к номеру IP указывают на испытания с работающим вентилятором или без него и с повышенной механической защитой от поражения электрическим током.
Зоны повышенного риска находятся во влажных или влажных условиях, в замкнутых пространствах или когда сварщик подвергается воздействию больших площадей оголенного металла. Для использования в такой среде важно использовать источник питания с отметкой S, что означает, что напряжение холостого хода ниже 48 В (среднеквадратичное значение). переменный ток или 113 В пикового напряжения постоянного тока Если источник питания имеет более высокое напряжение холостого хода, следует использовать устройство понижения напряжения, которое ограничит напряжение на держателе примерно до 25 В.
Соответствующие стандарты для источников питания, оборудования и принадлежностей для дуговой сварки:
EN 60974-1: 1998, IEC 60974-1: 1998, «Оборудование для дуговой сварки — Часть 1: Источники сварочного тока»
EN 60974-7: 2000, «Оборудование для дуговой сварки, Часть 7, Горелки»
EN 60974-11: 1995, «Оборудование для дуговой сварки, Часть 11, Держатели электродов»
EN 60974-12: 1995, «Оборудование для дуговой сварки, Часть 12, Соединительные устройства для сварочных кабелей»
EN 169: 1992, «Спецификация фильтров для средств индивидуальной защиты глаз, используемых при сварке и аналогичных операциях»
EN 60529: 1992, «Спецификация степени защиты, обеспечиваемой кожухами» (коды IP)
EN 470-1: 1995, «Защитная одежда.
для использования в сварке и родственных процессах — общие требования »
EN 50199: 1996,« Электромагнитная совместимость (ЭМС) — стандарт на оборудование для дуговой сварки »
EN 50060: 1989« Источники питания для ручной дуговой сварки металлическим электродом. с ограниченной нагрузкой »
Электродуговая сварка: значение, процедура и оборудование
Прочитав эту статью, вы узнаете: — 1.Значение электродуговой сварки 2. Методика электродуговой сварки 3. Электрический ток для сварки 4. Значение полярности 5. Оборудование 6. Подготовка кромки стыка 7. Электроды.
Значение дуговой сварки:Дуговая сварка — это процесс сварки плавлением, при котором тепло, необходимое для плавления металла, получается от электрической дуги между основным металлом и электродом.
Электрическая дуга возникает, когда два проводника соприкасаются друг с другом и затем разделяются небольшим зазором от 2 до 4 мм, так что ток продолжает течь через воздух. Температура, создаваемая электрической дугой, составляет от 4000 ° C до 6000 ° C.
Используется металлический электрод для подачи присадочного металла. Электрод может быть покрыт флюсом или без покрытия. В случае неизолированного электрода поставляется дополнительный флюсовый материал. Для дуговой сварки используются как постоянный ток (DC), так и переменный ток (AC).
Переменный ток для дуги получается от понижающего трансформатора. Трансформатор получает ток от сети от 220 до 440 вольт и понижается до необходимого напряжения i.е., от 80 до 100 вольт. Постоянный ток для дуги обычно получают от генератора, приводимого в действие электродвигателем, патрульным или дизельным двигателем.
Напряжение холостого хода (для зажигания дуги) при сварке на постоянном токе составляет от 60 до 80 вольт, а напряжение замкнутой цепи (для поддержания дуги) составляет от 15 до 25 вольт.
Порядок электродуговой сварки: В первую очередь свариваемые металлические детали тщательно очищаются от пыли, грязи, жира, масла и т. Д.Затем заготовку следует надежно закрепить в подходящих приспособлениях. Вставьте подходящий электрод в электрододержатель под углом от 60 до 80 ° к заготовке.
Выберите правильный ток и полярность. Пятна отмечаются дугой в местах проведения сварки. Сварка выполняется путем соприкосновения электрода с изделием и последующего разделения электрода на необходимое расстояние для образования дуги.
Когда возникает дуга, возникающее при этом сильное тепло расплавляет изделие ниже дуги и образует ванну расплавленного металла.В изделии образуется небольшое углубление, и расплавленный металл осаждается по краю этого углубления. Это называется дуговой кратор. После остывания стыка шлак легко удаляется щеткой. По окончании сварки следует быстро вынуть электрододержатель, чтобы гасить дугу и отключать подачу тока.
Электрический ток для сварки: И DC (постоянный ток), и AC (переменный ток) используются для создания дуги при электродуговой сварке. У обоих есть свои преимущества и приложения.
Сварочный аппарат постоянного тока получает питание от двигателя переменного тока, дизельного / бензинового генератора или от твердотельного выпрямителя.
Вместимость машины постоянного тока:
Ток:
До 600 ампер.
Напряжение холостого хода:
от 50 до 90 вольт (для образования дуги).
Напряжение замкнутой цепи:
от 18 до 25 вольт (для поддержания дуги).
Сварочный аппарат переменного тока имеет понижающий трансформатор, который получает ток от основного источника переменного тока. Этот трансформатор понижает напряжение с 220 В до 440 В до нормального напряжения холостого хода от 80 до 100 В. Доступен диапазон тока до 400 ампер с шагом 50 ампер.
Мощность сварочного аппарата переменного тока:
Текущий диапазон:
До 400 ампер с шагом 50 ампер.
Входное напряжение:
220–440 В
Фактическое требуемое напряжение:
80 — 100 вольт.
Частота:
50/60 Гц.
Значение полярности:Когда для сварки используется постоянный ток, доступны два типа полярности:
(i) Прямая или положительная полярность.
(ii) Обратная или отрицательная полярность.
Когда работа делается положительной, а электрод — отрицательной, тогда полярность называется прямой или положительной полярностью, как показано на рис. 7.16 (a).
При прямой полярности около 67% тепла распределяется на рабочем месте (положительный полюс) и 33% на электроде (отрицательный полюс).Прямая полярность используется там, где при работе требуется больше тепла. Эта полярность используется в черных металлах, таких как низкоуглеродистая сталь, с более высокой скоростью и надежной сваркой.
(a) Прямая полярность.
(б) Обратная полярность
С другой стороны, когда работа выполняется отрицательной, а электрод — положительным, тогда полярность известна как обратная или отрицательная полярность, как показано на рис. 7.16 (b).
При обратной полярности около 67% тепла выделяется на электроде (положительный полюс) и 33% — на рабочем (отрицательный полюс).
Обратная полярность используется там, где при работе требуется меньше тепла, как в случае сварки тонких листов. Цветные металлы, такие как алюминий, латунь и никель, свариваются с обратной полярностью.
Оборудование, необходимое для дуговой сварки:Различное оборудование, необходимое для электродуговой сварки:
1. Сварочный аппарат:
Используемый сварочный аппарат может быть сварочным аппаратом переменного или постоянного тока.Сварочный аппарат переменного тока имеет понижающий трансформатор для понижения входного напряжения с 220-440 В до 80-100 В. Сварочный аппарат постоянного тока состоит из электродвигателя-генератора переменного тока, дизельного / бензинового двигателя-генератора или сварочного агрегата трансформатор-выпрямитель.
Аппарат переменного тока обычно работает от источника питания 50 или 60 Гц. КПД сварочного трансформатора переменного тока варьируется от 80% до 85%. Энергия, потребляемая на кг. наплавленного металла составляет от 3 до 4 кВтч для сварки на переменном токе и от 6 до 10 кВтч для D.C. Сварка. Сварочный аппарат переменного тока обычно работает с низким коэффициентом мощности от 0,3 до 0,4, в то время как двигатель при сварке на постоянном токе имеет коэффициент мощности от 0,6 до 0,7. В следующей таблице 7.9 показаны напряжение и ток, используемые для сварочного аппарата.
2. Держатели электродов:
Электрододержатель предназначен для удержания электрода под желаемым углом. Они доступны в различных размерах в зависимости от номинального тока от 50 до 500 ампер.
3.Кабели или выводы:
Назначение кабелей или проводов — отводить ток от машины к месту работы. Они гибкие и изготовлены из меди или алюминия. Кабели состоят из 900–2000 очень тонких проволок, скрученных вместе для обеспечения гибкости и большей прочности.
Провода изолированы резиновым покрытием, армированным волокном и, кроме того, толстым резиновым покрытием.
4. Кабельные соединители и наконечники:
Кабельные соединители предназначены для соединения переключателей машины и держателя сварочного электрода.Используются соединители механического типа; как они могут он собирается и снимается очень легко. Разъемы разработаны в соответствии с допустимой токовой нагрузкой используемых кабелей.
5. Отбойный молоток:
Отбойный молоток предназначен для удаления шлака после затвердевания металла шва. Он имеет форму долота и заострен с одного конца.
6. Проволочная щетка, колесо с силовым проводом:
Функция проволочной щетки заключается в удалении частиц шлака после измельчения отбойным молотком.Иногда, если возможно, вместо ручной проволочной щетки используется силовое колесо.
7. Защитная одежда:
Используемая защитная одежда предназначена для защиты рук и одежды сварщика от тепла, искр, ультрафиолетовых и инфракрасных лучей. Используемая защитная одежда — кожаный фартук, кепка, кожаные перчатки для рук, кожаные рукава и т. Д. Сварщик должен носить кожаные туфли с высокими щиколотками.
9. Экран или лицевой щиток:
Экран и маска предназначены для защиты глаз и лица сварщика от вредного ультрафиолетового и инфракрасного излучения, образующегося во время сварки.Экранирование может быть достигнуто с помощью головного или ручного шлема.
Подготовка кромки стыка:Эффективность и качество сварного соединения зависит также от правильной подготовки кромок свариваемых листов. Перед сваркой необходимо удалить с поверхности всю окалину, ржавчину, жир, краску и т. Д.
Очистку поверхности следует проводить механически с помощью металлической щетки или проволочного колеса, а затем химически с помощью четыреххлористого углерода.Необходимо придать правильную форму краям пластины, чтобы обеспечить надлежащий стык.
Форма кромок может быть простой, V-образной, U-образной, измененной и т. Д. Выбор различных форм кромок зависит от вида и толщины свариваемого металла. Некоторые различные типы канавок для кромок изделия показаны на рис. 7.17. БАДД
(i) Квадратный стык:
Применяется при толщине плиты от 3 до 5 мм. Обе свариваемые кромки должны находиться на расстоянии примерно 2-3 мм друг от друга, как показано на рис.7.17 (а).
(ii) Одинарный клиновой стык:
Применяется при толщине пластин от 8 до 16 мм. Оба края скошены, образуя угол примерно от 70 ° до 90 °, как показано на Рис. 7.17 (b).
(Iii) Двойной V-образный стык:
Используется, когда толщина листов превышает 16 мм и где сварка может выполняться с обеих сторон листа. Оба края скошены, чтобы образовать двойной V, как показано на Рис. 7.17 (c).
(iv) Одинарный и двойной U-образный стык:
Применяется при толщине пластины более 20 мм. Обработка кромок сложна, но стыки более удовлетворительны. Для этого требуется меньше присадочного металла, как показано на рис. 7.17 (d) и (e).
Электроды для дуговой сварки можно разделить на две большие категории:
1. Неплавящиеся электроды.
2. Плавящиеся электроды.
1. Нерасходуемые электроды:
Эти электроды не расходуются в процессе сварки, поэтому они и были названы неплавящимся электродом. Обычно они изготавливаются из углерода, графита или вольфрама. Угольные электроды более мягкие, в то время как вольфрамовые и графитовые электроды твердые и хрупкие.
Углеродные и графитовые электроды можно использовать только для сварки на постоянном токе, в то время как вольфрамовые электроды можно использовать как для сварки на постоянном и переменном токе. При использовании электродов этого типа присадочный материал добавляется отдельно.Поскольку электроды не перегорают, дуга получается стабильной.
2. Расходные электроды:
Эти электроды плавятся во время сварки и подают присадочный материал. Обычно они изготавливаются из того же состава, что и свариваемый металл.
Длину дуги можно поддерживать, перемещая электрод по направлению к изделию или от него.
Накладные электроды могут быть двух типов:
(i) Электроды без покрытия:
Доступны в форме непрерывной проволоки или стержней.Их следует использовать только с прямой полярностью при сварке на постоянном токе. Открытые электроды не защищают ванну расплавленного металла от атмосферного кислорода и азота.
Следовательно, сварные швы, полученные этими электродами, имеют более низкую прочность, более низкую пластичность и более низкую стойкость к коррозии. Они находят ограниченное применение при мелком ремонте и некачественных работах. Раньше они сваривали кованое железо и низкоуглеродистую сталь. В современной практике они не используются или используются редко. Их также называют простыми электродами.
(ii) Электроды с покрытием:
Иногда их также называют обычными электродами. Покрытие (тонкий слой) флюса наносится по всему сварочному стержню и, следовательно, называется электродом с покрытием. Флюс во время сварки защищает зону расплавленного металла от атмосферного кислорода и азота. Этот флюс также предотвращает образование оксидов и нитридов. Флюс химически реагирует с оксидами, присутствующими в металле, и образует легкоплавкий шлак с низкой температурой плавления.
Шлак плавает в верхней части сварного шва и может быть легко удален щеткой после затвердевания сварного шва. Качество сварного шва покрытым электродом намного лучше, чем у неизолированного электрода.
В зависимости от коэффициента покрытия или толщины флюсового покрытия электроды с покрытием делятся на три группы:
(а) Электроды со слабым покрытием.
(б) Электроды со средним покрытием.
(c) Электроды с сильным покрытием.
Сравнение трех типов покрытых электродов приведено в таблице 7.10:
Преимущества электродов с флюсовым покрытием:
Флюсовое покрытие сварочных электродов имеет ряд преимуществ. Вот некоторые из них:
1. Защищает зону сварки от окисления, создавая атмосферу газа вокруг дуги.
2. Он производит шлак с низкой температурой плавления, который растворяет примеси, присутствующие в металле, такие как оксиды и нитриды, и плавает на поверхности сварочной ванны.
3. Уточняет размер зерна свариваемого металла.
4. Добавляет легирующие элементы в свариваемый металл.
5. Он стабилизирует дугу с помощью определенных химикатов, обладающих этой способностью.
6. Уменьшает разбрызгивание наплавленного металла.
7. Концентрирует поток дуги и снижает тепловые потери. Это приводит к повышению температуры дуги.
8. Замедляет скорость охлаждения сварного шва и ускоряет процесс закалки.
9. Увеличивает скорость осаждения металла и получаемого проплавления.
Состав электродных покрытий:
Покрытие электрода может состоять из двух или более ингредиентов. Различные типы покрытий, используемые для разных типов свариваемых металлов.
Состав типовых электродных покрытий и их функции приведены в таблице 7 11. Некоторые из них обсуждаются здесь:
1.Шлакообразующие составляющие:
Шлакообразующие ингредиенты: оксид кремния (Sio 2 ), оксид марганца (Mno 2 ), оксид железа (F e O), асбест, слюда и т. Д. В некоторых случаях оксид алюминия (Al 2 o 3 ), но он делает дугу менее стабильной.
2. Составляющие для улучшения характеристик дуги:
Ингредиенты для улучшения характеристик дуги: оксиды натрия (Na 2 O), оксиды кальция (CaO), оксиды магния (MgO) и оксид титана (TIO 2 ).
3. Раскисляющие компоненты:
Раскисляющие ингредиенты: графит, алюминиевый порошок, древесная мука, карбонат кальция, крахмал, целлюлоза, доломит и т. Д.
4. Связующие компоненты:
В качестве связующего используются силикат натрия, силикат калия и асбест.
5. Легирующие компоненты:
Легирующие элементы, используемые для повышения прочности сварного шва: ванадий, кобальт, молибден, алюминий, хром, никель, цирконий, вольфрам и т. Д.
Спецификация электродов:
Спецификация электродов предоставлена Бюро индийского стандарта IS: 815-1974 (вторая редакция).
В соответствии с этим, электроды с покрытием определяются по:
(i) Буква префикса.
(ii) Шестизначный кодовый номер.
(iii) Буква суффикса.
(i) Буква префикса:
Буква префикса указывает на способ изготовления электродов.
Эти буквы префикса с указанием способа изготовления электродов приведены в таблице 7.12:
(ii) Шестизначный кодовый номер:
Шестизначный кодовый номер указывает рабочие характеристики и механические свойства наплавленного металла.
Значение каждой отдельной цифры от одного до шести приведено в Таблице 7. 13:
(iii) Буква суффикса:
Буква суффикса указывает на особые свойства или характеристики электрода.
Они приведены в таблице 7.14:
Первые цифры кодового номера по существу объясняют тип покрытия, используемого на электроде, и это покрытие обозначает рабочие характеристики.
В таблице 7.15 представлены семь типов покрытий, представляющих первую цифру числа:
Вторая цифра кода указывает положение сварки согласно таблице 7.16 дано ниже:
Третья цифра номера кода указывает режим сварочного тока, рекомендованный производителем электрода.
Они приведены в таблице 7.17:
Четвертая, пятая и шестая цифры кодового номера обозначают предел прочности на разрыв, максимальный предел текучести и относительное удлинение со значением удара.
Они приведены в таблице 7.18:
В дополнение к кодировке, указанной выше, все электроды должны соответствовать требованиям испытаний IS: 814 (части I и II) — 1974. Каждый пакет электродов должен иметь маркировку с указанием кода и спецификации.
Пример:
IS: 815 кодировка: E 315 — 411K
Спецификация: Ссылка: 814 (Часть-1)
Значение приведенного выше примера таково:
(i) Электрод изготавливается методом сплошной экструзии и подходит для дуговой сварки низкоуглеродистой стали. [E].
(ii) Покрытие электрода содержит значительное количество титана с основными материалами и будет производить жидкий шлак.[3].
(iii) Электрод подходит для сварки в плоском, горизонтальном, вертикальном и верхнем положении. [1].
(iv) Электрод пригоден для сварки на постоянном токе с положительной или отрицательной полярностью. Также подходит для сварки переменным током с напряжением холостого хода менее 90 вольт. [5].
(v) Электрод имеет диапазон растягивающих напряжений наплавленного металла от 410 до 510 Н / мм 2 . [411].
(vi) Электрод имеет максимальный предел текучести наплавленного металла 330 Н / нм 2 . [411].
(vii) Электрод имеет минимальное удлинение в процентах при испытании на растяжение наплавленного металла, равное 20 процентам на измерительной длине 5,65 √S o , а среднее значение ударной вязкости наплавленного металла составляет 47 Дж при 27 ° C. [411].
(viii) Электрод имеет железный порошок в покрытии, обеспечивающем извлечение металла от 130 до 150 процентов.
(ix) Электрод соответствует IS: 814 (Часть-I) -1974.
Проволока порошковая из недрагоценных металлов для электродуговой сварки (HS: 831120) Торговля продуктами, экспортеры и импортеры | OEC
Обзор Эта страница содержит последние данные о торговле проволокой с сердечником из недрагоценных металлов для электродуговой сварки.В 2019 году Проволока с сердечником из недрагоценных металлов для электродуговой сварки заняла 1979-е место в мире по объему продаж в мире с общим объемом продаж 1,01 млрд долларов. В период с 2018 по 2019 год экспорт проволоки с сердечником из недрагоценных металлов для электродуговой сварки вырос на 3,09%, с 980 млн долларов США до 1,01 млрд долларов США. Торговля Проволока порошковая из недрагоценных металлов для электродуговой сварки составляет 0,0056% от общего объема мировой торговли.
Проволока порошковая из недрагоценных металлов для электродуговой сварки является частью продуктов для пайки металлов с покрытием.
Экспорт В 2019 году ведущими экспортерами Проволока порошковая из недрагоценных металлов для электродуговой сварки были США (179 млн долларов), Китай (137 млн долларов), Южная Корея (131 млн долларов), Япония ( 69,6 млн долларов) и Вьетнам (61,1 млн долларов).
Импорт В 2019 году основными импортерами проволоки из недрагоценных металлов для электродуговой сварки были Китай (79,3 млн долларов), США (72,6 млн долларов), Канада (71,5 млн долларов), Мексика (67,5 млн долларов) и Японии (54 млн долларов).
Тарифы В 2018 году средний тариф на Проволока порошковая из недрагоценных металлов для электродуговой сварки составляла 10,3%, что делает его 2144-м наименьшим тарифом по классификации продукции HS6.
Страны с самыми высокими импортными пошлинами на Проволока порошковая из недрагоценных металлов для электродуговой сварки — это Багамы (41,8%), Иран (32%), Судан (35%) и Малайзия (30%). ). Страны с самыми низкими тарифами — Маврикий (0%), Южная Африка (0%), Гонконг (0%), Шри-Ланка (0%) и Сингапур (0%).
Рейтинг Проволока порошковая из недрагоценных металлов для электродуговой сварки занимает 850-е место в Индексе сложности продукции (PCI).
Описание Дуговая сварка — это процесс, в котором для генерации тепла между электродом и сварочной ванной используется электрический ток или дуга. Электрод обычно представляет собой расходный стержень. Для сварки на поверхность основного металла электродом обычно является проволока с покрытием.
Основные меры безопасности и проверки
Безопасность судов в море зависит от знаний, навыков и самостоятельности экипажа при выполнении работ по техническому обслуживанию и ремонту во время рейса и между постановкой в сухой док. Для их владельцев суда также зависят от здорового и компетентного экипажа, чтобы свести к минимуму производственные травмы, непредвиденные расходы и время нахождения судна вне дома.
Техническое обслуживание во время рейса является неотъемлемой частью работы члена экипажа, а такие задачи, как сварка на борту, являются обычным делом. Даже в этом случае важно, чтобы бригада, выполняющая сварочные работы на борту, выполняла это в соответствии со строгими принципами безопасности. Последствия несоблюдения правил техники безопасности или обслуживания оборудования могут быть очень серьезными.Для экипажа существует риск получения травм и долгосрочной опасности для здоровья.
Для судна риски для безопасности и целостности оборудования столь же серьезны, и в конечном итоге, если судно будет повреждено или перенаправлено из-за проблем со здоровьем или оборудованием, последствия могут быть также финансовыми. Крайне важно, чтобы со сварочным оборудованием и газами обращались безопасно и надежно — безопасность при эксплуатации всегда должна быть приоритетом. Вот правила техники безопасности и меры предосторожности, которые экипаж должен соблюдать до и во время электродуговой сварки на борту.
Переменный ток
Переменный ток (AC) всегда будет доступен на борту судна от электросети, но экипаж должен принять во внимание оборудование, которое им предлагается использовать, и принять соответствующие решения.
Доступны два типа сварочных аппаратов; трансформатор, который принимает переменный ток и подает переменный ток, но с более низким напряжением, и выпрямительные / инверторные машины, которые преобразуют переменный ток в постоянный ток (DC) на выходе при более низком напряжении.
Мы советуем экипажу избегать использования переменного тока при сварке на борту судна.Это связано с тем, что в случае случайного поражения электрическим током через тело человека передается переменный ток, что может вызвать судороги, которые могут привести к остановке сердца. Напротив, по поверхности сварщика будет протекать постоянный ток, если он случайно окажется частью электрической цепи.
Напряжение и частота
Основное назначение всех сварочных аппаратов — снизить высокое напряжение до подходящего безопасного рабочего напряжения. Рабочее напряжение сварочного аппарата называется напряжением холостого хода (OCV) или иногда называется напряжением без нагрузки.Определение OCV — это напряжение между выводами сварочного аппарата, который включен, но не используется.
В Кодексе правил безопасной работы для моряков торговых судов Управления морского судоходства и береговой охраны Великобритании указано, что максимальное напряжение должно быть следующим:
Для выпрямителей и инверторов постоянного тока: макс. 70 В постоянного тока
Для трансформаторов переменного тока макс. 25 В переменного тока
Поэтому первое, что должен проверить любой член экипажа перед началом работы, — это соответствие сварочного аппарата на борту этим значениям.На большинстве сварочных аппаратов это указано на табличке оборудования.
WSS также рекомендует избегать использования сварочных аппаратов, использующих высокие частоты (HF) для запуска процесса вольфрамового инертного газа (TIG). ВЧ могут создавать помехи для оборудования радиосвязи, а также могут мешать управлению пуском / остановом оборудования с электронным управлением, такого как насосы. Доступны низковольтные системы пуска TIG, использующие процесс «подъемной дуги», и поэтому нет необходимости использовать ВЧ для запуска процесса сварки.
Соответствие
В Европейском Союзе и на судах, плавающих под флагом стран-членов ЕС, экипаж также должен проверить, соответствует ли машина знаку соответствия европейскому (CE). Это форма «паспорта», которая позволяет товарам беспрепятственно перемещаться в Европу и по всей Европе, а также гарантирует, что машина соответствует директивам и стандартам ЕС по электричеству.
Стандарты, которым должно соответствовать сварочное оборудование в странах-членах ЕС, следующие:
EN 60974-10 Европейские нормы электромагнитной совместимости.
EN 60974-1 / 5 Европейские нормы для аппаратов для дуговой сварки: источники тока для сварки.
Операторам также следует обратить внимание на знак «S», указывающий на то, что оборудование подходит для использования в областях с повышенной опасностью поражения электрическим током. Это особенно важно при работе в потенциально влажных, влажных и стесненных местах, таких как двойное дно или балластные цистерны.
Обратный кабель
Еще одна область, требующая определенности, — это использование таких терминов, как «земля» и «земля».Обратный кабель сварочного аппарата часто называют заземлением, но это не так.
Термины «земля» и «заземление» используются в электротехнике США для обозначения электрического оборудования, которое надежно соединено с землей по соображениям безопасности. В Великобритании эквивалентными терминами являются «земля» и «заземление».
Обратный кабель аппарата для дуговой сварки пропускает столько же тока, сколько и сам сварочный кабель. Сварочный и обратный кабели являются частью электрической цепи.В результате, для безопасной сварки бригадир должен использовать возвратный зажим и кабель, которые должны быть размещены как можно ближе к месту сварки.
Размещение возвратного зажима к ближайшей арматуре с лампочкой приведет к тому, что корпус корабля окажется в этой области, что создаст риск поражения электрическим током. Фактически сварщик будет стоять на обратном пути, возможно, в некачественной обуви, в грязных перчатках, во влажных условиях, возможно, в соленой воде (отличный проводник электричества).
Если он лежит на животе или на спине в вспотевшем комбинезоне, он подвергает большие части тела действию живой палубы.Если сварочный кабель плохо изолирован, то использование корпуса в качестве обратного кабеля также может вызвать короткое замыкание, создавая искры и риск взрыва. Этот вид работы в сочетании с использованием трансформатора, подающего переменный ток с высоким OCV, может быть фатальным для сварщика.
Также следует помнить, что подключение обратного кабеля непосредственно к корпусу судна может также вызвать прохождение тока через шарикоподшипники и поршни, что приведет к повреждению. При сварке оборудования двигателя бригадир всегда должен протягивать обратный кабель и зажим к месту сварки и закреплять его как можно ближе к зоне сварки.
Будьте в безопасности при сварке
Во избежание поражения электрическим током и риска поражения электрическим током, а также для обеспечения безопасной работы судовой персонал должен принимать следующие меры предосторожности:
- Используйте только источники питания постоянного тока с OCV ниже 70 вольт;
- Поместите возвратный зажим и кабель как можно ближе к месту сварки;
- Помните, что через обратный кабель проходит столько же тока, сколько через сварочный кабель;
- Использование корпуса в качестве возвратного кондуктора противоречит правилам государства флага;
- Носите сухую изолированную защитную одежду и перчатки в хорошем состоянии, меняя их по мере необходимости, чтобы они оставались сухими;
- Изолируйте себя от обрабатываемой детали и обратного кабеля, надев обувь на резиновой подошве или встаньте на сухой изолированный коврик.
Не прикасайтесь к возвратной коробке никакими другими частями тела;
- Используйте полностью изолированные держатели электродов;
- Не используйте изношенные, поврежденные кабели, кабели недостаточного размера или плохо сращенные;
- Не наматывайте кабели, по которым идет ток, вокруг вашего тела;
- Не прикасайтесь к электроду под напряжением голыми руками;
- Выключайте все оборудование, когда оно не используется;
- Используйте только исправное оборудование. Отремонтируйте или замените поврежденные детали перед дальнейшим использованием;
- Следует избегать влажных условий труда.Даже потоотделение снижает сопротивляемость организма поражению электрическим током.
Эти моменты могут показаться очевидными, но, по нашему опыту, часто бывают случаи, когда бригада работает небезопасно. Результаты могут быть серьезными — и наиболее серьезными для задействованного экипажа.
Пример 1
Судовой слесарь настраивал свое сварочное оборудование, и, когда он устанавливал хлыст на питатель, одна рука коснулась металлического сопла хлыста, а другая рука касалась проволоки из питателя. Это замкнуло электрическую цепь, которая позволила 80-вольтовому электричеству пройти через его грудь. Сотрудник получил ожоги рук и был доставлен в больницу для лечения.
Пример использования 2
Судовой слесарь прибыл на борт корабля в начале смены и обнаружил на палубе воду после ночного ливня. Он знал об опасности поражения электрическим током, поэтому остановился на комингсе вокруг дверного проема, прежде чем потянуться к сварочному аппарату. К сожалению, его ботинки и рабочие перчатки были уже мокрыми.Когда сотрудник прикоснулся к сварочному аппарату, он замкнул электрическую цепь, и ток прошел через него, получив травмы, которые потребовали лечения в больнице.
Пример 3
Член экипажа вернулся на палубу корабля после ливня. Он торопился перевезти сварочный аппарат и закончить работу до обеда. Слесарь знал, что нельзя стоять в воде при работе с электрооборудованием, но он не заметил, что тонкая фанера, на которой он стоял, погружалась в воду в тот момент, когда он наступал на нее. Его одежда и ботинки были уже мокрыми от бури. Когда он коснулся оборудования, цепь замкнулась, и по его телу прошел ток. Его тоже пришлось доставить в больницу на лечение.
Посетите наш каталог сварочной продукции
Электродуговая сварка | PMI
Что такое сварщик?Сварщик — это человек, который использует ручное или дистанционно управляемое оборудование для соединения или резки металлических деталей. Они также заполняют отверстия, углубления или швы в металлических изделиях.*
Чего я могу ожидать, если я студент, изучающий электродуговую сварку?
Обладая 50-летним опытом, инструкторами по сварке PMI являются сертифицированные сварщики MIG, TIG, STICK и FLUX-CORE. Студенты получат возможность узнать об основных процессах сборки и сварки и смогут сделать карьеру с устойчивой заработной платой.
Какой основной учебный план я буду принимать?
- Обычное чтение для печати
- Газовая дуговая сварка вольфрамом (GTAW)
- Дуговая сварка защищенного металла (SMAW)
- Газовая дуговая сварка металлов (GMAW)
- Дуговая сварка порошковой проволокой (FCAW)
- Газовая вольфрамовая дуговая сварка — Труба
- Сварочное производство
Свидетельство выпускников сварки
У нас отличная сварочная программа. Но не верьте нам на слово. Посмотрите видео ниже и послушайте рассказ одного из наших выпускников, который сразу после окончания учебы устроился на работу сварщиком!
С каким оборудованием я могу работать?
- 18 Кабины сварочные
- Ножницы, пробойники и гибочные станки по металлу для металлургов
- Ленточная пила по металлу
- Фрезерный станок Bridgeport
- Lincoln Precision Tig и Square Wave Machines
- Машины Lincoln Power MIG
- Системы кислородно-ацетиленовой и плазменной резки
- Токарный станок по металлу Клаузинга
Посетите наш сварочный цех
Каковы перспективы работы сварщиков?
Предполагается, что занятость сварщиков, резчиков, паяльщиков и паяльщиков вырастет на 6 процентов с 2016 по 2026 год, что примерно так же быстро, как в среднем по всем профессиям. Рост занятости отражает потребность в сварщиках на производстве из-за важности и универсальности сварки как производственного процесса. Базовые навыки сварки одинаковы в разных отраслях, поэтому сварщики могут легко переключаться из одной отрасли в другую, в зависимости от того, где они больше всего нужны. Стареющая инфраструктура страны потребует опыта сварщиков, резчиков, паяльщиков и паяльных машин, чтобы помочь восстановить мосты, шоссе и здания. *
Наших выпускников принимают на работу!
Мы гордимся нашей отличной программой трудоустройства здесь, в PMI.Посмотрите видео ниже, чтобы услышать мнение одной из многих компаний, которые нанимали наших выпускников PMI на протяжении многих лет.
* Информация предоставлена Бюро труда и статистики США.
Сварка — Дуговая сварка — Электрод, металл, основа и газ
Электрическая дуга, используемая в сварочных процессах, создается между покрытым или неизолированным металлическим электродом и основным металлом или заготовкой. При дуговой сварке в защитном металлическом корпусе (SMAC) электрическая цепь устанавливается между сварочным аппаратом (источник постоянного или переменного тока постоянного или переменного тока), заготовкой, электрическими кабелями, электрододержателем, электродом и заземляющим проводом.Для зажигания дуги электрод должен касаться основного металла; Обычно это делается путем царапания или расклевывания электродом основного металла. Когда электричество начинает течь, электрод удерживается от основного металла, создавая зазор. Электрический ток течет через зазор, вызывая дугу. Сильное тепло от дуги расплавляет заготовку и электрод, содержащий металлический порошок, который при расплавлении становится присадочным металлом. Покрытие или покрытие на металлическом электроде представляет собой плавящийся флюс, который удаляет загрязнения из сварного шва и иногда создает газ, который защищает область от атмосферного загрязнения .По сути, электрод и его защита контролируют механические, химические и электрические характеристики сварного шва.
Тепло — 6 000–9 000 ° F (3 351–4 982 ° C) — электрической дуги переводит основной металл и расходуемый электрод в расплавленное состояние за считанные секунды.
Газовая дуговая сварка металлическим электродом (GMAW или MIG) аналогична SMAW. В этом процессе всегда используется постоянный ток (DC) и есть устройство подачи газа. Расходуемый электрод помещен в сопло, которое подает инертный защитный газ, такой как гелий или аргон.GMAW имеет несколько преимуществ перед SMAW. Благодаря GMAW скорость сварки выше, шлак не образуется, проплавление становится глубже, а электродная проволока подается непрерывно, что позволяет выполнять более длинные сварные швы. Типом дуговой сварки, в котором не используется плавящийся электрод, является дуговая сварка вольфрамовым электродом в газовой среде (GTAW или TIG). Между основным металлом и вольфрамовым электродом образуется дуга, используется защитный газ, и для охлаждения горелки требуется подача воды . Вместо расходуемого электрода при необходимости используется металлический стержень или сварочный стержень для обеспечения присадочного металла. Этот вид сварки еще называют гелиосваркой.
Дуговая сварка: определение и источник питания
В этой статье мы обсудим следующее: — 1. Определение дуговой сварки 2. Источник питания для дуговой сварки 3. Дуговая сварка постоянным и переменным током.
Определение дуговой сварки:
По определению, дуговая сварка — это процесс, при котором свариваемые куски металла доводятся до надлежащей температуры сварки в точке контакта за счет тепла, выделяемого на выводах дуги и в потоке дуги, так что металлы полностью плавятся. друг друга, образуя единую твердую однородную массу, после ее застывания.
В этом процессе электрическая дуга создается путем приведения двух проводников (электрода и металлической детали) к подходящему источнику электрического тока, на мгновение в контакте, а затем на небольшом расстоянии друг от друга. Ток продолжает течь через небольшой промежуток и выделяет сильный жар. Вырабатываемое тепло используется для плавления части заготовки и присадочного металла и, таким образом, образует соединение. Итак, дуговой сварной шов представляет собой соединение металлических деталей, выполненных локализованным нагревом без какого-либо давления.Поэтому иногда этот вид сварки называют сваркой без давления. Вырабатываемое дугой тепло также используется для резки металла.
Напряжение, необходимое для зажигания дуги, выше, чем необходимое для ее поддержания. Температура составляет порядка 3600 ° C, при которой для соединения не требуется механическое давление. Согласно BSS 638 максимальное напряжение, указанное для сварки, составляет около 100 вольт для безопасности оператора. Напряжение дуги варьируется от 20 до 40 вольт, а сила тока от 50 А при работе с листовым металлом до 1000 А при тяжелой автоматической сварке.
Сварочная схема для процесса электродуговой сварки представлена на рис. 6.9. Сварочная схема состоит из сварочного аппарата, двух выводов, электрододержателя, электрода и самой работы.
Электродуговая сварка широко применяется для соединения металлических деталей, ремонта сломанных отливок и заливок путем напыления нового металла на изношенные детали.
Дуговая сварка снова подразделяется на пять групп, а именно: углеродная дуговая сварка, металлическая дуговая сварка, атомно-водородная дуговая сварка, дуговая сварка металла в инертном газе и дуговая сварка под флюсом.
Источник питания для дуговой сварки :Для дуговой сварки используются как постоянный, так и переменный ток, и у каждого из них есть свои особенности; в некоторых случаях подходит любой из них.
Электрические свойства дуги определяют требования, которым должен соответствовать источник питания для дуговой сварки. Для зажигания дуги требуется более высокое напряжение, чем для ее поддержания в нормальных условиях. По этой причине напряжение холостого хода источника питания (при отсутствии дуги между электродом и изделием) должно быть выше дуги или напряжения холостого хода (когда дуга возникает между электродом и деталью). Работа).
При постоянном токе напряжение холостого хода должно быть не менее 30 или 35 вольт, в то время как при переменном токе оно должно быть не ниже 50 или 55 В. Открытая дуга будет поддерживаться на уровне от 18 до 25 вольт. Напряжение холостого хода обычно составляет от 50 до 90 вольт.
Для зажигания дуги электрод прикасается к изделию, а затем отводит на небольшое расстояние. При контакте электрод замыкает сварочную цепь, и непреднамеренное короткое замыкание может вызвать чрезмерный ток в цепи, который может вызвать опасный нагрев и даже ожог изоляции.Следовательно, источник питания для сварки должен иметь возможность ограничивать выброс тока при возникновении дуги до небольшого процента выше желаемого значения.
При сварке металлической дугой шарики расплавленного электродного металла переносятся по дуге, таким образом изменяя сопротивление дуги и, следовательно, напряжение и ток дуги. Фактически сопротивление дуги постоянно изменяется в широких пределах за очень короткие периоды времени. Дело в том, что расплавленные глобулы металла проходят от электрода к пластине со скоростью 30 или более в секунду, постоянно вызывая приблизительно короткие замыкания от электрода к изделию. Если дуга не должна погаснуть, источник питания должен иметь возможность быстро изменять свое напряжение в зависимости от сопротивления дуги.
Особое значение имеет способность источника питания быстро восстанавливать напряжение после того, как шарик расплавленного металла откололся от электрода. Дуга возобновится только при напряжении не менее 25 вольт. Следовательно, напряжение должно восстановиться до 25 вольт в течение 0,05 секунды.
Для ручной сварки покрытыми электродами статическая характеристика (кривая, показывающая зависимость между напряжением источника и сварочным током) представлена кривой I на рис.6.25. Это падающая или отрицательная характеристика. OA представляет напряжение холостого хода, OB представляет напряжение дуги или замкнутой цепи, OD представляет ток дуги, а OE представляет ток короткого замыкания. Точка C на кривой I показывает момент зажигания дуги. Благодаря этому типу вольт-амперной характеристики ток короткого замыкания в сварочной цепи снижается до предела, достаточного для обмоток сварочного генератора или трансформатора.
Если дуга имеет плоскую (кривая III) или нарастающую вольт-амперную характеристику (кривая II), например, при сварке в защитной дуге, автоматической сварке большими токами, источник питания также должен иметь плоскую или возрастающую характеристику соответственно.
Таким образом, источник питания для ручной дуговой сварки должен соответствовать следующим требованиям:
1. Напряжение холостого хода должно быть достаточным для беспрепятственного зажигания дуги, но безопасным для оператора (ниже 80 вольт).
2. Ток короткого замыкания должен быть в пределах безопасности обмоток генератора или трансформатора.
3. Напряжение источника питания должно быстро меняться при изменении длины дуги.
4.Мощность источника питания должна быть достаточной для обеспечения желаемого тока дуги.
Дуговая сварка постоянным и переменным током : AC и DC могут использоваться в дуговой сварке, каждая из которых имеет свои отличительные достоинства и области применения.
Преимущества дуговой сварки на постоянном токе заключаются в более высокой стабильности дуги и степени нагрева изделия. Он лучше всего подходит для тонкого листового металла (менее 6 мм), а также для сварки цветных металлов.
Сваркана переменном токе из-за отсутствия «дугового разряда» считается лучшей для производственной сварки с использованием электродов большого размера.
Сварка переменным током имеет ряд экономических преимуществ, таких как указанные ниже:
1. Поскольку на заводах используется источник питания переменного тока, для сварки постоянным током требуется вращающийся генератор постоянного тока или выпрямитель, а для сварки переменным током требуется только трансформатор, который относительно дешевле по первоначальной стоимости.
2. Техническое обслуживание трансформатора менее сложно и дорого, чем обслуживание генератора постоянного тока.
3. Эксплуатационные расходы на оборудование переменного тока также ниже, чем на оборудование постоянного тока.