Ультразвуковая сварка нетканых материалов — УЛЬТРАЗВУКОВАЯ ТЕХНИКА — ИНЛАБ
С. С. ВОЛКОВ, канд. техн. наук
МГТУ им. Н.Э. Баумана
Изготовление нетканых материалов посредством скрепления волокнистых холстов ультразвуковой сваркой
В
последние годы большое значение приобрели изделия их химических волокон, в
частности нетканые материалы. Эти материалы обладают хорошими фильтрационными
свойствами и высокой прочностью. Сущность технологии изготовления нетканых
полотен заключается в получении волокнистых холстов и образовании между
волокнами прочных связей [1]. Холст – это определенным образом сформировавшийся
слой, состоящий из равномерно распределенных в нем нескрепленных волокон. К
преимуществам способов изготовления нетканых материалов можно отнести:
производительность, значительно превышающую производительность ткацких станков;
возможность автоматизации процессов и объединения в поточную линию агрегатов
для изготовления или подготовки волокон, формирования волокнистых холстов,
скрепление волокон в холсте и отделки материала; низкую стоимость получаемых
материалов; возможность использования в ряде материалов в качестве сырья
непрядевых отходов текстильного и других производств; широкий диапазон
пористости и плотности материалов.
Широко распространен клеевой способ изготовления нетканых материалов, при котором связь между волокнами определяется адгезией связующего к волокнам. Помимо этого способа, применяют различные механические технологии, когда скрепление волокон в холстах осуществляется вязально-прошивным, иглопробивным и валяльно-войлочным способами. Применяют также способы горячего прессования, бумагоделательный, получение нетканых материалов из расплава полимера и др.[1,2].
Наряду с несомненными достоинствами указанным способам присущи и недостатки, обусловливающие хаотическую ориентацию волокон, ограниченную толщину получаемого материала и его низкую прочность. В большинстве случаев прочность волокон не превосходит 20% прочности материала.
На
кафедре «Технологии сварки и диагностики» МГТУ им. Н. Э. Баумана ведутся
исследования в области создания нетканых материалов посредством ультразвуковой
сварки холстов, сформированных из термопластичных волокон либо из их смеси с
натуральными или химическими волокнами, а также разработки технологии и
оборудования для изготовления материалов с помощью ультразвука. Сущность
способа заключается в том, что волокна холста, которые могут быть ориентированы
или распределены случайно, скрепляются посредством ультразвуковой сварки. При
этом холст может состоять из термопластичных волокон (полипропилена, капрона,
лавсана, сарана, хлорина и др.) либо из их смеси с хлопком, вискозой, шерстью и
другими нетермопластичными волокнами. В последнем случае размягченная
термопластичная составляющая обволакивает нетермопластичные волокна, образуя
прочные соединения. С увеличением содержания нетермопластичных волокон прочность
нетканых материалов падает практически линейно. Причем предельно допустимым
содержанием нетермопластичных волокон считать 65%.
Из
всего разнообразия карбо – и гетероцепных волокон исследовали по одному типу
волокон каждого класса: полипропиленовые и полиэтилентерефталатные
(лавсановые). Такой выбор обусловлен исключительными свойствами этих волокон, в
частности, гидрофобностью, делающей их незаменимыми для изготовления
волокнистых фильтров, работающих во влажной среде [3]. Поскольку волокнистые холсты
характеризуются большим коэффициентом затухания, то их скрепление можно
выполнять по схеме контактной ультразвуковой сварки [4].
Для непрерывного осуществления процесса наиболее приемлем способ шовно-шаговой сварки, являющейся разновидностью прессовой сварки, с шаговым перемещением материала. При такой схеме сварки предотвращаются деформации и разрывы нескрепленного холста при сварке и транспортировке готового материала на заданный шаг. При этом сварные швы располагают как в направлении, перпендикулярном продольной оси холста, так и под углом к оси (рис.1,а,б). Протяженные швы можно получить при использовании нескольких сварочных головок, установленных таким образом, чтобы обеспечивалось перекрытие сварных швов (рис.1,в).
Первые
эксперименты по ультразвуковой сварке волокнистых холстов различного развеса
только из термопластичных волокон, проведенные на режимах для сварки сплошных
полимерных материалов, не дали положительных результатов.
На
первой – происходит частичное размягчение поверхности волокон, расположенных в
слоях, прилегающих к волноводу. Шов имеет спрессованную волокнистую структуру и
незначительное усилие разрыва. На второй стадии волокна, расположенные в слоях,
прилегающих к волноводу, полностью переходят в вязкотекучее состояние и
размягченный термопластичный полимерный материал вдавливается сварочным
давлением во внутренние слои холста, скрепляя их. Шов имеет при этом
характерный матовый оттенок и значительную прочность.
Все эксперименты проводили на лабораторной установке с использованием магнитострикционного преобразователя мощностью 1,6 кВт и резонансной частотой 22 кГц, с ножевым экспотенциальным волноводом из титанового сплава ВТ5. В качестве опоры использовали стальную плиту толщиной 20 мм.
Сварку
выполняли по циклу сварочное давление – ультразвук – сварочное давление. Такой
цикл позволяет охлаждать сварной шов под сварочным давлением после отключения
ультразвуковых колебаний, что существенно влияет на повышение прочности сварных
соединений холста и, кроме того, предотвращает расползание волокон в
расплавленном состоянии [4]. Сварку проводили на отработанных оптимальных
режимах: для холстов, сформированных их полипропиленовых волокон, амплитуда
смещений А=30 мкм, сварочное давление р
Можно предположить, что основным источником теплоты при ультразвуковой сварке волокнистых термопластичных материалов, являются гистерезисные потери от циклического деформирования. Явление разогрева полимерных материалов при циклическом деформировании изучалось до сих пор в связи с усталостной прочностью этих материалов [5]. Установлено, что интенсивное теплообразование в испытуемом образце происходит после достижения определенной критической температуры, что обусловлено резким изменением релаксационных характеристик волокнистого полимерного материала – динамического модуля и механических потерь [5,6]. Критическая температура не зависит от амплитуды нагрузки, круговой частоты, условий теплоотвода в волновод и опору и определяется только физико-механическими свойствами волокнистого полимерного материала, режимом нагружения и температурой окружающей среды [7].
Для
сравнения кинетики разогрева волокнистых полимерных материалов и сплошных
полимерных материалов при циклическом деформировании проводили
термографирование процесса ультразвуковой сварки волокнистых полимерных
материалов с помощью электронно-лучевого осциллографа [7]. К преимуществам
этого способа относится его практически полная безынерционность в отличие от
светолучевых способов осциллографирования. Длительное послесвечение
электронно-лучевой трубки позволяет наблюдать визуально и производить
фотографирование термограммы с экрана осциллографа.
В экспериментах использовали хромель-копелевые термопары, имеющие высокую термоэдс. Для одновременного наблюдения двух и более кривых термического цикла, помимо многолучевых осциллографов, можно использовать различные типы коммутаторов. В данном случае использовали коммутатор на шаговом искателе, что позволило получить четкие осциллограммы с двух или трех термопар при исследовании распределения температур по толщине свариваемого термопластичного волокнистого материала.
Из
сравнения кривых термических циклов
различных точек объема волокнистого материала, находящегося под волноводом, со
схематическими кривыми, приведенными в работах [3,7], следует, что режим разогрева
во всех точках волокнистого материала высокотемпературный.
Характер
термических циклов при сварке волокнистых холстов (рис.2) сходен с характером
термических циклов при сварке сплошных термопластичных мягких материалов,
например, полиэтилена толщиной до 5 мм (рис.3). Критическая температура Ткр перехода к интенсивному
разогреву составляет 100ОС при сварке материалов из полипропиленовых
волокон и 130ОС – материалов из полиэтилентерефталатных волокон при
температуре окружающей среды 23ОС. Время достижения Ткр в различных точках
неодинаково. Это связано с неравномерностью распределения амплитуд напряжений и
деформаций и температурными условиями на границах волновод — материал и
материал – опора. Интенсивность тепловыделения в некоторой степени зависит от
механических потерь ? в термопластичном материале, которые больше у волокнистых
полимерных материалов, чем сплошных.
Можно предположить, что разогрев волокнистых материалов при ультразвуковой сварке будет приближаться к адиабатическому, т. е. протекать без теплообмена с окружающей средой. Зону, выделенную сварочным давлением в волокнистом материале, можно представить как эквивалентный ему сплошной вязкоупругий стержень, по которому распространяются продольные колебания (рис.4).
Примем,
что стержень закреплен на конце х=0,
так как податливость материала опоры много ниже податливости полимерного
материала, боковая поверхность стержня теплоизолирована, теплофизические и
релаксационные характеристики материала не зависят от температуры, вся
механическая энергия, затрачиваемая на циклическое деформирование стержня,
переходит в тепловую. При этих допущениях задача о разогреве волокнистого
материала под действием ультразвуковых колебаний сводится к решению
дифференциального уравнения
dT/d?=d2T/d?2 + q(ch?1? + cos?2?),
где Т, ?, ?, q – безразмерные параметры; ?1,?2 – факторы механических потерь.
Предположим,
что в сечении х=0 температура
практически равна начальной температуре стержня, а в сечении х=l происходит
теплообмен между поверхностью нагретого полимерного волокнистого материала и
холодным волноводом. Для волокнистых полимерных материалов, толщина которых
превышает 5 мм, ?1 > 1,35,
поэтому наибольшая температура разогрева будет непосредственно под волноводом.
Исходя из этого, представим кинетику образования сварного соединения при ультразвуковой сварке волокнистых полимерных материалов следующим образом. В начальный момент сварки непосредственно под волноводом образуется вязкотекучая прослойка, поскольку здесь развиваются наибольшие температуры. Под действие м статического сварочного давления расплавленный полимерный материал вдавливается во внутренние слои волокнистого холста. При малой поверхностной плотности полимерного материала вязкая масса проникает на противоположную сторону, подогревая его по всей толщине, что значительно сокращает время сварки. Когда толщина волокнистого материала сравнима с расстоянием, на которое перемещается вязкая масса под действием заданного сварочного давления, время сварки должно изменяться незначительно. Дальнейшее увеличение поверхностной плотности волокнистого материала приведет к резкому возрастанию времени сварки.
При
проведении экспериментов волокнистые полимерные материалы с различной
поверхностной плотностью сваривали до полного проплавления, которое фиксировали
по образования сварного шва в виде характерной прозрачной пленки (рис. 5). При
этом амплитуду смещения рабочего торца волновода поддерживали на минимальном
уровне – 20 мкм, а давление, близкое к максимальному, составляло 4 МПа.
Поверхностную плотность образцов определяли на аналитических весах второго
класса. Наличие на кривых участков, соответствующих тем значениям поверхностей
плотности, при которых время проплавления изменяется незначительно, и точек
перегиба, после которых наблюдается резкое увеличение времени проплавления,
подтверждает правильность выдвинутого предположения о кинетике образования
сварного шва при ультразвуковой сварке волокнистых полимерных материалов.
Для
исследования структуры с помощью рентгенографического метода выполняли сварку
волокнистых полимерных холстов, из которых затем вырезали сварные швы. При этом
амплитуду смещения рабочего торца волновода и сварочное давление поддерживали
на оптимальном уровне (отмеченном выше), а время пропускания ультразвукового
импульса изменялось от 0,2 до 1 с.
Структуру сварных швов исследовали на приборах УРС-70 и ДРОМ-1 на медном излучении с никелевым фильтром. Степень ориентации кристаллов определяли по кривой азимутального распределения интенсивности рефлекса 110.
Для определения степени упорядоченности кристаллитов образцы быстро вращали вокруг первичного рентгеновского луча при медленном вращении счетчика.
Рентгенограмма
исходного волокна полипропилена свидетельствует о высокой степени ориентации
кристаллов в волокне. При воздействии
ультразвуком в зоне шва происходит локальный перегрев, температура при этом
достигает температуры плавления, что при времени воздействия 0,2 и 0,3 с
приводит к образованию пленки, в которой просматриваются отдельные волокна, а
при 0,4с – полной прозрачной пленки. При воздействии ультразвуком в течение 0,2
и 0,3с происходит значительная разориентация кристаллов, а дальнейшая выдержка
— приводит к их полной переориентации.
На
рис. 6 приведены дифрактограммы исходного волокна, подвергавшегося воздействию
ультразвука в течение 0,3 и 0,4с. Если при времени воздействия tи=0,3с
значительные изменения в дифрактограмме на наблюдаются, то при tи=0,4с
происходит резкое расширение рефлексов вплоть до их слияния. Полуширина
рефлекса возрастает в 2 раза, что свидетельствует об увеличении дефектности
кристаллитов. Степень кристалличности образцов практически не изменяется.
Поскольку сварные швы, полученные при времени протекания ультразвукового
импульса 0,3с и выше, имеют значительное разрывное усилие, можно предположить,
что это обусловлено отжигом и появлением ?-текстуры. Для проверки этого
предположения из полипропиленовой пленки толщиной 30 мкм, ориентированной в
двух направлениях, вырезали образцы размером 50х50 мм для проведения отжига. В
исходном состоянии в пленке выявили две кристаллические текстуры с осью С и осью ?. Вероятно ?-текстура
появилась при термофиксации пленки в процессе ее изготовления. Отжиг проводили
в термошкафу при температуре около 170ОС, близкой к температуре
плавления полипропилена, с выдержкой от 1 до 5 мин. Для предотвращения
коробления образцы закладывали между двумя фторопластовыми прокладками и
зажимали в специальном приспособлении.
Установили, что при выдержке в течение 2 мин текстура практически не изменяется. Увеличение выдержки сопровождается переориентацией кристаллов уже в течение 15 мин происходит полная разориентация кристаллитов.
Результаты
испытания образцов, вырезанные из исходной и отожженной пленок, на разрыв
показали, что прочность при этом изменяется незначительно. Следовательно, само
наличие ?-текстуры не должно проводить к резкому уменьшению разрывного усилия
сварного шва. Однако известно, что переориентация кристаллов и образование
?-текстуры сопровождается релаксацией полимерных цепей и возникновением
внутренних напряжений. Это приводит к росту дефектности кристаллитов, о чем
свидетельствует расширение рефлексов на дифрактограммах (см. рис. 6) и, по-видимому, к образованию
микротрещин, что обуславливает снижение разрывного усилия сварных швов.
Необходимо отметить, что с увеличение значений параметров режимов сварки
разрывное усилие швов не падает до нуля. Поскольку изменение разрывного усилия
в большей мере обусловлено уточнением полимерного материала в процессе сварки,
то и остаточная толщина шва остается неизменной при сварке на этих режимах. Это
явление, названное автостабилизацией толщины шва, впервые обнаружено при сварке
полимерных пленок [4]. Стабильность толщины шва в этом случае можно объяснить
тем, что в процессе утонения зоны сварки происходит постоянное
перераспределение теплоты, выделяющейся в полимере вследствие гистерезисных
потерь в материале, и теплоты, отводимой в холодные волновод и опору. Очевидно,
что при определенной минимальной толщине шва наступает тепловое равновесие или
количество отводимой теплоты даже превалирует над количеством теплоты,
выделяющейся в полимере, вследствие чего температура в зоне сварки начинает
падать.
Увеличение времени пропускания ультразвукового импульса при сварке волокнистых холстов из полиэтилентерефталатных волокон свыше 0,3 с практически не влияют на разрывное усилие и толщину шва. При воздействии ультразвуком от 0,2 до 0,5с значительные изменения в структуре зоны шва на рентгенограммах не зафиксированы.
Чтобы
уменьшить теплоотвод в волновод и опору проводили сварку лавсановых и
полипропиленовых волокон через целлофановые и бумажные прокладки. В результате
разрывное усилие сварного шва понизилось с 110 до 40 Н. При этом в структуре
материала шва наблюдали некоторую амортизацию и полную разориентацию
кристаллитов. Для выявления микротрещин и других дефектов проводили
электронно-микроскопическое исследование сварных швов. Предварительные
эксперименты по отработке методики испытаний показали, что для получения
качественных срезов необходима фиксация волокон. В качестве химического
фиксатора поверхности волокон использовали 2%-ный раствор четырехоксида осмия.
Фиксацию проводили при Т=4ОС
в течение 24 ч, а также 7, 21 и 30 суток. Затем волокна промывали дистиллированной водой,
обрабатывали 96О-ным спиртом и заливали смесью эпоксидных смол
ЭПОН-812. Полимеризацию проводили в термостате при 60ОС в течение 24
ч. Полученные блоки разрезали на ультрамикротоме фирмы «Рейхерт», а срезы
просматривали на световом и электронном микроскопах.
Установили, что только при фиксации в течение 30 суток в срезах довольно прочно удерживается более 90% волокон.
В электронном микроскопе срезы волокон полипропилена имели вид овалов или кругов с неправильным по толщине темным кругом. При очень больших увеличениях (50 000 – 80 000) на поверхности волокон четко видны частицы металла, располагающиеся неравномерным по толщине слоем.
Для
исследования сварных швов проводили предварительную фиксацию волокон указанным
выше способом. После фиксации, сварки на различных режимах и заливки смесью
эпоксидных смол сварные блоки резали на микротоме.
После просвечивания на электронном микроскопе получили типичную картину взаимодействия двух соседних волокон. В отдельных участках происходило полное слияние волокон до исчезновения границы раздела. Однако на некоторых участках такое слияние не происходило, и между волокнами сохранились пустоты, которые, по-видимому, снижали прочность сварного шва нетканых материалов.
Необходимо отметить, что нетканые фильтровальные материалы из ультратонких волокон, разработанные и изготовленные в соответствии с предложенным способом, отвечают всем требованиям, предъявляемым к материалам фильтров предварительной очистки и, следовательно, могут быть рекомендованы для использования в качестве предфильтров, в частности для фильтрации газовых сред от аэрозолей.
ВЫВОДЫ
Контактная
прессовая шовно-шаговая сварка наиболее приемлема для изготовления нетканых
материалов с помощью ультразвука и позволяет избежать деформаций и разрывов
волокнистых холстов при сварке и транспортировке. Такая схема позволяет также
создать универсальное сварочное оборудование.
При ультразвуковом воздействии наиболее интенсивно разогреваются слои волокнистого холста, прилегающие к волноводу, поэтому оптимальной является толщина волокнистого холста, соответствующая поверхностной плотности, равной 0,4 кг/м2.
Для образования прочного сварного соединения наибольшее количество нетермопластичных добавок не должно превышать 65% общего количества волокон в холсте.
Список литературы
- Назаров Ю. П., Афанасьев В. М. Нетканые
текстильные материалы. М.: Легкая индустрия, 1974. 200 с.
- Тихомиров В. Б. Физико-химические
основы получения нетканых материалов. М.: Легкая индустрия, 1971. 328 с.
- Справочник по сварке и склеиванию
пластмасс/А. Н. Шестопалов, Ю. С. Васильев, Э. А. Минеев и др./ Под. общ. ред.
А. Н. Шестопалова. Киев.: Технiка,
1986. 192 с.
- Волков С.
С., Черняк Б. Я. Сварка пластмасс ультразвуком. 2-е изд., перераб. и доп. М.: Химия, 1986. 256 с.
- Урожумцев Ю. С., Скалозуб С. Л.
Акустическая усталость полимеров//Механика полимеров. 1969. № 1. С. 108-111.
- Ратнер С. Б., Бугло С. Т. Влияние
режима нагружения на разогрев пластмасс при циклическом
деформировании//пластические массы. 1969. № 3. С. 465-469.
- Черняк Б. Я., Волков С. С., Орлов Ю. Н. Процесс теплообразования при ультразвуковой сварке пластмасс//Сварочное производство. 193. № 8. С. 53-55.
Ультразвуковая сварка металлов
Ультразвуковая сварка металлов (ultraschall-schweissen; ultrasonic welding) — это сварка давлением при воздействии ультразвуковых колебаний. Соединение образуется в результате совместного действия на детали сжимающего усилия и высокочастотных механических колебаний, что сопровождается относительным тангенциальным смещением малой амплитуды соединяемых поверхностей и нагревом метала в зоне сварки.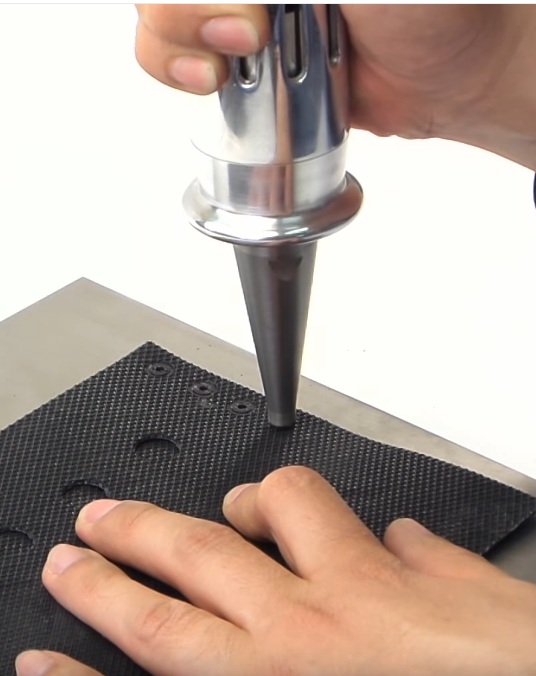
Рис. 1. Принципиальная схема точечной (я) и шовной (б) сварки ультразвуком: 1 — свариваемые детали, 2 — трансформатор упругих колебаний, Р — сжимающая сила, 3 — сварочный наконечник (ролик), 4 — маятниковая опора (опорный ролик), 5 — сварная точка (шов), у.з.к. — ультразвуковые колебания.
Сварочный наконечник 3 (при шовной сварке — ролик) определяет площадь и объем источника ультразвуковых механических колебаний непосредственно в зоне сварки. Он должен передавать колебания для осуществления трения между поверхностями соединяемых деталей с минимальными потерями между ним и верхней деталью.

Таким образом, процесс ультразвуковой сварки металлов происходит в условиях трения, вызванного микроскопическим относительным возвратно-поступательным перемещением участков поверхностей в зоне сжатия, что сопровождается выделением теплоты. Распространение ультразвуковых колебаний при сварке показано на рис. 2.
Рис. 2. Распространение у.з.к. при сваривании. а — начало сваривания; б — процесс сварки; в — окончание процесса.
Исследования показали, что при ультразвуковой сварке действуют два основных источника тепла. Один находится в зоне контакта сварочного наконечника (ролика) с деталью, второй — в зоне соединения деталей. Выделение теплоты у сварочного наконечника обусловлено его трением с деталью и приводит к пластическому деформированию наружной поверхности детали под наконечником. Выделение теплоты между деталями обусловлено действием нормальных сжимающих напряжений и напряжений сдвига, что приводит к внешнему и внутреннему трению в металлах и пластической деформации в зоне сварки.
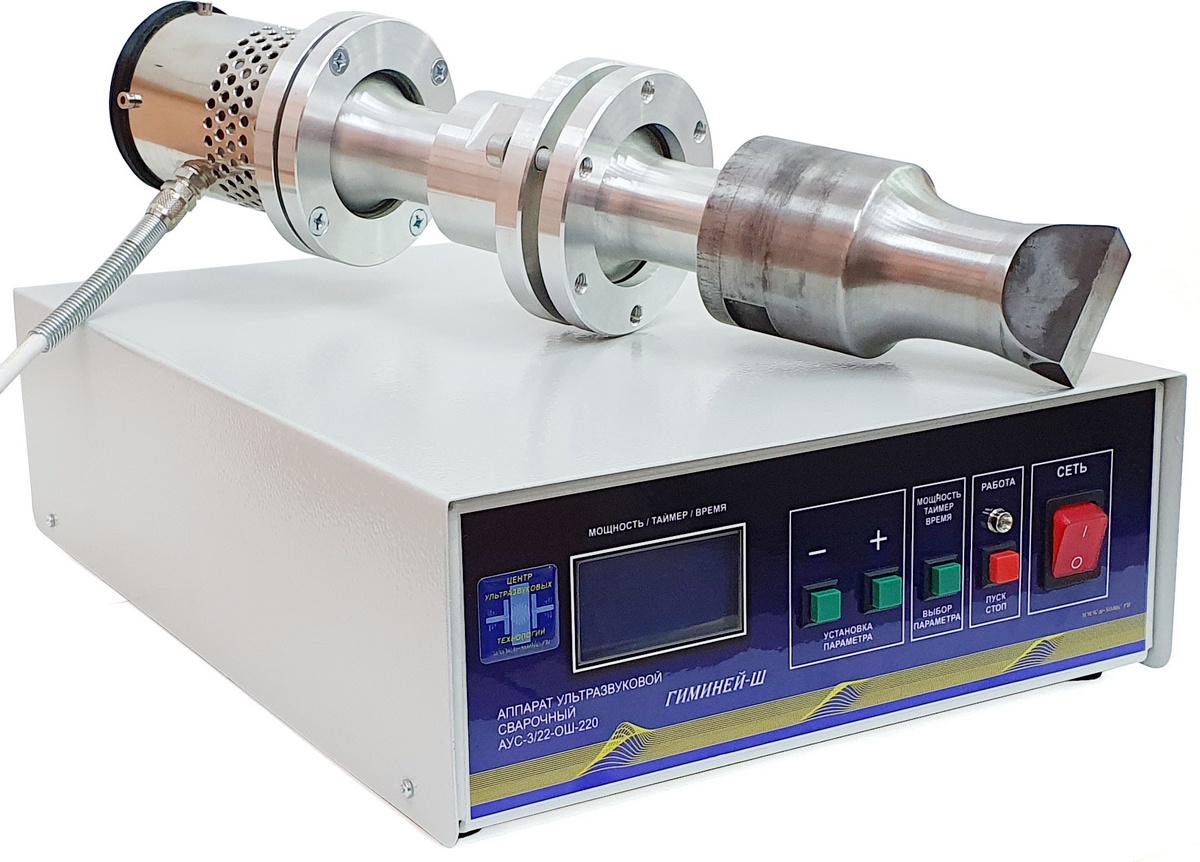
Вибрирующий сварочный наконечник в первый момент сварки развивает интенсивное выделение тепла в зоне его контакта с деталью. В зону сварки ультразвуковые колебания передаются с некоторым опозданием (см. рис. 2).
Усилие сжатия обеспечивает передачу ультразвуковых колебаний в зону сварки. Его минимальное значение, при котором начинают образовываться соединения, зависит от свариваемых материалов и их толщины, а оптимальное значение возрастает с увеличением амплитуды колебаний.
При увеличении контактного давления начальная скорость нагрева растет за счет улучшения связи между сварочным наконечником и деталями. Скорость нагрева деталей зависит также от формы и состояния поверхности наконечника.
Температура в зоне сварки зависит от твердости и теплофизических свойств свариваемых материалов, мощности колебательной системы и параметров режима сварки. Нагрев в зоне сварки обычно не превышает 0,6 температуры плавления. Под действием трения, нагрева и пластического деформирования пленки загрязнений разрушаются и удаляются из зоны сжатия, благодаря чему становится возможным образование узлов схватывания, их расширение и формирование сварного соединения.
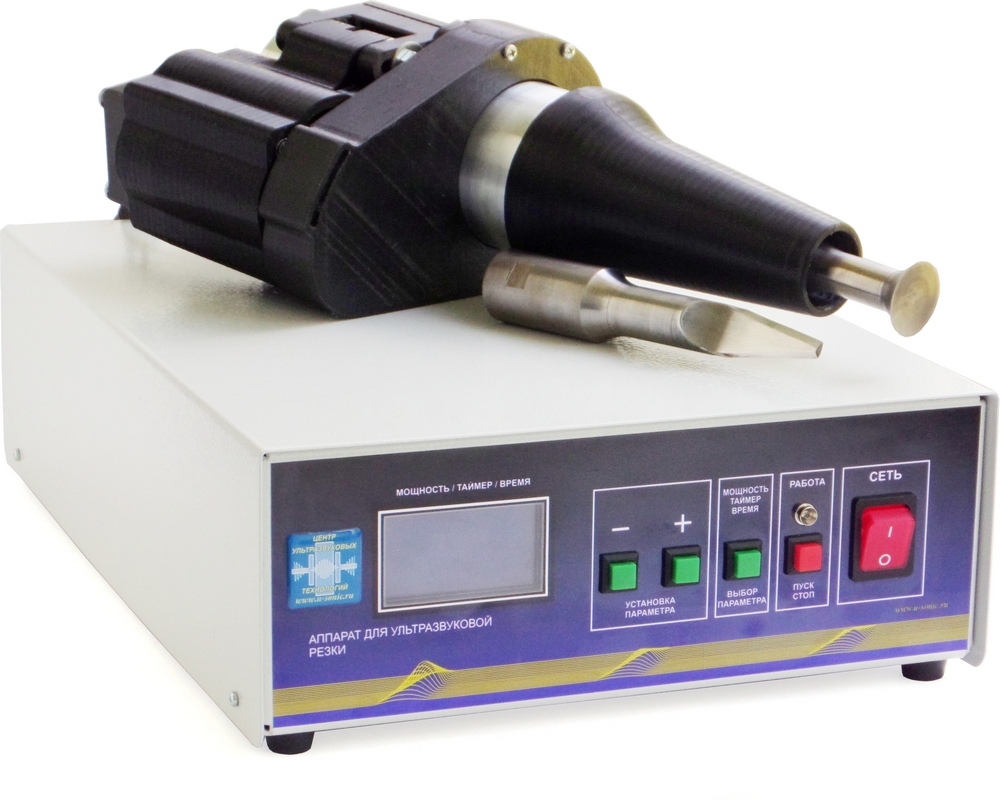
УЗ-сварка может выполняться с импульсным нагревом места сварки от отдельного источника тепла, что позволяет уменьшить усилие сжатия, амплитуду и время действия уз-колебаний, и деформацию металла. Такой способ разработан для ультразвуковой сварки микродеталей. Свариваемые элементы подлежат действию ультразвуковых колебаний и нагреванию одновременно или в определенной последовательности.
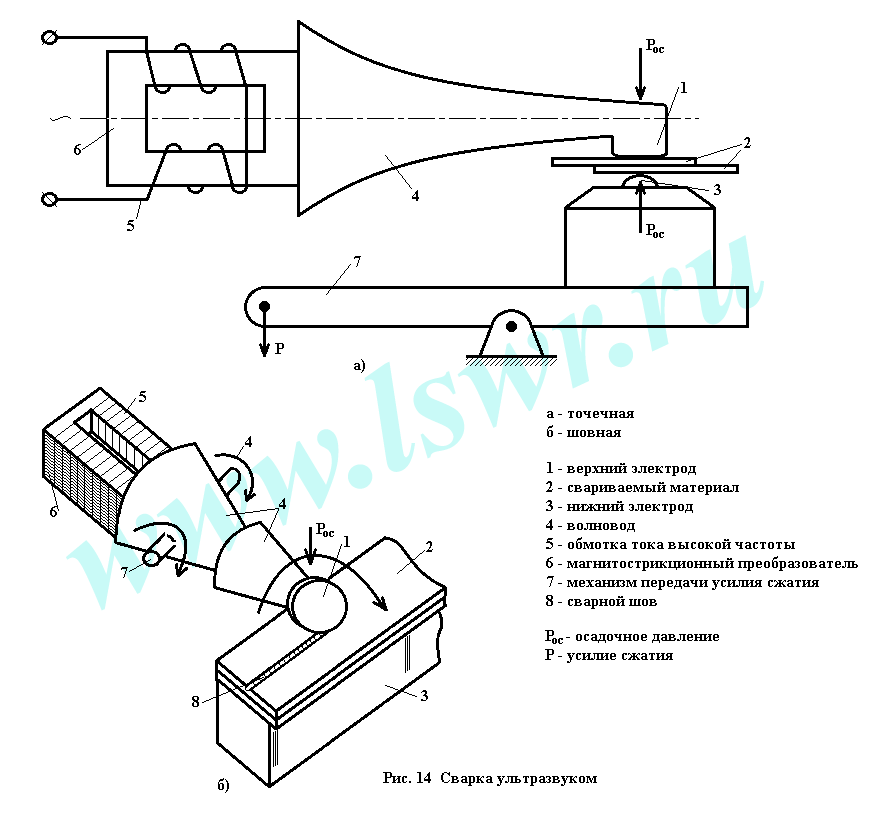
Процесс выполняется следующим образом. Сначала сварочный инструмент небольшим усилием прижимается к детали, затем через него пропускается электрический ток для его нагрева и одновременно (или с некоторым опережением или опозданием) включаются ультразвуковые колебания. Способ позволяет сваривать материалы с различными физико-химическими свойствами.
Существует мнение, что успешная ультразвуковая сварка разнородных материалов возможна при условии разности атомных радиусов соединяемых деталей не более 15 … 18%. Это условие соответствует общему представлению о существовании твердых растворов. При разности атомных радиусов в пределах 19 … 44% сварка металлов усложняется. Исследование А. О. Россошинского позволили получить с помощью ультразвукового сваривания надежные соединения между материалами с существенными различиями атомных радиусов и различиями физико-химических свойств, например, между керамикой и металлами. Образование соединений автор объясняет определенным перемещением металла в зоне сварки.

При ультразвуковой сварке можно выделить процессы образования физического контакта, активации поверхностей и объемного взаимодействия, несмотря на кратковременность процесса. Все эти процессы протекают в условиях действия ультразвуковых колебаний. Поэтому иногда отмечается возможность развития процессов усталости в зоне сварного соединения под влиянием длительного действия колебаний и снижение прочности соединений вследствие частичного разрушения узлов схватывания.
Кроме статьи «Ультразвуковая сварка металлов» смотрите также:
Сварка пластмасс ультразвуком
Рекомендуем приобрести:
Установки для автоматической сварки продольных швов обечаек — в наличии на складе!
Высокая производительность, удобство, простота в управлении и надежность в эксплуатации.
Сварочные экраны и защитные шторки — в наличии на складе!
Защита от излучения при сварке и резке. Большой выбор.
Доставка по всей России!
Метод сварки пластмасс ультразвуком — один из промышленных методов соединения полимерных материалов, основанный на преобразовании механических высокочастотных колебаний (более 20 000 Гц) в тепловую энергию. Выделяемое при этом тепло размягчает свариваемые поверхности, генерируясь в толще материала, а приложенное давление обеспечивает плотный контакт внутренних поверхностей материала.
Получение и передача ультразвуковых колебаний на материал осуществляется по следующей схеме (рис. 19). Вибратор 1 преобразует электрическую энергию высокой частоты в механические колебания сердечника с частотой ультразвука. Колебания очень маленькой амплитуды передаются от вибратора к концентратору 2, который усиливает механические колебания и благодаря своей особой конструкции концентрирует их в конце волновода. Конец волновода является сварочным инструментом (электродом) или опорой, когда в качестве электрода используют наконечники. Колебания от волновода передаются полимерному материалу 3, который укладывают на опору — отражатель 4. Отражатель может быть пассивным (ненастроенным) и активным (настроенным). В свою очередь, отражатель укладывают на опорную поверхность стола 5. Давление осуществляется со стороны электрода, как показано на схеме, или со стороны опорной поверхности стола.
Рис. 19. Схема сварки пластмасс ультразвуком:
1 — вибратор; 2 — концентратор; 3 — свариваемый материал; 4 — отражатель; 5 — опора.
Ультразвуковую сварку применяют в основном для соединения материалов с низкой электро- и теплопроводностью, большинство из которых трудно или вообще не возможно сваривать другими методами. Ультразвуком сваривают следующие полимерные материалы: органическое стекло, винипласт, полиэтилен, поливинилхлорид, полистирол и др.
Процесс образования соединения при ультразвуковой сварке можно условно разделить на две стадии. Вначале происходит нагрев соединяемых материалов. На второй стадии между нагретыми до вязкотекучего состояния контактирующими поверхностями возникают связи, которые и обеспечивают получение неразъемного соединения.
Особенности сварки ультразвуком состоят в следующем:
1) можно соединять детали, толщина одной из которых практически неограничена, и осуществлять сварку конструкций, в которых затруднен доступ к месту сварки; это объясняется тем, что сварка осуществляется с помощью одного электрода, односторонним способом, ультразвуковая энергия может подводиться на значительном расстоянии от места соединения;
2) высокая производительность процесса; так как максимальный разогрев происходит на свариваемых поверхностях, вследствие чего исключается значительный перегрев пластмасс по толщине или длине привариваемого стержня;
3) не создаются радиопомехи;
4) не подводится напряжение к свариваемым поверхностям;
5) возможна сварка более широкого ассортимента и больших толщин изделий из различных полимерных материалов, чем при сварке ТВЧ.
По характеру распределения вводимой механической энергии относительно свариваемых поверхностей ультразвуковая сварка? может быть разделена на контактную и передаточную.
В первом случае механическая энергия равномерно распределена по всей площади контакта свариваемых изделий. Этот вид ультразвуковой сварки обычно применяют для соединения эластичных пластмасс небольшой толщины (— 0,05—1,5 мм). Наиболее распространены соединения внахлестку.
При передаточной ультразвуковой сварке механические колебания вводятся в отдельной точке или на небольшом участке поверхности верхнего изделия. Передача и равномерное распределение механической энергии зависят в этом случае от упругих свойств свариваемого материала. Поэтому передаточную сварку применяют для соединения объемных деталей из жестких пластмасс, таких как полистирол, полиметилметакрилат и др. Наиболее рациональны соединения встык или втавр.
По степени непрерывности процесса ультразвуковую сварку можно разделить на прессовую и непрерывную. Прессовая сварка выполняется за одно рабочее движение волновода. По этой схеме может осуществляться как контактная, так и передаточная ультразвуковая сварка. Непрерывная сварка позволяет получить непрерывные протяженные сварные швы за счет относительного перемещения волновода и свариваемого изделия. Она используется для сварки изделий из пленок и синтетических тканей: мешков, фильтров, непромокаемой одежды и др.
По степени механизации непрерывная сварка делится на ручную и механизированную. При ручной сварке непрерывные швы любой конфигурации получают за счет перемещения сварочного пистолета, а изделие при этом остается неподвижным. Таким способом можно соединять многослойные пакеты из разных пленок с покрытием. При механизированной непрерывной сварке, как правило, перемещается свариваемое изделие, а сварочный волновод остается неподвижным.
Оптимальный режим, зависящий от свойств свариваемого материала, толщины и формы изделия, состояния контактируемых поверхностей и целого ряда других факторов, определяется в каждом конкретном случае экспериментально.
В связи с массовым характером производства и отсутствием простых и надежных методов неразрушающего контроля для сварных изделий из пластмасс особое значение приобретает надежность и стабильность технологического процесса сварки. Для повышения стабильности свойств сварного соединения и получения соединения с максимальной прочностью режим сварки в каждом отдельном случае может меняться.
На сварочном оборудовании могут быть установлены приборы контроля и регулирования технологическим процессом.
Схемы процесса
Способ предложен в 1958 г.
учеными МВТУ им. Н. Э. Баумана под руководством акад. Г. А. Николаева. Способ ультразвуковой сварки пластмасс заключается в том, что
электрические колебания ультразвуковой частоты (18—30 кГц),
вырабатываемые генератором, преобразуются в механические продольные
колебания магнитострикционного преобразователя, вводятся в свариваемый
материал с помощью продольно-колеблющегося инструмента-волновода,
расположенного перпендикулярно свариваемым поверхностям (рис. 29.5).
Здесь часть энергии механических колебаний переходит в тепловую, что
приводит к нагреву зоны контакта соединяемых деталей до температуры
вязкотекучего состояния. Надлежащие условия ввода механических колебаний
и создание тесного контакта свариваемых деталей, расположенных на
опоре, обеспечивается статическим давлением рабочего торца волновода на
свариваемые детали. Это давление способствует также концентрации энергии
в зоне соединения. Динамическое усилие, возникающее в результате
воздействия колеблющегося волновода, приводит к нагреву свариваемого
материала, а действие статического давления обеспечивает получение
прочного сварного соединения. Механические колебания и давление в этом
случае действуют по одной линии перпендикулярно к свариваемым
поверхностям. Такая схема ввода энергии применяется для ультразвуковой
сварки пластмасс, в отличие от «металлической» схемы, когда механические
колебания действуют в плоскости соединяемых поверхностей, а давление
прикладывается перпендикулярно к ним. Подвод энергии от волновода может
быть односторонним и двусторонним. По характеру передачи энергии и
распределению ее по свариваемым поверхностям ультразвуковая сварка
делится на контактную и передаточную.
Контактная сварка
Возможность передачи механической энергии в
зону сварки зависит от упругих свойств и коэффициента затухания
колебаний свариваемых материалов. Если полимер характеризуется низким
модулем упругости и большим коэффициентом затухания, то сварное
соединение можно получить лишь на малом удалении от плоскости ввода
колебаний. Для равномерного распределения энергии по всей площади
контакта свариваемых деталей необходимо, чтобы рабочий торец,
соприкасающийся с верхней деталью, имел форму и площадь, идентичную
площади и форме плоскости контакта свариваемых деталей. Контактная
ультразвуковая сварка обычно применяется для соединения изделий из
мягких пластмасс, таких как полиэтилен, полипропилен, поливинил-хлорид, а
также пленок и синтетических тканей небольшой толщины — от 0,02 до 5
мм. При этом способе сварки наиболее распространены соединения
внахлестку (рис. 29.6).
Передаточная сварка
Если полимер обладает высоким модулем
упругости и низким коэффициентом затухания, то сварное соединение можно
получать на большом удалении от поверхности ввода механических колебаний
(рис. 29.7). В этом случае ввод механических колебаний может
осуществляться в точке или на небольшом участке поверхности верхней
детали. Благодаря хорошим акустическим свойствам материала изделия
энергия ультразвуковой волны незначительно ослабляется при проходе через
деталь, контактирующую с волноводом, и почти полностью транспортируется
к границе раздела свариваемых деталей. Тепловыделение на границе
раздела в этом случае зависит от конфигурации изделия, а площадь сварки
значительно отличается от площади рабочего торца волновода. Передаточную
сварку рекомендуется применять для соединения объемных деталей из
жестких пластмасс, таких как полистирол, полиметилметакрилат, капрон,
полиамиды, поликарбонат. Наиболее распространены стыковые и тавровые
соединения. Удаление поверхности ввода механических колебаний от
плоскости раздела свариваемых деталей зависит от упругих свойств
материала, мощности ультразвука, подготовки кромок и может составлять от
10 до 250 мм. В случае необходимости передаточной сваркой можно
соединять и мягкие термопласты. Для этого свариваемые детали должны
находиться в жестком застекленном состоянии, что может быть достигнуто
путем охлаждения их до температуры
стеклования.
Оборудование
В МГТУ им. Н. Э. Баумана разработаны машины типа УПМ-21, УПК-15М, УПШ-12, ВНИИЭСО разработаны машины типа МТУ-1,5 и МТУ-0,4, которые серийно выпускаются заводом «Электросварка». Переносные установки РУСУ-50 и РУСУ-44-250 разработаны в НИАТ. Машины типа БШМ-1 разработаны ВНИИЛТЕКмашем совместно с ВНИИТВЧ им.. В. П. Вологдина и серийно выпускаются ПО Промшвеймаш (г. Орша).
Ультразвуковая сварка полиэтилена
Ультразвуковую сварку применяют при изготовлении емкостей, различных контейнеров и труб, предназначенных для хранения пищевых и других промышленных продуктов.
В большинстве случаев при упаковке продуктов в полиэтиленовую тару соединяемые поверхности загрязнены упаковываемым продуктом. Поэтому использование других методов сварки, кроме ультразвукового, в данном случае исключено. Загрязненность свариваемых поверхностей упаковываемым продуктом накладывает специфические требования к процессу ультразвуковой сварки, так как это оказывает влияние на прочность получаемого сварного соединения. Загрязнение поверхности приводит к понижению прочности сварного соединения.
Кроме того, при сварке изделий из полиэтилена следует учитывать особенности хранения и предшествующую обработку соединяемых изделий, которая также влияет на прочностные и эксплуатационные характеристики сварного шва.
Применение предварительной термообработки в интервале температур 50—100°С незначительно влияет на прочность сварных соединений (прочность уменьшается соответственно на 5—9% по сравнению с прочностью образцов, сваренных без предварительной термообработки).
С повышением температуры обработки до 115 °С наблюдается понижение прочности на 17%, и продолжительность сварки при этом увеличивается на 2—3 с.
Значительно влияет на качество сварного шва старение полиэтилена в условиях солнечной радиации. После 30 ч облучения ультрафиолетовыми лучами образец нестабилизированного полиэтилена низкой плотности толщиной 0,7 мм перестает свариваться. Полиэтилен, стабилизированный сажей или парафином, перестает свариваться после 60 ч облучения.
Ультразвуковая сварка полистирола
Ультразвуковую сварку изделий из полистирола применяют для изготовления различных контейнеров и сосудов, игрушек, спортивных товаров, а также для упаковки пищевых продуктов, медикаментов, косметики и т. д. В зависимости от формы изделия и свойств материала применяют контактную и передаточную сварку или комбинацию этих методов. Каждый из выпускаемых в настоящее время полистиролов (блочный, суспензионный, эмульсионный и ударопрочный) имеет различную способность свариваться — от наилучшей у блочного до наихудшей у ударопрочного полистирола.
При сварке изделий из полистирола одним из важных факторов, влияющих на процесс формирования сварных швов, является качество соединяемых поверхностей. Хорошая геометрическая форма и правильная подготовка поверхностей не только облегчает сварку, но и способствуют повышению прочности шва, увеличивают производительность процесса и позволяют строго фиксировать одну часть свариваемого изделия относительно другой его части.
Разделки кромок могут различаться по форме, по в основном одна из стыкуемых деталей должна иметь выступ, входящий по всей длине в соответствующий паз другой детали (рис. 20). Стыкуемые детали должны обладать наименьшей контактной поверхностью; поэтому паз выполняют плоским, а выступ — острым. Острие выступа должно контактировать с соединяемой поверхностью на очень небольшой площади, которая сводится почти к линии. Это способствует концентрации механической энергии на выступе, ускоряет процесс нагрева и сварки пластмасс.
Наилучшей является V-образная разделка свариваемых кромок, которая применяется для соединения деталей, показанных на рис. 20, а. На верхней детали делается V-образный выступ, а на нижней — V-образный паз. Высота выступа должна быть больше, чем глубина паза на 0,05—0,030 мм. При таком типе соединений достигается лучшая текучесть разогретого материала под действием давления и шов имеет хороший внешний вид.
При сварке соединений необходимо предусматривать допуски на текучесть размягченного полимера, который выдавливается из зоны шва, образуя грат. Если грат нежелателен, используют специальные конструкции шва, чтобы избежать выплесков полимера (см. рис. 20, 6 и в). Доведенный до вязкотекучего состояния полимер должен соединять две стыкуемые поверхности, заполняя зазор в несколько десятых долей миллиметра.
Рис. 20. Типы разделки кромок свариваемых поверхностей изделия.
Линия наплыва вдоль шва и выход наплыва за пределы шва свидетельствуют о том, что сварка произошла, В тех случаях, когда требуется герметичность изделия, необходимо, чтобы сварные детали имели линию наплыва. Однако линия наплыва большей частью ухудшает внешний вид изделия, поэтому ее следует избегать в особенности на полированных поверхностях.
Улучшение внешнего вида достигается ступенчатой конструкцией рабочей части волновода, при этом выступ изготовляют так, чтобы наплыв образовывался на внутренней стороне изделия. Малогабаритные детали несложной формы свариваются за один контакт волновода с изделием, причем волновод устанавливается перпендикулярно к свариваемым поверхностям по оси симметрии соединения. Если деталь сложная и длина сварного шва значительная, то количество точек и место введения ультразвуковых колебаний определяются экспериментально.
На свариваемость жестких пластмасс большое влияние оказывают условия хранения соединяемых деталей. Длительное хранение деталей до сварки приводит к уменьшению прочности сварного соединения. Особенно сильно уменьшается прочность соединения при сварке деталей, прошедших длительное хранение в атмосферных условиях. Таким образом, для получения качественных сварных соединений сварку необходимо производить либо сразу же после отливки деталей, либо хранить литые детали в темных холодных помещениях. Хранение деталей в атмосферных условиях при наличии солнечной радиации недопустимо.
Применение ультразвука для сварки деталей детских игрушек из полистирола позволило полностью исключить процесс склеивания дихлорэтаном, толуолом и другими растворителями, применение которых приводит к значительной загазованности воздушной среды. Использование ультразвуковой сварки повышает производительность труда и культуру производства.
Соединение пластмасс с металлами
В последнее время ультразвук применяется не только для сварки пластмасс, но и для соединения пластмасс с металлами и впрессовки металлических изделий в пластмассы.
При соединении металлических изделий с пластмассовыми в металлическом изделии делают отверстие, а в изделии из пластмассы — штифт, выполненный как одно целое с изделием. Металлическое изделие надевают на штифт, а на выступающую часть штифта накладывают ультразвуковой инструмент — волновод, торец которого имеет два сферических углубления, Под действием ультразвука выступающая часть штифта размягчается и деформируется инструментом в две полусферические головки, образующие замковое соединение, напоминающее собой соединение заклепками.
Лебедев Г.А. «Напыление. Сварка. Склеивание».
См. также:
Ультразвуковая сварка металла. Медных, алюминиевых проводов.
Наша компания разрабатывает новый станок для ультразвуковой сварки металлов. Данное оборудование используется для сварки различных, в основном, медных и алюминиевых проводов и контактов.
Преимущества ультразвуковой сварки металлических контактов
Данный вид сварки имеет ряд преимущества перед традиционными вариантами: сварка высокотеплопроводных металлов, таких как медь,серебро; металлов разной толщины;без использования флюса;без высоких температур; тонкой фольги;малая деформация деталей;
Оснастка для сварки изготавливается в соответствии с индивидуальными требованиями к свариваемым изделиям.
Станок для ультразвуковой сварки состоит из:
— источник питания
— ультразвуковой преобразователь
— сварочная оснастка для зажима деталей
— волновод
На данный момент УЗ сварка металла применяется в различных сферах промышленности, в особенности:
— производители бытовой электроники
— кабелей, электропроводки
— аккумуляторных систем
— микроэлектроника
Для чего нужна ультразвуковая сварка медных и алюминиевых проводов
Позволяет получить прочное и надежное соединение изделий, быстро, без лишних затрат на электроэнергию, нагрев и т. д. Преимущества данного вида сварки уже давно зарекомендовали себя на многих предприятиях. Например, на предприятии электротехнической промышленности успешно сваривают медную проводку и шины в электрошкафах, так же сваривают контакты проводов без снятия защитных покрытий, что ускоряет и удешевляет само производство. В аккумуляторном производстве сваривают тонкую фольгу из меди и никеля.
Характеристики станка для ультразвуковой сварки металла:
1. Частота 20кГц
2. Зона сварки (с текущим инструментом) 26х7 мм.
Если вы заинтересованы в получении более подробной информации, в том числе и по цене такого оборудования, просим отправить запрос на почту [email protected]
По завершению проектирования вам будет выслано КП.
Ультразвуковая сварка – ООО «ЦСК»
Главная|Энциклопедия сварки|У|Ультразвуковая сваркаУльтразвуковая сварка – сварка, источником энергии при которой являются ультразвуковые колебания.
Используется для сварки металлов, пластмасс, тканей, кожи, металлов со стеклом, полупроводниковыми материалами и др. Ультразвуковая сварка применяется при точечной, шовной и контурной сварке.
Сварочный метод реализуется благодаря специализированному оборудованию по работе с высокочастотными колебаниями. При этом используются продольные и изгибные механические колебания. В 1969 году был собран первый полностью пластиковый автомобиль, детали которого сваривались ультразвуковой сваркой.
Процесс ультразвуковой сварка отличается низкой себестоимостью и трудоекостью процесса сварки. Ультразвуковые установки имеют простую конструкцию.
Сущность ультразвуковой сварки
Ультразвуковая сварка осуществляется с использованием непрерывно генерируемого ультразвука с частотой 18-180 кГц. мощность 0,01-10 кВт. Сварка происходит с одновременным воздействием на свариваемые поверхности механических высокочастотных колебаний, внешним давлением, приложенным перпендикулярно к свариваемым поверхностям, и тепловым эффектом от высокочастотных колебаний. Тепловое воздействие высокочастотных ультразвуковых колебаний может сочетаться с дополнительным локальным импульсным нагревом заготовок от отдельного внешнего источника теплоты.
При воздействии высокочастотных колебаний происходит сухое трение частиц в свариваемых поверхностях. Под действием сухого трения поверхностные пленки (оксидные и их адсорбированных газов) разрушаются. Затем сухое трение заменяется чистым трением, при котором образуются узлы схватывания. Образуются общие зерна, принадлежащие двум свариваемым поверхностям, и общая границы между поверхностями зерна.
Процесс ультразвуковой сварки
С физической точки зрения ультразвуковая сварка проходит в три этапа:
— нагрев изделий, активизация диффузии в зоне соприкосновения
— образование молекулярных связей между вязкими поверхностными слоями
— затвердевание (кристаллизация) и образование прочного шва
Ультразвуковую сварку можно классифицировать:
1 По степени автоматизации:
— ручная. Оператор контролирует параметры установки и ведет сварочный пистолет по линии шва
— механизированная. Параметры задаются оператором и поддерживаются установкой, детали подаются под излучатель
— автоматизированная. Применяется на массовом производстве. Участие человека исключается
2 По методу подведения энергии к рабочей зоне:
— односторонняя
— двусторонняя
3 По методу движения волновода:
— импульсная. Работа короткими импульсами за одно перемещение волновода
— непрерывная. Постоянное воздействие излучателя, волновод двигается с постоянной скоростью относительно материала
4 По способу определения количества энергии, затрачиваемой на соединение:
— по времени воздействия
— по величине осадки
— по величине зазора
— по кинетической составляющей
В последнем случае количество энергии определяется предельной амплитудой смущения опоры.
5 По способу подачи энергии в рабочую зону различают следующие режимы ультразвуковой сварки:
— контактная. Энергия распределяется равномерно по всему сечению детали. Позволяет сваривать детали до 1,5 толщиной. Применяется для сваривания внахлест мягких пластиков и пленок
— передаточная. В случае высоких значений модуля упругости колебания возбуждаются в нескольких точках. Волна распространяется внутри изделия и высвобождает свою энергию в зоне соединения. Используется для тавровых швов и соединений встык жестких пластиков
Процесс ультразвуковой сварки пластика и металла имеет общую физическую основу, но значительно различается по параметрам.
Ультразвуковая сварка металлов требует нагрева до высоких температур и приложения больших сжимающих усилий. Для пластиков можно обойтись гораздо меньшими значениями этих параметров. Схема установки ультразвуковой сварки пластмасс также значительно проще.
Последовательность действий:
— подключение генератора ультразвука
— преобразование ультразвука, проходящего через конвертер, в продольные механические колебания волновода
— подсоединение волновода перпендикулярно плоскости шва и передача заготовкам колебательной энергии
— преобразование механической энергии в волновую, что обуславливает интенсивный нагрев области соприкосновения волновода и заготовки
— возрастание текучести в нагретом поверхностном слое
— нагрев зоны контакты посредством динамического усилия, прикладываемого со стороны излучателя
— образование прочной связи посредством статического усилия, приложенного в том же направлении – перпендикулярно поверхности контакта.
Технология и оборудование ультразвуковой сварки металлов (1часть)
Ультразвук находит широкое применение в науке для исследования некоторых физических явлений и свойств веществ. В технике ультразвуковые колебания используют для обработки металлов и в дефектоскопии.
В сварочной технике ультразвук может быть использован в различных целях. Воздействуя им на сварочную ванну в процессе кристаллизации, можно улучшить механические свойства сварного соединения благодаря измельчению структуры металла шва и удалению газов.
Ультразвук может быть источником энергии для создания точечных и шовных соединений. Ультразвуковые колебания активно разрушают естественные и искусственные пленки, что позволяет сваривать металлы с окисленной поверхностью, покрытые слоем лака и т. п. Ультразвук снижает или снимает собственные напряжения и деформации, возникающие при сварке. Им можно стабилизировать структурные составляющие металла сварного соединения, устраняя возможность самопроизвольного деформирования сварных конструкций со временем.
В качестве источника энергии при сварке металлов ультразвук еще не нашел широкого применения, хотя этот способ имеет ряд преимуществ и особенностей по сравнению с контактной и холодной сваркой.
При сварке ультразвуком неразъемное соединение металлов образуется при совместном воздействии на детали механических колебаний высокой частоты и относительно небольших сдавливающих усилий. В принципе этот метод сварки имеет много общего с холодной сваркой сдвигом.
Для получения механических колебаний высокой частоты обычно используется магнитострикционный эффект, состоящий в изменении размеров, некоторых металлов и сплавов под действием переменного магнитного поля. Для ультразвуковых преобразователей обычно используют чистый никель или железо-кобальтовые сплавы. Изменения размеров магнитострикционных материалов очень малы: так, для никеля магнитострикционное удлинение составляет 40-10-6. Поэтому для увеличения амплитуды смещения и концентрации энергии колебаний, а также Для передачи механических колебаний к месту сварки используют волноводы или концентраторы, которые в большинстве случаев имеют сужающуюся форму.
Эксперименты показывают, что для сварки металлов достаточно иметь волноводы с коэффициентом усиления около 5, при этом амплитуда на конце волновода при холостом ходе должна быть 20—30 мкм. Магнитострикционный преобразователь и волноводы должны быть рассчитаны и изготовлены на заданную частоту ультразвукового генератора.
Основной узел машины для выполнения точечных соединений с помощью ультразвука — магнитострикционный преобразователь (рис. 8).
Рис.8. Схема установки для точечной сварки ультразвуком:1—магнитострикционный преобразователь;2— диафрагма;3 — механизм нажатия;4 — выступ;5 — маятниковая опора;6 — волновод;7 — кожух водяного охлаждения;8 — изделие
Его обмотка питается током высокой частоты от ультразвукового генератора. Охлаждаемый водой магнитострикционный преобразователь 1 изготовлен из пермендюра (К49Ф2), он служит для превращения энергии тока высокой частоты в механические колебания, которые передаются волноводу 6. На конце волновода имеется рабочий выступ 4. При сварке изделие 8 зажимают между рабочим выступом 4 и механизмом нажатия 3, к которому прикладывают усилие, необходимое для создания давления в процессе сварки.
Сварка происходит при включенном преобразователе. Высокочастотные упругие колебания передаются через волновод на рабочий выступ 4 в виде горизонтальных механических перемещений высокой частоты. Длительность процесса сварки зависит от свариваемого металла и его толщины, для малых толщин она исчисляется долями секунды.
Основные узлы машины для выполнения шовных соединений при помощи ультразвука (рис. 9): вращающийся магнитострикционный преобразователь 1 н волновод 2. Конец волновода имеет форму ролика 3. Изделие 5, подлежащее соединению, зажимают между вращающимся роликом 3 волновода и холостым роликом 4, Высокочастотные упругие колебания передаются через волновод на ролик, который вращается вместе с волноводом.
Рис.9.Схема установки для роликовой сварки ультразвуком:1—магнитострикционный преобразователь; 2 — волновод; 3 — сваривающий ролик;4 — прижимной ролик; 5 — изделие; 6 — кожух преобразователя; 7 — подвод тока от ультразвукового генератора;8 — привод; 9 — подвод охлаждающей воды
Изделие, зажатое между роликами, перемещается, и одновременно создается герметичное соединение.
Сварка по контуру, разработанная в МВТУ — МЭИ, обеспечивает получение герметичного шва практически самого сложного контура. Простейший ее вид — сварка по кольцу. В этом случае конический штифт, вставляемый в волновод, имеет форму трубки (рис. 10). При равномерном поджатии деталей к сваривающему штифту получается герметичное соединение по всему контуру.
Процесс ультразвуковой сварки происходит при воздействии сдвигающих высокочастотных колебаний, давления, приложенного перпендикулярно к поверхности листа, и теплового эффекта, сопровождающего процесс сварки. В результате в зоне сварной точки наблюдается небольшая пластическая деформация.
Исследование процесса образования сварного соединения при ультразвуковой сварке медных пластин толщиной 0,35 + 0,35 мм показывает, что при малом времени пропускания ультразвука (менее 0,05 с) сварка не происходит.
Рис.10.Схема установки для ультразвуковой сварки по контуру:1— волновод;2 — сменный полый штифт; 3 — сменный прижимной штифт; 4 — прижимная опора; 5 — свариваемое изделие
Рис. 11. Макроструктура мест разрушения сварных соединений меди после различной продолжительности пропускания ультразвука. Х16
После разъединения образцов на их поверхности непосредственно под сваривающим выступом наблюдается пятно, имеющее полированную поверхность (рис. 11, а). Диаметр полированного пятна возрастает при увеличении времени сварки (рис. 11, а—д). При пропускании ультразвука в течение 0,1 с в местах контакта обнаруживаются не только зашлифованные поверхности, но и вы- рывы металла, свидетельствующие об образовании прочных соединений, так называемых узлов схватывания. На рис. 11, б виден один узел схватывания на зашлифованной поверхности.
Пропускание ультразвука в течение 0,73 с привело к дальнейшему увеличению площади зашлифованного пятна, при этом площадь узла схватывания также возросла. Вокруг основного узла схватывания возникли отдельные небольшие участки схватывания, удлиненные в направлении ультразвуковых колебаний. С увеличением времени пропускания ультразвука более 0,73 с площадь зашлифованного участка почти не изменяется (рис. 11, г, д), но площадь узлов схватывания начинает увеличиваться более интенсивно. При пропускании ультразвука свыше 1,06 с происходит разрушение сварного соединения с вырывом точки по всему контуру.
Проведенные измерения микротвердости поверхности зашлифованного пятна и основного металла вблизи пятна показали, что микротвердость поверхностного слоя зашлифованного пятна выше (Н50 42—44), чем у основного металла (Н50 28—30). Образование полированного пятна на свариваемых поверхностях указывает на то, что оно возникло вследствие трения под действием высокочастотных колебаний соприкасающихся поверхностей непосредственно под контактным выступом.
Таким образом, процесс ультразвуковой сварки происходит под действием трения, вызванного микроскопическим возвратно-поступательным перемещением трущихся поверхностей.
Сварка ультразвуком — Энциклопедия по машиностроению XXL
из «Технология металлов »
Ультразвуком хорошо свариваются медь, алюминий и многие другие пластичные материалы.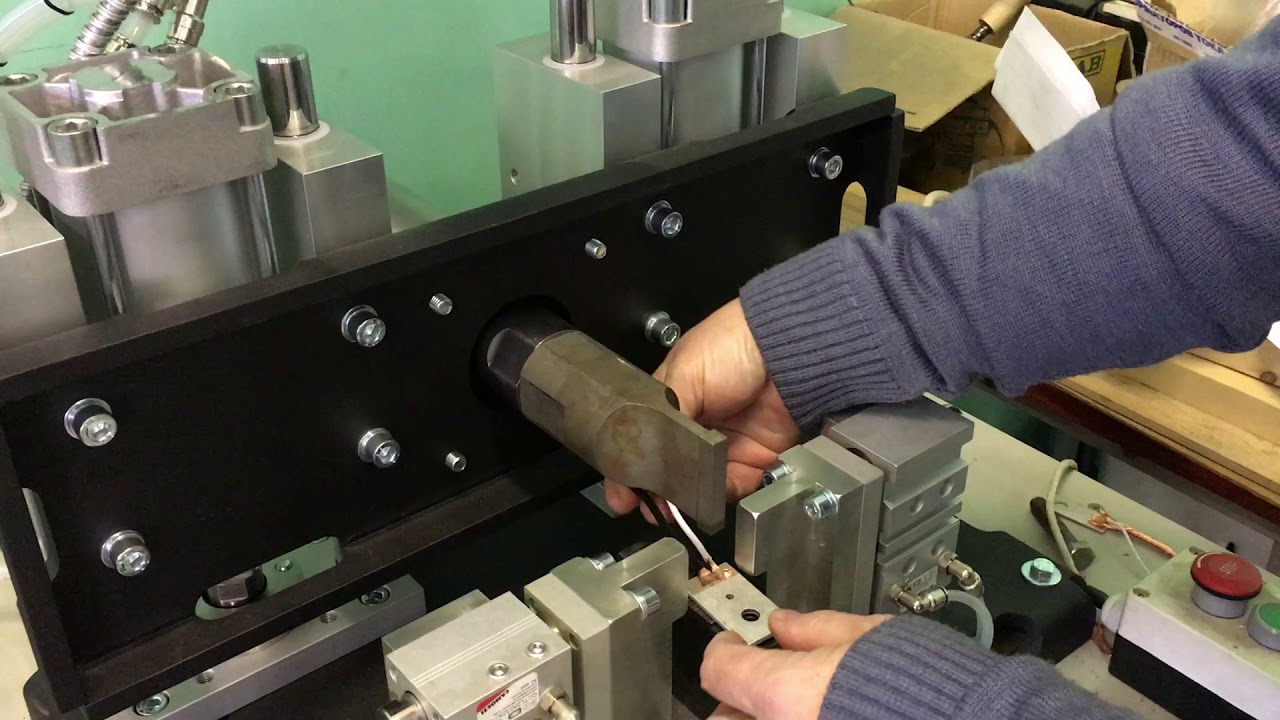
Перспективно применение ультразвуковой сварки для соединения металла в разнородных сочетаниях алюминия с нержавеющей сталью, алюминия с медью и т. д. [c.480]
Кроме соединения металлов, ультразвуковые колебания применяют для сварки пластмасс винипласта, полиэтилена, хлорвинила, капрона, нейлона и оргстекла толщиной от 0,5 до 10 мм. Установки для сварки этих материалов отличаются тем, что в месте сварки создаются не касательные напряжения, обусловленные трением свариваемых поверхностей, а нормальные, перпендикулярные к поверхности. Частота колебаний при сварке пластмасс равна 18—25 кГц. [c.481]
В настоящее время ультразвуковая сварка находит ограниченное применение в электронной технике, в приборостроении и радиоэлектронной промышленности, в авиа- и автомобилестроении для приварки тонких элементов к несущим конструкциям, в точном машиностроении, в электротехнической и других отраслях промышленности, а также в медицине.
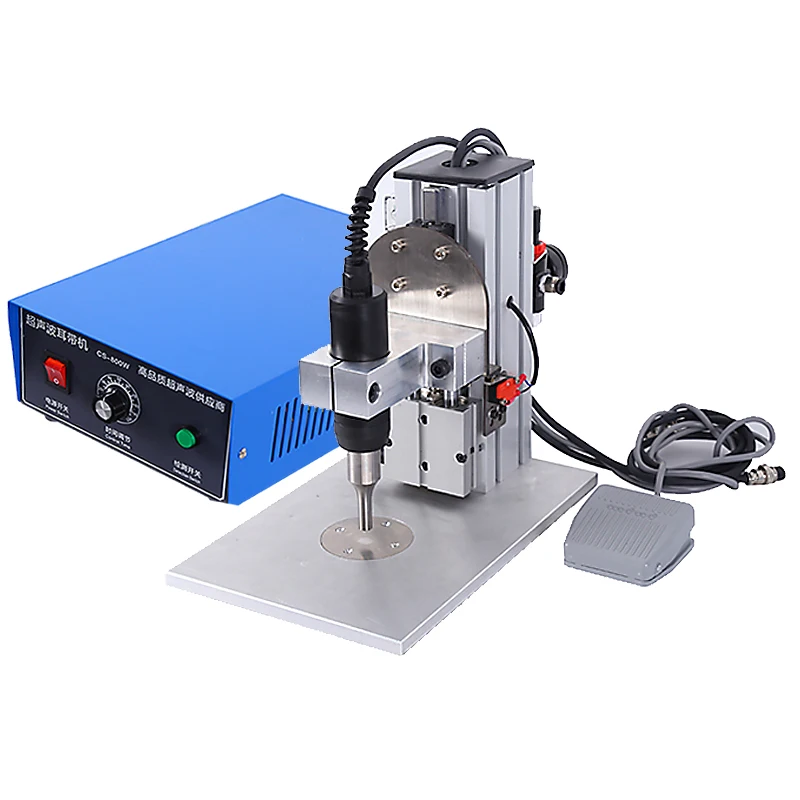
Одним из достоинств ультразвуковой сварки является простота изготовления изделий и невысокая стоимость сварочных машин. Для получения ультразвуковых колебаний используют магнито-стрикционный эффект, состоящий в изменении размеров некоторых металлов, сплавов и керамических материалов под действием переменного магнитного поля. Магнитострикционный преобразователь I выполняют в виде пакета штампованных пластин из магнитострик-ционных материалов (см. рис. 306), например чистый никель или железокобальтовые сплавы толщиной 0,1—0,2 мм с размещенной на нем обмоткой. [c.481]
При включении ультразвукового генератора 5 в пакете / возбуждается магнитное поле, которое вызывает колебания размеров сердечника с той же частотой. [c.481]
Колебания передаются через трансформатор продольных колебаний, присоединяемый к магнитострикционному преобразователю пайкой твердым припоем. Преобразователь / питается током высокой частоты от специального генератора 5.

Возможность разрушения ультразвуком окисных поверхностных пленок используют и для пайки металлов. При этом отпадает необходимость во флюсах, служащих для удаления окислов с поверхности металлов, что представляет собой большое технологическое преимущество, и улучшаются санитарные условия на рабочем месте. [c.481]
Вернуться к основной статье
Ультразвуковая сварка – обзор
13.4.1 Ультразвуковая сварка
Ультразвуковая сварка стала общепринятым методом соединения крупногабаритных относительно небольших пластиковых деталей. В этом процессе ультразвуковой генератор используется для создания колебаний одной подложки относительно неподвижной второй подложки. Это, в свою очередь, вызывает интенсивный фрикционный нагрев между двумя подложками, которого достаточно для быстрого образования расплавленной зоны сварки. При давлении и последующем охлаждении можно получить прочную связь.Основные части стандартного устройства для ультразвуковой сварки показаны на рисунке 13.6.
Рисунок 13.6. Оборудование, используемое в стандартном процессе ультразвуковой сварки.
Из Гримма (1995). Процесс ультразвуковой сварки состоит из четырех этапов. В фазе 1 рупор соприкасается с подложкой, прикладывается давление и начинается вибрационное движение. Выделение тепла из-за трения расплавляет точки непосредственного контакта, и расплавленный материал перетекает в поверхность соединения. На этапе 2 скорость плавления увеличивается, что приводит к увеличению смещения сварного шва и полному смыканию поверхностей деталей. Стационарное плавление происходит в фазе 3, так как в сварном шве поддерживается постоянная толщина слоя расплава. В фазе 4, фазе выдержки, вибрация прекращается, достигается максимальное смещение и возникает высокая прочность соединения по мере остывания и затвердевания сварного шва.
В процессе ультразвуковой сварки материал подается между вибрирующим ультразвуковым излучателем и неподвижной наковальней (режим погружения) или движущимся колесом (режим вращения). Высокочастотные механические вибрации (20–40 кГц) передаются через подложку для создания теплоты трения, накапливаемой на поверхности соединения, и для достижения температуры, достаточной для расплавления и соединения материалов.Поскольку тепло, необходимое для склеивания, производится на границе раздела, а не снаружи материалов, и передается к стыку посредством теплопроводности, процесс ультразвуковой сварки начинается точно на границе раздела, и термическая деградация волокон сводится к минимуму.
Ультразвуковые рожки могут различаться по размеру, максимум примерно до 24 см на 4 см, если они прямоугольные, или около 9 см в диаметре, если они круглые. Фактическая форма рупора зависит от конкретной операции сварки, которую необходимо выполнить. Одним из преимуществ ультразвуковой сварки является то, что тот же процесс может включать в себя ультразвуковую режущую кромку, позволяющую выполнять обработку «разрезать и сшить».
Технология ультразвуковой сварки вошла в швейное производство как передовой метод соединения синтетических материалов и смесей для получения непрерывных непроницаемых швов или локализованных точек соединения. Типичными применениями ультразвуковой сварки являются нанесение мотивов на одежду, отверждение и запечатывание лент и ремешков по длине, а также придание формы небольшим деталям одежды, шитье которых в противном случае было бы дорогостоящим и трудоемким.
Ткани могут быть 100% синтетическими или смесовыми с содержанием натуральных волокон до 40%.Для несинтетических тканей или смесей с содержанием натуральных волокон более 40 % термоактивируемые материалы (термопластичные клейкие пленки или тканевые покрытия) помещают между двумя кусками ткани. Материал должен иметь одинаковую толщину, плотность пряжи, плотность переплетения, эластичность основы и стиль вязания, которые являются факторами, влияющими на способность к сварке. Различные ткани, которые можно соединять ультразвуковой сваркой, показаны в таблице 13.15.
Таблица 13.15. Ткани, которые можно присоединиться с использованием ультразвуковой сварки
Группа ткани | Подгруппа ткани | Пригодность ультразвуковой сварки | Комментарии | |||||
---|---|---|---|---|---|---|---|---|
Да | Некоторые случаи | NO | ||||||
Natural | ||||||||
хлопок | тканые, трикотажные, флеки, нетканые | x | требуют клеевой пленки | |||||
целлюлозы | тканые, вязаные, флис, нетканые | x | требуют клейкой пленки | |||||
шерсть | тканые, вязаные, флис, нетканые | x | требуют клейкой пленки | |||||
Silk | тканые, вязаные, флис, нетканые | x | требуют клейкой пленки | |||||
стекло | Тканые, трикотажные | x | R equires клейкая пленка | |||||
углерода | Тканые, трикотажные | х | Требуется клейкую пленку | |||||
Synthetic | ||||||||
Акриловые | тканого, трикотажного | х | может быть разрезана с помощью ультразвукового Сварка, но склеивание требует клеевой пленки | |||||
регенерированная целлюлоза | • Acetate | Thetate | Thetate, Flece, нетканые | x | Требуется клейкая пленка | • Viscoseтканые, вязаные, флис, нетканый | x | требует клей |
NYLON | тканые, вязаные, флис, нетканые | x | с или без клейкой пленки | |||||
полиэстер | Ткань, трикотаж, флис, нетканый материал | x | с или без клейкой пленки | |||||
полипропилен | тканые, вязаные, флис, нетканые | x | с или без клейкой пленки | |||||
полиэтилен | тканые, трикотажные, флис, нетканые | х | С или без клейкой пленки | |||||
мелованной | х | без клеевой пленки | ||||||
• Полиуретан | х | без клеевой пленки | ||||||
• поливинилхлорид | х | Сварка ингибируется пластификаторов | ||||||
• политетрафторэтилена | х | Спрей пальто может быть приварена, толстых пленок нужна пленка межслойного | ||||||
ламинированная | х | Предпочтительно с пленочной прокладкой ER | ||||||
эластичные ткани | x | с эластичной пленки через | ||||||
натурально-синтетические смеси | x | синтетические расплавы в натуральном волокне или используют клейкий слой |
От Джонса (2013).
Несколько компаний производят автоматизированное ультразвуковое сварочное оборудование для швейной промышленности. Например, швейцарский производитель Schips (www.schips.com) представил несколько ультразвуковых машин для подшивки швов, непрерывной сборки двух тканей с помощью липкой ленты и приварки сложенной резинки к ткани одежды. Компания PFAFF (www.pfaff.com) разработала ультразвуковое оборудование для резки и сшивания.
Ультразвуковая сварка – процесс и оборудование
Профессиональные знания 61
Обзор процесса
Ультразвуковая сварка компонентов, отлитых под давлением из термопластов, представляет собой процесс, в котором используются механические вибрации выше слышимого диапазона.Вибрации, создаваемые сварочным сонотродом или, как известно, рупором, используются для размягчения или плавления термопластичного материала на линии стыка. Соединяемые компоненты удерживаются вместе под давлением и подвергаются вибрации, обычно с частотой 20 или 40 кГц.
Нажмите здесь , чтобы посмотреть наши последние технические подкасты на YouTube .
Возможность успешной сварки компонента определяется конструкцией оборудования, механическими свойствами свариваемого материала, а также конструкцией компонентов и соединений.Время ультразвуковой сварки короткое (обычно менее одной секунды), что делает этот процесс идеальным для массового производства. Этот процесс широко применяется во многих приложениях, начиная от автомобильных световых приборов и заканчивая продуктами бытовой электроники, такими как корпуса мобильных телефонов.
Оборудование
Оборудование для ультразвуковой сварки состоит из пресса, генератора, преобразователя или преобразователя, усилителя, сонотрода или рупора и инструментов для поддержки компонентов.
Генератор
Генератор преобразует электроэнергию из однофазной сети в нужную частоту и напряжение, чтобы преобразователь преобразовал их в механические вибрации.
Машинный пресс
Стойка станка предназначена для удержания сварочной системы или штабеля и приложения усилия, необходимого для сварки. Он состоит из опорной плиты, удерживающей инструментальное приспособление, и пневматического цилиндра для приложения усилия.Аппарат имеет манометр и регулятор для регулировки силы сварки.Следует отметить, что определенное манометрическое давление, установленное на одной части оборудования для ультразвуковой сварки, не обязательно будет обеспечивать такое же сварочное усилие, как другое устройство, настроенное на то же манометрическое давление.
Сварочное усилие должно быть откалибровано с помощью тензодатчика, чтобы можно было провести прямое сравнение сварочных усилий от машины к машине.
Также имеется клапан управления потоком, позволяющий регулировать скорость, с которой сварочная головка приближается к свариваемому компоненту. Некоторые производители оборудования внедрили систему приложения электромагнитной силы вместо традиционного пневматического цилиндра.Это дает лучший контроль скорости подхода и может быть полезным при сварке небольших или хрупких компонентов.
Сварочный блок
Это часть машины, обеспечивающая ультразвуковые механические колебания. Как правило, это блок из трех частей, состоящий из преобразователя, усилителя и сварочного рожка, установленный на сварочном прессе в центральной точке секции усилителя. Стек представляет собой настроенный резонатор, скорее похожий на камертон музыкального инструмента. Для работы резонансная частота настроенного сварочного блока должна близко совпадать с частотой электрического сигнала от генератора (с точностью до 30 Гц).Преобразователь
Преобразователь, также известный как преобразователь, преобразует электрическую энергию генератора в механические колебания, используемые в процессе сварки. Он состоит из нескольких пьезоэлектрических керамических дисков, зажатых между двумя металлическими блоками, обычно титановыми.
Между каждым из дисков находится тонкая металлическая пластина, образующая электрод. По мере того как синусоидальный электрический сигнал подается на преобразователь через электроды, диски расширяются и сжимаются, производя осевое движение от пика к пику от 15 до 20 мкм.
Датчики— это хрупкие устройства, с которыми следует обращаться осторожно. Как только элементы сломаны, преобразователь не будет работать.
Бустер
Усилительная секция сварочной колонны служит двум целям, в первую очередь для усиления механических вибраций, создаваемых на конце преобразователя, и передачи их на сварочный рожок. Его вторичное назначение — предоставить место для установки пакета на сварочном прессе.
Усилитель расширяется и сжимается по мере того, как преобразователь подает ультразвуковую энергию.
Усилитель, как и другие элементы сварочного аппарата, представляет собой настраиваемое устройство, поэтому он должен резонировать на определенной частоте, чтобы передать ультразвуковую энергию от преобразователя к сварочному рупору. Для успешного функционирования бустер должен быть либо половиной длины волны ультразвука в материале, из которого он изготовлен, либо кратным этой длине. Обычно это половина длины волны.
Сварочный рожок
Сварочный рожок — это элемент сварочного аппарата, который подает энергию на свариваемую деталь.Типичный сварочный рожок показан на рис. 4 . Конструкция сварочного рожка имеет решающее значение для успешной сварки. Настоятельно рекомендуется, чтобы изготовление сварочного рожка осуществлялось только компаниями, специализирующимися на ультразвуковой сварке.
Сварочный рупор, как и усилительный элемент, представляет собой настраиваемое устройство, которое в большинстве случаев также обеспечивает механическое усиление. Обычно он изготавливается из алюминия или титана. Алюминиевые сварочные рожки, как правило, используются для небольших объемов работ, поскольку износ может быть особой проблемой для этого материала.Некоторые сварочные рожки имеют специально закаленные наконечники для уменьшения износа во время сварки.
Как и в случае с бустерным элементом, длина сварочного рупора должна быть равна либо половине длины волны ультразвука в материале, из которого он изготовлен, либо кратна этой длине. Это обеспечивает достаточную амплитуду на конце сварочного рожка для осуществления сварки.
Амплитуда обычно составляет от 30 до 120 мкм. Форма сварочного рупора важна, так как напряжение, вызванное осевым расширением и сжатием рупора, может привести к растрескиванию в приложениях с большой амплитудой.В некоторых случаях сварочный рожок изготавливается с прорезями в осевом направлении. Это необходимо для обеспечения максимальной амплитуды вибрации в продольном направлении.
Наконечник сварочного рожка подает ультразвуковую энергию на свариваемый компонент. Наконечник должен быть специально разработан, чтобы соответствовать компоненту. Это обеспечит максимальную передачу энергии между рупором и компонентом. Обычно кончик рупора профилирован, чтобы соответствовать контурам компонента.
Опорный инструмент
Наконец, основание машинного пресса поддерживает инструменты, поддерживающие компоненты во время операции сварки. Опорный инструмент предназначен для предотвращения перемещения нижнего компонента во время применения ультразвука. Его часто обрабатывают, чтобы точно соответствовать контурам поверхности компонента.Следующая статья будет посвящена конструкции компонентов и параметрам сварки.
Часть 2: Конструкция компонентов
См. дополнительную информацию о сварке полимеров или свяжитесь с нами.
Как работает ультразвуковая сварка | HowStuffWorks
Ультразвуковая сварка имеет много преимуществ по сравнению с традиционными методами. Во-первых, сварка происходит при более низких температурах по сравнению с другими методами. Таким образом, производителю не нужно расходовать огромное количество топлива или другой энергии для достижения высоких температур. Это удешевляет процесс. Это также быстрее и безопаснее.
Процесс занимает доли секунды или секунды. Таким образом, это может быть сделано быстрее, чем другие методы. Фактически, он может склеивать пластмассы лучше и быстрее, чем клей.Например, новые смарт-ключи в автомобилях имеют чип-транспондер. Автомобиль может завестись только тогда, когда он обнаружит чип. Чтобы сделать ключ, один конец металлической заготовки ключа и чип помещаются в одну половину пластиковой крышки. Другая половина помещается поверх них и приклеивается к основной половине. Это склеивание обычно выполняется с помощью клея, для отверждения которого требуется время. Та же задача может быть выполнена с помощью ультразвуковой сварки менее чем за секунду.
Ультразвуковая сварка не требует легковоспламеняющихся видов топлива и открытого пламени, поэтому по сравнению с другими методами сварки это более безопасный процесс.Рабочие не подвергаются воздействию легковоспламеняющихся газов или вредных растворителей. В электронике медные провода обычно соединяются с электрическими контактами на печатных платах с помощью припоя. Та же задача может быть выполнена с помощью ультразвуковой сварки за короткое время и без воздействия на рабочих паров тлеющего свинцового припоя. Хотя слух рабочих может быть поврежден воздействием высокочастотного звука, эту потенциальную опасность легко уменьшить, поместив ультразвуковой сварочный аппарат в защитный бокс или клетку и/или используя средства защиты органов слуха.
Наконец, ультразвуковая сварка такая же прочная и долговечная, как и обычная сварка тех же материалов, что является лишь одной из причин, по которой этот метод используется в автомобилестроении. Чтобы сделать автомобили легче и экономичнее, автопроизводители обращаются к алюминию как основному металлу в кузовах автомобилей. Ультразвуковая сварка может использоваться для соединения металла за меньшее время и при более низких температурах, чем традиционная сварка.
Ультразвуковая сварка имеет свои ограничения. Во-первых, глубина сварных швов составляет менее миллиметра, поэтому этот процесс лучше всего работает на тонких материалах, таких как пластик, проволока или тонкие листы металла. Ультразвуковая сварка стальной балки для здания нецелесообразна. Во-вторых, он лучше всего работает при сварке подобных материалов, таких как аналогичные пластмассы или аналогичные металлы. Как вы видели на примере обуви New Balance, для ультразвуковой сварки разнородных материалов требуется дополнительный материал — в случае с обувью New Balance это пленка, которую можно приклеить между синтетической замшей и сеткой.
Несмотря на эти ограничения, популярность и потенциал ультразвуковой сварки продолжают расти.
Что такое ультразвуковая сварка и подходит ли она мне? — RevPart
Что такое ультразвуковая сварка и подходит ли она мне?
Изучая способы соединения пластиковых деталей, вы почти наверняка остановитесь на процессе, подпадающем под одну из следующих категорий: механическое соединение, склеивание или сварка. Механические процессы, такие как защелкивание, винты или заклепки, отлично подходят, если продукт необходимо разобрать в течение срока его службы или если продукт будет работать в небольшом объеме. Клеи, такие как клей, образуют более прочную связь и превосходно склеивают два разнородных материала. Процессы сварки пластмасс носят непрерывный характер, не требуют расходных материалов и используют комбинацию тепла и давления для сплавления деталей. При оценке методов производства нельзя упускать из виду один конкретный метод сварки: ультразвуковую сварку.
Что такое ультразвуковая сварка?
Проще говоря, ультразвуковая сварка использует высокочастотные вибрации для нагрева и соединения двух частей, соприкасающихся под давлением.Эти высокочастотные вибрации в большинстве случаев превышают предел человеческого слуха. Диапазон человеческого слуха составляет от 20 Гц до 20 кГц, в то время как ультразвуковые частоты, используемые в этих сварочных аппаратах, обычно находятся в диапазоне от 15 кГц до 75 кГц. Техника была запатентована в 60-х годах и впервые использовалась в индустрии игрушек. С тех пор технология продолжает развиваться и используется в таких отраслях, как медицина, электроника, упаковка и автомобилестроение. Ультразвуковая сварка может использоваться как для пластмасс, так и для металлов, но в этой статье основное внимание будет уделено сварке пластмасс.Чтобы лучше понять ультразвуковую сварку, давайте рассмотрим компоненты сварочного аппарата.
Блок питания . Каждый ультразвуковой сварочный аппарат начинается с источника питания. Источник питания иногда называют генератором частоты, потому что он потребляет стандартную электрическую мощность (обычно 115 В) с частотой 60 Гц и преобразует ее в рабочую частоту примерно 20 кГц или 20 000 циклов в секунду. Другие широко доступные выходные частоты находятся в диапазоне от 15 до 70 кГц.Затем этот высокочастотный ток направляется по специальному кабелю в ультразвуковой блок.
Ультразвуковой стек. Стек — это не одно целое, а комбинация трех основных компонентов: преобразователь, усилитель и сварочный рупор. В сварочном аппарате для пластика ультразвуковой блок выровнен вертикально и расположен над свариваемыми деталями в опорной колонне.
Преобразователь. Преобразователь представляет собой пьезоэлектрический преобразователь, на который подается ток высокой частоты от источника питания и который выдает механические колебания той же частоты.Преобразователь работает за счет пьезоэлектрического эффекта — вспомните кварцевые часы. Таким образом, пьезоэлектрический эффект возникает, когда механическая деформация (изменение формы из-за давления) возникает в материале-кандидате, который, в свою очередь, генерирует электрический заряд. Пьезоэлектрический эффект работает и в обратную сторону. Если к материалу приложить электрическое поле, он изменит форму. Пьезоэлектрические преобразователи, используемые в ультразвуковых преобразователях, состоят из множества пьезоэлектрических керамических дисков, покрытых с обеих сторон металлическими пластинами.Все они хранятся под давлением в титановом цилиндре. Источник питания посылает на это устройство высокочастотный ток, генерирующий быстро меняющиеся электрические поля. Эти быстро меняющиеся электрические поля вызывают быстрое изменение формы пьезоэлектрического материала, что приводит к высокочастотным вибрациям. Титановый цилиндр помогает передавать эту вибрацию усилителю.
Бустер. Усилитель является реактивным компонентом преобразователя и помогает усилить или ослабить вибрацию.Колебания, исходящие от преобразователя, имеют приблизительную амплитуду (от нуля до пика) 8 микрометров (диаметр эритроцита). Эта амплитуда должна часто изменяться, чтобы успешно передать требуемую энергию сварному соединению. Усилитель увеличивает или уменьшает
амплитуду вибрации в определенном соотношении. Это соотношение определяется геометрией и распределением массы ракеты-носителя, каждая из которых точно спроектирована для достижения этого соотношения. Например, бустеры с большей массой возле рупора уменьшают выходную амплитуду.Типичные передаточные числа бустера составляют 1: 0,6 (амплитуда уменьшения) и 1: 2,0 (двойная амплитуда), и обычно они изготавливаются из титана или алюминия. Отношение также может быть выражено как «усиление», где усиление равно выходной амплитуде, деленной на входную амплитуду. Бустер — не единственный компонент стека, который может изменять амплитуду акустических волн.
Горн или сонотрод. За пределами США рупор иногда чаще называют сонотродом.Рупор принимает вибрации от усилителя и дополнительно усиливает или ослабляет амплитуду акустических волн. Рог также отвечает за передачу этих вибраций на свариваемые детали путем прямого контакта. В пластиковом сварочном аппарате рупор и усилитель вибрируют в осевом направлении с рабочей частотой, установленной источником питания. Рупор контактирует с верхней пластиковой деталью и применяет эти вибрации перпендикулярно поверхности детали. Напротив, металлические рога сварщика лежат горизонтально, а вибрации прикладываются параллельно поверхности деталей.Рупор уникально спроектирован так, чтобы его концы постоянно двигались в противоположных направлениях, в то время как центр рупора оставался на месте. Умножая выходную амплитуду преобразователя на усиление усилителя и усиление рупора, вы можете найти эффективную выходную амплитуду стека, применяемую к части. Титан является предпочтительным материалом для изготовления рупора из-за его механических свойств, таких как высокая усталостная прочность и твердость, но также существуют экономичные алюминиевые и стальные рупоры для правильного применения.Существует множество форм рупора, каждая из которых имеет свое уникальное применение, и для особых случаев могут быть изготовлены специальные рупоры. Круглый рожок, например, полезен, когда детали должны быть сварены по окружности. Прежде чем рог сможет воздействовать на заготовку вибрацией, ее необходимо сначала опустить на место.
Привод. Привод отвечает за опускание пакета на свариваемые детали. Он также должен прикладывать усилие, соответствующее желаемому приложению.Ультразвуковые сварочные приводы обычно имеют пневматический или электрический привод и обеспечивают усилие сварки в диапазоне 50-750 фунтов. Приводы, используемые в аппарате для ультразвуковой сварки металла, могут приводиться в действие гидравликой и воспринимать большее усилие. Точное усилие будет определяться исходя из конструкции свариваемых деталей.
Гнездо или наковальня. Обычно свариваются две детали — верхняя половина и нижняя половина. Нижняя половина находится в приспособлении, называемом гнездом. Гнездо будет направлять вибрации на поверхность раздела между двумя частями.Когда приспособление, удерживающее нижнюю часть, более плоское, его можно назвать наковальней. При сварке длинных швов некоторые машины имеют подвижную наковальню, которая перемещает деталь, удерживая сварщика на месте.
Процесс ультразвуковой сварки. Теперь, когда вы знакомы с основными компонентами ультразвукового сварочного аппарата, пришло время понять, как работает типичный цикл сварки:
Первым шагом является загрузка деталей в гнездо вручную или с помощью автоматизации — автоматизация используется при выполнении больших объемов работ. Далее органы управления сварочным аппаратом будут работать в одном из четырех режимов:
Сварка по времени. Сварка по времени запускает последовательность сварки в течение заданного времени. В течение многих лет это был стандартный способ сварки. Недостатком этого процесса является то, что это система без обратной связи (без обратной связи). С появлением строгих требований к качеству в таких отраслях, как медицина, метод сварки по времени не всегда может обеспечить требуемый уровень стабильности. Если одна часть отличается от другой очень незначительно, обратной связи, объясняющей различия, не существует.Это приводит к изменению качества сварки и общих характеристик детали. Благодаря тому, что новые датчики и усовершенствованные элементы управления становятся более доступными, были разработаны более совершенные режимы сварки.
Общая энергия. Одна из теорий успешной сварки заключается в том, что для данной детали необходимо приложить определенное количество энергии к границе раздела деталей для получения удовлетворительного сварного шва. Режим полной энергии работает путем измерения мощности, потребляемой сварщиком, и регулировки продолжительности процесса сварки для достижения желаемого энергопотребления (мощность x время = энергия).Этот метод, хотя и хорош в теории, трудно предсказать фактическую энергию, приложенную к сварному шву, из-за потерь в машине (например, потери энергии в приспособлении).
Свернуть (относительное) расстояние. С помощью линейного энкодера система управления может измерять расстояние, на которое рог погружает верхнюю часть в нижнюю во время сварки. Измерение начинается, когда рупор впервые соприкасается с верхней частью (когда привод опускается), и заканчивается после достижения заданного расстояния. Это предустановленное расстояние представляет собой расстояние разрушения — величину, на которую плавится поверхность раздела между двумя частями.Этот метод является предпочтительным во многих ситуациях, поскольку позволяет точно контролировать глубину сварки.
Абсолютное расстояние. Когда габаритные размеры свариваемой детали являются критическими, предпочтительным методом является «абсолютное расстояние». Используя линейный энкодер, сварщик будет продолжать цикл сварки до тех пор, пока не будет достигнут определенный общий размер детали (обычно общая высота). Методы полной энергии, расстояния коллапса и абсолютного расстояния включают в себя петли обратной связи, что делает их системами с обратной связью.
После того, как выбран режим управления, привод опускает стек. В конце концов рупор соприкасается с верхней частью, и прикладывается нагрузка. Между тем, источник питания подает ток на преобразователь, который выдает высокочастотную вибрацию через усилитель и звуковой сигнал. Рог подает эту ультразвуковую волну на свариваемые детали. Одна из частей обычно имеет направляющую энергии на границе раздела. Энергетический директор представляет собой небольшой формованный гребень высотой чуть менее 1 миллиметра и углами сторон 60-90 градусов.Из-за вибраций и трения направляющая энергии расплавится и создаст молекулярную связь с поверхностью другой детали. Время сварки обычно занимает менее секунды, после чего сварной шов быстро охлаждается из-за того, что температура плавления остается локализованной на границе раздела деталей. Времени на лечение тоже нет. После этого привод полностью убирается, и детали можно снять вручную или с помощью автоматики.
Лучшие методы проектирования.
При оценке ультразвуковой сварки как метода изготовления важно помнить, что некоторые пластики свариваются лучше, чем другие.
• Благодаря своему химическому составу и тонкой структуре термопластичные пленки и ткани легко свариваются ультразвуковыми методами.
• Аморфные термопласты (такие как ABS) также являются идеальными кандидатами.
• Полукристаллические термопласты (такие как нейлон) получить сложнее, но можно.
• С другой стороны, термопластичные эластомеры очень плохо подходят для ультразвуковой сварки и, как правило, не рекомендуются.
Различные материалы имеют разные диапазоны амплитуд, необходимые для эффективной сварки. Большинство поставщиков ультразвуковых сварочных аппаратов могут предоставить эталонные настройки для различных материалов. Сварка двух разных пластиков может быть достигнута, если их настройки не слишком отличаются.
Размер деталей также является важным фактором. Ультразвуковая сварка отлично подходит для мелких деталей. Насколько велик слишком большой? Вот несколько практических правил:
• Чем сложнее материал, тем меньше может быть его максимальный размер. Нейлон (сложный) может быть только около 3,5 дюймов, а АБС (легкий) может быть около 10 дюймов.
• Для более низких частот (15 кГц) требуются более крупные инструменты (10 дюймов).Для более высоких частот (40 кГц) требуются инструменты меньшего размера (2,5 дюйма)
Геометрия детали влияет на возможность получения чистых сварных швов. Ультразвуковая сварка хорошо работает с тонкостенными деталями, длинными неподдерживаемыми стенками и внутренними сварными швами. Сложная геометрия и глубокие контуры плохо подходят для ультразвуковой сварки.
При проектировании интерфейса между деталями важно добавить направляющую энергии. Энергетический директор работает, чтобы сконцентрировать энергию от рога, чтобы инициировать быстрое плавление. Обычно это треугольный профиль, расположенный в центре стены по всей длине стены.Рекомендуется размещать регулятор энергии на части, касающейся рупора. Хорошей отправной точкой является угол 60-90 градусов высотой, равной 1/8 толщины стены. Эмпирическое правило для требуемой силы привода составляет 1 фунт-сила на каждый погонный миллиметр направляющей энергии. Дизайн деталей должен включать элементы, которые помогают их выравнивать. Эти предложения являются лишь отправной точкой и должны быть оценены инженером по применению. Проверенный набор эмпирических данных вместе с установленными процедурами сварки являются ключом к успешному проекту.
Преимущества
Ультразвуковая сварка имеет множество преимуществ по сравнению с альтернативными методами:
• Высокопрочные сварные швы
• Отсутствие расходных материалов — без крепежа или клея
— без отверждения. Сварка менее чем за секунду.
• Легко автоматизируется
• Чистота и точность
• Вентиляция не требуется
• Может выталкивать загрязнения из-под упаковочных швов
• Обеспечивает герметичное запечатывание с защитой от несанкционированного доступа
• 0004 • Низкое энергопотребление — работает короткими импульсами 90 005 90 Отлично подходит для летучих или термочувствительных продуктов
• Использует стандартную электрическую мощность (115 В при 60 Гц)
• Проверенная технология с большим выбором оборудования
• Относительно низкие капитальные затраты на оборудование
Ограничения и недостатки.
Вот некоторые ограничения, о которых следует помнить при оценке ультразвуковой сварки:
• Размер детали должен быть небольшим
• Геометрия не должна быть слишком сложной
• Ограничено некоторыми пластиками и комбинациями пластиков
• Ограниченный сварной шов depth
• Может издавать слышимый высокочастотный шум
При оценке способов соединения пластиковых деталей в вашем следующем проекте подумайте о преимуществах ультразвуковой сварки и посмотрите, подходит ли она для вашего применения.
Karl Hegna
Основы технологии ультразвуковой сварки пластмасс
Что такое ультразвуковая сварка?
Технология ультразвуковой сваркииспользует высокочастотные вибрации (ультразвук) для точного соединения двух термопластичных деталей за доли секунды. Под точным давлением соединение герметизируется менее чем за 0,2 секунды.
Ультразвуковые волны вибрируют десятки тысяч раз в секунду.Это колебание передается на контактную поверхность, непосредственно контактирующую с пластиковыми деталями. Поскольку граница зоны сварки имеет большое акустическое сопротивление, она создает высокие температуры. Пластик является довольно плохим проводником тепла и не может рассеивать тепло до тех пор, пока он не изменит состояние пластика с твердого на жидкое. При небольшом надавливании две части сливаются вместе, как если бы они были единым куском пластика. Как только ультразвуковой сигнал прекращается, детали снова становятся твердыми. Это магия, которая создает чистый и очень прочный сварной шов между двумя частями. Сварной шов будет иметь прочность, близкую к прочности исходных материалов, формируемых вместе в процессе литья под давлением.
Давайте немного покопаемся, чтобы увидеть, как выглядит каждый шаг! Мы поговорим о том, как работает этот процесс, каковы его преимущества и недостатки, а также о том, как спроектировать пластиковые соединения, чтобы максимально использовать эту технологию.
Основы ультразвуковой сварки
Этап 1 — Детали приспособления
Две детали из термопластика, которые необходимо собрать, помещаются вместе, одна поверх другой, в опорное гнездо, называемое приспособлением.
Этап 2 — контакт звукового сигнала
Компонент из титана или алюминия, называемый рупором, контактирует с верхней пластиковой частью.
Этап 3 — Приложено давление
К деталям прикладывается контролируемое давление, которое прижимает их к приспособлению.
Этап 4 — Время сварки
Рупор вибрирует вертикально 20 000 (20 кГц) или 40 000 (40 кГц) раз в секунду в течение точного времени, также называемого временем сварки.Различные части деталей точно спроектированы таким образом, чтобы энергия направлялась в определенные точки контакта между двумя частями.
Механические вибрации передаются через термопластичные материалы на поверхность соединения, создавая тепло от трения. Когда температура на границе стыка достигает точки плавления, пластик плавится и течет, а вибрация прекращается. Это позволяет расплавленному пластику начать остывать.
Этап 5 — Время удержания
Усилие зажима поддерживается в течение заданного периода времени, чтобы обеспечить сплавление деталей по мере охлаждения и затвердевания расплавленного пластика.Это известно как время удержания. Улучшенная прочность соединения и герметичность могут быть достигнуты за счет приложения более высокой силы во время выдержки. Это достигается с помощью двойного давления в различные моменты времени выдержки.
Этап 6 — Рупор втягивается
После затвердевания расплавленного пластика зажим снимается, а рупор убирается. Две пластиковые детали теперь соединены, как будто отлиты вместе, и снимаются с приспособления как одна деталь.
Ультразвуковая сварка для сборки пластмасс — это быстрый, чистый, эффективный и воспроизводимый процесс, потребляющий очень мало энергии.Не требуются растворители, клеи, механические крепления или другие расходные материалы, а готовые сборки прочны и чисты.
важные факторы ультразвуковой сварки пластмасс
Время сварки и давление сварочной головки можно регулировать с амплитудой, определяемой конфигурацией преобразователей и стержней. Как правило, основные переменные
- Амплитудные стержни и преобразователи
- Давление сварочной головки
- Время сварки
- Время удержания
Регулировка должна быть точной. Если частота слишком высока или время подачи сигнала слишком велико, пластик может легко деформироваться за пределами границ точек соединения. Если приложенная энергия слишком слаба, то образуется плохое соединение.
Преимущества и недостатки:
Преимущества ультразвуковой сварки пластмасс
Технология ультразвуковой сварки отличается высокой скоростью сварки, высокой прочностью сварки и хорошей герметичностью. Это подходящая замена традиционным процессам сварки/склеивания.Процесс является чистым, поскольку в нем не используются вредные растворители или клеи, а также не повреждается продукт. Эта технология также легко внедряется в производственный процесс и имеет низкий уровень брака. В качестве бонуса все эти преимущества помогают снизить производственные затраты.Недостатки ультразвуковой сварки пластмасс
При увеличении толщины и твердости пластиковых деталей мощность, необходимая для сварки, увеличивается экспоненциально в зависимости от параметров пластика. Это увеличивает стоимость изготовления ультразвукового сварочного аппарата.Если потребляемая мощность слишком велика, проектирование и изготовление акустической системы, а также технологические эффекты приведут к ряду трудноразрешимых проблем. Таким образом, эта технология обычно ограничивается тонкими деталями, такими как проволока, фольга и листы. Состояние этой технологии ограничивает форму соединения системы ультразвуковой сварки соединениями внахлестку и ограничено головкой инструмента. Детали могут выступать только в пределах допустимого диапазона размеров сварочной системы. Форма сварного соединения и размерный ряд ограничены.
Эти ограничения означают, что детали, подлежащие сварке, должны быть точно спроектированы, чтобы максимально использовать преимущества этого процесса.
Области применения
Ультразвуковая сварка пластика подходит практически для всех термопластов. При планировании сварки деталей из полукристаллического пластика важно помнить, что поведение при сварке этих пластиков значительно отличается от поведения аморфных пластиков.
Ультразвуковая сварка пластмасс в ограниченных пределах может использоваться для соединения двух различных термопластов (аморфных пластиков).Ультразвуковая сварка не подходит для термореактивных пластиков. Сегодня ультразвуковая сварка используется во всех отраслях промышленности, где перерабатываются пластмассы. Чаще всего они используются в автомобильной, медицинской, текстильной, пищевой, пластмассовой и упаковочной отраслях.
Как начать?
NexPCB предлагает эту технологию как часть наших полных предложений «под ключ». Если вы ищете этот тип приложения для своих текущих или новых проектов, вы можете перейти к нашему запросу проекта, чтобы представить свои проекты.Наша команда опытных инженеров-механиков оценит ваш проект и сообщит вам, подходит ли эта технология для вашего проекта!
Как решить распространенные проблемы ультразвуковой сварки
Ультразвуковая сварка является широко признанным и общепринятым процессом соединения термопластичных материалов. Он предлагает множество преимуществ, включая надежность и повторяемость процесса, более низкое энергопотребление по сравнению с другими методами соединения, экономию материалов (поскольку нет необходимости в расходных материалах, таких как клей или механические крепежные детали), а также экономию труда.
Но, как и в любом процессе, бывают ситуации, когда явные проблемы с этой техникой могут прервать производственный процесс. Ключом к решению и предотвращению этих проблем является понимание их вероятного происхождения. Процессоры, которые успешно используют ультразвуковую сварку, обычно имеют две основные черты: у них есть хорошо задокументированный и проверенный процесс сварки; и этот процесс поддерживается и поддерживается местным хорошо обученным «чемпионом». Если один или оба этих важных фактора отсутствуют, вы, скорее всего, очень скоро позовете на помощь.Даже если оба присутствуют, возможно, вам понадобится помощь или техническая помощь хотя бы время от времени.
ПРИНЦИП РАБОТЫ ПРОЦЕССА
Прежде чем рассматривать распространенные причины проблем с ультразвуковой сваркой, давайте на минутку разберемся в самом цикле сварки. При ультразвуковой сварке высокочастотные вибрации воздействуют на поверхности двух деталей с помощью вибрирующего инструмента, обычно называемого «рупором» или «сонотродом». Сварка происходит в результате теплоты трения, образующейся на границе раздела между деталями.Ультразвуковые колебания создаются рядом компонентов — источником питания, преобразователем, усилителем и звуковым сигналом, — которые передают механическую вибрацию деталям.
Как показано на рис. 1, блок питания берет стандартное сетевое напряжение и преобразует его в рабочую частоту. В следующем примере мы будем использовать обычную частоту ультразвуковой сварки 20 кГц, хотя сварка может выполняться в диапазоне от 15 до 60 кГц для удовлетворения особых потребностей. В процессе работы блок питания посылает электрическую энергию заданной частоты по ВЧ кабелю на преобразователь.В преобразователе используется пьезоэлектрическая керамика для преобразования электрической энергии в механические колебания на рабочей частоте источника питания. Эта механическая вибрация либо увеличивается, либо уменьшается в зависимости от конфигурации усилителя и звукового сигнала. Надлежащая амплитуда механических колебаний определяется инженером по применению и зависит от термопластичных материалов, используемых в деталях.
Свариваемые детали подвергаются механической нагрузке, как правило, с помощью пневматического привода, удерживающего усилитель и звуковой сигнал.При этой нагрузке механические колебания передаются на поверхность раздела между поверхностями материала, которая фокусирует колебания для создания межмолекулярного и поверхностного трения. Это трение создает тепло и последующий расплав, который затвердевает в сварное соединение.
Основными компонентами ультразвуковой системы являются источник питания, исполнительный механизм и стек (см. рис. 2). Блок питания принимает линейное напряжение номиналом 120-240В и преобразует его в высоковольтный высокочастотный сигнал.Он также содержит программирование, необходимое для управления приводом и пакетом контролируемым образом для достижения желаемого результата сварки. Привод с пневматическим или электрическим сервоприводом, доступный как автономный настольный блок или интегрированный в автоматизированную систему, перемещает ультразвуковой инструмент к соединяемым деталям. Он прикладывает необходимое усилие к материалам, чтобы помочь создать условия для сварки.
Ультразвуковой стек дополняет систему. Он передает вибрационную энергию посредством прямого контакта с деталями на уплотняемую/соединяемую поверхность.Стек обычно состоит из трех элементов: преобразователя или преобразователя (описанного выше), который содержит пьезоэлектрические керамические кристаллы, которые колеблются с частотой приложенного сигнала источника питания. Когда эти кристаллы колеблются, они физически расширяются и сжимаются, создавая измеримое механическое движение (называемое размахом амплитуды) на выходной стороне преобразователя.
Вторая секция, бустер, с прикрепленным кольцом в средней части, выполняет две функции: действует как точка крепления стека в приводе, а также служит для усиления или уменьшения выходного движения, создаваемого в преобразователе.
Третий и последний компонент пакета — рупор (сонотрод), который будет контактировать с соединяемыми частями. Рупор будет спроектирован так, чтобы соответствовать профилю соединяемых жестких частей, или может иметь уплотнительный профиль, добавленный к его контактной поверхности в приложениях с пленкой / текстилем. Для каждого применения рупор предназначен для объединения с другими компонентами пакета для достижения оптимального уровня выходной амплитуды, чтобы обеспечить максимально эффективную ультразвуковую сварку.
ТИПИЧНЫЕ ПРОБЛЕМЫ
Проблемы обычно возникают в одной из четырех областей:
1. Оборудование : Ультразвуковое сварочное оборудование или различные сварочные компоненты не подходят для данного применения.
2. Параметры процесса : Используемые параметры не подходят для соединяемых деталей.
3. Материалы : Изменения вносятся в тип, состав или физические/механические характеристики материалов, используемых в деталях.
4. Конструкция детали : Некоторые детали геометрии детали не подходят для воспроизводимой или успешной сварки.
Следует также отметить, что иногда проблема, выявленная в одной области, может выявить слабость или недостаток в другой области.
Начнем с снаряжения. Легко и, как правило, логично думать, что оборудование и подходы, обеспечивающие успешную сварку в одном приложении, будут такими же и в другом. Но это не всегда так. Во всем мире наиболее широко используются ультразвуковые сварочные аппараты с частотой 20 кГц; Благодаря своей универсальности эти сварочные аппараты могут обеспечивать высокую мощность (до 6000 Вт) и высокую амплитуду выходной мощности, а также они могут работать с широким диапазоном доступных размеров инструментов.Для контрактного производителя, который производит детали, сваренные ультразвуком, оборудование с частотой 20 кГц может стать отличной инвестицией, поскольку оно дает надежду на будущее использование во многих приложениях.
Однако в некоторых случаях, особенно при работе с небольшими и хрупкими деталями, мощные и высокоамплитудные возможности 20-кГц оборудования могут оказаться слишком «агрессивными» для определенных узлов, что может привести к повреждению. Одним из возможных решений является уменьшение входной амплитуды, но это не сработает, если применяемая амплитуда ниже рекомендуемого уровня для свариваемого полимера.
Вопросы об ультразвуковой сварке? Посетите зону сварки, склеивания и сборки PTOnline.com
Другим решением является поиск оборудования, работающего на более высокой частоте, возможно, 30 или 40 кГц, при условии, что инструменты, необходимые для приложения, доступны для использования на этой частоте. Высокочастотное оборудование производит меньшую выходную амплитуду, но компенсирует это резонированием на более высокой частоте. Таким образом, высокочастотные сварщики считаются «более щадящими» в применении ультразвуковой энергии к деталям. Электронные сборки, особенно с чувствительными таймерами/генераторами и другими компонентами, расположенными на печатных платах, выиграли от этого подхода. Аналогичным образом, детали, которые страдают от «диафрагмирования» или «масляного скопления» из-за чрезмерного перемещения одной из сопрягаемых частей, часто выигрывают от перехода на более высокочастотное оборудование.
Другим потенциальным фактором являются сбои в работе оборудования. Они редко происходят без предупреждения. Одним из очевидных примеров является изменение или усиление шума, создаваемого при работе сварочного аппарата.Опытные операторы и обслуживающий персонал часто настроены на такие тонкие гармонические колебания и должны всегда сообщать об этих изменениях руководителям. Своевременное обращение к «скрипучему колесу» вполне может позволить выявить и решить проблему до того, как это отрицательно скажется на производстве.
Аналогичным образом, более новое ультразвуковое оборудование позволяет пользователям выполнять интерактивные диагностические проверки функций, которые при правильной интерпретации и использовании в сочетании с другими предупредительными знаками, такими как шум, могут предупредить пользователя о тревожных тенденциях, прежде чем они станут серьезными проблемами. Источники питания с помощью усовершенствованных протоколов связи могут получать такие данные, как «результаты графика сварки» и «сканы рупора», которые можно сравнить с исходными данными, полученными, когда оборудование было новым, недавно обслуживалось или работало в соответствии со стандартами.
С помощью этой информации опытные пользователи могут сосредоточиться на устранении неполадок и определить, требуются ли дополнительные действия или дальнейший мониторинг. Как только проблемная область определена, замена подозрительных компонентов на заведомо исправные является одним из способов точной идентификации сварочного оборудования, требующего ремонта или корректирующих действий.Примеры полезных диагностических данных:
• Данные графика сварки . Это может помочь выявить различия между хорошими деталями и подозрительными деталями. Данные, отображаемые на графике сварки, как показано на рис. 3, включают амплитуду, потребляемый ток, мощность, частоту и фазу. Изменения амплитуды, фазы, частоты и тока могут указывать на проблему с блоком питания или стеком. Несоответствие потребляемой мощности может указывать на изменение процесса (например, давление сварки), изменение геометрии детали (могут измениться допуски, особенно в области соединения) или проблему компонента пакета (рупор или преобразователь начинают выходить из строя). .
• Диагностическое сканирование клаксона . Это определяет, потребляет ли рупор больше энергии (отображается как увеличение мощности, необходимой для работы в воздухе). Увеличение потребляемой мощности может указывать на образование трещины в рупоре. Такие трещины иногда бывают внутренними и поэтому не всегда видны невооруженным глазом.
• Случайные данные . Данные, которые кажутся хаотичными по сравнению с известными достоверными данными, могут указывать на неисправность преобразователя, рупора или радиочастотного кабеля, как показано на рис.4.
ПАРАМЕТРЫ ПРОЦЕССА И МАТЕРИАЛЫ
Тщательный контроль и документирование параметров процесса – еще одна область, которую нельзя упускать из виду. Производители медицинских и автомобильных компонентов знают об этом и следуют строгим процедурам, часто предписываемым регулирующими органами, такими как FDA, что приводит к высокой степени успеха при использовании ультразвуковой сварки.
К сожалению, переработчики других продуктов, таких как игрушки или одноразовые изделия, часто работают в соответствии с гораздо менее строгими требованиями и осуществляют гораздо более слабый контроль процесса.В подобных ситуациях операторы могут постоянно корректировать настройки в ответ на изменение деталей или производственных условий. Хотя такой подход может привести к удовлетворительному производству, любые возникающие проблемы труднее диагностировать, особенно дистанционно, когда параметры процесса часто меняются. Например, было ли последнее изменение параметра вызвано проблемой с оборудованием или изменением состава или качества детали?
Как правило, когда такое приложение требует помощи, инженер по ультразвуковой сварке, задав несколько основных вопросов, касающихся деталей (материал, конструкция соединения, требования к испытаниям и текущая настройка машины), может направить клиента к правильному решению. .Такой подход особенно удобен, если устранение неполадок может быть выполнено непосредственно на станке с использованием заводских деталей. Обзор процесса поиска и устранения неисправностей/настройки параметров показан на рис. 5.
Проблемы, связанные с материалами, являются частым источником несоответствий или проблем в производстве. Как показано в следующих примерах, даже небольшие различия в материалах могут существенно повлиять на качество сварки или производства:
• Полимерные заменители . Поскольку цены колеблются, переработчики обычно хотят переключаться между аналогичными полимерами по экономическим причинам.Тем не менее, перед внесением каких-либо изменений целесообразно проконсультироваться со специалистом по ультразвуковой сварке.
Одним из примеров распространенных, но потенциально проблемных изменений является переход от легко свариваемого аморфного материала, такого как АБС, к гораздо более трудносвариваемому полукристаллическому полимеру, такому как полипропилен. Для успешной сварки АБС-пластику требуется меньшая мощность ультразвукового пакета (30-70 микрон при 20 кГц), чем для ПП (90-120 микрон). Если это изменение приводит к тому, что детали не обладают той прочностью, которая была у них раньше, или их сварка занимает больше времени, или если сварные швы вызывают повреждение чувствительных поверхностей/компонентов сборки, проблема может заключаться в отсутствии выходного сигнала ультразвукового стека.Проверка компонентов пакета, в частности звукового сигнала и усилителя, необходима для определения того, позволят ли усовершенствования любого компонента эффективно сваривать новый полимер и вернуть приложение к «нормальному» диапазону успеха.
• Высокое содержание измельченного материала . Повторно измельченные термопласты, хотя их можно многократно плавить и реформировать, подвергаются некоторому ухудшению своих физических свойств с каждым последующим плавлением. Совокупный эффект слишком большого количества повторно измельченного материала может привести к тому, что детали не будут соответствовать спецификациям. По этой причине Брэнсон рекомендует использовать не более 10 % измельченного материала в деталях, подлежащих ультразвуковой сварке. В конкретных приложениях, требующих соблюдения строгих критериев тестирования и приемки, производителям следует серьезно задуматься о периодическом анализе производственных материалов для постоянной проверки качества материалов, из которых изготавливаются готовые детали.
• Наполнитель . Часто наполнители необходимы для обеспечения прочности и долговечности деталей. Однако различные типы и процентное содержание наполнителей в деталях могут повлиять на успешность процессов соединения пластмасс.Брэнсон рекомендует поддерживать содержание наполнителя на уровне менее 30%. Соединение деталей, содержащих более высокий процент наполнителя, особенно длинных волокон, иногда приводит к скоплению наполнителя в сварном шве, что может снизить прочность сварного шва.
Еще одна проблема – абразивные наполнители. Некоторые наполнители, придающие дополнительную прочность или ударную вязкость, включая карбонат кальция, диоксид кремния и тальк, также могут быть абразивными по отношению к контактным поверхностям оснастки. Длительное воздействие абразивных деталей на поверхности инструментов может вызвать износ, который может привести к косметическим повреждениям деталей и неадекватной передаче энергии на поверхности соединения деталей.
Рекомендуется переход на титановые рупоры с износостойкой поверхностью (например, из карбида или нитрида титана). Для крепления рекомендуется сталь или закаленная нержавеющая сталь.
КОНФИГУРАЦИЯ ДЕТАЛЕЙ И ПОИСК И УСТРАНЕНИЕ НЕИСПРАВНОСТЕЙ
Наличие всего остального — оборудования, материалов и процесса — не будет иметь большого значения, если детали, которые вы пытаетесь сварить, спроектированы неправильно. Но вместо того, чтобы пытаться рассмотреть здесь все детали хорошей конструкции детали, давайте сосредоточимся на некоторых основных причинах неправильной конструкции детали:
• Отсутствие четко определенных целей проекта или приложения .Многие прикладные проекты испытывают трудности, когда есть «движущаяся цель» для тестирования и принятия. Например, потребуется ли приложению тест на падение? Испытание давлением? И если да, то при каких значениях? Эти значения необходимы для эффективного проектирования уплотнительного соединения. Как правило, критерии приемлемости требуют раннего рассмотрения и принятия решений, если мы хотим, чтобы проектирование проходило гладко.
• Отсутствие понимания наилучших типов соединений для конкретных применений .Неоптимальные конструкции соединений часто возникают, когда главный проектировщик, который может иметь лишь поверхностное представление о процессах соединения пластмасс, продвигает проект вперед только для того, чтобы обнаружить, что было принято неправильное решение и что характеристики соединения деталей и сварки не были должным образом обдуманный.
Часто такие выводы делаются только после того, как были сделаны значительные инвестиции (завершение пресс-формы, производство деталей и первоначальные испытания сварных швов). Опять же, ключевые аспекты, связанные с деталями и сварными швами (контроль зазора сварного шва и тип уплотнения — герметичный, конструкционный или и то, и другое) должны быть определены на ранней стадии проекта.Сотрудничество с инженером по ультразвуковой сварке на начальных этапах проекта может помочь определить ключевые критерии деталей, лучше обучить проектировщиков и помочь минимизировать или, по крайней мере, выявить возможные риски.
• Износ пресс-формы, обычно вызванный использованием абразивных полимеров или наполнителей, со временем может привести к тому, что детали существенно и по размерам будут отличаться от ранее проверенных деталей. В результате основные элементы соединения, такие как направляющие энергии или соединения с натягом при сдвиге, больше не соответствуют спецификациям.Профили деталей могут больше не соответствовать набору инструментов. Результаты сварки могут становиться все более и более непостоянными. Средства для решения этой проблемы включают переработку существующей формы или изготовление новой формы.
В конечном счете, проблемы с деталями, сваренными ультразвуком, могут возникать из многих источников. Звонок местному представителю ультразвукового сварочного оборудования, как только возникнет подозрение на проблему, может позволить диагностику и рекомендации по устранению, которые часто выполняются по телефону или по электронной почте, что может помочь вам выявить, свести к минимуму или решить потенциальные производственные проблемы.Чтобы уменьшить потребность в устранении неполадок, следуйте этим рекомендациям:
• Сотрудничайте с инженерами-разработчиками вашего поставщика оборудования для ультразвуковой сварки на ранних стадиях проектирования (или редизайна, если предполагаются существенные изменения в материалах, форме или функциях).
• Всегда имейте в наличии резерв запасных компонентов производственного качества, особенно для критически важных приложений, где перерывы в производстве могут вызвать серьезные операционные или финансовые проблемы.Запасные части для производства являются жизненно важным помощником при устранении неполадок при соединении, а в случае дефицита поставок могут поддерживать производство с минимальным временем простоя.
• Воспользуйтесь возможностями обучения, которые позволят вам освоить технологию соединения пластмасс, которую вы используете. Брэнсон, например, предлагает семинары в различных корпоративных офисах и на объектах клиентов, предоставляя практическое обучение и техническую помощь, необходимые для того, чтобы ваш «чемпион» ультразвукового процесса был хорошо информирован о новейших технологиях и был готов обучать и поддерживать технологии по мере необходимости. средство.Инженеры-конструкторы, инженеры по качеству, персонал по обслуживанию оборудования и операционный/производственный персонал могут извлечь выгоду из времени, потраченного на обучение.
ОБ АВТОРЕ : Дэвид Дальстранд — старший сотрудник Emerson. региональный технический координатор/инженер по разработке текстиля для Branson Ultrasonics Corp., Данбери, Коннектикут. Он обладает прикладными знаниями и проектированием инструментов для ультразвуковых, вибрационных, орбитальных, термических и лазерных технологий соединения, используемых при сборке жестких термопластов, синтетических тканей и фильмы.Контакты: (770) 962-2111, доб. 17; [email protected]; www.emerson.com.
Процесс ультразвуковой сварки – принцип работы, составные части, преимущества и недостатки при применении
Что такое ультразвуковая сварка
Ультразвуковая сварка (USW) – это метод сварки, в котором для сварки двух деталей используется ультразвуковая вибрация высокой частоты. Он чаще всего используется для сварки термопластичных материалов и разнородных материалов.Металл с тонким сечением также можно сваривать УЗВ.
Принцип работы
Ультразвуковая вибрация высокой частоты (от 20 кГц до 40 кГц) используется для соединения двух пластмассовых деталей. Высокочастотная вибрация генерирует тепловую энергию на границе раздела двух частей и расплавляет материал. Расплавленный материал сплавлялся друг с другом, образуя прочный сварной шов при охлаждении и затвердевании.
Типичная используемая частота составляет 15, 20, 30, 35 или 40 кГц.
Основные детали
Различные основные детали или компоненты ультразвуковой сварки:
- Пресс A: Используется для приложения давления к двум соединяемым пластиковым деталям.Он может быть с пневматическим или электрическим приводом.
- Гнездо или наковальня или приспособление: Это зажимное устройство, которое используется для удерживания и зажима двух пластиковых деталей вместе. Он допускает высокочастотную вибрацию, направленную на поверхность раздела двух частей.
- Ультразвуковой стек : Он состоит из трех компонентов: преобразователя или пьезоэлектрического преобразователя, усилителя и рупора или сонотрода. Эти три элемента настроены на работу на резонансной частоте 15 кГц, 20 кГц, 30 кГц, 35 кГц или 40 кГц.
- Преобразователь: Преобразует электрические сигналы в высокочастотные механические вибрации. И делает это благодаря пьезоэлектрическому эффекту.
- Усилитель: Механически изменяет амплитуду вибрации. В некоторых стандартных системах используется для зажима стопки в прессе.
- Горн или сонотрод: Он вибрирует на высокой частоте и передает механическую вибрацию на две свариваемые детали. Он также механически изменяет амплитуду.Он принимает форму детали. Рог изготовлен из титана или алюминия.
- Ультразвуковой генератор: Он генерирует и подает высокочастотные электрические сигналы, соответствующие резонансной частоте стека.
- Контроллер: Используется для управления движением пресса и подачей ультразвуковой энергии.
Читайте также:
Рабочий процесс ультразвуковой сварки части.
Для лучшего понимания посмотрите видео ниже:
Применение
В основном используется в компьютерной и электрической, аэрокосмической и автомобильной, медицинской и упаковочной промышленности.
- Компьютерная и электротехническая промышленность: Здесь он используется для соединения проводных соединений и создания соединений в небольших чувствительных цепях.
- Аэрокосмическая и автомобильная промышленность
В автомобильной промышленности он используется для сборки крупных пластиковых и электрических компонентов, таких как дверные панели, приборные панели, воздуховоды, лампы, рулевые колеса, обивка и компоненты двигателя.
В аэрокосмической отрасли используется для соединения тонких листов и легких материалов, таких как алюминий.
- Медицинская промышленность
Не загрязняет сварной шов и не разрушает его.Именно поэтому его используют в медицинской промышленности.
Такие изделия, как фильтры для анестезии, артериальные фильтры, фильтры для крови, диализные трубки, пипетки, фильтры для крови/газа, резервуары для кардиометрии и т. д., могут быть изготовлены методом ультразвуковой сварки.
4 . Упаковочная промышленность
Используется для упаковки различных материалов в пищевой промышленности.
Используется для упаковки опасных материалов, таких как взрывчатые вещества, фейерверки и химикаты.
Читайте также:
Преимущества
- Это быстрый процесс сварки.
- Имеет быстрое время высыхания, т.е. изделия не остаются долго сохнуть в приспособлениях
- Может быть легко автоматизирована.
- Обеспечивает чистое и точное соединение.
- Обеспечивает чистые места сварки и не требует подкраски.
- Оказывает низкое термическое воздействие на материалы.
Недостатки
- Нельзя использовать для изготовления больших швов (более 250 х 300 мм).