Контактная стыковая сварка – технология и аппараты для сварки — статьи от «МЕЛТПЛАСТ»
Контактная стыковая сварка — способ соединения площадей сечений изделий путем глубокой деформации металлических поверхностей без плавки самого металла. Она применяется как в процессе строительства масштабных конструкций, например, космических аппаратов, массивных труб, так и при соединении миниатюрных деталей: микросхем, полупроводников и т. д. Преимущества этого способа сварки в широте использования и в универсальности соединения практически всех конструкционных материалов: легированной стали, низкоуглеродной, сплавы на основе титана, алюминия, магния и т. д.
Различаются два варианта контактной стыковой сварки: оплавлением и сопротивлением. Частота и использования сварки оплавлением составляет не больше 10 % общего количества технологических процессов сварки.
Cхема контактно-стыковой сварки: оплавлением и сопротивлением
Сварка — электродеформационный технологический процесс, согласно ГОСТ 2601—84, он относится к высокоэффективным вариантам стыка металлических поверхностей изделий.
Стыковая сварка — метод сцепления площадей двух изделий (стыков) путем воздействия сильного электротока. При таком способе соединения ввариваемые поверхности прочно соединяются, контактирование происходит без расплавления самих деталей, а за чет деформации их поверхностей — стыка.
Циклограммы стыковой контактной сварки
Где, I — сварочный ток; Р — усилие сжатия; S — перемещение подвижной плиты; t — время сварки; а — сопротивлением; б — оплавлением;
Главный физический процесс при стыковой сварке — нагрев и последующая деформация поверхности, за счет чего происходит удаление поверхностных пленок, происходит контактирование, затем получается высокопрочное соединение с заданными характеристиками. Стыковой сваркой соединяют полиэтилен, стыки труб, арматуры и пр. детали из конструкционных материалов.
Стыковая сварка выполняется на основе з-на Джоуля-Ленца. Процесс происходит под действием тока высокого значения путем очень сильного сжатия, прикладываемого к свариваемой поверхности.
Сварка сопротивлением — вид стыковой сварки, при которой процесс происходит с нагревом контакта до состояния пластичности. Если же технология происходит путем оплавления площадей контактирующих изделий — это способ стыковой сварки плавлением. Когда производится сварка сопротивлением, стык очень плотный — две площади сцепляются в замках сварочной машины, далее на них направляется сильный электр. ток. Когда площади деталей станут пластичными, происходит осадка — ток отключается.
Чтобы процесс происходил с соблюдением всех правил, сварное соединение было прочным, поверхности деталей необходимо предварительно подготовить:
- стык обезжирить;
- устранить все пленки, главным образом оксидные;
- выполнить пассивирование, нейтрализацию;
- просушить поверхности;
- выполнить контроль готовность деталей к процессу для прочного сварного контакта.
Поверхности, которые контактируют, должны отвечать следующим требованиям:
- создавать минимальное сопротивление сильному электротоку;
- на контакте значение сопротивления равное по всей его площади;
- площади изделий для сварки необходимы в максимально ровном виде к совпадающим плоскостям.
Существует два вида сварки оплавлением: непрерывным процессом, прерывистым.
Схема процесса стыковой сварки
непрерывным оплавлением
Схема процесса стыковой сварки
прерывистым оплавлением
При непрерывной стыковой сварке оплавлением
, изделия крепятся в спец. замках сварочной машины. Далее при подаче тока путем плавного передвижения изделия приводят в сцепление. При этом площадь изделий контактирует, они свариваются. Затем происходит осадка на необходимое значение, долее ток отключается. Этот вариант контактирования и сварки применяется при контактной сварке рельсов, труб с тонкими стенками, листов и т.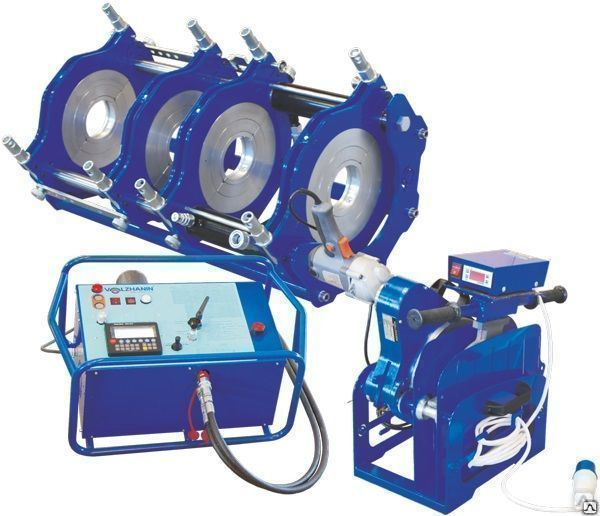
Такие поступательные и возвратные движения при воздействии тока замыкают цель, пока поверхности деталей на контакте не достигнут предела 800-900 градусов, при такой температуре происходит оплавление, осадка материала. Сварка плавлением используется при стыке изделий из низкоуглеродистой стали, когда контактная сварка оплавлением с помощью непрерывного соединения является недостаточной. Этот вариант требует доп. расхода материала, поэтому нагрев может дополнительно осуществляться сопротивлением — ток идет при замкнутой сварочной цепи, затем детали разъединяются, далее идет плавление, осадка.
Стыковая сварка оплавлением возможна с менее тщательной обработкой свариваемых изделий, чем при сварке сопротивлением, поскольку металл из области сваривания частично плавится — расходуется, поэтому место стыковки обрабатывается в технологическом процессе. Детали для оплавления могут резаться пресс. ножницами, с помощью кислородной резки, однако при последнем способе понадобится последующая очистка от шлака или окалины. Возможно отклонение поверхностей в торцевании в пределах 12-15 %. При норм. условиях контактно-стыковой сварки электроток, давление направляются прямо к месту стыкования.
Этот способ несколько отличается от других, его называют «электротермодеформационным». Сварка сопротивлением выполняется без плавления основания — в этом ее отличие и уникальность. Металл при контактно-стыковой сварке таким методом поддается сильной деформации на пластичность. Основа контактно стыковой сварки заключается в следующем: стержни для сварки оснащаются подключенным электротоком. При соприкосновении образуется замкнутая электроцепь. В зоне контакта происходит высокое сопротивление, в связи с этим выделяется небольшое количество тепла. Далее разогретые стержни прижимаются давлением друг к другу, затем подача электротока прекращается.
Cхема стыковой контактной сварки сопротивлением
Разогретые стержни постепенно отвердевают, в связи с этим технология и получила название сварки сопротивлением. Стоит сказать, что для распределенного повышения температуры материала и последующего использования стыковой сварки сопротивлением поверхность свариваемых деталей нуждаются в тщательной обработке. По существу детали очень сильно сцепляются, поэтому никаких мельчайших инородных тел на стыкуемой поверхности быть не должно. Через детали при очень плотном стыке дается сильный ток, при нагревании они переходят в пластичную форму, далее детали сжимаются с увеличивающимся нажатием до получения сцепления в твердом физсостоянии.
Контактная стыковая сварка сопротивлением подразумевает зачистку области механич. способом. Для прочих вариантов контактной стыковой сварки эта подготовка не нужна. Высокой квалификации и большого профессионализма сварка сопротивлением не предусматривает. Этот вид контактной сварки довольно востребован, он применяется в разных сферах производства, строительства. Применяется для площадей сечением от 1 до 20 квадратных мм. Ограничения касаются только алюминиевых (сечение до 500 кв.
Очень часто сварка сопротивлением используется для сварки труб, проволоки. Для контактной сварки сопротивлением может использоваться и сталь, однако низкоуглеродистая.
По мнению экспертов, с помощью контактной сварки сопротивлением можно сваривать металлы разных свойств, для примера, алюминий и чугун, медь и сталь. Можно встретить и критические замечания по поводу соединения. Оптимальный результат при сварке сопротивлением получается при использовании малоуглеродистых и низколегированных материалов, легких сплавов из металла.
Из практики многократного проведения технологии стыковой сварки полиэтиленовых труб она происходит чаще всего с помощью специальной машины стыковой сварки. Полимер, из которого выполнены трубы, прекрасно поддается контактной сварке. Большая популярность аппарата стыковой сварки полиэтиленовых труб обусловлена надежностью, безопасностью, а также возможностью взаимодействия с трубами разнообразного размера.
Машина для стыковой контактной
сварки КС-011
Контактный аппарат для стыковой
сварки HDL75-250-4
Стыковая сварка полиэтиленовых труб с помощью аппарата выполняется качественно и надежно. Сварочные машины для стыковой сварки труб бывают следующих разновидностей:
- стационарные;
- подвесные;
- передвижные;
- специализированные;
- универсальные.
Любая машина для стыковой сварки труб ПНД состоит из механической и электрической части, пневмосистемы, а также системы водяного охлаждения. Стыковая сварка труб ПНД немного отличается от стыковой, поскольку пластик не проводит сквозь себя ток, из-за этого торцы таких труб прогревают спец. контактными элементами для нагрева. А в остальном же технология соединения площадей изделий, затвердевание, кристаллизация в общем похожи.
Машины для стыковой сварки существенно ускоряют процесс сцепления поверхности двух деталей, поэтому на технология успешно применяется в разнообразных областях: в строительстве, в металлургии, в ж/д строительстве, в автомобильной промышленности, при производстве инструментов, при прокладке трубопроводов для соединения труб из пластика со стальными.
Вернуться в начало статьи
Стыковая сварка оплавлением: процесс, виды, области применения
Оборудование и приспособления
Для машин общего назначения ГОСТ 297—80 устанавливает, в частности, следующие основные параметры.
- Наибольший вторичный ток. Это ток, который проходит во вторичном (сварочном) контуре при его коротком замыкании на максимальной ступени регулирования при номинальных значениях раствора и вылета сварочного контура.
- Номинальное и (или) наименьшее и наибольшее усилия сжатия электродов – для точечных, шовных и рельефных машин.
- Требования к геометрическим параметрам электродов и консолям машины (размеры контура относятся к наиболее важным параметрам машины; контуры состоят из жестких и гибких токоведущих элементов, которые соединяют вторичные витки сварочного трансформатора с оснасткой машин).
Оснастка машин включает консоли, электрододержатели, электроды, токоподводящие губки и другие элементы, размеры и конструкция которых может меняться в зависимости от конструкции изделия. На этих элементах иногда устанавливают приспособления, фиксирующие или поддерживающие свариваемые, детали, загрузочные или съемные механизмы. Вторичный контур характеризуется такими параметрами:
- активное сопротивление;
- индуктивное сопротивление;
- полное сопротивление в режиме короткого замыкания.
В состав точечных, рельефных, шовных, подвесных и многоэлектродных машин входят приводы сжатия. В период протекания сварочного тока эти приводы формируют на электродах постоянное или изменяющееся во времени сварочное усилие. В необходимых случаях такие приводы создают на электродах усилие предварительного обжатия (до включения тока) и ковочное усилие (после выключения тока), превышающие уровень сварочного усилия. В большинстве машин приводы сжатия являются пневматическими, реже – пружинными.
Привода вращения роликов шовных машин – обеспечивают передвижение свариваемых деталей на шаг точек. Вращение роликов может быть непрерывным и прерывистым. Приводным может быть один из роликов, а в некоторых случаях крутящий момент передается сразу на оба ролика.
Электроды для точечной сварки и ролики для шовной сварки состоят из: рабочей части, части, обеспечивающей соединение с машиной, и средней (основной) части
Рабочая часть обеспечивает непосредственный контакт (электрический и механический) электрода со свариваемыми деталями и имеет рабочую поверхность, форма и размеры которой являются важной технологической характеристикой электрода (ролика). В настоящее время наиболее распространены две формы рабочей поверхности: плоская (цилиндрическая у роликов) и сферическая
Основной функцией электродов и роликов является подвод тока к деталям и передача к ним сварочного усилия. Внутренняя часть большинства электродов для точечной сварки имеет канал для подачи охлаждающей воды. Внутри охлаждающего канала находится трубка, по которой поступает вода.
Расходные материалы
Наибольшему износу в сварочных аппаратах подвергаются электроды, которые постоянно испытывают механические и термические нагрузки. Изготавливаются они из чистой меди, либо из медных сплавов с алюминием, цинком, кадмием и другими металлами, повышающими прочность и упругость изделия. Подобные сплавы делятся на несколько типов:
- Для работы при высокой температуре (около 500 градусов по Цельсию) и непрерывной подаче тока – такие электроды изготавливают из бронзы с добавлением никеля, кремния, циркония или хрома;
- Для работы при температуре до 300 градусов, сварки цветных сплавов, низколегированных сталей применяются сплавы МС (легированные серебром) и МК;
- Для работы при малых (до 200 градусов по Цельсию) температурах подходят сплавы бронзы с хромом и кадмием.
Быстрее всего изнашиваются электроды конической и цилиндрической формы, медленнее всего – плоские и широкие, применяемые в машинах для рельефной сварки.
Оборудование для стыковой сварки
Существует различное оборудование, используемое для контактной стыковой сварки. Его можно классифицировать в зависимости от конструктивных особенностей и признаков, характерных для оборудования, применяемого при точечной и шовной контактной сварке. Оборудование может быть классифицировано в соответствии с видами сварных работ (обработка сопротивлением и оплавлением). Кроме того, существует деление в зависимости от рода электротока, назначения и т. п.
Оборудование состоит из:
- станины;
- сварочного трансформатора;
- вторичного контура;
- подвижной и неподвижной плит;
- токопроводящих губок для фиксации заготовок;
- зажимных цилиндров;
- привода подачи;
- направляющих;
- блока системы управления.
Наиболее распространенными являются аппараты стыковой сварки переменного тока.
Детали некоторого сортамента обрабатываются при помощи специализированного оборудования. К примеру, выпускается специальная аппаратура для сварки ленточных пил, цепей, железнодорожных рельсов. Работы возможны как в стационарных условиях, так и на железнодорожном полотне.
Для стыковой сварки труб, диаметр которых не превышает 1 м, используется контактное соединение, выполняемое как в стационарных, так и в полевых условиях. Если необходимо работать с трубами, диаметр которых превышает 1,4 м, прибегают к использованию специального сварочного оборудования, внутрь которого вводятся трубы.
Стыковая
Во время данного вида работ в отличие от рельефной и точечной детали свариваются по всей поверхности их соприкосновения. Стыковая сварка имеет две разновидности:
- сопротивлением, при котором соединение нагретых практически до температуры плавления стыков деталей производится путем сильного сжатия деталей, в результате которого элементы соединяются в твердой фазе;
- оплавлением, которое, в свою очередь, имеет тоже два вида:
- непрерывное оплавление, при котором сближение деталей происходит во время работы сварочного трансформатора.
При сжатии элементов возникает контакт, и происходит нагрев стыка протекающим электрическим током. При снижении силы сжатия контактное сопротивление увеличивается, и за счет этого происходит снижение сварочного тока. Сплошное касание деталей заменяет точечное соприкосновение. При этом участки соединения выступают и оплавляются за счет повышения эффективности нагрева в них. Процесс оплавления продолжается до появления прослойки из жидкого металла, который образует сплошное соединение, а его излишки выдавливаются из пространства между деталями;
- стыковая сварка оплавлением с подогревом представляет собой процесс, при котором нагрев соединяемых элементов происходит путем кратковременных замыканий торцов деталей, после чего они оплавляются. Преимущества данного вида заключаются в более прочном соединении элементов, экономии электроэнергии, в возможности сваривать различные по составу детали, её часто можно встретить в кораблестроении. не требует большой механической обработки.
- непрерывное оплавление, при котором сближение деталей происходит во время работы сварочного трансформатора.
Принцип стыковой сварки
Технология контактной стыковой сварки представляет собой такой способ соединения металлических заготовок, при котором область стыка деталей равномерно нагревается. Горячие части деталей плотно соединяются друг с другом, полученный сплав является неразъемным.
Эта разновидность сварных работ характеризуется высокой производительностью за счет повышенной скорости соединения деталей. Стыковая контактная сварка отличается более быстрым и равномерным плавлением металла, что приводит к ускоренному образованию сварного шва. Сам процесс может быть автоматизированным и встроенным в конвейер. Благодаря этому контактная стыковая обработка деталей распространена на серийном производстве, например, при работе с трубами.
Для соединений, полученных при использовании этой технологии работ, характерны повышенная прочность и долговечность. Сварка используется в процессе производства автомобилей, самолетов и нефтепроводов. Еще одним достоинством данного способа является тот факт, что на качество шва не влияет квалификация сварщика, а значит, производство не зависит от наличия высококвалифицированных рабочих.
Рекомендовано к прочтению
- Резка меди лазером: преимущества и недостатки технологии
- Виды резки металла: промышленное применение
- Металлообработка по чертежам: удобно и выгодно
Стыковая обработка с использованием контактного оборудования подходит для работы с различными типами заготовок (стальными трубами, пластинами, свариваемыми встык, ПНД трубами и т. п.). Для получения удовлетворительного результата необходимо строго следовать технологии работы.
Существует две разновидности контактной стыковой сварки:
- оплавлением;
- сопротивлением.
Остановимся на этих разновидностях сварных работ подробнее.
youtube.com/embed/BeerMjstPo8?feature=oembed» frameborder=»0″ allow=»accelerometer; autoplay; clipboard-write; encrypted-media; gyroscope; picture-in-picture» allowfullscreen=»»>Технология стыковой сварки
Технология стыковой сварки включает в себя сильный разогрев свариваемой поверхности и механического воздействия на деталь для достижения сварного соединения. Предъявляемые требования чтобы технология стыковой сварки прошла успешно, включает в себя:
тщательная подготовка торцов поверхности металла. Они должны быть подогнаны максимально ровно. Это обеспечит прочность соединения. Удаление загрязнений на поверхности, окислов, что также повышает качество сварного соединения
Особенно это важно учитывать когда площадь поверхности 200 миллиметров квадратных;
закрепление свариваемых деталей в сварочной машине, установка их соосности;
пропускание электрического тока высокой частоты, который нагревает и расплавляет соединяемые поверхности;
механическое сжатие заготовок, при котором происходит пластическая деформация, разрушение оставшихся окислов и атомное соединение двух поверхностей;
процесс кристаллизации и образование кристаллической решетки сварного соединения.
Такая технология стыковой сварки дает возможность соединять детали различного предназначения. А качество соединения позволяет долгой эксплуатации изделия.
Способы стыковой сварки
На способы стыковой сварки влияют:
- марка свариваемого металла, его состав;
- какая площадь сечения в месте соединения металла;
- какие предъявляются требования к качеству сварного соединения.
Первый способ – это сварка сопротивлением.
Его используют когда соединяют деталь площадью сечения до 200 миллиметров квадратных. Для этого детали прочно закрепляют в специальных зажимах сварочной машины. Свариваемые поверхности плотно прижимают друг к другу. Затем пропускают электрический ток, который может быть 1000 – 10000 А. Температура нагрева торцов детали ниже температуры плавления металла. После нагрева производится сжатие заготовок с одновременным отключением тока. Сварка сопротивлением применяется при соединении стержней и труб из низкоуглеродистой стали малого сечения, а также проволоки.
Второй способ – это сварка оплавлением.
Сварочный процесс такого способа похож на первый способ. Только при этом методе сварки сначала подается ток, а потом следует соединение деталей. Перемещают при этом только одну из деталей с медленной скоростью. Средняя температура оплавления растет постепенно, достигая равномерного слоя расплавленного металла. Такой способ может быть непрерывным или прерывистым. Соединяемая заготовка в сечении может достигать 100000 миллиметров квадратных. Детали свариваемые таким способом: колеса, кольца, трубы, рельсы и др.
Такие способы стыковой сварки позволяют расширить номенклатуру свариваемых материалов.
Стыковая сварка металла
Стыковая сварка металла является практичным способом для соединения железнодорожных рельсов, чтобы получить соединение не имеющее стыка. Предоставляет возможность производства заготовок длинных размеров из стали, цветных металлов и их сплавов. Стыковая сварка металла применяется для изготовления якорных цепей, в производстве режущего инструмента, змеевиков больших холодильных установок. В целом, такой способ сварки имеет очень широкий спектр применения.
Устройства для осуществления процесса
Оборудование для контактной сварки может применяться для полной автоматизации проводимого процесса. В большинстве случаев достаточно лишь правильно разместить заготовки и нажать на одну клавишу. К другим особенностям аппаратов стыковой сварки можно отнести следующие моменты:
- Хорошая производительность.
- Возможность автоматизации процесса.
- Высокая стоимость оборудования.
- При проведении работы исключается вероятность допущения ошибки.
Аппарат для стыковой сварки
В продаже можно встретить оборудование самых различных производителей
Рекомендуется уделять внимание продукции лишь известных компаний
Виды стыковой сварки
Сварка пластин и других металлических изделий встык может проводиться несколькими способами – оплавлением и сопротивлением. Каждый метод имеет характерные особенности и нюансы, которые обязательно нужно соблюдать при проведении сварочных работ.
Сварка оплавлением
Стыковая сварка оплавлением является популярной технологией, которую используют в разных сферах промышленности. Ее суть состоит в том, что определенный объем напряжения, который подается на область обмоток трансформатора, прекращается, как только два свариваемых изделия соприкоснутся. Если говорить простыми словами, напряжение повышается и в момент наивысшей точки сразу же прекращается его подача. Но при этом сохраняется достаточный объем тепловой энергии для расплавления металлической основы.
На поверхности стыков двух изделий имеются небольшие неровности, именно они обеспечивают хороший контакт между изделиями. Но все же если вы хотите получить отличный результат, то лучше торцевые части сдавить и полностью их выровнять. Это улучшит площадь соприкосновения. Данные условия обеспечат быстрое разогревание и расплавление металла, он в прямом смысле закипит всего за несколько секунд.
Сварка оплавлением характеризуется тем, что при ее проведении могут появляться дополнительные неровности, в которых могут концентрироваться паровые смеси от расплавленных металлов. Но данные пары приносят пользу сварочному процессу, они оказывают защитное воздействие, а именно защищают сварочную зону от негативного воздействия кислорода.
Важно! Контактная стыковая сварка оплавлением проводится с использованием усилия или давления. Его прикладывать необходимо тогда, когда стыки свариваемых изделий уже немного расплавились
В момент, когда происходит сжатие двух изделий, лишний жидкий металл выходит за пределы. Как раз в это время происходит соединение двух элементов. В результате получается прочный и качественный шов, При его осмотре практически не обнаруживается видимых и скрытых дефектов. Дело в том, что продукты разложения, оксидная пленка удаляются вместе с излишками расплавленной металлической массы.
Контактная сварка оплавлением не требует предварительно подготовки и особой обработки металлических поверхностей. Для проведения не нужно подготавливать торцевые части изделий, это существенно экономит время. Если необходимо сварить элементы, которые имеют разное сечение, то заранее можно сделать противоположные скосы. Это намного улучшит контакт между заготовками, увеличит их площадь соприкосновения.
Сварка сопротивлением
Стыковая сварка сопротивлением существенно отличается от сварочного процесса оплавлением. Во время проведения этой технологии изделия прижимаются губками к поверхности электродов. Именно это позволяет получить хороший контакт, а губки отлично удерживают элементы, предотвращают их скольжение.
Затем элементы с усилием прижимают друг к другу, и после подается электрический ток. Именно он начинает постепенно разогревать металлическую структуру. Разогревание металла должно проводиться до той степени, когда он приобретает пластичные свойства. Под сильным давлением изделия соединяются друг с другом. Лишняя расплавленная металлическая масса выходит, вместе с ней удаляется оксидная пленка.
Обратите внимание! Сварка сопротивлением проводится с постоянным давлением, его подача не должна прекращаться пока металлическая структура полностью не остынет и не образуется прочное соединение. Если соблюдать все правила и принципы, то шов выйдет ровным, без изъянов, дефектов с хорошей износостойкостью
Контактная стыковая сварка сопротивлением машины и других изделий требует предварительно подготовки и обработки свариваемых изделий. Их необходимо хорошо зачистить. Кроме этого стоит учитывать, что детали, которые сваренные при помощи сварочного процесса сопротивлением имеют меньшую устойчивость к окислению, поэтому этот метод редко применяется. Также сварка подходит только для деталей с небольшим сечением.
Определение, схема и разновидности стыковой контактной сварки
Стыковая сварка — это способ контактной сварки, при котором сваривание деталей происходит по всех площади их соприкосновения. Схема контактной сварки показана на рисунке слева. Детали поз.1 закрепляют в токоподводящих зажимах поз.2,3, один из которых подвижен и связан с приводом усилия и перемещения машины. По характеру нагрева различают стыковую сварку оплавлением и сопротивлением.
Стыковая сварка сопротивлением
При этом способе сварки происходит сжатие деталей с довольно большим усилием, порядка 3-5 кН. Затем включают сварочный трансформатор поз.4 и либо нагревают электрическим током до высокой температуры (примерно 80-90% от температуры ликвидуса), либо расплавляют металл в стыке. Исходя из этого, стыковую сварку сопротивлением можно разделить ещё на два вида — без локального расплавления металла и с его расплавлением.
После нагревания сварочный ток выключают и резко создают усилие, равное усилию осадки, благодаря чему происходит либо интенсивная деформация твёрдого металла (выдавливание металла из стыка), вместе с которым происходит удаление оксидных плёнок, либо удаление жидкого металла и части нагретого твёрдого металла. При этом происходит формирование физического контакта и образование прочного соединения. После сварки на деталях образуется утолщение — грат, поз.5 на схеме.
Стыковая сварка оплавлением
При стыковой сварке оплавление на детали сначала подаётся напряжение в пределах 6-8 В от сварочного трансформатора. Затем детали сближаются до соприкосновения с небольшим усилием порядка нескольких деканьютонов. На отдельных участках контакта плотность тока получается очень высокая (до 3-5 кА/мм2), в результате чего металл в этих точках быстро нагревается и расплавляется с образованием перемычек жидкого металла между торцами соединяемых кромок. Происходит быстрый перегрев этих точек, и металл в них расплавляется с образованием перемычек жидкого металла между свариваемыми торцами. Далее перемычки быстро перегреваются и взрывообразно разрушаются.
Торцы продолжают нагреваться за счёт постоянного образования новых жидких перемычек и их разрушения, т.е. по сути, происходит оплавление торцов. К концу процесса на всей поверхности торцов образуется слой жидкого металла. В этот момент скорость сближения резко увеличивается и возрастает усилие. Торцы жидким слоем входят в контакт и бОльшая часть жидкого металла вместе с оксидными плёнками и частью твёрдого металла выдавливаются из стыка с образованием грата. Во время осадка происходит отключение электрического тока.
Также существуют счучаи сваривания одновременно двух стыков, нагрев токами высокой частоты, постоянным током и другие разновидности контактной стыковой сварки.
Преимущества стыкового соединения
Любой вид сварочных работ имеет свои технологические преимущества и недостатки. Сварка встык, по отзывам многих специалистов-сварщиков, обладает целым рядом положительных качеств, которые существенно выделяют ее по сравнению с другими технологиями.
К преимуществам контактной стыковой сварки относятся следующие:
- при использовании этого способа оплавления нет необходимости в предварительном нагреве места соединения и подготовке кромок стыкуемых деталей;
- при соблюдении сварочной технологии легко получить прочное и надежное соединение, которое способно прослужить несколько десятков лет без аварийных ситуаций;
- сохраняется высокий уровень химической однородности материала после сварочного соединения, что способствует увеличению прочности стыка;
- легкость и простота выполнения работы не требуют специальных знаний даже от начинающего сварщика;
- возможность производить процесс контактной стыковой сварки в полностью автоматическом режиме;
- высокая скорость выполнения технологических операций;
- универсальность использования практически всех материалов.
Все эти преимущества значительно превосходят незначительные недостатки процесса сварки стыковым способом.
Роль пластической деформации
Пластическая деформация металла вызывается как внешними, факторами – усилием со стороны электродов, так и внутренними – напряжениями, возникающими при несвободном расширении металла зоны сварки. При точечной, шовной, рельефной и стыковой сварке сопротивлением пластическая деформация металла присутствует на протяжении всего процесса сварки: от формирования холодного контакта до проковки соединения. При сварке оплавлением деформация происходит на этапе предварительного подогрева и осадки.
Основная роль пластической деформации при точечной, шовной и рельефной сварке заключается в формировании электрического контакта, в образовании пластического пояса для удержания расплавленного металла от выплеска и ограничения растекания сварочного тока во внутреннем контакте, в уплотнении металла на стадии охлаждения.
Основная роль пластической деформации при стыковой сварке заключается в удалении оксидов для образования металлических связей в стыке (второй этап цикла сварки) и электрических контактов (преимущественно в течение первого этапа нагрева). Деформация вызывается действием усилия сжатия, создаваемого приводом сварочной машины. Для образования начального электрического контакта достаточно небольшого давления, при котором происходит микропластическая деформация рельефа поверхности торцов. Для удаления оксидов и образования связей требуется относительно большая объемная пластическая деформация деталей. При стыковой сварке в большинстве случаев используется свободная схема объемной деформации, при которой металл течет без какого-либо внешнего ограничения. В процессе стыковой сварки о величине деформации судят по укорочению деталей, вызванному осадкой.
Что такое контактная стыковая сварка?
Екатерина
Порой на производстве бывают ситуации, когда необходимо выполнить сварку арматуры, рельсов или изготовить детали сложной формы (колеса, рычаги, обручи). В таких случаях дуговая сварка может просто не справиться с объемом работ. Сварщику придется потратить уйму сил и времени на изготовление одного изделия, а это точно не входит в планы предприятия.
Чтобы решить эту проблему можно найти дополнительных высококвалифицированных сварщиков, но тогда предприятие понесет убытки из-за необходимости их официального оформления. А можно добавить на производство всего один комплект нового сварочного оборудования. Для этих целей отлично подойдет стыковая сварочная машина для контактной сварки. С ее помощью можно выполнить большие объемы работ без потери качества. В этой статье мы подробно расскажем, что такое контактная стыковая сварка.
Содержание статьи
- Общая информация
- Технология
- Сварка оплавлением
- Сварка сопротивлением
- Вместо заключения
Общая информация
Контактная сварка стыковая — метод соединения металлов, суть которого заключается в равномерном нагреве всего стыка обеих деталей. После нагрева детали плотно стыкуются друг с другом, тем самым образуя неразъемное соединение. Есть два типа контактной стыковой сварки, но о них мы поговорим позже.
Отметим, что высокая производительность сварки таким методом связана именно со скоростью образования соединения. При контактной сварке металл плавиться быстрее и равномернее, поэтому шов образуется быстрее. Кроме того, процесс сварки можно автоматизировать и встроить в конвейер. По этой причине контактную стыковую сварку часто используют на серийном производстве, где необходима стыковая сварка труб, например.
Соединения, выполненные контактной стыковой сваркой, отличаются повышенной прочностью и долговечностью. Поэтому такое сварочное оборудование можно встретить на производстве автомобилей, самолетов и нефтепроводов. Кроме того, качество шва не будет зависеть от квалификации сварщика, что удобно на производстве с нехваткой квалифицированных кадров.
Технология
Метод стыковой сварки с помощью контактного оборудования позволяет варить самые разнообразные типы деталей. Вам доступна сварка стальных труб, сварка пластин встык, сварка ПНД труб и прочее. Но чтобы результат сварки был удовлетворительным нужно строго соблюдать технологию.
Как мы писали ранее, сварка стыковых соединений с помощью контактной сварки может быть двух типов — сварка оплавлением и сопротивлением. Далее мы подробно расскажем о каждом типе, опишем процесс сварки и расскажем об основных особенностях.
Сварка оплавлением
Контактная сварка оплавлением очень популярна и заключается в том, что напряжение, подаваемое на обмотки трансформатора, прекращается, как только две детали соприкоснутся. Проще говоря, напряжение нарастает и в момент своего пика как раз прекращается его подача. При этом тепловой энергии достаточно, чтобы металл начал плавиться.
На стыках двух деталей всегда есть небольшие неровности, как раз за счет них и происходит лучший контакт заготовок. Но лучшего результата можно достичь, если сдавить торцы, полностью их выровнять. Тогда площадь соприкосновения будет гораздо выше. Не нужно думать, что при такой сварке металл не может нагреться быстро. Наоборот, в таких условиях он способен буквально закипеть за считанные секунды.
Во время плавления образуются дополнительные неровности, в которых концентрируется пары расплавленных металлов. Эти пары оказывают защитное действие, они защищают сварочную зону от негативного влияния кислорода. Кстати, усилие или давление обязательно, его прикладывают только в тот момент, когда стыки деталей уже немного расплавились.
Во время того, как сдавливаются две детали, лишний жидкий металл выдавливается за пределы, в этот момент образуется соединение двух деталей. Сам шов получается очень прочным и качественным, в нем присутствует минимум видимых и скрытых дефектов, поскольку все продукты разложения и окисная пленка выходит вместе с выдавленным расплавленным металлом. По этой причине контактная стыковая сварка оплавлением часто используется на производствах с большими партиями продукции.
Также отметим, что сварка оплавлением не требует какой-то особой обработки или подготовки металла, в отличие от сварки сопротивлением. Не нужно подготавливать торцы, а значит и тратить производственное время. Лучше сделать еще одну или несколько единиц продукции. Это преимущество также играет большую роль на крупносерийном производстве.
Если нужно сварить детали, у которых разное сечение, то есть одна хитрость. Вы можете заранее сделать противоположные скосы. Таким образом вы улучшите контакт между заготовками, увеличив их площадь соприкосновения. А во время нагрева заготовки примут нормальную форму.
Пару слов хотим сказать про предварительный нагрев деталей. Мы не рекомендуем использовать этот метод в повседневной практике, поскольку он просто отнимет время, а производительности не добавит. Прогревайте только крупногабаритные детали, например, рельсы. Тогда это будет оправдано.
Есть несколько способов выполнить сварку оплавлением максимально быстро и качественно. Мы дадим несколько простых рекомендаций. Сначала нужно состыковать детали медленно, чтобы между ними постепенно образовался контакт. В такие моменты металл довольно быстро нагревается и начинает выделять пары. Потом нужно развести детали. В этот момент тепло начинает распространяться по всей поверхности заготовок.
Далее снова стыкуем детали. Ждем, пока они полностью нагреются. В результате получаем качественное соединение. Главное — выполнять все манипуляции без больших перерывов.
Сварка сопротивлением
Контактная сварка сопротивлением кардинально отличается от сварки оплавлением. Здесь заготовки прижимаются губками непосредственно к электродам. Так удается добиться хорошего электрического контакта, а губки в свою очередь надежно удерживают детали, препятствуя их скольжению.
Далее детали плотно прижимают друг к другу и подают сварочный ток, который начинает нагревать металл. Металл должен разогреться до той температуры, когда он приобретает пластичные свойства. Детали под давлением соединяются друг с другом, лишний расплавленный металл выдавливается, а вместе с ним уходит и окисная пленка.
Давление не прекращают, пока металл не остынет и не образуется твердое соединение. Чтобы выполнить такую сварку металл нужно предварительно зачистить и обработать. Также учтите, что детали, сваренные сопротивлением, обладают меньшей стойкостью к окислению в процессе эксплуатации, что сужает сферу применения. Также контактная стыковая сварка сопротивлением машины подходит только для сварки деталей с небольшим сечением. Поэтому ее редко используют на крупных производствах. Но ее все еще можно встретить в небольших цехах с маленькими тиражами продукции.
Вместо заключения
Похожие публикации
Контактная стыковая сварка сопротивлением машины
Контактная стыковая сварка сопротивлением машины – это сварочный процесс, где разрозненные ранее детали соединяются по всей плоскости касания.
Важно, что контакт и соединение происходит в результате нагрева.
В этом методе многое зависит от требований, предъявляемых:
- К сварному шву.
- Площади сечения.
- Определённой марки металла.
Силовое воздействие выполняется двумя способами:
- оплавлением;
- сопротивлением.
Данный метод используется в различных сферах деятельности человека. Об этом ниже.
Область применения
Сегодня стыковая сварка сопротивлением активно используется в авиационной отрасли и космической промышленности.
Она давно знакома сотрудникам, задействованным в области автомобилестроения.
Данная технология подходит для сварки труб газопроводов и нефтепроводов. Популярность технологии объяснить просто:
- Минимальная трудоёмкость.
- Скорость выполнения работ.
- Высокая прочность соединений.
Интересно, что этот метод позволяет соединять детали от сотых до десятков миллиметра.
В процессе используют системы с повышенной частотой питающего напряжения.
Как результат, появляется прекрасная возможность уменьшить размеры трансформатора.
«К сведению!
Для работы этим методом квалификация сварщика не выносится на первый план.
С заданием может легко справиться и новичок.»
Виды стыкового процесса
Существуют два вида – это метод оплавлением и сопротивлением.
- Сущность метода оплавления.
Данная технология характерна подачей напряжения на обмотку сварочного аппарата. Ток поступает до момента контакта рабочих элементов.
Кромки металлических рабочих поверхностей должны быть разогреты и чуть-чуть расплавлены ещё до соприкосновения. Современные сварочные аппараты дают возможность выполнить эту операцию практически мгновенно: за тысячные доли секунды.
Схема метода оплавления
- Сущность процесса контактной стыковой сварки сопротивлением
Технология характеризуется необходимостью прижимать детали к электродам оснащёнными специальными губками. Таким образом, достигается электрический контакт высокого качества. Исключается проскальзывание рабочего материала между электродами.
Метод стыковой сварки
Мощный ток, который подаётся на электроды, хорошо разогревает детали.
«Важно,
что первоначальный нагрев снижает вероятность наплава. В результате чего появляется возможность максимального нагрева металлических заготовок.»
Контактная стыковая сварка сопротивлением обладает рядом преимуществ. Основной положительный момент заключается в выдавливании металла в град при высоких рабочих t.
Швы после контактной стыковой сварки сопротивлением
«К сведению!
Нужно предварительно подготавливать торцы металлических элементов с целью прочного соединения.»
Именно подготовительные работы в дальнейшем определяют качество на завершающей стадии процесса.
Сварка стыковых соединений в вертикальном положении возможна двумя способами:
- Снизу вверх.
Когда выполняется сварка стыкового шва в вертикальном положении, дуга, направленная на основную металлическую поверхность, возбуждается в нижней точке. После образования ванночки расплавленного металла электрод под углом 20-25 к горизонту отводится вверх и немного в сторону. Дуга.
- Сверху вниз.
Изначально при возбуждении дуги в верхней точке шва электрод проводится перпендикулярно. После появления кратера характер проводки меняется и переходит в наклонное положение.
«Обратите внимание,
что метод рекомендовано использовать для соединения тонкого металла, прокладке первых слоёв и наличие разделки кромки.»
Сварка стыковых соединений в наклонном положении имеет свои особенности. На рисунке чётко видно как движется электрод при наклоне узких валков.
Сварка сопротивлением в наклонном положении
- По траектории острого угла.
- Пошагово, лесенкой.
- Перемещение вдоль пластины и обратный процесс, происходящий в сварочной ванне.
Какое оборудование необходимо?
Для выполнения работ используются стыковые контактные машины. Они работают с сечением от десятых долей до десятков тысяч мм2.
Машины разнообразны по конструкции осадочных и зажимных устройств, потребляемой мощности.
Машина контактной стыковой сварки сопротивлением
А также по приводу, который может варьироваться от ручного варианта, до автоматизированного процесса.
У машин предусмотрены литые станины или конструкции сварного типа с использованием стального листа или профиля.
Рабочий стол такой машины предусмотрен в нескольких вариациях:
- вертикальный вариант;
- наклонный вариант;
- горизонтальная поверхность.
Машины разнообразны по использованию зажимных приспособлений, предназначенных для фиксации рабочих деталей.
Технология контактной стыковой сварки и режимы сварки
Сварка стыковых соединений в нижнем положении с разделкой кромок и угловых швов предполагает выполнение процесса в стеснённых условиях.
Разделочные кромки не дают возможность жидкому шлаку стекать по краям.
От переизбытка жидкого шлака происходит накат на сварочную дугу.
Шлак движется впереди, опускается вниз разделки, затрудняя сварочный процесс. Это, в большинстве случаев, приводит в зашлакованности и некачественному провару соединений.
«Важно!
Сварку выполнять «углом назад».»
Когда проводится изготовление ответственных изделий, именно стыковым швам уделяется особое внимание.
Особое внимание уделяется корню шва, когда проводится разделка кромок под сварку стыковых соединений. Качество корневого шва зависит от тщательно оформленного валика на первоначальном этапе. А также от подготовительных работ с обратной стороны корневого шва для сварки другого валика.
Пример стыковой сварки
Техника безопасности
При проведении работ следует соблюдать пожарную, личную технику безопасности.
Перед началом работ проводится инструктаж, результаты которого заносятся в журнал.
К сварочному процессу допускаются лица старше 18 лет, прошедшие специальную подготовку.
В мероприятия по безопасности входят: подготовка рабочего места и средств личной защиты.
Работы и техника безопасности регламентируется общими положениями и инструкциями предприятия.
Заключение
Стыковая сварка листов один из наиболее качественных методов соединения металлов.
Не зря он активно работает в авиационной и космической отрасли, где необходимо выполнить большой объём сварочных работ.
Правильное выполнение того или иного процесса гарантирует надёжность соединения, а значит качество изготавливаемой детали.
Технология стыковой сварки сопротивлением. (Лекция 11)
1. КУРС ЛЕКЦИЙ-ПРЕЗЕНТАЦИЙ по дисциплине «ТЕХНОЛОГИЯ и ОБОРУДОВАНИЕ СВАРКИ ДАВЛЕНИЕМ» лекция №11
ПРЕПОДАВАТЕЛЬ:к.т.н., доцент кафедры «ОиТСП»
БЕНДИК Татьяна Ивановна
1
2. СОДЕРЖАНИЕ ЛЕКЦИИ №11
2СОДЕРЖАНИЕ ЛЕКЦИИ №11
Тема 11 . Технология стыковой сопротивлением
Технологические особенности процесса,
области применения
Подготовка деталей к сварке
Циклограмма процесса сварки
Основные параметры режима сварки
Особенности технологии сварки проволоки,
стержней, звеньев цепи и др.
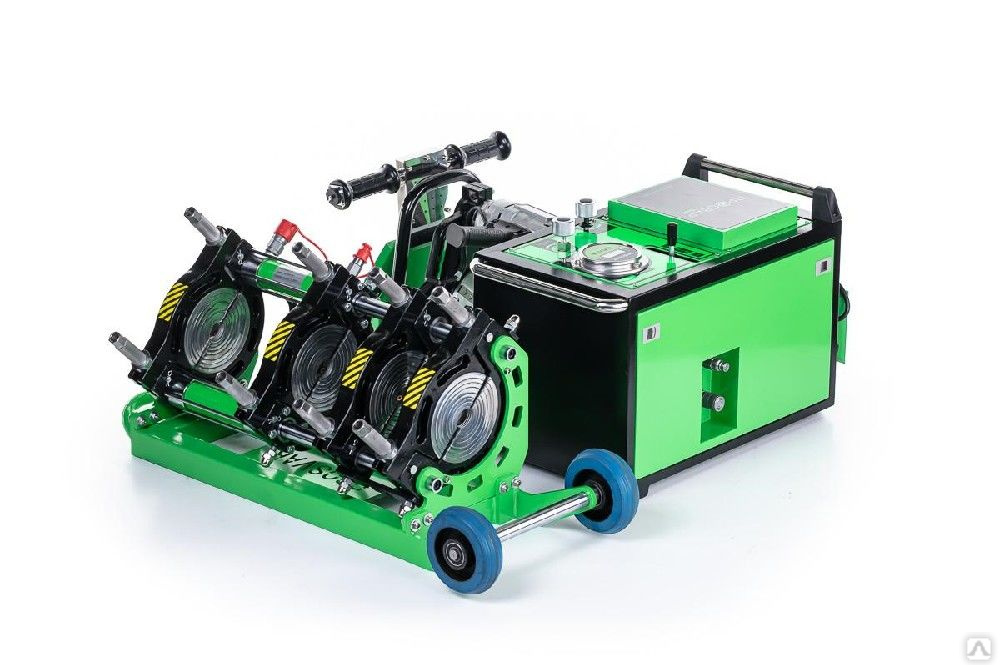
Послесварочные операции
Технологические особенности процесса, области применения
Контактная стыковая сварка – разновидность контактной сварки, при которой нагрев
металла осуществляется электрическим током до температуры сварки tсв, которая может
быть ниже или выше температуры плавления Тпл соединяемых материалов, а сварка
происходит по всей площади касания деталей.
Существует две разновидности стыковой сварки: стыковая сварка сопротивлением (tсв <
Tпл) и стыковая сварка оплавлением (tсв Tпл). Свариваемые детали закрепляются в
токоподводящих зажимах с усилием зажатия Fcж.
Стыковую сварку как сопротивлением, так и оплавлением относят по состоянию
металла в зоне сварки к сварке в твердой фазе, хотя в отдельных случаях, особенно при
стыковой сварке оплавлением деталей больших сечений, стыковое соединение
формируется в твердожидком состоянии.
Стыковой сваркой сопротивлением чаще всего соединяют детали небольшого сечения
из сталей (до 300 мм2), а также из вольфрама, молибдена, алюминия и меди (до 100
мм2).
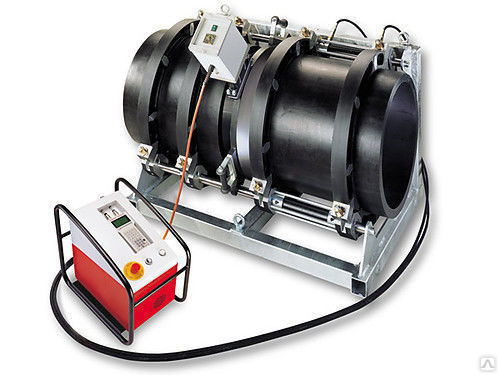
3
Технологические особенности процесса, области применения
При стыковой сварке сопротивлением торцы деталей вначале сжимаются, а затем к ним
подводится ток. Пока торцы не разогреты, они соприкасаются лишь по отдельным
небольшим площадкам, образовавшимся в результате деформации выступающих
частей микрорельефа их поверхностей.
Вследствие местного сужения поперечного сечения токоведущей части деталей, а также
наличия оксидных пленок контактное сопротивление между холодными деталями rдд
бывает значительным, оказывая решающее влияние на нагрев деталей в зоне сварки. В
общем балансе доля теплоты, выделяемой на этом сопротивлении, не превышает
10…15 %. Однако она выделяется в узкой приконтактной зоне за малый промежуток
времени и вызывает быстрое повышение в ней температуры. И хотя контактное
сопротивление rдд быстро становится равным нулю, в узкой приконтактной зоне попрежнему температура растет быстрее, чем в других зонах. Таким образом, при
cтыковой сварке cопротивлением rдд играет роль концентратора теплоты.

Типовые детали, получаемые стыковой сваркой
Нагрев деталей при сварке сопротивлением можно рассматривать как наложение двух процессов.
Нагрев до температуры Т1 бесконтактного стержня теплотой, равномерно выделяемой на собственном
сопротивлении на всей его длине;
дополнительный нагрев на величину Т2 теплотой, выделяемой в стыке и распространяющейся в
сторону токоподводящих электродов.
Нагрев зоны соединения осуществляется до температуры tсв, которая ниже температуры плавления
свариваемых металлов Тпл. Таким образом, сварное соединение при сварке сопротивлением
образуется в твердой фазе и происходит в течение трех стадий: активации контактных поверхностей,
образования физического контакта и объемного взаимодействия свариваемых металлов.
Типовая циклограмма процесса
стыковой сварки сопротивлением:
Iсв – сварочный ток;
τсв – время нагрева; S – передвижение
подвижной плиты машины; Fос– усилие
осадки; ∆св – припуск на сварку
Распределение температуры
при сварке сопротивлением
Неблагоприятным фактором при нагреве сопротивлением является его
неравномерность по сечению деталей, вызываемая случайным расположением токопроводящих микроучастков в стыке (особенно в
начальном периоде нагрева) и поверхностным эффектом.

Неравномерность нагрева по сечению деталей особенно резко
проявляется на деталях с развитым сечением: трубах, широких и тонких
листах.
Неравномерный нагрев является одной из основных причин
ограниченного применения сварки сопротивлением.
Формирование металлической связи происходит в ходе пластической
деформации. Металл зоны сварки нагревается до температуры tсв и
становится пластичным. В результате пластической деформации
разрушаются и вытесняются из зоны свариваемого контакта оксидные
пленки, образуются ювенильные поверхности, атомы металла
сближаются на расстояние действия межатомных сил. Нагрев
способствует повышению подвижности атомов. В процессе охлаждения
продолжаются диффузионные процессы, образование общих зерен,
изменение структуры и свойств металла, релаксация внутренних
напряжений.
Для получения качественных соединений проволоки и прутков из трудно
свариваемых тугоплавких металлов (молибдена, вольфрама и др.

могли бы выдержать операции прокатки, ротационной ковки и волочения,
используется сварка сопротивлением с двойной осадкой. Она заключается
в том, что на первой стадии свариваемые детали сжимаются при
небольшом начальном усилии F н, а на второй – увеличенным усилием
осадки Fос.
Основными параметрами режима сварки сопротивлением являются:
– величина сварочного тока Iсв;
– время нагрева τсв;
– начальное усилие сжатия Fн;
– усилие осадки Fос;
– установочная длина lo;
– припуск на сварку ∆св.
Между плотностью сварочного тока jсв и временем нагрева τсв существует
зависимость, которую можно использовать при определении параметров
режима сварки:
где k – коэффициент, зависящий от свариваемого металла; для сталей
k = 8…10, для алюминия k = 20, для меди k = 27.
Плотность сварочного тока jсв и время нагрева τсв колеблются в широких
пределах. При больших плотностях сварочного тока jсв наблюдаются выплески
расплавленного металла.

нельзя считать сваркой сопротивлением. Качество соединений при наличии
выплесков получается низким.
При малых значениях времени нагрева τсв наблюдается неравномерный нагрев
деталей по сечению и возможен непровар. Применение повышенных значений
τсв усиливает окислительные процессы. При недостаточной величине Fос
усиливается тепловыделение в зоне контакта, что может привести к выплескам
и усилению процесса окисления металла.
При большом Fос усиливается пластическая деформация, активируются
процессы разрушения окислов и образования ювенильных поверхностей.
При малой установочной длине lo (см. рис. 6.3) наблюдается большой отвод
теплоты в электроды. При чрезмерной установочной длине lo растет
потребляемая мощность, хотя и снижаются потери теплоты в электроды.
Возможно искривление свариваемых деталей и потеря их устойчивости.
Минимальная величина lo при сварке стержней равна их диаметру, а при сварке
листов lo min = (3…4) δ, где δ – толщина листа в миллиметрах.

При сварке низкоуглеродистых и низколегированных сталей давление при
осадке
рос
=
30…50
МПа,
при
сварке
легированных
сталей
рос = 100…150 МПа.
Плотность тока jсв при сварке сталей составляет 20…60 А/мм2 (мягкие режимы)
и 90…200 А/мм2 (жесткие режимы). Время нагрева τсв – 1…10 с (мягкие режимы)
и 0,6…1,5 с (жесткие режимы).
Подготовка деталей к сварке
Способ стыковой сварки выбирают в
зависимости от материала, размеров и
формы поперечного сечения свариваемых
деталей, масштабов производства, а также
требований, предъявляемых к качеству
изделий.
Форма детали должна обеспечивать
возможность надежного закрепления
ее в токоподводящих губках машины.
Необходимо создать условия для
равномерного нагрева и одинаковой
пластической деформации обеих
заготовок. Форму и размеры сечения
свариваемых заготовок следует
выполнять примерно одинаковыми.
Различие в диаметрах не должно
превышать 15 %, а по толщине 10 %.

Подготовка деталей к сварке заключается в получении
определен-ной формы торцов, очистке их поверхности и
поверхности деталей. Торцы деталей получают
механической резкой на ножницах, пилах, металлорежущих
станках, горячей или холодной высадкой на прессах, а
также с помощью плазменной, лазерной и газовой резки с
последующим удалением шлака.
Тщательная обработка торцов необходима при сварке
сопротивлением. Она должна обеспечить защиту торцов от
окисления и обеспечить вытеснение окисленного металла
из зоны стыка.
Для облегчения процесса возбуждения, оплавления и
снижения требуемой мощности машин при сварке деталей
больших сечений на торцовой поверхности делают скос под
небольшим углом (6…8º). Это уменьшает площадь
начального контакта и увеличивает плотность тока в начале
процесса.
Послесварочные операции
После выполнения сварочной операции
производится последующая обработка
сварного соединения, которая включает
удаление грата (усиления), правку и
термообработку.

Сварка стержня с устройством для
срезания грата: 1 – грат; 2 – нож;
3 – электрод; 4 – сваренная деталь
Способы удаления грата (усиления)
выбирают в зависимости от
конфигурации деталей, возможностей и
наличия специального оборудования.
При небольших компактных сечениях
(стержни, наружные швы труб) грат
(усиление) удаляют в зажимах
сварочной машины при нагретом
металле специальными стальными
ножами на металлорежущих станках,
вращающимся металлорежущим
инструментом. После сварки рельсов
грат срезают протягиванием горячего
стыка через специальные ножи.
Послесварочные операции
В прямых трубах малого и среднего диаметра грат срезают дорном, который
прикрепляют к штанге и проталкивают через горячий стык с использованием
пневматического цилиндра.
Удаление внутреннего грата с использованием дорна: 1 – стык трубы;
2 – труба; 3 – дорн; 4 – пневматический цилиндр; 5 – подача сжатого воздуха
Послесварочные операции
На рис.

кольцевых деталей, и – специальная фреза для обработки таких швов.
При стыковой сварке труб котлов и теплообменников внутренний грат удаляют
непосредственно после выполнения операций продувкой кислородом или
газовыми смесями.
При обработке стыков сложной формы, а также в единичном производстве
широко используют пневматические переносные зубила и вращающиеся
шлифовальные круги. У заготовок крупного сечения из легированных сталей
грат удаляют после термообработки.
Схема обработки шва после сварки
кольцевых деталей: 1 – стык; 2 –
изделие; 3 – фреза
Фреза для обработки внутреннего шва
трубы: 1 – нож; 2 – барабан
Вид и режим термообработки устанавливаются в зависимости от
конструкции и материала изделия. Нагрев осуществляется
электрическим током, пропускаемым через закрепленные в электродах
изделия, в печах, газопламенными горелками, с помощью индуктора и
др. В отдельных случаях изделия после стыковой сварки (кольца,
ободья колес и др.

установках.
СПАСИБО ЗА ВНИМАНИЕ
КАКИЕ БУДУТ ВОПРОСЫ?
Технология стыковой сварки сопротивлением. (Лекция 11) презентация, доклад
КУРС ЛЕКЦИЙ-ПРЕЗЕНТАЦИЙ
по дисциплине
«ТЕХНОЛОГИЯ и ОБОРУДОВАНИЕ СВАРКИ ДАВЛЕНИЕМ»
лекция №11
ПРЕПОДАВАТЕЛЬ:
к.т.н., доцент кафедры «ОиТСП» БЕНДИК Татьяна Ивановна
СОДЕРЖАНИЕ ЛЕКЦИИ №11
Тема 11 . Технология стыковой сопротивлением
Технологические особенности процесса, области применения
Циклограмма процесса сварки
Основные параметры режима сварки
Особенности технологии сварки проволоки, стержней, звеньев цепи и др.
Послесварочные операции
Контактная стыковая сварка – разновидность контактной сварки, при которой нагрев металла осуществляется электрическим током до температуры сварки tсв, которая может быть ниже или выше температуры плавления Тпл соединяемых материалов, а сварка происходит по всей площади касания деталей.
Существует две разновидности стыковой сварки: стыковая сварка сопротивлением (tсв
Стыковую сварку как сопротивлением, так и оплавлением относят по состоянию металла в зоне сварки к сварке в твердой фазе, хотя в отдельных случаях, особенно при стыковой сварке оплавлением деталей больших сечений, стыковое соединение формируется в твердожидком состоянии.
Стыковой сваркой сопротивлением чаще всего соединяют детали небольшого сечения из сталей (до 300 мм2), а также из вольфрама, молибдена, алюминия и меди (до 100 мм2).
Технологические особенности процесса, области применения
При стыковой сварке сопротивлением торцы деталей вначале сжимаются, а затем к ним подводится ток. Пока торцы не разогреты, они соприкасаются лишь по отдельным небольшим площадкам, образовавшимся в результате деформации выступающих частей микрорельефа их поверхностей.
Вследствие местного сужения поперечного сечения токоведущей части деталей, а также наличия оксидных пленок контактное сопротивление между холодными деталями rдд бывает значительным, оказывая решающее влияние на нагрев деталей в зоне сварки. В общем балансе доля теплоты, выделяемой на этом сопротивлении, не превышает 10…15 %. Однако она выделяется в узкой приконтактной зоне за малый промежуток времени и вызывает быстрое повышение в ней температуры. И хотя контактное сопротивление rдд быстро становится равным нулю, в узкой приконтактной зоне по-прежнему температура растет быстрее, чем в других зонах. Таким образом, при cтыковой сварке cопротивлением rдд играет роль концентратора теплоты.
Технологические особенности процесса, области применения
Типовые детали, получаемые стыковой сваркой
Нагрев деталей при сварке сопротивлением можно рассматривать как наложение двух процессов. Нагрев до температуры Т1 бесконтактного стержня теплотой, равномерно выделяемой на собственном сопротивлении на всей его длине;
дополнительный нагрев на величину Т2 теплотой, выделяемой в стыке и распространяющейся в сторону токоподводящих электродов.
Нагрев зоны соединения осуществляется до температуры tсв, которая ниже температуры плавления свариваемых металлов Тпл. Таким образом, сварное соединение при сварке сопротивлением образуется в твердой фазе и происходит в течение трех стадий: активации контактных поверхностей, образования физического контакта и объемного взаимодействия свариваемых металлов.
Типовая циклограмма процесса стыковой сварки сопротивлением:
Iсв – сварочный ток;
τсв – время нагрева; S – передвижение подвижной плиты машины; Fос– усилие осадки; ∆св – припуск на сварку
Распределение температуры при сварке сопротивлением
Неблагоприятным фактором при нагреве сопротивлением является его неравномерность по сечению деталей, вызываемая случайным распо-ложением токопроводящих микроучастков в стыке (особенно в начальном периоде нагрева) и поверхностным эффектом. Неравномерность нагрева по сечению деталей особенно резко проявляется на деталях с развитым сечением: трубах, широких и тонких листах.
Неравномерный нагрев является одной из основных причин ограниченного применения сварки сопротивлением.
Формирование металлической связи происходит в ходе пластической деформации. Металл зоны сварки нагревается до температуры tсв и становится пластичным. В результате пластической деформации разрушаются и вытесняются из зоны свариваемого контакта оксидные пленки, образуются ювенильные поверхности, атомы металла сближаются на расстояние действия межатомных сил. Нагрев способствует повышению подвижности атомов. В процессе охлаждения продолжаются диффузионные процессы, образование общих зерен, изменение структуры и свойств металла, релаксация внутренних напряжений.
Для получения качественных соединений проволоки и прутков из трудно свариваемых тугоплавких металлов (молибдена, вольфрама и др.), которые могли бы выдержать операции прокатки, ротационной ковки и волочения, используется сварка сопротивлением с двойной осадкой. Она заключается в том, что на первой стадии свариваемые детали сжимаются при небольшом начальном усилии F н, а на второй – увеличенным усилием осадки Fос.
Основными параметрами режима сварки сопротивлением являются:
– величина сварочного тока Iсв;
– время нагрева τсв;
– начальное усилие сжатия Fн;
– усилие осадки Fос;
– установочная длина lo;
– припуск на сварку ∆св.
Между плотностью сварочного тока jсв и временем нагрева τсв существует зависимость, которую можно использовать при определении параметров режима сварки:
где k – коэффициент, зависящий от свариваемого металла; для сталей k = 8…10, для алюминия k = 20, для меди k = 27.
Плотность сварочного тока jсв и время нагрева τсв колеблются в широких пределах. При больших плотностях сварочного тока jсв наблюдаются выплески расплавленного металла. Такой процесс из-за нагрева зоны сварки выше Тпл нельзя считать сваркой сопротивлением. Качество соединений при наличии выплесков получается низким.
При малых значениях времени нагрева τсв наблюдается неравномерный нагрев деталей по сечению и возможен непровар. Применение повышенных значений τсв усиливает окислительные процессы. При недостаточной величине Fос усиливается тепловыделение в зоне контакта, что может привести к выплескам и усилению процесса окисления металла.
При большом Fос усиливается пластическая деформация, активируются процессы разрушения окислов и образования ювенильных поверхностей.
При малой установочной длине lo (см. рис. 6.3) наблюдается большой отвод теплоты в электроды. При чрезмерной установочной длине lo растет потребляемая мощность, хотя и снижаются потери теплоты в электроды. Возможно искривление свариваемых деталей и потеря их устойчивости.
Минимальная величина lo при сварке стержней равна их диаметру, а при сварке листов lo min = (3…4) δ, где δ – толщина листа в миллиметрах.
При сварке низкоуглеродистых и низколегированных сталей давление при осадке рос = 30…50 МПа, при сварке легированных сталей
рос = 100…150 МПа.
Плотность тока jсв при сварке сталей составляет 20…60 А/мм2 (мягкие режимы) и 90…200 А/мм2 (жесткие режимы). Время нагрева τсв – 1…10 с (мягкие режимы) и 0,6…1,5 с (жесткие режимы).
Подготовка деталей к сварке
Способ стыковой сварки выбирают в зависимости от материала, размеров и формы поперечного сечения свариваемых деталей, масштабов производства, а также требований, предъявляемых к качеству изделий.
Форма детали должна обеспечивать возможность надежного закрепления ее в токоподводящих губках машины. Необходимо создать условия для равномерного нагрева и одинаковой пластической деформации обеих заготовок. Форму и размеры сечения свариваемых заготовок следует выполнять примерно одинаковыми. Различие в диаметрах не должно превышать 15 %, а по толщине 10 %.
Подготовка деталей к сварке заключается в получении определен-ной формы торцов, очистке их поверхности и поверхности деталей. Торцы деталей получают механической резкой на ножницах, пилах, металлорежущих станках, горячей или холодной высадкой на прессах, а также с помощью плазменной, лазерной и газовой резки с последующим удалением шлака.
Тщательная обработка торцов необходима при сварке сопротивлением. Она должна обеспечить защиту торцов от окисления и обеспечить вытеснение окисленного металла из зоны стыка.
Для облегчения процесса возбуждения, оплавления и снижения требуемой мощности машин при сварке деталей больших сечений на торцовой поверхности делают скос под небольшим углом (6…8º). Это уменьшает площадь начального контакта и увеличивает плотность тока в начале процесса.
Послесварочные операции
После выполнения сварочной операции производится последующая обработка сварного соединения, которая включает удаление грата (усиления), правку и термообработку.
Сварка стержня с устройством для срезания грата: 1 – грат; 2 – нож;
3 – электрод; 4 – сваренная деталь
Способы удаления грата (усиления) выбирают в зависимости от конфигурации деталей, возможностей и наличия специального оборудования.
При небольших компактных сечениях (стержни, наружные швы труб) грат (усиление) удаляют в зажимах сварочной машины при нагретом металле специальными стальными ножами на металлорежущих станках, вращающимся металлорежущим инструментом. После сварки рельсов грат срезают протягиванием горячего стыка через специальные ножи.
Послесварочные операции
В прямых трубах малого и среднего диаметра грат срезают дорном, который прикрепляют к штанге и проталкивают через горячий стык с использованием пневматического цилиндра.
Удаление внутреннего грата с использованием дорна: 1 – стык трубы;
2 – труба; 3 – дорн; 4 – пневматический цилиндр; 5 – подача сжатого воздуха
Послесварочные операции
На рис. представлена схема обработки двумя фрезами шва после сварки кольцевых деталей, и – специальная фреза для обработки таких швов.
При стыковой сварке труб котлов и теплообменников внутренний грат удаляют непосредственно после выполнения операций продувкой кислородом или газовыми смесями.
При обработке стыков сложной формы, а также в единичном производстве широко используют пневматические переносные зубила и вращающиеся шлифовальные круги. У заготовок крупного сечения из легированных сталей грат удаляют после термообработки.
Схема обработки шва после сварки кольцевых деталей: 1 – стык; 2 – изделие; 3 – фреза
Фреза для обработки внутреннего шва трубы: 1 – нож; 2 – барабан
Вид и режим термообработки устанавливаются в зависимости от конструкции и материала изделия. Нагрев осуществляется электрическим током, пропускаемым через закрепленные в электродах изделия, в печах, газопламенными горелками, с помощью индуктора и др. В отдельных случаях изделия после стыковой сварки (кольца, ободья колес и др.) подвергаются правке и калибровке в специальных установках.
СПАСИБО ЗА ВНИМАНИЕ
КАКИЕ БУДУТ ВОПРОСЫ?
Сравнение сварки оплавлением и стыковой сварки
Сварка оплавлением и стыковая сварка представляют собой процессы контактной сварки, при которых коалесценция производится одновременно по всей площади двух соприкасающихся поверхностей. В обоих процессах тепло для сварки получается за счет сопротивления электрическому току между двумя обращенными поверхностями.
В этой статье объясняются основные различия между процессом сварки оплавлением и процессом стыковой сварки. Эти термины иногда используются неправильно или взаимозаменяемо, и их применение может привести к путанице.
В любом процессе контактной сварки два или более куска металла соединяются под воздействием тепла и давления в течение контролируемого периода времени. Основная формула выражается следующим образом:
Тепло = I 2 RT
где: I = тепло или сварочный ток в амперах
R = электрическое сопротивление свариваемых деталей
T = время
И оплавление, и стык сварочные процессы могут выполняться с использованием вторичных токов переменного (AC) или постоянного тока (DC) с первичной входной мощностью однофазной или трехфазной.
Как работает стыковая сварка
Рисунок 1: Оплавление при сварке оплавлением выжигает неровности на поверхностях сварного шва. ![]() |
Одной из первых форм контактной сварки, использовавшейся в металлообрабатывающей промышленности, является стыковая сварка. Хотя сварка оплавлением и стыковая сварка выполняются на аналогичных сварочных машинах, наиболее заметными исключениями являются приложения давления и тока.
При обычном стыковом сварном шве две свариваемые детали сначала соединяются под давлением. Затем подается ток, который нагревает область контакта до такой степени, что приложенное давление позволяет сковать детали вместе. Другими словами, сварка встык представляет собой одностадийную операцию как тока, так и давления.
Давление и ток применяются на протяжении всего цикла сварки, пока соединение не станет пластичным. Постоянное давление (обычно от воздушного баллона) преодолевает размягченную область, создавая эффект ковки и последующего сварного соединения. Это делается без изменения тока или давления на протяжении всего цикла.
Настоящий стыковой шов не имеет брызг. Окончательная осадка на сварном соединении обычно ровная и симметричная. Видно очень небольшое рваное выталкивание металла.
Примерами современных применений процесса стыковой сварки переменным током являются соединение проволоки и стержней малого диаметра, таких как катушки для непрерывных операций, производство ленточных пил и проволочные каркасы.
Рис. 2: Сварку оплавлением можно применять, как показано здесь, на материале с неровными краями и двумя концами, которые не совпадают в точности. |
Разработки в области стыковой сварки
Хотя стыковая сварка широко использовалась в первые промышленные годы, она была ограничена из-за того, что для доведения концов больших заготовок до температуры ковки требовался большой ток. Также требовалась тщательная подготовка концов. Свариваемые поверхности заготовки должны были быть очень чистыми, гладкими и параллельными. Если надлежащая подготовка не была выполнена, горячие точки на поверхности сварного шва будут создаваться из-за неравномерного протекания тока.
Считалось, что сварка встык дает более слабые швы, чем сварка оплавлением. Развитие современных микропроцессорных средств управления и использование постоянного тока и конечного контроля над прилегающими поверхностями помогло развеять это убеждение.
Раньше стыковая сварка ограничивалась небольшими машинами мощностью от 5 до 100 кВА и однофазным переменным током. Более крупные приложения требовали больших токов. Этот высокий спрос на вторичный ток создавал нагрузку на первичный источник питания пользователя и требовал большого распределительного оборудования.
В последующие годы для стыковой сварки применялся трехфазный источник питания постоянного тока. Сварочный аппарат, оснащенный трехфазным источником питания постоянного тока, обеспечивает сбалансированную нагрузку на сеть, уменьшенный первичный ток и более равномерный нагрев зоны сварки. Индуктивные потери сведены к минимуму, что дает большую свободу при проектировании машин. Трехфазным стыковым швом на постоянном токе успешно свариваются материалы больших поперечных сечений как из черных, так и из цветных металлов.
Однако трехфазный источник питания постоянного тока с его выпрямлением, физическими размерами и соответствующими элементами, необходимыми для поддержки системы стыковой сварки, требует повышенных затрат. Требуется трехфазное управление, так как увеличена подача воды на выпрямленную вторичную обмотку трансформатора.
Научные исследования показали, что более узкая зона термического влияния (ЗТВ) может быть получена на машине для стыковой сварки на трехфазном постоянном токе. Дополнительные испытания показали, что нет существенной разницы в качестве сварки трехфазным стыковым швом на постоянном токе по сравнению с однофазной сваркой оплавлением на переменном токе.
Как работает сварка оплавлением
Термин «сварка оплавлением» говорит сам за себя — во время процесса происходит «оплавление». Тепло выделяется в процессе сварки оплавлением за счет сопротивления действию оплавлением поверхностей раздела, а не контактного сопротивления, как в процессе стыковой сварки. В то время как стыковая сварка представляет собой одноэтапную операцию, сварка оплавлением представляет собой двухэтапный процесс.
Первый этап — мигание. Ток, подаваемый на заготовки, вызывает вспышку или искрение на границе двух соприкасающихся концов материала. Действие оплавления возрастает вплоть до приведения материала в пластическое состояние. Это оплавление образует ЗТВ, очень похожую на стыковой сварной шов.
Рис. 3: Перед сваркой оплавлением включены дополнительные этапы: прожиг или предварительный оплавление и предварительный нагрев. |
После того, как участок стал пластичным и достиг нужной температуры, начинается второй этап операции – осадка или ковка. Затем два конца заготовок соединяются с очень большим усилием, достаточным для того, чтобы материал опрокинулся. Это вытесняет пластиковый металл вместе с большей частью примесей из соединения.
Гладкие, чистые поверхности заготовок не так важны для этого процесса, как для стыковой сварки, потому что оплавление выжигает неровности на поверхностях сварки (см. Рисунок 1 ). Это позволяет соединять самые разные материалы. Такие предметы, как широкие тонкие листы материала; трубки; поковки; и черные и цветные материалы могут быть успешно сварены.
С однофазными источниками питания переменного тока (трансформаторами) сварка с большими площадями поперечного сечения может выполняться с меньшим потреблением тока из-за действия оплавления.
Также можно применять сварку оплавлением, как показано на рис. 2 . Этот пример скоса двери имеет шероховатые края, и два конца не совпадают идеально. Последующая шлифовка и удаление излишков облоя и высаженного материала с помощью окончательной полировки устраняет любые признаки соединения. Вспышка устраняет любую подготовку срезанной кромки заготовки из экструдированного листового металла.
В других случаях взвесь или шлак можно выбить для удаления. Высадка под шлаком представляет собой твердый металл, похожий на стыковой сварной шов, и для его удаления требуется операция резки, обрезки или удаления заусенцев.
Недостатком этого процесса является сама вспышка. Оператор и окружающее пространство должны быть защищены, а дым и пары должны быть удалены. Образующиеся частицы шлака накапливаются вокруг поверхностей машины, и требуется частая очистка.
Управление процессом сварки оплавлением
Ключом к процессу сварки оплавлением является контроль двух заготовок по отношению друг к другу во время операции оплавлением.
Некоторые из первых механизмов контроля расстояния между двумя заготовками для надлежащего оплавления приводились в действие вручную. Оператор контролировал ток кнопкой большого пальца или автоматическим отключением.
Оператор стал очень опытным в управлении величиной давления двух заготовок и, как следствие, вспыхиванием. Наблюдая за тепловым цветом области и выбросом материала, оператор знал, когда следует приложить более сильное давление для второй стадии (или части высадки) сварки оплавлением.
Более поздние разработки включали моторизованную систему привода с регулируемой скоростью, связанную с редуктором и кулачком. Эта комбинация обеспечивала переменную скорость, сводя две заготовки вместе с ускорением к концу стадии сварки оплавлением. Это ускорение требуется из-за увеличения количества материала, выбрасываемого при повышении температуры, что, в свою очередь, увеличивает сопротивление между двумя материалами.
Блок высадки, предусмотренный на кулачке, позволял своевременно инициировать вторую стадию (высадки). Ток инициировался и впоследствии отключался концевыми выключателями, стратегически расположенными для работы вместе с кулачком, и его можно было включать или выключать для обеспечения надлежащего нагрева.
Поскольку в промышленности разрабатывались сплавы и специальные материалы, требовалась совершенно другая скорость подъема кулачка и изменение высадки. Это приводило к изменению или замене кулачка при переходе от одного поперечного сечения к другому или от одного сплава к другому. Например, алюминиевые сплавы требуют быстрой или высокоскоростной высадки из-за их более узкой ЗТВ. Это вызвало чрезвычайно быстрый подъем кулачка для размещения этих сплавов, и успех был в лучшем случае посредственным.
Затем использовались цилиндры с воздухом над маслом, но они были ограничены меньшим поперечным сечением заготовок.
Еще один способ управления движением двух заготовок при сварке оплавлением — это комбинация гидравлического клапана и сервоклапана. Это обеспечивает контроль и высокое давление с быстрым ускорением. Используемые сегодня машины для сварки оплавлением с гидравлическим приводом могут создавать давление осадки более 200 тонн.
Большинство сварочных аппаратов оплавлением используют однофазные источники питания переменного тока. Как и в случае стыковой сварки, также может использоваться трехфазный постоянный ток. Хотя это не устраняет мелькание, но приводит к уменьшению первичного тока, меньшим потерям материала и более узкой ЗТВ. Однако капитальные затраты выше, а требования к процессу такие же, как и для стыковой сварки на постоянном токе, упомянутой ранее.
Разработки в области сварки оплавлением
Элементы управления. Универсальность сварки оплавлением увеличилась за счет добавления электронных и микропроцессорных средств управления, которые точно контролируют и контролируют процесс сварки оплавлением. К этим элементам управления относятся:
1. Информация обратной связи для определения скорости и ускорения двух заготовок при их сближении.
2. Текущий контроль.
3. Действие импульсного напряжения.
Предварительная вспышка и предварительный нагрев. Другие разработки включают дополнительные этапы перед сваркой оплавлением (см. Рисунок 3 ). К ним относятся прожиг или предварительная вспышка, которые позволяют выровнять рваные концы неподготовленных деталей перед второй стадией предварительного нагрева. Часть предварительного нагрева операции сварки оплавлением позволяет генерировать тепло на границе раздела сварного шва без заметных потерь материала.
Этот предварительный нагрев представляет собой колебание двух заготовок относительно друг друга. После того, как два конца заготовок соединены вместе, сопротивление материала позволяет генерировать тепло, а два конца раздвигаются (до того, как они расплавятся), обеспечивая охлаждающий эффект на границе раздела материала.
Как только концы начинают остывать и затвердевать, процесс повторяется и продолжается в быстром движении до тех пор, пока тепло не вернется в обе заготовки. С помощью этого процесса:
1. Большая площадь поперечного сечения может быть сварена с меньшим потреблением тока.
2. В высокопрочных сплавах может выделяться тепло без больших потерь материала при воспламенении.
3. Температурный градиент остается более равномерным.
После достижения надлежащей зоны термического влияния на этапе предварительного нагрева на короткий период времени начинается этап сварки оплавлением, за которым следует осадка или усилие ковки.
Во многих случаях при сварке сталей с очень высоким содержанием легирующих элементов или углерода возможно растрескивание, если сварной шов слишком быстро охлаждается до комнатной температуры. Если предварительный нагрев недостаточен, растрескивание можно предотвратить с помощью заключительного процесса сварки оплавлением, называемого последующим нагревом. Цикл последующего нагрева может быть встроен в машину для сварки оплавлением и отрегулирован на желаемую температуру.
Заключение
Как и в случае других процессов контактной сварки, технология быстро меняет применение как стыковой сварки, так и сварки оплавлением. Постоянное совершенствование средств управления, источников питания переменного и постоянного тока, усовершенствованной гидравлики и сервоклапанов улучшило оба процесса. В то же время эта передовая технология расширила область применения, которую можно выполнять.
Из-за разнообразия продуктов и материалов, которые можно сваривать оплавлением или стыковой сваркой, каждое применение необходимо рассматривать отдельно. Производственные требования, полезность, чистота и внешний вид самого сварного шва играют важную роль в выборе этих двух процессов сварки сопротивлением.
При правильном применении оба обеспечивают качественные сварные швы без газовой защиты или присадочных материалов. Эти процессы используются сегодня для таких применений, как автомобильные, сельскохозяйственные и строительные колеса из различных сплавов, кольца турбин и реактивных двигателей, шасси самолетов, зубчатые колеса маховика и многое другое из различных сплавов, включая никелевую основу, алюминий, вольфрам и медь.
Сварка оплавлением и стыковая сварка являются отдельными частями семейства контактной сварки. Непонимание в первые годы разработки создало им необоснованную репутацию черного искусства. Сегодня развитие технологий позволило как стыковой сварке, так и сварке оплавлением стать строго контролируемыми, точными и надежными процессами плавления металлов.
Ларри Э. Мосс (Larry E. Moss) является директором по продажам и техническим вопросам компании Automation International, Inc. , Данвилл, Иллинойс, а также членом Ассоциации производителей сварочных аппаратов сопротивлением (RWMA). Мы с благодарностью признаем помощь RWMA в разработке этой статьи.
1. Бюллетень исследований в области сварки, 26 (2), стр. 49-53.
Сварка сопротивлением как основная компетенция
- Start (EN) ►
- Товары ►
- Технология сварки ►
- Сварочные процессы
Процессы контактной сварки в решениях по автоматизации
Вот уже более 50 лет контактная сварка является основным направлением деятельности Bihler. Нашими сильными сторонами являются:
— контактная стыковая сварка, сварка внахлест, выступающая сварка,
— контактная сварка, сварка благородных металлов, уплотняющая проволока,
— серебряно-графитовая сварка, сварка гаек, пайка.
Для полного обзора сварочных процессов Bihler мы рекомендуем вам приобрести бесплатное Руководство по сварке Bihler . Здесь подробно описываются все процессы сварки и иллюстрируются на успешно реализованных производственных примерах.
Стыковая сварка сопротивлением
При контактной стыковой сварке примыкающие поверхности заготовки 1 и заготовки 2 соединяются в месте соединения путем подачи достаточной энергии и нагрева (резистивный нагрев).
Стыковая сварка сопротивлением обычно используется для изготовления замкнутых колец. Разнообразие вариантов простирается от круглой проволоки до плоского полосового материала.
Сварка внахлест
При сварке внахлест, также называемой сваркой внахлестку, детали, которые прижимаются друг к другу (перекрывающиеся поверхности заготовки 1 и заготовки 2), соединяются после соответствующего нагрева (нагрев сопротивлением) соединения.
Требования и практические советы: материал электродов, как правило, W или WCu, хорошее охлаждение электродов, закрывающее движение электродов параллельно сварочному шву
Выступающая сварка
При рельефной сварке детали прижимаются друг к другу и соединяются посредством достаточного нагрева соединения . Нагрев шва (нагрев сопротивлением) осуществляется за счет концентрации тока в выступах сварки. Геометрическая формовка уменьшает контактную поверхность, увеличивая переходное сопротивление.
Текущая концентрация зависит от формы и объема выступа. Оптимальное согласование этих двух факторов может критически повлиять на поведение материала при плавлении, поэтому может быть достигнуто оптимальное качество сварки с максимально возможным сроком службы электрода.
Контактная сварка
Контактная сварка — это процесс локального нанесения драгоценных металлов, полученный методом рельефной сварки. В области промышленной коммутационной техники драгоценные металлы, также называемые контактами, обеспечивают более низкое переходное сопротивление контакта, высокую стойкость к сварке, хороший путь дуги и поведение при гашении дуги, хорошую стойкость к выгоранию, высокую коррозионную стойкость и высокие термические и электрическая проводимость.
Контакты, готовые к сварке, можно либо приобрести непосредственно в виде пластин, либо изготовить путем нарезки более привлекательных по цене полуфабрикатов (круглая проволока, профильная полоса) по размеру. Для оптимальной и гибкой обработки любого вида полуфабрикатов компания Bihler рекомендует использовать разработанные для этой цели устройства для контактной сварки.
Уплотнение прядей
Уплотнение прядей представляет собой процесс прессования отдельных проволок пряди вместе и уплотнения их под давлением после применения тепла (нагрев сопротивлением). Соединение (соединения) представляет собой контактные поверхности (площадь поверхности) отдельных проводников.
Установка/уплотнение в вертикальном направлении выполняется электродами. Это создает сварной шов на многожильном проводе, в результате чего получается пучок. Он придает скрученной проволоке оптимальную форму для последующих сварочных работ.
Сварка гаек
При сварке гаек детали прижимаются друг к другу (гайка и несущий материал) и соединяются путем нагревания соединения. Соединение нагревается (нагрев сопротивлением) за счет текущей концентрации вспомогательных средств для сварки. Эта геометрическая форма уменьшает площадь контакта и одновременно увеличивает переходное сопротивление. При этом приварной выступ может быть расположен на гайке и/или на несущей планке.
Требования и практические советы: массивный, устойчивый сварочный захват и конструкция инструмента (высокие усилия сварки), точное, воспроизводимое позиционирование гаек, минимизация разбрызгивания при сварке за счет хорошей подачи благодаря системе захватов, а также за счет точной регулировки сварочного усилия. и параметры сварки
Пайка сопротивлением
Требуется добавка припоя (обычно L-Ag15P)
Возможны соединения большой площади (> 90%)
В основном используется для медных материалов, напр. коммутационные контакты с поверхностью сплавления
Контакт
Мартин Отт Otto Bihler Maschinenfabrik Тел.: +49(0)8368/18-340 |
Петер Тиме Otto Bihler Maschinenfabrik Тел.: +49(0)8368/18-348 |
Исследование и контроль факторов, влияющих на стыковую сварку сопротивлением с осадкой.
Заголовок
Исследование и контроль факторов, влияющих на стыковую сварку сопротивлением с осадкой.
Автор
Керстенс, Н.Ф.Х.
Автор
Ричардсон И. М. (промоутер)
Факультет
Машиностроение, морское дело и материаловедение
Отделение
Материаловедение и инженерия, соединение и механическое поведение
Свидание
20. 01.2010
Абстрактный
Целью данной работы является исследование факторов, влияющих на процесс стыковой сварки сопротивлением с осадкой, чтобы получить представление о поведении металла и характеристиках процесса сварки, чтобы можно было сваривать новые автомобильные стали с меньшим временем разработки и меньшим количеством отказов в производстве. В принципе процесс сварки довольно прост, соединяемые материалы зажимаются между двумя электродами и прижимаются друг к другу. Поскольку имеется поверхность раздела с более высоким сопротивлением, чем у основного материала, при приложении сварочного тока и напряжения в месте соединения будет выделяться тепло. Как только материал становится достаточно теплым и мягким, прикладывается дополнительное (осадочное) давление и формируется сварной шов. При изготовлении колесных дисков после сварки высадку удаляют стамесками и ножницами, разрезая кромки сварного шва, с последующим вкатыванием остального материала в обод. После удаления высадки обод колеса в несколько этапов подвергается холодной штамповке до окончательной формы. В целях данного исследования сталь S460MC толщиной 2,0 мм и сталь HR45 толщиной 1,65 мм были исследованы на испытательном сварочном предприятии Fontijne Grotnes BV. Обе стали были специально разработаны для холодной штамповки и глубокой вытяжки и имеют в основном ферритную микроструктуру. Было проведено первоначальное исследование образования трещин в колесных дисках во время производства, доказавшее отсутствие твердых и склонных к растрескиванию микроструктур в зоне сварки исследуемых материалов. Идея о том, что обод колеса трескается, например, из-за присутствия бейнита и мартенсита, была отвергнута. Были обнаружены два основных типа трещин: большие трещины, которые образуются из-за первоначальной несоосности листов, смазки и/или масла на границе раздела во время сварки, и неравномерного распределения тепла во время сварки. Трещины другого типа представляли собой микротрещины, возникающие из-за насечек, образовавшихся при зачистке и прокатке кромок колесных дисков после сварки.
Чтобы свести к минимуму количество материала, вдавливаемого в обод колеса, необходимо правильное выравнивание долот и режущих инструментов. используется, это уменьшенная версия производственного сварочного аппарата, но без средств подачи материала или обработки после сварки. В процессе сварки было замечено, что образец сварного шва прогревается неравномерно, излучаемый свет на границе раздела в некоторых местах ярче, чем в других. Также после сварки окисление места стыка показало, что прогрев был неравномерным, с более теплыми и более холодными участками. Эта неравномерность приводит к неравномерным характеристикам сварного шва и различиям в качестве сварного шва по длине сварного шва. Испытания на растяжение образцов, взятых как с краев, так и из центра сваренных образцов, показали, что максимальная прочность на растяжение может достигать 95% от предела прочности основного материала. Однако деформация до разрушения сварных образцов составляла не более 60 % с разницей в 30 % между центральным испытательным образцом и краевыми образцами.
Испытание Эриксена также использовалось для определения качества сварного шва. Из-за конструкции тестера Эриксена тестировался только центр образцов. Высота по Эриксену составляла до 85 % от высоты основного материала для сварных образцов, и было обнаружено, что при отсутствии краевых дефектов испытание по Эриксену является быстрой и достоверной проверкой качества сварного шва. Из-за наблюдаемого неравномерного качества сварного шва и нагрева зоны сварного шва акцент исследования сместился на понимание причин неоднородности. Измерения температуры как тепловизионной камерой, так и термопарами показали, что действительно имеет место неравномерное распределение температуры во время сварки по границе стыка. Внешние края линии стыка имеют более высокие температуры, чем центральная часть сварного шва. Локальная разница может достигать 300 К на расстоянии всего 20 мм. Также имеются горячие точки на обоих концах линии стыка примерно в 10 мм от краев. Эти горячие точки могут вызывать локальное плавление в сталях с полосами сегрегации при низкой температуре плавления.
Были выяснены причины неравномерного распределения температуры. Использование локальных измерений тока во время сварки не представлялось возможным, однако, когда процесс сварки только начался и не было значительного нагрева образца сварного шва, можно напрямую связать распределение напряжения с распределением плотности тока. Измерить распределение напряжения относительно легко, датчики напряжения были приварены точечной сваркой к поверхности образцов сварного шва, и измерения показали, что во время сварки имело место неравномерное распределение напряжения. Эта неравномерность имела то же распределение, что и распределение температуры, низкие напряжения в местах, где температуры были низкими, и сигналы высокого напряжения там, где температуры были высокими. Поскольку неравномерное распределение напряжения было измерено как для однокомпонентных, так и для двухкомпонентных образцов (образцы с границей раздела и без него), можно сделать вывод, что основное влияние оказывают граничные условия, определяемые сварочным оборудованием.
Исследовано влияние системы зажима и контактной поверхности электродов для определения их влияния на нагрев зоны сварного шва. Было показано, что прижимное усилие образцов недостаточно велико для предотвращения скольжения образцов при сварке, и что образцы необходимо располагать по центру электродов, чтобы свести к минимуму неравномерный нагрев. В местах самого высокого местного давления контактное сопротивление самое низкое, и, следовательно, нагрев в этих местах будет медленнее. Самые высокие краевые температуры были измерены на дальнем конце электродов, где ожидается самое низкое давление зажима. Для получения более равномерного нагрева необходимо получить более равномерное распределение тока. Этого можно добиться, изменив границу раздела между электродом и поверхностью образца или поверхность раздела между образцами сварного шва. Адаптация электродов оказывает небольшое влияние, но также приводит к увеличению времени сварки из-за уменьшения площади контактной поверхности (уменьшение на 10 % приводит к увеличению времени сварки на 5 %).
Изменение границы раздела может сократить время сварки до 20% за счет локального более быстрого начального нагрева. К сожалению, изменение поверхности раздела привело к снижению повторяемости сварных швов. Также были исследованы остаточные напряжения в сварных образцах. Были измерены оба образца с присутствующей осадкой, а также образцы, где осадка была удалена. Образцы с присутствующим сварным швом показали растягивающие напряжения в центре линии стыка, но сжимающие напряжения по краям образца. После снятия осадки общее напряженное состояние листа стало более нейтральным, пики сжимающих и растягивающих напряжений стали меньше. Распределение напряжения было объяснено концептуально с помощью модифицированной модели стержня. В этом исследовании использовалось моделирование с помощью MS.Marc и ABAQUS, чтобы лучше понять сложные электрические, тепловые и механические взаимосвязи, наблюдаемые в ходе реальных экспериментов. Были разработаны три различные модели: тепловая модель, термомеханическая модель и модель локальной деформации.
Модель локальной деформации показала, что метод испытаний Эриксена является допустимым методом оценки качества сварного шва. Смоделированная общая деформация, наблюдаемая при развальцовке колесных дисков, была ниже, чем смоделированная и измеренная деформация во время испытаний Эриксена. Как тепловая, так и термомеханическая модели являются прогнозирующими. Первый основан на входных параметрах, поступающих непосредственно из измерений во время сварочных экспериментов. Термомеханическая модель основана на зависимости параметров материала от температуры. Первоначальная тепловая модель была разработана для определения того, может ли неравномерное распределение плотности тока, измеренное в ходе экспериментов, привести к неравномерному нагреву зоны сварки. Модель не включала ни параметры, зависящие от температуры, ни механическую связь. Это показало, что неравномерный ввод тока приводит к неравномерному нагреву образца. За счет более равномерного распределения тока по длине зоны соединения можно получить более равномерный нагрев.
Было также указано, что вокруг загрязнений на границе раздела, проводящих или изолирующих, локально существует более высокая температура. Механическая модель является более реалистичной моделью, поскольку она включает в себя осадочную силу. Модель прогнозирует образование осадки при перекосах листов при сварке. Поскольку эта модель включает параметры материала, зависящие от температуры, можно прогнозировать остаточные напряжения после сварки, которые качественно согласуются с измеренными остаточными напряжениями в реальных сварных швах.
Предмет
S460MC
контактная осадка встык
осадка
сварка
обод
обод колеса
неравномерный нагрев
распределение плотности тока
остаточное напряжение
Для ссылки на этот документ используйте:
http://resolver.tudelft.nl/uuid:468e3a2e-6f9c-4ebb-8570-a5750787bf64
Издатель
ГВО drukkers & vormgevers BV | Понсен и Лойен
ISBN
98772520
Часть коллекции
Институциональный репозиторий
Тип документа
докторская диссертация
Права
(c) 2010 Керстенс, Н. Ф.Х.
5 Различные типы контактной сварки [со схемой и PDF]
Главная » Электротехника » Сварка сопротивлением: типы, работа, области применения, преимущества и многое другоеСаифом М. . Различные типы контактной сварки объясняются схемами и преимуществами, областями применения и т. д.
Сварка сопротивлением и типы
Сварка сопротивлением представляет собой процесс сварки в жидком состоянии, при котором соединение металла с металлом выполняется в жидком или расплавленном состоянии. Сварка сопротивлением также известна как термоэлектрический процесс, в котором тепло вырабатывается на поверхностях раздела свариваемых пластин из-за электрического сопротивления, и к этим пластинам прикладывается контролируемое низкое давление для формирования сварного соединения.
В этом методе используется электрическое сопротивление для выработки тепла, поэтому он называется контактной сваркой. Сварка сопротивлением является очень эффективным и экологически чистым сварочным процессом, но его применение ограничено из-за высокой стоимости материала и ограниченной толщины материала.
Принцип работы контактной сварки
Это процесс сварки, при котором тепло вырабатывается за счет сопротивления, оказываемого заготовками протекающему через них электрическому току. В этом процессе свариваемые детали удерживаются вместе, и через них проходит сильный ток. За счет сопротивления потоку тока выделяется тепло, достаточное для плавления металла.
Одновременно к зоне сварки прикладывается давление, чтобы свариваемые детали соединились. Произведенное тепло определяется формулой H = I 2 Rt, где
- H = выделяемое тепло в джоулях
- I = ток, проходящий через работу в амперах
- R = электрическое сопротивление работы в омах
- t = be Время протекания тока в секундах
Сварка сопротивлением широко используется и состоит из точечной, выступающей, шовной, стыковой сварки и сварки оплавлением.
Типы сварки сопротивления
Следующие приведены 5 различных типов сварки сопротивления:
- Сварка с сопротивлением. также: Как выполняется дуговая сварка? Типы, оборудование, области применения и прочее
1. Точечная сварка
В этом процессе соединяемые детали прочно удерживаются между двумя тяжелыми электродами, которые включены во вторичную цепь понижающих трансформаторов. Максимальное сопротивление возникает на контактной поверхности двух соединяемых частей и выделяется сильный нагрев.
Выделившееся тепло расплавляет заготовку в месте электрода. При этом к заготовке через электроды прикладывается давление и происходит сварка. Подача тока и количество времени должны быть достаточными для надлежащего расплавления поверхностей раздела.
Ток прекратился, но давление электрода сохранялось доли секунды, а сварной шов быстро охлаждался. Затем электрод удаляют и подводят к контакту в другом месте. Это сформирует круглый самородок.
Размер самородка зависит от размера электрода. Обычно он составляет около 4–7 мм в диаметре.
2. Выступающая сварка
Выступающая сварка аналогична точечной сварке, но с использованием плоского электрода. При этом протекание тока и результирующий нагрев локализованы на выступе, поэтому можно соединять толстые детали, которые нельзя соединить точечной сваркой.
Заготовка удерживается между электродом и через него проходит большое количество тока. Небольшое давление применяется через электроды на сварочных пластинах. Ток проходит через углубление, которое расплавляет его и заставляет углубление давления выравниваться и образовывать сварной шов.
Читайте также: Как работает подводная сварка? и Типы подводной сварки
3. Шовная сварка
Аналогичен точечной сварке, но при этом непрерывный шов производится путем передачи работы между вращающимися электродами в форме колеса, которые создают сварочное давление, а также проводят сварочный ток. Он может быть непрерывным или прерывистым.
Сначала ролики прижимаются к заготовке. Через эти ролики проходит большое количество амперного тока. Эти интерфейсные поверхности расплавятся и образуют сварной шов. Теперь ролики начинают катиться по рабочим пластинам. Это позволит сформировать непрерывный сварной шов.
Время движения сварного шва и электрода контролируется, чтобы гарантировать, что сварной шов перекрывается, а заготовка не слишком горячая. Используется для создания герметичных соединений.
4. Сварка оплавлением
Это тип контактной сварки, который можно использовать для соединения концов листов, проволоки, стержней или труб. При этом в зазоре между заготовками возникает электрическая дуга до достижения температуры сварки. Затем прикладывается давление для получения непрерывного сварного шва.
5. Стыковая сварка
Стыковая сварка отличается от сварки оплавлением тем, что между соединяемыми поверхностями не возникает дугового разряда. Тепло производится исключительно за счет электрического сопротивления поверхности соприкосновения потоку тока.
Преимущества контактной сварки
Ниже перечислены преимущества контактной сварки:
- Присадочный металл не требуется.
- Можно сваривать одинаковые и разнородные металлы.
- Может сваривать как тонкие (0,1 мм), так и толстые (20 мм) металлы.
- Высококвалифицированный персонал не требуется из-за простого и полностью автоматизированного процесса.
- Обладает высокой производительностью.
- Это экологически чистый процесс.
- Этот процесс отличается высокой скоростью сварки.
Недостатки контактной сварки
Ниже перечислены недостатки контактной сварки:
- Стоимость оборудования для контактной сварки высока.
- Толщина заготовки ограничена в связи с текущим спросом.
- Менее подходит для материалов с высокой электропроводностью.
- Требуется высокая электрическая мощность.
- Сварные соединения имеют низкую прочность на растяжение и усталостную прочность.
Применение контактной сварки
Ниже приведены области применения контактной сварки:
- Она широко используется в автомобильной промышленности.
- Выступающая сварка обычно используется при производстве гаек и болтов.
- Сварка швов используется для выполнения соединений с защитой от утечек, необходимых в небольших резервуарах, котлах и т. д.
- Сварка оплавлением применяется для сварки труб и труб.
Скачать PDF этой статьи
Вот и все, спасибо за внимание. Если вам понравилась наша статья « Типы контактной сварки », поделитесь ею с друзьями. Если у вас есть какие-либо вопросы по этой статье, вы можете задать их в комментариях.
Читать далее:
- Пайка: типы, области применения, преимущества и недостатки
- Газовая сварка: типы, принцип работы, оборудование, применение и многое другое
- Пайка: типы, инструменты для пайки, безопасность при пайке и преимущества
О Саифе М.
Саиф М. по профессии инженер-механик. Он закончил инженерное образование в 2014 году и в настоящее время работает в крупной фирме инженером-механиком. Он также является автором и редактором на сайте www.theengineerspost.com
…
Предназначен для эффективного соединения стальных, алюминиевых и медных проводов.
Перейти к содержимомуСоединение проводов
Узнайте об этих машинах прямо сейчас!
Аппараты
Контактное лицо
Машины для стыковой сварки IDEAL серий DS и AS были специально разработаны для эффективного соединения стальной, алюминиевой и медной проволоки. Их сильные стороны заключаются в реализации точных, многократно точных и устойчивых к вытяжке стыковых сварных швов. Компактная и прочная конструкция машины с интуитивно понятным управлением предназначена для промышленного использования на проволочно-волочильных заводах, кабельных заводах и при обработке проволоки.
В зависимости от профиля требований 9Используются процессы стыковой сварки 0035 (DS), стыковой сварки оплавлением (AS) и сварки двойным усилием (DD/STS) . При разработке машин для стыковой сварки серий DS и AS особое внимание уделялось оператору с учетом простой и эргономичной работы. Используемые во всем мире машины для стыковой сварки IDEAL серий DS и AS ежедневно доказывают свое качество и надежность… и делают это на протяжении десятилетий.
Важные особенности всех машин серий AS и DS
- Корпуса машин прочной конструкции для долговечности в сложных производственных условиях
- Расположение электрических компонентов, а также элементов управления/настройки и переключателей, защищенных от загрязнения и повреждений
- Зажимное устройство с большим усилием зажима, понятное и эргономичное крепление
- Равномерное, высокая степень распределения давления без проскальзывания детали в процессе сварки с помощью регулируемых ручных, пневматических или гидравлических зажимных устройств (зависит от типа машины)
- Идеальное выравнивание сварных швов благодаря использованию износостойких, плавно движущихся линейных и высокоточных направляющих
- Быстросменные электроды с V-образными или фигурными канавками для быстрой установки
- Регулируемое усилие осадки, путь тока и расстояние между губками для оптимальных результатов сварки
- Процесс высадки с помощью пакета пружин или пневматических или гидравлических цилиндров (зависит от типа машины)
- Автоматическое управление сварочным процессом для точно воспроизводимых результатов сварки
- Точная многоступенчатая регулировка сварочного напряжения для оптимальных параметров процесса
Что бы ни случилось — с превосходной технологией IDEAL вы всегда будете на переднем крае и оптимально подготовлены для адаптации к постоянно меняющимся техническим требованиям.
Машины для стыковой сварки IDEAL типа DSH и DSF для соединения стальных, алюминиевых и медных проводов
С помощью машин для стыковой сварки IDEAL типа DSH и DSF можно получить точные, многократно точные и устойчивые к вытяжке стыковые сварные швы. Эта надежная концепция машины с интуитивно понятным управлением особенно подходит для использования на проволочно-волочильных заводах, кабельных заводах и при обработке проволоки. Благодаря точной линейной направляющей тележки машина также идеально подходит для соединения изделий из проволоки за одну операцию. Станки типа ДШ оснащены ручными прижимными устройствами; тип DSF — для лучшего обращения с проводами — оснащен зажимными устройствами с педальным приводом на шасси. Стандартно все машины для стыковой сварки типа ДШ и ДСФ уже оснащены устройством для отжига стали с низким содержанием углерода. В зависимости от конкретного применения машины могут быть дополнительно оснащены дополнительными устройствами для отжига.
Дополнительные опцииУстройства для отжига охватывают диапазон от простых до устройств с электронным управлением, а также с автоматическим контролем температуры отжига с помощью инфракрасного спектрального пирометра. В результате даже обработка проволоки из твердого сплава или специальных сплавов не вызывает никаких проблем. На машинах для стыковой сварки IDEAL в варианте оснащения NE — для обработки цветных металлов — расстояние между губками, давление осадки и путь тока могут устанавливаться отдельно друг от друга даже в базовой комплектации. Разумеется, эта функция доступна и для всех других машин серии DS.
- Отдельная настройка расстояния между кулачками, давления высадки и пути тока – альтернатива стандартной центральной регулировке (стандартно для варианта оснащения NE для обработки цветных металлов, таких как медь или алюминий)
- Устройство для отжига стальной проволоки с умеренным содержанием углерода СГВ
- Электронное устройство EGV для отжига стальной проволоки с повышенным содержанием углерода
- GTR автоматическая система отжига (с пирометрическим управлением) для стальной проволоки с высоким содержанием углерода
- Ходовая часть с двумя и четырьмя колесами (серийно для всех машин DSF, а также для DSH от 130 до 180)
- Шлифовальный мотор и складной напильник для удаления заусенцев со сварного шва
- Ножницы для концов проволоки дисковая пила
- Разделительное устройство, установленное на рабочем столе станка
- Лупа с подсветкой
- Процесс сварки двойным усилием для высокопрочных сварных швов (для DSH 130 и DSH 160)
Узнайте об этих машинах прямо сейчас!
Технические данные DSH 015 — DSH 180
Технические данные DSH 015 NE — DSH 160 NE
Брошюрные сварочные машины для проводов и цепей
Вариант
Dual Pictsid Welld.обработка цветных металлов
Типы DSH 130 и DSH 160 в варианте оснащения NE могут быть оснащены процессом сварки двойным усилием «DD». В процессе сварки двойным усилием в процессе сварки выполняется дополнительный осадочный удар. Это дополнительное приложение силы почти полностью выдавливает термически затронутый материал из зоны сварки. Таким образом достигается более мелкозернистая структура в околошовной зоне и, как следствие, улучшаются механические свойства сварного шва. Таким образом можно получить даже высокопрочные соединения! Ключевые преимущества процесса сварки двойным усилием «DD»:
- Мелкозернистая структура
- Высокая прочность на растяжение
- Высокая прочность на изгиб
Микрофотографии
Машины стыковой сварки ДСП тип для серийного производства изделий из проволоки в больших количествах Окружающая среда. Надежная концепция машины оснащена пневматическими зажимными устройствами, а также точными сварочными тележками с линейными направляющими.
Дополнительные опцииБлагодаря простому и интуитивно понятному управлению, а также автоматизированной последовательности сварки достигаются большие объемы производства колец, каркасов, фасонных деталей и других изделий из круглой и профильной проволоки. Машины типа DSP подходят как для ручного рабочего места, так и для интеграции в производственные линии. Для требовательной непрерывной работы электроды были подготовлены для водяного охлаждения — в зависимости от требований то же самое относится и к трансформатору. В дополнение к обычной стыковой сварке, с опцией MIS, можно получить сварку с несколькими пульсациями, сварные швы с низким уровнем заусенцев, которые практически не требуют последующей обработки.
- Многопульсационный контроль тока МИС для малозаусенцевых соединений стальных проволок с низким содержанием углерода, требующих минимальной или вообще не требующей последующей обработки соединения
- Плавная регулировка, а также деактивация сварочного тока в зависимости от пути или времени для индивидуальной настройки в соответствии с требованиями отдельных продуктов
- Электронное устройство для отжига EGV для стальной проволоки с высоким содержанием углерода для бесступенчатой регулировки напряжения и времени отжига
- Графическая панель управления для программируемого ввода параметров
- Интерфейс для интеграции в производственные линии
- Ручной упор для достижения воспроизводимых размеров
- Специальные электроды для колец, фасонных деталей и т.
д.
* Отдельные опции доступны не для всех размеров машин.
Технические данные DSP
Узнайте об этих машинах прямо сейчас!
Видео о продукте: IDEAL, тип DSP 120
Машина для стыковой сварки проволоки для производства серии
Тип IDEAL DST Машины для стыковой сварки для изготовления Т-образных и линейных сварных швов а также в линейных соединениях
в больших количествах. Надежная концепция машины оснащена пневматическими зажимными устройствами, а также точными сварочными тележками с линейными направляющими. Сильные стороны машины для стыковой сварки IDEAL типа DST заключаются в создании точных, устойчивых к вытяжке и многократно точных стыковых сварных швов, а также в интуитивно понятном, простом в освоении и эргономичном управлении. Автоматизированная последовательность позволяет сократить время цикла.Для требовательной непрерывной работы электроды были подготовлены для водяного охлаждения — в зависимости от требований то же самое относится и к трансформатору. Интеграция в производственные линии осуществляется легко и просто благодаря дополнительному интерфейсу. Бесступенчатая регулировка, а также деактивация сварочного тока в зависимости от пути или времени позволяют индивидуально учитывать требования обрабатываемого материала, тем самым обеспечивая оптимальные результаты сварки. Ввод параметров осуществляется через графический интерфейс пользователя. С опцией MIS — управлением током с несколькими пульсациями — можно получить сварные швы стальной проволоки с низким содержанием углерода с низким уровнем заусенцев, которые практически не требуют последующей обработки.
Технические данные Серии DSP и DST
Узнайте об этих машинах прямо сейчас!
Видео о продукте: IDEAL тип DST 120
Draht-Stumpfschweißen in T- und Linienstößen
Машины для стыковой сварки оплавлением типа
AS для высочайшей производительности при самых тяжелых промышленных соединениях 504Для достижения максимально возможной прочности на растяжение и соответствующего выполнения стандартных требований лучше всего подходят прошивные машины IDEAL типа AS.
Автоматизированная последовательность сварки начинается с предварительного нагрева концов проволоки с последующим оплавлением. Заканчивается процесс сварки. Даже в стандартной версии все станки типа AS оснащены гидравлическими зажимными устройствами. Оборудование машин типа АС может быть дополнено различными процессами отжига (в соответствии с требованиями обрабатываемого материала) и устройствами для удаления заусенцев, а также машинами и устройствами для предварительной и последующей обработки сварных швов. Преимущества стыковой сварки оплавлением стальной и алюминиевой проволоки на наших машинах типа AS:
- Наилучшее качество сварки с металлургически чистыми соединениями; силы ок. 90% (относительно основного материала)
- Короткое время сварки (в зависимости от диаметра проволоки требуется всего несколько секунд)
- Низкие требования к подготовке концов проволоки (любые неровности и загрязнения в месте соединения мало влияют на процесс)
- Высокая воспроизводимость параметров сварки; опционально возможны эффективный контроль и регулирование процесса сварки
- Высокая размерная точность свариваемых проволок благодаря жестким допускам по длине
IDEAL является одним из пионеров технологии стыковой сварки оплавлением — с 1923 года.
Для получения дополнительной информации об этом типе машины нажмите здесь.
Узнайте об этих машинах прямо сейчас!
Видео о продукте IDEAL AS0 15
Abbrennstumpfschweißmaschine zur manuellen Herstellung von zweiteiligen Zugstäben
Сварочный аппарат с двойным давлением для черных и цветных металловIDEAL STS 020 по DD0 104
Процесс сварки под двойным давлением используется, прежде всего, в цехах волочения проволоки.
Сварочный аппарат двойного давления DD0 104, а также STS 020 от IDEAL-Werk, после сварки с усилием почти полностью выдавливает из зоны сварки подвергающийся термическому воздействию материал из железа или цветного металла. Это улучшает механические свойства, а также конструкцию сварного шва. С сериями STS или DD0 можно достичь высокого качества сварки и огромной прочности. При этом машина отличается высокой воспроизводимостью параметров сварки.
9№ 0009
Идеальное решение для ваших задач по вертикальной вытяжке рулонов на линиях вытягивания и волочения.
Видео о машине IDEAL STS 020
Машина для стыковой сварки STS 020 – вертикальная
Видео о продукции
IDEAL DD0 104Машина для сварки цветных металлов и черных металлов двойным давлением Ссылка для загрузки страницы
Настройки конфиденциальности
Если вам еще не исполнилось 16 лет, и вы хотите дать согласие на дополнительные услуги, вы должны спросить разрешения у своих законных опекунов. Мы используем файлы cookie и другие технологии на нашем веб-сайте. Некоторые из них необходимы, в то время как другие помогают нам улучшить этот веб-сайт и ваш опыт. Персональные данные (например, IP-адреса) могут обрабатываться, например, для персонализированной рекламы и контента или измерения рекламы и контента.
Более подробную информацию об использовании ваших данных вы можете найти в нашей политике конфиденциальности. Здесь вы найдете обзор всех используемых файлов cookie. Вы можете дать свое согласие на целые категории или отобразить дополнительную информацию и выбрать определенные файлы cookie.
Принять все Сохранять Используйте только необходимые файлы cookie
Настройки конфиденциальностиОсновные (3)
Основные файлы cookie обеспечивают выполнение основных функций и необходимы для правильной работы веб-сайта.
Показать информацию о файлах cookie Скрыть информацию о файлах cookie
Имя Печенье Борлабс Анбитер Владелец этого сайта, Выходные данные Цвек Сохраняет настройки посетителей, выбранные в окне файлов cookie Borlabs Cookie. Имя файла cookie borlabs-cookie Печенье Laufzeit 1 Яр Имя Куформ Анбитер Куформ Цвек Сохранить информацию, введенную в формы, предоставленные плагином Quform для сеанса. Сохраняет только идентификатор сеанса (без личных данных) / Требуется по соображениям безопасности (защита от подделки межсайтовых запросов) / Требуется для нормальной работы плагина
Печенье Laufzeit quform_session Имя WPML Анбитер Владелец этого сайта Цвек Сохраняет язык последней просматриваемой пользователем страницы. Датеншуцерклерунг Privacy Policy and GDPR Compliance
Имя файла cookie WP-WPML_Current_Language Печенье Laufzeit 1 год Статистика (1)
Статистика
Статистические файлы cookie собирают информацию анонимно.
Эта информация помогает нам понять, как наши посетители используют наш веб-сайт.
Показать информацию о файлах cookie Скрыть информацию о файлах cookie
Акзептирен Гугл Аналитика Имя Гугл Аналитика Анбитер Google Ireland Limited, Gordon House, Barrow Street, Dublin 4, Ирландия Цвек Файл cookie Google, используемый для аналитики веб-сайта. Генерирует статистические данные о том, как посетитель использует веб-сайт.
Датеншуцерклерунг https://policies.google.com/privacy Хост(ы) google.com Имя файла cookie _ga,_gat,_gid Печенье Laufzeit 2 года Внешние носители (2)
Внешние носители
Контент с видеоплатформ и социальных сетей по умолчанию заблокирован.
Если файлы cookie внешних носителей принимаются, доступ к этому содержимому больше не требует ручного согласия.
Показать информацию о файлах cookie Скрыть информацию о файлах cookie
Акзептирен Карты Гугл Имя Карты Гугл Анбитер Google Ireland Limited, Gordon House, Barrow Street, Dublin 4, Ирландия Цвек Используется для разблокировки контента Google Maps. Датеншуцерклерунг https://policies.google.com/privacy Хост(ы) .google.com Имя файла cookie НИД Печенье Laufzeit 6 Монате Акзептирен YouTube Имя YouTube Анбитер Google Ireland Limited, Gordon House, Barrow Street, Dublin 4, Ирландия Цвек Используется для разблокировки контента YouTube. Датеншуцерклерунг https://policies.google.com/privacy Хост(ы) google.com Имя файла cookie НИД Печенье Laufzeit 6 Монате Настройки конфиденциальности Выходные данные
Перейти к началуВ чем разница между лазерной сваркой и сваркой сопротивлением?
Содержание
Определение сварки сопротивлением и лазерной сварки Сварка сопротивлениемСварка сопротивлением представляет собой производственный процесс и технологию соединения металлов или других термопластичных материалов, таких как пластмассы, путем нагревания.
Это метод сварки путем приложения давления через электрод после соединения заготовки и использования тепла сопротивления, генерируемого током, проходящим через контактную поверхность и прилегающую область соединения.
Лазерная сваркаЛазерная сварка — это высокоэффективный, точный, бесконтактный, экологически чистый и безызлучательный метод сварки с использованием лазерного луча высокой плотности в качестве источника тепла.
Классификация сварочного оборудования Классификация оборудования для контактной сварки.В зависимости от режима энергоснабжения он делится на:
Однофазный сварочный аппарат промышленной частоты, сварочный аппарат с вторичным выпрямителем, трехфазный низкочастотный сварочный аппарат, сварочный аппарат с накопителем энергии и инверторный сварочный аппарат.
Классификация оборудования для лазерной сваркиПо способу сварки подразделяется на:
Точечная сварка, сплошная сварка, сварка встык, сварка внахлест
В зависимости от режима светоотдачи его можно разделить на:
Чистая волоконная лазерная сварка, лазерная сварка с передачей жесткого оптического пути, лазерная сварка YAG, лазерная сварка полупроводников.
Классификация контактной сваркиМетоды контактной сварки в основном включают точечную сварку, шовную сварку, рельефную сварку и стыковую сварку (контактную стыковую сварку и стыковую сварку оплавлением)
1. Точечная сваркаТочечная сварка — это метод сварки сопротивлением, при котором сварное изделие собирается внахлестку, запрессовывается между двумя цилиндрическими электродами, а основной металл плавится под действием тепла сопротивления, образуя точку сварки.
Точечная сварка в основном используется для сварки листов.
Процесс точечной сварки
① Подпрессуйте, чтобы обеспечить хороший контакт с заготовкой.
② Включите питание, чтобы сформировать наггетсы и пластиковое кольцо в месте сварки.
③ Выключите ковку, чтобы самородок остыл и кристаллизовался под непрерывным действием давления с образованием паяного соединения с плотной структурой, без усадочных полостей и трещин.
2. Шовная сваркаПроцесс шовной сварки аналогичен процессу точечной сварки, за исключением того, что вместо цилиндрического электрода используется вращающийся роликовый электрод в форме диска.
Сварное изделие собирается внахлестку или встык и помещается между двумя роликовыми электродами, ролик оказывает давление на сварное соединение и вращается, непрерывно или прерывисто подавая мощность для образования непрерывного сварного шва.
Шовная сварка в основном используется для сварки конструкций с обычными сварными швами и требованиями к герметизации, а толщина листа обычно составляет менее 3 мм.
3. Выступающая сваркаВыступающая сварка является вариантом точечной сварки;
На заготовке имеются сборные выпуклости. Во время рельефной сварки на стыке одновременно могут образовываться один или несколько самородков.
4. Стыковая сварка сопротивлениемСтыковая сварка сопротивлением – это способ сборки сварных изделий в стыковые соединения, приведения их торцов в плотный контакт, нагревания их до пластического состояния нагревом сопротивления, затем отключения питания и быстрой осадки усилие для завершения сварки.
Стыковая сварка сопротивлением в основном используется для сварных соединений с простым сечением, диаметром или длиной стороны менее 20 мм и низкими требованиями к прочности.
5. Стыковая сварка оплавлениемСтыковая сварка оплавлением – это способ сборки сварного соединения в стык, подключения источника питания, постепенного приближения торца к локальному контакту, нагревания этих точек контакта теплом сопротивления, генерирования вспышка под действием большого тока, расплавление металла конца, а затем отключение питания и быстрое применение силы осадки для завершения сварки, когда конец достигает заданной температуры в пределах определенного диапазона глубины.
Качество соединения при сварке оплавлением лучше, чем при контактной сварке, механические свойства сварного шва эквивалентны свойствам основного металла, и нет необходимости очищать предварительно сваренную поверхность соединения перед сваркой.
Стыковая сварка оплавлением часто используется для сварки важных сварных конструкций.
Может сваривать один и тот же металл или другой металл;
Может сваривать металлическую проволоку 0,01 мм или металлический стержень и профиль 20000 мм.
Недостатки контактной сварки:В настоящее время по-прежнему отсутствуют надежные методы неразрушающего контроля, и качество сварки можно проверить только разрушающими испытаниями технологических образцов и заготовок, а также различными технологиями контроля.
Соединение внахлест при точечной и шовной сварке не только увеличивает вес детали, но и образует внутренний угол вокруг сварного шва двух пластин, что приводит к снижению прочности на растяжение и усталостной прочности соединения.
Оборудование имеет высокую мощность, высокую механизацию и автоматизацию, что делает оборудование дорогостоящим и сложным в обслуживании, а широко используемый мощный однофазный сварочный аппарат переменного тока не способствует сбалансированной работе энергосистемы.
Подводимая теплота может быть снижена до минимально необходимой величины, диапазон металлографических изменений зоны термического влияния мал, а деформация, вызванная теплопроводностью, также минимальна.
Заготовка может быть размещена в замкнутом пространстве (вакуумированном или под контролем внутренней газовой среды).
Легко выполнять высокоскоростную сварку с помощью автоматизации, а также можно управлять цифровым или компьютерным управлением.
При использовании перфорированной сварки отношение глубины к ширине наплавленного валика может достигать 10:1.
На него не влияет магнитное поле (дуговая сварка и электронно-лучевая сварка просты) и он может точно выровнять сварные детали.
Существует широкий спектр свариваемых материалов, а также различные разнородные материалы, которые можно соединять друг с другом.
Нет необходимости в использовании электродов, и не нужно беспокоиться о загрязнении или повреждении электродов.
Поскольку это не процесс контактной сварки, потери и деформации машин и инструментов могут быть сведены к минимуму.
Не требуется защита от вакуума или рентгеновского излучения.
Устройство переключения может передавать лазерный луч на несколько рабочих станций.
При сварке тонких материалов или проволоки малого диаметра будет непросто переплавить, как при дуговой сварке.
Параметры сварочного процесса при однопроходной сварке толщиной 32 мм были проверены на соответствие требованиям, что может сократить время, необходимое для сварки толстых листов, и даже сократить использование присадочного металла.
Лазерный луч может быть сфокусирован на небольшой площади и может сваривать небольшие и близко расположенные детали.
Лазерный луч легко фокусировать, выравнивать и направлять с помощью оптических инструментов, его можно размещать на соответствующем расстоянии от заготовки и направлять между станками и инструментами или препятствиями вокруг заготовки.
Другие правила сварки не могут быть воспроизведены из-за указанных выше ограничений по пространству.
Может сваривать более двух металлов с разными физическими свойствами (например, с разным сопротивлением).
Заключение
Можно видеть, что лазерная сварка намного лучше, чем традиционная контактная сварка, с точки зрения преимуществ сварки, качества сварки, стоимости сварки и преимуществ сварки.