высокотемпературная холодная сварка для металла
Технология холодной сварки для металла является широко известным и легким в применении способом соединить две однородные или даже разные по материалу детали. Фактически это склеивание деталей специальным пластичным составом, глубоко проникающим в материал и образующим высокопрочный шов.
Холодная сварка
При посредстве этой технологии можно сваривать детали из черных и цветных металлов. Метод прекрасно подходит для материалов и изделий, отличающихся склонностью к деформации при нагревании. Кроме того, возможно соединять и разные металлы, такие ка многослойные металлические ленты или алюминиевые проводники, усиленные полосками из меди.
Содержание
Характеристики и состав холодной сварки
Основными характеристиками холодной сварки являются:
- Наличие и состав наполнителя.
- Время первичного высыхания — время т.н. «схватывания», за это время состав должен быть нанесен на место склейки и разровнен.
- Время окончательного отверждения — раньше этого срока изделие нельзя эксплуатировать.
- Температура применения — рекомендуемая температура, при которой смесь можно наносить на поверхность.
- Максимальная температура эксплуатации.
Пластичный клеящий состав холодной сварки может состоять из одного или двух компонентов. Обязательными компонентами его являются:
- Клеевая основа в виде эпоксидной смолы, определяющей пластические свойства.
- Наполнитель — пудра из металла, равномерно распределенная по объему.
- Улучшающие качество добавки, например, сера.
Качество получаемого методом холодной сварки шва зависит от таких условий, как:
- Качество клеящего материала.
- Подготовка поверхностей деталей для склеивания.
- Соблюдение технологии.
Прочность получающегося шва в реальных условиях будет ниже, чем у шва, полученного горячим методом.
Поэтому технология лучше всего применима для локального ремонта малонагруженных изделий.
Как правильно пользоваться холодной сваркой
Для получения хорошего шва исключительную важность имеет аккуратное выполнение последовательности шагов:
Технологический процесс холодной сварки
- Очистить склеиваемые поверхности от масложировых и механических загрязнений. Очистка бывает механическая (абразивы, стальная щетка), химическая (растворители и обезжириватели) и комбинированная.
- Все действия проводятся только в защитных перчатках.
- Двухкомпонентный состав выдавить из туб и хорошо смешать компоненты.
- Пластилин образный состав отделить от бруска шпателем необходимое количество и тщательно закрыть оставшийся брусок.
- Размять состав.
Он должен слегка нагреться, сохраняя пластичность, как только требуемая консистенция достигнута, нанести массу на склеиваемые поверхности.
- Надежно прижать поверхности друг к другу, обмотав детали эластичным жгутом.
- Если ремонтируются трубы, состав надо наносить несколькими разглаживающими движениями.
- Через время, указанное в технических характеристиках как время первичного засыхания (схватывания 90% клея) жгут можно снять.
- Пользоваться отремонтированным изделием можно только по истечении времени окончательного затвердевания, как правило, это 24 часа.
Остатки клеящего вещества лучше убирать шпателем после нанесения и наложения жгута. Если же они успели затвердеть, то удалить их можно, слегка обстукивая молоточком.
Температурные характеристики
Состав клеящей массы определяет, какую температуру выдерживает холодная сварка. В руководстве пользователя всегда приводится это значение. Если тщательно выполнять все требования руководства, шов выдержит эту температуру без потери прочности.
Бюджетные марки обычно разрабатываются для максимальной температуры в районе 260 С. Специальные виды смесей имеют максимальную температуру эксплуатации свыше 1300 С. Стоят они заметно дороже, но зато позволяют ремонтировать детали и изделия, работающие в условиях высоких температур. Это отличное подспорье, если применение горячей технологии затруднено по причинам пожаробезопасности или доступности места ремонта.
Виды холодной сварки
Применяются следующие виды:
- Точечная. Для соединения алюминиевых и медных проводников, приклеивания медных кончиков на алюминиевые провода.
- Шовная. Для производства тонкостенных сосудов, герметичных емкостей и кожухов оборудования.
- Стыковая. Для соединения проводов или кольцеобразных изделий.
- Тавровая. Для соединения элементов прокатных профилей.
- Сдвиговая. Для соединения труб отопительных или водопроводных контуров, а также компонентов электрораспределительных сетей на железных дорогах.
В зависимости от способа расфасовки различают:
- Жидкая сварка — поставляется в виде двух отдельных компонентов, пластификатора и отвердителя, которые перемешиваются перед применением.
- Пластилинообразной, поставляется в виде бруска, который разминают и перемешивают перед применением.
Двухкомпонентная холодная сварка сложнее в использовании, но зато более экономно расходуется.
- Пластилинообразная холодная сварка
- Жидкая холодная сварка
По целевому назначению различают:
- жидкая сварка для металла служит для склеивания большинства металлов и содержит наполнитель в виде металлической пудры;
- жидкая сварка для ремонта автомобиля, отличается повышенной стойкостью к вибрациям, также имеет в своем составе наполнитель;
- универсальную, соединяющую металлы, дерево или пластик в любом сочетании.
Прочность такого соединения будет невысокой;
- для работы в специальных условиях, таких, как подводные, высокотемпературные, в агрессивных средах и т.п.
Термостойкая холодная сварка
Термостойкая холодная сварка весьма популярна среди автолюбителей, ремонтирующих глушители и другие элементы выпускной системы
Способы применения холодной сварки
Способ использования холодной сварки для металла подробно описан в инструкции по ее применению.
Для того чтобы применение холодной сварки прошло успешно, а шов прослужил долго, нужно тщательно следовать всем пунктам инструкции. Любая неаккуратность, экономия, подмена и т.п. приведут к снижению качества и долговечности шва.
Советы по применению холодной сварки
В частной жизни способ чаще всего используют для авторемонта и починки отопительного хозяйства. Прохудившийся и заклеенный глушитель или бензобак будет служить еще долгие годы, не требуя замены.
К сожалению, радиатор таким образом удастся только временно подлатать, чтобы доехать до сервиса своим ходом. Постоянно пользоваться им будет нельзя. Если место течи установить не удается, то можно опустить радиатор в ванну с водой. Выходящие пузырьки укажут место течи.
Для ремонта глушителя надо выбрать высокотемпературную марку. Если в инструкции указана комнатная температура применения, то для начала работ ремонта следует дождаться остывания детали.
Если вы ремонтируете отопительную систему, то следует выбрать состав, выдерживающий длительный контакт с водой. Следует помнить, что метод подходит для ремонта небольших отверстий. Если повреждения значительны, то лучше применить горячую сварку.
Способ категорически непригоден для склеивания деталей, работающих под большой нагрузкой.
Не стоит пытаться заменить марку, разработанную для конкретного материала, на ту, что есть под рукой. Наполнитель должен точно соответствовать склеиваемым материалам, иначе о прочности шва можно будет забыть.
Как работает холодная сварка
Растворитель, содержащийся в клеящем составе, растворяет не только слой окислов на поверхности, но и приповерхностный слой металла, сближая атомы двух деталей на расстояние, близкое к размерам кристаллической решетки, в холодном состоянии.
Это напоминает процессы, происходящие в сварочной ванне — зоне совместного плавления электрода и поверхностных слоев соединяемых деталей при горячей сварке.
Преимущества холодной сварки по металлу
Технология обладает неоспоримыми преимуществами:
- Нулевой расход электроэнергии или газа.
- Опрятный и прочный шов не требует последующей обработки.
- Нет нужды длительного обучения, наличия специальной аппаратуры.
- Дает возможность прочно соединять разные металлы, например, алюминий и медь, которые другими способами практически не соединяются.
- Дает возможность осуществлять ремонт деталей и трубопроводов без их демонтажа, не только в холодном, но и в горячем состоянии.
- Ремонт электроустановок под напряжением, емкостей и труб под небольшим давлением и даже с легковоспламеняющимися материалами.
- Отсутствуют деформации, вызванные остаточными напряжениями в металле, возникающими после горячей сварки.
- Высокая экологичность процесса, отсутствие вредных отходов.
Аккуратный шов холодной сварки линолеума
Кроме всего перечисленного, низкая трудоемкость и невысокая цена расходных материалов делают способ экономически выгодной.
Недостатки холодной сварки
Основным недостатком способа является низкая по сравнению с горячей сваркой прочность шва. Материалы все же не сплавляются, образуя единый поликристалл, а склеиваются. Поэтому метод непригоден для высоко нагруженных соединений.
Меры безопасности
Компоненты, из которых состоит смесь, отличаются высокой химической активностью и сильно раздражают кожу и слизистые оболочки действием. При попадании внутрь организма они вызывают опасное для жизни отравление. Поэтому при работе необходимо строго соблюдать меры безопасности:
Обязательно работать в резиновых или пластиковых перчатках
- Обязательно работать в резиновых или пластиковых перчатках.
- При работе с составом для пластика обязательно попробуйте действие компонентов на материал перчаток. Если они растворяются — перчатки следует взять из другого материала.
- Работать в защитных очках или в прозрачном защитном щитке. Особенно важно соблюдать этот пункт при работе снизу от ремонтируемого объекта — автомобиля, трубопровода и т.
п., чтобы исключить попадание кусочков вещества на лицо и слизистые глаз и рта.
- В случае случайного попадания на кожу — немедленно промыть большим количеством чистой проточной воды
- В случае попадания внутрь организма — выпить много жидкости, лучше молока и немедленно обратиться к врачу.
- Беречь от детей! Игра с похожим на пластилин веществом может закончиться в больнице или в морге.
- Не применять для ремонта посуды и емкостей, контактирующих с пищей.
После затвердевания компоненты смеси теряют химическую активность и абсолютно безопасны для прикосновения руками.
высокотемпературный водостойкий продукт, какой жаростойкий вариант выдерживает температуру 300 и 1000 градусов
Разнообразие клеевых составов
Клеи применяются и работают в широком диапазоне температур. Существуют составы для разнообразных температурных режимов
- температуру в пределах от -30 до +300 градусов выдержат термостойкие составы
- термопрочный клей выдержит воздействие от +140 градусов
- 180 минут без потери качеств и без химического взаимодействия с топливными частицами пламени продержится огнестойкий продукт
- огнеупорный материал может соприкасаться с огнем без временных ограничений
- жаростойкий (жароустойчивый, жаропрочный) клей может нагреваться до +1000 градусов
Минеральные вещества, имеющие наиболее высокие показатели термостойкости цементно-глиняная основа с добавлением шамотного волокна, песка в качестве пластификатора используется для кирпичной кладки в печах. Выдерживает нагрев до +1200 градусов.
Недостаток — невысокое качество сцепления. Плюс — недорогая стоимость цемент алюмосиликатный и каолин с добавками из кварцевого песка и жидкого стекла обеспечивают жаропрочность при температуре до +1360 градусов.
Применяется для отделки плиткой и керамогранитом каминов и печей алюмосиликатный цемент с горшечным камнем (талькохлоритовой мукой) является достаточно дорогим средством, но это оправдывается высоким качеством клеевых швов, высокими показателями адгезии и устойчивостью к температурам до +1500 градусов.
Состав способен преобразовать коротковолновое и, как следствие, жесткое тепловое излучение в мягкое длинноволновое. Отлично взаимодействует с какими угодно материалами в отделке и печных работах.
Критерии выбора
Современный рынок предлагает огромный ассортимент составов, предназначенных для работы с металлами, среди них есть и термостойкие. Выводы относительно качества вы сможете сделать сами после применения клея.
Следует с некоторой осторожностью отнестись к составам, относящимся к разряду универсальных
Поэтому обратите особое внимание на то, какие в нем компоненты. Также присмотритесь к:
- Диапазону температур, при которых клей не теряет полезных свойств. Уточните, при каких условиях будут эксплуатироваться готовые элементы, нуждаются ли они в проведении дополнительной обработки.
Если да, то при каких температурах.
- Периоду высыхания. Данный параметр полностью зависит от особенностей процесса нанесения и рабочего места.
- Методике нанесения. Помните, что она бывает разной: одни материалы склеиваются точечно, другие следует обработать полностью. В последнем случае расход клея увеличится.
- Технологиям нанесения. Они имеют отличия. Спросите совета у продавца-консультанта, убедитесь, что состав будет удобен в использовании.
- Консистенции. Любые клеи поступают в продажу, имея несколько исполнений: тубы либо пластиковые палочки. В первом случае придется самостоятельно делать смесь с двух компонентов, что далеко не всегда удобно и возможно. Готовые составы выделяет удобность применения.
- Уровню устойчивости к жидкостям и агрессивному воздействию окружающей среды. Этот параметр особенно важный, если склеиваемые компоненты будут располагаться вне помещений.
- С какими материалами может проводиться склеивание. Подбирайте определенные составы для выполнения конкретных задач.
Другие рекомендации
- Если на ярлыке указывают «для холодной сварки», это не значит, что состав предназначен для металлов. С его помощью могут скрепляться другие материалы: фаянс, керамика, древесина и им подобные.
- Не стоит покупать значительное количество клея про запас. Помните, что средний срок хранения — около года.
Виды и компоненты клея
Все термостойкие составы можно условно поделить на 3 большие группы. В первую входят средства для облицовки каминов, печей, варочно-отопительных приборов. Обычно они представляют собой клеевые растворы на основе минеральных составляющих, выдерживают температуру от +1000 градусов. Ко второй группе относятся клеи для теплых полов, их термостойкость – не более +140 градусов. Третью группу составляют клеи в небольших упаковках, прозрачные или матовые на вид, применяемые для ремонта бытовой техники, плит и иных нагревающихся изделий. Их основу составляют смолы.
По консистенции термостойкие клеи бывают:
- порошковыми – перед применением их нужно разводить согласно инструкции;
- готовыми – могут использоваться сразу, по текстуре напоминают мастику, гель, герметик, шпаклевку и т. д.
Клей может быть синтетическим и природным по происхождению, хотя в большинстве случаев имеют место смешанные составы. Средства обязательно включают пластификаторы – искусственные вещества, придающие прочность, эластичность, дополнительную влагостойкость и морозостойкость.
Основа для работы с металлами
Клей для металлов и сплавов применяется при монтаже конструкций, которые подлежат нагреванию и содержат металлические элементы. Одни составы наносят сплошным методом, другие – точечным. Минимальный предел термостойкости подобных средств составляет +370 градусов. Клей для металла также можно применять для установки теплого пола, при укладке плитки в банях, саунах.
Основа для стекла
Обычно такие термостойкие клеи используются для ремонта бытовой техники, содержащей стеклянные элементы, а также для различных нагревающихся приборов. В составе присутствуют органические соединения, обеспечивающие стойкость к повышенным температурам. Клеи для стекла всегда являются прозрачными.
Клей для печей
Если раньше для кладки печей применялась только глина, то сейчас ее с успехом заменили специальные термостойкие составы. Они не вызывают необходимости проводить грязную и долгую работу, имеют увеличенный уровень адгезии. Для усиления кладки и повышения газонепроницаемости нередко дополнительно обрабатывают швы термостойким силиконовым герметиком. Последний также предупреждает деформацию материалов при температурном расширении.
Обзор производителей
Положительные отзывы покупателей получает также «ТерракотСуперкамин», который используется в качестве кладочного состава, а также фиксирует облицовочную терракотовую плитку (для всех остальных типов облицовочных плит состав не подходит). Плитку нужно укладывать на этот глиняно-цементный с шамотным наполнителем состав следует рядами, давая время клею на схватывание после каждого 2-4 пояса. Для кладки печи подойдет также вариант «Плитонит СуперКаминОгнеупор».
Для металлических и стеклянных элементов каминных конструкций потребуется специальный клей. Термостойкие составы для металла представлены продуктом «Dow Corning Q3-1566» и красным клеем-герметиком от Belife Silicone . Первый выдерживает нагрев до 350 градусов, сохраняет высокие эксплуатационные свойства и долговечность в комнатных условиях, газонепроницаем, влагостоек.
Для отделки внешних стенок печи или каминного портала подойдет клей для высоких температур «Профикс». Он демонстрирует гармоничное соотношение стоимости и качества, выдерживает температуру до 1200 градусов. Благодаря возможности нанесения тонким слоем облицовка смотрится аккуратно, а расход клея заметно снижается. Популярностью пользуется еще один состав для отделки – «Geresit Flex CM 16», главным преимуществом которого является возможность облицовки даже неровной поверхности кладки.
Клей-герметик подходит для эксплуатации в пределах -70… +300 градусов, наносить его следует при температуре не ниже +18. В ассортименте «Плитонит» также можно найти состав для металла – «Premium +1500». Он представляет собой жаростойкий состав для склеивания металла, керамики, стекла, в том числе друг с другом.
Среди отечественных производителей термостойких составов следует выделить компанию «Диола». Термостойкий клей Д-314 предназначен для облицовки каминов и печей керамической плиткой и выдерживает нагрев до 850 градусов. Плитка надежно фиксируется, а при необходимости до момента застывания можно легко подкорректировать ее местоположение.
Еще одним отделочным составом (который, кстати, подходит и для кладки) является клей GM-215 от российского производителя «Геркулес». Температура нагрева достигает 1200 градусов, может фиксировать низкопористую керамическую и глазурованную плитки. Недостатком клея является его повышенная жесткость, из-за чего в процессе приклеивания плитки нельзя сдвигать. Если это все же необходимо, то следует убрать нанесенный до этого слой клея и положить новую его порцию.
Огнестойким вариантом для склеивания стеклянных поверхностей может стать клей «UHU Glas». Он может нагреваться до 125 градусов, отличается высокой скоростью схватывания, стойкостью к УФ-воздействию.
Для керамики можно использовать клей на цианоакрилатной основе «UHU Porzellan Keramik». Клей отличается хорошей пластичностью, высокой адгезией и прочностью, но только при склеивании небольших участков.
Холодная сварка для металла – применяем правильно
Что такое холодная сварка? Этот вопрос задают себе многие из тех, кто собирается воспользоваться данным средством для быстрого соединения металлов. О холодной сварке, без сомнения, слышали многие и достаточное количество людей уже успели признать все преимущества данной технологии. Но, к сожалению, не все из тех домашних мастеров, кто уже успел попробовать соединить металлические детали при помощи такого средства, смогли оценить все его уникальные характеристики.
Холодная сварка для металла
Основная причина такой ситуации заключается в том, что очень часто наши люди не считают нужным внимательно читать инструкции, в которых и оговорены все нюансы использования того или иного устройства или технологии. Именно поэтому мы и хотим посвятить данную статью всем вопросам, относящимся к правилам использования и области применения такого замечательного средства, каким, бесспорно, является холодная сварка.
Разновидности холодной сварки
По сути, холодная сварка — это клей с высокой степенью пластичности, изготовленный на основе всем известной эпоксидной смолы. По своей структуре этот клей может быть двухкомпонентным, тогда его можно хранить длительное время, либо однокомпонентным, который необходимо применить максимально быстро, чтобы не столкнуться с утратой им своих клеящих свойств.
Как правило, такое средство выпускается производителями в виде двухслойного цилиндра, внешняя оболочка которого состоит из отвердителя, а внутренний сердечник представляет собой эпоксидную смолу, смешанную с металлической пылью. Такая добавка в виде металлической пыли необходима для того, что придать получаемому соединению высокую прочность и надежность. Содержит холодная сварка и другие добавки, которые и придают ей, а также соединениям, полученным с ее помощью, уникальные характеристики. Основную часть таких добавок производители держат в секрете, но наиболее известной из них является сера.
Холодная сварка для металла
Такое средство активно и успешно используется не только домашними мастерами, но и автолюбителями, так как позволяет оперативно и эффективно решить многие проблемы, связанные с эксплуатацией автомобиля. Соединения, полученные с его помощью, дают возможность не только забыть о возникшей проблеме на короткое время, но и эксплуатировать восстановленные детали достаточно продолжительное время.
Однако следует иметь в виду, что холодная сварка оптимально демонстрирует себя при соединении тех деталей, которые не испытывают при эксплуатации значительных нагрузок. Широкое применение такое средство нашло и при ремонте сантехнических устройств, в которых необходимо оперативно устранить возникшую течь. Но насколько бы надежным оно не было, всегда следует помнить о том, что оно служит лишь для того, чтобы устранить возникшую проблему лишь на время. При первом же удобном случае следует воспользоваться методами капитального ремонта.
Клей «Холодная сварка» для различных видов пластика
Данное средство, которое является менее распространенным, используется, как следует из его названия, для выполнения оперативного ремонта пластиковых деталей. Находит применение такой клей как на производственных предприятиях, так и для выполнения ремонта в бытовых условиях. Чаще всего необходимость пользоваться таким средством возникает в тех случаях, когда нужно выполнить ремонт пластиковых труб и корпусов различных устройств.
Виды холодной сварки для различных материалов
Холодная сварка, используемая для соединения линолеума
Пользоваться таким клеем можно и в тех случаях, когда необходимо выполнить соединения изделий, изготовленных из жесткой резины. Естественно, что широкое применение такая сварка нашла при выполнении строительных и ремонтных работ. Следует отметить, что соединения линолеума, полученные с ее помощью, значительно превосходят по своим характеристикам те, для выполнения которых использовались клей или двусторонний скотч.
Мы перечислили лишь основные виды холодной сварки, но существуют и другие, которые менее распространены. Все эти средства отличает высокая оперативность получения и надежность соединений при условии, что при выполнении работ строго придерживались всех необходимых требований.
Инструкция по применению
Нанесение жаропрочной смеси проходит в 2 этапа. Сначала производится подготовка основания, а затем – заполнение швов и трещин.
Подготовительные работы
Предварительно поверхность тщательно очищается от всех видов загрязнений. При необходимости используются моющие средства или растворители. Далее места контакта с герметиком нужно обезжирить:
- Сольвентом;
- Бензином;
- Ксилолом;
- Универсальным обезжиривателем;
- Растворителем 646;
- Ацетоном.
Если работы производятся на улице, во избежание загрязнения пылью, рекомендуется заклеить малярной лентой подготовленную поверхность до начала заполнения огнеупорной пастой.
Слишком гладкие материалы обрабатываются наждачной бумагой, затем очищаются от крошки и остатков абразива, и обезжириваются.
Заполнение швов
Пошаговое руководство нанесения герметика:
- У картриджа срезается носик, сверху накручивается специальная насадка. Баллончик вставляется в пистолет. Металлическую тубу нужно просто проткнуть обратной стороной колпачка.
- Место контакта смачивается водой.
- Паста медленно выдавливается из контейнера. Надо следить за равномерным заполнением швов или трещин.
- Лишняя смесь удаляется влажной вискозной салфеткой или мягкой тканью.
Одни виды герметиков затвердевают самостоятельно в течение 1-3 суток, другие – полимеризуются при эксплуатации дымохода в разных режимах. Все данные об этой процедуре напечатаны на упаковке.
Заполнение швов и трещин проводится только при плюсовых температурах. Оптимальной является — +20 ºС, но работать можно и при +5 ºС.
Смесь не наносят на поверхности, пребывающие под водой, или находящиеся постоянно в условиях высокой влажности.
Техника безопасности
Хоть строительный материал и не относится к токсичным, но проветривать помещение во время работы необходимо.
Рекомендуется надевать прозрачные пластиковые очки, во избежание попадания герметика в глаза.
Желательно использование рабочих перчаток с заливкой, поскольку некоторые виды смесей на воздухе вступают в химическую реакцию, и могут вызвать ожог кожных покровов.
С волос состав смыть тяжело, особенно через несколько минут после попадания, поэтому их лучше скрыть под головным убором.
Где применяются термостойкие клеи
Термостойкие клеящие средства используются на нагревающихся поверхностях, а также на пластмассовых, керамических, металлических, графитовых, резиновых и прочих основаниях.
Свою популярность они заслужили отчасти благодаря технологической стабильности.
Даже новичку под силу выполнить работы с применением таких продуктов, не владея профессиональной техникой их нанесения.
Сегодняшние термостойкие клеи не потребуется мешать, как глину, добиваясь отсутствия комков. Огнеупорные термостойкие составы могут использоваться для кладки конструкции полностью.
Термостойкие клеи можно брать для облицовки и декорирования каминов, муфельных и жаровых печей, кузнечных горнов. Одинаково хорошо термостойкие составы работают на горизонтальных и отвесных основаниях.
Какой тип клея выбрать для металла
Производители выпускают ассортимент клеевых составов, которые справятся с задачей приклеивания металлических частей к плоскостям.
Эпоксидный клей
Эпоксидный клей для металла используется в домашних условиях, промышленности, на стройке. Имеет доступность, устойчивость к перепадам температур, водостойкость. Не подвергается воздействию ряда химических веществ: бензин, жидкость охлаждающая, керосин. Такие характеристики дают возможность к использованию клея в уличных условиях, для склеивания элементов, эксплуатирующихся в агрессивных средах.
Производится такой вид в двух тарах. В одной эпоксидная смола, во второй отвердитель. Непосредственно перед нанесением, два компонента смешиваются. Рабочее время зависит от типа эпоксидки и может продлиться от пары минут до пары часов.
Для придания прочности соединения, в эпоксидный клей добавляется стружка керамики или железа. Примером может служить восстановление эпоксидкой винтовой резьбы.
Что касается площади склеивания, она может быть от малых размеров до больших.
«Холодная сварка» – эпоксидный клей. Это не технология холодной сварки. Технологический метод приводит к деформации плоскости.
Анаэробный клей для металла
Склеить металл можно и анаэробной группой составов. Их действие начинает проявляться при прекращении поступления воздуха к сплаву. Начинается его полимеризация (проявляются химические реакции), он становится герметичным полимером.
В зависимости от использования в различных условиях, анаэробные клеи применяются:
- В отопительных системах – материал для уплотнения элементов. Свойства сохраняются при воздействии температур до 140 градусов.
- В средах с агрессивным влиянием химических элементов.
- В сферах повышенной сцепливаемости к смежной плоскости.
Смесь делится на одно-, двухкомпонентные. Второй вариант более надежен, но сложен в использовании в домашних условиях.
При недоступности проведения сварочных работ, однокомпонентные составы эффективно герметизируют стыки, которые далее противостоят ударам, вибрациям, имеют высокую сцепливаемость с любыми плоскостями.
Двухкомпонентный клей для металла смешивается непосредственно перед нанесением.
Цианакрилатный клей
Цианакрилатные клеи относятся к универсальным средствам, которые способны приклеивать сплавы к различным плоскостям. Также могут приклеить металл к металлу. К достоинствам относятся:
- Быстрое схватывание.
- Прочность соединения.
- Долговечность шва.
- Качественное соединение.
Если между частями есть зазоры, то качество и долговечность соединения гарантированы не будут. Также слабость проявляется в неспособности выдерживать температуру более 100 градусов, не соединении железа с силиконовыми плоскостями, полиэтиленом, пропиленом.
Большая часть органических соединений не влияют на состав, но растворяется в ацетоне. Проявляет диэлектрические способности, не содержит аллергенов. Но работы стоит проводить в средствах ИЗ.
Недопустимо прикасаться х/б тканями, так как возможно возгорание.
Для увеличения вибрационных свойств, добавляется абиетиновая кислота с глицерином.
Водостойкий
Водостойкий клей нужен для решения домашних работ, связанных с устранением течи в трубах, сантехнических оборудованиях, при заделывании потеков в аквариуме, пластике и пр.
Также производится такими смесями работа по герметизации швов и заделывание шумовых утечек в кондиционированных системах, отопительных, вентиляционных.
Производители
На отечественном рынке самыми популярными производителями являются иностранные компании, поскольку российская продукция имеет более низкое качество, о чем свидетельствуют многочисленные потребительские отзывы. Отечественная продукция представлена торговыми марками «Алмаз» или «Полимет», Henkel. Лидерами среди иностранных составов считаются Hi-Gear, Abro, Poxipol.
Abro Steel – американская двухкомпонентная сварка универсального назначения. Материал выдерживает воздействие разных агрессивных веществ и отлично сохраняет свои свойства вплоть до температуры +260 С.
Hi-Gear «Быстрая сталь» производится для работ с металлом, пластиком и камнем. Продукция обеспечивает прочное соединение, устойчива к механическому и химическому воздействию.
Henkel «Момент СуперЭпокси» широко используется для соединения сплавов из металла и других материалов. Свои свойства состав сохраняет до температуры +140 С.
Уругвайский Adefal Trading S. A. Poxipol – универсальная двухкомпонентная холодная сварка. Максимальной температурой для такой продукции является показатель +120 С.
Германская Wurth Liuguid Metal Fe 1 выпускается для работ с керамическими и металлическими деталями и конструкциями. Материал не горит и не содержит растворителей. Состав сварки обеспечивает ее устойчивость к агрессивным веществам. Максимальной температурой для подобной продукции считается +120 С.
Холодная сварка для батарей и водопроводных труб Mastix лучше всех остальных составов справляется с задачей заделывания трещин и других дефектов на подобных конструкциях. Температура в трубопроводах не превышает допустимую составляющую +120 С, поэтому продукцией можно пользоваться в домашних условиях. Такая сварка позволяет создавать утраченные части и новые детали.
Металлосиликатная продукция Kerry «Термо» обладает повышенной вязкостью. Она отлично зарекомендовала себя в работе с жаростойкими сплавами из стали, чугуна и титана. Состав устойчив к механическим воздействиям, поэтому рекомендован для ремонта автомобильных деталей. Продукт выдерживает перепады температур от +900 до -60 С.
Холодная сварка
Бездиффузионное соединение достигается применением так называемой «холодной сварки», выполняемой эпоксидными компонентами. При этом для такого типа соединений разработаны как обычные вязко-текучие составы, расфасованные в тюбики или флаконы, где в одной емкости находится эпоксидный компаунд, а в другой – отвердитель, так и более удобная форма в виде твердых брусков.
Перед работой от такого бруска ножом отрезается нужное количество состава, и мокрыми руками разминается в саморазогревающуюся массу, похожую на мягкий пластилин. Масса вытягивается в тонкий шнурок и в виде шва накладывается на предварительно очищенные и обезжиренные поверхности. Процесс полимеризации запускается уже в тот момент, когда мокрыми руками, чтобы состав не лип к ним, перемешиваются между собой изолированные до этого специальной прослойкой слои.
Полезно узнать > Что представляет собой эпоксидный клей и где он используется
Такая размятая рукам эпоксидка наносится в виде пасты тонким слоем на обе предварительно обезжиренные и зашкуренные для лучшей сцепляемости поверхности. Потом, после нанесения и размазывания слоя, склеиваемые детали прижимаются одна к другой так, чтобы обеспечить их неподвижное друг относительно другу состояние, и уже на исходе 40-60 минут можно убрать прижимную нагрузку.
Преимущества склеивания
- Не нужно обладать профессиональными навыками и специальным оборудованием.
- При работе свойства металла в местах соединения остаются без изменений.
- Равномерное распределение нагрузки на основу.
- Полноценная герметичность швов.
- Нет ограничений относительно типов обрабатываемых элементов.
- Работы возможны практически в любых местах.
- Швы не нуждаются в дополнительной финишной обработке (выравнивание, шлифовка), без которых не обойтись после завершения сварочных работ.
- Технологическая операция отнимает незначительное время.
- Металлы можно запросто склеить с любыми другими материалами, чего нельзя достигнуть с помощью других методов.
Область применения термостойкого клея
Домашние умельцы используют термоустойчивый клей не только для склеивания, но и в качестве герметика.
Герметизирующая смесь, основой которой является термостойкий силикон, очень удобна для заполнения соединений, щелей в дымоходе. Она используется также при ремонте бытовых нагревательных приборов.
Для электрических и газовых духовок
Если вы до сих пор не знаете чем приклеить стекло в духовке, то термостойкий клей будет. Некоторые герметизирующие средства устойчивы к открытому воздействию огня. К ним относится огнеупорный герметик Makroflex. Он, как никакой другой материал, эффективен при ремонте трещин и стыковок в электрических духовках и жаровнях.
Высокую популярность завоевал термостойкий клей Момент . Он востребован при склеивании различных материалов: стекла, керамики, фарфора, пластика, кожи.
Для отделки плиткой
Диапазон использования клеящих смесей, устойчивых к высоким температурам, очень широк. Но чаще всего их применяют как плиточное склеивающее средство.
- цемента;
- песка;
- полимерных добавок, придающих смеси клеящие свойства.
Термостойкий плиточный клей для печей может быть на полиуретановой или эпоксидной основе. Тот и другой вид смеси состоит из двух компонентов, которые имеются в упаковке. Их смешение следует производить перед самым употреблением в соответствии с указанной пропорцией.
Для каминов и печей
Подбирать клей и термостойкий герметик для печей следует в зависимости от области их применения.
При отделке печей и каминов применяется термопроводящий клей, способный выдерживать температуру до 125°C, но с высокой теплопроводностью. При выполнении облицовочных работ необходимо исключить сползание плитки. Поэтому используют смесь повышенной фиксации, позволяющей производить облицовку по разным направлениям, в том числе сверху вниз. А при кладке кирпича нужен высокотемпературный клей для печей, термоустойчивый к температуре до 1400°C.
Немаловажное значение при выборе клея имеет цена и экономичный расход. Покупателям нравится, когда этот товар предлагается в готовой к употреблению консистенции, с множеством вариантов фасовки, а на упаковке указываются нормы его потребления
В среднем поверхность в 1 м² требует 1,5 кг смеси с толщиной нанесения раствора 1 мм. А на практике эти показатели могут быть выше, особенно если склеиваемая площадь не идеально ровная.
К универсальным средствам, обладающим соединительными характеристиками, относят различные клеи. Сегодня промышленность выпускает разнообразные типы клеящих основ. Все они обладают своими специфическими свойствами. К одной из групп таких основ относят термостойкие клеи, предназначенные для работы с широким температурным диапазоном.
Изготовление высокотемпературного клея своими руками
Возможно, приготовить клей огнеупорный жаростойкий самостоятельно. Компоненты несложно найти. Для получения надежного клеевого раствора требуется 1 часть глины, 1 часть цемента, 3 части песка. Для придания влагостойкости добавляется обычная соль, пропорция соли к общей клеевой массе примерно равна 1 стакан/1 ведро. Лучше производить перемешивание мастерком. Важным является степень жирности глины. Определяют степень путем перемешивания ее с водой до сметанообразного состояния. Затем наносят на древесину, если прилипает 2 мм массы, то степень нормальная.
Важным является степень жирности глины.
Термостойкий клей имеет много разновидностей, для получения супер надежного соединения следует подбирать подходящий состав под вид материала, который будет приклеиваться. Работать с клеем необходимо, соблюдая меры безопасности, чтобы избежать проблем со здоровьем. Также можно создать раствор своими руками, процесс несложен.
Основные типы высокотемпературных герметиков
На рынке представлены разные виды герметиков, обладающих способностью противостоять высоким температурам. Для заделывания дефектов на печной кладке лучше покупать те, что содержат силикаты и силикон. Средства фасуются в небольшие цилиндрические картриджи, которые удобно вставлять в монтажный (клеевой) пистолет.
Также в продаже можно встретить небольшие упаковки в тюбиках, напоминающих пасту, которые применяются, как любой обычный клей. Разнообразные цвета позволяют подобрать состав под цвет основного материала, чтобы сделать «заплатку» эстетичной или вовсе визуально незаметной. Все герметики делятся на термостойкие, жаростойкие, уплотняющие и с облицовочными свойствами.
Термостойкие герметики
Основа таких средств – силикон, они выдерживают до +350 градусов. Для достижения такой стойкости к нагреванию в состав также вводится оксид железа, потому основным цветом массы становится оранжевый. Некоторые средства содержат уксусную кислоту, они категорически не подойдут для железа – создавая оксидную пленку, герметики не обеспечат достаточную адгезию. Зато для алюминия, прочих цветных металлов и нержавейки их применять можно, хотя для любого металла лучше приобрести бескислотный состав.
Обычно термостойкие герметики применяются для нанесения на наружные стенки каминов, печей. Также они годятся для открытых участков, где на шов будут воздействовать атмосферные факторы, ультрафиолет – например, для кровли из профнастила, черепицы. Можно использовать составы для устранения щелей в дымоходе или деталях автомобиля. Предел термической стойкости всегда указан на упаковке. Надо помнить, что +350 градусов – это верхний рубеж кратковременного повышения температуры. Постоянный же нагрев не должен превышать +250…+270 градусов.
Полимеризация герметика происходит за несколько часов, некоторые термостойкие средства застывают только через 1-2 суток. Чем ближе окончание срока годности, тем быстрее происходит этот процесс. Идеальными условиями для полимеризации герметика считаются температура +23…+25 градусов, влажность 50%. Иные условия замедлят или ускорят полное отверждение материала.
Жаростойкие герметики
Подобные средства содержат силикаты, потому рассчитаны на более серьезный нагрев – до +1500 градусов, причем возможно даже прямое воздействие пламени. Ремонтировать жаростойкими герметиками следует прокладочный слой между кирпичами, чугунными элементами печной кладки, швы топочной камеры, дефекты котлов отопления. Герметики не утрачивают свойств даже при экстремальном нагреве, но при действии открытого огня нужно найти в инструкции прямое указание производителя на такую возможность.
Окраска жаростойких герметиков обычно черная, серая из-за наличия силикатов. Они прекрасно сцепливаются с любыми материалами, и все-таки перед нанесением рекомендуется обработать поверхность наждачкой. Выполнение работ стоит осуществлять при температуре, близкой к +20 градусам. После высыхания шов будет жестким, поскольку такие герметики отличаются невысокой эластичностью. Лучше не применять их на изделиях, подверженных вибрации, зато для уже прошедших усадку сооружений они прекрасно подходят.
Силиконовые уплотнители
В продаже также можно найти полужидкую силиконовую пасту красного или синего оттенка. По мере застывания она формирует эластичный шов, который может растянуться в 2 раза. Такие герметики применяются для новых кладок, которые подвержены сильной усадке. Также можно использовать уплотнители для покрытия сэндвич-дымоходов с наружной стороны. Большого нагрева средства не выдерживают – они работают только в пределах -40…+250 градусов. Максимальная глубина шва не должна быть более 6 мм, нанесение осуществляется при +5…+30 градусах. Самые популярные марки силиконовых уплотнителей – Титан, Момент-Гермент, Пеносил.
Клеящие облицовочные составы
Материалы с клеящими способностями используются, если печная кладка покрывается сетью трещин, ведь обычным герметиком обработать всю площадь нереально. Облицовочные составы прекрасно проникают в самые узкие и глубокие трещинки, надежно пряча их. После ремонта камин, печь приобретут более эстетичный внешний вид. Обычно подобные смеси реализуются в ведерках в готовом виде или в мешках в форме сухого порошка. Термостойкость облицовочных составов может быть разной:
- смеси на основе каолиновой пыли, шамота – до +400 градусов;
- однокомпонентные клеи с минеральными добавками – до +800 градусов;
- мастики для приклеивания плитки, камня – до +1000 градусов.
Эпоксидный клей: свойства, разновидности, особенности использования
Фото: Instagram abroind
Состав эпоксидного клея
Эпоксидка считается универсальной. Она накрепко соединяет поверхности из различных материалов. Основной элемент клеящей массы — эпоксидная смола. Она способна проникать достаточно глубоко внутрь склеиваемых поверхностей, что обеспечивает прочное и долговечное соединение. Клей — это композиция из эпоксидной смолы и вспомогательных компонентов. Их характеристики представлены в таблице.
Доля вещества от массы сухой смолы | Вещество | Свойства | |
---|---|---|---|
Отвердители | до 15% | Полиамины, аминоамиды, отвердители-модификаторы из полимеров и др. | Изменяют состояние вещества из геля в твердое, определяют прочность соединения |
Растворители | 3-5% | Кселол, различные спирты или ацетон | Увеличивают скорость затвердевания клея |
Наполнители | от 50 до 300% | Порошковые (окиси металлов, алюминий, кремнезем), специальные ткани, волокна стеклянные или углеродные | Определяют характеристики материала, могут работать отвердителями и/или стабилизаторами |
Пластификаторы | до 30% | Эфиры фосфорной или фталиевой кислот | Определяют физические и механические характеристики смеси |
Ассортимент эпоксидных клеев очень широк, в них присутствуют описанные ингредиенты в разных пропорциях и комбинациях.
Свойства и сфера применения эпоксидных клеев
Застывший клей образует безусадочный шов, устойчивый к маслам, щелочам и растворителям. Эпоксидка отличается высокой адгезией к различным основаниям, легко переносит резкие перепады температур в диапазоне от -20 до +250 С, не является электрическим проводником. Шов эластичен, его можно шлифовать, окрашивать, лакировать и сверлить. Возможно добавление дополнительных компонентов к основному рецепту, что дает составу новые свойства.
Благодаря этим свойствам материал широко востребован во многих отраслях:
- Машиностроение. Производство абразивного инструмента, технической оснастки и др.
- Авиастроение и космонавтика. Производство солнечных батарей, установка теплозащиты, внутренней и внешней, сборка авиатехники.
- Строительство. Сборка мостовых конструкций из железобетона, трехслойных строительных панелей и многое другое.
- Судо- и автомобилестроение. Сборка корпусов из стеклопластика, закрепление деталей из разнородных материалов, монтаж высоконагруженных узлов и т.
Фото: Instagram madewithdots
Плюсы и минусы эпоксидного клея
Клеящие смеси на основе эпоксидных смол разнообразны, но все они имеют общие достоинства:
- Устойчивость к воздействию агрессивных химических веществ, среди которых масла, бензин, неконцентрированные кислоты и щелочи. Моющие средства и остальная бытовая химия не разрушают шов.
- Термостойкость. Переносит повышение температуры до +250 С.
- Эластичность. Возможны небольшие смещения склеенных фрагментов, сверление и шлифование шва.
- Полная водонепроницаемость.
- Хорошая адгезия с различными материалами, включая пластмассы, дерево, цемент, гипсокартон и др.
- Устойчивость усадке и к образованию трещин.
Есть у эпоксидных составов и некоторые недостатки, которые нужно учесть перед их применением. Смесь нельзя выбирать для работы с никелем, полиэтиленом, цинком, силиконом, хромом и тефлоном. Запрещено склеивать такими составами предметы, которые соприкасаются с продуктами.
Фото: Instagram aviora_sekunda_aktobe
Двухкомпонентный и однокомпонентный клей
Клеящий состав производится в двух формах, каждая из них является полноценным материалом.
Однокомпонентный состав
Готовая к использованию смесь, выпускается в расфасовке небольшого объема. Благодаря тому, что в массу уже введен отвердитель, клей начинает застывать сразу после того, как вскрывают упаковку. По этой причине материал не применяется для работы с большими объемами, но хорошо подходит для мелкого ремонта, герметизации швов и т.п.
Фото: Instagram mechtairealnost
Двухкомпонентная смесь
В упаковке находятся две емкости. Одна с композитным составом, другая с отвердителем. Перед работой их нужно соединить, строго соблюдая пропорции, которые производитель указывает в инструкции. Преимущество двухкомпонентного материала в том, что его можно смешивать по мере необходимости, получая состав для больших объемов работ.
Фото: Instagram hmstudio_com_ua
Разновидности клея на основе эпоксидки
Ассортимент материала очень широк, поэтому составы классифицируют по таким признакам:
Консистенция
Клеящие смеси производятся в виде жидкости либо пластичной массы, напоминающей глину. В первом варианте это гель, который очень удобно наносить на склеиваемые фрагменты. Пластичная масса достаточно плотная, фасуется в герметичные тубы. Перед работой ее извлекают, слегка смачивают водой и тщательно разминают руками. После этого ее можно наносить на основание.
Фото: Instagram autoshop_camaro_kemerovo
Способ отверждения
Исходя из типа отвердителей, составы делятся на три группы, различающиеся рекомендованной температурой затвердевания.
- Без нагрева. Раствор становится твердым при температуре порядка +20 С. На структурирование состава уходит довольно длительное время, больше 72 часов, для ускорения этого процесса рекомендуется термообработка.
- Модифицированные композиции с температурой затвердевания от +60 до +120 С.
Отличаются повышенной устойчивостью к растворителям органического типа и ударной вязкостью. - Сверхпрочные смеси горячего отверждения. Для затвердевания требуется температура от +140 до +300 С. Термоустойчивы, имеют высокие электроизоляционные характеристики.
Фото: Instagram avtomobilni_magazin
Расход клея и время его отверждения
Расход клеящего состава зависит от толщины слоя, которым он наносится, и от материала основания. Так, пористые поверхности, например бетон или дерево, значительно увеличивают расход материала. В среднем на один квадратный метр уходит порядка 1100 г клея при условии, что толщина слоя не выше 1 мм.
Скорость отверждения зависит от марки состава и температуры окружающей среды. Не рекомендуется работать с материалом на холоде. Оптимальная температура — от +10 до +30 С. Для ускорения процесса затвердевания клея шов можно подогреть. В среднем на отверждение жидких клеев ЭДП уходит около двух часов и около суток на полную полимеризацию. Холодная сварка твердеет намного быстрее — всего за 10-20 минут.
Фото: Instagram nail_anzhelika78
Универсальный или специализированный клей
Область применения клеев на основе эпоксидки очень широка. Они используются при производстве кораблей, самолетов, автомобилей и в строительстве. Востребованы составы в быту. С их помощью ремонтируют мебель, технику, предметы декора, напольные и настенные покрытия и другое. Эпоксидкой герметизируют различные инженерные коммуникации, ее используют для изготовления сувениров, бижутерии, поделок и многого другого.
Для применения в быту выбирают универсальные составы или специализированные материалы. Наиболее востребованы такие разновидности эпоксидного клея.
«Момент» от Henkel
Производится две линейки эпоксидных смесей. Однокомпонентный «Эпоксилин» и «Супер Эпокси», состоящий из двух компонентов. Для удобства смешивания последний выпускается расфасованным в два шприца. Это универсальные составы, образующие прочный шов, который после отверждения можно шлифовать, красить и даже сверлить.
Фото: Instagram kantstovary_perm
Холодная сварка
Специализированные смеси для ремонта предметов из различных металлов. Обладают повышенной прочностью, высокой скоростью отверждения. Чаще выпускаются как пластичная масса, но могу быть и в жидком виде. Продукция представлена разными брендами под названиями «Поксипол», «Эпокси-титан», «Эпокси-металл».
Клей ЭДП
Так сокращенно называется эпоксидно-диановый материал с полиэтиленполиамином. Относится к универсальным клеям, работает с различными основаниями: дерево, кожа, бетон, камень, керамика, резина и т.д. Приобретает заявленную прочность в течение 24 часов после нанесения. Выпускается разными компаниями под марками ЭПД, Химконтакт-эпокси, Эпокс-универсал.
Эпоксидный клей можно приготовить самостоятельно в домашних условиях. Как это сделать, показано в видеоматериале.
Инструкция по использованию эпоксидного клея
Для качественного склеивания деталей нужно точно выполнять рекомендации производителя смеси. В общих чертах такая инструкция выглядит так.
- Подготовка основания. Оно зачищается наждачкой, очищается от загрязнений и пыли, обезжиривается. В домашних условиях для обезжиривания используются растворители.
- Подготовка клеевого состава. Однокомпонентные смеси готовить не нужно. Двухкомпонентные смешиваются. Первой в емкость выдавливается эпоксидка, затем отвердитель. Пропорции должны быть точно соблюдены. Затем ингредиенты тщательно смешиваются.
- Склеивание деталей. Состав аккуратно наносится на одну из соединяемых поверхностей. Вторая накладывается на нужное место и плотно прижимается. В таком положении детали фиксируются на 7-10 минут, после чего остается подождать несколько часов, чтобы клеящий состав набрал необходимую прочность.
Полезные советы по хранению и удалению клея
Производитель рекомендует хранить состав в сухом месте, в вертикальном положении. Целостность упаковки не должна быть нарушена, иначе внутрь попадет воздух, что ухудшит качество клея. Хранить состав нужно только при комнатной температуре. Упакованная эпоксидка хранится от года до трех лет, но свойства ее со временем ухудшаются.
Работа с клеем предполагает использование защитных средств, поскольку отмыть его очень сложно. Пока состав еще жидкий, можно смыть его мыльной водой или ацетоном, если клей уже начинает полимеризоваться. Застывшую эпоксидку удалить очень сложно, можно попробовать такие методы:
- Нагрев утюгом или феном. Под воздействием высоких температур клей размягчается и его легче удалить.
- Замораживание хладагентом. После такой обработки состав делается хрупким и откалывается от поверхности.
- Применение растворителей. Клей смачивают анилином, толуолом, этиловым спиртом и т.п. Через некоторое время отскабливают пятно.
Фото: Instagram kamindustry.ru
Меры предосторожности
В состав клеящей смеси входят вещества с резким запахом, некоторые из них токсичны. По этой причине необходимо проводить все работы с эпоксидкой только в хорошо проветриваемом помещении. Желательно защитить дыхательные органы маской. Людям, склонным к аллергическим реакциям, рекомендуется надевать перчатки, чтобы предотвратить попадание вещества на кожу.
Если раствор все же попал на нее, нужно как можно быстрее смыть его мыльной водой. При попадании на слизистые используется только чистая вода. Если появилось раздражение, следует срочно посетить врача. Для смешивания клея запрещено использовать посуду, в которой будет храниться или готовиться пища.
Материал подготовила
Инна Ясиновская
Кварцвиниловая плитка отзывы вся правда. Советы по выбору.
Содержание:
1. Преимущества кварцвинила и ПВХ плитки
1.1 В чем разница кварцвинила и виниловой плитки
2. Виды Кварцвиниловой плитки — Клеевая
3. Виды Кварцвиниловой плитки — Со Smart лентой
4. Виды Кварцвиниловой плитки — Замковая
4.1 NEW Эко паркет — Замковый
5. Виды Кварцвиниловой плитки — С напылением FREE

7 Кварц виниловый ламинат с фаской или без какой лучше?
8. Толщина защитного слоя
9. Температура эксплуатации и использование с «теплыми полами»
10. Выводы и рекомендации
Что такое кварцвиниловая плитка?
Это синтетический материал, который изготавливается из ПВХ и специальных наполнителей. По слоям, упрощенно, это выглядит следующим образом : виниловая основа, сверху наносят декор-фактурную пленку на которую наносят защитный слой чистого ПВХ и полиуретана толщиной 0,1 — 0,7 мм. Максимальная толщина защитного слоя дает 43-й класс использования это максимальный класс изностостойкости для напольных покрытий.
По сравнению с линолеумом, внешний слой ПВХ плитки очень часто лучше передает расцветку и фактуры натуральных материалов:
- дерево
- мрамор
- гранит.
Можно сказать что кварцвинил сочетает в себе все преимущества четырех популярных напольных покрытий:
- от паркета — красоту
- от линолеума — практичность
- от ламината — модульность и вариативность укладки
- от керамической плитки — долговечность
К тому-же материал является антистатическим, не боится огня и устойчив к химическим веществам, не скользит и не деформируется от влаги в местах стыковки (в отличие от ламината). Обладает трехуровневым износостойким защитным слоем (PU — полиуретан, CB — керамический наполнитель, UV — ультра-компонент). Слой UV-ультра-компонента придает материалу высокую стойкость к образованию пятен и надежно защищает от солнечного ультрафиолета.
В чем разница между кварцвинилом и винилом?
Главная разница в наличии кварцевого песка. В первом случае песка в составе от 60-80%, в то время, как в ПВХ мела, песка и других наполнителей часто не более 20%. Кварц с одной стороны придает плитке прочность, при этом добавляет ей хрупкость. А так-как износу подвергается только внешний защитный слой, никакой разницы в эксплуатации плитки при равной толщине защитного слоя нет. Кварц винил с защитой 0,3 мм придет в негодность быстрее чем ПВХ с защитным слоем 0,5 и тем более 0,7 мм.
И тем не менее линолеум имеет более высокую герметичность и стабильность внешнего вида. При укладке плитки на недостаточно ровные полы, очень часто со временем будут появляться щели, избавиться от которых возможно только после полного перенастила кварцвинила. Что не представляется возможным при приклеивании на обычный клей, а не на фиксацию.
Четыре основных вида ПВХ и кварц винила:
Отличаются способом крепления между собой или к полу.
1. Клеевая плитка ПВХ
Укладываются на пол на специальный контактный клей или фиксатор. На подготовленное основание наносится клей, после чего плитку приклеивают к полу, а сверху прикатывают под нагрузкой
Как правило этот вариант выдерживает очень высокие эксплуатационные нагрузки, поэтому обычно применяется на больших коммерческих объектах. Данная плитка очень требовательна ровности основания.
2. ПВХ плиты SMART
Соединяются между собой с помощью SMART-ленты или клеевой ленты . К полу не клеится, SMART-лента выполняет роль тонкой подложки, поэтому допускается укладка на неровности до 1 мм на 2 метра длинны измерения.
Рекомендуется к применению дома, на даче, в небольших офисах, маленьких ресторанах и магазинах.
Основными условиями для качественного монтажа этого типа плиты, являются:
- правильная подстановка планок друг к другу как показано на рисунке
- температура во время укладки в помещении не ниже +20°С, температура пола не ниже +15°С
- после склеивании плит места стыков необходимо тщательно прикатывать прикаточным роликом.
3. Замковая плитка ПВХ
Виниловый ламинат или замковая плитка ПВХ. Планки соединяют между собой при помощи встроенного механического замка. Замки бывают разных типов, но по сути повторяют замок ламината. Приклеивать к полу нет необходимости, но приклейка дает большую надежность и увеличивает срок эксплуатации.
Подложку стелить не рекомендуется. Первое время (около месяца) все будет выглядеть ровно и красиво, но наличие мягкого слоя под замковой плиткой ускорит скорость разрушения замков, что, в конечном счете, приведет к расхождению швов плитки.
Рекомендуется к применению дома, на даче, в небольших офисах, маленьких ресторанах и магазинах.
Главными условиями надежной укладки кварц-винила с механическим клик-замком:
- наличие у плиты прочного замка
- подбивка каждой планки подбивочной плашкой.
Но если на длинной (продольной) стороне производители всегда нарезают замок типа КЛИК, то на короткой (поперечной) стороне могут быть два варианта замка. Замок «ШИП-ПАЗ» (на рисунке ниже первый вариант) и замок «КЛИК» (на рисунке ниже второй вариант). Оба замка очень хорошо работают на идеально ровном полу, но для качественного монтажа замка «ШИП-ПАЗ» требуется намного более ровный, фактически идеальный пол.
При незначительных перепадах высоты или неровностях основания, замок ШИП-ПАЗ» «отстреливает» от нижней планки. Бороться с этой проблемой можно только проклеиванием замка специальным клеем (но тогда теряется «мобильность» данного решения). Поэтому, когда покупателю нравится дизайн с таким замком, мы всегда заостряем внимание на том, что основание должно быть идеально ровное. Добиться этого возможно только выравниванием основания финишным самовыравнивающимся полом.
Замок «КЛИК» тоже требует ровного основания, но «прощает» небольшие перепады высоты. Но при перепадах больше 3 мм на 2 метра длинны замок, под нагрузкой, с течением времени все равно разрушиться.
Выводы и выбор делайте сами.
Еще одним очень важным моментом при выборе замкового кварц-винила является общая толщина плитки. Понять, почему, Вы можете внимательно посмотрев на рисунок ниже:
Если толщина плашки 5 мм или больше, то толщина самого тонкого «перешейка», на замке, составляет более 2 мм. А вот если общая толщина плитки составляет 4,5 мм или меньше, то технически не представляется возможным сделать толщину «перешейка» больше 1 мм (чаще даже меньше). Поэтому во время эксплуатации кварцвинила толщиной меньше 4,5 мм замки не выдерживают даже небольшой нагрузки!
Замок на перешейке просто отламывается, что приводит к образованию щелей, пол начинает «дышать».
Очень часто замки кварцвиниловой плитки толщиной 4,5 мм китайско-корейских производителей просто рассыпаются уже через несколько дней после укладки.
Если торцевые стыки кварцвиниловой плитки после укладки все-таки разошлись, значит Вы положили подложку толще 1 мм и плотностью ниже 250 кг/м3 и недостаточно внимания уделили ровности пола, а как известно — Скупой платит дважды!
Поэтому, выбирая замковую ПВХ плитку, лучше обратите свое внимание на продукцию хорошего европейского производителя (Quickstep, Tarkett, Forbo, Decoflooring и Wonderful Vinyl Floor). Кроме того:
- общая толщина плитки должна быть 5 мм и более
- толщина защитного слоя от 0,55 — 0,7 мм
В этом случае вы однозначно останетесь довольны покупкой, и на протяжении многих лет будете гордиться своим правильным выбором напольного покрытия. Вспомните народную поговорку: «Мы не настолько богаты, чтобы покупать дешево!» Если уж решили покупать ПВХ плитку, не экономьте, а если хотите сэкономить, купите хороший линолеум!
Думайте не о том как сэкономить сейчас, а как экономить на протяжении 10 лет! Ведь если сегодня вы сэкономите и купите дешевую виниловую плитку, то очень скоро наверняка пожалеете о таком своем решении. За качество нужно платить, причем не очень много. Стоимость кварц-винила примерно такая же, как стоимость ламината среднего класса, однако технические и эксплуатационные характеристики у кварцвинила намного выше.
Еще один тип ПВХ плитки на замке — так называемый «винил-гибрид». Эта плашка, 1/3 верхней части которой состоит из простого ПВХ, декоративной пленки и защитного слоя, а 2/3 нижней части — из композитного материала. Винил-гибрид обладает теми же преимуществами, что и простой кварцвинил с клик-замком, но благодаря композитному материалу он при этом намного легче, чем обычный винил с замком.
Не так давно на рынке напольных покрытий появилась новинка — ЭКОпаркет. Основной состав планок — природный материал Карбонат Кальция, который полностью безопасен для здоровья человека. Благодаря именно Карбонату кальция в сочетании с Черным углем- удалось добиться 3х ключевых характеристик: Экологичность. Надежность. Многофункциональность.
ECOparquet визуально похож на кварц-виниловую плитку ПВХ, однако это далеко не так, в рейтингах профессиональных специалистов, данный продукт находится в фаворитах!
Основные отличия:
- Состав. Полностью измененное содержание планок. Основная часть — Карбонат Кальция, который широко используется в таких продуктах как зубная паста, мел, стекло.
Для жесткости и стабильности покрытия был использован черный уголь (Carbon black) или как его еще называют технический углерод, чаще используется в обычном карандаше. Полимеры используемые для соединения веществ, относятся к той же группе, что и применяемые в медицине (пример искусственное сердце или капельница) или повседневной жизни (пластиковые бутылочки и пр.)
- Термостабильность и Жесткость. За счет добавления черного угля — планки жестче, стабильнее и устойчивее к температурным перепадам.
- Рельеф. За счет увеличения толщины защитного слоя (0,55 мм), планки обладают ярко выраженным, глубоким рельефом поверхности, который придает элегантности и изящности напольному покрытию.
- Замковое соединение. Толщина ламели составляет 5 мм поэтому замки очень надежны и плотно удерживают планки между собой даже при резких перепадах температур. При демонтаже покрытия шанс повредить замковое соединение гораздо ниже, чем у виниловых плиток с меньшей общей толщиной.
4. ПВХ винил «FREE» (фри).
Свободно лежит на полу за счет антискользящего резинового или клеевого напыления на нижней части плитки.
- подложка не применяется
- не требует приклейки к полу
- может собираться и разбираться несколько раз
- требуется идеально ровный пол Очень часто используется как мобильное покрытие для выставок или временных офисов.
Из какого сырья изготовлен?
Еще винил подразделяют на тот, который изготовлен из первичного сырья, и выполненный из вторичного сырья. ПВХ плитка из первичного сырья намного более качественнее, гораздо экологичнее и более стабильнее процессе эксплуатации (не расслаивается, не меняет геометрических размеров). Этот винил намного качественнее и в чаще всего изготавливается на европейских заводах.
Виниловая плитка, выполненная из вторичного сырья (обычно изготавливается на китайско-корейских заводах), всегда дешевле по цене, как правило, достаточно долго выделяет неприятный, а часто и небезопасный запах, и в процессе эксплуатации может расслаиваться, крошиться, терять геометрические размеры или вообще «гуляет» туда-сюда.
Объясняется это исключительно желанием сэкономить и снизить цену конечного продукта, ведь вторичный винил как сырье в два раза дешевле первичного качественного винила. Соответственно, заботясь о качестве, вашем здоровье и настроении, мы рекомендуем приобретать качественный продукт из первичного винила. Да, он немного дороже, чем аналогичный продукт из вторичного винила, но здоровье дороже, а неприятные случаи нам известны.
Кварц виниловый ламинат с фаской или без какой лучше?
Наличие фаски на стыках, позволяет скрыть небольшое расхождение планок, которое часто возникает на недостаточно ровном основании пола
поэтому, если у вас не получается сделать идеально ровный пол, берите плитку ПВХ только с фаской
Толщина защитного слоя является одним из важнейших параметров ПВХ винила.
Защитный слой является одним из самых главных составляющих напольного покрытия, так как он несет на себе самые большие нагрузки, но и здесь есть свои «подводные камни»:
- 4-е поколение — защитный слой из полиуретана с добавлением оксида алюминия
-
5-е последнее поколение (самое лучшее, и более износостойкое) — трехкомпонентный защитный слой состоит из: PU — полиуретан, CB — керамическая крошка, UV — ультра-компонент.
Защитный слой бывает от 0,1 до 0,7 мм. Чем толще защитный слой, тем дольше виниловое напольное покрытие сохранит свой внешний вид. Соответственно, если защитный слой у ПВХ плиты 0,3 мм, ее можно монтировать только для домашнего использования (ходить по нему желательно только в мягких носках).
А вот если толщина защитного слоя 0,55 мм и более, плиту можно укладывать в любых помещениях, в том числе коммерческого назначения, с большим потоком людей.
Отзывы экспертов: дешевой пвх плитка бывает обычно потому, что китайские производители экономят и на этом слое, ведь защитный слой составляет до 60% от стоимости конечного продукта. Если на китайском кварц виниле указано, что толщина защитного слоя составляет 0,4 мм, то со 100% вероятностью — в действительности защитный слой составляет лишь 0,3 мм, а то и 0,25 мм. На глаз такую разницу непрофессионалу определить невозможно.
Температура эксплуатации и использование для теплых полов.
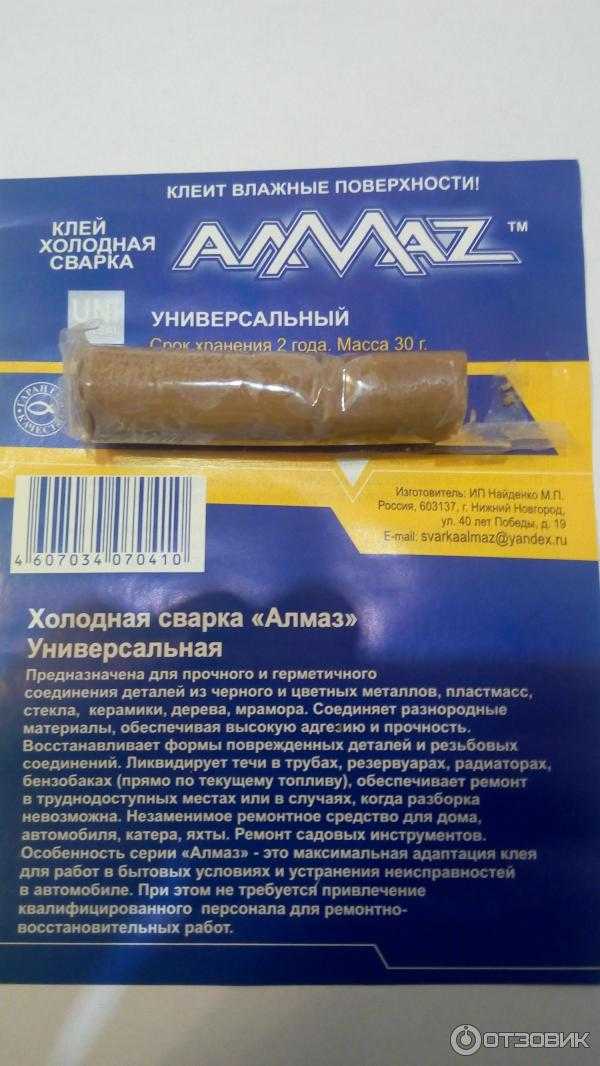
Кварцвинил можно укладывать в помещения с температурой эксплуатации от 0 до 40°С. ПВХ плитку можно укладывать поверх всех систем подогрева пола, кроме инфракрасной пленки. Нагревать материал можно не более чем 28-30°С. Почему нельзя греть кварцвиниловую плитку больше 28 градусов? При нагревании ПВХ выделяет винилхлорид, тяжелые металлы, фталаты, а это яд. Если Вам не страшно за свое здоровье, помните, что при нагреве может меняться геометрия плитки что приводит к возникновению щелей и «взбуханий».
Что теплее плитка ПВХ или линолеум? За счет своей структуры бытовой и полукоммерческий линолеум в своей структуре имеет больше воздушных пор. Для износостойкости это минус, но для звуко- и теплоизоляции большой плюс. Ну и ходить босиком по мягкому покрытию конечно комфортнее.
Выводы и рекомендации:
Все вышеперечисленные характеристики дают возможность успешно использовать кварц-винил как на объектах коммерческого назначения — торговые центры, аэропорты, банки, кафе, рестораны, офисные помещения, школьные, дошкольные и медицинские учреждения, склады, гаражи, так и в жилых помещениях — квартиры, коттеджи, дачи, сауны, бассейны.
Особенно интересен будет винилам владельцам домашних животных.
Производитель дает гарантию — 20 лет для домашнего использования, 10 лет — для использования в комерческих помещениях.
Что лучше кварц-винил или коммерческий линолеум? Конечно коммерческое рулонное покрытие более практично. Сваренный по швам линолеум герметичен на 100% на всем протяжении своей эксплуатации. Что не скажешь о плитке, в стыках которой со временем могут появляться щели, избавиться от который практически невозможно. Решением может являться густая холодная сварка, которой можно заполнить данные щели.
Аэрозольные краски в баллончиках KUDO
Аэрозольные краски в баллончиках получают все более широкое распространение.
Откуда же они взялись, какую выбрать, какими они бывают и чем хороши?
История появления аэрозольного баллона
Прорывом в развитии аэрозолей стало изобретение норвежцем Эриком Андреасом Ротхеймом в 20-х годах прошлого столетия прототипа современного аэрозольного баллона. Ротхейм искал самый эффективный способ равномерного нанесения воска на лыжи, и обнаружил, что лучше всего подходит аэрозоль. В 1927 году он получил патент на свое изобретение. Но коммерческий успех пришел позже.
В 1943 году американцы Лайл Гудхью и Уильям Салливан создали небольшой аэрозольный баллон, наполненный газом-вытеснителем и химическими веществами, предназначенными для борьбы с вредными насекомыми. Американские войска, в особенности те, что воевали на Тихом океане, восприняли новинку на ура – за оставшиеся два года войны было произведено примерно 50 000 000 баллонов.
А собственно аэрозольная краска появилась на свет в 1949 году: владелец компании Sycamore Эдвард Сеймур, чтобы наиболее эффектно продемонстрировать алюминиевое покрытие для радиаторов, по совету своей жены Бонни приспособил для этого банку-спрей от дезодоранта.
Преимущества красок в баллончиках
- Аэрозольные лакокрасочные материалы сразу готовы к применению. Их не нужно разбавлять, переливать в более удобную тару, достаточно лишь тщательно встряхнуть аэрозольный баллон перед применением.
- Наносить краски-спреи довольно просто, для этого не нужно каких-то специальных навыков. Но все же и здесь есть свои тонкости. Поэтому рекомендуем перед применением посмотреть небольшое обучающее видео.
- При помощи аэрозольных красок гораздо легче окрашивать сложные и труднодоступные поверхности.
- Аэрозольные краски можно использовать многократно. Если вы истратили не всю краску из баллона, достаточно продуть клапан и распылительную головку, чтобы они не засорились при дальнейшем хранении, и можно смело оставлять аэрозольный баллон на весь заявленный срок хранения – краска в нем не испортится. Такой подход невозможен для краски в обычных банках – если ее однажды вскрыть, долго храниться она уже не будет.
- Продолжительный срок хранения.
Если эмали в обычных банках имеют срок годности 1-2 года, то аэрозольные запросто могут храниться 5-8 лет. Все дело в том, что аэрозольный баллон герметичен, из него не испаряется растворитель и в него не проникает воздух, поэтому аэрозольная краска не портится от времени.
Недостатки красок в баллончиках
- Недостаток, по сути, всего один – наличие опыла во время окрашивания. Мельчайшие частицы краски-спрея при нанесении разлетаются по всему помещению, поэтому поверхности, которые вы не собираетесь красить, нужно обязательно защитить укрывными материалами.
Как устроен аэрозольный баллон
Аэрозольный баллон состоит из корпуса (1), клапана (2), трубочки (3) и распылительной головки (4). В баллон заправлены краска (5) и газ-вытеснитель (6) (он же пропеллент). Благодаря пропелленту в баллоне поддерживается давление, которое при нажатии на клапан и выталкивает краску через распылительную головку в виде спрея. При долгом хранении пигмент, входящий в состав краски, осаждается на дне баллона. Поэтому перед применением краски баллон нужно тщательно встряхнуть в течение нескольких минут, и в процессе нанесения регулярно встряхивать. Для того, чтобы состав эффективнее перемешивался при встряхивании, в аэрозольные баллоны вкладывают два небольших металлических шарика (7).
Подавляющее большинство аэрозольных красок – однокомпонентные. Существуют и двухкомпонентные аэрозольные краски, но они очень дорогие и потому встречаются очень редко. Поэтому дальше речь пойдет исключительно об однокомпонентных аэрозольных красках. По типу основы их можно разделить на несколько основных групп.
Акриловые
Акриловые аэрозольные краски в баллончиках быстро сохнут (2 часа в нормальных условиях), имеют яркие, насыщенные цвета, высокую эластичность и хорошую адгезию к пластикам. На акриловой основе выпускается множество аэрозольных красок: обычные, металлики со всплывающим и невсплывающим пигментами, флуоресцентные, фосфоресцентные, светоотражающие, с эффектом «хамелеон». Но по прочности, атмосферостойкости и стойкости к растворителям акриловые краски уступают алкидным. Следует развеять довольно частое заблуждение о том, что акриловые краски не пахнут, потому что они на водной основе. На водной основе выпускаются акриловые краски в банках, они действительно не пахнут. А вот аэрозольные акриловые краски изготовлены с применением органических растворителей, поэтому при распылении и при высыхании издают запах.
Посмотреть все →
Алкидные
Алкидные аэрозольные краски в баллончиках имеют высокую адгезию к металлам, высокие твердость, атмосферостойкость, светостойкость и стойкость к растворителям. Это очень популярные и самые стойкие эмали, алкидные краские не нужно дополнительно покрывать лаком.
Обратите внимание, они имеют длительное время сушки (от 5 до 24 часов), кроме того, под действием кислорода воздуха в них в течение двух недель после нанесения происходит полимеризация, в процессе которой алкидная краска набирает все свои свойства.
Есть несколько особенностей нанесения алкидных аэрозольных красок. Первое: каждый последующий слой нужно наносить «мокрым по мокрому», то есть в промежутке от 30 минут до 1,5 часов после нанесения предыдущего слоя. Второе: не наносить алкидную краску больше, чем в три слоя. При большой толщине покрытия верхние слои высохнут и полимеризуются раньше, закупорив нижние, не позволяя им до конца высохнуть и полимеризоваться. Получившаяся твердая корка на мягкой основе быстро разрушится. Третье: до полной полимеризации алкидные материалы нельзя подвергать сильному механическому воздействию, например, мыть контактным способом или полировать.
Более подробно об особенностях применения и совместимости алкидных и акриловых аэрозольных материалов можно почитать здесь.
Посмотреть все →
Эфиро-целлюлозные
Это так называемая автомобильная база «металлик». Имеет отличный декоративный эффект и обладает высокой стойкостью к выгоранию. Но образует матовое покрытие, нестойкое к механическому воздействию. Поэтому эфиро-целлюлозную краску «металлик» обязательно нужно покрывать лаком для придания прочности и глянца. Не следует путать эфиро-целлюлозные «металлики» с акриловыми — это разные эмали. Акриловые лаком покрывать либо не обязательно, либо и вовсе не нужно — все зависит от типа пигмента.
Посмотреть все →
Кремнийорганические
Самый яркий представитель кремнийорганических аэрозольных красок – термостойкая эмаль. Выдерживает нагрев до температуры от 400 до 800°C (в зависимости от цвета пигмента), но для достижения такой стойкости требует термозакалки. Режимы термозакалки могут быть разными, они указаны в инструкции к каждой краске. Но в любом случае эмаль после нанесения и высыхания необходимо нагреть до высокой температуры, например, 250°C и выдержать при этой температуре некоторое время. Без термозакалки эмаль заявленные высокие температуры выдерживать не будет. На кремнийорганической основе выпускаются также термостойкий (до 250°C) и водоотталкивающий лаки, имеющие отличную адгезию с камнем, бетоном и кирпичом. Прокаливать эти лаки не требуется.
Посмотреть все →
Аэрозольные краски на водной основе
Используются в качестве временных декоративных покрытий, с гладких поверхностей легко смываются водой. Смыть их с пористых поверхностей может оказаться проблематично, потому что удалить пигмент из пор довольно сложно. Краски-спреи на водной основе могут иметь обычные цвета, металлики, могут быть и яркими флуоресцентными.
Посмотреть все →
Таблица применимости аэрозольных красок
Акриловые | Алкидные | Эфироцеллюлозные | Кремнийорганические | На водной основе | |
Черные металлы | Хорошая адгезия | Отличная адгезия | Отличная адгезия | Хорошая адгезия | Легко удаляется |
Нержавеющая сталь | Слабая адгезия | Слабая адгезия | Слабая адгезия | Слабая адгезия | Легко удаляется |
Алюминий | Слабая адгезия | Только со специальным грунтом | Только со специальным грунтом | Слабая адгезия | Легко удаляется |
Дерево | Отличная адгезия | Отличная адгезия | Отличная адгезия | Хорошая адгезия | Трудно удаляется |
Пластик* | Отличная адгезия | С активатором адгезии | Хорошая адгезия | Слабая адгезия | Легко удаляется |
Камень, кирпич, цемент | Отличная адгезия | Отличная адгезия | Отличная адгезия | Отличная адгезия | Трудно удаляется |
Стекло | Только со специальным грунтом | Только со специальным грунтом | Только со специальным грунтом | Только со специальным грунтом | Легко удаляется |
*Кроме тефлона, силикона, полиэтилена и полипропилена.
Металлы с самыми низким температурами плавления: топ-10
Привычным стереотипом является, что металл – это обязательно нечто тяжёлое, прочное, блестящее. Из металлов делают инструменты и механизмы, оружие и украшения. Металлы используют для защиты от непогоды и хранения пищи. Даже в язык проник стереотип — фраза «возьми какую-нибудь железяку» имеет вполне конкретный и ёмкий смысл.
Однако, твёрдые, прочные и жаростойкие далеко не все металлы. И вещества, такие как натрий, галлий, ртуть — находят необычные применения.
Сегодня, поговорим о десяти металлах с самыми низкими температурами плавления.
Олово (231°C)
Химический элемент, занимающий в периодической таблице юбилейное, пятидесятое место известен человечеству с древнейших времён. Первые капли олова (латинское наименование Stannum) первобытные люди заметили в своих кострах ещё за 4 тысячи лет до нашей эры. Немудрено — ведь олово плавится при температуре всего при 231°C. При этом дерево ещё только-только начинает обугливаться и робко гореть.
После застывания «слёзы», которыми плакал в огне красивый тяжёлый камень кассидерит, сохраняли форму, в которой им довелось застыть. Так появились первые металлические предметы кухонного быта.
Когда же удалось вытопить из зелёного малахита рыжую медь, оказалось, что смесь меди с оловом гораздо прочнее любого из металлов по отдельности. Тут-то цивилизация и начала бурно развиваться. Оружие, доспехи, посуда, инструменты — всё делали из прочной и красивой бронзы.
При какой температуре плавится
Металлические элементы, какими бы они ни были — плавятся почти один в один. Этот процесс происходит при нагреве. Оно может быть, как внешнее, так и внутреннее. Первое проходит в печи, а для второго используют резистивный нагрев, пропуская электричество либо индукционный нагрев. Воздействие выходит практически схожее. При нагреве, увеличивается амплитуда колебаний молекул. Образуются структурные дефекты решётки, которые сопровождаются обрывом межатомных связей. Под процессом разрушения решётки и скоплением подобных дефектов и подразумевается плавление.
У разных веществ разные температуры плавления. Теоретически, металлы делят на:
- Легкоплавкие – достаточно температуры до 600 градусов Цельсия, для получения жидкого вещества.
- Среднеплавкие – необходима температура от 600 до 1600 ⁰С.
- Тугоплавкие – это металлы, для плавления которых требуется температура выше 1600 ⁰С.
Плавление железа
Температура плавления железа достаточно высока. Для технически чистого элемента требуется температура +1539 °C. В этом веществе имеется примесь — сера, а извлечь ее допустимо лишь в жидком виде.
Интересное: Как варить чугун
Без примесей чистый материал можно получить при электролизе солей металла.
Плавление чугуна
Чугун – это лучший металл для плавки. Высокий показатель жидкотекучести и низкий показатель усадки дают возможность эффективнее пользоваться им при литье. Далее рассмотрим показатели температуры кипения чугуна в градусах Цельсия:
- Серый — температурный режим может достигать отметки 1260 градусов.
При заливке в формы температура может подниматься до 1400.
- Белый — температура достигает отметки 1350 градусов. В формы заливается при показателе 1450.
Важно! Показатели плавления такого металла, как чугун – на 400 градусов ниже, по сравнению со сталью. Это значительно снижает затраты энергии при обработке.
Плавление стали
Плавления стали при температуре 1400 °C
Сталь — это сплав железа с примесью углерода. Её главная польза — прочность, поскольку это вещество способно на протяжении длительного времени сохранять свой объем и форму. Связано это с тем, что частицы находятся в положении равновесия. Таким образом силы притяжения и отталкивания между частицами равны.
Справка! Сталь плавится при 1400 °C.
Плавление алюминия и меди
Температура плавления алюминия равна 660 градусам, это означает то, что расплавить его можно в домашних условиях.
Чистой меди – 1083 градусов, а для медных сплавов составляет от 930 до 1140 градусов.
Литий (180°C)
Этот удивительный металл, открыли только в начале XIX века. Литий (Lithium, элемент №3) довольно легкоплавкий — жидкий метал температуры всего 180°C можно помешивать даже деревянной ложечкой.
Литий отличается очень малой плотностью — вдвое легче воды! Металл относится к группе щелочных и довольно активен химически (поэтому его так долго не могли открыть).
В современном мире литий широко используется для создания удивительных сплавов — твёрдых, лёгких и жаропрочных. Без лития не обходится ни одна современная электронная штучка. Ведь литий является ключевым компонентом компактных и ёмких аккумуляторов. А ещё, именно литий придаёт замечательный алый цвет фейерверкам.
Важность рассматриваемого показателя
Температура плавления материалов учитывается практически во всех сферах их применения. Примером можно назвать то, что на момент рождения авиации не могли использовать обычный алюминий, так как он быстро нагревался из-за трения и терял свои линейные размеры. Появление дюралюминия существенно изменило мир авиации. После его открытия все дирижабли и самолеты стали изготавливать при обширном применении этого сплава.
Нагреву подвергаются и многие другие ответственные детали различных механизмов. Примером назовем ведущие валы различных механизмов, звездочки и шестерни, которые из-за непосредственного контакта также теряют свою твердость, что приводит к повышенному износу.
Существует довольно большое количество справочников, в которых указывается температура плавления для всех металлов и иных сплавов. При рассмотрении этого показателя следует учитывать химический состав. Даже незначительное изменение концентрации одного из элементов приведет к повышению или понижению температуры перестроения кристаллической решетки.
Индий (157°C)
В конце XIX века химикам удалось открыть и выделить в чистом виде элемент, занявший в периодической таблице клетку №49. Индий (Indium) — довольно тяжёлый (почти как железо) металл, плавящийся при 157°C.
Этот материал поразительно мягок и пластичен. Мягче этого металла только тальк! Невероятное свойство сделало индий незаменимым в радиоэлектронике. Тонкие индиевые полоски, нанесённые на стекло, хорошо проводят электрический ток — но при этом совершенно прозрачны. Так делают уже привычные нам плоские экраны на основе «жидких кристаллов» (LCD).
Сплавы для пайки
На практике многие сталкиваются с плавлением при пайке деталей. Если поверхности соединяемых материалов очищены от загрязнений и окислов, то их нетрудно спаять припоями. Принято делить припои на твердые и мягкие. Мягкие получили наибольшее распространение:
- ПОС-15 — 278…282 °C;
- ПОС-25 — 258…262 °C;
- ПОС-33 — 245…249 °C;
- ПОС-40 — 236…241 °C;
- ПОС-61 — 181…185 °C;
- ПОС-90 — 217…222 °C.
Их выпускают для предприятий, изготавливающих разные радиотехнические приборы.
Твердые припои на основе цинка, меди, серебра и висмута имеют более высокую температуру плавления:
- ПСр-10 — 825…835 °С;
- ПСр-12 — 780…790 °С;
- ПСр-25 — 760…770 °С;
- ПСр-45 — 715…721 °С;
- ПСр-65 — 738…743 °С;
- ПСр-70 — 778…783 °С;
- ПМЦ-36 — 823…828 °С;
- ПМЦ-42 — 830…837 °С;
- ПМЦ-51 — 867…884 °С.
Использование твердых припоев позволяет получать прочные соединения.
Внимание! Ср означает, что в составе припоя использовано серебро. Такие сплавы обладают минимальным электрическим сопротивлением.
Натрий (97,8°C)
Натрий (Natrium, 11-й элемент) может расплавиться даже в кипятке — 97,8°C. Но мы бы не советовали позволить даже маленькому кусочку натрия упасть в воду (хотя бы и ледяную). Щелочной металл натрий очень активен химически и немедленно реагирует, отделяя от молекул воды водород и превращаясь в сильнейшую щелочь.
При этом выделяется много тепла, которое тут же поджигает освободившийся водород. Взрыв и пожар! Такие материалы как натрий хранят в керосине, что исключает их контакт с водой и влагой воздуха.
Как очень активный элемент, натрий в том или ином виде присутствует вокруг нас в огромных количествах. Взять хотя бы хлорид натрия — обычная поваренная соль.
Что такое температура плавления
Каждый металл имеет неповторимые свойства, и в этот список входит температура плавления. При плавке металл уходит из одного состояния в другое, а именно из твёрдого превращается в жидкое. Чтобы сплавить металл, нужно приблизить к нему тепло и нагреть до необходимой температуры – этот процесс и называется температурой плавления. В момент, когда температура доходит до нужной отметки, он ещё может пребывать в твёрдом состоянии. Если продолжать воздействие – металл или сплав начнет плавиться.
Интересное: Контроль неразрушающий соединения сварные методы ультразвуковые
Плавление и кипение – это не одно и то же. Точкой перехода вещества из твердого состояния в жидкое, зачастую называют температуру плавления металла. В расплавленном состоянии у молекул нет определенного расположения, но притяжение сдерживает их рядом, в жидком виде кристаллическое тело оставляет объем, но форма теряется.
При кипении объем теряется, молекулы между собой очень слабо взаимодействуют, движутся хаотично в разных направлениях, совершают отрыв от поверхности. Температура кипения – это процесс, при котором давление металлического пара приравнивается к давлению внешней среды.
Для того, чтобы упростить разницу между критическими точками нагрева мы подготовили для вас простую таблицу:
Свойство | Температура плавки | Температура кипения |
Физическое состояние | Сплав переходит в расплав, разрушается кристаллическая структура, проходит зернистость | Переходит в состояние газа, некоторые молекулы могут улетать за пределы расплава |
Фазовый переход | Равновесие между твердым состоянием и жидким | Равновесие давления между парами металла и воздухом |
Влияние внешнего давления | Нет изменений | Изменения есть, температура уменьшается при разряжении |
Калий (63,5°C)
Близкий родственник натрия — калий. Элемент №19 (Kalium) также бурно реагирует с водой, образуя щёлочь, и также легкоплавок — 63,5°C. А вот съедобных соединений калия почти нет, и в этом он полная противоположность натрию. Хотя в ограниченно малых количествах организму всё-таки необходим (микроэлемент).
В чистом виде калий практического применения не имеет. Но его многочисленные соединения с древних времён известны как удобрения, моющие средства, важные компоненты многих химических процессов.
Рубидий (39,31°C)
37-й элемент таблицы — рубидий (Rubidium) плавится всего при 39,31°C. Кусочек рубидия может растаять на блюдце как сливочное масло. Это лёгкий металл, его плотность лишь немного превышает плотность воды. Но реагирует с водой рубидий не менее бурно, чем его близкие родственники калий и натрий.
Рубидий удивителен своими химическими свойствами. Сам по себе щелочной металл очень легко вступает в разнообразные химические реакции. Но при этом соли рубидия и его сплавы с другими металлами являются хорошими катализаторами реакций. То есть, значительно ускоряют процесс, при этом совершенно не расходуясь сами по себе. Это делает рубидий ценным материалом для химической промышленности и радиоэлектроники.
Твердое и жидкое состояние металла
Многие знакомы с металлами и сплавами по их твердому состоянию. Они встречаются практически во всех сферах деятельности. Только в металлургии и в производственных цехах металл встречается в жидком состоянии. Это связано с тем, что для преобразования кристаллической решетки приходится проводить нагрев сырья до рекордных температур.
Твердое состояние характеризуется следующими качествами:
- Структура держит свою форму. Сталь известна тем, что может выдерживать серьезную нагрузку в течение длительного периода.
- Каждому материалу свойственны свои показатели прочности и твердости, вязкости.
- Постоянный химический состав. Поверхность стали или других сплавов может реагировать на воздействие химических веществ, окисляться или покрываться коррозий, но вот химический состав остается неизменным.
- Возможность обработки резанием. При повышении пластичности не образуется стружка на момент механической обработки, что существенно усложняет процесс.
В жидком или вязком состоянии металл приобретает совсем другие свойства:
- Высокая пластичность позволяет выполнять литье по форме, ковку или проводить другую обработку, связанную с пластической деформацией заготовок.
- Есть возможность изменить химический состав путем добавления легирующих элементов. За счет подвижной кристаллической решетки можно проводить насыщение структуры стали хромом, никелем, титаном и многими другими веществами.
- Термическая обработка проводится также при температуре, которая приводит к перестроению кристаллической решетки. Однако при закалке металл сохраняет свою форму, то есть структура остается твердой.
Существуют сплавы, которые можно разогреть до жидкого состояния и в домашних условиях. Примером можно назвать олово, применяемое при изготовлении припоя. Температура плавления олова находится в пределах 250 градусов Цельсия. Этот показатель нагрева можно достигнуть при применении обычного паяльника.
Цезий (28,5°C)
Очень мягкий серебристый металл буквально плавится в руках. При температуре 28,5°C цезий (Caesium) становится жидкостью и буквально утекает между пальцев. Но не вздумайте провести такой опыт! Из всех щелочных металлов элемент №55 самый химически активный (уступая лишь францию).
На открытом воздухе цезий моментально окисляется, образуя яркое пламя. А при попадании в воду просто взрывается. Цезий ухитряется поджечь даже лёд! Более того, образовавшийся при реакции с водой гидроксид цезия разъедает стекло — и потихоньку грызёт сосуды из золота и даже платины.
А вот в электронике такая активность цезия позволяет делать очень чувствительные фотоэлементы и часы поистине космической точности.
Франций (27°C)
Элемент, занимающий 89-ю ячейку периодической таблицы — франций (Francium) — очень похож на цезий. Франций плавится при 27°C, но до этого неимоверно активный щелочной металл ещё требуется сберечь.
Мало того, что франций бурно реагирует буквально со всем подряд — он ещё и очень радиоактивен! Буквально через полчаса от килограмма франция останется — хорошо если горстка — разнообразных сильно излучающих продуктов деления.
Впрочем, в таких количествах его никто никогда и не видел. Неудивительно, что в природе этот элемент один из самых редко встречающихся. Да и практического применения ему так и не нашлось.
Галлий (26,79°C)
А вот серебристый металл галлий (Gallium — ещё до открытия элемента Д.И. Менделеев заранее оставил ему в таблице клеточку № 31) встречается гораздо чаще и нередко применяется просто для забав. Плавится он почти как цезий, при 26,79°C, но в остальном разительно отличается от своего «нервного» братца.
Внешне и по механическим свойствам галлий очень похож на алюминий. Лёгок, теплопроводен, в чистом виде довольно хрупок. Мгновенно образующаяся на воздухе плотная плёнка окислов так же хорошо защищает его от разрушения.
В чистом виде галлий практически не находит применения. А вот его соли и, особенно, легкоплавкие сплавы нашли широчайшее применение в ядерной физике, радиоэлектронике, измерительной технике.
Ртуть (-38,87°C)
Все мы хорошо знакомы со ртутью — даже сегодня, в век электроники, вряд ли найдётся хоть один человек, которому не измеряли бы температуру тела ртутным термометром. Но мало кто задумывается, что очень текучая тяжёлая серебристая жидкость — самый настоящий металл!
Да-да, элемент №80, Hydrargyrum, плавится на самом лютом морозе — температура кристаллизации ртути почти минус сорок градусов (-38,87°C).
Человечество знакомо со ртутью с древнейших времён. Ртуть находит широчайшее применение в технике, химии, металлургии. Этот элемент достоин отдельного, немаленького рассказа — а сегодня он гордо венчает наш рейтинг.
1 0
Можно ли сваривать в космосе? Шокирующий ответ!
Последнее обновление
Сварка в космосе возможна с использованием процесса, известного как холодная сварка. На Земле вам нужно тепло, чтобы сварить два металла вместе. Это влечет за собой нагревание металлов до тех пор, пока вы не достигнете точки плавления. Но в космосе вам не нужно использовать тепло для сплавления двух металлов.
Холодная сварка — лучший процесс для сплавления металла в такой нестабильной среде. Он восходит к 1940-х годов и считается общим явлением материалов. В вакууме, таком как космос, два одинаковых материала, таких как металл, сплавляются вместе посредством контактной сварки.
В этой статье вы узнаете все о сварке в космосе. Продолжайте читать для более глубокого понимания.
Кто был первым космонавтом, совершившим сварку в космосе?
Первыми сварщиками в космосе стали российские космонавты Георгий Шонин и Валерий Кубасов. Это произошло еще в 1969 году, в то время, когда освоение космоса только набирало обороты. Целью этого первого испытания было проверить опасность сварки в космосе.
Эта российская команда провела серию экспериментов, в которых использовались три метода сварки. Они хотели посмотреть, какие из них эффективны для создания прочных связей, а также безопасны для использования в новой среде. Три метода сварки:
- Дуговая сварка плавящимся электродом
- Электронно-лучевая сварка
- Дуговая сварка сжатым воздухом под низким давлением
С тех пор в космической технике произошло много изменений, позволивших улучшить холодную сварку в открытом космосе. Существуют более продвинутые методы сварки внутри и снаружи космических аппаратов. Кроме того, космонавты лучше разбираются в материалах, которые хорошо подходят для холодной сварки.
Почему сварка в космосе сложна?
Сварка — это процесс соединения двух материалов, обычно металлов или термопластов, с использованием высокой температуры для расплавления частей и их сплавления. Сварка в космосе сопряжена с некоторыми уникальными проблемами, которые следует считать успешными.
Одной из самых больших проблем является тот факт, что в космосе нет атмосферы. Это означает, что нет воздуха, поддерживающего процесс сварки. Для сварки в космосе необходимо использовать специальное оборудование, способное обеспечить атмосферу для проведения сварки.
Еще одна проблема — отсутствие гравитации. Это может затруднить позиционирование свариваемых материалов в правильном положении. Для удержания материалов на месте могут потребоваться специальные приспособления и инструменты.
- Читать по теме : Сколько зарабатывают сварщики в аэрокосмической отрасли? Статистика заработной платы
Третья проблема — экстремальные температуры, которые могут быть в космосе. Это может привести к расширению или сжатию свариваемых материалов, что усложнит процесс сварки.
Несмотря на эти проблемы, сварка в космосе возможна и успешно используется во многих случаях. При правильном оборудовании и планировании сварка в космосе может стать успешным и надежным способом соединения материалов.
Холодная сварка в космосе
Сварка в вакууме требует иного мыслительного процесса, чем обычная тепловая сварка. В космосе астронавтам приходится использовать разные тактики, чтобы сплавлять металлические детали во время ремонта. Вместо тепла используют контактную или холодную сварку.
В открытом космосе существует большое давление, которое сплавляет две металлические детали. Но это может произойти только в том случае, если материалы чистые и однородные. Сплавить металл и дерево в пространстве не получится, поэтому необходимы другие способы крепления таких деталей.
Тем не менее, холодная сварка остается одним из самых эффективных способов сварки в космосе. Две металлические детали, которые необходимо прикрепить, всегда остаются цельными. Это отличается от стандартной тепловой сварки, когда расплавленное состояние необходимо для сплавления двух металлических частей.
Космонавтам предстоит пройти небольшой процесс, прежде чем они смогут использовать холодную сварку в космосе. Первым шагом является удаление любых оксидных слоев на двух металлических частях. Нередко на металле можно обнаружить оксидный защитный слой, препятствующий склеиванию.
Наилучший способ удаления оксидного слоя — чистка щеткой, обезжиривание или использование химических средств. После удаления оксида металла следующим шагом является соединение двух металлических частей под высоким давлением. Это то, что создает металлургические связи.
Контактная сварка требует, чтобы две металлические детали были в наилучшем состоянии. Это означает, что они не должны подвергаться закалке. В результате большинство астронавтов предпочитают работать с мягкими металлами, которые более пластичны и создают прочные связи.
5-этапный процесс холодной сварки
- Первым этапом является очистка поверхностей свариваемых материалов. Это важно для обеспечения хорошего соединения между двумя деталями.
- Далее материалы располагаются так, чтобы они были на одном уровне друг с другом. Еще раз, это важно для создания хорошего соединения.
- Затем используется аппарат для холодной сварки для создания электрического соединения между двумя деталями. Это соединение позволит току течь между двумя частями и создать сварной шов.
- Затем аппарат для холодной сварки подаст ток на две детали. Этот ток заставит две части нагреваться и в конечном итоге сварится вместе.
- После завершения сварки аппарат для холодной сварки убирается, и двум деталям дают остыть.
Изображение предоставлено: Vladi333, Shutterstock
Преимущества холодной сварки
Холодная сварка не создает ЗТВ (зоны термического влияния)
Тепловая сварка требует расплавления двух металлических частей, чтобы сплавить их вместе. Одним из недостатков тепловой сварки является создание зоны термического влияния (ЗТВ). Происходит это из-за воздействия высоких температур. Однако холодная сварка не вызывает этого и приводит к более сильному сплавлению.
Прочные соединения
Холодная сварка создает прочные соединения, которые сохраняются в вакууме, например в открытом космосе. Сварные швы также чистые и не приводят к слабым интерметаллическим связям.
Улучшенное соединение разнородных металлов
Некоторые металлы, такие как медь и алюминий, лучше всего подходят для холодной сварки, которая позволяет соединять разнородные металлы. Это также отличный способ соединения металлов, таких как алюминий серий 2xxx и 7xxx. Это невозможно сделать с помощью других методов соединения металлов.
Недостатки холодной сварки
Требует надлежащей подготовки металла
В открытом космосе космонавты не могут просто выполнять холодную сварку. Сначала они должны очистить металлы, чтобы избавиться от грязи и окислов. Весь процесс занимает время в опасной среде, особенно если соединяемые детали большие.
Холодной сварке могут подвергаться только определенные материалы.
Сварка в космосе — сложный метод, так как вы не можете соединить все типы металлов. Только пластичные металлы, которые не подвергались закалке, идеально подходят для сплавления в вакууме.
Подходят только ровные ровные поверхности
Холодная сварка имеет особое значение, когда речь идет о возможных типах сварных швов. Сварка неровных поверхностей невозможна. Этот метод применим только к плоским ровным поверхностям, которые соединяются без каких-либо затруднений.
Изображение предоставлено: Cergeus, Shutterstock
Может ли металл свариться в космосе?
На данный момент в космосе парит множество металлических конструкций. Теоретически части этих металлических конструкций можно сваривать в космосе.
Однако шансы на это ничтожны из-за смягчающих обстоятельств. Помните, что холодная сварка в вакууме может происходить только тогда, когда обе поверхности сплавления чистые. Это означает, что металл в космосе должен быть чистым и свободным от оксидов, чтобы иметь место холодная сварка.
Металл, доставленный в космос, имеет оксидные слои. У всех спутников и других кораблей, плавающих в открытом космосе, больше шансов столкнуться, чем слиться. Поскольку счищать окисные слои там некому, металл не может свариться в космосе.
Можно ли предотвратить нежелательную холодную сварку в космосе?
Случайная холодная сварка в космосе не исключена, но для этого должны присутствовать соответствующие условия. Тем не менее, вероятность нежелательного сплавления металла может привести к катастрофическим последствиям.
Так что лучше найти способы предотвратить нежелательную холодную сварку металла в космосе. Ниже приведены несколько способов, которыми астронавты могут предотвратить это.
1. Покрытие поверхности
Холодная сварка может происходить в космосе, если металлические поверхности не содержат оксидов, грязи и других покрытий. Лучший способ предотвратить расплавление металла — обеспечить покрытие металлических поверхностей этими веществами. Таким образом, космонавты могут очищать поверхности, если когда-либо возникнет необходимость в специальной холодной сварке.
2. Снижение воздействия на окружающую среду
Некоторые голые металлы подвержены высокой вероятности холодной сварки, даже если в этом нет необходимости. Примером могут служить теплоизолированные детали, которые выдерживают термоциклирование, повреждения от радиации и атомарного кислорода. В конечном итоге они разрушают защитное покрытие, защищающее от нежелательной холодной сварки в космосе.
3. Безопасные простые конструкции
На космическом корабле есть крепления, замки и защелки. Важно защитить их, чтобы предотвратить загрязнение и износ. Это происходит из-за наличия абразивных частиц, которые попадают между этими структурами.
4. Меньше движущихся частей
Для предотвращения холодной сварки без предварительных требований требуется меньше движущихся частей. Это поверхности, которые подвергаются трибоэлектрическому износу и воздействию окружающей среды.
Заключение
Сварка в космосе возможна с использованием процесса, называемого холодной сваркой. Эта форма сварки отличается от стандартной тепловой сварки, распространенной во всем мире. Поскольку сварка в космосе происходит в вакууме, нет необходимости использовать тепло для расплавления двух металлических поверхностей.
Холодная сварка сплавляет две металлические детали под высоким давлением. Этот процесс существует уже некоторое время и впервые был использован в 1969 году в космосе. Иногда в космосе может происходить нежелательная холодная сварка, поэтому очень важно предотвратить это.
Источники
- Космонавты используют контактную или холодную сварку в космосе
- Холодная сварка происходит только тогда, когда две металлические поверхности находятся в наилучших условиях
- Важно предотвратить нежелательную холодную сварку в космосе
- Только пластичные металлы, не подвергавшиеся закалке, допускают холодную сварку
Вас также может заинтересовать: Можно ли сваривать черные трубы? Все, что тебе нужно знать!
Авторы и права: Castleski, Shutterstock
- Кто был первым астронавтом, совершившим сварку в космосе?
- Почему сварка в космосе сложна?
- Холодная сварка в космосе
- 5-этапный процесс холодной сварки
- Преимущества холодной сварки
- Холодная сварка не создает HAZ (зона тепловизионного воздействия)
- Строительные соединения
- Лучшее соединение разнородных металлов
- Недостатки холодной сварки
- Требуется подготовка металла
- .
Специфические материалы могут в разделении холодной сварки
. - Только плоские правильные поверхности могут делать
- 1. Покрытие поверхности
- 2. Снижение воздействия на окружающую среду
- 3. Надежность простых конструкций
- 4. Меньшее количество движущихся частей
Холодная сварка труб из ковкого металла
Герметизация труб из пластичного металла (трубок) является важным и необходимым процессом при отделении устройства от вакуумной насосной станции. Инструменты, которые могут надежно выполнять функцию отсечки (холодной сварки), обеспечивают надежное уплотнение, способное выдерживать температуры прожига до 600 o C и устраняет необходимость использования дорогостоящих клапанов для выполнения того же процесса. С помощью этих эффективных инструментов отжим трубы и полученное в результате холодносварное (герметически запаянное) соединение выполняется за одну операцию. Хотя этот процесс отсечки чаще всего используется в вакуумных приложениях, он одинаково эффективен в приложениях, связанных с высоким или низким давлением.
Без сомнения, самым важным фактором в получении этого соединения холодной сварки является сама труба. Выберите неправильную трубку, и результаты будут действительно очень разочаровывающими. Выбор трубки имеет решающее значение и заслуживает более подробного обсуждения.
Выбор надлежащего материала трубок
Для получения надежного, воспроизводимого сварного соединения холодной сваркой при использовании механических отжимных инструментов требуется правильный материал трубки и ее подготовка. Для получения герметичного соединения должны быть соблюдены все условия. Без сомнения, материал труб и термообработка являются наиболее важным фактором во всем этом процессе.
Трубки, наиболее часто используемые для механических отводов, изготовлены из бескислородной меди с высокой проводимостью. Спецификации, химический состав и состояние пластичности сертифицированной заготовки (чистота 99,9%). Медь подробно описана в спецификациях ASTM B68-83, B75-84, B133-33 и B170-82. Другие одобренные и часто используемые материалы включают: никель высокой чистоты («никель A», NI 270, NI 200 или никель 99,4% чистоты ASTM-B161), алюминий (отожженный 3003 h24, 98% классифицируется как неподдающийся термической обработке), чистое железо, Золото, Платина, Серебро и Колумбий.
Медная трубка OFHC
Если учесть, что процесс отсечки деформирует и удлинит трубку на 350 % или более, а зона холодного сварного шва будет упрочняться во время процесса отсечки, создавая удлиненную зернистую структуру. в трубке важно, чтобы трубка была правильно обработана перед попыткой механического пережатия.
OFHC Медь отжигают при 650 o — 850 o C в течение 30 минут в атмосфере сухого водорода. Конечным результатом является ковкий материал трубки, который будет правильно пережиматься с помощью инструмента и не будет преждевременно отделяться. Слишком твердая трубка будет утомляться и отделяться до того, как инструмент для отсечения завершит свой цикл, что приведет к повреждению соединения холодной сварки и негерметичному или сомнительному уплотнению. С другой стороны, трубка также может быть отожжена слишком мягкой, что приведет к тому, что трубка не сможет отделиться, оставив очень тонкое полотно материала, которое требует от техника физического «покачивания» лишнего материала для достижения разделения.
Никелевая трубка
Никель высокой чистоты имеет несколько преимуществ для процесса холодной сварки: (1) Минимальное выделение газов во время отжига и отжима, (2) Минимальное окисление и, (3) Более высокие температуры отжига. Для выполнения механического холодного сварного соединения с механическим отжимным инструментом никель должен быть полностью отожжен при 1150 o C в течение 30 минут для достижения необходимой твердости трубы.
Дополнительные факторы выбора трубки
Другим фактором, влияющим на качество и стабильность отсечки, является толщина стенки. Как правило, трубы из меди и никеля OFHC имеют довольно тонкие стенки. Например, трубка диаметром 1/8 дюйма обычно имеет толщину стенки примерно 0,030–0,035 дюйма, тогда как трубка диаметром 1/2 дюйма будет иметь толщину стенки примерно 0,040–0,045 дюйма. Трубки с толстыми стенками, твердость которых также может превышать требуемую спецификацию, потребуют большего давления инструмента для сжатия, отрыва или разделения трубок. Поскольку все трубки в процессе пережатия подвергаются механической обработке, любое изменение твердости трубки или толщины стенки будет напрямую влиять на качество и надежность отрезанной трубки.
Проверка ваших трубок поставщиком инструмента является очень важным шагом в процессе, и его нельзя избегать. Все факторы, описанные выше, необходимо тщательно рассмотреть, прежде чем вы закончите работу над трубкой или источником отсечного инструмента.
Подготовка трубки к пережатию
Независимо от материала трубки, выбранного для вашего применения, правильная подготовка трубки является важным этапом в процессе. Тубуляция И.Д. не должно быть никаких загрязнений в месте защемления. Звуковые или механические методы очистки гораздо предпочтительнее химической очистки перед откачкой, поскольку они обеспечивают наиболее стабильные соединения холодной сварки. Тубуляция Н.Д. следует отполировать, чтобы удалить любое окисление, так как эти кристаллы оксида будут тверже, чем трубка, и могут повредить соединение холодной сварки.
Инструменты, предназначенные для производства пережимных трубок, оснащены набором прецизионных твердосплавных роликов, которые сжимают трубку для получения соединения холодной сварки. Между каждым циклом отжима остатки металла из трубки часто остаются на твердосплавных роликах, и это загрязнение следует удалить, слегка протирая твердосплавные ролики мягким полотенцем, смоченным легким машинным маслом, чтобы поверхность была чистой и готовой к работе. следующий цикл отжима.
После отжима
Процедуры испытаний будут различаться в зависимости от области применения герметизируемых трубок. Как правило, трубки, поддерживающие вакуум, подвергаются тесту на утечку гелия или исследованию под микроскопом в целях сравнительного анализа. Для применений с высоким или низким давлением процедуры испытаний часто включают испытание на утечку в той или иной форме. Какая бы процедура тестирования не использовалась, технологические процедуры должны быть точно продублированы, чтобы можно было отследить любые проблемы, связанные с отказом трубки.
После того, как трубка была успешно пережата и подтверждена герметичность, обработанный конец трубки должен быть защищен пластиковой крышкой, эпоксидной смолой или герметиком, так как край очень острый и запаянный конец может быть поврежден если ударился или погнулся. НИКОГДА не рекомендуется пайка или пайка конца трубы, сваренного методом холодной сварки, так как структура зерна может быть нарушена, что приведет к утечке.
Выбор инструмента для отщипывания
Наиболее эффективные инструменты для выполнения процесса отщипывания приводятся в действие гидравлическими насосами. Усилие смыкания зажимных кулачков, необходимое для успешного отсечения и холодной сварки одобренных НКТ, будет превышать 5000 фунтов на квадратный дюйм. Кроме того, твердосплавные отжимные ролики, соприкасающиеся с трубкой, должны быть прецизионно отшлифованы, чтобы обеспечить однородность поверхности защемления и устойчивость к износу. Несмотря на то, что существует несколько доступных ручных механических инструментов для отщипывания, отжим, производимый этими инструментами, непостоянен, ненадежен и не воспроизводим. Ручные инструменты просто не могут генерировать достаточное усилие закрытия, чтобы обеспечить герметичное уплотнение на постоянной основе для особо важных применений.
Гидравлические отщипывающие инструменты доступны в различных размерах и стилях, с различными гидравлическими насосами, в зависимости от области применения.
Модели с ручными и зажимными захватами доступны для труб диаметром от 1/16 до 1 дюйма. Гидравлические насосы доступны как в пневматических, так и в электрических моделях и могут быть дополнительно модифицированы для приложений с малым или большим объемом. Важно правильно подобрать комбинацию трубки и помпы для выполняемой работы.
Резюме
Области применения, связанные с необходимостью холодной сварки и герметизации труб, обычно являются критическими по своей природе. Другими словами, эти трубки должны быть герметично закрыты и оставаться в таком состоянии сколь угодно долго, в широком диапазоне температур и условий окружающей среды. В результате крайне важно, чтобы и трубка, и инструмент, выбранные для применения, были правильно подобраны. Если все сделано правильно, конечным результатом будет холодное сварное соединение, которое останется герметичным в течение всего срока службы производимого продукта.
Для получения дополнительной информации о Custom Products & Services, Inc. посетите веб-сайт www.custom-products.com
Manufacturing.net (MNET)
23 сентября 2022 г.
Видео распаковки промышленных носителей
4 августа , 2022
Ключевой индикатор инфляции достиг 6,8%, поскольку цены продолжают расти
29 июля 2022 г.
Когда слишком холодно для сварки?
Вопрос задан: Эшли Грейди III
Оценка: 4,8/5 (69 голосов)
При работе с трубопроводами и сосудами под давлением вы не можете работать, если температура падает ниже точки замерзания, что составляет 32 градуса по Фаренгейту . Сварочные нормы ASME еще мягче для сварщиков, не позволяя никому работать, если температура падает ниже 50 градусов по Фаренгейту.
Можно ли сваривать в холодную погоду?
Температура замерзания приведет к тому, что ваши сварные швы остынут намного быстрее , что может привести к растрескиванию и недостаточному проплавлению. Холодная погода также означает большую разницу температур между сварным швом и обрабатываемой деталью. Это может вызвать сильную деформацию. Простое решение — предварительный нагрев.
Как узнать, что мой сварной шов слишком холодный?
Поместите один из ваших образцов в тиски, возьмите молоток и посмотрите, сможете ли вы разорвать сварной шов. Если ломается с небольшим усилием то вы знаете, что у вас холодный сварной шов с небольшим проплавлением. Если у вас есть ленточная пила, вы также можете сделать поперечный разрез в заготовке, чтобы увидеть, насколько хорошо проварился сварной шов.
Можно ли сваривать на снегу?
Сварка для защиты от атмосферных воздействий
Сварка в арктических условиях может быть успешной только в том случае, если условия труда приемлемы. … Сварка MIG/MAG и TIG всегда должна выполняться в месте, защищенном от ветра, дождя и снега. Защита может быть обеспечена различными типами палаток (рис. 2) или даже обогреваемыми сварочными боксами (рис. 3).
При какой температуре выполняется сварка?
Электрические дуги очень горячие, поэтому дуговая сварка является эффективным процессом сварки. Хотя для разных металлов требуются разные температуры, дуговая сварка обычно выполняется при температуре дуги примерно 10 000 градусов по Фаренгейту .
Итак, я купил аппарат для холодной сварки
41 связанных вопросов найдено
До какой температуры вы нагреваете сталь перед сваркой?
Часто перед началом сварки деталь необходимо выдержать в определенном диапазоне температур в течение определенного периода времени, например, , от 250 до 400 градусов по Фаренгейту в течение 30 минут.
Зачем нужно подогревать перед сваркой?
Предварительный нагрев — это процесс , применяемый для повышения температуры основной стали перед сваркой . … Для замедления скорости охлаждения сварного шва и основного материала, что может привести к более мягкому металлу сварного шва и микроструктуре зоны термического влияния с большей устойчивостью к водородному растрескиванию при изготовлении.
Холодная сварка хороша?
Холодная сварка обеспечивает быстрое и прочное соединение проводов и обычно используется с алюминием, латунью 70/30, медью, золотом, никелем, серебром, серебряными сплавами и цинком. Холодная сварка также хороша для соединения разнородных металлов, которые в противном случае было бы трудно эффективно сварить.
Можно ли сваривать алюминий в холодную погоду?
Алюминий является отличным проводником тепла. … Предварительный подогрев алюминия часто не требуется, но он может предотвратить растрескивание сварного шва 0338, особенно при сварке в холодную погоду. Поддерживайте низкую температуру предварительного нагрева и размещайте прихваточные швы в начале и в конце сварного шва.
Почему при сварке важна скорость перемещения?
В большинстве случаев проникновение сварного шва в основной материал увеличивается при увеличении скорости перемещения сварного шва, и наоборот. … Это более прямое воздействие на основной материал приводит к более глубокому проплавлению сварного шва, поскольку ограничивает амортизирующий эффект сварочной ванны.
Как определить правильность сварки?
Хороший сварной шов легко отличить. Он будет прямым и однородным, без шлака, трещин и отверстий . Разрывов шва не будет. Он не должен быть слишком тонким, и на нем не должно быть провалов или кратеров.
Как узнать, достаточно ли прочен мой сварной шов?
Чтобы действительно проверить сварной шов, вам необходимо провести рентгеновский контроль , магнитный флюс, проникающий контроль или ультразвуковой контроль, который выявляет пустоты, непровары и т. д.
Чего нельзя делать при сварке?
Не носите одежду с короткими рукавами или одежду с манжетами во время сварки. Вы можете получить ожоги от искр или горячего металла. Не допускайте контакта рук с острыми краями при открытии банок с электродами. Не работайте в зоне с горючими материалами.
Деформируется ли металл в холодную погоду?
Проблема с холодной погодой и сварными швами
Даже в правильных условиях связанные с этим температуры очень легко деформируют металл. И когда этот металл остынет, более вероятно возникновение деформации . Сварные швы также более подвержены растрескиванию в этих условиях из-за плохого проплавления.
Как сварщикам сохранять прохладу?
Охлаждающие ленты — обычное средство для сварщиков, позволяющее избежать перегрева. Легкие коммерческие охлаждающие ленты и охлаждающие ленты — отличный способ охладить головку и сердцевину, направляя холодный воздух туда, где он нужен больше всего.
При какой температуре сварка MIG?
При сварке GMA (MIG) основной металл плавится и сплавляется с расплавленным присадочным металлом при температуре приблизительно 1650°C (3000°F) . Это считается процессом слияния.
Что произойдет, если основной металл слишком холодный?
В холодную погоду основной металл становится теплоотводом . В результате он будет высасывать тепло прямо из вашего сварного шва, как только вы перестанете его применять. Это плохая ситуация, потому что, если ваш сварной шов слишком быстро остынет после его нанесения, он в конечном итоге треснет.
Какой толщины можно производить холодную сварку?
Применение холодной сварки
Холодная сварка давлением обычно используется для соединения алюминиевых и медных проводов/стержней диаметром от 0,5 мм до 12 мм или более , а тип сварки — стыковое соединение. Комбинация проволочных металлов, таких как алюминий и медь, также может быть сварена методом холодной сварки.
Вам нужен газ для холодной сварки?
Холодная сварка, также известная как холодная сварка давлением или контактная сварка, представляет собой процесс сварки в твердом состоянии, при котором соединение двух металлов происходит без плавления или нагрева на границе раздела двух свариваемых частей. Это означает, что в процессе соединения и соединения не присутствует жидкая или расплавленная фаза.
Что такое дефект холодной сварки?
Холодный нахлест — это тип дефекта сварки, который возникает, когда расплавленный металл не полностью сплавляется с поверхностью холодной пластины . Это приводит к дефекту в виде трещины, часто очень маленькой, параллельной пластине. Дефект холодного сварного шва внахлест подразделяют на три типа: разбрызгивание, нахлест и холодный нахлест внахлест.
Откуда вы знаете, что температура предварительно подогрета?
Метод контроля твердости зоны термического влияния
1 предоставляет два дополнительных метода определения предварительного нагрева. Этими методами являются 1) Метод контроля зоны теплового влияния (HAZ) и 2) Метод контроля водорода.
Вы предварительно нагреваете чугун перед сваркой?
Предварительный нагрев чугунной детали перед сваркой замедлит скорость охлаждения сварного шва и области вокруг сварного шва. Всегда предпочтительнее нагревать всю отливку, если это возможно. Типичные температуры предварительного нагрева составляют 500-1200 градусов по Фаренгейту. … После сварки дайте детали медленно остыть.
Нужно ли предварительно нагревать нержавеющую сталь перед сваркой?
Предварительный нагрев стали замедляет скорость охлаждения в зоне сварки ; может быть необходимо избежать образования трещин в металле шва или в зоне термического влияния. … * эти стали не подвержены водородному растрескиванию, поэтому предварительный подогрев требуется редко, за исключением уменьшения риска возникновения усадочных напряжений в толстых сечениях.
Похожие вопросы
- 23 Работает ли сварка jb на морозе?
- 45Почему в космосе производят холодную сварку металлов?
- 15Сваривается ли металл в космосе?
- 33 Работает ли холодная сварка?
- 45Как работает аппарат для холодной сварки?
- 31Что такое холодная сварка?
- 44JB сварка будет работать на морозе?
- 38Затвердевает ли сварной шов jb на холоде?
- 42Как выполнить холодную сварку металла?
- 30Затвердевает ли сварной шов jb в холодную погоду?
Реклама
Популярные вопросы
- 19Почему джип-рэнглеры такие ненадежные?
- 21Что такое дриблинг?
- 36Когда начинают действовать налоговые льготы?
- 22Умеете ли вы плавать в озере Корпус-Кристи?
- 25Будет ли снова доступна клятва Эрианы?
- 32Что такое буддийский обход?
- 42Что такое добыча полезных ископаемых?
- 23Вялый значит апатичный?
- 20С кем сейчас встречается Локи?
- 27Почему инеосов назвали гренадерами?
сварка | Типы и определение
дуговая сварка
Просмотреть все материалы
- Связанные темы:
- дуговая сварка сварка взрывом холодная сварка диффузионное соединение электронно-лучевая сварка
Просмотреть весь связанный контент →
Резюме
Прочтите краткий обзор этой темы
сварка , метод, используемый для соединения металлических деталей, обычно с применением тепла. Этот метод был открыт во время попыток придать железу полезную форму. Сварные клинки были разработаны в 1-м тысячелетии нашей эры, самые известные из них производились арабскими оружейниками в Дамаске, Сирия. В то время был известен процесс науглероживания железа для производства твердой стали, но полученная сталь была очень хрупкой. Техника сварки, которая включала прослойку относительно мягкого и прочного железа с высокоуглеродистым материалом с последующей ковкой в молоте, позволила получить прочное и прочное лезвие.
В наше время совершенствование технологии производства железа, особенно внедрение чугуна, ограничило сварку кузнецом и ювелиром. Другие способы соединения, такие как крепление болтами или заклепками, широко применялись к новым изделиям, от мостов и железнодорожных двигателей до кухонной утвари.
Современные процессы сварки плавлением являются результатом необходимости получения непрерывного соединения на больших стальных пластинах. Было показано, что клепка имеет недостатки, особенно для закрытого контейнера, такого как котел. Газовая сварка, дуговая сварка и контактная сварка появились в конце 19 века.век. Первая реальная попытка широкомасштабного внедрения сварочных процессов была предпринята во время Первой мировой войны. К 1916 г. кислородно-ацетиленовый процесс был хорошо разработан, и применяемые тогда методы сварки используются до сих пор. С тех пор основные улучшения коснулись оборудования и безопасности. Дуговая сварка с использованием плавящегося электрода также была введена в этот период, но изначально использовавшаяся неизолированная проволока приводила к хрупким сварным швам. Решение было найдено путем обматывания оголенного провода асбестом и обвивкой алюминиевой проволокой. Современный электрод, представленный в 1907, состоит из неизолированной проволоки со сложным покрытием из минералов и металлов. Дуговая сварка не использовалась повсеместно до Второй мировой войны, когда острая потребность в средствах быстрого строительства для судоходства, электростанций, транспорта и сооружений стимулировала необходимые опытно-конструкторские работы.
Сварка сопротивлением, изобретенная в 1877 году Элиу Томсоном, была принята задолго до дуговой сварки для точечного и шовного соединения листов. Стыковая сварка для изготовления цепей и соединения стержней и стержней была разработана в XIX веке.20 с. В 1940-х годах был внедрен вольфрамово-инертный газовый процесс с использованием неплавящегося вольфрамового электрода для выполнения сварных швов плавлением. В 1948 году в новом процессе в среде защитного газа использовался проволочный электрод, который изнашивался при сварке. Совсем недавно были разработаны электронно-лучевая сварка, лазерная сварка и несколько твердофазных процессов, таких как диффузионная сварка, сварка трением и ультразвуковое соединение.
Сварной шов можно определить как слияние металлов, полученное путем нагревания до подходящей температуры с приложением давления или без него, а также с использованием или без использования присадочного материала.
При сварке плавлением источник тепла выделяет достаточно тепла для создания и поддержания ванны расплавленного металла требуемого размера. Тепло может подаваться электричеством или газовым пламенем. Сварку электрическим сопротивлением можно рассматривать как сварку плавлением, потому что образуется некоторое количество расплавленного металла.
Оформите подписку Britannica Premium и получите доступ к эксклюзивному контенту. Подпишитесь сейчас
Твердофазные процессы производят сварку без плавления основного материала и без добавления присадочного металла. Всегда используется давление, и обычно обеспечивается некоторое количество тепла. Теплота трения выделяется при ультразвуковом соединении и соединении трением, а нагрев в печи обычно используется при диффузионном соединении.
Электрическая дуга, используемая при сварке, представляет собой сильноточный низковольтный разряд, обычно в диапазоне 10–2000 ампер при напряжении 10–50 вольт. Столб дуги сложен, но, вообще говоря, состоит из катода, который испускает электроны, газовой плазмы для проведения тока и области анода, которая становится сравнительно более горячей, чем катод, из-за бомбардировки электронами. Обычно используется дуга постоянного тока (DC), но могут использоваться дуги переменного тока (AC).
Суммарное потребление энергии во всех процессах сварки превышает количество энергии, необходимой для изготовления соединения, поскольку не все генерируемое тепло может быть эффективно использовано. Эффективность варьируется от 60 до 90 процентов, в зависимости от процесса; некоторые специальные процессы сильно отклоняются от этой цифры. Тепло теряется за счет теплопроводности через основной металл и за счет излучения в окружающую среду.
Большинство металлов при нагревании вступают в реакцию с атмосферой или другими металлами поблизости. Эти реакции могут быть чрезвычайно вредными для свойств сварного соединения. Например, большинство металлов быстро окисляются в расплавленном состоянии. Слой оксида может помешать правильному соединению металла. Капли расплавленного металла, покрытые оксидом, захватываются сварным швом и делают соединение хрупким. Некоторые ценные материалы, добавленные для определенных свойств, так быстро реагируют на воздухе, что осажденный металл не имеет того же состава, что и изначально. Эти проблемы привели к использованию флюсов и инертных атмосфер.
При сварке плавлением флюс играет защитную роль, облегчая контролируемую реакцию металла, а затем предотвращая окисление, образуя защитный слой над расплавленным материалом. Флюсы могут быть активными и помогать в процессе или неактивными и просто защищать поверхности во время соединения.
Инертные атмосферы играют такую же защитную роль, как и флюсы. При дуговой сварке металлическим электродом в среде защитных газов и дуговой сварке вольфрамовым электродом в защитных газах инертный газ — обычно аргон — вытекает из кольцевого пространства, окружающего горелку, непрерывным потоком, вытесняя воздух вокруг дуги. Газ не вступает в химическую реакцию с металлом, а просто защищает его от контакта с кислородом воздуха.
Металлургия соединения металлов важна для функциональных возможностей соединения. Дуговая сварка иллюстрирует все основные особенности соединения. В результате прохождения сварочной дуги образуются три зоны: (1) металл шва или зона сплавления, (2) зона термического влияния и (3) неповрежденная зона. Металл шва – это та часть соединения, которая расплавилась во время сварки. Зона термического влияния – это область, прилегающая к металлу шва, которая не подвергалась сварке, но претерпела изменение микроструктуры или механических свойств под действием тепла сварки. Незатронутый материал — это тот, который не был нагрет достаточно, чтобы изменить свои свойства.
Состав металла шва и условия, при которых он замерзает (затвердевает), существенно влияют на способность соединения соответствовать эксплуатационным требованиям. При дуговой сварке металл шва состоит из присадочного материала и расплавленного основного металла. После прохождения дуги происходит быстрое охлаждение металла шва. Однопроходный шов имеет литую структуру со столбчатыми зернами, простирающимися от края ванны расплава к центру сварного шва. При многопроходном сварном шве эта литая структура может быть изменена в зависимости от конкретного свариваемого металла.
Основной металл, прилегающий к сварному шву или зоне термического влияния, подвергается ряду температурных циклов, и изменение его структуры напрямую связано с пиковой температурой в любой заданной точке, временем воздействия и охлаждением. ставки. Типов основного металла слишком много, чтобы обсуждать их здесь, но их можно сгруппировать в три класса: (1) материалы, не подверженные воздействию тепла сварки, (2) материалы, упрочненные структурными изменениями, (3) материалы, упрочненные процессами осаждения.
Сварка создает напряжения в материалах. Эти силы вызываются сжатием металла шва и расширением, а затем сжатием околошовной зоны. Ненагретый металл накладывает ограничения на вышеперечисленное, а поскольку преобладает усадка, металл шва не может свободно сжиматься, и в соединении накапливаются напряжения. Это обычно известно как остаточное напряжение, и для некоторых критических применений его необходимо устранить путем термической обработки всего изготовления. Остаточные напряжения неизбежны во всех сварных конструкциях, и если их не контролировать, произойдет изгиб или деформация сварного соединения. Контроль осуществляется методом сварки, приспособлениями и приспособлениями, технологиями изготовления и конечной термической обработкой.
Существует большое разнообразие сварочных процессов. Некоторые из наиболее важных обсуждаются ниже.
Использование только давления (например, холодная сварка) Патенты и заявки на патенты (класс 228/115)
Использование только давления (например, холодная сварка) Патенты (класс 228/115)
С предварительной обработкой работы (Класс 228/116)
Холодная прокатка (Класс 228/117)
Монолитные сорбенты с металлической оболочкой
Номер патента: 11268938
Реферат: Изобретение относится к монолитным сорбентам, покрытым трубками из металла. Металлическую оболочку можно наносить непосредственно на монолитные сорбенты методом холодного формования.
Это обеспечивает очень механически стабильную оболочку монолитных сорбентов с минимальным мертвым пространством.
Тип: Грант
Подано: 28 октября 2016 г.
Дата патента: 8 марта 2022 г.
Правопреемник: Merck Patent GmbH
Изобретатели: Карин Кабрера, Клаус Крехер, Гизела Юнг
Канистра и способ производства
Номер патента: 11260467
Реферат: Способ формирования канистры посредством механического соединения соответствующих слоев первого металлического материала (тантал) и второго металлического материала (ниобий) для формирования листового материала, таким образом формируя листовой материал в форме контейнера, в котором первый металлический материал содержит тантал, а второй металлический материал содержит по меньшей мере один из ниобия, молибдена или стали.
Готовая канистра содержит первый металлический материал, содержащий тантал, и второй металлический материал, механически связанный с первым металлическим материалом путем воздействия на первый и второй металлические материалы по меньшей мере 1 000 000 фунтов на квадратный дюйм, чтобы таким образом сформировать канистру, имеющую внутренний диаметр 13-19миллиметров (мм), причем второй металлический материал содержит по меньшей мере один из ниобия, молибдена или стали.
Тип: Грант
Подано: 28 июля 2020 г.
Дата патента: 1 марта 2022 г.
Правопреемник: Национальная сетевая компания
Изобретатель: Стивен А.
Чиполла
Соединение компонентов и способ выполнения соединения компонентов
Номер патента: 10654136
Abstract: Соединение компонентов включает в себя первый компонент, изготовленный из материала, притягивающегося к магниту, и второй компонент, непосредственно или косвенно примыкающий к первому компоненту и имеющий отверстие. Предусмотрен магнитный элемент, который закрывает отверстие и притягивает первый компонент, так что оба компонента сжимаются вместе.
Тип: Грант
Подано: 24 июня 2016 г.
Дата патента: 19 мая 2020 г.
Правопреемник: Bayerische Motoren Werke Aktiengesellschaft
Изобретатели: Майк Хаммер, Иоганн Ван Никерк
Уплотнение для микроэлектронной сборки
Номер патента: 10508030
Реферат: Типичные реализации методов и устройств обеспечивают уплотнения для герметизации соединений склеенных микроэлектронных устройств, а также склеенных и герметизированных микроэлектронных сборок. Уплотнения располагаются на стыкуемых поверхностях уложенных друг на друга штампов и пластин для герметизации стыкуемых поверхностей.
Пломбы могут располагаться на внешней периферии приклеиваемых микроэлектронных устройств или располагаться внутри периферии с использованием различных технологий.
Тип: Грант
Подано: 14 марта 2018 г.
Дата патента: 17 декабря 2019 г.
Правопреемник: Invensas Bonding Technologies, Inc.
Изобретатели: Раджеш Каткар, Лян Ван, Киприан Эмека Узо, Шаову Хуан, Гуилиан Гао, Ильяс Мохаммед
Двигатель, воздуходувка и компрессор
Номер патента: 10389215
Реферат: Двигатель, содержащий ротор и статор, имеющий множество катушек, намотанных вокруг пазов, причем по крайней мере одна из катушек включает один алюминиевый провод, соединенный одним медным проводом.
к алюминиевому проводу, многожильный провод (подводящий провод), соединенный с медным проводом, участок соединения, сваренный холодной сваркой давлением (участок соединения), соединенный между алюминиевым проводом и медным проводом с помощью сварки холодным давлением, и сварной шов без давления соединительная часть (стыковая часть), предусмотренная между медным проводом и многожильным проводом (подводящим проводом). Заусенец, покрытый изоляционным элементом (изоляционной трубкой), предусмотрен в соединительной части, сваренной методом холодной сварки давлением (соединительная часть). Толщина изоляционного элемента (изоляционной трубки) больше высоты заусенца.
Тип: Грант
Подано: 31 марта 2014 г.
Дата патента: 20 августа 2019 г.
Правопреемник: Mitsubishi Electric Corporation
Изобретатели: Кодзи Ябэ, Казухико Баба, Такахиро Цуцуми, Томоаки Ойкава
Узел градиентной катушки, градиентная катушка и система магнитно-резонансной томографии
Номер патента: 10295629
Резюме: Настоящие варианты осуществления обеспечивают сборку градиентной катушки.
Узел градиентной катушки включает корпус из алюминиевой проволоки и конец медной проволоки, соединенный холодной сваркой давлением с двумя концами корпуса из алюминиевой проволоки. Используя градиентную катушку согласно конкретному варианту осуществления, можно уменьшить вес градиентной катушки, а также уменьшить толщину внешней вакуумной камеры, используемой для магнита, тем самым уменьшив стоимость магнита и градиентной катушки и облегчив задачу. для установки и обслуживания магнита и градиентной катушки. Нет проблемы окисления, связанной с холодной сваркой давлением алюминиевой проволоки с концами медной проволоки, поэтому дефекты качества, возникающие в результате такого окисления, исключены.
Тип: Грант
Подано: 24 ноября 2014 г.
Дата выдачи патента: 21 мая 2019 г.
Правопреемник: Siemens Aktiengesellschaft
Изобретатели: Вэй Пинг Пэн, Стефан Стокер, Чао Ван
Способ формирования заготовки из листовой стали
Номер патента: 10118213
Реферат: Изобретение относится к способу формования заготовки, в частности заготовки, из листовой стали, в котором последовательно осуществляют следующие операции: состоящий из нескольких стальных слоев, неразъемно соединенных друг с другом путем прокатки, из которых по меньшей мере два стальных слоя имеют различную прочность и/или относительное удлинение при разрушении, нагрев заготовки и горячую штамповку заготовки.
Для обеспечения высокой прочности и в то же время максимально легкой формуемости в изобретении предлагается закаливать по меньшей мере один участок горячедеформированной заготовки, а затем заготовку подвергать холодной штамповке в области, в которой закалка уже закончилась. было выполнено. Изобретение также относится к соответствующей заготовке.
Тип: Грант
Подано: 27 августа 2015 г.
Дата патента: 6 ноября 2018 г.
Правопреемники: THYSSENKRUPP STEEL EUROPE AG, THYSSENKRUPP AG
Изобретатели: Стефан Графф, Давид Пьеронек, Маркус Цёрнак
Способ изготовления шкафа для бытовой техники.
Номер патента: 10017971
Реферат: Шкаф прибора может быть изготовлен с по меньшей мере первой металлической ванной и монтажным кронштейном, с помощью которого компонент прибора может быть установлен на корпусе. Кронштейн и первый металлический бак могут располагаться рядом друг с другом. Кронштейн может быть прикреплен к первому металлическому баку путем перемещения одной из частей первого металлического бака или кронштейна со скоростью, достаточно большой, чтобы вызвать пластическое течение части первого металлического бака вокруг части кронштейна.
Тип: Грант
Подано: 8 сентября 2014 г.
Дата выдачи патента: 10 июля 2018 г.
Правопреемник: Whirlpool Corporation
Изобретатели: Крис С.
Крейкрафт, Стивен Дж. Кюль, Джон Э. Меддлс, Аксель Хулио Рамм
Труба с механической футеровкой
Номер патента: 9885431
Реферат: Наматываемая труба с механической футеровкой (MLP) (30), имеющая по меньшей мере футеровку (32) и наружную трубу (34), наружная труба имеет внешний диаметр DH, с MLP, образованным из множества стыков труб, имеющих соединительные кольцевые сварные швы (36), при этом концы каждого стыка труб заканчиваются плакированными наплавными швами (40), имеющими длину в диапазоне Lmin=100 мм и Lmax=4DH, и при этом толщина футеровки, t, равна или меньше значения, рассчитанного по формуле I, как определено.
Тип: Грант
Подано: 13 ноября 2013 г.
Дата выдачи патента: 6 февраля 2018 г.
Правопреемник: TECHNIP FRANCE
Изобретатели: Орельен Пепен, Томаш Ткачик
Способ склеивания двух подложек и изготовленное им устройство
Номер патента: 9573804
Реферат: Изобретение относится к способу соединения по меньшей мере двух подложек, например из стекла, кремния, керамики, алюминия или бора, с использованием промежуточного тонкопленочного металлического слоя для обеспечения склеивание, при этом указанный способ включает следующие этапы: а) обеспечение указанных двух подложек; b) нанесение указанного тонкопленочного металлического слоя по меньшей мере на часть поверхности первой подложки из двух подложек; c) приведение поверхности второй подложки в контакт с указанным тонкопленочным металлическим слоем на указанной поверхности первой подложки, так что обеспечивается соединение между второй подложкой и тонкопленочным металлическим слоем на первой подложке; и d) по меньшей мере локальное усиление связи между второй подложкой и тонкопленочным металлическим слоем на первой подложке.
Изобретение также относится к устройству, содержащему две подложки, например, из стекла, кремния, керамики, алюминия или бора, и промежуточный тонкопленочный металлический слой.
Тип: Грант
Подано: 21 декабря 2012 г.
Дата выдачи патента: 21 февраля 2017 г.
Правопреемник: Micronit Microfluidics B.V.
Изобретатели: Ронни Ван ‘Т Увер, Марко Теодор Блом, Йерун Ханевельд, Йоханнес Оонк, Маринус Бернардус Олде Рикеринк, Петер Тийссен, Хендрик Ян Хильдебранд Тигелаар, Жан-Ноэль Фер, Жан-Кристоф Руле, Амитава Гупта
Высокочастотный кабель, высокочастотная катушка и способ изготовления высокочастотного кабеля
Номер патента: 9478328
Реферат: Способ изготовления высокочастотного кабеля, включающий покрытие центральной жилы из алюминия или алюминиевого сплава покровным слоем из меди; и волочение проволоки центрального проводника, покрытого покровным слоем, с использованием штампов в несколько этапов, причем каждый из штампов имеет коэффициент уменьшения поперечного сечения от 20% до 29% с полным углом обжатия 16 градусов, для образования волокнообразной структуры в продольном направлении в покрывающем слое и для образования слоя интерметаллического соединения, имеющего большее объемное сопротивление, чем покрывающий слой между центральным проводником и покрывающим слоем.
Тип: Грант
Подано: 21 июля 2014 г.
Дата патента: 25 октября 2016 г.
Правопреемник: ФУДЖИКУРА ЛТД.
Изобретатели: Такаши Синмото, Шотаро Ёсида, Синдзи Катаяма, Тайкоу Тода, Такамаса Като, Масанори Дайбо, Акио Кавакави
Система подачи соединительной проволоки и способ для нее
Номер патента: 9397066
Реферат: Система подачи соединительной проволоки имеет узел натяжения проволоки с камерой, имеющей входное отверстие для проволоки и выходное отверстие для проволоки.
Впускные и выпускные отверстия для проволоки имеют центры, совмещенные с центральной осью камеры. Зажим расположен для приема соединительного провода, подаваемого через выходное отверстие для провода. Зажим имеет по меньшей мере две губки, подвижные относительно друг друга и предназначенные для захвата проволоки для совмещения центральной оси проволоки с центральной осью камеры. Губки также могут перемещаться вдоль центральной оси проволоки, чтобы протягивать проволоку через узел натяжения проволоки.
Тип: Грант
Подано: 23 апреля 2015 г.
Дата патента: 19 июля 2016 г.
Правопреемник: FREESCALE SEMICONDUCTOR, INC.
Изобретатели: Чжицзе Ван, Чжиган Бай, Хучан Чжан
Способ приклеивания пористого металла к металлическим подложкам
Номер патента: 8951465
Реферат: Способ изготовления имплантата с пористым металлическим компонентом.
Готовят рыхлую порошковую смесь, включающую биосовместимый металлический порошок и прослойку, и прессуют на металлическую основу. После сжатия прокладку удаляют, в результате чего образуется компакт, включающий пористую металлическую структуру, прижатую к металлической основе. Компакт спекается, образуя узел, который выравнивается с частью металлической подложки имплантата. Процесс металлургического соединения, такой как диффузионное соединение, выполняется на границе раздела узла и металлической подложки для формирования имплантата, имеющего пористый металлический компонент.
Тип: Грант
Подано: 25 февраля 2013 г.
Дата выдачи патента: 10 февраля 2015 г.
Правопреемник: Biomet Manufacturing, LLC
Изобретатель: Гаутам Гупта
Магнитно-импульсная сварка и формовка пластин
Номер патента: 8899084
Реферат: Описан способ сварки двух заготовок вместе.
Предусмотрен проводник, имеющий электрическую связь с импульсной цепью. Часть второй заготовки расположена рядом с проводником. Две заготовки также располагаются вместе. Часть или вся одна заготовка приваривается к другой путем подачи импульсного тока на одну из заготовок. Раскрыт способ формирования заготовки с использованием импульсного тока для придания заготовке желаемой формы.
Тип: Грант
Подано: 9 октября 2012 г.
Дата патента: 2 декабря 2014 г.
Правопреемник: Dana Automotive Systems Group, LLC
Изобретатели: Борис А. Яблочников, Ева С. Штайгервальт, Том О’Нил, Джек А.
Куммероу
Сквозные отверстия в многослойных печатных платах
Номер патента: 8766107
Реферат: Примеры многослойных печатных плат («ПП») описаны, а также способы изготовления и использования таких ПП, которые включают слои ламината; по меньшей мере одно сквозное отверстие, пересекающее слои ламината, и сквозной проводник, содержащийся в сквозном отверстии, причем сквозной проводник содержит использованную часть и неиспользованную часть, сквозной проводник содержит медь, покрытую металлом, имеющим проводимость ниже, чем проводимость медь.
Тип: Грант
Подано: 13 апреля 2012 г.
Дата выдачи патента: 1 июля 2014 г.
Правопреемник: International Business Machines Corporation
Изобретатели: Мойзес Кейс, Тэ Хонг Ким, Рохан У. Мандрекар, Нусрат И. Шерали
Способ изготовления композитной стальной пластины
Номер патента: 8752752
Реферат: Составная стальная плита включает по крайней мере два стальных листа, прокатанных в плиту. Один из листов имеет состав, меняющийся по глубине от нанокристаллического до микрозернистого. Плиту изготавливают путем обработки стального листа для получения состава в листе, который варьируется в направлении по глубине листа от нанокристаллического до микронного зерна, укладки обработанного листа в штабель по меньшей мере с одним другим стальным листом и прокатки штабелированных листов в форму.
плита.
Тип: Грант
Подано: 9 марта 2009 г.
Дата патента: 17 июня 2014 г.
Правопреемник: Гонконгский политехнический университет
Изобретатели: Цзянь Лу, Цзюньбао Чжан, Айин Чен
Конструкции мишеней и соответствующие методы для сопряженных сборок мишеней, способы их производства и применения
Номер патента: 8702919
Реферат: Описаны мишени для распыления, которые содержат: a) компонент поверхности мишени, содержащий материал мишени; b) поддерживающий компонент сердцевины, имеющий контактную поверхность, заднюю поверхность и по меньшей мере одну открытую область, при этом контактная поверхность соединена по меньшей мере с частью компонента целевой поверхности; и при этом по меньшей мере часть целевого поверхностного компонента входит в по меньшей мере одну открытую область основного поддерживающего компонента.
В некоторых вариантах осуществления целевой поверхностный компонент, сердцевинный компонент подложки или их комбинация имеют по меньшей мере один элемент площади поверхности, соединенный или расположенный на задней поверхности сердцевинного поддерживающего компонента, целевой поверхностный компонент или их комбинация, при этом поверхность Функция площади увеличивает эффективность охлаждения компонента поверхности мишени.
Тип: Грант
Подано: 13 августа 2007 г.
Дата патента: 22 апреля 2014 г.
Правопреемник: Honeywell International Inc.
Изобретатели: Стефан Феррасе, Вернер Х.
Хорт, Джэён Ким, Фрэнк С. Элфорд
ФОРМИРОВАНИЕ ТРАНЗИСТОРА ХОЛОДНОЙ СВАРКОЙ
Номер публикации: 20140094006
Abstract: Устройство и способ изготовления включают получение первого узла подложки, включающего первую подложку и первый металлический слой, сформированный на первой подложке, и второго узла подложки, включающего вторую подложку и второй металлический слой, сформированный на второй подложке. Первый металлический слой соединяется со вторым металлическим слоем с использованием процесса холодной сварки, при этом одна из первой подложки и второй подложки включает в себя слой полупроводникового канала для формирования транзисторного устройства.
Тип: Заявка
Подано: 3 октября 2012 г.
Дата публикации: 3 апреля 2014 г.
Заявитель: International Business Machines Corporation
Изобретатели: Ченг-Вэй Ченг, Шу-Джен Хань, Масахару Кобаяши, Ко-Тао Ли, Девендра К. Садана, Куен-Тин Шиу
Сквозные отверстия в многослойных печатных платах
Номер патента: 8658911
Реферат: Примеры многослойных печатных плат («ПП») описаны, а также способы изготовления и использования таких ПП, которые включают слои ламината; по меньшей мере одно сквозное отверстие, пересекающее слои ламината, и сквозной проводник, содержащийся в сквозном отверстии, причем сквозной проводник содержит использованную часть и неиспользованную часть, сквозной проводник содержит медь, покрытую металлом, имеющим проводимость ниже, чем проводимость медь.
Тип: Грант
Подано: 17 апреля 2012 г.
Дата патента: 25 февраля 2014 г.
Правопреемник: International Business Machines Corporation
Изобретатели: Мойзес Кейс, Тэ Хонг Ким, Рохан У. Мандрекар, Нусрат И. Шерали
Склеивание при комнатной температуре с помощью напыления
Номер патента: 8602289
Реферат: Способ соединения множества подложек при комнатной температуре с помощью промежуточного элемента включает: формирование промежуточного элемента на поверхности, подлежащей склеиванию с подложкой, путем физического напыления множества цели; и активируют склеиваемую поверхность ионным лучом.
Предпочтительно мишень, состоящая из множества типов материалов, подвергается физическому напылению. Поскольку материалы промежуточного элемента напыляются из множества мишеней, расположенных в различных направлениях от склеиваемой поверхности подложки, промежуточный элемент может быть равномерно сформирован на склеиваемой поверхности. Кроме того, поскольку промежуточный элемент состоит из множества типов материалов, соединение при комнатной температуре подложек, которые трудно склеить вместе, когда промежуточный элемент состоит из материала одного типа, может выполняться без нагревания и чрезмерного прессования подложек во время склеивание.
Тип: Грант
Подано: 6 сентября 2007 г.
Дата патента: 10 декабря 2013 г.
Правопреемники: Mitsubishi Heavy Industries, Ltd.
, Национальный институт передовых промышленных наук и технологий
Изобретатели: Такаюки Гото, Джун Утсуми, Кенсуке Идэ, Хидэки Такаги, Масахиро Фунаяма
Способ соединения высокоуглеродистой стали для бесконечной горячей прокатки и устройство для него
Номер патента: 8584923
Реферат: Способ соединения бесконечных горячекатаных материалов сдвигом, позволяющий нарезать резьбу горячекатаных материалов в процессе чистовой прокатки без разрыва полосы путем контроля условий соединения горячекатаных материалов в бесконечной горячей прокатке. раскрыт процесс производства высокоуглеродистой стали и бесконечная установка горячей прокатки для него.
Способ соединения сдвигом бесконечных горячекатаных материалов из высокоуглеродистой стали включает соединение срезом металлических стержней из высокоуглеродистой стали, содержащих от 0,30% до 1,20% по массе С, неизбежных примесей и остатка Fe, или содержащих от 0,15% до 1,5% C, содержащий по крайней мере один из Cr, Ni, Mo, V, Ti, W, B, Nb и Sb, неизбежные примеси и остаток Fe, так что соединяемая поверхность соединенных металлических стержней формируется с наклоном в направление толщины металлических стержней на установке горячей прокатки с помощью столяра, приспособленного для соединения металлических стержней после наложения внахлест хвостовой части ведущего металлического стержня и верхней части заднего металлического стержня.
Тип: Грант
Подано: 20 ноября 2006 г.
Дата патента: 19 ноября 2013 г.
Правопреемники: POSCO, Mitsubishi-Hitachi Metals
Изобретатели: Чон-Суб Ли, Юн-Хи Кан, Чун-Су Вон, Чон-Бон Ли, Сан-Вук Ха, Кенджи Хории, Тосихиро Усуги, Хидэаки Фурумото, Сигенори Широгане, Такао Фунамото
ПЛАКИРОВАННЫЙ МАТЕРИАЛ ДЛЯ ИЗОЛЯЦИОННЫХ ПОДЛОЖЕНИЙ
Номер публикации: 20130292816
Реферат: Плакированный материал 1А для изоляции подложек снабжен слоем 4 никеля, выполненным из никеля или сплава никеля, слоем 6 титана, выполненным из титана или сплава титана и расположенным на одном стороне слоя Ni, и первый слой 7 алюминия, изготовленный из алюминия или алюминиевого сплава и расположенный на одной стороне слоя 6 титана, которая противоположна стороне слоя 6 титана, на которой расположен слой 4 никеля.
Слой 4 никеля и слой 6 титана соединяют плакирующей прокаткой. Слой 5 сверхэластичного сплава серии Ni-Ti, образованный путем сплавления по меньшей мере Ni из составляющих элементов слоя 4 Ni и по меньшей мере Ti из составных элементов слоя 6 Ti, помещают между слоем 4 Ni и слоем 6 Ti. слой 6 и первый алюминиевый слой 7 соединены плакированной прокаткой встык.
Тип: Заявка
Подано: 25 октября 2011 г.
Дата публикации: 7 ноября 2013 г.
Заявитель: ШОВА ДЕНКО К.К.
Изобретатели: Ацуши Отаки, Сигеру Ояма
ЭЛЕКТРОПРОВОДНИКИ И СПОСОБЫ ИЗГОТОВЛЕНИЯ ЭЛЕКТРОПРОВОДНИКОВ
Номер публикации: 20130248229
Abstract: Электрический проводник включает в себя основную подложку из по меньшей мере одного из меди, медного сплава, никеля или никелевого сплава и слоистую структуру, нанесенную на основную подложку.
Слоистая структура включает фольгу и слой графена, нанесенный на фольгу. Слоистая структура наносится на основную подложку после нанесения графенового слоя на фольгу. Способ изготовления электрического проводника включает в себя обеспечение основной подложки, обеспечение фольги, нанесение слоя графена на фольгу для определения слоистой структуры и нанесение слоистой структуры на основную подложку.
Тип: Заявка
Подано: 5 февраля 2013 г.
Дата публикации: 26 сентября 2013 г.
Заявитель: Tyco Electronics Corporation
Изобретатель: Родни И. Мартенс
МЕТОД СВАРКИ ВЫСОКИМ ДАВЛЕНИЕМ/ВЫСОКОЙ СКОРОСТЬЮ ИЛИ СОЕДИНЕНИЯ ПЕРВОЙ И ВТОРОЙ МЕТАЛЛИЧЕСКИХ ЗАГОТОВОК ПЕРЕД СВАРКОЙ/СОЕДИНЕНИЕМ; ИЗДЕЛИЕ ПРОИЗВОДСТВА
Номер публикации: 20130189025
Реферат: Предложен способ формирования металлургической связки.
Первую металлическую заготовку и одну или несколько вторых металлических заготовок сближают друг с другом таким образом, что первая часть первой заготовки, как правило, перекрывает вторую часть одной или нескольких вторых заготовок. Между указанной первой частью и указанной второй частью предусмотрен подходящий материал, причем указанный материал находится в форме частиц или фольги. По меньшей мере, первая часть указанной первой заготовки, включающая указанную первую часть, прижимается к указанной части одной или более вторых заготовок, включающих указанную вторую часть, с помощью любого из подходящего процесса соединения под высоким давлением и процесса соединения на высокой скорости, такого как чтобы заставить указанную первую металлическую заготовку и указанную одну или несколько вторых металлических заготовок соединиться или свариться друг с другом с образованием металлургической связи между ними.
Тип: Заявка
Подано: 26 февраля 2013 г.
Дата публикации: 25 июля 2013 г.
Заявитель: INFINITY IP COMMERCIALIZATION (ISRAEL) LTD.
Изобретатель: INFINITY IP COMMERCIALIZATION (ISRAEL) LTD.
ПЕЧАТНАЯ ПЛАТА И СПОСОБ ЕЕ ИЗГОТОВЛЕНИЯ
Номер публикации: 20130168144
Реферат: Настоящее изобретение относится к способу изготовления печатной платы, который включает: подготовку базовой подложки с электродной площадкой; обеспечение проводящего материала заданной высоты; размещение проводящего материала на электродной площадке; и формирование проводящего штифта на электродной площадке путем соединения электродной площадки и проводящего материала, что позволяет добиться мелкого шага и легко реализовать проводящий штифт с высоким соотношением сторон.
Тип: Заявка
Подано: 17 декабря 2012 г.
Дата публикации: 4 июля 2013 г.
Заявитель: Samsung Electro-Mechanics Co., Ltd.
Изобретатель: Samsung Electro-Mechanics Co., Ltd.
СОЕДИНИТЕЛЬНЫЙ МАТЕРИАЛ, СПОСОБ ИЗГОТОВЛЕНИЯ СОЕДИНИТЕЛЬНОГО МАТЕРИАЛА И ПОЛУПРОВОДНИКОВОГО УСТРОЙСТВА
Номер публикации: 20130127026
Резюме: В соединительном материале по настоящему изобретению слой сплава серии Zn сформирован на внешней поверхности слоя сплава серии Al.
В частности, в соединительном материале содержание Al в слое сплава серии Al составляет 9от 9 до 100 мас.% или содержание Zn в слое сплава серии Zn составляет от 90 до 100 мас.%. При использовании этого соединительного материала можно подавить образование пленки оксида алюминия на поверхности соединительного материала во время соединения, и можно получить предпочтительную влажность, которая не может быть достигнута со сплавом Zn-Al. Кроме того, высокая надежность соединения может быть достигнута, когда после соединения остается слой сплава серии Al, поскольку его мягкий алюминий действует как амортизирующий материал.
Тип: Заявка
Подано: 18 января 2013 г.
Дата публикации: 23 мая 2013 г.
Изобретатели: Осаму ИКЕДА, Масахидэ ОКАМОТО
Электродвигательные агрегаты и системы и способы соединения проводов электродвигательных агрегатов
Номер патента: 8436506
Реферат: Статор для электродвигателя включает катушку статора, включающую пару проводов с соответствующими концами, соединенными кольцом.
Кольцо располагается вокруг пары проводов и соединяется с парой проводов с помощью металлического соединения.
Тип: Грант
Подано: 13 апреля 2010 г.
Дата выдачи патента: 7 мая 2013 г.
Правопреемник: GM Global Technology Operations LLC
Изобретатели: Пей-Чунг Ван, Джон С. Агапиу, Джон Патрик Спайсер
Способ сварки высоким давлением/высокой скоростью или соединения первой и второй металлических заготовок перед сваркой/соединением; изделие, изготовленное таким образом
Номер патента: 8393525
Реферат: Предложен способ формирования металлургической связи.
Первую металлическую заготовку (10) и одну или более вторых металлических заготовок (15) помещают в непосредственной близости друг от друга, так что первая часть (12) первой заготовки (10) в целом перекрывает вторую часть (17). ) одной или более вторых заготовок (15). Подходящий материал (99) расположен между указанной первой частью (12) и указанной второй частью (17), причем указанный материал (99) имеет форму частиц или фольги. По меньшей мере, первая часть указанной первой заготовки (10), включающая указанную первую часть (12), прижимается к указанной части одной или более вторых заготовок (15), включающих указанную вторую часть (17), с помощью любого из подходящих процесс соединения под высоким давлением (95) и процесс соединения на высокой скорости, такие как обеспечение соединения или сварки указанной первой металлической заготовки (10) и указанной одной или нескольких вторых металлических заготовок (15) друг с другом с образованием металлургической связи между ними.
Тип: Грант
Подано: 20 июня 2007 г.
Дата патента: 12 марта 2013 г.
Правопреемник: Infinity IP Commericalization (Israel) Ltd.
Изобретатели: Орен Гафри, Юрий Лившиз
Холодная сварка
Номер патента: 8376206
Реферат: Холодный сварной шов образуется в многослойном материале. Первый штифт соединен с первым блоком. Второй штифт соединен со вторым блоком. Многослойный материал расположен между первым штифтом и вторым штифтом. Первый штифт противостоит второму штифту.
Многослойный материал удерживается в плоскости XY и плавает по оси Z.
Тип: Грант
Подано: 18 октября 2011 г.
Дата выдачи патента: 19 февраля 2013 г.
Правопреемник: Medtronic, Inc.
Изобретатели: Кристиан С. Нильсен, Тимоти Т. Бомстад, Энтони М. Часенски
Магнитно-импульсный импульсный луч из смешанного металла
Номер патента: 8360301
Реферат: Узел ударной балки включает балку из высокопрочной стали и пару концевых кронштейнов, изготовленных из материала, отличного от высокопрочной стали.
Кронштейны локально деформируются на балке, тем самым окружая часть балки. После деформации кронштейны образуют плоскую секцию, пригодную для приваривания к дверной панели автомобиля, а также секцию для удержания балки. Балка может иметь элемент поверхности, пригодный для удержания балки на концевых кронштейнах. Способ усиления дверного узла транспортного средства включает позиционирование балки по отношению к концевым скобам таким образом, чтобы скобы окружали часть балки, а затем приведение в действие магнитно-импульсной катушки (MPC) для деформации перекрывающейся части скоб на балку. . Кронштейны затем прикрепляются к поверхности дверного узла для усиления дверного узла.
Тип: Грант
Подано: 31 марта 2009 г.
Дата патента: 29 января 2013 г.
Правопреемник: GM Global Technology Operations LLC
Изобретатели: Кеннет Г.
Данай, Ричард М. Клебер, Джеймс К. О’Кейн, Джон Р. Брэдли, Джон Э. Карсли, Кевин К. Паркила, Джеффри М. Скрамлин
ПУТЬ ПРОВОДНИКА, ПОЛУПРОВОДНИКОВОЕ УСТРОЙСТВО С ИСПОЛЬЗОВАНИЕМ ЕГО И СПОСОБ ИЗГОТОВЛЕНИЯ ПУТЬ ПРОВОДНИКА И ПОЛУПРОВОДНИКОВОЕ УСТРОЙСТВО
Номер публикации: 20120299166
Реферат: Путь проводимости включает пластину (11), образующую первый путь проводимости, выполненную из первого металла и имеющую сквозное отверстие (13), и пластину, образующую второй путь проводимости (15). изготовлен из второго металла и имеет запрессовываемую часть (17), запрессованную в сквозное отверстие. Поверхность стенки сквозного отверстия и боковая поверхность запрессованной части образуют наклонную поверхность (18) соединения, наклоненную относительно нормали к поверхности перекрытия пластины, образующей первый путь проводимости, и пластины, образующей второй путь проводимости, и соединительный участок (25), образованный потоком металла, формируется в области, расположенной на периферии наклонной соединяющей поверхности.
Тип: Заявка
Подано: 30 ноября 2011 г.
Дата публикации: 29 ноября 2012 г.
Изобретатели: Масанори Минамио, Зюня Танака, Рётаро Имура
Композитный проводящий компонент и способ его изготовления
Номер публикации: 201202
Реферат: Способ изготовления композитного проводящего компонента, включающий этапы изготовления по меньшей мере двух заготовок из металлического материала, причем указанные заготовки состоят из разнородных металлических материалов; размещение указанных заготовок кромкой к кромке или с частичным перекрытием друг друга, твердофазное соединение указанных заготовок друг с другом путем прокатки или сварки с образованием составного тела, прокатка указанного составного тела вдоль стыка по всей ширине композитный корпус для уменьшения его толщины и разрезание прокатанного композитного корпуса поперек соединения для получения по меньшей мере двух композитных проводящих компонентов, каждый из которых содержит металлические материалы указанных по меньшей мере двух заготовок и имеет соединение между указанными по меньшей мере двумя различными металлическими материалами .
Композитный проводящий компонент содержит, по меньшей мере, первую часть первого металлического материала и, по меньшей мере, вторую часть второго металлического материала, при этом указанные первый и второй металлические материалы отличаются друг от друга и изготавливаются данным способом.
Тип: Заявка
Подано: 3 декабря 2010 г.
Дата публикации: 22 ноября 2012 г.
Изобретатель: Сёрен Каль
ПРИБОР ДЛЯ ИЗМЕРЕНИЯ ПОЛОЖЕНИЯ, ШКАЛА И СПОСОБ ИЗГОТОВЛЕНИЯ ШКАЛЫ
Номер публикации: 20120266478
Реферат: Способ представляет собой шкалу с индуктивно сканируемой градуировкой, при этом шкала включает последовательность элементов градуировки, расположенных в направлении измерения, и стопку слоев, включающую в себя последовательность металлических слоев.
Последовательность металлических слоев включает несущий слой из ферромагнитного металла и слой градуировки, который образует последовательность элементов градуировки. Несущий слой расположен между градуировочным слоем и металлической подложкой, и металлическая подложка имеет такие размеры, чтобы окончательно определить механические свойства набора слоев.
Тип: Заявка
Подано: 17 апреля 2012 г.
Дата публикации: 25 октября 2012 г.
Изобретатели: Александр Франк, Марк Оливер Тиманн, Мартин Хьюманн
МЕТОДЫ И УСТРОЙСТВА СЖАТИЯ И ХОЛОДНОЙ СВАРКИ
Номер публикации: 20120241216
Резюме: Предусмотрены методы холодной сварки сжатием, соединительные конструкции и герметичные защитные устройства.
Способ включает обеспечение первой подложки, имеющей по меньшей мере одну первую соединительную структуру, которая содержит первую соединительную поверхность, причем эта поверхность содержит первый металл; обеспечение второй подложки, имеющей по меньшей мере одну вторую соединительную структуру, которая содержит вторую соединительную поверхность, причем эта поверхность содержит второй металл; и сжатие вместе по меньшей мере одной первой соединительной конструкции и по меньшей мере одной второй соединительной конструкции для локальной деформации и сдвига соединяемых поверхностей на одной или нескольких границах раздела в количестве, эффективном для образования связи металл-металл между первым металлом и вторым металл соединяемых поверхностей. Нахлесты на соединяемых поверхностях эффективны для вытеснения поверхностных загрязнений и облегчения тесного контакта между соединяемыми поверхностями без подвода тепла. Герметично закрытые устройства могут содержать лекарственные препараты, биосенсоры или МЭМС-устройства.
Тип: Заявка
Подано: 4 июня 2012 г.
Дата публикации: 27 сентября 2012 г.
Заявитель: MicroCHIPS, Inc.
Изобретатели: Джонатан Р. Коппета, Курт Шелтон, Норман Ф. Шеппард-младший, Дуглас Снелл, Кэтрин М.Б. Сантини
Метод прессования и аппарат прессования
Номер патента: 8235278
Реферат: Пресс-аппарат включает в себя монтажный стол и прижимной элемент.
Заготовку, сформированную из множества ламинированных листов сердцевины, помещают на монтажный стол, а прижимной элемент используют для прижатия заготовки к монтажному столу сверху. Монтажный стол поддерживается базовым элементом с возможностью свободного перемещения в горизонтальной плоскости. Когда прижимной элемент опущен, позиционирующий элемент определяет положение заготовки таким образом, что основные листы заготовки выровнены вдоль одной вертикальной оси.
Тип: Грант
Подано: 5 октября 2010 г.
Дата патента: 7 августа 2012 г.
Правопреемник: Toyota Boshoku Kabushiki Kaisha
Изобретатели: Широ Фуджимура, Такума Ватанабэ, Хадзиме Банно
Герметичное уплотнение с использованием конструкции шпунт-паз холодной сварки
Номер патента: 81
Резюме: Предусмотрены методы холодной сварки сжатием, соединительные конструкции и герметичные защитные устройства.
Способ включает обеспечение первой подложки, имеющей по меньшей мере одну первую соединительную структуру, которая содержит первую соединительную поверхность, причем эта поверхность содержит первый металл; обеспечение второй подложки, имеющей по меньшей мере одну вторую соединительную структуру, которая содержит вторую соединительную поверхность, причем эта поверхность содержит второй металл; и сжатие вместе по меньшей мере одной первой соединительной конструкции и по меньшей мере одной второй соединительной конструкции для локальной деформации и сдвига соединяемых поверхностей на одной или нескольких границах раздела в количестве, эффективном для образования связи металл-металл между первым металлом и вторым металл соединяемых поверхностей. Нахлесты на соединяемых поверхностях эффективны для вытеснения поверхностных загрязнений и облегчения тесного контакта между соединяемыми поверхностями без подвода тепла. Герметично закрытые устройства могут содержать лекарственные препараты, биосенсоры или МЭМС-устройства.
Тип: Грант
Подано: 4 ноября 2005 г.
Дата патента: 5 июня 2012 г.
Правопреемник: MicroCHIPS, Inc.
Изобретатели: Джонатан Р. Коппета, Курт Шелтон, Норман Ф. Шеппард-младший, Дуглас Снелл, Кэтрин М. Б. Сантини
ХОЛОДНАЯ СВАРКА
Номер публикации: 20120125978
Реферат: Холодный сварной шов формируется в многослойном материале.
Первый штифт соединен с первым блоком. Второй штифт соединен со вторым блоком. Многослойный материал расположен между первым штифтом и вторым штифтом. Первый штифт противостоит второму штифту. Многослойный материал удерживается в плоскости XY и плавает по оси Z.
Тип: Заявка
Подано: 18 октября 2011 г.
Дата публикации: 24 мая 2012 г.
Заявитель: Medtronic, Inc.
Изобретатели: Кристиан С. НИЛЬСЕН, Тимоти Т. БОМСТАД, Энтони М. ЧАСЕНСКИЙ
СОЕДИНИТЕЛЬНЫЙ МАТЕРИАЛ, ПОЛУПРОВОДНИКОВОЕ УСТРОЙСТВО И СПОСОБ ИЗГОТОВЛЕНИЯ ПОЛУПРОВОДНИКОВОГО УСТРОЙСТВА
Номер публикации: 20120098134
Резюме: При соединении с обычным плакирующим материалом Zn/Al/Zn толщина соединительной части должна быть менее чем в два раза больше, чем у существующего припоя с высоким содержанием свинца (около 100 мкм) чтобы сделать теплостойкость в соединительной части, по крайней мере, эквивалентной уровню существующего припоя.
Более того, толщина алюминиевого слоя должна быть как можно большей, чтобы в полной мере продемонстрировать способность алюминиевого слоя к релаксации напряжений. Предложено полупроводниковое устройство, включающее в себя полупроводниковый элемент, раму и соединительную часть, которая соединяет полупроводниковый элемент и рамку друг с другом, в котором интерфейс между соединительной частью и полупроводниковым элементом и интерфейс между соединительной частью и рамки соответственно имеют площадь пленки оксида алюминия, которая составляет более 0% и менее 5% от всей площади соответствующих интерфейсов.
Тип: Заявка
Подано: 30 августа 2010 г.
Дата публикации: 26 апреля 2012 г.
Изобретатели: Масахидэ Окамото, Осаму Икэда, Юки Мурасато
МЕТОДЫ ИЗГОТОВЛЕНИЯ ПОРИСТЫХ ОРТОПЕДИЧЕСКИХ ИМПЛАНТАТОВ
Номер публикации: 20120067853
Реферат: Описан способ изготовления ортопедического имплантата с пористой наружной поверхностью.
В одном варианте осуществления имплантат включает пористый слой, промежуточный слой и твердую подложку. Пористый слой предпочтительно связывают с промежуточным слоем посредством холодного изостатического прессования. Промежуточный слой предпочтительно прикрепляют вакуумной сваркой к твердой подложке таким образом, чтобы пористый слой образовывал по меньшей мере часть внешней поверхности ортопедического имплантата. Предпочтительно диффузионная связь создается между склеенным промежуточным слоем и твердой подложкой путем горячего изостатического прессования. В другом варианте пористый слой создают на внешней поверхности твердого слоя путем селективного плавления. Предпочтительно твердый слой соединен с твердой подложкой таким образом, что пористый слой образует по меньшей мере часть внешней поверхности ортопедического имплантата.
Тип: Заявка
Подано: 16 сентября 2010 г.
Дата публикации: 22 марта 2012 г.
Заявитель: HOWMEDICA OSTEONICS CORP.
Изобретатели: Айгуо Ван, Дэниел Э. Лауринович, Хайтонг Цзэн, Наоми Мюррей, Баладжи Прабху
Разбухающий пакер и способ его изготовления
Номер патента: 8127978
Реферат: Пакер с набухающим элементом изготавливается с внутренними кольцами, которые могут быть разъемными или спиральными. После наращивания разбухающего элемента на временной оправке по элементу прорезают продольный шов различной конструкции.
Это позволяет быстро развертывать элемент на трубе, который будет частью колонны и будет служить в качестве конечной оправки. Затем узел сваривается или обжимается магнитным импульсом, чтобы заставить открытые концы колец двигаться навстречу друг другу и закрепляться друг с другом, а также открывать возможность прикрепления частей на самом кольце к нижележащему трубчатому элементу путем смещения или иным образом. удаление набухающего материала, который находился между кольцом и окончательной оправкой, когда начался процесс магнитного импульса. Кольца могут быть полностью встроены в элемент или могут выступать за противоположные концы или их комбинации.
Тип: Грант
Подано: 20 мая 2009 г.
Дата патента: 6 марта 2012 г.
Правопреемник: Baker Hughes Incorporated
Изобретатели: Роберт О.
Кастильо, Энтони П. Фостер
СПОСОБ ИЗГОТОВЛЕНИЯ МЕТАЛЛИЧЕСКОЙ ЛАМИНИРОВАННОЙ ПОДЛОЖКИ ДЛЯ ОКСИДНОГО СВЕРХПРОВОДЯЩЕГО ПРОВОДА И ОКСИДНОГО СВЕРХПРОВОДЯЩЕГО ПРОВОДА С ИСПОЛЬЗОВАНИЕМ ПОДЛОЖКИ
Номер публикации: 20120040840
Abstract: [Задача] Металлическая ламинированная подложка для оксидного сверхпроводящего провода предоставляется по низкой цене. Металлическая ламинированная подложка обладает высокой прочностью и стабильно высокой двухосной ориентацией в продольном направлении. [Средства разрешения] Металлическая ламинированная подложка для оксидного сверхпроводящего провода изготавливается таким образом, что немагнитная металлическая пластина Т1 толщиной не более 0,2 мм и металлическая фольга Т2 из сплава меди, формируемая холодной прокаткой при осадка не менее 90% и толщиной не более 50 мкм ламинируют друг с другом поверхностно-активным склеиванием при комнатной температуре, после ламинирования кристаллы металлической фольги ориентируют термообработкой при температуре не ниже 150°С.
и не более 1000°С, после чего на металлическую фольгу наслаивают эпитаксиальную ростовую пленку Т3 из никеля или сплава никеля толщиной не более 10 мкм.
Тип: Приложение
Файл: 11 ноября 2009 г.
Дата публикации: 16 февраля 2012 г.
Изобретатели: Хиронао Окаяма, Акира Канеко, Такеши Като, Масая Кониси
Низкотемпературная лазерная точечная ударная сварка с бесконтактным приводом
Номер патента: 8084710
Реферат: Лазер, направленный на язычок пластины, вызывает направление оптической энергии на язычок, а именно на его верхнюю поверхность.
Энергия, воздействующая на язычок, ускоряет язычок из исходного согнутого положения, выпрямляя его до удара о лист-мишень. Удар происходит со скоростью более 100 м/с, что приводит к металлургической связи между язычком и листом-мишенью. Лазер предпочтительно поражает верхнюю поверхность в нормальном направлении, исходя из начального углового положения выступа относительно цели. Лазерное излучение, предпочтительно в диапазоне от 1 до 100 Дж, доставляемое за микросекунду, может быть усилено абляционным слоем на верхней поверхности или прозрачным покрытием на верхней поверхности, которое реагирует на расширяющийся газ из-за абляционной активности на верхней поверхности. . Сварной шов формируется без физического контакта между сварочным аппаратом и язычком.
Тип: Грант
Подано: 9 марта 2009 г.
Дата патента: 27 декабря 2011 г.
Правопреемник: Университет штата Огайо
Изобретатели: Гленн С. Даэн, Джон С. Липпольд
Холодная сварка
Номер патента: 8038048
Реферат: Холодный сварной шов формируется в многослойном материале. Первый штифт соединен с первым блоком. Второй штифт соединен со вторым блоком. Многослойный материал расположен между первым штифтом и вторым штифтом. Первый штифт противостоит второму штифту. Многослойный материал удерживается в плоскости XY и плавает по оси Z.
Тип: Грант
Подано: 30 августа 2005 г.
Дата патента: 18 октября 2011 г.
Правопреемник: Medtronic, Inc.
Изобретатели: Кристиан С. Нильсен, Тимоти Т. Бомстад, Энтони М. Часенски
Способ твердофазного связывания и устройства, полученные с его помощью
Номер публикации: 20110151272
Реферат: Раскрыты способ твердотельного соединения множества металлических слоев и устройства, изготовленные этим способом. Первый и второй металлические слои соединены в твердом состоянии с использованием защитного покрытия на несклеенных поверхностях, которые взаимодействуют с устройством приложения давления, чтобы предотвратить прилипание поверхностей к устройству приложения давления и защитить поверхности от отпечатков во время процесса соединения.
Изобретение может быть использовано для изготовления микроканальных устройств с гладкими внешними поверхностями и устранения смазок для пресс-форм, используемых в обычных процедурах склеивания.
Тип: Заявка
Подано: 20 декабря 2009 г.
Дата публикации: 23 июня 2011 г.
Изобретатели: Рид Бреннен, Кевин Киллин, Карен Л. Сиворд
Инструмент и способ сборки металлических деталей ударным воздействием с помощью магнитной силы с использованием двух электромагнитных катушек, подвижных друг относительно друга
Номер патента: 7959057
Реферат: Инструмент для сборки детали из ферромагнитного материала с деталью из парамагнитного материала.
Инструмент включает в себя первую часть инструмента, включающую в себя первый упор и первую электромагнитную катушку. Инструмент также включает в себя вторую часть, включающую в себя второй упор, при этом вторая часть механически собрана с первой частью таким образом, что первый и второй упоры выборочно притягиваются или отталкиваются друг от друга. Первая электромагнитная катушка используется для создания электромагнитного потока, который позволяет подталкивать парамагнитную часть ко второму упору и/или притягивать к нему ферромагнитную часть, когда первая и/или вторая часть помещается между первым и вторым упорами.
Тип: Грант
Подано: 28 марта 2006 г.
Дата патента: 14 июня 2011 г.
Правопреемник: Рено С.
А.С.
Изобретатель: Бернар Крики
ПРЕСС-МЕТОД И ПРЕСС-АППАРАТУРА
Номер публикации: 20110095072
Реферат: Пресс-аппарат включает монтажный стол и прижимной элемент. Заготовку, сформированную из множества ламинированных листов сердцевины, помещают на монтажный стол, а прижимной элемент используют для прижатия заготовки к монтажному столу сверху. Монтажный стол поддерживается базовым элементом с возможностью свободного перемещения в горизонтальной плоскости. Когда прижимной элемент опущен, позиционирующий элемент определяет положение заготовки таким образом, что основные листы заготовки выровнены вдоль одной вертикальной оси.
Тип: Заявка
Подано: 5 октября 2010 г.
Дата публикации: 28 апреля 2011 г.
Заявитель: TOYOTA BOSHOKU KABUSHIKI KAISHA
Изобретатели: Широ ФУДЖИМУРА, Такума ВАТАНАБЭ, Хадзиме БАННО
Клемма аккумуляторной батареи холодного формования
Номер патента: 7
4Производство ячеистых материалов и конструкций из сплавов с памятью формы методом нестационарно-жидкостного реактивного соединения
Номер публикации: 20110009979
Реферат: Настоящее изобретение раскрывает способ использования чистого ниобия в качестве переходного жидкого реактивного припоя для изготовления сотовых или сотовых конструкций, проволочных пространственных каркасов или других разреженных сборных конструкций или отдельных изделий.
с использованием нитинола (почти эквиатомного сплава титана и никеля) и родственных сплавов с памятью формы и сверхэластичных сплавов. Нитиноловые сплавы с памятью формы (SMA), полученные в виде гофрированного листа, дискретных трубок или проволоки, могут быть соединены друг с другом с использованием недавно открытой технологии соединения. Чистый ниобий при контакте с нитинолом при повышенной температуре сжижается при температурах ниже точки плавления и легко затекает в капиллярные пространства между соединяемыми элементами, образуя прочное соединение.
Тип: Заявка
Подано: 7 августа 2010 г.
Дата публикации: 13 января 2011 г.
Соискатели: РЕГЕНТЫ МИЧИГАНСКОГО УНИВЕРСИТЕТА, СОВЕТ ПОПЕЧИТЕЛЕЙ МИЧИГАНСКОГО УНИВЕРСИТЕТА
Изобретатели: Джон А.
Шоу, Дэвид С. Граммон
НИЗКОТЕМПЕРАТУРНАЯ ТОЧЕЧНАЯ УДАРНАЯ СВАРКА БЕСКОНТАКТНАЯ
Номер публикации: 20110000953
Abstract: Лазер, направленный на язычок пластины, вызывает направление оптической энергии на язычок, а именно на его верхнюю поверхность. Энергия, воздействующая на язычок, ускоряет язычок из исходного согнутого положения, выпрямляя его до удара о лист-мишень. Удар происходит со скоростью более 100 м/с, что приводит к металлургической связи между язычком и листом-мишенью. Лазер предпочтительно поражает верхнюю поверхность в нормальном направлении, исходя из начального углового положения выступа относительно цели. Лазерное излучение, предпочтительно в диапазоне от 1 до 100 Дж, доставляемое за микросекунду, может быть усилено абляционным слоем на верхней поверхности или прозрачным покрытием на верхней поверхности, которое реагирует на расширяющийся газ из-за абляционной активности на верхней поверхности.
. Сварной шов формируется без физического контакта между сварочным аппаратом и язычком.
Тип: Заявка
Подано: 9 марта 2009 г.
Дата публикации: 6 января 2011 г.
Заявитель: УНИВЕРСИТЕТ ШТАТА Огайо
Изобретатели: Гленн С. Даэн, Джон С. Липпольд
Разбухающий пакер и способ его изготовления
Номер публикации: 20100294484
Реферат: Пакер с набухающим элементом изготавливается с внутренними кольцами, которые могут быть разъемными или спиральными.
После наращивания разбухающего элемента на временной оправке по элементу прорезают продольный шов различной конструкции. Это позволяет быстро развертывать элемент на трубе, который будет частью колонны и будет служить в качестве конечной оправки. Затем узел сваривается или обжимается магнитным импульсом, чтобы заставить открытые концы колец двигаться навстречу друг другу и закрепляться друг с другом, а также открывать возможность прикрепления частей на самом кольце к нижележащему трубчатому элементу путем смещения или иным образом. удаление набухающего материала, который находился между кольцом и окончательной оправкой, когда начался процесс магнитного импульса. Кольца могут быть полностью встроены в элемент или могут выступать за противоположные концы или их комбинации.
Тип: Заявка
Подано: 20 мая 2009 г.
Дата публикации: 25 ноября 2010 г.
Изобретатели: Роберт О. Кастильо, Энтони П. Фостер
Реферат: Предлагаются способ и устройство для холодной штамповки клеммы батареи, имеющей участок соединения с аккумулятором и участок электрического соединения. Участок соединения с батареей определяет первую продольную ось, а участок электрического соединения определяет вторую продольную ось, при этом первая ось отстоит от второй оси на некотором расстоянии. Соединительная часть батареи и электрическая соединительная часть могут включать в себя одно или несколько удлинений. Часть электрического соединения может дополнительно включать вставку.
Тип: Грант
Подано: 18 декабря 2009 г.
Дата патента: 15 марта 2011 г.
Правопреемник: Tulip Corporation
Изобретатели: Бернард Н. Шпигельберг, Терри Дж. Эвраец
Сварка горячим воздухом в изменяющихся условиях окружающей среды — стр. 2 из 2
По мнению Марка, все дело в том, что сварщик знаком со своим оборудованием. «Двигатели вентиляторов на некоторых новых сварочных аппаратах больше, а значит, ваша горелка горячее», — говорит он. «Другие ручные сварочные аппараты не дуют столько воздуха. Это означает, что если аппликатор возьмет в руки новый ручной пистолет, ему придется научиться работать с ним. В идеале это должно быть решено до того, как начнется настоящая сварка».
Обучение всегда должно включать обучение технике безопасности, отмечает Дэйв. «Я считаю, что безопасность — это работа номер один, и мне нравится тот факт, что есть сварочный аппарат, который избавляет вас от необходимости идти назад и, возможно, с крыши», — говорит он.
Более того, успешная ручная сварка — это навык, который требует индивидуальной техники, обычно развиваемой и совершенствуемой с течением времени. Это означает, что операторы должны иметь опыт работы с различными конфигурациями сопла, поскольку правильный выбор температуры сварщика и ширины сопла может существенно повлиять на качество ручной сварки.
«Не все пистолеты работают при одной и той же температуре и при одном и том же температурном режиме, поэтому я прошу подрядчиков нумеровать свои пистолеты», — добавляет Марк.
Способность выполнять удовлетворительные сварные швы под разными углами и в труднодоступных местах в основном зависит от опыта и подготовки. Фото: ГАФ.
Кристиан согласен с тем, что обучение и общение между руководителями и бригадами могут иметь жизненно важное значение, поскольку производительность робота-сварщика зависит от модели и условий окружающей среды.
При сварке в холодную погоду термопластическую мембрану необходимо «предварительно нагреть» перед сжатием сварного шва. В то время как автоматический сварочный аппарат имеет отверстия в сопле, которые предварительно нагревают мембрану, у ручных пистолетов их нет.
«Когда я наблюдаю за сваркой, большинство монтажников держат ролик слишком близко к соплу, что не позволяет предварительно нагреть мембрану», — говорит Марк. «Я предлагаю держать валик на расстоянии не менее 1 или 2 дюймов от кончика».
Способность выполнять удовлетворительные сварные швы, удерживая аппарат для сварки горячим воздухом любой рукой, облегчает сварку под разными углами и в труднодоступных местах. Поскольку немногие установщики по своей природе симметричны, в основном важен опыт работы с такими деталями. И в этом заключается основная проблема для кровельных подрядчиков в целом — поиск и удержание квалифицированной рабочей силы.
«Простая установка зонда в шов не гарантирует отсутствие утечек, особенно в холодную погоду, когда крыша также не «прощупывается», — говорит Марк. «Наиболее важное значение для водонепроницаемости кровельной системы имеет обучение монтажников».
При ручной сварке с помощью валика часто используется давление пальца для установки и «прихватки» верхней части мембраны на место. Однако для окончательной сварки всегда следует использовать твердый силиконовый валик. Полевые швы, сваренные прихватками, не проходят контроль.
Мембрана обычно сваривается при помощи двухпроходной сварки. Монтажник сваривает внутреннюю часть шва на первом проходе и завершает сварку вторым проходом.
Насадка помещается между двумя слоями мембраны, а ролик используется для сжатия мембраны и создания связи. В идеале сварные швы должны быть непрерывными, без пустот или частичных сварных швов.
Звучит просто, не правда ли? Это может быть, если ваше тело не искривлено вокруг приподнятого трубопровода, в тени 100 градусов по Фаренгейту, и горячий ветер собирает все виды потенциальных загрязнителей шва и уносит их в вашем направлении. Дефекты обычно исправляются путем тепловой сварки еще одного слоя армированной мембраны поверх места дефекта в тот же день, при условии, что внутренняя часть шва не была загрязнена.
Настройка оборудования и тестовая сварка
Специалисты по кровле знают все о важности настройки роботизированных сварочных аппаратов и выполнения пробных сварных швов перед тем, как утром приступить к работе. Тем не менее, производители мембран хотели бы, чтобы бригады проверяли сварные швы в начале каждого рабочего периода, в том числе после обеда во второй половине дня. Они также рекомендуют проводить тестирование при значительных изменениях погоды, включая изменения температуры воздуха, скорости ветра, облачности и т. д.
Низкие температуры воздуха и пасмурное небо обычно требуют меньшей скорости, чем при более высоких температурах и солнечном небе.
Для начальных настроек аппарата для автоматической сварки горячим воздухом один эксперт рекомендует приведенную ниже формулу. Она не является надежной, но является хорошей отправной точкой при средних погодных условиях:
Формула скорости: температура окружающей среды/10 + 2=FPM (футов в минуту).
Например: 80/10 + 2=10 кадров в минуту.
«Если сварщик ожидает резких перепадов температуры окружающей среды от горячей к холодной — вспомните осенний Чикаго, — он может настроить сварочный аппарат ближе к 1,5-дюймовому сварочному шву», — говорит Дэйв. «Таким образом, при понижении температуры сварной шов будет оставаться в пределах требуемых производителем параметров ширины шва».
Как правило, производители мембран хотят видеть расслоение тестового шва не менее 1 дюйма, но не более 1,5 дюймов.
Дейв считает, что добросовестный подрядчик будет выполнять не менее двух тестовых сварных швов в день. «В худшем случае они понимают, что то, что работало вчера, может не работать сегодня», — говорит он.
Многие факторы влияют на настройки сварочного аппарата, включая тип мембраны (TPO, ПВХ) и толщину. «ТПО и ПВХ свариваются по-разному, — говорит Дэйв. «Вы хотите, чтобы сварочный аппарат работал на более высокой температуре с ПВХ и видел дым и кровотечение на краю шва. Если вы задымите или вытечете ТПО, вы перегреете лист и в значительной степени повредите сварной шов».
Чтобы избежать такой ситуации, требуется тестовая сварка с использованием мембраны «свежий мешок» длиной примерно 18 дюймов. Для полноразмерных автоматических сварочных аппаратов один производитель мембран предлагает использовать приведенный ниже сценарий, учитывая комментарий Марка о том, что новое оборудование может работать быстрее или горячее, чем предполагалось.
Пример сценария: Начните с установки скорости сварки на 10 футов в минуту и температуры на 600°F и выполните пробную сварку. Поднимите температуру до 700 ° F, сохраняя скорость сварщика на уровне 10 футов в минуту, и выполните еще одну пробную сварку. Продолжайте этот процесс с шагом 100°F, сохраняя скорость неизменной, пока машина не достигнет максимума (обычно 1148°F) и не найдите окно сварки. Затем установите машину на середину окна сварки.
Наконец, приварите вместе два 18-дюймовых куска мембраны в согласованном режиме и дайте мембране остыть в течение не менее 10 минут. Отрежьте полоски шириной 1 дюйм поперек 18-дюймовой сварной мембраны и проверьте каждый сварной шов, прикладывая достаточное давление, чтобы шов разошелся.
Приемлемый сварной шов разрушится из-за того, что обнажится армирование холста, иначе называемое «связкой, разрывающей пленку». Частичный сварной шов не пройдет испытание на отслаивание из-за частичного разделения двух слоев мембраны.
Визуальный осмотр может помочь выявить перегрев или разрывы в зазорах в зоне сварки в швах. Фото: ГАФ.
Наконец, «холодный» или «ложный» сварной шов не будет выполнен из-за полного разделения двух слоев мембраны.
«Вы можете поместить образец на машину Instron (в испытательном центре) для большей точности, — говорит Дэйв, — но правильно проведенное испытание на отслаивание, проведенное на крыше, обычно удовлетворительно.
Кроме того, визуальный осмотр может определить достаточную ширину сварного шва; наличие крепежных деталей и пластин в зоне сварки; перегрев или разрыв в зоне сварки; указания на специальную герметизацию Т-образных стыков; а также серьезный недогрев или пропуск участков шва.
Физическое зондирование предполагает использование шовного зонда с тупым концом, такого как съемник шплинта с тупым концом. Сварному шву необходимо дать остыть перед измерением. Щуп с некоторым усилием прижимают к кромке сварного шва и проводят по шву. Инструмент-зонд войдет в зону термического сваривания между двумя слоями мембраны в местах, где швы частично сварены и обнаружена «пустота». Затем можно использовать измерительный инструмент для отслеживания проблемной области шва до тех пор, пока не встретится сплошной (заказной) сварной шов.
Инспектор кровельных работ может также попросить осмотреть контрольные сварные швы и провести зондирование и визуальное наблюдение, но большинство производителей избегают разрушающих испытаний при контроле прочности швов при монтаже кровли.
«Производительность сварки с годами улучшилась в результате активного общения и обучения», — заключает Кристиан. «В частности, обучение работе со сварочным окном и настройкой машины способствовало повышению производительности сварки».