Cварка под флюсом – ГОСТ 8713-79, технология, типы швов и флюсов
Какая связь между словами «окисление» и «бич»? Самая прямая, если они употребляются в контексте сварки металлов. Потому что окисление металла, которое является прямым следствием высочайшей химической активности в зоне высокой температуры во время электродуговой или газовой сварки, – настоящий бич современной сварки.
В дополнение к испарению материалов сварочной проволоки и снижению скорости процессов окисление металлов негативно сказывается на эффективности плавления. А с увеличением продолжительности процесса сварки в сварочной ванне начинает все больше и больше скапливаться шлак.
Спасение от этих сварочных бед – изоляция и защита рабочей зоны. Это выполняется с помощью специальных сварочных флюсов – композициями из неметаллических элементов с разнообразными свойствами.
Общая информация
Автоматическая дуговая сварка под слоем флюса — это технология, суть которой ничем не отличается от классической дуговой сварки. Металл плавится из-за высокой температуры, которая формируется благодаря электрической дуге. Ниже изображена схема автоматической дуговой сварки под флюсом.
Отличие автоматической сварки от любой другой заключается лишь в том, что большинство процессов выполняется не вручную, а с помощью специальных станков. Например, подача проволоки и движение дуги. Ну а в нашем конкретном случае все эти операции производятся под слоем флюса, нанесенного на поверхность металла.
Государственное регламентирование технологии, типов соединения, характеристики
ГОСТ 8713-79 классифицирует и маркирует буквенными обозначениями подвиды способа соединения под флюсом:
- АФ – на весу. Производится без средств, предотвращающих протекание металла в зазоры между соединяемыми кромками. Если требуется проварить на полную глубину, то это делают в два приёма с обеих сторон шва.
- АФф – на флюсовой подушке. Название способа иллюстрирует суть: под свариваемый стык подкладывают флюс, через огнеупорную подкладку прижимают к стыку прорезиненным шлангом.
Подают в трубку воздух под давлением – порошок плотно прижат к изделиям в области шва.
- АФм – на флюсомедной подкладке. Применяется для предотвращения пережога металла кромок, соединения угловых, стыковых и тавровых сопряжений с флюсомедными подкладками, формирующими обратную сторону шва.
- АФо – на остающейся подкладке. Применяется при односторонней сварке, когда нельзя сваривать на флюсовой подушке. Стальные подкладки – гарантия полного провара швов.
- АФп – на медном ползуне. Его конструкция обеспечивает соединение порошковой проволокой с принудительным образованием углового шва. Жидкий шлак образуется по ходу горения дуги, затем всплывает на поверхность.
- АФш – с предварительным наложением подварочного шва. Применяется реже из-за значительных трудозатрат. Упрощает процесс сборки изделия.
- АФк – с предварительной подваркой корня шва. Выполняют покрытым или плавящимся электродом в защитном газе.
Глубина провара достигает 1/3 толщины детали.
Роль флюса
С автоматической сваркой все ясно. А вот что насчет флюса? Что это такое?
Флюс — это специальное вещество (может выпускаться в виде порошка, гранул, паст и жидкостей), обладающее положительными свойствами. Флюсы толстым слоем подаются прямо в сварочную зону, защищая ее от негативного влияния кислорода. Также флюс защищает сам металл, способствует устойчивому горению дуги, уменьшает вероятность разбрызгивания металла и даже изменяет химический состав шва при необходимости.
Суть процесса
Как уже говорилось выше, автоматическая сварка подразумевает более основательную подготовку поверхности. Пыль, грязь, жировые разводы, остатки лакокрасочных материалов, ржавчина и прочий сор недопустимы в технологическом процессе. Сварочный процесс можно начинать только на чистый и обезжиренный металл.
Автоматический процесс с использованием флюса можно начинать после выставления настроек, которые задает оператор. Чтобы выставить правильные настройки, человек должен обладать теоретическими знаниями сварочного автомата. Чем толще металл, тем больший диаметр электрода используется. Вместе с тем увеличивается сила сварочного тока и напряжение дуги. А вот скорость работ снижается при большой толщине металла.
В интернете можно найти массу расчетов при работе с разными соединениями. Эта тема масштабна и мы не будем ее касаться в данной статье. Рекомендуем ее изучить самостоятельно.
В сварке принимает участие присадочная проволока, использующаяся для флюсового состава. Будет хорошим вариантом подобрать пруток из того же материала, из которого сделан сам элемент сваривания. Присадка подается в автоматическом режиме, от специалиста требуется лишь заправить ее в механизм.
Флюс засыпают с специально отведенный отсек на сварочном аппарате. Соответственно, расход флюса будет больше при сварке толстых металлов. Любой флюс расплавляется от температурного нагрева, а попадая на область шва, не вредит его свойствам, а зачастую, и улучшает их. Во время сварочного процесса флюс вспенивается и образует на поверхности стыка металлический шлак. Его необходимо убирать.
Сварка автоматическим режимом с помощью флюса ускоряет работу, но на качество шва быстрота не отражается.
Виды применяемых флюсов
Перед тем, как провести сварку под флюсом, неплохо было бы узнать, какие вообще бывать разновидности. Прежде всего, всю флюсы делятся по назначению. Они могут быть для сварки углеродистых и легированных сталей, для высоколегированных сталей и для цветных металлов. Это первое, на что стоит обратить внимание перед покупкой флюса.
Также флюсы могут быть плавлеными или керамическими. Их отличие в составе. В большинстве случаев используется именно плавленый флюс, поскольку он относительно универсальный и стоит недорого. С его помощью можно эффективно защитить сварочную ванну от кислорода. Но не ждите от плавленого флюса каких-то особых качеств. Если вам необходимы действительно отличные свойства шва, то выберите керамический флюс. Он обеспечивает отличное качество.
Также флюсы могут быть химически активными и химически пассивными. Активный флюс содержит в составе кислоты, способные не только защитить металл при сварке, но и привести к коррозии. Так что тщательно удаляйте флюс после работы. Пассивные флюсы в автоматической сварке не применяются, поскольку не обладают достаточными для этого свойствами. Зачастую вы встретите пассивный вещества при пайке в виде воска или канифоли.
Кстати, о производителях. Это давний спор всех начинающих и опытных сварщиков. Кто-то считает, что отечественные компании производят недорогой и эффективный флюс, а кто-то всеми руками за импортные комплектующие. Мы не будем однозначно говорить, что лучше, скажем лишь то, что на практике и отечественные, и импортные флюсы показывают себя хорошо, если соблюдена технология сварки.
Сварные соединения – как их определяет государственный стандарт
По ГОСТ 8713-79 сварные швы классифицируются как:
- стыковые;
- угловые;
- тавровые;
- нахлёсточные.
В свою очередь, они подразделяются на соединения:
- с отбортовкой кромки;
- без скоса;
- со скосом одной кромки;
- с криволинейным скосом одной кромки;
- с ломаным скосом одной кромки;
- с двумя симметричными скосами одной кромки.
Достоинства и недостатки
У автоматической сварки с применением флюса есть много плюсов. Ее главное достоинство — возможность полной автоматизации процесса сварки. От сварщика не нужно даже уметь варить, достаточно знать, как настроить оборудование. Также такой метод сварки гарантирует отличное качество сварочных соединений, поскольку отсутствует человеческий фактор.
У технологии сварки деталей автоматической наплавкой под слоем флюса есть и недостатки. Во-первых, вы сможете варить только нижний швы. Также детали должны быть очень точно подогнаны, ведь машина формирует шов в четко заданном месте, и любая ошибка при стыковке приведет к браку. Кроме того, нужна очень тщательная подготовка металла перед сваркой.
Учтите, что у вас не получится сварить металл на весу. Деталь нужно будет зафиксировать на горизонтальной поверхности и предварительно проварить корень сварного соединения. Еще один существенный недостаток — большая стоимость как оборудования для автоматической сварки, так и комплектующих.
Теперь, когда вам все известно, пора узнать, какова технология автоматической сварки под флюсом.
Где используется?
Автоматика применяется для разных целей. «Самодостаточное» оборудование сейчас имеет своё место на каждом крупном производстве, где детали изготавливаются большими партиями на конвейерах.
Сборка автомобилей, производство трубопроводных конструкций, балок, кораблестроение и прочие отрасли тяжёлой промышленности процветают благодаря работе автоматических сварочных аппаратов и станков.
Они способны делать плотные и надёжные соединения путем автоматической сварки с флюсом, которые высоко ценятся в данных сферах.
Технология сварки
Прежде всего, перед сваркой необходимо подготовить металл. Для каждого металла подготовка своя, но мы дадим общие рекомендации. Нужно очистить деталь от грязи, краски и коррозии. Затем нужна тщательная зачистка поверхности с помощью металлической щетки или шлифовального круга. Только после подготовительных операций можно приступать к сварке.
Технология сварки под флюсом проста за счет того, что многие процессы выполняет не человек, а машина. Мастеру не нужна зажигать дугу, следить за ее стабильностью, выбирать скорость подачи проволоки и так далее. Все, что от вас требуется — правильно настроить режимы сварки под флюсом. По сути, задать машине программу действий. Ниже таблица с перечислением режимов автоматической сварки под флюсом.
Это режимы автоматической сварки под флюсом для стыковых соединений. Естественно, существуют и другие типы соединений, поэтому для них нужно произвести расчет режимов сварки. Здесь мы не будем касаться этой темы, поскольку она очень обширна (сколько типов соединений, столько и формул), поэтому изучите эту информацию самостоятельно. В интернете много способов расчета.
При работе также используется специальная присадочная проволока для сварки под флюсом. Ее подача тоже автоматизирована, нужно лишь загрузить бобину в подающий механизм. Рекомендуем приобретать проволоку, изготовленную из того же металла, что и деталь.
Теперь немного о флюсе. Он тоже подается автоматически, только предварительно его нужно насыпать в специальный резервуар. Толщина слоя флюса зависит от толщины свариваемого металла. Чем металл толще, тем больше нужно флюса.
У вас может возникнуть закономерный вопрос: а плавится ли флюс? И влияет ли он на структуру шва? Да, конечно флюс плавится под действием температуры. Но при этом он никак не нарушает структура шва, а лишь улучшает ее. Но при этом застывший флюс превращается в шлак, который после сварки нужно удалить. Остатки неиспользованного флюса можно использовать повторно.
Подобная технология применения флюса при автоматической сварке позволяет существенно увеличить скорость работ, при этом не потеряв в качестве.
Оборудование
Производится оборудование 2 видов для сварки деталей под флюсом. В первом виде используют сварочную проволоку толщиной не более 3 мм.
Принцип устройства такого сварочного аппарата предполагает самостоятельную регулировку дуги (напряжения на ней), в то время как проволока подается с постоянной скоростью.
Второй вид – это оборудование, в котором автоматически регулируется сила тока, в зависимости от скорости подачи сварочных проволок. Диаметр электродной проволоки для такого оборудования начинается от 3 мм.
Производятся сварочные полуавтоматы и устройства для автоматической сварки. Выпускают универсальные аппараты, на которых можно проводить сварку порошковой проволокой, под флюсом, MIG, а также электродуговую строжку. Ток достигает значений 300…1500 A.
Современные автоматические модели оснащают механизмом, который позволяет собрать нерасплавившийся флюс и отправить его назад в емкость для загрузки. Существует функция контроля пропорциональности шва.
В промышленности распространены самоходные аппараты (трактора, подвесные головки), позволяющие автоматически варить объемные и протяженные конструкции. Если сварочный аппарат оснащен лазером, то это дает возможность отслеживать положение электрода. Причем экран можно устанавливать на расстоянии порядка 20 метров.
Используемые материалы
От правильности выбора проволоки электрода зависит качество сваривания. Химический состав проволоки определяет шовные характеристики. Желательно использовать проволоку из стали, соответствующую ГОСТ 2246-70. Она производится из легированной, высоколегированной, малоуглеродистой стали. Размеры готовой проволоки соответствуют стандарту (диаметр составляет 0,3-12 миллиметров).
Поставляется проволока обычно в восьмидесятиметровых бухтах. Иногда, с разрешения покупателя, используются кассеты, катушки. Перед применением проволоки, которая определенный период хранилась в складском помещении, эксперты рекомендуют очищать ее, обрабатывать бензином/керосином. Это дает возможность устранить с нее ржавчину и грязь.
Для соединения деталей из алюминия используется проволока, соответствующая ГОСТ 7871-75. Нередко используют проволоку, покрытую медью. Ее не нужно предварительно обрабатывать. Качество сварки, осуществляемой флюсовой проволокой без газа, прямо зависит от характеристик флюса. От состава флюса зависят показатели газовой среды, жидкого шлака. Взаимодействуя с деталью, шлак определяет структуру шовного металла. От его структуры зависит устойчивость изделия к растрескиванию.
Флюс используется для того, чтобы:
- легировать шовный металл;
- изолировать сварную ванну от внешних воздействий;
- создавать шовную поверхность;
- стабилизировать дуговой разряд.
Недостатки от применения флюса
Слабые места данной технологии обуславливаются более высокими требованиями к оборудованию, так как для эффективного расплава флюса требуется большая мощность. Сегодня выпускаются специальные модификации аппаратов для аргонодуговой сварки в среде флюса, имеющие специальную оснастку для его подготовки и подачи. Логично, что такие модели стоят на 15-20% дороже. Еще один недостаток связан с увеличением зоны расплава. Хотя ее можно контролировать в определенных границах, мелкие элементы точечно обрабатывать в таких условиях проблематично.
Сварка под флюсом различных типов сталей
Сварка конструкционных углеродистых сталей
При сварке конструкционных малоуглеродистых сталей используют флюсы марок АН-348А, ОСЦ-45, АНЦ-1 и другие в сочетании с малоуглеродистыми или марганцевыми проволоками марок Св-08А, Св-08ГА, Св-10Г2.
Сварку среднеуглеродистых сталей выполняют при пониженных режимах, что существенно сказывается на производительности, поэтому, при изготовлении конструкции из среднеуглеродистых сталей данный вид сварки не нашёл широкого распространения на практике.
Высокоуглеродистые конструкционные стали содержат 0,46-0,75% углерода и свариваемость их затруднена. Для сварных конструкций эти стали не используются и необходимость в их сваривании возникает, как правило, при ремонтных работах. В большинстве случае, ремонт выполняют методом наплавки.
Сварка низколегированных сталей
К низколегированным сталям относят группу сталей, содержащих в составе менее 5% легирующих элементов. Оценивая свариваемость сталей этой группы, можно сказать, что при сварке под флюсом их свариваемость существенно не отличается от нелегированных малоуглеродистых сталей. Но, легирующие элементы в составе стали повышают склонность сталей к росту зёрен в зоне термического влияния, а при высокой скорости охлаждения в них могут возникать неоднородные структуры закалочного характера.
Для сварки металлоконструкций из низколегированных сталей, с температурой эксплуатации до -40°C, используют высококремнистые марганцевые флюсы марок АН-22, АН-22М, АН-47, АН-67А и другие в сочетании с легированной сварочной проволокой марок Св-10НМА, Св-08ХМ, Св-08МХ и др.
Сварка среднелегированных сталей
Среднелегированными являются стали, содержащие в составе 5-10% легирующих элементов. Для современных среднелегированных сталей характерно легирование многокомпонентное, комплексное. Легирование этих сталей только одним элементом применяется редко.
К сварным конструкциям из среднелегированных сталей предъявляются требования повышенной прочности в условиях эксплуатации, а также, нередко, коррозионная стойкость, стойкость к импульсным (резко возрастающим, мгновенным) нагрузкам. Чем выше содержание легирующих элементов, тем труднее сваривать сталь.
Одной из главных проблем свариваемости среднелегированных сталей является их чувствительность к образованию горячих трещин в сварных швах, поэтому при их сварке необходимо тщательно выбирать композицию шва. Кроме этого, необходимо использовать технологические приёмы и выбирать режимы, которые позволят получить хороший коэффициент формы шва и снизить скорость охлаждения.
Для сварки конструкций из среднелегированных сталей сварка под флюсом получила достаточно широкое применение. Для такой сварки используются низкокремнистые флюсы марок Ан-15, АН-15М, АН-17М и бескремнистые марок АН-30, ОФ-6, АВ-4 и др.
Применение бескремнистых флюсов предпочтительно в тех случаях, когда к металлу шва предъявляются повышенные требования по ударной вязкости. В сочетании с вышеуказанными флюсами применяется сварочная проволока марок Св-20Х4ГМА, Св-08Х20Н9Г7Т, Св-10Х5М, Св-10ХГСН2МТ.
Сварка высоколегированных сталей
Высоколегированными считаются стали, содержащие в составе более 10% легирующих элементов. Сварка под флюсом высокоуглеродистых сталей нашла широкое применение в химической и нефтяной промышленности, где требуется высокая коррозионная стойкость сварных изделий и жаропрочность.
Своим широким применение для этих сталей сварка под флюсом получила благодаря постоянству процесса сварки и, как следствие, химической однородности металла шва. Это очень важно для высоколегированных сталей, учитывая, что даже незначительная химическая неоднородность металла шва может стать причиной образования в нём кристаллизационных трещин или заметно снизить коррозионную стойкость или жаропрочность.
Сварка под флюсом способна обеспечить швы с гладкой поверхностью и плавным переходом к основному металлу, что позволяет повысить стойкость к коррозии по сравнению со сваркой электродами.
При сварке под флюсом высоколегированных сталей обычно применяют проволоку диаметром 2-3мм. При этом могут использоваться почти все марки проволоки по ГОСТ 224, а также многие марки проволоки, выпускаемые по ТУ, например, Св-12Х11НМФ, Св-12Х13, Св-10Х17Т, Св-04Х19Н9, ЭП467, ЭП235, ЭП497 и другие.
Для сварки жаропрочных высоколегированных сталей применяются фторидные флюсы марок АНФ-5, АНФ-8, АНФ-24 и бескремнистые флюсы марок АНФ-17, АНФ-22. Для сварки коррозионностойких высоколегированных сталей применяют флюсы с низким содержанием кремния марок АН-26, АНФ-14.
Сварка под флюсом. Трактор Jasic-MK-1
Автоматическая SAW сварка под флюсом – это один из наиболее продуктивных способов сварки, при котором используется электродная проволока сплошного сечения, а для защиты дуги и сварочной ванны от воздуха применяют флюс. Сварка под флюсом характеризуется глубоким проплавлением основного металла. При сварке под флюсом образующийся шлак обеспечивает дополнительную тепловую защиту и снижает тепловые потери дуги, чем значительно повышает качество сварного шва и соединения в общем.
В процессе автоматической сварки под флюсом горение дуги происходит между проволокой и основным металлом. Столб дуги и сварочная ванна из жидкого металла со всех сторон плотно закрыты слоем флюса толщиной 30-35 мм. В процессе горения дуги часть флюса расплавляется, образуя вокруг дуги газовую полость, а на поверхности расплавленного металла – жидкий шлак, который надежно защищает сварочный шов от окружающей среды.
В статье мы рассмотрим сварочный трактор Jasic MK-1, производства мирового лидера сварочного оборудования Shenzhen Jasic Technology. На сегодняшний день компания Shenzhen Jasic Technology располагает четырьмя научно-исследовательскими центрами и тремя современными производственными площадками. Благодаря передовым исследованиям компания получила более 50 национальных патентов, а также 14 наград за вклад в национальную науку Китая и развитие технологий в сфере сварки, завод отмечен статусом «предприятие государственного значения». Производство компании имеет сертификат ISO9001, производственный процесс и продукция соответствуют мировым стандартам.
Сварочный трактор Jasic MK-1 для автоматической SAW сварки под флюсом подойдет для выполнения длинных прямолинейных и кольцевых швов в нижнем положении при серийном и массовом производствах. Минимальный ток сварки составляет 100А, а максимальный – 1000А или 1250А в зависимости от комплектации и модели источника питания. Продолжительность включения трактора Jasic MK-1 максимально возможна и составляет 100%.
Сварочный трактор Jasic MK-1 обеспечивает стабильную сварку всеми видами проволоки диаметром от 2 мм до 6 мм. Для обеспечения наилучшего позиционирования сварочную головку и поперечную балку можно перемещать по вертикальной и горизонтальной оси, а также вращать. Четырехроликовый механизм подачи проволоки обеспечивает стабильную подачу проволоки, качественную центровку, значительное усилие прижима и минимальные потери мощности, скорость подачи проволоки составляет 0.3 – 3.0 м/мин.
Каретка трактора представляет собой подвижную тележку на колесах. Она приводится в движение электродвигателем постоянного тока с плавно регулируемой скоростью. Скорость сварки можно изменять в широком диапазоне от 0.1 до 1.5 м/мин. На каретке находится рукоятка, которая позволяет переключать режимы перемещения – режим «AUTO» движение трактора осуществляется автоматически, в режиме «MANUAL» — трактор может перемещаться исключительно вручную, что необходимо для точного позиционировании трактора относительно свариваемых деталей.
Блок управления сварочного трактора Jasic MK-1 позволяет управлять всеми процессами непосредственно с пульта и состоит из таких основных узлов:
Кнопка экстренной остановки. Нажмите эту кнопку в случае возникновения чрезвычайной ситуации при сварке. Блок управления будет обесточен и сварочный трактор остановится. Когда опасность будет устранена – поверните кнопку в направлении, указанном стрелкой, блок управления включится и сварку можно будет продолжить.
Цифровые дисплеи. С высокой точностью отображают значение скорости перемещения автомата, напряжения сварки и тока сварки;
Сигнальные индикаторы
скорости сварки и скорости подачи сварочной проволоки;Энкодеры, предназначены для регулировки тока или скорости подачи проволоки, скорости сварки, напряжения сварки. Преимущество энкодеров по сравнения с типовыми потенциометрами это их долговечность, отсутствие механического износа и возможность точной регулировки параметров;
Переключатель направления движения каретки задает направление, в котором будет осуществляться сварка: вперед или назад;
Кнопка «FN» вызова подменю при помощи которой изменяются дополнительные параметры сварки, например, такие, как функция заварки кратера в конце сварки;
Кнопки «START» и «STOP», которые предназначены для начала или остановки процесса сварки соответственно.
При использовании на производстве сварочных тракторов JASIC MK-1 повышается продуктивность сварки в 10-15 раз по сравнению с другими способами сварки, достигается однородность шва и повышается качество наплавленного металла, значительно снижаются расходы сварочной проволоки в связи з уменьшением потерь металла на выгорание и разбрызгивание.
Сварка под флюсом значительно облегчает работу операторов и исключает негативное влияние сварочной дуги на органы зрения, поскольку весь процесс происходит в закрытой шлаковой коркой ванне, исключая световое загрязнение и позволяя работать оператору, который следит за процессом без маски.
Сварочный трактор Jasic MK-1 входит в комплект поставки систем автоматической сварки Jasic MZ-1000
и Jasic MZ-1250.По вопросу тестирования и приобретения оборудования обращайтесь к нашим менеджерам.
Автоматическая дуговая сварка под флюсом. Флюс сварочный.
Автоматическая дуговая сварка под флюсом
Для сварки используют непокрытую электродную проволоку и флюс для защиты дуги и сварочной ванны от воздуха. Для сварки под флюсом характерно глубокое проплавление основного металла.
Подача и перемещение электродной проволоки механизированы. Автоматизированы процессы зажигания дуги и заварки кратера в конце шва. Дуга 10 горит между проволокой 3 и основным металлом 8. Столб дуги и металлическая ванна жидкого металла 9 со всех сторон плотно закрыты слоем флюса 5 толщиной 30…50 мм. Часть флюса плавится и образуется жидкий шлак 4, защищающий жидкий металл от воздуха. Качество защиты лучше, чем при ручной дуговой сварке. По мере поступательного движения электрода металлическая и шлаковая ванны затвердевают с образованием сварного шва 7, покрытого твердой шлаковой коркой 6. Проволоку подают в дугу с помощью механизма подачи 2. Ток к электроду подводят через токопровод 1.
Автоматическая дуговая сварка под флюсом
Преимущества автоматической сварки под флюсом по сравнению с ручной дуговой сваркой: повышение производительности процесса сварки в 5…20 раз, повышение качества сварных соединений и уменьшение себестоимости 1 м сварного шва.
Флюс сварочный
Применяемые флюсы различают по назначению. Флюсы для сварки низкоуглеродистых и низколегированных сталей предназначены для раскисления шва и легирования его марганцем и кремнием. Для этого применяют высококремнистые марганцевые флюсы, которые получают путем сплавления марганцевой руды, кремнезема и плавикового шпата в электропечах.
Флюсы для сварки легированных и высоколегированных сталей должны обеспечивать минимальное окисление легирующих элементов в шве. Для этого применяют керамические низкокремнистые, безкремнистые и фторидные флюсы, которые изготавливают из порошкообразных компонентов путем замеса их на жидком стекле, гранулирования и последующего прокаливания. Основу керамических флюсов составляют мрамор, плавиковый шпат и хлориды щелочно-земельных металлов.Наши передовые возможности дуговой сварки под флюсом
2 июня 2020 г.
GSM Industrial специализируется на сложных проектах любого масштаба, и мы верим в постоянное совершенствование. Мы регулярно инвестируем в нашу команду и оборудование, чтобы расширить наши производственные возможности. Недавно мы добавили в наше производственное подразделение современную систему дуговой сварки под флюсом, включая трехосевой позиционер для удержания и соединения конструкций весом до 7,7 тонн. Эта система позволит GSM Industrial сваривать более тяжелые конструкции более эффективно и по конкурентоспособной цене.
Ценность и преимущества для наших партнеров и клиентов
НАСАДКА: Наша система SAW работает с чрезвычайно высокой скоростью наплавки с мощностью более 33 фунтов. в час по сравнению с обычными GMAW и FCAW. Скорость наплавки или количество нанесенного сварочного материала может увеличиваться на один, два и три электрода в зависимости от конструкции соединения и толщины материала. С SAW мы можем за один проход выполнить то, что в других сварочных процессах потребовало бы нескольких проходов.Это означает более короткое время выполнения и, возможно, более быстрое включение проектов. Быстрая работа означает экономию средств для наших клиентов и партнеров.
КАЧЕСТВО: Система SAW обеспечивает сварку с превосходными металлургическими свойствами и геометрией валика, значительно сокращая общее время сварки. Автоматически регулируемая скорость перемещения, напряжение и постоянная сила тока обеспечивают очень хорошую глубину проникновения, профиль валика и равномерное размещение. Поскольку дуга погружена в флюс, сварной шов не подвергается воздействию атмосферы, что означает меньшую вероятность появления примесей и загрязняющих веществ, которые, как известно, вызывают распространенные дефекты сварки.Результатом SAW является однородный сварочный наплав практически без брызг, с минимальным выделением сварочного дыма и воздействием ультрафиолетового излучения.
ВОЗМОЖНОСТИ: Добавление этой системы SAW расширяет наши возможности по изготовлению более крупных и толстых металлических компонентов. В то время как наши квалифицированные сварщики всегда могли сваривать сосуды с толстым покрытием и компоненты из конструкционной стали, мы расширили наши возможности с точки зрения толщины, эффективности, согласованности, точности и стоимости.
Наилучшие применения для дуговой сварки под флюсом
Процесс под флюсом позволяет соединять различные формы конструкций и идеально подходит для продольных или кольцевых швов на резервуарах, больших трубах, цилиндрах, дымовых трубах, турбинах и тяжелых сосудах ASME.SAW увеличивает нашу способность эффективно повышать ценность для наших клиентов в тяжелой промышленности, такой как производство электроэнергии, сталелитейные заводы и химические заводы.
GSM Industrial инвестирует в следующий уровень технологий, чтобы постоянно расширять наши возможности для наших клиентов и создавать возможности для нашей команды для повышения их квалификации. Мы потратили более 240 часов на обучение шести членов нашей команды системе SAW, чтобы обеспечить гибкость и своевременную реализацию проектов наших клиентов.Свяжитесь с нами сегодня, чтобы узнать больше об использовании SAW для ваших производственных проектов.
Исследование влияния параметров процесса дуговой сварки под флюсом на механические свойства стали для сосудов под давлением ASTM A283, класс A
Сталь для сосудов под давлением используется в котлах и конструкциях сосудов под давлением. В этом исследовании изучалось влияние параметров процесса дуговой сварки под флюсом (SAW) на механические свойства этой стали. Образец сварного шва был изготовлен из листа ASTM A283 класса A из 6 листов.00-миллиметровая толщина. Образец для сварки обрабатывали на ПАВ с изменением трех технологических факторов. Для первого фактора исследованы сварочные токи 260, 270 и 280 ампер. Второй фактор оценивал скорость движения, которая была протестирована как 10 и 11 миллиметров в секунду. Третий фактор исследовал параметр напряжения, который варьировался от 28 до 33 вольт. Каждое условие сварки проводилось случайным образом, и каждое условие тестировалось в общей сложности три раза с использованием полного факторного плана.Полученные материалы исследовали с помощью испытаний на прочность при растяжении и твердость, а также наблюдали с помощью оптической микроскопии (ОМ) и сканирующей электронной микроскопии (СЭМ). Результаты показали, что сварочный ток, напряжение и скорость перемещения значительно повлияли на прочность на разрыв и твердость (значение <0,05).
Оптимальными параметрами ПАВ были 270 ампер, 33 вольта и скорость перемещения 10 мм/с. Были обнаружены перлит высокой плотности и мелкозернистый, что привело к повышению прочности и твердости материала.
1. Введение
ASTM A283 марка А Сталь – это качественная сталь для корпусов котлов высокого давления, которая обладает хорошей свариваемостью и отличной ударной вязкостью. Он идеально подходит для применения при умеренных и более низких температурах. Этот материал широко используется производителями котлов и сосудов под давлением, которые обеспечивают производственную поддержку в нефтехимической, нефтяной и газовой промышленности. Стали, содержащие от 0,15% до 0,30% углерода, обычно называют мягкой сталью. При сварке углеродистых сталей, содержащих не более 0,0 трещины под валиком или недостаточной ударной вязкости в околошовной зоне обычно не наблюдается.2% углерода и 1% марганца. Такая сталь может быть сварена без предварительного нагрева, термообработки после сварки или специальных процедур сварки, когда толщина соединения составляет менее 1 дюйма, а ограничение соединения не является серьезным. Сосуд под давлением ASTM A283 Сталь класса A, которая используется как в сосудах под давлением, так и в промышленных котлах, является отличным выбором для работы при температурах ниже температуры окружающей среды и обладает превосходной ударной вязкостью [1, 2].
Параметры сварки, такие как ток, напряжение, скорость подачи проволоки и длина вылета электрода, являются основными параметрами сварки под флюсом (SAW).Напряжение или длина дуги определяют силу дуги. Короткая дуга фокусирует имеющуюся силу на небольшой площади сварочной ванны, что обеспечивает более глубокое проплавление и более узкие сварные швы. Скорость подачи проволоки также является фактором, определяющим проплавление и форму сварного шва. Скорость подачи электрода регулируется для получения желаемого напряжения для хорошего плавления и проплавления [3]. Ли и др. [4] экспериментировали с новым методом применения внешней цепи постоянного тока в процессах дуговой сварки под флюсом между шлаком и сварочной ванной для контроля включений и улучшения внешнего вида металла шва.
Полный факторный план особенно полезен на этапах экспериментальной работы. Факторный план часто используется для изучения влияния двух или более независимых переменных на одну зависимую переменную [5]. Мохсен и др. [6] применили факторный план 2 3 для изучения влияния дуговой сварки защитным металлом на чугунную сталь. Исследование было сосредоточено на трех факторах электрода, а также на условиях предварительного нагрева и охлаждения. Джафари и др. [7] протестировали полный факторный план 3 4 , чтобы определить важные производственные параметры, влияющие на свойства литья по выплавляемым моделям из сплава Al-Si-Cu.
В данной работе основное внимание уделяется влиянию параметров SAW на механические свойства стали класса A ASTM A283 для сосудов высокого давления. Оптимальные значения факторов в процессе ПАВ были определены с использованием полного факторного плана эксперимента. Это исследование может помочь в выборе подходящих параметров SAW для сварки сосудов высокого давления из стали ASTM A283 класса A.
2. Методология исследования
2.1. Материалы и методы
Сосуд высокого давления ASTM A283 стальной лист марки A был 6.толщиной 00 мм. Детальный материальный химический состав приведен в таблице 1.
|
Образцы сварки были сварными с помощью сосуда под давлением ASTM A283 класса сталь, с помощью сварочных токов 260, 270 и 280 ампер Сварочные напряжения были установлены на 28 или 33 вольта. Скорости сварки поддерживали на уровне 10 или 11 мм/с, а диаметр электрода (LC-72) составлял 2,00 мм.
После сварки образцы подвергались механическим испытаниям. Сварные образцы были разрезаны поперек сварного шва и отполированы стандартными металлографическими методами.Образцы сварных швов были исследованы и проанализированы с помощью перевернутого испытания на прочность на растяжение в соответствии со стандартом ASTM. Микротвердость определяли с нагрузкой 1000 g для наблюдения за влиянием факторов ПАВ в околошовной зоне [8, 9]. Отполированные для оптической микроскопии (ОМ) и сканирующей электронной микроскопии (СЭМ) образцы сварных швов под флюсом были протравлены HNO 3 (2 мл) и метанолом (98 мл) [9].
2.2. Схема эксперимента
Эксперименты были разработаны для определения оптимальных условий сварки.Полный факторный план эксперимента был использован для изучения основных эффектов и влияния факторов, влияющих на предел прочности при растяжении и твердость. Факторы сварки, изученные в этом исследовании, включали сварочный ток, напряжение и скорость перемещения, как показано в таблицах 2 и 3: «Гипотезы эксперимента (с достоверностью 95% (значение <0,05))»; указывает на то, что факторы сварки не влияют на прочность на растяжение и твердость ; указывает на то, что сварочные факторы и время влияют на предел прочности на разрыв и твердость
|
|
3. Результаты и обсуждение
3.1. Прочность на растяжение
Анализ результатов дисперсии и выводы суда, анализируя изменчивость в полном факториальном экспериментальном дизайне показан в таблице 4.
|
Влияние параметров процесса ПАВ на предел прочности при растяжении определяли с доверительной вероятностью 95% (значение <0.05) [10]. Результаты показывают, что данные могут быть предсказаны с использованием модели. собранных данных составляет приблизительно 92,59%, что показывает, что ответ может быть описан экспериментальными факторами, показанными в таблице 4.
На рисунке 1 показано распределение остатков в нормальном распределении для анализа прочности на растяжение. Нормальное распределение использовалось для проверки остаточного распределения. Результаты показывают, что остатки были распределены по прямой линии от середины гистограммы. Остаточное значение распределения имело нормальную форму, и остатки оценивались как имеющие нормальное распределение.
На рис. 2 показано влияние параметров сварки на предел прочности при растяжении. Взаимодействие между этими переменными становится очевидным, когда линии на графике не параллельны. Результаты показывают, что максимальная достигнутая прочность на растяжение составила 541 МПа при сварочном токе 270 ампер, напряжении 33 вольт и скорости перемещения 10 мм/с.
3.2. Анализ твердости
Из теста ANOVA, приведенного в таблице 5, анализ данных показал условия твердости в % и %, и, таким образом, решение удовлетворяет коэффициентам значения ANOVA, который равен , и мы отклоняем нулевую гипотезу. Результат показал, что два фактора ПАВ повлияли на твердость с доверительной вероятностью 95%.
|
На рис. 3 показан остаточный график для твердости. Статистический анализ данных был выполнен и подтвержден экспериментальными моделями.Гипотеза заключалась в том, что картина невязок, полученных из экспериментальных данных, соответствует принципу (0, ) [11]. Остатки считались независимыми и нормально распределенными. Средние значения 0 и стабильны в экспериментальных данных. Результаты показали, что данные носят случайный характер, что делает вывод об экспериментальных результатах твердости.
На рис. 4 показано влияние факторов ПАВ на твердость. Взаимодействие между этими факторами становится очевидным, когда линии на графике не параллельны.Линейный график показывает, что существует сильное взаимодействие между факторами сварки и твердостью. Результаты показывают, что самая высокая твердость, достигнутая при факторах ПАВ, составила 254 HV при токе 270 ампер, напряжении 33 вольта и скорости перемещения 10 мм/сек.
3.3. Наблюдения за микроструктурой
Как видно из зоны термического влияния (ЗТВ), микроструктура материала сварного шва представляет собой феррит в исходной и перлитной фазах после дуговой сварки металлическим электродом в среде защитного газа [12].
На рис. 5 представлено сравнение микроструктуры образца сварного шва из стали марки А ASTM A283 до и после сварки под флюсом. На рис. 5(а) показана микроструктура исходного образца, из которой видно, что микроструктура представляет собой феррит в исходной и перлитной фазах (черный цвет) [13, 14], а перлитная фаза имеет плотность 24,36 % и распределение в исходной фазе. . Исходная твердость исходного материала составляла 175 HV. На рис. 5(b) показано, что перлитная фаза превратилась в зерно матрицы ферритной фазы, которая имела плотность перлитной фазы 55.12%, после сварки SAM. Твердость наплавленного образца составляет 254 HV в ЗТВ. Сравнение микроструктуры исходного и сваренного образцов выявило явные различия. Произошло увеличение плотности крупного и пластинчатого перлита, что привело к повышению твердости материала и предела прочности при растяжении, что может повлиять на твердость в ЗТВ [15]. Следовательно, факторы, используемые при выборе подходящей сварки, также влияют на микроструктуру и механические свойства свариваемых материалов.
СЭМ-микрофотография на рис. 6 сравнивает плотность перлита в образцах. На рис. 6(а) также показана микроструктура образца, сваренного при токе 280 ампер, напряжении 28 вольт и скорости перемещения 11 мм/сек. Он показывает снижение плотности перлитной фазы с преимущественно крупным перлитом [16, 17], что вызвано недостаточным напряжением сварочного тока и скоростью перемещения. В этом случае образовался перлит, который способствовал снижению твердости и прочности на разрыв [18] сплава 226.96 HV и 511,4 МПа соответственно. На рис. 6(б) показан образец, сваренный при токе 270 ампер, напряжении 33 вольт и скорости перемещения 10 мм/сек, на котором также показана микроструктура образца с его исходной фазой в феррите и перлите и увеличением в плотности перлита и тонкого перлита, обеспечивающего максимальную прочность на растяжение и твердость. Также было обнаружено, что подходящие коэффициенты SAW улучшают как прочность на растяжение, так и свойства твердости, что влияет на плотность перлита в ферритной фазе, показанную на рисунке 6.Ойяравелу и др. В работе [19] сообщается, что самая высокая твердость и предел прочности при растяжении явно способствовали образованию мартенситной и перлитной фаз в металле шва и околошовной зоне. Соответствующие наблюдения были сделаны Lah et al. [20], где самые высокие механические свойства сварного шва стали для сосудов высокого давления были обусловлены плотностью перлита и мелкодисперсной перлитной фазой.
4. Заключение
В этом исследовании было изучено влияние факторов SAW на механические свойства стали ASTM A283 марки A.Сварку образцов проводили при сварочных токах 260, 270 и 280 А, напряжении 28 и 33 В и скорости перемещения 10 или 11 мм/с. Были проанализированы механические свойства и микроструктура. Результаты этого исследования суммированы следующим образом: (1) Факторный расчет сварочного тока с напряжением и скоростью перемещения привел к взаимодействию прочности на растяжение и твердости на 95% доверительном уровне (значение <0,05). (2) Оптимальный Факторами ПАВ были сила тока 270 ампер, напряжение 33 вольта и скорость перемещения 10 мм/сек, что привело к пределу прочности при растяжении 541 МПа и твердости 254 HV.(3) Микроструктура стали ASTM A516 марки A содержала перлит и феррит при оптимизации коэффициентов ПАВ, что влияет на плотность перлита в исходной фазе. (4) Было обнаружено, что прочность на растяжение и твердость, полученные для образцов сварного шва, соответствуют образование перлитной плотности и мелкодисперсного перлита в металле шва и околошовной зоне.
Конкурирующие интересы
Авторы заявляют об отсутствии конкурирующих интересов.
Благодарности
Эта работа выполнена при финансовой поддержке Национального исследовательского совета Таиланда в 2016 году.Авторы выражают благодарность Департаменту образования в области производственных технологий, Факультету промышленного образования и технологии Технологического университета Тонбури имени короля Монгкута (KMUTT) за вклад в это исследование.
Оператор вспомогательной дуги Описание работы и обзор Карьерный проект
Обязанности и ответственность
Оператор вспомогательной дуги отвечает за настройку и эксплуатацию аппаратов для дуговой сварки. Это машина, которая сваривает детали готовых металлических изделий.Их типичные обязанности и ответственность включают в себя:
- Настройка аппарата для дуговой сварки, в том числе выравнивание и регулировка аппарата
- Использование машины для сварки материалов в соответствии с чертежами, схемами, процедурами сварки и рабочими схемами
- Выбор правильного напряжения и мощности автомата
- Визуальный осмотр сварных швов на соответствие спецификациям
- Настройка станка в зависимости от размера, положения и проникновения валика
- Повторная сварка дефектных соединений с использованием оборудования для ручной сварки
- Предварительный нагрев поверхностей с помощью ручной горелки или нагревательных печей
Квалификация
Чтобы стать оператором Sub Arc, вам потребуется аттестат о среднем образовании или его эквивалент в сочетании с техническим обучением и обучением на рабочем месте. Они могут быть присуждены профессионально-техническими институтами, общественными колледжами, частными школами сварки и различными подразделениями вооруженных сил США.
Навыки и соответствующий опыт работы
Чтобы иметь наилучшие возможности трудоустройства, операторы Sac Arc должны стремиться получить как можно больше опыта в строительной и сварочной промышленности. Им также нужны навыки, такие как:
- Физическая подготовка и выносливость, , так как операторы Sac Arc должны будут поднимать тяжелые материалы, которые необходимо сваривать
- Навыки общения являются операторами Sac Arc, которые должны будут внимательно и четко общаться с другими сварщиками
- Ориентация деталей , так как операторам Sac Arc необходимо будет разрезать материалы и сваривать их с точностью до миллиметра
- Ловкость, , поскольку операторам Sac Arc потребуется хорошая зрительно-моторная координация для работы с оборудованием
- Критическое мышление , поскольку операторы Sac Arc должны уметь решать проблемы, возникающие в проекте
Часы
Операторы Sac Arc будут работать полный рабочий день, и сверхурочная работа является обычным явлением.
Зарплата
По данным Бюро статистики труда, средняя годовая заработная плата сварщиков, резчиков, паяльщиков и паяльщиков в 2019 году составляла 42 490 долларов. Самые низкие 10 процентов зарабатывали менее 29 470 долларов, а самые высокие 10 процентов зарабатывали более 64 240 долларов. Операторы дуги Sac могут рассчитывать на заработную плату в аналогичном диапазоне.
Важно помнить, что средний доход сварщиков зависит от их опыта и уровня квалификации, отрасли и размера компании, в которой они работают.
Прогресс
Ожидается, что рост занятости сварщиков, включая операторов Sac Arc, в ближайшие годы ускорится. Это связано с устаревающей национальной инфраструктурой, требующей опыта сварщиков. После прохождения начального обучения операторы Sac Arc могут пройти дополнительные курсы и получить сертификаты, чтобы улучшить свои перспективы трудоустройства и возможности
.
Высокопроизводительная дуговая сварка под флюсом с использованием бесшовной порошковой проволоки
Второй вебинар из серии из трех частей посвящен сварке в судостроении.Дуговая сварка под флюсом является одним из наиболее эффективных и производительных сварочных процессов, доступных производителю. Высококачественные сварные швы обеспечивают очень хорошую скорость наплавки и отличные механические свойства. Сам процесс не сильно изменился за прошедшие годы, но последние инновации в технологии производства проволоки доказали свою эффективность в повышении скорости и эффективности наплавки.
Одной из таких инноваций является появление технологии бесшовной порошковой проволоки для дуговой сварки под флюсом.Очевидно, что использование бесшовных порошковых проволок для дуговой сварки под флюсом по сравнению со сплошными проволоками позволяет значительно повысить скорость наплавки и сократить время, необходимое для получения качественных сварных швов с отличными механическими свойствами при использовании многопроходных и двухпроходных методов. без дополнительных капиталовложений. Используя двухпроходную технику в сочетании с соответствующим флюсом, проволоку можно использовать для соединения листов толщиной до ¾ дюйма. В этой презентации будут описаны принципы и производственный процесс бесшовной проволоки, обсуждены особенности и преимущества, а также подробные процедуры и результаты, включая использование двухпроходной технологии для листов толщиной от ⅜ до ¾ дюйма.
voestalpine Böhler Welding — ведущий мировой производитель высококачественной проволоки и флюсов для дуговой сварки под флюсом для различных областей применения в производстве, подъемно-транспортном оборудовании, нефтегазовой отрасли, производстве электроэнергии, транспорте и судостроении.
Динамики 9012
Russel FUCHS
VP Прикладная Инжиниринг, Voestalpine Bohler Сварка USA
Russel Fuchs является вице-президентом прикладной техники, наблюдая за США и Канадой, для вуээээлпинской сварки Bohler, один из мировых крупнейших производителей сварочных расходных материалов.
Рассел и его команда предоставляют обширные прикладные и технические знания для повышения эффективности процессов, разработки новых экономичных инженерных решений в технологии соединения и консультирования клиентов по оптимальному сочетанию наполнителя и основного материала для наилучшего соответствия техническим требованиям.
Рассел работает в компании voestalpine Bohler Welding уже 36 лет и более 42 лет работает в сварочной отрасли. Расположенный в Хьюстоне, штат Техас, Рассел является пожизненным членом Американского общества сварщиков и входит в несколько комитетов AWS.Он также активно сотрудничает с несколькими отраслевыми органами и организациями, такими как ASME, API и NACE.
Эрвин Геринг, IWE
Глобальный менеджер по продукции – проволока и флюс под флюсом, voestalpine Böhler Welding
один из крупнейших мировых производителей сварочных расходных материалов. В качестве старшего члена группы управления глобальной продукцией Эрвин отвечает за разработку новых продуктов, специализированные приложения для продуктов и общую бизнес-стратегию для бизнеса проволоки и флюса под флюсом.
С большим интересом к судостроению и ремонту, а также трубопрокатным заводам, ветряным башням/фундаментам и другим применениям высокопрочной конструкционной стали, Эрвин и его команда добились значительных успехов в технологии проволоки и флюса под флюсом для удовлетворения сложных требований к материалам и производительности. инициативы вместе с деловыми партнерами у своих конечных клиентов.
Имея степень в области машиностроения и степень магистра в области сварки (IWE), Эрвин применяет свой более чем 30-летний опыт в области сварки для оптимизации решений для проволоки/флюса под флюсом для удовлетворения конкретных отраслевых потребностей, поддержки повышения производительности и улучшения общей свариваемости.
MECHANICALFUNDA для инженера-механика
Введение:Сварка под флюсом — это распространенный процесс дуговой сварки, при котором образуется дуга между непрерывно подаваемым электродом и заготовкой. Он в основном используется для выполнения более быстрых сварных соединений.
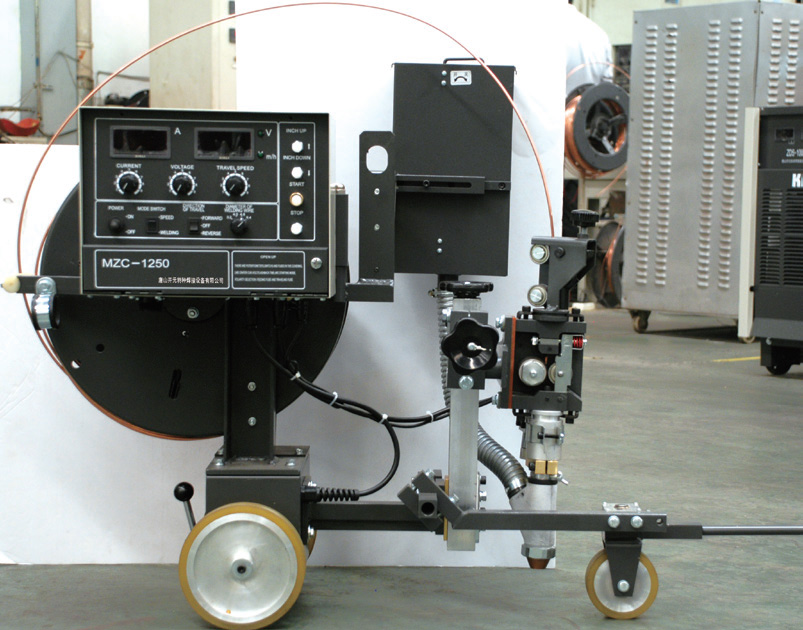
Как это работает?
Этот процесс сварки может быть автоматическим или полуавтоматическим. Основной принцип этого процесса заключается в том, что флюс начинает осаждаться на свариваемом стыке. Источником питания, используемым при дуговой сварке под флюсом, может быть переменный или постоянный ток.Могут эффективно использоваться машины как постоянного напряжения, так и постоянного тока. Дуга может зависнуть либо в результате касания электрода заготовкой, либо путем размещения стальной ваты между электродом и изделием перед включением сварочного тока.
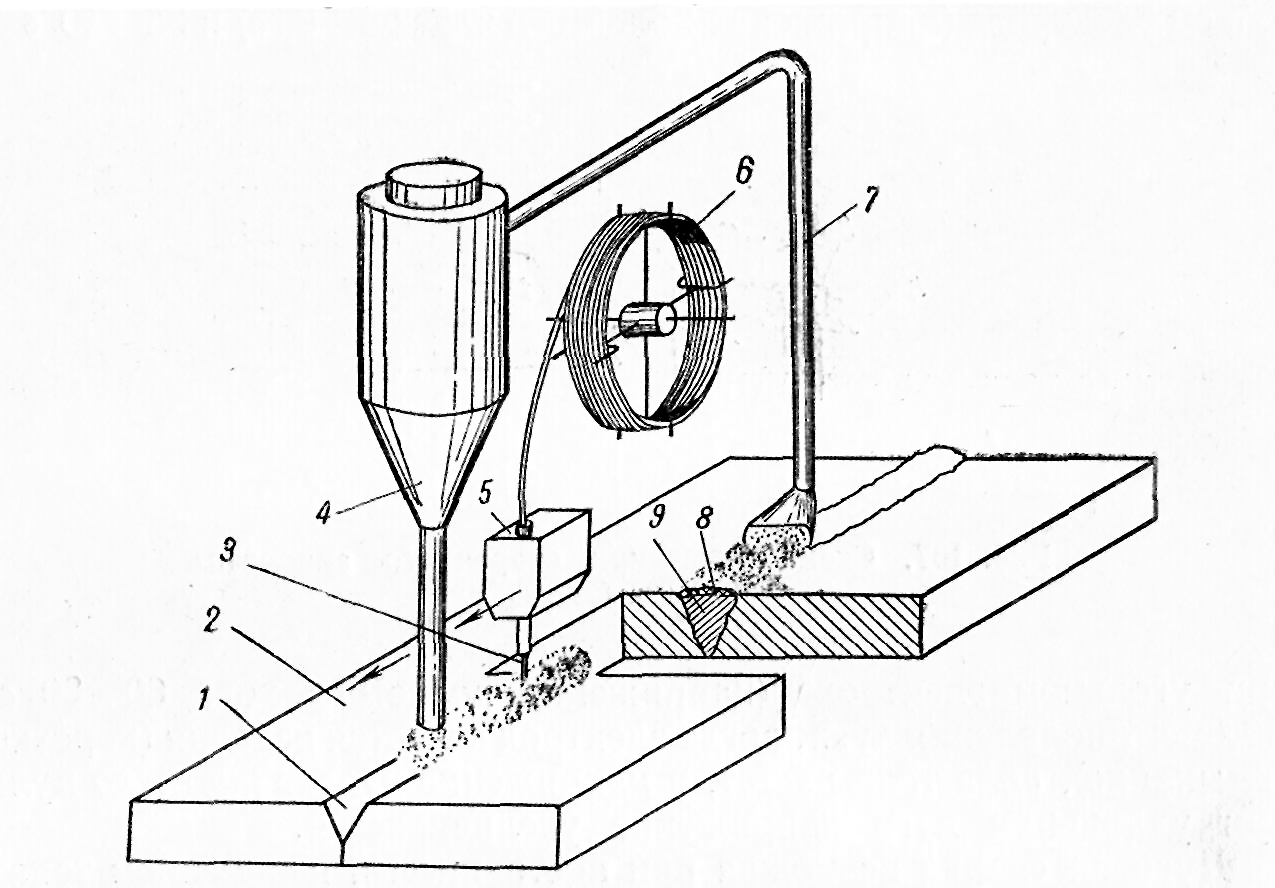
Электрод с постоянной заданной скоростью непрерывно подается к свариваемому стыку. Длина дуги также поддерживается постоянной за счет использования принципа саморегулирующейся дуги, потому что, если длина дуги уменьшается, напряжение увеличивается. Поэтому скорость выгорания будет увеличиваться.
В этом процессе также может использоваться некоторая опорная пластина из материала, такого как сталь или медь, для контроля проникновения и поддержки большого количества расплавленного металла, связанного с этим процессом.

Процесс SAW в основном зависит от следующих факторов:
- Напряжение дуги или длина дуги
- Скорость перемещения электрода
- Электрод торчит или контактный наконечник работает
- Тип тока переменного или постоянного тока
- Скорость подачи проволоки
Преимущества дуговой сварки под флюсом:
- Высокая скорость осаждения.
- Высокие эксплуатационные факторы в некоторых приложениях.
- Глубокое проплавление, обеспечивающее прочность сварных соединений.
- Предотвращает разбрызгивание и разбрызгивание горячих материалов на рабочих, поскольку дуга всегда покрыта слоем флюса.
- Высокоскоростная сварка тонких листов.
- SAW подходит для внутренних и наружных работ.
- Однопроходные сварные швы могут выполняться в толстых листах.
- Большая часть флюса повторно используется в этом процессе.
- Можно получить очень аккуратный внешний вид и гладкие формы сварных швов.
- В соединениях формируется хорошая пластичность и коррозионная стойкость, а также хорошая ударная вязкость.
- В этом процессе нам не требовалось добавлять давление, потому что оно уже создавалось электродом.
- Этот процесс ограничен сталью, нержавеющей сталью и никелем.
- Ограничено позициями 1F, 1G и 2F.
- Ограничено металлическими пластинами большой толщины. Флюс
- подвержен загрязнениям, которые могут вызвать пористость сварных соединений.
- Требуется замена флюса на стыке, что не всегда возможно.
- Требуются подкладочные полоски для надлежащего проникновения.
- Остатки флюса и шлака могут представлять опасность для здоровья и безопасности.
Комбинации проволоки и флюса для дуговой сварки под флюсом
Дуговая сварка под флюсом (SAW) — это распространенный и чрезвычайно полезный процесс дуговой сварки, который требует использования плавящегося сплошного или трубчатого электрода с металлическим сердечником с непрерывной подачей. В этом случае «погруженный» определенно не означает «погруженный в воду», а вместо этого относится к защитному полю гранулированного плавкого флюса, состоящего из таких соединений, как кремнезем, фторид кальция и известь. Эти материалы защищают расплавленный шов и зону дуги от атмосферного загрязнения во время процесса сварки, предотвращая брызги и искры, а также подавляя потенциально вредное УФ-излучение и пары, которые часто возникают в процессе дуговой сварки. Во время SAW дуга обычно погружается под флюс и поэтому не видна во время сварки.
Как правильно выбрать проволоку и флюс для дуговой сварки
Хотя процесс дуговой сварки сам по себе не сложен, существуют аспекты требований к процессу, которые следует рассмотреть, прежде чем двигаться дальше. Одним из наиболее важных является решение о том, какой тип проволоки и флюсовый материал следует использовать. Отличным источником информации такого типа почти всегда является Американское общество сварщиков, которое определяет широкий спектр классификаций и кодов и очень четко излагает спецификации для различных материалов на основе указанных требований к конструкции и изготовлению. Поскольку доступные комбинации флюса и проволоки практически безграничны, чрезвычайно важно понимать, как проволока и флюс будут взаимодействовать не только друг с другом, но и со свариваемым материалом. В конце концов, квалифицированные сварщики не только знают , как сваривать , но также понимают сложное взаимодействие многих материалов, которые могут использоваться при сварке, чтобы обеспечить желаемый результат.
Понимание потенциального использования и условий использования продукта, подлежащего дуговой сварке
Помимо полного понимания материалов, задействованных в SAW, также важно понимать, как и где будет использоваться готовое изделие после сварки, и, в частности, , какой тип нагрузки будет подвергаться изделию .Например, некоторые продукты должны быть в состоянии обрабатывать несколько изменений нагрузки, в то время как другие должны будут обрабатывать только один тип статической нагрузки во время использования. Другие продукты могут использоваться при экстремальных температурах или при наличии риска коррозии. Все эти варианты использования требуют совершенно разных типов сварных деталей , которые часто являются результатом различных комбинаций проволоки и флюса. Понимание того, какая комбинация лучше всего подходит для конкретной ситуации, и признание того, что цена не может быть единственным соображением, имеет важное значение для обеспечения того, чтобы конечный продукт мог последовательно соответствовать стандартам качества и безопасности после его использования.
EVS Metal — американский производитель прецизионного листового металла со штаб-квартирой в Ривердейле, штат Нью-Джерси. Наши механики и операторы используют новейшие технологии для резки, гибки и отделки отдельных изделий, а также деталей для интеграции или сборки в более сложные изделия. Наши четыре предприятия, сертифицированные по стандарту ISO 9001:2015, занимают более 250 000 квадратных футов вертикально интегрированных производственных площадей и оснащены самым современным доступным оборудованием, от лазеров и обрабатывающих центров с ЧПУ до автоматизированных линий порошковой окраски.