Ст3сп сталь: характеристики и расшифовка, применение и свойства стали
- Стали
- Стандарты
Всего сталей
Страна | Стандарт | Описание | ||||||||||
---|---|---|---|---|---|---|---|---|---|---|---|---|
Россия | ГОСТ 380-2005 | ![]() | ||||||||||
Россия | ГОСТ 535-2005 | Прокат сортовой и фасонный из стали углеродистой обыкновенного качества. Общие технические условия | ||||||||||
Россия | ГОСТ 4781-85 | Профили стальные горячекатаные для шпунтовых свай. Технические условия | ||||||||||
Россия | ГОСТ 5781-82 | Сталь горячекатаная для армирования железобетонных конструкций.![]() | ||||||||||
Россия | ГОСТ 8696-74 | Трубы стальные электросварные со спиральным швом общего назначения. Технические условия | ||||||||||
Россия | ГОСТ 10705-80 | Трубы стальные электросварные. Технические условия | ||||||||||
Россия | ГОСТ 10706-76 | Трубы стальные электросварные прямошовные.![]() | ||||||||||
Россия | ГОСТ 10707-80 | Трубы стальные электросварные холоднодеформированные. Технические условия | ||||||||||
Россия | ГОСТ 10884-94 | Сталь арматурная термомеханически упрочненная для железобетонных конструкций. Технические условия | ||||||||||
Россия | ГОСТ 10885-85 | Сталь листовая горячекатаная двухслойная коррозионно-стойкая.![]() | ||||||||||
Россия | ГОСТ 14637-89 | Прокат толстолистовой из углеродистой стали обыкновенного качества. Технические условия | ||||||||||
Россия | ГОСТ 14918-80 | Сталь тонколистовая оцинкованная с непрерывных линий. Технические условия | ||||||||||
Россия | ГОСТ 16523-97 | Прокат тонколистовой из углеродистой стали качественной и обыкновенного качества общего назначения.![]() | ||||||||||
Россия | ГОСТ 30136-95 | Катанка из углеродистой стали обыкновенного качества. Технические условия | ||||||||||
Россия | ГОСТ 32678-2014 | Трубы стальные бесшовные и сварные холоднодеформированные общего назначения. Технические условия |
Механические свойства Ст3сп
Механические свойства по стандарту ГОСТ 380-2005
Предел текучести, σ0,2, МПа |
Временное сопротивление разрыву, σв, МПа |
Относительное удлинение при разрыве, δ5, % |
205 — 255 | 370 — 490 |
23 — 26 |
Механические свойства по стандарту ГОСТ 535-2005
Толщина, мм |
Предел текучести для остаточной деформации, σт, МПа |
Временное сопротивление разрыву, σв, МПа |
Относительное удлинение при разрыве, δ5, % |
Изгиб до параллельности сторон* |
до 10 |
> 255 |
380 — 490 |
> 26 |
d=a |
11 — 20 | > 245 | 370 — 480 | > 26 | d=a |
21 — 40 | > 235 |
370 — 480 |
> 25 |
d=2a |
41 — 100 | > 225 |
370 — 480 |
> 23 | d=2a |
более 100 | > 205 |
370 — 480 |
> 23 | d=2a |
По согласованию с потребителем для фасонного проката толщиной более 20 мм допускается снижение предела текучести на 10 МПа
Допускается снижение относительного удлинения на 1% (по согласованию с потребителем)
Допускается превышение верхнего предела временного сопротивления на 49 МПа, а по согласованию с потребителем — без ограничения верхнего предела временного сопротивления при условии выполнения остальных норм.
* a — толщина образца, d — диаметр оправки
Нормы ударной вязкости KCU, Дж/см2
Толщина, мм |
При температуре +20 °C |
При температуре -20 °C |
После механического старения |
Категория стали 3 (Ст3сп3)** | |||
3 — 9,9 |
> 108 |
- | - |
10 — 25 | > 98 | - | - |
26 — 40 |
> 88 |
- | - |
Категория стали 4 (Ст3сп4) | |||
3 — 9,9 | - | > 49 | - |
10 — 25 | - | > 29 | - |
Категория стали 5 (Ст3сп5) | |||
3 — 9,9 | - | > 49 | > 49 |
10 — 25 | - | > 29 | > 29 |
** Категории стали:
3 — сталь с испытанием механических свойств на растяжение на образцах, изготовленных из нормализованных заготовок указанного в заказе размера, но не более 100 мм
4 — сталь с испытанием механических свойств на растяжение и ударную вязкость на образцах, изготовленных из термически обработанных (закалка + отпуск) заготовок указанного в заказе размера, но не более 100мм
5 — сталь с испытанием механических свойств на растяжение на образцах, изготовленных из сталей в нагартованном или термически обработанном состоянии (отожженной или высокоотпущенной)
Механические свойства по стандарту ГОСТ 5781-82
Сортамент |
Класс прочности |
Диаметр, мм |
Временное сопротивление разрыву, σв, МПа** |
Предел текучести, σ0,2, МПа |
Относительное удлинение при разрыве, δ5, % |
Испытание на изгиб в холодном состоянии* |
Арматура | А-I (А240) | 6 — 40 |
> 373 |
> 235 |
> 25 |
180 °C; c=d** |
* c — толщина оправки, d — диаметр стержня
** Для арматурной стали диаметром от 20 до 40 мм испытание на изгиб в холодном состоянии при 180 °C: c=2d
Механические свойства по стандарту ГОСТ 8696-74
Предел текучести для остаточной деформации, σт, МПа (кгс/мм2) |
Временное сопротивление разрыву, σв, МПа (кгс/мм2) |
Относительное удлинение при разрыве, δ5, % |
> 245 (25) |
> 372 (38) |
> 23 |
Нормы ударной вязкости KCV, Дж/см2 (кгс⋅м/см2)
Категория стали* | При температуре +20 °C |
При температуре -20 °C |
После механического старения |
3 (Ст3сп3) | > 59 (6) | ||
4 (Ст3сп4) | - |
> 29,4 (3) |
- |
5 (Ст3сп5) |
- |
> 29,4 (3) |
> 29,4 (3) |
Механические свойства по стандарту ГОСТ 10705-80
Сортамент |
Диаметр, мм |
Толщина, мм |
Временное сопротивление разрыву, σв, МПа |
Предел текучести, σ0,2, МПа |
Относительное удлинение при разрыве, δ5, % |
Термически обработанная продукция | |||||
Трубы | все | все |
> 372 |
> 225 |
> 22 |
Без термической обработки | |||||
Трубы | от 10 до 19 | не более 0,06*D |
> 441 |
> 216 |
> 13 |
Трубы | от 19 до 60 | не более 0,06*D |
> 392 |
> 216 |
> 13 |
Трубы | от 10 до 19 | более 0,06*D |
> 441 |
> 216 |
> 5 |
Трубы | от 19 до 60 | более 0,06*D |
> 392 |
> 216 | > 5 |
Трубы | от 60 до 152 | все |
> 372 |
> 216 |
> 20 |
Трубы | от 152 до 377 | не более 6 | > 353 |
> 216 |
> 17 |
Трубы | от 152 до 377 | более 6 |
> 353 |
> 216 |
> 14 |
Трубы | более 377 | не более 6 |
> 353 |
> 216 |
> 19 |
Температура испытания, °C |
Ударная вязкость KCU, Дж/см2 (кгс⋅м/см2) |
+20 | 78,4 (8) |
-20 | 39,2 (4) |
+20 (после механического старения) | 39,2 (4) |
Механические свойства по стандарту ГОСТ 10706-76
Сортамент |
Временное сопротивление разрыву, σв, МПа |
Предел текучести для остаточной деформации, σт, МПа |
Относительное удлинение при разрыве, δ5, % |
Трубы |
> 372 |
> 245 |
> 20 |
Толщина, мм |
Температура испытания, °C |
Ударная вязкость KCU, Дж/см2 |
Категория стали 3 (Ст3сп3)* | ||
5 — 9 |
+20 |
> 59 |
9 — 25 | +20 |
> 49 |
более 25 | +20 |
> 29 |
Категория стали 4 (Ст3сп4)* | ||
5 — 9 |
-20 |
> 20 |
9 — 25 |
-20 | > 15 |
Для магистральных тепловых сетей
Временное сопротивление разрыву, σв, МПа |
Предел текучести для остаточной деформации, σт, МПа |
Относительное удлинение при разрыве, δ5, % |
Условия испытаний |
Ударная вязкость KCU, Дж/см2 |
Категория стали 4 (Ст3сп4)* | ||||
> 372 |
> 245 |
> 23 |
-20 °C |
- |
Категория стали 5 (Ст3сп5)* | ||||
> 372 |
> 245 |
> 23 |
-20 °C |
> 30 |
> 372 |
> 245 |
> 23 |
механическое старение |
> 29 |
* Категории стали в зависимости от нормируемых характеристик:
3 — сталь с испытанием механических свойств на растяжение на образцах, изготовленных из нормализованных заготовок указанного в заказе размера, но не более 100 мм
4 — сталь с испытанием механических свойств на растяжение и ударную вязкость на образцах, изготовленных из термически обработанных (закалка + отпуск) заготовок указанного в заказе размера, но не более 100мм
5 — сталь с испытанием механических свойств на растяжение на образцах, изготовленных из сталей в нагартованном или термически обработанном состоянии (отожженной или высокоотпущенной)
Механические свойства по стандарту ГОСТ 10707-80
Сортамент |
Временное сопротивление разрыву, σв, МПа |
Предел текучести для остаточной деформации, σт, МПа |
Относительное удлинение при разрыве, δ5, % |
Термически обработанная продукция |
|||
Трубы |
> 372 |
> 225 |
> 22 |
Без термической обработки |
|||
Трубы |
> 314 |
> 216 |
> 5 |
Механические свойства по стандарту ГОСТ 10884-94
Сортамент | Класс прочности | Диаметр, мм | Диаметр оправки* |
Временное сопротивление разрыву, σв, МПа** |
Предел текучести, σ0,2, МПа |
Относительное удлинение при разрыве, δ5, % |
Испытание на изгиб в холодном состоянии |
Арматура | Ат400 | 6 — 40 | 3d |
> 550 |
> 440 |
> 16 |
90 °C |
* d — номинальный диаметр стержня
** В стержнях временное сопротивление разрыву не должно превышать 750 МПа
Механические свойства по стандарту ГОСТ 14637-89
Толщина, мм |
Предел текучести для остаточной деформации, σт, МПа |
Временное сопротивление разрыву, σв, МПа |
Относительное удлинение при разрыве, δ5, % |
Изгиб до параллельности сторон* |
Категории 1, 2, 3, 4, 5 (Ст3сп, Ст3сп2, Ст3сп3, Ст3сп4, Ст3сп5)** | ||||
4 — 20 |
> 245 |
370 — 480 |
> 26 |
d=1,5a |
20 — 40 |
> 235 |
360 — 460 |
> 25 |
d=2,5a |
40 — 100 |
> 225 |
360 — 460 |
> 23 |
d=2,5a |
100 — 160 |
> 205 |
360 — 460 |
> 23 |
d=2,5a |
Категория 6 (Ст3сп6)** | ||||
не более 20 |
> 295 |
> 430 |
> 16 |
d=4a |
более 20 |
> 295 |
> 430 |
> 16 |
d=5a |
Допускается превышение верхнего предела временного сопротивления не более чем на 50 МПа при соблюдении остальных норм; по согласованию с потребителем — без ограничения верхнего предела.
По согласованию с потребителем для проката толщиной более 20 мм допускается значение предела текучести ниже на 10 МПа.
Допускается снижение относительного удлинения на 1% абс. для проката толщиной более 8 мм и на каждый миллиметр уменьшения толщины для проката толщиной 8 мм и менее.
* a — толщина образца, d — диаметр оправки
** Категории стали в зависимости от нормируемых характеристик:
1 — механические свойства при растяжении и изгибе
2 — химический состав и механические свойства при растяжении и изгибе
3 — химический состав, механические свойства при растяжении и изгибе, ударная вязкость при температуре +20°С
4 — химический состав, механические свойства при растяжении и изгибе, ударная вязкость при температуре –20°С
5 — химический состав, механические свойства при растяжении и изгибе, ударная вязкость: при температуре –20°С, после старения и КСV при температуре +20°С
6 — химический состав, механические свойства при растяжении и изгибе, ударная вязкость: при температуре –40°С, после старения и КСV при температуре 0°С
Нормы ударной вязкости KCU, Дж/см2 (кгс⋅м/см2)***
Толщина, мм |
При температуре +20 °C |
При температуре -20 °C |
При температуре -40 °C |
После механического старения |
Категория стали 3,4,5 (Ст3сп3, Ст3сп4, Ст3сп5) | ||||
5 — 9 | > 78 (8) | > 39 (4) | - | > 39 (4) |
10 — 25 | > 69 (7) | > 29 (3) | - | > 29 (3) |
26 — 40 |
> 49 (5) | - | - | - |
Категория стали 6 (Ст3сп6) | ||||
все | - | - |
> 39 (4) |
> 29 |
*** Для проката категорий 1 (Ст3сп) и 2 (Ст3сп2) ударную вязкость не нормируют
Нормы ударной вязкости KCV, Дж/см2 (кгс⋅м/см2)
Толщина, мм |
При температуре -40 °C |
При температуре 0 °C |
Категория стали 5 (Ст3сп5) | ||
5 — 20 | 34 (3,5) | - |
более 20 | - | - |
Категория стали 6 (Ст3сп6) | ||
8 — 9 | - |
34 (3,5) |
10 — 20 | - | 30 (3,1) |
более 20 | - | - |
Механические свойства по стандарту ГОСТ 14918-80
Сталь группы ХШ*
Толщина, мм |
Временное сопротивление разрыву, σв, МПа |
Относительное удлинение при разрыве, δ4, % |
Категория вытяжки Н** | ||
до 0,7 | 300 — 490 | > 21 |
07 — 1,5 |
300 — 490 |
> 22 |
1,5 — 2 |
300 — 490 |
> 23 |
более 2 |
300 — 490 |
> 24 |
Категория вытяжки Г | ||
до 0,7 |
275 — 430 | > 23 |
07 — 1,5 |
275 — 430 | > 24 |
1,5 — 2 |
275 — 430 | > 25 |
более 2 |
275 — 430 | > 26 |
Категория вытяжки ВГ | ||
до 0,7 | 255 — 410 | > 26 |
07 — 1,5 | 255 — 410 | > 28 |
1,5 — 2 | 255 — 410 | > 29 |
более 2 | 255 — 410 | > 30 |
Сталь группы ХП, ПК
Толщина, мм |
Предел текучести для остаточной деформации, σт, МПа |
Относительное удлинение при разрыве, δ5, % |
до 0,7 |
> 230 |
> 20 |
07 — 1,5 |
> 230 |
> 22 |
1,5 — 2 |
> 230 |
- |
более 2 | > 230 | - |
* Группы стали в зависимости от назначения:
ХШ — сталь для холодной штамповки
ХП — сталь для холодного профилирования
ПК — сталь под окраску
** Категории вытяжки (в зависимости от степени к вытяжке):
Н — сталь нормальной вытяжки
Г — сталь глубокой вытяжки
ВГ — весьма высокой вытяжки
Глубина сферической лунки стали группы ХШ
Толщина, мм | Категория вытяжки Н | Категория вытяжки Г | Категория вытяжки ВГ |
0,5 |
> 6,9 | > 8 | > 8,5 |
0,6 | > 7,2 |
> 8,5 |
> 8,9 |
0,7 | > 7,5 | > 8,9 | > 9,2 |
0,8 | > 7,8 | > 9,3 | > 9,5 |
0,9 | > 8,2 | > 9,6 | > 9,9 |
1 | > 8,6 | > 9,9 | > 10,1 |
1,1 | > 8,7 | > 10,1 | > 10,3 |
1,2 | > 8,8 | > 10,3 | > 10,5 |
1,3 | > 8,9 | > 10,5 | > 10,7 |
1,4 | > 9 | > 10,6 | > 10,8 |
1,5 | > 9,1 | > 10,8 | > 11 |
1,6 | > 9,5 | > 11 | > 11,3 |
1,7 | > 9,6 | > 11,1 | > 11,4 |
1,8 | > 9,7 | > 11,2 | > 11,5 |
1,9 | > 9,8 | > 11,3 | > 11,6 |
2 и более | > 9,9 | > 11,4 | > 11,7 |
Механические свойства по стандарту ГОСТ 16523-97
Группа прочности ОК360В
Сортамент | Толщина, мм |
Временное сопротивление разрыву, σв, МПа* |
Относительное удлинение при разрыве, δ4, %** |
Испытание на изгиб в холодном состоянии*** |
Категория стали 1 (Ст3сп)*** | ||||
Труба | до 2 | - | - | d=a |
Труба | более 2 | - | - | d=2a |
Категория стали 4 (Ст3сп4) | ||||
Труба | до 2 | 360 — 530 | > 20 | - |
Труба | более 2 | 360 — 530 | > 22 | - |
Категория стали 5 (Ст3сп5) | ||||
Труба | до 2 | 360 — 530 | > 20 | d=a |
Труба | более 2 | 360 — 530 | > 22 | d=2a |
Группа прочности ОК370В
Сортамент | Толщина, мм |
Временное сопротивление разрыву, σв, МПа* |
Относительное удлинение при разрыве, δ5, %** |
Испытание на изгиб в холодном состоянии*** |
Категория стали 1 (Ст3сп)**** | ||||
Труба | до 2 | - | - | d=a |
Труба | более 2 | - | - | d=2a |
Категория стали 4 (Ст3сп4) | ||||
Труба | до 2 | 370 — 530 | > 20 | - |
Труба | более 2 | 370 — 530 | > 22 | - |
Категория стали 5 (Ст3сп5) | ||||
Труба | до 2 | 370 — 530 | > 20 | d=a |
Труба | более 2 | 370 — 530 | > 22 | d=2a |
* Допускается изготовление проката без ограничения верхнего предела временного сопротивления
** Для холоднокатаного проката относительное удлинение при разрыве +2%
*** a — толщина образца, d — диаметр оправки
**** Категории стали в зависимости от нормируемых характеристик:
1 — без испытания механических свойств на растяжение и ударную вязкость
4 — сталь с испытанием механических свойств на растяжение и ударную вязкость на образцах, изготовленных из термически обработанных (закалка + отпуск) заготовок указанного в заказе размера, но не более 100мм
5 — сталь с испытанием механических свойств на растяжение на образцах, изготовленных из сталей в нагартованном или термически обработанном состоянии (отожженной или высокоотпущенной)
Механические свойства по стандарту ГОСТ 30136-95
Сортамент | Способ охлаждения* | Временное сопротивление разрыву, σв, МПа |
Относительное сужение, ψ, % |
Катанка | УО1, ВО |
< 490 |
< 60 |
Катанка | УО2 |
< 540 |
< 60 |
*Способы охлаждения катанки:
УО1 — одностадийное охлаждение
УО2 — двухстадийное охлаждение
ВО — охлаждение на воздухе
Механические свойства по стандарту ГОСТ 32678-2014
Сортамент |
Временное сопротивление разрыву, σв, МПа |
Предел текучести для остаточной деформации, σт, МПа |
Относительное удлинение при разрыве, δ5, % |
Термически обработанная продукция | |||
Трубы |
> 372 |
> 225 |
> 22 |
Без термической обработки* |
|||
Трубы | > 315 |
> 216 |
> 5 |
* Механические свойства труб без термической обработки устанавливают по согласованию между изготовителем и потребителем. В случае отсутствия такого согласования производство сварных холоднодеформированных труб должно соответствовать нормам, указанным в таблице.
Дополнительные свойства Ст3сп
Сварка стали Ст3сп
Ст3сп характеризуется уникальной свариваемостью, что обеспечивает большой диапазон технических характеристик, которые можно улучшить при помощи легирующих добавок. Свойства стали дают возможность применять дуговую сварку – автоматическую и ручную, сварку по контактно-точечной и электрошлаковой технологии.
Важно для проведения всех сварочных работ, что сталь данной марки легко сваривается без подготовительных мероприятий – специальной подготовки, и изделия не требуют обработки после сварки. Хотя это касается только сварки изделий с толщиной менее 3,6 см. Стальные изделия с большей толщиной рекомендовано предварительно разогреть (100 °С) и выполнить термообработку после сварки.
Для сварки изделий из Ст3сп целесообразно использовать проволочные электроды (чаше всего, с большим сечением), плавящимися мундштуками.
Форма поставки стали Ст3сп
Поставляется данная сталь в различных формах — поковки и отливки, сортовая сталь – листы, трубы квадратные и круглые, прокат фасонный (двутавры, тавры, швеллеры, уголки), слитки, слябы и блюмы, сутунки, заготовки, метизы, проволока, ленты, штамповки и пр.
Область применения
Изготовление элементов несущих конструкций, сварных и не сварных деталей и изделий, эксплуатируемых при положительных температурных режимах. А также листовой и фасонный прокат, эксплуатация которого производится при условиях температур -40°С — +425°С, и/или нагрузок с переменными значениями (статических, динамических).
Применение стали Ст3сп с учётом характеристик и свойств
Сталь данного типа является одной из самых востребованных в строительстве и промышленности.
Отсутствие в сплаве кислорода, и однородная структура – это факторы, повышающие стойкость к образованию коррозии в агрессивных средах. Эти качества, а также большая пластичность делают данную сталь незаменимой при производстве конструкций, элементов, к которым предъявляются большие требования по жёсткости.
Это прокат – листовой и фасонный (швеллеры, двутавры и тавры, уголки), заготовки для арматуры, элементы трубопроводов (в частности, квадратные трубы), и пр.
Характеристики стали дают возможность возводить из неё опорные несущие конструкции, каркасы, эксплуатация которых ведётся в сложных условиях.
Из стали Ст3сп изготавливают элементы и детали без термообработки, что даёт возможность сохранить все характеристики сплава – фланцы, тройники, переходы.
Сталь используют также в качестве основного слоя при производстве горячекатаных 2-слойных листов, стойких к коррозии.
Аналоги Ст3сп
Марка ст3сп (аналоги — С255, ВСт3сп5-1 и 18сп, Е 235-C по ISO 630:1995)
×
Отмена Удалить
×
Выбрать тариф
×
Подтверждение удаления
Отмена Удалить
×
Выбор региона будет сброшен
Отмена
×
×
Оставить заявку
×
Название | |||
Отмена
×
К сожалению, данная функция доступна только на платном тарифе
Выбрать тариф
Сварка чугуна — Все о сварке
Этот способ газовой сварки чугуна применяют в тех случаях, когда место сварки и характер конструкции позволяют выполнять местный подогрев без появления трещин и напряжений в свариваемых изделиях. Местный предварительный подогрев применяют при сварке массивных деталей или деталей, конструкция которых не создает жесткого контура. В этих случаях участок местного подогрева выбирают так, чтобы в детали создавались тепловые деформации, равнозначные деформациям, которые возникнут на участке сварки, имеющей трещину на участке равномерную тепловую деформацию, необходимо осуществить, подогрев противоположного плеча на участке 2.
Сварка чугунной рамы
Местный подогрев свариваемых деталей выполняют до температуры 300—500°С сварочными горелками, паяльными лампами, индукционным электронагревом и другими способами. При сварке применяют нормальное сварочное пламя или пламя с небольшим избытком ацетилена. Мощность сварочного пламени выбирают из расчета расхода ацетилена 100—120 дм3/ч на 1 мм толщины свариваемого металла. В качестве присадки используют чугунные прутки марки Б диаметром 4, 6, 8, 10 и 12 мм, длиной 250—450 мм. Согласно ГОСТ 2671—80, чугунные прутки марки Б содержат 3,0—3,5% С, 3,5—4,0 Si, 0,5—0,8% Мп, не более 0,08% S, 0,3—0,5% Р, 0,05% Сr и 0,3% N. После сварки места подогрева медленно охлаждают, для чего прикрывают их асбестом и засыпают песком.
Холодная сварка чугуна
Холодная сварка чугуна используется если при нагревании и охлаждении детали свободно сжимаются и расширяются, не вызывая больших остаточных напряжений, в этом случае мощность пламени горелки должна быть максимально возможной. Технологический процесс сварки без предварительного нагрева почти аналогичен процессу горячей сварки, однако имеет и свои особенности. Перед заваркой дефекта необходимо подогревать пламенем горелки участки, прилегающие к дефекту. После окончания заполнения дефекта горелку в течение 2—3 мин медленно отводят, направляя пламя на участки, прилегающие к дефекту. Деталь или часть детали, на которой находится заваренный участок, для медленного охлаждения засыпают песком или покрывают асбестом.
Способ низкотемпературной пайки-сварки чугуна отличается от обычных способов тем, что основной металл не доводится до температуры плавления, а нагревается только до температуры 820—860°С, т. е. до температуры «смачиваемости». Этот способ разработан в институте ВНИИавтогенмаш и основан на применении специальных чугунных прутков и флюсов. Капли расплавленного присадочного металла под действием сварочного пламени легко растекаются по поверхности свариваемого металла, обеспечивая плотное соединение свариваемых деталей. Низкотемпературную сварку чугуна используют при заварке литейных дефектов деталей из серого чугуна, а также при заварке чугунных деталей в готовых изделиях в случаях их поломки, появления трещин и других дефектов. В качестве присадки для заварки тонкостенных отливок применяются чугунные прутки НЧ-2, а для толстостенных — чугунные прутки УНЧ-2. Для низкотемпературной пайки-сварки чугуна применяют специальные флюсы ФСЧ-2 и МАФ-1. Применяемые флюсы химически очищают нагретую свариваемую поверхность от оксидов, жиров и других загрязнений, увеличивают прочность сцепления наплавленного металла с основным, увеличивают жидкотекучесть расплавленного металла и защищают нагретую поверхность и расплавленный металл от кислорода и азота воздуха.
Состав флюсов для низкотемпературной пайки-сварки чугуна приведен в таблице.
Состав | Марка флюса | Состав | Марка флюса | ||
ФСЧ-2 | МАФ-1 | ФСЧ-2 | МАФ-1 | ||
Бура плавленая Сода кальцинированная Азотно-кислый натрий Селитра натриевая | 23 — 50 — | 33 12 — 27 | Углекислый литий Углекислый натрий Фтористый натрий Фторцирконий калия Оксид кобальта | 0,5 26,5 — — — | — — 12,5 8,5 7 |
Разделку дефектного, участка под низкотемпературную сварку выполняют фрезерованием, сверлением или строганием. Место сварки предварительно зачищают до металлического блеска. Профиль разделки кромок сквозных и несквозных дефектов представлен на рисунке. Угол разделки составляет 70—90°. Неглубокие поры и шлаковые включения вырубают зубилом или удаляют шлифовальным кругом. Перед сваркой изделие подогревают горелкой до температуры 300—400°С. Изделия сложной формы нагревают в печи.
Схема устранения сквозных дефектов (трещин) показана на рисунке. При устранении засверленных дефектов (пористость, раковины) присадочный металл наносят по винтовой восходящей линии. На нагретую наплавляемую поверхность равномерно наносят слой флюса. Место сварки нагревают горелкой до температуры 820—860°С, пламя должно быть строго нормальным. При этой температуре паста-флюс плавится, покрывая тонкой пленкой место сварки. Присадочный пруток также покрывают флюсом. Расплавляясь, присадочный металл стекает на завариваемую поверхность и растекается по ней. Сварку ведут левым способом. Расстояние между ядром пламени и концом прутка должно составлять 2—3 мм, угол между осью горелки и плоскостью детали — 20—30°.
После сварки изделие медленно охлаждают под слоем асбеста или в песке. Так как при данном способе основной металл не доводят до расплавления, то отсутствуют участки отбеленного чугуна и металл шва получается плотным, мягким и хорошо обрабатывается механическими способами.
Профиль разделки дефекта под пайкосварку: а — разделка несквозиого дефекта, б — сквозного дефекта с применением подкладки из огнеупорного материала
При низкотемпературной пайке-сварке чугуна вместо ацетилена можно применять газы-заменители. При применении в качестве горючего газа пропан-бутана мощность сварочного пламени выбирают из расчета пропан-бутана 60—70 дм3/ч на 1 мм толщины свариваемого металла. Пламя берется нормальное. При толщине металла до 6 мм сварку выполняют за один проход, при толщине 9—12 мм — в два прохода. При использовании в качестве флюса ФСЧ-2 рабочая температура составляет 900—950°С. При такой температуре не исключено появление структур закалки в зоне термического влияния, поэтому указанный флюс имеет ограниченное применение. Его используют в тех случаях, когда допускается повышенная твердость наплавленного металла. Флюс МАФ-1 позволяет вести процесс низкотемпературной пайки-сварки при рабочей температуре 750—800°С.
Схема устранения сквозных трещин (а) и засверленных дефектов (б)
В некоторых случаях целесообразно применять пайку-сварку чугуна латунными припоями. Этот метод используют при ремонтной сварке. Преимущество пайки-сварки чугуна латунью по сравнению со сваркой плавлением заключается в том, что нагрев чугуна до температуры плавления латуни (850—900°С) существенно не изменяет структуры металла, что исключает опасность отбела чугуна и не вызывает значительных термических напряжений. Кромки детали толщиной до 25 мм скашивают под углом 45°, а при большей толщине рекомендуется ступенчатая разделка; при пайке-сварке латунью лучше, когда поверхности соединяемых кромок шероховаты.
Углерод с поверхности соединяемых кромок выжигают на глубину 0,12—0,15 мм двумя способами: соединяемые кромки детали покрывают пастой из железных опилок и борной кислоты и нагревают пламенем горелки до 750— 900°С; кромки детали нагревают пламенем горелки, отрегулированным с избытком кислорода до той же температуры. Наибольшее применение нашел второй способ. Техника пайки-сварки состоит в следующем. Кромки нагревают до красного цвета, посыпают флюсом и облуживают участками. Сварочное пламя должно быть нормальным или с небольшим избытком кислорода. Деталь должна находиться в наклонном положении, пайку-сварку выполняют снизу вверх. Положение горелки и присадочного металла такое же, как при правом способе. Мощность сварочного пламени выбирается из расчета 60—75 дм3/ч ацетилена на 1 мм толщины.
Для пайки-сварки разработаны специальные флюсы ФПСН-1 и ФПСН-2, которые нейтрализуют действие свободного графита, частицы которого выступают на свариваемой поверхности и мешают ее смачиванию. В качестве припоя используется кремнистая проволока ЛОК 59-1-03, содержал в среднем до 0,3% Si. Для пайки-сварки изделий, к механическим свойствам которых предъявляются повышенные требования, применяют припой ЛОМНА 49-25-10-4-0,4, содержащий Сu, Sn, Mn, Ni и до 0,6% Аl. При пайке этим припоем металл паяльно-сварного шва имеет цвет чугуна, твердость НВ 180—200 и временное сопротивление разрыву 280—340 МН/м2.
Для пайки используют поверхностно-активный флюс марки ФПСН-2. Он содержит 45% борной кислоты, 22,5% углекислого лития, 22,5% соды кальцинированной и 10% солевой лигатуры. Его применяют в виде порошка или пасты. Флюс плавится при температуре 600—650°С. Пайку выполняют обычной сварочной горелкой, работающей на ацетилене или газах-заменителях. Вначале при пайке-сварке слегка окисленным пламенем нагревают место наплавки до 450—500°С, а затем в разделку вводят флюс. Пайку-сварку начинают в момент плавления флюса, направляя пламя на прилегающие к разделке участки. Расплавленный флюс прутком припоя равномерно распределяют по всей поверхности завариваемого места; затем пламя направляют на конец прутка, расплавляют его и заполняют разделку металлом припоя. Наплавленный металл сразу же после сварки проковывают ручным медным молотком.
Горячая сварка чугуна
Горячая газовая сварка чугуна нашла широкое применение при исправлении дефектов литья, а также ремонте небольших чугунных деталей. Способ горячей сварки чугуна является наиболее надежным, обеспечивающим лучшее качество сварного соединения. Выбор способа сварки определяется составом чугуна, конструкцией детали, характером дефекта и условиями работы. Процесс горячей газовой сварки разбивается на целый ряд отдельных операций, от которых зависит качество сварного соединения. К этим операциям относятся: подготовка деталей под сварку, предварительный подогрев деталей, сварка деталей, охлаждение деталей после сварки. Подготовка к сварке определяется видом дефекта отливки или характером поломки детали. Для предотвращения распространения трещин концы их перед сваркой рекомендуется засверливать. Раковины, трещины и другие поверхностные дефекты подготавливают разделкой места заварки. Разделку ведут вырубкой или другими механическими способами. Свариваемое изделие перед сваркой собирают и прихватывают по кромкам. Диаметр прихваток не должен превышать 5—6 мм. Без подготовки кромок сваривают детали толщиной до 4 мм. На деталях толщиной свыше 5 мм выполняют разделку кромок под углом 70—90°.
Температура общего предварительного подогрева определяется размером деталей, толщиной стенок, жесткостью конструкции, объемом наплавляемого металла и структурой чугуна. Общий подогрев свариваемых деталей ведется в электрических и газовых печах, а при единичных ремонтных работах — в специальных термических печах, ямах и горнах. Для общего нагрева, а также последующей термической обработки сваренных деталей используют горны и печи различного типа. На рисунке представлен горн, состоящий из металлического каркаса 1 и чугунной опоки 2 с колосниковой решеткой 3. Естественная тяга через колосниковую решетку обеспечивает такую скорость сгорания кокса, которая необходима для постепенного нагрева деталей.
При сварке чугуна используют также камерные печи и печи с выдвижным подом. При отсутствии специальных печей на месте сварки сооружают временные печи. При пользовании временными печами деталь обкладывают древесным углем и закрывают асбестом. Для поступления воздуха делают снизу отверстие или оборудуют специальную систему поддува. После того как свариваемая деталь нагреется до требуемой температуры, ее извлекают из печи и подают на рабочее место сварщика. Во избежание охлаждения свариваемой детали во время сварки ее закрывают листовым асбестом. Открытым остается только место сварки. После сварки изделие медленно охлаждают в яме или вместе с горном. Равномерное и медленное охлаждение предупреждает коробление, образование трещин и структур отбела.
Сварку чугуна выполняют нормальным пламенем или пламенем с небольшим избытком ацетилена. В начале сварки пламя горелки устанавливают почти вертикально, по мере сварки делают необходимый угол в зависимости от толщины свариваемого металла. Ядро пламени должно находиться на расстоянии 2—3 мм от поверхности свариваемого металла. Наконечник горелки выбирают из расчета расхода ацетилена 120 дм3/ч на 1 мм толщины свариваемого металла.
Печи: камерная (а) и с выдвижным подом (б)
В качестве присадки согласно ГОСТ 2671—80 для горячей газовой сварки применяют чугунные прутки марки А диаметром 4, 6, 8 и 12 мм, длиной 250—450 мм. Чугунные прутки марки А имеют следующий химический состав: 3,0—3,5% С, 3,0—3,4% Si, 0,5—0,8 Мп, не более 0,08% S, 0,2—0,4% Р, не более 0,05% Сr, 0,3% Ni. Чугунные прутки марки А с торца маркируют белой краской. Прутки должны храниться в сухом месте в ящиках или на стеллажах. При горячей сварке чугуна необходимо учитывать резкие переход из жидкого состояния в твердое и образование окисной пленки на поверхности жидкой ванны, что затрудняет выделение газа из жидкого металла. Для облегчения выделения газа сварочную ванну необходимо непрерывно помешивать присадочным прутком. При горячей газовой сварке чугуна применяют флюс, способствующий улучшению процесса сварки и удалению образовавшихся оксидов. В качестве флюса используют прокаленную буру или смесь 56% прокаленной буры, 22% углекислого натрия и 22% углекислого калия. Кроме того, при сварке чугуна можно применить газообразный флюс БМ-1 (ТУП 42—64).
В процессе сварки сварщику необходимо следить за тем, чтобы в наплавленном металле не оставалось шлака и расплавленный присадочный металл хорошо сплавлялся с основным металлом. Для получения сварного соединения, свойства которого равноценны свойствам основного металла, необходимо после сварки уменьшить скорость охлаждения. Для этого пламя сварочной горелки отводят от поверхности свариваемого металла на 50—60 мм, а наплавленный металл подогревают пламенем в течение 1—1,5 мин. Для уменьшения внутренних напряжений в массивных деталях сложной конфигурации рекомендуется сваренные детали подвергать вторичному нагреву до температуры 600—750°С и охлаждать вместе с печью.
Холодная сварка для металла — разновидности, помощь в выборе
Во время строительства и ремонта возникают ситуации, когда нельзя проводить соединение металлических конструкций и деталей сварным швом при высоких температурах. Альтернативным вариантом для получения надежного крепления является холодная сварка. В чем причины популярности метода, поможет понять подробное знакомство с особенностями используемых материалов и технологией проведения работ.
Содержание
- 1 Что представляет сварочный состав, характеристики и виды
- 1.
1 Состав клеящих композитов
- 1.2 Разновидности холодной сварки для металла
- 1.
- 2 Особенности холодной сварки для алюминия
- 3 Термостойкая холодная сварка для металла
- 4 Как выбрать холодную сварку для металла
- 5 Лучшая холодная сварка для металла
- 6 Инструкция проведения холодной сварки для металла
- 7 Секрет популярности холодного сваривания
- 8 Заключение
Что представляет сварочный состав, характеристики и виды
Основой для сцепления металлических частей друг с другом служит специальный клей. Он представляет собой пластичную массу, глубоко проникающую внутрь металла. Под влиянием составляющих компонентов разрушается оксидная пленка и образуется прочная кристаллическая решетка. Процесс склеивания схож со сваркой давлением. Технология применяется для соединения цветных, черных и нержавеющих металлов.
Состав клеящих композитов
Ингредиенты холодной сварки влияют на прочность шва, время застывания, параметры температурного режима, которые он выдерживает. От состава смеси зависит область ее применения. Основу клея различных производителей составляют:
- Эпоксидная смола. Компонент, обеспечивающий однородность структуры, сцепление частиц состава, и его пластичность.
- Отвердители. Вещества, ускоряющие полимеризацию и затвердевание клея.
- Наполнители. Металлические или минеральные порошки, повышающие прочность шва, устойчивость к воздействиям, температуру выдержки.
- Пластификаторы. Ингредиенты, придающие пластичность и увеличивающие сопротивляемость к ударам и механическим воздействиям.
Работу с каждым отдельным видом клея необходимо проводить в соответствии с технологической инструкцией. Эксплуатация обработанных объектов должна осуществляться с соблюдением условий, рекомендованных производителем.
Разновидности холодной сварки для металла
По консистенции клей для сваривания бывает жидкий и твердый. В первом случае продукт представляет собой два компонента, которые смешиваются друг с другом перед применением. Твердая клеевая масса продается в виде однородной или двухслойной пасты. Оба состава после высыхания образуют прочное крепление.
В зависимости от сферы применения холодная сварка бывает четырех видов:
- Универсальная. Клей, в состав которого входят полимеры. Материал подходит для сцепления металлических, пластиковых, резиновых поверхностей.
- Автомобильная. Композит, предназначенный для заделки щелей и ликвидации незначительных повреждений на металлических частях автотранспорта.
- Высокотемпературная. Сварка, отличающаяся повышенной вязкостью и стойкостью к воздействию высоких температур. Сварной шов после застывания выдерживает t от -60°C до +1500°C.
- Водостойкая. Данный вид клея имеет двухкомпонентный состав, не теряющий прочности при постоянном нахождении в воде. Это идеальный материал для ремонта коммуникационных сетей.
Готовая масса для склеивания быстро становится непригодной к применению. Поэтому нецелесообразно перед началом работ делать заготовки в большом объеме.
По назначению и месту нанесения композит бывает:
- Точечный. Используется для устранения небольших зазоров, сваривания мелких деталей с крупными объектами.
- Шовный. Для ремонта герметичных тонкостенных емкостей и сосудов.
- Тавровый. Применяется для фиксации шпилек, обмоток трансформатора, шинопроводов.
- Стыковой. Используется для сварки проводки, замыкания концов, образования колец.
- Сварка сдвигом. Подходит для ремонта водопроводов и труб системы отопления.
От состава клея зависит способность сварного шва выдерживать определенный диапазон температур. Эти величины указываются на упаковке продукта. Соблюдение допустимых минимальных и максимальных параметров гарантирует прочность и надежность крепления.
Особенности холодной сварки для алюминия
Соединение заготовок из этого металла с помощью гаек и болтов не всегда образует прочное крепление. В тех случаях, когда нет возможности использовать электродуговую сварку, алюминиевые заготовки скрепляются специальными клеевыми составами. С их помощью быстро и качественно образуется надежный сварочный шов.
Данный способ позволяет без подготовки быстро и качественно получить неразъемное соединение. Ее применение актуально для устранения аварийных ситуаций и поломок.
Клей для алюминия выпускается в виде мастики или густой жидкости. В его состав входят:
- эпоксидная клеевая основа;
- стиральный порошок, упрочняющий соединение;
- специальные присадки, повышающие устойчивость к высоким температурам и агрессивным средам.
Компоненты, содержащиеся в мастике, придают застывшему покрытию повышенную прочность. Сварной шов превосходит по прочности сам металл.
После завершения работы необходимо тщательно очистить инструмент и место сварки алюминиевых поверхностей от лишнего клея. Избавиться от излишков и наплывов материала после засыхания очень сложно.
Термостойкая холодная сварка для металла
Высокотемпературные клеевые составы широко используются в промышленной сфере и для ремонта в быту. Главное отличие термостойкого клея – способность образовывать шов, выдерживающий температуру свыше 1000°C. Компоненты, входящие в смесь, улучшают эксплуатационные характеристики материала. Под воздействием экстремально высоких температур, прочность сварного соединения увеличивается.
Композит поступает в продажу в готовом виде. Перед его применением не требуется специальной подготовки и перемешивания. Затвердевшая поверхность не поддается коррозии и воздействию агрессивных сред. Места склеивания легко шлифуются песком.
При выборе клеевого состава, необходимо учитывать температуру плавления самого металла. Не имеет смысла покупать клей с термостойкостью, превышающей этот показатель у обрабатываемых деталей.
Как выбрать холодную сварку для металла
Грамотный подход к подбору композиционного материала – залог получения надежного сварного шва. Перед покупкой посмотрите следующие характеристики:
- тип свариваемых поверхностей;
- минимальные и максимальные границы температур, подходящих для эксплуатации;
- срок годности;
- время, необходимое для проведения работы;
- период полного застывания композита.
Клей поступает в продажу в упаковке различного размера и объема. Расход материала рассчитывается исходя из минимально допустимой плотности нанесения состава.
Лучшая холодная сварка для металла
Различные марки клея имеют в своем составе одинаковую основу. Главным отличием являются модификаторы и пластификаторы, которые используются производителями. Отечественные композиты заслуживают внимания не меньше чем зарубежные материалы. Популярность у потребителей завоевали следующие марки:
- «Контакт». Двухкомпонентная холодная сварка из полиэпоксидной смолы и отвердителя. С ее помощью восстанавливают форму обрабатываемого объекта, устраняют полости и герметизируют соединения.
Клей-пластилин отличается стойкостью к воздействию воды, растворителей и нефтепродуктов. Материал поступает в продажу в готовом к использованию виде. Кроме металлов и сплавов склеивает: стекло, дерево, фарфор, камень, бетон, жесткий ПВХ, мягкие пластики. Сварной шов выдерживает эксплуатацию при t от-30°C до +160°C.
- Hi-Gear или «Быстрая сталь». Продукт производства США состоит из двух компонентов, в состав которых входит металлический порошок. Затвердевшая поверхность композита устойчива к температурам до +260°C и воздействию агрессивной среды.
- «Металлопластилин алюмополимерный». Клей повышенной вязкости содержит мелкодисперсную алюминиевую пыль. Материал отличается высоким сцеплением с цветными металлами, стойкостью к воздействию воды, антифриза и бензина. Его используют для сварки высоколегированных нержавеющих сталей, алюминия, латуни и меди.
- «Эпокси-титан». Особо прочный композит с регулируемой эластичностью.
Он применяется для соединения: металла, керамики, гранита, пластмассы, дерева. С его помощью надежно заделываются трещины, отверстия в трубопроводах, радиаторах, крепежных элементах. Предел прочности застывшего шва при сдвиге составляет более 30 МПа. Это позволяет проводить сварку объектов, подверженных вибрации, деформации на изгиб и ударным нагрузкам.
Инструкция проведения холодной сварки для металла
Производители клея обязаны прилагать к своему продукту руководство по применению. Перед началом работ необходимо ознакомиться с рекомендациями, указанными в нем. Общая схема проведения сварки любых марок состоит из следующих этапов:
- Место склеивания зачищается наждачной бумагой.
- Металлические поверхности обезжириваются спиртом или ацетоном.
- Композит подготавливается к работе. Если клей двухкомпонентный и находится в разных тюбиках, их содержимое смешивается в отдельной посуде.
- Клеевая масса наносится на место сварки и плотно прижимается.
- Затвердевшая поверхность шлифуется.
Нанесение композита рекомендуется проводить поэтапно, несколькими слоями. Это способствует повышению прочности соединения.
Секрет популярности холодного сваривания
Это универсальное средство для ремонтных работ в быту и промышленной сфере. Преимущества применения специального клея:
- простота в использовании;
- стойкость полученного соединения к коррозии и воздействию агрессивных сред;
- соответствие нормам экологической безопасности;
- экономия затрат на газ и электроэнергию;
- затвердевание поверхности в течение 3 часов;
- отсутствие отходов после завершения работ;
- податливость обработке песком.
Для того чтобы проводить холодную сварку, не требуется дополнительное оборудование и профессиональная подготовка.
Заключение
Применение холодной сварки не способно полностью заменить традиционные способы. Благодаря неоспоримым достоинствам композитных материалов, они подходят для восстановления и ремонта металлических конструкций и элементов.
Используемая литература и источники:
- Статья на Википедии
- Сварка металлов. Термины и определения основных понятий. — М.: ИПК Издательство стандартов, 1984.
- Гладков Э. А., Бродягин В. Н., Перковский Р. А. . Автоматизация сварочных процессов. — М.: Изд-во МГТУ им. Н. Э. Баумана, 2014.
- Howard B Cary; Scott C. Helzer Modern Welding Technology. Upper Saddle River, New Jersey: Pearson Education. (2005).
Ремонт бензобака своими руками — как отремонтировать бензобак
Во время эксплуатации автомобиля порой возникают различные неисправности, связанные непосредственно с бензобаком. Нужно заметить, что все проблемы следует решать сразу же, как только они обнаруживаются. В противном случае значительно снижается безопасность, а также эффективность работы. В некоторых случаях вполне можно провести ремонт бензобака своими руками. Однако необходимо соблюдать определённые требования, а также располагать некоторыми навыками.
Основные проблемы
Ржавчина
В ходе эксплуатации возникают разнообразные проблемы с бензобаком. Причиной может послужить ржавчина или регулярная езда по плохим дорогам. Стоит чиркнуть днищем или зацепить что-нибудь, как сразу же появляются трещины, пробои или иные повреждения.
Если в салоне начинает пахнуть бензином, то это явный признак того, что бензобак или топливная система повреждены. Также стоит обращать внимание на расход топлива – если он превышает норму, то, возможно, причина как раз кроется в этом.
Прохудившийся бензобак
В любом случае передвигаться на автомобиле, у которого протекает бензобак, не просто небезопасно, а запрещено. Именно поэтому следует сразу же принять соответствующие меры, чтобы восстановить всё.
Подготовка к ремонту бензобака
Иногда нужно снимать
Прежде чем начинать ремонт бензобака, следует ознакомиться с общими правилами и техникой безопасности:
- Опустошить бензобак, слив всё топливо.
- Демонтировать бензобак.
- Подготовить всё необходимые инструменты.
Тут необходимы некоторые пояснения. Во-первых, перед началом работы следует подготовить бензобак надлежащим образом. Чтобы слить полностью топливо потребуется приподнять автомобиль домкратом и наклонить его. После этого некоторое время следует подождать, чтобы он просох. В некоторых случаях лучше даже промыть его водой.
Во-вторых, нужно внимательно осмотреть повреждения. В зависимости от этого будет понятно, снимать ли бензобак или можно провести ремонт и так.
Как только всё это будет улажено, можно приступать непосредственно к ремонту. Существует множество различных способов. Каждый выбирает тот, который подходит под конкретную ситуацию лучше всего.
Ремонт методом пайки
Метод пайки
Если имеются не слишком значительные повреждения, то тогда стоит воспользоваться обычным паяльником и паяльным флюсом – канифолью и жиром.
Автомобильный бак подготавливается надлежащим образом к работе. Область вокруг повреждения следует хорошо зачистить и обезжирить. Для обработки используется ортофосфорная кислота (20%). Далее подготавливаются оцинкованные заплатки и припаиваются на место пробоя.
Данный способ вполне удобен и надёжен. Однако требуется тщательная подготовка, в том числе демонтаж непосредственно самого бензобака.
Использование эпоксидной смолы и стеклоткани
Стеклоткань и эпоксидная смола
В качестве заплатки, которая позволит устранить течь и заделать пробой, может использоваться эпоксидка и стеклоткань. В данном случае также происходит зачистка области вокруг повреждения, а затем наносится слой ткани, пропитанный в смоле. Подобным образом наносится несколько слоев. Каждый раз необходимо дать подсохнуть предыдущему. В конце следует всё отшлифовать, подровнять, обработать антикором и подкрасить.
В качестве временного способа можно использовать и другие материалы, например, обычную ткань и клей. Если пробой образовался в пути, то этот вариант наиболее оптимальный, чтобы устранить на время течь.
Вообще, этот способ один из самых лучших – ремонт занимается всего несколько часов, при этом не требуется использование каких-то специальных инструментов.
Установка заплаток «холодной сваркой»
Холодная сварка
Одним из наиболее популярных методов является так называемая «холодная сварка». В чём-то этот способ похож на предыдущий – с использованием смолы и ткани. Данное средство продаётся в любом специализированной магазине. Необходимо смешать два компонента, чтобы образовалась пластичная масса. Она затвердевает буквально за 10–20 минут, поэтому идеально подходит для заплаток. Предварительно также следует зачистить поверхность вокруг повреждения.
Метод достаточно простой и надёжный, так что подойдёт многим.
Устранение трещин сваркой
Приваренные заплатки
Это один из самых надёжных и радикальных методов решения проблемы. По сравнению с остальными это, без сомнения, самый надёжный и качественный способ. Однако есть определённые сложности: следует демонтировать бак автомобиля, слить топливо, просушить его.
Как правило, к сварке обращаются при достаточно серьёзных повреждениях, например, когда пробоина слишком большая, чтобы ставить обычную заплатку. Тогда повреждённый кусок буквально вырезается и на его место устанавливается новый.
В любом случае заваривать топливный бак следует предельно осторожно, соблюдая все меры предосторожности, так как вы будете работать с емкостью, в которой находился бензин.
Видео
Вот пример сварки бензобака:
REC Wiki » Как бороться с деформациями при 3D-печати
Любой производственный процесс, включающий охлаждение полимеров или металлов, будет сопровождаться усадкой материалов, будь то литье пластмасс под давлением, литье металлов или 3D-печать. В этой статье поделимся хитростями, помогающими бороться с нежелательными эффектами усадки — деформациями, растрескиванием и отлипанием.
Когда дело доходит до деформации при литье пластмасс под давлением, инженеры должны учитывать скорость охлаждения, давление и скорость заполнения. Деформации при работе с листовыми металлами устраняются с помощью отжига, угловой геометрии и особых методов сварки. В 3D-печати усадка возникает, когда более ранние и более поздние слои охлаждаются с разной скоростью.
Вытекающие деформация чреваты как проблемами с размерной точностью, так и эстетическими дефектами. Когда слои большой площади охлаждаются и сжимаются, они могут смещать элементы моделей. Подобные дефекты зачастую можно увидеть невооруженным глазом, и в тяжелых случаях усадка может приводить к искривлению поверхностей и дислокации посадочных мест и технических отверстий в печатаемых деталях.
Пример отрыва и закручивания из-за сильной усадки
На самом деле при 3D-печати усадка неизбежна, только проявляется она по-разному в зависимости от геометрии моделей, режимов печати и используемых материалов. По этой причине усадку стоит принимать во внимание еще на этапах проектирования и подготовки моделей к 3D-печати.
В этой статье мы поделимся советами по борьбе с усадкой, подходящими не только для FDM 3D-печати, но многих других методов аддитивного производства.
У 3D-печати и мультиков есть что-то общее
Процесс послойной 3D-печати в чем-то подобен кинеографам. Это такой старый метод мультипликации, когда отдельные кадры рисуются на листах бумаги, а затем складываются в стопку. Если их быстро пролистать, рисунки приходят в движение. Для того чтобы анимация была плавной, каждый кадр должен перетекать в следующий с минимальными изменениями.
Этот же принцип действует и в FDM 3D-печати, да и многих других методах аддитивного производства. Если дизайну 3D-модели не хватает «текучести», а тем более если геометрия сильно «прыгает» от слоя к слою, нужно постараться сгладить процесс либо изменением дизайна, либо изменением ориентации модели на рабочем столике. Чем плавнее переход от одного слоя к другому, тем лучше. Изделие выйдет не просто более эстетичным, но и геометрически более точным.
Большинство слайсеров позволяют предварительно просматривать построение модели слой за слоем еще до генерации G-кода. Воспользуйтесь этой возможностью, и если заметите резкие перепады в контурах слоев, внесите необходимые изменения в форму модели, либо постарайтесь повернуть ее так, чтобы переходы были более плавными.
Стремитесь к органичным формам
3D-печать органичной, бионической структуры на стереолитографическом 3D-принтере
Вы наверняка замечали по разным иллюстрациям, что в профессиональной 3D-печати часто используются бионические элементы, то есть навеянные природой: например, угловатые и плоские формы заменяются структурами, похожими на ветви деревьев.
Это не случайно, ибо замена углов скруглениями — один из наиболее простых и эффективных методов борьбы с усадкой. Это способствует более плавному переходу от слоя к слою, как описано выше. Наиболее важны скругления углов внутри модели, но если дизайн позволяет, можно закруглить и внешние углы и поверхности. Даже небольшие скругления могут сильно повлиять на результат. Например, скругления с радиусом 0,15 мм хватит, чтобы снять напряжение с кромки. Чем выше радиус, тем лучше, лишь бы он не влиял на толщину стенок. Берите пример с оплавленных свечек — это прекрасный пример натуральной геометрии. Собственно, поэтому в генеративном дизайне алгоритмы топологической оптимизации и генерируют структуры, подобные деревьям или кораллам — в природе идеально плоские поверхности и резкие углы встречаются крайне редко.
Углы и толщина стенок
Пример деформации и расслоения
Прямые углы на деталях обычно приводят к резким изменениям в площади сечений, что нежелательно. По мере возможности старайтесь заменять прямые углы двумя или несколькими, например двумя по 45 градусов.
Еще одна хорошая идея — равномерная толщина стенок. Если стенки быстро сужаются или утолщаются, это приведет как резкому изменению площади и неравномерному охлаждению, что может привести к деформациям и даже растрескиванию. Если стенки разной толщины регламентированы дизайном, постарайтесь хотя бы округлить углы.
Какой должны быть толщина стенок? Ответ зависит от материала, геометрии и процесса, но за отправную точку можно взять толщину в 1% от самого большого габарита самого изделия — длины, ширины или высоты, смотря что больше. Это правило стоит применять к изделиям размером больше 75 мм, но меньше 250 мм. Если деталь меньше, повышайте относительную толщину, а если больше — уменьшайте. Если речь идет о хрупкой детали, лучше пренебречь правилом в сторону утолщения стенок.
Ориентация модели
Пример закручивания
Во многих случаях нежелательные эффекты усадки можно смягчить изменением ориентации модели на рабочем столике. Например, зачастую более-менее плоские детали выгоднее печатать не плашмя, а под углом. Представьте деталь в форме буквы Н: когда принтер напечатает ножки и дойдет до перемычки, произойдет резкий перепад в площади сечения, и после усадки перемычка искривит ножки. Если же модель наклонить на бок, переходы будут более плавными, а значит снизится риск деформации. Угол наклона зависит от детали: наклонять на 45 градусов не обязательно, может хватить и 10-15. Минус в том, что 3D-печать под наклоном может повысить заметность слоев и расход материала на построение опорных структур. Некоторые технологии, например селективное лазерное спекание, не требуют построения поддержек, а потому метод снижения усадки за счет оптимальной ориентации в таких технологиях широко распространен.
Термокамеры и адгезионные средства
Помимо дизайна и ориентации модели бороться с деформациями помогают соблюдение температурного режима, вспомогательные структуры и адгезионные средства — клеи, лаки и специальные покрытия на столиках. Здесь все зависит от пластика для 3D-печати. Например, полилактид (ПЛА) обладает очень низкой усадкой, да к тому же низкой температурой плавления, поэтому подогрев столика и использование термокамеры при работе с этим полимером противопоказаны. Но бывает и наоборот: еще один популярный пластик для FDM 3D-принтеров — акрилонитрилбутадиенстирол (АБС), а он то как раз доставляет немало хлопот с усадкой, приводящей к деформациям, растрескиванию по слоям и даже отрыву моделей со столиков.
На примере АБС приведем несколько решений по борьбе с деформациями:
1. Перед печатью почистите столик изопропиловым спиртом. При необходимости, особенно если собираетесь печатать крупные изделия, нанесите адгезионное средство.
Вариантов тут множество: это может быть клей (специализированный состав, клей-карандаш или раствор ПВА-клея), лак для волос, раствор самого АБС в ацетоне (так называемый АБС-сок). Адгезионное средство необходимо наносить тонким, равномерным слоем.
2. По возможности используйте термокамеру. Многие FDM 3D-принтеры имеют закрытые камеры, помогающие стабилизировать фоновую температуру. В большинстве случаев это пассивные камеры, то есть воздух внутри нагревается столиком и хотэндом, но бывают и активные, термостатированные варианты с отдельными нагревателями и датчиками, позволяющими удерживать заданную температуру.
В крайнем случае можно смастерить или даже купить короб, накрывающий принтер целиком. Задача термокамер — удерживать печатаемую модель в более-менее равномерно разогретом состоянии до завершения работы, чтобы она могла остыть целиком, а не по слоям. Это, в свою очередь, помогает добиваться более равномерной усадки и тем самым избегать растрескивания.
3. Используйте подогреваемую платформу. Если без термокамер еще можно обойтись, подогрев столика почти всегда необходим при 3D-печати АБС. Усадка первых слоев, отвечающих за сцепление с рабочей поверхностью, приведет как минимум как закручиванию углов, а в худших случаях — к отрыву модели от столика.
Отчасти с этим помогают бороться упомянутые выше адгезионные средства, но немаловажную роль играет и нагрев столика. Используйте комбинированный подход: нанесите адгезионное покрытие и разогрейте столик примерно до 100-100°С для работы с АБС (другие полимеры требуются других температур).
4. Снизить риск отлипания от столика можно с помощью вспомогательных структур — рафтов и бримов. Рафты — отдельные слои увеличенной площади, поверх которых печатается изделие, бримы же наращивают площадь первых слоев самого изделия.
После 3D-печати рафты и бримы удаляются. Это повышает затраты как на расходный материал, так и постобработку, но с другой стороны значительно снижается риск отрыва модели и деформации из-за закручивания слоев — деформироваться буду рафты и бримы, а сама модель сохранит форму.
Идеальный вариант — использовать все четыре решения одновременно. Более подробно про повышение адгезии можно узнать в статье по этой ссылке.
рецепт приготовления кофе в турке
Мы собрали в одном месте наши статьи, посвященные различным способам заваривания кофе. Надеемся, вы найдете их полезными и будете применять, чтобы получить максимум от свежеобжаренного кофе.
Турка
Эспрессо
Мока
Френч-пресс
Кемекс
Пуровер
Сифон
Аэропресс
Необходимо
100 мл
Вода
10 г
Кофе
Сварить кофе в турке – это несложно. Это любимый способ приготовления кофе дома у многих. С
другой стороны это
тонкий, требующий особого подхода инструмент. По приготовлению кофе в ибрике, джезве, так ещё
называют турку,
проходят мировые чемпионаты. При всей своей простоте, процесс требует максимальной концентрации
внимания и
выполнения множества условий. Настоящая кофейная церемония, где каждое движение отзывается во вкусе.
Для того, чтобы приготовить кофе в турке, нужна хорошая жерновая кофемолка, способная производить
мелкий помол.
Помимо кофемолки нужна питьевая вода с низкой минерализацией (50–150 мг/л), комнатной
температуры, свежеобжаренный кофе, ложка для
перемешивания и сама
турка, или, как ее еще называют, ибрик или джезва. Советую использовать медную или керамическую
турку. Важно, чтобы у медной турки внутреннее покрытие было из
серебра или пищевого олова. Сосуд имеет широкое основание и сужается к верху,
имеет носик. Диаметр горлышка должен быть на 15-20% меньше основания, если джезва
стандартной геометрии (сужение ближе к верхней части, как на фото в нашей инструкции). Это
важно, чтобы сформировалась кофейная шапка.
Турки бывают разных размеров, от маленьких, на 1 чашку, до больших, на 6
или даже 8 чашек, но мы не рекомендуем использовать турку объемом свыше 300 мл.
В большой турке не получится выварить кофе, он скорее будет недоэкстрагированным (с травянистыми и
овощными оттенками во вкусе). Выбирайте джезву под объем вашей чашки.
Конечно, речь идет об условных чашках. Кроме того, важно, что в турке должно оставаться свободное
пространство при
приготовлении кофе, но не слишком много. При заваривании кофе будет подниматься в турке и
образовывать пену. Если
свободного пространства в турке будет слишком много, пена может пригореть к краям и придать
нежелательную
горечь.
При приготовлении кофе в турке обычно используется мелкий помол, как для эспрессо или чуть мельче. Мы рекомендуем отойти от слишком мелких фракций «в пыль» и попробовать помол покрупнее.
Когда кофе в турке приготовлен правильно, он очень насыщенный и густой. Очень важный совет – никогда не спускайте глаз с кофе, когда он заваривается в турке. Он может «убежать» в мгновение ока и запачкать вам плиту.
Если вы хотите разнообразить вкус напитка, в турку
можно добавить сахар и специи, например, кардамон, корицу или анис. В любом случае пользуйтесь правилом – добавляйте сыпучие ингредиенты (специи) к
молотому кофе, а жидкие (сироп) к воде.
Какой сорт кофе лучше использовать для приготовления в турке? Любой. Выбор сорта кофе – это дело вкуса. Не бойтесь пробовать робусту – она прекрасно ведет себя в турке. Для того, чтобы сварить кофе в турке, вы можете использовать кофе любой степени обжарки, какая вам нравится.
Вопрос о том, мешать или не мешать кофе, приготовляемый в турке, спорный. На наш взгляд, если кофе
помешать, когда он
уже снят с огня, то получается намного более чистая чашка, т.к. взвесь, присутствующая в пене,
оседает на дно.
Однако сторонники того, чтобы не мешать кофе во время приготовления, утверждают, что в каждую чашку
должно попасть
равное количество пены. Мешать или не мешать – дело предпочтений, но, в любом случае, процесс
перемешивания
происходит только на финальном этапе приготовления.
Итак, за дело!
*Встречаются турки, которые сужаются в середине, тогда диаметр горлышка может быть до 40% от диаметра дна.
Помните, что эти рекомендации по приготовлению кофе в турке – всего лишь отправная точка для ваших экспериментов. Смело меняйте их по вкусу!
Нам понадобятся:
- Чистая питьевая вода (общая минерализация 50-150ppm, комнатной температуры)
- Кофемолка – помол мелкий.
Помол визуально – «соль экстра». Для темной обжарки можно использовать покрупнее.
- Весы
- Турка
- Свежеобжаренный кофе
Чтобы сварить вкусный кофе в турке, мы рекомендуем соотношение кофе и воды 1:10 (на 20
г кофе – 200 мл воды). Это базовая пропорция, ее можно менять в зависимости от величины помола и
степени обжарки кофе.
Диапазон пропорции кофе к воде: от 1:8 до 1:12. Например, для светлой обжарки можно попробовать 1:8,
для темной – 1:12.
Пропорция влияет на интенсивность вкуса и плотность текстуры. Чем больше кофе по отношению к воде
– тем насыщеннее и ярче будет напиток, но важно не переусердствовать, чтобы не получить горькую
чашку». .
При расчете, ориентируйтесь на объём вашей турки, заполняйте её до точки сужения.
1 шаг
Отмерьте на весах и смелите необходимое количество кофе. Но весы использовать необязательно: например, в ладонь обычно помещается около 10 г зерна.
2 шаг
Засыпьте молотый кофе в турку и слегка потрясите, чтобы частицы легли равномернее.
3 шаг
Залейте чистую питьевую воду до точки сужения турки.
4 шаг
Поставьте турку на плиту на средний огонь (скажем, 5 из 9). Чем дольше будет вариться кофе, тем плотнее будет текстура. Для небольшой турки на 100-150 мл рекомендую 2-4 минуты, для 150-300 мл – 4–7 минут, но это уже дело вкуса.
5 шаг
Как только вы увидите, что кофе поднялся, уберите турку с огня. Если кофе начнет выбегать из-под шапки тонкой струйкой, аккуратнее: он вот-вот сбежит!
6 шаг
Слегка размешайте кофейную шапку и разлейте напиток по чашкам. Ничего сложного!
1. Кофе по-восточному
Кофе по-восточному готовится просто: берете кофе из группы B или R (однако ничто не мешает вам попробовать и светлую обжарку), добавляете зеленый кардамон, 2-3 коробочки, и сахар, лучше тростниковый. Кардамон используйте в зернах, но не смалывайте его в той же кофемолке, что и кофе. Вы получите замечательный крепкий напиток с пряным ароматом кардамона. Осторожно: он оказывает очень бодрящее действие!
2. Нежный кофе
Если вы хотите получить мягкий и сладкий напиток, этот рецепт – для вас! Для того,
чтобы сварить кофе в турке по этому рецепту, потребуется кофе сухой обработки, финиковый
(или
любой другой натуральный) сироп из расчета 3-5 г на 100 мл воды и палочка корицы. В принципе, сироп можно не использовать, так как кофе сухой обработки сладкий сам по себе.
Засыпьте кофе в турку, добавьте воду, предварительно размешав в ней сироп палочкой корицы.
Сварите напиток так, как вы обычно это делаете, но перед тем, как разлить по чашкам,
размешайте кофейную шапку не ложкой, а палочкой корицы. Тонкий пряный оттенок во вкусе
удивительным образом будет дополнять сладость, характерную для сухой обработки.
Читать статью на нашем канале в Яндекс.Дзен
Сварочное оборудование и автоматика Lorch
Решения, которые помогут вам двигаться вперед.
Узнать сейчас:
Умная сварка.
Во-первых, неважно, как вы это называете. Future Welding, Next level Welding… тоже хорошо, но: всегда ли можно выполнить требование? А о ком речь на самом деле? Единственное, что имеет значение, это то, что ВЫ получаете что-то от этого.
Итак, почему Смарт?
Дело только в хитрости в деталях продукта? Или речь идет об обдуманных решениях? Возможно, вы также думаете о людях, которых считаете умными.
Умный в Lorch означает:
Быть рядом с вами, понимать вас и ваши требования. Разработка высочайшего качества для практического использования. Быстрый в использовании и интуитивно понятный в управлении для неизменно высокого качества результатов сварки. Всегда стремитесь создавать для вас еще лучшие и экономичные решения — для требований завтрашнего дня. Потому что умным может быть только то, что делает вас более успешным!
Это разумно только тогда, когда улучшает ваше будущее.
Заявление, история, доказательство для вас.
Читать далее
Благодаря инновационным технологиям Lorch у вас есть все необходимое для любого применения.

Серия S
Настраиваемая импульсная производительность высокого класса: контроль, качество и совершенство.
Читать далее
Серия MicorMIG Pulse
Сварка с минимальным разбрызгиванием благодаря стабильной и контролируемой импульсной дуге.
Читать далее
Сварочный комплект Lorch Cobot
Версия MIG-MAG для еще большей эффективности сварки.
Читать далее
V-серия
Сварка ВИГ в тяжелых условиях для профессионалов.
Читать далее
Серия S-RoboMIG XT
Для максимальной производительности робота.
Читать далее
Ссылки, которые говорят сами за себя.
Практический. Универсальный. Экономичный.
Самый быстрый путь к правильной сварочной системе.
С помощью нашего удобного средства поиска продукции вы можете ускорить поиск и быстро найти устройства, отвечающие вашим требованиям.
Найти продукты сейчас
Действительно близко. Действительно практично. Настоящий Лорх.
Всегда лучшая консультация:
близко, лично и честно.
НАЙТИ СВОЕГО ПАРТНЕРА
Вопросы? Не стесняйтесь обращаться к нам.
СВЯЖИТЕСЬ С LORCH
Станьте партнером Lorch сейчас и пользуйтесь преимуществами.
Подробнее
Список сварочных процессов — Википедия, свободная энциклопедия
Список сварочных процессов — Википедия, свободная энциклопедия
http://en.wikipedia.org/wiki/List_of_welding_processes
Список процессов сварки
Из Википедии, свободной энциклопедии
Это список процессов сварки, разделенных на соответствующие категории. Связанные N ссылочных номеров (второй столбец) указаны в ISO 4063 (в Европейском Союзе опубликован как EN ISO 4063).[1] Цифры в скобках устарели и были удалены из текущей (1998 г.) версии ISO 4063. Справочные коды AWS Американского общества сварщиков обычно используются в Северной Америке.[2]
Содержание
1 Дуговая сварка 2 Газокислородная сварка 3 Сварка сопротивлением 4 Сварка в твердом теле 5 Другая сварка 6 Примечания и ссылки 7 См. также 8 Внешние ссылки флюс или защитный газ Угольный электрод, исторический Исторический Исторический Медь, ремонт (ограниченный) Промышленность, строительство Промышленность Применение Атомно-водородная сварка (149) AHW Дуговая сварка незащищенным металлом Углеродная дуговая сварка Дуговая сварка флюсовой проволокой Дуговая сварка металлическим газом [3] (113) BMAW (181) КАВ 136 137 131 135
FCAW Непрерывный плавящийся электрод, заполненный флюсом FCAW-S GMAW Непрерывный плавящийся электрод и защитный газ
1 из 5 ://en. wikipedia.org/wiki/List_of_welding_processes
Дуговая сварка вольфрамовым электродом в среде защитного газа
[4]
141 15 111 121 185
GTAW PAW SMAW SAW MIAB
дуга Расходуемый электрод, покрытый флюсом, может сваривать любой металл, если у них есть правильный электрод Автоматическая дуга, погруженная в гранулированный флюс, оба конца трубки являются электродами; нет защитного газа; дуга быстро вращается вдоль края под действием приложенного магнитного поля
Аэрокосмическая промышленность, строительство (трубопроводы), инструменты и трубы для штампов, контрольно-измерительные приборы Строительство, наружная работа, техническое обслуживание
Плазменно-дуговая сварка Дуговая сварка защитным металлом [5] Дуговая сварка под флюсом
трубопроводы и трубы
Газокислородная сварка
Название Воздушно-ацетиленовая сварка Кислородно-ацетиленовая сварка Кислородно-пропановая сварка Водородная сварка под давлением N AWS Характеристики Ограниченные Техническое обслуживание, ремонт Области применения (321) AAW Химический сварочный процесс, не популярный 311 312 313 OAW При сгорании ацетилена с кислородом образуется высокотемпературное пламя, недорогое оборудование Газовая сварка с кислородно-пропановым пламенем OHW При сгорании водорода с кислородом образуется пламя PGW Газовое пламя нагревает поверхности, а давление создает сварной шов Ограничено Трубы, железнодорожные рельсы (ограничено)
Сварка сопротивлением
Наименование Точечная сварка сопротивлением Сварка швом сопротивлением Выступающая сварка N 21 22 23 AWS RSW RSEW PW Характеристики Два остроконечных электрода применяют давление и ток к двум или более тонким заготовкам Два электрода в форме колеса катятся вдоль заготовок, применяя давление и ток Применение Автомобильная промышленность, аэрокосмическая промышленность Аэрокосмическая промышленность, стальные барабаны, трубы
2 из 5
24. 07.2013 20:39
Список сварочных процессов — Википедия, свободная энциклопедия
http://en.wikipedia.org/wiki/List_of_welding_processes
Сварка оплавлением Сварка с осадкой
24 25
FW UW Поверхности стыкового соединения нагреваются и соединяются под действием силы сварка Диффузионная сварка Сварка взрывом Электромагнитно-импульсная сварка Кузнечная сварка Сварка трением Сварка трением с перемешиванием Сварка горячим давлением Сварка горячим изостатическим давлением Роликовая сварка 47 (43) 42 FOW FRW 48 45 441 N AWS Характеристики Применение Соединение коррозионностойких сплавов с более дешевыми сплавами
CEW Разнородные металлы выдавливаются через одну и ту же головку CW
Соединение мягких сплавов, таких как медь и алюминий, ниже точки плавления их электрических контактов Титановые рабочие колеса насосов Переходные соединения для химической промышленности и судостроения. Биметаллические трубопроводы Автомобильная промышленность, сосуды под давлением, соединения из разнородных материалов Дамасская сталь Авиакосмическая промышленность, железная дорога, наземный транспорт Судостроение, аэрокосмическая промышленность, железнодорожный подвижной состав, автомобилестроение Аэрокосмические компоненты Авиакосмические компоненты Разнородные материалы
DFW Линия сварки не видна Соединение разнородных материалов, напр. коррозионно-стойкие сплавы к конструкционным сталям EXW Трубы или листы ускоряются под действием электромагнитных сил. Оксиды выбрасываются при ударе Старейший в мире процесс сварки. Оксиды должны быть удалены флюсом или пламенем. Тонкая зона термического влияния, оксиды разрушены трением, требуется достаточное давление
FSW Вращающийся расходный инструмент перемещается по линии стыка HPW HPW ROW Металлы спрессовываются при повышенных температурах ниже точки плавления в вакууме или в атмосфере инертного газа Горячий инертный газ создает давление внутри сосуда высокого давления, т. е. автоклава. Биметаллические материалы соединяются, заталкивая их между двумя вращающимися колесами 9
Список сварочных процессов — Википедия, бесплатная энциклопедия
USW
Высокочастотная вибрационная энергия воздействует на фольгу, тонкие металлические листы или пластик.
Солнечная промышленность. Электроника. Задние фонари автомобилей.
Другая сварка
Наименование Электронно-лучевая сварка N 51 511 72 AWS Характеристики Применение
ЭЛС Глубокое проплавление, высокая скорость, высокая стоимость оборудования. Быстро сваривает толстые детали, вертикальное положение, только сталь, плавящимся электродом непрерывного действия ЭШС. Производство толстолистового проката, строительство Строительство, судостроение.
Электрошлаковая сварка Поточная сварка Индукционная сварка Лазерная сварка
74 521 522
IW LBW Глубокое проплавление, быстрота, высокая стоимость оборудования Сочетает LBW и GMAW в одной сварочной головке, способной перекрывать зазоры до 2 мм (между пластинами), ранее это было невозможно только с LBW. Автомобильная промышленность Автомобильная, судостроительная, сталелитейная промышленность Компоненты распределительных устройств Железнодорожные пути
Лазерная гибридная сварка
Ударная сварка Термитная сварка Электрогазовая сварка Дуговая сварка стержнями
77 71 73 78
PEW TW
После электрического разряда применяется давление, которое склеивает материалы Экзотермическая реакция между порошком алюминия и оксидом железа порошок
Плавящийся электрод непрерывного действия, вертикальное расположение, только сталь Резервуары для хранения, судостроение Приваривает шпильки к основному материалу с помощью тепла и давления
Примечания и ссылки 9Также известна как ручная дуговая сварка металлическим электродом (MMA) или сварка электродом. Кэри, Ховард Б. и Скотт С. Хелцер (2005). Современные технологии сварки. Река Аппер-Сэдл, Нью-Джерси: Pearson Education. ISBN 0-13-113029-3. Линкольн Электрик (1994). Справочник по процедурам дуговой сварки. Кливленд: Линкольн Электрик. ISBN 99949-25-82-2.
См. также
Сварка Список кодов сварки Символы и условные обозначения, используемые в документации по сварке лазерная наплавка
Внешние ссылки Информация о процессе контактной сварки (http://www.keytometals.com/page.aspx?ID=CheckArticle&site=kts&NM=76). 553340803″ Категории: Списки, связанные с технологиями сварки Последнее изменение этой страницы: 3 мая 2013 г., 12:37. Текст доступен по лицензии Creative Commons Attribution-ShareAlike; могут применяться дополнительные условия. Используя этот сайт, вы соглашаетесь с Условиями использования и Политикой конфиденциальности. Wikipedia® является зарегистрированным товарным знаком Wikimedia Foundation, Inc., некоммерческой организации.
5 из 5
24.07.2013 20:39
Электросварка сопротивлением — Словарь героев Википедии Пожалуйста, помогите улучшить эту статью, добавив ссылки на надежные источники.

Искать источники: «Электросварка сопротивлением» – новости · газеты · книги · Scholar · JSTOR (ноябрь 2009 г.) ( Узнайте, как и когда удалить это шаблон ) 9000 999 9000 999. соприкасающиеся металлические части неразъемно соединяются путем нагревания их электрическим током, расплавляя металл в месте соединения. [1] Электросварка сопротивлением широко применяется, например, при производстве стальных труб и при сборке кузовов автомобилей. [2] Электрический ток может подаваться на электроды, которые также оказывают зажимающее давление, или может индуцироваться внешним магнитным полем. Процесс контактной сварки можно дополнительно классифицировать по геометрии сварного шва и способу приложения давления к соединению: например, точечная сварка, шовная сварка, сварка оплавлением, рельефная сварка.
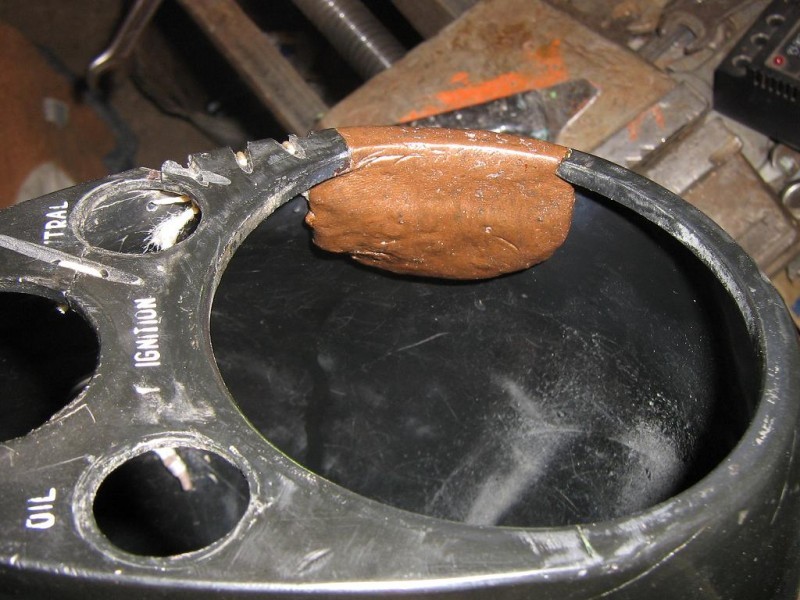
Содержание
- 1 Сталовая сварка
- 2 Сварка шва
- 3 Низкочастотная сварка.
- 8 Внешние ссылки
Точечная сварка , некоторые ребра теплообменника и некоторые трубки. Обычно источники питания и сварочное оборудование рассчитаны на определенную толщину и свариваемый материал. Толщина ограничена выходной мощностью источника сварочного тока и, следовательно, диапазоном оборудования из-за тока, необходимого для каждого применения.
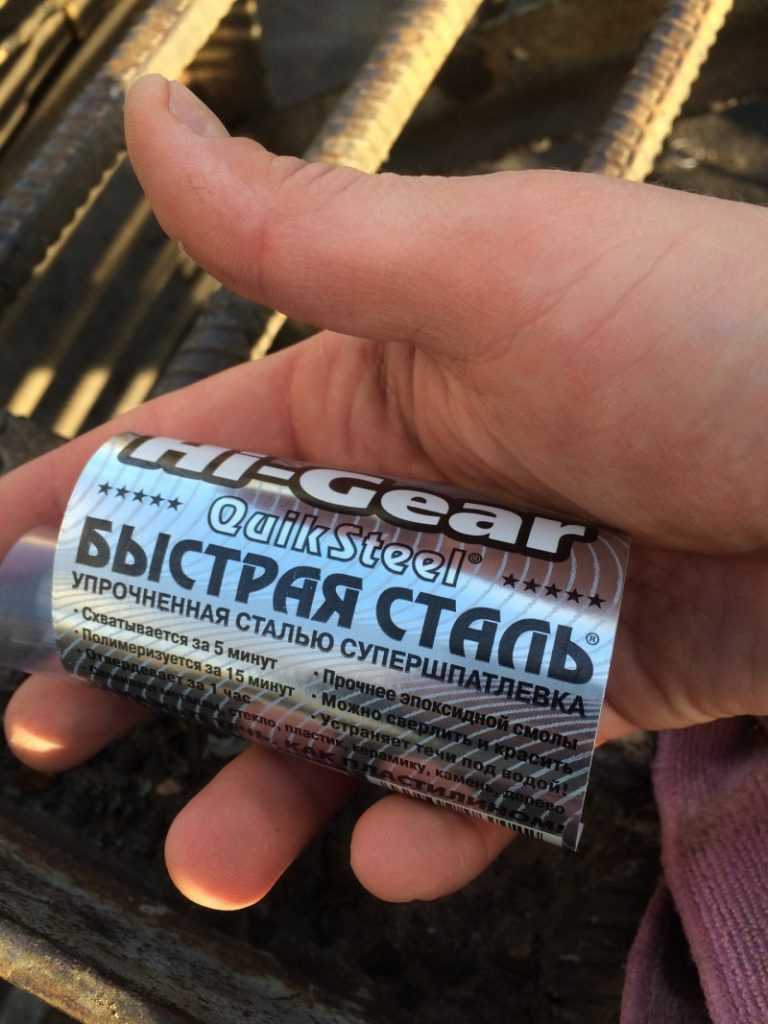

Если применяется чрезмерное или слишком быстрое нагревание, или если сила между основными материалами слишком мала, или покрытие слишком толстое или слишком проводящее, то расплавленная область может распространяться на внешнюю часть заготовок, избегая удерживающая сила электродов (часто до 30 000 фунтов на квадратный дюйм). Этот выброс расплавленного металла называется выбросом, и когда это происходит, металл становится тоньше и имеет меньшую прочность, чем сварной шов без выброса. Распространенным методом проверки качества сварного шва является испытание на отслаивание. Альтернативным испытанием является испытание на растяжение с защемлением, которое гораздо сложнее выполнить и требует калиброванного оборудования. Поскольку оба теста носят разрушительный характер (что приводит к потере пригодного для продажи материала), неразрушающие методы, такие как ультразвуковая оценка, находятся на разных стадиях раннего внедрения многими OEM-производителями.
К преимуществам метода относятся эффективное использование энергии, ограниченная деформация заготовки, высокая производительность, простота автоматизации и отсутствие необходимых присадочных материалов. Когда требуется высокая прочность на сдвиг, предпочтение отдается точечной сварке, а не более дорогостоящему механическому креплению, например клепке. Хотя прочность на сдвиг каждого сварного шва высока, тот факт, что точки сварки не образуют непрерывного шва, означает, что общая прочность часто значительно ниже, чем при других методах сварки, что ограничивает полезность процесса. Он широко используется в автомобильной промышленности — автомобили могут иметь несколько тысяч точечных сварных швов. Для точечной сварки нержавеющей стали можно использовать специальный процесс, называемый дробеструйной сваркой.
Существует три основных типа соединений контактной сваркой: твердое тело, плавление и пайка оплавлением. В твердотельной связке , также называемой термокомпрессионной связкой, могут использоваться разнородные материалы с разной зернистой структурой, т. е. молибдена к вольфраму, соединяются с использованием очень короткого времени нагрева, высокой энергии сварки и большой силы. Существует небольшое плавление и минимальный рост зерен, но определенная связь и поверхность раздела зерен. Таким образом, материалы фактически связываются, еще находясь в твердом состоянии. Склеенные материалы обычно демонстрируют превосходную прочность на сдвиг и растяжение, но низкую прочность на отрыв. В fusion bond , подобные или разнородные материалы с аналогичной структурой зерна нагреваются до точки плавления (жидкого состояния) обоих. Последующее охлаждение и комбинация материалов образуют «самородок» сплава двух материалов с более крупным ростом зерен. Как правило, для получения соединений плавлением используются высокие энергии сварки при коротком или длительном времени сварки, в зависимости от физических характеристик. Склеенные материалы обычно обладают отличной прочностью на растяжение, отрыв и сдвиг. В пайка пайкой оплавлением , резистивный нагрев низкотемпературного припоя, такого как золото или припой, используется для соединения либо разнородных материалов, либо самых разных комбинаций толстых/тонких материалов.
Твердый припой должен «смачиваться» с каждой деталью и иметь более низкую температуру плавления, чем две заготовки. Полученная связка имеет определенные границы раздела с минимальным ростом зерен. Обычно процесс требует более длительного (от 2 до 100 мс) времени нагрева при низкой энергии сварки. Полученная связка демонстрирует превосходную прочность на растяжение, но плохую прочность на отрыв и сдвиг.
Шовная сварка[править]
«Шовная сварка» перенаправляется сюда. Геометрическую конфигурацию сварки см. в разделе «Сварка».
Сварка контактным швом представляет собой процесс, при котором производится сварка на сопрягаемых поверхностях двух одинаковых металлов. Шов может быть встык или внахлест, и обычно это автоматизированный процесс. Он отличается от сварки оплавлением тем, что при сварке оплавлением обычно сваривается весь стык сразу, а сварка швом формирует сварной шов постепенно, начиная с одного конца. Как и точечная сварка, шовная сварка основана на использовании двух электродов, обычно изготовленных из меди, для приложения давления и тока. Электроды часто имеют форму диска и вращаются, когда материал проходит между ними. Это позволяет электродам оставаться в постоянном контакте с материалом для выполнения длинных непрерывных сварных швов. Электроды также могут перемещать или способствовать движению материала.
Трансформатор подает энергию на сварной шов в виде низковольтного сильноточного переменного тока. Соединение заготовки имеет высокое электрическое сопротивление по отношению к остальной части цепи и нагревается током до точки плавления. Полурасплавленные поверхности прижимаются друг к другу давлением сварки, которое создает соединение плавлением, в результате чего получается однородная сварная конструкция. Большинство шовных сварщиков используют водяное охлаждение через узлы электрода, трансформатора и контроллера из-за выделяемого тепла.
Сварка швов обеспечивает чрезвычайно прочный сварной шов, поскольку соединение проковывается под воздействием тепла и давления. Правильно сваренное соединение, образованное контактной сваркой, легко может быть прочнее материала, из которого оно выполнено.
Шовная сварка обычно используется при производстве стальных труб круглого или прямоугольного сечения. Сварка швов использовалась для производства стальных банок для напитков, но больше не используется для этого, поскольку современные банки для напитков изготавливаются из бесшовного алюминия.
Существует два режима шовной сварки: прерывистый и непрерывный. При сварке прерывистым швом колеса перемещаются в желаемое положение и останавливаются для выполнения каждого сварного шва. Этот процесс продолжается до тех пор, пока не будет достигнута желаемая длина сварного шва. При непрерывной шовной сварке колеса продолжают вращаться по мере выполнения каждого сварного шва.
Низкочастотная электросварка сопротивлением Он был снят с производства в 1970-х годов, но по состоянию на 2015 год некоторые трубопроводы, построенные этим методом, оставались в эксплуатации.
[3] Труба, сваренная методом контактной сварки (ERW), изготавливается путем холодной штамповки стального листа в цилиндрическую форму. Затем между двумя кромками стали пропускают ток, чтобы нагреть сталь до точки, в которой кромки соединяются вместе, образуя соединение без использования сварочного присадочного материала. Первоначально в этом производственном процессе для нагрева краев использовался переменный ток низкой частоты. Этот низкочастотный процесс использовался с 1920-х годов до 1970 года. В 1970 году низкочастотный процесс был заменен высокочастотным процессом ERW, который давал сварной шов более высокого качества.
Со временем было обнаружено, что сварные швы труб низкочастотных ВПВ подвержены селективной шовной коррозии, крюкообразным трещинам и неадекватному склеиванию швов, поэтому низкочастотные ВПВ больше не используются для производства труб. Высокочастотный процесс все еще используется для производства труб для использования в строительстве новых трубопроводов. [4]
Другие методы[править]
Другие методы ERW включают сварку оплавлением, сварку контактным выступом и сварку с осадкой. [5]
Сварка оплавлением — это тип контактной сварки, в котором не используются присадочные металлы. Свариваемые куски металла располагаются на заранее определенном расстоянии в зависимости от толщины материала, состава материала и желаемых свойств готового сварного шва. На металл подается ток, а зазор между двумя частями создает сопротивление и создает дугу, необходимую для расплавления металла. Как только куски металла достигают нужной температуры, они прижимаются друг к другу, эффективно сваривая их вместе. [6]
Выступающая сварка является модификацией точечной сварки, при которой сварной шов локализуется посредством приподнятых участков или выступов на одной или обеих соединяемых деталях. Тепло концентрируется на выступах, что позволяет сваривать более тяжелые сечения или уменьшать расстояние между сварными швами. Выступы также могут служить средством позиционирования заготовок. Выступающая сварка часто используется для приварки шпилек, гаек и других резьбовых деталей машин к металлической пластине. Он также часто используется для соединения скрещенных проводов и стержней. Это еще один высокопроизводительный процесс, и несколько выступающих сварных швов могут быть выполнены с помощью подходящего проектирования и приспособления. 9 Куглер, А. Н. (1977). Основы сварки . Международные заочные школы. LCCN 77360317.
Библиография
Дополнительная литература Справочник по сварке Vol. 2 (8-е изд.). Майами: Американское общество сварщиков. ISBN 0-87171-354-3
Внешние ссылки by American Welding Society
6 Типы стамесок, используемых в мастерских [Столярные работы, металлоконструкции] PDF
Главная » Мастерская » Что такое долото: типы, детали, методы, меры предосторожности с PDF и многое другоеавтор: Saif M
В этой статье вы узнаете, что такое долото и как его использовать в мастерской. с его частями , методами, мерами предосторожности и типами долота с PDF .
Долото используется для резки плоского, круглого или углового железа и толстых металлических листов. Он также используется для удаления ненужного металла с поверхности изделия путем разрезания его на мелкие кусочки. Этот акт известен как чипирование.
Автор Fishdecoy из английской ВикипедииРезка долотом грубая. Поэтому возникает необходимость в чистовой обработке после зачистки стамеской. Это экономит время. Зубила используются как для горячих, так и для холодных металлов. Как таковые долота были разделены на две категории.
Классификация долота
- Горячее долото
- Холодное долото
1. Горячее долото
Горячее долото используется для резки горячих металлов в кузнечной мастерской. В стамеске имеется отверстие, в котором закреплена деревянная ручка. Их режущая кромка выполнена под углом 30°. При использовании этой части ее часто окунают в воду для охлаждения, чтобы ее края оставались неповрежденными.
2. Холодное долото
Холодное долото обычно используется в мастерских по обработке листового металла и слесарных мастерских. С помощью холодного долота можно производить резку или скалывание металла, когда эти металлы находятся в холодном состоянии.
Предлагается с 4-мя, 6-ю или 8-ю сторонами. Они изготовлены из высокоуглеродистой стали, которая содержит от 0,75% до 1,00% углерода. Обычно используется долото длиной 150 мм. Практически размер долота известен по ширине режущей кромки долота.
Читайте также: 9Different Types of Sheet Metal Operations
Parts of a ChiselFollowing are the different parts of a chisel :
- Head
- Body
- Forging angle
- Cutting edge
- Cutting angle
1 Головка
Самая верхняя часть долота называется «Голова». Посередине он немного присосан, так что удар молотка приходится по центру долота. Таким образом, из-за повторяющихся ударов его головка становится грибовидной, как показано на рис.
В этом случае головка долота должна быть выправлена шлифовкой. При изготовлении головы верхняя часть туловища должна находиться под углом от 10° до 20°.
2. Корпус
Та часть долота, за которую мы его держим, называется корпусом или прикладом. Он состоит из четырех, шести или восьми сторон, чтобы его было удобно держать. Корпус сделан несколько плоским снизу.
3. Ковочный угол
Некоторая часть плоской поверхности под корпусом долота сужается. Этот угол конусности называется углом ковки. Он также известен как угол прорисовки.
4. Режущая кромка
Та часть долота, которая выполняет режущую функцию, называется режущей кромкой. Его ширина принимается за мерку стамески.
5. Угол резания
Угол, под которым заточена режущая кромка долота, называется углом резания. Для резки твердых металлов угол резания больше, а для резки мягких металлов угол резания меньше. При заточке стамесок для резки различных металлов их углы должны быть следующими:
- Мягкая сталь — 55 °
- чугун — 60 °
- Сталь инструментов — 65 ° до 70 °
- Медь — 45 °
- Алюминий — 30 °
- — 50280
- .
- Aluminum — 30 ° . Долото
- Плоское зубило
- Крестовое разрезок
- боковой срезанный зубил
- Круглый нос. , Это цельнометаллическое долото, используемое для получения плоской поверхности металла путем скалывания. Это долото используется для резки проволоки, тонких листов, круглых стержней и т. д.
Край этого долота имеет форму буквы «V» и является плоским, приподнятым от центра. Благодаря этому выступающие части не застревают в поверхности реза при скалывании.
2. Долото для поперечной резки
В основном используется для вырезания квадратных пазов и каналов. Этим зубилом делается шпоночный паз на валу. Его режущая кромка имеет ширину от 3 мм до 12 мм.
Для того, чтобы эта стамеска не застряла в канавках и щелях при работе в канавках и щелях, часть за ее кромкой выполнена сравнительно тонкой.
3. Долото с боковым резом
Там, где другие типы стамесок не могут быть легко использованы, используются стамески с боковым резом. Шпоночный паз и шплинт очищаются этим долотом.
Почти аналогичен плоскому долоту, но часть, выполняющая режущую функцию, повернута набок. Его поворачивают под углом, а затем куют. Его угол резания, как правило, и угол ковки под углом.
4. Круглое долото
Его край закруглен. Он используется для создания масляной канавки в подшипнике и для прорезания пазов в углах. Его угол ковки равен а, а угол резки составляет от 35 ° до 40 °. В таких работах, когда сверло смещается во время сверления и остается какое-то вещество, остатки металла исправляются этим долотом.
5. Долото с алмазным наконечником
Изготовлено из высококачественной стали. Его форма квадратная, а конусообразная. Его край заострен и имеет форму ромба.
На основе его квадратных концов определяется его размер. Им зачищаются квадратные углы и треугольные углы.
С помощью этого зубила мы можем сделать канавку на ровной поверхности.
6. Долото с коровьим ртом
У этих типов долота его форма напоминает широкий рот коровы. Вот почему он известен как долото коровьего рта. Из него делают кромки выступающих частей из простого металла и головки заклепок и большие круглые отверстия. Его угол ковки находится под углом.
Методы использования долотаДолото используется для резки и измельчения тонкого металлического листа, пластины, круглого стержня и других подобных материалов. На рис показан разрез металлической пластины. При использовании стамески следует помнить о следующих моментах:
- На разрезаемом металле необходимо нанести точную маркировку.
- Всегда правильно держите долото левой рукой, а молоток – правой.
- Правильно установите долото по отмеченной линии, затем ударьте молотком по его головке. Прежде чем нанести второй удар по стамеске, ее следует снова установить.
- При резке долотом следует концентрироваться на его режущей кромке.
- Нанесите удар молотком по центру головки долота.
- Во время измельчения мы всегда должны использовать защитные очки.
- Держите лицо лицом к стене во время сколов.
- Если кто-то работает впереди вас, закрепите защитный кожух сзади тисков, чтобы стружка не попала в него.
- Грибовидное долото никогда не должно использоваться для измельчения.
- На головке долота и поверхности молотка, используемого для рубки, не должно быть жирных пятен.
- Чрезвычайно длинное долото не должно использоваться для измельчения.
- Во время рубки мы должны продолжать наносить смазку на край долота.
Вот и все, спасибо за внимание. Если у вас есть какие-либо вопросы по « Виды долота » вы можете задать их в комментариях.
Подпишитесь на нашу рассылку БЕСПЛАТНО
Адрес электронной почты
Загрузите PDF-файл этой статьи отсюда:
Загрузить сейчас
Далее:
- Токарный станок: детали, типы, операции, приспособления
- 4 основных типа фрезерных станков
- Режущие инструменты для токарных станков
О Саифе М.
Чтобы режущая кромка прослужила дольше, даже коническая часть долота сделана твердой, а кромка закалена. Для этого долото следует нагреть при соответствующей температуре до половины его длины и охладить эту краевую часть долота в чистой воде.
Это сделало бы эту конкретную часть долота твердой. Затем его крайнюю часть следует зачистить наждачной бумагой. Опять же, его следует нагреть до соответствующей температуры.
Теперь цвет этой детали начнет меняться, и когда она станет соответствующего цвета, ее следует охладить в известковой воде. Это смягчит более длительный период.
Читайте также: Концепция прокатных станов с типами прокатных станов
Типы долота
Ниже приведены различные Типы долота :