Контактная сварка меди
Для меди и ее сплавов контактная сварка затруднена вследствие их высокой электрической проводимости и теплопроводности, а также узкого диапазона температур, в котором металл может свариваться давлением. Свариваемость медных сплавов лучше, чем технической меди, так как они обладают пониженной электрической проводимостью и теплопроводностью. Однако не все сплавы свариваются одинаково хорошо. Чаще контактная сварка применяется для латуней и кремнистых бронз. Среди них хорошо свариваются α-латуни (например, марки Л68), электрическая проводимость , которых не более 28% электрической проводимости меди. Повышение содержания цинка в латуни приводит к ухудшению ее свариваемости вследствие уменьшения пластичности сплава. Уменьшение концентрации цинка неблагоприятно влияет на свариваемость, поскольку понижается электросопротивление сплава. Хорошо свариваются кремнистая бронза (до 4% Si, электрическая проводимость равна примерно 10% электрической проводимости меди) и медно-никелевые сплавы, например мельхиор (80% Сu, 20% Ni, электрическая проводимость .
Для получения чистой контактной поверхности заготовок рекомендуется их очистка механическим способом, а также травлением в тетрахлорметане или растворе каустической соды с последующей тщательной промывкой в проточной воде. Для растворения пленки оксидов применяют травление в следующих смесях: 10% -ный раствор серной кислоты, бихромат натрия; серная кислота, фтористый алюминий и 6dхромат натрия.
Точечная и роликовая сварка меди.
Точечная и роликовая сварка меди возможна только с применением электродов из тугоплавких металлов, обладающих теплопроводностью и электрической проводимостью, более низкими, чем основной металл, для уменьшения отвода теплоты во время сварки (например, из вольфрама или молибдена). При использовании таких электродов поверхность деталей сильно нагревается, а местами расплавляется, портится внешний вид изделия и быстро изнашиваются электроды.
Качество сварных точечных швов можно повысить, используя теплоизолирующие прокладки (например, из нержавеющей стали), размещаемые между электродами и поверхностями свариваемых деталей, а также покрывая соприкасающиеся поверхности деталей, например, серебром.
Для медных сплавов применение мягких режимов нецелесообразно. Обычно длительность нагрева медных сплавов при точечной сварке ограничивается 0,2-0,4с. Точечная сварка латуни производится короткими импульсами при больших значениях сварочного тока. В связи с высокой электрической проводимостью латуни толщина свариваемых листов на одной и той же машине принимается примерно в 2 раза меньше, чем толщина листов из стали. Шовная сварка латуни требует относительно большого удельного давления электродов, чем точечная. При сварке латуни марки Л62 υ При ширине роликов, равной 3-5 мм, сварочный ток для латуни приблизительно определяется из уравнения
Таблица 1. Ориентировочные режимы точечной сварки латуни Л62
b, мм | Радиус поверхности электрода, мм | р, кПа | Р, кН | Iсв, кА | t, с | Потребляемая мощность, кВА |
0,5+0,5 | 50 | 67 | 1,3 | 1,6 | 0,1 | 68 |
1,0+1,0 | 50 | 98 | 1,8 | 18,3 | 0,2 | 95 |
1,5+1,5 | 70 | 78 | 2,6 | 26,8 | 0,2 | 167 |
3,0+3,0 | 150 | 117 | 3,9 | 38,6 | 0,35 | 290 |
Латунь малых толщин (0,05-0,5 мм) можно соединять конденсаторной сваркой.
При точечной сварке медных сплавов с высоким электросопротивлением (кремнистая бронза, мельхиор) по сравнению со сваркой малоуглеродистой стали ток увеличивают примерно на 25%, мощность на 50%, давление на электроды принимают близким давлению при сварке стали.
Стыковая сварка оплавлением.
Стыковая сварка оплавлением требует особой техники из-за трудности поддержания на торцах свариваемых деталей слоя жидкого металла, а также при прогреве их на значительную глубину для последующей осадки. Лучшие результаты получаются при осадке стыка под током. Установочную длину вылета медных деталей определяют по формуле:
где d — диаметр свариваемых стержней, мм. Скорость оплавления ориентировочно равна 10 мм/с. Цикл сварки не должен превышать 1-2 с. Прочность стыка прутков из меди марки Ml в среднем составляет 206-215,8 МПа, угол загиба 180°.
Таблица 2. Ориентировочные режимы шовной сварки латуни Л62
b, мм | Ширина роликов, мм | Р, кН | IСВ, кА | Потребляемая мощность, кВА |
0,5+0,5 | 3 | 2,45 | 22,3 | 110 |
0,5+0,5 | 3-4 | 2,45 | 25,5 | 140 |
1,0 + 1,0 | 4-5 | 3,7 | 27,0 | 160 |
Таблица 3. Ориентировочные режимы стыковой сварки оплавлением заготовок из меди
Параметр | Размер заготовки, мм | ||
Пруток, d=10 | Труба, 9,5×1,5 | Полоса, 44,5×10 | |
Установочная длина, мм | 20 | 20 | 20 |
Давление осадки, МПа | 372 | 284,5 | 216 |
Сварочный ток, к А | 33 | 20 | 60 |
Вторичное напряжение, В | 6 | 5 | 10 |
Удельная мощность, кВА/мм2 | 2,6 | 2,7 |
Медь соединяют стыковой сваркой сопротивлением. Провод и прутки из чистой меди диаметром 7-16 мм сваривают при i=380 А/мм2 и средней температуре нагрева 0,7-0,75Тпл. Начальное давление составляет 0,98-2,9 МПа, а конечное 343,4-392,4 МПа. Концентрированный нагрев контактной зоны и большие скорости осадки (150-250 мм/с) исключают разупрочнение металла и обеспечивают высокие пластические и электрические свойства соединений. Для соединения медных проволок успешно применяется стыковая конденсаторная сварка. Латунь и бронза соединяются стыковой сваркой легче, чем медь. Для их сварки требуются большие конечные скорости оплавления и осадки. Хорошо соединяются стыковой сваркой заготовки из деформируемых бронз марок Бр.Х0,5; Бр.ОФ6,5-0,15; Бр.АМц9-2. Поскольку скорость охлаждения бронзы значительно больше, чем стали, и бронза в интервале температур 750-770° С имеет достаточно высокую прочность, при ее сварке давление должно быть выше, чем при сварке стали. В ряде случаев для повышения пластичности сварных соединений рекомендуется их последующая термическая обработка: для соединений из бронзы типа Бр.
Таблица 4. Ориентировочные режимы стыковой конденсаторной сварки медной проволоки
dпр, мм | СК, мкФ | U, кВ | Усилие осадки, кН |
256 | 0,9 | 1,4 | |
2,0 | 380 | 1,0 | 1,4 |
2,8 | 380 | 1,4 | 1,5 |
3,0 | 540 | 1,5 | 1,6 |
3,2 | 550 | 1,5 | 1,8 |
Таблица 5. Ориентировочные режимы стыковой сварки латуни и бронзы
Параметр | Сплав | ||
Л 62 | Бр.ОФ6,5-0,15 | ||
Толщина металла, мм | 3-5 | 2-5 | 5-8 |
Установочная длина (суммарная), мм | 30 | 30 | 45 |
Припуск на оплавление, мм | 15 | 15 | 22 |
Длительность оплавления, с | 3 | 3 | 9 |
Скорость оплавления перед осадкой мм/с | 11 | 11 | 6 |
Средняя скорость оплавления, мм/с | 5 | 5 | 2,5 |
Длительность осадки под током, с | 0,3 | 0,3 | 0,5 |
Давление осадки, МПа | 157 | 177 | 137-157 |
Удельная мощность при оплавлении, кВА/мм2 | 0,05 | 0,07 | 0,03-0,035 |
Удельная мощность при осадке, кВА/мм2 | 0,4 | 0,4 | 0,2 |
Контактная сварка меди
Этот способ насчитывает несколько разновидностей. Они имеют свои технологические особенности и применяются в тех или иных случаях. Однако два способа, а именно шовная и точечная сварка медных элементов, практически не используется. Обработка стыков с помощью оплавления происходит с затруднениями, так как связана с некоторыми сложностями. Для такого способа на торцах изделия в местах сварочных работ требуется постоянно поддерживать слой расплавленного металла.
Также неудобство вызывает необходимость поддержания определенной температуры на торцах обрабатываемого изделия. Прогревать металл требуется довольно глубоко, иначе последующая его осадка будет затруднена. Чаще всего для осуществления такой осадки нужно воздействовать на медь с помощью довольно большого давления, примерно до 400 МПа.
Особенности стыковой контактной сварки
Этот вид обработки особо распространен при соединении медных трубопроводов, ленты или проволоки. Чаще всего медь выступает не в чистом виде, а в виде её различных сплавов.
При проведении стыковой контактной сварки образовывается намного меньше искр, чем при аналогичной обработке черных металлов. При обработке медных изделий искры похожи на крупные капли расплавленного металла, а не на искрящийся сноп огней. Для получения высококачественного шва нужно произвести осадку стыков под воздействием тока. В случае применения такой тактики вы получите довольно прочный шов. Он не будет уступать в прочностных характеристиках самой меди, поэтому детали с таким соединением будут выдерживать значительные нагрузки.
Широкое практическое применение имеет способ соединения проволоки методом разряда конденсатора с высоким вольтажом.
Примерные режимы стыковой контактной сварки
Параметры режима сварки | Пруток, диаметром 10мм | Труба 9,5х1,5мм | Лента 44,5х10мм |
Установочная длина, мм | 20 | 20 | — |
Припуск на оплавление, мм | 12 | — | — |
Припуск на осадку, мм | 8 | — | — |
Скорость оплавления, мм/сек | 8 | — | — |
Скорость осадки, мм/сек | 200 | — | — |
Удельное давление осадки, МПа | 372,2 | 284,4 | 215,7 |
Удельная мощность, кВт/мм2 | 2,6 | 2,66 | 1,35 |
Сила сварочного тока, кА | 33 | 20 | 60 |
Вторичное напряжение, В | 6 | 5 | 10 |
Ориентировочные режимы сварочных работ с помощью разряда конденсатора
Диаметр проволоки, мм | Ёмкость конденсатора, мкФ | Напряжение заряда, В | Начальное расстояние в стыке, мм | Усилие осадки, Н |
1,6 | 256 | 900 | 14 | 1373 |
2,0 | 380 | 1000 | 15 | 1373 |
2,8 | 380 | 1400 | 16 | 1471 |
3,0 | 440 | 1500 | 16 | 1569 |
3,0 | 1200 | 1000 | 9 | 1177 |
3,0 | 1200 | 800 | 5 | 1177 |
3,0 | 550 | 1400 | 5 | 1471 |
3,0 | 540 | 1300 | 8 | 1569 |
3,0 | 540 | 1500 | 12 | 1569 |
3,2 | 550 | 1500 | 14 | 1765 |
Относительная длина вылета элементов определяется по формуле L=(2,0. ..2,5)d.
Где L – длина вылета, а d – диаметр изделия. Считается в миллиметрах.
Оплавление происходит со скоростью около 10 миллиметров в секунду. Весь цикл сварочных работ в основном занимает 1-2 секунды. При сваривании медных прутков марки M1 прочность шва будет составлять от 206 до 216 МПа. Угол загиба составляет 180 градусов. Твердость сварного шва немного выше, чем твердость основного материала.
Контактная сварка меди
Медь является уникальным по своим физико-химическим свойствам материалом. Она имеет достаточно высокую коррозийностойкость в различных средах и агрессивных воздействиях на металл. Эти технологические качества обуславливают весьма широкое использование меди в легкой и тяжелой промышленности.
К выполнению сварки меди контактным способом выдвигаются достаточно строгие требования. При чем от чистоты наплавляемого металла зависят требования, выдвигающиеся к проведению сварочных работ по данному металлу.
По своим физическим и химическим свойствам медь, в обычных температурах является инертным металлом, но при воздействие процесса нагрева ее поверхности она имеет свойство вступать во взаимодействие с кислородом, галогенам, серой и фосфором. Все эти факторы значительно затрудняют выполнение контактной сваркой меди и ее сплавов.
При выполнении сварки давлением необходимо принимать во внимание весьма маленький температурный диапазон позволяющий выполнять сварные работы давлением. В своем большинстве контактную сварку применяют для сваривания не только меди, но и соединений меди с бронзой и латунью. Для получения чистой контактной поверхности заготовок, необходимо проводить некоторые механические действия по ее очистки.
Также необходимо применять химическое травление и последующее тщательное смывание всех используемых кислот и щелочек для травления в проточной воде. Применение электродов зависит от выбранного способа выполнения сварных работ.
Так для роликовой и точечной контактной сварке широко используются электроды, изготовленные из тугоплавким металлов состоящие из вольфрама и молибдена. Рекомендуется использовать медь без примесей для обеспечения повышенного качества сварного шва. Из-за плохих литейных свойств меди очень большую роль при выполнении контактной сварки играет присадочный материал.
В качестве присадочного материала широко используется сплавы меди с достаточно большим содержанием раскислителей, которые в свою очередь обеспечивают получение в процессе выполнения работ качественного и плотного и прочного литого соединения.
Техническая медь, используемая, в качестве присадочного материала при сварке делится на пять марок, которые отличаются друг от друга количеством примесей содержащихся в металле. Такие примеси как бериллий повышают теплопроводность металла, а алюминиевые примеси повышают устойчивость к коррозии. Есть и такие примеси, которые способны ухудшать свойства. К этим элементам относятся водород, мышьяк и свинец. При сварке меди необходимо принимать во внимания все перечисленные выше показатели.
Сварка меди и алюминия: обзор методов
Актуальность
Электромобили сегодня обсуждаются повсеместно. Немецкая автомобильная промышленность и предприятия снабжения активно адаптируются к новым разработкам. Создаются новые производства, в частности в области производства аккумуляторов.
Эффективная сварка алюминия с медью становится одной из центральных технических задач в сфере электромобилестроения. Компания METROM mechatronische maschinen GmbH ( имеет многолетний опыт соединения тугоплавких материалов и сплавов, которые не могут быть обработаны методом традиционной сварки плавлением, и способна предложить промышленности новые технологии соединения в области решения различных задач с участием меди и алюминия.
Процесс 1: Лазерная сварка динамическим отражением луча
Сварка разнородных материалов позволяет оптимально использовать их специфические качества. Лазерная сварка обеспечивает экономичный способ соединения комбинированных материалов. Однако различия термофизических характеристик и свойств материалов могут приводить к снижению качества сварки, поскольку возникающие интерметаллические фазы способны значительно ослабить прочность соединения.
Данная технология использует отражение яркого лазерного луча быстро вращающимися зеркалами для проекции на зону сварки. Высокая фокусируемость лазерных лучей позволяет добиться очень узкого сварочного шва, пропорционального соотношения сторон, сверхкороткого цикла сварочной ванны. Заготовка испытывает воздействие относительно небольшой энергии, что снижает продолжительность нестабильных интерметаллических фаз.
Такие результаты были достигнуты в рамках проекта федерального министерства образования и научных исследований Германии (BMBF) «WELDIMA — исследование и развитие лазерных и волновых сварочных технологий для разнородных материалов».
Рис.1. Лазерное плавление Al-Cu заготовок
Рис. 2. Микрошлиф Al-Cu заготовок после лазерного плавления
Процесс 2: Cварка трением с перемешиванием (FSW)
Сварка трением с перемешиванием — это технология механического соединения материалов в твердой фазе. Технология позволяет избежать такие нежелательные явления при плавлении металлов как продолжительные интерметаллические фазы.
Вращающийся инструмент оказывает давление на поверхность материала в зоне стыка при помощи заплечника и вызывает пластификацию металла за счет импульсного нагревания. Наконечник, внедренный в заготовку, регулирует перемещение материала. Термомеханическая сварка позволяет получить мелкозернистый шов с высокими показателями прочности.
Данный процесс был реализован компанией METROM на 5-ти осевом обрабатывающем центре с технологией параллельной кинематики.
Обрабатывающий центр выполняет 5-ти координатную сварку трением с перемешиванием сложных материалов и предварительную механическую обработку поверхностей стыка.
Преимущества метода сварки трением с перемешиванием:
- соединение тугоплавких материалов, не поддающихся традиционным методам сварки
- минимальная деформация заготовок
- дополнительный присадочный материал не требуется
- возможна сварка разнородных материалов
Преимущества концепции нового оборудования:
- упрощенная и экономичная наладка оборудования
- обширная рабочая зона
- высокая жесткость и точность позиционирования
- отзывчивое и гибкое управление
Сравнение сварочных методов:
Лазерная сварка отраженным лучом
Сварка трением с перемешиванием (FSW)
При лазерной сварке отраженным лучом сварка характеризуется контролируемой жидкой фазой, в случае сварки трением с перемешиванием — сварка происходит в твердой фазе.
Лазерная сварка отраженным лучом используется при изготовлении тонкостенных заготовок. Например, контактирование алюминия и меди в литий-ионных аккумуляторах. Другие материалы: Al + Mg, нержавеющая сталь + медь.
Сварка трением с перемешиванием (FSW) применяется для сложных линейных соединений, литейного алюминия, например для корпусов. Другие материалы: Al + Mg.
Рис.3. Cварка трением с перемешиванием технологией Pentapod
Рис.4. Лазерное индукционное плакирование винтовой прокаткой лент Al-Cu
Процесс 3: Лазерное индукционное плакирование прокаткой
Композитные заготовки из алюминия и меди, созданные для конкретных потребностей промышленности, могут открыть новые конструктивные возможности для разработки компонентов электроприводов, сделав их максимально компактными, легкими и устойчивыми к высоким механическим нагрузкам.
Процедура лазерного индукционного плакирования прокаткой, разработанная METROM, позволяет создавать такие композитные заготовки. Соединение алюминиевой и медной лент выполняется в процессе разовой прокатки с низкой деформацией (< 11 %). Уникальность технологии состоит в комбинировании традиционной дотермической обработки обеих лент и линейном лазерном луче. Он разогревает внутренние стороны лент до температуры необходимой для плакирования именно перед раствором валков. Так, например, эта технология хорошо подходит для производства биметаллических соединительных гильз (соединительных муфт). Локальная деформация дает относительно большую свободу при комбинировании заготовок, геометрия которых может не совпадать.
Результаты были получены в рамках проекта «DeLIZ — Производственно-технический демонстрационный центр для литий-ионных решеток», финансируемого федеральным министерством образования и научных исследований Германии.
Лазерное индукционное плакирование прокаткой
Лазерное индукционное плакирование прокаткой представлчет собой соединение методом деформации и локального повышения температуры. Используется для лентовых заготовок, в перспективе нанесение ленты на профиль. Например, сварка Al-Cu соединителей для литий-ионных решеток. Другие материалы: сталь + сталь, Al + сталь, Cu + сталь.
Электромагнитная импульсная сварка
Электромагнитная импульсная сварка — связывание атомов без зоны термического воздействия. Хорошо подходит для заготовок с симметричным вращением. Например, трубы, валы, прочные резервуары. Другие материалы: Al + сталь, Cu + сталь, Al + Ti.
Рис.5. Микрошлиф стыка Al-Cu методом электромагнитной импульсной сварки
Рис.6. Соединение заготовок Al-Cu
Процесс 4: Электромагнитная импульсная сварка
При создании зоны высокого давления электромагнитный импульс позволяет выполнить соединение практически без фазы плавления для большинства металлических заготовок.
Принцип технологии позволяет избежать возникновения интерметаллических фаз в зоне стыка. Так при соединении разнородных материалов разница точек плавления, толщины и теплопроводимости становится некритической. Локальное давление создается посредством бесконтактного воздействия электромагнитного поля.
Кроме того, данная технология открывает возможность экономически эффективной бесконтактной формовки металлов и производства высокопрочных соединений.
Сварка на атомном уровне позволяет выполнять обработку с заданными параметрами. Данная технология хорошо подходит для обработки труб и валов, продольная сварка также возможна. Обычно толщина стенки одной из свариваемых заготовок не должна превышать 2-4 мм. Сварочные швы испытывают крайне низкое влияние температуры и не попадают в зону теплового воздействия.
В дополнение к исследованию технологии IWS также изучает способы повышения качества соединений за счет точного подбора инструментов и геометрии выполнения сварки.
Данное исследование финансируется Европейским фондом регионального развития и федеральной землей Саксонией.
Переходное электрическое сопротивление комбинаций Al-Cu
Для дополнительных консультаций, пожалуйста, обращайтесь в компанию «ИНТЕРТУЛМАШ», которая является официальным представителем и поставщиком продукции и услуг компании METROM mechatronische maschinen GmbH в России и СНГ.
Ссылка на страницу компании METROM на русском языке:
https://www.itmash.ru/METROM
Контактная информация:
Телефон: +7 (495) 668-13-58
email: [email protected]
сайт: www.itmash.ru
Рис.1. Лазерное плавление Al-Cu заготовок
Рис.2. Микрошлиф Al-Cu заготовок после лазерного плавления
Технология EWM-spotArc® – контактная сварка методом TIG
В машиностроении очень часто возникает задача выполнить точечное одностороннее соединение тонких металлических листов. Обычно такую задачу решают точеной сваркой с помощью контактных сварочных машин, либо контактных сварочных клещей. Если доступ к соединению возможен только с одной стороны, используется точечная сварка сопротивлением на медном подслое (рис. 1).
Рис. 1 Односторонняя контактная точечная сварка
Но существуют производственные ситуации, когда применение точечной контактной сварки на медном подслое невозможно из-за недоступности обратной стороны детали или больших габаритов конструкции. Для сварки таких соединений в течение уже многих лет применяются MIG/MAG, TIG – сварка, плазменная сварка, при которых соединение происходит за счет сквозного проплавления верхнего листа и оплавления нижнего. Фирмой EWM разработана технология EWM-spotArc® – точечная сварка вольфрамовым электродом в аргоне (рис.2). Для реализации этого процесса были разработан специальный источник питания и аргонодуговая горелка.
Рис. 2 Принцип технологии EWM-spotArc®
Преимущества электродуговой точечной сварки
Одним из недостатков традиционной точечной сварки сопротивлением является образование сварной точки – для лучшей фиксации листа на медной подложке и обеспечения хорошего контакта (рис.1) необходимо прикладывать высокое давление, после которого на листе остаются вдавленные отпечатки от медных электродов. Кроме того, для такой сварки необходима специальная дорогостоящая установка, которая есть не на каждом предприятии.
В этом случае лучше всего применять аргонодуговую TIG–сварку точкой методом EWM-spotArc®.
Такая сварка имеет преимущества перед MIG/MAG – сваркой — лучшую поверхность точки и меньшее тепловложение. Так как сварка производится без присадочного металла, а расплавляется только основной металл, то точки получаются плоскими, без усиления, отсутствует необходимость последующей механической обработки места сварки. Благодаря меньшему времени сварки, по сравнению с MIG/MAG–сваркой, не происходит перегрев металла, что гарантирует отсутствие сварочных деформаций.
Установки для точечной сварки методом EWM-spotArc®
Для точечной сварки методом EWM-spotArc® можно применять стандартные инверторные источники питания для TIG–сварки фирмы EWM, они все оснащены функцией для метода EWM-spotArc® (рис. 3). Их необходимо лишь оборудовать специальными горелками (рис.4).
Рис.3
Рис.4
Сопло горелки для EWM-spotArc® имеют специальную форму, которая обеспечивает при сварке постоянство зазора между вольфрамовым электродом и изделием. Кроме того, сопло служит опорной поверхностью для прижима листов друг к другу, что улучшает качество сварочной точки и обеспечивает отсутствие зазора между свариваемыми листами. Для различных типов сварных соединений имеются различные по геометрии сопла (рис.5).
Рис.5 Сопло для сварки EWM-spotArc®
При сварке методом EWM-spotArc® лист, находящийся сверху, проплавляется насквозь сварочной дугой и приваривается к нижнему листу. Получаются плоские, гладкие сварочные точки без усиления (рис. 6), которые требуют последующей механической обработки.
Рис. 6 Внешний вид соединения выполненного методом EWM-spotArc®
Область применения EWM-spotArc®
Технология EWM-spotArc® применяется для:
- выполнения нахлесточных, тавровых, угловых, стыковых соединений или прихваток листов из углеродистых и нержавеющих сталей (рис. 7)
- выполнения сварки и прихватки разнотолщинных соединений
- выполнения сварки профилей, труб
Рис. 7 Сборка конструкции коробчатого сечения с применением EWM-spotArc®
Читайте также:
Высокопроизводительная TIG-cварка InFocus от Kjellberg
Сварочная технология InFocus разработана для сфер применения, недоступных для стандартных решений TIG-сварки. Высокосфокусированная сварочная дуга гарантирует эффективное соединение практически всех видов стали и цветных металлов, листов малой и большой толщины. Точная, надежная сварка обеспечивает высокое качество швов с ровной поверхностью.
…
EWM-activArc® – TIG-сварка сфокусированной дугой
Суть технологии EWM-activArc® заключается в поддержании постоянной энергии сварочной дуги не зависимо от воздействия внешних факторов, таких как, изменение расстояния между наконечником электрода и сварочной ванной. При этом можно добиваться высокой плотности дуги для гарантированного проплавления.
…
Поделиться ссылкой:
КОНТАКТНАЯ СВАРКА ( СПОТТЕРЫ )
Споттеры
Используя возможности точечной сварки, споттер позволяет заметно сократить время ремонта таких повреждений, как, например, вмятины или вздутие кузовных панелей, глубокие царапины. Полезность такого аппарата в кузовном цехе переоценить трудно.
Что это такое?
Споттер – это устройство для контактной сварки. По сути споттер является сварочным аппаратом, принцип действия которого основан на испускании значительного количества тепловой энергии в месте контакта свариваемых материалов при прохождении тока.
Споттер (от англ. spot – «точка») – аппарат односторонней точечной сварки, который нашел свое применение именно при ремонте кузовных панелей автомобиля. В Западной Европе споттеры применяются уже более полувека. Позже они стали появляться в США, Японии и других странах. В России эти устройства известны достаточно давно, но их активное распространение на отечественном рынке началось только в последние несколько лет.
Наиболее актуально применение споттера при ремонте объемных деталей кузова, к которым трудно подобраться с обратной стороны (двери, пороги и т. п.). Споттер позволяет приварить к поврежденной поверхности крепежный элемент, за который реально вытянуть вмятину, не тратя времени на разборку-сборку. Также с помощью ряда споттеров можно нагревать металл, что при некоторых небольших повреждениях позволяет вообще обойтись без вытягивания – металл сам принимает прежнюю форму (осаживается).
Как работает?
Режим 1:В этом режиме используется обратный молоток или пуллер. Пуллер — специальное устройство, подключаемое к разъему пистолета. Этот режим используется для исправления небольших, неглубоких вмятин. Это наиболее часто встречающиеся повреждения, они легко выправляются и составляют большую часть работ, принося «быстрыe» деньги. Особенно позволяют насладиться качеством работы, машины последнего поколения, т.к. применяемые новые упругие металлы прекрасно вспоминают свои первоначальные формы.
Режим 2: Используется для приварки тянущих элементов с помощью специальных электродов. К тянущим элементам, волнистая проволока, прямые или крученые кольца (сережки), можно приложить значительное усилие, которое и позволяет исправить сильные повреждения, вплоть до восстановления порогов с замятыми ребрами.
Режим 3: Используется со специальным коротким омедненным электродом для осаживания выпуклостей от обратного молотка, пуллера, клеммы массы или от следов отвертки, которой случайно выдавили, метал при арматурных работах.
У разных моделей споттеров предусмотрен разный набор приспособлений и аксессуаров для работы, но в целом все они действуют схожим образом. С помощью споттера к поврежденной поверхности приваривают специальный крепежный элемент, за который затем необходимо вытянуть деформированную поверхность.
Некоторые споттеры позволяют нагревать металл угольными стержнями. В случае небольших повреждений можно при нагревании восстановить форму металлической детали.
Режим 4: В этом режиме используется угольный электрод, с помощью которого разогревается значительная поверхность листа. Нагрев позволяет осадить метал, и избавиться от «хлопуна» получаемого при вытягивании большой поврежденной поверхности.
Режим 5: На этом режиме с помощью специальных омедненных электродов приваривают элементы крепления молдингов и шумоизоляции, которые могли быть удалены в процессе ремонта или как правило, отсутствуют на новых деталях
Режим 6: Режим используется для приварки шайбы с помощью, которой крепится клемма массы аппарата. Правда этот режим используют и для вытягивания с помощь тех же колец и крюка с 2,5 килограммовым обратным молотком.
Режим 7: На этом режиме с помощью специального омедненного электрода (с магнитом для удержания привариваемого болта) вы сможете приварить болты под резьбу или саморезы под пластик. С их помощью устанавливаются плашки тормозных трубок, жгутов электрики или клемм массы, которые отсутствуют на новых деталях или были срезаны при проведении восстановительных работ.
Также в комплект могут входить и сварные клещи, позволяющие сваривать листовой металл друг с другом по принципу контактной сварки. Принцип контактной сварки заключается в подаче сильного тока между двумя листами металла в строго определенной точке. Этот ток подается через медные электроды, причем свариваемые листы сильно прижимаются друг к другу с помощью рычажных сварочных клещей или ручной системы сжатия с усилением зажима. В течение около ¼ секунды листы нагреваются до предельной температуры плавления. Усилие, прилагаемое к электродам (около 150 кг), смешивает друг с другом молекулы металла, выполняя тем самым процесс сварки.
Металл не должен полностью разжижаться, так как в этом случае он будет выдавлен при внезапном расширении, что приведет к образованию низкоконсистентного, пористого или просто полого ядра сварной точки.
Фактически контактная сварка является просто современной аналогией метода, применяемого когда-то кузнецами: они нагревали два элемента докрасна, а потом ковали их молотом, чтобы прочно соединить. Сегодня электричество заменяет кузнечный горн, а усилие рычажных сварочных клещей пришло на смену молоту.
Многие устройства обладают готовыми программами: необходимо лишь выбрать тип сварки (с помощью сварочного пистолета – односторонняя точечная сварка), тип крепежного элемента, толщину свариваемого металла и продолжительность сварки. Интерфейсы современных аппаратов приближены к человеку, оттого выполнить вышеперечисленные операции очень просто.
Любой кузовщик может освоить работу споттером. Хотя, справедливости ради, стоит сказать: описание работы некоторых приборов будет представлять собой целый двухтомник. Однако на практике все не так страшно.
Виды аппаратов
Принцип действия споттеров – сварка сопротивлением. Это один из самых быстрых и простых видов сварки. Он не требует высокой квалификации оператора и дает надежное соединение.
Самые дешевые аппараты – это споттеры с отдельно стоящим трансформатором однофазного переменного тока. Они позволяют удалять вмятины, но малоэффективны при необходимости точечной сварки на оцинкованной стали и непригодны для стали с высокой ударной прочностью. Производители автомобилей такое оборудование не используют.
Более мощные – споттеры с трансформатором трехфазного постоянного тока. Но наиболее современная технология – это споттеры, где вместо обычного трансформатора используется инвертор. Эта технология позволяет получить ток высокой частоты 2000 Гц, что, в свою очередь, заметно снижает вес и размеры трансформатора. Но главное отличие инвертора – не мощность и компактность, а высокое качество сварного соединения, соответствующего заводским стандартам (нет падения силы тока в процессе сварки). Такие аппараты могут работать практически с любыми металлами, используемыми в автомобилестроении.
Впервые инверторную технологию в сварочных аппаратах применила в 1999 г. французская фирма Saitek. С тех пор многие производители сварочного оборудования применяют инверторы, которые обеспечивают большую мощность и силу тока на выходе при меньшем размере аппарата.
Процесс сваривания скоротечен, вручную осуществить дозирование сварочного импульса очень трудно. В большинстве случаев эта задача решается с помощью цифровой электроники, управляющей режимами сварки. Споттеры с электронным управлением режимами сварки принято называть цифровыми.
Что бы работа, не подкинула сюрпризов, необходимо помнить следующее:
1. При подключении к электрической сети необходимо учитывать следующее. Сечение проводов подведенных к электрической розетке должно быть сечением не менее 2,5мм² (для аппаратов с 32А мощности сечение должно быть не менее 4мм²), если используется удлинитель, то сечение кабеля должно быть увеличено в зависимости от длины. Автоматические предохранители на распределительном щите должны быть с индексом кривой отсечки «D» т.е. с задержкой по срабатыванию, для модели на 230В 25А, для модели на 400В 16А. Все эти рекомендации возникают из-за самого метода сварки – метод короткого замыкания, иначе потери по сопротивлению на кабелях не позволят получить желаемый результат.
2. Зачищенные места необходимо очистить от пыли после подготовки поверхности, иначе происходит сильное искрение, больший расход наконечников, меньше комфорта в работе.
3. Клемму массы «земля» необходимо устанавливать как можно ближе к месту работ и не в коем случае на ставить на соседнею деталь.
4. Следить за прочностью контактов в местах крепления инструмента и массы. Плохой контакт провоцирует пробои и выход из строя мест крепления инструмента.
5. Приварка – например, при приварке волнистой проволоки необходимо, начинать с дальней точки и двигаться к массе, иначе будет шунтирование, ток будет идти по наименьшему сопротивлению и каждая последующая точка буде слабей предыдущей. При этом необходимо следить за тем, чтобы проволока не касалась детали всеми точками, а только той которую привариваем в данный момент.
6. Сила нажатия инструментом на деталь при сварке – просто дотроньтесь уверенно. Контактную сварку также называют сваркой сопротивлением. Если нажатие будет очень сильным, то и сварки может не произойти, сопротивление в месте контакта может быть близка к нулю, будет легкое прилипание.
7. При значительной площади повреждения детали, начинать вытяжку необходимо с краю двигаясь к середине по спирали. Это позволит избежать провала вокруг центра, за который обычно начинают вытягивать. Металл растягивается и как следствие хлопун обеспечен. Постепенное вытягивание по спирали позволяет избежать чрезмерной растяжки металла и как следствие сэкономленное время.
Технология диффузионной сварки металлов
Диффузионная сварка — сварка за счёт взаимной диффузии на атомарном уровне свариваемых поверхностей деталей. Диффузионная сварки применяется в частности при производстве компенсаторов шинных медных пластинчатых КШМ для получения монолитной однородной контактной площадки из тонких медных пластин.
Определения и сущность диффузной сварки описаны в ГОСТ 26011-74. Диффузионная сварка производится воздействием давления и нагревом свариваемых деталей в защитной среде. Перед сваркой поверхность детали обрабатывают по 6 классу шероховатости и промывают для обезжиривания ацетоном.
Температура нагрева составляет 0,5 – 0,7 от температуры расплавления металла свариваемых деталей. Высокая температура обеспечивает большую скорость диффузии и большую пластичность деформирования металла. При недостаточной диффузии в сварке используют металлические прокладки (фольга из припоя ВПр7 толщиной 0,1 – 0,06 мм.) или порошок (фтористый аммоний), прокладываемые в месте сварки. Перед сваркой фольгу приваривают к поверхности одной из деталей с помощью контактной сварки. В процессе сварки прокладка расплавляется.
Процесс сварки осуществляется с использованием разных источников нагрева. В основном применяют индукционный, радиационный, электронно-лучевой нагрев, нагрев проходящим током, тлеющим разрядом или в расплаве солей
Сварка протекает при давление в камере – 10−2 мм. рт. ст. или в атмосфере инертного газа (иногда водорода). Вакуум или защитная атмосфера предохраняет свариваемые поверхности от загрязнения.
Сварка производится сжатием деталей с давлением 1 – 4 кгс/мм2. Давление, применяемое при способах сварки без расплавления материалов, способствует разрушению и удалению окисных пленок и загрязнений на поверхности металла, сближению свариваемых поверхностей до физического контакта и эффективного атомного взаимодействия, обеспечению активации поверхностей для протекания диффузии и рекристаллизации. Различается сварка с высокоинтенсивным силовым воздействием (свыше 20 МПа) и сварка с низкоинтенсивным силовым воздействием (до 2 МПа).
Диффузионная сварка проходит в две стадии:
- Сжатие свариваемых поверхностей, при котором все точки соединяемых материалов сближаются на расстоянии межатомных взаимодействий.
- Формирование структуры сварного соединения под влиянием процессов релаксации.
В отличие от традиционных способов сварки расплавлением, где к основному металлу вводится дополнительный металл в шве, диффузионная сварка позволяет получить однородный шов без серьезных изменений в физико-механическом составе места соединения.
Соединения обладают следующими показателями:
- наличие сплошного шва без пор и образований раковин;
- отсутствие окисных включений в соединении;
- стабильность механических свойств.
Благодаря тому, что диффузия — это естественный процесс проникновения одного вещества в другое, в зоне соприкосновения не нарушается кристаллическая решетка материалов, а следовательно, отсутствует хрупкость шва.
Недостатки технологии диффузионной сварки
- необходимость вакуумирования рабочей камеры;
- тщательная подготовка и очистка свариваемых поверхностей.
Преимущества технологии диффузионной сварки
- диффузионная сварка не требует сварочных припоев, электродов;
- не нужна дополнительная механическая обработка свариваемых поверхностей;
- высокое качество сварного соединения;
- малый расход затрачиваемой энергии;
- широкий диапазон толщин свариваемых деталей – от долей мкм, до нескольких метров.
Применение диффузионной сварки
К преимуществам данной технологии относят возможность диффузионной сварки разнородных материалов с получением равнопрочного шва без существенных изменений в физико-химических характеристиках, высокий уровень защиты и отсутствие необходимости в присадочном металле. Такая сварка позволяет создание прочных конструкций как из однородных металлов со сплавами, так материалов разного рода, в том числе резко отличающихся своими характеристиками, например пористых составов со слоистыми. Это не растворимые друг в друге, тугоплавкие или малопластичные металлы и сплавы, соединение которых довольно затруднительно. А применение диффузионного способа позволяет получать сварные конструкции даже из таких пар металлов и сплавов, которые практически невозможно соединить с помощью других видов сварки. Примером этого может служить диффузионная сварка титана со сталью, стойкой к коррозии, молибдена с медью или ниобия с вольфрамом, силикатов (кварц, стекло) с металлами, жестких углеводородов (графит и сапфир) со сплавами, стекла с ферритами и металлами.
Оборудование
Для проведения диффузионной сварки выпускается оборудование, различаемое по степени вакуумирования: с низким вакуумом (до 10-2 мм рт. ст.), со средним вакуумом (10-3…10-5 мм рт. ст.), с высоким вакуумом (свыше 10-5 мм рт. ст.), с защитным газом разной степени давления.
Для нагрева деталей применяют индукционный нагрев токами высокой частоты, электроконтактный нагрев током, радиационный нагрев электронагревателем.
В установках используют гидравлические или механические системы давления. Установки бывают с ручным управлением, полуавтоматические и автоматические с программным управлением. Автоматы применяются в крупносерийном или массовом производстве.
По теме
Компенсаторы шинные медные КШМ с диффузионной сваркой контактных площадок
Подключение трансформатора к шинопроводу
Популярные товары
Шины медные плетеные
Шины изолированные гибкие и твердые
Шинодержатели
Изоляторы
Индикаторы наличия напряжения
Введение Медь и медные сплавы являются важными инженерными материалами из-за их хорошей электрической и теплопроводности, коррозионной стойкости, износостойкости металла по металлу и отличительного эстетического внешнего вида. Медь и большинство медных сплавов можно соединять сваркой, пайкой и пайкой.В этом разделе мы поговорим о различных медных сплавах и дадим некоторые рекомендации о том, как соединить эти металлы без ухудшения их коррозионных или механических свойств и без появления дефектов сварных швов. Основные группы медных сплавов
Сплавы с высоким содержанием меди: (a) Медь, свободная механической обработкой — для улучшения обработки могут применяться низколегированные добавки серы или теллура.Эти сорта считаются несвариваемыми из-за очень высокой склонности к растрескиванию. Сварочные котлы соединяют пайкой и пайкой. Медно-цинковые сплавы (латунь): Медные сплавы, в которых цинк является основным легирующим элементом, обычно называют латуни. Медно-оловянные сплавы (фосфорная бронза): Медные сплавы, содержащие от 1% до 10% олова. Медно-алюминиевые сплавы (алюминиевая бронза): Содержат от 3% до 15% алюминия со значительными добавками железа, никеля и марганца. Обычные области применения сплавов алюминия и бронзы включают насосы, клапаны, другую водную арматуру и подшипники для использования в морской и других агрессивных средах. Медно-кремниевые сплавы (кремниевая бронза): Доступны как в кованой, так и в литой форме. Кремниевая бронза имеет важное промышленное значение благодаря своей высокой прочности, отличной коррозионной стойкости и хорошей свариваемости. Медно-никелевые сплавы: Медно-никелевые сплавы, содержащие 10-30% Ni, обладают средней прочностью, обеспечиваемой никелем, который также улучшает стойкость меди к окислению и коррозии.Эти сплавы обладают хорошей формуемостью в горячем и холодном состоянии и производятся в виде плоского проката, труб, прутков, трубок и поковок. Общие области применения включают пластины и трубки для испарителей, конденсаторов и теплообменников. Медно-никель-цинковые сплавы (никель-серебро): Содержат цинк в диапазоне 17% -27% вместе с 8% -18% никеля. Свариваемость меди и медных сплавов Сварочные процессы, такие как газовая дуговая сварка металла (GMAW) и газовая дуговая сварка вольфрамовым электродом (GTAW), обычно используются для сварки меди и ее сплавов, поскольку при сварке материалов с высокой теплопроводностью важен высокий локальный подвод тепла.Можно использовать ручную дуговую сварку металла (MMAW) меди и медных сплавов, хотя качество не такое хорошее, как при сварке в среде защитного газа. 2.1 Конструкции сварных соединений для соединения меди и медных сплавов:
2.2 Подготовка поверхности: 2.3 Предварительный нагрев: Газовая дуговая сварка (GMAW) меди и медных сплавов 3.1 GMAW меди: Таблица 1: Типичные условия для ручного GMAW
* см. Рекомендуемые защитные газы для GMAW меди и медных сплавов:
Подробнее см. Руководство по защитному газу . 3.2 GMAW медно-кремниевых сплавов: Сварочные материалы типа ERCuSi-A, а также защита аргоном и относительно высокие скорости перемещения используются в этом процессе. Aufhauser Silicon Bronze — это провод на основе меди, рекомендованный для GMAW медно-кремниевых сплавов. Важно убедиться, что оксидный слой удаляется проволочной щеткой между проходами. В предварительном нагреве нет необходимости, а температура между проходами не должна превышать 100 ° C. Эти сплавы имеют широкий диапазон затвердевания, что дает крупнозернистую дендритную зернистую структуру. Поэтому во время сварки необходимо соблюдать осторожность, чтобы предотвратить растрескивание металла шва. Горячее упрочнение металла шва снизит напряжения, возникающие при сварке, и вероятность образования трещин. Сварочную ванну следует сохранять небольшого размера, используя бусинки стрингера при высокой скорости движения. Газовая вольфрамо-дуговая сварка (GTAW) меди и медных сплавов 4.1 GTAW меди: Медные профили толщиной до 16,0 мм можно успешно сваривать с использованием процесса GTAW. Типовые конструкции соединений показаны на рис. По сравнению с аргоном смеси аргона и гелия обеспечивают более глубокое проплавление и более высокие скорости перемещения при том же сварочном токе.Смесь 75% He / 25% Ar обычно используется для обеспечения хороших характеристик проплавления гелия в сочетании с легким зажиганием дуги и улучшенными характеристиками стабильности дуги аргона. Для GTAW меди с бусинами стрингера или бортами с узким переплетением предпочтительна прямая сварка. Типичные условия для ручной GTAW меди показаны в таблице 2 ниже. Таблица 2: Типичные условия для ручной GTAW
* см. Рисунок 1 4.2 Газовая вольфрамовая дуговая сварка медно-алюминиевых сплавов: Присадочный стержень ERCuAl-A2 может использоваться для GTAW сплавов алюминия и бронзы. Пруток из кремниевой бронзы Aufhauser (ERCuSi-A) можно использовать для сварки кремниевой бронзы во всех положениях.Также можно использовать сварочный стержень из алюминиевой бронзы ERCuAl-A2. Сварка может выполняться на постоянном токе с использованием аргона или аргон / гелий, либо на переменном токе с использованием защитного газа аргона. Ручная металлическая дуговая сварка (MMAW) меди и медных сплавов 5. ![]() MMAW обычно используется для технического обслуживания и ремонтной сварки меди, медных сплавов и бронз. Электрод Aufhauser PhosBronze AC-DC (ECuSn-C) может использоваться в следующих целях:
Конструкции шарниров должны быть аналогичны показанным на Рисунок 1 .Положительный электрод постоянного тока (DC +) следует использовать с методом стрингера. Сечения более 3,0 мм требуют предварительного нагрева до 250 ° C или выше. 5.2 Ручная дуговая сварка медных сплавов металлом: Aufhauser PhosBronze AC-DC (ECuSn-C) может использоваться для сварки медно-оловянных и медно-цинковых сплавов. Требуются большие стыковые углы, и наплавка металла шва должна выполняться методом стрингера. Таблица 3: Рекомендации по MMAW латуни и фосфорной бронзы
Пайка меди и медных сплавов Принцип пайки заключается в соединении двух металлов сплавлением с присадочным металлом. Пайка широко используется для соединения меди и медных сплавов, за исключением алюминиевых бронз, содержащих более 10% алюминия, и сплавов, содержащих более 3% свинца. Пайка меди широко используется в электротехнической промышленности, а также в сфере обслуживания зданий и вентиляции и кондиционирования воздуха. Для достижения надлежащего сцепления во время пайки необходимо учитывать следующие моменты:
![]() Стандартные процедуры обезжиривания с использованием растворителя или щелочи подходят для очистки неблагородных металлов, содержащих медь. Необходимо соблюдать осторожность, если для удаления поверхностных оксидов используются механические методы. Для химического удаления поверхностных оксидов следует использовать соответствующий травильный раствор. 6.2 Соображения по конструкции соединения:
Используйте нейтральное пламя. Нейтральное пламя — это когда равные количества кислорода и ацетилена смешиваются с одинаковой скоростью. Белый внутренний конус четко очерчен и не имеет дымки. 6.4 Удаление флюса: Если использовался флюс, остатки необходимо удалить одним из следующих методов:
![]() Сварка меди припоем Сварка пайкой — это технология, аналогичная сварке плавлением, за исключением того, что присадочный металл имеет более низкую температуру плавления, чем основной металл. Прочность процесса пайки твердым припоем определяется пределом прочности на разрыв наплавленного присадочного металла, а также фактической прочностью связи, развиваемой между присадочным металлом и основным металлом.Кислородно-ацетилен обычно предпочтителен из-за его более легкого схватывания пламени и быстрого тепловложения. 7.1 Выбор сплава: Сплав, наиболее подходящий для работы, зависит от прочности соединения, устойчивости к коррозии, рабочей температуры и экономических характеристик. Обычно используются следующие сплавы: Aufhauser Low Fuming Bronze или Aufhauser Low Fuming Bronze (с флюсовым покрытием). Типичные конструкции швов показаны на Рисунок 4 ниже.
7.3 Регулировка пламени Используйте слегка окисляющее пламя. 7.4 Flux:Используйте Aufhauser Copper and Brass Flux , смешайте с водой до состояния пасты и нанесите на обе стороны стыка. Стержень можно покрыть пастой или нагреть и окунуть в сухой флюс. 7,5 Предварительный нагрев:Предварительный нагрев рекомендуется только для тяжелых секций. 7.6 Углы наклона горловины и стержня: Наконечник сопла к металлической поверхности от 40 ° до 50 °. Таблица 5: Данные для сварки пайкой меди
После предварительного нагрева или повышения температуры соединения до температуры, достаточной для сплавления присадочного стержня и меди, расплавьте шарик металла с конца стержня и нанесите его на стык, смачивание или лужение.
Для удаления остатков флюса можно использовать любой из следующих методов:
Aufhauser Filler Metals Aufhauser производит полную линейку сплавов для пайки и сварки меди. |
Сварка меди и ее сплавов — часть 1
Ремонт котла медного от Flying Scotsman
Из всех металлов медь — самый древний, ее впервые использовали для изготовления инструментов и оружия примерно с 3500 лет до нашей эры.Поэтому сварщики и металлурги могут претендовать на очень долгую родословную! Чистая медь мягкая, пластичная и легко обрабатывается, но ее можно укрепить только холодной обработкой. Он не претерпевает фазовых превращений, поэтому его нельзя упрочнять термической обработкой, как сталь. Это также относится ко многим медным сплавам, так что любое приложение тепла размягчит холоднодеформированный сплав, что приведет к значительной потере прочности в зонах термического влияния.
Две дополнительные характеристики меди и некоторых ее сплавов:
- высокая теплопроводность, что означает, что для многих стыков требуется предварительный нагрев даже при довольно скромной толщине, и
- имеет высокий коэффициент теплового расширения, что означает, что деформация может быть проблемой из-за того, что корневые зазоры быстро закрываются во время сварки.
Легирование различными металлами может использоваться для улучшения механических свойств и / или коррозионной стойкости. Эти сплавы можно удобно разделить на девять отдельных групп, как указано ниже. В дополнение к перечисленным существует несколько марок сплавов для свободной механической обработки, содержащих свинец (Pb) или селен (Se). Эти сплавы для свободной механической обработки являются короткозатратными и очень чувствительны к образованию горячих трещин. Сварщику их лучше избегать, хотя их можно успешно соединить пайкой или пайкой.
- Чистая медь с остаточными элементами менее 0,7%
- Сплавы с высоким содержанием меди с содержанием легирующих элементов менее 5%
- Медные сплавы с содержанием цинка (Zn) до 40% (латуни)
- Медные сплавы с содержанием олова менее 10% (бронзы)
- Медные сплавы с содержанием алюминия (Al) менее 10% (алюминиевые бронзы часто сокращаются до союзно-бронзовых)
- Медные сплавы с содержанием кремния (Si) менее 3% (кремниевая бронза)
- Медные сплавы с содержанием никеля (Ni) менее 30% (медно-никелевые сплавы)
- Медные сплавы с содержанием цинка менее 40% и никеля менее 18% (никель-серебро)
- Медные сплавы с содержанием Sn менее 10% и Zn менее 4% (красная латунь или бронза)
- Специальные сплавы, содержащие
- 0.
1-1,5% кадмия (Cd)
- менее 2,7% бериллия (Be)
- 0,6-1,2% хрома (Cr)
- 0,1-0,2% циркония (Zr).
Эта группа специальных сплавов способна к дисперсионному упрочнению.
Медные сплавы можно сваривать с помощью большинства традиционных сварочных процессов, хотя из процессов дуговой сварки наиболее распространены методы дуговой сварки в среде защитного газа.
Сплавы чистой меди
Существует три отдельных сорта чистой меди: Бескислородная медь с содержанием менее 0.02% кислорода; медь с твердым пеком, которая содержит <0,1% кислорода, представленного в виде оксида меди, и медь, раскисленная фосфором (P), с 0,05% P до 0,05% мышьяка (As). Бескислородная медь имеет самую высокую электрическую проводимость, медь, раскисленная фосфором, является сплавом, наиболее часто используемым для изготовления сосудов высокого давления и теплообменников. Бескислородная медь является наиболее легко свариваемой, хотя при использовании не раскисленных присадочных металлов может возникнуть проблема с пористостью.
Оксиды меди в меди с твердым пеком могут привести к охрупчиванию зон термического влияния из-за образования оксидных пленок на границах зерен.Пористость металла сварного шва, даже при использовании полностью раскисленных присадочных металлов, также является серьезной проблемой, вызванной диссоциацией оксида меди, особенно когда присутствует водород (H).
Медь, раскисленная фосфором, представляет меньшую проблему пористости, хотя пористость металла сварного шва все еще может образовываться, особенно в автогенных сварных швах. Поэтому важно, чтобы присадочные металлы содержали сильные раскислители, наиболее распространенными из которых были кремний (Si) и марганец (Mn). Также необходим контроль содержания водорода, поэтому при ручной дуговой сварке металла необходимы правильно обожженные электроды с низким содержанием водорода.При сварке TIG или MIG требуется чистая, обезжиренная проволока и стержни, а также защитный газ высокой степени чистоты.
Два присадочных металла, наиболее часто выбираемых для сварки сплавов чистой меди, — это AWS A5. 7 ERCu, C7 теперь замененного BS 2901 Часть 3 и ERCuSi-A, старый C9 из BS 2901. ERCu обычно содержит 0,4% Si и Mn с 0,8% Sn для улучшения текучести; ERCuSi-A содержит 1% Mn и 3% Si и является предпочтительным присадочным металлом для вязкого пека и P-раскисленной меди. BS 2901 Часть 3 была заменена BS EN ISO 24373: 2009 Сварочные материалы.Проволока и прутки сплошного сечения для сварки плавлением меди и медных сплавов .
Защитные газы для сварки: аргон, гелий и азот или их смеси. Чистый аргон можно использовать для сварки TIG толщиной примерно до 2 мм и для сварки MIG примерно до 5 мм — при большей толщине смесь аргона и гелия даст лучшие результаты с большим тепловложением и меньшим риском отсутствия дефектов плавления.
Газовые смеси азота и аргона с азотом использовались в прошлом, с некоторыми преимуществами, полученными с точки зрения повышенного тепловложения от высоковольтной азотной дуги, но такие газы коммерчески недоступны, и в настоящее время предпочтительными являются защитные газы аргон-гелий или гелий. выбор.Высокая теплопроводность меди означает, что при увеличении толщины требуются не только защитные газы с высоким тепловложением, но и предварительный нагрев при толщине сечения, превышающей 2 мм. В таблице приведены очень приблизительные рекомендации по рекомендуемым уровням предварительного нагрева и сварочного тока для сварки TIG и MIG.
Процесс | Толщина (мм) | Защитный газ | Предварительный нагрев, ° C | Сварочный ток (амперы) |
---|---|---|---|---|
TIG | ||||
1.0 | аргон | > 10 | 20–60 | |
1,0 — 2,0 | аргон | > 10 | 50–160 | |
2,0 — 5,0 | аргон / 75 гелий | 50 | 120–300 | |
6,0 — 10,0 | аргон / 75 гелий | 100–200 | 250–375 | |
12,5 | аргон / 75 гелий | 350 | 350–420 | |
15.![]() | аргон / 75 гелий | 400–450 | 400–470 | |
МИГ | ||||
<5,0 | аргон | 10–100 | 175–240 | |
5,0 — 7,0 | аргон / 75 гелий | 100 | 250–320 | |
10,0 — 12,5 | аргон / 75 гелий | 200–300 | 300–400 | |
> 16.0 | аргон / 75 гелий | 350–450 | 350–600 |
При сварке толстой меди с предварительным нагревом более 250 ° C и сварочным током более 350 ампер необходимо учитывать здоровье и безопасность сварщика и персонала, работающего поблизости.
Важное значение имеет изоляция свариваемого изделия с помощью тепловых одеял, а также обеспечение надлежащего экранирования от очень мощной дуги TIG или MIG. Сварщик должен выбрать плотное стекло с фильтром не менее 13 тона при сварочном токе выше 300 ампер, чтобы снизить нагрузку на глаза.
Типичные виды подготовки под сварку встык: —
- толщиной до 1,5 мм — квадратный край, без зазора
- От 1,5 до 3 мм — квадратный край с зазором 1,5 мм
- От 3 до 12 мм, одинарный -V, угол наклона от 60 ° до 90 °, кромка пера и зазор до 1,5 мм
- Одинарный V-образный вырез от 12 до 25 мм, угол наклона от 60 до 90 °, поверхность основания от 1,5 до 3 мм, максимальный зазор 1,5 мм
- Двойной V-образный вырез толщиной более 25 мм, угол наклона от 60 до 90 °, поверхность основания от 1,5 до 3 мм, максимальный зазор 1,5 мм
Углерод, нержавеющая сталь или керамическая плитка или лента могут использоваться в качестве временных поддерживающих полос и помогают контролировать форму корневого валика.
Серия «Рабочие знания» предназначена для сварщиков и поэтому имеет тенденцию концентрироваться на традиционных процессах дуговой сварки. Следует иметь в виду, что электронно-лучевая сварка и сварка трением, включая трение с перемешиванием, широко и очень успешно использовались для сварки толстослойной меди без необходимости в присадочных металлах, высоких температурах предварительного нагрева и дорогостоящих защитных газах.
Эту статью написал Джин Мазерс .
Для получения дополнительной информации свяжитесь с нами.
Что такое точечная сварка? (Полное руководство по процессу сварки)
Количество тепла зависит от теплопроводности и электрического сопротивления металла, а также от продолжительности воздействия тока. Это тепло можно выразить уравнением:
Q = I 2 Rt
В этом уравнении «Q» — это тепловая энергия, «I» — ток, «R» — электрическое сопротивление, а «t» — время, в течение которого применяется ток.
Материалы для точечной сварки
Благодаря более низкой теплопроводности и более высокому электрическому сопротивлению сталь сравнительно легко поддается точечной сварке, а низкоуглеродистая сталь лучше всего подходит для точечной сварки.Однако стали с высоким содержанием углерода (углеродный эквивалент> 0,4 мас.%) Склонны к низкой вязкости разрушения или образованию трещин в сварных швах, поскольку они имеют тенденцию к образованию твердых и хрупких микроструктур.
Для оцинкованной стали (оцинкованной) для сварки требуется немного более высокий сварочный ток, чем для стали без покрытия. Кроме того, в случае цинковых сплавов медные электроды быстро разрушают поверхность и приводят к потере качества сварки. При точечной сварке сталей с цинковым покрытием необходимо либо часто менять электроды, либо поверхность кончика электрода «одевать», когда резак удаляет загрязненный материал, обнажая чистую медную поверхность и изменяя форму электрода.
Другие материалы, обычно свариваемые точечной сваркой, включают нержавеющую сталь (в частности, аустенитные и ферритные марки), никелевые сплавы и титан.
Хотя алюминий по теплопроводности и электрическому сопротивлению близок к медным, температура плавления алюминия ниже, что означает, что сварка возможна. Однако из-за его низкого сопротивления при сварке алюминия необходимо использовать очень высокие уровни тока (в два-три раза выше, чем для стали эквивалентной толщины).
Кроме того, алюминий разрушает поверхность медных электродов в очень небольшом количестве сварных швов, а это означает, что добиться стабильного высокого качества сварки очень сложно. По этой причине в настоящее время в промышленности можно найти только специализированные области применения точечной сварки алюминия. Появляются различные новые технологические разработки, которые помогают обеспечить стабильную высококачественную точечную сварку алюминия.
Медь и ее сплавы также могут быть соединены точечной сваркой сопротивлением, хотя точечная сварка меди не может быть легко достигнута с помощью обычных электродов для точечной сварки из медных сплавов, поскольку тепловыделение в электродах и заготовке очень похоже.
Решением для сварки меди является использование электрода, изготовленного из сплава с высоким электрическим сопротивлением и температурой плавления, намного превышающей точку плавления меди (намного выше 1080 ° C). Материалы электродов, обычно используемые для точечной сварки меди, включают молибден и вольфрам.
Где используется точечная сварка?
Точечная сварка находит применение в ряде отраслей, включая автомобилестроение, авиакосмическую, железнодорожную, бытовую технику, металлическую мебель, электронику, медицинское строительство и строительство.
Учитывая легкость, с которой точечную сварку можно автоматизировать в сочетании с роботами и системами манипуляции, это наиболее распространенный процесс соединения на производственных линиях большого объема и, в частности, был основным процессом соединения при строительстве стальных вагонов на протяжении более 100 лет. .
Сварка кузова на автомобильной производственной линии.
Вопросы и ответы по теме
Класс 1 | Медно-циркониевый | C15000 | Цирконий Медь используется в электродах для точечной сварки и колесах для шовной сварки.Он особенно полезен при сварке оцинкованных материалов из-за его высокой теплопроводности, предотвращающей прилипание. |
Класс 2 | Медь-Хром | C18200 | Хром Медь — это первичный медный сплав для высокотехнологичной точечной и шовной сварки чистой низкоуглеродистой стали, низколегированных сталей, нержавеющей стали, латуни и бронзы с низкой проводимостью, нейзильбера, никеля, никелевых сплавов и монеля. |
Класс 2 | Медь-хром-цирконий | C18150 | Хром Цирконий Медь используется в качестве электродного материала для сварки оцинкованной стали и других материалов с металлическим покрытием. Он обладает улучшенным сопротивлением ползучести при высоких рабочих температурах. |
Класс 3 | Медь-никель-кремний-хром | C18000 | Медь, не содержащая бериллия, класс 3 — это очень твердая, термообрабатываемая медь с умеренной электропроводностью, которая идеально подходит для использования в качестве роликов для шовной сварки, штампов для выступающей сварки, штампов для стыковой сварки оплавлением и стыковой сварки, токопроводящих валов и втулок, конструктивных элементов с высокими нагрузками. токопроводящие элементы, электрододержатели и электроды высокого давления, в которых свариваемый материал имеет высокое электрическое сопротивление. |
Класс 3 | Медно-никель-бериллиевый | C17510 | Бериллиевая медь класса 3 поддается термообработке с умеренной электрической и теплопроводностью и высокой прочностью на разрыв. Он рекомендуется для штампов для выступающей сварки, штампов для оплавления и стыковой сварки, токоведущих элементов и сверхмощных держателей электродов со смещением. Также обычно рекомендуется для точечной и паровой сварки сталей с высоким электрическим сопротивлением, таких как нержавеющая сталь. |
Класс 4 | Медно-бериллиевый | C17200 | Бериллиевая медь класса 4 имеет чрезвычайно высокую твердость и предел прочности на разрыв, но меньшую электропроводность, чем сплавы класса III. Его рекомендуется использовать в качестве электродного материала для специальных сварочных работ оплавлением, стыковой сваркой с высаживаемыми кромками и выпуклой сварки, в которых чрезвычайно высокое давление и значительный износ, но при этом незначительный нагрев. |
C101 | Бескислородная медь | C10100 | Бескислородная медь имеет самую высокую проводимость среди всех котлов. Он используется для электрических и электронных проводников, волноводов, объемных резонаторов, сверхпроводниковых матриц, вакуумных ламп и твердотельных устройств, а также уплотнений стекло-металл. |
C110 | Электролитическая медь | C11000 | Податливость электролитической меди позволяет легко гнуть, паять, просверливать, сваривать и формовать практически любую конструкцию. В основном он используется для сантехнической арматуры и некоторых электрических компонентов, не требующих обширной механической обработки. |
Контактный наконечник Forney 60165 для сварки MIG, наконечники для дуговой сварки меди
15 долларов.

Высококачественные электроды для точечной сварки с медным наконечником по оптовым ценам Сертифицированные продукты
Воспользуйтесь преимуществами широкого ассортимента высококачественных электродов для точечной сварки с медным наконечником , доступных в Alibaba.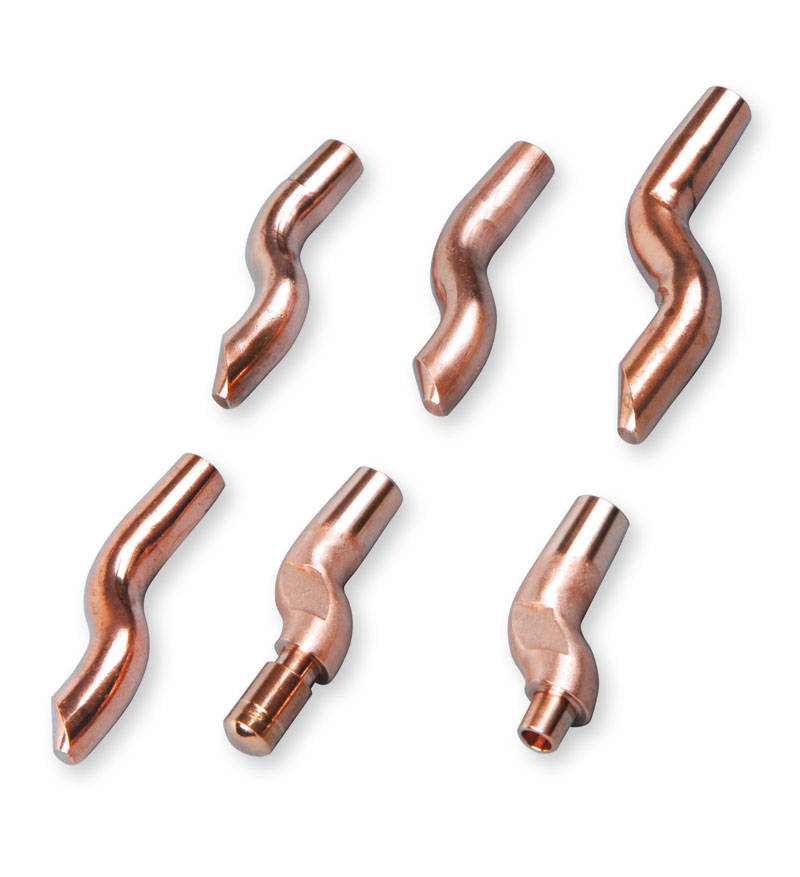
электроды для точечной сварки медный наконечник обычно относятся к концу одиночного сигнала или провода. Они отличаются по сложности и объему от более крупных соединительных устройств, которые работают с несколькими каналами.Наиболее распространенные электроды для точечной сварки с медным наконечником соединяются с концом проволоки различными способами, включая, помимо прочего, скребок, винт, припой или сварку. Электроды для точечной сварки с медным наконечником обычно предназначены для простого подключения к другим устройствам посредством проводящих разрывов. Это обеспечивает непрерывный поток электрического сигнала.
Дополните свой набор инструмента любым из электродов для точечной сварки медным наконечником от Alibaba.com. Они были классифицированы, чтобы удовлетворить любые ваши конкретные желания и потребности. Выберите из огромной коллекции электродов для точечной сварки с медным наконечником , доступных в различных вариантах, включая морской и автомобильный. Вы найдете огромное разнообразие материалов, таких как медь, латунь и т. Д., Чтобы удовлетворить все ваши электрические требования. Некоторые из этих электродов для точечной сварки с медным наконечником также предлагают дополнительное преимущество индивидуальной настройки, позволяя персонализировать этот элемент в соответствии с вашими предпочтениями.
Оцените поразительную надежность электродов для точечной сварки, медный наконечник , делая покупки на Alibaba.com. С легкостью выполняйте свой следующий электрический проект с любым из электродов для точечной сварки , медным наконечником , предлагаемых нашими надежными поставщиками, производителями и оптовиками.
Как производить детали быстрее, чем сегодня — Feature Part — M4 Sciences
«Feature Part Series» — это краткий обзор того, как производственные компании по всему миру могут изготавливать детали быстрее, надежнее и с меньшими затратами ресурсов. Модулированная вспомогательная обработка (МАМ).Сегодня мы рассмотрим наконечники для сварки MIG или любые наконечники для медной сварки с питающим отверстием в центре. Сварочные наконечники являются расходным материалом в больших объемах, поэтому снижение производственных затрат даже на небольшой процент может очень быстро привести к значительному увеличению прибыли. Многие производители, поставщики комплектного оборудования или многоуровневые поставщики уже оптимизировали и сбалансировали процесс обработки с учетом существующей технологии станков, доступной сегодня … так как же добиться еще большей экономии? Обратите внимание на новые производственные технологии.
Как вы, наверное, уже знаете, медные сплавы могут быть очень сложным материалом для сверления из-за их мягкости. Обычно вы используете цикл сверлильного сверления, чтобы удалить неоднородную стружку, которая увеличивает время цикла. Попробуйте увеличить скорость подачи, и стружка начнет скапливаться в точке сверла, что увеличивает частоту поломки инструмента. Или, может быть, вы используете дорогой канюлированный пруток для изготовления наконечников и нуждаетесь в альтернативном процессе обработки, который является более экономичным и позволяет вам более гибко реагировать на запросы ваших клиентов.Откройте для себя новую производственную технологию под названием обработка с модуляцией (MAM). Добавление MAM в микс обеспечивает очень контролируемую модуляцию инструмента по оси Z, позволяя вам бурить быстрее с минимальным клеванием или без него, увеличивать срок службы ваших инструментов и иметь более контролируемый процесс, который подходит для вашего существующего оборудования. Наука, лежащая в основе этой новаторской технологии, началась в Университете Пердью, и после 5 лет разработки M4 Sciences с 2010 года помогает клиентам по всему миру, установив более 100 установок.